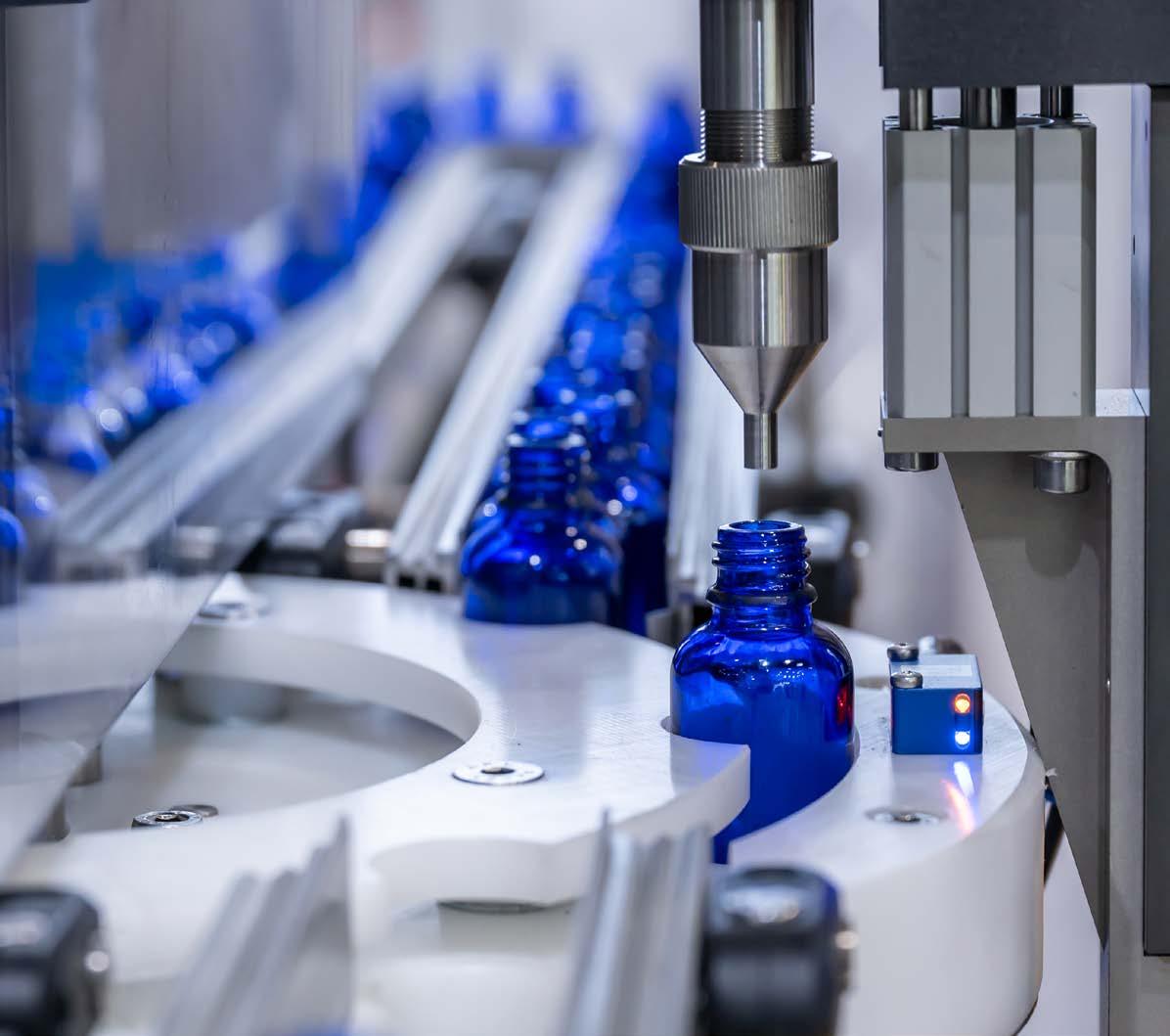
ABB - 12
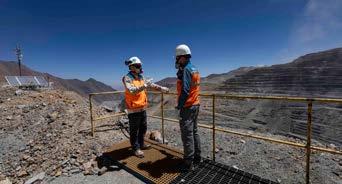
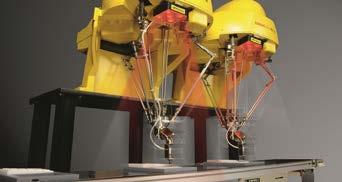
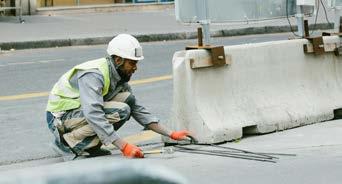
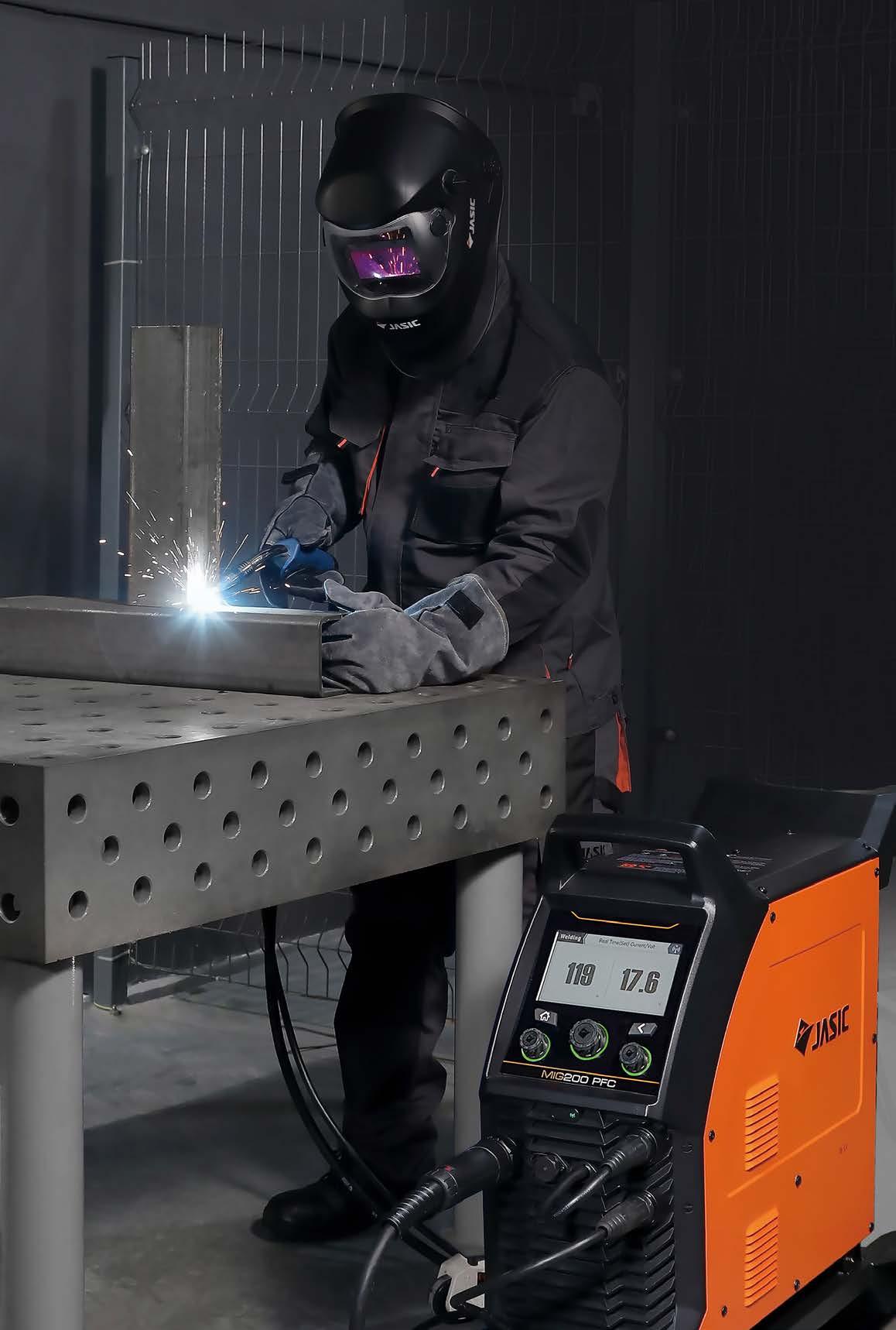
ABB - 12
Editor’s Choice
PPMA SHOW PREVIEW
Coatings
Connectors & Fittings
Control & Automation
Electrical & Electronics Health &
Machining & Machinery Measurement &
ABB
ABB to upgrade gas turbine control system to boost reliability and efficiency at Singapore power plant
RENISHAW
Renishaw strengthens global presence with the opening of facilities in India and Japan
BURKERT
Bürkert modulating control valves help UK brewery secure productivity
PRIME VISION
How Prime Vision’s Flow Projector benefits warehouse staff for streamlined sorting processes
FANUC
Boosting aerospace manufacturing outputmanufacturing output
ADVANCED ENGINEERING
Two-day event includes talks from over 150 industry experts
MAPAL
Empower your aluminium machining
DYNE TESTING
Quick, easy, low-cost surface measurement technology
ENGINEERING DESIGN SHOW
Discover your next supplier at The Engineering Design Show
GOUGH ENGINEERING
Manufacturers can reduce material waste and enhance product quality
HANNOVER MESSE 2025
HANNOVER MESSE 2025 will feature a strong presence by drive technology and fluid power
• Continuous diagnostic: Full coverage of your critical assets at all times.
• Early diagnostics: Monitoring of imbalance, wear and overall vibration.
• Maximum efficiency: Permanent diagnostics helps keep your assets running efficiently.
• Easy integration: ifm provides individual solutions suited to different types of machines. Reducing costs, avoiding unplanned downtime and optimising processes: The ifm application solutions. ifm – close to you!
The leading source for innovators in Technology, Manufacturing and Maintenance within the Engineering & Processing industry worldwide.
Published bimonthly, a subscription to PECM magazine is essential for Process Engineers, Chemical Engineers, Instrumentation Engineers, Mechanical Engineers, Plant Engineers, Precision Engineers, Environmental Engineers & General Engineers, Companies and Organizations in the Food, Dairy, Beverage, Brewing, Semiconductor, Pharmaceutical, Biotechnology, Chemical, Oil & Gas, as well as all UK's major manufacturing units.
Every issue of the magazine contains the latest news, in-depth features, together with product innovations and case studies showing how process engineers are implementing new technologies to reduce costs and impact on the environment.
With over 158,000 readers worldwide the publication is widely read, recognized, and well respected within the Process, Engineering & maintenance industries.
A subscription to PECM magazine is the industry's 'must have' publication.
SUBSCRIBE TO 6 BIMONTHLY ISSUES OF PECM FOR JUST £27
• The magazine gets delivered directly to your door once every issue is published
• The quality of the hard copy enhances the reading experience
To Subscribe please call 01304 806039
SUBSCRIBE TO OUR DIGITAL EDITION COMPLETELY FREE OF CHARGE
Designed for the digital age, the magazine has been created for easy viewing on all electronic devices. All our issues stored in one place: get unlimited access to our previous and future issues.
To Subscribe please visit www.pecm.co.uk/subscribe
EDITOR IN CHIEF
Antony Holter editor@mhmagazine.co.uk
BUSINESS MANAGER
Josh Holmes josh@mhmagazine.co.uk
SALES DIRECTOR
Jake Page jake@pecm.co.uk Tel: 01227 937174
SALES MANAGER
Martin Richardson martin@pecm.co.uk Tel: 01304 086039
DIGITAL MANAGER
Jamie Bullock jamie@mhmagazine.co.uk Tel: 01227 936971
Please
EDITOR
Elizabeth Hutton elizabeth@pecm.co.uk
STUDIO DESIGNER
Richard Bland richard@mhmagazine.co.uk
ACCOUNTS DEPT
Alison Holmes accounts@pecm.co.uk Tel: 01227 936976
PUBLISHING DIRECTOR
Martin Holmes martin@mhmagazine.co.uk Tel: 01304 806039
DIGITAL ASSISTANT
Stacey Goodwood Tel: 01227 936971
MH Media Global Ltd. 18/20 Newington Road, Ramsgate, Kent, CT12 6EE Tel 01304 806039 l Fax: 08721 152240 l www.pecm.co.uk
Expromet Technologies Group is opening a new base within the Philippine Economic Zone Authority (PEZA). The new facility will offer customers extended sourcing solutions, inventory management, faster delivery times and local precision CNC machining capability.
De-risking
Expromet Group companies provide UK-manufactured precision casting and machining solutions alongside extensive supply chain partnerships with global manufacturers. Global economic, political and social considerations now make it more important than ever to offer an increasingly wide range of sourcing options.
Expromet Asia Inc will initially provide a new logistics and inventory call-off facility. CEO Robert Guest confirms this is part of the group’s drive to optimise Expromet’s end-to-end supply chain from trusted manufacturers:
“Expromet’s increased presence in Southeast Asia will enable us to reinforce existing supply routes and establish direct links with a more extensive manufacturing base. Local warehousing and call-off will further de-risk the supply chain for our customers.”
Worldwide customers will benefit from:
• increased security of supply, minimising risk in the supply chain
• reduced lead times through warehousing and inventory
management
• cost efficiencies and enhanced operational reliability.
Expromet is further investing in state-of-the-art CNC machining technology with the aim of offering CNC machining on-site in the Philippines. This will deliver expertise directly where it is needed, helping to optimise the speed and efficiency of Expromet’s worldwide manufacturing supply chain. It will also provide opportunities to eliminate tariffs and benefit from significantly lower taxes, giving customers a competitive edge.
Expromet Asia will ultimately provide an umbrella service that encompasses product development, sourcing and inventory management. The Philippines facility will provide local technical and engineering expertise to accelerate product development, alongside advice on manufacturing methods to
optimise cost and lead times without impacting on quality. With suppliermanaged inventory and flexible scheduling, Expromet Asia will provide a turnkey solution that adds significant value to customers’ supply chain management.
Expromet group companies supply precision engineered solutions for performance-critical applications to a wide range of industry sectors, including Aerospace, Automotive and Electronics.
“Expromet’s base in the Philippines will improve supply options and reduce lead times, providing a fantastic opportunity for customers across demanding sectors to benefit further from strategic sourcing,” says Jason Tyas, responsible for building and developing Expromet’s presence in Southeast Asia.
“Building a strong presence in Asia means that Expromet can meet local customers and manufacturers face to face, ensuring that we develop robust relationships and meet customer expectations. It enhances Expromet’s ability to provide turnkey solutions sourced from international supply chain partners, building on Expromet’s reputation as a fully integrated, leading-edge supplier of engineered solutions.”
To find out more about overseas sourcing through Expromet Technologies Group, please call +44 (0)1271 866200 or email enquiry@expromet.com
Cross+Morse is a Birmingham based manufacturer of Mechanical Power Transmission products and solutions with over 100 years of history, right in the centre of the engineering hub in the West Midlands region in the United Kingdom. We operate in a 5000m2 fully integrated factory with a dedicated and loyal staff who have amassed a depth of technical expertise and engineering experience over their many years of continued service.
Cross & Morse are Mechanical Power Transmission solution specialists and at this present time we have £1.5m worth of finished stock on our shelves such as Roller Chain and Sprockets in both stainless and carbon steel, Gears, Racks, Couplings, Torque Limiters, Sprag Clutches, Timing & V belt Pulleys, timing & V Belts, Inverted Tooth Chain, Silent Chain, Sealmaster Bearings, McGill Cam followers, Shaft Clamping Elements, Freewheel & Overload Clutches.
We value innovation highly at Cross+Morse, which is why we constantly invest in new machinery and technology as well as training programmes and apprenticeships to maintain the highest standards of quality and service we are well known for. With our
in-house team of application and design engineers at your disposal Cross+Morse are able to provide bespoke technical solutions to your power transmission problems in the most cost-effective way.
Have a specialised or ambitious requirement? Send us your drawings and
application details and we will do our utmost to find the best solution possible, we welcome a challenge! We have been providing solutions for the food and drink, oil & gas, agricultural, pharmaceutical, quarrying, energy and environmental industries, bottling and packaging plants and many more for over 100 years. Our customers come from the widest range of industries and include original equipment manufacturers for packaging, conveying systems and material handling applications. We also export our quality products all over the world, through our network of long standing distributors or directly to the manufacturers and end users of mechanical power transmissions on every continent.
At Cross+Morse we consider customer support along with in-house design and manufacture an essential element in our service to industry, please browse our website for details and more information on our manufacturing capabilities as well as our stringent quality control. We are certified to ISO 9001:2015 and have been for over 30 years.
Call or email us now to solve your mechanical power transmission problems.
PENICO ROTARY GRINDING TABLE
Converts surface grinders to rotary work
For further details contact Penico Guages Limited info@penico.com 01274 511044 www.penico.com
Since 1977, Smiths Fire LLP has been providing essential fire safety solutions and maintenance services. Specialising in a comprehensive range of services, including fire extinguishers, safety signage, fire alarms, emergency lighting, fire safety training & fire risk assessments, we excel in safeguarding your premises against fire hazards.
What distinguishes us is our commitment to reliability, professionalism and quality service, all delivered at exceptional value. At Smiths Fire LLP, we combine professional expertise with a personalised touch, ensuring the highest standards of safety for our clients across various sectors.
We can offer tailored solutions to meet your specific needs, whether you require equipment installation, regular maintenance, or comprehensive training - trust Smiths Fire LLP to deliver excellence every step of the way.
Contact us today to elevate your fire safety standards and enjoy unparalleled peace of mind with our trusted solutions and expertise.
01536 484846 | sales@smithsfire.com
Scan to learn more:
new generation of valves, precisely tailored to your needs
• Leaner and faster production using cleverly designed modules which are standadized across different product categories.
• Modular and flexible design with a wide range of configuration options, optimizing response time to your specialized requirements.
• More agility, products can be ordered and manufactured faster than ever before with item prices and availability information easily accessible.
• The platform-base design enables faster conformity adjustments to ensure GEMÜ products are always optimized with the latest features.
www.gemu.co.uk
Versatile Controls Ltd was established in October 1987 by the current owner Mr Jon Slim and the late Mr Edward Dowty.
The Company started as a distributor for The Versa Products Inc of New Jersey to serve the Oil and Gas industry in The North Sea with high quality pneumatic and hydraulic control valves.
During the following years, the company acquired other distribution rights with ITT Neodyn pressure switches, ITT Conoflow regulators, Ruelco switches and regulators and Deltrol flow control products.
In recent years, the company has made progress in the manufacture of high quality mixing systems for The Pharmaceutical industry and was responsible for many of the systems required during the recent covid epidemic.
AUTOMATION & CONTROL SYSTEMS
INNSWORTH TECHNOLOGY PARK
sales@versatilecontrols.co.uk
In today’s manufacturing landscape, water supply limitations, an increase in water charges, and stringent environmental regulations are pressing concerns for industries worldwide. These challenges are driving the adoption of sustainable practices, including exploration into new, more environmentally friendly wastewater treatment solutions.
With water shortage fears growing across the UK, companies are re-examining their production processes with a view to reduce the waste of this valuable global resource.
“Without a rapid, effective treatment option, liquid effluent can become a costly issue to tackle,” says Jamie George, Projects & Business Development Director at Axium Process.
While effluent composition varies with the industry, it is usually composed of microplastics, fats, oils, grease and many other unsavoury particulates. Membrane filtration is able to selectively separate these suspended solids, leaving behind high-quality water that is immediately available for reuse in upstream or downstream processes.
Eliminating the need for damaging chemical flocculants, membrane filtration reduces the risk of damage to our rivers and waterways and could potentially reveal the presence of valuable materials that would otherwise be destroyed using alternative methods.
Jamie George states “Initial pilot trials on the feed material are carried out, either at our Swansea test facility, or at the manufacturer’s premises. These are instrumental in how we identify and adjust process parameters for optimal filtration results.”
Able to provide a reliable, cost-effective solution to reducing discharge volumes with the potential to recovering up to 90% of wastewater, membrane filtration is a tried-and-true solution for water recovery needs. Plants can be constructed in a variety of setups, from containerised units to small, compact systems that can be moved to other areas as needed and can also be designed with future expansion in mind.
Axium’s extensive expertise allows for the design and manufacture of crossflow membrane filtration solutions tailored for diverse applications, all while adhering to international regulations and maintaining the highest of hygienic standards.
For further information, please visit www.axiumprocess.com
Antofagasta Minerals partners with ABB to drive real progress in its mining industry decarbonization initiatives
Antofagasta Minerals and ABB have signed a Memorandum of Understanding (MoU) to accelerate decarbonization initiatives by electrifying and automating mining operations in Chile. The collaboration aims to develop and implement a net zero emission haulage solution by leveraging ABB’s expertise as well as its eMine™ solutions.
The mining industry is striving to close the gap in demand for copper driven by the energy transition, while simultaneously wrangling the challenge of decarbonizing their own operations. Currently, anticipated mine supply from announced projects is expected to meet only 70 percent of copper requirements by 2035[1]. Net zero emission haul trucks have been identified as a ABB
key solution for achieving large scale decarbonization for mines around the world. This collaboration between ABB and Antofagasta Minerals represents a significant step toward advancing the adoption of electrification in mining and defining best practice for the industry.
Under its purpose to “develop mining for a better future”, Antofagasta Minerals is at the forefront of decarbonization. It is working towards reducing its emissions by 50 percent by 2035 and achieving carbon neutrality by 2050, having already reduced its Scope 1 and Scope 2 carbon dioxide emissions by 928,000 tons[2].
Through the development of the trolley trial at its Los Pelambres operation, the company has played a pivotal role in advancing
the implementation of electrical solutions in the mining ecosystem. Antofagasta Minerals expects electrification will present viable solutions for reducing emissions in its haulage processes and is aiming to test battery powered trucks and trolley assist technologies in the next few years.
ABB is supporting Antofagasta Minerals with its decarbonization roadmap by supplying advanced technology solutions from its eMine portfolio. Specifically, the parties intend to utilize ABB’s eMine consultative studies to define the techno-economic optimum for the all-electric mine, evaluating decarbonization technologies, impact on mine operation and design, as well as power distribution.
Furthermore, in recognition of the critical role net zero emission haul trucks play in meeting the greenhouse gas emission reduction goals, ABB and Antofagasta Minerals will collaborate, alongside other third parties, to accelerate the development of net zero emission haulage solutions. Antofagasta Minerals will act as an early adopter and test site for technology and has committed to using ABB’s eMine Trolley System. The system is known to reduce diesel consumption by up to 90 percent in specific environments while lowering energy costs and overall environmental impact. This technology not only reduces emissions in the short term, but also enables the future implementation of battery technology in the mining industry.
“Our shared vision in achieving more sustainable processes and operations in the mining industry drives us to innovate and push the boundaries of what is possible,” said Max Luedtke, Global Business Line Manager Mining, ABB. “Industry collaboration is vital to achieving the progress needed to reduce the industry’s environmental impact. As one of the industry’s largest copper players, Antofagasta Mineral’s support is invaluable to this pursuit. Combined with ABB’s holistic eMine framework, this is a major step towards achieving the all-electric
Our shared vision in achieving more sustainable processes and operations in the mining industry drives us to innovate and push the boundaries of what is possible
mine of the future and fuelling decarbonization efforts. We are fully invested in the collaborative journey to develop further solutions.”
An anaerobic digestion plant operator contacted North Ridge Pumps who were looking to reduce fertiliser use, and utilise digestate throughout their farm.
Digestate is an excellent fertiliser containing all the nutrients and micronutrients required for successful modern farming, including nitrogen, potassium and phosphorus. What’s more, none of these nutrients are lost during anaerobic digestion, so farmers can close what’s called the nutrient cycle and reuse these essential minerals.
What our client wanted
They wanted to improve the transfer rates from their digestate pond to a nursing tank at their anaerobic digestion plant.
The liquid being transferred was mechanically-separated anaerobic digestate which contained screed at less than 1mm and only 5% solids. The mixture also contained a small amount of sand.
They were struggling to achieve a flow rate of 100m³h, and wanted to double this up to 200m³h. The digestate transfer pipeline was 300m long and fed into a nursing tank, as well as into digestate tanks as a feedstock or seed for future batches.
They were extracting the digestate liquid from a lagoon 4m in height and 18m away. Their objective was to double their existing flow rate and hydraulically mix their lagoon, they were looking for a heavy duty transfer pump to achieve this.
Here at North Ridge Pumps, our wide-ranging expertise means we can specify from a wide range of pumps for a variety of industrial and commercial applications.
Moreover, we’re not limited to a single pump technology. Our knowhow enables us to offer a bespoke solution, not something just picked off the shelf. This means we can select the most appropriate pump for any application at the lowest lifetime cost.
For this demanding application, we specified our XR625, and built and supplied it in just over 6 weeks. This is a 6” self-priming pump manufactured from ductile iron and hard faced seal unsusceptible to solids such as sand for this application.
Our pump is designed to deliver a digestate transfer flow rate of 200m³h with only an 18.5Kw motor. To maximise output flow, we advised the client to run the pump at 60Hz via a frequency inverter to achieve the required flow and pressure.
Our XR pump range
These are heavy-duty self-priming pumps which are solid handling, efficient and extremely durable. This is thanks to the armoured volute which surrounds the impeller, improving
pump efficiency and protecting the pump casing from wear.
What’s more, the XR’s double curved impeller helps improve pump efficiency. For example, in this particular application, the existing pump achieved a flow rate of just 100m³h with a 25kw motor. Our new pump delivered 200m³h with a motor power of only 18.5Kw.
Protected against corrosion
Another important consideration was the properties of the digestate itself. It can vary in quality and be very corrosive. So when selecting a pump type, we had to make sure that all internal parts were easily accessible and aren’t held in place by screws which can corrode over time.
Our XR pump series has design features including oversized inspection ports, and no internal screws in the pump unit.
Another clear advantage of our XR range is that traditionally self priming pumps have a wear plate covering the impeller which is replaced as it wears.
The issue with this design is that when the wear plate is replaced pump performance is not restored to that of the original design as the casing has worn. Our range features an armoured volute covering the impeller which when replaced ensures the pump works to the original performances.
If you have an application needing smooth transfer of fluids, viscous liquids or solids and don’t know which pump is best for you, talk to North Ridge Pumps and get expert help and advice.
For further information, please visit www.northridgepumps.com/contact-us
Optimise performance with specialist support
Industry knowledge and application expertise across dispensing, dosing, full containment, gentle handling, blending and transfer, means whatever the problem, it’s likely we’ve seen it before. So we can help you solve it sooner.
+ Accelerated stator wear
+ Clogging
+ Changes to fluid consistency
+ Flow Reduction
+ Inconsistency in finished product
+ Inaccurate transfer of chemicals
+ Leakage | Liquid separation
+ Product Wastage
+ Seal wear or failure
+ Valve Blockage or unintended Opening
We’ve been engineering sanitary pumps for sectors such as distilling, brewing, food manufacturing/processing, and more, for 20+ years. We understand industryspecific processes and know what it takes to optimise performance through bettersuited pump design - giving you complete peace of mind.
Our expert engineers understand your process and guide you through the options, so you can confidently select the most suitable chemically resistant pump.
EXAMPLE PRODUCTS:
+ Acids
+ Alkalis
+ Coagulants
+ Corrosive
+ Chemical Sludge
+ CO2
+ Flammable
+ Flocculants
+ Oxidisers
+ Pyrophoric
+ Refrigerants
+ Solvents
+ VOC with low NPSH
+ Water Reactives
Motor customers in the UK are currently particularly pleased with the fast delivery capability of German manufacturer Menzel Elektromotoren. In early June, the family-run company received two orders for large machines within one week.
Due to motor failures, the water supply to 30,000 households was threatened and production in a cement plant was halted. After delivery times of only six and ten days, respectively, both the pump and the cement mill could be restarted in the shortest imaginable time. Faced with unexpected downtime due to equipment failures, customers often cannot afford to wait for a motor manufactured from scratch – standard delivery times in higher output ranges start at six months. Menzel has proven itself to be a strong partner in an emergency, quickly configuring suitable motor systems for a wide range of highoutput applications from its large, diverse stock of motors, cooling units and ancillary equipment –such as the current two jobs for British customers. The squirrel cage pump motor has a nominal output of 1380 kW operating at 3300 V. The slip-ring motor for a cement mill delivers 2000 kW at 11 kV. Its special features are increased ingress protection rated IP55 and a closed cooling system with a top-mounted air-to-air heat exchanger (cooling type IC 611), ideal for dusty environments and large temperature fluctuations.
Large industrial motors from stock and quickly tailored to order.
After delivery times of only six and ten days, respectively, both the pump and the cement mill could be restarted in the shortest imaginable time.
NEW ELECTRIC MOTOR PLANT FROM JANUARY 2024
SUPPLIER OF LARGE MOTORS FOR ALL UK APPLICATIONS
MORE THAN 20.000 MOTORS AVAILABLE FROM STOCK!
MORE THAN 20.000 MOTORS AVAILABLE FROM STOCK!
Motors up to 25 MW and 13.8 kV
Motors up to 25 MW and 13.8 kV
• Low voltage slip-ring and squirrel cage motors up to 3,000 kW
• Low voltage slip-ring and squirrel cage motors up to 3,000 kW
24,000 m 2
24,000 m 2
• Medium voltage slip-ring and squirrel cage motors up to 15,000 kW
• Medium voltage slip-ring and squirrel cage motors up to 15,000 kW
• Direct current motors up to 2,000 kW
• Direct current motors up to 2,000 kW
• Frequency converter-proof drives
• Frequency converter-proof drives
• In-house load test facility up to 13.800 V, 2.300 kVA, 120 Hz
• In-house load test facility up to 13.800 V, 2.300 kVA, 120 Hz
Customized special designs
Customized special designs
• Custom designs for special applications and operating conditions
• Custom designs for special applications and operating conditions
• Optimized motor design for higher efficiency
• Optimized motor design for higher efficiency
• Mechanically and electrically interchangeable motors
• Mechanically and electrically interchangeable motors
• Commissioning worldwide
• Commissioning worldwide
MENZEL Great Britain Ltd. | UK Branch Office
27 Hunt Drive | Melton Mowbray | Leicestershire LE13 1PB
Martin Rooney | Tel.: +44 1664 500 844 | Mobil: +44 7957 618046
martin.rooney@menzelgb.co.uk NEW ELECTRIC MOTOR PLANT FROM JANUARY 2024
MENZEL Great Britain Ltd. | UK Branch Office 27 Hunt Drive | Melton Mowbray | Leicestershire LE13 1PB Martin Rooney | Tel.: +44 1664 500 844 | Mobil: +44 7957 618046 martin.rooney@menzelgb.co.uk
MENZEL Elektromotoren GmbH
German Headquarters
MENZEL Elektromotoren GmbH German Headquarters
Am Alten Walzwerk 2 | 16761 Hennigsdorf | Germany
Am Alten Walzwerk 2 | 16761 Hennigsdorf | Germany
menzel-motors.com info@menzel-motors.com
menzel-motors.com info@menzel-motors.com
AROUND THE CLOCK, AGAINST THE CLOCK!
AROUND THE CLOCK, AGAINST THE CLOCK!
ABB has been commissioned to upgrade one of the turbine control systems at the 1,300 MW Keppel Merlimau Cogen (KMC) combined cycle gas turbine on Jurong Island in Singapore, to improve efficiency and reliability. The scope includes replacing the existing Egatrol 8 turbine control system with Egatrol X, which is based on the ABB Ability™ System 800xA® flagship distributed control system (DCS) and modern AC800M portfolio.
Transferring full functionality from the existing application to the updated solution allows the customer to avoid downtime and install the control system in the shortest possible time. The project involves upgrading DCS components while keeping the overall structure as far as possible. Instead of having to rebuild the entire system in one go, ABB will provide a flexible, customized approach whereby older components are replaced as and when needed. This prevents unnecessary downtime, avoids the costs associated with loss of operation, and ensures a stable, reliable energy supply with high availability.
All control settings are adopted through an in-house software code conversion process, eliminating timeconsuming adjustments of system parameters. The user interface, based on System 800xA, only requires minor adjustments, which eliminates operator retraining. The hardware design, featuring ABB’s latest I/O evolution kit, significantly reduces commissioning time and eliminates the risk of re-wiring errors.
As part of Singapore’s commitment to
achieving net zero emissions by 2050, the government is driving business transformation through grants for energy efficiency and emissions reduction. It is also investing in low carbon technologies to progress the energy transition . With power generation currently accounting for 40 percent of carbon dioxide emissions, the country plans to diversify its energy supply with a focus in four areas: solar, regional power grids, emerging low-carbon alternatives including hydrogen, and natural gas.
While natural gas continues to play an important role, as the country expands its energy portfolio, the KMC project showcases how ABB enables customers to enhance energy and carbon efficiency in gas power generation. This initiative not only safeguards current energy security but also supports the integration of renewable energy into the grid, driving forward shared energy transition goals.
customized upgrade installations in the fastest and safest way available,” said Per Erik Holsten, President of ABB Energy Industries. “Turbines sit at the heart of a power plant and our gas turbine control systems have been helping utilities to provide electricity to households across the world in the most efficient and sustainable way possible.”
“We are pleased to renew the longstanding partnership between Keppel and ABB with the latest turbine upgrade project. Leveraging ABB’s strong domain knowledge, we are confident that KMC will experience a smooth and seamless migration to the updated system, which is critical to our productivity and ability to provide reliable power supply to the grid,” said Miguel Benito, Assistant Managing Director, Technical and Operations, Power & Renewables, Infrastructure, Keppel.
This is part of KMC’s ongoing initiatives to adopt automation solutions to boost system reliability and responsiveness, to achieve enhanced efficiency, lower fuel costs, and a reduced environmental impact.
“As a global leader in the DCS market, ABB has both the expertise and technology to deliver flexible, For further information, please visit www.abb.com
A manufacturer of vape liquids and flavours contacted Castle Pumps looking to upscale their production. Part of this involved improving the efficiency of transferring the concentrated flavours from the IBCs where they are stored.
They were looking for a number of container emptying solutions for fitting onto the IBCs and dispensing the favours without manually handling the fluid that takes up more operator time, is less accurate and is more likely to result in waste and spills. They wanted to be able to remove these when not in use and store them away, and needed them to be food grade due to the final product being for human consumption.
When it comes to container emptying, Castle Pumps’ first port of call is to consider a Flux barrel pump. All Flux drum pumps benefit from being lightweight and easily fitted to a container and removed just as easily. With various immersion tube lengths available to suit the container size, a 1200mm downtube would be able to be selected for use on their IBCs.
The good news was that this customer already had Flux pumps on site for another process, which meant they were a natural option as they were already familiar with their maintenance and operation.
Given the low viscosity, clean nature of the product, Castle Pumps knew that the Flux F400 impeller style pumps were suitable as they can handle up to 1200cP. The F430 model with mechanical seal was specified to protect the pump’s inner tube from the fluid and prevent cross contamination between flavours. The ensure that they last with the aggressive nature of the concentrated flavours, the seals were upgraded to FFKM to prevent them from being eaten away.
The Flux F430 selected was ATEX approved, fully food grade, constructed of stainless steel and supplied with tri-clamp
fittings for a hygienic connection. We supplied a full solution for dispensing the vape flavours from their IBCs including motor, pump with 1200mm immersion tube, screw cap, compression gland, earthing wire and clip, trigger nozzle, hose and swaged fittings.
The customer ordered three of these food grade pumps for use and one to hold on site as a spare to prevent any risk in production downtime when maintenance is required! These solutions have been in use for several months now and are successfully delivering the customer’s process.
Getting the wrong pump for your process can result in inconsistency in the finished product, crushed solids, clogging, excessive wear, loss of productivity, waste of costly product or at worst, contamination. Always trust technical experts to specify the right pump for your application.
Manufacturing is one of the UK’s success stories. With an output valued at £224bn , we are now the eighth largest manufacturing nation in the world. But our position is vulnerable unless we significantly increase our level of automation.
Helping manufacturers to increase their productivity, reduce waste, improve product quality and alleviate labour shortages, the benefits of automation are myriad. And as the only G7 country to sit outside the top 20 in terms of robot density (we are actually 25th in the IFR global robot league table), accelerating our automation uptake is essential if we are to retain our place as a leading manufacturing nation.
It is therefore important that when designing a new product, planning a new production line or upgrading your existing facility, automation is factored in from the very start of the process, not just as an afterthought. Not only does this keep down costs, it also ensures that any automation will be right first time, minimising downtime, boosting productivity and resulting in a solution that is fit for purpose.
Here, Oliver Selby, Head of Sales for FANUC UK, outlines six key design considerations for seamless automation integration…
1. Embrace the automation process
It may sound obvious, but keep front of mind the fact that your product’s manufacturing process will need to benefit from automation. This can generally only be done by incorporating automation into the design of the product, whether that’s by giving the part a feature that allows it to be picked up by a robot, located or inspected by a vision system, or allowing access for a welding torch or fixturing, for example.
This mindset also translates to the wider production line. We see products designed using multiple materials, joining techniques and production methods which won’t all necessarily work together to produce something that is easily automated,
but which designers are reluctant to give up. However, it can be better to take a hit on one material or process to make things easier to automate, thereby reducing overall production costs.
2. Prioritise parts
Focus on part delivery methods within the complete solution. Often, customers will come to us looking for an automated solution, but with their component parts delivered in no ordered way. As much as 20-30% of the cost of the project can be spent on getting those parts located or fixtured and ready to process before the real automation process can actually begin. It makes more commercial sense to keep parts in order, whether that’s in a nested box, on a conveyor or in a stack.
Also think about part handling and fixturing. Significant costs could end up being channelled into part
Incorporate automation into the design of the product, whether that’s by giving the part a feature that allows it to be picked up by a robot, located or inspected by a vision system.
fixturing – even more so if you are working with a range of parts due to multiple fixtures. A good example of best practice here is to focus on one-way assembly; for example, where parts stack on top of each other to create the complete product or common part features that allow common fixturing.
Consider TCO
Concentrating on the wrong drivers for automation is a major error but one that we sadly see all too frequently. Some customers are more focused on fitting an automation solution into a defined payback period (often under two years) instead of looking at the value it will bring to the business over its lifetime. A total cost of ownership model is a far better measure. Purchase price only accounts for between 15-25% of the total cost of ownership; the remainder is made up of factors such as maintenance, energy usage, repairs, and even end of life. Measuring TCO rather than ROI will ensure you get the right automation solution for your business, resulting in real long-term value.
4. Remember the process, not just the consumer
It can be tempting when developing a new product to prioritise what’s easiest for the consumer, without realising that this may negatively impact the automation process. A prime example of this is shelfready packaging. The current trend within food manufacturing for front-facing packaging with tearoff flaps or loose fitting lids allows retailers quick and easy restocking of shelves. However, this seemingly simple change in packaging design has made it extremely difficult for automation to be exploited for endof-line palletising, as the loose fitting lid or tear-off flap is not conducive to staying in place. Therefore, before making any packaging changes – no matter how seemingly minor – think carefully about how they may impact your ability to automate, and the effect this will have on production efficiency and labour demand.
5. Talk to automation suppliers Engage with automation suppliers as early as possible. At FANUC, we
For further information,
are more than happy to support designers that are beginning their journey towards automation and will readily provide guidance on what the process is going to involve. We’ve done this countless times throughout the years as different sectors have started to embrace automation – from manufacturers of low-cost products to high-value goods; companies in the food industry; and more recently, with EV battery manufacturing for the automotive sector. We have rounded experience across lots of different applications within a wide range of industries that we are happy to share, and which designers can learn from.
6. Try before you buy
Finally, as in many industries, some automation suppliers are now starting to offer low-cost/ low-risk routes into automation for companies taking their first steps into automation. Robots as a Service (RaaS) is a subscription-based option that enables manufacturers to pay a set fee over a specified period of time, and effectively lease a robot to use in their facility. The limitation of this offering is that it will only suit certain simple applications, for example, palletising, or particular welding options. The upside is that the robot can be repurposed for multiple product types – palletising a box of cakes is effectively the same process as palletising a box of dishwasher tables, for instance. Talk to your automation supplier to determine if RaaS could be right for your needs in the short-term –by allowing firms to test the water and experience the benefits before making their own investment, it can represent an affordable route into automation for some first-time users.
In conclusion, when designing or upgrading any production line, make sure to consider automation as one of the cornerstones of your project from the outset. By working with a reputable automation supplier, you can ensure your manufacturing facility is optimised for success, not just for today, but for years to come.
It couldn’t be more flexible: solenoid interlock now with new functions
The world’s smallest electronic solenoid interlock AZM40 now offers even more versatile application options with new accessories and new features. With dimensions of 119.5 x 40 x 20 mm, it is particularly suitable for small safety gates or maintenance hatches and confined installation spaces. Despite its compact design, the AZM40 achieves a remarkable locking force of 2,000 N.
With the new lockout tag, the AZM40 can now also be used for larger, accessible machines and systems. Service staff can attach a lock to the lockout tag when entering the danger zone. This means that the door of the safety guard cannot be closed, and unintentional start-up of the machine is prevented.
In addition, the new versions of the AZM40 solenoid interlock can be extended with an emergency exit or emergency release. Two different versions - with lever or push-button - are available. The lever is available both as an emergency exit and as an emergency release and can be mounted directly on the AZM40. The push button is also available as an escape release or emergency release. Its similarity to an emergency stop button makes it intuitive to operate. The emergency exit ensures that any trapped persons can free themselves from the machine area. The emergency release is used to ensure that the danger zone in a machine can be reached quickly in an emergency - e.g. in the event of a fire.
The new “inner values” of the AZM include the addition of the high degree of protection IP69 and the
The new versions of the AZM40 solenoid interlock can be extended with an emergency exit or emergency release.
With the new lockout tag, the AZM40 can now also be used for larger, accessible machines and systems.
temperature range of -20 °C to +55 °C, which open up additional application possibilities.
Another advantage is the long service life with now 500,000 switching cycles (actuator cycles) and 1,000,000 switching cycles (locking cycles).
The bistable interlock principle of the AZM40 is also sustainable, with the advantage of permanently lower power consumption. Compared to monostable solenoid interlocks, more than 50% of the power
consumption can be saved. A further advantage is the added safety: even in the event of a power failure, the safety door remains securely closed during hazardous run-on movements.
Thanks to the 180-degree angle flexibility, the actuator can approach the AZM40 continuously so that the interlock can also be used on flaps that do not close at a 90 degree angle or that open upwards at a 45 degree angle. The angle flexibility ensures that the interlock can be easily installed even in confined and difficult-to-access locations.
The AZM40 can be easily mounted on standard 40mm profiles with no overhang. For other profile system widths (20 mm, 30 mm, 45 mm, 50 mm and 60 mm), a set of two universal mounting plates can be used for the AZM40 and actuator. This ensures quick and cost effective installation for a wide range of profile system widths.
The Huck® fastening system exemplifies innovation and excellence in the fastening industry; the diverse product range plays a crucial role in high-demand applications ensuring reliability, durability and efficiency.
In the ever-evolving landscape of industrial manufacturing, efficiency, reliability, and durability are paramount. The Huck® fastening range is a brand synonymous with innovation in the fastening industry. Renowned for LockBolt® and structural blind fastener technologies, Huck® fasteners provide solutions that enhance manufacturing processes across a multitude of industries where structural integrity is critical and where a strong, permanent, and tamper-resistant joint is required.
The Legacy of Huck® Fasteners
With over 80 years of fastener innovation, Huck® fasteners have consistently delivered performanceengineered solutions designed to withstand extreme conditions and demanding applications. This legacy of innovation and reliability has made Huck® fasteners a trusted name in the industry. The Huck® LockBolt, based on Lou Hucks’ original design, provides high stability and facilitates lightweight, stronger and more durable structures. Hucks’ ever evolving LockBolt and structural blind fastener capabilities continue to solve problems in in a wide variety of applications – no torque, easier evaluation, maintenance free and high corrosion standards are some of the benefits of using the Huck® fastener product range.
Speed of Installation: Huck® fasteners are designed for rapid installation. The installation process is often faster compared to traditional fasteners such as bolts and nuts, reducing assembly time.
Consistency and Reliability: The installation process of Huck® fasteners is consistent and reliable, reducing the likelihood of installation errors and rework, which saves time and resources. They benefit from rigorous testing, certifications, and quality management systems, ensuring consistent performance and building confidence in their use.
Cost Reduction
Reduced Labor Costs: Huck® fastener installation offers significant advantages in terms of efficiency and speed due to the straightforward process and visual inspection methods.
Reduced Material Costs and Weight reduction: Huck® fasteners are designed to create strong, durable joints, often requiring fewer fasteners compared to traditional fastening methods.
Maintenance and Longevity: Huck® fasteners typically have a long service life and require less maintenance, leading to cost savings over the product’s lifecycle.
Performance
Strength, Durability and Performance
Evaluation: Huck® fasteners provide high joint strength and are resistant to vibration and loosening; they are subjected to various tests to assess their performance under static and dynamic loads. Depending on the
fastener type, tests include tensile, shear, slip-load and creep testing as well as fatigue testing to emulate realworld conditions.
Aesthetic and Structural Integrity:
They can be installed without causing significant distortion or damage to thin sheet metal, preserving the material’s integrity and appearance.
Corrosion Resistance: Huck® fasteners are perfect for safety-critical applications; they are often subjected to harsh environmental conditions, including moisture, saltwater exposure, and chemical agents. Huck® fasteners are manufactured with coatings that resist corrosion, enhancing the longevity and performance of the final product. The coatings act as a barrier, shielding the fasteners from corrosive elements and preventing the onset of rust and degradation. By effectively sealing the surface of the fasteners, coatings significantly extend their lifespan, reducing maintenance requirements and replacement costs over time. This is particularly crucial in industries such as marine, offshore, and transportation, where corrosion can pose significant safety risks.
Advanced LockBolt Technology
Huck® LockBolts are renowned for their strength and vibration resistance. Unlike traditional nuts and bolts, Huck® LockBolts form a permanent joint that resists loosening, even under extreme conditions. This makes them ideal for high-vibration environments.
Huck® LockBolts are installed using direct tension and swaging. The Huck® installation tool grips the pintail of a LockBolt and then pulls to close the gaps in the materials being joined.
One standout product is the Huck® BobTail®, which has been proven to increase manufacturing efficiency. The BobTail® LockBolt eliminates the need for torque and re-torque procedures, ensuring consistent and reliable installations while significantly reducing labour costs, and unlike traditional LockBolts® no pin-break is required, therefore leaving no corrosion-prone area of bare metal or spent mandrels to be collected.
Huck LockBolts
Positive Locking Mechanism: Threaded bolts rely solely on frictional forces, in contrast, LockBolts consist of a pin and a collar and are installed using direct tension and swagingthere are no gaps between collar and pin ‘threads’ – a common source of loosening in conventional nuts and bolts.
Huck® LockBolt brand names include, BobTail® Magna-Grip®, C6L®, C50L®, C120L® and Hucktainer® (also available in encapsulated Hucktainer which can be colour matched to customers’ requirements).
When accessibility is an issue, Huck® structural blind fasteners offer a robust solution. Designed for applications where only one side of the joint is accessible, these fasteners provide high-strength, reliable joints often replacing welding. A key benefit is their internal locking mechanism that retains the ‘pin’ after installation.
Huck® structural blind fastener brand names include, Auto-Bulb®, BOM®, FloorTight®, HuckLok®, MagnaBulb®, Magna-Lok®, Magna-Tite®, and Penta-Lok™
Standard Nut and Bolt Frictional Force compared with Huck LockBolt Direct Tension Swaging
Huck® LockBolts High and Consistent Clamp Force: The installation process ensures a precisely controlled clamp force. This high and consistent clamp force minimises any potential movement within the joint, further enhancing the resistance to vibration.
Star Fasteners are the UK’s largest distributor of the Huck® fastener product range and stock a wide range of sizes, head styles, materials, and plating’s; this versatility ensures a wide range of applications and industries are accommodated. As industries evolve, Star Fasteners remains committed to providing advanced fastening solutions that meet the rigorous demands of modern engineering and manufacturing.
Complementing their extensive range of fasteners, Star Fasteners offers a suite of installation tools designed for ease of use and efficiency – offering a versatile range of battery and air-powered
options that enhance productivity on the shop floor. These tools ensure that Huck® Fasteners are installed correctly and efficiently, further boosting the overall performance of the fastening system.
Star Fasteners prides itself on its customer-centric approach. Through detailed case studies and customer feedback, the company continuously improves its product range to meet realworld challenges. This commitment to excellence ensures that Huck® fasteners remain at the forefront of the fastening industry, providing solutions that drive success for their customers.
In conclusion, Huck® fasteners represent the pinnacle of fastening technology. Their innovative designs, superior performance, and proven customer satisfaction make them an invaluable asset in modern manufacturing. Whether it’s enhancing the efficiency of assembly lines, ensuring the reliability of components and safety critical products, or supporting the sustainability of green energy projects, Huck® fasteners deliver solutions that meet and exceed industry demands.
Markforged Holding Corporation (NYSE: MKFG), the company strengthening manufacturing resiliency by enabling industrial production at the point of need, today announced the FX10 Metal Kit, a print engine that brings metal printing capability to the FX10. With this kit, the FX10 becomes the world’s first industrial 3D printer that can print both metal filaments and composites with continuous fibre reinforcement.
“Customers no longer have to choose between a metal and a composite
printer. Years of R&D investment and field experience have come together to provide an all-in-one solution for 3D printing to provide immediate return on investment once installed on a factory floor,” said Shai Terem, CEO of Markforged. “The FX10 supercharges other equipment on the factory floor to be better utilized and run more efficiently, increasing productivity and reducing potential line down events.”
The FX10, released in November 2023 as a composite only printer, was
designed to be the most versatile tool on the factory floor and has received tremendous feedback from early customers. With its modular architecture, upgrades like the Metal Kit enable customers of the FX10 to gain additional value from the machine after purchase.
Markforged also announced a new 316L stainless steel metal filament to be used with the FX10 Metal Kit. Users will also be able to print in 17-4PH with additional support for other Markforged metal filaments in the future.
“We designed the FX10 to be a modular platform, so that we are able to release new innovations and upgrades without customers having to purchase a new printer every year,” said Terem. “Along with new software capabilities we release regularly, the FX10 Metal Kit is poised to provide continuously growing value on factory floors for years to come.”
The FX10 Metal Kit consists of a swappable print engine that includes a metal-specific print head, material feed tubes, routing back, and dual pre-extruders. An FX10 can be swapped between metal and composite as many times as needed, and the swap takes about 15 minutes.
Years of R&D investment and field experience have come together to provide an all-in-one solution for 3D printing to provide immediate return on investment once installed on a factory floor.
Similar to the 5th Generation Continuous Fiber Reinforcement (CFR) print system in the FX10 that prints nearly twice as fast as previous composite printers, the 2nd Generation Metal FFF engine, built on years of Markforged’s experience printing metal, prints significantly faster than previous Markforged metal systems. FX10 combines faster print speed with a print volume twice as large compared to Markforged’s prior industrial metal printers.
Metal prints are built from the metal filament and a ceramic release filament. The ceramic release is extruded as an interface between the part and supports for ease of separation and removal. Once metal prints are complete, they must be washed and sintered in Markforged’s Wash-1 and Sinter-2 solutions.
Eiger, Markforged’s slicer and print management software automates the process, including scaling parts to account for shrinkage during sinter.
The Digital Forge is the additive manufacturing platform that enables every aspect of the FX10 and is purpose-built to integrate into existing manufacturing ecosystems. With the Digital Forge, users can share parts across their organization, and monitor fleet performance from a central location.
Markforged will showcase the FX10 Metal Kit at the International Manufacturing Technology Show in Chicago, Illinois from September 9-14 at booth 432305 where it will be printing in both continuous fibre reinforced composites and metal.
Markforged (NYSE:MKFG) is enabling more resilient and flexible supply chains by bringing industrial 3D printing right to the factory floor. Our additive manufacturing platform The Digital Forge allows manufacturers to create strong, accurate parts in both metal and advanced composites. With over 10,000 customers in 70+ countries, we’re bringing ondemand industrial production to the point of need. We are headquartered in Waltham, Mass where we design the hardware, software and advanced materials that makes The Digital Forge reliable and easy to use.
Whether bitter, ale, lager or craft –the incredible choice of beers makes competition between brewers fierce. To gain share in a saturated market and meet consumer demand, breweries need production equipment such as control valves to operate with the utmost reliability. Consequently, when a UK brewery noticed its mechanical interface modulating control valves were becoming very maintenance intensive, it approached Bürkert for a better solution.
Brewing is a complex process encompassing hop and grain selection, mashing, boiling, heating,
cooling, fermentation and bottling – and valves play a crucial role in delivering the perfect bottle, can or pint.
At a brewery in the UK, an array of modulating control valves was responsible for regulating various processes such as glycol supply to the chillers, steam control to the heat exchangers, as well as CO2 and O2 supply for fermentation and storage. As required in the food and beverage industry, equipment was subjected to regular chemical washdowns. Furthermore, the need
to meet supply agreements placed high operational demands on the whole process, including the valves.
Traditional modulating control valves rely on a mechanical interface, with the valve’s position controlled via a series of levers or pivots. This has limitations. First, mechanical wear on components can compromise valve accuracy over time,
affecting processes and overall product quality. Chemicals from repeated washdowns can also clog the mechanisms, reducing valve performance.
Bürkert’s
Built-in LED indicators provide process information at a glance.
The brewery was suffering from all these issues, resulting in deteriorating valve accuracy and increasing failures. While repair work could be completed during scheduled maintenance, the valves were becoming a time sink, with every planned shutdown dedicated to fixing them. Diaphragm actuators in the valves were adding to the problem, as they were not suitable for use with ingredients used in the brewing process. The situation was having an adverse effect on other projects and greatly increasing operating expenditure (OPEX) – a position operators couldn’t tolerate.
Looking for a long-term solution, the brewery approached Bürkert, a leading manufacturer of fluid control solutions for the brewing sector. After dialogue with the customer, Bürkert recommended its ELEMENT range of pneumatically actuated continuous control valves – which directly addressed the limitations of the previous equipment.
Kieran Bennett, Industry Manager, Food, Beverage, Chemical & Petrochemical at Bürkert, explains why: “These valves are fully sealed and feature air recycling technology, which prevents ingress of ambient
Specifically designed for hygienic environments, the ELEMENT valves
feature a stainless steel exterior for ease of cleaning and inherent chemical resistance.
air, chemicals and contaminants. The clean dry air used to pressurise the actuator is fed back into the spring chamber via a pilot valve, which helps to prevent internal contamination and corrosion. This ensures a long service life.
Specifically designed for hygienic environments, the ELEMENT valves feature a stainless steel exterior for ease of cleaning and inherent chemical resistance. The smooth, robust design ensures no purchase for bacteria or contaminants. Combined with ingress protection ratings up to IP67, the design is ideal for production environments with regular washdowns. The system installed at the brewery included digital leakage alerts, as well as intuitive read-outs for flow, temperature, pH levels and operating pressure.
Bürkert began the process of replacing all the valves at the brewery around five years ago, and during that time, the new replacements have required no maintenance. This has saved time, allowing brewery staff to engage in other projects, and reduced OPEX, improving overall profitability. One valve even had a large quantity of chemical spilt over it and was left for several days. The brewery was impressed to discover that it was completely unaffected.
Additionally, Bürkert has provided the customer’s engineering team with training regarding the maintenance process for the new valves. All involved were impressed with the easy, straightforward procedures. Furthermore, ELEMENT valves can be remotely monitored, so the condition of each unit can be discerned without time consuming inspections at each valve.
With the profusion of beers available to consumers, getting products on the shelves or to the pumps is imperative for breweries to achieve success. With its new, highly reliable and accurate Bürkert ELEMENT valves, this brewery can reach the productivity levels required to get ahead.
“A contactless position control system eliminates wear and clogging issues. The piston actuator is smaller and lighter, while offering better compatibility with brewing processes than competing diaphragm designs. Users can expect 0.1% accuracy over seven million cycles, more than three times longer than conventional alternatives. An LED digital display on top of the valve also provides key process information to operators.” For further information, please visit www.burkert.co.uk
Learn more about the advantages of Bürkert ELEMENT valves here: https://www.burkert.co.uk/en/ Landingpage/long-life-and-long-termaccuracy-for-continuous-controlvalves
Renishaw strengthens global presence with the opening of facilities in
To help service its growing customer base in India and Japan, global engineering technologies company, Renishaw, has recently opened two state-of-the-art technology centres — one in Chennai, India, and one in Nagoya, Japan. These upgraded facilities will strengthen Renishaw’s presence in both countries and improve customer access to the company’s engineering expertise and innovative technologies.
Renishaw unveiled its upgraded Nagoya facility at a two-day event, attended by over a hundred guests including its largest distributors, machine builder customers, Japanese metrology academics, representatives from the British Embassy, and employees from the company’s Tokyo office. Over the two days, Renishaw showcased the centre’s demonstration and office spaces, calibration laboratory, warehouse and despatch areas. The event also included demonstrations of the full range of metrology and spectroscopy products offered by Renishaw, including the new Renishaw Central smart manufacturing software suite which allows manufacturers to collect, present and action accurate process data to enhance their production.
“The event was a chance for us to show visitors how far Renishaw has come since opening our first Nagoya office in 1986,” explained Jason Taylor, Managing Director of Renishaw Japan. “We bought the current Nagoya building in 2019 and moved our offices there, and we’ve now turned the first floor into a brand-new technology centre with
a customer demonstration area, seminar room and applications development areas. Now it’s up and running, we’ll use the centre with our customers, developing and demonstrating new solutions.”
Renishaw also recently opened a new office and demonstration centre in Chennai, India, attended by hundreds of customers, machine tool builders, channel partners and journalists. The new facility will support Renishaw’s customers and partners in the Tamil Nadu region, as well as host potential buyers so that they can test the application of Renishaw products on their components before investing. The Chennai site will also serve as a training hub for students, machine builders, end user customers, channel partners and Renishaw employees.
“India is currently experiencing a dynamic period of growth, making it an exciting time to be part of this market,” explained Paul Weaver, Director of Sales and Marketing at Renishaw India. “The machine tool industry is expanding, new investments are flowing in from abroad, and both the domestic and
export markets are seeing significant demand. Renishaw is at the heart of this growth, actively supporting the precision manufacturing sector.”
“Our new office and technology centre in Chennai marks a new phase in Renishaw’s development,” added Weaver. “This new facility demonstrates our latest innovations, including the NC4+ Blue non-contact laser tool setter, the REVO® 5-axis multi-sensor measurement system, and EquatorTM shop-floor gauging systems. It also showcases our precision encoders and calibration devices — and we’ll use these for customer demonstrations and training sessions.”
Renishaw is continuing to invest in upgraded and new facilities to better support its customers. In addition to the facilities in India and Japan, within the past year it has also opened new offices in Brazil and created its first subsidiary operation in the United Arab Emirates, to serve the rapidly growing manufacturing and advanced engineering sectors in the Gulf Cooperation Council region and Egypt.
We specialise in CONNECTING skilled contractors with manufacturing businesses
Our platform seamlessly BRIDGES THE GAP, facilitating collaborations that enhance project efficiency and quality.
With a focus on streamlining communication and fostering valuable partnerships, CONTRACTORS 4 INDUSTRY LTD is the go-to hub for engineering professionals and manufacturing enterprises seeking successful collaborations.
ADVANTAGES FOR INDUSTRIAL ENGINEERING CONTRACTORS:
• High quality leads targeted audiences
• Data-driven insights efficiency
• Enhanced reputation cost-effective marketing
ADVANTAGES FOR INDUSTRIAL
PROJECT/ENGINEERING MANAGERS:
• Verified expertise enhanced productivity
• Cost-efficiency flexibility
• Specialised network streamlined process
Recognising that there’s a problem in an industry run by giants is the first step to ending customer complacency, but recognising that there are viable alternatives to these giants without the perceived hassle opens huge opportunities to change the way you do business. Andrew Jones, Technical Director at Axair Fans examines the benefits of stepping out of complacency.
As customers we often get so conditioned to an industry that we assume there is only one way of doing something. But as we all understand, there’s rarely one way. In an industry where there are a handful of excellent companies with a strong complete team, there are also small to medium businesses in the industry who don’t have the advantage of being completely autonomous in their component sourcing. They lack resource or confidence in their own technical selections, integration techniques, or have a fear of trusting unknown suppliers, creating barriers to future competitive advantage.
Fear is a huge driver of complacency. A procurement department tasked with finding components, may turn down a lesser-known company that in culture, value and service, is a better fit for their needs. The reason? Fear, whether real or perceived, that their job would be on the line if something went wrong. This causes teams to ignore the express purpose of their job and even do something that was not in the company’s best interests.
Imagine approaching a new component sales organisation for technical assistance and having one single contact for technical
Reports show that 84% of technical buyers prefer purchasing from a company that understands their goals, they clearly want to be understood.
and commercial questions, without getting passed around when you just need the answer that enables you to move onto the next step. Large companies struggle with this, especially as they’ve grown quickly and lost that attentive value. Customer requests are initially dealt with by customer service, escalated to senior levels, then passed to technical with weeks of delays and customer chasing before being brushed aside. The same message is rung around multiple industries. That larger companies often don’t have the time or care for customers spending below a certain threshold. Standards change if you allow them to, when companies start working more with larger customers. The
cost of that choice falls on the value added for customers outside of these golden eggs. For small to medium company issues, this poor level of service continually creates complacency. These large companies can stop caring and begin to take customers for granted. That’s an indication that the industry itself has become complacent.
From my experience of working in the tech and engineering industries in my career, similar sized business clients have similar needs; to work collaboratively, to be listened to, to have access to an attentive and focused contact, and to rely on the resourcefulness of the technical team in helping to integrate solutions. Focusing on our niche clients in the value-added customer centric approach we have at Axair leads to trust, quick decisions and everything just moves at a faster pace.
Customers are individuals, they’re not companies they work in. We identified early on that our purpose was to help customers to build better systems, and almost 32 years on from our incorporation date, we continue to embed our values into the team, forming long lasting relationships and partnerships with key industry stakeholders.
If your business is coasting by working with existing suppliers who haven’t stepped up the mark, then it’s time to think about how you can end the complacency. Yes, its always tempting to go after the biggest fish in the pond, thinking it will clearly be the best, but if you’re falling short, then consideration should be given to better value-added smaller players who just might be the right fit for your needs.
Following recent turmoil in the global employment market, countless businesses have reported problems in find the quantity and quality of workers needed to keep operations running smoothly. This labour shortage is being felt particularly strongly across the warehousing, logistics and e-commerce sectors, which are having to handle more packages than ever with fewer workers. Fortunately, both challenges can be partly addressed by a single piece of technology – the Prime Vision Flow Projector.
Almost three-quarters of warehouse operators in the U.S. say they can’t find enough staff1. On top of that, even when they can find new employees, it’s often hard to retain them. For instance, Amazon struggles to keep warehouse workers for long periods, reporting that only one in three of their employees remain for more than 90 days after being hired2.
There’s no single reason for this. Rather, there is a broad combination of factors that make the job both physically and mentally demanding. High turnover rates are driven by the repetitive and sometimes strenuous nature of manual sorting tasks, which can lead to job dissatisfaction and burnout.
This leaves warehouse operators with two key challenges. Firstly, they need to find a way to reduce turnover by improving worker satisfaction by alleviating the monotony and strain of manual
sorting tasks. Secondly, they need to find a way to address the issues they are facing right now and find a solution that can help workers operate effectively with minimal training and experience. These are two areas where Prime Vision’s Flow Projector can help.
The Prime Vision Flow Projector is an advanced technological solution designed to optimise the efficiency and accuracy of parcel sorting processes in warehouses and e-commerce fulfilment centres. Essentially, it is a compact unit that houses a combination of recognition sensors, laser projection technology, and vision recognition software. When installed above a sorting area, the Flow Projector can immediately identify the destination of a parcel by reading its barcode. Using a laser beam, it projects the sorting
destination directly onto the parcel, providing clear and precise guidance for the sorting personnel.
As parcels move along the conveyor, the system tracks their movement, maintaining the projected sorting number on each parcel until it is collected. This continuous tracking ensures that workers can easily and accurately sort parcels without the need for handheld scanners or other additional tools, significantly streamlining the process.
Moreover, the display be configured to not only show the final sorting destination, but also the sequence in which packages should be loaded into trucks. This feature is particularly beneficial for optimising loading efficiency and ensuring that parcels are loaded in the correct order for delivery routes.
By reducing the physical strain and monotony associated with traditional sorting methods, the Flow Projector enhances job satisfaction.
The technology’s plug-and-play capability means that it can be easily integrated into most existing sortation systems without requiring extensive modifications or large investment costs.
The Prime Vision Flow Projector significantly boosts productivity, with users usually experiencing at least a 50% increase. This improvement stems from the ability to project information onto multiple parcels simultaneously, allowing operators to handle several items at once. This capability drastically reduces the time spent on repetitive tasks, such as scanning each parcel individually with a handheld device.
By enabling workers to sort multiple parcels in a single action, the Flow Projector optimizes the workflow and increases the throughput of the sorting process, leading to more efficient overall operations.
The Flow Projector eliminates the need for handheld scanners or other cumbersome technology, freeing workers from repetitive and physically demanding tasks. This means employees spend less time manually sorting parcels and always have both hands free, making it much easier to pick up and manipulate the items.
By reducing the physical strain and monotony associated with traditional sorting methods, the Flow Projector enhances job satisfaction. Workers appreciate the intuitive nature of the technology, which simplifies their tasks and reduces stress. As a result, they are more likely to find their work engaging and fulfilling, leading to higher morale and lower turnover rates.
One of the standout benefits of the Flow Projector is its ability to quickly onboard staff, including those who may not speak the local language. Traditional training methods can take up to three days, but this is reduced to about half an hour with the Flow Projector.
Indeed, the technology is so intuitive that workers often require no formal training at all - they can simply observe the system in operation and immediately understand how to use it. This makes the Flow Projector an excellent tool for environments with high turnover or when employing temporary staff.
The Flow Projector is designed to be affordable to install and does not require a redesign of the existing warehouse infrastructure. Installation is quick, typically completed within a day, making it accessible for businesses of various sizes. Unlike other solutions that may take weeks or months to implement, the Flow Projector can start delivering real, tangible benefits within an hour of coming
online. Its plug-and-play nature ensures minimal disruption during deployment.
Additionally, its scalability allows for gradual implementation across multiple warehouse exits, enabling businesses to expand its use as needed without significant upfront costs. This quick return on investment (ROI) makes the Flow Projector a highly attractive option for improving efficiency and productivity in warehouse operations.
Another great benefit of the Flow Projector is its ability to optimise sequencing. By ensuring that parcels destined for early delivery are loaded first, it enhances delivery efficiency and streamlines the process. This smart sequencing reduces fuel consumption and lowers CO2 emissions, making it a win for both logistics operations and the environment.
The Prime Vision Flow Projector is a key solution for warehousing and e-commerce businesses grappling with labour shortages. By integrating advanced recognition sensors, laser projection technology, and vision recognition software, it addresses the dual challenges of reducing worker turnover and enhancing operational efficiency.
This allows it to not only solve immediate operational challenges but also position warehouses for long-term success by fostering a more efficient, satisfied, and stable workforce. As Prime Vision continues to innovate and support the warehousing sector through technological innovations, businesses can look forward to even greater enhancements in productivity and efficiency.
More from Prime Vision: https:// primevision.com/how-primevisions-flow-projector-benefitswarehouse-staff-for-streamlinedsorting-processes/
In an ever more competitive and connected world, marketing has increasingly become a tool which manufacturers and engineers choose to use.
And, as the digital revolution transforms how we manufacture and engineer, it’s little surprise companies appreciate its role in engaging with customers too.
Often overlooked by marketing specialists, a new breed of marketing agency is focusing on the needs of those who make or engineer products and solutions.
Sarah West, award-winning Chartered Marketer and founder of B2B marketing experts, Full Mix Marketing, shares her experience identifying the best marketing tactics for companies in manufacturing and engineering.
Is marketing more important than ever for manufacturers and engineers?
The answer to this question may depend on your perspective.
Amidst rising competition, companies in nationwide and international segments often feel an investment in marketing is critical to keep their name in customers’ minds.
Many smaller manufacturing and engineering firms remain reliant on word-of-mouth, reputation and existing relationships. As such, a website, brochure or regular trade show may be the extent to which they consider marketing.
In our experience, regardless of whether marketing is more important than ever, it is certainly more effective than ever.
Though it can feel like some traditional marketing tactics have less relevance, they can still deliver results.
Whether targeting growth - or to simply maintain your current size –actively focusing on your marketing makes either outcome much more likely.
An investment in equipment to boost your capabilities is rarely effective without the accompanying marketing to grow your order book.
What are the marketing challenges for manufacturers or engineers?
There are a number of unique challenges which can impact the marketing tactics for manufacturers and engineers:
1. Complex offerings
Many companies provide complex products or services which can be difficult to communicate.
The challenge is not only doing this succinctly but making sure you focus on addressing your customers’ needs and highlighting what makes what you deliver different.
2. Long sales cycles
Both manufacturing and engineering frequently involve long and intricate sales cycles, where valuable relationships are forged over time.
This typically means that to build trust, marketing too must be maintained over a lengthy period and its ultimate aim - to increase sales - can take time to achieve.
3. Competition
Manufacturing and engineering sectors are often highly competitive, with multiple companies vying for the same customers and contracts.
Price can be a significant driver. However, increasingly long and complex supply chains mean that quality and dependability are also more important than ever.
Successful marketing needs to stand out from competitors and communicate the right qualities.
Keeping up with rapidly developing technology can be essential for staying competitive – as can communicating your advances through your marketing.
Manufacturing can be particularly influenced by consumer trends and companies sometimes need to adapt their marketing to reflect changing buying behaviours.
Perhaps the greatest example of change is sustainability, with companies using marketing to
highlight their environmentally friendly practices.
There are an increasing number of marketing channels which can be used to promote modern businesses.
Our experience working with manufacturers and engineers has helped us identify several which frequently feature in a successful marketing mix.
Though digital marketing may not be as critical as it is for consumer marketing, it is increasingly important for manufacturing and engineering. Many potential customers will visit your website when researching or considering what you deliver and it may be the likely destination for much of your marketing.
Search Engine Optimisation (SEO) can help elevate your business to the first page of search engine results. However, it’s worth using tools to analyse the number of potential customers who are searching as it may be low if what you deliver is niche.
SEO takes time, so online advertising such as Pay-Per-Click (PPC or Google Ads) can also help target those searching - if sufficient volume exists.
Content marketing is perhaps the biggest growth areas of modern marketing.
Content such as blogs, guides, opinion pieces and videos can have multiple benefits, including establishing your expertise and boosting website traffic. Showcasing successful projects via case studies and testimonials can quickly build trust in what you deliver.
Trade publications and websites are often crying out for press releases and stories about any developments within businesses in their sector.
Social media - and LinkedIn in particular - can help you share industry news, product updates and engage with your audience, including decision-makers in the businesses you’d like to work with.
For many manufacturers and engineers, their number of
target clients is small and clearly identifiable. This can make direct marketing particularly effective.
Data can often be purchased to create a comprehensive list of businesses and key individuals to target. Industry membership organisations can be a good source too.
Email campaigns can promote products or services, share updates, disseminate useful content and nurture leads. In an online world, receiving a sales letter, mailer or physical brochure in the post can often have a greater impact than many might imagine.
Though it can feel like some traditional marketing tactics have less relevance, they can still deliver results.
Many manufacturers and engineers believe their business emanates from industry connections – and they’re often correct. However, it is also something which can be encouraged through marketing channels which boost awareness of your capabilities and expertise.
Participating in trade shows, exhibitions and other industry events can be a highly effective way to showcase your capabilities and meet the clients you wish to work with. An after-show strategy to follow up the contacts made is essential.
When it comes to successful marketing, tailoring the right tactics to your specific business and sector is critical.
As East Anglia’s leading B2B marketing agency, we work with businesses across the UK in manufacturing, engineering, technology and similar sectors. We go to great lengths to understand what they do, what makes it great and how best to reach their customers through marketing.
Daysoft only makes and sells daily disposable contact lenses because these are the healthiest type of contact lens to wear.
• From just 20p per lens delivered
Here at daysoft® we’re focused on what matters: providing simple, affordable vision solutions that are kinder to the planet without compromising on quality.
• Made in the UK; over 1 billion sold
We believe healthy eyesight should be affordable for everyone
So we cut out the middleman and pass the savings to you. daysoft® lenses are made to rigorously high standards in our UK lab and then sold online, straight to you. As the only company in the world that design, make and sell contact lenses directly to customers, we’re able to replace other brands for half the price without compromising quality.
• Simple to use; no cleaning so no cleaning solutions
• Brand switch to daysoft® with no optician refitting needed Order
We’re the environmentally conscious choice
daysoft® is a Registered Trade Mark of DAYSOFT Limited
We’re conscious that single-use daily disposables have an impact on our planet. That’s why we’re working towards innovative solutions to reduce our carbon footprint.
We’re trailblazers in innovation and expertise
We’ve always been ahead of the curve when it comes to innovation and design. Our chairman, Ron Hamilton, invented daily disposables and built the world’s first laboratory dedicated to making them. We continue to innovate and improve, using patented daysoft® technology and our unique SoftEdge™ design to offer you the safest way to wear lenses at an amazingly affordable price.
Our unique INPAC technology enables us to reduce excess plastic waste by up to 50%.
Designed and manufactured in the UK, our contact lenses have a lower carbon footprint than those that are shipped from across the globe.
Quality made medical devices
Safe, accessible, healthy eye care for everyone is at the heart of our vision at daysoft®. Our contact lenses are
• From just 20p per
• Easy to buy; either subscription or pay-as-you-go
We’ve always been ahead of the curve when it comes to innovation and design.
• Simple to use; no
• Easy to buy; either
• Made in the UK; over
• Brand switch to daysoft® refitting needed
medical devices, and as such are required to meet strict standards, measured through a rigorous regulatory framework.
Daysoft only makes contact lenses because healthiest type of Order online at
daysoft® is a Registered Trade
1
ALL OF OUR CONTACT LENSES ARE:
• Manufactured under the control of a certified Quality Management System, compliant with ISO 13485:2016.
• Approved under the European Medical Devices Regulations (Directive 93/42/EEC) under The Medical Device Regulations (Canada), licence #61427
• We’re also subject to regular audits by SGS Belgium Ltd, to ensure we continue to meet regulatory requirements, including stringent checks on the effectiveness of our sterilisation process.
we
daysoft’s® manufacturing process has been designed around the high specification details of the contact lens itself. Our state-of-the-art facility in Blantyre, Scotland only makes daily-disposable lenses and our processes, along with a highly skilled workforce allow us to supply you with the highest quality lenses at the most affordable price.
70,000+ repairs annually:
Proven reliability with thousands of successful repairs every year.
Quality since 1984 thanks to knowledge and experience: Decades of experience ensure in-depth knowledge and craftsmanship.
Comprehensive test centre:
More than 1,400 test rigs for thorough and reliable testing.
A ‘green’ choice:
Contribute to CO2 reduction by choosing repair.
Fast repairs:
Thanks to an extensive stock of time-sensitive components.
We carry out more than 70,000 repairs annually and have an extensive test centre with more than 1,400 test stands.
We can fully test your industrial electronics!
A repair takes place at our headquarters in the Netherlands and/or at our repair sites in Poland, China, Brazil and the UK. Skilled technicians repair at component level, supported by advanced measuring and testing equipment.
UNIS Group specialises in the repair of both end-of-life, used and new electronics. Since 1984, we have offered quality thanks to our extensive knowledge and experience.
We carry out more than 70,000 repairs annually and have an extensive test centre with more than 1,400 test stands. Moreover, we are a ‘green’ choice by reducing our CO2 footprint. Thanks to an extensive stock of time-sensitive components, we can guarantee fast repairs.
Interested?
Contact us at uksales@unisgroup. com or +44 1604 499 777 and we will be happy to discuss the possibilities with you.
For further information, please visit www.unisgroup.co.uk
70,000+ REPAIRS ANNUALLY:
Proven reliability with thousands of successful repairs every year.
SINCE 1984:
Proven reliability with thousands of successful repairs every year.
70,000+ REPAIRS ANNUALLY: COMPREHENSIVE TEST CENTRE:
Decades of experience ensure in-depth knowledge and craftsmanship.
Decades of experience ensure in-depth knowledge and craftsmanship.
More than 1,400 test stands for thorough and reliable testing.
More than 1,400 test stands for thorough and reliable testing.
Contribute to CO2 reduction by choosing repair.
Contribute to CO2 reduction by choosing repair.
COMPREHENSIVE TEST CENTRE: A ‘GREEN’ CHOICE: FAST REPAIRS: QUALITY SINCE 1984:
Thanks to an extensive stock of time-sensitive components.
Thanks to an extensive stock of time-sensitive components.
We can fully test your industrial electronics!
We can fully test your industrial electronics!
UNIS Group specialises in the repair of end-of-life as well as used and new electronics. Skilled technicians repair at component level, supported by advanced measuring and testing equipment. Contact us for more information!
UNIS Group specialises in the repair of end-of-life as well as used and new electronics. Skilled technicians repair at component level, supported by advanced measuring and testing equipment. Contact us for more information!
www.unisgroup.co.uk
www.unisgroup.co.uk
uksales@unisgroup.com +44 1604 499 777
uksales@unisgroup.com +44 1604 499 777
Quirepace manufacture the BVC range of Industrial Vacuum Cleaners. BVC is the original “British Vacuum Cleaners”, and the majority of the current range is manufactured here in the UK in Quirepace’s Fareham factory.
The BVC range of Industrial Vacuum Cleaners is specifically designed to meet the demanding requirements of manufacturing and processing operations by offering robustness, efficiency, heavyduty construction and excellent after-sales back-up.
There are two separate and distinct applications for Industrial Vacuum Cleaners within manufacturing facilities. The first is for general housekeeping; a clean environment is a safe environment. The BVC range offers vacuum cleaner solutions for all products and environments, and in particular offers M-Class and H-Class machines designed specifically to collect hazardous materials or which are designed to operate in ATEX designated zones.
The second application for Industrial Vacuum Cleaners within process and manufacturing is where the machine is integrated directly in to the workflow.
With design and production in-house, Quirepace are able to customise standard machines for bespoke applications.
This integration may be physical adaptations to direct the vacuum to a particular part of the work area and/or may be control integrations to enable the
equipment to be actuated directly by the process controls. For example, BVC models in the IV62, Ti60 and Ti80 ranges all offer the option for control through contacts suitable for interface to external control systems.
A huge range of hoses, tools and accessories are available, and Quirepace carry extensive stocks of consumables and spare parts ensuring BVC Industrial Vacuum Cleaners can be relied upon to deliver robust performance whenever and wherever needed.
Quirepace offer demonstrations on site, and the knowledgeable and experienced sales team will guide the user to the perfect solution for the application.
Industrial Processing includes a vast range of potential applications for perforated products. RMIG Solutions has extensive experience in the chemical, pharmaceutical, paper, and offshore industries, to name a few. From small, high precision perforation in thin materials to large holes in thick sheets used in the mining industry, RMIG Solutions has the knowledge, versatility, and tooling to deliver products according to customers’ requirements.
One particular area of Industrial Processing is dealing with waste water. The water industry presents a number of unique challenges in the use of perforated products. A key consideration here is the aggressive nature of the water towards the materials being used. RMIG Solutions has vast experience in servicing the waste water industry, and produces high flow, burr-free perforated waste water screens, offering accurate screen tolerances and effective separation.
Another area of Industrial Processing is medical and pharmaceutical, where RMIG Solutions’ perforated materials are able to give firm tolerances during their manufacture, and are well suited for use in sterile environments.
RMIG Solutions’ perforated products also have numerous uses in the petrochemical sector, from industry specific applications such as filtration, to oil and gas exploration, as well as more general applications such as walkways in processing plants.
The Bridge Slot sheet from RMIG Solutions play an essential role when it comes to the design and manufacture of biomass drying floors. The combination of sheet thickness and opening size allows RMIG Solutions’ sheets to be used either as a suspended floor in wood chip drying containers and trailers, or as drive-on drying floors in outdoor buildings.
The bridge slot opening size determines the products that can be dried, which range from fine oilseed rape through to larger grains and cereals, as well as logs and wood chip drying.
RMIG Solutions’ food processing market sector meets the high levels of hygiene demanded by the food processing industry. Perforated screens are also strong with important thermal capabilities, making them useful for a wide range of food processing applications. RMIG Solutions’ tailor made perforated solutions are ideal for cleaning, heating and steaming in food production environments. Whether it’s baking trays, cereal cleaning or ingredient conveyors, all of RMIG Solutions’ perforated materials can be customised for each application.
Control leader Promtek returning for PPMA 2024 after hit debut last year
Stand E32, PPMA Show, 24-26 September 2024, NEC Birmingham
Automation specialist Promtek Ltd will be returning to the PPMA show this September, showcasing its pioneering cloud-based process control solutions for intelligent weighment management, recipe handling and production monitoring. Stand E32, PPMA Show (24-26 September 2024, NEC Birmingham).
Following the success of last year’s debut at the show, the company’s Condor CloudTM and MicroManTM control systems will once again be demonstrated to visitors. Together they provide a complete strategic overview of every aspect of production, taking the fuss out of managing ingredient reformulations, equipment utilisation, climate impact and energy costs.
As a cloud-based alternative, Condor Cloud offers IT/OT integration for ingredient and recipe handling without the need for expensive IT infrastructure, making it ideal for fast-growing SME manufacturers with a weighing process. With no need for onsite servers or network requirements, the browser-based Condor Cloud will help grow a business, reduce costs, and optimise production facilities without the need for overly complicated software or paper trails.
Promtek’s unrivalled all-in-one platform uses predefined algorithms to calculate energy efficiency accurately, bringing all the benefits of large-scale manufacturing systems to smaller-scale facilities. Using the
system’s time-in-motion capabilities, each step in the production process is analysed and measured, and a standardised time for each stage is established. By analysing the data in Condor from each connected motor and input, the MES can trim down production waste and reduce energy usage by fine-tuning individual equipment settings – significantly lessening the amount of kWh/t.
MicroMan, a hand weighing platform, collates ingredient and recipe information from manual adds, either as part of a bigger batch using Promtek’s signature process control platform StoraWeigh or the integration platform Condor, to generate bespoke production control and data. Businesses can use the data to create customer-specific trusted records of weights and measurements of ingredients and materials, manage recipe control, improve ingredient traceability, prevent cross-contamination and assist with order scheduling.
Promtek’s Marketing Manager, Lani Scholtz, explained: “Promtek is thrilled to be heading to the PPMA once again. We are truly excited to showcase our next-level innovations, and as well as this, there’s the opportunity to discuss the customised solutions we can offer, like a system we created in conjunction with Schneider Electric recently based on the Tesys Island.
“By combining our expertise and technology with Schneider’s Tesys, we were able to set up a system where a feed mill’s machinery was completely controlled and monitored via a network connection, without the need for contactors or a costly PLC. We love what we do and we’re looking forward to making some fabulous new connections within the industry.”
Formed in 1972, Staffordshirebased Promtek has over fifty years of expertise designing and integrating process control and automation systems for various bulk material handling industries. The Potteries-based company is proud of its heritage and is the go-to provider of management solutions for developing, integrating and supporting process controls. Its automated solutions serve with distinction in the production facilities of top-notch companies all around the globe.
To learn more, visit Promtek on Stand E32 at PPMA Show, 24-26 September 2024, NEC Birmingham.
For further information, please visit www.promtek.com
Sidel’s advanced agile packing and palletising solutions will be showcased on stand E84 at the PPMA Show, at the NEC Birmingham, UK, 24 – 26 September.
PPMA is the UK’s leading exhibition for processing and packaging machinery, attracting engineers, production and processing specialists, project managers, and buyers.
Sidel will be showcasing on-stand agile packing and palletising solutions designed for the food, home, and personal care (FHPC) sector, alongside innovative turnkey packaging solutions.
“Explore Sidel’s packaging expertise at PPMA 2024 this September,” comments Bastien Carcenac, Account Manager of Sales for FHPC UK. “Improving line performance is no easy task, but Sidel’s solutions can help manufacturers reduce downtime and operational costs while adapting to market demands – supercharging efficiency.”
Sidel will present agile packing and palletising solutions tailored to meet the evolving needs of modern manufacturing environments, highlighting advanced automated machines such as the RoboAccess_ Pal S and the CoboAccess™_Pal. Both machines replace manual palletising with short payback, typically in 1-2 years, ensuring a quick return on investment.
The RoboAccess_Pal S handles up to 2,400 products per hour, delivering high performance and flexibility in a compact footprint. This solution maximises space utilisation achieving speeds of up to 12 cycles per minute and accommodating a case payload of up to 25 kg.
The CoboAccess_Pal™ enhances working conditions and maintains high-level safety standards. These solutions are engineered to optimise the end-of-line packaging process.
From standalone to turnkey solutions for wide production
At the show, discover how the Sidel range of packaging solutions is adapted to all production rates, ensuring the flexibility needed to meet diverse industry demands. As a single supplier of advanced packaging technologies, Sidel ensures seamless system integration with its complete packaging lines, optimising overall production
The CoboAccess_Pal™ enhances working conditions and maintains high-level safety standards.
efficiency. For those looking to enhance specific production areas, Sidel’s standalone machines offer high performance and flexibility.
Bastien Carcenac concludes: “Sidel’s offerings cover all aspects of the packaging process, from PET blowing to filling, labeling, packing, and palletising. This integrated approach enables Sidel to deliver tailored solutions that meet the unique needs of each client’s packaging requirements, space constraints, and production speeds.”
For further information, please visit www.sidel.com
For over 35 years the annual PPMA Show has been a highlight of the processing and packaging industry’s calendar. This event, between 24-26 September at the NEC in Birmingham, is renowned for bringing together thousands of visitors and exhibitors from the FMCG sector. It is anticipated that hall 5 will once again be filled with excitement and anticipation, providing visitors with a perfect platform to network with wellknown exhibitors and learn about their latest state-of-the-art technologies and solutions.
Owned and organised by Automate UK, the PPMA Show is recognised as
the industry leading event. It brings together the very best suppliers of processing and packaging machinery, robotics and industrial vision systems with the capability to deliver significant benefits to a wide range of businesses. These include cost reductions, increased efficiency, quality improvements, and reduced downtime and turnaround, all of which can deliver a healthy return on the investment in these technologies.
The show provides a unique opportunity for visitors to experience a complete production line with every aspect of it being represented, from labelling, filling
and packaging to processing, robotics, automation and industrial vision systems.
Visitors will be able to see the latest innovations from an impressive lineup of over 350 exhibitors, comprising over 1,500 brands. These exhibiting companies will be showcasing their latest cutting-edge solutions for the full spectrum of the manufacturing industry, including pharmaceuticals, food and beverages, building materials and suppliers, pet care, and microbrewers and distillers.
The show floor is expected to be vibrant with live demonstrations and product launches, along with
experts on hand to help the visitors find the right solutions for their needs. It is anticipated that the show will deliver impressive results with many business transactions taking place during the three-day show.
Aaron Moore, Asset Maintenance Manager, Nestle, said this about the 2023 PPMA Show: “Fantastic day here at the PPMA Show, lots of suppliers that we work with. Some really innovative solutions, and a lot of relatable things for us, so we are taking lots of lessons home.”
Here are just some of the hundreds of exhibitors taking part in the show:
Reiser (D110) has been a leading supplier of processing and packaging equipment for the meat, food, pet food, bakery, and cheese industries for over 60 years. From single machines to complete process-topackaging production lines, their solutions combine specialised equipment, custom engineering, and in-depth expertise to meet customer challenges.
Visitors will be able to see the latest innovations from an impressive lineup of over 350 exhibitors, comprising over 1,500 brands.
Videojet (E30) is one of the worldleading manufacturers of coding and marking systems. The company’s portfolio includes its full end-toend suite of primary, secondary and tertiary equipment, including printing date or batch codes onto a food package and labelling full traceability information on a pallet.
ULMA (B20) provides the most extensive selection of packaging machinery and applications on the market. ULMA’s product range also includes fully automated solutions encompassing crate/case loading,
product handling, pick and place, palletizing, end-of-line, and comprehensive turnkey project management.
Ishida (B50) is a world leader in the design, manufacture and installation of end-to-end weighing, packing and safety solutions for the food industry. The company helps manufacturers increase automation and compliance, reduce cost and downtime, increase operational efficiencies and brand protection, and maximise profits.
The comprehensive exhibitor listing is available online to help visitors plan their visit: https://www.ppmashow.co.uk
One of the show highlights is its informative and inspiring expert talks which provide visitors with a wealth of knowledge to take with them to consider how they can apply this to improve their businesses. This year’s keynote speakers are:
Jessica Sansom, Huel: The manifestations of climate changerising to the challenge and adapting to a new normal
The food industry is responsible for more than a quarter of all global greenhouse gas emissions. Without significant change in this industry, it will be impossible to limit global warming to under 2 degrees.
134 countries at COP 28 signed a declaration on sustainable food systems, meaning that they must now include food in their national climate action plans, including a commitment to shift from higher greenhouse gas-emitting practices to more sustainable production and consumption approaches.
Jessica’s presentation explores what needs to happen in the processing equipment and packaging machinery sector in order to meet those targets.
Stefan Casey, Nestlé: The digital transformation of FMCG industry: How digital technology is bringing both challenges and opportunities in packaging across the whole value chain
Stefan’s talk will focus on affordable personalisation and customisation in packaging design through to production. His presentation will cover points such as the needs for more flexible packaging production solutions, cost effective solutions by optimising end-to-end from design through to manufacturing, and quality control and safety. Visitors will also have an opportunity to hear from leading industry speakers including Matt
Androsiuk - Cobots and Machinery Safety Ltd, Dr Martin Kidman – SICK UK Ltd, Adam DickinsAD Frameworks Ltd, and Chris Whyborn - Thornton Tomasetti. The seminars provide a wealth of valuable insights covering a wide range of topics, such as industry standards, CE and UKCA marking, automation to reduce carbon footprint, and many more inspiring subjects.
In addition to the seminars UK Automation Forum will be hosting a panel discussion on ‘What would make UK food businesses adopt more robots?’. The panel is hosted and facilitated by Gail Hunt from Automate UK, who will be joined by industry experts including Mike Loughran - Rockwell Automation, Chris Rooum - MTC - Manufacturing Technology Centre (MTC), Mike Wilson - Manufacturing Technology Centre (MTC), Prof Phil WebbCranfield University, and Oliver
Selby - FANUC UK. The discussion will focus on the positive impact that adopting automation can have on the sector as well as sharing advice and learnings that can help to deliver successful outcomes.
In addition to discovering and exploring various innovations and solutions, experiencing live demonstrations, seeing product launches first-hand and learning at seminars, visitors will have plenty of opportunities to make new business connections and network with industry peers.
Automate UK wants to ensure that visitors have a standout show experience; one of the new features at this year’s show is the free PPMA Show app. This will allow visitors to plan their day, have easy access to their entry ticket and discover all aspects of the show, from exhibitors and products through to a complete list of seminars and speakers.
Scott McKenna, Chief Operating Officer at Automate UK, said:
“We’ve been working hard to ensure that the PPMA Show continues to live up to its reputation as the UK’s largest event showcasing innovative technology from the processing and packaging industry. Our aim is to ensure that the show continues to evolve and as such we’ll be introducing new features to enhance the show experience for both visitors and exhibitors.”
APPLICATIONS
Compressor blades and vane tips
Repair of combustion and flame tubes
Replacement of honeycomb seals
Turbine blades, vanes and NGVs
Compressor Casings
Compressor Discs
Exhaust Unit Components
Bolts and Fasteners
Shafts and Studs
SERVICES WE PROVIDE:
Chemical Cleaning/Stripping, Dry Grit
Blasting & Glass Bead Burnishing
Machining, milling, turning and grinding
Dimensional Inspection and Non-Destructive Testing
Metallurgical Assessment and laboratory reports
Application and/or replacement of Engineered Coatings and Thermal Spray
Dressing and blending of compressor and turbine blades
Heat Treatment
Welding: Tungsten inert gas (TIG) and Spot and Stitch
Vacuum Brazing
Rotaflow are into our fourth decade of designing and manufacturing Swivel Joints. We solve engineering problems where fluids need to be transferred across rotating interfaces, without leakage. Our units are in most engineering sectors: From Brewery, Dairy, Food & Drink, Process & Plant, Drilling & Mining, Oil, Gas and Subsea, Nuclear and Chemical.
Through design and in-house manufacture our swivel joints can allow one or more different flows through a single unit, enabling the pipework to rotate 360 degrees whilst carrying fluids (including hydraulic and pneumatic) of different pressures without cross-contamination or leakage.
There are many different forms of Swivel Joint… from very straight forward designs of our F and FS series, Compact swivels or Heavy Duty to Articulated Pipework configurations, Floating Suction Arms, Jacketed, High Pressure. A Swivel Joint reduces costs by reducing the risk of leakage with its associated downtime.
We are specialists in taking your bespoke requirements and being able to design a solution that can fit your budget, dimensions, materials, FAT/witness testing, hygienic and pressurised environments. We regularly test to Hyperbaric, Seal Life and conduct Temperature/Pressure/ Load Cycle Testing. We are ISO 9001:2015 certified.
With off-the-shelf solutions that are ready to go, or we can redesign and in-house manufacture to enable a quick turn-around with minimal fuss and maximum design experience.
To find out more please visit our website and/or give us a call. Tel: +44(0)1663 735003 | sales@rotaflow.com www.rotaflow.com
Articulated Pipework Torsion In Hoses
Rotating Cylinders
Swivel joints allow pipework to pressure 1/4” to 40” and beyond. Vacuum to over 20,000psi
Stock and bespoke production. Unique bearing/seal design for longer life.
ISO 9001 CE marked where applicable.
Tel: +44(0)1663 735003
E-mail:
Engineering business acquires historic boiler firm creating first-of-its-kind solution GREEN’S
Ropsley Ltd, the holding company of PJD Mechanical Engineering, announces that it has acquired Green’s Power, who invented the Economiser in 1841 and is now a global provider of heat transfer, economiser and industrial boiler products.
The parent company of PJD, who also owns Teesside-based fabrication business, Piper Services, amongst others, has made the strategic move to acquire the esteemed Green’s Power in order to provide a unique, end-to-end solution.
This acquisition will mean the expansion of one of the largest independent groups in the UK Power and Industrial markets, with a team of more than 250 specialists and an annual turnover exceeding £40m.
This merging of businesses, whose offerings will see the launch of a fully integrated solution,
We’re pleased to announce this acquisition and are keen to begin integrating the businesses and offering a seamless solution to customers new and old.
from steam boiler and pressure part design and engineering, to manufacture, installation and then repair and maintenance for a variety of sectors.
David Hayle at Ropsley Ltd comments: “We’re pleased to announce this acquisition and are keen to begin integrating the businesses and offering a seamless solution to customers new and old.
“Now that the economic challenges of the past few years are behind us, we’re very much setting our sights on further exponential growth and look forward to supporting this iconic business with the next phase of its development.”
Chris Wright, Operations Director of Green’s Power adds: “Green’s has been operating within the industry since 1821 and over this period, it established itself as a global leader in the provision of boiler equipment and services”
PJD’s strengths lie in site installation, equipment repairs, and servicing, while Green’s is a pioneer in design, engineering and manufacturing; creating a turnkey solution, with multiple locations across the UK and global manufacturing reach. For more information about PJD, visit pjdltd.com and Green’s Power visit heatexchangegroup.co.uk
“We’re now very much looking forward to the future, and our partnership with the Ropsley portfolio, to continue being a truly progressive developer of solutions within the group’s core sectors.”
SRC North-West Limited are a well experienced, Greater Manchesterbased roofing refurb and Solar PV company, covering the entirety of the UK. We primarily work in the commercial & industrial sector, with different types of businesses ranging in size, in a wide range of industries, but commonly within the high energy usage sector, such as manufacturing, fabrication, engineering and printing.
As a business, we offer fully managed, turnkey solutions, that take away the stress of arranging the project and various components within it.
SRC North-West Limited are a well experienced, Greater Manchesterbased roofing refurb and Solar PV company, covering the entirety of the UK. We primarily work in the commercial & industrial sector, with different types of businesses ranging in size, in a wide range of industries, but commonly within the high energy usage sector, such as manufacturing, fabrication, engineering and printing.
As a business, we offer fully managed, turnkey solutions, that take away the stress of arranging the project and various components within it.
We have a demonstratable, proven and historic track record in delivering high value contracts covering multiple disciplines. Our main focus is on providing safe projects at great value, finished to the highest of standards and calibre.
We have a demonstratable, proven and historic track record in delivering high value contracts covering multiple disciplines. Our main focus is on providing safe projects at great value, finished to the highest of standards and caliber.
SRC is unlike most, we are not just a Solar PV installer or a Roofing Contractor. From inception, we set out to be both, which often provides greater value for money and financial savings, instead of having to instruct two or more companies to carry out work. We manage the entirety of the project with one point of contact.
Given that often businesses are facing budgetary restrictions due to the rises we have seen in previous years, we are also pleased to offer the very commonly used £0 outlay option of having a PV system installed using a Power Purchase
SRC is unlike most, we are not just a Solar PV installer or a Roofing Contractor. From inception, we set out to be both, which often provides greater value for money and financial savings, instead of having to instruct two or more companies to carry out work. We manage the entirety of the project with one point of contact.
Agreement (PPA) which, if required, can also include roof repairs/refurbs within the package. This method is becoming more popular with large blue-chip companies due to the minimised risk.
As an engineer with over
Commercial Solar Panels are becoming increasingly popular amongst businesses in the UK, with the benefits being a way to save money on energy bills, whilst reducing carbon footprint and assisting with sustainability goals. With unpredictable energy costs, and growing pressures to demonstrate your green credentials, achieve Net Zero and your ESG commitments, installing Solar Panels can combat all points in one.
Jono
Garton – CBRE
They never once hesitated to go that extra mile in order to meet our clients expectations. Responsive , reactive and reliable - quite simply one of the best contractors I’ve dealt with in recent memory.
We offer free no-obligation site surveys and quotations to advise on the available solutions and the efficiency of them, as well provide you with 3D-deisgn and full system output simulations.
Commercial Solar Panels are becoming increasingly popular amongst businesses in the UK, with the benefits being a way to save money on energy bills, whilst reducing carbon footprint and
35 years in the industry I am extremely critical of contractors however I can honestly say that I am struggling to find any faults with any of their work.
on the available solutions and the efficiency of them, as well provide you with 3D-deisgn and full system output simulations.
To discuss the various funding options, and to see how they’ll suit your business get in touch using the details below or, why not come to visit our stand at the Advance Engineering Exhibition on 30th-31st October 2024, at stand F142.
To discuss the various funding options, and to see how they’ll suit your business get in touch using the details below or, why not come to visit our stand at the Advance Engineering Exhibition on 30th-31st October 2024, at stand F142.
You can contact us by:
Telephone: 0333 772 3015
Emai: Ryan@srcnwltd.co.uk
Linkedin: SRC North West LTD
You can contact us by: Telephone: 0333 772 3015 Email: Ryan@srcnwltd.co.uk Website: www.srcnwltd.co.uk
Instagram: SRCNWLTD
Linkedin: SRC North West LTD Instagram: SRCNWLTD
In the face of unprecedented demand for new aircraft, robotics specialist FANUC is helping the aerospace industry to increase production efficiency and boost output. Over the past five years, FANUC has supported Airbus with its in-house robotics strategy, culminating in Airbus developing a robotic drilling system which employs a FANUC M-800iA/60 sixaxis robot. The system has improved drilling accuracy and increased productivity for Airbus, while freeing up human employees to work on more creative and valueadded tasks.
The start of this year (Q1 2024) saw the global aircraft order backlog hit record-breaking heights, reaching 15,812 . Automation and robotics are considered key levers to support this increasing demand. FANUC has long championed the use of its industrial robotic solutions as a way for aerospace manufacturers to boost production rates, streamline their operations and cut cycle times.
“Automation has become crucial in closing the gap on the backlog in aircraft orders as it significantly enhances production efficiency,
reducing the time needed for manufacturing complex components,” says Oliver Selby, Head of Sales for FANUC UK.
“Additionally, automation minimises human error and allows for more consistent quality control, ensuring faster turnaround times and enabling manufacturers to meet demand more effectively.”
Boasting advanced automation technology and an experienced team of robotics experts, FANUC was the ideal company to support Airbus in the development of its
in-house robotics division. With its multiple drilling applications still largely completed manually, automating this process was a priority – but sourcing a robot that was robust enough to meet Airbus’ requirements initially proved a challenge.
“The specific solution that Airbus was looking for did not exist anywhere in the market,” explains Oliver. “The robot in question needed to be extremely rigid and stiff but also highly accurate, and with a minimum 60kg payload. We therefore worked together with Airbus to develop a prototype and refined this until it precisely matched their specifications for lower payload/small hole drilling.”
This prototype has gone on to become the M-800iA/60 six-axis model, which is now part of FANUC’s standard industrial robot range. Also suitable for laser cutting, welding or other applications which require extremely high levels of accuracy, it offers outstanding precision without slowing down the production process.
Following rigorous testing and validation with FANUC, Airbus placed the first commercial order for the M800iA/60. The robot is now part of Airbus’ proprietary automated mobile drilling system. This system has now gone into production and represents the first of a new generation of robotic solutions for Airbus that have been custom designed by its in-house experts, with technical support provided by FANUC. Now on its way to being integrated into the A320 Family pre-assembly line, it adds value to Airbus’ manufacturing processes by reducing costs and stoppages, all while improving quality and saving time.
Since the introduction of the M800iA/60 to the market, FANUC and Airbus have further developed the technology and implemented it into larger robots in the high accuracy/high stiffness range – 190kg and 270kg payload versions are now available, with a reach of 2m and 2.7m respectively. These additional FANUC robots could allow for further adoption in other applications within Airbus as they move to higher rate production to meet increasing global demand.
“There are numerous benefits to aerospace manufacturers of automating their drilling applications with the M800iA/60,
Showcasing the benefits of automation and robotics to the aerospace industry is vital in helping the sector to reduce the current backlog.
including improved accuracy and repeatability, increased output, and better use of personnel for more value-added tasks,” states Oliver. “Longer term, the development of an in-house robotics division should also enhance the industry’s ability to attract high-level talent to technologydriven, innovative and future-ready companies.”
The future of aerospace manufacturing Oliver continues: “From FANUC’s perspective, working with Airbus has been an extremely positive and rewarding experience. Showcasing the benefits of automation and robotics to the aerospace industry is vital in helping the sector to reduce the current backlog. This project demonstrates how important it is to collaborate with a robotics partner that will provide the right experience, knowledge, training and technology to support companies to achieve their commercial aims. We hope this will be the first of many such collaborations between FANUC and Airbus to increase efficiency within their manufacturing applications.”
To learn more about the future of aerospace manufacturing, visit FANUC on stand 4900 at the Farnborough International Airshow, 22-26 July 2024.
Sourcing high-end and highperforming electrical components for the product(s) you design or sell, is a challenge faced by many industries. Whether it’s home appliances, office equipment, medical solutions or any one of a vast range of products requiring power supply solutions, quality assured components have never been in higher demand.
Here at Ideal Power, our job is to make the process easier for you through our expert knowledge in specifying, sourcing and supplying a complete range of power supply solutions. This ranges from typical external power supplies and battery chargers to internal power supplies and DC/DC converters.
We also specialise in providing tailored power supply solutions that precisely align with your unique and specific requirements. Our expert team works closely with you to understand your needs and develop custom solutions that optimise performance, efficiency, and reliability.
Why Choose Ideal Power?
Expert Knowledge: Our team of specialists possess extensive expertise in power supply technology, ensuring that we provide our clients with the most suitable and advanced solutions for their projects. Whether you need assistance with product selection or technical support, we are here to help.
Fully Certificated Products: All our products come fully certificated with relevant approvals, ensuring compliance and peace of mind.
Large Variety of Products: Our extensive product range includes everything from AC-DC power supplies and DC-DC converters to battery chargers and custom power solutions. Whatever your power supply needs, we have the right product for you.
Bespoke Products: We understand that every project is unique. That’s why we offer customised power supply solutions designed to meet your exact specifications. From standard products to fully bespoke designs, our solutions are engineered to deliver optimal performance.
Design-In Distribution: As designin distributors, we offer seamless integration of our products into your systems.
Product Supply Management:
Managing your power supply inventory can be challenging. Our supply management services streamline this process, ensuring that you always have the right components when you need them. We handle everything from procurement to logistics, so you can focus on your core business.
12 Month call-off service: No room for storage, no problem. Our service ensures you always have the power solutions you need, when you need them
Stay ahead with our expert knowledge and bespoke products tailored to your business needs.
Benefit from our reliable worldwide distribution and convenient call-off service, ensuring you get the components you need, when you need them.
Your electronic design and manufacturinng partner
Workingwithourengineers,wescopeoutyour electronicdesignfromconcepttoreality,ensuring qualityateverystage.
Ourengineersdesignschematics,PCBlayoutsand createelectronicmanufacturingprocessesthat meettheneedsofyourelectronicdesign.
Ourin-houseassemblycapabilitiesdeliveryour high-qualityelectronicdesignprototypes,ready foruse.
www.gspkdesign.ltd.uk sales@gspkdesign.ltd.uk
Scantovisitourwebsite MD652323 FM541918 ATEX 7422
FORTEC UK is proud to unveil the Litemax IPPS-4851-APL9, a cutting-edge 48.5” Panel PC tailored specifically for the transportation sector by Litemax, a renowned manufacturer in the outdoor market. This innovative solution is engineered from the ground up to excel in outdoor environments, boasting a remarkable brightness of 3000 cd/m² that ensures exceptional visibility even in challenging lighting conditions.
Key Features of the Litemax IPPS-4851-APL9 include:
• HiTni Panel for Direct Sunlight: Engineered with HiTni technology, this panel prevents blackening of the TFT polariser and maintains display clarity when exposed to direct sunlight for extended periods, making it ideal for outdoor and transportation applications.
• Auto DLS Dimming with IR Remote Controller: Advanced Auto DLS Dimming adjusts screen brightness based on ambient light levels, enhancing visibility and reducing power consumption. The IR remote controller adds convenience and ease of operation.
• 3mm AG Glass with Waterproof Full Flat Design: Featuring 3mm Anti-Glare (AG) glass and a waterproof full flat design, the IPPS4851-APL9 ensures durability and reliability in diverse environmental conditions, guaranteeing longevity and consistent performance in harsh settings.
• UVIR Film for Outdoor Harsh Environments: Specially designed UVIR film protects against UV and IR radiation, further extending panel lifespan and suitability for outdoor use.
• Slim and Sleek Design: With a slim 25mm display thickness and a sleek 1.5mm border, the IPPS-4851-APL9 combines functionality with a modern aesthetic, perfectly suited for contemporary transportation environments.
• Versatile Power Input Options: Supporting multiple power input options (AC110/220V, DC9-36, and optional DC110V), the Panel PC
Benefit from a perfectly harmonised complete system for the DC 24 V control voltage level. The modular REX system flexibly adjusts to your application. It saves up to 60 % space in the control cabinet and can be easily installed thanks to its patented connection technology.
features M12 connectors built to withstand vibrations, shocks, and environmental factors like dust and moisture.
Brendan O’Reilly, Display and Embedded Solutions Manager at FORTEC UK, expressed enthusiasm about the IPPS-4851-APL9’s introduction to the UK market: “Its exceptional brightness, size, and robust features make it an ideal solution for transportation applications, where visibility and reliability are paramount. This addition to our product lineup underscores our commitment to providing innovative and high-quality display solutions.”
The Litemax IPPS-4851-APL9 is now available for order. For further details, please click here.
GSPK Design, based in Knaresborough, North Yorkshire has delivered outstanding electronic design and manufacturing services for over 24 years. Our commitment to quality has earned us an outstanding reputation amongst clients both domestically and internationally. We are delighted to say that in 2024, we are seeing continued growth in all aspects of our work.
The team will bring new ideas that will further enhance our wide range of capabilities.
This growth is highlighted by the addition of a new head electronic design engineer who will take the lead on electronic design projects. The team will bring new ideas that will further enhance our wide range of capabilities. Additionally, we’ve expanded our production workforce, which will help bolster our collective skills to produce fully assembled PCBs to a wide range of sectors.
Some of the sectors we work within include medical, automotive, defence & instrumental control. Working on such a variety of projects has allowed us to expand our quality accreditations to include iso 13485:2016, for the design and manufacture of medical devices, as well as SGS ATEX certification, for the design and manufacture of electronic equipment for use in potentially explosive environments.
At GSPK Design we want to be at the forefront of the ever-changing technology landscape to best support our client’s needs. To match the high demand for our services, we have expanded our production area. This has allowed space for two new SMT lines and many more new pieces of cutting-edge equipment. These improvements will help us achieve quicker turn arounds and even higher quality.
To discuss your electronic design and manufacturing requirements, email us at sales@gspkdesign.ltd.uk.
Manufacturing precision gears, gearboxes and assembled components for suppliers in the aerospace industry
Providing engineering expertise and precision parts for commercial aircraft
Manufacturing an extensive range of electro-mechanical components for the medical industry
Providing engineering expertise and precision parts for medical scanners & radiotherapy machines
Our world class engineers deliver global solutions utilising cutting edge technology for critical industries including: Medical, Aerospace, Oil & Gas, Off-Highway and Defence
Contact us today and see how we can deliver your vision
Advanced Engineering, the UK’s premier annual event for the engineering and manufacturing sectors, has announced this year’s keynote speakers. The six industry leaders — and 150+ other speakers — will share their expertise and insights on critical industry issues during talks across several different forums. The two-day show will take place at the NEC in Birmingham on October 30 and 31, 2024.
The first of this year’s keynote speakers, Brian Holliday, is a leading figure in industrial technology and digital manufacturing. As the head of Siemens Digital Industries for the UK and Ireland, he oversees advanced automation, industry software, systems integration and R&D. He is an expert on productivity, digital manufacturing and industrial strategy, often contributing to media discussions.
The next speaker Matthew Atkinson, lead research engineer at Jaguar Land Rover, is an expert in automotive engineering, specialising in replacing metallic structures with injection moulded composites. His work focusses on interior mechanical commodities like cockpit, seating and loadspace features and his innovative approach has earned him multiple patents, including for the Range Rover 18MY Executive Seating.
Next, Shaun Harris CBE is currently director of support and chief engineer at the Royal Air Force. With a distinguished 37-year career in the RAF, Shaun has held numerous leadership roles. His extensive experience
This year’s speaker lineup brings together some of the brightest minds in the industry.
spans engineering, logistics and information warfare. Shaun has served around the world, from the UK and USA to Afghanistan and Iraq.
Also set to speak are Solange Baena, UK lead for the aviation environmental roadmap at Airbus, and Leonie Moffat, laser radar sales account manager at Nikon. Last but most certainly not least is Stefan Lawrenson, senior polymer chemist at Scott Bader, who specialises in sustainable technology and polymer chemistry. His research focusses on enhancing nanoparticles and synthesising eco-friendly materials.
“This year’s speaker lineup brings together some of the brightest
minds in the industry,” said Alison Willis, CEO of the show’s organiser, Easyfairs UK & Global. “Their diverse expertise will provide deep insights into pressing issues like Industry 4.0, supply chain management and sustainability.
“This lineup highlights the spirit of innovation that Advanced Engineering is all about, and our commitment to fostering knowledge exchange within the engineering community,” concluded Willis. “I’m sure the knowledge and inspiration they’ll bring to the event will be of value to all visitors.”
Advanced Engineering brings together industry leaders and professionals to explore the latest innovations across multiple sectors, including aerospace, automotive, defence and security, marine and more. Attendees can expect presentations on a wide range of topics, from digitally enabled supply chains to advanced propulsion technologies. The full speaker program will be announced soon.
Union Industries, the UK’s leading manufacturer of high-speed industrial roller doors, is celebrating its 10th anniversary as an EmployeeOwned Trust (EOT).
Incorporated as Union Industries in 1972, the Leeds-based manufacturer has gone from strength to strength since founders Isobel and Paul Schofield took the decision to safeguard the future of the company by selling their majority share to the Union Industries EOT.
In the last decade, the business has paid more than £3m in tax-free bonuses; in the last five years alone, employees have each received an annual bonus of £3,600, and in 2024 that rose to £6,500 per employee. It has also achieved record levels of revenue and profit, with profit soaring from £130,000 in 2013/2014 to £2.4m in 2023/2024.
10 years of success for any business is a major milestone, but 52 years of business and for 10 of those, the most profitable ones, to be as an Employee-Owned Trust is remarkable.
Employees also have a vested interest in its success, particularly following the establishment of an Employee Council, full voting rights and representation on the board of Trustees.
Under the scheme, every employee can buy into the business at an annual dealing day, while new starters receive shares after 12 months of employment.
Andrew Lane, Managing Director at Union Industries, said: “10 years of success for any business is a major milestone, but 52 years of business and for 10 of those, the most profitable ones, to be as an Employee-Owned Trust is remarkable.
“Although we have always benefited from a committed workforce, becoming employee-owned has further empowered the team; everyone now also has an added financial incentive as a result of an annual tax-free bonus and the Employee Council ensures everyone is involved.”
Weetabix opts for best of British with high-speed door installations by
Union Industries, the UK’s leading manufacturer of bespoke highspeed doors, is helping one of Britain’s most iconic cereal brands maintain its high standard of hygiene with the installation of more Bulldoors and Matadoors.
Weetabix initially approached Union Industries in 2023 to maintain and elevate hygiene standards at its site at Burton Latimer near Kettering. Recognising the superior quality and reliability of Union’s Bulldoors, it expanded its partnership by installing a further six doors around its facilities, including Burton Latimer and Corby, making eleven Union doors across the two sites in total to date.
The bespoke doors, tailored to fit each individual opening, address specific challenges such as tight spaces and sloping floors, ensuring a perfect seal and optimal functionality.
In addition to maintaining hygiene standards, some entries and exits in Weetabix’s production and warehouse areas utilise a two-door solution of airlocks. This system interlinks the doors electronically to allow only one door at a time to be open, effectively prevents the ingress of insects, dust, and other foreign bodies, further safeguarding product integrity.
Union’s Bulldoors are regarded as the ‘reliable workhorse’ of rapid roll doors and are known to perform more than 1.4 million cycles per year, making it a popular
choice across multiple sectors. They feature specialist ‘CrashOut’ and ‘Auto-Reset’ damage protection facilities, and offer control outputs for options such as airlocks, traffic control systems and remote monitoring, whilst aiding temperature control for ambient and chilled environments.
The market-leading, bespoke, high-speed roller doors help to prevent the severe drop of ambient temperature in buildings, especially evident in the winter months, eliminating any potential impact on production environments.
Alan Hirst, Sales Director at Union Industries, said: “We are delighted to continue our partnership with Weetabix in enhancing their
operational efficiency and hygiene control. Our rapid roll doors are renowned for their reliability and performance, making them the ideal choice for Weetabix’s production environments.”
Anthony Brawn, Facilities Contracts Manager at Weetabix, said: “We are proud to partner with Union Industries in maintaining the highest standards of hygiene and operational efficiency across our facilities. The installation of Union’s high-speed doors ensures a seamless flow of operations
“With Union Industries, we are confident in achieving our longterm goals of reduced downtime, enhanced productivity, and minimised costs.”
Whether degreasing, classic component cleaning or high-purity applications - the demands on cleaning solutions have increased in all areas of the manufacturing industry. Ecoclean is responding to these changed market requirements with an even broader and more modularized product range. The focus is on higher cleaning quality, improved costs, and more energyefficient processes.
Component cleaning is a critical step in manufacturing, ensuring that downstream processes meet quality standards across all industrial sectors. The diversity in cleaning applications has increased, driven by factors like new and modified products, increasingly compact and complex geometries, and a broader variety of materials. Workpiece dimensions can vary from less than a millimeter to several meters. Depending on production stage, product, and industry, requirements for cleanliness and process complexity differ. For instance, final cleaning in high-tech industries, such as semiconductor manufacturing, medical technology, and precision optics, requires the removal of particulate contamination at the nanometer level and nanolayers of residual film. Conversely, in general industries, the focus is often on removing large quantities of chips and machining media at high speed. In all cases, cleaning processes must be economical.
To effectively tailor cleaning solutions to specific tasks, it is essential to consider various product and company-specific criteria in addition to cleanliness
standards. This necessitates a flexible product range in terms of cleaning media, plant design, and process technologies. Ecoclean, as a full-range supplier, covers the entire spectrum of wet-chemical processes using water-based media, solvents, and modified alcohols. This comprehensive approach allows the company to efficiently customize cleaning processes and systems to meet specific product and company requirements, whether for batch or individual part cleaning. Ecoclean’s process design is supported by in-house Test Centers, including cleanroom facilities for high purity applications.
Modular systems, such as EcoCvela for water-based cleaning and EcoCstretch for solvent-based cleaning, offer efficient solutions for tasks requiring special equipment. The modular concept includes different chamber sizes and a variety of process technologies, such as spray cleaning, ultrasonics, injection flood washing (IFW), Pulsated Pressure Cleaning (PPC), and plasma cleaning. These
systems are designed for both general industry and high-purity applications, ensuring short process times, high cleanliness levels and energy-saving operation.
In the field of multi-stage ultrasonic immersion cleaning, Ecoclean offers modular solutions through its UCMSmartLine, UCMPerformanceLine, and UCMHighLine series. These systems, comprising standardized modules for cleaning, rinsing, drying, and more, can be easily configured and commissioned. They are also designed for high-purity applications, with appropriate equipment for cleanroom operation.
With its diversified portfolio, Ecoclean enables companies across various industrial sectors to adapt to changing cleaning requirements in a cost-effective, energyefficient, and future-oriented manner. This approach not only ensures compliance with stringent cleanliness standards but also supports sustainable and resourceefficient manufacturing practices.
EFFICIENT CLEANING AND DEBURRING SYSTEMS FOR VARIOUS INDUSTRIAL PARTS AND COMPONENTS.
Aqueous Cleaning
Solvent Cleaning
Ultrasonic Cleaning
High-pressure
Waterjet Deburring
Surface Processing & Selective Cleaning
Machine safety is critical in industrial settings to protect workers, ensure operational efficiency, and comply with legal regulations. Recognising that each machine and operations have specific demands, Safety Systems has designed and delivered a diverse range of safety solutions that comply with current machinery safety legislation including PUWER, BS, EN & ISO Standards.
“All our projects focus on enhancing the safety of often aging machinery, and updating both guarding and electrical systems to meet current standards. As safety regulations have advanced significantly since many of these machines were originally constructed, our work ensures they comply with today’s stringent requirements,” stated Allan Harris, Director.
Safety Systems, in its current form, has been operating since 2014 when Mark Smailes took over as Director after the company was divested from TUV SUD Ltd. However, the roots of Safety Systems trace back to 2001, when Roger Scott founded the company as a supplier of machinery safety components, including interlocks, safety relays, and light curtains. Since then, the company has grown organically, evolving from a component supplier to a full-service provider, offering design, supply, installation, and validation of comprehensive safety solutions using products from a wide range of leading safety component manufacturers and innovators.
“We are a specialist engineering company dedicated to upgrading the safety of both new and existing machinery to ensure full compliance with current UK and EU machinery safety standards and regulations.
This includes modernising older machines with outdated safety devices and adapting new machinery, often manufactured outside the European Economic Area, that does not meet UK/EU standards. Recently, we successfully re-engineered three new machines built to American standards, bringing them into compliance with key UK regulations such as EN60204-1, EN ISO 13849, and EN ISO 14120, ensuring they can be safely put into service,” added Allan.
Safety Systems are experts in delivering bespoke machinery safety solutions and effectively act as a one-stop shop for machinery safety issues, offering everything from initial assessments such as PUWER and CE/UKCA audits, design and implementation of safety upgrades through to final signoff and validation. Unlike other machinery safety companies that only focus on guarding or electrical safety, Safety Systems offer a full package with complete turnkey solutions.
Recently, the company has invested in a couple of upgrades to its test equipment, enabling them to offer Stop Time Testing for ESPE devices. Stopping time is crucial for machines with dangerous motions when positioning protective devices like light curtains, safety scanners, and two-handed controls because it determines the safety distance
needed to prevent the operator from reaching the danger point before the machine stops. Using the HHB Safetyman® DT2 time meter means stopping time and distance can be tested to ensure safety devices are correctly positioned and functioning. The company’s Functional Safety Engineers can perform this testing on-site, or provide the equipment for hire if you prefer to conduct the tests yourself.
What’s more, Safety Systems also provide testing of permanently installed electrical systems to machinery in accordance with EN60204-1. Section 18 of EN60204-1 outlines the need to verify the safety of a machine’s electrical equipment through inspection, testing, and proper documentation. This includes checking for compliance with electrical documentation, examining equipment for damage, ensuring protection from electrical contact, and conducting tests like continuity of the earthing system, insulation resistance, and functional performance. Using the company’s advanced GOSSEN METRAWATT ProfiTest Prime testing machine, they can thoroughly check and validate the electrical safety of your machinery, ensuring it meets the required standards.
Safety Systems is dedicated to enhancing workplace safety with its expertly designed and supplied machine guarding solutions. We asked Allan, how do they tailor machine guarding solutions to meet the unique needs of different industries. He responded:
“With extensive experience across various industries, we design tailored safety solutions that meet specific requirements, such as
hygiene standards for food and pharmaceuticals or corrosion resistance for chemical and saline environments. Our skilled Design Engineers use the latest Autodesk Inventor Professional 3D software to custom design all guarding systems. This advanced modelling allows us to visually represent machinery and solutions, helping to ease operator concerns by demonstrating how the guarding will impact their interaction with the equipment. This visualisation is also valuable for business leaders when implementing safety upgrades.”
Of course, every industry comes with its own challenges. We asked Allan what are the current compliance challenges companies face and how does Safety Systems help businesses to overcome them. He answered:
“Understanding how to address issues in a timely, cost-effective, and compliant way is crucial. While many companies have on-site engineering teams, these teams are often focused
on keeping machines running and may not have the time to delve into the complexities of machinery safety standards. Since we work with these standards daily, we are well-versed in interpreting them and can quickly develop solutions that align with the latest guidelines, ensuring their machinery stays safe and compliant.”
Safety Systems is a tight-knit group made up of colleagues that have worked together for between 10-30 years. Evolving from a safety component supplier to a comprehensive safety solutions provider, their combined deep industry knowledge and adaptability underscores their expertise in the industry. Their proactive approach to solving safety issues ensures that solutions are both timely and compliant.
“When collaborating with clients, we begin with a comprehensive risk assessment of their machinery, conducted by a qualified professional to identify potential
hazards in accordance with relevant standards. Following this assessment, we apply innovative engineering to develop tailored safety solutions. This often involves integrating various technologies to create a robust and effective Safety System that addresses the identified risks,” said Allan.
Looking ahead, Safety Systems is currently investing in new software to help its internal processes and to streamline workflows. “From this, we will hopefully see an improvement in our productivity and reduction in our paper work,” added Allan.
In conclusion, Safety Systems exemplifies excellence in machinery safety through its unwavering commitment to innovation and compliance. By seamlessly integrating advanced technologies and tailoring solutions to meet specific industry needs, they not only enhance safety but also ensure operational efficiency across diverse environments.
In hygiene-critical environments, such as food processing facilities, the risk of contamination poses significant challenges. One of the most serious risks is the presence of foreign bodies in food products, which can lead to health hazards, costly product recalls, and damage to a brand’s reputation. To mitigate these risks, the use of detectable products has become increasingly important. These products are designed to be easily identified by metal detectors and X-ray inspection systems, providing an added layer of safety and quality control.
Foreign body contamination can occur at various stages of the production process. Common sources include broken equipment, stray stationery items such as pens, and personal protective equipment (PPE) such as gloves. When these items enter the production line undetected, they could find their way into the final product, posing a serious risk to consumers.
Detectable products are engineered to address this issue. Made from materials that are metal detectable and x-ray visible, these products can be identified and removed before they reach the consumer. This capability is crucial in maintaining the integrity of the food supply chain and ensuring that products are safe for consumption.
In the food processing industry, compliance with rigorous safety
standards is mandatory. Many regulatory bodies, including the British Retail Consortium (BRC) and the Food and Drug Administration (FDA), require manufacturers to have systems in place to prevent foreign body contamination. The use of detectable products supports compliance with these standards, as they are specifically designed to be identified by the detection systems that are integral to food safety protocols.
Moreover, using detectable products demonstrates a company’s commitment to due diligence. By implementing these products, manufacturers can show that they are proactively taking steps to prevent contamination, which can be crucial during audits and inspections.
The primary benefit of using detectable products is the enhancement of food safety. However, there are also significant cost-saving advantages. Product
recalls due to contamination can be extremely costly, not only in terms of direct financial loss but also in terms of the damage to brand reputation and customer trust. By integrating detectable products into the production process, companies can significantly reduce the likelihood of such events, thereby safeguarding both their bottom line and their reputation.
Detectable products are not limited to a single type of item; they encompass a wide range of tools, stationery, utensils, and PPE, including pens, gloves, scoops, and brushes. These products are designed to withstand the demanding conditions of food processing environments, often being resistant to wear and tear, chemicals, and temperature fluctuations. Their durability ensures that they remain effective over time, providing ongoing protection against contamination.
In hygiene-critical environments such as food processing, the use of detectable products is not just a safety measure; it is a critical component of a comprehensive food safety strategy. These products provide an essential line of defence against foreign body contamination, helping to ensure that the food reaching consumers is safe. By enhancing safety, supporting regulatory compliance, and reducing the risk of costly recalls, detectable products play a vital role in maintaining the integrity and reputation of food processing operations.
P
P
P
P
Comfortable fit with textured fingers
Suitable for all types of food Light,
P Light, durable and resistant to chemicals
P Three sizes available
BST
BST Detectable Products are the original pioneers in metal detectable plastic technology. Since 1985 BST have refined our materials to increase both performance and the range of products available to the food industry. BST detectable products are developed using highly advanced food grade materials, tested on x-ray inspection and metal detection systems, produced in hygienic environments and migration tested to the FDA and EU standards for food contact. Our products are designed to be as safe as possible for food production environments and if
materials
Environmentally friendly practices are crucial in today’s market. I’ll assist you in crafting a realistic approach to lower GHG emissions and meet regulatory standards, strengthening your brand image and opening up new growth avenues.
High sales don’t always translate to healthy cash flow. Together we’ll review your finances and craft a strategy to keep cash moving smoothly, ensuring your business has the financial flexibility it needs to grow.
Lets assess your current processes to pinpoint areas for growth, such as optimizing sales strategies, improving team skills, or adopting the latest technologies.
Stuart Ovington, Business Advisor
Leachate Solutions is an industryleader in closed landfill engineering and leachate treatment plants. With over 35 years’ experience working with Local Authorities (LA’s) on discharge from closed landfill sites, Leachate Solutions was founded in 2015.
The Preston-based company is the UK’s only designer and supplier of the state-of-the-art Airless Methane Stripping Plants for customers around the country, specialising in all closed landfill site services, and solutions for the process and wastewater industries.
The traditional method of using forced air 24/7 to remove methane continues to be widely used but the technology is old, has a high energy usage, significant maintenance costs, and is not environmentally friendly.
The new cutting-edge Fully Automated Airless Methane Stripping Plant System utilises ondemand principals, saving spiralling energy costs and uses stainless steel instead of plastic.
“This technology drastically reduces energy usage and harmful emissions, with a low visual impact and reduced noise pollution. The reduced sludge production and combined low maintenance and operational costs combined makes this the technology of choice for dissolved methane stripping in a wide range of applications from farming to construction across the UK.” explained Jane Rostock: Director.
This technology drastically reduces energy usage and harmful emissions, with a low visual impact and reduced noise pollution.
Leachate Solutions also provide a number of services – for managing water & wastewater, whether it is in the Process industry/ agriculture & farming or closed landfill.
• Control & monitoring services –pump control / management
• Pumping services – supply & Installation / repairs / pump Hire
• Specialise engineering projects
– Treatment & Management of Attenuation Lagoons
From supply & installation of a variety of pumps for most situations – to – managing & servicing Lagoon projects & pumps
All our pumps and associated equipment are sourced from trusted manufacturers that can support all projects from dewatering to emergencies. Our size ranges from 2” to 12” we have an extensive range of environmentally friendly pumping products to support companies with a variety of pumping options.
“All companies need to apply for and comply with environmental permits from the Environment Agency to discharge liquid effluent or wastewater into surface waters, or into storage lagoons, We offer full consultancy for all closed landfill and process industry work. Our chief Solutions Engineer, Carl has been designing & creating bespoke solutions for many years and can provide onsite assessment for your situation
With many companies looking for sustainable best practices, and a route to Net Zero, our Fully Automated Airless Methane Stripping System has been designed to meet the latest regulations, and we welcome any enquiries from new and existing customers.
Businesses in the food and drink sector are replacing printed and painted signs with projected alternatives which improve food hygiene and safety. That’s according to Projected Image, who have worked with companies including Coca-Cola and Dunbia.
Projected Image supplies LED gobo projectors that shine bright safety signs onto surfaces, including floors, walls and doors. The image is provided by a glass ‘gobo’ which can be customised for specific health and safety signage needs.
“Projected signage tackles many challenges faced by the food and drink industry. Unlike painted signage and safety markings, projected signs don’t risk producing contaminants, such as paint chips, when cleaned regularly or subjected
to heavy foot and forklift traffic. They don’t fade or harbour bacteria either” says Ian Spoors, MD of Projected Image.
The experts say LED projected signs are clearer, brighter and more consistent than traditional signage, reducing ‘sign blindness’ for a safer, more hygienic workplace.
“For Dunbia, we produced projected signage for handwashing stations and
they’ve reported an increase in sign visibility throughout their factory. Many companies are finding that projected safety signs are the long-term, lowmaintenance solution for safer, cleaner workspaces” says Ian.
Projected Image is the UK’s only dedicated provider of LED projectors and custommade gobos. The low-energy projectors can be installed by qualified electricians in any commercial or industrial environment.
never-fade,
Our LED projected safety signs are harder to ignore, longer lasting & more cost-effective than painted & printed signage. No contamination
and never-fade
Teknomek’s Hygienox furniture range offers an ultra-sterile solution for the strictest of hygiene requirements.
Standard Teknomek:
Hygienic high-standard
304L-grade stainless steel
Physically chemical resistant
Designed for easy cleaning
Clean and smooth welds
Long-lasting
Hygienox tables & lecterns:
316 electropolished <0.3RA finish
provided as standard - also available without electropolishing
Chemical-resistant design for harsh sterilisation processes
Tubular legs and table tops with open corners
Extra clean polished welds
(0)1603 788 833.
For many years now, aluminium materials have been becoming more and more prevalent in many industries. This trend continues unabated. While light-weight construction and corresponding materials and structures have always been an important aspect of aerospace, the use of aluminium to reduce weight in automobile manufacturing has increased steadily, and has really taken off now due to electromobility. MAPAL is a leading technology partner for machining aluminium components thanks to its many years of experience designing, producing and applying tools for aluminium machining.
Aluminium and aluminium alloys are in principle easy to machine. As the cutting forces are low, high cutting data and in particular long tool life can be achieved with appropriate process planning. However, aluminium alloys have some special features which must be mastered. The geometry of the component and ever-increasing demands on tolerances and process capability pose additional challenges when machining aluminium.
Aluminium alloys can basically be subdivided into the principal categories of cast alloys, wrought alloys and powder-metallurgical alloys, whereby mainly the first two play a role in machining. For cast alloys, various alloy elements and corresponding casting methods are utilised to create the desired properties of a component. When casting, it is important to come as close as possible to the component’s final form to simplify mechanical machining. This “near net shape” technology has become established
Machining rates of over 90% are standard in parts production in the aerospace industry. The NeoMill-AluQBig indexable insert milling cutter from MAPAL performs outstandingly for volume machining of aluminium. ©MAPAL
in mass production in particular.
When machining casted parts, the silicon content is decisive with regard to the alloy element as it has a powerful effect on wear and tool life. For wrought alloys as well, the desired properties can be brought about by the alloy elements. The silicon content is lower here, though, enabling chipless ductility. Other alloy elements are used here though to achieve good strength and stability as well as fatigue strength. Cold- or warm-worked alloys are the result, which can be processed into wrought material and then be machined.
The aerospace industry deploys MAPAL tools both for part machining – i.e. manufacturing components that are assembled to form sections of the fuselage or wing – as well as for the final assembly where the individual sections of the entire aeroplane are put together.
When part machining aluminium parts, the part is frequently machined from solid material. Machining rates of over 90% call for an efficient
volume machining to machine as much raw material in as little time as possible. Powerful tools are key here. The tools must meet a widely variety of requirements in final assembly. Not only is aluminium frequently utilized here, other light-weight materials like titanium and fibrereinforced plastics are also used in one machining step. These so-called stacks are material combinations that pose a particular challenge as the machining characteristics of the combined materials are very different and the tools have to meet their varying requirements.
The aerospace industry has been using aluminium for many years to save weight. Besides the favourable relationship between stability and weight, this material also meets other requirements such as corrosion resistance, fatigue strength and low embrittlement. Therefore, there is high demand for machining solutions for aluminium in part production as well as in final assembly for aeroplanes.
More range with every kilogramme saved
Weight reductions are a primary concern in the development of electric vehicles as well. After all, every kilogramme saved means more range and less CO2. In mechanical machining for electric vehicles, established processes and tools are very good for producing some of the parts. However, there are inevitably new systems and components in e-vehicles that have to be redeveloped due to their function in terms of geometry and precision and/or material properties. Precision tool makers are called upon to deliver answers when it comes to scaling production volumes in the automotive industry and the habitual
Stator housings of an electric motor place particular demands on precision for machining. The weight-optimised fine boring tool with HPR400 technology for machining the stator housing fulfils all requirements for process reliability. ©MAPAL
where large-scale structural parts are no longer made of individual parts but are cast as a single piece. The components’ large size and tendency to vibrate call for special tool geometries for low-vibration machining with a high degree of precision. New long-chipping aluminium alloys whose machining characteristics must first be mastered represent a further, related challenge.
MAPAL has developed an extensive product and application portfolio thanks to many years of experience and countless proven solutions in the field of aluminium machining.
demands on process stability, consistent parts quality and attractive price levels.
One example of special requirements are the electric motor housings. The large stator bore with a diameter tolerance in the IT6 to IT7 range as well as circularity and cylindricity of 20 to 30 µm or less, combined with other functional surfaces for accommodating rotors and transmission elements, requires the highest degree of precision with regards to shape and precision tolerances.
The large battery trays are another example. Their main structure consists of extruded profiles made of aluminium with low silicon content. The challenges here are to keep chip and burr formation under control and to machine the very large parts using economical cutting data without vibration. This also applies to the trend towards mega and giga casting
Aluminium is also used in many other industries thanks to its properties. Depending on production volume and number of variants, manufacturers use standardised machining solutions for parts where a significant amount of machining is required. Here too there are aluminium parts produced in high quantities, which require very sophisticated customised concepts. In fluid power, for example, parts like pneumatic valve housings and pneumatic cylinders are produced in large quantities. For industries with high variance and small quantity, standardised tool solutions make sense.
Wide-ranging product and application portfolio for aluminium MAPAL has developed an extensive product and application portfolio thanks to many years of experience and countless proven solutions in the field of aluminium machining. The range includes established bore machining applications like fine boring, reaming and boring. MAPAL’s guide pad technology for fine boring achieves the highest degree of precision for diameter, circularity and cylindricity. For tools with fixed blades for reaming and boring, MAPAL offers a one-of-a-kind range for PCD tools. It includes everything from tools for a single diameter with chamfer to very complex tools for multi-stage bore geometries. For drilling into solid, there is also a large selection of solid carbide drills and drills with indexable inserts. Deep drilling and dry drilling are a particular challenge as special geometries and expertise are required for both.
includes face milling cutters, highvolume milling cutters, end milling cutters and special designs. Series with cassettes, inserts or a fixed design are available for face milling cutters, for example. PCD and different varieties of carbide are used as cutting material and can be supplied for various cutting depths in combination with the required surface finishes and profiles. In this way special cross-cut structures can be created for sealing faces, for example. In addition to the universally applicable range of end milling cutters made of solid carbide or with PCD blades, MAPAL has products that cater to special requirements such as high precision, parts vulnerable to vibration or highvolume machining.
The product range and extensive manufacturing expertise form the basis for optimal machining processes for aluminium parts. But the tool itself is not the only factor. Only through the art of engineering can the wide-ranging product and application portfolio provide the perfect solution. And this is where MAPAL’s true strength lies. Considerable experience developing new solutions time and again for the production of aluminium parts make the tool manufacture a first-class solution provider in this area. And the customer takes centre stage here.
According to the MAPAL philosophy, the perfect solution can only be the one that is precisely tailored to the needs and requirements of the customer. The expectation is not over-engineering but rather machining processes designed based on requirements. MAPAL sees itself as a solution provider and technology partner and, as opposed to a conventional tool supplier, does not only consider technical aspects but also tries to put itself in the customers shoes. This customercentred focus is behind the “Basic - Performance - Expert” solution approach and enables MAPAL to tailor the tools to the customer’s requirements.
For the milling of aluminium, MAPAL offers a broad range that For further information, please visit mapal.com/en-int/
Using T Slot Extruded Aluminium Profile is a convenient and cost-effective way to build a machine framework
Using T-Slot extruded aluminium profiles for building machine frames offers numerous advantages over traditional steel welding methods. Here’s an in-depth look at why this method stands out:
Advantages of T-Slot Extruded Aluminium Profiles
1. Eliminates Welding and Surface Preparation
• No Welding Required: T-Slot extrusions can be connected using various fasteners and connectors, eliminating the need for welding.
• Anodized Finish: The profiles come pre-anodized, providing a superior and durable surface finish compared to traditional paint jobs. This also eliminates the need for messy and toxic painting processes.
2. Ease of Use and Flexibility
• Easy Cutting and Assembly: Aluminium profiles are much easier to cut and handle compared to steel. The assembly process is straightforward, requiring simple tools.
• Modular Design: The T-Slot system allows for easy modifications and adjustments. Frames can be dismantled and reassembled if design changes are needed, providing flexibility during the build process.
3. Precision and Reduced Rework
• No Distortion: Unlike welding, which can cause distortion due to heat, T-Slot assemblies maintain their precision and alignment, reducing the need for rework.
• Consistent Tolerances: The precision machining of T-Slot extrusions ensures that all components fit together accurately, maintaining consistent tolerances throughout the build.
4. Cost and Time Efficiency
• Reduced Labour Costs: By eliminating welding, grinding, and painting, labour costs are significantly reduced.
• Quicker Turnaround: Preparation and assembly times are reduced, leading to faster project completion.
5. Safety and Environmental Benefits
• No Hazardous Processes: The absence of welding, grinding, and painting reduces the exposure to hazardous fumes and materials, creating a safer working environment.
• Environmentally Friendly: The anodized aluminium finish is more environmentally friendly compared to traditional painting processes that involve solvents and chemicals.
6. Durability and Strength
• High Strength-to-Weight Ratio: Aluminium profiles provide a strong and lightweight solution for machine frames, ensuring durability and ease of handling.
• Corrosion Resistance: The anodized surface of the aluminium provides excellent corrosion resistance, ensuring the longevity of the frame.
Conclusion
Switching to T-Slot extruded aluminium profiles for your machine
frames can greatly enhance the efficiency, precision, and flexibility of your build process. The elimination of welding and painting not only reduces costs and time but also improves safety and environmental impact. With the added benefit of modularity and ease of assembly, T-Slot extrusions offer a superior alternative for high-quality machine frame construction.
Whether you are a seasoned builder of complicated machinery or a complete novice, building a frame with T-Slot Aluminium extrusions is easy.
As the only UK & Ireland distributor of the mk Technology Group aluminium profile range, let AdaptTech Manufacturing Solutions help you create your ideal machine frame. The range includes:
• 40 x 40 profile - ideal for lightweight machine frames.
• 50 x 50 profile - for heavy-duty machine frames with high static loads.
• 60 x 60 profile - the most robust profiles which are the perfect choice for machine frames required to handle the heaviest loads, multi-axis gantries and lifts.
We can assist with your design and help you to select the best connection method. We can provide a fully assembled solution or a kit of parts if you prefer to assemble yourself.
Contact AdaptTech now and let us help you realise your manufacturing solution!
The mk Technology Group is one of the leading suppliers of profile and conveyor technology. Using their own aluminium profile system as a common base technology, mk provides a comprehensive modular system for factory automation.
WISEMAN THREADING TOOLS LTD
We have been supplying threading tools and gauges since 1987.
Together with supplying plain plug and ring gauges this is all that we do, we therefore consider ourselves to be specialists in this field.
We supply worldwide.
We hold extensive ready stocks that include all of the standard stuff that others offer, but also includes taps, dies, die nuts, die head chasers, thread rolls and gauging for threads not normally available 'off the shelf '.
Our real time stocks can be checked and purchased online at www. threadtools.com Just enter the thread details into the search box on the home page.
You will be directed to the item, if stocked, or to our specials, (custom manufacture), sales team. who will quote to supply at competitive rates, in good time.
As an account holder you can also order online from our listed in stock items, at your normal terms. We realise that you need the right item at the right price and quality, and in a reasonable time frame.
We are geared to provide that.
We can ship stocked items same day.
Our experienced sales staff can assist and advise you on any technical issues.
We welcome enquiries from resellers and can offer terms to suit.
WISEMAN THREADING TOOLS LTD
11 Padgets Lane, South Moons Moat, Redditch B98 0RA UK
+44(0)1527 520 580 sales@threadtools.com www.threadtools.com
HSS DIES & DIE NUTS
Large shelf stocks for all Standard and many Special Threads. Check our stocks online.
THREAD CUTTING AND ROLLING HEADS and parts and repair service
THREAD ROLLS FOR ALCO & FETTE HEADS. READY STOCKS CUSTOM MANUFACTURURE
THREAD GAUGES all types. Large stocks for standard and SPECIAL threads. Any non stocked can be quoted for custom manufacture.
HSS TAPS
Huge Stocks for all Standard threads
CUSTOM MADE taps our SPECIALITY!
We stock taps for many non standard (SPECIAL) threads
All types; Spiral flute and point, Fluteless, Left Hand, etc, etc.
CHASERS FOR COVENTRY & LANDIS TYPE DIE HEADS
Ready stocks for most size heads most standard and some special threads Geometry available for most materials. Custom manufacture our speciality!
Over the last 30 years there has been a boom in the traceability and identification of manufactured components. Many industries want to directly laser mark these, however there are some parts that are just getting larger and larger.
Casting and pressing companies sometimes have such large parts that they simply cannot fit these into a standard sized Class 1 laser enclosure leaving many companies wondering how they can mark them.
Even though they launched a new range of large XXL-Box class 1 enclosures in 2022, SIC Marking saw this problem as a new challenge for 2023. They have now launched their Funnel Integrated Technology (F.I.T. for short) as a complete all in one solution that combines all of the necessary components and settings to mark larger parts in a simple, safe and economic way within the customers production line and budget.
The FIT tunnel eliminates the need to enclose the entire part for the laser marking process by enclosing just the marking area. The compact design allows for the FIT system to be retrofitted easily into an existing robotic cell.
This ready to integrate and secured laser marking system comes as a ‘Tunnel Style’ Class
1 compliant enclosure. It is a compact and easy to integrate solution with a single connection to a PLC. The F.I.T. can be mounted to a robot head for presenting to a stationary part – or fixed in position allowing the robot to present the part for marking.
Not only is the F.I.T. adapted for production environments with its maintenance drawer for the cleaning of the lens, it has built-in shock protection preventing the funnel from damage. The F.I.T. tunnel can be adapted to your marking needs with three window sizes available as standard: 24mm x 32mm, 100mm x 32mm and 100mm x 100mm. Custom sizes can also be accommodated.
The F.I.T. is available as a basic chassis or as a complete solution with protective covers, a cooling system, electrical cabinet and tooling as well as an optional integrated Cognex vision system for 2D verification / validation or 3D lens for marking curved or angled surfaces.
For a demonstration of the new F.I.T. and / or any of the other laser marking systems in SIC Marking’s extensive range, please get in touch with SIC Marking UK in Warwick, UK on 01926 830372 where one of the very knowledgeable engineers will
be happy to talk to you.
The SIC Marking Group was formed in 1992 and has been growing ever since, as a result of its development in new sectors, winning many local and international customers, in addition to many takeovers. The increasing number of its distributor partners and the opening of subsidiaries on the 3 continents have given it an acknowledged presence and international reputation.
It has 10 subsidiaries, mobilised for promotion, implementation and customer support in France, Spain, Italy, UK, Germany, Canada, USA, Mexico, China and Korea. They also deploy its marking and traceability solutions locally on behalf of international groups.
Furthermore, its 40 exclusive distributor partners enable it, overall, to serve more than 50 countries worldwide.
SIC Marking UK is one of 10 subsidiaries around the World. SIC Marking Group has developed innovative, permanent marking solutions and automated identification systems for the complete traceability of industrial components for over 30 years. SIC Marking has a wide range of the most robust and state of the art Dotpeen, Scribe and Laser Marking machines available on the market today. Whether Column Mounted, Integrated or completely Portable like our battery powered cordless eMark for example, we can provide a machine that is suitable for both your application and budget. SIC Marking is constantly adding to the range and re-investing into R & D. The new eTouch portable Dotpeen marker offers Icon style Touch screen technology and the Laser systems now have a range of modular Class 1 enclosures with the XXL-Box range – offering the ability to mark parts up to 1500mm in length as a standard product.
Our UK Team is based in Warwick, where we have dedicated Sales and Aftersales engineers with over 50 years’ experience who would welcome a call to discuss your marking application.
Please call 01926 830372 for further details or email us on salesuk@sic-marking.com
INDUS Engineering Services is proud to offer a wide range of custom control panels, automation systems and special purpose machinery. After working on major control and automation projects for several of the south’s leading brands, the company has recently acquired a new premises with the aim of increasing production capacity of bespoke and sub-contract, control panel manufacture. The new premises will also allow us to support the wider range of engineering
activities carried out by the company, such as the design, manufacture, and testing of special purpose machinery. Also, to further our goals to reduce our carbon foot print we will be installing a high efficiency solar PV array in the coming months. For more information on the services that are available please do not hesitate to contact and we will be happy to discuss your project needs and requirements.
www.indusengineering.co.uk
Konecranes has launched its range of EX C-series chain hoists for explosion proof lifting in hazardous environments. The models are suitable for a wide range of industrial applications where gases, flammable substances, dust and other ignition sources create the potential for explosions. The models have been designed and tested specifically to fulfil ATEX and IECEx requirements for use in Zone 1, 2 and 21 explosive environments.
Konecranes has launched its range of EX C-Series chain hoists for explosion proof lifting in hazardous environments.
Ergonomics, operational efficiency, versatility and ease of use have been the driving factors in the development of the hoists. The compact design and low headroom allow maximum use of available
workspace. Inverter controlled trolley movement and 2-step hoisting facilitate smooth and accurate load handling. EX C models are available with SWLs from 320 kg to 2,500 kg.
Smart engineering techniques have been employed in the manufacture of the EX C-series with the use of Konecranes ‘Core of Lifting’ components, including a purpose-built motor, gearbox and controls. The robust and durable hoists provide reliable performance over extended periods, ensuring maximum operational availability, reduced maintenance requirements and extended life cycle.
www.konecranes.co.uk
Totalkare’s ergonomic positioners are single or double column devices that enable the lifting and rotation of a product during welding and assembly operations.
With overall capacity from 2,000 - 90,000kg to suit, they are both compact and flexible.
Eislingen, Germany. The Fair Friend Group (FFG) has initiated a comprehensive strategic realignment to address the current global challenges in the machine tool industry and to strengthen its competitive position. At the International Exhibition for Metalworking (AMB) 2024, the group will emphasize innovation, efficiency, and an enhanced global presence under the motto “Let’s Start the Journey.” As part of this transformation, FFG has appointed Dr. Sebastian Schöning as its new Chief Executive Officer (CEO). Dr. Schöning, who holds a PhD in mechanical engineering, brings over 20 years of professional and management experience. Since 2021, he has served as the Group’s Chief Operating Officer and as CEO of MAG IAS GmbH. In his new role, Dr. Schöning will spearhead global strategy development and lead the group’s operations. He will be supported by Ms. Rong-Rong Liu, who has been appointed Chief Financial Officer (CFO) and will be responsible for overseeing the group’s financial management.
A key element of the realignment is the increased leveraging of synergies among Fair Friend Group’s globally operating companies. This enables FFG to provide customers with even more integrated and customized solutions. Additionally, FFG plans to expand its range of standard machines and develop new technologies in emerging industries such as humanoid robotics and energy. By deeply integrating
artificial intelligence, smart manufacturing, energy efficiency, and decarbonization,
https://ffg-ea.com/amb
FFG aims to ensure future-oriented and environmentally friendly production. Customers will benefit from a wide range of highly specialized machines and manufacturing systems, allowing manufacturing companies to respond flexibly to both regional and global market demands.
“Our clear vision, strong management team, and relentless drive to help our customers succeed are the keys to future growth,” said Sebastian Schöning. “With the measures we are now implementing, we are ideally positioned to further expand FFG’s market presence in the global machine tool industry.” Founder and Chairman Jimmy Chu shares this optimism and adds: “I have complete confidence that under the leadership of Dr. Sebastian Schöning and Rong-Rong Liu, FFG will play a leading role in innovative technologies and achieve its goals.”
FFG at AMB 2024 in Stuttgart Hall 6, Booth B11
Rondean Ltd are here to help with any of your machinery needs….
By listening carefully to the needs of our customers we have been successful in providing only the right solution on every occasion.
We believe that only by investing in a quality machine can you sustain a competitive edge and so avoid a costly breakdown or even an expensive replacement.
By listening carefully to the
The fact that most of our sales are repeat business from current satisfied customers is testimony that our approach to finding a solution rather than merely making a sale proves to be the right one.
company that has the knowledge, experience and ability to take the stress out of much in demand services such as; loading, off-loading, positioning, installation, product training and servicing.
New stock arriving daily CALL US 0191 410 5886
We believe that only by investing in a quality machine can you sustain a competitive edge and so avoid a costly breakdown or even an expensive replacement.
We have been supplying machinery since 1984 so you can be confident you’re dealing with a machine company that has the knowledge, experience and ability to take the stress out of much in demand services such as; loading, off-loading, positioning, installation, product training and servicing.
Email: info@rondean.co.uk Units 11 & 13, First Avenue, Drum Industrial Estate, Birtley, County Durham, DH2 1AG
Once identified we can arrange for a free full-power test before you buy.
The fact that most of our sales are repeat business from current satisfied customers is testimony that our approach to finding a solution rather than merely making a sale proves to be
Once identified we can arrange for a free full-power test before you buy.
stock arriving daily CALL US 0191 410 5886
TTV Industrial Ltd, formed in 1989, is a family owned and run precision engineering business situated near Ipswich in Suffolk.
Our ethos is to build a customer base, by working towards a long term mutually beneficial relationship. We understand that one of the hardest parts of running a business is to find suppliers that will work with you, a good supplier is as important as the customer.
TTV gained a reputation in various industries for re-engineering parts to eliminate unacceptable failure and plant down time and this continues today. Our design and reverse engineering team have many years of experience. A priority in any design is to design for manufacture this helps to ensure that the parts can be quickly and therefore economically produced.
In 1989 we bought pre-owned machines, Mazak mainly, as even then we recognised the speed of programming was essential, particularly for short order production efficiency and never dreamt of a situation where we found it essential to have the latest machine tools at hand. The Mazak rep came around for years before he gained an order. Starting the business was hard work, if you’re awake, you’re at work and in poor condition rented Ex WW2 USAF buildings. Being able to design and build a purpose-built facility in 2010 was a dream come true. Working all day, building at night and weekends has paid off. A facility that we are so proud of where visitors say, “have you got a
self-loading and turning during the machining operation.
TTV gained a reputation in various industries for re-engineering parts to eliminate unacceptable failure and plant down time and this continues today
job for me?” when you hear that it is very satisfying.
It important to us that our customers know we are happy to help with a one-off part or a production run and just in time batch delivery. With this in mind, we are set up to manufacture efficiently as it’s that one off part that so often leads to ongoing work and batch production where we utilise our machines that feature
Quality Control is high on every one’s agenda, but TTV have taken this to a high with in process, on the machine, dimensional checks recorded using wireless enabled measuring devices and pre-loaded tolerances that must be met to proceed, every part has its own record that corresponds with the laser etched part number suffix.
We have 23CNC spindles and our machining capacity is best described by saying that chucking work on the lathes is currently limited to 600mm diameter that’s both horizontal and HD vertical machines with simultaneous 4th axis milling machines “paired” with the lathes with spindle speeds up to 24k RPM. Grinding and balancing is also an important part of our in-house ability.
We are always happy to quote and what have you to lose.
TTV Industrial Ltd is located in the East of England, a family run business dedicated to supporting its customers around the world in a multitude of Industries such as Oil and Gas, Automotive, Motorsport and Agriculture.
All under one roof we design, reverse engineer and manufacture components, problem solving and supporting our customers in ever changing markets.
One off’s, prototypes and batch work is all undertaken with a 100% inspection system and tracability.
Expert supplier of new and used sheet metal machinery: Supporting the circular economy with exceptional customer service
Machinery Supplies UK Ltd is a supplier of new and used sheet metal machinery, service spares consumables and accessories.
Established in 2020, though still a new company, owner Andy Naylor brings a wealth of experience spanning over 35 years. The resident expert team of machine operators, software engineers and electronic & hydraulic engineers are on hand to help match customers with the right machinery and parts, even if they aren’t in stock.
With a focus on premium customer service, Machinery Supplies UK offers a 24/7 Support Network for customers around the country and prides itself on its ‘can do’ winning attitude.
“I have been working with sheet metal machinery since I left school in the mid-1980’s and now we sell the machines I used to operate. With a truly international outlook, we have sold machinery to the USA, Taiwan, Europe as well as all over the UK. The latest cutting-edge laser welding machinery is coming from China and I travel there regularly to meet with these high-end manufacturers,” explained Andy.
With a focus on premium customer service,
Machinery Supplies UK offers a 24/7 Support Network for customers around the country and prides itself
on its ‘can do’ winning attitude.
Machinery Supplies UK provides the following new and used machinery and solutions to customers, both in stock and on-site available for demonstration with our team of experts:
• Fiber Laser cutting machines
• CNC Punching Machines
• Press Brakes
• Used Machinery
• Material storage solutions
• Deburring equipment
• Laser cleaning equipment
• Fiber laser welding
• Laser parts and maintenance
• Laser accessories
We are delighted to showcase Machinery Supplies UK Ltd with our Production innovation Award.
Machinery Supplies UK Ltd is a supplier of new and used sheet metal machinery, service spares consumables and accessories.
Fiber Lasers are widely used across industrial environments for a range of actions from marking, welding, cutting, cleaning, drilling, and much more and are renowned for advanced-precision. Furthermore, many companies appreciate the smaller carbon footprint, low maintenance and operating costs of Fiber Lasers. The engineers at Machinery Supplies UK offers support across most makes of Fiber Lasers and currently have the following two machines for sale:
Established in 2020, though still a new company, owner Andy Naylor brings of experience spanning over 35 years. resident expert team of machine operators, software engineers and electronic & engineers are on hand to help match customers with the right machinery even if they aren’t in stock.
With a focus on premium customer Machinery Supplies UK offers a 24/7 Network for customers around the country prides itself on its ‘can do’ winning attitude.
“I have been working with sheet metal machinery since I left school in the mid1980’s and now we sell the machines to operate. With a truly international we have sold machinery to the USA, Europe as well as all over the UK. The cutting-edge laser welding machinery coming from China and I travel there to meet with these high-end manufacturers,” explained Andy.
• NEW compact 3M x 1.5M 3kW Fiber Laser: Manual pullout table complete with chiller, extraction filtration system, with Maxphotonics laser source. Full price: £59,000: including installation and warranty.
Machinery Supplies UK provides the new and used machinery and solutions customers, both in stock and on-site for demonstration with our team of S Fiber Laser cutting machines
S CNC Punching Machines
S Press Brakes
S Used Machinery
• NEW 3M X 1.5M 6kW Fiber Laser: Changeover table, chiller, extraction filter, with Raycus laser source. Full price: £119,000: including installation and warranty.
S Material storage solutions
S Deburring equipment
S Laser cleaning equipment
S Fiber laser welding
S Laser parts and maintenance
S Laser accessories
Innovation Award
There is also a selection of used laser machines available of various kw and size ranges with chiller, extraction, software and fully installed package. This is a great addition to the circular economy, for those looking to invest in second-
Fiber Lasers are widely used across industrial environments for a range of actions marking, welding, cutting, cleaning, and much more and are renowned for advanced-precision. Furthermore, many companies appreciate the smaller carbon footprint, low maintenance and operating costs of Fiber Lasers. The engineers at
Expert supplier of new and used sheet metal machinery: Supporting the circular economy with exceptional customer service
Machinery Production supplier machinery, accessories.
new
a wealth years. The operators, hydraulic match and parts, service, Support country and attitude.
metal midmachines I used outlook, Taiwan, The latest machinery is there regularly manufacturers,” following solutions to on-site available experts:
industrial from drilling, for many carbon operating at
Machinery Supplies UK offers support across most makes of Fiber Lasers and currently have the following two machines for sale:
S NEW compact 3M x 1.5M 3kW Fiber Laser: Manual pullout table complete with chiller, extraction filtration system, with Maxphotonics laser source. Full price: £59,000: including installation and warranty.
S NEW 3M X 1.5M 6kW Fiber Laser: Changeover table, chiller, extraction filter, with Raycus laser source. Full price: £119,000: including installation and warranty.
There is also a selection of used laser machines available of various kw and size ranges with chiller, extraction, software and fully installed package. This is a great addition to the circular economy, for those looking to invest in secondhand, reconditioned machinery, as part of sustainable best practice.
cartridges, multitools, collars, die adaptors and expert advice as well as spares and consumables.
“Our DEBURRING machines also offer exceptional value, adding the final finish and touch to the laser cut parts. From simple deburring to regraining, our process of materials solutions are available to fit customer requirements.”
“We are forever liaising with our NEW equipment suppliers in order to bring only the premium UK market high quality sheet metal working equipment, coupled with our faultless aftersales support.”
“Our new state of the art East Yorkshire showroom will be opening later this year, when we will invite new and existing customers from across the industry. Watch this space!” added Andy.
For more information, please see the contact details below:
T 01482 420491
T 07743 989565
info@ukmachinery.uk https://ukmachinery.uk https://www.linkedin.com/in/andy-n-629859a0 https://twitter.com/usedmach
Machinery Supplies UK goes further than other suppliers by offering additional services such as Laser Slat Cleaners: designed to reducing part scratching and keep extraction flowing, part and parcel of laser bed longevity. This includes the 240v/415 v models for varying kW laser powered machinery. Furthermore, the Rhino Parter Hammer is renowned for making the removal of tabbed laser cut parts much easier, using a handy automation impact vibration to break the tabs.
hand, reconditioned machinery, as part of sustainable best practice.
The wide selection of Press Breaks include makes such as Amada, Trumpf and Bystronic from small compact to large tonnage and bed sizes, all fully checked tested, serviced and prepared and comes with a full warranty. The team can provide tooling at an extra cost and all machinery is installed on-site, with full training given to operators. These press brakes can bend thick materials across various applications from construction, automotive, aerospace, agriculture to oil and gas.
TRUMPF is widely considered to be the pinnacle of German machinery manufacturing across the entire machine tool, laser and electronics sectors. Regarded as a worldleader in machine tools for flexible sheet metal processing, the TRUMPF CNC Punching Machines are in high demand across the UK and further afield. The expert engineering team at Machinery Supplies UK provides an extensive range of TRUMPF accessories from
Machinery Supplies UK goes further than other suppliers by offering additional services such as Laser Slat Cleaners: designed to reducing part scratching and keep extraction flowing, part and parcel of laser bed longevity. This includes the 240v/415 v models for varying kW laser powered machinery. Furthermore, the Rhino Parter Hammer is renowned for making the removal of tabbed laser cut parts much easier, using a handy automation impact vibration to break the tabs.
automotive, aerospace, agriculture to oil and gas.
team at Machinery Supplies UK provides an extensive range of TRUMPF accessories from cartridges, multitools, collars, die adaptors and expert advice as well as spares and consumables.
“Our DEBURRING machines also offer exceptional value, adding the final finish and touch to the laser cut parts. From simple deburring to re-graining, our process of materials solutions are available to fit customer requirements.”
“Our new state of the art East Yorkshire showroom will be opening later this year, when we will invite new and existing customers from across the industry. Watch this space!” added Andy. sponsors this issue of Best Practice – see them on pages 4-5 9
The wide selection of Press Breaks include makes such as Amada, Trumpf and Bystronic from small compact to large tonnage and bed sizes, all fully checked tested, serviced and prepared and comes with a full warranty. The team can provide tooling at an extra cost and all machinery is installed on-site, with full training given to operators. These press brakes can bend thick materials across various
TRUMPF is widely considered to be the pinnacle of German machinery manufacturing across the entire machine tool, laser and electronics sectors. Regarded as a world-leader in machine tools for flexible sheet metal processing, the TRUMPF CNC Punching Machines are in high demand across the UK and further afield. The expert engineering
“We are forever liaising with our NEW equipment suppliers in order to bring only the premium UK market high quality sheet metal working equipment, coupled with our faultless aftersales support.”
Non-machinable or non-conveyable items are the bane of any postal or e-commerce sorting operation. Whether large, heavy, fragile, unstable or oddly shaped, these goods can’t be automatically sorted and instead require inefficient, manual processing. However, with new automation technologies like computer vision and robots, businesses have an opportunity to change this. In the near future, every item could be machinable.
Lars Pruijn, Innovation Director, and Mart Ruijs, Product Manager at Prime Vision explore how computer vision and robotics could make nonmachinable items a thing of the past.
Items that don’t fit in
Non-machinable items, often called ‘uglies’ because of the difficulties they pose, can take many different forms – from big TVs, brooms and car tyres to large pots of paint. What they all have in common is that, due to their characteristics, they can’t be accommodated in a standard, automated sorting system. As postal services and e-commerce companies invest heavily in fixed infrastructure that is optimised for smaller items, non-machinables present a sizeable problem. They must be identified, separated, and accommodated in a different process.
Traditionally, this has been accomplished manually. Warehouse staff identify non-machinables by eye, then move them by hand to a separate chute or destination. This is time consuming and costly, placing unnecessary strain on workers.
Furthermore, a manual approach isn’t fact based, raising the possibility that a non-machinable item might slip through.
The ability of computer vision to accurately identify problematic goods and the inherent flexibility of robots will soon ensure that every item is machinable
Improving the identification and transport of these goods has long been an uphill battle, but computer vision and robotics can provide a solution.
Eyes on the oversized prize
Computer vision technology offers the capability to quickly and accurately identify non-machinable items at the beginning of the sorting process. This eliminates any manual intervention, greatly improving efficiency.
Correct identification of a wide range of items is possible thanks to machine learning. By training artificial intelligence (AI) models using examples from a business’s real-world operations, a computer vision system can not only recognise objects based on dimensions and weight, but other characteristics such as shape, stability, packaging type and more. The more items the system is exposed to, the better it becomes at recognition.
As well as relying on hard data to correctly determine nonmachinable items, the system can assist in automatically pre-sorting them to an appropriate chute, conveyor, area or robot – so no
unsuitable packages slip through. Furthermore, computer vision seamlessly integrates within the brownfield environment of existing processes too, relying on camera hardware and standalone software.
Ultimately, computer vision speeds up the processing of nonmachinable items. Effective presorting means manual intervention is not required, with items that were initially unsuitable for automation now accounted for in a fast, costeffective process.
With pre-sorting complete, the next question is how to efficiently move non-machinable items to a desired destination? A manual approach is slow and places strain on employees, and by their very nature, these items are unsuitable for fixed conveyor systems.
Robots are famed for enabling incredibly flexible sorting operations, but their versatility in terms of payload provides a unique opportunity to automate the handling and transport of traditionally non-machinable items. The latest robots are highly autonomous, using a combination of computer vision and ranging to safely navigate a pre-mapped area, picking up and dropping off items to any destination within it. Able to handle anything from a single letter to a 2-metre square parcel weighing well over 30 kg, robots can be equipped to move a wide range of items that would be totally unsuitable for a conveyor system.
With customised systems for gentle loading, transport and unloading (depending on what is being
carried) robots can efficiently deliver non-machinable items to the next stage of the sorting process without human intervention. Robots are equally adept working with other installed infrastructure in small- or large-scale operations – allowing almost universal application. Navigation software and a talent for working in tight spaces means that robots carrying large items could even coexist next to others moving smaller ones, uniting sorting operations within a single, highly efficient and flexible ecosystem.
Any sortation process is interlinked, and it is at the end of the process where computer vision and robotics can be further integrated to ensure reliable delivery of non-machinable items to customers.
After pre-sorting and transport, non-machinable items need to be placed in chutes or storage areas
ready for final dispatch. However, due to their size and awkward shapes, more space needs to be allocated in chutes to accommodate them. Failure to do so risks blockages or items being damaged.
However, by harnessing a computer vision system to check available capacity in each chute, robots can be directed to unload at a destination where room is available, like a game of logistical Tetris.
Blockages and damage can be avoided, while providing a healthy buffer for simplified loading into cages, pallets and delivery vehicles.
Currently, nearly every sorting operation has a percentage of nonmachinable items which represents a reduction in profit. This will not be the case for much longer. The combination of computer vision and robotics promises to end the era of non-machinable items and consign the term to history.
The ability of computer vision to accurately identify problematic goods and the inherent flexibility of robots will soon ensure that every item is machinable. Manual intervention will be a thing of the past, as these parcels and products will be accommodated in an efficient, automatic process that is tailored to their unique requirements. In some cases, the movement of smaller and larger items may be possible in the same areas.
Tantalisingly, this can be achieved in conjunction with existing operational infrastructure, as computer vision and robotics can be integrated with installed hardware and software rather than replacing it. Combined with the inherent flexibility and scalability of both solutions, the entire postal, e-commerce and logistics sector could soon see an end to the era where size and shape mattered.
Street works carried out in England between 2022 and 2023 cost the economy some £4 billion in journey disruption. Infrastructure work is essential, but how can we minimise its impact on drivers and residents? In this article, Stewart Goulding, managing director of drive system supplier EMS, explores how robotics could be the solution.
Maintenance work carried out by gas, water and telecoms companies is necessary for the provision of essential services. But less welcome is the disruption that these street works often bring. Speed restrictions, closed pavements and temporary traffic lights can cause mile-long tailbacks at worst, and a mild inconvenience at best.
To tackle this issue, the Government proposed plans earlier in 2024 to crack down on street works, with increased fines on utility companies allowing works to overrun into the weekend and bank holidays. If successfully implemented, the scheme could have a massively positive impact for drivers, deterring utility companies from causing unnecessary disruption.
But there is something the plan doesn’t address — the speed of these repairs. While awarding late fines to companies might encourage them to complete works more quickly, it could also lead to work being rushed. Substandard quality repairs could result in work needing to be redone, which only adds to the issue of disruption.
Evidently, a more rounded approach is needed to tackle the challenge of infrastructure maintenance. So, what else should be considered?
Developments in drone technology, including the commercialisation of drones with advanced camera systems mean that building powerful, lightweight drones is becoming increasingly possible.
To address the speed and responsiveness of repairs, integrating more autonomous technology into maintenance processes could be advantageous. One project led by the University of Leeds is investigating this with its concept of ‘self-repairing’ cities. This £4.2m research project aims to minimise street disruptions using specially designed maintenance robots.
Maintenance robots offer several advantages. For example, repairs at
height, such as broken streetlamps often require a specialist vehicle with a crane-like mechanism to lift the worker up to the street light. Not only does this require dedicated equipment — which is often limited in number — but it also means that part of the road or pavement is obstructed while work is being carried out.
The self-repairing city concept presents a more streamlined solution, using drones. These can be stationed around cities and dispatched as required to quickly fix such problems. Health-and-safety risks of lifting workers up at height are decreased, with minimal disruption to road users in the process.
These drones may also be useful for inspection. Conducting road condition surveys manually is timeconsuming. And it’s unsafe to slow down to inspect the condition of a pothole on a road when surrounding traffic is moving much more quickly.
It’s possible that some cars will be able to record and transmit data on road condition on their own — Mercedes Benz trialled this with its own vehicles in the Netherlands. But until then, drones can offer a much more streamlined solution. Able to work around the clock, drones can quickly identify small cracks and potholes before they escalate into more serious problems.
Robotics can also be used to inspect areas we can’t see. Underground water pipes in the UK lose thousands of litres each year due to cracks and leaks. In this application, robots could be used to crawl through pipes too small for human workers, and remotely operated for safe and thorough inspection.
The benefits of these maintenance robots are clear to see. With more systematic inspections, faults — whether on our roads, on-street infrastructure, or underground — can be picked up far more quickly, enabling faster, cheaper repairs. The integration of automation technology into a utility company’s toolkit could be hugely advantageous, but it all begins with the right robot.
Whether it’s a small DC motor powering drone propellers or carefully positioning a robotic arm, how well these tasks are performed is down to the capabilities of the drive system.
There are several key elements for design engineers to consider when specifying a suitable drive system for maintenance robot applications. Weight is a vital consideration. Drones, for instance, need to be lightweight for several reasons. A lighter device will have more power efficiency, but heavier drones can also demand specialist licenses when being flown in built-up areas.
Developments in drone technology, including the commercialisation of drones with advanced camera
systems mean that building powerful, lightweight drones is becoming increasingly possible. But for drones carrying out repairs on their own, the weight and size of the tools required must also be considered. As a result, design engineers might find themselves with more weight restrictions than initially thought.
For robots operating in compact spaces, such as within pipework, size is another key consideration. The drive system must be as compact as possible to reduce the overall size of the robot, else they introduce another source of obstruction. Yet, despite a smaller size, the motor must still be able to provide enough torque to carry out repair tasks effectively, such as tightening screws or applying filler paste.
To help maintain a high torque, engineers can make use of precision gearheads. These small gearboxes sit between the motor and point of power transfer, slowing high motor speeds while significantly increasing available torque. They also help to improve movement control, ideal for high-precision work.
For compact applications such as
those in small maintenance robots, planetary gearheads are the ideal solution. These make use of toothed planetary gears that rotate around the centrally mounted sun gear, with the number of teeth determining the reduction ratio. Planetary gearheads have an increased number of contact points thanks to the toothed gear design, making them especially robust, with a long service life.
And this access to higher torques can be achieved with minimal extension of the drive length. FAULHABER offers a variety of planetary gearheads, distributed exclusively in the UK and Ireland by EMS. The smallest gearhead in the micro range has a diameter of just 3.4 millimetres, with the smallest standard gearhead still only a diameter of six millimetres.
While infrastructure repair work is essential for many core services, there’s no denying the social and economic impact it can have. Updating maintenance strategies with the latest technologies, including advanced robotics, can help to minimise negative effects of repair work all while building better, more reliable infrastructure for the future.
For further information, please visit www.ems-limited.co.uk
To help industrial and research users measure surface energy with a quick, easy, and low-cost methodology, Dyne Testing, an Intertronics company, supplies Dyne Pens and Inks. Dyne Pens and Inks are a convenient way of measuring a polymer’s surface energy or wettability, and of identifying filmic contamination of metals. This can benefit engineers and researchers in packaging and converting, automotive, aerospace, medical device manufacturing, and battery technology applications.
The Dyne Pen test is a simple method of determining the surface energy of most polymer-based materials in line with ISO 8296 and ASTM D257884. It is used to help understand the surface energy and wetting characteristics of polymers, and their suitability for bonding, coating, painting, or printing. Test results will inform the need for surface preparation, such as cleaning, or plasma, corona, or flame surface treatment.
Dyne Pens are available in a range of values from 30 to 72 “Dynes”. To perform the test, the user selects a pen, and draws a line on their substrate. The test ink will either form a continuous film on the surface or draw back into droplets. If the test ink stays as a film for 3 seconds or more, then the substrate’s minimum surface energy (measured in mJ/m², mN/m, or dyne/cm) is lower than the test ink. The surface energy of the substrate can be determined within a tight tolerance by applying a range of increasing or decreasing values of test inks and observing the wetting. Users can also purchase inks
The Dyne Pen test is a simple method of determining the surface energy of most polymerbased materials in line with ISO 8296 and ASTM D2578-84.
in bottles, which can be spread using a brush, spreader or drawdown bar to perform the test.
There are two types of Dyne Pen, the ISO Type, which is based on ISO 8296:2003 ink specifications, and a Non-Toxic range, an ethanol-based alternative. The ISO Type is available both in pen format and as bottles of ink, which are purple in colour. The non-toxic range is available as ink only and is yellow in colour. Test inks also have application in assessing contamination on metal surfaces.
“For bonding/printing to be a success, the liquid’s surface tension must be less than the substrate’s surface energy, so that wetting occurs” said
Ben Swanson, Chief Commercial Officer at Intertronics. “While most metals wet fine, many plastics do not. Metals, however, can become contaminated during handling, and this can impact their ability to be processed.
“There are many ways to improve a plastic’s surface energy, including cleaning, treatment with plasma/ corona or by using a primer,” continued Swanson. “Plasma treatment can increase the substrate’s surface energy and clean it simultaneously, making it useful to treat both metals and plastics.”
“Originally designed for use in packaging applications to test the surface energy of polyethylene film before printing, Dyne Pens have been used successfully in many applications,” said Alison Fox, Brand Manager at Dyne Testing. “Before and after surface treatment, the Dyne Pen test can be extremely helpful to understand a substrate’s surface tension. Customers who want to ensure a successful printing or bonding process can order Dyne Pens from us for next day delivery.”
For environments where a move advanced test is needed, Dyne Testing supplies instrumentation for contact angle measurement and optical tensiometers.
For customers looking to use surface measurement to improve their understanding of wetting and adhesion, Intertronics and Dyne Testing can support with developing a reliable, repeatable, and safe process.
Vision Engineering, UK designer, manufacturer and exporter of ergonomic microscopes and measuring systems, has announced a new sub £1k entry point for its patented optical stereo microscope technology with the global launch of OPTA, plus it has enhanced a number of its product ranges.
Available for only £900, with a choice of three stands and two lenses, OPTA redefines the entry point for users to benefit from Vision Engineering’s exceptional image quality, ergonomic design and ease of use.
Additionally, Vision engineering announces exciting advancements across its popular EVO Cam, Lynx EVO, and Swift PRO product lines. These enhancements broaden the appeal and applications of these powerful tools, making them more accessible to a wider range of industries and users.
The EVO Cam series now boasts a wider range of configurations, offering even greater flexibility for digital inspection tasks. With the launch of a new, simplified ICON model, users can now choose from multiple software
These products are the combined result of listening to our customers and continuously developing our innovative products.
configurations and ergonomic stands to perfectly tailor their EVO Cam system, enabling effortless image comparison, capture, measurement, and reporting.
Award-winning Lynx EVO range extended for Superior 3D Viewing
Building upon its reputation for unparalleled ergonomic design and stunning 3D stereo imaging, the Lynx EVO series has been extended to include a simpler, non-zoom variant to appeal to a more price conscious market. This makes the benefits of Lynx EVO accessible to a much wider audience who have applications demanding exceptional image quality and clarity, useable working distance, and exceptional user comfort.
Vision Engineering has enhanced the Swift PRO metrology line, its flagship range of bench-top optical measuring systems, with the release of the new Swift PRO EDGE. Featuring a 6.5x zoom, the EDGE enables quick, precise measurements of a wide range of part sizes and features without
time-consuming lens changes for different measurement tasks. Using our industry standard, user-friendly Metlogix software, operators of all skill levels will operate the EDGE more efficiently and more productively.
Commenting on the upcoming product launches, Paul Newbatt, Group Sales and Marketing Director at Vision Engineering says “These products are the combined result of listening to our customers and continuously developing our innovative products. By bringing OPTA to market now, and enhancing the value propositions of our EVO Cam, Lynx EVO and Swift PRO ranges, we are confident that these new solutions will significantly broaden the appeal of our Inspection and Metrology portfolio. This enables a much wider range of customers in existing and new markets to better achieve their inspection and measurement objectives with Vision Engineering solutions.”
9-10 October 2024
Coventry Building Society Arena
The UK’s biggest event dedicated entirely to engineering, electronic and embedded design
Join thousands of design engineers this October! Source the latest products, services and innovations available to the sector. Register today.
@EngDesignShow #EngDesignShow www.engineeringdesignshow.co.uk
HEADLINE SPONSORS
Discover your next supplier at The Engineering Design Show (SOLD-OUT exhibition floor)!
EDS 2024 is back on the 9th – 10th October at The Coventry Building Society Arena. PECM readers are invited to join thousands of engineers at the UK’s number one free exhibition of mechanical, electronic and embedded design.
Headline Sponsors, Powell Electronics, Solsta and Wurth Electronics, return to the show for two unmissable days. They will be joined by Dassault Systemes, sponsors of The Engineer Conference Theatre, QRA, sponsors of the very-popular EDS Party and ConeX, sponsor of our new Start-Up Zone.
Visitors can expect to meet with 200+ exhibitors covering everything from 3D printing, fasteners and adhesives, design software, drives and controls, embedded systems, labeling, laser marking, motion control, PCB manufacture and assembly, and much more.
Visit the website (www.engineeringdesignshow. co.uk) for the full list of exhibitors and read below to hear about everything else you can’t afford to miss!
Unlock 50+ hours of free learning across the 3 conference theatres. Highlights include:
• 11:15 am | 9th October - Socially assistive robots and the UH Robot House – Patrick Holthaus, Senior Research Fellow and Robot House Manager, University of Hertfordshire / The Robot House
• 1:15 pm | 9th October - Protecting intellectual property in the age of AI – Katy Sayer, UK and European
Patent Attorney, Venner Shipley
• 11:15 am | 10th October - British Olympic track bike developmentBen Collins, Lead AM Applications Engineer, Renishaw
• 12:15 pm | 10th October - The Fight to Repair: why you don’t truly know your product until someone else has tried to repair It! - Jude Pullen, Creative Technologist, RS DesignSpark
Join practical workshop sessions. Takeaway inspiration to apply to your business
• 10:30 am | 9th October - How high-speed data communication is used on industrial machinery –Ryan Milligan, Director Business Development, Powell Electronics
• 11:30 am | 9th October - How to maximise the potential of multiphysics simulation – Dr Ross Hubble, Technical Manager, COMSOL Ltd
• 1:30 pm | 9th October - Realising productivity and innovation through inclusive working environments - Poppy Harrison, Engineer, Maira Bana, CFD Manager and Laura Hoang, Human Factors Engineer at SheCanEngineer
• 1:30 pm | 10th October – The devil is in the detail - Martin Dinmore, Distribution Channel Manager, Pico Technology
Meet the next generation of engineering superstars!
Nottingham Trent University will be showcasing the next generation of over 25 product designers. Featuring graduates from 2024 who have exhibited recently at New Designers in London, whereby their work has secured outstanding recognition from prestigious brands such as Dyson, Kenwood and Unilever.
Additionally, second year product design students will be exhibiting their collaborative project with industry partner Trampboards (www.trampaboards.com) showcasing the use of the VESC power system. The Trampaboard
team will be on hand to describe the innovative VESC system and how students have applied their technology in their robots.
Explore cutting-edge advancements from across the world of engineering design at the Innovation and Start-Up Zones
The Innovation Zone will be displaying an exciting selection of design work. This includes Creative Hubb Limited’s EOD Bomb Disposal Suit, a complex garment made up of multiple layers of meta and/or para aramid materials required per
panel/area to achieve the specified level of protection.
At the Start-Up Zone visitors can meet with an exceptional lineup of companies. Explore new products from Structural Evolution, Electrogear Solutions, Infinicity and HAL Robotics. Plus, 3D printers and scanners from Construct 3D, Nexa 3D, Central Scanning.
There are plenty of other exciting things you won’t want to miss:
• Stop by The Robot House from the University of Hertfordshire - The ground floor has been adapted into a unique research facility for human-robot interaction. It is equipped with the latest generation of robotics platforms, including state-of-the-art care robots for assisted living.
• Race to place at the EDS Games Zone – enjoy the immersive F1 racing simulators, take your shot on the basketball shoot the hoop or check out our other fun games and activities.
• Take a break at our Chill and Charge Zone – offering a quiet spot to relax and recharge both yourself and your devices.
• Enter the free EDS raffle – back by popular demand. Last year’s prizes included a FitBit, Apple AirPods, Amazon vouchers and much more!
• Join the party (4:30 pm – 6:00 pm | 9th October) - We’re inviting all visitors, exhibitors, and speakers to join us at the EDS Party. Enjoy complimentary drinks, nibbles, and live music. This year, we’ve expanded our space to include a quieter area away from the music, providing the perfect spot to catch up with friends, clients, and colleagues after a bustling day.
There is no better opportunity in the UK for design engineers to source the latest products and suppliers, find inspiration and network. Use the QR code below to confirm your free place, we can’t wait to see you there!
Tinytag Ultra 2 thermocouple data loggers are used to record temperature data during the heat curing of medical grade acrylic at Manchester Royal Eye Hospital.
NHS ocularists working in the Department of Ocular Prosthetics at Manchester Royal Eye Hospital are responsible for fabricating and fitting ocular prostheses, cosmetic shells and facial prostheses. Part of the fabrication process is the heat curing cycle, in which the medical grade acrylic which the prosthetic eyes are made out of is exposed to high temperatures so that it hardens and is suitable for wear.
The ocularists use Tinytag Ultra 2 thermocouple data loggers to monitor temperatures during the heat curing cycle to ascertain that the acrylic has been cured at the optimum temperature (a temperature range of 200°C to 1300°C for the correct amount of time).
If the acrylic is not cured properly, the material does not harden fully and remains porous, resulting in monomer leaking out of the acrylic and causing irritation for the wearer. It is therefore imperative that temperatures are recorded during the cycle. Tinytag thermocouple data loggers are ideal for use in this application, as their thermocouple probes offer fast response monitoring in temperatures from -200°C to +1370°C.
To monitor the heat curing cycle,
If the acrylic is not cured properly, the material does not harden fully and remains porous, resulting in monomer leaking out of the acrylic and causing irritation for the wearer.
the data logger’s thermocouple probe measures the temperature within the heat curing tank, while the data logger itself remains outside the tank recording the readings taken by the probe. The data from each cycle is downloaded, viewed and analysed using Tinytag Explorer software. If the temperatures are found to
have fallen outside the desired parameters, indicating that the acrylic may have not cured properly, the cycle is repeated to ensure that the prosthesis is properly cured.
Using Tinytags to monitor temperatures during the heat curing cycles gives the team at Manchester Royal Eye Hospital peace of mind that the acrylic has cured properly and therefore will give the best possible results for their patients.
Data loggers for indoor, outdoor and industrial/process applications
• Rugged and compact
• Rugged and compact
• Easy to use
• Easy to use
• Dust, splash or waterproof
• Dust, splash or waterproof
• Data downloaded to PC
• Data downloaded to PC
• Cost-effective
• Cost-effective
Accompanying probes are available for monitoring extremes of temperature, and for awkward to reach areas such as pipework.
Accompanying probes are available for monitoring extremes of temperature, and for awkward to reach areas such as pipework. For larger sites, Tinytag Radio and LAN loggers automatically gather data for viewing on a PC, across a
Logger
For larger sites, Tinytag Radio and LAN loggers automatically gather data for viewing on a PC, across a LAN or remotely across the internet.
or remotely across the internet.
Most customers will tell you just how efficient Sepura oil-water condensate units are. But did you know that our patented filtration media found inside every genuine Sepura unit is made from recycled glass bottles?
This not only makes the outputs from our units environmentally friendly but also our manufacturing process too.
Going green and achieving your targets doesn’t have to be a compromise.
The UK hospitality sector is set for a positive 2024, fuelled by favourable economic conditions, evolving culinary trends, and strategic industry efforts. Despite high energy prices, consumer demand for beer and spirits remains strong. The rising popularity of craft beers and a growing market for artisan and flavoured gins partly drives this trend. For brewing and distilling operations, managing costs while maintaining product quality is crucial.
In the brewing and distilling industry, challenges can be categorised into three key areas: raw materials handling, production, and waste management. Efficient product flow control is essential in each area to ensure highquality output. Progressive cavity (PC) pumps provide significant advantages in efficiency, productivity, and energy savings, helping producers navigate high energy costs.
gravity fed into a masher where it is mixed with hot water before entering the mash tun. However, newer or smaller breweries often use conveyors, adding complexity and cost. Inconsistent mixing due to uneven water addition can also reduce yield.
The brewing or distilling process begins by mixing milled grain (grist) with water in a vessel called a mash
SEEPEX’s BT range offers a streamlined alternative, combining a feed hopper and adjustable auger feed screw to ensure homogenous mixing and stable yield. These offer installation and mashing-in flexibility, mixing the grist with hot water and then pumping into the mash tun. This pump can reduce transfer times by half and double mashing capacity.
The inclusion of Smart Conveying Technology (SCT) enabling rapid dismantling and cleaning, increasing pump stator life by up to 200% and reducing maintenance time by up
Fermentation, where yeast is added to the wort to convert simple sugars into alcohol, is a critical stage. Yeast is shear-sensitive and requires gentle and hygienic handling to preserve its quality. Traditional peristaltic pumps can damage yeast with their pulsating action, which has a detrimental effect on the taste of the beer or spirit.
SEEPEX’s BCF range of PC pumps provides a gentler alternative, moving yeast through a series of cavities with minimal shear. This preserves yeast quality and ensures better fermentation outcomes. This is because PC pumps move the product through the pump in a series of cavities, preventing slip from the discharge back through the pump. Slip creates shear, so PC pumps have extremely low shear compared to other pump designs that have clearances between the lobes, screws or gears. They are also good at handling entrained air and foam, which is important for brewers and distillers as the yeast can become foamy at this stage.
The low shear action is also beneficial for recovering yeast for reuse, enhancing efficiency over manual or less effective methods. At the end of the fermentation process, yeast can also be recovered for re-use (known as harvesting) by draining from the conical base of closed vessels (bottom cropping) or skimming from the surface of open vessels (top cropping). In both cases, the low shear characteristics of the BCF range offer advantages over alternative pumped methods or inefficient manual processes.
Precise addition of flavours and colours is essential for consistent product quality. Pulsation from positive displacement pumps can disrupt even distribution, leading to quality issues. This is because once these pumps have dispensed a product, there is a pause before they can dispense again. This creates a gap in the process that can lead to uneven distribution of ingredients.
SEEPEX’s D range of PC dosing pumps delivers virtually pulsationfree performance, ensuring linear accuracy and consistent metering of additives. This linear accuracy, which varies with pump speed, allows easy calibration and control. Its ability to dose low flow rates means that colours, flavours and portions are consistent. These pumps can manage a wide range of viscosities and consistencies, from thin liquids to sticky substances, always ensuring precise and reliable dosing.
By transitioning to innovative PC pump solutions, brewers and distillers can enhance product quality, reduce energy consumption, and boost production capacity.
Spent grains, draff, and hops need efficient removal post-mashing to maintain production flow. These by-products must be quickly transferred to storage tanks or silos to allow production to continue. They are then transported for use as animal feed, as additives in bakery products, for energy generation in biogas plants or to produce biofuel.
these manually, larger operations often use pneumatic expeller units, which are energy intensive. However, brewers and distillers can significantly reduce their costs by pumping these residues instead.
Open hopper PC pumps with auger feed systems provide a cost effective and energy efficient solution for conveying spent grain or draff through closed pipe systems. SEEPEX’s Smart Air Injection (SAI) technology further optimises this process by combining progressive cavity pumping with pneumatic dense phase conveying, significantly reducing air consumption and energy costs. The system solution can efficiently convey 60-85% moisture content spent grains, draff and hops in 20-30m long plugs over distances of up to several hundred metres using controlled pulses of air. Trials at a UK brewery showed potential air consumption reductions of up to 90% for spent grains and 80% for hops compared to the existing pneumatic expeller.
By transitioning to innovative PC pump solutions, brewers and distillers can enhance product quality, reduce energy consumption, and boost production capacity. This optimisation helps maintain profitability despite the pressures of high energy costs, ensuring that the industry can thrive in a challenging economic landscape.
By Nikolay Biba, MICAS Simulations Ltd, Oxford, UK and Pavel Mordvintsev, QForm Group FZ, UAE
Numerical simulation has become an indispensable tool for the development of metal-forming technology. It eliminates the need for expensive metal trials by accurately predicting the product shape and identifying technological defects. Nonetheless, the engineer must specify the parameters of the technological process and the shape of the deforming tools before the simulation starts. Thus, the search for the best technology still relies on an engineer’s skills and experience, even though they can now try different variants much faster.
With multi-stage forging or rolling processes through several passes, the real challenge is to find the best sequence of intermediate shapes between forging blows (preforms) or the sequence of roll grooves. In this case, we face the problem of finding the optimal workpiece shape transformation from the initial stock to the finished product. This transformation is not a simple alteration of some drafts or radii. We must consider the shapes of deformed workpiece and forming tools as the integrity of interconnected geometrical entities and alter them to achieve the best performance. The material volume constancy requirement also restricts the variation of the deformed workpiece. The creation of such intermediate shapes must be done using specialised CAD software that uses precise simulation as an optimisation and verification tool to
Fig. 1. The automatically created geometry shape for the top die cavity (a), the preform operation simulation (b), photos of the industrial defect-free aluminium preform and finished forged part before flash trimming.
achieve the best performance, and this must be done using established technological process design rules and practical experience. With this approach, we came to the next level of manufacturing digitalisation, which is called the simulation-driven design of processes. Its outcome includes finish die fill, absence of material flow defects, minimum material loss, and guaranteed material workout, all while staying within the admissible load. We have special simulation-driven software products for aluminium profile extrusion, shape rolling, ring rolling and open-die forging, however here we illustrate our approach with an example of a hot closed-die forging.
In practice, very few forgings are produced in a single impression. Usually, one or two preforming
operations are necessary to transform the billet material into a shape that fills completely without defects in the finish die cavity. Our unique software, QForm UK Direct, develops a preform shape based on potential flow approximation. An explanation of the method and its history can be found in [1]. As an output, the program creates the optimal preform shape and the complete CAD model of the preforming dies. Then, this model can be verified by simulation and CNC machined for regular forging manufacturing, as shown by the complex aluminium forging example in Fig. 1.
[1] N. Biba, A. Vlasov, D. Krivenko, A. Duzhev, S. Stebunov, Closed Die Forging Preform Shape Design Using Isothermal Surfaces Method, In Proceeding of ESAFORM 2020, ISBN: 978-1-7138-1028-5, pp. 268-273.
Prediction of phase composition and mechanical properties
Prediction of phase composition and mechanical properties
LONGITUDINAL ROLLING
LONGITUDINAL ROLLING
11th-12th September 2024 | NEC Birmingham, UK
Alex Stewart International attendees:
Stephen Russell (ASI UK)
Adam Leadbetter (ASI UK)
Cameron Finley (ASI UK)
For meeting requests and metal inspection & analysis enquiries, please email: stephen.russell@alexstewartinternational.com
Alex Stewart International provide a comprehensive range of inspection and analysis services for all metals
www.alexstewartinternational.com
Four Speedor high-speed doors have been installed by Hart Door Systems at a major frozen and cooked meat manufacturing in northern England. The doors, at just 1.5m wide and 1.95m high, are the second smallest Speedors ever manufactured by Hart.
“The contract demonstrates two things,” says Gordon Kipling, regional sales manager for Hart. “Not only is our Speedor range available in distinctly different types of doors but where applicable the doors can be available in reduced sizes for precise requirements.
“In this case there was a need to protect the production environment against drafts, humidity, dust and dirt by installing our Speedor Cleanroom with its fast opening and closing speed. Our pharmaceutical standard Cleanroom Speedors control airflow thus reducing contaminants.”
Designed specifically for manufacturing and research facilities, Speedor Cleanroom works
in strictly controlled environments where hygiene standards are high, such as pharmaceuticals, food processing, electronics and micromechanics industries.
The main features of Speedor Cleanroom include maintaining strict air leakage requirements over specified pressure differentials. Complete with an intelligent control panel with digital display each Cleanroom has a reliable and clean in-line drive system complete with an integral safety brake and a non-touch safety light curtain ensures maximum protection to personnel.
Seals minimise pressure drops and protect the manufacturing environment against drafts, humidity, dust and dirt.
Hart’s shutters shut out villains
A major contractor has chosen Hart’s shutters to protects its new building in a high crime area in the North West of England.
Brian Woodcock, Hart’s regional sales manager, said the client moved to purpose-built premises located in an area known for high levels of criminal activity. “The client chose to protect themselves
from theft by installing tubular driven window/door shutters around the entire building,” explains Mr Woodcock.
“A total of 14 shutters have been installed along with two Sectional overhead doors all finished in a mixture of anthracite grey and goosewing grey. These provide comprehensive protection. This order shows that we are capable of delivering a comprehensive range of door products all manufactured by Hart which is the crucial point.
“Hart has invested heavily in designing and testing exceptional high security rolling shutter systems. Hart high security shutters are tested and certified by the BRE under LPS1175 and to BSEN 12453:2005; BSEN 12604:2000; BSEN 12635:2002; BSEN 12978.2003
“ In particular Hart’s Terror Screen, which is not relevant to the North West order, has set exceptional standards of protection of up to 20 minutes against cutting, drilling, crowbars and axes due to its exceptional robustness. This allows enough time for security teams to arrive on site.
“Hart’s Terror Screen SR1-4 high security roller shutters have been installed at a number of high security locations worldwide including power stations, nuclear facilities, government buildings, data centres, banks and museums.
“A further development is Hart’s Typhoon shutter which has an enhanced guide channel, heavier gauge curtain and Hart manufactured wind locks.
The metals industry, characterised by the handling of long and heavy materials, is continually pushing the boundaries of efficiency and safety. With the introduction of HUBTEX’s new sensory aisle entry assistant, the sector is set to make a significant leap forward in warehouse operations. This innovation, designed for narrow-aisle environments, addresses a critical challenge faced by companies handling bulky goods—navigating tight spaces without causing damage to the materials or the equipment.
HUBTEX’s sensory system utilises advanced 2D lidar technology to guide multidirectional sideloaders with unprecedented precision. For companies in the metals industry, where even minor errors can lead to costly damages, this technology is a game-changer. The system ensures that sideloaders align perfectly with narrow aisles, reducing the risk of collisions and enhancing the safety of both the operators and the goods.
This advancement is not just about reducing damage—it’s about improving overall operational efficiency. By minimising errors during aisle entry, companies can streamline their processes, reduce downtime, and ultimately save costs. The ability to integrate this system with existing pedestrian safety sensors further enhances its value, offering a cost-effective solution for modernising warehouse operations.
Safety, precision, and efficiency are the pillars upon which the future of the metals industry will be built. HUBTEX’s innovation is a clear example of how embracing
This advancement is not just about reducing damage—it’s about improving overall operational efficiency
cutting-edge technology can lead to significant improvements in these areas. As the industry moves forward, those who invest in such technologies will not only improve their operations but also gain a competitive edge in a demanding market.
In an industry where every millimetre counts, the adoption of HUBTEX’s sensory aisle entry assistant is more than just a smart move—it’s a necessity for any company looking to stay ahead in an increasingly competitive environment.
Research by the National Association of Manufacturers (NAM) found that 58 per cent of manufacturers considered sustainability essential for competitiveness. Sustainability is a strategic imperative, including in material handling processes. Here, Carl Hodges, business development manager at Gough Engineering, the materials handling specialist, explores five ways manufacturers can reduce their environmental footprint.
NAM’s research, conducted in 2022, marked a sharp increase from 38 per cent the previous year, demonstrating that sustainability is moving up manufacturers’ agendas. However, manufacturers face a dual challenge in their pursuit of sustainability: balancing environmental goals with operational efficiency and costeffectiveness.
Transitioning to greener practices often requires substantial investments in new technologies or equipment, which can pose financial challenges and disrupt established workflows. Despite these hurdles, integrating sustainable solutions into material handling processes is crucial for reducing environmental impact and maintaining competitiveness.
Here, we delve into five methods through which material handling equipment can advance sustainability while enhancing operational efficiency.
1. Lowering energy consumption
Reducing energy consumption is pivotal to sustainable
Gough Engineering’s Vibrecon® vibratory separators feature an energy-efficient design, minimising power use while efficiently handling materials.
manufacturing practices. Energyefficient equipment, such as motors equipped with variable frequency drives (VFDs) and high-efficiency conveyor systems, plays a critical role in achieving this goal. VFDs allow precise control over motor speed and torque, optimising energy usage during varying operational demands.
Gough Engineering’s Vibrecon® vibratory separators exemplify energy-efficient design. Engineered to minimise power consumption while transferring product efficiently, these separators utilise advanced vibratory technology tailored to specific material handling requirements. This gives consistent, reliable performance so motors run smoothly and efficiently, minimising environmental impact. The approach not only reduces operational costs but also contributes to a lower carbon footprint while securing production quality objectives.
Effective management of material waste is imperative for sustainable manufacturing. Accumulated waste and spillage can create risk zones that affect not only the wear and overload on mechanical systems and safety risks for operators, but also pose potential fire hazards for certain materials.
To mitigate these effects, industrial sieves, such as vibratory and centrifugal separators, are instrumental in classifying and sorting raw materials, ensuring uniformity and minimising waste during production processes.
In a recent project for Gough Engineering, a pharmaceutical manufacturer wanted to optimise their production line efficiency. By integrating vibratory screening equipment, the manufacturer achieved precise separation of active pharmaceutical ingredients (APIs), while recovering product that was
unfit for further processing and then recycling or reconditioning it within the production infeed lines. This process reduced material waste and enhanced product quality.
3. Preventing leakages and spillage
Minimising leakages and spillage is a critical aspect of sustainable material handling, as it directly impacts both resource conservation and safety. An example of this in practice is tubular feeders in handling fine powders. These systems are designed with sealed tubes and extraction points to ensure that no dust escapes into the atmosphere.
The enclosed design prevents product spillage and contamination, thus safeguarding the integrity of the material being handled and reducing the risk of potential hazards associated with airborne dust. This focus on minimising leakages not only enhances operational efficiency but also contributes to a more sustainable and environmentally friendly production process.
4. Precise control over product transfer
Precision in material handling not only minimises waste but also
supports recycling efforts and promotes resource efficiency. Advanced vibratory separators, such as the Vibrecon® GVC5 with a diameter of 1,380mm, offer precise particle size classification, facilitating the recycling of materials within food, chemicals, plastics and other suitable products.
A recycling facility in Norfolk, UK, implemented Gough Engineering’s Vibrecon® GVC5 separator to process glass fibers efficiently. The system’s dual-deck design allowed for effective separation of oversize particles, fine materials and quality fibers, contributing to enhanced recycling rates and reduced landfill waste.
5. Minimising downtime through easy maintenance
Reliable equipment operation is fundamental to sustainable manufacturing practices. Material handling solutions engineered for easy maintenance, with robust components and proactive service support, ensure continuous operation and minimal downtime.
It’s important to partner with a material handling specialist
Effective management of material waste is imperative for sustainable manufacturing.
that provides comprehensive maintenance programs that include regular service checks and component replacements to optimise equipment performance and longevity. By adhering to service schedules, manufacturers mitigate operational disruptions and maintain high productivity levels with excellent machine performance and utilisation.
By implementing these five strategic steps towards sustainable material handling, manufacturers not only reduce their environmental footprint but also enhance operational efficiency and competitiveness in a rapidly evolving market.
To learn more about how Gough Engineering’s material handling equipment can benefit sustainability initiatives, visit its website.
Storage and order picking equipment are essential for maintaining efficient material flow. Creating the ideal system will give manufacturers a massive increase in storage capacity and pick rates within the space they have available, says Edward Hutchison, Managing Director of BITO Storage Systems.
Without effective and reliable storage and order picking systems, production and assembly lines will grind to a halt. The Just In Time (JIT) supply of parts, semi-finished products and raw materials to production machines requires flexible and scalable warehouse storage and retrieval systems. Systems can be manual or automated, working in combination with continuous units, such as overhead conveyors and conveyor belts, or discontinuous systems, such as Autonomous Mobile Robot (AMRs), Automated Guided Vehicles (AGVs) or forklift trucks.
Such systems must not only provide a smooth flow of parts through the plant, from storage to feed the line, but also accommodate future growth. And with assembly areas claiming priority over space in most factories, storage and order picking will often need to fit into a constrained footprint. Fortunately, there are many ways that these objectives can be achieved successfully.
A good example of a lower cost and space saving method to achieve ‘right first time’ part delivery to the line comes in the form of carton or
pallet live systems, comprising flow shelves created from racking. With clear labelling, flow shelves help create effective pick zones because the design provides a density of storage that results in a greater number of pick face locations than would be possible with tradition shelving and racking. Because cartons or pallets are loaded into the flow lane on a first in, first out (FIFO) basis, when an empty unit is removed another full carton or a pallet full of parts flows into place on rollers in the inclined lane, ready to pick from.
Compared to a traditional wide aisle configuration, Very Narrow Aisle (VNA) racking provides a more space efficient solution for holding general parts, usually on pallets and is served by VNA lift trucks. This is a pretty standard solution these days, though a narrow aisle can be designed to feed a carton live structure, integrated into the rack, running alongside the aisle and providing a dense pick face for parts.
Picking small parts is a vital element in most factory warehouses, and where the goal is to keep things
simple, this can be easily integrated within pallet racks. One option is to create small parts pick locations on the reachable ground level, with upper storage levels serving as a buffer store for replenishment. Plastic small parts storage containers will help to store and organise small items and C-parts – making them available for quick and easy picking. This will result in a reasonably efficient picking process but ground floor locations within a pallet rack will, of course, be limited. Flow shelves, however, can be easily installed into pallet racking to increase the number of pick locations and volume of SKUs located on the ground level pick face. Adding standard shelving within pallet racking is another option to create flexible small item pick faces. Using mobile shelving will maximise the available space, though moving the shelves increases pick times. Inclined shelving within a pallet racking bay will make items clearly visible for picking.
Plastic bins and containers will keep parts protected throughout the intralogistics process and during transport to ensure they are delivered to the line in prime condition. It is worth seeking out storage system supplier such as BITO, which in addition to offering racking, shelving and flow lanes, also provides a plastic container range comprising a variety of sizes and a broad choice of accessories. This will ensure the optimum system is designed to fit a given space, maximising the potential for small parts picking and, ultimately, improve manufacturing efficiency.
With up to 4.2m bending length and up to 3,200 kN press force, electro-hydraulic press drive from HAWE Hydraulik, 69S top control from Delem, up to 8-axis backgauge with pneumatically movable supports, hydraulic tool clamps and CNC-controlled crowning from technology leader WILA, iMeasure angle measuring system from ACCURL, laser bending line and CNC-controlled bending aids and much more!
ACCURL®’s Top level EuroMaster hybrid press brake built with highend specifications and execution, advanced motion technologies and is still impressively quiet. With the integration of advanced safety equipment and options the EuroMaster is the best in creating
complex parts.
Press Brake servicing you can depend on
Here at Axe & Status, we take pride in offering top-quality press brake servicing to ensure the optimal performance and longevity of your valuable equipment.
As a trusted provider of comprehensive maintenance and repair solutions, we understand the critical role that press brakes play in your sheet metal fabrication processes.
https://axestatus.com/press-brakeservicing/
Why choose ACCURL?
ACCURL is widely recognised for
its state-of-the-art technology and inventive solutions within laser machinery. Boasting 33 years of experience and a remarkable record of over 12,000 installed machines, ACCURL’s expert R&D team works tirelessly to research the most competitive technology for their customers. This dedicated approach aligns seamlessly with Axe & Status’s commitment to providing exceptional solutions to their clients.
ACCURL conducts exhaustive studies to offer a diverse range of fibre laser cutting technology, tailored to meet unique customer needs. This results in the production of ultralight, high-precision, and high-energy 2D fibre-laser cutters suited for a variety of industries.
SIZES OFFERED
1,300 x 1,300mm
2,000 x 1,000mm
2,500 x 1,250mm
3,000 x 1,500mm
● Up to 12kW
● Fully Protected Enclosure ● High Precision Rack & Pinion
● Max Power Laser Resonator
● Welded Tubular Construction
● Slide out table for easy load/unload, up to 900kg
● Autofocus Laser Head
The introduction of Green Hybrid Servo and Electric Servo bending technology for manipulating sheet metal gives ACCURL a substantial edge over competitors. The integration of the IPG Fiber Resonator, offering power ranging from 1kW to 30kW, further solidifies ACCURL’s position as a top-tier manufacturer in the sheet metal machining industry.
Axe & Status exclusively import the large range of fabrication machinery from Accurl in China, which includes Fibre Laser Machines, Pressbrakes and Guillotines.
We install all the imported machinery and provide comprehensive Service Support ongoing.
Metal Machinery Expertise
With decades of experience in the industry, our skilled technicians possess in-depth knowledge of sheet metal machinery and understand
ACCURL conducts exhaustive studies to offer a diverse range of fibre laser cutting technology, tailored to meet unique customer needs.
the intricate workings of the various equipment types.
Whether it’s a Press Brake, Fibre Laser, CNC plasma cutter or shearing machine repair that you require, Axe & Status can help.
We appreciate how crucial it is to get your sheet metal machinery back in operation quickly and reduce downtime. Our team will provide a prompt response to carry out timely repairs without compromising on quality. We prioritise our customer’s
needs and strive to deliver an exceptional service that will exceed your expectations.
https://axestatus.com/sheetmetal-machinery-repairs/
ACCURL SMART CUBE FIBRE LASER up to 12kw
Experience precision and efficiency with the Cube Compact Laser cutting machine, an ideal solution for compact cutting.
This innovative system seamlessly integrates precise 2D laser cutting into a sleek, space saving design.
Compact Design – Minimize floor space without compromising cutting quality
Range of Laser Sources – up to 12kw for versatility in production
Manually retractable cutting table –Simplifies loading and unloading for increased efficiency
High precision – Achieve highly precise cuts at high speeds, perfect for intricate parts production
Introduce Revive | RF314 safety boot, Rock Fall’s latest edition to the world of engineering and manufacturing, ‘to be blunt’ the Revive | RF314 is becoming the hottest topic in safety footwear!
Just like the original engineer boot of the 50’s, & 60’s the toe is bulbus and the sole is thick, and in keeping with the retro feel the Rock Fall development team have given the Revive | RF134 an extraordinary, sustainable, and contemporary twist!
Developed using groundbreaking Next-gen material innovation by Generation Phoenix (www. genphoenix.com). The uppers are made with highly durable material, derived from pre-consumer recycled leather fibre. Using this lightweight material has reduced the weight of the boots considerably.
Designed for use in electronics, aerospace and logistic industries the design of the Revive safety boot prioritises health, safety, comfort and performance – basically the Revive has been designed to reduce fatigue during extended shifts.
What other features went into the
The outsole incorporates an injection moulded scuff cap to give enhanced protection to the toecap area of the boot.
para-aramid anti-perforation protective midsole developed by Activ-Step® Footwear Components to protect the feet.
The outsole incorporates an injection moulded scuff cap to give enhanced protection to the toecap area of the boot.
ESD Certified, this built-in technology works discreetly to dissipate static electricity, safeguarding any electronic components in the workplace. This translates to a safer work environment and reduced risk of accidental damage to sensitive equipment.
The Revive | RF314 ESD certified, ankle height, mid-boot, lace-up, scored a perfect 10 throughout our working trials. We believe the Revive engineering safety boot will become a welcome addition to PPE supplies across automotive and aerospace, manufacturing environments, freight, and logistic industries.
Available through Retail Stockists Nationwide
Direxpander® Diamond Precision Reamers by DK HoldingsSmoothing the way in the reaming of hydraulic components and more
Phil Wares, Electroplating/ CAD Manager at DK Holdings Limited, introduces the company’s Direxpander®, a diamond coated precision reamer and long-standing engineering gem that has become the definitive tool for sizing and straightening the bores of cast components such as Hydraulic Transfer Valves.
“We have been supplying this tool for many years to our customers to fulfil their requirements. As an engineer and manufacturer I can say that this tool is a joy to produce, encompassing several skills and technologies, which ultimately results in a tool fit for the application which has been proved time and time again”, Phil explains.
What makes the Direxpander® Diamond Precision Reamer a perfect tool?
‘’This dependable engineering masterpiece consists of a diamond coated sleeve mounted on a tapered mandrel which allows the final diameter of the tool to be adjusted to very fine limits. It is a tool of great rigidity which is vital to the application. The precision diamond coating ensures consistent sizing and surface finish over thousands of components, producing accurate bores every time. We can supply the tool in a standard range of sizes from 6mm to 60mm with other sizes available on request. The reamer is easy to use on conventional or fully automatic machines and has replaced many honing tasks, resulting in quicker, more reliable and accurate bore production”, Phil continues. “Design, Manufacture, Supply – to us
The precision diamond coating ensures consistent sizing and surface finish over thousands of components, producing accurate bores every time.
this means to work in partnership with our customers worldwide, offering precision engineered Diamond Tooling such as the Direxpander® Diamond Precision Reamer from inception to the supply”, Phil concludes.
This is just one of many quality diamond tools that D.K. Holdings produces and has been producing for decades.
Get in touch with one of the team at DK Holdings and find out how they can support your requirements no matter how large or small, or request their free Engineering product guide and Direxpander® Diamond Precision Reamer product focus, the team is always on hand to help!
DK Holdings Limited Station Approach Staplehurst TN12 0QN
Telephone: 01580 891662
Email: info@dk-holdings.co.uk
Twitter: @DK_Holdings
Tel: +44(0)1580
info@dk-holdings.co.uk
www.dk-holdings.co.uk
Save energy
Save money
Integrate the LHS 210/410 series air heaters with Leister’s new CHINOOK blower.
get in touch
Tel: +44 (0)1707 331111 info@welwyntoolgroup.co.uk www.welwyntoolgroup.com
Specifically designed to feed process air at inlet temperatures of up to 350°C
Quiet operating sound level of 58dB(A)
Capable of delivering air flow of 1,640 l/min at 50Hz with a static pressure of 14.6kPa
Deltec is the leading Impact Socket and Bespoke tool manufacturer in the UK and specialises in Impact Sockets, Specialised Sockets, accessories and related tools for various applications in different industries, such as Automotive, Construction, Bridge, Marine building and maintenance, Wind, Oil & Gas, Mining etc.
With 45 years of experience, Deltec aims for the goal of zero defects. Deltec has gained confidence and long-term support from many global clients due to its excellent quality, service, competitive price, reliability and on-time delivery. Deltec is well reputed with its excellent products all over the world.
All our products are manufactured to International DIN standards. Deltec’s Technical & Design Department designs and develops custom sockets and prototypes. Deltec is also a pioneer in product research and development, engineering and manufacturing – Fast track service also available.
Factory Tours available Please enquire
– See British Manufacturing at its Best.
www.deltecindustries.co.uk
• ‘By Industry, For Industry’, practical guidance for everyday and irregular situations and tasks
• Readily accessible for all in the industry –wherever they are, whatever time they have
• FREE task and procedure checklists
To make EEMUA’s guidance, training, events and other
– ask@eemua.org or visit www.eemua.org
• professional development
• Webinars and seminars for knowledge sharing
• This selection of specialist publications and many
For engineers and technicians working in many industrial sectors FOD will always be a real and present danger.
Keeping track of every tool and piece of equipment, especially when several storage cabinets are in simultaneous use, can be challenging.
Snap-on Industrial’s Level 5™ automated total asset management system minimises the risk of FOD by constantly tracking every tool, detecting which tools have been removed or returned.
It also enables engineers and technicians to quickly find every tool they need, when they need it, saving time and easing stress. Engineered to track individual tools by user, without bar codes, scanners, RFID tags or other add-ons, the system works at the speed its users demand.
Level 5™ boxes are network ready, using either Ethernet or wireless connection.
Powerful software enables users to review activity at all boxes in their location from one central computer, avoiding the need to inspect each box.
Major benefits of the system include:
• No individual tool scanning required;
• No RFID tags to install or replace;
• Intuitive interface, via touch screen;
• Audible voice confirmation of tool removal and replacement;
• Automatic locking for maximum security;
• Errors announced and displayed to
indicate incorrect tool position or advise when a drawer is not closed;
• Keyless access control for easy access by authorised users.
Says Richard Packham, Director UK & Europe for Snap-on Industrial: “Snap-on’s automated system takes tool management to an entirely new level, giving workshop managers and other authorised users easy access to the tools they need, while protecting against foreign object damage.
“The ability to monitor several boxes from one central computer offers managers a huge time saving advantage.”
Developed and verified ‘for industry, by industry’, EEMUA 231 Mechanical Integrity courses are for industrial engineers at every career stage – to aid efficient hands-on work with primary containment and prevent loss of hazardous substances, including with pressure systems.
• Satisfy industry requirements at each competency level – Awareness, Basic application, Practitioner.
• Certificated up to 5 years.
• CPD-approved
• Flexible delivery to suit Learners and companies – Blended, Live online, Classroom, E-learning, or In-house.
• Available to all – free or discounted to EEMUA Members.
• Courses throughout each year, including:
Mechanical Integrity Practitioner Certificate (MIPC®) – Blended, live online learning, with 1:1s and Mentor Support – for on-site application of EEMUA 177, 231 and 232 guidance, and PSSR ACOP – certificated for 5 years via exam and portfolio assessment – Continuing Professional Development approval – in-depth learning for 27 weeks, 4 hours per week, flexibly – on-site or on-call. The MIPC course adapts to engineering needs of each Learner their company and site/s via a 2-hour induction (to fit work schedules ahead of the course) – the next course starts 21 October 2024.
EEMUA 231 Mechanical Integrity Basics
Blended, online learning – set at Basic application competency level – 4 hours of learning per week for 3 weeks – certificated via exam – next course starts 30 September 2024
EEMUA 231 Mechanical Integrity e-learning
Awareness level – with Continuing Professional Development approval – available – on-demand.
EEMUA 231 Mechanical Integrity In-house training – 1 day or 2 half-days – set at the Awareness level – for your choice of time, location , method of learning – by arrangement
Also... External Corrosion Seminar – by EEMUA and AMPP Benelux – Haarlem, NL – 10 October 2024 online-learning@eemua.org
In the pharmaceutical, food, and biotechnology industries, GEMÜ multi-port valves are essential for integrating diverse process requirements and functions within compact spaces. GEMÜ’s blockand-bleed solutions significantly enhance process reliability and safety during maintenance and calibration, as well as prevent cross-contamination by reducing dead-legs.
Depending on the application, various configurations are available for shutting off (block) and draining or venting (bleed), with each differing in construction. This eliminates the need for complex piping systems. With minimal welds, not only are leak paths reduced, but weight and installation time are also significantly decreased.
The different design versions of the block-and-bleed functions can be categorized into the following groups:
1. Simple block-and-bleed valves
2. Double block-and-bleed valves
3. ‘Sterile cross’ valves (steam barrier)
4. Complex block-and-bleed valves
For more in depth information on the block-andbleed function groups, please see on below page 10:
>> Customer magazine (gemu-group.com)
Precision in every flow!
Bene t from the advantages of the low ow control valve Type 7042 from Schubert & Salzer Control Systems for micro ow rates and high operating pressures:
• ultra compact
• precise control
• safe shut-off
Visit us at PPMA Show 24 - 26 September 2024
NEC, Birmingham, UK Stand: G70
www.schubert-salzer.com
In cooling water systems, water is used to remove heat from an industrial process or air conditioning equipment. Neil Hannay, Senior R&D Engineer with Titan Enterprises, says: “Selecting an appropriate flow meter for a cooling water system is just as vital as the operational process itself.” Flow monitoring helps to optimise plant or system efficiency, save energy, control chemical costs and enhance overall profitability.
1. Water coolant for glass bottle production
Graphoidal Developments manufacture advanced lubrication and coating systems for glass container industries where accurate application of a coolant is critical to the reliability of the machine. Titan’s Industrial Process Atrato® ultrasonic flowmeters are installed in the water lines to monitor the coolant flow to the shears which cut semi-molten glass in bottle making machines. This robust flowmeter has no moving parts and is packaged to address the more challenging industrial process and control environments.
2. Metering laser coolant flow
Industrial and medical lasers used in cutting, welding, micro-machining, cosmetic and eye surgery, generate a significant amount of heat. Water circulated through a chiller or heat transfer system is a popular method to quickly and effectively dissipate heat to ensure stable long-term performance of the laser. Titan’s
800 series turbine flowmeters are integrated into leading industrial and medical laser systems to provide consistent laser cooling through accurate and repeatable water flow measurement.
3. Cooling systems for medical treatment applications
An innovative liquid-based cooling system by Paxman Coolers Ltd utilises Titan’s NSF-approved mini turbine flowmeters to monitor the rate of coolant flow around their patented cooling cap during chemotherapy treatment. Titan’s mini turbine flowmeter offers an excellent balance of measurement accuracy, long term resistance to coolant fluids, high reliability and is cost effective.
4. Cooling the world’s most sensitive astronomical camera
The world’s largest optical telescope, the 10.4m Gran Telescopio Canarias (GTC) on La Palma, is equipped with a powerful astronomical camera, called HiPERCAM. The five light sensors used in HiPERCAM are ultrasensitive charge-coupled devices which require cooling to 183K (-90°C) to minimise noise in the images. This cooling is achieved using very
high performance thermo-electric (peltier) coolers, which in turn require a liquid coolant (a waterglycol mixture at +5°C) to remove the heat they extract. Titan’s FT2 optical flow sensor that uses an LED and photo-diode to measure flow was used successfully without being affected by the undesirable properties of the telescope’s cooling fluid.
5. Measuring Refrigerant Flow
Reliable flow monitoring of refrigerant liquids is vital for cooling equipment used in data centre facilities. Using steel reinforced polymer components, the low inertia turbines of Titan’s 900 and 1000 Series turbine flow sensors are ideal for measuring the low viscosities encountered with volatile refrigerant fluids measured in liquid form.
The bottom line for cooling liquid water systems is for reliable monitoring and ensuring there is adequate flow of coolant to the downstream instrument or process, thus mitigating against serious problems caused by over-heating, such as degradation of operational performance, damage to critical equipment and shutdowns.
Titan Enterprises is a leading design and manufacturer of innovative end user and OEM high-performance flowmeters and flow measurement instrumentation, used within a wide range of processes, environments and applications.
• Compact, robust, reliable
• Excellent accuracy and repeatability
• Measure low to high flow ranges
• High chemical resistance
• NSF-Approved mini turbine flowmeters
• ATEX-compliant and high pressure Oval Gear models
• OEM bespoke design capability Titan’s liquid flowmeters are designed and manufactured to ISO 9001 with traceable calibrations.
+44 (0)1935 812790 sales@flowmeters.co.uk www.flowmeters.co.uk
The established process for fluid and oil condition monitoring is to periodically take a sample and have it analysed in a laboratory. Customers rely on this periodic data to react to trends to plan servicing and maintenance and to reduce asset downtime from failure.
Driven by the constant market economic pressure to reduce costs and eliminate unplanned maintenance time, Spectrolytic has developed a measurement solution to match the market needs of our customers in all our sectors.
Spectrolytic’s FluidInspectIR® series - are OEM proven, robust and affordable fluid condition monitoring equipment that gives customers meaningful and understandable real-time data in the same parameters and in the same units as they are commonly receive it from their laboratory analysis.
Our products are already monitoring 100’s of plant assets over 1000’s of operational hours and managing millions of litres of industrial oils and fluids every day across the globe.
Oils, lubricants, cooling fluids play a critical role in industry in the operation of plant assets.
Conventionally, plant engineers operating and maintaining high value assets rely on taking fluid samples periodically and sending them to a laboratory for analysis. It can take up weeks and sometimes even months from sampling to receiving the sample report and
introduces a large time lag in the reporting of the fluid condition.
The benefit of having real-time monitoring of the fluid condition is vast. Customers will not only have the satisfaction of being in complete control of their asset, but have substantial cost savings by
• Extending Asset Viability and Prolonging Asset Life:
• Reducing Oil / Fluid Usage Costs:
• Eliminating Unplanned Maintenance:
• Lowering Labor Costs:
• Minimizing Machine-Human Interface:
• Cutting Reliance on External Laboratories:
FluidInspectIR® Analyser systems
Spectrolytic has developed a unique technology platform with the FluidInspectIR® (see figure 1) that can be seamlessly installed in-line or at-line(portable), and that utilises the powerful analytical technique of mid-infrared spectroscopy to measure the chemical composition of a fluid. Additional sensors can be added to measure physical properties such as viscosity and contamination.
With each measurement the sensor determines the changes of the fluid at a molecular level using
the same analytical technique and data extraction as employed by laboratories around the world.
The FluidInspectIR® series of systems are being used many different application areas such as Oil Condition Monitoring on marine fleets, power plants, turbomachinery, steel and aluminium rolling and industrial fluids.
The systems are being employed on cooling fluids for metal working and data centres, fuel screening such as gasoline, biodiesel and jet fuel and where there is a requirement for fast, high resolution measurements in pharmaceutical, and biochemical manufacturing processes.
The systems are ATEX certified and can be installed in Zone 1, Group 2C explosive environment.
The power of the real time data via the FluidInspectIR® inline sensor can be exemplified in a use case on a VLSFO engine on a dredging vessel.
The sensor detected unusual pattern of water content in the lube oil which was traced back to a failure of the cooler and caught in time to prevent catastrophic engine failure.
The real-time and accurate measurement provided by our sensor saved the customer potentially £10,000s of repair cost and unplanned down time
It would NOT have been possible to pick this failure mode up with conventional lab-based oil analysis.
FluidInspectIR® offers cutting-edge oil and fluid condition monitoring systems, delivering accurate, real-time data to prevent equipment failures and reduce downtime. Perfect for marine, power generation, industrial machinery, and more.
Fluids
FluidInspectIR® offers cutting-edge oil and fluid condition monitoring systems, delivering accurate, real-time data to prevent equipment failures and reduce downtime. Perfect for marine, power generation, industrial machinery, and more. Extend
Real-time monitoring for the Marine, Power Generation, Industrial Fluids and Steel & Aluminium Rolling industries.
Real-time monitoring for the Marine, Power Generation, Industrial Fluids and Steel & Aluminium Rolling industries.
Remotely monitor FAME levels in BioDiesel, Ethanol in Gasoline and Water content in Jet Fuel.
Remotely monitor FAME levels in BioDiesel, Ethanol in Gasoline and Water content in Jet Fuel.
Extend Asset Life: Early failure warnings prolong machinery lifespan.
Dynamically analysing cooling fluids for Data Centres and Metal Milling and Cutting.
Dynamically analysing cooling fluids for Data Centres and Metal Milling and Cutting.
Powerful, real-time fluid monitoring for the pharmaceutical, biochemical and chemical industries.
Powerful, real-time fluid monitoring for the pharmaceutical, biochemical and chemical industries.
Cost Savings: Reduce oil usage and dependency on labs, saving money.
Operational Efficiency: Minimise human involvement with fully automated systems.
Operational Efficiency: Minimise human involvement with fully automated systems.
Transform your fluid condition monitoring and maintenance approach with FluidInspectIR and save $10,000's annually on operational and consumable costs.
Transform your fluid condition monitoring and maintenance approach with FluidInspectIR and save $10,000's annually on operational and consumable costs. Oil Condition Monitoring
Product quality, product safety. The guiding mantra in dairy production. That’s why the world’s leading dairy producers rely on the products and solutions developed by DMNWESTINGHOUSE. Our rotary valves and diverter valves offer the highest level of precision engineering, preventing bridging and possible contamination during conveying processes. At the same time, they guarantee unparalleled cleanability, drastically increasing product safety while reducing downtime for maintenance and repairs.
Through years of experience and valuable partnerships, DMNWESTINGHOUSE has gained a deep understanding of the global dairy industry and its challenges. We have earned the trust of an industry where hygiene, cleanability, and safety are paramount. In our R&D department, we leverage innovative technology, setting the dairy industry standard. In our factories, we control every step in the manufacturing of heavy-duty rotary valves and diverter valves.
Just like you, we strive for unparalleled quality and consistency. A commitment underscored by our compliance with current certifications, including USDA, EHEDG-ED Class II and ATEX. Whether it’s about infant formula, lactoferrin, (plant-based) milk powders, caseinates or probiotics, at DMN-WESTINGHOUSE, we help you maintain the highest quality standards in dairy.
Many producers of dairy products, ranging from baby formula to
lactoferrin, rely on our renowned heavy-duty rotary valves. These valves come in two types and various sizes: the drop-through type (AL/AXL/AML) and the blowthrough type (BL/BXL/BXXL). They comfortably comply with the stringent hygiene standards the dairy industry needs to maintain. All product contact surfaces consist of food-grade material, polished to perfection. They are all radiused and polished to an astonishing 0,8 µm Ra (150 grit), and the rotor vanes have precisely chamfered edges preventing the build-up of conveyed dairy powders.
Cleaning intervals will vary depending on which dry dairy substances are processed. To reduce cleaning time and resulting downtime, we developed the MZC rotary valves based on our AL— and BL-series. The MZC-I and MZC-II are equipped with supporting rails
so the rotor and end cover can be removed. The MZC-II opens on two sides for unprecedented easy access and superior cleanability.
These valves facilitate premium process handling, raising the bar in cleanability, hygiene, and safety. The rotor body clearances are set automatically when the rotary valve is closed after cleaning.
Adding innovative solutions can take your dairy production to the next level.
We offer:
· Rotor Interference Detection (RID 3.0) is our third generation, detecting unwanted contact between the rotor and body or end covers. This prevents major damage and provides insight into product contamination. RID 3.0 offers 50 times more accurate resistance measurement than its predecessors.
Through years of experience and valuable partnerships, DMN-WESTINGHOUSE has gained a deep understanding of the global dairy industry and its challenges.
· Shaft seal flow control boosts the reliability of our AL and BL heavyduty rotary valve series even more. Precise flow control prevents the build-up of powder residue on the shaft seals, minimising the risks of seal failure, contamination, leakage, damage and downtime.
· Rotary valves equipped with the Sanitary Air Seal (SAS) outboard bearing shaft seal minimise leak risks due to pressure changes inside the valve, thus maintaining the right airflow.
For maintaining hygiene and preventing contamination, cleaningin-place (CIP) is indispensable. CIP is about cleaning the interior of pipelines, valves, tanks and other equipment without the need for disassembly. In the dairy industries it’s a necessary, often automated method to maintain the highest levels of hygiene and prevent contamination.
Handling dry dairy solids is about maintaining the strictest standards and requirements 24/7. Are you currently operating Niro rotary valves needing replacement any time soon? Our NR347 rotary valves (NR = Niro replacement) match the outer dimensions of the Niro valves operating within your system, which means they are usually a perfect fit. The NR347 is based on our heavyduty AL250 model and is made of stainless steel. Meeting all hygiene and safety standards, the NR347 will
prove its value day in and day out.
Our diverter valves: boosting efficiency and hygiene
Diverging and converging powders or granulates is a daily routine in dairy production. Safety, efficiency and maximum hygiene are key. That’s why our 2-TDV, 3-TDV, M-TDV, and GPD diverter valves are very much in demand.
· Our 2-TDV and 3-TDV diverter valves are designed for quick disassembly and streamlined distribution. The 2-TDV effortlessly handles two destinations, while the 3-TDV targets three.
· The M-TDV efficiently handles the
pneumatic transport of powders or pellets, diverging and converging flows to multiple destinations. Available in different sizes, offering up to 14 ports.
· Our diverter valves are the perfect choice for systems needing regular, quick cleaning with minimal downtime.
Would you like to know more about DMN-WESTINGHOUSE rotary valves or diverter valves and discover why we are the dairy industry’s choice worldwide?
Please get in touch with the DMNWESTINGHOUSE: +44 1249 818 400 or dmn.uk@dmnwestinghouse.com.
GARDENA has always proven to be a particularly sustainable innovator. Thanks to a partner, the basic requirements for future-oriented and sustainable production have been met: With the latest linear rotary and linear technology from the drive specialist LinMot, GARDENA has succeeded in redefining the precision, speed and sustainability of its production systems.
The Micro-Drip System (MDS) is a resource-efficient irrigation solution that delivers water drop by drop to where plants need it: to the roots thus greatly reducing water consumption.
The new generation of production should offer more process reliability, increased precision in force control and process parameters as well as sustainability and energy efficiency, which led GARDENA to choose LinMot.
PR02 – Linear /Rotary modules.
Implementing industrial systems for precise and dynamic locking, screwing or assembly is an extremely complex challenge with conventional servo solutions.
The LinMot PR02 provides both the rotary and linear servo motion combined in one compact motor avoiding the need for more complex and heavy servo motors and guides.
Precision with Feedback Force and Torque sensors are available as options for the LinMot PR02 which enable real-time monitoring and evaluation of process parameters with an accuracy of equal or better than 1% of the demanded value.
Thanks to the precision of the LinMot PR02 motors, GARDENA have found their systems are 3 to 4 times faster than their older process.
Parameters and contours can change fundamentally and quickly on both the product and the machine side, so that the re-teaching of the individual positions must be done quickly, easily and precisely. Thanks to their flexibility, the LinMot motors adapt to all adjustments to the production machines at lightning speed and all changes can be made very quickly.
DM01 / SM01 – Linear modules
The modularity of the LinMot linear modules such as the DM01 and SM01 also impressed the GARDENA engineers.
This provides a way for X and Y pick and place units to be quickly and easily assembled.
Sustainability or efficiency?
The question of having sustainability and efficiency working together has been well and truly answered as the collaboration between GARDENA and LinMot proves.
We were called to consult on several flow applications on board a multimillion-pound new generation of catamaran hybrid passenger ferry. These fabulous low emission ferries will operate on the Thames and be future proofed incase an ultra-low emission zone is introduced for river traffic.
The vessels designer identified a requirement for three flow measurements to be made. The first was on the diesel fuel consumption on the common rail engine. The second was for the battery cooling circuit and the third was the diesel engine cooling circuit. These ferries have a hybrid motor in each of the two hulls, so that was four measurement points per hull, eight in total. The battery cooling fluid was a water / glycol mix cooled indirectly via a heat exchanger, whilst the diesel engine cooling was raw sea water, drawn up and passed through a strainer. The pipework was all Nickel Copper alloy, DN25 (fuel lines) DN50 and DN100 line sizes for the two cooling circuits.
For the diesel flow measurement, a gear flow meter was already installed, but iCenta realised that it was sized incorrectly and was causing a significant pressure loss. A precision OVAL FlowPet 5G gear meter was selected for the task of flow measurement from the diesel flow.
Then the cooling circuits were surveyed, and the ultrasonic sensors were installed within the bilge, access was tight, the space was about 60 cm at its largest point and a person could not turn around. After a risk assessment and gas safety check, the ultrasonic meters were set-up and
the sensors installed. It is in such space critical applications a quick setup and small meter, in a rugged bumper case is a definite advantage!
Both the Metri Pro-Lite and the Precision Flow PD190 measured the flow well, particularly on the water glycol mix for the battery cooling. However, it was found that as the engine approached full power, a great deal of entrained air was mixed into the engine cooling fluid which is not ideal for ultrasonic meters, or many other flow measurement technologies, for that matter. Entrained air is not a good conductor of heat and would therefore also affect the performance of the cooling circuit.
The ultrasonic flowmeters proved unsuitable (due to entrained air) on the diesel engine cooling circuit, so a different flow technology was required. This remains a natural strength of iCenta, we have all the flowmeter technologies, so we can honestly recommend the best flowmeter technology choice for a particular application, and we represent the best flow instrumentation from around the World.
In terms of diagnostics, the ultrasonics did give us valuable insight into the flow conditions. A combined Doppler – Transit time flow meter is available via iCenta, and this would have been a good application for that device, automatically switching between Doppler and transit-time techniques.
Metri Pro-Lite was fast to set up and easy to operate, having a backlit graphics display for use in low light conditions. Signal diagnostics are available so you can see the acoustic signals in real time. The meter, after the signal amplification is fully digitised, using correlation detection, has effectively become an industry standard signal processing technique for transit-time flowmeters. All these features really help when working with a range of fluids in demanding situations. The Metri Ultra Pro-Lite also sits in a powerful position in the market. Due to intelligent modern design, it is perfectly engineered to provide a capable clamp-on flowmeter, at a realistic cost to the user. iCenta recommend clampon ultrasonic flow meters on site, especially useful for verifying other meters, and for general spot flow readings. The meter also has a fully configurable datalogger for post testing analysis.
Initially we thought that it was a good application for ultrasonics, but due to entrained air on the diesel cooling water it was felt that a magnetic flowmeter was a better choice. Post trial, the new meters were correctly specified sized and delivered, so the overall solution involved Oval geared meters and C-Mag Comac Cal 316L Magnetic flowmeters.
Rotaflow provide solutions that enable different fluids (including oils, fuels, corrosives, food) and/ or air/steam to be transferred through awkward, and often, already established production infrastructure. With 40 years of experience, we have designed and manufactured swivels to withstand and perform effectively when faced with many tricky environmental factors: Overcoming issues with heat, pressure, size and material choice.
Swivel joints will allow the movement on a slowly rotating drum or remove the damaging effect of twisting on hoses.
Swivel joints will allow the movement on a slowly rotating drum or remove the damaging effect of twisting on hoses.
We manufacture in Carbon Steel and 316 SS with “specials” in any grade of metal to suit customer specification: Titanium, Super Duplex, etc. With bores ranging from 0.25” to 40”; Vacuum duty to 20,000PSI and multi passaged designs allowing multiple
flows of fluid though a single unit.
The photo attached is of a secondgeneration swivel design for use on cleaning rigs where acid is a factor.
Rotaflow is a global leader in swivel joint design and manufacture. We engage with clients all over the world to produce swivel joints for a wide range of industrial uses, from drilling and mining, food and drink production, pharmaceutical, process and plant, to subsea oil and gas extraction.
To find out more please visit our website and/or give us a call. Tel: +44(0)1663 735003
For further information, please visit www.rotaflow.com or email sales@rotaflow.com
Articulated Pipework Torsion In Hoses
Swivel joints allow pipework to pressure 1/4” to 40” and beyond.
Vacuum to over 20,000psi.
Stock and bespoke production.
Unique bearing/seal design for longer life.
ISO 9001 CE marked where applicable.
Tel: +44(0)1663 735003
E-mail:
HANNOVER MESSE
HANNOVER MESSE 2025 will feature a strong presence by drive technology and fluid power
Traditionally, drive technology and fluid power has been represented at HANNOVER MESSE by a large number of companies from Germany and abroad, especially in odd-numbered years. This will also be the case in 2025 when manufacturers will present their latest applications and components for intelligent and sustainable production. All this, under the Motion & Drives label, will be focused in Halls 4, 5 and 6. Drive technology and fluid power plays a key role in many industries, because nothing can move without these technologies. For the strongly export-oriented industry, HANNOVER MESSE is the ideal platform for boosting global business thanks to its highly international character. Companies that have already registered include Atos, Bosch Rexroth, Cantoni, Festo, Flender, IMM Hydraulik, SEWEURODRIVE and Schaeffler.
“With HANNOVER MESSE, we are offering exhibitors the opportunity to be embedded in a unique industrial innovation ecosystem. It is one in which companies from the engineering, electrical and digital industries as well as the energy sector present efficient and sustainable solutions for current and future industrial value creation. The mix of representatives from research, business, start-ups and politics meeting in one place at the same time is unique. This results in unique business potential and access to top-level decision-makers, technology scouts, experts and media representatives from all over the world,” says Hubertus von
With HANNOVER MESSE, we are offering exhibitors the opportunity to be embedded in a unique industrial innovation ecosystem.
Monschaw, Global Director Trade Fair and Product Management HANNOVER MESSE at Deutsche Messe AG.
“In 2025, HANNOVER MESSE and its Motion & Drives community will be the driver of innovation and center of gravity when it comes to the best new solutions for the engineering world. The Motion & Drives companies supply power, torque, positioning, data, and solutions for our real and virtual worlds,” emphasizes Hartmut Rauen, Deputy Managing Director of the Machinery and Equipment Manufacturers Association (VDMA).
According to the VDMA, German drive technology companies alone exported goods worth EUR 17.9
billion last year. The most important customer countries were China, the USA, France, Italy, Poland, Austria, the Czech Republic and the UK.
Fluid power is also a very exportoriented segment: in 2023, goods worth EUR 8.4 billion were exported, corresponding to an export quota of 60 percent. The most important customer countries are the USA, China, Italy, France, Austria, the UK and the Netherlands.
In addition to the individual stands, the Motion & Drives area will offer an exclusive joint stand for VDMA members as well as a forum accompanying the trade fair, the “Motion & Drives Conference Stage”, which will be organized by the VDMA Drive Technology and Fluid Power associations. Current industry topics will be discussed there, including digitalization, interconnectivity, Manufacturing-X, OPC UA, umati as well as energy monitoring and efficiency, carbon footprint, digital product passport and recycling management. In addition, a special show organized by the EU-funded Fluid 4.0 research project will demonstrate digital and sustainable solutions in fluid and drive technology. One focus will be on the challenges of system architecture, energy consumption, PCF calculation, and recycling management.
With umati, the VDMA has launched an interface initiative to make data more easily accessible. With umati, data – including from drive technology – can be used without additional outlay.
For further information, please visit www.hannovermesse.de/en
Process Engineering Control & Manufacturing is a lively, engaging, insightful independent publication & directory which offers practical advice & solutions on the technical and management challenges faced by engineers and managers in the process & manufacturing industries.
Subscription enquiries: Call 01304 806039
Email: editor@mhmagazine.co.uk
Advertising enquiries: Jake Page – 0203 907 9166
Email: jake@pecm.co.uk
Editorial submissions or enquiries: Antony Holter – 01304 806039
Email: editor@mhmagazine.co.uk
The Schmersal Group is an approved course provider for the “Functional Safety of Machinery” training course of the TÜV Rheinland Functional Safety Training Program.
Are you an engineer, tester, project lead or quality representative involved in machinery safety? Improve your expertise with our TÜV Rheinland Functional Safety Professional training course.
Our four-day (eight-day online) program, equips you with essential skills for work in the machinery and factory automation sectors. Functional Safety Professional is the main qualification from the functional safety certification program (FSCP).
Engineers with proven experience in machine safety and functional safety will go in-depth into the requirements and demands of international standards, and by passing a final exam, will receive an o cial Functional Safety Engineer (TÜV Rheinland) certificate.
Detailed information can be found in our brochure, scan the QR code to download your copy.