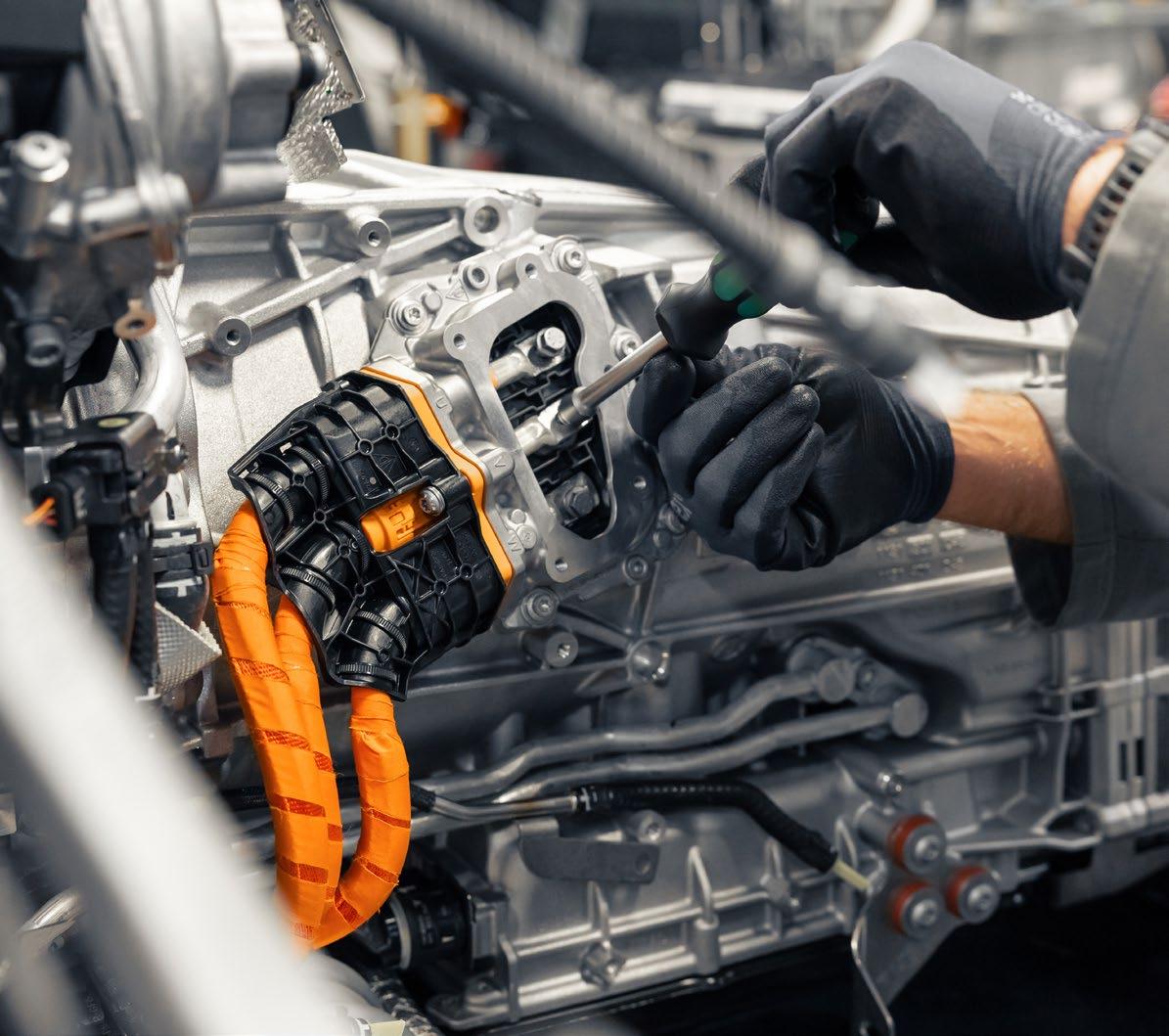
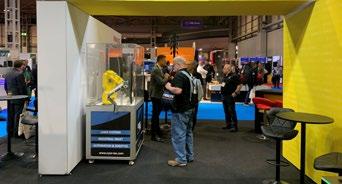
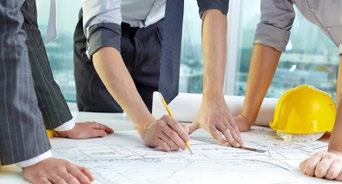

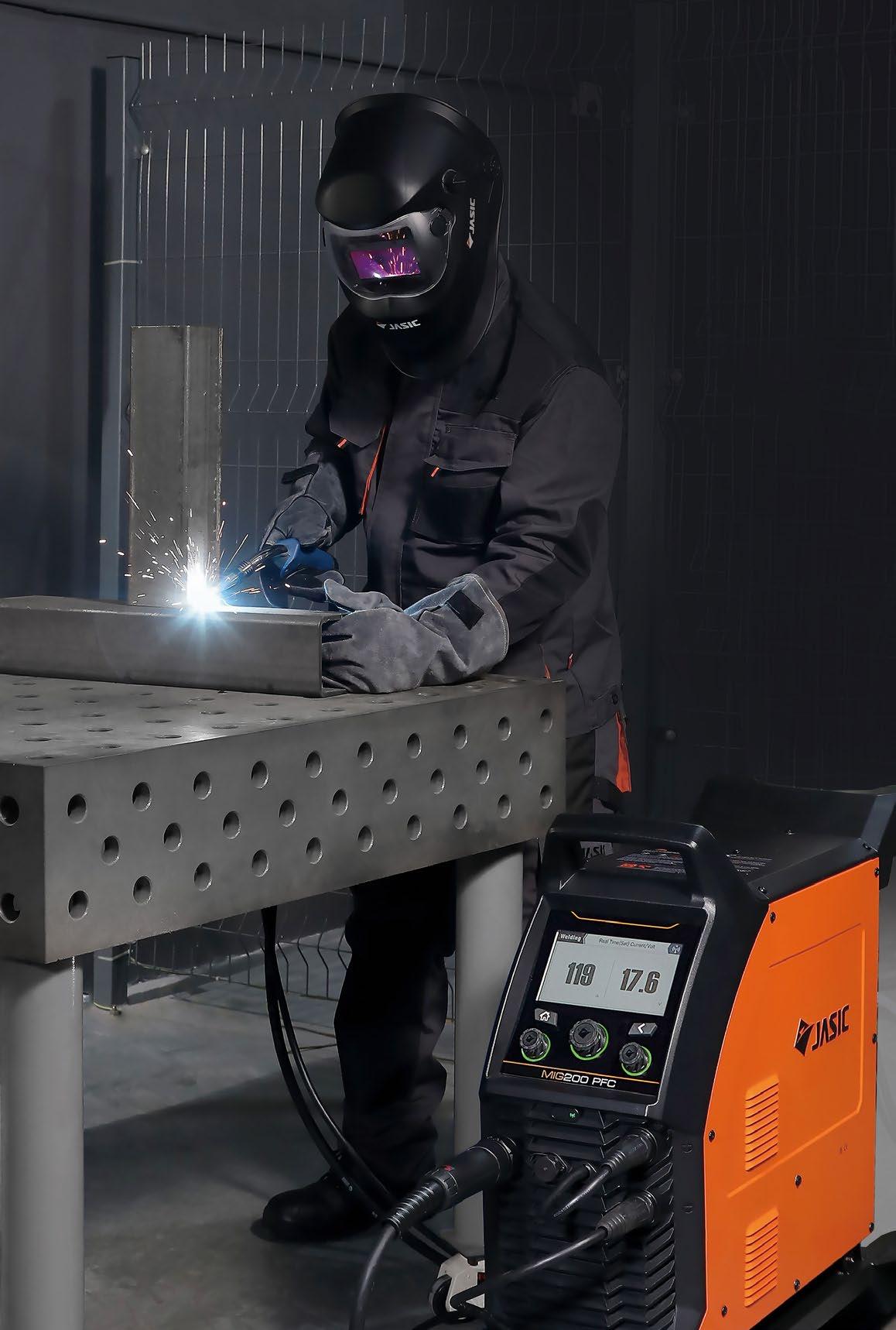
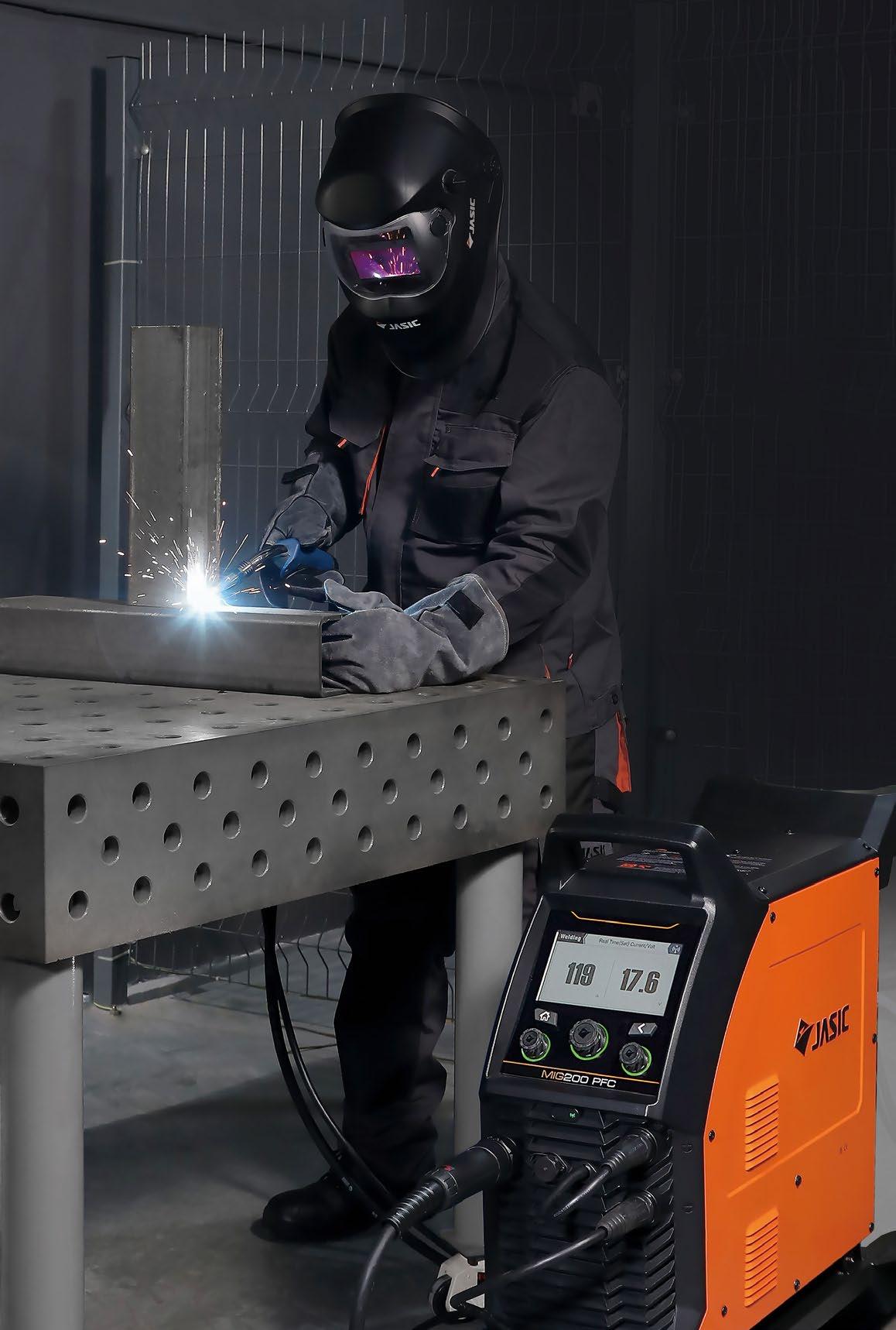
Editor’s Choice
Coatings
Connectors & Fittings
Control & Automation
Electrical & Electronics
Gears, Drives & Motors
Machining & Machinery
BENTLEY
Ultra performance V8 hybrid succeeds W12 as Bentley’s pinnacle powertrain
ALFA LAVAL
New report highlights rethinking maintenance as key to enhancing industry’s commercial resilience
FANUC
FANUC says ‘commitment’ is needed to change UK culture around automation
GOUGH ENGINEERING
Customised material handling equipment improves manufacturing efficiency
OMNIFLEX
Ensuring reliable long-distance critical signal delivery in mining applications
PORTESCAP
Miniature motor selection and the role of inertia
SUMITOMO
Revealing the real value
PRIME VISION
Prime Vision robots help Babydump take first steps in automated order picking
ERS HUB
ERS Hub issues grassroots rallying call as it looks to young people to fill the 100,000+ electrification jobs void
EMIS GLOBAL
Three Phase EMC filters from EMIS designed for motor and power drive systems
BURKERT
Optimising chromatograph performance
• Continuous diagnostic: Full coverage of your critical assets at all times.
• Early diagnostics: Monitoring of imbalance, wear and overall vibration.
• Maximum efficiency: Permanent diagnostics helps keep your assets running efficiently.
• Easy integration: ifm provides individual solutions suited to different types of machines. Reducing costs, avoiding unplanned downtime and optimising processes: The ifm application solutions. ifm – close to you!
The leading source for innovators in Technology, Manufacturing and Maintenance within the Engineering & Processing industry worldwide.
Published bimonthly, a subscription to PECM magazine is essential for Process Engineers, Chemical Engineers, Instrumentation Engineers, Mechanical Engineers, Plant Engineers, Precision Engineers, Environmental Engineers & General Engineers, Companies and Organizations in the Food, Dairy, Beverage, Brewing, Semiconductor, Pharmaceutical, Biotechnology, Chemical, Oil & Gas, as well as all UK's major manufacturing units.
Every issue of the magazine contains the latest news, in-depth features, together with product innovations and case studies showing how process engineers are implementing new technologies to reduce costs and impact on the environment.
With over 140,000 readers worldwide the publication is widely read, recognized, and well respected within the Process, Engineering & maintenance industries.
A subscription to PECM magazine is the industry's 'must have' publication.
SUBSCRIBE TO 6 BIMONTHLY ISSUES OF PECM FOR JUST £27
• The magazine gets delivered directly to your door once every issue is published
• The quality of the hard copy enhances the reading experience
To Subscribe please call 01304 806039
SUBSCRIBE TO OUR DIGITAL EDITION COMPLETELY FREE OF CHARGE
Designed for the digital age, the magazine has been created for easy viewing on all electronic devices. All our issues stored in one place: get unlimited access to our previous and future issues.
To Subscribe please visit www.pecm.co.uk/subscribe
EDITOR IN CHIEF
Antony Holter editor@mhmagazine.co.uk
BUSINESS MANAGER
Josh Holmes josh@mhmagazine.co.uk
SALES DIRECTOR
Jake Page jake@pecm.co.uk Tel: 01227 937174
SALES MANAGER
Martin Richardson martin@pecm.co.uk Tel: 01304 086039
DIGITAL MANAGER
Jamie Bullock jamie@mhmagazine.co.uk Tel: 01227 936971
Please
EDITOR
Elizabeth Hutton elizabeth@pecm.co.uk
STUDIO DESIGNER
Richard Bland richard@mhmagazine.co.uk
ACCOUNTS DEPT
Alison Holmes accounts@pecm.co.uk Tel: 01227 936976
PUBLISHING DIRECTOR
Martin Holmes martin@mhmagazine.co.uk Tel: 01304 806039
DIGITAL ASSISTANT
Stacey Goodwood Tel: 01227 936971
Media Global Ltd. 18/20 Newington Road, Ramsgate, Kent, CT12 6EE Tel 01304 806039 l Fax: 08721 152240 l www.pecm.co.uk
Ultra performance V8 hybrid succeeds W12 as Bentley’s pinnacle powertrain
Bentley’s future is being brought another step closer with the announcement that its iconic W12 engine will be succeeded by an all-new, performance-focused V8 hybrid powertrain. Producing the highest power output ever offered in a Bentley, the new powertrain will also be the most dynamic, most responsive and most efficient system in Bentley’s history, befitting a new generation of daily supercars.
Christened the Ultra Performance Hybrid, the new powertrain follows Bentley’s long-standing tradition of supplementing classleading combustion engines with technology to increase performance.
Supercharging in the 1920s was the early forebear to the use of turbocharging from the 1980s to present day. From this summer, Bentley goes one step further –bringing even more performance through ‘electrocharging’ – using a potent hybrid system to create what will be the most advanced and most powerful powertrain in Bentley’s 105-year history. The new system builds on Bentley’s existing hybrid powertrains, but goes even further in the level of performance and efficiency it brings – with more than 750 PS and a 50 mile (80 km) electriconly range. That represents at least 91 PS more than the W12 engine previously offered in the Flying Spur and GT W12 Speed derivatives.
As Bentley’s iconic 6.0-litre twin turbo W12 engine heads towards retirement this summer, with 105,000 engines built over the last two decades, the new Ultra Performance Hybrid will take on the mantle as Bentley’s leading powertrain, establishing the new family of Bentleys it will power as the world’s best electrified luxury
performance vehicles. While developing more power than the W12 and four-figure torque over a wider plateau, the Ultra Performance Hybrid will also deliver a WLTP drive cycle CO2 figure of under 50 g/km.
The character of the new engine is also previewed today, with the release of an engine sound clip that reveals an exquisite combination of cross-plane bass with a free-revving growl. This represents one end of the audio spectrum offered by the
powertrain; the polar opposite to the absolute silence the system will offer in electric mode.
More details on Bentley’s new electrified powertrain, which will drive the next phase of its Bentley’s Beyond 100 journey and deliver the promise of every car in the range being available as a hybrid, will be released over the coming weeks. Meanwhile, customers can continue to enjoy the final few remaining examples of Bentley’s W12 and nonhybrid V8 engines, available through Bentley’s global retailer network.
New report highlights rethinking maintenance as key to enhancing industry’s commercial resilience
Production, process, and plant managers operating across various industries have been urged to rethink their approach to heat exchanger maintenance following updated insight from a new industry whitepaper.
The message comes at a pivotal point for industry, as increasing energy costs, aggressive competition from overseas, and decarbonisation targets risk limiting industry recovery.
In particular, high-energy users are being warned that running key equipment to failure will result in additional costs in the form of equipment repair and poor efficiency levels.
To provide practical guidance, global engineering company, Alfa Laval, has launched the whitepaper Taking the Heat – which aims to make proactive maintenance of plate heat exchangers (PHEs) a priority for manufacturers.
According to the report, poor maintenance of PHEs across industry plays a major role in increased global carbon emission levels. Although viewed as ‘one piece of a larger puzzle’, without proper servicing and maintenance, the risks of production line failure, low levels of output and unsightly balance sheets are dramatically increased for businesses.
Relying on reactive maintenance not only perpetuates a false economy but increases the risk of
Poor maintenance of PHEs across industry plays a major role in increased global carbon emission levels.
unpredictability in machinery and costs. Remarkably, an academic report from 2013 found that around 15% of all factory maintenance costs are credited to heat exchangers, with half of that figure due to fouling.
A report from OneServe also found that machine downtime is costing manufacturers in excess of £180 billion each year. Experts at Alfa Laval say taking a groundup approach to PHE maintenance could drastically lower the chance of line failure and downtime.
PHEs are also commonly specified years ahead of becoming fully operational within a plant, making Alfa Laval’s case for energy-hunting and lean manufacturing even
more pertinent. Energy-hunting uses calculations to estimate energy savings and aims to find new ways of reusing waste energy by changing the cleaning and maintenance program or updating configurations.
The report continues to highlight the measures businesses can implement to achieve lean manufacturing and a proactive maintenance schedule.
Rachel Bridges, Managing Director at Alfa Laval says: “Now is the time for renewed focus on effective maintenance strategies, not only to make the most of installed assets, but also to correct the course as commercial resilience is stretched to its limit. We project there are thousands of PHEs in operation that are not working efficiently which could be unnecessarily draining businesses. It is now time to make maintenance a priority for PHEs, not a reactive response to failure.
“The current situation makes it critical that businesses manage the issues that remain in their control,” Rachel continues. “We hope this new report reinforces the importance of establishing a proactive and considered maintenance strategy and that PHEs are acknowledged as a significant part of a complex picture.”
1 Fouling In Heat Exchangers: A Costly Problem | IMPO (impomag.com)
2 Machine downtime costs UK manufacturers £180bn a year (theengineer.co.uk)
To download the full report, www.alfalaval.co.uk/takingtheheat
The World’s First In-line Large Gauge Laser Wire Stripper.
Engineered for:
Electric Vehicle Wires and Cables
Tough Fiberglass Construction
Aerospace Shielded Cable
Microwave Antennae
ALRAD Instruments Limited (established 1970) has been serving the Industrial, Automation, Scientific, Medical and Instrumentation markets for over 50 years and has a wealth of experience in all aspects of Machine Vision, Automation and Scientific Imaging.
Our product areas cover imaging, machine vision and automation components, Industrial and Scientific cameras for UV, Visible and Infrared wavelengths, thermal cameras, image sensors, photonics components including laser products, vacuum and related products, embedded AI and deep learning vision systems. We also provide standard and bespoke imaging software and complete system solutions together with our integration partners.
Our imaging technology operates in a wide spectrum from Ultraviolet through Visible to Infrared and Thermal wavelengths. We supply the latest camera technology and vision components including illumination products covering the complete spectrum from ultraviolet through visible to Infrared. These products are suitable for applications in Machine Vision, Automation, Scientific Research, Medical imaging, Agriculture, UAV/Drone, security and Search and Rescue applications.
For further information, please visit www.alrad.com
Scan to learn more:
A new generation of valves, precisely tailored to your needs
• Leaner and faster production using cleverly designed modules which are standadized across different product categories.
• Modular and flexible design with a wide range of configuration options, optimizing response time to your specialized requirements.
• More agility, products can be ordered and manufactured faster than ever before with item prices and availability information easily accessible.
• The platform-base design enables faster conformity adjustments to ensure GEMÜ products are always optimized with the latest features.
In this case study, we’re discussing a new horizontal self-priming spill control pump we recently supplied to an industrial client. They had several silos and tanks on site and needed an effective and reliable pump to minimise potential damage from any spills.
In the UK, the accidental spillage of oils and other chemicals from industrial sites causes a significant amount of pollution every year.
Many spills can be prevented with rigorous production processes and strict monitoring. But if there is an accidental leakage, it’s important to act quickly to:
• Minimise possible damage: spills can spread rapidly and seriously harm the environment
• Avoid prosecution: court fines and clean-up costs after a spill can be expensive
• Reduce negative PR: a spill can mean very bad publicity for a company, its directors and clients, as BP discovered in the US after the Deepwater Horizon incident
What’s the difference between spill control, primary and secondary containment?
Spill control tactics are designed to reduce the amount of contact the spilled material has with people, property and the wider environment.
Primary containment is the actual vessel or container holding a substance - solids, liquids, chemicals or waste. It’s the first line of defence
against spills, leaks or accidental releases.
Secondary containment serves as a back-up in case the primary containment is breached. It is a regulatory requirement for any primary container if the contents are hazardous, and a breach of that containment would endanger life, soil or water around it.
By law, the secondary containment system, ‘must have sufficient capacity to contain at least 10% of the total volume of the primary containers or 100% of the volume of the largest container, whichever is greater.’
Our specification for this client
For this particular project, our client asked for a pump which
would be corrosion resistant not only to a number of differing fluids but also resist deterioration overtime from exposure to air, and water which can be common with pumps manufactured from Cast Iron. We specified the pump to be manufactured from AISI316 stainless steel to ensure that there were no issues with pump corrosion during its operation lifetime.
We specified a 3’ horizontal selfpriming pump made from cast AISI 316 stainless steel. This material is widely used in industrial applications. It’s also well suited to even harsher environments needing greater corrosion resistance, having more tensile strength at higher operating temperatures.
Our stainless steel self-priming pump was specially designed for spill containment at the client’s site where there are several tanks and silos housed within a bund – this is a
A key feature of this spill control and tanker loading pump is the self-priming function which primes the pump in just 45 seconds – vitally important when a spill has to be contained quickly.
type of embankment or wall of stone or earth, built to stop the area being covered by a large amount of water.
Also suitable for tanker loading
In addition, the pump will be used as a tanker loading pump and to feed discharge into a sewage plant. If the silos or tanks ever leak, the pump will
evacuate the bund of any wastewater, milk or other low viscosity liquid.
We supplied the pump with a builtin control panel so that users had convenient local control of the pump’s operations on site.
A key feature of this spill control and tanker loading pump is the self-priming function which primes the pump in just 45 seconds – vitally important when a spill has to be contained quickly. In addition, it can handle solids up to 30mm and dry run for up to 30 minutes once the head is filled with liquid.
If you’re looking for a spill control, tanker loading or sewage plant feed pump, and aren’t sure which one’s right one for you, contact us on 01773 302 660, email sales@northridgepumps.com or visit North Ridge Pumps at www.northridgepumps.com to see how we can help.
For further information, please visit www.northridgepumps.com
FANUC says ‘commitment’ is needed to change UK culture around automation
At Smart Factory Expo (5-6 June 2024, NEC Birmingham), FANUC UK named ‘commitment’ as the number one driver to help inspire a change in culture towards robotics and automation among British manufacturers. FANUC’s Head of UK Sales Oliver Selby gave the keynote speech at the event’s Automation & Robotics Acceleration Symposium and said a change in culture was needed to ensure continued UK manufacturing success, calling for commitment towards skills and education across all levels –from students to C-Suite – as well as commitment to a long-term automation investment strategy.
“Despite being the eighth largest manufacturing nation, we are 25th in terms of robotics adoption,” said Oliver. “Just imagine what we could achieve if we raised our automation levels.”
Citing a difference in attitude towards investment in robotics between the UK and many of the leading automated nations, Oliver believes the UK has much to learn in terms of best practice: “In countries such as Germany, Japan and the US, automation is prioritised from the outset of any new manufacturing project – it’s not an afterthought,” he stated. “And in Scandinavia, a
realistic view on payback periods (as well as a realisation that total cost of ownership is a better measure of value than ROI) sees companies prioritising a long-term investment strategy around automation. Of course, government support also plays a large part, and in this regard, we are playing catch-up. However, it’s not too late to make a change if all stakeholders work together.”
Increasing education around automation – at every level – is also crucial to boosting our robotics uptake. “Within firms, particularly SMEs, it’s essential that a range of staff are trained and educated
on the benefits that the right automation solution can deliver,” said Oliver. “Whether that’s the finance department, engineering or operational staff, management, board members and even the owner, everyone has something to learn.”
This commitment to education also extends to inspiring the next generation of engineers and ensuring they are equipped with the skills that will be needed by modern manufacturers. To this end, FANUC has partnered with WorldSkills UK for fourth time, in the Industrial Robotics competition. The qualifying rounds for this year’s contest took place live at Smart Factory Expo and saw the 12 highest ranking teams compete in a 3.5hour challenge to pick and place 10 cylinders, following a pre-set robotic pathway.
“We are extremely proud of our partnership with WorldSkills UK and watching the talented young competitors complete the qualifying challenge was very rewarding,” said Oliver. “The five best teams will go
winners will have the chance to represent Squad UK in the global competition.”
Attracting over 7,000 visitors on day one alone, Smart Factory Expo showcased the finest technologies and solutions available to manufacturers today. For FANUC, the event proved highly successful, bringing multiple new leads across sectors as diverse as medical, semiconducting, bakery, confectionery and plastics.
With over 35 system integrator partners, we are well placed to support manufacturing firms from every corner of industry
on to compete in the WorldSkills UK final at the FANUC Open House event at our Coventry HQ in November, while the ultimate
“With over 35 system integrator partners, we are well placed to support manufacturing firms from every corner of industry,” added Ollie. “Our stand featured five of our key partners and enabled us to showcase the added value that FANUC can bring beyond supplying automation technology. The event was busy across both days and brought quality leads to our door, as well as allowing us to demonstrate the value of the WorldSkills UK initiative. We are already looking forward to what next year’s show will bring.”
For further information, please visit www.fanuc.eu/uk/en
The hydrogen industry is poised to revolutionise the global energy landscape, promising reduced carbon footprints and mitigating climate change. Accurate and reliable pressure measurement is critical in harnessing hydrogen’s potential, ensuring safety, efficiency, and precision. Silicon-on-sapphire (SoS) pressure transducers and transmitters are at the forefront of this advancement, transforming pressure measurement technology in the hydrogen industry.
Understanding Silicon-onSapphire Technology
Silicon-on-sapphire technology integrates a thin layer of silicon on a sapphire substrate, combining silicon’s semiconductor properties with sapphire’s mechanical strength and thermal stability. This results in a robust and highly sensitive pressure measurement device capable of performing in extreme environments.
Advantages of Silicon-onSapphire Pressure Transmitters
High Precision and Sensitivity: SoS pressure transmitters offer superior precision and sensitivity, essential for hydrogen systems where minor pressure variations can significantly impact safety and efficiency.
Temperature Stability:
Operating in extreme temperatures, hydrogen systems benefit from SoS technology’s minimal thermal drift. The sapphire substrate’s low thermal expansion coefficient ensures accurate pressure readings across a wide temperature range.
Durability and Corrosion Resistance:
Hydrogen environments can be harsh. Sapphire’s chemical inertness and mechanical robustness make SoS pressure transmitters highly resistant to corrosion and wear, ensuring long-term reliability and reduced maintenance costs.
High Pressure Capability:
Designed to withstand highpressure conditions, SoS pressure transmitters are ideal for hydrogen applications demanding robust performance under stress.
in
Hydrogen Production:
In methods like water electrolysis, precise pressure control is crucial. SoS pressure transmitters ensure optimal performance and safety by providing accurate monitoring and control.
Storage and Transportation: Accurate pressure management
is essential in hydrogen storage and transportation. SoS pressure transmitters monitor storage tanks and vessels, ensuring safe operation and alerting operators to potential issues.
Fuel Cells:
Hydrogen fuel cells require precise pressure regulation for optimal performance. SoS pressure transmitters maintain the necessary conditions, enhancing efficiency and longevity.
Hydrogen Refuelling Stations: Refuelling hydrogen-powered vehicles demands accurate pressure control. SoS pressure transmitters provide real-time data to manage the refuelling process safely and efficiently.
Enhancing Safety through Reliable Pressure Measurement
Safety is paramount in the hydrogen industry due to hydrogen gas’s high flammability and potential hazards. SoS pressure transmitters enhance safety with features such as:
Leak Detection:
Early detection of leaks through accurate pressure monitoring allows prompt intervention, preventing accidents and ensuring the safety of personnel and equipment.
System Integrity Monitoring:
Continuous pressure measurement helps maintain hydrogen systems’ integrity, identifying and addressing potential issues that could compromise safety.
Compliance with Regulations:
The hydrogen industry must adhere to stringent safety regulations. SoS pressure transmitters provide reliable data to ensure systems operate within prescribed safety parameters.
Contributing to Efficiency and Sustainability
SoS pressure transmitters also enhance hydrogen systems’ efficiency and sustainability by providing accurate and reliable pressure data. This contributes to:
Optimal System Performance:
Precise pressure control ensures hydrogen systems operate at their best, maximising energy efficiency and reducing waste.
Reduced Downtime:
Reliable pressure measurement minimises unexpected failures and downtime, crucial for maintaining continuous operation in critical hydrogen applications.
Lower Maintenance Costs:
The durability and corrosion resistance of SoS pressure transmitters reduce maintenance frequency and costs, contributing to long-term sustainability.
Case Studies and Real-World Applications
Hydrogen Refuelling Stations in Europe:
Adopting SoS pressure transmitters has enhanced the accuracy and reliability of pressure measurement systems, resulting in safer and more efficient refuelling operations.
Early detection of leaks through accurate pressure monitoring allows prompt intervention, preventing accidents and ensuring the safety of personnel and equipment.
Hydrogen Production Facilities in Asia:
Utilising SoS pressure transmitters in electrolysis processes has improved efficiency, supporting the region’s energy sustainability goals.
Aerospace Applications in the United States:
Incorporating SoS pressure transmitters in hydrogen propulsion systems for spacecraft ensures safety and performance in demanding environments.
Future Prospects and Innovations
The role of silicon-on-sapphire pressure transmitters in the hydrogen industry will continue to expand. Future innovations may include:
Enhanced Miniaturisation:
Advances in microfabrication techniques could lead to even smaller, more sensitive SoS pressure transmitters for compact hydrogen systems.
Integration with IoT:
Integrating SoS pressure transmitters with the Internet of Things (IoT) could provide realtime data analytics and remote monitoring, enhancing safety and efficiency.
Research and development may yield SoS pressure transmitters with multi-parameter measurement capabilities, offering comprehensive monitoring solutions for hydrogen applications.
Conclusion
Silicon-on-sapphire pressure transmitters are transforming pressure measurement technology in the hydrogen industry. Their high precision, temperature stability, durability, and high-pressure capability make them indispensable for a wide range of hydrogen applications. By enhancing safety, efficiency, and sustainability, SoS pressure transmitters drive the hydrogen industry forward, contributing to a cleaner and more sustainable energy future.
ViSWIR Hyper APO Features:
• Capable of fully corrected focus shift in visible and SWIR range (400nm - 1700nm)
• Achieves spectral imaging with a single sensor camera by simply syncing the lighting Floating design adjusts focus for different wavelengths 8mm, 12mm, 16mm, 25mm, 35mm* and 50mm* (*2023)
ViSWIR Lite Features: High transmittance at whole wavelength of 400nm - 1700nm by adopting hyper wideband AR coat
Outstanding cost-performance for single-wavelength lighting & narrow-band imaging Compact design 5mm, 8mm, 12mm, 16mm, 25mm, 35mm, 50mm
A bakery and confectionary goods producer contacted Castle Pumps looking for some pumps to help them move away from the manual handling of some of their ingredients, and upscale their production.
They required a pump for transferring the fillings of their doughnuts and apple fritters, as well as a model for dosing vanilla essence and other flavourings. It wasn’t long before it became clear that peristaltic pumps were the perfect choice!
The beauty of the peristaltic design is that its inner tube is the only part that encounters the fluid. Not only does this make it simple and low cost to maintain compared to other pump technologies with multiple wearing parts such as impellers and seals and bearings, but it also makes it highly versatile in terms of the fluids it can handle.
Why did peristaltic pumps “rise” to the occasion?
For the doughnut and fritter filling, an AMP peristaltic pump with an inverter was supplied. The addition of the inverter was important to allow the bakery to adjust the speed of the motor when being used with the fillings of differing viscosities. For example, when pumping the more viscous jams, the motor speed needs to be slowed considerably compared to when transferring the apple pulp.
Due to there being a single wetted part as previously mentioned, there are no valves to clog or impellers to jam. This design means that the
The beauty of the peristaltic design is that its inner tube is the only part that encounters the fluid.
peristaltic pump can easily handle the apple chunks and stringy solids present within the fillings without damage or downtime to the bakery’s process. Infact, peristaltic pumps’ solid handling capabilities are only limited to the diameter of their internal hose, meaning if it fits, it can usually be pumped!
When it came to the dosing of the flavourings, Castle Pumps
specified a DS-M peristaltic dosing pump. This model has excellent accuracy even at low flow rates, making it ideal for handling small volume transfer and highly precise quantities.
For both models, Castle Pumps specified a food grade thermoplastic internal hose and tri-clamp connections for a smooth, non-contaminating pipework joint, ensuring that the pumps are safe for handling products for human consumption.
Getting the wrong pump for your process can result in inconsistency in the finished product, crushed solids, clogging, excessive wear, loss of productivity or waste of costly product. Always trust technical experts to specify the right pump for your application.
A pump may do the job, but only the right pump will save you excessive wear, process failures, product waste & operator time.
Get the RIGHT pump with our 15 years’ experience in:
✓ Solid-laden, viscous fluids without clogging/wear
✓ Safe handling of chemicals, fuels & flammables
✓ Highly accurate dosing of chemicals & ingredients
✓ Difficult to pump or delicate, shear sensitive fluids
✓ 99.98% barrel emptying to prevent product waste
Contact our technical sales engineers now!
According to Deloitte’s 2024 Manufacturing industry outlook report, “technology will likely remain a pivotal force in driving efficiency, resilience and innovation in the supply chain.” On fast-paced production lines where time is of the essence, integrating new equipment demands swiftness. So, how can manufacturers proactively tackle these challenges? Here, Stephen Harding, managing director of Gough Engineering, explains why the answer lies in customised material handling equipment.
Investments in new machinery and processes will be vital if manufacturers are to navigate industry challenges, foster growth and remain competitive. However, investing in new equipment is far from straightforward. Securing budget allocations can be a challenge, requiring meticulous consideration of the potential returns on investment (ROI), as well as financial metrics such as profitability and cash flow.
To calculate the ROI, manufacturers must identify their reasons for investing in the new machinery in the first place. These goals and objectives might include increased production efficiency, improved product quality or enhanced production capacity. Next, a comprehensive cost analysis is needed that encompasses the initial investment and related ongoing operational costs.
In other words, investing in new equipment necessitates a delicate balance between capital expenditures
(CAPEX) and operating expenditures (OPEX). The former includes purchase costs, installation, training and any necessary infrastructure changes on the factory floor. OPEX encompasses the ongoing costs associated with dayto-day operations, such as utilities, planned and unplanned maintenance, salaries and supplies for expected reliability and performance.
These decisions must also be made quickly so that manufacturers can swiftly integrate advanced equipment into their lines. So, how can manufacturers get ahead of the game when investing in new machinery and processes? Fortunately, a solution lies in customised equipment.
Let’s look at the impact customised equipment can have on production lines. A food producer/distributor wanted to meet rising demands and expand its market reach across Europe and the Far East. The company sought to enhance its process for unloading big bags with high levels of quality control; with the possibility to load the product into silos, tankers, or even back into big bags.
Challenges included accommodating various big bag sizes, maintaining a fast throughput in excess of 20 tons per hour, and adhering to ATEX, the European safety standard for explosive atmospheres.
To overcome these operational complexities, the company enlisted the expertise of Gough Engineering to implement a tailored material handling system. Gough Engineering’s approach is to address specific challenges encountered
Investments in new machinery and processes will be vital if manufacturers are to navigate industry challenges, foster growth and remain competitive.
by customers, aiming to minimise manual handling, reduce energy consumption, and optimise cleanliness while ensuring product integrity throughout the process.
Gough Engineering selected a range of solutions from its portfolio. That included the use of big bag discharging units, the use of temporary storage using silos and hoppers, followed by check screening processes to remove any conglomerates or debris.
Product elevation would be crucial to the new material handling system, lifting product between each quality checking process for final delivery. A system’s design can include a Gough Swinglink bucket elevator, Floveyor aero-mechanical conveyors or vacuum transfer systems.
These systems would work alongside
vibrational screening as well as different over-band or ‘in-line’ metal detection systems — an over-band metal detector unit is positioned above the conveyor belt, or with an ‘in-line’ metal detection systems during product conveying and transfer.
Gough Engineering provided comprehensive design consultancy and engineering support services. This included factory acceptance testing and mechanical installation, to ensure smooth implementation of the system.
Amid the surge in investments to enhance efficiency and innovation, decision-makers face the critical task of balancing CAPEX and OPEX to ensure optimal returns. Gough Engineering delivers tailored solutions that not only meet but
Gough Engineering’s tanker loader with big bag, screening and Floveyor elevation.
exceed client expectations. From standalone units to complex integrations, the solutions are crafted to meet the diverse needs of modern production environments, offering controlled distribution of products tailored to each client’s unique processes.
The integration of advanced and customised technology into manufacturing processes has become paramount, as highlighted by Deloitte’s industry report, and will be key to driving progress within industry.
Gough Engineering’s solutions are all designed and manufactured in Staffordshire, UK. To find out more about these, including its FIBC Big Bag Discharger systems and elevation solutions like the Floveyor F4 aero-mechanical conveyor system, visit its website.
For further information, please visit www.goughengineering.com
Here at daysoft® we’re focused on what matters: providing simple, affordable vision solutions that are kinder to the planet without compromising on quality.
We believe healthy eyesight should be affordable for everyone
So we cut out the middleman and pass the savings to you. daysoft® lenses are made to rigorously high standards in our UK lab and then sold online, straight to you. As the only company in the world that design, make and sell contact lenses directly to customers, we’re able to replace other brands for half the price without compromising quality.
We’re trailblazers in innovation and expertise
We’ve always been ahead of the curve when it comes to innovation and design. Our chairman, Ron Hamilton, invented daily disposables and built the world’s first laboratory dedicated to making them. We continue to innovate and improve, using patented daysoft® technology and our unique SoftEdge™ design to offer you the safest way to wear lenses at an amazingly affordable price.
We’re the environmentally conscious choice
We’re conscious that single-use daily disposables have an impact on our planet. That’s why we’re working towards innovative solutions to reduce our carbon footprint.
Our unique INPAC technology enables us to reduce excess plastic waste by up to 50%.
Designed and manufactured in the UK, our contact lenses have a lower carbon footprint than those that are shipped from across the globe.
made medical devices
Safe, accessible, healthy eye care for everyone is at the heart of our vision at daysoft®. Our contact lenses are
We’ve always been ahead of the curve when it comes to innovation and design.
medical devices, and as such are required to meet strict standards, measured through a rigorous regulatory framework.
ALL OF OUR CONTACT LENSES ARE:
• Manufactured under the control of a certified Quality Management System, compliant with ISO 13485:2016.
• Approved under the European Medical Devices Regulations (Directive 93/42/EEC) under The Medical Device Regulations (Canada), licence #61427
• We’re also subject to regular audits by SGS Belgium Ltd, to ensure we continue to meet regulatory requirements, including stringent checks on the effectiveness of our sterilisation process.
How we make daysoft® contact lenses
daysoft’s® manufacturing process has been designed around the high specification details of the contact lens itself. Our state-of-the-art facility in Blantyre, Scotland only makes daily-disposable lenses and our processes, along with a highly skilled workforce allow us to supply you with the highest quality lenses at the most affordable price.
• ‘By Industry, For Industry’, practical guidance for everyday and irregular situations and tasks
• Readily accessible for all in the industry –wherever they are, whatever time they have
• FREE task and procedure checklists
To make EEMUA’s guidance, training, events and
– ask@eemua.org or visit www.eemua.org
• professional development
• Webinars and seminars for knowledge sharing
• This selection of specialist publications and many
Rubbertech has been supplying technical mouldings to the electronics industry for over 30 years.
Our range includes protective covers for electronic devices, seals & gasket mouldings, plastic injection mouldings, keypad assemblies that include flexible circuits with LED backlighting and Liquid Silicone over-moulding assemblies.
Custom keypads
All keypads are unique, so custom solutions are in demand. Rubbertech help to develop the customers design to best solve their requirement and ensure ease of manufacture.
Keypads can be designed to operate using carbon contacts, metal dome and tactile switches. Where required keypads can be supplied assembled with flexible circuits or PCB’s.
Keypads can be backlit with LEDs using spray and laser etching processes or can be screen printed and pad printed. With several options for protective coatings keypads offer excellent life often into the millions of operations.
If operating environments require then keypads can be supplied with either plastic or metal keycaps assembled.
As well as liquid silicone moulding, Rubbertech can now offer overmoulding onto plastics.
Many injection moulded components require IP rated sealing, with LSR over-moulding a seal can be
Rubbertech help to develop the customers design to best solve their requirement and ensure ease of manufacture.
incorporated into a plastic case mould.
Keypads can also be manufactured using this process where a silicone keypad is over-moulded to a plastic front case moulding.
We supply rubber seals, gaskets, bellows and many more mouldings.
Our rubber mouldings can be manufactured in silicone, Neoprene, Nitrile, EPDM, Viton / FKM, Fluorosilicone and TPE materials. We mould many grades for use in Pharmaceutical / medical environments, Food Safe, Water Industry Grades as well as UL approved options.
High value equipment incorporating easily damaged touchscreens require protection. Our custom designed covers offer impact protection and can be further enhanced by printing and spray finish options. Using component CAD we create initial designs and images that can then be worked on with the customer to create a final design.
Complementing our keypad mouldings, seals and instrument covers Rubbertech also supply injection moulded components. Utilising latest CAD software, mould flow analysis software and finishing options such as spray coatings, printing, chrome plating and laser etching we work with our customers to ensure products are cost effective to manufacture and add value to the customers product.
Where possible we look to supply customers with the accompanying keypad or sealing mouldings as a complete assembly to ensure no design issues with fit and function and improve cost efficiencies.
In mining applications, coal-carrying conveyor belts can be up to 20 km long and, if they break and do not immediately stop, cargo can be spilled everywhere and cause a major safety risk. Conveyors usually come equipped with contacts that indicate problems like breakages, but, with the extreme distances involved, these can be unreliable. Here Ian Loudon, international sales manager at remote monitoring specialist Omniflex, explains why new fibre optic modules are game changes in mining applications in terms of reducing downtime and improving safety.
The mining industry is the backbone of modern civilisation, providing the raw materials essential for everything from buildings and infrastructure to electronics and medicine. The global coal mining industry specifically has grown by nearly 20 per cent on average for each of the last five years, meaning conveyors in the industry are carrying more coal than ever. However, these mining operations often take place in remote and challenging environments, where reliable communication is paramount.
Modern mining conveyor belts can extend for tens of kilometres, carrying tonnes of material daily. These mammoth systems are crucial for transporting extracted resources from the mine to processing facilities or stockpiles. Therefore, ensuring efficient and uninterrupted operation is vital for maintaining production quotas.
However, conveyor belt safety is an equally important
Wireless telemetry systems play a vital role in ensuring the smooth and safe operation of conveyor belts.
consideration. Belt breakages can have catastrophic consequences –causing damage to infrastructure, environmental spills and, even, worker injuries or fatalities.
Wireless telemetry systems play a vital role in ensuring the smooth and safe operation of conveyor belts. These systems continuously monitor belt tension, speed and alignment, and can detect anomalies that could indicate potential problems. Real-time data transmission allows
for early intervention, preventing minor issues from escalating into catastrophic failures. In the unfortunate event of a belt breakage, sensors can trigger emergency shut-off mechanisms immediately, minimising damage and potential injuries.
Getting switch contact signals point-to-point can be a matter of life and death. When an operator hits the conveyor’s emergency stop button, they need to be confident that the system will shut down as intended. If someone is in danger in a mining environment, the risk of signal failure must be mitigated to an acceptable level.
However, maintaining reliable longdistance signal delivery in mining environments can be challenging for several reasons. First, signal strength can be limited in any underground operations where rock formations hamper radio wave transmissions.
Next, mining activities can generate a significant amount of electromagnetic interference (EMI), which can interfere with wireless signals. Furthermore, mining applications often take place in harsh environments where temperature, humidity and dust levels can place excessive strain in communication equipment.
Finally, the distances involved are also a big hurdle to overcome for many transmission options. Copper wiring is extremely costly and, when required to run over many kilometres, the costs are often prohibitive. Furthermore, copper systems do not even guarantee reliable transmission over those distances. For example, standard communication links on copper wires like RS 485 are generally limited to about a kilometre of reliable transmission.
Therefore, to overcome all these challenges and ensure ongoing worker safety, the mining industry must source signal transceiver modules that can operate
reliably even in the harshest of environments.
Bidirectional fibre optic modules offer new possibilities Omniflex’s new FCX module is a bidirectional transceiver, meaning it combines both transmission and reception capabilities into one device. This eliminates the need for separate modules, halving the number of modules required in any given setting and dramatically reducing costs for purchasing and installation. Costs are reduced further because fibre optic cabling is much cheaper than copper, so, as well as needing less modules, the cost per module is also lower.
To set the units up, users should place one module at either end of a duplex fibre optic link and when the contact on the first is closed, the other module is energised replicating the contact signal.
The transceiver is compatible with either 850 nm multi-mode or 1310 nm single mode fibre optic cabling; the latter can send switch contact
signals up to 20 km of range. The FCX is powered from a 10-30 Vdc power supply and the device can operate in a range of 0-60 degrees Celsius.
The FCX can also be used in nuclear radiological safety warning signals and monitoring and controlled shutdown of electrical substations. The FCX is certified for use in SIL-2 applications, meaning system designers can trust that the risk associated with transmitting switch contact signals over long distances can be limited to appropriate levels using the module.
With many years of experience in providing SIL-rated safety systems across mission critical industries, Omniflex is well placed to identify and provide the most suitable solution for any given application.
To find out more about the FCX’s remote safety applications in the mining industry, visit Omniflex’s website: https://www.omniflex. com/dsview.php?hid=C2477A.
By Andrew Jones
Business leadership teams constantly talk about how they can improve their processes and systems, but how many spare a thought for those customers in roles where they are buying solutions for organisations. Believe me, as the technical head of an engineering company I speak to a lot of customers who are buyers of industrial fans and the positive feedback following the first interaction is often overwhelming. The thing is they have a long, arduous, and heavy process that sales teams really don’t appreciate or take on board when interacting with them. From self-educating and intense research to ultimately becoming subject matter experts in many niche components or applications. Then, only after they’ve conducted extensive self-serve research do they think they can clearly and confidently express what they need from suppliers. They want to speed this process up of course, but admittedly, none of us like to speak to a salesperson who doesn’t add value or understand our specific requirements, it’s a painful experience, especially when we feel we know more about the component than the very people who are meant to be the experts. The one biggest issue for these buyers isn’t finding suppliers, it’s having trust in the information available, the people giving that information and mitigating the risk associated with the solutions or suppliers offering them. Today’s buyer journey, made more difficult by the vast amount of information online, has reached a point where it’s now difficult to navigate in the right direction without a significant amount of help.
Reports show that 84% of technical buyers prefer purchasing from a company that understands their goals, they clearly want to be understood.
Our buyers don’t want more information that would distract from the task of sourcing, they want the right information to help them to pinpoint the right solution. Reports show that 84% of technical buyers prefer purchasing from a company that understands their goals, they clearly want to be understood. I‘ve spoken about the benefits of collaborative working in previous articles, but this statistic really resonates with me. Our company, Axair Fans, has a set of values that every employee embodies in their everyday activities. A key value we live by is that “We Understand, Apply and Give Back”. This means that we focus on understanding our customers’ needs before offering a
solution. Our team are taught and reminded regularly that listening starts and ends with respect. It means we’ll actually hear and digest our customers points as they make them and wait for them to finish before offering our take. In an industry such as ours there are lots of old school salespeople, they’re keen to speak, talk about product features or ask the next question, and they forget to listen to what their customers are saying. This creates a huge gap in communication in a stage that is highly significant to the buyer who wants to ask questions about specifications, implementations, and the expected challenges if they transitioned to our solution.
You must be genuinely interested in your clients’ challenges to operate in this way, because ultimately customers don’t buy products, they buy the results that the product gives. To appreciate this, you must show empathy for the customers plight and build authentic, trusting relationships that take away any perceived risk of changing supplier or product. In my experience giving the buyer the control in the selection process ensures they can focus on their goals rather than being swayed down a road that is more biased towards the suppliers’ own objectives around product targets and revenue goals. This doesn’t only help the buyer to navigate to the right decision using their own goals as the compass, it benefits the supplier too. Our employees who understand, apply and give back learn more about the industry we operate in and stay up to date with the latest trends. Ultimately our customers ensure we have one foot in the real world and don’t make assumptions about buyer or customer behaviour.
The Huck® fastening system exemplifies innovation and excellence in the fastening industry; the diverse product range plays a crucial role in high-demand applications ensuring reliability, durability and efficiency.
Revolutionising Industrial Fastening
In the ever-evolving landscape of industrial manufacturing, efficiency, reliability, and durability are paramount. The Huck® fastening range is a brand synonymous with innovation in the fastening industry. Renowned for LockBolt® and structural blind fastener technologies, Huck® fasteners provide solutions that enhance manufacturing processes across a multitude of industries where structural integrity is critical and where a strong, permanent, and tamper-resistant joint is required.
The Legacy of Huck® Fasteners
With over 80 years of fastener innovation, Huck® fasteners have consistently delivered performanceengineered solutions designed to withstand extreme conditions and demanding applications. This legacy of innovation and reliability has made Huck® fasteners a trusted name in the industry. The Huck® LockBolt, based on Lou Hucks’ original design, provides high stability and facilitates lightweight, stronger and more durable structures. Hucks’ ever evolving LockBolt and structural blind fastener capabilities continue to solve problems in in a wide variety of applications – no torque, easier evaluation, maintenance free and high corrosion standards are some of the benefits of using the Huck® fastener product range.
Speed of Installation: Huck® fasteners are designed for rapid installation. The installation process is often faster compared to traditional fasteners such as bolts and nuts, reducing assembly time.
Consistency and Reliability: The installation process of Huck® fasteners is consistent and reliable, reducing the likelihood of installation errors and rework, which saves time and resources. They benefit from rigorous testing, certifications, and quality management systems, ensuring consistent performance and building confidence in their use.
Cost Reduction
Reduced Labor Costs: Huck® fastener installation offers significant advantages in terms of efficiency and speed due to the straightforward process and visual inspection methods.
Reduced Material Costs and Weight reduction: Huck® fasteners are designed to create strong, durable joints, often requiring fewer fasteners compared to traditional fastening methods.
Maintenance and Longevity: Huck® fasteners typically have a long service life and require less maintenance, leading to cost savings over the product’s lifecycle.
Performance
Strength, Durability and Performance
Evaluation: Huck® fasteners provide high joint strength and are resistant to vibration and loosening; they are subjected to various tests to assess their performance under static and dynamic loads. Depending on the
fastener type, tests include tensile, shear, slip-load and creep testing as well as fatigue testing to emulate realworld conditions.
Aesthetic and Structural Integrity:
They can be installed without causing significant distortion or damage to thin sheet metal, preserving the material’s integrity and appearance.
Corrosion Resistance: Huck® fasteners are perfect for safety-critical applications; they are often subjected to harsh environmental conditions, including moisture, saltwater exposure, and chemical agents. Huck® fasteners are manufactured with coatings that resist corrosion, enhancing the longevity and performance of the final product. The coatings act as a barrier, shielding the fasteners from corrosive elements and preventing the onset of rust and degradation. By effectively sealing the surface of the fasteners, coatings significantly extend their lifespan, reducing maintenance requirements and replacement costs over time. This is particularly crucial in industries such as marine, offshore, and transportation, where corrosion can pose significant safety risks.
Advanced LockBolt Technology
Huck® LockBolts are renowned for their strength and vibration resistance. Unlike traditional nuts and bolts, Huck® LockBolts form a permanent joint that resists loosening, even under extreme conditions. This makes them ideal for high-vibration environments.
Huck® LockBolts are installed using direct tension and swaging. The Huck® installation tool grips the pintail of a LockBolt and then pulls to close the gaps in the materials being joined.
One standout product is the Huck® BobTail®, which has been proven to increase manufacturing efficiency. The BobTail® LockBolt eliminates the need for torque and re-torque procedures, ensuring consistent and reliable installations while significantly reducing labour costs, and unlike traditional LockBolts® no pin-break is required, therefore leaving no corrosion-prone area of bare metal or spent mandrels to be collected.
Huck LockBolts
Positive Locking Mechanism: Threaded bolts rely solely on frictional forces, in contrast, LockBolts consist of a pin and a collar and are installed using direct tension and swagingthere are no gaps between collar and pin ‘threads’ – a common source of loosening in conventional nuts and bolts.
Huck® LockBolt brand names include, BobTail® Magna-Grip®, C6L®, C50L®, C120L® and Hucktainer® (also available in encapsulated Hucktainer which can be colour matched to customers’ requirements).
When accessibility is an issue, Huck® structural blind fasteners offer a robust solution. Designed for applications where only one side of the joint is accessible, these fasteners provide high-strength, reliable joints often replacing welding. A key benefit is their internal locking mechanism that retains the ‘pin’ after installation.
Huck® structural blind fastener brand names include, Auto-Bulb®, BOM®, FloorTight®, HuckLok®, MagnaBulb®, Magna-Lok®, Magna-Tite®, and Penta-Lok™
Standard Nut and Bolt Frictional Force compared with Huck LockBolt Direct Tension Swaging
Huck® LockBolts High and Consistent Clamp Force: The installation process ensures a precisely controlled clamp force. This high and consistent clamp force minimises any potential movement within the joint, further enhancing the resistance to vibration.
Star Fasteners are the UK’s largest distributor of the Huck® fastener product range and stock a wide range of sizes, head styles, materials, and plating’s; this versatility ensures a wide range of applications and industries are accommodated. As industries evolve, Star Fasteners remains committed to providing advanced fastening solutions that meet the rigorous demands of modern engineering and manufacturing.
Complementing their extensive range of fasteners, Star Fasteners offers a suite of installation tools designed for ease of use and efficiency – offering a versatile range of battery and air-powered
options that enhance productivity on the shop floor. These tools ensure that Huck® Fasteners are installed correctly and efficiently, further boosting the overall performance of the fastening system.
Star Fasteners prides itself on its customer-centric approach. Through detailed case studies and customer feedback, the company continuously improves its product range to meet realworld challenges. This commitment to excellence ensures that Huck® fasteners remain at the forefront of the fastening industry, providing solutions that drive success for their customers.
In conclusion, Huck® fasteners represent the pinnacle of fastening technology. Their innovative designs, superior performance, and proven customer satisfaction make them an invaluable asset in modern manufacturing. Whether it’s enhancing the efficiency of assembly lines, ensuring the reliability of components and safety critical products, or supporting the sustainability of green energy projects, Huck® fasteners deliver solutions that meet and exceed industry demands.
High performance temperature control for Biotechnology and Pharmaceutical engineering, the new LAUDA Ultratemp range is here:
Typical biotech and industrial applications for the new LAUDA Ultratemp process circulators require high heating and cooling output within a moderate temperature range. High External volumes can be quickly heated up and cooled down again with outputs from 25 to 50kW.
The devices are available with a 400 V;3/PE; 50Hz & 460 V; 3/PE; 60 Hz bi-frequency power supply and can therefore be used worldwide. There is also a device model with 400;3/ PE; 50Hz, which has been optimised for mains frequency at 50Hz. All variants can be operated within an ambient temperature range of -15 to 50°.
The Ultratemp process circulators are available with protection level IP 54 as standard. The high-quality stainless steel housing is protected against splash water and allows for easy cleaning of the surface.
Intuitive operation is provided directly at the device via the function buttons and an LCD. Furthermore, the devices can be controlled via PC with an integrated web server. The devices are prepared for the cloud-based digital applications from LAUDA. These offer intelligent analysis and monitoring tools, as well as remote maintenance functions that maximise the operating time,
to the environment. Use with nonflammable liquids such as water or water/glycol provide easy handling and low operating costs.
The Ultratemp process circulators round off the LAUDA portfolio in the upper performance range of biotech and industrial applications.
High External volumes can be quickly heated up and cooled down again with outputs from 25 to 50kW.
reliability and performance for all LAUDA devices.
Application optimised equipment
The Ultratemp process circulators enable exact regulation to an external temperature within a range of -5 to 60°C. Their high temperature stability of +-0.5K guarantees a precise temperature in the application. The water-cooled design minimises any heat emitted
The Ultratemp portfolio includes three models of constant temperature equipment with high heating and cooling capacities, especially for bioreactor applications with reactor volumes from 2000 to 5000 litres.
LAUDA offers temperature control solutions in all the requisite performance classes for applications in the biopharmaceutical industry and for the biotechnical processes.
The Microcool circulation chillers and PRO process circulators are available for laboratory reactors. The temperature of reactors with 200 to 2000 litres can be controlled with process circulators from the Variocool and Integral lines. The new Ultratemp line means that LAUDA now offer solutions for reactors and mixers with a volume of up to 5000 litres.
For further information, please visit www.lauda.de/en
For design applications that depend on motion, whether that’s a robot, a surgical power tool, or a satellite control system, miniature DC motors are commonly used thanks to their performance and compact footprint. To accurately specify a miniature motion solution, understanding the role of inertia is crucial. While sizing tools can assist in this process, a thorough analysis of the application’s wider design, combined with targeted customisations, can help optimise performance.
When specifying a miniature motor, inertia is a key consideration. As a measure of a motor’s resistance to changes in rotational speed, its inertia value is based on a calculation involving the mass and radius of its rotor. High rotational inertia presents a greater challenge in accelerating the system, whereas a lower inertia indicates ease of acceleration. As less energy is required to accelerate or decelerate a motor with lower inertia, they are more energy-efficient, and this can make a significant difference in applications with frequent start-stop cycles. Motors with lower rotational inertia also usually offer improved control, which is a positive attribute for applications that require precise positioning.
While it may seem that lower inertia is optimal, matching the motor’s inertia with the load’s inertia is essential. In the most basic terms, if the load’s inertia is significantly greater than that of the motor, the motor will struggle to control the outmatched mass or size. The closer the inertia match, the more accurately the motor and drive system can control the load, especially in applications requiring precise movements.
As a measure of a motor’s resistance to changes in rotational speed, its inertia value is based on a calculation involving the mass and radius of its rotor.
Although a 1:1 inertia ratio is theoretically perfect, it’s neither practical or necessary to achieve. In real-world applications, striving for an inertia ratio close to 1:1 can
result in oversized components, higher system costs, and increased energy consumption. Instead, each use case has an acceptable range, although for applications that demand dynamic control and positioning, like high-speed assembly or textile yarn guides, a low load-tomotor inertia ratio is crucial.
The common challenge is an inertia mismatch caused by a high loadto-motor inertia ratio. This kind of imbalance can introduce stability issues that cause increased response times and lower system bandwidth. It can also result in wasted energy as the motor works harder to move the load. At its most serious level, it causes oscillations and resonance that could damage the motor as well as the load and connections.
Many motor manufacturers provide online tools and calculators to assist design engineers when selecting a miniature motor, including those such as Portescap’s MotionCompass™. However, a comprehensive awareness of the contributing factors to inertia is useful in motion design and integration. While a motor catalogue and sizing tool can provide the inertia rating, holistic design tactics can improve overall application design and help close the inertial gap.
Gear reduction is a common step, and this technique reduces the load
inertia in proportion to the square of the gear ratio. Moreover, modern control systems with advanced algorithms and high-resolution feedback devices can address inertia mismatch issues. However, the adverse effects of inertia mismatch, or a high load to motor inertia, can become worse by a lack of stiffness in the system, also known as load compliance. To minimise these issues, we can look to wider components of the application or machine to optimise rigidity.
Load compliance challenges are more common in indirect drive systems. Here, the motor is not directly coupled with the load but is connected through one or more power transmission elements such as a gear mechanism, pulley belt systems, chain drives, or ballscrews. To simplify an indirect system to increase stiffness, as well as
reduce further potential causes of inertia, it is useful to consider the effect of each connected component beyond the motor shaft.
For demanding applications that would significantly benefit from a close motor-to-load inertia ratio, starting with the possibility of a direct drive system is advisable. This motion design approach will keep the number of power transmission elements to a minimum while optimising compliance.
With a direct drive, the motor is directly coupled to its load. This
connection removes the inertia resulting from power transmission components, and the less inertia the motor needs to overcome, the less torque it requires to meet the desired acceleration rate. A direct drive system also minimises effects such as backlash, the play between mechanical components that can also impact power transfer and system reliability.
To minimise the overall inertia within an application or machine, as
well as optimize the inertia balance between the motor and the load, a comprehensive review of all design aspects impacting the motion cycle is advisable. To effectively achieve this, involving motion engineers early in the overall design process is preferable.
Firstly, engineering input can help to improve the wider machine or application design and advise on the best motion solution approach. Secondly, early involvement of motion designers means that if customisation is required for the motor or transmission, the most effective results can be reached early in the process with no impact in time to market.
Portescap provides a ready supply of tools and motor data to help guide original equipment manufacturer (OEM) engineers in their specifications. Most importantly, the company’s motion specialists are available to discuss design and customisation needs across a range of applications.
The key benefits of manufacturing components using this versatile process
Investment casting allows us to create highly intricate and complex components with virtually any alloy. It produces excellent dimensional accuracy, high integrity, and a fine surface finish, capable of meeting the demanding specifications of a wide range of industry sectors.
What is investment casting?
Investment casting derives its name from the process used to form the moulds. A series of wax patterns is assembled together and dipped (‘invested’) in tanks of liquid slurry alternated with ceramic stucco. This builds up layers that dry to form a ceramic mould.
The wax is melted away, then molten metal is carefully poured into the mould. After cooling under controlled conditions, the ceramic shell can be removed, and the cast metal parts finished to requirements.
The key benefits of investment casting
• Versatility of design
Investment casting offers exceptional design flexibility. Complex components can be cast to near net shape, including internal shaping, undercuts and slots, and complex passageways. Thinner walls may be cast than is possible in other processes such as sand casting, leading to lower overall weight and improved efficiency.
• Versatility of materials
Most alloy bases, such as ferrous, aluminium, nickel, copper and cobalt, are well-suited to investment casting. At Investacast, we are expert in air investment casting nickel-base
superalloys. These alloys can be difficult to machine from solid, or to machine post-casting, and expensive to forge. Investment casting is the more economical manufacturing process of choice for components in these materials.
• Range of sizes and applications
At Investacast we have cast components weighing from 10g to 30Kg, for applications from turbine blades to camera housings, for a wide range of industries.
Tight tolerances
Investment castings can be held to much tighter tolerances than sand castings or forgings: close dimensional tolerances down to +/ - 0.15mm/25mm can be achieved.
• Exceptional surface finish
Investment casting gives a very smooth finish thanks to the ceramic mould, typically offering 1.6 Ra to 3.2 Ra surface finish as cast. This can significantly reduce the amount of secondary machining, and therefore time, required compared to other manufacturing processes.
• Rapid prototyping
Investacast’s rapid prototyping service allows companies to turn ideas
into products quickly and efficiently. We offer casting simulation and rapid production of prototypes to mitigate any risks when transitioning to production tooling.
• Low tooling costs
The investment casting process has much lower tooling set-up costs than gravity die or high pressure die casting, which require permanent casts to be manufactured. This makes it suitable for pre-production runs for high-volume pressure die cast products.
• Repeatability
The quality of investment castings is maintained, providing a very reliable product and low-cost repeat runs.
• Sustainability
Investment castings are created to near net shape, and we recycle our wax, so production waste is minimal. Advice from the investment casting experts
Our expert team can advise on DfM and whether investment casting is the right manufacturing method for your components. Call+44 (0) 1271 866200 or email info@investacast.com
Developed and verified ‘for industry, by industry’, EEMUA 231 Mechanical Integrity courses are for industrial engineers at every career stage – to aid efficient hands-on work with primary containment and prevent loss of hazardous substances, including with pressure systems.
• Satisfy industry requirements at each competency level – Awareness, Basic application, Practitioner.
• Certificated up to 5 years.
• CPD-approved
• Flexible delivery to suit Learners and companies – Blended, Live online, Classroom, E-learning, or In-house.
• Available to all – free or discounted to EEMUA Members.
• Courses throughout each year, including:
Mechanical Integrity Practitioner Certificate (MIPC®) – Blended, live online learning, with 1:1s and Mentor Support – for on-site application of EEMUA 177, 231 and 232 guidance, and PSSR ACOP – certificated for 5 years via exam and portfolio assessment – Continuing Professional Development approval – in-depth learning for 27 weeks, 4 hours per week, flexibly – on-site or on-call. The MIPC course adapts to engineering needs of each Learner their company and site/s via a 2-hour induction (to fit work schedules ahead of the course) – the next course starts 21 October 2024
EEMUA 231 Mechanical Integrity Basics
Blended, online learning – set at Basic application competency level – 4 hours of learning per week for 3 weeks – certificated via exam – next course starts 30 September 2024.
EEMUA 231 Mechanical Integrity e-learning
Awareness level – with Continuing Professional Development approval – available – on-demand
EEMUA 231 Mechanical Integrity In-house training – 1 day or 2 half-days – set at the Awareness level – for your choice of time, location , method of learning – by arrangement
Also... External Corrosion Seminar – by EEMUA and AMPP Benelux – Haarlem, NL – 10 October 2024
online-learning@eemua.org +44 (0) 20 7488 0801 www.eemua.org
Cost pressures are frequently cited by companies as a reason for not investing in new machinery. Put off by the upfront price tag, many persist with tried and tested systems. But this can often be at the detriment of long-term performance and profits. Ashlee Gough at Sumitomo (SHI) Demag UK reviews the tipping point when injection moulding machinery loses its value, becomes financially unviable to maintain, and can hit you where it hurts most … on the bottom line.
Let’s face it, we’ve all learned the ‘get what you pay for’ lesson the hard way. It is a universal and age-old dilemma. We want to pay less. But equally, we want a product, service or experience to deliver more.
By nature people are wired to choose cost over value. Yet, by flipping this narrative, value can actually save you money and make you more. It is understandably a hard concept to grapple with. But when we start to really analyse the cost of ownership in full context, what is the real value to you and your business? What results would you see, and when?
What’s your worth?
Warren Buffet famously said: “Price is what you pay; value is what you get.” Although he was applying this statement to stock investments, it was still money driven. In the case of fast-paced manufacturing, the same proclamation rings true. When quality and speed underpin commercial success, reliability is paramount. Investing in new equipment yields direct benefits through lower service requirements as well as higher quality parts and greater output.
When unplanned downtime occurs, no value is being produced. Yet, operational overhead costs continue to grow - directly impacting the bottom line.
Calculating the real value in polymer processing really comes down to machine reliability, looking beyond the explicit costs and weighing in all the likely expenses you may incur across the lifespan of your equipment.
Sumitomo (SHI) Demag estimates that there are currently 15,000 injection moulding machines in the field throughout the UK and Ireland. However, these are only being replaced at an average of 200 to 250 new machines per year. Although many moulding machines can last 20+ years, the value question moulders should ask themselves is
whether a machine that’s older that 20 years is economical to run?
Avoid circling the downtime drain
For most processors, downtime is the single largest source of lost production time. Every product that comes off the line after processing and finishing has a value attached to it.
Unplanned downtime is the biggest drain. When unplanned downtime occurs, no value is being produced. Yet, operational overhead costs continue to grow - directly impacting the bottom line.
Whatever machine architecture you opt for, reliability will, to a large degree, be dictated by build quality. Additionally, equipment that is poorly maintained will likely breakdown more frequently. This impacts quality, as well as productivity and Overall Equipment Effectiveness (OEE).
Adopting a ‘run to failure’ mindset can be risky. Especially when customer schedules and stock holdings are so reliant on quick, seamless component deliveries.
Make reasonable rationalisations
Reliability can be notoriously difficult for a processor to quantify. It really does depend on cycle time, process demand (materials processed, quality of tooling, tool weights, number of functions utilised etc.,) and whether the machine is properly and regularly maintained.
It might sound obvious, but the single biggest thing users can do to ensure machine reliability and longevity is to carry out the service work that is highlighted on the machines’ HMI, or in the instruction manual. Planned maintenance invariably has a lesser
impact on line efficiency than unscheduled downtime caused by a failing part.
Until recently, machine manufacturers would recommend set intervals to conduct certain tasks e.g. oil changes or lubrication. Using machine data such as loads, cycle times etc., recommendations can now be adjusted and scheduled according to usage – providing a far more customised and responsive plan than a traditional ‘fixed’ approach.
Electric machines now have even more inbuilt data gathering capabilities. Parameters such as machine acceleration and deceleration and forces and motor duty are all checked via sensors, which provides a more detailed and complete optimisation picture.
Evaluating the relative merits of cost versus value is a balancing act. It also requires understanding economies of scale and where trade-offs might support or compromise seemingly sound financial decisions.
By discerning which costs are truly significant, processors can make better and more informed decisions about equipment investments.
Relevant costs are future-oriented. These are the ones that affect future expenses and revenue, and can change as a result of a decision. Irrelevant
The original Ergo Tech Extra, like many moulding machines of its generation, may still produce components, but the value question is are these older machines economical to run?
costs (also known as sunk costs) on the other hand have already been incurred and cannot be recovered, for instance machine depreciation. Hidden costs are those that are omitted intentionally or otherwise, and can add up over time. “This is why TCO is so important as an equation, as it considers all of these direct and indirect costs,” reports Ashlee.
One of the best ways to make an informed purchasing decision based on value is to ask yourself these four questions:
1. What production issues will this new machine solve for me and how does this fit with my overall business strategy?
2. What are measurable results? And can I compare my existing process like-for-like and run a tool trial on the machine I am considering?
3. What additional effort, or features,
do I need to gain these results and are there any hidden costs?
4. What service and support capabilities are offered by the OEM, e.g. training, process support, optimisation and energy consumption field studies, locality of engineers and target response times versus KPIs.
High-end machines naturally deliver value-add processing features. But what if you are a mass technical moulder that doesn’t require this panoply of offerings? By focusing on all-electric, Sumitomo (SHI) Demag grasps that best value comes from offering a full gambit of choices. It’s why the company is reviving its most popular series in history – the IntElect X-tra. Available in 100, 130 and 180, manufacturers can now benefit from the IntElect elite performance, with a direct drive platform that offers improved efficiencies and responsiveness, the stability and repeatability of electric drives, and parallel functions that can significantly improve productivity. Without paying for features that aren’t warranted.
Short-term thrift is rarely worth it. Instead, try to base your machine decision on reliability and selecting technical features that actually add value. There’s also a hefty element of psychology attached to cost and perceived value cautions Ashlee.
“When people feel valued they tend to push themselves harder. The same can be said for machines. Cost is the price; Value is the benefit. The question is, which one will exceed your expectations?”
The European productivity roadshow arrives in the UK and Ireland this July. Discover how manufacturing counterparts are adopting a coordinated approach to increase value and foster sustained productivity growth. View how digital tools are helping to deliver better processing control, less machine downtime and are addressing spiralling costs. Setting up in Athlone, Limerick, Silverstone and Glasgow, to attend this unmissable event register at https://roadshow.sumitomo-shidemag.eu/register or contact Ashlee Gough or Dave Raine direct.
APPLICATIONS
Compressor blades and vane tips
Repair of combustion and flame tubes
Replacement of honeycomb seals
Turbine blades, vanes and NGVs
Compressor Casings
Compressor Discs
Exhaust Unit Components
Bolts and Fasteners
Shafts and Studs
Rotaflow are into our fourth decade of designing and manufacturing Swivel Joints. We solve engineering problems where fluids need to be transferred across rotating interfaces, without leakage. Our units are in most engineering sectors: From Brewery, Dairy, Food & Drink, Process & Plant, Drilling & Mining, Oil, Gas and Subsea, Nuclear and Chemical.
Through design and in-house manufacture our swivel joints can allow one or more different flows through a single unit, enabling the pipework to rotate 360 degrees whilst carrying fluids (including hydraulic and pneumatic) of different pressures without cross-contamination or leakage.
There are many different forms of Swivel Joint… from very straight forward designs of our F and FS series, Compact swivels or Heavy Duty to Articulated Pipework
configurations, Floating Suction Arms, Jacketed, High Pressure. A Swivel Joint reduces costs by reducing the risk of leakage with its associated downtime.
We are specialists in taking your bespoke requirements and being able to design a solution that can fit your budget, dimensions, materials, FAT/witness testing, hygienic and pressurised environments. We regularly test to Hyperbaric, Seal Life and conduct Temperature/ Pressure/ Load Cycle Testing. We are ISO 9001:2015 certified. With off-the-shelf solutions that are ready to go, or we can redesign and in-house manufacture to enable a quick turn-around with minimal fuss and maximum design experience.
To find out more please visit our website and/or give us a call. Tel: +44(0)1663 735003 sales@rotaflow.com www.rotaflow.com
Articulated
SERVICES
Chemical Cleaning/Stripping, Dry Grit
Blasting & Glass Bead Burnishing
Machining, milling, turning and grinding
Dimensional Inspection and Non-Destructive Testing
Metallurgical Assessment and laboratory reports
Application and/or replacement of Engineered Coatings and Thermal Spray
Dressing and blending of compressor and turbine blades
Heat Treatment
Welding: Tungsten inert gas (TIG) and Spot and Stitch
Vacuum Brazing
Rotating Cylinders
Swivel joints allow pipework to pressure 1/4” to 40” and beyond. Vacuum to over 20,000psi. Stock and bespoke production. Unique bearing/seal design for longer life.
ISO 9001 CE marked where applicable.
Tel: +44(0)1663 735003
E-mail:
When you require something special, Helapet offers unrivalled flexibility in developing and manufacturing inline filter devices, specialising in custom-made designs. For over 35 years we have supplied filters for a range of vital applications across a wide variety of industries.
Designed for precise micron level filtration and clarification of particulates in air and liquids, each filter is produced in close consultation with our clients to ensure you receive the perfect filter first time.
Our selection of housing sizes, media options and connector types allow our clients to create the best filtration solution that can be used efficiently within or alongside several types of instrumentation, devices and equipment.
What we offer:
• A selection of disc housing diameters to suit sample flowrate and filtration requirements
• Wide media choice with pore sizes ranging from 0.1 to 100 micron. We can even use
You design, we create
Helapet knows that no single filter can be suitable for the varied filtration applications that are used across industries. Our new online design tool provides customers with a simple-to-use design wizard, combined with enhanced information to guide customers through the 100’s of available filter combinations.
clients’ own media
• Up to 10 inlet/outlet connector choices including hose barb, luer lock and pipe thread
• Tampo single colour printing of logos, instructions or part numbers on both inlet and outlet sides of the filter in a range of colour options
• Manufactured trial samples to test your prototype before final approval
• On-site cleanroom packing and testing. We also offer sterilisation services to optimise compliance
Founded in 2001, Brunos produces cooled salad dressings and gourmet butters. Since its inception, sales have risen steadily, prompting this progressive family business to employ increasingly sophisticated production methods to keep up with demand. Now a 45-employee enterprise, Brunos produces four million products each year at its 3,500m2 production facility in Sarnen, central Switzerland.
Although its production line was already automated, until recently, Brunos’ packaging and palletising
function was still a manual process. This resulted in bottlenecks at the final stage of the process, as employees struggled to match the speed of the automated line. Unable to meet increased order levels and at the limit of its capabilities, the firm began to look for an alternative solution – but complex palletising patterns and limited space made their search a potential challenge.
into cardboard boxes, but they could hardly keep up with the speed of our production line. We began thinking about an automated solution for the palletising process, but our space was rather tight. We needed to find a solution with a compact footprint that would tie in with our existing automated processes in terms of quality and productivity.”
manually
“We had reached our limits,” explains Managing Director Michael Arnold. “By this point, we had two or three employees
Brunos turned to Robotec Solutions AG, a local provider of robot-assisted automation, with more than 800
successful installations to its name across a diverse range of sectors.
Jörg Lanz, Head of Sales at Robotec Solutions AG, says: “Working together with our customers, our most important task is to find the best automation solution for the application. In this project to palletise the bottled salad dressings, our main challenges were cycle time, space constraints and palletising patterns.”
With regards to the palletising patterns, Brunos’ production line fills bottles individually before placing them in groups of 6, 10 and 12. These groups then undergo shrink-wrapping in foil. “We needed to devise an innovative palletising pattern based on the pre-grouping of bottle packs and involving part-rotation,” reveals Jörg. “After completing each layer, we required the robot to place an additional intermediate layer on top. This operation would have to take place without changing the gripper to help minimise cycle time.”
Working
together with our customers, our most important task is to find the best automation solution for the application.
Robotec regularly leverages the quality of FANUC’s range of industrial robots and collaborative robots (cobots) to fulfil its customers’ requirements. In this instance, the ideal robot for the task was the strong, lightweight and compact FANUC M-710iC/50 6-axis industrial robot with 50kg payload and 2,050mm reach.
“It was clear from the start that we would choose a FANUC robot,” states Jörg. “We’ve been a FANUC partner for over 20 years and often
say we have ‘yellow blood’ flowing through our veins. The FANUC M-710iC/50 fits Brunos’ requirements perfectly. Capable of carrying heavy loads, its long reach allows optimal processing of the palletising pattern – and always at full speed. Further plus points include low energy consumption, a small footprint and good availability of spare parts.”
capacity
For Brunos, automating its palletising function with the help of the FANUC M-710iC/50 robot has allowed it to keep pace with the production line, enabling the company to fulfil its ever-growing order book. Michael Arnold adds: “We are very happy with the results and success achieved following the introduction of the FANUC robot. It fulfils our expectations in terms of quality and productivity. We are completely satisfied.”
Check out the video here: https://www.youtube.com/ watch?v=t9KOhG0ZYuM
Versatile Controls Ltd was established in October 1987 by the current owner Mr Jon Slim and the late Mr Edward Dowty.
The Company started as a distributor for The Versa Products Inc of New Jersey to serve the Oil and Gas industry in The North Sea with high quality pneumatic and hydraulic control valves.
During the following years, the company acquired other distribution rights with ITT Neodyn pressure switches, ITT Conoflow regulators, Ruelco switches and regulators and Deltrol flow control products.
In recent years, the company has made progress in the manufacture of high quality mixing systems for The Pharmaceutical industry and was responsible for many of the systems required during the recent covid epidemic.
AUTOMATION & CONTROL SYSTEMS
INNSWORTH TECHNOLOGY PARK GLOUCSTER, GL3 1DL sales@versatilecontrols.co.uk 01452-731447
Unicar and Multicar are network monorail track systems with autonomous trolleys or cars which can move anywhere on the track network. The track can be installed horizontally, vertically and at any gradient. Unicar has a carrying capacity of up to 15kg, whilst the larger Multicar system can carry up to 45kg including any load handling device.
The ability to transport payloads both horizontally and vertically without any requirement to transfer the payload to a separate lifting mechanism delivers an innovative and extremely flexible intralogistics solution.
Both Unicar and Multicar can be routed at high level and within service areas where the track can be kept well away from production floors and other logistics systems, only dropping to load/unload areas in the immediate vicinity of the process to be served. This has the significant benefit of keeping the working floor clear of obstructions and traffic, and makes the most efficient use of the process space.
Both Unicar and Multicar transactions can be initiated either through HMI
(touchscreen terminals) or integrated with SCADA and WMS for automated control. Interface with other automated systems, such as automated load/unload stations is easily delivered through local PLC interfaces. The trolleys themselves also present both power and digital I/O for sophisticated load handling systems if required.
A feature of both Unicar and Multicar is the ability to keep the payload perfectly
horizontal during transportation, no matter whether the trolley is moving horizontally or vertically. This can be achieved either using a gravity pendulum system or a dynamic powered solution.
Both Unicar and Multicar are well established solutions in Europe and beyond and are now available in the UK through Quirepace. Contact us today and find out more about these innovative and flexible systems.
In this issue of PECM, we are delighted to showcase Sibor as our New Year Spotlight company.
Sibor has a long history, spanning over thirty years providing leading process control, engineering and project management expertise. Established in 1992, to originally provide process control systems and industrial automation to many industrial applications, such as large blue-chip companies, the company has been focusing on the energy sector more recently, notably the anaerobic digestion renewable energy sector.
Sibor provides turnkey design and build service solutions across manufacturing and automation control, including the following services:
• EIC/mechanical design and installation services
• Process control services
• Process instrumentation services
• Atex design and installation services
• Project management services
• Software development services
• Support services
With a vision for providing automated control systems that provide manufacturing benefits and added assurance throughout, Sibor are trusted professionals throughout the project. From initial requirements analysis, expert software engineers define user-needs from the offset, through to application design and software, component selection and assembly for a successful outcome.
Sibor runs applications as local stand-alone systems or alternatively, as Ethernet/IP networked solutions.
Utilising cutting-edge Supervisory Control and Data Acquisition (SCADA), Sibor ensures streamlined services across all customer applications.
We caught up with Managing Director: Rob Mockridge to find out more,
“We have always enjoyed organic growth and over the last 12 months, the company has gone through a major transition and has now been accredited with ISO 9001 and 14001 and we have also been accredited by safe contractor.
We have gone from strength to strength completing many major
upgrade projects for the MOD and several renewable energy companies, ranging from replacing old for new to major electrical infrastructure and controls installations.
We have seen a 40% increase in business over the last 12 months- an accolade to our strong team.
We are very excited for the year ahead in the anaerobic digestion renewable energy sector and we have just signed two major contracts with renewable energy companies to provide LV power distribution design and installation combined with control and instrumentation design and installation. With a pipeline of projects to follow, allowing us to keep investing in our staff and business activities.
Our growth in control and automation projects is a tribute to our innovative approach to design and comes from our long history in many industrial sectors.”
With 134 million babies born globally in 2023, demand for baby products is high. This birth rate, combined with the rise of e-commerce, has forced suppliers to rapidly expand. To alleviate its growing pains, Babydump, a leading European retailer of baby products, automated its order picking operations at Sint-Oedenrode in the Netherlands to increase throughput and sustainability. For efficiently moving orders through the facility, it relies on 12 autonomous guided robots (AGRs) from Prime Vision.
A baby boom for business
Babydump is part of the FTH group and was founded in the 1970s as a retailer of baby products. It’s now market leader in its segment with a thriving online operation and 14 stores throughout the Netherlands and Belgium. The business offers baby rooms, prams, car seats, buggies, high chairs, baby clothing and many more baby essentials.
Experiencing rapid growth and looking to meet new environmental legislation, Babydump searched for ways to improve the efficiency and sustainability of its order picking operations. At its site in SintOedenrode, online orders and stock deliveries for its stores were picked manually by employees.
Having reached the limits of this set up, Babydump installed an automatic storage and retrieval system (ASRS) from Autostore to streamline the process. The ASRS holds 15,000 crates containing specific items. Instead of employees travelling along the racks, the system delivers the correct items for each order directly to a picking
station, allowing workers to easily pack products.
With regards to sustainability, Babydump worked on optimising its packaging. Instead of relying on standard box sizes that rarely matched the volume of the shipment, the company purchased two box erector machines. These produce two different types of boxes, which once packed by employees at the picking station, are cut to the exact size of the order and fitted with a lid by box closing machines. This minimises wasted space and improves sustainability. The order then travels via chutes to the conveyors, which sort it for dispatch to a particular store, route or delivery service.
Robots connect the dots
However, the success of the system relied on efficiently moving boxes between all the different machines, picking stations, conveyors and chutes. There were other complications too.
Beyond the ASRS, prams and other non-machinable products that can’t be handled by automation needed to be accommodated in a different process flow. Furthermore, the facility handles both online and store orders. Supporting 14 physical locations as well as e-commerce customers added more complexity. Clearly, static conveyors would be unable to accommodate these multiple demands, so a more flexible solution was required.
Following discussions with the supplier of the ASRS, Babydump approached Prime Vision to provide a fleet of 12 robots and an additional spare to support the newly automated facility. Based in the Netherlands, Prime Vision is a global supplier of automation, computer vision and robotics technology for the logistics sector. It currently operates over 700 robots at customer facilities around the world. Its local presence and industry
expertise were critical advantages to Babydump.
Richard Hagen, Account Director at Prime Vision, says: “While we are used to operating fleets of up to 88 robots for sorting operations for courier and express services, the complexity of operations at Babydump presented a challenge. Our experience in this area meant that we could offer a flexible, cost-effective solution.”
Prime Vision robots have a 35 kg carrying capacity and a 50 x 70cm loading surface, ready to carry a wide variety of boxes. Using light detection and ranging (LIDAR) for guidance and safety, the robots can travel without QR markers or metal on the floor. An overarching fleet management system plots the most efficient route for each robot, ensuring maximum efficiency and productivity. Smoothly travelling at between 0.8 to 1.1 m/s, Prime Vision robots quickly move items to the correct destinations.
Richard explains the setup process: “What’s important to us during implementation is the floor and what interactions will take place on it. Working with the customer, we will map out the floor in special patterns, then upload these maps to the robots so they can navigate. The other element is marking out the pick-up and drop off points such as conveyors, box machines, picking stations and chutes.
“Information from the warehouse management system tells each robot which destination to travel to, and we facilitate this with bespoke software that seamlessly communicates with the customer’s infrastructure. Any robot can drive to any destination, so they are much more flexible than conveyors. We can have the entire system up and running in less than weeks, providing quick installation and smooth processes.”
The robots have been operating at Sint-Oedenrode since the start of 2024. As well as facilitating the movement of items, the robots have the flexibility to accommodate stock orders for stores. With a battery
a leading European retailer of baby products, automated its order picking operations at Sint-Oedenrode in the Netherlands to increase throughput and sustainability.
Prime Vision robots have a
35 kg carrying capacity
and
a 50 x 70cm loading surface,
ready to
carry a wide variety of boxes.
life of over 10 hours, each robot covers multiple shifts, while the interchangeable batteries can be fully charged within 2 to 3 hours. For maintenance, Prime Vision offers remote assistance and preconfigured spare robots ready for rapid deployment to reduce downtime.
Since the system has gone live, Babydump has recorded a 400 to 500% improvement in the productivity of its order pickers. This increased throughput has meant the company can comfortably meet
rising demand. As well as simplifying order picking for employees, it has also reduced errors and returns, saving costs, lowering emissions and improving customer satisfaction. Meanwhile, optimised packaging has saved space and materials, enhancing sustainability at Babydump. Prime Vision robots have made a significant contribution to these successes.
Richard adds: “For complex logistics processes where efficiency is paramount, robots are often the best solution, and I think the market is becoming aware of the benefits.”
Managing Director of Babydump, Henk Timmer, says: “For us, being at the forefront of innovation, continuity and sustainability is in our DNA. Prime Vision’s solution fits perfectly with that.”
More from Prime Vision: https:// primevision.com/prime-vision-robotshelp-babydump-take-first-steps-inautomated-order-picking/
For further information, please visit www.primevision.com/
ALRAD Instruments Limited (established 1970) has been serving the Industrial, Automation, Scientific, Medical and Instrumentation markets for over 50 years and has a wealth of experience in all aspects of Machine Vision, Automation and Scientific Imaging.
Our product areas cover imaging, machine vision and automation components, Industrial and Scientific cameras for UV, Visible and Infrared wavelengths, thermal cameras, image sensors, photonics components including laser products, vacuum and related
products, embedded AI and deep learning vision systems. We also provide standard and bespoke imaging software and complete system solutions together with our integration partners.
Our imaging technology operates in a wide spectrum from Ultraviolet through Visible to Infrared and Thermal wavelengths. We supply the latest camera technology and vision components including illumination products covering the complete spectrum from ultraviolet through visible to Infrared. These products are suitable for applications in Machine Vision, Automation, Scientific Research, Medical imaging, Agriculture, UAV/Drone, security and Search and Rescue applications.
For further information, please visit www.alrad.com
PRODUCT NUMBER
PRODUCT NUMBER
6ES7136-6DB00-0CA0
6ES7136-6DB00-0CA0
6ES7155-6AU01-0BN0
6ES7136-6RA00-0BF0
6ES7155-6AA01-0BN0
6ES7510-1SJ01-0AB0
6ES7550-1AA01-0AB0
6ES7193-6BP00-0BA0
6ES7331-7PF01-0AB0
6AV2124-0JC01-0AX0
6ES7322-1FF00-0AA0
6ES7138-6AA01-0BA0
6ED1052-1CA00-0BA1
6ES7392-1BM01-0AA0
6ES7135-6HD00-0BA1
6ED1052-1CC00-0BA4
6ES7515-2AM02-0AB0
6ES7331-7KB02-0AB0
6ES7212-1CA00-0XB0
6ES7134-6GF00-0AA1
6AG2511-1AK02-4AB0
6ES7511-1AK02-0AB0
6ES7510-1DJ01-0AB0
6SL3210-1KE14-3UF2
6ES7212-1AA00-0XB0
6ES7131-6BH01-0BA0
6ES7511-1FK02-0AB0
6ES7332-5HF00-0AB0
6ES7393-4AA10-0AA0
6ES7132-6BH01-0BA0
6ES7241-1AH32-0XB0
6SL3210-1KE15-8AF2
6SL3210-1KE15-8AF2
6ES7513-1AL02-0AB0
6ES7393-4AA00-0AA0
6ED1053-1CA00-0BA1
6ES7392-1AJ00-0AA0
6ES7390-5BA00-0AA0
6AV2124-0QC02-0AX1
6AV2124-0GC01-0AX0
6ES7972-0BA40-0XA0
6ES7315-2EH14-0AB0
6ES7131-6BF01-0BA0
6ED1056-4BA00-0AA0
6SL3211-0AB21-1AB0
6SL3210-1KE12-3UF2
6SL3210-1KE11-8AF2
6ES7232-4HD32-0XB0
6ES7155-6AU01-0CN0
6ES7134-6JD00-0CA1
6SL3210-1KE21-7AF1
6SL3210-1KE18-8AF1
6ES7368-3BB01-0AA0
6SL3210-1KE21-3AF1
6SE6410-2UB12-5AA0
6ES7972-0BB51-0XA0
6ES7515-2FM02-0AB0
6ES7513-1FL02-0AB0
6ES7315-2AH14-0AB0
6ES7153-2BA10-0XB0
6ES7134-6GD01-0BA1
6ED1053-1BB00-0BA1
6ES7512-1CK01-0AB0
6ES7512-1CK01-0AB0
6ES7511-1CK01-0AB0
6SL3244-0BB12-1FA0
6ES7518-4FP00-0AB0
6ES7518-4AP00-0AB0
6ES7532-5NB00-0AB0
6ES7517-3TP00-0AB0
6ES7517-3FP00-0AB0
6ES7517-3AP00-0AB0
6ES7513-1FL02-0AB0
6ES7511-1FK02-0AB0
6ES7511-1AK02-0AB0
6SL3210-1KE14-3UF2
6SL3210-1KE15-8AF2
6ES7516-3UN00-0AB0
6ES7516-3TN00-0AB0
6ES7522-1BL10-0AA0
6ES7522-1BH10-0AA0 1071153 10713518 1044125 1023546 1041114 1056430 1018601 1023891 1026287 1026820 1028934 1028936
ERS Hub issues grassroots rallying call as it looks to young people to fill the 100,000+ electrification jobs void
Engaging and boosting inclusivity at grassroots level with young people is going to be essential if the UK is going to fill the hundreds of thousands of expected job opportunities in electrification.
That’s the rallying call from Coventry University’s Deepak Farmah, who is currently helping to connect the emerging community through the Electric Revolution Skills Hub (ERS Hub), an integrated digital platform for providing inclusive access to training, development, and jobs in an electrified and greener future.
The Commercial Director for ERS Hub believes his team has made significant headway in creating an intuitive platform that has brought together education, training providers, employers and the future workforce all in one place, and with clear routes to courses and jobs.
However, he also feels that the big challenge now is to reach out to young people at primary and secondary schools, colleges and hard-to-reach youth groups to get them excited about the world of electrification as a diverse and inclusive sector.
“It is still a fledgling industry. The career paths and the type of jobs available are difficult enough to understand for adults, let alone young people trying to work out what the future holds,” explained Deepak.
“In a Gigafactory alone there are more than17 different roles you can aspire to, whilst in PEMD there are up to 80 knowledge profiles,
We want to start conversations with youngsters from different backgrounds, who may not have access to mainstream career advice or opportunities.
ranging from motor engineer and design lead through to testing and validation. Our role is about showcasing these and demystifying how you get there.”
He continued: We’ve already started this work, with the aim of engaging with tens of thousands of pupils and hundreds of schools and groups already, but this is just the beginning.
“Our experts have been attending career fairs, industry events, launching podcasts and providing curiosity boxes to educational establishments. These are a great way to start the conversation and encourage young people to build a motor from scratch following a simple lesson plan that can be delivered by any teacher – not just a STEM one.”
The ERS Hub, which is co-funded by Coventry University and UKRI, is keen to support more STEM related activities at grassroots levels and recently threw its weight behind ProtoEV, the ultimate motorsport competition for schools, colleges, youth clubs and apprentices in the UK.
Organised by the Blair Project, five youth teams from South London spent twelve weeks of tireless work and testing to retrofit a fully electric e-kart, before putting it
through its paces to try to claim the fastest lap at TRAQ Motor Racing in Croydon.
Leaways School took the first prize for its combined efforts on design, innovation, teamwork and speed, with Liam Palmer also securing the best teacher award. Oasis Play’s two teams finished second and third, as well as claiming the fastest lap accolade.
Experts from the ERS Hub joined Formula 1, Teamsport Karting and Innovate UK in a career session to raise awareness of possible jobs and careers in electrification.
“By providing hands-on experience in clean tech, we not only equip young people with essential skills but also ignite their passion for sustainable solutions and diversity in engineering. Witnessing their creativity and
determination reassures me that the future of motorsports and clean technology is in capable and diverse hands,” added Deepak.
Richard Lane, Product Development Director at the ERS Hub, said: “Events like the ProtoEV Challenge are crucial in inspiring the next generation of engineers and innovators.
“Equality, Diversity and Inclusion is a major focus. We want to start conversations with youngsters from different backgrounds, who may not have access to mainstream career advice or opportunities.
“That is the only way we are going to create the pipeline of talent the UK is going to need to grasp the opportunity of electrification. Reducing barriers to entry is key and – the next generation can’t do it, if they can’t see their own path to get there.”
ERS Hub is in the early stages of its grassroots journey and the longerterm plan involves ‘educating the educators on the opportunities’ and pressing the button on a more youthfriendly platform that will appeal to young people.
For further information, please visit www.ershub.co.uk or follow it across its social media platforms.
The demand for high-voltage cables to distribute electricity is high and growing fast. Supply is outstripped and new factories are being built all over the world. Look at the audacious Morocco project to link sunny and windy Morocco with the UK. And see “The surprising key to a clean energy future” in Bill Gates’ blog.
High voltage is necessary to minimise the energy loss in transmission. It means that the insulation in the cables, whether under the sea or over land must be flawless. Especially for submarine cables repairing defects or damage on a cable is very expensive. So you would think that online quality checking in manufacture would be vital and commonplace. Yes and no. Yes it is vital, no it is not commonplace. In fact there is only one system that can examine HV cable insulation as it is being made, and that is Acuity’s ultrasonic Ultrascreen. An offline system for manual inspection of cable joints, Ultraprofilor, uses the same technology to 3-D visualise joints in even more detail.
Our technology is in factories of several global cable-makers. All our clients jealously guard the
knowledge of the presence of our technology – hence the title of this piece. We have enabled recovery of cable worth millions by identifying defective lengths to cut out of reels that would otherwise have been scrapped.
Cable buyers have therefore not been aware of the benefits of having cable scanned in detail prior to shipment, although this is now beginning to change.
High voltage is necessary to minimise the energy loss in transmission. It means that the insulation in the cables, whether under the sea or over land must be flawless.
The professional bodies in the industry are showing interest in using our data, potentially for certification.
As the cable market expands so must we. To learn more about our products and about collaboration get in touch at info@acuityproducts.co.uk.
ViSWIR Hyper APO Features:
• Capable of fully corrected focus shift in visible and SWIR range (400nm - 1700nm)
• Achieves spectral imaging with a single sensor camera by simply syncing the lighting
Floating design adjusts focus for different wavelengths 8mm, 12mm, 16mm, 25mm, 35mm* and 50mm* (*2023)
computar-global.com
ViSWIR Lite Features:
High transmittance at whole wavelength of 400nm - 1700nm by adopting hyper wideband AR coat
Outstanding cost-performance for single-wavelength lighting & narrow-band imaging Compact design 5mm, 8mm, 12mm, 16mm, 25mm, 35mm, 50mm
info@cbcuk.com 020 8457 2618 catalyst of optics
Manufacturing precision gears, gearboxes and assembled components for suppliers in the aerospace industry
Providing engineering expertise and precision parts for commercial aircraft
Manufacturing an extensive range of electro-mechanical components for the medical industry
Providing engineering expertise and precision parts for medical scanners & radiotherapy machines
Our world class engineers deliver global solutions utilising cutting edge technology for critical industries including: Medical, Aerospace, Oil & Gas, Off-Highway and Defence
Contact us today and see how we can deliver your vision
Menzel Elektromotoren has celebrated the opening of its new headquarters near Berlin with a grand inauguration party. In honor of company founder Kurt Menzel, the date was set for his 120th birthday on 14 May 2024. With increasing numbers year on year, the German manufacturer successfully markets its industrial motors and tailor-made drive systems worldwide. This continued success, now required more space with modern production facilities designed for efficient processes, and larger, heavier machines. In addition to stateof-the-art machinery, efficient paint shops and test fields that can accommodate even the largest motor configurations, the new plant is prepared for further growth. In coming years, the workforce at this site can be expanded from around 100 to 150, allowing the manufacturer to meet all customer requests.
Menzel manufactures its own motor series and also specializes in custom models and exact replicas of existing machines. Menzel builds new motors with outputs up to and beyond 25 MW from scratch, stocks a large range of motor variants up to 15 MW and adapts them at short notice for various drive tasks.
The company also offers testing of motors, generators and rotary converter sets. Since the official factory commissioning on 2 January 2024, the quality management system has already been certified according to DIN EN ISO 9001:2015.
More information: www.menzel-motors.com/article/ moving-to-new-motor-plant/
Dates and figures on the construction of the new plant:
- Foundation stone laying: 11 June 2022 at > 30 °C
- Topping out ceremony: 16 December 2022 at -10 °C
- Construction period: 17 months, completion on schedule
- Official commissioning: 02 January 2024
- Hall floor space: 6416 m²
- Office floor space: 2096 m²
- Plot size: 22928 m²
- Earmarked expansion area: ~ 4000 m²
- Modules and material:
o 96 windows
o ~ 300 steel sandwich panels
o ~ 36 km low voltage cables
o ~ 24 km communication lines
o ~ 1,3 km building management system cables
o ~ 500 sockets
o ~ 600 data ports
o ~ 500 lighting, inside and outside
- Staff at headquarters:
o Currently almost 100 employees from over 20 nations with a combined 933 years of work experience at MENZEL
o Capacity for 150 employees
- Relocation cargo:
o ~ 300 truckloads
o ~ 2000 moving boxes
- Broken tethers: ~ 10000
- Satisfaction barometer from handover to today, 5 months after commissioning (mean value): 100 %
NEW ELECTRIC MOTOR PLANT FROM JANUARY 2024
24,000 m 2
SUPPLIER OF LARGE MOTORS FOR ALL UK APPLICATIONS
MORE THAN 20.000 MOTORS AVAILABLE FROM STOCK!
MORE THAN 20.000 MOTORS AVAILABLE FROM STOCK!
Motors up to 25 MW and 13.8 kV
Motors up to 25 MW and 13.8 kV
• Low voltage slip-ring and squirrel cage motors up to 3,000 kW
• Low voltage slip-ring and squirrel cage motors up to 3,000 kW
24,000 m 2
• Medium voltage slip-ring and squirrel cage motors up to 15,000 kW
• Medium voltage slip-ring and squirrel cage motors up to 15,000 kW
• Direct current motors up to 2,000 kW
• Direct current motors up to 2,000 kW
• Frequency converter-proof drives
• Frequency converter-proof drives
• In-house load test facility up to 13.800 V, 2.300 kVA, 120 Hz
• In-house load test facility up to 13.800 V, 2.300 kVA, 120 Hz
Customized special designs
Customized special designs
• Custom designs for special applications and operating conditions
• Custom designs for special applications and operating conditions
• Optimized motor design for higher efficiency
• Optimized motor design for higher efficiency
• Mechanically and electrically interchangeable motors
• Mechanically and electrically interchangeable motors
• Commissioning worldwide
• Commissioning worldwide
MENZEL Great Britain Ltd. | UK Branch Office
27 Hunt Drive | Melton Mowbray | Leicestershire LE13 1PB
Martin Rooney | Tel.: +44 1664 500 844 | Mobil: +44 7957 618046
martin.rooney@menzelgb.co.uk NEW ELECTRIC MOTOR PLANT FROM JANUARY 2024
MENZEL Great Britain Ltd. | UK Branch Office 27 Hunt Drive | Melton Mowbray | Leicestershire LE13 1PB Martin Rooney | Tel.: +44 1664 500 844 | Mobil: +44 7957 618046 martin.rooney@menzelgb.co.uk
MENZEL Elektromotoren GmbH
German Headquarters
MENZEL Elektromotoren GmbH German Headquarters
Am Alten Walzwerk 2 | 16761 Hennigsdorf | Germany
Am Alten Walzwerk 2 | 16761 Hennigsdorf | Germany
menzel-motors.com info@menzel-motors.com
menzel-motors.com info@menzel-motors.com
AROUND THE CLOCK, AGAINST THE CLOCK!
AROUND THE CLOCK, AGAINST THE CLOCK!
The global EMC solutions provider EMIS offer a range of three phase, dual stage EMC filters designed for motor and power drive systems. The TMF3221/TMF3222 family can provide superior attenuation performance and suppress conducted noise even when high interference levels are present.
The TMF3221/TMF3222 are housed in a convenient and space saving slim book-shelf enclosure which may be installed next to inverters, converters or motor drives. The devices are designed to meet the needs of power drive applications, including machinery and machine tools, worldwide.
Typical applications include variable speed drives (VSD), power drive systems (PDS), three-phase servo drives machine tool and machinery, IT power distribution networks, inverters and converters, wind turbines, process automation equipment, elevators, and three phase power supplies.
The TMF3221 provides standard attenuation performance and the TMF3222 offers high attenuation performance. The TMF3222HV are HV version filters particularly designed for high voltage applications.
Standard features include:
• Operating Voltage520VAC/760VAC
• Current Rating - 10A to 230A
• Operating Frequency - 50/60 Hz
• Operating temperature rangeC+100° to C-40°
The devices are designed to meet the needs of power drive applications, including machinery and machine tools, worldwide.
• Compliance with Class 1C or 2C limits
EMIS aims to offer an end-to-end solution to meet industry’s ongoing EMI Challenges. Customers are supported by a very experienced consulting team, a fully equipped Pre-Compliance Lab and a huge
safety certified standard product offering of over 2500 part-numbers produced in their own very efficient facility.
Designing and manufacturing EMI filters for more than 40 years EMIS is a global source for efficient EMI and EMC solutions across all industries, applications and the frequency spectrum. With a robust global supply footprint across eight industry segments, EMIS is continuously investing in technology and skills to deliver its promise of efficiency with seamless customer support.
Products available include EMI/ EMC Components, Feedthrough Components, Power Quality, Military Grade Filters and Surge Protection.
James Technical Services (JTS), one of the UK’s few remaining manufacturers of environmental test chambers, has transitioned into Employee Ownership (EO) via an employee ownership trust (EOT) nearly 30 years since it was founded.
Established in Talgarth near Brecon by Glen and Sue James in 1995, the business started with engineer and designer Glen refurbishing second hand chambers, and Sue looking after company finances and business development.
Three decades on, JTS employs 10 people from its purpose-built factory and makes test chambers that can re-produce the harshest of environmental conditions, temperatures, humidity and vibration serving industries including aerospace, automotive, pharma and many more.
Glen and Sue have been looking to retire, however, and thought they had explored all options before resigning themselves to closing down their successful business – until they came across the employee ownership model.
Now, twelve months on from starting the process of closing JTS, they have taken on a new Managing Director, David Hunter, and have ambitious growth plans to double their turnover in three years’ time, having fully transitioned into an employee-owned business instead.
Glen said: “JTS is a successful business providing much needed jobs and skills in Mid Wales, but Sue and I had
come to the point where we wanted to retire. We explored a trade sale, but we knew that we’d run the risk of the factory function being moved to another area.
“We thought our only other option was to close the business, which was a last resort as it is doing really well, but as we were winding down the business, we heard about the EOT model and realised it was perfect for us.
“So, we contacted Cwmpas who talked us through the process and set about making the arrangements for the EOT. We quickly realised that we’d need someone to drive the business forward under this model and so David Hunter joined the team as our new Managing Director.”
Glen added: “Sue and I will remain at the business on a part-time basis during the transition period, but we are so pleased that David has hit the ground running with some ambitious growth plans, and that the rest of the
team has welcomed the EOT. It is the perfect solution for us, and the future of the business.”
Managing Director, David Hunter, added: “The fact JTS was transitioning into an employee-owned business was a big attraction for me. Having worked a lot of my life as a small cog in major automotive companies, to know that as employees we all have a vested interest in the performance of the business was a real boon.”
“I’m also pleased to welcome Richard Lewis back into the JTS team as our Sales Director. Rich has a wealth of experience in this industry and is looking forward to working with old and new contacts to push JTS to be the biggest and best manufacturer of environmental test chambers in the UK.
For further information or to discuss a project please contact Rich on 07535 426129 or richard@jts-testchambers.co.uk
• Standard and bespoke specification chambers designed to meet any needs.
• Sizes ranging from containers, walk in rooms, floor standing & bench top.
• Temperature, humidity or combined solutions available.
• Service, Calibration and Installation.
Since 1977, Smiths Fire LLP has been providing essential fire safety solutions and maintenance services. Specialising in a comprehensive range of services, including tire extinguishers, safety signage, fire alarms, emergency lighting, fire safety training & fire risk assessments, we excel in safeguarding your premises against fire hazards.
What distinguishes us is our commitment to reliability, professionalism and quality service, all delivered at exceptional value. At Smiths Fire LLP, we combine professional expertise with a personalised touch, ensuring the highest standards of safety for our clients across various sectors.
We can offer tailored solutions to meet your specific needs, whether you require equipment installation, regular maintenance, or comprehensive training - trust Smiths Fire LLP to deliver excellence every step of the way.
Contact us today to elevate your fire safety standards and enjoy unparalleled peace of mind with our trusted solutions and expertise.
01536 484846 | sales@smithsfire.com
WISEMAN THREADING TOOLS LTD
We have been supplying threading tools and gauges since 1987.
We have been supplying threading tools and gauges since 1987.
Together with supplying plain plug and ring gauges this is all that we do, we therefore consider ourselves to be specialists in this field.
Together with supplying plain plug and ring gauges this is all that we do, we therefore consider ourselves to be specialists in this field.
We supply worldwide.
We supply worldwide.
We hold extensive ready stocks that include all of the standard stuff that others offer, but also includes taps, dies, die nuts, die head chasers, thread rolls and gauging for threads not normally available 'off the shelf '.
We hold extensive ready stocks that include all of the standard stuff that others offer, but also includes taps, dies, die nuts, die head chasers, thread rolls and gauging for threads not normally available 'off the shelf '.
Our real time stocks can be checked and purchased online at www. threadtools.com Just enter the thread details into the search box on the home page.
Our real time stocks can be checked and purchased online at www. threadtools.com Just enter the thread details into the search box on the home page.
You will be directed to the item, if stocked, or to our specials, (custom manufacture), sales team. who will quote to supply at competitive rates, in good time.
You will be directed to the item, if stocked, or to our specials, (custom manufacture), sales team. who will quote to supply at competitive rates, in good time.
As an account holder you can also order online from our listed in stock items, at your normal terms. We realise that you need the right item at the right price and quality, and in a reasonable time frame.
As an account holder you can also order online from our listed in stock items, at your normal terms. We realise that you need the right item at the right price and quality, and in a reasonable time frame.
We are geared to provide that.
We are geared to provide that.
We can ship stocked items same day.
We can ship stocked items same day.
Our experienced sales staff can assist and advise you on any technical issues.
Our experienced sales staff can assist and advise you on any technical issues.
We welcome enquiries from resellers and can offer terms to suit.
WISEMAN THREADING TOOLS LTD
11 Padgets Lane, South Moons Moat, Redditch B98 0RA UK
We welcome enquiries from resellers and can offer terms to suit. WISEMAN THREADING TOOLS LTD 11 Padgets Lane, South Moons Moat, Redditch B98 0RA UK +44(0)1527 520 580 sales@threadtools.com www.threadtools.com
+44(0)1527 520 580 sales@threadtools.com www.threadtools.com
HSS DIES & DIE NUTS
HSS DIES & DIE NUTS
THREAD ROLLS FOR ALCO & FETTE HEADS. READY STOCKS CUSTOM MANUFACTURURE
Large shelf stocks for all Standard and many Special Threads. Check our stocks online.
Large shelf stocks for all Standard and many Special Threads. Check our stocks online.
THREAD GAUGES all types. Large stocks for standard and SPECIAL threads. Any non stocked can be quoted for custom manufacture.
CUSTOM MADE
All
THREAD GAUGES all types. Large stocks for standard and SPECIAL threads. Any non stocked can be quoted for custom manufacture. CHASERS FOR COVENTRY &
Ready
Ready stocks for most size heads most standard and some special threads Geometry available for most materials.
Gas and liquid chromatography are indispensable techniques used in the pharmaceutical and clinical fields. They are essential for the separation, identification, and quantification of complex mixtures. These methods offer high sensitivity and precision, making them ideal for analysing a wide range of substances, from small organic compounds to large biomolecules. Creating new pieces of equipment to carry out these tasks requires numerous flow control components and it is important to focus on those that deliver the best results.
Troy Stehr, Industry Account Manager at Bürkert, looks at the challenges of creating chromatographs that deliver the accuracy and repeatability demanded by medical and pharmaceutical applications.
In the pharmaceutical industry, chromatography is crucial for drug development, quality control, and ensuring the purity of active pharmaceutical ingredients (APIs). Clinically, it aids in the diagnosis and monitoring of diseases through the analysis of biomarkers, therapeutic drugs, and metabolites.
The development of new chromatographic systems, however, presents several challenges. A primary obstacle is the precise control of gas and liquid flow, which is fundamental to achieving accurate and reproducible results. Inconsistent flow rates can lead to poor separation, compromised detection limits, and unreliable quantification, ultimately affecting the integrity of the analytical results.
Ensuring a stable and precise flow rate is essential to ensuring precision and repeatability.
Variations in flow can cause peak broadening or tailing, affecting resolution and sensitivity. Using advanced flow control technologies such as electronic pressure control (EPC) in gas chromatographs and precision dosing in liquid chromatographs can maintain consistent flow rates. In addition, real-time monitoring and feedback systems can adjust parameters dynamically to ensure flow stability.
Temperature stability is equally important; fluctuations can affect the viscosity of the mobile phase and the interaction between analytes and the stationary phase, leading to inconsistent retention times. By implementing precise temperature control systems, such as oven temperature programming or thermostat-controlled column compartments, these issues can be mitigated.
Durability and maintenance
Increasing demand for highthroughput analysis and point-ofcare testing is driving the need for compact, automated chromatographic systems. Microfluidic technology as well as automated sample preparation and injection systems can reduce sample and reagent consumption, improve throughput, and enable portable applications.
Clearly, for equipment that is used regularly, a robust build quality and simple maintenance procedures are important. Frequent interventions for maintenance caused by system wear and tear can lead to downtime and increased operational costs. Developing durable materials and components, along with automated maintenance protocols, can enhance system longevity and reduce downtime.
The choice of valve can also have a significant effect on maintenance costs and process availability. In a laboratory with an eight-hour working day, valves clocked at 1 Hz, operating for six hours will perform 21,600 switching operations per day.
Using a conventional solution, the valve reaches 10 million operations
and can be used for 463 days.
However, selecting a Bürkert solution that can achieve 100 million operations means the equipment can operate for 4,630 days. This equates to a potential saving of 90 million circuits, a service life of more than 4,100 days and seven hours less maintenance, resulting in a more productive solution.
There are also challenges within the individual fields of liquid chromatography. Analytical work can be affected by vague switching behaviour of the liquid control valves, which leads to imprecise mixing in the mobile phase, leading to an inaccurate gradient. The valves and their control blocks play a vital role in delivering accuracy and cleanliness to the process.
A similar situation exists for gas chromatography as well. Designing and building analysis equipment for laboratories is a complex task, needing to combine a
compact footprint with precision, speed of analysis and reliability. As a manufacturer, sourcing all the various components to create a gas control solution, as well as configuring and installing them can be a painstaking process.
This can be made much simpler by engaging with an expert in the field, such as Bürkert, that has the expertise to design, specify, source, assemble and test all the required components. The result is a task-specific device, optimised for performance and reliability, that delivers stable measurement results with excellent repeatability.
Increasing demand for high-throughput analysis and point-of-care testing is driving the need for compact, automated chromatographic systems.
The quality of valve blocks is determined by the design and manufacturing expertise that goes into the complex process of machining as well as the quality of the surface finish. Mass produced valve blocks may not have the optimum level of quality or the best design features for a particular application.
It is better to have a range of options for materials and valves to ensure the most effective design is achieved. For example, incorporating pulse valves enables solvent bottles to be changed during operation, saving time for operators. In the same design, cleaning processes can be automated and valve blocks designed to optimise this activity as well.
Furthermore, the gas control system can be designed with simple integration interfaces to match both the mechanical and electronic/ communication protocols. More complex systems can include multichannel mass flow controllers, bespoke manifolds and integrated control systems, all of which can be developed and supplied by specialists such as Bürkert.
Chromatographs offer clinical and pharmaceutical laboratories the means to conduct vital research and development work. The precise control of gas and liquid flow in chromatography is paramount to obtaining reliable analytical results. Overcoming the challenges in developing new chromatographs requires a multifaceted approach, incorporating advanced technologies and innovative solutions.
By addressing these topics with the support of experts such as Bürkert, the pharmaceutical and clinical sectors can continue to rely on chromatography for critical analyses, ensuring the safety and efficacy of drugs as well as the accuracy of clinical diagnostics.
Sulzer is meeting growing demand from critical energy markets in APAC by opening a new service center in Rayong, Thailand. The facility is strategically positioned to provide rapid, efficient maintenance and upgrade services to the region’s growing refining, petrochemical and power generation sectors.
The Rayong Service Center will increase Sulzer’s repair capacity in the area by 80%. It provides customers access to advanced engineering and maintenance capabilities, allowing it to deliver world leading retrofit, reverse engineering, and service projects for rotating equipment including industrial steam turbine units up to 10MW.
Li Jian, President, APAC at Sulzer, said: “Our new facility in Rayong is a direct response to the local market’s need for specialized, rapid support. By establishing operations close to our customers, we will ensure that we boost the speed of delivery for tailored solutions that address the unique needs and challenges of our local customers, enhancing the reliability and performance of their operations.”
Our new facility in Rayong is a direct response to the local market’s need for specialized, rapid support.
As part of Sulzer’s plan to meet the needs of local industry, the service center offers streamlined retrofitting capabilities. This allows it to cut typical lead times for critical pump models used in oil and gas production and power generation by 50%.
The Rayong facility will also act as a hub for technology and knowledge transfer from Sulzer’s premier turbomachinery service point in Indonesia. This initiative will elevate
the local capabilities in industrial steam turbine services, solidifying Sulzer’s commitment to building regional industrial resilience.
Sulzer’s investment in Rayong marks a strategic expansion in the APAC region, setting the stage for further growth across the area over the coming years.
Cross+Morse is a Birmingham based manufacturer of Mechanical Power Transmission products and solutions with over 100 years of history, right in the centre of the engineering hub in the West Midlands region in the United Kingdom. We operate in a 5000m2 fully integrated factory with a dedicated and loyal staff who have amassed a depth of technical expertise and engineering experience over their many years of continued service.
Cross & Morse are Mechanical Power
Transmission solution specialists and at this present time we have £1.5m worth of finished stock on our shelves such as Roller Chain and Sprockets in both stainless and carbon steel, Gears, Racks, Couplings, Torque Limiters, Sprag Clutches, Timing & V belt Pulleys, timing & V Belts, Inverted Tooth Chain, Silent Chain, Sealmaster Bearings, McGill Cam followers, Shaft Clamping Elements, Freewheel & Overload Clutches.
We value innovation highly at Cross+Morse, which is why we constantly invest in new machinery and technology as well as training programmes and apprenticeships to maintain the highest standards of quality and service we are well known for. With our
in-house team of application and design engineers at your disposal Cross+Morse are able to provide bespoke technical solutions to your power transmission problems in the most cost-effective way.
Have a specialised or ambitious requirement? Send us your drawings and
application details and we will do our utmost to find the best solution possible, we welcome a challenge! We have been providing solutions for the food and drink, oil & gas, agricultural, pharmaceutical, quarrying, energy and environmental industries, bottling and packaging plants and many more for over 100 years. Our customers come from the widest range of industries and include original equipment manufacturers for packaging, conveying systems and material handling applications. We also export our quality products all over the world, through our network of long standing distributors or directly to the manufacturers and end users of mechanical power transmissions on every continent.
At Cross+Morse we consider customer support along with in-house design and manufacture an essential element in our service to industry, please browse our website for details and more information on our manufacturing capabilities as well as our stringent quality control. We are certified to ISO 9001:2015 and have been for over 30 years.
Call or email us now to solve your mechanical power transmission problems.
Report reveals ‘True Impact’ of manufacturing is nearly a quarter of UK GDP MTA
Manufacturing is having a far greater impact on the UK economy than first thought according to a major new report released today.
‘The True Impact of UK Manufacturing’, was unveiled at MACH 2024 in Birmingham, shows industry is worth £518billion and supports 7.3million UK jobs directly and across the supply chains/ communities it operates in.
This represents nearly a quarter of total GDP (23%) and far bigger than the direct contribution of 8.2% that is usually quoted by economists.
Carried out by Oxford Economics and the Manufacturing Technologies Association (MTA), the in-depth report also shows that ‘making things’ accounts for 34.5% of all UK goods and services exports, whilst the median wage is £31,300 – 11% higher than the national median wage.
The findings are even more impressive when you consider the sector has had to navigate a myriad of challenges outside its control in recent years, including changing relations with the European Union, the Covid-19 pandemic, unprecedented increases in energy costs and global supply chain fragility and international conflicts.
MTA’s Chief Executive Officer, James Selka is now urging the sector to build on this report by exploring ways in which it can address the skills shortage and develop successful programmes, such as the High Value Manufacturing Catapult
The results illustrate that manufacturing accounts for £518bn of GDP and supports 7.3m jobs, most of which enjoy higher than average wages.
Centres, to increase wealth creation by commercialising more of the great ideas and innovations born in the UK.
“This is a fantastic insight into the true impact of manufacturing in the UK and reinforces what many of us already know – that industry is a far greater contributor to GDP and jobs than listed in national accounts,” commented James.
“Our report has been designed to take a ‘deeper dive’ and looks at the direct, indirect, and induced impacts of manufacturing, which is a far more comprehensive overview of what we make, the complex nature of our supply chains and the economic benefit gained from the spending of wages by those employed in our sector.”
He continued: “The results illustrate that manufacturing accounts for £518bn of GDP and supports 7.3m jobs, most of which enjoy higher than average wages.
“We are also a part of the economy that invests heavily in new technologies, with nearly half (47%) of total R&D investment made by manufacturers. You only have to visit MACH this week to see this firsthand, with more than 500 companies showcasing the latest in automation and robotics, additive manufacturing, latest software, advanced CNC machining and measurement and inspection solutions.”
The MTA is now calling on a wellintegrated commitment from the whole nation to help industry realise its potential, ranging from business leaders and academics to policymakers so crucial in developing a cross-party industrial strategy.
The recent Advanced Manufacturing Plan - accompanied by support worth £4.5bn - has been welcomed as a step in the right direction and an important vehicle in helping to cultivate the new technologies and industries being born, such as electrification, lightweighting, less carbon intensive materials and renewable energy.
Introducing new measures that increase exports should also be a priority and there is an unprecedented opportunity to deliver critical sovereign capabilities from public health to defending our realm.
For further information, please visit www.mta.org.uk
INDUS Engineering Services is proud to offer a wide range of custom control panels, automation systems and special purpose machinery. After working on major control and automation projects for several of the south’s leading brands, the company has recently acquired a new premises with the aim of increasing production capacity of bespoke and sub-contract, control panel manufacture. The new premises will also allow us to support the wider range of engineering
activities carried out by the company, such as the design, manufacture, and testing of special purpose machinery. Also, to further our goals to reduce our carbon foot print we will be installing a high efficiency solar PV array in the coming months. For more information on the services that are available please do not hesitate to contact and we will be happy to discuss your project needs and requirements.
www.indusengineering.co.uk
Totalkare’s ergonomic positioners are single or double column devices that enable the lifting and rotation of a product during welding and assembly operations.
With overall capacity from 2,000 - 90,000kg to suit, they are both compact and flexible.
Faller Packaging produces folding boxes in record time for pharmaceutical manufacturer Pohl-Boskamp
Pharmaceutical manufacturer G. Pohl-Boskamp urgently needed packaging materials for its main product Gelomyrtol. Faller Packaging helped the company to keep its remedy for colds available – in the shortest possible time and using all available resources.
Sometimes things need to move really quickly. Last autumn, the pharmaceutical manufacturer G. Pohl-Boskamp faced a major challenge: Based in Hohenlockstedt, SchleswigHolstein, the medium-sized company produces medicines and medical products for the treatment of acute and chronic illnesses – and it found itself suddenly confronted by a huge demand for folding cartons for its main product Gelomyrtol. The packaging design also had to be adapted at the same time. The situation was unexpected and a fast and effective solution was urgently needed – so G. PohlBoskamp turned to its partner Faller Packaging in Waldkirch.
Swiftly mobilising all its resources
Faller Packaging, the specialist company for folding cartons, package leaflets, labels, and combination products from a single source, responded promptly to support its long-standing customer. The remedy had to remain available on the market during the cold season, so speed was crucial. Working closely and diligently together, the Faller sales, order service, pre-printing, planning, material planning and production teams got the job
The remedy had to remain available on the market during the cold season, so speed was crucial.
done. Within just a few days, three million folding cartons were dispatched to northern Germany. “Faller’s assistance was truly vital. Without their fast response, we’d certainly have faced delivery bottlenecks. We’re fully convinced
that Faller will also be the right partner for Pohl-Boskamp in the future,” says Sandra Matthießen of Purchasing at G. Pohl-Boskamp GmbH & Co. KG.
Most customers will tell you just how efficient Sepura oil-water condensate units are. But did you know that our patented filtration media found inside every genuine Sepura unit is made from recycled glass bottles?
This not only makes the outputs from our units environmentally friendly but also our manufacturing process too.
Going green and achieving your targets doesn’t have to be a compromise.
Industrial Processing includes a vast range of potential applications for perforated products. RMIG Solutions has extensive experience in the chemical, pharmaceutical, paper, and offshore industries, to name a few. From small, high precision perforation in thin materials to large holes in thick sheets used in the mining industry, RMIG Solutions has the knowledge, versatility, and tooling to deliver products according to customers’ requirements.
One particular area of Industrial Processing is dealing with waste water. The water industry presents a number of unique challenges in the use of perforated products.
A key consideration here is the aggressive nature of the water towards the materials being used. RMIG Solutions has vast experience in servicing the waste water industry, and produces high flow, burr-free perforated waste water screens, offering accurate screen tolerances and effective separation.
Another area of Industrial Processing Metal Products
is medical and pharmaceutical, where RMIG Solutions’ perforated materials are able to give firm tolerances during their manufacture, and are well suited for use in sterile environments.
RMIG Solutions’ perforated products also have numerous uses in the petrochemical sector, from industry specific applications such as filtration, to oil and gas exploration, as well as more general applications such as walkways in processing plants.
Additionally, RMIG Solutions works with biomass drying applications. The demand for alternative sources of sustainable and renewable energy is always growing.
Bridge Slot sheets from RMIG Solutions are the most effective way of drying woodchip to an optimum moisture content, ensuring boilers operate efficiently to benefit farming and agriculture.
The Bridge Slot sheet from RMIG Solutions play an essential role when it comes to the design and manufacture of biomass drying floors.
Industrial Processing
The combination of sheet thickness and opening size allows RMIG Solutions’ sheets to be used either as a suspended floor in wood chip drying containers and trailers, or as drive-on drying floors in outdoor buildings.
The bridge slot opening size determines the products that can be dried, which range from fine oilseed rape through to larger grains and cereals, as well as logs and wood chip drying.
we make ideas come to life
RMIG Solutions’ Food Processing market sector meets the high levels of hygiene demanded by the food processing industry. Perforated screens are also strong with important thermal capabilities, making them useful for a wide range of food processing applications. RMIG Solutions’ tailor made perforated solutions are ideal for cleaning, heating and steaming in food production environments. Whether it’s baking trays, cereal cleaning or ingredient conveyors, all of RMIG Solutions’ perforated materials can be customised for each application.
As consumer demand increases for plantbased products and proteins, manufacturers are turning their attention to tried-andtrue technology in hope of unearthing new discoveries for financial growth and company expansion. Many manufacturers are turning to crossflow membrane filtration in search of answers.
Able to provide high-quality protein yields without the risk of altering the macromolecules’ structure, crossflow membrane filtration provides a way to separate desired molecules, like protein, from the undesired molecules. Using membrane filtration avoids the loss of functional and nutritional properties, as opposed to other processes such as acidleaching or thermal treatments. Research indicates membrane filtration can achieve a protein retention rate of up to 97%.
Axium Process has been helping such companies on the road to success.
“This is not new technology,” said Jamie George, Projects & Business Development Director at Axium Process, “this is a trusted
technology applied in new ways. For over 20 years we’ve helped market-leading manufacturers achieve results. The premise is the same, but the execution is a different matter entirely; we have the knowledge and experience to know where things diverge, and what to do when that happens.”
“At Axium, we tailor our solutions to customers’ specific needs, whether it’s maximising pea protein isolate for plantbased burgers or extracting soy protein for shakes.”
Research indicates membrane filtration can achieve a protein retention rate of up to 97%.
For companies looking to create plantbased products, membrane filtration can provide a cost-effective solution within a small footprint, helping maximise production output and efficiency. By embracing the automation of membrane filtration, companies can focus on product development and market demands, confident that their production line is up to the task.
For further information please contact: Jamie George, Axium Process Ltd, Hendy Industrial Estate, Hendy, Swansea SA4 0XP Tel 01792 883882
Email: jamie.george@axiumprocess.com
Smart Air Injection (SAI), SEEPEX’s patented sludge pumping system, is delivering cost savings to wastewater treatment plants (WWTP) around the world. One of the many satisfied customers of the energy-efficient technology is the WWTP Hetlingen, near Hamburg, Germany, which will now save around 20-25% of energy in thick sludge pumping alone.
Environmental and economic considerations play a decisive role when municipal water utilities are considering the purchase of new pumping technology. Worldwide, SEEPEX’s energy-efficient and low-maintenance SAI-system
ensures that thick sludge reaches its destination at low pressure, even over distances of one kilometre.
Two conveying technologies for a
With SAI, SEEPEX, the world’s leading specialist in progressive cavity pumps, pump systems and digital solutions, has launched a customised system solution. It uses a combination of progressive cavity pumping and dense phase pneumatic conveying to transport highly dewatered sludge discontinuously in short plugs in a particularly energyefficient manner, unlike any other conventional conveying technology.
In principle, it’s just like the good old pneumatic mail. As a result, friction losses only occur along these plugs and not in the entire pipe, resulting in numerous unique advantages, such as the ability to transport up to 1 kilometre with a low-pressure pump and PN10 piping.
For municipal water utilities in the UK, the alternative to conventional processes, which has been tried and tested worldwide for years, can quickly pay for itself. More than 80 customers already benefit from this innovation, which is patented in Europe, the USA and China.
The wastewater board operates the Hetlingen WWTP northwest of Hamburg, Germany. Serving more than 40 towns and communities, the Hetlingen plant treats more than 31 million cubic metres of wastewater per year and processes about 46,000 Mg of sludge per year, which is anaerobically stabilised, dewatered in centrifuges and pumped into silos. After anaerobic stabilisation, the digested sludge is dewatered in centrifuges in a separate building and then falls through a hopper into the pump cellar. From there, it was previously pumped by two piston pumps to two silos located 60 metres away and 30 metres higher. The dewatered sludge is then trucked to an off-site incinerator for thermal recovery. When the centrifuges were replaced in a planned rebuild, the piston pumps were found to be undersized. In addition, maintenance requirements and energy costs were very high.
Hetlingen WWTP turned to SEEPEX when it needed to improve its solids handling technology following the replacement of centrifuges and feed pumps. The main challenge was to find a new thick sludge conveying system that would fit into the existing infrastructure along with the replanning of the thickening sludge
silos. The result, as envisioned by the plant operators, was a system that would minimise maintenance and energy costs, as well as downtime for servicing. The goal was to significantly reduce the total cost of ownership (TCO) in direct comparison to installed piston pumps. In addition, the wastewater authority wanted a much more flexible system that would be suitable for future upgrades. As the centrifuges for dewatering had already been ordered, a quick solution had to be found to transport the 5 - 15 m³/h
With SAI, SEEPEX, the world’s leading specialist in progressive cavity pumps, pump systems and digital solutions, has launched a customised system solution.
After extensive consultation and a comprehensive review of the plant’s specific conditions, SEEPEX experts set about developing a solution that was perfectly tailored to the plant. In the end, SEEPEX was chosen as the general contractor to supply and install two redundant systems. The scope of supply included installation, piping and cabling. Delivery was completed within 6 months. The bespoke SAI system was supplied with a hopper pump (BTHE 13012) with a moveable stuffing part for easy removal and access to the rotor side joint and screw conveyor (Rotor Joint Access), a dosing pump for lubricant supply, a compressed air system consisting of a compressor and air receiver, and a control cabinet with integrated control. In addition, SEEPEX installed two separate pipelines (PN16, DN250 in stainless steel) over a length of 90 metres (60 metres horizontal, 30 metres vertical), including the necessary sensors and isolation valves. The integrated automation technology - the SAI controller - allows the two outdoor silos to be fed as required.
Pneumatic dense phase conveying with supporting lubricant minimised friction losses in the pipeline. The characteristic pressure behaviour of SAI is also evident in Hetlingen, where the pipeline pressure in operation is only 2-3 bar. In contrast, hydraulic operation using a piston pump was achieved at up to 70 bar.
By reducing the operating pressure, it was possible to use a PN16 stainless steel pipeline. Due to the low pressure level compared to conventional solutions with much higher operating pressures, it was possible to save costs in the purchase of piping.
In addition, the low operating pressure significantly increases the service life of all pump and pipework components. Overall, SAI saves around 20-25% of energy per year compared to a piston pump. The Rotor Joint Access maintenance concept, with its moveable stuffing part, simplifies pump maintenance and saves costs. It allows quick and easy access to the rotor-side joint for easy maintenance without dismantling the pressure branch or stator. In this way, the innovative SAI system solution greatly simplifies maintenance.
Application
• Sewage sludge up to 25% dry matter content
• 90 metre conveying distance (30m vertical, 60m horizontal)
• Flow rate up to 15 m³/h
Benefits
• Efficient transport of dewatered sludge with energy savings of 20-25%
• Low operating pressure
• Minimal maintenance costs (Maintain in place)
• Overcomes height differences and changes of direction with ease
• Smart Air Injection system incl. software (SAI-controller)
• Open hopper pump BTHE 130-12
• PC pump for dosage of lubricants BN 05-12
With these new pumps up and running, the WWTP Hetlingen will have to intervene less frequently during operation and the entire operational side runs more smoothly. Significant energy savings during pump operation will reduce the plant’s carbon footprint, boosting their climate protection measures.
A new jet-mixing pump system has significantly reduced capital, installation, maintenance and energy costs at Moove, the leading global lubricants manufacturer and distributor, in the UK.
For a closed-top 50m3 tank used in the manufacturing process of quality lubricating, engine, hydraulic and gear oils, Moove wanted to trial a set-up that would not only be better economically, but also provide more redundancy.
Ian Lowe, Moove’s Manufacturing General Manager, explained; “A motor failure on a blender could mean as much as four days impact on production, so it was important for us to take the opportunity to prove a different technology.”
‘A better option’
He added: “The performance of our existing paddle mixers has been good, but Borger were recommended as a company that would work with us to provide a better option; one that could be easily replicated.”
The team at Moove drew up a logic for Borger to examine, outlining their objectives, which ultimately resulted in
a pump (plus two nozzles), for a 3-bar application with a flow-rate of up to 60m3/ hr. To meet the space requirement at the Gravesend site in Kent, Borger also provided the system as a skid-mounted unit, working closely with Moove to supply a customised control panel with a specially written program.
“The fact that Borger were able to deliver a complete, all-in-one package was a real bonus,” continued Ian.
‘So simple to look after’
“With a 9kW motor (compared to 12kW for the paddle mixers), we are automatically saving on energy, but one of the other main benefits is that the Borger equipment is so simple to look after. There’s easy access to the pump-head, and no special tools required. Retrofit to an existing tank is also very straightforward.
“We’re very pleased with solutions provided by Borger that allowed us to achieve the goals of our project.”
CloudNC, the manufacturing technology company, has announced the release of Cutting Parameters AI, a new solution that automatically generates appropriate physics-based feeds and speeds for virtually any CNC machining scenario, in moments.
Defining new feeds and speeds for CNC machining operations is an arduous and time consuming task, involving considerable manual experimentation. As a result, many CAM programmers are forced to rely on a ‘one-size fits all’ approach towards machining components, instead of tailoring specific settings
for every toolpath - resulting in lower productivity, inefficient cycle times, and sub-optimal surface finishes.
Cutting Parameters AI resolves that problem by employing models that allow users to easily set physicsbased feeds and speeds for every unique toolpath in moments, within their existing CAM software packages and workflows. With Cutting Parameters AI, the largest constraints to removing material faster in any unique cut are always visible to the machinist, enabling them to take immediate action to increase productivity.
In addition, Cutting Parameters AI can provide safe starting feeds and speeds for materials and with tools that the user has never worked with, dramatically increasing right-firsttime operations.
As a result, CloudNC expects users of Cutting Parameters AI - provided as a new module of its existing CAM Assist solution, which generates machining strategies for 3-axis and 3+2 axis components - to immediately benefit from instant cutting parameters tailored to any scenario, resulting in productivity optimisations of at least 20% in their machining operations.
Theo Saville, co-founder and CEO of CloudNC, said: “Cutting Parameters AI is the first solution to automatically provide sensible feeds and speeds that can be applied in virtually any machining scenario, by a user of any ability level. It’s a step change in accelerating one of the most time consuming, tricky aspects of machining and will substantially reduce the time that CAM users spend setting up, while also substantially increasing what it’s possible for them to achieve with a CNC machine.”
When making new components with a CNC machine, there are so many factors to consider when selecting feeds and speeds that determining the best option is very time consuming for an experienced CAM engineer, and bewildering for someone new to the industry. Cutting parameters that are too aggressive cost money through broken or worn out tools and scrapped parts. Equally, sticking to a conservative, safe range of cutting speeds leaves time and money on the table with slow toolpaths.
Defining new feeds and speeds for CNC machining operations is an arduous and time consuming task, involving considerable manual experimentation.
Furthermore, what are good cutting parameters for one toolpath may be less suitable for other toolpaths - but programming different parameters for every operation is too intricate and difficult for all but the largest batch sizes. Additionally, introducing new types of tooling (or materials) comes with the overhead of creating presets and populating the data into CAM software.
Cutting Parameters AI resolves those problems by applying AI. When using the software, the physics model immediately
recommends appropriate feeds and speeds by combining both its embedded domain knowledge and an understanding of the cutting context.
It identifies and models factors that ultimately limit the machining process, including cutting dynamics, workpiece and tool material, tool holder geometry, and surface finish models. It then combines machine learning models and a detailed three-dimensional model of the physics of the cutting process to provide a recommendation to the user.
The user interface also allows the applicable constraints to be configured in a flexible and intuitive way, allowing the user to rapidly reach a recommendation tailored to their specific usage and specifications.
Cutting Parameters AI is available now as a module for CloudNC’s CAM Assist solution, which is available today via www.cloudnc.com, and the Autodesk App Store.
Storage and order picking equipment are essential for maintaining efficient material flow. Creating the ideal system will give manufacturers a massive increase in storage capacity and pick rates within the space they have available, says Edward Hutchison, Managing Director of BITO Storage Systems.
Without effective and reliable storage and order picking systems, production and assembly lines will grind to a halt. The Just In Time (JIT) supply of parts, semi-finished products and raw materials to production machines requires flexible and scalable warehouse storage and retrieval systems. Systems can be manual or automated, working in combination with continuous units, such as overhead conveyors and conveyor belts, or discontinuous systems, such as Autonomous Mobile Robot (AMRs), Automated Guided Vehicles (AGVs) or forklift trucks.
Such systems must not only provide a smooth flow of parts through the plant, from storage to feed the line, but also accommodate future growth. And with assembly areas claiming priority over space in most factories, storage and order picking will often need to fit into a constrained footprint. Fortunately, there are many ways that these objectives can be achieved successfully.
A good example of a lower cost and space saving method to achieve ‘right first time’ part delivery to the line comes in the form of carton or
pallet live systems, comprising flow shelves created from racking. With clear labelling, flow shelves help create effective pick zones because the design provides a density of storage that results in a greater number of pick face locations than would be possible with tradition shelving and racking. Because cartons or pallets are loaded into the flow lane on a first in, first out (FIFO) basis, when an empty unit is removed another full carton or a pallet full of parts flows into place on rollers in the inclined lane, ready to pick from.
Compared to a traditional wide aisle configuration, Very Narrow Aisle (VNA) racking provides a more space efficient solution for holding general parts, usually on pallets and is served by VNA lift trucks. This is a pretty standard solution these days, though a narrow aisle can be designed to feed a carton live structure, integrated into the rack, running alongside the aisle and providing a dense pick face for parts.
Picking small parts is a vital element in most factory warehouses, and where the goal is to keep things
simple, this can be easily integrated within pallet racks. One option is to create small parts pick locations on the reachable ground level, with upper storage levels serving as a buffer store for replenishment. Plastic small parts storage containers will help to store and organise small items and C-parts – making them available for quick and easy picking. This will result in a reasonably efficient picking process but ground floor locations within a pallet rack will, of course, be limited. Flow shelves, however, can be easily installed into pallet racking to increase the number of pick locations and volume of SKUs located on the ground level pick face. Adding standard shelving within pallet racking is another option to create flexible small item pick faces. Using mobile shelving will maximise the available space, though moving the shelves increases pick times. Inclined shelving within a pallet racking bay will make items clearly visible for picking.
Plastic bins and containers will keep parts protected throughout the intralogistics process and during transport to ensure they are delivered to the line in prime condition. It is worth seeking out storage system supplier such as BITO, which in addition to offering racking, shelving and flow lanes, also provides a plastic container range comprising a variety of sizes and a broad choice of accessories. This will ensure the optimum system is designed to fit a given space, maximising the potential for small parts picking and, ultimately, improve manufacturing efficiency.
Hart Doors has completed two more contracts featuring its Speedor high-speed doors on one contract and a large double reduction chain operated shutter on the other contract.
John Loftus, a senior manager at Hart Doors, says the recent contracts show the flexibility the company offers. “Hart’s durable rolling shutter doors have been installed for a leading supplier of construction and building materials in the UK and Hart’s high speed door, Speedor, has been installed for the UK arm of a global company in the specialised eatery sector.”
“Our product choice is an immensely attractive option for a very wide range of business categories which inevitably are faced with many different requirements. Hart’s roller shutters are available in a wide range of sizes, specifications and colours to suit virtually any application. Further they are designed and manufactured in the UK to the highest quality and safety standards in solid steel or aluminium, with optional insulation.
“As a result we supply a huge range of industrial and commercial premises, in fact anywhere that requires protection from physical attack or fire. Our shutters are available in sizes up to 10m. Hart’s roller shutters can be manufactured with light or heavy-duty wind resistance, for low or high use or standard opening/closing or high speed.
“The shutters can be manufactured in a choice of plastisol or powder coat finishes, in a variety of colours. Automatic or manual electric operation is available, as are a range of safety devices for pedestrian use, all complying with the Machinery Directive 2008.”
The Speedor has been installed at a UK facility for an international specialist retailer within the eatery sector. “The company is viewed as one of the most innovative and scientific in the World,” says Mr Loftus. “Our Speedor has been installed for the UK & Ireland arm of the business.”
www.hartdoors.com
e-t-a.co.uk
Deltec is the leading Impact Socket and Bespoke tool manufacturer in the UK and specialises in Impact Sockets, Specialised Sockets, accessories and related tools for various applications in different industries, such as Automotive, Construction, Bridge, Marine building and maintenance, Wind, Oil & Gas, Mining etc.
With 45 years of experience, Deltec aims for the goal of zero defects. Deltec has gained confidence and long-term support from many global clients due to its excellent quality, service, competitive price, reliability and on-time delivery. Deltec is well reputed with its excellent products all over the world.
All our products are manufactured to International DIN standards. Deltec’s Technical & Design Department designs and develops custom sockets and prototypes. Deltec is also a pioneer in product research and development, engineering and manufacturing – Fast track service also available.
Factory Tours available Please enquire – See British Manufacturing at its Best. www.deltecindustries.co.uk
Save energy Save money Integrate the LHS 210/410 series air heaters with Leister’s new CHINOOK blower.
get in touch Tel: +44 (0)1707 331111 info@welwyntoolgroup.co.uk www.welwyntoolgroup.com
Specifically designed to feed process air at inlet temperatures of up to 350°C
Quiet operating sound level of 58dB(A)
Capable of delivering air flow of 1,640 l/min at 50Hz with a static pressure of 14.6kPa
With business booming at Wetherbybased fabrication specialist Kellys Welding, the company wanted to replace its pre-owned CO2 laser cutter with a new fibre laser. With a shortlist of ‘wants’ that included quality, speed, energy efficiency and a very competitive price, Kellys Welding spent nearly 12 months assessing the UK market. The company discovered that only an ACCURL fibre laser cutter from Axe & Status could meet its requirements and provide the impetus for further growth. Such has been the impact of the ACCURL Masterline 3105 that the monthly savings on electricity consumption alone pay for the finance on the machine. According to Kellys Welding, “it’s like having a laser cutter for free”.
Kellys Welding is a family-run business launched by Owner Joe Kelly in 2017. In just seven years the company has grown from a one-man start-up to a 10-employee enterprise that is on track for a turnover of £1.3 million in 2024.
The reasons behind this impressive growth are many, but ironically the company gained its first real break during the pandemic. Although welding jobs came to a halt, Kellys Welding was also selling raw material online, an activity that boomed.
“After the pandemic we had enough money to buy our first laser cutter, a pre-owned CO2 model,” says Joe Kelly. “It was perfect at the time but we soon ran out of capacity due to our growing workload and the machine’s lack of speed. It also consumed a lot of electricity, so we started thinking about a replacement.”
By then, Kellys Welding had built up a robust customer base; sufficient to afford a brand new laser cutter. Around the same time, the company relocated to the unit next door, which at double the footprint would provide the perfect home for its new laser cutter. The question now, was which one to buy?
“We looked at lots of machines over a 12-month period,” states Joe. “At first we only considered brands that were familiar to us, but soon realised they were way out of our price range. We started looking at other brands, including from Asia, but
they were poor. We even went to see one in action. Although it was cheap and did the job, it seemed unsafe. It had a CE mark, but it only stood for ‘Chinese Export’.”
He continues: “Then we came across the ACCURL Masterline and knew it was the one for us. It’s had all of the right parts. A lot of machines from Asia come with parts we’ve never heard of. The ACCURL is different with its PRECITEC cutting head, for example. The machine also carries an official CE mark and features integrated Class IV safety systems. Axe & Status did some test cuts for us and we were very happy to proceed.”
Kellys Welding estimates that the ACCURL Masterline 3015 6kW fibre laser cutter from Axe Status is about eight times faster than the company’s previous CO2 laser cutter. Moreover, the ACCURL offers far more economic running costs.
“The ACCURL Masterline uses around five times less electricity than our CO2 machine, which equates to a saving of around £4000 a month,” reveals Joe. “These savings pay for the finance on the machine, so it’s like having a laser cutter for free!”
The company also reports that the ACCURL fibre laser uses far less gas and requires a lot less clean-up: parts come off the machine ready to weld. The CADCAM nesting software for the ACCURL brings further savings.
“We nested a job the other day for 5mm thick stainless steel. Whereas previously we would need three sheets, now it’s just two because the software can place parts closer together. At £500 a sheet, it’s a big saving.”
Kellys Welding laser cuts mild steel from 1 to 20mm thick, stainless steel from 1-12mm and aluminium up to 6mm. The company processes everything from 1-offs and small batches up to thousands. Investing in the ACCURL fibre laser is not only good news for Kellys Welding, but also for its customers.
“Keeping our CO2 laser would have created such a backlog with
ACCURL Masterline fibre laser cutters offer high dynamics, achieving a positioning speed of up to 180m/min and acceleration of 3G.
our workload today,” explains Joe Kelly. “Our customers need a quick response and if we weren’t in position to meet their requirements they would quickly go elsewhere.”
Kellys Welding has a strong and growing pool of local customers in sectors that span construction, automotive and retail, with many now trusting the company as its main supplier. The business has seen its turnover double every year for the past five, based on an ethos of short lead times, competitive prices and top-quality products.
“As a small company we usually have the flexibility to price match and win orders. In contrast, many of our competitors have expensive monthly machine payments to meet. We looked at a European machine with the same specification as the ACCURL and it was over £500,000. The ACCURL was less than a third of that, with a three-year warranty for parts and labour.”
ACCURL Masterline fibre laser cutters offer high dynamics, achieving a positioning speed of up to 180m/min and acceleration of 3G. Thanks to high-quality components, such as an IPG laser fibre source, PRECITEC ProCutter laser head and Rexroth servo drive, ACCURL laser cutters can operate continuously seven days a week, 365 days a year supported by automatic nozzle cleaning and graphite anti-burn technology. The machine is Industry 4.0 ready.
Kellys Welding is pleased to report that the ACCURL Masterline has proved totally reliable since its arrival, with the company enjoying high-level support from both Axe & Status and ACCURL.
“During commissioning we had the engineer from ACCURL optimise the parameters for every single material we cut here,” says Joe Kelly. “Since then, Axe & Status set up a What’s App group. If we ever had a query we simply post a message and get a reply around two minutes later. The group is even linked with the ACCURL factory, which will be useful if we ever need their input in the future.”
Innovative design, rigorous testing and high precision engineering are why Oliver Hydcovalves are the most trusted valves for Hydrogen and Carbon Capture applications.
The range has grown rapidly to include instrumentation, Double Block and Bleed, Pipeline, and Subsea Gate Valves. Shown here is the 1” Hydraulic Gate Valve with manual override, DBB with 20mm bore, 3” Flange, and the 1/2” Hydraulic Gate Valve equipped with Remote Operated Vehicle bucket capability.
These valves, showcased for their diverse features, are en route for deployment in Carbon Capture (CC) injection applications.
For information on how Oliver Hydcovalves can provide Hydrogen and Carbon Capture valve solutions for your green renewable energy project, telephone +44(0)1565 632 636 or visit our website.
The range has grown rapidly to include instrumentation, Double Block and Bleed, Pipeline, and Subsea Gate Valves.
your
Designed to provide hot water instantaneously whatever the load conditions, up to 2100kW without the need for water storage.
Designed to provide hot water instantaneously whatever the load conditions, up to 2100kW without the need for water storage.
Reliable, Efficient and Cost Effective
■ Reduced Heat Loss
Efficient and Cost Effective
■ Improved Temperature Control
■ Thermal Efficiency
■ Operational Savings
• Reduced Heat Loss
ARI-Armaturen UK Ltd
steam systems, thermal oil and hot water and is a subsidiary of a large German engineering company, reputed to have the largest valve stock in Europe.
• Improved Temperature Control
• Thermal Efficiency
• Operational Savings
Deltec is the leading Impact Socket and Bespoke tool manufacturer in the UK and specialises in Impact Sockets, Specialised Sockets, accessories and related tools for various applications in different industries, such as Automotive, Construction, Bridge, Marine building and maintenance, Wind, Oil & Gas, Mining etc.
With 45 years of experience, Deltec aims for the goal of zero defects. Deltec has gained confidence and long-term support from many global clients due to its excellent quality, service, competitive price, reliability and on-time delivery. Deltec is well reputed with its excellent products all over the world.
All our products are manufactured to International DIN standards. Deltec’s Technical & Design Department designs and develops custom sockets and prototypes. Deltec is also a pioneer in product research and development, engineering and manufacturing – Fast track service also available.
Factory Tours available Please enquire – See British Manufacturing at its Best. www.deltecindustries.co.uk
Reliably tight, durable and versatile triple offset valve with zero leakage, even in harsh industrial environments.
Changing from single to double isolation made easy with the small face-to-face dimensions of the ZETRIX®
ZETRIX® Double block and bleed arrangement
www.ari-armaturen.com
Founded in 1981 in West Sussex, Flotronic Pumps is a worldleading manufacturer of air operated double diaphragm pumps (AODP). With the invention of our ground-breaking ‘One Nut’ pump design, Flotronic have revolutionised the application of diaphragm pumps throughout the industry.
Over the last 30 years our ‘One Nut’ double diaphragm pump has proven its success in an incredibly diverse range of international industries including but not limited to pharmaceuticals, food & beverage, cosmetics, personal and household care and chemical manufacturing.
Our global customer base can rely on our expertise in delivering the highest quality products as well as our abilities to provide engineering excellence, thus enabling them to achieve their competitive edge.
For more information please contact: +44 (0)1444 881871 or email salesteam@flotronicpumps.com
After years of intensive research and development, GEMÜ are expanding their product range considerably with a platform-based design that will ensure a faster and more tailored service for customers. The new products share a common feature – their modularity. Synchronized interfaces allow flexible combination of the new modules. This means that the modularly configured products can be ideally customized for a wide range of operating and system conditions.
GEMÜ 12A0 INTELLIGENT POSITION INDICATOR
As an automation module, the GEMÜ 12A0 electrical position indicator is compatible with all pneumatically operated process valves with linear actuator of the new platform generation. Regardless of actuator size and control function, the GEMÜ 12A0 can be retrofitted to either device.
GEMÜ D40 | D41 HIGH-PERFORMANCE
DIAPHRAGM VALVES
The pneumatically actuated GEMÜ D40 and D41 diaphragm valves are designed for use in aseptic manufacturing processes. GEMÜ D40 is mounted using four collar nuts, while the GEMÜ D41 valve type equipped with EasyLock technology and is mounted completely without loose components using a central screw connection.
GEMÜ S40 MODULAR GLOBE VALVE
Pneumatically operated GEMÜ S40 2/2-way globe valve with proven GEMÜ globe valve sealing principle and innovative modular linear actuator. The GEMÜ S40 globe valve is available in both angle seat and straight seat versions.
GEMÜ P40 EFFICIENT TANK BOTTOM VALVE
The pneumatically actuated GEMÜ P40 PD tank bottom valve is designed for use in sterile applications. The sealing principle of the valve is based on the GEMÜ PD sealing technology, which hermetically separates the actuator from the medium. All actuator parts (except the sealing and design elements) are made from stainless steel.
Process valves, including diaphragm valves, used in the pharmaceutical industry are subjected to some of the toughest conditions in manufacturing. Reliability and consistency of every component is crucial for pharmaceutical companies because it directly influences the overall product quality and process reliability. What factors, then, should be considered to ensure the correct selection of manual valves every time?
Avoiding contamination and dosage errors
From standard two-port valve setups to configurations that incorporate multiple valves into a single solution, choosing the right design can affect product quality, the overall process footprint, pipework complexity, as well as minimizing dead space. Optimising valves for their application ensures the best performance, precision dosing and repeatability, all of which deliver process reliability and uniformity. Similarly, valves need to be able to handle the process fluids as well as the sterilisation processes used between production runs.
Valves that include visual position indicators enable precise control and repeatability, which are important as each adjustment can impact the final product. The ability to set limits on the valve’s stroke length enables extreme settings to be avoided, ensuring minimum and maximum flows are maintained.
To ensure that maintenance and safety procedures are also adhered to, Bürkert valves include locking features such as lock out, tag out (LOTO) to protect against accidental and unauthorized adjustments during operation and maintenance.
When a diaphragm valve is required, the choice of materials impacts the reliability of the component and the mean time between failures (MTBF). Designers of pharmaceutical processes should ensure that the diaphragms used in valves are capable of offering the longest possible service life, can withstand the ingredients used in production, and can be easily replaced when necessary.
However, when the time does come to replace a diaphragm, it’s vital that the correct procedure is carried out as quickly as possible and only by trained personnel. Bürkert offers a diaphragm replacement service or can provide training for a customer’s existing team. You
To ensure that diaphragm valves are constructed with the most appropriate materials for a long, reliable service life, Bürkert provides access to its multi-medium testing facility. Here, valves with orifice sizes up to DN100 are tested under realistic conditions to optimise the service life and reliability of all components in direct contact with the media.
With a deep understanding of the challenges affecting its customers’ operations, particularly in specialised sectors like pharmaceuticals, Bürkert offers a diverse range of products available in a variety of materials to suit any application. Each component is crafted with precise, repeatable machining accuracy and undergoes rigorous testing procedures, such as delta ferrite testing.
Bürkert also ensures full traceability of all materials and compounds used in its production process. This meticulous attention to detail allows Bürkert valves to be seamlessly integrated into a customer’s existing setup.
Process Engineering Control & Manufacturing is a lively, engaging, insightful independent publication & directory which offers practical advice & solutions on the technical and management challenges faced by engineers and managers in the process & manufacturing industries.
Subscription enquiries: Call 01304 806039
Email: editor@mhmagazine.co.uk
Advertising enquiries: Jake Page – 0203 907 9166
Email: jake@pecm.co.uk
Editorial submissions or enquiries: Antony Holter – 01304 806039
Email: editor@mhmagazine.co.uk