MANUFACTURING Engineering Process

Issue 62 2023 £4.95
www.pecm.co.uk
Effective and reliable throughout the entire product lifecycle
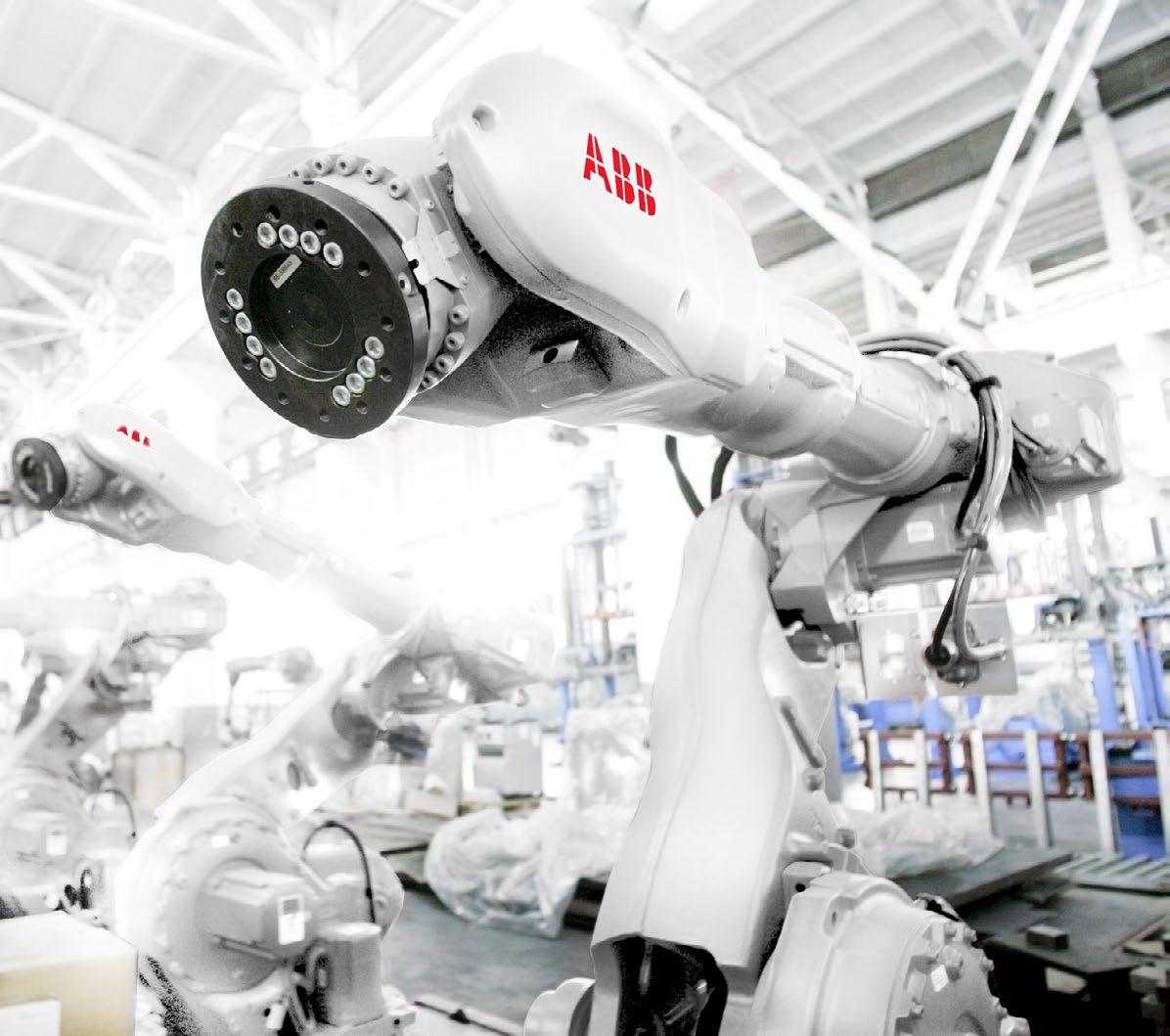

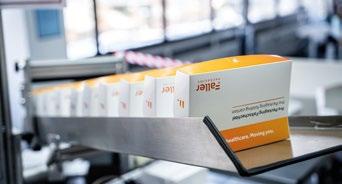
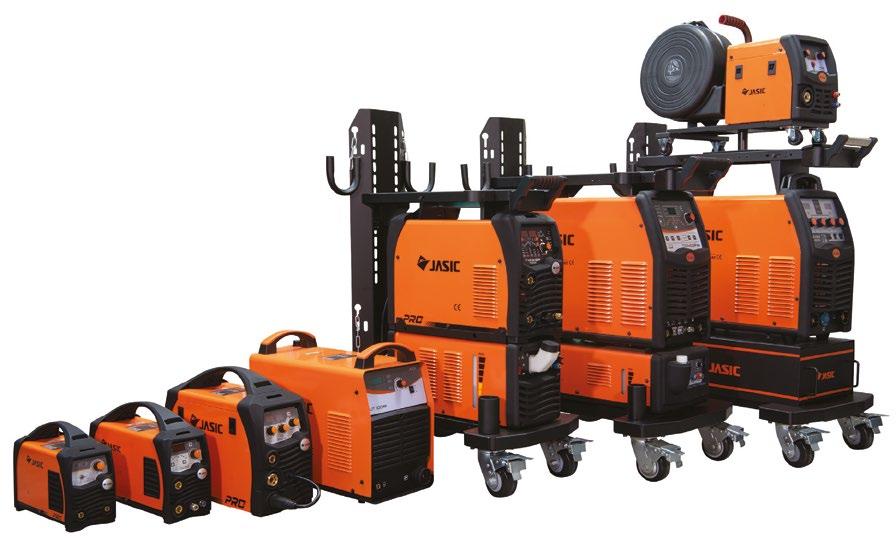
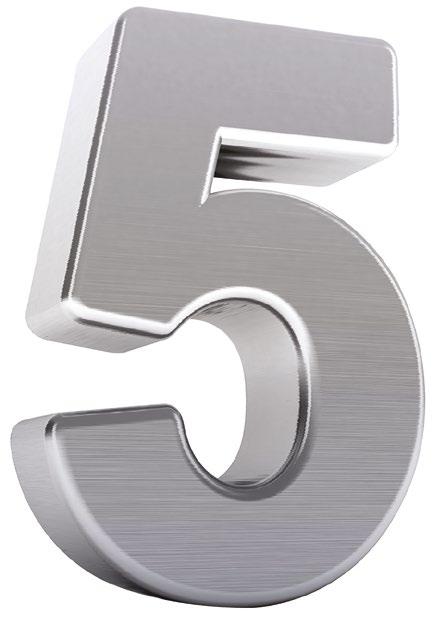
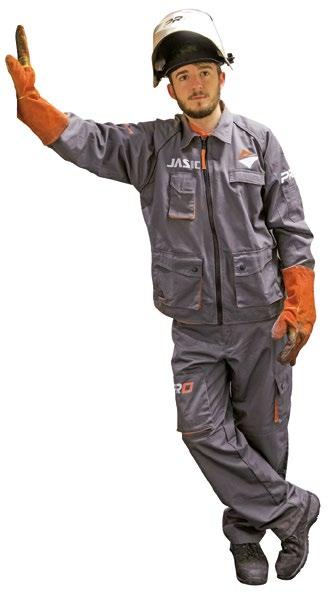
Issue 62 2023 £4.95
www.pecm.co.uk
Effective and reliable throughout the entire product lifecycle
Inside Issue 62
TEEPEE ELECTRICAL
One of the UK’s longest serving engineers celebrated 76 years working in industry this week and insisted he wants to carry on until he is 100
WATLOW
Dennis Long, chief system designer at industrial electric heater manufacturer, Watlow, explores the possibilities of electric process heaters
SHELL ENERGY
What does the IETF mean for energy intensive users?
GLOBAL HEAT TRANSFER
Turning back time on marine fluid degradation
ASG GROUP
Leading Manufacturing Group Awarded Aerospace Certifications
FANUC
How we can secure the future of automation?
EK ROBOTICS
ek robotics transport robot wins renowned iF Design Award 2023
SANDVIK COROMANT
Secure and high-quality aluminium threading with next-generation CoroTap® 100 and CoroTap® 400
ABB
ABB technology to help tackle methane leakages from orphan oil and gas wells
FLUKE
Saudi Electricity Company improves service and reduces costs with Fluke inspection equipment
INFOR
Nine ways consumable, democratised data improves factory operations
The widest range of accessories on the market. Future-proof
Suitable to any environment, application and industry. Concept workbench
Multiple sizes and combinations available. Productivity and well-being
DESIGN YOUR PERFECT WORKSTATION
The Treston 3D Configurator can be used to design an industrial or technical workstation that best meets your needs. To get started, all you need is a mobile phone or a computer with an internet connection; no downloading is required and using the software is free.
Subscribe
The leading source for innovators in Technology, Manufacturing and Maintenance within the Engineering & Processing industry worldwide.
Published bimonthly, a subscription to PECM magazine is essential for Process Engineers, Chemical Engineers, Instrumentation Engineers, Mechanical Engineers, Plant Engineers, Precision Engineers, Environmental Engineers & General Engineers, Companies and Organizations in the Food, Dairy, Beverage, Brewing, Semiconductor, Pharmaceutical, Biotechnology, Chemical, Oil & Gas, as well as all UK's major manufacturing units.
Every issue of the magazine contains the latest news, in-depth features, together with product innovations and case studies showing how process engineers are implementing new technologies to reduce costs and impact on the environment.
With over 140,000 readers worldwide the publication is widely read, recognized, and well respected within the Process, Engineering & maintenance industries.
A subscription to PECM magazine is the industry's 'must have' publication.
SUBSCRIBE TO 6 BIMONTHLY ISSUES OF PECM FOR JUST £27
• The magazine gets delivered directly to your door once every issue is published
• The quality of the hard copy enhances the reading experience
To Subscribe please call 01304 806039
SUBSCRIBE TO OUR DIGITAL EDITION COMPLETELY FREE OF CHARGE
Designed for the digital age, the magazine has been created for easy viewing on all electronic devices. All our issues stored in one place: get unlimited access to our previous and future issues.
To Subscribe please visit www.pecm.co.uk/subscribe
EDITOR IN CHIEF
Antony Holter editor@mhmagazine.co.uk
BUSINESS MANAGER
Josh Holmes josh@mhmagazine.co.uk
SALES DIRECTOR
Harrison James harrison@pecm.co.uk
Tel: 0203 907 9166
SALES MANAGER
Martin Richardson martin@pecm.co.uk
Tel: 01304 086039
DIGITAL MANAGER
Jamie Bullock jamie@mhmagazine.co.uk
Tel: 01227 936971
EDITOR
Elizabeth Hutton elizabeth@pecm.co.uk
STUDIO DESIGNER
Richard Bland richard@mhmagazine.co.uk
ACCOUNTS DEPT
Alison Holmes accounts@pecm.co.uk
Tel: 01227 936976
PUBLISHING DIRECTOR
Martin Holmes martin@mhmagazine.co.uk
Tel: 01304 806039
DIGITAL ASSISTANT Stacey Goodwood
Tel: 01227 936971
Please mention Process Engineering Control & Manufacturing when responding to items in this issue.
Bentley has announced that it will cease production of its 12-cylinder petrol engine in April 2024, by which time more than 100,000 examples of the iconic W12 will have been handcrafted in the company’s Dream Factory in Crewe, England.
The decision comes as part of Bentley’s acceleration towards a sustainable future through its Beyond100 strategy which will see the company’s entire model line fully electrified by the start of the next decade, reducing fleet average emissions to 0 g/ km CO2. This journey has already begun, with the introduction of the Bentayga and Flying Spur Hybrid models for which demand is exceeding the company’s expectations. When production of the W12 ceases next year, Bentley’s entire model line will be available with the option of a hybrid powertrain. Meanwhile, an engine first made available in the sector-defining Continental GT, which has been powering Bentley both metaphorically and literally for the last 20 years, will be consigned to history.
Bentley isn’t letting the W12 bow out without a dramatic send-off. Development work has concluded recently on the most powerful version of the W12 ever created. The ultimate iteration of this mighty engine – destined for just 18 examples of the Bentley Batur to be handcrafted by Mulliner – is now confirmed as developing 750 PS and 1,000 Nm of torque. The increased torque figure forms the typical Bentley ‘torque plateau’, running from 1,750 rpm to 5,000 rpm – with peak power at 5,500 rpm.
Bentley’s Chairman and Chief Executive, Adrian Hallmark, comments:
“Our progressive journey towards sustainable luxury mobility means making changes to every area of Bentley Motors. When we first launched the W12 back in 2003, we knew we had a mighty engine that would propel both our cars and the brand forwards at speed. 20 years and more than 100,000 W12s later, the time has come to retire this now-iconic powertrain as we take strides towards electrification –but not without giving it the best send-off possible, with the most powerful version of the engine ever created.
“The 750 PS titan that Mulliner has created for the Batur marks the end of a development journey of which our engineering and manufacturing colleagues should be extremely proud, and when production finishes in April next year we aim to retrain and redeploy all of the skilled craftspeople who still build each engine by hand.”
Battling through an exceptionally gruelling series of durability tests, the uprated engine has proven to be as reliable as ever and so will equip the most powerful road-going Bentley ever built. While all Baturs are sold, a limited number of the 659 PS version of the W12 engine offered in the Speed versions of Continental GT, Bentayga and Flying Spur as well as the Continental GT Mulliner and Flying Spur Mulliner can still be ordered. Demand for these final W12powered Speed and Mulliner models is expected to be high, and customers eager to secure one of the last ever 12-cylinder Bentleys should contact their retailer with equal speed.
Bentley’s aim is to retrain and redeploy all 30 of the skilled craftspeople that handassemble and test every single W12 engine at Bentley’s carbon-neutral factory in Crewe.
Meanwhile, the W12 engine production facility will make way for an expanded line for the completion of other Bentley engines used for the plug-in hybrid models.
Since the first introduction of the 6.0-litre, twin-turbocharged W12 in 2003, the engineering team in Crewe has continually improved the performance of the engine in terms of power, torque, emissions and refinement. Over the last 20 years, power has increased by 37 per cent and torque by 54 per cent, while emissions have been reduced by 25 per cent. Initially this was through evolution and optimisation of the control systems, improvements in the oil and cooling designs, turbocharging technology and more effective injection and combustion processes. For the launch of the Bentayga in 2015, the W12 was completely redesigned from the sump up, and it’s that version of the engine that remains in production today – featuring cylinder deactivation, direct and port injection, and twin-scroll turbos.
Each W12 engine is hand-built over 6.5 hours by a team of craftspeople before undertaking a highly sophisticated test regime of over an hour via three specialist diagnostic machines. Every week, one
engine is run over an extended test cycle and then fully stripped for inspection.
The W12 engine facility will have delivered over 105,000 engines before reaching its 20th anniversary this year.
For the final and ultimate version of the W12, Mulliner’s engineering team has reworked the intake, exhaust and cooling systems to liberate more power and torque than ever before. Under the watchful eye of Mulliner’s Chief Technical Officer, Paul Williams (who previously led the development of the second-generation W12), the engine is now signed-off at 750 PS and 1,000 Nm of torque – both record-breaking figures for the engine.
The turbocharger compressors are of a new design to improve efficiency, while the ducts that feed air to them are 33 per cent larger – at peak power, the new engine ingests more than a ton of air (1,050 kg) per hour. Larger charge-air coolers, with a depth increased by 10 mm and a new core geometry, reject 35 per cent more heat from the pressurised intake air, reducing intake temperature to a greater extent meaning a denser charge for more power.
The new intake and turbocharging system is matched with a heavily revised engine calibration to liberate the extra torque available, and the complete engine system is then paired with a new transmission calibration to deploy the additional power and torque and enhance the driving experience.
Bentley’s legendary 6.0-litre twinturbocharged W12, created in 2002, has evolved into the latest iteration of W12 engine used across today’s current model range. The unique W-configuration means that the engine is 24 per cent shorter than an equivalent V12, benefitting packaging and maximising usable cabin space.
The latest generation of W12 was launched in the Bentayga in 2015. A thoroughly reworked engine included a crankcase 30 per cent stronger than its predecessor, while the cylinder surfaces were coated
to reduce friction and improve corrosion resistance. A low-alloy steel coating is applied to the bores using an Atmospheric Plasma Spray (APS) process.
Improvements were also made to the cooling system, with the engine featuring three separate coolant circuits. The first is designed to bring the cylinder heads up to optimum operating temperature as quickly as possible for best engine performance and low emissions. The second cools the engine block and oil system, while the third handles the thermal load of the turbochargers. Each system has a dedicated water pump, allowing optimised individual control.
The W12 combines high-pressure direct fuel injection (200 bar injection pressure) with low-pressure port injection (six bar). The combination of these two systems maximises refinement, lowers particulate emissions and optimises power and torque delivery.
Twin-scroll turbochargers minimise turbo response time and provide a more efficient exhaust package. The exhaust assemblies for the three front and three rear cylinders are separate from one another which then feed the twin-scroll impellers. The turbocharger housing is welded directly to the exhaust manifolds and feature integrated speed sensors, allowing the engine to monitor turbo performance for maximum efficiency.
Bentley’s Variable Displacement system shuts down half of the engine under defined conditions. Intake and exhaust valves, fuel injection and ignition are all shut down on defined cylinders, with the engine running as a six-cylinder for improved efficiency. The system will run in this mode in gears three to eight, below 3,000 rpm and up to 300 Nm torque output.
For further information, please visit www.bentleymotors.com
Our progressive journey towards sustainable luxury mobility means making changes to every area of Bentley Motors.
One of the UK’s longest serving engineers celebrated 76 years working in industry this week and insisted he wants to carry on until he is 100.
Vic Sutton, a Calibration Engineer at harness and wiring looms specialist Teepee Electrical in Bloxwich, turned 90 on Tuesday and spent his big birthday playing a role in daily production and enjoying a surprise party with colleagues he openly calls ‘family’.
It marked what has been a rollercoaster career for the former mechanical engineering apprentice, who started work just four years after the end of the second world war and has spent time at English Electrical, as a radio engineer in the Royal Air Force, with British Electronic Products, Thorn EMI and a local Staffordshire start-up.
He has combined his love of manufacturing with an insatiable appetite for Northern Soul music that has seen him become one of the scene’s most loved DJs with more than 700 gigs under his belt.
It was only the weight of equipment that saw him pack up his decks a few months ago, but Vic readily admits he still gets pulled into doing some guest spots by friends.
“My family keep asking me when I’m going to stop, but I genuinely just love coming to work,” explained Vic, who still works three days per week.
“Teepee Electrical is a fantastic company. We all get on really well and it’s like one big family - the fact we are doing such great work for the ‘blue light’ sector is the icing on the cake.
“I’ve been here two decades, starting off doing the drawings for the wiring harnesses for some big-name customers. These days I’m responsible for the calibration of more than 428 hand tools used by my colleagues to crimp the wires.”
He went on to add: “We’ve got our own testing room that’s like my own den and my
problem-solving skills are definitely put into good use as the management team tend to bring me in to make things more efficient at our Leamore Road Factory.”
Vic, who witnessed the final days of the Battle of Britain from the family home in Walthamstow, believes the biggest change in manufacturing has been the emergence of technology and the fact everything is done on computers - including his calibration work.
However, his message to the engineers of the future is ‘education, education, education’, making sure that young people take every opportunity to learn, whether that is at school, college, university or on the shopfloor.
Steve Clarke, Managing Director of Teepee Electrical, added his support: “Vic is a walking, talking inspiration…it’s as simple as that.
“Everyone loves him, and he really brings a feel-good factor to the factory, not to mention years of manufacturing and problem-solving experience that makes a real difference on our shopfloor.
“His stories are amazing, from overcoming tuberculosis as a child and playing in two bands in Stoke-on-Trent to rubbing shoulders with Alvin Stardust and Billy Fury.”
Vic received an early 90th birthday present in March when he welcomed his fourth great-grandchild to the world, with Elliot James joining Nevaeh, Harlow and Nixon.
He also has four grandchildren (Ashleigh, Amy, Ellie and William) from his daughter Joanne and son Darren.
“I love my family to bits, but I have no intention of giving up work just yet. As long as I remain fit enough - both in body and mind - I hope to still be working at Teepee Electrical when I hit the big century.”
For further information, please visit www.teepeeelectrical.co.uk
Your all-in-one solution
YOUR BENEFITS:
• Increased machines availability: Clear error detection, high transparency and remote diagnosis
• Flexibility: Easy assembly, modularity and convenient adjustment
• Time saving: Innovative and flexible connection technology
• Cost efficiency: No further accessories necessary
E-T-A Circuit Breakers Ltd. +44 (0) 1296 420336 info@e-t-a.co.uk
www.e-t-a.co.uk
• The cost-effective and flexible way to ensure uninterrupted power supply without CAPEX costs.
• UPS hire, for businesses, data suites and stadiums.
UPS rental systems on a weekly basis, depending on the site requirements. OPEX allows the benefits today without waiting for high level approval that comes with CAPEX expenditure.
UPS RENTAL SYSTEMS-FLEXIBILITY
UPS Rental systems offer:
Containerised: UPS rental systems can be customized to meet the specific power requirements of site requirement, ensuring backup power for your site. Each container comes with Battery Autonomy backup, independent air conditioning, internal lighting, secure lockable with remote monitoring.
Installed: Temporary UPS installation, ensuring that businesses get power protection, without the wait.
Within the building: Temporary UPS Installation can be within your building. Level access and floor weight loading will allow us to provide a temporary UPS installation indoors.
24/7 support and maintenance services, Businesses rely on uninterruptible power supplies.
Emergency Call-out to site 24 hours a day across the UK.
Remote monitoring
UPS RENTAL FOR EVENTS
• Football Stadiums
• Music Concerts
• Outdoor events
• Light shows create powerful harmonic surges that generators alone can’t handle without falling over. An uninterrupted power supply ensures hassle free concerts and light shows, throughout the gig.
• Hospitals and other healthcare facilities
Data centres: UPS Failure happens. UPS Hire systems can be deployed to site, ensuring uninterrupted power supply to data centres, with emergency generators, before power loss damages the reputation of your brand. Call Power Continuity immediately for resilience needs.
Manufacturing: Power disruptions can suddenly stop production.
We can install short term UPS rental systems to eliminate power spikes & brown outs.
Football Stadiums: Loss of Stadium lighting.
UEFA televised matches must have UPS power protection.
UPS RENTAL systems protect media events from power disruptions.
Universities
Loss of power resilience at Data Comms hubs.
Rapid delivery and installation of our temporary UPS solutions , keep Universities operational
Outside broadcasts
Hiring a UPS system can be more costeffective than purchasing and installing a UPS system, especially for short term filming.
Government Departments
Resilience is the back bone of Governmental Oversight of the UK economy. Government servers must have clean unfailing power.
UPS rental containers rapidly deployed to power protect the UK infrastructure.
Cost-effectiveness: Hiring a UPS system can be more cost-effective than purchasing and installing a UPS system, especially for small and medium-sized businesses.
UPS RENTAL systems are cost-effective to ensure uninterrupted power supply resilience on a temporary basis without incurring long term capital costs of CAPEX.
Power Continuity has containerised UPS resilient rental systems from 30KVA N+1 up to 2 Megawatts; all available installed on a temporary basis.
For more information call us on 0845 055 8455
Power Continuity
UPS Rental for Short & Long Term Hire
Any Where - Any Event - Any Time | www.powercontinuity.co.uk
Processing and refining hydrocarbons requires high heat for a number of critical steps, and heaters based on fossil fuels have traditionally filled those roles. But with mounting pressure to mitigate carbon dioxide emissions and advance long-term decarbonization goals, engineers have been exploring the potential for electric process heaters. This would allow several heating steps to be completed using “clean” electricity from renewable sources.
Replacing fossil fuel heaters with electric heaters would allow for a reduction in “Scope one” carbon dioxide emissions. As defined by Buehler, Scope one emissions are the direct result of burning fuels like natural gas or fuel oil for process heating. Scope two emissions result from the need to import energy, while Scope three emissions are produced while using a product. For example, emissions from vehicles on the road. All three types must be reduced to hit decarbonization targets.
What’s holding back Scope one emission reduction?
A survey conducted by Watlow for its customers and prospects has revealed that a full 90 per cent of oil and gas leaders are already actively engaged in decarbonization efforts. Hydrocarbon processors are no longer focused on if they should decarbonize, but how they will decarbonize.
So why aren’t electric process heaters more ubiquitous in the energy sector today?
Surprisingly, familiarity might be the main reason. Until now, such heaters have played only very narrow roles in hydrocarbon processing and were usually smaller, operating at lower voltages. Although larger heaters are easily imaginable, engineers recognize that a number of questions arise when it comes to their control and maintenance. In short, no one wants to be first into the water when it comes to running larger medium-voltage thermal systems.
The good news for industry is that modern electric heaters can provide the same, or improved, performance that hydrocarbon
engineers have come to expect from fossil fuel powered heaters and can therefore play a key role in decarbonization efforts.
Some of the most common questions about larger process heaters have to do with control. What additional elements are needed to ramp up the heater? How is temperature monitored and controlled? What additional safety precautions are needed?
Just because larger electric heaters have not traditionally been used to heat all processes in the petrochemical industry does not mean that the technology is untested. In fact, field-proven power switching devices have been in use for low voltage electric process heaters and electric medium voltage motors in numerous industries for years, and the ability to control voltage is well established.
PLCs and similar power management systems bring heaters online in ways that prevent problems for other devices connected to the same power source. The heater and controller are part of one closedloop system, which streamlines integration and yields more control over the entire system.
Dennis Long, chief system designer at industrial electric heater manufacturer, Watlow, explores the possibilities of electric process
Industry leaders like Watlow are solving the world’s most challenging and essential thermal problems. Its work includes breaking down the barriers to energy transition to provide clean, efficient and reliable ways to electrify processes traditionally heated with fossil fuels. This includes Watlow’s POWERSAFE™ solution — a medium voltage heating solution that combines both an electric heat exchanger and a control system. The system has been proven to operate safely and reliably at 4160V and higher. It also offers a flexible combination of a siliconcontrolled rectifier and contactor circuits up to 25 megawatts within a single control package, delivering high-efficiency power to reduce the size and weight of the solution, while providing a clean, safe asset for
engineers tasked with decarbonizing thermal systems.
Gaining familiarity with electric process heating systems now will reduce the burden of energy transition later. Engineers are realizing two things. First, there are far more opportunities to use electric process heating systems with far fewer size constraints than energy and environmental engineers previously imagined. Second, control of these megawatt size heating systems is demonstrated in field applications, with precise control of process and skin temperatures. But, by working with a reliable partner to electrify process heating systems is one of the surest ways to progress toward climate action goals without interrupting productivity or profitability.
Industry leaders like Watlow are solving the world’s most challenging and essential thermal problems.
Heatsense Cables, www.heatsensecables. co.uk, established in 1984, is regarded as the UK’s leading specialist high-performance thermocouple and signal cable manufacturer. Its manufacturing capabilities cover a broad range of specialist cables that operate in extreme environments, -196°C to +1250°C. The company is a technology leader in fluoropolymer extrusion, high-performance taping and cable wrapping. Related processes include cover sintering, colouring, etching and the application of various specialist coatings. The range covers cables that are resistant to flame, oils & chemicals and which operate in ultra-high vacuum, cryogenic and high radiation environments.
The company offers a bespoke advanced technical design and manufacturing service and undertakes development work on new cable designs and materials.
PFA, FEP, PTFE, ETFE, EFGLAS, SILICONE, PE, PU, PVC, Taped & Sintered PTFE, Polyimide & Aramid Yarns, PTFE impregnated yarns and Mica. Braiding materials include glass, quartz & ceramic fibres, other specialist yarns and various metals.
The high-performance cable range includes thermocouple cables, RTD cables & PRT
wires, sensor wires & cables, micro-wire & miniature cables, cryogenic cables, heat resistant cables & wires – the INTEMP™ range of cables, glass fibre, quartz, ceramic & pure nickel cables, radiation resistant wires & cables, equipment wires, UHV & low outgassing cables, high-voltage wires & cables, micro-coaxial cables, bespoke cables, multicore cables, high flex braided cables, PTFE yarns and PTFE cable tapes & cords.
See our base online catalogue https://www.heatsensecables.co.uk/products/ heatsense-cables-product-catalogue
Heatsense continues to add and upgrade specialist plant & equipment, build on internal
systems & software, add accreditations and undertake development work on new materials and processes to support customer needs and requirements, including keeping abreast of changes in legislation.
Markets include aerospace, space, nuclear, automotive, medical, R&D, oil & gas and general industry.
Heatsense is EN9100:2018, ISO9001:2015, ISO14001:2015 Accredited, F4N (Fit for Nuclear) Approved, Cyber Essentials Plus Certified, JOSCAR Approved and a Member of ADS
SPECIALIST HIG HPE R FORMANCE SO L UTIONS
SPECIALIST HIG HPE R FORMANCE SO L UTIONS
For further information please visit www.heatsensecables.co.uk and/or contact sales@heatsensecables.co.uk
SPECIALIST HIGH-PERFORMANCE SOLUTIONS
SPECIALIST HIGH-PERFORMANCE SOLUTIONS
SPECIALIST HIGH-PERFORMANCE SOLUTIONS
Heat Resistant Cables & Wires for Extreme Temperatures
Fibre, Quartz, Ceramic & Pure Nickel Cables
& Low Outgassing Wires & Cables
Bespoke Cables Multicore Cables
High-Voltage Wires & Cables Micro-Coaxial
High Flex & Braided Cables
PTFE Yarns, Lacing Tapes & Cords
Regardless of how diverse your task is, a thermography automation solution from InfraTec allows you to master the challenge efficiently and cost-effectively. The proven modular system, consisting of a thermographic camera, transmission, display, interface, industrial PC and software components, allows flexible adaptation to your specific requirements.
InfraTec offers you exactly the system solution that meets your requirements. Starting with a single high-end infrared camera including thermography software up to the delivery of a complex, customised thermographic automation solution, you will receive the right product for your application.
We offer a comprehensive range of more than 30 infrared camera models. Our product range comprises entry-level devices, professional and universal cameras, high-end solutions as well as industrial thermal cameras and infrared imager. The range includes the high-end camera series ImageIR®, which is developed and manufactured at the InfraTec headquarters in Dresden. For fixed installation, e.g. in harsh industrial environments, as well as for mobile use, the powerful uncooled thermographic systems VarioCAM® High Definition are suitable.
The core of the turnkey thermography automation solutions are the innovative, robust thermal imaging cameras with detector formats up to (1,920 × 1,536) IR pixels and frame rates into the kilohertz range. In conjunction with InfraTec modular hardware and software system, you receive tailored solutions for virtually all fields of industry and research.
Automated thermography solutions from InfraTec provide you with reliable knowledge about even the smallest temperature developments and distributions. Over 30 years of thermal imaging experience and more than 6,000 satisfied customers worldwide confirm InfraTec’s competence in this field. InfraTec infrared cameras are available in the UK and Ireland exclusively from Quantum Design UK and Ireland.
Our product range comprises entry-level devices, professional and universal cameras, high-end solutions as well as industrial thermal cameras and infrared imager.
Applications include:
Applications include:
UK/Ireland Distributors for
UK/Ireland Distributors for
Tel: +44 (0)1372 378822 | Email: info@qd-uki.co.uk
Tel: +44 (0)1372 378822 | Email: info@qd-uki.co.uk
www.qd-uki.co.uk
www.qd-uki.co.uk
Rapeseed meal extract or meal is a byproduct of rapeseed oil manufacture. It is created when seeds are pressed to extract oil from the plant, creating a byproduct of rapeseed meal. It is used as protein source and soya replacement which can be fed to animals or used to alter the fatty acid composition of milk.
An agricultural processing facility contacted us who were looking to recycle rape meal as a way of generating an income stream from waste by product, as well as work towards meeting net zero and sustainability targets.
They had discovered that during the cold pressing of oils large amounts of meal were being generated, which was not being utilized efficiently. The meal was gathering in pits, or containers with water and the customer wanted to be able to move it easily across their plant into containers for resale and transport. There were various sources of the meal, and they wanted the ability to move a pump kit between various points to easily decant containers or empty pits of the liquid.
North Ridge worked with the customer to fully understand the distances in which the fluid would be pumped, the liquids characteristics and solid concentration and viscosity. It is important to understand the nature of a waste liquid as quite often its nature can vary between plants making it difficult to transfer as it can be viscous, or contain abrasive solids which can quickly wear pump parts or seals. We can quickly determine what pump may be best for an application or which technology may be best suited for a particular fluid often by seeing pictures or videos of the fluid being poured, stirred or agitated without having to wait for an engineer to visit site.
We specified and supplied a self priming mobile pump kit which could be used to draw the fluid located in tanks below the pump, or take the liquid directly from vessels transferring it up to 10M horizontally and 6M vertically. We worked with the customer to ensure the process
water could be pumped at its processing temperature – 50°C without waiting, as well as handle the suspended solids which were up to a few mm in diameter. The pump was supplied with a local on
off switch for ease of control and a 10M 3 phase power cable.
Utilising a pump kit not only enables operators to work more efficiently and recover waste product but they can be designed to eliminate manual handling, and automate fluid transfer. Pump sets can be customised to accommodate almost any process, be made mobile for ease of portability and supplied complete with accessories for easy all-in-one fluid transfer such as hosing, flowmeters and dispensing nozzles. As North Ridge Pumps are not limited to a single pump technology, it enables us to specify more than one solution for your particular process, and handle virtually any kind of fluid.
If you are looking at methods of waste recovery and processing to generate new revenue streams, visit www.northridgepumps.com or call 01773 302 660 to see how we can help.
For further information, please visit www.northridgepumps.com
North Ridge worked with the customer to fully understand the distances in which the fluid would be pumped, the liquids characteristics and solid concentration and viscosity.
Industry knowledge and application expertise across dispensing, dosing, full containment, gentle handling, blending and transfer, means whatever the problem, it’s likely we’ve seen it before. So we can help you solve it sooner.
+ Accelerated stator wear
+ Clogging
+ Changes to fluid consistency
+ Flow Reduction
+ Inconsistency in finished product
+ Inaccurate transfer of chemicals
+ Leakage | Liquid separation
+ Product Wastage
+ Seal wear or failure
+ Valve Blockage or unintended Opening
We’ve been engineering sanitary pumps for sectors such as distilling, brewing, food manufacturing/processing, and more, for 20+ years. We understand industryspecific processes and know what it takes to optimise performance through bettersuited pump design - giving you complete peace of mind.
EXPERT GUIDANCE:
Our expert engineers understand your process and guide you through the options, so you can confidently select the most suitable chemically resistant pump.
EXAMPLE PRODUCTS:
+ Acids
+ Alkalis
+ Coagulants
+ Corrosive
+ Chemical Sludge
+ CO2
+ Flammable
+ Flocculants
+ Oxidisers
+ Pyrophoric
+ Refrigerants
+ Solvents
+ VOC with low NPSH
+ Water Reactives
The space race didn’t get off to the best start this year, with the UK’s first ever satellite mission ending in disappointment. The launch highlights how the failure of just one component can lead to the demise of an entire mission. But space waits for no one, and as the race continues, how can we best ensure that future missions are successful? Here, Dave Walsha, sales manager at DC motor supplier EMS, explains.
Virgin Orbit’s Start Me Up mission hoped to be historical: being the first orbital launch from the UK, the first international launch for Virgin Orbit, and holding the first satellite built in Wales.
Investigations into the reason for the project’s failure are still ongoing, but
preliminary evidence suggests that the problem lies with a filter in the rocket’s second-stage propulsion system. The filter was dislodged, causing issues downstream and ultimately leading to premature shutdown of the engine.
The project highlights the complexity of space missions, and the importance of every single component — including micromotors — in ensuring a safe and successful mission. But what can reliable micromotors do for space applications?
Most orbital launch vehicles, including Virgin Orbit’s rockets, rely on RP-1 fuel for power. RP-1 is a highly refined form of kerosene, which has had additional
unwanted compounds removed to produce a cleaner burn and prevent engine damage.
RP-1 is mixed with liquid oxygen (LOX) to create a combustion reaction. The nature of this reaction means precise ratios aren’t required, provided both reactants are present in some capacity. But if the ratio does begin to stray significantly from the ideal, then one reactant is likely to run out before the other, leaving the remainder as dead weight.
To avoid this from happening, butterfly valves are installed onto the fuel tank pipes. Controlled by servo motors, these valves allow precise control of reactant flow, which means that the fuel mixture can be kept as close to its ideal ratio as possible.
Micromotors aren’t only helpful in ensuring an efficient launch — they can be just as important when it comes to making the return journey.
Since the first unmanned space mission Sputnik in 1957, unmanned space probes have been used for a more cost-effective and safer method of space study. Small samples of rock and dust are collected from other planets in the hopes that they contain some clues about planet formation and potential signs of life.
Return capsules are responsible for bringing these samples safely back to Earth for analysis. Their smooth, dome-like shape offers them greater aerodynamics. But one might ask: with no exterior flaps, how can the capsule retain its stability and avoid spinning off course?
The answer is to use linear DC servo motors within the capsule. By moving up and down the X and Y axes, the motors can help to shift the capsule’s centre of mass and help to stabilise it in flight. In some cases, the weight of the motor can be sufficient to act as a counterweight,
but additional weights can be added if a higher mass is needed.
Expectations of these motors are high. They must be able to operate in the harshest of conditions, whether it’s the extreme heat of re-entry or the absolute zero temperatures of space. They must also be able to withstand extreme force and vibrations, with no loss of integrity. In the case of providing stability in real-
time, the motors need to be able to quickly change direction. The linear servo motors in sample return capsules may need to travel along their axes up to four times a second.
The motors must also be as compact as possible, with free space often a commodity. High reliability is another necessity, as the role these motors play can be significant in ensuring safe and efficient spacecraft operation.
FAULHABER motors, supplied in the UK and Ireland exclusively by EMS, are able to deliver to such a specification. In fact, there are already numerous FAULHABER motors hard at work in space, in applications ranging from seismometers and rovers to satellites and artificial assistants.
We never know what we’ll find in the cosmos, or even if we’ll find anything at all. The complexity and unpredictability of space means it’s almost impossible to guarantee the success of one mission to the next. But by choosing components carefully to match the harsh conditions and requirements of such missions, each spacecraft can be given the best possible chance of success.
For further information, please visit www.ems-limited.co.uk
Micromotors aren’t only helpful in ensuring an efficient launch — they can be just as important when it comes to making the return journey.
Rozone’s bioremediating ROwasher range outperforms every parts washer on the market and beats our previous machine’s running costs by 54.5% and uses 30%-37% less consumables. * The ROwasher is the first innovation in parts washing for decades. It is UKdesigned and manufactured, together with the bioremediating filter mat and the ROwash degreaser. Find out how the ROwasher works here: https://www.rozone.co.uk/ rowasher/how-it-works
Contaminants such as oils and grease are always present in engineering and workshop environments. Current legislation makes us improve our sustainability, environmentally friendly and health and safety credentials.
The ROwasher reduces toxic solvent use, cuts any toxic waste and improves the technicians’ working environment, whilst reducing operating costs. All ROwasher features and benefits can be found here https://www. rozone.co.uk/rowasher/features
Discover more about bioremediation here: https://www.rozone.co.uk/ bioremediation
Look at the science. The Science Behind the ROwasher by Dr Ibrahim Khalil https://youtu.be/tmDkeLOvuJs
Call Rozone’s ROwasher experts on 0121 514 0607. Or contact us here www.rozone.co.uk/contact/ or email info@rozone.co.uk
*Based on data from controlled laboratory trials in 2022
RMIG is the world’s largest manufacturer and supplier of perforated metal and its related products.
We know our customers’ requirements for price and quality and meet their demands with uncompromising service.
Not only do we offer standard and bespoke perforated metal sheets, we are able to offer you a range of secondary operations as detailed below.
Complete solutions
With a continued investment in the latest equipment and a network of professional partners we are able to produce prime quality products and solutions – from a simple perforated sheet to the fully formed and coated custom made part.
Cutting
We can cut and shape perforated sheet to meet the needs of your nal application.
Levelling
For some applications a high degree of atness is required, we have processes in place to ensure our perforated coils and sheets meet with your most demanding requirements.
Rolling and forming
We can roll, bend and form perforated sheets to match your design.
Aesthetic nishes and protective coating
We can offer powder coating and hot dip galvanizing solutions to meet your speci cations.
For more information please contact us tel: 01925 839610 | email: info.uk@rmig.com | www.rmig.com
•Gain or renew your 5-year Certificates of Competence*
•Courses based on EEMUA 159
• English, Dutch, German and French language options
•Select from courses throughout 2023, including:
TankAssessor courses*
22-25 May 2023 – in English
– classroom – London, UK
5-8 June 2023 – in Dutch
– classroom – Rotterdam, NL
2-6 October 2023 – in French – classroom – Près de Lyon, FR
6-9 November 2023 – in German
– live online
TankInspector courses*
22-24 May 2023 – in Dutch – classroom – Rotterdam, NL
16-18 October 2023 – in English
– live online
Storage Tanks e-learning
On-demand – in English or Dutch
In-house courses
By arrangement for your choice of: time, language, location, or live online
More choices, information and registration at www.eemua.org and events@eemua.org
we make ideas come to life
Selective soldering typically uses a wettable nozzle to apply solder to the underside of PCBs. This methodology allows the process to be tailored for specific joints and allows multiple nozzle types to be used on the circuit board. Controlled application of the solder is achieved by wetting (adhesion) of the solder to the nozzle.
Wettability is the study of the adhesion of liquids to solids as a result of the surface energy of the solid and the surface tension of the liquid. Generally, wettability is characterised by observing the contact angle of a stationary (sessile) droplet. In soldering, flux serves to clean the interface between the solder and nozzle and remove oxides that may impede the wetting process. After cleaning, a chemical reaction between the solder and nozzle determines the extent of the wetting but this interaction also limits the lifetime of the nozzle. It causes wear of the nozzle as the metal is leached into the solder bath.
A good nozzle must have good wettability to maintain a controlled process as well as balance the wettability and wear of the nozzle. Material composition must be carefully controlled to achieve this. A new nozzle material will reduce operation and maintenance costs for manufacturers by reducing the number of nozzles required overall and reducing downtime caused by nozzle failure. Improving the wettability of nozzles will allow for more challenging joints to be tackled using the selective method. This project has been undertaken due to customer requests to increase nozzle lifetime and reduce the maintenance required.
There has been limited development of improved selective soldering nozzles. This is due to the electronics industry being conservative in many respects and rightly so; “why fix what isn’t broken” especially when reliability is paramount. However, there has been some research carried out on the application of surface treatments for extending nozzle life.
This ground-breaking research project, part funded by Innovate UK and Pillarhouse International Ltd. is partnered with Coventry University through a knowledge transfer partnership scheme. The aim is to develop a new, longerlasting nozzle with excellent wetting properties. By applying the studies of tribology and materials science, fundamental work looking at different materials and surface engineering techniques has selected a number of potential candidates that show improved performance.
Prototype testing has been used to confirm compatibility with existing solders and fluxes. The new AP Master Nozzle will be available in June of 2023.
For further information, please visit www.pillarhouse.co.uk
A good nozzle must have good wettability to maintain a controlled process as well as balance the wettability and wear of the nozzle.
Benets of the AP (All Purpose) Master Nozzle include...
•
Improved initial wetting for faster nozzle start-up and more user friendly operation
Innovative surface treatment improves long-term wetting
• Lifetime predicted to be at least 8x longer than standard AP Nozzle
•
• Surface treatment resists oxidation at high temperatures allowing for easier nozzle rewetting
• Compatible with all current solders and uxes
Improved pull-off performance enables soldering of ne-pitch components
• Compatible with current Pillarhouse nozzle mounting system
•
• Exclusively available on all Pillarhouse machines using wettable nozzles
Nottingham-based Vestatec supplies unique styling solutions for premium brands like Bentley, Porche and Lamborghini. Its longstanding relationship with photochemical etching specialist Precision Micro is key for supplying speaker grilles to many of the world’s most luxurious vehicles.
Why photochemical etching?
Photochemical etching allows Vestatec to bring intricate designs to life while also adding clear cost-saving benefits. Chemical etching also means that finished metal speaker grilles maintain their sleek appearance and tactile perception for longer, as well as offering improved sound quality and durability.
An alternative to traditional stamping and laser cutting, photochemical etching uses chemical etchants to create complex but highly accurate precision components from almost any metal. With hundreds of holes to cut in the average speaker grille, and the need for consistent, pinpoint accuracy, laser cutting is simply not viable.
Made in the Midlands
Vestatec’s journey with Birminghambased Precision Micro began a decade ago but Vestatec did offshore its supply briefly while Precision Micro was actioning a £5.1m recovery plan following a fire in 2019.
While Precision was back to full manufacturing potential within three months, reconfiguring its processes and
increasing its overall capacity, Vestatec was facing difficulty importing product from the continent due to Brexit and the impact of the pandemic.
Precision’s rapid recovery, combined with importing woes, soon gave Vestatec the confidence to switch back to using Precision Micro as its primary supplier. Another key reason for the switch was Precision Micro’s product quality and service offering, while the geographical proximity of the two Midlands-based businesses presents significant benefits
for prototyping and makes complex designs more feasible.
In automotive, continuous innovation and strong collaboration is key. Improving the driving experience requires creative thinking throughout the supply chain –something which Vestatec’s Adam Jay believes Precision Micro always helps to deliver.
“We really push Precision Micro to explore the limits of what’s possible because ultimately, that’s how you innovate. We’ve often sent them designs which are theoretically impossible to manufacture but they always give their best efforts to make them a reality. This desire to go beyond what’s possible has helped us deliver some truly unique products,” says Adam.
Precision Micro’s value proposition ‘etching enhanced’ is something, by Vestatec’s own admission, that perfectly describes the business’s ability to explore the limits of its technology.
Adam Jay continues: “The etching process is high quality and it’s efficient for many reasons. Pushing boundaries and working collaboratively together stack up to provide USPs for both of us and I think the customers we deal with recognise our efforts to innovate and deliver consistent quality.”
To find out more about photochemical etching visit: precisionmicro.com
Why photochemical etching is the ideal solution for Vestatec’s
This desire to go beyond what’s possible has helped us deliver some truly unique products.
The government has officially announced the recipients of more than £12m in grant funding to help energy intensive industries cut their carbon emissions and streamline energy costs. Awarded as part of the Industrial Energy Transformation Fund (IETF), capital has been split between 22 pioneering projects across sectors including pharmaceuticals, steel, paper and food and drink.
Aiming to future-proof British businesses and accelerate the UK’s green industrial revolution – a wider ambition to decarbonise industrial processes and reduce national reliance on fossil fuels – funding will be used to deploy new technologies and improve efficiencies. So far, more than £34m has been awarded through the framework since its introduction in June 2020, with additional phases to be announced later this year.
Commenting on the announcement, Jodie Eaton, CEO of Shell Energy, said:
“It’s positive news indeed to see further government support given to energy intensive industries. Grant funding is essential to help drive the future of British industry, especially when it comes to innovation, efficiency and the roll-out of new technology.
“While the IETF should be celebrated, it’s just one of several government-backed initiatives created to support energy intensive industries. From the £289m Industrial Energy Transformation Fund, which offers support for businesses with high energy use to cut bills; and the £1bn CCUS Infrastructure Fund, which supports transport, storage and industrial carbon capture projects; to the £240m Net Zero Hydrogen Fund, which aims to accelerate low carbon hydrogen production initiatives, grant funding is playing a key role in decarbonising industrial processes.
“But despite such a plethora of support
options available, there are thousands of large businesses across countless industries where energy plays a significant operational role. Government funding alone can’t provide all the support needed, which means that planning and accelerating net-zero strategies is quickly becoming business-critical.
“That said, according to a recent poll of major energy users undertaken on a Shell Energy webinar, just 37% of attendees considered themselves on track to meet business decarbonisation goals. The vast majority saw clear room for improvement, with 11% admitting to not being on track at all.
“The fact of the matter is simple. Navigating the road to decarbonisation is complex, yet essential in both cutting carbon emissions and streamlining energy costs. Businesses must ask themselves the challenging questions – how are you fairing on the journey towards net-zero?
How can you steer through the complexities? What investment is needed? What’s more, how can you secure c-suite buy-in when planning for the future?
“Having the right expertise available to help optimise energy efficiency, drive procurement performance and guide you through all the upcoming changes will deliver significant business benefits. Working collaboratively with your supplier is therefore crucial to developing a long-term strategy that will keep you in control.
“We are already helping businesses with simple and reliable solutions for managing energy costs and planning their netzero roadmap. From offering renewable electricity, gas and cleaner energy options to a comprehensive suite of energy products and solutions for businesses, we are seeing rapid growth in demand for our services.
“For energy intensive users, market volatility will continue for the foreseeable future. Embracing change to maximise
efficiencies, while getting ahead of regulatory change, will prove pivotal in maintaining competitiveness at a time when transformation of operations across the board will be critical to success in 2023 and beyond.”
To find out about Shell Energy and its integrated energy solutions offering for businesses, visit www.shellenergy.co.uk/ business/energy-solutions.
Navigating the road to decarbonisation is complex, yet essential in both cutting carbon emissions and streamlining energy costs.To find out about Shell Energy and its integrated energy solutions, visit www.shellenergy.co.uk/business/energy-solutions.
Adopted as THE Food Safety Standard by 30,000 food manufacturers in over 130 countries, the ‘Brand Reputation Compliance Global Standards’ standardises quality, safety, and operational conventions to ensure that manufacturers fulfil their legal obligations to the consumer. Whilst it’s not yet a legal requirement in the UK, most large food retail brands insist that their suppliers are BRCGS-certified.
Key changes outlined in Issue 9 are heavily influenced by the most frequent non-conformities discovered throughout 2021, the most prevalent of which was 4.11.1 - Premises & Equipment Hygiene. Given its dubious honour as the most common type of non-conformity, equipment compliance is a major focal point in Issue 9.
There is far more emphasis on manufacturers responsibilities concerning equipment management than in Issue 8. This includes a documented purchase specification, as well as any relevant legislation, food contact approved requirements, and details of intended use of the equipment. Companies with a dedicated Food & Beverage team such as Thorite, the UK’s leading independent supplier of pneumatic and fluid power process products are now able to supply EHEDG certified components & equipment that ensure compliance with these new clauses.
Another of the most frequent reasons for an audit non-conformance is contamination - In particular biological, allergenic, or ingress of a foreign body. Contamination can occur in small parts of food manufacturing machinery, hence Issue 9 states a requirement for ‘the use of correct seals, impervious surfaces, or smooth welds and joints’. To combat this, Thorite offers products such as hydroformed diaphragm vales, constructed from a single piece of stainless steel with no welds or crevices for contamination.
Although not as prevalent, another of the BRCGS’s new fundamental requirements
is process control which is essential for ensuring full compliance with a HACCP (Hazard Analysis & Critical Control Points) or food safety plan. This is especially apparent in the clause 6.1.3.
This standard outlines the critical nature of process monitoring for ensuring products are manufactured to the mandated specification. Comprehensive monitoring systems are proven to provide highly accurate, real-time temperature data, support food safety compliance, and cut costs. Temperature, time, pressure, and chemical properties are all included as some examples of key parameters to
measure. Leading monitoring systems will typically also measure:
• Humidity
• CO2
• Energy consumption
• Concentration
• Flow
• Viscosity
In this instance, products from Thorite’s premier partners such as the FLOWave from Burkert can be used as a multi-parameter measuring device, where measurement is independent of flow direction and does not require conductivity of the medium.
Since it does not have any moving parts in the measuring tube, it thus has;
• No pressure drop
• No leakage problems
• No dead spaces
• No replacement parts
No matter the unique challenge your Food & Beverage Facility faces in light of the Issue 9 updates, Thorite has a solution. Contact their dedicated Food & Beverage team on FBFTeam@thorite.co.uk today to discuss how these changes will impact your business.
For further information, please visit www.thorite.co.uk
There is far more emphasis on manufacturers responsibilities concerning equipment management than in Issue 8.
EFFICIENCY &
& SAVINGS
Unparalleled efficiency and energy savings with Thorite tailored solutions for the manufacturing and engineering industry.
Unparalleled efficiency and energy savings with Thorite tailored solutions for the manufacturing and engineering industry.
All your pneumatic needs in one place:
All your pneumatic needs in one place:
Tubing, Hose & Quick-Connect Fittings
Tubing, Hose & Quick-Connect Fittings
Air Treatment & Filtration Systems
Air Treatment & Filtration Systems
Valves, Sensors & Switches
Valves, Sensors & Switches
Vacuum Pumps, Blowers & Accessories
Vacuum Pumps, Blowers & Accessories
Actuation, Automation & Control Systems Compressors, Nitrogen Generators & Ancillary Equipment
Actuation, Automation & Control Systems Compressors, Nitrogen Generators & Ancillary Equipment
There is no compromise on the quality of JASIC equipment..such is our confidence in this technology we can offer an unparalleled 5 year ‘true’ warranty on all models. Jasic’s manufacturing site is over 80,000m2 and is arguably the largest and most modern inverter manufacturing base in China.
How do Wilkinson Star provide such an industry leading product guarantee?
WE ARE SERIOUS ABOUT PRODUCT QUALITY. SOUND PERFORMANCE AND RELIABILITY IS WHAT YOU CAN EXPECT FROM JASIC PRODUCTS
• The manufacturer has invested millions of dollars into cutting edge integrated test laboratories on site – JASIC undergoes 42 individual tests to meet high quality standard.
• Jasic’s 4 centre strong R & D facilities has been ranked as the most progressive facility along with being the first welding laboratory awarded UA certification by China from TUV Rhineland.
NO OTHER DISTRIBUTOR CAN MATCH US ON THE LEVEL OF SERVICE FACILITY INVESTMENT MADE IN THE UK
• Wilkinson have 50 years’ experience in servicing welding equipment. Our state of the art service workshop facility and our 16 strong after sales service team offer the most recognised technical support in the welding industry. All equipment is fully supported by Wilkinson Star trained technicians.
• No other UK wholesaler can repair inverter boards to component level. At Wilkinson Star we have a dedicated
CARE IS OUR BYWORD AND YOUR PRODUCTIVITY IS OUR PRIORITY
• We provide a dedicated technical support line which you can call for any technical support queries
• If on site support is needed we provide this through our highly trained technicians who cover the country
• We can also interchange power sources to keep you up and running
• If required, Wilkinson Star will arrange at its expense to collect and return your JASIC product to carry out service or repair in our workshops
BE VIGILANT WHEN PURCHASING EQUIPMENT WITH EXTENDED WARRANTY
WITH JASIC 5 MEANS 5
JASIC’s warranty is a true 5 years; this means a problem at 6 months, 3 years or 4 years 11 months is treated with the same level of care.
No extensions. No additional costs…… just 60 rolling months of product peace of mind
ALL YOU NEED TO DO IS REGISTER YOUR PURCHASE AT JASIC.CO.UK FOR 5 YEARS PEACE OF MIND – IT’S REALLY THAT SIMPLE
For further information, please visit www.jasic.co.uk
MIPC® helps practitioner-level engineers stay on top of the latest industry developments and reinforces good practice in primary containment of hazardous substances, including in pressure systems
Using a blend of live, online classes, one-to-one sessions with expert tutors, and e-learning, enhanced by a mentor’s support and guidance, EEMUA’s Mechanical Integrity Practitioner Certificate course delivers in-depth training to engineers where they work – giving flexibility to learn on-site, on-call, or working from home
Registration open now for the next MIPC course. Learning starts 24 October 2023.
Induction of 2 hours to fit diaries from September 2023 adapts coursework to the engineering needs of each learner and their site/s.
For more information please contact EEMUA
online-learning@eemua.org
+44 (0)20 7488 0801 www.eemua.org
MIPC® shortlisted for the Best E-learning/ Online Education Initiative memcom membership excellence awards 2020 and 2022
ViSWIR Hyper APO Features:
• Capable of fully corrected focus shift in visible and SWIR range (400nm - 1700nm)
• Achieves spectral imaging with a single sensor camera by simply syncing the lighting Floating design adjusts focus for different wavelengths 8mm, 12mm, 16mm, 25mm, 35mm* and 50mm* (*2023)
ViSWIR Lite Features:
High transmittance at whole wavelength of 400nm - 1700nm by adopting hyper wideband AR coat
Outstanding cost-performance for single-wavelength lighting & narrow-band imaging Compact design 5mm,
The Tooling Division team at Pentagon were excited to take delivery of the highly anticipated FORM E 600 last week.
This new EDM Spark Eroder is the second of three new machines purchased from GF Machining Solutions with delivery phased between March and May this year. To make way for the new plant equipment the Tooling Division has undertaken a major reshuffle of machines providing a new layout to ensure adequate working space and support LEAN manufacture processes.
Investment into the FORM E 600 will enable the team to deliver further efficiencies in tool manufacture and optimise production with an integrated six station Linear Tool Changer and our System 3R holders. The EDM’s C Axis delivers high positioning precision (0.001°) regardless of electrode weight (up to 25kg). The four axes simultaneous interpolation allows easy machining of curved recesses and undercuts by rotating the C axis and widening the 3D vector which will be a huge asset for our in-house toolmaking services with finite detailing.
The final machine that will be added to the facility is the FORM E 350, completing a combined £500,000 investment, and is the largest one-time machinery investment that the business has made to date. Driven by consistent business growth and planning for the future of Pentagon’s UK based tool making capabilities the machines will deliver significant advancement in technology.
Customers to Pentagon will benefit from this investment on all levels as lead times are driven down and high-quality precision engineering is driven up.
Pentagon’s unique offering of both full mould tool manufacture and plastic injection moulding production, all from on site of UK manufacture delivers seamless service to customers. The collaborative approach between both the Moulding and Tooling divisions ensure process optimisation is delivered at every stage, from design through to finished product.
Pentagon Tooling is building for a sustainable future through machinery investment and continued commitment to training and upskilling of the engineering team. If you are looking for the services of an expert UK Toolmaker for your next plastic injection moulding project or you have existing mould tooling in need of repair, servicing or maintenance contact pentagon at sales@pentagonplastics. co.uk or call the Tooling Team on 01403 264397.
For further information, please visit www.pentagonplastics.co.uk
Customers to Pentagon will benefit from this investment on all levels as lead times are driven down and high-quality precision engineering is driven up.
TOOLING
BEYOND THE MOULD
BEYOND THE MOULD
Pentagon delivers a full turnkey solution for plastic injection moulding from one site of UK Manufacture.
Pentagon delivers a full turnkey solution for plastic injection moulding from one site of UK Manufacture.
With over 50 years’ experience you can be confident that your Bespoke Moulding project is in the hands of the experts for both mould tooling and repeat production.
With over 50 years’ experience you can be confident that your Bespoke Moulding project is in the hands of the experts for both mould tooling and repeat production.
Meet us at this years’ Interplas UK –26- 28 September at the NEC, Birmingham.
Meet us at this years’ Interplas UK –26- 28 September at the NEC, Birmingham.
Seeley International has announced the appointment of Mr. Fabio Marioni as the new Sales Manager for United Kingdom and Ireland, in an important move to expand business in these two key countries.
Mr. Marioni will implement crucial aspects of the company’s growth strategy, including coordinating contractors’ network and promoting Seeley International’s premium quality evaporative cooling technologies.
Mr. Marioni comes to Seeley International with significant experience working in the HVAC industry, such as Epta Refrigeration, Galileo TP and Ziehl-Abegg.
In welcoming the appointment, General Manager Sales EMENA, Mr. Sam Peli, said the addition of Mr. Marioni to the team would drive sales growth and reinforce Seeley International reputation as an industry leader.
“Seeley International’s success is achieved through a combination of attracting and retaining only the very best people, and an unwavering commitment to developing innovative and high-quality products,” Mr. Peli said.
“As part of the role, Fabio will promote awardwinning climate control solutions developed by Seeley International, as they will help the environment and achieve serious savings for users, because they cost less to run than other products on the market.”
“I am proud to be part of this market-leading & award-winning company. Seeley International offers an impeccable reputation for innovation, quality, reliability and safety, and I look forward to working with customers to showcase the unrivalled technology and energy efficiency benefits offered by Seeley International’s products.” Mr. Marioni said. “I am ready to play a role in taking the business to the next level in the UK and Ireland.”
www.seeleyinternational.com
Why choosing evaporative cooling for your industry?
Evaporative cooling is fast becoming the preferred option when cooling industrial and commercial spaces. Only using water and electricity to run, this solution is extremely cost-effective. Air conditioning is not such a viable option, because in warehouses and industrial plants the capital and running costs would be extremely prohibitive: for this reason, facilities managers are choosing evaporative cooling, which can cool at a fraction of the cost of refrigerated systems.
Easy to install and maintain, these coolers bring 100% fresh air from outside (they don’t recirculate indoor air). They are therefore perfect to enhance Indoor Air Quality (IAQ) and improve ventilation, positively impacting on workforce wellbeing and productivity. Illnesses such as heat stroke, asthma and other diseases connected to high temperatures are reduced.
Traditional air conditioning systems normally use chemical refrigerants to cool the air, whereas evaporative cooling only needs water and little electricity to run. Thus, every time a customer chooses to install evaporative coolers over a refrigerated system, the benefits for the environment are significant.
Helapet knows that no single filter can be suitable for the varied filtration applications that are used across industries.
Our new online design tool provides customers with a simple-to-use design wizard, combined with enhanced information to guide customers through the 100’s of available filter combinations.
When a customer in the marine industry realised that they had not been effectively monitoring their heat transfer system and fluid they contacted thermal fluid experts Global Heat Transfer, for support. After sampling the fluid and determining the extent of degradation, experts at Global Heat Transfer worked with the customer to find the most effective solution. Reducing the carbon levels in the system was not a simple task, but the final results provided the customer with a reliable and efficient heat transfer system.
Thermal fluids can be used for a diverse range of applications in the marine industry, from maintaining the temperature of heavy fuel oils and heating liquid cargo to providing a variety of heating services in the engine room and accommodation areas. The customer contacted Global Heat Transfer, to take a sample of its thermal fluid from a large tanker.
Heat transfer fluids operate at high temperatures for long periods of time, and naturally degrade over time. If engineers do not regularly test the thermal fluid and get the specialist support and advice needed, they will not understand its condition. Degradation, caused by oxidation, causes sludge which is a thickening of the fluid which will block system pipes. To better understand its condition the marine customer sent a representative sample of the vessel’s thermal fluid for analysis.
The initial analysis of the thermal oil sample was very concerning because the carbon percentage weight level was so high it was unreadable. Before this point, the previous highest recorded level for over 30 years was eight per cent weight of the fluid. It is important to note that one per cent weight of the fluid is the typical action point for changing out a fluid.
Due to the severe level of degradation, the lab couldn’t perform any of the eleven tests normally used to determine oil condition. As a result, fluid experts determined that the pumps, drains and strainers in the system were blocked with carbon debris. The system was covered with irremovable
hard baked carbon fouling, which acts as an insulator, reducing heat transfer efficiency and causing hot spots on coils. The high levels of acidity in the system, caused by oxidation, was corrosive to the internal components of the system and drastically increased the risk of leaks and health and safety risks as pipe corroded.
If fluid condition continues to deteriorate and the system is not regularly maintained, the fluid can increase the risk of fire. Under the Dangerous Substances & Explosive Atmospheres Regulations (DSEAR) and the Explosive Atmosphere Directive (ATEX) regulations and health and safety laws, businesses must take steps to protect
workers against risks from fire, explosion and similar events arising from dangerous substances present in the workplace, such as thermal fluids.
It was noted that some parts of the system were not heating up, indicating that the system was blocked. Given the fluid condition, it was also noted that when a hot sample was collected, the fluid solidified as it cooled. Due to this the system could not be switched off as the system would completely fail.
Once the marine customer understood the severity of its fluid issues, it looked for support to ensure oil condition met acceptable parameters and had a consistent flow, ensuring the vessel and crew could operate efficiently and safely onboard.
Global Heat Transfer consulted with the marine customer and carried out multiple system flushes over several days to remove the degraded product. Due to the level of carbon fouling in the system, the risk of coils, pipework and components seizing if the fluid was cooled was too high. Instead, Global Heat Transfer engineers flushed the system at its regular operating temperature, and carefully managed the additional risks of working with a hot fluid.
Global Heat Transfer initially used cleaning and flushing fluid Globaltherm C1, which is specially formulated to remove any harsh by-products of organic and most synthetic thermal fluids. This product cleans and flushes as it passes through the system. The system was then refilled with fresh Globaltherm M oil, which operates up to 320 degrees C for extended periods.
After the whole system was cleaned and refilled, Global Heat Transfer took a sample that showed first viscosity levels were at 36.6 @40 degrees C mm2/s (est), compared to the first measurable level of
142. A typical system would expect a score of 32 for a mineral oil, like Globaltherm M oil, so considering the state of the system originally, this was a positive result.
The health and safety risks associated with the fluid drastically reduced. Flow was improved inside the system, reducing the risk of failure and burst pipes that could harm workers on the vessel and improving efficiency. The artificially low flash point of the fluid returned to a measurable and acceptable limit, significantly reducing the risk of fire.
To avoid issues like this in the future, the marine customer now routinely draws a live, hot circulating representative sample at operating temperature. The sample is
then tested and analysed to ensure the oil is within safe and acceptable limits and maintenance is proactively carried out if needed.
Regular, proactive maintenance of thermal fluids will help marine vessels avoid any unexpected downtime and ensure their heat transfer system is reliable. By investing in regular fluid sampling, marine engineers will have the peace of mind that their system is running as efficiently as possible, reducing health and safety issues and costs.
To find out more about thermal fluid analysis and maintenance packages, visit the Global Heat Transfer website https://globalhtf.com/ thermal-fluid-lifecycle-maintenance.
For further information, please visit www.globalhtf.com
Flow was improved inside the system, reducing the risk of failure and burst pipes that could harm workers on the vessel and improving efficiency.
In 2013 Winn & Coales (Denso) Ltd. supplied their Steelcoat 100/400™ System to protect a gas pipe on the Craigavon Bridge in Derry City. The successful application led to the use of the same system by Northern Ireland Water to protect 281m of a wastewater pumping main, including flanges and support brackets, on the same bridge in 2022.
The Steelcoat 100/400 System has been used by water companies throughout the UK to provide effective, long-term protection from corrosion to exposed and above ground pipework. The ease and speed with which the system can be applied, alongside minimal surface preparation requirements, also helped to reduce traffic disruption on the bridge during the works. The final layer of Denso Acrylic Topcoat was also supplied in the same shade of blue to match the colour already featured on the bridge structure.
Winn & Coales (Denso) Ltd. provided training and site support during the application which was carried out by BSG Civil Engineering Ltd and O’Kane Civil Engineering over a 10-week period. The products were supplied by one of Winn & Coales (Denso) Ltd.’s distributors, APP Fusion Group, Lisburn.
In process and manufacturing industries, equipment reliability can’t be left to chance. Perlast® Perfluoroelastomers (FFKM) have been developed to provide exceptional sealing performance in environments where other materials might fail. From O-rings to hygienic gaskets, Perlast® is the name to trust for process industry leaders around the world. Here’s why…
1. Universal chemical resistance
Perlast® FFKM is chemically inert. In tests and in situ, Perlast® FFKM materials are proven in the most aggressive chemical environments – across process media as well as chemical (CIP) and steam (SIP) sterilisation routines.
2. High temperature resistance
The molecular structure of Perlast® FFKM results in extraordinary stability in high temperatures. Perlast® FFKM can withstand operating temperatures of up to 327°C (620°F). Perlast® FFKM is not only resistant to high temperatures – some grades seal down to -46°C (-51°F)
3. Mechanical strength
The low compression set of Perlast® FFKM means that across both static and dynamic applications, Perlast® FFKM seals can be specified within fast-paced process lines that cannot be undermined by material weakness and unreliability.
4. Full regulatory compliance
Perlast® FFKM is certified compliant to important standards across several industries, including food, dairy and pharmaceuticals (FDA, 3-A Sanitary Standards and USP), and energy (NORSOK M710, NACE, ISO23936, and ISO10423).
5. Availability
In recent months, the excellent availability of Perlast® FFKM has been a critical factor for equipment operators. An industry-wide shortage of FFKM ingredients has led to significant increases in lead times for major manufacturers and prominent FFKM grades. Perlast® FFKM has remained relatively unaffected by this supply chain complexity. Perlast® FFKM sealing components can
be manufactured to order in as little as a month – up to six times quicker than some competitor grades.
Switching to Perlast® FFKM
PPE sealing specialists understand the difficulties involved in specifying and implementing a new sealing material. Arrange an initial consultation with a Perlast® specialist at www.perlast.com, or
take a look at our videos and resources to explore the benefits of using Perlast® FFKM.
Precision Polymer Engineering are exhibiting at CHEMUK 2023 at the Birmingham NEC (10-11 May) – so if you’re attending, we’d love to welcome you to Stand M34 where our specialist sealing engineers have answers to all your industrial sealing questions.
The molecular structure of Perlast® FFKM results in extraordinary stability in high temperatures.
Linear motors are ideal for fast and accurate motion in a machine.
Linmot, the leading manufacturer of cylindrical linear motors, has made them even more suitable for demanding food and pharmaceutical applications. For these environments, any mechanism needs to have a high protection class and be easy to clean and require little maintenance.
The motors have been developed to be fully sealed and are made in High grade Stainless Steel. The cylindrical design allows the motor to be completely smooth and does not require seals. There are no food or particle traps and they can be fully washed down.
This is a big advantage over screw, belt actuators or pneumatic cylinders.
The motors are available in Linear modules with protection class IP64S and stainless steel linear modules with protection class IP69 consisting of a linear guide and an integrated LinMot linear motor.
Motor series in stainless steel (EN 1.4404/ AISI 316L) for wash down applications. The motors are characterised by their hygienic design and the high motor protection class IP69 according to DIN EN 60529. Perfectly suited for «in-place» cleaning processes like CIP and SIP.
Food processing with LinMot
LinMot linear motors have been used in the food industry for years. They score here with
industry-specific advantages, such as simple integration, flexible programmability, dynamics and hygienic design. The motors can be connected to common control platforms in synchronous operation or simple point-to-point motion. The advantages of servo technology enable the gentle and dynamic processing of
Website: www.quin.co.uk/linmot
food. With the help of stored motion profiles, frequent product changes can be achieved simply by pressing a button. LinMot linear motors are available in stainless steel with a high protection class, meaning they can be cleaned under high pressure and with caustic cleaning solutions.
The demand for automation solutions across all sectors is surging following the impact of the pandemic on global production. Automation technology and hardware play a crucial role in safeguarding processes and people and ensuring efficient operations and business continuity, even when human resource is in short supply.
The automation of industrial processes has considerable benefits in a range of areas:
• It enables 24/7 operations, driving down customer costs
• It provides improved safety for workers, reducing down-time
• It provides opportunities for upskilling the workforce
• It limits worker exposure to chemicals, heavy loads or repetitive operations
• Automated processes are often faster, increasing turnover
• Automated processes can be more consistent, improving quality.
A significant portion of Expromet Technologies Group’s production output is for industrial automation applications. Our customers provide a range of systems designed to help gain process efficiencies and develop sustainable business models by improving operating efficiency and reducing sensitivity to labour market fluctuations.
Expromet companies manufacture a variety of components for integrated safety control systems for safety sensing, industrial control and motion control. For example, Investacast manufactures investment and pressure-die cast metallic housings for electronic systems which combine safety functions with motion control. Investacast and sister companies
Haworth Castings and Metaltech Precision also produce components for automated fire detection systems on oil rigs – in fact, much of the group’s production is destined for
safety-critical applications where customers know they can rely on our expertise to meet demanding specifications.
The global pandemic forced industry to invest in robust systems which automate production and logistics processes, ensuring continuity of output in the face of social distancing and other restrictions.
Expromet is contributing to industrial automation in this sphere by manufacturing a variety of components for warehousing operations infrastructure that facilitate the storage, picking and packing of goods for home delivery.
www.expromet.com
Expromet group companies are themselves investing in industrial automation at their UK manufacturing facilities, including the acquisition of robot-loaded CNC machines which can operate 24/7 at high levels of output. These technologies improve processes and increase efficiency, allowing them to provide a faster, cost-efficient service to customers.
Expromet and its businesses each have a team of expert UK engineers who will work with you to design and develop your components for industrial automationadvising you on design for manufacture (DFM) and selecting the best manufacturing method.
Investacast, Haworth Castings and Metaltech Precision are among the world’s leading suppliers of investment castings, sand and pressure die castings, and precision machining. With their skill and expertise you can share in the benefits of automation technology and hardware, helping to safeguarding your processes and people and ensuring efficient operations.
For more information on how we can support you with industrial automation applications please visit our website, email enquiry@expromet.com or call +44 (0)1271 866200.
A significant portion of Expromet Technologies Group’s production output is for industrial automation applications.
After a few years of rethinking the way they work together, European Springs & Pressings have been reaping the rewards of increased collaboration with its sister companies. Making their mutual platform of products and services more accessible has enabled the spring and stamping firm to deliver a wider range of manufacturing capability and products to their customers than ever before.
Working more closely with UK manufacturing partners Metrol Springs and Lesjöfors Heavy Springs UK has brought significant benefits for the respective companies, as well as allowing the group to offer an unrivalled portfolio of springs, pressings, wireforms, gas struts and industrial hardware.
Shared attendance at exhibitions, pooling experience at cross-company strategy meetings and developing a mutual knowledge of each other’s products and specialisms has broadened the shared capability the companies can offer and increased their sales reach considerably.
This support brings tangible benefits to their clients as well. European Springs’ commitment to providing the coiling and pressing expertise that customer’s need - in order to find custom-made solutions for their manufacturing processes - remains unchanged, with the added assurance that when they claim to have the required capability in the UK to design and produce the optimal component at the most competitive price, they make good on that promise.
This culture of collaboration has been fostered by their parent company, Lesjöfors Springs & Pressings. Although not a household name in the UK, since its conception 150 years ago Lesjöfors has patiently and practically built from its manufacturing base by acquiring a broad network of companies with specialist capabilities and strengths.
Lesjöfors is now the biggest spring manufacturer in the Nordic region, the third largest in Europe, and has a strong
and growing presence in the US and Asia. Their culture of supporting innovation, and developing capability is why European Springs & Pressings Ltd. joined the group in 2007.
Lesjöfors’ dedication to investment, both in people and technology, mirrors ESP’s, and has allowed them to develop as a business, as well as recruit and retain the talent, and acquire the machinery required, to continually provide the high quality manufacturing that client’s demand.
The culture of collaboration developed within European Springs’ UK manufacturing family, alongside the market-leading portfolio of products and services across the Lesjöfors group, means that customers can continue to rely on the ESP promise - to provide innovative design solutions, reliable service and custom-made, quality components.
For further information, please visit www.europeansprings.com
Working more closely with UK manufacturing partners Metrol Springs and Lesjöfors Heavy Springs UK has brought significant benefits for the respective companies.
Stockport based ASG Group has announced their ongoing commitment to quality and accreditation approvals, showcasing their growing capability in the aerospace industry. The group has received a group-wide AS9100 approval following recent audit by NQA.
Since its formation in 2019, ASG Group has collaborated with partners to provide services to aerospace and space customers. However, the company has now obtained independent certification, enabling it to directly supply certified private and government aerospace, space, and defence organizations with additive manufactured components. This certification ensures that ASG Group meets the rigorous requirements of these sectors within an international framework.
The AS9100 approval is an internationally recognised Quality Management System (QMS) for organisations working in the design, development, production, installation and servicing of the aviation, space and defence sector, demonstrating that ASG Group is capable of delivering world-class products and services to their customers. The groupwide accreditation is a testament to the quality management systems in place across all of their seven globally based business units.
In addition to the AS9100 approval, ASG Tooling has also recently announced its achievement of the JOSCAR register approval. The Joint Supply Chain Accreditation Register (JOSCAR) is a collaborative tool used by major aerospace and defence companies to manage risk in their supply chains. The approval means that ASG Tooling has met the high standards required by JOSCAR and can now supply tooling to the aerospace and defence industry.
ASG Group has now also achieved coded welder approval, which means that they are qualified to perform welding on aerospace components to strict industry standards. The approval is a significant achievement for ASG Group and demonstrates their commitment to quality and safety in their operations.
Commenting on the recent approvals, ASG Group Managing Director, Simon Weston, said, “We are proud to have achieved these important accreditations, which demonstrate our commitment to quality and excellence in everything we do. These approvals are a testament to the hard work and dedication of our team and showcase our growing capability in the aerospace industry. Given the demands placed upon us by our world class customers in the aerospace and defence sectors, these approvals continue to separate us from our competition and
reflects our ongoing commitment to quality and excellence across the group and firmly validates ASG Group as an integral part of the global aerospace supply chain.”
ASG Group’s commitment to accreditations and quality approvals has helped to establish them as a trusted partner for the world’s leading aerospace companies. With their world-class capabilities, multi sites and more than 150 machine tools, ASG Group is well positioned to meet the growing demand for high-quality aerospace components and services globally, and is continuing to grow, invest and create new roles as well as continue its proud tradition of developing its own apprentices.
For more information about ASG Group please visit the company’s website at https://www.asg-group.co/
ASG Group has now also achieved coded welder approval, which means that they are qualified to perform welding on aerospace components to strict industry standards.
Around 50% of UK steel construction work incorporates portal frames. Thanks to the durability, adaptability, cost-effectiveness and low maintenance that steel frame building offer, they are an excellent choice as they are so adaptable for both commercial and domestic requirements.
The building industry together with construction methods have seen a technological revolution in recent years driven by the need to make construction faster, cheaper and safer. With the use of clever technology such as Building Information Modelling (BIM), drones and artificial intelligence (AI) architects and contractors have increasingly detailed information at their fingertips.
Images and precise measurements of a site taken by drones can be used to create detailed graphics and full-colour digital models / 3D site maps. AI algorithms are able to analyse data from a wide range of sources, including building plans, weather patterns, and traffic data, to make predictions about how a building will perform in the ‘real’ world. This has enabled architects to design buildings that are more energy-efficient, resilient, and sustainable as well as manage information on construction projects throughout their life cycle, right through to disposal.
The creation of geometric models as part of this process has allowed buildings to be conceived collaboratively and tested virtually before they are built. These detailed virtual models make it possible to live and breathe the construction and operation of a building before the production has even started.
Modern volumetric modular off-site construction continues to develop at a fast pace; consisting of two distinct industry segments, re-locatable modular and permanent modular - both are built off-site in controlled environments to high standards. Often manufactured as a series of structural units, stacking and / or adjoining factoryfinished modules - these then make up the finished combined structure of a building once assembled on-site.
Re-locatable modular - temporary modular buildings are ideal for situations that demand quick construction, they must also be
durable enough for future relocation and repurposing. Examples include, temporary classrooms, Sanitary and WC cabins, communication pods, show rooms, job / site trailers and glamping pods.
Permanent modular Construction (PMC) - are designed to remain in one location for an extended period of time. Examples include, schools / student accommodation, healthcare facilities, hotels, and restaurants.
Enhanced on-site productivity during the assembly phase ensures that the cost savings of modular builds can increase with production scale. Factory assembly based on ‘template’ builds means that approved designs can be reused and mass produced quickly and easily. These savings can grow rapidly, making it easy to achieve much faster output with less waste, downtime due to environmental effects, reduced labour and energy costs – all significantly lowering production / installation costs per unit.
Sustainability and identifying technology solutions that benefit the environment and manufacturing processes has become increasingly important to both consumers and businesses. With all of the new technological advances it makes sense for manufacturers to review their construction materials; fastening solutions are sometimes overlooked in this process; Huck® fasteners offer a wide range of permanent joining solutions that will both maximize factory efficiencies and offer maintenance-free, vibration-resistant joints for the full servicelife of the structure.
Because Huck® fasteners offer relatively high tensile, shear and clamp properties
vibration-resistant fastening solutions, additional benefits include: -
Performance and quality - Quality fasteners engineered to deliver optimal and consistent joint performance. Modular buildings need to withstand the vibration of rumbling down the roads on the back of a truck whilst being delivered to site, and then whatever the elements throw at them, from wind loads to corrosive substances in the air.
Lifetime costs –Construction projects built today need to be built to withstand the tests of time for years to come. Huck® high performance joints can deliver considerable cost savings over product lifetime.
As new construction methods emerge the range of fasteners must keep pace.
Hucks® DIBt approved range of grade 10.9
LockBolts offer maintenance-free vibrationresistant joints for the full-service life of the joint. Other benefits include fast and easy installation, and an installed dynamic performance providing up to five times greater fatigue life than conventional HV* bolts. (*The ‘HV’ mark comes from the German term ‘Hochfest Vorgespannt’. This refers to a HV preloaded bolt, applied in a bolt/nut/washer assembly according to the EN 14399/4-6 standard. These bolt connections are used in preloaded steel constructions).
When installed HuckBolt® performs identically in terms of strength and clamping force; other mechanical fasteners such as nuts and bolts must be installed using torque, which varies with friction.
BobTail® consist of two parts – a pin and a collar, but uses an entirely different installation method to nuts and bolts. As with nuts and bolts, BobTail® can be preassembled by hand to ‘lightly’ assemble the structure, they are then swaged with the installation tool (driven by pneumatic, pneudraulic or battery power). During installation the clamp force is determined by the stretching of the hardened metal pin and the swaging of the collar into the pins locking grooves. Installation is quick and unlike traditional LockBolts® no pin-break is required, BobTails® pintail-less design means reduced noise, no waste, and improved corrosion resistance. This direct metal-tometal contact of the collar swaged into the grooves of the pin eliminates the loosening effects of transverse vibration.
BobTail® can be installed in as little as two seconds.
When the installation tool is applied and the tool is activated, the action of the puller engaging onto the pin, together with the anvil swaging the collar completes the installation. The swage and eject sequence are programmed to complete the cycle without any additional installer input. The process ensures excellent gap closing capability.
BobTail® technical approval has been extended by 5 years. The approval gives BobTail® Lockbolts the verification of ‘static load-bearing capacity and fatigue strength’ in the context of Eurocode 3 for applications in construction. The extension of the approval means BobTail® Lockbolts
can be used in areas regulated by the building authorities as a replacement for non-preloaded structural bolting assemblies (acc. to EN 15048) or high-strength structural bolting assemblies for preloading (acc. to EN 14399). The values published can also be used in many other applications, including rail, commercial vehicles (chassis), lattice towers or wind turbines.
In addition to the load-bearing capacities, which are superior to that of a threaded bolt, BobTail® offers other advantages, such as the low scatter when applying the preload force, the non-detachable connection, vibration resistance and high fatigue strength. BobTail® Lockbolts are also characterized by the fact that they are mechanically maintenance-free (no retightening required) and are easy, quick and quiet to install.
The extent to which the regulations can be applied outside of Germany or in other areas of application must be clarified on a case-by-case basis with the regulatory authority or a certifier in the country in which the construction is to be undertaken.”
Two types of Huck® blind fasteners that are widely used in modular construction are the HuckLok® (6.4mm diameter) and the MagnaLok® (9.5mm and also 12.7mm diameters) as well as the Magna-Lok MX, which has been specifically designed to Replace M10 Bolting. Both of these products have a unique mechanical lock that ensures the integrity of the fastener in loaded conditions, and complete hole-filling properties to ensure moisture resistance.
Modular construction is not a new concept. Today’s volumetric modular off-site construction is a far cry from the pre-fab buildings of the nineteen forties / fifties.
When only one side of the joint material is accessible, performance-engineered Huck® structural blind fasteners have a solution. Each designed and engineered with a unique set of features and delivering solutions to common manufacturing challenges; for example, hole-filling, water-resistance, wide grip ranges, welding replacement - all offering high-speed assembly.
They have undergone a series of innovative improvements and have attracted significant investment. Modern construction methods are shaping the way we work and live and will help us to meet the needs of the twentyfirst century in terms of sustainability and efficiency.
By installing HuckBolts® and Huck® structural blind fasteners, an engineer can count on many benefits including maintenance free joints; lower lifetime cost of joint; will not loosen even under extreme vibration; high speed, easy to install systems that can reduce production time by 75%; improvements to health and safety; as well as being tamperproof.
Star Fasteners engineering support services enhance customers experience – we can assist with design, development and testing right through to choosing installation tooling, correct fastener installation and process optimisation.
Huck® fasteners can deliver modular build projects more efficiently and effectively with high-quality, dependable, fastening solutions.
For further information, please visit www.starfasteners.co.uk
Though it may seem initially like a simple task, adhesive bonding may be a vital and challenging part of your product design. Every application is different, and establishing what works best involves detailed discussions and testing. For design engineers without specialist adhesives experience, participating in dedicated training can help set a project up for success. This gives them a foundation of knowledge that can help them progress a project with their adhesives partner more smoothly.
Here Kevin Brownsill, Head of Technical: Learning and Development at adhesives and dispensing equipment supplier Intertronics, discusses the importance of training.
With a shortage of UK engineers, and around 20% of the workforce due to retire by 2026 according to the Engineering and Construction Industry Trade Body, training and upskilling is on the minds of many British manufacturing leaders. In addition, as the boundaries between traditional engineering fields like mechanical engineering and electrical engineering are beginning to blur, engineers may take on more multidisciplinary roles. Training in areas outside of an engineer’s core competencies can help project teams progress faster when they are faced with new challenges.
Selecting an appropriate adhesive is key to the success of a design project - it will help the product pass testing and ensure that the bond lasts the lifetime of the product. Alongside material choice, designing a suitable bonding process with simplicity and robustness is critical to the productivity of the manufacturing process.
Selecting adhesives, dispensing and curing equipment is difficult to get right using desk research alone; what works in practice doesn’t always work in theory — the data sheet may not always give the same insights as practical observations and tests. However, many design engineers have not had dedicated training or experience working with adhesives and processing equipment.
and development around adhesives and dispensing will help design projects in British manufacturing businesses run more smoothly. It will help engineers understand at what point to contact their adhesives partner, and what questions to ask to help the project progress smoothly. So, what areas are most important to prioritise training in?
Specifying a structural adhesive is both an art and a science. There are an increasing number of structural adhesives on the market, so it can be difficult to keep up with industry advances and choose the best materials to evaluate. There are various factors to consider that influence the decision, and these may differ depending on the priorities of an individual application. A good starting point for engineers is to know what questions to ask when specifying an adhesive, as well as to invest time in training on the different types of adhesive chemistries and their advantages.
Developing a robust, consistent, and validatable adhesives process depends on choosing appropriate dispensing and curing methodology. There are always choices, from manual to semi-automated and automated, with varying levels of speed, accuracy and repeatability. Training is available that covers the variables to consider when specifying application equipment, as well as provide an understanding of the advantages and limitations of available dispensing and curing options.
One particularly important area is productivity, so manufacturing teams may wish to arrange sessions that highlight the particular areas of a process that could be improved. It is difficult to change materials once a process is up and running, so training may cover handling, dispensing, and automation in detail. For example, there is a common misconception that automating a process requires a complete overhaul. We’d like to educate the market that you can incrementally improve a process from manual to automated or semi-automated in a way that is manageable and delivers return on investment.
As the shortage of engineering talent continues to affect British manufacturers, specialist training is a useful tool to bridge knowledge gaps in specialised areas.
Intertronics has always recognised the role training plays in helping its customers establish successful processes. To share the knowledge and insight we’ve gained from more than 30 years in the industry, and from our work with thousands of UK SMEs, we’re now offering a broader number of seminars, webinars, and 1-2-1 training. These can be delivered online or in person at a customer’s site or at our Technology Centre near Oxford.
To view some technical resources to enhance your learning, click here. To arrange some dedicated training on adhesives and dispensing, call 01865 842842 or email kevin.brownsill@intertronics.co.uk.
For further information, please visit www.intertronics.co.uk
In times where clean air is more important than ever, air cleaning systems from Zehnder Clean Air Solutions are a key factor in protecting people at work.
They complement existing ventilation perfectly and flexibly to remove airborne contaminants, particulates, dust, oil/mist, fumes/gases and micro-organisms.
And at the same time, they also save you money on cleaning (up to 70 %), maintenance (up to 30 %) and sick leave (up to 50 %). We offer an effective, flexible and reliable solution that meets your individual needs.
Get in touch with our experts to improve the air quality at your site!
Give us a call on 0800 0430100
Lanemark gas burner systems offer users reliable, high efficiency, process heating solutions.
FD Series Packaged Oven/Dryer Burners
•Speci cally designed for process air heating applications in convection ovens and dryers
•High turndown/short ame lengths providing accurate process temperature control
•High ef ciency gas + air modulation, gas only modulation and simple high/low control options
•Heat Input Range: 9 kW – 1550 kW
TX Series Gas Fired Process Tank Heating Systems
•High ef ciency (80%+) heating of all types of spray and dip process tanks
FD-C high turndown oven/ dryer air heating burners.
FD-GA modulating gas + air process air heating burners.
FD-E low cost high turndown oven/dryer air heating burners.
•Compact high ef ciency small diameter immersion tube heat exchangers occupying minimum tank space
•Accurate performance modelling using Lanemark TxCalc design software
•Heat Input Range: 15 kW (1½") – 1150 kW (8")
Midco HMA Series Air Replacement or “Make-Up” Air Heating Burners
•Direct red, high ef ciency burner systems, for high volume air heating applications such as paint spray booths, ovens and dryers.
•Supplied either as Midco burner heads for OEM system integration or as Lanemark DB or FDB complete packaged systems including modulating gas valve trains and controls
•Wide range of ring rates to suit alternative temperature rise and air velocity system requirements
Midco HMA high efficiency, high turndown, air replacement or “make-up” air heating burners.
TX high efficiency small diameter immersion tube tank heating systems.
•DbCalc system design software
Pioneers of heat pump technology for over 25 years
Achieve efficiencies up to 800% with process heating and cooling recovery and ability to simultaneously redistribute heating (up to 84°c) and cooling (down to 0°c) for other uses
Master/slave configurations up to 2MW
Internet connected for remote monitoring, control and diagnostics
MasterLAN software for control of multiple set points of each unit
Equipped with Modbus communication protocol
7 year warranty as standard
At MasterTherm we specialise in high efficiency heat pumps for commercial and industrial energy systems. For over 25 years we’ve been pioneering heat pump technology and our products have been used for projects all around the world including the cooling of supercomputers, heating of historic buildings and heat recovery for scientific research
devices. Our ground source heat pumps are the most advanced in the UK and can offer outputs up to 92kW for a single fixed output heat pump, 7-45kW for a single inverter heat pump or up to 2MW in a cascade system. By developing and manufacturing both fixed output and inverter ground source heat pumps we can ensure the best possible
solution is presented based on your business needs and building specification. Each of our heat pumps is constructed by hand using premium components, enabling us to offer customisation options, altering the performance of our heat pumps to specifically cater to your requirements.
www.mastertherm.co.uk
COATING SERVICES:
l Thermal Spray & HVOF Coatings
l Dry film lubricants - MoS2, PTFE, Graphite, WS2
l Coatings for corrosion, chemical & environmental protection
l Titanium anodising
l Zinc rich coatings for corrosion protection
l Impingment coating processes for ultra thin solid film lubricants
l Nonstick/release coatings for low coefficients of friction
l Primers for rubber and plastics for sound absorbing and dampening materials
l High temperature resistant coatings
l Rare earth magnet coatings
l Coatings for EMI/RFI shielding provide highly conductive coatings and platings to control electromagnetic interference
l Ultra thin conformal parylene coating to reduce friction and protect against contamination
l Pre-treatments including Ti Anodising, Phosphate Conversion Coating and Chilled Iron Blasting, Aluminum Oxide Blasting and Vapour Degreasing
According to ONS data , almost one fifth of all workers in the UK manufacturing industry is aged 55 or over. Less than 10% are aged between 16 and 24. Over the next decade, 20% of the workforce will retire, taking with them years of engineering and manufacturing expertise.
If UK manufacturing is to remain internationally competitive, we need to prioritise the development of a skilled pipeline – that is, people who can design, build, programme, integrate, operate and maintain manufacturing technologies. We also need to heavily embrace automation as a route to countering unskilled personnel shortages and increasing productivity.
Despite having a strong manufacturing industry, the UK lags behind other industrialised nations in its uptake of automation. According to the International Federation of Robotics’ 2022 report, robot density in the UK manufacturing industry was
111 robots per 10,000 employees in 2021, which is very low for a Western European country (Germany, in comparison, has 397 per 10,000 employees).
I believe that together, investment in education and expertise can accelerate our adoption of automation and go a long way towards addressing the problems facing UK manufacturing.
FANUC firmly believes that education is the key to securing and nurturing a pipeline of new manufacturing talent. The content of university degrees is already changing to become more industry related, and school leavers now have the option of studying for degrees such as an MSc in Artificial Intelligence and Robotics and a BEng in Robotic Engineering. However, there are still only 30 universities in the UK offering undergraduate courses in robotics and automation. In addition to this, we can see a widening gap in the provision of post-
GCSE technical education, where there is a need for more hands-on training in real life engineering settings.
We are deeply committed to supporting automation education at lower foundation level through both our Training Academy and the delivery of robotic equipment to training locations such as schools and technical colleges. In the last 12 months, we have supplied more than 25 robots to learning centres in the UK to support current and future education requirements.
Our Training Academy at our Coventry HQ is currently undergoing independent validation, after which FANUC UK will become one of the first automation companies to offer accredited courses that can feed into mainstream education, with credits obtained against a particular skill. Students will gain valuable hands-on experience in areas such as operating, programming, troubleshooting and integrating robots whilst securing credits towards their qualifications. This industry-led methodology will greatly benefit the new T-Level awards, which have been designed to try and solve the ever-growing skills gap conundrum.
This new engagement between education and industry, which will launch in the UK in the coming months, will mirror the US model where FANUC has been blazing a trail in the roll-out of certified education programmes for robotics and automation. It is hoped that fostering a close, mutually beneficial cooperation between industry and education providers will be the key to the success of the new T-Level system and be precisely the direct intervention we need to attract younger people to manufacturing.
But attracting new blood to the industry is just one part of the challenge. Developing that talent into real industry expertise that becomes a source of competitive advantage is equally important. And this is what investment in automation is really about – not just buying a robot and waiting for it to pay back in the traditional laboursaving sense but establishing automation as a core function within business models.
There are a number of benefits to building strong in-house automation capabilities. As well as reducing reliance on third parties, this approach supports staff retention and promotes innovation from the inside. Companies can identify where the opportunities lie within their own businesses, understand how automation can enhance their facilities and use it to increase their productivity levels; something which the UK currently struggles with on the international stage (a German worker is around 30% an hour more productive than a UK worker).
This trend is already starting to play out in industries such as automotive production and the distribution and e-commerce fulfilment sector, where high-profile businesses are reaping the rewards of building internal automation teams. As the UK adopts more robotics and automation across different facets of industry and manufacturing, our prediction is that more companies will look at establishing their own internal automation teams.
As manufacturing companies embark on net zero roadmaps to meet the Government’s 2050 ambitions, sustainability is higher than ever on the agenda. Therefore, if automation is to play a key role in addressing the labour crisis, it needs to demonstrate that it represents a sustainable solution and can feed into net zero efforts.
In this respect, FANUC is a vanguard. We have been making our own servo drives for over 50 years and have now reached the point where we have achieved bestin-class energy efficiency. For example, our ROBOSHOT series of electric injection moulding machines uses up to 70% less energy than hydraulic machines and up to 20% less than other electric machines, thanks to servo technology and intelligent power regeneration capabilities.
FANUC also takes a circularity-driven approach to innovation and after-sales care in order to maximise resource use by prolonging the useful life of equipment. As a company, we operate a lifetime promise that as long as a machine is still in service, we will provide customers with original spare parts for a minimum of 25 years. As well as this long-standing commitment, our research
and development team focuses on improving the lifespan of our products to reduce waste. One example is our CRX Collaborative Robot – with a heritage of nearly one million industrial robots, FANUC has designed the CRX to outlast its competition, with very minimal maintenance needed across its lifespan.
Automation presents a solution to several challenges facing manufacturers today, from unskilled labour shortages and increasing product quality to waste reduction. However, realising its potential will require a serious joint commitment by the manufacturing and automation communities to build skills and nurture the next generation of engineers. Here at FANUC UK, we are determined to be a key driving force for change.
For further information, please visit www.fanuc.eu/uk/en
As manufacturing companies embark on net zero roadmaps to meet the Government’s 2050 ambitions, sustainability is higher than ever on the agenda.According to the International Federation of Robotics’ 2022 report, robot density in the UK manufacturing industry was 111 robots per 10,000 employees in 2021, which is very low for a Western European country SOURCE: WORLD ROBOTICS 2022
ABB Robotics has been selected by Nobia - the leading kitchen specialist in Europe –to supply robotic automation solutions for their new factory in Jönköping, Sweden. By securing the contract, ABB Robotics furthers its expansion into new industry segments, helping to make production more efficient and sustainable.
“ABB’s contribution to Nobia’s new stateof-the-art factory clearly illustrates how we are helping companies unlock flexible automation to transform their business, supporting with unique global industry expertise and innovative, tailormade products,” said Andrea Cassoni, Managing Director, General Industry, ABB Robotics.
“Working with Nobia, our robotics solutions will enable fast mass-production of customized kitchens, meeting consumers’ increased demand for tailored and personalized product choices”.
The supply of ABB robots will enable Nobia to achieve its vision for more flexible and more automated manufacturing that’s capable of producing customized products at scale. By taking on the dull, dirty and sometimes dangerous tasks, the range of robots will enable Nobia’s workers to take on safer, more rewarding work. The robots included are IRB 7600, ideal for heavy applications, IRB 4600, a generalpurpose robot that increases production capacity and improves productivity, and IRB 6700, the highest-performance robot in the 150–300-kilogram class which, on average, takes about 2.5 tons per day off the shoulders of an employee. The robots will enable the factory to produce customized cabinets with 75-80% higher efficiency (time) in comparison to non-automated processes.
Combining ABB’s technological leadership in automation with Nobia’s segment insights and knowledge of their customers’ needs, the relationship will lead to more flexible and digitalized manufacturing processes. Together, the companies strengthen the competence development within automation for the region around Jönköping. In the local area, ABB Robotics will support and educate Nobia’s existing and future employees as
well as students at Jönköping University and neighboring Linköping University. The training will be held in ABB Robotics’ recently opened training center in Jönköping.
“We are very excited about this partnership with ABB. We are building a future-proof, high-capacity factory that will support our leading position. It is a real game changer for the whole industry. The factory will manufacture customized, made-to-order kitchens at the highest speed and at the same time highest possible quality. The unique combination of technique solutions
combined with our expertise will enable us to offer kitchens with leading design, and sustainability performance to customers in the Nordic region. To achieve this we will utilize ABB’s market leading technology for highly automated and flexible processes, and extensive logistics consolidation,” said Jon Sintorn, CEO, Nobia.
The region around Jönköping is characterized by extensive know-how and expertise in manufacturing, with ABB Robotics further enhancing this through its work with Nobia. The factory will be fully operational in the course of 2024, to become one of Europe’s most modern kitchen factories.
For further information, please visit www.new.abb.com
By taking on the dull, dirty and sometimes dangerous tasks, the range of robots will enable Nobia’s workers to take on safer, more rewarding work.
The tec.nicum academy offers a comprehensive range of seminars and training on machine and plant safety worldwide.
The Machinery CE Expert seminar is held over four days, the course provides a compact overview of all knowledge required to satisfy legal and normative requirements in the EU single market. The tec.nicum academy’s speakers make it easy for seminar participants to understand the complex compliance assessment requirements of the EU Machinery Directive.
Participants will receive all of the information they need to be able to correctly apply CE marks to machinery and systems. After passing the test, participants will be able to use the title “Machinery CE Expert with TÜV Rheinland Certified Qualification” www.schmersal.co.uk
SAB Bröckskes was quick to recognize the requirements and the demand of industrial users for end-to-end Ethernet (IIoT) down to the smallest production level, for example sensor or actuator, and developed rugged and economical solutions in response. The new cable range CATLine SPE created by SAB Bröckskes offers new solutions for diverse application areas.
Single Pair Ethernet cables can be used for different applications within diverse industries. The intended application is the key factor in the development of SPE cables.
For example, Single Pair Ethernet cables are suitable for fixed installation, mobile applications, and even highly flexible applications. For many industrial applications, high temperature-resistant and rugged SPE cables for indoor and outdoor installation are also required.
SAB’s focus is on two Single Pair Ethernet cables, which have been specially developed for the increasing data transmission rates in automation. In addition to the CATLine C-Track, a drag chain-compatible Single Pair Ethernet cable, SAB Bröckskes has also developed a robot-compatible SPE cable with UL recognition, the CATLine SPE Robot
The drag chain- or robot-compatible SPE cables ensure safe and reliable data transmission over a bandwidth of 1-600 MHz. These cables are also PWIS non-critical, oil resistant, UL recognized, and RoHS compliant.
As an early member of the SPE network, SAB Bröckskes’ ambition is to help establish SPE technology on the international market and drive new fields of application in the different industries. To this end, the cable specialist from Viersen has developed a complete product range for diverse applications:
Due to the high mechanical and transmission requirements of Single Pair Ethernet cables,
CATLine SPE C-Track
CATLine SPE Robot
CATLine SPE HT
CATLine SPE Rugged
CATLine SPE Rail
Single Pair Ethernet cable, drag chain compatible
Single Pair Ethernet cable, robot compatible
Single-Pair Ethernet cable, high temperature resistant
Single Pair Ethernet cable for rugged indoor & outdoor use
Single Pair Ethernet cable for railway applications
the demands on design and production are also significantly higher compared to multi-pair stranded Ethernet cables. The manufacturing specifications must be complied with to the letter.
All Single Pair Ethernet Cables are designed as single pair cables (2 x AWG 26/7) and can also be designed as hybrid cables depending on the application. SAB expects a lot of application-related special solutions, e.g. with power supply for motors and sensors. SAB considers itself well positioned in this area and would like to offer custom solutions. Design requirements differ depending on the application. For drag chain applications, a permanently flexible design with a specially adapted stranding technique was chosen for the CATLine SPE C-Track cable. For robot applications, the design was adapted to guarantee flexible use for a torsional application of +/- 180°.
Compared to a traditional 4-pair Ethernet cable, SPE cables save up to 30% on space and are up to 35% lighter. Considering the amount of cable that would be laid in km, the resulting cost savings are considerable. Over the life cycle of a railroad, for instance, you would be looking at savings somewhere within the 6-digit euro range.
A T1 SPE C-Track cable must meet the electrical and transmission requirements of draft standard CD IEC 61156-12 Ed. 1.0. Connectors are available from Harting, for example with which SAB Bröckskes works closely. Used in combination, full compliance with the standard is then assured.
Based on current information, SPE requires no more bandwidth than Cat.7A. SAB cables have already been successfully tested.
SAB’s manufacturing capabilities extend not only to basic types and standard dimensions, but, in particular, to special cables designed according to each customer’s requirements. Production can also be carried out in small batch sizes, which are of interest for small and pilot series.
SAB Bröckskes is one of the world’s leading cable manufacturers and suppliers of cables assemblies as well as temperature measurement technology. In over 75 years, a one-man operation has grown into a company with over 550 employees, which today more than ever guarantees outstanding quality made in Germany.
Our expertise lies in the design of highly flexible cables according to customer specifications for a wide range of applications, for example in the fields of automation, robotics, crane engineering, and railway technology. Subsidiaries and offices around the world work hard to find the optimal solution for our customers from more than 1,500 new developments per year.
An innovative cable specialist already in its third generation, we focus on continuously developing and further developing our products through intensive research and development as well as tests and inspections. Because not only do we produce cables, we also deliver solutions to problems.
For further information, please visit www.sab-cable.com
Cupio Services provides x-ray, acoustic, optical and electronic test, inspection and analysis services.
If you only require inspection, test or analysis services occasionally throughout the year, the requirement to purchase our equipment may not be necessary, this is where Cupio Services is the answer.
• Cutting-edge inspection and test equipment
• Functional testers and counterfeit part detection
• High resolution x-ray with multiple CT imaging options
• Acoustic microscopes for delamination detection within boards or complex devices
• Full failure analysis reports.
Speak to one of our experts today:
Cupio Services Ltd
+44 (0) 1256 262800 info@cupioservices.co.uk www.cupioservices.co.uk
Beechwood, Chineham Business Park, Basingstoke, Hampshire, RG24 8WA
The VARIO MOVE transport robot has been awarded this year’s iF Design Award. This is the third time that the flexibly configurable automated guided vehicle (AGV) from ek robotics, with its sophisticated industrial design, has received a coveted design award.
The industrial design of the VARIO MOVE series has convinced an international design jury for the third time: After receiving the Red Dot Award 2022 and German Design Award 2023, the VARIO MOVE transport robot from ek robotics has also been honored with the globally renowned iF Design Award in the category “Industry / Tools”. The number of submissions was large: The 133-member jury had to choose between 11,000 applicants from 56 countries, for the winners who may carry the popular design label in the future.
“We are very pleased and proud of the third award for the VARIO MOVE. All three design awards confirm the postitive feedback from our global customers who use the VARIO MOVE to optimize their material flows,” says Andreas Böttner, CEO of ek robotics. “Our goal for this transport robot series was to develop an appealing and smart design that conveys our new distinctive corporate
design. With the versatile VARIO MOVE, we have succeeded in this.” The VARIO MOVE AGV has been designed for the sustainable optimization of transport and material flows and meets a wide range of transport requirements. The modular concept, maximum availability, maintenance-friendly design and an exceptionally long life cycle are just as striking features as its design. “As a high-tech transport robot, the VARIO MOVE combines power and performance with a compact but friendly appearance and helps minimize fear of contact between humans and robots,” adds Ronald Kretschmer, CSO at ek robotics.
Together with industrial designer Meike Hahr from Creative Specialists, the engineers from ek robotics deliberately focused on a friendly appearance when developing the VARIO MOVE. Right from the start, people should experience the transport robot as a working partner and not as a disruptive factor. The iF DESIGN AWARD is awarded once a year by the world’s oldest independent design institution, iF International Forum Design GmbH. Since 1954, the iF DESIGN AWARD
has been a globally recognized trademark when it comes to excellent design.
Depending on the application profile, the three-time award winner can be equipped with different trolleys, various load handling devices and all major navigation technologies available on the market. The VARIO MOVE modular system consists of five defined lift masts, with which a transfer height of up to 5 meters can be achieved. At the same time, it has a high load capacity of up to 1,600 kg. Inside, an intelligent sensor system ensures maximum safety during operation, while the intelligent Li-Ion energy system is designed for 24-hour use, 365 days a year. This results in a multitude of possible combinationsone of the strengths of the Infinite Colors of Transport from ek robotics.
On April 25 - 27, visitors to LogiMAT will be able to experience the transport robot VARIO MOVE, which has won the Red Dot 2022, German Design Award 2023 and iF Design Award, in action under real conditions. You will find ek robotics in hall 6 at booth B05.
For further information, please visit www.ek-robotics.com/en/
SPD Ltd and our partners have been solving problems in Lightning & Surge Protection for over 50 years. Our devices are European designed and manufactured, state of the art products, which exceed the requirements of the latest standards. With over 3000 products in our range, we are the markets Surge Protection specialists, with a device to suit every installation.
We carry out many seminars with consultants and specialist training organisations as well as attending exhibitions and conferences both in the UK and overseas, where our knowledge is renowned. We also hold regular contractor training sessions online, some of which are live webinar sessions, where you can ask our Technical Director any questions, and some are on-demand, so can be accessed at a time to suit yourself.
If you have any questions at all please give us a call on 01484 851 747 or email info@surgedevices.co.uk.
NORTH SOMERSET based Famatel UK Ltd is one of the leading producers and suppliers of electrical products for over 10 years with Head office in Spain, factories across Europe and we are one of 7 Subsidiaries around the world and the group is growing every year. Famatel group ultimate objective is to intergrade group under one system offering global view of inventory and sales world wide enhancing its ability to change to market needs in every country at a moment notice.
As a distributer and assembler of industrial power distribution products and systems it holds a full range of BS4343 / IEC 309 electrical distribution products and manufactures a wide range of enclosures from IP20 to IP67 along with its new GRP range.
The company also has the ability to integrate its distribution products together to offer its customers a custom build solution to meet specific requirements. Famatel UK Ltd says that it employs a strict system of quality control that flows thought the Famatel SPA group.
We pride ourselves on producing system to our customers’ needs on time and on budget, within the time frames needed.
We produce Electrical distribution systems in Plastic , Metal, Staines Steel , GRP, with or with our transformers if necessary single and three phase.
We pride ourselves on producing system to our customers’ needs on time and on budget, within the time frames needed.
More than 25 years of experience in the international electric sector
By believing in this project we’ve truly crossed borders. We’ve become a global business where people, their attitude and their knowledge are the backbone to the Famatel project. Our corporate strategy rests on the pillars of teamwork and respect for diversity; it’s led us to have a presence in over 60 countries with 3 production centers and 7 subsidiaries. A demanding, honest and well-motivated team strive every day to consolidate our position on the national and international market by strengthening our relationship with clients and suppliers alike
Sales/General Enquiries
01934 412133 | sales@famatel.co.uk
Custom Build
custombuild@famatel.co.uk
Humidity - condensation - corrosion:
This chain of adverse conditions often adds up to cause failure in sensitive electrical and electronic components. The use of modern electric enclosure heaters is an effective and economic countermeasure that addresses these frequently neglected causes of defect and avoids damage or even breakdowns.
Operational reliability and longevity are attributes every customer expects from an enclosure. The controllers increasingly feature sensitive electronics. For some electronic components, the service life is directly related to the ambient temperature. This requires the interior temperature of switching cabinets to be lowered and unwanted excess heat to be removed. This is achieved through ventilation via filter fans.
The danger arising from condensation in electric cabinets is often disregarded, however, even if the resulting defect characteristics are usually very dramatic. Short circuits cause damages in individual units that must then be replaced. This cause of defect occurs - under certain climate conditions - even in well encapsulated enclosures.
Condensation - a rarely recognized cause of faults or even complete breakdowns of an entire control system
In combination with aggressive gases and dust particles, condensation causes atmospheric corrosion. Affected are, e.g.:
• bus bars • contactors
• relays • protective motor switches
• transformers • frequency inverters
• programmable controls
• semiconductors/circuit boards
• solder, crimp and screw connections
Condensation is thus a source of faults that must be taken seriously. The biggest risk in practice occurs when relatively high humidity and temperature fluctuations coincide in an encapsulated enclosure - e.g., during round-the-clock operation or in outdoor installations. Failure causes triggered by condensation in systems can be:
• changing contact resistances • indefinable stray currents • reduced insulation properties • arcing up to total short circuit • corrosion occurring
There’s something in the air
Humidity arises when the sun extracts water from waterways and plants by evaporation. This share of water vapor in the atmospheric air is referred to as “absolute” humidity (in g/m³). How much water can be stored in the air depends on a variety of factors, such as temperature or air pressure. The higher the air temperature, the more invisible water parts can be absorbed by and stored in the air. The ratio of “absolute” humidity to the max. possible humidity is referred as “relative” humidity (in %). At 100% RH, the air is saturated, and the so-called dew point is reached. No further water vapor can be stored in the air. The excess water vapor share is dumped into the environment as condensation.
At constant absolute humidity (water quantity in g/m³) and falling temperature, the air becomes saturated and can no longer hold the water vapor: the dew point is reached, and fine water droplets are deposited. This process can easily be observed on windows, spectacles and drinking glasses when the condensation occurs on the cold surfaces. This is when the danger of component failure in enclosures begins.
Outdoor installations are particularly at risk: condensation already forms as a result of temperature changes between mild daytime temperatures and overnight cool down, but even more so as a result of seasonal climate change or sudden temperature drops - such as during thunderstorms in summer.
Even in indoor installations, temperature changes trigger condensation. The culprits are bus bars, relays and other heatgenerating installations mentioned at the beginning that work in a day-night cycle.
If these are switched off at night, they no longer heat the air inside the electric cabinet. This cools down and the relative humidity rises. The consequence is the formation of condensation.
The formation of condensation only starts when a relative humidity of 100% is reached. But even values lower than that can present a danger for switching cabinets. Corrosion can already occur at much lower values. This is the result of various long-term studies. The empirical limit thus determined is at around 65% RH. From this threshold on, one has to expect corrosion in electric cabinets, even without condensation being formed.
Optimal conditions can only be achieved for constant temperature. Condensation and corrosion are not the only factors that significantly reduce the lifetime of the components - so does the mechanical stress brought about by continuous temperature change.
The “life insurance” for switching cabinets: electric enclosure heaters
The state-of-the-art solutions are electric enclosure heaters that have been developed specifically to avoid condensation and temperatures that are too low or fluctuate too much. The air in the electric cabinet is heated to the point where it can hold the entire water vapor and condensation is avoided. Just this is what would happen when equipment is switched off and no excess power is dissipated. Without heater, the relative humidity increases and condensation occurs on the components.
Conclusion:
Electric cabinet heaters are a reliable protection against condensation and temperatures that fluctuate or are too low. When comparing the cost caused by failures to the purchase price of electric cabinet heaters and controllers, the latter represent little additional cost that nevertheless makes a big difference.
For further information, please visit www.stego.co.uk
The technology that powers our smartphones is also driving electric vehicles, including materials handling equipment. Michael Burns, National Sales Manager at Grant Handling takes a look at Lithium-ion battery powered forklifts to discover why more businesses are making the switch to the Heli Lithium Lite range.
When you rely on your electric forklift for loading, unloading and transporting goods over short distances and in warehouses, you need maximum availability, reliability and convenience.
Over recent years, the cleaner, greener and quieter electric-powered forklift has increased in popularity across the engineering, food and beverage sectors.
Today, advances in battery and charger technology have seen Lithium-ion batteries transform the electric forklift market, and take up is growing fast.
Several factors are driving the Lithiumion revolution. When it comes to energy efficiency, Lithium-ion batteries offer excellent performance. Where lead acid burns 45-50% of its energy in heat, Lithiumion only loses 10-15%. It also has a longer life span, with over 75% capacity reserved after 4000 charge-discharge cycles, which helps keep running costs down. Lower noise pollution and zero emissions make it a better solution for the environment, too.
Add to this less time spent changing batteries, faster charging times and lower maintenance, it’s easy to see why so many businesses are switching to Lithium-ion.
Convenience and flexibility are built in, as Lithium-ion batteries can be opportunity charged or recharged as necessary - a 15 minute top up when staff are on a tea break or a quick 30 minutes during lunch. The Heli Lithium Lite range uses a conventional 3 pin socket to charge, so wall plugs can be placed at convenient spots around the business, ideal to get a short boost in
will not damage the Lithium-ion battery or shorten its lifespan. Add to this the batteries are completely maintenance free.
Lithium-ion batteries are completely sealed, so there is no risk of acid spills or corrosion. There’s also virtually no chance of overcharging and overheating thanks to the intelligent Battery Management System that tracks cell temperatures, ensuring they remain in safe operating range to minimise risk to operators, staff and customers.
Our new lithium-lite range consists of 3- and 4-wheel lithium-ion counterbalance forklifts
intensity applications, these compact forklifts are allrounders, setting the benchmark for quality and value. The Heli Lithium Lite range offers a performance comparable to internal combustion trucks, with zero emissions.
Easy to drive, comfortable and manoeuvrable, the Heli Lithium Lite works effortlessly in tight spaces. Precise handling and intelligent steering with multiple speed modes ensures you get the job done efficiently. Onboard operator protection systems on the hydraulics and drive ensure safer operation.
Ultra-low torque steering gear and lighter steering operation reduce driver fatigue,
while the truck’s optimised mast and pressed overhead guard offer improved visibility and safety for confident handling. Tough and durable, the integrated cast drive axle and reinforced cast steering axle is built to last.
Equipped with side shift as standard for faster and more accurate lifting and placement, with the versatile Heli Lithium Lite any attachment can be fitted to suit your needs.
The convenient anytime, any socket built-in charger ensures you keep
running all day. And with easy access for maintenance, the electrics are concentrated on the top of the lithium battery with centralised maintenance points for simple inspection and maintenance.
With the geopolitical factors that are currently affecting the global supply chain, at Grant Handling we have invested in stock of the Heli Lithium Lite range to help combat these challenges for our customers, offering immediate
shipment for both new equipment and spare parts. That means your next forklift is always readily available, right when you need it.
We know that a forklift breakdown can cause immense stress for your business, and that’s why you need an expert forklift service and maintenance team by your side. At Grant Handling, all your materials handling service requirements are taken care of with one call. With a network of local engineers that come to you wherever you are to get your operation running again as quickly as possible. A full range of flexible forklift services packages is available, tailored to your specific business needs, for total peace of mind.
For more on what the Heli Lithium Lite forklift range could do for your business, contact us.
Excelling in light applications, this fantastic entry-level forklift, with the latest in lithium-ion technology, boosts productivity while saving you money!
From MAK CLEANEX, a strong NSF K1 registered degreasing agent with no hazardous substances such as Ketones and N-Hexanes.
To MAK FOX, a unique multi-purpose, non-flammable degreaser with no hydroxide, phosphate or any hydrocarbons. And MAK WELDING, a Silicone-free anti-spatter liquid that is biodegradable and non-toxic. These products deliver RESULTS!
AutoStore is a global provider of the fastest, most flexible and densest automated storage system per square foot. It harnesses the power of warehouse robots for 24/7 order fulfilment within a cubic layout so dense that it can actually quadruple storage capacity and unlock the true potential of storage floorspace.
With a 99.6% uptime and bestin-class energy consumption, AutoStore is the modern solution to modern business
Through design and in-house manufacture our swivel joints allow one or more different flows through a single unit, enabling the pipework to rotate 360 degrees whilst carrying fluids (including hydraulic and pneumatic) of different pressures without crosscontamination or leakage.
There are many different forms of Swivel Joint… from very straight forward designs of our F and FS series, Compact swivels, or Heavy Duty to Articulated Pipework configurations, Floating Suction Arms, Jacketed, High pressure. A Swivel Joint reduces costs by reducing the risk of leakage with its associated downtime. By fitting a quality designed swivel, you are improving your production capacity.
With almost 40 years of experience, Rotaflow, are specialists in taking your bespoke requirements and being able to design a solution that can fit your budget, dimensions, materials, FAT/witness testing; hygienic and pressurised environments. We regularly test to Hyperbaric, Seal Life and conduct Temperature/Pressure/ Load Cycle Testing. We are ISO 9001:2015 certified.
The photo attached shows a burner boom swivel, complete with Norsok paint specification, being readied for despatching.
To find out more please visit our website and/or give us a call. Tel: +44(0)1663 735003 | sales@rotaflow.com www.rotaflow.com
constraints, all while keeping things simple with only 5 components; Bins, Robots, Ports, the Grid, and the AutoStore Controller.
AutoStore is designed for easy system expansion. Grow your capacity gradually without shutting down operations or experiencing downtime, so you are expanding your operation in line with actual business growth.
jon.brewin@autostoresystem.com
www.autostoresystem.com
In a tough competitive commercial environment finding ways to win new business is more important than ever.
Use Millmax EE* 46 HV as a cost-effective solution that improves both profitability and sustainability.
- Excellent temperature viscosity profile providing improved mechanical efficiency of the whole system.
- High viscosity index contributes to lower fluid leakage losses and greatly improves pump efficiency leading to lower energy usage.
- Excellent oxidation and thermal stability, improving oil cleanliness for longer operating life.
- Viscosity stability provides effective power transfer in hydraulic systems.
- Excellent low-temperature performance allowing use across a wide temperature range.
- Advanced anti-wear and corrosion chemistry protect equipment for longer component life.
- Low foaming formulation minimises aeration and cavitation for consistent power transfer.
- Good compatibility with elastomers and seals for longer seal life and reduced maintenance.
With CAPEX conditions restricting response time to unscheduled process and production downtime, Axium Process, specialists in liquid filtration solutions, have launched a new service that can now be funded through OPEX channels. Designed to meet a range of liquid processing concerns, Axium’s UF & RO2Go rental plants meet industrial scale demand for many different industries including pharmaceutical, food, beverage, dairy and water recycling. The systems are built on tried-and-tested technology and have been developed for rapid deployment with minimal operator training, allowing them to be up and running in a matter of hours following installation. Offering great flexibility, and backed by extensive technical expertise, Axium’s rental range can fulfil high-priority requirements swiftly, while reducing capital expenditure risk by allowing the technology to be assessed over the long term.
For further information, please contact: Derek Davies
Axium Process, Hendy Industrial Estate, Swansea, SA4 0XP Tel: 01792 883 882
Email: derek.davies@axiumprocess.com
info@axiumprocess.com
With the advancement of power electronic components in general gives rise to increased heat dissipation, resulting in more hotspots within control cabinets where traditional methodology of construction is employed. Separating the wiring from the components allows for free air movement, resulting in passive cooling within the cabinet.
A live on-site test was conducted to prove effectiveness of this approach. The first cabinet was equipped with a traditional back plate and cooled using an air conditioning system with a 1.5 kW heat loss. In the second cabinet a 1.45kW heat exchanger was fitted, and the mounted components were separated from the wiring using the Lutze AirSTREAM wiring frame. (shown in figure 1).
Measurements were taken for six hours at a time in each cabinet. The measurements were carried out over two days, with 10 sensors recording the ambient and internal temperatures. In the cabinet using the back plate the temperatures fluctuated between 29 degrees C and 43 degrees C. In
the cabinet using AirSTREAM, the temperatures fluctuated between 30 degrees C and 34 degrees C (as shown in figure 2). The test demonstrated that using AirSTREAM can achieve noticeable cooling and a consistent climate inside the control cabinets. This not only protects the components but reduces the amount of energy needed to cool the cabinets.
Visit https://www.luetze.com/en-gb/airstream-climb-c
Separating the wiring from the components allows for free air movement, resulting in passive cooling within the cabinet.
Available from NSK is a range of deep groove ball bearings adapted to the specific requirements of servomotors. Thanks to the development of special greases and a highly effective, low-friction seal, NSK solutions overcome the limitations of conventional electric motor bearings when used in servomotor applications.
For rolling bearings, servomotors present a challenge. With their frequent start, stop and reversing operations – as well as tiny corrective movements prompted by the sensor system – the typical motion profile of servomotors places bearings under intense stress. Furthermore, the frequent reversing and associated micro-vibration cause the lubricant film between the rolling element and running surface to be wiped away (without the opportunity for afterflow re-lubrication) to a greater extent than would be the case with continuous rotating bearings used in conventional electric motors.
Potential consequences include the generation of local micro-friction points on the raceways. This friction is caused when the lubricant film is insufficient and metal-tometal contact occurs between the raceway and ball.
To surmount these issues, NSK has developed a special grease known as EA7. Compared with conventional greases, EA7 offers improved lubricating properties when subject to micro-vibrations. The grease also helps to ensure that the bearings operate with low frictional torque and correspondingly minimal power loss. In practice, the use of EA7 lubricated bearings in servomotor applications leads to longer operating life and the doubling of service intervals.
Another factor that increases the service life of servomotors is cleanliness during operation. If the bearing grease releases particles (such as metal or sulphur) that migrate to surrounding components, the encoder may become dirty. Over time, this contamination will render the motor incapable of detecting precise position. A further consequence of escaping lubricant
Servomotors present specific challenges that can compromise conventional electric motor bearings
can be slippage during braking, which again might promote inaccurate positioning.
To provide a solution to the contamination issue, NSK has developed another grease for servomotor applications, called LGU. Compared with lithium soap grease, LGU emits around 90% less sulphur and metal particles, thus contributing to the long-term cleanliness of the bearing environment. The result: service intervals are extended by a factor of 1.5.
www.nskeurope.com
NSK has developed special greases and seals for its range of servomotor-specific deep groove ball bearings
Companies building or integrating servomotors can choose whichever grease is most suitable. EA7 extends the service life of deep groove ball bearings when subjected to the micro movements typical of servomotors, while LGU minimises the release of particles on to surrounding components, preventing imprecise positioning. These two high-performance greases are available as an option for the deep groove ball bearing series that NSK has developed for use in servomotors.
A further feature of these bearings is NSK’s DW seal, which offers a combination of exceptionally good sealing and low frictional torque. With DW seals, the company’s designers have developed an effective solution to the conflicting requirements of reliable sealing and energy-efficient bearing operation.
The range of deep groove ball bearings for servomotors is described in a new catalogue entitled ‘Bearings for Electric Motors’, which is available in print or as a PDF download at: www.nsk-literature.com/ en/industrial-motor-bearings
Menzel is an independent company, established in the UK and International market as a specialist in electric motor technology for industrial applications. It has over 95 years’ experience in production and delivery of custom electric drive solutions. Offering a wide range of services, it is several steps ahead of its competitors with regards to speed, service, and engineering.
Menzel is renowned for its reliability, flexibility, and most importantly, its speed of response. From personal advice regarding planning, development, design, and production, Menzel provides a total service from a single source. These include standard motors for industrial applications, identical, interchangeable replicas, custombuilt designs, mechanical and electrical augmentation, special designs for special drive operations and more.
The company’s main customer base is users of industrial AC and DC motors. They are often tasked with urgent replacement of failed motors no longer available from existing OEMS, Menzel step in to replace an asset helping to restart production quickly after an emergency failure occurs where no spare exists.
Menzel, operates the largest stock of ready built motors and components offering fast delivery for urgent need and up to 20 MW of power from stock. As specialists in all aspects of industrial sectors, Menzel ensures it caters for all with established references worldwide in cement, steel, water, paper, food and beverage, utility power and petro-chem markets.
Menzel Elektromotoren GmbH was established in 1927. Currently, Menzel has a new plant under construction on the outskirts of Berlin, which will help them to cope with the increased market demand and larger capacity. This operation will begin towards the end of 2023. It also has a UK based office in Melton Mowbray, Leicestershire, East Midlands to support British customers who needed to replace outdated and obsolete products which were no longer available from established manufacturers.
Menzel, operates the largest stock of ready built motors and components offering fast delivery for urgent need and up to 20 MW of power from stock.
Custom Solutions for Electric Motors Around the Clock, Against the Clock!
Whenever existing mechanical and electrical interfaces are key coupled with fast delivery
Motors up to 15 MW and 13.8 kV
• Low voltage slip-ring and squirrel cage motors up to 3,000 kW
• Medium voltage slip-ring and squirrel cage motors up to 15,000 kW
• Direct current motors up to 2,000 kW
• Frequency converter-proof drives
• In-house load test facility up to 13.800 V, 2.300 kVA, 120 Hz
Customized special designs
• Custom designs for special applications and operating conditions
• Optimized motor design for higher efficiency
• Mechanically and electrically interchangeable motors
• Commissioning worldwide
MENZEL Great Britain Ltd. | UK Branch Office
27 Hunt Drive | Melton Mowbray | Leicestershire LE13 1PB
Martin Rooney | Tel.: +44 1664 500 844 | Mobil: +44 7957 618046 martin.rooney@menzelgb.co.uk
MENZEL Elektromotoren GmbH | German Headquarters
Neues Ufer 19-25 | D–10553 Berlin | Germany
New electric motor plant in 2024
More than 20.000 motors available from stock!
24/7 emergency service
www.menzel-motors.com
Leaks and spills onto floors and surfaces are a common occurrence in industrial workplaces, which can increase the risk of slips plus exposure to hazardous liquids such as solvents and degreasers.
MEWA’s reusable, rentable cleaning wipe service helps companies ensure spills are mopped up quickly and efficiently by always having exceptionally absorbent cloths
to hand. Used cloths are then stored in MEWA’s SaCon safety container until collected and replaced with clean ones, giving companies peace of mind that soiled and contaminated wipes are stored safely in a fireresisting closed container and are compliant with hazardous waste regulations and will be cleaned safely in line with legal requirements.
www.mewa.co.uk
• World-class two-day conference agenda
• Solution Theatres
• Guitar Legends competition (win a 3D guitar)
• Masterclasses
• STEM features (next-gen talent)
• Sustainability initiatives (plant a tree in our forest)
• Future of Manufacturing
• 400+ exhibitors providing the latest innovations/ industry solutions
• Expert-Led sessions
• Post-event drinks and networking
Wednesday 7 & Thursday 8 June 2023
NEC Birmingham
Nineteen Group has announced a range of innovative activities that will take place during Manufacturing & Engineering Week 2023 www.mandeweek.co.uk. The week-long festival has four centrepiece exhibitions and combines both live and digital events, celebrating the best that the UK industrial sector has to offer.
A major part of Manufacturing & Engineering Week 2023 is the free conference programme that will take place across two Keynote Conferences and six Solutions Theatres. Emphasising the importance of M&E Week is the fact that on Day 1 the keynote address in the main theatre will come from Government on the topic of their plans for supporting
UK manufacturing while on Day 2 the shadow government will talk on the same subject.
Highlighting innovation is a key part of M&E Week. Made Smarter’s Innovation Alley, for example, will showcase the developing technologies that will change the landscape of manufacturing over the next five to ten years. Similarly, the Innovation Village, run by the seven High Value Manufacturing Catapult research and technology centres, is an immersive and interactive demonstration area that will take visitors on a journey from fossil fuels to renewables, demonstrating the technological advances that will transform industry for a sustainable world.
he week-long festival has four centrepiece exhibitions and combines both live and digital events, celebrating the best that the UK industrial sector has to offer.
Recognising the fact that the future of the industrial sector is as much about people as it is about technology is the Manufacturers of the Future programme developed with partners Engineering UK, Make UK, Engineers Without Borders UK and the IMechE. Taking place on the afternoon of Day 2 (8th June) the event enables students and apprentices, about to take the first step into their careers, to engage with the rapidly evolving world of manufacturing.
The week beginning 5th June 2023 is Manufacturing & Engineering Week with the centrepiece exhibitions Design & Engineering Expo, Smart Factory Expo, Maintec and the Drives & Controls zone taking place at Birmingham’s NEC on 7th and 8th June. Other exhibitions are also taking place at the NEC during the week run by other event organisers and these include Automechanika run by Messe Frankfurt; Med-Tech Innovation Expo and TCT 3Sixty from Rapid News Group and Subcon from the Mark Allen Group. A Visitor pass provides access to all events.
For more information visit: www.mandeweek.co.uk
WISEMAN THREADING TOOLS LTD
We have been supplying threading tools and gauges since 1987.
Together with supplying plain plug and ring gauges this is all that we do, we therefore consider ourselves to be specialists in this field.
We supply worldwide.
We hold extensive ready stocks that include all of the standard stuff that others offer, but also includes taps, dies, die nuts, die head chasers, thread rolls and gauging for threads not normally available 'off the shelf '.
Our real time stocks can be checked and purchased online at www.threadtools. com Just enter the thread details into the search box on the home page.
You will be directed to the item, if stocked, or to our specials, (custom manufacture), sales team. who will quote to supply at competitive rates, in good time.
As an account holder you can also order online from our listed in stock items, at your normal terms. We realise that you need the right item at the right price and quality, and in a reasonable time frame.
We are geared to provide that.
We can ship stocked items same day.
Our experienced sales staff can assist and advise you on any technical issues.
We welcome enquiries from resellers and can offer terms to suit.
WISEMAN THREADING TOOLS LTD
11 Padgets Lane
South Moons Moat
Redditch B98 0RA UK
+44(0)1527 520 580 sales@threadtools.com www.threadtools.com
HSS DIES & DIE NUTS
Large shelf stocks for all Standard and many Special Threads. Check our stocks online.
THREAD CUTTING AND ROLLING HEADS and parts and repair service
HSS TAPS
Huge Stocks for all Standard threads
CUSTOM MADE taps our SPECIALITY!
We stock taps for many non standard (SPECIAL) threads
All types; Spiral flute and point, Fluteless, Left Hand, etc, etc.
THREAD GAUGES all types. Large stocks for standard and SPECIAL threads. Any non stocked can be quoted for custom manufacture.
CHASERS FOR COVENTRY & LANDIS TYPE DIE HEADS
Ready stocks for most size heads most standard and some special threads Geometry available for most materials. Custom manufacture our speciality!
Leeds Plastic Engineering Ltd, are specialists in CNC machining and turning of all types of engineering plastic and non-ferrous materials. The company prides itself both on the quality of output and reliability of service so is well placed to create long lasting partnerships.
At Leeds Plastic Engineering Ltd we produce high quality, precise plastic components to a wide variety of industries across the UK. Whether it be a one off component or a run of thousands the standard, consistency and attention to detail will not be compromised.
We can produce anything from simple wear strips to complex 3D components in an extensive range of materials including but not limited to Nylon, polypropylene, acetal, Delrin, UHMWPE, HDPE, PTFE, PEEK, acrylic, PET, Tufnol, PVDF and polycarbonate.
We are happy to manufacture and quote for components using anything from 2D
hard copy drawings through to 3D cad models and can also reverse engineer from existing parts.
We supply many bespoke plastic conveyor and change parts for use in automation applications within the bottling, packaging, printing, food processing and materials handling industries. Example items we manufacture include:
• Chain tracks
• Wear strips
• Guides
• Change parts
• Sprockets
• Starwheels
• Machine Guards
• Washers
• Bushes
• Metal detectable components
• Feedscrews
• Conveyor parts
• Gears
• Paddles
From launching the business in March 2015, we have experienced rapid growth, and with this, we have continuously invested in new machinery to expand our capabilities and increase the capacity of our CNC precision machining services. We have the latest CNC machinery, up to date, state of the art cad cam software and modern tooling which enables us to produce excellent surface finishes whilst working to the tightest tolerances the material allows.
Having also invested in the latest, stateof-the-art inspection machines to ensure the quality of our output is truly second to none. Our fully equipped and calibrated Inspection Department is working to IS09001:2015 standards.
We are proud to have been awarded the prestigious ISO9001:2015 certification recognising our commitment to total quality throughout our business.
Contact Details:
Gareth Baker, Director Tel: 0113 345 3150
Email: sales@leedsplasticengineering.co.uk
For further information, please visit www.leedsplasticengineering.co.uk
We supply many bespoke plastic conveyor and change parts for use in automation applications within the bottling, packaging, printing, food processing and materials handling industries.
Global metal cutting specialist Sandvik Coromant introduces a new generation of CoroTap® 100 and CoroTap® 400 for short-chipping and chip-free tapping of aluminium. The taps offer high process security and predictable tool life.
Threading is often the last operation in your component, and the last thing you want is for the tap to break. That is why process security and predictable tool life are of the highest importance when it comes to tapping. The next-generation CoroTap® 100 and CoroTap® 400, with optimized performance in aluminium, can meet very strict process security demands and offer a high level of reliability and consistent tool life.
The CoroTap® 100 straight flute tap features a refined edge rounding that helps to remove burrs and improve surface finish. The combination of core thickness, rake/relief angles and land width gives an optimal flute geometry with great chip evacuation. If threading deep holes, the back chamfer helps to improve the threading capacity.
The CoroTap® 400 forming tap has an optimized lobe shape developed for aluminium machining and a low frictioncoefficient surface treatment for a smooth and polished thread surface finish. With a reduced thread length, the tap is less in contact with the material, reducing power consumption and torque. Finally, staggered coolant holes offer excellent coolant flow into the thread-forming zone and a safe forming process.
In a production process, tapping can be a bottleneck and increased productivity is often a demand. For example, a typical aluminium cylinder block can have up to 12 different threads in its structure and tapping is the most time-consuming process. With the new straight flute tap and forming tap, you can increase productivity and reduce cost per part.
“Both geometries are combined with the latest surface treatments, substrates
and coatings, which gives the ability to use higher cutting data with significantly improved tool life, resulting in lowering your cost per part.” says Robert Smith, Offer Manager for Hole Making and Composites at Sandvik Coromant.
Both taps can be used for blind and through holes in many different components, such as cylinder blocks, cylinder heads, electric motor housings, transmission housings and battery racks. Robert continues: “These products are beneficial for anyone who machines aluminium, including automotive, E-mobility and general engineering.”
For further information, please visit www.sandvik.coromant.com
The CoroTap® 100 straight flute tap features a refined edge rounding that helps to remove burrs and improve surface finish.
◊ Manufacturing up to 1450mm diameter
◊ Turning - CNC lathes, Vertical Machining Centres
◊ Gear Cutting - Hobbing, Shaping, Gears, Sprockets & Pulleys
◊ Bevel Gears, Helical, External & Internal cut Gears
◊ Rack Shaping, Broaching, Keywaying
◊ Vertical Boring, Centreless & Rotary Grinding
◊ Bore Honing ◊ Induction Hardening
◊ Drilling & Tapping ◊ Marking ◊ Blacking
◊ Toothed Timing Belts stocked and cut to size
◊ Roller Chain in carbon steel, stainless steel in stock
◊ Large stocks of all products ◊ CAD - CAM Design & Development
◊ ISO 9001 : 2015
Boxford are a long established manufacturing equipment brand, who supply professional, affordable and reliable laser cutting, engraving and CNC machines to a range of industries. The Boxford team are looking forward to being part of the MACH 2022 show at NEC, Birmingham from 4th – 5th April and will be providing live demonstrations using a selection of their laser cutting, engraving and marking equipment. Included in their comprehensive display will be a BFL2010 2KW fibre metal cutting laser, a BFM110 30W fibre marking laser and a compact C02 laser complete with integrated 4K camera for design positioning, image tracing and live monitoring.
Boxford’s range of machines are capable of cutting and engraving a whole host of materials, including metals, wood, plastics, paper, card, foam, rubber and more. Their friendly team of experts will be on hand to answer any of your questions on the day!
As part of the launch of our new chain cutting service, Donghua is offering distributors free carriage (UK mainland only) on all orders of cut to length chain.
Donghua Limited is part of the Hangzhou Donghua Chain Group of Companies which is one of the world’s largest manufacturers of industrial chain, producing in excess of 40 million metres of finished chain per year.
Based in the West Midlands since 2009, we have created a comprehensive workshop on site in our warehouse and distribution centre, for the production of bespoke inhouse built attachment chain.
The new automatic chain cutting machine is the most recent addition to our workshop which includes a range of tools and machines which measure the length of chain; pre-load chain; match chain, cut large pitch chain and special attachment chain, plus features our highly popular hot dip chain lubrication facilities.
The new machine, which has been designed by Donghua and is the only machine of its kind in the UK, automates the chain cutting process enabling us to supply our distributors with cut to length Leaf Chain and Roller Chain.
Designed for speed and accuracy, the new machine cuts chain very quickly providing our customers with a cost-effective solution to buying cut to length chain. It cuts Leaf Chains from ½” pitch to 11/4” pitch in AL, BL, LL, FLC series; and cuts Roller Chains from ¼” pitch to 11/4” pitch in simplex, duplex and triplex in British and American standards.
To see Donghua’s new automated chain cutting machine in action watch our latest video, available on our website.
For more information about our chain cutting service call 01902 866200 or email sales@donghua.co.uk.
For more information visit: www.donghua.co.uk
A new in-house chain cutting service is now available from UK based Donghua Limited following the installation of our new automatic chain cutting machine
Designed for speed and accuracy, the new machine cuts chain very quickly providing our customers with a cost-effective solution to buying cut to length chain.
As surgical instrument manufacturers pursue greater throughput while facing increased labor costs, automating the
Workpiece length, shape and configuration determine where it is gripped by the robot when loaded into a machine, moved from spindle to spindle for drilling, residual cutting fluid removed, and returned to the pallet. Where a part is gripped impacts where it is clamped for drilling to ensure accuracy. Every variable along the process chain must be considered and accounted
for, and the calculus is detailed and complicated.
Then there are unique customer needs and requirements. The equipment and process must accommodate a variety of part families and hundreds of parts to increase runtime and efficiency. Operators must be able to change over part types and programming without calling in an automation specialist, and the entire process must be controlled from a central interface. Add to the mix that everything must be packaged in as small a footprint as possible, and the scope of the engineering challenge comes into focus.
ease your mold manufacturing versatility wer of gundrilling with the leaders in deep hole drilling, UNISIG. Offering complete solutions for everything fr simple to complex mold components, UNISIG machines help moldmakers improve efficiency, throughput and precision with outstanding part-processing versatility at an exceptional value.
Increase your mold manufacturing versatility using the power of gundrilling with the leaders in deep hole drilling, UNISIG. Offering complete solutions for everything from simple to complex mold components, UNISIG machines help moldmakers improve efficiency, throughput and precision with outstanding part-processing versatility at an exceptional value.
TAKE YOUR MOLDMAKING OPERATIONS FURTHER WITH UNISIG TODAY.
TAKE YOUR MOLDMAKING OPERATIONS FURTHER WITH UNISIG TODAY.
The robot automatically repositions the workpiece from the front of the first spindle into the rear of the second spindle without operator input. The process of drilling a part from both ends in a single-piece flow is unique to UNISIG. Workpieces with enlarged features on one side are loaded from the rear of the collet, solving a common problem in gundrilling medical surgical instruments with full automation.
Find out more at www.UNISIG.com
Find out more at www.UNISIG.com
UNISIG’s approach to solving these problems, however, results in targeted automation that enhances the existing benefits of gundrilling, ensuring a solid foundation for reliable process-wide automation.
At its core, the automated UNE6-2i is a purpose-built machine with automation embedded in its design, not added as an afterthought. Flexibility and adaptability are maximized by a harmonious, interdependent mechanical, software and operational planning scheme.
To meet size constraints, a 6-axis robot was embedded in the machine with a pallet system on the backside of the machine, allowing easy operator access from the front to setup the machine without compromising ergonomics. The configuration enables quick setup changes between prototype and proving operations and full production runs.
Control of the UNE6-2i and a computer are consolidated into the Human Machine Interface (HMI), a menu-driven touch screen system for easy, intuitive operation. Training and operator engagement with the system is significantly reduced due to user-friendly UNISIG controller menus and prompts.
UNISIG’s comprehensive and integrated approach to automating medical part manufacturing is a vison that sets it apart in the industry. It’s more than drilling the impossible hole. It’s a commitment to understanding and to the research that drives continuous improvement and innovation for automated part production at its full potential.
Further information on all machines and the complete UNISIG machine program is available at: www.unisig.com or follow the company on LinkedIn and Twitter (@UNISIG).
You will also meet us at the EMO 2023 show in Hannover, Germany, from 18–23 September.
For further information, please visit www.unisig.com
Gundrilling and BTA deep hole drilling for highly productive shops.
Gundrilling and BTA deep hole drilling for highly productive shops.
Whether your shop needs on-center or off-center holes, specialized job shop work or fully automated production, UNISIG has a deep hole drilling solution with the accuracy and performance you need.
Whether your shop needs on-center or off-center holes, specialized job shop work or fully automated production, UNISIG has a deep hole drilling solution with the accuracy and performance you need.
Take your shop’s production further - learn more at UNISIG.COM.
Take your shop’s production further - learn more at UNISIG.COM.
Plastic Omnium Automotive Ltd. used to encounter issues with stock management, slow stock access as well as low stock accuracy and lack of space. Today, its MRO materials are continuously accessible, the location of each required item is easily identified, and no transaction goes unnoticed as each pick is recorded. The benefits brought by a Konecranes Agilon® automated warehouse bring substantial savings of approximately £70,000 annually. The investment payback time was less than six months.
Plastic Omnium operates globally with 135 production plants in 25 countries and 25 R&D centres. Its diversified customer portfolio, industrial excellence and innovation strategy make it a major player in the automobile sector. The Edison Road facility supplies tailgates to Jaguar Land Rover.
“We were looking for better control of our maintenance spares. The main driver was knowing if we had a spare or not for parts and related transactions. We needed to reduce the occurrence of spare parts not being available at the time of breakdowns. Space reduction was another consideration,” says Duncan Lewis, Plant Engineer and the main user of Agilon at Plastic Omnium.
The company looked at several traditional alternatives to solve its stock management issues. “We visited a site where we saw Agilon in action”. Upon further investigation, the Agilon system seemed to suit best for storing smaller maintenance spares because of transaction accountability, the photo and weight options, and the accountability by secured logon.”
Plastic Omnium made a detailed ROI calculation to find the total savings potential. They added up the time taken up by the current manual process of searching for spares and the value of manual work that Agilon does automatically plus the future savings potential through an automatic replenishment process. “We estimated that we could pay back the Agilon system in six months and save up to £69,600 per year. It is
a massive saving for any business,” Duncan points out.
Agilon has improved our response time to breakdowns as people know where to go to get a spare. Currently, there are some 2,600 parts stored in the system.
The 14-metre long and 6.1-metre high Agilon system at Plastic Omnium was installed only in three days whereas installing a traditional stock management system takes from six to eight weeks. Members of our staff have been very impressed seeing it in action and using it.
Deploying Agilon in the Plastic Omnium warehouse has brought significant benefits. “Agilon has improved our response time to breakdowns as people know where to go to get a spare and if we have one or not and act accordingly if we don’t. It has also helped us pass financial and system audits. We have quick access to the parts through the portal, and control over P&L and stock levels. It improves budgeting, accountability and working with suppliers. We are all very impressed with it,” Duncan Lewis concludes.
For further information, please visit https://www.konecranes.com/en-uk/agilon
accountability, traceability and 100% stock accuracy with Agilon warehouse automation - Savings up to nearly £70,000 annually
Agilon has improved our response time to breakdowns as people know where to go to get a spare.
Obviously, one can do it gravimetrically, by trickling material onto a scale with an integral feedback loop continuously monitoring and controlling the rate feed. Admittedly, this way of filling is very accurate. But it is also an agonizingly slow process and not well suited to high output production. Furthermore, it is fair to point out that a manufacturing process will rarely call for this ultra-precise level of accuracy. For processes which require only from ±1% to ±5% repeat accuracy per dose, and/or requires higher productivity outputs, volumetric powder filling is a far better choice! However, volumetric filling of powdered materials is not without its own challenges.
By definition, all volumetric filling processes are called to deliver the same volume of material in each and every dose. In liquid filling applications, the weight of each delivered amount holds very closely from dose to dose because liquids are essentially incompressible.
By contrast, powders are compressible substances. In the process of filling powders volumetrically, the apparatus must somehow ensure not only that the same volume of powder is delivered in each dose, but also that it is delivered at a consistent density. This means that the density of the powder held within its volumetric chamber must somehow be compacted and delivered at a uniform constant density. We don’t necessarily need to know what the density will be for any volumetric powder charge, only that its value is consistent from dose to dose. We control the delivery weight by adjusting the volume of the chamber.
All Kinematics’ powder fillers are volumetric fillers. They all operate on the same core principle. Powder is picked up and simultaneously compacted in its allotted volumetric chamber by means of a uniform vacuum force. The open end of the chamber is then doctored of any excess powder to insure an exact and repeatable volume is delivered.
Finally, a gentle puff of low-pressure air is then exchanged with the vacuum to expel the charge into its designated container.
Kinematics & Controls Corporation has been designing and building both liquid and powder fillers for more than forty years. We have long since abandoned all efforts at turning out liquid fillers. They are too easy to make. We prefer the added challenge of building low-dose, high precision, powder filling equipment.
For further information, please visit www.kcontrols.com
Dispensing accurate dose weights of powdered materials is always challenging
Kinematics & Controls Corporation has been designing and building both liquid and powder fillers for more than forty years.
Kinematics and Controls Corporation manufactures high-precision, low-dose, dry product fillers for tank monitoring, level control and leak detection.
Our products include both standard “off-the-shelf” products, and custom-designed components and machines for O.E.M. applications.
4400/TX Automatic Benchtop Rotary Shuttle
Features:
• Fills Bags or Bottles
• Eliminates Costly Hand Weighing
• Single Fill Chamber is Easy to Calibrate
• Vacuum/Volumetric Dosing Principle>
• Handles Free-Flowing or Sticky Materials
• Built-In Product Agitation
• Dose Range: Approx. .05 gm. – 75 gm.
• >Repeat Accuracy: Approx. ±1%
• Fill Rate: 25 Fills/Min. (Max.)
4400/VC Semi-Automatic, Portable Powder Filler
Features:
• Low cost
• Eliminates Costly Hand Weighing
• Vacuum/Volumetric Dosing Principle
• Fills Free-Flowing or Sticky Materials
• Repeat Accuracy: Approx. ±1%
• Fill Rate: Approx. 15-18 Fills/Min.
Extremely accurate, low-weight powder
Custom configured linear powder delivery
The self-contained vacuum-pressure control module
Certified 316 S.S. construction
5500/TX Semi-Automatic, Bench Top Powder Filler
Features:
• Delivers Free-Flowing or Non-Free Flowing, Dense or Fluffy Powders
• Accurate/Repeatable Dose Weights of up to 180 gm.
• Production Rates of up to 25 Fills/Min.
• User Selectable Operating Modes
• Modern Drive Technology
• Certified 316 S.S. Construction
5500/MO Modular Powder Filling System
… Designed for systems integrators.
Kinematics’ Model 5500/MO, modular powder filling system was designed to provide a simple, turn-key solution for machine builders who need to integrate a precision, small-dose powder filling station into a larger, more fully featured, custom automatic packaging line.
Literally, be “UP” and filling powders within 24 hours of uncrating the system. The complete 5500/MO system comprises three (3) plug-andplay modules.
In 1999, Russell Flory established Central profiles with an ambition to create a lasercutting company that would stand out from the others in the West Midlands. His vision was to build a trusted brand, with a dedicated team committed to engineering excellence. Fast forward to the present day and we are proud to say this vision has come to fruition. Throughout the years, we have continued to invest in machinery, software, and personnel - even during challenging economic times. And, we don’t plan on slowing down any time soon.
At our 40,000sft premises in Kidderminster, we not only provide Laser cutting, but a range of services in house. Including metal bending, manual welding and even robots for higher volume repeatable bends & welds. By offering all of these services in-house, we have complete control over each stage of the production process and can guarantee the highest level of quality for every metal component we manufacture.
Primarily, we do sub-contract work, working with a range industries. Including Automotive & Transport to Security, Medical Equipment, and even Garden Furniture.
We develop close relationships with our customers that go beyond what you would expect. Striving to offer a personalised service, no matter the size or frequency of their orders.
Our team takes pride in delivering the same level of attentive service every single time.
We have recently made a considerable investment in a top-of-the-line, fully automated powder coating track, something that we have wanted for some time to meet customer demand.
Powder coating is highly sought-after in the industry for its durability and its ability to protect metal from rust, as well as for its attractive finish. Whether it be for interior or exterior use, there is a powder coating option that is suited to your needs.
Thanks to our recent investment, we are now able to offer powder coat only services to new customers.
For further information, please visit www.central-profiles.co.uk
Our team takes pride in delivering the same level of attentive service every single time.
We are the experts when it comes to providing laser cut parts for your business
TO LEARN HOW WE CAN HELP WITH YOUR LASER CUTTING NEEDS.
01562 744788
sales@centralprofiles.co.uk
Kidderminster DY11 7QN
We have heavily invested in obtaining the best equipment in the industry, allowing us to offer our customers laser cutting on either low to high production scale
With five press brakes in house, we can take on any metal bending job, no matter the complexity or size With our commitment to excellence, you can trust that your metal bending projects will be completed with precision
Our newly installed fully automated powder coating track will give your parts an unparalleled finish, free from rust, scratches, and the exact colour you desire Our state-ofthe-art system ensures your parts will look perfect every time, giving you peace of mind and exceptional quality results
"Making Metal Work For You Since 1999"
Silverson Laboratory mixers have been sold all over the world and are used by companies from small start-ups to larger international brands. The popularity of Silverson Laboratory mixers can be attributed to their versatility; they can be used to mix, emulsify, homogenise, disintegrate and dissolve, with an efficiency and flexibility unmatched by other machines.
Silverson Laboratory mixers are used for a variety of mixing processes from simple liquid/liquid blending, forming emulsions and reducing particle size to more complex mixing applications. They are ideal for all routine laboratory work, research and development, QA analysis and small-scale production.
Silverson offers a comprehensive range of Laboratory scale mixers which are used across industries as diverse as pharmaceuticals and chemicals. Whether you are processing 1ml or mixing batches of 50 litres, whatever your application, you’ll be sure to find a mixer to suit your needs.
The advantage of a Silverson over simple agitators and stirrers stems from the specially designed rotor/stator workhead; the high-speed rotation of the rotor blades draws materials into the workhead where they are intensively mixed, before being projected back into the body of the mix at high velocity. With this method, ingredients are fully incorporated and any agglomerates are eliminated.
The Silverson L5M-A laboratory mixer will soon be available with the body finished in white engineered polymer for increased durability and ease of maintenance. The updated radiused edges allow for easier cleaning. With its integral tachometer, ammeter and programmable timer, the L5M-A offers a level of instrumentation invaluable in applications where process validation and repeatability are required.
There are over 40 workheads, screens and assemblies available for Silverson Laboratory mixers. These easily interchangeable workheads enable any machine to perform a wide range of mixing operations and allow one mixer to perform duties that in the past may have required several different pieces of processing equipment.
One of the main advantages when choosing a Silverson Laboratory mixer for R&D or pilot-scale production is the ability to scale up from the laboratory to full-scale production models with ease.
Silverson offers the largest range of capacities from a single manufacturer - from 1ml up to 30,000 litres - and because all Silverson mixers are manufactured to the same precisionengineered tolerances anything you produce in the laboratory can be replicated in production and scalable results are achievable across the entire product range, without the need for reformulating.
mixer is suitable for the widest range of applications
With a capacity from 1ml up to 12 litres and the ability to mix in-line with flow rates up to 20 litres/minute, the L5 Series offers excellent reproducibility when scaling up to full-scale production and provides an accurate and easy means of forecasting the performance of larger Silverson machines under full-scale working conditions.
For more information please visit: www.silverson.co.uk
ABB
ABB’s emissions monitoring technology which is typically used for gas leak detection by oil and gas companies and natural gas utilities is now employed to identify and monitor orphan wells in the United States.
With the help of ABB technology, organizations such as The Well Done Foundation, the nonprofit that works to plug orphan oil and gas wells in the US, can detect leaking wells and, once the
wells are capped, continue to monitor the sites to ensure they no longer emit harmful greenhouse gases.
Orphan wells are oil or gas wells that have been deactivated and no longer have legal owners responsible for their care. Due to their age and deteriorated condition, the wells can leak methane and other harmful greenhouse gases through their “plugs”.
The United States Environmental Protection
Agency estimates that methane emissions from over 2 million inactive, unplugged wells, of which orphan wells are a subset, range from a CO2 equivalent of 7 to 20 million metric tons per year (approximately the emissions of 2 to 5 million cars).
Methane has more than 80 times the warming power of carbon dioxide over the first 20 years after it reaches the atmosphere, according to the Environment Defense Fund.
Many wells are situated on farmland, and could contaminate land, air and water, potentially harming ecosystems, wildlife, livestock, and people.
In some parts of the United States where towns are growing, housing has been built where oil and gas wells once stood. The Environment Defense Fund estimates that 14 million Americans live within a mile of an orphan well.
“It is extremely rewarding to see our technologies employed in the endeavor of fixing such a pressing environmental problem. We remain focused on accelerating the pace of environmental programs that reduce emissions, especially in the oil and gas industry. Our work on this initiative is a great example of how technology can benefit the environment and help countries achieve their sustainability goals,” says Jacques
Mulbert, Division President, ABB Measurement & Analytics.Together with channel partner WinnMarion, ABB worked to create a comprehensive approach that enables the identification, on-site qualification, and monitoring of orphan wells. At the heart of the system are ABB’s gas leak detection solutions as well as suite of flow computers, both used in tens of thousands of industrial plants worldwide to measure and report on emissions.
Initially, ABB’s gas leak detection system is used to find the orphan wells. Depending on their location, the high sensitivity analysers using OA-ICOS™ technology are transported by vehicle (using ABB Ability™ MobileGuard™), drone (HoverGuard™), or backpack (MicroGuard™) to the site. The system can detect methane emissions down to 1 part per billion (ppb).
Once on-site, it measures methane concentration and flow with a measuring range as low as 180kg/h. The flow from the thermal mass is logged and visualised on ABB’s gas flow computers, the control devices known in the industry for their extreme accuracy and reliability. In the post-plugging phase, methane emissions continue to be monitored.
A key advantage of ABB’s emissions monitoring technology is that it is fully audited by the Bureau of Land Management, which manages the Federal government’s onshore oil and gas program in the United States.
ABB’s Process Automation business automates, electrifies and digitalizes industrial operations that address a wide range of essential needs – from supplying energy, water and materials, to producing goods and transporting them to market. With its ~20,000 employees, leading technology and service expertise, ABB Process Automation helps customers in process, hybrid and maritime industries improve performance and safety of operations, enabling a more sustainable and resource-efficient future. go.abb/ processautomation
ABB is a technology leader in electrification and automation, enabling a more sustainable and resource-efficient future. The company’s solutions connect engineering know-how and software to optimize how things are manufactured, moved, powered and operated. Building on more than 130 years of excellence, ABB’s ~105,000 employees are committed to driving innovations that accelerate industrial transformation.
For further information, please visit www.abb.com
ABB is a technology leader in electrification and automation, enabling a more sustainable and resource-efficient future.ABB’s high sensitivity analysers are transported by vehicle (using ABB Ability™ Mo-bileGuard™), drone (HoverGuard™), or backpack (MicroGuard™) to the site.
Macsa ID UK is targeting the engineering and industrial markets with its newly launched SPA2 series of modular laser coders. Featuring several technologies and multiple power options, the simplified platform delivers maximum marking resolution and definition at higher speeds, more consistently over time. The advanced systems are versatile and reliable, as well as cost effective to own, maintain and operate. Kind to the environment, laser coder technology is fume, waste and consumable free, and uses less power and energy.
Boasting a modular design, Macsa’s flexible SPA2 lasers can be easily integrated with any production line or application, and adapted to meet changing needs of the user. Providing high quality marking on a range of materials, such as wood, thermal labels, board, metallised board, glass, ceramics, metals, rubber and plastics, the SPA2 platform is available with CO2, DPSS and Fiber technologies (several wavelength options). Plus, laser power from 3w-250w, enclosures for standard, dusty and wash down environments, extra powerful performance and high speed heads.
Macsa’s SPA2 F pulsed fiber laser model in particular is widely used for marking onto plastic or metal-coated materials, such as aluminium beverage cans, making it ideal for engineering and industrial applications. The new XQS high precision printhead ensures clear and legible codes even on curved surfaces with information applied continuously at high speed while maintaining integrity of the substrate.
The SPA2 series is also available with a HPD printhead for high resolution images, difficult substrates, product modification and marking areas above 250mm2. Digital galvos make calibration, trouble shooting and replacement much easier. A UHS printhead is available for very high speed lines and longer, more complex messages.
Due to the innovative EEP® (easy exchange printhead) feature, operators can switch printer heads on site using just two
connectors, allowing the laser system to be adapted to the requirements of the production line at all times.
Exceptionally easy to install, program and operate, online help videos, technical guides and tips can be accessed via a new 10- inch handheld touchscreen controller designed to make programming quicker and to eliminate operator errors. The lasers can also be controlled direct from a PC via an ethernet link or PLC with Profinet or OPC-UA.
The enclosure has been redesigned with a flat front surface allowing simple integration of vision systems and other devices. With models that meet IP54 and IP65 standards, the SPA2 lasers are designed to operate in dusty or damp environments and in extremes of temperature.
The novel RAF® (reverse airflow cooling) system means that filters are changed
less frequently and not at all in some circumstances. A sealed air system transfers heat from the laser to the cooling air itself. This eliminates the risk of dust being deposited directly into the system component. Part of the exhaust air is blown over the focusing lens keeping it dust free so that print quality is maintained without the need for operator intervention.
The surface recognition feature, which is included within its 3D printing kit, allows printing on multi-level surfaces, ensuring an optimal focal point at all times. An external Z-axis controller enables operators to adapt the SPA2’s vertical coding axis in order to vary the height between print cycles and adapt it to different products.
The SPA2 connector box offers a wide range of communication ports, enabling the system to be integrated with all elements of the production line. The lasers support Macsa’s Optima software for real time control and compatibility with desktop printers, label printer applicators and label applicators.
Macsa’s SPA2 laser coders are available with a comprehensive range of software, accessories and services, and backed by advice and consultation services, installation assistance, training, technical support and extended warranty.
For product information please contact: sales. uk@macsa.com or telephone 01462 816091.
For further information, please visit www.macsa.com/en-uk
Kind to the environment, laser coder technology is fume, waste and consumable free, and uses less power and energy.
SIC Marking UK is one of 10 subsidiaries around the World. SIC Marking Group has developed innovative, permanent marking solutions and automated identification systems for the complete traceability of industrial components for over 30 years. SIC Marking has a wide range of the most robust and state of the art Dotpeen, Scribe and Laser Marking machines available on the market today. Whether Column Mounted, Integrated or completely Portable like our battery powered cordless eMark for example, we can provide a machine that is suitable for both your application and budget. SIC Marking is constantly adding to the range and re-investing into R & D. The new eTouch portable Dotpeen marker offers Icon style Touch screen technology and the Laser systems now have a range of modular Class 1 enclosures with the XXL-Box range – offering the ability to mark parts up to 1500mm in length as a standard product.
Our UK Team is based in Warwick, where we have dedicated Sales and Aftersales engineers with over 50 years’ experience who would welcome a call to discuss your marking application.
Please call 01926 830372 for further details or email us on salesuk@sic-marking.com
www.sic-marking.co.uk
The Macsa ID SPA2 Fiber range codes and marks product information without damaging the substrate, at very high speeds while maintaining excellent definition.
The Macsa ID SPA2 Fiber range codes and marks product information without damaging the substrate, at very high speeds while maintaining excellent definition.
With a life span of more than 100,000 hours, the environmentally-friendly SPA2 F is ideal for coding onto plastic or metal coated materials such as aluminium beverage can
With a life span of more than 100,000 hours, the environmentally-friendly SPA2 F is ideal for coding onto plastic or metal coated materials such as aluminium beverage cans.
High powered lasers for coding on the fastest production lines
High powered lasers for coding on the fastest production lines
The XQS high precision printhead ensures clear and legible codes even on curved surfaces
The XQS high precision printhead ensures clear and legible codes even on curved surfaces
DUO dual processor technology enables high speed and high quality printing with variable data
DUO dual processor technology enables high speed and high quality printing with variable data
Extra protection enclosures and touchscreen for dusty and washdown environments
Extra protection enclosures and touchscreen for dusty and washdown environments
Contact Us : tel: 01462 816091
Contact Us : tel: 01462 816091
The Saudi Electricity Company (SEC) has reduced its yearly operational costs by 20% and improved its service levels to customers by upgrading its maintenance capabilities with inspection equipment from Fluke, the global technology leader in professional electronic test and measurement tools and software. SEC’s value-based maintenance strategy, which was implemented in 2014, has transformed its maintenance routines with the use of Fluke Ti32 definition thermal imaging cameras and Ti400/Ti450 portable infrared cameras, leading to a reduction in power outages.
Infrared cameras are invaluable for detecting small temperature differentials and can demonstrate progressive heat changes over time, allowing maintenance professionals to detect critical issues before they become failures. Fluke has recently relaunched its popular range of thermal imaging cameras, Ti300+, Ti401PRO and TiX501, all of which offer the quality expected from Fluke products and industryleading Lasersharp® autofocus technology which allows users to get the images they require in focus every time. Designed with field use in mind, the cameras are rugged and able to be used with one hand for simple and easy operation. The built-in laser distance meter calculates and displays the distance to the designated target on the camera screen and snaps the image in focus. Most importantly, temperature readings from in-focus images will be highly accurate. Each tool allows the user to record imagery for reports and record notes to the device so there is no need to carry paper and pen.
With the implementation of Fluke equipment, the SEC has been able to transform its maintenance routines and improve the reliability of its networks. The thermal cameras have been instrumental in identifying hot spots and detecting
temperature differences between phases, which have helped in reducing the number of unplanned outages. The use of precision acoustic imagers for corona discharge detection is expected to further enhance the company’s predictive maintenance strategy and help it achieve its goal of providing an uninterrupted power supply to its customers.
Increased reliability
Zakaria Al-Ramadhan, who has over 20 years’ experience at SEC and is the Distribution Engineering Specialist, says “Reliability is the key issue when supplying
power. Customers pay the company to supply power with no outages, which is why minimising disruption to supply is the most important focus for us.”
As a result of the successful implementation of Fluke equipment, the SEC is planning to purchase more corona cameras and deliver training to more of its technicians.
In addition to the thermal imaging equipment, the SEC has also taken on a range of rugged hand-held maintenance tools, which have increased the efficiency of its maintenance teams and reduced downtime. These include 49 Fluke 1736 three-phase power loggers alongside nearly 1000 Fluke 376 AC/DC clampmeters, 470 Fluke 1507 insulation testers and 600 1ACII non-contact voltage detectors. The move from condition-based maintenance to valuebased maintenance has not only resulted in significant cost savings, but it has also improved the sustainability of the company’s networks.
The SEC’s successful implementation of predictive maintenance has set an example for other utility companies both locally and around the world.
For further information, please visit www.fluke.com
With the implementation of Fluke equipment, the SEC has been able to transform its maintenance routines and improve the reliability of its networks.
Do you have a material whose viscosity, rigidity, stiffness or molecular mobility is important ? Or do you need to know if the quantity of material changes ?
Lab-Tools design and sell an extremely good value (£8,000) palm-top sized Time-Domain NMR Spectrometer that can measure these properties in solids, polymers, liquids and porous materials. Variable temperature NMR probes are available, that cover -60C to +80C. LabTools offer instruments that can measure pore-size distributions over 1nm to 1µm.
They have versatile Graphical User Interfaces to control the measurements, and to analyse and display the results. Analysis may be both on-line and off-line.
These instruments have been purchased by a range of national and international companies and universities, for their scientific measurements and publications: [http://www.lab-tools.com/publications/ Webber_JBW.html].
It can come with a Mandhalas NMR low-homogeneity magnet with 36mm clear Bore (£2,800), as in this photo, or a larger Halbach NMR magnet of good homogeneity and 55mm clear Bore (£6,800).
This spectrometer is robust and compact enough for use in the field, and with NMR Magnet and an optional 8 hour battery fits in a lap-top bag. It has a solid metal case, is gold flashed, and weighs under 1kg.
This spectrometer is robust and compact enough for use in the field, and with NMR Magnet and an optional 8 hour battery fits in a lap-top bag.LAB-TOOLS Lab-Tools Mk3 NMR Spectrometer with Mandhalas NMR Magnet.
Lab-Tools CryoP4 NMR Cryoporometer for measuring nano-metre to micron Pore-Size Distributions.
This nano-pore-size measuring instrument uses the above Mk3 NMR Spectrometer and one of the above NMR Magnets, to measure pore-size distributions in a range of porous materials.
The variable-temperature NMR Probe uses only electricity to both cool and heat the sample.
The above boxed CryoP4 version uses the Mandhalas NMR Magnet and has precision
thermal control (£22,000). The CryoP6 version with Halbach magnet measures down to sub-nanometres (£29,000).
Porous materials previously studied [Papers] :
Sol-gel & CPG silicas
MCM templated silicas
SBA templated silicas
Activated carbons
Biochar
Zeolites & MOFs
Catalysts
Cement & Concrete
Fired & unfired clays
Marine Sediments Hydrogels
Chalks, Shales
Sandstones
Oil-bearing rocks
Meteorites
Wood & Wood pulp
Paper
Rubbers
Emulsions & Paint
Artificial skin
Bone
Melanised fungal cells
Lab-Tools Ltd. (nanoscience)
+44 (0) 7805 437 241
nmr@lab-tools.com
For further information, please visit www.Lab-Tools.com | https://nmrspectrometer.lab-tools.com/
ADVANCED
In most foundries, the temperature of the metal melt is typically measured by thermocouple immersion probes. These immersion measurements can only be made in the crucibles or the transfer ladles where the melt is stationary, but not in the pouring stream where insertion of a probe would disturb the flow into the cast. However, the direct temperature of the pouring stream is critical to the quality of the final casting. Continuous monitoring of the pouring steam temperature and pour quality enables better control of the casting process.
Accurate and undisturbed temperature measurement of the pouring stream
can only be obtained by non-contact measurement via pyrometers. When castings are made of different alloys, conventional pyrometers and ratio pyrometers often cannot be used to measure the pouring stream due to considerable differences in measuring conditions and metal characteristics.
Due to extremely high ambient heat, fixed measurement systems require rugged industrial designs to overcome the challenges that hinder accurate temperature measurement of the pouring steam – from changes in stream location and width, start and stop time variation, as well as slag interference.
Advanced Energy’s specialized Impac® pyrometer solutions address these challenges and provide robust and accurate temperature measurement by using a special measurement system for this application. The Impac ISR 12-LO/GS measures the exact casting temperature of each pouring process and displays them online. Corrective action can be taken immediately if defined limits are exceeded, which maintains the narrow process window for quality castings.
Designed specifically for accurate measurement of pouring streams, the Impac ISR 12-LO/GS features:
• Armored fiber optic cables with hightemperature precision optics lens head that enables it to be securely mounted in difficult installation areas.
• Line spot shape optical beam that minimizes the effects of pour stream location variation. An integrated laser targeting function eases alignment. An automated lens-contamination warning function is also included.
• A short wavelength ratio detector that maximizes signal from low emissivity metals and minimizes systematic errors due to emissivity changes, as well as interference from dust and vapor.
• Advanced algorithm that determines the exact pouring stream temperature. This robust tuning procedure includes start and stop pour signals, as well as pouring time calculation. It is immune to random slag events and pre/post pour drips.
• Custom TQCS (Temperature Quality Control System) software for visualization of each pouring stream result, and online presentation. It integrates with foundries control systems to allow casting
Advanced Energy's SCR power controllers, optical temperature pyrometers, and thermal imagers set the standard for thermal processing precision, repeatability, and reliability.
advancedenergy.com
www.advancedenergy.com
optimization. Full digital and analog output functions are also included.
SUMMARY:
The Impac ISR 12-LO/GS pyrometer is a solution designed for the accurate measurement of pouring streams in foundries. This system can be used in both automatic and semi-automatic pouring machines and displays the temperature after each single pouring process. Measured values can be stored and displayed via analog and digital output. Thanks to its special functionalities and accessories, the Impact ISR 12LO/GS enhances safety and reduces employee interactions compared with immersion lance measurements using thermocouples.
Advance Energy is exhibiting at Thermprocess, Messe Düsseldorf (June 12-16). Visit our booth 9 A50.
Accurate and undisturbed temperature measurement of the pouring stream can only be obtained by noncontact measurement via pyrometers.
A range from 300 °C to 3000 °C: With the new CSvision series of ratio pyrome-ters from Berlin-based infrared specialist Optris, it is possible to measure the temperature of metals, melts or ceramics non-contact, safely and reliably from different distances.
Infrared pyrometers must meet high demands: Especially in metallurgy, they are often used under harsh conditions in which they must deliver reliable results at any time. Smoke, steam, or dust often impede a clear view of the measured object and affect the measurement signal. In these conditions, ratio pyrometers nevertheless provide stable measured valuescompared to single-channel pyrometers, even with dirty optics or with objects that move within the measuring field (e.g. metal rods or wires).
The new CSvision is equipped with the innovative Smart Ratio Mode (SRM) and can thus master even challenging applications with variable emissivity ratios. The built-in video sight and the motorized focus, which can be operated via software or app, allow the CSvision novelties to be focused very
conveniently on the respective object. The switchable two-stage brightness reduction filter ensures optimum viewing conditions even with very hot and therefore bright objects. Together with the crosshair laser, which is also standard, this ensures simple sensor alignment un-der all conditions.
The CSvision R1M offers an optical resolution of up to 150:1 and a measuring range of 600 to 3000 °C with a spectral range of 0.8 to 1.1 µm - in harsh industrial environments up to 65 °C without cooling. The R2M has an optical resolution of 75:1 and a spectral range of 1.45 to 1.75 µm. This allows temperatures to be meas-ured from as low as 300 °C to 1400 °C (up to 60 °C without cooling).
Easy sensor setup and monitoring via app
Optris creates an easy-to-use solution with the CSvision series that can be set up quickly and easily. The infrared thermometers have an interface to the IRmobile Android app and
CompactPlus Connect software. This allows easy video align-ment and real-time process monitoring. Two analog outputs are available for pro-cess integration, as well as digital interfaces such as RS485 or Modbus RTU.
A variably programmable I/O pin can optionally be used as alarm output, for signal triggering or e.g. for external emissivity/slope settings.
For further information, please visit https://www.optris.global/
• Load Monitoring and Automation Systems for manufacturing equipment
• Process monitoring and control for assembly machines
• Manufacturing Execution Systems including downtime analysis
• Production recording systems
• Bespoke control systems
• Calibration services
• Repair/Maintenance
Decade Monitoring Solutions Ltd Unit 3, Octagon Business Centre, Miller St, Birmingham, B6 4NH
Telephone: +44(0)121 359 3978
E-mail: sales@decade.co.uk www.decade.co.uk
ODIN is a new, compact, and reliable deep UV resonant
Raman instrument developed by IS-Instruments (IS-I) and TOPTICA for measurement of biopharma products.
ODIN is a new, compact, and reliable deep UV resonant
Raman instrument developed by IS-Instruments (ISI) and TOPTICA for measurement of biopharma products. TOPTICA’s Industrial CW Laser TopWave 229 enables new Deep UV Raman Spectrometer ODIN.
The system combines the newly developed solid state diode laser TopWave 229 and a spatial heterodyne spectrometer integrated into a single instrument with a unique all-reflective backscatter Raman collection probe. Sample damage caused by extended laser exposure has been mitigated via the introductiwww. toptica.comon of a dynamic sample positioning stage.
www.toptica.com
After introducing a new medication to the market, it is always a challenge for pharmaceutical manufacturers to calculate production capacities without incurring economic losses. With support from packaging specialist Faller Packaging machine and manufacturer SchubertPharma, manufacturers now have two strong partners whose solutions can help minimise investment risk: With the right packaging, biopharmaceuticals can be produced reliably, efficiently and in the highest quality throughout the entire product lifecycle – thanks to solutions ranging from manual packaging to fully automated top-loading lines.
To obtain approval for a new medication, pharmaceutical manufacturers have to provide packaging that meets all regulatory requirements. And when it comes to market launches, every day counts.
The sooner a product is available everywhere, the sooner patients will benefit and the high development costs can begin to pay off. However, pharmaceutical production has to be adapted quickly to increasing demand. Manually loaded packaging may be sufficient in the beginning, but a solution that can be automated is needed as quickly as possible following a successful launch. Many months can pass before a new approval with a machine-compatible packaging and the commissioning of a new line. On the other hand, manufacturers who build up a high production capacity even before the launch take on a significant investment risk.
With the right partners, this challenge can be turned into an economic benefit: Faller Packaging and Schubert-Pharma can support manufacturers from the Clinical Trial Phase 3 onwards – with a customised packaging solution which is already designed for the entire product lifecycle. This eliminates the need to change the format of the packaging at a later date. Karin Kleinbach, Sales Director at Schubert-Pharma, explains: “Our customers benefit from seamless service for every level of automation, from launch to series production.”
Together with their customers, the experts from Faller and Schubert-Pharma develop pharma-compliant, fully recyclable carton packaging for all parenterals and a wide variety of dosage forms such as vials, ampoules, syringes, medical devices or combination products. The partners design and implement top-loading packaging processes that range from manual to fully automated.
Pharmaceutical manufacturers can achieve medium packaging volumes with semi-automated processes thanks to Schubert’s mobile cobots.
Faller’s PrePackaging Service is available to bridge machine delivery times and for smaller quantities: With the delivery of pre-assembled pharmaceutical packaging, manual filling is possible at the customer’s site. For medium packaging volumes, manufacturers can partially automate filling using Schubert’s mobile cobots. For full automation, Schubert-Pharma develops customised and highly reliable top-loading packaging lines in compliance with international standards. The more closely the machine and packaging are matched to each other, the more efficient and reliable the automated packaging process becomes.
“This is why it is so important to plan the packaging materials – i.e. folding carton, leaflet and label – at an early stage in the development of a new medication,” explains Kerstin Löffler, Vice President Marketing, Corporate Communications & ESG at Faller. With this approach, pharmaceutical manufacturers, together with Faller and Schubert-Pharma, can not only shorten time-to-market, but also package their products more reliably and cost-effectively throughout the entire product lifecycle.
More information to PrePackaging can be found here: https://www.faller-packaging.com/en/services/prepackaging-service
The more closely the machine and packaging are matched to each other, the more efficient and reliable the automated packaging process becomes.
As a leading global protective packaging supplier Storopack recognizes the importance of ensuring goods are protected during transit and arrive in perfect condition.
Damaged goods not only incur costs for replacement orders but also affect businesses’ reputations. So while costs need to be kept to a minimum it is vital to choose the correct protective packaging type.
Usually a void fill packaging medium will suffice. However when the product is more sensitive to shock and vibration, such as engineering, electronics, aeronautical, and many other expensive products then more consideration has to be given to using the right type of in-the-box protective packaging.
Storopack’s FOAMplus® range is a perfect solution for companies that manufacture or ship products that require this highest degree of protection eliminating transit and handling damage.
The success of FOAMplus® polyurethane foam is based upon its huge versatility as a packaging medium. The foam can either be dispensed directly into the carton where the expanding foam will mould itself to the contours of the product shape or can be made into pre-moulded cushions to enhance presentation. The product will satisfy the most rigorous cushioning demands for high value, fragile and awkward shaped products. The light weight foam packaging also ensures that shipping costs are kept to a minimum whilst providing customers with total product protection.
As a space saving solution FOAMplus®, polyurethane foam packaging is ‘on demand’ and mixes two components together which then expands up to 200 times its liquid volume negating the necessity for large storage areas required for pre-fabricated packaging.
The benefits for customers are numerous. As well as an ideal solution for protecting awkward and valuable products, customers with product
design changes and new product line additions are able to quickly adapt the packaging without the need to carry a large range of bespoke cartons or fabricated packaging.
There are two dispensing methods available for the insitu protective packaging solution. Either FOAMplus® Hand Packer, a manually operated system, with a fully electronic microprocessor control to maintain consistent quality that delivers the foam direct into polythene lined carton via a foam dispensing gun.
Alternatively the Bag Packer² Foam-in-Bag dispensing system is fast, easy to use, efficient and economical. The machine can produce up to 23 foam-filled bags per minute at the touch of a button. Polyol B 5504R, foam B component is made from 30 percent recycled polyurethane.
www.storopack.co.uk
PAPERplus® - Paper pads provide maximum performance, high density, and strength. Ideal in-the-box protection for heavy products.
100% recycled content and 100% recyclable
In manufacturing, efficiency is key to success. Improved efficiency results in greater productivity, less waste, fewer hours lost to downtime and lower costs. This is why automated technology such as sack-filling machines and palletisers is so valuable – these machines feature specialist gripping heads to handle items with speed and precision.
The gripping heads found on palletisers are designed to hold bags, sacks and packages securely, allowing them to be moved quickly and efficiently without causing damage. Different gripping heads are available for handling different products and the most appropriate one will depend on the item’s shape, size, weight and handling requirements.
Common gripping heads may be vacuum operated, feature side clamps or magnets, or use a combination of all three.
Where there is a flat top surface, such as on boxes and cartons, a vacuum gripper is often used. However, at PALpack, we prefer to use a physical mechanical gripper, for reasons from changes in porosity to stability. All of PALpack’s palletisers are designed so that there are no change parts for different pack types.
World-leading manufacturer Lita offers gantry-style Cartesian palletisers which can pick and place items, often in complex pallet patterns. Several different gripping heads are available for handling different products. Because of the different gripping heads, both can handle RSC cases and shrink-wrapped packs of varying sizes and Robodue can also manage jerry cans.
Suitable for handling RSC cases, shrink wrapped packs, metal drums, bags, and sacks, Logico by Lita features a single arm with different gripping heads for different products. They can insert pads between
layers and handle empty pallets as well as move packages.
Different types of bags or sacks have different handling requirements and gripper heads can be designed accordingly. Europack’s rotating beam palletisers have a 360o rotating gripper head that can be changed to suit different packages, while combined heads can deal with more than one type of product.
Using sack-filling and palletising technology along with specific gripping heads improves processes, saving time, reducing manual labour and helping manufacturers to improve their overall operations. PALpack can supply not only sack palletisers, but also VFFS sack filling machinery.
For more information about PALpack’s automatic palletising solutions, please visit www.palpack.co.uk
Common gripping heads may be vacuum operated, feature side clamps or magnets, or use a combination of all three.PALPACK
PALpack work with our UK and Irish clients to offer practical, technical advice on automated palletising. With over 25 years' experience in the field, we understand all levels of food and beverage production, from low-speed, simple operations, to super high-speed, complex, multi-product manufacturing. PALpack are agents for top-of-the-range machinery supplied by European manufacturers
PALpack work with our UK and Irish clients to offer practical, technical advice on automated palletising. With over 25 years' experience in the field, we understand all levels of food and beverage production, from low-speed, simple operations, to super high-speed, complex, multi-product manufacturing. PALpack are agents for top-of-the-range machinery supplied by European manufacturers
Since our machine was installed, our line efficiency has improved dramatically, with little or no downtime recorded for technical issues, and their aftersales service is the best we have had from anyone in the 16 years of bottling production. I thoroughly recommend PALpack to anyone looking for some automatic palletisation on their production lines
Since our machine was installed, our line efficiency has improved dramatically, with little or no downtime recorded for technical issues, and their aftersales service is the best we have had from anyone in the 16 years of bottling production. I thoroughly recommend PALpack to anyone looking for some automatic palletisation on their production lines
UK premium gin manufacturer
UK premium gin manufacturer
Europack invented the rotating beam palletiser. Manufactured using only the highest quality components such as Siemens and SMC, these simple and easy-to-use palletisers have an extremely small footprint, with prices starting from as little as €60k
Europack invented the rotating beam palletiser. Manufactured using only the highest quality components such as Siemens and SMC, these simple and easy-to-use palletisers have an extremely small footprint, with prices starting from as little as €60k
VAI has designs, produces and supplies automatic and semi-automatic sack filling solutions, with machines that are used for decades. Their highly reliable solutions are made bespoke to customer requirements
VAI has designs, produces and supplies automatic and semi-automatic sack filling solutions, with machines that are used for decades. Their highly reliable solutions are made bespoke to customer requirements
One of the world’s most experienced and established manufacturers of automatic palletisers, Lita specialise in conventional medium to highpaced palletisers. These include Cartesian palletisers, layer palletisers and de-palletisers, as well as pallet de-stackers and layer card applicators.
One of the world’s most experienced and established manufacturers of automatic palletisers, Lita specialise in conventional medium to highpaced palletisers. These include Cartesian palletisers, layer palletisers and de-palletisers, as well as pallet de-stackers and layer card applicators.
With CAPEX conditions restricting response time to unscheduled process and production downtime, Axium Process, specialists in liquid filtration solutions, have launched a new service that can now be funded through OPEX channels.
Designed to meet a range of liquid processing concerns, Axium’s UF & RO2Go rental plants meet industrial scale demand for many different industries including pharmaceutical, food, beverage, dairy and water recycling.
The systems are built on tried-and-tested technology and have been developed for rapid deployment with minimal operator training, allowing them to be up and running in a matter of hours following installation.
Offering great flexibility, and backed by extensive technical expertise, Axium’s rental range can fulfil high-priority requirements swiftly, while reducing capital expenditure risk by allowing the technology to be assessed over the long term.
For further information, please contact:
Derek Davies
Tel: 01792 883 882
Email: derek.davies@axiumprocess.com
info@axiumprocess.com
As well as our industry leading condensate filtration range, SEPURA™ also manufacture high performance replacement filter service kits for all brands of oil-water separators.
PLUS our unique media provides a host of major advantages:
• Cleaner, lightweight handling
• Rapid installation
• Fast, easy servicing
• Outlet quality discharge down to 5ppm
M&C Engineering has helped a water company bring an end to a costly and time-consuming diesel pump application, by introducing a new skid-mounted unit from Borger.
Whilst a tank was being replaced at a treatment works, the water company were paying significant hire and running costs, as well as dealing with excessive noise – but the flow is now being diverted by a 24.4kW Borger EL 1550 pump, which has been skid-mounted by M&C Engineering, who also supplied valves, control panel and canopy.
Richard Shipp, Director at M&C Engineering, a full turnkey services provider, said: “We’re very impressed with Borger, as is our customer. The new pump has been running 24/7 with no problems whatsoever. The diesel pumps that were at the plant were very hungry and expensive to run – and although this is a temporary set-up to keep the RAS (Return Activated Sludge), moving, the Borger pump is lined up for a permanent installation with our customer, making good use of CAPEX”.
Benefitting from its Maintenance-In-Place design, which requires only basic tools for servicing, Borger’s self-priming rotary lobe pumps are proven worldwide across a multitude of industries, as well as in municipal wastewater treatment. With a reversible flow option, Borger’s rotary lobe pumps are also suitable for loading and unloading applications.
www.mandcengineering.co.uk
The BLUEline Nova sets new standards in pump technology. With or completely without casing protection – the BLUEline Nova achieves unrivaled volumetric efficiencies.
Made for one another – the newly developed DIUS rotors in combination with the flow-optimized pump chamber ensure perfectly smooth running at pressures of up to 12 bar.
Natasha’s Law, passed in 2019 after the tragic death of 15-year-old Natasha Ednan-Laperouse in 2016, as a result of a severe allergic reaction to sesame oil in a baguette, came into effect on 1st October 2021 to allow manufacturers and retailers time to comply with the new labelling requirements. Natasha had a known sesame allergy and was careful when selecting food. Despite believing she had chosen an allergen-free sandwich, she suffered a severe anaphylactic reaction to the sesame oil baked into the baguette, which was not listed on the label, and sadly died later that day.
Other examples of tragedies include Celia Marsh, who suffered anaphylactic shock after eating a “dairy-free” super-veg rainbow flatbread from Pret A Manger, which contained traces of milk protein, leading to her collapse and subsequent death.
A further example is that of teenager Megan Lee, who died after suffering a severe allergic reaction to nuts contained in a takeaway meal in 2016.
Though there are only approximately ten deaths in the UK from food allergies each year, the effect of allergic reactions is much wider. Hospital admissions due to serious allergic reactions, caused by food, have more than tripled over the past 20 years. Despite this, deaths from food-induced anaphylaxis have decreased during the same period (ref. The BMJ Today).
It is possible that the increase in food varieties and other factors may be contributing to the rise of food-related allergies, with reported cases even extending beyond the 14 known allergen groups (e.g. kiwi fruit).
In the UK, around 2 million people have food allergies, and there has been a four-fold increase in prescriptions for adrenaline auto-injectors like Epipen in the last two decades. About 10% of adults and children have a food sensitivity, with
20% of the population experiencing some form of reaction to food, suggesting a food hypersensitivity. On average, two school children per class in the UK have food allergies.
Millions worldwide suffer from food allergies, with up to 8% incidence among young children. In England and Wales alone during 2021, over 7,000 businesses were found to misdescribe or not declare allergens in their food. (Trading Standards Review, 2022 Winter edition) Despite Natasha’s Law being in effect for over a year, only 37% of Britons find allergen labelling easy to understand, while 48% are unsure and 15% lack confidence in them. (Mintel)
The number of annual deaths in the UK due to food allergies is still low (10 on average), but even one death is too many. Addressing this issue consistently can also
reduce the suffering of those with less serious allergic reactions. However, as a consumer, I am not aware of significant changes since the introduction of Natasha’s Law. Manufacturers still rely heavily on emboldened allergen information on packaging, and many fast-food outlets have made few changes.
What if pre-packaged products with allergens emboldened on the packet use the wrong packaging, and the label doesn’t include the allergens? In a recent survey of 14 UK supermarket chains, only 3 showed improvement in reducing incorrect labelling.
Problems caused by inaccurate labelling for pre-packers are easy to solve with a modest investment. It will come as no surprise to many to learn that this is one of Harford Control’s specialities.
Share your packaging control concerns with us and we will help eliminate your future risks permanently.
For further information, please visit www.harfordcontrol.com
Millions worldwide suffer from food allergies, with up to 8% incidence among young children.
Manufacturers are increasingly turning to smart manufacturing principles, hoping to turn the shop floor into highly efficient, data-driven operations humming with synchronised precision. Unfortunately, lineof-business managers, team leaders, and shift supervisors—the shop floor heroes— often lack easy access to the ERP system and the relevant data needed to keep production on track.
Deskless workers play a vital role in operational efficiency. Democratising data—making data consumable for a wider population—will give these frontline users valuable decision-making insights. With role-based dashboards and reporting tools, they can drive better performance up and down the production line, from smart use of resources to reduction in rework and scrap.
Countless critical decisions are made on the shop floor every shift. The setting— notoriously noisy and fast moving—isn’t conducive to careful, prolonged pondering of influences. Fast-moving production lines require fast decisions and expedient action. At the same time, errors can be costly, eating away at profitability, wasting resources, and jeopardising aspromised delivery times. Decisions based on guesses, one random exception, or anecdotal stories can send a team into spirals of wasted time, frustrating workers and managers alike.
The answer is to put data in the hands of every decision-maker in the organisation, even those who aren’t advanced data analysts with skills in report writing and applying artificial intelligence (AI) algorithms. Modern digital platforms provide interface tools to help users apply advanced functionality to everyday situations. Featuring low-code and nocode capabilities, the digital platform provides front-line users with rolebased dashboards to track relevant key performance indicators (KPIs) and custom reporting to investigate emerging trends. Quickly, dynamic insights are within reach of machine operators, maintenance technicians, and material handling engineers, scheduling clerks, and shift leaders.
Operational-level access to data is especially helpful in preventing gaps in workflows and avoidable delays. Frontline workers can get immediate answers to design questions or specifications on a custom work order. Access to information keeps production lines moving as planned, with minimal interruptions because of questions, disconnects between departments, or stockouts.
Advanced analytics can go even further to keep the shop floor operating smoothly and profitably. Managers can delve into exceptions and track influencing variables. They can find opportunities for improvement, such as eliminating quality roadblocks or controlling down time.
As artificial intelligence (AI) and machine learning (ML) have moved into the mainstream, manufacturers are increasingly seeking practical applications for data insights. Proof of concept projects are being replaced by ones which promise a timely, measurable return on investment. The shop floor offers many practical applications for AI-driven insights. Routine processes can be automated, streamlining the need for human interaction. Only anomalies or exceptions need to be routed to supervisors
for individual attention. Streamlining the data flow will also help keep various teams apprised of real-time updates and needs. No one is out of the information loop, falling behind on evolving expectations. One datadriven digital thread will connect every stage in shop floor operations.
Here are nine examples of how democratised data helps boost productivity:
1. Custom quotes and bill of materials. Efficiently managing make-to-order, engineer-to-order, and configured products requires an automated system for generating rules-based quotes and matching bills of materials. Once the customer has approved the order, the specifications must flow from sales to operations to ensure the right dimensions, features, and finishes are applied. Access to the customer order helps managers verify details, eliminating reworks or customer returns.
2. Projecting raw resources needed
Synchronising production planning and availability of raw resources requires access to data and AI-driven predictive capabilities to prevent stock-outs. Data helps procurement managers make sure the warehouse is stocked with necessary components. Too much inventory can be just and dangerous, tying up capital and risking obsolescence.
3. Accurate scheduling. Synchronising production runs to fulfill customer orders depends on accurate account data as well as sales, delivery promises, inventory of raw materials, and machine capacity. Working with co-manufacturers or subcontractors also requires access to information. Collaboration portals can help share information while protecting security.
4. Strategic scheduling of the workforce. With data insights, managers can track and understand performance of shifts and crews, identifying essential staffing requirements and tracking expenses. With the acute labor shortage manufacturers face today, careful scheduling of rightskilled workers is especially important.
5. Workflows. Keeping operations running smoothly with no gaps, delays, or roadblocks requires coordination among teams and sharing data on job status, equipment performance, and scheduling. Reporting can help identify trends and analyse variables, allowing managers to delve deeper into influencing factors that can be improved. Decisions can be made, changes executed, results monitored, and further refinements made. Continuous improvement can be part of the system and standardised workflows.
6. Compliance and quality control. Managers need to track, monitor, and evaluate quality standards, with a continuous feedback loop in place. As new products are introduced, specifications need to be easily updated and accessible to relevant teams. Regulation compliance, too, is critical in many industries and demands accurate reporting. Democratised access to data helps keep the details in view when and where they are needed most.
7. Waste reduction. As manufacturers strive to be more sustainable, they place a high priority on reducing waste, including energy, water, and raw resources. Reducing scrap is essential. By improving consistency and quality control, fewer units will need to be scrapped or reworked. Access to data will help crews verify proper machine settings, consult knowledge banks for typical resolutions of issues, and verify proper specifications and variables.
8. The call centere. The aftermarket service operation needs real-time access to account and product details to answer customer questions about deliveries, service agreements, warranty status, and scheduled preventive maintenance. Service dispatch needs to access the location and availability of technicians to dispatch the right person to the right job based on geography, service level agreements and urgency.
9. First-call resolution. Field technicians at the job site need remote access to details on the unit, as-serviced history, inventory status of parts, and availability of replacement or upgrade units. A technician with the right data is seen as a trusted advisor and can often make sales in the field.
For further information, please visit www.infor.com/en-gb
As artificial intelligence (AI) and machine learning (ML) have moved into the mainstream, manufacturers are increasingly seeking practical applications for data insights.
DIN11864 and 11853 unions were developed to meet the exacting needs of the food, chemical and pharmaceutical industries.
This range of unions has been developed from the three most common systems used in the hygienic and sanitary industries; namely the “Aseptic” screwed union to DIN11864-1; the “Aseptic” flange union to DIN11864-2 and the “Aseptic” clamp union to DIN11864-3.
Available with optional lengths to suit both orbital and manual welding, these unions have been designed to match tube and pipe specifications to DIN11866 Table A (DIN11850); DIN11866 Table B (ISO 1127) & DIN11866 Table C (ASME BPE).
Size range: 10mm to 150mm and 1” to 4” Specials are available up to 304mm
Materials: 316L SS 1.4404 and 1.4435
Specials available in Duplex and Alloy 22
Subcon is back with a real bang for 2023, bringing together the full manufacturing ecosystem for companies to source, subcontract, benchmark and learn all under one roof.
Combining the UK’s biggest and longestrunning subcontract manufacturing supply chain exhibition with more than 20 hours of free-to-attend conference sessions, Subcon is engineered to help future-proof your business.
More than 200 solution providers representing the best of British manufacturing engineering capability, alongside a wealth of market-leading international suppliers, will be present to help optimise your supply chain strategy and keep costs down.
Thousands of new products and innovations will be on display across the full range of advanced engineering technology, systems and services – from Additive
Manufacturing and Metrology solutions to Frictionless bearings, cables and controls, and everything in between. This is a show geared to helping you increase capacity, optimise productivity, improve flexibility and remain competitive.
New for Subcon 2023 are two conference theatres showcasing our industry-leading engineering and manufacturing journals,
The Engineer, Manufacturing Management and Machinery.
Together, they will convene dedicated conference streams for two days of highquality, case study-led discussions about hot technology and business process trends for you to apply directly to your business.
Drawing on a combined 340+ years of manufacturing journalism and insight, our editorial teams have curated a conference agenda that addresses the key opportunities and challenges facing UK businesses.
Two theatres will run in parallel, a dedicated Supply Chain Theatre in conjunction with Machinery Magazine and a second theatre co-led by The Engineer and Manufacturing Management magazine.
Our revered line-up of industry leaders are set to deliver insightful sessions covering Automation; Cybersecurity; Energy Storage; Net Zero; Recruitment & Retention, Supply Chain Resilience and much more.
Thousands of new products and innovations will be on display across the full range of advanced engineering technology, systems and services.
1. Are manufacturers ready for the challenges of moving to a net zero world? – Keynote by Professor Paul Monks, Chief Scientific Advisor to the Department for Energy, Security and Net Zero
When and Where - Theatre 1, Thursday 8 June, 10:35am – 11:05am
2. UK recovery: What are the new markets and how accessible are they? –
Panel discussion led by Mike Wilson, Chief Automation Officer at the MTC
When and Where - Theatre 1, Wednesday 7 June, 11:10am – 11:50am
3. Reimagining the skills shortage: From education to employment – Panel Discussion with expert insights from Innovate UK KTN, MTC and Sempai
When and Where - Theatre 1, Thursday 8 June, 11:55am – 12:35pm
4. Bringing home the supply chain – Panel discussion on the logistics of reshoring led by Aristides Matopoulos, Professor of Supply Chain Design at Cranfield University
When and Where - Theatre 2, Wednesday 7 June, 2:10pm – 2:45pm
5. Why should additive manufacturing be used in designing your supply chain – Panel discussion with expert insights courtesy of Digital Manufacturing centre, Prototal and AM-UK and CECIMO Trade Associations
When and Where - Theatre 2, Wednesday 7 June, 11:55am – 12:35pm
*subject to alternation
Your single-source provider for all manner of metal and plastic fabrication, casting, machining, finishing, assembly and other manufacturing services, from concept to completion.
Omnidex is a British-owned and managed company driven by a passion for quality. For more than 20 years, our company has provided world-class engineering outsourcing services at a competitive price.
Our experience and expertise spans almost all sectors, including aerospace, automotive, consumer products, medical, oil and gas, and more. Our customers include companies in the UK, United States, South Africa, Australia and many other countries.
We pride ourselves on utilising and investing in the latest equipment and technologies to deliver cutting-edge, high-quality products and services to our global customer base. Our highly skilled engineers, supported by a vetted network of subcontractors and stringent quality control processes, ensures everything we deliver meets the highest standard requirements and tolerances.
For a free quote for your next project –whether complex or simple, metal or plastic, high or low volume – contact us via our website: www.omnidexcn.com
Or come see us on Stand C141
The voice of Europe’s sixth-largest machinery sector
Machinery Exporters’ Association (Turkish Machinery) represents and promotes the interests of its 18,000 members. It does so by coordinating and delivering sectorspecific networking opportunities, business intelligence, and international events and trade missions.
The Turkish machinery sector has recorded robust growth over the past decade and has increased by more than 400% since 2003. It is now Turkey’s second largest exporter, worth some $25.5bn in 2022 –equivalent to 10% of total exports.
Centrally situated between Europe and Asia, Turkey is ideally located close to several of the highest-growth industrial machinery markets. Turkish machines operate in more than 200 countries around the world with a particularly strong presence in the United States and Europe.
Buyers are drawn to the strong emphasis Turkish machine manufacturers place on R&D activities, the rapid adoption of international manufacturing standards and new technologies, the highly educated and skilled engineering workforce, and highquality aftersales support.
Learn more about how Turkish machinery is MAKING THE WORLD WORK by visiting our website: httpwww.turkishmachinery.org/En
Or speak with us on Stand D121.
For further information, please visit www.subconshow.co.uk
At its core Sapman v12 is a sophisticated Manufacturing, Warehousing and Stock Control solution. This modular product provides extensive facilities for Stock Control, Sales and Purchase Order Processing, Warehouse Management, Bill of Materials, Works Order Processing, Engineering Control, MRP and CRP. With the Microsoft SQL database engine at its core this product provides a leading edge business management solution.
Our highly skilled team has 20 years of experience resolving our customers’ Assembly, Manufacturing Control and ERP requirements, their Stock Control and Warehouse Management needs using our advanced, effective and efficient software solution.
Sapman v12 fully integrates with Sage’s Accounting solutions: Sage 50 and Sage 200. It also provides an upgrade path from Sage 100.
Sapman v12 is highly customisable to operate with virtually any business model. With successful installations in a huge range of industry types from manufacturers of Medical Products to
Electronics Manufacturing our customers rely on Sapman v12 to run their businesses.
Sponsored development of specific functionality is possible where customers require some modification to allow the software to exactly map their business’s operational model.
Quotations: Quote ( including price breaks)& Drawings & Pricing : v12 can attach drawings to the Quote
SoP : The Sales Order Processing gets underway
Stock : Stock Enquiry : Check material Needs : Make to Order or Ex Stock?
If not it may generate a Purchase Order for more Stock
If the Sale item is Make To Order (MTO) then the Works Order Processing routine kicks in v12 is suitable for Batch Manufacturing, Make to Stock, make to Order, Kanban & service works
Stock values from v12 update Sage50 Nominal Ledger
PoP Purchase Order Raised
Purchase Invoice received & Sage 50 updated for Nominal Codes, Purchase Ledger and VAT
WoP The confirmed order has to be manufactured & v12 produces the works order
BOM V12 produces the BoM : tree-view with collapsible/expandable nodes
SFDC Shop Floor Data Capture : using barcodes v12 manages the job though the shop floor
WiP With Shop Floor Data Capture SFDC v12 knows :
What Material/Subcomponents have been used, Who has worked on the job and on what machine - Get Material, Labour & Machine Variances & produce management reports -
Every stock issue is linked to an original GRN - ensuring full Serial Number and Batch Traceability
Stock Finished item is booked into Stock v12 knows where it is; it covers multiple sock locations and stock with Sub Contractors
Stock values per client defined categories can be up dated to Sage50 Nominal at client defined times
Stock Stock records updated, Despatch note raised; Certificates of conformity produced
Sales Invoice raised & Sage 50 updated for Nominal Codes, Sales Ledger & VAT
“We enhanced our customer service with a highly innovative Sapomanv12 ERP System.The technology loads sales orders automatically from an EDI, analyses stock across multiple locations and reviews what’s available from suppliers to automatically calculate lead-times, allocate available stock, produce picking tickets and control scanner-based warehouse activities.”
“V12 offers us greater productivity, improved communications with third parties and the interconnectivity between the various menus and our Sage Accounting software makes operating our company infinitely easier.”
Colin Mallard, Finance Director, Lakeland LaboratoriesFor more information on Sapman v12 please visit our website at Sapmanv12.co.uk. Email us on info@sapmanv12.co.uk or please telephone us on: 0333 456 12 12.
Limited
• Customer Enquiries, Quotations, Sales Order Processing & Invoicing
• Purchase Order Processing & Trial Kitting
• Fully Traceable Stock Control (Multi Depot)
• Bill of Materials (Multi- Level)
• Shop Floor Data Capture & Planning Board
• Warehouse Management (WMS)
• Integration to Accounts Software
• 100+ Standard Reports & Business Intelligence (BI) Options NO upfront capital cost NO minimum contract length Immediate
The KD485-ADE-4XX-4XX from KK Systems is a DIN rail mounted interface converter with two serial ports which both support 2-wire or 4-wire RS485.
A common application is attaching new 2-wire RS485 devices to an existing 4-wire RS485 bus. The KD485 is protocol transparent and RS485 driver control is performed transparently.
Other port types available are RS232 and 20mA TTY.
User programmable versions also support data/protocol conversion.
The KD485 is powered from 7-35V DC and its 3-way isolation makes it ideal for industrial applications which require a robust unit with the full RS485 drive capability.
Custom products are also available, including C userprogrammable versions.
www.kksystems.com
Rotech Motion Sensor’s can be used whenever information or monitoring of shaft rotation, position, direction, speed, slip etc is required!
Rotech Motion Sensor’s can be used for indication, control, interlocking, protection, sequencing, alarm initiations and many more functions!
Rotech Motion Sensor’s can be used wherever materials are transported or processed By conveyors, elevators, screws, mixers, etc!
Patterson & Rothwell Ltd
Bee Works, Shaw Road, Royton, Oldham, OL2 6EH
enquiries@patterson-rothwell.co.uk
T 0161 621 5000
patterson-rothwell.co.uk
Product Design Tool Design Toolmaking ProductionDrallim is an innovative technology driven British engineering company with global presence. With experience in providing comprehensive turnkey assembly & test solutions covering electronic, electromechanical, engineering, and mechanical products. We offer our customers a total contract manufacturing service, offering design, and manufacturing solutions, providing engineering skills, manufactured equipment & custombuilt systems for the Aerospace, Industrial and Utility Markets.
Prototyping and New Product Introductions; From the initial enquiry, our Business Development Team analyses the specifications and requirements of a product or project and issues a comprehensive and detailed quotation. When an order is received, a project plan is then developed; our team uses detailed documentation, engineering change and reporting control to ensure continued information integrity.
An experienced project manager acts as the interface between Drallim and our customers although, at the same time, we actively encourage engineer-to-engineer communication. We have had customers engineers based at our headquarters signing off drawings as they are produced to meet urgent deadlines for manufacture. The designated project manager ensures that resources are allocated appropriately and that all tasks are tracked and recorded. The result is a controlled transition into the manufacturing process.
When it comes to product manufacturing, a substantial proportion of the end product’s total cost is determined at the design stage. As a result, this part of the manufacturing process presents the perfect opportunity to
identify improvements that will lead to cost reductions. A thorough understanding of each element will enable the product to be designed and optimised for procurement, manufacturing and test. We provide an extensive Design for Manufacture service to help our customers achieve substantial improvements, including:
• Improved manufacturing productivity
• Enhanced product quality and reliability
• Minimal/simplified maintenance
• Lower Cost
• Reduced time to market
• Increased customer satisfaction
• Manufacturing
• Precision assembly
We regularly produce complex assemblies that demand high levels of skill, precision, accuracy and consistency. The engineering and manufacturing teams at Drallim are highly skilled in this type of work, with awareness of critical engineering tolerances when producing assemblies of this complexity. Our skills-base extends to include testing of electrical, electronic, mechanical, hydraulic and pneumatic assemblies. Following rigorous approval processes Drallim’s supply chain partners for custom parts, such as plastics, machined and fabricated metalwork etc, are monitored closely for quality and delivery performance. Tight control of the material supply chain ensures the availability of high quality mechanical parts is maintained for timely production.
Many of the assemblies produced require wire and cable interconnection between boards and sub-assemblies. This can be via cable forms or point to point wiring. As part of our electro-mechanical assembly service we are often called on to produce products that require critical cable routing. We also undertake electrical wiring of switch and instrument panels plus sophisticated control cabinets. We have highly trained engineering and assembly teams to assist with design and the assembly and support for all your cable and loom requirements.
• Electro-mechanical Assembly
• Pneumatic & Hydraulic Assembly
• Racks & Cabinets
• Box-Build Assembly
• PCB Assembly
• Prototype Wiring
• Cable Assembly
• Testing
If you are interested in British Manufacturing and looking for a Contract Manufacturer, then maybe Drallim Industries could assist you.
For further information, please visit www.drallim.com
We take pride in overseeing the entire manufacturing process, from design, prototyping and manufacture to delivery, installation, full product certification and after-sales service
Small Batch Manufacture Electrical | Electronic Pneumatic | Hydraulic Mechatronics Concept Design
Oliver Hydcovalves have announced the design and manufacture of three new valves for hydrogen transportation and refuelling. Using high performance polymer bearings and seals in partnership with DuPont™, valves have been qualification tested to 102,000 cycles of operation while maintaining a fugitive emissions leakage class of BH.
Another unique feature of the valves is their full-bore design. This avoids restrictive flow, which appears to be a common problem in many valves on the market. Nick Howard, Engineering Director at Oliver Hydcovalves stated; “By maximising the flow rate, it will deliver a more continuous and consistent flow of hydrogen medium. This will allow for hydrogen fuel to be dispensed and refilled onsite much more quickly, which will deliver dramatic time-saving benefits.”
As the world continues to move towards sustainable energy sources, hydrogen is emerging as the promising fuel option for vehicles and industrial transportation on land, sea, and air. The transporting and dispensing of hydrogen fuel in working environments such as fuel stations and onsite fuel storage facilities, require specialist valves that have been designed and engineered for continuous high cycle operative use and meet the requirements of ISO 19880-3.
When dispensing hydrogen fuel onsite, it generally requires a large area to be closed
off while in progress, and can even involve a whole site closure, dependent on size of area. Therefore, the time it takes to dispense hydrogen fuel is crucial. Oliver’s full-bore valves deliver hydrogen much faster than other transportation valves that have a restrictive flow. This significantly reduces the downtime at a site, and in most cases, can be halved - minimising disruption to the forecourt and business operations.
Hydrogen fuel is stored and transported using pressurised tanks. Therefore, it’s of paramount importance that valves can handle extreme pressures too. Since 1979, Oliver has been synonymous with valve safety and reliability, even relied upon by the world’s largest energy producers, suppliers,
and end-users for its precision engineered solutions. As Oliver’s company mantra suggests ‘Reliability Under Pressure’, they’re well-positioned to provide the necessary assurances required.
This latest engineering achievement firmly places Oliver Hydcovalves at the forefront for hydrogen transportation valves. Built to the highest specifications using premium quality materials, and tested to the highest standards, it’s logical to see how Oliver’s claim to offer the best valve solution for hydrogen transportation and refuelling applications, certainly holds up.
Bore sizes include; 10mm, 14mm and 20mm. To learn more about hydrogen transportation and for guidance on hydrogen specifications, applications, qualifications and pricing, contact Oliver Hydcovalves on +44 (0) 1565 632636 or visit their website.
For further information, please visit www.valves.co.uk
This latest engineering achievement firmly places Oliver Hydcovalves at the forefront for hydrogen transportation valves.
World-leading
Valves for Hydrogen, Carbon Capture, Topside, Subsea, and Pipeline Applications.
Instrument & DBB Valves
• Manifolds, Needle, Check and DBB Valves to 22.5K psi
• Cryogenic
• Severe Service 650ºC, 10K psi
• Forged & Bolted Construction
Hydrogen & Carbon Capture Valves
• Instrumentation, Ball, Needle and DBB Valves for Hydrogen and Carbon Capture Applications
• Pipeline Ball Valves upto 18”
• 10K Ball Valves for Hydrogen Fuelling Stations
Pipeline Valves
Pipeline Valves
• 1” to 20” Bore Size
• 1” to 20” Bore Size
• High Temperature
• High Temperature
• High Pressure
• High Pressure
• Cryogenic
• Cryogenic
• API 10K Design
• API 10K Design
Subsea Valves
Subsea Valves
• Diver & ROV Operated Needle Valves
• Diver & ROV Operated Needle Valves
• Ball Valves Upto 15K
• Ball Valves Upto 15K
• Manual & Hydraulic Parallel Slide Gate Valves 3/8”, 1/2”, 3/4” and 1”
• Manual & Hydraulic Parallel Slide Gate Valves 3/8”, 1/2”, 3/4” and 1”
We Manufacture Valves for Global Energy Projects. To Find Your Local Supplier, Contact Us Today.
We Manufacture Valves for Global Energy Projects. To Find Your Local Supplier, Contact Us Today.
ARI-Armaturen – your answer to all your valve needs
A COMPLETE SOLUTION FOR STEAM TO WATER HEAT EXCHANGE
A COMPLETE SOLUTION FOR STEAM TO WATER HEAT EXCHANGE
Designed to provide hot water instantaneously whatever the load conditions, up to 2100kW without the need for water storage.
Designed to provide hot water instantaneously whatever the load conditions, up to 2100kW without the need for water storage.
■ Reduced Heat Loss
■ Improved Temperature Control
■ Thermal Efficiency
■ Operational Savings
• Reduced Heat Loss
ARI-Armaturen UK Ltd steam systems, thermal oil and hot water and is a subsidiary of a large German engineering company, reputed to have the largest valve stock in Europe.
• Improved Temperature Control
• Thermal Efficiency
• Operational Savings
Founded in 1981 in West Sussex, Flotronic Pumps is a world-leading manufacturer of air operated double diaphragm pumps (AODP). With the invention of our ground-breaking ‘One Nut’ pump design, Flotronic have revolutionised the application of diaphragm pumps throughout the industry.
Over the last 30 years our ‘One Nut’ double diaphragm pump has proven its success in an incredibly diverse range of international industries including but not limited to pharmaceuticals, food & beverage, cosmetics, personal and household care and chemical manufacturing.
Our global customer base can rely on our expertise in delivering the highest quality products as well as our abilities to provide engineering excellence, thus enabling them to achieve their competitive edge.
For more information please contact: +44 (0)1444 881871 or email salesteam@flotronicpumps.com
Reliably tight, durable and versatile triple offset valve with zero leakage, even in harsh industrial environments.
Changing from single to double isolation made easy with the small face-to-face dimensions of the ZETRIX®
ZETRIX® Double block and bleed arrangement
The innovative 900 Series Monitor/Controllers include everything you need to simplify water quality management and chemical dosing in industrial operations in one compact userintuitive instrument.
Monitor 7 critical water quality parameters simultaneously from easily configured inputs: 2 Conductivity/Resistivity/TDS/Salinity; 1 pre-amplified pH/ORP; 1 BNC pH/ORP; 1 0/4-20 mA; 1 RTD Temperature; and 1 Flow/Pulse.
% Rejection is available as a derived value. Outputs include up to 3 relays; 2 remote alarms; 1 0/4-20 mA; 1 0-10 VDC; and 1 RS-485 ASCII Serial Output.
Flow Switch input can disable all relay outputs when triggered by loss of flow.
Relays output to any user-supplied control equipment requiring up to 250V each and can trigger on any input parameter.
www.myronl.com
Pressure surges are recurrent problems in many production plants that occur as a result of turning on pumps, changes in temperatures of enclosed liquids or switching the valves too quickly. Among other things, opening the valves can also result in pressure surges if the media supply is at a high level and the fluid column to lower plant components suddenly starts increasing. The possibility that pressure surges may damage plant components, such as filters, sensors, pumps and piping is very high.
Furthermore, the pressure surges can also cause the shut-off valves to accidentally open for a brief moment, and the media may then get contaminated as a result of this. In the worst situation, this could lead to product loss or downtime due to necessary repair work that must be carried out.
GEMÜ has developed a new innovative solution, the GEMÜ 652 Pulsation Damper, to compensate pressure and volume fluctuations such as water hammer or vapour pressure surge. Based on the tried and tested diaphragm valve technology and reliable actuator design, the GEMÜ 652 is therefore ideal for use in sterile applications (maximum 150°C). This means that it is completely drainable and CIP/SIP capable, taking the specified draining angle into account. Furthermore, it is also suitable for use with corrosive liquid and gaseous applications.
The main function of the GEMÜ 652 pulsation damper is to dampen as much volume as possible within a specific operating range. The body is designed without a sealing weir (full bore design), and for this reason, it won’t shut off the media and therefore the actual expansion volume is compensated by the moving diaphragm.
The operating range and the volume compensated can be adjusted by using different actuator sizes and spring sets. Therefore, the increased expansion volume can be achieved by installing multiple pulsation dampers in series, which will compensate for larger volumes.
The GEMÜ 652 is self-acting as its function is accomplished solely using a spring force, therefore it does not require an electric or pneumatic supply. The control air connector is only used for the assembly and maintenance of the diaphragm.
The GEMÜ 652 pulsation damper is available in the nominal sizes DN15 to DN80 (diaphragm size 25 to 80). To ensure flexibility and a high range of applications, the valve bodies and diaphragms are available in various materials. Furthermore, it also complies with the current standards in the foodstuffs and pharmaceutical industry, such as BSE/TSE, FDA, USP Class VI and Regulation (EC) no. 1935/2004. This ingenious solution by GEMÜ will solve multiple problems in many varied
applications. Please contact us to speak to one of our local product specialists for further information about this product.
See below for more technical information on the GEMÜ 652:
>> Product Flyer
>> Data-sheet
>> Operating Instructions
The main function of the GEMÜ 652 pulsation damper is to dampen as much volume as possible within a specific operating range.
Workbenches and tool storage from Benchtek Modular Systems deliver real benefits that contribute to the overall success and efficiency of your workshop or manufacturing facility:
1. Customisation and flexibility: Benchtek modular workbenches and storage systems are designed to be easily customised and adapted to specific needs, making them ideal for a wide range of applications and industries. This flexibility allows for seamless integration into existing workflows and processes.
2. Modular to suit your needs: Benchtek workbenches prioritise ergonomics, incorporating adjustable features to ensure optimal working conditions in a wide range of production environments. CNC tool storage is an optional addition for machine shops.
3. Durability and quality: Benchtek workbenches and storage systems are built with high-quality materials and construction techniques, ensuring long-lasting durability and reliability. This investment in quality reduces the need for frequent replacements or repairs, leading to cost savings in the long run.
4. Organisation and accessibility: Benchtek storage systems are designed to keep tools organised and easily accessible, improving workflow and reducing time spent searching for the right tool. This increased organisation directly impacts productivity and efficiency in the workplace.
5. Tool protection: Benchtek storage systems offer protection for cnc tools from damage, such as rust, corrosion, and impact. This protection extends the life of the tools and lowers the overall cost of ownership.
6. Space optimisation: Benchtek modular workbenches and storage systems can be easily rearranged, expanded, or adapted as needs change, making efficient use of available space in workshops and manufacturing facilities with limited floor space.
7. Professionalism and aesthetics: Benchtek workbenches and storage systems offer a clean, organised, and professional appearance, reflecting positively on the company’s image. This attention to detail can be particularly
important when working with clients or partners who may visit the facility.
Benchtek high-quality modular workbenches and tool storage offer customisation, flexibility, ergonomic design, durability, organisation, tool protection, space optimisation, safety, and professionalism.
Investing in Benchtek solutions can help deliver increased efficiency, cost savings, and a positive reputation within the industry.
Benchtek workbenches and storage systems are built with highquality materials and construction techniques, ensuring long-lasting durability and reliability.