

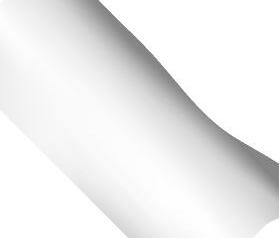
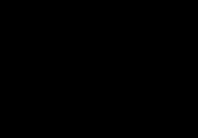

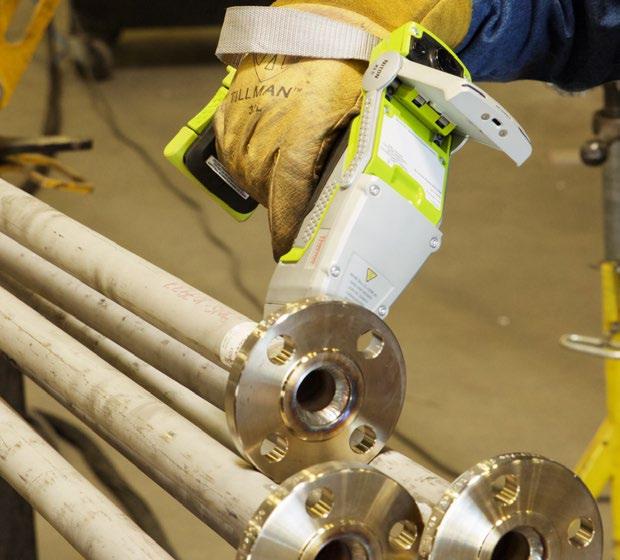
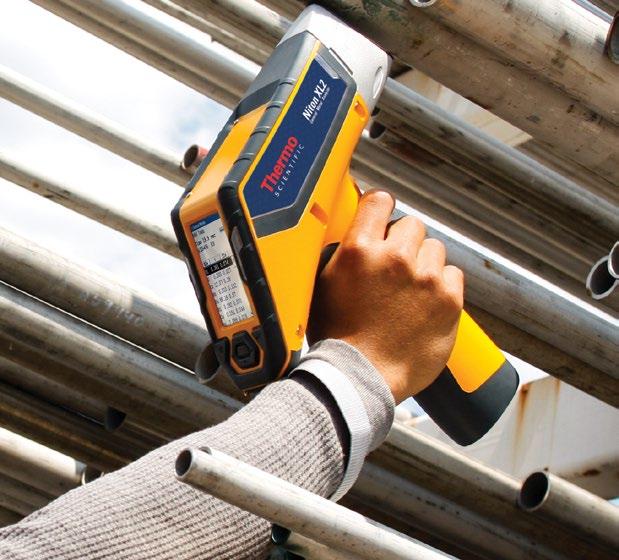
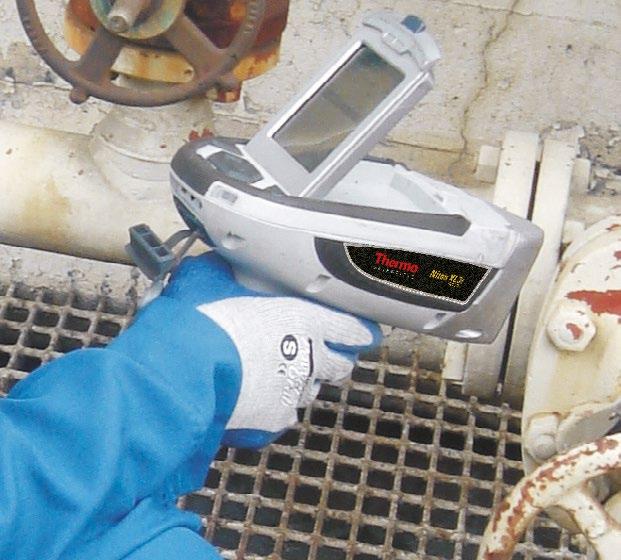
Martin

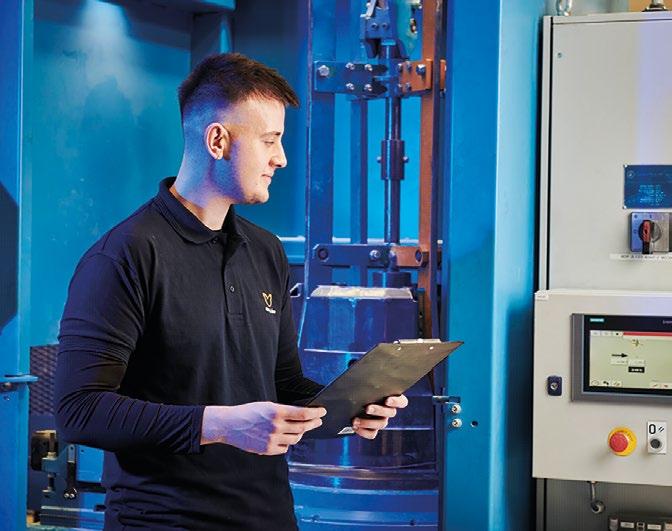
Josh
Alison
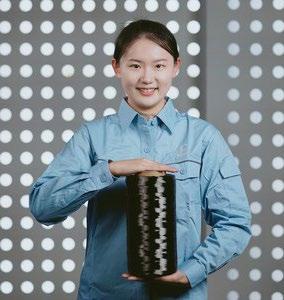
Martin
Josh
Alison
Three ranges of Roller Chain is available from chain manufacturer, Donghua Limited, and the new categorisation helps UK customers identify the right chain solution quickly and easily.
Donghua Limited is the UK arm of the Hangzhou Donghua Chain Group which is one of the world’s biggest chain manufacturers producing over 30 million metres of chain per year. Donghua Ltd has operated directly in the UK since 2009 and we have categorised our extensive Roller Chain products into three ranges: Standard, Solution and Premium.
The Standard Range features a variety of standard Roller Chain manufactured with precision to suit simple drives with large diameter sprockets or complex drives with multiple sprockets and high load bearings.
Chains within this range include: standard and stainless steel hollow pin bush roller chain; works norm roller chain; cottered type short pitch roller chain; driving chain; double pitch roller chain; heavy duty roller chain; oil field roller chain and short pitch roller chain.
The Solution Range offers customers a genuine solution to problems with chain wear, chain fatigue, high speed, lubrication, chain length accuracy and chain strength offering optimum performance in extreme conditions.
Chains within this range include: chromized pin (CP) chain, heavy duty chain, self-lubricated roller chain and our new EXL chain.
EXL Chain offers significant benefits over standard Roller Chain. It utilises different materials, material treatments and layer technologies, to offer the best possible quality/price ratio for all applications.
Aimed specifically for the after-market, EXL Chain is designed, manufactured and tested for unbeatable accuracy and performance in arduous conditions, offering enhanced wear and fatigue resistance and greater precision.
The chain is designed with a new hardened, shot-peened wide-waist plate for increased fatigue strength and a seamless cold forged solid bush and roller to give full contact between the pin, bushing and roller for higher durability.
The EXL Chain has optimised cylindrical parts which improve sliding contacts to help increase service life. It also incorporates Donghua’s unique ‘Easy Break Technology’ which enables the EXL Chain to be cut in the field using Donghua’s Plate Extractor tools.
To watch our video showing how to cut the EXL Chain using our Plate Extractor tools, visit: https://youtu.be/UD6rtBEJrkM
The Premium Range offers our customers a deluxe solution to problems with chain wear, chain fatigue, corrosion, high speed, lubrication, chain length accuracy and chain strength with specific build features designed to enhance durability and withstand a range of arduous environments.
Our new X3 Chain which was launched in the UK in 2022, is exceptional and delivers three times the performance for wear resistance, fatigue resistance and high speed performance for comparable Roller Chain. Its superior quality, durability and outstanding wear and fatigue resistance are realised by the new hardened, shotblasted plate shape, calibrated pin and bushing holes, special heat-treated and surface coated pins, seamless rollers and bushings and high performance prelubrication.
Our X3 Chain is supplied pre-loaded and pre-lubricated as standard and is available in British Standard 06B to 24B in simplex and duplex, ex-stock from our 25,000 sq ft warehouse in the West Midlands.
Manufactured on its own purpose-built production line which encompasses new production techniques and new surface treatments. Designed with a unique pin coating, optimised plate geometry and high precision stamping, X3 offers a new deluxe chain solution and is designed for sectors that use high demand drives such as Timber, Waste & Recycling and Mining & Quarrying.
To download our X3 catalogue visit:
Technology is constantly changing our day-to-day lives and has had a particular impact on the working world. Automation is fast becoming a key conversation within multiple industries in Great Britain, including manufacturing with robotics emerging as the solution.
Over the past few years, a need to move towards more automation in the manufacturing industry has been seen. In fact, a survey done by ABB Robotics found that of 250 SME and manufactur ing companies, 81.2% were considering incorporating robotics into their pro cesses to combat issues with workforce shortages and supply chain disruptions.
In this article, we’ll look at how, in order to keep up with the demand British manufacturing faces, more businesses are adopting robotics as a solution. We’ll also dive into what they can do for your business.
A big question from businesses still on the fence about bringing in robots is what can they do to improve processes. By automating sections of your manu facturing processes with robots, you’re given an opportunity to stay com petitive within a constantly evolving industry.
Substituting traditional labour with ro bots within your processes can help to provide added efficiency. Robots don’t require breaks, and they’re programmed to carry out specific practices with much smaller margins for error than
humans. This results in a more cost-ef fective output from your business, which could see greater revenue for less paid labour.
Robotics can also be useful when it comes to tasks that require a steadi ness that can’t always reliably come from humans. Whether it’s handling or removing materials that can be harmful or dangerous, welding, or separating materials from one another, robotics makes those tasks much easier to carry out.
The UK’s manufacturing industry has leant into a ‘quality over quantity’ men tality, focusing on top value from each product made, and robotics are now being incorporated into processes.
Between 2020 and 2021, the UK became one of the top 15 for sales of industrial robots globally. The Inter national Federation of Robotics (IFR) found that 2,205 industrial robots were installed throughout 2020, which brought the total in the country to around 23,000.
These robots are primarily found in the automotive manufacturing indus try in the UK with around 875, making up 16% of those that were installed in 2020. Several sectors are seeing a benefit in robot application due to a lack of workers, including the food and beverage sector, which already uses industrial machinery and hydraulic cylinders, has seen an increase to 304 robots in 2020. This is a 96% increase in volume since the previous year.
Though these numbers continue to rise, the IFR still ranked the UK outside of the top 20 countries with robot density within manufacturing. We can take from this that there is still room for robotics presence in manufacturing to grow on our shores.
The government itself outlined how much growth was possible in a Business, Energy and Industrial Strategy (BEIS), estimating that there was a potential 40% annual growth for robotics and autonomous systems in the UK between 2020 and 2030. This could in turn mean an extra £6.4 billion in value for the UK economy by 2035. And if our creation and sale of autonomous robots is set to increase, our use of them across a num ber of industries may be set to increase alongside it.
Automating your business process with robotics is not something to be scared of. The myth that robotics steals jobs has long since been debunked, and there is plenty of room for improvements within the manufacturing industry that they can help solve. Implementing robotics can help keep your business competitive in the global market, as well as provide an efficiency that is impossible to achieve with manual labour. There are currently a record number of robots installed; however, there is still room for growth, and the amount of revenue that could stimulate the UK economy if more is installed is staggering.
www.new.abb.com/products/robotics
Cyntech are pleased to announce
and Foshan in
who are located in
with
Cyntech Director Dave Mellor said - ‘we are very pleased and
to have Vitalconn amongst our connector
are a vital part of any system and
to the
in
They are a
team enables us to
can
Their
•
ABlack Country manufacturer has shaken off the Brexit blues to post a major increase in European sales.
Alloy Wire International (AWI), which supplies round, flat and profile wire, has seen orders soar to nearly a third of its predicted £13m annual turnover, with the firm’s commitment to short lead times and security of supply securing a string of new clients.
Investment in creating a strong network of sales offices across the globe is really paying off, with local on-theground knowledge now present in forty countries and proving crucial to building strong relationships in the automotive, aerospace, high value engineering, medical, oil and gas and nuclear sectors.
AWI’s shipping department also put in place a number of contingency plans with some of the world’s best transport
carriers, ensuring its material can be anywhere in Europe within three weeks of the order being placed.
Tom Mander, Managing Director Designate, commented: “We’ve seen all
the newspaper headlines around Brexit and the complications it is causing, but we’re bucking the national trend it seems.
“Yes, it hasn’t been easy, and we’ve had to spend a lot of time and money in getting
the processes right. However, the results speak for themselves with European sales up 20% over the last twelve months, underlining the importance of supply chain resilience.”
He continued: “A lot of our growth has come through our ability to meet supply requirements when we say we are going to do it. Our lead times are three weeks, and this is among some of the fastest in industry, thanks predominantly to our investment in 400 tonnes of stock at any one time, the quality of our production capabilities in the UK and our logistical operation.”
Alloy Wire International, which operates from two factories in the West Midlands and Yorkshire, has seen similar growth outside of Europe, with the buoyant oil and gas industry encouraging a major surge in North American business.
Demand for round and profile wire - manufactured in corrosion resistant
and/or high temperature resistant alloys such as Inconel X-750, Phynox, Inconel 718, Hastelloy C-276 - is coming from customers producing springs and fasteners that are used deep underground or under the ocean.
The medical device sector continues to buy wire made in alloys like MP35N, Phynox and, vacuum melted grades of
stainless steel for their metallographic purity.
Tom went on to add: “Customers in these high-tech sectors stipulate raw material from selected approved sources and the wire being manufactured to specific AMS and ASTM specifications. We adopt these practices, making it easy for customers to select AWI as their programme partner.
“This is further strengthened by our quality and operational systems being accredited to AS 9100 (Aerospace) and ISO 13485 (Medical devices).”
“This is further strengthened by our quality and operational systems being accredited to AS 9100 (Aerospace) and ISO 13485 (Medical devices).”
For further information, please visit www.alloywire.com or follow @alloywire on twitter.
We’ve seen all the newspaper headlines around Brexit and the complications it is causing, but we’re bucking the national trend it seems.
Global filtration specialist Bowman Stor, has announced the launch of a new SEPURA Technologies app for its extensive oil/ water separator range.
With a growing number of customers wanting genuine SEPURA™-branded units, the UK-based company has developed a unique mobile application. The new app allows users to access a handy OEM Comparison Tool to find the most suitable product for their needs - all by simply searching for their current manufacturer.
Available on both Android and Apple platforms, the application also includes an easy-to-use oil/water calculator which helps establish the right size of filtration unit for the customer’s compressor system.
Bowman Stor’s Managing Director, Richard Potts said: “The free SEPURA™ app makes life even easier for distributors, resellers
and endusers in every industry. We believe this is the first app of its kind in the filtration industry and users can now source the best separator products for their needs from any location.”
Only genuine SEPURA-branded products contain the groundbreaking SILEXA™ media - a revolutionary patented media developed through years of research in Bowman Stor’s own laboratories. The SILEXA material has major environmental
benefits, achieving outlet quality discharges as low as 5ppm.
With SEPURA’s comprehensive range of oil/water separator units and third party service kits covering low, medium and high capacity requirements for multiple industries, the app is the perfect way to find the ideal product for each specific use and send enquiries direct to the distributor.
To download the app Go to your App Store and search “Sepura Technologies”.
To place an order or for further information on SEPURA’s unique range of filtration products contact: Multi Factor Europe Ltd., t: 01978 855995 e: sales@mfeuk.co.uk or visit our website.to discover more about Vacuubrand vacuum technology solutions. www.sepura-technologies.com
We have developed a mobile App that will make it easy to identify the right SEPURA™ product to fit your current oil/water filtration system.
Not only that, we have also built in a calculator so you will know straight away which product from our comprehensive range is the correct one for you.
Our unique SILEXA™ filtration media is made from recycled materials and is more effective than any other filtration media currently available. Many users are now switching to our products over their existing OEM suppliers to meet their environmental commitments.
Amajor £500,000 investment drive has reached its final stage at a Telford-based precision manufacturer, with the arrival of two new state-of-the-art etching machines.
Advanced Chemical Etching (ACE), which has recently boosted its workforce by 12%, has taken delivery of two Chemcut Etch machines at its Hortonwood 33 facility in a bid to meet increasing global demand from the aerospace, electric vehicle, and hydrogen fuel cell markets.
The acquisitions will increase the firm’s etching capacity by 30% and will help customers bring their designs and proto types to market quicker, a decisive selling point that the business hopes will help it meet its two-year plan to hit £10m in sales.
It has been a busy twelve months for ACE, with turnover now back past Covid-19 levels and its best-ever month recently recorded after an influx of domestic and international orders were completed for customers keen to avoid international supply chain disruption.
Ian Whateley, Managing Director of Advanced Chemical Etching, commented: “We are always looking at ways where we can reduce lead times and have greater control over the tolerances we can offer, and this latest investment reinforces that.
“The two etching machines are currently being installed and should be fully up
and running by late summer. When they go live, we’ll have a third more produc tion capability, which means we can go after new opportunities and there’s plenty of those currently, whether its sup plying busbars and lead frames to EV or critical components to the medical sector.
“This latest technology will make us faster, guarantee repeatable quality and, with energy costs rising, will reduce our electricity and water consumption considerably.”
ACE specialises in the development of precision components to customers in more than 25 countries, spanning aero space, space, general engineering, auto motive, electronics, medical, telecoms and renewables.
The scope of its activities is far and wide and can include anything from safety critical components for aircraft and F1 cars, to meshes and electronic connectors, battery interconnectors, fuel cell bi-polar plates, cooling plates and heat exchang ers.
All parts are developed and manufac tured at its main site in Telford or at the company’s dedicated sister business, ACE Forming Limited, in Kingswinford.
It works to the most exacting tolerances and can manufacture components in materials, such as stainless steel, nickel alloys, copper, beryllium copper, phosphor bronze, brass and, thanks to new process es, aluminium, molybdenum, titanium, nitinol and elgiloy.
Chris Ball, Executive Director, went on to add: “We operated throughout the pandemic and, thankfully, have emerged with an even stronger order book than what we went into Covid-19 with…that’s a great position to be in, especially with the amount of reshoring opportunities heading back to the UK.
“In addition to our recent investment drive, we have also strengthened our workforce with eight new people joining across our inspection, facility and plant maintenance, and our sales and market ing departments.
“There has been an increase in the number of special operation products we are getting involved in and this would necessitate the need for people to be multi-skilled and internally work across numerous projects. That’s why investment in ongoing training will be so crucial.”
Advanced Chemical Etching is planning more exhibitions this year, with its next appearance coming at the Precision Fair in the Netherlands in November (16-17th)
It is also seeing requests to do mini trade shows of its capability to many several design departments at existing and new customers.
For further information, please visit www.ace-uk.net or follow Advanced Chemical Etching on LinkedIn.
Labtex
We specialise in glass batch reactors, Huber thermoregulators, IKA stirrers and rotary
Vacuubrand
Asecos
and fluoroplastic PTFE labware by Bola and Cowie. Labtex also specialises in Juchheim high-pressure reactors, SICCO desiccators, Adam analytical and precision
flammable and other
overhead and magnetic stirrers and automation
the laboratory by Hitec Zang.
We also offer a wide range of general laboratory equipment which includes balances, heating mantles, ovens, refrigerators and desiccators, as well as standard laboratory glassware and consumables. Labtex manufactures a Laboratory Scale Spray Dryer, for the production of freeflowing powders, and Buchner rings which aid safe and efficient vacuum filtration.
Labtex design and supply stainless steel fabrications for the process industries. Our work ranges from simple fabrications and machining to high specification bespoke projects for the pharmaceutical, food processing, water, paper and chemical industries. Working in conjunction with
skilled fabricators and finishers, Labtex ensures that work is completed to the highest standard.
With over 30 years’ experience in the scientific and laboratory equipment supplies industry, Labtex can provide a complete maintenance and technical support service that is second to none.
Our qualified and professional support personnel and service engineers will provide you with a fast, efficient response to your technical queries, ‘return-to-base’ repairs or on-site maintenance and servicing needs. www.labtex.co.uk
Si
nce the time of Henry Ford, the consensus among manufacturers has been that bigger is better. Economies of scale would provide increasing profits, and this necessitated ever larger manufacturing facilities. For some, the emergence of automation technology will power ever larger factories, or gigafactories as Elon Musk called them. For others though, automation opens the opportunity to do things in a radically different way. Here Stephen Hayes, managing director of Beckhoff Automation UK, explains why some manufacturers are using automation to operate on a smaller footprint.
A long-standing staple of economic thinking is the benefits of economies of scale. Put simply, this refers to the idea that when you scale up production, the cost of each unit of production comes down. In laymen’s terms, bigger is better.
Despite its association with innova tion and ‘breaking things’, Tesla has not strayed too far from Ford’s original meth od. The company’s approach retains the production line, it simply relies on much higher levels of automation, with robots working around the clock.
As for the mantra that bigger is better, Tesla’s celebrated gigafactory in the Ne vada desert is clear evidence that Musk subscribes to this maxim. It is expected that, once completed, Tesla Giga Nevada, or Gigafactory 1, will have the largest footprint in the world.
However, for many manufacturers, greater automation is offering the benefits of operating with a smaller footprint. This is especially so for those embracing the microfactory concept. At its heart, this approach dispenses with the traditional production line, using automation to underpin a modular approach on a much smaller footprint.
British EV start up Arrival has quickly emerged as the standard bearer for the microfactory. Like Tesla, the company is an innovative EV maker whose produc tion processes involve high levels of automation. However, whereas Tesla is building ever larger production facilities, for Arrival the answer is manufacturing
on a smaller footprint, with multiple microfactories deployed closer to the markets the company will serve.
An Arrival microfactory can be built in a standard 200,000 sq ft warehouse. It can be up and running in a matter of months, and in contrast to the extortion ate capital costs of gigafactories, it costs a mere £38 million. For Arrival CEO Mike Abelson, this will be key to the company’s success and will mean greater flexibility in reacting to market changes. With such a vast reduction in capital costs and the ability to deploy rapidly, those adopting the microfactory approach will not need to plan ahead years in advance.
It’s interesting that automation is paving the path for both gigafactories and microfactories, given the two concepts are polar opposites. At Beckhoff UK, we’re happy to cheer on both approaches, given the obvious benefits to mankind of increasing manufacturing efficiency.
However, even if you own a large facility, we’ve been working on solutions that allow manufacturers to take advantage of automation without having to sacrifice excessive space in their existing facility. Our automation without cabinets tech nology is intended to make automation
on a smaller footprint possible. Traditionally, new machines required control cabinets to house cabling and control systems, increasing the overall footprint of the machine. By reducing the cabling commitments via our automation without cabinets, we can deliver prod ucts and solutions that are inherently more mobile and suitable for relocation in comparison to cabinet-reliant coun terparts. Other benefits include reduced shipping costs and installation times, as well as higher output per square meter of production space.
Will automation lead to the largest building in the world, or will it lead to a factory in a box? So far, it looks like the answer will be both. The beauty of auto mation is its power to unlock different paths to more efficient and sustainable approaches to manufacturing. At Beckhoff UK, our solutions are designed to support this goal, whether your factories are micro or giga, we believe automation should be as simple as possible.
To find out more about automation without cabinets, check out Beckhoff’s website here
There is no compromise on the quality of JASIC equipment..such is our confidence in this technology we can offer an unparalleled 5 year ‘true’ warranty on all models. Jasic’s manufacturing site is over 80,000m2 and is arguably the largest and most modern inverter manufacturing base in China.
How do Wilkinson Star provide such an industry leading product guarantee?
WE ARE SERIOUS ABOUT PRODUCT QUALITY. SOUND PERFORMANCE AND RELIABILITY IS WHAT YOU CAN EXPECT FROM JASIC PRODUCTS
• The manufacturer has invested millions of dollars into cutting edge integrated test laboratories on site – JASIC undergoes 42 individual tests to meet high quality standard.
• Jasic’s 4 centre strong R & D facilities has been ranked as the most progressive facility along with being the first welding laboratory awarded UA certification by China from TUV Rhineland.
NO OTHER DISTRIBUTOR CAN MATCH US ON THE LEVEL OF SERVICE FACILITY INVESTMENT MADE IN THE UK
• Wilkinson have 50 years’ experience in servicing welding equipment. Our state of the art service workshop facility and our 16 strong after sales service team offer the most recognised technical support in the welding industry. All equipment is fully supported by Wilkinson Star trained technicians.
• No other UK wholesaler can repair inverter boards to component level. At Wilkinson Star we have a dedicated team of technicians in our JASIC Technology Centre.
• We have the facility to test products extensively on load banks and can validate machines to certification requirements.
CARE IS OUR BYWORD AND YOUR PRODUCTIVITY IS OUR PRIORITY
• We provide a dedicated technical support line which you can call for any technical support queries
• If on site support is needed we provide this through our highly trained technicians who cover the country
• We can also interchange power sources to keep you up and running
• If required, Wilkinson Star will arrange at its expense to collect and return your JASIC product to carry out service or repair in our workshops
JASIC’s warranty is a true 5 years; this means a problem at 6 months, 3 years or 4 years 11 months is treated with the same level of care.
No extensions. No additional costs…… just 60 rolling months of product peace of mind
ALL YOU NEED TO DO IS REGISTER YOUR PURCHASE AT JASIC.CO.UK FOR 5 YEARS PEACE OF MIND – IT’S REALLY THAT SIMPLE
For further information, please visit www.jasic.co.uk
is our confidence in this
offer an unparalleled
The rise of non-linear loads in industrial environments over the last two decades has resulted in the growing problem of harmonic currents and utility-level voltage distortion. Facing a lack of awareness, the industry has struggled to implement effective mitigation techniques. Here, global sales & marketing director of CP Automation, John Mitchell, discusses useful tips for mitigating harmonics.
Voltage distortion, caused by current harmonics can wreak havoc in a plant, damaging its equipment and the mains power supply. Damage can be serious and varied with the most common symptoms including voltage notching, motor vibration, arcing on bearings, nuisance tripping, electromagnetic interference (EMI/RFI) and overheating.
The very first place to start is to ensure you comply with regulations. International harmonic control requirement, IEEE-519, limits “the maximum frequency voltage harmonic to 3 per cent of the fundamental and the voltage total harmonic distortion (THD) to 5 per cent for systems with a major parallel resonance at one of the injected frequencies.” Some form of filtering is subsequently recommended.
We’re lucky in the UK to have a stiff power grid, but this is not true everywhere. Developing countries often aren’t as lucky. Weak grids with an unreliable supply and inadequate infrastructure are common in other parts of the world. The power ratings on products are often based on calculations performed in ideal conditions. Buyers would be wise to note that these products may perform adversely in weak grids and may not perform to IEEE-519 standards in these conditions.
Remember to always stay on your toes. The last few decades have seen a rise in the use of non-linear loads such as transistor based variable speed drives (VSDs) and line commutated DC drive systems. The processes of high frequency switching and pulse width modulation (PWM), introduce unwanted multiples of the fundamental 50hz frequency in the form of harmonics.
Knowing what options are available to you, can help the overall efficiency of the harmonic mitigation process.
Passive and active harmonic solutions can be installed in both series and parallel (shunt) configurations within a system. Series solutions operate in line with the load, meaning that units must be sized for the full current load. Shunt units can be sized only for the harmonic disturbance. There is a clear decision to be made between series-passive, shuntpassive, series-active and shunt-active solutions.
The most straight forward seriespassive solution can be achieved using a line reactor. This is a low cost way to reduce current harmonics, while adding a level of protection to the rectifier.
Shunt passive is power factor correction, often using fixed capacitor banks, tuned and detuned contactor based units, thyristor capacitor banks and fine tuned passive filters. These methods were principally developed to resolve reactive power and not specifically for harmonic mitigation. Today, I would hope no one is installing capacitor banks by themselves and, at the very least, using de-tuned ones – with an inductor for example.
Series-active takes the form of an Active-Front-End (AFE) VSD. It replaces the rectifier diodes in a regular VSD with an IGBT controlled rectifier to eliminate switching based signal noise.
AFEs are great at significantly lowering THD and maintaining good power factor. However, AFEs have some serious drawbacks. In order to maintain a small form factor, lower switching frequencies are used, which result in high switch ripples on the voltage waveform. This can cause other sensitive equipment like PLCs and telemetry and communications networks to nuisance trip and malfunction.
In addition, although this unit may at first seem to eliminate harmonics, it must be noted that with the AFE in addition to the VSD, there are now two drives in the circuit producing twice the heat. This means twice the heat and with a 200kW AFE it soon adds up. For the panel builder or system integrator, bigger cooling systems are needed to cope with the excessive heat.
Active filters provide the most efficient harmonic compensation in a compact unit that has little loss, is insensitive to grid conditions, cannot be overloaded and is easy to retrofit. All of this comes at a slightly higher cost, which is offset by the better return on investment over the longer term.
Understanding the often subtle differences between various harmonic filtering technologies can yield better cost savings, reduce complexity and prolong equipment life. Getting your head around what options are available really is worth it in the long run.
www.cpaltd.net
Linear motors are ideal for fast and accurate motion in a machine.
Linmot, the leading manufacturer of cylindrical linear motors, has made them even more suitable for demanding food and pharmaceutical applications. For these environments, any mechanism needs to have a high protection class and be easy to clean and require little maintenance.
The motors have been developed to be fully sealed and are made in High grade Stainless Steel. The cylindrical design allows the motor to be completely smooth and does not require seals. There are no food or particle traps and they can be fully washed down.
This is a big advantage over screw, belt actuators or pneumatic cylinders.
The motors are available in Linear modules with protection class IP64S and stainless steel linear modules with protection class IP69 consisting of a linear guide and an integrated LinMot linear motor.
Motor series in stainless steel
(EN 1.4404/ AISI 316L) for wash down applications. The motors are characterised by their hygienic design and the high motor protection class IP69 according to DIN EN 60529. Perfectly suited for «in-place» cleaning processes like CIP and SIP.
LinMot linear motors have been used in the food industry for years. They score here with industry-specific advantages, such as simple integration, flexible programmability, dynamics and hygienic design. The motors can be connected to common control platforms in synchronous operation or simple point-to-point motion. The
advantages of servo technology enable the gentle and dynamic processing of food. With the help of stored motion profiles, frequent product changes can be achieved simply by pressing a button. LinMot linear motors are available in stainless steel with a high protection class, meaning they can be cleaned under high pressure and with caustic cleaning solutions.
Users wishing to combine the advantages of dosing based on flow measurement with those of piston dosing in a rotary filling machine now have clean design LinMot motor options. Using LinMot stainless steel motors, the stroke movement of the filling needles can be mechanically decoupled from the movement of the carousel. Even highly dynamic needle raising applications are possible.
Unlike mechanical lifting curves, electrical direct drives do not exert any destructive forces on the bearing shafts.
www.quin.co.uk/linmot
The Rotary Selector Valve or RSV is a multiport, sprung loaded poppet valve, driven by a stainless steel profiled internal cam (spindle), with each port configurable in multiple banks. It stacks allowing different fluids to pass through each bank, in a variety of sequences, with indexing, key locks, actuation, switch outputs and a host of other options.
Used in small bore piping systems in the range -1bar to 10bar it is a simple and extremely reliable unit, of modular design, configurable for a multitude of applications. Available in both brass and stainless steel, with stem and seal materials chosen to suit the process media.
In complex pneumatic control systems for high integrity applications, it eliminates the cross-port leakage issues found with multiport ball valves. Also used in hydraulic applications such as drain and purge, or hydraulic actuation and many other control applications, where process sequences and interlocking can be easily configured in one device, providing a highly adaptable solution to a wide range of fluid control applications.
When being used in processing plants, where the flow is controlled by inline valves, pneumatic control of the actuators that open or close is achieved using electrical solenoid valves, that, in turn, pressurise or vent the actuators. As an emergency safety feature or to carry out planned maintenance, it is necessary to by-pass those solenoids and using an RSV enables a manual override.
Single acting actuators (spring return) are controlled by a single pneumatic signal and are bypassed using a single bank RSV, having one airpath.
Double acting valves require one side to be pressurised with the other vented, employ a two-bank.
Multiple actuators can be controlled by a single RSV, the series 40 having up to eight separate banks.
Drallim Rotary Selector Valve (RSV) is a flexible solution for process control
In complex pneumatic control systems for high integrity applications, it eliminates the cross-port leakage issues found with multiport ball valves.
The Volkswagen Group has placed an order with FANUC for 1,300 robots, demonstrating the strength of its relationship with the leading industrial automation specialist. Throughout 2022 and 2023, FANUC will supply four VW plants across Europe with a variety of robotic solutions to support production of both Audi and VW models.
The majority of the robots will be installed at Volkswagen’s manufacturing facility in Bratislava, Slovakia. “We are delighted that we can now extend our longstanding and trusted cooperation with Volkswagen to the Bratislava plant,” says Ralf Winkelmann, Managing Director of FANUC Deutschland GmbH.
As well as the Bratislava facility, the main VW plant in Wolfsburg will also receive a significant percentage of the 1,300 newly ordered robots. Volkswagen’s all-elec tric ID.3 is due to roll off the Wolfsburg
production line from 2023, and FANUC robots will be integral in assisting with body construction.
Further contributing to the expansion of e-mobility, the new FANUC robots will also be installed at Audi’s battery assem bly plant in Ingolstadt. The fourth facility
benefitting from the contract is the Audi plant in Györ, Hungary.
With a 40-year history of automating pro duction lines, a portfolio comprising over 100 models, and a monthly production capacity of around 10,000 robots, FANUC is ideally placed to supply major auto motive projects on time and on budget, despite the ongoing global supply chain crisis.
The company’s offering includes SCARA robots, which are in high demand for electric vehicle battery production due to their payload and proven reliability, as well as a newly launched model capable of handling loads of up to 1,000 kg, mak ing FANUC the go-to automation partner for automotive manufacturers.
www.fanuc.eu/uk/en
We are delighted that we can now extend our longstanding and trusted cooperation with Volkswagen to the Bratislava plant.
The COVID-19 pandemic, a tense socio-political global climate, and an increasingly demanding customer base have all contributed to a growing need for flexibility in manufacturing. As a result, manufacturers need equipment that can be quickly and easily reconfigured, rather than fixed production lines where every change may require weeks of downtime. Here Neil Ballinger, head of EMEA at EU Automation, a global supplier of quality automation components, explains the role of automation cells in transitioning to a more agile business model.
Customisation and high-mix lowvolume (HMLV) production are not new concepts in manufacturing. Both have risen to prominence in the last decade, with the demand for increasingly personalised products and services. These trends require manufacturers to rapidly adapt to changing market
conditions, and to reconfigure their production and assembly lines accordingly.
The need for adaptability intensified during the pandemic, when many
production plants experienced a boom in demand and needed to set up extra lines to produce critical supplies such as respirator components and personal protection equipment (PPE). On the other hand, some companies needed the flexibility to switch their production to entirely new items — from alcoholic drinks to hand sanitiser, from luxury fashion to medical gowns.
In this context, closed-loop automation cells have become increasingly popular. Automation cells, or robot cells as they are often called, are closed systems containing equipment that can automate several stages of the production process. For example, they may include robotic arms that load and unload the parts to be machined, in-feed and out-feed conveyors, and machine vision systems that determine what part is being fed-in, and that measure and inspect postprocessed items.
Since the days of factory pioneer Henry Ford, manufacturing plants have worked in a similar way — with long, linear production lines where items pass from station to station, being processed and finally inspected and shipped. In these lines, every change requires the intervention of multiple experts and can lead to several weeks of expensive downtime.
On the other hand, automation cells allow for a modular and easily scalable factory structure. These cells can be quickly rearranged on the factory floor whenever manufacturers need to restructure the production process — some models even come on wheels.
Another great advantage of automation cells is that they can be placed in any building where there is enough floor space. This means facilities like empty warehouses can be easily repurposed to set up a new production plant in record times.
This approach is perfect for manufacturers that need to establish a new production line very quickly, for example to respond to a sudden surge in demand. However, it will also facilitate those who are planning to bring production closer to the final customer to save on logistics costs, reduce lead time and minimise the company’s overall carbon footprint.
For example, British electric vehicles (EVs) start-up Arrival uses flexible automation cells in its microfactories, which are small-scale production plants that the company is planning to set up on the outskirts of cities worldwide. The use of automation cells allows the company to set up new production lines very quickly, so instead of relying on production sites overseas, Arrival has chosen this innovative approach to reduce costs by bringing production closer to where its vehicles are needed.
A further advantage of automation cells is that a factory structured this way can be very easily scaled up and down according to market demand, by simply adding or subtracting cells. This is a great approach for start-ups and smaller manufacturing companies who might not be in the position to invest in a huge and cost-prohibitive facility but want to give themselves space to grow.
The beauty of automation cells is that they contain everything the plant needs to automate the production process — or at least some of its core aspects — in an extremely compact architecture. Like Lego building blocks, the components in the cells are structured so that they all fit together to occupy the least possible space.
This is leading to an interesting phenomenon in equipment manufacturing — the standardisation of automation machinery. Traditionally, production and assembly lines were bespoke projects that required the expertise of several high-skilled professionals, such as design engineers and systems integrators. Designing, building and testing the line took several months, was extremely expensive, and required long periods of downtime.
On the other hand, automation cells can be realised in less than one week, although up to three weeks may be needed to map out the necessary tasks within the cell and establish the optimal workflow. There are even useful digital tools to help users in the process.
For example, FANUC’s Build Your Cell configurator guides users at every step to create the ideal cell for their application.
The benefits of automation cells are clear — production can start shortly after the manufacturer perceives the need for new workstations, either because of unprecedented demand, or because of the necessity to adapt production to new specifications. As well as this, costs are minimised and the overall agility of the plant is increased.
It seems clear that manufacturing is evolving from an industry based on cumbersome, bespoke projects to one that requires extreme flexibility through the use of modular architectures and standardised components. Automation cells offer a great chance to innovate manufacturers’ business models and keep up with the ever-evolving needs of an increasingly demanding global market.
For weekly updates on the new trends in smart manufacturing, and to order a wide variety of quality automation components from all major brands, visit www.euautomation.com.
Compared to traditional production lines, automation cells offer unprecedented flexibility.
At its core Sapman v12 is a sophisticated Manufacturing, Warehousing and Stock Control solution. This modular product provides extensive facilities for Stock Control, Sales and Purchase Order Processing, Warehouse Management, Bill of Materials, Works Order Processing, Engineering Control, MRP and CRP. With the Microsoft SQL database engine at its core this product provides a leading edge business management solution.
Our highly skilled team has 20 years of experience resolving our customers’ Assembly, Manufacturing Control and ERP requirements, their Stock Control and Warehouse Management needs using our advanced, effective and efficient software solution.
Sapman v12 fully integrates with Sage’s Accounting solutions: Sage 50 and Sage 200. It also provides an upgrade path from Sage 100.
Sapman v12 is highly customisable to operate with virtually any business model. With successful installations in a huge
range of industry types from manufacturers of medical products to disposable BBQs our customers rely on Sapman v12 to run their businesses.
Sponsored development of specific functionality is possible where customers require some modification to allow the software to exactly map their business’s operational model.
SELL IT
Quotations: Quote ( including price breaks)& Drawings & Pricing : v12 can attach drawings to the Quote
SoP : The Sales Order Processing gets underway
MAKE IT
Stock : Stock Enquiry : Check material Needs : Make to Order or Ex Stock?
If not it may generate a Purchase Order for more Stock
If the Sale item is Make To Order (MTO) then the Works Order Processing routine kicks in v12 is suitable for Batch Manufacturing, Make to Stock, make to Order, Kanban & service works
Stock values from v12 update Sage50 Nominal Ledger
PoP Purchase Order Raised
Purchase Invoice received & Sage 50 updated for Nominal Codes, Purchase Ledger and VAT
WoP The confirmed order has to be manufactured & v12 produces the works order
BOM V12 produces the BoM : tree-view
with collapsible/expandable nodes
SFDC Shop Floor Data Capture : using barcodes v12 manages the job though the shop floor
WiP With Shop Floor Data Capture SFDC v12 knows :
What Material/Subcomponents have been used, Who has worked on the job and on what machine - Get Material, Labour & Machine Variances & produce management reports -
Every stock issue is linked to an original GRN - ensuring full Serial Number and Batch Traceability
Stock Finished item is booked into Stock
v12 knows where it is; it covers multiple sock locations and stock with Sub Contractors
Stock values per client defined categories can be up dated to Sage50 Nominal at client defined times
SEND IT
Stock Stock records updated, Despatch note raised; Certificates of conformity produced
Sales Invoice raised & Sage 50 updated for Nominal Codes, Sales Ledger & VAT
“We really like the Shop Floor Data Capture system which enables us to see the current status of any Works Order live and onscreen.”
Alan Saitch, Managing Director, Lada Engineering Services Ltd
“V12 offers us greater productivity, improved communications with third parties and the interconnectivity between the various menus and our Sage Accounting software makes operating our company infinitely easier.”
Colin Mallard, Finance Director, Lakeland Laboratories
For more information on Sapman v12 please visit our website at Sapmanv12.co.uk. Email us on info@sapmanv12. co.uk or please telephone us on: 0333 456 12 12.
Buying an ERP system used to be a major capital expense, potentially running to tens of thousands of pounds for an up and running system.
The cost of the software purchase and associated consultancy made it a hugely considered financial outlay.
For manufacturers looking for a rapid Return On Investment – this was a major obstacle for many businesses : together with the desire to spend their CapEx budgets on modern machinery and increased manufacturing capacity rather than software!
For companies that want the software
“out of the tin” - and do not require any bespoke programming – a system install and set-up, including training and data conversion would be around £2,950. Our licencing is £95-£20 per month (depending on user numbers) with no minimum contract obligation. Additional users can be added as required and, indeed, reduced.
A key market for us is Sage users. Sapphire Manufacturing Systems Ltd. The developer of Sapman v12 has been an Authorised Sage Developer for over 20 years. So most of our users run on Sage50 and Sage200, and we still have some clients on Sage
Line 100 yet to upgrade.
One of the great advantages of Sapman v12 for Sage users is that users can benefit from multi depot stock and full Serial Number and Batch Traceability without the need to upgrade their accounting engine from Sage50 to Sage200. This is an additional cost saving benefit
We can demo the software remotely via Team Viewer or organise a visit to your premises or you can visit our Bristol Demo Suite: call us on 0333 456 12 12 to have a chat.
As Emmert Wolf said, a man is only as good as his tools, so operators and rental companies should focus on maintaining their machinery to make them as effective as possible. With some replacement parts costing thousands, extending the lifespan of each part in a surface removal machine is key to reducing downtime, costs and increasing productivity. Here Geoff Putz, vice president of manufacturing at surface preparation expert, National Flooring Equipment, answers some common questions about loading and maintaining equipment.
To remain efficient and cost effective, operators must remember to protect their machines during the floor removal process to reduce damages and help extend the lifespan of each machine component. A lack of care with machin ery could create health and safety risks to the operator and rapidly decrease the lifespan of parts. Here are some of the main ways to protect your machinery.
During loading and unloading, opera tors risk slamming a walk-behind into the floor as it moves up a ramp, which can drastically shorten the lifespan of the machine. Contractors should always attach and use transport wheels when manoeuvring walk-behind scrapers to limit damage and remove them while in transit to limit additional movement when in a vehicle.
Operators can load the machines in dif ferent ways depending on what’s availa ble. For example, if there is an electrical outlet, operators can simply drive the machine up a ramp and onto the trailer. If electricity is not available, take the drive pins off the wheels to allow free movement, check the tilt is up and use a winch cable to pull it onto the vehicle. Check local laws when securing the machine to ensure it meets regulation, but we also recommend using a chain to tie the machine down to stop it getting damaged during transportation.
When the transport wheels are attached flat to a ride-on scraper, the machine will tilt back a little to stop the wheels spinning around as it moves, altering the centre of gravity. Operators should always back ride-ons into the trailer, so the centre of gravity is more stable and
The weight and size of the ride-on ma chines can be a risk to the operator, so we recommend that any operator wears personal protective equipment when using the machinery, like steel toe shoes, to protect them from any accidents. The weight also needs to be taken into consideration when choosing a trailer to use. The weight of some machinery could easily damage a trailer if not properly reinforced, costing businesses large sums to replace damaged equipment.
The lifespan of components is heavily reliant on how regularly you use the ma chinery. If there is an accident, we do see new machines needing repair work. More
commonly, if a machine is rented out, it can be five or six years before parts need maintaining or replacing. If the machine is owner operated, some will never need replacements and other we will see ten years after purchase for battery replace ments or new chargers.
National Flooring Equipment has surface preparation experts around the globe who are always available for after sale support on any surface preparation issue, from choosing the right machine to effective transportation.
To talk to our experts, contact National Flooring Equipment today https://nationalequipmentdirect. com/contact.
There are many different forms of Swivel Joint… from very straight forward designs of our F and FS series, Compact swivels or Heavy Duty to Articulated Pipework configurations, Floating Suction Arms, Jacketed, High-pressure. A Swivel Joint reduces costs by reducing the risk of leakage with its associated downtime. By fitting a quality designed swivel you are improving your production capacity.
Rotaflow are specialists in taking bespoke requirements and being able to design a solution that can fit your budget, dimensions, materials, FAT/witness testing; hygienic and pressurised environments. We regularly test to Hyperbaric, Seal Life and conduct Temperature/Pressure/ Load Cycle Testing. We are ISO 9001:2015 certified. We have off-theshelf solutions that are ready to go, or we can redesign and in-house manufacture to enable a quick turn-around with minimal fuss and maximum design experience. Rotaflow have built up a reputation for providing reliable and quality designed products that resolve your engineering needs and we are proud to say many customers request our services over and over again.
To find out more please visit our website and/or give us a call. Tel: +44(0)1663 735003
sales@rotaflow.com
+44(0)1663
Sustainability is at the heart of a partnership between robotics and automation specialist
FANUC UK and machinery refurbishers Electron Engineering Services. By retrofitting a cutting-edge FANUC CNC into a lathe for a subcontract machinist, as well as a FANUC digital spindle motor and drive, servo drives and new electrical interface, this legacy machine has been upgraded ready for the digital age. As well as boosting productivity by delivering improved functionality, faster programming and enhanced reliability, the partnership is helping to cut waste by breathing new life into old machines, repurposing them for today’s smart manufacturing needs.
Based in Halifax, West Yorkshire, Electron Engineering Services Ltd (EES) has been refurbishing machinery for over 30 years. “The majority of
the machines we refurbish – that we essentially remanufacture – are actually of a higher build quality than many of their more modern counterparts,” explains Richard Vogel, EES Sales Director. “They are of robust, predominantly high integrity cast iron
construction, and would have been at the cutting-edge of technology when first commissioned.
“The refurbishment service we provide brings these machines in line with modern day requirements, whilst ensuring that the brilliant engineering that went into them in the first place isn’t discarded. This includes making sure they are compliant with modern standards and regulations, as well as incorporating the latest software, motors and control technology to maximise efficiency.”
An important part of the machine refurbishment process is retrofitting a new CNC. Short for Computerised Numerical Control, CNC is an electronic process for controlling machine tools. From improved functionality and faster programming, through to
The refurbishment service we provide brings these machines in line with modern day requirements, whilst ensuring that the brilliant engineering that went into them in the first place isn’t discarded.Sustainability is at the heart of a partnership FANUC UK and Electron Engineering Services. The partnership is helping to cut waste by breathing new life into old machines, repurposing them for today’s smart manufacturing needs
enhanced reliability, CNCs play a vital role in boosting productivity in a manufacturing facility.
As part of its latest project, EES is completely stripping down and rebuilding a Binns & Berry Data 90 CNC Lathe, for a customer with a subcontract machine shop. By retrofitting it with a new FANUC 0iTF CNC, as well as a FANUC digital spindle motor and drive, FANUC digital axis servo drives, and a completely new electrical interface, this legacy machine will be completely remanufactured and ready for the digital age.
“When it comes to selecting the CNC, there are a number of factors to be considered, such as whether it will provide the required functionality and whether it will seamlessly integrate with the client’s existing manufacturing processes and requirements,” explains Richard. “In this case, the client was already using FANUC controls, which made this a straightforward decision. But even when this is not the case, FANUC CNCs are often the client’s control of choice. FANUC is a globally recognised name, and its products – both firmware and software – are reliable and user-friendly, which are absolutely key in the type of projects that we undertake.”
Alongside the environmental benefits of machine refurbishment, there are also significant cost-saving implications, as EES’ projects typically involve highcapital machinery. Richard continues: “A full remanufacture solution usually delivers around a 50% cost-saving compared with a customer buying an
equivalent, brand-new machine. That means the potential productivity gains can be accessed by a wider range of manufacturers, as well as improving our customers’ ROI.”
As a result, EES is starting to see an increased demand for its services, both for retrofitting as well as for new, bespoke machine solutions. “We are definitely seeing signs of confidence from customers looking to invest in equipment and from our perspective, it’s great to know we can count on FANUC’s ongoing support to help meet this demand,” says Richard. “There are still a significant number of high-quality, older machines with great potential, provided they are updated to ensure compliance with the latest regulations and given modern CNCs, motors and drives to get the most out of their inherent mechanical capabilities.”
Ray Timberlake, Sales Manager at FANUC UK, adds: “The work that EES do is brilliant in terms of providing premium manufacturing equipment at a competitive price point. We’ve been working in partnership with them for over a decade, and every single project is an exciting opportunity to breathe new life into old machinery.”
PTC has announced the availability of cloud-native simulation as part of its Onshape® product development platform.
Onshape Simulation enables designers and engineers to perform finite element analysis (FEA) in a fast and simple way and to make informed design decisions with structural analysis throughout the product development process.
It is the only computer-aided design (CAD) and product data management (PDM) tool to offer simulation that is interwoven with the core design and assembly environment, which helps reduce the time, effort, and workflows required to set up and calculate structural analysis.
“This is the first time that CAD, PDM, and simulation have all been unified in one cloud-native environment,” said Greg Brown, Vice President of Onshape Product Management.
“This is an extremely efficient way for designers to simulate full assemblies, helping them make important time, material, and quality decisions earlier in the design process.”
Features and benefits of Onshape Simulation include:
• Designers receive accurate mechanical guidance, such as strength and rigidity, without ever leaving the design environment. The CAD model and the
simulation model are the same definition, which dramatically simplifies the assembly set-up for simulation
• Onshape uses the existing assembly mates in the definition of the part-topart interactions, eliminating the need to defeature, simplify, or set up connections for their models before running simulations
• Explore design variations quickly by simultaneously designing and analysing assemblies with no pre-processing or
meshing required. Simulation results are automatically refreshed when changes are made to Onshape models
• As part of an Onshape document, simulations are version-controlled with built-in PDM – including simulations for all design variations – and can be shared instantly with other users for simple collaboration and decision making
• Cloud computing allows simulations to be conducted fast and interactively, with no need for specialised local hardware.
Simulation is available now for Onshape Enterprise users, with availability for Onshape Professional users to follow shortly.
For more information, please visit our simulation page on Onshape.com.
This is the first time that CAD, PDM, and simulation have all been unified in one cloud-native environment.
ocess
Ltd., is announcing a major
distributor in South Korea. The link with Shinsung Ener-Tech Co., Ltd., based in Seoul, South Korea
a
create opportunities for both organisations in one of the most active markets in the region.
is very well established in the field of HVAC and process burners which are used within a variety of applications,” says Jeff Foster, Sales Director at Nuneatonbased Lanemark. “We share a commitment to quality, efficiency and environmental optimisation so are confident that, jointly, we can bring proven performance and key benefits to the regional customer base.”
The agreement with Shinsung is set to strengthen Lanemark’s own burner sales in the new distributor’s markets. The company’s (TX) tank heating burners, (FD) forced-draught oven burners, (FDB) forced-draught duct burners and its (DB) duct burners – each used extensively in processing and manufacturing operations from aluminium anodising to food processing – will, in turn, all enhance Shinsung’s own market strength.
“We are committed to building on the close relationships
that we have with distributors around the world, and we are, therefore, delighted to be able to add Shinsung to this list,” concludes Jeff Foster, Sales Director at Lanemark. “The area within which both companies have developed leading reputations is highly specialist so we are confident that the link between us will offer major gains to our respective customers.”
www.lanemark.com
China Petroleum & Chemical Corporation (HKG: 0386, “Sinopec”) has successfully produced China’s first batch of large tow carbon fiber at the company’s production base in Shanghai, making the company the first in the country and fourth in the world to possess large tow carbon fiber technology.
Sinopec’s production line has adopted its self-developed PAN (polyacryloni trile) base large tow precursor and carbon fiber technologies. The project is being implemented in two phases and expects to be in full production in 2024, projecting an annual production capaci ty of 24,000 tons of protofilament and 12,000 tons of large tow carbon fiber. Large tow carbon fiber refers to roving that contains 48,000 filaments or more. The high-performance material is often referred to as the “king of new material” and “black gold.” The product developed
and manufactured by Sinopec Shanghai is a new type of high-strength carbon fiber with a carbon content of over 95 percent. It has outstanding excellent mechanical properties and a specific gravity that’s less than one fourth of the steel, yet a strength that’s seven to nine times stronger. It is also corrosion resistant.
As the material can be widely used in producing parts and components, it is expected to be used for an increasing amount of industrial infrastructure pro jects in China, including ones related to wind power, solar power, high-speed rail, and aviation.
“Sinopec has customized a special pro duction line for large tow carbon fiber, including production equipment and techniques, which has enabled us to design oxidizing furnaces and carbide furnaces that revolutionizes not only the core technology of temperature field control, but also has a revolution
ary energy-saving design, marking a major milestone in the development of China’s carbon fiber industry,” said Huang Xiangyu, carbon fiber expert and deputy general manager of Sinopec Shanghai.
Sinopec now owns 251 patents related to carbon fiber and 46 patents for car bon fiber composite materials, the larg est number in China and third in the world, and through scaled up invest ment and industrial layout, Sinopec is committed to being a major contributor to the development of China’s carbon fiber industry.
Stavian Chemical, the 22nd largest global chemical distributor, is showcasing its exceptional ‘One-Stop Shop’ solution’ and a wide range of polymers, affirming its leading position in the global plastics industry, especially in Europe, at booth C12, hall 7.2, during the K 2022.
The K 2022 is taking place from October 19 - 26 at the Fairground Düsseldorf to present new products and innovations from all sectors of the industry – from production to processing, to mechanical engineering while guided by three main themes: Circular Economy, Climate Protection, and Digitalization.
In line with this, Stavian Chemical’s ‘One-Stop Shop’ concept is a crucial business solution connecting oil refineries and chemical manufacturers to hundreds of thousands of plastic manufacturers that contribute to the sustainable growth of each partner.
The ‘One-Stop Shop’ solution, comprising 12 specific business solutions, from in-depth customercentricity advisory and financial support to warehousing and customs handling and clearing, provides a world-class full-service package for Stavian Chemical’s customers and
partners. This is in addition to the brand’s strategic relationships with oil and gas conglomerates, top global multi-industrial corporations, and its decades of expertise in the logistics industry.
“The European plastics market is forecasted to grow by around 2% annually, reaching a volume of US$108 billion in 2031. As an international polymer distributor, and a major manufacturer of eco-friendly biodegradable packaging with high trustworthiness in the chemical industry, Stavian Chemical is proud to showcase One-Stop Shop at the K 2022 and become a strategic partner supporting the sustainable growth
of European clients,” said Stavian Chemical representative.
Proving its value to European clients, Stavian Chemical delivers innovative and sustainable solutions for customers and partners while maximizing values and prosperity for all stakeholders. In 2021, the company has developed a network of more than 21 offices and 40 warehouses across 30 countries. It also has served 14,000 partners across more than 100 countries, and this exponential business growth resulted in revenues of US$1.2 billion last year.
“Spurred on by the European Union –Vietnam Free Trade Agreement (EVFTA), Stavian Chemical has entered Europe with a strong proposition, bringing premium quality polymers from Vietnam, China, South Korea, and other countries that are priced competitively. We have also developed a bonded warehouse ecosystem in Europe. This expansion is ongoing and we want to ensure effective logistics, timing, and cost efficiency not only in the European market but also for our clients worldwide,” he added.
For more information, visit the Stavian Chemical website at https://stavianchem.com/.
As microprocessors continually get smaller, manufacturing becomes more accurate, working on the nanometer scale which is highly intolerant to disruption. To create the environment needed to facilitate precision manufacturing, it is essential to control vibration, temperature, humidity and particulates. Here’s how vibration control specialist, Mason UK, designed a sophisticated vibration isolation system to ensure conditions at an advanced manufacturing site in Ireland were ideal for high-precision manufacturing.
Mason UK was commissioned to provide vibration isolation support at a vast site upgrade project in Ireland. In fact, the site is one of the most technologically advanced manufacturing locations in Europe and the facility has undergone an upgrade that has enabled production of 14nm process technology.
However, these cutting-edge chips could not be realised without very precise manufacturing conditions. This requires a vast array of heating, cooling and filtration systems, all of which must be correctly isolated, since even exceptionally low levels of vibration can cause errors in fabrication. To achieve the stable environment required in the fabrication clean rooms, mechanical processes such as cooling, heating, ventilation and filtering systems are necessary — all of which generate unwanted vibration at every pump, fan, valve, duct and pipe support. Systems are vast, some ducts being over four metres in diameter, so the project is challenging.
Mason UK was brought on board by the contractor early to support the design. What makes this project unique is the scale of the facility and volume of vibration control required. As a result,
not only the vibration but factors such as wind loading, thermal expansion and the clash of services in a crowded area had to be considered.
As one of the biggest construction projects that Ireland has ever seen, the shear amount of product that Mason UK supplied was staggering. In total the vibration specialist has so far supplied 3800 spring mounts, 1600 hangers and 400 flexible pipe connectors for the site. With such an unprecedented undertaking ahead, it is little wonder that there was a very onerous specification.
“The first requirement is ensuring quality of the engineering design, for example, specifying a particular spring geometry or housings made in a certain way,” explained Adam Fox, director at Mason UK. “The second requirement is ensuring the product has the correct vibration isolation properties. This is determined
initially by the location in the building and the experienced product selection of the Mason UK engineering team.
“The closer you get to the fabrication, the more urgent the need for vibration isolation. Similarly, the higher up you go in the building, the more lightweight the structure gets, and more vibration isolation is necessary. Down in the foundations, vibration is minimal, but if you’re on the roof, that roof structure can be quite sympathetic to vibration. The vibration isolation properties can also be equipment driven. By and large, the bigger the diameter of your pipe, the bigger your pump or your ducting gets and the more energy it is able to carry. Consequently, larger pipes require a higher level of vibration isolation.”
Not only was Mason UK brought on board to supply the vibration control products, but the team was also invited to conduct associated design work. Mason UK has unrivalled design capabilities in this area, so this was a welcome invitation for its experienced engineers.
The team took 3D models of the ducts and supporting steels and generated their own drawings using building information modelling software, Revit. Mason UK also produced detailed 2D drawings using AutoCAD. These were used to calculate how much each component weighs, how much it expands and how much it contracts. This process was repeated for hundreds of pieces of plant equipment and kilometres of building services, for all locations and configurations, to show which products were required where. Crucially, this removed some responsibility from the contractor.
However, the project was not without its engineering challenges. Instead of simply supplying a standard catalogue product, Mason UK made bespoke spring mounts with different housing to meet the needs of this project. This allowed for clearance on vertical ducts when they grow and shrink thermally.
As with any project of this magnitude, smooth installation is key. The physical size of the products, some of which were half a metre in height and a vast range of sizes, could have proved tricky. Mason UK went above and beyond to help simplify the process. The company anticipated that it would be difficult to detail all duct supports and created bespoke spring mounts, with consistent dimensions and attachments. This ultimately made the installation cheaper and easier.
Mason UK also supplied flexible connectors for the project to isolate the pumps from the ground. The flexible pipe connectors selected were the Safeflex variety, using a uniquely robust flange design and reinforced with Kevlar, which has immense strength and fantastic resistance to becoming brittle over time. Cheaper variations use nylon and can become brittle if heated water passes through it. This can lead to failure which is absolutely unacceptable for a
continually running fabrication process.
“No one else builds connectors in this way,” continued Fox. “With the vast majority of connectors, you snap them on to their flange — but if you can snap them on, you can also snap them off. We use a solid steel ring which is bolted in place so that there’s no way it can snap out and fail.
“Our connectors can accept steam or chemicals passing through at high pressure and temperatures. If it were to burst, severe injury or flooding can result. From damage to equipment, to whole buildings being written off — the repercussions would be huge. Our Safeflex flexible pipe connectors are such a reliable design that we’ve never had a failure.”
While this project was clearly a massive engineering exercise, the quality and reliability of Mason UK’s products, coupled with the company’s unrivalled design expertise, proved invaluable to ensure the upgrade will be a success.
For more information about Mason UK’s design services or its comprehensive range of vibration control products visit www.mason-uk.co.uk.
Designing, manufacturing, installing and maintaining bespoke machinery for production lines in demanding sectors such as automotive, rail and general industry may seem like a complex process. However, expert machine manufacturers offer customers an integrated approach to every tailored machine build, ensuring that your custom equipment is delivered in a cost-effective and timely manner.
Adrian Degg, Group Engineering Director at KMT, explores the key stages of machine build projects and how turnkey engineering providers can support in delivering optimised equipment to factory floors.
An essential part of every project is the design phase, in which expert engineering teams closely collaborate with customers to scope out application requirements. Virtually any machine design is possible when working together with a turnkey service provider that has design engineers
highly experienced in meeting the requirements of OEM production lines. Blueprints and CAD models are provided for sign-off in customer specified formats. This ensures that your process and performance requirements are met with an application specific machine design.
With design completed, a machine builder with an in-house fabrications facility can quickly produce custom equipment frames and tooling.
Experienced fabricators and welders using state-of-the-art machinery, including in-house laser cutters and press brakes can manufacture to the highest quality standards. This ensures truly custom designs that meet the customer and industry relevant requirements with high reliability.
Machines are more than just metal though, which is where skilled machine builders come in. A complete electromechanical approach offered by a machine builder means that almost any system can be integrated into a machine design. This includes the implementation of powertrains, hydraulics, pneumatics, electronics, controls and instrumentation. Some builders even have the ability to produce custom software or create user interfaces that match your existing equipment to ensure operator familiarity. As a result, new or upgraded machines will not only offer exceptional efficiency, but will be optimised to the needs of each customer process.
A complete electromechanical approach offered by a machine builder means that almost any system can be integrated into a machine design.
As well as offering custom machinery, machine builders can renew older equipment too. A cost-effective method to extend the service life of existing assets, a refurbishment service allows you to rejuvenate a dependable machine with new controls, instrumentation and tooling – greatly improving efficiency and reliability.
Learn more about the benefits of machine refurbishment here
With your perfect machine built and tested, managing delivery and installation at your production facility is the next step. A complete in-house approach allows some machine builders to offer reduced lead times, with engineers familiar with a wider range of
industry requirements providing turnkey installation services. This ensures a swift and straightforward machine installation, reducing downtime for your operations.
That is not the end of the story though. Some machine builders can also support the future reliability of your equipment with around-the-clock maintenance support services. Maintenance personnel can be made available to proactively service machines, troubleshoot any issues and ultimately ensure availability. This can even include stationing dedicated teams at your facility, allowing the fastest possible response, helping to improve manufacturing operations.
Sourcing your perfect machine needn’t be complex when you choose the right machine builder. KMT offers all of the aforementioned services under one roof, backed by decades of experience and a flexible, high capacity engineering capability.
With a structured, in-house approach, KMT can provide a truly bespoke engineering service that delivers an optimal machine for your production process. With a proven track record in wide range of industries, including the automotive, rail and industrial sectors – KMT has the solutions and expertise ready to help you maximise your manufacturing productivity.
One of the UK’s leading manufacturers of round, flat and profile wire has named a new Managing Director as it looks to build on a record twelve months.
Alloy Wire International (AWI), which employs 33 people at factories in Brierley Hill and Batley in Yorkshire, has promoted Tom Mander to the role after being with the company for more than 17 years.
The move will see previous MD Mark Venables move upstairs to Chairman, remaining in the business to guide and advise for the foreseeable future.
This is an exciting next step in the AWI journey and will accelerate its ambition to increase sales from its current £13m level to £15m by 2025, with most orders now coming from clients overseas.
“Alloy Wire International is a very special business and I’m honoured to take the reins and help guide the company to the next stage,” commented Tom Mander. “We’ve come through the pandemic in a good position and, as a critical supplier, continued to provide our material to customers involved in power generation
and healthcare, the latter resulting in our wire being used in the VentilatorChallen geUK.”
He continued: “The last twelve months has seen us increase sales to £13m and achieve significant growth in internation al markets, including the US where orders have risen from $1.8m dollars to $4.2m dollars.
“All the foundations are in place to continue this growth and we’re just about to complete a £1m investment drive that will boost stock levels to one of the high est in our sector, whilst adding three new dry drawing and one wet drawing ma chines to increase production capacity.”
Alloy Wire International manufactures round, flat and profile wire in over 60 Exotic alloys, such as Inconel, Monel, Hastelloy, Nimonic and Waspaloy.
Founded in 1946 by John Stockdale in an old ambulance station in Old Hill in the Black Country, the company’s founding principles of ‘manufacturing quality, delivering reliability’ has stood the test of time and remains a crucial part of how it deals with its 6000-strong global client base.
Today, the firm continues to operate across 15 different market sectors and, despite global supply chain disruption, is still delivering material in just four weeks from the order being placed.
Mark Venables, who becomes Chairman, added his support: “The senior man agement team wanted to protect the core values that make AWI so special, so we took the decision last year to make Tom, Adam Shaw and Andrew Du Plessis, MD Designate, Finance Director and Technical Director respectively.
“This was paving the way for the next generation to take over and Tom’s promotion to MD this week is the next step in that process.
“He has been with us for 17 years and understands the culture and our people. It’s a natural appointment and I’m looking forward to seeing the fresh skills and insights he will bring to the role.”
For further information, please visit www.alloywire.com or follow @alloywire on twitter.
use,
and
are
air
environment, so can be used in more open
don’t rely on a
as warehouses,
and sports arenas.