MANUFACTURING Engineering
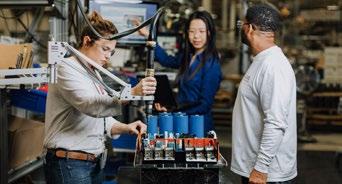
Innovation
Issue 64 2023
£4.95
www.pecm.co.uk
ROCKWELL AUTOMATION - 16
ROTZINGER GROUP - 42
PPMA SHOW - 1 1 1
Packaging and processing innovations on display at the 2023 PPMA Show
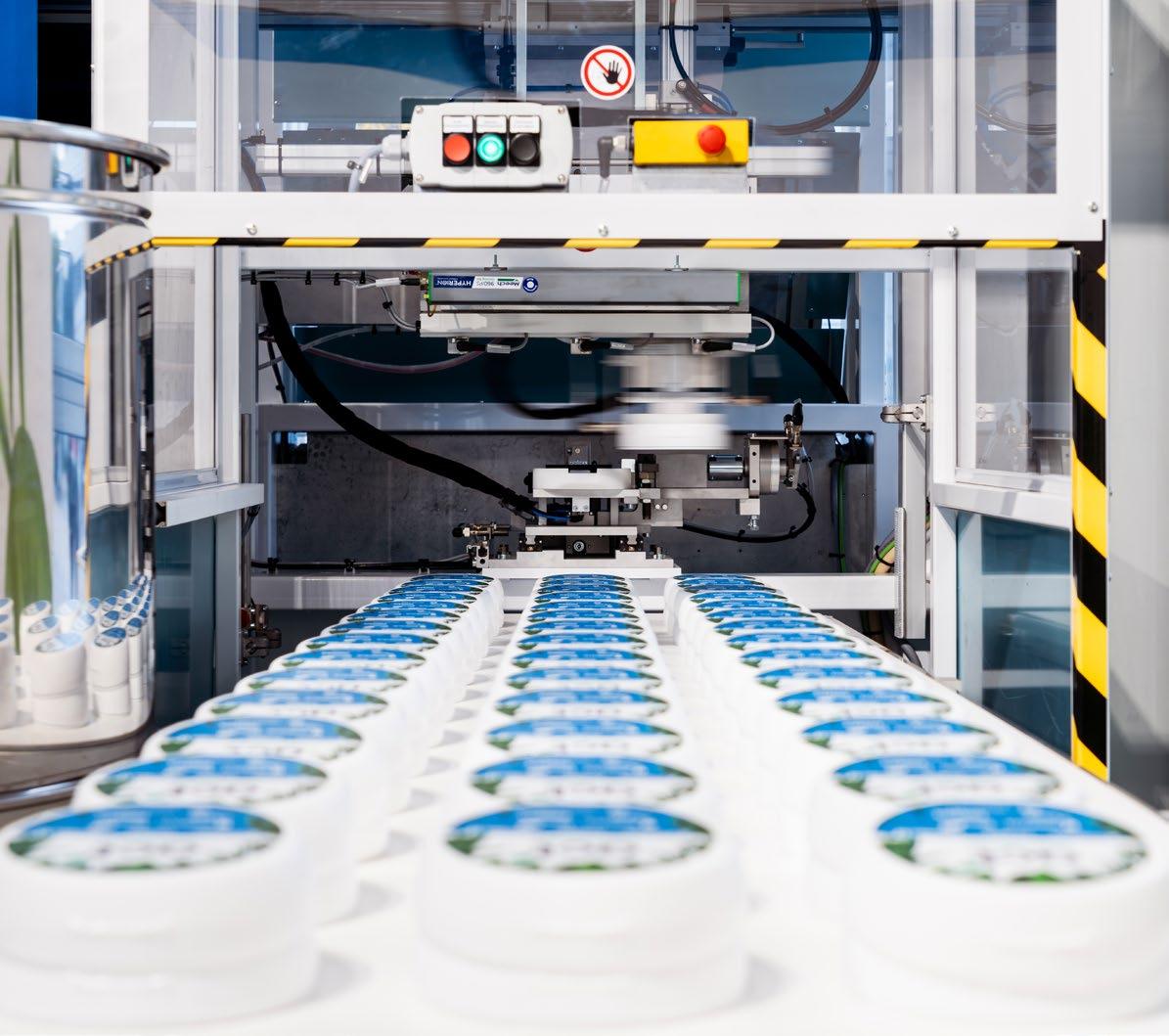

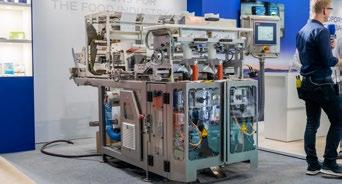
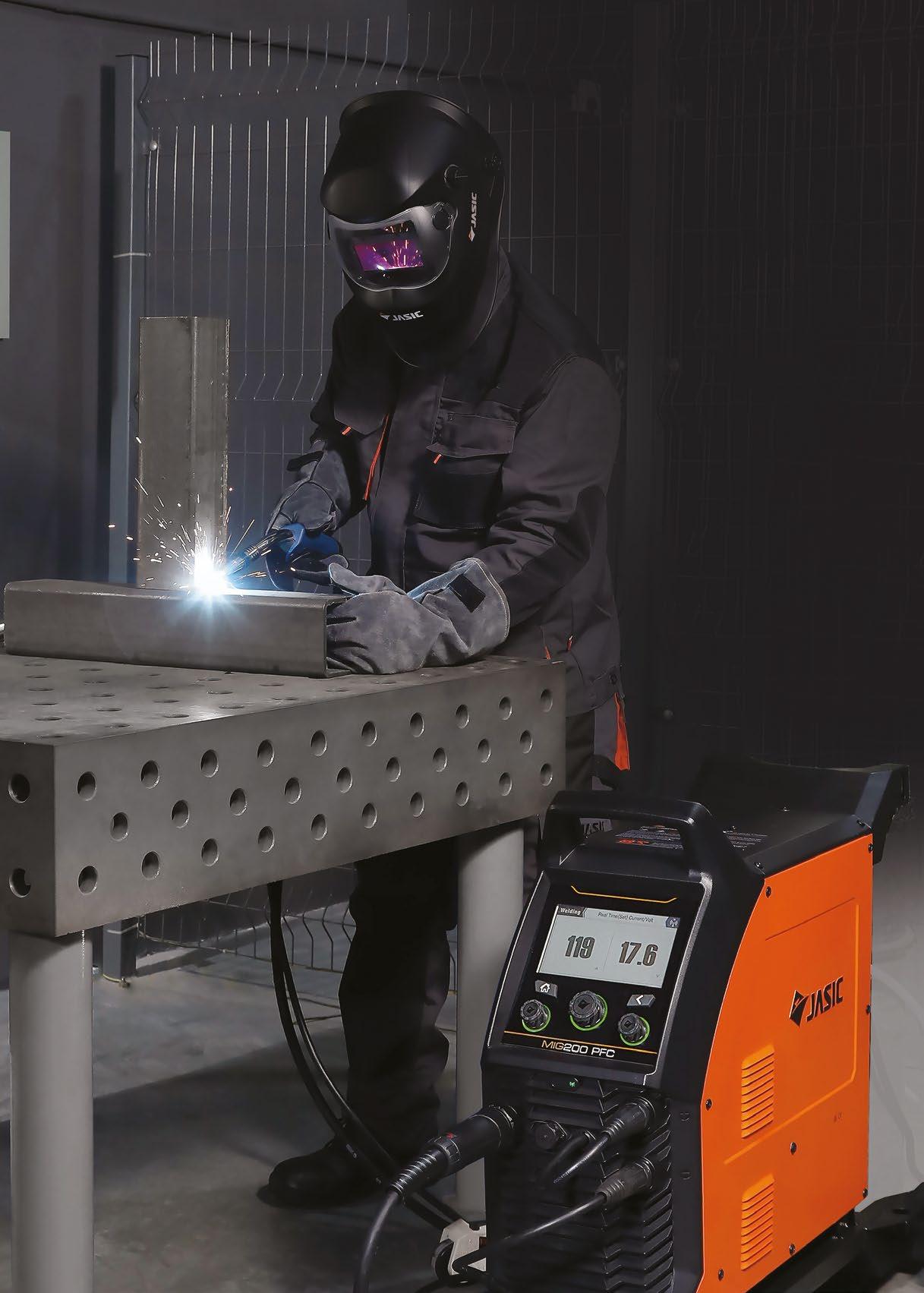
Innovation
Issue 64 2023
£4.95
www.pecm.co.uk
ROCKWELL AUTOMATION - 16
ROTZINGER GROUP - 42
PPMA SHOW - 1 1 1
Packaging and processing innovations on display at the 2023 PPMA Show
Inside Issue 64
CP AUTOMATION
CP Automation helps GA Pet Food Partners ensure uptime
GLOBAL HEAT TRANSFER
New coils increase solenoid valve energy efficiency by 80%
RE-FLOW
How to Strike the Right Balance in Business
PRIME VISION
Barcode reading between the lines
SPELSBERG
Ticking all the boxes for control systems
ABB
ABB expands large robot family with four energy saving models, 22 variants
FAMATEL UK LTD
Quality, service and a competitive product
KASTO
Retrofitting acrobatics under the roof
BURCKHARDT COMPRESSION
Burckhardt Compression’s Response to Hydrogen Production
SWINDON SILICON SYSTEMS
How ASICs can help businesses maintain and prove compliance
EMS LIMITED
Micromotors driving 3D measurement systems
SICK
SICK Announces Major Upgrade to Colour Sensor Portfolio
Meet Mantis, THE stereo microscope brand trusted by thousands of customers globally to deliver excellent high quality images for a wide range of magnification applications, in an easy to use ergonomic system.
To see what you’ve been missing search vision engineering mantis, scan the QR code or call us on 01483 248300.
Subscribe
The leading source for innovators in Technology, Manufacturing and Maintenance within the Engineering & Processing industry worldwide.
Published bimonthly, a subscription to PECM magazine is essential for Process Engineers, Chemical Engineers, Instrumentation Engineers, Mechanical Engineers, Plant Engineers, Precision Engineers, Environmental Engineers & General Engineers, Companies and Organizations in the Food, Dairy, Beverage, Brewing, Semiconductor, Pharmaceutical, Biotechnology, Chemical, Oil & Gas, as well as all UK's major manufacturing units.
Every issue of the magazine contains the latest news, in-depth features, together with product innovations and case studies showing how process engineers are implementing new technologies to reduce costs and impact on the environment.
With over 140,000 readers worldwide the publication is widely read, recognized, and well respected within the Process, Engineering & maintenance industries.
A subscription to PECM magazine is the industry's 'must have' publication.
SUBSCRIBE TO 6 BIMONTHLY ISSUES OF PECM FOR JUST £27
• The magazine gets delivered directly to your door once every issue is published
• The quality of the hard copy enhances the reading experience
To Subscribe please call 01304 806039
SUBSCRIBE TO OUR DIGITAL EDITION COMPLETELY FREE OF CHARGE
Designed for the digital age, the magazine has been created for easy viewing on all electronic devices. All our issues stored in one place: get unlimited access to our previous and future issues.
To Subscribe please visit www.pecm.co.uk/subscribe
EDITOR IN CHIEF
Antony Holter editor@mhmagazine.co.uk
BUSINESS MANAGER
Josh Holmes josh@mhmagazine.co.uk
SALES DIRECTOR
Harrison James harrison@pecm.co.uk
Tel: 0203 907 9166
SALES MANAGER
Martin Richardson martin@pecm.co.uk
Tel: 01304 086039
DIGITAL MANAGER
Jamie Bullock jamie@mhmagazine.co.uk
Tel: 01227 936971
EDITOR
Elizabeth Hutton elizabeth@pecm.co.uk
STUDIO DESIGNER
Richard Bland richard@mhmagazine.co.uk
ACCOUNTS DEPT
Alison Holmes accounts@pecm.co.uk
Tel: 01227 936976
PUBLISHING DIRECTOR
Martin Holmes martin@mhmagazine.co.uk
Tel: 01304 806039
DIGITAL ASSISTANT Stacey Goodwood
Tel: 01227 936971
Please mention Process Engineering Control & Manufacturing when responding to items in this issue.
If you were to put a figure on enhanced productivity, what would your ultimate manufacturing output goal be? Five percent, maybe ten? Given the current challenges, some processors may even push for 20 percent! Research by Sumitomo (SHI) Demag reveals that when all the productivity production stars align –including optimising all-electric technology, engaging people, utilising automation and other digital tools, and reducing production downtime – 50 percent or higher is entirely reachable.
Productivity is the hot topic at Interplas 2023, with a number of seminars and panel discussions already scheduled. Inevitably, these programs will showcase and share best practice on how to ‘achieve more output with the same or less effort’. After-all, this is the ultimate quest.
Ahead of the productivity curve is Sumitomo (SHI) Demag. Gathering information and data when visiting customers following new all-electric and machinery installations, the team reveals everything they’ve learned. Including how both small and large polymer processors can lean on their technology and team to unlock more untapped productivity opportunities.
All of this information is being captured in an insightful new Whitepaper. However, given the significance of this trailblazing evidence and yield-boosting benefits, the team shares a taster of how mass moulders can, with just a bit of expert support and guidance, double their manufacturing capacity and productivity.
Imagine the profit possibilities if each all-electric injection moulding machine within your fleet delivered an extra six months of processing capacity. How many extra projects could you take on? How much machine footprint could this save? What would this mean for your delivery schedules and customer satisfaction?
Phased Total Factor Productivity improvements to manufacturing processes holds huge promise. For many UK moulders, this could finally be the
golden egg to change the operational landscape and future prosperity of polymer manufacturing firms of all sizes?
Integrating an all-electric machine into production lines, alongside intelligent utilisation of digital tools and automation, combined with investing in training and development, can decrease cycle times by up to 55% percent. This can equate to an extra 168 days of production, illustrates the Processing Productivity whitepaper.
It doesn’t require doing everything all at once. Instead, the Sumitomo (SHI) Demag team assures customers that in a short space of time, marginal gains can unlock accumulative enhancements to boost profit margins.
It’s widely considered a ‘given’ that energy efficiency and reduced pollution are the benefits of all-electric injection moulding machines. Especially in today’s ecoconscious manufacturing world. However, beneath the hood of these machines are a number of velocity and injection power features that, when used correctly and repeatably by moulding operatives, result in faster cycle times and more stable start-ups. Even before any process optimisation steps have been introduced and expert setting knowledge has been imparted.
The advanced direct drive technology deployed by the IntElect series illustrates this point. Reducing a 10 second dry cycle time by just 0.55 seconds, for instance, can equate to an additional 2,274 cycles every day. Multiplied, this productivity improvement alone can add up to 14.3 extra production days!
MGS Technical Plastics is just one customer that observed an instant dry cycle time improvement of six seconds after switching from a Demag Ergotech 50ton to an IntElect2 50ton. “From these figures we can deduce that it equates to a 20 percent increase in cycles per year, giving MGS over 53 days of extra production capacity,” notes area sales manager Ashlee Gough.
When teams feel like you are invested in their development and future, they champion further process improvements.
As efficient as these state-of-the-art machines are, they are only as good as the people operating them. For teams and individuals to put their best efforts into their work, they need to feel engaged, confident and valued. When they do, quality rises and
productivity soars. These are the people you want to keep. They work harder, complete tasks to the best of their ability, deliver better customer service, question processes and are innovative problem solvers.
In-person field support and professional development courses plays a huge role in delivering the right diffusion of skills to maintain this proactive level of productivity engagement. “When teams feel like you are invested in their development and future, they champion further process improvements. This, in turn, has a lasting and invigorating effect,” reports MGS Technical Director Judson Smythe.
Nothing illustrates this point better than the eyewatering results gained when MGS participated in post-installation training. By optimising the machine set up, the Lancashire firm improved their ‘before training’ dry cycle times on the IntElect by a further 10.1 seconds. Compared to the original 29 second cycle time process, the optimised IntElect after training ran at 12.9 seconds. Resulting in over 761,000 more cycles per year, equating to 168 days of extra production “This on-site training helps even the most astute and skilled operatives to explore the full potential of features like parallel functions and how this supports the mould opening and closing speeds,” affirms Ashlee.
Adding robotics into the mix generates at least another five percent in higher productivity. More, if manufacturers can
introduce ghost shifts. To demonstrate the potential untapped after-hours production opportunities, this year’s Interplas showcase premiers a compact, fully-automated, compact IntElect75 ton turnkey cell. “Rather than operate split shifts or keep people in the factory until late at night, this cell illustrates to trade moulders and SMEs how they can confidently harness the benefits of automation when manufacturing standard components. To save costs, moulding firms may introduce ‘ghost’ night shifts to ramp up their manufacturing capacity even more. Equally, day-shift teams benefit from augmented workflow processes,” points out Managing Director Nigel Flowers.
For productivity to be sustained, marginal gains is the best approach. Every incremental improvement boosts productivity that little bit more. Providing polymer manufacturers with greater capacity to take on new customers and more projects. “Even in the most profitable organisations, there’s great potential for improving efficiency and workforce competence. The key is to start with the basics; correct operation and setup times; review manual and automated routines; optimise machine cycle times, etc.,” states Nigel.
Find out more and pick up your copy of the Sumitomo (SHI) Demag Processing Productivity Whitepaper at Interplas, Hall 4, Stand C40 or download it today here: https://uk.sumitomo-shi-demag.eu/makemore-for-less
For further information, please visit www.sumitomo-shi-demag.uk
In any industrial facility, electric motors and drives are a strong source of harmonic currents and utility-level voltage distortion. Together, these can wreak havoc with plant equipment and the mains power supply. When GA Pet Food Partners, a dry pet food manufacturer, began designing a new treatment plant at its Preston site, it knew that it needed to design harmonic mitigation into the plans to prevent unplanned outages from occurring. During the design process, it approached power quality specialist CP Automation to find a solution.
Beginning its journey in 1972 as a mixed arable and livestock farm, GA Pet Food Partners is a private label family-owned and family-run business specialising in the production and delivery of pet foods. The company is headquartered in Preston, alongside an additional Preston facility and two sites in Chorley, Lancashire.
As part of the company’s expansion, GA was developing a new water treatment plant and an odour abatement plant with biobeds, to address any environmental impact the expansion may incur. Following treatment, GA would then sell these products onto its consumers. During the site design process, GA knew that the site would contain many drives, and that this could introduce risks associated with harmonics and adverse noise unless properly addressed.
Harmonic frequencies are multiples of the fundamental frequencies and usually cause distortion in the voltage and current waveforms. Any drive, power supply or other load causes a nonlinear current draw, which generates harmonics at various frequencies. For example, single phase switches, such as those found in computers, predominantly generate third order harmonics, while AC drives generate fifth and seventh order harmonics.
Third order harmonics are undesirable for GA’s operations, because they cause a sharp spike in the zero-sequence current, and therefore increase the current in the neutral conductor. Meanwhile, fifth and seventh order harmonics will go straight to
the transformer and can cause derating, as well as premature insulation when present in excessive amounts.
The need was also legislative. The latest Engineering Recommendation G5/5 raised the limit on the measurement of voltage harmonics, total harmonic distortion (THD) and sub-groups from the 50th harmonic (2.5 kHz) to the 100th (5 kHz). Given that the new water treatment site would include at least 40 motors — one of GA’s sites also had over 300 drives — it was clear that harmonic mitigation would need to be designed into any future facility. At this point, the pet food manufacturer turned to power quality specialist CP Automation for support.
To support GA’s engineering team with the design, CP Automation supplied five P300 active harmonic filters from Swedish cleantech company Comsys. Some were used for the design of the new site, while other filters were retrofitted to replace legacy units.
“The active harmonic filters are a specialist type of inverter that measure the harmonic load on the mains and generate the exact inverse to cancel out any noise,” explained Jayne Whittaker, engineering director at GA Pet Food Partners. “In doing so, the Comsys filters can correct power factor, which is
vital as power factor capacitors are highly vulnerable to harmonics and the insulation failure they cause.
“As we’ve continued to expand and add more to kit to our sites, this growth has compounded power quality issues,” continued Whittaker. “I first realised these challenges 24 years ago, but only in recent years has mitigation technology caught up so that we can now resolve them constructively and cost effectively. Previously, we would have to overrate equipment to account for harmonics, but this had cost and efficiency implications.”
By supplying the active dynamic filtering (ADF) units, CP Automation could help GA achieve Engineering Recommendation G5/5 compliance while reducing the premature failure rate of equipment, nuisance tripping and other issues.
The new ADF P300 units are designed for all size loads and are functioning as intended — eliminating harmonics and reactive displacement at GA’s site. Unlike other mitigation technologies, the Comsys units can correct both harmonics and power factor, which not only improves resilience against noise but also reduces the current drawn from the mains, meaning less power is consumed.
“One of the unique selling points of the P300 is its compact build and that it can deliver significant value with a minimal footprint,” added John Mitchell, global sales and marketing director at CP Automation.
“This was especially important for GA, who was looking for ways to expand sustainably and in a way that would futureproof its sites from adverse load behaviour.
“On one site, we managed to save the space of four large panels by retrofitting two in their place, achieving a 50 per cent reduction in footprint,” continued Mitchell. “The P300 units are an investment in GA’s future growth, freeing-up floorspace for additional equipment while protecting its sites from harmful power quality issues. We really enjoyed being a part of this project.”
For further information, please visit www.cpaltd.net
Your all-in-one solution
circuit protection solution for mechanical and plant engineering. The REX system combines power supply, communication, circuit protection and power distribution in one system.
Benefit from the comprehensive DC 24 V circuit protection solution for mechanical and plant engineering. The REX system combines power supply, communication, circuit protection and power distribution in one system.
E-T-A Circuit Breakers Ltd. +44 (0) 1296 420336 info@e-t-a.co.uk
www.e-t-a.co.uk
E-T-A Circuit Breakers Ltd. +44 (0) 1296 420336 info@e-t-a.co.uk
www.e-t-a.co.uk
YOUR BENEFITS:
Clear error detection, high transparency and remote diagnosis
BEYOND THE MOULD
Pentagon delivers a full turnkey solution for plastic injection moulding from one site of UK Manufacture.
With over 50 years’ experience you can be confident that your Bespoke Moulding project is in the hands of the experts for both mould tooling and repeat production.
Meet us at this years’ Interplas UK –26- 28 September at the NEC, Birmingham.
• Flexibility: Easy assembly, modularity and convenient adjustment
• Increased machines availability: Clear error detection, high transparency and remote diagnosis
• Time saving: Innovative and flexible connection technology
• Flexibility: Easy assembly, modularity and convenient adjustment
• Cost efficiency: No further accessories necessary
• Time saving: Innovative and flexible connection technology
• Cost efficiency: No further accessories necessary
www.pentagonplastics.co.uk | websales@pentagonplastics.co.uk Tel: +44 (0) 1403 264 397 |
Containerised UPS systems provide emergency backup power on a temporary basis. Power Continuity UPS containers available for various scenarios. From 100kVA to 3000 kVA temporary Uninterruptible Power systems for ‘must have’ critical contingency to prevent power loss during planned site works. ensuring reliable power supply to sensitive electronics, servers, and site operations.
UPS HIRE CONTAINERS FOR TEMPORARY POWER
UPS hire containers offer installation, maintenance, and support services, ensuring you can rely on an uninterrupted power supply throughout the temporary deployment.
All our containers are ‘walk inside’. Weather protected. Resilient Air Conditioning and remote monitoring.
UPS HIRE SYSTEMS - FLEXIBILITY
UPS hire temporary systems offer multiple advantages, including:
EMEGENCY POWER: UPS failure can happen anytime. Deployment can be arranged to position our UPS container on your site, complete with 25 metres of cabling to allow us to temporarily install our UPS system to support your site load.
BESPOKE CONTAINER: UPS hire systems can be customised to meet the specific power requirements of power requirement. Plan in advance to ensure we provide the right level of resilient UPS power for your critical site.
INSTALLATION: Whether temporary or long term hire, Power Continuity offer professional installation services, working day or out or hours.
REMOTE MONITORING: Power Continuity remote monitoring support with maintenance services, ensuring that businesses have uninterrupted power supply throughout the temporary hire installation.
UPS HIRE SYSTEMS- COMBINED WITH OUR EMERGENCY GENERATOR
Power Continuity UPS hire systems combined with our emergency generators:-
Healthcare: Hospitals and other healthcare facilities just don’t have enough power to ensure uninterrupted power supplies to their energy consuming medical equipment. UPS rental containers bridge that power gap. Especially with generator back up.
Emergency Generator: UPS rental containers have battery autonomy for up to 20 minutes but for extra resilience we recommend installing our temporary diesel generators to allow running for up to 72 hours. Back up power to the Back up UPS container.
Manufacturing: We can install short term UPS rental systems to increase your output capacity, without worrying about power spikes or brown outs.
www.powercontinuity.co.uk
Football Stadiums: UEFA televised matches must have UPS power protection. UPS hire systems to protect from power disruptions during high value ticket international events.
Data centres: UPS Failure happens. UPS hire systems can be deployed to site, ensuring uninterrupted power supply to data centres, with emergency generators, before power loss damages the reputation of your brand. Call Power Continuity when you need resilience immediately today.
Rotary Fly Wheel UPS systems
Rotary Flywheel UPS hire systems for motor drives and heavy loads.
Only Power Continuity has long term hire Rotary Flywheel UPS systems available
Power Continuity has containerised UPS resilient system from 30KVA N+1 up to 2 Megawatts all available, to be delivered to site, installed on a temporary basis.
Your Reputation requires reliable UPS temporary when you need it most-which can only mean – Power Continuity Ltd. – There when you need us 24-7.
For more information call us on 0845 055 8455.
Reliable temporary UPS hire when you need it most, can only mean –Power Continuity.
MICRONEL
Micronel dc blowers save space, energy and money compared to other air sources such as bulky side channel blowers and compressed air systems.
Saving energy not only conserves resources but is also good for the balance sheet. That is why machine and plant manufacturers as well as production companies rely on Micronel high-performance blowers in process control and automation applications. The reliable high-tech solutions enable new and more efficient application possibilities and promote independence in comparison with previous compressed air systems.
Thanks to their very small compact sizes, Micronel blowers are suitable for decentralised installations and can be placed adjacent to the relevant process reducing pressure losses incurred in long air supply lines and allows flexible installation without the need to install or relocate air lines. Dynamic blower control allows air supply to be called up as on demand as required, increasing the efficiency of the application.
Here is a simple example: compared to
and ease of use, M16 connector and has G¾ inch pipe threads for 32mm tight hose connections. The housing complies with protection class IP67 with connected suction and discharge ports.
The 2 stage U100H4 can generate over 165 mBar (16,500 pascals) of pressure and achieve free blowing air flow over 900 litres per minute (54 metres cubed per hour) all from a very compact small size package of 107mm x 107mm x 118mm. With typical power consumption of 100 – 180 watts depending on working point they can pay for themselves in energy savings after only a few months.
Micronel blowers are also extremely advantageous in suction and extraction processes, such as pick & place processes or vacuum holding or conveying technology. A full range of accessories are also available including air knives, filters, and anti-vibration mountings.
a conventional Air-Knife compressed air application, with an annual consumption of 60000 m³ air volume, a Micronel Radial Blower U100H4 (pressure 165 hPa, flow volume 820 l/min) with a power consumption of 100 watts pays for itself in energy savings after only half a year.
The compact U100 dc blower family features a tough full aluminium IP67 housing, efficient brushless dc motor with integrated electronic driver for plug n run capability
The performance and cost savings of the blowers is particularly evident in applications such as drying and cleaning processes, where high pressure and a considerable volume of air are constantly required.
Micronel specialise in High Performance Blowers and Fans, their fan and blower products meet the needs of industries with special performance characteristics – Medical, Electronics Cooling, Personal Protection, Packaging, Gas Analysis, Laboratory, Transportation, Process Control and many more applications. Micronel offer customers the widest choice of standard ultra-slim fans, axial fans and high performance high pressure radial blowers from UK stock and provide technical design support for modified products and client specific designs.
For further information, please visit www.micronel.co.uk
Micronel reduce operating costs with decentralised compact dc blower solutions
In a rapidly changing world, customers need the flexibility to source their cast and machined products from a range of locations to satisfy different requirements. Expromet Technologies Group makes it easy for customers to find the right casting and machining solution by providing a range of options and expert advice.
Expromet businesses are market leaders in their respective fields and offer extensive UK casting, machining and fabrication capabilities:
• Investacast is one of the leading suppliers of investment castings in the UK, with a manufacturing base in Devon
• Haworth Castings specialises in fullyfinished aluminium sand and gravity die castings from two production facilities in Hampshire
• Metaltech Precision offers high quality precision CNC machined components and fabrications from its state-of-the-art facilities in Somerset.
Expromet also has an extensive global supply chain, enabling each of the Group companies to help customers source high quality castings products from a range of international manufacturing partners.
Customers may opt to outsource their requirements for a range of reasons, such as leveraging lower labour costs and greater economies of scale. Haworth Castings, Investacast and Metaltech Precision each provide clear advice and guidance on the relative benefits of overseas manufacture for specific types of products.
Where outsourcing supply is the best solution, Expromet Technologies Group companies will provide a turnkey solution, taking ownership of technical development, logistics and relationship
management to deliver a fully integrated service to the customer.
Expromet is proud of its skilled workforce across all three businesses, and continues
to expand its capacity to deliver worldclass casting and machining solutions both within the UK and overseas.
“As a leading group of advanced precision casting and machining businesses we understand the need to manufacture quickly, efficiently and to the highest quality, safety and environmental standards,” says Expromet CEO Alistair Schofield. “Our customers know we will help them find the best solution for manufacturing their casting products, be it local manufacturing or international sourcing, and know they can trust us to deliver.”
To take advantage of Expromet’s UK manufacturing capabilities and global supply chain contact us on + 44 (0) 1271 866200 or email enquiry@expromet.com.
For further information, please visit www.expromet.com
Expromet Technologies Group makes it easy for customers to find the right casting and machining solution by providing a range of options and expert advice.
Industry is facing a multitude of diverse challenges to remain competitive amid skills shortages and greater product variety. In such a fast-changing market, flexibility, and the ability to make changes rapidly is crucial to success. Manufacturing is becoming increasingly automated, and robots need to be integrated into machines to improve resource utilization and enhance data availability across different components. Traditionally, robot control systems were fragmented and tailored for specific robot applications. However, that is now changing with an integrated robot approach that can help accelerate robot deployments, simplify work, and improve productivity.
Maximizing the full benefit of robots is becoming even more crucial as competition increases. There is a greater expectation on the production teams, whether that means achieving higher output, shorter lead times, or more product customization. But improving operational performance can be complex and challenging when robots, although a crucial part of the solution, are often on the boundary.
To ensure that production is flexible and optimized, robots must be fully integrated as a core piece of the control system. At first glance, that increases the complexity and adds further challenges to manufacturing. This integration must be as simple as possible to be a viable solution. In today’s
more-intelligent production operations, integrated robots can help speed up deployment with a simplified control system that allows organizations to build and validate programs more efficiently using digital engineering tools and a single, integrated design environment.
When embarking on a robotic integration plan, two approaches can be followed. The robot and control system can be connected via EtherNet/IP, or you can combine them into a single, unified system. The best methodology depends on each precise use case and will depend on the operation’s specific needs.
Better coordination between robots and other equipment in manufacturing can make operations more responsive to demands. In addition, connecting robots with information solutions, such as analytics, can help optimize processes and reduce downtime. Connectivity can transform more than how robots operate. Centralizing control in a single design environment and using the latest digital tools can improve how robots are programmed, deployed, and supported.
Speed is always crucial when designing a new cell or production line. When that involves coordinating separate robot and machine control systems, that can eat up the time and increase the pressure on delivery schedules. In the traditional scenario, both the core and robot control systems must be programmed individually. Trying to align their performance can be cumbersome and involve a lot of trial and error.
There are two paths you can take to achieve integrated robots. The first is to connect a dedicated robot controller to a Logix PLC via the standard, unmodified EtherNet/ IP protocol. Robot programs are written in either the robot vendor’s programming environment or via Rockwell Automation’s Studio 5000® robot integration features. The other option is to use a Logix controller and Kinetix® drives to control a robot arm directly. The Logix controller hosts the robot kinematics, and the entire program is made in Studio 5000 to direct all robot movement without a dedicated robot controller.
EtherNet/IP connection allows the robots to be effortlessly added to the control network
with a simple, single-cable connection. This makes it easy to meet different application requirements while providing access to the Logix platform. It facilitates more centralized control by sending commands that initiate robot movement, obtain status, change recipes, and modify configurations. The platform can operate with more clarity and control by performing essential functions from an HMI without needing a robot pendant.
EtherNet/IP allows organizations to deploy faster and streamline advanced safety functionalities. It speeds up identity configuration, communications, and I/O data transfer using EtherNet/IP Add-on Profiles. In addition, it creates a simplified, more easily managed safety network using CIP Safety. The robot appears and is handled like any other EtherNet/IP network safety device. Integrated robots help people across job functions do more with robots by significantly reducing the effort for programmers by writing, testing, and refining in the Studio 5000 environment. It allows organizations to leverage skilled engineers who are already proficient with Studio 5000 software to bring systems up to speed faster, with no need to train or wait for the availability of a specialized robot programmer.
To meet the needs of the smart factory, it is vital that robots can be rapidly deployed and that they are flexible and easily integrated into the entire plant network. The challenge here is that this entails workers being comfortable with multiple systems. This is where unified robot control comes to the fore, to provide a more straightforward catalogue-number-driven approach. It eliminates the need for dedicated robot controllers and programming environments. Instead, unified control is an out-of-the-box, catalogue-number-driven solution based
on configuration instead of programming. It is possible to select a robot vendor, drag and drop it into an Ethernet/IP network, and generate an automatic bill of materials. Dedicated robotics libraries can generate project files and faceplates for overall robot device status, diagnostics, path configuration, homing and brake control.
Digital engineering allows the control code to be tested and validated so that the mechanics and logic work harmoniously before the robot cell is built. It offers the ability to stress test the real-world performance of the robot system digitally, to confirm cycle rates and recognize any potential bottlenecks before implementing any changes. Working in a digital environment using digital twins, engineers can design, iterate, test, and prove solutions faster.
The benefits of a digital platform do not end at the design stage; it offers advantages across the entire cell lifecycle. By designing with Rockwell Automation’s Emulate3D™ software, it is possible to create more efficient, practical robot applications and advanced tools using data to better control, operate, and support the system.
Utilizing the digital twin allows programmers to reduce design time and costs by shifting essential controls programming tasks earlier in the project. This strategy lowers the risk by using virtual commissioning to diagnose and remedy late-stage issues early.
By better connecting the controllers or unifying them into one system, you can create robot applications with less time and effort. This has multiple benefits, including reducing engineering time and costs by programming the robot and machine together in one place and reducing complexity and footprint with a centralized control architecture. It allows organizations to deliver high-speed, highprecision operations more efficiently with better synchronization of the devices on the machine network.
For more info, please visit www.rockwellautomation.com/en-gb/capabilities/industrial-automation-control/robot-automation.html
Maximizing the full benefit of robots is becoming even more crucial as competition increases.
ViSWIR Hyper APO Features:
• Capable of fully corrected focus shift in visible and SWIR range (400nm - 1700nm)
• Achieves spectral imaging with a single sensor camera by simply syncing the lighting
Floating design adjusts focus for different wavelengths
8mm, 12mm, 16mm, 25mm, 35mm* and 50mm* (*2023)
ViSWIR Lite Features:
High transmittance at whole wavelength of 400nm - 1700nm by adopting hyper wideband AR coat
Outstanding cost-performance for single-wavelength lighting & narrow-band imaging
Compact design
5mm, 8mm, 12mm, 16mm, 25mm, 35mm, 50mm
The widest range of accessories on the market. Future-proof
Multiple sizes and combinations available. Productivity and well-being
YOUR PERFECT WORKSTATION
Suitable to any environment, application and industry. Concept workbench
The Treston 3D Configurator can be used to design an industrial or technical workstation that best meets your needs. To get started, all you need is a mobile phone or a computer with an internet connection; no downloading is required and using the software is free.
How do you know when a kitchen sink is about to clog and overflow? Most residential pipes are hidden, so food waste and product build-up can go unnoticed until it leads to damage. In manufacturing, leaving pipework unmonitored can lead to unexpected downtime and safety issues, particularly when working with thermal fluids, so proactive monitoring is the best way to prevent these problems. Here Clive Jones, managing director of thermal fluid supplier and condition management expert, Global Heat Transfer, outlines the steps of thermal fluid analysis for proactive fluid monitoring and how businesses can use the results to increase fluid lifespan.
Thermal fluids are designed to operate effectively for many years, but over time, operating at and maintaining high temperatures means that the oil will naturally degrade. Thermal fluid analysis provides a deep dive into the condition of the oil and allows businesses to gain expert advice about how to effectively maintain the fluid and the system. Analysis also ensures health and safety compliance with The Dangerous Substances and Explosive Atmospheres Regulations (DSEAR) of 2002 and UKEX (formally the Explosive Atmosphere Directive ATEX 137 in the UK).
To comply with relevant safety regulations, such as DSEAR in the UK, manufacturers must take proactive steps to reduce the risk of fire or explosion caused by working with dangerous substances. If this fluid is left unattended, for example, fluid degradation — where thermal oils can be broken down into carbon molecules that stick to the pipes — can occur, reducing heat transfer efficiency. If not monitored effectively, degradation may go unnoticed until it causes significant production issues and system failure, leading to costly downtime and risk to health and safety.
Instead of reacting to issues, regular thermal fluid sampling and analysis enables businesses to proactively monitor fluid condition and intervene before issues impact production, extending thermal oil lifespan and reducing maintenance costs.
Effectively monitoring heat transfer oil condition requires engineers to regularly
take samples of the oil and send it to a specialist for analysis. Historically, thermal fluid experts conducted seven tests, however, in our experience conducting eleven tests provides results that best reflect the reality of what’s happening inside the system.
Once the sample arrives to an impartial lab for testing, an analytical chemist will look at its appearance, looking at the colour and for any particulates in the fluid. Fluid colour can range from clear and bright, which is common to newer fluids, to hazy, which can be a sign of high-water levels, to dark, which shows there is a high level of carbon build up in the system. These initial observations are confirmed in later steps to ensure the thermal fluid specialist provides the best recommendations.
Testing the water content of the oil is vital to regulatory compliance. Any water in the system and oil will convert to steam and expand, increasing the pressure in the system. By analysing water content, analysts and heat transfer fluid specialists can advise on how best to reduce the risks associated with high pressure.
The next step is to test viscosity and assess the impact the fluid has on the system pumps. If a fluid is too thick, flow rate will reduce, increasing the pressure on the pumps. This reduced flow rate can
create hot spots in the system, leading to inconsistent heating or cooling of products that results in waste products, increased damage to the system and rising maintenance costs.
Measuring the level of carbon in the system is key to understanding the degree of system fouling. If the thermal fluid expert detects high levels of carbon deposits, it suggests that there is more carbon in the system, which can harden in the pipes, acting as an insulator. As a result, the entire system heat transfer efficiency will reduce and more energy is required to heat up the system. Manufacturers should consider how they can prevent carbon build-up as it can create hot spots that accelerate wear on the pipes and increase the risk of leaks.
Analytical chemists will then test the total acid number (TAN). If there is a high level of acid in the fluid, it can lead to increased corrosion of the system and accelerated carbon creation. By measuring this parameter, manufacturers can understand how the fluid impacts the pipes of the system, ensuring that they can slow down degradation and reduce the frequency of scheduled maintenance needed to replace corroded parts.
Particulate quantity and iron tests highlight the degradation of components of the heat transfer system. Both tests can show signs that there is wear in the system that needs addressing so that manufacturers can intervene before the wear turns into a dangerous leak.
Manufacturers should also look at the results of the Pensky-Martens Closed Cup flash point, Cleveland Open Cup flash point and fire point tests to reduce health and safety risks. The industry standard suggests that closed flash point of the fluid cannot be below 100 degrees Celsius, because it means the fluid could ignite at lower temperatures, so these tests are vital to understanding if the fluid is safe for use.
Once analysis is complete, the thermal fluid expert delivers a report to the plant manager, organising points into cautions, actions, or serious findings. At this point engineers
To comply with relevant safety regulations, such as DSEAR in the UK, manufacturers must take proactive steps to reduce the risk of fire or explosion caused by working with dangerous substances.
can take the recommendations and plan interventions based on the priorities in the report. Making a record of each result will also help plant managers in the long term. By monitoring thermal fluid condition over time and looking for trends, helping them to anticipate when the system will require maintenance before downtime occurs.
Maintaining an efficient heat transfer system is integral to productivity, so unlike domestic
pipes where a blockage may cause a minor overflow, manufacturers should consider how they can effectively monitor fluid inside the system. Thermal fluid testing can be complex, so manufacturers can work with thermal fluid experts, like Global Heat Transfer, to ensure they complete the process effectively and get an accurate representation of what’s happening inside the system. For example, by including Global Heat Transfer’s Thermocare® as part of a
preventative maintenance programme that aligns with the ATEX triangle, experts can offer both on-site and remote technical support to help manufacturers rapidly sample and analyse fluid. From this, manufacturers can track fluid condition, anticipate and resolve issues quickly and implement preventative measures to extend fluid lifespan, reduce downtime and the facility’s environmental impact, and ensure system compliance.
For further information, please visit www.globalhtf.com/heat-transfer-management/heat-transfer-fluid-analysis/.
Rotaflow swivels are regularly utilised in the following engineering sectors with tailored or stock designs for specific needs: Brewery, Chemical, Dairy & Farming, Food & Drink, Nuclear, Process & Plant, Drilling & Mining, Oil & Gas, Subsea, Water & Waste.
A Swivel Joint reduces costs by reducing the risk of leakage with its associated downtime. By fitting a quality designed swivel, you are improving your production capacity. Rotaflow are specialists in taking your bespoke requirements and being able to design a solution that can fit your budget, dimensions, materials, FAT/witness testing; hygienic and pressurised environments. We regularly test to Hyperbaric, Seal Life and conduct Temperature/Pressure/ Load Cycle Testing. We are ISO 9001:2015 certified.
We have off-the-shelf solutions, or we can redesign and in-house manufacture to enable a quick turn-around with minimal fuss and maximum design experience. Photo attached shows a batch of 3” Hardened Carbon Steel Swivels mid machining. These will be stocked and ready for the drilling industry when requested. Rotaflow have built up a reputation for providing reliable and quality designed products that resolve your engineering needs and we are proud to say many customers request our services over and over again.
To find out more please visit our website and/or give us a call. Tel: +44(0)1663 735003 | sales@rotaflow.com www.rotaflow.com
Swivel joints allow pipework to pressure 1/4” to 40” and beyond. Vacuum to over 20,000psi. Stock and bespoke production. Unique bearing/seal design for longer life.
ISO 9001 CE marked where applicable.
Tel: +44(0)1663
RMIG is the world’s largest manufacturer and supplier of perforated metal and its related products.
We know our customers’ requirements for price and quality and meet their demands with uncompromising service.
Not only do we offer standard and bespoke perforated metal sheets, we are able to offer you a range of secondary operations as detailed below.
With a continued investment in the latest equipment and a network of professional partners we are able to produce prime quality products and solutions – from a simple perforated sheet to the fully formed and coated custom made part.
Cutting
We can cut and shape perforated sheet to meet the needs of your nal application.
Levelling
For some applications a high degree of atness is required, we have processes in place to ensure our perforated coils and sheets meet with your most demanding requirements.
Rolling and forming
We can roll, bend and form perforated sheets to match your design.
We can offer powder coating and hot dip galvanizing solutions to meet your speci cations.
For more information please contact us tel: 01925 839610 | email: info.uk@rmig.com | www.rmig.com
Helapet
Our
For over 50 years, SeaShield™ corrosion control systems have provided enduring protection on jetty piles and marine structures from the devastating effects of corrosion. The recent addition of the SeaShield 70/80™ System is a response to the industry’s need for a robust, UVstable, easy-to-apply system designed specifically for submerged and shoreline pipelines situated in aggressive marine environments.
The SeaShield 70/80 System, from Winn & Coales (Denso) Ltd, was created by combining a waterdisplacing petrolatum tape and primer with a tough PVC-backed bitumen tape (the SeaShield 80™ System) and a moisture-cured glass-fibre reinforced outerwrap (from the SeaShield 70™ System). The resulting system provides exceptional mechanical and impact strength and is available in three variations to suit the level of protection required.
The flexibility offered by the SeaShield 70/80 System marked it as the ideal choice for a recently completed project on the West Sussex coast. Leith Hill Plant Ltd., on behalf of Arun District Council, applied the heavy-duty version of the system in stages, both off-site and in-situ, to protect newly laid pipe sections on two outfall pipes that had previously suffered significant damage from shingle movement.
Global chemical etching supplier Precision Micro has unveiled a further expansion of its manufacturing capacity and capability with the addition of a second new etch room at its Fort Dunlop-based site in Birmingham, UK.
In an investment totalling £1.8 million, the etch room is home to three new highly efficient etch machines alongside a bespoke semi-automated print frame.
Believed to be an industry first, the business’s new print frame boasts a design that minimises human input in printing photoresists onto larger sheet metals up to 1500mm x 600mm in size, increasing throughput and delivering cost savings to its customers. Furthermore, the shift towards a more automated approach enhances component quality by eradicating the issue of foreign object debris which can impact the photochemical etching process, as well as reducing the manual handling of heavier materials.
Driven by global demand for nextgeneration energy technologies such as hydrogen production and storage, carbon capture, green energy buffering, electric and hydrogen electric vehicles, the expansion enables Precision Micro to supply larger, thicker etched sheets in higher volumes. Supplying enabling components such as printed circuit heat exchanger flow plates for waste energy recovery and hydrogen pre-coolers, busbar battery interconnects for EVs and bipolar plates for fuel cells and
electrolysers used for hydrogen production, the investment will support companies looking to productionise these products and overcome capacity constraints in the existing supply chain.
Karl Hollis, Precision Micro’s Director of Engineering, said: “We’ve worked closely with our suppliers to ensure all the new equipment is developed in line with our ESG strategy, automating many parts of our manufacturing process using less power to achieve the same consistent results. Chemical etching is often the only appropriate method for manufacturing the precision components needed for many emerging renewable technologies. This latest £1.8 million investment marks the next stage of our expansion, and we are excited to be able to support our customers’ rapid growth.”
In 2019, Precision Micro invested £5.1 million in plant and new equipment, a move which increased the business’s etching capacity by 30% which in turn opened new opportunities within sustainable energy markets. The latest addition has increased this by a further 40%.
Precision Micro also plans to add a fourth etch machine to its new etch room in early 2024.
For further information, please visit www.precisionmicro.com
This latest £1.8 million investment marks the next stage of our expansion, and we are excited to be able to support our customers’ rapid growth.
As a company that specialises in industrial 3D printing for low volume manufacture and batch production, 3DPRINTUK continues to grow at an impressive rate. The Londonbased company is unwavering in its use of high-end 3D printing systems to bridge the significant gap that exists between prototype and injection moulding. 3DPRINTUK provides an invaluable service for a wide range and growing number of customers where tooling costs are prohibitively expensive for their product or the volume demanded by injection moulding is excessive.
According to Nick Allen, 3DPRINTUK’s CEO: “Our primary focus is absolutely low volume and batch production. As a result, we are seeing new and repeat customers using our service to manufacture their parts. We are consistently manufacturing more than 1 million parts annually and the numbers keep going up. However, because of the nature of the 3D printing processes and our focus on quality, we can produce parts in volumes of 1, 10, 100, 1000 or 10,000 parts, so we can still offer a high-quality prototyping service for our customers that are in a new product development phase. They can test and quickly iterate their parts using our service, before using the same machines for manufacture.”
Over the last 12 months, 3DPRINTUK has taken the company to an even higher level, not least by becoming part of the Trimech Group through acquisition by Solid Solutions. With an approach based on the premise “if it’s not broken, don’t fix it” this move has solidified 3DPRINTUK’s position as a leading 3D printing service provider while extending its resources and supporting further growth.
Some key goals have been the foundation of 3DPRINTUK’s success over the last year, notably the company achieved ISO 9001 certification at the end of 2022. Quality has always been at the heart of the 3DPRINTUK service, but this certification provides reassurance to customers that the company operates at the highest levels for quality assurance and validation of 3D printed parts on a daily basis, in full compliance with the ISO 9001 standard.
Alessandro Catania, Quality and Compliance Manager at 3DPRINTUK stated at the time: “It is really gratifying after going through the extensive ISO 9001:2015 process to be notified that there are zero findings. Quality and quality assurance are a central feature
of all of the manufacturing and production services that we offer. And now we can prove it. By achieving ISO 9001 certification, we can demonstrate that all of our systems, processes and procedures meet the high demands that this certification requires for all of our 3D printed parts.” Following this successful outcome, 3DPRINTUK is in the process of qualifying for ISO 14001.
3DPRINTUK has also strived to ensure the company is run in full alignment with its stated values. Undertaking its Road to Net Zero initiative was essential to this and earlier this year, 3DPRINTUK set itself an ambitious target to become the first fully certified, net zero 3D printing bureau by the end of 2023 and to be the first 3D printing service to offset 100% of its plastic output. Achieving certified net zero is no easy task, but the company takes climate change and its impact seriously and this is the driving force behind its roadmap.
Allen went on the record, saying: “As a manufacturer of plastic parts, we cannot hide from the environmental impact of plastic on the environment. However, we also believe that plastic materials continue
to offer benefits and do have a part to play in a sustainable economy. This can be seen in the way that plastics can replace some metals making parts and components that are lighter in weight.”
Just a few months later, in June, 3DPRINTUK was able to announce that it had indeed achieved certified carbon neutral status and is the first 3D printing service bureau to do so.
It is not all that surprising then that 3DPRINTUK has continued to experience significant growth. One independent testament to this, was 3DPRINTUK being named as one of Europe’s fastest growing companies in 2023 on the FT 1000. This appearance was based on an absolute growth rate of 171.6% over the last four years. The list also highlighted how 3DPRINTUK is the third fastest growing manufacturer in the UK.
Inside the facility, the company’s fleet of 3D printers has grown significantly and now includes 14 in-house EOS SLS machines, four HP 5210 systems and a recently installed Stratasys SAF H350 industrial 3D printer. These machines are all complemented by a full DyeMansion suite of post processing equipment, which has also expanded significantly over the last 12 months. So much so, that the company is currently in the process of expanding the facility’s footprint to 15,000 square feet, adding an additional 5,000 square feet in the form of a new building in the same location, that will become a dedicated post processing hub.
The heart of 3DPRINTUK, however, is the team of talented and experienced people that offer a wealth of expertise. This expertise is not just dedicated to running the machines for optimum, high-quality output, but also
for software development and customer partnerships and liaison. The core team at 3DPRINTUK has now grown to 25 people, with sound leadership in each department.
The low entry cost of the 3DPRINTUK service sets it apart from other manufacturing options. With a minimum order of just £40, the service is open to a vast potential client base spanning across diverse sectors, and enabling the company to cater to a wide range of industries, as mentioned above, from volumes of 1 through to 10,000. 3DPRINTUK partners with clients working in sectors ranging from Cycling & Sport Technology to Marine & Subsea equipment; across Academia and the Creative industries; as well as Green Energy, Autonomous & Electric Vehicles, VR, Prosthetics & Robotics. The company also supplies a significant number of Design Consultancies with high end, functional prototypes and low volume production parts.
Third party testimonials are perhaps the surest way to garner understanding of how a company operates and delivers for its clients.
Below are just a couple, that speak to the capabilities and capacity of the 3DPRINTUK service:
Andrew Magnier, Founder of MagCAD, has utilized the company’s service for a number of years to develop and manufacture parts for his cycling business: “3DPRINTUK’s instant online pricing model showed us that its costs were very competitive and would scale well with our business. Initial test runs also demonstrated that the quality of parts is outstanding and the 3DPRINTUK team is very communicative and knowledgeable.” MagCAD now regularly places repeat orders for production parts.
Jeremy Sitbon, Chief Robotics Engineer – Marine Robotics Systems at ecoSUB Robotics also regularly use the 3DPRINTUK service for the production of some key parts for their underwater, autonomous vehicles. He said, “We are constantly on the look-out for the most cost-effective 3D printing solution for our underwater vehicles, but we cannot compromise on quality at all…. We will continue to use 3DPRINTUK as we have not found an on-line ordering system that comes close to theirs in terms of ease-of-use, and the team has an enormous depth of knowledge in material selection, DfAM, and print optimisation that benefits us on every level.”
The future is looking bright for 3DPRINTUK with continued growth and strengthened client partnerships for production applications featured high on the agenda.
For further information, please visit www.3dprint-uk.co.uk
3DPRINTUK’s instant online pricing model showed us that its costs were very competitive and would scale well with our business.
Linear motors are ideal for fast and accurate motion in a machine.
Linmot, the leading manufacturer of cylindrical linear motors, has made them even more suitable for demanding products that require exceptional cleanliness in the production environment. This has always been demanding for machine designers, but has been made much easier by using the Linmot DM01 Linear motor modules.
The DM01 Linear modules provide high precision positioning while supporting high loading with the following features:
• Stroke up to 575mm and peak force up to 572N
• Direct load mounting up to 30kg
• Clean Design
• No Slider lubrication is required.
• Higher stiffness / lower bending
• Load balance (MagSpring) & pneumatic holding brake option
• Can be combined to form two-axis systems
• Are available certified for Clean Room Applications.
The latest option that has just become available is the addition of a force sensor combined with force control software.
This is an option that can be added to any of the DM01 modules.
Just to demonstrate how sensitive, you can place an egg between two DM01 modules, one equipped with the new Force sensor.
One DM01 module moves with a programmed movement while the other follows while maintaining a precise 5 N force at all times to hold the egg without breaking it as shown in the picture.
A video of this application is available on our website (see below).
Using a regular force sensor requires precision alignment or measurement error will occur.
Linmot’s special design provides excellent
measurement accuracy even with axially offset loads or with side loading from an attached load (such as a gripper for example).
Here is a section through the sensor to show how the load is guided combined with the special design of the sensor itself.
While handling such delicate tasks, it can also handle up to +/- 500N of force combined with an accuracy of 1%.
This exciting new option opens up many new applications and makes the Linmot DM01 a unique and powerful new tool for the machine designer who needs sensitivity as well as force and dynamic speed.
For more information, please contact Quin Systems on 0118 977 1077 or sales@quin.co.uk. Website: www.quin.co.uk/linmot
…
EEMUA's MIPC® course helps practitioner-level engineers to be where needed on-site, and to stay on top of the latest industry developments and good practice in primary containment of hazardous substances – including in pressure systems. Blending live online classes, e-learning, and one-to-one sessions with expert tutors, enhanced by a mentor’s support and guidance throughout, EEMUA’s Mechanical Integrity Practitioner Certificate course delivers in-depth training to engineers where they work – giving professionals the flexibility to learn, on-site or on-call, for industry-recognised 5-year certification.
Registration open now for the next MIPC course. Learning starts 23 October 2023.
Induction of 2 hours to fit diaries from September 2023 adapts coursework to the engineering needs of each Learner and their site/s.
For more information please contact online-learning@eemua.org
+44 (0)20 7488 0801 www.eemua.org
Cupio Services provides x-ray, acoustic, optical and electronic test, inspection and analysis services.
If you only require inspection, test or analysis services occasionally throughout the year, the requirement to purchase our equipment may not be necessary, this is where Cupio Services is the answer.
• Cutting-edge inspection and test equipment
• Functional testers and counterfeit part detection
• High resolution x-ray with multiple CT imaging options
• Acoustic microscopes for delamination detection within boards or complex devices
• Full failure analysis reports.
Speak to one of our experts today:
Cupio Services Ltd
+44 (0) 1256 262800
info@cupioservices.co.uk
www.cupioservices.co.uk
Beechwood, Chineham Business Park, Basingstoke, Hampshire, RG24 8WA
We design and manufacture disc-based gravimetric blending equipment as well as material loaders for all plastics processing. Our equipment is engineered to make plastics processing easier and more cost efficient.
We put our combined 75 plus years of experience in plastics processing to use in the development of Plastrac’s Auto-Disc™ systems to provide you with versatile and effective machinery that will exceed all of your blending requirements.
Plastrac was established in 1995 in order to provide the best, most affordable, most effective, easy-to-operate blending systems available to market. We continually strive to keep our customers online and producing only the best product which fully meets the requirements of their respective customers and consumers.
We surround ourselves with outstanding employees who take the utmost care in the assembly of all Plastrac machinery and take pride in their work. Our knowledgeable staff is available to provide assistance should the need arise. Plastrac is here to supply your company with the latest blending technology available and is committed to support it for years to come.
Plastrac offers a variety of gravimetric material blenders and loader systems that are ideal for a multitude of plastic processing methods. Our plastic processing machines and auxiliary equipment is engineered
and loading systems synchronize in real-time with plastics molding machines to provide an accurate and consistent material mixture with no mechanical mixing. The Auto-Disc™ material feeder is engineered for quick material changeovers to reduce downtime. Our gravimetric blending systems will handle just about any injection, extrusion, or injection blow molding application. Disc based metering allows our equipment to cost-effectively feed at a wide range of throughputs without compromising consistency. The Auto-Disc™ can be configured into self-contained systems with material feeders and loaders that are all operated from a single controller.
Our newest innovation – ColorStream™ –is a Blending Revolution.
ColorStream is not just another cart system. It feeds colors and additives from the plant floor in real-time and transports them to the machine throat to blend with the main resin still being flood-fed out of the central loading system. ColorStream eliminates the need for climbing to the top of process machinery to change canisters or perform maintenance. It increases safety, slashes capital equipment costs, saves time, labor, and energy, and allows even faster color changes. So no more climbing on top of presses to perform maintenance or move blenders! ColorStream can easily be moved from machine to machine, and is nearly 100% maintenance-free. It also works for almost all injection molding, injection blow molding, extrusion, and PET applications.
LED performance, efficiency and durability are tied not only to the lights themselves, but also to the drivers that operate them. Russell Parr, CEO at PowerLed, highlights what to look for when sourcing LED drivers.
Innovations in LED technology are providing lighting designers and contractors with increasingly sophisticated options. However, a crucial component of bringing these options to life is driver technology.
Drivers are responsible for converting, regulating, and supplying the appropriate electrical power to ensure the optimal performance and longevity of LEDs. As with LED systems, driver technology is not static or universal – every application requires a specific driver, the quality of which has a significant impact on the project’s result. This makes it vital to assess LED driver suppliers and their products when scoping a project.
Because LEDs must operate failure-free in a variety of conditions, the drivers that power them should be durable, reliable, stable, and efficient. As such, there are several factors to consider when selecting drivers to ensure optimal performance. These include voltage and current ratings, power capacity, dimming capability, compatibility, efficiency, and reliability.
Higher-grade components should not be a nice to have but ‘non-negotiable’, particularly when selecting LED drivers. This is because it will ensure they:
• Offer good thermal behaviour, meaning all facets function safely
• Can withstand voltage spikes, which pose a particular challenge for control gear
• Boast a reduced ripple value, which serves as a solid performance indicator
• Have no-load, overload, thermal and short-circuit protection, to resolve potential installation issues
• Are EMC compliant, with the appropriate testing and certification
What’s more, the quality of the components used to manufacture drivers has an immense impact on power factor – the ratio of real power used compared to apparent power into the circuit or more simply put, how efficiently the electrical power is consumed. While there may be several contributing factors, inefficiency can often be attributed to poor driver design or low-quality components.
As a key element of any LED lighting system, the quality of the driver is crucial. Ultimately, LED drivers built with premium components will help to achieve the optimal performance, safety, longevity, and sustainability of a LED lighting system.
The range of available LED drivers can make it challenging to choose the right solution – and the right supplier. This is further complicated by the fact that not all manufacturers provide the same quality or depth of technical information on their products, leaving electrical contractors unable to make accurate comparisons.
With this mind, a good place to start is by looking for best-in-class solutions from accredited suppliers with a reputation for honesty, and excellence. Also add Energy-related Products (ErP) compliance to the list of criteria.
The ErP directive is an eco-design directive intended to encourage manufacturers and importers to provide products that are more energy and resource efficient, and adherence to this directive shows that a supplier’s products meet the energy guidelines set out by the EU.
In addition to product peace of mind, working with reputable and compliant suppliers will result in other benefits, from energy savings and reduced maintenance costs to longer LED lifetime, overall reduction in the cost of ownership, and reduced environmental impact.
Working with a trusted and established supplier like PowerLed, part of Sunpower Group Holdings LTD, will result in a dependable, high quality ‘fit and forget’ solution.
The company’s range of drivers is suited to both indoor and outdoor installations and, in addition to standard features such as power factor correction, high efficiency, compact size and isolated or non-isolated design, boasts unique advantages – they are CE approved, meet stringent safety certification, and offer a warranty of up to 5 years.
Besides its status as an official Tier 1 MEAN WELL partner, meaning it provides access to more than 4,000 products from one of the largest switching power supply manufacturers in the world, the ErP compliant company’s UK-wide network offers expert advice, bespoke technical design support, as well as premium LED drivers and lighting solutions for a range of residential, commercial, and industrial projects. Moreover, all its products meet both environmental and performance criteria while offering value for money.
For more information, visit https://www.powerled.uk.com/
As with LED systems, driver technology is not static or universal – every application requires a specific driver, the quality of which has a significant impact on the project’s result.
Retaining all the features of the standard (steel, aluminium and stainless steel) version of the Huck® Magna-Lok® structural blind fastener, the 316 A4 stainless steel Magna-Lok® also offers corrosion resistance beyond anything else in the Huck® blind fastener range.
Huck® Magna-Lok® structural blind fasteners are mechanical fasteners designed to join two or more materials together in situations where access is limited to only one side of the joint.
What is the difference between a Rivet and a Huck® structural blind rivet?
A Huck® structural blind rivet retains the pin in the rivet body (sleeve) post-installation for extra tensile and shear strength. This 360° internal locking technology enables the pin to be mechanically locked to the sleeve as it expands during installation, giving excellent joint tightness and highquality resistance to liquid penetration.
The Huck® 316 (A4) stainless steel MagnaLok® is available in 6.4mm (1/4’’) diameter, with a wide grip range to accommodate variations in joint thickness (2.03mm -15.88mm).
316 Marine Grade (A4) stainless Steel fasteners are specialised types of fasteners made from stainless steel alloy 316, which is also known as A4 stainless steel. These fasteners are designed to provide excellent corrosion resistance, making them particularly well-suited for use in corrosive environments. Here’s more information about them.
Key advantages of 316 marine grade, non-magnetic Huck® fasteners: Non-Magnetic Properties: Non-magnetic fasteners are essential in environments where magnetic fields can disrupt sensitive electronic components or equipment. Industries such as medical imaging, telecommunications, and aerospace benefit from non-magnetic fasteners to maintain equipment performance. MRI scanners operate using powerful magnetic fields, and any magnetic interference can disrupt the accuracy and quality of the images. 316 stainless steel in non-magnetic variants, is chosen to prevent unwanted interactions with the magnetic field,
ensuring that the material does not affect the scanner’s performance
1. Flush pin break eliminates grinding and filling, leaving an even surface
Strength and Durability: Huck® fasteners provide strong and reliable joints, often with load-carrying capabilities comparable to or even exceeding traditional fasteners. 316 stainless steel offers high tensile strength and durability, allowing fasteners to withstand significant loads and stresses.
2 Unique solid-circle lock ensures maximum strength and resistance to vibration. The potential for pin push-out is virtually eliminated
3. Excellent gap pull-out and high retained clamp
Ease of Installation: Huck® Magna-Lok® structural blind fasteners are relatively easy to install, requiring minimal access to only one side of the joint.
Vibration Resistance: Huck® fasteners offer excellent resistance to vibration, making them suitable for applications where the joint might experience movement or mechanical stress.
Corrosion Resistance: The primary advantage of using 316 stainless steel fasteners is their exceptional resistance to corrosion, making them ideal for applications exposed to moisture, saltwater, and other corrosive elements, such as marine environments.
Aesthetic Appeal: The smooth and polished appearance of stainless steel 316 gives a visually appealing finish to the fasteners, making them suitable for applications where aesthetics matter.
Wide Range of Applications: 316 stainless steel fasteners find use in various industries, including marine, construction, outdoor structures, architectural projects, and more.
Low Maintenance: Thanks to their corrosion resistance, Huck® fasteners generally require minimal maintenance over their lifespan.
Versatility: They can be used to join different materials, including metals and composites, expanding their applicability across industries.
Replaces Welding: In some cases, 316 Magna-Lok’s can replace the need for welding. 316 stainless steel is susceptible to weld decay; the welded area can be more vulnerable to corrosion, weakening the bond of the weld. Weld decay primarily affects the microstructure of the material around the weld joint. When 316 stainless steel is heated to certain temperatures (typically in the range of 800 to 1600°F or 425 to 870°C)
welding,
steel combines with chromium to form chromium carbides. This process depletes the chromium content in the immediate vicinity of the weld joint, leading to a reduced ability to form a protective chromium oxide layer that provides the stainless steel’s corrosion resistance.
1. Flush pin break eliminates grinding and filling, leaving an even surface
2 Unique solid-circle lock ensures maximum strength and resistance to vibration. The potential for pin push-out is virtually eliminated
3. Excellent gap pull-out and high retained clamp
4 The sleeve expands during installation to fill the hole and create a moisture-resistant joint
Mechanical advantages: these include, excellent gap closure capability, a flush pin break and outstanding hole filling on the blind side and is capable of filling irregular, slotted, oversized, or misaligned holes, whilst providing strong, vibration resistant joints.
Composition of 316 (A4) Stainless Steel: 316 is an austenite stainless steel which contains 18 percent chromium and 12 percent nickel. Steel is considered stainless when its chromium content is at a minimum of 10.5 per cent. Therefore, a higher content will result in an enhanced corrosion resistance. Unreactive chromium III oxide can form on a component’s surface, protecting the metal beneath from the environment. Nickel further increases the corrosion resistance of the resultant alloy.
Applications of 316 Marine Grade (A4)
Stainless Steel Fasteners: Marine Industry: These fasteners are extensively used in the marine industry due to their ability to resist corrosion caused by saltwater and exposure to the marine environment (but it is not resistant to warm seawater). They are used in boat construction, docks, piers, off-shore equipment and other maritime applications.
Outdoor Construction: Stainless steel 316 fasteners are popular for outdoor construction projects like solar plants, wind energy application, bridges, guardrails, and outdoor furniture, where exposure to the elements is a concern.
Chemical Processing: The corrosion resistance, along with its ability to withstand extreme temperatures, makes 316 stainless steel suitable for use in chemical processing plants where exposure to corrosive chemicals is common.
Food and Beverage Industry: In facilities where hygiene and non-toxic materials are crucial, 316 stainless steel fasteners are used for equipment, machinery, conveyors / packing (trolleys) and structures.
Medical Applications: 316 stainless steel fasteners are commonly used in medical applications where corrosion resistance and durability are essential. Medical devices and equipment often require materials that can withstand the harsh conditions of sterilization processes, and long-term use without compromising safety or performance.
While 316 stainless steel provides excellent corrosion resistance, no material is entirely immune to corrosion. It’s essential to
choose the appropriate grade based on the specific environment and type of exposure the fasteners will face. In certain extremely harsh environments, specialized coatings may need to be considered for added protection. Grade 316 stainless steel stands out as an extremely adaptable substance, presenting remarkable mechanical traits and unparalleled resistance against corrosion in contrast to alternative steel variants presently accessible in the market.
The Huck® Range Force® (GBB-BV4500118KT) is the latest addition to the Huck® battery installation tool range. Designed to revolutionise the world of battery installation tooling by providing flexible, durable, and consistent installations of structural fasteners for use on the production line or in the field, there are also hydraulic and pneudraulic (air) options available.
Star Fasteners engineering support services enhance customers experience – we can assist with design, development and testing right through to choosing installation tooling, correct fastener installation and process optimisation.
For further information, please call +44(0)1159324939 or visit www.starfasteners.co.uk
Thanks to their corrosion resistance, Huck® fasteners generally require minimal maintenance over their lifespan.
HEATSENSE CABLES
Heatsense Cables, www.heatsensecables co.uk, established in 1984, is regarded as the UK’s leading specialist high-performance thermocouple and signal cable manufacturer. Its manufacturing capabilities cover a broad range of specialist cables that operate in extreme environments, -196°C to +1,250°C. The company is a technology leader in fluoropolymer extrusion, high-performance taping and cable wrapping. Related processes include cover sintering, colouring, etching and the application of various specialist coatings. The range covers cables that are resistant to flame, oils & chemicals and which operate in ultra-high vacuum, cryogenic and high radiation environments.
Heatsense Cables, www.heatsensecables. co.uk, established in 1984, is regarded as the UK’s leading specialist high-performance thermocouple and signal cable manufacturer. Its manufacturing capabilities cover a broad range of specialist cables that operate in extreme environments, -196°C to +1250°C. The company is a technology leader in fluoropolymer extrusion, high-performance taping and cable wrapping. Related processes include cover sintering, colouring, etching and the application of various specialist coatings. The range covers cables that are resistant to flame, oils & chemicals and which operate in ultra-high vacuum, cryogenic and high radiation environments.
technical design and manufacturing service and undertakes development work on new cable designs and materials.
The company offers a bespoke advanced technical design and manufacturing service and undertakes development work on new cable designs and materials.
INSULATION & BRAIDING EXPERTS
PFA, FEP, PTFE, ETFE, EFGLAS, SILICONE, PE, PU, PVC, Taped & Sintered PTFE, Polyimide & Aramid Yarns, PTFE impregnated yarns and Mica. Braiding materials include glass, quartz & ceramic fibres, other specialist yarns and various metals.
PFA, FEP, PTFE, ETFE, EFGLAS, SILICONE, PE, PU, PVC, Taped & Sintered PTFE, Polyimide & Aramid Yarns, PTFE impregnated yarns and Mica. Braiding materials include glass, quartz & ceramic fibres, other specialist yarns and various metals.
The high-performance cable range includes thermocouple cables, RTD cables & PRT
The high-performance cable range includes thermocouple cables, RTD cables & PRT
wires, sensor wires & cables, micro-wire & miniature cables, cryogenic cables, heat resistant cables & wires – the INTEMP™ range of cables, glass fibre, quartz, ceramic & pure nickel cables, radiation resistant wires & cables, equipment wires, UHV & low outgassing cables, high-voltage wires & cables, micro-coaxial cables, bespoke cables, multicore cables, high flex braided cables, PTFE yarns and PTFE cable tapes & cords
wires, sensor wires & cables, micro-wire & miniature cables, cryogenic cables, heat resistant cables & wires – the INTEMP™ range of cables, glass fibre, quartz, ceramic & pure nickel cables, radiation resistant wires & cables, equipment wires, UHV & low outgassing cables, high-voltage wires & cables, micro-coaxial cables, bespoke cables, multicore cables, high flex braided cables, PTFE yarns and PTFE cable tapes & cords.
See our base online catalogue https://www.heatsensecables.co.uk/products/ heatsense-cables-product-catalogue
See our base online catalogue https://www.heatsensecables.co.uk/products/ heatsense-cables-product-catalogue
Heatsense continues to add and upgrade specialist plant & equipment, build on internal
Heatsense continues to add and upgrade specialist plant & equipment, build on internal
systems & software, add accreditations and undertake development work on new materials and processes to support customer needs and requirements, including keeping abreast of changes in legislation.
systems & software, add accreditations and undertake development work on new materials and processes to support customer needs and requirements, including keeping abreast of changes in legislation.
Markets include aerospace, space, nuclear, automotive, medical, R&D, oil & gas and general industry.
Markets include aerospace, space, nuclear, automotive, medical, R&D, oil & gas and general industry.
Heatsense is EN9100:2018, ISO9001:2015, ISO14001:2015 Accredited, F4N (Fit for Nuclear) Approved, Cyber Essentials Plus Certified, JOSCAR Approved and a Member of ADS.
Heatsense is EN9100:2018, ISO9001:2015, ISO14001:2015 Accredited, F4N (Fit for Nuclear) Approved, Cyber Essentials Plus Certified, JOSCAR Approved and a Member of ADS
For further information please visit www.heatsensecables.co.uk and/or contact sales@heatsensecables.co.uk
Thermocouple Cables RTD Cables & PRT Wires Sensor Wires & Cables Micro Wires & Miniature Cables
Thermocouple Cables RTD Cables & PRT Wires Sensor Wires & Cables Micro Wires & Miniature Cables
Heat Resistant Cables & Wires for Extreme Temperatures
Heat Resistant Cables & Wires for Extreme Temperatures
Glass Fibre, Quartz, Ceramic & Pure Nickel Cables
Glass Fibre, Quartz, Ceramic & Pure Nickel Cables
Equipment Wires & Cables UHV & Low Outgassing Wires & Cables
Equipment Wires & Cables UHV & Low Outgassing Wires & Cables
INTEMPTM Range of Cables
INTEMPTM Range of Cables
Radiation Resistant Wires & Cables
Radiation Resistant Wires & Cables
High-Voltage Wires & Cables
High-Voltage Wires & Cables
Micro-Coaxial Cables
Micro-Coaxial Cables
Bespoke CablesMulticore CablesHigh Flex & Braided Cables
Bespoke Cables Multicore Cables High Flex & Braided Cables
PTFE Yarns, Lacing Tapes & Cords
PTFE Yarns, Lacing Tapes & Cords
A member of
Rotzinger Group, a leading provider of automation solutions, is set to showcase its advanced Hygienic Conveyor for dry cleaning and the Robot with an Integrated Buffer at two upcoming events. One of the first customer projects utilizing the groundbreaking Hygienic Conveyor technology will be presented at an in-house show by Transver, located at Zürcherstrasse 42, 8852 Altendorf, Switzerland, on 17-18 August. In addition, the innovations will be highlighted from 22 to 26 October at iba Munich, booth B-470. Designed for confectionery and bakery products, the hygienic conveyor is optimized for dry cleaning, ensuring compliance with stringent food safety regulations in European food manufacturing. Leveraging decades of expertise in pick and place delta robots, buffering and conveying, the new integrated solution from Rotzinger combines flexibility, compactness, and ease of operation to boost uptime and reduce the total cost of ownership.
“We are thrilled to have the opportunity to connect with our European customers and prospects in the food sector at the inhouse show and iba Munich,” says Christian Vouillamoz, product manager, Rotzinger Group. “Our Hygienic Conveyor for dry cleaning and Robot with an Integrated Buffer have been specifically designed to tackle the escalating concerns regarding efficiencies and heightened sanitary requirements in food production. With their intuitive controls and streamlined design, these solutions aim to enhance productivity and optimize operations.”
Foodborne illnesses affect a significant number of individuals in Europe each year, highlighting the importance of preventing contamination and bacterial buildup in food production facilities.
Rotzinger has developed a Hygienic Conveyor for dry cleaning, specifically designed to address food safety concerns and adhere to the highest hygienic standards. This innovative conveyor incorporates an intelligent cleaning design,
featuring a foldable belt and beveled or rounded horizontal surfaces that prevent the accumulation of dirt particles and crumbs, thereby reducing the risk of mold infestation. The side panels no longer run horizontally parallel to the belt, but are inclined at 45 degrees to allow easier shedding of product residue. A hinged belt support enables easy access for efficient cleaning and maintenance. The conveyor’s stainless-steel construction ensures durability and long-lasting performance.
Furthermore, the Hygienic Conveyor provides flexibility in size range, accommodating a wide range of requirements. It offers width options ranging from 150 to 1800 mm; and length options from 400 to 35,000 mm, allowing it to meet the most challenging layout requirements with ease.
The Covid-19 pandemic has significantly impacted Europe’s economy and labor market, causing a precipitous decline, as highlighted in the EURES Report on labor shortages and surpluses 2022 . This downturn has been further emphasized by projections from the Institute for Employment Research (IAB) , which predicts a potential workforce reduction of seven million in Germany by 2035. In response to these challenges, Rotzinger Group has developed the Robot with an Integrated Buffer. This advanced machine is capable of efficiently picking and placing both unpacked and packed products into various packaging formats, including cartons, cases, thermoforms, flow-wrappers, and cartoning machines. In doing so, it offers a viable
solution to address labor shortages, while also optimizing production processes in the face of adversity.
With its modular design and flexibility, this integrated solution combines delta robots, buffers and conveyors in one cell with a reduced footprint, enabling greater efficiency, productivity and cost-effectiveness. The use of a single controller and a unified setup philosophy enables hassle-free maintenance and straightforward operation, eliminating the need for complex programming or extensive training. The Robot with an Integrated Buffer can be operated by a sole operator, offering simple changeovers facilitated by recipe selection, which automatically adjusts the necessary parameters with just a few clicks.
In response to the growing demand for improved efficiencies to counteract rising energy and raw material costs, European food manufacturers are turning to automation for their packaging processes. The Robot with an Integrated Buffer increases line efficiency and eliminates the need for additional linking conveyors and frames, resulting in cost savings and improved layout.
Equipped with vision-guided highspeed robots, this innovative machine accurately identifies incoming products on the conveyor belt and precisely places them in the feeding process. It utilizes optimal counterflow or co-flow techniques, providing versatile solutions to meet diverse production requirements. By consolidating these capabilities within a single solution, manufacturers can optimize their production lines and achieve early production start-up.
Rotzinger combines profound knowledge and experience in robotics, buffering, and
conveying from Demaurex, Rotzinger, and Transver, resulting in efficient systems or even new integrated products based on proven solutions. European food manufacturers can benefit from the intuitive Gemini control software platform and local service support, enhancing their operations and maximizing efficiency.
Visit booth B-470 to experience these game-changing solutions at iba Munich 2023. To register your interest in attending the Transver in-house show at Zürcherstrasse 42, 8852 Altendorf, Switzerland, on 17-18 August, please visit https://share.hsforms. com/1JQ3_8wHrRqelGpyzSVWwfw4h865.
Want to know more? Please visit www.rotzingergroup.com.
With their intuitive controls and streamlined design, these solutions aim to enhance productivity and optimize operation.
JASIC EVO is the new standard of UK in welding and is supported with an unparalleled 5 year out of the box warranty.
JASIC is a forerunner of IGBT inverter welding technology and its products have been used in some of the most ambitious
products in modern history such as the historic Beijing Bird’s Nest Stadium.
JASIC is driven by its passion for the worlds welding needs and strives to deliver reliable and ecological solutions.
JASIC’ EVO range offers a redefined industrial design and human machine interface. Solid welding performance and high standards in sustainability, safety and reliability.
From MAK CLEANEX, a strong NSF K1 registered degreasing agent with no hazardous substances such as Ketones and N-Hexanes.
To MAK FOX, a unique multi-purpose, non-flammable degreaser with no hydroxide, phosphate or any hydrocarbons. And MAK WELDING, a Silicone-free anti-spatter liquid that is biodegradable and non-toxic. These products deliver RESULTS!
Whether you’re a customer in need of specific fastening solutions or an industry professional seeking insights, our video library is tailored to meet your needs.
Whether you’re a customer in need of specific fastening solutions or an industry professional seeking insights, our video library is tailored to meet your needs.
Ever wondered what a Self Clinch Fastener looks like cut in half, or have you tried to visualise the appearance of a product or part when it is fully assembled?
Ever wondered what a Self Clinch Fastener looks like cut in half, or have you tried to visualise the appearance of a product or part when it is fully assembled?
Explore TR Fastenings’ media library for a comprehensive understanding of our wide range of fastening products and manufacturing processes. Access videos and resources tailored for engineers, designers and specifiers.
Explore TR Fastenings’ media library for a comprehensive understanding of our wide range of fastening products and manufacturing processes. Access videos and resources tailored for engineers, designers and specifiers.
Scan QR codes for more information
Scan QR codes for more information
TR’s Product Visualisers assist companies at the design stage. A range of options enables the user to interact with the products in a variety of ways such as assemblies, cutaways, magnification, material types and installation.
It’s intuitive, clear and a great training tool too!
TR’s Product Visualisers assist companies at the design stage. A range of options enables the user to interact with the products in a variety of ways such as assemblies, cutaways, magnification, material types and installation. It’s intuitive, clear and a great training tool too!
Pressure surges are recurrent problems in many production plants that occur as a result of turning on pumps, changes in temperatures of enclosed liquids or switching the valves too quickly. Among other things, opening the valves can also result in pressure surges if the media supply is at a high level and the fluid column to lower plant components suddenly starts increasing. The possibility that pressure surges may damage plant components, such as filters, sensors, pumps and piping is very high.
Furthermore, the pressure surges can also cause the shut-off valves to accidentally open for a brief moment, and the media may then get contaminated as a result of this. In the worst situation, this could lead to product loss or downtime due to necessary repair work that must be carried out.
GEMÜ has developed a new innovative solution, the GEMÜ 652 Pulsation Damper, to compensate pressure and volume fluctuations such as water hammer or vapour pressure surge. Based on the tried and tested diaphragm valve technology and reliable actuator design, the GEMÜ 652 is therefore ideal for use in sterile applications (maximum 150°C). This means that it is completely drainable and CIP/SIP capable, taking the specified draining angle into account. Furthermore, it is also suitable for use with corrosive liquid and gaseous applications.
The main function of the GEMÜ 652 pulsation damper is to dampen as much volume as possible within a specific operating range. The body is designed without a sealing weir (full bore design), and for this reason, it won’t shut off the media and therefore the actual expansion volume is compensated by the moving diaphragm.
The operating range and the volume compensated can be adjusted by using different actuator sizes and spring sets. Therefore, the increased expansion volume can be achieved by installing multiple pulsation dampers in series, which will compensate for larger volumes.
The GEMÜ 652 is self-acting as its function is accomplished solely using a spring force, therefore it does not require an electric or pneumatic supply. The control air connector is only used for the assembly and maintenance of the diaphragm.
The GEMÜ 652 pulsation damper is available in the nominal sizes DN15 to DN80 (diaphragm size 25 to 80). To ensure flexibility and a high range of applications, the valve bodies and diaphragms are available in various materials. Furthermore, it also complies with the current standards in the foodstuffs and pharmaceutical industry, such as BSE/TSE, FDA, USP Class VI and Regulation (EC) no. 1935/2004. This ingenious solution by GEMÜ will solve multiple problems in many varied
applications. Please contact us to speak to one of our local product specialists for further information about this product.
See below for more technical information on the GEMÜ 652:
>> Product Flyer
>> Data-sheet
>> Operating Instructions
The main function of the GEMÜ 652 pulsation damper is to dampen as much volume as possible within a specific operating range.
Automated machinery in the process and packaging industries are constantly developing. Here at OEM, we offer industrial automation components to support this development.
We offer components such as control panel components, machine vision cameras and scanners, motors, drives and linear products; process instrumentation and safety equipment.
sales@oem.co.uk
+44 (0) 0116 284 9900
www.oem.co.uk
OEM AUTOMATIC
OFFICES
Drammen, Pärnu, Riga, Vilnius, Trnava
SALES OFFICES
Stockholm, Malmö, Umeå, Aarhus, Oulu, Gdansk, Sosnowiec, Bedford
OFFICES & WAREHOUSES
Tranås, Allerød, Leicester, Turku, Warsaw, Prague, Budapest, Shanghai, Jönköping, Nässjö, Göteborg, Dublin, Cork and Dungannon
EASYFAIRS
In late July 2023, Kenya’s Government faced a huge cyber attack that affected services on a key government online platform called eCitizen portal, which is used by the public to access over 5,000 government services. The hackers claimed to have stolen passport data, which has not only raised concerns over the common ransomware attacks but has also compelled us to address the imminent danger presented by artificial intelligence (AI). Here, Simon Farnfield, event director for Advanced Engineering, explores the landscape of generative AI and cyber resilience, as we must pave the way towards a future where innovation thrives against the encumbrances of cyber threats.
In today’s digital landscape, engineering companies stand at the forefront of innovation, harnessing the potential of generative AI to revolutionise their design processes. Unlike traditional AI systems that are based on rules or pre-defined patterns, generative AI systems use machine learning to create new content that shares similar characteristics with the data they were trained on.
The advent of such technology has brought forth a new era of creativity and efficiency, enabling engineers to design intricate structures, optimise systems and come up with innovations like never before. However, as we embrace generative AI, the paramount concern that looms large is the increasingly growing risk of cyber attacks.
In fact, the UK’s cyber security agency has warned that the number of “hackers for hire” is set to grow over the next five years, leading to more cyber attacks and increasingly unpredictable threats. Not only has the likelihood of these attacks become greater, but they are also less predictable, as more ‘hackers for hire’ are tasked with going after a wider range of targets and off-theshelf products.
According to research analysis conducted by Darktrace, there has been a whopping 135 per cent rise in social engineering attacks driven by generative AI. Cybercriminals are exploiting these AI-powered tools to
Visit
hack passwords, expose sensitive data and deceive users across various platforms. As a result, the emergence of these sophisticated scams has sparked a surge of apprehension among employees, with as many as 82 per cent expressing heightened concerns about becoming victims of these manipulative tactics.
AI poses a formidable threat by significantly reducing or even eradicating barriers to fraud and social engineering tactics. Individuals, who are not native speakers or lack proficient language skills, can therefore exploit generative AI to engage in text conversations without errors. Therefore, phishing schemes become increasingly challenging to identify and protect against, heightening the risk of successful attacks that undermine traditional defences.
The well-known Chat GPT platform is a prime example of generative AI. Using the Transformer architecture, which is designed to process sequential data, GPT is a language model that is pre-trained on vast amounts of text data from the internet, allowing it to learn the statistical patterns, syntax and context of human language.
Unfortunately, cybercriminals have now begun to leverage AI technologies, like ChatGPT, to develop sophisticated spear phishing attacks. In fact, AI-driven spear phishing attacks targeting professionals, such as chief information security officers who oversee an organisation’s information, cyber and technology security, are becoming increasingly sophisticated and challenging to detect.
Here, attackers employ generative AI models to craft highly personalised and convincing phishing emails. These emails are tailored to each target, using their name, interests, recent online activity and even writing style to make them appear genuine and trustworthy. What’s more, these cybercriminals also use AI-generated emails to launch a spear-phishing campaign, targeting individuals within an organisation or specific groups. These emails may contain malicious attachments
or links leading to fake login pages that mimic legitimate services.
It is no surprise to learn that most successful infiltrations come from the targeting of employees, who inadvertently fall for the sophisticated phishing emails and become a victim of a cyber attack.
Avoiding generative AI attacks requires a comprehensive cybersecurity strategy that includes proactive measures to detect and defend against evolving threats. In keeping with our aforementioned scenario, it is wise to regularly train employees on the latest cyber threats, including generative AI attacks. Teach them to recognise suspicious emails, websites and content and encourage them to report any potential security risks promptly.
While we can somewhat accommodate for human error or misjudgement, it also necessary to invest in advanced cybersecurity solutions that incorporate AI and machine learning to detect and block AI-generated threats. These systems can analyse patterns, behaviours and anomalies to identify potentially malicious content.
After all, the world must look ahead and confront the emerging threat posed by AIbased cybercriminals. The attack on Kenya’s eCitizen portal serves as a reminder of the growing sophistication of cyber threats, as AI-driven techniques could play a destructive role in future of cyber security breaches.
With every obstacle comes an opportunity. As generative AI continues to advance, the cyber resilience becomes paramount, meaning that the relentless pursuit of innovation should not be hindered by the ever-present encumbrances of cyber threats. Instead, this must kickstart a proactive approach in developing robust defences against the malicious use of AI technology.
For cyber security specialists wanting to attend Advanced Engineering, held at the NEC in Birmingham from November 1-2, you can book your stand or register for a visitor pass today.
Vibration monitoring 24/7
Monitoring and Condition Based Maintenance of rotating machinery. This complete solution makes your machines fit for Industry 4.0
• Continuous diagnostic: Full coverage of your critical assets at all times.
• Early diagnostics: Monitoring of imbalance, wear and overall vibration.
• Maximum efficiency: Permanent diagnostics helps keep your assets running efficiently.
• Easy integration: ifm provides individual solutions suited to different types of machines. Reducing costs, avoiding unplanned downtime and optimising processes: The ifm application solutions.
ifm – close to you!
KMF
One of the biggest challenges in metal fabrication is supply bottlenecks. Long wait times, high demand and rises in associated costs all cause delays. Keith Nicholl, Commercial Director at sheet metal fabricators KMF looks at how metal manufacturers can boost the reliability of their supply chains to mitigate associated challenges.
Inefficiencies can be apparent across every aspect of a production line in all types of industries. Increasing efficiency in producing metal components and applications helps to keep up with the rising demands, cited as 5% between 2023 and 2027 in an industry report.
What’s more, as machine development rapidly advances, so does the pressure to follow suit. Industry 4.0 technology is a trend that sheet metal manufacturers must embrace in its infrastructure or run the risk of being left behind.
In fact, adding automation in a production line boosts productivity, reduces waste and helps in quicker decision making.
Including robotic bending machines can help in boosting efficiency within production. The time saved on the manual process helps to increase productivity and reduce wastage.
Reducing wastage is also a good way of lowering costs, an important way of remaining profitable in a time with rising costs for businesses.
Achieved by a multifaceted approach, costs of manufacturing can be managed by a combination of bulk creation, energy efficiency, preventative maintenance and quality control.
Preventative maintenance is one of the most important ways of reducing associated costs in the sheet metal manufacturing process. Regularly maintaining and servicing machinery can
prevent costly breakdowns and repairs which means uptime is higher and the lifespan of the equipment is longer.
Government regulations and accreditations go a long way in boosting the quality in metal production. For component purchasers, one way to ensure quality in your desired metal components is to look for specific ISO accreditation.
To find out more about KMF visit: www.kmf.co.uk
Having accreditations in key industries is a perfect way of making sure that the final component will undergo intensive quality control and inspection procedures. For example, if a manufacturer was consistently creating parts for aerospace, it would work towards the AS9100 group of standards. Alternatively, a creator of food processing equipment might require different health and safety accreditations or quality equivalent to BS EN 1672-2:2005.
Optimising sheet metal production supply chains is an imperative step to keeping up with growing demand placed on the industry.
To ensure a smooth world-class process from start to finish, it is important to use a combination of industry-leading technology and technical expertise. This infrastructure and person power put additional agility, efficiency, and quality to the final components meaning that your supply chain is as close to perfect as possible.
Adding automation in a production line boosts productivity, reduces waste and helps in quicker decision making.
Many businesses struggle to find a balance between productivity and efficiency – and no they aren’t the same thing. So, what is the difference between the two, and how do you strike the right balance?
Efficiency - refers to the quality of work and how well allocated resources are utilised.
Productivity – is the volume of output over a set period.
Productivity can be quite abstract and tends to be influenced by a variety of outside factors beyond the control of a business, such as the state of the economy and competitors. Nonetheless, obtaining an estimate can help managers appropriately allocate resources and plan ahead.
The basic formula for productivity is the following:
Productivity = Total Output / Total Input
Efficiency
If productivity is about maximising the amount of work product, then efficiency measures the quality of it. To do this, you need a standard to measure it against. With that, you can measure efficiency using the formula:
Efficiency = (Standard Labour Hours / Amount of Time Worked) * 100
Productivity can sometimes take precedence over efficiency. The need to complete a large volume of work, in a set time period, to turn a profit can mean businesses aren’t effectively utilising their resources and sacrificing efficiency.
Appropriate allocation of resources and labour is key to ensuring efficiency and productivity on-site.
Inefficiencies, although sometime minor issues, can add up. A few lost minutes here, a manual process there, and they can amount to large losses both in time and money.
Inefficient workflows can lead to:
• Returning to a job - re-doing rushed, poor-quality work, means resources are being siphoned away from other projects. In extreme cases, this can come at the cost of clients and contracts, which has a direct effect on staff morale and employee retention.
• Wasted work hours – manual processes can take double the time meaning less hours on the worksite and delays to the job.
• Misplaced resources – not keeping track of all equipment and vehicles means time lost in tracking down what is needed for a certain job. Also, if defects aren’t logged, precious time and money is spent on delays in works and finding a replacement.
• Scheduling clashes – if you don’t have information about jobs, upcoming and ongoing, all in one place, this can lead to clashes, double bookings and even missed opportunities of new work.
• Customer dissatisfaction – in such a competitive market, upsetting a client can mean they will look elsewhere to meet their needs. Poor communication, delays and missed appointments could all be reasons a client loses faith in your business.
• Declines in worker safety - cut corners can lead to injury or in the worst cases death. In 2021/22, 36.8 million days were lost due to work-related ill health and nonfatal injuries.
That’s why optimising your company’s operational processes to improve efficiency is crucial to achieving sustainable business growth. Many businesses are now trading in their current processes for a digital field management solution. With a more efficient foundation that streamlines many repetitive administrative processes, teams on all sides of the business can benefit from more time, where productivity can increase as well.
The main way field management software increases productivity is by automating repetitive admin tasks and streamlining workflows. Rather than physically transporting job packs, forms and communications to remote sites, instant communication between the dashboard and app components of the system allows users to receive all necessary work information through their mobile device.
With digital form completion through said app, automated workflows can be triggered based on submitted data. This means actions such as recording vehicle defects or scheduling servicing no longer need to be done by a staff member, enabling resources to be diverted elsewhere.
Meanwhile, efficiency is also improved. Asset management ensures that equipment is serviceable, workers are properly qualified to carry out work, and materials are being properly accounted for and stocked as needed. Enabling compliance through forms helps reduce errors in reporting. This, coupled with evidencing work through capture, sign-off, and tracking ensures work is completed to standard. All this feeds into live data reports, facilitating forward planning and data-driven decisions that help to measure and improve efficiencies across the business.
To summarise, productivity is measured by the quantity of work done, while efficiency is measured by the quality of this work. Neglecting one in favour of the other can have serious consequences but luckily, the increased adoption of new technologies is offering an accessible way for businesses to find that healthy balance and grow sustainably.
For further information, please visit https://re-flow.co.uk
From supermarkets to warehouses, barcodes are ubiquitous for identifying and tracking items. The widespread adoption of barcodes is due to almost flawless reliability, with read rates exceeding 99.9% in perfect conditions. However, in parcel sorting, external factors can affect this almost seamless process, resulting in barcode no-reads and, consequently, rejected parcels. To limit such instances, Prime Vision has developed Barcode Vision, a unique solution that reduces the number of rejected parcels.
Sjaak Koomen, Senior Researcher at Prime Vision, a global leader in computer vision integration and robotics for logistics and e-commerce, explains more.
In warehouses and fulfilment centres, barcodes allow businesses to identify and sort parcels by destination. Typically, an array of five cameras positioned around a
conveyor will scan the barcode, with the parcel then moved to the appropriate area. This is the case for most items, but a small number of barcodes aren’t read the first time.
There are multiple reasons for these noreads. A barcode may be damaged beyond identification. The surface of the parcel could be non-planar, such as a deformable plastic bag, a cylindrical item or a closed lid with the label placed over the top. The barcode may only be partly visible as the label has been stuck round a corner. Printer errors or low ink levels, as well as camera issues can also render a label unreadable.
In all mentioned cases, the parcel can’t be sorted, which means intervention is required. The first option is to rescan the barcode, sending the goods round the warehouse again, reducing sorting capacity. If this fails,
(Source: Shutterstock_170861873)
the item is rejected. A warehouse operative must rescan it or type the ID number, print a new label, apply it, store the parcel, and refeed it into the sorting system – an approach very similar to a barcode reading failure at the supermarket. This this costs time and money.
For example, in a real-world scenario, let’s say that rejects make up 5% of the total parcel stream at a large sorting centre processing 40,000 parcels per hour. This equates to a drop in capacity to 38,000 parcels per hour. However, it also means that manual handling is needed to cater for this 5%. In this case, 2,000 rejected parcels are sorted per hour. If handling each of them takes 20 seconds, 11 employees are required to process all the rejects1. The drop in capacity and extra investment in personnel adds up to millions in lost revenue every year - so reducing barcode no-reads is definitely worthwhile, especially for large scale sorting operations.
Barcode Vision offers a proven digital solution for reducing no-reads by providing an additional, special barcode scan for a second chance of identifying an item before it is returned for manual handling. Taking a different approach to a traditional system, Barcode Vision uses multiple methods to reconstruct damaged or unreadable barcodes.
By assessing the barcodes utilised at a site, it can learn the types to expect. Therefore, if one symbol is missing at the start or the end, it can be reconstructed and validated. Furthermore, Barcode Vision can read text below the barcode and combine it with symbols for a successful read.
Beyond using customer information to enable accurate reconstruction, Barcode Vision harnesses deep learning technology. Programmed in-house by Prime Vision, this system can intelligently reconstruct barcodes from blurry images, helping to overcome camera or printing errors.
The integration of Barcode Vision is straightforward too. It is compatible with existing scanning cameras, which means that the no-read issue can be resolved without replacing or retrofitting any hardware or conveyor components. Barcode Vision interfaces with a smart integration management (SIM) system that collects images and results from existing barcode readers. If the default reader is unsuccessful, this information is sent to Barcode Vision
for a second try. As well as using a common Prime Vision interface, the system is delivered as a Windows dynamic link library (.dll) for widespread compatibility.
The effectiveness of the system can be further improved by identifying specific
customer problems. Eliminating printer errors, changing packaging to be more reader-friendly and expanding the scanner area also assist the software in minimizing no-reads.
Barcode Vision is no panacea for parcel rejects, but it doesn’t need to be to deliver great results. The success of the technology differs between sorting operations, but even reading 25% of rejected parcels can offer a significant cost saving every year by lowering manual intervention, improving warehouse capacity and making processes more efficient.
With access to a unique, tailored solution that reads between the lines of barcode no-reads, sorting operations now have a second chance to reduce rejected parcels.
(Source: AdobeStock_169385238)
For more information, visit https://primevision.com/
Taking a different approach to a traditional system, Barcode Vision uses multiple methods to reconstruct damaged or unreadable barcodes.Image 1: In warehouses and fulfilment centres, barcodes allow to identify and sort parcels by destination. AI-driven analytical software platforms can help to identify correlations across order data
The first reinvention of air compressor technology in more than 85 years has rolled off the production line of a £17m new smart factory in Doncaster.
Lontra, an engineering technology company led by innovator Steve Lindsey, is committed to answering increasing demand by quadrupling the production of their innovative LP2 Blade Blower year-on-year until 2025.
This ambitious plan is designed to meet growing industry requirements and provides the market with a new, environmentally sustainable solution for air delivery in industrial settings all over the world.
Backed by the design and product lifecycle management capability of PTC’s Creo and Windchill platforms, the company has integrated its unique, patented and proven Blade Compressor® positive displacement technology within the custom engineered LP2 Blade Blowers.
This delivers a world-class performance, reduced noise and, importantly electricity savings of up to 34% compared with traditional products.
Demand is already coming from the US, which accounts for nearly 25% of the global market, and a further recruitment push is expected to increase a workforce that has already doubled in the last year.
“Seeing the first LP2 Blower come off the production line was a real milestone moment for the business,” explained Steve Lindsey, who formed the company in 2004.
“This is the first commercial innovation seen in the air compressor market in 85 years and it can’t come soon enough. Heavy industry uses these products to deliver power to manufacturing lines, to drive furnaces, convey material and blow away granules in cement factories and crumbs in biscuit factories.”
He went on to add: “All that blowing comes at a heavy cost to the environment. Compressors account for a staggering 10% of Europe’s industrial electricity use, which equates to
more than 10TWh (Terawatt-hours) of power per year and some 4.3million tonnes of CO2 emissions.
“We have an innovation that has been designed and now manufactured in the UK, with the investment in our Smart Manufacturing Centre giving us the capability to scale up quickly to meet what we expect to be huge demand.”
Inneo Solutions introduced Lontra to PTC’s cloud-based 3D CAD Design software Creo and this platform has been critical in achieving the complex geometry that makes the LP2 Blade Blower so different to its predecessors.
This includes add-ons covering finite element analysis (FEA) and behaviour modelling, which were used by up to 10 designers to achieve the necessary stillness and distortion requirements that deliver the environmentally sustainable performance.
“Where simultaneous optimisation of mechanical and thermodynamic performance is required, data from PTC Creo feeds directly into BladeSim, a software suite built in-house at Lontra for the virtual prototyping of positive displacement compressors, vacuum pumps, and their ancillaries,” pointed out Daryl Koch of Inneo Solutions.
“As well as improvements to compression, internal leakage and heat transfer, these tools tune silencers, and ancillaries for optimisation of the complete system.”
Another key element of the portfolio is Windchill, PTC’s product lifecycle management (PLM) suite, which makes a big difference in Lontra’s efficiency and sustainability, by saving not only time but also waste.
Windchill ensures that the record of materials and components used in its products are kept up to date, helping it capture learning from the design and development process, as well as reducing errors, scrap, and waste on the factory floor.
Elliot Clarke, UKi Director at PTC, added his support: “Both of Lontra’s sites have access to Windchill, as does the firm’s teams who work remotely – designers, purchasing, manufacturing engineers, CNC, assembly, and quality.
“The power of the software ensures that everybody is working off the most up-to-date data. In the future, we know the company is planning to provide certain suppliers with access to this too.”
The digital thread is at the heart of the next exciting stages of Lontra’s expansion, bringing to life all the benefits of the connectivity built into the LP2 Blower’s design, with its 25-plus internal smart sensors.
This work will be overseen by Lontra Digital, a new arm of the business responsible for the design and development of a proprietary state-of-the-art cloud-based technology stack (LontraEDGE) and its next-generation UI platform (LontraLENS) that powers HMIs, tablets and mobile apps.
This will enable the company and its customers to remotely monitor the health and efficiency of the units once they’re installed onsite in manufacturing and water treatment facilities.
“Almost every factory will have a maintenance person or team, whose job it is to keep machines running. They spend their days in and around those machines and, regardless of whether an alarm has been triggered or not, they can tell when something doesn’t sound right or is running hot, signalling that there may be a potential problem,” added Steve.
“That kind of experience is in short supply and dwindling fast as older members of the workforce retire. Now, thanks to data collection and machine learning, instead of that expert walking around just one factory, they can be maintaining 30 factories all around the world from one centralised location.”
He concluded: “In this way, Lontra Digital will help to increase reliability and efficiency, and reduce downtime for customers.”
For further information, please visit www.lontra.co.uk.
LONTRA
Advanced Engineering, the UK’s largest annual gathering of engineering and manufacturing professionals, is set to open its doors in a few weeks. Now in its 14th year, this year’s show comes with a fresh rebrand, removing the previous show zones and introducing a main stage for the event’s wellattended forums.
Advanced Engineering, taking place on November 1 and 2 at the NEC, Birmingham, was previously divided into several zones. However, in order to meet the future demands of the engineering and manufacturing sectors, the show has been re-engineered to encourage even more cross-industry collaboration.
This year, the long-established composite zone will remain, but the automotive, aerospace and connected manufacturing zones will be removed. However, these
sectors will still have a strong presence at the event, with the industry-specific forums remaining. There will also be a central stage on this year’s floor plan where discussions about key challenges in the industry will be discussed.
“Making these changes wasn’t an easy or a quick decision,” explained Alison Willis, director of Easyfairs, the organiser of Advanced Engineering. “We spoke to over 200 exhibitors, visitors and speakers to make sure that any changes made were futureproof and reflective of all stakeholders. We realised that many of the issues that our exhibitors and visitors are facing align. Take sustainability for example — we wanted to make sure that our floor plan allows attendees to share ideas and solutions to challenges like this,”
“Advanced Engineering has expanded
greatly over the years, starting as a specific aerospace event 14 years ago. 2023 felt like the right time to fully encourage collaboration across industries and to prepare the show for a new era of manufacturing and engineering.”
With the rebrand, Advanced Engineering returns with a speaker programme made up of some of the leading figures in UK engineering and manufacturing. This year’s day one keynote is Richard Noble, OBE, former holder of the world land speed record and serial innovator at ThrustWSH. Also on the main stage, Eman MartinVignerte, Director of External Affairs and Government Relations at Bosch, will share her thoughts on digitalisation and automation. In the afternoon, there will be a women in manufacturing panel, followed by a discussion from a Make UK representative on how new industrial technologies are affecting the skilled workforce.
On day two, the opening keynote will be given by Make UK, and will be followed by talks from Made in Britain on innovation in British engineering and design, and a second panel on women in composites. Two exciting competitions will also be held on the main stage, with the Enabling Innovation competition in the morning and the SAMPE Design and Make competition in the afternoon.
At the aerospace forum, visitors can meet experts from H2FLY, Rolls-Royce, YEET Aerospace, MGI Engineering, ADS, Midlands Aerospace Alliance, Satellite Applications Catapult and more, who will cover topics ranging from digitally enabled supply chains to propulsion technologies.
Meanwhile, exhibitors can learn about composites circularity, the future of composites and digitalisation being the key to productivity at the composites forum. Attendees can also see Pim van Baarsen, CEO at Silverstone Technology Cluster, and
Lucy Parsons, Sales Account Manager at Nikon Metrology UK, who will be discussing and showcasing innovative products at the automotive forum.
Advanced Engineering will also showcase groundbreaking innovations throughout its exhibition area. One of these is the prototype of the ThrustWSH boat. In what is a collaborative effort with PRF Composites, ThrustWSH has achieved the world land speed record and will allow visitors to see whether the boat can conquer the water speed record at the show.
In addition, MGI Engineering is speeding ahead in their journey to net zero and will demonstrate never seen before technologies to the sector, including an
F1 car and eVTOL drones. Meanwhile, SCU Motorsport has also booked up an exclusive exhibitor spot, pioneering its 3D learning environment for students that will involve augmented reality, virtual reality and mixed reality technologies.
It’s clear to see why this year’s expanded floor plan is quickly filling up. One of last year’s exhibitors, George Chetwood, Business Development Manager at Cognitiv Spark, said, “The show has been great — we’ve met so many new people and had great conversations. We’ve met clients that we’ve already been in talks with and have advanced those conversations. Our director has secured a spot next year, so we’ll be back then.”
Lee Brent, Sales Manager for Southwest Fabrications, commented, “This is our first year exhibiting at Advanced Engineering but it will not be our last. After a friendly and helpful team helped us decide on our stand in the most appropriate location, we have seen a tremendous amount of visitors flow through our stand, with over 100 individual companies interested in the products and services we offer. We have been so pleased with our experience and look forward to exhibiting for many years to come.”
To secure your visitor pass, see a current exhibitor list and check out the growing list of confirmed speakers, visit the Advanced Engineering website.
For further information, please visit www.advancedengineeringuk.com
2023 felt like the right time to fully encourage collaboration across industries and to prepare the show for a new era of manufacturing and engineering.
Now available from industrial process heating specialist Babcock Wanson is the Navinergy digital platform for 24/7 boiler room performance monitoring. This innovative system allows customers to monitor their boiler room from any device, anywhere in the world, to optimise energy and water efficiency, and ensure regulatory compliance.
The Navinergy platform integrates all the components needed to supervise and operate the boiler room, including control, regulation, recording, visualisation and communication.
Using a local Modbus TCP network, Navinergy gathers, records and stores field data from all the connected boiler room equipment. The data is presented in the form of graphs or a performance report, which can be customised to customers’ precise needs. These are sent to customers at regular intervals, but can also be easily generated
whenever required, for up to date information.
Where deviations in the operation of boiler room equipment are identified by Navinergy, alerts are sent to customers directly to enable them to assess the situation and decide if action is required. Alert levels are customisable to best manage and prioritise them.
In this way, Navinergy not only delivers information to be acted upon and periodically reviewed, but also provides customers with complete traceability.
www.babcock-wanson. com/2023/02/09/navinergythe-connected-boiler-room/ info@babcock-wanson.com.
Element™ GRP Housing incorporates modular panels to aid with flexibility and growth. Customers can choose from 10 standard sizes. Further customisation of the Element building is available with a choice of optional fittings. A vent or gland plate extends Element’s usage opportunities and a wide range of locking systems provide extra security and peace of mind for housing sensitive equipment.
Element’s corrosion, vandal and
weather resistant GRP panels feature a semi-gloss, light grey outer laminate, which is easy to maintain throughout its long service life. The inner laminate layer provides flame retardancy.
Delivered fully assembled and ready for anchoring into position with self-tapping masonry bolts, Element offers optimum flexibility for your application.
Glasdon UK Limited
E-mail: enquiries@glasdon-uk.co.uk
Website: www.glasdon.com
Lanemark gas burner systems offer users reliable, high efficiency, process heating solutions.
FD Series Packaged Oven/Dryer Burners
•Speci cally designed for process air heating applications in convection ovens and dryers
•High turndown/short ame lengths providing accurate process temperature control
•High ef ciency gas + air modulation, gas only modulation and simple high/low control options
•Heat Input Range: 9 kW – 1550 kW
TX Series Gas Fired Process Tank Heating Systems
•High ef ciency (80%+) heating of all types of spray and dip process tanks
FD-C high turndown oven/ dryer air heating burners.
FD-GA modulating gas + air process air heating burners.
FD-E low cost high turndown oven/dryer air heating burners.
•Compact high ef ciency small diameter immersion tube heat exchangers occupying minimum tank space
•Accurate performance modelling using Lanemark TxCalc design software
•Heat Input Range: 15 kW (1½") – 1150 kW (8")
Midco HMA Series Air Replacement or “Make-Up” Air Heating Burners
•Direct red, high ef ciency burner systems, for high volume air heating applications such as paint spray booths, ovens and dryers.
•Supplied either as Midco burner heads for OEM system integration or as Lanemark DB or FDB complete packaged systems including modulating gas valve trains and controls
•Wide range of ring rates to suit alternative temperature rise and air velocity system requirements
Midco HMA high efficiency, high turndown, air replacement or “make-up” air heating burners.
TX high efficiency small diameter immersion tube tank heating systems.
•DbCalc system design software
SEW-EURODRIVE has established efficient and flexible processes to achieve its vision for Industry 4.0. SEW’s new design for automated guided vehicles at its main U.S. location includes integrated timing belt conveyors from mk. These vehicles serve as mobile workbenches for mounting individual gearboxes.
Classic interlinked conveyor technology is the most efficient way to automate processes in mass production. In customised production, however, the requirements are ever-changing – with “lot size one” being the key word. This is where the flexibility of automated guided vehicles can be put to good use.
At its American headquarters in Lyman, South Carolina, SEW-EURODRIVE has built a flexible production facility that is optimised for precisely such custom production – where classic conveyor technology is combined with flexible workstations. The autonomous vehicles drive through the hall independently, picking up pre-assembled gearboxes from a belt conveyor and taking them to the workers, who can then continue mounting them on the vehicle itself as if they were at a mobile workbench. The vehicle then travels to the next station and transfers the gearbox back to a belt conveyor. It is thus possible to mount individual gearboxes, with efficient and flexible processes.
Through its “MAXOLUTION System Solutions” business segment, SEW offers scalable and future-proof system solutions in the field of mobile and rail-guided conveyor technology. As an overall solution supplier for automated guided vehicle systems, it focuses not only on the vehicles themselves but also on all the services associated with them, from system planning to commissioning and servicing. The vehicles and system components are produced at SEW-EURODRIVE’s headquarters in Bruchsal, Germany. Alongside SEW’s world-renowned modular system for gearmotors and electronic products, it also engineers autonomous vehicles based on an innovative modular technology and software system.
This system makes it possible to configure individual vehicles while keeping complexity low.
To autonomously pick up and then set down the gearmotors with a belt conveyor, the vehicles need an appropriately powered load handling device. “We had initially considered a chain conveyor that we could integrate into our vehicles,” says Aaron Bronner. However, working with the conveyor technology experts at the mk Technology Group (mk), the team found a better solution. “We decided on a dual-line timing belt conveyor instead of a chain conveyor,” says Ulrich Klein, one of the field representatives at mk who assisted with
the project. A timing belt conveyor is more economical and requires less maintenance than the chain conveyor in the original plan. Furthermore, the timing belt has a higher contact area than the chain. That also provides greater stability for the product on the vehicle, even when navigating sharp corners or making abrupt (emergency) stops. The ZRF-P 2010 timing belt conveyor from mk was the ideal solution for the project: it can safely carry the maximum load of 160 kg, and the drive variants available also allow for reverse operation (in both directions).
Because mk uses SEW drive technology as standard, integrating the drive was not a problem. The experts at MAXOLUTION programmed the controller and coordinated it with the overall system.
To find more contact mk Profile Systems on (01949) 823751, email info@mkprofiles.co.uk or visit www.mkprofiles.co.uk
A timing belt conveyor is more economical and requires less maintenance than the chain conveyor in the original plan.
Conveying, feeding and positioning up to 250 kg
Available as a single, dual or multiple line conveyor
While the enclosure might seem a humble component of a control system, for designers correct selection is vital to ensure suitability for the intended application. Nobody knows this more than Lawtronic, a renowned electrical control solutions provider for the past 36 years. It has a long-term relationship with Spelsberg, a market leader in enclosure technology that has supplied a wide range of boxes for Lawtronic projects.
Chris Lloyd at Spelsberg spoke with Dave Tester, Managing Director at Lawtronic Ltd., to discover how it has collaborated with Spelsberg to help overcome modern challenges in control system design and supply.
“We offer a complete service for control systems in applications across many industries, encompassing design, manufacture, testing and installation. Typically, we use Spelsberg enclosures for our marine, refrigeration, and baggage handling systems amongst others. There are obviously big application differences, so having a wide variety of boxes to choose from is important to us,” says Dave.
As control systems have diversified, a one-size-fits-all enclosure solution simply
doesn’t exist anymore. Consequently, designers need a wide range of sizes, models, materials and characteristics to choose from to ensure suitability. While a high ingress protection rating might be an important feature for a marine application, for a baggage handling machine it’s less so. If a Lawtronic customer requires a compact enclosure that can fit within a small footprint, having a multitude of sizes to choose from is beneficial. Having quick access to all the options simplifies procurement and expedites a control system design project.
Dave expands on the importance of options: “We had one customer who required an enclosure with a transparent lid so that engineers could easily view the electronics within. In the end, Spelsberg recommended an IP66 AKL 4-t, as it features a clear lid. This meant we could easily meet the customer request with an off-the-shelf item.”
Even with varied options, an off-the-shelf solution can’t always solve everything for a control system designer, and one Lawtronic project illustrates this.
“We developed a custom control system concept for a tray return conveyor installed
on X-ray security machines destined for an airport in Dubai. A standard enclosure solution wouldn’t fit within the constrained footprint of the machine, so we worked with Spelsberg during the design phase to produce one that would, and at the same time would dramatically reduce our labour during build,” Dave explains.
Having an in-house engineering capability ensures that enclosure manufacturers can support control system designers early in development with bespoke solutions.
CNC machining allows new enclosures to be prototyped quickly, so that the design team can carry out testing and meet a specific brief. Ultimately, an enclosure that exactly matches the unique requirements of the control system is achieved.
“Repeatability is a big thing for us too,” Dave expands. “We typically design control systems for volume production machine builders. For example, the system for the airport was required for over 100 individual machines. Not only do we need custom enclosures, but we sometimes need lots of them.”
Therefore, it’s important that enclosure manufacturers can not only produce custom items on reduced lead times for the development process, but also offer the manufacturing capacity and flexibility required to deliver short production runs of unique designs.
Modern trends don’t just apply to the engineering of control systems, but to supply as well. Across industry, suppliers and manufacturers are looking to localise their logistics operations to improve availability and minimise the effects of delays and increased costs.
“Everyone is working to make supply chains more robust through reshoring, and Spelsberg offering us local availability in the UK is beneficial. Our approach, like many, has been to hold more stock, and Spelsberg has supported this by providing us with increased enclosure inventory capacity. This gives us a more responsive and resilient supply chain.”
Local availability ensures that control system manufacturers can insulate supply chains from external shocks. The advantages of increased stockholding and reliable delivery also benefit their customers, helping to streamline projects and adding value.
“Ultimately, what we need from an enclosure supplier is efficiency and value. Efficient supply of custom products ensures that we can produce unique control systems faster. Having a UK enclosure supplier with off-the-shelf solutions reduces
costs, savings which we can pass onto our customers. These are the two key reasons why we have a long-term relationship with Spelsberg,” concludes Dave.
Clare McCusker, National Sales Manager at Spelsberg els UK Ltd., adds: “We are proud to work with Lawtronic, providing enclosures from our TG, TK, AK and Abox range. Our versatile products, rapid customisation service, engineering support, UK-based manufacturing and availability allows us to support the complex enclosure requirements of control system designers. Due to this we can assist in meeting the unique industry challenges they face.”
For further information, please visit www.spelsberg.co.uk
Having a UK enclosure supplier with off-the-shelf solutions reduces costs, savings which we can pass onto our customers.
With the HV 1000 C series, SAB Bröckskes, one of the world’s leading manufacturers of special cables, has developed new highly robust single-core (SC) and multicore (MC) cables for high-voltage wiring in construction, agricultural, and special vehicles. The HV single-core, available in eight standard dimensions with nominal cross-sections from 6 mm2 to 95 mm2, meets the special requirements for safety and reliability in electrically or hybrid-driven utility vehicles. The multi-core version is available in dimensions from 2 x 2.50 mm² to 5 x 6.00 mm². Due to its high mechanical strength and resistance to environmental influences as well as its very good oil and temperature resistance, the HV single core solution designed for nominal voltages of up to 1,000 V AC/DC is suitable, for example, for the electrical connection of inverters and electric motors.
The HV multi-core cable is used, for example, as a connecting cable to the cabin heater, the e-compressor or the HV heat pump in electric and hybrid vehicles. The double EMC-shielded high-voltage cables with bare copper stranding and orange-colored TPE-U sheathing have a low-temperature resistance down to -50°C according to DIN EN 60811-506 and withstand temperatures of up to +125°C for a operating time of up to 2,000
hours. The extremely tensile, abrasion and shear resistant outer sheath allows tight bending radii and, in many cases, eliminates the need for installation with additional protective tubing. Other quality and safety features include flame-retardant and self-extinguishing material properties in accordance with IEC 60332-1-2 as well as standardized high resistance to mud, UV, ozone, and salt water. All materials are free of harmful substances and meet RoHS criteria. In addition to the standard designs, SAB Bröckskes also offers intermediate cross-sections of e.g. 8 mm2 as well as sheaths in other color variants on request.
For further information, please visit www.sab-cable.com
The extremely tensile, abrasion and shear resistant outer sheath allows tight bending radii and, in many cases, eliminates the need for installation with additional protective tubing.Robust, process-safe high-voltage cable for connecting electric motors in mobile machinery, agricultural and special vehicles.
ABB Robotics is expanding its large robot range with four new models and 22 variants offering more choice increased coverage and greater performance. The next generation models include the IRB 6710, IRB 6720, IRB 6730 and IRB 6740, suitable for payloads ranging from 150kg to 310kg, with a reach from 2.5m to 3.2m, offering customers greater choice and significant performance and energy efficiency improvements.
“Sustainable production is a major priority of automotive manufacturers, with 78 percent of companies identifying it as important to their business and a further 77 percent identifying it as a priority for their customers1” said Marc Segura, President of ABB’s Robotics Division. “ABB’s four new robots offer 22 variants and energy savings of up to 20 percent, responding to our customer’s needs; offering more choice and greater flexibility for more sustainable production. These new robots will help our customers build resilience across a range of industries including automotive, general manufacturing, foundry, food and beverage and logistics.”
The improved energy efficiency is driven by ABB’s OmniCoreTM controller, and lighter robot design leading to energy savings of up to 20 percent. OmniCore also offers high motion control accuracy. Featuring ABB’s TrueMove and QuickMove motion control technology, the robots can achieve class-leading repeatability with a minimum of 0.03mm deviation. These capabilities make the new series of robots ideal for complex tasks such as spot welding, laser welding, screwdriving and riveting, allowing automotive manufacturers to achieve high quality assembly.
“Our new robot range meets the needs of the rapidly growing electric vehicle (EV) industry. As manufacturers ramp up production of EVs and batteries, they can choose from a wide range of ABB robots to ensure they have the right variant to handle batteries of varying sizes, from individual cells and modules to complete packages. They can also perform tasks such as highprecision car body assembly and spot welding and enter restricted areas within a vehicle to install seats or dashboards.” said Joerg Reger, Managing Director of ABB Robotics Automotive Business Line.
ABB’s new large robots will make their debut at ABB’s stand at Automatica 2023 (Hall B5, booth 319, June 27th-30th). They will be working in a fully functional battery production cell on ABB’s stand, performing spot welding tasks, loading and unloading EV-battery tray parts, which are provided by one of ABB’s fully autonomous mobile robots.
Watch the digital launch on LinkedIn on Jun 29th 2023, 4:00pm CEST. https://www.linkedin.com/ events/enablingsustainabilityperforma7065595544387084288/ comments/
For further information, please visit https://go.abb/robotics
The improved energy efficiency is driven by ABB’s OmniCoreTM controller, and lighter robot design leading to energy savings of up to 20 percent.
Support from automation specialist FANUC UK has helped a growing recycling tech company revolutionise the waste management sector with its AI-powered approach to sorting recyclable materials. London-based Recycleye uses proprietary AI vision technology in conjunction with FANUC 6-axis LR Mate robots to automate the detection and sorting of dry mixed recyclables, traditionally a largely manual process. This ground-breaking system, called Recycleye Robotics, is producing impressive results including an increase in sorting accuracy of up to 12% and improved line output of up to 10%, helping waste operators to boost their bottom line and providing a solution to ongoing labour shortages in the waste management industry.
Founded in 2020 with just four members of staff, Recycleye now employs over 45 people and has an install base that reaches across the UK and Europe. According to CEO Victor Dewulf, having FANUC by its side from day one as a strategic partner has been instrumental to the company’s rapid growth trajectory: “FANUC has been a key enabler in the success we’ve achieved so far, and they’re central to our future ambitions. They really put their faith in us and the product we set out to deliver.” Recycleye’s rapid journey took another step forward recently when it announced a $17m Series A financing round, led by deep-tech venture capital firm DCVC
Recycleye Robotics uses AI-powered computer vision to identify every single item in complex waste streams. The FANUC LR Mate robot which sits at the heart of the system then automatically separates those recyclables into different material classes such as plastics, aluminum, paper and cardboard. The most accurate and efficient AI robotic picking solution globally available today, it can operate 24/7, picking up to 33,000 items per robot over a 10-hour shift.
For Recycleye, choosing the right automation supplier and the right robotic solution was critical to their technology’s success. “In the early days of our journey, we worked with the MTC. They recommended that we speak to FANUC when we were looking for our robot
This ‘retrofitability’ was a main draw of the LR Mate – as a compact, short arm, mini robot it is easy to integrate into confined spaces, making it the perfect choice for Recycleye Robotics. As a result, the Recycleye team can install a system over a weekend, with no need for the facility to shut down or operations to be suspended.
partner and from day one, we knew we’d made the right choice,” says Chief Technical Officer Peter Hedley. “The FANUC LR Mate 200 iD/4SC is the perfect accompaniment to our vision system. We were looking to bring new technology into a very established, traditional industry. Although mostly reliant on manual pickers, any robots already being used to sort dry, mixed recyclables tended to be large, heavy Delta robots. The ability to retrofit our lightweight system into customers’ existing lines at a reasonable price point was therefore crucial.”
Peter continues: “In addition, the FANUC LRMate is ultra-efficient, using five times less energy than a Delta robot. And thanks to its sophisticated sensors, there’s no wasted travel – if it’s not gripping anything, it won’t move to the bin. Reliability was another a key factor for us. It can operate 24/7 for eight years and still come back to the same millimetre point it has been told to move to.”
For materials recycling facilities (MRFs), the benefits of Recycleye’s technology are myriad; not least that it offers a solution to the industry-wide labour crisis. A recent report by the CIWM revealed that 60% of survey respondents had struggled to recruit staff in the past year, forecasting 89,000 vacancies across the waste and recycling sector by 2028.
Recycleye Robotics uses AI-powered computer vision to identify every single item in complex waste streams.London-based Recycleye uses proprietary AI vision technology in conjunction with FANUC 6-axis LR Mate robots to automate the detection and sorting of dry mixed recyclables, traditionally a largely manual process
“The LR Mate robot can pick as accurately as a human worker, and the vision system is as accurate as a human eye,” explains Peter. “Robots don’t need to take a break, don’t slow down or get tired, and don’t leave the job or need replacing. This is crucial as it can be very hard to find manual workers for waste picking. Recycleye Robotics is more consistently accurate than a human worker and can work safely alongside human employees, thanks to its safety guarding. It can also easily handle the hazardous materials that are routinely found in sorting facilities, which can injure human pickers. It’s therefore an ideal complement to the existing workforce.”
Another benefit for MRFs is that materials that are sorted to the highest purity will command a higher price. Recycleye Robotics is usually used at the quality assurance stage of the recycling process, comprising both positive picking (e.g. any recyclables that have been missed) and negative picking (removing any contaminants such plastics in an aluminum line). This boosts sorting accuracy, increasing purity. And thanks to the system’s transparent traceability function – every item is scanned and the resulting data is visualised on a dashboard –demonstrating pick levels and proving the purity of the batch are made simple.
“Quite simply, for our customers in the MRF sector, investing in a Recycleye Robotics system ensures the future of their business
by giving them a competitive edge,” adds Peter.
FANUC UK has been part of the Recycleye journey from the start. With an install base of 14 systems across Europe in just three years and 25 FANUC LR Mates already purchased, FANUC UK’s Head of Sales, Oliver Selby, is confident that this is just the beginning for Recycleye:
“We wanted to be at Recycleye’s side from
day one. We had very early engagement with them and put in place a plan that allowed them to de-risk their offering to the market. We conducted simulations and physical trials to make sure that when the product was finally released, it was going to work exactly as planned. The result is a solution that allows a higher throughput than anything else on the market today and offers a superb, automated alternative to traditional sorting methods using a compact robot, which is easy to deploy, easy to install and with low lifetime costs.”
High-quality manufacturing can only be guaranteed by paying exceptional attention to detail. KRAUSNAIMER.COM
Benefit from our experience to increase your success!
Discover the new generation of Schubert & Salzer Control Systems pneumatic control valves with IO-Link positioner and learn about the future of valve technology.
Visit us at PPMA 26th - 28th September 2023
NEC, Birmingham, UK Stand: G72
www.schubert-salzer.com
Designed for manufacturers needing to add or retro-fit Eddy Current inspection to an Additive Manufacturing CNC or Robotic System.
• Dual Frequency High Performance Eddy Current Flaw Detector with C-Scan Capability.
• Wall mountable for ideal and easy process inclusion.
• No couplant, no effluent and no radiation.
• Supports X/Y and R/Theta manual scanners with an easy scan calibration and enoder configurations.
• Viewing and analysis of C-Scan Data e.g. Phase Rotation Adjustment, Gain Adjustment.
e:sales@ethernde.com
t: +44 (0)1727 648050
www.ethernde.com
The tec.nicum academy offers a comprehensive range of seminars and training on machine and plant safety worldwide.
academy
The Machinery CE Expert seminar is held over four days, the course provides a compact overview of all knowledge required to satisfy legal and normative requirements in the EU single market. The tec.nicum academy’s speakers make it easy for seminar participants to understand the complex compliance assessment requirements of the EU Machinery Directive.
Participants will receive all of the information they need to be able to correctly apply CE marks to machinery and systems. After passing the test, participants will be able to use the title “Machinery CE Expert with TÜV Rheinland Certified Qualification”
We’ll be exhibiting at Machine Building Live 2023. Visit us on stand 29, talk to us about our services and how we can assist you to achieve your safety goals.
www.schmersal.co.uk
www.uksupport@schmersal.com
In the challenging realm of food manufacturing, the need for resilient touch monitors in harsh processing environments is evident. These monitors must withstand water, chemicals, and extreme temperatures to prevent screen damage from contaminating production.
Partnering with Harford Control, renowned for its effective stainless steel touch terminals, Display Technology embarked on a close collaboration to formulate a solution. Harford Control’s terminals are tailored to meet the demands of the food industry by streamlining workflows, enhancing data accuracy, and upholding safety standards. This collaboration extended to Zytronic, a leading touch sensor company, resulting in the development of an exclusive touch screen solution.
Supplied Components:
AUO 15” Panel with 15” ZYTRONIC PCAP
Touch Sensor: The AUO panel provided clarity, while Zytronic’s PCAP touch sensor, layered with 0.75mm polycarbonate, ensured resilience in challenging conditions.
Embedded - ASROCK SBC-210N: Coupled with custom gold-plated LVDS and LED cables,
the ASROCK SBC-210N effectively powered the LCD display.
Advantages:
• Durability: The PCAP touch sensor’s polycarbonate overlay guaranteed longevity, mitigating the risk of glass contamination or substrate damage.
• Hygiene and Safety: Harford Control’s stainless-steel touch screen terminals, combined with Zytronic’s PCAP touch sensor, facilitated easy cleaning while adhering to food safety standards.
• Data Accuracy: Harford Control’s direct data capture, in tandem with dependable touch input from Zytronic’s sensor, minimized human
errors during data entry, ensuring precise information recording.
Conclusion: The collaboration involving Display Technology, Harford Control, and Zytronic yielded a groundbreaking touch screen solution. This innovation bolsters operational efficiency, reduces contamination hazards, and guarantees a safer food production process. It serves as a prime example of expertise’s transformative role in reshaping safety and reliability standards within the food industry.
For more information visit www.displaytechnology.co.uk
• IoT, electronics and plastics design and manufacture
• Firmware, software and App development, Cloud integration
• Low and high volume manufacture (UK and Far East)
• Unbeatable cost-effectiveness and lead time reductions
• Supply chain and stock management
Pre Assembled and Modular Light Towers
Multifunction Light and Acoustic Options
36mm, 50mm & 70mm Ø, Round & Elliptical
Super bright LED Technology
LED Beacons - Rotating, Flashing & Steady Light Output
Multi Tone Sounders
IP65/66 Ingress Rating
UL, UKCA & CE Approved
NORTH SOMERSET based Famatel UK Ltd is one of the leading producers and suppliers of electrical products for over 10 years with Head office in Spain, factories across Europe and we are one of 7 Subsidiaries around the world and the group is growing every year. Famatel group ultimate objective is to intergrade group under one system offering global view of inventory and sales world wide enhancing its ability to change to market needs in every country at a moment notice.
As a distributer and assembler of industrial power distribution products and systems it holds a full range of BS4343 / IEC 309 electrical distribution products and manufactures a wide range of enclosures from IP20 to IP67 along with its new GRP range.
The company also has the ability to integrate its distribution products together to offer its customers a custom build solution to meet specific requirements. Famatel UK Ltd says that it employs a strict system of quality control that flows thought the Famatel SPA group.
We pride ourselves on producing system to our customers’ needs on time and on budget, within the time frames needed.
We produce Electrical distribution systems in Plastic , Metal, Staines Steel , GRP, with or with our transformers if necessary single and three phase.
We pride ourselves on producing system to our customers’ needs on time and on budget, within the time frames needed.
More than 25 years of experience in the international electric sector
By believing in this project we’ve truly crossed borders. We’ve become a global business where people, their attitude and their knowledge are the backbone to the Famatel project. Our corporate strategy rests on the pillars of teamwork and respect for diversity; it’s led us to have a presence in over 60 countries with 3 production centers and 7 subsidiaries. A demanding, honest and well-motivated team strive every day to consolidate our position on the national and international market by strengthening our relationship with clients and suppliers alike
Sales/General Enquiries
01934 412133 | sales@famatel.co.uk
Custom Build
custombuild@famatel.co.uk
The Engineering Design Show (EDS) returns to The Coventry Building Society Arena on the 11th – 12th of October 2023, bringing together thousands of design engineers to source, learn and network.
Expect to discover 200+ exhibitors, thousands of the latest innovations and products and 30+ hours of free-to-attend conference sessions and workshops. Plus, don’t miss the dedicated robotics zone, an interactive VR display with Nottingham Trent University, ‘The EDS Race to Place’ games area (and a chance to win some fantastic prizes) and the end of day-one party, where all visitors, exhibitors and speakers are invited for free food, refreshments and live music!
There are so many huge names attending, with confirmed headline sponsors, Powell Electronics, Würth Electronics and Solid State Supplies. Dassault Systèmes are also sponsoring a new lounge area, creating a relaxing, networking space for visitors. Plus, we are pleased to welcome Mouser Electronics, Silicon Motion, Arrival Electronics and AWE, all sponsors for this year’s show.
EDS is the only show in the UK that caters specifically and entirely for the modern design engineer from all market sectors, making it the ‘must attend’ event for the UK design engineering community.
Meet with over 200 world class suppliers, representing the very best of engineering design. The packed exhibition hall will feature the latest technologies, materials, tools, software and services enabling visitors to source products and review supply chains.
Thousands of new products and innovations will be on display across the full mechanical, embedded and electronics landscape, including 3D printing, fasteners & adhesives, design software, drives and controls, embedded systems, labelling, laser making, motion control, PCB manufacture & assembly and many more. EDS provides a dynamic environment in which to interact with these suppliers, all under one roof at one time.
EDS has three conference streams that will run in parallel across the two days. Curated by the editors of the industry-leading titles The Engineer, New Electronics and Eureka!, and drawing on a combined 340+ years of engineering journalism and insight, the three streams will deliver multiple case studies and practical sessions that address the key opportunities and challenges facing UK design engineers.
Topics that will be covered include, AI for Design; Robotics; Sustainability in Design; Standards and Compliance; Advanced Materials; PCB Design, IoT Cybersecurity and much more! The 30+ sessions will provide a perfect setting for inspiration, learning and debate.
Visitors can also join practical, exhibitorled, workshop sessions that will be taking place across two separate theatres. The workshops are a brilliant opportunity to see the latest design innovation in action and put your questions to the experts.
1. Identifying Development Strategies Through Ethnography
Francesca Stephens, Head of Design, 42 Technology
When and Where: Eureka Theatre, Wednesday 11 October, 11:15am - 12:00pm
2. From Smart Sensors to AI: the New Frontier for IoT Applications
Dr Davide Di Palma, Engineering and Projects Director, HWM-Water
When and Where: New Electronics Theatre, Wednesday 11th October, 1:15pm - 2:00pm
3. The Impact of AI on Robotics Design and Deployment
Mr Rob Knight, Founder, The Robot Studio
When and Where: Eureka Theatre, Thursday 12th October, 10:15am - 11:00am
4. The Need for IoT Cybersecurity
Simon Loynes, Enterprise Sales Executive IoT/IIoT/Cybersecurity, Aeris Communications inc
When and Where: The Engineer Theatre, Thursday 12th October, 12:15pm - 1:00pm
Professor Amin Al-Habaibeh, Professor of Intelligent Engineering Systems, Nottingham Trent University
When and Where: The Engineer Theatre, Thursday 12th October, 2:15pm - 3:00pm
*subject to alternation
Win an award-winning, ‘best in design’, Good Housekeeping Institute, Hoover! The new HOOVER HL5 Home Upright Bagless Vacuum Cleaner will be raffled off at this year’s Engineering Design Show, courtesy of Smallfry Industrial Design in conjunction with Hoover.
The winner will be announced at the EDS after-show party, taking place on the 11th of October straight after the show closes. Visit Hoover on Stand E50 and be sure to check out their ‘evolution of the Hoover’ display.
The Robot Studio will be showcasing some of their incredible designs at EDS 2023
The Robot Studio’s goal is to create ‘a future where robots in daily life are as ubiquitous as websites are to the internet’. By developing designs as close to the human form as possible, The Robot Studio aims to create general-purpose ‘robot(s) that can turn (their) hand to a wide range of human-centric tasks’.
The Robot Studio uses ‘innovative mechanical designs with the latest NVIDA powered AI-at-the edge solutions’.
Come and meet them and their amazing designs at Stand C72
The future of deign with Nottingham Trent University NTU product design show case will be demonstrating the creative , innovative projects of the next generation of product design engineers. Recent graduates of NTU’s product design course will be on hand to overview their innovative projects and discuss their ideas with industry professionals at the show. Furthermore, we will be demonstrating the latest in visualization tools - Gravity sketch. The immersive technology will be demonstrated and available to test supported by our team of designers on hand to take you through your first steps to introduce you to the exploratory tool used in product design engineering.
Visit them on stand D1
POSITAL will be demonstrating their nextgeneration range of magnetic encoders & their energy harvesting device WINK POSITAL is a global manufacturer and technology leader in the world of sensing and energy harvesting.
Tracing its history back to 1918, as FRABA GmbH, the company has been at the forefront of rotary encoder technology since the technology was first conceived. The expanded range now includes absolute and incremental encoders, absolute kit encoders (for motor applications), inclinometers and linear draw wire sensors.
Come and meet WINK and the NEXTGEN encoders at Stand E41!
JPR Electronics is joining forces with WAGO, market leader in the field of spring clamp technology
JPR Electronics are independent distributors with a global network of franchises, enabling them to offer an extensive range of products from recognised quality manufacturers, such as WAGO.
At EDS, they will showcase an exciting range of products including: PCBs, Relays, Tooling, Installer Accessories etc. Alongside this, you will be able to win some amazing instant prizes in their exclusive SPIN TO WIN section!
And if that wasn’t enough, you can come to get some FREE WAGO Connectors and Accessories in their Pick N Mix area on Stand B54
For further information, please visit www.engineeringdesignshow.co.uk
Expect to discover 200+ exhibitors, thousands of the latest innovations and products and 30+ hours of free-to-attend conference sessions and workshops.
Motor customers in the UK are currently particularly pleased with the fast delivery capability of German manufacturer Menzel Elektromotoren. In early June, the family-run company received two orders for large machines within one week.
Due to motor failures, the water supply to 30,000 households was threatened and production in a cement plant was halted. After delivery times of only six and ten days, respectively, both the pump and the cement mill could be restarted in the shortest imaginable time. Faced with unexpected downtime due to equipment failures, customers often cannot afford to wait for a motor manufactured from scratch – standard delivery times in
above slip-ring motor delivers 2000 kW operating at 11kv, 6pole speed.
higher output ranges start at six months. Menzel has proven itself to be a strong partner in an emergency, quickly configuring suitable motor systems for a wide range of high-output applications
from its large, diverse stock of motors, cooling units and ancillary equipment –such as the current two jobs for British customers.
The squirrel cage pump motor has a nominal output of 1380 kW operating at 3300 V. The slip-ring motor for a cement mill delivers 2000 kW at 11 kV. Its special features are increased ingress protection rated IP55 and a closed cooling system with a top-mounted air-toair heat exchanger (cooling type IC 611), ideal for dusty environments and large temperature fluctuations.
Large industrial motors from stock and quickly tailored to order:
For further information, please visit www.menzel-motors.com
The
Custom Solutions for Electric Motors Around the Clock, Against the Clock!
Whenever existing mechanical and electrical interfaces are key coupled with fast delivery
Motors up to 15 MW and 13.8 kV
• Low voltage slip-ring and squirrel cage motors up to 3,000 kW
• Medium voltage slip-ring and squirrel cage motors up to 15,000 kW
• Direct current motors up to 2,000 kW
• Frequency converter-proof drives
• In-house load test facility up to 13.800 V, 2.300 kVA, 120 Hz
Customized special designs
• Custom designs for special applications and operating conditions
• Optimized motor design for higher efficiency
• Mechanically and electrically interchangeable motors
• Commissioning worldwide
MENZEL Great Britain Ltd. | UK Branch Office
27 Hunt Drive | Melton Mowbray | Leicestershire LE13 1PB
Martin Rooney | Tel.: +44 1664 500 844 | Mobil: +44 7957 618046 martin.rooney@menzelgb.co.uk
MENZEL Elektromotoren GmbH | German Headquarters
Neues Ufer 19-25 | D–10553 Berlin | Germany
New electric motor plant in 2024
More than 20.000 motors available from stock!
24/7 emergency service
www.menzel-motors.com
Rupture discs and safety valves have become indispensable for manufacturing companies in the chemical industry. However, there is a need to catch up in terms of signalling.
The opportunities offered to operators here are both diverse and economically interesting. With non-invasive signalling that can be integrated into the rupture disc, even processes with critical pressures and demanding media can be reliably monitored.
Processes involving high temperatures and highly corrosive media are widespread throughout the chemical industry. In the past, conventional signalling was not always compatible with such extreme conditions, which is why it is now often overlooked as an additional process monitoring system.
The use of modern signalling equipment not only helps to improve productivity and safety but is also helpful in terms of addressing environmental concerns. The German manufacturer REMBE is a European leader in the production of pressure relief devices, explosion protection systems and
the associated signalling devices. The company’s product range includes some of the most robust rupture discs and signalling systems available on the market. These solutions create significant operational added value in the chemical industry by reliably monitoring safety systems and critical pressure relief devices.
In processes involving potentially harmful media, the risk of leakage can be reduced via a quick and safe shutdown. REMBE’s
well-designed signalling systems comply with both industry-relevant standards for explosive atmospheres and the intrinsic safety standards. By providing rapid notification of a burst rupture disc, they help to safely control the process while minimising downtime. High-quality signal transmitters can be easily integrated into the existing control systems in order to transmit a visual or acoustic signal when the rupture disc bursts and to shut down the system if necessary.
The NIMU (non-invasive rupture disc monitoring) signal transmitter is suitable for systems exposed to harsh operating conditions. This reusable monitoring system is explicitly designed to provide rapid notification of a burst rupture disc. The REMBE NIMU sensor does not come into contact with the process itself, so it is not affected by harsh process conditions or corrosive media and ensures maximum tightness even for systems containing extremely corrosive chemicals.
The NIMU is mounted in a blind tap in the outlet on the rupture disc holder. Thus, the signal transmitter is completely isolated from the process. Potential leakage after the rupture disc has burst is also prevented – this is essential for customers in the chemical industry where leaks cannot be tolerated.
The signal transmitter is fully reusable not only after the rupture disc has burst, but also after scheduled maintenance work. During such maintenance work, the closed circuit of the rupture signalling system makes it easy to perform a function test – the rupture disc can then be reinserted into its holder. Furthermore, the operator can do this without external assistance, which simplifies and speeds up the maintenance process. This is simply a must in the chemical industry due to the demanding productivity requirements.
For further information, please visit www.rembe.de
REMBE’s well-designed signalling systems comply with both industryrelevant standards for explosive atmospheres and the intrinsic safety standards.
MTM Products have been established for over 40 years and are a leading manufacturer and supplier of industrial graphics products including self-adhesive labels, metal nameplates, graphic overlays, engraved labels and vinyl cut decals.
We have the knowledge and experience to advise you on the optimum graphics solution for your application, taking account of operating environment. We supply to many sectors including industrial machinery, electrical, automotive, rail, construction, medical and audio equipment. We offer excellent quality and
service at competitive prices. MTM are certificated to ISO9001 and ISO14001. Our products comply with the current RoHS and REACH requirements
MTM – the industrial graphics specialists
Let us share our expertise to make your life easier
Contact us at sales@ mtmproducts.co.uk or www.mtmproducts.co.uk
WISEMAN THREADING TOOLS LTD
We have been supplying threading tools and gauges since 1987.
Together with supplying plain plug and ring gauges this is all that we do, we therefore consider ourselves to be specialists in this field.
We supply worldwide.
We hold extensive ready stocks that include all of the standard stuff that others offer, but also includes taps, dies, die nuts, die head chasers, thread rolls and gauging for threads not normally available 'off the shelf '.
Our real time stocks can be checked and purchased online at www.threadtools. com Just enter the thread details into the search box on the home page.
You will be directed to the item, if stocked, or to our specials, (custom manufacture), sales team. who will quote to supply at competitive rates, in good time.
As an account holder you can also order online from our listed in stock items, at your normal terms. We realise that you need the right item at the right price and quality, and in a reasonable time frame.
We are geared to provide that.
We can ship stocked items same day.
Our experienced sales staff can assist and advise you on any technical issues.
We welcome enquiries from resellers and can offer terms to suit.
WISEMAN THREADING TOOLS LTD
11 Padgets Lane
South Moons Moat
Redditch B98 0RA UK
+44(0)1527 520 580 sales@threadtools.com www.threadtools.com
HSS DIES & DIE NUTS
Large shelf stocks for all Standard and many Special Threads. Check our stocks online.
THREAD CUTTING AND ROLLING HEADS and parts and repair service
HSS TAPS
Huge Stocks for all Standard threads
CUSTOM MADE taps our SPECIALITY!
We stock taps for many non standard (SPECIAL) threads
All types; Spiral flute and point, Fluteless, Left Hand, etc, etc.
THREAD GAUGES all types. Large stocks for standard and SPECIAL threads. Any non stocked can be quoted for custom manufacture.
CHASERS FOR COVENTRY & LANDIS TYPE DIE HEADS
Ready stocks for most size heads most standard and some special threads Geometry available for most materials. Custom manufacture our speciality!
The stacking cradle system at SÜLZLE Hagmeyer GmbH, a member of the SÜLZLE Group, has been in operation for an impressive 21 years. The steel distributor from Swabia opted to have KASTO’s storage technology experts retrofit their bar stock storage system to ensure it continues functioning efficiently for another 252 months. Within 15 working days, the storage specialist worked at incredible heights to replace the drive technology, finishing precisely according to schedule.
When a premium stainless steel pipe leaves Geislingen an der Steige, it likely originated from Hall 9 of the SÜLZLE Hagmeyer GmbH factory grounds. The company has been part of the SÜLZLE Group since 2018 and supplies numerous industrial and craftsmen’s businesses in the region with high-quality steel and other metal products from Geislingen. The interior of the warehouse with its blue walls is impressive. There are pipes of various sizes stacked closely together, reaching a height of almost ten metres. A crane hovers under the hall roof, moving from one location to the next, lifting, lowering, storing and retrieving filled load carriers.
With its team of around 100 employees and extensive machinery, SÜLZLE Hagmeyer in Geislingen is the steel and metal distributor for, e.g., pipes, flat and round bar steel and profiles made of stainless and high-grade steel as well as aluminium and other nonferrous metals. To protect finely ground and polished products from soiling and mechanical damage, the long-established company stores the semi-finished products in its stacking cradle system before shipping. The KASTO UNIBLOC A bar stock storage system was installed in the warehouse, which was built in 2001 for this purpose. Since then, it processes between 50 and 100 items per day. The steel and metal distributor stocks up to 2,000 tons of steel and aluminium in the approx. 98-metre long and 10-metre wide storage area.
Stacking cradle systems are characterised by their high-density storage capability. In this case, the UNIBLOC A offers more than 1,530 cassette spaces for three different stored goods lengths between four and six metres. A maximum of ten stacking cradles can be placed on top of each other. Up to
three cradles can be moved simultaneously with the multiple transport crossbeam. The storage and retrieval process begins and ends at two stations. The KASTOlogic warehouse management software ensures the most efficient routing. This system assists employees in their daily tasks, visualises storage and inventories, and communicates with the HOST system from SÜLZLE Hagmeyer, ensuring optimum overall performance.
After 21 years in operation, only a few spare parts were available, new or used, for the system’s electrical and electronic components. This was true, especially for the crane that carries out the storage and retrieval. The effects of wear and
ageing required constant creative and costly customised solutions. As a result, an extensive overhaul was necessary. The risk of a malfunction in the storage system was too great. “Longer unscheduled downtimes in the warehouse jeopardised the ability of the entire division to supply,” explains Hans Gekeler, Director of IT at SÜLZLE Hagmeyer. SÜLZLE Hagmeyer enlisted the help of KASTO to improve the output reliability of the plant in Geislingen.
The storage, sawing and automation specialist from Achern shares the mediumsized steel distributor’s approach to conserving resources. “The machine components and stacking cradles were still in excellent condition,” reported Alfred Schwörer, Retrofit Team Leader at
KASTO, during the status analysis. These components are not expected to malfunction in the next few years. However, the system’s controls were severely outdated and could become a concern. The replacement of specific parts “would not have worked because they were not compatible with the remaining components in the control chain” Gekeler adds. Therefore, the experts from Swabia opted for a retrofit.
At the end of February 2022, KASTO updated the complete control electronics at stations and crane bridge. “We replaced the entire drive technology on the crane,” Schwörer reports. This included switch components as well as motor and encoder cables. The existing measuring systems were replaced by an absolute encoder with integrated cable pull and an optical laser measuring system. In addition, the technicians updated the optical data light barrier and installed two climate control units in the control cabinets on the crane bridge. They also swapped out two frequency converters at the stations. The new components come with a service agreement to support the plant’s internal maintenance department. “The retrofit not only eliminates the cause of many malfunctions, minimising the risk of downtime,” Gekeler explains, comparing before and after. “At the same time, the new technology equips us for the future.”
Even the experienced automation expert from Achern rarely undertakes retrofit projects on stacking cradle systems. The project also faced challenges due to the physical conditions. “Normally, we prefer to work with up to 15 employees on retrofit projects. This allows us to carry out several measures in tandem,” explains Schwörer. “Unfortunately, that was not so straightforward in Hall 9.” The crane bridge did not provide nearly enough work space for the amount of personnel required. The KASTO team overcame the challenging conditions and limited space under the hall roof by using three articulated aerial platforms and a truck-mounted crane to transport loads efficiently. The safety of technicians was given utmost importance due to the significant working height. Protecting them from falling or other incidents
was the number one priority. “For obvious reasons, work safety preceded maximum speed,” Schwörer strongly emphasizes.
The retrofit at the beginning of the year was already the third project of this kind at SÜLZLE Hagmeyer. In 2011, KASTO upgraded a KASTO Unicompact 4000 honeycomb storage system, which was put into operation in 1993. In 2010, retrofit measures on a sheet metal storage system from a third-party supplier lead the way. The positive experience from previous interactions influenced the decision to place the new contract. Gekeler praised its project partner by saying “KASTO always demonstrated exceptional project planning skills”. “Goals are defined for each day and met consistently. The resources provided are selected to meet the current challenges faced taking into consideration the team size and the required auxiliary equipment.” As a result, this project was also executed flawlessly as per schedule. “The fast and dependable execution of projects like this helps us to better coordinate with customers and suppliers.,” reports the IT Director. KASTO completed the retrofit measures within three weeks and, most importantly, handed over a turnkey, reliable system in mid-March.
Left, SÜLZLE Hagmeyer’s treasure chest: In 2001, the metal distributor built a hall for its high-quality steel and aluminium products. The storage system was updated in 2022. Above, from the SÜLZLE Hagmeyer team (from left): Hans Gekeler, Director of IT, Gerhard Mehlmann, Maintenance Manager, and Ralf Thierer, Supervisor and Warehouse Manager.
The retrofit at the beginning of the year was already the third project of this kind at SÜLZLE Hagmeyer.
An environmental solutions company that was committed to implementing circular economy principles in managing waste to preserve finite natural resources, faced a challenge in maintaining its hydrogen production process due to low natural gas supply. To overcome this issue, Burckhardt Compression supplied a quick, cost-effective solution involving expansion technology, enabling the gas supply to be restored to the required level. This ensured that the hydrogen production process could continue smoothly while meeting sustainability goals.
As part of its commitment to sustainable waste management practices, an environmental solutions company produces hydrogen through steam methane reforming, which is used in various applications such as fuel cell vehicles, power generation, and industrial processes, contributing to the reduction of greenhouse gas emissions.
Originally, the company received natural gas at a supply pressure of 16 bar (232 psi). However, it was later advised that the pressure would be gradually reduced to 8 bar (116 psi) and then to 4 bar (58 psi). To maintain hydrogen production, a solution was needed to maintain the natural gas supply at the original pressure of 16 bar. The customer’s on-site engineering team had the task of sourcing two compressors quickly, and on a limited budget, which could handle the gradual change in process gas pressure and ensure that the hydrogen production process remained unaffected.
After evaluating their options, the engineering team identified an ideal solution available from Burckhardt Compression, the leading company for compression solutions across a wide range of applications.
Burckhardt Compression supplied and installed two second-hand Laby® 2K90-2E gas compressors, which had never been used before, allowing for a faster delivery time of only five months, much shorter than that offered by other companies.
The two Laby® compressors were delivered from stock in Switzerland as bare shaft compressors. Site installation
and commissioning were carried out by experts from Burckhardt Compression Brazil with support from the engineering team in Switzerland.
Burckhardt Compression delivered a fit-forpurpose, future-proof turnkey solution with a long operational life, maintaining the gas at its original pressure, ensuring sustainable long-term customer investment. The project was also delivered on budget, which allowed it to achieve its goals without incurring more costs.
When the project was completed, a spokesperson for the company concluded:
“Burckhardt Compression exceeded expectations throughout the entire project, from quotation to commissioning, operation, and final delivery of the compressors. Our partnership and commitment were critical to the success of the project, ensuring that we met all project expectations, including budget, deadline, safety, operational availability, and equipment quality. This project is an excellent example of our ability to deliver exceptional results and will serve as a model for future projects.”
For further information, please visit www.burckhardtcompression.com
Burckhardt Compression exceeded expectations throughout the entire project, from quotation to commissioning, operation, and final delivery of the compressors.
◊ Manufacturing up to 1450mm diameter
◊ Turning - CNC lathes, Vertical Machining Centres
◊ Gear Cutting - Hobbing, Shaping, Gears, Sprockets & Pulleys
◊ Bevel Gears, Helical, External & Internal cut Gears
◊ Rack Shaping, Broaching, Keywaying
◊ Vertical Boring, Centreless & Rotary Grinding
◊ Bore Honing ◊ Induction Hardening
◊ Drilling & Tapping ◊ Marking ◊ Blacking
◊ Toothed Timing Belts stocked and cut to size
◊ Roller Chain in carbon steel, stainless steel in stock
◊ Large stocks of all products ◊ CAD - CAM Design & Development
◊ Crossbore rework on all products - fast delivery
Increase your mold manufacturing versatility using the power of gundrilling with the leaders in deep hole drilling, UNISIG. Offering complete solutions for everything from simple to complex mold components, UNISIG machines help moldmakers improve efficiency, throughput and precision with outstanding part-processing versatility at an exceptional value.
TAKE YOUR MOLDMAKING OPERATIONS FURTHER WITH UNISIG TODAY
Find
software. The software and training for the company’s workforce were part of the investment, along with the hiring of additional personnel.
The company’s new fabrication capabilities will also serve as an inspiration and catalyst for ongoing development and advances in machine design that will have an immediate impact on the value UNISIG brings to its customers now and in the future, said UNISIG CEO Anthony Fettig.
UNISIG’s fabrication enhancements also include MIG and TIG welding with advanced digital process control and weld boom with power assist. A modular fixture system provides precision component setup from 3D models, while a vertical pallet system stores raw sheet material. To assist department personnel, vacuum sheet lifting equipment and updated bridge crane controls make for easy material handling.
quality and quantity of its components while optimizing the mix of parts that are made internally versus those that are outsourced for production.
The investment includes the installation of fiber laser cutting equipment, and a 242-ton capacity press brake with a 7-axis programmable back gage, all of which utilizes 3D programming and simulation
“The most exciting part of this investment from my view is the opportunity to fundamentally change how we think about the design of fabricated components,” Fettig said. “Our engineers will be inspired by the manufacturing innovations generated by the precision fabrication team and what we can do with these state-of-the-art production capabilities,” Fettig said.
Further information on all machines and the complete UNISIG machine program is available at: www.unisig.com or follow the company on LinkedIn and Twitter (@ UNISIG).
You will also meet us at the EMO 2023 show in Hannover, Germany, from 18–23 September.
For further information, please visit www.unisig.com
Gundrilling and BTA deep hole drilling for highly productive shops.
Gundrilling and BTA deep hole drilling for highly productive shops.
Whether your shop needs on-center or off-center holes, specialized job shop work or fully automated production, UNISIG has a deep hole drilling solution with the accuracy and performance you need
Whether your shop needs on-center or off-center holes, specialized job shop work or fully automated production, UNISIG has a deep hole drilling solution with the accuracy and performance you need
Take your shop’s production further - learn more at UNISIG.COM.
Take your shop’s production further - learn more at UNISIG.COM.
Hall 13, C21
Hall 13, C21
How do you prove your facilities are compliant? Gathering data, reports and logs from every inch of the manufacturing shop floor can take time, and it might not be as comprehensive as one might wish. Here, Richard Mount, Director of Sales at ASIC design and supply company Swindon Silicon Systems, explains how ASIC-driven smart sensors can help businesses maintain and prove regulatory compliance.
The manufacturing sector is a major UK industry, accounting for around eight per cent of the workforce and just under ten per cent of the country’s total economic output. With millions of employees across
the country, and vast amounts of products manufactured each day, there must be an element of standardisation to ensure that work is performed safely, and that products meet specifications.
Regulations are crucial in achieving this. Government and industry bodies set standards across areas including health and safety, environmental impact, and process quality. Meeting these standards often requires extensive reporting on the part of the manufacturer, which may include historical data, detailed process methods, and maintenance logs.
Penalties for non-compliance are typically fines, but if the business is not proven to meet other regulations, such as ISO, these certifications may also be lost. On top of that, businesses may need to cover the cost of inspection. Government agency HSE will recuperate costs for inspection of health and safety legislation breaches at £163 per hour, a significant financial cost to businesses.
Additional implications such as reduced consumer trust and damaged reputation also come with non-compliance. So, how can manufacturers ensure they are compliant — and prove it?
Implementing sensor technology into the shop floor can help, continuously measuring metrics such as temperature, humidity, air quality and noise. These sensors are used in a variety of applications. Perishable goods and chemicals that need to be stored under specific conditions can be monitored to ensure quality and prevent wastage. They can also benefit worker safety, by ensuring noise remains at safe levels or for monitoring the presence of toxic or harmful gases.
Combining these sensors with IoT technologies means that this data can be accessed real-time, ensuring operators can pick up faults almost immediately and take necessary action. It can also make reporting much easier, collating data from multiple connected sensors across the factory into one location.
With the important role that smart sensors play, they themselves must meet strict requirements. Sensor technology relies on ICs to perform the signal conversion, processing and digitisation to transform analogue signals obtained into digital
ones that can be reported. For some applications, standard, off-the-shelf ICs may be sufficient to perform these tasks. But to give smart sensors a technical and competitive edge, opting for a custom Application Specific IC, or ASIC instead can elevate sensing technology to the next level.
ASICs are designed exactly to the customer’s specification, resulting in a fully optimised chip for the specific application. This level of optimisation helps give ASICs a smaller footprint, as well as reduced power consumption. The smaller size of an ASIC helps broaden the number of potential applications where it can be used. For example, wearables such as wristbands and headsets are made more viable, offering workers an increased level of protection and safety compliance.
The low power consumption of an ASIC also means that battery-operated sensors have a much longer lifetime, lessening the need for battery replacements. It also prevents downtime of the sensor itself to ensure that there are no gaps in or loss of any data.
As new regulations continue to emerge in response to changing industry standards, it can be tricky for manufacturers to keep up. Making the most of smart sensor technology with ASIC-improved capabilities can help manufacturers ensure compliance across the whole of their plant not just on inspection day, but for the remaining 364 days of the year.
For further information, please visit www.swindonsilicon.com
Combining these sensors with IoT technologies means that this data can be accessed real-time, ensuring operators can pick up faults almost immediately and take necessary action.
Ongoing supply chain issues, skill gaps and ever-changing customer demands mean that now — more than ever — manufacturers are increasingly adopting ‘smart’ manufacturing mindsets to keep up. In this article, Richard Mount, Director of Sales at ASIC design and supply company Swindon Silicon Systems explores the role of position sensors within smart manufacturing, and how ASICs can drive the technology further forwards.
The concept of smart manufacturing has been around for some time. Essentially, its aim is to make processes more efficient and adaptable to changing market needs. This is all achieved while maintaining high production quality, worker safety and equipment uptime.
By making a manufacturing plant or process smarter, customer expectations are also met with greater swiftness. This could include the creation of more tailored, bespoke products to fit specific needs, which would otherwise be inefficient or unprofitable to manufacture. In highly competitive sectors, having a smarter, more agile mindset could be the make-or-break difference between staying ahead or falling behind the curve. But when it comes to executing smart methodologies at the production level, what technologies are available?
Position sensing is a crucial element of many smarter manufacturing processes, particularly with enabling factory automation. Tasks like pick-and-place or product assembly require the equipment to very accurately know its position in order to move precisely — information that can be obtained using position sensors. Depending on the type, these sensors may determine an object’s position either directly by finding its absolute location, or indirectly by measuring its relative displacement.
One common example is the inductive position sensor. Relying on principles of electromagnetic induction, these position sensors allow for non-contact detection of metallic objects. Conductive targets cause disturbances in the magnetic field, which are detected by the sensing element. Because
only metallic objects will affect the magnetic field, inductive position sensing can’t be used to detect non-metals like plastic. But the upside of this is that the sensor is less likely to be affected by dust or dirt build-up because these won’t affect the magnetic field. This makes them ideal for operation within dirtier industrial environments.
Another type is the optical position encoder. These typically consist of an LED and photodetector, with either an optical disc or scale depending on whether the encoder is measuring linear or rotary displacement. Optical encoders can perform to high resolutions, making them ideal for applications where high precision matters, such as a CNC machine.
When photons of light are captured by the photodetector, a weak electrical signal is generated. This must be amplified using a signal-conditioning circuit before being digitised with an analogue-to-digital converter (ADC). It can then be received by a CPU or microcontroller, which is able to calculate object position based on the signal. The processing unit is capable of recognising events such as reference marks being passed and can immediately take remedial action within a closed-loop system.
It’s vital that these processes of sensing, conditioning, and digitising are up to scratch. Sensor failure or inaccuracies could lead to the incorrect manufacture of products,
leading to a drop in productivity and wasted materials and time.
When an encoder is first developed, it may be comprised of off-the-shelf discrete components or integrated circuits (ICs). And for low production volumes, this may be an adequate solution. But for a sensor solution that outstrips its competition, it’s preferable to opt for an Application Specific IC, or ASIC.
An ASIC is simply an IC that has been designed and manufactured with its exact application in mind. This bespoke approach to IC design results in a chip fully optimised for its role, often with reduced power consumption and smaller chip size as additional benefits to its improved performance.
Choosing ASIC design also offers IP protection to reassure sensor manufacturers that their IP will not be made available to the competition, keeping them one step ahead. The nature of custom IC development and design also makes it much harder to reverse engineer than a standard IC, offering another level of defence.
Manufacturers are increasingly looking for methods to maximise efficiency of the shop floor. And in critical applications, even the tiniest fraction of a millimetre could mean the difference between success and failure. By utilising ASIC-based technologies, it’s possible to optimise sensor solutions right from chip level for a superior performance, no matter the process.
To learn more about Swindon Silicon and its custom IC solutions, visit https://www.swindonsilicon.com/news/
EMS
Quality means doing it right when no-one is looking,” said industrialist and Ford Motor founder Henry Ford. Quality assurance and verification are important steps in any production process, but how can we carry out these inspections? 3D measurement technologies are one such approach to getting a closer look at individual products as Stewart Goulding, Managing Director at DC motor supplier EMS explains.
In any manufacturing process, it’s crucial to ensure that the final product has been produced to its specification and to the desired quality. Any discrepancies in shape or surface metrology may negatively affect the way the product functions, as well as its efficiency and fit.
Visual inspections performed by a human or a camera robot may be sufficient for some manufacturing processes. But there are certain applications where inspections must be more comprehensive. One such example is the automotive sector. Gears, crankshafts and engine blocks must be tested thoroughly to ensure component integrity and that pieces will fit as desired with the rest of the car’s components.
Achieving this detailed view and examination is possible using 3D measurement technologies. A variety of techniques are available, which can be loosely split into two types — contact and non-contact.
Optical 3D scanning methods are a popular method of non-contact measurement. These offer protection for fragile surfaces that may otherwise be easily damaged by contact methods.
Typically performed using laser scanner or fringe projection systems, optical scans can measure thousands of points per second for a quick, complete scan of the finished product. The digital nature of optical method scanning combined with its speed makes it ideal for integration within highly automated manufacturing processes.
But not all products are best suited to
optical methods. Items made from materials with reflective or translucent properties, like glass or synthetic resin, can be difficult to measure using light-based methods. While coating sprays are available to allow optical-based measurements, applying and removing this layer can create unwanted additional steps in the manufacturing process.
An alternative option is to use a coordinate measuring machine (CMM). Generally regarded as the most accurate form of 3D measurement, these machines can take readings with a tolerance of just one micron, making them ideal for applications where high precision is of utmost priority.
CMMs rely on a probe or stylus with a ballshaped measuring tip that is positioned onto mapped reference points on the test object. A controller detects this contact to determine the precise shape of the object. It’s possible to manipulate the arm of the probe not only around the object, but also within it for access to cavities that would be difficult to access via an alternative method.
However, there are some disadvantages when it comes to using CMMs. This includes the long measurement time caused by the need to physically move the probe across and around the product. There is also the problem of reference points. CMMs typically measure on several pre-set reference points or along a single line, highlighting specific areas of interest rather than the whole product.
So, how can we maintain the high quality of CMM data, while achieving the speed of an optical-based method? This is where combination or multisensor methods come into play. By using a traditional CMM machine alongside an optical technique like laser scanning, manufacturers can make the best of both approaches.
Whichever method is used for imaging, it’s clear that they all rely on one thing — the accurate positioning of the sensor elements. Whether it’s rotating the arm of the CMM or directing a fine laser, all this positioning can be done using a drive system.
When selecting a drive system for such applications, it’s crucial that the precision of these small DC motors is on par with what the final measurement technology is expected to deliver. This includes the use of encoders, which can generate position signals based on the motor shaft rotation or linear movement. Crucial to allowing achieving precise positioning, these also allow for closed loop control of the motor.
Manufacturers face constant pressure to always maintain high product quality. And while it’s sometimes possible to verify product standard by eye, making use of 3D technologies offers a far more detailed and in-depth view of every inch of product, ensuring that every single product that leaves the factory is as good as the last.
For further information, please visit www.ems-limited.co.uk
In any manufacturing process, it’s crucial to ensure that the final product has been produced to its specification and to the desired quality.
Over the last 30 years there has been a boom in the traceability and identification of manufactured components. Many industries want to directly laser mark these, however there are some parts that are just getting larger and larger.
Casting and pressing companies sometimes have such large parts that they simply cannot fit these into a standard sized Class 1 laser enclosure leaving many companies wondering how they can mark them.
Even though they launched a new range of large XXL-Box class 1 enclosures in 2022, SIC Marking saw this problem as a new challenge for 2023. They have now launched their Funnel Integrated Technology (F.I.T. for short) as a complete all in one solution that combines all of the necessary components and settings to mark larger parts in a simple, safe and economic way within the customers production line and budget.
The FIT tunnel eliminates the need to enclose the entire part for the laser marking process by enclosing just the marking area. The compact design allows for the FIT system to be retrofitted easily into an existing robotic cell.
This ready to integrate and secured laser marking system comes as a ‘Tunnel Style’ Class 1 compliant enclosure. It is a compact
and easy to integrate solution with a single connection to a PLC. The F.I.T. can be mounted to a robot head for presenting to a stationary part – or fixed in position allowing the robot to present the part for marking.
Not only is the F.I.T. adapted for production environments with its maintenance drawer for the cleaning of the lens, it has built-in shock protection preventing the funnel from damage. The F.I.T. tunnel can be adapted to your marking needs with three window sizes available as standard: 24mm x 32mm, 100mm x 32mm and 100mm x 100mm. Custom sizes can also be accommodated.
The F.I.T. is available as a basic chassis or as a complete solution with protective covers, a cooling system, electrical cabinet and tooling as well as an optional integrated Cognex vision system for 2D verification / validation or 3D lens for marking curved or angled surfaces.
For a demonstration of the new F.I.T. and / or any of the other laser marking systems in SIC Marking’s extensive range, please get in touch with SIC Marking UK in Warwick, UK on 01926 830372 where one of the very knowledgeable engineers will be happy to talk to you.
www.sic-marking.co.uk
The SIC Marking Group was formed in 1992 and has been growing ever since, as a result of its development in new sectors, winning many local and international customers, in addition to many takeovers.
The increasing number of its distributor partners and the opening of subsidiaries on the 3 continents have given it an acknowledged presence and international reputation.
It has 10 subsidiaries, mobilised for promotion, implementation and customer support in France, Spain, Italy, UK, Germany, Canada, USA, Mexico, China and Korea. They also deploy its marking and traceability solutions locally on behalf of international groups.
Furthermore, its 40 exclusive distributor partners enable it, overall, to serve more than 50 countries worldwide.
Three years time storage
3 years rolling data retention
Live dashboards
Create real-time dashboards to analyze data and control devices
Events engine
Keep operators on-the-ball and informed
Synthetic Variables
Transform raw data into insights
User management
Build applications to best fit the operator’s needs
Interface Force Measurements Ltd
Ground Floor, Unit 19, Duke’s Ride, Wellington Business Park
Crowthorne, Berkshire RG45 6LS
Tel: +44 (0)1344 776666 | Email: info@interface.uk.com | www.interface.uk.com
Infrared Camera System for Continuous Reformer Tube Monitoring and Temperature Measurement Inside Furnaces
Advanced Energy’s FurnaceSpection™ system provides real-time continuous temperature measurement inside hightemperature furnaces in refining, metals, and glass production processes. By utilizing this accurate system, users are equipped to identify process abnormalities before they develop into problems that can lead to unplanned outages.
FurnaceSpection measures the temperature of product, refractory, and heat transfer surfaces inside natural gas-fired furnaces. It also enables the monitoring of flame condition, helping users reduce the production of NOX, which results in less environmental impact and longer furnace lifetime.
The system consists of an accurate 640 x 480 focal-plane array thermal imaging camera with high-quality optics and builtin flame filter, which reduces the influence of furnace chamber flame, as well as CO2.
FurnaceSpection is covered by a highly efficient housing, enabling air or optional water cooling to resist high ambient temperatures.
• Load Monitoring and Automation Systems for manufacturing equipment
• Process monitoring and control for assembly machines
• Manufacturing Execution Systems including downtime analysis
• Production recording systems
• Bespoke control systems
• Calibration services
• Repair/Maintenance
E-mail:
With the FurnaceSpection system, multiple measuring points on the furnace ceiling, end wall, and side wall can be independently monitored by adding measuring regions of interest.
The system helps operators monitor and control process temperature uniformity by streaming images documented by a powerful software for analysis and historical trends. In
www.advancedenergy.com | info@aei.com
addition, outputs to automation and DCS and a real-time web server broadcast these images on the plant’s local network.
At a cost of several thousand dollars per furnace and re-tubing costs in the millions, the system is designed to save a significant amount of capital by preventing complete furnace failure, as well as maximizing the lifetime of the refractory linings.
Before-and-after power/energy usage analysis is vital in energy audits and for organisations to validate energy-saving measures, especially for high consumers of electricity. The Tinytag Energy Logger is a portable data logger which can be used to monitor electricity consumption in individual pieces of equipment to help identify where potential energy usage savings can be made, improving energy performance and cost savings.
For a small initial investment, the Tinytag Energy Logger provides businesses with information about significant areas of energy usage, informing energy savings and leading to reduced costs. Recording data before energy-saving implementation can inform your strategy by revealing areas of high power consumption that could feasibly be reduced, as well as the peak times for energy usage in your facility. Data recorded after energy-saving plans are executed verify the energy savings of the methods in place, providing useful historical data to refer back to and report on.
Specialist industrial lubricants manufacturer Interflon uses the Tinytag Energy data logger in electrical monitoring to show its customers how using its products results in energy
savings. Before-and-after monitoring using the Tinytag Energy Logger demonstrates how Interflon’s lubricants can significantly lower friction levels in electrically-driven machinery, in turn lowering energy consumption.
Gemini Data Loggers designs and manufactures comprehensive building monitoring equipment, including temperature
• Rugged and compact
• Easy to use
• Dust, splash or waterproof
• Data downloaded to PC
• Cost-effective
Accompanying probes are available for monitoring extremes of temperature, and for awkward to reach areas such as pipework.
For sites requiring remote data access, Tinytag Radio and LAN loggers gather data automatically for viewing on a PC, across a LAN, or remotely across the inter net.
and relative humidity data loggers for assessing occupant comfort, data loggers for monitoring energy usage and efficiency, and carbon dioxide data loggers for monitoring indoor air quality. The Tinytag Connect system – comprising Radio and LAN data loggers and Tinytag Explorer Connect software – allows wireless, automatic environmental monitoring, ideal for large sites and applications.
SICK has announced a major advance in its colour sensor portfolio, with the launch of its CSS and CSX high resolution and highspeed devices. SICK’s newly developed flagship CSS colour sensor leads the way with best-in-class colour resolution and the ability to distinguish even the slightest nuances in shade. Its capability to identify subtle differences in surface structures and textures opens up wide-ranging applications in automotive manufacturing.
The SICK CSS Colour Sensor detects colours precisely, regardless of the distance from the object, at lengths of up to 500mm. Its unique distance regulation capability dispenses with the need for strict guidance of the target. It therefore accommodates changing sensing distances automatically on a production line, e.g. to account for differing orientations of a product on a conveyor, and to handle varying object sizes with ease.
Live L*A*B* or RGB colour values are displayed directly on the CSS’s on-sensor full-colour display. An innovative teach-in method enables the sensor to assess the similarity between the detected colour and expected colour in real time. Up to 15 colours can be output directly via the sensor’s four switching outputs. The SICK IO-Link CSS Colour Sensor also offers the unmatched capability to output up to 24 colours to a machine controller. The SICK CSS goes far beyond sensing homogenous colours,
opening up a wide field of applications, and is an even an attractive alternative to expensive colour measurement devices, in some cases.
With a switching frequency of 13.8kHz, the SICK CSX High Speed sensor works at double the pace of its predecessor device, while still offering customers the option of full mounting compatibility for direct replacement. As well as typical applications such as the detection of colour marks, labels and splices, the CSX now masters new highspeed production tasks such as rapid sorting of objects according to colour.
“SICK’s colour sensor portfolio has undergone a major overhaul, culminating in some of the best colour sensing capability currently available,” explains David Hannaby,
SICK’s market development manager for presence detection.
“These two devices now offer best-inclass performance, as well as combining unmatched colour recognition with ease of set-up and the ability to adjust the colour sensitivity precisely. The sensors are therefore ideal for wide-ranging colour sensing applications, such as colour verification for quality control, sorting and separation, as well as object and print mark positioning.
“The automatic sensing distance regulation enables the CSS to detect colours reliably, despite the difference that changing distances have on the perceived colour; it can handle differences in distance between 50mm and 500mm with ease.”
The CSS and CSX colour sensors help to achieve higher process speeds and higher throughputs with outstanding detection repeatability in automotive manufacturing, for example to differentiate components such as seat covers, or detect glued areas.
The SICK CSS colour sensors can be quickly and precisely configured for the specific application using the setup assistant in SICK’s SOPAS software. The IO-Link version offers additional advantages for quick and simple commissioning, as well as rapid diagnosis, process monitoring and fine adjustment of the process set-up.
For further information, please visit www.sick.co.uk
The SICK CSS Colour Sensor detects colours precisely, regardless of the distance from the object, at lengths of up to 500mm.
OMNIFLEX
To rescue, rehabilitate and protect rhino populations, highly specialised conservation programs have been set up in some of the biggest national parks in Southern Africa. In fact, over 44 per cent of protected land in South Africa is dedicated to nature reserves, which all need to manage the continuous supply of clean, filtered water and process waste water to run efficiently. Here, Ian Loudon, international sales and marketing manager at remote monitoring specialist Omniflex, explores how South African rhino sanctuaries are using wireless tank monitoring to keep conservation programs running.
According to Save The Rhino, there are just 6,195 black rhinos and 15,942 white rhinos left in the world, the largest populations being in South Africa. Worryingly, ongoing poaching of rhinos means that both species face extinction if they are not adequately protected.
Because protection sites will span over tens of thousands of hectares, installing water tank monitoring systems for a conservation site isn’t easy. Water tanks and reservoirs are often located in difficult-to-access, unsafe areas and installing control cables over large areas is expensive. Therefore, facilities managers are turning to wireless systems to monitor and manage the potable (consumable) and grey (waste) water levels for the camps, facilities and feeding stations for convalescent rhinos.
When choosing a system for water monitoring facilities managers have several options, including license free band radio telemetry. This system uses restricted radio band frequencies, controllers and separate radio remote terminal units (RTUs) with data interfaces to monitor and control a site’s water tanks. The license free band allows as many devices as necessary to be connected without regulatory approval. The band used is free from other radio traffic that can interfere and disrupt communications for managing water reticulation.
With impractical cable distances and expensive instrumentation costs, managers on conservation sites have no feasible way of monitoring water conditions in their tanks using traditional solutions.
By exploring wireless products that blend radio and controllers into a single package, it is possible to monitor and control water tank levels remotely over a conservation site. Products like these use licence free band frequencies to avoid unnecessary engineering and costly administration.
A reliable solution is a system comprising of multiple RTUs wirelessly interfaced into a big screen television at a central administration point, which, due to security levels required for anti-poaching, is manned 24/7. This screen provides an overview of all water tanks located in the facility, many of which are located several kilometres away. Each RTU is configured to detect high and low water tank levels in real-time and will trigger an on-screen alarm when abnormalities are detected.
Due to the remote location of the potable water reservoir, it is impractical to connect the RTUs in these tanks to the mains power. Therefore, each terminal has a built-in solar panel and requires no additional power
connections. Because the RTUs monitoring grey water are located closer to the manned station, they can be hardwired using a single cable to the mains power. However, to be off-grid and independent, the entire facility is powered by a solar system and backup generator for emergencies. This ensures that the remote monitoring of water levels is independent, despite nationwide grid outages.
The system ensures conservation sites can monitor the conditions of their water tanks over distances of up to 15 kilometres. The RTUs are also robust, housed in weatherproof casing with power supply charger units and backup batteries. What’s more, the low power consumption of the system makes it suitable for solar powered out-stations at remote reservoirs.
Conservation programmes are crucial to maintaining breeding populations and protecting endangered species from poachers. Therefore, every process from the installation of security fences to the monitoring of water levels must be carefully and efficiently controlled. When facility assets are spread over a large area, wireless remote monitoring technology makes control and management more simple, efficient and costeffective.
For further information, please visit www.omniflex.com/tank.php.
We are LAUDA – the world market leader for precise temperature control. WE are the reliable partner for electromobility, hydrogen, chemicals, pharmaceuticals/biotech, semiconductors and medical technology.
Get in touch to discuss your own temperature solutions: info@lauda-technology.co.uk
+44(0)1780 234 118 www.lauda-technology.co.uk
Visilume present our tried and tested UK manufactured sight flow indicators.
Our standard range, with a choice of stainless steel and carbon steel castings can be supplied with a flap or spinner to offer additional visual indication.
We have vast experience with custom requirements, whether that be special materials, overall lengths or pressure ratings.
As a leading global protective packaging supplier Storopack recognizes the importance of ensuring goods are protected during transit and arrive in perfect condition.
Damaged goods not only incur costs for replacement orders but also affect businesses’ reputations. So while costs need to be kept to a minimum it is vital to choose the correct protective packaging type.
Usually a void fill packaging medium will suffice. However when the product is more sensitive to shock and vibration, such as engineering, electronics, aeronautical, and many other expensive products then more consideration has to be given to using the right type of in-the-box protective packaging.
Storopack’s FOAMplus® range is a perfect solution for companies that manufacture or ship products that require this highest degree of protection eliminating transit and handling damage.
The success of FOAMplus® polyurethane foam is based upon its huge versatility as a packaging medium. The foam can either be dispensed directly into the carton where the expanding foam will mould itself to the contours of the product shape or can be made into pre-moulded cushions to enhance presentation. The product will satisfy the most rigorous cushioning demands for high value, fragile and awkward shaped products. The light weight foam packaging also ensures that shipping costs are kept to a minimum whilst providing customers with total product protection.
As a space saving solution FOAMplus®, polyurethane foam packaging is ‘on demand’ and mixes two components together which then expands up to 200 times its liquid volume negating the necessity for large storage areas required for pre-fabricated packaging.
The benefits for customers are numerous. As well as an ideal solution for protecting awkward and valuable products, customers with product
design changes and new product line additions are able to quickly adapt the packaging without the need to carry a large range of bespoke cartons or fabricated packaging.
There are two dispensing methods available for the insitu protective packaging solution. Either FOAMplus® Hand Packer, a manually operated system, with a fully electronic microprocessor control to maintain consistent quality that delivers the foam direct into polythene lined carton via a foam dispensing gun.
Alternatively the Bag Packer² Foam-in-Bag dispensing system is fast, easy to use, efficient and economical. The machine can produce up to 23 foam-filled bags per minute at the touch of a button. Polyol B 5504R, foam B component is made from 30 percent recycled polyurethane.
www.storopack.co.uk
PAPERplus® - Paper pads provide maximum performance, high density, and strength. Ideal in-the-box protection for heavy products.
100% recycled content and 100% recyclable
For food processors seeking fullyintegrated, paperless and automated data collection from across their entire inspection machine fleet, PPMA 2023 is a must-visit event. This year, Fortress Technology presents its latest data communication solutions, engineered to work on all their inspection machinery, as well as a number of other makes, models and brands.
Responding to repeatable calls by food manufacturers for a single centralised data collection package that can work across an unlimited number of inspection machines - including checkweighers, metal detectors, x-ray and even label and coding machines - Fortress Technology has sourced a compatible and affordable solution.
Featuring a simple front-end system, manufacturers can connect as many or as few inspection devices on one software system, even non-Fortress machines. Giving food and beverage factories total quality control and oversight across their entire production lines. Machine data connections can even be made across multiple sites and monitored remotely.
Once installed, the subscription-style data collection package can be easily scaled up to incorporate more machines. Options range from an industry-standard weight and quality monitoring system that captures and records incoming data against pre-determined target ranges by product, to monitoring and reporting COP checks. All data is date and time stamped, logged, and reports all non-conformities. Alerts by email can be issued when corrective actions are required.
Report and analysis tools can be displayed on any business PC via internet browsers. Reducing manual paperwork and eliminating unreliable, labour-intensive record-keeping.
“With these new data package options, the front-end structure has been kept
simple. This is intentional as it helps to keep data manageable, as well as delivering meaningful quality oversight for production and quality managers. In addition to recording data, the software analyses the data generated in real-time, immediately highlighting any critical parameters, such as contaminant reject
trends and weight overfill costings, as well as red flagging processes that might be drifting from specification,” explains Fortress Europe’s Commercial Manager, Jodie Curry.
Additional reports that can be extracted include line efficiency, production rates, batch performance, Trading Standards records and audit data. Detailed records can be produced for any defined timeframe detailing what was happening during the inspection of product packs.
Available on an affordable monthly subscription, once the software has been installed, additional devices, locations and sites can be added without having the repurchase the software.
For a full demonstration on how to quickly implement a more robust data collection package that suits your real time food and beverage processing needs, visit Fortress Technology, Stand B01, PPMA 2023.
For further information, please visit www.fortresstechnology.com
Featuring a simple front-end system, manufacturers can connect as many or as few inspection devices on one software system, even non-Fortress machines.
The UK’s largest processing and packaging machinery exhibition, the PPMA Show, returns to the NEC Birmingham in September. This is the ultimate event for anyone involved in the industry to see the latest processing and packaging machinery, robotics and industrial vision systems.
The exciting three-day event on 26-28 September will be showcasing the latest innovations to visitors from numerous different sectors involved in processing and packaging. Some of these sectors include food and beverages, pharmaceuticals, household products and toiletries, building materials and supplies, pet care, and microbrewery and distilleries as well as contract packers and more.
In less than two months, the show opens its doors to thousands of visitors, who will have the opportunity to hear from a range of dynamic speakers. They are all eager to share with the visitors their extensive industry knowledge and some fascinating insights into future developments. These seminars are designed to inspire visitors to think about how they can improve their businesses.
The content rich seminar programme topics will include food packaging innovation, the importance of sustainability, successful selling and how manufacturing is evolving to meet the needs of the processing and packaging sector.
The show already has a line-up of exciting keynote speakers, including Cassandra Stavrou MBE, Proper Snacks Founder, who shares her entrepreneurial journey, including some takeaway “rules for business” and the importance of innovation in processing and packaging machinery.
Joining her will be Dimitrios Spiliopoulos, Industrial IoT Lead for Manufacturing at Amazon Web Services, and Philip Hooker, VP Strategic Programmes at Cumulocity IoT, who will share their vision and expertise in empowering packaging and processing enterprises to tackle critical smart production and smart connected product challenges head-on.
This must-attend show will offer plenty of brilliant meeting opportunities with over 300 exhibitors, representing more than 2,600 brands. In addition, visitors can expect to see numerous exciting new product launches and live demonstrations at the show. This provides an ideal chance to get an up-close look at the latest technological innovations and products helping to shape the various markets.
Scott McKenna, Group Exhibitions and Membership Manager at the PPMA Group, said: “We are pleased to have once again such an array of exhibitors representing the full spectrum of the industry. These leading companies will be eager to demonstrate to visitors how they can improve their
The exciting three-day event on 26-28 September will be showcasing the latest innovations to visitors from numerous different sectors involved in processing and packaging.
businesses with the latest cutting-edge technologies. This can help businesses stay ahead with the latest trends, improve efficiency, and make better use of resources.”
Here are just some of the hundreds of exhibitors taking part in the show:
Reiser (D100) have been for over 60 years a leading supplier of processing and packaging equipment for the meat, food, pet food, bakery, and cheese industries. Their
solutions can range from single machines to complete process-to-packaging production lines. They provide solutions that combine specialised equipment, custom engineering and expertise to meet their customers’ challenges.
ULMA (B32) offer a variety of packaging machinery and applications that are available on the market, including Flow Pack, Thermoforming, Traysealing, Vertical, Shrink Wrapping and Stretch Film packaging
technologies. They also provide a range of automated solutions that can streamline your packaging process, including crate/ case loading and product handling, pick and place, palletising, end of line and full turnkey project management.
Omori UK (G20) are suppliers of packaging and processing equipment, specialising in tempering, mixers, grinders, and coating equipment. In addition, they supply a variety of packaging options such as
flowrapping, stretchwrapping, stick packing and pouch (Doy Pack) filling and end of line checkweighing, metal detecting and X-ray inspection.
Ishida Europe (A104) are amongst leading companies in the design, manufacture, and installation of complete weighing, packing and inspection solutions for the food industry. They specialise in helping manufacturers increase automation, reduce cost and downtime, increase operational efficiencies, and maximise profits.
Visitors can take advantage of the comprehensive exhibitor listing on the PPMA Show website to help plan their visit.
The PPMA Show will offer a rare opportunity for visitors to see a complete production line in action from start to finish, from labelling, filling and packaging to processing, robotics, automation and industrial vision systems.
Those looking for new solutions will be impressed with a wide variety of cuttingedge innovations on display. By integrating new solutions into their own businesses, they can streamline processes, improve efficiency, increase productivity, which when all put together benefits businesses by saving time and money.
Visitors can also connect with leading industry experts and gain access to an invaluable source of knowledge and insight. These experts can provide the
latest information and trends, help identify opportunities and challenges, and offer guidance and advice. In addition, whether looking to make new business connections or network with industry peers, this is the perfect event for all.
The PPMA Show is the premier event of the processing and packaging industry, providing insights into the latest innovations designed to improve efficiency, minimise costs and increase sales. Here’s the video of last year’s PPMA Show to see why this year’s show is not to be missed: https://www.youtube.com/ watch?v=rEnA4bsBTGM
To register for a free ticket to this year’s show, visit: https://ppma-show-2023-visitor.reg.buzz/website
For the last 25 years Bowman Stor have been leading the development and refinement of condensate filtration products and technology.
From our industry leading filtration media to our in house development lab and prototyping facilities we are, and always have been, at the forefront of the Oil-Water Filtration industry.
• OEM SEPURA™ Separators & service kits
• Design and Development facilities
• ISO9001 & 14001 Accreditations
• Own brand options available
• Filter bags to fit all systems
• Free Product Finder App to download
• All manufactured on site in the UK
www.sepura-technologies.com
With CAPEX conditions restricting response time to unscheduled process and production downtime, Axium Process, specialists in liquid filtration solutions, have launched a new service that can now be funded through OPEX channels.
Designed to meet a range of liquid processing concerns, Axium’s UF & RO2Go rental plants meet industrial scale demand for many different industries including pharmaceutical, food, beverage, dairy and water recycling.
The systems are built on tried-and-tested technology and have been developed for rapid deployment with minimal operator training, allowing them to be up and running in a matter of hours following installation.
Offering great flexibility, and backed by extensive technical expertise, Axium’s rental range can fulfil high-priority requirements swiftly, while reducing capital expenditure risk by allowing the technology to be assessed over the long term.
For further information, please contact: Derek Davies
Tel: 01792 883 882
Email: derek.davies@axiumprocess.com info@axiumprocess.com
Page 1
Ecoseal is approved to Gas Industry Standard (GIS) Leakage Control (LC) 25. It is the only product on the market to have achieved the specification set out in GIS LC25. The specification sets out the requirements for flexible joint penetrating sealant repair systems for external application to ferrous distribution pipes with either lead/yarn or mechanical type joints. The maximum operating pressure must be equal to or less than 2 bar, in areas where pipe movement might be experienced.
There are three viscosities of Ecoseal, thick, thin and ultra-thin. Each variety is designed to repair a different leaking, corroded or damaged joint. This includes mechanical, lead yarn and tightly packed joints.
Ecoseal is a two-part Polyurethane resin. This means a chemical reaction takes place when the two parts meet and combine. The process is user and environmentally friendly as no toxic fumes or chemicals are released.
Ecoseal provides an alternative to encapsulation repair systems. It is time-saving and costsaving because it eliminates the need for site assessments and measuring for encapsulation muffs. It provides an option to inject through the socket or directly through the lead joint face. Ecoseal can be used on spigots, mechanical joints, socket joints, and valves. It can be used on a range of pipes up to 2 bar pressure.
The picosecond pulse laser series FPYL-QPS is offered with peak power up to 100W at a repetition rate of 1MHz and a pulse width of <10ps. Available wavelengths are 266nm (1-8W), 355nm (1-50W), 532nm (180W) and 1064nm (1-100W). The repetition frequency range is between 400kHz and 2MHz. The power stability is <3% (<1% optional). The pulse-to-pulse stability is <2%. Both are measured in rms and over 4 hours. The output beam is transverse mode TEM00 and has high beam quality of M2<1,2. With a beam diameter of ~3mm and a divergence <1mrad the output beam is very well collimated.
The laser will be delivered with an appropriate power supply for the voltage range 100-240V as well as a water chiller.
Due to the high power with pulse widths <10ps these lasers are excellent suited formicro material processing. Typical applications are:
Applications:
♦ Flexible Materials Processing
♦ Brittle Materials Processing
♦ OLEDs Processing
♦ Glass & Ceramic Cutting and Drilling
♦ Semiconductor Industry
www.frlaserco.com | sales@frlaserco.com
The laser will be delivered with an appropriate power supply for the voltage range 100-240V as well as a water chiller.
Our latest case study focuses on a request we received to replace two ageing pumps which had first been installed within a around 1970.
Our client was looking to continue transferring water from ponds located on the site where it was then used for a range of processes within the quarry. This included the cooling of mechanical equipment such as saws, generators and plant equipment, as well as for the washing of sand and aggregate products like gravel and stones used in construction and landscaping.
The ponds are used because they recycle water, minimising the impact the quarry has on local water courses, and enabling the most cost-efficient operation of the plant. The pond water reused after treatment via the use of screens, and flocculation to remove contaminants.
The client’s existing pumps were being used to draw water from the ponds located 4.5m below the pump suction. They wanted to use their existing pipework which was DN150 outlet and DN200 inlet. In addition, they had also had problems with non-return valves on the inlet pipework, and wanted to see if these could be removed as they had failed in the past.
Vertical inline pumps can be made selfpriming through the addition of air ejectors or a separate priming pump installed on the pump head. This evacuates the air enabling the pump to perform suction lifts at up to 6m.
The client looked at both of these options. However, because of the risk of solids being caught up in the water, we could not recommend an electric priming pump, and the client was not keen on using an airdriven ejector.
At North Ridge Pumps, we’re not tied to a single pump technology, but provide the best pump for a particular application and designed for the lowest lifetime cost. In fact, we can use our expertise to offer a bespoke solution, not something straight off the shelf.
We recommended vertical long-coupled inline pumps as they are a great spacesaving pump with a reduced footprint size. They are easy to maintain through the addition of a spacer coupling bracket, which makes it possible to access the pump head without removing the motor.
This pump design is also more robust and designed for continuous use, thanks to the extra bearing bracket installed between the pump and motor. This takes a great amount of strain away from the motor during operation.
The vertical compact design means that the long-coupled pump can be installed where there is limited space. In addition, the back pull-out design allows the motor to be removed while the pump is still connected
to the pipework. This in turn means that time can be saved while the pump is serviced and maintained.
On this design, the centrifugal pump and motor have independent shafts. This means that only the pump shaft will need to be replaced if it breaks. Other less robust vertical centrifugal pumps on the market only use the motor shaft. So if the shaft breaks, the entire motor needs to be replaced.
A large spacer coupling is installed between the vertical inline pump and motor. This extra space protects the motor from fluid getting in if the seal fails. In addition, wear rings can be installed in the pump head. These are sacrificial parts that wear first, protecting the impeller and casing from wear, and prolonging the life of these parts and therefore the pump.
To make maintenance and servicing easier, access to the inner parts like the mechanical seal and impeller is done by simply removing the outer cover screen on the spacer coupling bracket. Then the pump and motor shafts can be separated without taking the motor out.
The pumps were specified for transferring pond water at a rate of 319m³h, and around 50m head at a speed of only 1400rpm making the pumps ideal for operation for long periods.
The motor specification required operation via VFD, as well as twin wired thermistors and insulated bearings. Due to the motors being 75KW and working in conjunction with a VFD, the insulated bearings prevent the circulation of current through them which can damage them and contribute to their failure.
If you have any application needing the transfer, circulation or injection of viscous solid-laden liquids and aren’t sure which pump to specify, speak to North Ridge Pumps to see how we can help.
For further information, please visit www.northridgepumps.com
At North Ridge Pumps, we’re not tied to a single pump technology, but provide the best pump for a particular application and designed for the lowest lifetime cost.
Industry knowledge and application expertise across dispensing, dosing, full containment, gentle handling, blending and transfer, means whatever the problem, it’s likely we’ve seen it before. So we can help you solve it sooner.
+ Accelerated stator wear
+ Clogging
+ Changes to fluid consistency
+ Flow Reduction
+ Inconsistency in finished product
+ Inaccurate transfer of chemicals
+ Leakage | Liquid separation
+ Product Wastage
+ Seal wear or failure
+ Valve Blockage or unintended Opening
We’ve been engineering sanitary pumps for sectors such as distilling, brewing, food manufacturing/processing, and more, for 20+ years. We understand industryspecific processes and know what it takes to optimise performance through bettersuited pump design - giving you complete peace of mind.
EXPERT GUIDANCE:
Our expert engineers understand your process and guide you through the options, so you can confidently select the most suitable chemically resistant pump.
EXAMPLE PRODUCTS:
+ Acids
+ Alkalis
+ Coagulants
+ Corrosive
+ Chemical Sludge
+ CO2
+ Flammable
+ Flocculants
+ Oxidisers
+ Pyrophoric
+ Refrigerants
+ Solvents
+ VOC with low NPSH
+ Water Reactives
The BLUEline Nova sets new standards in pump technology. With or completely without casing protection – the BLUEline Nova achieves unrivaled volumetric efficiencies.
Made for one another – the newly developed DIUS rotors in combination with the flow-optimized pump chamber ensure perfectly smooth running at pressures of up to 12 bar.
A rotary lobe pump made by Börger has helped solve a wastewater processing problem at a textile manufacturer.
Taking effluent from the bleaching process into a storage tank, the Börger pump has to contend with significant fibrous material that also contains elements of hydrogen peroxide and caustic soda.
When the defined fill level of the wastewater has been reached in the collection tank, the Börger rotary lobe pump automatically conveys the liquid in measured amounts from the collecting tank into the sewage system. Made of Duplex stainless steel and equipped with a maintenance-free mechanical seal, the compact Börger rotary lobe pump is very easy to service, requiring only basic tools.
Thames Water owns and operates Basingstoke Sewage Treatment Works. This regional sludge treatment centre processes sludge from various locations in either liquid or cake form. The Basingstoke Sludge Treatment Centre (STC) houses advanced facilities, including thermal hydrolysis and anaerobic digestion plants, capable of processing 53tDS/day of sludge from Basingstoke, Farnham, Fleet, Guilford, and Newbury. The site now generates enough energy from waste to power itself and export to the national grid.
The pulper feed pumps from another supplier were experiencing stator failures every four months, which caused breaks in the processing of the sludge, leading to reduced energy production and time-consuming, costly repairs. Thames Water approached SEEPEX with the task to offer a more reliable pump, capable of efficiently transferring up to 30 m3/ hr of 6-10%DS high-temperature sludge.
Following detailed discussions with the on-site process engineers and maintenance manager, SEEPEX selected its BNM pump – fitted with smart maintenance solutions, and also incorporated its advanced digital monitoring package.
The SEEPEX BNM maintain-in-place pump range is designed to make maintenance for large and challenging-to-maintain pumps simple. By leveraging innovative design features, maintenance time is significantly reduced, up to 80%. Fast and straightforward maintenance of pump components ensures streamlined preventative inspections and improves operational reliability and service life, effectively eliminating unscheduled downtime.
Since its installation, the BNM pump with integrated pump monitoring, has been operating 24/7 without requiring any service intervention. Real-time data collected through
the monitoring sensors has allowed SEEPEX to provide the site with invaluable, real-time information on the pumps performance. Any deviation from the pumps design parameters triggered an investigation.
This proactive approach highlighted fluctuations in the sludge temperature and the time of day these fluctuations occurred. Analysis of the data by SEEPEX enabled the correct rotor/stator combination to be selected which will again reduce the downtime of this asset even more.
The incorporation of SEEPEX innovative pump solution with monitoring capabilities has enabled Thames Water’s Basingstoke to benefit from reduced downtime and cost savings. The elimination of frequent stator failures and prompt detection of potential issues drastically increased uptime, maximising operational efficiency while the streamlined maintenance process has reduced spend on costly spares, ensuring cost-effectiveness and improved overall financial performance.
As the Basingstoke Sewage Treatment Works continues to set new benchmarks in sustainability and efficiency, the collaboration between Thames Water and SEEPEX serves as a glowing example of how cutting-edge technology and expertise can drive positive change in the wastewater industry.
Improve your efficiency like Thames Water’s success story. Contact SEEPEX today to unlock innovative pump solutions designed for the water and wastewater industry to solve your unique pumping challenges.
For further information, please visit www.seepex.com
SEEPEX
SEEPEX, a leading worldwide specialist in progressive cavity pump technology and digital solutions has secured a framework agreement with Anglian Water. This agreement solidifies SEEPEX’s expertise and positions the company as a key player in the field of Condition-Based Monitoring (CBM).
The framework agreement involves the supply, installation, and management of CBM systems for Anglian Water. SEEPEX’s cutting-edge technology will enable Anglian Water to move towards a more proactive approach to maintenance and monitoring the condition of rotating and pumping assets. This condition-based approach will optimise asset performance, minimise costly repairs, and maximise the lifespan of their critical infrastructure.
SEEPEX and Anglian Water have enjoyed a long-standing collaboration since the Eighties. SEEPEX’s expertise in providing progressive cavity (PC) pumps has made
them one of the nominated framework suppliers for PC pump technology: 700 SEEPEX pumps are installed across Anglian Water’s sites in environmental applications including thermal hydrolysis, sludge cake pumping and back mixing, pumping stations and chemical/flocculent dosing.
SEEPEX’s success in winning the framework agreement highlights its remarkable achievements in the digital field. The comprehensive tender process involved navigating new horizons, incorporating IIoT capabilities and cybersecurity. SEEPEX’s dedicated team, including digital experts and cybersecurity specialists, demonstrated SEEPEX’s forward-thinking approach to digital innovation.
Being awarded the framework agreement places SEEPEX in an elite league of companies, shows that SEEPEX’s can compete with the specialists in the digital space and re-affirms SEEPEX’s superior digital ecosystem and portfolio within the CBM domain.
SEEPEX’s digital ecosystem – integrating digital monitoring and cloud-based services – will provide information to Anglian Water on their equipment’s condition, with reports showing the actual status quo of the equipment and process, enabling predictive and forward planned maintenance.
With the framework agreement in place, SEEPEX is positioned to revolutionise Anglian Water’s asset management strategies. By leveraging advanced CBM systems and comprehensive analytics, SEEPEX will empower Anglian Water to proactively monitor asset health, achieve greater operational efficiency, and deliver an exceptional level of service to millions of customers across the region.
Contact us today to explore how SEEPEX monitoring solutions can transform your company’s asset management, unlock the potential of proactive maintenance and ensure the longevity of your critical equipment.
For further information, please visit www.seepex.com
SEEPEX and Anglian Water have enjoyed a longstanding collaboration since the Eighties.
The KD485-ADE-4XX-4XX from KK Systems is a DIN rail mounted interface converter with two serial ports which both support 2-wire or 4-wire RS485.
A common application is attaching new 2-wire RS485 devices to an existing 4-wire RS485 bus. The KD485 is protocol transparent and RS485 driver control is performed transparently.
Other port types available are RS232 and 20mA TTY.
User programmable versions also support data/protocol conversion.
The KD485 is powered from 7-35V DC and its 3-way isolation makes it ideal for industrial applications which require a robust unit with the full RS485 drive capability.
Custom products are also available, including C userprogrammable versions.
www.kksystems.com
Rotech Motion Sensor’s can be used whenever information or monitoring of shaft rotation, position, direction, speed, slip etc is required!
Rotech Motion Sensor’s can be used for indication, control, interlocking, protection, sequencing, alarm initiations and many more functions!
Rotech Motion Sensor’s can be used wherever materials are transported or processed By conveyors, elevators, screws, mixers, etc!
Web: rotechsystems.co.uk
Email: sales@rotechsystems.co.uk Tel: +44 (0)151 356 2322
During the first half of 2023, 56 food and drink companies went into administration, constituting 9% of the total UK administrations for this year according to Food Manufacture. The manufacturing sector has been under significant cost pressure due to Brexit, the pandemic and the war in Ukraine.
To boost productivity and save costs, businesses increasingly develop in-house software. Yet, for true cost savings, in-house development has proven ineffective and costly. Here’s why:
1. Managing Uncertain Risks and Costs
Developing an in-house system presents great risks of exceeding the project’s scope, budget, and timelines, which could even threaten to put the business into administration. McKinsey reveals that IT projects exceed budgets by 45%, timelines by 7%, and deliver only 56% of expected value. Opting for customisable off-the-shelf MIS/MES solutions smartly saves time, resources and risk.
2. Balancing Integration and Scalability
Complex factory operations require diverse improvement areas. Building homegrown systems diverts time and capital. However, comprehensive MIS/MES solutions like Harford’s deliver real-time insights across the factory, enhancing production with quality, performance, labour, wastage and energy data available in one system. Inhouse system development has proven time and again to be the most costly solution.
3. Amplifying Real-Time Data Analytics
Can internal dashboards prompt action?
Does a 65% to 40% OEE drop matter?
In-house software often lacks root cause analysis for data-driven decisions. In contrast, Harford’s MIS/MES system tracks production end-to-end, offering granular insights for swift root cause identification. Both managers and operators leverage real-time data for instant actionable responses, ensuring lasting solutions, rather than short lived ‘quick fixes’.
4. Ensuring Reliable Maintenance and Support
All systems demand training, but staff turnovers create extra challenges for inhouse developers. Opting for dedicated solution providers, like Harford, ensures 24/7 local support across 6 continents. Expert engineers offer rapid responses and on-site help if needed.
5. Focusing on Continuous Improvement
In-house advancement demands ongoing research and development, but what if the system developer has left the company? Engaging solution suppliers reallocates internal resources for innovation. Harford invests in MIS/MES systems annually, continually adapting to customer needs and market trends.
Don’t just take our word; hear from our client: “One year after implementation and Harford has supported us in reducing our bottling losses to less than 0.1% and has taken our overall end to end liquid losses down by more than 50%. This alone has delivered sufficient savings back to the business to pay for Harford.” --- Tony Brewerton, Plant Director, Loch Lomond Distillers
Opting for a reliable solution provider is more cost-effective and offers scalable benefits: risk and cost monitoring, advanced functionality, real-time insights and continuous improvement.
Meet us on Stand B46 at the PPMA event to explore how we can drive your continuous improvement and competitive edge.
For further information, please visit www.harfordcontrol.com
Opting for a reliable solution provider is more cost-effective and offers scalable benefits.
We help factories... by with End-to-End MIS/MES
When we help, the Harford system is built to scale across each factory, from goods-in to despatch. With Harford's MIS/MES solutions, all production-related information is available within a single system. All collected data is analysed, prioritised & distributed to networked factory screens, PCs, laptops, tablets and mobile phones, in real time, so that operators can make immediate adjustments to improve performance. Nothing is left to chance. See us on Stand B46
Phil Wares, Electroplating/CAD Manager at DK Holdings Limited, introduces the company’s Direxpander®, a diamond coated precision reamer and long-standing engineering gem that has become the definitive tool for sizing and straightening the bores of cast components such as Hydraulic Transfer Valves.
“We have been supplying this tool for many years to our customers to fulfil their requirements. As an engineer and manufacturer I can say that this tool is a joy to produce, encompassing several skills and technologies, which ultimately results in a tool fit for the application which has been proved time and time again”, Phil explains.
What makes the Direxpander® Diamond Precision Reamer a perfect tool?
‘’This dependable engineering masterpiece consists of a diamond coated sleeve mounted on a tapered mandrel which allows the final diameter of the tool to be adjusted to very fine limits. It is a tool of great rigidity which is vital to the application. The precision diamond coating ensures consistent sizing and surface finish over thousands of components, producing accurate bores every time. We can supply the tool in a standard range of sizes from 6mm to 60mm with other sizes available on request. The reamer is easy to use on conventional or fully automatic machines and has replaced many honing tasks, resulting in quicker, more reliable and accurate bore production”, Phil continues.
“Design, Manufacture, Supply – to us this means to work in partnership with our customers worldwide, offering precision engineered Diamond Tooling such as the Direxpander® Diamond Precision Reamer from inception to the supply”, Phil concludes.
This is just one of many quality diamond tools that D.K. Holdings produces and has been producing for decades.
Get in touch with one of the team at DK Holdings and find out how they can support your requirements no matter how large or small, or request their free Engineering product guide and Direxpander® Diamond Precision Reamer product focus, the team is always on hand to help!
DK Holdings Limited
Station Approach Staplehurst
TN12 0QN
Telephone: 01580 891662
Web: www.dk-holdings.co.uk
Email: info@dk-holdings.co.uk
Twitter: @DK_Holdings
For further information, please visit www.dk-holdings.co.uk
The precision diamond coating ensures consistent sizing and surface finish over thousands of components, producing accurate bores every time.
Drallim is an innovative technology driven British engineering company with global presence. With experience in providing comprehensive turnkey assembly & test solutions covering electronic, electromechanical, engineering, and mechanical products. We offer our customers a total contract manufacturing service, offering design, and manufacturing solutions, providing engineering skills, manufactured equipment & custom-built systems for the Aerospace, Industrial and Utility Markets.
Prototyping and New Product Introductions; From the initial enquiry, our Business Development Team analyses the specifications and requirements of a product or project and issues a comprehensive and detailed quotation. When an order is received, a project plan is then developed; our team uses detailed documentation, engineering change and reporting control to ensure continued information integrity. An experienced project manager acts as the interface between Drallim and our customers although, at the same time, we actively encourage engineer-toengineer communication. We have had customers engineers based at our headquarters signing off drawings as they are produced to meet urgent deadlines for manufacture. The designated project manager ensures that resources are allocated appropriately and that all tasks are tracked and recorded. The result is a controlled transition into the manufacturing process.
When it comes to product manufacturing, a substantial proportion
of the end product’s total cost is determined at the design stage. As a result, this part of the manufacturing process presents the perfect opportunity to identify improvements that will lead to cost reductions. A thorough understanding of each element will enable the product to be designed and optimised for procurement, manufacturing and test. We provide an extensive Design for Manufacture service to help our customers achieve substantial improvements, including:
• Improved manufacturing productivity
• Enhanced product quality and reliability
• Minimal/simplified maintenance
• Lower Cost
• Reduced time to market
• Increased customer satisfaction
• Manufacturing
• Precision assembly
We regularly produce complex assemblies that demand high levels of skill, precision, accuracy and consistency. The engineering and manufacturing
teams at Drallim are highly skilled in this type of work, with awareness of critical engineering tolerances when producing assemblies of this complexity. Our skills-base extends to include testing of electrical, electronic, mechanical, hydraulic and pneumatic assemblies. Following rigorous approval processes Drallim’s supply chain partners for custom parts, such as plastics, machined and fabricated metalwork etc, are monitored closely for quality and delivery performance. Tight control of the material supply chain ensures the availability of high quality mechanical parts is maintained for timely production.
Many of the assemblies produced require wire and cable interconnection between boards and sub-assemblies. This can be via cable forms or point to point wiring. As part of our electro-mechanical assembly service we are often called on to produce products that require critical cable routing. We also undertake electrical wiring of switch and instrument panels plus sophisticated control cabinets. We have highly trained engineering and assembly teams to assist with design and the assembly and support for all your cable and loom requirements.
• Electro-mechanical Assembly
• Pneumatic & Hydraulic Assembly
• Racks & Cabinets
• Box-Build Assembly
• PCB Assembly
• Prototype Wiring
• Cable Assembly
• Testing
So, if you are interested in British Manufacturing and looking for a Contract Manufacturer, we are sure Drallim can meet your needs.
For further information, please visit www.drallim.com
We take pride in overseeing the entire manufacturing process, from design, prototyping and manufacture to delivery, installation, full product certification and after-sales
Small Batch Manufacture Electrical | Electronic Pneumatic | Hydraulic Mechatronics Concept Design
Oliver Hydcovalves have announced the design and manufacture of three new valves for hydrogen transportation and refuelling. Using high performance polymer bearings and seals in partnership with DuPont™, valves have been qualification tested to 102,000 cycles of operation while maintaining a fugitive emissions leakage class of BH.
Another unique feature of the valves is their full-bore design. This avoids restrictive flow, which appears to be a common problem in many valves on the market. Nick Howard, Engineering Director at Oliver Hydcovalves stated; “By maximising the flow rate, it will deliver a more continuous and consistent flow of hydrogen medium. This will allow for hydrogen fuel to be dispensed and refilled onsite much more quickly, which will deliver dramatic time-saving benefits.”
As the world continues to move towards sustainable energy sources, hydrogen is emerging as the promising fuel option for vehicles and industrial transportation on land, sea, and air. The transporting and dispensing of hydrogen fuel in working environments such as fuel stations and onsite fuel storage facilities, require specialist valves that have been designed and engineered for continuous high cycle operative use and meet the requirements of ISO 19880-3.
When dispensing hydrogen fuel onsite, it generally requires a large area to be closed
the time it takes to dispense hydrogen fuel is crucial. Oliver’s full-bore valves deliver hydrogen much faster than other transportation valves that have a restrictive flow. This significantly reduces the downtime at a site, and in most cases, can be halved - minimising disruption to the forecourt and business operations.
Hydrogen fuel is stored and transported using pressurised tanks. Therefore, it’s of paramount importance that valves can handle extreme pressures too. Since 1979, Oliver has been synonymous with valve safety and reliability, even relied upon by the world’s largest energy producers, suppliers, and end-users for its precision engineered solutions. As Oliver’s company mantra suggests ‘Reliability Under Pressure’, they’re well-positioned to provide the necessary assurances required.
This latest engineering achievement firmly places Oliver Hydcovalves at the forefront for hydrogen transportation valves. Built to the highest specifications using premium quality materials, and tested to the highest standards, it’s logical to see how Oliver’s claim to offer the best valve solution for hydrogen transportation and refuelling applications, certainly holds up.
Bore sizes include; 10mm, 14mm and 20mm. To learn more about hydrogen transportation and for guidance on hydrogen specifications, applications, qualifications and pricing, contact Oliver Hydcovalves on +44 (0) 1565 632636 or visit their website at: www.valves.co.uk
As the world continues to move towards sustainable energy sources, hydrogen is emerging as the promising fuel option for vehicles and industrial transportation on land, sea, and air.
World-leading
Valves for Hydrogen, Carbon Capture, Topside, Subsea, and Pipeline Applications.
Instrument & DBB Valves
• Manifolds, Needle, Check and DBB Valves to 22.5K psi
• Cryogenic
• Severe Service 650ºC, 10K psi
• Forged & Bolted Construction
Hydrogen & Carbon Capture Valves
• Instrumentation, Ball, Needle and DBB Valves for Hydrogen and Carbon Capture Applications
• Pipeline Ball Valves upto 18”
• 10K Ball Valves for Hydrogen Fuelling Stations
Pipeline Valves
Pipeline Valves
• 1” to 20” Bore Size
• 1” to 20” Bore Size
• High Temperature
• High Temperature
• High Pressure
• High Pressure
• Cryogenic
• Cryogenic
• API 10K Design
• API 10K Design
Subsea Valves
Subsea Valves
• Diver & ROV Operated Needle Valves
• Diver & ROV Operated Needle Valves
• Ball Valves Upto 15K
• Ball Valves Upto 15K
• Manual & Hydraulic Parallel Slide Gate Valves 3/8”, 1/2”, 3/4” and 1”
• Manual & Hydraulic Parallel Slide Gate Valves 3/8”, 1/2”, 3/4” and 1”
We Manufacture Valves for Global Energy Projects. To Find Your Local Supplier, Contact Us Today.
We Manufacture Valves for Global Energy Projects. To Find Your Local Supplier, Contact Us Today.