FOOD & DRINK PROCESSING & PACKAGING
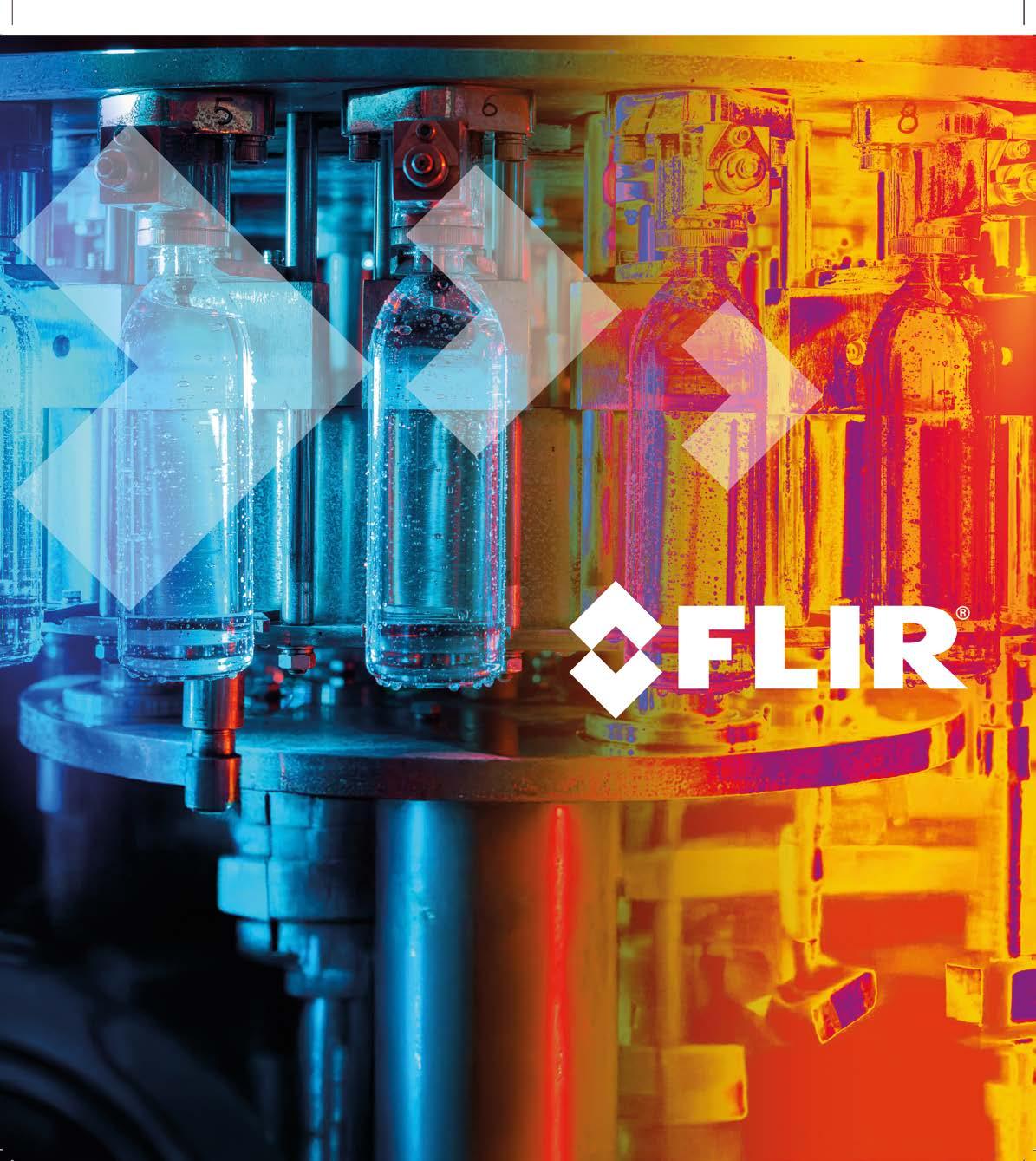
FLIR: Your strategic ingredient in strategic food and beverage production Mettler-Toledo introduces next-level flexibility with new combination inspection systems
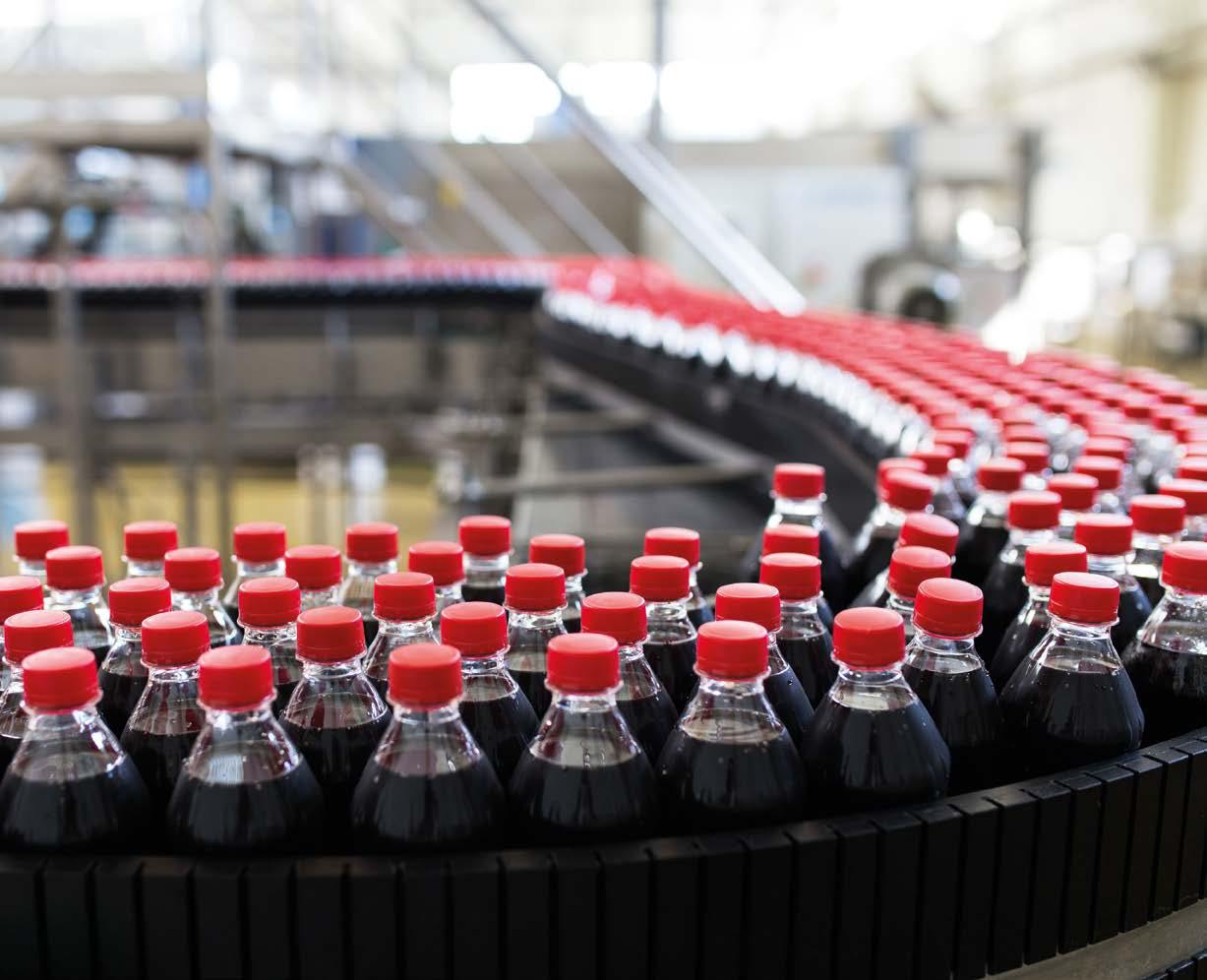
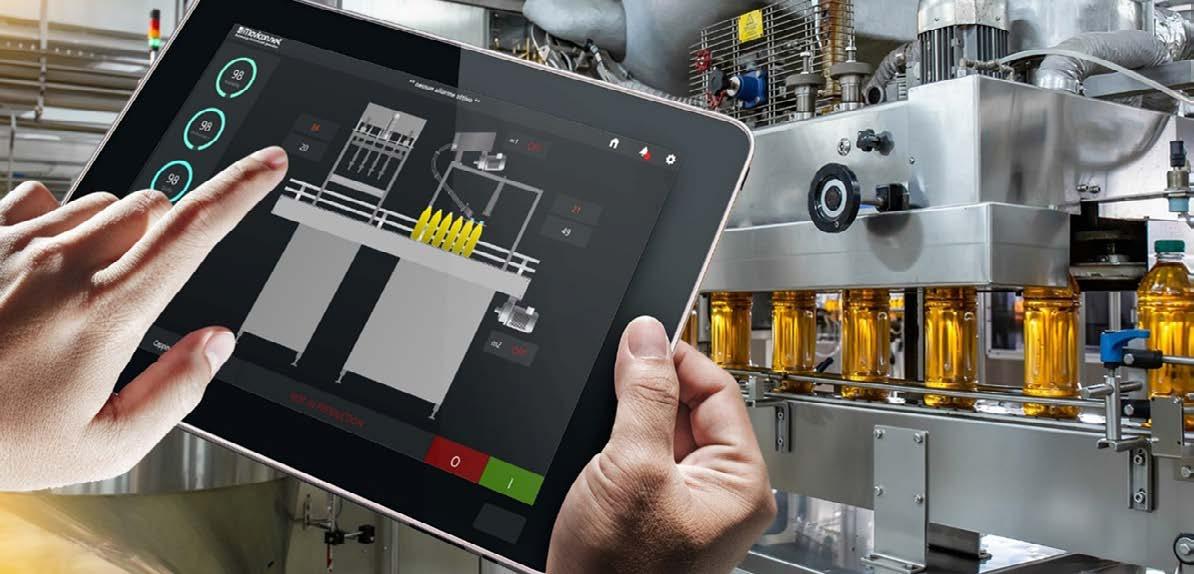
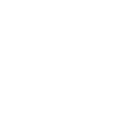
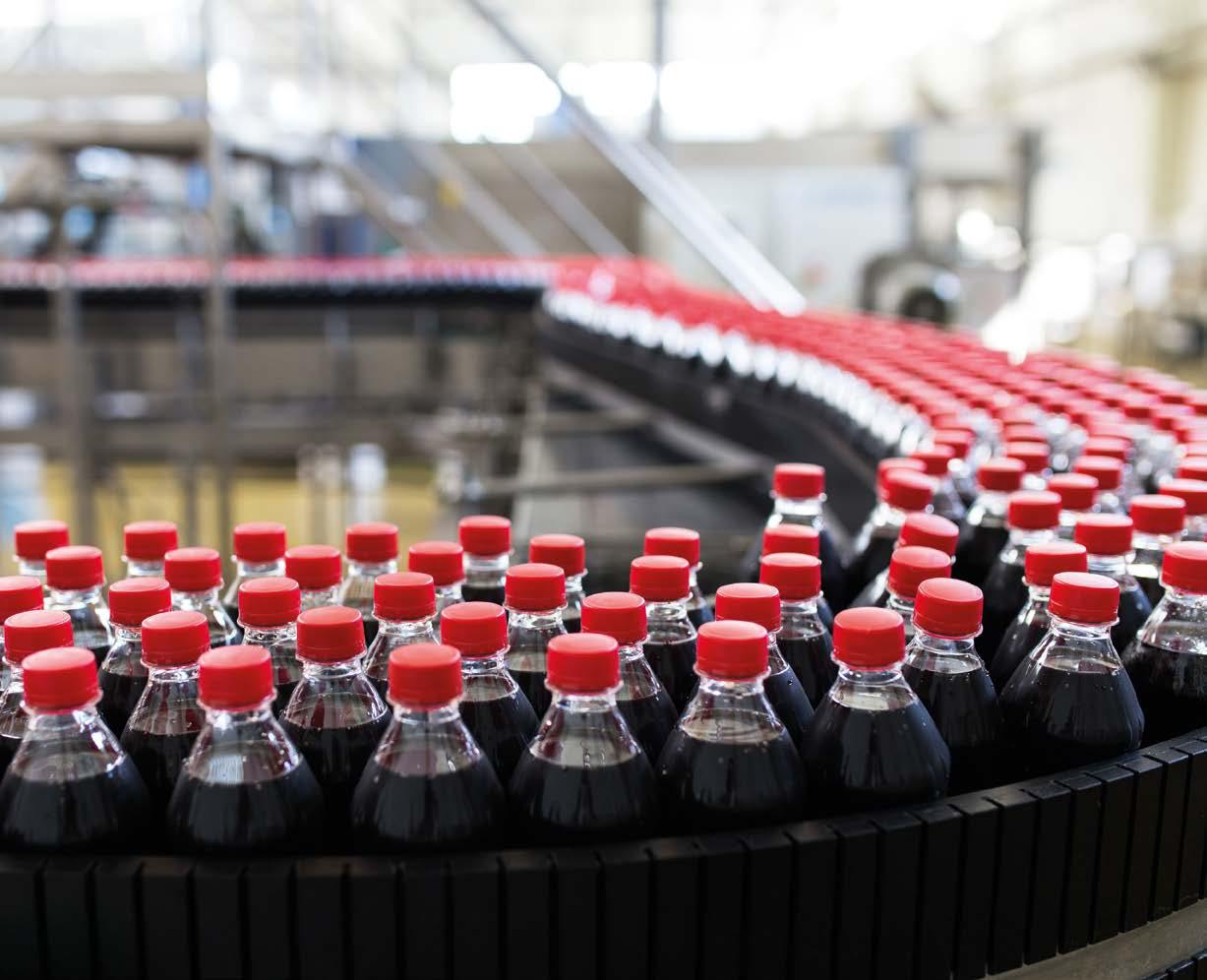
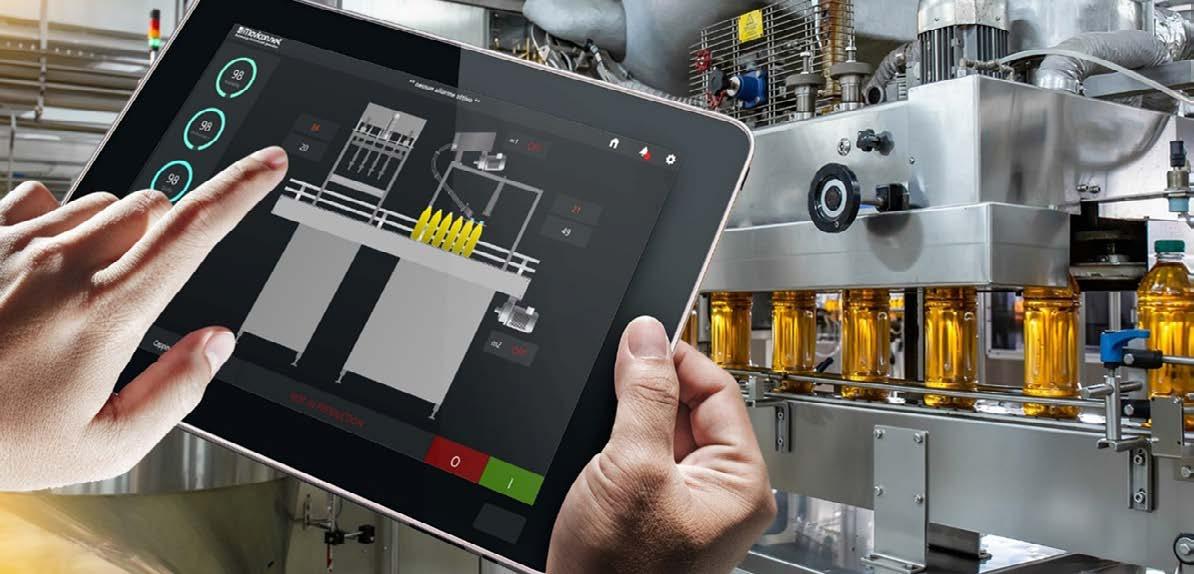
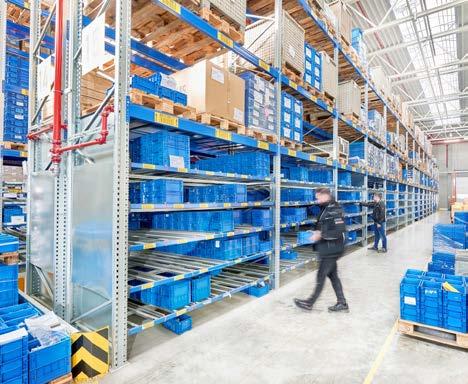
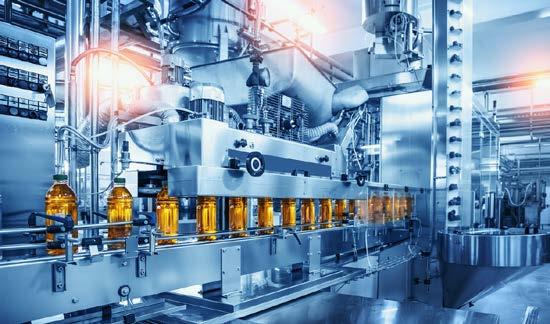
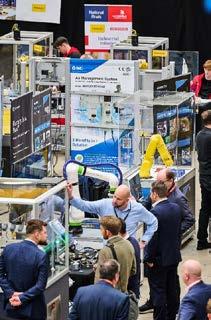
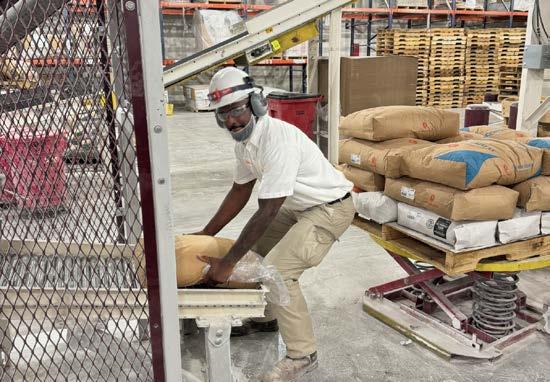
FLIR: Your strategic ingredient in strategic food and beverage production Mettler-Toledo introduces next-level flexibility with new combination inspection systems
Viscosity is defined as the “interaction between the different molecules in a fluid – this can be also understood as friction between the molecules in the fluid” and can be measured with various types of viscometers and rheometers using the measurement of centipoise (cP). When creating produce for consumption, manufacturers need to understand the effect created by food and beverage viscosity, which can be affected by the conditions within which it’s used, and are an important consideration when determining manufacturing methods.
Examples of different food and beverage items and their approximate viscosities are noted in the table to the right:
Depending on the viscosity of the product, the pressure and flow rate needed to propel the produce out of its primary container and into its intended location will differ. For example, a thicker, more viscous product will require an increased force versus that of a runnier, more water-like product. The latter is generally easier to transfer because it can be helped by gravity and has less resistance. For many products, however, consumer perception is that the ‘thicker’ a product is, the more superior it is, as it is perceived to have been made with higher quality ingredients. This leads to many products being more viscous than they may actually need to be due to consumer perception driving sales, especially for example, beauty products like creams, hair conditioner or shower gel; and even household products like bleach, washing up liquid or laundry detergent. Working with high viscosities is usually far more challenging for flow-control engineers who need to move fluids through manufacturing lines, ensuring that the liquid is transferred at the correct speed,
Product
-
(49°C)
Cocoa butter (60°C)
Condensed milk (75% solids)
Corn syrup
- 3,000 Fabric conditioner
garnish
Orange Juice Concentrate - 30 Brix
Orange Juice Concentrate - 60 Brix
Peanut butter
Printers Ink
Resin solution (from 18°C to 24°C)
Salad cream
Tomato ketchup
Toothpaste
Varnish paint
Yoghurt
without damage and without waste. But it’s not just the baseline viscosity of the produce that needs to be taken into consideration,
- 3,000
- 250,000
- 2,200
- 7,140
- 2,600
- 70,000
- 100,000
there are a few scenarios that can impact the viscosity and therefore change the properties of the product:
At Quantex, we understand the importance of viscosity, especially during manufacturing or within a retail or food service environment.
Temperature – a colder temperature significantly increases the viscosity of a product making it more solid and less smooth/runny
Head-height – should a product need to be propelled upwards, it’s working against gravity and will need a higher level of force to move it versus if it was to be released downwards or from above
Molecular levels – gases and liquids hold different levels of viscosity and generally speaking, fluids with larger, more complex molecules or long-chain polymers (e.g proteins, starches, hydrocolloids or gums, etc) will also have higher viscosities
Consistency – fluids with larger, more complex and inconsistentsized ingredients will have higher viscosities e.g soup with ‘chunky’ components versus water
Pressure – the lower the pressure applied to expel a food or beverage item, the slower it will run and the harder it is to drive and maintain the continuous momentum of the product
Freshness/age – if not sealed aseptically, produce can deteriorate
and break down either making the produce ‘runnier’, or it could solidify/ crystallise to cause blockages.
Rheology – some fluids shear thicken or shear thin as their flow velocity increases. Ketchup is a good example of shear thinning where it takes a lot of energy to start the fluid moving and then it becomes thinner. This is why you need to shake the bottle vigorously and then it suddenly pours out. Cornflower slurry is an example of shear thickening – the faster you stir it the stiffer it gets.
The optimal achievement of any pump is a near-vacuum (1 Bar negative pressure) so for a pump to self-prime the fluid must have a sufficiently low viscosity so that it can supply the inlet of the pump. The output of a pump is not constrained and may be several Bar. For extremely viscous liquids the fluid needs to be supplied to the pump using an independent pressure source.Overall, the key to moving viscous fluids is to choose the right pump. There are not many pump designs that can handle highly viscous fluids with precision. Quantex pumps use a positive displacement rotary action, so fixed volumes of fluid (boluses) are carried from inlet to outlet around a rotor – which produces inherently accurate doses and is much less sensitive to variables such as line pressure, fluid viscosity and flow rate. The positive displacement rotary action generates a high inlet vacuum and high pressure on the outlet.
This means that, unlike other pumps, Quantex is able to transfer highly viscous liquids such as ketchup and mayonnaise, sour cream, jam, face cream, hair conditioner and even relish etc whilst being self-priming and with better bag evacuation and less waste. Quantex can even manage very thick fluids such as peanut butter with particulates, but it is necessary to encourage the fluid to the inlet side of the pump as the fluid is too thick to self-prime. The below videos show different solutions at various viscosity levels being expelled with the aid of a Quantex pump:
QX25-SD pump dispensing milk and hot coffee from concertina bottles
QX100-SD dispensing relish condiments
The QX 120-Dl dispensing detergent and various dilutions
Bag-In-Box dispensing ketchup and mayonnaise
Bag-In-Box pump dispensing yoghurt dairy products
Bag-In-Box pump dispensing wine and alcoholic beverages
At Quantex, we understand the importance of viscosity, especially during manufacturing or within a retail or food service environment. And to serve these markets, we’ve developed a range of pumps to suit different flow rate ranges, viscosity levels and dispense applications and the technology holds over 100 global granted patents. Our HighSpeed Eco Pumps use air pressure to activate the diaphragm and seal the pumps instead of a silicone spring, so they are more easily recycled, and can run almost three times as fast as our standard or highpressure pumps.Microdosing Pump
• Low Flow Pump Range
• Bag-In-Box Pump Range
• High Flow Pump Range
If you’d like to learn more or discuss how a Quantex pump could work for you, please email Quantex. GeneralSupport@psgdover.com or call +49 (2065) 89205-0.
www.quantex-arc.com
Operating a business is always a challenge, especially so now, with inflation, disruption in supplies and increased energy prices. Therefore, asset reliability and maintenance efficiency are as important as they’ve ever been.
You want to reduce maintenance costs, cope with disrupted supplies of lubricants and spares, and maintain operations without doing long-term harm to your assets.
How? Through ConditionBased Maintenance (CBM) and Reliability-Centred Maintenance (RCM) strategies.
Oil Analysis can supply the data you need to:
• Prioritise maintenance for the critical plant that needs it most.
• Rectify issues relating to lubricant condition, contamination and quality (poor lubrication is one of the primary causes of machine wear).
• Extend service intervals for plant that does not need servicing.
• Identify root causes of contamination and wear and take steps to eliminate them.
• Greatly extend the useful life of your machinery.
• Maximise reliability and availability of your critical assets.
• Rationalise oil stocks and reduce spares inventory.
Talk to us about how Oil Analysis can help you reduce cost, improve reliability and take control of your resources and machinery. Whether it is lubricating and hydraulic oil, or electrical insulating oil, coolant, or fuel or even grease, you can rely on us.
We will provide prompt and clear oil analysis reports with comments and recommendations, with further advice only a phone call or an email away.
We will provide prompt and clear oil analysis reports with comments and recommendations, with further advice only a phone call or an email away. Our online results portal is easy to use and gives access to all of your data in one place, with great tools for monitoring trends and leaving feedback. We use intuitive images to relay cleanliness levels, so you will never be left confused by raw data from particle counts and ISO Codes.
Oil Analysis does not require any up front capital investment and is easily scalable with your needs.
Don’t delay, get in touch to see how you can improve reliability and save money with our Oil Analysis Services.
in your oil?!
Get in touch within a month of publication to take advantage of our offer! Quote “FDPP” to request a free oil sample or get 30% off your first order!
Swansea Tribology Services Ltd. www.oas-online.co.uk/FDPP oiltest@trib.co.uk +441792 799036
Industrial Processing includes a vast range of potential applications for perforated products. RMIG Solutions has extensive experience in the chemical, pharmaceutical, paper, and offshore industries, to name a few. From small, high precision perforation in thin materials to large holes in thick sheets used in the mining industry, RMIG Solutions has the knowledge, versatility, and tooling to deliver products according to customers’ requirements.
Industrial Processing includes a vast range of potential applications for perforated products. RMIG Solutions has extensive experience in the chemical, pharmaceutical, paper, and offshore industries, to name a few. From small, high precision perforation in thin materials to large holes in thick sheets used in the mining industry, RMIG Solutions has the knowledge, versatility, and tooling to deliver products according to customers’ requirements.
One particular area of Industrial Processing is dealing with waste water. The water industry presents a number of unique challenges in the use of perforated products. A key consideration here is the aggressive nature of the water towards the materials being used. RMIG Solutions has vast experience in servicing the waste water industry, and produces high flow, burr-free perforated waste water screens, offering accurate screen tolerances and effective separation.
One particular area of Industrial Processing is dealing with waste water. The water industry presents a number of unique challenges in the use of perforated products. A key consideration here is the aggressive nature of the water towards the materials being used. RMIG Solutions has vast experience in servicing the waste water industry, and produces high flow, burr-free perforated waste water screens, offering accurate screen tolerances and effective separation.
Another area of Industrial Processing is medical and pharmaceutical, where RMIG Solutions’ perforated materials are able to give firm tolerances during their manufacture, and are well suited for use in sterile environments.
Another area of Industrial Processing is medical and pharmaceutical, where RMIG Solutions’ perforated materials are able to give firm tolerances during their manufacture, and are well suited for use in sterile environments.
RMIG Solutions’ perforated products also have numerous uses in the petrochemical sector, from industry specific applications such as filtration, to oil and gas exploration, as well as more general applications such as walkways in processing plants.
RMIG Solutions’ perforated products also have numerous uses in the petrochemical sector, from industry specific applications such as filtration, to oil and gas exploration, as well as more general applications such as walkways in processing plants.
The Bridge Slot sheet from RMIG Solutions play an essential role when it comes to the design and manufacture of biomass drying floors. The combination of sheet thickness and opening size allows RMIG Solutions’ sheets to be used either as a suspended floor in wood chip drying containers and trailers, or as drive-on drying floors in outdoor buildings.
The Bridge Slot sheet from RMIG Solutions play an essential role when it comes to the design and manufacture of biomass drying floors. The combination of sheet thickness and opening size allows RMIG Solutions’ sheets to be used either as a suspended floor in wood chip drying containers and trailers, or as drive-on drying floors in outdoor buildings.
The bridge slot opening size determines the products that can be dried, which range from fine oilseed rape through to larger grains and cereals, as well as logs and wood chip drying.
The bridge slot opening size determines the products that can be dried, which range from fine oilseed rape through to larger grains and cereals, as well as logs and wood chip drying.
RMIG Solutions’ food processing market sector meets the high levels of hygiene demanded by the food processing industry. Perforated screens are also strong with important thermal capabilities, making them useful for a wide range of food processing applications. RMIG Solutions’ tailor made perforated solutions are ideal for cleaning, heating and steaming in food production environments. Whether it’s baking trays, cereal cleaning or ingredient conveyors, all of RMIG Solutions’ perforated materials can be customised for each application.
RMIG Solutions’ food processing market sector meets the high levels of hygiene demanded by the food processing industry. Perforated screens are also strong with important thermal capabilities, making them useful for a wide range of food processing applications. RMIG Solutions’ tailor made perforated solutions are ideal for cleaning, heating and steaming in food production environments. Whether it’s baking trays, cereal cleaning or ingredient conveyors, all of RMIG Solutions’ perforated materials can be customised for each application.
Belvoir Farm, known for its premium soft drinks, recently took a major step in-house by investing £2 million into a canning line at its Leicestershire facility. Key to this expansion was T. Freemantle’s Automatic Beverage Multipack Machine, which offers unmatched flexibility to carton various can sizes and multipack configurations. This adaptability has allowed Belvoir to produce innovative canned drinks at high speed, including RTD (Ready-To-Drink) mocktails, light sodas, and botanicals, making it easier to capture consumer interest and elevate its brand presence.
The popularity of canned drinks has surged recently, driven by sustainable packaging trends and a shift towards outdoor gatherings. Previously reliant on a co-packer, Belvoir sought to manage production in-house to meet growing demand, particularly in the non-alcoholic RTD sector.
The popularity of canned drinks has surged recently, driven by sustainable packaging trends and a shift towards outdoor gatherings.
The new cartoning machine, with its ability to handle various pack sizes and configurations, helped Belvoir launch a range of multipacks—such as four-packs and six-packs—to suit diverse consumer preferences.
The implementation of T. Freemantle’s machine delivered impressive results, consistently meeting the required speed of 55 cartons per minute and easily accommodating potential production increases. This machine’s design uses pre-glued cartons, facilitating faster packaging with minimal downtime for cleaning and format changes, which can be completed in under 15 minutes. In its first six months of operation, Belvoir produced 1.5 million cans, a significant increase over previous co-packing output.
Looking ahead, Belvoir aims to produce up to 10 million cans in 2025, including exports to markets such as the US and Australia. The flexible cartoning solution is key to Belvoir’s growth strategy, allowing the company to adapt quickly to changing market demands.
www.tfreemantle.com
The Schmersal Group has designed a new safety light barrier especially for hygiene-sensitive uses in the food processing industry, such as milk and meat processing.
This version has evolved with the demands of standard cleaning operations in the industry as the sophisticated design helps to ensure IP69 degree of protection (protection against the ingress of water from high-pressure of steam cleaning).
The protective enclosure with external gaskets satisfies stringent standards and is designed to cope with frequent cleaning with water, foam, lyes, high-pressure or hot steam.
SCHMERSAL | Enigma Business Park Malvern, Worcestershire, WR14 1GL
www.schmersal.co.uk
uksupport@schmersal.com
By Antoine Billardello, Food & Beverage Industry Specialist, FLIR
In the food industry, it’s essential to carefully control the temperature of perishable goods throughout production, transportation, storage, and sales. Safe, consistent, reliable production at speed and scale is critical. Failure of production assets and processes don’t just hit operations but can impact public safety, brand reputation and credibility.
Frequent warnings about illnesses caused by contaminated or improperly prepared foods emphasize the urgent need for stronger process controls.
Given that human error is often a contributing factor, food processors must implement strategic, real-time response tools that automate critical operations. This approach minimizes human factors, reduces risk while managing costs effectively.
Thermal imaging cameras are such a tool. Using FLIR thermal imaging cameras, you can make automated non-contact temperature measurements in many food processing applications. Analog video outputs can be viewed on video monitors, and digital temperature data, including MPEG4 video outputs, can be routed to a computer via Ethernet.
The main elements doing non-contact temperature measurements in the food processing industry are a thermal imaging camera and associated software. They act as “smart” non-contact sensors to perform 100% inspections, measuring the temperature of equipment, refrigerated products, and cooked foods as they exit the cooking process. These are not only give you real-time visibility of your production processes and assets but they’re also offering proactive insights.
Thermal imaging cameras are easy to use, small, and can be positioned
almost anywhere as needed. They can also be used to inspect package sealing, and improve efficiency in other food processing operations.
FLIR thermal imaging cameras have firmware and communication interfaces that enable their use in automated process control. Third-party software makes it easy to incorporate these tools into automated machine vision systems without the need for extensive custom-written control code.
The use of thermal imaging cameras in food processing is growing for applications such as:
• Oven baked goods
• Microwave cooked meats
• Microwave drying of parboiled rice and other grains
• Inspecting ovens for proper temperature
• Proper filling of frozen meal package compartments
• Checking integrity of cellophane seals over microwave meals
• Inspecting box flap glue of overwrap cartons
• Monitoring refrigerator and freezer compartments
Thermal imaging is first and foremost a quality assurance (QA) tool. Controlling the quality and safety of cooked meat products is an excellent use of this technology.
FLIR thermal imaging cameras have firmware and communication interfaces that enable their use in automated process control.
A permanently mounted thermal imaging camera can record the temperature of, for example, chicken tenders as they exit a continuous conveyor oven.
The objective is to make sure they are done enough but not overcooked and dried out. Reduced moisture content also represents yield loss on a weight basis. Thermal imaging cameras can also be used for inspection on microwave precooking lines. Besides improving product quality and safety, overall throughput can be increased. An additional benefit is reduced energy costs.
In addition to product inspections, thermal imaging cameras can monitor equipment and production assets. The drive to producer higher quality goods faster and at lower prices is increasing pressure on asset and process efficiency and in turn the assets themselves. When there’s a risk that equipment failure could be rapid failure the need for consistent and reliable monitoring is critical.
Within the cooked food sector for example, thermal imaging cameras can be part of a feedback loop to help control oven temperature.
Another use of thermal imaging cameras for conveyor ovens is monitoring temperature uniformity across the width of the conveyor oven cooking belt. If a heating element inside an electric oven fails, or you get uneven heating across an air impingement oven, one side of the product stream may be cooler. This can be quickly discovered with thermal imaging cameras.
Quality inspections of this sort are much more difficult with conventional contact type temperature sensors. Thus, thermal imaging cameras can help correct variability and improve quality before a lot of product is scrapped.
Software is available that allows thermal imaging cameras to locate objects and patterns in the images. One application for pattern matching is in the production of frozen meals. Thermal machine vision can use pattern recognition software to check for proper filling of food tray compartments.
A related application is automated 100% inspection of the heat-sealed cellophane cover over finished microwave meals. A thermal imaging camera can see heat radiating from the lip of the container where the cellophane heat-seal is formed. The temperature along the entire perimeter of the package can be checked by using the thermal image with machine vision software. This type of program matches the geometric pattern in the image and its temperatures against the temperatures in a pattern stored in a computer memory. An added function in such a system could be laser marking of a poorly sealed package so it can be removed at the inspection station.
An issue affecting product safety indirectly is the integrity of cartons that overwrap and protect food containers. One of the most costeffective ways of sealing overwrap cartons is to use heated glue spots on the carton flaps. In the past,
the integrity of the spot gluing was determined by periodically doing destructive testing on several samples. This was time-consuming and costly.
Because the glue is heated, a thermal imaging camera can “see” through the cardboard to check the pattern and size of the applied glue spots. The camera can be set up to look at predefined areas of the flaps where glue should be applied, and verify spot sizes and their temperatures.
The digital data collected is used for a pass/fail decision on each box, so bad boxes can be immediately removed from the production line. The data is automatically logged into the QA system for trend analysis, so a warning can be generated if an excessive number of boxes begin to fail.
Yet another application for thermal imaging cameras is monitoring container filling operations. Although this is seldom a product safety issue, it does affect yield and compliance with regulations. Different areas on the bottle can be defined and used to trigger an alarm and remove bottles that are overor under-filled. Thermal imaging cameras are a better alternative to visible light cameras when a bottle or jar is made of dark colored glass or plastic.
Application software currently available for thermal imaging cameras includes a wide variety of functions that support automated food processing applications. This software complements and works in conjunction with firmware built into thermal imaging cameras. The imaging tools and libraries in these packages are hardware- and language-independent, making it easy for food processing engineers to quickly implement thermal monitoring and control systems.
Thermal imaging cameras themselves provide the user with different operating modes that support correct temperature measurements under various conditions. Two functions commonly found in these cameras are a spotmeter and area measurements.
Thermal imaging cameras themselves provide the user with different operating modes that support correct temperature measurements under various conditions.
The spotmeter finds the temperature at a particular point. The area function isolates a selected area of an object or scene and usually provides the maximum, minimum, and average temperatures inside that area. The temperature measurement range typically is selectable by the user. As an adjunct to the temperature range selection, most cameras allow a user to set up a color scale or gray scale to optimize the camera image.
In conveyor oven applications, the area function is typically used because pieces of cooked product are often randomly located on the conveyor. The camera can be programmed to find and measure the minimum and maximum temperatures within the defined area. If one of those setpoint temperatures were to fall outside the user-defined limits, an application program running on a PC or PLC would instantly trigger an alarm, alerting the operator to check the thermal image on a video monitor or PC to find and remove the bad product, and/or adjust the cooking temperature.
In the case of local monitoring, an IR camera’s digital I/O can be used to directly trigger an alarm
device without additional software. However, food processing often benefits from higher level analytics that are available in third-party software that runs on a PC.
These out-of-the-box solutions do not require the writing of application source code. By adhering to commonly used machine vision interface standards such as GigE Vision® and GenICam® a wide range of functionality is supported by this software.
A simplified block diagram of conveyor monitoring is shown. One thermal imaging camera is adequate for many applications, or a thermal imaging camera may be combined with a visible light camera to record other target object attributes, such as color.
Incorporating thermal imaging monitoring in food and drink production offers significant strategic advantages. This technology enables consistent quality and compliance with safety standards while reducing the risk of contamination. By leveraging real-time data and details to make proactive adjustments, minimize product waste, and enhance operational efficiency it is driving streamlined, reliable production processes that can build consumer trust, optimize resource use, and contribute to a stronger competitive edge.
To discover how you can unlock the advantage of thermal imaging contact Antoine to learn more. Antoine.Billardello@Teledyne.com www.FLIR.com
November 26 – 28, 2024
For more than 75 years Silverson Machines has specialised in the manufacture of quality high-shear mixers for the food and beverage industries.
Silverson offer a wide range of high-shear mixers available that are ideal for food applications, ranging from the most popular L5M-A multi-purpose Laboratory mixer up to in-tank mixers that can process batches of up to 30,000 litres. And as of 2024, Silverson Machines can now offer customers even more mixing options with the launch of a new range of small-scale mixers. This new range includes an “Ultra Hygienic” small-scale mixer, a small-scale unit suitable for higher viscosity mixes, a small-scale Multi-stage In-Line mixer and a small-scale powder/ liquid mixer. These new additions complement the different types of laboratory and production models already available from Silverson, but importantly offer customers more options in terms of batch sizes and processing requirements.
With the exceptionally rapid mixing action of a Silverson high shear mixer, all mixers in the product range can benefit manufacturers of food and beverage applications. The high shear rotor/stator workhead at the heart of every Silverson mixer substantially reduces processing times when compared to conventional agitators and stirrers. For food and beverage applications Silverson mixers are ideal for:
• Hydrating and deagglomerating gums and thickeners
Agglomerates are instantaneously broken down as they pass through the rotor/stator workhead, resulting in an agglomerate-free mix with maximum yield.
• Reclaiming waste or out-of-spec product
• Dissolving
For example, Silverson mixers can produce a 66 Brix sugar solution at ambient temperature
• Homogenising
In many cases, a Silverson mixer can replace a high-pressure homogeniser in a processing line. They can also be used to create a uniform premix that will pass through a high-pressure homogeniser at a much faster rate and often in a single pass.
• Reducing particle size
• High Viscosity mixing
The innovative pumping rotor design of Silverson’s HV range mixers allows them to process higher viscosity products, these are
In our latest case study, we’re delving into the world of vegan leather – innovative alternatives to animal and plastic leathers which are more sustainable and have less impact on the environment.
This client of ours designs and produces transformative, sustainable biomaterials like vegan leather from natural resources like collagen, herbal extracts, minerals and oils.
They approached us with a need for a mobile high viscosity transfer pump to help test and ramp up their production of these sustainable biomaterials.
A massive growth market
According to a 10-year market forecast by Cambridge-based tech analysts IDTechEx, the vegan bio-based leather industry will grow by around 37.4% from 2024 to 2034.
To put this in perspective, new technologies developed to create sustainable alternatives to animal and plastic leather have already attracted investment worth over $1 billion. In fact, IDTechEx has discovered over 70 companies worldwide who are bringing viable vegan leather products to market.
Most of these businesses have sprung up in the last 3 to 5 years, and range from small startups like our client, to businesses that have secured hundreds of millions of pounds in funding. They are using this to scale up their production of vegan shoes, boots, clothing, fashion accessories and many other innovative new products.
What did our client need?
Our start-up client got in touch asking for advice on the best way for them to begin process testing, production and small-scale manufacturing.
The beginning of any testing and prototyping process is full of risks and challenges. Carefully considered plans which look workable on computer screens can often have wildly different outcomes in the real world.
To assist with testing, they were looking for a high viscosity transfer pump which would
would be difficult to predict but could change rapidly during the initial phases.
They needed a mobile high viscosity pump which would be domestic mains-powered and could handle high viscosity material at elevated temperatures. It should also easily manage solids, be simple to clean between batches and be able to run without fluid.
Initially, the pump might run for just an hour a day. But over time this would increase to several
be feeding a mixing vessel a few metres off the ground and drawing from a small 200L drum. The pump needed to transfer as much as possible from this drum without drawing in air or creating shear forces in the mixture.
we’re experts at providing engineered pumps for a vast range of applications. We use this specialist knowledge to deliver a tailor-made solution for each client, not a standard product picked off the shelf.
At North Ridge Pumps, we’re not limited to choosing just one pump design.
For this project, we specified an FMP40 roller peristaltic pump close-coupled on a trolley with a 1.5Kw inverter suitable for use with a 230V single phase supply.
This set-up would be able to transfer the bio-based materials at a rate of 774 to 2735 litres per hour or 12.9 to 45 litres a minute. We made the pump connections from stainless steel so the unit was easy to clean. In addition, the reinforced textile inlay hose within the pump was made from natural rubber.
FMP hose pumps are our biggest peristaltic pumps fitted with roller technology. These rugged units are fitted with reinforced hoses and rotors, heavily engineered integrated bearings, enlarged PU rollers plus our patented clamping system.
Thanks to its robust design and broad capacity range, peristaltic hose roller pumps like this are generally chosen for heavy duty industrial applications where the pump is a vital component in the whole process. Proven reliability is therefore paramount.
In addition, these pumps are easy and economical to maintain. This is because the hose is the only component that can wear, and the only component that is in contact with the fluid.
If you need to transfer sensitive fluids, solids or viscous materials, and aren’t sure which pump is the most suitable, speak to North Ridge Pumps to see how we can help.
www.northridgepumps.com/ contact-us
Tom Parker Ltd, an authorised distributor of CEJN products for over 50 years, is thrilled to introduce the new 208 Detect range of FDA-approved blow guns. This groundbreaking product range, a global first in the food and beverage industry, is poised to transform food production safety. These metal and X-ray detectable compressed air blow guns will reduce the risk of accidental contamination, product rejection, and expensive recalls.
One of the most significant risks faced in the food and beverage industry is physical foreign body contamination, particularly from unwanted metal and plastic fragments. To address this issue and safeguard product integrity, CEJN has engineered an innovative patented solution. The 208 Detect compressed air blow gun is the first metal and X-ray-detectable plastic blow gun available globally. It is manufactured entirely of foodgrade plastic and materials, and all
components are detectable, helping to dramatically minimise the risk of product contamination and waste in production.
The 208 Detect blow gun is engineered to provide comprehensive protection. Even if it is damaged, metal detectors and X-ray inspection systems can detect fragments as small as 2x2 mm (dependent on the system and sensor calibration). This next-generation product range also complies with many international food regulations,
One of the most significant risks faced in the food and beverage industry is physical foreign body contamination, particularly from unwanted metal and plastic fragments.
including HACCP, IFS, BRC, and GFSI standards like FSSC 22000.
The CEJN 208 Detect blow gun features stainless steel AISI 303 (1.4305) valves that resist corrosion, high temperatures, and chemicals, including those commonly used in industrial cleaning and disinfection
www.tom-parker.co.uk
• Metal & X-ray detectable
• Food grade plastic
• Stainless steel valves with food grade grease
• Detectable & food approved seals
• High chemical resistance
• Compliant with Reg. (EC) No. 1935/2004 & FDA CFR 21.170-199
& X-ray
& food
The CEJN 208 Detect blow gun range is a groundbreaking innovation made of food-grade plastic. It is the first metal and X-ray-detectable plastic blow gun to be introduced to the global market, reducing the risk of accidental contamination, product rejections, and expensive recalls. Even if the 208 Detect blow gun is crushed or a piece breaks off, contaminating F&B production lines, pieces as small as 2x2 mm can be detected.
www.tom-parker.co.uk
www.tom-parker.co.uk
sales@tom-parker.co.uk
sales@tom-parker.co.uk
blow gun for food industry
01772 255109
01772 255109
A Stainless Steel fabricating company, who specialise in the design and manufacturer of equipment for the food processing equipment, contacted Castle Pumps looking for advice on a solution. A project they were commissioned to work on required a pump to be installed onto the equipment they were manufacturing for an ambient food manufacturer.
The pump was needed to transfer soup, which could contain both meat and vegetable pieces. It was highly important to the end client that the chunks are passed whole without damage. Due to the pump being used for handling food products, they of course need this to be a food grade pump and able to be cleaned in place to ensure the soup remains safe for human consumption at all times.
A Soup-er Smooth Flow
The requirement for a food grade pump was no problem for Castle Pumps; with the food and drink industry being one of their specialities, What was important to carefully consider was the gentle handling of the meat and
This fully stainless steel model is of complete sanitary design, free of dead zones, ideal for clean in place and fully compliant with FDA, EHEDG and 3A.
vegetable chunks within the soup. Not only did the selected model need to be able to pump these solids without clogging, but also be able to keep them fully intact so that they weren’t crushed and turned to slurry within the soup.
Given the above point and the duty requirements at hand, Castle Pumps specified a food grade progressive cavity pump. The progressive cavity pump design is known for handling viscous, solid laden fluids without clogging thanks to its large cavities and absence of valves and reciprocating parts. The smooth, gentle motion of its rotor also means the pump applies low shear to the fluid as it passes through, fulfilling the
With production of the soup relying on this pump, reliability for this customer’s application was paramount. These models of progressive cavity pumps have a patented pin joint designed for 8000 hours before maintenance is required and consumes 20% less power than other models thanks to its long pitch rotor.
This fully stainless steel model is of complete sanitary design, free of dead zones, ideal for clean in place and fully compliant with FDA, EHEDG and 3A. The pump was supplied mounted on a Stainless Steel base plate for ease of integration into the wider system.
Getting the wrong pump for your process can result in inconsistency in the finished product, crushed solids, clogging, excessive wear, loss of productivity, waste of costly product or at worst, contamination. Always trust technical experts to specify the right pump for your application.
www.castlepumps.com
pump will save you excessive wear, process failures, product waste & operator time.
Get the RIGHT pump with our 15 years’ experience in:
Get the RIGHT pump with our 15 years’ experience in:
✓ FDA & 3A hygienic solutions for food and drink
✓ Highly accurate dosing of ingredients & additives
✓ Delicate fluids sensitive to consistency changes
✓ Solid-laden products without crushing or clogging
Contact our technical sales engineers now!
A pump may do the job, but only the right pump will save you excessive wear, process failures, product waste & operator time. Contact our technical sales engineers now!
Although better known for the durability and performance of its counterbalanced machines, Cat® Lift Trucks has a long and impressive history of delivering pioneering warehouse handling solutions.
Exclusively distributed in the UK and Ireland by Impact Handling, part of Aprolis UK, Cat Lift Trucks can trace its warehouse equipment roots all the way back to 1958. Over the years the company has focused heavily on cutting-edge product development and innovative production capabilities – investing heavily in organic growth and acquisition – to ensure it continues to provide its warehouse customers with market leading equipment.
A recent flurry of new product developments sees Cat now offer one of the widest and smartest warehouse equipment ranges in the marketplace. Yet despite the
history, the pedigree and all the exciting customer benefits the brand seems to remain one of the industry’s best kept secrets. So perhaps it’s time to take a deeper dive…
The first surprise is the incredible scope of applications the Cat Lift Trucks offering can support, thanks to its wide range and almost endless customisation options. The core equipment range includes, VNA, reach trucks, low and high level order pickers, ride on powered pallet trucks, powered pallet trucks, stackers, 4-way multi directional trucks, turret trucks and tow tractors.
Richard Root, National Sales Manager at Impact Handling comments: “We support warehouse customers across a really diverse range of sectors, everything from transport and haulage and retail to
manufacturing and 3PL. We offer true end-to-end solutions, with dedicated machines for every step in the chain, right down to the back of store or kerbside delivery.”
Cat Lift Trucks has a particular strong VNA offering in the UK, where Impact operates a dedicated in-house team of high density storage experts. The team includes a UK-based VNA factory specialist from Cat, permanently on hand to support customers. Unsurprisingly, the Cat Lift Trucks VNA range has generated significant interest amongst UK customers, combining numerous advantageous benefits such as 19 metre maximum lift heights, wire or rail guide options, superior ergonomics and low running costs.
The range builds on Cat Lift Trucks’ long held belief in developing products based firmly around customer needs.
A quick fact check shows that a commitment to flexibility is something Impact Handling takes very seriously indeed, featuring as a recurring theme throughout all of its offerings.
Indeed, Cat operates one of the most comprehensive on-going customer consultation programmes in the material handling sector. These values are echoed in its UK partnership with Impact Handling, extending into the ongoing support and back-up its customers can rely on across their sites, on a daily basis. Mr Root elaborates:
“The warehousing and logistics industries have changed at a remarkable pace over recent year. This has been driven by a number of factors, such as the remarkable rise of e-commerce, the step-change in health & safety attitudes, a continued drive to optimise every last inch of space, environmental concerns and, of course, numerous technological advancements.
“At Impact, we recognise that these changes aren’t something that has happened, but rather they are factors that continue to happen. And that these changes in the logistics industry – and the subsequent requirement from the customers handling fleet –are a continual and fast-moving evolution. This means that aside
from an extensive range, marketleading innovation and premium product quality, the most important thing we can bring to our customers is flexibility. Which is exactly what we do.”
A quick fact check shows that a commitment to flexibility is something Impact Handling takes very seriously indeed, featuring as a recurring theme throughout all of its offerings.
Most notably, Impact extends unique levels of flexibility to its long-term rental contracts. Meaning that customers can change equipment to meet changing needs throughout the contract term, without penalty. Effectively futureproofing their fleet in the process.
The flexibility continues with the equipment itself, where, aside from the extensive range of new Cat equipment, Impact can also blend a combination of manufacturerapproved refurbished machines
and short-term rental equipment into its agreements. Allowing yet further flexibility which ensures the fleet remains optimised, at all times, to the operation’s needs and budget – Including adjusting for seasonal demand.
As you might expect from Impact, the short-term rental fleet includes a broad selection of machines, covering all key models, and is held, primed for rapid despatch, to assist customers anywhere in the country.
Maintenance and ongoing support from impact is equally comprehensive and flexible, delivered by a nationwide team of xxx dedicated service engineers, all equipped with state-of-the-art service vans carrying all common parts and specialist tools. The service engineers are further supported by 20 regional service centre teams.
All-important up-time has proved to be another strength of the Cat Lift Trucks – Impact partnership, helped by Impact holding a reassuringly extensive UK-based parts inventory for warehouse equipment as well as Cat operating an expedited delivery system from the factory for all specialist parts requirements.
So, with such an incredible amount to offer warehouse handling equipment users, and such a strong and proven track record, this is one secret where the ‘Cat’ really does need to be let out of the bag!
www.impact-handling.com
Offer consistent product quality at the point of use for a wide range of applications, guide rails position the IBC and the mixer is raise and lowered into the IBC with a push button operated electrical actuator.
Fixed or mobile mixing stations are supplied complete with a control panel and safety interlocks.
Standard IBC mixing stations can be adapted to integrate with systems on site including pumps, valves, weighing and measuring instrumentation and controls to meet specific site requirements.
With 25 years experience, Paramount Waste Extraction Ltd. specialises in designing, installing, and upgrading waste extraction systems tailored for a wide range of industrial, process and manufacturing sectors, including carton manufacturing, printing, packaging, foil and film production.
With a focus on efficiency and sustainability, Paramount Waste offers custom solutions to optimise waste handling, reduce production downtime, and enhance operational productivity with automated systems reducing labour involvement. Our services range from complete turnkey installations to system assessment, modifications and upgrades.
A complete range of proven designs including Chopper Fans, Separators and Filtration equipment combine with many years experience to create efficient and effective designs that work.
Paramount Waste collaborates closely with clients to ensure each project is completed within budget while delivering lasting improvements. Known for our expertise and commitment to quality, we provide dependable solutions to meet all types of modern industrial waste handling challenges.
As customers, investors, and regulatory bodies mount pressure on businesses to become more sustainable, and an increased focus on ESG responsibilities, technology can be a valuable partner in achieving these goals.
By taking an insights-driven approach to their waste streams, businesses can create additional revenue streams, reduce waste management costs, and boost their green credentials.
At the recent PPMA Show, Waste Mission, a leading UK-based waste management company, unveiled its custom-built Waste Management Portal. This innovative platform is designed specifically for contracted customers, enabling them to manage their waste more effectively and sustainably than ever before, staying up to date with waste streams, compliance and ESG targets.
“These features are groundbreaking for our clients,” says Nicola Guest, Group Marketing Manager. “People have been blown away by the simplicity of use and the ease of understanding the data. Everything you need is at your fingertips and simplifies what has historically been a complex process - making sustainability simple.”
Waste Mission’s Waste Management Portal offers a comprehensive dashboard overviewing key metrics, including disposal routes, carbon savings, and the latest invoices. Customer data is attractively summarised through pie charts that detail various waste types, tonnages, and CO2 savings. This feature enhances transparency and empowers manufacturers to make informed decisions that align with their sustainability goals.
People have been blown away by the simplicity of use and the ease of understanding the data.
Navigating the financial aspects of waste management can be daunting. Waste Mission’s new portal simplifies this process by allowing users to download all invoices as PDFs, alongside waste transfer notes and multimedia evidence, ensuring compliance and clarity. A dedicated section for compliance documents also guarantees that contracts are being managed within legal parameters, giving customers peace of mind.
Understanding the specifics of waste generation is crucial for manufacturers aiming to reduce their environmental impact. The bespoke reporting feature allows customers to create tailored
reports that cater to their unique needs. This functionality enables businesses to track and manage their waste streams effectively, driving them towards more sustainable practices.
The commitment to keeping customers informed extends beyond waste management. The portal features a dynamic education/news section that updates users on the latest legislation and industry news sourced from our website, wastemission.com. This resource equips manufacturers with the knowledge necessary to stay compliant and adapt to evolving regulations.
The portal’s transport calendar displays all scheduled collections, complete with vehicle registration numbers and driver names, fostering transparency and accountability. Additionally, multiple communication options ensure customers can easily reach out for inquiries or support.
Waste Mission believes that effective waste management is a cornerstone of sustainable manufacturing. The new Waste Management Portal streamlines the waste management process and empowers British manufacturers to take significant strides towards their sustainability objectives, building a future a few shades greener.
To see the portal in action click here
Book a waste review at wastemission.com
Emerson: Global technology, software and engineering leader
Emerson will exhibit its latest Floor to CloudTM packaging solutions at PACK EXPO Chicago, November 3-6,
2024. Advancing the boundless future of automation, Emerson factory automation solutions and its Floor to Cloud approach empower smarter packaging lines and more efficient processes that make it possible for manufacturers to continuously improve plant productivity, sustainability and safety.
Visitors to North Building Level, Booth 5345, can view highlights from the extensive portfolio, which includes AVENTICSTM, BransonTM, MoviconTM, PACEdge and PACSystemsTM solutions. Packaging automation experts will demonstrate how a Floor to Cloud approach unlocks trapped data and connects islands of automation, giving manufacturers the visibility and control to solve critical challenges and ambitious goals. Attendees will learn how to accelerate net zero progress, raise overall equipment effectiveness (OEE) asset by asset, and empower teams with data to drive continuous improvement across the factory floor.
Presentation and event highlights:
In addition to showcasing its innovative packaging automation solutions, Emerson will also sponsor two events, the annual Packaging & Processing Women’s Leadership Network (PPWLN) breakfast and the Amazing Packaging Race.
All women who are registered for
PACK EXPO Chicago are invited to the free PPWLN breakfast and program on Tuesday, November 4, at 7:30 a.m. in West Building, Room W-375. Following the breakfast, attendees will have the opportunity for a private show floor tour and participate in a Q&A with Lisa Propati, Vice President and General Manager of Weiler Labeling Systems, as well as other packaging executives.
As part of the Amazing Packaging Race, teams from U.S. colleges, trade schools and universities race to complete tasks and solve problems at booths across the PACK EXPO show floor.
Product highlights:
Emerson Energy Manager
The Energy Manager is a preengineered hardware and software solution designed to simplify
energy monitoring from quick set up to intuitive operation. Ready out of the box, the Energy Manager monitors asset energy use in real time, allowing manufacturers to gain deeper insight into energy consumption and operating costs. Through its easy-to-use dashboard, operators can access asset-specific consumption, associated costs and carbon dioxide (CO2) emissions for up to 10 end points (expandable to 50 with a license). This level of immediate visibility can empower facility teams to reduce packaging
utility costs, lower carbon dioxide emissions and maximize energy and operational efficiency. For more extensive media and utilities monitoring, the Energy Manager can be paired with the Emerson Compressed Air Manager. The combined solution provides a streamlined view of energy costs and compressed air usage across a packaging line, factory and site.
AVENTICS Series XV Pneumatic Valves
Next-generation AVENTICS Series XV Pneumatic Valves provide greater automation flexibility and optimized flow for packaging lines, including compact handling systems and complex automation solutions. Series XV valves feature multiple interoperable valve sizes, higher flow rates in a compact design and an extensive portfolio of accessories. With broad connectivity, Series XV valves support leading fieldbus protocols to simplify integration into machine control networks. They come in multiple pneumatic connection directions with metal threads, parallel wiring and aluminum base plates that make Series XV valves easier to integrate into equipment designs.
Simple to commission, engineers can use the AVENTICS online configurator to quickly design
valves to specification and speed up machine development.
For more information, visit: https:// www.emerson.com/en-us/catalog/ aventics-xv03.
The award-winning AVENTICS Series Advanced Valve (AV) system with Advanced Electronic System (AES) is the first pneumatic valve system with an integrated Open Platform Communications Unified Architecture (OPC UA). The AES helps interoperability challenges and accesses data more easily, while the digital twin integration improves productivity efficiency and reduces costs.
For more information, visit: https:// www.emerson.com/en-us/catalog/ automation-solutions/aventics-aes.
AVENTICS Series AF2 Flow Sensors have helped plants around the world successfully reduce compressed air consumption and improve energy efficiency. By monitoring air consumption in pneumatic systems, AF2 sensors enable rapid intervention if leaks occur, helping optimize energy
consumption, reach net-zero targets, prevent machine downtime and reduce costs. Emerson now offers a high flow model of this advanced sensor that propels compressed air monitoring beyond individual machines to benefit larger air lines and systems. This expanded capability allows users to easily optimize energy consumption across an entire packaging facility and improve overall plant sustainability.
For more information, visit: https:// www.emerson.com/en-us/catalog/ aventics-af2.
The multimedia monitoring solutions, including CoreTigo wireless communication, analyze water, compressed air, gases, electricity, steam (WAGES) and other utilities. The Edge Analytics Dashboard measures efficiency, optimizes productivity and avoids or reduces downtime. Emerson experts will demonstrate the multimedia monitoring cabinet solution and the insights it offers, which will support meeting sustainability goals.
For more information, visit: www.Emerson.com/SustainableAutomation.
Movicon.NExT™ HMI/SCADA is a highly modular, highly scalable platform that goes beyond SCADA to solve automation problems for both CPGs and original equipment manufacturers (OEMs), from
the single machine level to a complete plantwide IIoT project implementation. Among Movicon. NExT modules, Movicon Pro. Lean™ provides performance data and analytics for evaluations of OEE and Movicon Pro.Energy™ measures and tracks consumption, while the advanced Movicon NExT. AR solves operational problems through visualization tools that allow personnel to evaluate previously unreachable equipment. For maximum flexibility, Emerson also provides Movicon WebHMI, an HTML5-based visualization tool that can be used as a stand-alone HMI product running on Windows or Linux operator panels, or as a Web Client for Movicon.NExT SCADA applications, as well as Connext™, an industrial protocol gateway.
For more information, visit https:// www.emerson.com/movicon.
Industrial edge software and solutions help analyze and solve problems where they occur — at the machine edge. PACSystems Edge Solutions is the most advanced portfolio of edge computing and control systems and includes edge hardware and software that help significantly simplify problem-solving at the machine level and allow easy, cost-effective analytics and communication at the edge. Included in the panel is the PACSystems RSTi-EP CPE200 compact controller family, which delivers large PLC capability in a compact, rugged
design. It provides security-bydesign, open programming and open communications built in, significantly reducing cost and complexity.
For more information, visit: www.emerson.com/PACSystemsedge and www.emerson.com/ PACSystems-Compact.
AVENTICS Series SPRA electric rodstyle linear actuator is an efficient, high-performance actuator that offers improved load capacity, accuracy and reliability. In addition to outstanding precision and repeatability, the Series SPRA is also extremely versatile and flexible, with a choice of three different screw technologies that allow implementation in a wide variety of (demanding) applications. Compliance with the ISO-15552 standard, easy-to-use online sizing and selection tools and a wide range of mounting accessories ensure simple selection of the appropriate linear motion solution for the application.
For more information, visit:
https://www.emerson.com/en-us/ catalog/automation-solutions/ aventics-spra.
AVENTICS Advanced Valve Systems form a reliable basis for both compact handling systems and complex automation solutions. Especially in the area of machine safety, the AV family offers intelligent solutions that significantly reduce effort when creating a safe design. The valves of the AV family — AV03 and AV05 — have set standards with their diagonal spool in both sizes. They are characterized by an excellent volume flow ratio and a record-breaking energy balance. With the serial Advanced Electronic System (AES) interface, the AV valve system communicates effortlessly with modern controllers via all common fieldbus systems. The modular electronics form the basis for high networking, flawless data transmission and integration into Internet-of-Things concepts.
For more information, visit:
https://www.emerson.com/ en-us/automation/fluid-controlpneumatics/pneumatic-valves-valvesystems.
Emerson edge devices combine the best deterministic controllers on the market with secure, nondeterministic controllers for analytics and machine learning algorithms to proactively optimize business outcomes. These rugged devices are designed for remote industrial areas and equipped with our vendor-agnostic PACEdge software to safely run nondeterministic applications. This reduces latency and meets all application performance requirements.
For more information, visit: https://www.emerson.com/ en-us/automation/control-andsafety-systems/programmableautomation-control-systems/ industrial-edge-software-solutions.
In today’s highly automated machines, the AVENTICS valve system of the Series G3 electronic fieldbus platform replaces conventional, hardwired solutions. It integrates communication interfaces with pneumatic valve systems that have input/output (I/O) capabilities. This nextgeneration electronic platform provides easy access to connections. It is easy to assemble, install, commission and maintain. The functionality of the G3 enables programmable logic controllers to turn valves on and off more efficiently and transmit I/O data
from sensors, indicator lights, relays, individual valves or other I/O devices on a channel basis over various industrial networks. The G3 has an easy-to-read graphic display, which can be used for configuration, commissioning and diagnostics. It offers application, performance and serviceability improvements for Original Equipment Manufacturers (OEMs) and end users alike.
For more information, visit: https://www.emerson.com/en-us/ catalog/aventics-g3.
The Compressed Air Manager provides visualization and benchmarking for compressed air and gas consumption for a machine, production line or across multiple sites. A pre-designed Edge enabled cabinet solution powers the monitoring and serves as a foundation to connect and scale across multiple machines and lines via the AVENTICS Series AF2. The Compressed Air Monitoring App, which comes pre-installed on the Edge Device is easily configurable and continuously monitors and analyzes data coming from the sensors. The Compressed Air Manager transforms available data via an embedded dashboard with KPIs where operators can easily visualize consumption trends, costs, benchmarks and CO2 impact. This data empowers users with greater insights to help
reduce energy costs, improve sustainability and streamline maintenance.
For more information, visit:
https://www.emerson.com/en-us/ catalog/automation-solutions/ emerson-compressed-air-manager.
The Branson GSX-E1 ultrasonic welder, and the advanced automation systems it enables, helps manufacturers improve efficiency and reach sustainability goals. Controls automatically monitor critical weld parameters in real time, delivering actionable performance and diagnostic data to help determine OEE (overall equipment effectiveness), enable traceability and optimize maintenance.
The welder’s market-leading encryption technology ensures data integrity and security. Compared to joining techniques like heat sealing, adhesives or mechanical fasteners, ultrasonic welders like the Branson GSX-E1 use less electricity, require no consumable materials and yield less waste, cutting assembly-line carbon footprints.
For more information, visit: https://www.emerson.com/en-us/ catalog/branson-gsx-e1.
Optimize every stage of the manufacturing process with realtime control, monitoring and data analysis provided by nextgeneration wireless automation solutions from Emerson and CoreTigo.
These wireless automation solutions connect devices and unlock trapped data. The combination of expertise from Emerson and industrial wireless technology from CoreTigo results in a fully connected ecosystem that can reduce inefficiencies and help customers get to market faster.
Wireless automation systems feature IO-Link Wireless, a deterministic, highly reliable and scalable universal wireless communication protocol with low latency (5 milliseconds) and low synchronization rates (tens of microseconds).
For more information, visit: https://www.coretigo.com/ products/.
www.emerson.com
Cordless tools have revolutionised industry; the convenience of being able to carry out tasks unencumbered by the need to find power and plug in, or to leave trailing leads around as trip hazards has resulted in almost all personal tools now being cordless.
In the World of vacuum cleaners, however, cordless options have been restricted to smaller machines with limited power and performance. This is because for anything other than the lightest applications, efficient vacuum cleaning requires a minimum of 1-1.5kW of power; something that is not easily achievable for useable durations with small batteries.
The new BVC IV60 eGX breaks the mould and has revolutionised the ability to provide cordless industrial vacuum cleaning power wherever and whenever it is required. This has been achieved through the unique combination of the proven BVC YP3 multistage vacuum turbine and the new Honda eGX electric engine with swappable battery power.
The Honda eGX is an engine that provides power in the 2hp class, powered by an on-board 750Wh lithium battery. When fitted to the BVC IV60 eGX industrial vacuum cleaner this power unit delivers around 1.5kW of power with a ½ hour run time, and around 1 hour of run time on a very useful half power setting. With a fast charger, and swappable battery continuous operation is achievable.
Since it’s introduction, the BVC IV60 eGX is finding diverse applications in several different markets. Examples include warehouse spillage cleaning in areas not serviced with power outlets, high-bay cleaning with high-reach kits, use in areas for wet recovery and cleaning; in fact, many applications where the lack
Since it’s introduction, the BVC IV60 eGX is finding diverse applications in several different markets.
of available power outlets is the motivation to look for cordless alternatives.
Apart from the elimination of the need to find local power outlets for industrial vacuum cleaning, the other significant benefit the BVC IV60 eGX offers is the elimination of trailing leads. In an operational processing area, e.g. if there is a need to clean up spillages without interrupting the process or causing a hazard with trailing leads, BVC IV60 eGX can be simply pushed to the location and turned on for efficient cleaning.
Like all BVC Industrial Vacuum Cleaners, BVC IV60 eGX is available
in different versions and with a wide range of hoses and tools. The first two versions available are the dry tank and wet tank versions. The dry tank version can be optionally fitted with HEPA filtration and offered in M-Class and H-Class configurations. The wet tank version, can be fitted with a sludge separator bucket, and has a tipping tank and drain hose for easy emptying.
Both versions are provided with 51mm (2”) inlets allowing the use of the full range of BVC 51mm and 38mm hoses and tools available from Quirepace. The range of tools includes various crevice tools, bench and brush tools, and robust floor tools. BVC IV60 eGX is also suitable for use with carbonfibre high-reach cleaning tools for cleaning at high level whilst the operator stays at ground level, avoiding the need to “work at height”.
The BVC IV60 eGX is manufactured by Quirepace at the factory in Fareham, Hampshire, alongside the rest of the BVC Industrial Vacuum range of heavy-duty machines. UK manufacture means a UK source of spare parts and after sales services. In addition, BVC IV60 eGX has been validated by Honda as an officially approved product meaning that the warranty and any service requirements on the Honda eGX motor itself is available through any Honda service centre.
Quirepace have a specialist sales team covering the UK, so if you have a potential application, a member of the team can visit site with a demonstration unit for an on-site trial.
To find out more, contact Quirepace today.
Quirepace Ltd
www.quirepace.co.uk
BVCsales@quirepace.co.uk
Tel +44 (0) 23 9260 3700
Gellert freeze dryers are the perfect solution for manufacturers looking for a reliable and scalable option for regulated food production. With a notable shift towards the freeze-dried product market, manufacturers and consumers alike are recognizing the benefits of this process. By reducing, or removing, the need for cold chain handling, manufacturers can reduce transportation and storage costs, and as freeze-dried material is much lighter than frozen or refrigerated product, this further lowers costs. Additionally, freeze dried products not only take less energy and cost to store, but they also maintain the biological benefits and flavours of the raw product whilst extending shelf life.
Gellert freeze dryers offer a controlled and repeatable manner for in-situ freeze drying directly on the shelves, ensuring the product maintains its shape, structure, and nutritional value. Gellert has developed a range of freeze dryers with ease of scale-up, user requirements, and operation in mind, making them versatile and popular in the industry.
Some of the beneficial features of Gellert equipment include AutoDry, an intuitive feature that allows users to input their desired temperature differential between the product, sample, and shelves, ensuring the sample can be dried using the AutoDry feedback mechanism, optimizing drying cycles.
The chamber, condenser, shelves, and shelf stack can all be constructed from 316L stainless steel for product contact, and a hybrid cooling system is also available on larger equipment, to utilize defrost water by re-heating via the freeze dryer compressors, saving energy and costs.
The most common applications that Gellert’s freeze dryers are used for include: -
• dairy products • fruits and vegetables
• pet food and pet treats
All Gellert systems are manufactured in Europe and strictly adhere to compliance regulations such as F-gas.
Biopharma Group is the exclusive distributor of Gellert freeze dryers across the UK, Ireland, and France. Both Biopharma Group and Gellert well respected and renowned companies, combining years of lyo industry experience. This winning combination allows the Biopharma group team to help you select the best freeze dryer to meet your specific need and Gellert has accrued a high level of practical experience and in-house expertise, developing an array of different models and configurations to satisfy a broad range of food production purposes.
Contact Biopharma Group’s product specialists to discuss your requirements or request more information.
www.biopharma.co.uk
• Improved efficiency & reduced drying time
• Replicable batches
• Replicable batches
• Improved efficiency & reduced drying time
• Replicable batches
Fox Venturi Eductors, for blending powders into liquids – have been used in food and beverage manufacturing for over 35 years. They are an ideal way to continuously produce well blended solutions, brines and beverages. Applications of Fox slurry eductors range from adding few pounds per hour of whey added to a milk stream to blending favour additives into liquids flows of 500 GPM or more.
bags and their accompanying dust and spillage still often surround powder addition to tanks and vessels, which often require staff climbing ladders with bags on their shoulders.
orange juice producer in the USA. Calcium Citrate is metered into a 2” food-grade Fox slurry eductor at 65 GPM at 70 psig. This venturi has been in service for over fifteen years with zero maintenance.
Coco Powder, Whey, and Spice Additives into Milk: Here a dairy manufacturer needed continuously blend pulverized coconut meat, whey, and flavorings into milk on its way to an interim process.
From Batch to Continuous liquid/solid blending with Fox Slurry Eductors The addition of powdered products is often left as a manual operation in otherwise highly automated production environments. Scoops, buckets and
As plant production rates increase, processes often evolve from batch to continuous, for which Fox Venturi Slurry Eductors are ideal. Liquid flow is maintained at a constant flow rate by the precision machined nozzle within the venturi. A screw feeder can then dose powder – from a bulk bag, bin, or silo – at a controlled rate. For example, Case Study 9 shows the installation at the largest
The motive nozzle in the slurry eductor maintains milk at a fixed, constant flow rate, enabling three in-weight feeders to drop additives into the washdown hopper at a constant feed rate, producing the desired mixture with uniform solids/liquids ratio.
Some of the largest global beverage manufacturers now use Fox slurry eductors to blend the ever-increasing variety of flavours that consumers are looking for. And a slurry eductor is not limited to powder feed from just one feeder. Up to six feeders can be arranged to deliver powder in different combinations, or one at a time, to meet continually changing production schedules. Fully hygienic CIP (Clean In Place) eductors, polished and ground in 316 ss, can be rapidly diassembled
Fox slurry eductors blend
Additives needed to whey, interim maintains the three losswashdown desired
have pellets from pelletizers.
Coco Powder, Whey, and Spice Additives into Milk:
Here a dairy manufacturer needed to continuously blend pulverized coconut meat, whey, and flavorings into milk on its way to an interim process.
The motive nozzle in the slurry eductor maintains the milk at a fixed, constant flow rate, enabling three lossin-weight feeders to drop additives into the washdown hopper at a constant feed rate, producing the desired mixture with uniform solids/liquids ratio.
Some of the largest global beverage manufacturers now use Fox slurry eductors to blend the everincreasing variety of flavours that consumers are looking for.
Plastic pellets from pelletizers been used for twenty years to transport plastic pellets from the end of extruder lines and various types of pelletizers.
for quick clean-outs between product runs to eliminate crioss contamination. See attached photo of an electropolished, fully hygienic venturi eductor.
Fox can supply the right properly engineered powder-feed hopper – adjusted per downstream piping geometry. Rather short distances can use a dry hopper. Longer distances , or systems with substantial vertical pipe downstream, need a washdown hopper - to both sweep powders into the eductor, but more importantly, to inhibit air from being sucked in . See attached graphic and photo of a slurry eductor with a washdown hopper.
A 3 inch Food-grade , electropolished SLURRY eductor for use in beverage manufacturing
in sauces, ketchup, etc This application requires what we call coaxial eductors, and eliminates the lumps and clumps common if these powders are just added to a tank.
– which we will be happy to send upon request from our website ( foxvalve.com) A few simple limits : a) Max solids loadfing is about 15 –18% solids by weight, b) Max liquid viscosity about 200 centipoise
An important niche for Fox slurry eductors is the instant hydration of hard-to-wet powders, used as emulsifiers, such as guar, carrageenan and xanthum gum. These are commonly used
Of course, there are distinct limits to whether a slurry eductor can work in each application. These are discussed in detail in the “10 Most Commonly Asked Questions” in our bulletin on Slurry eductors
Please contact us with details of your application.
USDA-Approved slurry eductors have been used to blend powders into pharmaceutical solutions for consumer products since the 1970ʼs.
Fox Venturi Eductors Dover , NJ, USA www.foxvalve.com
Manufacturing processes continue to evolve from the human-centred methods of the past to machine reliant assembly lines, moving into the highly automised processes of today. As the industry continues to evolve it is imperative to stay ahead of the competition, continually improving processes and creating solutions to maximise efficiency. With the highest quality equipment, Volkmann create innovative solutions to transfer bulk material with Multijector® Vacuum Conveyors. Driving drastic efficiency improvements, reducing waste and creating significant costsavings.
Due to constant development and improvement in technology, removal of explosion risks and with a focus on good hygienic solutions, Vacuum Conveyors today are a preferred choice in many industries. They can transfer nano-sized material and fine dust with particles size from 0,1 µm up to bigger sized pellets, sweets, or bottle caps, for example. Alongside bulk material transfer, Volkmann also create the most effective solutions for loading materials, including Drum Discharge Systems, Big Bag Unloading Stations and Rip-and-Tip Dump Stations. Consistently creating the optimum processing solution for food, pharma, AM and chemical industries.
What stands Volkmann apart is their ability to create custom solutions for each application. As specialists in the design and manufacture of pneumatic vacuum conveyors and systems, their experience and expertise ensure that you get the right solution. Pneumatic powder-transfer systems are replacing more and more conventional mechanical conveying methods like screws, augers, lifts, belts and bucket conveyors.
Because many production processes require multiple powders or granulates to be conveyed with the same equipment, it is important to have a receiver with a simple assembly to allow quick and easy manual dismantling and cleaning to avoid cross contamination.
The Volkmann VS and PPC series of vacuum conveyors feature a unique, stainless steel modular design with clamp rings allowing no-tools assembly and disassembly for cleaning and fast product changes.
Volkmann’s ranges of Vacuum Conveyors were the first on the market that were fully certified under European ATEX regulation for all dust and soon after, also gas explosion zones.
Customers can trust that Volkmann care about safety. Providing profound expertise and support for all hazardous applications relying on decades of experience and knowledge. The full range of VS and PPC Vacuum Conveyors are ATEX-certified as standard and
can be regarded “explosion-safe” for all dust explosion areas/zones (for conveying materials with MIE >1 mJ; MIE = minimum ignition energy) and if no inflammable gases are present.
Volkmann provide reliable, hygienic, and efficient material handling solutions that enhance the safety, productivity, and quality of the manufacturing processes. Volkmann UK offer free on-site trials of their Multijector® Vacuum Conveyors, with no obligations. To find out more email mail.uk@volkmann.info.
VOLKMANN UK Limited Unit 4 Anglo Office Park, Lincoln Road, High Wycombe, Bucks, HP12 3RH, United Kingdom +44 (0) 1494 512228 | mail.uk@volkmann.info | https://uk.volkmann.info
Drive technology specialist
ENEMAC from Germany has felt at home in the food production and packaging sector for more than 40 years. Again and again, customers place special requirements on the manufacturer’s products.
This was also the case for a food packaging company. They were looking for a solution to safeguard a cup filling machine.
Cup filling machines are an indispensable component in the modern food industry. They enable efficient and precise filling of food into cups or other containers of various sizes and materials. They play a crucial role in the automation of filling processes, which not only increases production speed, but also improves the accuracy and consistency of filling.
The versatility of cup filling machines makes it possible to fill a wide range of food products, including liquids such as yoghurt, sauces and drinks, semi-solid products such as puddings and fruit pieces, as well as solid products such as salads, snacks and confectionery. Adaptable to different packaging sizes and types, cup filling machines can meet the requirements of different products while maximising efficiency on the production line.
If a cup is damaged or positioned imprecisely during the filling process, this can disrupt or even interrupt the entire production process. There is also a considerable risk of contamination, which can lead to recalls by the manufacturer, resulting in high costs. The mechanics of the machine can also be damaged in the further course of the process.
To prevent this damage and stop further operation of the machine, a stainless steel ENEMAC safety coupling type ECG_ES was used in the drive train. A safety clutch generally transmits the torque up to a preset disengagement torque. If this torque is exceeded, for example due to a blockage in the filling process, it separates the input and output so that no more forces are transmitted.
The ECG_ES offers a reliable solution for disengagement torques between 2 and 900 Nm. With 14 different sizes and 2 designs - with and without axial locking - this product offers maximum flexibility and adaptability.
ENEMAC offers a wide range of stainless steel torque limiters for applications in the medical, food, beverage and chemical industries. All products are:
1. robust and durable: manufactured from high quality stainless steel to ensure a long service life and high performance in hygienic applications.
2. versatility: with a temperature range of -30° to +150°C, these couplings are suitable for a wide range of environments, from extreme cold to hot operating conditions
3. reliable safety: protection is purely mechanical, with positive disconnection within fractions of a second, regardless of power failures
4. easy cleaning: All parts are stainless and can thus be cleaned in the process.
5. easy restart of the machine: ENEMAC safety couplings are selfengaging and can continue to be used without disassembly when the motor starts up slowly
E-mail: sales@enemac.de web: https://enemac.eu/
Product compass/ product finder: https://compass.enemac.de/home
Tel: +49 6022 71070
When you buy machinery for use in the Great Britain (England, Wales or Scotland), do you know what to look for to ensure it is legal and safe?
If the manufacturer is based in GB and selling to GB customers, the machine should be UK CA marked to the Supply of Machinery (Safety) Regulations. Manufacturers in the EU and Northern Ireland might UK CA mark the machinery if only selling to GB, or they might CE mark it to the EU Machinery Directive if they are selling to the EU and GB. Fortunately, CE marking is still accepted in GB.
However, if the machine is CE marked, the manufacturer must have an EU Authorised Representative (EUAR) established in the EU, even if the manufacturer and customer are both in GB.
Hold Tech Files is based in the Republic of Ireland and can act as an EUAR for non-EU manufacturers selling machinery or other CE marked products.
Hold Tech Files Ltd www.holdtechfiles.eu
Automation is no longer just a tool for increasing efficiency; it brings extensive benefits to the entire production process. During times of labour shortages, automation offers a solution to optimize workflows while ensuring favourable working conditions. Automated systems not only help minimize human error and increase production speed but also play a crucial role in conserving resources.
Implementing automation technology can significantly reduce energy consumption and the amount of production space needed. This not only makes production more cost-effective but also helps reduce the ecological footprint. Additionally, automated processes allow for the manufacture of more durable machine components, which reduces material requirements and minimizes waste. Automation, therefore, is not only a response to labour market challenges but also a critical step towards more sustainable and eco-friendly production.
Our latest developments are focused on packaging efficiency optimisation, we have developed packaging machines for confectionery products, which are able to replace many packaging units due to their capacity. For example, our machines for double twist of chocolate candies can pack the products with the speed up to 1 800 candies per minute or hard caramel candies with the speed up to 2 300 products per minute. Such machinery saves power and packaging material consumption, production space and do not require to keep huge amount of the spare parts and require minimum labour force. One of our automation innovations is a robot-assisted packing head cleaning system that opens new possibilities in production, such as in the manufacture of confectionery with beneficial additives. In these areas, it is crucial to prevent foreign substances, even in trace amounts,
from entering the products. With this innovation, we offer our customers not only greater efficiency but also maximum product safety.
Environmental sustainability has become a pervasive topic in today’s packaging industry. Manufacturers worldwide are increasingly required to transition to packaging that is recyclable, compostable, or biodegradable. This shift is driven not only by regulatory requirements, such as European, American, and UK environmental standards, but also by the growing ethical awareness among consumers.
The goals of these initiatives are clear: they seek not only to reduce waste but also to create infrastructure for so-called “circular” materials. This allows raw materials to remain in circulation and creates new jobs, benefiting both the environment and the economy.
Interestingly, the shift to ecofriendly packaging is being driven not only by governments and regulators but also by consumers. According to recent market research, more and more consumers are making purchasing decisions based on ethical criteria. Products manufactured with ecological and social standards are gaining importance.
Consumers today are paying attention not only to the price or quality of a product but also to its environmental impact. Environmental certifications and labels, such as “carbon neutral” or “produced with alternative energy sources,” are crucial factors for many buyers. A product’s packaging plays a central role, as it reflects how seriously a company takes
its environmental responsibility. Packaging trends are most evident in labelling symbols, especially on confectionery items, which increasingly convey information on how the product was manufactured.
In recent years, regulatory requirements for packaging have become significantly stricter in Europe and the USA. These new laws address not only the materials used in packaging but also their efficient use of space.
A key focus of this legislation is the optimization of packaging space. The European Directive 94/62/EC, as well as international standards like OIML R 87 “Quantity of product in prepackages” and OIML D9 “Principles of Metrological Supervision”, set strict requirements for fill levels within packaging. A primary aspect of these regulations is the control of “slack fill,” meaning that unused space within packaging must be minimized wherever possible.
According to these guidelines, having unutilized space in packaging is nearly prohibited. The purpose is to reduce waste and optimize resource use. Consequently, there are increasing legislative recommendations for minimizing empty space and improving spatial efficiency in packaging.
These new regulations aim to encourage the packaging industry toward more responsible resource management and reduce environmental impact. Manufacturers and packaging designers are urged to develop innovative solutions that maximize the available space within packages and increase the overall efficiency of packaging processes.
www.theegarten-pactec.com
The first cartoning system that can keep up with our high-performance machines.
The first cartoning system that can keep up with our high-performance machines.
BLM ensures maximum productivity without interface problems!
BLM ensures maximum productivity without interface problems!
Cartoning bottlenecks lead to productivity tailbacks – which is why Theegarten-Pactec is introducing the BLM, the first direct-feed cartoning system that keeps pace with our primary packaging machines. That‘s boxing clever! Because with an intake of up to 2,000 single products or 120 cartons per minute, the extremely flexible modular dockable system can now also process the high-performance output of the primary packaging.
Cartoning bottlenecks lead to productivity tailbacks – which is why Theegarten-Pactec is introducing the BLM, the first direct-feed cartoning system that keeps pace with our primary packaging machines. That‘s boxing clever! Because with an intake of up to 2,000 single products or 120 cartons per minute, the extremely flexible modular dockable system can now also process the high-performance output of the primary packaging.
Discover the value-creation potential of our innovative and durable machines at first hand!
Discover the value-creation potential of our innovative and durable machines at first hand!
ProSweets Cologne 02. – 05.02.2025
ProSweets Cologne 02. – 05.02.2025
Cologne, Germany
Cologne, Germany
Hall 10.1, Booth F011
Hall 10.1, Booth F011
MANUAL & AUTOMATIC BOOT WASHER
Manual boot wash stations, like the ones we supply at Stainless Steel Manufacturing & Equipment, are great for small to mediumsized processing areas and plants.
Manual boot wash stations, like the ones we supply at Stainless Steel Manufacturing & Equipment, are great for small to mediumsized processing areas and plants.
handheld boot brush that enables you to clean the top and sides of your boots and shoes. How to use the Manual Boot Washer:
How to use the Manual Boot Washer:
Our manual boot washer can be used for all types of footwear worn in production areas and is often used on entry and exit to prevent employees from walking debris into changing rooms and corridors.
Our manual boot washer can be used for all types of footwear worn in production areas and is often used on entry and exit to prevent employees from walking debris into changing rooms and corridors.
Manual boot wash stations, like the ones we supply at Stainless Steel Manufacturing & Equipment, are great for small to mediumsized processing areas and plants.
Manual boot wash stations, like the ones we supply at Stainless Steel Manufacturing & Equipment, are great for small to mediumsized processing areas and plants.
Manual boot wash stations, like the ones we supply at Stainless Steel Manufacturing & Equipment, are great for small to mediumsized processing areas and plants.
To activate the manual boot washer, you simply place your foot on the base brushes within the trough, which actuates a valve mounted on the underside of the boot washer. Water the flows through the hose brush and enables you to effectively clean the boot from all angles–ensuring all dirt is removed.
How to use the Manual Boot Washer: To activate the manual boot washer, you simply place your foot on the base brushes within the trough, which actuates a valve mounted on the underside of the boot washer. Water the flows through the hose brush and enables you to effectively clean the boot from all angles– ensuring all dirt is removed.
304/316 stainless steel, providing you with the reassurance that it’s up to standard. What’s more, we aim to accommodate the requirements of all our customers, ensuring that you find a suitable boot cleaning station for your hygienic setting.
To activate the manual boot washer, you simply place your foot on the base brushes within the trough, which actuates a valve mounted on the underside of the boot washer. Water the flows through the hose brush and enables you to effectively clean the boot from all angles– ensuring all dirt is removed.
• Automatic & Semi-Automatic Boot washer.
How to use the Manual Boot Washer:
• Automatic Sensor Operated or Semi-Automatic button operated.
Available in 1-4 stations, the manual boot washer comes with a high-density nylon base brush for scrubbing the soles of shoes and includes a convenient, water-fed, handheld boot brush that enables you to clean the top and sides of your boots and shoes.
Available in 1-4 stations, the manual boot washer comes with a high-density nylon base brush for scrubbing the soles of shoes and includes a convenient, water-fed, handheld boot brush that enables you to clean the top and sides of your boots and shoes.
Our manual boot washer can be used for all types of footwear worn in production areas and is often used on entry and exit to prevent employees from walking debris into changing rooms and corridors.
Our manual boot washer can be used for all types of footwear worn in production areas and is often used on entry and exit to prevent employees from walking debris into changing rooms and corridors.
Investing in a manual boot wash station will ensure your employees perform the necessary washing and disinfecting steps required for hygiene regulations.
Investing in a manual boot wash station will ensure your employees perform the necessary washing and disinfecting steps required for hygiene regulations.
Investing in a manual boot wash station will ensure your employees perform the necessary washing and disinfecting steps required for hygiene regulations.
Manual boot wash stations, like the ones we supply at Stainless Steel Manufacturing & Equipment, are great for small to mediumsized processing areas and plants.
Our manual boot washer can be used for all types of footwear worn in production areas and is often used on
How to use the Manual Boot Washer: To activate the manual boot washer, you simply place your foot on the base brushes within the trough, which actuates a valve mounted on the underside of the boot washer. Water the flows through the hose brush and enables you to effectively clean the boot from all angles– ensuring all dirt is removed.
To activate the manual boot washer, you simply place your foot on the base brushes within the trough, which actuates a valve mounted on the underside of the boot washer. Water the flows through the hose brush and enables you to effectively clean the boot from all angles– ensuring all dirt is removed.
Our manual boot washer can be used for all types of footwear worn in production areas and is often used on entry and exit to prevent employees from walking debris into changing
• Cleaning boots by the action of rotating brushes.
• Automatic dosing of water and detergent.
How to use the Manual Boot Washer:
Investing in a manual boot wash station will ensure your employees perform the necessary washing and disinfecting steps required for hygiene regulations. MANUAL BOOT WASHER
• Removal of the brush is done without the need for tools and makes cleaning the brush and the brush housing simple.
Our automatic stations provide continual performance but are easy to dismantle, requiring no extra tools. In turn, the automatic boot washer is easy to clean, and the rotating tray and brushes can be cleaned individually, allowing you to clean your equipment thoroughly.
Available in 1-4 stations, the manual boot washer comes with a high-density nylon base brush for scrubbing the soles of shoes and includes a convenient, water-fed, handheld boot brush that enables you to clean the top and sides of your boots and shoes.
To activate the manual boot washer, you simply place your foot on the base brushes within the trough, which actuates a valve mounted on the underside of the boot washer. Water the flows through the hose brush and enables you to effectively clean the boot from all angles– ensuring all dirt is removed.
Available in 1-4 stations, the manual boot washer comes with a high-density nylon base brush for scrubbing the soles of shoes and includes a convenient, water-fed, handheld boot brush that enables you to clean the top and sides of your boots and shoes.
The modular belt conveyor offers a reliable versatile solution to many conveying applications.
Investing in a manual boot wash station will ensure your employees perform the necessary washing and disinfecting steps required for hygiene regulations.
Available in 1-4 stations, the manual boot washer comes with a high-density nylon base brush for scrubbing the soles of shoes and includes a convenient, water-fed, handheld boot brush that enables you to clean the top and sides of your boots and shoes.
Investing in a manual boot wash station will ensure your employees perform the necessary washing and disinfecting steps required for hygiene regulations.
The modular belt conveyor introduces a flexible conveying solution that can, due to the nature of the belt itself, convey
Here at Stainless Steel Manufacturing & Equipment Ltd, we can supply a boot washer that is made from Grade
We supply the Lazy Susan Turntable, which is a Stainless Steel Turntable, to meet and exceed the requirements of all industries. We aim to satisfy even the most diverse demands, including those based in the food, drink, pharmaceuticals, packaging and production industry, ensuring that all equipment is manufactured to the highest quality and made to last.
We supply the Lazy Susan Turntable, which is a Stainless Steel Turntable, to meet and exceed the requirements of all industries. We aim to satisfy even the most diverse demands, including those based in the food, drink, pharmaceuticals, packaging and production industry, ensuring that all equipment is manufactured to the highest quality and made to last.
• Supplied with a venture metering system for accurate dosing of the detergent
A turntable that’s made from stainless steel is a cost-efficient investment to make, especially if you’re looking to maximise the efficiency of production.
A turntable that’s made from stainless steel is a cost-efficient investment to make, especially if you’re looking to maximise the efficiency of production.
The Stainless Steel Turntable is just one of the products that we are proud to supply at SSME and is available in various sizes.
The Stainless Steel Turntable is just one of the products that we are proud to supply at SSME and is available in various sizes.
We supply the Lazy Susan Turntable, which is a Stainless Steel Turntable, to meet and exceed the requirements of all industries. We aim to satisfy even the most diverse demands, including those based in the food, drink, pharmaceuticals, packaging and production industry, ensuring that all equipment is manufactured to the highest quality and made to last.
products through inclined as well as horizontal and helical paths.
products through inclined as well as horizontal and helical paths.
We supply the Lazy Susan Turntable, which is a Stainless Steel Turntable, to meet and exceed the requirements of all industries. We aim to satisfy even the most diverse demands, including those based in the food, drink, pharmaceuticals, packaging and production industry, ensuring that all equipment is manufactured to the highest quality and made to last.
We supply the Lazy Susan Turntable, which is a Stainless Steel Turntable, to meet and exceed the requirements of all industries. We aim to satisfy even the most diverse demands, including those based in the food, drink, pharmaceuticals, packaging and production industry, ensuring that all equipment is manufactured to the highest quality and made to last.
We supply the Lazy Susan Turntable, which is a Stainless Steel Turntable, to meet and exceed the requirements of all industries. We aim to satisfy even the most diverse demands, including those based in the food, drink, pharmaceuticals, packaging and production industry, ensuring that all equipment is manufactured to the highest quality and made to last.
We supply the Stainless Steel Turntable in a range of sizes to make it easier for you to find products that will fit perfectly within your industrial setting. When it comes to accumulating products evenly, you cannot go wrong with the Stainless Steel Turntable- it’s specifically designed to bring work closer to the user.
We supply the Stainless Steel Turntable in a range of sizes to make it easier for you to find products that will fit perfectly within your industrial setting. When it comes to accumulating products evenly, you cannot go wrong with the Stainless Steel Turntable- it’s specifically designed to bring work closer to the user.
A turntable that’s made from stainless steel is a cost-efficient investment make, especially if you’re looking to maximise the efficiency of production.
A turntable that’s made from stainless steel is a cost-efficient investment to make, especially if you’re looking to maximise the efficiency of production.
A turntable that’s made from stainless steel is a cost-efficient investment to make, especially if you’re looking to maximise the efficiency of production.
A turntable that’s made from stainless steel is a cost-efficient investment to make, especially if you’re looking to maximise the efficiency of production.
We supply the Stainless Steel Turntable in a range of sizes to
We supply the Stainless Steel Turntable in a range of sizes to make it easier for you to find products that will fit perfectly within your industrial setting. When it
The Stainless Steel Turntable is just one of the products that we are proud to supply at SSME and is available in various sizes.
Space and loads permitting, 90 and 180 degree turns enable products to be conveyed on winding routes through production areas.
The Stainless Steel Turntable is just one of the products that we are proud to supply at SSME and is available in various sizes.
The Stainless Steel Turntable is just one of the products that we are proud to supply at SSME and is available in various sizes.
Space and loads permitting, 90 and 180 degree turns enable products to be conveyed on winding routes through production areas.
We supply the Stainless Steel Turntable in a range of sizes to make it easier for you to find products that will fit perfectly within your industrial setting. When it comes to accumulating products evenly, you cannot go wrong with the Stainless Steel Turntable- it’s specifically designed
The Stainless Steel Turntable is just one of the products that we are proud to supply at SSME and is available in various sizes.
We supply the Stainless Steel Turntable in a range of sizes to make it easier for you to find products that will fit perfectly within your industrial setting. When it comes to accumulating products evenly, you cannot go wrong with the Stainless Steel Turntable- it’s specifically designed
Steel Turntable- it’s specifically designed
The modular belt conveyor offers a reliable versatile solution to many conveying applications.
The modular belt conveyor offers a reliable versatile solution to many conveying applications.
The modular belt conveyor introduces a flexible conveying solution that can, due to the nature of the belt itself, convey
The modular belt conveyor introduces a flexible conveying solution that can, due to the nature of the belt itself, convey
2 FDPP - www.fdpp.co.uk
sizes.
products through inclined as well as horizontal and helical paths.
products through inclined as well as horizontal and helical paths.
Space and loads permitting, 90 and 180 degree turns enable products to be conveyed on winding routes through production areas.
Space and loads permitting, 90 and 180 degree turns enable products to be conveyed on winding routes through production areas.
Stainless steel mixer tumblers are available in three sizes, including 300 Litre, 450 Litre and 600 Litre. They are perfect for mixing dry and wet ingredients.
A mixer tumbler for food can effectively save on labour costs and increase production efficiency. Instead of mixing ingredients in smaller batches by hand, the mixer tumbler will automatically rotate a larger quantity of products at a faster rate.
Features
• 304 stainless steel construction
• Open frame to aid cleaning & maintenance
• Direct shaft drive operation
• Available with stainless steel lid if required
• Variable speed controls
• Mobile or free standing
Description:
Description:
• Tip height to customer specification
Operation:
Our Atomiser Sanitising Conveyors have been designed for the sanitization of the outer surfaces of various products being transferred between low and high care areas.
Our Atomiser Sanitising Conveyors have been designed for the sanitization of the outer surfaces of various products being transferred between low and high care areas.
Though stainless steel mixers are designed to boost productivity in the food processing industry, they come with variable speeds – allowing you to choose how quickly the drum rotates. With the addition of a timer control panel you can also program the tumbler to shut off after a specific number of revolutions, saving time and effort.
Description:
A huge variety of products can be transported through the Sanitising Conveyor, such as boxed or bagged food ingredients like vegetables, sauces, coatings, blocks of cheese, the list is endless
Description:
Description:
Our Atomiser Sanitising Conveyors have been designed for the sanitization of the outer surfaces of various products being transferred between low and high care areas.
A huge variety of products can be transported through the Sanitising Conveyor, such as boxed or bagged food ingredients like vegetables, sauces, coatings, blocks of cheese, the list is endless
Operation:
As well as conveniently marinading ingredients, a stainless steel mixer tumbler enhances the safety of your food processing plant by ensuring no food ends up on the floor.
Operation:
Operation:
a sensor gives a signal to the control panel and the conveyor belt will start. Then using compressed air the mixture is then supplied to five atomiser nozzles which are positioned above and below the conveyor belt. These produce a mist within the tunnel giving total coverage of all surfaces of the products that are
The solution tank is automatically filled with a pre-dosed mixture of water and sanitiser using a Dosatron water powered dosing pump. When a product is placed on the in-feed roller conveyor a sensor gives a signal to the control panel and the conveyor belt will start. Then using compressed air the mixture is then supplied to five atomiser nozzles which are positioned above and below the conveyor belt. These produce a mist within the tunnel giving total coverage of all surfaces of the products that are
The drum can also be tilted to make it easier to unload food goods. This not only helps to keep
Our Atomiser Sanitising Conveyors have been designed for the sanitization of the outer surfaces of various products being transferred between low and high care areas.
Our Atomiser Sanitising Conveyors have been designed for the sanitization of the outer surfaces of various products being transferred between low and high care areas.
A huge variety of products can be transported through the Sanitising Conveyor, such as boxed or bagged food ingredients like vegetables, sauces, coatings, blocks of cheese, the list is endless
The solution tank is automatically filled with a pre-dosed mixture of water and sanitiser using a Dosatron water powered dosing pump. When a product is placed on the in-feed roller conveyor a sensor gives a signal to the control panel and the conveyor belt will start. Then using compressed air the mixture is then supplied to five atomiser nozzles which are positioned above and below the conveyor belt. These produce a mist within the tunnel giving total coverage of all surfaces of the products that are
product wastage to an absolute minimum but it makes it easier to clean too.
To prevent cross-contamination, you must give the drum a quick wipe-down inside between uses. Then, at the end of the day, it will need to be thoroughly cleaned, ready for the next day. As a result of being made from grade 304 stainless steel (a material that’s resistant to both corrosion and oxidation), all you need is warm water, a mild soap or detergent, and a soft cloth or sponge to gently wipe the surface clean.
carried out quickly and reliably. Atomising sanitization is very efficient as each nozzle only uses .8 litres of solution per hour and with the integral gravity recirculation system the use of solution is kept to a minimum and your products will not come out of the tunnel dripping with water.
conveyed through the tunnel. The control panel has a built in inverter which allows you to control the speed of the belt and ensures that a wide range of products can be safely passed through the system ensuring that hygiene routines can be carried out quickly and reliably. Atomising sanitization is very efficient as each nozzle only uses .8 litres of solution per hour and with the integral gravity recirculation system the use of solution is kept to a minimum and your products will not come out of the tunnel dripping with water.
conveyed through the tunnel. The control panel has a built in inverter which allows you to control the speed of the belt and ensures that a wide range of products can be safely passed through the system ensuring that hygiene routines can be carried out quickly and reliably. Atomising sanitization is very efficient as each nozzle only uses .8 litres of solution per hour and with the integral gravity recirculation system the use of solution is kept to a minimum and your products will not come out of the tunnel dripping with water.
A huge variety of products can be transported through the Sanitising Conveyor, such as boxed or bagged food ingredients like vegetables, sauces, coatings, blocks of cheese, the list is endless
The solution tank is automatically filled with a pre-dosed mixture of water and sanitiser using a Dosatron water powered dosing pump. When a product is placed on the in-feed roller conveyor a sensor gives a signal to the control panel and the conveyor belt will start. Then using compressed air the mixture is then supplied to five atomiser nozzles which are positioned above and below the conveyor belt. These produce a mist within the tunnel giving total coverage of all surfaces of the products that are
At stainless steel Manufacturing & Equipment ltd, design and manufacture a wide range of stainless steel equipment for the food and pharmaceutical industries. Our design team have over 25 years of experience and have worked on projects for many of the major food and pharmaceutical manufacturers. We are based in the West Midlands, just 3 minutes form Junction 10 of the M6. All our products are manufactured in house and we are the UK agent for the SCM boot washer and hygiene station range. We pride ourselves in manufacturing good quality products at competitive prices and as well as our standard range
At stainless steel Manufacturing & Equipment ltd, design and manufacture a wide range of stainless steel equipment for the food and pharmaceutical industries. Our design team have over 25 years of experience and have worked on projects for many of the major food and pharmaceutical manufacturers. We are based in the West Midlands, just 3 minutes form Junction 10 of the M6. All our products are manufactured in house and we are the UK agent for the SCM boot washer and hygiene station range. We pride ourselves in manufacturing good quality products at competitive prices and as well as our standard range
At stainless steel Manufacturing & Equipment ltd, design and manufacture a wide range of stainless steel equipment for the food and pharmaceutical industries. Our design team have over 25 years of experience and have worked on projects for many of the major food and pharmaceutical manufacturers. We are based in the West Midlands, just 3 minutes form Junction 10 of the M6. All our products are manufactured in house and we are the UK agent for the SCM boot washer and hygiene station range. We pride ourselves in manufacturing good quality products at competitive prices and as well as our standard range
We will manufacture items to meet customer specific requirements.
We will manufacture items to meet customer specific requirements.
We will manufacture items to meet customer specific requirements.
A huge variety of products can be transported through the Sanitising Conveyor, such as boxed or bagged food ingredients like vegetables, sauces, coatings, blocks of cheese, the list is endless
For more information or the place an order
At stainless steel Manufacturing & Equipment ltd, design and manufacture a wide range of stainless steel equipment for the food and pharmaceutical industries. Our design team have over 25 years of experience and have worked on projects for many of the major food and pharmaceutical manufacturers. We are based in the West Midlands, just 3 minutes form Junction 10 of the M6. All our products are manufactured in house and we are the UK agent for the SCM boot washer and hygiene station range. We pride ourselves in manufacturing good quality products at competitive prices and as well as our standard range
The solution tank is automatically filled with a pre-dosed mixture of water and sanitiser using a Dosatron water powered dosing pump. When a product is placed on the in-feed roller conveyor a sensor gives a signal to the control panel and the conveyor belt will start. Then using compressed air the mixture is then supplied to five atomiser nozzles which are positioned above and below the conveyor belt. These produce a mist within the tunnel giving total coverage of all surfaces of the products that are
Please Call: 0121-661-6346 or Email: sales@ssmeltd.co.uk
For more information or the place an order
For more information or the place an order
About Us At stainless steel Manufacturing & Equipment ltd,
conveyed through the tunnel. The control panel has a built in inverter which allows you to control the speed of the belt and ensures that a wide range of products can be safely passed through the system ensuring that hygiene routines can be carried out quickly and reliably. Atomising sanitization is very efficient as each nozzle only uses .8 litres of solution per hour and with the integral gravity recirculation system the use of solution is kept to a minimum and your products will not come out of the tunnel dripping with water.
conveyed through the tunnel. panel has a built in inverter you to control the speed of ensures that a wide range of can be safely passed through ensuring that hygiene routines carried out quickly and reliably. sanitization is very efficient nozzle only uses .8 litres of per hour and with the integral recirculation system the use is kept to a minimum and your will not come out of the tunnel with water.
Please Call: 0121-661-6346 or Email: sales@ssmeltd.co.uk
Please Call: 0121-661-6346 or Email: sales@ssmeltd.co.uk
We will manufacture items to meet customer specific requirements.
the food and pharmaceutical industries. Our design team have over 25 years of experience and have worked on
IMA serves the international dairy market with the best platforms and machines available to satisfy industry needs, consistently providing tailored technologies for the packaging of dairy products and alternatives.
From a wider perspective, IMA gathers within the IMA FOOD entity, an impressive number of brands offering technologies for the food industry, but focusing on the dairy market it grants proven expertise and know-how thanks to the following brands:
IMA Benhil (Germany), IMA Corazza (Italy), IMA Erca (France), IMA Fillshape (Italy), IMA Gasti (Germany), IMA Hassia (Germany), IMA Ilapak (Italy / Switzerland), IMA Intecma (Spain).
The above IMA FOOD companies offer dedicated and cutting-edge solutions to respond to the packaging needs of the following dairy products and alternatives.
Machines for dosing and wrapping of butter and margarine bricks and sticks, from single-serve up to 500g portions, from low to highspeed production output. Efficient performance and a top-quality fold, using different wrapping materials, from standard aluminium to paperbased solutions.
Filling and sealing machines designed to fill pasty products with high hygiene requirements into preformed containers in different sizes, and shapes.
Forming, filling and sealing machines (FFS) for a huge variety of portion cup designs and materials such as PS, PET and PP. They offer maximum accuracy, precise product cut-off and gentle product handling.
Complete lines for dosing and wrapping of processed and spreadable cheese in triangular, rectangular, and square portions of different weights, including mini portions.
State-of-the-art technology to preserve cheese properties and package integrity. Hot fill solutions as well as cold fill systems are included in the range that also comprehends dedicated secondary packaging equipment.
IMA’s range for processed and spreadable cheese also includes fill and seal machines (FS) for pre-formed containers and FFS machines for cups, and portion packs.
IMA provides horizontal FFS flow wrapping machines to pack portioned, blocks and pre-wrapped sliced cheese and vertical FFS baggers and weighing solutions suitable for shredded, grated, and diced cheese.
Our FS as well as FFS solutions are known for their outstanding filling accuracy. Covering a wide range of filling styles, countless customized and tailor-made design possibilities for cups are available to satisfy any customer demand. Fillers benefit from automatic, fully controlled SIP/CIP systems
for maximum hygiene, and are supplied in full compliance with European regulations.
Filling systems for flexible standup pouches - with and without spout - complete our machine portfolio, guaranteeing top hygiene design with ultra-clean and aseptic solutions.
Turnkey solutions for sustainable production
Taking advantage of synergies and integrations within the IMA Group, the IMA FOOD companies are able to supply complete turnkey packaging solutions: from dosing to wrapping and cartoning, from forming, filling, and sealing to display boxing up to any secondary and end of line equipment tailored specifically for dairy products.
IMA Group companies stand out not only for their manufacturing capabilities but also for the competence in supporting customers in the research and development of new sustainable packaging styles and materials as well as Smart Manufacturing products and services.
www.ima.it/foodanddairy
IMA serves the international dairy and dairy alternative industries with the best platforms and machines, consistently providing tailored technologies for the packaging of cheese, butter, margarine, yoghurt, desserts, UHT milk and more.
IMA serves the international dairy and dairy alternative industries with the best platforms and machines, consistently providing tailored technologies for the packaging of cheese, butter, margarine, yoghurt, desserts, UHT milk and more.
From stand-alone machines to fully-integrated solutions, our advanced technologies and expert consultancy ensure tailored support for every need, from primary to end of line packaging solutions.
From stand-alone machines to fully-integrated solutions, our advanced technologies and expert consultancy ensure tailored support for every need, from primary to end of line packaging solutions.
Make the most, with us.
Make the most, with us.
Hart Door Systems, the original British manufacturer of the highspeed door concept, is confident that there are considerable prospects for another successful year for its Speedor and Typhoon brands.
“Despite global uncertainties on the political front and the ever present debate on Climate Change I believe our leading Speedor and Typhoon brands will continue to be in demand,” says Doug Hart, Hart’s chairman. “The fundamentals delivered by Hart are quality throughout manufacture to installation as well as service back-up to comply with changing national and international safety standards.
“We are cognisant of Climate Change issues and the need to keep both Hart’s and our clients’ carbon footprints to a minimum by using the latest manufacturing technology to streamline the manufacturing process. Where possible we would use recyclable materials.”
“Looking more closely at the Speedor brand, as Britain’s original manufacturer of the automatic high speed door, Hart has always
We are cognisant of Climate Change issues and the need to keep both Hart’s and our clients’ carbon footprints to a minimum
led the way with developments in commercial door technology by being aware of issues facing industry. Speedor is a good example of an engineered door system for frequent use in hightraffic situations. This rapid roll door is robust, requires low maintenance and delivers exceptional wind resistance in exposed areas.
“While its high-speed opening and closing action improve efficiency, the energy-saving potential of this rapid roll door is high, controlling internal temperatures, escaping dirt, odours and noise. Special features include; moisturecontrolled electrics, mechanical components shielded from dust and dirt, and a unique guide system offering exceptional wind resistance up to class 5 as defined by DIN EN 12424.
“There are several options with the Speedor brand namely ECO, Storm, Mini, Conveyor and Cleanroom which together strengthen Hart’s overall high-speed door offer. Speedors are ideal for challenging applications where reliability is essential. Its increasing success is based on its improved, rugged, design predominately for external use up to 8m x 6m/6m x 8m often in robust operating conditions with high wind loads.
“We have always had quality as our prime driver and our success with new variants, not just in high-speed doors but shutters such as our new Typhoon range, the fundamentals are quality throughout manufacture to installation and service to comply with changing national and international safety standards.”
“Hart Door Systems is a global business supplying door and shutter systems to sectors such as automotive, agriculture, communications, consumer foods, energy, environment, exports, food, logistics, manufacturing, power, sport, transport and utilities.
www.hartdoors.com
The Kennet Crayfish Company has had a successful season including being nominated as one of three finalists in the main category “Food Producer of the Year” at the BBC Food and Farming Awards 2024.
The company has created the largest processing facility for crayfish in Britain, it is eco-friendly, humane and uses pure, chalk-stream water to handle wild crayfish from the River Kennet. Cooked to order, then chilled and vacuum packed in microwaveable trays by a process that gives them up to 21 days refrigerated shelf life. Each pack is 500 grams and the current range includes packed in brine, Sichuan or Swedish style sauces. Crayfish are smaller, freshwater cousins of lobsters and thought by many to have a superior flavour, much prized by top chefs and foodies around the world. Most crayfish currently sold in the UK are imported from fish farms in the polluted rivers of China.
www.kennetcrayfish.com
and manufacture, wide range of models covering high security, large doors with high wind resistance (3,000 to 5,000 pascals), fire and high speed automation with systems’ interface.
As part of any Food processors HACCP program validation of cook and chill processes is a critical and significant task taking time, effort, and resources.
PhoenixTM have developed a thruprocess temperature monitoring technology specifically for this task designed to meet the challenges of the food processing market. Ideal for the validation process for any new cook regime, new product, or annual process certification. Whether performing an oven survey “oven mapping to identify cold spots” or validating the cook under production conditions, the thru-process profiling solution gives you the accuracy, efficiency, and reliability you need to satisfy your HACCP demands.
As its name suggests thru-process profiling is the method by which product and or process temperature is monitored throughout the complete cook / chill process.
Monitoring of continuous conveyorised linear and spiral ovens and semi-continuous or rotational batch cooks is feasible where the use of external recorders with trailing thermocouples is tedious, impractical, and unsafe.
Employing the thru-process principal process monitoring can be performed under true production conditions without compromising line productivity .
At the heart of the thru-process monitoring system is the PhoenixTM data logger.
The PhoenixTM NT data logger range has been designed specifically for the challenges of monitoring food processing applications with an IP67 case design protecting from moisture. Type K or Type T data logger options allow accurate measurement of both cook and chill processes. The data logger itself can operate between -40 °C to 80 °C with a data logger accuracy of ±0.3 °C operating below +50 °C.
Data logger and thermocouple correction factors can be further applied to maximise measurement accuracy.
PhoenixTM offer a family of thermal barriers to suit the process type, duration, and temperatures of a wide range of cook regimes.
An extensive range of different thermocouple types is also available to suit different product types , sizes and monitoring demands.
The PhoenixTM Thermal View Food Software provides a comprehensive suite of analysis tools to convert the raw profile temperature data into useful process information. The analysis tools include the ability to calculate Fo/Pu values for the process against target microorganisms.
The information gathered, further to process validation, can be used to allow informed process problem solving and optimisation to maximise product quality, yield, process productivity and efficiency.
Contact PhoenixTM to help Find, Fix and Forget your Food Cook Problems!
Further Information www.phoenixtm.com
Newman Labelling Ltd, a leader in pharmaceutical labelling solutions, proudly introduces the S125 Labelling System, a fully automatic self-adhesive labelling machine engineered for cylindrical containers. This entry-level addition to Newman’s renowned range promises efficiency, precision and affordability, making it ideal for labelling lines.
The S125 is perfect for start-ups and short production runs, accommodating cylindrical containers in various sizes. It is designed for ease of use and adaptability without compromising on Newman’s signature quality and durability.
“The S125 reaffirms Newman's commitment to delivering excellent quality labelling solutions to start-ups and mid-size operations.”
-Martyn Bell, General Manager
With its exceptional features designed specifically to facilitate reliable and efficient labelling of cylindrical containers, the S125 is a practical and affordable solution for operation lines of all sizes. Its key specifications include:
Speed: The S125 boasts an impressive labelling speed of up to 60 containers per minute, making it an ideal choice for entry-level production environments.
Container Diameter Range: Versatility is a hallmark of the S125, which is designed to accommodate containers with diameters ranging from 12 mm to 75 mm. Such a wide labelling range ensures that users can meet all their labelling requirements without the need for additional machinery.
Energy Efficient: In an era where energy efficiency is paramount, the S125 shines with its power consumption of less than 2 HP.
The S125 is a testament to Newman’s ongoing commitment to delivering innovative, accessible and reliable solutions.
Ruland stainless steel oldham coupling with PEEK center disk for high temperature and corrosion resistance
Food processing equipment require a diverse range of components due to various requirements in the operating environment such as washdown, high temperature, and caustic chemicals. Oldham couplings are an ideal coupling for food and beverage equipment due to their misalignment accommodation, zerobacklash properties, and balanced design. Ruland manufactures hubs in aluminium for general purpose applications and 303 stainless steel for high corrosion and temperature applications, giving designers an offthe-shelf coupling suitable for various servo-driven applications such as connecting a motor to a ball screw, lead screw or gearbox.
Ruland stainless steel oldham coupling, ideal for food and beverage equipment due to its misalignment accommodation, zero-backlash properties and balanced design
to maintain consistent corrosion resistance. Ruland adds a proprietary surface treatment to hardware to prevent galling.
Ruland oldham couplings are available in bore sizes from 3 mm to 32 mm. Disks can be manufactured with a center hole to allow further shaft penetration or slots for retention hardware to attach the disk to a hub so it can stay in place during disassembly.
Oldham couplings are comprised of two hubs that mate to a center disk. This three-piece design allows food and beverage equipment designers to customize oldham couplings with a clamp or set screw hub with inch, metric, keyed, and keyless bores. They have a balanced design for reduced vibration at speeds up to 6,000 rpm and operate with low bearing loads, protecting these sensitive components from premature failure. In addition, Ruland uses a proprietary hub machining process that leaves a smoother surface for interaction between the hub and disk, resulting in longer life and reduced downtime.
The oldham disk is available in acetal for zero-backlash and high torque capacity, PEEK for high temperature and corrosion resistance, and nylon for dampening and noise reduction. In the event of failure or wear, the disk is replaceable, restoring the original performance characteristics of the coupling. Oldham couplings also act as a mechanical fuse during torque overload situations, with the disk breaking cleanly and stopping power transmission.
The use of 303 stainless steel combined with a PEEK disk allows designers to use standard oldham couplings in a wider variety of servodriven applications. Stainless steel hubs have hardware of like material
Oldham couplings are carefully manufactured in Ruland’s factory in Marlborough, Massachusetts under strict controls using proprietary processes. Ruland manufactures couplings and shaft collars for food processing and packaging equipment in a variety of sizes, styles and materials, and supplies adjustable handles, modular mounting systems, universal joints and other components to meet the demands of this industry. Design engineers benefit from using Ruland because they can select many standard instock parts from a single source. 3D CAD files, full product specifications, and additional technical information are available on www.ruland.com.
Specially designed for the frozen pastry industry, a recently developed packaging line by Gampack guarantees optimal handling of delicate products, even in continuous-cycle production
In the competitive confectionery sector, companies face significant challenges related to secondary packaging. These challenges include the need to maintain food integrity and freshness while ensuring high production speeds to meet market demand without compromising quality.
This year, Gampack Group, a leader in designing, developing, and manufacturing machines for secondary and tertiary packaging, is adding an innovative line dedicated to the secondary packaging of frozen pastries to its portfolio. This 100 percent tailor-made packaging solution was conceived to overcome the complex challenges associated with managing delicate products in continuous-cycle production.
The equipment erects corrugated cardboard boxes from flat blanks, into which a bag is inserted to prevent direct contact between the products and the secondary packaging. All materials in contact with food are strictly food-grade. “This line, beyond standard packaging operations, performs timely and accurate quality checks on products. It can handle an infeed speed of up to 500 products per minute across various sizes, with an output of up to 50 boxes per minute,” explains Gaetano Giuri, Gampack’s Area Manager for the UK.
This sophisticated, high-tech packaging system ensures a process that preserves product integrity and appearance while optimizing production efficiency. With a strong focus on flexibility and automation, Gampack’s solution significantly enhances several crucial aspects of
the production process. Thanks to dedicated high-speed pick-and-place robots for frozen foods, Gampack achieves precise, delicate handling that prevents product damage during packaging, ensuring that products reach consumers in perfect condition and enhance brand perception.
Moreover, the line is designed for extreme flexibility, adapting easily to variations in product sizes and packaging types. This versatility allows producers to respond promptly to market trends and consumer demands, enabling the swift launch of new products or variants without additional equipment investment.
“With this new packaging line, Gampack not only strengthens its
presence in the confectionery market but also sets new standards of quality and innovation,” Giuri says. As a systems provider and manufacturer of packaging machinery, Gampack Group is based in Piacenza, in Italy’s renowned Packaging Valley. The company comprises two key divisions: Mechatronics and Robotics. The Mechatronics division specializes in automatic machinery for secondary packaging, primarily for rigid products like beverage cartons, cans, and glass jars. The Robotics division focuses on developing and producing both traditional machines for secondary packaging (e.g., forming, closing, and clustering machines) suitable for both rigid and flexible products, such as doypacks, flow packs, and pouches, as well as palletising lines. Together, these divisions enable Gampack to deliver complete, highly customizable end-of-line systems across various industries, including food, beverages, cosmetics, pharmaceuticals, and more.
https://gampackgroup.com/en
Menzel pitch up with yet another quick delivery to UK.
When a customer on the Wirral suffered a failure of a critical 600kw, 6000V, 4pole compressor motor his immediate response was to ask the compressor packager for a replacement.
With a like for like OEM replacement not available in under 30 weeks and his only alternative to hire diesel driven plant at extremely high monthly rentals it was not looking good!
However, one call to Menzel Motors from his Service Partner and frowns turned to smiles as Menzel confirmed they had configured a similar set up for other seemingly captive customers before.
A review of current available stock, a drawing and images showing how the motor would be configured in 2-3 weeks and an order was placed.
Within fourteen days the motor was delivered to the UK site ready to be installed!
Within fourteen days the motor was delivered to the UK site ready to be installed!
“ Thank you for the excellent turnaround with this motor. We have exceeded the customer’s delivery expectations and they are extremely pleased with the service
we were able to offer with Menzel’s close support.
Once again, we appreciate all of your efforts and look forward to working with you in the future.”
Menzel continue to be the go to brand in time of real need for quick replacement motors.
Performance data of the squirrel cage compressor motor
• Menzel motor type: MEBKGR400L-04
• Motor standard: IEC / EN 60034-1
• Nominal power: 600 kW
• Nominal voltage: 6000 V (6 kV)
• Nominal frequency: 50 Hz
• Number of poles: 4 poles
• Nominal speed: 1490 min-1
• Design: IM B5
• Frame Size / Shaft height: 400 mm
• Degree of protection: IP 55
• Cooling type: IC 411 TEFC Totally Enclosed Fan Cooled
• Weight 4200kg
www.menzel-motors.com
NEW ELECTRIC MOTOR PLANT FROM JANUARY 2024
24,000 m 2
SUPPLIER OF LARGE MOTORS FOR ALL UK APPLICATIONS
MORE THAN 20.000 MOTORS AVAILABLE FROM STOCK!
MORE THAN 20.000 MOTORS AVAILABLE FROM STOCK!
Motors up to 25 MW and 13.8 kV
Motors up to 25 MW and 13.8 kV
• Low voltage slip-ring and squirrel cage motors up to 3,000 kW
• Low voltage slip-ring and squirrel cage motors up to 3,000 kW
24,000 m 2
• Medium voltage slip-ring and squirrel cage motors up to 15,000 kW
• Medium voltage slip-ring and squirrel cage motors up to 15,000 kW
• Direct current motors up to 2,000 kW
• Direct current motors up to 2,000 kW
• Frequency converter-proof drives
• Frequency converter-proof drives
• In-house load test facility up to 13.800 V, 2.300 kVA, 120 Hz
• In-house load test facility up to 13.800 V, 2.300 kVA, 120 Hz
Customized special designs
Customized special designs
• Custom designs for special applications and operating conditions
• Custom designs for special applications and operating conditions
• Optimized motor design for higher efficiency
• Optimized motor design for higher efficiency
• Mechanically and electrically interchangeable motors
• Mechanically and electrically interchangeable motors
• Commissioning worldwide
• Commissioning worldwide
MENZEL Great Britain Ltd. | UK Branch Office
27 Hunt Drive | Melton Mowbray | Leicestershire LE13 1PB
Martin Rooney | Tel.: +44 1664 500 844 | Mobil: +44 7957 618046
martin.rooney@menzelgb.co.uk NEW ELECTRIC MOTOR PLANT FROM JANUARY 2024
MENZEL Great Britain Ltd. | UK Branch Office 27 Hunt Drive | Melton Mowbray | Leicestershire LE13 1PB Martin Rooney | Tel.: +44 1664 500 844 | Mobil: +44 7957 618046 martin.rooney@menzelgb.co.uk
MENZEL Elektromotoren GmbH
German Headquarters
MENZEL Elektromotoren GmbH German Headquarters
Am Alten Walzwerk 2 | 16761 Hennigsdorf | Germany
Am Alten Walzwerk 2 | 16761 Hennigsdorf | Germany
menzel-motors.com info@menzel-motors.com
menzel-motors.com info@menzel-motors.com
AROUND THE CLOCK, AGAINST THE CLOCK!
AROUND THE CLOCK, AGAINST THE CLOCK!
Direct Adhesives are proud UK Premium Partners of Henkel. Our experienced team can help you unlock the benefits of the outstanding innovations in sustainable adhesive technology that Henkel bring to the packaging market. Launched at Fachpack in September, Technomelt Supra 079 ECO Cool is the latest product helping you reduce your carbon footprint.
Technomelt Supra 079 ECO Cool is the world’s first low temperature running carbon-negative hot melt adhesive. This innovative product offers not only high performance but also an exceptional environmental profile, representing a major leap forward in reducing carbon footprint in your packaging operations.
Designed for end-of-line cardboard packaging, Technomelt Supra 079 ECO Cool is developed from bio-based raw materials, certified to remove more CO2 from the environment than is emitted during its entire life cycle. This carbonnegative status sets it apart from traditional adhesives, which add to your carbon footprint. Henkel’s development is a clear response to the packaging industry’s growing focus on environmental impact, helping businesses meet regulatory
requirements and sustainability goals more effectively.
Key Benefits for Users of Cardboard Packaging
1. Carbon-Negative Footprint
The adhesive’s formulation, of bio-based and ISCC certified mass balanced materials means that a reduction of up to 32% of CO2 emissions is achievable compared to other polyolefin based hot melt adhesives, which allows companies to align with ambitious decarbonisation targets and ESG (Environmental, Social, and Governance) commitments.
2. Energy Efficiency through Cool Technology
As part of Henkel’s Cool Technology range, Technomelt Supra 079 ECO Cool can be applied at lower temperatures, reducing energy consumption by up to 40% compared to conventional hot melts. This translates into cost savings for manufacturers while also supporting their efforts to minimise operational energy use.
3. Superior Adhesion and Stability
Technomelt Supra 079 ECO Cool offers the same reliable performance as Henkel’s premium adhesives. It
ensures strong, durable seals for cardboard packaging, even under demanding conditions such as varying temperatures or extended storage.
4. Minimised Waste and Maintenance
The adhesive’s clean running properties reduce char buildup, ensuring smooth operations and lowering the need for frequent equipment maintenance, thus increasing productivity.
The introduction of Technomelt Supra 079 ECO Cool sets a new benchmark for the industry. This adhesive enables businesses to achieve both sustainability and operational efficiency; without compromising on performance, marking a transformative moment in packaging solutions.
Direct Adhesives are ideally located to serve your adhesive needs, with extensive stock availability and an experienced, professional team.
We can add our adhesive expertise to your operation, helping you deliver your sustainability goals. Please get in touch by calling 01525 381111, email us on info@directadhesives.co.uk or visit our website www.directadhesives.co.uk
WE’VE GOT AUTOMATED PACKAGING ALL WRAPPED UP...
• Materials & machinery for the complete solution
• Transit & display packaging
• Fully-recyclable, sustainable, anti-fog, barrier, MAP packaging and more...
• High-speed equipment for demanding environments
• Supported by expert engineers, across the UK & Ireland
DISCOVER THE RIGHT INGREDIENTS FOR FOOD PACKAGING SUCCESS.
THE COMPLETE SOLUTION T 01484 715111 E enquiries@yps.co.uk YPS.CO.UK
The UPSI-2412DP2 from Bicker Elektronik is a powerful DC UPS designed to protect 24VDC industrial, medical, and security systems from powerfailure and data loss. Utilizing maintenance-free Supercapacitors (Supercaps), it ensures long-term reliability and reduced maintenance comparedto traditional batteries. Supercaps charge quickly and offer a service life up to 10 times longer than lead-acid batteries.Housed in a compact DIN rail mount, this UPS supports applications like IPCs, controllers, and sensors, functioning across a wide temperaturerange (-20 to +70°C) for continuous 24/7 operation. The UPSI-2412DP2 features intelligent input current detection, ensuring optimal powerdistribution between the load and Supercap charger. In backup mode, it provides regulated output, maintaining consistent voltage during powerinterruptions.The system includes advanced features such as minimum load detection, a PowerFail relay, and automatic shutdown and reboot for IPCs duringpower failure. Users can monitor and configure the UPS via the included UPSGen2 software, which offers real-time status and parameter settings. Designed for reliability, the UPSI-2412DP2 ensures seamless protection for critical applications and comes with a 3-year warranty.
www.bicker.de/en/upsi-2412dp2
21 Sefton Business Park, Olympic Way, Aintree, Liverpool, Merseyside L30 1RD UK T: +44 (0) 151 525 1488 E: laboratory@alexstewartagriculture.com Your global network of inspection and analytical services www.foodtestlab.co.uk
In the high-demand, precisiondriven world of food processing, efficient energy management is key to operational success. Elcomponent Ltd, a leading provider of energy monitoring solutions in the UK, has empowered companies for over 30 years with innovative tools designed to maximise energy efficiency. Specialising in tracking energy metrics across electricity, gas, water, steam, and other essential resources, Elcomponent offers solutions that provide comprehensive oversight of energy usage. Their state-of-theart MW2 energy software and LoRaWAN (Long Range Wide Area Network) technologies deliver tailored solutions for the unique demands of the food processing sector.
Food processing presents distinct energy challenges: strict regulatory requirements, intensive water and electricity usage, and the need for accurate temperature and humidity control. Inefficiencies in these areas can escalate costs and operational issues, and Elcomponent’s solutions are engineered to help producers overcome these challenges. With specific experience with multiple processing and manufacturing companies, Elcomponent understands how to deliver energy monitoring solutions in this challenging sector.
Elcomponent’s MW2 energy software is a powerful solution for multi-site, complex operations, providing real-time data visualisation, analysis, and reporting to help food processors identify energy waste and optimise consumption. Designed to handle
everything from machine-specific energy data to main incoming supplies, MW2 helps facilities cut energy costs and comply with strict industry regulations. Managers can set alarms, track historical trends, and consolidate data across multiple locations, allowing for precise control over every aspect of production energy use.
Elcomponent’s LoRaWAN solutions bring advanced connectivity to energy monitoring, enabling long-range, low-power communication across large facilities. This setup is ideal for extensive food processing plants where monitoring every asset is essential yet challenging. LoRaWAN sensors capture data from remote or hard-to-reach locations—cooling systems, ovens, refrigeration units— without complex wiring, reducing installation time and disruption.
Scalable and adaptable, LoRaWAN enables processors to add sensors as operational needs grow, avoiding major overhauls. This adaptability is invaluable as food processors respond to evolving regulatory and operational requirements.
Elcomponent combines its technological expertise with handson support, offering training, implementation, and ongoing maintenance to help clients optimise their energy use. Beyond collecting data, Elcomponent partners with clients to interpret and act on it, reducing waste and aligning operations with sustainability goals.
With Elcomponent’s robust MW2 software, scalable LoRaWAN solutions, and extensive expertise in food processing, companies can achieve unparalleled energy efficiency. Take control of your energy, streamline processes, and make strides towards sustainability with Elcomponent’s advanced monitoring solutions. Connect with them today to explore how they can support your energy management journey.
Elcomponent Ltd
Unit 5, Southmill Trading Centre, Southmill Road, Bishops Stortford, Herts, CM23 3DY sales@elcomponent.co.uk www.elcomponent.co.uk
Kecolhaveover25yearsof experienceinhandlingalltypes ofviscousproductsinthefood, pharmaceuticalandcosmetics markets,aswellasgeneral industrialapplications.
Asampleofproductswealreadypump…
Asampleofproductswealreadypump…
Kecolhaveover25yearsof experienceinhandlingalltypes ofviscousproductsinthefood, pharmaceuticalandcosmetics markets,aswellasgeneral industrialapplications. T:+44(0)1746764311
TeethingGel
From June, Palletower, the UK’s leading manufacturer and stockist of storage and logistics equipment have transitioned the production of their plastic box pallets and collars to the UK. In the past, these have been manufactured and imported from Europe and China. At present, a fully lorry load of plastic boxes (104) weighing 4.6 tonnes distributed from Istanbul to the UK generates almost 2.6 tonnes of carbon emissions.
The shift in production not only allows Palletower to have more control over materials, but means that the company can offer the environmental and cost benefits to its wide customer base.
The impact that overseas distribution has on your carbon footprint
The average SME company in the UK generates around 15 tonnes of carbon emissions annually, making up 44% of the UK’s nonhousehold emissions. Palletower has partnered with Positive Planet, a sustainability business advisory, revealing the carbon impact of distribution to the UK, depending on location. Birmingham was chosen as the distribution centre of choice as it is a central UK distribution location.
As the majority of boxes were manufactured in Istanbul, by transporting just 607 plastic boxes to the UK, this generates the same amount of carbon emissions as an average SME. However, with the exclusive mould allowing
manufacturing of Palletower plastic boxes in the UK, they will be saving up to 2,569.7 KgCO2e per 104 boxes produced, as distribution emissions will be eliminated.
While businesses may opt to source products from Europe rather than Asia in an effort to become more environmentally conscious, the research has revealed that transporting primarily by road, over a much shorter distance can produce significantly more emissions than transporting by sea from further afield.
In fact, road freight produces nearly 10 times (9.7) the amount of emissions as sea freight. For example, a lorry travelling 1995km from Rome to Birmingham produces 1,586KgCO2e compared to Shanghai which produces 1580KgCO2e over 19,374km distance. Therefore, by shifting manufacturing to the UK, businesses could reduce distribution emissions by 1000-2,600KgCO2e per shipment.
The multi-purpose use of Palletower’s plastic boxes make them widely used in an array of industries to distribute products locally and globally. While Palletower’s customers might focus on their individual sustainability goals, the climate impact and change that Palletower has made by moving their production to the UK benefits the industry as a whole.
Matthew Palmer, Managing Director at Palletower says, “In an industry which is typically known as having its environmental challenges, we are keen to lead the way and spread awareness to our customers about the importance of investing in sustainable practices from the ground up, starting with the equipment they use to transport their goods.’’
For more information about Palletower’s UK manufacturing, please visit: Contact Us for Your Storage & Logistics Solutions | Palletower
Edge network architectures move compute, storage and analytics near the point of data generation allowing reduced latency, improved performance and optimised transmission costs. Transitioning to Edge creates its own set of challenges, sites can be remote or geographically distributed, which can mean a lack of dedicated onsite IT personnel and OT spaces may have limited environmental controls.
Whether the location is environmentally protected or not, there will be characteristics that define the type of technology infrastructure required to achieve a secure and high functioning OT resource. Specific capabilities are required to match the physical attributes of chosen OTE (operational technology equipment), include
Security – Physical - users must control the physical access in non-traditional IT spaces, ensuring that data (GDPR compliance) and equipment are protected. Locks, keypads, secure housing and video are essential for off-site or open site equipment.
Data – transmission and processing of sensitive industrial data must be secure and appropriate levels of access and encryption implemented to reduce the vulnerability to cyberattacks as hackers target possibly less secure industrial networks. Cybersecurity systems that protect industrial embedded devices and data from malicious updates during regular software, firmware and configuration updates are increasingly available.
Power – technology requires more monitoring and protection of power sources and delivery. It is essential that OT can be remotely monitored, and the power delivery managed within the specific requirements of the equipment as power surges
AI drives predictive maintenance and swarm intelligence, and with cognitive and contextaware computing manufacturing is becoming more efficient and effective.
can disrupt, and even destroy sensitive circuit boards. PDU (power distribution units) within OT cabinets/enclosures will ensure power is constantly monitored and alerts can be set in situations where a service visit is required. Power ratings for edge computing application like retail stores are typically ranging from 5kVA to 10kVA.
Environmental – Sensors around sensitive technology help monitor and respond to extreme temperatures, humidity and other environmental conditions that can impact network performance.
System Software – Increasing processing power is allowing OT to collect, filter and process realtime data from Edge deployments, meaning better understanding of the operation of the equipment.
Connectivity – Intelligent network patching solutions simplify remote management and updates.
Hardware - The Edge environment and equipment needed will dictate the enclosure required for any deployment. In highly protected areas, standard ITE
cabinets maybe suitable, while in harsh environments specific rated enclosures will be required to ensure protection and security.
Increasing trends toward preconfigured and populated intelligent enclosures make installation fast, and consistent. A trend is to have identical BOM, ensuring identical Infrastructure components are installed globally. This is becoming a key advantage when deployment is across multiple locations that must communicate, but where dedicated on-site IT staff are not available.
Cabling and Connectivity in a mixed IT/OT environment means standards-based cabling and connectivity solutions guarantee a robust deployment operates as specified and to the highest level of equipment and data performance.
Factory data silos are being replaced as their data lakes offer the capability for AI and machine learning to drive innovations in OT and factories are beginning to integrate AI across production systems. AI drives predictive maintenance and swarm intelligence, and with cognitive and context-aware computing manufacturing is becoming more efficient and effective. Power rating, per cabinet housing AI installations, is on average 50kVA today. With 100kVA predicted for future installations.
Industry 4.0 may finally be with us, as network and connectivity developments, such as edgeto-cloud, low-power wide-area networks (LPWAN), gigabit ethernet, unified IoT frameworks and others become critical to the success of industrial networks and the organisations that deploy and rely on them.
www.panduit.com/edge
Next-generation cabinet with custom configurations to meet your network needs.
Next-generation cabinet with custom configurations to meet your network needs.
Next-generation cabinet with custom configurations to meet your network needs.
Scalability
Scalability
Configuration platform to create cabinet to meet your specification and requirements
Configuration platform to create cabinet to meet your specification and requirements
Scalability
Configuration platform to create cabinet to meet your specification and requirements
Ease of Use
Ease of Use
Easy to adjust E-rails, PDU installation and accessories to reduce installation time
Ease of Use
Easy to adjust E-rails, PDU installation and accessories to reduce installation time
Easy to adjust E-rails, PDU installation and accessories to reduce
Maximum Cooling 80% perforated doors for increasing power density in newer deployments
Maximum Cooling 80% perforated doors for increasing power density in newer deployments
Maximum Cooling 80% perforated doors for increasing power density in newer deployments
Universal design for server or network applications
Flexibility
Universal design for server or network applications
Flexibility
Universal design for server or network applications
Integrated Intelligence Turnkey deployment with pre-configured PDU, access control and environmental monitoring
Integrated Intelligence Turnkey deployment with pre-configured PDU, access control and environmental monitoring
Integrated Intelligence Turnkey deployment with pre-configured PDU, access control and environmental monitoring
www.panduit.com
Robust
Robust
Solid construction with Best-in-Class load rating for secure installation
Robust
Solid construction with Best-in-Class load rating for secure installation
Solid construction with Best-in-Class load rating for secure installation
Security
Choice of key lock, 3-digit combo or HID electronic and/or keypad lock.
Security
Security
Choice of key lock, 3-digit combo or HID electronic and/or keypad lock.
Choice of key lock, 3-digit combo or HID electronic and/or keypad lock.
Enhanced Cable Management
Choice of tool-less fingers, vertical cable manager and front-to-back cable manager
Enhanced Cable Management
Enhanced Cable Management
Choice of tool-less fingers, vertical cable manager and front-to-back cable manager
Choice of tool-less fingers, vertical cable manager and front-to-back cable manager
As logistics operations and warehouses grow older, not only does the technology contained within wear out, incurring more regular downtime, it also naturally becomes outdated – unable to keep pace with modern requirements driven by omnichannel logistics, e-commerce, the demand for small order sizes and handling faster order picking speeds.
It makes sense to plan modernisation in good time, before a system or equipment reaches service life expiry. For those concerned about the cost and convenience of a major replacement or modernisation programme, consider retrofitting.
Modernisation offers the opportunity to adapt intralogistics systems to meet new requirements and to make them more efficient and reliable. This means maintaining the basic structure of a warehouse in terms of storage zones, layout, conveyor and storage systems, but modernising individual items of materials equipment and creating new processes. This will increase performance and improve overall warehouse system availability. Sometimes the modernisation of a warehouse can even avoid the need to construct a new building or an expensive extension of an existing facility.
A retrofit is a refurbishment and modernisation of existing intralogistics systems. The advantages of retrofitting include lower planning and implementation costs compared to
a new purchase or new installation. The risk of failure is also reduced compared to completely new systems. Not only is modernisation in this way resource-friendly, but also employees can continue to work in the existing facility for as long as possible.
There are many individual areas that can benefit from retrofitting. One important area to focus on is picking operations. If a picking system no longer proves efficient and ergonomic, a company must be able to react quickly to adapt their existing storage system to the new conditions. Given that most warehouses have pallet racking as their major item of materials handling equipment, this presents a great opportunity for modernisation, with a number of picking options that can be retrofitted in pallet racking at ground level, which is the prime order picking area.
BITO pallet racking has been designed to allow fast adaptation to different needs, providing customers with a maximum amount of flexibility. There is a vast range of accessories and ancillary products, which allows many easyto-implement reconfiguration
If a picking system no longer proves efficient and ergonomic, a company must be able to react quickly to adapt their existing storage system to the new conditions.
variants. For example, by fitting flow levels at floor height, pallet racking can be adapted for picking individual packaging units or single items whereas the pallet storage levels on top are used as a buffer store.
Retrofitting options for pallet racking include drop in sections of roller tracks for unit or piece picking, push-back roller track levels also for unit or piece picking, full-width roller lanes for pallets, container pick walls, shelving, dropon wire shelves, chipboard panel decking, inclined shelving and steel panel decking.
These options provide numerous advantages such as a substantially higher number of reference lines, shorter travel routes, reduced pick times, maximum configuration
flexibility and excellent ergonomic conditions for strain-free working.
Of course, modernisation does not result in a new warehouse, but it will bring it up to date and extend its service life. The project will involve investment, a detailed concept and preliminary planning. The new components have to be coordinated with the existing ones. It is also important to ensure that existing components are not overloaded by the performance of the new ones, which might cause them to fail. The implementation of retrofitting measures during ongoing operation must also be planned in detail so that warehouse operations are not disturbed or even interrupted.
It is worth seeking out a storage system supplier, such as BITO, which in addition to offering racking, shelving and flow lanes, also provides a plastic container range comprising a variety of sizes and a broad choice of accessories. This will ensure the modernised system is designed to fit a given space, maximising the potential for improved picking efficiency and material flow.
www.bito.com
Warrington based Christeyns Food Hygiene (CFH) has acquired H&M Disinfection Systems Ltd, who design, manufacture and install cleaning and disinfection systems for the Food, Dairy and Beverage industries.
In operation since 1989, H&M’s modern manufacturing site near Northwich manufactures high quality pump sets, control panels and hygiene systems as well as bespoke units built to individual requirements. With over 30 years of experience in their respective fields the two firms have been partners for many years, providing a turn-key solution for effective cleaning and disinfection operations.
The acquisition will see the H&M facility continue to operate from their existing premises with all staff in place.
Christeyns Food Hygiene is highly regarded in the industry for its effective formulations of detergents and disinfectants for all
This acquisition will increase CFH’s engineering team and significantly bolster our service offering to clients across the UK and Eire
applications in the food, dairy and beverage industries with customers from across a range of household consumer brands and suppliers to the UK’s food retailers. CFH is part of the Belgium owned Christeyns group.
“As we continue our growth strategy, we are delighted to confirm that H&M has become part of the Christeyns family. This acquisition will increase CFH’s engineering team and significantly bolster our service offering to clients across the UK and Eire,” commented CFH Operations Director & Managing Director, Andy Bethel.
“We regard H&M as an expert in its field, with a reputation for
providing high quality, bespoke hygiene application equipment, the cornerstone of many customer’s food safety management systems. Already working with us as a partner, this was a natural move forward and will ensure a broader, highly enhanced service and health and safety offering for all our customers,” concludes Bethel.
The current CFH engineering offering for the optimisation of water, energy consumption, dosing, time and labour will be further strengthened, combining both chemical and engineering expertise including an expanded equipment portfolio, CIP sets, Washdown Systems, Bulk tanks and bespoke engineering.
Stephen Hall, H&M comments: “This is an exciting development for all parties with new opportunities and a further blending of skills and experience that will create a stronger engineering division overall.”
www.christeyns.com www.hmdis.co.uk
• New handheld printers from Bentsai
• Print up to 24.5mm high on any surface
• Programmable with barcodes, QR codes, logos, date and time info
• Solvent black ink come as standard but aqueous and coloured inks available
• Prices start from just £325
The coupling specialist Enemac from Kleinwallstadt has developed stainless steel overload clutches especially for torque limitation in chain and timing belt drives in filling, cleaning and packaging systems. The ECI_ES and ECR types fulfil the strict hygiene requirements of the food, pharmaceutical and medical industries.
The ECI_ES torque limiter is designed for use with wide toothed belt pulleys, sprockets or gear wheels. Thanks to the extra-wide bearing position, it is easier to fit these components in conveyor and packaging systems. Precise torque limitation is achieved via disc springs, which enable large adjustment ranges without the need for changes. These range from 2Nm to 900Nm for 14 sizes.
Type ECR, on the other hand, is ideal for narrow attachments
Enemac is now offering a new product compass that makes it easier for users to select the right safety and shaft couplings.
such as toothed discs, cardan shafts or components with a connecting flange. This coupling is made entirely of stainless steel and has detent balls with lifetime lubrication that are NSF-registered. With 5 sizes and adjustment ranges
from 50Nm to 350Nm, the ECR is particularly suitable for use in clean rooms in the medical and pharmaceutical industries as well as in the food sector.
Enemac is now offering a new product compass that makes it easier for users to select the right safety and shaft couplings. This digital compass enables intuitive and fast navigation through the extensive product range. Users can select couplings based on specific criteria such as torque range, size, area of application and hygiene standards. The product compass also provides detailed information on the technical properties and application options to find the optimum solution for individual requirements.
www.enemac.eu
High-precision X-ray sources and detectors for the most demanding inspection applications.
Hamamatsu Photonics provide the fastest and highest quality X-ray inspection technology for non-destructive testing. By obtaining top-level precision in detection and visualisation, our extensive product range is assisting OEM and systems integrators in a wide range of unique and demanding applications. Our products have advanced the detectability and measurement of defects and contaminants at unprecedented speed, resolution, and power.
Shining a spotlight on the key challenges facing UK manufacturers and the ways in which automation can address them, FANUC UK’s annual Open House returns this autumn. Taking place at the company’s UK headquarters in Ansty Park, Coventry on 12-14 November 2024, the event will bring together speakers from global giants such as Airbus, Amazon and Cummins with automation influencers from Make UK, Automate UK and FANUC Europe. In addition to 30+ exhibitors, live robot demonstrations and the live final of the WorldSkills UK Industrial Robotics competitions, visitors can enjoy presentations, panel debates and discussions from over 20 automation experts on such hot topics as the current state of UK manufacturing, how to attract young people into manufacturing, and the adoption of robotics into SMEs.
Hands-on robot experiences
FANUC’s Open House has now firmly cemented itself as an unmissable highlight of the automation calendar, attracting a mix of over 600 manufacturers, robotics experts, academics, students, MPs and press. Each morning is focused on speaker presentations and panel debates, while the afternoon sessions are devoted to hands-on robotics experiences. Visitors are encouraged to take part in FANUC Academy taster sessions, enjoy live demonstrations of the latest automation innovations, network with peers, seek solutions from FANUC’s exhibitor partners, and support the talented young people competing in the WorldSkills UK finals.
FANUC’s Open House has now firmly cemented itself as an unmissable highlight of the automation calendar, attracting a mix of over 600 manufacturers, robotics experts, academics,
In-depth presentations: Airbus’ automation journey
Reflecting the key challenges facing today’s manufacturers, each day has a distinct theme:
• Day 1 (Tues 12 Nov): Enabling Step Change for Automation Adoption
Following the opening address by Managing Director Tom Bouchier, Marco Chacin of Airbus will take to the floor with FANUC’s Oliver Selby to discuss the aerospace company’s automation journey in conjunction with FANUC.
Further sessions will focus on ‘Successes and Challenges of Global Automation’, ‘The Current State of UK Manufacturing and the Future for the Sector’, plus a panel debate focusing on an SME stakeholder’s perspective, featuring speakers from Cummins and Hennik Research.
• Day 2 (Weds 13 Nov): Education for Automation Adoption
Highlighting the importance of inspiring and supporting the next generation of manufacturers, Day 2 will feature presentations from current Amazon apprentices, Rosa Wells of University College Birmingham, and the 2023 winners of the WorldSkills UK Industrial Robotics competition.
A panel debate with insight from automation influencer Mike Wilson and other UK Automation Forum members will also discuss what needs to be done to attract more young people into manufacturing.
• Day 3 (Thurs 14 Nov): UK Automation 2030
The final day of Open House 2024 will begin with an address from FANUC’s European President, Marco Ghirardello. Chris Corkan
After the success of last year’s event, which attracted a record number of visitors, I am even more excited to open our doors this November and show the manufacturing community just what automation can do for their business.
of Make UK will then consider the ‘State of the Nation: UK Manufacturing’, before Automate UK’s Peter Williamson discusses ‘Changing Culture and Policy to Drive Greater Robot Adoption in the UK’.
The event’s seminar programme will close with a panel debate by the West Midlands Robotics Cluster – featuring Mike Wilson, Tom Bouchier and Rachael Eade MBE –into ways to increase the adoption of robotics into SMEs.
Inspirational young talent “After the success of last year’s
event, which attracted a record number of visitors, I am even more excited to open our doors this November and show the manufacturing community just what automation can do for their business,” says FANUC’s UK Managing Director, Tom Bouchier.
“From alleviating labour challenges and increasing productivity to improving sustainability credentials, there are so many ways in which automation can empower British manufacturers to futureproof their enterprises
and ensure that as a nation, we can continue to compete on the world stage. Encouraging young people into the industry is essential to this vision, and the array of burgeoning manufacturing talent on display at Open House will be an inspiration to many. I look forward to welcoming visitors to our Coventry HQ this November.”
To register your interest in attending the FANUC UK Annual Open House (12-14 November 2024, Ansty Park, Coventry), go to https://ukopenhouse.fanuc.eu
The event will bring together speakers and over 30+ exhibitors. Visitors can seek solutions from FANUC’s exhibitor partners and support the talented young people competing in the WorldSkills UK finals.
Vision sensors are the ‘eyes of industrial automation’. That is because the devices enable machines to see and interpret their surroundings. Anyone looking for a particularly powerful sensor for print quality verification can now find what they need in the DCR 1048i OCV from Leuze: It can read 1D/2D codes within one application and also check quality using the OCV process. This makes it possible to reliably determine whether the best-before date, batch or other printed information is present, complete and legible. Optimal visual verification
OCV stands for “Optical Character Verification”. Users can teach the vision sensor for OCV print quality verification quickly and easily. All you need to do is present it with a
Users can teach the vision sensor for OCV print quality verification quickly and easily.
reference image of the optimum print.
The DCR 1048i OCV then reliably detects defective printing – for example due to, clogged print heads, low ink cartridges, or
adhesion problems. Once the threshold value is set, products recognized as defective can be rejected. The DCR 1048i OCV offers an efficient and flexible solution for production processes.
Simple Vision: Simple setup, efficient detection
Performance, flexibility and usability are what count when it comes to image processing sensor technology for industrial automation. Simple Vision sensors meet these requirements. They are as easy to operate as optical sensors, plus they are as powerful as camera systems. The Sensor People from Leuze offer this concept as a quick and straightforward introduction to vision technology.
www.leuze.com
During a recent upgrade of their previous packaging line, one food development company discovered significant improvements in usability and flexibility. In addition, they experienced further benefits from discussing the whole project with their suppliers, Yorkshire Packaging Systems (YPS).
“The company’s previous line had been purchased from YPS some considerable time ago and has served them well, with extensive use,” explained YPS MD Glyn Johnson. “It had come time for the company to replace it and, as they’d appreciated the service and support we delivered last time, they returned to discuss their new requirements with us.”
The company produces bespoke baked goods, with a focus on ingredients with nutritional benefit. As their products are developed and created on behalf of other food companies, there is a wide variety in finished size of product. Packaging requirements such as collations required and materials used, including branded and non-branded films, are all defined by the onward customer to their own needs.
Full discussions of their requirements followed by demonstrations of the latest models led the company to opt for a Pratika MPE X2 fully-automatic l-sealer, plus a new shrink tunnel and conveyor.
Key to their decision was the ease of use of the new l sealer, especially the simple way to save recipes for different products. This feature of the new line makes for quick and easy changeovers, vital when their product range includes such differing items.
Additionally, the HMI is especially user friendly, with 180° movement so it can be positioned for the
The
customer is delighted with the equipment supplied, which delivers more benefit than they’d originally hoped for.
operator’s convenience. The HMI is paired with the compatible shrink tunnel for total control of the whole operation from the same spot. The low-level film holder, batwing doors and extended infeed conveyor make loading of film and products much safer and easier.
The versatility of the l sealer, including its height adjustable sealing jaw, has proved ideal for the variety in the producer’s range and is also significantly quicker than the previous line, delivering improvements in production speed.
To complete the package, YPS helped the customer to specify an appropriate film for optimal
performance of the system. The film selected contains 30% recycled content and is ultra-thin for savings in plastic use.
“The customer is delighted with the equipment supplied, which delivers more benefit than they’d originally hoped for,” stated Glyn. “The included service contract also gives them peace of mind that they can get to grips with the new system with our support. It was a pleasure to work with them again and to find a solution that has helped to move their production forward.”
www.yps.co.uk
Mettler-Toledo Product Inspection, a global leader in precision instruments and product inspection technology, has extended its Combination inspection portfolio with the launch of new CM (checkweighing and metal detection) and CX (checkweighing and x-ray) Combination Systems. This significant advancement integrates the new M30 R-Series metal detectors and X2 Series of high performing x-ray inspection systems into high-precision C-Series checkweighers, providing customers with maximum flexibility to choose the right system to suit their individual application, packaging and budget requirements.
With the introduction of the next generation of the CM and CX Combination Systems, MettlerToledo delivers powerful 2-in-1 inspection solutions that manage Critical Control Points (CCPs) by combining precision weighing with contamination detection in an integrated solution. These new systems offer simplified operation, a space-saving design and reduced total cost of ownership. The integration of the new M30 R-Series and X2 Series also offers higher detection sensitivity, providing an added layer of security and quality control.
The CM Combination System (Checkweighing and Metal Detection)
The CM Combination System integrates the precision weighing C-Series checkweighers with the advanced M30 R-Series metal detectors, creating a completely flexible solution that enhances the portfolio of combination
systems with an optimised priceto-performance ratio. The C-Series checkweighers deliver unparalleled accuracy and precision in weight measurement, facilitating compliance with regulatory standards and minimising product giveaway. They feature intuitive user interfaces and advanced data management capabilities, allowing for seamless integration into existing production lines, plus a smaller machinery footprint accommodates limited factory floor space. For high-end applications, these innovative systems can be configured with the new FlashCell™ load cell technology, this means that the checkweighers can complete precision weighing checks at higher product throughputs.
The M30 R-Series and Profile metal detectors are equipped to detect a range of ferrous, nonferrous, including aluminium and stainless-steel contaminants
optimising for both wet and dry applications. They offer the highest level of product safety and quality. Utilising advanced signal processing and intelligent detection algorithms, the metal detectors provide superior sensitivity and reliability, improving the capability to detect smaller contaminants and significantly reducing false reject rates.
The combination of these advanced technologies allows manufacturers to tailor inspection solutions to their specific application, packaging and budget needs. By merging precise weighing capabilities with state-of-the-art metal detection, customers achieve maximum flexibility to meet diverse packaging requirements. The system also boasts a spacesaving design with full integration on a single frame, facilitating easy cleaning and maintenance while optimising production floor space.
The integration of the new M30 R-Series and X2 Series also offers higher detection sensitivity, providing an added layer of security and quality control.
The CX Combination System integrates the high-precision C-Series checkweighers with state-of-the-art X2 Series x-ray inspection systems, creating a powerful solution for comprehensive quality control. The X2 Series x-ray inspection systems feature innovative ContamPlus™ Software, which runs over 30 inspection algorithms continuously and in parallel, detecting hard-to-find foreign bodies while reducing waste. Also featuring the HiGain detector technology, which generates sharper images to deliver outstanding contaminant detection, these systems are capable of identifying a wide range of contaminants, including metal, glass, stone, calcified bone and high-density plastics, while also performing quality assurance checks such as detecting missing or broken products.
Combined with the precision weighing capabilities of the C-Series checkweighers, equipped with FlashCell™ technology, this integration offers unparalleled accuracy and consistency for various packaging needs. By bringing these two technologies together, manufacturers can benefit from increased productivity and decreased total cost of ownership. The smart industrial design features easy operation with quick, toolless access to components, enabling belt and curtain removal in less than five minutes. Intuitive user interfaces further simplify operation. An additional option is a Smart Catch Bin, the intelligent separation of contaminated or incorrectly weighed products can also help to enhance both safety and efficiency. This integrated solution not only improves detection sensitivity but also optimises overall production line performance.
Flexibility: Multiple inspection combination options provide manufacturers with maximum flexibility to find the right solution for their packaging, application and budget needs. This flexibility is achieved by combining the latest advanced contamination detection technologies i.e. M30 R-Series metal detectors and X2 Series x-ray inspection systems, meaning that every need is met.
One-touch operation via the checkweigher supports easy and automated product changeovers. Statistical and status information for the contamination detection solution and checkweigher are available via one Human Machine Interface (HMI), reducing operator training requirements and minimising the risk of user errors. The advanced HMI design improves usability, making the Combination System user-friendly.
Space
Shared components, such as conveyors, provide space savings, and having less feet on the floor facilitates easy cleaning.
A single vendor solution provides documentation, installation, configuration support, training and service for two technologies in one, reducing costs over the long term.
Checks: Vision inspection technology is available as an additional option, making a powerful 3-in1 system which can provide comprehensive quality control by detecting packaging defects, verifying label information and maintaining product integrity.
Industry 4.0 Ready: Both Combination systems can be connected to ProdX™, a stateof-the-art product inspection management software. This complete quality inspection data management system delivers full digital management of product inspection equipment for realtime monitoring and food safety compliance. Visibility of the data can help improve productivity, food safety traceability and facilitate regulatory compliance.
Joern Migge, Head of Product and Market Management, MettlerToledo, says, “We are excited to introduce the new CM and CX Combination Systems to our customers. These innovative solutions provide unparalleled flexibility, enhanced efficiency and significant cost savings. By integrating the latest M30 R-Series metal detectors and X2 Series x-ray inspection systems, we are able to deliver maximum protection and quality assurance for our customers’ products.”
For more information, click here or visit www.mt.com/pi-ideal-combipr
One of the largest premium flour and ingredient companies in North America, Ardent Mills, recently implemented automatic testing on several of its conveyor Fortress Technology metal detectors. A number of the company’s packaging lines are now also using digital reporting to enhance efficiency, food safety and traceability.
Ardent Mills has an expansive national footprint. Comprising over 40 locations producing flour, quinoa and pulses, organic and gluten-free products, Ardent Mills recognises the importance of embracing the newest digital technologies to ensure that every aspect of its operations remain true to its quality standards. Processing around 22.4 million bags of packed milled product annually, over the last 12 months Packaging Engineer Manvine Bharj and her team, supported by local Fortress food safety specialists, has set up Halo Automatic Testing on six inline conveyor packaging lines.
At the mills that ship packed product direct to retailers and commercial bakeries, Ardent implements an end-of-line HACCP testing point, just before palletising. “We intentionally test our inspection equipment more often than our customers’ conformance requirements stipulate, as it provides extra quality assurance and fills us with confidence that our products are the safest they can be,” notes Manvine.
Activating the technologies preinstalled on their Halo Ready Fortress metal detectors has proven to be an efficiency and safety gamechanger for many of the mills’ quality managers. The resulting operational savings have been equally rapid. Manvine estimates the ROI on the original
Ardent Mills requested a blue light system to alert operators when a Halo test is running.
Stealth Metal Detector investment has been achieved in six months or less. “Halo provides the perfect blend of inspection continuity, contaminant detection, machine performance and safety,” adds the Packaging Engineer.
Like many mills and bulk processors, one of the greatest challenges when performing repeatable manual tests is the amount of time and labour it requires and simulating the same conditions for each test. UK Sales Director Phil Brown explains:
“Manual testing in milling environments often requires placing a test sample in the exact middle of each grain bag, passing this through the metal detector, removing it from the line, opening the packaging and removing the test sample, and inspecting it again. Testing all three metals, every two hours is a lot of heavy lifting, sifting, repacking and potential waste. Not to mention, replicating this test manually is extremely challenging to do accurately.”
Halo Automatic Testing instead independently tests all three
Activating the technologies preinstalled on their Halo Ready Fortress metal detectors has proven to be an efficiency and safety gamechanger for
many of the mills’ quality managers.
metals in the exact geometric centre of each Stealth metal detector aperture. The technology then mimics the disturbance caused by a test contaminant calibrated to the precise size, metal type and speed of each product bag as it passes through the metal detector aperture.
“With automated tools like Halo and Contact 4.0 we are proactively preventing issues for our team members, all while improving customer service and overall food safety,” reports Manvine.
In order to distinguish between a real metal detection reject and when a Halo test is being performed, the milling business requested one customisation – a blue light system to alert operators when a test is running.
“This feature alone has made a huge impact on our labor demands and potential product waste. Without this blue light we would have to either sift and rework every 50lb test sack assuming it was contaminated, or simply reject and waste it. That could have added up to re-inspecting 12 sacks, 600lbs of flour, per line, every shift,” highlights Manvine
With many sites moving towards paper-lite processes, automating QA documentation has been a crucial step in maximising both equipment and operator efficiency, reports the milling business.
As a web-based networked system, Contact 4.0 allows operators to monitor multiple metal detectors. “Our quality managers loved Contact 4.0 as soon as it was implemented. As a networked system, it’s so easy to go into the centralised browser, select and email shift reports and view when tests were performed. Having this complete oversight allows them to immediately address issues and ensure the inspection process doesn’t cause a bottleneck,” exalts Manvine.
The cohesive Contact 4.0 reporting system allows authorised employees to troubleshoot performance issues remotely. Test failure, fault or non-conformity events can trigger an automatic email alert, detailing when an event occurred on a specific machine.
With more facilities eager to switch and activate similar efficiency-enhancing programs, the packaging engineer anticipates ongoing integration projects. Citing real-time information as being the enabler for smarter decision making, Manvine believes that rolling out new technology also ignites curiosity and drives operators to do even better.
Food safety has never been subject to more scrutiny than now. According to the World Health Organisation (WHO), an estimated 600 million people fall ill each year after eating contaminated food. In the UK, contamination and allergen issues are the biggest cause of food recalls, showing a lot still needs to be done to improve around maintaining food safety.
So, how can manufacturers ensure they follow best practices in ensuring our food is safe?
If we look at the production of processed food products on a large commercial scale, there is generally good practice in most factories.
The food and beverage industry has been slower to adopt a formal regulatory framework than industries such as pharmaceuticals, for example. If we look at global trends, the tendency is to hold suppliers responsible for all aspects of the supply chain, in the case of ‘from farm to fork’. Even the best-managed factory depends on the quality of its raw materials. But sometimes processes can be interfered with, making vigilance along the supply chain as important as inside the processing plant.
Around the world, most food safety regimes rely on a Hazard Analysis of Critical Control Points (HACCP) methodology. This requires a supplier to evaluate risk areas in the production and supply chain and ensures measurements and tests at critical points detect problems before the product is shipped. For example, if a sterilisation process is required, a record of temperature against time must be maintained and reviewed before shipment. And with this comes an increasing focus on prevention rather than detection.
Digitised data is easily transmitted from place to place and may be backed up without compromising integrity
Food safety management systems are multifaceted, making them complex. They will incorporate everything from hygiene and plant organisation through to maintaining records of production parameters and equipment calibration, as well as the traceability of batches in case a product is recalled.
As a result, facilities will obtain a huge quantity of data each week. But for a long time, the industry has relied on manual ways of data logging and monitoring, usually involving paper. Yet, the experience of other regulated industries is that however attractive paper might seem, digital records will always come out on top. Particularly in the case of audits by the governing regulator.
Take for example, the logging of refrigeration temperature. Good manufacturing practices (GMP) require reliable record-keeping to demonstrate that air temperatures, pack temperatures and door open and closed signals are kept within certain parameters. This is extremely important to prove that safety criteria for refrigeration
during food storage and processing has been monitored and adhered to.
Keeping paper records onsite without any possibility of backup is problematic in any case. For example, documents can be falsified, particularly if operators at various process steps record temperature readings in handwriting.
The solution is the digitisation of data, as well as the automated recording of process data around critical control points. Digitised data is easily transmitted from place to place and may be backed up without compromising integrity. It also creates a ‘digital thread’ running from ‘farm to fork’ that provides suppliers with instant access to critical data for audit and for internal quality check tests.
Producers seeking to implement digital data logging can opt for a system like the F4T® temperature controller, which has data logging built in. With these options, users can record pre-set data, cutting down on setup time and hassle. Watlow’s tools also include a list of common setups to help producers find the best way to log data that fits their needs, making implementation as easy as possible.
Food safety should be the first concern of any responsible supplier, but with over half a billion people falling ill each year to the food they consume, it’s clear there is room for improvement. The industry must rid itself of all manual and paper processes, and instead implement digital solutions that are reliable, more efficient and make tracking food through the supply chain easier to monitor.
www.watlow.com
www.ndc.com/food-bulk-materials-processing/
The new product VisioPointer® is one of ree new Vision Inspection products from Minebea Intec and fur er enhances e already popular inspection portfolio. It is also one of e key products at helps drive automation wi in food production and manufacturing. Combined wi e Automatic Weigh Price Labeller WPL-A customers can automate eir entire end of production line where labelling plays a significant part of e manufacturing.
The new product VisioPointer® is one of ree new Vision Inspection products from Minebea Intec and fur er enhances e already popular inspection portfolio. It is also one of e key products at helps drive automation wi in food production and manufacturing. Combined wi e Automatic Weigh Price Labeller WPL-A customers can automate eir entire end of production line where labelling plays a significant part of e manufacturing.