FOOD & DRINK PROCESSING & PACKAGING
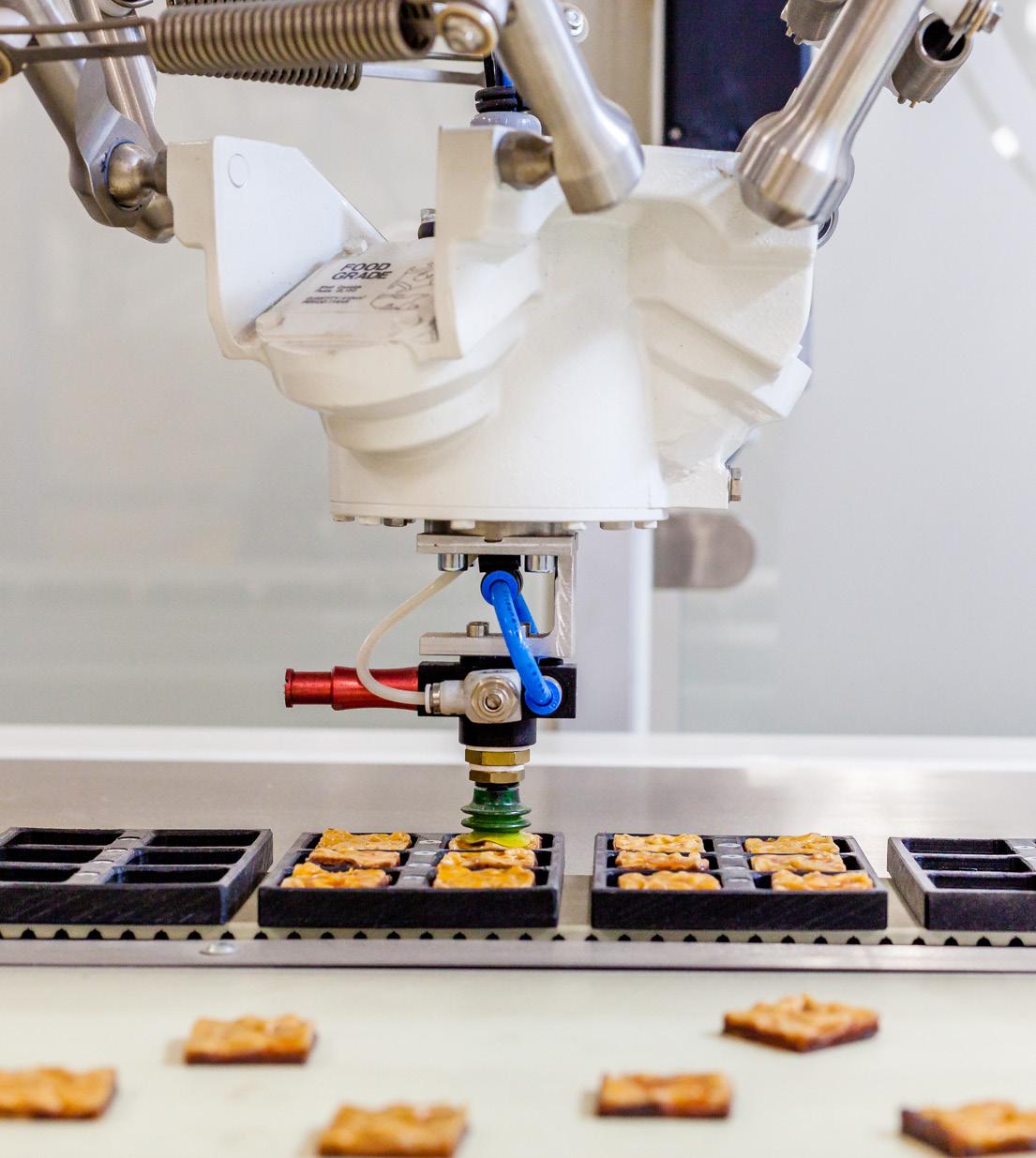
How robots are set to shape the future of food manufacturing
NOMOQ revolutionises the beverage can industry
How robots are set to shape the future of food manufacturing
NOMOQ revolutionises the beverage can industry
Our UK based Product Advisory team and in-house IT developers offer end-to-end food and consumer product brand and reputation protection.
Our services are scalable and flexible to meet your needs and budget. For an exclusive 15%* off your first invoice with SGS United Kingdom Ltd please quote FDPPSGS15.
Our services include:
Product label review
Pack copy generation
Specification writing and review
Product legislation consultancy
Crisis management support
Bespoke Product Lifecycle Management system
Project management
Horizon scanning
Contact us
+44 (0) 151 350 6666
ukenquiries@sgs com
www sgs com/foodsafety
www sgs com/linkedinfood
For an automated, wet Clean-in-Place process, a technician can push a cart with pre-programmed recipes and integrated water line hookups to tubular drag conveyors, facilitating quick sanitary compliance and production changeover
To promote food safety and sanitary compliance, processors are increasingly seeking the ability to Clean-in-Place (CIP), an automated method of cleaning the interior surfaces of tubular drag conveyors without disassembly. Now, with the advent of mobile tools like an innovative “smart cart” that quickconnects to any tubular conveyor and enables simple, customizable “single button cleaning recipes,” CIP is becoming easier, faster, less laborintensive, more repeatable, and almost fully automated.
Tubular drag conveyor systems gently move product through a sealed, enclosed tube using a drag cable and circular discs pulled through on a loop, so are ideal for delicate items. In a wet CIP process, the system is flooded with water, flushed, rinsed, cleansed, and thoroughly sanitized. The process thoroughly flushes out any potential allergens like nuts or gluten from conveying equipment and can be used with a variety of food types such as nuts, grains, cereals, powdered soups, and frozen fruits and vegetables.
Although the CIP process is very effective, streamlining its automation and simplifying the process for all of a facility’s tubular drag conveyors has been a priority for leading innovators in the industry.
“The standard system required port hookups to water lines and installing piping. The processor also had to make decisions such as which water temperatures to utilize, or whether to use a cleaning solvent - and the correct amount to add manually,”
For an automated, wet Clean-in-Place process, a technician can push a cart with pre-programmed recipes and integrated water line hookups to tubular drag conveyors, facilitating quick sanitary compliance and production changeover.
Once it is set up, all you do is press a button and it will bring in the required amount of water at the correct temperature with the necessary amount of solvent for cleaning.
says John Adair, Engineering and Quality Director for Cablevey Conveyors, an Oskaloosa, Iowabased conveyor manufacturer that has designed, engineered, and serviced enclosed cable and disc tube conveyors for 50 years, and is in more than 65 countries.
To simplify the wet cleaning process, Adair and his engineering team at Cablevey have developed a small, mobile “smart cart” with
integrated water line hookups that a single technician can easily take to any tubular drag conveyor in a facility. The cart is specifically designed to be a fraction of the size of similar carts on the market to facilitate mobility. When the cart is in position and connected to water lines, the CIP process is automated and controlled by a programmable logic controller (PLC) that reduces the need for manual labor and virtually eliminates the risk of improper cleaning.
“Once it is set up, all you do is press a button and it will bring in the required amount of water at the correct temperature with the necessary amount of solvent for cleaning,” says Adair.
The smart cart is designed to store and utilize pre-programmed CIP recipes to flush various residual materials from the tubular drag cable conveyors in a facility before new production runs. The cleaning
Once it is set up, all you do is press a button and it will bring in the required amount of water at the correct temperature with the necessary amount of solvent for cleaning
recipes enable even those with very little training to use the cart. This is helpful in today’s tight labor market and allows the technician to move on to other tasks once the cleaning process begins.
The use of easily executable recipes ensures a superior, repeatable clean that essentially “error proofs” the process. This is particularly important when the technician may be new or less familiar with the production equipment.
“Depending on the product being conveyed, sometimes all you need is a wet rinse, or sometimes you need a specific cleaning solvent. All that information is saved, so after the first cleaning, it can be automatically repeated. Just push a button to start the appropriate recipe, whether you have one conveyor running multiple products, or dozens of conveyors running various products,” says Adair.
To facilitate food safety compliance, the smart cart also documents all critical CIP information such as water volume and temperature, chemicals used, and cleaning time by date in an easily retrievable data log.
Since decreasing production downtime between conveyor cleanings is a priority for food processors, Cablevey provides new capabilities with the cart that expedites the CIP process.
Currently, the CIP process floods the tubular conveyor system but is not designed to specifically clean the discs. “Operators would manually clean each disc and advance the system [disc by disc] when the discs had to be cleaned of particularly viscous substances,” says Adair.
Now, as an option on the cart, a disc washer can be integrated with the conveyor turnaround to spray a pressurized cleansing solution on the discs. This helps to remove stickier substances like chocolate that could remain after routine CIP cleaning.
“The disc washer sprays highpressure water directly on the discs, so it acts like an automatic car wash. At the push of a button, the discs and cable are run through and spray cleaned, which reduces CIP time and eliminates the need to manually clean the discs,” says Adair.
To further reduce downtime, Cablevey also offers a new sanitary blower option.
“After the wet CIP process, a sanitary blower attachment on the smart cart can dry the discs and other parts of the system 75% faster than typical air drying,” says Adair. He points out that the faster the conveyor is cleaned and dried after a product change, the sooner it can be put back into service, which improves profitability.
While the food processing industry is aware that automated CIP can improve conveyor system production uptime, barriers to implementation have slowed adoption. Utilizing a mobile smart cart with integrated water hookups will help processors to easily implement CIP in tubular drag conveyors throughout their facilities: expediting conveyor cleaning, production changeover, and sanitary compliance.
For more info, call +1 (641) 6738451; in U.S. call toll free: +1 (800) 247-3344; fax: +1 (641) 673-7419; email: info@automatedhandling.com; or visit www.cablevey.com.
The use of easily executable recipes ensures a superior, repeatable clean that essentially “error proofs” the process.Carrier AquaSnap® 30RBP aircooled scroll chillers operating on lower global warming potential (GWP) refrigerant R-32 are providing high-efficiency cooling and heating for the world’s largest vertical farm in Lydney located in the Forest of Dean district in Gloucestershire, operated by Jones Food Company. The vertical farm, the size of seventy tennis courts, offers 148,000 square feet of growing space for stacking crops 15 layers high, and is expected to supply 1,000 tonnes of fresh produce a year to UK supermarkets. Carrier is a part of Carrier Global Corporation (NYSE: CARR), global leader in intelligent climate and energy solutions.
Contractor Brooktherm Refrigeration Ltd was tasked with providing an HVAC solution capable of delivering a constant supply of efficient heating and cooling to the pressurised warehouse. It was essential that the chillers specified were compatible with Brooktherm’s control system.
“One of the key challenges was the requirement to achieve four different temperature and
humidity set points,” said Ben Doherty, Projects Coordinator, Brooktherm Refrigeration Ltd. “With the support of Carrier, we achieved them all.”
Carrier recommended its flexible and compact AquaSnap 30RBP air-cooled scroll chillers with refrigerant R-32, which operate from -0oC up to +48oC, and come with Greenspeed intelligence® variable-speed pumps to reduce pumping energy consumption by up to two-thirds. The innovative solutions support Carrier’s ESG
goal of helping customers avoid more than 1 gigaton of GHG emissions by 2030.
The Carrier chillers have a heat recovery system that enables waste heat to be captured and used for various heating applications on site, saving energy while maintaining optimum growing conditions. The cultivation warehouse is served by two HVAC plants, one on the north side and one on the south side, each equipped with two Carrier chillers, delivering a total of 2.2 megawatts of cooling and heating to the growing room.
“This exciting project is an efficient and environmentally-responsible way to produce food and Carrier was delighted to be part of such a pioneering, sustainable new approach to growing the nation’s food,” said Paul Hill, Regional Sales Manager, Carrier UK. “The HVAC plant was fully commissioned summer of 2023, and by October the entire growing area was fully planted, allowing the operator to harvest a tonne in weight of basil and leafy greens every 19 days.”
“With our new facility, we further accelerate Britain’s position as a world-leader when it comes to vertical farming,” said James LloydJones, Chief Executive Officer, Jones Food Company. “We already supply thousands of British retail stores with basil grown in our first facility in Lincolnshire, but our Lydney site is three times bigger and will allow us to supply a greater range to more stores.”
For more information about the cooling and heating solution delivered to Jones Food Company, visit: www.carrier. com/commercial/en/uk/products/ air-conditioning/air-cooledchillers/30rb--30rbp/
Being flexible is good, being fast and flexible is even better. Schubert packaging machines are leading the way. Intelligent control and precise robotics can now replace complex mechanics to ensure maximum flexibility in all packaging processes. In fact, 80% of the leading FMCG companies count on us and our flawless packaging combined with the lowest possible consumption. In line with our Mission Blue Sustainability Initiative: A winning proposition – for our planet and for you. www.schubert.group/en/food.html
Being flexible is good, being fast and flexible is even better. Schubert packaging machines are leading the way. Intelligent control and precise robotics can now replace complex mechanics to ensure maximum flexibility in all packaging processes. In fact, 80% of the leading FMCG companies count on us and our flawless packaging combined with the lowest possible consumption. In line with our Mission Blue Sustainability Initiative: A winning proposition – for our planet and for you. www.schubert.group/en/food.html
The baked goods industry is facing a fundamental transformation.
As are many other sectors, it is struggling under the currently challenging economic environment, with increased energy prices, supply bottlenecks and inflation. There are also fewer and fewer smaller traditional artisan bakeries, which are now being squeezed out by large industrial bakeries. Most market players are facing a shortage of staff. As a result, steps that used to be carried out manually now have to be performed by machine – and as quickly as possible. Although many baking processes have already been automated, this is not yet the case when it comes to packaging. Moreover, consumers want more and more product diversity and are demanding more sustainability. In this dynamic environment, bakeries of all sizes need reliable, expert support. As a packaging specialist with many years of experience, Gerhard Schubert GmbH is a partner that accompanies companies on the challenging path to profitability, efficiency and automation.
In addition to a fast-paced market environment, the challenges bakeries are facing today also lie
in the production and packaging processes themselves. For instance, many baked goods are very sensitive when it comes to handling, while others have to be cooled throughout or packaged in a modified atmosphere. As a rule, however, baked goods come directly from the oven. So the downstream packaging process needs to run as smoothly as possible, because the baking process cannot be interrupted. With its innovative top-loading machines and customised consulting services, Schubert is ideally positioned to ensure precisely coordinated automated processes. This enables assortments with high production quantities as well as changing formats with small batches to be handled smoothly and seamlessly. By the same token, switching between conventional and more
sustainable packaging materials also needs to be carried out as quickly as possible.
Packaging baked goods –Schubert machines guarantee flexibility
With Schubert, all processes ranging from primary to secondary and tertiary packaging can be combined into a modular yet compact linear system. Various packaging steps can be flexibly integrated into the overall process. The Flowmodul flow-wrapping unit can be incorporated into the TLM line at various points – for example, to pack freshly baked goods directly into flowpacks, or further along in the packaging process, for example, to wrap tray-packed baked goods into flowpacks. Packing into transport cartons and subsequent palletising can also be integrated into a Schubert TLM line.
Pick & place robots: accurate and always precise
With Schubert, pick & place robots play an important role in the packaging processes. They pick up baked goods and place them into trays, cartons or thermoformed
Although many baking processes have already been automated, this is not yet the case when it comes to packaging.
packs – with millimetre precision. They can achieve this thanks to the vision system developed in-house by Schubert, which, as a quality control system, reduces waste, cuts costs and significantly increases the efficiency of the entire packaging process. In addition to determining the exact position, the pick & place vision system ensures that baked goods that do not meet the quality specifications or are damaged are not picked up and further processed.
Moreover, thanks to their customised tools, the pick & place robots are extremely flexible when it comes to processing baked goods of different consistencies, shapes or sizes. With the complete PARTBOX 3D printing system from Schubert Additive Solutions, bakeries can quickly and easily produce the tools they need themselves using certified print jobs. Furthermore, the pick & place machines bring their strength to bear with various assortment configurations such as mixed biscuit packs: The baked goods are fed to the packaging line via several lateral conveyor belts so that bakeries can introduce different product variations into the packaging process. From the infeed conveyors, the pick & place robots pick up the baked goods
and pack them into the respective assortment packs.
With the Flowpacker, all types of baked goods can be packaged into different flow-wrapped packs. The flexible packaging machine combines pick & place robots, the flow-wrapping unit and a quality control system. It makes it easy to switch between baked goods of different shapes and sizes as well as between different packaging formats and materials. For example, the Flowpacker can package baked goods directly from the oven, either individually, in groups or stacked into flowpacks, or place them in different formations into trays or U-boards before packaging them into flowpacks.
Thanks to Schubert’s various advanced sealing technologies, manufacturers of baked goods also have the option of using extra-thick high-barrier films. The use of environmentally friendly paper-based films or recyclable monofilms is also possible with the exceptionally flexible flowwrapping machine.
The topic of sustainability plays a key role for Schubert. To provide its customers with the best possible advice, the packaging specialist has bundled its far-reaching expertise into its Packaging Perspectives programme. By providing consulting, packaging development and research, the technology leader aims to actively support producers of baked goods along their sustainability journey. In practical terms, this means that the Schubert experts help with material selection and packaging design to develop a packaging solution that is both machine-compatible and environmentally friendly. By using Schubert’s modular, automated packaging machines, bakery businesses can not only respond flexibly to new requirements, but also produce sustainably and ideally position themselves for the future.
www.schubert.group/en/bakerypackaging/
A good fork lift truck battery maintenance regime will maximise productivity, enhance site safety and help minimise fleet costs.
A good fork lift truck battery maintenance regime will maximise productivity, enhance site safety and help minimise fleet costs.
Here is our top ten list of the everyday things fleet managers and operators can do to get the most out of their lead-acid battery powered equipment.
Here is our top ten list of the everyday things fleet managers and operators can do to get the most out of their lead-acid battery powered equipment.
Maintaining the correct battery fluid levels is an essential part of extracting the full performance potential from any battery. Levels should neither be too low nor too high –top up the cells so that the plates and separators are just covered by electrolyte. However, this is di erent if your truck has autofill. If the white disc in the clear window has dropped then top up. If the white disc is at the top, then don’t top-up Battery manufacturers recommend that levels are regularly checked. Doing so will also help prevent premature damage or failure. Always make sure that only distilled, deionised water is used when topping-up any lead acid battery.
Maintaining the correct battery fluid levels is an essential part of extracting the full performance potential from any battery. Levels should neither be too low nor too high –top up the cells so that the plates and separators are just covered by electrolyte. However, this is di erent if your truck has autofill. If the white disc in the clear window has dropped then top up. If the white disc is at the top, then don’t top-up Battery manufacturers recommend that levels are regularly checked. Doing so will also help prevent premature damage or failure. Always make sure that only distilled, deionised water is used when topping-up any lead acid battery.
As the water in batteries is critical to the transfer of energy, the introduction of fresh water must occur at the correct time during its charging cycle, which is after the battery has completed its charge and never before. Electrolyte expands when it gets warm so topping up before a charge can result in spillage of electrolyte.
As the water in batteries is critical to the transfer of energy, the introduction of fresh water must occur at the correct time during its charging cycle, which is after the battery has completed its charge and never before. Electrolyte expands when it gets warm so topping up before a charge can result in spillage of electrolyte.
There is an important di erence between a charger that simply works and one that is specifically designed to correctly charge a given type and make of battery. Check with battery suppliers to confirm that the correct charging equipment is being used. Using incorrect chargers can be extremely dangerous, can damage batteries and may also compromise insurance cover. Always follow the charging procedure shown in your charger’s manual.
There is an important di erence between a charger that simply works and one that is specifically designed to correctly charge a given type and make of battery. Check with battery suppliers to confirm that the correct charging equipment is being used. Using incorrect chargers can be extremely dangerous, can damage batteries and may also compromise insurance cover. Always follow the charging procedure shown in your charger’s manual.
Batteries will always perform best after a full charge. Avoid the temptation to partially charge them, or to interrupt a charging cycle. Doing so could damage the battery permanently, reducing its capacity as well as potentially shortening its life.
Batteries will always perform best after a full charge. Avoid the temptation to partially charge them, or to interrupt a charging cycle. Doing so could damage the battery permanently, reducing its capacity as well as potentially shortening its life.
A typical lead acid battery needs to be left for a good two hours to cool after every charge. Build this time into your charging schedule and make it a mandated part of your health and safety best practice.
A typical lead acid battery needs to be left for a good two hours to cool after every charge. Build this time into your charging schedule and make it a mandated part of your health and safety best practice.
Equipment operators should continually monitor the status shown on Battery Discharge Indicators. Batteries should ideally be recharged when their indicator shows around 25% charge remaining. Doing so will keep them in optimum condition and allow the battery to deliver its maximum capacity for longer. Newer machines are also programmed to cut out the hydraulic function when 80% discharge is reached, preventing lift, however drive functions remain una ected.
Equipment operators should continually monitor the status shown on Battery Discharge Indicators. Batteries should ideally be recharged when their indicator shows around 25% charge remaining. Doing so will keep them in optimum condition and allow the battery to deliver its maximum capacity for longer. Newer machines are also programmed to cut out the hydraulic function when 80% discharge is reached, preventing lift, however drive functions remain una ected.
Battery leads can be prone to damage or corrosion, as can plugs and chargers. Check all equipment and connections and report any frayed wires or worn insulation. A weekly visual inspection will help identify any issues before they can a ect the operation of the machinery.
Battery leads can be prone to damage or corrosion, as can plugs and chargers. Check all equipment and connections and report any frayed wires or worn insulation. A weekly visual inspection will help identify any issues before they can a ect the operation of the machinery.
When operating more than one battery, such as in multiple shift environments, make sure that they are all used and charged evenly. This will avoid the risk of any one battery being over-cycled, which could result in a decrease in performance and shortening of its useful life. Implementing Battery Monitoring System technology will keep operators informed of batteries’ status and ensure even use.
When operating more than one battery, such as in multiple shift environments, make sure that they are all used and charged evenly. This will avoid the risk of any one battery being over-cycled, which could result in a decrease in performance and shortening of its useful life. Implementing Battery Monitoring System technology will keep operators informed of batteries’ status and ensure even use.
The lids of battery cells should always be kept clean and free from debris. Doing so will prevent potential earth leakage and any subsequent reduction in capacity.
The lids of battery cells should always be kept clean and free from debris. Doing so will prevent potential earth leakage and any subsequent reduction in capacity.
Whenever working with batteries always wear suitable protective clothing and use appropriate safety equipment. Ensure spill kits and an eye wash station is located within your charging area. Remember to also provide good ventilation to all batteries and chargers when charging and keep battery compartment lids open if charging the battery in situ. And don’t forget to safely store the charge cables when not in use, this will avoid unnecessary damage as well as removing any potential trip hazards.
Whenever working with batteries always wear suitable protective clothing and use appropriate safety equipment. Ensure spill kits and an eye wash station is located within your charging area. Remember to also provide good ventilation to all batteries and chargers when charging and keep battery compartment lids open if charging the battery in situ. And don’t forget to safely store the charge cables when not in use, this will avoid unnecessary damage as well as removing any potential trip hazards.
Recent advances in its in-house developed robotic technology has enabled Cama Group to further enhance its machine portfolio, with a solution designed to address some of industry’s most pressing concerns in terms of smaller packaging sizes and available plant real estate.
At the heart of many of Cama’s machines are its robotic solutions. Developed in-house to cater for the precise needs the packaging industry, this robotic technology sets Cama apart from other suppliers, giving it the capability to offer far greater performance, accuracy, consistency and repeatability than many other machine suppliers.
Thanks to significant research and development efforts, a new smaller, faster variant of its robotic solutions – in conjunction with an innovative approach to its phasing conveyors – has given Cama the opportunity to reinvent the capabilities of its popular IF range, with the introduction of the new IF20 monoblock machine.
Francesco Riva, Sales Engineer Director at Cama explains: “These new technologies have been under development for a while now and are key to helping us address a major demand from our global customers. They are looking for broader capabilities in the smallto-medium-box packaging segment
as end consumers migrate towards smaller portion sizes, not just because of demographic changes, but also to reduce waste from unused products supplied in larger formats.
“Key to the evolution is the newformat robot we have created. Not only is it faster, but its smaller installed size means it can be
clustered closer to other robot base units. This means we can shrink the overall size of the machine and, just as importantly, change its shape to match available real estate and product flows.”
Hand in hand with the new robot is a new design of phasing conveyor. “A typical box-forming, robot loading, and box-closing machine is linear, with a vertically mounted phasing conveyor. But by laying the phasing conveyor on its side – but still using the topmost face – we create a horizontal track within the envelope of the machine that can be exploited from two sides.
“New carriage designs take this new flexibility to another level too. By using pneumatic ‘suckers’ or specially designed grippers instead of fixed, carton-specific lugs, we can supply platens/carriages that will cater for a variety of carton sizes without the need to replace or re-engineer them between batches. We have also the vacuum on board feature that hold the boxes and avoid format change.”
Key to the evolution is the new-format robot we have created. Not only is it faster, but its smaller installed size means it can be clustered closer to other robot base units.
Operationally, the packaging stages are the same as with the company’s very popular IF318 monoblock packaging machine. Boxes are formed, placed into/onto the phasing conveyor, robots then pick and place the products before the boxes are closed and sealed. In the new IF320 these stages occur in a loop as opposed to a line, and because of this layout, a ‘spare’ or ‘empty’ station is created within one quadrant of the machine.
“This is where the flexibility really shines through,” explains Riva. “We can populate this empty quadrant with existing packaging stages to match the layout or infeed of the existing plant, or we can add supplemental processes, such as printing or leaflet insertion,
without increasing the overall envelope of the machine.”
At just 5.2 m long, the IF320 is 30% shorter than equivalent machines, but can still offer a throughput of up to 75 boxes per minute, depending on the box size and the dynamics of the products being packaged, while quality levels and forming, closing & glueing precision are just as high as with other Cama machines.
“Thanks to this combination of robots, conveyors and expandable
capacity all optimizing the in-machine real estate,” Riva concludes, “we can deliver modular solutions that can be tailored to match the precise needs of the customer applications – be it speed, space, accessibility or, indeed, special/supplemental processes.”
The IF320 takes advantage of Cama’s Breakthrough Generation (BTG) concept too, which sees modular, scalable frameworks that offer easy entry and access, coupled to a hygienic machine design. Within this framework, contemporary automation solutions, including advanced rotary and linear servo technology, is tightly coupled to the robot, to deliver the all-important flexibility and adaptability required by modern packaging operations. This machine is cross categories: can be applied to cosmetic industry, personal care, home care, confectionery, bakery, coffee, dairy…
Finally, the machine also benefits from Cama’s Industry 4.0 offering, which makes operator training, machine interactions and maintenance routines simpler, thanks to immersive augmented reality (AR). And to keep uptime to an absolute maximum, it exploits Cama’s ‘toolless’ RFID-managed changeover solution, which results in some of the fastest batch-swap/ re-engineering routines in the industry.
For more information: www.camagroup.com
From farm to fork, the quest for efficiency, safety and sustainability drives new technologies and methodologies in the food sector. The Hangzhou Donghua Chain Group is a leading manufacturer of high quality chain solutions. Through its ongoing commitment to R&D, the company has developed a range of cuttingedge chain solutions for the Food Processing industry.
Like many sectors, the Food Processing industry demands chain that offers the maximum working life with the minimal maintenance downtime. Any downtime, but especially unplanned maintenance, adversely impacts productivity.
Donghua Limited is the UK subsidiary and we stock an extensive portfolio of Conveyor chain, Roller chain and Attachment chain in our 25,000 sq ft warehouse in the West Midlands. Our range of chain is supplied in a variety of materials and finishes including:
Donghua’s food industry chain includes special alloy coatings to protect against corrosion caused by aggressive wash down procedures.
H1 Food Grade lubrication is applied to the chain (subject to application requirements) in our UK workshop. By hot-dipping lubricant, it reaches parts of the chain that normal lubrication does not reach.
Attachment chain is preloaded as standard to help reduce fatigue and extend the wear life of inhouse built chain. Chain with little or no pre-load will suffer significant elongation during initial use and will need to be changed sooner.
Attachment chain is matched to within very close tolerances to ensure the attachment links engage with the sprockets simultaneously, thereby
Any downtime, but especially unplanned maintenance, adversely impacts productivity.
eliminating undue stress which is a major cause of fatigue failures on attachments.
Innovative food production chain includes:
Polymer Conveyor chain –designed to prevent the ingress of foreign matter and reduce maintenance costs and downtime. Manufactured using food grade engineering plastic, the lightweight Polymer chain is lubefree.
Universal Attachment chain – a ‘one chain fits all’ solution which replaces 99 per cent of other manufacturer’s chain. Built in the UK specifically for the distribution market.
Drytec chain – built to specific customer requirements and manufactured to the highest standards with bespoke attachments.
Donghua chain is compatible with the leading food equipment manufacturers, and has quickly become the chain of choice for companies in the food processing industry. Produced to very narrow tolerances, chain from the same production batches are on average within 1/3 DIN standards.
Our Food Chain is supplied through a growing network of Product Partners, Stockists and Distributors.
To find out more about our Food Chain, visit www.donghua.co.uk/food-industry/
Supplied in a variety of materials and finishes, with H1 food grade lubrication, Donghua Chain is the chain of choice for maximum working life and reduced maintenance downtime.
Donghua supplies the food production industry with a range of high quality chain compatible with leading food equipment manufacturers including:
Baker Perkins, Bradman Lake, Ishida, Johnson, Krones, Meurer, Panamat, Rademaker, Raque and more...
donghua.co.uk/food-industry
The right step towards automating your warehouse!
“Modula, a leading company in the field of vertical automated warehouses, ideal for saving time, space, and reducing picking errors, introduces two new products with Lift features but new applications.
The first is Modula Pallet, a groundbreaking automatic vertical solution, revolutionizing the way businesses handle 1200x800 mm pallets. Designed to operate seamlessly without the need for traditional forklifts, this innovative system streamlines warehouse operations and enhances efficiency.
The key feature of Modula Pallet is its ability to handle pallets directly from the ground, eliminating the reliance on forklifts for lifting. The load is smoothly transported on the ground and then efficiently loaded into the lifting section of the storage system. This not only ensures a more straightforward workflow but also relieves operators from the challenges associated with handling materials at heights.
Modula Pallet enables the strategic storage of pallets at elevated positions while ensuring convenient groundlevel delivery. The use of a pallet jack or manual forklift suffices for internal warehouse movements, simplifying the overall logistics process. This makes it the optimal solution for businesses dealing with a moderate number of pallets, ranging from a few tens to a few hundred, aiming to maximize warehouse organization by capitalizing on vertical storage space.
A notable feature of Modula Pallet is its facilitation of piece picking, allowing operators to access individual items directly through the picking window without the need to move the entire pallet. This represents a significant innovation, enhancing speed, precision, and ergonomic considerations in the picking process.
The key feature of Modula Pallet is its ability to handle pallets directly from the ground, eliminating the reliance on forklifts for lifting.
In the ever-evolving landscape of warehouse automation, the new Modula Next emerges as a gamechanger, not just as a conventional lift system, but as a versatile vending machine catering to diverse industry needs.
Modula Next operates like a Lift but thinks like a vending machine. Thanks to a system of movable windows, managed by dedicated software, only the compartment where the operation needs to be performed becomes available to the picking operator.
This has two advantages:
1. the operator cannot make a mistake in retrieval even among similar items,
2. every movement is tracked, you know exactly who took what and when, with no margin for error.
One innovative application of Modula
Next is its capability to function as a vending machine, facilitating the one-to-one distribution of personal protective equipment or personal effects. This feature makes it an invaluable asset for companies keen on optimizing the management of individualized items.
Consider the scenario of companies supplying parts or components to other businesses. By strategically placing a fully stocked Modula Next unit at the client’s facility, the client can efficiently retrieve spare parts or components only when necessary and in the required quantities. This approach brings numerous advantages, including the elimination of time wasted on excess inventory, meticulous inventory control, and the ability to trace every withdrawal. Most notably, for the supplying company, it becomes a guarantee that the client exclusively purchases its products, eliminating the need to explore alternatives from competitors.
This utilization of Modula Next represents a paradigm shift in inventory management, providing businesses with a level of precision and efficiency that was previously hard to achieve.
As industries continue to seek innovative solutions for their logistical challenges, Modula stands out as a reliable and adaptable tool, reshaping the way companies approach inventory distribution and ensuring a seamless and streamlined process for clients and suppliers alike. www.modula.eu
From serial & identification labels to complicated control panels & mimics, Brunel Engraving specialise in providing a tailored service to suit every different requirement. Flexible and dependable, we can advise you on the best material and process to use for your application or we can engrave materials you supply to us.
Our team of highly skilled engravers use the very latest technologically advanced machinery to undertake sophisticated print processes and to tackle the most intricate engraving procedures with a fast turn around and guaranteed quality.
Brunel Engraving are one of the most successful and experienced industrial engraving businesses in the UK and continue to grow within the food & drink processing / packaging industry. Established in 1989, we have the resources and the technical expertise to provide bespoke engraving services to a wide spectrum of industrial clients, supplying products to suit your every engraving requirement from a range of materials.
When you deal with Brunel you can be assured of a fast response, a quality product, a competitive price and a “can do” attitude!
www.brunelindustrialengraving.co.uk
Midco
Lanemark gas burner systems offer users reliable, high efficiency, process heating solutions.
FD Series Packaged Oven/Dryer Burners
•Speci cally designed for process air heating applications in convection ovens and dryers
•High turndown/short ame lengths providing accurate process temperature control
•High ef ciency gas + air modulation, gas only modulation and simple high/low control options
•Heat Input Range: 9 kW – 1550 kW
TX Series Gas Fired Process Tank Heating Systems
•High ef ciency (80%+) heating of all types of spray and dip process tanks
•Compact high ef ciency small diameter immersion tube heat exchangers occupying minimum tank space
•Accurate performance modelling using Lanemark TxCalc design software
•Heat Input Range: 15 kW (1½") – 1150 kW (8")
Midco HMA Series Air Replacement or “Make-Up” Air Heating Burners
•Direct red, high ef ciency burner systems, for high volume air heating applications such as paint spray booths, ovens and dryers.
•Supplied either as Midco burner heads for OEM system integration or as Lanemark DB or FDB complete packaged systems including modulating gas valve trains and controls
•Wide range of ring rates to suit alternative temperature rise and air velocity system requirements
•DbCalc system design software
Orkla Confectionery & Snacks responds to new case packing demands with highly flexible Syntegon equipment
Among the many factors of success, adapting to market changes is probably the most vital. In this regard, Orkla Confectionary & Snacks took a decisive step to stay abreast of competition. The Finnish confectionery producer decided to tweak its secondary packaging to meet international export requirements. With Syntegon’s Elematic 3001 WA Compact, a flexible and modular case packing solution, Orkla is securing its competitiveness.
Whether sweet or salty, liquorice is highly popular throughout Scandinavia. The company Orkla Confectionary & Snacks Finland AB belongs to the Oslo-based Orkla Group, which comprises a wealth of consumer goods companies and totals 70 brands for chocolate and liquorice. The Panda brand is a mainstay in the portfolio and is the market leader for Finnish liquorice and known for its countless varieties
since 1927. With its tasty liquorice creations, Orkla Confectionery & Snacks mainly targets the markets in Scandinavia, the UK, the US and Canada, and Central Europe.
Having multiple export countries means different packaging requirements. Due to changing transport conditions in the US and Canada, Orkla had to switch from packing two products side-by-side to packs in a row while increasing the production capacity. To save space, a new case packer should be compact and able to handle ten different case formats, while operating at double the speed compared to the previous case packer. Quick changeover times are required to efficiently switch between the different formats.
When Orkla heard about Syntegon and the Elematic 3001 WA Compact, they were thrilled: the machine seemed to be the perfect fit for packing a broad variety of bag sizes into different case formats. “After the first
presentation, it was obvious that the machine delivers what its name suggests – a compact, easy-to-clean and accessible case packer,” Arto Liimatainen adds. One thing in particular caught the manager’s attention: the case packer’s format flexibility and speed.
The Elematic at Orkla can handle ten case formats at an infeed rate of around 150 bags per minute. Thanks to the machine’s modularity, the operators can easily adapt the collating chain for the next case format. Moreover, Syntegon kept the overall number of format parts to a strict minimum for a time-saving format changeover. “The machine’s unmatched flexibility tipped the scales for Syntegon, but so did the company’s service support,” Jari Leinonen explains.
Orkla relies on ten case formats to pack different counts of bags standing upright in rows. “However, it quickly became clear that one of the formats could not
Thanks to the new machine, Orkla was able to revamp its production line without having to expand its footprint.
be processed on the Elematic,” explains Bernhard Vaihinger, product manager for case packers at Syntegon. “We then redesigned the format and shared our proposal, together with explanatory videos on “How to handle the case” with the customer.” It was important to keep the blank’s dimensions and to ensure that the full wrap-around case with perforation remained feasible and the case easy to open.
“We were impressed with the fast and efficient solution from Syntegon,” says Arto Liimatainen. “In total, we are now able to pack ten case formats with different bag configurations, including 2 times 6 bags, 3 times 6 or even 1 times 8.”
Thanks to its case flexibility, the Elematic 3001 WA Compact can produce full wrap-around, ledge tray and tray cases for various applications.
Because the bags do not have a fixed, stable shape, they posed another challenge Syntegon was willing to take on. Case forming, placing the bags inside and closing the bag thus required gentle handling and accurate grouping to literally “build” the case around
the bags, that beneficial is for the Elematic 3001 WA Compact. The Elematic currently runs every day and is changed to a new format twice a day on average.
Thanks to the new machine, Orkla was able to revamp its production line without having to expand its footprint. “We are very pleased to have secured our competitiveness with a much leaner set-up,” says Arto Liimatainen. “This fruitful cooperation has not only benefitted our production. We also built a strong bond with Syntegon which we are eager to maintain for many years to come.”
www.syntegon.com
processes
PhoenixTM have developed a thru-process temperature monitoring technology specifically for this task designed to meet challenges of the food processing Ideal for the validation process new cook regime, new product, process certification. Whether performing an oven survey “oven mapping identify cold spots” or validating the cook production conditions, the thruprofiling solution gives you the efficiency, and reliability you need your HACCP demands.
As part of any Food processors HACCP program validation of cook and chill processes is a critical and significant task taking time, effort, and resources.
As part of any Food processors HACCP program validation of cook and chill processes is a critical and significant task taking time, effort, and resources.
name suggests thru-process is the method by which product process temperature is monitored throughout the complete cook / chill process.
PhoenixTM have developed a thruprocess temperature monitoring technology specifically for this task designed to meet the challenges of the food processing market. Ideal for the validation process for any new cook regime, new product, or annual process certification. Whether performing an oven survey “oven mapping to identify cold spots” or validating the cook under production conditions, the thru-process profiling solution gives you the accuracy, efficiency, and reliability you need to satisfy your HACCP demands.
PhoenixTM have developed a thru-process temperature monitoring technology specifically for this task designed to meet the challenges of the food processing market. Ideal for the validation process for any new cook regime, new product, or annual process certification. Whether performing an oven survey “oven mapping to identify cold spots” or validating the cook under production conditions, the thruprocess profiling solution gives you the accuracy, efficiency, and reliability you need to satisfy your HACCP demands.
Monitoring of continuous conveyorised and spiral ovens and semi-continuous rotational batch cooks is feasible where of external recorders with trailing thermocouples is tedious, impractical, and
As its name suggests thru-process profiling is the method by which product and or process temperature is monitored throughout the complete cook / chill process.
As its name suggests thru-process profiling is the method by which product and or process temperature is monitored throughout the complete cook / chill process.
The PhoenixTM NT data logger range has been designed specifically for the challenges of monitoring food processing applications with an IP67 case design protecting from moisture. Type K or Type T data logger options allow accurate measurement of both cook and chill processes. The data logger itself can operate between -40 °C to 80 °C with a data logger accuracy of ±0.3 °C operating below +50 °C.
Monitoring of continuous conveyorised linear and spiral ovens and semi-continuous or rotational batch cooks is feasible where the use of external recorders with trailing thermocouples is tedious, impractical, and unsafe.
Employing the thru-process principal monitoring can be performed true production conditions without compromising line productivity .
Monitoring of continuous conveyorised linear and spiral ovens and semi-continuous or rotational batch cooks is feasible where the use of external recorders with trailing thermocouples is tedious, impractical, and unsafe.
An extensive range of different thermocouple types is also available to suit different product types , sizes and monitoring demands.
Data logger and thermocouple correction factors can be further applied to maximise measurement accuracy.
Employing the thru-process principal process monitoring can be performed under true production conditions without compromising line productivity .
heart of the thru-process monitoring the PhoenixTM data logger.
Employing the thru-process principal process monitoring can be performed under true production conditions without compromising line productivity .
The PhoenixTM NT data logger range has been designed specifically for the challenges of monitoring food processing applications with an IP67 case design protecting from moisture. Type K or Type T data logger options allow accurate measurement of both cook and chill processes. The data logger itself can operate between -40 °C to 80 °C with a data logger accuracy of ±0.3 °C operating below +50 °C.
The PhoenixTM NT data logger range has been designed specifically for the challenges of monitoring food processing applications with an IP67 case design protecting from moisture. Type K or Type T data logger options allow accurate measurement of both cook and chill processes. The data logger itself can operate between -40 °C to 80 °C with a data logger accuracy of ±0.3 °C operating below +50 °C.
An extensive range of different thermocouple types is also available to suit different product types , sizes and monitoring demands.
An extensive range of different thermocouple types is also available to suit different product types , sizes and monitoring demands.
The PhoenixTM Thermal View Food Software provides a comprehensive suite of analysis tools to convert the raw profile temperature data into useful process information. The analysis tools include the ability to calculate Fo/Pu values for the process against target micro-organisms.
PhoenixTM offer a family of thermal barriers to suit the process type, duration, and temperatures of a wide range of cook regimes.
At the heart of the thru-process monitoring system is the PhoenixTM data logger.
At the heart of the thru-process monitoring system is the PhoenixTM data logger.
Data logger and thermocouple correction factors can be further applied to maximise measurement accuracy.
Data logger and thermocouple correction factors can be further applied to maximise measurement accuracy.
The PhoenixTM Thermal View Food Software provides a comprehensive suite of analysis tools to convert the raw profile temperature data into useful process information. The analysis tools include the ability to calculate Fo/Pu values for the process against target microorganisms.
The PhoenixTM Thermal View Food Software provides a comprehensive suite of analysis tools to convert the raw profile temperature data into useful process information. The analysis tools include the ability to calculate Fo/Pu values for the process against target micro-organisms.
PhoenixTM offer a family of thermal barriers to suit the process type, duration, and temperatures of a wide range of cook regimes.
PhoenixTM offer a family of thermal barriers to suit the process type, duration, and temperatures of a wide range of cook regimes.
The information gathered, further to process validation, can be used to allow informed process problem solving and optimisation to maximise product quality, yield, process productivity and efficiency.
The information gathered, further to process validation, can be used to allow informed process problem solving and optimisation to maximise product quality, yield, process productivity and efficiency.
The information gathered, further to process validation, can be used to allow informed process problem solving and optimisation to maximise product quality, yield, process productivity and efficiency. Contact PhoenixTM to help Find, Fix and Forget your Food Cook Problems!
Contact PhoenixTM to help Find, Fix and Forget your Food Cook Problems!
Contact PhoenixTM to help Find, Fix and Forget your Food Cook Problems!
Further Information
www.phoenixtm.com
www.phoenixtm.com
Are you prepared to turbocharge your sales pipeline, empower your employees, and seize control of your business growth strategy?
Look no further than Oomph CRM.
Our cutting-edge customer relationship management tool is specifically designed for small businesses like yours.
• Identify who should take action on sales opportunities.
• Determine the necessary actions to be taken through our contact and lead management feature.
• Track the progress of each prospect within your sales pipeline with intuitive dashboard visualisations.
Best of all, Oomph CRM is incredibly user-friendly, ensuring a smooth and hassle-free experience for all users.
In the face of today's market challenges, Oomph CRM serves as an ideal and cost-effective solution.
Our affordable plans can be tailored to meet the unique needs of your business.
As far as appetising names go, ‘fake meat’ is one that hardly gets the mouth watering.
Perhaps that’s part of the problem. Even as vegetarian and vegan lifestyles are more popular than ever and more than 61% of
consumers want to increase the number of plant-based foods in their diets, almost 40% are cutting out meat alternative products . Increasingly, fake meat is not on the menu.
Just a few short years ago, fake meat was the next big thing in food. Today, it is reporting falling sales and tumbling revenues . So, can the plant-based meat industry stem the bleeding and find its place in a world increasingly open to vegan food, or is it simply a flash in the frying pan?
While it’s easy to write off fake meat as all sizzle and no artificial steak, the scale of its early success would indicate that it was more than a simple fad. The environmental angle – livestock rearing and meat production account for a huge chunk of global carbon emissions – means that
alternatives to traditional meat are necessary. But, before plantbased products can become a true alternative to meat, they must become more appetising.
In the short term, the cost-ofliving crisis cannot be overlooked. Plant-based meat is a relatively young industry and its products are still being refined with new innovations. This means R&D costs continue to eat into margins, and the economies of scale have not yet been optimised. In short, fake meat tends to be priced at a premium when many consumers are finding their budgets squeezed. However, the industry still has some more fundamental problems that must be solved before it can reach its full potential.
Notably, the quality of the products on offer is yet to truly match consumer expectations. Some of this can be resolved
Despite all the bad news surrounding fake meat, there remains untapped potential in the market.
with clearer communication on the distinction between vegan and plant-based foods. A vegan consumer who mistakenly assumes a plant-based meat product meets their dietary needs will need some convincing before they trust a similar product again.
Consumers may also be going cold on fake meat as a consequence of the negativity surrounding ‘ultra-processed’ foods. This issue became such a controversy that ‘ultra-processed’ was nominated as dictionary publisher Collins’ word of the year for 2023 .
And, of course, it is important to clarify that not all ultra-processed foods are created equal. Food processing is more about the ingredients involved than anything else. A recent WHO-backed study found that some ultra-processed foods, including plant-based meats, are not inherently unhealthy. In fact, foods like bread and cereal reduce the risk of certain diseases, as they are high in fibre.
Despite all the bad news surrounding fake meat, there remains untapped potential in the market. Exciting new developments are occurring daily,
such as 3D-printed plant-based meat, which can help improve quality and cost efficiencies in the production process. And the exploration of pea proteins continues to deliver real results, with its excellent functional properties driving improved flavours, textures, and nutritional value in plant-based products. There is even talk of injecting animal fat into plant-based alternatives to help deliver on taste – a controversial topic, of course.
Despite its downcast recent past, solving these issues could lead to a brighter future for plantbased meat. By rethinking their supply chains, manufacturers can find efficiencies that unlock new possibilities, including finding alternative ingredients that may offer new benefits, such as a higher amount of protein per gram, a subtly different texture that can
change the eating experience, or simply a lower cost.
This is where partnering with a distributor, which possesses indepth knowledge of ingredient properties and global supply chains, becomes critical to success. It will help manufacturers add flex to their supply chains through dual sourcing, and route around disruptions caused by extreme weather, geopolitical instability, and material shortages.
It can also help manufacturers find ingredients that better suit their sustainability goals. For European manufacturers looking for soy protein, they may feel their only option is to pay for expensive, locally-made soy products to lower transit emissions. However, alternative products may be available at a lower cost from Canadian or Brazilian suppliers that invest in carbon offsetting and renewable energy, offering a lower overall carbon footprint. This could involve using a different kind of soy product, or pea and wheat proteins, which are both proven alternatives. The options are out there – and a distributor can help find them.
Plant-based meat may no longer be the next big thing in the food industry. But that doesn’t mean it can’t be important, successful, and profitable. Consumers have shown they do have an appetite for the potential of fake meat – it just needs a little longer in the oven.
In today’s case study, we’re drilling down into a project we worked on for an overseas wine manufacturer. As well as making a range of wines, the company turned some of its product into vinegar to create another regular income stream.
They contacted North Ridge Pumps looking for a proven and effective way to decant intermediate bulk containers (IBC) containing vinegar with an acidic content up to 8%. The company wanted an all-inone pump kit designed to quickly transfer the vinegar from the container.
Turning good wine into great vinegar is surprisingly easy. In fact, you may have accidentally made wine vinegar in the past by leaving out an opened bottle of wine too long.
Wine can be left in a warm place for two weeks allowing the natural oxidation process to undertake the rest. Too much alcohol will hamper the growth of the bacteria that turn the wine into vinegar. Too little alcohol and the vinegar won’t keep very well.
To make large quantities of wine vinegar, a ‘mother’ vinegar is needed. This is fermenting bacteria culture which turns alcohol into acetic acid working in combination with oxygen. It can be bought as ‘live’ or ‘mother’ vinegar, or simply as an unpasteurised vinegar. Mother vinegar can also be made by combining wine and vinegar and leaving it to ferment.
As part of this client’s production process, bulk deliveries of vinegar were being made and had to be transferred into drums on site. To do this, a pump was needed.
Barrel or drum pumps are usually chosen for applications like this. They provide an easy and safe way to transfer or dispense virtually any fluid or chemical from containers like barrels, tanks, IBCs and drums. In addition, many different models, lengths, tubes and accessories are available to meet the demands of a variety of different sectors.
This particular application was just right for a sanitary barrel pump, also known as a drum pump. But which one to specify?
Here are 7 factors we look at when specifying a barrel pump for a client:
Barrel pumps don’t usually decant all of the contents from a container, and sometimes leave as much as 5% of the fluid at the bottom.
If this fluid is expensive, this level of waste can add up to tens of thousands of pounds worth of lost product and profit every year. On the flip side, significant savings can be made by taking out all of the contents of every container.
That’s why special types of pumps have been developed to totally remove these contents, and one specifically designed to do this is the North Ridge Pumps 99.98% Barrel Emptying Kit.
Obviously, fluids come in a wide variety of viscosities, from some similar to water to others which have the consistency of a paste or sludge. The properties of the liquid also need to be taken into account such as whether it is rheopectic or thixotropic.
Here at North Ridge Pumps, we’re not tied to a single pump technology. We use our expertise to offer a tailor-made solution, not something taken off the shelf.
Rheopecty is the characteristic of some fluids to become more viscous if they undergo shearing forces. The longer these forces are operating, the higher the viscosity. In short, rheopectic fluids, such as some lubricants, thicken or solidify when agitated or shaken.
The opposite and much more common type of behaviour is called thixotropy. Here, some fluids that are thick or viscous when static will begin to flow when they’re agitated, shaken, shear-stressed or just put under stress. It then takes a while for them to return to their original viscous state.
3. Power source
Sanitary drum pumps can use a range of different power sources. They can use electricity working on differing voltages such as 110V/230V or 3 phase, air power or even be hand-operated.
Something else to factor into the decision is whether the unit is to be installed in a safe area away from flammable liquids or vapours. Or perhaps it’s to go into an ATEX zone which would require a full ATEX Pump kit. This can play a major part in deciding the pump and motor type we specify.
4.
Some liquids have the property of crystallising when they come into contact with air. In this case, mechanically-sealed pumps are essential to ensure that air doesn’t get into the pump. In addition, certain chemicals like solvents evaporate, so the unit needs to be sealed to stop the contents getting out into the atmosphere.
Seal-less sanitary drum pumps are best for certain liquids which are
aggressive and where the exact breakdown of chemical composition is unknown, making the right choice of seal more difficult.
5. Size of container
Fluids are transported in a multitude of containers ranging from small tote boxes of 25L and bigger 205L drums, all the way up to Intermediate Bulk Containers (IBC) and bespoke tanks. The size of the tank and the properties of the fluid it’s transporting will dictate the type of pump specified, and the method used to extract its contents.
6. Hygiene standards and cleanability
For this specific project, the client would need a sanitary drum pump which was completely hygienic. This meant that a stainless steel pump could certainly have been an option.
Alternatively, a third partyaccredited hygienic pump could be a solution. This would need certification by an independent organisation such as 3-A, FDA or EHEDG as meeting food hygiene standards. These state that pumps used for transferring food or fluids must not affect the taste or composition of the material being transferred, must be fully traceable and inert.
7. Bulk
Barrel or drum pumps can be configured to carry out bulk transfer of fluids, or more precise metered batching. They incorporate a flowmeter hose and can incorporate a batching facility with a range of pre-sets enabling batches to be decanted at the touch of a button.
With transfer accuracy levels of 99%, these units take away a great deal of time-consuming weighing and measuring of liquids, and help boost productivity and profitability.
In addition, barrel pumps can be set up by the operating company to provide different levels of access for users and managers with varying levels of access.
Our specification for this client The overseas wine manufacturer
told us they wanted a sanitary pump kit designed to quickly decant vinegar from intermediate bulk containers (IBC) into smaller drums.
Here at North Ridge Pumps, we’re not tied to a single pump technology. We use our expertise to offer a tailor-made solution, not something taken off the shelf. So we always choose the most costeffective pump for any specific client and project.
For this application, we specified a sanitary barrel pump manufactured in highly polished and hygienic 316 stainless steel. It’s fully configurable and comes with a variety of options to give the client greater production flexibility.
Due to the low viscosity of vinegar, we specified an impeller pump type which is specially designed for liquids with low viscosities which flow easily and are not affected by shear forces.
All connections are tri-clamp ensuring that they are fully sanitisable for maximum levels of food hygiene. We supplied the pump with 2m of food grade hose and a dispensing nozzle for full control of every fluid transfer.
Looking for a quick and easy way to empty containers without having to use manual handling? We can specify a bespoke solution for your business.
Visit www.northridgepumps.com or call 01773 302 660 to see how we can help.
E/M Coating Services pride themselves on being able to offer customers high quality coating applications and processes for a wide range of industrial sectors. We are uniquely placed to design and manufacture bespoke protective coating solutions in our own highly specialised industrial coating facilities. We have over 40 years of experience in surface technologies and are pioneers in the development and application of solid dry film lubricant coatings.
Our products and services are utilised by high technology markets including the aerospace and oil and gas sectors, ensuring that we are always at the forefront of the latest designs, materials and technologies.
E/M Coating Services, under their brand name Everlube® Products, offers a complete engineered coating development service and our own in house formulation chemists are continually developing new coatings and surface
We have over 40 years of experience in surface technologies and are pioneers in the development and application of solid dry film lubricant coatings.
technologies that are designed to satisfy todays ever increasing engineering requirements.
Our Everlube® range of branded dry film lubricant products have been specifically designed to enhance and improve the performance of critical components and meet a wide variety of industry, defence and customer specifications for critical components.
Our technical services team will work with you to find the product
most suited to your requirements or if you know which product you need please visit our Everlube® Product website directly, we have also produced an Everlube® dry film coatings matrix as a quick reference guide.
Coating removal services are used to ensure that critical components, fabrications or surfaces are completely clean and free from any residual rust or coating residue. By utilising our surface coating removal services you can restore your components or fabrications to near their original condition.
We offer an array of surface, paint and powder coating removal techniques including: burn off, localised high temperature removal, grit blasting, selective blasting, sponge blasting and chemical stripping.
www.emcoatingsuk.co.uk
l Thermal Spray & HVOF Coatings
l Thermal Spray & HVOF Coatings
l Dry film lubricants - MoS2, PTFE, Graphite, WS2
l Dry film lubricants - MoS2, PTFE, Graphite, WS2
l Coatings for corrosion, chemical & environmental protection
l Coatings for corrosion, chemical & environmental protection
l Titanium anodising
l Titanium anodising
l Zinc rich coatings for corrosion protection
l Zinc rich coatings for corrosion protection
l Impingment coating processes for ultra thin solid film lubricants
l Impingment coating processes for ultra thin solid film lubricants
l Nonstick/release coatings for low coefficients of friction
l Nonstick/release coatings for low coefficients of friction
l Primers for rubber and plastics for sound absorbing and dampening materials
l Primers for rubber and plastics for sound absorbing and dampening materials
l High temperature resistant coatings
l High temperature resistant coatings
l Rare earth magnet coatings
l Rare earth magnet coatings
l Coatings for EMI/RFI shielding provide highly conductive coatings and platings to control electromagnetic interference
l Coatings for EMI/RFI shielding provide highly conductive coatings and platings to control electromagnetic interference
l Ultra thin conformal parylene coating to reduce friction and protect against contamination
l Ultra thin conformal parylene coating to reduce friction and protect against contamination
l Pre-treatments including Ti Anodising, Phosphate Conversion Coating and Chilled Iron Blasting, Aluminum Oxide Blasting and Vapour Degreasing
l Pre-treatments including Ti Anodising, Phosphate Conversion Coating and Chilled Iron Blasting, Aluminum Oxide Blasting and Vapour Degreasing
Offer consistent product quality at the point of use for a wide range of applications, guide rails position the IBC and the mixer is raise and lowered into the IBC with a push button operated electrical actuator.
Fixed or mobile mixing stations are supplied complete with a control panel and safety interlocks.
Standard IBC mixing stations can be adapted to integrate with systems on site including pumps, valves, weighing and measuring instrumentation and controls to meet specific site requirements.
Sappi Rockwell Solutions specialise on the development, formulation and production of high-performance heat seal, high barrier, and anti-fog coatings, supplying high performance lidding films to the food industry.
We are a leading provider of single-ply heat seal coated lidding films suitable for any food application in the market and service major food manufacturers and packaging convertors globally. Based in Dundee, Scotland we possess extensive knowledge and experience of over 35 years.
StarPaper GP, our new and innovative paper lidding, provides universal peelable seals to all tray types, allowing for high quality graphics and potential replacement of cardboard sleeves.
PermaClear is our proprietary high clarity, non-migratory anti-fog. A unique coating unlike any other anti-fog in the market today.
Rocklid SPX-LT-AF is our low seal initiation lidding film specially designed for 100% recycled content PET trays, ideal for highspeed production lines.
Sappi Rockwell Solutions are heavily focused on developing coating formulations to manufacture highly specialised packaging with strong ambitions towards mono material and paper lidding structures.
High frequency electromagnetic field induction sealing is the process to apply metallic film cover on plastic cups by the use of heat only.
The heating up of the aluminum film is a touchless process, controlled, selective, quick, homogeneous, clean, programmable, safe and sure, energy saving and environment respectful.
Sinergo is an Italian company that has been designing and manufacturing automation since 1991.
Thanks to the specific know-how, rigorous working method and high-quality standard, Sinergo develops innovative and customized industrial solutions and equipment.
Sinergo is supplying the main Companies worldwide in electronics, electro-mechanic, power semiconductor, e-mobility, medical, food & packaging, defense and aeronautics … and others avant-garde sectors.
Sinergo electromagnetic field sources are ready to be used in the food & drink industry especially for the cup sealing.
Complete handling, filling, dispensing, sealing, packaging … production processes can be performed by the use of Sinergo fully automatic lines
Participating in MACH 2024 offers Torus Technology Group an excellent platform to connect with industry professionals, showcase their latest innovations, and network with potential clients and partners. It’s a valuable opportunity to stay at the forefront of industry trends and demonstrate their commitment to engineering excellence.
Torus Technology Group are a global group of companies centred on engineering excellence, providing measurement, automatic, metrology
Torus Manufacturing transforms ideas into reality with cutting-edge technology, expertise, and turnkey solutions.
and manufacturing solutions. This year Torus are pleased to be exhibiting at MACH 2024 – bringing focus to 3 key divisions, Torus Metrology, Torus Manufacturing and Torus Modular Frameworks.
Torus Metrology provide professional services which include Calibration, Sub-Contract Programming and Inspection, Verification, Training and Support to all industries. By offering these services through a UKAS accredited calibration laboratory, Torus Metrology positions itself as a reliable and internationally recognised provider in the field. It also demonstrates a commitment to maintaining the highest standards in calibration, which is essential for industries where precision is paramount.
Torus Manufacturing transforms ideas into reality with cuttingedge technology, expertise, and turnkey solutions all whilst delivering contract manufacturing services to customers who are looking for high quality manufacturing at highly competitive prices. Our contract manufacturing solutions and services include Machining, Design, Assembly, Fabrication, Calibration and Inspection, Stock Management and Replenishment, Repair and Overhaul, Tooling Care and Maintenance, and Global Shipping and Freight.
Torus Modular Frameworks offer a range of flexible, highquality, robust aluminium profile solutions for commercial and industrial environments including office, production, manufacturing, and factory facilities. Our range includes workstations, enclosures, controlled environments, partitioning, and bespoke solutions, all designed, machined, and managed from our factory in Telford, UK.
Our interactive, engaging stand at MACH (18-410) will showcase all 3 divisions, so please pop by.
www.torus-group.com
Torus Metrology have over 25 years experience within the Metrology Industry, providing comprehensive solutions to your metrology requirements. Join us at Mach 2024.
CMM Training
UKAS CMM Verification & Service
UKAS Arm/Height Verification
CMM Sub-Contract Inspection
CMM Sub-Contract Programming
CMM Overhaul/Moves/Breakdowns
On-Site Arm Inspection Spares & Accessories
Whether you require a turnkey, 1 off, or high volume manufacturing solutions, you can be assured that Torus Manufacturing has the answer.
Design Services
Machining Services
Machined Assemblies
Fabrication & Finishing Processes
Our products are designed & built to suit your needs and requirements by offering a completely bespoke solution, with a range of options and accessories to choose from for all products.
CMM / Machine Enclosures
Metrology Workstations
Partitioning / Walkways
Controlled Environments Workstations
Bespoke Projects
Quality & Inspection
Stock Holding Services
UK Manufacturer Ceratech
Accuratus have been making keyboards, mice, and other computer peripherals for over 40 years. This innovative company specialises in devices built to make your life easier – and now, they’re entering the world of kitchen automation.
Upgrade your kitchen with the Accuratus Bump Bars!
Introducing a new way to control your kitchen setup – the Accuratus Bump Bars! Designed to suit highpressure cooking environments, these steam-proof bump bars will make running your operation smooth and efficient.
The Accuratus bump bars are designed to seamlessly integrate with your existing interface, making running a kitchen easier than ever. Program the bar using our Matrix Maker software to meet your specifications, then use the intuitive design to sort through orders quickly and easily, without
having to touch screens and other equipment where grease and dirt can build up.
These space saving bump bars are available in two models: 15 key or 20 key.
The 15 key bump bar (KYB500BB15F) features a fully programmable 15 key interface, made from high quality and durable materials. The bump bar is designed to be spill proof, with sealed holes stopping spillages from entering and damaging the
bump bar. The USB cable has 15Kg strain relief, preventing it from being pulled out of the bump bar.
The 20 key bump bar (KYB500BB20A) is a combo USB & RF fully customisable bump bar which uses high quality mechanical key switches, with up to 50 million actuations per key. This bump bar is made from high quality materials and sealed inside a metal shell with a sealed membrane input. A paper legend sheet can be easily inserted to customise your layout.
The Accuratus bump bars are designed to seamlessly integrate with your existing interface, making running a kitchen easier than ever.
Both bump bars can be customised with your own colour, legends, interfaces, and logos to create an interface tailored to you and your kitchens needs.
Construct your own setup with the Accuratus Programmable Range
Looking for something a bit more customisable? The Accuratus Programmable Range has got you covered! This suite of fully programmable keyboards is available in a variety of different models - including sleek, space saving “B” versions - and range from models with 24 keys to 128 keys!
Whether you’re crunching numbers, accepting orders, or sorting data - the programmable keyboard range can make your business life straightforward and hassle-free. Every key can be programmed with up to 8 layers of code, and on each layer a key can have up to 256 characters programmed, giving you unparalleled customisable options.
Every model in the Accuratus programmable range is made with EPOS grade membrane keys or Chery MX Mechanical, making every button press soft and tactile. The relegendable keys come with their own transparent keycaps, allowing you to label each key
as you need to. Additionally, all programmable units come with an assortment of 1x2 and 2x2 replacement keys and transparent keycaps, allowing you to create a custom large button keypad. The Accuratus programmable range – the ultimate in customisable interface creation.
Control your production with ease using the Accuratus Stainless Steel “all-in-one” solution
For more complex automation tasks, the Accuratus Stainless Steel Suite has the perfect tools. These rugged, mountable keyboards can be pre-programmed for more complex operations such as activating and deactivating food processing automation units. The water-proof, spill-proof, vandalproof stainless steel keys are designed to be resistant to dirt, dust, and liquid – ideal for a food preparation environment. The keyboards themselves can be easily cleaned with water, disinfectant, and other cleaning agents.
Available in either PS2 or bespoke USB connection, and with a choice of integrated input method (trackpad or trackball), these keyboards are the ideal control unit for a large-scale kitchen setup. The keyboards can be directly mounted to a wall or surface to sit in your ideal location. These units can even be integrated directly into surfaces, sitting flat and taking up as little space as possible.
For an all-in-one kitchen automation control unit, look no further than the Accuratus Stainless Steel Suite.
For more information on any of the products talked about, please email Sales@ceratech.co.uk, call 01420 85470, or visit www.ceratech.co.uk.
Not found what you’re looking for? Ceratech Accuratus have a long history of bespoke and OEM product manufacturing, including custom logos, printing, and even whole products. If you have an idea for a product, get in contact – Ceratech will find a solution!
The way food and drink manufacturers print traceability information on their products is changing. According to non-profit barcode provider, GS1, 2D or data matrix codes are set to become the new global standard in traceability marking by the end of 2027. The new format codes contain much more data as they include a greater number of characters than their barcode counterparts.
But does it matter as much to those that have to measure it?
However, providing so much information in a relatively small area means the data matrix code needs to be sharply printed in high resolution.
Thermal inkjet (TIJ) printers offer a simple solution to these printing requirements. The printers print 300dpi at a print height from 1mm –51mm and can use water or solventbased inks to print data onto a variety of substrates.
They use a cartridge-based ink delivery system to print supersharp high-resolution logos, QR codes and date and batch code information at speeds of up to 200m/min.
Compressed air quality audits are rarely carried out in strict compliance with ISO 8573 and a lot can happen in between them that can seriously affect your reputation and profitability. For many companies, in-house verification of compressed air quality supplements their external ISO 8573 audits to give a more regular understanding of delivered air quality.
For primary packaging, which needs to be marked with batch codes and best before dates, the Sojet MoTix printers are ideally suited.
Removing the need for sending samples away for laboratory analysis through the use of modern sensors, provides a quick assessment of quality and an almost instant response to changes. Not all
T-Mark is a supplier of TIJ printers from Chinese manufacturer, Sojet, and is supplying more and more of them into the food and drink sector.
For primary packaging, which needs to be marked with batch codes and best before dates, the Sojet MoTix printers are ideally suited.
With the MoTix range, up to four printheads can be combined to print up to 51mm high at the same resolution.
The basic model in this range uses 1 printhead to print up to 12.5mm high. The printer uses HP ink cartridges, each with an integrated printhead, giving a lowmaintenance, high quality print solution in a range of ink colours. The Moli MoTix range is new from Sojet and offers a darker print at higher print speeds than Sojet’s previous best-selling range, the Sojet Elfin series.
AAK Foods has bought two Sojet printers to mark its bottles with traceability information and is impressed with the reliability of the machines. Engineering Manager, Neil Heselwood, said: “The Sojet has incurred zero line downtime in 18 months, the only maintenance is a wipe of the head and replacement ink cartridges. So the fact that the printer costs less to purchase than a service pack used in a (continuous) inkjet coder is remarkable.”
T-Mark can supply across Europe from its offices in the UK and in Belgium. For more information, visit www.t-mark.co.uk
Ideal for verifying desiccant or refrigerant dryer performance anywhere. No waiting for the sensor to react through the innovative park festure that keeps the sensor dry between tests.
Portable S600 Compressed Air Purity Analyser
Measure Dew Point, Particle Concentration and Residual Oil Vapour with one easily portable instrument. Produce reports directly for each test point and move to the next.
Wall Mounted S601 Compressed Air Purity Analyser
Designed for 24/7 continuous monitoring of Dew Point, Particle Concentration and Residual Oil Vapour. Communicates with plant SCADA systems through Ethernet or RS-485 and has an integral data logger for record security.
Whether water is being used as part of a production process or for cleaning down areas and process equipment, recycling water can save food manufacturing plants thousands of litres every year. Implementing a wastewater treatment system can therefore significantly reduce water bills, and Castle Pumps have been playing their part in delivering these systems.
Enquiry
Castle Pumps received an enquiry from a fabricator of fluid storage tanks who were designing a waste storage and recycling system. Their steel container encloses a water tank with pressure washers connected, used to wash down site equipment. Once used, the collected water is passed through a Lamella Separator and Filtration system to remove any large solid particles and returned to the original water tank to use again.
They were looking for Castle to specify a wastewater pump that would remove the filtered-out sludge at the bottom of the Lamella Settlement Tank and transfer it into a separate container to be disposed of.
Solution
When specifying a wastewater sludge pump for this Lamella Separator application, the nature of the fluid was the first thing to consider. 2-3% solid content was estimated and
so it was important the pump in question could handle this, as well as the viscous sludge consistency. Due to its only wetted part being the internal tube, a peristaltic pump is ideal as the passing of solids is only limited to the diameter of the tube. There are no valves to clog or seals to wear, making it low maintenance for even more challenging, solid laden fluids.
After discussing the flow rate and pressure requirements, Castle Pumps specified the model of peristaltic pump that would meet the duty range. To provide the user with flow control for
There are no valves to clog or seals to wear, making it low maintenance for even more challenging, solid laden fluids.
when the contents of the Lamella settlement tank differ, the pump was also specified with an integrated inverter.
Its dry run capabilities means that there would be no damage if the pump is accidentally left running after the settlement tank is emptied of sludge. Peristaltic pumps are also self-priming which was important as the pump was to be installed above the settlement tank and needs to draw the fluid up.
The final tick in the box was that peristaltic pumps are low maintenance in design, thanks to the inner tube being the only wearing component. Given the often-harsh nature of waste products, this is an excellent feature when handling wastewater, sludge or effluent.
www.castlepumps.com
PPT is an initiative aimed at reducing the use of plastic packaging and increasing recycling rates. It applies to plastic packaging produced in or imported into the UK that does not contain at least 30% recycled plastic. As a food packaging manufacturer, you can mitigate costs associated with the PPT by incorporating recycled plastic into your packaging materials.
Metrohm offer a solution to help you avoid PPT costs by ensuring compliance with recycled plastic content requirements. With the DS2500 Near-Infrared Analyser and pre-calibration models, you can accurately determine the recycled plastic content in your packaging materials. By utilising recycled plastic above the 30% threshold, you can minimise or eliminate PPT liabilities.
Additionally, Metrohm’s solution streamlines quality control processes, saving time and costs associated with traditional chemical or physical measurements. With rapid, chemical-free analysis provided by NIR Spectroscopy, you can efficiently verify the recycled plastic content in your packaging materials, ensuring compliance with PPT regulations. Optimise production efficiency, minimise costs, and contribute to sustainability goals by increasing the use of recycled materials in your food packaging products.
To learn more visit: wwww.metrohm.com/ppt Or contact info@metrohm.co.uk
At Tunable, we transform invisible gases into actionable insights. Our advanced gas sensing instruments analyze free-moving molecules, impacting environments, processes, and products. We deliver realtime, multi-gas analyzers by combining micro and nanotechnology with infrared spectroscopy, ensuring fast, reliable, and precise measurements for diverse applications.
Our technology is grounded in MEMS, featuring no moving parts, which guarantees our devices’ robustness and reliability. Designed for ease of use, our analyzers require minimal maintenance, operate without calibration gases, and offer low operational expenses. The analyzers provide continuous, realtime gas data, enabling process control and non-invasive quality assurance.
The novel technology is capable of quantifying gases in the 2µm – 14µm range allowing true multi-gas capability. In addition, we have also introduced an exciting new approach to gas analysis - Gas Fingerprint Recognition. This approach extends beyond measuring concentrations, utilizing unique spectral “fingerprints” and machine learning to analyze patterns associated with gases or odors emitted from a product or process. This technique allows for detailed insights into the state, performance, and quality of your products or processes, improving quality control and process optimization in food manufacturing and beyond.
contact@tunable.com or visit www.tunable.com
Award winning Smart Storm is a leading UK Manufacturer of Wastewater Monitoring and Treatment Instrumentation, additionally supplying bespoke solutions for the complex demands of industrial trade effluent. Built on a history of systematic research and development capability, the company has long been at the forefront of innovative products for water and wastewater industries. This has resulted in multiple prestigious awards for developments in technology in the UK and across Europe.
The head office is located in Caernarfon, Wales, with cutting edge R&D and production departments; the Yorkshire office in Halifax operates the wastewater solutions sector for trade effluent.
The company business is effectively organised into three separate areas which offer a unique hybrid benefit to all customers:
The expert product range includes : Level, Flow, Sampling, and Water Quality measurement, with IOT capability.
Smart Storm products, manufactured in house, offer a simpler and more cost effective means of measuring and controlling waste and enable wastewater to be managed and treated at source more easily, reducing carbon footprints and providing a positive social impact through an enhanced and cleaner environment.
For three decades, Smart Storm ’s Solutions Sector have supplied industrial wastewater monitoring, treatment solutions, and services to Food and Drink Manufacturers. The bespoke solutions for trade effluent, empower clients from all industries to be environmentally compliant whilst reducing effluent bills.
Large or small systems, Smart Storm Solutions can meet your Wastewater Treatment and monitoring needs.
Ready made pH Balancing system
Design and manufacture of unique and innovative solutions for the removal of fats, oils, and grease from wastewater. Generate Income from your recovered FOG!
Smart Storm’s unique Greasebuster FOG skimmer is able to remove up to 20m3 litres (or more) of fats, oils or grease per day, The Greasebuster uses a unique material to attract the FOG onto an extraction belt whilst rejecting water, allowing the FOG to be reclaimed and sold for Biodiesel, generating income for you!
Click on the QR code to see the video! Greasebuster
There is hardly a week goes past when the inflation rate and the rising living costs are not in the news headlines. Increases are due largely on material cost increases during manufacture. Whilst these increases have varied widely, depending on the product in question, few raw materials will have increased as much as carbon dioxide gas. According to the Energy and Climate Intelligence Unit, the price of CO2 rose by as much as 3,000% in 2022. Several different factors were to blame for the increase but clearly the ongoing war in Ukraine is a key attributing factor. But the increased price is only part of the issue. During recent years, there have been significant shortages of the gas for use across various industries. In Europe a major portion of CO2 comes from making ammonia for fertilizer, but the escalating cost of natural gas, due to geopolitical changes, has caused manufacturers to scale
back production with one industry observer stating that up to 70% of production has been affected.
As the largest user of CO2 across the globe, the food and beverage industry has been severely affected by both escalating costs and availability of carbon dioxide gas. The beverage industry alone consumes more than a quarter of the global CO2 production every year. Add the food segment into the equation and the figure increases significantly.
As a result of these issues, the food and drinks industry is exploring all possible ways of reducing CO2 consumption. Often stored in bulk tanks, the gas is delivered to various points of use via steel lines often generically referred to as air lines. Traditionally these air lines contain a significant number of screw connections, elbow joints, reducers etc. All these can be prone to leaks over time, allowing gas to escape into the working environment. A single leak might not be considered very significant but as lines get older, it is not uncommon for many joints to develop small leaks that cumulatively give rise to a significant loss of gas. In most centralised systems, the compressor will compensate for the loss by working harder, ensuring that pressure is maintained, therefore drawing more gas from the bulk tank. Of course, although production
The camera works on the principle that even the smallest of gas leaks has an associated noise.
might not be affected in terms of quality, the issue certainly reduces overall efficiency and negatively impacts the all-important bottom line. Another issue that is often overlooked is related to health and safety. As carbon dioxide gas is 1.5 times heavier than air it has the potential to be a health hazard amongst workers in confined spaces. As the gas is colourless and odourless detection can be difficult and the deadly hazard goes unnoticed.
These problems are compounded as the lines delivering the gas are often in hard-to-reach locations such as elevated positions coupled with the fact that they are frequently situated in noisy environments making leak detection extremely difficult.
FLIR Teledyne are pleased to announce the launch of the new FLIR Si2-LD acoustic imaging camera. Following on from the highly successful Si124, the camera forms part of the FLIR Si2 next generation of imaging cameras with a specific focus on air and gas leak
detection. The camera works on the principle that even the smallest of gas leaks has an associated noise. The highly sensitive microphones on the FLIR Si2-LD can detect even the slightest of sounds with an extremely high degree of accuracy and precision. Compared to its predecessor, the FLIR Si2-LD represents a quantum leap in terms of gas leakage detection and overall performance. For those hard-toreach areas, detecting gas leaks is no problem with the extensive range of the FLIR Si2-LD. At 10 metres the acoustic camera can detect gas leaks as small as 0.05 litres per minute. At a distance of 2.5 metres the camera is capable of detecting minute leaks down to 0.0032 litres per minute. Difficult to reach areas of a production plant are often dark or dimply lit. For this reason, the FLIR Si2 comes complete with
two extremely powerful LED lights that illuminate the area, allowing specific gas lines to be identified and analysed.
A new high definition five-inch 1280 x 720 screen which is both sharper and brighter than the FLIR Si124 brings alive the images captured by the 12MP camera with its 8x zoom lens.
Of course, FLIR recognise that senior management will want to quantify the gas leaks in terms of a monetary value. A key feature of the FIR Si2 is the camera’s ability to not only detect the gas but to quantify the leakage rate and furthermore calculate the economic penalty. Termed Industrial Gas Quantification, the incorporated software can calculate losses for a variety of gaseous systems including ammonia, nitrogen, helium, hydrogen, argon, compressed air and of course carbon dioxide. This unique software coupled with the new advanced features of the FLIR Si2-LD provide valuable information regarding gas leaks enabling the maintenance engineer to perform remedial action that has an immediate and lasting effect on the company’s bottom line.
To find out more about this exciting new acoustic camera and other new developments within the FLIR product line contact your local Teledyne FLIR agent.
www.flir.co.uk
For more than 50 years we’ve been leading the way in temperature measurement excellence. We’re passionate about providing an exemplary service for our customers, our experienced sales team provide expert technical advice and support.
The launch of our new brochure sees us celebrating the Labfacility journey, from a small family venture back in 1971 to the prominent name we’ve become in the industry today.
Trusted by Industries Worldwide
From our humble beginnings, we’ve evolved into the UK’s leading ISO 9001-accredited manufacturer and supplier for the complete temperature chain, offering an everexpanding range of products. With a state-of-the-art UK manufacturing hub in Dinnington, South Yorkshire, and partnered with worldwide distributors Farnell, we are your GOTO source for all things related to temperature measurement.
As Europe’s largest manufacturer of thermocouple connectors and accessories in IEC, ANSI, and JIS calibration standards, we serve major PLCs and worldwide distributors, exporting our products daily to over 85 countries, including Australia, China, India and the Americas. Our products cater to a diverse range of industries, from engineering, agriculture, and automotive to brewing, cold chain, pharmaceuticals, plastics, and medical applications.
Labfacility products are exported daily to over 85 countries including Australia, China, India, mainland Europe and the Americas…a truly global reach.
Who do we work with?
We’re trusted by major PLCs and worldwide distributors alike.
Labfacility products are exported daily to over 85 countries including Australia, China, India, mainland Europe and the Americas…a truly global reach. We meet the temperature measurement needs of a vast range of industries from engineering, agricultural, automotive and brewing, to cold chain, pharmaceutical, plastics, and medical, to name but a few.
Our products in a nutshell...
Labfacility manufacture a wide range of temperature sensors to suit your application. A large range of Thermocouples in IEC, ANSI and JIS calibration, PRT’s, Detectors,
Environmental Sensors and HandHeld Sensors/ Thermometers are available to buy, for immediate despatch, from www.labfacility.com
We are Europe’s largest manufacturer of thermocouple connectors and accessories in IEC, ANSI and JIS Colour codes. The full range of connectors is available from stock for immediate despatch.
Labfacility manufacture an extensive range of thermocouple and PRT temperature sensors. Thermocouples include Exposed junctions, Mineral Insulated, Surface, Hermetically sealed and Handheld probes. PRT Sensors include Industrial head sensors, Stick-on patch sensors, Autoclave and M12 industrial automation temperature sensors.
We offer a wide range of thermocouple, PRT and extension cable/wire in stock for immediate despatch. Thermocouple cables are available in IEC, ANSI and JIS Colour codes. Insulation types include PFA, PTFE, PVC & Fiberglass.
The Thermocouple Welder, manufactured by Labfacility, is a compact, simple-to-use instrument designed for thermocouple and fine wire welding.
https://www.labfacility.com/ labfacility-company-brochure For all sales enquiries, please contact us as follows:
Email: sales@labfacility.com
Tel: +44 (0) 1243 871280 Web: www.labfacility.com
Schmersal is set to launch four new electromechanical safety switches with separate actuator: the AZ215/AZ216 and AZ315/AZ316 switches handle safety guard position monitoring of sideways or rotating guard doors. Their stand-out feature is the rotating actuator head made from diecast zinc, which can be easily rotated in 90° increments before installation. This allows the head to be approached from the side from four different directions, as well as from above. With this versatile approach position and possibility of combination with different actuators, the AZ series offers maximum flexibility in installation, as well as a range of universal usage options to the user. The designer can use the AZ switch both for right-hand and
Their stand-out feature is the rotating actuator head made from diecast zinc, which can be easily rotated in 90° increments before installation.
left-hand design on rotating and sliding guard doors.
The plastic or metal switch housing is consistent in design and size with the PS 215/216 and PS 315/316 series position switches, giving the AZ switches an equally compact design and easy integration into the surrounding construction. The small AZ215 and AZ216 switches are consistent with standard EN
50047, while the larger AZ315 and AZ316 switches satisfy standard EN 50041.
In addition to the standard version with M20 cable entry and connection terminals, versions with 4 or 8-pin M12 connector are also available, depending on the number of contacts. With the inbuilt 8-pin connector, AZ switches can be connected to the SFB Safety Fieldbox. Device versions with three contacts in a wide range of combinations can also assume a signalling role in addition to their safety function. The connection terminals on the switch elements, which are rotated by 45°, enable quick and easy wiring.
www.schmersal.co.uk
uksupport@schmersal.com
The AM-T100 Time-of-Flight camera (ToF) uses a Sony DepthSense™ sensor to create 3D depth images with millimetre accuracy. The ToF technology enables high-speed 3D imagery of the scene.
With powerful IR illumination and a high image rate of up to 60fps at 640 x 480 pixel image resolution, the AM-T100 achieves a 67° x 51° field of view with a range of up to 6m.
This camera can be used to support, box filling, stacking, volume detection and labelling in logistics and packaging as a means of boosting the efficiency and accuracy of processes.
www.schmersal.co.uk
uksupport@schmersal.com SCHMERSAL
Malvern,
WR14 1GL
For decades, robots have been helping to increase production efficiency, improve quality and consistency, and alleviate labour shortages in industries such as automotive, machinery, and plastics. Other sectors however, including food and beverage, have been slower to wake up to the benefits of automation, with many food producers still heavily reliant
on manual labour and semiautomated equipment. Figures from the IFR 2022 World Robotics Industrial Robots Report show that only 3% of global industrial robot installations are for food and beverage applications, compared with 23% for automotive.
Fortunately, the tide is beginning to turn – global robot installations in the food and beverage industry grew by 12% year on year from 2016 to 2021. And in the UK, of the 2,054 industrial robot installations in 2021, 164 were in the food and beverage industry, representing a total of 8% – well above the global average.
Most robot installations in food production lines are for packaging, picking and placing tasks. However, there is a lot more that robots can do. At FANUC, we believe the adoption of robotics
is set to change the face of food manufacturing for the better, both for primary and secondary processing and packaging tasks. Here, we look at four ways in which food production lines could look very different in 2033 thanks to the increased use of robots and automation…
Lightweight and simple to use, collaborative robots, or cobots, are becoming increasingly popular within food factories, especially where space is restricted. Extremely slimline and with a base not much bigger than an A4 sheet of paper, they fit easily into crowded areas, such as loading/ palletising environments, and can work alongside humans. Despite their size, they lend themselves well to lifting applications, such as palletising and material handling
In the UK, of the 2,054 industrial robot installations in 2021, 164 were in the food and beverage industry, representing a total of 8% – well above the global average.
tasks – the FANUC CRX-25iA, for example, has a 25kg payload and a 1,889mm reach. We are continuing to develop our cobot range and in the future, we expect to see cobots with increasingly high payloads and longer reaches, to cope with growing customer demand.
Since Covid and Brexit, labour shortages in the food industry have worsened and companies are looking to remove manual handling wherever possible. While a number of the individual processes in a food factory may already be automated, in many cases, people are still required to move products from one stage to another. Robots are ideally placed to help in these scenarios. Inherently flexible, they can easily be repurposed to cope with product changes enabling the factory to remain agile in the face of labour shortages.
Packing is another area which is traditionally very labour intensive.
There is now a clear trend of using robots to pack ingredients into trays, trays into boxes and boxes onto pallets, freeing up human workers to carry out more valueadded tasks. In the future, food factories will resemble automotive factories more and more, with robots carrying out the majority of manual handling tasks. There will also be an increased use of autonomous robot vehicles to move stock around the warehouse, and for loading/unloading.
Another area which is ripe for automating is quality control. Robotic vision inspection systems using AI and machine learning can detect product faults quickly, accurately and reliably, helping to speed up production lines. This technology can also be used for product sorting and grading, eg potatoes. Repetitive, manual tasks such as this are ideal for being completed by AI-powered visionguided robots, helping to free up valuable human employees.
Finally, robots are moving out of the factory and helping to replace labour shortages in the fields. There are already trials of robots being placed onto tractors and incorporated with a vision system to inspect produce in the field. They can assess the stage
of growth/ripeness, and then pick the fruit or vegetable when they’re ready to be harvested. Expect to see many more of these applications in the future.
Automation in action: Meet Bakisto, the robot baker FANUC has joined forces with baking oven manufacturer WIESHEU and retail specialist Wanzl to develop the automatic Bakisto system. Comprising three interconnected systems –a FANUC cobot; Wanzl’s smart baked goods presenter ‘BakeOff i’ featuring artificial intelligence and a network-enabled baking oven; and the WIESHEU TrayMotion automatic loading and unloading system – Bakisto automates important tasks for retail bakeries, such as loading baking trays, inserting and removing trays from the oven, and restocking displays.
Based on historical data and current stock levels, the AIpowered BakeOff i estimates daily baked goods demand and predicts when peak baking should take place. The FANUC cobot then carries the baking trays loaded with frozen baked goods from the refrigeration unit and pushes them into the transport trolley, which runs on rails in front of the preheated oven. The TrayMotion loading system pulls in the loaded trays, enabling the baking process to begin. After baking, the system pushes the baking trays back into the transport trolley, which moves to the side, allowing the baked goods to cool down while also making space for subsequent production. The FANUC cobot then fills the predefined compartments of the BakeOff i with the finished and cooled baked goods. Feeding new data into the AI system ensures the process is continuously being optimised.
FANUC believes that Bakisto is ripe for addressing labour shortages in the food industry by relieving retail workers from repetitive tasks and unsociable working hours, as well as increasing product consistency and reducing food waste.
Gellert freeze dryers are the perfect solution for manufacturers looking for a reliable and scalable option for regulated food production. With a notable shift towards the freezedried product market, manufacturers and consumers alike are recognizing the benefits of this process. By reducing, or removing, the need for cold chain handling, manufacturers can reduce transportation and storage costs, and as freeze-dried material is much lighter than frozen or refrigerated product, this further lowers costs. Additionally, freeze dried products not only take less energy and cost to store, but they also maintain the biological benefits and flavours of the raw product whilst extending shelf life.
Gellert freeze dryers offer a controlled and repeatable manner for in-situ freeze drying directly on the shelves, ensuring the product maintains its shape, structure, and nutritional value. Gellert has developed a range of freeze dryers with ease of scale-up, user requirements, and operation in mind, making them versatile and popular in the industry.
Some of the beneficial features of Gellert equipment include AutoDry, an intuitive feature that allows users to input their desired temperature differential between the product, sample, and shelves, ensuring the sample can be dried using the AutoDry feedback mechanism,
freeze dried products not only take less energy and cost to store, but they also maintain the biological benefits and flavours of the raw product whilst extending shelf life.
optimizing drying cycles. The chamber, condenser, shelves, and shelf stack can all be constructed from 316L stainless steel for product contact, and a hybrid cooling system is also available on larger equipment, to utilize defrost water by re-heating via the freeze dryer compressors, saving energy and costs.
The most common applications that Gellert’s freeze dryers are used for include: -
• smart foods e.g., supplements and nutraceuticals
• food and beverages
• dairy products
• fruits and vegetables
• pet food and pet treats
All Gellert systems are manufactured in Europe and strictly adhere to compliance regulations such as F-gas.
Biopharma Group is the exclusive distributor of Gellert freeze dryers across the UK, Ireland, and France. Both Biopharma Group and Gellert are well respected and renowned companies, combining years of lyo industry experience. This winning combination allows the Biopharma Group team to help you select the best freeze dryer to meet your specific need and Gellert has accrued a high level of practical experience and in-house expertise, developing an array of different models and configurations to satisfy a broad range of food production purposes.
Contact Biopharma Group’s product specialists to discuss your requirements or request more information.
www.biopharma.co.uk
A split frame machine that features a line of new anti-deformation rounding pads to protect highpurity thin-wall tubing in food and pharmaceutical process applications has been introduced by Esco Tool of Holliston, MA.
The Esco COHOG® Split Frame Machine has a robust stationary ring machined from 7075 aluminum alloy that is hard coated and supports a custom steel forged, heat-treated, and nickel-plated rotating ring using precision tuned eccentric bearings. Featuring new anti-deformation rounding pads to prevent thin-wall pipe and tubing from being crushed, this clamshell style machine is ideally suited for use in food and pharmaceutical process applications.
Easy to set-up using indexable tooling that squares itself to the tube O.D. with the antideformation pads attached, the Esco COHOG ® Split Frame Machine incorporates a one-piece module that mounts to the tool slide and holds a pre-angled bit of 30, 37-1/2 degree or custom angles. Pneumatic, hydraulic, and electric motors are offered, and most of the cutting inserts have multiple cutting edges for long life and are simple to replace.
The Esco COHOG® Split Frame Machine is priced from $10,500.00 up, depending upon size and is available for sale or rent.
For more information contact:
Esco Tool, A Unit of Esco Technologies, Inc.
Matthew Brennan, Marketing Director
75 October Hill Rd. Holliston, MA 01746
TEL (508) 429-4441 / FAX (508)429-2811
e-mail: matt@escotool.com www.escotool.com
Featuring new antideformation rounding pads to prevent thinwall pipe and tubing from being crushed, this clamshell style machine is ideally suited for use in food and pharmaceutical process applications.
The Aerox-Injector removes the odours that arise during production of animal feed. Our units help our clients to minimise their emissions in order to comply with industry legislation and laws. The key industries we are specialised in are:
Animal feed | Pet food | Aqua feed | Oil seed
The Aerox-Injector destroys the odours coming from extruders, pelletizers, dryers and coolers and is now also available in ATEX1.
The advantages for the end-user are:
• Small footprint required, so easy to implement
• No requirements of Gas, Water or Chemicals
• Injection principle allows treatment of large volumes of process air
Aerox b.v.
+31 30 – 6779180 info@aerox.nl www.aerox.nl/en
Alex
Hygiene-sensitive production and packaging processes require sensors that meet the most stringent requirements. Leuze makes this possible with sensor series intended for the food industry and with its many years of application knowhow.
There are few industries where the demands placed on the sensor systems are as great as they are in the food industry. Whether sausage or cheese, confectionery or pastries, dairy or beverages: Hygiene is always a key factor when processing and packaging the products. Sensors in these areas must be resistant to intensive cleaning and disinfection cycles. The technology must also be able to withstand considerable fluctuations in temperature. With its new miniature sensors in stainless steel housings, Leuze fulfills all the important requirements of the food industry: chemical and thermal resistance, leak tightness and a
In the food industry, hygiene requirements are most strict wherever the food product or beverage is not yet protected by primary packaging.
hygienic product design. Protection classes such as IP67, IP68 and IP69K as well as ECOLAB, CleanProof+ and JohnsonDiversey certifications confirm that the devices operate properly at all times even in extremely harsh environments.
In the food industry, hygiene requirements are most strict wherever the food product or beverage is not yet protected by primary packaging. “This places high demands on sensors that are used for automation in these areas,” says Steffen Hundt, Product Manager at Leuze. “Sensor systems
must be high performance and hygienic, but also robust so that they can operate reliably in harsh environmental conditions.” With its new solutions, Leuze ensures the following four key requirements for sensor systems used in the food industry:
Chemical requirements: high resistance Cleaning plays a major role in the packaging area of the food industry. Intensive cleaning processes, particularly after production runs, are necessary in order to remove food residue and to prevent bacterial carry-over. There are many cleaning cycles, long exposure times as well as preliminary and main cleaning.
Furthermore, the sensor systems must be able to deal with a broad range of different cleaning agents – from ECOLAB cleaners to various foam and disinfectant cleaners that may be acidic or alkaline. To make
sure that the sensors optimally withstand the cleaning agents, Leuze checks the devices using the ECOLAB test and also CleanProof+ and Johnson Diversey procedures. This ensures the long-term resistance of the sensor housing.
Thermal requirements: major differences in temperature Major differences in temperature exist particularly when food is placed in its primary packaging. For example Owing to the sensitive foodstuffs handled in meat processing, the temperatures often range from 5 to 10°C. In contrast, however, cleaning is performed at extremely high temperatures. “Here, we again play it safe with our sensors and always test the products in several ways: in the climate chamber, by thermal shock testing and also by means of a steam jet test,” explains Steffen Hundt.
Leak tightness: reliably waterproof
As the sensors are exposed to continuous wet conditions and humidity during cleaning and because highpressure water jets are additionally used, absolute leak tightness is essential. Leuze always tests all sensors using leak testing equipment. The sensors intended for the food industry meet the demands required for IP69K approval: They are tested using a steam jet with an extremely high water pressure of up to 10,000 kPa and a temperature of up to 80 °C. The distance to the sensor during testing is very close at just ten centimeters. Furthermore, the sensor is exposed to the steam jet from different angles in order to simulate cleaning as realistically as possible.
Materials/product design: hygienic and food-safe
Sensors installed in packaging machines should be made of material that is approved for contact with food. Furthermore, the devices must be designed in such a way that they can be cleaned easily. In addition, no bacteria and no food residue are allowed to accumulate. For this reason, smooth surfaces without gaps and cavities are required.
Leuze meets these requirements by implementing a hygienic product design and using selected FDAcompliant materials. This means that Leuze sensors for the food industry have a stainless steel housing as well as glass-free and scratch-resistant optics covers.
The requirements make it clear that suitable sensor systems are needed for hygiene-sensitive production
and packaging processes. Leuze has specially developed the 53C and 55C sensor series for this purpose.
They are characterized by the housing made of high-quality, particularly smooth V4A stainless steel and the glass-free, scratch resistant optics cover. The sensors can thus withstand demanding cleaning and disinfection cycles as well as large temperature fluctuations.
Anyone wanting to be on the safe side when it comes to sensor systems used in the food industry should opt for a sensor manufacturer with extensive expertise in this area. Steffen Hundt explains: “Leuze not only understands the challenges in hygiene-sensitive environments, but has for decades worked closely with its customers from the food industry. We implement the Sensor People’s comprehensive application knowledge in optimum sensor solutions for every requirement.” The high-tech product range includes a number
of different sensors for the field of automation technology. For example, switching and measuring sensors, identification systems, data transmission and image processing solutions as well as safety components, services and holistic solutions. Another advantage: Leuze covers not only a sub-process, but provides its customers from the food industry with assistance from the first to the last step in the packaging process completely and at all times.
Leuze has developed the sensors of the 53C and 55C series especially for hygiene-sensitive production and packaging processes. They can be used very flexibly as through beam photoelectric sensors, retroreflective photoelectric sensors or diffuse sensors. Depending on the model, Leuze solutions reliably detect glass, PET, film or small parts. The fill level of aqueous liquids can also be easily detected. The 53C and 55C sensor series are dustproof and waterproof and meet the requirements of protection classes IP67, IP68 and IP69K. The housing is consistently designed to prevent bacterial carry-overs and contamination. Smooth contours without fastening holes prevent deposits. A special fastening concept of the 53C series in hygienic design also contributes to this: The sensor and the machine have a gastight connection via the mounting trunnion. Useful: The sensors can be configured, operated and maintained via IOLink.
www.leuze.co.uk
In one of Peterborough’s foremost business parks, two hours north of London sits one of the giants in the Dryer manufacturing industry. Planet Dryers, a member of the CPM family of brands, is known for its high-quality range of specialist equipment, sleek designs, sanitary innovations and operational efficiency.
“Every piece of equipment we make, we do it with the customer’s needs in mind,” said CPM Operations Manager Ross Vinten. “We take a lot of pride in our brand, designs and build quality.”
One design has stood out above the competition and keeps on improving. The Triple Pass Dryer is the line’s top selling machine and can be found in snack extruder lines around the world. The Triple Pass Dryer works with a wide range of applications, including extruded snacks, nuts, rice cakes and breakfast cereals.
It’s a modern design, focused on hygiene for food, and driven by customer feedback,
“It’s a modern design, focused on hygiene for food, and driven by customer feedback,” Vinten said. “Each machine provides excellent drying performance ensuring a uniform product which is fully tested and validated. The laboratory SAT testing at factory sign-off yields process performance figures right in the centre of the target range, which is great for everyone involved”.
Being flexible and solution oriented are also traits of the Planet Dryers line. When one large-named customer wanted to improve their sustainability standing, the Triple Pass electric version was offered: aptly known as the TPe.
“It’s about giving the customers more options and proving that
we have an adaptable design, while maintaining performance,” Vinten said.
Previously purchased gas-powered machines can be refurbished to electric, and by design, a customer could switch between both power sources. Planet Dryers is very much focussed on continued innovation and development of the range, and as such, new R&D exercises are being carried out on a Hydrogen design, known as the TPh.
“You’ve got to continually deliver to the needs of the market and strive to excel. That’s why we’re the best in class and a recognised standard in extruded snack lines globally,” Vinten said.
For more information, contact planetdryers.info@cpm.net or visit www.onecpm.com.
Measurement Challenge/Difficulty:
Steam being used in breweries had always been overlooked as a source or “reusable” or “capturable” energy. Averaging Pitot tubes typically used were not only inaccurate, but still required costly pipe runs along with very regular and expensive maintenance and replacement. In generating steam, thermal mass meters had been used but presented some of the same problems. Brewers looking to improve their efficiencies needed a new method to obtain and measure a thermal mass balance around the plant for steam generation and usage. Specialty gases such as Carbon Dioxide, Nitrogen, and Chlorine were being used in the utilities and process areas of the brewery. All of these were measured with previously mentioned flowmeter technologies, usually inadequately. The brewers needed a better flowmeter that would reduce the use of expensive purchased gases or be able to monitor use of generated steam and energy demands more accurately.
In beer production, accurate temperature control is critical to any wort boiling kettle since it is a sensitive process and one of the most energy-intensive aspects of beer production. In this case, the kettle is a large vat with tubing coiled around the exterior wall. The tubing carries a mix of steam and water to heat the wort in the kettle. Modulating the proportion of steam vs. water in the tubing enables the brewery to control the thermal transfer profile of the batch process.
The wort boiling process demands a high volume of steam in its initial phase, enough to bring the large batch up to temperature quickly but without burning the wort at points of direct heat transfer. Once the entire contents of the wort kettle reach a boil, a much lower rate of steam feed can then be used to maintain a desirable temperature for the remainder of the heating cycle.
In beer production, accurate temperature control is critical to any wort boiling kettle since it is a sensitive process and one of the most energy-intensive aspects of beer production.
Previous Method:
Steam measurement was made with orifice plates, then averaging pitot tubes. Specialty gases were measured with thermal mass dispersion meters. All of these technologies had similar problems with pipe diameter restriction, maintenance and replacement frequency and costs, and inaccuracies of the devices. Vortex meters especially could not generate accurate readings at low flows in a condensed environment crowded with fittings and tight turns.
Solution:
V-Cones were installed, reducing operating costs and virtually eliminating replacement expenses. The accuracy of the flowmeters helped the brewery to better calculate their steam/heat balance. V-Cones on specialty gas lines helped reduce usage and more accurately measure produced Carbon Dioxide, resulting in a more economical production. V-Cones measuring Chlorine gas aided in the cleansing cycles thereby reducing gas purchases. V-Cones used in Nitrogen applications measured the gas more accurately, reducing the overall use of gas. Date Installed: 1997.
The industry’s leading showcase for packaging, warehouse and logistics management solutions has expanded its programme, resulting in an exhibition packed with more shows, innovation, insights and inspiration than ever before.
IntraLogisteX 2024 offers unprecedented opportunity for those looking to stay one step ahead in a competitive global market place. Now in its 10th year, the show thrives on its reputation as the go-to connective for industry leaders and innovators to propel businesses to more productive, cost-effective levels. The journey continues with 2024’s event, which adds a Sustainable Supply Chain exhibition to the two-day multi-experience show that also features a Robotics
and Automation exhibition and an ‘Intralogistics’ space showcasing the smartest moves in warehousing and logistics.
Stephen Brooks, IntraLogisteX’s managing director, said: “There is no question that IntraLogisteX 2024 will be our biggest and best show to date. The Sustainable Supply Chain Exhibition is a particularly exciting addition to the programme. It’s our response to the industry call for a show that offers tangible, results-driven solutions that businesses can enact immediately. It’s an opportunity not to be missed for companies looking to engage with experts and get the inside track on sustainablybased supply chain solutions and trends.”
Featuring more than 350 exhibitors, 60 conference sessions and an expected 8,000plus attendees from across the industry, IntraLogisteX is expertlycurated to maximise business profit through the optimisation of intralogistics management. Brother, Ocado Intelligent Automation, Körber Supply Chain Automation, SEE (formerly Sealed Air), Carlton Packaging, Protega Global, Exotec, Hai Robotics, Locus Robotics, Springpack, and Siemens are among the global brands exhibiting at this year’s event, with more leading names in the logistics, packaging, and automation sector due to confirm their attendance in the coming weeks.
Now in its 10th year, the show thrives on its reputation as the go-to connective for industry leaders and innovators to propel businesses to more productive, costeffective levels
The newly-created Sustainable Supply Chain Exhibition is aimed at compliance-focused supply chain professionals, as well as companies committed to achieving ‘above and beyond’ environmental outcomes. It includes an array of exciting, enterprising spaces including a Start-Up Hub that offers small and medium-sized businesses an exclusive opportunity to promote revolutionary services and solutions that will help businesses to achieve sustainability goals.
The brand-new exhibition focuses on pivotal sectors such as packaging, last-mile logistics,
cold-chain logistics, software and more – all crucial components of the supply chain ecosystem. As well as developments in sustainable delivery and materials, the Startup Hub will shine a light on new systems to improve traceability.
A Sustainability Theatre will also form part of the Sustainable Supply Chain Exhibition Space, providing
a platform for industry thought leaders and influencers to share their aspirations for the sector’s future sustainability.
IntraLogistex 2024 takes place on March 19th and 20th at NEC Birmingham.
For more details visit: www.intralogistex.co.uk
Storage and order picking equipment are essential for maintaining efficient material flow. Creating the ideal system will give manufacturers a massive increase in storage capacity and pick rates within the space they have available, says Edward Hutchison, Managing Director of BITO Storage Systems.
Without effective and reliable storage and order picking systems, production and assembly lines will grind to a halt. The Just In Time (JIT) supply of parts, semi-finished products and raw materials to production machines requires flexible and scalable warehouse storage and retrieval systems, whether manual or automated, working in combination with continuous units, such as overhead conveyors and conveyor belts, or discontinuous systems, such as Autonomous Mobile Robot (AMRs), Automated Guided Vehicles (AGVs) or forklift trucks.
Such systems must not only provide a smooth flow of parts through the plant, from storage to feed the line, but also accommodate future growth. And with assembly areas claiming priority over space in most factories, storage and order picking will often need to fit into a constrained footprint. Fortunately, there are many ways that these objectives can be achieved successfully.
A good example of a lower cost and space saving method to achieve ‘right first time’ part delivery to the line comes in the form of carton or pallet live systems, comprising flow shelves created from racking. With clear labelling, flow shelves help create effective pick zones because the design provides a density of storage that results in a greater number of pick face locations than would be possible with tradition shelving and racking. Because cartons or pallets are loaded into the flow lane on a first in, first out (FIFO) basis, when an empty unit is removed another full carton or a pallet full of parts flows into place on rollers in the inclined lane, ready to pick from.
Without effective and reliable storage and order picking systems, production and assembly lines will grind to a halt.
Compared to a traditional wide aisle configuration, Very Narrow Aisle (VNA) racking provides a more space efficient solution for holding general parts, usually on pallets and is served by VNA lift trucks. This is a pretty standard solution these days, though a narrow aisle can be designed to feed a carton live structure, integrated into the rack, running alongside the aisle and providing a dense pick face for parts.
Picking small parts is a vital element in most factory warehouses, and where the goal is to keep things simple, this can be easily integrated within pallet racks. One option is to create small parts pick locations on the reachable ground level, with upper storage levels serving as a buffer store for replenishment. Plastic small parts storage containers will help to store and organise small items and C-parts – making them available for quick and easy picking. This will result in
a reasonably efficient picking process but ground floor locations within a pallet rack will, of course, be limited. Flow shelves, however, can be easily installed into pallet racking to increase the number of pick locations and volume of SKUs located on the ground level pick face. Adding standard shelving within pallet racking is another option to create flexible small item pick faces. Using mobile shelving will maximise the available space, though moving the shelves increases pick times. Inclined shelving within a pallet racking bay will make items clearly visible for picking.
Plastic bins and containers will keep parts protected throughout the intralogistics process and during transport to ensure they are delivered to the line in prime condition. It is worth seeking out storage system supplier such as BITO, which in addition to offering racking, shelving and flow lanes, also provides a plastic container range comprising a variety of sizes and a broad choice of accessories. This will ensure the optimum system is designed to fit a given space, maximising the potential for small parts picking and, ultimately, improve manufacturing efficiency.
Nordson Measurement & Control Solutions (formerly NDC Technologies) allows international food companies to maximize process performance and KPIs through the measurement of moisture, fat/oil, protein and color.
The NDC Products brand from Nordson Measurement & Control Solutions features both at-line and on-line non-contact, NIR gauging solutions to meet the manufacturing challenges faced by the food industry.
The InfraLab Series 9 family groups the benchtop analyzers to the Series 9 on-line gauge. It offers two instrument designs (standard and the NEW Top-Loader) to cover the full range of food applications, including powders, beans, grains, and semi-solid products. The InfraLab Series 9 analyzers are available in single- or multicomponent formats and allow for rapid color, moisture, fat/oil, and protein analyses (only 5 seconds) in process environments, replacing time-consuming laboratory methods or at-line instruments such as loss-on-drying or gravimetric moisture testing. With their greater processing power and measurement capability, the InfraLab Series 9 analyzers deliver deeper process insight into the operation, enabling a significant reduction in a company’s operational expenditure (OPEX).
The Series 9 gauge is a nextgeneration process optimization solution for measuring color, moisture, and other key constituents on-line. It is specially engineered for 24/7 duty, helping manufacturers to meet product quality demands and efficiency goals. The Series 9 delivers
The NEW Top-Loader facilitates sample presentation & reduces human error - it is ideal for powders, beans, grains and semi-liquids.
unparalleled measurement performance while maintaining simplicity and versatility in design and operation. The flexible, futureproof platform harnesses the full power of infrared spectroscopy. The user-friendly format requires no special operator skills or expert knowledge, yet it allows expert users to access the enhanced interaction capabilities as desired.
Overall, the Series 9 Color Gauge keeps you ahead with:
• Evolutionary technology that is flexible, adaptable and scalable to meet your changing needs.
• Enterprise-level intelligence compatible with Industry 4.0.
• Easier operation and maintenance.
• Lower cost of ownership over a long lifetime of operation.
More information available on: www.ndc.com/food-bulk-materialsprocessing/
IFE Manufacturing, part of Food, Drink & Hospitality Week, returns to ExCeL London on 25-27 March to showcase the very latest products and innovations in the world of food & drink.
A must-attend event for brand owners and manufacturers to source new packaging, ingredients, technology, and manufacturing solutions, IFE Manufacturing is packed with opportunities to discover a wide range of products and meet directly with brand owners.
Visitors to the show will have the opportunity to connect with brands including ingredients leaders Belazu, Biospringer by
Ingredients, packaging innovators Elopak UK, Magnum Packaging (N.E) Ltd and MM Packaging, and organisations such as Make UK, QAD Redzone and Ashbury.
IFE Manufacturing will also showcase suppliers such as Kecol Pumps, the leading manufacturer
of piston pumps and priming systems for viscous products, smart weighing technology experts MARCO Limited and moisture measurement brand MoistTech Corp.
Plus, the Trends & Innovations Platform will play host to a wide range of presentations, discussions and debates on the most important topics in the food & drink manufacturing sector including sessions covering precision fermentation, allergens, the potential impact of AI on the industry, consumer insights and some of the disruptive forces impacting on the world of food & drink in 2024.
Mark Thompson, Co-Founder of Edinburgh-based insight and innovation company TRKR, and panellist for the session, ‘Ultra Processed Foods: What is all the fuss about?’, says: “I’m looking forward to attending IFE Manufacturing and sharing my thoughts and views on the topic of ultra-processed foods.
“It’s an important topic as whilst many of the foods that fall under the umbrella of ‘ultra-processed’ are everyday staples for most consumers. A loaf of bread for example, the very fact that these items are part of our weekly diet means that as an industry, we need a measured and informed approach to tackling their uptake.”
The Trends & Innovation Platform will also see the winners announced for the inaugural IFE Manufacturing Ingredients Awards, in partnership with the Institute of Food Science & Technology. These new awards were created to highlight innovation in early-stage food development and celebrate trailblazers at the forefront of food science and technology.
Each year IFE Manufacturing also works with a number of key partners in the manufacturing sector including the British Contract Manufacturers and Packers Association (BCMPA).
CEO Emma Verkaik comments: “The BCMPA is delighted to be exhibiting again at IFE Manufacturing 2024 on behalf of our 200-plus membership and to be able to have the opportunity to talk face to face with visitors about their production and outsourcing needs.”
IFE Manufacturing takes place alongside IFE, The Pub Show, HRC and International Salon Culinaire as part of Food, Drink & Hospitality Week on 25-27 March at ExCeL London. Don’t miss out on your chance to be part of the UK’s biggest celebration of industry innovation, register for your complimentary trade ticket at www.ifemanufacturing.co.uk.
The newly introduced AC/DC UPS solution UPSI-2406IP-38AC from Bicker Elektronik, Donauwoerth/ Germany, ensures uninterruptible power supply of safety-relevant 24VDC applications, such as control and regulation modules, embedded box IPCs, drives, actuators, sensors, lighting and safety technology in case of AC mains failure and voltage dips. The particularly safe and long-life LiFePO4 battery technology is used as energy storage and enables up to 100h long-term bridging. The intelligent DC emergency power supply with AC wide-range input thus reliably avoids system failures, downtimes and data loss. The particularly robust design with IP65 protection makes the new UPSI-2406IP-38AC the ideal choice for demanding environmental conditions. Typical applications include heavy industry, petrochemicals, tunneling and mining, security and building services, energy, infrastructure, environmental technology, communications, lighting technology, commercial and special vehicles, food industry, chemicals and agriculture.
Robust aluminium housing with protection class IP65
The high-quality aluminium housing protects all components of the emergency power supply from mechanical impact: Both the intelligent DC UPS control and charging electronics (24V/6A) with upstream AC/DC converter and the integrated lithium iron phosphate battery pack. The sealed housing elements and connections are resistant to water, ice, oil and dust in accordance with protection class IP65. An integrated pressure compensation element with membrane prevents condensation inside the unit. The operating temperature range of the UPSI-2406IP-38AC extends from -20 to +50°C. The high-quality ÖLFLEX® input and output cables are permanently installed on the
housing. Four slotted holes allow safe and flexible wall or pole mounting of the AC/DC UPS. A pole-mounting kit is available as an option.
24VDC long-term bridging up to 100 hours
Uninterruptible power supply (UPS) of sensitive or safety-related 24VDC systems supplied from the AC mains is particularly important in case of blackouts, brownouts or flicker. For international use, the UPSI-2406IP-38AC has a wide-range AC input from 90 to 264 VAC with active PFC and high-efficiency AC/DC converter topology. In AC mains operation, which is automatically set after the input voltage is applied, the 24VDC output is activated and the integrated LiFePO4 energy storage is charged at the same time. In case of a voltage drop of the input voltage below the smallest nominal value, the UPS is switched to battery operation with regulated DC output voltage within fractions of a second and enables backup times of up to 100h. When the AC input voltage returns, the UPS is automatically switched back to regular mains operation and charging of the energy storage continues.
Integrated LiFePO4 highperformance battery pack
The LiFePO4 energy storage (lithium iron phosphate) with 330Wh convinces in safety-relevant applications with a particularly stable battery chemistry, a long service life of at least 10 years and more than 6000 full charge and discharge cycles. Bicker Elektronik deliberately uses the particularly safe lithium iron phosphate chemistry for all highperformance battery packs, which makes thermal runaway almost impossible. The UPSI-2406IP-38AC also meets the safety requirements of the IEC/EN 62040-1 standard. The battery management system (BMS) monitors and controls the complete charging and discharging process of each battery cell of the energy storage unit. The integrated cell balancing ensures a balanced and even charge of all cells so that the full capacity of the lithium iron phosphate battery pack remains permanently usable. In addition, the UPSI-2406IP-38AC offers a battery start function, which makes it possible to start a 24V application from the battery by pressing a button on the UPS (up to 6 A max. load current), without the AC voltage supply being present. www.bicker.de/en/upsi-2406ip-38ac
NOMOQ, the pioneer and leading provider of digitally printed cans in Europe, today announces the launch of blank (undecorated) aluminium beverage cans on NOMOQ.com, expanding its product offering beyond the core business of digitally printed cans.
Recognising the diverse needs of their customers, NOMOQ is introducing ‘Blank Cans’ to cater to those who seek unprinted cans for their filling lines. This service allows customers the flexibility to maintain labelled productions in combination with digitally decorated cans, both directly sourced from NOMOQ in the same
transportation system.
The UK beverage industry was projected to reach over £8 billion in revenue at the end of 2023 with 22.2million users by 2027 as Brits are set to become a nation of canned beverage consumers due to changing drinking habits post pandemic and a desire for fully recyclable packaging. This shows the demand for canned products will remain strong throughout 2024 and beyond.
NOMOQ’s growing portfolio of blank cans allows craft beverage businesses to consolidate their packaging supply chains whilst
maintaining high quality and environmentally friendly solutions as the demand for aluminium cans remains high.
Alongside each order, the experts at NOMOQ are also offering personalised business advice, providing information to ensure all transport, packaging and labelling is as environmentally friendly as it can be, and that the end result can be indefinitely recycled whilst not compromising on brand quality.
The benefits of NOMOQ providing both, undecorated blank cans and printed cans are:
We are excited to launch this new service after listening to customer feedback requesting more packaging options from one supplier.
1. Sustainable logistics: Customers can now streamline their supply chain by sourcing both digitally printed and unprinted cans from a single distributor, simplifying the procurement process and enhancing overall efficiency. Bulk shipments from a single source reduce overall CO2 impact, aligning with NOMOQ’s own commitment to eco-friendly practices.
2. Cost Efficiency: By consolidating can orders from a single warehouse, customers stand to benefit from reduced transportation costs. Filling a delivery lorry with cans from the same location ensures a more cost-effective shipping solution.
3. 24/7 Convenience: Customers can order blank silver cans and digitally printed, branded cans through NOMOQ’s e-commerce platform in one simple location at any time.
NOMOQ Co-Founder, Patrick Schweizer, comments: “We are excited to launch this new service after listening to customer feedback requesting more packaging options from one supplier.
“Aluminium cans are one of the world’s most recycled beverage packaging and a shining example of a circular economy in action, and we are happy to offer our expertise to a wider group of customers whilst offering more to our current customers. Ordering a wide range of beverage cans 24/7 has never been easier and the service will be fully integrated on our platform in the coming weeks.”
Contact hello@nomoq.com to find out more about blank cans or visit www.NOMOQ.com to request a digitally printed can for free.
As industries embrace digitalization, new and innovative ways to cut costs are emerging, and one key approach is through energy optimization. A crucial aspect of this strategy involves closely monitoring instances of high energy demand. Unexpected spikes in electricity usage can result in significant additional expenses, particularly in energy-intensive production settings. This is where STEGO’s ESS 076 Smart Sensor Current steps in. In this article, we will explore how this intelligent current sensor, equipped with an IO-Link interface, provides an effective solution for keeping a close eye on load peaks. Not only does it help in monitoring these peaks, but it also plays a role in enhancing overall energy efficiency.
For manufacturing companies, unexpectedly high electricity bills are among the most unwelcome surprises. December, in particular, can turn into a financial pitfall.
Speaking of December: why is this month so crucial when it comes to the total cost of electricity consumption? The reason is that a high peak load in December can result in a subsequent increase in electricity costs for the entire year, imposed by the grid operator. But what if there was a way to avoid these unpleasant surprises? Combine the measuring of electricity consumption per machine and employing peak shaving – a you get a smart strategy to prevent peak loads and shield yourself from unwanted additional payments. This article dives into how precise electricity measurement, especially with the ESS 076 Smart Sensor Current from STEGO, holds the key to a stress-free year-end.
Current sensors like the ESS 076 offer straightforward real-time
monitoring of power consumption in systems and machines. The potential for efficiency gains is significant, especially in energyintensive applications. This becomes evident in our case study with STEGO client, LEGROM. Specializing in plastic injection moulding, LEGROM operates an extensive array of injection moulding machines, known for their high energy demands as they heat and process plastic granules under high pressure. In the past, the immediate or simultaneous activation of injection moulding machines at LEGROM resulted in unexpected additional electricity costs. Retrofitting the machines with a current sensor proved to be a much more cost-effective solution compared to dealing with additional payments. This is crucial, considering that in an industrial setting, these extra electricity costs can quickly escalate into five-digit sums.
From the outset, LEGROM recognized that advancing energy flow monitoring would depend on peak shaving. Kim Waldmann, Managing Director at LEGROM and an industry expert in injection moulding, drew on his experience across various injection moulding companies to understand that
information is the key resource for more efficient processes and risk mitigation.
For LEGROM, the digitization process was carefully planned as a well-thought-out use case. However, the approach needed to be “minimally invasive.”
An intelligent retrofit application for current measurement became crucial for their operational technology (OT). Integrating sensors into the numerous machines in the injection moulding shop floor had to be quick and straightforward to minimize both time and complexity. The goal was to keep machine downtimes to a minimum to avoid disruptions to production capacity and productivity. Waldmann explained, “The integration of the STEGO current sensors was uncomplicated. We only needed to disconnect the machines from the power supply and route the live cable through the ESS 076. The sensor can measure up to 100 A AC without direct contact, perfectly fitting our current condition monitoring needs. The sensors’ practical latching mechanism ensures secure and simple attachment to the power line.”
Visit www.stego-group.com for more information
Products and solutions from STEGO protect sensitive electronic components against heat, cold and humidity. Take a look at our product range.
www.stego-group.com
We were called to consult on several flow applications on board a multimillion-pound new generation of catamaran hybrid passenger ferry. These fabulous low emission ferries will operate on the Thames and be future proofed incase an ultra-low emission zone is introduced for river traffic.
The vessels designer identified a requirement for three flow measurements to be made.
The first was on the diesel fuel consumption on the common rail engine. The second was for the battery cooling circuit and the third was the diesel engine cooling circuit. These ferries have a hybrid motor in each of the two hulls, so that was four measurement points per hull, eight in total. The battery cooling fluid was a water / glycol mix cooled indirectly via a heat exchanger, whilst the diesel engine cooling was raw sea water, drawn up and passed through a strainer.
The pipework was all Nickel Copper alloy, DN25 (fuel lines) DN50 and DN100 line sizes for the two cooling circuits.
For the diesel flow measurement, a gear flow meter was already installed, but iCenta realised that it was sized incorrectly and was causing a significant pressure loss.
A precision OVAL FlowPet 5G gear meter was selected for the task of flow measurement from the diesel flow.
Then the cooling circuits were surveyed, and the ultrasonic sensors were installed within the bilge, access was tight, the space was about 60 cm at its largest point and a person could not turn around. After a risk assessment and gas safety check, the ultrasonic meters were set-up and the sensors installed. It is in such space critical applications a quick setup and small meter, in a rugged bumper case is a definite advantage!
Both the Metri Pro-Lite and the
Metri Pro-Lite was fast to set up and easy to operate, having a backlit graphics display for use in low light conditions.
Precision Flow PD190 measured the flow well, particularly on the water glycol mix for the battery cooling. However, it was found that as the engine approached full power, a great deal of entrained air was mixed into the engine cooling fluid which is not ideal for ultrasonic meters, or many other flow measurement technologies, for that matter. Entrained air is not a good conductor of heat and would therefore also affect the performance of the cooling circuit.
The ultrasonic flowmeters proved unsuitable (due to entrained air) on the diesel engine cooling circuit, so a different flow technology was required. This remains a natural strength of iCenta, we have all the flowmeter technologies, so we can honestly recommend the best flowmeter technology choice for a particular application, and we represent the best flow instrumentation from around the World.
In terms of diagnostics, the ultrasonics did give us valuable insight into the flow conditions.
A combined Doppler – Transit time flow meter is available via iCenta, and this would have been a good application for that device, automatically switching
between Doppler and transit-time techniques.
Metri Pro-Lite was fast to set up and easy to operate, having a backlit graphics display for use in low light conditions. Signal diagnostics are available so you can see the acoustic signals in real time. The meter, after the signal amplification is fully digitised, using correlation detection, has effectively become an industry standard signal processing technique for transit-time flowmeters. All these features really help when working with a range of fluids in demanding situations. The Metri Ultra Pro-Lite also sits in a powerful position in the market. Due to intelligent modern design, it is perfectly engineered to provide a capable clamp-on flowmeter, at a realistic cost to the user. iCenta recommend clamp-on ultrasonic flow meters on site, especially useful for verifying other meters, and for general spot flow readings. The meter also has a fully configurable datalogger for post testing analysis.
Initially we thought that it was a good application for ultrasonics, but due to entrained air on the diesel cooling water it was felt that a magnetic flowmeter was a better choice. Post trial, the new meters were correctly specified sized and delivered, so the overall solution involved Oval geared meters and C-Mag Comac Cal 316L Magnetic flowmeters. www.metricmeasurements.co.uk
ORBIS Europe will be presenting its sustainable and durable plastic transport packaging solutions for use in various industries at LogiMAT (March 19-21 in Stuttgart, hall 4, stand 4C80). These include the manufacturing and automotive industries, the food and beverage industry and the transportation of hazardous goods. “Our sustainable and durable packaging solutions improve the product flow along the entire supply chain. In this way, we help companies to minimize costs in the long term and reduce CO2 emissions at the same time,” says Jürgen Krahé, Senior Commercial Director EMEA.
ORBIS is presenting the XXLPak for use in the automotive and manufacturing industries. Measuring 1638 x 1219 mm, the extra-long
PlastiCorr® enables companies to replace corrugated cardboard boxes.
container can transport particularly large and bulky components and is also ideal for use in automated production processes. The maximum load capacity is 900 kilograms. The XXLPak is foldable and therefore enables a return ratio of 1:2.6. Thanks to its stackability (1+4 static and 1+3 dynamic), trucks are optimally utilized during
transport. As a result, fewer vehicles are on the road – which reduces greenhouse gases. Users can adapt the XXLPak to their supply chain using different height and door configurations.
The GitterPak large load carrier measuring 1200 x 800 mm can also be used to transport heavy components efficiently, replacing steel mesh boxes. Unlike steel, plastic does not rust, which prevents components from being damaged or scratched. The smooth inner walls offer additional product protection. When folded, 272 GitterPaks can be transported per truckload.
In the food and beverage industry, packaging must meet high hygiene standards. This is what the plastic
Our sustainable and durable packaging solutions improve the product flow along the entire supply chain.
pallets from ORBIS are designed for. Compared to wooden pallets, plastic is less susceptible to damage, splintering or breakage, which means that the goods are better protected. This allows primary packaging such as aluminum cans, glass and plastic bottles to be transported safely. The non-porous surface makes it easier for users to clean the pallets. The upper deck of the pallets also has ventilation holes, making them suitable for automated washing and drying systems. The long service life means that companies need to replace the pallets less frequently, which conserves natural resources and saves costs at the same time.
The PlastiCorr® reusable packaging solution also ensures more sustainable transportation in the FMCG segment. It replaces corrugated cardboard boxes 1:1 and is suitable for use in automated
packaging lines. Even after several cycles, the plastic solution retains its quality and functionality. Companies can reuse PlastiCorr® 70 times or more, significantly improving their return on investment and carbon footprint.
ORBIS also offers solutions for the hazardous goods segment: The hazardous goods container IonPak® has been specifically developed for the transportation of lithium-ion batteries and other solid hazardous goods and can be used for up to 400 kg net hazardous goods in accordance with RID/ADR. An inner packaging solution optimized for hazardous goods provides additional protection for the transported goods and can be adapted to individual customer requirements. The IonPak® is also suitable for use in fully and semi-automated production facilities.
ORBIS Europe at LogiMAT, March 1921 in Stuttgart: hall 4, stand 4C80
www.orbiseurope.eu/en/
The
is UN-certified (UN4H2/UN50H) and suitable for the transportation of lithium-ion batteries.
It’s frustrating to witness the frequent recalls of products in recent years, causing significant wastage, all testimony to the need for paramount control of food safety and quality. One recent example was the recall of four cheese products due to potential contamination with E. Coli bacteria. Tragically, one person in Scotland died from the infection, whilst 11 others were hospitalised.
Ensuring food safety and quality is crucial in the food and drink manufacturing industry. Most factories already carry out laboratory testing to assess the quality of materials, checking for compliance with specified tolerances and ensuring they are free from contamination.
Despite these precautions, a significant challenge can arise in bridging the gap between laboratory tests and the busy factory floor. This gap manifests in issues such as isolation, rejects, rework and costly product recalls, the inability to track raw materials, human errors, lost documentation, delayed data and downtime. The breakdown in communication poses a considerable risk to both the efficiency of the manufacturing process and, more critically, to consumer safety.
The Crucial Role of LIMS
Some key benefits of implementing LIMS:
• Ensure Quality Control
Automated data collection and analysis help identify deviations from quality standards, enabling timely corrective actions to maintain high-quality standards.
• Track and Trace Materials from start to finish.
Ensuring food safety and quality is crucial in the food and drink manufacturing industry.
• Automated Sampling & Labelling helps reduce the likelihood of sample mix-ups, thereby enhancing efficiency and safety.
• Schedule Batches
• Heldware
LIMS can help capture vital information quickly, conduct root cause analyses, evaluate downtime and calculate additional labour hours needed due to material failures, thereby allowing factories to detect batch rejections early, understand root cause, quarantine and possibly destroy product before despatch and thereby protect the consumer.
• Integration with Existing Lab Machinery
Eliminate the need for keyboard entries and further minimise risks of operator error.
Harford LIMS
Harford Control developed Laboratory Information
Management Systems (LIMS) to help food and beverage manufacturers optimise the laboratory testing process and provide real-time actionable information, as stand-alone or a fully integrated part of Harford MES. By automating tasks such as material usage confirmation, bulk material tracking and informing laboratory teams of sampling requirements, we help factories ensure material safety and quality, reduce risks and enhance efficiency. Real-time monitoring and seamless integration of lab equipment with Harford LIMS enables proactive management of non-compliant products.
Contact Harford Control by calling +44 (0) 1225 764461 or send an email to info@harfordcontrol.com
Southgate Global, a leader in the supply of packaging equipment, consumables and servicing in operational logistics and fulfilment, has launched a new Water Activated Tape Dispenser (WAT) to help speed up operations and reduce costs as the demand for e-commerce rises.
The Optimax OM700 WAT Dispenser has been designed specifically by Southgate’s specialist team for fast-paced operational logistics environments, as customers look to increase staff productivity to meet demand.
With UK e-commerce sales expected to reach £160.6 billion in 2024 and continue to grow at 4.1 per cent year on year to 2026 resulting in forecast sales of
£194 billion by 2027 , the need for efficiency in every aspect of operations is vital to give companies a performance edge.
Developed with high-volume, fastpast shipping in mind, the OM700 has quick tape output, outputting 60 metres per minute, pre-set buttons to auto dispense from 15cm to 145cm, a programme mode – to allow configuration of up to 6 different lengths in sequence via the digital display - plus the largest tape capacity in the industry - up to 255mm long and 80mm wide.
Phil O’Driscoll, Head of Innovation & New Product Development, explained how the expectation from customers to have deliveries that are quick, secure, and convenient is pushing operations
and warehouse managers to find new ways to optimise their packing operations.
He described how this played a key part in the development of the OM700, “We recognised the pressures that fulfilment and distribution sites were under and looked to produce a product that would ensure fast and continuous packaging operations, while also offering considerable capital cost savings on other options.
“To find a solution that is informed by demand, we asked our customers to review their current equipment and share with us what is, and isn’t, working well. This is a process we follow with all new product development at Southgate, and
Our solution allows operators to improve workflow with fewer interruptions such as having to consistently refill the water tank, refill the tape or adjust the tape dimensions.
ensures we are bringing products to the market that are going to make a difference.”
WAT Dispensers offer a multitude of benefits for packing and shipping operations as it ensures consistent and accurate sealing, reducing the time and effort required compared to manual methods. The strong bond formed by water-activated tape creates a permanent seal making it highly tamper resistant as well as removing the need for multiple layers of retaping, further speeding up the packing process. m/f
Setting it aside from the industry standard, the OM700 has nine new customer inspired features
including the largest water bottle capacity in the industry of up to 2l, eliminating the need for frequent refilling.
O’Driscoll added, “It was important when designing the OM700 that we weren’t just matching, but exceeding the benefits of other options at a lower more cost-effective price that doesn’t compromise on performance.
“Our solution allows operators to improve workflow with fewer interruptions such as having to consistently refill the water tank, refill the tape or adjust the tape dimensions. Small interruptions such as these can have big knockon effects on the entire logistics operation. And in a world where there is no longer room to be behind on operation speed, such constraints can be detrimental in staying ahead.”
The OM700 also provides an optional automatic measuring sensor which will auto-dispense tape to fit the exact size without wasted tape and a foot pedal for hands free operation.
Equipped with a safety interlock switch to disable the cutting blade when the front cover is open, O’Driscoll explained how the OM700 is built with the safety of staff at the forefront.
“At Southgate, we’re continuously looking for ways to introduce new products which make our customer’s operations work even more efficiently, while at the same time are affordable, high quality and kind on the planet. The OM700 offers exactly that, and we’re delighted to now be offering this new product to our new and existing customers.”
Serving over 3,000 customers in more than 20 countries around the world Southgate has a range of operational logistics and fulfilment solutions that support some of the biggest organisations in the key sectors including 3PL, e-commerce, retail, post & parcel and general manufacturing.
For more information on Southgate’s OM700 WAT Dispenser, click here
We
talk to the experts at IKO Nippon Thompson about how linear rail and carriages can be easily adjusted and modified, and how projects can be redesigned around standard products, to save customers time and money
Alinear rail and carriage system is many a design engineers first choice for transporting a load, and for good reason. It provides a rugged and precise solution that is inherently self-aligning, offers high load handling capabilities, and can operate in some of the most challenging environments. But the temptation to over-engineer a system can add significant cost to a project, while asking a vendor to supply a non-standard arrangement can dramatically lengthen the lead time.
For applications where reductions in weight are paramount, IKO offers the cost-effective precision linear slide range. Made from stainless steel, and available in recirculating (BSR) and non-recirculating (BSP) options, this range is highly flexible. It features a simple two-row, four-point contact structure, high motion accuracy and stable load carrying capacity.
This is where IKO Nippon Thompson’s in-house design and adjustments service becomes invaluable, with the UK team of applications engineers able to suggest design amendments that can reduce lead times from months to days, and/or remove significant cost from a project. Mark Ross, technical sales engineer at the company’s Milton Keynes UK headquarters, says: “There are a wide range of things we can do at local level, from the everyday to the more unusual, to deliver an application-specific solution, providing a key service that can save UK customers time and money.”
This can be further enhanced using a built-in rack and pinion system in the BSP variant (BSPG) for applications where there is potential for cage creep. This phenomenon is generally seen in many vertically orientated, highspeed applications, and IKO’s design reduces the chance of this occurring.
our various global locations, and we can tap into that free stock and have it delivered within a couple of days,” says Mark.
even ended up with a design that uses non-standard length carriages.
A prime example is the company’s ability to assess the key parameters in a project, and look at what can be easily amended without compromising the performance criteria, so that the project can be serviced from the company’s free stock. “For any supplier, manufacturing a system to order is going to take time, but IKO Nippon Thompson will always have standard products available as free stock at
For applications that may receive fluctuating and complex loads, but still need to see consistent repeatable results, the BWU range may be more appropriate. The high rigidity, precision linear slide units offer design engineers the possibility of adding a secure mounting position that can handle loads of up to 12,100N. They are also exclusively made of stainless steel, making them suitable for potentially corrosive environments or cleanrooms. In addition, they are suitable for applications where rust prevention oil is not preferred.
“From there we have the in-house capabilities to modify standard products to meet specific customer requirements.”
Examples include cutting rail to specific length at the simplest level, or changing the e-dimension –the measure from the end of the rail to the first mounting hole. “As standard, this e-dimension would be half the normal hole pitch, but that might not suit the application,” Mark explains.
Such adjustments and amendments can be important time savers for customers, particularly when they are building a prototype as proof of concept. But IKO Nippon Thompson’s design services can also save customers significant amounts of money, for example when it is clear that the design engineer has over-specified the project, perhaps as a belt and braces approach to meeting particular lifespan requirements.
For designers and machine builders looking to increase load ratings further, while keeping the overall machine size to a minimum, IKO can then offer its crossed roller ways (CRW). This range is available in three different variants, including a rack and pinion option (CRWG) and a heavier-duty variant that increases the strength of the internal components (CRWH). These products all utilise cylindrical rolling elements instead of ball bearings, and provide increased load rating capacity and improved rigidity. This, in turn, increases the stability of the overall product.
“We can quickly drill down to the customer’s most important considerations and then look at how that impacts on the rail and carriage dimensions,” says Mark. “By talking through load and stroke requirements, that might lead us to propose alternative carriage lengths. For example, has the designer opted for a shorter carriage to increase
Despite the variation in materials and structure, all of the models share a similar design. With single linear caged bearings consisting of ball or roller elements running along inner and outer tracks. These bearings are arranged in parallel, one on each side of the slide, to support the weight of the table (or carriage) and its mounted load as it moves.
The various designs all provide precise accurate motion, normally over short stroke lengths. In the BSP, BWU and CRW ranges, this motion is further enhanced by their non-recirculating design. Due to the compression and release of the rolling elements as they pass in and out of contact with
“By adjusting the rail and carriage dimensions, we can often find a much more cost-effective approach, selecting more appropriate and standard products or better cost products,” he continues. “We can play
the raceways seen in recirculating designs, there is no chance of the balls causing any background distortions in the data gathered. For the same reason, the bearings run very quietly. In addition, maximum speeds of 50m/min can be achieved.
with parameters such as preload to see if this provides a better way to meet specific application criteria. Or we can butt together standard rails to deliver longer, non-standard lengths at given profile dimensions without impacting precision.
“In addition, we can add seals and scrapers to protect the rolling elements on some product types, as well as offering different coating options to protect against rust or to alter the products’ aesthetic appearance if that’s a requirement too. The addition of rail caps can also be a further simple (yet cost-effective) way to increase the longevity of the system, and is something which, whilst basic, is often overlooked.”
All of this comes hand in hand with the capability to provide CAD drawings and models, and to port those designs straight into customers’ models.
IKO Nippon Thompson is conscious, too, of the cost of logistics for its customers, and so can supply pre-packaged sets to reduce packaging, handling and stock management. And then there is the company’s on-site training in addition to its telephone and web video support.
“It’s all part of a service that means we are much more hands-on with our customers than perhaps other suppliers are willing or able to be,” concludes Mark. “We want to be more involved because it benefits all of us – we get to deliver the most appropriate solution and customers get time- and cost-saving benefits.”
While IKO prizes quality over pricing, one thing for customers to keep in mind when buying precision linear ways is how many parts are included. This is particularly important when specifying the CRW range. While, for historical reasons, many competitors sell these parts in what is essentially only half of a full set required for any motion profile –two ways with one cage and rolling elements – IKO always sells CRWs as a complete kit: four ways with two cages and rolling elements. For that reason, a price that is perhaps 75% higher for an IKO full set (for example) when compared to a competitor’s set might prove to be a more cost-effective option, as two sets of the competitor’s product would be needed to make up the same quantity as IKO’s offering.
www.ikont.eu • Email: enquiries@iko.co.uk
Tel” 01908 566144
By offering the right bearings in an installation-friendly manner, IKO aims to meet its customers’ needs –and often exceeds them.
Contact IKO UK today at 01908 566144, or email enquiries@iko. co.uk to discuss your motion control needs. Alternatively, visit the IKO website
The VeloBlade Flow Runner is an automatic feeding system that is retro ttable onto all VeloBlade Nexus models. This time saving automated production process has a stacking capability of up to 100kg. The Flow Runner removes the need for sta to load the system manually saving you both time and money.
Your KHS line optimization service gets more performance out of your existing production lines.
The longer a machine is in operation, the more its level of efficiency drops. There are many reasons for this which are not always immediately recognizable. Our line optimization service thoroughly screens your lines, pinpointing all weak points and optimizing your machine efficiency by up to 30%. Interested? khs.com/line-optimization