
www.nzmanufacturer.co.nz
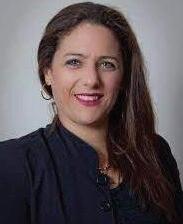

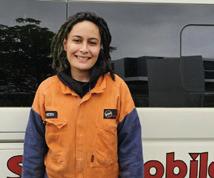
www.nzmanufacturer.co.nz
Datum Machines stand
The last three months were very intense and at times very challenging. We learned a lot and realised some of our business processes and engineering production will need to change going forward.
But that’s how we learn. As the crated machine left Waiwhetu on a Mainfreight Truck heading to Auckland, Zak commented that there was 11 months of our lives in that box.
We have had a great deal of support over the last eight months or so with other small businesses helping and wanting to see Zak succeed. They recognised his determination, design talent and self-taught engineering skills which have resulted in the finished DGM-S1 Gantry Mill CNC machine. Support from others like Hutt Valley Chamber of Commerce, NZ Manufacturer and Engineering News magazines wanting to give Zak’s business exposure to help get it out there.
Exhibiting at the EMEX Engineering and Mechanical trade show was an expensive exercise and such a venture always costs a big percentage more than what you first imagine. The stand alone was $11K but I think all up it would have cost us at least $16,000, probably more.
That said, the show was a great success. The contacts made with other NZ businesses, potential suppliers, future collaborators, as well as prospective customers was worth it alone.
Everyone was impressed with the DGM-S1 and even
more impressed to realise it has been Aotearoa New Zealand designed and manufactured. Pretty much single handed by Zak.
Other exhibitors of CNC machines came by to check it out and meet Zak. They recognised and commented on the machines look and build quality. They congratulated Zak and could see the machines capabilities in its build and realised that the Gantry Mill CNC has real potential.
While all exhibitors are there to sell their own machines and there is an element of competition, many play in very different leagues with some machines in the many hundreds of thousands of dollars or more.
Ooverall, it’s a very friendly, encouraging and supportive show. The show organisers were also very supportive and keen to see Zak get as much exposure and so generated interest where they could.
They pointed many people in the direction of the Datum Machines stand and brought over people from education organisations and industry manufacturing groups every day.
Secure supply of energy and data to moving industrial equipment.
• Large size range
• Vertical travels
• Energy tubes
• Hygienic chains
• Solutions for long travel
• Guide troughs
• Readychain
• Robotic, 3D
• Circular movement
HUGE range of high quality flexible cables
• Control cables
• Single cores
• Data cables
• Sensor/Actuator
• Intrinsically Safe
• VSD/EMC cables
• Halogen Free cables
• High temperature
• Harsh Conditions
• Crane cables
• Profibus cables
• Bus/DeviceNet
• Solar cables
• Instrumentation
• Flat cables
• Curly cords
Largest range of flexible conduits for cable protection
• Conduits
• Conduit fittings
• Divisible systems
• Jumbo systems
• Conduit Accessories
• Braided cable protection
• Fire barrier solutions
• Food and beverage
• EMC systems
• Ex, ATEX, IEC EX
Industrial connectors for many industries
• Rectangular multipole connectors from ILME
• Single pole Powerline connectors from TEN47
• EPIC connectors from Lapp Group
• M23 circular connectors from Hummel
• Circular connectors specifically for the entertainment/stage lighting industry from Socapex
Safety engineering solutions from EUCHNER
• Multifunctional Gate Box MGB
• Transponder-coded safety switches
• Electromechanical safety switches
• Magnetically coded safety switches
Sensor technologies for automation
• High-Precision Laser Distance Sensors
• Ultrasonic Sensors
• Inductive Sensors
• Fluid Sensors
LEAD
EMEX 2024 – One company’s reflections.
EDITORIAL
How about a ‘Blue Sky’ innovative vision for manufacturing in New Zealand?
BUSINESS NEWS
Tightening purse strings hit NZ SME manufacturers.
The Scope 3 ripple effect.
How to capture the hidden upside of green manufacturing.
SMART MANUFACTURING
Efficiency v Productivity.
Navigating manufacturing’s shiftwork environments with digital workforce management.
ANALYSIS
What matters more, excellence or impact?
SMART MANUFACTURING
Mimic joins race to develop AI-driven collaborative robot.
Using Industry 4.0 to improve maintenance.
COMMENT
Transferable skills the key to unlocking productivity benefits.
ANALYSIS
Balancing innovation and growth.
EMEX 2024 reflections.
DEVELOPMENTS
Three Kiwi cleantech ventures make list of top 25 in Asia-Pacific.
Long-term future for Tiwai Point aluminium smelter secured
SUSTAINABILITY
Can I see your (product) passport please?
WORKSHOP TOOLS
Shaking hands with a robot.
CBS rotary screw blowers a compact solution.
WOMEN GOING PLACES
Patsy Gadsby making her mark.
THE LAST WORD
Is NZ ‘offshoring its environmental footprint’ –is that fair?
Ian Walsh Ian is a Partner, Argon & Co. NZ, a master black belt improvement specialist and global lean practitioner. He is passionate about improving productivity and helping to create world class New Zealand businesses.
Dr Barbara Nebel CEO thinkstep-anz Barbara’s passion is to enable organisations to succeed sustainably. She describes her job as a ‘translator’ – translating sustainability into language that businesses can act on.
Lewis Woodward Is Managing Director of Connection Technologies Ltd, Wellington and is passionate about industry supporting NZ based companies, which in turn builds local expertise and knowledge, and provides education and employment for future generations.
Mark Devlin
Having owned food manufacturing and distribution businesses for a decade, Mark Devlin now runs Auckland public relations agency Impact PR. Mark consults to several New Zealand manufacturing firms including wool carpet brand Bremworth, aircraft exporter NZAero and cereal maker Sanitarium.
Insa Errey Insa’s career has been in the public and private sectors, leading change management within the energy, decarbonisation, and sustainability space. Insa holds a Chemical and Biomolecular BE (Hons) from Sydney University. She is a member of the Bioenergy Association of NZ and has a strong passion for humanitarian engineering, working with the likes of Engineers Without Boarders Australia.
5 7 14 16 18 22 27
Insa is a member of Carbon and Energy Professionals NZ, been an ambassador for Engineering NZ's Wonder Project igniting STEM in Kiwi kids and Engineers Australia Women in Engineering, increasing female participation in engineering.
PUBLISHER
Media Hawke’s Bay Ltd, 121 Russell Street North, Hastings, New Zealand 4122.
MANAGING EDITOR
Doug Green
T: +64 6 870 9029
E: publisher@xtra.co.nz
CONTRIBUTORS
Holly Green, EMA,
Business East Tamaki, Ian Walsh, Adam Sharman, Jarrod Adam
Insa Errey, Stephanie Pretorius
Damien Durston, Dr. Troy Coyle
Craig Carlyle, Mario Rodriguez
Wes Brunnen, Martin Brook, Ross Thompson, David O’Connor
ADVERTISING
T: + 64 6 870 9029
E: publisher@xtra.co.nz
DESIGN & PRODUCTION
:kim-jean:
E: kim.alves@xtra.co.nz
WEB MASTER
Julian Goodbehere
E: julian@isystems.co.nz
PUBLISHING SERVICES
On-Line Publisher
Media Hawke’s Bay Ltd
DIGITAL SUBSCRIPTIONS
E: publisher@xtra.co.nz
Free of Charge.
MEDIA HAWKES BAY LTD
T: +64 6 870 9029
E: publisher@xtra.co.nz
121 Russell Street North, Hastings
NZ Manufacturer ISSN 1179-4992
Vol.16 No.5 June 2024
Copyright: NZ Manufacturer is copyright and may not be reproduced in whole or in part without the written permission of the publisher. Neither editorial opinions expressed, nor facts stated in the advertisements, are necessarily agreed to by the editor or publisher of NZ Manufacturer and, whilst all efforts are made to ensure accuracy, no responsibility will be taken by the publishers for inaccurate information, or for any consequences of reliance on this information. NZ Manufacturer welcomes your contributions which may not necessarily be used because of the philosophy of the publication.
How about a ‘Blue Sky’ innovative vision for manufacturing in New Zealand?
Three weeks ago, Australian prime minister, Anthony Albanese announced a $22.7 billion agenda for Future Made in Australia, to meet the challenges facing Australia, which require a big national response.
In the NZ Budget 2024, the prime announcement was tax reductions across the population. A noble effort but money that will continue to be gobbled up by inflation, insurance and vehicle registration increases and more…all applied by companies who know how to extract the last gold filling from the client.
As a small economy we don’t have lots of money to spare and we need to be smarter. The National Government is easing the puss, putting plasters on sores and trusting that through inflation reducing by the end of the year all will improve.
However, we need something similar to Australia. A Future Made in NZ or Build the Future Together is purposeful. To improve the economy, conditions for workers, to cover the cost of living and incentives ( a decent salary, shares) and opportunities for our smart companies to sell their products overseas.
We need smart, trained people to be rewarded for effort and not move to Australia. We need to keep on finding markets in this troubled and weird world we live in.
We need a Business Council of successful, proactive people who can drive the country forward from their own life experiences and trials and tribulations. Aspirational business people who know ‘how to get there’. Using private and public sector money on projects that will truly make a difference for the better.
A regular comment is that ‘if not as much money was invested in property, but into manufacturing, we would be a lot better off’.
Doug Green , PublisherThe recession is taking a bite out of New Zealand manufacturers’ sales revenue, according to new data from inventory management software brand Unleashed.
Unleashed’s first Manufacturing Health Index since New Zealand officially entered a recession found sales revenue dropped by 7% in the first quarter of this year, but is still up 18% year-on-year, aided by superb growth in the Energy, Medical Supplies, and Personal Care subsectors.
The report looks behind the curtains of SME manufacturers in New Zealand, Australia, and the UK, across 12 subsectors.
Unleashed head of product Jarrod Adam says high interest rates will continue to put downward pressure on firms, but the data shows the sector is able to respond positively to these headwinds.
“The beginning of the year has been a speed bump for Kiwi manufacturers, but we need to keep in mind that overall revenue is actually up on the same period as last year. These companies are nothing if not dynamic, and in this current environment it is crucial to react to the cards you are dealt,” said Adam.
“One really positive sign in the data is the much lower lead times, which will help these businesses be as productive as possible when conditions change for the better.”
The report notes that firms have drastically improved their lead days to just 14 to begin the year, from 30 days in the final quarter of 2023, and 37 in the same quarter of last year. Lead time improvements are both a sign of normalising supply chains globally and the knock-on effect of New Zealand business’ laser focus on logistics over the past three years.
At the pointy end of the disposable income problem, local Kiwi Food and Beverage producers have been confronted with difficult times with little reprieve on the horizon as interest rates and inflation stay stubbornly high.
For beverages, sales dipped 12% since the previous quarter, but year-on-year still saw a marginal 1% revenue increase.
As is the case in Australia, the Food manufacturing sector has been hit worse than their contemporaries in beverages. Last quarter saw sales revenue plummet 23%, with a year-on-year constriction of 10%.
Clean Collective Beverage company CEO David McGrath says economic factors have been hitting industry players both big and small.
“What is clear of the beverage industry is that volumes are down across the board. Over the past couple of years inflation has masked a lot of it, but talk to sellers or manufacturers and they’ll tell you this is an industry-wide issue,” McGrath said
“For Clean Collective, we’re in the lucky position of continuing to grow, but like other manufacturers we are seeing a tough 12 months ahead. For consumers to open up their wallets again, the key factor is going to be interest rates coming down to encourage spending.”
A success story for the broader manufacturing industry has been the continued growth of Kiwi chemical and energy manufacturers, who have enjoyed a bumper year off the back of continued investment in renewables. Overall sales revenue within the sector has grown 39% year-on-year, including a 14% spike during the first quarter of this year.
Taking one of the biggest revenue hits was the Building and Construction industry, which saw sales drop 26%, as inflationary pressures and a slowdown in projects combined to put serious strain on the industry.
However, the industry has taken time over the slower period to reinvest in logistics and other productivity gains. Lead times reduced to just 16 days on average, after a 38 day blow out during the tail end of last year, as the wider construction industry was hampered by a shipping crisis in the Red Sea.
“The Building and Construction industry has been hit hard by current economic conditions, but they have responded in kind. Quiet times are a period to reinvest in improved systems and productivity, which will allow the industry to build back better than before,” said Unleashed’s Jarrod Adam.
Sales were down 24% in the Clothing industry, far below the country average of 7%, following the trend of retail-oriented industries being susceptible to drop offs in discretionary spending.
Although the majority of the manufacturers in the report are B2B firms using traditional sales channels, New Zealand manufacturers are increasingly diversifying their sales models. 48% of Kiwi and Australian firms are using or have used eCommerce tools, up from just 4% in 2021.
For more information and the full research, visit: https://www.unleashedsoftware.com/industry/manufacturing-inventory-management/manufacturinghealthindex
The Manufacturing Health Index assesses SME manufacturer performance via a big data approach. Starting with a cohort of 1,790 manufacturers in the UK, Australia and New Zealand, the Q1 2024 report draws on data from every purchase, sale and stock movement made by each business in the study between Q1 2018 and Q1 2024.
8 Hannover Place, Rolleston is a single level 2,552sqm office/ warehouse/cleanroom facility constructed circa 2019.
The building was purpose built for plastic injection moulding of packaging for supplying to local and national dairy processors. The smart modern warehouse with a stud height of 7.5 metres to the portal knee with Kingspan roof and wall panels. The moulding cleanroom is ISO certified and temperature controlled with positive airflow.
Call today to learn more.
bayleys.co.nz/5524078
Jeremy Speight 027 655 5647
021 225 2130
In the ever-evolving landscape of regulations, New Zealand manufactures find themselves connected to the regulatory frameworks of key trading partners such as the European Union (EU). The EU has positioned itself as a global leader in climate action, with ambitious targets set under the European Green Deal and the European Climate Law.
As part of its efforts to reduce greenhouse gas emissions, the EU has implemented regulations on Scope 3 emissions reporting through directives such as the Non-Financial Reporting Directive (NFRD) and the EU Taxonomy Regulation.
Understanding the impacts of Scope 3 regulations in these markets is crucial for New Zealand manufacturing. Let’s delve into how regulations in the EU can shape the strategies and operations of New Zealand manufacturers.
Scope 3 emissions refer to indirect greenhouse gas emissions that occur in the value chain of a company, including both upstream and downstream activities. These emissions often result from activities such as the production of purchased goods and services, transportation and distribution, and waste disposal.
For any EU customer this may just be your manufacturing sites Scope 1 or 2 emissions. Meaning
What does this mean for NZ manufacturers?
Market Access and compliance pressure to adhere to these standards is required for exporting to the EU which governs Scope 3 emissions disclosure and reduction. Failure to meet these requirements can result in barriers to market entry.
In a global market increasingly, prioritising emissions reduction is becoming an advantage, as exporters can face competition from countries with lower carbon footprints. Failure to manage or measure emissions can put NZ manufacturers at a competitive disadvantage and could impact market share.
Even if you are not directly exporting to the EU you might find that your product ends up selling in these markets and as such the supply chain now requires supply chain transparency on scope 3 emissions. Supply chain transparency means gaining comprehensive visibility of the supply chain to identify emission hotspots and opportunities for improvement.
associated with raw materials, production processes, and distribution channels, which may just include your site.
Nestlé, a global food and beverage company, has responded with thorough supply chain transparency measures to trace the origin of raw materials and assess environmental impacts. By working closely with suppliers, Nestlé aims to reduce Scope 3 emissions associated with its products and promote sustainable sourcing practices across its supply chain.
Putting pressure on the likes of their major NZ suppliers which include Fonterra. Fonterra has responded with their own scope 3 targets. Targeting a 30% intensity reduction in on-farm emissions by 2030 which aims to accelerate emissions reduction and provide transparency within their own local scope 3. Addressing your emissions is not just a matter of environmental responsibility, it’s now a strategic
A decision to move towards green manufacturing is often analysed as a business case on a spreadsheet. However as NZ Manufacturer business advisor and Impact PR director Mark Devlin has found, there are intangible benefits that may manifest once companies embrace a more sustainable future.
According to Stats NZ data, the manufacturing sector produces the second-highest level of emissions of all industries. While accounting for 14% of all greenhouse gases produced in the country annually, this was down 10% on the previous year.
Latest seasonally adjusted quarterly data shows a further reduction of 39 kilotonnes of gas emissions across Kiwi manufacturers.
Whether it is nurdles on the beach or nitrous oxide in the atmosphere, putting products on retail shelves can be associated with a steep environmental impact - and the manufacturing industry is often the public face of this.
The recent decline in emissions may suggest a fall in manufacturing volumes as a result of lower demand or we could be seeing more widespread adoption of green production practices and technology.
The latter is certainly something worth celebrating and in many cases may present a brand development opportunity that can be leveraged for both individual manufacturers and the entire sector.
Having worked with hundreds of companies over the past two decades we have seen numerous examples of how embracing sustainable manufacturing models can result in unexpected and often significant upsides for brands.
Recently, I was approached by producers from the world’s largest public broadcasting network - The Association of Public Broadcasting Corporations in the Federal Republic of Germany (ARD).
The offshore production team had seen publicity around a transformative move one of my clients, Bremworth, had made to eliminate 2,500 tonnes annually of synthetic yarn from the production of carpets and replace them with New Zealand wool.
The producers requested their documentary crew travel to NZ to film at Bremworth’s South Auckland factory and showcase what the company was doing and why they had so heavily bet on an all-wool future.
ARD is producing the new current affairs documentary for its flagship Das Erste (The First) channel. Around 50 million people, approximately 60% of Germany’s population, watch Das Erste live to air every week. (In comparison New Zealand’s TV One has around 1.2 million weekly viewers - less than a quarter of Kiwis.)
The 71-year-old Das Erste is seen as Germany’s most credible TV network and the exposure in the eight-minute documentary, estimated to be worth over $7.2 million in advertising value, would be otherwise cost-prohibitive for Bremworth (and most Kiwi companies) to access.
Given the market size of Germany, for the wool
industry, this opportunity could be the equivalent of the impact the Lord of the Rings films had on New Zealand tourism.
Germany is also one of the world’s most environmentally conscious countries and their interest in how New Zealand is transforming its wool sector to meet growing global demand for natural fibres, could help open new export channels in the EU’s largest population centre.
The documentary is scheduled to air later this year in Germany to what is seen as a relatively untapped market for New Zealand wool - presenting a significant opportunity within a well-aligned consumer group that is highly focused on sustainable living.
While the significant reduction of the majority of synthetic materials from the production process is a significant achievement for any manufacturer, it is also possible to address environmental concerns in other ways.
We have also been working with Waikato aeronautical manufacturer NZAero, to position their new SuperPac 750XL-II utility aircraft, which is capable of being outfitted for fighting wildfires, rainmaking, reducing the size of locust populations and pollution control, as uniquely suited to help nations fight the growing impact of climate change.
Following the nationwide publicity around international interest in the new model, the company was invited to join Prime Minister Christopher Luxon and a delegation of senior business leaders on a
seven-day mission to Singapore, the Philippines and Thailand.
During the Southeast Asian mission, NZAero signed a multi-million dollar export agreement to supply the Royal Thai Air Force with parts and maintenance services.
In addition, the company is now looking to sell a fleet of its SuperPac aircraft, which each has a multi-million dollar price tag, to Thailand’s Department of Royal Rainmaking and Agricultural Aviation.
The government agency has an annual cloud-seeding programme to stimulate artificial rain and dampen down fine particulates in the air caused by vehicle emissions and agricultural practices.
While we know that building a brand is a complex process, manufacturers who make a conscious move towards sustainable production or provide a solution to the impact of environmental degradation in some way are often seen as leaders in their field - and subsequently afforded unique opportunities to build awareness of their brand.
Leveraging these initiatives requires an understanding of their news value. What we look for to determine whether a story has merit for media is not necessarily that the initiative is at scale or even fully implemented - it can be a small trial, prototype or even just a concept under development. What makes something newsworthy is often centred around how novel it is and its potential to make an impact.
In today’s fast-paced world, businesses and individuals often chase productivity, believing it to be the hallmark of success. However, the relentless pursuit of productivity—defined as the sheer volume of tasks completed—can overshadow a more crucial metric: efficiency. Efficiency, which emphasises the optimal use of resources to achieve desired outcomes, offers a more sustainable and effective path to long-term success.
Improving productivity is a common catch cry for many organisations heard from Governments to Boards and CEO’s. Productivity measures how much work is done in a given period. It’s a quantity-focused metric, often leading to a “more is better” mentality. It’s also an internally focussed metric ultimately linked to the sales growth aspirations of most organisations. Productivity growth leads to more output, therefore more sales, therefore more revenue.
Who wouldn’t want to grow and improve productivity? However the caveat is: Does productivity lead to higher profitability, financial sustainability and adequate margin? Does it lead higher customer satisfaction that will create a long-term success?
In contrast, efficiency measures the quality of the work done – including how well resources, such as time, money, and effort, are utilised to achieve desired outcomes. As a quality-focused metric it prioritises doing things right rather than merely doing more.
There are some pitfalls of prioritising productivity alone. Productivity-driven models often ignore process optimisation, resource optimisation and right first time considerations which can inadvertently create higher cost.
For example, using overtime to achieve an increase in output can harm profitability but tick the productivity box, or perhaps the production or planning process has not been optimised so more output results in more defects, wasted material or other inefficiencies that already existed.
Producing more without regard optimisation can lead to higher cost and increased waste ultimately harming the organisation’s bottom line.
Focusing on efficiency offers a more balanced approach to better business outcomes. Efficiency eliminates the unwanted and the unnecessary to reduce cost and improve quality. Pursuing it supports a culture of ongoing improvement to how the work gets done. It ensures any growth is both sustainable and profitable.
Emphasising efficiency has the potential to protect the bottom line and business outcomes:
1) A focus on efficiency brings quality improvement that ensures “doing things right” and ultimately producing products or services that meet or exceed customer expectations. This focus on quality can enhance brand reputation, customer loyalty and competitive advantage.
2) Minimising waste and optimising processes through efficiency improvement can significantly reduce costs while maintaining output. This not only improves profitability but also positions the company as a sustainable entity.
Shifting from a productivity-centric to an efficiency-centric approach requires strategic changes:
• Quality Focus: Set clear, quality-focused goals rather than merely quantitative targets. For example, instead of aiming to produce a certain number of units, aim to improve customer satisfaction ratings, reduce waste, reduce costs or defect rates.
• Improvement: Regularly improve processes to eliminate waste and improve resource utilisation. Equip employees with the knowledge and skills needed to both identify waste and inefficiency, and take effective action.
• Performance Metrics: Create the right metrics. The simplest course is to make inefficiency highly visible. Good visibility will naturally foster the ownership and accountability necessary to drive improvement.
While productivity has long been celebrated as the key to success, it is efficiency that offers a more sustainable path forward. By prioritising the optimal use of resources and focusing on quality over quantity, individuals and organisations can achieve superior results, increase innovation, and ensure long-term success.
In an era where resources are increasingly precious, embracing efficiency is not just a strategic advantage but a necessity.
Regardless of how much automation, number robots or AI are helping New Zealand’s manufacturing industry, the sector can’t survive without a human workforce. Skilled staff shortages are an issue worldwide for businesses, including in Aotearoa.
As the sector contends with an aging skilled labour pool, complex shift schedules, and balancing productivity with worker well-being, the role of effective workforce management becomes paramount.
According to the 2023 New Zealand Advanced Manufacturing Report New Zealand’s manufacturing sector employs more than 220,000 people, which is about 12 per cent of the national workforce, almost double the percentage employed in Australian manufacturing.
Of the manufacturing subsectors, food and beverage, followed by machinery and equipment, employ the most people.
With so many people employed across different regions and subsectors, critical factors such as interpreting complex award systems, managing overtime rules, ensuring efficient onboarding, handling leave and accruals and maintaining accurate time and attendance records are essential for manufacturers.
These elements are vital for Human Resources (HR) departments to master, so they can streamline operations and foster a happy workplace.
The transition away from manual, paper-based workforce management practices has been a significant leap forward for the manufacturing sector. Embracing digital HR solutions not only enhances organisational efficiency but also unlocks a host of benefits such as time and cost savings and improved resource allocation.
Yet, despite these advantages, some manufacturers retain outdated manual and paper-based processes that inhibit productivity and hamper operational agility.
In the quest for improved efficiency, accurate management of shop floor activities and a
strategic approach to workforce deployment are indispensable.
This includes leveraging technological advancements like a Time and Attendance system tailored for diverse manufacturing environments.
Such systems facilitate precise tracking of employee hours, streamline rostering and support dynamic shift patterns, thereby reducing administrative loads and enhancing payroll accuracy.
Misinterpretation of awards and improper management of overtime often leads to workforce payment errors, which we have seen result in significant legal and financial repercussions for large manufacturing firms since legislation was introduced. Last year, former Labour MP Ibrahim Omer Crimes (Theft by Employer) Amendment Bill passed its first reading and included penalties of a fine of up to $5000 and/or up to one year’s imprisonment for individuals, and a fine of up to $30,000 for companies and other employing entities.
In its Briefing for the Incoming Government last year, the New Zealand Council of Trade Unions (CTU) Te Kauae Kaimahi, which represents over 320,000 New Zealand union members in 27 affiliated unions, says that wage theft is an ongoing problem.
According to the CTU, the government should prioritise action against wage theft as it is widely underreported, and disproportionately impacts low-income workers.
A Time and Attendance system can play a crucial role in mitigating these workforce underpayment risks by ensuring accurate recording of working hours and compliance with a complex set of labour laws and industry awards across New Zealand.
The manufacturing sector is characterised by its continuous operations and potential safety hazards, which necessitates vigilant monitoring of work hours
to prevent employee fatigue, reduce error rates and minimise the risk of workplace incidents.
Implementing an Auto Rostering system simplifies the creation of equitable and compliant shift schedules, taking into account worker preferences and requests, skill sets and legal obligations, thereby promoting a healthy work-life balance and preventing employee burnout.
Easing HR’s administration work with workforce management
Digital workforce management systems offer comprehensive visibility and control over employee data, from leave entitlements to accrual management, enhancing decision-making and operational transparency.
This not only benefits HR departments by easing administrative burdens but also empowers manufacturing sector employees with real-time access to their entitlements, fostering a more engaged and happier workforce.
New Zealand’s manufacturing sector stands to gain a lot from the digital transformation of its workforce management practices because it remains extremely labour intensive. By adopting integrated digital solutions, manufacturers can achieve a harmonious balance between operational efficiency and employee satisfaction.
This strategic approach to workforce management not only saves time and money but also cultivates a more dynamic and productive workforce, setting the foundation for sustained success in a highly competitive environment.
Industry 4.0 refers to the fourth industrial revolution taking place right now. This revolution is driven by the convergence of digital technologies such as the Internet of Things (IoT), robotics, artificial intelligence (AI), augmented and virtual reality, 3D printing and more. Adopting these technologies is enabling manufacturers to enhance their performance, output, monitoring, quality and control on a global scale.
The challenge for New Zealand businesses starting out on their Industry 4.0 journey is knowing when, how and what technologies to adopt to improve efficiency, quality, documentation, business intelligence and sustainability.
This Government initiative enables Kiwi manufacturers to experience Industry 4.0 technologies first-hand via nationwide showcase events, manufacturing site visits, interacting with and learning from industry leaders.
The Smart Factory Showcase is a free, interactive session designed to demystify and break down Industry 4.0 with a world leading NZ example. The session will highlight how incorporating smart technologies improves efficiencies, productivity, connectivity, solves common manufacturing issues and streamlines systems and processes. The Showcase provides an ideal introduction to kick-start or progress your own Industry 4.0 journey.
This event is designed for CEO’s, Digital Technology Managers, Operations Managers, Design Engineers and Managers seeking an in-depth understanding of the latest available technologies for businesses. It is a valuable forum to get buy-in from stakeholders and the events are relevant across all sectors. Teams are encouraged to attend together.
The Smart Factory Showcase highlights Nautech Electronics’ Auckland facility and what the future of advanced manufacturing looks like – You will be inspired, gain powerful insights to enhance your manufacturing agility and be armed with the knowledge to join the Industry 4.0 revolution.
Showcases
It can really help by providing concrete examples of how you can actually apply this stuff and get value from it, and network with others to find out what they’re doing to implement Industry 4.0
Mitchell Sanson, Engineering Manager, Hansa ProductsThe Employers and Manufacturers Association (EMA) has appointed John Fraser-Mackenzie as its new Chief Executive.
EMA Board spokesperson David Welsh says the Board is delighted to have appointed someone of Fraser-Mackenzie’s calibre.
“John brings significant senior leadership and commercial acumen to the EMA and has the experience we need as we continue to update our systems, processes and services to best support our members,” says Welsh.
Fraser-Mackenzie has previously been Chief Financial Officer and Interim Chief Executive at Metro Performance Glass, Executive Director at Pacific Harvest Limited, Finance Director at Goodman Fielder, and Head of Finance Eastern Europe at HJ Heinz.
During his time at Metro Performance Glass, Fraser-Mackenzie refocussed the business and oversaw an increase in revenue, implemented a new procurement structure and led strategic finance, investor relations and governance through a period of significant business growth.
Fraser-Mackenzie says he is excited to have been
appointed as the EMA’s new Chief Executive and is looking forward to taking up the role.
“The EMA is New Zealand’s largest business association and has a long and proud history supporting businesses in the upper North Island,” says Fraser-Mackenzie.
“It’s an honour to have been appointed the new Chief Executive and I am looking forward to getting started and helping build on the work done to date and strongly position the EMA to support and deliver the services businesses need.”
Fraser-Mackenzie, who starts the role on 10 June, replaces Brett O’Riley, who is standing down after five and a half years as EMA Chief Executive.
Welsh thanked O’Riley for his commitment and service to the EMA.
“Brett successfully led the EMA through a period of significant change,” says Welsh.
“The past five years have been some of the most challenging the Association has experienced, with a pandemic followed by a major economic downturn. Brett has done a fantastic job navigating the EMA through these challenges, working more closely than ever with other associations, while supporting
members and overseeing a major upgrade of the Association’s digital platform.
“As a result, Brett ends his time with the EMA poised for growth helping business succeed, which John and the executive team will be in a perfect position to drive.”
The Employers and Manufacturers Association (EMA) is encouraging all manufacturing business owners, managers and workers to take part in a short survey about state of health and safety in the sector.
Head of Advanced Manufacturing Jane Finlayson says the survey is a key part of the research gathering phase of Project Whakahaumaru, which is focussed on developing a harm reduction action plan for the manufacturing sector.
“If we want to create meaningful change, we need to hear from as many people as possible – business leaders, workers and unions,” says Jane.
“By capturing as much lived experience as possible from all those involved in manufacturing, the more informed we will be to understand what is happening on the ground and how we can work together to look at potential solutions.”
To complete the survey, you simply scan the QR code or click here
facilitated by Novona and funded by ACC.
“We’re delighted by the feedback and input we’ve received to date from all parts of the sector and from across the country,” says Jane.
“The conversations we have had to date, including at EMEX, shows there is a strong commitment from manufacturing businesses of all shapes and sizes to work together to create real change to reduce harm and help businesses reduce risks and increase their productivity and competitiveness.”
Jane says the first phase of the project, which included taking a deep dive into ACC injury data, confirmed many of the assumptions the project team had, as well as the insights being provided by manufacturers participating in working groups.
“For example, by far the most common injury in manufacturing is a soft tissue injury mostly resulting from lifting and carrying. We also found that the age group with the highest injury rate was aged between 44-55,” explains Jane.
The ACC data also confirmed the following sub-sectors as warm “hot spots”:
Machinery and equipment manufacturing
· Furniture and other manufacturing
Seafood, meat and poultry, and grain products
Metal products
Wood products manufacturing and dealing
Dairy, sugar and confectionary
Petroleum, coal, chemical and associated product manufacturing
Non-metallic mineral product manufacturing.
“The data from ACC is important because it allows us to not only identify the types of injuries that are most often reported, but also helps us identify how these injuries might contribute to lost productivity due to time taken off work,” says Jane.
“To create meaningful change, we need to reduce both the rate and impact of injuries in manufacturing. This means we will be aiming to help more businesses and their workforces better manage risk and achieve lower rates of harm. This helps uplift the sector in terms of attractiveness for skills and investment.”
Jane says the data tells us so much and the current phase of the project involves seeking insights into what is happening in the manufacturing sector at all levels.
“We have established several Focus Groups and are currently conducting one-to-one interviews with a wide range of people working in the sector. This will build on, and add depth, to the information we are collecting through our surveys and other research activities.
“From here, we’ll move onto the third phase of the project, which will look at analysing and reporting back the findings of our research and working together to start building and testing a harm action reduction plan that will support the sector to reduce workplace harm and keep our workers safe.”
If can learn more about Project Whakahaumaru, including how you can get involved, by visiting www. ema.co.nz/services/manufacturing /project-whakahaumaru.
Sandra Lukey
Sandra Lukey is the founder of Shine Group, a consultancy that helps science and technology companies accelerate growth. She is a keen observer of the tech sector and how new developments create opportunity for future business. She has over 20 years’ experience working with companies to boost profile and build influential connections.
Mike Shatford is an expert in the field of technology development and commercialisation. His company Design Energy Limited has completed over 100 significant projects in this vein by consulting for and partnering with some of New Zealand’s leading producers.
Among Mike and his team’s strengths are industrial robotics and automated production where the company puts much of its focus.
Sean O’Sullivan
Has a B Com (Hons) Otago University. In 2000 - 2001 introduced PCs on the workshop floor and job and staff tracking and a productivity software App to Fletcher Aluminium Group and 100 manufacturers NZ nationwide. In 2001 – 2022 Founding Director Empower Workshop Productivity & Scheduling Software App. 236 manufacturing and engineering clients mainly throughout NZ and Australia, also UK and US.
Iain Hosie
Iain Hosie is a respected figure in the NZ Advanced Manufacturing and Materials sectors, with extensive experience in product development, research projects and commercializing tech products. Iain is a Director and Founder of Nanolayr Ltd, Director for the NZ Institute for Minerals and Materials Research, Commercial Director for Fabribotics Ltd, and Executive Council of BiotechNZ.
Catherine Lye
Is the first Chief Executive Officer of the newly formed cross-sector incorporated society, Advanced Manufacturing Aotearoa (AMA). Catherine has been Head of Manufacturing and Export Communities at the 7,100-member Employers and Manufacturers Association for the past two years. As part of that she has guided the Advanced Manufacturing and Industry 4.0 initiatives.
Adam Sharman
Is a Senior Partner at Dsifer. With a background in technology implementation, manufacturing and strategy, Adam and the team at Dsifer are on a mission to support New Zealand’s manufacturing sector transform using technology, data and analytics to outcompete on the world stage. Combining expertise in data engineering, data science & analytics and visualisation.
Siemens will deepen its collaboration with NVIDIA to help build the industrial metaverse. Siemens is bringing immersive visualisation powered by new NVIDIA Omniverse Cloud APIs to the Siemens Xcelerator platform, driving increased use of AI-driven digital twin technology.
At the NVIDIA GTC, Siemens and NVIDIA demonstrated how generative AI can revolutionize the visualisation of complex data, making photorealism possible, and showcased how sustainable shipbuilder HD Hyundai can use it to develop new products.
“We will revolutionise how products and experiences are designed, manufactured and serviced. On the path to the industrial metaverse, this next generation of industrial software enables customers to experience products as they would in the real world: in context, in stunning realism and – in the future – interact with them through natural language input,” said Roland Busch, President and CEO of Siemens AG.
“In collaboration with NVIDIA, we will bring accelerated computing, generative AI, and Omniverse integration across the Siemens Xcelerator portfolio.”
“Omniverse and generative AI are driving massive transformation for industrial enterprises,” said Jensen Huang, founder and CEO of NVIDIA. “Siemens is bringing NVIDIA platforms to their customers and opening new opportunities for industry leaders to build the next wave of AI-enabled digital twins at every scale.”
In the next phase of this collaboration,
Siemens will release a new product later this year for Teamcenter® X, Siemens’ industry-leading cloud-based Product Lifecycle Management (PLM) software, part of the Siemens Xcelerator platform. Powered by NVIDIA Omniverse technologies, it will provide engineering teams with the ability to create an ultra-intuitive, photorealistic, real-time, and physics-based digital twin that eliminates workflow waste and errors.
Setting up and adjusting details in photorealistic renderings – such as material definitions and lighting environments, along with other supporting scenery assets – will be accelerated dramatically using generative AI.
Tasks that previously took days can be completed in hours, with engineering data contextualised as it would appear in the real world. In addition to engineering, other stakeholders – from sales and marketing teams to decision-makers and customers – will benefit from the deeper insight and understanding of real-world product appearance, enabling more informed and quicker decision-making.
In collaboration with NVIDIA, Siemens demonstrated the creation of real-time, photorealistic visualisation for HD Hyundai, a market leader in sustainable ship manufacturing.
HD Hyundai has been developing ammonia- and hydrogen-powered ships, a complex process requiring oversight of ships that can contain over seven million discrete parts. HD Hyundai can use the new product to unify and visualise these massive engineering datasets interactively.
This is a landmark research effort which brings to life the company’s first experimental generative AI model.
The Bernini model is acutely geared to geometric precision and scale, and can rapidly generate multiple functional variations of a 3D shape from a given input.
Project Bernini was devised by the Autodesk AI Lab within Autodesk Research, which comprises a diverse team of scientists and specialists working on applying AI to aid in difficult tasks in design, manufacturing, architecture, engineering, and construction, as well as the creative processes in media and entertainment.
The model has been trained on ten million diverse 3D shapes – a composite dataset made up of publicly available data, a mixture of CAD objects and organic shapes. Autodesk is also applying a truly
generative approach that produces several variants, giving a designer choice and contributing to their creative workflow. According to Autodesk’s 2024 State of Design & Make report, 78 per cent of business leaders believe AI will enhance their industry and 79 per cent agree that AI will make their industry more creative.
As the team works to refine this technology, Autodesk is actively engaging potential partners to further study and improve the performance of generative models for design and make.
The Aotearoa New Zealand research, science and innovation (RSI) system is one that purportedly values and rewards research excellence and research impact equally. Despite this, the current system favours an approach that focuses on excellent research that has impact vs impactful research that is excellent.
It is a subtle difference but let me explain how that plays out in practice and why there is an inherent bias. For me, this is an important discussion to have as it has flow-on impacts for industry-led researchwhich is mostly impact-led.
According to MBIE “the Endeavour Fund plays a unique role in the science system through an open, contestable process with a focus on both research excellence and a broad range of impacts”. The indicative investment in the 2024 investment round is $57 million per year (projects range 2-5 years).
This makes it a key, if not the key, research investment mechanism for research organisations in Aotearoa. It is highly competitive, with most Universities, Crown Research Institutes and Independent Research Associations competing for this pool of funding. As a result, the success rate is very low (usually below 20%). The application process is onerous and it is run in set rounds, with only one round per year. Missing out on funding can have crippling effects for many organisations. The two main criteria for assessment are excellence and impact. However, excellence is assessed first and then only the top ranking submissions are progressed to the next step where they are assessed for impact.
Essentially, this means that research excellence is given priority in practice. There could be an amazingly impactful research proposal that misses out because it rates less highly in terms of excellence. It won’t even get considered. The fact is that it can’t progress, no matter how impactful it is, even if it is still pretty decent in terms of excellence.
I am not at all advocating that we support projects with low research excellence. What I am asking is, why are we OK with a process that allows this to happen? Are we happy with a process that potentially knocks out the most impactful science before it can even be considered?
Let’s say that we have two projects. Project A is high in research excellence (let’s say it would be assessed
as being a 5/5 for research excellence) and slightly less high in research impact (let’s say it would be assessed as being a 4/5 for research impact).
On the other hand, Project B is less high in research excellence (let’s say it would be assessed as being a 4/5 for research excellence) and high in research impact (let’s say it would be assessed as being a 5/5 for research impact).
In the current assessment process, they are both rating 9/10. However, project B has a higher chance of not being considered for funding as it is more likely to be knocked out of the first stage of assessment because it has rated 4/5 for research excellence.
This is not fair. It is also not sensible.
An alternative approach is to ensure that all proposals are assessed for both impact and excellence or that impact is the first hurdle. Surely, all research must be high impact? Is there any point doing the most excellent research in the world if it has no impact? Conversely, I can see many reasons why it would be important to do the most impactful research in the world, despite it being less “excellent” (noting that excellence is generally described as “the best people, a rigorous approach and optimum results”.
How have we got it so wrong? Is this a sensible way to do things? I can see why it is done this way… it leads to less resources being required for project assessment. However, is that the best outcome for how our major RSI funding is allocated?
This is only one example amongst many where impact is touted as being equivalent but is actually subservient to excellence.
In a 2021 report titled “Excellence in Research” it was pointed out that MBIE uses a definition of “Science excellence”, from the National Statement of Science Investment 2015-2025 (NSSI) “that differs from international practice in excluding non-academic impact.” This report also states the critical point that “Research excellence and impact (seen as the second pillar, alongside excellence, of a healthy RSI sector) are assessed separately”. Unfortunately, this document only focused on discussing the “concept of
research excellence: what it is, how it can be assessed and why it matters”. It did not address research impact, despite noting “excellence and impact are closely linked: in mission-led research, for instance, we want both excellence and impact and these are likely to be correlated”.
In a 2019 position paper titled “The Impact of Research” MBIE introduced a definition of research impact as “A change to the economy, society or environment, beyond contribution to knowledge and skills in research organisations”. Surely, that is the hurdle whereby we should be first assessing where our national research funding is directed. At the very least, it shows why research impact should be considered equal to academic measures of research worthiness for funding.
So where to from here?
In my summation of these two reports; the definitions used in Aotearoa for “research excellence” and “research impact”; and the practical ways that excellence and impact are assessed, there is one very concerning outcome. We are favouring measures of research excellence that largely assess the value of research to the academic community over measures of research impact that assess the value of the research to the whole community.
The National Statement of Science Investment is due for review. I hope that the system is revised to either assess impact and excellence simultaneously or is amended to favour impact. After all, what actually is the point of research without impact… even if it is performed by the best researchers, in the best facilities, with the best methodologies and technologies, and then published in the best journals?
Dr Troy Coyle brings more than 20 years’ experience in innovation management across a range of industries including materials science, medical radiation physics, biotechnology, sustainable building products, renewable energy and steel. She is a scientist with a PhD (University of NSW) with training in journalism and communications.
The race to develop the first commercially available humanoid robot has been primarily concentrated in the US – until now.
Mimic, a Switzerland-based startup, is challenging US dominance and joining the robotics race to be the first to take a robotic arm and humanoid hand combination to market using generative AI, as it raises a pre-seed round of $2.5M. mimic’s $2.5M round is led by early stage Swiss investor Founderful, together with participation from German-based fund another.vc, UK-based Tiny.vc and an all-star lineup of specialised angel investors.
Spinning out from the research university ETH Zurich, mimic was founded by researchers Elvis Nava, Stefan Weirich,Stephan-Daniel Gravert and Benedek Forrai in 2024.
The founding team were working at the intersection of robotics and AI under Professor Robert Katzschmann’s Soft Robotic Labs when they became increasingly convinced that the latest developments in large scale generative AI models would upend a multitude of industries, beyond just language and image generation.
The team set out to develop a foundation model for robotic manipulation and quickly realized how much value their idea held to revolutionise the way robotics fit into our everyday lives and economy.
Today, global labour shortages are rocking businesses across multiple sectors and employers are struggling to find, hire and retain workers.
Against the backdrop of a pronounced shift in work preferences, like reduced hours and enhanced flexibility to work from home, lab or shortages are especially severe in the case of menial, repetitive, and demanding manual tasks.
mimic plans to ease these shortages with dexterous, human-like robotic hands that fit seamlessly into existing manual labour workflows, driven by state-of-the-art AI models trained directly from human demonstrations.
This solution will enable a robot with humanoid hands to understand and imitate any behaviour, simply by watching a human perform it.
This marks a departure from conventional robotic solutions, which focus on being
purpose-built for narrow use cases. Since each use case requires expensive ad-hoc engineering and comprehensive pre-programmed movements, robots are only able to complete the narrowly specific task they are designed for.
In contrast, mimic is developing robots with a unified, general- purpose approach to achieve a variety of tasks with a single robot design.
mimic’s robots will be powered by a foundation AI model, meaning they will be able to reason and understand the physical world. The downstream effect is that robots can execute tasks with minimal demonstrations and without requiring expensive, complicated programming by engineers for each new task.
These robots are designed for any industry employing workers in repetitive but hard-to-automate tasks involving complex motor skills.
Already, the team has been approached by a wide range of initial customers, from supermarkets, industrial baking and gastronomy to manufacturing, recycling and pharmaceutical lab automation.
“Conventional automation leaves a huge gap of tedious, low to medium volume manual labour tasks that often fall under the table because they are too complex or not economical to automate. For companies from retail to manufacturing, it becomes increasingly harder to find the right staff for these tasks. Taking AI-driven robotic manipulation to the next level, we can now address these challenges with unparalleled flexibility and ease of use”, says co-founder Stefan Weirich.
Looking forward, the team will spend the coming months further developing their robot and AI model to prepare for mimic’s official product launch this year.
Taking steps to become more energy efficient and making the switch to clean energy can have plenty of benefits for your bottom line. It doesn’t have to be costly to implement, either.
EECA provides free tools and advice to help your business take the next step – including energy efficiency checklists, energy calculators and advice on the best clean and clever tech on the market.
Discover more at eeca.govt.nz/manufacturing
We have been hearing about Industry 4.0 for some time now, and like any fashion, stories of innovation and success abound. However, some of us are still left scratching with the concepts and applications.
More so, in the rush to adapt tech fashion it is important to understand how the technology fits into your overall systems and processes.
In the maintenance management world, Industry 4.0 offers two powerful advantages, Cloud based maintenance management systems and integrated machine data. The opportunities are endless, but the application of the technology is where the real learning will take place.
Industry 4.0 (IOT 4.0) is the name for the current trend of automation and data exchange in manufacturing technologies. The term comes from the Fourth Industrial Revolution, (or 4.0) and generally involves putting terrestrial intelligence into the internet (Cloud) where it can be integrated, or plugged in, to other systems.
If your vehicle dashboard was weaponised to IOT 4.0, when your warning light illumined to warn of an issue, the same information would be uploaded to the Cloud. Imagine getting a call from BP in response to your low fuel warning light coming on?
As engineers have evolved from gaining respect for their technical ability to gaining respect for their ability to run a maintenance management process, computerised maintenance management systems (CMMS) have become the pivotal tool in enhancing efficiency, productivity, and reliability. CMMS’s have evolved from the 1980’s paper-based maintenance management systems, to floppy disks, hard drives, LANs, WAN’s and finally thin clients.
Now with the internet delivering bandwidth, Cloud driven systems are a reality, offering speed, transparency, and transportability as well as the “plugging in” of contiguous systems, either machine or finance based. The new breed of Cloud (IOT) based CMMS offer the opportunity to integrate seamlessly into this interconnected ecosystem, ushering in a new era of predictive maintenance, data-driven decision-making, and asset optimisation.
The modern maintenance engineer must bridge between reliability engineering and the operational realities to form a coherent work schedule that avoids reliability embarrassment and financial rabbit holes.
Conventionally this would be achieved with strategies including task optimisation (as found results), and condition monitoring (in service feedback). Direct connection to the plant is a paradigm shift in the role, but it must be understood it is simply another tool in the toolbox. Connected machinery is not in itself a maintenance plan.
The ability to harness real-time data from sensors, devices, and equipment from the production environment leverages the ability to gather, analyse, and interpret vast amounts of operational data, enabling proactive maintenance strategies.
By continuously monitoring equipment performance and health metrics, the CMMS can predict potential issues before they escalate, allowing maintenance teams to intervene pre-emptively and schedule repairs during optimal downtime windows.
Cloud based maintenance management systems like MainTrak offer a whole new level of transparency and transportability for the engineer.
Cloud based CMMS offer a number of benefits:
• Low cost of ownership
• Easy to maintain
• User friendly interface (web browser)
• Remote system access
• Faster more efficient support from the vendor
• Open architecture and interfaces
Connected CMMS facilitate condition-based maintenance strategies, wherein maintenance activities are triggered based on the real-time condition of assets. By monitoring factors such as temperature, vibration, and performance metrics in real time, CMMS can dynamically adjust maintenance schedules and prioritise tasks according to the current state of equipment.
This dynamic approach not only optimises resource allocation but also minimises unnecessary maintenance interventions, reducing downtime and operational disruptions.
The trap is in managing the flow of data so that you are driving the maintenance management process, not being driven by feedbacks.
As an example, a Kiwi dairy company was forced to pare back their IOT 4.0 outputs after a flood of overzealous system alarms threatened to swamp their scheduling.
We can however reap the benefits of the IOT 4.0 era to embrace predictive analytics and machine learning algorithms to unlock actionable insights from historical maintenance data. Through pattern recognition and anomaly detection, trends, patterns, and correlations that may go unnoticed by human operators can be recognised and used to trigger work schedules.
This predictive capability enables organisations to transition from reactive and preventive maintenance approaches to a more proactive and data-driven maintenance paradigm, ultimately driving down maintenance costs and extending asset lifespan.
Moreover, CMMS integrated with IoT devices enable remote monitoring and control capabilities, allowing maintenance teams to oversee equipment performance and execute maintenance tasks from anywhere with an internet connection.
This remote accessibility enhances operational flexibility, accelerates response times, and empowers maintenance personnel to address issues promptly, regardless of their physical location.
Where to from here? The application of computerised maintenance management systems in the Internet 4.0 world represents an opportunity for a paradigm shift in maintenance practices, leveraging process feedback to drive efficiency, reliability, and cost savings.
By integrating these advanced technologies logically into the CMMS, organisations can optimise asset performance, mitigate risks, and stay competitive.
Internet 4.0 is like your car telling BP via the internet that it needs refuelling.
Having had the opportunity to attend a number of industry conferences over the past few weeks and network with a variety of industry players, I can’t help but reflect on the role training plays in the Manufacturing sector. I find myself questioning whether there is a reset needed in order for the industry to see the desired value and outcomes from the training investment.
Traditionally, the Manufacturing sector believed that ‘qualifications’ are the currency when it comes to training staff, and while there is a place for qualifications, we need to challenge ourselves on whether we are seeing the outcomes deemed so essential in the current environment through this means of training.
The general feeling amongst the industry at the moment is that there is a need to lift productivity, create a more dynamic workforce and work on the softer skills which ultimately create a more engaged and efficient organisation. Unfortunately it’s commonly agreed that the current qualification based training is not hitting the mark.
With increasing commentary about the need for NZ Manufacturers to invest and adapt to smart technology it has been encouraging to hear the
conversation evolve into the importance of investing and developing in smart human capital as well.
We need to start talking about how we create smart people, and in doing so create a NZ wide training approach that prioritises skills development and transferable skills , creating a team who are fully engaged and adequately equipped to meet the evolving demands of today’s work.
Focussing on transferable skills in critical areas like leadership and problem solving, rather than task based, role specific skills is the step change the industry needs. Not only will this result in positive productivity and engagement benefits, but will no doubt improve employee retention too. According to Gallup’s 2022 global workforce survey, engaged workers are 23% more profitable than non-engaged workers.
With the disestablishment of Te Pukenga and an unclear picture of what the future of the vocational Education system might be, businesses now feel like they are having to shoulder the burden of a system which is not fit for purpose, and we don’t have the
luxury of time to wait for central government to solve this.
The evidence is clear, having a workforce that is capable of learning and applying a wide range of skills leads to increased efficiency and productivity. Rather than being constrained by narrow job descriptions, and traditional task focussed, qualification based training pathways, lets focus on creating teams who have a broader skill set, the ability to handle complex problems, individuals who are constantly looking for opportunities to make things better, with transferable skills enabling them to support different teams and projects, and with the confidence and skills to lead, coach and mentor.
The question is, what now? The answer is simple: invest in your people, invest in creating development pathways to grow their transferable skills, and give them the opportunity to apply them across a range of roles, tasks and experiences.
As a sector, we have an obligation to do right by our people and businesses, rather than live in hope that a pot of funding becomes available to support this.
The EMEX Exhibition happens every other year at the Auckland Showgrounds and is both a chance for vendors to showcase the latest in manufacturing technology, systems and services, but also an opportunity for the industry to comes together to share perspectives on the challenges facing the industry, and the opportunities available through evolutions in approaches, technologies and markets.
The 2024 edition of the EMEX Exhibition was no exception. Following on from the highly attended 2022 edition as the industry came together for the first time since the COVID pandemic, this year’s event had a more grounded feel to it as vendors and manufacturers alike seek to balance innovation and growth for the long term with capital and market constraints in the short term.
One notable change since 2022 was the presence of New Zealand’s first minister for manufacturing, Andrew Bayly. Whilst it is still early days in the establishment of the portfolio, the fact that the industry now has ministerial representation is seen as a positive development as New Zealand struggles to keep pace with the investment in the industry that is being demonstrated overseas.
Whilst there may have been little directly for manufacturers to shout about in the May budget (announced on the final day of the exhibition), Minister Bayly has indicated some positive moves already, notably an extension of the Smart Industry Readiness Assessment funding to support manufacturers identify opportunities for acceleration through the adoption of industry 4.0 technologies.
This visibility of the industry at the ministerial level was welcomed by the exhibitors and visitors to EMEX this year. However, in speaking with attendees, the focus remains on navigating through a challenging economic environment, whilst not limiting potential future growth and agility for the long term.
Whilst every business has its own context, three key challenges were repeatedly identified across industry players.
The challenge of labour capacity availability in 2022, during which, the problem was one of finding the right number of people, appears to have largely dissipated. However, it has been replace by the challenge of quality talent availability.
Organisations are repeatedly reporting that they have enough people, however, labour remains a constraint through higher rates of absenteeism, lower levels of engagement and productivity and lower levels of relevant skills to support future strategic ambitions.
As a result of these constraint, organisations are, in some cases, accelerating their automation strategies to reduce dependence on humans in order to focus on developing their key talent on those higher value, strategic tasks that require skills and capabilities that are harder to automate.
Whilst there are some positive indicators for New Zealand manufacturers, for example an increase in exports to the US market, most organisations are still working within a paradigm of a constrained economic environment, resulting from high inflation and interest rates, supply chain challenges and labour quality constraints.
As a result, most organisations reported a conservative approach to capital outlay, growth targets and investment in R&D and new product development. On the positive side, a significant number of organisations,
recognise the need to use this time to review their operational efficiency, process discipline and strategic priorities to establish a stronger foundation from which to accelerate as the market returns.
With the increasing propagation of connected systems, machines and HMIs, impact of increasing potential frailty points in IT and OT networks is being recognised as a high priority across the industry. This comes at a time when there increasing examples of IT/ OT integration being exploited.
This concern was also reflected the recent State of the Industry report from Rockwell Automation that showed cybersecurity in the top 5 external obstacles for manufactures for the first time.
The prevalence of IoT connected robots and co-bots on display at EMEX this year shows that device and system integration is a fundamental part of the future of manufacturing.
However, as organisations scale up their adoption of IoT connected devices, protecting organisation data and mitigating the cyber security threat resulting from multiple frailty points will only increase in priority.
Whilst these challenges remain a concern for many, there were many opportunities evident through the presenters, exhibitors and attendees that provide grounds for optimism.
More and more organisations are placing data at the centre of the enterprise and operational strategies. As the quality and volume of data increases, and the sophistication of organisations to use it to drive insight develops, many are seeing exponential gains through a data-driven approach to prioritisation, optimisation and strategic advantage.
With the wide-spread adoption of AI, this data is now being put to work to solve optimisation problems previously put in the too hard basket.
The potential use cases and benefits of AI are continuing to emerge. However, the priority for organisations should remain on ensuring that AI tools are being adopted on top of high-quality data. Unfortunately, poor quality data continues to hold back many from reaping these benefits.
Walking round the halls of EMEX this year showcased the variety of lower-cost, modular options for automation. The availability of agile, lightweight co-bots demonstrates an increasing trend in organisations taking a modularised approach to automation, one in which a co-bot is able to perform multiple functions to remove bottlenecks, address skills gaps and/or increase through-put for a manufacturing line.
For New Zealand’s SME business landscape, these tools provide a logical fit for organisations for whom the ROI full automation of a line does not stack up. Using a modularised approach allows for line efficiency and flexibility with a lower payback period; an attractive proposition in capital constrained times.
A notable change from EMEX 2022 to this year’s exhibition was the presence of representatives from, what have been lesser served markets, for New Zealand businesses. This was particularly true of the defence industry, for example with presence from AUKUS.
New Zealand’s reputation as a highly trustworthy and secure country makes our businesses well positioned to support markets for whom security is a priority.
This has been a trend recognised over the last few years and is now accelerating with New Zealand businesses winning work away from cheaper labour economies due their ability to ensure security and privacy, for example in automotive electronics and defence.
It will always be hard for New Zealand businesses to compete on price alone. However, through a focus on process efficiency, quality, flexibility and security we are able to find an alterative competitive advantage. There is no doubt that, for most organisations, the short-term economic conditions will be challenging. However, through a focus mitigating the challenges and exploiting the opportunities described above, there is reason to be optimistic about the medium to long term, so we will wait with interest to see where we are as an industry for EMEX in 2026.
Advertising Booking Deadline – 7 July 2024
Advertising Copy Deadline – 7 July 2024
Editorial Copy Deadline – 7 July 2024
Advertising – For bookings and further informa
Media Hawkes Bay Limited 06 870 9029
Articles to be sent to: publisher@xtra.co.nz www.nzmanufacturer.co.nz
Kayne Mulcahy, Managing Director, Mulcahy Engineering:
This was our ninth time exhibiting at EMEX, with our first being back in 2007. It is always great to reconnect with existing and potentially new customers, suppliers and business partners directly. Having the opportunity to share knowledge and experiences with industry peers is also an invaluable outcome of the show.
Graeme Evans, Regional Vice President (ANZ), Epicor: We support manufacturers across Australasia to optimise their end-to-end operations through enterprise resource planning (ERP) solutions that deliver real-time intelligence. EMEX 2024 was a terrific opportunity for us and a wide variety of individuals and organisations to collaborate around the themes of engineering, manufacturing technology and electronics.
As the largest trade show of its kind in New Zealand, it is integral for cultivating relationships and fostering a culture of innovation and growth, driving the entire sector forward.
Was the energy positive, potential for sales?
Mulcahy:
There was a really positive energy amongst both exhibitors and attendees at this years show, which is pleasing considering the current economic conditions faced by many.
A real sense that businesses are feeling that we may be past the bottom of the cycle and are looking forward to the climb back up to a more favourable trading environment.
Evans: EMEX has now been in operation for more than 40 years – an incredible milestone. There were more than 200 exhibitors and an estimated 5,000 buyers in attendance.
Naturally, there is always potential to drive sales at EMEX, but Epicor’s priority for the three-day event was to meet with our existing customers and establish new relationships with organisations that we can empower in the short and long term.
Mulcahy: Access to talent and labour shortages, particularly over the past two years have presented major challenges to manufacturers and has undoubtably impacted productivity in our industry.
Also, NZ’s manufacturing economy is typically a high mix, low volume environment, this requires business systems and processes to be agile so they can flex with demand.
Evans: It’s no secret that New Zealand is currently undergoing its second recession in 18 months. Demand is slow, and supply chain issues continue to hurt manufacturers and the business landscape more broadly. In particular, labour shortages have been a real challenge for manufacturers as there is a lack of talent in the local market, and that is having a real impact on productivity.
Evans: The perception is that a smaller portion of manufacturers use advanced technology, and this leaves them at a significant disadvantage compared to global peers.
The instinct for companies to cling on to older factories or equipment to try and save on costs can impact on medium to long term business performance.
A thoughtful re-design of production facilities can make a company more efficient and help it to save more money in the long run. Deploying powerful digital solutions that enable manufacturers to quickly convert real-time data into actional insights, helping to ensure greater business agility and resilience.
The latest Gartner survey showed 80% of CEOs plan to increase digital technology investments to counter current economic pressures. In such a competitive economic environment, NZ manufacturers need to innovate, or risk being left behind.
If NZ companies exported more manufactured products, not just tech software, would this make it easier?
Neither Mulcahy nor Epicor exports technology software out of New Zealand. For context, here are short descriptions of Mulcahy and Epicor:
Mulcahy: A metals-based contract manufacturing company, partnering with innovative product leadership companies who have developed products and IP but can’t or don’t want to manufacture them themselves - Mulcahy is their manufacturing arm.
Epicor: A leading provider of ERP software for the manufacturing and logistics sectors in NZ. Epicor’s IoT, data, and AI/Cognitive ERP capabilities helps its customers to drive efficiency, productivity, and growth.
Our productivity level is low, partly due to us being large importers of products. Your thoughts?
Evans: Labour shortages are an ongoing concern within the NZ manufacturing and logistics sectors. Wages and productivity are also key concerns, with manufacturers struggling to attract and retain new staff.
For NZ manufacturers to prosper in times of global economic uncertainty, they must invest in process improvements and technology, in-house staff training and development, and supply chain resilience.
New Zealand’s educated workforce, high production standards, and stable regulatory environment are a particularly attractive value proposition for companies looking to diversify their supply chains.
With the help of technology, NZ manufacturers can capitalise on Industry 4.0, digitising their operations and processes to better support and attract employees, which will help to enable them for growth.
Evans: Labour shortages are an ongoing concern within the NZ manufacturing and logistics sectors. However, as mentioned, with the help of technology, NZ manufacturers can capitalise on Industry 4.0, digitising their operations and processes to better support and attract employees, which will help to enable them for growth.
While digitisation can be a long process, manufacturers that invest in upskilling their workforce and automating their processes, will ultimately enable their employees to do more, and attract those who want to work in organisations using the latest technology that will not only help the business but also advance their career.
Mulcahy: Absolutely, NZ is full of innovative product leadership companies who punch above their weight on a global scale.
We are exposed to many companies who fly below the radar domestically but are true product leaders internationally. Our vision is to partner with as many of these as we can to leverage off their growth.
Our value proposition is that we allow our customers to focus on their core business activities, R&D, product development and sales channels, whilst our investment in our people, process and technology supports their success, that’s our purpose to ‘enable innovation’.
Mulcahy: Yes, we export manufactured products both directly and indirectly through our New Zealand based customers. We see ourselves as an enabler to the New Zealand export community.
Seequent, The Bentley Subsurface Company headquartered in Ōtautahi Christchurch, has launched Visible Geology, a free web application to teach earth science students how the earth works – in 3D.
Seequent, New Zealand’s largest software solutions company and a former Hi-Tech Company of the Year, engaged game development studio CerebralFix, whose clients include Disney, Pixar, and DreamWorks, to build the Visible Geology app.
Together, they have created an immersive, intuitive gaming experience that is set to transform the way earth science students are taught the key concepts of geology.
Geology is a foundational science for understanding the earth. The app moves beyond traditional 2D and paper-based teaching methods into immersive 3D modelling in the cloud via a simple, intuitive interface. Anyone with access to the internet can access Visible Geology for free – no subscription required.
Graham, Grant, CEO, Seequent, said: “Everyone at Seequent is passionate about inspiring the next generation of earth scientists. We know how critical earth scientists are to understanding the earth’s resources and solving some of the world’s most urgent and complex challenges – from climate resilience to the energy transition.
“With falling enrolments and older professionals retiring, there is a workforce crisis ahead that is set to impact our way of life. That’s why we have taken our world-leading expertise in earth science software and brought in gaming experts CerebralFix to build Visible Geology and have decided to make it available to everyone, for free.”
Around the globe, universities are reporting a significant decline in earth science enrolments and courses are being cut. Australia has witnessed a 40% slump in
geoscience students completing degrees in the last eight years*, and in 2020 the UK reported a 43% decrease** in students studying geology since 2014. The American Geosciences Institute has reported a workforce deficit of 130,000 geoscientists in the US by 2030***.
CerebralFix Co-CEO Chelsea Rapp said: “Video games have an incredible ability to transform education by blending immersive experiences with interactive learning. They are much more than just entertainment; applications like Visible Geology are dynamic tools that empower learners to explore and experiment in ways that traditional methods cannot match.”
Dr Kate Pedley, Geology Lecturer, University of Canterbury, New Zealand, was part of the Visible Geology testing process with her students and is already incorporating Visible Geology into her undergraduate courses.
Dr Pedley said: “Visible Geology is intuitive and easy to use. Students can play around with it and have a bit of fun and it builds understanding in a way that complicated 2D maps can’t. Visible Geology builds a
bridge for students to the professional geoscience software they will use in their careers.”
Visible Geology complements Seequent’s academic program, an international network of students, educators, and researchers using Seequent’s professional software for low or no cost to advance our understanding of the earth at more than 500 leading universities.
References
*Australian Geoscience Council’s Australian Tertiary Geoscience Education Profile
** Enrolment in crisis: A UK-wide strategy for exciting, engaging and retaining students in the geosciences A joint report from The Geological Society of London and University Geoscience UK
*** Geoscience Workforce Projections 2019-2019, American Geosciences Institute data sheet
Seequent, The Bentley Subsurface Company, helps organisations to understand the underground, giving them the confidence to make better decisions faster.
Seequent builds world-leading technology that is at the forefront of Earth sciences, transforming the way customers work.
Zak was asked to be involved with manufacturing and education organisations with interests in engineering and design. As an example of what is possible and for his input and experience in manufacturing machine building.
Of the smaller businesses exhibiting we met some really good people. Running their own NZ businesses they fully understood how we were feeling, would we be successful after 12 months of very hard work and total investment, or not.
There was an element of Imposter Syndrome before arriving at EMEX and during the setup. Seeing all the serious CNC machines there such as HASS and Mazak with their sales teams and glossy stands. The giant stands of those like Amada which we were told by their team cost over $350K.
However Zak’s machine only ever received great comments - on its finish, build quality and its potential. People from the big CNC players all came over to check it out and to meet Zak.
Everyone agreed there is nothing like it, no machines with the same capabilities available in New Zealand or Australia. All were impressed.. Great feedback.
But are we in business or are we broke?
We had been told by more experienced exhibitors not to expect confirmed sales during the show. This proved to be the case.
However, there was a great deal of interest in the DATUM Series One Gantry Mill CNC. Some hot prospects. From a few different business types as
Every day Seequent helps them develop critical mineral resources more sustainably, design and build better infrastructure, source renewable energy, and reduce their impact on the environment. Seequent operates in 150 countries while proudly maintaining headquarters in New Zealand.
CerebralFix is a leading game development studio based in Christchurch, which specialises in casual, social and mobile gaming.
well as from the government & education sector. Over the three days quite a few people came back to view it again, often bringing colleagues and co-workers to check it out.
We are quietly, nervously hoping the next 10 days will bring more serious enquiries and confirm our belief that visitors did make decisions at the EMEX show to place orders.
We will start some follow up with the hot prospects next week, after everyone has waded through the many follow up emails, they and we, are getting from exhibitors.
lead times are 8 – 12 weeks for the first four machine orders. It will stretch out a bit after this.
Three Kiwi cleantech startups seeking to follow in the footsteps of Nasdaq-listed waste-to-value leader Lanzatech have been included in a list of those to watch in the Asia-Pacific.
Geo40, Aspiring Materials and Zincovery are part of the most recent Cleantech APAC25, a list of the 25 startups most likely to make significant market impact over the next five years.
The list is compiled by a multi-national panel of experts and curated by the Cleantech Group, an international cleantech market research and events business advisory and consultancy.
“It’s great to see these ambitious Kiwi cleantech ventures recognised again on the world stage hot on the heels of Neocrete, Tectonus and bspkl. making the 2023 CleanTech Forum 50 to Watch list of the most promising startups globally,” says Phil Anderson, Callaghan Innovation Business Innovation Advisor, and New Zealand Cleantech Mission Lead.
Zincovery has developed an industry-disrupting technology to recycle zinc with 20 times fewer emissions and with 45% lower production costs, compared to current solutions. This makes Zincovery the world’s only producer of low-carbon, high-purity, and fully recycled zinc.
Geo40 develops unique, innovative technologies for mineral recovery from underground fluids for deployment in the global transition towards cleaner energy and critical minerals. Aspiring Materials is building Aotearoa New Zealand’s first carbon mineralisation facility.
All three startups were part of the Cleantech Trek USA, a New Zealand Cleantech Mission that connected Kiwi cleantech ventures with corporates and investors at networking events in Silicon Valley, and at the 2024 Cleantech Forum North America, in San Diego, in January.
“For our cleantech founders the value of getting in-market face-time with investors, potential partners, and multinationals at events like the Cleantech Group Forum is absolutely huge.
“Having three of these startups make the APAC25 shows how important it is to have a physical presence internationally at trade shows, and other cleantech industry events.
“The quality of our science and technology is up there with the very best but Kiwi cleantech founders also need to overcome distance from markets, and limited access to capital at home. Additionally, the small size of our domestic market means most of our cleantech founders need to look off-shore from day one. This is why it is crucial that they’re represented at big in-market events where they can gain such great exposure.
“Cleantech Trek USA is an example of how several Government agencies can work together to support our globally ambitious cleantech startups. I’m looking forward to continuing to work closely with Cleantech Mission partners NZTE, Auckland Unlimited, Are Ake, and Uniservices, as well as MacDiarmid Institute, Kiwinet and NZGCP, to support Kiwi cleantech founders at similar events in the near future,” he says.
Recently, eight cleantech ventures attended the Cleantech Forum Asia in Singapore. “It’s fantastic to see NZTE leading this trek – we have great momentum,” says Phil Anderson.
In May, the New Zealand Cleantech Mission launched at Parliament Profiling the Cleantech Sector in New Zealand, a new report outlining the current size and impact of this growing sector. It will also take deep dives into key topics such as investment, regulation,
Looking for a marketing edge?
70% of licence holders say signing on has positively affected sales.
Queenstown Lakes’ commitment to a carbon-zero visitor economy will be brought to life for business owners and tourism operators at the region’s inaugural Electrifying Queenstown business summit on June 24th at Millbrook Resort.
A collaboration between Destination Queenstown and Queenstown Business Chamber of Commerce, the initiative is powered by Aurora Energy, inviting local businesses to unlock the economic benefits of electrification, saving on costs and growing their business while decarbonising.
The one-day event will bring together industry leaders and specialists from a range of sectors including energy, finance, transport, climate and tourism. Destination Queenstown Chief Executive,
Mat Woods, says the summit caters to all businesses, no matter what stage of the regenerative journey they’re at.
“Queenstown Lakes’ visitor economy reaching carbon-zero by 2030 relies on local businesses and tourism operators recognising the rewards of switching to renewable energy solutions such as hydrogen, wind and solar to enable fully electric heating, cooking and transport.
“One of the most effective ways to decarbonise is by going electric. We’re excited to have experts joining Electrifying Queenstown to share knowledge and practical ideas to support the tourism and business community to shift to a sustainable future,” Woods said.
Courts have imposed more than half a million dollars in penalties since mid-March, in cases where workers have lost fingers on machinery that wasn’t kept safe by businesses.
“Businesses must manage their risks to keep workers safe. In each of these cases there was a failure to follow basic machine safety standards. WorkSafe investigated and prosecuted the cases as part of our role to hold businesses to account when they fall short on health and safety,” says WorkSafe principal inspector Mark Donaghue.
“All three cases are from the manufacturing sector – which has a persistent problem with machine safeguarding and is one of the country’s high-risk industries.”
One worker had two fingers amputated and a third degloved in a punch and shear machine, when the regular machine was out of order at Thompson
Engineering in Timaru in January 2022. The business was recently fined $247,500 and ordered to pay reparations of $35,000.
Another worker had three fingers partially amputated while using a punch and forming press at Auckland’s Anglo Engineering in March 2022.
In sentencing, Judge Lisa Tremewan referred to “an unintended complacency” and that “it is critical that robust practices are employed by those within the relevant industries”. A fine of $200,000 was imposed, and reparations of $35,337 were ordered.
And a third worker was cleaning a machine when it amputated two fingers and degloved a third at Flexicon Plastics in Auckland in August 2022. The machine’s on/off switch had been knocked into operation because the interlock wasn’t functioning. A fine of $74,392 was imposed, and reparations of $33,000 ordered.
Guest speakers include Mike Casey, CEO Rewiring Aotearoa and Forest Lodge Orchard; Finn Ross, Lake Hawea Station and Founder of Climate Action Company; and Glenn Coates, General Manager Asset Management and Planning Aurora Energy. During an interactive tradeshow exhibit, businesses can speak with experts about low interest finance options, carbon counting, electric transport, charging solutions and solar.
Queenstown Business Chamber of Commerce Chief Executive Officer, Sharon Fifield, says Electrifying Queenstown aims to transform the question of ‘why should I decarbonise my business’ to ‘how do I get started’, equipping business owners with information they need to start decarbonising and save money while doing it.
“If you are unsure whether your safeguarding is up to scratch, engage a qualified expert as soon as possible,” says WorkSafe’s Mark Donaghue.
“These sorts of incidents are avoidable. Workers should not be suffering harm like this in 2024, and businesses have no excuse. WorkSafe is notified of machine guarding incidents from across the country every week, and is regularly prohibiting dangerous machinery as part of its proactive and targeted assessments. WorkSafe has a role to influence business to make sure they keep people healthy and safe – that’s why we’re speaking out on this issue.”
Workplaces have been required to safeguard machinery since the Machinery Act 1950 took effect. But more than 70 years later, workplaces still aren’t getting it right, with too many workers in Aotearoa being injured and killed from unsafe machinery.
New Zealand Aluminium Smelters (NZAS) has signed 20-year electricity arrangements that secure the future of the Tiwai Point aluminium smelter to continue competitively producing high-purity, low-carbon metal, backed by a diversified mix of renewable electricity from New Zealand’s South Island.
NZAS, which owns and operates Tiwai Point, has signed contracts with electricity generators Meridian Energy, Contact Energy and Mercury NZ to set pricing for an aggregate of 572 megawatts (MW) of electricity to meet the smelter’s full electricity needs. The agreements, which are subject to regulatory approvals and other conditions, are expected to commence in July 2024 and run until at least 2044. Rio Tinto Aluminium Chief Executive Jérôme Pécresse said “We are pleased the long-term future of the Tiwai Point smelter has been secured with these agreements, which were reached with a genuinely collaborative spirit between all parties.
“They give us confidence that our New Zealand workforce and assets can continue competitively producing the high purity, low-carbon aluminium needed for the global energy transition.
“This is an exciting new chapter, and we would like to thank everyone involved, including our new energy partners, our local Indigenous partners Ngāi Tahu, the Southland community, the New Zealand government and our NZAS workforce for their support in getting us here today.”
The new electricity arrangements include 20-year demand response agreements with Meridian Energy and Contact Energy, under which NZAS may be requested to reduce electricity consumption by up to a total of 185MW. This will help ensure secure electricity supply to New Zealand homes and businesses when it is most needed.
In a separate transaction, Rio Tinto has entered into an agreement to acquire Sumitomo Chemical Company Limited’s (SCC’s) 20.64% interest in NZAS
for an undisclosed price. On completion of the transaction, NZAS will be 100% owned by Rio Tinto. Rio Tinto has also entered into an agreement, for an undisclosed price, to acquire SCC’s 2.46% interest in Boyne Smelters Ltd (BSL), which owns and operates the Boyne Island aluminium smelter in Gladstone, Australia. On completion of this acquisition, Rio Tinto’s interest in BSL will be 61.85%.
The sale and purchase transactions are part of SCC’s business portfolio transformation. Each transaction is subject to various conditions precedent, including regulatory approvals from New Zealand’s Overseas Investment Office and Australia’s Foreign Investment Review Board, as applicable.
NZAS contributes about NZ$400 million to the Southland economy annually, or 6.5% of Southland’s GDP.
About 1000 full time-equivalent employees and contractors work at the smelter, with around a further 2200 people offsite employed indirectly.
Digital Product Passports are coming! In the next few years, expect to share your products’ sustainability credentials on a scannable label that explains how consumers can repair and recycle them. It’s another step towards a circular economy that makes the most of resources, extends the life of products, recovers materials and reduces waste.
In time, these passports are likely to apply to many products as the world moves to a more circular economy. New Zealand manufacturers need to get ready.
What is the circular economy and why does it matter?
‘The circular economy changes how we produce and consume goods,’ says thinkstep-anz circular economy expert Dr Jim Goddin. ‘It moves us from the current ‘linear’ way of making things, using them and throwing them away. Instead, we’ll remanufacture products and reuse them and the materials that make them up.’
The circular economy is about more than recycling
‘Recycling can convert waste into reusable material. That’s important but it often devalues material,’ says Jim.
For example, much recycled food packaging includes a layer of virgin plastic to maintain food safety and hygiene. The recycled material loses value through the recycling process because its origins cannot be certain.
Alternatively, a material’s properties can degrade and need to be restored.
‘We can’t make a milk bottle from just recycled materials. We need to add virgin materials. So it’s far better to design products that avoid creating waste in the first place.’
A successful circular economy relies on data. As manufacturers, you need to understand the materials and intermediate goods that go into your products. Where do they come from? What environmental impacts do they create? How can you design your products to make best use of materials and goods – and reuse them?
Consumers need data about the products they buy. What are they made of? What environmental impacts are involved? How can they use these products as sustainably as possible, by repairing and reusing them?
A lack of data currently hinders progress.
‘We need to know what materials products are made of, to keep them in service for longer’, says Jim. ‘This information helps us work out how to reuse or repair products, compost them safely, and separate materials to maximise
the value of recycled materials.’
This is where Digital Product Passports come in.
A DPP is a digital record of a product’s ‘journey’ over its lifecycle and explains what it is made of. It typically answers these questions:
• How durable is the product? Can it be reused, upgraded or repaired?
• Does it contain substances that cannot be passed on? Examples include coatings that prevent composting and chemicals that must be kept out of food.
• How energy- and resource-efficient is it?
• How much recycled content does it contain?
• Can it be remanufactured or recycled?
• What is its carbon footprint?
What do DPPs mean for Aotearoa
New Zealand’s manufacturers?
This depends on the markets you supply. If you supply domestically, be aware that the Ministry of Business Innovation and Employment (MBIE) is investigating DPPs.
If you supply materials, intermediary goods or final goods to the European Union, get ready for DPPs. Last year the European Parliament agreed the new Ecodesign for Sustainable Products Regulation (ESPR) in principle. As a result, suppliers must prove that materials and goods are sustainable, durable and recyclable.
1. See this as an opportunity
Tell your product’s story. What do you want
customers to know about your product, beyond its obvious features? Share the work you are doing to make it more sustainable!
Think about your competition too. How does your product stack up for ‘sustainable’ and ‘circular’? Could you do more?
2 Prepare your data
You’ll need data to back up your story. It will take time to collect. For example, to disclose your carbon footprint or how circular your materials are, you may need to talk with an expert. You may also need a qualified third party to verify your data against international standards.
The good news? Delving into your supply chain and production processes to find this data can uncover opportunities to reduce risks and costs and improve your product and processes.
3 Consider the lifetime of your data
How will you maintain your data? What extra value could you get from it? For example, could you redesign your product to be repairable?
4 Investigate how you’ll structure, store and share your information
Many digital platforms are emerging to help you do this. The platforms need to work together. You’ll also need to make sure your passports ‘talk’ with other systems, such as your production system.
The EU is working on the timeline. Batteries and vehicles, textiles, electronics and ICT, furniture, plastics, construction materials and chemicals will need passports first, likely from 2026/2027. Other industries are expected to follow by 2030. www.thinkstep-anz.com
Things don’t always run smoothly in a production environment. In your sheet metal manufacturing company, you take a lot of care to plan the manufacturing workflow through the different machines you have in your workshop, carefully nesting parts to optimise material utilisation on the machine you have chosen for the cutting.
If that machine is suddenly unavailable it can cause significant delays replanning the nesting and production to suit another machine. What is required is a system that will adapt the nest and the cutting operations to suit another machine in your workshop – resolving a manufacturing headache with a few clicks.
Whatever the reason, breakdown, maintenance, rush job, planning error, the result is the same and the job you have carefully planned, all its nesting and cutting sequences need to be redone for another different machine at short notice to avoid disrupting delivery times and the remainder of the planned workflow.
Machines are rarely 100% compatible so all the nesting and cutting operations need to be started again to generate the right CNC code and methods that suit the substitute machine.
Lantek provides a solution with its ‘Modify Machine’ feature, which will quickly resolve your workflow problems, seamlessly adapting the existing nesting and cutting plans for a new machine.
This capability will save hours of delay, taking away the need to manually recreate programs for a new machine, solving a real-world problem that can happen in a dynamic and fast-moving manufacturing environment.
Manufacture is up and running again without delay and with very little effort.
Additionally, the constraints of having to use a particular machine are removed, further adding to the flexibility and efficiency of a factory and its equipment.
The ability to make changes to the selected machinery at very short notice and with little effort will also have an effect on the mindset during production planning.
Modern production involves a dynamic and constantly changing environment, so Lantek’s ‘Modify Machine’ feature is not just clever technology to solve an immediate problem.
Its benefits can be far reaching, in making the best possible use of the machinery available in the workshop, maximising machine utilisation and increasing the options for using ingenuity to solve production requirements.
By combining the skills of your engineers with the intelligence in the software, Lantek has created a solution for a problem that can also revolutionise how a company investigates ways to use its available machinery to the full.
www.lantek.com
Robots have become an integral part of industry and are increasingly finding their way into small and medium-sized companies in the form of cobots, such as the ReBeL.
They sort, pick and move with the help of cameras, suction devices and gripper systems. igus has now developed a finger gripper for the ReBeL cobot so that it can also perform humanoid tasks. It is made entirely of lubrication-free plastics, and is therefore very cost-effective and easy to integrate.
With the ReBeL, igus has brought a compact and lightweight cobot onto the market, which allows for a cost-effective way to start working with robotics.
It is ideal for assembly tasks, quality inspections and jobs in the service sector. So that the robot can actually perform tasks, it requires grippers and suction devices. For this purpose, igus offers a wide selection of suitable end effectors from various manufacturers on the RBTX.com marketplace.
The ReBeL is light and inexpensive with a weight of around 8 kilogrammes and is often used in humanoid applications. Requests were made for a robot hand that can be easily connected to the ReBeL via plug and play. Precise movements thanks to high-performance plastics
All components, including the flange, cables and control unit, are provided directly from igus in Cologne. This gives the customer a solution that is 100% compatible. Lubrication-free high-performance plastics keep the price low. The plain bearings in the joints made of iglidur polymers are not only cost-effective and lubrication-free, but also ensure smooth and precise movements of the individual fingers. Extensive tests in the company’s own 3,800-square-metre laboratory guarantee the longevity of the humanoid hand.
They are extremely flexible and can be controlled via various interfaces, including USB, TTL (5V) serial and internal scripting. In addition to the finger gripper, igus offers other products for the ReBeL environment. These include, for example, fire-resistant smoke hoods, a 7th axis, gripper sets, adapter plate sets, energy supply systems, a finished workstation and connection cables. www.treotham.com.au
igus has developed a finger gripper for the ReBeL cobot. The ReBeL can perform a variety of simple humanoid tasks with the new low-cost robotic hand. (Source: igus GmbH)
TechRentals® is an IANZ endorsed Calibration Laboratory We offer both IANZ Endorsed and Traceable Calibrations of test and measurement equipment inluding:
As the demand for laser processes with higher throughput is increasing across all industries, quality standards are being tightened. As a result, conventional laser scanning systems quickly reach their limits.
Aerote is addressing this issue by upgrading AGV laser scan head performance through a powerful controller feature, Enhanced Scanner Control (ESC). The new ESC feature for Automation 1-GL4 2-axis laser scan head drives is a totally passive control loop enhancement that ensures higher accuracy during the most dynamic motion.
Aerotech’s 2-, 3- and 5-axis laser scan heads all benefit from this feature, which enables higher accelerations with less tracking error so users see significant enhancement in laser process throughput.
The ESC feature increases the performance of all AGV laser scan head products without the user needing to change the trajectory or how the motion is commanded.
Users need to push their scan head products to faster and more dynamic limits without decreasing precision. This upgrade enables productivity increases because units per hour can increase with no drop in quality.
A wide range of laser applications are already benefiting from ESC, including:
• Percussive laser drilling for electronics & semiconductor applications: ESC delivers increased hole drilling efficiency with strict hole profile quality requirements.
• Laser cutting and micromachining of display glass for automotive and mobile applications: Increasing cutting velocity without sacrificing on-edge quality means higher throughput and steady quality yields.
• Laser welding of medical devices: Higher frequency wobble motion during welding profiles enables higher weld quality and minimises post processing.
Up to 35 percent more efficient when compared to conventional rotary blowers, the CBS series from Kaeser brings all the advantages of rotary screw blower technology to lower flow rate applications, such as those found in wastewater treatment plants, and all in a compact solution.
For municipal or industrial wastewater treatment plants requiring compressed air with differential pressures of up to 1100 mbar, the CBS series rotary screw blower from Kaeser is the perfect solution – with motor powers from 7.5 to 22 kW and flow rates from 2.3 to 12.2 m³/min.
Thanks to its many advantages, the CBS also shines in applications such as the production of aeration air in water treatment processes including bioreactors, flotation and fluidisation. It’s up to 35 percent more efficient compared to conventional rotary blowers and offers significant energy advantages in the two-digit range compared to other screw and turbo blowers on the market. Thanks to its broad flow rate control range, the CBS can also cover extremely low air demands in such a way that no wasteful oversupply occurs.
This impressive efficiency is achieved in part through the use of two screw rotors featuring the renowned Sigma Profile which are taken directly from Kaeser’s rotary screw compressor segment. Even at maximum speeds, these rotors ensure minimal transmission losses, delivering the operator the lowest-possible energy costs.
The energy efficiency of the CBS, its low maintenance requirement and the ability to set up CBS units directly adjacent to one another make this series especially advantageous for continuous operation.
They come equipped with either an integrated frequency converter or star-delta starter, as desired. The non-slip synchronous reluctance motors in versions equipped with a frequency converter also increases the overall efficiency.
The rotary screw blowers are delivered as connection-ready machines (with power electronics and the Sigma Control 2 controller) that can be put into operation immediately, with minimal time and effort.
The Sigma Control 2 blower controller, which is also integrated, ensures comprehensive monitoring and straightforward connection of each individual machine to the operator’s communication network, compliant with the principles of Industrie 4.0. This smart controller also makes it possible to rapidly integrate the blowers into the Sigma Network, unlocking the advantages of the Sigma Air Manager 4.0.
Novacel, a Chargeurs company, is a 40-year-old worldwide leader in surface solutions. Present in 90 countries, with more than 750 employees, Novacel, under the signature ‘Beyond the Surface’, is deeply committed to sustainability and innovation.
Novacel’s purpose is to improve its customers’ industrial efficiency. They offer complete solutions to its B2B customers with industrial processing films, technical tapes, paper products, machines and a set of technical services.
Novacel provides the Glass market with several solutions : process and protective films with specific features (international outdoor resistance up to 12 months, low peel films and film compatible with acid etching process), technical tapes for IGU manufacturing (temperature resistance up to 180°C) and premium vertical lamination machines.
Waste and expense involved in window replacement is a challenge in the glass market. Processing and protective films are used to ensure window glass is not damaged and in need of replacement.
Due to the increasing value and technical capabilities of glass, more than ever before, glass needs to be preserved all the way through the supply-chain.
From handling and transport to site, processing films can be used to ensure the glass surface is supplied to the customer in the condition it left the factory.
Increasingly, with extended Outdoor resistance, Novacel can protect the glass once on construction sites for longer periods of time.
On the worksite, external pollution and degradation of the glass or profiles can lead to the replacement of the window, resulting in both economic and environmental costs for the manufacturer.
In the best case, even if the windows are not damaged on site, cleaning may be necessary (paint, silicone adhesive, cement spots or grinding sparks…), which can result in costly onsite cleaning and the use of cleaning products that can be harmful to the environment and human health.
With these issues in mind, Novacel works closely with its customers and partners to analyse their needs from the beginning of the glass fabrication up to its installation, in order to offer the best range of process & protective films that protect against damage and soiling.
So companies are not using the right product over all?
Windows protection is already widely used for window profiles but it is still in its infancy on glass. Too often, where film is used, it is done so to ensure windows are delivered in good condition to site –but the full lifecycle of the construction site is not considered.
Today, other protection methods like plastic bags
or heat-shrinkable covers are only a transport solution between the factory and site. These are not solutions that offer any protection once the window is installed.
Novacel’s process and protective film solutions stay on the surface through the construction process, with outdoor resistance of up to 12 months, without any disturbance to the ongoing build surrounding the windows. Removal is simple and fast and the film is fully recyclable.
Novacel’s product solutions on glass deliver a reduced carbon footprint and eliminate the need for:
- the use of secondary packaging
- the use of harmful products to the environment (cleaning agents and chemicals).
- damage and, as a consequence, the complete replacement of a window unit which results in the reuse of raw materials, energy and capital in replacing the unit as well as the waste component of the damaged unit
Your approach to safety in volatile environments?
Novacel has developed an eco-responsible range: Oxygen
Novacel’s Oxygen products embody a promise to:
- Reduce fossil raw material usages as far as possible, in order to save these non-renewable resources
- Use as many Renewable resources as possible for a more favorable carbon balance
- Reduce carbon emissions
- Be 100% recyclable
- Be more focused on human well-being
The Novacel Oxygen range offers 3 technology-driven products:
- Oxygen Recycled: a minimum of 25% of recycled Low Density Polyethylene in the formulas of compatible films. Ideal for pre-coated metals, laminates, carpets, glass...
- Oxygen Lean: a reduction of 20% in the quantity of Low Density Polyethylene included in the film. The solution for aluminum composite panels and laser cutting.
- Oxygen Vegetal: minimum 30% of plant oil waste & residue via Mass Balance approach. The most versatile solution for all markets: aluminum, stainless steel, laminates, glass...
How is your company finding current business conditions?
As the market leader in protective and processing films, Novacel has many exciting projects ongoing in the region in our core markets including Stainless Steel and Aluminum, Decorative Laminates and Plastics and Pre-Coated Metals, especially in Appliances and Electronics industries.
Post Covid, and the supply chain issues that followed, we increasingly see Governments and Business in
Australia and NZ wanting to rely less on imported materials and turning back to local manufacturing. Even as inflation suppresses the construction market, we are seeing strong investment in local manufacturing and risk mitigation.
As a result, our technical know-how is in high demand to collaborate and deliver solutions for increasingly challenging projects in the market.
Our core market remains our growth focus. Growth in these sectors is delivered by Novacel’s experience and technical knowledge. Increasingly, we are seeing a trend towards more technical and challenging surfaces and transformations in need of surface solution - 3D laser cutting, textured low energy paint systems and specialized anti-fingerprint coatings are a few examples where our technical knowhow is fueling growth in existing markets.
Secondly, the emergence of technical glass in our challenging regional climates is a massive opportunity. In glass, as already outlined we have an expansive range.
But, we also offer our Vertical Film Laminating Units capable of applying our range of surface solutions vertically within existing glass processing lines - the game changer being the ability to apply our film with the window frame margin unfilmed.
Novacel has embraced the challenge we all face with the warming of the planet. Our mission is to eventually reduce the overall cost and carbon footprint of our customers from our standard range of processing films.
2024 is very much taking the next step by continuing to collaborate with our customers, markets and partners with our innovative new Oxygen range. The ability for us to value add and assist with the challenges we all face is our ‘number one’ priority this year.
www.thinkstep-anz.com
inspired by an animated character in a fantasy television series.
Once a jack of all trades and now an aspiring engineer, Patsy attributes Avatar The Legend of Korra to propelling her into the trade.
“I worked as a cleaner and in a bakery, I studied to be a make-up artist and spent three years as a postie, but it was during the six months I spent jobless watching Avatar that I finally worked out what I wanted to do,” she says.
“One of the characters in the series was an engineer and she was so badass. It really inspired me to see a female doing a job that’s traditionally done by men.”
Fast-forward a few years and the Manurewa 30-year-old is now halfway through an engineering fabrication apprenticeship, and is blazing a trail at Black Steel Mobile (BSM), one of Auckland’s leading steel fabricators.
“I spent the first 18 months as a trades assistant; I was green, I didn’t know anything! After that they put me in a bay to do some basic fabrication and welding, which I was actually pretty good at, so they asked me if I wanted to do an apprenticeship.”
She jumped at the chance.
“Doing a trade gives you a new skill set, you can work overseas, and you don’t have to pay back a massive student loan. There are so many benefits.”
One of eight apprentices currently in training at BSM, Patsy is the only female – but that’s never held her back.
“They don’t treat me any different just because I’m a girl. If they see I’m struggling because I’m not as strong, they come and help me, but they don’t treat me like a damsel in distress. I feel like I’m respected. It all comes down to the effort you put in; if you can prove yourself it doesn’t matter what gender you are.”
Patsy has taken to the practical side of the trade like a duck to water, and her well-honed eye for detail is highly valued in the fabrication bay.
“I’m suited for architectural stuff that requires finesse, anything that needs to look pretty! When we have jobs that require an eye for detail that’s where I flourish.”
The bookwork is proving more challenging, but with plenty of support from BSM and Competenz, Patsy is thriving.
“I can’t say I enjoy the bookwork but there’s an end game. My foreman and supervisor are always here to answer any questions, and so are our qualified apprentices. Then every Monday BSM puts on two hours of evening classes to cement our learning. I feel lucky to have this help; I don’t know if I’d be able to get through it on my own.”
BSM General Manager Steve Powell is thrilled with her progress.
“Patsy is great, and her attention to detail is a huge strength,” says Steve. “The paperwork and relearning how to learn new things academically
has been more of a challenge, but that’s why we have our weekly group training sessions – they’re designed to facilitate that transition from working to working and learning.”
As well as nurturing apprentices through their training, BSM encourages them to attend industry events, further boosting confidence and industry connections. For Patsy, the mentoring is clearly paying off.
“She has so much more confidence now than she did when she started with us,” adds Steve.
Competenz Training Advisor Jonathan Newsome has also noticed the transformation.
“I was really impressed with how Patsy offered to take the stage and share her experience at a recent Women in Trades event; she’s a great role model for other women considering careers in the trade,” says Jonathan, who helps guide Patsy through her apprenticeship by providing personalised support and ensuring her unique needs and goals are addressed.
On-the-job learning in an industry she loves has finally given Patsy a career to be excited about.
“The first day I walked into this workshop I was like a scared little rabbit, but now I have so much more confidence and faith in my abilities. I can weld and make things from steel. Last year I even made a set of stairs. It was really difficult and at the time I questioned whether I’d actually be able to finish it, but once it was done and installed I felt so proud.
“I’m really glad I watched that Avatar cartoon and it inspired me to become a steel fabricator!”
By not mining vital minerals, NZ is ‘offshoring its own environmental footprint’ – is that fair?Martin Brook, Associate Professor of Applied Geology, University of Auckland, Waipapa Taumata Rau
When Resources Minister Shane Jones recently unveiled his draft strategy for mineral mining, it was quickly criticised by the Labour opposition as “taking New Zealand backwards”. One environmental group even called it a “love letter to mining companies”.
But the government’s ambition to double the sector’s export value to NZ$2 billion by 2035, with flow-on effects for local employment and regional economies, deserves a broader debate.
In particular, New Zealanders opposed to mineral mining must ask whether it is ethically fair and reasonable to effectively outsource the risks of mining to other countries, while benefiting from the modern technologies those minerals make possible.
The government’s mining strategy aims to produce a list of “critical minerals” for exploration. The International Energy Agency identifies minerals such as copper, lithium, nickel, cobalt and rare earth elements as essential components in many of today’s rapidly growing clean energy technologies – from wind turbines and electricity networks to electric vehicles.
Our mission is to share knowledge and inform decisions.
About us
Indeed, according to the United Nations Environment Programme, these critical minerals are increasingly necessary for decarbonising energy systems. One of the three pillars of the draft minerals strategy is the delivery of minerals “for a clean energy transition”. How we source those minerals is an important question.
New Zealand has a rich mining history, with a wide variety of resources still extracted from underground and opencast mines. There is also a long history of opposition to mining, especially in national parks and on conservation land, as well as on privately owned hill country.
And there are legitimate concerns about the environmental, social and governance implications of mining. First, it can have devastating environmental
effects, especially the extraction of high-value critical minerals that often require enormous “strip ratios” and generate huge volumes of waste rock tailings that must be stored.
Put simply, the strip ratio represents the amount of waste material (also known as overburden) that must be moved to extract a given amount of ore. For example, an overburden thickness of 100 metres and an ore thickness of 50 metres would yield a strip ratio of 2:1.
The actual concentration (known as the “grade”) of the target metal within the ore is the other factor to consider. For example, copper ore usually contains about 0.5% to 2% copper. A high-grade ore may be extracted from a mine with a high strip ratio, potentially generating enormous volumes of waste rock.
The waste is crushed, liquidised into slurry and pumped behind tailings dams, where it desiccates over time. Tailings dams are constructed to grow in height over decades as the mine progresses. Effective management is integral to the safety of a mine and any downstream population. Tailings dam failures can lead to high-velocity flood disasters. But the well managed and stable tailings storage facility at OceanaGold’s Martha mine at Waihi shows what can be achieved with sufficient engineering and environmental regulation.
Second, mineral extraction has caused and fuelled decades of unrest and civil war in some countries. The minerals most associated with funding conflict – the “three Ts” of tin, tungsten and tantalum –are present in many everyday products such as smartphones and laptops. Tantalum in particular is listed as a “conflict mineral” by the European Union. According to the US Geological Survey, the source of tantalum has dramatically changed in recent years. In 2000, Australia produced 45% of global tantalum
concentrates, but by 2014 this had dropped to 4%, offset by extraction in the mineral-rich but war-torn Katanga province of the Democratic Republic of Congo.
New Zealand is hardly in the same category. But the country’s mineral deposits are often found in mountainous areas, formed by the heat and pressure associated with tectonic processes over millions of years. Often these upland areas are beautiful national parks.
At the same time, New Zealand will need to use extracted minerals – either from its own mining operations or those of other countries – to make the transition to green energy and maintain present standards of living.
By not exploring the mineral mining potential in its own backyard, while simultaneously consuming those minerals from other sources, New Zealand is conveniently offshoring its own environmental footprint.
To assume foreign landscapes and environments are more expendable raises serious ethical and moral questions that need to be addressed within the current debate over the government’s draft mining strategy.
One response might be for New Zealand, where it can, to look at extracting and exporting minerals within its own strict safety and environmental regulations. This would help share the global environmental burden of mineral extraction in a more sustainable way.
Such an approach (which might also be applied to the countries from which we source minerals) also fits with the Māori ethic of reciprocity, tauutuutu. This has been applied to modern economic and environmental thinking, and defined as:
an indigenous concept that places an ethical obligation on communities and enterprises to emphasise balance, reciprocity, and symbiosis in their social and environmental relationships.
Behavioural economics has shown that reciprocal behaviour builds trust, which is crucial for long-term relationships. Countries that embrace reciprocity are better positioned to navigate complex global challenges, achieve UN sustainable development goals, build resilient supply chains, and work toward a green future that energy transition will allow.
In anticipation of the critical minerals list the government has requested, New Zealand needs to consider how it can meet the demands of a new economy, practically as well as morally and ethically.