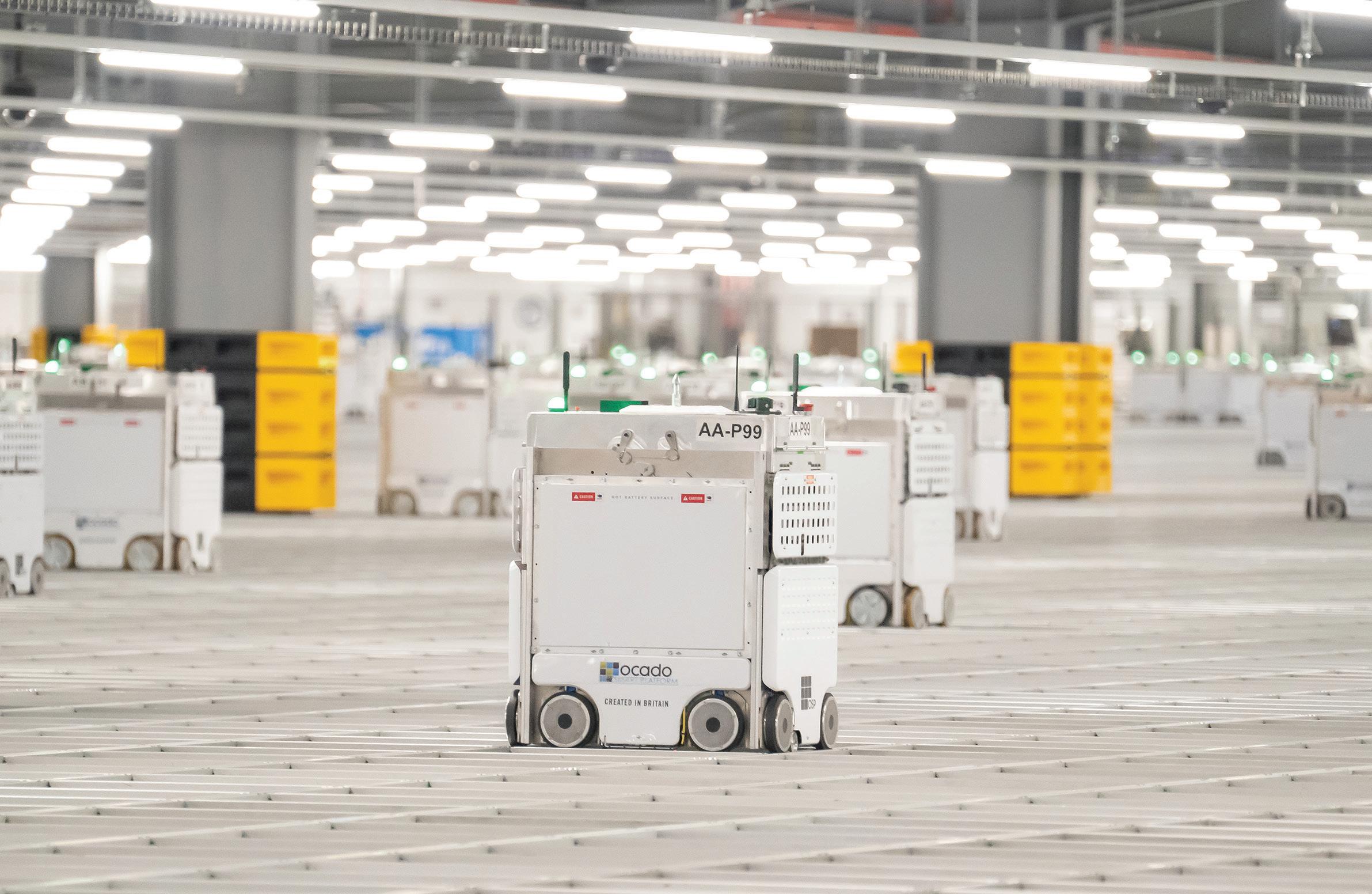
4 minute read
HOW OCADO TECHNOLOGY AUTOMATED COVID TEST SCHEDULING
ANNA MOSS
OCADO GROUP IS A UK BASED TECHNOLOGY COMPANY that provides end-to-end online grocery fulfilment solutions to some of the world’s largest grocery retailers and holds 50% of Ocado Retail Ltd in the UK in a Joint Venture with Marks & Spencer. Ocado has spent two decades innovating for grocery online, investing in a wide technology estate that includes robotics, AI and machine learning, simulation, and forecasting.
Ocado Retail Ltd is the world’s biggest online-only grocery retail business. It offers a range of over 50,000 products and serves over 639,000 active customers across the UK, shipping 325,000 orders per week.
Its fulfilment is based on Customer Fulfilment Centres (CFCs), highly automated warehouses powered by cutting edge technology.
Ocado Group employs over 15,000 people, many of whom perform frontline roles such as picking and packing in CFCs, delivering orders to customer homes, providing customer service in the contact centre etc.
TEST SCHEDULING CHALLENGES AND AUTOMATED SOLUTION At the beginning of the COVID-19 lockdown, Ocado Group took a decision to test all frontline employees on a weekly basis in order to protect the health of the staff. This task presented the business planning team with a large-scale logistical problem of scheduling frontline employees at each site to available test slots determined by room and testers’ availability subject to operational constraints.
These constraints included, for example, the requirements that each employee should be scheduled for a test within their working shift, a spacing between tests performed on the same employee should be within given bounds, only a limited share of employees from the same work area could be scheduled for a test on the same day etc.
The problem proved too difficult to be solved manually, and the Ocado Technology’s Data Science team was approached for help, with extremely tight time limitations. The team leveraged their prior experience with constraint optimisation problems, e.g. staff rostering. The COVID-19 test scheduling problem was solved using Constraint Programming technology, by creating an efficient constraint model of the problem and feeding it to a Constraint Solver. The task also involved a significant implementational effort. Good design practices allowed partial reuse of the existing code base and enabled execution of all stages of the project from requirement collection through research, implementation, refinement to deployment in less than two weeks.
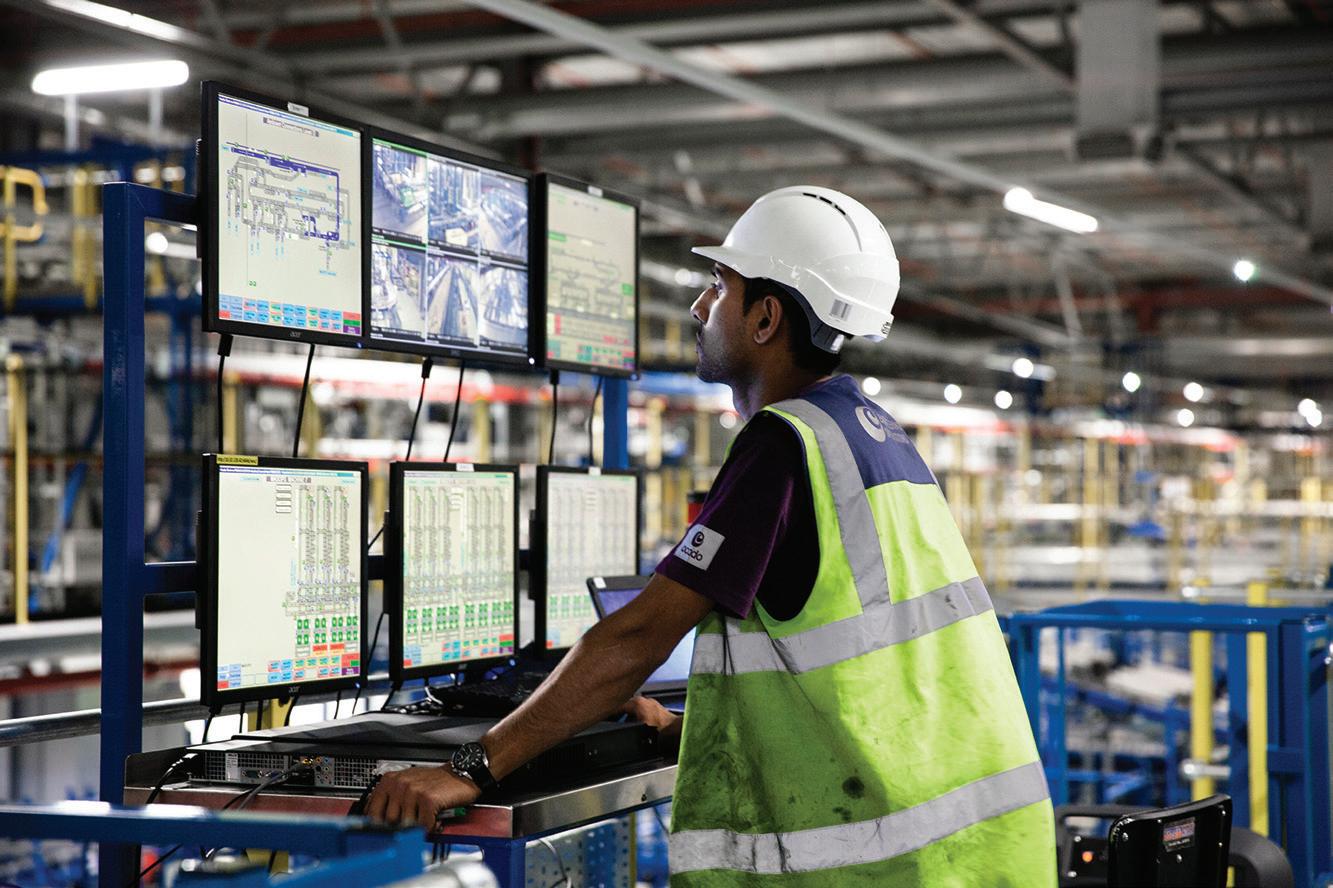
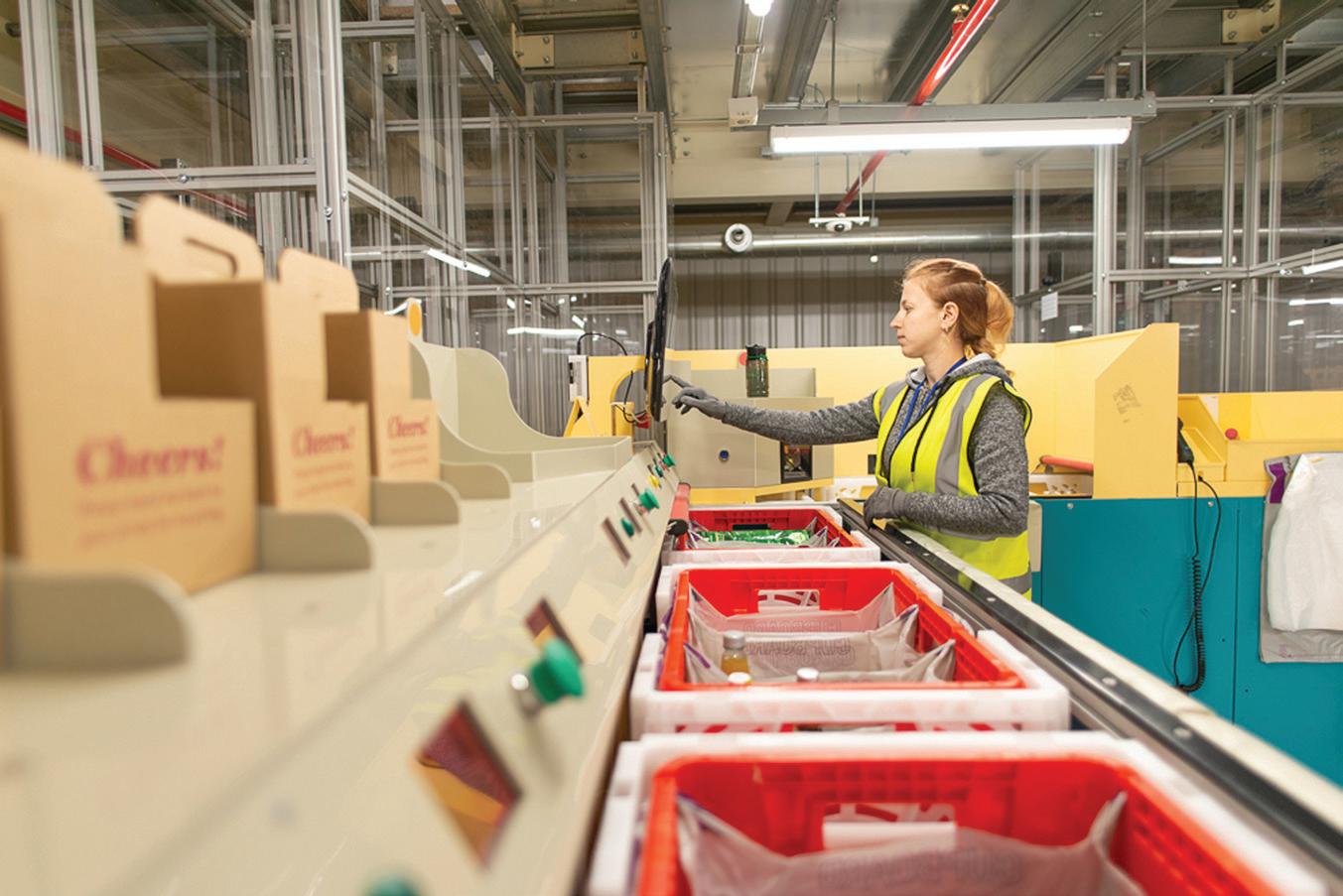
© Ocado Group
AUTOMATED TEST SCHEDULING ROLL OUT AND IMPACT
As a result, the business planning team was able to automatically create test schedules for different Ocado sites which complied with the specified constraints. The tool has been used to automate a substantial share of the test scheduling tasks in different business areas producing schedules for up to 3500 employees across 4 sites. The automated test scheduling tool thus became a significant part and an enabler of the COVID-19 testing process in Ocado.
James Norton, a planning analytics manager, observes: “Our analytical teams in Logistics have always had a close working relationship with Data Science, collaborating on automation projects to add significant value to our delivery and fulfilment operation. This meant we were already aware of the potential they had to support our challenge, and they had a working knowledge of how we operate. Being able to react quickly in an environment of mutual understanding resulted in a rapid proof of concept, created with flexibility to adapt to the inevitable changing circumstances.”
Lewis Momen, a business analyst, says: “The COVID-19 Scheduling Tool that Ocado Technology’s Data Science department built for us has been and continues to prove immensely useful. When we first approached the test scheduling problem, it quickly became apparent that, given the scheduling constraints, the vast number of employees to be tested and the time pressures we were under to rollout the programme, a long-term and resilient solution was required.
“We approached Ocado Technology’s Data Science team with the problem, and they were quickly able to build a tool that outputted an optimised solution. Since its development, the tool has been refined to meet changing programme requirements, and it is used several times a week to produce weekly testing schedules across several of Ocado’s sites. Ultimately the tool has facilitated an organised and efficient testing programme, helping to keep Ocado’s employees safe during these unprecedented times.” Anna Moss is a Principal Data Scientist at Ocado Technology. She obtained a PhD in Computer Science from Technion, specialising in Combinatorial Optimisation. During her fifteen years of industry experience, Anna has worked on several challenging projects applying optimisation techniques to realworld applications.
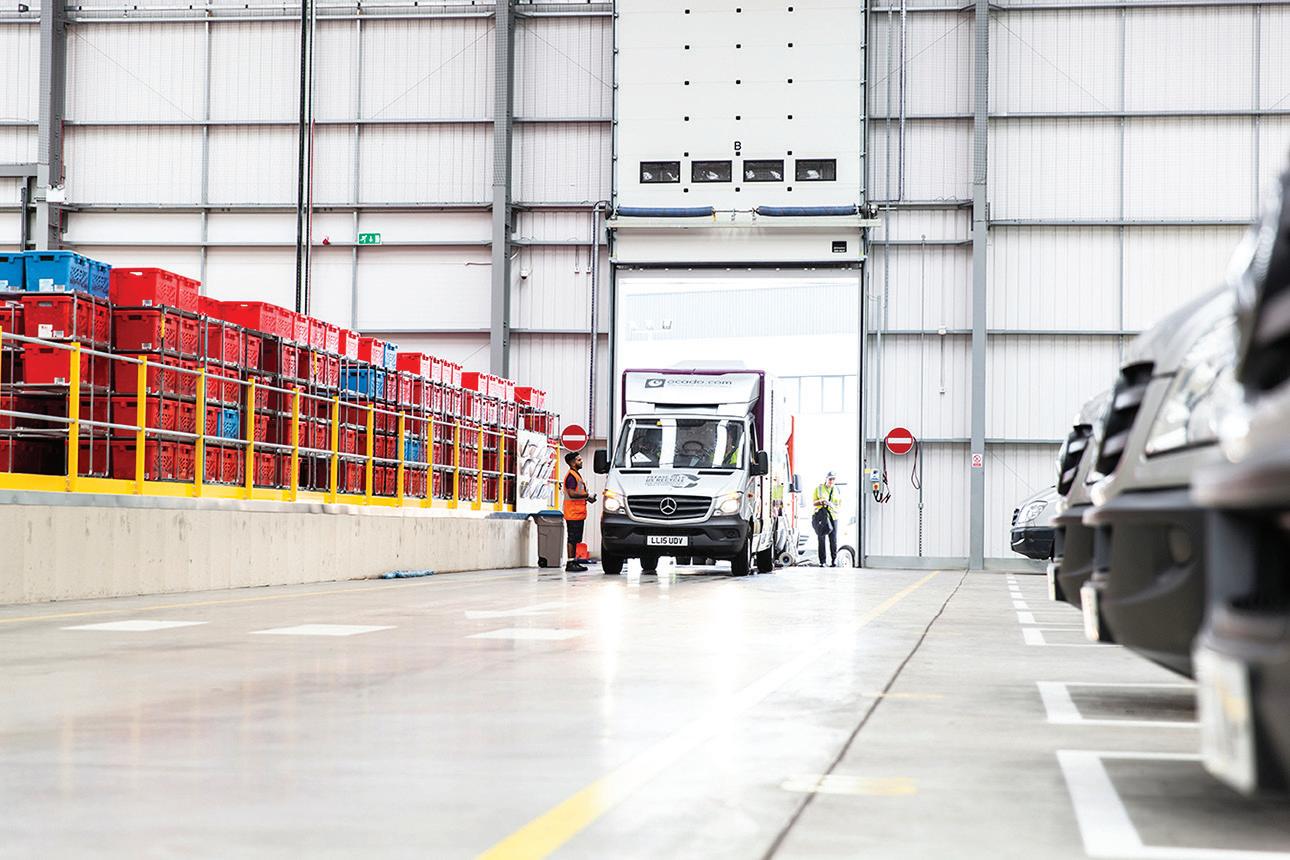
A shorter version of this article appeared in the December 2020 issue of IFORS News.