
21 minute read
OPHANGING EN STUURINRICHTING 30
Flensmoeren en bouten
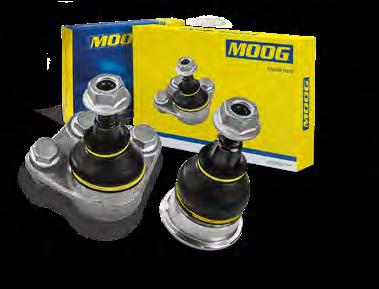
Advertisement
Links verzinkte kogelpen; rechts kogelpen met chromium 3 coating.
Johnny Vanzeebroeck vertelt dat ze zo de oorzaak van het soms vroegtijdig stuk gaan van de draagarmrubbers hebben ontdekt: “Een vaak voorkomende fout is om bij het vernieuwen van de draagarmen de bouten en moeren volledig vast te draaien terwijl de auto nog met naar beneden hangende wielen op de hefbrug staat. Als dan de auto met de wielen op de grond wordt geplaatst, worden de rubbers extra belast. Beter is om de bouten en moeren terwijl de auto op de brug staat slechts gedeeltelijk vast te draaien. Het helemaal vastdraaien met het gepaste koppel gebeurt dan beter in een tweede fase als de auto effectief met de wielen op de grond staat.”
Goeie materiaalkeuze
Om de kwaliteit te verzekeren zijn dus de montage in de garage en de productie -zeg maar de assemblagekwaliteit- van cruciaal belang. Maar er zijn nog twee andere aspecten en dat zijn de materiaalkeuze en de innovatie. Daarvoor nemen we het voorbeeld van een kogelgewricht. Moog kiest er voor om de kogelpennen via inductie te harden waardoor ze tweemaal harder worden en vijfmaal langer meegaan. Harden door inductie is een van de meest doeltreffende manieren om staalsoorten te harden. Dat gebeurt door een aanzienlijke verwarming van het materiaal en dat is mogelijk door een hoge stroom en spanning door het metaal te laten gaan gevolgd door een onmiddellijke koeling. Johnny Vanzeebroeck voegt daaraan toe dat een dergelijke techniek ook op sommige OE-onderdelen wordt toegepast. Bij Moog wordt de geharde kogelpen gecombineerd met een kogelstofvezel lager. Deze lagers zijn heel duurzaam en daarmee afgestemd op de lange levensduur van de kogelpennen. Bovendien laten deze lagers een soepele beweging van de pen toe. Het gewricht wordt gemonteerd met verzinkte flensmoeren die betrouwbaarder zijn dan de combinatie van een traditionele moer met een afzonderlijk vlot. Om corrosie geen kans te geven, krijgt de behuizing van de kogelpen een duurzame coating. Naargelang het type is dat met zink of chromium 3 dat trouwens ook voor het coaten van stabilisatorstangen wordt gebruikt. Inwendig in het kogelgewricht kiest Moog voor een synthetisch vet dat beschermd wordt door een rubberen hoes die op zijn beurt vast zit met een metalen -en geen kunststof- ring. Kunststofringen verliezen immers sneller hun spankracht waardoor de kans vergroot dat stof, zand en water na verloop van tijd in het
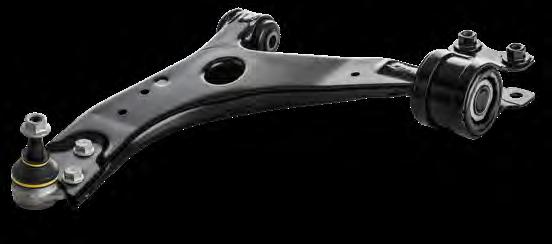
Plaatstaal draagarm met inwendige en uitwendige cataphorese coating.
gewricht terecht komen. De onderkant van het kogelgewricht wordt afgedekt door een metalen plaatje. Ook bij draagarmen zijn er specifieke technieken om de duurzaamheid te bevorderen. Bij de draagarmen uit plaatstaal gebruikt Moog staal met dezelfde metaalsterkte als OE. Tijdens het productieproces wordt de ganse draagarm ondergedompeld om zowel uitwendig als inwendig een cataphorese coating te krijgen. Draagarmen die uit aluminium zijn vervaardigd, worden gezandstraald om mogelijke imperfecties van het gietproces te verwijderen en de buitenkant van de draagarm te harden. Daarmee vermindert de kans op metaalmoeheid met 40%.
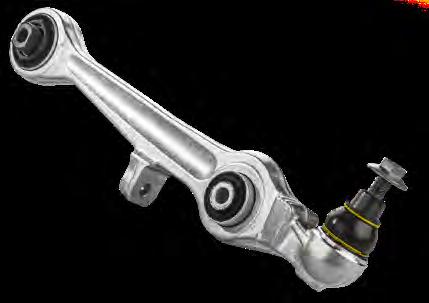
Elektrische auto’s
Bij Moog gaan ze er prat op dat ze met hun producten een grote marktdekking hebben en bijvoorbeeld ook onderdelen hebben voor de meest recente elektrische auto’s. Volgens Johnny Vanzeebroeck vraagt dat om bijzondere aandacht: “Elektrische auto’s zijn zwaarder en hebben een sterk acceleratievermogen. Dat zorgt voor extra belasting van de ophanging en de stuurinrichting.”
Gezandstraalde aluminium draagarm.
Bestel aan de bron
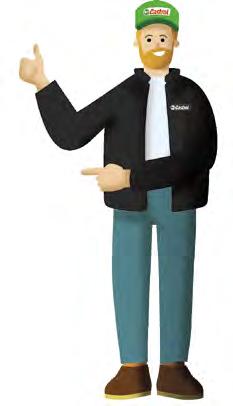
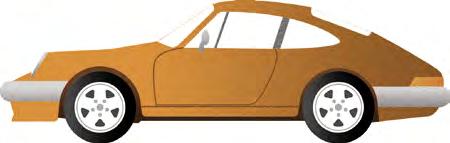
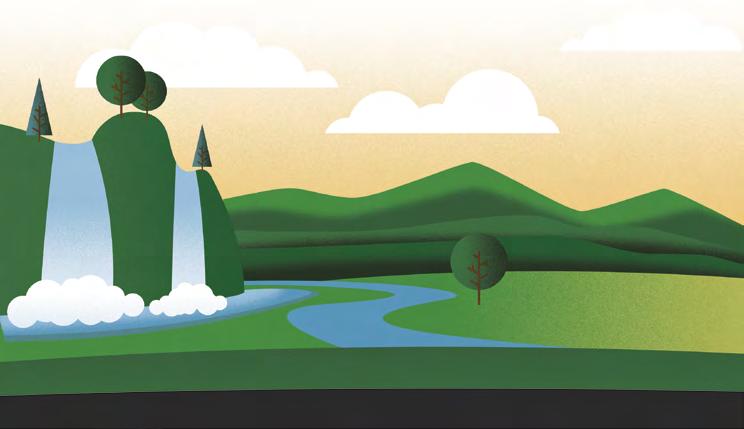
Een gratis jas bij uw eerste bestelling*
Congres Future Repair - Repair the Future
Technologie neem hoge vlucht, maar de uurlonen volgen niet
Effective Media organiseerde op 9 juni in Kinepolis Antwerpen voor de 2de keer Future Repair - Repair the Future. Een evenement dat zich volledig op de carrosseriesector richt. Info Garage was ook aanwezig en luisterde aandachtig.
Het congres werd geopend met een debat waarin vier carrosserienetwerken vertegenwoordigd waren: Stijn Davignon (ABS), Philippe Bovijn (Axial), Johan Van Deursen (Cryns Carrosserie) en Frank Deroy (Wondercar). Er werden enkele belangrijke topics aangekaart. Goed opgeleid personeel vinden, zowel voor administratieve functies als technische profielen blijkt nog steeds een groot probleem voor heel de sector. Vooral in het licht van elektrificatie en de toenemende techniciteit van de voertuigen (bvb calibratie van ADAS) blijken die profielen heel moeilijk te vinden. Daaraan is bovendien een hogere kost verbonden voor herstellingen. Waarbij de panelleden zich afvroegen wie dat uiteindelijk zal betalen. Philippe Bovijn haalde daarbij de uurlonen aan die te laag zijn. De verhouding met leasingmaatschappijen en verzekeringen is op dat vlak zeker een heet hangijzer. Maar daar werd tijdens het debat jammer genoeg niet dieper op ingegaan. Van de organisatoren kregen we ondertussen te horen dat dit het hoofdthema wordt voor de editie van volgend jaar.
Sprekers
Na het debat was het aan de sprekers om elk hun expertise te delen.
Patrick Bonni van Educam beet de spits af met een gedetailleerde uiteenzetting van hedendaagse hersteltechnieken in een snel veranderende automobielwereld. Hij moet echter ook vaststellen dat er nog een grote lacune is op het vlak van bijscholing. Slechts gemiddeld 11% van de carrosseriebedrijven leidt zijn eigen personeel op, terwijl dat 30% is in garagebedrijven. Nog veel (opleidings)werk aan de winkel dus! Koen Silverans van Axalta had het over innovatie in autolakken. Een technische uiteenzetting met als centraal thema Fast Cure Low Energy Technology en de voordelen van deze laktechnologie. Boris Koster van Fixico ging dieper in op de herstellingskosten van elektrische auto’s en waarom die hoger zijn. Daarbij een aantal evidente zaken, zoals extra expertise inzake het spanningsvrij maken van voertuigen. Maar ook het gebruik van specifieke materialen (aluminium, glasvezel, …). Kurt Vandecasteele van Lechiffre Automotive Innovation bracht de meest diverse presentatie. Hij had het onder andere over de war on talent, efficiënter werken, nieuwe tools voor klantencommunicatie en nieuwe technische tools (bvb high definition fotopoorten met analysesoftware). Al bij al de meest gesmaakte presentatie van de namiddag. Het laatste woord was voor Kristof Eraly van Febelcar. Hij had het o.a. over de snelle technische evolutie in de sector. Maar ook over de toegenomen klantenverwachtingen en hoe daaraan te voldoen. Hij haalde ook het punt aan dat onderbelicht was in het debat: het gemiddelde uurloon in de sector is 55 €/ uur, terwijl het economische break-even punt 80 à 90 €/uur zou moeten zijn.
Conclusie
Al bij al een interessante namiddag maar er is zeker ruimte voor verbetering. Een aantal sprekers herhaalden wat anderen al gezegd hadden. En vooral het debat had scherper gemogen. We kijken dan ook uit naar de editie van volgend jaar waarbij de carrosserienetwerken in rechtstreeks debat zullen gaan met de leasingbedrijven en verzekeraars.
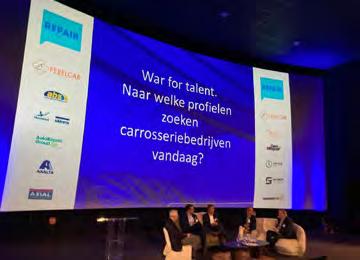
A Plus Carrosserie
A Plus Carrosserie is de samensmelting van Carrosserie Bart Eyckmans en Carrosserie Willemen, maar in de eerste plaats het geesteskind van Bart Eyckmans. Een ondernemer pur sang die zijn bedrijf future proof maakt door te innoveren en in zijn bedrijfsvoering verstandige keuzes te maken. Een gesprek!
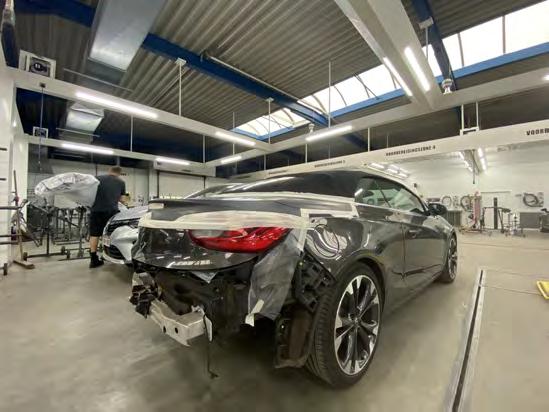
Na een carrière van 10 jaar bij Total, kon Bart Eyckmans niet langer ontkennen dat er een behoorlijke dosis ondernemersbloed door zijn aderen stroomt. Daarom nam hij in 2014 Carrosserie Eyckmans van zijn vader over. Een business die hij al behoorlijk goed kende, omdat hij altijd al had meegeholpen in het bedrijf. De belangrijkste voorwaarde om het bedrijf over te nemen, was dat hij zijn eigen visie mocht uitwerken. Bart Eyckmans: “Voor ik het bedrijf overnam, was het een vrij kleinschalige carrosserie met twee medewerkers op de vloer. Ik zag het toch groter en groeien doe je in de eerste plaats door meer opdrachtgevers te krijgen. We hebben eerst de infrastructuur van het gebouw gemoderniseerd om meer productiecapaciteit te creëren. Dan ben ik naar de verzekeringsmaatschappijen en opdrachtgevers gestapt om conventies af te sluiten. Een tweede belangrijke pijler van mijn visie is consulting in schadeherstel. We werkten al in onderaanneming voor een grote concessie uit Antwerpen. Ik heb toen een business plan uitgeschreven over hoe zij hun schadeherstel konden optimaliseren. Uiteindelijk hebben we daar een contract getekend om hen volledig te servicen op het vlak van autoschade. We hebben in de concessie een schadebeheerder gedetacheerd om 100% het schadebeheer te doen. Ik denk dat we dat in de toekomst ook voor andere bedrijven kunnen doen.” Het verhaal van A Plus Carrosserie begint in 2017 wanneer Carrosserie Willemen uit Kapellen wordt overgenomen. Beide bedrijven bestaan nog een tijdje apart maar de activiteiten worden uiteindelijk in oktober 2019 samengevoegd onder de naam A Plus Carrosserie in de KMO-zone Vloeiende in Kapellen.
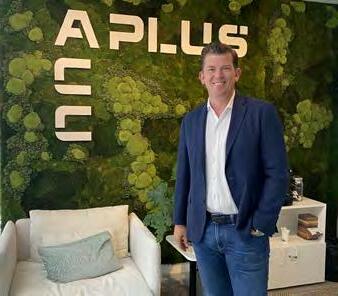
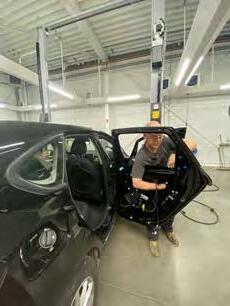
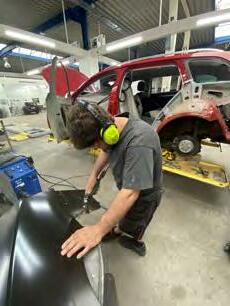

Juiste montage
A Plus Carrosserie heeft de afgelopen jaren flink geïnvesteerd in zijn infrastructuur. Het bedrijf heeft drie volwaardige spuitcabines, een kleinere, een middelgrote en een grote. “Daarmee dekken we zowat heel de markt af tot en met lichte bedrijfsvoertuigen”, zegt Bart Eyckmans. Daarnaast ook nog een smart box voor spot repair, zeven voorbereidingszones, acht demontage- en montagezones en vier plaatwerkzones. “Die investeringen zijn gebeurd vanuit mijn visie dat we meer volume willen. En dan moet je daar ook iets tegenover kunnen stellen qua productiecapaciteit”, legt Bart Eyckmans uit.
Productiviteit en processen
Iedereen in de carrosseriesector is zich bewust van de krappe marges, dat is enerzijds te wijten aan de te lage uurlonen (zie kaderstuk Philippe Bovijn) maar toch moet je zelf ook je verantwoordelijkheid nemen in de bedrijfsvoering, zegt Bart Eyckmans: “Optimalisatie van processen en de productiviteit van de medewerkers zijn factoren waar je niet genoeg de nadruk op kan leggen in het huidige economische klimaat. Daarom werken wij bijvoorbeeld met een volledig gedigitaliseerde planning en werkproces. Alle medewerkers hebben een iPad waarmee ze on the job foto’s kunnen nemen, opmerkingen kunnen toevoegen en ineens naar de administratieve medewerkers sturen, die dan bijvoorbeeld onderdelen kunnen bestellen. Dat bespaart heel wat tijd en maakt de processen korter en efficiënter. Daarnaast is energiebeheer ook een belangrijke factor vandaag. Zo gaan wij de komende maanden investeren in zonnepanelen om energie te voorzien aan onze technische installaties. We voegen ook geen gasverwarming meer toe in onze spuitcabines. We werken uitsluitend met UV grondverven en aan de lucht drogende vernissen. Dat zijn allemaal kleine winsten die op het einde van de rit een groot verschil maken.”
Alles in eigen huis

De filosofie van A Plus Carrosserie is om alles in eigen huis te doen. Uitlijnen, ADAS-calibratie, coderingen, … Wanneer dat niet lukt met de eigen systemen, wordt er gewerkt met een externe partner. Dat betekent echter niet dat de voertuigen daarom noodzakelijk naar die externe partner moeten gebracht worden. Dit kan vandaag immers ook op afstand. “Dat we een voertuig naar die partner brengen, gebeurt eigenlijk hoogst uitzonderlijk”, zegt Bart Eyckmans. “Je kan eigenlijk stellen dat we 95% zelf in huis doen. En ja, dat is belangrijk. Alles wat je moet uitbesteden, betekent immers tijdverlies en kost geld.”
Een gespreide portefeuille
A Plus Carrosserie heeft een diverse portefeuille aan klanten: particulieren, vloten, leasingmaatschappijen, …
Iets waar Bart Eyckmans veel belang aan hecht: “Ik vind risicospreiding belangrijk in de bedrijfsvoering. In mijn visie mag één klant niet meer dan 10 à 15 procent van je zakencijfer vertegenwoordigen.”
Antwerp Car Center: op zoek naar synergie
Naast het gebouw van A Plus Carrosserie bevindt zich Antwerp Car Center, waarvan Bart Eyckmans eveneens eigenaar is. Deze onafhankelijke garage is een afzonderlijk bedrijf, maar dat neemt niet weg dat er vanzelfsprekend naar synergieën wordt gekeken. Bart Eyckmans: “Ik ben er van overtuigd dat er een toekomst is voor onafhankelijke garages. Zeker in combinatie met een carrosserie zoals bij ons. In het verleden kregen wij al regelmatig vragen van klanten om remblokken of olie te vervangen, de auto klaar te maken voor de technische keuring en dergelijke. Met Antwerp Car Center kunnen we perfect inspelen op die behoefte door onderhoud aan te bieden. Beide bedrijven hebben trouwens een gemeenschappelijke receptie, wat de klantenervaring ook ten goede komt. Wat de doelgroepen betreft, hanteren we eigenlijk dezelfde filosofie als bij A+ Carrosserie: een goede spreiding. Dus naast particulieren, mikken we ook op vloten en leasingmaatschappijen. Daarom hebben we ook in dit bedrijf forst geïnvesteerd om een zeer professionele service te kunnen aanbieden, zowel technisch qua installaties als qua klantenopvolging. We zijn ondertussen ook lid geworden van 123 AutoService, het garagenetwerk van Doyen. Ook wat deze activiteit betreft, vinden we het nuttig om deel uit te maken van een netwerk. We werken ondertussen al voor een aantal grote leasemaatschappijen, er zit dus ook duidelijk groei in dit deel van onze business.”
Waarom Axial?
A Plus Carrosserie is in 2019 lid geworden van Axial. Een keuze die Bart Eyckmans als volgt uitlegt: “Axial is eigenlijk een coöperatieve waarbij alle leden aandeelhouder zijn. We hebben nog voldoende vrijheid om een onafhankelijke koers te varen. We zijn een groep van KMO-bedrijfsleiders die vanuit die groepering gecoached worden naar vloten toe. En dat is een hele belangrijke doelgroep om in je

portfolio te hebben qua volume en recurring business. Die twee aspecten waren voor mij het belangrijkste. Solidair met elkaar, maar toch nog ons eigen ding kunnen doen. En vooral: een volwaardige professionele service kunnen bieden in een aangename omgeving voor de klanten. Met die persoonlijke touch proberen alle Axial leden het verschil te maken. Customer experience is een belangrijke factor in alle segmenten van de automobielmarkt, dus zeker ook bij koetswerkherstel.” Wat zijn de hete hangijzers binnen de carrosseriesector? We vroegen het aan Philippe Bovijn. “Ongetwijfeld de uurlonen. Heb je een conventie met een verzekeringsmaatschappij, dan ben je verplicht te werken aan de uurlonen die zij opleggen. Daarbij zie ik twee problemen. Niet iedere carrossier krijgt dezelfde voorwaarden opgelegd, zelfs al is dat bij dezelfde verzekeringsmaatschappij. Daardoor worden wij eigenlijk tegen elkaar uitgespeeld. Daarnaast zijn de uurlonen ook systematisch te laag. Om rendabel te zijn, moet je ergens tussen de 65 en 75 euro zitten, terwijl dat in de praktijk dikwijls nog 50 à 55 euro per uur is. Dit is niet vol te houden. Als Axial willen wij dat debat wel aangaan, maar uiteindelijk zie ik daar toch een grotere rol weggelegd voor Febelcar.” “Een tweede trend die ik zie is binnen onze sector is de opkomst van Artificiële Intelligentie bij expertise. De mensen van Informex staan daar al heel ver in. Zeker voor blikschade zou AI experts kunnen vervangen op termijn. Is er onderliggende schade aan de structuur van het voertuig, dan is dat al minder evident. We zullen dus nog experts nodig hebben in de toekomst, maar het zullen er minder zijn.”
Philippe Bovijn, General Manager Axial Belgium
AFDICHTING
STAAT GARANT VOOR DE KWALITEIT VAN ELK STUK. ONGEACHT HET TYPE VOERTUIG.
VIBRATIE CONTROLE CABINE FILTRATIE
AFDICHTING TRILLINGSCONTROLE CABINE FILTRATIE
RAADPLEEG ONZE CATALOGUS ONLINE

CORTECO, ORIGINELE KWALITEITS ONDERDELEN
Corteco is een van de toonaangevende leveranciers van onderdelen voor de onafh ankelijke vervangingsmarkt van automotive onderdelen. Deel uitmakend van de wereldwijd gekende Freudenberg groep levert Corteco meer dan 27 000 OEM kwaliteitsproducten. Onafh ankelijke garages vertrouwen op Corteco onderdelen en profi teren zo van de originele Freudenberg kwaliteit.
KENNIS & OPLEIDING ATC weet er raad mee
Nico Bourgois geeft intro over ‘metal shaping’
ATC België geeft jaarlijks een tiental lezingen die de kennis, het kunnen en de nieuwsgierigheid bij iedereen die actief is in de autosector aanscherpen. De maand juni stond in het teken van carrosserie met twee thema’s. Eén daarvan was ‘metal shaping’ ingeleid door specialist Nico Bourgois.
‘Metal shaping’ of plaatbewerking brengt je terug tot de basistechnieken van de carrossier en al gauw wordt duidelijk dat deze vaardigheden een puur ambacht zijn. De ATC-bijeenkomst rond dit thema duurde twee uur en vond plaats in het atelier van Nico Bourgois uit Merchtem. Op die tijd word je geen vakman maar wel scherpt het je interesse aan voor die bekwaamheid en de opleidingen die Nico in zijn werkplaats geeft. Nico vertelt dat zijn opleiding vier volle dagen duurt. Per opleiding laat hij vier tot maximum vijf mensen toe zodat hij iedereen perfect kan opvolgen en bijsturen. Want laten we wel wezen, plaatbewerking of ‘metal shaping’ heeft voor een groot deel te maken met praktijkervaring en oefening. Er komt wel theoretische kennis bij te pas maar die wordt en passant door Nico gegeven.
Weinig plamuur
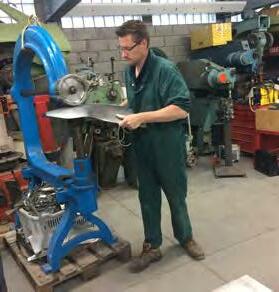
Nico Bourgois geeft een demonstratie met het Engels wiel.
In de vier dagen van de opleiding besteedt Nico aandacht aan verschillende zaken. In de eerste plaats aan het lassen. Voor elke bewerking is een aangepaste manier van lassen aangewezen. Het meeste vakmanschap en zeker feeling wordt gevraagd bij het TIG-lassen (Tungsten Inert Gas of wolfraam) omdat je eigenhandig materiaal moet toevoegen. Het komt er op neer niet te veel materiaal toe te voegen. De uitdaging bestaat erin om twee platen aan elkaar (boord tegen boord zonder flens) aan elkaar te lassen en daarbij de temperatuur te beheersen om vervorming te voorkomen. Op afwisselende plaatsen lassen, het inkloppen van de las, het hoort er allemaal bij. Het is al gauw duidelijk. Nico houdt van het zuivere werk en heeft het niet begrepen op het overvloedig gebruik van plamuur. “Met een perfect afgewerkte plaat is geen plamuur nodig,” zo weet hij. Verder vult hij aan met “te veel plamuur geeft op termijn altijd problemen zoals inzakkingen, barsten en andere ongewenste effecten.”
Engels wiel
De andere dagen van de opleiding worden besteed aan het puur vormgeven van een plaat. Daarbij gaat eerst de aandacht naar het aloude plaat kloppen. Eén van de oefeningen bestaat erin om een bolvormig kommetje te kloppen. Als ondergrond kan een boomstam met holle bovenkant gebruikt worden of een zandzak. Ter loops geeft Nico uitleg wat het krimpen en rekken van een plaat is en wat de effecten daarvan zijn. Bij het vakmanschap van het ‘metal shaping’ of vorm geven van een metaal plaat hoort zonder twijfel het leren werken met het fameuze Engels wiel. Nico heeft verschillende exemplaren in zijn werkplaats staan. Hij raadt af om te werken met Chinese exemplaren omdat deze een minder stevig gietijzeren frame hebben dat kan flexen. De beste exemplaren zijn nog de echte Engelse wielen die uit Londen of Birmingham komen. Het rollen van een plaat op het Engels wiel kun je niet op één dag onder de knie krijgen, wel leer je in de opleiding de basistechniek en dan komt het er op neer door vele uren oefening zich verder te bekwamen. Met een Engels wiel is het de bedoeling om een platte plaat tot een waar koetswerkpaneel te vormen. Nico doet ook autorestauraties en heeft in de praktijk ondervonden dat gerolde platen heel wat preciezer kunnen gemaakt worden dan geperste panelen die je in de after market kunt kopen. Het persen gebeurt nu vaak met verouderde mallen die niet meer in optimale staat verkeren. Belangrijk bij het plaat vormen is ook het kunnen maken van een FSP-mal en boogplaten die verschillende
Hamers zijn essentieel in de plaatslagerij.

vloeilijnen in het paneel weer geven. Op die manier kun je je werk regelmatig toetsen aan de vormgeving die je wilt bekomen. Laatste deel van de opleiding bestaat erin om het gevormde koetswerkpaneel aan de rand van bevestigingsflenzen te voorzien.
Ervaring
Na de introductie van Nico wordt ons duidelijk dat ‘metal shaping’ een ambacht is dat respect verdient en in ere moet gehouden worden. Het is dan ook lovenswaardig dat Nico zijn kennis en ervaring met anderen wil delen tijdens de opleidingen die hij geeft. Nico heeft bovendien ervaring als voormalig trainer bij Educam en momenteel werkt hij als trainer bij Gates. De trainingen ‘metal shaping’ doet hij in eigen beheer, net als restauratieprojecten van auto’s.
Eén van de oefeningen tijdens de opleiding bestaat erin om een kommetje te kloppen uit een staalplaat. Belangrijk bij het plaat vormen is ook het kunnen maken van een FSPmal en boogplaten die verschillende vloeilijnen in het paneel weer geven. Belangrijk bij het plaat vormen is ook het kunnen maken van een FSPmal en boogplaten die verschillende vloeilijnen in het paneel weer geven.
ATC: wat doet je er mee?
ATC is van oorsprong een Nederlandse vereniging voor autotechnici en viert dit jaar zijn 75ste verjaardag. Sedert 1985 is er ook een Belgische afdeling met als voorzitter Hendrik Moyson. In totaal telt ATC België 18 subafdelingen. Wie lid wordt, kan per jaar van een tiental lezingen genieten met telkens een interessant onderwerp uit de autobranche. Deelnemers leren over nieuwe technieken of kunnen weer kennis maken met ‘oude’ technieken die dreigen verloren te gaan. Met ATC wordt kennis uitgewisseld en de interesse in het autovakmanschap gestimuleerd. Het is bovendien een uitgelezen gelegenheid om aan netwerking te doen. Meer info op www.atc-belgium.be
XTREME ENERGIEBESPAREND.

© 2022 Axalta Coating Systems. All rights reserved. HET XTREME-SYSTEEM: EFFECTIEVE DROGING BIJ 40°C OF 20°C.
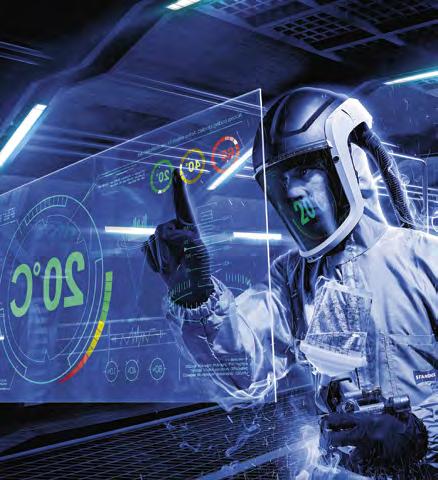
Met het Xtreme-systeem kan het volledige droog-proces worden uitgevoerd op 40°C of zelfs 20°C, waarmee u tot wel 70% aan energiekosten kunt besparen.
De VOC-Xtreme-Nass-in-Nass Füller U7650 is klaar voor de basislak na slechts 5 minuten drogen. Nadat u de VOC-Xtreme Klarlack K9580 hebt aangebracht, kunt u het voertuig na slechts 15 minuten drogen op 40°C verplaatsen uit de cabine, zodat u door kunt met de volgende reparatie-opdracht. Zelfs zonder geforceerde droging is de verwerkingstijd slechts ongeveer 75 minuten, waardoor het uitermate kostenefficiënt is!
NIEUW!
Waarom herstellingskosten bij elektrische voertuigen vaak hoger zijn
Doordat de automobielsector zich de afgelopen jaren enorm heeft ontwikkeld, worden voertuigen steeds innovatiever. Deze ontwikkelingen zorgen uiteraard voor veiligere wegen, hoger gemak en dragen bij aan de duurzaamheid. Echter, voor de herstellingsindustrie hebben deze snel veranderende ontwikkelingen een ander effect.
Een opiniestuk door Boris Koster, Director of Business Development Fixico
Carrosseriebedrijven dienen zich namelijk constant aan te passen om te zorgen dat zij in staat zijn om bepaalde herstellingen adequaat uit te kunnen voeren. Onder deze aanpassingen vallen bijvoorbeeld het trainen van personeel, het aanschaffen van nieuw apparatuur en het behalen van vereiste certificeringen. Dit alles bij elkaar, heeft ervoor gezorgd dat het herstellen van cosmetische autoschade aan nieuwere voertuigen een stuk duurder is geworden. Volgens gegevens van Fixico zijn de gemiddelde herstellingskosten voor voertuigen van één jaar oud tussen 2016 en 2019 met 29% gestegen. Daarbij blijft het thema e-mobiliteit een groeiende trend. Elektrische voertuigen (EV) worden door hun lage energieverbruik en dalende prijzen steeds populairder. Tegelijkertijd neemt de complexiteit van zelfs kleine EV herstellingen toe, wat vaak leidt tot hogere kosten en een langere herstellingsduur. Wat is de reden achter deze hogere kosten en hoe kan het herstellingsmanangement van EV’s worden geoptimaliseerd?
Reden 1: Vereiste voorzorgsmaatregelen
De meeste elektrische voertuigen rijden op kostbare lithium-ionbatterijen die extra veiligheidsmaatregelen met zich meebrengen. Indien carrossiers niet zijn opgeleid om met elektrische voertuigen te werken, kunnen ze de batterij beschadigen of zichzelf ernstig verwonden. In sommige gevallen moet de gehele batterij uit het voertuig worden verwijderd of van het systeem worden losgekoppeld. Stel dat bijvoorbeeld het voertuig wordt overgespoten en onder grote lampen wordt geplaatst om te drogen, dan moet de batterij wel eerst worden verwijderd. Als dit namelijk niet gebeurt, kunnen de lampen oververhitting veroorzaken en de levensduur van de batterij drastisch verkorten. Gezien niet alle carrosseriebedrijven beschikken over de juiste kennis of middelen om herstellingen aan elektrische voertuigen uit te kunnen voeren, is de zoektocht naar een geschikt carrosseriebedrijf ingewikkelder geworden. Indien een bedrijf wel gecertificeerd is, zullen de kosten vaak hoger uitvallen. Door het nemen van extra veiligheidsmaatregelen is er meer tijd nodig voor de herstelling, wat leidt tot het in rekening brengen van extra tijd van de carrosserie en een langere herstellingsduur.
Reden 2: Aanwezigheid van rijhulpsystemen in elektrische voertuigen
Terwijl autofabrikanten hun auto’s blijven innoveren, blijven ook de rijhulpsystemen zich verder ontwikkelen. Carrosseriebedrijven hebben daardoor nieuwe apparatuur, faciliteiten, training en vaardigheden nodig om herstellingen uit te voeren indien er rijhulpsystemen bij betrokken zijn. Sensoren van rijhulpsystemen worden over het algemeen verwerkt in juist die onderdelen van het voertuig die vaak worden geraakt tijdens een schadegeval, denk hierbij aan de bumper, zijspiegels, voorruit, of banden en wielen. Het zorgvuldig kalibreren van rijhulpsystemen nadat de herstelling is voltooid, is nodig om er zeker van te zijn dat ze nog steeds correct werken. Gezien EV’s vaak zijn uitgerust met een breed scala aan rijhulpsystemen is dit proces steeds vaker wel dan niet onderdeel van een EV-herstelling. Omdat het kalibratieproces de herstellingsduur verlengt en een bepaalde expertise vereist, zal de carrossier meer uren en kosten rekenen. De gegevens van Fixico laten zien dat, afhankelijk van het onderdeel en het rijhulpsysteem, het kalibratieproces tot 2 uur meer tijd in beslag kan nemen en herstellingen waar rijhulpsystemen bij zijn betrokken gemiddeld zo’n 40% duurder zijn dan een herstel van een voertuig zonder rijhulpsystemen.
Voor de zoektocht naar de juiste carrosserie kan beginnen, is het belangrijk om te achterhalen wat het voertuig precies nodig heeft.
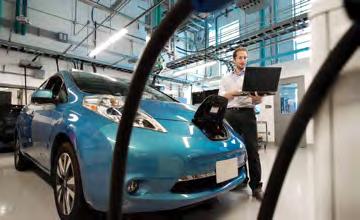