
9 minute read
Inspect To Avoid The Unexpected

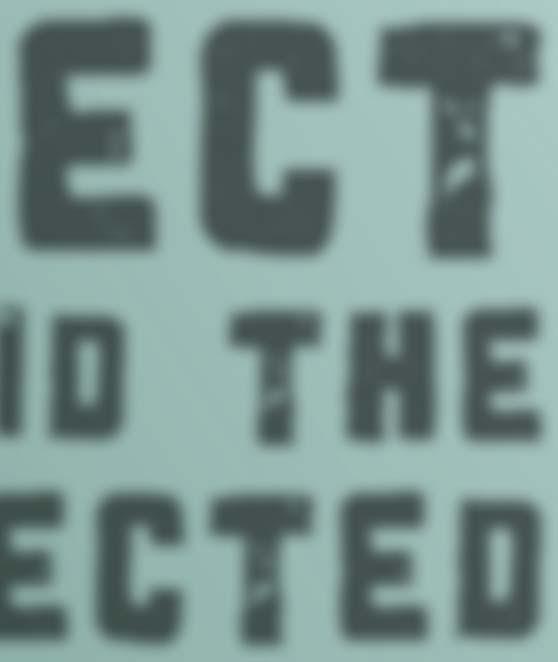

Dennis Blauser, Marietta Silos, USA, outlines how professional silo inspection and maintenance are fundamental for fi scally and socially responsible silo ownership.


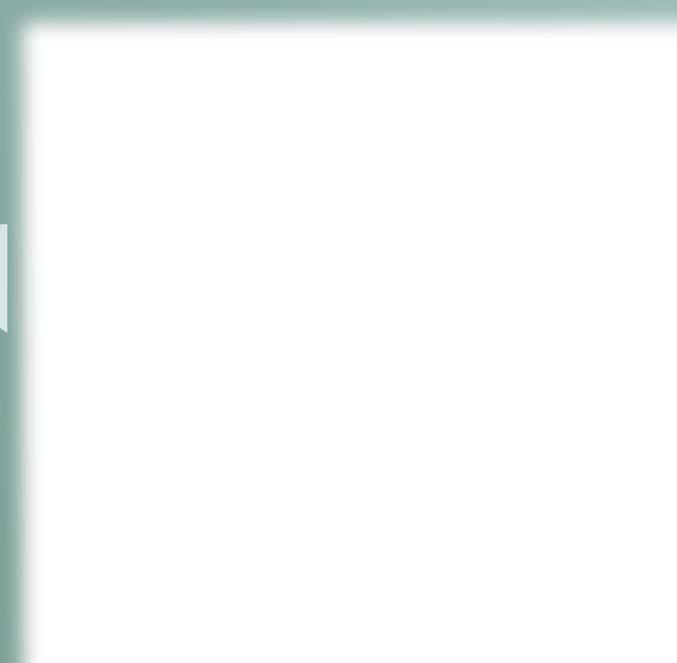
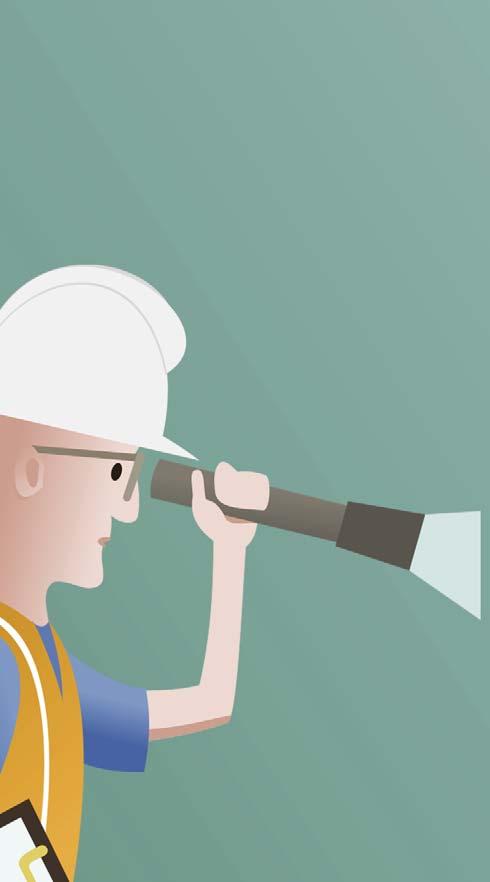
In the past, silo engineers and construction experts recommended inspections at least every two to fi ve years. Yet, without Occupational Safety and Health Administration (OSHA), Health and Safety Executive (HSE), or other safety standard requirements, plant and facility managers would often opt for in-house inspections or skip the process altogether. After a rise in silo failures over recent years, many insurance companies now require silo inspections. Regular silo inspections can help reduce the liability issues that arise after a structural failure.
All silos, regardless of age, stored material, or construction type, must be inspected by a professional specialising in silo construction annually or semi-annually. Though it is important to keep an eye on silos by inspecting key elements regularly, there are too many limitations to in-house inspections to warrant skipping a professional assessment. A professional inspection by a qualifi ed silo engineer or contractor is the only way to ensure a silo remains operational and safe.
A silo inspection includes a thorough examination of the structure to identify current and potential issues. After the inspection is complete, the customer receives a detailed report of fi ndings that outlines all discoveries in order of importance. This allows customers to identify essential repairs easily. Full-service companies provide this fi ndings report, recommended repairs list, and a proposal for the cost of repairs.
Maximising scheduled inspections
While the majority of silos should follow an annual or semiannual inspection programme, there are situations when a more frequent inspection schedule is necessary.
Concrete stave silos designed for industrial storage require frequent inspection. Heavier stored materials like aggregates increase the loads placed on internal components, including

walls and cones. This, coupled with pressure or vacuum loading and unloading, all increase the strain on a silo. With these loads constantly cycling in the silo, it may be diffi cult for the silo to withstand the stresses; silo failure becomes only a matter of time.
Even silos that were purpose-built for industrial storage can pose serious threats to safety as they age. Many older silos were constructed with outdated design methods, like steel suspended cones, which carry a high failure rate. When suspended cones collapse, they can cause complete silo failure. While it is true that material can sometimes be recovered and silos can occasionally be repaired after failure, companies often face additional costs from clean-up, possible environmental damage, and liabilities.
Even for newer silos, there are other factors that can result in a more frequent inspection schedule. As a result of extreme weather – including high winds, heavy rain or flooding, other natural disasters, or fi res – silos should be inspected before normal operations resume. Though concrete silos are typically able to withstand high winds, steel silos are highly susceptible to failure from wind damage (Figure 2).
A silo that shows signs of new or worsening damage should be inspected as soon as possible. Regularly viewing the silo exterior can help facilities fi nd new or worsening issues that might necessitate earlier or more frequent inspections.

Figure 1. The image shows a failing wall on a stave silo.
Figure 2. Damaged hoops on this stave silo led to a structural failure.
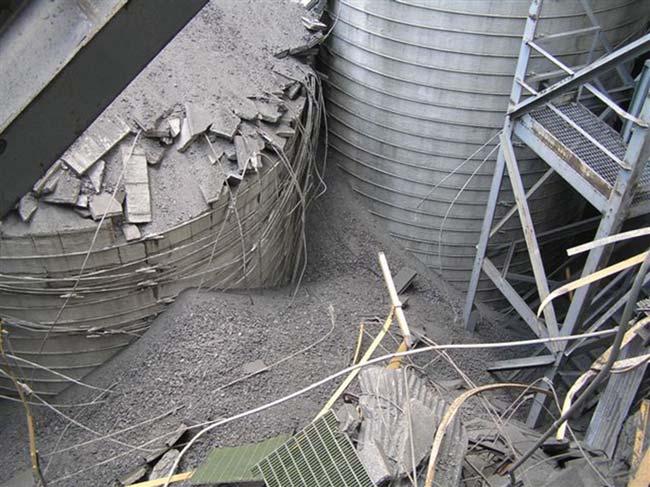
Exterior damage
Cracks — while cracks can seem like a small problem, they are a sure sign of stress. They can also allow moisture into the silo or allow moisture to attack steel reinforcement. When storing clinker, raw or kiln feed, and finished product, moisture prevention is vital.
For silos storing cement, fly ash, and lime, moisture intrusion can lead to hydration of the stored material.
Not only does this degrade product quality, it also causes material build-up, blockages, and material flow issues. Spalling — spalling of exterior walls can expose reinforcing steel and lead to corrosion of the reinforcement. Corrosion — galvanised hoops used on stave silos for structural integrity are susceptible to corrosion.
Without proper maintenance and regular inspections, the hoops deteriorate and jeopardise silo wall integrity and risk failure. Bowing walls — silo walls with visible bowing indicate a serious issue that can lead to wall collapse.
Repurposed agricultural silos commonly experience bowing walls due to the added stresses they face in an industrial application. Bowing walls can also be caused by asymmetric flow that places increased pressure along the wall. This bowing can quickly lead to wall failure and silo collapse.
Hidden issues
A professional silo engineer can check for issues that are not visible to the untrained eye. In addition to problems located out of sight high up on the silo exterior or rooftop, professionals are also trained to look for internal problems.
Silo roofs
Though silo roofs often house equipment used to operate the bulk storage system, they are easy to overlook when it comes to preventive maintenance. They must be constructed to withstand the equipment load, vibration from loading and unloading, environmental extremes, and light foot traffi c. While cracking and peeling of rooftop coatings can be easy to spot, membrane coatings may allow water into the silo even when they appear unscathed. Because membrane coatings do not bond directly to the silo surface, a small pinhole leak can allow moisture between the barrier and across the entire silo roof causing unseen damage, including corrosion of metal silo components and stored material hydration. Stored cement and lime are particularly susceptible to hydration. Beyond causing product degradation, hydration causes the stored product to expand, which increases pressure on silo walls. It also causes material build-up, leading to
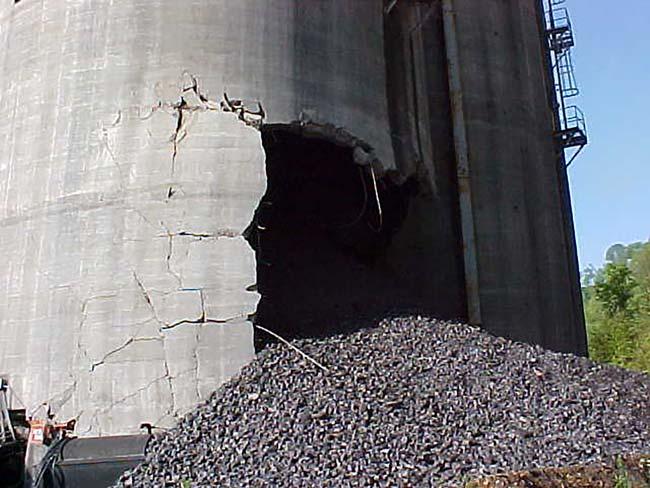
Figure 3. This image shows a silo with a wall failure that resulted from a failed suspended cone.
material flow issues that further increase silo wall pressure and the chance of structural failure. Silo roofs that show signs of ponding or pooling water can indicate possible structural problems that should be addressed immediately.
Roof beams and pockets
The roof slab is supported by internal roof beams that rest inside beam pockets. These components must be regularly inspected and properly maintained to prevent roof collapse. Spalling concrete around the beam pocket indicates a weakening of the concrete. If this continues, the pocket will no longer be able to support the roof beam, leading to collapse.
Cones
Professional silo inspections include an examination of the silo cone as it impacts the performance and safety of the silo. Inspectors look for signs of rust, weld quality, check cone thickness, and ensure the design complies with current best practices. Inspections of silos that have suspended cone designs will include this as a fi nding. When an experienced, full-service company conducts the inspection, the repair proposal will include the necessary remediation to bring the silo up to best practices and ensure safe operation.
Delamination of silo walls
Though concrete spalling can be a clear sign of silo damage, delamination of the concrete’s interior layers is not always visible. The delaminated, unbonded layers and loss of bond to reinforcement steel of the concrete walls reduce the structural integrity of the silo. Experienced silo engineers use a hammer to check for delamination through concrete sounding.
Material flow issues
Issues with the material flow can arise due to improper design for the stored materials or as a result of material build-up. A sure sign of material flow issues is decreased production. If this is not addressed early, it can increase pressure on silo walls and cause bowing and structural failure. It is important to understand the particulars of silo design to identify causes of material flow issues correctly. When material build-up is the suspected cause of material flow issues, it is essential to schedule a professional cleaning and inspection. Using inexperienced workers to attempt to address blockages or build-up is extremely dangerous and can lead to injury and death.
Crack migration
Without the proper experience and technology, it can be diffi cult to map the changes in cracks, spalling, and other signs of silo damage.
Conclusion
Regular, professional silo inspection and maintenance is a requirement of fi scally and socially responsible silo ownership. Unexpected silo failure has caused numerous operations to close their doors due to halted production and resulted in injury and loss of life. As more stories of silo failure, injuries, or fatalities are reported in the news, silo owners and the general public have become more aware of the possible dangers that ageing, unmaintained silos pose. Ageing silos, repurposed agricultural silos, and those designed with suspended cones need to be inspected more frequently to ensure structural integrity.
Regular, professional inspections by a fi rm specialising in silo construction or engineering are the most effective way to fi nd potential problems early. Fixing problems quickly, before they become an emergency, helps save money and can reduce or eliminate safety issues. The long-term savings, reduced liability, and reduction of unplanned downtime that results from professional silo inspections should be seen as an investment. It is far cheaper to address issues early on than to address a silo failure. Between regularly scheduled professional inspections, facilities should observe the silo exterior for any obvious signs of damage. This will help determine if the schedule needs to be revised to include more frequent inspections.
While silo inspections help uncover issues, regular repairs and preventive maintenance are the only way to remediate and prevent problems like structural failure. Facilities must follow through with recommended repairs to prevent failures due to inadequate maintenance. Important silo maintenance includes airflow unit inspection and regular, professional silo cleaning to avoid material build-up issues. Though silos that are regularly emptied and refi lled do not experience as many problems as silos that are kept topped off, it is still important to set a regular cleaning schedule. Sticking to a schedule also allows facilities to plan for silo cleaning during less busy times in the production schedule and avoid unplanned downtime. By scheduling a silo cleaning simultaneously with a silo inspection, facilities can save money and ensure they receive the most thorough examination of the silo interior.