
www.nzmanufacturer.co.nz
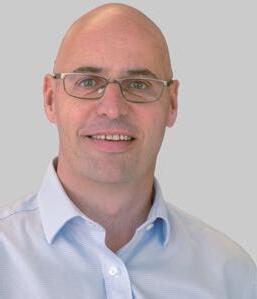
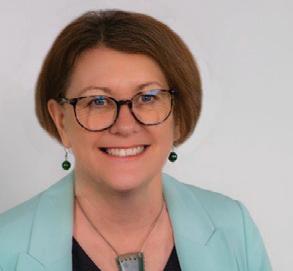
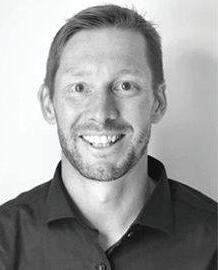
www.nzmanufacturer.co.nz
SmartSat Cooperative Research Centre (SmartSatCRC) has announced the first four new jointly funded space research projects and opened further funding opportunities in partnership with New Zealand’s Ministry of Business, Innovation and Employment (MBIE).
The four initial research projects, commencing in this month, include research into monitoring methane emissions, enhancing real-time monitoring of greenhouse gases, managing free space optical communication nodes across Australia and New Zealand, improving the tracking of space objects, and developing a joint AUS-NZ concept for maritime domain awareness.
Professor Andy Koronios, CEO of SmartSat CRC, emphasised the importance of this collaboration and stated, “In a significant advancement for Trans-Tasman space collaboration, this partnership between Australia and New Zealand in the space sector demonstrates our commitment to leveraging our combined strengths and resources.
“These projects are a testament to our shared vision of driving innovation and developing capabilities that will not only benefit our respective countries but also contribute to global advancements in space technology.”
The partnership between SmartSat and MBIE aims to establish enduring partnerships between Australian and New Zealand researchers to create platforms for larger-scale future research
collaborations, help develop talent, joint expertise and support R&D in alignment with industry and end user needs.
Additionally, the research addresses major environmental, economic and social challenges through scientific collaboration while leveraging the unique geographical advantages of Australia and New Zealand, such as the southern hemisphere location, clear skies, and varied topography.
Dr Carl Seubert, Chief Research Officer of SmartSat CRC, added: “We’re excited to be driving international research collaboration, and bringing Australian and New Zealand research organisations together to tackle significant issues through innovative space R&D.
“Initiatives such as this are essential to foster the development of space technology and amplify its impact to solve environmental, economic, and social challenges on Earth.”
In addition to announcing the initial projects, SmartSat also opened a call for submissions
for funding opportunities for further research activities under the program.
SmartSat CRC and MBIE are inviting proposals for collaborative six-month feasibility studies with up to AUD $100,000 for Australia-based research activities, or up to NZD $100,000 for New Zealand-based research activities.
This funding opportunity aims to harness complementary resources and expertise to develop innovative research and development projects in the area of Earth Observation that will drive the growth of the space industry in both countries.
Open to public and private Australian and New Zealand research organisations, projects should align with industry and end-user needs, addressing major environmental, economic, and social challenges.
For more information and to submit proposals, please visit the SmartSat CRC website
Secure supply of energy and data to moving industrial equipment.
• Large size range
• Vertical travels
• Energy tubes
• Hygienic chains
• Solutions for long travel
• Guide troughs
• Readychain
• Robotic, 3D
• Circular movement
HUGE range of high quality flexible cables
• Control cables
• Single cores
• Data cables
• Sensor/Actuator
• Intrinsically Safe
• VSD/EMC cables
• Halogen Free cables
• High temperature
• Harsh Conditions
• Crane cables
• Profibus cables
• Bus/DeviceNet
• Solar cables
• Instrumentation
• Flat cables
• Curly cords
Largest range of flexible conduits for cable protection
• Conduits
• Conduit fittings
• Divisible systems
• Jumbo systems
• Conduit Accessories
• Braided cable protection
• Fire barrier solutions
• Food and beverage
• EMC systems
• Ex, ATEX, IEC EX
Industrial connectors for many industries
• Rectangular multipole connectors from ILME
• Single pole Powerline connectors from TEN47
• EPIC connectors from Lapp Group
• M23 circular connectors from Hummel
• Circular connectors specifically for the entertainment/stage lighting industry from Socapex
Safety engineering solutions from EUCHNER
• Multifunctional Gate Box MGB
• Transponder-coded safety switches
• Electromechanical safety switches
• Magnetically coded safety switches
Sensor technologies for automation
• High-Precision Laser Distance Sensors
• Ultrasonic Sensors
• Inductive Sensors
• Fluid Sensors
New joint research projects under Australia –New Zealand Collaborative Space Program.
EDITORIAL
“We haven’t the money, so we’ve got to think.”
BUSINESS NEWS
Digital Capability – A Critical Lever for Success.
NZ Wool Industry to benefit from multi-million dollar marketing investment.
SMART MANUFACTURING
It’s all about the people.
Cisco and Rockwell to accelerate digital transformation in Asia Pacific industrial market.
NZAero flying the flag for Kiwi aircraft manufacturing.
Coming full circle.
Digital Factory Accelerator: Driving Northern Ireland’s Manufacturing into the Future.
Reducing manufacturing emissions.
Robotic Integration and the future of Supply Chains.
SUSTAINABILITY
Nature is in the business news.
COMPANY PROFILE
Oasis Engineering – energy and fuel transfer specialist to the world.
THE INTERVIEW
Sam Cotter-Dephoff, Scale Studios, Wellington.
ENERGY
Trans-Tasman aviation shipments decarbonised via SAF programme.
WOMEN IN TECHNOLOGY
Breaking barriers: Paving the way for women in tech.
WORKSHOP TOOLS
Lower costs and higher productivity for shot peening processes.
NZ welders a step ahead on safety.
Igus launches compact, energy e-chain DEVELOPMENTS
Accelerating the battery industry.
Gas production forecast to fall below demand. AI raises privacy issues for SMEs and eCommerce.
THE LAST WORD
Building an engineering culture and resilient technology.
Ian Walsh Ian is a Partner, Argon & Co. NZ, a master black belt improvement specialist and global lean practitioner. He is passionate about improving productivity and helping to create world class New Zealand businesses.
Dr Barbara Nebel CEO thinkstep-anz Barbara’s passion is to enable organisations to succeed sustainably. She describes her job as a ‘translator’ – translating sustainability into language that businesses can act on.
oodward
Is Managing Director of Connection Technologies Ltd, Wellington and is passionate about industry supporting NZ based companies, which in turn builds local expertise and knowledge, and provides education and employment for future generations.
Mark Devlin
Having owned food manufacturing and distribution businesses for a decade, Mark Devlin now runs Auckland public relations agency Impact PR. Mark consults to several New Zealand manufacturing firms including wool carpet brand Bremworth, aircraft exporter NZAero and cereal maker Sanitarium.
Insa Errey
Insa’s career has been in the public and private sectors, leading change management within the energy, decarbonisation, and sustainability space. Insa holds a Chemical and Biomolecular BE (Hons) from Sydney University. She is a member of the Bioenergy Association of NZ and has a strong passion for humanitarian engineering, working with the likes of Engineers Without Boarders Australia.
Insa is a member of Carbon and Energy Professionals NZ, been an ambassador for Engineering NZ's Wonder Project igniting STEM in Kiwi kids and Engineers Australia Women in Engineering, increasing female participation in engineering.
Jane Finlayson is Head of Advanced Manufacturing at the EMA, and has 25-years’ experience in business and economic development. She is passionate about empowering businesses to grow, innovate and embrace Te Ao Māori.
PUBLISHER
Media Hawke’s Bay Ltd, 121 Russell Street North, Hastings, New Zealand 4122.
MANAGING EDITOR
Doug Green
T: +64 6 870 9029
E: publisher@xtra.co.nz
CONTRIBUTORS
Holly Green, EMA,
Business East Tamaki, Ian Walsh, Adam Sharman, David O’Connor, Mark Devlin, Nicholas Russell, Jane Finlayson, Andrew Bayly, Terry Smagh, Isabel Naidoo, Tim Mazzarol
ADVERTISING
T: + 64 6 870 9029
E: publisher@xtra.co.nz
DESIGN & PRODUCTION
:kim-jean:
E: kim.alves@xtra.co.nz
WEB MASTER
Julian Goodbehere
E: julian@isystems.co.nz
PUBLISHING SERVICES
On-Line Publisher
Media Hawke’s Bay Ltd
DIGITAL SUBSCRIPTIONS
E: publisher@xtra.co.nz Free of Charge.
MEDIA HAWKES BAY LTD
T: +64 6 870 9029
E: publisher@xtra.co.nz
121 Russell Street North, Hastings
NZ Manufacturer ISSN 1179-4992
Vol.16 No.7 August 2024
Copyright: NZ Manufacturer is copyright and may not be reproduced in whole or in part without the written permission of the publisher. Neither editorial opinions expressed, nor facts stated in the advertisements, are necessarily agreed to by the editor or publisher of NZ Manufacturer and, whilst all efforts are made to ensure accuracy, no responsibility will be taken by the publishers for inaccurate information, or for any consequences of reliance on this information. NZ Manufacturer welcomes your contributions which may not necessarily be used because of the philosophy of the publication.
“We haven’t the money, so we’ve got to think”
These words were spoken by Lord Sir Ernest Rutherford, Nobel Laureate.
Since he spoke them, some inspiring products have been made. These include The Martin JetPack, The Yike Bike, The Springfree Trampoline, Woollen Shoes, The Pavlova, Richars Pearse’s Flying Machine, Hamilton Jet, The Buzzy Bee…and the list goes on.
What is significant about these products is that they were made at a time when there wasn’t the money available. Through sheer determination and effort, they found markets and advanced New Zealand’s name on the world stage as an innovative and go-ahead nation.
There are a lot more products that have made the country proud and celebrated the entrepreneurs determined to get ahead.
However, times have been changing and the lack of attention being given to our manufacturers today is shameful. Financial corrections have been made to get the books in order without the productive sector getting a look in. Nowhere in the Budget did we hear of the importance of the manufacturing sector to the economy, that all efforts were appreciated and when times get better, assistance would be offered to keep the backbone of the country strong.
It seems that Government has gone too far with its slash and burn. The country of 5,000,000 can’t all dance on the top of the designated pin.
Anyway, back to the inventions: The Britten Motorcycle, Wave Power, Conducting Polymers, Carbon Nanotubes, The Electric Fence, the Hamburger Holder…
Doug Green , Publisher
David O’Connor, Commercial Manager, The Learning Wave
One of the greatest challenges for any organisation is the cost and effort of onboarding a new employee . This is further amplified in a tight job market where you may need to recruit individuals who do not have the core skills you would normally deem essential to be productive and work safely in your environment.
The need to have a pipeline of skilled and capable workers with a broad range of transferable skills, strong work ethic and the right attitude is critical to enable long term business success.
The training and educational sector have a role to play in enabling access to the right training pathways to ensure the continual development and upskilling of the team to prepare them for that next career step or business change.
In Manufacturing, the productivity challenge is clearly rooted in a skills deficit, with many individuals lacking the essential skills and capability needed to fully leverage modern manufacturing practices. This skills gap has a significant impact on team work, employee engagement, safety and operational efficiency, leading to poor staff retention, low efficiency, higher error rates and increased waste
As Manufacturing plants become increasingly technology dependent, this skill gap is unfortunately amplified and an urgent fix becomes even more
essential. Foundational digital literacy is often inaccurately assumed as a skill held by most kiwis. According to the 2014 Survey of Adult Skills survey (PIAAC) the reality of this is that 55% of workers do not have the right level of digital competency to be successful in their roles. Meaning that over half of our workforce has low/poor Problem solving skills in technology rich work environments.
If Digital literacy is deemed critical to success, then we have to question why those who set the rules for access to workplace literacy funding continue to stipulate that digital literacy is one of the ‘other’ literacies, maintaining that access to funded training programmes is based on competency levels in reading and numeracy only.
Digital skills and digital literacy training for today’s worker is essentially the ticket to the game, and many are being turned away at the gates, or made to sit on the bench because we are not able to provide them access to the training they need.
Assuming we agree that productivity and innovation are the drivers of business growth, and growth leads to expansion, and expansion leads to the need for more people, then underpinning this is talent.
The training and educational sector in New Zealand therefore needs an ecosystem that delivers the right training programmes to businesses, fit for our modern ways of working, rather than being constrained by the rules of a vocational education system.
If we can co-create this with the sector we can effectively prioritise access to the right skills based training, empower a digitally capable workforce, enhance our manufacturing capabilities, build talent and create successful businesses.
Unfortunately for now, we are left sitting in the dark ages while we patiently await for the system to catch up and prioritise digital skills, like they do reading and writing.
New Zealand’s rural sector is set to benefit from a multi-million dollar marketing investment by one of the country’s largest wool carpet manufacturers, designed to address misconceptions about the natural fibre and grow exports.
New Zealand is the world’s third largest producer of wool, accounting for 9% of global production, however, the country’s export revenue from wool is projected to fall by 3% to $380 million over the coming year.[1][2]
The planned $2 million plus advertising investment from Bremworth is believed to be one of the highest ever from a Kiwi company to support a wool product brand. The spend will also provide a financial boost for local print, billboards, online and broadcast media titles, in an otherwise flat local advertising market.
The company has appointed New Zealand’s largest independent media agency, Together, to help develop and implement a series of new campaigns for the domestic and trans-Tasman markets to help elevate wool flooring.
The move follows ongoing upgrades to the manufacturer’s supply chain, which are expected to lift production volumes and help meet growing domestic and global demand for Bremworth’s wool carpet.
Rochelle Flint, chief brand and product officer of Bremworth, says it is hoped one of their largest-ever investments in developing their brand will also help stimulate demand for New Zealand wool and help address the decline in domestic production.
She says their research shows while three-quarters of homeowners would prefer to have wool in their homes, a similar proportion are not actually purchasing wool - with synthetic flooring continuing to dominate the market.
Flint says with their expanded supply chain now in place, manufacturing volumes can be scaled significantly in response to demand, presenting an opportunity to increase conversion and grow market share in both the domestic and Australian markets.
“Our research has identified a segment of homeowners that don’t put as much focus on the flooring as they do in rooms like their kitchen or bathroom. They may spend thousands on a benchtop but when it comes to carpet, it doesn’t enjoy the same prestige.
“This new campaign is about elevating wool as a flooring option and becoming part of the consideration set for more consumers, and growing wool carpet’s market share through greater conversion at the retail level. We want this audience to understand that you live your life on carpet and
it is an architectural surface worthy of much more attention.
“A large part of our campaign messaging will be dedicated to addressing misconceptions about wool that are part of the barrier to purchasing wool. Included among these myths are that it’s not suitable for kids, it doesn’t last as long, it’s hard to care for etc.
“Generations of Kiwis have lived on wool flooring and it has performed extremely well, however, there is a younger generation becoming homeowners now that have never experienced the quality and longevity of wool.
“This natural insulating fibre is incredibly durable and has a natural stain resistance, which is how sheep stay white on the farm, however despite living in a nation globally renowned for the calibre of wool production, there is an emerging segment of the market that we have yet to reach with these messages.
“This campaign will be about raising awareness and educating these consumers on the benefits of this natural fibre,” she says.
Penelope Brown, Together’s managing director of Media, says the latest evolution of Bremworth’s brand strategy will reach hundreds of thousands of homeowners and design influencers over the coming year.
She says the first of the new campaigns will launch in August - introducing new messaging inspiring consumers to emotively engage with New Zealand wool across out-of-home, TV, print and digital mediums.
“Our intention is to align ourselves more with design partners and work towards further premiumisation of the Bremworth brand.
“Research shows the brand is already the most trusted in the industry by consumers, however, this is only one element of the decision to purchase and we want more New Zealanders and Australians to understand this incredible journey that Bremworth has been on, the exceptional product that they produce and their relentless dedication to the elevation of NZ wool over synthetics, which are essentially plastics.
“To achieve this we will be implementing a series of highly targeted trans-Tasman campaigns designed to ensure the brand is front of mind for both the new home build and renovation markets,” she says.
Rochelle Flint.
Flint says Together will join their incumbent public relations agency Impact PR and, creative agency Kindred, in supporting Bremworth to grow wool carpet’s share of the flooring market.
“We know that the Bremworth story is now attracting global interest, and this investment will have a flow on benefit in helping to reposition New Zealand’s wool sector.
“With our new hybrid supply chain set to help deliver substantially higher volumes of finished product, we now have the confidence to increase our annual marketing spend. This investment will help significantly expand the number of homes with wool carpet, in Australasia and beyond,” she says.
[1] IBISWorld - industry market research, reports, and statistics. (n.d.). https://www.ibisworld. com/nz/bed/wool-production/141/#:~:text=Recent%20Trends%20%E2%80%93%20Wool%20 Production,are%20expected%20to%20be%20 stable.
[2] Statista. (2024b, February 6). Wool export revenue in New Zealand FY 2017-2025. https://www.statista. com/statistics/1295200/new-zealand-wool-export-revenue/#:~:text=In%20the%20year%20 ended%20June,New%20Zealand%20dollars%20 by%202025 mark@impactpr.co.nz
Ian Walsh, Partner, Argon & Co
Last month, I wrote an article on productivity (Productivity – The Only Game in Town) and I received a few questions and comments relating to the skills gaps we have in New Zealand.
I’d really encourage you to read that article if you haven’t yet, and I can hopefully address those questions and comments here. https:// nzmanufacturer.co.nz/2024/07/productivity-isthe-only-game-in-town/
As I noted in my last article, a skilled workforce is vital for productivity growth. If we want to have a great place to live, bring up families and enjoy the best economy that both New Zealand can offer, then we must have great people with the right skills leading our businesses, creating value and growth.
Of course I’m not the only person who knows this; I’m regularly asked by hiring managers whether I know of a good candidate to join their company. Sometimes I can help, but more often than not, I simply don’t know enough people to fill all the vacancies in these companies.
Recent macroeconomic analysis is showing clearly that differences in education and skills explain much of the international differences in long-term growth rates.
Improvements in skills at all levels of ability seem to matter. Increases in both the proportion of top achievers and the proportion with at least a minimal level of literacy and numeracy are correlated with higher economic growth rates.
However, the current approach in industry seems to be to promote the best operator to foreperson, team leader etc. and assume they will know what to do and how to do it.
The other approach is to hire someone, under the assumption that the market is teeming with highly capable and skilled individuals. Little-to-no training and development is offered by most employers, and we have among the lowest post-secondary education participation rates in the OECD.
The data also shows that the capability of New Zealand’s first level leaders in terms of people management and skills is among the lowest in the OECD.
This is especially true in smaller organisations with less resources and capability to train and develop.
As such, the notion that the market is teeming with capability is nonsense. The capability there is typically no better than what you already have. The “stars” aren’t waiting for job adverts; they have already been offered multiple opportunities.
There are many factors involved here, one of them being the standard of our education system. It’s poignant to discuss this, as the government is taking action to address the underperformance of our students compared to international benchmarks. New Zealand’s results showed a decrease in high performers and an increase in low performers over the past 20 years in all three “core” subjects.
This was most pronounced in mathematics, where the percentage of low performers increased from 15 percent of kiwi 15-year-olds in 2003 to 29 percent in 2022 while the percentage of high performers dropped from 21 to 10 percent in the same period.
The Curriculum Insights and Progress Study (CIPS) study revealed that only 22 per cent of Year 8 students in New Zealand met the expected curriculum benchmarks for mathematics. Prime Minister Luxon said approximately 50,000 Year 8 students did not meet the expected standards last year. He described the results as a “total system failure.”
If we don’t do the basics well, we won’t have the right foundations for the future, and in a rapidly accelerating technological world, science, maths and reading are fundamental. This decline in New Zealand’s education has been going on for 15 years, and whilst we are still above the OECD average, we are not where we want to be.
continued on Page 15
Cisco, a worldwide leader in networking and security, and Rockwell Automation, the world’s largest company dedicated to industrial automation and digital transformation, has announced a collaboration to propel digital transformation of the industrial market in the Asia Pacific, Japan and Greater China region.
The announcement was made as the two companies signed a Memorandum of Understanding (MOU) on the same.
Cisco and Rockwell Automation provide technologies and services that enable manufacturers to optimise operations, enhance productivity, and ensure the security of their industrial networks. This collaboration will see the two companies coming together to facilitate the implementation of advanced automation solutions, such as connected factories and industrial IoT, while also addressing the unique challenges and requirements of manufacturing environments.
“As industries across APJC embark on their digital transformation journeys, our collaboration with Rockwell Automation is poised to deliver significant value for our customers,” said Kartika Prihadi, Vice President, Partners & Routes to Market Sales, Cisco.
“By joining forces, we aim to empower industrial enterprises with cutting-edge secure connectivity solutions that drive operational efficiency, enhance productivity and unlock new growth opportunities.”
The MOU signifies a deeper commitment to fostering collaboration and innovation between Cisco and Rockwell Automation, as they work together to harness the power of digital technologies and automation solutions to meet the unique challenges of the APJC industrial market.
“At Rockwell we firmly believe in the idea of better together and we are excited to embark on this journey with Cisco to accelerate digital transformation in Asia and the Pacific,” said Shovan Sengupta, regional vice president, Market Access, Rockwell Automation.
“By combining our strengths and capabilities, we are well-positioned to help industrial enterprises in the region navigate the complexities of digitalization and achieve sustainable growth.”
Cisco and Rockwell Automation will also work towards training and building a wider talent pool to address the digital skills gap in the manufacturing sector. This will be done by leveraging Cisco’s
Networking Academy program and Rockwell Automation’s partnerships with universities across the region.
Cisco Networking Academy is one of the longest-standing IT skills-to-jobs programs in the world. Cisco Networking Academy provides high-quality IT and cybersecurity courses, learning simulators, and hands-on learning opportunities via a learning platform to support instructors and engage learners in 190 countries.
To date, over 20 million global learners have taken Cisco Networking Academy courses to gain digital skills. Additionally, 95% of students that have taken Cisco certification aligned courses have attributed obtaining a job or education opportunity to Cisco Networking Academy.
Rockwell Automation is a global leader in industrial automation and digital transformation.
Cisco is the worldwide technology leader that securely connects everything to make anything possible.
EMA Communications Advisor Nicholas Russell
From cloud seeding to fire fighting and emergency evacuations, the efficiency and versatility of turboprop aircraft has meant they remain in strong demand around the world.
Compared with jet engine aircraft, they offer many benefits such as lower operating costs, shorter take-off and landing distances, and better performance in adverse weather conditions.
NZAero is New Zealand’s only commercial aircraft manufacturer. Its SuperPac 750XL-II is the latest iteration of the Hamilton aircraft manufacturer’s hugely successful airframe. With added power, a quieter propeller and touchscreen glass cockpit flight systems and avionics, it can climb faster and burn less fuel than its previous models.
The SuperPac 750XL-II was launched in November last year and is currently certified in New Zealand, Israel and Papua New Guinea. Australian certification is very close, and the European Aviation Safety Agency (EASA) process is also well advanced. American Federal Aviation Administration (FAA) certification is progressing, along with Canada and Thailand.
Stephen Burrows, CEO of NZAero, says having regulations in each region complicates the process of bringing products to market.
“Aircraft manufacture is a heavily regulated industry, and you can’t sell the aircraft until you have certification,” says Burrows.
“If everyone in the world operated on the same certification basis, it would be easy. You just do the
certification once and you’d be away. But because each region has its own set of requirements, you then have to certify it multiple times in order to reach all of those markets.
Some countries use the big regulators to predicate their own certification, so that can speed the process up.
“We’ve seen bilateral agreements put in place with numerous countries that accept other countries’ certification, so that’s where governments can help.”
The development of bilateral agreements such as these is one of the aims of the EMA’s Advocacy team.
Head of Advocacy Alan McDonald says the EMA advocates on behalf of its Members, including NZAero, for the removal of non-tariff barriers to trade, such as the red tape surrounding aircraft certification.
While some non-tariff barriers exist for good reasons – such as regulations to promote safety – foreign governments can agree to accept New Zealand’s regulations as equivalent, says McDonald.
“Government-to-government discussions or longer-term free trade agreements can help to facilitate this.”
New Zealand is a signatory to several bilateral and multilateral agreements with other countries that support a commitment to harmonise aviation standards, rules, procedures and processes. But it’s a slow, expensive process and this is why you
don’t see a flood of new designs in the sector, says Burrows.
For its part, NZAero continues to innovate and develop new products, with the SuperPac and EFIS Flight Deck both recent examples, and other projects include future green energy aircraft.
However, a lot of designs are quite old, and this means that emerging technologies, such as batteries and hydrogen fuel, are built into existing aircraft designs.
“There are aircraft operating in the northern hemisphere with lithium-ion power plants that are on 80-year-old airframes,” says Burrows.
“The 750XL is a 20-year-old design. I mean, if you looked at car manufacturing, that would be a very old design. But in the aviation world, that’s nothing.”
By EMA Head of Manufacturing Jane Finlayson
Global demand for sustainable goods is increasing, and among New Zealand manufacturers there’s an urgent need to innovate to remain competitive.
From SMEs up to huge multinationals, ‘business as usual’ won’t be enough to meet the sustainability challenges the world faces.
Legislation both in New Zealand and overseas will force the hand of many manufacturers. In New Zealand, regulations such as the Emissions Reduction Plan will place an increasingly high cost on manufacturing emissions.
Overseas, the likes of the EU’s Carbon Border Adjustment Mechanism (CBAM) will have an impact on our exported products.
The CBAM is a tool that puts a price on the carbon emitted during the production of carbon-intensive goods that are entering the EU, and to encourage cleaner industrial production in non-EU countries.
But sustainability is also good business. Like any strategic initiative done right, it can reduce costs, increase revenue and mitigate risks. Sustainability is about futureproofing.
In late July, Minister for Small Business and Manufacturing Andrew Bayly launched a report with compelling new research on the circular economy. It is intended to support the growth and resilience of New Zealand’s advanced manufacturing sector by identifying and mapping the sector’s emissions and waste patterns and finding ways for businesses to adopt net-zero circular manufacturing practices.
The aim is to move away from a linear economy to one that ‘designs out’ waste and pollution, keeps resources in use for as long as possible, then recovers and regenerates products.
The EMA and other industry experts fed into the report, ‘Mapping Emissions and Waste Data in the Manufacturing Sector’, which found that circular economy practices do exist in New Zealand, within and across all the manufacturing subsectors, but they differ greatly.
The key similarity was in challenges around waste. Of the 17 million tonnes of waste produced annually in this country, 92% ends up in landfill.
Most of the manufacturing subsectors depend on imports and as a result ‘offshore’ their emissions.
Circular supply chains enable businesses to become more resilient by decoupling operations from the extraction of natural resources, thereby increasing material security and reducing exposure to price volatility.
The report found that opportunities exist to use more local products, but clear emissions policies were needed to encourage the shift.
Barriers to adopting the circular economy model include access to capital, risk aversion and a lack of knowledge and understanding of waste reporting – there needs to be better understanding of where materials end up at the end-of-use, and how they can be recovered.
From fashion and textiles to cosmetics and food products, consumers are increasingly seeking sustainable goods. This is an opportunity for Kiwi manufacturers to promote a sustainable ‘brand New Zealand’ to the world.
The report on manufacturing emissions is the macro part of that sustainability journey, and it will help to inform policy in areas such as encouraging government policies to help businesses adopt the circular economy, foster collaboration across agencies and aid in setting national targets for circularity.
There is also practical help for individual manufacturers. Along with the report, the Sustainable Business Network announced an updated Climate Action Toolbox, which is a free online resource to help small and medium businesses reduce emissions.
This includes tailored guidance for manufacturers on how to fund climate initiatives, making it easier to take action.
The toolbox can be found on the business.govt.nz and Sustainable Business Network websites.
One of the companies that provided a case study in the toolbox was Auckland sustainable cabinetry and furniture manufacturer Spacebar Design.
Director Anson Kong says that sustainability is about changing mindsets, and this includes convincing clients to repurpose furniture rather than replace it.
A set of Spacebar drawers at the Sustainable Business Council offices was made out of recycled plywood, with a vivid green tabletop made from recycled fishing nets and other plastics.
‘Ghost nets’ are fishing nets that have been lost or abandoned in the ocean. These nets continue to trap everything in their path, presenting a major problem for the health of our oceans and marine life. An initiative that encourages the recycling of materials such as damaged or ageing fishing nets is part of the circular economy.
Creating durable, practical materials out of a waste product that can often cause harm in our oceans is a win-win.
Technology can also play a huge role in sustainable business models, and over the past four years the EMA has been heavily involved in upskilling manufacturers and encouraging them to embrace technology to help with productivity. There are also very clear benefits in other areas including safeguarding and caring for your people and the environment.
Many of the case studies featured from this programme highlight cost and energy savings, making the case for change even more compelling. The EMA has a full-day course to think through this topic, called Introducing Sustainability: The What, the Why and the How for Businesses
Make the most of these resources and tap into the experts to speed up a sustainability journey and develop circular practices that benefit not only the environment but the bottom line as well.
Regulations such as the Emissions Reduction Plan will place an increasingly high cost on manufacturing emissions.
Sandra Lukey
Sandra Lukey is the founder of Shine Group, a consultancy that helps science and technology companies accelerate growth. She is a keen observer of the tech sector and how new developments create opportunity for future business. She has over 20 years’ experience working with companies to boost profile and build influential connections.
Mike Shatford
is an expert in the field of technology development and commercialisation. His company Design Energy Limited has completed over 100 significant projects in this vein by consulting for and partnering with some of New Zealand’s leading producers. Among Mike and his team’s strengths are industrial robotics and automated production where the company puts much of its focus.
Sean O’Sullivan
Has a B Com (Hons) Otago University. In 2000 - 2001 introduced PCs on the workshop floor and job and staff tracking and a productivity software App to Fletcher Aluminium Group and 100 manufacturers NZ nationwide. In 2001 – 2022 Founding Director Empower Workshop Productivity & Scheduling Software App. 236 manufacturing and engineering clients mainly throughout NZ and Australia, also UK and US.
Iain Hosie
Iain Hosie is a respected figure in the NZ Advanced Manufacturing and Materials sectors, with extensive experience in product development, research projects and commercializing tech products. Iain is a Director and Founder of Nanolayr Ltd, Director for the NZ Institute for Minerals and Materials Research, Commercial Director for Fabribotics Ltd, and Executive Council of BiotechNZ.
Adam Sharman
Is a Senior Partner at Dsifer. With a background in technology implementation, manufacturing and strategy, Adam and the team at Dsifer are on a mission to support New Zealand’s manufacturing sector transform using technology, data and analytics to outcompete on the world stage. Combining expertise in data engineering, data science & analytics and visualisation.
-Adam Sharman, Senior Partner, Dsifer
As New Zealand’s manufacturing industry continues to evolve in the face of global challenges, it’s crucial to look beyond our shores for inspiration and insights. In this article, we review the approach taken in Northern Ireland, where a pioneering initiative is reshaping the manufacturing landscape.
This case study offers valuable lessons for New Zealand manufacturers seeking to navigate the complexities of digital transformation and Industry 4.0.
In an ambitious move to boost the competitiveness of Northern Ireland’s manufacturing sector, a groundbreaking initiative called the Digital Factory Accelerator (DFA) has recently concluded its pilot phase.
This innovative program, spearheaded by the Advanced Manufacturing Innovation Centre (AMIC) and Invest Northern Ireland in partnership with the High Value Manufacturing Catapult (HVMC) and LMAC Group, aims to accelerate the adoption of Industry 4.0 technologies across the region’s diverse manufacturing landscape.
The DFA pilot, which wrapped up in June 2024, involved 32 companies ranging from small enterprises to large multinationals.
Using the internationally recognised Smart Industry Readiness Index (SIRI) assessment tool, the program provided participating companies with a comprehensive evaluation of their digital maturity and a roadmap for future transformation.
One of the differentiators of SIRI is the ability to benchmark globally based on company size, and by sector.
The DFA pilot used the XIRI analytics platform provided by INCIT to develop meaningful insights that are crucial in shaping strategies for manufacturing within regions.
Key findings from the pilot revealed that Northern Ireland’s manufacturing sector, while producing world-class products and services, lags behind international benchmarks in terms of digital adoption.
The average SIRI score for UK manufacturing companies was 1.12, significantly lower than the peer group average of 1.84 (on a scale of 0-5). This gap highlights both the challenges and opportunities facing the sector as it aims to compete on the global stage.
The assessment identified several critical areas for improvement:
1. Leadership awareness: There’s a pressing need for business leaders to enhance their understanding of Industry 4.0 principles to drive transformation effectively.
2. Investment in technology: Northern Ireland manufacturers have opportunities to leverage better technologies to improve productivity and efficiency, potentially leading to lower labour costs in the back office and the shop floor.
3. Connectivity: Enhancing connectivity across manufacturing operations emerged as a key enabler for digital factories, with a focus on strategic data collection and analysis.
The program also revealed sector-specific insights. The agri-food industry, for instance, showed higher digital maturity due to its repetitive production processes and regulatory requirements. In contrast, sectors dealing with custom or engineer-to-order products faced unique challenges in digital adoption.
Despite the gaps identified, the DFA pilot has been met with overwhelming positivity from participants. Companies reported improved understanding of Industry 4.0 concepts, clearer strategic alignment, and a sense of direction for their digital transformation journeys.
As the global manufacturing landscape continues to evolve, programs like the Digital Factory Accelerator will play a crucial role in ensuring Northern Ireland’s manufacturing sector remains competitive, innovative, and future-ready.
By bridging the digital divide and fostering a culture of continuous improvement, Northern Ireland is positioning itself at the forefront of the fourth industrial revolution.
For New Zealand manufacturers, the experiences of our Northern Irish counterparts offer both cautionary tales and inspiring possibilities. While our local context differs, many of the challenges— and opportunities—in digital adoption are universal.
As we in New Zealand continue to chart our own course towards a more digitally mature manufacturing sector, initiatives like the Digital Factory Accelerator provide a compelling model for collaborative, data-driven transformation.
By learning from international experiences and adapting them to our unique needs, New Zealand’s manufacturers can position themselves at the forefront of the global Industry 4.0 revolution, driving innovation, productivity, and competitiveness in the years to come.
Hon Andrew Bayly, Minister of Manufacturing
Manufacturing is a significant sector for New Zealand. It employs 230,000 people and accounts for nearly 10 per cent of GDP and 60 per cent of exports. I often describe it as a “sleeping giant” for New Zealand’s economy, because its significance is not well understood.
When I travel around the country promoting the manufacturing sector, one of the things I often remind people is that a career in manufacturing is a career in a highly advanced, technical field.
A lesser-known fact is that approximately a quarter of all New Zealand’s business-led research and development comes from the manufacturing sector, meaning manufacturing is a key driver of innovation. However, to support this innovation, manufacturers need the right tools and resources.
I know from talking to manufacturers that access to information and expert guidance on how to upskill and improve productivity is challenging. Which is why I was delighted to recently launch a set of tools to help empower manufacturers to grow their business and reduce their emissions.
The first is a report that identifies and maps the manufacturing sector’s emissions and waste patterns. Titled ‘Mapping Emissions and Waste Stream Profiles, and Opportunities for Achieving Net-Zero Circular Advanced Manufacturing’, the report is based on waste and emissions data from 2019 (the most recent data available).
It provides a comprehensive picture of waste, emissions, and opportunities to improve sustainability across the seven main manufacturing subsectors: food and beverage, machinery and equipment, other manufacturing, metal and metal products, chemicals and refining, wood and paper, and plastics and rubber.
The report details challenges and opportunities for the sector with a goal of helping manufacturers identify opportunities to adopt low-emissions technology and increase circular manufacturing practices which, in turn, will help us reduce our net greenhouse gas emissions.
While this report details some challenges for the sector – such as significant supply chain emissions, and many subsectors’ dependence on imports which then ‘offshore’ their emissions – it also highlights many opportunities.
These include reducing risk and cost, more resilient supply chains, better use of waste as inputs, meeting customer demand, extending service lives, the three R’s (reuse, reduce, repair) and improved brand and relationships.
Barriers exist around access to capital, risks with emerging technologies and approaches, lack of knowledge, and lack of central standardised waste data.
The demand for low-carbon-manufactured products is increasing globally, and New Zealand is in a strong position to take advantage of this through our agile and innovative manufacturers and relatively low-carbon electricity grid.
There are many examples of our manufacturers already innovating in this way. For example, I understand there is a company making gumboots in Wellington that collects old gumboots from companies that use a lot of this product, like meat works. They then shred them up into small pellets and turn them into new gumboots. This is 100 per cent gumboot-to-gumboot manufacturing!
Reducing waste through adopting circular economy principles will also increase efficiency in our resource use and ease supply-chain pressures.
The second tool is the Climate Action Toolbox’s Manufacturing Pathway, which includes an emissions calculator to help businesses set targets and monitor progress.
A two-minute assessment, based on simple information about a manufacturer’s business, provides tailored recommendations of areas to focus on. Manufacturers can browse the priority areas to focus on actions that would make the biggest difference or choose from suggested ‘quick wins’ to get going straight away.
Designing products, site operations, manufacturing processes, and moving goods are all likely to be priority areas. The Toolbox suggests actionable changes across these topics, with information on the benefits, steps to follow, links to helpful resources,
and case studies from other businesses that are leading the way.
Providing businesses with the tools to grow and innovate is a key part of our Government’s Climate Strategy. We will not accept shutting down productive sectors of the economy to meet emissions targets. Instead, we are committed to an innovation and technology-led approach which enables production to increase as our emissions come down.
We need businesses to grow and thrive because without businesses the Government has no income, and without an income we cannot invest in the public services New Zealanders rely on every single day.
To have a world class education, health and transport system, we must have world-class businesses that export and compete on the world stage.
I truly believe the manufacturing sector has a vital role to play in building a sustainable and prosperous future for all New Zealanders.
The Climate Action Toolbox can be accessed at www. tools.business.govt.nz/climate
Hon. Andrew Bayly is the Minister for Manufacturing in the National-led Coalition Government; he can be contacted at andrew.bayly@parliament.govt.nz
By Terry Smagh, Senior Vice President and General Manager, Asia-Pacific and Japan at Infor
Robotics has commanded headlines for its role in manufacturing and final assembly operations, with some of the world’s largest manufacturers reporting massive robotics-led ROI in their quest to automate and innovate across the factory floor.
Robots vary significantly in size, functionality, mobility, dexterity, artificial intelligence, and cost. They can be fixed, mobile or fly, in the form of drones, and increasingly, they are programmed to recognise and learn from their surroundings.
Their ability to capture information and make decisions independently, means that they can often perform tasks with little to no human intervention.
Robotics’ deployment in the warehouse was, until recently, restricted to only the largest of organisations as they typically came in the form of fixed assets with high price tags. The emergence of robotics-as-a-service has, however, changed the game somewhat, bringing robotics-led innovation to warehouses of all different sizes and profiles.
Testament to this, is that robotics is expected to see strong growth over the next five years, particularly within supply chain operations that include lower-value, potentially dangerous or high-risk tasks.
The opportunity for ROI is huge, as travel and movement of goods across the warehouse typically commands the most time and money.
And against a backdrop of a global labour shortage, organisations are having to look at ever more creative ways to bridge skills gaps, and robotics represents a pivotal solution in this area.
In the wake of a rise in online shopping, and associated SKU proliferation, merchandise has increased in both volume and diversity.
Robots in the warehouse make it simpler and more efficient to move both batches and individual picks, not only reducing reliance on labour, but mitigating risk through increasing safety on the shop floor.
Similarly, drones can undertake detailed stock counts at night, eliminating a need for people to physically check inventory.
As many organisations bring their warehouse operations back in-house to realise greater control in the wake of unprecedented complexity and uncertainty, robotics can instil flexibility.
In a similar vein, it can give 3PLs an advantage as they move complex merchandise mixes across numerous categories for high volumes of customers.
Yet despite this shift, many organisations are realising that in order to realise the full potential of robotics, it has to go hand in hand with a modern, cloud-based WMS platform.
Without a system which can be easily integrated via APIs, and seamlessly talk to the robots, interpret data, and inform workflows, robotics can only extend so far, limiting potential and impeding ROI.
While robotics can represent a game changer in automation and efficiency, allowing people to shift to more strategic, less dangerous, and higher value work, an effective WMS platform is the core foundation of the warehouse. Through facilitating seamless flow of data and insights spanning sales orders, picking, packing and fulfilment, the potential of robotics can be truly maximised.
In fact, according to Gartner 95% of supply chain organisations have either invested, or plan to invest, in cyber-physical automation, with a significant proportion of those planning on using intralogistics smart robots (ISRs).
Labour availability constraints are the primary driver behind investments in robotics according to 66%.
As technology continues to improve, robotics-as-a-service gains further momentum, and prices decrease, the question is no longer whether to capitalise on robotics, but in what way, and how soon.
What is certain, is that the success will depend largely on the extent to which a modern WMS is leveraged to integrate and optimise workflows.
There is no doubt that the supply chain of the future is likely to see continued growth of autonomous robots.
Those who get it right will not only improve the speed and accuracy of routine operations right now,but ensure flexibility and agility to adapt in the future as market conditions and dynamics dictate.
New York’s Architizer Inc has awarded Kaynemaile’s RE/8 architectural mesh an A+ Jury Award for ‘Building Envelopes, Cladding, and Roofing’ in its 12th annual awards honouring the world’s best architecture and spaces. Kaynemaile was also the A+ Popular Choice Winner for ‘Sustainable Design.’
The design-led Petone company is on an awards roll following its naming in the U.S. Architectural Record Products of the Year Awards saluting the best building and design products introduced to the US market within the last year.
In 2023 Kaynemaile won ‘Global Gold’ for exporting at Wellington’s Gold Awards and has featured in multiple New Zealand architectural awards won for the Invercargill Central which has transformed the city centre into a vibrant community hub with a beautiful indoor shopping complex.
The U.S. awards are for Kaynemaile’s new RE/8 product launched in San Francisco a year ago. RE/8 is made from 88% bio-circular content from Covestro, the world-leading provider of high-tech polymers. Kaynemaile’s mesh is extremely lightweight, uses 20% of the energy needed to produce steel, and is 100% recyclable.
“Today Kaynemaile is a global leader in specialised architectural product applications that can be found on building exteriors and interiors all over the world,” says Kaynemaile founder and CEO Kayne Horsham. Over 90 per cent of sales are generated through exports.
Horsham says RE/8 has achieved a rare certification from the International Sustainability and Carbon Certification (ISCC) organisation covering its entire product cycle from ‘cradle to grave.’ RE/8 features a reduction in the carbon footprint of the base polymer material by up to 80%.
Kaynemaile’s focus on the US has seen the recent completion of exterior and interior projects in Atlanta, Dallas, Des Moines, Los Angeles, Orlando, and Santa Clara in Silicon Valley where 1,000 square metres of Kaynemaile 3D kinetic screens cover an 800 space parking garage features almost 1,000 square metres of Kaynemaile mesh screens across the facade.
Horsham says a major building wrap for a high-tech manufacturer has just unveiled in Belgium, with designs in currently progress for retail and hotel installations in the Philippines, Singapore, and Dubai.
Wellington technology investor Movac is lead shareholder in Kaynemaile. Movac founding partner Phil McCaw has been chair of Kaynemaile since 2016 and says the flow of awards to the Petone represents the success of a “wonder product” created by founder Kayne Horsham.
In 2023 Kaynemaile doubled the size of its production facility and commissioned a new injecting moulding machine to enable 24/7 shifts as the company closes on some of the largest order enquiries they have experienced. The company works closely with architects throughout the world to customize its mesh systems whether it is a mega carpark façade or a highly decorative atrium chandelier.
Kayne Horsham says a key benefit of Kaynemaile is what he calls the ‘WonderCool Effect.’ “With nearly a quarter of the USA’s population projected to live in extreme heat conditions, there is an urgent need for passive heat mitigation technology in new building designs. Kaynemaile delivers up to a 70% reduction in solar gain on exterior installations. It’s a product made for a hot world.”
continued from Page 8
Singapore had the highest average scores in all three subjects and it is no co-incidence they have a vibrant economy and standard of living.
Of course just educating our people is not enough, we have to give them skills in leadership, management and best practices, so they can lead teams, grow capability, develop innovative solutions to problems and improve their processes. World class companies develop leadership capability, harness it, retain it and treat it as a strategic competitive advantage.
Many will only promote from within, forcing them to have a talent pipeline and ready now successors. Others have specific programs to drive capability and
With its origins in the Creatures, Armor, and Weapons department of The Lord of the Rings film trilogy, Kaynemaile has evolved into an international business based on its patented liquid-state manufacturing process coupled with compelling design aesthetics and a team focused on providing custom-made design solutions at scale.
Established in 2006, Kaynemaile designs and manufactures highly versatile architectural mesh systems for commercial, public, and residential building facades, and interiors through to public artworks, lighting effects, and stage shows.
Kaynemaile has been awarded the IF Material Award, NYCxDesign Award for Best New Architectural Product, Architecture MasterPrize for Building Envelope and Construction Materials, and Civil+Structural Engineer Yearbook of Engineering Achievement 2021 and 2022 for Environmental and Sustainability. Most recently Kaynemaile was awarded in Architectural Record’s best building systems and components 2023 and Architizer’s 2024 A+ Awards for Building Envelopes, Cladding, and Roofing, and Sustainable Design.
Architizer is a portfolio database, media site, and architectural manufacturer search engine that is transforming the architecture community. With over 86,000 projects from around the world, Architizer’s vision is to bring more innovation, efficiency, and quality to the world of architecture and design.
accelerate top performers. Some even have their own universities! They invest in this capability and nurture it because it has massive payback.
If we want to change the outcomes, we have to change our systems. This means ensuring all people achieve a good standard of education, and providing the pathways for people to develop all the skills and competencies they need to help NZ business achieve its potential.
Hopefully the latest initiatives by government regarding education and Te Pukenga will help in these directions, but it is also up to New Zealand’s business and educational institutions to step up.
With good reason. In the next few years, New Zealand manufacturers can expect to be called on to answer these two questions. How is your business reducing your impacts on nature? How will changes to nature affect your business?
Who’ll be asking these questions? Governments, regulators and financiers like lenders. They’re realising that centuries of degrading nature (the ecosystems that make up land, oceans, freshwater and the atmosphere) is not only depleting biodiversity. It’s having financial and economic impacts on businesses too.
These parties are adding weight to environmentalists’ calls for urgent change. In this article we explain what this means for manufacturers in Aotearoa New Zealand.
The World Economic Forum’s 2024 Global Risks Report ranks dwindling biodiversity and collapsing ecosystems among the five most severe risks to business in the next ten years.
The UK Green Finance Institute’s recent report makes sobering reading. It identifies and measures the country’s nature-related risks.
The report confirms that these risks are as harmful as the risks of climate change, and that nature and climate are linked. Zoonotic diseases, declining soil health, slips, floods, food insecurity and lost production will affect all sectors – including manufacturing. The economic impacts could be worse than the Global Financial Crisis or Covid-19. The report concludes that the UK must transition its economy urgently to valuing and investing in the environment. As 50 percent of the country’s risks come from overseas (including New Zealand), UK regulators and financial institutions will require businesses to scrutinise their supply chains. We expect other trading partners, including the EU, to take a similar stance.
The world has agreed a biodiversity equivalent for the global goal that limits global warming. Nature Positive is made up of three goals that result in full recovery of nature by 2050. The Kunming-Montreal Global Biodiversity Framework, adopted by 196 countries including New Zealand, supports these goals.
What does this mean for New Zealand manufacturers?
New Zealand manufacturers rely heavily on nature. Food and beverage manufacturing accounts for around 32% of our GDP; forestry and wood products contribute a further 9%. All sectors need stable land, a safe and healthy workforce, reliable supply chains and buoyant markets to be productive and profitable.
We can learn from Mātauranga Māori. The Māori relationship with the land is about kinship. Mātauranga Māori values respect and honour nature. All aspects of nature, including people, are intertwined and connected through whakapapa. Get ready for changes
Some changes will be ‘transitional’. Markets, products and laws will change as our economy and our trading partners’ move to be more nature-positive. For example, regulations and taxes on our exports will become more stringent. Central banks and financial institutions will expect companies to explain how they are managing the risks they face. Companies may diversify their suppliers to reduce supply chain risks.
Other changes will be physical. For example, continuing deforestation may cause land to erode. Severe weather, and our human compulsion to pave natural surfaces, may cause flooding. Flooding may destroy buildings. Secondary impacts may affect the property market, insurance premiums and mental health.
1. Understand the changes ahead
Research what changing global regulations and nature-related disclosures mean to your business.
2. Understand the benefits for your business
This is an opportunity to reduce your risks and make your business more resilient. There’s also potential to build relationships and be known as a business that ‘takes nature seriously’.
3. Identify your business’s relationships with nature Map the activities involved in creating, producing, delivering, using and disposing of your products. Identify activities where your business affects nature in material ways and vice versa.
Look for risks and opportunities. How do you manage runoff into soil (an impact on nature)? How secure is your supply of natural resources (e.g. crops, an impact that nature has on your business)?
Could you become known as a manufacturer who is ‘doing your bit’ for nature (an opportunity)?
4. Make a plan
You are probably managing your relationship with nature already. For example, you may be using Forest Stewardship Council (FSC®) timber or supporting local wetlands.
Build these activities into your plan and expand on them. Consider redesigning your product to reduce the natural resources you use. Redirect run-off away from soil. If you use agricultural materials, ask suppliers to find an alternative to pesticides. Set goals and collect data.
5. Strengthen your governance
Make sure nature features in your policies and is on the agenda at management and Board meetings.
6. Communicate – and act
Share what you’re doing to enlist others’ support. Talk with your suppliers, team and customers. Make sure they understand that improving your relationship with nature is a priority. You’ll make fastest progress together.
www.thinkstep-anz.com
Export award winning, Tauranga based Oasis Engineering continues to expand its international market as a specialist manufacturer delivering world leading solutions to those pushing the boundaries of energy and fluid transfer for the benefit of humanity and the environment.
The company originally began as the maintenance division of a soft drink brand but was separated during a restructuring during the 1980’s. The new company quickly established a strong reputation as a machine shop that reliably produced high tolerance precision machined parts in difficult to work materials such as stainless steel and titanium. This led to work manufacturing valves and couplings that were required for the new and emerging Compressed Natural Gas (CNG) fuel market for a major CNG supply company and this quickly expanded to every major CNG supplier and to every significant CNG market in more than 40 countries.
Today Oasis Engineering is part of the ELAFLEX Group of Companies of Hamburg and is manufacturing precision CNG, LPG and Hydrogen reticulation products for the world market with approximately 80% of production going to the USA, 10% to other world markets and 10% to the local New Zealand market.
The company is well placed to meet the demands of emerging markets including Hydrogen and Methane for heavy transport vehicles and renewable Natural Gas with sales doubling within the last two years. Oasis also produces specially designed high quality fluid couplings for the milk industry trailers.
This state-of-the-art manufacturer is fully accredited to ISO 9001:2015 with product testing facilities including a Hydrostatic test rig rated to 4000 BAR and an Environmental Test Chamber rated between -800C and +1850C. A new addition will be a Hydrogen product test laboratory which is scheduled to be commissioned by the end of the year.
Meeting the demands for the highest precision
and ultimate efficiency from day one, the company invested early on in an Okuma CNC machine and today this high-tech machine shop has fourteen Okuma CNC Machines including Multi-tasking CNC Machines, 5-axis Machining Centres, CNC Lathes, Bar Feeders and Robotics.
“Okuma has always been at the centre of our precision manufacturing machine shop, providing unparalleled reliability, easy programming, time saving multi functions and the highest quality output, coupled with the high level of service backup directly from the manufacturer,” said Managing, Director Kevin Flint.
Keeping abreast with products of the future and also meeting the demands of special applications and solutions for clients, is a team of ten engineers in the internal design office covering industrial design, hydraulics, environmental and future product development. ELAFLEX Germany also supports the design centre in product development. The design team also look into and implement design changes and make recommendations on improvements for clients to increase efficiency or improve the manufacturing process.
Some of the latest Oasis products include Hydrogen quick couplers, cylinder valves, ball valves and trailer load/unload manifolds.
Kaizen methodology plays an important part in increasing productivity in the manufacturing plant and in teaching people to perform experiments on their work using scientific methods to identify waste processes. Kaizen is an ongoing daily process in all areas of the business producing measurable outcomes.
The team of skilled engineers at Oasis Engineering have many years of experience in working with different materials including stainless steel, titanium, brass, aluminium and engineering plastics and from its inception and continuing today it provides precision contract manufacturing services to external clients worldwide.
Overall the company employs some 50 personnel and has at least two apprentices under training at any time with one or more taken on each year and this is leading to a high retention rate of skilled labour.
“Following the long-term relationship that recently retired Okuma General Manager Fred de Jong has built up with this outstanding company it will be a pleasure for me to continue with this close relationship to ensure that the right machines always meet their requirements and market needs,” said newly appointed Okuma New Zealand Manager Karl Medley.
“The newly appointed Okuma Service Engineer will also play an important role in further strengthening our services in this area,” he said.
Sandvik Coromant has a new grade in its new generation steel turning series. Grade GC4405 is first choice for high metal removal rates in stable conditions, especially in harder steels. The possibility to machine dry in softer steels opens up for more sustainable machining.
They recently introduced steel turning grades GC4425 and GC4415. The new generation grades have been refined in every aspect, delivering an average 25% increase in tool life compared to previous grades.
Grade GC4425 delivers wear resistance, heat resistance and toughness in a wide application range, while grade GC4415 complements GC4425 with enhanced performance when more heat resistance is needed.
Grade GC4405 should be applied as a high feed productivity optimizer with high metal removal rates in stable conditions where plastic deformation
properties are demanding.
Among the features coming with the new grade is a new carbide substrate with optimised microstructure, which will reduce plastic deformation in high feed applications. The substantial increase in plastic deformation resistance has enabled a drastic expansion in the application range towards harder steels and higher productivity compared to existing grade GC4305.
New grade GC4405 features second generation Inveio technology coating, with this coating version designed specifically to combat crater wear common to P05 applications. What makes second generation Inveio different from the earlier generation is the alumina coating, where the crystals are lined up in an even more vertical orientation towards the top surface to improve wear resistance, bringing a more consistent quality and performance.
The new grade provides a considerable increase in productivity and tool life, particularly when machining steels above 300 HB. The grade is also suitable for machining softer steels — in this case without the need of coolant, which is a noteworthy opportunity from a sustainability point of view.
Comprehensive tests conducted between existing GC4305 and next generation steel turning grade GC4405 indicate an increase in tool life ranging from 30% up to 130%, mainly a result of significantly improved plastic deformation and crater wear resistance.
Grade GC4405 is recommended for continuous roughing to semi-finishing in stable conditions and long time in cut. It is suitable for high feed machining with medium, roughing or wiper geometries in harder steels above 300 HB or for high feed and/or high speed machining in softer steels below 300 HB.
It’s been an interesting year. We have been fortunate enough to have been working on our largest project to date for the majority of the year (delivered at the start of July) which has meant that we have been unusually stable.
A large percentage of our work comes from the film industry (specifically American productions looking to shoot here) and we have certainly experienced more challenging years, working through Covid and the 2024 Hollywood Writers Strike.
Comparatively this year has been more reliable.
We have noticed a change in the type of screen work entering the country since the writer’s strike ended. The large genre blockbusters we were famous for hosting have been replaced by more medium sized contemporary productions which offer less work to a prop house than the former.
However, the volume of productions has certainly helped keep things from getting too concerning.
Interesting projects currently being worked on?
We are in the middle of a really fun project, building props and other elements for a New Zealand feature film.
It is a hilarious genre comedy by a very talented team that we are really excited to be a part of. We can’t give too much away but we will say it’s not every day we get to work on such wacky builds.
They’re the kinds of things that when we are discussing them in the workshop we sometimes have to just stop and wonder how what we are doing can be a real job.
We have just come off the back to back production of a large public sculpture for the Wellington
Waterfront and several full size dinosaur sculptures for a museum in South Africa (the largest of which is 11 metres long and 4 metres tall).
We have managed to produce these by investing in large 3D printers (largest able to print 1200x1200x1600) and recently moving into a larger workshop to accommodate these builds.
We are hoping we can market these builds domestically and globally to land more work producing large sculptural pieces for promotional events or museum exhibitions.
It has been very difficult to keep staff on this year. Due to a significantly larger number of film productions in Auckland than Wellington, we have, understandably, seen a lot of the talent move up the country.
This, coupled with the fact that the productions have needed to outsource less builds due to budget and genre, has meant that the work we take on has been smaller and less frequent resulting in shorter contracts and less job security for staff.
This has also meant we have less time with crew on the floor to upskill them before we have to let them go which we anticipate could have long term consequences for the future of the art department and their ability to find experienced technicians.
In many ways a majority of the work we produce involves solving unique problems. We specialise in building bespoke items that normally haven’t existed beyond the digital design phase before we get involved.
Once we do, we like to point out that there are often several ways to produce any practical item and this can change based on the requirements of the piece, the time available to build it and the budget.
From there it’s just a matter of reaching an agreement with the client on the best approach. We like to say that the best and worst part of our job is that no two jobs are alike.
It makes every project feel fresh and exciting but it also means the pressure is on to get it right the first time!
Your creative staff must have met some interesting challenges?
One could argue that if something isn’t a challenge then it isn’t interesting. Again, we are lucky in that a lot of the creative work we do, specifically for the film industry, is wholly unique.
We have made chomping killer alligators for American horror films, muppet bird babies for Wellington Paranormal, oversized Marvel props, film festival trophies, bronze landscapes using geographical data, miniature forests, cities and mountains.
We have modelled and manufactured never before seen dinosaurs working alongside paleontologists, produced a snow leopard sculpture for Wellington Zoo and designed and manufactured stages for music festivals.
We have found it particularly challenging to crack the international market but if the opportunity arises we will provide work for any country that is enquiring.
We have produced builds for Australia and South Africa and are currently in the process of making collectables for an artist in the United States. We were also recently involved with Studio Sabine Marcelis, a Dutch/Kiwi artist.
We facilitated the installation of several pieces of her work in Wellington, outside Te Papa at the start of the year.
matters: why it is important for an economy to have a manufacturing base
Australian analysis which matters to New Zealand. Manufacturing is an on-going journey and needs to be the central focus for a recovering economy -ed.
The loss of manufacturing jobs at Ford Australia generated a lot of debate about the long-term viability of the Australian car industry, and manufacturing in general.
This debate included arguments that manufacturing is important and needs more government support. It has also seen some commentators argue that Australian’s have no right to expect jobs in manufacturing.
While most of this debate focused on the automotive manufacturing sector, there is a wider question that needs to be answered.
This relates to the issue of whether it is feasible for an advanced economy to grow and prosper without a manufacturing sector?
Kaldor’s Laws
Economist Nicholas Kaldor (1908-1986) proposed that economic growth and enhanced standards of living were positively correlated with national industrial activity.
He suggested that growth in GDP was positively related to growth in the nation’s manufacturing sector. Productivity in the manufacturing industries was also positively related to growth in this sector.
He also suggested that the productivity of the non-manufacturing sector was associated with growth in manufacturing.
Kaldor was a controversial figure in economics. He criticised mainstream economists for what he saw as an excessive focus on “equilibrium” approaches, condemning them as “barren and irrelevant”. He preferred to focus on the creative function of markets rather than their ability to simply allocate existing resources.
His analysis of the decline of the United Kingdom’s manufacturing sector argued in favour of greater economies of scale and expansionary fiscal stimulus by national governments combined where necessary with import controls.
Not surprisingly this “supply-side Keynesian” approach was roundly condemned by monetarists and neoliberal economists.
The problems facing manufacturing in industrialised nations such as the UK were attributed to poor industrial relations, inadequate investment in R&D, insufficient investment in technical education and training and poor management.
Kaldor’s theories on economic growth and the role played by manufacturing are therefore not without their critics.
However, they raise some interesting questions as to the overall importance of manufacturing to the long-term economic growth and general productivity of a national economy.
They also highlight the protracted, and often bitter, disputes that occur within the circles of economists as to how a national economy should be managed.
Why manufacturing matters
The issue of what has been termed the “deindustrialisation” of the developed world has been exercising academics and policy makers since at least the 1980s.
Low productivity growth and the emergence of new challenger nations such as Japan and Taiwan led to a shift in the majority of industrial economies.
As manufacturing jobs were moved offshore there was a significant amount of structural unemployment.
By the end of the 1980s the majority of employment was to be found in the services sector and there was talk of a “post-industrial society”.
Over the past two decades the emergence of China as a global manufacturing powerhouse has further challenged the existing manufacturing base within other countries. This raises further concerns over whether or not it matters that an economy retains a manufacturing sector.
According to some analysts manufacturing does matter and the loss of manufacturing jobs is not good for an economy. Such a view over the importance of manufacturing was articulated recently by Professors Gary Pisano and Willy Shih of Harvard University’s Business School.
According to Pisano and Shih, without a manufacturing sector it is very difficult for aneconomy to sustain innovation.
They point to the offshoring of semiconductor manufacturing by American companies in the past. This led to the competencies within the workforce and production systems for the production of such technology to be largely lost to American industry.
Over time this provided an opportunity for the Taiwanese, South Koreans and increasingly the Chinese to build their manufacturing base. From semiconductors there was a transition to the production of flat screens.
This trend is now moving to LED technology and they suggest that soon high-efficiency lighting will be largely sourced to Asian manufacturers.
According to the US Council on Competitiveness manufacturing in the United States directly employs over 11 million and contributed around US$1.7 trillion to the national economy in 2010.
It also has one of the highest multiplier effects of all industry sectors and is a provider of skilled and well-paid jobs.
The key to a competitive manufacturing sector is the ability to draw together a range of macro and micro level elements.
Government policy plays an important role. However, so does the cost of labour, energy and the quality of infrastructure, legal and regulatory systems.
The list of recommendations emerging from this substantial report is lengthy, but in essence they call for action by both industry and government.
There is a call for fiscal reform to transform the taxation system and reduce regulatory and structural costs that impede innovation and new venture creation.
The report also calls for changes to the protection of Intellectual Property (IP) laws, international standards
for interoperability and export control regimes to enhance exports. A key feature of this is to work more closely with trading partners to enact anti-counterfeiting programs.
The report also calls for a substantial investment in education and training targeted at encouraging more students to enter the fields of engineering and relevant technology and production areas.
In the development of human capital it seeks to use the mechanism of international education to attract more skilled and talented students to the United States, with a view to retaining them within the workforce.
Support for small to medium enterprises (SMEs) is also highlighted. This includes enhanced management development support and apprenticeship schemes to help boost the capacity of these firms.
It also seeks to build up the level of innovation through the creation of advanced manufacturing clusters, networks and partnerships.
This involves the modernisation of factories to include more technology-enabled smart manufacturing processes. Finally, the report seeks an investment in transport, production and telecommunications infrastructure that is smart, sustainable and resilient.
Australia’s manufacturing sector is significantly smaller than America’s. However, it employs around 945,600 people or 8.5% of the workforce.
This is about five times more than the mining sector. Despite a declining investment in capital equipment and R&D over recent years, the manufacturing sector also contributes significantly more to innovation than other industry sectors.
Although the economic growth created by Australia’s mining and energy sector cannot be ignored what is inevitable about such resources booms is that they inevitably reach a peak.
A more diversified economy is essential for the longer term, and manufacturing has an important role to play.
The key to enhancing our manufacturing industries is to address a series of macro and micro level issues simultaneously.
Fiscal policy, including taxation rules need to be overhauled to encourage industries to transition into a more competitive future through investment in capital equipment and R&D.
There must be greater assistance, particularly to SMEs, to help local manufacturers connect with global supply chains.
Education and training of the workforce is also a critical area that requires future investment.
DB Schenker is participating in Cathay’s Corporate Sustainable Aviation Fuel Programme
DB Schenker has officially announced its participation in Cathay’s Corporate Sustainable Aviation Fuel (SAF) Programme, aiming to advance sustainability in the logistics industry by partnering to reduce emissions in cargo shipments.
To help tackle climate change, Cathay established a Corporate SAF Programme in 2022. It enables members to purchase SAF for uplift on Cathay Pacific and Cathay Cargo flights, from Hong Kong and other ports on the network.
By joining and committing to buy 878 metric tons of SAF (the equivalent of 290,000 US gallons), DB Schenker has become one of the biggest contributors to the scheme to date, which demonstrates its commitment to sustainable logistics.
further expands DB Schenker’s network of biofuel partners.
In total, DB Schenker’s SAF program is available globally for all flights on all airlines and has attracted a wide range of customers including Lenovo and Nokia.
The Australian government has committed to a Net Zero Plan, guiding the country’s transition to a legislated target of net zero greenhouse gas emissions by 2050. New Zealand has a similar 2050 Net Zero target.
Advertising Booking Deadline – 6 September 2024
Advertising Copy Deadline – 6 September 2024
Editorial Copy Deadline – 6 September 2024
Advertising – For bookings and further informa
Media Hawkes Bay Limited 06 870 9029
Articles to be sent to: publisher@xtra.co.nz www.nzmanufacturer.co.nz
In the logistics sector, warehousing, packaging, and transportation consume large amounts of energy and generate significant greenhouse gases (GHG). Optimising energy consumption to reduce carbon emissions is a pressing issue for logistics companies.
Back in 2020, DB Schenker became the first company in the logistics industry to cover a commercial full charter round trip flight with SAF. As of spring 2021, all direct emissions of a weekly charter rotation between Frankfurt and Shanghai onboard Lufthansa Cargo were avoided by fully covering the fuel consumption with SAF.
Since then, the global logistics service provider continued to push the boundaries of sustainability in air freight. The new collaboration with Cathay
Daniel Andersen, Director, Air Freight, DB Schenker Australia & New Zealand Cluster, says the focus on reducing greenhouse gases in the air freight industry is integral, and requires collaboration between airlines and logistics companies, as well as their customers.
“This major partnership with Cathay on SAF opens the door to more sustainability collaboration in the region. SAF is available throughout Australia and New Zealand on DB Schenker air freight, for customers looking to elevate their contributions to a more sustainable aviation industry,” says Andersen.
We are dedicated to providing readers the best information for business success and stimulation.With a strong team of writers, contributors and researchers, JEZ Media is deliberate in its forward-planning of issues to make them more easy to understand and our world a better place for doing business
We are a network of magazines and websites of diversified business and manufacturing news, political, community and creative information.
Our Publications and Websites include:
Across Asia, the Pacific and around the world Asia Manufacturing News keeps you in touch with the latest in manufacturing trends and developments. Our team ensures that the best of technology information is available to you, the reader, through case studies and product and business news as soon as it is released. You can read it on our website www.asiamanufacturingnewstoday.com and of course, in the magazine. We talk to and interview industry leaders, monitor the trends and share the information to benefit your company in the future. We are a media partner for trade fairs across Asia.
Australian Manufacturing News brings you the latest in product developments and success stories from leading companies manufacturing for world markets. The best and the brightest of Australian ingenuity is read about here. A media partner for the annual AMTIL Australian Manufacturing Week.
www.foodinnovationist.com brings you news on developments on world food markets which assist in meeting market demands. Food being pivotal to our way of life and well-being comes to us in many forms, from growers, suppliers and food entrepreneurs from all parts of the world. A rich and healthy life is what it is all about.
www.asiamanufacturingnewstoday.com
Advertise
If you wish to advertise on the Asia Manufacturing News site or in the magazine, then please view our rate card for advertising details and send us an email if you require further information. View Media Kit
www.australianmanufacturingnews.com
Advertise
If you wish to advertise on the Australian Manufacturing News site please email publisher@xtra. co.nz for further information.
View Media Kit
www.foodinnovationist.com
Advertise
If you want to advertise contact: publisher@xtra.co.nz for further information.
www.themirrorinspires.com
Advertise
The Mirror looks at issues affecting society and our world today. These include the education, environment, political and economic realms where we constantly need to consider the quality of life we have and the influences which bring about change, we are constantly faced with.
The Mirror is the ideal forum for you to share with other readers your ideas and thoughts on what matters to you most, and how we can learn from your experiences.
Everywhere you look factories are becoming smarter. Modern manufacturing means greater productivity with people and machines using technologies for more profitable manufacturing centres. We bring to you the tools to succeed, to plan ahead, to be creative and to control the future of your business.
Publishes NZ Manufacturer, the leading monthly manufacturing, engineering and technology magazine and website in New Zealand. Articles on AI, robotics, Industry 4.0, sustainability, green energy appear regularly, as well as a strong focus on Women in Manufacturing. Aspirational stories on companies finding success as well as analysis and developments. A media partner for trade fairs EMEX and SouthMACH.
If you want to advertise on The Mirror site, please contact publisher@xtra.co.nz
Download Media Kit
smartmanufacturingtoday.com
Advertise
If you want to advertise on the Smart Manufacturing site please email publisher@xtra.co.nz
www.nzmanufacturer.co.nz
Advertise
If you want to advertise
In the magazine or on the website email publisher@xtra.co.nz
Isabel Naidoo, Chief People Officer at Wise, New Zealand
Despite progress and international efforts in diversity and inclusion, the technology industry remains a male dominated space. We still see imbalances from graduate intakes, through to seasoned executives, and it’s a trend that’s yet to significantly shift.
With only 27% of the New Zealand tech industry made up of women, it’s apparent that more needs to be done to attract and retain female talent in the industry.
For women who do choose to pursue a career in the tech industry - they may be up against a range of problematic challenges: from pay inequity and a lack of representation, to gender bias and the inevitable act of balancing a career with family. And sadly, for a lot of working women - some of these challenges span far beyond just the tech sector.
While some steps toward closing the gap have been made - truly meaningful progress is happening at a glacial pace. According to The World Economic Forum, it will take more than 150 years to close the global economic gender gap.
The world is currently losing out on approximately $12 trillion USD of global GDP, and frankly - we
cannot afford to wait over a century to close the economic gender gaps while still calling on more women to join the tech-force.
It’s crucial the tech industry takes on more responsibility to foster an inclusive culture where women and other underrepresented talent are supported and empowered.
Strategies for taking control and driving progress
It’s not just enough for women to consider what’s in their best interests, we need to be a part of an industry which does the same. The progressive nature of the tech industry has meant that progress has already been made to enable a more inclusive environment, but there’s still plenty of room to grow. Company culture plays a big part in this.
As a global player in the fintech industry, our team feels not only a responsibility - but also a desire - to ensure our workplace is doing all we can to close any gaps or address any barriers.
It’s important for employers to not settle for standard practice, they need to break barriers and go beyond traditional norms to foster an inclusive environment. For example, a workplace which values employees should be going beyond the Government’s minimum wage parental leave policy and offer something more substantial.
We offer 18 fully paid weeks of gender inclusive parental leave for birth or adoption. We also offer 3 paid ‘me days’ a year, for staff who just need a dedicated few days for life admin.
But fostering an inclusive culture comes down to more than just leave entitlements. Work is a big part of our lives, yet work-life balance remains a key challenge for many people, but especially women who often take on more child-caring responsibilities.
Having worked in a flexible working model for many years now, I’ve seen first hand the value it brings to helping women balance personal and professional responsibilities, and also improving wellbeing and productivity across the board. 69% of New Zealanders consider themselves ‘hybrid workers’, almost double the global average of 37%, which is a really positive step in the right direction.
It’s also no secret that women are still largely under-represented in executive level roles. Our Board consists of 44% women and 45% of the Leads in the organisation being women - but not all tech companies would be able to say the same.
That’s why we’re passionate about initiatives that work to directly uplift and upskill women - to continue the trajectory we’ve established thus far. Wise Women Code is a good example of this, where each year we welcome women, non-binary folks and trans women to our offices for 3 days of knowledge sharing, side-by-side coding sessions and networking to provide a glimpse into the fintech industry.
It’s just one example of how we’re trying to encourage more women into the industry.
It’s also crucial for businesses to review data on their own gender pay gap so they can tackle the issue head on and roll out tactics to reduce it.
Fostering Diversity: Women Drive Innovation and Growth in the Tech Sector
As a Chief People Officer, I know that businesses simply can’t achieve the things they want to do without their people. The tech industry is renowned for being progressive, innovative and future-focused — but this is generally viewed through a product, not a people lens.
Diverse teams design for diverse customers best, and everyone - including women - have a role to play in building a stronger, more resilient and diverse industry.
The economy benefits from diversity. Having women in the workforce not only supplies new or untapped labour sources, but it brings in fresh perspectives, valuable skill sets and helps companies grow exponentially.
The industry is changing for the better and there has been strong progress over the past few years, but we mustn’t mistake progress with success.
We’re in 2024 and still talking about women in the workplace. The time is ripe for change. Only then will the tech industry truly be able to excel.
Shot peening, the “hammering” of work pieces with precisely defined blast media, is an indispensable operation in industries such as automotive and aerospace.
By inducing a residual compressive stress into the work pieces, the shot peening operation substantially improves their long-term resistance against tensile and bending loads.
The process is used for treating toothed, steering and transmission components, also for springs, driveand crankshafts and all kinds of turbine blades. A significant advantage of the shot peening operation is that the component weight can be reduced without impacting its mechanical load capabilities.
This is particularly beneficial in electric vehicles, because it increases their operating range and reduces their energy consumption. Due to changing work piece structures and shapes E-mobility frequently necessitates the alteration of manufacturing processes.
Moreover, the customers are demanding significantly higher energy-, resource- and cost-efficiency. In other words, significant improvements in productivity and sustainability. Rösler can provide comprehensive support for such optimization projects.
Lower energy consumption by using turbines instead of compressed air blast systems Compressed air blast systems have been the pre-dominant shot peening tools to consistently achieve the specified residual compressive stress values. A downside of the compressed air method is that it requires a lot of energy.
Today innovative technical improvements of the turbine technology allow the precise and high-quality shot peening of a broad range of components with energy-efficient, highly productive turbines. For
many peening applications costly compressed air blast systems are no longer required.
The most important factors to be considered in peening operations are the work piece shape and size, the required peening results and the blast media. Based on these factors Rösler runs computer simulations of the blast pattern as well as the entire process.
The simulations are followed by actual peening trials in our Customer Experience Center (CEC). Since the CEC is equipped with a broad range of turbine and compressed air blast systems, the shot peening trials can be conducted under actual production conditions.
With an in-house X-ray diffractometer the peening trials can be quickly evaluated to determine which process parameters and blast media will generate the required results.
A joint optimiSation project between a leading European automobile manufacturer and Rösler resulted in energy savings of 30 % and a 50 % increase of the shot blast capacity. Based on the convincing project results, in the meantime this customer purchased four shot peening machines equipped with turbines.
Sometimes a review of the existing shot blasting parameters can help to significantly improve the entire peening process. Once they are established, the process parameters are frequently no longer
Operating at exceptional levels of e ciency, the state-of-the-art PillAerator series magnetic bearing turbo blowers from Kaeser, can save up to 25% of the energy costs associated with conventional technologies.
They are ideal for aeration and flotation processes with high air demand, delivering energy-e cient and reliable operation for low life-cycle costs. With flow rates up to 1600 m3/h and differential pressures up to 1.3 bar, the PillAerator series turbo blowers are ideal for applications with a high demand for oil-free low-pressure process air. These cutting edge blowers can therefore meet the
requirements of many applications across a diverse range of industries, such as; biological aeration in municipal and industrial wastewater treatment plants to yeast fermentation in food production, fluidisation and the generation of blast and combustion air.
PillAerator turbo blowers stand out not only for their exceptional efficiency - saving up to 25% of the energy costs associated with conventional technology - but also for their intelligent design. The turbo impeller is driven directly by a high-speed motor inside a shaft supported by magnetic bearings, making the system completely
questioned.
Such carelessness can result in high equipment wear and unused potential for process improvement.
Perfectly calibrated process parameters, including the optimal media selection, guarantee high peening qualities, less equipment wear and low operational costs. If a review of the shot blasting parameters in an existing machine is not sufficient, a retrofit can be the right solution.
Among other things this includes upgrading the machine with more productive components such as more powerful turbines or the development of work piece fixtures for new or modified work pieces. Optimisation of the blast pattern must always be part of the considerations
In all instances shot peening trials in the CEC along with the evaluation of the results by X-ray diffraction, special tests of the peening coverage and, if needed, surface roughness and light-microscopic measurements, will ensure that the required peening specifications are achieved.
Very important for resource and cost efficiency of the process is the selection of the right blast media. A blast media analysis will always help to determine if the current media is right for the respective application.
wear-free. This means that no lubrication is required, saving both work time and costs when it comes to maintenance.
The intelligent magnetic bearings, which are protected against unexpected mains power failure, actively control the rotor position at every operating point, thereby achieving a very broad control range for the flow rate.
Magnetic levitation of the bearings from start-up through to standstill enables completely wear-free operation, allowing an unlimited starting frequency for the turbo blower. To stop the process air supply, the motor can be brought to a standstill, thereby saving energy.
Occupational health and safety is a critical matter in New Zealand and internationally, and particularly so in the welding industry. Regulations governing the safety of welders and their working environment have continued to be tightened as awareness of the hazards posed by metal fumes has increased within the welding industry.
Manufacturers of welding equipment are also taking note and have responded by introducing safety gear and welding equipment to minimise exposure to welding hazards, while New Zealand welders, with an eye on the future, are already implementing these solutions.
The metal fumes produced during the welding process can be especially dangerous when inhaled by welders. The fumes consist of microscopic particles of hot metal and gases, and can contribute to carcinogenic conditions.
In March 2017, the International Agency for Research on Cancer (IARC) reclassified welding fume from Group 2B (Possibly Carcinogenic to Humans) to Group 1 (Carcinogenic to Humans). This assessment was published in IARC’s Monograph 118 in July 2018.
Ultraviolet radiation from welding can also have negative consequences on the wellbeing of welders. It too was evaluated and similarly classified to Group 1 (Carcinogenic to Humans) in Monograph 118.
While many countries around the world such as Germany, the Netherlands and Great Britain already have strict welding fume policies, these are being further scrutinised and intensified in order to protect employees effectively.
In Australia, the Work Health and Safety Ministers recently agreed to an immediate reduction in the workplace exposure standard for welding fumes, from an 8-hour time weighted average of 5 mg/m3 to 1 mg/m3.
As the exposure standard for welding fumes is carefully reassessed by governing bodies and industry stakeholders in individual countries around the world, New Zealand welders are already evaluating and implementing solutions that will help meet higher standards.
These solutions include welding guns that feature on-gun fume extraction capability. Leading welding equipment manufacturers such as Kemppi, have introduced a range of options for New Zealand welders to choose from.
The Kemppi Flexlite GF series of MIG/MAG welding guns extract the welding fumes directly from the gun nozzle without disturbing the shielding gas flow, to provide a safer and cleaner working environment for the welder.
New Zealand’s MHM Automation started using GF fume extraction guns because of the overall feel and usability of the torch, but also to help minimise welding fumes in its workshop. “On-gun fume extraction is particularly handy as it lets you maximise the level of fumes captured at the point of generation to help protect the welder,” says Rowan Lyons, Workshop Foreman, MHM Automation. Kemppi’s subsidiary, Trafimet, has also released a range of guns with on-board fume extraction functionality. According to Trafimet, the ERGOFRESH
fume extraction MIG guns remove 94% of welding fumes at the point of creation.
In addition to on-gun fume extraction, New Zealand welders are also investing in welding helmets that feature Powered Air Purifying Respirators (PAPRs). These respiratory protection systems have battery powered filters that provide the welder with continuous clean and fresh air as they weld, while blocking out harmful contaminants.
PAPR helmets such as Kemppi’s new Zeta Fresh Air range offers TH3-level breathing protection to guard against harmful fumes, particles and gases. The TH3-level classification blocks out 99.8% of hazardous fumes.
Apart from providing clean air, the PAPRs also tend to be equipped with auto-darkening lenses to protect welders against ultraviolet radiation which can cause ocular melanoma and conjunctivitis.
Shaun Beck has recently launched one of New Zealand’s latest Hydraulink Owner-Operator businesses, establishing Hydra Medic to serve the Hawkes Bay region.
He is joined by Hamish Blue, Hydra Medic’s newest Hydraulink Service Technician.
The choice of the business name Hydra Medic reflects the thoroughness and professionalism that this qualified diesel mechanic and man of many skills is investing in the business he has established to secure his family’s future, working in conjunction with Hydraulink Hawkes Bay distributor, KRS.
Shaun’s enthusiasm
for the job reflects the experience of skilled people who want to set themselves up for life with the backing of a premier brand with 400 service points throughout New Zealand, Australia, and the Asia-Pacific – and which actively encourages its people to advance their skills and business experience.
“I love getting the job exactly right and hearing the compliments from customers. They notice when you not only do the big things on the job right – safety, quality compliance, and performance – but also the little things that show you care about your work.
“You must treat the machinery as if it was your own – even down to a detail like lining up the hoses so the brands and specs all align. Not only does this presentation look good, but it also makes it easy for owners to specify replacements when the time comes.”
Tired of the lifestyle in crowded Auckland, and wanting to set up his own business, but with the strong backing and training from a national network, he chose Hawkes Bay and Hydraulink.
“I chose Hawkes Bay because of the pleasure of living in a rural setting in Taradale, but with bustling
industries and opportunities all around. A place where we want to be, while being able to do what I love to do with machinery of all types.
“I chose Hydraulink because of the quality brand they are, with the ongoing training and support they give you as you need it. I knew as soon as I had my first chat with them that we shared the same deep values, attitudes and knowledge.
“Plus, they do a lot of motor racing sponsorship, as well as supporting the America’s Cup Challenge with precision hydraulics. That’s talking my language, so it was like joining a family of like-minded people.
“If I needed any further proof, it came within two weeks after Cyclone Gabrielle struck, and floodwaters cut off access to our property completely.
“Hydraulink and KRS stepped in immediately to put us back on our feet – they accommodated our family in Hasting for a month, at their expense, until things settled down.
“This immediate support enabled me to get to work immediately on the huge range of machinery in industries affected by the catastrophe – which was just about all of our customer base.”
Kaeser Compressors has revolutionised condensate treatment with the introduction of its next-generation Aquamat oil-water separator.
Available for delivery volumes up to 90 m³/min, the innovative Aquamat i.CF features an advanced internal controller - the Aquamat Control - which undertakes active management of the treatment process whilst simplifying maintenance planning and making service work cleaner.
The active, intelligent Aquamat i.CF – clean, safe and modular.
Liquid condensate is an inevitable by-product of compressed air generation which must be disposed of in an environmentally responsible manner. Before this can happen, the oily condensate must first be separated out. Conventional oil-water separators rely on gravity to facilitate the separation process, allowing the condensate to trickle through a filter that absorbs the oil.
The new Aquamat i.CF, however, has revolutionised condensate treatment by actively and intelligently optimising process efficiency and functional reliability.
The internal Aquamat Control controller is entirely new. It monitors the condensate level in the oil-water separator and, when the maximum level is reached, uses short bursts of compressed air to push the condensate through the filter cartridges. This method maximises the absorption capacity of the cartridges, resulting in reliable and resource-efficient operation of the Aquamat i.CF, even under high operational demands. In the unlikely event of a problem, the controller detects it and issues a notification.
For the first time, this active mode of operation allows the remaining service life of the filter cartridges to be accurately determined based on load.
The network-capable Aquamat Control controller not only simplifies maintenance planning for the oil-water separator but also guides the operator through the necessary work steps.
Another intelligent design feature is the pressurisation of the cartridges, which ensures they are already empty when replacement is needed, making them much lighter and easier to handle.
The overall design of the Aquamat i.CF sets
new standards when it comes to hygiene. No contact with the condensate is necessary when changing the cartridges and the whole procedure is contaminant-free, thereby protecting both the environment and service personnel.
The Aquamat i.CF is available in five new model variants for compressors with delivery volumes from 8 to 90 m³/min. For added practicality, all models use cartridges of the same size. This considerably simplifies spare parts stocking and supply, thereby saving time and money.
The different capacities of the five model variants are achieved by connecting multiple cartridges in parallel; this modular design concept enables simple, retrospective adjustment of the respective capacity.
The Aquamat i.CF is certified and approved by the Berlin Institute for Construction Technology for state-of-the-art treatment of compressor condensates containing mineral and synthetic oils, providing operators with the highest possible level of technical and legal security.
For cable guidance in drawers and pull-outs of all kinds, igus has launched the draw e-chain. Thanks to the minimalist design, the price of the compact energy chain is 30 per cent lower than the most cost-effective standard e-chains. This protects against expensive oversizing, especially if the application is only moved a little.
From drawers in camper vans to pull-outs in server racks in data centres: industrial energy chains for hundreds of thousands of cycles are oversized for guiding cables in applications where movement only occurs occasionally. Users would pay for features that they do not need.
The new energy chain has a bend radius of 45mm, an external width of 45mm and an external height of just 22mm. This makes it 13 per cent flatter than igus’s flattest standard e-chain B17.1.048.0 to date. Minimalist design makes draw e-chain particularly
cost-effective
The draw-e-chain is not only more compact than standard models, it also costs less. The reason: there are no mechanically complex components. The injection-moulded e-chain does not need any chain links to fold. Instead, the segments are flexible enough to allow the required bending.
Thanks to this absence of chain links, the draw-e-chain consists of just six segments per metre, which can be connected via a simple connector system, which reduces effort and costs. “Due to this minimalist design, the draw e-chain costs 30 per cent less than our most cost-effective standard e-chain,” says Ottersbach.
Assembly completed in just a few minutes
The draw e-chain is designed so that users can assemble it by hand in a very short time. The low-cost
energy chain is designed for installation rotated by 90 degrees, for example on the inner side of a drawer. Connection elements are not necessary. The segments of the cable guidance have holes for screws. Inserting cables is also done quickly, unlike standard e-chains, there are no crossbars that users have to open first.
You simply push the cables through the bendable tabs of the energy chain from above. That takes just a few seconds. www.treotham. com.au
Integrals Power has started production of high-performance Lithium Iron Phosphate (LFP) and Lithium Manganese Iron Phosphate (LMFP) cathode active materials at its pioneering new UK pilot plant.
This milestone for the UK battery industry will help to accelerate the development of the domestic battery industry and achieve net zero ambitions.
Following successful laboratory trials, Integrals Power is now launching the UK’s first pilot plants producing the company’s proprietary high-performance LFP and LMFP nanomaterials. The new facility has an annual capacity of 20 tonnes, the equivalent to 250 electric cars, which will primarily be used for evaluation by cell suppliers, battery and vehicle manufacturers worldwide.
Establishing manufacturing in the UK is also a boost for the domestic battery industry by reducing its carbon footprint, enhancing supply chain security and transparency, and mitigating geopolitical issues such as import tariffs on EVs and their components.
Quality is equally important: Integrals Power’s LFP materials have been assessed as ultra-high purity in a third-party analysis using cutting-edge X-ray
diffusion technology to study attributes such as chemical composition and lattice structure of the molecules – these are key to the performance of the material when built into battery cells.
Developed in-house, Integrals Power has created a modular production facility which can be readily scaled to higher volumes in the future to meet growing customer demand, and also to enable a range of different chemistries to be made. The process takes place over seven stages, and from raw materials to packaged samples ready for customers takes up to 48 hours:
Integrals Power sources all its raw materials from European and North American suppliers which ensures a purer, higher performance LFP and LMFP cathode materials with greater energy density compared to the Chinese-manufactured cathode materials which currently account for around 90%1 of production worldwide.
Natural gas production in New Zealand is expected to drop below demand, according to the latest oil and gas reserves data released by the Ministry of Business, Innovation & Employment (MBIE).
“For at least the next three years, data shows New Zealand’s natural gas reserves will produce 10 petajoules (PJ) less than recent demand levels,” says MBIE Markets Manager Mike Hayward.
“New Zealand has used around 150 PJ of natural gas
per year for the last two years. While New Zealand holds 8.7 years of natural gas in useable reserves, field operators only expect to extract up to 140 PJ each year for the next three years.”
‘Reserves’ refer to natural gas which operators expect to extract over the lifetime of the field, given technical and economic constraints.
“The amount of natural gas in New Zealand’s reserves has decreased by 335 PJ or 20% between 1 January 2023 and 1 January 2024, to 1,300 PJ,” says Mike Hayward.
“44% of this reduction is due to gas extracted and used over the course of 2023. The remaining 56% is a result of revisions to reserves figures from gas field operators. Operators revise their reserves figures as they get a better idea of exactly how much gas exists in – and can be extracted from – their fields.”
This year’s revisions are split fairly evenly between downgrades to contingent resources, where operators believe the gas is there, but it’s too hard to extract (100 PJ), and revisions to existing figures, where operators believe there is less total gas than previously thought (88 PJ).
“New Zealand’s natural gas reserves have been steadily declining since 2019 and are expected to remain on this pathway unless there are new discoveries or innovation which enables commercially feasible production from contingent resources,” says Mike Hayward.
“Limited gas supply is already impacting industrial users: for example, Methanex’s reported production at its Motunui plant was down 31 per cent in the March 2024 quarter compared to the same quarter last year.”
Of all the gas used in New Zealand in 2023, the majority was used by the industrial sector, either being burned for heat (35% of all use) or being used as a feedstock (26%) in factories. Around 29% of gas use was for electricity generation, and the remaining 10% of use represented use by households, schools, hospitals, and other businesses.
The full oil and gas reserve data can be read on the MBIE website: https://www.mbie.govt.nz/building-and-energy/energy-and-natural-resources/ energy-statistics-and-modelling/energy-statistics/ petroleum-reserves-data
With the retirement of Okuma’s highly respected New Zealand General Manager Fred de Jong, the company has appointed Karl Medley as his preplacement.
Karl’s appointment will further expand the already strong business development of Okuma CNC machines in the New Zealand manufacturing sector with many customers becoming internationally competitive resulting in strong export growth.
To continue this strong market presence, Karl Medley joined the New Zealand Okuma team in May this year. Karl who hails from the UK, and comes with an extensive background and a wealth of experience
in precision machine applications with major manufacturers within medical, military, aerospace and general engineering industries.
With responsibilities for Okuma New Zealand’s overall management, focusing on sales and managing service, Karl is a qualified mechanical engineer trained in CNC and CAD/CAM programming. Previously from hands-on engineering experience to production and management Karl was ultimately responsible for CNC machine sales throughout Northern England.
Further strengthening technical and service support for its customers, Okuma New Zealand has also
announced the appointment of an additional Service Engineer, Rodel Estoya to the New Zealand team based in Auckland. Rodel has an extensive service background and knowledge of many CNC machine tool brands including Okuma which will further benefit New Zealand customers.
With the capability to access unprecedented levels of data on customers—the equivalent of more than 26 trillion DVDs of data are generated each year globally—it is time for New Zealand SMEs, retailers and eCommerce sites to have a conversation about the challenge of leveraging data to enhance customer experiences while maintaining trust and respecting privacy.
Mark Presnell, Managing Director at Convergence, an eCommerce tech integration firm in Auckland, says research tells us that the world will generate about 147 zettabytes of data in 2024. Given New Zealand’s population size, he estimates Kiwis generate more or less 1.62 petabytes of data per day.
“AI is fuelled by data, so this is a massive opportunity that few retailers and eCommerce sites are taking, but it is also imperative that those who are will be respectful of a person’s privacy. I think 2024 is an important time for us to address the difference between adding value and invading privacy.
“Data on customer insights, behaviour and preferences offers an unprecedented opportunity to connect and engage customers in a way that builds business success, but it should not be used clumsily or exploited because that’s not good for the business and it’s not good for the customer.”
Presnell says New Zealanders have all largely surrendered much of their privacy to live in a digital society, but nevertheless, smart retailers and
eCommerce sites will see the need for customer awareness, acknowledgement, and permission to use their data in exchange for a more personalised approach.
He says generative AI can personalise communications and offerings to create meaningful interactions. Understanding specific customer preferences, such as those of a left-handed golfer, allows for tailored product recommendations rather than irrelevant promotions.
However, personalisation must provide real value. If a customer purchases an eBike, follow-up communications might include information on local biking tracks rather than a relentless push of service and parts.
Presnell says that research suggests half of retailers and eCommerce sites struggle to access and integrate data, while customers have ethical concerns.
“Retailers and eCommerce sites should explore integrating various data sources—such as their point-of-sale software, CRM and inventory management—to provide data insights and improve AI accuracy,” he says.
There is a significant portion of Kiwis who worry about AI producing biased results. Transparent AI practices are essential to build customer trust.
“Ensure that customers opt-in to data collection and usage, and that they understand and agree to
The Gold Coast will be home to Australia’s first factory capable of producing both community lithium batteries and EV chargers as eLumina’s $20 million manufacturing facility approaches completion.
The factory will produce 300 batteries a year and create 300 jobs on the Gold Coast, capable of serving up to 100 Queensland households with reliable and cheaper renewable energy.
Chief Executive Officer of eLumina, Lisa Marsh, said on-shore manufacturing of critical EV technology, such as chargers and batteries, was essential to Australia’s energy future.
“Global demand for batteries is soaring. We have record solar uptake and energy generation in Australia, but we need battery storage at scale to harness its full potential,” she said.
“Through battery storage we can capture this energy and ensure reliable and cheaper off-grid power to all Australians. This insulates communities from power outages and saves them money.”
Ms Marsh said eLumina was proud to be building the factory in Queensland and grow the local industry.
“Queensland has the potential to become a world leader in next-generation battery manufacturing and research and development. Our centre is just the start of that. We are committed to making a fundamental difference to Australia’s clean energy economy,” she said.
“We’re building this facility using local talent and locally sourced parts and materials. Once it’s
completed, it will support 300 high-skilled jobs, which will draw on the region’s talent.”
“Our world-class research and development training centre will also upskill hundreds of Queenslanders with the expertise to contribute to our evolving battery and EV charging sector.”
Gold Coast Mayor Tom Tate said the Gold Coast had an ambitious plan to secure a larger slice of the clean energy sector and the high skilled jobs it’s creating.
“Our Economic and Climate Resilience and Sustainability Strategies are all about backing the Gold Coast to use renewable energy and boost the uptake of renewables.”
“eLumina choosing the Gold Coast as home for Australia’s first factory building both lithium community batteries and EV chargers shows our city has the right settings, ambitions and support for businesses for advanced manufacturing to thrive.”
“I’m excited to see the thousands of EV chargers and batteries set to be deployed in Australia over the coming years to be stamped - ‘Made on the Gold Coast’.
To accelerate the deployment of its EV chargers across the country, eLumina has partnered with Addelec (formerly known as Gemtek), a leading installer of EV charging stations with national asset management capabilities.
“The number of EVs on Australian roads is growing rapidly and charging infrastructure needs to keep
how their information will be used. I am aware that there is legislation around this, but I would suggest your average SME retailer has very little understanding of the legislation.”
1. Ask for Permission
Ensure customers are aware of and consent to data collection. Use clear opt-in tick boxes and avoid using cameras for anything other than security purposes without explicit consent.
2. Personalise Thoughtfully
Use the data to offer genuine value and provide useful information that aligns with customer interests without always trying to make a sale.
3. Maintain Transparency
Clearly communicate how customer data will be used. Build trust by ensuring data is only used for its intended purpose and is kept secure.
Retailers need to focus on integrating various data sources to improve AI accuracy and personalisation, but make sure your approach is ethical and transparent,” Presnell says.
pace with that. The eLumina D1 with built in battery storage is a great option to have, especially considering the power challenges we have across Australia” Addelec’s General Manager – Chris McPherson said.
“Producing EV chargers in Australia will make it easier to meet demand and to support the exciting transformation to more sustainable transport.”
Ms Marsh said building Australia’s sovereign capability in battery storage and EV technology would support the growth of green energy and electric vehicles.
“By producing this technology in Australia, we can provide families with cheaper power and give more people confidence to drive an EV.”
The factory is set to be operational by August this year.
eLumina, an Australian-owned company, manufactures top-of-the-line EV chargers known for its superior efficiency and reliability. It offers a wide range of battery energy storage systems (BESS) in various capacities to cater to the diverse requirements of industrial and commercial settings. Operated by Australians with a global presence, eLumina’s dedicated team of engineers strives to create a one-stop shop for innovative energy solution, redefining energy interactions and preparing businesses for the new generation of energy infrastructures.
The pace of change in technology has created many opportunities—and raised as many challenges.
Driving this shift requires modern technology leaders to expand from their traditional role as “guardians of IT” to become closer partners with the business.
So says David Pedreira, CTO of Santander Argentina, in this interview with Jorge Machado, he reflects on his long experience leading technology organisations and the key actions that have allowed him to transform the technology function.
Jorge Machado: How did you go about building up an engineering culture? What was the biggest change in terms of how you managed technology as a result?
David Pedreira: To build an engineering culture, you need to bring together people who like to challenge traditional processes—we went from requiring 15 signoffs for a road map to getting it approved in one meeting and adopting agile resource management—and who understand what is required to enable a better developer experience, such as using APIs to create services.
I’ve also prioritised technology leaders who like to manage people over experienced managers with less technical experience; it’s critical to have deep experience in technology first.
Second, I’ve invested in tools, particularly an integrated developer portal. The right tool
enforces process standardisation and helps with communications. When you try to organise engineering in a portal, you learn that all your engineering processes need to be easy.
To help your developers build, you need to go from what has traditionally been a confusing series of requests and hurdles to a much simpler self-service model, where approved code and services are ready to go and easy to integrate. A developer portal also handles all the aspects of an application’s life cycle, from the code to managing incidents in production.
By embracing an engineering portal, we’ve established that everything, even core enablers, are products and should be treated as such. And products, in the engineering core, are not designed to be closed. Everything should be composable, even at this very core level.
Finally, I’ve invested in metrics. I created a small business intelligence team that ensures that every single thing is measured. That created a data-driven culture and helped both in making decisions and in handling the continuous improvement of all activities.
Jorge Machado: What are two or three of the most successful initiatives you’ve led to improve IT resiliency at Santander?
David Pedreira: I truly believe IT resiliency is the offspring of discipline in demanding well-executed processes. Two areas where I was able to make an immediate impact were fixing the “crisis of the first day” and the site reliability engineering (SRE) practice.
Let me explain. We have a significant level of inflation, which leads many Argentinians to buy dollars. In 2020, restrictions were placed on the monthly access to US dollars. This led many Argentinians to go to the online bank to buy dollars at the earliest possible moment, the first banking day of the month.
Traffic would spike 20 times higher from one minute to the next—I’ve never seen anything like it. It occurred only four hours a month, but we had an outage every single month because our mainframe was not designed to handle so many transactions. We did not want more downtime, and we had just four weeks to fix it. Scaling the mainframe or offloading the transactions elsewhere wasn’t an option.
So we buffered the mainframe by introducing a “virtual queue” to the site, which gave our teams time to offload the transactions from the mainframe and decreased downtime by 70 percent.
I also created the SRE team and moved to a true no operations (NoOps) approach. The reliability team,
for example, introduced observability and automated the generation of alarms and the escalation process. We also changed the main monitoring from technical measurements to detecting anomalies in customer behavior—for example, we no longer depend on percentage of CPU usage but on number of logins to detect incidents.
We also broke up our monolithic system to create small “failure” domains—you cannot imagine how many times I have seen different microservices sharing a database—and accelerated the migration of applications to the cloud, which, in my experience, is by far the most stable environment.
These actions reduced the number of incidents by 90 percent, significantly improved our response time to incidents, from hours to seconds, and also improved the management of technical debt in the road map.
Jorge Machado: How did you improve infrastructure automation and adopt infrastructure as code (IaC)?
David Pedreira: To automate infrastructure, I’ve adopted two key principles: abstraction and “zero tickets.” In terms of abstraction, the less a developer knows about the details of the infrastructure the better.
I wanted to make sure that the development teams focused only on the code. The engineering teams are the ones that handle the IaC and “hide” it behind the developer portal, where developers can get prebuilt templates to work with.
The “zero tickets” principle is based on the idea that the ticket is the physical realization of waste. We leveraged a ticketing tool and established a path to zero requests over two to five quarters. That was the KPI.
We also introduced a zero-ticket goal on the developer employee-satisfaction score, so that we
could track if the goal was being achieved. In the end, all infrastructure teams started automating everything.
That not only reduced the number of people in charge of these activities from more than 400 to less than 90 but also reduced the resolution time from weeks to minutes or seconds.
Jorge Machado: Could you discuss your experience in adopting FinOps practices and optimising cloud infrastructure spend?
David Pedreira: I’m going to talk about my previous role at Mercado Libre. I’m quite proud of what we built while I was CTO there.
Cloud expenses are complex. The cost of a simple compute instance is a function of memory, CPU, and storage. In addition, if you pay in advance and commit consumption (reserve instances, saving plans), you get savings, and if you are willing to sacrifice quality, you can purchase spot instances. The virtual machine (VM) will have indirect costs, such as support, networking, monitoring, backup, and security. The cost ends up including more than 100 different components, and it’s hard to understand what is relevant and what is not.
Controversially, our first step was to do some math to arrive at a good-enough approximation of the price of the VM and find the three main components that made a difference. In our case, they were CPU, memory, and persistence.
With that, we set a reference price for the VM. We did it for the main costs in the cloud provider and mapped it to the costs of our engineering products. The second step was to split the problem of efficiency into “How much are you consuming (quantity)?” and “How cheaply can you provide the service to your customer (price per unit)?”
The former was made an objective for the developer
teams: “You cannot use more than X US dollars per month.” The latter was made an objective for the engineering teams: “Your average VM cost cannot exceed Y US dollars per month.”
Our third step was to create the right operating model. We created a center of excellence around FinOps to analyse more-complex scenarios and push for optimizations all across the board. We brought our finance and control teams on board, since this initiative needed to be shared with the organization.
Once these were in place, the evolution was natural and required little effort. As a result, over the year it took to bootstrap this practice, we reduced expenses by 40 percent.
Jorge Machado: How has the CTO role changed in the past five years? How do you think it will evolve?
David Pedreira: Over the years, many organisations have viewed the technology function as “the others.” We handled tools, provided efficiency, and often reported to the CIO.
Now, we’re moving toward being IT strategists who set the direction the organisation should move toward, such as how to use generative AI or how to evolve a product. We define how product development teams should work and where they should focus, speaking directly on the go-to-market plan, not as an “order taker” but as an equal.
We need to focus more on the strategy side and become better internal communicators about what is relevant and what technologies matter to help transform the company.
The solution to New Zealand’s gas shortage sits on the country’s doorstep and can come on stream far quicker than imported LNG options suggested by government ministers this week.
Brian Cox of the Bioenergy Association said importing Liquid Natural Gas (LNG) fails to provide New Zealand communities with the economic and wellbeing benefits that can come almost immediately from investing in this country’s own long term biogas production.
Biogas is sourced from amassing waste streams including the likes of food, crop and wood, and when broken down release gas suitable for combustion, usually methane. Methane can also be captured from existing landfills and is often wasted by being burnt off into the atmosphere, also contributing to global warming in the process.
“Indications are that the production and supply of gaseous biofuels is likely to be a similar cost to imported LNG. Even the gas produced from existing landfills can be refined and simply injected into our existing gas pipeline,” he said.
Importing LNG would mean New Zealand steps away from being self-sufficient for its gas supply and immediately becomes reliant upon overseas market prices, supply routes and availability in an increasingly energy hungry world.
Cox said biomethane produced from the likes of food waste and agricultural crop residues meets the same quality standards as gas extracted from the ground as a fossil fuel.
“Anywhere natural gas is used it can be used without any conversion costs for consumers. Any current natural gas equipment can continue to be used.”
Estimates are almost ten percent of New Zealand’s current renewable energy could be sourced simply by taking the biogas from waste processes and piping it into the gas grid. This would be split evenly between both the North and South Islands.
The recently commissioned Ecogas Reporoa Organics Recycling facility in the central North Island is proving the viability of biogas as a high value energy option.
“Last month Ecogas sold its first supply of biomethane to Nova Energy. The sector is well on the path for
expansion, and support from Government would speed this up significantly.”
Cox said an investment in domestic biogas not only saved valuable dollars being invested offshore. It also integrated well with other policies including waste minimisation, job creation, and climate change response.
“If tapped, it means NZ could produce enough biogas to represent a reduction of 3.7 million tonnes of CO2 emissions, and equates to as much as 27% of NZ’s lower end of targeted gas reduction of 14m tonnes of CO2.
“None of these benefits would be achieved by importing LNG.”
The Bioenergy Association has calculated 40% of fossil gases in New Zealand could be replaced by biogases by 2050.
Cox said New Zealand has been slow to adopt the waste policies widely employed in many other countries which involve food waste being processed to make other products, rather than left for landfill.