
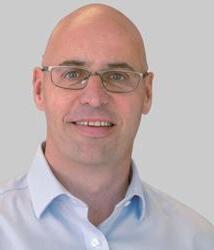
BUSINESS NEWS
Lifting productivity; Why investment in talent and technology must go hand in hand.
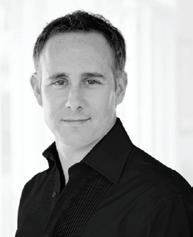
BUSINESS NEWS Manufacturers have unique opportunity to bank talent
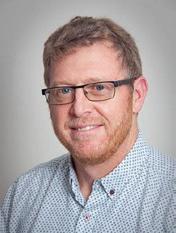
www.nzmanufacturer.co.nz
and ladders.
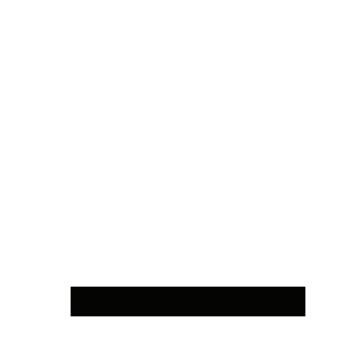
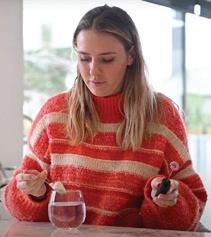
BUSINESS NEWS
Lifting productivity; Why investment in talent and technology must go hand in hand.
BUSINESS NEWS Manufacturers have unique opportunity to bank talent
www.nzmanufacturer.co.nz
and ladders.
Mackwell & Co. of Christchurch was established in 2016 by Founder Sam Mackwell. The company’s purpose is to “empower energy sovereignty” with a focus on energy resilience and fossil-fuel-free transport.
Mackwell realised the two concepts needed to address this are the use of accessible and low value biomass as fuel, and a technology that can safely and cleanly convert this to useful work without relying on extensive infrastructure.
The Mackwell A35 features a unique biomass fired water tube boiler that is compact and responsive enough for use in transport as well fixed shaft power or electricity generation. The A35 traction engine is designed for horticultural and small farm towing up to seven tonnes at 40 km/h, and the same boiler and engine will be produced as a 26kW generator set offering up to 180kW of heat.
Once this concept is proven in the market the design will be scaled to 600kW for industrial and marine use.
Mackwell & Co. technology has shown to have a number of other applications. Earlier this year Mackwell partnered with Biocare Pty Ltd. to design and manufacture four large combustion chambers for a project in Kangaroo island which is set to be one of the largest biochar projects globally.
Discussions are now underway with New Zealand forestry operators to use large steam engines to directly drive equipment such as disc chippers. The A35 has attracted five pre-orders for businesses including portable sawmills and essential oils distillation.
Customers can expect more than 35% in overall cost savings where replacing diesel engines, and a 96% reduction in CO2 emissions. Small engines are suitable for manual fueling, and larger applications will require a mechanical feed system to maintain the 2.5kg/kWh input requirement. Mackwell engines are of additional value where heat is needed, such as hydronic underfloor heating or food processing. In this way Mackwell engines go beyond traction to compliment a range of renewable energy systems, but without the need for expensive storage or distribution.
The development of a unique hardgoods product continues to challenge Mackwell in many ways. The small A35 engine was chosen as a technically viable starting point for the six engineering staff to deliver, with all design in-house and manufacturing shared with local businesses. However, running a workshop, continually training staff in a ‘new’ field, and the effects of Hofstadter’s law on project deadlines are real challenges familiar to all manufacturers. The result is a need for significant capital investment to deliver each prototype and scale it to production.
Secure supply of energy and data to moving industrial equipment.
• Large size range
• Vertical travels
• Energy tubes
• Hygienic chains
• Solutions for long travel
• Guide troughs
• Readychain
• Robotic, 3D
• Circular movement
HUGE range of high quality flexible cables
• Control cables
• Single cores
• Data cables
• Sensor/Actuator
• Intrinsically Safe
• VSD/EMC cables
• Halogen Free cables
• High temperature
• Harsh Conditions
• Crane cables
• Profibus cables
• Bus/DeviceNet
• Solar cables
• Instrumentation
• Flat cables
• Curly cords
Largest range of flexible conduits for cable protection
• Conduits
• Conduit fittings
• Divisible systems
• Jumbo systems
• Conduit Accessories
• Braided cable protection
• Fire barrier solutions
• Food and beverage
• EMC systems
• Ex, ATEX, IEC EX
Industrial connectors for many industries
• Rectangular multipole connectors from ILME
• Single pole Powerline connectors from TEN47
• EPIC connectors from Lapp Group
• M23 circular connectors from Hummel
• Circular connectors specifically for the entertainment/stage lighting industry from Socapex
Safety engineering solutions from EUCHNER
• Multifunctional Gate Box MGB
• Transponder-coded safety switches
• Electromechanical safety switches
• Magnetically coded safety switches
Sensor technologies for automation
• High-Precision Laser Distance Sensors
• Ultrasonic Sensors
• Inductive Sensors
• Fluid Sensors
Mackwell & Co. – Empowering energy sovereignty with advanced steam engines.
BUSINESS NEWS
Lifting productivity: Why investment in talent and technology must go hand in hand.
Manufacturers have unique opportunity to bank talent.
SMART MANUFACTURING
Improvement snakes and ladders. Feeding the machine.
Co-Intelligence: Living and working with AI. Stop calling workplace safety failures ‘accidents’.
America’s Cup expected to deliver 1.5 billion audience.
Interface: Locally developed planet-saving operating system.
GovGPT pilot promises faster access to Government business.
ANALYSIS
Has Industry 4.0 left your operations vulnerable? How can manufacturers combat rising interest rates and optimise efficiency?
SMART MANUFACTUING
2024 KiwiNet Awards finalists.
Navigating the manufacturing technology landscape: MES vs MDH vs MMP.
SUSTAINABILITY
How your business can benefit from the circular economy.
ANALYSIS
Why BIM hasn’t reached its full potential in Aotearoa – yet…
COMMENT
Paying a ‘unique’ price.
WOMEN GOING PLACES
Alexandra Vranyac – Wheeler, CEO, Master Electricians NZ.
SAFETY
Kemppi launches lightweight welding helmets with maximum breathing protection. Call for cutting – edge solutions and collaboration to address safety in electrical industry.
Reducing refrigeration energy and carbon emissions.
Mobile robots reduce costs for SMEs.
DEVELOPMENTS
Daikin creates cutting-edge warehouse and distribution centres.
New Dunedin trade school boosts local options.
THE LAST WORD How industry can accelerate momentum.
Ian Walsh Ian is a Partner, Argon & Co. NZ, a master black belt improvement specialist and global lean practitioner. He is passionate about improving productivity and helping to create world class New Zealand businesses.
Dr Barbara Nebel
CEO thinkstep-anz
Barbara’s passion is to enable organisations to succeed sustainably. She describes her job as a ‘translator’ – translating sustainability into language that businesses can act on.
oodward
Is Managing Director of Connection Technologies Ltd, Wellington and is passionate about industry supporting NZ based companies, which in turn builds local expertise and knowledge, and provides education and employment for future generations.
Mark Devlin
Having owned food manufacturing and distribution businesses for a decade, Mark Devlin now runs Auckland public relations agency Impact PR. Mark consults to several New Zealand manufacturing firms including wool carpet brand Bremworth, aircraft exporter NZAero and cereal maker Sanitarium.
Insa Errey
Insa’s career has been in the public and private sectors, leading change management within the energy, decarbonisation, and sustainability space. Insa holds a Chemical and Biomolecular BE (Hons) from Sydney University. She is a member of the Bioenergy Association of NZ and has a strong passion for humanitarian engineering, working with the likes of Engineers Without Boarders Australia.
Insa is a member of Carbon and Energy Professionals NZ, been an ambassador for Engineering NZ's Wonder Project igniting STEM in Kiwi kids and Engineers Australia Women in Engineering, increasing female participation in engineering.
Jane Finlayson is Head of Advanced Manufacturing at the EMA, and has 25-years’ experience in business and economic development. She is passionate about empowering businesses to grow, innovate and embrace Te Ao Māori.
PUBLISHER
Media Hawke’s Bay Ltd, 121 Russell Street North, Hastings, New Zealand 4122.
MANAGING EDITOR
Doug Green
T: +64 6 870 9029
E: publisher@xtra.co.nz
CONTRIBUTORS
Holly Green, EMA,
Business East Tamaki, Ian Walsh, Adam Sharman, David O’Connor, Mark Devlin, Nicholas Russell, Jane Finlayson, Frank Phillips, Dr Troy Coyle, Paul Jarvie, Trevor Dearing, James Robinson, Alexandra Vranyac
ADVERTISING
T: + 64 6 870 9029
E: publisher@xtra.co.nz
DESIGN & PRODUCTION :kim-jean:
E: kim.alves@xtra.co.nz
WEB MASTER
Julian Goodbehere
E: julian@isystems.co.nz
PUBLISHING SERVICES
On-Line Publisher
Media Hawke’s Bay Ltd
DIGITAL SUBSCRIPTIONS
E: publisher@xtra.co.nz Free of Charge.
MEDIA HAWKES BAY LTD
T: +64 6 870 9029
E: publisher@xtra.co.nz
121 Russell Street North, Hastings
NZ Manufacturer ISSN 1179-4992
Vol.16 No.8 September 2024
Copyright: NZ Manufacturer is copyright and may not be reproduced in whole or in part without the written permission of the publisher. Neither editorial opinions expressed, nor facts stated in the advertisements, are necessarily agreed to by the editor or publisher of NZ Manufacturer and, whilst all efforts are made to ensure accuracy, no responsibility will be taken by the publishers for inaccurate information, or for any consequences of reliance on this information. NZ Manufacturer welcomes your contributions which may not necessarily be used because of the philosophy of the publication.
We lead this issue with an energy story (Page 1) to “empower energy sovereignty”, the purpose of Mackwell & Co of Christchurch, with a focus on energy resilience and fossil-fuel-free transport.
Mackwell realise the two concepts to achieve this are the use of accessible and low value biomass as fuel and a technology that can safely and cleanly convert this to useful work without relying on existing infrastructure.
I have been trying to get my head around the deep concern being felt around the country regarding the cost of energy and the damaging effects this is having on domestic and business users at this time.
With companies not being able to see a way ahead and closing, with the exorbitant price to the domestic market (where those disconnected have to find the money to be reconnected when they cannot pay the bill) what is the country meant to do?
One thing, the energy companies need to be challenged on their pricing and why the return to shareholders is, at this time, more important than the wellbeing of the future of business in New Zealand.
Another thing, make it affordable for all New Zealanders to have solar panels on their buildings and homes.
How does a smart, innovative country like New Zealand find itself in the situation where with high power costs, imports will become more expensive?
Where our reliance on the rural sector to succeed on export markets becomes a challenge; when the price of energy means their products become more expensive on world markets?
Higher energy prices assist government coffers. But at what cost?... regions losing the financial input of (now) closed businesses whose staff leave and look afield to Australia.
Doug Green , Publisher
-David O’Connor, Head of Emerging Markets, The Learning Wave
In the evolving landscape of the manufacturing sector in New Zealand, the adoption and successful implementation of smart technology are undeniably key drivers of productivity.
However, without parallel investments in upskilling the workforce, the potential gains from such technological advancements may be left unrealised.
At a recent industry event, a business owner shared their experience of raising significant capital to introduce cutting-edge technology in their food manufacturing business.
The implementation, however, came to a halt as it became clear that the existing staff lacked the necessary skills to operate the new systems, which led to multiple challenges to meet production requirements.
This scenario raises the question: Is this an isolated incident, or a reflection of a broader trend where businesses overlook the critical need for workforce readiness in their technology strategies?
Investment in both areas —developing your talent and adopting the new advanced technologies— must be seen as complementary rather than separate business strategies.
Business leaders must ensure that their HR and training teams are fully integrated with their Operations and IT efforts, creating a seamless
approach to lifting staff capability that aligns with technology implementation plans.
When these efforts are given equal priority, they create a cycle where skilled and engaged workers drive technological adoption, and in turn, the technology enhances the capabilities and productivity of the workforce—a win-win situation.
One client likened their smart technology experience to “buying a Ferrari but then handing the keys over to kids on their learner’s license in full knowledge that they would crash it’.
While this analogy might be an apt description of their workforce’s current skill level, it also serves as a cautionary tale for business owners.
The cost and potential setbacks of implementing advanced technology without a focused and skilled workforce can be significant and detrimental.
For New Zealand’s Manufacturing Sector to fully capitalise on the financial benefits of technology, it must be supported by a skilled and adaptable workforce. Talent and technology must go hand in hand.
In a recent article, Sean Gear offered valuable insights into what a successful 21st-century vocational education system could look like, if we dare to think differently. One of his key points was the need for a system that fully integrates technology and future
skills, prioritising digital literacy, critical thinking, and adaptability as core components of all training programs.
This vision requires significant investment in technology infrastructure and professional development to equip training providers with the tools to deliver these essential skills effectively in the workplace.
New Zealand, with its relatively small ecosystem, presents a unique opportunity for closer collaboration between systems/technology providers and training providers.
By working together, they can offer businesses comprehensive solutions that ensure talent and technology are valued equally. Bridging this gap between talent and technology will not only lead to more successful technology implementations but also drive a more skilled, innovative, efficient, and sustainable manufacturing industry in New Zealand.
The future of manufacturing hinges on the seamless integration of advanced technology and a skilled, adaptable workforce.
Investing in the upskilling of your people is not just essential—it’s the key to unlocking the full potential of your technology investments.
Business East Tāmaki (formerly the Greater East Tāmaki Business Association) is here to make it easier to do business; working alongside business
With forecasts from the Hanga-Aro-Rau Workforce Development Council showing the manufacturing, engineering, and logistics (MEL) sectors will need to fill over 157,000 jobs over the next 5 years, existing recruitment strategies need to be widened to include those with transferable skills from other industries.
As NZ Manufacturer business advisor and director of Auckland public relations agency Impact PR Mark Devlin has found, recent government cost-cutting measures could provide an opportunity for manufacturers to access a resource critical for the sector’s future growth.
With thousands of government and private sector workers made redundant during the recession and from public sector cuts in recent months, the opportunity exists for the manufacturing sector to create a talent bank of skilled workers.
This could help futureproof the sector by accommodating thousands of new employees in manufacturing firms nationwide.
A large proportion of the 6,000+ Government workers who are losing their jobs as a result of public sector cuts have highly transferable skills that are in short supply and could be absorbed by a wide range of manufacturing firms that contribute directly to the country’s economic growth.
What we know of government workers is that they are well-trained in many of the key competencies in desperate need within the manufacturing sector. This includes people from government departments with an existing relationship with industry such as WorkSafe, NZTE, ACC, and MPI.
With Māori and Pacific Peoples expected to make up a growing proportion of the workforce the sector needs to be looking to bring in greater diversity and more cultural awareness - and the Government workforce has an abundance of expertise in this area.
As a nation, we have invested heavily in developing our government workforce and it is critical we move to retain these skills, many of which are unique to our ethnic and demographic makeup in New Zealand. Most of these workers will be basing their understanding of the job market on what they can see advertised, as their filtered searches for new roles may be limited to government or administrative positions.
They may have underestimated how transferable their skills are to other sectors and may also be feeling despondent and potentially desperate given media reports of high numbers of applicants for the
available roles.
In addition, thousands more private sector workers are finding themselves displaced from their jobs due to restructuring or business insolvency.
This spike in labour supply could form part of a move to fill 158,000 roles (an average of 31,500 per year to 2029) that the Hanga-Aro-Rau Workforce Development Council’s research has shown will be required in the manufacturing, engineering and logistics sectors over the next five years - a hurdle that is set to impact industry growth if not addressed. With this volume of supply entering the job market at effectively the same time, and with little forward notice, some form of support may be needed to proactively reduce the cost of finding skilled workers for businesses, address misconceptions about the sector, improve diversity awareness and help reduce the number of Kiwis moving to Australia - due to the perceived lack of opportunity within New Zealand. There are messages that need to be delivered to this potential workforce, many of whom would never have considered the manufacturing sector as part of their career.
One of these is that new technology is reshaping the manufacturing industry and helping it shed its legacy image of dirty workshops and machinery. They also need to know sector needs employers in every business function including finance, HR, marketing, sales, health and safety and IT and it needs to see more underrepresented groups move into the industry - including women, Māori and Pacific peoples and disabled workers.
With the manufacturing industry moving rapidly towards automation, which is bringing in robotics, AI and other technologies, the skills required to manage this transformation are diverse and in short supply.
We are seeing more remote working now as wellwhere equipment can be managed virtually which is helping to pave the way for increased diversity within the sector.
This means if a worker wants to stay in Wellington or is physically challenged with poor mobility there may be opportunities available.
It is also important to let the workforce know most employers will offer some sort of on-the-job training - helping transition workers who are new to the sector within a matter of weeks.
For many, this will mean they can finish their current role one day and walk into another in manufacturing the next day – with no loss of salary or external retraining required.
Manufacturers now have a unique opportunity to match thousands of highly qualified employees entering the job market within another sector of the economy that they may otherwise have never considered.
We know that many firms have been looking for more employees since the pandemic. Over time it has become cost-prohibitive to advertise roles for an extended period and these businesses have learned to adapt - often by turning away domestic and export orders and downsizing their production.
There is a clear opportunity to connect a large highly skilled workforce with businesses that can once again scale up production and take on new contracts.
It is a once-in-a-lifetime opportunity to migrate large numbers of workers, who are well-trained with respect to cultural sensitivity and other core skills needed to help increase the number of Māori & Pacific peoples to a sector with critical skills shortages.
The message the industry needs to deliver is there is a hidden layer of work opportunity here that they are inherently well suited to and there may be no need to disrupt their whānau by looking for work offshore.
-Ian Walsh, Partner, Argon & Co NZ
As we head into Spring 2024, it’s encouraging to see fresh growthboth in nature and in the economy.
I appreciate it’s too early to celebrate from the rooftops, but I’m invigorated by the growing number of activities emphasising what matters most – productivity!
The recently repurposed National Infrastructure Agency (NIA) has a remit to drive better practices through New Zealand’s industry sectors. Done right, the promotion of growth in capital investment should lead to an overall improvement in business performance.
But to lock this in as a reality, we know that dedicated investment in people and processes is the only true way to lead to a better performance culture.
I thought it might be timely to call out some of the “myths and misunderstandings to avoid” and to talk through what a good continuous improvement program looks like, as you may be contemplating what your business can do to ride this wave.
Here is my Improvement Snakes and Ladders. Unfortunately, it is not a touch it once and let it go fix; like fitness, use it or you lose it!
1. We don’t need to do this. In NZ less than 20% of businesses know what a continuous improvement or transformation programme truly is. In more competitive markets it’s 100%. Can you wait to find out if you have a competitor who is significantly better than you? Your call, but it sounds risky. Why wouldn’t you do it? At this point, you haven’t even put your piece on the board.
2. We did that. It didn’t work. If you believe you have “done” lean, you don’t understand lean. It is not a project; it is a continuous improvement programme designed to create a culture of high performance. A subset of this is “we did 5S”, which again displays a deep lack of understanding. You are at the start line.
3. We can do it ourselves. Yes, you can, but almost no one succeeds this way. Improvement requires significant change from leaders and throughout the organization, the right knowledge, and the right application of this knowledge. Doing it yourself is like climbing Everest without a Sherpa. Most will fall off and end up taking the snake back to number 2.
4. We have some better options to improve performance quickly and deliver great results. Do those! Most will be one-offs and will give you a small ladder. But none of these are a journey of improvement.
5. We can’t afford an improvement programme. A good improvement programme should be self-funding: it should break even (at worst) in year one and be 5-10 times ROI by year three. Can you afford not to do it and let your competition steal a lead? Your call here could be your ladder or your competition’s ladder.
6. We have too many higher priority initiatives and can’t resource this. This may well be true, but how many of those deliver a 10-to-1 return in three years with little-to-no capital investment? Do they develop and engage your people, improve morale, and create capability and capacity to survive and grow? These would have to be some impressive priorities to avoid a trip down a snake.
7. I can delegate this programme to a continuous improvement expert who can manage this transformation. Even with good sponsorship, how good is your expert? Are they a genuine Sherpa or a weekend rock climber? Most are the latter. Make sure you know they have climbed the mountain many times with many organisations. Have they worked in a truly world class company? Have they got proven and trusted references? Are they up to date with global best practice?
You need all of these to get a Sherpa who knows the mountain, knows what the top looks like and can lead a climbing team. If you have this person, you have a ladder. If not, continued on Page 26
From Wharton professor and author of the popular One Useful Thing Substack newsletter
Ethan Mollick comes the definitive playbook for working, learning, and living in the new age of AI.
Something new entered our world in November 2022 -- the first general purpose AI that could pass for a human and do the kinds of creative, innovative work that only humans could do previously.
Ethan Mollick immediately understood what ChatGPT meant: after millions of years on our own, humans had developed a kind of co-intelligence that could augment, or even replace, human thinking.
Through his writing, speaking, and teaching, Mollick has become one of the most prominent and provocative explainers of AI, focusing on the
practical aspects of how these new tools for thought can transform our world.
In Co-Intelligence, Mollick urges us to engage with AI as co-worker, co-teacher, and coach. He assesses its profound impact on business and education, using dozens of real-time examples of AI in action.
Co-Intelligence shows what it means to think and work together with smart machines, and why it’s imperative that we master that skill.
Mollick challenges us to utilize AI’s enormous power without losing our identity, to learn from it without being misled, and to harness its gifts to create a better human future.
Wide ranging, hugely thought-provoking, optimistic, and lucid, Co-Intelligence reveals the promise and power of this new era.
For readers of Naomi Klein and Nicole Perlroth, a myth-dissolving exposé of how artificial intelligence exploits human labour, and a resounding argument for a more equitable digital future.
Silicon Valley has sold us the illusion that artificial intelligence is a frictionless technology that will bring wealth and prosperity to humanity. But hidden beneath this smooth surface lies the grim reality of a precarious global workforce of millions labouring under often appalling conditions to make A.I. possible.
This book presents an urgent, riveting investigation of the intricate network that maintains this exploitative system, revealing the untold truth of A.I.
Based on hundreds of interviews and thousands
of hours of fieldwork over more than a decade, Feeding the Machine describes the lives of the workers deliberately concealed from view, and the power structures that determine their future.
It gives voice to the people whom A.I. exploits, from accomplished writers and artists to the armies of data annotators, content moderators and warehouse workers, revealing how their dangerous, low-paid labour is connected to longer histories of gendered, racialised, and colonial exploitation.
A.I. is an extraction machine that feeds off humanity’s collective effort and intelligence, churning through ever-larger datasets to power its algorithms.
This book is a call to arms that details what we need to do to fight for a more just digital future.
7A new Callaghan Innovation-led initiative will support Kiwi businesses of all sizes and stages to boost productivity and competitiveness through the transformative power of artificial intelligence.
Science Innovation and Technology Minister Judith Collins launched the AI Activator at the Aotearoa AI Summit in Auckland. The AI Activator is designed
to boost economic growth and exports via the rapid adoption of AI. The initiative is a collaboration between Callaghan Innovation, NZTE and NIWA.
“Globally, there are significant and growing opportunities to harness the power of AI. There is a growing gap between those who understand and use AI, and those who don’t. Some businesses find it
hard to know where and how to start – that’s where the AI Activator comes in,” says Sarah Sun, Callaghan Innovation Head of AI and Digital.
“The AI Activator is here to support the success of all growth-focused Kiwi businesses, wherever they are on their AI journey. It’s an exciting time to be in business, and we
continued on page 13
By Paul Jarvie, EMA Manager of Employment Relations & Safety
With the Government signalling that significant reform of our workplace health and safety regulations are on the way, it’s time to look at the language we use around preventable harms. For too long, ‘accident’ has been a blanket term that absolves responsibility. Whether at home, on the road, or in our workplaces, we’ve grown accustomed to shrugging off incidents as ‘accidents’. But are they truly random acts beyond our control, or is there more to the story?
When we label something an ‘accident’, we imply innocence and inevitability. It’s a linguistic shrug that suggests nothing could have been done differently. But the reality, backed by extensive research, paints a different picture.
Insurance companies that provide cover for ‘accidental damage’ base their premiums entirely on historical data of such events. They know these events will happen, how many, when and how. The premium setting process uses vast databases to ensure the number of claims do not exceed their premium income – that’s how they remain in business. It’s a similar system to ACC for injury claims. In 2023, ACC handled nearly 200,000 workplace claims, with many stemming from repeat incidents that were likely to have been identified in companies’ hazard registers.
As such, they were neither unknown nor unforeseen. This data underscores the need for a more nuanced approach in our safety lexicon.
In workplaces, terms like ‘incident’ or ‘near miss’ are often used interchangeably with ‘accident’. Yet, these terms don’t adequately capture the essence of what really happened: a failure in systems, procedures or human judgement that resulted in harm or damage.
Take aviation, where research from the Pilot Institute found that pilot error accounted for 69.1% of plane crashes, with 17.2% due to mechanical issues and 13% of unknown cause.
Even legally, the term ‘accident’ can be problematic. In cases of dangerous driving leading to convictions, calling them accidents undermines the severity of the offense and diminishes accountability.
The British Medical Journal, among others, has moved away from using ‘accident’ precisely because it fails to acknowledge the preventable nature of most injuries.
When we say ‘accident’, we obscure the fact that hazards and risks were often identified beforehand –through hazard registers, risk assessments and safety protocols.
Let’s reframe our approach. Instead of accidents, let’s call them what they often are: failure events.
This term not only reflects a more accurate depiction of what occurred but also shifts our focus to improving systems and processes to fail safely when incidents do occur.
By embracing terms like ‘failure event’, we acknowledge that incidents are not inevitable but
are often the result of foreseeable risks and inadequate mitigations.
This shift isn’t just about semantics – it’s about fostering a culture of proactive risk management and continuous improvement.
As we move forward, let’s celebrate successes in risk mitigation rather than merely recording failures. Let’s invest in safer systems that reduce the likelihood of failure events occurring.
And let’s hold ourselves accountable by using language that reflects the realities of workplace safety.
Finally, let’s retire ‘accident’ from our vocabulary where it inaccurately masks preventable harm. Instead, let’s embrace ‘failure event’ – a term that compels us to learn, adapt, and prioritise safety above all else.
Because, in the end, what we call things matters. And calling incidents what they truly are – failure events – moves us closer to a safer, more accountable future.
We invite you to take part in an EMA initiative to inform our submission to Government on the upcoming health and safety review. The 10 minutes it takes to fill in this survey could alter the future of health and safety in New Zealand. Be a leader and make a difference.
Seeing the skills and technology of Emirates Team New Zealand and Kiwi companies
The estimated 1.5 billion-plus global audience for this year’s Louis Vuitton 37th America’s Cup will witness not only spectacularly fast races from the AC75 competitors, including Emirates Team New Zealand, but also a showcase of the New Zealand engineering skills supporting the biggest-ever programme of Cup races, also including women’s and youth events.
“What people see on the surface, with yachts such as Emirates Team New Zealand reaching speeds of more than 50 knots, is just part of a wonderful story for local skills,” says long-time Emirates Team New Zealand supporter Lee Short, Director of Hydraulink Fluid Connectors.
“Inside the boats there is a wealth of technical and engineering input from a host of New Zealand companies that put us right up there with the world’s best. The quality of engineering of hydraulics systems in these boats, is right up there with the standards of Formula One racing cars. The 350kg foil canting system that enables the boats to respond quickly to changes and inputs has to be able to raise and lower the yachts’ 1.5 ton foils inside three seconds.
“Some of the hydraulic systems involved are every bit as complex and critical as the construction, civil engineering, and mining machinery we work on throughout Australia and New Zealand. The pedal-powered cyclor pumps, provide the hydraulic power for the AC75 boat control systems – including control of the twin skinned mainsail, foils, and rudder functions of the AC75s.
“Kiwi engineers have developed amazing systems for all the boats – the AC75s, plus the smaller AC40s for the Puig Women’s and UniCredit Youth America’s Cup, which collectively comprise the biggest racing fleet ever of Cup and supporting event yachts over
the leadup to the final series starting on October 12.
“Then there are hydrogen technological advancements led by Emirates Team New Zealand, the Defender of the 37th America’s Cup, and their innovative developments of ‘Chase Zero’: the hydrogen-powered foiling chase boat. This is an outstanding development to boost the use of this sustainable zero emissions source of energy in the marine industry,” says Lee.
Hydraulink has been supplying hydraulic hoses, componentry, and fittings to Team New Zealand Cup defences and challenges since 1995 and has been there through the entire series of four Cup events leading up to this event.
Hydraulink is just one of the many New Zealand companies contributing its skills to support the defence – for example, providing hoses and fitting for the one design foil canting systems used by the AC75’s and AC40’s, in addition to all hydraulic hoses and fittings used by Emirates Team New Zealand in their boat ‘Taihoro’.
“The pressures on hydraulics are so much greater than when we first got involved – the days of muscular manpower and sheer grunt are no longer enough to handle the loads on the crews as the boats go ever-faster.
“So, there is an engineering challenge to produce the lightest, most compact, powerful, and responsive hydraulic systems with engineering innovations such as titanium rams and 550 bar (8000psi) systems, with hose assembly pressure ratings up to 700 bar (10,000 psi), to deliver the best power for peak performance.
“The precision of these systems is up there with the engineering standards of Formula One racing –
all our hoses, of which there are 23 in each of the cant system in all the AC75s, are all individually painstakingly inspected and marked exclusively for their intended use. “
A total of more than 2,000 Hydraulink hose assemblies are involved in the Americas Cup fleets, including AC75s, AC40s, Hydrogen chase boats, and spares. All are meticulously inspected and classified for particular uses.
The hose types all feature Kevlar reinforcement to minimise expansion at elevated pressure, and ultra-smooth tube surfaces to provide low Delta P pressure drops to enhance activation response times of the circuit cylinders.
Port adaptors and hose connections are primarily DIN2353 metric c/w elastomeric sealing elements to provide maximum integrity of retention and sealing where elevated pressures may be experienced.
Lee Short says the whole engineering effort taking place above and below the yachts’ decks has flow-on benefits for the myriads of Kiwi companies involved in helping to mobilise resources for this world-class event.
“I know that our role in our specialisation – hoses, fittings, and service – tests our mettle and presents us with challenges, and we take pride in ensuring the highest level of performance, reliability, and safety in all our markets, whether on land or at sea.’
“With the 600 media outlets attending – and with the event going live broadcast free to air globally and on YouTube – numerous New Zealand skills and achievements will be showcased. These will have a lasting impact on our engineering capabilities for years to come.
Hydraulink considers its involvement in high-tech ventures as reinforcing the company’s strong focus on safety and reliability for industrial users in New Zealand and Australia.
Sandra Lukey
Sandra Lukey is the founder of Shine Group, a consultancy that helps science and technology companies accelerate growth. She is a keen observer of the tech sector and how new developments create opportunity for future business. She has over 20 years’ experience working with companies to boost profile and build influential connections.
Mike Shatford is an expert in the field of technology development and commercialisation. His company Design Energy Limited has completed over 100 significant projects in this vein by consulting for and partnering with some of New Zealand’s leading producers.
Among Mike and his team’s strengths are industrial robotics and automated production where the company puts much of its focus.
Sean O’Sullivan
Has a B Com (Hons) Otago University. In 2000 - 2001 introduced PCs on the workshop floor and job and staff tracking and a productivity software App to Fletcher Aluminium Group and 100 manufacturers NZ nationwide. In 2001 – 2022 Founding Director Empower Workshop Productivity & Scheduling Software App. 236 manufacturing and engineering clients mainly throughout NZ and Australia, also UK and US.
Iain Hosie
Iain Hosie is a respected figure in the NZ Advanced Manufacturing and Materials sectors, with extensive experience in product development, research projects and commercializing tech products. Iain is a Director and Founder of Nanolayr Ltd, Director for the NZ Institute for Minerals and Materials Research, Commercial Director for Fabribotics Ltd, and Executive Council of BiotechNZ.
Catherine Lye
Is the first Chief Executive Officer of the newly formed cross-sector incorporated society, Advanced Manufacturing Aotearoa (AMA). Catherine has been Head of Manufacturing and Export Communities at the 7,100-member Employers and Manufacturers Association for the past two years. As part of that she has guided the Advanced Manufacturing and Industry 4.0 initiatives.
Adam Sharman
Is a Senior Partner at Dsifer. With a background in technology implementation, manufacturing and strategy, Adam and the team at Dsifer are on a mission to support New Zealand’s manufacturing sector transform using technology, data and analytics to outcompete on the world stage. Combining expertise in data engineering, data science & analytics and visualisation.
Windows 10 is approaching its end-of-life date, which has spurred a new initiative aimed at extending the usability of older computers. Kauricone has developed a new operating system named interface, targeted at preventing the disposal of potentially millions of PC’s and Laptops
The New Zealand-based company’s founder, Mike Milne, was driven by concerns about the environmental impact and the practicality of discarding operational hardware.
“This is a brand-new lightweight, secure, and efficient operating system, requiring a fraction of the compute and memory requirements demanded by bloated modern operating systems,” he indicated.
Kauricone is recognised for its machine learning technology and sustainable server solutions. Milne stated that Interface continues the company’s efforts to deliver low-cost, high impact computing by making older computers viable again. Interface aims to operate efficiently on systems that no longer meet the high requirements of new operating systems such as Windows 11.
“We’ve stripped down the PC to its essentials. Where a Microsoft Windows 11 install consumes 24GB of hard drive, Interface requires just 2GB - and that includes productivity applications.” Milne specified.
The release of Interface is particularly timely, given that Microsoft will cease support for Windows 10 in October 2025. This change is estimated to make around one million computers in New Zealand and 250 million globally redundant. “That’s incredibly bad for the environment, made worse when considering there is nothing wrong with these devices beyond software incompatibility” Milne remarked.
Milne highlighted that Interface could provide these computers with an additional five to ten years of useful life. The operating systems is designed for ex-lease fleet and refurbished machines and is expected to appeal primarily to environmentally conscious and budget sensitive groups. This includes educational institutions, small businesses, non-profits, and charities.
Interface has a very fast learning curve – not like Linux. You can use all your programs from just three screens. Users can either upgrade their existing computers at a Kauricone reseller or purchase refurbished laptops or PC’s pre-installed with Interface.
Interface comes with several pre-installed applications, including Firefox browser, Folder Manager, open-source LibreOffice, and the GIMP graphic design program. Additionally, a developer suite is also available, for those looking to customise their software experience.
Beyond its eco-friendly appeal, Interface is designed for versatile use, covering browser-based Software as a Service applications, education, and computing tasks like word processing and spreadsheets.
A variety of pretested hardware is available to ensure compatibility with Interface. Among these are HP T530 Thin Client (AMD), Lenovo ThinkCentre (i5 Intel), Dell Latitude Laptop (i7 Intel) Toshiba Portege laptop (i7 Intel), Samsung Ultrabook (Intel i7), among others. Milne noted that Interface is also compatible with brand new hardware.
When installed by a reseller, the operating system, along with its bundled applications, is priced at just $99.00 including installation. “And it will run quite happily on just 4GB RAM and a 32GB disk, demonstrating the very wide range of older hardware which can get a new lease of life with an appropriate operating system and applications.” he mentioned.
With four resellers already appointed, Interface is steadily entering the local market, with a focus on operators involved in upgrading and refurbishing computers - and who recognise the obsolescence and waste problem.
“If we’re going to get real about saving the planet, there’s a lot the IT industry can do. Too much hardware is given short shrift thanks to ever-expanding software requirements. With Interface, we’re saying enough is enough – let’s put perfectly good computers back into classrooms and offices, rather than poisoning the environment with yet more waste,” Milne concluded.
Callaghan Innovation will pilot GovGPT, an AI conversational companion, to help businesses get the information they need from several Government websites much faster.
GovGPT provides accurate and referenceable information from a range of different Government websites through natural language conversations.
“We know there’s a lot of Government support and information out there to help businesses thrive. But it can be hard to find and is often located across a number of different sites. Businesses often don’t have time to hunt around for what they need from Government, so there’s a risk of missing out on support or crucial information,” says Sarah Sun, Callaghan Innovation Head of AI and Digital.
“Ultimately, our vision is for a simple, digital front-door where Kiwis can quickly and easily get answers to their questions about Government support and services. Anyone should be able to access important information in a way that’s most intuitive to humans – natural conversations in their preferred language. GovGPT is a first step.”
Callaghan Innovation partnered with Whāriki Māori Business Network and a technology provider to develop the GovGPT proof of concept in less than two months and by combining the existing functionality of large language models (LLMs) and a library of existing software modules.
GovGPT features multilingual support in many common languages, including text-based Te Reo Māori. “It’s great to have Whāriki Māori Business Network on board to help us ensure the cultural relevance, and appropriateness of content so we can offer a comprehensive, valuable tool for all users,” says Sarah Sun.
The GovGPT pilot is already ‘multimodal’ so it can support both text and speech chats. But the pilot will also be updated and improved rapidly over the next few months to create a seamless user experience, including customisation options for the conversational companion, such as different voices, tone and speech speed.
“We are keen to ensure GovGPT meets the varying needs of the diverse business community in Aotearoa
New Zealand so that finding important Government information is as easy as having a conversation with someone,” she says.
GovGPT uses a technique called “Retrieval Augmented Generation” (RAG) to enhance the accuracy and reliability of the generative AI model by fetching relevant facts from a set of Government websites.
GovGPT will be demonstrated at the AI Summit on the Callaghan Innovation stand, where the GovGPT project team will encourage feedback from conference attendees to support the development of the pilot.
Callaghan Innovation is planning to make the GovGPT pilot available on its website in October. Businesses and organisations interested in this technology are encouraged to contact Callaghan Innovation for assistance implementing a version of GovGPT for their own websites.
AI Activator to support rapid adoption of transformative technologies continued from page 9
are looking forward to helping support the success of more Kiwi AI innovators,” she says.
The AI Activator is based on the highly effective ‘activator’ model developed by Callaghan Innovation for ecosystem-wide support.
“Activators, including the HealthTech and AgriTech Activator, have been really successful in supporting the needs of early-stage and innovation-intensive companies in Aotearoa New Zealand,” says Sarah Sun.
“The new AI Activator initiative provides access to AI expertise, R&D resources, AI tools for businesses and interactive learning modules. We are keen to work with businesses who want to know the basics and understand opportunities and risk mitigations for AI-solutions. There is something for everyone,” she says.
Judith Collins also announced GovGPT, a new proof of concept product that is part of the AI Activator, at the AI Summit. GovGPT is an AI conversational companion to help businesses get the information they need from Government websites, faster. GovGPT makes information available from a range of business-related Government websites through a simple, chat-like interface. Callaghan Innovation is planning to make the GovGPT pilot available on its website in October.
“We are delighted to be working with our partners at NZTE and NIWA to help more ambitious businesses integrate AI and expand their growth horizons,” she says.
“NZTE is committed to supporting Kiwi businesses to grow; AI holds significant potential to increase productivity and efficiency and enable businesses to compete and expand on the global stage.
“NZTE is excited to host in-person workshops, as part of the AI Activator, aimed at enhancing AI knowledge and capabilities among all export businesses.
We believe these workshops will help businesses pinpoint high-value AI opportunities within their models and accelerate AI adoption where it is most beneficial.”
“In addition, we are seeing a growing number of our tech exporters embrace AI technology to build new products and augment services to their customers around the world,” says NZTE Sector Lead, Manufacturing, Technology and Services, Richard Cotman.
NIWA will play a crucial role to support stronger relationships between researchers and scientists who can support businesses to take advantage of the latest advances in AI.
“NIWA continues to develop its AI capabilities and is already using AI extensively in the science research sphere, especially in climate research where we work with massive amounts of data,” says Warrick Johnston, NIWA’s General Manager Technology & Innovation.
“NIWA has many active AI projects that are integral parts of the research across our science fields. Most notable is our use of AI for operational forecasting and flood management.
“The AI Activator is a tremendous initiative to help keep New Zealand at the forefront of research and NIWA is privileged to be a partner.”
Two innovative startups, Prosaic and Script Sense are showcasing very different AI-use cases at the AI Summit. Both are targeting global markets with their AI solutions.
Prosaic is an AI-powered app that uses AI and open banking to help small businesses, sole traders, and their accountants, to automate the process of finding deductible expenses and income tax credits.
Script Sense is an award-winning AI platform that helps pharmacists to overcome workforce challenges, enhance efficiency, and improve patient care using the transformative power of AI.
Visit the AI Activator
Trevor Dearing, Director of Critical Infrastructure Solutions, Illumio
For three years running, manufacturing has been a top-attacked industry, according to the IBM X-Force Threat Intelligence Index 2024.
Attackers see manufacturers as an increasingly attractive target. Smart factories open new attack vectors, and as new industrial control systems (ICS) become more connected, the opportunity for malware to spread grows.
This is placing increasing pressure on manufacturers to make their operations resilient enough to withstand attacks, with the 2024 World Economic Forum Global Cybersecurity Outlook revealing that operational disruption is the greatest cybersecurity concern for almost half (45%) of leaders.
Here I will discuss how Industry 4.0 is changing manufacturing cybersecurity and why deploying a Zero Trust approach can help protect against vulnerabilities from smart factories and ICS.
Industry 4.0 has revolutionised manufacturing through automation and connectivity. Now, enterprise resource planning (ERP) systems handle everything from taking orders to overseeing production.
New ICS technology provides more data and control by using smarter applications built on standard platforms which in turn extends the operational life of the systems.
Because of Industry 4.0, manufacturers are improving how well their supply chains work. But this also means their systems are more connected and vulnerable to cyber threats. These threats can target ICSs and cause serious problems.
In the past, ICS attacks were mostly simple malware and known weaknesses. But with smarter systems now available, attackers have more opportunities. These new systems connect and communicate in complex ways that leave security gaps and blind
spots.
They also connect to the internet which opens even more ways for attackers to breach and exploit systems.
These changes have led to more sophisticated attacks such as zero-day exploits and targeted hacks. There’s also more use of social engineering to gain access to critical systems. Now, attackers can find and use weaknesses faster and often go undetected longer. This makes it easier than ever to carry out attacks on manufacturing operations.
Cyberattacks can do more damage than just halting production lines. Manufacturers are also seeing several other effects of breaches and ransomware attacks. The five most common attacks we see are:
1 Stolen intellectual property: Manufacturers spend a lot of time and money on research and development (R&D) to stay innovative and keep ahead of their competitors. Many recent breaches in manufacturing have led to the theft of patents, designs, formulas, manufacturing processes.
2. Stolen data: Besides R&D, manufacturers also often have sensitive information about customers, vendors, and employees. When this data is breached, they can face legal problems, fines, and a loss of trust from their customers and partners.
3 Damaged physical assets: Attacks on ICSs and operational technology (OT) can cause physical damage to machines and equipment and cause periods of downtime. Attackers can manipulate ICSs to operate machinery in dangerous ways. This can lead to equipment failure, the destruction of goods or even endangering human life.
4. Compliance violations and legal consequences: Manufacturers in regulated industries can face more problems from cyberattacks due to compliance issues. If a cyberattack happens and data is not protected, companies can face large fines, legal trouble, and more attention from regulatory groups.
5. Compromised supply chain: Attackers are increasingly targeting manufacturers to get into larger supply chains. Hacking one manufacturer can give attackers access to the systems of connected suppliers, partners, and customers. This can damage business relationships and cause loss of business.
Securing ICS environments requires a comprehensive, risk-based approach. To secure these environments, manufacturers need to move from traditional network security approaches to protecting individual assets and applications.
This approach establishes communication and security rules per system and makes decisions based on risk.
The Zero Trust security model, supported by NIST and used by top manufacturers, makes changes to the traditional way of protecting manufacturing networks. Zero Trust is a cybersecurity model that assumes no part of the network is inherently trustworthy – “never trust, always verify.” Nothing is trusted by default which makes it harder for attackers to get in and spread inside the network.
Central to a Zero Trust strategy is Zero Trust Segmentation (ZTS), segmentation that uses the principles of Zero Trust. With ZTS, manufacturers can get a clear view of network traffic, enforce security rules, and quickly contain threats.
Many attacks in manufacturing rely on being able to reach the target assets from the initial point of entry. Industry 4.0 is making systems so interconnected that the traditional trust-based model no longer applies. Manufacturers must adopt a Zero Trust security model to protect modern industrial control systems.
James Robinson, Head of Services Asia Pacific, Syspro
Over the past five years, the manufacturing sector has demonstrated remarkable resilience, enduring many different challenges. Today, manufacturers face a renewed and formidable challenge with unexpected higher inflation raising the risk of yet another rate hike, threatening to destabilise the core economics of manufacturing businesses across Australia and the Asia Pacific region.
The challenging economy has dominated the news for over two years, placing the manufacturing industry in the spotlight as it grapples with the challenges it presents.
SYSPRO’s recent Global CFO Manufacturing Survey showed that over 80 per cent of respondents across the Asia Pacific region cited high inflation and interest rates as a cause of drag in the manufacturing industry.
Meanwhile, 67 per cent of companies surveyed have been buffeted by economic uncertainty and supply chain disruptions. Yet, as history has shown, within every challenge the manufacturing sector has faced lies an opportunity for innovation and efficiency improvements.
To counteract the effects of rising costs, manufacturers need to optimise their operational efficiency. Integrating their ERP (Enterprise Resource Planning) and MOM (Manufacturing Operations Management) systems can be a game-changer in achieving this goal. continued on Page 18
The 12th annual KiwiNet Research Commercialisation Awards honours 18 finalists who are transforming scientific discoveries into new technologies, businesses and real-world solutions. These innovations, emerging from outstanding research within New Zealand’s universities, Crown Research Institutes and other research organisations, are driving significant economic and societal benefits for Aotearoa.
The KiwiNet Awards celebrate deep tech heroes from across New Zealand, including research entrepreneurs, innovators and commercialisation professionals.
This year, innovations in the spotlight include novel botanical drugs, synthetic dairy proteins, sustainable surfactants, waste-to-resource technology, plant-based polystyrene replacement, UV water cleaning technology, plant-based dairy alternatives, medtech AI for eye exams, implantable brain sensors, waste minimisation innovations, ball monitoring tech for sports, and advanced engineering innovations for health and building resilience.
KiwiNet CEO Dr James Hutchinson says, “The KiwiNet Awards highlight the powerful economic impact of research commercialisation and showcase the collective strength of our science and innovation sector. Our 2024 finalists are exceptional.
“From tackling climate change to improving health outcomes, they’re solving problems that matter for New Zealand and the world. This year, we’re excited to introduce the Commercialisation Rising Star category, shining a light on emerging commercialisation professionals shaping the future of our sector. Together, we’re creating lasting benefits for our communities, economy and environment.”
The 2024 KiwiNet Research Commercialisation Awards finalists are:
• Jean-Luc Ellis – WasteXpert/ Waipapa Taumata Rau, University of Auckland: Reducing construction and demolition waste with on-site systems
• Jenny Zhu – LineBuddy/ Te Whare Wānanga o Waitaha | University of Canterbury: Umpiring ball monitoring tech for accurate line calls
• Dr Arup Nag – ANDFOODS/ Riddet Institute/ Te Kunenga ki P rehuroa Massey University: Innovating tomorrow’s food today
• Emily McIsaac - Daisy Lab/ Te Kunenga ki P rehuroa Massey University: Making dairy proteins - without the cows
• Cynthia Hunefeld – Evithé Biotechnology/ Te Herenga Waka—Victoria University of Wellington: Putting nature back into medicine with botanical drugs
• Dr Jack Chen – Spherelose/ AUT: Sustainable surfactants for a brighter future
BNZ Researcher Entrepreneur Award
• Distinguished Professor Harjinder Singh - Riddet Institute, Te Kunenga ki P rehuroa Massey University: Research entrepreneurship icon and food science leader
• Distinguished Professor Geoff Chase - Te Whare Wānanga o Waitaha | University of Canterbury: Engineering better medicine and a more resilient New Zealand
• Ella Moffat - Massey Ventures: An emerging leader in the commercialisation ecosystem
• Ben Pearson - UniServices: Building connections and collaboration for exceptional outcomes
• Abi Thampi - AUT Ventures: A highly effective and relatable commercialisation champion
• ANDFOODS - Riddet Institute/ Te Kunenga ki P rehuroa Massey University/ Massey Ventures: Breakthrough dairy-alternatives taking the world by storm
• Cetogenix - Pacific Channel/ Scion: Building renewable futures — with no waste left behind
• Kitea Health - Auckland Bioengineering Institute/ Waipapa Taumata Rau, University of Auckland: World-first implantable brain sensor set to transform patients’ lives
• ZealaFoam® - AgResearch/ Plant & Food Research/ Scion: Breaking the mould with sustainable plant-based polystyrene replacement
• NovoLabs and Massey Ventures: Advanced UV technology bringing cleaner water to the world
• Toku Eyes and Waipapa Taumata Rau, University of Auckland: Medtech AI: Using the eye as a window to our health
The 2024 KiwiNet Awards judging panel comprises Cather Simpson – CEO of Orbis Diagnostics and Partner at Pacific Channel; Greg Sitters – Managing Partner at Mat Group; Guy Royal – Director of Tuia Group; Suse Reynolds – Angel Investor; and Olivia Ogilvie – CEO and co-founder of Opo Bio.
The Kiwi Innovation Network (KiwiNet) is a consortium of 19 universities, Crown Research Institutes, an Independent Research Organisation and a Crown Entity established to boost commercial outcomes from publicly funded research by helping to transform scientific discoveries into new products and services.
The 2024 KiwiNet Awards are supported by MBIE, PwC NZ, Sprout Agritech, BNZ, KCA, Campus Plus and AJ Park as well as Return On Science, Momentum, and Mat , the sponsor of the Momentum Student Entrepreneur.
KiwiNet Awards winners for 2024 will be announced at an evening reception on 9 October in Auckland.
Adam Sharman, CEO LMAC Group, APAC
As manufacturing organisations strive to optimise their operations, the adoption of technology has always been a key focus. In the last 10 years, developments in digital technologies for manufacturers have increased pace and, whilst most organisations recognise the opportunity presented by these developments, the rapidly changing ecosystem of systems can make it difficult to identify the best fit for the business.
The landscape of manufacturing or operational management systems has evolved considerably in recent years, with multiple options available to fit the needs of the business based on scale, complexity and requirements.
Three solutions that have gained significant traction are Manufacturing Execution Systems (MES), Manufacturing Data Hubs (MDH), and Machine Monitoring Platforms (MMP). Each offers unique benefits and comes with its own set of limitations. This article aims to provide a comprehensive comparison to help manufacturers make informed decisions on which of these solutions is the best fit when considering investment in OT software.
Manufacturing Execution Systems (MES)
MES is a comprehensive software solution that manages and monitors work-in-process on the factory floor. It operates in real time to enable the control of multiple elements of the production process, including:
- Resource allocation and status
- Production scheduling
- Dispatching production units
- Quality management
- Labor and material tracking
- Performance analysis
MES serves as a bridge between planning systems like ERP (Enterprise Resource Planning) and the actual production processes, providing a holistic view of how current conditions on the plant floor can be optimised to improve production output.
1. Comprehensive Production Management: MES provides end-to-end visibility and control over production processes, from order release to finished goods.
2. Real-time Decision Making: Offers real-time data and analytics, enabling quick responses to production issues.
3. Quality Control: Integrates quality management processes, reducing defects and improving overall product quality.
4. Resource Optimisation: Helps in optimising the use of materials, labour, and equipment.
Limitations
1. Complex Implementation: MES can be complex to implement, often requiring significant time and resources.
2. Cost: Generally more expensive than other solutions, both in terms of initial investment and ongoing maintenance.
3. Rigidity: Some MES solutions may be less flexible in adapting to rapid changes in manufacturing processes.
A Manufacturing Data Hub (MDH) is a centralised data management system designed to collect, store, and organise data from various sources across the manufacturing environment. It acts as a single source of truth for all manufacturing-related data, including:
- Production data
- Quality data
- Supply chain information
- Machine performance data
- Energy consumption data
MDH focuses on data integration, normalisation, and accessibility, enabling manufacturers to break down data silos and facilitate more comprehensive analytics and reporting.
Manufacturing Data Hubs can provide a virtual centralisation of data across multiple systems, machines and PLCs for the purposes of monitoring and analysis of real-time performance. MDH differ from a data warehouse or data lake where the data is centralised into a physical (not-virtual) centralised data repository.
Benefits
1. Data Centralisation: MDH excels at collecting, storing, and organising data from various sources across the manufacturing environment.
2. Improved Data Accessibility: Provides a single source of truth, making it easier for different departments to access and utilise manufacturing data.
3. Enhanced Analytics: Facilitates advanced analytics and reporting by consolidating data from multiple systems.
4. Scalability: Generally more scalable than MES, allowing for easier integration of new data sources.
1. Limited Process Control: Unlike MES, MDH typically doesn’t provide direct control over manufacturing processes.
2. Data Quality Dependence: The effectiveness of MDH relies heavily on the quality and consistency of input data from various sources.
3. Potential for Data Overload: Without proper management, the vast amount of data collected can become overwhelming and difficult to navigate.
Machine Monitoring Platforms (MMP) are specialised systems, focused on collecting and analysing data from manufacturing equipment in real-time. MMP typically include:
- Real-time machine status monitoring
- Production counting and cycle time tracking
- Downtime tracking and analysis
- OEE (Overall Equipment Effectiveness) calculations
- Predictive maintenance alerts
Machine Monitoring Platforms are primarily concerned with machine performance, efficiency, and maintenance, providing deep insights into equipment utilisation and potential issues. MMPs are a good fit where the priority is understanding the production, rather than controlling machines, as in a Supervisory Control and Data Acquisition (SCADA) system.
1. Focused Insight: Provides deep, real-time insight into machine performance and status.
2. Predictive Maintenance: Enables predictive maintenance strategies, reducing downtime and maintenance costs.
3. Easy Implementation: Generally easier and quicker to implement compared to comprehensive MES solutions.
4. Cost-Effective: Often more affordable, especially for smaller manufacturers or those focusing primarily on equipment efficiency.
1. Limited Scope: Primarily focused on machine performance, lacking the broader production management capabilities of MES and the control capabilities of SCADA.
2. Integration Challenges: May require additional effort to integrate with other manufacturing systems for a holistic view.
3. Data Context: While rich in machine data, MMP may lack the broader context of production processes and business objectives.
The choice between MES, MDH, and MMP depends on various factors including the size of the operation, specific industry needs, existing technology infrastructure, and budget constraints.
• Large, Complex Operations: May benefit most from a comprehensive MES solution, despite the higher cost and complexity.
• Data-Driven Organisations: Might find MDH most valuable for its ability to centralise and analyse data from multiple sources.
• Equipment-Centric Manufacturers: Could see significant ROI from an MMP, especially if machine efficiency is a primary concern.
Many manufacturers are also exploring hybrid approaches, combining elements of these solutions to create a tailored system that meets their specific needs. For example, an engineering shop may run an automated line using a machine monitoring platform and an analogue production process that is run with a project management system both of which are reported, scheduled and analysed through an MES.
Small Business and Manufacturing Minister Andrew Bayly, along with Climate Change Minister Simon Watts, introduced a new MBIE report showing circular opportunities for the manufacturing sector.
“Manufacturing is a sleeping giant for New Zealand’s economy; with the right tools and support, manufacturing has the potential to supercharge our economic growth,” Bayly said. “The manufacturing sector accounts for 10 per cent of GDP, 60 per cent of our exports, and employs 230,000 people.”
“Globally there is increasing demand for low-carbon manufactured products. Our agile and innovative manufacturers with their strong green reputation and access to relatively low-carbon electricity are well positioned to take advantage of this demand,” he added.
Watts emphasises that the manufacturing sector is already heading in the right direction and is supporting New Zealand in meeting its climate change targets. However, there is still more to be done. “That’s why we are providing manufacturers with information to support them to adapt their business to be less carbon-intensive, with the launch of a new online toolbox, report and dataset.”
The circular economy is critical component of modern manufacturing. Adopting circular economy principles can help you to significantly reduce costs while making your business more sustainable.
The circular economy (CE) is a concept that changes how we produce and consume goods. It uses systems thinking to design out waste and pollution, keep products and materials in use and regenerate natural systems. CE moves us away from the current ‘linear’ model of producing and consuming goods and services: ‘take-make-dispose’. It has economic, environmental and social benefits. It is also closely linked to the Bioeconomy, which uses renewable biological resources to produce food, products, and energy.
➙ Identify your risks: The circular economy is an economic model. Think about the value in your products and equipment. How can this be maintained for longer? How can you recover manufacturing value so you can benefit from it again? How can you reduce your exposure to price volatility and ensure access to needed resources?
➙ Implement waste reduction strategies: Conduct a thorough audit of your waste streams and understand the waste your suppliers and customers produce. Identify materials that can be eliminated, reused or substituted for more
recyclable alternatives. Invest in technologies that reduce the waste you produce during the manufacturing process.
➙ Use waste as a resource: Explore ways to repurpose waste materials into new products or inputs for other processes, create additional revenue streams and reduce what goes to landfill.
➙ Adopt renewable energy sources: Transition to renewable energy sources such as solar, wind, or biomass. Fossil fuels are part of the linear economy and are non-renewable. It also reduces your carbon footprint, creates energy security and leads to long-term cost savings on energy bills.
➙ Optimise resource use: Use resources more efficiently by improving your production processes. Implement Industry 4.0: Incorporate smart manufacturing technologies like IoT, AI, and machine learning. These technologies can improve your business’ operational efficiency, reduce downtime and enhance product quality and traceability.
➙ Anticipate Industry 5.0: The future is based on greater collaboration, customisation, and the delivery of sustainable products and services. This involves greater traceability and transparency. Digital product passports are part of this and require preparation.
➙ Invest in durability: New Zealand relies on imported technology and equipment. Looking after what we import, maintaining and refurbishing it, saves money and increases resilience. It’s a balance between keeping things going and keeping up as technology advances.
➙ Work with supply chain partners: Working closely with suppliers and customers to implement sustainable practices throughout the supply chain can amplify impact and lead to shared benefits, such as cost reductions and improved resilience.
➙ Leverage government incentives: New Zealand’s government offers various grants, tax incentives, and support programs to encourage sustainable manufacturing practices. Taking advantage of these can offset the costs of green initiatives.
➙ Invest in Research and Development: New sustainable technologies, materials and processes can lead to long-term competitive advantages and open up new market opportunities.
➙ Educate and train your workforce: Developing a skilled workforce that is knowledgeable in sustainable practices and advanced manufacturing techniques can improve operational efficiency and help implement new technologies effectively.
As manufacturing continues to evolve in the digital age, the choice of technology solutions becomes increasingly critical. Understanding the strengths and limitations of each technology option is crucial in making an informed decision that aligns with
manufacturing goals and challenges.
A thorough requirements definition process that captures user information requirements, system and technology integration, flexibility and scalability of the solution, investment required, and industry
The report Mapping Emissions and Waste Stream Profiles, and Opportunities for Achieving Net-Zero Circular Advanced Manufacturing supports the growth and resilience of Aotearoa New Zealand’s advanced manufacturing sector.
It found that circular economy practices exist in New Zealand within and across manufacturing subsectors. Subsectors differ greatly. However, they are connected through resource flows and face similar challenges, particularly around waste. The report highlights opportunities for each subsector to adopt net-zero practices.
Learn more in the new report delivered by thinkstep-anz, Aurecon and the Sustainable Business Network for the Ministry of Business, Innovation and Employment. Download the summary report here: https://lnkd.in/gpz5fkMa https://www.thinkstep-anz.com/reports/
Main manufacturing subsectors and manufacturing GDP share (2020) Source: thinkstep-anz
specificity is critical to identifying the best fit. Ultimately, the optimal solution will be one that not only meets current needs but also positions the organisation for future growth and adaptation as the industry and market evolves.
Here are several strategies for manufacturers to consider:
1. Invest in technology and automation
Embracing advanced technologies and automation is essential for the manufacturing sector. Innovations like ERP and MOM systems can significantly enhance operational efficiency by reducing reliance on manual labour, minimising errors and centralising information.
Together with advanced technologies like the Internet of Things (IoT), artificial intelligence (AI), and machine learning, provide real-time data and insights, enabling informed decision-making and improved productivity.
2. Optimise supply chain management
Efficient supply chain management is crucial for minimising costs and ensuring a steady flow of materials. ERP systems help manufacturers enhance supply chain efficiency by diversifying their supplier base, leveraging digital supply chain solutions and improving inventory and warehouse management.
Building relationships with suppliers and exploring local sourcing options can also reduce reliance on international suppliers and mitigate the impact of future global disruptions.
3. Implement lean manufacturing principles
Lean manufacturing principles focus on eliminating waste and optimising processes. With the support of ERP and MOM systems, manufacturers can enhance productivity and reduce costs by streamlining
operations, reducing unnecessary steps and improving workflow.
4. Invest in workforce training and development
A skilled and motivated workforce is essential for operational efficiency. Manufacturers should invest in training programs to enhance employee skills and knowledge.
ERP systems facilitate the cross-training of employees, improving flexibility and reducing downtime on the production line. Additionally, encouraging a culture of continuous improvement and employee engagement can drive innovation and productivity.
5. Implement predictive maintenance
Unplanned downtime and equipment failures can be costly. Implementing predictive maintenance strategies through MOM systems helps identify potential issues before they lead to breakdowns.
By leveraging data analytics and IoT sensors, manufacturers can monitor equipment health, schedule maintenance proactively and minimise downtime, ultimately reducing costs and improving efficiency.
6. Optimise production planning and scheduling
Effective production planning and scheduling help maximise resource utilisation and minimise idle time. ERP and MOM systems enable manufacturers to implement advanced planning and scheduling (APS) systems, optimising production processes, efficiently allocating resources and reducing lead times. This ensures smooth production runs, reduces
bottlenecks and improves overall efficiency.
7. Adopt sustainable practices
Sustainability is not only beneficial for the environment, but it also enhances operational efficiency. Implementing sustainable waste reduction, recycling and eco-friendly packaging can reduce costs and improve brand reputation.
ERP systems support sustainable sourcing practices, ensuring a stable supply of raw materials and mitigating the impact of price fluctuations and global supply chain disruptions.
The manufacturing industry has faced numerous challenges in recent years, and the current inflationary pressures and rising interest rates are no exception.
However, manufacturers can counteract these rising costs by optimising their operational efficiency through the adoption of advanced technology.
Investing in ERP and MOM solutions is crucial in times of economic uncertainty. These systems help manufacturers survive and thrive in the face of rising costs by enhancing operational efficiency and turning challenges into opportunities for growth and innovation. The resilience and adaptability that have defined the manufacturing industry for decades will continue to drive its success in the future.
Looking for a marketing edge?
By Dr Troy Coyle, HERA CEO
Building Information Modelling (BIM) has been a promising tool in the manufacturing and construction industry for decades, yet it remains underutilised in Aotearoa. So, why isn’t it embedded more broadly in our industry? And more importantly, what can we do to unlock its potential?
Since the 1980s, BIM has provided a comprehensive repository of data, enabling better decisions during design, build, and maintenance phases. Unlike traditional CAD models, BIM integrates information that allows computers to perform complex simulations. Yet in New Zealand, BIM’s capabilities are largely untapped.
Old habits die hard
One of the key issues is the way BIM is being used— or not used. Many in the industry continue to treat BIM as an enhanced version of 2D or 3D CAD, using it primarily for its visual modelling capabilities. While there’s certainly value in that, it misses the real power of BIM: its ability to drive collaboration across teams and improve project efficiency.
To maximise BIM’s benefits, we need to adopt it as a process, not just a tool - one that promotes early involvement of all stakeholders, open communication, and collaboration. This means breaking down silos and ensuring all stakeholders,
from designers to asset owners, work with the same integrated information. This means looking beyond isolated areas such as clash detection or design coordination, and instead – using it throughout the entire lifecycle of a project.
One of the reasons for slow uptake is the perception of BIM as a costly, complex tool that only large commercial projects can afford. The reality is that BIM can drive significant cost savings— with global studies suggesting time and cost reductions of 20% to 30% on projects that use it effectively. However, there’s hesitancy to invest in the necessary technology and training. The upfront costs of implementing BIM often obscure its long-term benefits, particularly for small to mid-sized firms. In a heavy engineering industry known for being risk-averse, this short-term thinking can stifle innovation.
For BIM to transform Aotearoa New Zealand’s construction and manufacturing sectors, we need more than just individual adoption—we need industry-wide collaboration. This includes comprehensive training, greater investment in
The six raw materials that shape modern civilisation
Sky News economics editor Ed Conway, an inhabitant of the “ethereal world” in which ideas and services are bought and sold, opens his account with an eye-opening visit to a Utah gold mine where an entire mountain range is being removed in the quest for earthly riches.
That hugely destructive pit is a comparative scratch in the ground, though, compared to a vast Chilean copper mine that “can produce comfortably more copper each year…as the amount of gold produced by every mine on the planet since the beginning of time.”
Gold is somewhat inconsequential, while copper is essential to electronics. So is sand, one of the six commodities Conway examines in rich detail without his prose ever sliding into the miasmas of the dismal science.
Sand contains silicon, which yields computer chips and “the fiber optics from which the internet is woven.” Silicon combines with cement and asphalt
to make buildings and roads; iron provides the infrastructure of the built material world; salt yields hydrogen chloride, another component of computer chips and even solar panels; and oil is implicated in just about everything, including greenhouse-grown vegetables that feed the world.
Even in an energy and material regime weaned from fossil fuels, Conway argues, fossil fuels will play a part—and getting that weaning accomplished, he adds, “will mean building untold new energy capacity across the world: solar panels, wind turbines and nuclear plants, a rate humankind has never before achieved.”
Yet, he adds at the conclusion of this erudite exploration, which ably describes how his chosen commodities interact, it’s not an impossibility, thanks to his sixth element: lithium, the basis for the batteries that may lead the way to a renewable energy future.
Of course, copper and glass will be involved, too.
technology, and a shift in mindset that sees BIM as essential for projects of all sizes.
At HERA, we’re leading the charge in showing how BIM, combined with Construction 4.0 technologies like AI and IoT, can improve project outcomes. Through our research, we’re developing case studies that demonstrate how BIM can be applied in New Zealand’s unique environment, providing a roadmap for the industry to follow. The technology is here, and the benefits are clear—it’s up to us to embrace this change.
The Hook
“But we’re unique, no one else takes bespoke orders that morning, processes and ships them that afternoon.”
“Not even your competitors?”
“Yes, they do….but they are much bigger and can afford to develop systems that are perfect for themselves”.
“Is there anyway to test how bespoke these orders really are?”
The Problem
This conversation, in various guises happens regularly with clients, and sometimes it’s true, but often, we’re not as unique as we think. And that’s a good thing!
The more unique we are, or decide to be, in our operations the more expensive our journey to digitisation becomes.
This becomes particularly salient against the backdrop of New Zealand’s beating heart of manufacturing SME’s being in the midst of a perpetual battle when it comes to digitisation.
Firstly, weighing up the challenging costs of developing digital systems and automated processes that are fit for purpose with realistic return on investment. Whilst secondly, being touted the value of Industry 4 technologies but facing a skills barrier to adoption.
The Solution
So what advice would I give to any manufacturing business looking to digitisation and automation be? It’s simple. Start thinking about your internal operations differently. Or paradoxically, not different at all.
Whilst there is widespread appreciation for needing a clear competitive advantage, that thing or things that set you apart and make you unique.
Extending this thinking to everything about your business can hamper digital progress, driving you to look for or build bespoke solutions that match your processes perfectly.
Frank Phillips, Managing Director, Fulcrum
Where competitive advantage should be ‘up in lights’ externally. Internally we should be asking ourselves the question ‘how can we make this process as similar as possible to other operations’.
This is for two reasons:
1. It’s cheaper to borrow than build.
2. If that’s the standard, there’s usually good reason for it.
Without doubt there are exceptions to the second, but challenging ourselves with the question ‘why do we do it this way’ can only ever be a positive exercise.
This is brought to life by a couple of recent examples for me.
The first was a client who’s manufacturing operation used non-standard pallet sizes for storage and logistics. Whilst there was previous good for this, it became insignificant when weighed up against the downsides of manual container loading; unique pallet racking and impractical cost to automate.
Changing to standard pallets opens the door for quicker and cheaper automation where the return on investment is more attractive.
Whilst automating palletising would be unlikely to feature as a competitive advantage, few would argue against the value of the associated productivity gains.
The second example was a client in the healthcare industry, manufacturing products unique to individual patients.
Every order must be checked multiple times by hand to verify all the details match, ensuring patient safety and optimum results.
When building their technology roadmap we explored software that could ‘read’ the orders and verify the details automatically.
Drawing on proven technology, namely Optical Character Recognition (OCR) and Robotic Process Automation (RPA), the build and testing process would be lengthy and costly.
Challenging the status quo, we analysed how many orders were actually unique. It turned out that figure was only around 23%.
This insight opened the door to establishing SKUs in the ERP system that could be ordered by specific ‘part number’, allowing a vast reduction in the manual checks taking place.
By looking for ways to align our internal operations to industry standards (or even the standards in a parallel industry) costs will decrease and whilst the chance of successful implementation increases.
So, if like many manufacturers, you are looking to: Track products through the shopfloor; Measure real time performance; Go paperless on the shopfloor
Or one of a myriad of other challenges, remember it pays to look at how you can use what’s already on offer and challenging the business to align to that, rather than developing something bespoke.
Being careful to invest in processes and technology that meet our competitive advantage is imperative. Understanding the price that we pay for being unique is vital when looking towards setting the foundations of Industry 4 in your operations,
Frank Phillips is an experienced manufacturing consultant. Based in Taranaki he runs Fulcrum, a platform that allows New Zealand Manufacturers to connect to Manufacturing Technology Partners. To find out more, visit: https://fulcrumnz.com/
continued from Page 28
Take bottled water: this format that became a convenient alternative to tap water expanded the beverage industry without all its growth coming from the cannibalization of other offerings.
While their paths differ, the leading market builders do share some common characteristics. Critically, their CEOs and boards had strong convictions in the moves’ potential, giving management the ability to act boldly and bring the full organization along.
For example, early in his tenure as Microsoft CEO, Satya Nadella committed to launching a new growth phase through big investments in cloud computing, a success the company is now trying to reproduce with investments in AI.6 Another commonality is these companies’ reliance on strategic advantage to
choose their innovation bets.
Semiconductor manufacturer TSMC, for example, uses its foundry capabilities to out-innovate and outcompete potential rivals in the new markets it creates.
To reduce the risks involved in pursuing breakout innovations, companies can consider the four following strategies:
• Identify a ‘two-fer.’ This involves finding an opportunity that can offer an immediate benefit while also making a new offering available to customers.
• Look for a structural opening. Factors such as excess capacity (which companies like eBay have used), government subsidies, and other incentives can also reduce the risk of the innovation investment.
• Strike a partnership. Big companies often watch start-up activity to gauge new market trends and are increasingly partnering with or acquiring smaller companies to fuel their own breakout growth.
• Provide tools to enable others’ growth. Some companies, rather than trying to be gold miners, are embracing the concept of selling picks and shovels instead.
Industry momentum—and, by extension, business portfolio momentum—is a function of both broad external factors and individual companies’ actions. By investing in bold innovations that create new customers and markets and thus spark new waves of industry growth, innovative business leaders can not only expand their companies’ headroom for growth but also change the trajectories of their industries.
How are you finding life as CEO of Master Electricians NZ?
I’m loving working with passionate people who are committed to advancement of this industry, which in many ways is at the centre of the energy transition. I’ve found that the people around me share many of the same values – a desire to support members in a proactive way and grow the industry, and a willingness to take risks and innovate so that electrical contractors are future-ready.
What are the challenges in this role?
The electrical industry is undergoing rapid change - from technological innovation and sustainability imperatives to regulatory shifts and evolving consumer demands. In this dynamic environment I see every challenge as an opportunity. There are opportunities to enable technology adoption at a faster rate. There are opportunities that flow from convergence of industries and infrastructure in terms of dynamic careers for electrical contractors and diversified business opportunities.
We need to lean into regulatory reform and having the funding needed to keep up with rapid changes in standards – both in terms of product and practices.
Another step up is that the industry is currently served by multiple ministers and parts of government which often means we never have the ability to communicate about the impact across the value chain!
Do your members have issues recruiting the right staff?
Yes and no. We have got a workforce skill shortage, and the economic situation does mean we don’t recruit and train enough. There is also the need and desire to innovate and adopt new technologies – the electrification of the NZ economy relies on individuals and businesses who can pick up micro skills faster than ever before and in ways that meet their needs in terms of experiential learning.
That is why we are investing in a new training
entity – Trade Master. It’s a one-stop CPD shop that will partner with wholesalers, suppliers and other industry leaders to promote and support the adoption of new products and services that are innovative and emerging. There is a desire to recruit individuals who have the right mix of aligned values, soft skills, and aspirations to grow.
Being a team player with an eagerness to learn and take risks, and learn quickly on the job, are all critical traits at a time when the half-life of skills is less than 18 months.
Keeping members up to date with technology, especially in training – is this an issue?
Emerging technologies will transform electrical system design, installation, and management. The electrical industry needs to embrace cutting-edge technology and sustainable practices to meet the evolving needs of clients and address global challenges.
Rapid technological change is the reason the half-life of skills is now estimated to be 18 months or less, so our workforce must quickly master new technologies. We need to upskill current electricians and train new entrants in EV technology, energy storage, and smart grid management. Flexible training options are needed to quickly equip the workforce with new skills.
The answer lies in a multifaceted approach by the electrical industry, involving strategic partnerships, continuous education and training, and a commitment to diversity and inclusion.
How do you use your business experience to advocate for members?
My background spans academia, the public sector, and the business world. I’ve had the opportunity to hone skills across policy, strategy, training, communication and management, and this is proving to be a good value proposition for successful advocacy.
quote?
Feel the fear and do it anyway!
Last book read?
Range by David Epstein
What do you draw inspiration from?
In terms of personal goals and dreams, setting a goal and working toward achieving it can be a great source of inspiration. The process of overcoming obstacles and seeing progress really fuels my drive to keep pushing forward. Learning something new and gaining a deeper understanding of something new ignites curiosity and inspires me to try new things.
Leading international welding equipment manufacturer, Kemppi, has released its new Zeta Fresh Air welding and grinding helmets. The brand-new lightweight helmets come with a respirator for maximum breathing protection while also offering complete eye and face safety and a range of additional must-have features.
The Zeta Fresh Air helmets are equipped with a respirator for TH3-level breathing protection.
The synergy between the helmet and powerful certified respirator stops 99.8% of harmful fumes, gases and particles to help keep the user safe. The helmets also deliver comprehensive face protection. Both the grinding and welding helmets are certified to AS/NZS 1716:2012. Plus, the best-in-class auto-darkening welding filter (ADF) delivers maximum eye protection.
Although tough and robust, the new Zeta Fresh Air range of helmets is remarkably lightweight. The helmets’ lightweight design delivers maximum comfort and reduces neck fatigue. Plus, the narrow shape of the helmets makes it easier to move around on-site or in the workshop.
All welding helmets in the Zeta Fresh Air series provide enhanced visibility. The welding models come
with VISION+ technology for an accurate view of the environment and a best-in-class auto-darkening filter – a 2.5 DIN shade makes it easier to see bright colors and details when the arc is turned off. There are also grinding and surface-finishing Fresh Air helmets with a 200mm high viewing area and 180° viewing angle.
Each model in the Fresh Air range is specifically designed for one-hand use. Well placed buttons and controls are easy to reach and operate with one hand for no-nonsense usage.
The Zeta Fresh Air W201x helmet features integrated LED lights. These built-in automatic work lights increase safety while providing you with the best visibility for the task at hand. The lights are powered by the blowing unit and they automatically turn off or on based on the ambient light. Alternatively, they can be easily controled manually by hand.
Zeta Fresh Air helmets come with a respirator to prioritize welder health. They offer comprehensive eye, face and breathing protection while remaining comfortable and easy to use. For more details call Matt on 0220 200 626
Users can choose from 6 helmet models within the range. These include the:
• Zeta Fresh Air W201x PFU210e welding helmet
• Zeta Fresh Air W201 PFU210e welding helmet
• Zeta Fresh Air W201 RSA230 welding helmet
• Zeta G201x PFU210e grinding helmet
• Zeta G201 PFU210e grinding helmet
• Zeta G201x RSA230 grinding helmet
New Zealand’s dedication to the safety of people in the electrical industry, sees us already implementing various protection requirements to fight against the dangers posed by arc flash incidents.
These are notably outlined in the AS/NZS 4836:2023 standard, which emphasises that protective clothing worn during work on or near exposed energised conductors must be appropriate, correctly fitted, cover the full body, and be in working condition. Despite these standards, there exists a notable gap in federal regulation regarding the mandated frequency of testing or inspections related to arc flash hazards.
While electrocution often takes centre stage when we talk about electrical hazards, there is another more explosive risk facing the electrical industry. According to New Zealand worksafe, 2-4 incidents involving arc faults occur in New Zealand every year. Far from minor, these incidents pose a significant risk of severe burns or even death.
One company that has taken a proactive approach to mitigating this risk engaged Schneider Electric as experts to undertake an Arc Flash assessment at all their plants and, in doing so, identified a level 3 arc flash rating in some switchboards. The company then proceeded to design and install an ARC Flash protection solution, effectively mitigating the risks associated with potential arc flash incidents.
Schneider Electric then stepped in promptly to implement engineering controls that protect employees tasked with equipment maintenance,
while ensuring minimal disruption to daily operations. In fact, collaborating with stakeholders, it has executed installation in a single shutdown.
Arc flashes can result in explosive events, generating extreme temperatures and posing significant threats to those who are operating systems with such hazards. It’s known that the only way to counter a potential arc flash is through regular monitoring, service, and maintenance. Unfortunately, many companies tend to delay these measures, unintentionally exposing their workforce to heightened risks.
When asked about the reasoning behind these delays, Vice President of Power Systems and Services James Hunt at Schneider Electric said, “It comes down to human behaviour – worrying about the ‘what if’ and potential associated costs. These risks are there, and business owners are potentially exposing their people and assets without knowing.
“The current regulatory regime doesn’t mandate the frequency of testing. So, it is up to proactive businesses to monitor and manage that risk. This is where Schneider Electric brings additional value by providing highly-skilled consultants who audit, evaluate, and map electrical and automation assets and systems on an ongoing basis.”
To rectify such issues, Schneider Electric installs an advanced ARC
Flash protection system that makes the switchboard safe by monitoring critical sections and tripping the incomer circuit breaker at the first indication of an ARC Flash, preventing potential incidents.
Hunt emphasised an ongoing commitment to providing cutting-edge solutions and called for industry collaboration to address the absence of federally mandated regulations on the frequency of arc flash hazard monitoring.
He stated, “Preventing arc flashes can save many New Zealand lives every
year, and without regulations, we need to band together as an industry to break human behaviour, instilling more preventative safety measures in this area into our everyday work environment.”
The important focus now for New Zealand electricians is to shift towards fostering a proactive safety culture that advocates for united efforts in minimising the risks associated with arc flash incidents.
For more information on arc flashes or the ARC Flash protection solution, visit: www.se.com/nz/en/
The demands placed on EMC cable glands are multifaceted: they must not only effectively dissipate electromagnetic interference fields, but also undesirably high shield currents. Furthermore, compact dimensions are needed to fit them in limited installation spaces. In response to market requirements, EMC cable glands also need to be simple, quick and dependable to install.
Addressing these needs, the new UNI Dicht TRI from PFLITSCH combines the top EMC bonding capabilities of the TRI spring – familiar from the blueglobe series – with the compactness and individuality of the UNI Dicht modular system.
The UNI Dicht TRI achieves maximum screening attenuation across the entire frequency range, facilitated by its patented triangle spring that enables 360° bonding with the cable shield over a large area. The mechanical separation of the shield contacting from the sealing element guarantees constant and enduring EMC properties for the UNI Dicht TRI. A further advantage is the very high current carrying capacity that reliably dissipates undesirably high shield currents thanks to the large contact area of the solid stainless steel TRI spring.
The assembly process is both straightforward and reliable. All the user needs to do is to remove the cable sheath at the contact point where the shielding braid is to be bonded. The TRI spring reliably bonds the cable shield as soon as the cable is inserted in the cable gland – even with out-of-round or off-centre cables.
Importantly, this bonding method from PFLITSCH means that the cable shield only needs to be exposed at the actual connection point inside the control cabinet. As the shielding braid remains fully intact, maximum screening attenuation is achieved and the useful signals are transmitted without being unnecessarily affected by interference signals.
The interlocking of the double nipple and sealing insert prevents the cable from twisting when the pressure screw is tightened. This feature makes the UNI Dicht TRI particularly suitable for applications where the cable is already bonded, for example connectors and sensors.
Huge screening ranges ensure a reliable EMC connection.
The UNI Dicht TRI is available in sizes from M16 to
AoFrio, a global refrigeration technology company headquartered in New Zealand, has launched AoFrio® INSIDE™, a first-to-market complete refrigeration solution designed to accelerate the industry’s journey
towards Net-Zero. AoFrio INSIDE offers customers the ability to sharply reduce their fleet’s energy consumption and includes data-driven tools to remotely analyse and optimise fleets for additional efficiency gains.
The refrigeration sector is responsible for 10% of global total carbon emissions, with cooling technologies alone consuming 17% of total electricity usage worldwide. This, combined with the release of harmful greenhouse gases, has made the refrigeration sector a significant contributor to climate change.
To combat these challenges, AoFrio INSIDE offers exceptional benefits, including:
• Contributes up to 64% energy savings: Externally validated against standard refrigeration systems, the AoFrio INSIDE high-efficiency hardware and software package is proven to contribute to overall energy reductions of up to 64%*.
• Connected ecosystem: The only solution on the market that gives customers a dashboard view of their assets’ real-time energy usage, enabling fast and accurate fleet-wide reporting.
• Identify and act: Data-driven insights allow customers to identify coolers consuming energy outside their usual operating range, remotely determine the cause, and resolve the issue.
M25 for cable diameters from 4.0 mm to 20.5 mm. Thanks to its large sealing ranges, wide diameters can be reliably sealed with IP 68. The huge screening range of the UNI Dicht TRI furthermore ensures a reliable EMC connection. For example, in the M25 very thin shield diameters from 3 mm up to 17 mm can be bonded.
The large sealing area in PFLITSCH cable glands prevents constriction of the cable sheathing to guarantee durable and safe installation. The UNI Dicht TRI made of nickel-plated brass or stainless steel is approved for the temperature range from –40 °C to +130 °C with a TPE sealing insert and from –55 °C to +200 °C with a silicone sealing insert.
PFLITSCH EMC cable glands are an important element of the EMC protection concept for electrical systems, safeguarding against interference and failures.
www.treotham.co.nz
The UNI Dicht TRI expands the comprehensive PFLITSCH range of solutions relating to EMC and helps users to implement a seamless EMC concept. (Photo: PFLITSCH)
food and drinks at the optimal serving temperature, it’s about driving a more sustainable industry for generations to come. This inspired us to combine the best hardware, software and cloud-based services to create an industry-leading innovation,” says Balla.
AoFrio INSIDE received global recognition last year through its winning in the ‘Incremental Change in Energy efficiency’ category at The Cool Challenge, an initiative led by the Beverage Industry Environmental Roundtable (BIER). It has also been announced as a finalist in two categories in the upcoming global RAC Cooling Awards 2024: ‘Refrigeration Innovation of the Year’ and ‘Refrigeration Product of the Year— System or Standalone’.
“AoFrio INSIDE can reduce and accurately measure a cooler’s energy use, leverage machine learning to understand how to improve performance and use remote management tools to implement data-driven insights on a large scale,” adds Balla.
• Accelerate Net Zero goals: Reporting on actual energy usage and associated carbon emission reductions allows customers to track their pathway to Net Zero.
• Future-proofed system: AoFrio INSIDE leverages AI-powered actionable insights for long-term benefits.
Greg Balla, CEO of AoFrio, says, “AoFrio INSIDE is a game-changer. It contributes to potential energy savings of up to 64%, significantly reduces carbon emissions, and provides real-time reporting and actionable insights on further improvements.”
“This solution empowers our customers to reduce their environmental impact and enhance their profitability. Refrigeration is much more than keeping
As a hardware-enabled SaaS company, AoFrio’s mission is to lead the charge towards a more sustainable and efficient food and beverage industry. With over 2.7 million coolers connected to the AoFrio cloud and over eight years of actionable data acquired, AoFrio is the global leader in the market, creating and manufacturing cutting-edge and sustainable solutions for commercial refrigeration.
AoFrio provides solutions to its customers to keep food and drinks fresh and safe at the point of sale. Global beverage brands such as Coca-Cola, Pepsi, and Heineken already use its technology to manage their fleets of commercial bottle coolers.
*Based on Independent testing from Re/Gent. Actual results may vary depending on usage conditions and other factors.
DEWALT has introduced its most innovative and versatile storage system to date with the launch of Toughsystem 2.0 DXL. This world-first redefines portable, stackable storage, offering the latest in large-scale solutions designed to enhance productivity, efficiency, and safety on the jobsite.
The DXL range includes heavy-duty drawers, a rolling base and a work top. These components provide a durable, mobile workshop solution ideal for work sites, workshops, garages, or any location where equipment is used and security is paramount.
Each product in the new lineup is designed for enhanced organisation efficiency, mobility, and durability, ensuring that tools are always accessible and secure on the jobsite. The range offers quick tool access, easy transport, and customisable workspace options.
The DXL System comprises of four new products; Deep Drawer, Shallow Drawer, 4-Wheel Dolly and Work Top. Each features auto-stacking latches for quick connectivity with each other and previous
TOUGHSYSTEM modules, allowing users to create and customise combinations that meet the specific tool and accessory needs of each job. The system is also available in a 5-in-1 Tower pre-stacked combination modular workstation.
Perfect for accommodating larger tools and equipment, Toughsystem 2.0 DXL Deep Drawers features removable dividers for customisable organisation and heavy-duty aluminium carry handles for convenient transportation. The deep drawer includes an integrated locking bar with a unique metal secure lock mechanism for secure storage, providing quick and easy lock/release and acting as a deterrent to theft.
The locking aluminium drawer levers prevent accidental opening during transit. A weather seal protects tools from water and dust, ensuring durability and longevity in challenging jobsite conditions. The deep drawers also feature auto-stacking latches that connect seamlessly with all DXL and Toughsystem 2.0 modules. It has a total load capacity of 25kg.
This unit features two drawers with ball-bearing slides for smooth operation, removable dividers for flexible organisation, and ample storage for smaller tools and accessories. It includes an integrated locking bar for secure storage, locking aluminium drawer levers, and heavy-duty aluminium carry handles.
Integrated ToughTrack provides quick access to tools and accessories, while auto-stacking latches enable fast connectivity. The unit has a total load capacity of 25 kg (12.5 kg per drawer).
There is also the Toughsystem 2.0 DXL Dolly,Toughsystem 2.0 DXL Work Top, and Toughsystem 2.0 DXL 5 in 1 Tower.
“ReBeLs on Wheels” make driverless transport systems affordable thanks to modern
Mobile robotic systems are being used in more and more work areas, from e-commerce warehouses to modern restaurants. However, widespread use is often unaffordable for small and medium-sized companies due to the high prices. igus wants to change this with new low-cost robotics offerings and is presenting a series of low-cost mobile plastic robots.
The market for automated guided vehicles (AGV) and autonomous mobile robots (AMR) is booming: the global market for mobile robotics, including service robotics, currently totals around $20.3 billion, and experts expect this figure to almost double by 2028. Mobile robots are particularly widespread in material handling and industrial applications.
igus launches a new series of cost-effective mobile AGVs and AMRs for education, logistics and service with the aim of making mobile robotic systems affordable for SMEs.
And these smart helpers are even increasingly making their rounds in catering and hospitals. The plastics experts at motion plastics specialist igus have also been successfully testing AGVs in-house for four years - driverless shelves that deliver mail and shipments to offices as well as mobile robots in production that move transports and rotary stacking containers.
The experience gained flows directly into the development of a new Low Cost Automation product line, the “ReBeL on Wheels”. The goal: to pave the way for small and medium-sized enterprises (SMEs) to cost-effective mobile robotics.
The foundation of any mobile robotic system is the ReBeL. Using plastic makes the robot particularly affordable and, with a net weight of 8.2kg, the lightest service robot with cobot function in its class. Without exception, igus develops and manufactures all mechanical components that make up the ReBeL. Its payload amounts to 2kg and it has a reach of 664mm. Various moving systems are planned in which the ReBeL is centrally integrated: igus is launching an affordable version for the education sector, which includes the robot arm. Based on open-source software and equipped with a gripper, the ReBeL EduMove serves as an autonomous learning platform for educational institutions. It has a modular design, so that other functions can be added, such as lidar, camera technology or a slam
algorithm. Another version is an automated guided vehicle for SMEs, which can transport up to 30kg. With the optional ReBeL, simple A to B positioning tasks can be carried out. It dispenses with expensive sensor technology and instead relies on 3D sensor technology developed in-house. The ReBeL Butler is suitable for simple but time-consuming pick-up and delivery services, for example, in the hotel and catering industry.
The goal of all these developments is the lighthouse project, a mobile robot with integrated HMI and vision that would even be able to tidy up an office on its own. “With this project, we are pursuing a bottom-to-top strategy in which certain components such as safety laser scanners are not included in the basic package so as to keep the price low,” explains Alexander Mühlens, Vice President and Head of the Low Cost Automation Business Unit at igus.
“Nevertheless, the solution can be retrofitted for industrial requirements.” This year, igus will be presenting an affordable gripper with a large stroke and travel that offers a high degree of flexibility when gripping different geometries, among other things. Says Mühlens: “The areas of application for this planned low-cost AMR are extremely diverse and go far beyond simple transport tasks. They cover a huge range of use cases in different areas of life, such as cleaning tasks or serving coffee directly at the workplace.”
www.treotham.com.au
Leading heat pump company Daikin New Zealand is expanding with two purpose-built facilities in Auckland and Christchurch to meet customer demand and improve services nationally.
Daikin Park will consolidate all four of the company’s Auckland locations on a 12,150m2 site in Mt Wellington, making it the largest Heating, Ventilation, and Air Conditioning (HVAC) warehouse in the country. The Christchurch facility will start construction in the next 18 months to service the growing South Island market.
Managing Director, Ryuta Hayashibara, said Daikin Park will help reinforce its position as the market leader in New Zealand by supporting faster response times and improving customer experience.
“The expansion will enable us to be more agile and improve our operation resulting in greater customer satisfaction while continuing to drive customer growth and focusing on technology and product innovation to improve indoor air quality and ensure all Kiwi homes are warm, dry, and sufficiently
heated.”
Outbound operations from the Auckland facility start on August 19 and the full company will be relocated and operational by mid-October.
Supply Chain and facilities Manager, Andy Heydon, said to streamline operations, the new site has 10 docks, a capacity of 10,900 pallet spaces, and capacity to distribute 470,000 cubic meters of freight per year.
“We are taking control of our own supply chain with Daikin Parks being a significant investment in the company’s future,” he said.
Daikin Park is a partnership with industrial property experts PFI whose projects include Sistema Plastics manufacturing facility near Auckland Airport.
Daikin’s new Auckland facility is targeting a 5 Greenstar rating to support Daikin Global’s ambitious sustainability goals, aiming to achieve carbon neutrality by 2050. The new building includes environmentally friendly elements such as electric vehicle charging stations, a 100kw solar system, and rainwater harvesting tanks.
The opening of Daikin Park Auckland follows Daikin Australia’s successful expansion recently with the launch of similar facilities in Melbourne, Adelaide, and Brisbane.
Beyond its warehousing and office capability, the facility houses Daikin’s sales team, Trade Centre, and showroom.
The location also features a Training Academy offering courses to develop, upskill and increase the knowledge of technicians, Daikin’s specialist dealers, and the sales team.
New Zealand’s banking sector is set for a new phase of competition, as a local fintech moves to become the first locally owned bank designed for an open banking environment and artificial intelligence (AI).
Financial services company Debut has begun discussions with the Reserve Bank of New Zealand and is now preparing an application to become a registered bank.
There are currently 27 banks registered in New Zealand, however, only five are locally owned - with the last registered over a decade ago.
A recent Commerce Commission report into NZ’s banking industry highlighted significant concerns about the lack of competition. The report found that the market is dominated by the four major Australian-owned banks, which are highly profitable but do not compete aggressively for customers - resulting in higher costs, fewer choices, and poorer service for consumers compared to other countries with open banking. Open banking is a system where banks allow third-party providers such as fintechs to access customers’ financial data with their approval. The model is designed to give consumers greater control over their financial information and provide them with more personalised products and services.
The Government has accepted the commission’s recommendation to allow the introduction of open banking and allow consumers greater access to next-generation banking services and more competition throughout the sector.
continued from Page 8
While not a registered bank, Debut has launched an array of new financial services into the market through a mobile app.
The Commission’s report also found some consumers, such as Maori, were particularly vulnerable to financial exclusion under the current banking system. Debut representatives say their technology is designed to reduce geographic and other barriers to access - with customers able to set up an account online, without the need to enter a physical branch, for key services like a digital Mastercard debit card, Apple Pay, and Google Pay within minutes.
These services also include allowing customers to set up multiple virtual debit cards on-demand that control the type of transactions that can be made. The card can be deleted at any time - preventing hard-to-cancel subscriptions from recurring and providing more protection when shopping on unfamiliar websites.
Experts say open banking will also allow the entry of service providers with leaner operating modelsreducing fees and improving returns for consumers.
In a first for the industry, a 5.10% per annum universal interest rate is currently applied to both transaction and savings accounts offered by Debut. There are no penalties, lock-ups, or minimum deposit requirements, ensuring that all customers can benefit equally from this rate. In addition, there are no foreign exchange fees applied to purchases while travelling offshore or through international e-commerce sites.
you’re likely to take a snake back to 1.
8. I don’t personally need to be involved in the continuous improvement programme. Delegating authority for a major transformation programme to the CI team or an external consultant typically results in failure, as they do not have the direct authority to drive change.
Typically, when the programme is delegated in this way, the sponsor is too busy to lead it, and so they aren’t invested. This becomes apparent quickly
to the wider team who then become uninvested themselves. This is a snake back to 1.
9. We’re already world class. Of course, you don’t need an improvement programme if you’re already world class… but why does every single world class company have one? And continue to do it? Are you truly world class? If so, you’ve won! Otherwise, take the snake back to 2.
10.We already have an established programme with great support, sponsorship, and
Artificial intelligence and automation are also set to play a significant role in fraud detection and helping consumers manage their finances, with new AI-driven budgeting tools introduced by the company automatically categorising transactions with 91% accuracy.
Sulabh Sharma, Debut co-founder, says the introduction of open banking will be transformative for the industry and how New Zealanders manage their finances.
He says while New Zealand has been slower in adopting open banking compared to other countries, the introduction of the Consumer and Product Data Bill marks a significant step towards broader data sharing.
“The Bill will extend beyond the banking sector to include industries such as energy, telecommunications, and insurance, creating a more integrated and comprehensive data-sharing ecosystem.
“We have modelled Debut’s offering on highly successful neobanking services that emerged in markets like the UK, Brazil and Australia - following changes to their regulatory environment.
“By building this technology from the ground up with this framework in mind, we can integrate a new suite of financial services and work towards our goal of putting $1 billion back in Kiwi pockets.”
engagement. We’re achieving great results and have been doing this for years. If this is true, then take the ladder to the top. You win! And you should share your great achievements with others.
If you want to know where you really are at, on your journey, give me a call. A quick chat should be able to give you some direction.
An industry-leading trades training facility will create exciting new opportunities for aspiring electrical and plumbing trades in the region.
The first of its kind in New Zealand, the Skills Group Skills Hub incorporates a three-trades model, housing the Group’s three specialist trades brands— Etco for apprentice and electrical training, Industry Connection for Excellence (ICE) for plumbing, gasfitting, and drain laying apprentice training, and E-tec for advanced electrical training.
The Bradford-based hub is located in the former Tamahine Knitwear factory that initially opened in 1970, and utilising the same building footprint, the education institution is designed to accommodate up to 140 apprentices at once.
The newly modernised campus will supercharge trades training in the area – and, as the only Level 4 apprenticeship training facility in Dunedin, will eliminate the need for apprentices to travel to Invercargill or Christchurch for Level 4 training.
Skills Group Director of Specialist Trades, Ben Stevens, says the Group is delighted to support Dunedin and the Central Otago area by giving South
Island-based apprentices and their employers more training choices with less travel.
“This is a real positive for the region and will help meet the significant apprentice training demand across the South Island,” says Stevens. “It’s great to have a presence here and create something new, something modern, using the best quality gear and technology so that we can equip our apprentices for success.”
ICE General Manager Antony Russell says the extensively renovated campus will offer state-of-the-art, purpose-built training facilities, with industry-standard equipment including large roofed drainlaying pits, modular bathroom pods, new hand and battery tools, new workshop equipment, multiple 4+ assessment sets for each task, large bright touch-enabled displays and class sets of laptops.
AI will also be front and centre.
“The online component of our programmes includes additional learning activities featuring videos, animations, and interactive scenarios to support trainees’ knowledge development,” explains
Russell. “We are also initiating a new project to explore the potential of augmented reality devices for gathering evidence during on-the-job assessments.”
Tutors will come directly from industry and have extensive on-the-job experience, ensuring apprentices gain all the skills they need to succeed in the sector.
Skills Group’s first specialist trades school looks set to change the landscape for South Island tradies. Apprentices and electrical and plumbing employers will have even greater choices with opening a second three trades campus in Hornby in tautahi Christchurch in September.
Rotorua based Hayes International was founded by Tom Hayes in 1960 and this private company became part of the Bradbury Group of Kansas, USA in 1999.
Today the New Zealand Company is internationally known as a market leader for quality and performance with in excess of 1,820 Hayes machines exported to more than 90 countries worldwide.
Hayes originally started producing corrugated sheet machines for roofing and cladding, however products produced by this amazing 64-year-old New Zealand manufacturer today include Panel Mills, Purlin Mills, Stud Mills Roll-Forming Accessories, Purlin Mill Accessories, Auto-Curvers, Folding Machines, Coil Handlers and more recently Finished Product Handling Equipment including automated Purlin Stacking Equipment.
“In purchasing a Hayes machine our clients get the best in the industry in terms of reliability and performance which also provides them with a competitive advantage with whole of life cost, reduced machine down time and waste minimization,” commented Managing Director, Nick Looijen.
“90% of our business is repeat customers or direct referrals from existing customers with our principal markets being Australia, UK, USA and New Zealand” he said.
Okuma has been an integral part of this advanced manufacturing business with the first Okuma CNC Machining Centre purchased in the early 1970’s. Since that time a further ten precision CNC Machining Centres and Lathes have been added to the Hayes machine shop including the latest Okuma Double Column CNC Machining Centre Model MCR-A5C 25 x 65 resulting in the highest precision component output and significant production benefits.
The Okuma Double Column machine
producing 5.6 metre purlin chassis sections has reduced production time of five days to one shift with complete accuracy.
“The Okuma machines provide us with complete accuracy of the highest quality standard with significant time savings making us internationally competitive,” said Nick Looijen. “We have experienced staff and the Okuma machines are easily programmed yet we take full advantage of Okuma’s specialised training especially with new machines to ensure that we take full advantage of each machine’s capabilities,” he said.
Engineers and apprentices under training are excited with the new machines enabling them to achieve new skills and expand their personal development.
With the advantage of an in-house design team using the most advanced software in industrial design, electrical, hydraulics and engineering disciplines the company can change designs, expand product development etc. with time savings and accuracy to provide precisely what the customer requires and expects.
With more automation the lead times are being
drastically reduced in the manufacture of major plants and equipment with rapid replacement parts for worn components on roll-forming lines shipped directly to customers wherever they are in the world.
Hayes International also assists customers on upgrading their roll-forming machinery to improve efficiency, add features or update specifications. This has many advantages over purchasing a new machine according to the company, including lower up-front costs, shorter manufacturing lead time and reduced down time etc. providing customers with greater flexibility and options.
Upgrade options can be many and varied such as additional guards for a machine to meet local regulations when changing locations, additional punch heads for Hayes purlin mills forming stations for sloping eaves or sigma purlins, coil handling or upgrading the control system for efficiency, improved control or vision. Coil handling can be added or adapted to existing equipment and machine lines. Today the company employs more than 90 personnel with a strong commitment to apprenticeships with six under training at any time. It has a commendable record of staff retention with more than 20% with 20 or more years of service and one long serving member of 43 years and offers many incentives particularly on safety and workplace training.
Export sales for Hayes International now represent approximately 95 % with the remaining 5% to New Zealand customers. “It is exciting for Okuma to be working together in partnership with Hayes International as the company continues to expand and develop new precision products for world markets and we look forward to the future in tandem,” said Okuma New Zealand Manager, Karl Medley.
People often speak of industry momentum as if it were a force of nature independent of individual companies’ actions—like the mysterious “ether” scientists once believed filled the universe and allowed light to travel.
While demographics and macroeconomic factors outside organisations’ control do contribute to momentum, the trajectory and pace of industry growth very much rely on the innovation efforts of a sector’s constituent businesses.
By harnessing technology and creating new offerings or business models, companies can forge new markets and propel new consumption.
Roughly 80 percent of a typical company’s growth comes from its core business. This is often interpreted to mean that if a business happens to be in a high-momentum industry, simply riding that wave will yield significant growth.
However, even within high-momentum industries, there is a distribution of winners and losers. Companies that rebalance their business portfolios toward high-momentum segments can boost those portfolios’ performance and thus their chances of being among the winners.
But that’s not the whole story.
What are sometimes missed in that narrative are the factors behind this momentum and the role that industry members play in accelerating it. Momentum stems partly from the amount of growth headroom that remains in an industry. Just as companies or products follow an S-curve wherein a period of investment is succeeded by a stretch of steep growth that eventually tapers off, so do industry value pools.
A new market experiences a period of rapid growth until it becomes saturated, causing its growth to slow. In an industry made up of mature markets, growth momentum declines to the rate determined by macroeconomic factors. Beyond this point, the growth of a company within that industry will tend to come at the expense of other companies’ market share or consumers’ wallets.
This is where innovation comes in—and those who make the boldest moves often gain the biggest
benefits.
The degree to which an organisation proactively shapes its industry’s growth momentum can significantly boost its performance and longevity.
How breakout innovations feed growth momentum
The pace of an industry’s growth is partly propelled by broad trends such as the rate of population growth, the purchasing power of that population, the rate of inflation, and GDP growth.
While some industries, such as utilities and healthcare, are less affected by macroeconomic factors, they are exceptions rather than the rule.
However, there is another set of factors that relates to actions individual companies take to spur the growth and expansion of their industries. Notably, sectors with high proportions of companies that develop new categories of products, services, and experiences or invent new business models outperform other industries on economic profit.
That’s because these types of innovations—breakout, instead of incremental—create entirely new markets rather than merely new versions of existing products or experiences, thereby expanding the industry’s economic pie rather than just increasing one company’s slice of it.
While industries such as biotechnology and software have the highest rates of such breakout growth because of the rapid proliferation of new technologies and their applications, slower-growing sectors can experience similar innovation-based bursts.
Industries with many innovation pockets typically outperform others in part because breakout innovations can create entirely new markets rather than just increase the revenues from existing ones.
The development of the HPV vaccine, for example, which prevents a viral infection correlated with several types of cancer, did not replace or cannibalise tetanus vaccines or even broad sections of oncology product portfolios. Instead, it created an additional revenue category that expanded the overall industry’s size.
This pattern doesn’t apply solely to patent-heavy industries. In the early 2000s, telecommunications was considered a mature industry, yet it experienced a surge of growth when innovations in wireless technology created a new value pool. These advances launched the industry—and the companies in it—on a new growth curve since most customers, at least initially, added wireless service to their landlines instead of replacing them.
Breakout innovations can involve business models and processes instead of offerings. The introduction of endcap shelving units, for instance, at the entrances to supermarket aisles dramatically increased companies’ use of in-store displays by reducing the time it took to set up in-store promotions from weeks to days.
Just as breakout innovations expand industries’ overall pies rather than merely shifting market share from one company to another, so do they boost companies’ growth momentum through the acceleration of companies’ constituent businesses. That’s because each business that makes a big innovation advancement gives the parent company more headroom to grow.
Breakout innovations are great for industry momentum, but do you need to be the one to carry them out or can you just ride the wave of another industry member’s successful big bet? It turns out that those who take the risks gain significant advantages in the markets they create.
This strategic move is so powerful because creating a market without competitors, or one in which only indirect substitutes exist, enables the innovator to generate much faster growth than it could in a crowded segment, assuming the new offering satisfies sizable unmet demand. Companies that do this essentially create their own high-momentum markets.
They also ensure that they have the capabilities to capture value, instead of just defining an opportunity that better-positioned competitors can seize. Tencent, for example, started as a messaging software company but was able to build on its strategic advantages of a broad customer base and experience building “sticky” applications to expand into numerous industries, from e-commerce to video games.
It leveraged its more than one billion active monthly users to innovate new offerings across a broad, device-agnostic platform and has spent over $20 billion on R&D in the past three years and filed more than 62,000 patents.5
Breakout innovations need not invent entire categories. Telehealth—fed by the rapid advance of healthcare apps, AI-enabled medical imagery for remote diagnosis, and wearable biosensors—was more of a tactical expansion than a new market.
Incremental innovations, such as the semiconductor industry’s steady stream of novel chips that have revolutionized numerous devices, can also create new markets but at a regular, repeatable pace rather than with a big bang. Sometimes, innovation requires minimal R&D.
continued on Page 20