FOOD & DRINK PROCESSING & PACKAGING
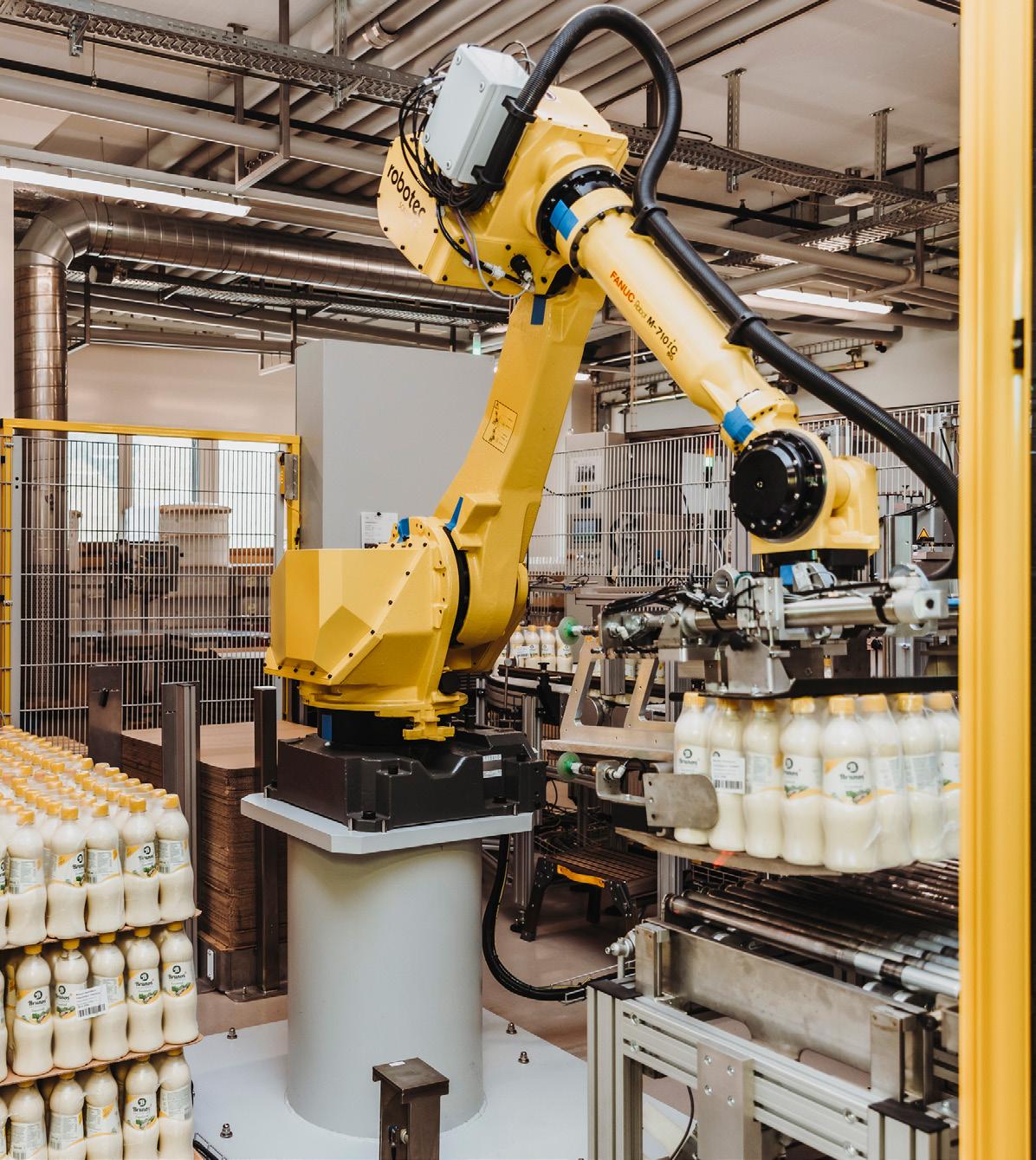
Tosca expands European operations with new service centre in Ingolstadt, Germany
Dairy inspection sensitivity gets smarter
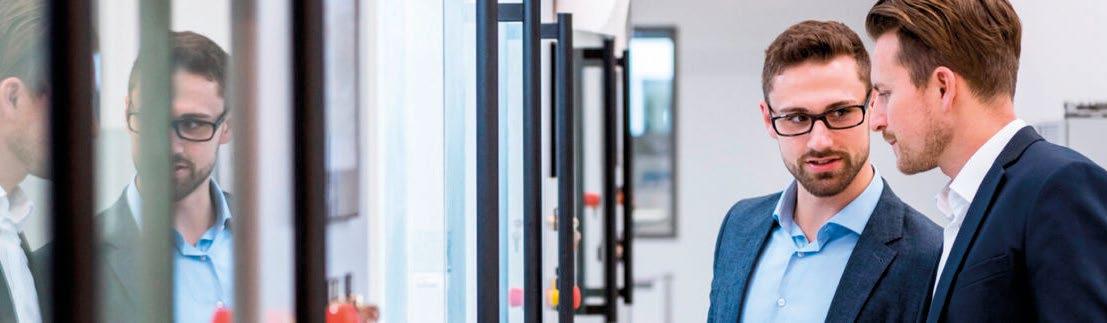

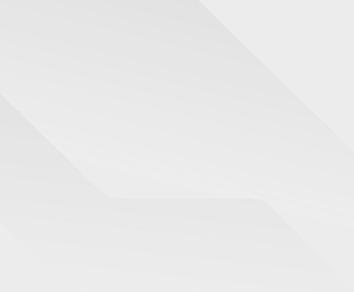
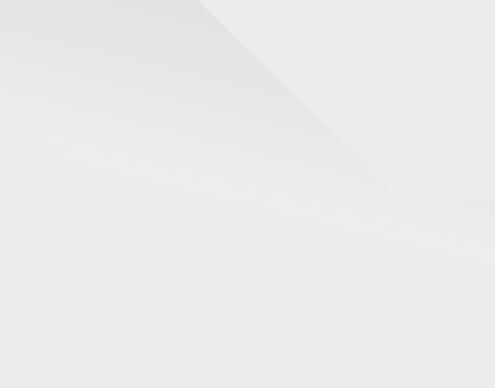











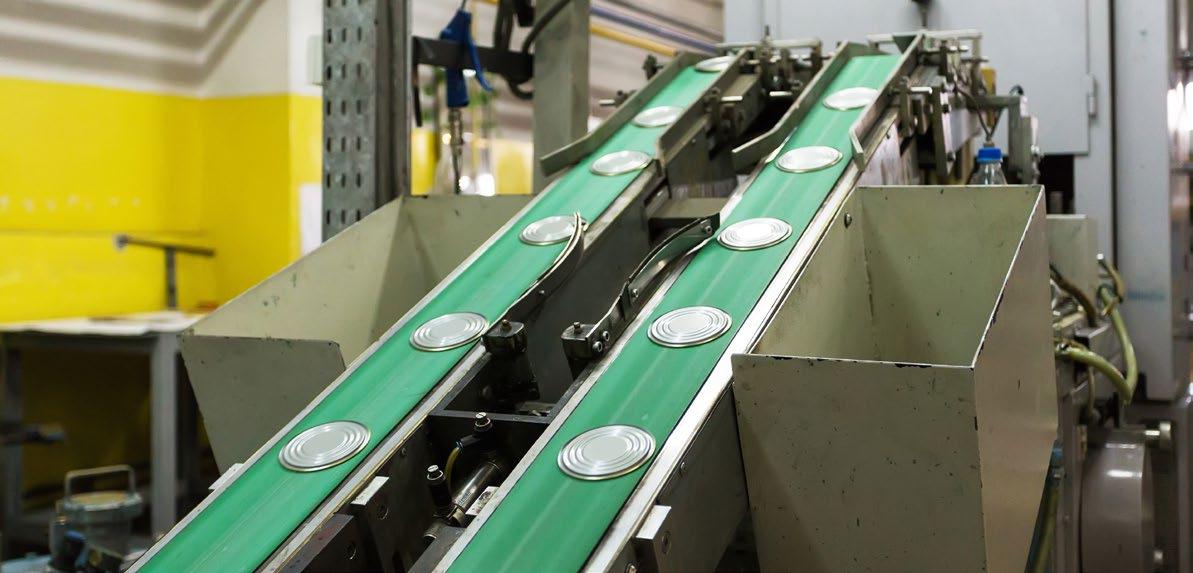
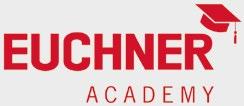

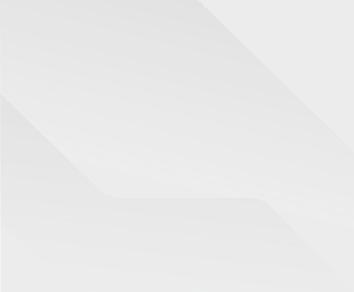
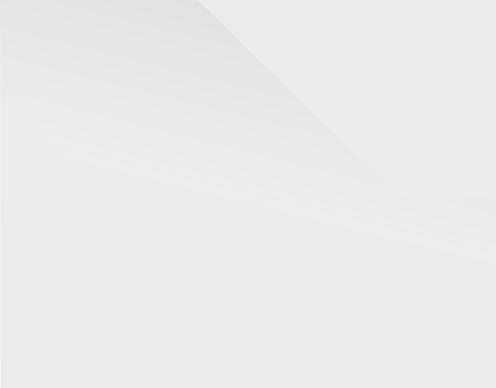
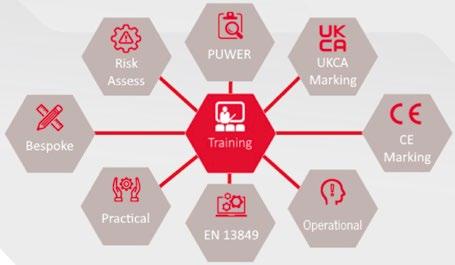
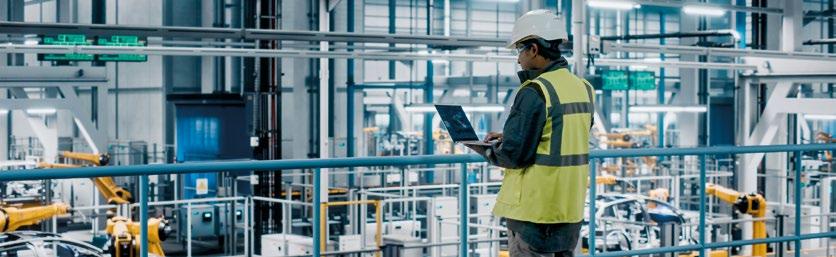
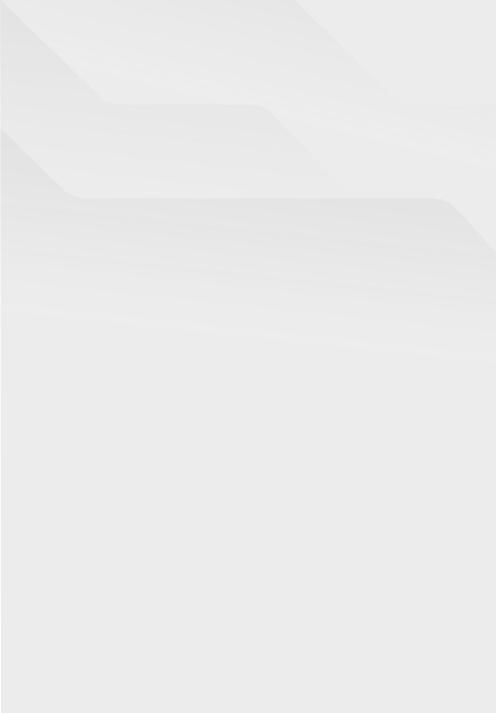
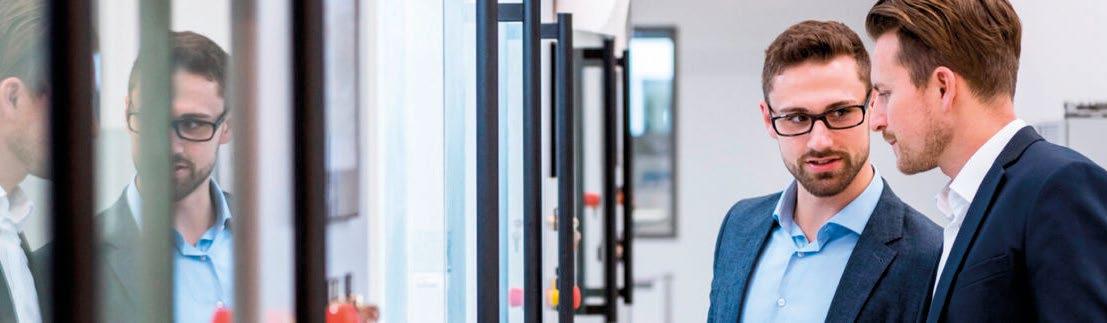
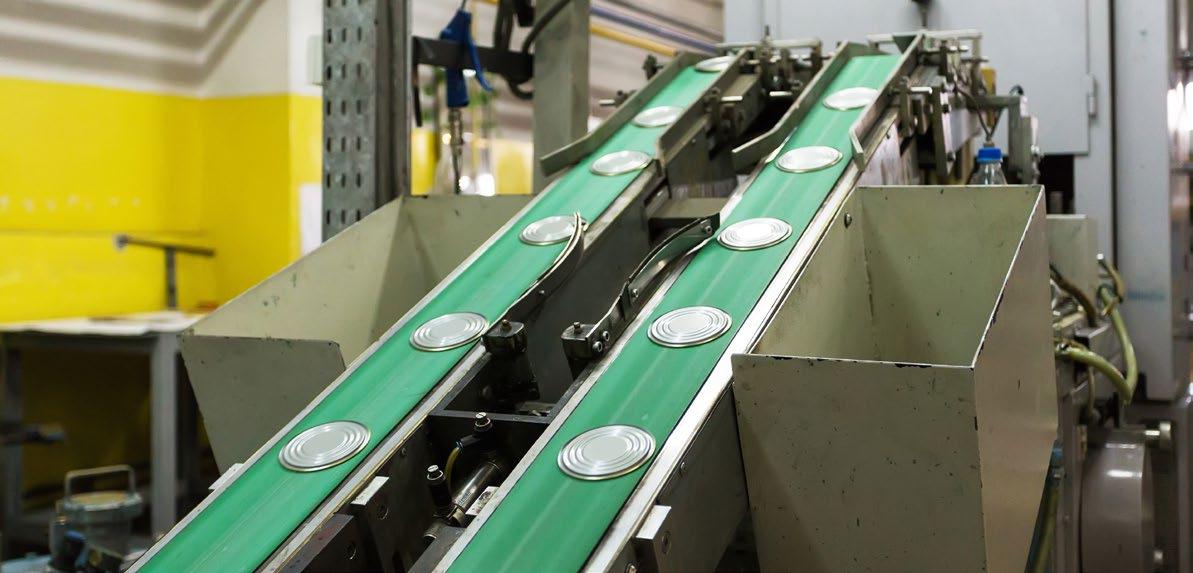

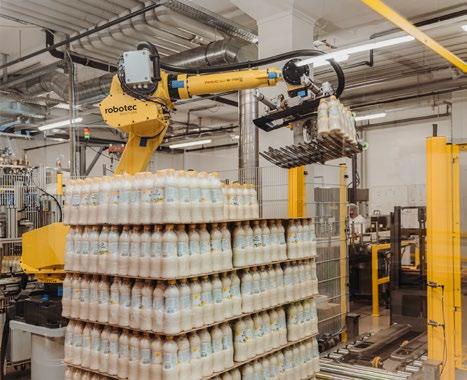
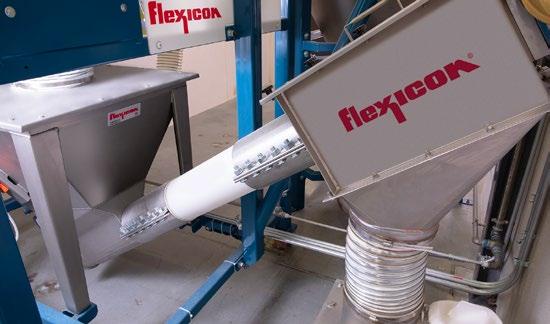
Business
01227 392571
Newington Road, Ramsgate
CT12 6EE
01304 806039 www.fdpp.co.uk



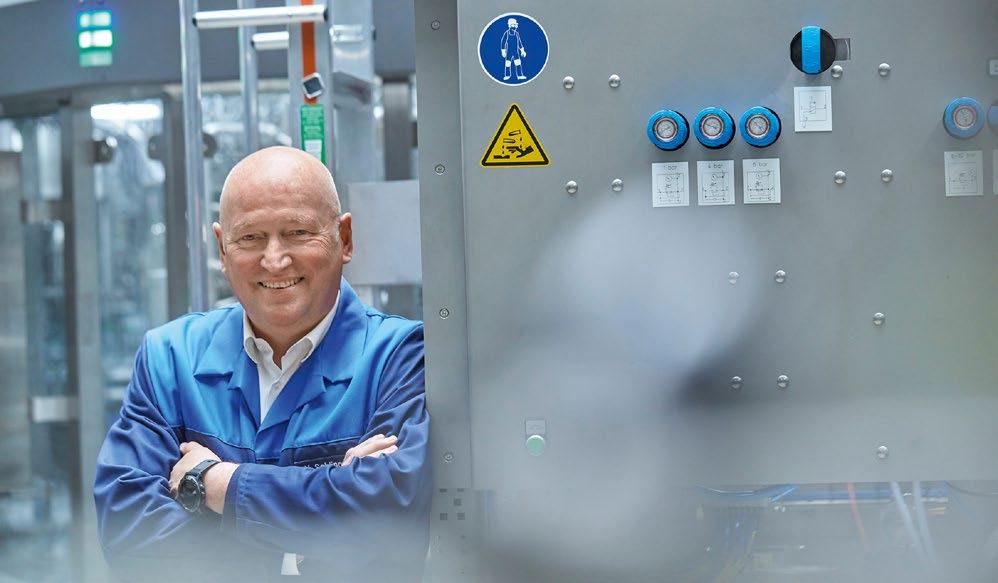
Tosca expands European operations with new service centre in Ingolstadt, Germany
Dairy inspection sensitivity gets smarter
Business
01227 392571
Newington Road, Ramsgate
CT12 6EE
01304 806039 www.fdpp.co.uk
With ultrasound, deposits on bottle washing machines, for instance, can be clearly reduced, cleaning intervals lengthened and downtimes shortened – not to mention the savings in energy and resources. German mineral water bottling plant Staatlich Bad Meinberger has put this simple principle into practice – and is delighted with the results.
“When it comes to sustainability and resource efficiency, we’re one of the pioneers,” explains Robert Mühlenweg, technical and logistics plant manager for the beverage producer. “Our colleagues in the sector thus like to come and see how we’re cutting down on our consumption of water and energy.” As an SME bottler it’s important to move with the times, he believes. And that’s not all: “As we frequently push ourselves to the limit, we tend to be noticed
in our branch of industry.” When he and his colleague Jannis Maas, the plant manager responsible for production and supply at BAD MEINBERGER, talk about cutting down on their carbon emissions, they mean genuine climate neutrality – and not mere compensation through the purchase of certificates. Their attitude and resulting success has earned them great trust and plenty of freedom among the managing directors. “In order to further improve our various consumption values, we often try new things out and sometimes even dare to experiment.”
They began exploring one such new avenue with KHS in March 2022 – incidentally not for the first time, for the mineral water company enjoys a long technological partnership with the Dortmund systems supplier.
The bottler has repeatedly acted as an extended workbench and pilot customer to the nearby machine and systems manufacturer, enabling new and further developments to be tested under real conditions and fine adjustments made where necessary.
This time the technology isn’t new, however, but a procedure that’s been in use for many years in a completely different sector, namely shipbuilding, and is now being applied to the beverage industry. KHS HASYTEC Dynamic Biofilm Protection is a simple plug-and-produce product where ultrasonic transducers cause the liquid in certain components of the machine to gently vibrate. The system is currently available for both bottle washing machines
and pasteurizers – whether for new machines or as a conversion for existing systems.
At BAD MEINBERGER Dynamic Biofilm Protection reduces deposits of biofilm, limestone and fibrous material from paper labels in the spray pipes on the KHS Innoclean EE bottle washer, for example. In the past, without this system machinery often became clogged with deposits that required a considerable amount of effort to remove. “The combination of paper and limestone in particular presented us with a real challenge,” says Maas. “Our colleagues often had to get to work with a chisel!”
not muscle power
It’s not just the time-consuming physical labor that’s hard work when it comes to cleaning machine parts. In the peak season especially, with the plant running at full capacity, finding an appropriate slot for cleaning often proves something of a headache. “Before we installed the ultrasonic converter, the level of calcification on the machine had to be checked at the latest every two months and the machine then descaled and partly dismantled in order to remove the deposits formed. This took up an entire day that had to be blocked off in the production schedule or moved to a weekend. And even if the team is basically motivated to put in a shift on a
When it comes to sustainability and resource efficiency, we’re one of the pioneers.
Saturday or Sunday during the peak season if this is necessary, they’re understandably not desperate to do this work that’s strenuous and unproductive,” Maas emphasizes.
The Dynamic Biofilm Protection system, complete with two control units and twelve ultrasonic transducers, has been in operation at BAD MEINBERGER for about 18 months now. “It was primarily our trust in KHS that prompted us to install the system,” Mühlenweg remembers. “And of course we were also convinced by the fact that the process has been in use for many years without any problems, even in huge shipping containers.” The reason for this is easy to comprehend: the liquid is oscillated, thus keeping the particulate matter contained in it in motion, not by a constant permanent frequency but by intermittent pulses.
In the end, the engineers’ curiosity won them over, resulted in the mineral water bottling plant being one of the first beverage operations to use this technology.
“This was one of the best decisions we’ve ever made,” says Mühlenweg happily. “We often filled an entire wheelbarrow with deposits in the past; now we barely need a 20-liter bucket. And this year we haven’t yet had to carry out a single acid treatment. The system is completely autonomous and practically maintenance free.” Maas smiles that “the new system is making itself noticeable here by being unnoticeable. Or, to put it another way, the best service is the service you don’t need.”
BAD MEINBERGER is also being supported in its striving for greater sustainability by the use of the new procedure. “On the one hand, the Dynamic Biofilm Protection system considerably lengthens the time between cleaning operations and reduces downtime, thus enabling a significant increase in production,” stresses Kathrin Gareis, service product manager at KHS. “On the other, the consumption of water, heat, electricity and chemicals such as citric acid used to descale components is greatly decreased by this system. Besides the cuts in operating costs this results in, this also helps to save energy and resources – an issue which is so important to our customers.”
In this context, Mühlenweg and Maas monitor the quality of the caustic in their bottle washer extremely carefully. They use about 40 cubic meters of it which
– should it have to be discarded –first needs to be brought up to the right temperature and then dosed with new chemicals each time. There’s thus constant filtration during filling and only the exact same amount of fresh water or caustic is added as is lost through the removed labels, for instance. At the same time, owing to specific process parameters that have a high risk of forming deposits, the caustic temperature at BAD MEINBERGER has been lowered through close cooperation with the laboratory. “Most beverage producers use higher temperatures but that’s not our intention,” Mühlenweg states. “In view of the high costs for heat generation, at the moment our sector is undergoing a rethink. Lots of colleagues could follow our lead here.”
Gareis totally agrees and not only sees deposits being greatly reduced and intervals between cleaning cycles becoming longer for both current and future KHS customers thanks to Dynamic Biofilm Protection but also potential for saving on energy and resources.
Ultrasonic transducers to reduce deposit formation on heat exchangers, process water baths, pipes and sprays; option for new machines or as a retrofit for existing KHS systems.
• Longer cleaning intervals
• Less downtime
• Increased production
• Fewer personnel hours needed for cleaning
• Water, electricity, heat and chemical savings
• Lower operating costs
For more information go to: www.khs.com/en/media
How can you package confectionery and baked goods flexibly in a wide variety of pack formats? With pick & place robots that accurately position each product and systems that effortlessly switch between different packaging materials. Saving precious resources –with virtually no waste. This is our Mission Blue. A true benefit for the climate and the many FMCG manufacturers who have been relying on us since 1966. And for you too. www.schubert.group/en/confectionery-snacks.html
How can you package confectionery and baked goods flexibly in a wide variety of pack formats? With pick & place robots that accurately position each product and systems that effortlessly switch between different packaging materials. Saving precious resources –with virtually no waste. This is our Mission Blue. A true benefit for the climate and the many FMCG manufacturers who have been relying on us since 1966. And for you too. www.schubert.group/en/confectionery-snacks.html
Founded in 2001, Brunos produces cooled salad dressings and gourmet butters. Since its inception, sales have risen steadily, prompting this progressive family business to employ increasingly sophisticated production methods to keep up with demand. Now a 45-employee enterprise, Brunos produces four million products each year at its 3,500m2 production facility in Sarnen, central Switzerland.
Although its production line was already automated, until recently, Brunos’ packaging and palletising function was still a manual process. This resulted in bottlenecks at the final stage of the process, as employees struggled to match the speed of the automated line. Unable
to meet increased order levels and at the limit of its capabilities, the firm began to look for an alternative solution – but complex palletising patterns and limited space made their search a potential challenge.
“We had reached our limits,” explains Managing Director Michael Arnold. “By this point, we had two or three employees packing bottles manually into cardboard boxes, but they could hardly keep up with the speed of our production line. We began thinking about an automated solution for the palletising process, but our space was rather tight. We needed to find a solution with a compact footprint that would tie in with our existing
automated processes in terms of quality and productivity.”
Fulfilling complex palletising patterns
Brunos turned to Robotec Solutions AG, a local provider of robot-assisted automation, with more than 800 successful installations to its name across a diverse range of sectors. Jörg Lanz, Head of Sales at Robotec Solutions AG, says: “Working together with our customers, our most important task is to find the best automation solution for the application. In this project to palletise the bottled salad dressings, our main challenges were cycle time, space constraints and palletising patterns.”
We’ve been a FANUC partner for over 20 years and often say we have ‘yellow blood’ flowing through our veins.
With regards to the palletising patterns, Brunos’ production line fills bottles individually before placing them in groups of 6, 10 and 12. These groups then undergo shrink-wrapping in foil. “We needed to devise an innovative palletising pattern based on the pre-grouping
of bottle packs and involving part-rotation,” reveals Jörg. “After completing each layer, we required the robot to place an additional intermediate layer on top. This operation would have to take place without changing the gripper to help minimise cycle time.”
Strong, long and lightweight Robotec regularly leverages the quality of FANUC’s range of industrial robots and collaborative robots (cobots) to fulfil its customers’ requirements. In this instance, the ideal robot for the task was the strong, lightweight and compact FANUC M-710iC/50 6-axis industrial robot with 50kg payload and 2,050mm reach.
“It was clear from the start that we would choose a FANUC robot,” states Jörg. “We’ve been a FANUC partner for over 20 years and often say we have ‘yellow blood’ flowing through our veins. The FANUC M-710iC/50 fits Brunos’
requirements perfectly. Capable of carrying heavy loads, its long reach allows optimal processing of the palletising pattern – and always at full speed. Further plus points include low energy consumption, a small footprint and good availability of spare parts.”
For Brunos, automating its palletising function with the help of the FANUC M-710iC/50 robot has allowed it to keep pace with the production line, enabling the company to fulfil its ever-growing order book. Michael Arnold adds: “We are very happy with the results and success achieved following the introduction of the FANUC robot. It fulfils our expectations in terms of quality and productivity. We are completely satisfied.”
Check out the video here: https://www.youtube.com/ watch?v=t9KOhG0ZYuM
Nordson Measurement & Control Solutions (formerly NDC Technologies) allows international food companies to maximize process performance and KPIs through the measurement of moisture, fat/oil, protein and color.
The NDC Products brand from Nordson Measurement & Control Solutions features both at-line and on-line non-contact, NIR gauging solutions to meet the manufacturing challenges faced by the food industry.
The InfraLab Series 9 family groups the benchtop analyzers to the Series 9 on-line gauge. It offers two instrument designs (standard and the NEW Top-Loader) to cover the full range of food applications, including powders, beans, grains, and semi-solid products. The InfraLab Series 9 analyzers are available in single- or multicomponent formats and allow for rapid color, moisture, fat/oil, and protein analyses (only 5 seconds) in process environments, replacing time-consuming laboratory methods or at-line instruments such as loss-on-drying or gravimetric moisture testing. With their greater processing power and measurement capability, the InfraLab Series 9 analyzers deliver deeper process insight into the operation, enabling a significant reduction in a company’s operational expenditure (OPEX).
The Series 9 gauge is a nextgeneration process optimization solution for measuring color, moisture, and other key constituents on-line. It is specially engineered for 24/7 duty, helping manufacturers to meet product quality demands and efficiency goals. The Series 9 delivers
The NEW Top-Loader facilitates sample presentation & reduces human error - it is ideal for powders, beans, grains and semi-liquids.
unparalleled measurement performance while maintaining simplicity and versatility in design and operation. The flexible, futureproof platform harnesses the full power of infrared spectroscopy. The user-friendly format requires no special operator skills or expert knowledge, yet it allows expert users to access the enhanced interaction capabilities as desired.
Overall, the Series 9 Color Gauge keeps you ahead with:
• Evolutionary technology that is flexible, adaptable and scalable to meet your changing needs.
• Enterprise-level intelligence compatible with Industry 4.0.
• Easier operation and maintenance.
• Lower cost of ownership over a long lifetime of operation.
More information available on: www.ndc.com/food-bulk-materialsprocessing/
• Minimal product degradation
• No product de-mixing
• Low remaining product
• Any angle possible
• Minimal power consumption
• The conveying takes place in a tubular system which is sealed and completely dust-free.
Aero-mechanical conveying was introduced to the UK market by Entecon in 1963. Since then, thousands of these systems have been sold throughout the world to handle powders and granular materials cleanly, efficiently and in an enclosed environment.
Entecon conveyors are built to endure conditions in which materials may contain particularly abrasive or corrosive properties.
The fully enclosed construction helps to maintain a dust-free working environment as required by health and safety legislation, as well as energy-efficient running costs.
Entecon is active in the market not only with the Aero Mechanical Conveyor, but also with other types of transport systems. The Entecon product range includes – dust-free Automatic Sack Openers and Sack Tip Stations, Big Bag Fillers and Dischargers, Flexible Dosing Feeders, as well as complete projects.
The Aero-mechanical Conveyor can be fully integrated and used in combination with existing Entecon equipment.
Entecon Industries Ltd, 8 Lawrence Way, Camberley, Surrey, GU15 3DL Company no: 07041873
In one sense buying material handling equipment has never been easier, with the help of Google a new truck could be on its way in just a few clicks! On the other hand, with the widest ever choice of machinery, as well as ever tightening legislation, selecting equipment has probably never been more complicated.
In one sense buying material handling equipment has never been easier, with the help of Google a new truck could be on its way in just a few clicks! On the other hand, with the widest ever choice of machinery, as well as ever tightening legislation, selecting equipment has probably never been more complicated.
The successful navigation of all these variables, while daunting, does have the potential to deliver a handling solution to a business that is a far better fit for its needs than has ever been possible before. And it is at this point where the di erence between equipment that is nearly right and equipment that is exactly right can deliver the biggest wins for all businesses and unlock ‘true value’. This is also where the idea of buying a truck online, or without taking professional advice, starts to seem a lot less attractive.
The successful navigation of all these variables, while daunting, does have the potential to deliver a handling solution to a business that is a far better fit for its needs than has ever been possible before. And it is at this point where the di erence between equipment that is nearly right and equipment that is exactly right can deliver the biggest wins for all businesses and unlock ‘true value’. This is also where the idea of buying a truck online, or without taking professional advice, starts to seem a lot less attractive.
The biggest variable of them all is actually the operational application and the customer site itself. Whether this is one location or multiple, the combination of material flow factors, and the nature of the handling environment, is often the biggest area of opportunity to realise optimisation and value from a handling fleet. It is also a critical area for health and safety, as well as environmental considerations. Yet, almost unbelievably, this is one of the most overlooked areas by equipment users.
The biggest variable of them all is actually the operational application and the customer site itself. Whether this is one location or multiple, the combination of material flow factors, and the nature of the handling environment, is often the biggest area of opportunity to realise optimisation and value from a handling fleet. It is also a critical area for health and safety, as well as environmental considerations. Yet, almost unbelievably, this is one of the most overlooked areas by equipment users.
Consulting an experienced material handling specialist can bring enormous benefits in these areas, and is absolutely essential from
Consulting an experienced material handling specialist can bring enormous benefits in these areas, and is absolutely essential from
a safety perspective. At Impact Handling, for example, we have vast experience and practical data from managing handling equipment for 1000’s of customers across the UK. Our active direct rental fleet alone includes over 6,500 units and we additionally service and maintain customer-owned fleets containing another 15,000+ machines, covering all major brands and specialist handling equipment. These machines are deployed across many diverse sectors and all nature of sites – meaning there aren’t many scenarios we haven’t seen.
a safety perspective. At Impact Handling, for example, we have vast experience and practical data from managing handling equipment for 1000’s of customers across the UK. Our active direct rental fleet alone includes over 6,500 units and we additionally service and maintain customer-owned fleets containing another 15,000+ machines, covering all major brands and specialist handling equipment. These machines are deployed across many diverse sectors and all nature of sites – meaning there aren’t many scenarios we haven’t seen.
This real-world experience has given us a deep practical working knowledge which our customers, both old and new, are able to benefit from – Helping them to identify the perfect solution for their needs and bringing better value to their operation. We believe so strongly that professional site surveys are essential to any handling equipment purchase that we provide these as an entirely complimentary service to all our customers.
This real-world experience has given us a deep practical working knowledge which our customers, both old and new, are able to benefit from – Helping them to identify the perfect solution for their needs and bringing better value to their operation. We believe so strongly that professional site surveys are essential to any handling equipment purchase that we provide these as an entirely complimentary service to all our customers.
Once the handling environment and application have been professionally assessed, attention can be turned to the choice of equipment
Once the handling environment and application have been professionally assessed, attention can be turned to the choice of equipment
itself. It is important that this choice is led by the customer’s priorities. Do not allow an equipment supplier to restrict the range of choice - be that power source, the handling capacity or the ability to fully customise the equipment to exactly fit the need.
itself. It is important that this choice is led by the customer’s priorities. Do not allow an equipment supplier to restrict the range of choice - be that power source, the handling capacity or the ability to fully customise the equipment to exactly fit the need.
Although statistically, the current momentum is clearly towards electric as the power source of choice, 44% of all new machines sold are still internal combustion (IC) powered, based on the 2023 UK Materials Handling Association market data. It is worth keeping an open mind and appraising all options, as not every business is ready, willing or able to make the change to electric. The biggest hurdle often proving to be power supply restrictions.
Although statistically, the current momentum is clearly towards electric as the power source of choice, 44% of all new machines sold are still internal combustion (IC) powered, based on the 2023 UK Materials Handling Association market data. It is worth keeping an open mind and appraising all options, as not every business is ready, willing or able to make the change to electric. The biggest hurdle often proving to be power supply restrictions.
If that is the case for your operation, don’t be afraid to embrace the new generation of diesel- and gas-powered machines. The technology has made significant strides, with the current stage V generation of engines meeting all of the current stringent emission legislations, as well as delivering exceptional fuel e ciency. The operational performance benefits of IC over electric can also prove beneficial in many site environments.
If that is the case for your operation, don’t be afraid to embrace the new generation of diesel- and gas-powered machines. The technology has made significant strides, with the current stage V generation of engines meeting all of the current stringent emission legislations, as well as delivering exceptional fuel e ciency. The operational performance benefits of IC over electric can also prove beneficial in many site environments.
While electric machines do incur an initial price premium, for those ready to make the switch they also generally o er a lower Total Cost of ownership (TCO), thanks primarily to the fuel savings. Electric truck technology continues to advance at remarkable speed and previous limitations are improving every day. The battery changeover process, for example, has been refined to the point where it can take as little as five minutes on the latest Cat machines.
While electric machines do incur an initial price premium, for those ready to make the switch they also generally o er a lower Total Cost of ownership (TCO), thanks primarily to the fuel savings. Electric truck technology continues to advance at remarkable speed and previous limitations are improving every day. The battery changeover process, for example, has been refined to the point where it can take as little as five minutes on the latest Cat machines.
Do also keep an open mind about the di erent battery technologies – Lithium-ion and Lead Acid – both of which remain highly relevant depending on the application and environment.
Do also keep an open mind about the di erent battery technologies – Lithium-ion and Lead Acid – both of which remain highly relevant depending on the application and environment.
Richard Root, National Sales Manager at Impact Handling notes: “Although 90% of the electric truck conversation is about Lithium-ion, it still only represents around 20% of sales”. This fact is supported by the UK Materials Handling Association, whose 2023 figures show that 72% of all all-new electric equipment sales are specified with Lead Acid batteries. The largest uptake of Lithium-Ion batteries being in the powered pallet truck segment, where the split is approaching 50/50.
Richard Root, National Sales Manager at Impact Handling notes: “Although 90% of the electric truck conversation is about Lithium-ion, it still only represents around 20% of sales”. This fact is supported by the UK Materials Handling Association, whose 2023 figures show that 72% of all all-new electric equipment sales are specified with Lead Acid batteries. The largest uptake of Lithium-Ion batteries being in the powered pallet truck segment, where the split is approaching 50/50.
Don’t lose sight of what really matters When considering new equipment, it is very easy to overlook the factors that are the most critical to the business. Namely reliability and up-time. Many operations will grind to a halt if the material being handled cannot be moved, or if the goods cannot be loaded. And the cost of this interruption can be significant.
Don’t lose sight of what really matters When considering new equipment, it is very easy to overlook the factors that are the most critical to the business. Namely reliability and up-time. Many operations will grind to a halt if the material being handled cannot be moved, or if the goods cannot be loaded. And the cost of this interruption can be significant.
This is why the choice of service provider and the quality of their equipment may just be the single most important MHE decisions you make. So, look carefully at the geographical
This is why the choice of service provider and the quality of their equipment may just be the single most important MHE decisions you make. So, look carefully at the geographical
reach of your supplier’s service network and at their response time. At Impact we have over 250 dedicated service engineers, who are deployed as a mobile response force, equipped with state-of-the-art service vans, carrying stock of all common service parts. Collectively this team provides nationwide coverage and industry leading response times. This is supported by regional depots which hold comprehensive parts inventories, all configured for rapid delivery.
reach of your supplier’s service network and at their response time. At Impact we have over 250 dedicated service engineers, who are deployed as a mobile response force, equipped with state-of-the-art service vans, carrying stock of all common service parts. Collectively this team provides nationwide coverage and industry leading response times. This is supported by regional depots which hold comprehensive parts inventories, all configured for rapid delivery.
Make sure you carefully appraise your supplier and make sure that they can respond to your needs and locations. Try to choose a supplier for the long term. Avoid those who are just looking for a one-o sale, they will not be motivated by your best interests.
Make sure you carefully appraise your supplier and make sure that they can respond to your needs and locations. Try to choose a supplier for the long term. Avoid those who are just looking for a one-o sale, they will not be motivated by your best interests.
As Richard Root from Impact adds: “A common mistake we see is the overestimation of the capacity of a truck required for a given application. This results in the customer paying more than they need for a machine that will subsequently cost more to run and maintain, with no practical benefit to the business.”
As Richard Root from Impact adds: “A common mistake we see is the overestimation of the capacity of a truck required for a given application. This results in the customer paying more than they need for a machine that will subsequently cost more to run and maintain, with no practical benefit to the business.”
is your friend
Flexibility is your friend
We are living in a fast-moving world and that demands a fleet that can respond to, and keep up with, that rate of change. Flexibility, in all its forms, from your MHE supplier has never been more important.
We are living in a fast-moving world and that demands a fleet that can respond to, and keep up with, that rate of change. Flexibility, in all its forms, from your MHE supplier has never been more important.
The ability to change your fleet during the term of your agreement is a good example, as Richard Root explains:
The ability to change your fleet during the term of your agreement is a good example, as Richard Root explains:
“The benefits of our flexibility were really highlighted during the COVID pandemic, when we were able to support customers
“The benefits of our flexibility were really highlighted during the COVID pandemic, when we were able to support customers
whose needs changed dramatically, almost overnight. It allowed them to rapidly change the profile of their fleet to meet their new needs, without cost penalty.”
whose needs changed dramatically, almost overnight. It allowed them to rapidly change the profile of their fleet to meet their new needs, without cost penalty.”
A flexible supplier will also give you more options when you come to plan your fleet, as Richard continues:
A flexible supplier will also give you more options when you come to plan your fleet, as Richard continues:
“A good supplier will be able to o er you a wide range of new equipment from high quality brands. They should also carry a strong fleet of short-term hire machines to supplement the core fleet as and when required AND at short notice. At Impact we run a fully approved refurbished programme too, meaning we take the best equipment coming out of contract and refurbish it back to its original specification. Giving customers yet another purchase option.”
“A good supplier will be able to o er you a wide range of new equipment from high quality brands. They should also carry a strong fleet of short-term hire machines to supplement the core fleet as and when required AND at short notice. At Impact we run a fully approved refurbished programme too, meaning we take the best equipment coming out of contract and refurbish it back to its original specification. Giving customers yet another purchase option.”
Financial flexibility is also an important consideration. Balancing long term rental contracts versus outright purchase with maintenance agreements, or even hybrid models can provide yet more areas for a business to realise economies and savings. Self-funding suppliers, like Impact, can o er greater financing flexibility too, so be careful to do your homework here as well.
Financial flexibility is also an important consideration. Balancing long term rental contracts versus outright purchase with maintenance agreements, or even hybrid models can provide yet more areas for a business to realise economies and savings. Self-funding suppliers, like Impact, can o er greater financing flexibility too, so be careful to do your homework here as well.
So, in summary, there is more to choosing the right equipment than you might at first think. However, the right supplier can do most of the leg work for you, without any additional charge, and the e ort will be well worthwhile.
So, in summary, there is more to choosing the right equipment than you might at first think. However, the right supplier can do most of the leg work for you, without any additional charge, and the e ort will be well worthwhile.
Approached correctly, the outcome has the potential to deliver benefits to all areas of your fleet, operation and business, and to do so while reducing costs – now that’s ’True Value’.
Approached correctly, the outcome has the potential to deliver benefits to all areas of your fleet, operation and business, and to do so while reducing costs – now that’s ’True Value’.
A bakery and confectionary goods producer contacted Castle Pumps looking for some pumps to help them move away from the manual handling of some of their ingredients, and upscale their production.
They required a pump for transferring the fillings of their doughnuts and apple fritters, as well as a model for dosing vanilla essence and other flavourings. It wasn’t long before it became clear that peristaltic pumps were the perfect choice!
The beauty of the peristaltic design is that its inner tube is the only part that encounters the fluid. Not only does this make it simple and low cost to maintain compared to other pump technologies with multiple wearing parts such as impellers and seals and bearings, but it also makes it highly versatile in terms of the fluids it can handle.
Why did peristaltic pumps “rise” to the occasion?
For the doughnut and fritter filling, an AMP peristaltic pump with an inverter was supplied. The addition of the inverter was important to allow the bakery to adjust the speed of the motor when being used with the fillings of differing viscosities. For example, when pumping the more viscous jams, the motor speed needs to be slowed considerably compared to when transferring the apple pulp.
Due to there being a single wetted part as previously mentioned, there are no valves to clog or impellers to jam. This design means that the peristaltic pump can easily handle the apple chunks and stringy solids present within the fillings without damage or downtime to the bakery’s process. Infact, peristaltic pumps’ solid handling capabilities are only limited to the diameter of their internal hose, meaning if it fits, it can usually be pumped!
The beauty of the peristaltic design is that its inner tube is the only part that encounters the fluid.
When it came to the dosing of the flavourings, Castle Pumps specified a DS-M peristaltic dosing pump. This model has excellent accuracy even at low flow rates, making it ideal for handling small volume transfer and highly precise quantities.
For both models, Castle Pumps specified a food grade thermoplastic internal hose and tri-clamp connections for a smooth, non-contaminating pipework joint, ensuring that the pumps are safe for handling products for human consumption.
Getting the wrong pump for your food grade process can result in inconsistency in the finished product, crushed solids, clogging, excessive wear, loss of productivity, waste of costly product or at worst, contamination. Always trust technical experts to specify the right pump for your application.
www.castlepumps.com
A pump may do the job, but only the right pump will save you excessive wear, process failures, product waste & operator time.
Get the RIGHT pump with our 15 years’ experience in:
✓ FDA & 3A hygienic solutions for food and drink
✓ Highly accurate dosing of ingredients & additives
✓ Delicate fluids sensitive to consistency changes
✓ Solid-laden products without crushing or clogging
✓ 99.98% barrel emptying to prevent product waste
Contact our technical sales engineers now!
The use of refillable flavoured hot and cold drinks and the bulk-refill of liquid grocery products is on the rise with 60% of people in the UK carrying refillable drinks bottles compared to that of only 20% in 2012. In this piece, we’ll explore some key business benefits of refillable drinks and bulk-refill and how technology can be used to propel the movement even further.
It’s not just retailers who are getting behind this movement (with an increase in the number of zero waste shops), but Governments seem to be actively encouraging it with incentives such as:
• The French Government started to make bulk refill mandatory for shops – Convention Citoyenne pour le Climat (in French)
• The European Commission’s Packaging and Packaging Waste Directive recently included a proposed target for 95% of cold and hot beverage cups to be reusable by 2040
• In February 2022, Chile signed into its single-use plastics law that all supermarkets with more than three checkout points must offer and receive refillable beverage bottles in their physical and online stores).
With more consumers wishing to reuse their containers to bulkrefill or refill their drinks, some industries have started taking matters into their own hands and integrating refill machines within their premises for either product purchase (bulk dispense liquid refill), or food service use (food and
beverage solutions) for drinking. Places where this is starting to happen include:
• Restaurants and cafes – these venues can save money on the cost of disposable cups and lids by offering refillable drink options. They can also increase customer satisfaction by appealing to customers who are concerned about the environment.
• Gyms and fitness facilities –health-focused facilities can provide a valuable service to their members by not only offering refillable water dispensers but also flavour and nutrientenhanced product offerings. This can potentially support members’ workout performance and can also help the gym to reduce its single-use plastic waste.
Businesses that offer refillable drinks can differentiate themselves from their competitors, giving them a competitive advantage and helping to attract and retain new customers
• Retail environments – where space is at a premium, retailers are looking to install bulk-refill machines which take up less space yet supply their customers with a wide variety of products. Retailers need easy and low-costto-maintain equipment with quick and simple methods for product replenishment.
• Offices – large offices can save money on the cost of individual bottled drinks by providing refillable flavoured water dispensers for employees. This can also help the office to reduce its waste and appeal to employees who are concerned about the environment.
• Educational establishments –schools and universities can help to reduce their waste and educate
students about the importance of sustainability by offering refillable flavoured water dispensers and other refillable drink options.
There are many business benefits of offering refillable drinks or bulkrefill, however, we’ve condensed our list to the top 10:
1. Reducing environmental impact –meeting sustainability goals is high on the agenda for a growing number of businesses. By using refillable drink containers, or eliminating individually packaged goods with refill machines, companies are reducing the amount of single-use plastic waste produced, which is good for the environment.
2. Reducing plastic consumption for health – throughout the world, single-use plastic is having a detrimental effect on the planet and our health. Not only is plastic pollution a huge problem in our oceans and rivers, but as the littered plastics are breaking down into smaller and smaller particles (or ‘nanoplastics’), it is becoming a widely reported health concern. This publicity is causing a rise in the popularity of plastic waste-free options.
3. Materials cost savings – refillable drinks can save businesses money in the long run as long as machines can be low-cost and easy-tomaintain. Whilst setting up the system takes initial investment, the elimination of the ongoing cost to purchase single-use containers/ bottles/cups will amortise this capex over time and turn into savings.
4. Machine footprint and shelfspace savings with more consumer choices – by not having to provide single-use cups inside a machine, the machine size can reduce dramatically. Similarly, by using bulk-refill where one large bag replaces individually packaged bottles or cartons, the shelf-space required for each product line can be reduced. Furthermore, where ingredients such as flavours or fragrances can be mixed with base products at the point of dispense, more choice can be offered to the consumer with less SKUs and reduced shelf-space. Lastly, and perhaps most significantly, dispensing also provides the opportunity to use higher concentrations of products and mix with water at the point of dispense, which, for certain products is a viable way to reduce footprint per product line.
5. Transportation cost savings – similar to points mentioned in no.4 above: the space and potential additional weight that bulk packaging saves can also reduce shipping costs and by shipping a smaller volume of highly concentrated solution and diluting with water onsite, transportation space and weight can also be far smaller, resulting in a massive reduction in shipping and packaging costs.
6. Increased customer satisfaction and loyalty – many customers appreciate businesses that are committed to sustainability and that offer refillable drink options. This can lead to increased customer satisfaction and loyalty.
7. Harnessing technology –consumers are beginning to make use of technology to aid their sustainability efforts. The Refill App is a free app connects them to a global network of places to reduce, reuse and refill. It has over 400,000 app downloads to date (October 2023) and details a growing 300,000 refill stations offering refills for water, coffee, food containers and plasticfree shopping. Thousands of independent retailers, cafes and businesses already use the technology seeing an increase in their footfall, along with some bigname brands including Starbucks, Costa Coffee, Lush and National Trust.
8. Competitive advantage –businesses that offer refillable drinks can differentiate themselves from their competitors, giving
them a competitive advantage and helping to attract and retain new customers. An example of this could be gyms that offer refillable drinks with the aid of in-pump dilution and mixing. By offering highly tailored drinks that are enhanced depending on their customer’s needs e.g. a dose of vitamin C could be added to the usually-standard water, helping fitness people supplement their nutrition.
9. Marketing opportunities –businesses can use refillable drinks as a marketing opportunity for both brand-building and sales, especially if a machine has an interactive screen and a central IoT cloud service. For example, the screen can offer more story around a brand and catch people’s attention, but for sales support, they can offer discounts to customers who bring their own reusable cups or bottles, or if there is a surplus of a particular product flavour in the supply chain, promotional discounts can help to shift that product type.
10. Market retention and loyalty –by installing a refillable machine, consumers are likely to respond positively and return to the venue or brand for additional purchases and repeat business. Consumers become loyal to specific products if their goals are aligned and sustainability pushes them to develop a climate-conscious mindset and lean towards sustainable businesses.
So, with demand for bulk-refill or refillable drinks on the rise,
multiple benefits for brands and retailers and with governments starting to push for change, why has there been such a slow deployment of liquid dispensing machines?
The main problem is the upkeep required of the machines themselves: individually packed goods can be far easier to manage and less expensive. It is particularly a problem for retailers because they are on a mission to reduce the number of shop-floor staff required and are not already resourced to maintain equipment:
Typical pain points include:
• Regular cleaning / maintenance and pumps inside the machines need regular calibration which is expensive and time-consuming.
• Servicing machines takes considerable staff training which is expensive for businesses, especially those with high churn like supermarkets or fast food restaurants.
• Replenishing products can take too long vs stacking shelves.
• Drinks can be of inconsistent quality and brands/retailers can lose market share.
• Dispensers tend to generate mess from drips and spillages.
• Machines can break down or not function properly causing consumer complaints
However, there is good news for bulk-refill and refillable drinks…
Consumers become loyal to specific products if their goals are aligned and sustainability pushes them to develop a climate-conscious mindset and lean towards sustainable businesses.
Quantex is a new, game-changing recyclable pump technology that solves all of the pain points listed above. These lightweight, compact pumps are attached to the liquid packaging, and can either be connected in-line or directly to the liquid pack. If you are familiar with a tap used on a bag-in-box of wine, the ‘Bag-in-Box’ range of Quantex pumps can directly replace this Vitop tap – and, instead of pressing the tap and letting the product dribble out using gravity, the pumps are clicked into a small motor drive which doses the product accurately at various flowrates, with high vacuum and self-priming.
Unlike other pumps, Quantex can handle highly viscous solutions
(including melted chocolate, condiments (i.e. ketchup and mayonnaise) and yoghurt) and accurately dose and perform inpump dilution to enable brands to use higher concentrations of their products and save money on shipping costs by taking water out of the distribution channel. For drinks dispensing, gone are the days when only water could be dispensed, Quantex pumps allow consumers to add a variety of enhancements including liquid minerals and vitamins, syrups, coffee, milk, chocolate, flavouring etc). These added options open up the market for many businesses and create a chance for them to increase their ROI, as well as help their environmental measures.
Quantex pumps come in a variety of sizes and flow rates depending on the application:
• Precision Pumping
• In-Pump Dilution and Mixing
• High Vacuum Pump
• High Pressure Pump and Spray Capability
• Reverse Cycling
• Customer Lock-in
With many organisations and news outlets reporting on the benefits of utilising refillable drinking bottles and machines, it’s safe to say
that this trend is set to continue to rise. Furthermore, local and national UK governments are putting further incentives in place including:
• In 2019, the European Union approved a ban on certain single-use plastics which will be implemented in all EU member countries.
• The UK government will implement a new cash incentive system, placing deposits on drinks bottles and cans to help boost recycling from 2025.
• The Welsh Government is committed to making Wales the world’s first ‘Refill Nation’.
Overall, bulk-refill and dispense solutions offer several benefits for businesses. They can help to reduce environmental impact, save money, increase customer satisfaction, and differentiate from competitors.
If you’d like to learn more or discuss how a Quantex pump could help your organisation create a game-changing refill platform, please email quantexinfo@psgdover.com or call +49 (2065) 89205-0.
www.psgdover.com
Healthy vision shouldn’t cost the earth
Daysoft only makes and sells daily disposable contact lenses because these are the healthiest type of contact lens to wear.
Here at daysoft® we’re focused on what matters: providing simple, affordable vision solutions that are kinder to the planet without compromising on quality.
• From just 20p per lens delivered
We believe healthy eyesight should be affordable for everyone
Quality made medical devices
Safe, accessible, healthy eye care for everyone is at the heart of our vision at daysoft
Daysoft only makes contact lenses because healthiest type of
• Simple to use; no cleaning so no cleaning solutions
So we cut out the middleman and pass the savings to you. daysoft® lenses are made to rigorously high standards in our UK lab and then sold online, straight to you. As the only company in the world that design, make and sell contact lenses directly to customers, we’re able to replace other brands for half the price without compromising quality.
• Made in the UK; over 1 billion sold
Our contact lenses are medical devices, and as such are required to meet strict standards, measured through a rigorous regulatory framework.
• From just 20p per
• Simple to use; no
• Easy to buy; either subscription or pay-as-you-go
• Easy to buy; either
ALL OF OUR CONTACT LENSES ARE:
• Brand switch to daysoft® with no optician refitting needed Order online at daysoft.com
daysoft® is a Registered Trade Mark of DAYSOFT Limited
We’re trailblazers in innovation and expertise
We’ve always been ahead of the curve when it comes to innovation and design. Our chairman, Ron Hamilton, invented daily disposables and built the world’s first laboratory dedicated to making them. We continue to innovate and improve, using patented daysoft® technology and our unique SoftEdge™ design to offer you the safest way to wear lenses at an amazingly affordable price.
We’re the environmentally conscious choice
We’re conscious that singleuse daily disposables have an
We’ve always been ahead of the curve when it comes to innovation and design.
impact on our planet. That’s why we’re working towards innovative solutions to reduce our carbon footprint.
Our unique INPAC technology enables us to reduce excess plastic waste by up to 50%.
Designed and manufactured in the UK, our contact lenses have a lower carbon footprint than those that are shipped from across the globe.
• Made in the UK; over
• Brand switch to daysoft® refitting needed
• Manufactured under the control of a certified Quality Management System, compliant with ISO 13485:2016.
Order online at
daysoft® is a Registered Trade
• Approved under the European Medical Devices Regulations (Directive 93/42/EEC) under The Medical Device Regulations (Canada), licence #61427
• We’re also subject to regular audits by SGS Belgium Ltd, to ensure we continue to meet regulatory requirements, including stringent checks on the effectiveness of our sterilisation process.
daysoft’s® manufacturing process has been designed around the high specification details of the contact lens itself.
Our state-ofthe-art facility in Blantyre, Scotland only makes dailydisposable lenses and our processes, along with a highly skilled workforce allow us to supply you with the highest quality lenses at the most affordable price.
For further information, please visit www.daysoft.com
The New EC Series conveyors integrate with the M30 R-Series metal detectors to offer Affordable Quality Inspection Solutions for Small to Medium-Sized
Mettler-Toledo Product Inspection, a global leader in product inspection solutions, is proud to announce the launch of the EC Series conveyors designed to meet the product quality control needs for small to midsized food manufacturers. The EC Series conveyors seamlessly integrate with the M30 R-Series metal detectors, to offer a reliable inspection solution at an affordable price point for small and mediumsized packaged products in standard production environments. The integrated metal detection solutions are ideal for inspecting a wide range of both wet and dry applications, including meat, bakery and confectionery, ready meals and snack foods.
The simplified EC Series conveyor specifications include a range of options to suit production line integration needs while still meeting BRCGS requirements. Standard components are specified for reliability and ease of maintenance, facilitating maximum uptime and productivity. For example, the modular belt design and streamlined features enables easier cleaning – complemented by an ingress protection IP65 rating – quick servicing, and reduced operator time. Reporting capabilities include OPC UA, USB and connectivity to Mettler-Toledo ProdXTM software for enhanced data management and traceability.
The new conveyors are the result of the commitment by Mettler-Toledo to respond to market demands by providing innovative solutions for customers. By listening to the needs of small and mid-sized manufacturers, the development of the new conveyors meets both
budget and regulatory compliance needs at a time when combatting rising costs matters the most.
“An EC Series conveyor coupled with an M30 R-Series metal detector is the perfect detection solution for small to mid-sized businesses seeking affordable quality and compliance,” said Ben Pimblett, Head of Market Management at Mettler-Toledo. “Designed with simplicity and ease of use in mind, our new conveyors suit various production needs while providing maximum uptime due to reduced cleaning and maintenance time.”
The EC Series is compatible with three of the M30 R-Series metal detector models, which identify a range of metals, both magnetic and non-magnetic including all
ferrous, non-ferrous, stainless steel and aluminium, matched to different production and compliance needs, and budget considerations:
• M31R StandardLine – entry-level versatile and reliable inspection in all food segments; high frequency, tuned technology with eDrive that delivers up to 10% spherical sensitivity improvement over legacy models.
• M33R PlusLine – enhanced performance with very high frequency tuned technology and eDrive to deliver an up to 20% improvement in spherical sensitivity performance, ideal for dry applications such as cereal bars, dry pasta, confectionery and snacks.
The new conveyors are the result of the commitment by MettlerToledo to respond to market demands by providing innovative solutions for customers.
• M34R PlusLine – enhanced performance using DualSimultaneous Frequency and Product Signal Suppression technology to improve spherical sensitivity performance by up to 25% and reduce false rejects in wet or conductive applications; tailored to wet, challenging and conductive applications such as meat, poultry, seafood, dairy, products with high salt content and those packed in metallized film.
The EC Series conveyors are and at a cost-effective price point, making it an ideal choice for manufacturers looking to combat rising manufacturing costs quickly.
offers the GC Series conveyors, suitable for larger products and high-volume production environments. Both conveyors can be fully integrated with the M30
Innovia Films, a leading material science pioneer and major producer of BOPP films, has announced the launch of an extension to their range of sustainable films, that have been marketed under the Encore brand name.
“One big cornerstone of the Packaging and Packaging Waste Regulation (PPWR) is the integration of a certain percentage of recycled post-consumer content into plastic packaging. This regulation will have a huge impact on how brands are going to design their packaging and the motivation for this regulation is to reduce the per capita quantity of packaging”, says Simon Huber, Managing Director Innovia Europe.
“Flexible packaging, being lightweight and highly resource
The environmental credentials of the films can be improved further, by reducing the quantity of fossil based virgin materials and replacing with bio based polypropylene.
efficient, can help reduce the total amount of packaging being used and has a much lower CO2 footprint regarding transportation than many rigid alternatives. Innovia is working with the whole value chain in initiatives like CEFLEX (Circular Economy for Flexible Packaging) to increase the recycling of this flexible packaging back into film. The inclusion of recycled content in new films is top of the list for much of the industry – moving from a linear to a more circular system” explains Steve Langstaff, Head of Recycling at Innovia Films.
The extension to the Encore range of sustainable BOPP films include the use of chemical recycled polymer for food contact applications and the addition of mechanically recycled PCR for non-food. Innovia are also working
closely with Prevented Ocean Plastic and have developed a film with 30% POP material. In all cases the key functionality of the BOPP remain intact and are comparable to virgin grade materials.
The environmental credentials of the films can be improved further, by reducing the quantity of fossil based virgin materials
and replacing with bio based polypropylene. This reduces the carbon footprint of the films further and again with no detrimental effect on film properties.
“All products are now available for trialling”, Innovia announced.
www.innoviafilms.com
If you’re looking to reduce the number of different sensors used in your systems, the 420B and 412B series from Leuze are the right choice: The new ultrasonic sensors are available with adjustable sound cone and as switching (HTU) or measuring (DMU) sensors – this allows extremely flexible application. The sound cone can be set via an IO-Link interface to the three ranges “narrow”, “medium” or “wide” and thus adapted to the respective application. As a result, the ultrasonic sensors operate with maximum precision: They are able to detect reliably in situations where optical sensors are pushed to their limits. They also detect glossy, reflective, very dark or transparent surfaces as well as liquids without problem. The 420B series includes ultrasonic sensors in compact cubic plastic housings. It replaces the 420 series. With the new devices, users benefit from smaller dead zones with the same or a higher sensor operating range. The 412B series complements the range of cylindrical sensors in M12 housing with devices featuring IO-Link and analog output.
Maximum flexibility in the red housing
Thanks to their adjustable sound cone, IO-Link interface and two switching outputs, the HTU420B ultrasonic sensors in the red housing are suitable for challenging detection tasks. For example, two fill levels
The ultrasonic sensors of the 420B series have an adjustable sound cone. A narrow, medium or wide sound cone can be selected depending on the application. This allows, for example, fill levels to be monitored through differently sized container openings
With the new devices, users benefit from smaller dead zones with the same or a higher sensor operating range.
can be detected or two positions can be monitored simultaneously. The adjustable sound cone turns the sensors into flexible all-rounders. A narrow sound cone, for example, is suitable for detecting a fill level through small container openings. In its wide setting, the sound cone in turn captures larger areas – ideal in the case of bulk material or diffusely reflective objects with complex surface or structure. Practical: An interruption filter detects brief changes in measurement within a certain interval caused by interfering objects (e.g. an agitator). The sensor suppresses these interfering signals via the IO-Link interface, thereby
Thanks to an adjustable sound cone and small dead zone, the new Leuze ultrasonic sensors of the 420B and 412B series can be used for many different applications.
ensuring a seamless production process.
For the precise measurement of distances
Moreover, to measure distances, system operators can make use of the DMU420B and DMU412B ultrasonic distance sensors. The devices have an analog output (either current or voltage), an IO-Link interface as well as an adjustable sound cone.
Economical solution in the black housing
The Sensor People from Leuze also offer the HTU420B ultrasonic sensors in a standard design with black plastic housing. As an economical solution with one switching output (push-pull), they are suitable for simple detection tasks. Both variants are available in the operating ranges from 10 to 250 millimeters, 15 to 500 millimeters as well as 20 to 1000 millimeters. The HTU412B series has an operating range of 15 to 500 millimeters.
The cubic sensors measuring 20.5 x 41.0 x 15.0 millimeters are extremely compact. The cylindrical sensors of the HTU412B series too are just 50 millimeters long. They are therefore also particularly suitable for applications in constrained spaces. All types can be parameterized quickly: Easy setup and operation is possible using the teach button, via the teach input or via IO-Link.
www.leuze.com
With 134 million babies born globally in 20231, demand for baby products is high. This birth rate, combined with the rise of e-commerce, has forced suppliers to rapidly expand. To alleviate its growing pains, Babydump, a leading European retailer of baby products, automated its order picking operations at Sint-Oedenrode in the Netherlands to increase throughput and sustainability. For efficiently moving orders through the facility, it relies on 12 autonomous guided robots (AGRs) from Prime Vision.
A baby boom for business
Babydump is part of the FTH group and was founded in the 1970s as a retailer of baby products. It’s now market leader in its segment with a thriving online operation and 14 stores throughout the Netherlands and Belgium. The business offers baby rooms, prams, car seats, buggies, high chairs, baby clothing and many more baby essentials.
Experiencing rapid growth and looking to meet new environmental legislation, Babydump searched for ways to improve the efficiency and sustainability of its order picking operations. At its site in SintOedenrode, online orders and stock deliveries for its stores were picked manually by employees.
1 How many people die and how many are born each year? – Our World in Data
Prime Vision robots have a 35 kg carrying capacity and a 50 x 70cm loading surface, ready to carry a wide variety of boxes.
Having reached the limits of this set up, Babydump installed an automatic storage and retrieval system (ASRS) from Autostore to streamline the process. The ASRS holds 15,000 crates containing specific items. Instead of employees travelling along the racks, the system delivers the correct items for each order directly to a picking station, allowing workers to easily pack products.
With regards to sustainability, Babydump worked on optimising its packaging. Instead of relying
Babydump, a leading European retailer of baby products, automated its order picking operations at Sint-Oedenrode in the Netherlands to increase throughput and sustainability.
on standard box sizes that rarely matched the volume of the shipment, the company purchased two box erector machines. These produce two different types of boxes, which once packed by employees at the picking station, are cut to the exact size of the order and fitted with a lid by box closing machines. This minimises wasted space and improves sustainability. The order then travels via chutes to the conveyors, which sort it for dispatch to a particular store, route or delivery service.
However, the success of the system relied on efficiently moving boxes between all the different machines, picking stations, conveyors and chutes. There were other complications too. Beyond the ASRS, prams and other nonmachinable products that can’t be handled by automation needed to be accommodated in a different process flow. Furthermore, the facility handles both online and store orders. Supporting 14 physical locations as well as e-commerce customers added more complexity. Clearly, static conveyors would
Prime Vision robots have a 35 kg carrying capacity and a 50 x 70cm loading surface, ready to carry a wide variety of boxes.
be unable to accommodate these multiple demands, so a more flexible solution was required.
Following discussions with the supplier of the ASRS, Babydump approached Prime Vision to provide a fleet of 12 robots and an additional spare to support the newly automated facility. Based in the Netherlands, Prime Vision is a global supplier of automation, computer vision and robotics technology for the logistics sector. It currently operates over 700 robots at customer facilities around the world. Its local presence and industry expertise were critical advantages to Babydump.
Richard Hagen, Account Director at Prime Vision, says: “While we are used to operating fleets of up to 88 robots for sorting operations for courier and express services, the complexity of operations at Babydump presented a challenge. Our experience in this area meant that we could offer a flexible, costeffective solution.”
Prime Vision robots have a 35 kg carrying capacity and a 50 x 70cm loading surface, ready to carry a wide variety of boxes. Using light detection and ranging (LIDAR) for guidance and safety, the robots can travel without QR markers or metal on the floor. An overarching fleet management system plots the most efficient route for each robot, ensuring maximum efficiency and productivity. Smoothly travelling at between 0.8 to 1.1 m/s, Prime Vision robots quickly move items to the correct destinations.
Richard explains the setup process: “What’s important to us during implementation is the floor and what interactions will
take place on it. Working with the customer, we will map out the floor in special patterns, then upload these maps to the robots so they can navigate. The other element is marking out the pickup and drop off points such as conveyors, box machines, picking stations and chutes.
“Information from the warehouse management system tells each robot which destination to travel to, and we facilitate this with bespoke software that seamlessly communicates with the customer’s infrastructure. Any robot can drive to any destination, so they are much more flexible than conveyors. We can have the entire system up and running in less than weeks, providing quick installation and smooth processes.”
The robots have been operating at Sint-Oedenrode since the start of 2024. As well as facilitating the movement of items, the robots have the flexibility to accommodate stock orders for stores. With a battery life of over 10 hours, each robot covers multiple shifts, while the interchangeable batteries can be fully charged within 2 to 3 hours. For maintenance, Prime Vision offers remote assistance and preconfigured spare robots ready for rapid deployment to reduce downtime.
Order picking operations reborn Since the system has gone live, Babydump has recorded a 400 to 500% improvement in the productivity of its order pickers. This increased throughput has meant the company can comfortably meet rising demand. As well as simplifying order picking for employees, it has also reduced errors and returns, saving costs, lowering emissions and improving customer satisfaction. Meanwhile, optimised packaging has saved space and materials, enhancing sustainability at Babydump. Prime Vision robots have made a significant contribution to these successes.
Richard adds: “For complex logistics processes where efficiency is paramount, robots are often the best solution, and I think the market is becoming aware of the benefits.”
Managing Director of Babydump, Henk Timmer, says: “For us, being at the forefront of innovation, continuity and sustainability is in our DNA. Prime Vision’s solution fits perfectly with that.”
Prime Vision has released a video of the robots in action, which can be viewed here.
More from Prime Vision: https://primevision.com/primevision-robots-help-babydumptake-first-steps-in-automatedorder-picking/
Hart Door Systems has completed two more contracts for leading UK manufacturers supplying a range of door systems from Hart’s Speedor range of high speed doors to Hart’s roller shutters.
“Both clients are leading manufacturers in their respective sectors, one specialising in roofing and cladding, the other in wall, roof and landscaping innovations,” says Gordon Kipling, Hart’s Northern Sales Manager. “Their requirements were dissimilar which resulted in Hart supplying a range of doors for different purposes.
“For example we supplied Speedor Cleanroom, high speed, doors for one contract and Speedor Minis for another. Cleanroom is designed to work in environments in which
pressure differentials need to be maintained and where hygiene standards are high, whereas Speedor Mini is for high traffic, frequent use internal applications. This is a low cost access option.”
Mr Kipling added: “In all over both contracts were supplied a total of 10 doors. Once again our range of door solutions gives clients many options and as manufacturers they very often have highly individual needs. Hart is a logical supplier with considerable expertise.
“Our product choice is superb and manufactured to required standards. We expect more orders for fast action doors to follow in the near future.”
www.hartdoors.com
Since 1977, Smiths Fire LLP has been providing essential fire safety solutions and maintenance services. specializing in a comprehensive range of services, including tire extinguishers, safety signage, fire alarms, emergency lighting, fire safety training & fire risk assessments, we excel in safeguarding your premises against fire hazards.
What distinguishes us is our commitment to reliability, professionalism and quality service, all delivered at exceptional value. At Smiths Fire LLP, we combine professional expertise with a personalized touch, ensuring the highest standards of safety for our clients across various sectors.
We can offer tailored solutions to meet your specific needs, whether you require equipment installation, regular maintenance, or comprehensive training - trust Smiths Fire LLP to deliver excellence every step of the way.
Contact us today to elevate your fire safety standards and enjoy unparalleled peace of mind with our trusted solutions and expertise.
01536 484846 | sales@smithsfire.com
The latest generation of flame treatment systems designed and manufactured by CEC is already being extensively used in the automotive industry where modification of the surface of plastic components is required. Now, CEC announces their new Hybrid Treating System operating on Gas and Electricity, offering much better, quicker and long lasting surface treatment prior to painting, foaming, or printing or other surface applications ensures that complete adhesion bonding is achieved.
Application: The machine can be used for flame-treating cables, automotive parts, plastic containers, food containers, car bumpers and a wide range of other products to improve printing and adhesion.
Dancing Goat Distillery has come a long way since barreling its first batch of rye whiskey in 2017. It’s now a destination that offers a range of distillery experiences from tours to hands-on distilling classes. The Dancing Goat Gin Academy lets students distill and bottle their own 750 ml bottle of gin to take home. The distillery also boasts a rusticchic tasting room where patrons can watch corn and rye become drinkable spirits, including the company’s flagship Limousin Rye and Death’s Door gin.
While the company’s rye whiskey can spend six years barrel-aging, Dancing Goat needed only about five years to orchestrate three expansions. The most recent, which doubled the facility’s footprint to 3,159 m2, moves grain nine-times faster using a Flexicon pneumatic conveying system.
Employing modern techniques
With each expansion, the company strives to preserve the traditional art and science of distillation as it adopts modern techniques. Thus, an old-school copper pot remains in service beside sleek distillation columns. At the cookers, where grains and malt are turned into a mash for fermentation, the company has twice upgraded its loading methods. Originally, workers hoisted dozens of 23 kg bags of grain to load three 908 L cookers. When those were replaced by two 7,192 L cookers, Dancing Goat began receiving grain in bulk bags, unloading them into the vessels using a bulk bag discharger and flexible screw conveyor from Flexicon.
After its latest expansion added a third 11,356 L cooker, Dancing Goat installed a 26 m long PNEUMATI-
The distillery combines modern methods with traditional aging in oak barrels.
CON® pneumatic conveying system, also from Flexicon. The system transports the grains to two 0.2 m3 hoppers, one feeding the two existing cookers and one feeding the new cooker. “The pneumatic system can load three times as much grain in one-third the time,” says Mike Reiber, former director of operations. “Instead of driving fork trucks to the bulk bag discharger at the cookers and charging the cookers there, we created a grainhandling room and based our pneumatic conveying system there. It improves the process and is less painful for the operators.”
Weigh batching from a distance Located on the opposite side of the facility from the cookers, the grain room houses the intake and terminus of the pneumatic circuit, and a bulk bag discharger mounted on load cells. With a forklift, workers load the bags into the discharger using a lifting frame that nests into receiving cups atop the discharger’s frame posts.
Once the bag spout is secured to a SPOUT-LOCK™ clamp ring, the grains—milled to a flour-like consistency—flow into a 155 L floor hopper, from which a 1.5 m long flexible screw conveyor, inclined at 45 degrees, feeds the grain into the pneumatic conveying line via a pickup adapter, which includes an air inlet filter. Load cells supporting the discharger transmit loss-ofweight signals to a PLC that stops the screw conveyor once a pre-set batch weight has been fed into the pneumatic line.
With each
expansion,
the company strives to preserve the traditional art and science of distillation as it adopts modern techniques.
The 125 mm diameter pneumatic line—under negative pressure generated by a 23.3 kW vacuum pump—transports the entire batch with no residual, across the facility to the two 0.2 m3 capacity hoppers installed over the cookers. Inline fill/pass valves, located above each hopper, guide the grain to one hopper or the other, depending on the recipe.
The grain discharges into each cooker through a rotary valve. Above the twin cookers, a diverter valve controls whether the grain discharges from the hopper to the first or second cooker. The second hopper discharges to the third, larger cooker.
On the return side, the line runs from the hoppers back to the grain room to a 122 cm diameter filterreceiver whose cartridge filters separate the conveying air from carry-over grain dust. Reverse-pulse air nozzles dislodge accumulated material, which enters a 0.5 m3 floor hopper with rotary valve that returns it to the conveying line feeding the cookers.
“That means I don’t have to worry about grain being aged at the bottom of my conveying line or about grain backing up in the filter-receiver,” Reiber says. “It also minimises any concerns about attracting bugs or other pests and it gets the maximum amount of grain into the cookers.”
The pneumatic conveying system— which can move as much as 6,350 kg per hour—reduces the time operators spend loading and discharging the bulk bags. “Instead of taking the bags to the use point, they’re now taken to the grain handling room near to where they’re stored,” Reiber says. “The
Dancing Goat Distillery produces rye, gin, brandy, schnapps and other spirits.
forklifts travel maybe 15.2 m now, so the amount of handling, the forklift time, has been cut by 80 percent.”
Corn and rye, the grains Dancing Goat uses the most, flow from the bulk bags faster. “We were delivering a bag in roughly 15 minutes before. Now it’s in the 5-minute range for a bag of corn and 7 minutes for rye, with both bags weighing 794 kg,” Reiber says. A typical batch requires discharging six to eight bulk bags. “The operators who were here before we upgraded are amazed at how much less work and how fast the pneumatic system transfers the grain. We’re doing more with less work and in less time.” The operators are freed to perform other tasks in the distillery.
The operation is also cleaner and safer because the batching system is contained and operates under vacuum, preventing the grains from spreading dust. “We already make a flammable product, ethanol, and we don’t want to add potential fuel—airborne dust—to a zoned and classified space,” Reiber says.
In the grain room, the bulk bag discharger contains dust and ensures reliable flow using several subsystems. At the bag spout interface a SPOUT-LOCK™
clamp ring makes a dust-free connection to the floor hopper. As the bag empties, a TELE-TUBE™ telescoping tube lowers the clamp ring, applying continual downward tension to keep the spout taut promoting flow. Meanwhile, FLOWFLEXER™ bag activator plates raise and lower the opposite bottom edges of the bag into a V shape, directing all of the grain out the spout.
“We use the bag activator plates every day on every grain. It helps break up the cube that can form during transport,” Reiber says. The company also relies on the discharger’s POWER-CINCHER™ flow control valve, whose pneumatically driven bars close concentrically on the spout. “It’s a great tool when we need to restrict the flow or tie off a bag before it’s empty. It’s ideal for handling malt, which starts out blocky but then flows like water once it gets moving.”
In addition, the discharger’s posts can be raised or lowered to accommodate off-size bulk bags. “Our malt supplier’s bulk bags are about 14 inches longer than the normal ones,” Reiber notes. “But it only takes maybe five minutes to adjust all four posts.”
While the distillery has become a destination for whiskey and spirits lovers, Reiber says the company is only partway into its journey, with plans to load the grains from bulk silos instead of bulk bags.
“We plan to tie in the silos to piggyback on the pneumatic conveying system,” Reiber says. “The goal is to cook, ferment, and distill around the clock, and this system has brought us much closer to doing that.”
Dancing Goat Distillery welcomes guests to explore the new grounds. To book a distillery experience, go to www.dancinggoat.com and follow @DancingGoatDistillery on social media for updates, events and new experiential offerings.
sales@flexicon.co.uk www.flexicon.com
In any business world, data is reshaping the landscape. Food processing is no exception. If we consider the next big technology development, it will inevitably be a non-incremental, non-organic, move away from human labour and towards automation. In food production humans generally perform two sub-tasks for each primary task. In virtually every case, one of these sub-tasks is checking/quality control.
After biological contamination, label related defects are cited as the second most common cause behind costly and brand-damaging product withdrawals and retailer returns. There are several powerful reasons to ensure that the labelling of food products is correct. From the perspective of a food processor, the reasons broadly fit into three categories – improved production efficiency, waste reduction and regulatory compliance.
Using technology to verify the label offers far greater benefits compared to manual inspection.
Automated label verification has a huge part to play in increasing production line efficiency in food factories. Many applications which were previously deemed uneconomic to automate are now being automated based solely on the unavailability of a skilled workforce.
Using technology to verify the label offers far greater benefits compared to manual inspection. Given today’s production speeds, it’s impossible for one human to accurately read and process all the data for an entire shift. Let alone
check all elements of the label integrity, use by dates, country of origin, special promotions and cooking time. Operative fatigue swiftly kicks in. A few minutes is more realistic.
Having decided to automate the two main questions that follow are “How to go about it?” and soon after “what’s the risk?”. Most automation tasks should be achievable and contacting organisations such as BARA can help guide projects.
Among some of the many automation risks, one of the most significant is removing the final visual check due to labour shortages. For instance, a food operative putting meat steaks into a retail tray will inevitably check a multitude of critical factors, such as general appearance, colour, fat content etc. as they pick up and place the steaks into the tray.
However, inspecting established quality parameters in each piece of meat on processing lines can be further enhanced with the use of automated vision solutions. Machine vision companies can almost replicate (and in many cases outdo) a human operative. It is non-destructive, easy and quick. It is entirely feasible that inspection processes on meat and poultry processing and packing lines will be dominated by cameras in the next decade.
In the case of checking the label is correct, the case for automation is much stronger. The label not only identifies the product but contains critical variable information such as “use by” dates and pricing. A welldesigned label verification system should be able to verify 100% of the data on 100% of the products against validated source production data. Typically via the factory MRP system, not from a production line operative. As well as guaranteeing its accuracy, having this complete audit trail provides proof that all data or labels are verified.
A study by climate action NGO WRAP titled “Quantification of
food surplus, waste and related materials in the UK grocery supply chain” calculated that approximately 1.7 million tonnes of food were wasted in the UK prior to it reaching the consumer, almost half of which was preventable.
A further study by Rentokil determined that mislabelling was the second most common cause of food recalls in the US, and the third in the UK. A well-designed label verification system would be able to detect not only that an incorrect label was being used but also any incorrect data necessitating a recall.
Food labelling errors fall in to two categories, systematic errors, and random errors. A systematic error is where the label and/or data is manifestly incorrect. Random errors are generally a problem relating to the vagaries of the production process, such as a foreign body becoming attached to a printer. Label verification facilitates this full end of line automation and is critical to the whole quality control picture. JentonDimaco label verification systems are the only
ones that meet all UK labelling requirements and provide the data to prove it.
Stay right side of labelling laws
Almost all aspects of food production are subject to strict legal and customer compliance regulations.
Food labelling requires that many parameters must be checked, from the basics of is it the correct packaging, to the more complex of weights, prices and country of origin. Typically, this information is recorded at intervals (often every 30-60 minutes) on paper check sheets with labels then affixed as proof.
Companies that have stuck with a manual approach to label verification are often tethered to a system that generates little, if any, benefit to themselves over and above meeting their compliance obligations.
A fully automated label verification system should offer several benefits over a manual system.
• 100% of the data is verified • 100% of the packs are verified
Designing a label verification system that meets the requirements of the cases described above requires careful consideration. Our infographic (figure 1) provides an overview. Each numbered point correlates to the system diagram.
1 – It’s all about the data! The diagram shows the label verification server linking to an MRP server, a proprietary server, and spreadsheets. Ideally all the data would come from an MRP server, but it is usually a combination of some or all of them. Wherever the data is sourced from it is important that the following rules are observed
- The data should not be duplicated across multiple sources
- The data must be the latest version available - The data source must be secure and traceable
2 – The hardware. This should be able to read the label concerned. In our experience “smart” cameras are to be avoided as they present too many compromises. Different packaging solutions may necessitate multiple cameras located in different locations.
3 – The label technology. Currently almost 100% of label verification systems are camera based for use on printed labels. To be ‘future-proofed,’ systems should be able to use alternative media such as RFID and NFC.
4 – The label. The ability to read many forms of label is important. As a minimum a system should have a good OCR to read text and printed characters, as well as 1D, 2D and data embedded codes. Many do not, instead relying on an off the shelf vision toolbox with
• The label data is verified against a known correct standard
• Both systematic errors (incorrect data) and random errors (e.g., misplaced label / missing label / print head contamination) are captured.
Additionally, these systems provide:
• Proof of compliance
• Facilitates fast audit responses
• Tracks manual overrides against individual user and time/date
• Easily allows the data to be fed back as part of continuous improvement programs.
An automatic label verification system should provide the data not only for compliance but to help guide the business.
inherent compromises! The ability to read encrypted codes such as those from MagVision can aid future proofing.
5 - QA / Technical. These teams generally have primary and secondary needs that can be helped by automating label verification. The primary need is to ensure compliance throughout production. From a central location, they must have a complete overview of what’s happening whilst being fed key process information, such as pass/fail percentages.
The secondary function is being able to check labels offline to the same standard as the online system. An offline label verification system utilising the same data allows new products / labels to be verified prior to them going into production.
6 – Remote access. Authorised remote access is critical for three principal activities. It allows remote technical support to help lineside operators diagnose problems on seemingly correct labels. In Dimaco’s experience, over 85% of all remote access requests due to continuous rejection is a result of lineside operators working from obsolete data sources, such as printed spreadsheets. Remote access also enables senior technical personnel to monitor different production sites. Thirdly, it facilitates quick and easy on the job training.
7 – The Supermarket. Providing the capability to respond to changing requirements. In many applications it is common for pricing to change during a production run. If this happens then it is essential that the label verification is automatically updated.
Dr Russell Sion, Director, JentonDimaco
An automated label verification can deliver multiple benefits to a food producer. It can increase efficiency, reduce staff count, reduce waste, and improve compliance.
To achieve these significant benefits, care and attention must
be taken when designing and implementing the system. Simply attaching a smart camera and entering data into a local terminal will not deliver anything close to the same benefits. For example, if a lineside operator sets a printer up to print a use-by date of “Feb 30” and sets the smart camera up to verify “Feb 30”. Guess what? The so called, verification system passes all the packs!
In label verification there are no shortcuts to success. Yet, for those businesses prepared to make the investment there is the prospect of numerous benefits. Everything always circles back to one thing –It’s all about the data!
For more information go to: www.dimaco.co.uk
Manufacturers face more pressure than ever to deliver quality products quickly, but any number of variables can throw off the bestplanned production schedule— from machine and human error to unexpected downtime and materials shortages. Real-time production monitoring and process monitoring work in concert to provide immediate insights that enable manufacturers to rapidly identify and address potential issues before they impact the ability to deliver on customer commitments. In this article, Lynn Loughmiller, Software Engineering Manager at DELMIAWorks, takes a closer look at how production and process manufacturing monitoring systems work to improve shop floor performance.
Understanding Manufacturing Monitoring Systems: Production Monitoring vs. Process Monitoring
Production monitoring and process monitoring both rely on real-time
data from smart machines and sensors on equipment. However, they are effectively two different parts of a recipe for gaining insights into what is happening on the shop floor at any given time.
• Production monitoring is similar to the top part of a recipe that lists the ingredients, centering around parts and materials. It tracks the production of parts starting from the raw material used, such as a plastic pellet or metal sheet, to counting parts as they are created, tracking their movement into inventory, and recording any associated scrap.
• Process monitoring is much like the bottom of the recipe that looks at how things are being done. It focuses on conditions that affect processes, such as whether machine cycle times, temperatures, amperages, and lubrication levels are within specified parameters.
When real-time data from manufacturing monitoring systems is shared with a manufacturer’s enterprise resource planning (ERP), manufacturing execution system (MES), and other related software, the information can automatically trigger actions and support decision-making throughout the business. The following are five examples of how production monitoring and process monitoring—either separately or working together—can be used to improve operations.
Production monitoring plays an integral role in ensuring that enough raw materials are in inventory because it tracks machine cycle times, which can be used to predict when a manufacturer will run out of a specific material. Production monitoring can also capture when
Production monitoring of machine cycles can help manufacturers get raw materials to the correct machine when they’re needed and avoid downtime.
more scrap than projected is being produced, signaling not just a potential production problem but also the need to re-order a raw material sooner. An MES storing real-time production and process monitoring data can feed this information into the purchasing model of an ERP system, which then auto-generates purchase orders for materials, ensuring the availability of materials to support production runs while also improving utilization.
Warehouse Management –
Production monitoring of machine cycles can help manufacturers get raw materials to the correct machine when they’re needed and avoid downtime. Here, real-time data in the integrated MES system is fed into warehouse management software, which uses this information to automatically direct forklift operators or other workers on where to deliver raw materials for use at a specific machine.
3. Quality Control and Compliance – Manufacturers can use both monitoring approaches to ensure quality. For example,
production monitoring together with a vision system can trigger a programmable logic controller (PLC) to detect bad parts. Similarly, process monitoring can capture factors, such as machine temperatures falling below acceptable parameters. In either case, the data can be used to automatically trigger automatic rejections of the affected parts. Additionally, process monitoring data fed into ERP and quality management systems can simplify compliance and certification by automatically verifying and documenting that parts were made in accordance with specified parameters.
The two types of monitoring can be used to indicate when to perform machine maintenance. For example, production monitoring can capture that a particular machine has just produced 300,000 parts over several work orders and trigger a maintenance work order for that machine. On the other hand, when process monitoring captures a machine’s cycle counts, the number of cycles or length of cycles can indicate wear or a problem with the machine, again triggering an alert to schedule maintenance at a time that minimally impacts production.
5.
– In those cases when a machine goes down, the part still needs to be produced. Production monitoring can show
how long a work order is going to take. The data can then be shared with auto-scheduling functionality in the MES system. If the downtime is minimal, auto-scheduling may simply update production timing on the current machine. However, if the downtime will impact delivery to the customer, autoscheduling can re-assign the part production to another machine.
The applications of production and process monitoring will continue to grow as manufacturing monitoring systems take advantage of advances in generative artificial intelligence (AI). Both forms of monitoring have made it possible to build huge historian stockpiles of data from machines on the shop floor, which can be used to build predictive models. Then, when mapped against real-time data in ERP, MES, and other manufacturing applications, these models will make it possible to forecast what is or will happen on the shop floor with much greater accuracy.
The resulting AI-driven insights will provide a strategic resource for training engineers and operators on how effectively their product “recipe” is working. Moreover, these AI-powered analytics and forecasts will become a critical factor in empowering manufacturers to make timely, highly informed decisions across their business. And that’s a recipe for success.
The food processing industry demands chain solutions that maximise working life and minimise maintenance downtime. Donghua Limited, the UK arm of the Hangzhou Donghua Chain Group, is at the forefront of high-quality chain solutions, ensuring that food processing operations achieve performance and reliability.
Unplanned maintenance can significantly disrupt production schedules, leading to decreased productivity and increased costs. Donghua chains are designed to meet these challenges head-on, offering robust performance under the most demanding conditions.
From their 25,000 sq ft warehouse in the West Midlands, Donghua Limited stocks an extensive range of Conveyor Chains, Roller Chains, and Attachment Chains. These chains are available in a variety of materials and finishes, ensuring they meet the diverse needs of customers in the food processing industry.
Donghua’s chains are available with special alloy coatings that protect against corrosion caused by aggressive wash-down procedures, ensuring longevity and reliability.
To further enhance chain performance, Donghua applies H1 food grade lubrication through a hot-dipping process in their UK workshop. This method ensures the lubricant reaches part of the chain that standard lubrication cannot, provides superior protection, and extends the chain’s life.
All Attachment Chains are preloaded as standard, reducing fatigue and extending wear life. Chains with insufficient pre-load experience significant elongation during
Unplanned maintenance can significantly disrupt production schedules, leading to decreased productivity and increased
costs.
initial use, necessitating in early replacement.
Donghua ensures Attachment Chains are matched to very close tolerances, allowing attachment links to engage with sprockets simultaneously. This precision eliminates undue stress, a major cause of fatigue failure in attachments.
Donghua’s Food Industry chain solutions include:
Polymer Conveyor chain – designed to prevent the ingress of foreign matter and reduce maintenance costs and downtime. Manufactured using food grade engineering plastic, the lightweight Polymer chain is lube-free.
Universal Attachment chain – a ‘one chain fits all’ solution that replaces 99 per cent of other manufacturer’s chain. Built in the UK specifically for the distribution market.
Drytec chain – custom-built to specific customer requirements and manufactured to the highest standards with bespoke attachments.
Donghua chains are compatible with the leading food equipment manufacturers, and have quickly become the preferred choice for companies in the food processing industry. Produced to extremely narrow tolerances, chains from the same production batches consistently meet or exceed 1/3 DIN standards.
Donghua’s Food Industry chains are supplied through a growing network of product partners, stockists and distributors, making it easier than ever to access these high-quality solutions. To learn more about how Donghua can enhance your food processing operations, visit www.donghua.co.uk/food-industry/.
From farm to fork, many food safety assurance systems rely on robust Hazard Analysis Critical Control Point (HACCP) programmes. But, how do you verify that the steps you’ve taken to ensure conformance to food safety standards are working? Can you wait until the next periodic audit, or should you act sooner?
Successful, industry-leading food manufacturers don’t wait for a crisis to happen before taking steps to improve their food safety culture. They regularly use audits to identify gaps and potential risks and verify the effectiveness of their internal controls to strengthen customer trust and satisfaction. Performed internally, or by a knowledgeable food safety consultant, a typical audit review can last up to three hours – dependent on the organisation’s size. A well-structured review can reveal the respective strengths and weaknesses of food processing practices, keeping unforeseen conformity surprises from adding further disruptive pressures to already complex, and sometimes fragile, food supply chains.
The distinction between a food inspection and a food safety audit can get clouded. In food safety circles especially, the two terms are frequently interchangeable. They both help to improve operational performance. And they both assess conformance to set standards. There are, however, subtle differences.
A food safety audit is a systematic evaluation of food factory documentation to determine if food safety practices, programmes and related activities, including procedures and record keeping, are meeting expectations. Generally, an auditor looks at
Food safety audits are used by processors to identify gaps and potential risks and verify the effectiveness of internal controls.
Poor record-keeping and non-compliance with established Food Safety Plans are some of the top reasons that food and beverage manufacturers fail their audits.
data over a period of time to see if positive or negative trends are developing.
Food safety inspections, on the other hand, provide a thorough physical review of a food facility to assess what is actually happening in production during a precise moment in time. This snapshot – typically lasting between two and four days –gives a realistic assessment of conditions. These can be both positive and negative.
When inspecting a Critical Control Point (CCP), an inspector may look for any potential contaminant events that if left unaddressed could prompt an
investigation. When conducting an audit, qualified personnel will review the effectiveness of a HACCP plan and ensure it is being implemented correctly.
The Food Standards Agency evaluates the effectiveness of the official audit controls systems managed by enforcement officers and local authorities in England, Wales and Northern Ireland. Although food safety audits are not a legal requirement, by conducting internal or external audits, food processors can be assured their processes are conforming to these defined food safety standards.
Any failure can feel like the end of the road. However, in audit terms, a non-conformance issue simply notifies a food processor that something needs to be addressed in order to comply with food safety rules, regulations and supplier contractual obligations.
Poor record-keeping and noncompliance with established Food Safety Plans are some of
the top reasons that food and beverage manufacturers fail their audits. When equipment and surfaces deteriorate, they can present a possible contamination risk. Auditing highlights these issue and ensures they are resolved before an inspection. Additionally, end-of-line inspection equipment can expedite the process of tracing a contaminant entry-point and correcting the non- conformance.
In order to assess performance and knowledge of good manufacturing practices, a Traceability Performance Assessment can also be conducted. This timed traceability recall exercise can be added to any GMP inspection and helps to promote food safety compliance amongst staff, highlights Phil Brown, Sales Director of Fortress Technology Europe.
When choosing an external consultant, look for professionals who are experienced and familiar with the latest regulations in your food sector, such as meat or dairy. It is also advisable to request customer references, notes Phil. “Other qualities to look for are good problem solvers. Food safety audit consultants should feel comfortable working unsupervised and monitoring everything from documentation processes to daily practices. And they should be able to do all of this without placing undue burden on your production and quality control teams and processes.”
An audit checklist should cover all aspects of production that affect food safety practices and HACCP compliance. Most auditors will expect to examine documentation,
records, premises, practices, equipment, and processes. Signs of pest infestation, hygiene protocols, temperature control, and food handler and machine operative training and competence will all be scrutinised.
To assist food manufacturers, Fortress published a typical audit-conformance checklist in its latest Food Equipment Audits Whitepaper. Download a free copy from https://fortresstechnology. co.uk/food-equipment-audits/.
Post-audit, the successes and non-compliances flagged by the investigation should be examined by the relevant staff and auditing personnel. Once a course of action to address and prevent future non-conformances is established, food processors can implement these changes.
For inspection equipment, specific GFSI standards should be followed. Particularly the testing of industrial food metal detectors.
Food safety audits play an essential role in supporting safe food consumption, brand integrity, regulatory compliance, supply chain management, risk assessment and prevention, and promoting operational excellence. Given the numerous critical control points in a processing plant, Fortress advises routinely and systematically revisiting potential hygiene and contamination hazards as part of a regular risk assessment and food safety programme.
As more good practice is adopted, the food safety goalposts will inevitably move. “Food safety is reliant on continuous improvement. Once any changes are reviewed and implemented, HACCP plans should be modified. This ongoing effort drives advances in processes and efficiency, as well as enhancing product quality,” emphasises Phil Brown.
+44 (0) 1295 256266 www.fortresstechnology.co.uk
As part of any Food processors HACCP program validation of cook and chill processes is a critical and significant task taking time, effort, and resources.
PhoenixTM have developed a thruprocess temperature monitoring technology specifically for this task designed to meet the challenges of the food processing market. Ideal for the validation process for any new cook regime, new product, or annual process certification. Whether performing an oven survey “oven mapping to identify cold spots” or validating the cook under production conditions, the thru-process profiling solution gives you the accuracy, efficiency, and reliability you need to satisfy your HACCP demands.
As its name suggests thru-process profiling is the method by which product and or process temperature is monitored throughout the complete cook / chill process.
Monitoring of continuous conveyorised linear and spiral ovens and semicontinuous or rotational batch cooks is feasible where the use of external recorders with trailing thermocouples is tedious, impractical, and unsafe.
Employing the thru-process principal process monitoring can be performed under true production conditions without compromising line productivity .
At the heart of the thru-process monitoring system is the PhoenixTM data logger.
The PhoenixTM NT data logger range has been designed specifically for the challenges of monitoring food processing applications with an IP67 case design protecting from moisture. Type K or Type T data logger options allow accurate measurement of both cook and chill processes. The data logger itself can operate between -40 °C to 80 °C with a data logger accuracy of ±0.3 °C operating below +50 °C.
Data logger and thermocouple correction factors can be further applied to maximise measurement accuracy.
PhoenixTM offer a family of thermal barriers to suit the process type, duration, and temperatures of a wide range of cook regimes.
An extensive range of different thermocouple types is also available to suit different product types , sizes and monitoring demands.
The PhoenixTM Thermal View Food Software provides a comprehensive suite of analysis tools to convert the raw profile temperature data into useful process information. The analysis tools include the ability to calculate Fo/Pu values for the process against target microorganisms.
The information gathered, further to process validation, can be used to allow informed process problem solving and optimisation to maximise product quality, yield, process productivity and efficiency.
Contact PhoenixTM to help Find, Fix and Forget your Food Cook Problems!
Further Information
Kadant PAAL Ltd are based in Derbyshire with an advantageous reach throughout the UK and this is where we produce our Dicom Range of waste solutions. We prioritise our relationships with our customers to assist you to understand your waste and provide the best solutions for your waste management.
Acknowledging businesses such as Food Manufacturers, Hotels, Hospitals, Retail and many more we are able to provide an efficient, reliable solution for the types of waste streams produced by these business sectors, our KPX32 Portable Compactor.
In the design of the KPX32 we appreciate the outcomes of the compaction of these types of waste and have therefore covered all angles, with the self-contained body and it is liquid retentive. We are ensuring you have no unwanted mess on your site and that the contents of the compactor are retained, securing a hygienic waste transportation system. Even a detail such as the
hydraulic lid specification completes the picture by deterring rodents.
Considerations within the footprint of your business can often be key, where will everything go? The KPX32 steps up to the challenge enabling it to be easier to locate and relocate to different areas of your facility, of course if there is power available for operation.
Enabling optimum Waste Management functionality, the KPX32 is equipped with the Dicom Connect Platform, RMS, with many features such as email notifications of machine status, intelligent service scheduling and Remote diagnostic functionality. These attributes ensure a smooth operation for this area of your business.
We have an expert team, let us listen to your needs and offer you the solutions to enable you to move forward with your waste management requirements.
www.kadantpaal.com | www.dicompaal.co.uk
In the food and beverage packaging industry, the demand for highquality products is inseparable from the need for impeccable hygiene and efficient processing. Traditional bearing materials often fall short in meeting these critical requirements. Enter ceramic bearings — a solution that offers not only enhanced performance but also addresses the stringent hygiene standards demanded by food and beverage environments. Here Chris Johnson, managing director at ceramic bearings supplier, SMB Bearings explains the benefits of opting for this material type.
Food packaging settings demand the highest levels of hygiene to ensure products are not just safe for consumption but also maintain their quality. Traditional steel bearings, often prone to corrosion, wear, and particulate generation,
present a contamination risk that is unacceptable in these sensitive environments.
Unplanned stops in filling, packaging, or palletising assets in food processing can have cascading negative impacts that severely limit operational efficiencies. These interruptions not only disrupt production schedules but can also lead to compromised product quality and increased costs. In the pursuit of maintaining hygienic conditions, cleaning procedures can inadvertently damage seals and promote bearing corrosion, undermining the bearings’ integrity and longevity.
Furthermore, excessive re-greasing, often a consequence of attempting to mitigate wear and friction, can inadvertently contaminate products and packaging materials.
In this intricate ecosystem, ball bearings play a critical role. Their malfunction due to inadequate maintenance or improper cleaning practices can trigger a domino effect of delays, reduced productivity, and compromised food safety standards.
Ceramic bearings, with their nonreactive and non-porous nature, offer a robust solution. They remain impervious to chemical reactions, thereby eliminating the risk of contaminant introduction and safeguarding the integrity of packaged goods.
Characteristics that count
Ceramic bearings exhibit exceptional resistance to corrosion, a paramount trait when considering exposure to cleaning agents and washdown procedures. This characteristic ensures that the bearings maintain their structural
Unplanned stops in filling, packaging, or palletising assets in food processing can have cascading negative impacts that severely limit operational efficiencies.
integrity over extended operational cycles, thus contributing to prolonged equipment lifespan and minimised downtime.
Food packaging processes often involve exposure to elevated temperatures. Ceramic bearings thrive in these conditions due to their high thermal stability. This property prevents dimensional distortions and ensures consistent performance even under temperature fluctuations, crucial for maintaining precision in packaging operations.
What’s more, ceramic bearings’ ability to operate without lubrication at lower speeds, translates into lower friction and reduced heat generation during operation. This contributes to energy savings and improved efficiency in the packaging line, making them an asset in highthroughput environments.
In the realm of food packaging lines, bearings may encounter a multitude of challenges, including extreme temperatures and exposure to excessive moisture and chemicals.
In such settings, the bearings employed need to adhere to a variety of unconventional standards. The presence of contaminants further compounds the situation, manifesting in various ways. In the meticulously regulated domain of food and beverage production, the introduction of contaminants can result in substantial losses in production efficiency. Moreover, the copious moisture stemming from regular washdown cycles can lead to the displacement of lubricants from the component.
Likewise, the bearings must withstand chemical exposure arising from detergents and sanitisers, which can trigger corrosion and expedite the wear of components. For applications that are too corrosive for 440 stainless steel ball bearings, or where the load is too high for 316 grade stainless steel bearings, full ceramic bearings in zirconia or silicon nitride are advised. These bearings are also suitable for much greater temperature extremes.
Ceramic bearings are often costlier to manufacture, so design engineers must evaluate the benefits they bring to the specific packaging application and determine if the enhanced performance and longevity justify the investment.
Alternatively, plastic acetal resin bearings present a cost-effective choice and are also resistant to corrosion. Where bearings are suitable for applications involving low loads and speeds. To enhance resistance against corrosion and withstand extreme temperatures, it is possible to employ alternative materials for the rings or cages, such as polyether ether ketone (PEEK), polytetrafluoroethylene (PTFE), or polyvinylidene fluoride (PVDF).
The slender nature of bearings often used in packaging applications necessitates meticulous attention to the circularity of the rings themselves. Consequently, the manufacturing procedure demands an exceptionally precise approach to ensure optimal circularity in both rings, along with favourable noise levels within the bearing. This invariably mandates the utilisation of fine grinding and machining
techniques, complemented by an exceedingly high standard of quality in both the manufacturing process and the raw materials employed. Any imperfection in the formation of the rings, no matter how minuscule, can impede the smooth operation of the bearing, resulting in excessive noise and disturbances along the food packaging line.
Ceramic materials, though highly resilient, have inherent brittleness. Design engineers must strike a balance between optimising loadbearing capacity and safeguarding against potential fractures or surface damage during high-impact events.
In the evolving landscape of hygienic and efficient food packaging, ceramic bearings emerge as a transformative force. Their corrosion resistance, temperature stability and friction-reducing properties make them pivotal in safeguarding product quality while optimising packaging line performance. However, the journey towards full integration entails addressing challenges related to precision manufacturing, load-bearing capabilities and costeffectiveness. By leveraging the distinct characteristics of ceramic bearings and conquering these design engineering hurdles, the food packaging industry can embrace a new era of efficiency, reliability and product integrity.
Interested in ceramic bearings for a food and beverage application? For more information about SMB Bearings’ ceramic bearings offering, visit the website or contact a specialist today.
www.smbbearings.com
Earthly Labs’ small-scale carbon capture technology is designed to serve the needs of emission sources such as craft breweries, wineries, distilleries, commercial greenhouses and other small to medium sized industries. We offer a full solution including CO2 capture hardware, software, installation, engineering and real-time remote monitoring services – capturing the CO2, purifying, monitoring and recycling, to keep it out of the atmosphere. With each customer, we focus on converting molecule to value, reducing emissions, reducing costs, and creating new market opportunities in the circular CO2 economy. The first commercial application for our CiCi® CO2 capture technology was CO2 recovery and reuse for craft breweries, reducing CO2 emissions while reducing CO2 costs and supply chain volatility.
CiCi® CO2 emissions monitoring and reporting software controls gas processing, while providing real-time alerts so customers can let our units run 24x7 unmanned. The remote dashboard also allows the team to track via mobile phones or desktops, running reports offline and assessing CO2 capture volumes. As the carbon market develops for CO2 incentives and credits, the software is ready to provide traceability and transparency to the molecule.
Earthly Labs believes CO2 technology is a buttress to support our customers’ goals – emission reduction, cost reduction and value creation.
Earthly Labs believes CO2 technology is a buttress to support our customers’ goals – emission reduction, cost reduction and value creation. We have developed a customer onboarding and implementation process that tracks and monitors customer success –from kick-off meeting to delivery to installation and post-sale support. Our team members have a deep
understanding of the industries we serve so we can integrate our solution knowledgeably, train team members effectively, and install equipment confidently, with minimal disruption to your processes. With more units in operation than any supplier at our scale, we have developed installation processes and training tools that enable quick time-to-value and sustained CO2 capture performance. During commissioning, our team helps build piping manifolds, install piping, tie in CO2 capture equipment to your fermentation tank, set up remote monitoring software, capture and liquify CO2, and train your team and ensure your continued success. We also have a catalog of tips and tricks in our manual and customer service portal, with post-sale customer support from industry and engineering experts. In addition, the cloud-based performance monitoring dashboard allows our customer service team to troubleshoot or offer proactive feedback to maximize CO2 capture. While our CO2 capture technology is unparalleled, our people and yours will ensure your success.
Available in three different CiCi® CO2 capture models; Oak, Elm and Teak, according to capacity and site requirements.
Contact an expert at earthlylabs@chartindustries.com or go to www.earthlylabs.com to find out which model is best for your operation.
Jim Bligh, FDF’s Director of Corporate Affairs and Packaging, on spearheading a sustainable packaging revolution, advocating for innovation, and the need for regulatory clarity in the industry
In the rapidly evolving packaging world, enhancements in food packaging persistently surface and bring revolution to the industry, which is shifting towards a more transparent, reliable, and socially responsible future.
A quick web search around any key headwinds that the packaging sector can expect in the coming years regularly throws up the Food & Drink Federation (FDF) and one man in particular: Jim Bligh, Corporate & Public Affairs Director.
The packaging landscape is expected to undergo significant changes driven by Extended Producer Responsibility (EPR) and similar policies. Clearer regulations are anticipated to spur innovation and investment in sustainable practices. Whilst Bligh envisions a future where supermarket shelves feature products made from different, more recyclable materials, reflecting shifts in consumer behaviour and manufacturing practices, a quick rummage around his current and rather busy in-tray shows challenges remain.
Whether it’s ensuring a consistent supply of recycled content or governmental focus on fee collection over system efficiency, Bligh believes the pending transformation of the entire packaging value chain isn’t just about materials—it’s about revolutionising the entire packaging ecosystem, from production to disposal.
“I think it’s accelerating,” Bligh told London Packaging Week. “I think with the changes in material science, the advances we’re making on different types of materials in all parts of the economy present huge opportunities. The biggest opportunities we’ve seen for decades in packaging! Having clarity on rules, more investment, direct financial incentives through EPR, and various other things will mean that we’re at the cusp of a new leap in how we package our products. I think we’ll see less plastic, and replacing plastic is a long-term challenge that no one has completely solved. So, watch that space, particularly in the material science world.”
Bligh, a recently appointed member of the London Packaging Week Innovation Awards 2024 Jury, sees vast opportunities
emerging from advances in material science, anticipating a shift away from plastics towards more sustainable alternatives. However, uncertainties persist, particularly regarding implementing EPR and Deposit Return Schemes (DRS). Despite consultations starting seven years ago, progress has been slow, leaving industries unsure about the recyclability of innovative packaging materials.
“You’d expect that we’ll see quite rapid progress over the next two or three years,” said Bligh. “But what that will mean for the industry then is standard rules on recyclability in particular. So, when we’re innovating, creating new packaging, and creating new products, we’ll know whether they’ll be recyclable or not. One of the problems at the moment is that there’s a whole load of innovation going on, but, for example, if you’re making paper packs for your crisps, we don’t know when they’ll even be able to be recycled under the new systems that we’ll have in place in the coming years. We just need to get on with it and work with the government to build systems that work and attract the right investment to get that circular economy going.”
As the United Kingdom grapples with the pressing issue of improving its recycling rates, the conversation around EPR becomes ever more crucial. EPR schemes, which place the onus on producers to manage the
lifecycle of their products, have seen remarkable success in various countries. However, the UK faces unique challenges in adapting these systems to its context. Key concerns include the current government’s focus on fee collection over system efficiency and the critical role of producer leadership in driving sustainable packaging innovations.
“I think EPR has worked really well overseas,” he added. “If you go to Canada or parts of the United States or Belgium, you see highfunctioning systems that have pushed up their recycling rates. Our concern in the UK is that the government has done a lot of thinking about how to invoice businesses for the fees and not a lot of thinking about building a system that creates circularity. We are pretty confident that there’ll be a system that invoices us for £1.7 billion a year and that will happen in the next couple of years. The challenge for the next government after the election is going to be driving investment, attracting investment into new technologies, consolidating existing recycling infrastructure, encouraging and enabling packaging innovation, and spending that money wisely.
“It’s not good enough for us that we’ll pay extra money that ultimately pushes up food prices. It’s not good enough for us that we’ll spend all those extra billions, and nothing comes out of it at the other end. So, the challenge for us and the government is how to create an efficient system that
When there are costs involved at the level that we’re going to see with EPR - well into the billions - the incentive is there to create new types of packaging that will work.
creates that circularity. For us that involves taking the best of overseas schemes, which generally involve producer leadership, where producers are good at running EPR systems and that’s why we see double the UK’s recycling rates in places like Belgium. So, we want to inject a bit of producer leadership into the systems to make it happen. I think that will happen over the coming years, but the system that will be in place from next year will be more cash collection than waste collection and we need to shift it so there’s more waste collection going on and more recycling over the first five years of the scheme to make it work.
“The cost is borne by us and so it’s in our interest as producers that we make a system that really works and that we don’t just accept the status quo. In England, we’ve got a 44% recycling rate and that is not good enough when it comes to the cost that we’re about to start paying. Producers have an incentive to reduce the packaging they use, but also to
build that system to get more recycled content into packaging in the future. And that means that we have a clear behavioural driver to make this work, so it’s critical that industry is at the heart of this.”
The landscape of packaging and recycling is poised for significant transformation, driven by the implementation of policies like EPR. By establishing clear regulations, EPR aims to foster an environment where producers are motivated to reduce plastic usage and overall packaging volume. This regulatory clarity is expected to spur innovation and attract investment capital, propelling the industry towards sustainable practices. According to Bligh, when new technologies are guided by well-defined frameworks, they generate substantial investment and momentum.
“When there are costs involved at the level that we’re going to see with EPR - well into the billionsthe incentive is there to create new types of packaging that will work,” said Bligh. “I think having clarity in the rules will create the space for us to innovate and to develop those new products. It’s going to require a considerable amount of capital but if we get this right, then there’ll be investment capital coming in that will enable real innovation quite quickly, which is what we’ve seen in other places.”
Over the next decade, we can expect a noticeable shift in the packaging of supermarket products. While the contents may remain unchanged, the packaging materials will likely be different, more sustainable, and designed to be more easily recyclable.
“What we buy in the supermarket will look and feel different and be in different materials and hopefully then consumers will then recycle it in the right way as well,” he added. “There’s a big job of work for us all to do there to get people to think differently about the products they’re putting in their recycling bin. We need to make sure that we’re driving up those rates with the buy-in of citizens as well as the buy-in of manufacturers.
“From a food and drink perspective, how we make our products, how we grow them, how we ship them, and how we sell them is all changing, and how we package them is changing at the same pace. Every element of our food system is transforming, and you can really feel that when it comes to the packaging. You see it in the supermarkets, particularly where you walk around and it feels very different. I think we’ll see different materials, things like seaweed, coming into packaging and a lot more paper being used than plastic. I think people’s mindset is in the right place but it’s now about having the clarity of the rules and making sure that we got the right investment going in.”
The true measure of innovation lies in the satisfaction of its end users. In the packaging industry, this often means experimenting with various materials until finding a solution that works well for consumers and manufacturers alike. For largescale producers, such as major crisp manufacturers, the demand for stable, reliable packaging is immense. The challenge is not just in developing sustainable options but also in securing a consistent supply of recycled content. According to Bligh, it’s crucial for producers to work with other stakeholders and
for governments to help facilitate the development of a more robust market for recycled materials.
“There’s more to it, I think, than just being sustainable, but that’s an important driver,” he continued.
“I think one of the problems that we face as producers is the supply of recycled content has not been consistent. There are only a couple of factories in Europe that produce, for example, chemically recycled plastic that you can use again as food-grade packaging. They do not produce anything like enough for the global demand that exists. They don’t produce enough for the European demand that exists. So, it’s hard to make the big changes you want to make with enough content to make it happen. What we need to do as producers is to challenge the other players in the ecosystem to create enough supply because there is really enough demand and that’s where I think the government can come in to try and co-facilitate the market.”
Bligh was keen to praise manufacturers and the packaging sector for their advancements, stressing the need for a circular economy and underscoring the importance of future generations
by advocating for packaging that prioritises sustainable materials.
“It’s really exciting to be part of this panel and to see the innovations that are happening and to see everybody coming together to celebrate,” he said. “I think where the industry is at and how it’s transforming will make for a fantastic process. We’ve got some brilliant brands involved in the panel, some real deep experts who are leading the change and to be among them is a great opportunity for me and the FDF as well to help move us on as an industry and to get a lot more sustainable as we change in the next few years.”
As the packaging industry strides towards a more sustainable and environmentally conscious future, the journey ahead is both challenging and promising. But with leaders like Bligh advocating for innovation, collaboration, and regulatory clarity, there’s optimism for significant progress in the years to come.
The first London Packaging Week Innovation Awards winners will be announced on the second day of the show, September 12. Find out more about the awards at www.londonpackagingweek.com/ innovation-awards
When investing in new machinery and processes, manufacturers can get ahead of the game with customised equipment.
According to Deloitte’s 2024 Manufacturing industry outlook report, “technology will likely remain a pivotal force in driving efficiency, resilience and innovation in the supply chain.” On fast-paced production lines where time is of the essence, integrating new equipment demands swiftness. So, how can manufacturers proactively tackle these challenges? Here, Stephen Harding, managing director of Gough Engineering, explains why the answer lies in customised material handling equipment.
Investments in new machinery and processes will be vital if manufacturers are to navigate industry challenges, foster growth and remain competitive. However,
investing in new equipment is far from straightforward. Securing budget allocations can be a challenge, requiring meticulous consideration of the potential returns on investment (ROI), as well as financial metrics such as profitability and cash flow.
To calculate the ROI, manufacturers must identify their reasons for investing in the new machinery in the first place. These goals and objectives might include increased production efficiency, improved product quality or enhanced production capacity. Next, a comprehensive cost analysis is needed that encompasses the initial investment and related ongoing operational costs.
In other words, investing in new equipment necessitates a delicate balance between capital expenditures (CAPEX) and operating expenditures (OPEX). The former includes purchase costs, installation, training and any necessary infrastructure changes on the factory floor. OPEX encompasses the ongoing costs associated with day-to-day operations, such as utilities, planned and unplanned maintenance, salaries and supplies for expected reliability and performance.
These decisions must also be made quickly so that manufacturers can swiftly integrate advanced equipment into their lines. So, how can manufacturers get ahead
Investments in new machinery and processes will be vital if manufacturers are to navigate industry challenges, foster growth and remain competitive
of the game when investing in new machinery and processes? Fortunately, a solution lies in customised equipment.
Let’s look at the impact customised equipment can have on production lines. A food producer/distributor wanted to meet rising demands and expand its market reach across Europe and the Far East. The company sought to enhance its process for unloading big bags with high levels of quality control; with the possibility to load the product into silos, tankers, or even back into big bags.
Challenges included accommodating various big bag sizes, maintaining a fast throughput in excess of 20 tons per hour, and adhering to ATEX, the European safety standard for explosive atmospheres.
To overcome these operational complexities, the company enlisted the expertise of Gough Engineering to implement a tailored material handling system.
Gough Engineering’s approach is to address specific challenges encountered by customers, aiming to minimise manual handling, reduce energy consumption, and optimise cleanliness while ensuring product integrity throughout the process.
Gough Engineering selected a range of solutions from its portfolio. That included the use of big bag discharging units, the use of temporary storage using silos and hoppers, followed by check screening processes to remove any conglomerates or debris.
Product elevation would be crucial to the new material handling system, lifting product between each quality checking process for final delivery. A system’s design can include a Gough Swinglink bucket elevator, Floveyor aero-mechanical conveyors or vacuum transfer systems.
These systems would work alongside vibrational screening as well as different over-band or ‘inline’ metal detection systems — an over-band metal detector unit is positioned above the conveyor belt, or with an ‘in-line’ metal detection systems during product conveying and transfer.
Gough Engineering provided comprehensive design consultancy and engineering support services.
This included factory acceptance testing and mechanical installation, to ensure smooth implementation of the system.
Amid the surge in investments to enhance efficiency and innovation, decision-makers face the critical task of balancing CAPEX and OPEX to ensure optimal returns. Gough Engineering delivers tailored solutions that not only meet but exceed client expectations. From standalone units to complex integrations, the solutions are crafted to meet the diverse needs of modern production environments, offering controlled distribution of products tailored to each client’s unique processes.
The integration of advanced and customised technology into manufacturing processes has become paramount, as highlighted by Deloitte’s industry report, and will be key to driving progress within industry.
Gough Engineering’s solutions are all designed and manufactured in Staffordshire, UK. To find out more about these, including its FIBC Big Bag Discharger systems and elevation solutions like the Floveyor F4 aero-mechanical conveyor system, visit its website.
www.goughengineering.com
BVC Industrial Vacuum Cleaners and Central Vacuum Cleaning Systems manufactured by Quirepace, are used by many of the UKs leading food and drink manufacturers and processors. The reasons why BVC equipment is chosen are many, and in this article, we will focus on some of the principal benefits of the equipment.
Industry demands robust equipment that can be relied upon to perform day after day, week after week, and when service is required expects efficient backup from the factory and easy access to spare parts. This is where BVC equipment excels; since the equipment is manufactured in the UK, spare parts are held at Quirepace’s Fareham warehouse, and because Quirepace supports customers with local area account managers, customers can rely on BVC Industrial Vacuum Equipment to clean up wherever and whenever required without significant interruption and downtime.
The food industry places particular demands on equipment, not least because in many cases the environment is rated as an ATEX zone due to the organic nature of the products. Dusts from flour, cereals, sugar, etc. can all be potentially explosive if the conditions are right, and hence machines intended to be used within ATEX rated areas must be constructed to minimise the risks of inadvertent ignition.
Similarly, many dusts are also potentially hazardous to health when inhaled, and hence appropriate levels of filtration must be incorporated in to any vacuum cleaner designed to recover potentially hazardous dusts.
The range of BVC Industrial Vacuum Cleaners suitable for the Food and Drinks industry extends from the 1kW IV40, which is available in several different versions including M & H Class and ATEX rated, to the 15kW Ti80 designed for fast recovery of bulk products. All machines can be used with intermediate
interceptors to increase the volume of material that can be collected.
In addition to portable equipment, BVC also supply and install fixed pipework systems. In smaller installations this may just be a small quantity of fixed pipework which can be connected to a portable vacuum cleaner. For example, this allows for easy cleaning of mezzanine and upper floors using short and therefore lightweight hoses, whilst the main vacuum unit remains on the ground level.
In larger Central Vacuum Cleaning Systems, not only the pipework, but also the plant is fixed. The plant itself usually including a cyclonic separator combined with various types of discharge arrangement –for example direct discharge in to FIBCs. The installation is carefully designed around the installation parameters and number of operators.
Hoses and tools form an essential part of the system, and again Quirepace offer a very wide range of options for their BVC Industrial Vacuum Cleaners. Hoses come in different diameters for use with different density products, and also offer choices such as anti-static and conductive, heat resistant, and very heavy duty. Likewise, tools to use with the machines must be selected for the most efficient material recovery, whether that is a robust floor tool or an aerating bulk handling tool which helps to aerate
the product being recovered and keep it moving in the vacuum hose.
One of the most popular tool ranges is the high-reach equipment. These are very lightweight carbon fibre poles which can be extended up to 15m high, combined with various end-tools and brushes – for example shaped brushes for cleaning pipework.
The latest innovation in the BVC range of Industrial Vacuum Cleaners is the new Honda eGX powered version of the mid-range IV60. This revolutionary power unit is a battery-electric engine with a quickly changeable battery (just like any cordless tool), and which delivers up to 1.5kW of power. This unique configuration means a powerful and truly cordless solution for industrial cleaning is now available, which with a spare battery enables continuous run time. Eliminating trailing leads means that cleaning jobs can be carried out without considering the trip hazard caused by trailing leads.
Quirepace’s knowledgeable area sales team is available to carry out on-site demonstrations of equipment. Site visits enable the job to be assessed and appropriate recommendations made to ensure that the BVC machine supplied is always the right machine for the job.
Quirepace Ltd. www.bvc.co.uk bvcsales@quirepace.co.uk 023 9260 3700
FD-GA modulating gas + air process air heating burners.
Lanemark gas burner systems offer users reliable, high effi ciency, process heating solutions.
FD Series Packaged Oven/Dryer Burners
•Speci cally designed for process air heating applications in convection ovens and dryers
•High turndown/short ame lengths providing accurate process temperature control
•High ef ciency gas + air modulation, gas only modulation and simple high/low control options
•Heat Input Range: 9 kW – 1550 kW
TX Series Gas Fired Process Tank Heating Systems
•High ef ciency (80%+) heating of all types of spray and dip process tanks
•Compact high ef ciency small diameter immersion tube heat exchangers occupying minimum tank space
•Accurate performance modelling using Lanemark TxCalc design software
•Heat Input Range: 15 kW (1½") – 1150 kW (8")
Midco HMA Series Air Replacement or “Make-Up” Air Heating Burners
•Direct red, high ef ciency burner systems, for high volume air heating applications such as paint spray booths, ovens and dryers.
•Supplied either as Midco burner heads for OEM system integration or as Lanemark DB or FDB complete packaged systems including modulating gas valve trains and controls
•Wide range of ring rates to suit alternative temperature rise and air velocity system requirements
•DbCalc system design software
Lanemark Combustion Engineering Limited
Lanemark House, Whitacre Road, Nuneaton, Warwickshire CV11 6BW United Kingdom
Tel: +44 (0) 24 7635 2000 Fax: +44 (0) 24 7634 1166 E-mail: info@lanemark.com
LensConnect … Zoom, Focus & Iris remote-controllable from PC
Introducing the award-winning computar LensConnect Series
• Easy Installation
Precise adjustment of Focus & Iris
USB connector standard
Inspection while moving focus
• Outstanding repeatability
• High Resolution at any position
• Superb stopping accuracy
Connection Diagram
• Low voltage and current
info@cbcuk.com
• Superior and versatile interface computar-global.com
020 8457 2618 catalyst of optics
Lotan, a UK-based manufacturer of packaging solutions, turned to TM Robotics to help achieve a balance between functionality, cost-effectiveness and eco-friendliness through automation.
As demand and reliance on plastic injection moulding rises, so are concerns about its environmental impact and energy consumption. Here, Nigel Smith, managing director at TM Robotics, the official distribution partner of Shibaura Machine injection moulding machines in the UK and Ireland, highlights the role of all-electric moulding machines in advancing sustainability in UK manufacturing.
According to Grand View Research, forecasts suggest that the compound annual growth rate (CAGR) for the injection moulded plastics market will rise by 4.6 per cent through 2028. The anticipated growth is being driven by the growing demand for plastic components
across various industries including automotive, packaging, home appliances, electrical and electronics and medical devices.
The market growth will be especially fuelled by rising investments in the packaging and automotive sectors, with automotive companies increasing their production capacities and prioritising weight reduction to enhance fuel efficiency. For instance, the increasing use of plastics to replace metals and alloys in automotive components is predicted to drive product demand among end users — and will offer significant opportunities for injection-moulded plastics to enter the market.
But, as demand and reliance on injection moulding rises, so too are concerns about its environmental impact and the energy consumption of moulding processes. Combining high temperatures, pressures, cooling requirements and equipment operation, injection moulding can be a very energy-intensive manufacturing process.
Fortunately, all-electric injection moulding machines are offering an alternative to more energyintensive hydraulic models. Let’s look at how all-electric machines can support the rise of injection moulding, while addressing environmental concerns.
The market growth will be especially fuelled by rising investments in the packaging and automotive sectors, with automotive companies increasing their production capacities and prioritising weight reduction to enhance fuel efficiency.
One company that is embracing the advantages of all-electric injection moulding machines is Lotan, a UK-based manufacturer. The manufacturer specialises in sustainable packaging solutions for various industries including food and beverage, cosmetics, pharmaceuticals and retail. Lotan wanted to achieve a balance between functionality, costeffectiveness and eco-friendliness in its packaging solutions.
The company turned to Shibaura Machine all-electric injection moulding machines, supplied by TM Robotics. Performance benefits of the machines include
a range of clamping force from 50 to 2,500 tons, which can be calibrated by a digital direct screw transfer (DST) control for added production flexibility. Other advantages included faster injection speeds and improved cycle times. In addition, the machines’ user-friendly interface and Internet of Things (IoT) integration could help to simplify Lotan’s operations and support its preventive maintenance.
Performance tests conducted by Shibaura Machine ensure the energy efficiency of all-electric injection moulding machines. In one instance, the performance of an all-electric Shibaura Machine’s EC650SX-61B IMM, which boasts a clamping force of 650 tons, was evaluated against hydraulic servo alternatives. The EC650SX61B IMM showcased a notable 51 per cent reduction in energy consumption.
In another test, Shibaura Machine’s 1,800 ton EC1800SX155B model was put against a rival all-electric injection moulding machine. Both machines exhibited similar energy consumption levels — but Shibaura Machine’s EC1800SX155B showcased a superior cycle
time and an impressive 30 per cent overall energy efficiency gain.
Lotan’s use of Shibaura Machine all-electric injection moulding machines has yielded substantial energy savings of up to 40 per cent compared with traditional hydraulic counterparts. The company has also reported significant improvements in performance, and costeffectiveness, and ordered several more Shibaura Machine injection moulding machines from TM Robotics — specifically its newest SXIII range.
As the demand for plastic components continues to grow, so too is the imperative to adopt sustainable manufacturing practices. Fortunately, all-electric injection moulding machines have a significant role to play in industry’s ambitions for better sustainability and operational efficiency.
To learn more about how Shibaura Machine’s all-electric injection moulding machines support sustainable manufacturing, visit TM Robotics’ website.
www.tmrobotics.com
New research from Industrial Physics reveals that less than a quarter of organisations are currently taking an innovative approach to packaging
New research from Industrial Physics, the leading packaging and material test and measurement provider, has revealed the extent of innovation within the food and beverage packaging industry, and how this is impacted by internal operations.
Last year, Industrial Physics’ report found that there is a desire for innovation, with 96% of packaging professionals in food and beverage expressing that new developments in packaging were important, and with 71% believing it was very important. However, this year’s data highlights that in reality, less than a quarter (24%) of organizations are currently taking an innovative approach.
The international survey of packaging professionals operating in the food and beverage packaging sector found that more than 1 in 5 (22%) packaging professionals said that their company does not usually follow up on the innovative ideas it comes up with, and half of respondents (49%) said that too many teams are involved in the innovation process, which slows them down.
The report also found that 35% of packaging professionals using organic material said that they didn’t feel they had the appropriate expertise to facilitate growth and innovation in their business.
As Steve Davis, Global Director of Product Management at Industrial Physics explains in the report, there is limited capacity for innovation despite the desire for it being there: “Overall the mechanisms, the capacity and the direction aren’t quite there yet. Packaging companies understand the significant resource and investment required for the majority of
innovation opportunities, therefore the decision to go ahead is not a quick or an easy one.”
When respondents were asked how their business had fared over the past five years, almost half (47%) said their company has had to make layoffs. This is more likely to be the case with US based respondents at 58%, compared with an average of 44% in Europe and 45% in Asia. The proportion of those making layoffs varies between material type – the highest being those working with paper (62%).
Davis adds: “Many companies within the packaging sector have been operating for decades and currently do not have the capacity to pursue innovative ideas whilst maintaining their regular manufacturing output which already satisfies a consistent demand. We’re noticing that companies who want to pursue innovation are running into internal barriers. In a period where budgets are extremely tight and layoffs are being made, unless a company can guarantee the ROI, there simply isn’t enough justification to assign resource to innovation.”
Davis concludes: “Our report
highlights that pursuing opportunities in innovation is not as straightforward as it seems. With continued turbulence and both internal and external factors contributing to uncertainty, organizations need more support than ever to remain resilient and assess opportunities for innovation in packaging without compromising on the quality or safety of their products.
“With 41% saying their company is planning to take an innovative approach in the next three years, companies should start planning ahead and assessing their internal operations to make careful, considered decisions about how they’re going to pursue innovation, as these changes cannot be made overnight.”
To learn more about food and beverage packaging innovation and the internal environment, download Industrial Physics’ free report here. To understand more about the wider factors impacting innovative approaches in food and beverage packaging, look out the next report in Industrial Physics’ research series, coming this year.
www.industrialphysics.com
The Concept agitator system processes a 25kg block of raisins every seven seconds and can feed them into any production line Scan & watch the Concept Agitator in action
Designed, manufactured and installed by Concept
Produces signi cant savings in labour costs
The new machine was developed after one of the UK’s leading suppliers of speciality nuts, dried fruit and confectionery required a bespoke solution to improve e ciency.
Concept Engineering of Hull were approached and they designed what is believed to be the only machine of its kind capable of breaking blocks of dried fruit without causing damage.
The Concept Fruit Breaker features an agitator to break up solid blocks of dried fruit, a task that previously had to be carried out manually.
2-6 GB Business Park, Wiltshire Road, Hull, HU4 6PA. 01482 351267
Domino Printing Sciences (Domino), trusted global provider of complete variable data printing solutions, is pleased to announce the launch of its new automated product printing and label verification solutions to help manufacturers reduce the risk of costly product labelling errors. Domino’s latest solutions include advanced coding automation software that removes the need for manual intervention and integrated machine vision to check the accuracy of every printed code.
As legislation surrounding the labelling of consumer products becomes stricter, ensuring efficiency and accuracy in product identification operations has never been more important, but product printing errors due to inefficient processes and overreliance on human labour continue to be a significant issue.
“In January 2024 alone, the FDA issued 19 recalls for food products in the US, with 18 of them attributed to undeclared allergens due to labelling errors,” says Adem Kulauzovic, Director of Automation, Domino. “These figures highlight that printing and labelling inefficiencies are still very much present within a significant number of manufacturing facilities, despite recent advances in product coding automation.”
Recent industry reports support these findings, with Automate UK’s recent Industry Insights Survey 2024 finding that over 81% of industry workers identified automation as their primary challenge for 2023. The cost of adoption, lack of internal knowledge, and the inability to find the right suppliers stand out
as some of the top barriers to adoption.
“When it comes to adopting automation, designing a solution that integrates various technologies while managing relationships with multiple suppliers can be costly and complex, posing a challenge for many businesses,” continues Kulauzovic. “Our closed-loop solutions have been designed to offer all the benefits of automated product coding from a single trusted source, helping to reduce complexity and costs associated with lengthy project timelines. In addition, our flexible finance options – encompassing both subscription models and product leasing – mean businesses can upgrade without significant capital investment.”
When it comes to adopting automation, designing a solution that integrates various technologies while managing relationships with multiple suppliers can be costly and complex, posing a challenge for many businesses.
Domino focuses on supplying complete end-to-end solutions for variable data printing so manufacturers can ensure that the energy, time, and funds they invest are spent creating highquality, sellable products. End-
to-end solutions encompass two newly launched products, Domino Automation, and the R-Series i-Tech, plus remote monitoring from Domino’s cloud-based services – all of which are designed to work alongside Domino’s full range of variable data printing solutions:
• Domino Automation –centralised message storage and automated printer management software
• R-Series i-Tech – label verification and quality inspection system optimised for high-speed production lines
• Domino’s cloud-based services – machine monitoring tools for remote diagnostics, troubleshooting, and optimisation Domino’s solutions can be tailored
to customer requirements, with all components available as standalone products, or integrated as part of a full, closed-loop solution.
As part of Domino’s extended customer testing, end-to-end product printing and label verification solutions were delivered to a number of sites across Domino’s existing customer base. The ease of integrating a complete solution from a single provider received significant positive feedback.
“The market has told us that cost and complexity are huge factors preventing manufacturers from adopting automation – we are here to tell you that coding automation doesn’t need to be costly or complex,” says Tony McNulty, Chief Product Officer, Domino. “Our end-to-end solutions are designed so manufacturers can easily automate their product labelling, reducing the risk of errors, without the hassle of managing multiple vendors or conflicting technologies.”
Please visit the website to find out more information about Domino’s automated product printing and label verification solutions.
For further information on Domino please visit www.domino-printing.com
In this case study, we’re discussing a new horizontal self-priming spill control pump we recently supplied to an industrial client. They had several silos and tanks on site and needed an effective and reliable pump to minimise potential damage from any spills.
In the UK, the accidental spillage of oils and other chemicals from industrial sites causes a significant amount of pollution every year.
Many spills can be prevented with rigorous production processes and strict monitoring. But if there is an accidental leakage, it’s important to act quickly to:
• Minimise possible damage: spills can spread rapidly and seriously harm the environment
• Avoid prosecution: court fines and clean-up costs after a spill can be expensive
• Reduce negative PR: a spill can mean very bad publicity for a company, its directors and clients, as BP discovered in the US after the Deepwater Horizon incident
What’s the difference between spill control, primary and secondary containment?
Spill control tactics are designed to reduce the amount of contact the spilled material has with people, property and the wider environment.
Primary containment is the actual vessel or container holding a substance - solids, liquids, chemicals or waste. It’s the first line of defence against spills, leaks or accidental releases.
Secondary containment serves as a back-up in case the primary containment is breached. It is a regulatory requirement for any primary container if the contents are hazardous, and a breach of that containment would endanger life, soil or water around it.
In the UK, the accidental spillage of oils and other chemicals from industrial sites causes a significant amount of pollution every year.
By law, the secondary containment system, ‘must have sufficient capacity to contain at least 10% of the total volume of the primary containers or 100% of the volume of the largest container, whichever is greater.’
Our specification for this client
For this particular project, our client asked for a pump which would be corrosion resistant not only to a number of differing fluids but also resist deterioration overtime from exposure to air, and water which can be common with pumps manufactured from Cast Iron. We specified the pump to be manufactured from AISI316 stainless steel to ensure that there were no issues with pump corrosion during its operation lifetime.
We specified a 3’ horizontal self-priming pump made from cast AISI 316 stainless steel. This material is widely used in industrial applications. It’s also well suited to even harsher environments needing greater corrosion resistance, having more tensile strength at higher operating temperatures.
Our stainless steel self-priming pump was specially designed for spill containment at the client’s site where there are several tanks and silos housed within a bund – this is a type of embankment or wall of stone or earth, built to stop the area being covered by a large amount of water.
In addition, the pump will be used as a tanker loading pump and to feed discharge into a sewage plant. If the silos or tanks ever leak, the pump will evacuate the bund of any wastewater, milk or other low viscosity liquid.
We supplied the pump with a built-in control panel so that users had convenient local control of the pump’s operations on site.
A key feature of this spill control and tanker loading pump is the selfpriming function which primes the pump in just 45 seconds – vitally important when a spill has to be contained quickly. In addition, it can handle solids up to 30mm and dry run for up to 30 minutes once the head is filled with liquid.
If you’re looking for a spill control, tanker loading or sewage plant feed pump, and aren’t sure which one’s right one for you, contact us on 01773 302 660, email sales@northridgepumps.com or visit North Ridge Pumps at www.northridgepumps.com to see how we can help.
Optimise performance with specialist support
Whether you’re dealing with clogging, separation, downtime, or other issueit’s costly. Time wasted troubleshooting and lower production mean missed targets and less profit. A sanitary pump is the solution but choosing the right one feels like stepping into a minefield. You know what you need it to do but with so many options, it’s difficult to know which is best for your process and parameters.
+ Accelerated stator wear
+ Clogging
+ Changes to fluid consistency
+ Clean-in-place and sterilise-in-place hygiene issues
+ Crushing of sensitive products
+ Inconsistency in finished product
+ Inaccurate transfer of flavourings or ingredients
+ Liquid separation
+ Seal wear or failure
We’ve been engineering sanitary pumps for sectors such as distilling, brewing, food manufacturing/processing, and more, for 20+ years. We understand industry-specific processes and know what it takes to optimise performance through better-suited pump design - giving you complete peace of mind.
Our expert engineers understand your process and guide you through the options, so you can confidently select the most suitable sanitary pump.
EXAMPLE PRODUCTS:
+ Abrasive mixtures
+ Creams, milk & ice cream
+ Edible oils & fats
+ Fish & meat
+ Fruits eg. cooked apples, plums, berries, grapes
+ Grains & seeds
+ Pastes & purees
+ Syrups, juices & alcohols
+ Vegetables & peelings
+ Waste eg. trimmings, packaging & offcuts
+ Sheer sensitive liquids
+ Solid laden or viscous mixtures
The BCMPA – the Association for Contract Manufacturing, Packing, Fulfilment & Logistics, will be hosting its first full conference since 2018, focusing on the latest industry trends and challenges in third-party outsourcing.
Held at the Delta by Marriot Nottingham Belfry on the 10th of July, the conference will be an opportunity for BCMPA members and other professionals to network, share their knowledge, and gain insight into the ever-evolving landscape of the third-party outsourcing sector.
Key topics that will be discussed throughout the day include the rising demand for sustainable practices across the supply chain, recent changes surrounding environmental regulations and effective strategies for carbon reduction, digitalisation and trends within the fulfilment sector.
Emma Verkaik, CEO at the BCMPA said; “Our recent member survey highlighted an increasing want for networking opportunities. This conference is designed to meet that need, offering a platform for face-to-face collaboration, knowledge exchange, and partnerships, as well as tackling some of the challenges currently facing the world of contract manufacturing, packing, fulfilment and logistics.
“Our hope is that all attendees will gain a valuable overview of the most pressing industry challenges
Our recent
member
survey highlighted an increasing want for networking opportunities.
and leave with an understanding of how to combat these within their own business.”
Speakers include Josephine Coombe, CCO of Nulogy, colead sponsor of the conference alongside the exhibition organiser of Packaging Innovations and the Contract Pack & Fulfilment Show, Easyfairs. Additionally,
Kevin Vyse, Head of Technical at ProAmpac RAP and Jude Allen, Interim Managing Director at OPRL, will shed light on sustainable packaging and navigating the challenges of EPR legislation in outsourcing. In addition, there will be a presentation on the global economic outlook from respected economist Trevor Williams, and a look at the consumer trends in fulfilment by Andrew McLelland of IOM3 as well as others.
Additionally, the event sponsors will offer delegates a chance to learn more about the services they offer in supporting the third-party
outsourcing industry and include Acopia Group Ltd, AddParts, Autopack, Benchmark, Element Logic, Keystone Law and Two Blue Solars.
Tickets for the conference are now available to both members and non-members, with an option for overnight accommodation and an informal networking dinner on the 9th of July. Those interested in attending are invited to contact the BCMPA for more information and pricing, by email at conference@ bcmpa.org.uk. or visit the BCMPA website: bcmpa.org.uk/events/ bcmpa-conference
Easy entry into industrial VGA thermography
Reliable temperature measurement is a requirement for the success of many industrial processes. Berlinbased manufacturer Optris presents the Xi 640 in-frared camera, a new member of its Compact Line, which enables reliable, af-fordable and noncontact temperature measurement in VGA resolution for me-chanical engineering and the supplier industry.
With its Xi Compact Line, Optris combines the advantages of precise thermal imag-ing cameras with the benefits of infrared thermometers.
The compact Xi 640 VGA infrared camera offers comprehensive, non-contact condition monitoring for indus-trial applications. With a high optical resolution of 640 x 480 pixels and a frame rate of 32 Hz in
the spectral range of 8-14 µm, the VGA infrared camera can be used to monitor fast thermal processes at temperatures between -20 °C and 900 °C. Optris has equipped the Xi 640 with an “Auto spot finder” function, which can also be used to measure the temperature of moving objects without having to readjust the camera.
Motorized focus ensures a sharp image
Like the other models in the Xi family, which has now grown to six models, the Xi 640 uses a motorized focus for convenient focusing from a distance. The image processing is carried out using the free PIX Connect software with line scan func-tion, which is also included. Important parameters are configured via a USB 2.0 in-terface; a USB-to-GigE converter is optional. The Xi 640 is supplied with a process
interface cable and a USB cable. The thermal imaging camera can be used in am-bient temperatures between 0 °C and 50 °C as standard. Optris offers a wide range of accessories for the camera, from the air purge unit and mounting bracket to the water cooled housing, which enables ambient temperatures of up to 250 °C.
Suitable for mechanical engineering and many other industries
Thanks to its high precision, robustness and flexibility, the Xi 640, like its sibling models in the Compact Line, is predestined for use in mechanical engineering or the OEM sector. The compact camera is the simple and reliable introduction to VGA thermography for various industries.
www.optris.com
Completing the Advanced X2 Series of X-ray Inspection Systems: Affordable, Future-Proof Solutions with Enhanced Sensitivity, Dual Functionality and Unmatched Capabilities
Mettler-Toledo Product Inspection proudly announces the release of the innovative X52 Dual Energy x-ray inspection system to complete its X2 Series. Designed to meet the demands of challenging applications in packaged products, the X52 sets a new standard in detection capabilities at an incredible price point. The X52’s proprietary software provides increased adaptability by seamlessly transitioning between single energy, dual energy or both modes, optimising the performance of the system depending on the application.
In single energy mode, the X52 identifies a wide range of contaminants including glass, metal, mineral stone, calcified bone, dense plastic and rubber compounds based on their material composition, offering thorough inspection for product safety and quality. Dual energy mode further enhances accuracy by analysing materials’ densities, providing an advanced level of detection to preserve consumer well-being and uphold industry standards.
The X52 x-ray inspection system excels in both efficiency and accuracy by seamlessly detecting foreign body contaminants while simultaneously completing a broad range of quality assurance checks. Through its advanced technology, the X52 significantly reduces false rejects, distinguishing between genuine contaminants and product variations with ease. This precision
minimises unnecessary production halts and disruptions, allowing manufacturers to maintain operations and reduce unnecessary downtime. By maximising uptime and minimising waste, the X52 boosts productivity and reduces overall costs, setting a new standard in x-ray inspection technology.
The X52 single and dual energy x-ray system is designed to futureproof manufacturing operations, instantly accommodating evolving product lines and applications. Its adaptable nature not only offers long-term reliability but also promotes sustainability and cost savings by consolidating multiple detection capabilities into a single machine, reducing the need for additional equipment. This approach provides
manufacturers with peace of mind as they navigate changing industry landscapes, meaning they can meet both current and future production demands efficiently and effectively.
Equipped with state-of-the-art features, the X52 offers increased sensitivity, thanks to its use of proprietary Advanced Material Discrimination (AMD) and ContamPlus™ software. Using advanced x-ray technology, the X52 inspects the contents of packaged products with exceptional accuracy. The AMD dual energy software enhances the system’s ability to differentiate between materials, offering
The X52 x-ray inspection system excels in both efficiency and accuracy by seamlessly detecting foreign body contaminants while simultaneously completing a broad range of quality assurance checks.
precise contaminant detection even in challenging scenarios such as products that are overlapping or vary in thickness. This helps provide peace of mind that your end products safer, more reliable and high-quality.
Further showcasing its capabilities, the X52 incorporates HiGain+ DE detector technology, surpassing conventional solutions with enhanced accuracy and reliability. The HiGain+ DE detector, by Mettler-Toledo, provides exceptional sensitivity and resolution, enhancing material analysis with accuracy. This advanced technology offers thorough inspection without compromising efficiency, meeting the evolving needs of manufacturers across industries.
Beyond its cutting-edge detection capabilities, the X52 also brings practical benefits to manufacturers, starting with its space-saving design. Engineered with a compact footprint, it maximises floor space in production facilities without compromising on performance. Additionally, the X52 is available with comprehensive service and support from the Mettler-Toledo global network of service experts, offering remote and on-site support, so manufacturers can maximise uptime and performance.
Manufacturers can now easily comply with industry standards and streamline regulatory compliance through ProdX™, a data
• X12 High Performance X-ray System: This high performing singlelane x-ray inspection system comes as a standard configuration and is available at an attractive price point, featuring the HiGain detector, which generates sharper images to deliver outstanding contaminant detection.
management software from MettlerToledo providing full regulatory documentation. The X52’s userfriendly interface allows for easy access to inspection data, enabling quick decision-making and proactive quality control measures.
The X52 embodies the MettlerToledo commitment to excellence, combining smart industrial design with streamlined approaches.
From elevating Overall Equipment Effectiveness (OEE) to reducing Total Cost of Ownership (TCO), the X52 operates at peak performance for extended periods of time.
The X52 completes the line-up for the X2 Series of x-ray inspection systems.
In addition to the X52, the X2 Series consists of two other models – the X12 and X32. All are available in multiple line configurations 800, 1300, 1800 and 2000 millimeter line lengths:
• X32 Advanced X-ray Solution: Offering enhanced sensitivity and product integrity performance, this x-ray inspection solution features the HiGain+ detector and is available in standard and custom configurations, with single or multilane capabilities.
“The X52 x-ray inspection system marks a pivotal leap forward in product inspection technology,” says Mike Pipe, Head of Global Sales and Product Management at Mettler-Toledo Safeline X-ray. “With its forward-thinking design, the X52 future-proofs manufacturers by detecting unwanted contaminants in even the most challenging packages. Its unmatched performance, innovative features and comprehensive support set a new standard for product integrity and reliability. We are thrilled to provide manufacturers with the tools they need for enhanced product safety, quality and compliance now and in the future.”
For more information about the X52 X-ray Inspection System and other Mettler-Toledo products, please click here or visit www.mt.com/xray-x52-pr
Industrial Physics, a leading test and measurement instrument provider, announces the acquisition of Torus Group, a UK-based expert in quality control measurement systems and metrology.
The acquisition marks a significant development for Industrial Physics and will increase its ability to serve as a quality partner to customers across several key end markets. The latest move supports the company’s ambitious growth strategy as laid out by Chief Executive Officer, Barry Lyon, upon his appointment in July 2023.
Torus Group, known for its strong portfolio in measurement for metal and rigid packaging in the food and beverage industries, has recently expanded into plastic packaging and medical devices. Following the acquisition, Industrial Physics customers across the globe will have access to an even wider
Our shared commitment to quality, safety, and innovation will deliver significant benefits for our customers.
range of solutions, including test and measurement equipment, metrology services and machine enclosure support.
Speaking on the announcement, Barry Lyon, CEO of Industrial Physics, shared: “Packaging innovators need reliable test and measurement solutions to navigate rapid development across the packaging industry today and ensure the quality and safety of their products. We are proud to be guiding customers with this across various end markets, and remain active in sourcing opportunities to widen the range of our solutions. With more than 20 years of
experience in the industry and localised support teams in place for customers across industries globally, Torus Group is a perfect addition to support our purpose: protecting the integrity of brands and products.”
Chris Freshman, Torus Group’s group director of business development, commented: “Joining Industrial Physics is an exciting opportunity for Torus Group. Our shared commitment to quality, safety, and innovation will deliver significant benefits for our customers. With the acquisition now completed, we look forward to integrating with Industrial Physics’ global infrastructure to offer an even greater suite of measurement systems and localised support to our customers.”
Website: www.industrialphysics.com
LinkedIn: industrial-physics
Twitter: @IndustrialPhys
Alex Stewart Food Test Lab is a fully UKAS accredited laboratory and is part of Alex Stewart Agriculture. We provide a complete range of food testing and microbiological analysis including food and dairy products, water and beverages, seeds, cereals, oils & fats, raw & refined sugar and other consumable products.
21 Sefton Business Park, Olympic Way, Aintree, Liverpool, Merseyside L30 1RD UK T: +44 (0) 151 525 1488 E: laboratory@alexstewartagriculture.com Your global network of inspection and analytical services www.foodtestlab.co.uk
Food safety specialist Fortress Technology addresses the main metal detection challenges that arise when inspecting dairy applications for contaminants, reviewing how the latest technology is smarter and overcomes a number of sensitivity challenges.
Applying the company’s longstanding metal detection expertise, European Sales Director Phil Brown explains how changing characteristics, product and orientation effect can disrupt product signals and affect detection sensitivity if not addressed. The food inspection specialist also touches on how digital technologies and machine learning are pushing the innovation boundaries and streamlining inspection processes.
Due to high levels of automated processing machinery, the use of tools for maintenance, and other mixing equipment, metal remains the most prevalent contaminant risk in food manufacturing, potentially causing product quality and consumer safety issues. Metal detectors can be deployed to reduce this food safety
risk. However, due to the physics of disturbing the electromagnetic field, the orientation of a metal contaminant can affect whether a contaminant is effectively detected.
This phenomenon is known as orientation effect. It occurs most noticeably when long, thin wiretype metal contaminants are more easily detected if they pass through the metal inspection system in one orientation rather than another. However, this orientation effect is exhibited by any non-spherical contaminant, not just wires.
A typical occurrence could be when equipment is calibrated to detect a stainless-steel sphere measuring 2mm in diameter. While it may identify and reject this contaminant, the machine may fail to detect a stainless-steel wire that is slightly smaller in diameter, but longer than 2mm. It does depend on the orientation of the wire as it travels through the detector.
Often, it can be easier to detect stainless steel and non-ferrous wires when they pass through the aperture
Reducing the aperture size in relation to the product size can be a simple and effective way to increase metal detector sensitivity
space sideways or upright, rather than in alignment with the conveyor. This is because of the magnetic permeability of the metal, which is much lower for stainless steel than ferrous metals.
Reducing the aperture size in relation to the product size can be a simple and effective way to increase metal detector sensitivity. This is because sensitivity is expressed as the smallest detectable spherical contaminant travelling through the geometric centre of the aperture. The centre of aperture is always the least sensitive position in the aperture. The idea is to challenge the worst-case scenario. So, if the contaminant is detectable in this position, then it will be more easily detected closer to the aperture walls.
Features like single pass product learning and automatic calibration can also help, as operators are easily able to overcome a potentially changing product effect which will result in maintaining the highest performance levels and lowest levels of false detections.
Dairy product applications are typically wet and conductive, which can present an additional challenge for metal detectors. Cheese, for example, with its high moisture content, combined with salt, can be highly conductive and cause a reaction like metal being present. This product effect can result in the product being rejected and good food being discarded.
To identify a metal contaminant within conductive products, a metal detector must remove or reduce this product effect. Single pass calibration is meant to do this. However, the underlying operating frequency of the metal detector impacts how effective a calibration can be at eliminating the product effect. With single frequency metal detectors running ‘wet’ products there is often a trade-off between ferrous and stainless-steel performance depending on the selected frequency. Typically, higher frequencies exhibit increased performance in detecting stainless-steel versus ferrous metals. The best approach is to find a frequency that provides a balance between the lowest product effect and the detection of target contaminants.
Using simultaneous multi-frequency technology is the most reliable way to remove product effect without compromising the sensitivity of a metal detector. This processing technology powers the Fortress Interceptor, enabling it to run realtime analysis of the low-frequency and a high-frequency signals in parallel.
The increased sensitivity was one of the primary reasons why dairy processor Vepo Cheese selected seven Interceptor metal detectors
to integrate with their vertical packing machines. The cheese giant specifically requested “state of the art inspection equipment that could deal with variations in density and product effect.”
Technical Operations Manager at Vepo, Hugo van Put recounts: “These metal detectors are really sensitive. This helps us to feel confident that the risks of contaminants are minimal, with less chance of a food safety issue. Having the double readings within the Interceptor system also lowers the risk of falsepositive rejects, which saves on food waste.”
The standard technique for measuring the sensitivity of metal detectors in food inspection is to use metal test spheres. Yet, metal contaminants typically enter the production line as flat metal flakes, shards, swarf or thin wires, rather than globular shapes. So why test using spheres?
The main rationale is it provides machinery suppliers and food processors with a comparative sensitivity control. A sphere does not exhibit orientation effect and will always produce the same signal when passed through the same position of a
metal detector’s aperture.
The food metal detection industry has general sphere size guidelines. For example, a wet block of cheese measuring approximately 75mm high, currently has sphere size parameters of 2.0mm for ferrous metals, 2.5mm for non-ferrous and 3.5mm for stainless steel. However, these levels are not always one size fits all, as the product effect from different types of cheese as an example, can vary greatly.
There are multiple variables that can affect a metal detector’s performance, from the potential size and composition of possible contaminants to the liquid content and consistency of the product matrix.
It’s equally important to note that there is no ‘best’ metal detection frequency. There are only ranges of frequencies, each better for different purposes. As with any aspect of food safety, there’s always a cause and a consequence. Having sufficient scientific understanding about how dairy products behave and conditions that can trigger a false positive reaction is important. If in doubt, seek expert guidance. www.fortresstechnology.co.uk
Thanks to its compact design, E-BOX GRIPPER allows increased storage volumes within the automated warehouse, enabling higher storage capacity for the same amount of space. The use of sensors and IoT components makes it a “plug-in” solution that is quick and easy to install, maintain and, most importantly, can collect data for predictive maintenance.
Watch Eurofork’s solution in action: https://youtu.be/nrF2mjFztjk
Using IO-Link Wireless based communication enabled Eurofork to control the conveying unit’s and boxholding grippers wirelessly with full flexibility, rather than having complex and malfunctionprone wired connectivity. The motors controlling the grippers are connected via a TigoBridge IOLink Wireless Bridge device, which enables the simplest and most reliable wireless communication from the moving E-BOX GRIPPER. The TigoBridges communicate over the air with the TigoMaster IO-Link Wireless Master which also enables a seamless integration to the PLC and to enterprise applications such as WMS or ERP systems. This setup is particularly suited for environments with densely packed warehouse shelving aisles, where interference is a common challenge.
This Industry 4.0 design approach, empowers the E-BOX GRIPPER to offer a variety of benefits and advantages:
• Operational Excellence: Overstocking reduction, increased efficiency, error reduction and enhanced traceability.
• Industrial IOT Ready: Thanks to IO-Link and IO-Link Wireless, the system provides full control and bidirectional communication for control and monitoring (including
predictive maintenance).
• Non-Stop: Power transmission embedded into the belt system ensures continuous operation of the grippers, and wireless connectivity enables fewer cables, less wear and tear, and less maintenance.
• High Performance: Simultaneous handling of two boxes built into the system, additional expansions upon request.
• Customizable & Scalable: Enable variable distances between tines (for boxes of different widths) and operate with all Eurofork’s accessories (belt system, chain system, roller tracks, etc.).
• Adaptable & Flexible: Can be easily integrated on a variety of stacker crane and shuttle systems.
• Silent: Designed to minimize noise during handling operations.
“The integration of CoreTigo’s IOLink Wireless technology into the E-BOX GRIPPER was simple and straightforward”, says Giuseppe Testa, CCO of Euroforkat Eurofork”. “Having this flexibility with a wireless solution enabled us to fulfill the needs of the market and provide the E-BOX Gripper which addresses key industry challenges”.
“CoreTigo’s IO-Link Wireless solution is specially designed for control and monitoring on moving components in harsh industrial environments, which made it the perfect solution for Eurofork’s E-BOX GRIPPER”, says Matteo Orlandelli, Italy Country Director at CoreTigo. “We’ll be showcasing these and many other capabilities at the upcoming SPS Italia 2024”.
www.coretigo.com
Tosca, a global leader in reusable packaging solutions, is pleased to announce the opening of a new, state-of-the art service centre in Ingolstadt, Germany. This downstream-focused facility, equipped with solar panels for sustainable energy usage and advanced technology capabilities, is designed to support Germany’s largest retailers with efficient, datadriven services.
The opening of the Ingolstadt service centre marks a significant expansion of Tosca’s footprint across Europe. With a total area of approximately 2,700 m², the centre is strategically positioned to cater to the growing demand for Tosca’s innovative reusable plastic products and pooling services in the region. With the addition of the Ingolstadt centre, Tosca currently operates 10 service centres across Central Europe.
Ingolstadt is equipped with advanced technologies, including RFID gates, scanning equipment, and automation systems. These innovations ensure optimal data accuracy and provide customers with deep insights into their supply chain performance, underscoring Tosca’s commitment to futureproofing supply chains. This technology enables Tosca to increase the efficiency and accuracy of their customers’ supply chains, driving growth, operational excellence and sustainability.
Driven by the increasing business in plastic half pallet operations, the decision to establish the Ingolstadt centre underscores Tosca’s dedication to supporting its downstream customers across
The opening of the Ingolstadt service centre marks a significant expansion of Tosca’s footprint across Europe.
Europe. By optimising operations and reducing transport costs, the new centre will enhance efficiency while facilitating further growth in the region. Importantly, the centre is positioned to serve Tosca’s largest downstream customer in Central Europe and one of its key suppliers.
In August/September, Tosca will install a fully automated wash line at their site, including a conveyor reader on the wash line to automatically update asset status and monitor performance. These investments highlight Tosca’s commitment to enhancing operational efficiency and providing
their customers with superior supply chain solutions.
“We’re excited to unveil our newest service centre in Ingolstadt, a testament to our ongoing commitment to delivering exceptional service and value to our customers,” said Marco Gonzalez, Managing Direct for Central Europe at Tosca. “This expansion highlights our ability to adapt quickly to market demands, as well and our dedication to growth in reusable plastic packaging solutions across Europe’.
Notably, Tosca achieved an impressive lead time of just four months from the start of site search to operational readiness, showcasing the company’s agility and collaborative working across all departments.
As Tosca continues to solidify its presence in the European market, the opening of the Ingolstadt service centre represents a significant milestone in the company’s journey towards continued growth and innovation.
www.toscaltd.com/en-gb/
Pharmaceutical manufacturer G. Pohl-Boskamp urgently needed packaging materials for its main product Gelomyrtol. Faller Packaging helped the company to keep its remedy for colds available – in the shortest possible time and using all available resources.
Sometimes things need to move really quickly. Last autumn, the pharmaceutical manufacturer G. Pohl-Boskamp faced a major challenge: Based in Hohenlockstedt, SchleswigHolstein, the medium-sized company produces medicines and medical products for the treatment of acute and chronic illnesses – and it found itself suddenly confronted by a huge demand for folding cartons for its main product Gelomyrtol. The packaging design
Faller’s assistance was truly vital. Without their fast response, we’d certainly have faced delivery bottlenecks.
also had to be adapted at the same time. The situation was unexpected and a fast and effective solution was urgently needed – so G. PohlBoskamp turned to its partner Faller Packaging in Waldkirch.
Faller Packaging, the specialist company for folding cartons, package leaflets, labels, and combination products from a single source, responded promptly to support its long-standing
customer. The remedy had to remain available on the market during the cold season, so speed was crucial. Working closely and diligently together, the Faller sales, order service, pre-printing, planning, material planning and production teams got the job done. Within just a few days, three million folding cartons were dispatched to northern Germany. “Faller’s assistance was truly vital. Without their fast response, we’d certainly have faced delivery bottlenecks. We’re fully convinced that Faller will also be the right partner for Pohl-Boskamp in the future,” says Sandra Matthießen of Purchasing at G. Pohl-Boskamp GmbH & Co. KG.
www.faller-packaging.com
Registration has opened for Fi Europe 2024, allowing forward planners to lock this unmissable food & beverage industry event into their schedules and benefit from an early bird discount. Those who register before 14 July qualify for an introductory rate of €49, which includes entry to the Fi Europe Conference. The 2024 edition will offer a host of new features, including an expanded Food Manufacturing Technologies & Solutions Area and the Pet Food Suppliers’ Hub.
A vast and vibrant show floor is the core of Fi Europe’s value proposition and the format is constantly evolving in line with market trends. Informa is expanding the Food Manufacturing Technologies & Solutions Area for 2024, dedicating a larger space to solutions that can help food & beverage businesses secure their supply chains and future-proof their operations. This year will also see the introduction of the Pet Food Suppliers’ Hub – a new area showcasing ingredients
Fi Europe’s content programme is always a highlight, with expert speakers offering exclusive insights on the challenges, trends and technologies shaping the food & beverage industry.
and technologies that can support the pet food industry in developing nutritious, safe and innovative products. In addition, there will be a number of new country pavilions, providing visibility for products and solutions from markets around the world. Denmark, Thailand and Latin America will be among the countries participating in this capacity for the first time this year.
Fi Europe’s content programme is always a highlight, with expert speakers offering exclusive insights on the challenges, trends and technologies shaping the food & beverage industry.
This year, for the first time, entry to the Fi Europe Conference will be free of charge for visitor pass holders, making this knowledge gathering forum accessible to all.
Yannick Verry, Brand Director, Food ingredients Europe & Americas, at Informa Markets, says: “The food & beverage industry never stands still; there are always new narratives unfolding. We strive to evolve the Fi Europe platform to reflect these changes and challenges, whilst constantly looking for ways to enrich the experience and add value for visitors and exhibitors alike. We look forward to seeing how attendees use the different facets and features of this year’s event to support innovation, solve problems and develop profitable connections.”
Registration for Fi Europe 2024 is now open. Click here to register.
Discover more about Fi Europe here.
Established in 1978, Isoclad & sister company Securiclad have been supplying panel systems for over 40 years. Part of the Resource family of businesses since 2017, Isoclad and Securiclad operate from two sites employing over 60 highly trained staff.
Our Isoclad operation plus Securiclad sales, design and technical teams are located in our North Shields HQ, with Securiclad production and Customclad operation located in our brandnew state of the art facility in Monmouth, South Wales.
Isoclad is the largest independent manufacturer of insulated panels and ancillaries in the UK. Renowned for our products globally, we place user-friendly service at the heart of our offering, ensuring your project receives ongoing advice and support at every stage from our team of professionals.
In addition to our industry leading insulated panels, as a business we offer a much wider service; from initial project planning through to blueprints and installation, we liaise with your team to enable a smooth project timeline from start to finish.
Innovation is part of what makes us who we are and what drives us. We continue to invest in innovative products and production methodologies, recognising that the built environment is continually changing and that our processes and products must move with it.
Our Thermocore panel range delivers excellent thermal performance and are designed to offer superb structural integrity, lending itself to hygienic and temperature controlled applications amongst others.
The thermally-efficient, closed cell foam core provides excellent performance and cost savings
through reduced demand on utilities and excessive heating & cooling which limits the carbon footprint of our products.
Our internal wall and ceiling insulated panels deliver a flexible, lightweight product that combines functionality, reliability and durability. These products are suitable for an array of sectors such as Cold & Chill Stores, Freezers, Food Processing and Clean Room facilities. Designed to
be installed with ease, Thermocore can be used for permanent walls, temporary partitions and demountable solutions.
Our specifications allow for control of mould and bacterial growth and resist moisture ingress. Hygienic and safe product faces make this product ideal for very demanding requirements.
The Thermocore range has a low environmental footprint and is made from part-recycled materials including environmentally friendly steel, increasing your building’s eco-credentials.
www.isoclad.co.uk
Founded in 2000, Puma Engineering specialises in designing, manufacturing, and installing high-precision engineering products for customers in the food & beverage, pharmaceutical, petro-chemicals, power generation, oil and gas, cryogenics, and subsea industries.
Drawing on our deep technical expertise and problem-solving skills, we can help you to find effective technical solutions to the most challenging engineering requirements.
With an unwavering customer focus, we deliver high-quality products on time, every time.
Operating from our specialised 1,400m2 facility in Southampton we can ensure products are manufactured using the very best productive methodology, with direct engagement from our highly technical management team.
Segregated clean section to fabricate exotic materials in a ferrous-free environment.
Contact our team today: 02380 675975 Unit 9, Westwood Business Park, Brunel Road, Southampton, SO40 3YS Webenquiry@puma-eng.co.uk www.puma-eng.co.uk