SMART MANUFACTURING
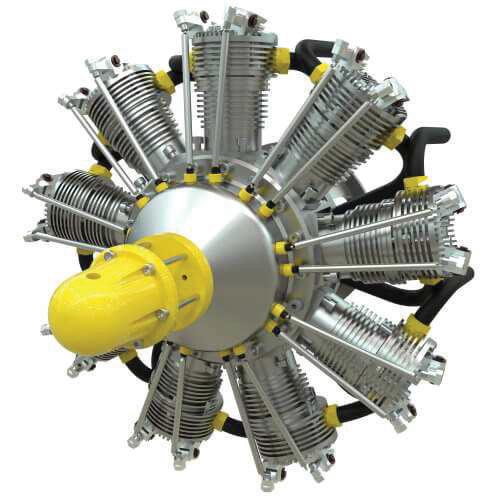
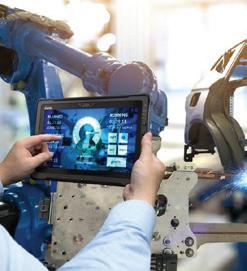
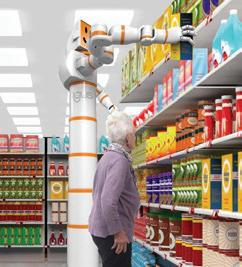
Humanoid robots with low cost automation.
MANUFACTURING The new landscape of the manufacturing industry.

Humanoid robots with low cost automation.
MANUFACTURING The new landscape of the manufacturing industry.
Reflecting on the journey, Industrial Tube general manager Ian Foster says the company has made great progress and achieved a huge amount in 10 years.
“Initially, we operated the stainless mills in Auckland, and then in 2014, added a purpose-built extension for the new stainless plant to our existing facility here in Hamilton,” he says.
“Once the Auckland machinery refurbishment was completed and functioning, we installed a second polisher and added a larger mill from STM Australia. This enabled us to produce 5, 6 & 8-inch tube, all requiring considerable effort to ensure we had the right equipment, capability and capacity to support our customers.”
In 2017, Industrial Tube’s mill team shifted their focus to efficiency, adjusting the plant to enable the production of regular sizes and lengths of tube up to 20 metres, and polishing up to 12 metres, which the company continues to offer today.
“Most recently, we commissioned an internal polisher for the larger sizes of tube, which was designed and built by our internal engineering team. Combined with our BLM LT7 3D tube laser cutter, we are now able to produce almost any requirement in the market,” says Mr Foster.
“We are seeing real benefits from this, recently being awarded two large contracts for stainless steel components, involving several of our processing solutions,” he adds.
Throughout Industrial Tube’s journey, Foster says the
team has strived for quality, and at times, have had to supply replacement products when they missed the mark.
“We have always stood by our service promise, which is the basis of our business philosophy, and are grateful that our long-term suppliers Acerinox (Bahru) and Thyssenkrupp operate with a similar ethos,” he says.
Foster says Industrial Tube is in the stainless tube business for the long haul and will continue to offer all merchants and customers the same Industrial Tube high-quality product and service we are renowned for.
Industrial Tube is a privately owned and operated company, founded in 1985 with its manufacturing base in Hamilton. Industrial Tube began as a manufacturer of precision carbon tube.
More than three decades on, Industrial Tube offers a wide range of value-added services, as well as the production of the stainless hygienic and architectural tube, pre-galvanised tube, and the Ag-Steel horticulture product range.
Industrial Steel celebrates a decade in the stainless tube market.
Improving productivity brings about success.
How to successfully deliver your CRM project with Clarity, Simplicity and Certainty. Safeguarding business from being victimised by money-traps.
Igus accelerates humanoid robotics with low cost automation.
Manufacturers preparing for digital future. The new landscape of the manufacturing industry.
New research to develop first overarching data connectivity standardisation.
Winstone Wallboards uses circular economy to reduce carbon emissions in plasterboard.
Robot scissors snip ribbon at tech hub launch. Robots help customers pick up online purchases.
Robotics Plus modular vehicle to alleviate labour shortages.
Autostore expands local footprint to meet supply chain demands.
Lantek’s version has advances in flexibility and manual process automation.
Euchner Industry 4.0 – ready with ultra-modern safety.
Automated smoke alarm has push notifications.
Zincovery raise brings ‘Green Zinc’ a step closer.
Diversity Works NZ to host international inclusion conference in February 2023. MilkTechNZ brings home Company-X Innovation Award.
Steel awards showcase local industry’s strength and innovation.
Steel Construction NZ Apprentice of the Year.
THE LAST WORD Is low-code the future of manufacturing?
Brett
Media
Doug
T:
Holly
Quality 4.0 is about readying manufacturers
for the future, by equipping them with connected, advanced, purpose-built tools.
So says Scott Philbrook. MD of RS Australia and New Zealand in his article on Page 9. And yes, Quality 4.0 is the digital transformation of quality management, and the alignment of software and digital processes, with the capabilities of Industry 4.0.
The Page 1 story is worth a shout out because of longevity and Industrial Tubes fits the bill, having been ten years in the stainless-steel market.
Copyright: NZ Manufacturer is copyright and may not be reproduced in whole or in part without the written permission of the publisher. Neither editorial opinions expressed, nor facts stated in the advertisements, are necessarily agreed to by the editor or publisher of NZ Manufacturer and, whilst all efforts are made to ensure accuracy, no responsibility will be taken by the publishers for inaccurate information, or for any consequences of reliance on this information. NZ Manufacturer welcomes your contributions which may not necessarily be used because of the philosophy of the publication.
Based in the mighty Waikato, the company entered the stainless market in 2013, purchasing stock and machinery from Stainless Steel Mill.
EMA has been focussed on Industry 4.0 this year and the Network Site visit is a program to encourage sharing of Industry 4.0 knowledge, understanding the technologies and learning from others who have embarked on the journey.
We know that improving productivity with enhanced technology brings about success. So, their efforts are to be celebrated as they support business in the challenging manufacturing environment their members face.
When I look forward to 2023, I consider the key issues business will be facing to include cyber security, renewable energy, supply chain and the circular economy – all areas of focus to ensure business processes work efficiently, maximising materials and minimising waste in time and application.
On Page 2 of this issue, you will find contact details so your company can receive a copy of the Media Kit 2023.
Well worth your while to plan ahead and get involved in one of the better manufacturing and technology magazines in New Zealand and Trans-Tasman.
This is the 4th in a series of 6 articles looking at how to successfully deliver your CRM project. The full series contains:
The development of Business Requirements will, if done right, clearly dictate the functional definition of the solution. This however must be accompanied by an equally clear and complementary data definition. Separate teams should be created for Customer data and Product data as well as Functionally aligned User Teams.
The Product data, to be designed/developed for import, will need to reflect current definitions, additional fields for enhanced usage and the structures and capability of the CRM or operational systems being deployed.
The Customer data will reflect the core business processes of Sales and Transaction processing and the necessary requirements for Marketing to understand the customer sufficiently to generate lead campaigns based on current and potential value as well as fields that reflect the nuances of the customer.
Importantly the Data Dictionary will also include, and match the Business Requirements, the rules pertaining to when and by whom fields will be updated and the mandatory requirements. This is where the devil in the data can be exposed or tamed.
All this happens, and is signed off by all parties, in design prior to work being started or at least completed in the new platform
The model below is the Solution Architecture. Each system will receive, hold and generate data. It is important to define:
• Data will be held within each system. Duplication of data is not optimum but is acceptable as long as data maintenance is automated
• Data will be transferred. Data should be transferred, or better still presented, on an “As Required’ basis. Ie Customer data will be delivered to the Marketing Automation system for activities. The CRM will be the master for all Customer data; Product data will be represented in the Ecommerce solution, The PIM will be the master for all Product data
• Data will be generated. Data will be created as each Customer engagement occurs. Ie A customer will be included in a Marketing Segment for either analysis or activity. That the customer is part of that segment will be flagged and that they were
contacted as part of a campaign will also be flagged against the record
The rules to manage this data proliferation are what will allow the complexity to provide the business value while supporting each process and team.
is here to make it easier to do business; working alongside business leaders and property owners in the region on security, advocacy, development and growth.
These are CSFs for the Selection Process, not the Project: 1. Data design supports all Business Processes
A CRM solution will support multiple Business Units who will have diverse and potentially conflicting
With the New Zealand dollar falling and inflation at record highs, now more than ever, every cent counts.
At times like these, it’s imperative businesses are more critical of where their money is going and know exactly what they’re paying for.
But where to start? Right now, Kiwi businesses are losing thousands every year to one simple yet overlooked issue: currency conversion fees. This issue isn’t just important to large global organisations, it’s important to nearly every Kiwi business.
Whether you’re paying international suppliers or employees, importing materials from overseas, spending while travelling, or even purchasing goods from international websites - you’re most likely paying your bank both a service fee and a marked up exchange rate for each transaction.
The service fee is straightforward. If you use your bank for an international purchase, it will charge a fee for the service it provides. For example, when you use a standard credit or debit bank card you will likely be charged around 2% of every international transaction.
The marked up exchange rate is more complex. It’s typically hidden and you most likely don’t even realise you’re not paying the mid-market exchange rate (i.e. the currency exchange rate you can find on Google). When you make an international purchase, all major New Zealand banks have their own exchange rate which you pay. This ensures your
bank profits beyond just the service fee for each international transaction.
This adds up - previous research from Wise, the global technology company building the best way to move and manage money around the world, shows these hidden fees have cost Kiwis billions of dollars over time. Money that is better kept to spend on your business.
We know that these fees can be a minefield for Kiwi small businesses. Our research, which saw YouGov poll over 4,800 micro small and medium businesses (MSMBs) across the world, revealed more than half (51%) of New Zealand’s MSMBs who felt discouraged from expanding overseas, reported the cost and complexity of international banking as a major deterrent from conducting international operations.
Next time you use your bank to pay an international invoice, travel for work, or pay for something overseas online - educate yourself on the additional fees and charges involved. Know that as a business owner, there are options outside of your traditional bank when it comes to helping your business go global.
As we continue through these difficult economic times, every cent counts. I implore you to take the time to find the best solution for your business. Get it right now, and it will save you a lot down the line.
By Tristan Dakin, Wise Country ManagerAmong
Man, machine – or both? Humanoid robots are no longer science fiction, they are reality. igus has been researching humanoid robotics for some time and has now presented a prototype of the motion plastics bot: a humanoid robot that combines the advantages of high-performance plastics and Low Cost Automation. The robotics components are available from Treotham Automation.
Robots have become an integral part of our everyday lives. Since the transition to Industry 4.0, more and more tasks have been automated – and new forms of robotics are benefiting. But robots can also make things easier in our daily routines.
A humanoid that is both functional and friendly and has human features can support humans not as a machine, but as a partner. There has been steady progress in humanoid robotics research and
development. For example, a research team at the Chemnitz University of Technology is developing an e-skin – a touch-sensitive electronic skin that could make humanoid robots even more human-like.
Driven by the question of the direction into which robotics can develop, igus has spent some time working on its own vision of a humanoid robot – the motion plastics bot.
“With the igus ReBeL and our drytech range, working components were already available to enable a robot to move. The humanoid robot is a project we worked on with the robotics experts from TruPhysics, a Stuttgart-based start-up, who assembled the intelligent humanoid from our motion plastics and other components. It is available there under the name Robert M3”, says Alexander Mühlens, Head of the Automation Technology and Robotics Business Unit at igus. “We hope the bot will demonstrate the interplay between integrated intelligence and our products made of high-performance plastics – at an affordable price.”
Lightweight, maintenance-free low-cost humanoid
For a long, trouble-free service life without maintenance, the igus tribo-polymers in the motion plastics bot offer a clear advantage: no lubricants needed.
At the same time, high-performance plastics allow a lightweight design. They reduce the motion plastics bot’s weight to just 78 kilograms at heights of up to 2.70 metres and a span of 1.50 metres.
The motion plastics bot features a self-propelled AGV (automated guided vehicle), a telescopic body and a head with an integrated screen and avatar for interactive communication.
Another central component is the igus ReBeL, a service robot with cobot capabilities that is used as the bot’s arms. The fully integrated tribo strain wave gear with motor, absolute-value encoder, force control system and controller constitute the core of the ReBeL.
The motion plastics bot moves at a walking pace and has a load capacity of 2kg per arm. It is controlled as an open-source solution via the Robot Operating System (ROS). This is because the entire igus Low Cost Automation product range can be mapped in the ROS.
By studying the motion plastics bot, igus is combining the advantages of their high-performance plastics for movement and their Low Cost Automation expertise to further advance the development of the next generation of robots.
“We see a lot of potential in humanoid robots. But our world is built by people for people. So instead of just using individual automation parts, it makes sense to study humanoids and androids. The question is when the market will be ready”, says Alexander Mühlens.
Human-like robots can perform dangerous as well as simple and monotonous tasks. In a professional environment, work can go beyond the mere pick & place performed by robot arms. In the household sector, a bot can replace several robots: it could vacuum autonomously, mow the lawn, go shopping, cook, do laundry and perform all sorts of other tasks – even caring for the sick.
It would be not just a machine, but a companion that could provide people relief for a long time. “Such a robot has so far been associated with high costs, but if you take into account the possible service life, it would pay off in the long term”, says Mühlens.
“It is our goal to use motion plastics components to demonstrate simple, cost-effective solutions for humanoid robotics.”
Quality 4.0 is the digital transformation of quality management and the alignment of software and digital processes with the capabilities of Industry 4.0.
*Scott Philbrook, Managing Director of RS Australia and New Zealand discusses its elements, implementation, and outcomes in the AU/NZ manufacturing environments:
The manufacturing sector has embraced the digitisation and connectivity of Industry 4.0. Smart, connected technologies have revolutionised all aspects of our manufacturing processes. The ongoing evolution of Industry 4.0 technology, integration, and digitalisation has seen quality management become even more vital to manufacturers; the merging of new technologies and capabilities married to traditional quality management has seen the emergence of Quality 4.0.
This is about readying manufacturers for the future by equipping them with connected, advanced, purpose built tools. Companies that invest shrewdly in Quality 4.0 will not only see increases in operational efficiency, but they will also benefit from maintaining a quality driven culture and increased customer satisfaction.
Quality 4.0 does not replace traditional quality management principles: it instead enhances them to partner with the Industry 4.0 manufacturing environment. There are
elements that support Quality 4.0; they include the ability to effectively collect multiple sources of data promptly so decisions can be made in an agile manufacturing environment as data has always underpinned improvements in quality management. This is supported by connectivity between engineering, manufacturing, and quality teamsand the application of machine intelligence for data analysis.
Implementation and enhancements of Quality 4.0 requires systems including artificial intelligence and machine learning, blockchain, cloud technology, connected and edge devices, and big data that
replaces paper based methods: thus allowing collaboration between all shareholders throughout the manufacturing process. However, Quality 4.0 is not just software: it requires engagement from the top management down, and processes created by those who use the system.
To successfully implement Quality 4.0 a few factors need consideration prior to investment. Identifying areas where Quality 4.0 technology will have the biggest impact, whilst setting expectations is an intuitive way to chart a direction to success. Also, identifying what core competencies of Quality 4.0 that are most relevant to the company’s needs will mitigate against unnecessary expenditure.
Ensuring that Quality 4.0 aligns with the company’s broader digital transformation strategy is also essential.
Quality 4.0 is more than an Industry 4.0 quality management ideology. It is about manufacturers being prepared for the digital future through equipping themselves with advanced, connected tools that enhance quality processes and allow for agile decision making from all stakeholders within the company.
*Scott Philbrook is an expert in digital transformation in manufacturing.
A raft of sustainability initiatives have earned the Liggins Institute’s laboratory the highest level of international sustainability certification.
The University of Auckland research lab is the first university lab in Aotearoa New Zealand to gain My Green Lab certification and only the second lab of any sort across New Zealand.
My Green Lab is a not-for-profit, run by and for scientists, that sets standards for sustainability and supports labs to reach them.
The green lab award comes as Waipapa Taumata Rau, University of Auckland is placed tenth in the 2023 QS Sustainability Rankings, as well as placing sixth in the Times Higher Education 2022 impact rankings
A My Green Lab survey of lab users kicked off the
accreditation process, finding the laboratory was doing well but there were areas for improvement.
“It has been a matter of educating people about what we were already doing, as well as making some key shifts in laboratory practice,” says Liggins technical services manager Eric Thorstensen. The laboratory had been recycling for some time, for example by sending old lab coats to schools and ice packs to the Rec Centre. However, it stepped up its efforts to earn the accreditation.
The ice pack initiative started about 18 months ago as a way of reusing the cold packs that come
with refrigerated deliveries by sending them to the University’s Recreation (Rec) Centre.
Labs are very energy intensive, with two items alone – incubators and tissue/cell culture hoods – using as much energy in a year as an average household. Signs around the lab now alert people to which items can be safely turned off, and timers and sensors are being introduced.
A Property Services electrician calculated that changing all the lab lighting to LED would save $23,000 over ten years; however, this initiative hasn’t been actioned yet.
Digitalisation is transforming the entire realm of the manufacturing industry, from production to delivery. The ongoing shortage of skilled workers, increased competition, supply chain challenges, and changing customer expectations are the driving force behind the persistent digitisation, encouraging manufacturers to deliver better work efficiencies and do more with less.
Technologies such as the Internet of Things (IoT), artificial intelligence (AI), machine learning (ML), and data analytics have played a key role in predictive maintenance, quality control, and real-time transparency in operations while delivering condition-based maintenance insights into systems.
As the manufacturing landscape continues to change, it’s pushing manufacturers to explore new ways of doing business with emerging technologies. Some of the key trends that are shaping the future of the sector include:
• Industry 5.0: the next iteration of smart manufacturing is here. Industry 5.0 brings personalisation and human touch back to the centre of factory operations.
On the production floor, collaborative robots will work alongside employees and help with tasks such as welding, painting, and buffing. By pairing collaborative robots with humans, manufacturers reduce operator workload and enhance job satisfaction.
• Manufacturing as-a-Service (MaaS): the marketplace is seeing an increasing demand for
custom manufacturing, especially from customers who want to reduce high capital expenditures.
The MaaS concept is growing in popularity and is helping manufacturers focus on product innovation while outsourcing the manufacturing process, 3D printed or otherwise, to a third party.
With MaaS, manufacturers save investment expenses, cost of labour, maintenance, and upgrades. It also lends itself to faster time-to-market and enhanced innovation and customisation.
• Internet of Things (IoT): IoT-driven digital transformation can help manufacturers open new value chains in generating valuable data for product design and development and enhance customer experiences. IoT, coupled with data analytics from connected devices, can identify errors and fix them before a customer even notices.
For example, data relayed from IoT sensors can tell when a dishwasher is on the brink of failure. From there, customer services teams can set up a service call, creating a seamless experience for the customer.
• Increased focus on cybersecurity: cyber breaches in manufacturing can shut down production for weeks and cost an excessive amount of money dealing with the consequences.
As manufacturers embark on their digital transformation, it’s essential to consider the digital security risks and measures to take.
Building resilience into digital initiatives, underpinned by zero trust principles, will ensure businesses can anticipate, protect, withstand, and recover from adverse conditions.
• Augmented reality (AR) applications: AR technology through rugged mobile devices helps manufacturers control shop-floor automation systems and other automation solutions directly on the mobile workstation from anywhere within the facility.
This eliminates manual data collection, reduces errors, and streamlines multiple operations.
Rugged devices also support floor operators in challenging environments and can withstand substantial impact. AR technology is developing at a rapid pace and will continue to help the manufacturing industry overcome challenges to become more efficient, innovative, and cost-effective.
Digital transformation is revolutionising all aspects of the manufacturing industry, driving improvements in efficiency and productivity, and helping manufacturers to do more with less.
In fact, the industry has been one of the biggest testing grounds for digital transformation so far and has sought to improve processes, enhance operational efficiency, and provide better insight into supply chain issues including inventory levels and demand cycles. Investing in new digital technologies such as AI, IoT, ML, data analytics, and AR applications will continue to ensure manufacturers drive more growth and innovation for future business success.
Nathan Knight, Hitachi Vantara’s Managing Director for Australia and New Zealand, makes the case for a coordinated approach to decarbonisation and digitalisation
Imagine that manufacturers have a character on each shoulder, one with the word PROGRESS emblazoned across its chest, and the other, SUSTAINABILITY. When deciding where to invest precious resources like time, expertise and money, they can feel like two competing priorities.
“Pick me,” says Progress. “More digital services, more automation, more cloud, more diversification, more data analytics, more!” The other voice pleads, “But what about me? You have to consider the planet, responsible resource management, diversification of your staff and your supply chain. You have to reduce your emissions.” Sustainability’s voice is getting louder and more insistent.
In the pursuit of digitalisation in the name of progress and competitive edge, the two do not have to be at odds with one another. In fact digitalisation is a powerful tool that can help manufacturers achieve the critical sustainability goal of decarbonisation.
Many Eyes on the Manufacturing Sector
Australia strengthened emissions reduction targets with the goal of net zero by 2050.
According to Grattan Institute, decarbonising Australian industry is an “industrial revolution against a deadline” and the scale and pace of change required is unprecedented. The think tank has called for government policy change, stricter emissions limits and a focus on decarbonising heavy manufacturing and mining, which reportedly produce a third of Australia’s carbon emissions.
The heavy industry sector collaborated with decarbonisation experts to form the Australian Industry Energy Transitions Initiative (ETI), which says that regional Australia’s industrial economy could cut greenhouse gas emissions by more than 80% and become centres for multibillion-dollar investments in renewable energy. It would take an unprecedented transformation of the energy system, they say.
Acknowledging that the agriculture, mining, manufacturing, data centre and other sectors will be essential to Australia meeting emissions reductions goals, the government has established a $43M Industrial Energy Transformation Studies Program.
It makes funding available to encourage manufacturers and others to consider decarbonisation efforts including technologies that enable greater flexibility and responsiveness of energy demand, such as digitalisation.
All of this points to the expectation that Australian manufacturers must do what they can to actively decarbonise Australian industry.
The Role of Digitalisation Application modernisation and digitisation of workloads are already underway at many organisations, partly because applications have advanced and requirements have changed, but also to reduce operational overhead.
More efficient workloads and data sharing allow the business to extract and enhance data insights across the organisation and automate daily tasks, both of which can offer savings and agility in the organisation, particularly relevant for the manufacturing sector. A reduced infrastructure footprint can save on power costs.
That’s an excellent business case for app modernisation, but let’s not forget the associated contribution to ESG goals.
Data centres must be powered and cooled 24/7, whether housed within your own premises, or accessed via cloud or managed services. This significantly contribute to the business’ overall carbon footprint. The global carbon footprint for data centres accounts for more than 2% of global carbon emissions, which is reportedly the equivalent of global airline industry.
That number is expected to rise, but your business can take steps to reduce its own infrastructure footprint. App modernisation can provide up to 50% savings in terms of server capacity, reducing the energy consumption of the data centres that service the business, and cutting carbon emissions along with the power bill.
Smarter Data Management involves avoiding unnecessary duplication of data sets (and storage of multiple versions of data sets) as well as leveraging technology such as object storage which makes it less costly to store large volumes of data. Both can contribute to a smaller infrastructure footprint. Applying the right storage virtualisation technology to existing storage environments can also reduce CO2 emissions.
If you opt for an operating system with enhanced data reduction technology, you can store more data within your existing storage capacity. In some use cases a 65% reduction in electricity consumption will reduce CO2 emissions by 65%.
It also makes sense to remove the need for data migration during digital transformation efforts such as upgrades to next generation storage systems. Not only is it time consuming and considered risky in terms of potential data loss or service interruption, but it requires old and new systems to run in parallel throughout the migration phase. Such processes consume a lot more power, require additional cooling and floorspace and can take months to complete.
Assess your options, along the digitalisation process. We recently conducted a data center assessment for a customer and showed that one option under consideration – a storage NVMe flash configuration – created 2.5 times more CO2 compared to the other, an SSD with SAS interface solution. The point is, with the right insight and guidance, CO2 emissions can be driven down.
Replace infrastructure with eco-friendly systems. More than 80% of the value-chain CO2 emissions of a storage product are related to its use after it is sold. At Hitachi Vantara, we are decarbonising our own offices and factories as well as developing new low-carbon infrastructure for our customers.
In fact, between generations of our storage solutions, we cut carbon emissions between 30% to 40% compared to previous models – this includes in the procurement of raw materials, production, transportation, five years of use and final recycle.
Digitalisation and decarbonisation are important drivers for business and for the planet. With the right approach to infrastructure modernisation, an organisation can accomplish both at the same time.
Advertising Booking Deadline – 5 December 2022 Advertising Copy Deadline – 5 December 2022
Editorial Copy Deadline – 5 December 2022
Advertising – For bookings and further information contact: Doug Green, P O Box 1109, Hastings 4156, Hawke’s Bay Email:
Editorial material to be sent to : Doug Green, P O Box 1109, Hastings 4156, Hawke’s Bay Email: publisher@xtra.co.nz Tel: 06 870 9029
At NZ MANUFACTURER our aim is to keep our readers up to date with the latest industry news and manufacturing advances in a tasty morsel, ensuring they do not get left behind in the highly competitive and rapidly evolving manufacturing world.
www.nzmanufacturer.co.nz
Featuring
The Smart Factory Showcase
Your chance to experience the future of advanced manufacturing by immersing yourself in the Smart Factory Showcase.
Transform your business
Understand how Industry 4.0 can transform a business and see first-hand what a high level of maturity in Industry 4.0 technologies looks like, based on a real ‘smart factory’ in New Zealand.
The sessions
Feature a digital twin of Nautech Electronics’ Auckland facility which enables us to deliver real content and stories directly to you. The interactive session examines how Nautech integrated smart technology to enhance efficiency, connectivity, and processes. They also highlight how you can engage and improve employee experiences and enhance manufacturing agility.
Our aim is that you will leave the showcase feeling inspired by the solutions offered and armed with the knowledge needed to kick-start your own Industry 4.0 journey
The Network Site Visits is a programme to encourage sharing of Industry 4.0 knowledge across the sector. Whether you are well into your Industry 4.0 journey or just starting out, the programme provides a range of opportunities to expand your understanding of Industry 4.0 technologies and learn from others who have already embarked on their Industry 4.0 journey. Join us for events, undertake an assessment or expand your knowledge through resources and case studies.
Companies can apply for a fully funded Smart Industry Readiness Index (SIRI) Assessment process to help accelerate their own journey towards Industry 4.0, the result of which will be a benchmark against other companies in their sector and a high level prioritisation roadmap.
Apply for the assessment
The tours provide an opportunity to see first-hand what businesses have implemented as a result of the SIRI Assessment. They will showcase developments, specific technologies and learnings on their Industry 4.0 journey. Targeted at local manufacturers, these events are delivered across New Zealand and are a great way to network and connect with others in the region.
Upcoming events
The webinar series is an opportunity to hear stories from all stages of the Industry 4.0 journey, focusing on the benefits of implementing these technologies, what challenges you may need to overcome along the journey and specific examples of Industry 4.0 technologies, all based on the experience of New Zealand companies.
Upcoming events
Documented as part of the SIRI Assessment, the case studies provide an opportunity to understand a specific example of how Industry 4.0 technology has been implemented in a manufacturing environment. They will provide you with key learnings to take away and inform your own journey.
Resources
Last month I shared the news of the Endeavour Fund’s support for HERA’s four-year research project focused on transforming the construction sector in Aotearoa New Zealand. Today, I wanted to introduce the key research themes and programs which will interact and interconnect as part of the overarching research.
The wider program will develop New Zealand’s first standardisation infrastructure for vertical integration of construction participants’ systems, as well as horizontal integration of the value chain and collaborative networks.
• Circular Design: Using Construction 4.0 enabled data to identify target areas for optimisation and creating a better design. The hypothesis is that structural synthesis system can fulfil optimisation requirements, in which a cost/environmental impact function is minimised considering constraints on design and manufacturability.
• Smart Construction: Investigating intrinsic properties and invariant signatures of construction objects, such as footings, slabs, and beams , as well as their synergistic structural performance, to create a new end-to-end computational platform for design and manufacture.
• Monitoring 4.0: Developing a framework for objective/improved monitoring and performance assessment of structural systems using in-situ data and numerical models, as well as optimal instrumentation plans to maximise the information gain while limiting cost.
• Matauranga Maori and Construction 4.0: Addressing the gap of knowledge by building a uniquely Maori framework. This will create new knowledge domestically and be an international example of indigenous knowledge. As no Construction 4.0 framework currently exists, this is an exciting opportunity to build in Matauranga Maori from the onset.
• Construction 4.0 Technology Transfer: Developing an alternative to traditional linear knowledge/technology transfer in New Zealand construction. This new approach will draw on the principles of co-creating value and models
for knowledge flows in innovation ecosystems, including regulatory governance models and related policy by and for the sector.
• Sustainable Future: Adapt and extend existing greenhouse gas emission datasets (e.g. ecoInvent, BRANZ CO2NSTRUCT) for building materials and products. These will be used to calculate the carbon footprint of the alternative prefabrication and modularisation solutions, and compared with existing approaches using a whole-of-life and whole-of-building modelling approach.
• Computing Technologies for Construction 4.0: Investigating emerging and applicable artificial intelligence approaches and adapt emerging computing techniques to the complex
requirements of Construction 4.0 data. To consolidate work in this area for dissemination across the sector, we are also creating the Construc tion4.0Hub, which you can find and join on LinkedIn https://www.linkedin.com/showcase/construc tion4-0hub/
Separately, we have recently launched the Engine Room, a new series focused specifically on SMEs and their post-pandemic innovation journey. Hosted on HERA’s MetalMind app, the Engine Room is a place for SME owners to connect with each other and subject matter experts to demystify and address a different topic each week. You can find out more by visiting https://www.hera.org.nz/steel-innovation/.
When tackling i4.0, food manufacturing and processing industries are all on a journey of discovery.
Industry supplier NZ Controls includes itself in this bracket, describing the company as a service provider rather than a manufacturer. “We are also working out how it all fits together so that we can help our customers. We want to add value. It’s our responsibility to be informed and ready to help guide our customers into the world of Industry 4. We work hard to battle the hype and drill down into real and practical applications with measurable returns,” says Nikk King, director business development, NZ Controls. NZ controls believes that the best approach is to consider the i4.0 technologies as a set of tools and concepts to enhance what it is already doing. Thus, i4.0 is more an evolution than a
revolution. Nikk says that while the results can be revolutionary, “We don’t need to ditch everything and start again or even make significant physical changes”.
Perhaps the best way to take advantage of the i4.0 tools and techniques is to change or broaden the mindset to one of iterative and continuous improvement. While there’s nothing revolutionary there, says Nikk, NZ Control’s ability to apply emerging technologies leads to newly discovered opportunities for improvement. In some other cases, i4.0 tools may just provide the data needed to prove what you may already suspect, finally giving the justification to get those projects moving.
Another key application for the i4.0 toolkit is to allow more flexibility and potentially ‘revolutionise’ some aspects of production. For example,
evolving from a very linear and inflexible workflow to a more adaptive cell or modular approach, perhaps using collaborative robots and automated guided vehicles to move components instead of traditional conveyors filling up the floor.
“From NZ Controls perspective we must provide measurable value. We seek to collaborate on developing a measurable business case, delivering i4.0 technology solutions and help our customers realise their return on investment. In doing so, we maintain our customers’ trust and in some small way help to evolve the local manufacturing sector into one which is incrementally more productive.”
“You
Circular economy thinking is helping Winstone Wallboards (WWB) reduce carbon in Aotearoa New Zealand’s built environment. Around 15% of our country’s greenhouse gas (carbon) emissions relate to our buildings. Knowing that construction waste contributes heavily to these emissions, WWB set itself a challenge.
WWB manufactures plasterboard under the GIB® brand. It is New Zealand’s only manufacturer of this product. The company wanted to reduce plasterboard wasted in construction across New Zealand by 30% without changing the design of its product.
Its Designing out Waste programme (supported by the Ministry for the Environment, Canterbury Joint Waste Committee, Auckland Council, WasteMINZ, AUT and BRANZ) and circular economy practices have helped WWB reduce waste, emissions, costs and business risks and build relationships and the resilience in the industry.
The circular economy changes how we produce and consume goods. It designs out waste and pollution, keeps products and materials in use, and regenerates natural systems. In a circular economy, sending construction waste to landfill is a ‘leakage’ from the product’s ‘system’ (the processes involved in converting inputs to outputs).
Our thinkstep-anz team helped WWB identify five ‘hotspots’ of greenhouse gas emissions (GHGs) for construction waste across their product’s lifecycle. The diagram below shows the emissions created when the manufacturer makes and transports its product to its customers, and when its customers use and dispose of the plasterboard.
The emissions these activities release are examples of ‘embodied carbon’ in building products. The link between all these sources of emissions? Waste.
-thinkstep-anzof all materials, including 700kg of plasterboard waste, end up in a skip bound for landfill (source: Wastage Rate Report (Construction Resources and Waste Platform), REBRI – BRANZ).
Much of this waste is created when builders cut down sheets of plasterboard. Even when things go to plan, this results in waste: they cannot typically reuse the offcuts. Add in mistakes such as cutting a board to the wrong size or damaging it during storage and the waste ratchets up fast.
To reduce these leakages, WWB now offers a wide range of plasterboard lengths and widths. Customers can order custom sizes if they buy 100 boards or more. This means they can use a size that is most efficient for their project and reduces or eliminates offcuts.
WWB is also pushing for changes across the industry. These include clauses in construction contracts to focus project teams on minimising waste, and encouraging modular design. The manufacturer also supports ‘materials logistics plans’ so that builders receive the right amount of materials at the right time. This reduces the risk of mislaying product, over-ordering, and damaging plasterboard stored on site.
High rates of construction waste mean building projects often use more plasterboard than they need to. As the industry reduces the amount of plasterboard it wastes, WWB can reduce the volume of plasterboard it needs to make and transport to support the same amount of building activity.
These activities help WWB maintain market position: it can adapt its production processes and offer customers value with ‘make to order’ plasterboard. Aotearoa New Zealand benefits too. We can construct more buildings from the same amount of plasterboard, with lower average carbon emissions.
Gypsum is a mineral that contains sulphur and calcium and improves soil structure.
WWB wanted to give this gypsum a ‘second life’. Its partnerships in Auckland, Bay of Plenty, Waikato, Nelson, Canterbury and Central Otago recycle gypsum for agricultural and horticultural uses. Instead of sending waste to landfill, WWB contributes to a circular, biological system.
The manufacturer will continue to extend circular economy in the coming year. When it opens its new plant in Tauriko, Tauranga, the company will be able to recycle waste plasterboard into new plasterboard. This is an example of a circular technical system.
On an average residential building site, around 23%
The manufacturing process creates waste gypsum.
By reducing the factors that cause these leakages, WWB has reduced its greenhouse gas emissions too. These emissions include emissions in the natural gas the manufacturer uses to dry plasterboard, in the electricity, paper and gypsum it buys to make plasterboard, and in buildings around New Zealand.
By reducing its waste, the company pays lower landfill fees. It has reduced its risks by anticipating changes in government policy such as higher waste charges. WWB has built more resilience in the industry by increasing its capacity to meet its customers’ demand.
Circular economy helps WWB build relationships. Customers value the opportunity to make their plasterboard go further, spend less to dispose of their waste, and ‘buy more responsibly’. Employees appreciate being part of a business that is ‘doing the right thing’. The programme helps WWB meet its ESG (environmental, social and governance) targets and keep its investors happy.
www.thinkstep-anz.com
The Business School has unleashed the 5G-powered technology hub Te Ahi Hangarau powered by Vodafone. The hub is already helping to spark innovative ideas by enabling students to harness emerging technologies thanks to significant financial and technological investment from Vodafone in partnership with Nokia.
At the launch of cutting-edge 5G technology hub it was fitting that a pair of voice-activated, 5G-connected robot scissors cut the ceremonial ribbon.
When the magic words - “Alexa, open the technology hub,” were spoken, developer Hayden Moore says a smart home device picked them up, a message was then sent to the internet over Vodafone’s 5G network and on to the Internet of Things (IoT)-powered robot scissors before a motor was activated enabling the scissors to snip the ribbon - sans finger power.
The build, which took around ten hours, utilised emerging tech, including 3D modelling and printing, a custom smart-home routine, and finally, lots of testing, says Hayden. The unique ceremony was just a small demonstration of the impact 5G can have.
Before the cutting-edge ribbon-cutting ceremony,
Business School dean Susan Watson, Vodafone’s Chief Technology Officer Tony Baird and commerce student Isabella Bouwer shared their thoughts on the value of the future-focused tech hub.
Isabella told those gathered that when she put on a Virtual Reality (VR) headset in the hub for the first time, she knew it wouldn’t be her last.
The Bachelor of Commerce student said she was stoked to explore the power of the metaverse and VR during her Business School studies.
“Within the Business 202 ‘Future of Work’ module, we were assigned a task to create a virtual office space using the platform Spatial. Spatial is a software app that enables people to build their own spaces in the metaverse, both for personal and business reasons,” she said.
“My parents often ask me what I’m up to at uni, so when I told them I was creating a business space in the metaverse, they said - when did you get a job at Facebook?
“When they asked me to explain the metaverse, I initially struggled to find the words. I believe the clearest way to tell someone about the metaverse is to think about what it isn’t – it’s not a new
technology, app, or tool; it’s a way of thinking about combining many technologies to experience how we use tech and interact with it across our lives in an entirely new way.
“It’s likely the metaverse and the utilisation of VR technologies will soon transform the workplace as we know it.”
Along with expansive virtual experiences, Te Ahi Hangarau offers students across the University the chance to utilise 3d-printing technology and the IoT.
“By engaging with these emerging technologies now, our students can develop the skills they need to succeed in the future,” Business School dean Susan Watson said at the launch event on 2 November.
Te Ahi Hangarau is already meeting its potential as a hub of inspiration and collaboration - over 800 students have explored the business potential of the metaverse, while students from across campus have participated in a week-long sustainability innovation sprint, and hundreds of students have participated in equipment training – learning about 5G, IoT, VR and more.
The buy-online-pickup-in-store trend is quickly becoming an attractive alternative to “last-mile” delivery. With the first-ever public-facing technology from AutoStore shoppers across Australia and New Zealand can pick up their online purchases quickly with the help of robots.
AutoStore has launched its latest innovation, the PickUpPort, a public-facing port that lets customers shop online and pick up their order directly from the AutoStore System. This technology streamlines retail operations, negating the need for a third-party delivery/courier service to close the last mile, as well as the integration solutions that enable smooth processing of orders from retailer to delivery driver and to customer.
“These potential cost savings and efficiencies benefit the retailer, as well as the shopper,” explains Jason Wu, Business Development Manager for AutoStore Australia and New Zealand. “Customers living or working near the retailer enjoy the benefits of ‘click and collect’ shopping, without the added costs associated with courier or delivery services”.
“With the new PickUpPort, retailers can offer a hassle-free pick-up option in-store, and customers can see how Robots pick, organise, and store items. When retailers adopt this technology, their customers get even more flexibility and freedom,” says Carlos Fernández, Chief Product Officer at AutoStore.
The PickUpPort is an intuitive technology that doesn’t demand extensive implementation and user training. When a customer places an order and chooses in-store pickup, a Controller function asks the AutoStore Robot to pick the Bins that contain the products. The warehouse operator consolidates the order, and the order is stored in the AutoStore System. When the customer arrives at the store, a robot will bring the Bin holding their correct order items to the PickUpPort for easy collection.
The new technology is a direct response to the evolving demand for greater efficiency in the way customers receive products. Adding public-facing
ports to stores can drive additional in-store purchases and enable retailers to provide a frictionless omnichannel shopping experience for customers. “An enhanced customer experience is a significant
Robotics Plus’ autonomous multi-use, modular vehicle platform for agriculture is designed to carry out a variety of orchard and vineyard machine tasks - to alleviate ongoing labor shortages and transform the industry.
The multi-purpose Unmanned Ground Vehicle (UGV) can be supervised in a fleet of vehicles by a single human operator. The vehicle uses a combination of vision systems and other technologies to sense the environment - to optimise tasks and allow intelligent and targeted application of inputs such as sprays.
Growers will be able to rotate multiple tools on the highly adaptable and configurable agriculture platform, depending on the day’s work - for jobs such as spraying, weed control, mulching, mowing and crop analysis.
Steve Saunders, Co-founder and CEO of Robotics Plus, says its world-class team worked alongside growers, researchers and best-in-class technology suppliers to deliver the unique modular architecture for its multi-purpose UGV, which can operate in a range of environments.
“We’ve created a flexible agricultural platform with the power to adapt to different crop types with tools for various applications, providing year-round automation benefits and maximizing machine utilization.
Saunders says that for automation to be adopted, it must also provide a good return on investment.
“Our multi-purpose vehicle replaces tractors and
other tools. But, it does much more than just replacing labor – it’s loaded with intelligence to improve efficiencies,” he says.
The first application for the technology is intelligent spraying. The system intelligently varies the flow rate to ensure spray efficacy whilst reducing inputs. Spray rates and airspeed is controlled in zones and responds as the sprayer moves along orchard or vineyard rows.
The highly manoeuvrable UGV has a small footprint and unique steering configuration, incorporating electric steering and independent motors, which increases productivity - allowing significantly more ground to be covered than machines which turn on every second row or greater, depending on row configuration. The UGV can be deployed in a range of applications in various crop types with a minimum row spacing of 1.8M/6ft.
Dr Alistair Scarfe, Co-founder and CTO of Robotics Plus, says its hybrid electric diesel UGV delivers outstanding performance in the field.
“Electric drive motors give superior torque and control, whilst a Tier 4 diesel generator means the vehicle can operate for extended periods. Fuel consumption is minimized by electrically driving all systems, including tools. Regenerative braking and high-capacity batteries also extend efficiency and range.
“In addition, the vehicle’s lightweight design and intelligent all-wheel-drive system, with independent
wheel motors to ensure grip and control - while significantly reducing ground compaction to protect the soil,” he says.
Robotics Plus has partnered with best-in-class technology suppliers, including Yamaha Motor Company, Autonomous Solutions Inc., and Croplands, to significantly increase the robustness and support for the product in a demanding environment such as agriculture.
Robotics Plus has developed multiple autonomous systems for use in agriculture and automation for intelligent fruit-packing to address significant industry issues, including global labor shortages, rising costs, and yield security. In addition, its robotic automatic log scaling machines are transforming port logistics with improved safety and productivity.
needs. Simple field structure like location may be different for Sales Territory Management and Marketing Segmentation. It is better to have a single view of customer, but not compromised, than multiple fields for the same purpose.
2. Import Clean Data – Time consuming but essential process
a. If importing from multiple sources, consolidate externally adding a source code to each file. Select a master file and build rules for when data conflicts
b. Identify breadth and depth of data to import.
i. Many fields, included when source systems were deployed, will no longer be relevant and/or data has not been maintained so as to not have any value
ii. Historical data will be more valuable for analytics than operational/sales staff, the value therefore needs to be assessed especially if the system has a contact record fee structure
c. Clean duplicates. Be certain on tight vs loose matching criteria. It is better to use loose criteria and run a report for records that would have been picked up in a tight match and have sales staff
manually clean
d. Import Unsubscribe flags
e. Assign / reassign appropriate Sales Team members
3. Maintenance
The day the data is loaded it will start to be out of date. There will be fields that need no maintenance (Date of Birth) Fields that are automatically maintained via business processes (Transaction Data; Marketing Activity) and fields that require additional processes to maintain (Customer Contacts; Opt Outs). Automation of data maintenance creates major efficiencies.
Sometimes it is subtle variances that make the difference in approach and each industry has its own idiosyncrasies:
1. Complexity of SKUs
The complexity of product options driving the proliferation of SKU’s needs to be allowed for in the selection of Products for customers and then the analysis of Sales compared to Market Segments
and Sales Channels. The SKU needs to be to built up and then broken down again.
The interface to the ERP, as well as potentially a PIM and CPQ, requires the data to be transferred and stored for multiple purposes. All data must be clearly identified as to its Master and transfer protocols, unless contained a single system.
Clarity – The Clarity comes from Design. There are so many potential pitfalls in manipulating and structuring the data that a precise, agreed design is absolutely imperative. It is easier to amend functions than it is to change the data model post go live.
Simplicity – Simplicity again comes from design but slightly different in that working through all the pitfalls can produce a simpler data model, with less fields, less rules but still supporting the business requirements.
Certainty – Deploying the data to enable each team the flexibility to deliver on their accountabilities, after rigorous design, will give the solution and business benefits Certainty of being achieved. Flexibility can also require complexity, but by this stage the design will have tamed the Devil exposed by the Detail.
scott@xception.co.nz
In a move that is set to disrupt the warehouse automation industry, AutoStore has announced its strategic penetration of the market, in line with the company’s bold plans for global growth. Through the recent appointment of local Business Development Manager, Jason Wu, the company is well-positioned to expand its footprint across Australia and New Zealand.
AutoStore, which has delivered more than 900 systems across 40-plus countries, is a leader in cubic storage automation, offering innovative Automated Storage and Retrieval Systems (ASRS).
Wu believes there is great potential for a wide range of Australian industries. “Although we are widely accepted in ecommerce there is also potential for everything from grocery and healthcare to industrial and manufacturing industries to take advantage of AutoStore technology”.
Wu believes a new modernised approach to warehousing is required to help business overcome the challenges arising from global megatrends. “This is an opportunity to up-scale and have the competitive upper hand.”
Megatrends: An evolving market demands smart solutions
AutoStore has identified several global megatrends, set to emerge in the local market:
• eCommerce: The swift rise of eCommerce which, according to AutoStore’s research, is expected to represent 25% of global consumer spending within the next few years.1
• Rapid delivery: Rising consumer demand for same-day delivery - in turn, prompting the rapid emergence of micro-fulfilment centers (MFCs), particularly in cities.
• Robotics in logistics: An upswing in demand for supply chain automation, using robotics and related technology. Wu says that the Australian market is yet to catch up to the likes of Europe and the USA, where automation technology has already been widely implemented. “We expect demand for industrial robots will grow at a
compound annual rate of 13% over the next few years.”
• Sustainability: Growing demand for energy efficient, sustainable solutions.
“In response to these trends, customers are in search of flexible, scalable solutions that will enable enhanced operational efficiency, for maximum throughput,” states Wu.
AutoStore is poised to meet the evolving demands of the market with its technology, innovative solutions, customer service and various software packages.
“We customise to the customer’s application - be it inventory and stock management, in-store retail design, warehouse pick processing, or software systems.”
Among these is the ASRS – a system that uses warehouse robots for 24/7 order fulfilment within a cubic layout. Its modular design enables 90% space utilisation. It makes use of cloud-based technology and real-time data collection to facilitate inventory management and predictive maintenance.
In addition, the ASRS comprises intelligent robots, each fitted with up to 50 on-board sensors. These self-diagnose and self-correct, ensuring optimal performance. “The ASRS achieves efficient throughput, of up to 650 bin presentations per hour,” adds Wu.
The integration and implementation of the ASRS is relatively fast - usually taking between 12 to 16 weeks. “This is thanks to the open API architecture of our proprietary software, and the strength of our local integration partner network,” explains Wu. “Our customers achieve ROI within two to
three years of their investment, compared with the average four to five years for shuttle solutions.”
He adds that worldwide, AutoStore achieves 99.7% uptime across its installed base, meaning that its solutions are highly reliable . “This is a very secure system that, at the same time, is very green. It’s one of those rare systems that can run 100% on solar energy,” says Wu.
Confident in its offering to the local market, AutoStore is set to further bolster their offering through a new product launch taking place later this year. “As the Australian market refines its focus on supply chain management, it’s time for companies to think smart about their supply chain. AutoStore is firmly committed to the local supply chain and logistics sectors. We are eager to partner with customers on the development of solutions that fit their footprint, their business, and their objectives,” says Wu.
Jason Wu, AutoStore Business Development Manager, ANZNotes:
1. Source: Premium management consulting company eMarketer, Statista. Global market representing US, Europe and Asia.
The Waikato’s technology sector is in growth mode and emerging agri-tech MilkTechNZ just proved it.
The Te Rapa, Hamilton, company invented wireless milking shed cup removers in the last year, earning it a double whammy at the Waikato Chamber of Commerce Business Awards on November 4.
MilkTechNZ chief executive Gustavo Garza was presented with the Chief Executive of the Year Award after receiving the Company-X Innovation Award from Company-X co-founder and director Jeremy Hughes.
MilkTechNZ’s CR-1 Electronic Milking Cup Removers can be fully customised and programmed from any Wi-Fi enabled device and include a built-in diagnostic system that alerts dairy farmers to any issues that arise during the milking cycle.
Digital technology innovation is the area that Company-X works in and MilkTechNZ’s innovation and export success is another strong affirmation that New Zealand has the capacity to produce world leading digital technology.
The Waikato technology sector’s contribution to gross domestic product (GDP) is around $1.1 billion and climbing. New, innovative, companies like MilkTechNZ show this will continue to grow as they bring new innovations to market.
Cultivate Trust chair Erin Wansbrough said it was great to see an emerging Hamilton agri-tech company take out such a prestigious award for an innovative product sold here and overseas.
“The fact that MilkTechNZ was able to conceive and deliver an award-winning product during such a
disruptive time shows how resilient the tech sector is, particularly here in the Waikato,” Wansbrough said.
“The future is bright.”
The trust recently launched the Tech in the Tron initiative to attract 500 skilled workers and their families to the Waikato from within New Zealand and overseas to grow the region’s technology sector.
The Company-X Innovation Award judges said Garza and the MilkTechNZ team had taken deep industry knowledge and built a business that provided innovative solutions to meet the market.
Previous winners of the Company-X Innovation Award include Yardmaster Effluent Pumps, Montana Group, and the Spring Sheep Milk Co.
Lantek, a multinational pioneer in the digital transformation of the sheet metal, metal cutting and processing industry, has presented over 80 new improvements and advances in its latest software version, Lantek Global Release 2022.
This new update of its product family incorporates significant improvements in flexibility, making it adaptable to the different circumstances of all types of company; usability, for a better user experience and process visibility; and efficiency and automation, to accelerate the speed of the tasks, reducing manual steps.
Several months of intense work, thousands of hours of development, with almost a dozen teams involved, has resulted in more than 80 new functionalities within its portfolio, as well as other internal and architectural improvements that will allow the company to continue guaranteeing the evolution of its products.
To meet these requirements, the new machine configuration module has been completely redesigned for faster system start-up on any type of machine where it is implemented.
Additionally, its innovative process automation module allows users to easily create unattended or guided workflows, and even use the entire Flex3d architecture as a big “black box”, with countless possibilities.
Furthermore, Lantek’s new advanced milling technology management supports different tooling and cutting strategies for machines that incorporate this technology, expanding the available machining possibilities.
Power Sync integration engine, in order to export production information from your MES to external systems, both for cutting processes and for any type of operation.
Quoting has become one of the key processes for many of Lantek’s customers, with new needs as their businesses evolve. Better integration of Lantek MES and Lantek Integra with Lantek Flex3D allows new options for importing, nesting, and time and cost calculation in the tube/profile parts quoting module. Support for assembly quoting has also been improved, thanks to a new, intuitive ability to browse the entire assembly structure of components and the operations involved in the calculation of costs and prices for a quote.
Finally, Lantek Integra perfects material planning, thanks to the ability to “pre-reserve” sheets or profiles in sales orders. This is fully integrated with the Warehouse and Purchasing modules, so the right material can be used later during the nesting process.
The commercial launch of Lantek Analytics in 2021 saw the incorporation of the first SaaS (Software as a Service) application to Lantek’s product portfolio. This business intelligence application collects relevant business data every day. It can be accessed from any device at any time and allows users to see what is happening in the factory with more than 70 predefined KPIs and dozens of metrics and dimensions available. It has never been easier to transparently observe the data of any business, all aggregated into meaningful KPIs.
The Lantek Expert CAD/CAM nesting software solution incorporates multiple improvements, so that its users can use them on a daily basis from different areas of the system. It also has a redesigned module that allows automatic tagging technology to be applied, this provides improved configuration options to adapt to any part geometry or cutting quality, thus avoiding possible imperfections in the final result.
The new version also facilitates the native interpretation of bending line technology from the import stage, as well as the automatic import of nests created by external systems including the automatic detection of repeated parts. Additionally, new options have been added for the semi-automatic generation and modification of scraps.
The market for machining structural tubes and profiles continues to grow strongly, as does the number of new machines, devices and technologies designed to cut these types of part. Lantek’s new update reflects the latest industry demands as scenarios for greater digital maturity evolve.
Lantek MES and Lantek Integra handle workshop management, accurately track resource loading, orders, delivery dates, quality and stock levels, maintaining traceability and flexibility to react to changing circumstances.
To improve traceability, the capabilities for recording information on downtime and reasons for parts scraped during production has been improved optimising their subsequent analysis.
The operator will also have the ability to record changes made to the sheet format ultimately used during the production of a nest, maintaining traceability for any change within the software system.
In this new version, multiple improvements have been made to the
In recent months, Lantek has incorporated numerous improvements into this Cloud-based Business Intelligence module. These allow the creation and visualisation of customised widgets and KPIs, as well as stability and performance improvements.
All these innovations and additions will allow Lantek to position its products at a new level, with the aim of providing its customers with great visibility and control, facilitating and speeding up production.
The proliferation of automation in production is placing new demands on machinery safety and the associated safety engineering while connectivity is becoming all the more important in this sector. As a force for innovation in industrial safety engineering and automation, EUCHNER continues to develop practical, pioneering products that perfectly fit the IoT world. One device, many applications: the CKS2 safe key system
The CKS2 is a new, safe key system that is simple to integrate into the overall control system and suitable for a wealth of applications. By selecting the appropriate RFID key during initial setup, the user decides whether the device should be used as a simple means of starting and stopping machines and processes, as an electronic authorization system for multiple operators or as a trapped key system, for example.
Configuration takes place when the key is taught-in for the first time. The system can be reconfigured to perform different functions at any time. EUCHNER calls this versatility “FlexFunction.” Highly coded, transponder-based keys ensure the highest possible safety level. The system can be connected to IO-Link using the Gateways.
This enables users to implement comprehensive diagnostic and communication functions, such as determining which key was used to operate the installation. The CKS2 is also available as a submodule
for the MGB2 Modular, opening up many new applications for this successful door locking system.
MGB2 Modular – EtherCAT P with FSoE
The highly flexible MGB2 Modular safety door protection system includes the aforementioned submodule for integrating the CKS2 safe key system and a new bus module for the safe EtherCAT P with FSoE, providing users with yet another connection option in addition to PROFINET/PROFIsafe and Ethernet/IP with CIP Safety.
By developing the new bus module for EtherCAT P with FSoE, EUCHNER confirms its pioneering role in the sector of safety engineering for bus systems.
The comprehensive diagnostic functions in the form of EtherCAT messages and the integrated web server provide a fast and detailed overview of the device status. Setting the parameters is easy, so even replacing the module for servicing is a simple task taking no more than a few minutes.
With the Multifunctional Gate Box, users benefit from a highly functional safety door system with guard locking. It not only meets the highest safety level up to PL e, but above all offers a broad scope of customization thanks to countless variants and functions plus diverse options for networking and Industry 4.0 applications.
The CTS safety switch features an impressive locking force, a compact design and flexible mounting options. Measuring only 135 x 31 x 31 mm, the CTS
provides a maximum locking force of 3,900 N. For hinged or sliding doors or extremely small door radii – three different switch mounting directions and a universal actuator with floating bearing enable the CTS to be used almost anywhere. An extendable escape release can be added at any time.
The transponder-based safety switch with guard locking guarantees maximum safety because it meets all requirements for category 4/PL e according to the EN ISO 13849-1 and EN ISO 14119 standards.
With its new FlexFunction, the CTS combines in a single device multiple functions that are otherwise available only in separate variants. This means users can choose whether the CTS operates with or without guard lock monitoring and evaluates the actuator code using a high or low coding level. Functions are selected via the matching actuator. Industry 4.0-ready with the CTS: in addition to communicating intelligently when connected in series with other EUCHNER devices, the new switch can also connect to IO-Link. The CKS2 system is available from Treotham.
The CTS is ideal for applications requiring a high locking force in a confined space. With the new FlexFunction, the CTS combines in a single device multiple functions that are otherwise available only in separate variants.
BFM® Global, the team behind the snap-fit flexible connector, the BFM® fitting, have released a new product enhancement that offers a quick, easy access option for in-stream metal-detector testing and product sampling.
The Quick Access Port is a new add-on option that can be inserted in the BFM® Seeflex 040E or 060ES range of flexible connectors. It gives easy access to product flow to perform metal detector drop-testing, take product samples or even add small-volume ingredients.
Provides fast, easy access to product flow without product spillage.
The Quick Access Port consists of a 56mm polyurethane thread port hole with a stainless-steel screw in plug. The port can be inserted in the side wall of BFM® fitting connectors made from the popular Seeflex 040E and 060ES materials.
The plug can be unscrewed and re-screwed easily without interrupting product flow and without spilling product. This means customers don’t need to remove a flexible connector to do testing or access difficult pipe hatches or doors where there is potential for product loss.
The concept for the Quick Access Port came about from a discussion about the difficulty some customers had accessing product flow for metal detector testing. “They were having to remove the connector each time they tested – which in some cases was hourly - and this was a significant interruption to production” said Matthew Bailey, BFM® Global’s Technical Lead.
By adding a port in the wall of the BFM® fitting connector, it serves as both the chute for product to pass through the detector and as the testing access portal, without product loss or any significant downtime.
It’s taken quite a bit of development to get this innovative new product modification to market and the team are excited about the application possibilities.
“It’s great we’ve managed to solve the initial challenge for use in metal detector testing” said Bailey. “The new port option also means that BFM® fitting flexible connectors can act as easy access hatches for in-stream product sampling and for adding small volume ingredients during processing which is a bonus!”
The Quick Access Port is now available as an optional extra to add to any Seeflex 040E and Seeflex 060ES flexible connector of 150mm / 6” (diameter and length). Both materials are compliant with FDA, USDA & EU food safety regulations.
Time is of the absolute essence when dealing with a fire or smoke event, and the Wiser Lithium Battery Smart Smoke Alarm from Schneider Electric offers peace of mind, with the extra protection layer of push notifications. Sent upon the detection of smoke from the Wiser by SE app, notifications mean people can be alerted even while away from their home or premises so they can take action. The app also provides confidence allowing people to check their alarm is online, has a good battery level and be able to set optional test reminders.
The Wiser Smart Smoke Alarms can be used alone, interconnected wirelessly with other Wiser smoke alarms or as part of a PDL Wiser smart home system. The alarm has many intelligent features, meeting the increasing demand for technical capability in the home.
For tech-savvy customers and those who want a sure sense of safety and reliability, Wiser Smoke alarms can be integrated with other elements in the home for an enhanced warning procedure.
Wiser Automations can be programmed to trigger lights to come on in the bedrooms and illuminate a path to the doorway at night if smoke is detected, helping to ensure maximum time for an escape to safety and property protection. The new dual spectrum photoelectric smoke-sensing technology helps to mitigate false alarms for added confidence.
The Wiser Smoke Alarm has already been recognised globally as a red dot
winner of the 2022 iF Design Awards, which acknowledges excellent design around the world. Every year, an international jury panel of 100 experts honours achievements in products, packaging, communication and service design.
The sleekness of the Wiser Smoke Alarm contrasts with the tiredness and clunkiness of traditional smoke alarms, and the extra-large test/hush button makes it simple to routinely perform a safety check.
Wiser Smoke Alarms are available through local electricians or an approved Wiser Approved Installer’.
Icehouse Ventures and Outset Ventures co-led oversubscribed funding round.
Zincovery has received a $3m NZD investment, led by Icehouse Ventures and Outset Ventures, marking a significant milestone on the path to the world’s first ‘green zinc’.
Zinc, a popular galvanising agent in the metal industry, has a messy environmental record. It’s a rare example of a metal that is more emissions intensive to recycle than it is to mine in the first place, as well as being incredibly expensive, with a high waste profile.
Zincovery has invented a way to salvage zinc from waste using 70% less energy than current methods, at a 30% cost reduction.
“Metal manufacturers are striving to hit the carbon zero 2050 target, but zinc remains a stubborn barrier to achieving these goals. Zincovery’s technology has the promise to significantly improve the environmental footprint of the multi-billion dollar zinc recycling industry,” said Zincovery CEO Jonathan Ring.
Icehouse Ventures CEO Robbie Paul says he is excited to invest in another promising waste to value start-up, the twelfth such investment for Icehouse Ventures.
“Zincovery is very aligned to our objective of doing well and doing good. It is particularly attractive as an investment proposition because the Zincovery team can tap into the experience, connections, and resources of other waste to value trailblazers like Mint Innovation and LanzaTech.” said Paul.
Imche Fourie, CEO of deep-tech investor Outset Ventures, is pleased to support a New Zealand-grown company innovating in a niche, globally relevant field.
“By reclaiming metals from the toxic dust generated from electric arc furnaces, Zincovery has developed technologies that finally make zinc recycling viable.
This speaks to a trend we’re seeing of startups in Aotearoa working to create clean innovations in traditionally “dirty” manufacturing operations, like steel reprocessing.” says Fourie
For Zincovery, building a large-scale plant capable of processing large quantities of waste zinc is a long and difficult road, with a potential $10 Billion pot of gold at the end, says Jonathan.
“The last few years have been about proving Zincovery works as advertised in the lab, which we have been able to do. Our next phase is about proving it at one hundred times scale in our first pilot facility,” said Ring.
The pilot facility, which will be built over the coming year in Zincovery’s Christchurch home-base, will provide the blueprint for a future commercial factory, capable of turning tonnes of zinc dust into a variety of zinc products.
In addition to the investment from Outset Ventures and Icehouse Ventures, Zincovery’s raise saw reinvestment from existing shareholders K1W1, Christian Albrecht, and Wolfgang Leitner, as well as new investment from Climate Venture Capital Fund.
Dr Jez Weston of Climate Venture Capital Fund says the stake in Zincovery underpins the importance of backing companies with genuine emission reduction solutions.
Diversity Works New Zealand is hosting the Whiria Nga Kaha Workplace Inclusion Aotearoa international conference in February next year.
This three-day conference in Rotorua will bring together international and national speakers and will feature a mix of diversity, equity and inclusion practitioners, leaders and people who supported vulnerable groups in the workplace during the Covid-19 pandemic.
The theme for this year, Courage to Connect, reflects
the need to reconnect after the pandemic years, and invites delegates to weave together our strengths to increase economic and social prosperity in New Zealand.
The conference brings together international and local speakers sharing the latest trends and what organisations around the world are doing to advance cultures of inclusion.
It will be an opportunity to reconnect after the pandemic years and weave together our strengths
Zincovery is a company on a mission to decarbonise zinc recycling, with a proprietary technology that significantly reduces the energy required to extract zinc from zinc dust. ZIncovery’s resulting zinc product is at a high grade of purity, gathered at a lower cost than the existing method.
The start-up has already had early success with future customers, signing an agreement with AW Fraser once a commercial plant is operational.
Zincovery was founded by Jonathan Ring (co-founder, CEO) and Aaron Marshall (co-founder CTO) in 2019 while Jonathan was an engineering student at the University of Canterbury and Aaron was his supervising professor.
to increase economic and prosperity in New Zealand. The conference will also launch the Global Inclusion & Diversity Alliance (GIDA) and Diversity Works New Zealand’s professional accreditation programme.
The three-day programme includes presentations from across the public and private sectors, panel sessions and breakout sessions. Early bird registration is available until 16 December.
The Waikato’s technology sector is in growth mode and emerging agri-tech MilkTechNZ just proved it.
The Te Rapa, Hamilton, company invented wireless milking shed cup removers in the last year, earning it a double whammy at the Waikato Chamber of Commerce Business Awards on November 4.
MilkTechNZ chief executive Gustavo Garza was presented with the Chief Executive of the Year Award after receiving the Company-X Innovation Award from Company-X co-founder and director Jeremy Hughes.
MilkTechNZ’s CR-1 Electronic Milking Cup Removers can be fully customised and programmed from any Wi-Fi enabled device and include a built-in diagnostic system that alerts dairy farmers to any issues that arise during the milking cycle.
Digital technology innovation is the area that Company-X works in and MilkTechNZ’s innovation and export success is another strong affirmation that New Zealand has the capacity to produce world leading digital technology.
The Waikato technology sector’s contribution to gross domestic product (GDP) is around $1.1 billion and climbing. New, innovative, companies like MilkTechNZ show this will continue to grow as they bring new innovations to market.
Cultivate Trust chair Erin Wansbrough said it was great to see an emerging Hamilton agri-tech company take out such a prestigious award for an innovative product sold here and overseas.
“The fact that MilkTechNZ was able to conceive and deliver an award-winning product during such a
disruptive time shows how resilient the tech sector is, particularly here in the Waikato,” Wansbrough said.
“The future is bright.”
The trust recently launched the Tech in the Tron initiative to attract 500 skilled workers and their families to the Waikato from within New Zealand and overseas to grow the region’s technology sector.
The Company-X Innovation Award judges said Garza and the MilkTechNZ team had taken deep industry knowledge and built a business that provided innovative solutions to meet the market.
Previous winners of the Company-X Innovation Award include Yardmaster Effluent Pumps, Montana Group, and the Spring Sheep Milk Co.
Steel Construction New Zealand (SCNZ) is pleased to announce the results of 2022’s SCNZ Excellence in Steel Awards. The winners were announced on 4 November in Nelson, where more than 200 structural steel industry leaders and specialists gathered to celebrate the best of the best at an event that showcases the sector’s commitment to innovation, best practice and collaboration.
Judges whittled 56 award entries down to 21 finalists, which demonstrate the exceptional design and execution possible when steel is used as the principal construction material. The 2022 winners are:
• Supreme Winner and $1.5M-$3M category winner: D&H Steel Construction for NL2A Shared Pathway Steel features heavily in the Shared Path, which
boardwalks, balustrades and handrails, and a new pedestrian bridge. Sited over rough terrain and waterways, D&H Steel provided value engineering to make the 2.9km mostly off-road pathway buildable and practicable.
• Under $500K category: John Jones Steel for Te Aika Sculpture
The sculpture, which is 8m high and 10m wide, was fabricated in one piece to ensure it was symmetrical before being split apart for transport and painting. Designed by two Ngāi Tahu artists, it will sit on the Avon riverbank and form a ngutu, or entranceway, to the Te Pae convention centre in Christchurch.
• $500K-$1.5M: John Jones Steel for the tākaro Avon River Corridor Bridges
The three architecturally designed bridges that cross the Avon River in Medway, Avondale and Snell, are an important feature in the area’s regeneration. To achieve the desired look, the hollow steel sections were induction bent and an anti-graffiti, UV-resistant topcoat of paint was applied. The 45m-long, 4.5m-high, 3m-wide bridges were trial assembled in John Jones Steel’s workshop to ensure accuracy before being seamlessly installed.
options. The steel structure was driven by bold architectural requirements, which included complex structures like curved welded beams, V-shape columns, three-dimensional trusses and difficult connection geometries.
• Earthquake Strengthening: Petone Engineering for Generator – Waring Taylor
The façade of this heritage building in Wellington has been retained and character features including exposed structural steel, timber and brickwork have been incorporated into the design. Strengthening work brought the structure up to 100 percent of the New Building Standard and involved adding new five-storey shear walls and a full-height structural steel K-frame. The new skeleton preserves the original 1920’s steelwork and adds substantial strength in a visually appealing way.
• Standalone Residential: VIP Structural Steel for Rocking Horse Road
follows the geometry of the existing KiwiRail tracks. The pathway comprises several different steel applications including elevated helical
• Over $3M: Aurecon and D&H Steel Construction for Puhinui Station Interchange Puhinui interchange is a striking transport hub that supports the shift to low-carbon transport
The home’s design references Christchurch buildings of the 1960s with its use of embossed blockwork and structural steel. The external spiral staircase and internal floating stairs are the main structural features of this build and could only be achieved using steel. Both staircases were completely assembled off site and transported as one. The home’s design has resulted in a smart structure to overcome the challenges of building in a floodplain.
The
The Steel Construction New Zealand (SCNZ) awards acknowledge the growing number of highly capable individuals emerging in the structural steel industry, and celebrate those whose skills, drive and willingness to learn has helped them to achieve outstanding outcomes. They recognise well-rounded people who demonstrate not only talent and a good attitude, but display traits important to the industry – commitment, innovation and agility.
More than 10 percent of the total workforce employed by local structural steel contractors are in a training programme, and 70 percent of structural steel contractors employ an average of five apprentices.
The 2022 winners and finalists are: Apprentice of the Year Winner: Zayne Pullan, Red Steel
Zayne started his apprenticeship in 2019 and promptly impressed with his can-do attitude, and his ability to learn and grow. He quickly became proficient at interpreting drawings and ensuring the safe handling of structural steel components.
Red Steel Workshop Manager Alister Varcoe says that Zayne has constantly grown in his ability to fabricate and weld complex, heavy structural steel items. “Zayne is now one of our leading fabricators and completes with ease some of the most challenging fabrication and welding projects that Red Steel has ever seen.”
Mr Varcoe says that Zayne’s positive and reliable attitude towards work, coupled with his ability to bring fresh ideas to the table, make him a highly valuable employee.
Apprentice of the Year finalists:
- Sam Grearny, Patton Engineering
- Dylan Lee, John Jones Steel
Young Achiever of the Year Winner: Abishai Tupuola, Grayson Engineering
Abishai entered the industry with an unusual skillset, but quickly adapted and has instigated some significant projects for Grayson Engineering. He graduated from university as a graphic design, and worked as a labourer for Grayson Engineering while he searched for a job in his chosen field. Finding a job in line with his qualification proved difficult yet Abishai remained positive.
An early project involved creating a new company profile for Grayson Engineering. Abishai exceeded the company’s expectations and he was offered a new role as its Communications Officer, responsible for creating advertising and marketing content, and keeping the website up to date.
Abushai has assumed responsibility for maintaining Grayson Engineering’s environmental system and is currently training to become its Health and Safety Manager.
Young Achiever of the Year finalists:
- Anson Alexander, Black Steel Mobile
- Riti Sharma, Alrite Steel & Services
structural steel sector recently came together in Nelson to applaud the bright new talent in the industry with the Apprentice of the Year and Young Achiever of the Year awards.
Business leaders have been losing sleep in face of various challenges within the manufacturing industry. Decreasing production output, labour shortages, ongoing supply chain disruptions and inflation are just a few to be named.
As noted by the Australian Bureau of Statistics, almost a third of all Australian employing businesses are having difficulty finding suitable staff, and more than two in five businesses have been facing supply chain disruptions since January 2022.
In the past, low-code application development has been deployed by manufacturing companies as a ‘nice-to-have’, connecting peripheral devices and supporting logistics. However, business leaders are progressively recognising the extended value in low-code, rapidly adopting low-code platforms throughout all core domains and business activities, including engineering, product design, and quality control.
According to Gartner, by 2024, 65 percent of all app development functions will use low-code application building, with 66 percent of big companies using at least four low-code platforms at once.
But what makes low-code the future when it comes to improving manufacturing and supply chain efficiencies?
For many IT leaders, there is still some confusion between Business Process Management (BPM) software and low-code. It’s important to note that, while they share some similarities, low-code and BPM have some fundamental differences when it comes to capabilities and application.
While BPM models and streamlines business processes and has a less-targeted application, low-code simplifies the creation and delivery of apps and functions, often addressing specific customer needs and allowing for greater flexibility and customisation.
While manufacturers are trying to integrate on manufacturing floors IoT devices that can be controlled from anywhere, any time, the rapid adoption of these devices means that they must now develop supporting applications at an ever-faster pace, straining the traditional development process to its limit.
That’s where low-code platforms come into play. A low-code application development platform uses pre-built modules, drag and drop visual environments and automation to enable users to create mobile and web applications with speed - even if they have
minimum knowledge of coding.
By using this model-driven approach, companies are cutting down time spent on application development and enabling their digitisation project, building apps up to ten times faster than before.
This rapid app development system is not only important for building software from the ground, but it also enables companies to customise existing technologies and rapidly adapt to evolving customer and industry needs.
Requiring less engineering efforts, low-code platforms eliminate the need for experienced programmers and open the doors for citizen developers to fill in the gaps left by the tech skills shortage.
Industry analyst firm Gartner anticipates that, by 2024, 80 percent of technology products and services will be built by people who are not necessarily technology professionals.
This means a narrowing of the gap between business functions and app development, with experts in the manufacturing domain becoming directly involved in the creation of the software they use - and therefore able to tailor it to their real needs.
In terms of mobility, this system provides cross-platform compatibility, requiring much less effort from companies and programmers to develop robust applications.
By giving access to third-party APIs and modules for different platforms, it can be used to build apps in the backend that will improve manufacturing and supply chain efficiencies - like connecting with transportation suppliers - and in the frontend to guarantee order fulfilment and customer satisfaction - for example tracking the status of an order.
This means the ability to easily create purpose-built and customisable apps for every process, workforce and application.
processes, problem-solving skills and a logical approach.
Some of the biggest challenges manufacturers face today are the inclusion of millions of legacy systems, which are costly to deploy, extend and maintain, and monitoring production and execution.
With low-code application development, the long-term goal is to use a friendly interface to gain real-time visibility not only into manufacturing processes, but also the larger ecosystem, including customers and partners - so that important data can flow more quickly.
Slowly but surely, low-code is moving into the core of manufacturing operations. The advantages of using this method - less dependence on experienced developers, faster development of worker-specific apps and the flexibility of adding functionality as required - all cater to the needs of manufacturers who need to quickly respond to market changes and customer needs.
Essentially, low-code has evolved from a crisis management technology to a core technology that helps manufacturers improve efficiencies, empowering companies to thrive rather than just survive.
Like many other industries, manufacturing comes with its own set of specificities and challenges to be considered when designing high-tech solutions.
To successfully implement and enjoy the many benefits of low-code application development, organisations need a detailed understanding of
A method built for agility, mobility and scalability
Is low-code application development the future for manufacturing businesses?
Essentially, low-code has evolved from a crisis man agement technology to a core technology that helps manu facturers improve efficiencies, empowering companies to thrive rather than just survive.
Is low-code the future of manufacturing?
Jornt Moerland, Regional Vice President APAC of Mendix.