
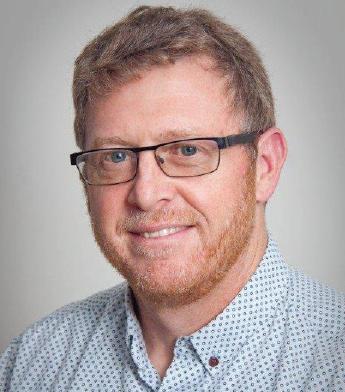
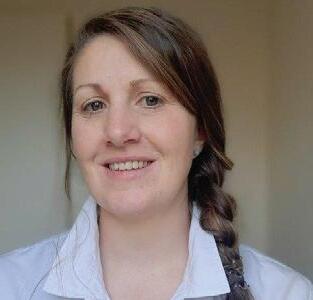
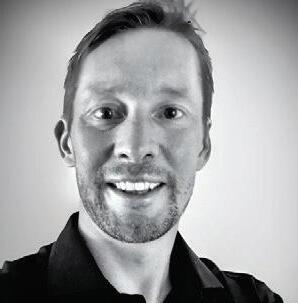
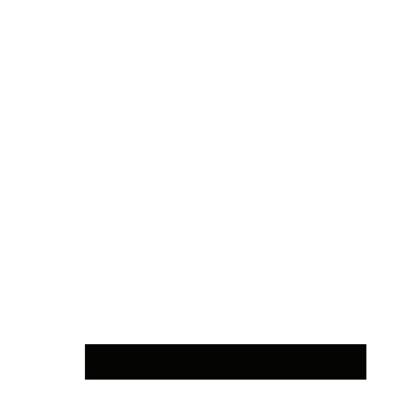
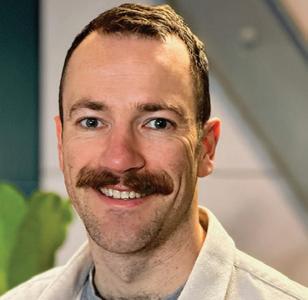
By Mark Devlin, Managing Director, Impact PR
New Zealand’s food manufacturing sector has long been the pride of our nation—an industry built on innovation, quality and a deep-rooted commitment to sustainability.
Yet, in an increasingly competitive global market, even our best ideas need a boost to flourish on the world stage. The recent announcement of a Government-backed export initiative with Canada is a significant step in that direction.
The latest initiative, which saw the recent signing of a Memorandum of Understanding between the Canadian Food Innovation Network (CFIN) and its local counterpart New Zealand Food Innovation Network (NZFIN), promises to accelerate the commercialisation of Kiwi food innovations.
It is designed to give our food and beverage firms access to emerging technologies, comprehensive market intelligence and robust research and development support. With Canada’s 40 million consumers within reach, this collaborative programme could open a new frontier for New Zealand’s agricultural exports—a sector that accounts for nearly half of all goods and services sold offshore.
The move is part of a broader strategy to double the value of New Zealand food exports by 2030. Recent forecasts predict that our
food and fibre exports will reach a staggering $56.9 billion by mid-2025.
For an industry that already invests over half a billion dollars annually in agri-food research, such ambitious targets underline the urgency of transforming research outputs into commercially viable products.
At the heart of this initiative lies the innovative ‘Catalyst Model’ developed by NZFIN. This model is engineered to create a domestic international ecosystem, seamlessly integrating food innovation facilities across
Auckland, Waikato, Otago, Palmerston North and Canterbury with applied innovation hubs in Australia, Singapore, Indonesia and now, Canada.
This interconnected network will support every stage of product development—from ideation and prototype development through to pilot scale trials, market launch and export expansion.
What excites me most is the potential this ecosystem holds for reducing the barriers that have traditionally stifled the growth of value-added food products.
continued on Page 20
Secure supply of energy and data to moving industrial equipment.
• Large size range
• Vertical travels
• Energy tubes
• Hygienic chains
• Solutions for long travel
• Guide troughs
• Readychain
• Robotic, 3D
• Circular movement
HUGE range of high quality flexible cables
• Control cables
• Single cores
• Data cables
• Sensor/Actuator
• Intrinsically Safe
• VSD/EMC cables
• Halogen Free cables
• High temperature
• Harsh Conditions
• Crane cables
• Profibus cables
• Bus/DeviceNet
• Solar cables
• Instrumentation
• Flat cables
• Curly cords
Largest range of flexible conduits for cable protection
• Conduits
• Conduit fittings
• Divisible systems
• Jumbo systems
• Conduit Accessories
• Braided cable protection
• Fire barrier solutions
• Food and beverage
• EMC systems
• Ex, ATEX, IEC EX
Industrial connectors for many industries
• Rectangular multipole connectors from ILME
• Single pole Powerline connectors from TEN47
• EPIC connectors from Lapp Group
• M23 circular connectors from Hummel
• Circular connectors specifically for the entertainment/stage lighting industry from Socapex
Safety engineering solutions from EUCHNER
• Multifunctional Gate Box MGB
• Transponder-coded safety switches
• Electromechanical safety switches
• Magnetically coded safety switches
Sensor technologies for automation
• High-Precision Laser Distance Sensors
• Ultrasonic Sensors
• Inductive Sensors
• Fluid Sensors
April and May issues of NZ Manufacturer magazine www.nzmanufacturer.co.nz, as Media Partner, will include Previews of SouthMACH 2025.
We have, again, put together Special Packages to celebrate SouthMACH at below normal rates. We also welcome articles on your company’s innovations and developments, published at no charge. This is also the event to celebrate the Minister for Manufacturing Awards.
Quarter Page advertising space:
$320 per insertion (Normal rate $440) Article space as well at No Charge.
Half Page advertising space: $420 per insertion (Normal rate is $550) Article space is available at No Charge.
Full Page advertising space: $550 per insertion (Normal rate $750) Article space is available at No Charge.
For April issue: advertising artwork and article: 4 April 2025
For May issue: advertising artwork and article: 4 May 2025.
Article length: up to 600 words plus a picture.
If you have special requirements or need assistance with your material, please contact us. Only too happy to help!
Regards,
Doug Green, Publisher NZ Manufacturer
www.nzmanufacturer.co.nz
publisher@xtra.co.nz 027 625 6166
LEAD
NZ-Canada initiative to drive food export growth.
BUSINESS NEWS
Manufacturing a key player in our export story.
A tale of two sectors.
How to reconstruct manufacturing and productivity.
SMART MANUFACTURING
Company Profile: Uniplas.
EMA FOCUS
Long Covid’s legacy of uncertainty.
SMART MANUFACTURING
Sea sponge inspires super strong compressible material.
Fabrum and Sumitomo expand liquid hydrogen technology to industry.
Smart manufacturing starts with Plex. Launch of pilot Earn as You Learn NZ Certificate in Manufacturing Level 3.
SUSTAINABILITY
Energy efficiency: a bright way to power up your savings!
SMART MANUFACTURING
Robotics Plus acquisition to enable precision agriculture for growers.
Inaugural Minister for Manufacturing Awards 2025 - entries are open!
COMMENT
Why the Right to Repair will benefit New Zealand manufacturers.
ANALYSIS
Smart Industry Readiness Index: Key Themes and Findings.
Navigating Industry 4.0 - The Essential Guide for SME Manufacturers.
WORKSHOP TOOLS
Advantages of cobot welding.
Holding system to streamline small part machining.
Master Lock launches key storage products.
TRAINING
The digital skills gap: A business risk.
DEVELOPMENTS
World’s largest oil pipeline expansion to boost Kiwi surveillance aircraft exports, Daikin Park Christchurch: Green star focus for a sustainable future in Hornby.
THE LAST WORD
No more excuses: Manufacturers need to lead NZ productivity shift.
Walsh Ian Walsh is a leading expert in designing and implementing transformational improvement programmes, with over 30 years of experience helping businesses drive operational excellence and long-term success. A Six Sigma Master Black Belt, he has worked with both New
Zealand’s top organisations and global multinationals including Kimberley Clark, Unilever, Guinness to unlock productivity, reduce costs, and optimise business performance. Ian has been at the forefront of operational improvement, working at all levels—including Boards—to deliver high-impact change. Ian continues to play a key role in advancing business excellence, supporting Auckland University and The Icehouse with expert insights on productivity, operational improvement, and best-practice methodology.
Dr Barbara Nebel CEO thinkstep-anz
Barbara’s passion is to enable organisations to succeed sustainably. She describes her job as a ‘translator’ – translating sustainability into language that businesses can act on.
Mark Devlin
Having owned food manufacturing and distribution businesses for a decade, Mark Devlin now runs Auckland public relations agency Impact PR. Mark consults to several New Zealand manufacturing firms including wool carpet brand Bremworth, aircraft exporter NZAero and cereal maker Sanitarium.
Errey
15 16 23 21
Insa’s career has been in the public and private sectors, leading change management within the energy, decarbonisation, and sustainability space. Insa holds a Chemical and Biomolecular BE (Hons) from Sydney University. She is a member of the Bioenergy Association of NZ and has a strong passion for humanitarian engineering, working with the likes of Engineers Without Boarders Australia.
Insa is a member of Carbon and Energy Professionals NZ, been an ambassador for Engineering NZ's Wonder Project igniting STEM in Kiwi kids and Engineers Australia Women in Engineering, increasing female participation in engineering.
Jane Finlayson is Head of Advanced Manufacturing at the EMA, and has 25-years’ experience in business and economic development. She is passionate about empowering businesses to grow, innovate and embrace Te Ao Māori.
PUBLISHER
Media Hawke’s Bay Ltd, 121 Russell Street North, Hastings, New Zealand 4122.
MANAGING EDITOR
Doug Green
T: 027 625 6166
E: publisher@xtra.co.nz
CONTRIBUTORS
Holly Green, EMA,
Business East Tamaki, Ian Walsh, Adam Sharman, Mark Devlin, Nicholas Russell, Jane Finlayson, Chris Penk, Richard Whitmore, Paul Jarvie, Insa Errey, Frank Phillips, Richard Morton, David Altena, Rob Bull
ADVERTISING
T: 027 625 6166
E: publisher@xtra.co.nz
DESIGN & PRODUCTION :kim-jean:
E: kim.alves@xtra.co.nz
WEB MASTER
Julian Goodbehere
E: julian@isystems.co.nz
PUBLISHING SERVICES
On-Line Publisher Media Hawke’s Bay Ltd
DIGITAL SUBSCRIPTIONS
E: publisher@xtra.co.nz Free of Charge.
MEDIA HAWKES BAY LTD
T: 027 625 6166
E: publisher@xtra.co.nz
121 Russell Street North, Hastings NZ Manufacturer ISSN 1179-4992
Vol.17 No.2 March 2025
Andrew Bayly was the instigator of the concept and within the last month the inaugural Minister for Manufacturing Awards 2025 have been launched (Page 15). The baton has now been passed to the new minister, Chris Penk.
The aim is to celebrate outstanding individuals and businesses driving productivity, workforce prosperity, and global competitiveness across New Zealand’s manufacturing sector.
The success of our ‘creative class’ in manufacturing can well and truly be celebrated.
Winners will be announced on Wednesday 28th May 2025 at SouthMach, Christchurch.
New Zealand-based company Robotics Plus, a specialist in agricultural automation solutions, has been bought by Yamaha Motor Co., Ltd. to form the foundation of Yamaha Agriculture Inc.
This new company will be focused on delivering autonomous equipment and AI-powered digital solutions that help growers in the specialty crop market become more sustainable, profitable and resilient in the face of scarcer resources and climate change.
A New Zealand success story which again brings overseas ownership into the equation.
Ian Walsh in his column (Page 8) doesn’t mince words when he says the global construction sector has seen little-to-no productivity growth over the last 50 years, and in New Zealand it’s no different.
There is a unified view that productivity needs to improve, however little or no concerted action has been taken to adopt best practices.
The tales of late delivery, cost overruns and underperformance on completion are now so common that these outcomes are expected. Indeed 94% of construction projects do not achieve cost, time, or quality objectives.
When a job is costed at $2 billion, it is no longer a surprise when it ends up costing $6 billion or more!
Adam Sharman (Page 17) talks SIRI and how New Zealand manufacturers seek to optimise and accelerate their productivity through Industry 4.0. They face several distinctive challenges:
Scale and Investment Capacity, Talent Acquisition, Connectivity Infrastructure, Integration with Legacy Systems.
New Zealand manufacturers exhibit a characteristically pragmatic approach to technology implementation. Rather than pursuing cutting-edge technologies for their own sake, Kiwi businesses tend to prioritise practical solutions with clear returns on investment.
This approach serves many companies well but can sometimes limit exploration of more transformative technologies that might deliver longer-term competitive advantages.
-Chris Penk, Minister for Small Business and Manufacturing
Starting 2025 by taking on the role of Minister for Small Business and Manufacturing has been an exciting time. As readers of NZ Manufacturer will be well aware, these areas lie at the heart of the New Zealand economic engine.
Manufacturing is a key player in our export story and the vast majority of NZ businesses are “small” (with 97% having fewer than 20 FTE employees).
So let me start by saying how grateful I am to everyone in the sector who is producing the goods, quite literally(!), to ensure New Zealand’s economic growth.
My initial approach is to listen carefully to what manufacturers see as their challenges and opportunities. This will provide a countrywide perspective, on top of what I hear from constituent businesses within Kaipara ki Mahurangi.
The area that I represent in northwest and the rural north of Auckland includes some significant industrial zones, so I appreciate manufacturing is a key enabler of employment and social cohesion in local communities.
My “starter for 10” would be making sure that manufacturing businesses can navigate bureaucratic roadblocks and – wherever possible - removing those roadblocks.
I have observed that the compliance burden is too
our watchword as a government.
Trade is another key pillar to aid growth, and it’s our ambition to double the value of New Zealand exports within a decade.
We’re getting on with signing new trade agreements across the globe – knowing the quality of our great Kiwi products will always be their own key selling point.
So far, one of the most pressing concerns I hear from manufacturers is workforce gaps. That’s why the Government has partnered with Advancing Manufacturing Aotearoa to launch an ‘earn as you learn’ pilot in Waikato.
This initiative connects high school students with local manufacturers to gain hands-on experience while earning a competitive wage and an NZ Certificate in Manufacturing Level 3.
It is fantastic to see educators and industry leaders working together to address challenges and provide young Kiwis with rewarding career pathways. While it is only one initiative, its success could provide a blueprint for other regions, and I look forward to seeing the progress these students make.
I recently visited Grayson Engineering in Wiri, Auckland, a recognised leader in steel fabrication. They’ve won multiple awards for excellence in steel
improving their workers’ quality of life in New Zealand.
Some of their team members have been with them for over 15 years, and they also employ local apprentices.
Learning from industry leaders like Grayson Engineering is essential as, we the Government, work to address skill shortages and develop policies that support long-term workforce stability.
On a related note, I have been hearing that visa settings remain an area of frustration for manufacturers looking to bring in skilled workers, and addressing these challenges will require collaboration across Government.
Advocacy is a key part of my role, and I am committed to ensuring that the voices of manufacturers are heard at the decision-making table.
In summary, my focus as Minister is on breaking down barriers, fostering growth and ensuring this sector continues to thrive. I look forward to working closely with industry leaders, educators, and policymakers
Ian Walsh, Partner, Argon & Co NZ
I was reminded last week of the level of complexity and difficulty to solve our productivity crisis. It’s clear to me that we have a multi-speed economy, with certain sectors having made great progress over the last 10 years with others still on the starting blocks.
The dairy sector has been developing and implementing best practices, training leaders, building capability and employing appropriate technology for over 25 years.
Fonterra has lead the charge and most other dairy companies have followed this lead, by developing and employing solutions to improve productivity, reduce waste, improve yield and reduce costs. It has led to fantastic outcomes, with the most recent payout reflecting both the great work on the farm and the much improved off-the-farm processing capability. It would be untenable to consider competing globally with the capability the sector had in 1999.
The payout would have been significantly lower and dare I say many processors would have been seriously impacted. This is, of course, not to say the job is finished, because it isn’t, but the direction of travel for the sector looks good.
In contrast, the global construction sector has seen little-to-no productivity growth over the last 50 years, and in New Zealand it’s no different. There is a unified view that productivity needs to improve, however little or no concerted action has been taken to adopt best practices.
The tales of late delivery, cost overruns and underperformance on completion are now so common that these outcomes are expected. Indeed 94% of construction projects don’t achieve cost, time or quality objectives.
When a job is costed at $2 billion, it’s no longer a surprise when it ends up costing $6 billion or more!
There are some examples of progress, but in a recent focus group of 20 construction companies, 4 were implementing some practices, 2 were performing well and 2 were just starting.
This is representative of my experience over the last 10 years with 10% or less making significant progress.
This is concerning when we consider that over the next 10 years there are many upcoming and ongoing projects of national significance to improve NZ’s infrastructure.
These projects are to enable our exporters better access to markets, and reduce costs associated with our congested or unreliable road networks. We’re also looking for foreign direct investment to help us fund this, but in order to execute these projects we will be relying on our most underperforming sector, in terms of productivity.
The underperformance we’ve become used to is not the expectation everywhere however.
For example, Highways England deployed Lean as a key strategy over 15 years ago, and now have billions of dollars of savings documented in their roading developments. They are measured on reducing their costs to deliver more, given the savings they generate.
The UK government drives this and the tier one suppliers now all have best practice programs to deliver the outcomes expected.
It was clear that the dairy sector in the 1990s was going through aggregation; the mega merger was on the horizon and the leaders were willing to embrace and lead change to drive competitive advantage and shareholder returns.
We have seen the same change in the technology sector, where competitive pressure has driven rapid adoption of best practice for over 40 years, and of course the automotive sector, with the Toyota journey being well documented since the 1960s.
The construction sector has not had the same pressure applied, with risk being passed through layers of bureaucracy, and traditional procurement practices building contingencies and passing risk resulting in higher costs.
This is as opposed to value-based pricing, and
incentives to collaborate and share risk to reduce costs and improve outcomes.
There are great overseas examples of where this has been applied and with significantly improved outcomes.
The reality is only the government has enough buying power to drive a change in traditional practices. Given that this money is coming from the pockets of taxpayers, and the aforementioned potential foreign investment, we should surely be looking to achieve a significant improvement in our construction sector so that these stakeholders get the best returns.
We need to go into these construction projects with an approach that leaves us not just with the infrastructure, but also with minimised debt, and increased performance capabilities that we can take into future projects, so we can undertake future projects with confidence and certainty.
Surely, we should learn from our own local experience, the global learning and require our leading organisations (this includes government) to adopt these proven practices to drive better outcomes for all New Zealanders.
Reconstructing manufacturing and productivity can be quite the undertaking, but it’s definitely doable with a clear strategy. Here are some key steps to consider:
• Assess Current Processes: Start by evaluating the existing manufacturing processes and productivity levels. Identify bottlenecks, inefficiencies, and areas for improvement.
• Adopt Lean Manufacturing Principles: Lean manufacturing focuses on minimizing waste and maximizing value. Implement principles like just-in-time production, continuous improvement (Kaizen), and value stream mapping.
• Invest in Technology: Embrace advanced manufacturing technologies such as automation, robotics, and the Industrial Internet of Things
(IIoT). These can enhance efficiency, accuracy, and flexibility.
• Enhance Workforce Skills: Invest in training and upskilling your workforce to ensure they can effectively utilize new technologies and processes. Foster a culture of continuous learning and improvement.
• Implement Data Analytics: Use data analytics to gain insights into production processes, identify trends, and make informed decisions. Predictive maintenance and real-time monitoring can prevent downtime and improve productivity.
• Optimize Supply Chain: Evaluate and optimize your supply chain to ensure timely delivery of raw materials and efficient distribution of finished products. Consider strategies like supplier
collaboration and inventory management.
• Sustainability Practices: Integrate sustainable practices into your manufacturing processes to reduce environmental impact and improve efficiency. This can also enhance your brand reputation and appeal to eco-conscious consumers.
• Set Clear Goals and Metrics: Define clear goals for productivity improvements and establish key performance indicators (KPIs) to measure progress. Regularly review and adjust your strategies based on performance data.
These steps can help transform your manufacturing operations and boost productivity. Remember, it’s a continuous process, so always be on the lookout for new opportunities for improvement!
Richard Whitmore – Managing Director, Uniplas NZ Ltd
How is Uniplas finding current business conditions?
The business environment was challenging in 2023-2024, but we observed a positive shift towards the end of last year. Our business focuses on supplying other manufacturers and retailers.
Through COVID, business boomed, but high interest rates and inflation impacted people’s spending. Companies reduced stock levels, placed last-minute orders, and generally ordered lower volumes.
There seemed to be a lack of ‘mojo’ in New Zealand, but we are determined to lead the charge and make 2025 a year of growth and innovation.
Where do you see development for your company’s products and services?
We are excited about our sustainability growth. Designing products with their end of life in mind and de-carbonising our power supply help us work towards carbon zero certification.
Along with new rooftop solar, we’ve been investing in our plant with new moulding machines, lathes, and grinders, maintaining our constant investment in the future.
Do you export…if so, where to?
We directly and indirectly export all over the world, but predominantly to Australia and the United States. We have always enjoyed our relationship with our Australian importers, but we are very interested to see how the new international trade policies elsewhere are going to affect exports here in Aotearoa, New Zealand.
How are you finding staff retention at present?
The financial pressures are not just on the company but on the employees themselves. Trying our best to look after our staff during tough times has really helped us retain our core team over the years, and we can’t see that changing anytime soon.
What ‘one thing’ would make business better for you?
Getting kiwis to stay local when it comes to developing products. It too easy for many to chase the cheapest tooling and production deals abroad; we have heard too many horror stories of stolen IP for our liking.
So, in short, getting people to choose New Zealand first, for their design and manufacturing needs.
readers about the new solar system?
We are installing Wellington’s largest and one of the country’s biggest rooftop solar arrays. The system consists of 1,620, 580w panels, producing enough to power 123 average homes per year.
This is our first major step towards reducing reliance on the grid, decreasing carbon emissions, and hedging against future rising energy costs.
Your road to success …is it going to plan?
Our road to success includes tapping into new industries within New Zealand and abroad, bringing Kiwi ingenuity and innovation to add value. This has been progressing well, with plans to extend our product range, launching in mid-2025. Along with our in-house products, we are increasing the national visibility of our range of machines and services. Located in the centre of the country, Uniplas NZ Ltd is perfectly positioned to manufacture larger, less freight-efficient items, reducing shipping costs and ensuring efficient distribution nationwide.
Kiwi businesses are keen to restart growth this year. After a couple of conservative years, there’s renewed motivation, especially in the Hutt Valley, to get things moving again
Investment in the manufacturing sector is sadly lacking. Your thoughts on this?
During COVID-19, Kiwis benefited from strong onshore manufacturing, enabling production of essential items without delays or shortages. This perspective has waned with the cost-of-living crisis, pushing people to opt for cost-effective options regardless of origin.
However, this motivates the industry to enhance efficiencies and cut costs, making manufacturing leaner and more competitive internationally.
Investments in automation, manufacturing techniques, and plastic recycling plants are crucial for boosting and sustaining New Zealand’s manufacturing sector.
By EMA’s Paul Jarvie, Manager of Employment Relations & Safety
The Covid-19 lockdowns of 2020/21 may be fading into memory, but for long-Covid sufferers, the difficulties of that unusual period in our recent history carry on to today.
New Zealand was first hit by Covid-19 on February 28, 2020, and by March 25, we were in full lockdown, implementing some of the strictest measures in the world to contain the virus.
Borders closed, businesses shut, and only essential workers were allowed to leave their homes. Over time, vaccinations helped mitigate the spread, but Covid did not disappear – it mutated, persisted, and for some, left lasting health challenges.
Most people recovered from Covid-19 within weeks, experiencing symptoms such as fever, cough, and temporary loss of taste or smell.
But for an estimated 10-15% of those infected, the effects linger.
Long Covid, as it has come to be known, brings a host of debilitating symptoms, including brain fog, chronic fatigue, joint pain, and respiratory issues.
For New Zealand, this translates to between 207,000 and 405,000 people potentially affected.
For businesses, this creates a complex challenge. The workforce is already under strain, and managing employees who are on long-term leave due to Long Covid presents difficulties in productivity, team cohesion, and operational planning.
Unlike a typical illness where recovery follows a predictable trajectory, Long Covid remains uncertain. Symptoms fluctuate, meaning employees may seem fit one day and struggle the next. This inconsistency complicates business planning, as employers must juggle staffing levels while maintaining fairness to all employees.
From an employer’s perspective, the legal framework in New Zealand provides clear guidelines.
The Human Rights Act prohibits discrimination based on medical conditions, meaning an employee suffering from Long Covid cannot be unfairly dismissed, demoted, or treated differently due to their illness.
However, this does not negate the strain businesses feel when a key team member is absent for months.
Unlike a broken leg, with a defined healing timeline, Long Covid’s uncertain recovery period leaves employers in limbo, struggling to balance compassion with the practical needs of running a business.
Employers must approach this situation with a proactive strategy. First, maintaining open communication is key. Checking in with employees
about their health, medical updates, and possible return-to-work plans allows businesses to anticipate staffing needs.
Employers should also encourage affected employees to explore flexible working arrangements. Adjusting work hours, enabling remote work, or modifying duties can allow employees to contribute within their capacity rather than being completely sidelined. Another important factor is managing leave entitlements.
Sick leave in New Zealand allows for 10 days per year, which is insufficient for a Long Covid sufferer. Once sick leave and annual leave are exhausted, continued on Page 26
Inspired by the humble deep-sea sponge, RMIT University engineers have developed a new material with remarkable compressive strength and stiffness that could improve architectural and product designs.
The double lattice design was inspired by the intricate skeleton of a deep-sea sponge known as Venus’ flower basket, which lives in the Pacific Ocean.
Lead author of the latest RMIT study into the structure, Dr Jiaming Ma, said extensive testing and optimisation revealed the pattern’s impressive combination of stiffness and strength, mixed with an ability to contract when compressed.
It’s this last aspect – known as auxetic behaviour –that opens a whole range of possibilities to apply the design across structural engineering and other applications.
“While most materials get thinner when stretched or fatter when squashed, like rubber, auxetics do the opposite,” Ma said.
“Auxetics can absorb and distribute impact energy effectively, making them extremely useful.”
Natural auxetic materials include tendons and cat
skin, while synthetic ones are used to make heart and vascular stents that expand and contract as required. But while auxetic materials have useful properties, their low stiffness and limited energy absorption capacity limits their applications. The team’s nature-inspired double lattice design is significant because it overcomes these main drawbacks.
“Each lattice on its own has traditional deformation behaviour, but if you combine them as nature does in the deep-sea sponge, then it regulates itself and holds its form and outperforms similar materials by quite a significant margin,” Ma said.
Results published in Composite Structures show with the same amount of material usage, the lattice is 13 times stiffer than existing auxetic materials, which are based on re-entrant honeycomb designs.
It can also absorb 10% more energy while maintaining its auxetic behaviour with a 60% greater strain range compared to existing designs.
Dr Ngoc San Ha said the unique combination of these properties opened several exciting applications for their new material.
“This bioinspired auxetic lattice provides the most solid foundation yet for us to develop next generation sustainable building,” he said.
“Our auxetic metamaterial with high stiffness and energy absorption could offer significant benefits across multiple sectors, from construction materials to protective equipment and sports gear or medical applications,” he said.
The bioinspired lattice structure could work as a steel building frame, for example, allowing less steel and
concrete to be used to achieve similar results as a traditional frame.
The structure could also form the basis of lightweight sports protective equipment, bullet proof vests or medical implants.
The team at RMIT’s Centre for Innovative Structures and Materials has tested the design using computer simulations and lab testing on a 3D printed sample made from thermoplastic polyurethane.
They now plan to produce steel versions of the design to use along with concrete and rammed earth structures – a construction technique using compacted natural raw materials.
“While this design could have promising applications in sports equipment, PPE and medical applications, our main focus is on the building and construction aspect,” Ma said.
“We’re developing a more sustainable building material by using our design’s unique combination of outstanding auxeticity, stiffness, and energy absorption to reduce steel and cement usage in construction.
“Its auxetic and energy-absorbing features could also help dampen vibrations during earthquakes.”
The team is also planning to integrate this design with machine learning algorithms for further optimisation and to create programmable materials.
‘Auxetic behavior and energy absorption characteristics of a lattice structure inspired by deep-sea sponge’ is published in Composite Structures (DOI: 10.1016/j. compstruct.2024.118835)
Sandra Lukey
Sandra Lukey is the founder of Shine Group, a consultancy that helps science and technology companies accelerate growth. She is a keen observer of the tech sector and how new developments create opportunity for future business.
Mike Shatford
is an expert in the field of technology development and commercialisation. His company Design Energy Limited has completed over 100 significant projects in this vein by consulting for and partnering with some of New Zealand’s leading producers. Among Mike and his team’s strengths are industrial robotics and automated production where the company puts much of its focus.
Sean O’Sullivan
Has a B Com (Hons) Otago University. In 2000 - 2001 introduced PCs on the workshop floor and job and staff tracking and a productivity software App to Fletcher Aluminium Group and 100 manufacturers NZ nationwide.
Founding Director Empower Workshop Productivity & Scheduling Software App.
Iain Hosie
Iain is a Director and Founder of Nanolayr Ltd, Director for the NZ Institute for Minerals and Materials Research, Commercial Director for Fabribotics Ltd, and Executive Council of BiotechNZ.
Adam Sharman
Is a Senior Partner at Dsifer. With a background in technology implementation, manufacturing and strategy, Adam and the team at Dsifer are on a mission to support New Zealand’s manufacturing sector transform using technology, data and analytics to outcompete on the world stage. Combining expertise in data engineering, data science & analytics and visualisation.
Patrick McKibbin
CEO – Hutt Valley Chamber of Commerce
Patrick joined the Hutt Valley Chamber of Commerce in September 2021. His passion is identifying and connecting with manufacturing & technology businesses, other businesses, local government, central government and industry associations.
New Zealand company Fabrum, a global leader in zero-emission transition technologies, has partnered with Sumitomo Australia Pty Ltd, a leading global integrated trading and investment business enterprise, to provide Sumitomo’s financing solutions for Fabrum’s hydrogen liquefier customers in Australia.
The strategic collaboration addresses the growing demand for liquid hydrogen in the heavy transport and aviation sectors, which are actively pursuing decarbonisation and new energy sources.
Fabrum’s containerised portable liquefiers—available in configurations producing either 35 kg, 75 kg or 400 kg of liquid hydrogen per day—offer a sustainable solution for transport through liquid hydrogen fuel.
Housed in 20-foot and 40-foot containers, the systems offer maximum flexibility and mobility for customers.
Under the Memorandum of Understanding (MOU), Fabrum—renowned globally for its expertise in industrialised small to medium-scale liquefaction systems and composite vessels for liquid hydrogen, liquefied natural gas, and other gases—will introduce a financing option for its portable liquid hydrogen systems.
This option will be made available through Sumitomo Australia, a specialist equipment importer and solution provider, and a wholly owned subsidiary of Japan’s Sumitomo Corporation
Fabrum has a proven track record in delivering liquid hydrogen production systems worldwide. Recently, they commissioned Australia’s largest liquid hydrogen production facility on a mine site for Fortescue, and are soon set to ship another system to Germany –among other projects.
Through this partnership with Sumitomo, they aim to further reduce barriers to adoption by offering a financial solution for our technology, helping the industry advance toward a hydrogen-powered future without the burden of upfront capital costs.
Sumitomo’s partnership with Fabrum paves the way for a greener future for Australian industry by introducing flexible financing solutions for hydrogen liquefication technology.
This collaboration aligns with Sumitomo’s commitment in sustainable business activities that support their long-term objectives for climate change mitigation and achieving Net Zero by 2050.
Rockwell Automation will be showcasing its Plex cloud-based manufacturing platform at this year’s Australian Manufacturing Week (AMW) in Melbourne from May 6-9. Demonstrations will be held at stand MS210 (Manufacturing Solutions Zone).
Plex Manufacturing Execution System (MES), integrated with Rockwell’s suite, offers comprehensive manufacturing software, providing real-time production management, enhancing compliance, quality, and efficiency.
“Plex is a cloud-based platform, that enables future-focussed manufacturers to achieve real-time integration, high levels of availability and flexibility, cybersecurity, and scalability,” says Anthony Wong, vice president, enterprise software sales, Asia Pacific, Rockwell Automation
Plex has been used by Australian and New Zealand companies to enhance operational efficiency, with examples including:
• STM Brands, a manufacturer of high-quality, award-winning accessories for tablets, laptops, and phones with a worldwide retail presence and offices in Sydney, San Diego, London, and Kuala Lumpur. As air freight costs began to rise, STM Brands realised its supply chain and spreadsheet-based planning was not accurately keeping up with demand volatility, and this was eating into the company’s margins.
After implementing Plex, STM Brands increased gross profit margin by 5%, improved operating margin by 20%, reduced costly air freight by 50%, and decreased overall freight to sales ratio by 25% year-over-year. Importantly, Plex’s Supply Chain Planning (SCP) integrated into STM’s existing Enterprise Resource Planning (ERP) software, allowing for seamless data transfer.
• Tasti Products Limited, New Zealand, a snack bar and wholefood ball manufacturer. Recognising
their legacy ERP system could no longer support an expanding business, Tasti Products searched for a smart manufacturing solution that would allow the company to scale in size and improve the speed in which business analytics could be performed. Tasti sought a manufacturing solution that was cloud-based and could help drive its end-to-end digital transformation.
With the ability to offer world-class food safety and its established presence in the food and beverage industry, Plex provides Tasti Products with a connected plant floor, digital product tracking capabilities, and real-time data to support the company as it continues to grow.
• Miraka, New Zealand, a Māori owned dairy company and the world’s first dairy processor to be powered by renewable geothermal energy. Miraka is using Plex to enhance the company’s business and operations with a business-wide ERP system.
In real time, Plex seamlessly integrates and manages all of Miraka’s transactions and systems from the farm, to factory, to customer. It will help make the dairy processor more efficient, resilient, agile and, sustainable. Plex is also a modular system, so it can grow and adapt as needs change in the future, allowing companies like Miraka to remain agile and stay ahead of the competition.
launched Catherine Lye – CEO, Advancing Manufacturing Aotearoa
Nineteen high school leavers embarked on a transformative educational journey in mid-February, starting the highly anticipated Earn as You Learn NZ Certificate in Manufacturing Level 3 pilot programme in Hamilton.
This innovative 30-week, industry-led initiative is a fantastic collaboration between Waikato’s leading manufacturers—Action Manufacturing, APL Manufacturing, ES Plastics, Hansa Products, Gallagher Group, Loadscan, Longveld, NZ Aero, PPL Plastic Solutions, Stafford Engineering, Stainless Design, and Supreme Sheetmetals—along with Advancing Manufacturing Aotearoa, Wintec, Hanga Aro Rau, and WECA.
The program aims to bridge the gap between formal education and hands-on manufacturing experience, while addressing the sector’s evolving workforce needs.
Learners split their week between two days of classroom learning at WINTEC’s Rotokauri Campus in Hamilton and three days of paid, on-the-job training
with some of the country’s top manufacturers.
Over the 30-week course, students rotate through three different companies, spending ten weeks with each. This ensures they gain diverse, well-rounded experience while earning a wage. Upon completing the course, students will graduate with a New Zealand Certificate in Manufacturing Level 3 and valuable hands-on experience to help them secure their first full-time role.
Howard Fountaine, GM of APL Manufacturing, shared: “Our decision to get involved stems from a desire to grow a skilled talent pool in manufacturing. We want to raise the profile of the industry, showing young people that manufacturing is more than just factory labour. It offers diverse opportunities, from logistics specialists to CNC programmers, and this programme is key to unlocking those pathways.”
The Earn as You Learn programme comes at a critical time as New Zealand’s manufacturing sector faces a skills shortage.
The initiative addresses the lack of hands-on, practical training while ensuring students are work-ready by the time they finish their studies.
In announcing the programme, Small Business and Manufacturing Minister Chris Penk highlighted the
vital role manufacturing plays in New Zealand’s economy.
“Manufacturing contributes around 8.4 percent of New Zealand’s GDP and employs 10 percent of our workforce. But businesses are telling us that skill shortages are limiting productivity. Manufacturing can supercharge our economic growth and strengthen our global competitiveness, but it needs the right support to thrive and increase its exports.”
Justin Brien, Commercial Manager at Stainless Design, emphasised the programme’s real-world value: “This programme offers students exposure to real-world scenarios, helping them develop essential skills like problem-solving, teamwork, and adaptability—skills that employers seek in the manufacturing sector. Our company sees immense value in giving students the chance to apply what they learn in a real manufacturing environment.”
Stephen Burrows, CEO of NZ Aero, also expressed his support: “By participating in this programme, we’re not just investing in the future of our business but in the future of the manufacturing industry. We need a workforce that is not only skilled but adaptable, capable of navigating the challenges of a rapidly evolving sector. The Earn as You Learn programme is a critical step in building that workforce.”
In the business of manufacturing? Here are clean and clever ways to save.
Taking steps to become more energy efficient and making the switch to clean energy can have plenty of benefits for your bottom line. It doesn’t have to be costly to implement, either.
EECA provides free tools and advice to help your business take the next step – including energy efficiency checklists, energy calculators and advice on the best clean and clever tech on the market.
Discover more at eeca.govt.nz/manufacturing
-Insa Errey, Advisor to NZ Manufacturer, Genesis, Senior Manager Future Fuels.
Energy efficiency is increasingly becoming a key factor to drive cost reductions, especially in the manufacturing sector. As manufacturers seek ways to remain competitive and reduce operational expenses, energy costs should become the primary target for cost-cutting measures. By improving how energy is used, it can reduce bills, boost productivity, and contribute to long-term sustainability.
In manufacturing energy cost can account for up to 20% of total operational expenses, these costs can vary depending on the industry and the energy intensity of the product. Energy costs, in many cases, are second only to labour in terms of operational spending. Leading to improving energy efficiency delivering substantial financial benefits.
Energy efficiency involves the reduction of energy consumption without compromising output or quality. The savings generated from these measures can translate directly into reduced operational costs and higher profit margins.
Significant savings can be realised with low to no cost process optimisation. While other opportunities may involve initial investment which can seem significant, the return on investment (ROI) is often reached quickly through reduced energy costs.
Global insights from the International Energy Agency (IEA) show that in some industries, energy efficiency projects can pay for themselves in as little as 2-3 years.
Beyond immediate savings, energy efficiency improvements can provide long-term financial benefits. Energy efficiency can help mitigate the impact of rising energy prices, making it easier for manufacturers to predict future costs and avoid unexpected increases in energy expenses.
Even small reductions in energy
Another consideration is that energy efficiency can also provide manufacturers with a competitive edge in the global market. As international consumers and businesses become more focused on sustainability,
manufacturers that prioritise energy efficiency and reduce their environmental impact are more likely to attract customers and partners who value responsible production practices.
The IEA call energy efficiency the ‘first fuel’ and has long advocated for energy efficiency to reduce costs and improve global competitiveness. According to the IEA, improving energy efficiency in industrial processes could save billions of dollars annually. For example, upgrading industrial motors and optimising production lines could reduce energy consumption in manufacturing by 10-20%.
The IEA also emphasises the importance of implementing best practices in energy management and fostering the adoption of low-carbon technologies. The IEA’s annual Energy Efficiency Market Report outlines how energy efficiency measures can save billions in energy costs globally over the coming decades.
Germany are leaders in manufacturing and industrial production and has set ambitious goals for energy consumption reductions as part of its Energiewende (energy transition). Germany set a binding target to reduce energy consumption by 30% by 2030.
The manufacturing sector in Germany is already undergoing significant transformations, with companies integrating energy-efficient technologies and working in energy efficiency networks to reduce energy use and cut operational costs.
These networks bring together businesses, local authorities, and other stakeholders to collaborate on improving energy efficiency across various sectors.
The idea behind these networks is to foster
knowledge exchange, best practices, and joint solutions for reducing energy consumption.
By participating in these networks, organisations can set and achieve energy efficiency goals, benefiting from shared experiences and resources.
This collaborative approach helps companies identify and implement cost-effective energy-saving measures, which ultimately supports Germany’s goal of reducing greenhouse gas emissions and becoming less reliant on fossil fuels.
Energy efficiency is a game-changer for reducing operational costs in manufacturing. With energy consumption being a major expense, manufacturers can realise significant savings by adopting energy-efficient technologies and practices. EECA (Energy Efficiency and Conservation Authority) Sector programme have tools a resource to help businesses optimise their energy.
By embracing these strategies, manufacturers can not only reduce operational costs but also increase their competitiveness, contribute to a sustainable future, and position themselves as leaders in a rapidly changing market.
New Zealand-based company Robotics Plus, a specialist in agricultural automation solutions, today announced it has entered into an agreement to be acquired by Yamaha Motor Co., Ltd. to form the foundation of Yamaha Agriculture, Inc., a new company focused on delivering autonomous equipment and AI-powered digital solutions that help growers in the specialty crop market become more sustainable, profitable and resilient in the face of scarcer resources and climate change.
Robotics Plus specialises in developing automation solutions for agriculture, combining expertise in robotics, automation, sensing, and data analytics.
With a proven track record of delivering innovative technologies to global markets, the company continues to push the boundaries of agricultural automation. Its latest development, Prospr, is a robust, autonomous, multi-purpose hybrid vehicle designed to perform a range of orchard and vineyard tasks.
Built to tackle labour shortages and enhance efficiency, precision, sustainability, and safety, Prospr is capable of multiple activities including spraying and weed control, with additional attachments such as mowing in development.
Robotics Plus’ innovations also includes the poro Fruit Packer, which automates fruit packing, and a robotic log scaler to automate log measurement for trucks and trains.
Since 2017, Yamaha Motor, the parent company of newly launched U.S.-based Yamaha Agriculture has supported Robotics Plus with strategic investment to drive development of agricultural automation technologies and to expand its presence in the agtech sector.
Following Robotics Plus’ acquisition, the company will continue to operate its core business at its headquarters in Tauranga, retaining high value skilled jobs and IP development in New Zealand, while benefiting from the support of Yamaha Agriculture, to grow globally.
Robotics Plus’ autonomous hybrid vehicle Prospr, capable of multiple activities including spraying, weed control, with further attachments coming such as mowing - addresses key labor challenges faced by growers.
Another recent Yamaha Agriculture acquisition, The Yield, brings advanced data analytics and AI-powered models to deliver yield predictions and optimize on and off-farm operations. Yamaha Agriculture will combine Robotics Plus’ robotic solution Prospr with advanced data analytics to support producers of wine grapes, apples, and other specialty crops across
The inaugural Minister for Manufacturing Awards 2025 have been launched to celebrate outstanding individuals and businesses driving productivity, workforce prosperity, and global competitiveness across New Zealand’s manufacturing sector.
The launch marks a significant milestone in the growth of New Zealand’s manufacturing industry, highlighting its potential in an increasingly competitive global marketplace.
However, many people are unaware of the immense potential and success within New Zealand’s manufacturing sector.
It’s time to showcase the brilliance of New Zealand manufacturing. Let’s stand proud and be recognised for the incredible work we do. It’s time to make some noise!
“The manufacturing sector is vital to New Zealand’s economic success. It drives productivity, supports technological progress, generates high-quality employment opportunities and underpins 60% of NZ’s exports,” said Catherine Lye, CEO of Advancing Manufacturing Aotearoa.
“The Minister for Manufacturing Awards 2025 will inspire the next generation of talent and help
boost the sector’s global competitiveness through investment in advanced technologies.”
The awards will feature four key categories:
• Excellence in Process Innovation: Recognising innovative manufacturing processes that improve efficiency, sustainability, and product quality.
• Manufacturing Apprentice of the Year: Honouring an outstanding apprentice who shows exceptional promise and skill in the manufacturing industry
• Manufacturer of the Year: Awarded to a business demonstrating excellence in production, innovation, and overall contribution to the industry.
• Excellence in Manufacturing Leadership: Recognising leaders who have made a significant impact on their business and the industry through visionary leadership and strategic growth. Nomination Information Pack email info@amanz. nz for the nomination form.
Hon Chris Penk – Minister for Manufacturing will officiate the awards ceremony on 28th May 2025 at SouthMach Christchurch, the South Island’s premier industry trade event, showcasing the latest
North America, Australia, and New Zealand.
Leveraging Yamaha’s long heritage as a trusted manufacturer of high-performance products, the new agriculture business will integrate the complementary technologies to create a comprehensive platform that enables precision farming for growers.
By combining autonomous equipment with intelligent data insights, Yamaha Agriculture helps growers reduce input costs, optimize resource utilization and improve overall farm productivity and sustainability.
From the outset, founders Steve Saunders and Dr. Alistair Scarfe built Robotics Plus with a global vision. The company has rapidly grown into a team of 130, with its robotic innovations deployed in markets worldwide.
developments in manufacturing, engineering, and technology.
We look forward to recognising the manufacturers who are shaping the future of New Zealand’s manufacturing industry
The inaugural Minister for Manufacturing Awards 2025 is proudly supported by Advancing Manufacturing Aotearoa and the New Zealand Government through the Minister of Small Business and Manufacturing Hon Chris Penk.
Key Dates
• Entries Open: Friday 28th February 2025
• Entries Close: 5pm, Friday 28th March 2025
• Finalists Notified: Friday 25th April 2025
• Winners Announced: Wednesday 28th May 2025 at SouthMach, Christchurch
The recent first reading of the Consumer Guarantees (Right to Repair) Amendment Bill in New Zealand’s Parliament marks a pivotal moment for businesses, consumers, and the environment.
If enacted, this legislation will require manufacturers to provide spare parts, repair manuals, and software access to consumers and independent repairers. While some manufacturers may be concerned about potential costs or intellectual property risks, the right to repair presents significant benefits for New Zealand’s manufacturing sector.
It can drive business innovation, reduce waste, enhance customer loyalty, and build a more resilient, circular economy.
Understanding the Right to Repair
The right to repair ensures that consumers and independent repairers have access to the tools, parts, and information necessary to maintain and fix products. It challenges restrictive policies that limit repairs to authorised service providers, often increasing costs and contributing to e-waste.
Key elements of the Right to Repair include:
• Access to spare parts and manuals – Manufacturers should provide genuine replacement parts and repair guides.
• Repair-friendly design – Products should be designed to allow easy repairs without specialised or proprietary tools.
• Protection against restrictive policies – Consumers should not be locked out of repairs due to software restrictions or warranty clauses.
The legislation is particularly relevant to industries such as electronics, appliances, vehicles, and agricultural machinery, where manufacturers traditionally limit repair options, increasing costs for businesses and consumers alike.
The Right to Repair and its Impact on manufacturers
Some manufacturers may worry that making spare parts and repair information available will reduce profits from new product sales or increase compliance costs. However, international experience shows that embracing repairability can be a strategic advantage rather than a financial burden.
1. Enhancing customer loyalty and brand reputation
Consumers are becoming increasingly conscious of sustainability. A commitment to repairability fosters customer trust and long-term brand loyalty. When consumers know they can repair their products affordably, they are more likely to invest in high-quality, durable goods from brands they trust. This can help New Zealand manufacturers differentiate themselves in both local and international markets.
2. Strengthening the domestic economy
A thriving repair industry keeps money circulating within New Zealand rather than flowing offshore for replacement products. Cutting down on the need to import, benefits our trade balance. By supporting local repair services, manufacturers contribute to job creation and skills development, benefiting small and medium-sized enterprises (SMEs) and fostering
economic resilience.
In Australia, the Productivity Commission’s Right to Repair Inquiry highlighted the economic advantages of accessible repair services, while the UK has implemented regulations requiring manufacturers of household appliances to provide spare parts for up to ten years. These policies have led to a boost in domestic repair industries and reduced reliance on imported goods.
3. Encouraging innovation and competitive advantage
The shift towards repairable, durable products drives design innovation. Manufacturers that integrate modular, repair-friendly designs can tap into new markets, offering premium, long-lasting products. Brands that invest in repairability can also diversify their business models, offering subscription-based services, extended warranties, and repair programs that create new revenue streams.
Global companies like Apple have started to respond to the EU’s Right to Repair regulation by providing access to over 200 genuine Apple parts and tools as well as repair manuals and diagnostics tools. While there is still room for improvement, the regulation has also started influencing their designs - for example the adhesives used for safer battery replacements.
Internationally there are also businesses like the Dutch company Repeat (formerly Gerrard Street) who have built a loyal customer base by offering modular, repairable headphones as a service: Repeat Audio - Headphones that last a lifetime.
The Environmental and Resource Security Benefits
1. Reducing waste and improving sustainability New Zealand faces significant challenges in managing electronic and industrial waste. The right to repair extends the lifespan of products, preventing them from becoming waste prematurely and reducing the environmental burden of constantly manufacturing new goods.
While recycling is part of the solution, it is not a silver bullet. Many valuable materials—such as those in electronic devices—are difficult to recover efficiently. A circular economy that prioritises repair over disposal is a more sustainable and cost-effective way to manage resources.
2. Addressing resource scarcity and supply chain risks
New Zealand is highly dependent on imports for many raw materials and finished goods. The government recently published a list of critical minerals. Supply chain disruptions, such as those seen during the COVID-19 pandemic, highlight the risks of over-reliance on global production networks. A repair-friendly economy mitigates these risks by reducing the need for constant imports and ensuring that existing materials and products remain in use for longer.
New Zealand is not alone looking at right-to-repair policies.
Australia has already implemented the Motor Vehicle Service and Repair Information Sharing Scheme,
requiring car manufacturers to provide independent repairers with service and repair information at a fair price.
The European Union has introduced a Right to Repair Directive, ensuring manufacturers provide spare parts and repair manuals for appliances and electronics to extend product lifespans. The bloc also introduced the EU Batteries Regulation (2023/1542) that mandates user-replaceable batteries in laptops, smartphones and other electronic devices.
The United States has seen state-level right-to-repair legislation, with growing federal momentum to expand repair rights across multiple industries.
Aligning with these global shifts positions New Zealand manufacturers amongst the leaders of regulatory changes, making their products more competitive internationally and reducing compliance risks in export markets.
Turning challenges into opportunities
While the right to repair may require some adjustments, it ultimately presents a growth opportunity for New Zealand manufacturers. By embracing repairability, businesses can:
• Build stronger customer relationships through repair services and extended warranties.
• Reduce waste disposal costs and increase sustainability credentials.
• Foster local job creation in repair, refurbishment, and remanufacturing industries.
• Gain a competitive edge by leading in circular economy practices.
Supporting the right to repair is about creating a self-sufficient, future-proof economy. It empowers consumers, strengthens local businesses, and reduces environmental harm. Instead of viewing repairability as a cost, manufacturers should see it as an investment in resilience, innovation, and long-term growth.
*Author: Jim Goddin, Head of Circular Economy at thinkstep-anz.
Jim is a specialist in circular economy systems design, co-authoring the widely adopted Material Circularity Indicator with the Ellen MacArthur Foundation.
A Chartered Engineer, he has led major R&D programs in eco-design, additive manufacturing, and critical materials. Jim advises organisations like APCO and UKRI and is an implementation partner for the Circular Transition Indicators framework. He holds a PhD in materials engineering.
www.thinkstep-anz.com
Adam Sharman, CEO LMAC Group APAC
The Smart Industry Readiness Index (SIRI) has emerged as a critical tool for manufacturing organisations seeking to navigate their digital transformation journeys.
At LMAC Group we have supported over 200 business across New Zealand and the UK to define, start and optimise their Industry 4.0 journeys through our digital transformation approach using the Smart Industry Readiness Index.
Reflecting on this experience, in this article we will discuss the key themes and insights into the current state of Industry 4.0 adoption and their implications for manufacturing business across the industry
As New Zealand manufacturers seek to optimise and accelerate their productivity through Industry 4.0, they face several distinctive challenges:
1 Scale and Investment Capacity: With most New Zealand manufacturers being SMEs, many face challenges in securing sufficient capital for comprehensive digital transformation initiatives.
2 Talent Acquisition: The limited local talent pool for specialised digital skills creates a significant barrier, with many organisations struggling to attract and retain experts in areas like industrial IoT, data science, and automation engineering.
3 Connectivity Infrastructure: Regional manufacturers sometimes contend with limited high-speed internet access, constraining their ability to implement cloud-based solutions or real-time monitoring systems.
4 Integration with Legacy Systems: Many established New Zealand manufacturers operate with older equipment and systems that present integration challenges for newer digital technologies.
New Zealand manufacturers exhibit a characteristically pragmatic approach to technology implementation. Rather than pursuing cutting-edge technologies for their own sake, Kiwi businesses tend to prioritise practical solutions with clear returns on investment. This approach serves many companies well but can sometimes limit exploration of more transformative technologies that might deliver longer-term competitive advantages.
SIRI assessments across New Zealand have consistently highlighted several dimensions that manufacturers identify as top priorities for improvement. These priority areas reflect both the specific challenges facing New Zealand’s manufacturing sector and the greatest opportunities for competitive advantage.
The connection between operational technology (OT) and information technology (IT) systems presents a significant opportunity for New Zealand manufacturers. Priority areas within vertical integration include:
• Creating seamless data flows between shop floor equipment and enterprise systems through IoT connectivity for real-time data collection and analysis
• Implementing manufacturing execution systems (MES) to bridge the gap between ERP and operational systems
• Developing digital twins of production processes to enable better simulation and optimisation
This dimension is especially important for export-focused manufacturers who need to demonstrate complete traceability and compliance with international standards.
Many New Zealand manufacturers identify shop floor automation as a critical priority, particularly given the country’s persistent labour shortages and relatively high labour costs. Assessments reveal that while basic automation exists in many facilities, there are significant opportunities to:
• Implement more advanced robotics solutions, especially collaborative robots that can work alongside human operators
• Automate material handling and internal logistics to reduce manual movement of goods
• Deploy machine vision systems for quality inspection, reducing reliance on manual inspection processes
• Integrate automated guided vehicles (AGVs) for more efficient movement of materials within facilities
This dimension becomes particularly important for manufacturers in sectors like food processing and assembly operations, where labour-intensive processes remain common.
Data collection, centralisation, integration and analytics capabilities consistently emerge as a high-priority area from SIRI assessments. New Zealand manufacturers recognise significant untapped potential in their operational data, with specific focus areas including:
• Implementing predictive maintenance systems to reduce unplanned downtime
• Creating real-time performance dashboards to enable faster decision-making
• Building quality prediction models to identify potential defects before they occur
The gap between data collection and data utilisation is particularly pronounced in New Zealand, with many companies possessing extensive operational data but limited capabilities to derive actionable insights from it.
With New Zealand’s geographic isolation and distributed supply chains, enterprise connectivity consistently ranks as a high-priority dimension.
Key focus areas include:
• Implementing cloud-based platforms to enable remote monitoring and management
• Developing better connectivity between manufacturing sites and distribution networks
• Creating digital collaboration tools to connect with international customers and suppliers
• Building robust cybersecurity frameworks to protect increasingly connected systems
For manufacturers with multiple sites across New Zealand or international operations, this dimension becomes particularly critical for maintaining operational visibility and coordination.
Perhaps the most consistently identified priority across all SIRI assessments in New Zealand is workforce development. Specific focus areas include:
• Creating structured training programs for digital skills development
• Implementing augmented reality tools for knowledge transfer and remote assistance
• Developing clear career pathways for employees transitioning to more technical roles
• Building partnerships with educational institutions to create talent pipelines
This dimension represents both the greatest challenge and opportunity for New Zealand manufacturers, as successful digital transformation ultimately depends on having skilled personnel who can implement and operate new technologies.
Given New Zealand’s relatively small market size, manufacturers often need to produce a wider variety of products in smaller volumes than their international counterparts. This makes process flexibility a critical priority, with focus on:
• Implementing modular production systems that can be rapidly reconfigured
• Developing digital work instructions that adapt to different product variants
• Creating flexible automation solutions that can handle product variation
• Building scheduling systems that optimise changeovers and setup times
This dimension is especially important for contract manufacturers and those serving multiple export markets with varying product requirements.
Understanding these priority dimensions helps create more targeted improvement strategies for New Zealand manufacturers and allows for better allocation of limited transformation resources. The SIRI framework provides not just assessment capabilities but also a roadmap for addressing these key areas in a structured, prioritised manner.
One of the most striking findings from SIRI assessments to date is the significant variation in digital maturity across different manufacturing sectors. While industries like semiconductors, pharmaceuticals, and automotive manufacturing typically score higher, traditional sectors such as textiles, food processing, and raw materials often lag behind. This disparity reflects different competitive pressures, regulatory environments, and historical investment patterns in digitalisation.
Companies consistently score higher on technology adoption than on process redesign or organisational transformation. While many organisations have invested in advanced technologies like IoT sensors, data analytics platforms, and automation systems, they often struggle to adapt their processes and organisational structures to fully leverage these technological capabilities. This disconnect creates a significant barrier to realising the full potential of Industry 4.0 investments.
Interestingly, company size doesn’t always correlate with digital maturity. While large enterprises often have greater resources to invest in digital transformation, some smaller and medium-sized enterprises demonstrate remarkable agility
in implementing Industry 4.0 solutions. These high-performing SMEs typically succeed by focusing on specific, high-impact
Perhaps the most significant finding from SIRI assessments is the crucial role of leadership commitment and workforce engagement in successful digital transformation.
Organisations with strong leadership support for Industry 4.0 initiatives and comprehensive strategies for workforce development consistently outperform their peers, regardless of industry or region.
Many organisations struggle to demonstrate clear returns on their Industry 4.0 investments. This challenge often stems from inadequate planning, insufficient metrics for measuring success, or failure to align digital initiatives with broader business objectives.
Successful organisations address this by establishing clear KPIs for their transformation efforts and focusing on initiatives with measurable business impact.
New Zealand manufacturers consistently identify workforce development as a critical challenge. The transition from traditional manufacturing skills to digital competencies requires significant investment in training and cultural change.
continued from Page 19
More successful organisations are developing multi-pronged approaches that combine upskilling existing workers, recruiting new talent, and partnering with educational institutions.
SIRI assessments suggest that New Zealand manufacturers are at an inflection point in their Industry 4.0 journey. While most remain in early to middle stages of digital maturity, the path forward is becoming clearer.
Leading organisations are demonstrating how targeted digital investments can overcome geographical isolation, address labour shortages, and create distinctive competitive advantages in global markets.
SIRI assessments indicate that most manufacturing organisations are still in the early to middle stages of their Industry 4.0 journey. However, leaders are emerging across all sectors who demonstrate how comprehensive digital transformation can drive significant competitive advantage. These organisations typically succeed by:
• Taking a holistic approach that addresses technology, processes, and organisational culture simultaneously
• Focusing on use cases with clear business value
• Building robust data infrastructure that can support advanced analytics and AI applications
• Developing comprehensive workforce development strategies
Navigating industry 4.0 - The essential guide for
include having detailed process documentation and a clear vision of your automation goals.
When engaging automators, it’s crucial to ensure that you’re automating the right processes. Automating a non-bottleneck process might not deliver the expected ROI. Additionally, consider the scalability and supportability of the solution. Ask questions like:
• Can the solution grow with my business?
• What are the maintenance requirements?
• How quickly can we get support if something goes wrong?
Commercial arrangements with automators can vary. Some offer turnkey solutions with a one-time payment, while others might propose a subscription model for ongoing support and upgrades. Be clear about your expectations and negotiate service-level agreements (SLAs) that ensure timely support and maintenance.
In conclusion, automators are invaluable partners in the journey towards Industry 4.0. Their expertise in designing and implementing automation solutions can transform your manufacturing processes, leading to increased efficiency, higher quality, and a safer workplace. While there are considerations to keep in mind, the benefits of partnering with a reputable automator far outweigh the challenges. Embrace the future of manufacturing with the right automation partner by your side!
If you have an automation project in mind, find the right partner to deliver it Fulcrumnz.com
-Frank Phillips, Director, Fulcrum
Welcome to the first of our exclusive series on Industry 4.0 and automation, tailored specifically for small and medium-sized manufacturers in New Zealand.
Over the course of this series, we’ll dive into the world of Industry 4.0, exploring the various types of companies that can help you revolutionize your manufacturing processes. From automators who design and build cutting-edge robotic systems, to data experts who transform raw data into valuable insights, each article will provide an in-depth look at the key players in your digital transformation.
Our goal is to equip you with the knowledge and insights needed to make informed decisions and unlock the full potential of your business. Whether you’re looking to automate a bottleneck process, integrate disparate systems, or harness the power of data for continuous improvement, we’ve got you covered.
Join us on this journey as we explore the exciting opportunities and challenges of Industry 4.0. Together, we’ll discover how the right partnerships and strategies can drive your business towards greater efficiency, productivity, and success.
Without further ado – here’s our first instalment: Automation Experts. What you need to know.
When it comes to the cutting-edge world of Industry 4.0 and automation, automators are the wizards behind the curtain. These companies specialise in analysing manufacturing processes and designing custom equipment and robotics to automate tasks efficiently and safely.
Think of them as the architects and engineers who transform manual operations into streamlined, automated workflows.
Engaging an automator can be a game-changer for manufacturers facing challenges such as labor shortages, inconsistent quality, and inefficient production lines. By automating key processes, manufacturers can achieve higher productivity, improved product consistency, and a safer working environment. The real value lies in targeting the right processes for automation—typically those that are bottlenecks or prone to human error.
Working with an automator usually begins with a thorough analysis of your current processes. This phase involves site visits, data collection, and collaborative discussions to understand your goals and pain points. The automator then designs a custom solution, which could range from robotic arms to fully integrated automated lines.
Expect to dedicate internal resources to this collaboration, including process engineers, IT personnel, and operations managers. The engagement can span several months, from initial analysis to full implementation. Pre-requisites
continued bottom of on Page 18
Looking for a marketing edge?
continued from Page 1
By linking local businesses with global expertise, specialised technologies and significant capital, this programme offers a defined pathway for turning promising research into export success stories. In an industry where only a fraction of innovations ever reach the market, such support could prove transformative.
Entrepreneurs in the food sector often face a steep climb when attempting to commercialise their innovations.
The NZFIN initiative is uniquely positioned to change that narrative. By offering tailored support—from guiding firms through the intricacies of scaling production to providing access to a global network of food scientists and process engineers—this new initiative ensures that even the most nascent ideas can be nurtured into market-ready products.
Grant Verry, NZFIN Co-CEO, has articulated the vision succinctly: Kiwi food and beverage firms can now bring an idea to the table and receive the guidance needed to transform that idea into a tangible export.
The initiative’s comprehensive approach— extending beyond territorial and regulatory boundaries—ensures that
businesses can compete on the global stage with the same level of support they receive domestically.
These initiatives are more than just an export programme; it is a clear statement about New Zealand’s future in food manufacturing. Our industry has always been about more than just food—it’s about innovation, sustainability and a commitment to quality that the world admires.
By harnessing our local ingenuity and connecting it with international expertise, we can not only meet global demand but also drive transformative change across the sector.
For manufacturers and food innovators, this is an opportunity to reimagine what is possible.
It offers a chance to move away from the traditional, often fragmented approach to product development and embrace a model that is integrated, forward-thinking and truly global.
This, in turn, will generate not only increased export earnings but also foster a healthier, more dynamic food manufacturing landscape here at home.
As someone who has spent over two decades in FMCG public relations and business transformation, I am thrilled to see our government and industry leaders taking such decisive action.
Now is the time for Kiwi manufacturers to capitalise on this initiative, to optimise their operations, embrace new technologies and ultimately, to lead the charge in global food innovation.
Sarah Wynn-Williams
This book by Kiwi, Sarah Wynn-Williams has caused a storm. The master of free speech doesn’t want it published.
Power and corruption - the power system we live in - accountability. Think about the systems you are a part of. Being careless can have huge consequences. Working for Mark Zuckerberg may not be the best option and did Sheryl Sandberg “Lean In’ too far?
An explosive memoir charting one woman’s career at the heart of one of the most influential companies on the planet, Careless People gives you a front-row seat to Facebook, the decisions that have shaped world events in recent decades, and the people who made them. From trips on private jets and encounters with world leaders to shocking accounts of misogyny and double standards behind the scenes, this searing memoir exposes both the personal and
the political fallout when unfettered power and a rotten company culture take hold. In a gripping and often absurd narrative where a few people carelessly hold the world in their hands, this eye-opening memoir reveals what really goes on among the global elite.
Sarah Wynn-Williams tells the wrenching but fun story of Facebook, mapping its rise from stumbling encounters with juntas to Mark Zuckerberg’s reaction when he learned of Facebook’s role in Trump’s election. She experiences the challenges and humiliations of working motherhood within a pressure cooker of a workplace, all while Sheryl Sandberg urges her and others to “lean in.”
Careless People is a deeply personal account of why and how things have gone so horribly wrong in the past decade―told in a sharp, candid, and utterly disarming voice. A deep, unflinching look at the role
In my view, the success of this initiative will be measured not only in export dollars but in the broader impact it has on the competitiveness and resilience of New Zealand’s food sector.
This is a critical opportunity to build a more connected, innovative and prosperous industry that reflects the very best of what New Zealand has to offer.
that social media has assumed in our lives, Careless People reveals the truth about the leaders of Facebook: how the more power they grasp, the less responsible they become and the consequences this has for all of us.
A tailored, thoughtful combination of cutting-edge technologies, stronger contracting skills, and deep supply chain capabilities can get a new factory up and running—without costly delays.
Today’s environment is giving manufacturers even more reasons to reassess their footprint strategies. For some, localisation of production may now seem increasingly attractive—particularly amid rising volatility in tariff and trade policy, evolving incentives for manufacturers
Manufacturers know that building new factories— and doing so quickly—can be incredibly complex. It is possible for the chief manufacturing officer to have never overseen the expansion of an existing factory—let alone the development of an entirely new “greenfield” site.
The construction industry’s capacity for new factory construction is also constrained, especially by the demand for skilled workers.
The sheer scale of the capacity gap is daunting even before confronting the very real risks that major projects face, from spiralling labour costs to vulnerable supply chains.
There’s no single technology or template that manufacturers can deploy in response. Instead, to close the gap, manufacturing leaders need an integrated approach to factory building, one that encompasses thoughtful factory design, a reassessment of the supply chain, and effective construction management.
The first step is undertaking a meticulous factory design process that seeks to ensure consistent flow of production, with adequate redundancy in capital assets
Heightened competition for capital under current market conditions means it’s more critical than ever for manufacturers to deliver major capital projects on time and on budget.
Higher labour costs in a new location require a company to rethink the entire value chain for the new plant—and with it, core production processes. Executives need to recognise that a greenfield development offers a unique chance to invest in Industry 4.0 technologies, maximising ROI and minimising production disruption
Industry 4.0 user cases can show high potential for a very different production line, with heavier use of robotics and other forms of automation.
An even more advanced application of Industry 4.0 that many companies have already deployed is to build a digital twin of the future production line, as a medical-products company did in designing a new plant for its high-mix, high-volume product portfolio.
Leveraging a digital twin allows a company to optimise a new factory’s layout by simulating future production so that engineers can build in additional flexibility and minimise the impact of frequent changeovers.
Advanced technology alone can only achieve so much. Too often, new factories run into a highly analogue problem: suppliers that can’t keep up, whether because of difficult logistics, their own capacity constraints, or broader issues in the supply relationship.
To mitigate these risks for a new assembly site, an aerospace and defence manufacturer developed an in-depth analysis that combined factors such as suppliers’ available production capacity, geographic footprint, and applicable transportation modes and routes with forecasts of component demand at both the market and individual-part levels.
The company used the insights from this analysis to develop its supplier strategy, identifying where existing suppliers could meet demand and where additional suppliers were needed.
Because timely project delivery also depends on effective design and construction management, leaders need a robust contracting strategy that seeks risk-sharing opportunities with vendors and builds incentives for punctual completion.
In parallel, companies can also define applicable governance models, establish a construction stage-gate process, and start addressing one of the largest risks to major construction projects: skilled-labour availability.
Well before starting its fab project, a semiconductor manufacturer revisited and revamped its contracting strategies, systematically building new capabilities so that it could better understand its contractors’ costs and constraints.
The insights helped the fab’s leaders adopt a new negotiation stance, which ultimately led to a genuine partnership with the fab’s general contractor—along with a more intelligent allocation of risk and about a one-quarter reduction in bid price.
At the same time, a team of analysts developed an integrated trade labour strategy to identify top labour risks and better manage talent scarcity.
A detailed assessment reviewed how labour needs would evolve for every trade over the project’s duration, and for each area and building in the sprawling facility.
Next, the team identified the labour needs of the major trade contractors, ranking potential vendors by their capacity, proximity to the site, and potential
for long-term relationships.
Finally, for the largest packages of work, the team evaluated the most likely bidders, with recommendations to split up some packages so that more contractors would be able to work in parallel on-site. These steps saved more than $50 million.
The fab’s careful use of advanced construction technologies, including the latest modular-building techniques and generative-scheduling and performance transparency tools, helped it mitigate other risks. Leaders used a generative-scheduling model to test a range of alternative construction program designs—such as resequencing the structural packages or reallocating labour to boost utilisation.
The model identified more than 90 optimization opportunities that together cut timelines and total project costs by more than 10 percent.
This use of technology has also proven successful for an automotive OEM in constructing a new battery facility. Leaders explored “what if” scenarios and opportunities to optimise the tooling installation schedule, which allowed the company to shave more than a month from its delivery schedule and saved more than $40 million.
Project leaders at each of these companies undertook a strategic review of four essential issues to guide their greenfield expansion strategy.
One of the primary considerations was site flexibility: how much leeway the company has in choosing the greenfield site.
For example, changing a company’s geographic footprint can have a dramatic effect on its suppliers’ capacity to support the expanded business. Some companies face additional location constraints due to specialized transportation or skill requirements, customer proximity, or the necessity of being near other plants.
Understanding the risks to supply chain and workforce availability is crucial when selecting a site and can involve difficult trade-offs. One high-complexity manufacturing company’s supply chain requirements left it little choice but to enter markets that were already short on skilled workers.
continued on Page 26
Sandvik Coromant has introduced the QS Micro — a new quick-change holding system developed specifically for sliding head machines. It promises exceptional precision, security and repeatability and maximised machine utilisation.
The QS Micro holding system is specifically designed for small part machining and sliding head machines. It covers the majority of industry segments, such as general engineering, automotive, aerospace and medical. With an extensive range of cutting heads and shank adaptors, the system offers a multitude of configurations and quick tool changes.
The assortment includes rectangular shaft adaptors in sizes 10 × 10 mm up to 20 × 20 mm, and equivalent inch sizes. It also features cutting heads for general turning, parting and grooving, and threading in
families CoroTurn 107, CoroCut 2, CoroCut XS and CoroThread 266. CoroTurn 107 and CoroCut XS provide cutting heads designed for Y-axis machining, offering advantages such as higher stability and better chip evacuation.
One of the main benefits of the QS Micro holding system is that it is possible to quickly change cutting heads with high precision, which reduces the machine downtime.. Another benefit is the modularity, which enables the fitting of different types of cutting heads in different adaptors, reducing the need for a large tool inventory.
Other benefits include a rigid holding mechanism that minimizes vibrations, enabling unprecedented precision in sliding head machines without compromising process security. High indexing
Cobot welding is a game changer for the manufacturing industry. A flexible solution that can be tailored to the needs of individual manufacturing firms, cobot welding delivers numerous benefits including increased productivity, quality-control, cost efficiency, scalability, real-time monitoring and an enhanced working environment.
Cobot welders automate the welding process and work alongside humans to perform welding tasks. Capable of working continuously with minimal maintenance and without the need for breaks, cobot welders can help boost production output. They can handle repetitive tasks quickly, as well as more intricate work efficiently to improve productivity. Plus, requiring minimal oversight and monitoring, they can also free up workers so that they can focus on more complex or higher-value tasks.
“Cobots have the capability to run 24/7 and to also work in automated cycles,” says Stuart Orr, Sales Director, Kemppi Australia. “As a result, they can enhance manufacturing processes and deliver significant productivity benefits.”
Cobot welding systems also maintain precise control over welding parameters such as temperature, pressure and so on. This leads to more uniform welds, while minimising the potential for variation in quality.
Kemppi, a leading global welding manufacturer, has an extensive range of cobot-ready welding solutions, including the Master M 353, Master M 355 and Master M 358, and the X5 FastMig and X5 FastMig Pulse.
“In a cobot environment, all of our cobot-ready
machines follow pre-programmed steps to ensure consistency and precision when welding,” explained Stuart.
The delivery of consistent welds also means fewer defects, which can reduce the need for rework and any associated costs.
Thanks to the accuracy of cobot welding systems, they tend to reduce material waste and hence, overall production costs for manufacturers.
Cobots can also lead to the need for less manpower on the shop floor as they can handle a range of tasks with ease, and therefore, help reduce labour costs.
Further, unlike traditional manufacturing equipment, cobots are often less expensive, and because they require less integration and infrastructure, can result in a faster return of investment.
Manufacturers also have significant choice when it comes to choosing a cobotic welding solution that aligns with both their needs and budget. For instance, manufacturers who do not require their cobotic welding system to be frequently reprogrammed can consider a more cost-effective option such as the Kemppi Master M 353 and 355 models. For those requiring a system for more intricate cobot applications and superior performance, the Kemppi X5 FastMig series offers sound value.
Cobots may also be the answer in a tight labour market. “In the current welding labour shortage environment, cobots are a viable option that allow manufacturers to access the welding skills they need and maintain control over their operations with a low capital investment,” said Stuart.
Cobots are also highly flexible and adaptable, and can accommodate the shifting demands of various manufacturing environments.
“They can be quickly reprogrammed for welding tasks or product designs, which is especially beneficial in small-batched or customised production runs. They are also scalable. When the manufacturer’s production volumes increase, additional cobot welders can be quickly and easily integrated into the existing system,” said Stuart.
Today, many cobots are equipped with sensors and software to collect data regarding the welding
precision (+/- 3µm) also ensures supreme component quality, exceptional accuracy and repeatability across various operations.
Furthermore, efficient chip control is crucial in small part machining. All QS Micro shank adaptors provide through-coolant functionality,allowing easy coolant connection to the cutting heads, and the precision coolant is delivered directly to the insert.
Effective chip evacuation is critical. Chip smearing can significantly impact the intricacy of the machined parts. Fortunately, our through-coolant functionality results in exceptional chip control, extended tool life and increased productivity.
process in real-time. This allows manufacturers to monitor weld quality and performance, and make any desired adjustments to optimise welding processes.
Kemppi’s WeldEye is a comprehensive and universal welding management software that helps optimise production processes. WeldEye consists of various modules which can be combined with any brand of equipment to provide live monitoring. The ArcVision module, for instance, when combined with the Kemppi Master M 358 or X5 FastMig, provides real-time monitoring and data insights from the cobot welding station that can be accessed directly within the cloud-based platform.
The information ArcVision provides can be visualised in customisable tables and graphs. Manufacturers can then adjust welding parameters on the fly to reduce the likelihood of errors, ensure quality output and maximise uptime. The data can also help identify areas for improvement to optimise the welding process.
Cobots can also help minimise human exposure to welding hazards such as heat, smoke, fumes and UV radiation. The metal fumes produced during the welding process can be especially dangerous when inhaled. The fumes consist of microscopic particles of hot metal and gases, and can contribute to carcinogenic conditions.
Cobots can make welding environments safer and meet Australia’s tightening welding fume exposure standards because they can remove workers from direct exposure to welding arcs. This, together with on-torch fume extraction solutions, such as the Kemppi Flexlite GF series, extract the welding fumes straight from the torch nozzle, to provide a safer and cleaner environment for workers.
Typically, cobots are easy to operate and require little programming experience. Most cobot welding manufacturers also provide training and support. “Our cobot welders are user-friendly and do not require the operator to have any deep or specialised programming knowledge. They have an intuitive interface which helps make operating them simple and easy. In essence, their simplicity helps empower manufacturing firms to be more productive and efficient,” said Stuart.
Richard Morton CEO, The Learning Wave
One of the biggest challenges for organisations in this increasingly digital world is employees who lack essential digital skills. In a tight job market, hiring workers who are already digitally proficient is difficult, making upskilling the best solution.
In today’s rapidly evolving workplace, digital capability is no longer optional - it is a critical factor for business success, but it is not always at the level it needs to be.
Despite digital literacy being critical for modern work, a surprising 55% of workers in New Zealand lack the right level of digital competency to thrive in technology-rich environments.
Equipping frontline workers with digital skills is crucial. Leaders who invest in digital upskilling for their teams will see direct benefits in productivity, efficiency and workforce resilience.
This skills gap directly impacts workplace safety, efficiency, and retention. Manufacturing suffers from low digital adoption, leading to higher error rates, increased waste, and lower overall productivity.
Employees and or workforces can often become the barrier to digital adoption meaning untapped productivity opportunities are left behind or not even considered. As workplaces become more technology-dependent, leaders who fail to prioritise digital training risk falling far behind.
Investing in digital skills for frontline workers is a direct contribution to business success. Organisations that integrate digital upskilling into their workforce strategy see measurable returns:
• Increased Productivity - employees who can efficiently navigate digital tools complete tasks faster and make fewer errors
• Higher Engagement and Retention - workers who receive ongoing training feel valued and more likely to stay
• Improved Operation Efficiency - a digitally capable workforce reduces downtime and optimises processes
We know New Zealand manufacturing companies that introduce structured digital and leadership training report a 3:1 return on investment. Their employees not only gained practical digital skills but also contributed to measurable workplace improvements.
Effective Solution: Digital Transformation for Frontline Workers
Leaders who want to future-proof their organisations should prioritise structured digital training and help is out there. One effective solution is the EMA Micro-Credentials Programme delivered
by The Learning Wave, specifically designed to equip frontline workers with essential digital skills for manufacturing, engineering and industrial sectors.
It is a two-day face to face workshop with a follow-up online session or in-house options are available for larger workforces wanting to provide this opportunity to groups of employees.
This proven and effective approach not only provides workers with practical digital capabilities but also ensures they can apply their learning in real workplace scenarios, contributing to overall business improvement.
As businesses navigate an increasingly digital world, leaders must ensure their workforce is equipped to thrive. Digital capability is no longer a “nice to have” rather, it is essential for competitiveness, efficiency and long-term success.
By investing in digital upskilling today, organisations can create a workforce that is agile, adaptable and prepared for the challenges of tomorrow. The businesses that act now will be the ones leading the future.
He kickstarted his career studying maritime engineering, but it’s only since pursuing an apprenticeship as a fabricator that Sam McLean has found his fit.
Now, just four years on, he’s a qualified tradie, a workshop supervisor, and a highly valued employee at Onehunga-based steel fabrication specialists JP Engineering Services. The Mt Albert 25-year-old says he’s living the dream.
“The feeling of accomplishment and satisfaction looking at something you’ve created keeps bringing me back,” says Sam. “Every day is challenging in a different way, especially starting on a design I haven’t attempted to fabricate before.“
It’s challenges like these that cement Sam’s passion
for the sector and employers like JP Engineering who give him the support he needs to thrive.
Like Sam, Vaitai (Tai) Sakaio has excelled under John’s headship. Originally from Tuvalu, the hardworking 29-year-old was drawn to welding “like a moth to a light”. He, too, has recently completed his apprenticeship, giving cause for a double celebration at JP Engineering Services - complete with staff barbecue and speeches.
“During my apprenticeship I had some personal challenges. My mum had breast cancer, and I fell hard. I knew I wasn’t performing my best at work, and I almost left the company, but fortunately, I had plenty of words of wisdom and support from John. He has always been keen on upskilling and putting
me through my tickets.
“I’ve gained a lot of knowledge and life lessons from him, and in the last two years of my apprenticeship, when I got a bit lazy, he gave me a deadline. That’s what helped push me through to the end; that’s what motivated me to stop mucking around and complete my apprenticeship.”
Support from Competenz further fuelled Tai’s success.
Enthusiasm, adaptability, and initiative: these are qualities that have earned Ngāruawāhia apprentice Zander Pringle the prestigious Stuart Tolhurst Memorial Award for 2024 in Hamilton this month.
Announced at the Maintenance Engineering Society New Zealand (MESNZ) Awards dinner, the honour places Zander at the apex of his field, cementing his place as New Zealand’s top mechanical maintenance engineering apprentice. Needless to say, he’s “stoked”.
It’s a remarkable achievement for the 22-year-old, who fell in love with the trade beginning through the Gateway programme when he was at Hamilton Boys’ High School.
“Bookwork never interested me, so I’d pretty much ruled out uni – I always preferred doing more hands-on stuff. One of the Gateway options was to go into Fonterra and follow a fitter or sparkie around for two months, so I thought I’d give it a go.
“ I didn’t have any expectations, but I ended up loving it. I did my first two weeks with a sparkie and the next two weeks with a fitter. That was when I thought, that’s me. I want to become a fitter, and I want to do it at Fonterra.
“I’ve always loved figuring out how things work –pulling things apart to see what’s inside and putting
them back together, and that’s essentially what the job is. There’s so much variety! My daily tasks can include anything from replacing mechanical seals and motors, to preventative maintenance checks and rebuilding actuators. I really enjoy the problem-solving aspect of the job – trying to diagnose what’s wrong and then fixing it. Being able to successfully finish a job is very satisfying.”
Mechanical maintenance engineering is the perfect fit for Zander, and three-and-a half years into his journey, he’s excelling. Alongside thriving in his apprenticeship, he has taken on several additional responsibilities including being the health and safety representative for the maintenance department, and union delegate for Fonterra apprentices. This year he has also assisted in the hiring of new apprentices. His boss Todd McKay is justifiably proud.
Balancing the demands of high-level sport with work and study, Zander truly has it all—one of the many reasons Competenz Training Advisor Samuel (Sam) Bay nominated him for the Stuart Tolhurst Memorial Award.
“This trade provides an opportunity to travel the world. Already a trip to Australia to do a 17-day meat works shut down using my annual leave, and once I’m qualified, I’m keen to do a longer stint overseas, travelling and working.”
Hill Labs has strengthened its food safety and drinking water compliance services with the acquisition of Canterbury-based companies Food and Health Standards (FHS) and Auditing Solutions (AS), in partnership with experienced auditor and business leader Sam Brooks.
This strategic move enhances Hill Labs’ ability to support local councils, food producers, and industry clients, particularly in the South Island.
As part of the transaction, Hill Labs has also acquired FHS’s water compliance monitoring operations, which will be integrated into its own services. This expansion establishes Hill Labs’ position in municipal
water sample collection and compliance monitoring, supporting councils with a seamless, high-quality solution.
FHS and AS, founded by Ian and Gail Shaw, have built a strong reputation over 30 years for their commitment to quality, integrity, and service. Ian will continue in a senior role, ensuring continuity, while Gail will retire.
Brooks, who has nearly two decades of experience in food auditing, will take on the role of CEO for FHS and AS.
Hill Labs Managing Director Jonno Hill describes the acquisitions as a logical next step in the company’s growth.
Brooks sees the transition as a win for both businesses and their clients.
“Embarking on this new venture with such a competent team fills me with confidence. It has been wonderful getting to know the team and being welcomed into the family culture within the business. I’ve also had the opportunity to meet customers and understand their needs, and I’m excited to lead FHS and AS into this next chapter alongside Hill Labs.”
Ian Shaw also expressed his enthusiasm for the transition.
“This is an exciting development for FHS and AS. Our legacy, built over three decades, is now secured
for the future. Hill Labs, with Sam at the helm, is the perfect partner to continue delivering the high standards our customers rely on. Our values align closely, and I look forward to continuing in a senior role.”
Alongside the acquisition, Hill Labs is expanding its municipal water compliance services, bringing FHS’s water team, led by Lisa Shaw, into its operations. Lisa and her team have earned a reputation for being reliable, supportive, and responsive in delivering essential water compliance services.
Lisa’s team will move into Hill Labs’ Christchurch site at Print Place, working closely with Business Manager Jared Halstead, who will now oversee both asbestos and water compliance services.
Hill Labs’ investment in these acquisitions aligns with its long-term vision to be New Zealand’s leading food and water testing provider, with a strengthened presence in the South Island.
FHS and AS will continue operating under their existing branding, with Hill Labs providing support through shared services. The transition will be carefully managed to ensure continuity for employees and clients while unlocking new opportunities for innovation and growth.
Heat pump company Daikin is incorporating its ambitious global sustainability goals into a new purpose-built facility in Christchurch.
Daikin New Zealand’s new development in Hornby, which is due for completion in October 2025, is targeting a 5 Green Star rating to support Daikin Global’s aim to achieve carbon neutrality by 2050.
The development makes Daikin the first international company in the Canterbury region to follow its global sustainability charter to have all its facilities around the world meet an accredited sustainability rating.
Once the facility – known as Daikin Park Christchurch – is occupied, it also aims to achieve a 5-star NABERS rating which shows a building’s energy performance.
“This project represents a significant investment in sustainable development and innovation within the Canterbury region,” said Ben Lagan, Managing Director of Christchurch-based developer Carbon Property.
“Sustainability is top of mind for Daikin globally and we are working closely with Daikin New Zealand to ensure it meets the organisation’s key sustainability targets on a local level,” said Mr Lagan.
Daikin Park’s sustainability features include a 100kw solar system, energy efficient fittings and fixtures, low VOC environmentally friendly paints and sealants, facilities for cyclists and EV charging stations, and rainwater harvesting.
To significantly reduce the operational impact on the environment, Daikin is installing industry-leading HVAC systems in the Christchurch facility. This technology includes advanced heat recovery technology and predictive fault detection to ensure maximum energy efficiency and indoor air quality.
The Christchurch facility also includes a comprehensive training academy to support the development of skilled workers in the HVAC industry.
As part of improving sales and installation skills in the industry, Daikin also aims to collaborate with vocational training schools and local universities.
Michael Trad, Director of Daikin New Zealand, said: “Along with Daikin Park Auckland, the facility will lead the way in raising the level of skills development in the entire heat pump market which is set to continue expanding in the future.”
Mr Trad said Daikin’s vision was to establish state-of-the-art facilities that further enhance the support it provides customers.
“Building on the success of four Daikin Park’s in Australia and one in Auckland, the Christchurch project provides an opportunity to demonstrate Daikin’s global supply chain excellence in New Zealand and redefine the standard for customer experience.”
Daikin Supply Chain and Facilities Manager, Andy Heydon, said Daikin Park Christchurch would support the company’s supply chain vision for the long term.
The expansion of the world’s largest oil and gas pipeline throughout North America is set to provide part of a $70 million boost to exports of New Zealand-made amphibious-capable aircraft over the next decade.
The 29,000 km pipeline, the world’s longest and most complex oil and liquids transportation system, carries over 5.8 million barrels of oil and 0.70 billion cubic meters per day of natural gas. The network extends from the Gulf of Mexico through the US and into Canada - transporting 30% of crude oil produced in North America and a fifth of all natural gas consumed in the United States.
The expansion of the pipeline network is set to increase demand for New Zealand-made E-350 Expedition aircraft.
The North American pipeline company operates a fleet of six E-350 aircraft, a model that was first made in Canada but is now produced by Hamilton-based aeronautical manufacturer NZAero.
Under a US$1.5 billion system fitness and leak detection annual programme, the aircraft are used to protect the local environment from damage to the subterranean pipeline due to land movement and erosion following weather events as well as unauthorised construction in the area.
A team of pilots fly sorties at an altitude of 200 metres along the network, identifying hazards and helping to prevent damage that could result in environmental contamination. The aviation patrols have helped the company maintain an almost impeccable safe delivery record of 99.999959% with nearly 37 billion barrels of oil transported over the past decade.
Stephen Burrows, CEO of NZAero, says the US pipeline operator has recently taken delivery
of the first E-350 sold by the Waikato manufacturer, with a second order currently in production at their facility.
He says the potential growth in the pipeline network represents a multimillion-dollar export opportunity for the New Zealand aeronautical manufacturing sector.
“The E-350 Expedition is a highly versatile utility aircraft that is ideal for carrying passengers and large cargo items. It excels in various environments, functioning as a cross-country cruiser, backcountry bush plane, or floatplane, with rugged landing gear and short takeoff and landing (STOL) capabilities.
“Now the aircraft is back in production, we are seeing a significant enquiry from around the world including Northern Europe, the Middle East and Asia - as a low-cost aircraft to access isolated villages and humanitarian applications such as medivac.
“There is also strong demand coming from North America where most of the aircraft are used in tourism operations taking people into the wilderness. As they can be easily converted to land on water, many of the 80 aircraft in existence are used to access fishing lodges on remote lakes in
Canada and Alaska.
“We expect this model to account for around a quarter of our aircraft exports over the next decade and we are aiming to produce around 30 units during this period. This would represent over $70 million in export earnings from this aircraft and its parts and maintenance alone.
“This entry-level offering would complement the global sales of our SuperPac750XL-II, the world’s first XSTOL (Extremely Short Take-Off and Landing) utility aircraft,” he says.
Burrows says the E-350 was selected for its ability to handle heavy turbulence at low altitudes and visibility for the pilots.
He says the addition of another two New Zealand-built E-350s to their fleet over the next two years will standardise the pipeline owner’s fleet across the U.S. and Eastern Canada.
“What sets these aircraft apart for their operations is how tough they are at low altitudes - around 500 to 700 feet. In strong turbulence and during 60-degree bank turns around valve and compressor station sites, they perform flawlessly.
“Some of their planes have nearly 9,000 hours of low-altitude surveillance and show minimal wear. They handle turbulence better, thanks to their beefier wings, which cut the bumpiness in half compared to lighter aircraft. They’re smoother, more durable, and outperform anything they’ve used before.
“The fleet standardisation will allow them to operate seamlessly, as all the planes will be practically identical, meaning their pilots can move between aircraft easily. Plus, having just one set of stock parts makes maintenance far more efficient,” he says.
continued from Page 21
Despite the location’s other benefits, the company had to develop additional plans to attract and retain talent.
Another critical factor is timeline: the time required to meet the production schedule and potential opportunities for investment to accelerate the completion date. Identifying where investments can expedite processes is vital.
Each region and industry has unique requirements, and companies should understand the standard timelines and which actions or investments could help accelerate them. For example, if equipment production can be accelerated, could the future workforce begin training on new processes earlier?
Does the company have sufficient training capacity, and are there other sites with experienced workers
who can provide initial leadership? The complex manufacturer found that even with investment, “time to talent” remained challenging, delaying the site’s ability to operate at full capacity.
Third, companies should consider new processes and technology. Up-front investments in automation and robotics not only improve performance but also attract a future-ready workforce.
With Industry 4.0 advances, some manufacturers are already implementing two-way supplier connectivity by fitting lines with sensors and deploying digital work instructions. The complex manufacturer found ways to implement technologies that could assist the workforce without requiring extensive process redesign and certification.
Last, leaders should continue looking for ways to
transform existing production during greenfield design and development. At least initially, new facilities may not be more efficient than current sites.
Leaders should therefore keep exploring potential capacity improvements at existing facilities even as greenfield expansion is underway. The complex manufacturing company, for instance, wasn’t projected to be fully operational with its greenfield facility for over three years.
To meet growing demand, it had to find efficiencies in its current locations by continually reexamining equipment utilisation, staffing, and overall efficiency metrics.
By addressing these issues, companies can effectively shape their greenfield expansion strategy to minimize risks and maximise operational efficiency.
continued from Page 10
employees may request unpaid leave or changes to their working conditions.
This is where businesses must assess their options carefully. Dismissing a staff member due to Long Covid should be a last resort, only after extensive discussions, medical evaluations and legal guidance. The idea of ‘frustration of contract’ – where an employment agreement is ended due to an inability to perform duties - is problematic in the case of Long Covid, as many people eventually recover and can return to work.
Businesses must also consider the cost of replacing staff. Losing experienced workers means losing valuable institutional knowledge.
Training new employees is expensive and time-consuming, often causing more disruption than finding ways to support existing staff through their recovery.
Employers should view this as an investmentby helping staff gradually reintegrate into the workplace, they retain skills and loyalty while fostering a supportive work culture. There are steps businesses can take to mitigate these challenges. Encouraging employees to prioritise their health, offering wellness initiatives, and promoting access to occupational therapy, physiotherapy, and mental health support can speed up recovery.
Simple accommodations, such as allowing rest breaks, reducing strenuous tasks, or providing hybrid work options, can make a significant difference in an employee’s ability to function.
Employers should also be mindful of team morale. When one employee is on extended leave, others may feel the pressure of increased workloads. Open discussions with teams about workload distribution and temporary staffing solutions can ease frustrations and ensure fairness.
Long Covid is not just an individual health issue, it is a business challenge that requires careful handling. Employers who adapt and show flexibility will retain skilled workers, maintain productivity, and foster a work culture that values people over short-term profit.
While Long Covid presents hurdles, businesses that take a long-term view and support their employees will ultimately benefit from a more engaged and resilient workforce.
If you’d like more information on how to manage Long Covid in your business, contact the EMA’s employment relations team at ema.co.nz/services/ employment-relations or call 0800 300 362.
New Zealand’s productivity crisis has dragged on for decades, waiting hasn’t worked.
Our productivity lags other OECD nations, with clear consequences: stagnant wages, reduced competitiveness, declining living standards, weak business investment, an over-reliance on commodities and low-value industries. We work longer and harder, not smarter.
The Treasury has called it our biggest economic challenge, yet we continue to treat it as an abstract problem rather than an urgent, business-led priority.
To make any meaningful progress and catch our peers, businesses en masse must focus actively on performance improvement. Even with that level of action and momentum, it would still take three to five years before we begin seeing national productivity improvements.
To achieve this, we’re not talking about “some manufacturing businesses” making incremental improvements. We need to redefine New Zealand’s economic landscape… According to Statistics NZ (2023) there are ~ 23,000 NZ manufacturing businesses. For meaningful change we need 15,000 manufacturers, or two-thirds, to make this their top priority for the next five years.
Our government has set ambitious targets spanning:
• Doubling exports
• Improving R&D
• Strengthening skills
• Reducing crime rates
• Improved healthcare
• Focusing on sustainability
But these span every sector and shift with the political cycle. While government policy provides a foundation, it’s not enough. Business leaders must take charge. Without individual businesses improving their performance, national productivity will remain stagnant.
What if prioritising productivity delivered more impact than today’s scattergun approach?
• Without productivity gains, even billions in funding won’t move the needle
• Businesses, not policymakers, are the primary drivers of change
• Waiting for ‘the right conditions’ is exactly why we’re failing
Labour shortages, rising costs and global competition are often seen as barriers. In reality, they are forcing functions that should push businesses to innovate and:
• Improve leadership and strategic alignment to lift performance and sustainability
• Define, systemise and automate operations to reduce reliance on manual effort.
• Use data intelligently, moving beyond gut feel to tracking performance and driving continuous improvement.
The reason nothing has changed for generations isn’t a lack of solutions, it’s a failure to act at scale. Too many businesses haven’t prioritised operational improvements and view them as optional or “nice-to-haves.” In reality, they are the only way forward.
We’re living with a problem that each of us can fix for long enough. It’s time to shift the focus from waiting on the Government or talking about lifting productivity, to making it a daily business priority.
At a recent event, the Mahi Tahi TechFest, focused on supporting businesses to underpin innovation with technology, I laid out the core principles needed to improve business performance. If you haven’t already:
• Defined clear, measurable KPIs for your business
• Adopted a continuous improvement mindset at every level
• Leveraged technology to support innovation to free up time for higher-value work …then you’re not working toward your full potential and run the risk of competitors passing you by.
This isn’t just about your business, it’s about New Zealand Inc. If 15,000 manufacturers take their business performance seriously, we can transform New Zealand’s economic trajectory and national productivity.
But that change starts with individual decisions. What will you do today to make building a higher-performing team and business a reality?
If this resonates with you, don’t just nod along, you need to act. The difference between businesses that thrive or struggle is execution, you could:
• Attend an ASB Manufacturers Workshop run by the EMA across NZ until June to discover the benefits of becoming a data-driven business. It is a small investment but provides insights into what a high-performance manufacturing business looks like.
• Apply for a Callaghan Innovation Smart Industry Assessment, if you qualify, to understand your next
steps and have a pro in your corner to support you on the journey (currently only available until June 30, 2025, due to disestablishment of Callaghan Innovation)
• Get a step-by-step breakdown of the core productivity principles David shared at the Mahi Tahi TechFest if you’re not sure where to start
You don’t need funding to get started. Putting time aside to learn the fundamentals of continuous improvement such as Lean Thinking, is free.
Start with blogs, YouTube and explore best practices from businesses on a Lean journey. Inspiration is everywhere, here are a couple of examples from Rob:
A practical look at why improvement should always be a priority.
Simple ways to introduce Lean principles into your business.
As your business grows and you look to scale, investment will be needed, whether in automation, technology or workforce development.
There is a perception that securing funding for initiatives can be tough, that banks don’t support businesses and prefer to lend on housing. But the reality is different, banks are data-driven. To approve lending, they need high-quality information. The businesses securing funding today meet lending requirements. It’s that simple.
Our businesses have underperformed for decades, and now we lack the capital needed to invest in transformation. We need the support of the banking sector to make meaningful progress, but businesses must present a strong investment case.
Start with what’s free. Learn, act and build momentum. When you’re ready to scale, be prepared to engage lenders with a clear, data-driven business case.
Your business’s performance isn’t just an economic issue, it’s about you - your leadership, your edge, your workforce and your legacy.
The time for talk is over: Act now, or watch others pass you by.
This is the challenge, and opportunity, of our time. Businesses that act now will define the future of the manufacturing industry and national economy.