
www.nzmanufacturer.co.nz
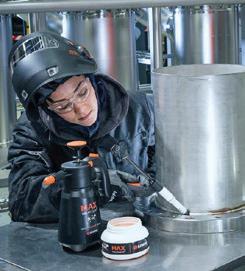
BUSINESS NEWS
Productivity stagnation requires long-term plan.
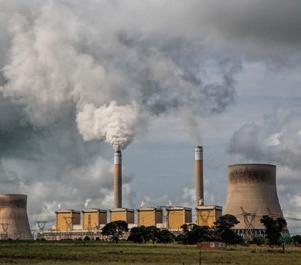
SMART
MANUFACTURING
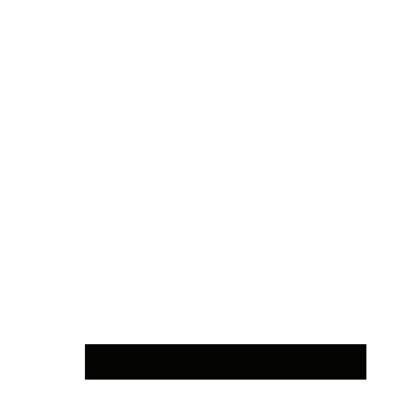
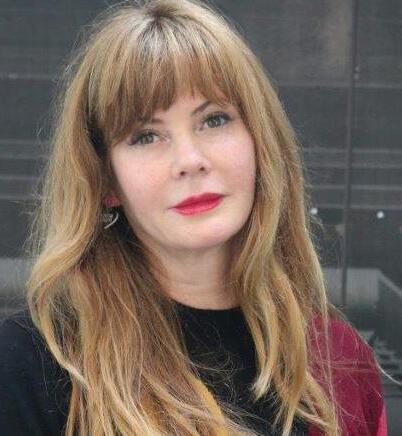
Emission plan requirements for industrial process heat. SMART
MANUFACTURING
The Tohu App – how cultural mapping can boost industry growth!
www.nzmanufacturer.co.nz
BUSINESS NEWS
Productivity stagnation requires long-term plan.
SMART
MANUFACTURING
Emission plan requirements for industrial process heat. SMART
MANUFACTURING
The Tohu App – how cultural mapping can boost industry growth!
Ian Walsh, Partner, Argon & Co
It is great to see that finally we are talking as a nation about the need to be more productive. Our poor performance in productivity terms is not a new issue or problem, but given the current economic environment, it has become clear to everyone that we have a significant gap to countries with which we compare ourselves.
The consequences of this are significant, with many young New Zealanders leaving for foreign shores for better pay, conditions and quality of life.
This problem has been disguised for decades by global financial crises, pandemics, earthquakes and media misdirection (“We are the most liveable country!”, “Auckland is one of the top 10 cities!” etc.).
Like climate change it has been possible to ignore for a long time. However, most of us are aware that our infrastructure is creaking. We can’t invest in health education, police, transport and other programs to the extent that we would like to, as we can’t afford it.
Productivity is essential for economic growth, competitiveness, profitability, job creation, resource efficiency, and work-life balance. Focusing on productivity improvements at individual, organizational, and national levels can lead to numerous benefits and contribute to overall prosperity
I have been to many business meetings, and the focus for any improvement drive is return on investment – they are asking whether investing in an activity makes the business more profitable, more competitive and ultimately whether it will result in better return for shareholders, so they
can invest in future programs to improve the product or service, grow the business and offer better products or services.
The same is true at a national level, the government can only spend what the economy generates (balanced budgets and low debt). Profit (or in more political termianology, surplus) needs to be re-invested in productive infrastructure, skills and aassets that allow for future returns in societal benefits.
Just like a business, when profit is not generated by a government, we see job cuts in the form of unemployment, and a cheapening of the product (NZ inc.) in the form of inflation.
So what do we do about New Zealand’s poor productivity? The main causes for the differences between us and those much more productive countries are:
• Low levels of investment: One major factor contributing to New Zealand’s productivity gap is the historically low levels of investment in physical capital, research and development, and innovation.
To address this, there needs to be a shift in mindset towards long-term investment, both by businesses and the government. Encouraging increased investment in technology,
manufacturer expanding overseas.
infrastructure, and skills development will help boost productivity levels.
• Small and fragmented market: New Zealand’s small domestic market makes it challenging for businesses to achieve economies of scale, hindering their ability to compete globally.
To counteract this, businesses should focus on exporting and expanding into international markets. The government can also support businesses by promoting trade agreements, providing export incentives, and investing in marketing campaigns to raise New Zealand’s profile abroad.
continued on Page 8
Secure supply of energy and data to moving industrial equipment.
• Large size range
• Vertical travels
• Energy tubes
• Hygienic chains
• Solutions for long travel
• Guide troughs
• Readychain
• Robotic, 3D
• Circular movement
HUGE range of high quality flexible cables
• Control cables
• Single cores
• Data cables
• Sensor/Actuator
• Intrinsically Safe
• VSD/EMC cables
• Halogen Free cables
• High temperature
• Harsh Conditions
• Crane cables
• Profibus cables
• Bus/DeviceNet
• Solar cables
• Instrumentation
• Flat cables
• Curly cords
Largest range of flexible conduits for cable protection
• Conduits
• Conduit fittings
• Divisible systems
• Jumbo systems
• Conduit Accessories
• Braided cable protection
• Fire barrier solutions
• Food and beverage
• EMC systems
• Ex, ATEX, IEC EX
Industrial connectors for many industries
• Rectangular multipole connectors from ILME
• Single pole Powerline connectors from TEN47
• EPIC connectors from Lapp Group
• M23 circular connectors from Hummel
• Circular connectors specifically for the entertainment/stage lighting industry from Socapex
Safety engineering solutions from EUCHNER
• Multifunctional Gate Box MGB
• Transponder-coded safety switches
• Electromechanical safety switches
• Magnetically coded safety switches
Sensor technologies for automation
• High-Precision Laser Distance Sensors
• Ultrasonic Sensors
• Inductive Sensors
• Fluid Sensors
LEAD
Productivity is the only game in town.
BUSINESS NEWS
Managing your online reputation.
NZ’s productivity stagnation requires a long-term plan.
SMART MANUFACTURING
Embracing digital technologies without losing craftsmanship.
Creative HQ, fuelling innovation.
Kiwi drivers ready to embrace wireless EV technology.
An explanation of emission plan requirements for industrial process heat.
How leveraging smart factories optimises products and operations for manufacturers.
Leadership development – showing the real return on investment.
The Tohu App – how cultural mapping can boost industry growth!
COMPANY PROFILE
Seaview manufacturer expanding presence in New Zealand and internationally.
SUSTAINABILTY
Ten tips to make your business case for sustainability stack up.
CASE STUDY
More than meets the eye.
ANALYSIS
How to unlock the potential of your team.
COMMENT
International study: governance failing NZ workplace safety.
WORKSHOP TOOLS
Igus launches new compact, low-cost energy chain.
Sense-2 monitors oil life.
DEVELOPMENTS
Wesley Lewis is Plastics Apprentice of the Year. Electronic governor enhances marine engine speed control.
Engineering New Zealand supports shared vision to infrastructure investment.
ENERGY
Fabrum collaborates with Toyota for liquid hydrogen storage.
THE LAST WORD
Power-hungry AI driving a surge in tech giant carbon.
Ian Walsh Ian is a Partner, Argon & Co. NZ, a master black belt improvement specialist and global lean practitioner. He is passionate about improving productivity and helping to create world class New Zealand businesses.
Dr Barbara Nebel CEO thinkstep-anz
Barbara’s passion is to enable organisations to succeed sustainably. She describes her job as a ‘translator’ – translating sustainability into language that businesses can act on.
oodward Is Managing Director of Connection Technologies Ltd, Wellington and is passionate about industry supporting NZ based companies, which in turn builds local expertise and knowledge, and provides education and employment for future generations.
Mark Devlin
Having owned food manufacturing and distribution businesses for a decade, Mark Devlin now runs Auckland public relations agency Impact PR. Mark consults to several New Zealand manufacturing firms including wool carpet brand Bremworth, aircraft exporter NZAero and cereal maker Sanitarium.
Insa Errey
Insa’s career has been in the public and private sectors, leading change management within the energy, decarbonisation, and sustainability space. Insa holds a Chemical and Biomolecular BE (Hons) from Sydney University. She is a member of the Bioenergy Association of NZ and has a strong passion for humanitarian engineering, working with the likes of Engineers Without Boarders Australia.
Insa is a member of Carbon and Energy Professionals NZ, been an ambassador for Engineering NZ's Wonder Project igniting STEM in Kiwi kids and Engineers Australia Women in Engineering, increasing female participation in engineering.
6 10 13 14 17 21 26
Jane Finlayson is Head of Advanced Manufacturing at the EMA, and has 25-years’ experience in business and economic development. She is passionate about empowering businesses to grow, innovate and embrace Te Ao M
PUBLISHER
Media Hawke’s Bay Ltd, 121 Russell Street North, Hastings, New Zealand 4122.
MANAGING EDITOR
Doug Green
T: +64 6 870 9029
E: publisher@xtra.co.nz
CONTRIBUTORS
Holly Green, EMA,
Business East Tamaki, Ian Walsh, Adam Sharman, Dr. Troy Coyle
David O’Connor, Mark Devlin
Dennis Wesselbaum, EMA
Mei Dent, Nathan Hight
ADVERTISING
T: + 64 6 870 9029
E: publisher@xtra.co.nz
DESIGN & PRODUCTION
:kim-jean:
E: kim.alves@xtra.co.nz
WEB MASTER
Julian Goodbehere
E: julian@isystems.co.nz
PUBLISHING SERVICES
On-Line Publisher
Media Hawke’s Bay Ltd
DIGITAL SUBSCRIPTIONS
E: publisher@xtra.co.nz
Free of Charge.
MEDIA HAWKES BAY LTD
T: +64 6 870 9029
E: publisher@xtra.co.nz
121 Russell Street North, Hastings
NZ Manufacturer ISSN 1179-4992
Vol.16 No.6 July 2024
Copyright: NZ Manufacturer is copyright and may not be reproduced in whole or in part without the written permission of the publisher. Neither editorial opinions expressed, nor facts stated in the advertisements, are necessarily agreed to by the editor or publisher of NZ Manufacturer and, whilst all efforts are made to ensure accuracy, no responsibility will be taken by the publishers for inaccurate information, or for any consequences of reliance on this information. NZ Manufacturer welcomes your contributions which may not necessarily be used because of the philosophy of the publication.
Readers are invited to contact NZ Manufacturer and share their thoughts on Productivity.
If Ian Walsh from Argon & Co is saying so succinctly the importance of Productivity (Page 1) then where are the rest of you with your observations and the way forward for the country?
I am sure you have pictures to share, actions you would like to see taken and examples of where your business is currently. The CPI does not lie, and the picture for manufacturing is less than stella!
One major factor contributing to New Zealand’s productivity gap, as Ian sees it, is the lack of investment in physical capital, research and development and innovation.
We have all heard the comment that “if the amount of money invested in (dormant) property was invested in manufacturing, things may be quite different.”
Dennis Wesselbaum, Associate Professor, Department of Economics, University of Otago says that by embracing innovation, up-skilling our workforce and implementing targeted policy interventions, New Zealand can chart a path towards a more productive and prosperous future for all. (Page 7)
Share your present experiences with Productivity. We want to know what is going on for your company.
Enjoy the read.
Doug Green , Publisher
In business, first impressions matter. New research by NZ Manufacturer business advisor and Impact PR director Mark Devlin has found many of the country’s manufacturers are failing to manage their online reputation - an oversight that could have repercussions for their growth.
For manufacturers, business relationships can be multi-faceted and, given the technical nature of the industry, at times they can also be highly complex.
Whoever your target consumer is when you enter a business relationship at some level, even a rudimentary transactional one, you need them to have confidence in your brand from the outset - a promise you can deliver in a way that aligns with their understanding of what constitutes value.
If you fail to reassure a potential customer that you can adhere to this expectation, your chances of entering a relationship are greatly diminished.
I recently toured a local manufacturing facility where I was shown a piece of cutting-edge technology destined for the export market that was worth around $1 million.
This is not an insignificant amount of money to spend on a single product and it occurred to me that if I was buying something of that value from an overseas company I would want to have the highest level of trust in that firm.
This begs the question - how does a manufacturer create digital ‘trust signals’ so that when a potential customer, employee or other stakeholder begins
to research their company, it provides the requisite reassurance necessary for them to move to the next stage of interaction and purchase?
While all manufacturers have customers, few would have walked in their digital shoes to understand what they see during any initial desktop research process.
At the same time, an even smaller number of customers will pass on the feedback that what they found online put them off progressing a purchase any further.
Impact PR conducted a somewhat scientific study of New Zealand’s 50 largest manufacturers (by shipment volume) to better understand how well they managed their online reputation.
The scope of this sentiment study included analysis of both the first page of Google as well as that of Google News. Each of these two pages contains 10 search results. This is a total of 1,000 search results and each was manually reviewed and categorised.
Essentially this gave us a ‘first impression’ view of how a potential customer would see and evaluate a manufacturing firm from their online presence.
While most of us will be familiar with Google’s standard search results, Google News, a news
aggregator, is a valuable measure of what others are saying about a firm - usually, this manifests as news articles.
The acid test we applied here is whether there is anything on the first page of search results that may be considered negative or in some way be detrimental to the image of the company.
You may be forgiven for assuming that large, well-resourced manufacturers with teams of experts dedicated to maintaining their reputation would have impeccably well-manicured search engine results.
The results of the study tell a different story.
Of the 50 manufacturers we looked at, almost a quarter (24%) had a negative piece of content on the first page of their search results.
This type of content included; details of court cases or convictions (including Commerce Commission rulings), negative employee reviews, media stories about financial loss, negative content within their
continued on Page 21
East Tāmaki (formerly the Greater East Tāmaki Business Association) is here to make it easier to do business; working alongside business
- Dennis Wesselbaum, Associate Professor, Department of Economics, University of Otago
In the ups and downs of the global economy over the last decade, New Zealand has had one relatively consistent challenge: persistent productivity stagnation.
Productivity compares the amount of goods and services produced (output) with the amount of inputs used to produce them.
Since the Productivity Commission was set up in 2011, annual productivity growth has averaged at just 0.2% – one of the worst in the OECD.
In 2023, New Zealand experienced declines across key metrics: labour productivity dropped by 0.9%, multifactor productivity (which includes labour, capital, energy, materials and purchased services) fell by 2.2% and capital productivity by 3.8%.
There has also been a sharp decline in small business productivity, with a 19% drop from its peak in November 2022.
Productivity is not only an abstract concern. It directly impacts income growth, exacerbates inequality and hampers overall welfare.
The productivity puzzle
But New Zealand’s stagnation doesn’t have to be inevitable. There are tangible approaches the government can take to boost the country’s productivity. Here’s how.
There are at least two ways New Zealand can improve human capital – the sum total of the skills and education a worker has to do their job.
In the short-term, the government needs to allow more high-skilled migrants to enter the country. This type of migration can reduce skill mismatch and create knowledge spillovers.
That is, migrants bring valuable knowledge, expertise and innovative ideas from their home countries, which can spread to local firms, industries, or individuals via collaboration and competition.
Over the long-term, investing in education and cultivating STEM and digital skills will be crucial for combating the country’s productivity stagnation and future-proofing the workforce.
Technological advancement is a key driver of progress, yet its integration requires careful planning.
Artificial intelligence (AI), in particular, holds immense potential to boost productivity. One study found generative AI, for example, could boost a worker’s performance by almost 40%.
But the widespread use of AI demands not only technological infrastructure but also a skilled workforce and the ability of organisations to adapt.
Regulation, reducing adjustment costs and barriers, taxation, and industrial policy are interrelated elements of the productivity puzzle.
But regulation, in particular, must be balanced carefully. The government needs to ensure worker and environmental safety while also encouraging innovation.
The government also needs to encourage the development of new businesses – a key factor to boost productivity. To do this, policy makers need to reduce entry and exit costs of doing business.
Industrial policies, such as subsidies or tax incentives, if appropriately targeted, can also increase productivity by supporting innovative firms rather than stifling competition.
An example is to provide research and development tax credits to encourage innovation in high-tech industries.
Industrial policies can also reduce productivity growth, particularly when they slow down the shift of elements such as labour and capital from less productive or declining sectors to more productive or growing sectors.
To be effective in addressing productivity, industrial policies need to be targeted at the most competitive sectors.
They also need to apply to a broad number of firms with the purpose of benefiting the most competitive in each sector.
Tax policy is another important driver which needs to be carefully designed.
For example, if the tax policy subsidises the use of equipment while taxing the employment of labour, policy makers will have increased the incentives for automation and reduced incentives to create new ideas.
This would put a damper on increasing productivity. Instead, policy makers could look at an automation tax, applicable to technologies which automate tasks above a certain level.
Despite a 17% increase in spending on research and development (R&D) in New Zealand last year, one study found it is not that effective for increasing productivity. Rather than supporting widespread innovation, poorly targeted R&D funding can prop up otherwise unsustainable businesses.
Instead, the government needs to tax all firms uniformly, encouraging less innovative firms to exit. This would free up resources for more innovative firms to intensify their R&D efforts. Implementing targeted taxes could further support this selective process.
Productivity growth is also influenced by where people work and the density of networks. Research has found tech clusters like Silicon Valley in the United States can play an important role in innovation, business competitiveness, and economic performance.
This is not a new idea. As far back as 1991, manufacturing clusters were touted as the key to improving New Zealand’s export competitiveness. But in 2018, a report found the cluster theory had failed to take hold – in large part due to infrastructure issues and the spread of businesses across the country.
Despite recognising the importance of these factors, New Zealand has faced persistent challenges in implementing comprehensive reforms.
In part, this is due to institutional inertia, lack of expertise among government officials in integrating research into policy formulation, fragmented policy approaches across different sectors, insufficient funding and a historical reliance on traditional industries.
If we really want to address our lagging productivity levels, an integrated approach is needed.
Improving labour market flexibility, infrastructure, and housing regulations enhances mobility and efficiency, unlocking potential across industries.
Furthermore, trade liberalisation policies aimed at increasing foreign direct investment and cross-border mergers and acquisitions can increase productivity.
By embracing innovation, up-skilling our workforce and implementing targeted policy interventions, New Zealand can chart a path towards a more productive and prosperous future for all.
Adam Sharman, Senior Partner, Dsifer
In an era where digital transformation is reshaping industries across the board, bespoke engineering and machine shops face a unique set of challenges and opportunities.
These specialised manufacturers, known for their ability to create custom, one-off products, are now grappling with how to embrace digital technologies without losing the craftsmanship that sets them apart.
As they step into this brave new world, several key considerations emerge, along with significant benefits.
At LMAC and Dsifer, we work with a lot of custom engineering organistions, and recognise the unique challenges these shops face. At the heart of the digital transformation is the need to maintain and enhance customisation capabilities, whilst optimising production and front-end processes to remain competitive on time to deliver and cost. Bespoke engineering thrives on flexibility, and any digital system must be flexible enough to accommodate diverse client demands. Advanced product configuration tools and parametric design software are becoming essential, allowing engineers to quickly adapt designs while maintaining the personal touch that customers expect.
Data integration stands as another cornerstone of this digital revolution. By connecting design, production, and quality control systems, shops can create a seamless flow of information from concept to finished product.
Product Lifecycle Management (PLM) software is increasingly becoming the central nervous system of these operations, ensuring that every stakeholder has access to the latest information.
The adoption of advanced manufacturing technologies is reshaping the landscape, offering substantial benefits. With Computer-Aided Design (CAD) and Computer-Aided Manufacturing (CAM) systems well-established to significantly reduce design time and errors, additive manufacturing, opens new doors for prototyping and small-batch
continued from Page 1
production, allowing for rapid iteration and reduced waste.
These technologies enable machine shops to take on more complex projects and deliver them faster, increasing competitiveness and profitability.
Digital manufacturing also brings remarkable improvements in efficiency and productivity. Machine shops can now utilise digital twin technology to simulate design and optimise production processes before physical implementation.
This leads to reduced setup times, minimised material waste, and improved overall equipment effectiveness (OEE). Real-time monitoring and data analytics enable predictive maintenance, reducing downtime and extending the life of expensive machinery.
For the workforce, while there’s a growing need for building capability uplift, digitisation also brings benefits. Digital tools can automate repetitive tasks, allowing skilled machinists to focus on more complex, value-added work. Augmented reality (AR) training tools are making it easier to transfer knowledge and skills, addressing the industry’s persistent skills gap.
Quality control, always critical in bespoke engineering, is being enhanced through digital means. Advanced inspection technologies and digital testing methods are improving accuracy and consistency.
Moreover, digital systems make it easier to maintain detailed documentation and traceability, which is particularly valuable for shops serving regulated industries like aerospace or medical devices.
Supply chain management is another area ripe for digital transformation. By digitising inventory and procurement processes, shops can reduce lead times and improve communication with both suppliers and customers. This enhanced connectivity is particularly valuable in an industry where timing and precision are everything.
As shops become more digitally integrated,
• Skills and education gaps: A skilled workforce is vital for productivity growth. Addressing the skills and education gaps in New Zealand is essential. Initiatives such as vocational training programs, apprenticeships, and partnerships between businesses and educational institutions can help bridge these gaps.
Encouraging lifelong learning and upskilling will also ensure that workers have the necessary skills to adapt to changing work environments.
emerges as a critical concern. Protecting intellectual property and sensitive customer data is paramount, as is ensuring the reliability and integrity of digital systems.
Machine shops must now consider cybersecurity as an integral part of their operations, not an afterthought.
The customer interface is being revolutionised, offering new ways to add value. Online platforms for order placement and tracking are becoming standard, as are digital collaboration tools that allow clients to be more involved in the design and specification process.
This increased transparency and interaction can lead to better outcomes and stronger customer relationships.
One of the most significant benefits of digital manufacturing for machine shops is the ability to tap into new business models. With digital technologies, shops can offer rapid prototyping services, engage in distributed manufacturing networks, or even provide digital design services. This diversification can lead to new revenue streams and increased resilience in a competitive market.
As bespoke engineering and machine shops navigate this digital frontier, the key to success lies in embracing technology while preserving the unique value proposition that sets them apart.
By carefully considering these factors and implementing digital solutions thoughtfully, these shops can not only survive but thrive in the digital age. The benefits – increased efficiency, improved quality, enhanced customer satisfaction, and new business opportunities – make the digital transformation journey not just necessary, but exciting and full of potential.
Additionally, providing businesses with access to funding and resources to adopt new technologies will contribute to increased productivity.
• Regulatory environment: Streamlining regulations and reducing bureaucracy can significantly improve productivity. Creating a business-friendly environment by reducing red tape, simplifying compliance processes, and removing barriers to entry will support entrepreneurship and innovation.
• Workplace culture and management practices: Improving productivity also requires
• Innovation and technology adoption: New Zealand has been slow in adopting new technologies and embracing innovation compared to other countries. Encouraging a culture of innovation, providing support for research and development, and fostering collaboration between industry and academia can help drive technological advancements.
a focus on workplace culture and management practices. Encouraging flexible work arrangements, promoting employee engagement, and investing in employee well-being will lead to increased productivity and better business outcomes.
It’s important to note that addressing these challenges requires a collaborative effort from businesses, government, and other stakeholders. By prioritising investment, innovation, skills development, and fostering a supportive business environment, we can start to work towards closing the productivity gap and providing the quality of life that we used to treasure. I’m already working on it –what will you do today?
Industry 4.0 refers to the fourth industrial revolution taking place right now. This revolution is driven by the convergence of digital technologies such as the Internet of Things (IoT), robotics, artificial intelligence (AI), augmented and virtual reality, 3D printing and more. Adopting these technologies is enabling manufacturers to enhance their performance, output, monitoring, quality and control on a global scale.
The challenge for New Zealand businesses starting out on their Industry 4.0 journey is knowing when, how and what technologies to adopt to improve efficiency, quality, documentation, business intelligence and sustainability.
This Government initiative enables Kiwi manufacturers to experience Industry 4.0 technologies first-hand via nationwide showcase events, manufacturing site visits, interacting with and learning from industry leaders.
The Smart Factory Showcase is a free, interactive session designed to demystify and break down Industry 4.0 with a world leading NZ example. The session will highlight how incorporating smart technologies improves efficiencies, productivity, connectivity, solves common manufacturing issues and streamlines systems and processes. The Showcase provides an ideal introduction to kick-start or progress your own Industry 4.0 journey.
This event is designed for CEO’s, Digital Technology Managers, Operations Managers, Design Engineers and Managers seeking an in-depth understanding of the latest available technologies for businesses. It is a valuable forum to get buy-in from stakeholders and the events are relevant across all sectors. Teams are encouraged to attend together.
The Smart Factory Showcase highlights Nautech Electronics’ Auckland facility and what the future of advanced manufacturing looks like – You will be inspired, gain powerful insights to enhance your manufacturing agility and be armed with the knowledge to join the Industry 4.0 revolution.
Showcases
It can really help by providing concrete examples of how you can actually apply this stuff and get value from it, and network with others to find out what they’re doing to implement Industry 4.0
Mitchell Sanson, Engineering Manager, Hansa Products
New Zealand’s largest and only national stone benchtop fabricator, AGB, is continuing its fight against silicosis with the announcement that it will be the first in the country to supply zero-silica engineered stone.
AGB, a family-run business, has been a persistent and staunch advocate for safer products, and a safer working environment for their staff and customers.
AGB was the first New Zealand business to ban high-silica engineered stone – shifting from up to 95 percent silica 12 months ago, to market-leading low-silica engineered stone with less than 40 percent silica.
Now AGB is again a driving force in the industry, becoming the first supplier in New Zealand to offer zero-silica engineered stone, with slabs expected to land in the country in September.
“If low-silica was the revolution, zero is the evolution. It’s actually not that big of a step to make. This is the next advancement of us being at the forefront of health and safety of workers – and our customers,” Cam Paranthoiene, co-owner of AGB Stone, says.
AGB owners Cam and Christine Paranthoiene have for many years led the way stone fabricators should operate – including creating proprietary processes, investing millions of dollars in state-of-the-art machinery and being early adopters of wet-cutting and air monitoring as a safeguard against the potentially-fatal lung disease silicosis.
As part of phasing out high-silica slabs they stopped working with suppliers who chose not to meet the company’s standards of less than 40 percent silica. AGB has now taken a bold step of saying they will work with only those suppliers who commit to transition to zero-silica in its engineered stone range.
The Australian government has imposed a total ban on engineered stone following a 2021 report that claimed one in four stonemasons or joiners working with fabricated stone before 2018 had been diagnosed with silicosis.
The ban took effect from July 1 this year, however fabricators have until the end of 2024 to fulfil pre-orders.
Paranthoiene believes this is an unnecessary step – that zero-silica is an excellent solution. “There has been significant investment in researching and developing a zero-silica product overseas. It continues to improve and is now a better alternative to natural stone or the other products that are exempt from the Australian ban,” he says.
The scale of the danger of silicosis from dust emitted when stone is dry cut or polished was not fully known in the industry until 2019. The New Zealand Engineered Stone Advisory Group (NZESAG), supported by ACC and WorkSafe was established that year to ensure the safe practice guidelines for stone fabricators, with AGB instrumental in setting up those standards.
WorkSafe has previously estimated 60,000 engineered stone slabs are imported each year, and there are believed to be approximately 130 businesses that fabricate them into benchtops for kitchens, bathrooms and commercial premises.
In April 2023, the New Zealand Council of Trade Unions urged the Government to protect workers exposed to hazardous material in engineered stone, emphasising that terminal illnesses such as lung cancer, silicosis and other autoimmune diseases are preventable if proper action is taken.
Better Benchtop’s zero-silica will have a 10-year warranty and will be available initially in 12 colours. Orders are being taken now with stock expected in September.
“It really is no different to fabricate. You’re not having to work any harder and it’s safe for everyone from the manufacturer to the installer, to the home owner.”
AGB has six factories across the country and employs more than 130 people. However it is the smaller operators that have not invested in the same level of safety precautions that worries Paranthoiene.
The New Zealand Startup Council’s UpStart Nation report sets ambitious targets for the nation’s startup ecosystem, envisioning Aotearoa as a global leader in generating sustainable value creation by 2030. To achieve this vision, the report calls for doubling the number of current startups to 5,000 and securing $2 billion in new capital.
Creative HQ, the innovation hub based in Wellington, is at the forefront of this movement. It has been nurturing New Zealand’s tech ecosystem for the past 20 years, driving innovation and creating an environment in which startups can thrive.
Since its inception in 2003, Creative HQ has had a singular mission: to empower innovators to transform their ideas into real-world solutions. Its programmes have supported 417 startups to date, helping them raise an impressive $300 million in capital and create 1,300 active jobs, with 801 jobs based in Wellington alone.
Collectively, the startups that have emerged from Creative HQ’s programmes now boast a valuation of $1.3 billion.
Creative HQ’s work was recently recognised at the prestigious Hi-Tech Awards, where it took home the award for Best Contribution to the NZ Tech Sector.
By equipping entrepreneurs and intrapreneurs with the capability, confidence, and connections they need through the various startup programmes,
Creative HQ has catalysed innovation and become a high-performing, impact-creating launching pad for New Zealand’s most ambitious entrepreneurs.
One such programme is the 12-week Climate Response Accelerator, which brought together nine startups focused on cleantech innovation and solutions in the climate and energy space. With mentorship from industry experts and the opportunity to secure a $100k investment from
Motion Capital, a former programme alumnus, at the Showcase event in Wellington on 20 June, the Climate Response Accelerator has helped create momentum for Kiwi entrepreneurs looking to make meaningful change for Aotearoa and beyond.
Startups that have gone through this and other Creative HQ accelerators have secured significant funding, expanded internationally, and made a lasting impact in their respective industries. Success stories include well-known brands such as Sharesies, Hnry, FTNMotion, Optimal Workshop, Marsello, Tapi, Silverstripe, Publons, Pledge Me and many more that fly under the radar publicly but make a difference in the lives of many.
Part of the ripple effect of this success, and other initiatives active throughout the country, is the tech sector’s growing contribution – currently around $20 billion annually – to New Zealand’s GDP.
Creative HQ recognises that there is even more potential for the tech industry to drive economic growth, create jobs, attract international investment, and enhance New Zealand’s global reputation. But realising this potential requires ongoing collaboration between the public and private sectors, particularly during challenging economic times.
Catherine Jones, Chief Executive at Creative HQ, emphasises the importance of practical and strategic collaboration. She told us, “It is critically important that the public and private sectors work together during these tough economic times to ensure that
industries have the conditions, connectivity, capital, capability, and culture to thrive.”
“And through fostering such collaboration and harnessing the expertise and resources of mentors, coaches, industry experts, funders, and investors across New Zealand, Creative HQ aims to elevate the tech sector to new heights”, Ms Jones says.
“As New Zealand looks to the future, increasing investment in innovation is crucial. The University of Auckland recently drew comparisons with Finland, which invests 3% of its GDP into innovation, resulting in less income inequality, a higher GDP per capita, and a higher score on the Human Development Index.
“By increasing our innovation investment to a similar level [from 1.4% of GDP currently], New Zealand could add another $59 billion to its GDP annually, and in doing so have the means to address critical funding and delivery challenges in housing, health, education, and infrastructure. It could truly be a game-changer for our society, economy, and people.”
Creative HQ’s work over the past two decades has laid the foundation for a vibrant startup ecosystem in New Zealand. And as Aotearoa navigates the challenges and opportunities of the 21st century, Creative HQ will undoubtedly continue to drive innovation, nurture startups, and shape a future where technology serves as a powerful tool for sustainable value creation and positive change.
Sandra Lukey
Sandra Lukey is the founder of Shine Group, a consultancy that helps science and technology companies accelerate growth. She is a keen observer of the tech sector and how new developments create opportunity for future business. She has over 20 years’ experience working with companies to boost profile and build influential connections.
Mike Shatford is an expert in the field of technology development and commercialisation. His company Design Energy Limited has completed over 100 significant projects in this vein by consulting for and partnering with some of New Zealand’s leading producers. Among Mike and his team’s strengths are industrial robotics and automated production where the company puts much of its focus.
Sean O’Sullivan
Has a B Com (Hons) Otago University. In 2000 - 2001 introduced PCs on the workshop floor and job and staff tracking and a productivity software App to Fletcher Aluminium Group and 100 manufacturers NZ nationwide. In 2001 – 2022 Founding Director Empower Workshop Productivity & Scheduling Software App. 236 manufacturing and engineering clients mainly throughout NZ and Australia, also UK and US.
Iain Hosie
Iain Hosie is a respected figure in the NZ Advanced Manufacturing and Materials sectors, with extensive experience in product development, research projects and commercializing tech products. Iain is a Director and Founder of Nanolayr Ltd, Director for the NZ Institute for Minerals and Materials Research, Commercial Director for Fabribotics Ltd, and Executive Council of BiotechNZ.
Catherine Lye
Is the first Chief Executive Officer of the newly formed cross-sector incorporated society, Advanced Manufacturing Aotearoa (AMA). Catherine has been Head of Manufacturing and Export Communities at the 7,100-member Employers and Manufacturers Association for the past two years. As part of that she has guided the Advanced Manufacturing and Industry 4.0 initiatives.
Adam Sharman
Is a Senior Partner at Dsifer. With a background in technology implementation, manufacturing and strategy, Adam and the team at Dsifer are on a mission to support New Zealand’s manufacturing sector transform using technology, data and analytics to outcompete on the world stage. Combining expertise in data engineering, data science & analytics and visualisation.
Dynamic wireless charging technology allows electric vehicles to charge while in motion, offering a promising solution to the limitations of fixed charging stations. Although it’s not available yet, how do Kiwi drivers feel about this innovative technology?
A survey of 1150 existing and prospective electric vehicle (EV) drivers shows that although people have concerns about the safety and charging cost of dynamic wireless charging, it’s viewed positively overall.
On-road charging systems could revolutionise how we think about EV charging, making it more convenient and less time-consuming for users, say the University of Auckland researchers behind the study: Analysing electric vehicle users’ intention to use dynamic wireless charging facilities: A study from New Zealand.
Doctoral candidate Ramesh Majhi, senior lecturer Prakash Ranjitkar (Faculty of Engineering) and senior research fellow Selena Sheng (Business School) designed a survey to explore people’s views of wireless charging technology.
The results showed that 93 percent of respondents are optimistic about dynamic wireless charging technology and would like to try it in the future.
The most compelling advantage of wireless charging, according to those surveyed, is its usefulness, mainly due to the ease and convenience it offers to EV users, potentially transforming the current charging experience by complementing stationary charging stations.
The study shows that people who prioritise sustainability are more inclined to support and use dynamic wireless EV charging.
Additionally, urban users are more likely
to adopt the technology than their rural counterparts.
Social influences, including the behaviour and choices of peers, were also found to affect drivers’ decisions to use the tech.
But despite the overall enthusiasm, the findings reveal concerns about data privacy, electromagnetic radiation and the potential costs associated with the adoption and use of wireless in-road technology.
“Dynamic wireless charging may not be practical for meeting urban transportation demands. However, it offers significant advantages for intercity travel by reducing EV drivers’ reliance on plug-in charging stations that often cause detours on highways,” says primary investigator Dr Majhi.
The study insights are crucial for developing effective measures and policies for the successful integration of dynamic wireless charging into the transportation network, says Dr Sheng.
“The movement toward adopting EVs for their sustainability in reducing greenhouse gas emissions faces hurdles regarding inadequate charging infrastructure.
“This is where in-road charging lanes will be of benefit, and it’s essential for policymakers to know how best to manage the rollout of this kind of technology in future and to ensure people’s concerns are understood, and hopefully alleviated.”
Selena Sheng.
Do you use fossil fuels to produce industrial heat in your manufacturing processes? Then chances are that recent regulatory changes might require you to start producing an emissions plan as part of the consenting process with your regional council.
EMA Head of Advanced Manufacturing Jane Finlayson says a new National Policy Statement for Greenhouse Gas Emissions from Industrial Process Heat, which came into force in July 2023, aims to support New Zealand in reaching its Paris Climate Agreement target of net-zero by 2050.
“Process heat currently contributes just over 10 percent of New Zealand’s gross emissions, and about 85% of emissions from processed heat come from the manufacturing sector,” says Jane.
“The new National Policy Statement aims to reduce these emissions by phasing out the use of coal for industrial process heat by 2037 and will require many manufacturers to develop emissions plans when using other forms of fossil fuels, such as natural gas, for process heat.”
Beca Industrial Sustainability Consultant Sarah Bacon says that process heat is defined as energy used as heat, primarily in the form of steam, hot gases or hot water; specifically for industrial and manufacturing processes.
“These new regulations will impact industrial and manufacturing companies using process heat to convert any raw materials into a final product. They also capture the indoor cropping sector when heat is produced via fossil fuels to grow plants,” says Sarah.
“Importantly, devices that burn fossil fuels to warm spaces and heat water within the commercial building sector are not captured under the new regulations as defined in the National Policy Statement.
“But if you are in the industrial, manufacturing or covered crop sector, and are producing more than
500 tonnes of carbon dioxide equivalent per year on your site, through fossil fuel-fired heat devices you will now be required to prepare an emissions plan as part of a consent application.”
These emissions plans, and who is required to produce them, were the focus of a recent webinar hosted by the EMA, with support from Beca and EECA.
“Your emissions plan is essentially a step-by-step pathway outlining all the projects or upgrades you intend to make to your site to reduce your emissions over time and needs to be submitted to your Regional Council,” says Sarah.
“It is important to note the regulations are not specific about how fast you need to make these emissions reductions except for the use of coal, which needs to be phased out by 2037.
“Another key consideration is if you are looking to replace your heat generating device. If you are doing this in the near-term, you will need to do a more extensive assessment of any technically feasible and financially viable lower-emissions alternative to your current device.”
Sarah says within your emissions plan you need to paint a picture for your regional council as to why you require your process heat device such as a boiler, furnace or oven, and the steps you will be taking to minimise their environmental impact.
“Within the emissions plan, you will need to include information about why you require process heat at your site, what you are producing with it, details about the age of your heat generating device such as how long it has been operational, and how it has been maintained,” says Sarah.
“Your plan will also need to identify and prioritise emissions reduction opportunities across three
key categories, which include energy efficiency, heat recovery, and alternative technology and fuel switching.
“This might mean looking at how you can optimise your existing assets, or it might involve reviewing your processes to understand if there is any waste heat that you can recover and then reuse it in your process.
“Finally, you will need to set out your transition pathway, which will include the best practicable option for replacing your heat generating device when it gets to end-of life, along with appropriate targets leading up to this point on how the site’s emissions will be reduced over time.”
Jane says while one of the big challenges for businesses when it comes to reducing emissions is cost, decarbonising your industrial processes can have significant benefits.
“Improving your energy efficiency will often lead to reduced expenses. The technology to support you to do this is advancing quickly and decreasing in price, while the cost of fossil fuels is only likely to increase as supplies tighten,” says Jane.
“But decarbonisation can also help future proof your business as both consumers and large corporates demand more sustainable products and a better understanding of your emissions profile.”
Jane says that there are a range of resources available to support manufacturers on their decarbonisation journey, including on the EECA website, while organisation like Beca can support companies to develop their emissions plan.
The EMA has also made its recent webinar, which contains further information about emissions plan, freely available here
Mei Dent, Chief Product and Technology Officer, TeamViewer
Manufacturing processes and supply chains have become more complex over the past few years, making traditional methods insufficient to meet the demand for greater customisation and shorter production cycles.
Manufacturers feel pressured by rising labour and material costs to find more efficient ways to produce high-quality goods. Additionally, the increasing need to meet environmental regulations and sustainability goals pushes manufacturers to adopt greener practices. As global competition intensifies, manufacturers must find ways to innovate and stay agile to respond quickly to market changes.
Smart factories address these challenges by integrating advanced technologies to create a more responsive, efficient, and sustainable production environment.
By leveraging technologies like artificial intelligence (AI), machine learning (ML), and the Internet of Things (IoT) to deliver predictive analytics and big data, manufacturers can optimise processes, manage inventory in real time, streamline logistics, and improve factory management.
Smart factories collect, process, and use this data to gain valuable insights. Real-time production monitoring and closed-loop optimisations, along with collaboration between advanced robotics and humans, help create these transformations.
However, a significant challenge in smart factory implementation is the disconnect between IT professionals and plant managers, particularly regarding data collection, outcome creation, and data protection.
IT professionals often advocate for comprehensive data collection to optimise predictive maintenance, while plant managers are more concerned with the practical, immediate concerns such as knowing which machines are currently in production, how production is running, and maintaining seamless operations.
IT professionals’ preference for leveraging cloud solutions can also clash with plant managers’ concerns about security and the usability of hyper-scale offerings. For example, IT professionals may push for automated updates and virtualisation, whereas plant managers worry about if production is operating at the level needed and the potential disruptions to long-established production systems. Bridging these differing perspectives is crucial for achieving successful IT and operational technology (OT) convergence in smart factories.
Manufacturers can leverage the benefits of smart factory technologies fully by aligning the objectives and addressing the concerns of both IT professionals and plant managers. These benefits include:
Manufacturers can significantly boost productivity and efficiency by using predictive analytics and big data insights.
This provides optimised processes and just-in-time inventory management, reducing downtime and improving operational flow.
For instance, remote connectivity solutions provide detailed views of all IT and OT hardware assets, helping manufacturers manage warranties, patch information, and potential security risks while troubleshooting issues remotely.
Smart factories create safer work environments by reducing the risk of injuries from harmful objects, heavy lifting, and repetitive tasks.
Advanced robotics and automated systems handle these dangerous jobs, ensuring worker safety. Additionally, industrial augmented reality (AR) solutions enhance frontline workers’ skills by providing step-by-step instructions and remote assistance, empowering them to perform complex tasks more efficiently.
• Optimised sustainability efforts
Real-time data helps manufacturers adopt sustainable practices by optimising energy consumption and reducing waste.
Consumers are increasingly willing to pay more for products made responsibly, making sustainability a competitive advantage. Implementing a central industrial IoT platform facilitates seamless communication between machines and IT systems across multiple factory sites, creating a strong foundation for sustainable operations.
Manufacturers can respond to trends and customer demands quickly by integrating cloud connectivity and real-time insights into the manufacturing process.
This leads to higher product quality and a better customer experience as companies can deliver customised and up-to-date products. Advanced platforms structure and analyse manufacturing data, turning it into a powerful foundation for AI-driven insights, which allows manufacturers to make informed, data-driven decisions and maintain an updated view of production.
Automated material handling systems streamline logistics and material flow within the factory, minimising manual handling and reducing cycle times.
Leading manufacturers’ smart factories interconnect humans, robots, and logistics using digital twin technology—a virtual representation of a physical object, process, or service—and AI-driven systems to optimise production plans and inventory management. This ensures high efficiency and responsiveness to customer demands.
Facilitating
A successful smart factory relies on the seamless convergence of IT and OT. Although they have different focuses—IT on data processing and communication, and OT on monitoring and controlling physical devices—both domains must work together to fully realise smart factory innovation’s benefits. There are four critical steps to facilitate this convergence:
IT and OT need to understand each other’s priorities and challenges to collaborate effectively. IT professionals should spend time on the plant floor to gain insights into daily operations and manufacturing practicalities.
IT professionals should use practical, easy-to-understand language when communicating with plant managers, avoiding technical jargon and buzzwords. Solutions should be user-friendly and easily comprehensible by operators, not just IT administrators.
Manufacturers can adopt private cloud and edge architectures to balance data processing needs and security concerns. These technologies offer scalable solutions that meet the plant’s real-time demands while ensuring robust data protection.
To measure smart factories’ success, IT and OT departments must agree on common key performance indicators (KPIs) across productivity, timeliness, quality, resilience, innovation, and costs. Aligning these metrics ensures both teams work
towards shared goals and enhances overall factory performance.
While the scope of smart factory applications is broad, it is important to note that most vendors focus on specific areas and the industry is still learning to find the best ways forward.
Current use cases in smart factories might be limited; however, there are significant strengths in areas such as warehouse picking and after-sales services, like remote support and training, where innovation and value delivery are well-positioned to drive progress.
Embracing smart factory innovation puts manufacturers at the cutting-edge of industrial
David O’Connor, Commercial Manager, The Learning Wave
While it is a comparatively easy exercise for businesses to show the Return on Investment on additional plant or machinery, being able to crunch the numbers of the real impact of leadership development training has traditionally been seen as more subjective, and made even harder when faced with the current headwinds of tight economic conditions.
Businesses that continued to prioritise investment in their people during the earlier 2020s are now repeating the rewards of increased leadership bench strength, higher levels of staff engagement, and little or no employee churn.
And many of our clients can now confidently calculate the return on their training investment.
Much was made of the ‘Great Resignation’ during 2020 and the impact this would have on businesses losing their best talent, we all know businesses that stopped leadership development training while others doubled down on their investment to upskill their leaders.
It is interesting that the commentary around the great resignation disappeared from HR and business reporting without much noise at all, and has been replaced with plenty of articles on the VUCA eraa trendy managerial acronym short for volatility, uncertainty, complexity, and ambiguity.
In this VUCA era, it is reported that businesses need leaders - at all levels - with strong resilience, who can actively engage a wide and diverse group of staff, manage multiple projects and demands, and have a curious mindset to be able to lead their teams through constant change.
So it is the businesses that continue to invest in their people leaders who will be reaping the rewards in the VUCA era, and being able to not only retain their top talent but also have a bench of talented leaders ready to step in and take on more responsibility. And it is these businesses that can measure the real return on their leadership training investment.
As a training provider, we find that helping develop their leadership capability is often the burning platform and the area of urgent need for business owners and training managers.
We have always focused on linking learning to business outcomes and making sure that development is not only practical for today’s leaders but also able to be applied back on the job.
Being able to take seemingly complex leadership theories and concepts and turn them into real workplace tools is one of the biggest challenges for the training industry.
A failure to see a real return is often sighted in HR and industry research as the reason why companies don’t invest in leadership development.
With two decades of experience in New Zealand workplaces, we know that leaders today need practical leadership tools that can be easily applied. They want leadership skills that are relevant to the Kiwi context and able to fit a range of small and medium businesses, and they want to be able to show that they are learning and applying their skills. We do this by having an individual or team productivity improvement project as a key aspect of the leadership training package.
The project provides leaders the chance to not only show what leadership skills they have learned and applied, but also show the impact of their improvement project on team performance and dynamics, workplace efficiency, and workplace culture.
And importantly, for business owners, and those
progress, unlocking impressive improvements in productivity, efficiency, safety, sustainability, and product quality.
By seamlessly merging IT and OT, companies can break down barriers and adopt practical, data-driven solutions that optimise operations and build resilience. Leveraging real-time data, predictive analytics, and advanced automation, manufacturers can quickly adapt to market demands, minimise downtime through predictive maintenance, and boost sustainability by reducing waste and optimising energy usage.
signing off the training spend, they can calculate the return on investment.
One client who has committed to running their leadership development (NZQA aligned) programme over the past 6 years - reaching over 70 leaders - has been able to report to their senior leadership team a 3:1 ROI on their training investment, this comes directly from the projects.
Coupled with this, all of those leaders who completed their development have been promoted within the business, and are now nominated their direct reports to be in the next cohort.
So while 2024 is proving to be economically tight for many businesses, we are looking at it as the year of “Great potential” for business who invest in leadership development that unlocks that potential in their people.
We believe that it will provide Kiwi Manufacturing businesses with a significant return in both the short and long term, making them more productive, and more able to navigate the challenges and constant change of todays world of work.
For more on the impact of leadership development check out the Freightways - LEAD Case Study https:// vimeo.com/906515117
By Dr Troy Coyle, HERA CEO
Our engineering, construction and manufacturing sectors are struggling to find talent. We need to be far more inclusive so we can unlock the potential of a diverse future workforce and all the benefits they bring to our mahi (work).
I have for some time spoken about this based on my own experience, being female. I have fast realised that wāhine Maori are even more under-represented and indeed Māori generally.
The reasons as to why women and Māori (and Pacific for that matter) are not attracted to these sectors are varied and complex. However, one key issue is that high school children (and even down to intermediate and primary) are not engaging with STEMM (Science, Technology, Engineering, Mathematics and Mātauranga Māori).
They are not aware of the plethora of disciplines in STEMM or the future careers that are available to them. They don’t know how exciting, engaging and rewarding careers in these disciplines can be and how they contribute in so many different ways to inter-generational wellbeing. Importantly, they don’t know what will match with their own individual wants and needs from a future career.
For Māori, this requires a matching process where rangatahi (youth) can identify careers that map to their values in a kaupapa Māori way. If there is one thing we have learnt at HERA over our years holding space for Matauranga Māori, it is that Māori need to be engaged in a Māori way.
Prevailing career matching tools do not consider cultural differences and they don’t consider a person’s values either. They often simply match a person to a career based on their perceived academic aptitude.
This fails so many of our rangatahi and leaves many behind. It also, likely, pushes rangatahi towards careers that they may not actually find personally fulfilling. Further, the prevailing methods are clearly not working as we have such low STEMM participation rates. We are not selling careers in our sectors in a way that appeals to many, including Māori!
The Tohu App – a way forward
I saw a need, a gap and an opportunity to better link rangatahi with our sectors - to prepare both for the future of work. What I didn’t know, was how to do it.
Enter Naomi Manu MNZM. Naomi, now Founder of Auraki Group, was at the time, the Founder of Pūhoro STEMM Academy, whom HERA has had a strong relationship with over several years. Naomi had also seen this need, gap, and opportunity. We agreed that we would create a solution together.
The result is the Tohu App. Tohu is a web-based kaupapa Māori app, developed by Auraki group and partners, and supported by HERA, that guides rangatahi through a series of patai (questions) to help them to identify their values, match them to an associated atua who are then linked to STEMM career options which then lead users to study pathways to these career options.
Future developments of the Tohu app will broaden it out to encompass more atua, as well as further kaupapa Māori guidance and links to te ao Māori (Māori worldviews).
We believe the Tohu app will revolutionise career planning for rangatahi in Aotearoa New Zealand and may even change the way that career mapping is done globally. Naomi saying: “Being culturally anchored provides a sense of identity and belonging, which is crucial for career success in a globalised world...integrating these values into career planning supports not only individual success but also the sustainability of Māori culture and principles in the modern workforce.”
The Tohu App aligns with our commitment to Vision Mātauranga through our Endeavour funded project “Construction 4.0: an industry 4.0 transformation of the Aotearoa New Zealand construction sector,” known as “Ngākopa Construction 4.0” for short.
As the heavy engineering, construction, and manufacturing sectors grapple with talent shortages, it’s clear that inclusivity is no longer just a goal—it’s a necessity.
To bridge this gap and ensure a robust future workforce, we must broaden our horizons and actively include diverse backgrounds, particularly those of Māori and Pacific peoples who will account for 20% of our future workforce.
The impending release of Minister Simmonds’ cabinet paper on vocational education offers a timely opportunity to reflect more strongly on how rangatahi not only identify potential career pathways into our sectors through the Tohu App, but also how they navigate through the learning and upskilling
requirements needed so they can contribute more meaningfully to our sectors.
The identification of drop off in traditional educational pathways identified when developing the Tohu App raises the importance of creating a range of career pathways both in academia and industry training to better engage Māori and Pacific youth.
This approach will not only address current talent shortages but also pave the way for a more diverse and innovative future workforce.
I personally am looking forward to more Māori participation in engineering, construction and manufacturing. I am also looking forward to a world where people have greater career satisfaction because the career mapping tools consider, not just what rangatahi are good at, but what will make them fulfilled.
Dr Troy Coyle brings more than 20 years’ experience in innovation management across a range of industries including materials science, medical radiation physics, biotechnology, sustainable building products, renewable energy and steel.
She is a scientist with a PhD (University of NSW) with training in journalism and communications.
and long-term
business New Zealand Tube Mills is a leading manufacturer specialising in carbon & stainless steel precision tubes.
Established in the 1950s as an exhaust system producer for the automotive industry, the company pivoted to horticultural trellising solutions in the early 2000’s as the local car manufacturing industry declined.
Today, they produce the ECO TRELLIS® and ECO BEAM™ systems, widely used in vineyards and orchards. In recent years they have expanded their work to include Apple orchards across New Zealand & Australia with their ECO V trellis.
Patrick McKibbin, CEO of the Hutt Valley Chamber of Commerce, sat down with Terry Carter, General Manager of New Zealand Tube Mills to discuss their business and their role in the Seaview business community.
“The middle of each year is traditionally a busy time for New Zealand Tube Mills, and this year is no different’ said Terry Carter, ‘This is when we have our production at high capacity, and we are certainly in that position this year.
“But we are still doing things a little bit differently to most of the manufacturing community. Our factory team work 4 days, Monday to Thursday, still at 40 hours a week, but having Friday off, unless there is overtime to do. We have found this model works well, and our productivity is still really good.”
There is lots going on for this leader in environmentally and sustainable trellising solutions for the agricultural and horticultural industries.
Terry explained that Cyclone Gabrielle, whilst devasting for the Hawkes Bay region and some of their main customers in the wine and hort sectors, has meant that some customers have been looking for different solutions as part of the rebuilding process.
‘Whilst some of the more traditional methods of trellising were washed away, the steel trellis was more easily reclaimed. This additional advantage of our solution was interesting. We of course have supported our customers through this difficult time but have seen new customers seek our option as they look to replace’ says Terry.
Coming out of the Covid pandemic has also seen New Zealand Tube Mills prosper. However, a lack of RSE workers in 2022 for the Kiwifruit sector and higher interest rates meant a poor quality of crop in 2023 and these producers were reluctant to further invest. Now this has improved, and quality, yields and higher prices are being seen this sector is starting to open up.
In recent years, New Zealand Tube Mills has focused on expanding its market presence internationally. They have secured substantial business in the U.S., supplying major wine brands in California, and are now exploring opportunities in Europe with the assistance of MBIE and ALTIOS, a global business consultancy. This strategic expansion aims to balance their seasonal sales by targeting both Northern and Southern Hemisphere markets. Their team are working hard in Tasmania as that wine sector starts to grow, and their mainland market in the traditional wine producing areas of Australia are also continuing to look for environmental solutions.
They have been well supported by New Zealand Trade and Enterprise in many of their markets.
The environmental nature of the New Zealand Tube Mills solution is really paying dividends as customers start to look for options which are sustainable.
The New Zealand Tube Mills solutions meets the needs of customers in the USA and Europe as their regulations increase their emphasis in this area. The company recently signed up to Toitu Envirocare, to progress its Carbon Zero initiatives.
Situated in Seaview means that New Zealand Tube Mills are also thinking about the longer term impacts of climate change; sea level rise, the cost of insurance and the future of their business.
For the time being though they have just resigned their lease for the next 8 years and are very happy to be located in the Seaview area of the Hutt Valley, close to their skilled workforce.
Its definitely onwards and upwards for this great Hutt Valley manufacturer.
This information is based on a guide we wrote with the Sustainable Business Council and Kaitiaki Collective.
It’s a situation we know many manufacturers face. You want to make your business more sustainable. (Bravo!) You can see the many benefits of manufacturing products that reuse resources, avoid modern slavery and create fewer environmental impacts.
But – here’s the kicker – you’re struggling to get the business case for making these changes ‘over the line’ with your accountant or finance team. These ten tips will help you.
Tip 1. See becoming more sustainable as an investment
Sustainable businesses are excellent businesses. They create value in the short and long terms –economically, environmentally and socially. Treat your sustainability programme as an investment and manage it as one.
Tip 2. Identify your stakeholders
Consider the many people who have a ‘stake’ in your business succeeding sustainably. You will naturally think of your investors, customers, suppliers, team, local community and regulators.
Think longer term and wider too. Include the environment and people who will live many years in the future.
Tip 3. Confirm where to focus with a materiality assessment
Your business case needs to reflect the views of all these stakeholders and your business too. Start with a ‘materiality assessment’. It’s a practical way, using interviews and surveys, to home in on the sustainability activities that your stakeholders and business care about and to prioritise the ones that matter most.
A materiality assessment takes a broad view of sustainability and covers environmental, social and economic topics. Include your top priority topics in your business case.
Tip 4. Understand who you need to convince
Who do you need to influence to get your business case over the line? What are they interested in? What are they concerned about? Who else has their ear?
Some people’s sustainability concerns may need time to work through. Acknowledge concerns, address them with data and examples and reach consensus. These conversations will pay off in the long run. Find your allies. Is there
someone in your business who truly ‘gets’ the long-term, intergenerational value of sustainability and will champion your ideas? Look beyond roles and titles. The most effective champion may be someone from your factory floor.
Tip 5. Do your research
Desk-based research is a good place to start but will get you only so far. Talk with the people who understand what operating more sustainably involves in a practical sense.
What does it mean for the people who design your products? Operate your machinery? Buy your materials? Deal with your customers? Manage your transport supplier?
Let’s assume you’re thinking of investing in new energy-efficient equipment. Start by listing the benefits. For example, if you use less energy, you’ll reduce your carbon footprint and the risk of being ‘pinged’ with a carbon tax.
Your new equipment will be more reliable and fewer breakdowns will reduce your costs. Customers will value your lower-carbon products and you may increase your sales.
Then consider your costs. They’ll include the costs of investing in your new equipment, retraining your team and adapting your processes. Bring all these costs and benefits together in your business case.
Tip 7. Do the numbers
A business case supports a business decision. That means it’s about numbers. Your finance team or accountant can help you with the traditional measures that decision-makers want to see, such as Net Present Value (NPV) and Return on Investment (ROI).
Attach numbers to every part of your business, including your ‘intangible assets’ (e.g. the value of your brand). These assets are becoming increasingly important. Be careful not to double-count. Use sensitivity analysis to test how robust your figures are.
Tip 8. Make your business case inspiring, strategic and practical
Create a vision of what your business will look like when you’re operating more sustainably. Show how the investment supports your wider business strategy. Tell a story.
What will your people be doing (and feeling)? How will your suppliers and customers be involved in your new ways of working? What will your business be known for?
Tip 9. Show that you know how to manage the investment long term
Show your decision-makers that you have a plan to maintain your investment. If it’s a physical investment like machinery, you’ll need a maintenance plan. If it’s an intangible investment like a responsible procurement strategy, you’ll need to show who will manage the strategy and how, plus how you’ll know your strategy’s working.
Tip 10. Focus on action and create a sense of urgency
Your decision-makers want results. Confirm a simple plan that shows you’ve considered the roadblocks you need to overcome and the opportunities you need to grasp. Who will lead this work? Where will you start? What needs to happen in years one, two and three?
We wish you success in this important step to becoming a more sustainable business!
www.thinkstep-anz.com
What started as an unexpected failure on a key piece of machinery has ended as one of the most ambitious and successful recycling projects Meridian has ever undertaken.
A failure in one of two transformers at Meridian’s West Wind site last May left the team with one working transformer and scratching their heads about what to do with the other one – all 100 tonnes of it.
“We decided that it wasn’t cost effective to repair,” says West Wind Site Owner Hamish Walker.
“One of the questions we asked was, what’s best for business? Do we pick this failed transformer up, plonk it next to it, and just leave it there?”
Ultimately, the decision was guided by a combination of economics and environmentalism. Senior Project Manager Jade Lloyd says the team quickly found that the best and only acceptable option was to salvage as much of the failed transformer as possible.
Of the roughly 100-tonne transformer and 36,000 litres of oil, it’s estimate that just three tonnes of wood, oil-soaked wood and paper were unable to be repurposed, recycled or reused.
Lower Hutt-based supplier Macaulay Metals was engaged to assist with the removal of the transformer. Because its enormous size made it very hard to transport it on the winding rural roads leading from West Wind, it was dismantled into its component parts on site.
“They took the tank away, pulled all the copper out, and that’s going away and getting recycled. And they pull all the steel laminations, which is the majority of the weight there.
Then they get chopped into smaller laminations and get reused in smaller transformers,” says Hamish Walker.
Following five months of meticulous planning, the scrapping process took just two weeks, starting with 36,000 litres of oil being drained for recycling.
“We sent that off to eNZoil, a transformer oil company in New Zealand that regenerates the oil so that we can buy it back and reuse it in our new transformer, which is an awesome sustainable win for us,” says Jade Lloyd.
And the team was also focused on ensuring workers were kept safe in the challenging conditions.
“I’m very proud of the project managers and the
engineers and the team that carried out the work,” says Hamish Walker.
“We had adverse weather conditions while we were doing it. We did it safely, and we did it with minimal environmental impact.
“And what we’ve learned throughout this process is incredibly valuable for the next time we’re looking to replace major pieces of machinery or equipment.”
A replacement T2 transformer is expected to arrive at West Wind in early 2025.
Looking for a marketing edge?
70% of licence holders say signing on has positively affected sales.
In the ever-evolving landscape of the manufacturing industry, enhancing operational efficiency is paramount to staying competitive and meeting the demands of modern consumers.
Software has become increasingly important in defining organisations as teams and technologies merge, and company software applications become synonymous with business operations.
Traditional tools for point solution monitoring or log management lack the capability to provide comprehensive observability across the organisation’s digital infrastructure. These tools also fail to deliver a cohesive, near-real-time performance view across the entire manufacturing landscape.
Unified observability has gained prominence in recent years as it provides a clear view of an organisation’s infrastructure, enhancing productivity and facilitating proactive issue resolution.
Integrating artificial intelligence (AI)-driven automation within unified observability further enhances its capability to address challenges like global disruptions, resource shortages, and unpredictable demand.
This technology provides actionable insights for agility and efficiency, aligning with the goals of Industry 4.0 to create smart factories with interconnected systems and advanced technologies. While unified observability effectively monitors point solutions and manages logs, the quality of the outcomes depends on the connectivity of manufacturing equipment to supply the necessary data.
Unified observability offers significant advantages for manufacturers, especially when optimising manual handling. These benefits include:
observability might detect equipment overheating so maintenance teams can intervene before any breakdowns occur.
Unified observability helps manufacturers streamline manual handling workflows by offering a clear view of operations. Manufacturers can analyse data from various processes to identify bottlenecks and optimise workflows, leading to reduced manual handling times and increased productivity.
For instance, a manufacturer might identify and eliminate redundant steps in a handling process by using observability data, enhancing overall workflow efficiency. On a production line, observability can reveal unnecessary waiting times between stages, leading to reconfiguration that speeds up the entire process.
updated to better support OT machinery, resulting in smoother manual operations.
A broad oversight across the entire supply chain management and materials handling process helps identify bottlenecks, optimise workflows, and respond to disruptions more effectively.
This integrated approach aligns with the principles of Industry 4.0, letting manufacturers maintain a competitive edge. AI-driven insights can enhance supply chain forecasting and risk management, providing more accurate and timely responses to supply chain challenges.
For example, a manufacturer might use unified observability to monitor supply chain performance, identifying and resolving delays or inefficiencies that could impact manual handling operations. In a warehouse, observability might pinpoint delays in deliveries, leading to proactive adjustments that keep manual handling operations on track.
Real-time data improves safety and efficiency in manual handling, empowering manufacturers to proactively address potential hazards. For example, monitoring equipment and processes can alert operators to issues, reducing the likelihood of accidents and injuries.
AI algorithms can predict equipment failures or safety risks, providing preventive actions. This technology streamlines workflows and eliminates inefficiencies, contributing to a safer and more productive environment. In a factory setting,
Aligning IT and operational technology (OT) management lets manufacturers streamline processes and improve efficiency by breaking down data silos and providing a holistic view. This empowers teams to troubleshoot and optimise both IT and OT environments simultaneously, enhancing manual handling processes and overall operational performance.
AI facilitates predictive maintenance and automated adjustments, ensuring IT and OT systems operate harmoniously. In a plant, IT systems might be
Without unified observability, manufacturing operations often face fragmented data and limited visibility, leading to inefficiencies, increased downtime, and compromised safety standards.
Misaligned IT and OT management can result in operational silos and missed opportunities for process optimisation, and the lack of centralised data often hinders effective supply chain management and materials handling, causing delays, bottlenecks, and disrupted operations.
However, with a complete view of operations from factory floor to supply chain, unified observability transforms how manufacturers address challenges in manual handling, maintain operational resilience, and deliver exceptional digital experiences.
The integration of AI-driven automation further enhances these capabilities, ensuring manufacturers can respond swiftly and efficiently to any operational challenges.
Wikipedia page and the impact of natural disasters on business operations.
When we look at their Google News results, the proportion of large-scale manufacturers with negative content increased to 48%.
One of these companies had 80% negative content.
While there was some overlap with the first page of search results (ie media stories about financial loss/ receiverships or legal stoushes) there was noticeably more diversity in the types of news angles found.
Health & safety issues (including workplace fatalities and penalties awarded as a result), environmental concerns/pollution, misleading labelling, industrial action, a facility fire, executive bullying allegations, theft from the business, and restructuring leading to job loss were common themes.
Unfortunately for the businesses, some of these news articles dated from several years prior, even as far as 2015 in one case.
Increasingly we are being approached by companies wanting to own their online search results.
While Google’s algorithm is constantly evolving, management of this digital real estate is achievable and prudent.
Generally speaking, it is easier to control a search engine’s results than it is to control news media. This is because journalists are tasked with providing a balanced view of a story.
However, there are strategies that can be implemented to allow a business to shape its online reputation.
Creating a foundation of positive content is a great way to dilute any negative content that is present or may manifest in the future.
The first step is assessment.
Have a look at your search results - what sort of image do they send about your company? How consistent is this with how you want your brand to be portrayed? The second step involves remedial or, preventative action.
Here you may need to enlist a PR specialist for this one, who can help create a series of targeted news articles and seed these in media for you. As an example, our agency is a Google News publisher and can post positive content directly to the aggregator.
CSR initiatives are increasingly valuable as a mechanism for delivering good news stories about your brand. One of the manufacturers in our study produced a range of stories about their community initiatives that helped colour the brand effectively. Another suggestion, the video appears in Google’s search results, consider getting a corporate video scripted, filmed and uploaded to YouTube - (tip it will need to be optimised for the search engine to ensure it ranks for your brand name).
The third step is the introduction of a regular programme of monitoring.
Appoint someone either internally or use an external agency to keep an eye on online reputation and to flag any issues that arise.
Your company’s online reputation matters, and investing resource into its management can help attract new customers. Make your reputation management a foundation part of your marketing strategy, and ensure that all employees are aware of the potential for their social media profiles to appear in search results about your company.
By the end of 2024, Tork paper towels and napkins, used every day by businesses across New Zealand and Australia, will be produced at the Essity Kawerau paper mill using renewable geothermal steam.
Tissue making is energy intensive, the decarbonisation project, which will require a temporary closure of a paper machine, will replace a natural gas component of the machine with a new drum dryer that will use geothermal steam for heat and drying.
Essity has been on a programme of continuous improvement at Kawerau to reduce its emissions for more than a decade.
With this transition from natural gas to geothermal steam, the total carbon footprint for Essity’s Kawerau site will be about 66% lower in 2025 than it was in 2009.
The emissions reduction delivered by this shift to geothermal steam will be equivalent to removing over 2,200 cars from Kiwi roads.
Essity’s Kawerau plant is the only manufacturer of toilet tissue, paper towel, and kitchen towel in New Zealand.
The site produces Tork paper products which are used in hospitals, schools, hotels, and workplaces throughout the region. Each year, around 55,000 tonnes of tissue and paper towel rolls out of the plant.
A paper machine that is wholly using geothermal steam for tissue drying is a world first in the paper manufacturing industry.
Investing in renewable energy sources is an important part of Essity’s ongoing commitment to sustainability and 2030 science-based carbon reduction targets.
The rebuild at Kawerau by Essity, a global hygiene and health company, will mean consumers will be
able to access locally produced, sustainable and low carbon tissue products.
The geothermal project at Kawerau will improve the paper machine efficiency, product range capability and, importantly, continue the journey of reducing carbon emissions from the plant.
The partnership with Ngāti T wharetoa is contributing to the socio-economic health of the local community and the supply contract helps fund local marae, housing and education.
The significant steam supply contract is due to increase by approximately half when the rebuilt machine is commissioned later this year.
Around 80 contracting staff will be involved in the project as well as 25 Essity employees from engineering, operations, safety and management teams.
With a total investment of NZ$20 million, the Paper Machine Project is largely funded by Essity alongside industrial co-funding from EECA (Energy Efficiency and Conservation Authority).
around one common goal: 20% more women engineers by 2021. www.diversityagenda.org
- Ishan Galapathy
Employee engagement is the Holy Grail that most employers are searching for in order to have everyone in the team working to their full potential - contributing to a productive workforce, delivering meaningful outcomes, creating a happier workplace, and delivering a better bottom line.
Sadly, the statistics aren’t great. If we look at 2022 data from Gallup (the global authority on all things related to employee engagement), only 23% of our workforce accounts for engaged employees.
The disgruntle and actively disengaged category represents 18%; and the fence-sitting, quietly quitting, unengaged group accounts for a whopping 59%.
Imagine having a team of ten rowers on your boat, with three people rowing their heart out, five just sitting with their arms crossed adding dead weight, and two people rowing in the opposite direction. How fast do you reckon your boat can go?
If this rowing team represented the entire workforce around the world, the impact of the fence-sitters on the global economy is a staggering US$ 8.8 trillion or 9% of the global GDP. That’s a lot!
So, how can we tap into this underutilised potential of the team? The good news is, it’s easier than you think.
Reviewing the Gallup trends over the last 15years, it highlights the issue in black and white. We’ve worked really hard to reduce the actively disengaged category – the disgruntled, disruptive, disenchanted. Yet, the fence-sitting, quietly quitting category has more or less remained the same over the years. Even though we’ve seen fairly consistent upward
trends in engaged employees, it’s the overwhelming volume of the disengaged workforce that signals our greatest source of untapped potential.
Having worked across multiple companies and countries over the last 25 years, I know for a fact that the fence-sitting, quietly quitting employees are only seemingly disengaged.
While you might think that these employees only turn up in body, leaving their brains behind, I’ve found that they are waiting to be discovered, leveraged and motivated.
Below is a three-step framework that will help you to unlock the true potential of your team, leveraging the few engaged team members, involving the majority fence sitters and ignoring the disgruntle.
Build Momentum – Leverage belief and the trust of your few diligent team members. They are willing to work hard but there are getting tired, overwhelmed and on the brink of quitting or falling into the disengaged category.
The main reason is that they are the only ones who have to deploy initiatives, solve problems, generate new ideas and deliver the day-to-day results.
The key in this step is to involve a few quietly quitting fence-sitters into some key improvement initiatives that are led by an engaged team member. Ensure the disengaged are involved in resolving matters and are not just sitting idle – like those adding dead weight in our rowing team example.
Gain Traction – Expedite results and help the team to make faster progress. I find progress to be the antidote for disengagement. When everyone gets involved and the team starts to make progress, even the quiet ones will start to feel proud of the team’s
contribution.
If they follow any structured problem-solving methodologies, chances are over a two-to-threemonth period they would deliver exceptional results that would even surprise the engaged few. You’re starting to make a difference.
Expand Followers – You cannot keep this success a secret. Leverage every possible opportunity –townhall meetings, newsletters, bulletin boards, canteen posters, team meetings – to share the team’s success.
The best approach is to get the team to present, not you the leader. What you will find is that progress and positivity to be infectious. Celebrate together. Soon, your quietly quitting fence sitters cannot not become engaged. Then you can leverage them to lead more initiatives on their own, involving the next layer of fence sitters.
The key to unlocking team’s full potential is involving the quiet quitters. If you repeat the above cycle each quarter, within a year you’ll notice that the ship is turning faster than you expected. With the fence-sitters starting to become believers, teams will start feeling happier, more productive, better engaged and running on all six-cylinders – their full potential.
*Ishan Galapathy is an operational excellence strategist, author, speaker and mentor renowned for his simple techniques that deliver big change. With more than 25 years of experience across seven countries, Ishan helps businesses unlock their hidden capacity and true capability. His latest book UNLOCK delivers techniques to convert seemingly disengaged employees into change drivers. Download your free introductory overview from UnlockBook.com.au.
An analysis of health and safety data from more than 2,600 companies across three countries reveals significant leadership failures at governance and executive management levels may be contributing to New Zealand’s failure to reduce workplace incident rates to better match Australia and the United Kingdom.
Insights from the Safe365 Safety Culture Maturity Report 2024—the first of its kind to analyse the current maturity of safety culture in New Zealand, Australia, and the United Kingdom—found that lack of director and manager knowledge is holding safety culture maturity back, particularly in New Zealand.
Overall, the report found that director and management knowledge of risk management practice and the depth of awareness around their own industry-specific safety landscape falls short of what is needed, scoring 48% in maturity for director knowledge and 46.3% for manager knowledge.
Nathan Hight, co-founder and managing director of the New Zealand-owned and operated health and safety tech platform, Safe365, says there is a systemic issue with the level of director knowledge regarding good governance within organisations.
This includes a lack of the necessary understanding to effectively question and account for organisational spending, compliance with management practices and whether or not we’re focused on the right areas to truly impact worker safety.
“Nobody is questioning the best intentions of senior leadership, nor are we suggesting indifference, but rather a lack of understanding of effective governance of work health, safety and well-being.
“The solutions are often not complex. Directors need to be equipped with the knowledge to ask good questions that check and challenge senior management, and to exercise visible leadership on health, safety and well-being within the business and, importantly, possess a willingness to address and solve these problems.”
Hight says directors and senior management need visibility into effective insights, including risk assessments, incident reporting, compliance monitoring, and safety audits. Such data can help them offer oversight and leadership that leads to better workplace risk management, incident reduction, and regulatory compliance–but that’s not enough either.
“There is a prevalent assumption that meeting legal compliance obligations with health and safety regulation equates to safe outcomes for workers. Company directors and senior management need to realise that regulatory compliance represents the minimum viable threshold and does not necessarily reflect a comprehensive safety picture.
“Unfortunately, health and safety training is often focused on meeting compliance requirements, which does not reflect the systemic changes needed in the profession.”
Hight says it is imperative that organisations invest in training and developing their directors, senior management and even safety professionals to meet modern governance and safety standards so that the senior leadership can look beyond compliance requirements and instead strive for excellence in leadership and accountability.
Recent prosecutions of board members and senior management for health and safety failures, including the former chief executive of Ports of Auckland Limited (POAL), Whakaari Management Limited (WML), and Whangārei Boys’ High School’s Board of Trustees (WBHS BOT), are unlikely to improve outcomes.
Hight says that prosecutions are unlikely to change behaviour because the current plateau in harm statistics, despite increasing regulations, points to a compliance-focused approach that is creating a culture of complacency and failing to make workplaces safer.
“However, demonstrating the business value in health and safety might (change behaviour). For example, if insurance companies (including ACC) take greater steps to reward proactive organisations with better insurance terms and benefits, such as risk management rebates, instead of generally treating them all the same.”
Alongside the need for stronger management and director knowledge, the report shows that, while systems and processes are in place to tackle potential risks or incidents, verification that these risk management practices are actually in place and performing as intended is inconsistent due to low levels in internal audit and verification maturity. In other words, in the absence of proper assurance, many companies are operating under the illusion of safety, and as a result, we will continue to see preventable harm continue.
“Workers and/or contractors that role-model best practices in health and safety are usually only informally recognised.
“This report is a reminder that a true safety culture goes beyond compliance and requires a commitment to continuous improvement and excellence in leadership, accountability and organisation-wide engagement in safety outcomes, leading to reduced harm and improved overall business performance,” says Hight.
Advertising Booking Deadline – 8 August 2024
Advertising Copy Deadline – 8 August 2024
Editorial Copy Deadline – 8 August 2024
Advertising – For bookings and further informa
Media Hawkes Bay Limited 06 870 9029
Articles
By downsizing, the draw e-chain saves 30 per cent of costs in applications with a low degree of movement.
For cable guidance in drawers and pull-outs of all kinds, igus is launching the draw e-chain. Thanks
The draw-e-chain offers a flat, simple and cost-effective design for cable routing in pull-outs and drawers of all kinds, for example in server racks. (Source: igus GmbH)
to the minimalist design, the price of the compact energy chain is 30 per cent lower than the most cost-effective standard e-chains. This protects against expensive oversizing, especially if the application is only moved a little.
From drawers in camper vans to pull-outs in server racks in data centres: industrial energy chains for hundreds of thousands of cycles are oversized for guiding cables in applications where movement only occurs occasionally. Users would pay for features that they do not need.
“We have therefore developed the draw e-chain, a new compact low-cost energy chain for cable guidance in drawers and pull-outs of all kinds,” explains Jörg Ottersbach, Head of the e-chain Business Unit at igus. The new energy chain has a bend radius of 45mm, an external width of 45mm and an external height of just 22mm. “This makes it 13 per cent flatter than our flattest standard e-chain B17.1.048.0 to date.”
The draw-e-chain is not only more compact than standard models, it also costs less. The reason: there are no mechanically complex components. The injection-moulded e-chain does not need any
The Sense-2 is plug-and-play and accurately identifies when oil reaches the end of its life, superseding traditional time-based maintenance schedules which can result in oil being discarded prematurely – with the potential of wasting up to 50 per cent of its useful life.
For the manufacturing and lubrication industries, Sense-2 ‘s ability to extend maintenance intervals by monitoring equipment condition in real-time, results in answering the actual equipment needs rather than maintenance being driven by time-based scheduling. This, in conjunction with reducing the business’s carbon footprint, will help support sustainability goals by reducing oil consumption by approximately 30 per cent per year, as well as reducing parts consumption and extending equipment life.
Sense-2 detects any issues before damage occurs, identifying subtle changes in equipment condition early. It can be fitted easily and efficiently to any existing equipment in any application and is configurable to any oil type.
Although oil analysis is not new, traditional lab sampling is expensive and impractical with other sensors focusing on specific parameters while missing others.
This system ensures the industry has access to superior quality information in an easy-to-use format, preventing excessive wear of components resulting in increased productivity and reduced machine downtime and maintenance costs.
The real-time aspect of the system is what sets it apart, utilising unique active molecular-level analysis to detect all changes in oil condition and any contamination.
The Tan Delta sensor works by providing a
full-spectrum holistic (FSH™) oil quality analysis, which continuously monitors the ratio of two key measurements, capacitance and conductance, to provide real-time insight.
This molecular analysis taking place every few seconds, enables accurate tracking of oil degradation as well as detecting contamination and early signs of internal equipment problems.
This allows for precise predictions of maintenance points crucially optimising maintenance scheduling, and reducing costs and downtime.
The OQSx-G2 oil quality sensor within the Sense-2 kit is also available as a Mobile Oil Tester (MOT) kit, created with workshops and mobile maintenance teams in mind. Any oil from any equipment can
chain links to fold. Instead, the segments are flexible enough to allow the required bending.
Thanks to this absence of chain links, the draw-e-chain consists of just six segments per metre, which can be connected via a simple connector system, which reduces effort and costs. “Due to this minimalist design, the draw e-chain costs 30 per cent less than our most cost-effective standard e-chain,” says Ottersbach.
The draw e-chain is designed so that users can assemble it by hand in a very short time. The low-cost energy chain is designed for installation rotated by 90 degrees, for example on the inner side of a drawer.
Connection elements are not necessary. The segments of the cable guidance have holes for screws. “Inserting cables is also done quickly,” says Ottersbach. Unlike standard e-chains, there are no crossbars that users have to open first.
“You can simply push the cables through the bendable tabs of the energy chain from above. That takes just a few seconds.”
www.treotham.com.au
be sampled and tested simply and easily on-site in seconds.
The sensor is used in conjunction with the MOT software, which operates on any Windows-based laptop, tablet or PC. Users simply install the MOT app, connect it to the sensor, collect the sample in one of the bottles provided and follow the steps in the software to test the sample. www.tandeltasystems.com.
TechRentals® is an IANZ endorsed Calibration Laboratory
We offer both IANZ Endorsed and Traceable Calibrations of test and measurement equipment inluding:
0800 832 473
www.techrentals.co.nz
Kemppi Australia has launched its Art of Welding Competition for 2024. The competition showcases “welding art” which can take the form of a welded sculpture, pattern design, a motif or an object. The welding process involved to create the art piece can be manual or use more advanced techniques such as robotics, lasers or friction welding.
Now in its fifth year, the competition is keenly contested by both professional artists and amateurs alike. “It’s great to see the artistic talent that is flourishing not just among professional metal artists but also welders, apprentices, teachers, tinkers and hobbyists,” said Mark Shaw, Managing Director, Kemppi Australia.
This year, the competition again features a dedicated amateur category. Entrants can win from a pool of four great prizes. The prizes include state-of-the-art Kemppi welding equipment and helmets, as well as clothing and gloves.
The competition will run until Monday 30th September and is open to anyone in Australia
and New Zealand over the age of 18. For more information on how to enter visit the Kemppi Australia Facebook, Instagram or LinkedIn pages
or message Kemppi Australia’s social media pages directly. Alternatively, email skettos@skettos.com.au for a copy of the competition flyer.
Is the laser cutting industry evolving and automating as quickly as its customers?
By Bruce Thomas, Product Executive, Tempus Tools
In a fast moving industry such as laser cutting, no-one can afford to be complacent. Laser shops have to ensure they are up to date with the best technologies available to them. Suppliers, in turn, have to ensure they are very closely attuned to the rapidly changing needs of customers large and small. You have to have an ear to the group continuously. This is a dynamic business. The global laser cutting machine market size is current more than a staggering USD 5.59 billion and predicted to a phenomenal growth trajectory. By 2030, the market is expected to reach a monumental USD 11.32 billion, exhibiting a remarkable Compound Annual Growth Rate (CAGR) of 9.6%.
With that amount of money out on the shop floor, no businesses can afford not to be at the head of the field.
So, is our industry evolving and automating as fast as our customers? In the 50 years I’ve worked in the laser cutting industry, customers and vendors alike have been racing to out-compete each other with faster and superior technologies.
Laser cutting vendors are now automating throughout their operations, from manufacturing to invoicing, and everything in between.
So it comes as no surprise that these highly automated organisations are seeking an automated quoting experience when they need to request a laser cutting job.
Getting an instant online quote is far more efficient than having to request information, which comes back hours, or days later. By that point, the end customer may have gone elsewhere.
A trend that’s ubiquitous across all industries is the demand for faster service, faster deliveries, and faster turnaround times. As technology has improved,
Is our industry evolving and automating as fast as our customers? Laser cutting vendors are now automating throughout their operations, from manufacturing to invoicing, and everything in between.
services have become faster, and the consumer has developed a taste for “instant” service – and they want more.
This has been a major driver for companies to invest in automation to keep up with demand.
This is just as true in the laser cutting industry as may be for groceries or retail products. A vendor that can return a quote faster, and subsequently deliver a laser cutting job faster, is more likely to win the work, because this gets the final product to the end customer faster.
And with the end customer wanting the product increasingly quickly, faster quoting is going to go from being desirable, to being necessary for business growth.
With the trends towards automation and faster service in mind, Tempus Tools has introduced its Web Store feature to ToolBox, its cloud-based laser cutting quoting software.
Web Store is an online quoting portal that ToolBox subscribers can use on their own website, with their own branding, to allow customers to receive instant online quotes and instant pricing 24/7.
This is a game-changer for laser cutting companies. A customer working different hours might put a
request in on a Sunday afternoon. Previously, this would have to wait until normal business hours on Monday, but now that customer gets an instant quote and can choose whether they are ready to proceed to an order.
It’s a win-win scenario. The customer gets information quicker, and the laser cutting business can win more orders with quoting available around the clock. It even frees up staff who would previously have been preparing quotes to work in other vital areas of the business to further add to growth and expansion.
A major barrier to entry for new automated technologies has been long or complicated setups, where the business has to suffer while the transition occurs.
But with ToolBox, the setup takes minutes, not weeks or months, so laser cutting job shops can get back to doing what they do best. And the Tempus Tools team can assist right through the setup process (at no extra charge), using their decades of experience from the job shop floor, through to management of large laser cutting enterprises.
With a low monthly subscription fee and fast setup, ToolBox has been designed to give even the smallest job shops the same advantages as the major players in boosting efficiency and responsiveness to customer quotes.
Upgraded operations are well underway at Whakatane Mill Limited’s (WML) paperboard mill following the businesses official grand re-opening celebrated back in March.
The initial months of the year were spent installing new state-of-the-art machinery, as well as upgrading its facilities, and since its re-opening WML is now fully equipped to service its local and global customer chain with premium quality board products.
Customers from across the globe attended the in-person event alongside numerous local and government officials, such as Minister of Manufacturing and Small Business, Andrew Bayly and Local MP Dana Kirkpatrick.
Representing more than mere upgrades to facilities, over NZD$100m worth of private funding has been poured into the business, ensuring the growth and prosperity of both the mill and the local Whakatane community for years to come.
On the day of the grand re-opening, guests were invited to take a tour through the mill to view the new machinery upgrades which will enable WML to produce an additional 50,000 tonnes of premium folding box boards, along with improved environmental and energy systems to further embed the business’ long-term success.
The upgrade seeks to increase WML’s total production capacity of up to 200,000 tonnes of premium folding box board in the future. WML is the only folding box board producer in the Australian/New Zealand geography.
A New Zealand Apprenticeship in Plastics Engineering has opened the door to a wealth of unexpected opportunity for Dunedin’s Wesley Lewis.
The talented 27-year-old has just been named Plastics Apprentice of the Year 2023, and now he’s on the fast track to success at food packaging business Packit Packaging.
Since joining Packit as a casual packer Wesley has made his mark, impressing General Manager Jamie Hodgins with “his can do attitude, work ethic and high standards of workmanship”. Now he is continuing to blaze a trail, developing his managerial capabilities through the Dunedin Leadership Academy.
“Wesley went from packing parts into cartons in our factory, to now managing the plant and daily production over the space of four years through his apprenticeship,” says Jamie. “He is a key member of our business and we’re looking forward to moving him into a managerial position in the future.”
which was pretty satisfying.”
It was also “pretty satisfying” when he found out he had won Plastics Apprentice of the Year at the recent New Zealand Plastics Industry National Conference.
“It was a bit of a shock to be honest, but it means a lot to have all my hard work and effort recognised. There were some stressful times during my apprenticeship. I loved the technical side, but I found the business side of things pretty challenging. Going into it I had no knowledge of business systems, flow systems and stuff like that, but it does all get explained really well throughout the training.”
With the mentorship of a great employer and a dedicated Competenz training advisor for additional guidance, plastics apprentices are well supported as they work their way through their Level 4 qualification.
The grand re-opening event is a stark contrast to the uncertain future that the business faced only three years ago where an unfortunate closure was looming over WML. Since acquiring the business, the new owners have invested significantly in the mill’s capabilities, committing to its successful future and the continued prosperity of Whakatane’s local economy.
Executive Chairman of Whakatane Mill Limited Ian Halliday, conveyed the immense pride he had in re-opening the business, setting its course for a fruitful future.
“Looking back to when we first acquired the mill, and to where the business is at now, it’s incredibly fulfilling. We have invested heavily in upgrading the business as we always believed in its potential, and to see it now come to fruition is truly rewarding. As the largest private employer in Whakatane, with 80 years of exporting history, we are proud to see the mill step forth into its next evolution.
“We want to thank our team, commercial partners and local contractors who have helped with the upgrade, along with our customers who continue to partner with us. We remain committed to further advancements, ensuring a bright future for our business and community alike,” concludes Halliday.
Currently in the role of Supervising Production Technician, Wesley is responsible for the day-to-day operations of the factory and the technical staff workload, also overseeing the training of Packit’s newest plastics apprentices. Although he never intended to go down the management path, Wesley says his quick career progression has come as a pleasant surprise.
“As a kid I always enjoyed tinkering with things and my apprenticeship gave me the chance to immerse myself in the technical side,” says Wesley.
“It’s very easy to look at a machine and assume you know what it’s doing, but there’s actually so much to it, like maintenance, how it operates, and chemical breakdowns.
The apprenticeship covers all that and gives you a really good broad understanding.
“Now I’m working my way up in the company and going down the leadership route. I started out with no management skills at all, and it has been a real eye opener learning how different people operate.”
Does he miss the tool time?
“Yeah I do a little bit, it’s very rewarding. But I’m always on hand for higher level diagnostics when my team needs me, and Jamie has me doing more of the bigger projects now which I really enjoy. Earlier this year we installed a whole new chiller system, and I did all the labour around that
Quarterly visits, phone and email assistance, marking of units, study groups, and drawing classes are just some of the support offered by Competenz training advisor Stuart Hewson who says he is “very proud” that Wesley’s work ethic and high levels of achievement have been recognised at a national level.
“Wesley has a lot of enthusiasm for learning and the plastics industry, and genuinely shares his knowledge and experience with his trainees,” says Stuart.
“He is the future of the industry, the next business manager and owner, and future trainer in such a technical area.”
Although Wesley didn’t realise it at the time, the New Zealand Certificate in Plastics Engineering (Level 4) has been the perfect springboard to an exciting career.
“People think that if you get a plastics apprenticeship you only ever work in plastics but that’s not the case,” he says. “It’s very engineering based, it’s very broad and there are lots of different routes you can take. I for one, thoroughly recommend it!”
Due to a failure of a Caterpillar Hydraulic Governor on the Tug Vessel “Te Matua”, operated by South Port NZ, Emee NZ Ltd of Mossburn, was consulted to check out the possibility of an improved, reliable, readily available, cost-wise and serviceable system. Having deliberated and sourcing suitable and reliable hardware involved to substitute the original system, it was found that the movement of the Caterpillar 3606 Engines Fuel Injection Pumps mechanisms demanded a high torque to move such from idle to full throttle.
The requirement was also to have a system that originally was air control to the Bridge, superseded by simple “Rotational Dial” and have simple 4–20mA wiring connection. Other air control levers and parts subject to age failure were removed.
It was decided to use a combination of a GAC ACB 2001 12Ft Lb Actuator and an AXIOMATIC AX100310 Unidirectional Digital Control for each engine to supersede the original equipment.
The combination of both these products together with suitable developed programed firmware and a mechanically driven encoder has now made reliable use of this vessel.
This equipment was fitted to both Engines and
to date has more than proved their worth in speed control which incidentally this vessel is used extensively for moving large ships within the Island Harbour complex and narrow channel entrance.
Installation of the Emee System is very simple, with a Manufactured Actuator Bracket fitted to each engine with linkage, also an enclosure for the required wiring and having the Axiomatic Controllers externally mounted for access.
The Axiomatic units are totally encapsulated protecting the internal hardware from the sea environment. This is a major plus to eliminate corrosion and damage. A further feature is an emergency “override key switch” which in the event of Bridge Control failure will put the engine RPM to working speed.
Used only in this emergency state. The EMEE System is simple and maintenance free.
The vessel’s propulsion incorporates 2 x 1000 HP Caterpillar 3606 Marine Diesel Engines which are the prime movers for 2 Voith Schneider Units. The EMEE system has other aspects of inbuilt engine control including “PID” and “CAN” which are essential for precise engine tuning and monitoring.
Smoke Limiting etc. The GAC Actuator has rotational movement and bearings on each end of the output shaft.
For engines requiring greater torque for moving the fuel pump rack another Actuator could be attached in parallel using the same above Axiomatic Controller. This Controller is capable of driving two above Actuators together.
Emee NZ Ltd would like to thank those Engineers of Both Axiomatic Technologies, GAC (Governors America Corporation) and especially the team from South Port Bluff NZ for their patience and undivided assistance in helping to achieve the goal of developing this unique control system.
Engineering New Zealand Chief Executive Dr Richard Templer welcomes a new report from the Helen Clark Foundation and WSP that recommends a shared vision and bipartisan support for infrastructure projects.
Bridging the Infrastructure Gap – Funding and financing for a resilient Aotearoa New Zealand was launched, with both National and Labour talking about being open to a bipartisan approach to long term infrastructure.
“I’m really encouraged by what I’ve heard from both major parties regarding a bipartisan approach,” says Templer.
“A shared vision for infrastructure investment and a clear commitment to projects will serve Kiwis far better,” he says.
Templer says engineers have a core role in helping deliver a resilient New Zealand and that a shared vision for infrastructure investment will help the country access and use those skills.
“New Zealand is currently facing a shortfall of about 2,500 new engineers every year and uncertainty around major projects may be contributing to a deepening skills shortage, with engineers leaving for overseas,” he says.
“We need to be growing our pool of skills and Engineering New Zealand is keen to support a
solution. We met with Minister Stanford about how we can help ensure our education system is configured to deliver the skills we need in engineering and other STEM subjects,” he says. Templer thinks there’s never been a better time for a shared vision for infrastructure. “We need to build for our future. Commitment to a shared vision for infrastructure is a ‘win-win’ that would really allow our country to increase our productivity and resilience,” he says.
Tentech, a leading Australian information management consultancy, is excited to announce its expansion into New Zealand, responding to increasing demand from organisations across the Tasman.
With a robust reputation in Australia for delivering cutting-edge technology solutions, Tentech aims to empower more businesses in New Zealand to harness the power of effective information management to boost productivity, enhance efficiencies, and drive substantial growth.
“Tentech has always been at the forefront of technology innovation, specialising in design and engineering data management. As we navigate this pivotal year for data management, our expansion
into New Zealand is a strategic move to address the evolving needs of businesses in the digital era,” said James Tennent, Managing Director of Tentech. Tentech’s vendor-agnostic approach ensures that each client receives the most suitable technology solutions, tailored to their unique needs without the limitations of vendor-specific restrictions. This flexibility allows Tentech to integrate and automate systems effectively, making business operations more efficient and competitive.
Central to Tentech’s service offering is the MinuteView platform. This unified platform enhances information management capabilities through comprehensive integrations, automations, and advanced data management tools, setting a new standard in the industry.
With this strategic move across the ditch, Tentech is well-positioned to lead and influence the future of information management in the region.
New Zealand company Fabrum, a world leader in zero-emission transition technologies to enable a lower-carbon economy, is set to supply Toyota with its proprietary liquid hydrogen storage technology. Fabrum has established a reputation globally as a leader in end-to-end hydrogen production and refuelling systems. The green hydrogen project adds to a number of others under construction internationally, with global players in aviation, heavy transport, and industry.
Dr Ojas Mahapatra, CEO of Fabrum, says: “We’re delighted to be working with Toyota to advance their hydrogen projects with our liquid hydrogen storage technology. This order is significant as it’s our first from Toyota, which is at the forefront of new technologies and innovations for its future mobility projects – and it signals the beginning of our relationship.”
Their work with Toyota represents Fabrum’s second Japan-New Zealand hydrogen project. They
are also working with Obayashi Corporation, one of the world’s leading construction companies, to deliver unique dual-pressure hydrogen refuelling technology for an Auckland-based refuelling station project.
For 20 years, Fabrum’s patented cryogenic technology has enabled the global movement towards clean energy transition.
Representatives from Toyota in Japan recently visited Fabrum in Christchurch..
Left to right: Dr Ojas Mahapatra (CEO, Fabrum), Yoshichika Shimane (Toyota), Christopher Boyle (Executive Chair, Fabrum), Sangkun Lee (Toyota), and Barry Prince (Vice President – Hydrogen, Fabrum).
Fabrum delivers solutions to support a zero-emission future for mobility in aviation, marine, heavy transport, and heavy industry. The Fabrum patented cryocooler technology has been applied in electrolysers, hydrogen liquification plants, boil off gas management systems, and hydrogen refuelling stations.
Fabrum’s composite technology has also been
adopted into heavy industry mobility, on-board aviation fuel tanks, and superconductivity. Fabrum has built an impressive list of global IP and solution success, applying its sustainable solutions to enable humanity to tread lightly.
The Gold Coast will be home to Australia’s first factory capable of producing both community lithium batteries and EV chargers as eLumina’s $20 million manufacturing facility approaches completion.
The factory will produce 300 batteries a year and create 300 jobs on the Gold Coast, capable of serving up to 100 Queensland households with reliable and cheaper renewable energy.
Chief Executive Officer of eLumina, Lisa Marsh, said on-shore manufacturing of critical EV technology, such as chargers and batteries, was essential to Australia’s energy future.
“Global demand for batteries is soaring. We have record solar uptake and energy generation in Australia, but we need battery storage at scale to harness its full potential,” she said.
“Through battery storage we can capture this energy and ensure reliable and cheaper off-grid power to all Australians. This insulates communities from power outages and saves them money.”
Ms Marsh said eLumina was proud to be building the factory in Queensland and grow the local industry.
“Queensland has the potential to become a world leader in next-generation battery manufacturing and research and development. Our centre is just the start of that. We are committed to making a fundamental difference to Australia’s clean energy economy,” she said.
“We’re building this facility using local talent and locally sourced parts and materials. Once it’s completed, it will support 300 high-skilled jobs, which will draw on the region’s talent.”
“Our world-class research and development
training centre will al so upskill hundreds of Queenslanders with the expertise to contribute to our evolving battery and EV charging sector.”
Gold Coast Mayor Tom Tate said the Gold Coast had an ambitious plan to secure a larger slice of the clean energy sector and the high skilled jobs it’s creating.
“Our Economic and Climate Resilience and Sustainability Strategies are all about backing the Gold Coast to use renewable energy and boost the uptake of renewables.”
“eLumina choosing the Gold Coast as home for Australia’s first factory building both lithium community batteries and EV chargers shows our city has the right settings, ambitions and support for businesses for advanced manufacturing to thrive.”
“I’m excited to see the thousands of EV chargers and batteries set to be deployed in Australia over the coming years to be stamped - ‘Made on the Gold Coast’.
To accelerate the deployment of its EV chargers across the country, eLumina has partnered with Addelec (formerly known as Gemtek), a
leading installer of EV charging stations with national asset management capabilities.
“The number of EVs on Australian roads is growing rapidly and charging infrastructure needs to keep pace with that. The eLumina D1 with built in battery storage is a great option to have, especially considering the power challenges we have across Australia” Addelec’s General Manager – Chris McPherson said.
“Producing EV chargers in Australia will make it easier to meet demand and to support the exciting transformation to more sustainable transport.”
Ms Marsh said building Australia’s sovereign capability in battery storage and EV technology would support the growth of green energy and electric vehicles.
“By producing this technology in Australia, we can provide families with cheaper power and give more people confidence to drive an EV.”
The factory is set to be operational by August this
eLumina, an Australian-owned company, manufactures top-of-the-line EV chargers known for its superior efficiency and reliability. It offers a wide range of battery energy storage systems (BESS) in various capacities to cater to the diverse requirements of industrial and commercial settings. Operated by Australians with a global presence, eLumina’s dedicated team of engineers strives to create a one-stop shop for innovative energy solution, redefining energy interactions and preparing businesses for the new generation of energy infrastructures.
Gordon Noble, Research Director, Institute for Sustainable Futures, University of Technology Sydney. Fiona Berry, Research Principal, Institute for Sustainable Futures, University of Technology Sydney.
Since the release of ChatGPT in November 2022, the world has seen an incredible surge in investment, development and use of artificial intelligence (AI) applications.
According to one estimate, the amount of computational power used for AI is doubling roughly every 100 days.
The social and economic impacts of this boom have provoked reactions around the world. European regulators recently pushed Meta to pause plans to train AI models on users’ Facebook and Instagram data.
The Bank of International Settlements, which coordinates the world’s central banks, has warned AI adoption may change the way inflation works. The environmental impacts have so far received less attention. A single query to an AI-powered chatbot can use up to ten times as much energy as an old-fashioned Google search.
Broadly speaking, a generative AI system may use 33 times more energy to complete a task than it would take with traditional software.
This enormous demand for energy translates into surges in carbon emissions and water use, and may place further stress on electricity grids already strained by climate change.
Most AI applications run on servers in data centres. In 2023, before the AI boom really kicked off, the International Energy Agency estimated data centres already accounted for 1–1.5% of global electricity use and around 1% of the world’s energy-related CO emissions.
For comparison, in 2022, the aviation sector accounted for 2% of global energy-related CO emissions while the steel sector was responsible for 7–9%.
How is the rapid growth in AI use changing these figures? Recent environmental reporting by Microsoft, Meta and Google provides some insight. Microsoft has significant investments in AI, with a large stake in ChatGPT-maker OpenAI as well as its own Copilot applications for Windows.
Between 2020 and 2023, Microsoft’s disclosed annual emissions increased by 40%, from the equivalent of 12.2 million tonnes of CO to 17.1 million tonnes.
These figures include not only direct emissions but also indirect emissions, such as those caused by generating the electricity used to run data centres and those that result from the use of the company’s products. (These three categories of emissions are referred to as Scope 1, 2 and 3 emissions, respectively.)
Meta too is sinking huge resources into AI. In 2023, the company disclosed is Scope 3 emissions had increased by over 65% in just two years, from the equivalent of 5 million tonnes of CO in 2020 to 8.4 million tonnes in 2022.
Google’s emissions were almost 50% higher in 2023 than in 2019. The tech giant’s 2024 environmental report notes that planned emissions reductions will be difficult “due to increasing energy demands from the greater intensity of AI compute”.
Data centres generate a lot of heat, and consume large amounts of water to cool their servers.
According to a 2021 study, data centres in the United States use about 7,100 litres of water for each megawatt-hour of energy they consume.
Google’s US data centres alone consumed an
estimated 12.7 billion litres of fresh water in 2021.
In regions where climate change is increasing water stress, the water use of data centres is becoming a particular concern.
The recent drought in California, where many tech companies are based, has led companies including Google, Amazon and Meta to start “water positive” initiatives.
These big tech firms have announced commitments to replenish more water than they consume by 2030. Their plans include projects such as designing ecologically resilient watershed landscapes and improving community water conservation to improve water security.
Where data centres are located in or near cities, they may also end up competing with people for resources in times of scarcity. Extreme heat events are one example.
Globally, the total number of days above 50°C has increased in each decade since 1980. July 2023 was the hottest month ever recorded.
Extreme heat translates to health impacts on local populations. A Lancet 2022 study found that even a 1°C increase in temperature is positively associated with increased mortality and morbidity.
On days of extreme heat, air conditioning can save lives. Data centres also like to keep cool, so their power use will spike with the temperature, raising the risk of blackouts and instability in electricity grids.
So what now? As we have seen, tech companies are increasingly aware of the issue. How is that translating into action?
When we surveyed Australian sustainability professionals in July 2023, we found only 6% believed data centre operators provided detailed sustainability data.
Earlier this year we surveyed IT managers in Australia and New Zealand to ask what they thought about how AI applications are driving increased energy use. We found 72% are already adopting or piloting AI technologies.
More than two-thirds (68%) said they were concerned about increased energy consumption for AI needs. However, there is also significant uncertainty about the size of the increase.
Many IT managers also lack the necessary skills to adequately address these sustainability impacts, regardless of corporate sustainability commitments. Education and training for IT managers to understand and address the sustainability impacts of AI is urgently required.