

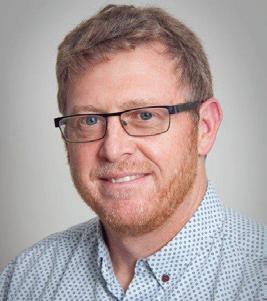
SMART MANUFACTURING
Funding Growth
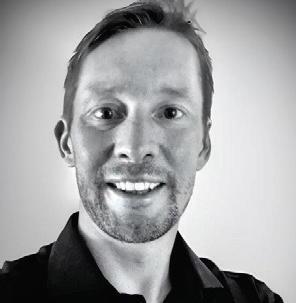
SMART MANUFACTURING
Building a comprehensive business case for factory technology investment.
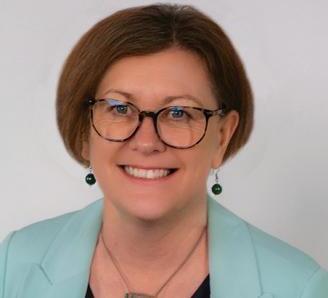
9 10 11
SMART MANUFACTURING
Funding Growth
SMART MANUFACTURING
Building a comprehensive business case for factory technology investment.
9 10 11
By Mark Devlin, Managing Director, Impact PR
Auckland is the industrial heart of New Zealand, but an emerging scarcity of industrial-zoned land is poised to have far-reaching implications for the manufacturing sector. As businesses increasingly seek larger, purpose-built facilities to house state-of-the-art technology and automated processes, the land supply constraints could prevent growth and innovation in one of the country’s most essential industries.
New Zealand’s manufacturing sector, which contributes over 10% to GDP and employs more than 240,000 people, is under increasing pressure to modernise and scale up. Global trends in automation, robotics, and smart logistics demand facilities that are capable of supporting high ceilings, expansive footprints, and advanced connectivity.
Stephen Hughes, CEO of Drury South Crossing—New Zealand’s largest mixed-use property development—says that half of the second phase of their industrial development has already been sold. Manufacturing companies and industrial operators are vying for what remains of the land, recognising the unique advantages that sites like Drury offer. According to Hughes, “Large-scale manufacturing facilities require contiguous greenfield sites with close access to major transport arteries like motorways and rail. The diminishing availability of such land in Auckland is beginning to limit the options for industrial expansion.”
A major shift in the manufacturing sector is the adoption of Automated Storage and Retrieval Systems (ASRS) and other advanced technologies. These systems optimise operations by automating warehousing processes, reducing labour costs, and improving efficiency. However, the infrastructure for such systems cannot simply be retrofitted into existing warehouses; they demand purpose-built facilities with ceilings as high as 30 metres and footprints of two hectares or more.
Ben Stewart, Associate Director of Property at Calder Stewart, explains that Auckland’s geography and regulatory landscape are significant obstacles. “The region is constrained by natural barriers, including internal waterways and hilly terrain, as well as policy-driven limits on rezoning arable land. The availability of contiguous industrial-zoned land with favourable ground conditions is increasingly scarce,” Stewart says.
Manufacturers and distributors looking to consolidate operations into single, efficient hubs—similar in size to Briscoes’ planned $100 million 3.2-hectare distribution centre at Drury South Crossing—are now realising that opportunities to secure such sites are limited.
The rise of energy-intensive industries, such as data centres and high-tech manufacturing, adds another layer of complexity to the equation. At Drury South Crossing, over $30 million has been allocated to building a 60MW substation to future-proof the site’s energy supply. Hughes says “This facility will be one of Auckland’s largest, capable of powering the equivalent of 45,000 homes. Such investments are critical to supporting the next generation of industrial users, including manufacturers integrating AI and advanced
continued on Page 26
Secure supply of energy and data to moving industrial equipment.
• Large size range
• Vertical travels
• Energy tubes
• Hygienic chains
• Solutions for long travel
• Guide troughs
• Readychain
• Robotic, 3D
• Circular movement
HUGE range of high quality flexible cables
• Control cables
• Single cores
• Data cables
• Sensor/Actuator
• Intrinsically Safe
• VSD/EMC cables
• Halogen Free cables
• High temperature
• Harsh Conditions
• Crane cables
• Profibus cables
• Bus/DeviceNet
• Solar cables
• Instrumentation
• Flat cables
• Curly cords
Largest range of flexible conduits for cable protection
• Conduits
• Conduit fittings
• Divisible systems
• Jumbo systems
• Conduit Accessories
• Braided cable protection
• Fire barrier solutions
• Food and beverage
• EMC systems
• Ex, ATEX, IEC EX
Industrial connectors for many industries
• Rectangular multipole connectors from ILME
• Single pole Powerline connectors from TEN47
• EPIC connectors from Lapp Group
• M23 circular connectors from Hummel
• Circular connectors specifically for the entertainment/stage lighting industry from Socapex
Safety engineering solutions from EUCHNER
• Multifunctional Gate Box MGB
• Transponder-coded safety switches
• Electromechanical safety switches
• Magnetically coded safety switches
Sensor technologies for automation
• High-Precision Laser Distance Sensors
• Ultrasonic Sensors
• Inductive Sensors
• Fluid Sensors
How Auckland’s land crunch threatens growth.
EDITORIAL
Talk fests do not help the bottom line.
BUSINESS NEWS
Mexican tariffs to increase costs. Trade shows and events 2025.
SMART MANUFACTURING
Funding growth.
SMART MANUFACTURING
Building a comprehensive business case for factory technology investment.
EMA
How do we turbocharge manufacturing?
SMART MANUFACTURING
Technology department collaboration with Real Steel.
Why AI will not accelerate productivity growth.
Superconducting space technologies rolled out in Japan.
ANALYSIS
From survive to thrive.
AI
Operationalising AI for manufacturing in ASEAN.
How to build the skills needed for the age of AI.
COMMENT
Countries successfully growing their manufacturing.
ANALYSIS
The Silent Threat.
COMMENT
Manufacturers must adapt.
WORKSHOP TOOLS
Wireless charging for small applications. New integrated lithium-ion battery-powered forklifts
Green hydrogen production on Kite Ships. KANDO Innovation, a manufacturing innovation.
SUSTAINABILITY
Sustainability outlook 2025: Six tips for manufacturers.
DEVELOPMENTS
ENZ says Government urgently needs to firm up infrastructure pipeline.
THE LAST WORD
Manufacturers can adapt to workplace changes by being flexible.
Walsh
Ian Walsh is a leading expert in designing and implementing transformational improvement programmes, with over 30 years of experience helping businesses drive operational excellence and long-term success. A Six Sigma Master Black Belt, he has worked
New
Zealand’s top organisations and global multinationals including Kimberley Clark, Unilever, Guinness to unlock productivity, reduce costs, and optimise business performance. Ian has been at the forefront of operational improvement, working at all levels—including Boards—to deliver high-impact change. Ian continues to play a key role in advancing business excellence, supporting Auckland University and The Icehouse with expert insights on productivity, operational improvement, and best-practice methodology.
Dr Barbara Nebel CEO thinkstep-anz Barbara’s passion is to enable organisations to succeed sustainably. She describes her job as a ‘translator’ – translating sustainability into language that businesses can act on.
Business and Manufacturing.
Mark Devlin
Having owned food manufacturing and distribution businesses for a decade, Mark Devlin now runs Auckland public relations agency Impact PR. Mark consults to several New Zealand manufacturing firms including wool carpet brand Bremworth, aircraft exporter NZAero and cereal maker Sanitarium.
Insa’s career has been in the public and private sectors, leading change management within the energy, decarbonisation, and sustainability space. Insa holds a Chemical and Biomolecular BE (Hons) from Sydney University. She is a member of the Bioenergy Association of NZ and has a strong passion for humanitarian engineering, working with the likes of Engineers Without Boarders Australia.
Insa is a member of Carbon and Energy Professionals NZ, been an ambassador for Engineering NZ's Wonder Project igniting STEM in Kiwi kids and Engineers Australia Women in Engineering, increasing female participation in engineering.
Jane Finlayson is Head of Advanced Manufacturing at the EMA, and has 25-years’ experience in business and economic development. She is passionate about empowering businesses to grow, innovate and embrace Te Ao Māori.
Copyright: NZ Manufacturer is copyright and may not be reproduced in whole or in part without the written permission of the publisher. Neither editorial opinions expressed, nor facts stated in the advertisements, are necessarily agreed to by the editor or publisher of NZ Manufacturer and, whilst all efforts are made to ensure accuracy, no responsibility will be taken by the publishers for inaccurate information, or for any consequences of reliance on this information. NZ Manufacturer welcomes your contributions which may not necessarily be used because of the philosophy of the publication.
PUBLISHER
Media Hawke’s Bay Ltd, 121 Russell Street North, Hastings, New Zealand 4122.
MANAGING EDITOR
Doug Green
T: +64 6 870 9029
E: publisher@xtra.co.nz
CONTRIBUTORS
Holly Green, EMA,
Business East Tamaki, Ian Walsh, Adam Sharman, Mark Devlin, Nicholas Russell, Jane Finlayson, Shane Ponraj, Chris Foord
Liam Merrick, Geerten Lengkeek
ADVERTISING
T: + 64 6 870 9029
E: publisher@xtra.co.nz
DESIGN & PRODUCTION
:kim-jean:
E: kim.alves@xtra.co.nz
WEB MASTER
Julian Goodbehere
E: julian@isystems.co.nz
PUBLISHING SERVICES
On-Line Publisher
Media Hawke’s Bay Ltd
DIGITAL SUBSCRIPTIONS
E: publisher@xtra.co.nz
Free of Charge.
MEDIA HAWKES BAY LTD
T: +64 6 870 9029
E: publisher@xtra.co.nz
121 Russell Street North, Hastings NZ Manufacturer ISSN 1179-4992
Vol.17 No.1 February 2025
We are not short of commentators in New Zealand telling us what is wrong. Some even prefer ideas on how we can fix things. These commentators appear in our newspapers and whatever they say – does it matter? – does not bring about change. They do not affect policy.
They keep their Profile and allowance – the newspapers keep their commentators as added value for the paper they write for, seemingly to satisfy the subscriber.
If they believe they can make a difference to our way of life, they need to talk less about (say) real estate, where so much money is invested that does not go into the productive sector.
People buying up property are, generally, not the creative class, innovators, developers, forward- thinking in their view on the nation’s future.
This is where a cloud hangs over our prime minister; he owns properties and whatever he says for the direction the country does not affect his back pocket. He is in a regal position where decisions made will not lessen his financial situation.
We have Chris Plenk, the new Minister for Small Business and Manufacturing who does not have a budget, A minister outside cabinet who answers to Judith Collins.
We have the dis-assembling of Callaghan Innovation and its functions moved to other entities.
We need to come to grips with where the country is heading and how we are going to get there. Is it more overseas investment, hopefully in businesses and not real estate. Is it public sector and private sector investment – and what will the investment focus on?
We continually discuss the rail, road and sea transport systems as to help make the economy stronger. But just what is around the corner?
We know agriculture and land-based enterprises continue to succeed, great export earners. Our top 10 exports accounted for over three-quarters (76.4%) of the overall value to global markets:
Dairy, eggs, honey: US$12.2 billion (30.7% of total exports)
Meat: $5.4 billion (13.6%)
Wood: $2.9 billion (7.2%)
Fruits, nuts: $2.2 billion (5.4%)
Beverages, spirits, vinegar: $1.53 billion (3.9%)
Cereal/milk preparations: $1.52 billion (3.8%)
Modified starches, glues, enzymes: $1.4 billion (3.4%)
Machinery including computers: $1.19 billion (3%)
Fish: $1.19 billion (3%)
Aluminium: $949.8 million (2.4%)
We need a Minister for Productivity!
Shane Ponraj, CFA, Equity Analyst
The United States announced a 25% tariff on products imported from Mexico from Feb. 4, 2025.
Roughly 42% of narrow-moat Fisher & Paykel’s full-year revenue is attributable to the US, and approximately 60% of US volumes are supplied from Mexico.
As a result, we decrease our fiscal 2026 gross margin forecast by roughly 230 basis points to 60.9% versus an estimated 62.3% in fiscal 2025.
However, we leave our midcycle gross margin forecast of 65% unchanged, consistent with Fisher’s long-term target.
The firm intends to mitigate the impact of tariffs through cost reductions, manufacturing efficiencies or price increases over time.
We maintain our NZD 25 fair value estimate, or AUD 23, at current exchange rates. Shares appear overvalued.
Fisher’s opportunity lies in increasing the utilisation of nasal high-flow therapy for broader respiratory applications. While it greatly expanded the hardware base due to covid demand, we contend that changing clinical practices remains a gradual and difficult process.
Our midcycle group revenue growth and EBIT margin forecasts of 12% and 30%, respectively, are unchanged and consistent with Fisher’s long-term
targets. We expect scale efficiencies and a growing contribution of higher-margin consumables to drive a five year earnings per share compound annual growth rate of 20%.
We don’t expect Fisher’s market position to be significantly affected. Fisher’s internally developed proprietary technology has helped maintain over 70% market share in humidified ventilation in the hospital setting and leading innovation in nasal high-flow therapy.
Switching costs derive from the challenges each hospital would face in retraining staff on new machines and maintaining a continuum of care for patients.
We think competitors would be challenged to offer original products that are comparable in quality without infringing on Fisher’s patents while also having to compete with Fisher’s entrenched relationships.
-Morningside Research
by Guido Tonelli
What are we made up of? What holds material bodies together? Is there a difference between terrestrial matter and celestial matter – the matter that makes up the Earth and the matter that makes up the Sun and other stars?
When Democritus stated, between the fifth and fourth centuries BCE, that we are made up of atoms, few people believed him. Not until
By Vince Beiser
Power Metal sounds the alarm on the environmental and social consequences of electronic and digital energy—and how the ways we are combating climate change come at a cost.
When we bring our mobile phone to life with a tap or settle in behind the wheel of our car, few of us give much thought to the raw materials required to make these sometimes miraculous- seeming devices work.
Journalist Vince Beiser has reflected deeply on that subject, and the result, Power Metal: The Race for the Resources That Will Shape Our Future, is a sharp cautionary tale about the dilemmas facing humanity as we advance deeper into what he calls the Electro-Digital Age, especially as we pursue the essential transition to an energy-renewable future.
Everything comes with a cost, Beiser reminds us, even when it comes to the use of so-called critical metals like lithium, cobalt and nickel. These resources are fundamental to the massive expansion of electric cars and the clean energy sources (namely solar and wind power) that are necessary to combat climate change.
Galileo and Newton in the seventeenth century did people take the idea seriously, and it was another four hundred years before we could reconstruct the elementary components of matter.
Everything around us – the matter that forms rocks and planets, flowers and stars, even us – has very particular properties. These properties, which seem quite normal to us, are in fact very special, because the universe, whose evolution began almost fourteen billion years ago, is today a very cold environment.
In this book, Guido Tonelli explains how elementary particles, which make up matter, combine into bizarre shapes to form correlated quantum states, primordial soups of quarks and gluons, or massive neutron stars.
New questions that have emerged from the most recent research are answered: in what sense is the vacuum a material state? Why can space-time also vibrate and oscillate?
Can elementary grains of space and time exist? What forms does matter assume inside large black holes?
In clear and lively prose, Tonelli takes readers on an exhilarating journey into the latest discoveries of contemporary science, enabling them to see the universe, and themselves, in a new light.
What makes that truth problematic, he argues, is that the inevitable price of progress often falls most heavily on the residents of impoverished countries who bear the burden of first extracting these materials and later disposing of the batteries and printed circuit boards, for example, in which they’re used.
Beiser’s journey to this insight takes him from the streets of his hometown of Vancouver, British Columbia, where he tracks an “urban miner” digging through dumpsters for salvageable products like copper wiring, to a lithium mining operation in Chile’s Atacama desert, to a garbage dump in Lagos, Nigeria, where “e-waste scrappers” work in hazardous conditions to recycle electronic products.
Power Metal is a concise, but thoroughly researched, work crammed with eye-popping statistics—among them the fact that 75 pounds of ore must be mined to build one four-and-a-half ounce iPhone. It investigates highly touted technologies like sea mining, whose promised benefits may conceal massive environmental risks.
In the final section of his book, Beiser offers some
prescriptions to reduce the planet’s insatiable demand for resources that go beyond costly and energy-intensive recycling, including broadening the scope of right to repair laws, making urban spaces more friendly to bicyclists and deeply questioning our infatuation with the automobile.
Whatever one thinks of the practicality of some of his proposals, Beiser has performed a vital service by alerting both policymakers and ordinary citizens to some of the critical choices facing us.
I have been considering the approach to drive growth in NZ as we move into 2025. Overall, this is a positive direction, and business needs growth to fund investment, to improve its product and service and create a virtual cycle.
This is very much what Dr Edwards Deming laid out to Japan in the 1950’s. However, he described this as a quality circle with the start being to focus on improving your product or service, leading to happier customers, better product, lower cost, then more sales and the cycle is virtuous and repeats.
Expecting growth for growth’s sake by encouraging investors, without improving your product or service, or a clear strategy (Ireland or Singapore for example) is a recipe for failure. This investment is only one part of the puzzle. The other parts are aligning your businesses and universities and research capabilities with the areas in which the nation can win.
The restructure of Callaghan and research institutes goes some way to this, but aligning universities and business and research, I would suggest is still a work in progress.
This of course is common practice in Japan, America and other “successful” countries with major corporates invested in universities and research in a synergistic manner.
As Doug Green outlined in his article, our top 10 exports accounted for over three-quarters (76.4%) of the overall value to global markets:
• Dairy, eggs, honey: US$12.2 billion (30.7% of total exports)
• Meat: $5.4 billion (13.6%)
• Wood: $2.9 billion (7.2%)
• Fruits, nuts: $2.2 billion (5.4%)
• Beverages, spirits, vinegar: $1.53 billion (3.9%)
• Cereal/milk preparations: $1.52 billion (3.8%)
• Modified starches, glues, enzymes: $1.4 billion (3.4%)
• Machinery including computers: $1.19 billion (3%)
• Fish: $1.19 billion (3%)
• Aluminium: $949.8 million (2.4%)
These would seem to be a good space to start, to align business, research and universities in terms of creating a pipeline of innovation and talented capable people to drive our economy forward.
Only the government can bring these parties together, effectively and create the right framework and support to deliver the right outcomes for the whole country not just specific parts or entities within it.
It is great we now have a minister for manufacturing. There is now some growing recognition of the need for greater profile for manufacturing however, the budget is still controlled elsewhere and the rate of progress is slow.
There are signs of some engagement but we could do so much more. For example, a quick review of funding available to support manufacturing in Australia reveals
• Industry growth program giving SME’s access to grants of between $50k to $250k for early-stage commercialisation projects and $100k to $5 Million for commercialisation and growth projects, all designed to help build manufacturing capability.
• National reconstruction fund, $15 Billion into priority sectors to boost Australia’s domestic manufacturing and economic base
• Manufacturing modernisation fund, with $50 Million available from 2021 to 2023 designed to support transformation in small to medium manufacturing business (up to 199 employees)
• Modern Manufacturing Initiative $200 Million to help business collaborate with research institutions, translate innovation into commercial projects and integrate into international markets
• State funding, each State has specific initiatives as well
Unfortunately, a quick study of funding available for NZ, is not as productive, with the Callaghan Lean fund now discontinued, training initiatives such as TTAF now stopped.
There are regional business partner funds usually 50:50 funded up to $5k and similar initiatives with NZTE and funding for numeracy and literacy training.
A comparison of the two approaches is very stark. The reality is many NZ SME’s need support to develop the capability they need and they do not have the resources or capacity to deliver this requirement.
Government and universities and other institutions need to provide better more capable candidates and we need to provide support and funding to commercialisation of innovation to drive the growth.
We have some of the pieces of the jigsaw on the table but not the complete picture as yet and talking growth without the detailed roadmap may only lead to further frustration.
We can and must do better.
Adam Sharman, CEO LMAC Group, APAC
As the imperative for technology adoption in manufacturing increase, investment decisions are becoming increasingly complex. Gone are the days when a simple ROI calculation could justify major capital expenditure. Forward-thinking manufacturers are now developing comprehensive business cases that look beyond immediate financial returns to consider broader strategic implications, particularly around workforce sustainability and competitive positioning.
One of the most compelling arguments for technology investment lies in addressing the looming demographic crisis facing manufacturing. Across developed economies, the manufacturing workforce is aging rapidly, with experienced workers retiring faster than they can be replaced. This isn’t just a temporary staffing challenge – it represents a fundamental shift in labour market dynamics that will persist for decades.
Modern automation and digital technologies offer a powerful response to this demographic challenge. Rather than viewing technology merely as a cost-saving measure, manufacturers should consider how it helps future-proof their operations against workforce scarcity.
Advanced robotics and automation systems can maintain productivity even as skilled labor becomes harder to find. More importantly, they can make manufacturing more attractive to a new generation of workers who expect to work with cutting-edge technology.
When building a business case for technology adoption, it’s crucial to move beyond the simplistic narrative of automation replacing workers. Instead, focus on how technology transforms and elevates human roles. Modern manufacturing technologies create opportunities for workers to develop new skills and take on more engaging responsibilities. Repetitive, physically demanding tasks can be automated, allowing workers to focus on higher-value activities that require human judgment and creativity.
This transformation has important implications for workforce development and retention. Younger workers are often more attracted to workplaces that offer opportunities to work with advanced technology.
By investing in modern systems, manufacturers can position themselves as employers of choice in an increasingly competitive labor market.
While workforce considerations are crucial, financial analysis remains at the heart of any business case. However, this analysis needs to be comprehensive, looking beyond simple cost reduction metrics.
Consider how technology investments can drive revenue growth through increased capacity and flexibility. Factor in how improved quality and consistency can strengthen customer relationships and open new market opportunities.
The cost analysis should also be thorough, incorporating all aspects of ownership. This includes not just the initial purchase price, but also installation, training, maintenance, and eventual decommissioning costs.
However, it’s equally important to consider cost avoidance – how technology investments can help sidestep future expenses related to workforce shortages, quality issues, or competitive disadvantage.
A compelling business case must address how new technology will be implemented successfully. This means developing detailed plans for integration with existing systems, training programs for current workers, and strategies for maintaining production during the transition period.
It’s particularly important to consider how implementation timing aligns with workforce demographics – phasing in new technology as experienced workers retire can create natural opportunities for transition.
Risk assessment should go beyond technical considerations to examine workforce and organizational impacts. How will existing workers
adapt to new technologies? What new skills will be required?
How can knowledge be effectively transferred from experienced workers to automated systems? These human factors often determine the success or failure of technology implementations.
No technology investment decision exists in isolation. A thorough business case must consider industry trends and competitive dynamics. Are competitors making similar investments? How will technology adoption affect your market position?
What are the risks of falling behind industry standards? These strategic considerations often provide compelling justification for technology investments beyond pure financial returns.
Perhaps most importantly, a comprehensive business case should paint a picture of how technology investment positions the organization for future success. This means considering not just current challenges, but emerging trends in manufacturing technology, workforce demographics, and market demands.
How will the investment support long-term strategic objectives? How does it help build a sustainable competitive advantage?
Successful technology adoption in manufacturing requires more than just buying new equipment – it demands a thoughtful approach to transformation that considers both technical and human factors.
By developing business cases that address the full scope of benefits and challenges, manufacturers can make better investment decisions and increase their chances of successful implementation.
In an era of demographic change and increasing competition, the ability to effectively evaluate and implement new technologies may well determine which manufacturers thrive and which struggle to survive.
By EMA Head of Advanced Manufacturing Jane Finlayson
Economic growth appears to be the focus for 2025 following a tough year of recession and rising unemployment.
But one of the key drivers of national growth, our manufacturing sector, has been struggling due to high operational costs, increasing global competition, outdated technology, skills shortages and a lack of R&D to drive innovation.
The BNZ-Business New Zealand Performance of Manufacturing Index (PMI), a monthly survey providing insight into levels of activity in the sector, has been in contraction for 22 consecutive months. This signals declining production, low new orders, and falling profits across the manufacturing landscape.
Recent government efforts to fast-track infrastructure development, stop wasteful spending, push through RMA reforms, sign new trade deals, and make foreign investment easier have laid the foundation for a more competitive future, but that’s peripheral to the direct challenge facing manufacturers.
A key task facing incoming Manufacturing Minister Chris Penk is to assess how the government can help the sector stay competitive with our global peers and drive productivity.
For many New Zealand manufacturers, the path forward is clear: investment in technology, particularly software and hardware, is essential. As we progress deeper into the Fourth Industrial
Revolution (Industry 4.0), the convergence of artificial intelligence, cloud connectivity, and real-time data analytics will prove crucial in shifting New Zealand’s manufacturing sector from lagging to leading in the global market.
Yet, many manufacturers are struggling to keep up with international standards and this particularly, but not exclusively, affects our smaller companies.
New Zealand’s manufacturing sector includes some very advanced manufacturers, but many small and medium-sized businesses have fallen behind our Asian and European counterparts.
As a result, despite the government’s aspiration to double the value of exports in the next decade, manufacturers are at risk of losing ground without investment in automation and productivity improvements.
There was little in Budget 2024 for the manufacturing sector, and the government’s grim Half-Year Economic and Fiscal Update late last year suggests there is little in the coffers for new spending. Meanwhile, countries similar in size to New Zealand, such as Singapore, Ireland and Denmark, have offered substantial funding to help their manufacturers with technology uptake.
For New Zealand to stay competitive, the government will need to follow suit, providing targeted funding and mechanisms to support manufacturers who must embrace technology/Industry 4.0 but currently
lack the knowledge and financial means to make the leap.
We hope that, despite the fiscal constraints, the government will find ways to continue to support productivity growth, if not through direct funding, then via mechanisms such as accelerated depreciation.
Practical and financial assistance will be crucial. The EMA, through the Industry 4.0 Demonstration Network (a partnership with Callaghan Innovation, BECA, and LMAC) and now through the ASB Manufacturers Workshops, is committed to educating and inspiring manufacturers to adopt technology and boost productivity.
continued on Page 26
Sandra Lukey
Sandra Lukey is the founder of Shine Group, a consultancy that helps science and technology companies accelerate growth. She is a keen observer of the tech sector and how new developments create opportunity for future business.
Mike Shatford
is an expert in the field of technology development and commercialisation. His company Design Energy Limited has completed over 100 significant projects in this vein by consulting for and partnering with some of New Zealand’s leading producers. Among Mike and his team’s strengths are industrial robotics and automated production where the company puts much of its focus.
Sean O’Sullivan
Has a B Com (Hons) Otago University. In 2000 - 2001 introduced PCs on the workshop floor and job and staff tracking and a productivity software App to Fletcher Aluminium Group and 100 manufacturers NZ nationwide.
Founding Director Empower Workshop Productivity & Scheduling Software App.
Iain Hosie
Iain is a Director and Founder of Nanolayr Ltd, Director for the NZ Institute for Minerals and Materials Research, Commercial Director for Fabribotics Ltd, and Executive Council of BiotechNZ.
Adam Sharman
Is a Senior Partner at Dsifer. With a background in technology implementation, manufacturing and strategy, Adam and the team at Dsifer are on a mission to support New Zealand’s manufacturing sector transform using technology, data and analytics to outcompete on the world stage. Combining expertise in data engineering, data science & analytics and visualisation.
Patrick McKibbin
CEO – Hutt Valley Chamber of Commerce
Patrick joined the Hutt Valley Chamber of Commerce in September 2021. His passion is identifying and connecting with manufacturing & technology businesses, other businesses, local government, central government and industry associations.
Head of the Technology Department. (Belinda Curran)
Over the past two years the Engineering Department at St Patrick’s College Silverstream has been collaborating with Real Steel, an ever changing dynamic company which offers a wide range of career pathways from a school leaver to a university trained mechatronic expert.
A company where all are working together to produce cutting edge technology for manufacturing components, to designing and building specialist machinery for industry.
This collaboration originated from an introduction made by Patrick McKibbin of the Hutt City Chamber of Commerce. This organisation is doing a tremendous amount of work connecting high schools with local industries.
Real Steel has been operating in the South Pacific
year we
This press brake will be forming all bends in students’ design.
Industrial Park since 2007 at 24 Railway Avenue, Upper Hutt: a local industry interested in giving back to the community and trying to change the perception of how an engineering career is commonly perceived.
Luke Mathieson, the Managing Director of Real Steel, approached a number of high schools in the Upper Hutt vicinity in 2022. We traded visits and it became apparent that our engineering department was operating with technology from the 1950’s and therefore not properly preparing students for a future pathway into the engineering profession.
However, I had just upgraded our computer suite with the intention of engaging 3D software. So, when Luke suggested a collaboration, we jumped at the opportunity to get involved.
Luke, myself, and Aaron Gamble (lead designer at Real Steel) met to discuss potential projects and thus the collaboration was born. Students were given the opportunity to build a toolbox and then go on to design a firepit.
The year starts off with the students learning how to build their toolbox using Solidworks, specifically the sheet metal function. This is a predetermined design and Real Steel has laser cut the sheet metal ready for
us to fabricate and assemble, supplying the class set of parts.
Without the ongoing support, guidance and technology of Real Steel, the students would not have had the opportunity to study and produce engineering components that reflect real-world experiences and learning. Their generosity has enabled the boys to engage in tool box and firepit manufacturing at Level 1, and the opportunity to machine ‘stems’ and ‘triple clamps’ for the Level 2 mini bikes.
At the end of 2023, St Patrick’s College Silverstream invested in purchasing the licence for Solidworks, a software that is used extensively throughout all industries.
Thanks to Aaron I managed to do a quick upskill over the summer and instigated the teaching and learning of Solidworks into our department’s curriculum. Students learnt how to use the basics of this program to create the toolbox and then they went on to utilise the knowledge to develop their own design of a firepit. We used Solidworks and our little laser cutter here at Stream to do some rapid prototyping of scale 1:1 cardboard model firepits. Aaron was available to help me if there was anything I needed, which gave me the confidence to embark on this venture. It was a privilege to have access to such valuable knowledge and I would like to thank Aaron and Luke for their continued support.
on student laser cut cardboard models before the designs go to Real Steel to be cut and formed.
Once the designs were signed off by Aaron, the students then prepared their digital files for industry. There is a very specific criteria required as the machinist on the factory floor will need to use these files to produce the outcomes the students want. Great real world learning for these lads.
Through this incredibly generous collaboration with Real Steel students are able to produce some quality outcomes.
Students learning
Geerten Lengkeek, Managing Director, Productivity People
While I desperately want to believe that the burgeoning AI tools will massively improve productivity in New Zealand and the world, there is decades of evidence that this will not be the case. We humans have been outstanding in wasting tech opportunities; will it be the same with AI?
I present exhibit A: the graph showing a steady decline in productivity growth (in the US) since 1950, overlaid with the tech innovations we all expected to change the world forever.
Did we see wholesale change from the introduction of the PC and the Internet in the 80’s, Wi-Fi in the 90’s, the iPhone and social media in the 2000’s, and other innovations such as Cloud computing and Bitcoin the 2010’s? Absolutely yes! Did we see a corresponding increased rate of productivity growth? I’m afraid this is an unequivocal emphatic no!
Productivity growth has been steadily declining over the past seventy years, despite the new tools we have at our fingertips. Changing from typewriters to PC word processing, microfiche research to the Internet, mailing lettings to email and IM, trial and error product development to quantum computing modelling: these should be all massive leaps towards higher productivity.
Why are we not seeing this in the productivity numbers?
There is a hypothesis amongst some thinkers that I find compelling. Gary Hamel calls it ‘bureausclerosis’.
Peter Weill calls it ‘silos and spaghetti’. I believe we are not intentional– we don’t plan for the benefits to occur and therefore waste them.
An example: tech is supposed to bring info at our fingertips, but who recently had to step through a convoluted process to authenticate yourself or to come to the precise piece of information we were looking for – from our bank, our government agency, our airline… the list goes on.
Rather than supercharge our productivity with more value-adding activities, we redirect our freed-up time to inefficient, wasteful activities. It is our tendency to build policy, regulation, fiefdoms, and overly complicated processes. We build up the bureaucratic plagues in the arteries of healthy businesses to stop the flow of ideas, resources, motivation – and value. We are not intentional with the deployment of tech; we don’t express expectations of benefits in terms of “if we achieve X, we should be doing more Y, and less Z”.
Will it be any different with AI? I sure hope so. But the human behaviour that has wasted our previous opportunities has not fundamentally changed, so
the outcome could well be more bureausclerosis, and the continuation of the downward trendline of productivity growth.
To unlock the value of tech in general and AI specifically, we need to address the underlying problem, and become intentional with reaping the benefits of AI. This can be expressed in many ways, but a start is to change the conversations at leadership and board level.
All too often when AI or other innovative tech is first discussed, the focus is first on risk: how do we keep our data safe, protect our intellectual property, safeguard our reputation. Sometimes the conversation moves on to all the cool things we can do with the new tech, maybe even benefits.
Rarely do we discuss how the tech should change how we act, backfill our new-found time with value-adding activities and stop us from introducing more bureausclerosis.
So, be intentional, change the conversation and reap the rewards of tech and AI. I’d love to be proven wrong in my prediction – please make this happen.
New Zealand-headquartered Zenno Astronautics (Zenno), the space superconductor company, has signed a Memorandum of Understanding (MOU) with ANA Trading to deploy Zenno’s superconducting technologies for space applications in the Japanese market.
ANA Trading is a member of ANA Group, Japan’s leading airline group. With the slogan “Next Stop, Space”, ANA Group has identified the expansion of its business field into space as one of its strategic priorities.
Under the terms of the agreement, ANA Trading, with deep knowledge of aerospace industries, will create business opportunities in Japan for Zenno
that contribute to the Japanese space industry. The initial focus is to deploy Zenno’s Z01 superconducting magnetic torquers for high-precision satellite positioning in the Japanese market.
Z01 scales to address demanding positioning requirements for satellites - from 50kg and up to space station sized - and the ongoing need for satellites to reposition in orbit to maximise commercial value.
In the future, the partnership will collaborate to bring an exciting roadmap of other technologies to the market, opening up new possibilities and increasing the competitiveness of the Japanese space industry.
Zenno co-founder and CEO Max Arshavsky says, “We are excited to be part of the Japanese space ecosystem with our partnership with ANA Trading. This collaboration will accelerate our growth in the
Japanese market and supports Zenno’s vision to build for life in space.
“Our mission is to create enabling and highly scalable technologies that will allow humanity to prosper in space without dependence on Earth’s resources, such as the need for fuel, radiation shielding, and frequent resupply of spacecraft in orbit.”
Chris Foord, Partner, Argon & Co New Zealand
As we look forward to 2025 the outlook for business and NZ are improving. Many businesses in 2024 were focused on the “survive till 2025” mindset, controlling costs and avoiding discretionary spend. Very few though forgot about the consumer/customer and the need to continue to serve, surprise and delight with excellent product, service and pricing. Most FMCG businesses will be looking to return to better margin positions in 2025 and indications are favourable that this is achievable.
The inflation beast has been tamed, so interest rates have fallen and are predicted to drop further (albeit not by a huge amount) through 2025. Business sentiment is on the rebound. Consumer confidence is at its highest level for two years, which in turn improves business confidence. Whilst the signs are positive, navigating from the survival mindset to a thrive mindset doesn’t happen without intent.
So, what are some helpful tips to consider as FMCG businesses transition into what should be a period of growth, and importantly how to create value and embed sustainable profitability. Here are some areas to consider and explore:
• Align operations to execute your business strategy
• Plan to drive profitable growth
• Unlock, deliver and celebrate quick wins
• Create and embed a continuous improvement culture
• AI: Proof of Value
Align operations to execute your business strategy
Operations is where the rubber hits the road for your business strategy. Are your operational teams involved in the key decisions as you launch new products, drive innovation, review range, pricing and promotional plans? If not, they should be. They
operationalise strategy, plans and tactics into reality. Get them onboard early and you will realise value faster and more effectively.
Continue your focus on productivity. 2024 taught most to drive efficiency through their existing business operating model as very few invested in capital options due to the cost of borrowing. With more capital projects likely in 2025 remember and retain the behaviours that got you through 2024. Growth should be profitable, but if not done correctly it can cost you as bottlenecks, capacity constraints, people/process/system capability gets challenged. Plan it out, assess your readiness to change, model outcomes, test and learn and integrate your teams to ensure success is embedded and sustained.
With large scale transformations and major capital projects (infrastructure, digital, automation) likely back on the cards for 2025 don’t forget to capture value on the way through. There is no better way to drive and sustain a transformation than getting runs on the board early, celebrating the success and showing yourselves, your teams and your customers that you are driving change in the right way.
Adopt lean techniques and tools, adapt them to your business, your team and ways of working. They are proven globally over many decades and stand true today as fundamental to value creation and growth mindsets. Build and nurture this capability in your leaders and teams – and most importantly don’t stop….it is called continuous for a reason.
Is it possible to write an article on trends and predictions for 2025 without referencing AI? Probably not. It is here, it is real, and it can and should be super valuable. It can also be daunting to know where to start and some have spent lots of money or time for little benefit.
Our recent survey of the Food & Grocery sector told us that 74% of businesses have or are planning to invest in Generative AI over the next 3 years. AI adoption is no longer polarised by age group – we are all giving it a go. Get clear on your use cases for AI, where and how it can add value, reduce repetitive tasks, provide deeper more holistic insight. Start small, build it, proof the value, then keep going. Here’s to 2025.
Karen Kim, CEO Human Managed
While the hype around Gen-AI will shift to the buzz around agentic-AI in 2025, traditional sectors such as manufacturing will still be coming to terms on deploying AI strategies to become participants of Industry 4.0 or the Fourth Industrial Revolution. This is the next phase where disruptive trends including data, connectivity, analytics, robotics and human-machine interaction is said to transform manufacturing significantly.
According to a Kearney study , while over 70% of ASEAN manufacturers polled claimed to be “non-leaders/followers” of AI adoption, 47% believe investment in AI is “very critical” for their business. Gartner’s Prism use case of GenAI in Manufacturing encourages leaders to evaluate AI use cases on a strategy that addresses both value generation and feasibility .
• Value parameters include increased revenue, increased efficiency, managed risk and non-financial gain.
• Feasibility parameters include technical feasibility, internal readiness, external readiness. So how can leaders operationalize AI, keeping value and feasibility in mind? At Human Managed, we believe it begins with an understanding of data. A framework to understand the highest impact for manufacturing businesses in the age of AI, would be to understand “3 Ops”-DataOps (Feeding AI), MLOps (Tuning AI), IntelOps (Applying AI).
In the manufacturing sector, data can be provided through assets in an interconnected ecosystem. From a range of sensors, machine data on temperature, vibrations, pressure, power consumption, operating hours etc are collected. Industrial machines, robotic arms and assembly lines can provide process data includes information on production rates, cycle times, error rates, material usage. Image and video data from cameras capture data for product dimensions and defect detection. ERP systems provide information on inventory levels, order information, transportation data.
Given the vast array of data, manufacturing enterprises have to first solve for the issues around understanding the data itself. These can be clubbed into 5 buckets –
1. The visibility problem – to have a current view of assets, their posture and behaviours to be able to track business changes.
2. The verification problem – to ensure that data outputs generated by tools and solutions are verifiable and trusted.
3. The foresight problem – to predict accurately based on large volumes of reliable data, effective models and quick feedback loops.
4. The prioritisation problem – to prioritise quickly, which data, events and alerts are essential and need attention.
5. The orchestration problem – to bring together multiple tools and technologies into cohesive operational pipelines to detect, react and respond effectively given the volumes and velocity of increasing data.
After establishing the ground reality from a data perspective, manufacturing enterprises need to zoom out to see opportunities in business models from an AI modelling perspective. Manufacturing data can train machine learning models for a vast array of use cases including predictive maintenance, quality control, supply chain optimization, process optimization, robotics and automation.
While there have been significant advances in foundation models and large language models, with many plug-and-play AI tools, operating AI at scale across multiple use cases and business processes, requires custom-trained models. However, this is also where most MLOps and LLMOps challenges occur, such as:
1. Choice paralysis : with AI developments evolving so quickly, deciding what direction to take and what models to use is challenging.
who will give the feedback and the associated mechanism. There is also a responsibility to check for and reduce bias and prejudice.
Even when you make headway with the DataOps and MLOps problems, one big piece of the puzzle is left in operationalized AI: presenting and serving the AI outputs to the correct recipient (humans or machines) at the right time.
For manufacturing enterprises, these could include real-time monitoring and alerts to track machinery, production and supply chain in real time, predictive analytics for planning and resource allocation, integrating AI-driven analytics to support decision in quality control, inventory management and workforce allocation.
While the outputs of DataOps (insights & intel) and MLOps (labels) are important, what is also essential—but often deprioritized—is how they get generated, delivered, and tuned to be usable across the business.
At Human Managed, we call this continuous process of data-to-intel, intel-to-labels, and labels-to-serving pipelines: IntelOps. To get the most out of AI in your day-to-day business processes, it’s crucial to build in the specifics of the distribution of labor between humans and machines.
• What Human or AI processes analyze what type of data and use cases? (Logic, model)
• What Human or AI processes generate outputs (insights, recommendations)?
• What Human or AI processes do you use to execute actions? (Functions, tasks)
• Finally, how and where do you present the AI outputs? (API, report, notification)
There is no one mode of AI; it will be different based on the type of implementation, function and the level of automation required.
Conclusion: Balancing value and feasibility of AI in manufacturing depends on data, context, and processes
Advertising Booking Deadline – 7 March 2025
Advertising Copy Deadline – 7 March 2025
Editorial Copy Deadline – 7 March 2025
Advertising – For bookings and further informa
Media Hawkes Bay Limited 06 870 9029 Articles to be sent to: publisher@xtra.co.nz
2. Lack of technical expertise : even after identifying use cases and models, deep technical knowledge and capacity for experimentation is needed.
3. Siloed data flow : to achieve holistically contextualised intel from data, data sources and management which are typically isolated in enterprises, need to be integrated.
4. No context models: For machine learning to be operational, AI models must be trained, tuned, and improved with data, logic, and patterns unique to your business.
5. Feedback loop: AI models only improve with proper feedback, so decisions must be made about
The future of AI in manufacturing will belong to companies that prioritize building a robust, data-driven foundation, making data, models and their outputs operationalized and always production-ready- not just once, but every day By breaking away from reliance on isolated, human-held knowledge and fostering collaboration with a distributed ecosystem of partners and suppliers, these forward-thinking manufacturers will not only harness AI to enhance efficiency but also gain a strategic edge in innovation, making Industry 4.0 a reality.
We believe that the companies that continuously build the context of their business as distributed and scalable data (instead of tribal knowledge in individuals’ minds) and work with a distributed ecosystem of partners and suppliers will be the ones that grow with AI, balancing dual parameters of value and feasibility.
New technologies can be exciting and disruptive at the same time. Over the past few years, no innovation has been more contentious than artificial intelligence (AI). It is changing the way we think about when, where and how we work and what skills workers need to thrive in a world of intelligent machines and cognitive computing. But it comes with a colossal caveat.
How will it affect jobs and livelihoods? And, what steps can we take now to futureproof our workforces and equip them with the skills and know-how they’ll need to succeed in a more digital, automated and fast-paced jobs market?
Job displacement – or job reconfiguration – is a primary concern. Labour-intensive work, such as assembling electronics or automobiles, handling materials and overseeing supply chains – careers that employ tens of millions of workers, which are critical to the economies of many developing countries –will certainly be impacted as AI-powered activities, such as quality control and robotics, replace some jobs.
Knowledge-based in industries such as banking, marketing, and human resources may already need to skill-up to coexist with sophisticated technologies for financial analysis, algorithmic trading, predictive analytics and software development.
The IMF recently estimated that almost 40% of jobs will be impacted by AI. This effect varies by a country’s income level, however. About 60% of jobs in advanced economies may be impacted by AI, while exposure in emerging markets is 40% and in low-income countries it’s 26%.
While the near-term disruptions from AI are lower in emerging and developing economies, there is also a risk that workers in these countries miss out on the potential benefits.
The ramifications of AI’s deployment reaches well beyond job disruption. Advanced economies are embracing AI more rapidly than in the developing world, posing challenges for emerging economies, where insufficient skills and a lack of familiarity with essential innovative technologies could hinder progress.
Already there are hints that a deficit of technically skilled workers in some countries is discouraging investment in the supply chains for important industries, such as EV battery manufacturing and assembly.
Left unaddressed, the north-south skills chasm will widen, potentially exacerbating income inequality, limiting some economies from high-value opportunities and enflaming a host of other problems that can spill over borders.
It is now a given that workers – almost anywhere and in almost any job – need to be more proficient in technical and digital skills than ever before. Even while some jobs may be displaced, demand for technicians, technologists and engineers is steadily rising. In a recent survey of stakeholders in Ontario’s automotive industry, two-thirds of respondents identified a “lack of appropriate education and training options” for students and recent graduates
as a main reason for expected future skills shortages. More than half of respondents identified “a lack of reskilling and retraining options for current workers” as another challenge. The gaps in emerging markets are likely to be similar or worse.
That reality is reflected in the fast-growing education market. Today, only a sliver of education initiatives and investments are devoted to emerging technologies such as machine learning, cognitive computing, robotics and next-generation systems, and these are not yet integrated into education systems at large.
Traditional education or edtech products alone, however, are not going to cut it. With the pace of technological innovation today, applied technical training, lifelong learning programmes and continuous upskilling are necessary to equip workers with the ability to understand and operate evolving technologies and business models and, ultimately, to stay gainfully employed.
Policy-makers need to prioritise skills-based training with the AI-infused economy in mind. Successful economies from the past, such as Germany, South Korea, Singapore and Japan, offer valuable lessons. These countries emphasised engineering excellence, technical innovation and robust technical training to propel their economies, improve the employability of workers and provide the skills needed to compete in the global economy.
They created skills frameworks and incentivized
companies to invest in training. The results are well known.
In the age of AI, industry participation and collaborative approaches are critical for narrowing the gap between traditional tertiary education and the reality of work.
Workers need hands-on experience with state-of-the-art technologies. Educators and education institutions need to reimagine pathways and craft learning programmes that align with the technical and practical reality of today’s job market. In some cases, traditional educational credentials and formats must be reimagined and updated.
Stakeholders need to collaborate to identify new skill requirements and create sustainable models to upskill and reskill workers at scale and fast.
By forging partnerships and investing in human capital, emerging and developing economies can grow out of poverty and transition into more vibrant, equitable and modern economies.
Nurturing human capital is essential for a prosperous future. New approaches for rapid and continuous upskilling and reskilling are needed. Online learning platforms, micro-credentials and collaborative initiatives between educational institutions and industry can support this effort and accelerate the transition to a greener, more efficient and inclusive world where jobs and skills development pathways are readily available.
From the climate crisis and geopolitical headwinds to next-generation technologies, a series of complex challenges are rewriting the rulebook for global value chains.
Against this backdrop, what are manufacturers and supply chain companies doing to ensure their operations are fit for future success?
Most successful firms are moving away from making location decisions based on cost alone to a more complex process that considers factors including performance, resilience and sustainability.
Countries that want to remain competitive and position themselves as manufacturing hubs must embrace this shift. By adopting innovative policies across key country-level readiness drivers, nations can boost their appeal for foreign investment, potentially increasing GDP and their share of global value chains, the report suggests.
Here are some examples of those archetypes and how they are growing their manufacturing.
While Brazil’s GDP per capita and manufacturing’s share of GDP are below average, the country is making efforts to boost manufacturing’s economic role. The service sector now has a larger share of the GDP than the manufacturing sector.
Brazil is the world’s leading source of coffee and a major producer of sugar, soy, and beef. It also exports significant amounts of steel, automobiles, and electronics. For decades, Brazil has been actively promoting manufacturing to diversify its production and reduce its reliance on agricultural exports. In early 2024, the country launched a new policy plan to drive this effort – called Nova Indústria Brasil. This policy defined strategic areas for investment to stimulate technological development and increase the competitiveness of the Brazilian industry.
Key initiatives under this plan include measures to digitally transform industrial companies and invigorate the country’s semiconductor industry.
Like Brazil, India is in the adapter quadrant of the country archetypes. It also boasts a sizeable service sector, which is the main contributor to its overall GDP.
Alongside, it is making significant strides in manufacturing, with some states positioning themselves as key hubs for industries such as automotive. The country is expected to become a global player in light vehicle production, textiles, and electronics.
It is working to create a more stable and investment-friendly trade manufacturing environment through efforts such as the Production Linked Incentive Scheme. This public-private partnership initiative, launched in 2020, provides industry incentives for sales of domestically made products. This has increased the country’s reliance on domestic sourcing components, reducing imports and benefitting the country’s manufacturing capabilities. It has led companies, including Apple and its suppliers, to work closely with the Indian
government to increase operations in the country.
Manufacturing has become a critical part of Bangladesh’s economy, thanks to rapid industrialisation.
Once dependent on jute and subsistence farming, the country has halved poverty and significantly boosted GDP by becoming a powerhouse in global supply chains for textiles and garments.
Government initiatives to attract foreign investment have been at the heart of this effort. Through policies such as allowing duty-free importation of machinery in export zones and signing trade agreements with the US and Europe, Bangladesh has created a garment sector that employs 4 million people in more than 3,500 factories and exports goods worth $43 billion to 167 countries.
The country has also undertaken major infrastructure initiatives to develop its network of waterways and ports, strengthening its role as an
Mexico has developed a strong manufacturing base in sectors such as electronics and automotive. This is partly due to trade agreements such as the North American Free Trade Agreement, now known as the US-Mexico-Canada Agreement.
The country’s proximity to the US makes it an attractive destination for manufacturing, especially as more supply chain leaders look to mitigate risk with a nearshoring strategy, in which they look to move production closer to the customer. In 2023, Mexico passed China as the top exporter to the US.
However, the new Donald Trump administration’s potential tariffs on goods made outside the US could influence supply chain strategies and impact Mexico’s manufacturing competitiveness.
Streamlined regulatory frameworks and tax incentives are also boosting manufacturing – for example, in securing carmaker Audi’s investment to build a ‘smart factory’ – equipped with the latest technology – in San José Chiapa. This partnership has created thousands of jobs and last year produced nearly 200,000 vehicles.
A global leader in high-technology and innovation-driven manufacturing industries, the US is an example of a converger.
The number of manufacturing firms and plants in the US has fallen by about 25% since 1997. But in recent years, the country has prioritized reinvestment in advanced manufacturing.
The Inflation Reduction Act, which signed into law investments in clean technologies, also addressed the offshoring of US industry and promised to reinvest in US manufacturing at scale.
The law sparked an uptick in manufacturing, with manufacturers of battery components, wind and solar equipment, and EVs announcing tens of billions of dollars in new investments.
However, to realise the full benefits of these investments and cement its competitive edge, the US
must also scale up its industrial workforce to meet rising demand.
The US is also reinforcing its leadership in advanced technologies through initiatives such as the Creating Helpful Incentives to Produce Semiconductors (CHIPS) Act and is boosting supply chain resilience through the Promoting Resilient Supply Chains Act.
Such government support is a critical component in enabling countries to become attractive destinations for manufacturing, the Forum report notes.
Singapore exemplifies a scaler. It boasts a strategic location, a pro-business government and advanced infrastructure. It has developed a highly sophisticated manufacturing sector, particularly in chemicals and electronics – where it is the world’s fifth largest exporter of high-tech goods.
Under its Manufacturing 2030 plan, Singapore aims to become a leading industrial hub and increase its manufacturing output by 50% by the end of the decade. The focus is on both physical and digital transformation, accelerating innovation in advanced electronics and adopting Industry 4.0 technologies such as AI and robotics. Singapore also invests in smarter, more sustainable manufacturing through research, development, and talent partnerships.
For example, Singapore’s SkillsFuture Initiative, designed alongside the private sector, provides financial incentives and subsidies for training programmes to enhance workforce capabilities. The country is also engaging in public-private collaborations, including one with Siemens to advance sustainable manufacturing through the integration of renewable energy.
investing in and adopting policies across a holistic array of readiness factors, will help countries enhance their attractiveness for next-generation manufacturing and gain a competitive edge amidst the rewiring of global value chains.
While these systematic changes take time, their long-term success depends on collaboration between the public and private sectors to ensure that industrial strategies reinforce investment in core areas critical to the future of manufacturing and supply chains.
While these systematic changes take time, their long-term success depends on collaboration between the public and private sectors to ensure that industrial strategies reinforce investment in core areas critical to the future of manufacturing and supply chains.
In the current challenging business environment, people are looking to technology to provide insights into operations and identify opportunities to improve efficiency.
By leveraging advanced technology and data analytics, Teletrac Navman enables businesses, including those in the manufacturing sector to optimise their operations, enhance safety protocols, and maximise productivity.
Using telematics can address key business drivers such as efficiency, safety and sustainability. Across a business, Teletrac Navman’s solutions can optimise operations in:
• Vehicle tracking: Real-time location data helps optimise routes, minimise delivery times, and improve fuel efficiency.
• Driver behaviour monitoring: Identify and address risky driving habits to enhance safety, reduce accidents, and lower insurance premiums.
• Maintenance scheduling: Predictive maintenance alerts can prevent costly breakdowns and ensure vehicles are always in optimal working condition.
• RUC management: Efficient electronic RUC management means operators only buy the RUC they need and can easily claim rebates for mileage off road.
Asset tracking:
• Equipment location: Track valuable equipment like forklifts, generators, and construction machinery to prevent theft and ensure proper utilisation.
• Inventory management: Monitor the movement of goods within the manufacturing facility and across the supply chain for improved inventory
control.
Supply chain visibility:
• Real-time tracking: Gain visibility into the entire supply chain, from raw material sourcing to finished goods delivery.
• Improved delivery times: Optimise logistics and meet customer delivery expectations more effectively.
• Reduced delays: Identify and address potential disruptions proactively to minimize delays and maintain production schedules.
• Driver safety programs: Implement safety programs with features like driver coaching and fatigue monitoring to enhance driver safety and reduce accidents.
• Compliance with regulations: Ensure compliance with relevant regulations, such as work time regulations for drivers.
• Detailed reports: Generate comprehensive reports on fleet performance, fuel consumption, driver behaviour, and other key metrics.
• Data analysis: Analyse data to identify areas for improvement, optimise operations, and make informed business decisions.
As network operators prepare to shut down their aging 3G infrastructure later this year, many businesses still need to transition to newer 4G enabled telematics devices.
Making the transition to 4G is a great time to reassess all your telematics requirements and check that your provider understands and is able to meet your
changing business needs now and into the future.
Research shows that a more diverse, equitable and inclusive culture in a workplace brings innovation, creativity, boosts morale and improves employee engagement. This helps increase productivity and collaboration to result in better decision making and problem solving.
Teletrac Navman is a member of Diversity Works NZ and is committed to supporting an inclusive industry made up of all people from diverse communities. By fostering a supportive work environment, offering professional development opportunities, and recognising employee contributions, the company ensures that its team remains motivated and committed to delivering excellence in service and innovation.
Teletrac Navman’s new range of asset trackers can play a crucial role in asset protection by enabling businesses to track the location, maintenance schedules, and costs of their assets.
With advanced features such as extended battery life and indoor tracking capabilities, these devices provide real-time visibility and control, ensuring optimal security and operational efficiency. These battery-powered trackers utilise 4G communication technology, providing businesses with the capability to monitor both powered and unpowered assets seamlessly.
They’re designed to withstand harsh environmental conditions, ensuring reliable performance for extended periods of time. This makes them ideally suited to construction, mining, transport and equipment rentals as well as manufacturing.
By: Glenn Dobson, CEO of The Drug Detection Agency (TDDA)
Would you feel safe if your child’s school bus driver had been drinking before their shift? Or if a surgeon operating on a loved one was under the influence? The answer is no. Yet, on shop floors, in industrial plants, and across workplaces in the country, employees impaired by drugs or alcohol put themselves and others at risk.
Data from The Drug Detection Agency (TDDA) highlights concerning trends. Of workplace drug tests conducted by TDDA in New Zealand, 4.55% detected drugs. THC, cannabis’s active component, accounted for 72.9% of cases, followed by amphetamines at 34.2%, with opioid detection rising.
New substances, including fentanyl and tramadol, are appearing in workplaces. Fentanyl, a synthetic opioid 80 times stronger than morphine, and tramadol, a potent painkiller, are highly addictive and can impair judgment.
Identifying substance abuse in employees is difficult, and symptoms like poor concentration, absenteeism, and behavioural changes often mimic stress or fatigue. Long-term cannabis use can impair memory and attention.
Fentanyl poses extreme danger in the manufacturing space as it involves heavy machinery and dangerous equipment, where impaired judgment can lead to catastrophic outcomes.
A common problem is that managers lack training or the confidence to address drug concerns without risking legal disputes. The difficulty lies in moving between suspicion and verification without triggering a personal grievance. Educating them on handling such situations within legal boundaries is essential.
Substance abuse silently erodes productivity, increasing absenteeism, workplace errors, and injuries. Impaired employees take unnecessary risks and exhibit poor judgment, undermining safety and efficiency.
According to the 2023 Drug Harm Index, drug-related harm cost New Zealand $1.9 billion in 2023. For manufacturing businesses, where precision and safety are non-negotiable, the stakes are even higher. A single incident caused by impaired judgment can result in significant financial losses, reputational damage, and legal liabilities.
Under the Health and Safety at Work Act 2015, employers have a duty to manage drug and alcohol workplace risks. Here are some easy steps businesses can take to mitigate these risks:
1. Establish a clear policy: Implement a robust drug and alcohol policy that outlines expectations, testing procedures, and support mechanisms. Ensure this policy is communicated clearly to all employees, starting from the interview stage.
2. Focus on prevention and protection: Emphasise a culture of safety and well-being rather than punishment. Provide education on the dangers of substance abuse and offer support for those seeking help.
3. Regular testing: Introduce a regular drug testing programme tailored to business needs. Ensure all testing is conducted in compliance with the policy to avoid legal grievances.
Professional training: Equip managers with the skills to identify and address substance abuse confidently. This includes understanding the signs, conducting difficult conversations, and knowing the legal implications.
5. Seek expert advice: Partner with professionals like TDDA to design and implement accredited drug and alcohol screening programmes. This means compliance with legal standards and minimises risks.
Rushing into drug testing without preparation can lead to legal complications. To prevent this, find an accredited testing partner, like TDDA, that offers tailored solutions, including policy design, training, and 24/7 mobile testing, allowing businesses to manage risks, on site and with less downtime for the business.
New Zealand’s manufacturing sector has a strong reputation, but recent events put it at risk. Now is the time to review workplace safety measures.
After all, a robust substance management programme ensures a safer, healthier, and more
It will now be easier to identify and evaluate landslides risk thanks to new guidance for geotechnicians from the New Zealand Geotechnical Society (NZGS).
Landslides are New Zealand’s deadliest and costliest natural hazard on average but, until now, there hasn’t been a consistent approach for evaluating landslide hazards.
“The lack of a good practise document can sometimes lead to the same slope being evaluated by different people with completely different results,” says Richard Justice, the lead author of the guidance and an expert in geotechnical risk assessment.
“For years, New Zealand’s geotechnical community has been calling for clear and consistent advice on how to conduct site investigations and hazard assessments for landslides, and we’ve made a big step in that direction through this new guidance.
“This guidance reflects the huge amount of knowledge and research in New Zealand and internationally ranging from land use planning, investigation, model development, stability assessment and mitigation.
“We have pulled together the best of what’s currently available and added our own insights as experienced practitioners,” he says.
The NZGS has released the first part of its Slope Stability Guidance, which outlines the best practise on identifying landslide hazard and recommendations on what to do if a landslide or unstable land is identified.
Subsequent units, which will be released throughout 2025, will provide more details on recognising landslides, field investigations, analysing unstable slopes and mitigation strategies.
Richard hopes the guidance can support practitioners but cautions that it does not replace the need for technical expertise or location-specific advice.
The guidance, which was funded by the Natural Hazards Commission (NHC) Toka Tū Ake with additional support from MBIE, aligns with NHC’s goal
of supporting stronger homes built on better land. Dr Wendy Saunders, NHC’s principal advisor and land-use planning champion, says, “many of us live on slopes, especially in cities where space is limited. This can be a problem after an earthquake or heavy rainfall, because if slopes become unstable and slip, they can cause damage to property and infrastructure. With an increase in both urban development and extreme weather events, we can expect to see more landslips if nothing is done to mitigate risks.”
NHC currently receives more claims for damage due to landslips than any other natural hazard. Since the Auckland anniversary floods in January 2023, losses from landslips have totalled $302 million – over four times the cost from all other natural hazards combined.
James Robinson, Head of Services for Asia Pacific at Syspro
Manufacturers, face challenges magnified by geographical distance from key international markets and higher labour and production costs, demanding a relentless focus on agility and efficiency. Navigating global market dynamics
Australasian manufacturing sectors operate within a complex, rapidly evolving global economy. Supply chain disruptions, geopolitical tensions and fluctuating commodity prices continue to reshape the industry.
According to BHP’s latest economic outlook, major economies are experiencing varying growth rates. Developed economies are stabilising after grappling with high interest rates, while India remains on a rapid growth path.
Meanwhile, China’s uneven recovery underscores ongoing challenges within its industrial sectors, though it is expected to meet 2024 growth targets. Geopolitical risks are expected to remain elevated, adding uncertainty to global trade. Industrial activity in 2023 remained sluggish due to subdued global demand and the lasting impacts of the energy crisis. However, BHP projects a recovery in demand for key commodities like steel, copper and nickel by 2025, presenting growth opportunities for Australian manufacturers aligned with these sectors. For local manufacturers, this volatile landscape brings both challenges and opportunities. Higher interest rates continue to suppress domestic demand, but the recovery in commodity markets offers a chance to supply essential components to industries such as construction, transport and energy production.
In considering the shifting market challenges, manufacturers must adopt flexible, data-driven operational strategies to capitalise on opportunities. Enterprise Resource Planning (ERP) systems can help manufacturers respond effectively to shifts in demand by improving processes and enhancing efficiencies to remain competitive.
ERP systems help manufacturers integrate essential processes, including procurement, production, inventory management and financial reporting, into a unified platform that offers real-time visibility across operations.
This operational visibility empowers them to optimise workflows, identify bottlenecks early and synchronise production schedules with demand forecasts. The ability to pivot swiftly and adjust to shifting market conditions will enable Australian manufacturers to be competitive in a dynamic environment.
ERP systems build resilience
Manufacturers can use an ERP system to gain real-time insights into its supply chain to prevent avoidable issues from impacting it.
If raw material delays arise, the system can detect and flag them before they become costly disruptions. With this valuable data, a manufacturer can reallocate resources, adjust production timelines, or source alternative suppliers to maintain continuity and build resilience.
In addition, an ERP system will align production planning with demand forecasts, ensuring machinery and resources are optimally utilised, minimising downtime and reducing operational waste.
These efficiencies translate directly into lower costs, higher productivity, and a stronger competitive position in domestic and international markets.
ERP systems also open doors for new growth opportunities, such as expanding into new international markets. Manufacturers can use their ERP platform to streamline cross-border operations, manage currency risks and to ensure compliance with trade regulations, which are key enablers for seizing global market opportunities.
ERP as the foundation for operational excellence
ERP systems go beyond enabling agility; they provide a foundation for continuous improvement and innovation. Key benefits include:
• Production planning and scheduling: ERP systems create data-driven production schedules that adapt in real-time to changing demand forecasts, ensuring efficient resource allocation and minimising downtime.
• Innovation and product development: ERP platforms facilitate collaboration between R&D teams and market analysts, helping manufacturers align new products with customer needs and accelerate time-to-market.
Embracing the future of manufacturing
The ability to pivot quickly and respond proactively to market disruptions will be critical in this era of uncertainty and opportunity. Manufacturers that invest in ERP systems will enhance operational efficiency and position themselves for long-term success, reducing waste, improving productivity and gaining a sustainable competitive edge. Looking
Hyster’s new series delivers robust performance comparable to internal combustion engine (ICE) lift trucks. The Hyster J2.0-3.5XTLG series, capable of lifting up to 3.5 tonnes, is designed for both indoor and outdoor operations, providing a durable and flexible option with zero exhaust emissions.
The new electric series features up to 34% better through-mast visibility, a spacious weatherproof cabin, large superelastic tires, and high ground clearance. These design elements allow operators to maintain productivity over uneven surfaces and in challenging weather conditions.
The new models can be used both inside industrial warehouses and outside in yards or loading areas, particularly in industries such as wood, metals, chemicals, and construction materials.
The lithium-ion battery technology in these forklifts also delivers significant productivity advantages. With opportunity charging during breaks, businesses can maximize uptime across shifts.
The battery itself is maintenance-free, eliminating the need for engine servicing or battery changes, thus saving operational time and reducing total cost of ownership.
Compared to lead-acid battery charging, lithium-ion charging offers greater efficiency, giving users more power at no additional energy cost. Additionally, energy costs with the new Hyster models can be halved compared to ICE counterparts. These forklifts provide long-lasting value with an extended battery life and a standard 5-year warranty.
Wittenstein smart gearboxes from the TPK+ series with cynapse functionality, are those deployed by startup company Ocean Energy on its Kite Hydrogen Ship Prototypes and implemented for the production of green hydrogen.
When wind energy is harvested for electrolysing seawater directly on board, these power-dense, intelligent and communication-enabled hypoid gearboxes perform important functions controlling the four up to 1200 meter-long ropes of the Kite Propulsion system’s 60 square meter kite.
Ocean Energy opted for a reliable, future-proof technology comprised of robust TPK+ gearboxes and their cynapse functionality, i.e. with integrated sensors, logic and an IO-Link data interface in the gearboxes.
These smart gearboxes will supply essential operating and status data, while the energy ships that produce green hydrogen in the six permanent oceanic trade wind zones will be smartly navigated there according to the wind forecast..
Kite Hydrogen Ship – inspired by kitesurfing
The basic idea was to harness the forces acting on the kite that pull the kite’s ropes and convert them into electricity.
At the heart of the Kite Hydrogen Ship concept is the patented K1 Kite Propulsion system, which
can be imagined as a green power socket for the on-board electrolysis process. The challenge for the smart hypoid gearboxes is to control the kite’s four frequency converter-driven ropes as they generate electricity during the harvesting journey by launching and pumping the kites.
A large part of the energy that is generated in this way by the K1 Kite Propulsion system is utilised directly on board for the production of green hydrogen.
A hydrogen plant of this kind is designed to produce around 1000 tons of green hydrogen during its eight-week harvesting journey. That adds up to a good 6000 tons per year – enough to supply about 40,000 hydrogen cars or power an Airbus for almost twelve months.
The aim of the energy ship fleet now in the pipeline is to produce green hydrogen costing just 2 euros per kilo by 2035 – in other words, significantly more economically than with any other green technology known to date.
Dynamic wind loads of up to four tons per rope – no problem for a TPK+ hypoid gearbox
Hypoid gearboxes from the TPK+ series were selected to control the four steering ropes while pumping the kite based on simulation and application data. Their right-angle design is central to the ultra-space-saving principle of the entire K1 Kite Propulsion system and its integration into a seaworthy container.
Customers can choose from models equipped with either 154V or 115V batteries to match their operational intensity. The Hyster J2.0-3.5XTLG also includes a larger battery capacity than many competitors, enabling longer run times and minimizing downtime.
These size 300, two-stage gearboxes have a ratio of i=100 and are characterized by high torsional rigidity, low torsional backlash and greater absorption of external forces. The high-quality hypoid teeth simultaneously ensure high torque and exceptionally smooth running.
When a Kite Hydrogen Ship sets off semi-autonomously on a harvesting journey, the kites – and hence the propulsion system’s main axis – will be subjected to extremely diverse movements and forces. It was this that tipped the scales for Ocean Energy in favor of the TPK+ with cynapse functionality.
Transmission functions and operating data like acceleration values can be monitored and analyzed remotely in this way on the high seas. www.treotham.com.au
Auckland based KANDO Innovation headed by Keith Blenkinsopp is a New Zealand manufacturing inspiration in innovation and success with world leading design and technology leading to major export sales in the competitive international markets of America and Europe.
KANDO Innovation began with drive and an objective to make New Zealand and international markets safer, more efficient and confident, leading to a safer workplace through the development and implementation of the latest technology.
Leveraging the latest in engineering, automation, machining, vision technologies and more, the idea was to maximise competitive advantage whilst meeting the challenges of safety, skilled labour shortages and minimising downtime and wastage in industry.
Advanced Okuma CNC machines and robotics today play an important part in this strategy with the first Okuma machine purchased in 2019 and now with an additional four machines following the Okuma Monozukuri philosophy in “The Art of Making Things Better’.
KANDO Innovation is the home of the Guardian Bandsaw and the world’s first and only automated mussel opener each developed with engineers working closely with industry leaders on innovative ways to automate and improve repetitive manual and potentially dangerous processes.
The Guardian Bandsaws are manufactured in a range of sizes to meet the market demand in the
meat industry and supermarket butcheries and these machines incorporate world leading safety technology to keep workers safe.
Today the company employs more than eighty personnel plus ten in the USA and has an in-house design team of twenty covering such disciplines as software, mechanical, electrical and industrial design. KANDO has a positive approach to training with five apprentices under training in machining, fabrication and assembly operations.
The latest innovation from the KANDO design team is a meat membrane skinner which incorporates world leading safety vision technology that is designed for the meat industry and about to be released. This advanced machine will be welcomed by the industry due to its safety features and innovative technology.
With exports already a major part of its manufacturing output KANDO Innovation is poised for further major expansion and has geared up ready for the rapid uptake of its tested and proven Guardian Brand Bandsaws and the latest membrane skinner machine with advanced orders from the USA and new markets opening up in Europe.
“Once we build and install the systems and technologies for our clients, the same team that
was first engaged with the customer to capture and incorporate the lessons for success, are involved in the installation, training and on-going service and support,” said Keith Blenkinsopp.
The ThinkTop V55 offers unmatched peace of mind to users. Its durable, maintenance-free design ensures reliable performance even in the most demanding environments. Tamperproof construction and built-in self-diagnostics maximize uptime, making it a dependable choice for critical operations.
With its advanced features and compact design, the ThinkTop V55 sets a new standard for diaphragm valve monitoring and control, optimising performance and efficiency.
The ThinkTop V55 supports fast, reliable installation and quick commissioning. Onsite auto setup takes
less than a minute, while live setup – enabling quick remote valve configuration – requires only a minute or two.
Exchanging or hot-swapping control units can take place without disrupting production, ensuring operational and product safety.
The slim profile of the ThinkTop V55 optimises space utilisation, making integration into new or existing installations effortless. It is easy to mount in any position on the valve actuator to ensure ideal connection.
Moreover, the ThinkTop provides 360° LED visual status indication, making the valve position clearly visible from the factory floor. It delivers highly reliable performance in demanding environments thanks to its self-diagnostic features that boost uptime and productivity.
The ThinkTop V55 provides real-time diaphragm valve monitoring through digital, ASI 3.0, or IO-Link interfaces, ensuring accurate valve position readings. Its point-to-point IO-Link communication protocol integrates sensors and actuators into any automation system, regardless of fieldbus.
This integration makes it easier to capture, store, analyse, and act upon meaningful real-time data thereby supporting Industry 4.0 initiatives, streamlining configurability and process control.
The ThinkTop V55 is designed for Alfa Laval diaphragm valves, offering a true one-size-fits-all solution. It shares the same robust and reliable features as the ThinkTop V series, trusted by hygienic industries worldwide. Moreover, it simplifies purchasing, setup, operation and maintenance
Sustainability is no longer a “nice-to-have”—it’s a must-have. For New Zealand manufacturers, 2025 will bring new challenges and exciting opportunities. As the world grapples with climate change, resource scarcity, and shifting regulations, businesses that embrace sustainability will not only keep up but thrive.
To stay competitive, manufacturers need to navigate changes in climate adaptation, the circular economy, transparency, and stakeholder expectations. It’s about planning ahead, staying flexible, and taking action. Here are six practical tips from thinkstep-anz’s sustainability experts to help you lead the way in 2025.
1. Stay financially, environmentally and socially sustainable 2025 is expected to bring continued disruption and uncertainty on the global stage. Political and economic turbulence may distract some industries from their sustainability goals. However, maintaining focus on long-term objectives is critical.
“Succeeding sustainably means being financially sustainable as well as environmentally and socially,” explains Emily Townsend, Services Director at thinkstep-anz.
For manufacturers, this means building resilience by investing in sustainable practices that match up with stakeholder priorities and market expectations. Even if external pressures temporarily lessen, pushing forward with sustainability can pay dividends in the long run.
Your Action: Review your sustainability strategy to ensure it balances environmental goals with financial and social resilience. Focus on initiatives that will have long-term benefits for your business and stakeholders.
2.Prepare for the circular economy to go mainstream
The circular economy is no longer a niche concept. In 2025, manufacturers exporting to the EU will face increasing requirements to quantify and communicate the circularity of their products.
Aligning with standards like ISO 59020 and incorporating circularity metrics into Environmental Product Declarations (EPDs) will become essential to maintaining market access.
“We’ll see the circular economy go mainstream,” predicts Jim Goddin, Head of Circular Economy at thinkstep-anz. This trend is also gaining traction locally, with Green Star for Buildings introducing circularity metrics. Manufacturers who act now to measure and improve circularity will gain a competitive edge.
Action: Start gathering data to assess your products’ circularity. If you’re already working on an EPD, consider adding circularity metrics like the Material Circularity Indicator (MCI). Even without an EPD, measuring circularity will position your products to stand out in the market.
3. Focus on climate resilience and adaptation
With the reality of surpassing the 1.5°C warming threshold becoming increasingly likely, climate
adaptation will take centre stage in 2025.
“Adaptation, transparency, and innovation will define the sustainability landscape in the year ahead,” says Katharina Bauch, Head of Carbon at thinkstep-anz. High-quality carbon data and transparent reporting will be essential as businesses strengthen their resilience to climate risks. Working with your suppliers to get better data on your Scope 3 emissions does more than just improve accuracy. It builds stronger relationships and helps you find ways to cut emissions together.
Your action: Collaborate with your suppliers to collect accurate emissions data and improve your carbon disclosures. Explore how you can simplify and improve your GHG reporting processes.
4. Be transparent about your sustainability commitments
In a world of increasing scrutiny, transparency is non-negotiable. Consumers, investors, and employees are becoming more selective, favouring businesses that “walk the talk” on sustainability. Martin Fryer, Head of Strategy and Disclosures at thinkstep-anz, highlights this trend: “Consumers, employees, and investors will increasingly vote with their feet and wallets.”
For manufacturers, this means embedding stakeholder needs into your strategy and communicating your progress clearly. Authenticity and accountability will help build trust and loyalty.
Your action: Conduct a stakeholder analysis to understand what matters most to your customers, employees, and investors. Use this information to guide your sustainability initiatives and reporting.
5. Prepare for regulatory and market shifts
Regulations around sustainability and climate-related financial disclosures are ramping up globally and locally. While political uncertainty may create short-term delays, the long-term trajectory is clear: businesses need to act now to meet future expectations.
Nicole Sullivan, Impact Director at thinkstep-anz, warns that 2025 may start with a sense of waiting but will end with an urgent need for action. “Get
your house in order so that you can respond quickly to changing expectations when they arrive,” she advises.
Your action: Identify gaps in your current sustainability practices and address them proactively. Ensure you’re ready to meet new regulatory requirements and market demands as they arise.
6. Avoid greenwashing by focusing on credible claims
Greenwashing is under increasing scrutiny, with regulators, consumers, and stakeholders expecting businesses to back up their sustainability claims with evidence. “Misleading claims can erode trust and lead to reputational damage,” warns Senior Sustainability Communicator Jule Scherer.
To avoid these pitfalls, make sure that your sustainability initiatives are measurable and transparent. Clear communication about your progress, backed by robust data, will help you build credibility and stand out as a trusted manufacturer. Your action: Review your marketing materials and sustainability claims to check that they’re backed by verifiable data. Use recognised frameworks and standards to guide your reporting and communication.
For New Zealand manufacturers, 2025 is a year to embrace sustainability as a core part of your business strategy. By focusing on financial resilience, circularity, climate adaptation, transparency, regulatory readiness, and innovation, you can position your organisation for success in a rapidly changing world.
The challenges may be significant, but so are the opportunities. With proactive planning and a commitment to sustainability, your business can not only survive but thrive in the year ahead.
Photo by Nathan Maduta on Unsplash www.thinkstep-anz.com
An Australian-led scientific breakthrough to increase oil yield from plants will help advance the production and use of biofuels, such as sustainable aviation fuel.
Developed over a decade by scientists from Australia’s national science agency, CSIRO, the technology was acquired by Australian agricultural innovation company Nufarm.
The Biomass Oil Project has Nufarm leading a new global research partnership to further develop the technology.
Oils from plants are produced by specialised seeds and fruits, but CSIRO scientists looked at extending that to the biomass of the plant, including the leaves and stem.
CSIRO’s Dr Thomas Vanhercke, who has been working on the project for more than a decade, said the technology would have the potential to create an important new global energy source.
“We were inspired to develop this technology in response to the world’s need for increased production of plant oil without impacting on food security,” Dr Vanhercke said.
“With CSIRO’s existing expertise in the area and the
partnership with Nufarm on the Omega-3 canola project, we started thinking about how to extend that to the challenge of developing industrial scale feedstock oil from plants.
“We took the genetics for seed oil production and incorporated them across a range of crops with promising success.”
Current project lead, Dr Xue-Rong Zhou, said the world-leading research in boosting oil yield from plants is a major breakthrough for Australia and beyond.
“This development of new biofuels and renewable oils will support a sustainable future,” Dr Zhou said.
“We are looking forward to working with Nufarm and our global research partners to deploy the technology into high biomass energy cane and sorghum varieties and make it a reality.”
Nufarm CEO, Greg Hunt, said the company is now bringing together researchers from CSIRO, the University of Florida (UF), USA and the Instituto
Agronomico (IAC), Brazil to take the work to the next level.
“We have assembled a consortium of world-class R&D and technical partners who bring unique experience to develop this technology,” he said.
“Nufarm is also working with key strategic partners to further support the technical project development and future downstream commercialisation.”
Nufarm is a global agricultural innovator providing crop protection and seed technology solutions. Established over 100 years ago, Nufarm is listed on the Australian Securities Exchange (ASX:NUF) with its head office in Melbourne, Australia.
X3S FastMig Synergic and X3P FastMig Pulse are your fast route for completing high-quality welds in wide ranging welding and fabrication environments.
For more details call Matt on 0220 200 626
robotics into their operations.”
However, this level of investment underscores the cost barriers that smaller manufacturers might face. Without access to well-resourced industrial hubs like Drury, smaller players may struggle to remain competitive in a global market increasingly defined by automation and efficiency.
The industrial land shortage in Auckland has implications far beyond manufacturing. The lack of suitable sites may stymie growth in associated sectors such as logistics, warehousing, and even retail. Manufacturers unable to expand domestically might look offshore, taking jobs and investment with them.
As Auckland continues to grow, the competition for land will intensify. Stats NZ recently reported that Auckland’s population is projected to reach two million by 2030, adding further pressure on infrastructure and land resources.
The Need for Investment in Transport Infrastructure
Hughes says there is a growing need to invest in critical roading infrastructure in the region to support Auckland’s manufacturing and logistics sectors.
He highlights the proposed Mill Road project as an essential initiative to strengthen Auckland’s transport resilience and ensure better connectivity between the city and the Waikato.
continued from Page 11
“This type of infrastructure is vital for enabling the efficient movement of goods and services, particularly for businesses operating in South Auckland and the Waikato region.
“By providing an alternative to heavily congested routes like State Highway 1, Mill Road would reduce travel times, lower freight costs, and improve supply chain reliability— key factors for the region’s economic growth,” Hughes says.
Despite these challenges, the situation presents opportunities for innovation within the manufacturing sector. Businesses can explore solutions such as:
• Vertical Integration: Maximising the use of smaller land parcels by building upward with multi-level facilities.
• Decentralisation: Expanding operations to regions with more available land, such as Waikato or Bay of Plenty, while leveraging improved transport links to Auckland.
• Collaboration: Sharing resources such as energy infrastructure and logistics hubs within industrial clusters like Drury South Crossing.
Technology will also play a role in mitigating land scarcity. The rise of additive manufacturing (3D printing) could enable smaller, decentralised production sites, reducing the need for massive industrial facilities.
How do we turbocharge manufacturing?
ASB is focused on enabling higher productivity, and this new partnership will help manufacturers invest in upgrading their factories more easily.
We’ve seen how readily available software and hardware can help manufacturers move ahead. Software such as Manufacturing Execution Systems (MES) and Enterprise Resource Planning (ERP) are having a profound impact on efficiency and productivity.
MES helps track and manage production in real time, providing real-time insights into operational inefficiencies and helping optimise processes.
ERP systems integrate data from all parts of the business, giving manufacturers a comprehensive view of operations and enabling more informed decision-making. With these tools, manufacturers can scale more easily, manage growth more effectively, and improve decision-making by tapping into data-driven insights.
The ability to leverage artificial intelligence (AI) will further boost productivity, allowing manufacturers to predict maintenance needs, optimise supply chains, and even design more efficient products.
Right now, many New Zealand businesses have yet to digitise their processes sufficiently to take advantage of AI, so many will continue to miss out on these
game-changing opportunities.
On the hardware side, technologies such as vision systems, robotics, and smart products offer even more opportunities for growth. Vision systems, powered by machine learning, enable faster, more reliable quality control, ensuring high quality standards are met across the board.
These systems are invaluable in industries like electronics and consumer goods, where precision is paramount.
In addition, smart PPE such as wearable exoskeletons, fall detection suits and safety glasses with integrated sensors can keep your skilled workforce safe from harm.
Robotics and automation solutions, particularly collaborative robots (cobots), are helping to improve productivity by working alongside human workers and digitising manual processes.
Cobots can be redeployed across multiple tasks, offering flexibility and cost-effectiveness to small manufacturers that may have previously been unable to justify large-scale automation.
Smart products are another exciting area of growth. These products capture and analyse data in real time, giving manufacturers valuable insights into how their products are performing and how they
To ensure the continued growth of New Zealand’s manufacturing sector, policymakers and industry leaders must address the industrial land shortage with urgency. This includes:
• Proactive Rezoning: Identifying areas where industrial land can be expanded without compromising environmental or agricultural priorities.
• Incentivising Innovation: Providing grants or tax incentives for manufacturers adopting space-saving or sustainable technologies.
• Future-Proofing Infrastructure: Investing in power, transport, and connectivity to attract high-tech industries
The industrial land shortage in Auckland is not just a real estate issue—it is a strategic challenge that will shape the future of New Zealand’s manufacturing sector. As global competition intensifies and technological demands increase, businesses must adapt quickly to remain competitive. Developments like Drury South Crossing offer a glimpse of what’s possible when long-term planning and investment align with industry needs.
However, the question remains: will Auckland’s manufacturing sector seize these opportunities, or will the constraints of geography and planning hold it back? With collaboration between government, industry, and innovators, the potential to thrive in the face of this challenge is well within reach.
can better serve customer needs.
Companies like Tesla and Apple are already benefiting from this trend, as they use data collected from their smart products to inform everything from design to after-market services. New Zealand manufacturers who adopt similar technologies will be able to unlock new opportunities for growth and improve their product offerings.
Governments and manufacturers across the globe are investing, and if New Zealand is to succeed in doubling its export value, it must do the same.
To achieve a globally competitive manufacturing sector, New Zealand must embrace advanced manufacturing technologies to enhance and support our skilled workforce.
Despite the current struggles with limited resources and low digital maturity, it’s clear that collaboration between business and government remains vital to lifting our capacity and capability to keep producing amazing products.
For the future of the industry, and the jobs and wealth it contributes to society, the convergence of smart people, smart government support, and smart factories is essential.
Only then can New Zealand truly turbocharge its manufacturing growth and compete on the global
Seequent, The Bentley Subsurface Company, has announced a strategic partnership with the International Geothermal Association (IGA) to boost geothermal energy’s role as a sustainable and reliable renewable energy source.
Geothermal draws energy from hot fluids travelling through the Earth’s subsurface. These fluids are utilised to drive turbines producing electricity, directly to heat homes or in industrial processes.
Traditionally, geothermal energy has been viewed as energy restricted to environments where it is visible - however new technological breakthroughs and the realities of needing 24/7 access to energy are changing the investment landscape.
The International Geothermal Association is the leading global platform on geothermal energy.
Seequent software supports more than half of the world’s geothermal electricity production, bringing
clarity to a complex unseen challenge of managing subsurface resources. The company has long been at the forefront of technical advancements in the industry, for example, bringing geothermal energy directly to heat homes in Paris and Munich.
Seequent’s latest innovations include adding new physics capabilities to its software to trace fluids more accurately, ultimately leading to more efficient resource management and a more sustainable geothermal operation.
An emerging use case for geothermal is the rise of hyperscale AI-enabled data centres which represent a rapidly emerging new form of power demand requiring reliable baseload, or consistent, power supply.
Geothermal is the cleanest form of renewable energy able to provide this baseload power and should play a key role in future data centre strategy globally.
Seequent customer Fervo Energy is applying oil and gas technology to find new ways to produce geothermal energy for Google’s data centres in the Nevada desert.
The latest UN Emissions Report found geothermal energy had the potential to mitigate more energy emissions by 2035 than carbon capture and storage, or bioenergy, or the reduction of methane emissions from coal mining.* The UN’s assessment did not include unique downstream benefits in horticulture and agriculture, or the potential opportunities related to technological advances in mineral extraction.
Engineering New Zealand says government must “urgently firm up the infrastructure pipeline”
Engineering New Zealand Chief Executive Dr Richard Templer says the delay on infrastructure projects coming to market is impacting Kiwis. He says the Government must “urgently firm up the infrastructure pipeline and free up funds for delivery.”
“We know funds are ringfenced for projects – like schools, hospitals, roads, energy and water – but we need them to come to market so New Zealanders get the services they need,” he says.
Templer says the impact of the “stop works” on infrastructure projects really began to hit home in March when money earmarked for projects wasn’t released by the Government, with housing and transport projects most affected. High interest rates have also cut into client budgets, resulting in projects not being commissioned or scaled back.
Anna Bridgman, Water NZ Operations Manager at Stantec, says engineers understand that work may look different but firms need “certainty” to be able to plan and respond. “Certainty of work would allow companies to invest in people … even if the quantum is smaller.”
She says there is “a focus on delivery and value rather than excellence, and clients needing to show costs coming down.”
Although fiscal restraint is a sign of the times, Templer says this focus “could cost Kiwis in the long run if decisions are taken too quickly and prioritise cost over quality.”
New Zealand needs up to an additional 2,300 engineers annually to support its growth, even before replacing those who retire or move overseas. But the homegrown supply of engineers is desperately short of what’s needed. Worryingly, the number of NCEA graduates being assessed for and achieving senior maths and physics papers has dropped by over 20 percent in the past decade.
The same trend is seen in higher education, where the proportion of STEM graduates is below the OECD average.
Engineers – like doctors, teachers, nurses and other professionals with skills in demand – are leaving to countries like the United Kingdom and Australia, where the demand for jobs is immediate. Yet New Zealand is struggling to recruit or retain talent, and
the halt to projects is making things worse.
Templer says engineers are vital for our country’s growth and productivity, generating about $18 billion each year for our economy. “We simply can’t afford to lose more engineers. Once they’re gone, they’re gone – it can take years for engineers to come back,” he says.
Bridgman thinks “community-wide long-term vision” and apolitical, regional solutions would be timely. “I’d like to see what is best for each region and how we might work towards that,” she says.
Templer is keen to see funds for infrastructure projects released. “This Government has high hopes for productivity and growth – but engineers are needed to help deliver major projects so that New Zealanders enjoy prosperous lives.
“That’s why Engineering New Zealand is calling on the Government to do what it can to bring much needed infrastructure projects back online,” he says.
Liam Merrick, sales engineer, ECI Solutions
New Zealand’s manufacturing sector faces a significant challenge amid an ongoing skills and labour shortage. The Employers and Manufacturers Association (EMA) reports that 71 per cent of employers can’t find skilled people, an increase from 40 per cent in 2022, and 90 per cent are struggling to fill vacancies (1).
Employers also face difficulties in hiring trainees and apprentices due to the lack of technical staff to train them. This issue is exacerbated by the shifting preferences of workers, who increasingly seek flexible work arrangements.
The nature of production processes has long dictated that the traditional manufacturing environment requires onsite work. However, workers across industries now expect greater flexibility in their work arrangements, and manufacturers must respond to these changing expectations to remain competitive in the labour market.
Consequently, manufacturers must adapt their practices and embrace flexible working models that can attract and retain talent, such as exploring innovative solutions to maintain productivity and growth or investigating hybrid models for supporting staff. This is particularly relevant for manufacturing workers that will benefit from modern technology augmenting their onsite responsibilities, while administrative roles may not require workers to be onsite.
For example, certain roles will always require a physical presence on the factory floor, particularly in smaller operations, though some supporting functions can be partially or fully performed remotely such as finance, management, and even sales staff in the field.
Offering hybrid options for these less-fixed roles lets manufacturers expand their talent pool beyond geographical constraints to attract professionals who may not have considered a career in manufacturing due to perceived inflexibility.
Onsite, this may involve creating more collaborative spaces, improving ergonomics, and enhancing safety measures. Offsite, it involves providing employees with the latest technologies to perform their duties remotely and create an innovative environment that attracts new talent. This dual approach ensures that all employees can work effectively regardless of location.
There are two ways manufacturers can employ
technology to achieve greater flexibility: data analytics and automation. Enterprise resource planning (ERP) solutions are particularly valuable in this context.
These comprehensive systems give workers real-time access to critical data to make informed decisions. Manufacturers can use ERP solutions for seamless communication and collaboration between team members across locations.
ERP solutions also let manufacturers automate routine processes, reducing the workload on existing employees. This increases efficiency and enhances job satisfaction by eliminating mundane tasks and providing opportunities for skill development. Manufacturers can use ERP solutions to prepare for the future by addressing several key challenges associated with workforce changes and knowledge management, such as reducing the dependency on tribal knowledge, or the unwritten, undocumented information held by experienced employees.
Centralising data and standardising processes within an ERP system lets manufacturers capture and preserve critical operational knowledge that might otherwise be lost when seasoned workers retire or leave the company. This systematic approach to knowledge management delivers continuity and consistency in operations, regardless of staff turnover or movement between locations.
Importantly, it also makes onboarding processes seamless and encourages employee retention by reducing the friction around processes and knowledge sharing.
Manufacturers can also use ERP systems to enhance process control and error prevention when integrating less-experienced workers into the workforce. These solutions provide structured workflows, automated checks, and real-time monitoring capabilities that guide employees through complex processes, reducing the likelihood of mistakes.
An ERP system acts as a safety net as new workers are brought up to speed, offering prompts, alerts,
and validation steps that help maintain quality standards and operational efficiency. This accelerates the onboarding process and gives manufacturers the confidence to expand their onsite and offsite workforce without compromising on quality or productivity.
Embracing flexible working practices can reduce the strain of labour shortages on manufacturers by attracting a wider range of talent into supporting roles and functions, including those who may have previously been unable to commit to full-time work. This could include skilled administrative and financial professionals with caregiving responsibilities, living in remote areas, or seeking a better work-life balance.
Manufacturers must carefully assess which roles and tasks can be augmented by technology to transition to a more flexible working model. For example, while production line workers need to remain onsite, roles in areas such as design, finance, and administration are well-suited to hybrid arrangements, as are business owners themselves.
Identifying these opportunities and making changes to make them more desirable lets manufacturers create a balanced workforce that maximises both productivity and flexibility.
Flexible working practices will be crucial to address the skills and labour shortage as the New Zealand manufacturing sector evolves. Those who adapt to this new way of working sooner, rather than later, will be better positioned to overcome labour challenges and drive innovation in the industry.
References
(1) https://emalive.co.nz/documents/advocacy/ Skills-Shortage-Survey-Results-2023.pdf