www.kunststofenrubber.nl
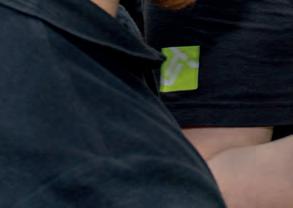
‘Je krijgt maar één kans om een goede matrijs te maken’
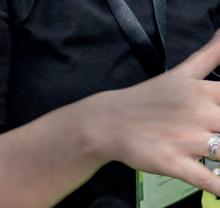
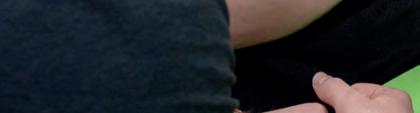
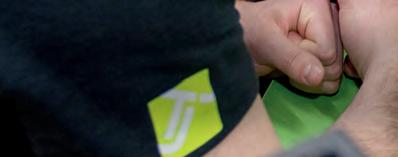
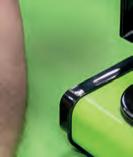
Innovatie en digitalisering must voor spuitgieters
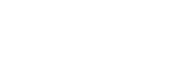
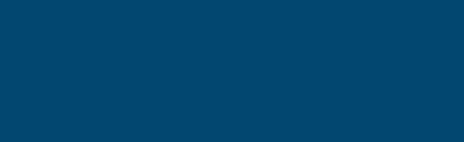

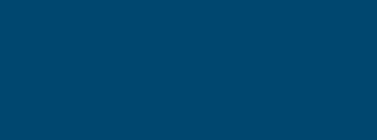
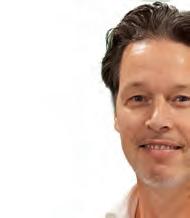
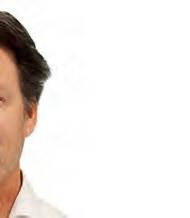

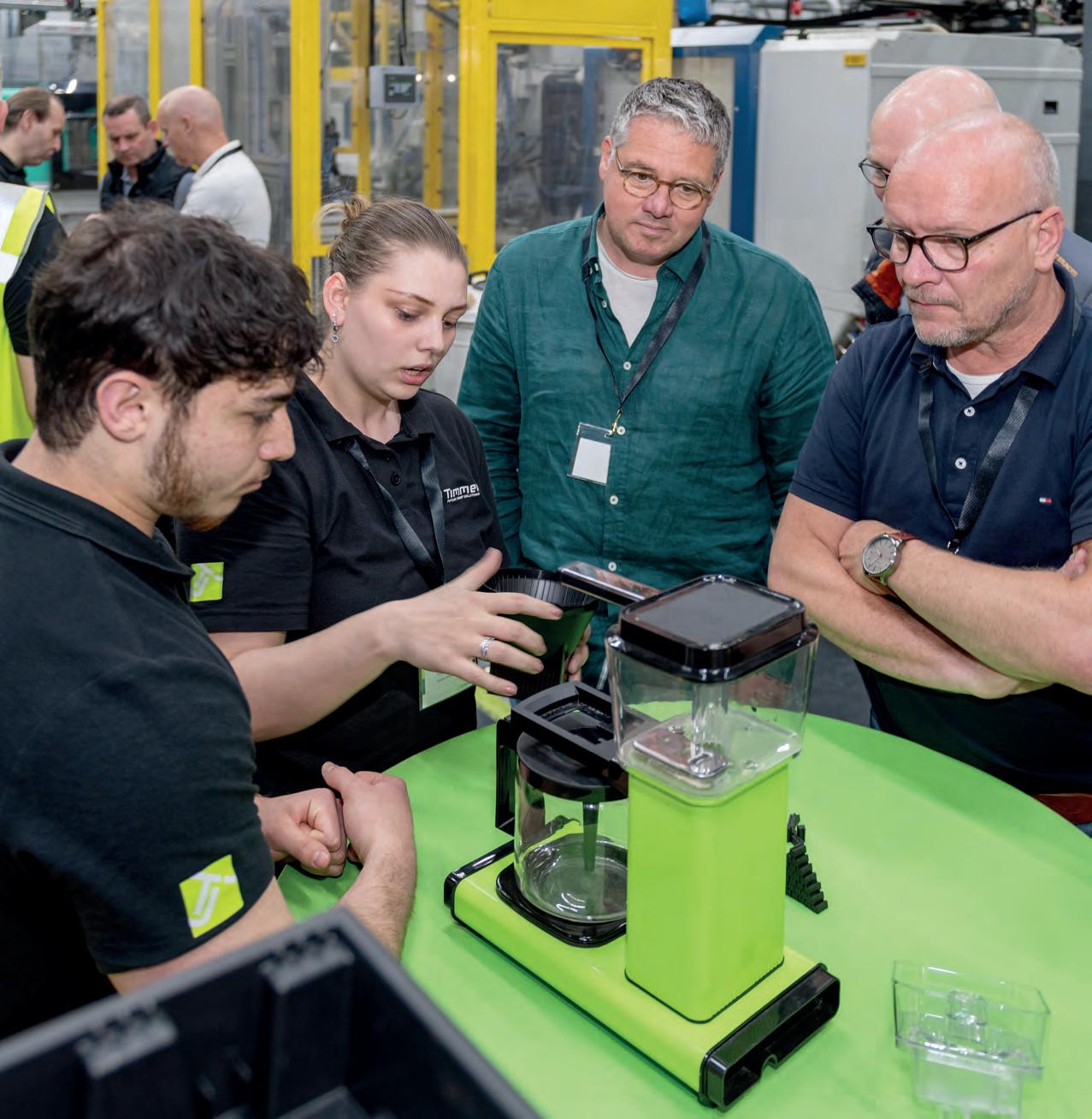
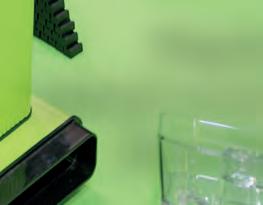
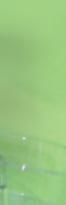
www.kunststofenrubber.nl
‘Je krijgt maar één kans om een goede matrijs te maken’
Innovatie en digitalisering must voor spuitgieters
www.arburg.nl
Kunststof & Rubber is een uitgave van Mybusinessmedia.
Uitgever: Arjan Stoeten
Redactie:
• Maartje Henket (+31 570 504 302, m.henket@mybusinessmedia.nl)
• Kasper Weigand (+31 570 504 374, k.weigand@mybusinessmedia.nl)
• Robin Zander (+31 6 222 080 34, r.zander@mybusinessmedia.nl)
Webredactie: Maartje Henket
Redactieadres:
Postbus 58, 7400 AB Deventer redactie.kunststofenrubber@mybusinessmedia.nl www.kunststofenrubber.nl
Advertentieverkoop:
Marc Nühn (+31 6 536 301 20, m.nuhn@mybusinessmedia.nl)
Alle advertentiecontracten worden afgesloten conform de Regelen voor het Advertentiewezen gedeponeerd bij de rechtbanken in Nederland.
Abonnementenadministratie
Abonnementen, bezorging en of adreswijzigingen: MYbusinessmedia Holding bv, abonnementen Kunststof & Rubber, Postbus 58, 7400 AB Deventer
klantenservice@mybusinessmedia.nl
Abonnementstarieven (excl. 9% btw)
• Jaarabonnement Nederland: € 275,-
• Jaarabonnement buitenland: € 299,-
• Proefabonnement (drie edities): € 29,50
• KIVI-leden: 45% korting
• Studentenabonnement: € 50,00 (inschrijvingsbewijs verplicht)
Jaarabonnement geldt tot wederopzegging. Beëindiging van het abonnement kan schriftelijk gebeuren, uiterlijk drie maanden voor het einde van de abonnementsperiode; nadien vindt automatisch verlenging plaats.
Druk: Drukkerij Roelofs, Enschede Basisontwerp / opmaak: Bureau OMA, www.bureauoma.nl
Hoewel de informatie gepubliceerd in deze uitgave zorgvuldig is uitgezocht en waar mogelijk gecontroleerd, sluiten de uitgever en de redactie uitdrukkelijk iedere aansprakelijkheid uit voor eventuele onjuistheden en/of onvolledigheid van de verstrekte gegevens.
MYbusinessmedia legt uw gegevens vast voor de uitvoering van de abonnementenovereenkomst. Uw gegevens kunnen door MYbusinessmedia of zorgvuldig geselecteerde derden worden gebruikt om u te informeren over relevante producten. Indien u hiertegen bezwaar hebt kunt u contact opnemen met de uitgever.
Voor u ligt het zomernummer van Kunststof & Rubber. En na een natter dan nat voorjaar is de zomer nu dan echt begonnen, schrijf ik op de eerste tropische dag van het jaar. Nou heb ik een goed geïsoleerd huis, maar tegen deze brandende eind juni-zon is mijn zolderkamertje niet opgewassen. Maar ik klaag niet.
Het nieuws van dit moment? Vanaf 3 juli is de vaste flessendop verplicht in de Europese Unie. Irritant, is toch de vaakst gehoorde reactie. Eerlijk is eerlijk, het was mij eigenlijk ook nooit zo opgevallen dat de flessendop een van de grootste vervuilers is. Toch blijkt dit uit onderzoek. Zo stelt stichting De Noordzee in hun doppenrapport dat doppen wereldwijd in de top 5 van meest gevonden items op stranden staan. En doppen behoren ook tot de top 5 van meest dodelijke afvalitems voor het zeeleven. Een kleine moeite dan, voor ons consumenten, toch? Ik klaag niet. Voor de sector was het een grotere uitdaging, maar ook die is nu voltooid. In ander nieuws hebben onderzoekers nu onmiskenbaar microplastics gedetecteerd in het bloed van Nederlandse testpersonen. Het is dus ook in ons eigen belang om gebruikte plastics goed op te ruimen en niet te laten rondslingeren.
Het zomerse thema deze maand is Matrijzen en Spuitgieten. Ik ben altijd blij verrast als ik zie wat voor leuke onderwerpen zich aandienen in reactie op onze inspiratiemail, die we sturen ter
Het is dus ook in ons eigen belang om gebruikte plastics goed op te ruimen
voorbereiding van een nieuwe editie. Sommige verhalen liggen voor de hand. Hasco, de uitvinder van de modulaire matrijs, bestaat 100 jaar. Leuk. Daar moeten we iets mee. Maar Formal Molding stond nog niet op mijn netvlies. Deze start-up 3D-print kunststof matrijzen waar het prototypes mee spuitgiet. Een matrijs van kunststof? Hoe dan?
Veel leesplezier en een goede zomer. Wij van de redactie hebben nog even geen vakantie maar kijken vast vooruit richting nazomer, met als belangrijkste agendapunt de Kunststoffenbeurs. Ik klaag niet.
KASPER WEIGAND, HOOFDREDACTEUR k.weigand@mybusinessmedia.nl
6
‘Je hebt één kans om een goede matrijs te maken’
Timmerije
BIJ HET OMSLAG
Timmerije maakt sinds jaar en dag onderdelen voor de Nederlandse producent van koffiezetapparaten Technivorm.
Artech Rubber vier keer zo groot in zes jaar tijd
30 Innovatie en digitalisering must voor spuitgieters
Aandachtspunten kunststof spuitgietindustrie richting 2030
Start-up Formal Molding 3D-print matrijs en spuitgiet prototype
GRATIS NIEUWSBRIEF
UPPACT verwerkt gemengd plastic afval tot homogene massa
Hasco viert 100-jarig jubileum
EN VERDER:
De Kunststof en Rubber-nieuwsbrief brengt u wekelijks op de hoogte van allerlei ins en outs uit de sector. Bedrijfsnieuws, materialen, machines, toepassingen, prijzen, vacature en human interest.
Aanmelden kan via www.kunststofenrubber.nl/nieuwsbrief
10 25ste editie van de kunststoffenbeurs
15 Online
21 Innovatie
22 Branchebreed
35 Brancheregister
In het oosten van het land, in het schilderachtige Neede, bevindt zich een van de mooie maakbedrijven van Nederland. Timmerije is een spuitgietbedrijf met een eigen matrijzenmakerij en een engineeringafdeling die er niet om liegt. Timmerije heeft 200 medewerkers en levert veelal hoogwaardige producten, die het van meet af aan met de klant engineert.
MAARTJE HENKET
‘Je
Wij spraken met sales & marketing manager Frank Bruins en projectleider engineering Hans van Oudheusden. “De workflow bij ons is als volgt”, steekt Bruins van wal: “Het voortraject start met een klantidee dat vertaald wordt naar een concept – en daarbij hoort bij ons al een flink stuk engineering. Wij gaan zitten met de klant, kijken naar het programma van eisen en als het project kansrijk is, vertalen we zijn ontwerp naar maakbaarheid. En we zorgen dat de klant weet wat hij gaat krijgen. Dat is de reden dat ze bij ons komen, want het is een gigantische investering. Met dat eerste stuk kan je zo een jaar bezig zijn. Of twee weken, dat kan ook, afhankelijk van de aard en omvang van het gevraagde.
Vervolgens komt er een offerte met de matrijsprijs en de productprijs en als de klant die accepteert, gaat de opdracht naar Van Oudheusden. De matrijsprijs en de gereedschapsmaker liggen dan al vast, net als de keuze voor het staal voor de matrijs en natuurlijk de grondstof voor het eindproduct. “Bij ons zitten de offerte engineer, de projectleider, de accountmanager, de inkoop, de grondstofleverancier en de gereedschaps
Frank Bruins en Hans van Oudheusden in de fabriek.
Timmerije maakt onder meer sinds jaar en dag onderdelen voor de Nederlandse producent van koffiezetapparaten Technivorm. Met deze klant wordt ook veel samen gedaan aan productontwikkeling. Zo is Timmerije op een gegeven moment de rubbervoetjes gaan maken voor in de zijstukken “Eerst kocht Technivorm die in Azië, maar er waren altijd problemen. Geen constante kwaliteit en lange levertijden. Nu maken wij ze en toen konden we de productielijn meteen zo aanpassen dat ze geautomatiseerd op hun plek worden geschoven. Dat scheelt de klant weer een handeling, plus het is gunstig in opslag en logistiek.” Ook worden de waterreservoirs van de apparaten in de productiecyclus bedrukt en zijn trays ontwikkeld om deze reservoirs veilig te transporteren.
BEELD: BJORN STAPS
maker allemaal in één team en ze communiceren allemaal rechtstreeks met elkaar. Er zijn daarbij geen wisselingen; ook de grondstofsoort zit bevroren in het project want we moeten erop kunnen rekenen dat de krimp vaststaat.”
In het voortraject wordt bijvoorbeeld ook met de engineers gekeken welke toleranties haalbaar zijn. Vaak vraagt de klant om toleranties volgens een nauwkeurige klasse van de DIN 16742norm, die niet altijd realiseerbaar zijn. Krimp zit tussen de 0,3 en 2,5%, afhankelijk van het materiaal. Dat moet eerst met de klant goed afgestemd worden. Vervolgens wordt de matrijs steel safe gemaakt: extra staal, zodat je er nog wat af kan halen, want bijlassen maakt kwetsbaar. Ook wordt er gekeken waar het gereedschap sowieso kwetsbaar wordt en of er inserts moeten komen, die later makkelijk vervangen kunnen worden. Bijvoorbeeld voor ontluchting en klikhaakjes. Van Oudheusden zorgt dan weer dat die vervanging kan plaatsvinden terwijl de matrijs op de machine zit, want je wilt hem er ook liever niet af halen.
Van Oudheusden werkt ruim 30 jaar in de spuitgietbusiness en sinds 2011 bij Timmerije, Hij bracht onder meer kennis in van de matrijzenmakerij in China. Hij vertelt: “In de eigen gereedschapsmakerij doen we vooral het onderhoud van de matrijzen – hoewel we ook geregeld matrijzen zelf maken, om te zorgen dat de kennis behouden blijft. Maar het grootste deel van onze matrijzen kopen we in bij geselecteerde partners. Volgens onze specs natuurlijk, wij hebben de knowhow en ze worden ook pas hier in de gereedschapsmakerij vrijgegeven. Onze partners zitten onder andere in Portugal, daar bestellen we de grotere matrijzen en de matrijzen voor producten waar een label ‘Made in Europe’ op moet. Verder hebben we Nederlandse en Chinese gereedschapsmakers waar we zaken mee doen.”
Hoe ze Chinese gereedschapsmakers hebben geselecteerd? Door Van Oudheusden werd een query gehouden om uit te vinden welke Chinese partners het meest geschikt waren. Daar is een document uitgekomen met een aantal potentiële partners voor verschillende soorten matrijzen. Van Oudheusden is vervol
Om toekomstbestendig te zijn en blijven, wordt de kennis op het gebied van matrijzen in eigen huis op peil gehouden. Twee jaar geleden zijn er twee jonge collega’s aangenomen van een technische opleiding. “Die jongens kunnen goed CNC-frezen en -draaien, alles met computers kunnen ze goed”, zegt Bruins. “Maar om een
complete matrijs te bouwen, heb je ervaring nodig. Die doen ze hier op.”
Daartoe is onlangs gestart met een vernieuwd opleidingstraject. “Ze leren hetzelfde als voorheen, maar de manier waarop is gemoderniseerd. De nieuwe generatie wil nu alles zelf kunnen vinden en indelen en bepalen. Daarom heb-
LINKS Yann Hubers bij de CNC-freesbank.
RECHTS Marc Heinneman tijdens matrijsonderhoud.
BEELD: BJORN STAPS
ben we een modulair cursuspakket gemaakt dat geheel online beschikbaar is. Ze kunnen zelf kiezen welke modules ze wanneer doen.”
Dat helpt om aantrekkelijk te zijn voor jonge mensen, evenals een goed klimaat, het feit dat Timmerije alles van A tot Z in huis heeft, en doorgroeimogelijkheden.
gens zelf meermalen in China geweest, voor het eerst in 2006, om de gereedschapsmakerijen te bekijken, hun processen te beoordelen en de beste te selecteren. Met een aantal daarvan doet Timmerije nu ook zaken. Het grote voordeel van bestellen in China, is dat ze tempo kunnen maken, doordat er eindeloos veel capaciteit is, zowel in machines als in mensen. “Als we dertig matrijzen nodig hebben voor een project, dan kunnen we dat in Nederland niet bij één gereedschapsmaker kwijt. Maar in China wel.”
Nadeel is de hogere staalprijs. “De klant eist vaak Europees staal, maar China moet dat eerst importeren. En door handelsbeperkingen, kost dat hen behoorlijk. Een grote matrijs kan daardoor duurder zijn in China dan in Portugal.”
Timmerije is IATFgecertificeerd, dus mag producten leveren voor de automobielindustrie. Daar zijn de eisen het hoogst. Een dashboardddeel moet bijvoorbeeld altijd matchen met de rest; vandaar dat Timmerije grondstof, proces en staal specificeert. Want een klein verschil in het staal van de matrijs kan leiden tot een totaal ander uiterlijk van het eindproduct. Sowieso is Timmerije vooral interessant voor hoogwaardige producten. “Klanten kiezen ons om de kwaliteit, leverbetrouwbaarheid en prijs”, zegt Bruins.
“Sommige producten zijn zo complex dat je de productie niet eens kán verplaatsen. Je moet de volgorde van de matrijs kennen, je moet een machine hebben die het kan...” Van Oudheusden vult aan: “Sommige matrijzen eisen heel veel. Bijvoorbeeld als je verticaal twee componenten wilt spuiten, moet je de machine hebben, de lay out moet passend zijn (dus hoe de tweede unit staat); de koppeling tussen machine en matrijs moet precies goed zijn, de delen moeten precies op tijd bewegen. Als die volgorde niet goed is, is de machine niet aan te sturen. De matrijs is van de klant, maar de knowhow zit vaak in de 3D van de matrijs en het proces.”
De matrijs wordt zoals gezegd meestal elders gemaakt en daar wordt hij vrijgegeven op de vorm van het product. De gereedschapsmaker doet een proefspuiting met de grondstof die Timmerije opstuurt. Het product komt naar Timmerije, waar het wordt gemeten en besproken met de klant en de feedback gaat terug voor aanpassingen. Vervolgens worden de wijzigingen geïmplementeerd, volgt een tweede proefspuiting die weer wordt gecontroleerd en zo door tot alles past. Dan komt de matrijs naar Nederland (met de boot kost dat vanuit China acht tot tien weken) en wordt hij gelost en geïnspecteerd in Timmerije’s gereedschaps
makerij. Daar worden de koelnippels, hot runners en elektrische aansturing aangesloten. Als alles goed is, wordt hij vrijgegeven voor productie en ingepland voor een eerste proefspuiting intern. Dan wordt een nulserie gemaakt, van een paar honderd tot duizend exemplaren en als die voldoet aan alle meetrapporten en kwaliteitseisen en Timmerije hem goedkeurt,
Mart Brummelhuis bij de CNC-draaibank.
BEELD: BJORN STAPS
Als de matrijs niet meteen goed is, komt
wordt hij gedeeld met de klant. Als die akkoord gaat, wordt de matrijs vrijgegeven voor productie. Dit is een enorm traject en het moet per se goed gaan. “Bij een matrijs heb je één kans om het goed te doen”, benadrukt Van Oudheusden. “Want als het niet goed gaat, komt je klant niet terug.”
25 – 1400 ton
Timmerije bezit spuitgietmachines met een sluitkracht van 25 tot 1400 ton, dus het bedrijf kan een breed pakket aan producten maken. Onlangs zijn er vijf machines bij gekocht van Krauss Maffei: energiezuinige hybride machines in de range 250 900 ton. Middelgroot dus, want kleine machines koopt Timmerije elektrisch. Kraus Maffei is goed in de TCO (total cost of ownership). Zij doen ook het onderhoud –afgezien van het dagelijks onderhoud, dat wordt gedaan door de eigen technische dienst.
Timmerije draait 5 dagen per week, 24 uur per dag in drie shifts. Er is altijd een gereedschapsmaker, een grondstoffenspecialist en iemand van de technische dienst aanwezig. Door het Manufacturing Execution System (MES) is er minder uitval dan voorheen, terwijl ze meer draaien. Alle machines en gereedschappen zijn erop aangesloten, dus je weet precies wat wanneer moet gebeuren. Het systeem houdt de draaiuren bij, maar ziet het ook als een bepaald product veel uitval genereert. Dan kan je gaan onderzoeken of het aan de machine ligt, aan de matrijs, of aan iets anders. Uitdaging is nog wel de dataanalyse. “Die moeten meerdere disciplines gaan beheersen”, besluit Bruins.
www.timmerije.nl
“Gelukkig is de N18 gereed gekomen, van Enschede naar Doetinchem. We zitten hier op een prachtige plek, maar erg handig is het niet qua bereikbaarheid. Als we willen dat jongens uit de omtrek hier komen werken, moeten we wel echt iets te bieden hebben. En het helpt dat ze hier nu makkelijker kunnen komen.”
Ook voor de afvoer van producten – bij voorkeur voor bedrijven in een straal van 300 kilometer rond Neede – is de nieuwe N18 een uitkomst. “We hebben een deel opslag op het eigen terrein en een deel extern, bij de rondweg. Dat betekent al dat veel vrachtwagens hier niet meer tot op het terrein hoeven te komen.”
Sinds 1999 staan tijdens de Kunststoffenbeurs de mogelijkheden voor duurzame productontwikkeling en productie met kunststof en rubber centraal. In 25 jaar uitgegroeid tot de grootste vakbeurs in de Benelux, viert de Kunststoffenbeurs dit jaar haar jubileum op 18 en 19 september in de Brabanthallen te ‘s-Hertogenbosch. Deze editie wordt groots aangepakt met verschillende themapleinen en een nog grotere beursvloer.
Programmamanager Charlotte de Jong bij organisator Mikrocentrum en verantwoordelijk voor de Kunststoffenbeurs, deelt haar visie over de aankomende editie: “Het afgelopen jaar slaagden we erin de gehele kunststofketen opnieuw samen te brengen. De stijging van het aantal bezoekers geeft duidelijk aan dat er veel interesse is in deze branche om elkaar te ontmoeten. Met een groei van 25% in bezoekersaantallen ten opzichte van 2022, zien we nog steeds een stijgende lijn.”
Al 25 jaar is de Kunststoffenbeurs een plek waar je de mogelijkheden ontdekt voor innovatieve, slimme en duurzame productontwikkeling en productieprocessen. Tijdens de jubileumeditie van dit jaar staat de slogan ‘Endless possibilities of circulair plastics’ centraal.
“In de afgelopen 25 jaar heeft de Nederlandse kunststofverwerkende industrie aanzienlijke veranderin-
gen ondergaan”, aldus De Jong. “Globalisering heeft geleid tot meer uitbesteden en verplaatsen van productie en ontwikkeling. We zien ook weer een beweging naar reshoring. Als het gaat om duurzaamheid en milieu ligt de focus op energiezuinige machines en het toepassen van steeds grotere percentages recyclaat.
De marktvraag is veranderd door de behoefte aan lichtgewicht constructies, functie-integratie, mogelijkheden voor decoratie en veel nauwere maattoleranties. Dat betekent dat er de komende jaren heel veel zal veranderen in de verwerking van kunststoffen. Wat precies, dat laten we graag zien tijdens de 25e editie van de Kunststoffenbeurs.”
Endless possibilities
Bedrijven in de kunststof- en rubberbranche produceren een grote variatie aan onderdelen, modules en eindproducten die onmisbaar zijn in onder andere verpakkingen, (consumenten)producten en machines.
Er wordt hard gewerkt aan de duurzame toekomst van kunststoffen
Dankzij de unieke en veelzijdige eigenschappen kun je met kunststof namelijk alle kanten op: in kleur, vorm en gewicht, maar het is ook combineerbaar met andere materialen en toepasbaar in vele productietechnieken. Dit maakt dat kunststof een grote impact en waarde heeft op onze samenleving. “Een wereld zonder kunststoffen is dan ook ondenkbaar, maar de wereld vraagt ook om toekomstbestendige oplossingen. Bijvoorbeeld thermoplastische kunststoffen die uitstekend gerecycled kunnen worden.”
Verbonden met de Kunststoffenbeurs
Al jaren verbinden ook diverse brancheorganisaties zich met de Kunststoffenbeurs. Toonaangevende autoriteiten zoals de NRK, Equip Plast, Plastics Europe en Polymer Science Park zetten zich jaarlijks actief in om de belangen in de branche te vertegenwoordigen. Dat de Kunststoffenbeurs hiervoor een uitgelezen gelegenheid is, concludeert de organisatie uit de ruim 3.500 professionals uit de kunststof- en rubberindus-
trie die samenkwamen tijdens de vorige editie in 2023. “De diversiteit aan exposanten en bezoekers toont aan dat er hard wordt gewerkt aan de duurzame toekomst van kunststoffen”, aldus De Jong.
210 exposanten
Bezoekers, zoals merkeigenaren en kunststofverwerkers, krijgen via het tweedaagse congresprogramma en een bezoek aan de beursvloer met ruim 210 exposanten antwoord op actuele ontwikkelingen en uitdagingen. Denk hierbij aan onderwerpen en thema’s op het gebied van regelgeving, machinebouw, verpakkingen, medische technologie en inzichten over de (duurzame) ontwikkeling van consumentenartikelen.
kunststoffenbeurs.nl
Tijdens de vorige editie kwamen
3.500 professionals uit de kunststof- en rubberindustrie samen.
Na een succesvolle 24e editie met een groeiend aantal bezoekers, meer exposanten dan ooit op de beursvloer en vertegenwoordiging van gerenommeerde partijen op de Live Stage, staat de volgende Kunststoffenbeurs gepland op 18 en 19 september. Als bezoeker ontmoet je in korte tijd belangrijke spelers uit de kunststof- en rubberwereld in de Benelux en daarbuiten. Meer informatie en je gratis bezoek direct aanmelden kan via de website.
Anno Visser werkt met zijn eigen gebouwde automatische spuitgiet-machine.
Industrieel productontwerper Anno Visser wilde zijn getekende producten graag als daadwerkelijk gespuitgiet product testen, maar de hoge kosten en tijdsinvestering van traditionele spuitgietmatrijzen maakten dit vrijwel onmogelijk. Het moest gewoon in één keer goed. Hij bedacht een methode om spuitgietmatrijzen die geschikt zijn om prototypes mee te spuitgieten te 3D-printen van een thermoharder.
KASPER WEIGAND
Anno Visser startte zijn eigen bedrijf Formal Molding bij incubator Zwinc in Zwolle, waar veel start-ups bij elkaar zitten. Daarnaast werkt hij voor Scope Design, een gerenommeerd designbureau in Amersfoort, waar hij zich inzet om, voornamelijk spuitgietproducten, maakbaar te krijgen. Hij zocht naar een manier om prototypes realistisch te testen voordat er een definitieve matrijs wordt gemaakt. “Een ge-3D-print prototype wijkt vaak te veel af om eigenschappen van het uiteindelijke product goed te kunnen testen. Je hebt bijvoorbeeld niet dezelfde sterkte en stijfheid, vezelrichting of afwerking hardheid, softness en transparantie”, legt hij uit. Maar het 3D-printen van een matrijs, dat zou wel eens interessant kunnen zijn, bedacht hij.
Risico
“Het ontwikkelen van een spuitgietmatrijs brengt risico's met zich mee”, zegt Visser. “Het kost zóveel kennis,
expertise, tijd en geld. Een nieuw product moet je van tevoren goed testen. Als ik het straks ga maken en ik ontwikkel een dure matrijs, dat moet dat product ook echt worden zoals ik heb ontworpen. Iteraties zijn kostbaar, maar vooral tijdrovend, aangezien de matrijs telkens terug moet naar de matrijzenmaker voor aanpassingen.”
Hoogwaardige matrijs
Door een matrijs te 3D-printen met een harsprinter, maakt Visser een hoogwaardige matrijs die heel nauwkeurig is en bestand tegen de hoge temperaturen en hoge druk van het spuitgietproces. “Met de matrijs kan ik een kleine serie producten spuitgieten met als doel die als prototype te gebruiken. Ik vervang niet de uiteindelijke productiematrijs”, benadrukt hij. De hars, die uithardt onder invloed van UV-licht, heeft extra goede eigenschappen op het gebied van temperatuur en druk. Het is een thermoharder en meer wil Visser niet kwijt over zijn geheime recept.
De matrijs (boven) is ge-3D-print met een harsprinter en wordt gemonteerd op een moedermatrijs (onder).
“ Het spuitgieten bestaat al zo lang, het is zo’n uitgedokterd proces, dat best wel wat bedrijven in het conventionele vastzitten
Met de matrijs kan hij vervolgens 100 tot 150 shots spuitgieten met een PP of PE. Daarna degradeert het en is de kwaliteit niet meer toereikend. “Spuitgiet ik met een polyamide glasgevuld, dan haal ik maar 20 tot 30 stuks. Omdat dat gewoon veel meer slijt. En qua temperatuur is dat ook een grotere shock voor de thermoharder matrijs.”
Visser gebruikt deze manier van werken natuurlijk tijdens zijn eigen ontwerpproces, maar heeft Formal Molding opgericht omdat hij denkt dat het voor veel meer bedrijven interessant kan zijn. Hij startte ruim drie jaar geleden met experimenteren en heeft nu de machines en het proces zover onder controle dat hij ermee naar buiten treedt en opdrachten aanneemt. Dat is ook gelijk een uitdaging. “Want het spuitgieten bestaat al zo lang, het is zo’n uitgedokterd proces, dat best wel wat bedrijven in het conventionele vastzitten. Het is niet voor niets dat de iteraties bij de first out
Anno Visser met een demonstrator, een matrijs voor een klikgesp en het gespuitgiete product.
of tool (FOT) second out of tool (SOT), de eerste producten uit de matrijs, eigenlijk altijd ingecalculeerd zitten in de prijs. Daar houdt men gewoon rekening mee. Terwijl ik denk dat dit niet per se hoeft”, stelt Visser. “Doordat je van tevoren veel meer kan testen en valideren, is je product bijna in één keer goed. Er zijn ieder geval veel minder iteraties nodig. En die besparing probeer ik met Formal te verkopen.” Visser noemt dit proces het PreFOT proces, namelijk; de First Out of Tool (FOT) voordat de productiematrijs überhaupt gemaakt is.
Het concept is dat een bedrijf dat een nieuw product ontwikkelt, het prototype niet, zoals nu vaak gebeurt, hoogwaardig laat 3D-printen, maar door Visser laat spuitgieten. Klanten hoeven alleen maar de geometrie van het product aan te leveren. Visser ontwerpt zelf de matrijs. Na een week is er dan een kleine serie gespuitgiete prototypes van productiekwaliteit, om mee te testen. Iteraties die hieruit voortkomen, kunnen snel door Visser worden verwerkt, waarna er een nieuwe matrijs wordt geprint. Net zo lang totdat het
“
Ik denk dat het nog veel beter kan, en groter, nauwkeuriger en goedkoper. Er is nog veel winst te behalen
product perfect is en er met veel meer onderbouwde kennis geïnvesteerd kan worden in een productiematrijs.
Spuitgietmachine
Visser werkt met zijn zelfgebouwde automatische spuitgiet-machine. In eerste instantie omdat het project heel geleidelijk is opgebouwd, en hij daarom niet meteen kapitaal had voor een complete machine. Maar het gaf hem ook de mogelijkheid om zijn machine helemaal af te stemmen op de eigenschappen van de ge-3D-printe thermoharder matrijzen. “Met mijn matrijzen heb ik niet per se de sluitkracht nodig die een stalen matrijs wel nodig heeft.” Daarnaast heeft hij de hopper zo aangepast dat je heel snel en gemakkelijk materiaal kan uitwisselen. Je kunt hem afsluiten, eraf halen en verwisselen.
80 procent van de werkzaamheden van Formal Molding bestaat uit trajecten voor prototypes. Maar daarnaast kan het soms interessant zijn een kleine hoeveelheid nieuwe producten mee te nemen naar een presentatie of beurs. “Omdat je een reactie wilt testen, maar je niet al wil investeren in een matrijs.” Ook daar richt Visser zijn pijlen op. En hij ziet nog een kans. “Conventioneel spuitgieten wordt meestal interessant bij zo’n 3000 stuks. Er zit dus een kloof tussen waar ik zit en die 3000 stuks”, erkent hij. “Maar als ik nou 1000 stuks met één matrijs kan maken, dan wordt het al interessant voor een serie.” Hij kan namelijk vrij eenvoudig meerdere matrijzen printen. “Dan print ik er gewoon drie.”
In tegenstelling tot het spuitgieten, wat al behoorlijk is uitgeoptimaliseerd, is er binnen het 3D-printen nog volop ontwikkeling. Zijn nieuwe harsprinter, de nieuwe versie van zijn drie jaar oude printer, is alweer veel beter dan de vorige. “De innovatie gaat heel snel. Ik denk dat het nog veel beter kan, en groter, nauwkeuriger en goedkoper. Er is nog veel winst te behalen”, gelooft hij. Visser heeft een subsidieaanvraag lopen om onderzoek te kunnen gaan doen naar het verlengen van de levensduur van de matrijs.
www.formalmolding.com
Altijd op de hoogte van het laatste nieuws in de kunststof- en rubberbranche? Bezoek de website.
www.kunststofenrubber.nl
AI binnen de maakindustrie, wat is er mogelijk?
Tijdens de Maakindustrie Expo in Hardenberg was er ook aandacht voor AI. Voor de een een compleet nieuwe technologie, terwijl de ander er al dagelijks gebruik van maakt. Maar wat kun je ermee als maakbedrijf? Daar gingen Giel Cuijpers (senior cloud solutions architect bij Microsoft) en Jeroen Paters (business consultant customer engagement bij Prodware) dieper op in tijdens een kennissessie. Onze Jorine van Knippenberg deed verslag.
Lees verder
De Vereniging Nederlandse Gemeenten (VNG) heeft de overeenkomst met het voormalig Afvalfonds Verpakkingen, Verpact, opgezegd. ‘Vergoedingen die gemeenten van Verpact ontvingen bleken niet kostendekkend. Ook hekelt de VNG de transparantie bij de organisatie. De VNG zet in op nieuwe afspraken vanaf 2025’, aldus de site.
Lees verder
Waarom wordt er niet meer gerecycled materiaal gebruikt? Hoe kan het gebruik van secundaire materialen worden vergroot? Het Duitse SKZ Plastics Center en plastship GmbH identificeerden obstakels voor het gebruik van secundaire materialen en ontwikkelden aanbevelingen voor actie, rekening houdend met beperkende factoren. Een en ander heeft geleid tot een gratis online tool voor verwerkers.
Iets geniaals bedacht? KVK roept alle innovatieve mkb-ondernemers in Nederland op zich aan te melden voor de KVK Innovatie Top 100 2024, de grootste innovatie-etalage van Nederland.
De innovaties worden onder andere beoordeeld op originaliteit, groeipotentie, duurzaamheid en impact voor de branche en de samenleving. Het product of de dienst dient op de markt te zijn gebracht. Inschrijven kan tot en met 1 augustus.
https://bit.ly/45rfZgZ
Dijkhuis,
directeur/eigenaar
Artech Rubber vier keer zo groot in zes jaar tijd
Is het mogelijk om de grotendeels naar het verre buitenland verhuisde rubberproductie, deels, weer terug naar Nederland te halen, vroeg Richard Groot zich af. Met de nodige automatisering, waarom niet? Zes jaar geleden nam hij Artech Rubber uit Zutphen over om zijn plan mee te verwezenlijken.
KASPER WEIGAND
Richard Groot zag in de 27 jaar die hij werkte bij een grote handelaar in rubberproducten de rubberproductie verdwijnen van Noordwest-Europa, naar Zuid-Europa, en toen naar Oost-Europa en Azië. De behoefte naar rubber is alleen maar vergroot, maar de productie ervan verdween naar verre landen. Toen Artech Rubber BV, een bedrijf ingericht op kleinere series met korte levertijden, op zijn pad kwam, zag Groot mogelijkheden. Ik dacht, als we hier met grotere machines en meer kunnen automatiseren, dan moet het mogelijk zijn om de productie van bepaalde rubberproducten terug te halen naar Nederland. Efficiënt en margetechnisch op een goede manier”, vertelt hij.
Kort na de overname, stopte een grote Duitse concullega met zijn rubberproductie. “Die hebben we toen ook overgenomen, waardoor we de beschikking kregen over een aantal verder geautomatiseerde en volautomatische rubber injectiemachines. Dat maakte dat we onze propositie naar de markt verder konden uitbreiden.” Artech Rubber maakte altijd al relatief kleine series en klantspecifieke producten of specials, maar was nu ook in staat competitief grote series aan te bieden. Inmiddels is het zes jaar later, is Artech Rubber vier keer zo groot en groeide het personeelsbestand van acht naar ruim twintig medewerkers.
Het verschil tussen de productie van rubber en dat van kunststof is aanzienlijk. Kunststof verwarm je tot het thermoplast zacht is, vervolgens wordt het gegoten in de juiste vorm en daarna afgekoeld. “Rubber werkt precies andersom. We moeten het rubber bak-
hadden al een matrijzenmakerij, maar maakten ook gebruik van uitbesteding. Inmiddels hebben we flink geïnvesteerd in twee nieuwe machines en maken we nagenoeg alle matrijzen zelf”, vertelt Groot. Artech heeft met de aanschaf van twee Style CNCbewerkingscentra de capaciteit van de matrijzenmakerij verdubbeld. Ook het tekenen van de matrijzen in CAD-software gebeurt tegenwoordig intern. “Dan heb je het proces meer in eigen hand.”
Voor een proefserie maakt Artech een kleine proefmatrijs. “Blijven de aantallen klein, dan werken we met een enkelvoudige matrijs. Gaan die aantallen
ken om een vulkanisatieproces op gang te brengen waardoor je een veel langere cyclustijd hebt. Dat kan variëren van 2 tot 3 minuten tot wel een uur voor onze dikste producten. Al die tijd moet het product op constante temperatuur en druk worden gehouden en bezet het ook de pers natuurlijk”, omschrijft Groot.
De matrijstechniek voor kunststof spuitgieten is lastiger. Wanddiktes moeten gelijk zijn en er zitten overal koelkanalen. Dat is voor rubbermatrijzen niet nodig. Omdat de cyclustijden zoveel hoger ligger, ga je voor rubber wel sneller kijken naar een matrijs waarmee je meerdere delen per cyclus produceert, dus met meerdere caviteiten. “We maken veel nieuwe producten en voor elk nieuw product heb je een matrijs nodig. We
omhoog, dan gaan we naar een matrijs met meerdere caviteiten. Worden de aantallen nog hoger? Dan kijken we misschien naar injectie in plaats van het veel arbeidsintensievere conventioneel persen. Worden de aantallen nog hoger? Dan kunnen we kijken of we hem volautomatisch kunnen maken. Dan wordt het rubber geïnjecteerd en wordt de matrijs ook automatisch geleegd.”
Artech wil breed operationeel zijn en richt zich daarom op zowel enkelstuks als kleine en grotere series. En kleine, maar ook grote producten. “Dat is juist onze markt, zegt Groot. “Grote producten haal je niet gemakkelijk met de boot uit Azië. Daarnaast doen we veel rubber-metaal verbindingen. Bedrijven sturen
Invoer van rubber strip voor volautomatische productie.
dan hun metalen delen, die wij vervolgens berubberen. Ook iets wat je niet zomaar in Azië laat doen. Verder produceert Artech ook meer en meer producten voor een hoogwaardigere toepassing, waar meer en specifiekere eisen aan zitten. Te denken valt dan aan specifieke keuren, maar ook specialistische materialen zoals Aflas, siliconen en FFKM. Deze compounds worden deels in huis ontwikkeld door onze rubbertechnoloog en technisch directeur Dr. Ir. Kuno Dijkhuis”
Soorten
Er is namelijk nogal wat variëteit in rubber en Artech ziet nagenoeg alle soorten langskomen, van natuurrubber (NR) tot EPDM en van NBR tot FFKM. Van natuurrubber, wat van rubberplantages komt, worden hoofdzakelijk banden gemaakt, een van de weinige producten die Artech niet produceert. “Natuurrubber is heel slijtvast, maar niet zo verouderingsbestendig”, weet Groot. “Dat moet je niet gebruiken voor raamrubbers, dan zijn ze zo weg. Daar kies je voor een synthetische rubber als EPDM. Ben je op zoek naar een voedingsmiddellenkwaliteit of werk je met stoom, dan kijk je vaak naar siliconen of Aflas. Je hebt ook kwaliteiten die uitermate geschikt zijn voor hydrauliek en pneumatiek, bijv. NBR of FKM. Daar werken we allemaal mee”, vertelt hij. Sommige rubbers waar Artech mee produceert, kosten 3 euro per kilo en andere kosten 5.000 euro per kilo.
Zichtbaar
Rubberproducten in het algemeen, komen in tal van markten terecht, maar zijn in hun uiteindelijke functie overigens nauwelijks zichtbaar. Afdichtingen, die een groot gedeelte van de toepassingen van rubber vormen, zitten altijd ergens in en zie je dus niet. “In een verwarmingsketel, koffiezetapparaat of kraan zitten veel rubbertjes, maar die zie je niet.” Artech maakt
producten voor bijvoorbeeld pompen in de agrarische sector, maar ook voor de algemene maak- en voedingsmiddelenindustrie. In Nederland en soms daarbuiten.
Technische directeur Kuno Dijkhuis signaleert dat de industrie het nog steeds lastig heeft. “We zien dat onze bestaande klanten iets minder doen. Maar we hebben veel aanvragen van nieuwe potentiële klanten en voor nieuwe projecten, dat zijn wel kansen.” “Vroeger was alles wat van ver kwam, lekker”, zegt Richard Groot weer. Maar dat is niet meer zo. “Vanwege duurzaamheid, corona, de blokkade van het Suezkanaal. Omdat een rubbermatrijs niet zo heel erg duur is, zeggen sommige bedrijven: ik wil voor 50 procent van mijn behoefte een matrijs in Nederland hebben liggen. En die maken wij graag.” Dijkhuis: “Dan hebben ze een tweede leverancier dicht bij huis, die ook in nood kan inspringen en opschalen. We hebben dan niet alleen de matrijs hier liggen, maar maken ook een bepaald percentage van de producten standaard. Dat is wel iets wat wij voor ogen hebben en wat we ook voor een groot aantal klanten al doen.”
Op het gebied van recycling is er ook met rubber van alles mogelijk en Artech is er volop mee bezig. Groot legt het proces uit: “Neem een autoband. De banden worden ingezameld en er zijn bedrijven die de producten goed kunnen sorteren en uit elkaar kunnen houden. De loopvlakken van die band worden eraf gehaald, gegranuleerd en gedevulkaniseerd. Dat devulkanisaat krijgen wij vervolgens binnen en daar kunnen wij nieuwe rubberen producten van maken,
We bakken het rubber om een vulkanisatieproces op gang te brengen
mits we daar de juiste ingrediënten aan toevoegen om het vulkanisatieproces weer op gang te krijgen.”
Omdat het rubber tijdens dit proces toch wat inboet aan kwaliteit en voor banden juist een hele hoge kwaliteit rubber is vereist, kan het vaak niet meer terug in zijn originele functie. “Rubber dat niet meer geschikt is om opnieuw als bandenrubber te gebruiken, kan nog wel gebruikt worden in andere producten, waarvoor de veiligheidseisen iets lager liggen.”
De infrastructuur voor het recyclen van natuurrub-
Een bewerkingscentrum in de matrijzenmakerij.
van een matrijs.
ber is redelijk goed op orde. Maar voor synthetische rubbers niet. “En bandengranulaat of devulkanisaat, wat 80 procent van de rubberconsumptie wereldwijd vormt, kan niet in een EPDM of NBR, dat moet terug in de band of in producten waarin gelijkwaardige rubbersoorten worden gebruikt”, weet Dijkhuis, die gepromoveerd is op het devulkaniseren van rubber. Er zijn nog geen partijen in de markt die synthetische rubbers verzamelen, sorteren, vermalen, granuleren en devulkaniseren. Dat is een probleem. “De bedrijven die dit voor de bandenwereld doen, vragen hoeveelheden van minimaal 10 ton materiaal. Maar ik heb niet zomaar even 10 ton productieafval liggen, want we doen er juist alles aan om het percentage afval zo
Gerecycled rubber, klaar voor verwerking.
laag mogelijk te houden”, legt Groot uit. Groot en Dijkhuis zijn dan ook blij dat de bijmengverplichting voor kunststoffen vanaf 2027, vooralsnog niet gaat gelden voor elastomeren. “We kunnen al heel veel. Maar we zijn ook beperkt, omdat we afhankelijk zijn van wat er vóór ons in de supply-chain gebeurt. Dat komt wel, maar dat kost tijd”, verwacht Groot. Inmiddels verwerkt Artech al zo’n 100 tot 150 ton gerecycled rubber per jaar. En daar gaat het gewoon mee door. “We blijven verbeteren en optimaliseren”, besluit Dijkhuis.
www.artechrubber.nl
Geen enkel bedrijf heeft de gereedschaps en matrijzenbouw zo sterk vormgegeven als de fabrikant HASCO. De uitvinder van de standaard normdelen en pionier in de matrijzenbouw, viert in 2024 zijn 100jarig bedrijfsjubileum met klanten, medewerkers en partners.
Een verhaal dat begon in 1924 toen oprichter Hugo Hasenclever in zijn kelder in Lüdenscheid/Duitsland de eerste matrijzen vervaardigde voor de verwerking van het toen nog nieuwe materiaal bakeliet. Een verhaal dat later een beslissende verandering onderging dankzij zijn zoon Rolf Hasenclever, hij vond het modulaire systeem uit met standaard normdelen en vroeg in 1960 hiervoor het patent aan. Zijn idee bracht een revolutie teweeg in de branche. Het was een mijlpaal die de weg vrijmaakte van een puur ambachtelijk bedrijf naar een mondiaal bedrijf.
Vele mijlpalen
Vanaf dat moment zouden er vele mijlpalen volgen die keer op keer de reputatie van
een baanbrekend bedrijf zouden aantonen. Wat gold voor het analoge tijdperk van de matrijzenbouw, heeft HASCO met de start van de digitalisering in de jaren 80 nog meer bereikt. HASCO heeft innovatieve normen gesteld om producten en processen steeds eenvoudiger te maken voor ontwerpers, matrijzenmakers en spuitgieters.
Het team van HASCO Benelux heeft dit bijzonder jubileum samen gevierd met haar klanten uit België, Nederland en Luxemburg in de CMine te Genk.
HASCO
info.benelux@hasco.com www.hasco.com
Upcycling: een kozijn beschermt je huis; een antipipingscherm het hele land
Zorgen dat hoog water je dijk niet ondermijnt? Dat kan nu met het Prolock Delta filterscherm. Het anti-pipingscherm van gerecyclede kozijnen was dit jaar genomineerd voor ingenieursprijs Vernufteling. Bij piping stroomt water met zand vanaf de rivier onder de dijk door en komt het achter de dijk weer omhoog. Doordat zandkorrels en andere gronddeeltjes mee stromen, ontstaan er kanaaltjes onder de dijk door. Dat verhoogt het risico op het bezwijken van de dijk.
Het nieuwe scherm laat het water door, maar houdt het zand en andere gronddeeltjes tegen. Het wordt gemaakt van gerecyclede PVC-elementen en gevuld met fijn zand, dat het filterende werk doet. Ze zijn volgens de makers zeker honderd jaar onderhoudsvrij en zijn ze niet meer nodig, dan kunnen ze worden hergebruikt. De aanleg gebeurt trillingsvrij en kan ook elektrisch; dit in tegenstelling tot traditioneel gebruikte metalen damwanden, die veel zwaarder zijn.
Traditioneel wordt piping bestreden door grote hoeveelheden zand onder aan de dijk te storten, zodat er een extra breed dijklichaam ontstaat. Deze oplossing vraagt veel ruimte en het zand moet met vrachtwagens worden aangevoerd, wat tot overlast leidt.
Het Prolock Delta Filterscherm is begin 2024 voor het eerst toegepast bij dijkversterkingsproject Sterke Lekdijk, deelproject Salmsteke.
bit.ly/3xmZdCW
De productie van de Nederlandse industrie, inclusief de rubber en kunststofsector, opnieuw is gedaald in april 2024.
De productie in de rubber- en kunststofindustrie daalde met 1,4 procent. In totaal daalde de productie in de industrie in Nederland in april met 3,5 procent. Daarmee blijft de Nederlandse industrie voor de negende maand op rij krimpen. In de kunststof- en rubber industrie is zelfs al langer dan een jaar sprake van krimp. De NRK maakt zich al langere tijd zorgen over de dalende productiecijfers van de rubberen kunststofindustrie.
In mei waren de producenten in de industrie minder pessimistisch dan in april. Fabrikanten waren vooral optimistischer over de verwachte bedrijvigheid. Het vertrouwen van Duitse producenten, een belangrijke afzetmarkt voor de Neder-
Er gebeurt veel branchebreed: opleidingen, bijeenkomsten, bedrijfsbezoeken, noem maar op. Aan alles deelnemen gaat niet, maar alles overslaan is ook geen optie. Harold de Graaf, algemeen directeur van NRK, benoemt de belangrijkste actuele onderwerpen. www.nrk.nl
landse industrie, bleef in mei net zo negatief als in april (Eurostat). De kalendergecorrigeerde productie van de Duitse industrie was in april 3,5 procent lager dan een jaar eerder. Vergeleken met maart steeg de Duitse productie met 0,3 procent (Destatis).
Helft
CBS: ‘Bijna de helft van alle bedrijfsklassen in de industrie produceerde in april minder dan in dezelfde maand een jaar eerder. Van de acht grootste branches noteerde de reparatie en installatie van machines de grootste productiedaling. De elektrische en elektronische apparatenindustrie had de grootste stijging.’
De NRK maakt zich nog steeds grote zorgen over de dalende productievolumes in de industrie. De druk op de gehele Nederlandse industrie neemt toe. Steeds meer leden van de NRK krijgen te maken met afnemende orders, wat resulteert in lagere productievolumes. Deze situatie
Steeds meer leden van de NRK krijgen te maken met afnemende orders.
BEELD: WIKIMEDIA/ACMEDRINKTECSOLUTIONS
houdt al meer dan een jaar aan en brengt steeds meer ondernemers in moeilijkheden. Dit kan mogelijk ten koste gaan van werkgelegenheid. Bovendien komen investeringen in de verduurzaming van de kunststofsector in Nederland hierdoor steeds verder onder druk te staan. De NRK bespreekt deze zorgen in al haar gesprekken met stakeholders
RVO heeft bekendgemaakt vanuit de Circular Plastics NLsubsidieregeling vijf projecten te steunen. Ook NRKleden profiteren hiervan.
Onder de deelnemende bedrijven aan deze projecten zijn ook onder meer de NRKleden Trioworld, Morssinkhof Plastics en NRK-partner RecyBem, iets waar we trots op zijn. De subsidie is gericht op het bevorderen van recycling en het creëren van een economie waarin grondstofstromen circulair worden ingezet. Ondernemers konden subsidie aanvragen voor onderzoeksprojecten of showcases die knelpunten oplossen en de kwaliteit van recyclaat
verbeteren. De subsidie is verdeeld over verschillende onderwerpen binnen de plasticindustrie. Verschillende onderwerpen zijn aanvragen goedgekeurd die voldoen aan specifieke voorwaarden en beoordeeld zijn op onder andere de relevantie van het project en de samenwerking met ketenpartners.
Nieuwe regelingen
In 2024 wordt door CPNL opnieuw 30 mil-
De NRK heeft namens alle leden bezorgdheid geuit over de voorgestelde wijziging van de Wet milieubeheer voor het instellen van een Nationale Circulaire Plastic Norm. In haar reactie op de internetconsultatie van de NCPN benadrukt de NRK dat het wetsvoorstel een ongelijk speelveld creëert voor Nederlandse verwerkers en zal zorgen voor forse negatieve economische gevolgen en tegenvallende milieueffecten.
In een uitgebreide brief uit de NRK op een aantal belangrijke punten haar zorgen over de NCPN. De grootste knelpunten van het huidige ontwerp van de norm zijn:
Ongelijk speelveld: Het huidige ontwerp van de wet stelt import vrij van de norm. Daarmee wijkt de voorgestelde nationale norm af van Europese regelgeving, wat leidt tot een ongelijk speelveld voor Nederlandse verwerkers in de kunststofindustrie in vergelijking met hun Europese concurrenten.
Recyclaat niet altijd mogelijk: Voor veel
De NRK pleit voor aanpassingen op Europees niveau om een gelijk speelveld te behouden.
specifieke toepassingen is de inzet van recyclaat vanuit andere wet- of regelgeving niet toegestaan. Voorbeelden zijn voedselverpakkingen, persoonlijke verzorging, waterleidingen en technische toepassingen.
Economische gevolgen: Uit onderzoek van Ecorys, uitgevoerd in opdracht van de NRK, blijkt dat één op de zes verwerkers overweegt de productie naar het buitenland te verplaatsen bij invoering van de nieuwe norm. Kleinere en lokaal gewortelde verwerkers geven aan dat verplaatsing geen optie is in verband met lokale connecties, zij kiezen dan voor het stopzetten van de activiteiten.
Handelssysteem: Het voorgestelde handelssysteem in circulaire plasticeenheden
zal zorgen voor een verschuiving van het productportfolio in Nederland. Het zal voor producten waar de inzet van recyclaat niet mogelijk is alleen maar kostprijsverhogend werken en daardoor voor klanten aanleiding zijn waar mogelijk om deze producten buiten Nederland in te kopen.
Beperkte milieu-impact: De NRK betwijfelt of de milieuvoordelen zoals voorgesteld haalbaar zijn. Met de te verwachten grote weglek van economische activiteiten uit Nederland verdwijnt ook een belangrijk aandeel van de potentiële CO2-winst. Daarnaast is de berekende CO2-winst voornamelijk gebaseerd op de inzet van mechanisch recyclaat en niet realistisch als er chemisch recyclaat moet worden gebruikt waarvan de CO2-winst lager is.
Belemmering: Nederlandse verwerkers worden met dit wetsvoorstel onevenredig hard geraakt door de importvrijstelling en doordat export als gevolg van de forfaitaire norm ook onder de NCPN valt.
De NRK ondersteunt de stappen op weg naar een circulaire economie en trekt hierin graag samen met op met haar leden, de overheid, beleidsmakers en andere stakeholders. De NRK roept de overheid op om dit wetsvoorstel te heroverwegen en in te zetten op een Europese norm, zodat het gelijk speelveld in de EU wordt gegarandeerd.
joen euro beschikbaar gesteld voor een subsidieronde. Deze regeling wordt mede vormgegeven door het inventariseren van belangrijke onderwerpen en knelpunten in de markt. Na een positieve beoordeling van de tussentijdse evaluatie van het programma, wordt er voor de periode 2025 en 2026 een budget van 43 miljoen euro verwacht.
Ook het NTCP is betrokken bij verschillende projecten. BEELD: NTCP
Oprichter en ceo Jan Jaap Folmer (links) en mede-oprichter Michel Walstock tonen enkele producten van UPPACT.
Een van de problemen in de kunststofrecycling is dat de grondstof vaak gemengd en vervuild is. Kunststoffen scheiden en reinigen voordat de eigenlijke recycling plaatsvindt, is meestal gewoon te duur. Dan zit er weinig anders op dan de partij in de verbrandings-oven te gooien. Het Nederlandse bedrijf UPPACT brengt daar verandering in met een Australische techniek.
JAN VAN DEN BERG
Het liefst zou een recycler een hele partij plastic in één keer in een machine willen gooien, waar de verschillende soorten plastic netjes gescheiden uit tevoorschijn komen. Omdat dit niet kan, wordt plastic afval van tevoren gescheiden. Als dat bedrijfseconomisch en technisch kan tenminste. Veel afval is immers te zeer gemengd of vervuild om efficiënt verwerkt te kunnen worden. Dan rest slechts verbranden.
“Binnenkort hoeft dat niet meer”, zegt Jan Jaap Folmer. Hij is oprichter en directeur van UPPACT. Dit bedrijf heeft de afgelopen vier jaar een technologie geperfectioneerd waarmee het mogelijk is van kunststofmengsels bruikbare producten te maken. De installatie die dit kan, heet de Unwastor. De oorsprong hiervan ligt in Australië.
Lange carrière
Folmer kent de wereld van de kunststof recycling goed. Hij heeft intussen een lange carrière in de
kunststof achter zich. Zo was hij commercieel directeur bij Lankhorst Recycling Products. “Daar zag ik mogelijkheden om plastic afval te verwerken, die Lankhorst niet wilde oppakken. In goed overleg zijn we uit elkaar gegaan en ben ik voor mezelf begonnen. Vijf jaar geleden kwam ik in contact met een Australisch bedrijf dat claimde een technologie te hebben, waarmee reststromen van gemengde kunststoffen verwerkt kunnen worden. Dat leek ook mij aanvankelijk een beetje te mooi om waar te zijn, maar bij nader inzien kreeg ik er vertrouwen in.”
Commercieel
In Australië bleek deze technologie goed te werken. Toch kwam het project commercieel niet van de grond, omdat er in dat land nauwelijks een markt bestond voor plastic recycling. “Ze waren hun tijd vooruit”, oordeelt Folmer. “Maar voor Nederland en
Europa komt deze technologie op een goed moment. We kunnen in ons land veel kunststoffen recyclen, maar er is nog altijd een probleem met gemengd en vervuild plastic afval.”
Trommel met gaatjes
Hoe werkt het proces? Het gemengde plastic (en textiel) wordt tegen een ronddraaiende trommel met gaatjes geduwd. Door de wrijving en druk loopt de temperatuur van het plastic op en wordt het zacht. Door de rotatie en druk worden de plastics door elkaar heen gesmeerd en door de gaatjes in de trommel geperst. En komt vervolgens als een taaie maar homogene massa uit de mixer-melter waarna het via de extrusielijn in de matrijzen terechtkomt.
Brandbreedte
Verschillende soorten plastic hebben uiteraard uiteenlopende smelttemperaturen. Dat maakt, binnen een zekere bandbreedte, voor de effectiviteit van het proces niet uit, zegt Folmer. “Er ontstaat een homogene massa waarin de verschillende soorten plastic uit het afval goed gemengd zijn. De molecuulslierten worden als een soort spaghetti door elkaar gemengd. Kleine vaste deeltjes die niet van plastic zijn, zoals zandkorrels, maken gewoon deel uit van het eindpro-
In Eemshaven zet UPPACT een Australische mixer-melter aan het werk.
Er is meer dan voldoende gemengd plastic afval voor UPPACT beschikbaar.
duct. Dat geldt ook voor bijvoorbeeld kleine metalen deeltjes die je overhoudt als je chipszakken of mondkapjes verwerkt.”
Zuren
Het proces kan de meeste thermoplasten verwerken en kan in de praktijk in ieder geval overweg met plastic afval met de codes 1 tot en met 7. PVC kan in principe verwerkt worden, maar er zijn twee praktische bezwaren om dit te doen, zegt Folmer. “Er zitten zuren in, die de equipment kunnen aantasten. Bovendien komen er chloordampen vrij. Wij accepteren dan ook geen PVC in onze aangeleverde kunststof afvalstromen.” Er mag tot tien procent PET in het aangeleverde plastic zitten. Dat zullen vooral trays zijn, want voor PET-flessen is er immers een statiegeldsysteem. Vocht is een andere factor van belang, legt Folmer uit. “Te veel vocht verstoort het proces. Het aangevoerde plastic afval moet daarom zo droog mogelijk zijn. Alle vocht wordt in de mixer-melter verdampt, maar dat vertraagt het proces en kost veel energie. Zolang er water in het de mixer-melter zit, koelt dit de plasticmassa. Dat helpt zeker niet.“ De werking van het proces, van afvalinzameling tot eindproducten, is de afgelopen vier jaar ontwikkeld, met de oorspronkelijke Australische mixer-melter als uitgangspunt. Nu is het moment om de stap te maken naar een demofabriek.
Die wordt gebouwd in het Chemport Innovation Center van Groningen Seaports in Delfzijl.
Finetunen
Het hart van de fabriek in Delfzijl is een grote mixermelter van het Australische bedrijf Plastech. De capaciteit bedraagt 800 tot 900 kilo per uur, hetgeen zal uitkomen op een jaarlijks productie van 4.000 ton. “Hiermee zullen we het proces verder gaan finetunen”, aldus Folmer. De kern van de fabriek zal naast de mixer-melter bestaan uit een extrusielijn met een dubbele carrousel met twaalf posities voor matrijzen elk.
De variatie in afvalstromen is enorm, zegt Folmer. “We hebben van alles geprobeerd, waaronder visnetten. Die bestaan uit verschillende soorten plastic, waarvan de netten en de drijvers gemaakt zijn. Ook zit er altijd wat zand in afgedankte visnetten. Dat kunnen we prima verwerken.” Dat geldt ook voor bijvoorbeeld ziekenhuisafval, dat UPPACT mag verwerken als het niet in aanraking is geweest met mensen, organische materialen of ziekteverwekkers. “Ik keek ervan op hoeveel verpakkingsafval ziekenhuizen genereren”, merkt Folmer verbaasd op. De belangrijkste stroom, in volume gemeten, is het gemengde plastic afval van verpakkingsmateriaal van de huishoudens. Al met al is er in beginsel een grote aanvoer van
reststromen beschikbaar, die bestaat uit vooral HDPE, LDPE en PE.
Wat maak je daar vervolgens van? De variatie in mogelijke eindproducten blijkt groot te zijn. Denk aan eenvoudige objecten als planken, palen en afvoergoten. Maar ook tuinmeubilair hoort tot de mogelijkheden. “Er zijn zeker meer producten mogelijk”, zegt Folmer. “Wat we uiteindelijk allemaal zullen produceren, is een vraag die we in overleg met afnemers moeten gaan beantwoorden.”
Milieubelasting
De kwaliteit van de tot nu toe gemaakte producten is goed. Zo laten de elementen voor de grond- weg- en waterbouw zich goed frezen, zagen en boren. Positief is ook dat de milieubelasting van het proces laag is. “Onafhankelijk onderzoek laat zien dat we ten opzichte van virgin materiaal veel minder CO2-uitstoot hebben. Op elke ton gebruikt plastic besparen we zo 3 ton aan CO2. Dat komt grotendeels doordat we het materiaal maar één keer hoeven te verhitten voor zowel met mengen als het extruderen.”
Tussenstap
De fabriek in Delfzijl is een tussenstap op weg naar grootschalige commerciële productie. “De volgende stap wordt dan een fabriek van 15.000 ton per jaar. Groter heeft geen zin, omdat er geen behoefte is aan
meer productie binnen een gebied dat je qua afstand goed kunt bedienen.”
Een en ander betekent dat er in Noordwest-Europa ruimte is voor veel meer installaties. Het hoeft dan ook geen verrassing te zijn, dat UPPACT de vertegenwoordiger is van de Australische producent voor deze regio. En om tot slot nog even terug te keren naar dat land: De recyclingmarkt in Australië is intussen zodanig verbeterd, dat daar inmiddels een commerciële mixer-melter staat.
www.uppact.com
Een impressie van de nieuw te bouwen installatie in Delfzijl.
masterbatches & special compounds
knowledge and full focus on your process we develope masterbatches and special compounds that optimize and colorize your products.
Het maken van een spuitgietmatrijs is een ingewikkeld proces dat een hoge investering vereist en waarbij elke stap van groot belang is voor het eindresultaat. Het maakt niet uit of je spuitgietmatrijzen ontwikkelt, produceert, gebruikt of onderhoudt; actuele kennis van matrijstechnologie en de juiste toepassing van kunststoffen is altijd essentieel. Onze cursussen zijn gericht op het ontwikkelen van jouw kennis en talenten die leiden tot een maakbaar product.
ONZE MATRIJZENCURSUSSEN:
• Matrijzen voor kunststoffen A | Start 1 oktober in Veldhoven en 3 oktober in Utrecht
• Matrijzen voor kunststoffen B | Start 30 september in Veldhoven en 3 oktober in Utrecht
ONZE SPUITGIETCURSUSSEN:
• Kunststof-, matrijs- en spuitgiettechnologie | Start 28 oktober in Veldhoven
• Spuitgieten 1 (sprintklas) | Start 10 oktober in Veldhoven
• Spuitgieten 1 (sprintklas) | ENGELSTALIG | Start 4 oktober in Veldhoven
• Spuitgieten 2 (sprintklas) | Start 4 november in Veldhoven
MEER INFORMATIE OVER DEZE CURSUSSEN? NEEM DAN CONTACT OP MET:
Barend Blom
Programmamanager Opleidingen
M +31 (0)6 22 98 79 84
E b.blom@mikrocentrum.nl
BEKIJK AL ONZE 120 CURSUSSEN:
Bezoek www.mikrocentrum.nl voor meer informatie en direct inschrijven
En u ontvangt 1x per week dé nieuwsbrief specifiek gericht op uw vakgebied.
• Samenvoeging van meerdere temperatuurregelingssystemen in één werkgang
• Eenvoudige bediening
U blijft op de hoogte van:
• Nieuws uit de branche
• Productinnovaties
• Marktontwikkelingen
• Leveranciers
Ga naar: www.kunststofenrubber.nl/ nieuwsbrief
• Vermindering van insteltijden
• Snelle, veilige en foutloze vergrendeling
• Verkrijgbaar in alle gangbare profielsoorten op de markt
• Beschikbaar in 6/12/20-voudige uitvoering Multi-Coupling System
Q Plus is uw Lüdecke importeur. Ga naar qplus.nl voor multikoppelingen en meer!
De Nederlandse kunststofverwerkende industrie kan haar productiviteit alleen vergroten door het succesvol implementeren van innovatieve oplossingen en verregaande digitalisering. Data-analyse en zelfsturende machines zijn cruciale middelen om de concurrentiepositie te versterken en te voldoen aan strengere regelgeving, stelt Barend Blom, programmamanager opleidingen bij Mikrocentrum.
BAREND BLOM
Het overgrote deel van de kunststofverwerkende bedrijven in Nederland zijn kleine en micro mkb-bedrijven. Zonder ondersteuning van buitenaf wordt het voor hen moeilijk om die stap te maken Vrijwel ieder bedrijf in de kunststof spuitgietproductie beschikt over een softwaresysteem om de belangrijkste bedrijfsprocessen te automatiseren en te beheren voor optimale prestaties,
zoals Enterprice Resource Planning (ERP). Dit is niets nieuws. Er is echter meer nodig.
Het spuitgietproces beheersen is in feite via de parameters de controle houden op steeds veranderende omstandigheden. Omgevingscondities en de samenstelling van het materiaal kunnen veranderen, waardoor het proces aangepast moet worden om te voldoen aan de productspecificaties. In de praktijk zien we vaak dat operators instellingen handmatig aanpassen, wat betekent dat menselijk ingrijpen in het productieproces nog steeds noodzakelijk is. Het gebruik van digitale oplossingen kan leiden tot het zelfstandig (bij)sturen van het spuitgietproces. Vergelijkbaar met het instellen van cruise-controle van een auto.
Per cyclus genereren spuitgietmachines enorm veel data. Niet alle data is echter relevant voor het in stand houden van een optimaal proces. Door data te analyseren met behulp van software wordt het mogelijk om de grenzen van het productieproces vast te stellen. Binnen deze grenzen kan de besturing automatisch waarden aanpassen. De huidige stand van techniek
met artificial intelligence (AI) is perfect geschikt voor dit doel.
Energiemanagement
Randapparatuur is vaak verantwoordelijk voor een relatief hoog energieverbruik. Het vermijden van het toepassen van aanspuitingen leidt tot lager energieverbruik, minder benodigde ruimte en vermindering van logistieke bewegingen.
Het Digital Product Passport biedt toegevoegde waarde voor consumenten, bedrijven en beleidsmakers door antwoord te geven op vragen zoals: waar het product vandaan komt, hoe het gemaakt is, hoe het hergebruikt kan worden en welke duurzaamheidslabels het heeft. De KU Leuven – Polymer Processing & Engineering Group heeft een opstelling van een productiecel waarbij ieder product voorzien wordt van
Randapparatuur is vaak verantwoordelijk voor een relatief hoog energieverbruik
een QR-code, bijvoorbeeld voor een medisch onderdeel met een unieke identificatiecode (UDI). Met behulp van “in-proces” sensoren die alle data vastleggen als een soort productievingerafdruk.
Lang Ontwikkelen (LLO). Het borgen van kennis en sociale vaardigheden zijn succesfactoren.
Inwerken, training en begeleiding
Er zal een grotere behoefte ontstaan aan technische specialisten die binnen projectteams werken en begrijpen dat “een idee net zo waardevol is als de uitvoering ervan”. Om nieuwe medewerkers te werven, in te werken en te behouden, zijn een inwerkprogramma, korte trainingen en begeleiding essentieel. Gebruik van Learning Management System (LMS), Academy, E-learning, Virtual Reality en Werkplekleren zal verder toenemen. Praktische training aan de machine blijft belangrijk. Niet nabootsen, maar werkelijk doen en ondervinden met een coach (docent) om je te helpen.
‘Kunststof spuitgieten is het specialisme van het omgaan met parameters, dit is te automatiseren.’
Het spuitgietproces beheersen is in feite via de parameters de controle houden op steeds veranderende omstandigheden.
BEELD: BRAM SAEYS
Logistieke processen rondom productiemachines zijn goed te automatiseren, vooral als in ploegen wordt gewerkt. Een AMR is intelligentere variant van een Automated Guided Vehicle (AGV). Deze volgt geen vaste routes, heeft slimme software aan boord en vergelijkt de omgeving om op de plaats van bestemming te komen. Alle data die bij dit soort processen hoort, moet beveiligd worden. Dat is geen kwestie van eenmalig iets instellen maar van continu up-to-date houden.
Persoonscertificering
mikrocentrum.nl
De operatorfunctie zal steeds meer worden overgenomen door geautomatiseerde systemen ondersteund met software, sensoren en AI. Dat betekend echter niet dat er minder kennis gevraagd wordt. Integendeel! Samenwerking tussen specialisten om tot mooie zinvolle en duurzame technische oplossingen te komen, vereist een Leven
Barend Blom is sinds 2012 werkzaam bij Mikrocentrum Opleidingen. Door bedrijfsbezoeken, bezoeken van evenementen en gesprekken met cursisten en docenten heeft hij een goed beeld van wat zich afspeelt in de markt. Naast specifieke opleidingen voor de kunststofverwerkende industrie helpt Mikrocentrum met andere trainingen zoals cyber security voor de industrie, artificial intelligence voor managers, artificial intelligence voor engineers, data science starten in productieomgevingen, enzovoort.
Hasco, de uitvinder van de standaard matrijsunit, viert dit jaar zijn 100-jarig bedrijfsjubileum. De geschiedenis begon in 1924. Beslissend keerpunt was de uitvinding van de modulaire matrijs door zoon Rolf Hasenclever in 1960: een mijlpaal die de weg vrijmaakte voor de ontwikkeling van een kleine ambachtelijke onderneming tot een wereldwijd opererend bedrijf.
MAARTJE HENKET
De geschiedenis begon in 1924 toen bedrijfsoprichter Hugo Hasenclever in een kelderwerkplaats in Lüdenscheid de eerste mallen bouwde voor de verwerking van het toen nieuwe materiaal bakeliet. Het was een geschiedenis die later via zijn zoon Rolf Hasenclever een beslissend keerpunt onderging, toen deze het modulaire systeem voor standaardvormeenheden uitvond en in 1960 liet patenteren.
Meer vernieuwingen zouden volgen: Hasco claimt er nu 100 op zijn naam te hebben staan – en belooft dat er nog minstens 100 zullen volgen. “Bijna niemand weet nog dat gangbare producten zoals de afsluitkoppeling of de vergrendeling gepatenteerde creaties zijn uit het Duitse Lüdenscheid. Met 100 ideeën in het verleden en 100 ideeën voor de toekomst gaan we verder op de ingeslagen weg! Ons doel is om als pionier op het gebied van de matrijzenbouw ook de komende 100 jaar innovatieve mijlpalen voor de industrie te zetten”, zegt CEO Christoph Ehrlich.
Het begin
De meeste mensen kunnen zich het begin van de matrijzenbouw niet meer herinneren, toen elke fabrikant zijn eigen exemplaar op de werkbank creëerde en het beroep nog sterk gekenmerkt werd door vakmanschap. Rolf Hasenclever zou de manier van denken, ontwerpen en werken van de hele industrie veranderen. In 1957, na de vroege dood van zijn vader, nam hij het bedrijf over. Als een echte vernieuwer werd hij gedreven door de wens om een antwoord te vinden op de vraag hoe de constructie van een matrijs eenvoudiger en eenvoudiger kon worden gemaakt. De oplossing was het creëren van standaarden. En voor deze normen heeft hij de basis gelegd in de vorm van een systeem dat functioneert als een bouwdoos: de Hascovormeenheid. In 1960 patenteerde hij het modulaire systeem voor standaardvormeenheden.
Zijn idee was destijds baanbrekend en vormt vandaag nog de basis voor alle vormeenheden. “In elke matrijs die vandaag de dag wordt gebouwd, zit gegarandeerd
een stukje Hasco”, aldus Ehrlich. Hasenclever definieerde het gestandaardiseerde dimensiespectrum met metingen die waren gericht op de afstanden tussen de trekstangen van de spuitgietmachines. Het systeem raakte snel ingeburgerd, eerst regionaal in Sauerland, vervolgens in heel Duitsland en kort daarna internationaal. Het is dankzij de bedrijfsvisie van Rolf Hasenclever dat dit systeem tot op de dag van vandaag nog steeds overleeft. Ondanks veel weerstand en ook een aantal sceptici in de branche werd het assortiment standaardcomponenten en accessoires van Hasco in de jaren zestig verder uitgebreid. Tegelijkertijd zette hij zich in voor het stroomlijnen van de productie en de ontwikkeling van de bedrijfsstructuur. In 1965 opende hij in Lüdenscheid/Duitsland de eerste productiefabriek ter wereld voor standaardplaten. Vanaf dat moment konden standaardplaten besteld worden en snel uit voorraad geleverd worden. De vier boorgaten werden gelijktijdig in de op elkaar gestapelde platen geboord, terwijl het laatste spindelen individueel werd uitgevoerd op boormachines die voor onderwijsdoeleinden werden gebruikt. In 1966 werd een automatische precisieboormachine met 4 assen in gebruik genomen, die speciaal volgens de ontwerpen van Hasco was vervaardigd. In combinatie met een NC-ponsbandmachine zette Hasco de norm in de serieproductie van precisieproducten. De vraag was zo groot dat al snel moest worden overgeschakeld op een drieploegendienst.
Rolf Hasenclever vernieuwde de technologie, maar ook de marketing. Hij bedacht de modulaire matrijs en ook het ‘postordersysteem’ wat klanten wereldwijd eenvoudig toegang bood tot de producten.
1967 – catalogus
Na de uitvinding van het modulaire systeem werd in 1967 's werelds eerste standaard catalogus met vormeenheden gedrukt. Uiteraard weer uit de koker van Rolf Hasenclever, die zich liet inspireren door de catalogi van gerenommeerde postorderbedrijven. Wat bij huishoudelijke producten vanuit de huiskamer functioneerde, zou ook bij matrijzenbouwproducten moeten werken, zo meende hij. Hij wilde de keuze van de producten, het bestellen en de snelle levering zo gemakkelijk mogelijk maken voor zijn klanten. Later werd het mogelijk om producten per post of telefonisch te bestellen; in de jaren tachtig ook per teletekst en fax. Wat in gedrukte vorm beschikbaar is op ruim 2.000 pagina's, in inmiddels vijf boeken, is nu ook in digitale versie beschikbaar. Via het Hascoportaal www.hasco.com kunnen wereldwijd 100.000 standaardcomponenten worden besteld.
Groei
Dit duikelaartje zette Rolf Hasenclever aan het denken: wat niet mogelijk lijkt, kan het toch wel zijn. Zo speelde het een sleutelrol in de ontwikkeling van het bedrijf.
Met het catalogusbestelsysteem ontstonden nieuwe interne uitdagingen. Hasco ontwikkelde zich snel tot een wereldspeler; er werden locaties geopend in Europa en daarbuiten en steeds meer klanten wilden steeds meer producten in de kortst mogelijke levertijden. Er werden nieuwe productieconcepten ontwikkeld en geïmplementeerd die op moesten voldoen aan de kwaliteits- en precisie-eisen voor
LINKS Hasco vond de snelkoppeling uit.
RECHTS Recente innovatie: Shadowfreetechnologie.
serieproductie en de holistische ondersteuning van de klanten met technische service voor een voortdurend groeiend aantal producten.
Begrip van de praktische kant van de matrijzenbouw en de eisen van matrijzenmakers in hun dagelijkse werk heeft geleid tot vele innovaties. In de jaren zeventig lanceerde Hasco een reeks producten, die nog steeds op de markt zijn. Het begon met de uitvinding van de afsluitkoppeling onder artikelaanduiding Z80. Daarna volgden onder meer innovatieve vergrendelingseenheden (1977), nieuwe soorten naaldafsluitmechanismen (1983) en vele kleinere hulpmiddelen zoals afsluitpluggen (1984), datumstempels voor productmarkering (1985) en de additief vervaardigde hotrunner Hasco Streamrunner.
Het komt niet zelden voor dat de klanten van het bedrijf mede inspiratie voor nieuwe technologieën leveren. Zo werd in 2011 samen met een bedrijf uit het verpakkingssegment een tweetraps ejector met
Hasco implementeerde de mogelijkheden die digitalisering het bedrijf bood vanaf begin jaren tachtig in het ontwerp en de productie van matrijssystemen. Een ‘blauwdrukboek’ hielp op de CADtekentafel - naast de papieren handleiding met ontwerpvoorbeelden. De eerste stappen op de digitale weg werden binnen het bedrijf gezet op de afdeling matrijstechniek en machinebouw, toen datakoppeling met machines, productiedata-acquisitie en producttraceerbaarheid werden geïntroduceerd. In 1982 volgde de aanschaf van het eerste CAD-systeem van Unigraphics en de
een destijds innovatieve DLC-coating (Diamond Like Carbon) tot marktrijpheid ontwikkeld. Deze coating is sindsdien een Hasco-standaard.
Een recente innovatie is de Shadowfree-technologie. Bij conventioneel spuitgieten ontstaan er vaak ongewenste, slecht stromende plekken in de hotrunner als gevolg van ruwheid rond de kleppen. Dit resulteert in afbraakreacties in de kunststofsmelt en uitzonderlijk lange kleurovergangen. Het Shadowfree spruitstuk van Hasco Hot Runner bestrijdt dit probleem.
Het 3D-geprinte, vastgeschroefde systeem splitst de materiaalstroom in gestroomlijnde kanalen om gelijkmatig rond de naald te spoelen en herenigt ze op het punt waar de valve pin het smeltkanaal binnengaat. Volgens tests maakt het systeem een overgang van zwart naar wit materiaal mogelijk in 25 cycli en presteert het drie tot vier keer beter dan conventionele klepafsluitersystemen.
Naast het elimineren van dode hoeken en een bijzonder zachte materiaalstroom – met als gevolg een merkbare vermindering van drukverliezen - biedt de Shadowfree-technologie nu ook een oplossing voor extreem gevoelige materialen in termen van hittestabiliteit in combinatie met kleppoortsystemen. Met tot 70% snellere kleurveranderingen zorgt het systeem ervoor dat materiaalverliezen worden verminderd en de productkwaliteit wordt verhoogd. Welke 100 innovaties het bedrijf nog in petto heeft? Dat wordt wijselijk niet met ons gedeeld. Hasco gebruikt dit hele jaar om stukje bij beetje en beurs na beurs vernieuwingen voor het voetlicht te brengen. Wij wensen hun veel inspiratie!
www.hasco.com
introductie van de Hasco standaard matrijsmodule, waarmee ontwerpers en matrijzenbouwers complete matrijssystemen met de betreffende accessoires rechtstreeks vanuit het meegeleverde systeem konden configureren. Het basisconcept van de standaard matrijsmodule werd vanaf dat moment voortdurend uitgebreid en geoptimaliseerd. In 1997 verscheen de eerste versie in 3D – compleet met de driedimensionale gegevens die vandaag de dag nog steeds de basis vormen voor het ontwerp van vormgereedschappen. Een jaar later werd het digitale systeem uitge-
breid met een online bestelservice. Via de homepage, destijds bekroond als modernste website, was het mogelijk om alle plaat- en accessoirecomponenten op de eigen computer te bestellen. Tegelijkertijd vereenvoudigde dit de prijsberekening van een matrijssysteem.
GRONDSTOFFEN
Biesterfeld
Rolweg 27
4104 AV Culemborg +31 (0)345-687878 plastic-benelux@biesterfeld.com www.biesterfeld-plastic.com
Distributeur van kunststof granulaten. Leverancier van: BASF (PS, TPU), Chi Mei (o.a. ABS, M-ABS, SAN, PC), Celanese (o.a. PA, PBT, TPC-ET, TPE-V), DuPont (o.a. POM, PI), ExxonMobil (o.a. Vistamaxx, Vistalon, Exxelor), Idemitsu (o.a. PC, SPS), INEOS (o.a. PE, PP, HDPE, L(L)DPE, R-TPO), LG Chem (o.a. M-ABS, ASA, PC Compounds, PMMA, POE, NBR, SBR), SK Chemicals (o.a. PETG), Solvay (o.a. PFA, MFA, PPSU, PPS, PSU,PES, PEEK), Cabot (o.a. Roet), KumYang (o.a. Blaasmiddelen Cellcom), Master Additives (o.a. Rubber), EVA.
Distrupol BV
Schouwburgplein 30-34
3012 CL Rotterdam
P.O. BOX 21407
3001 AK Rotterdam
The Netherlands
+31 (0)10 - 2757880 info-benelux@distrupol.com www.distrupol.com
Leverancier van: CHIMEI (ASA, PC, PC/ABS, SAN, SBC), Kureha (PVDF), LG Chem (ABS, PA6, PC, POM, PBT, copolyester), Lucite International (PMMA), MOL group (PP), Neutrex (Purgex reinigings- middel), SIBUR (PP), Poliblend (PA, POM-H, PBT), Teknor Apex (TPE, TPV), Toray (ABS, trans- parante ABS, POM, PPS), Versalis (PE, EVA), Wells Plastics (additieven), Distrupol Colour (kleurcompounds, masterbatch).
Resinex Netherlands BV
Leeuwenbrug 105 B
7411 TH Deventer, Nederland +31 (0)570-677584 info.benelux@resinex.com www.resinex.com
Resinex Benelux NV
Moerenstraat 85a B2370 Arendonk, België +32 14 67 24 96 info@resinex.be www.resinex.com
Ultrapolymers BV
Galvanistraat 14-2
Postbus 138 6710 BC Ede 0318 - 641216 info@ultrapolymers.nl
Ultrapolymers Group NV
Gerard Mercatorstraat 90 3920 Lommel, België +32 11 57 95 57 info@ultrapolymers.be www.ultrapolymers.com
Fournier Polymers
Hoevestein 36 4903 SC Oosterhout
+31 (0) 162 - 491650
+32 (0) 251 - 33313 info.bnl@fournierpolymers.com www.fournierpolymers.com
Officieel distributeur voor o.a. ExxonMobil Chemical, Borealis, Eni Versalis, Radici Plastics, Polimarky, Polychim, Ducor en Wiwax.
Resinex Netherlands BV
W & R Plastics BV
Jean Monnetpark 73 7336 BB Apeldoorn 055 - 5335224 info@wenrplastics.nl www.wenrplastics.nl
Masterbatches & Additieven: Viba, Cabot, Unnox Iberia, Ultrabatch, Cabamix.
Colorex Master Batches BV Achterdijk 12 5705 CB Helmond +31(0)492-524252 post@colorex.nl www.colorex.nl
Unique Qolors BV Masterbatches
Oerstroom 50 5421 WV Gemert 085-076 13 63 info@uniqueqolors.nl www.uniqueqolors.nl
KUNSTSTOFRECYCLING
ARBURG BV
Krommewetering 81 3543 AM Utrecht +31 (0)30 24 26 06 0 netherlands@arburg.com www.arburg.nl
ARBURG NV
Herrestraat 8
3294 Molenstede, België +32 16 44 12 90 belgium@arburg.com www.arburg.be
Elektrische, hybride en hydraulische spuitgietmachines met sluitkrachten van 125 tot 6.500 kN. Robotsystemen, geïntegreerd in de SELOGICA direct machinebesturing.
OPLEIDINGEN & EVENEMENTEN
Mikrocentrum
De Run 1115, 5503 LB Veldhoven +31 (0)40 – 296 99 11 info@mikrocentrum.nl www.mikrocentrum.nl
Mikrocentrum is het verbindende platform voor de hightech- en maakindustrie. We hebben een fascinatie met technologie. En als onafhankelijke stichting kunnen wij als geen ander de juiste verbinding leggen om die fascinatie door te vertalen naar alle lagen van de waardenketen. Samen met onze leden, klanten en partners zetten we ons in voor een sterk innovatief ecosysteem, voor talentontwikkeling en voor de grote maatschappelijke uitdagingen. Dit doen we door op te leiden, ontmoetingen te stimuleren en door te verbinden met onze cursussen, evenementen en ons ledenplatform. Want met kennis, talent, skills en connecties als brandstof, maken we de wereld van morgen, vandaag al een beetje beter.
Get connectedmet oplossingen van ENGEL
Zelfs vlokken kunnen direct worden verwerkt op onze spuitgietmachines.
Bianca Gubi, Recyclingdeskundige bij ENGEL, Oostenrijk
…voor iedereen die recyclaten verwerkt!
Eisen en specificaties veranderen. Veel producten moeten nu al een vast aandeel aan gerecycled materiaal bevatten. Met het ENGEL-recyclingpakket voor conventionele spuitgietmachines, of door het filteren en ontgassen van de smelt in het ENGEL tweestapsproces proces kan uw restmateriaal direct worden verwerkt. Dat betekent: tot 100% gerecycled materiaal waardoor hoge materiaal kosten, energie- en CO 2 -besparingen verwezenlijkt kunnen worden! Get connected – en neem contact op met onze experts. engelglobal.com/circular-economy