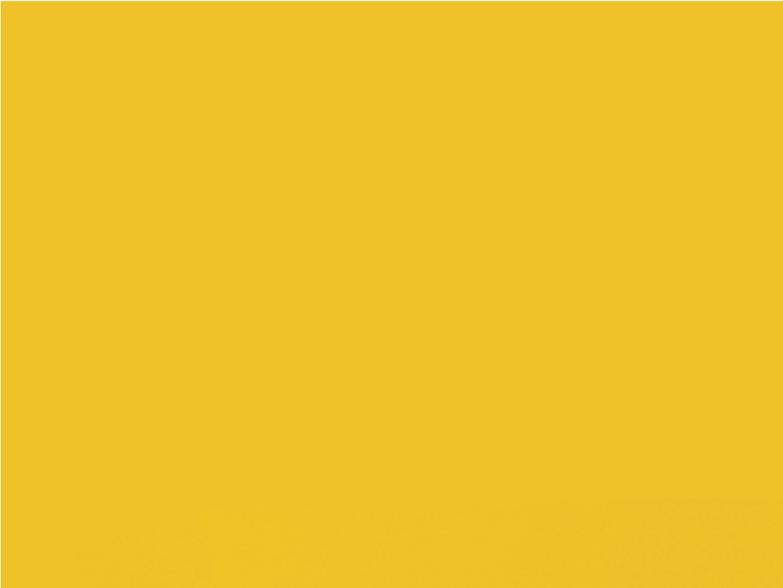
6 minute read
Check Out This Toolbox
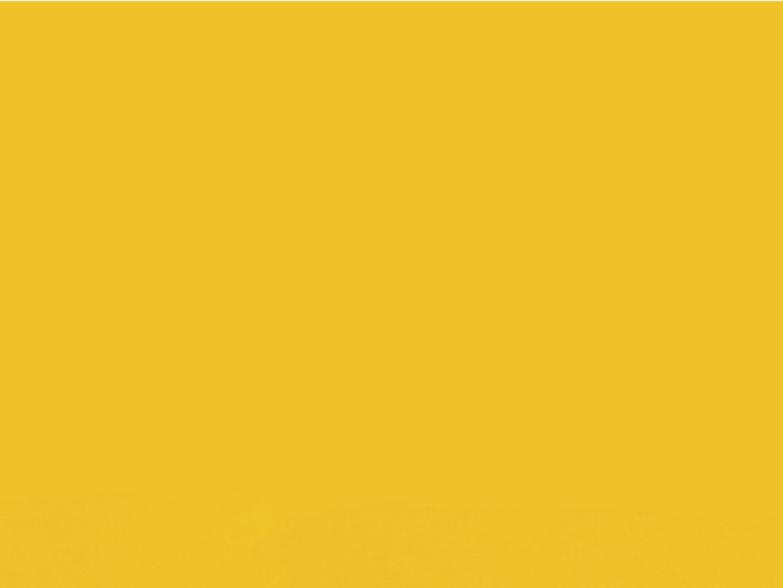
Greg Bierie, Benetech, USA, discusses how cutting-edge conveyor technologies can improve safety, maintenance, and compliance for dry bulk material transport.

Cargo includes a variety of dry bulk products or materials in need of transportation, storage, and transfer involving the use of belt conveyor systems. Although cargo could be anything from forest products to mining materials, the issues are similar. The systems and components are similar but vary in design and performance characteristics depending on the transported material. This article will discuss some of the problems and solutions that have benefitted from the Benetech design philosophy of total dust management.
Stringent environmental and occupational health and safety regulations require attention to spillage and dust that is generated from handling dry bulk cargoes. The Benetech approach uses an entire box of tools it has developed to attain total dust and spillage management
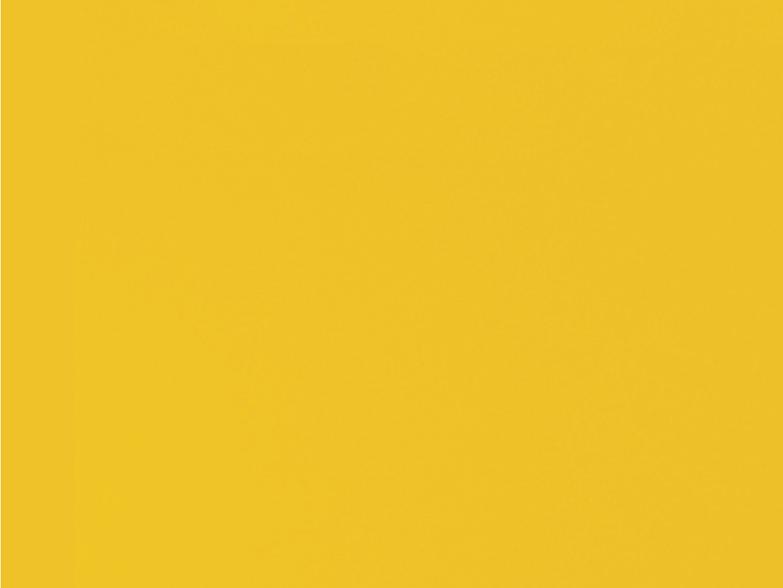
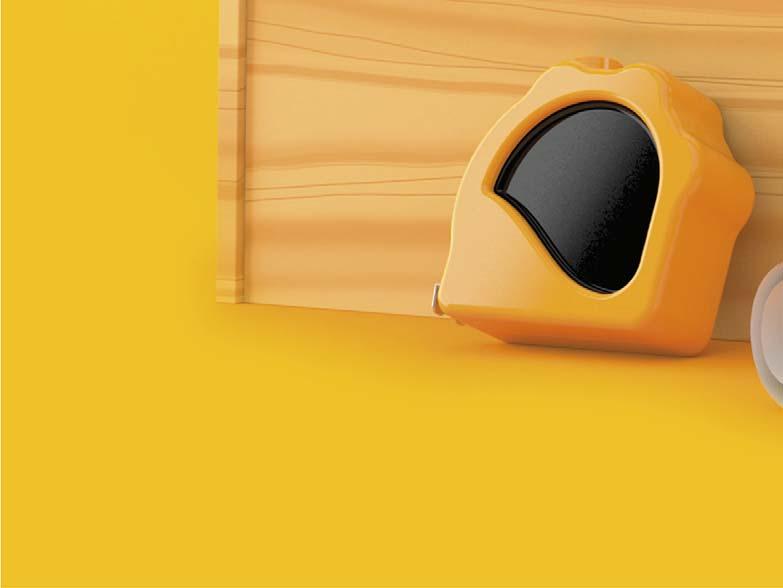
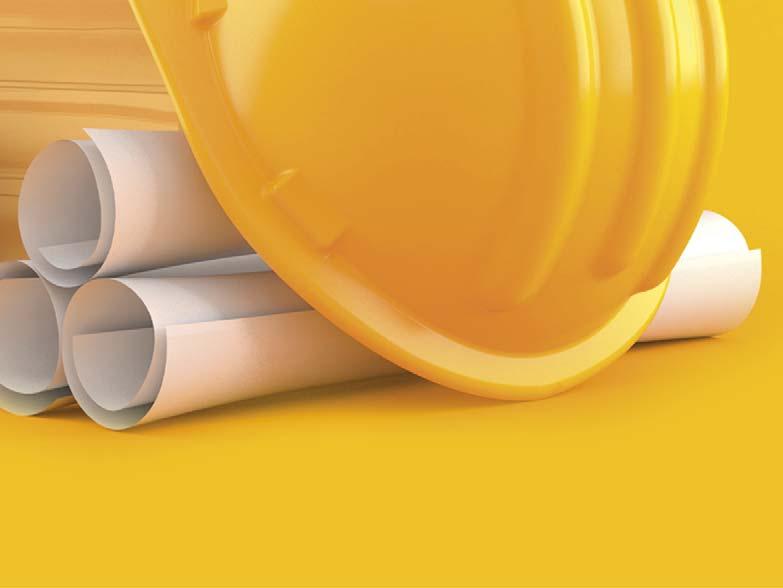
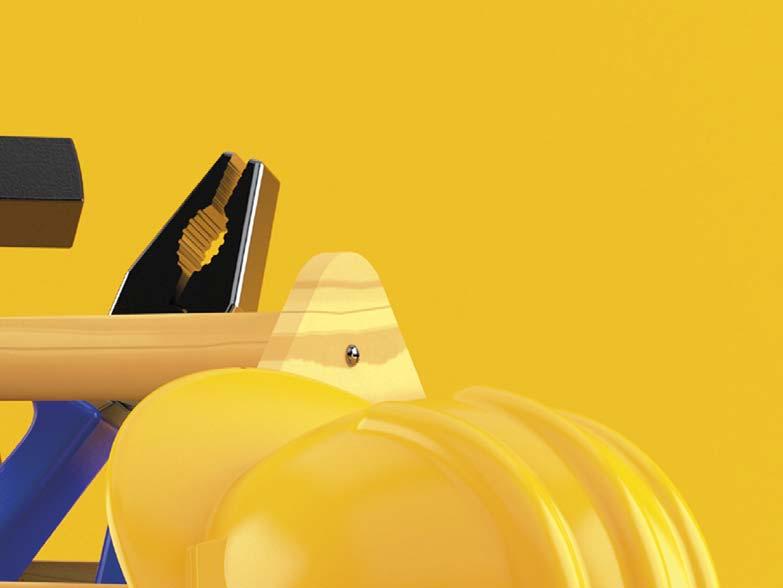
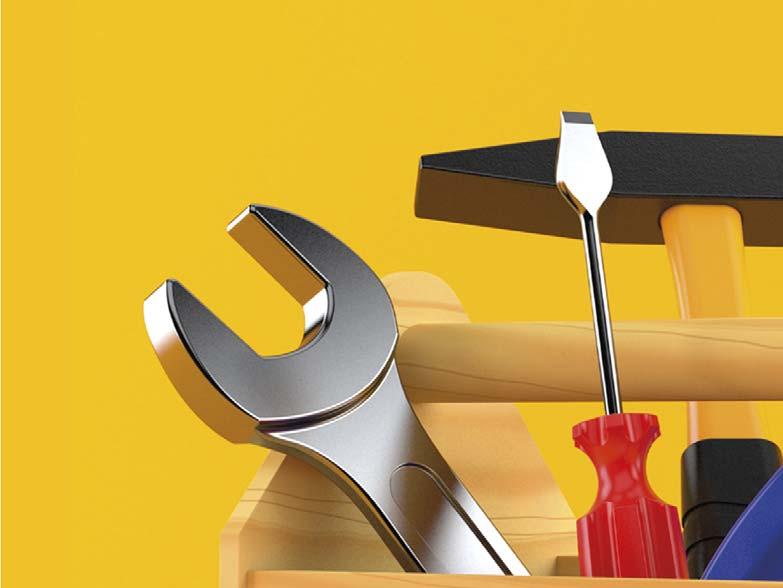
goals. Because these tools have been created specifically by plant professionals for use in the field to address various concerns, particular attention has been devoted to easing maintenance and safety in service. Lifecycle costing is a paramount consideration in achieving robust products and efficient systems to combine safety by design with improved performance characteristics and regulatory compliance. This article will look at specific applications making a difference to: Reduce dust – lower risk, increase safety. Prevent spillage – reduce clean-up and transfer cost. Improve material flow – enhance productivity and earnings. Ensure compliance – regulatory agencies, NGOs, and community.
Transfer and bulk storage
To avoid demurrage and facilitate the loading process, it is often required to have a readily available supply of dry bulk cargo that can safely and effi ciently move from the stockpile to the ship while meeting all environmental and regulatory requirements. Dust and spillage are concerns that are inherent with the movement of materials to and from storage. With most ports, there is also the added pressure from neighbours, NGOs, and environmental agencies.
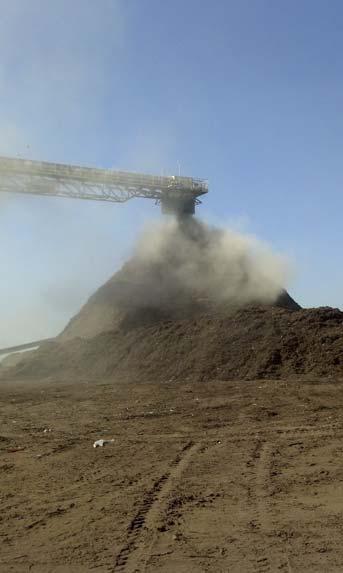
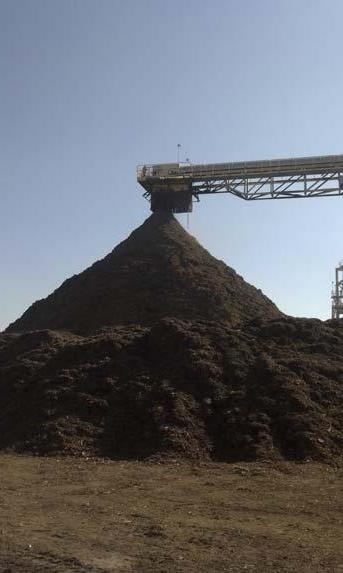
Figure 1. Biomass stack out and storage. Left: before; right: after.
Figure 2. Covered storage and transfer of wood pellets. Left: before; right: after.
Figure 3. GreenTarp™ – pile sealant for taconite pellets.
Biomass and renewables
There is currently a shift in energy resource materials that is seeing more and more need for biomass, pellets, and alternative sources than fossil fuels such as coal. These products bring their own set of problems with storage, loading, and transfer. Storage is accomplished in both outside and covered storage. Combustible dust is an additional factor that must be addressed in many cases.
Several applications are illustrated in the fi gures, defi ning both the problems and solutions for uninterrupted operations and production carried out safely within environmental guidelines.
Dust suppression
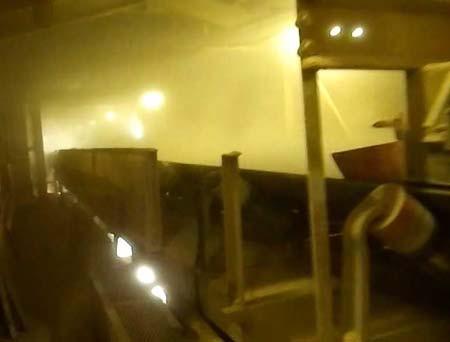

The installation in Figure 1 was under intense pressure from California (US) state environmental agencies for air quality management concerns and scrutiny from neighbours. There were also combustible dust concerns for dust accumulation on adjacent structures with wood dust, causing a fi re or explosion risk.
Engineered transfer points and modular load zones
Combustible dust was a signifi cant concern in Figure 2. This client decided that its best opportunity to reduce combustible dust issues in an enclosed area was to cure the problem at the source instead of putting band aids on the problem. A fully engineered chute and load zone design was chosen for that task. As can be seen in Figure 2, a signifi cant difference was achieved. No additional dust control measures were necessary to eliminate the problem in this enclosed conveyor system. By controlling
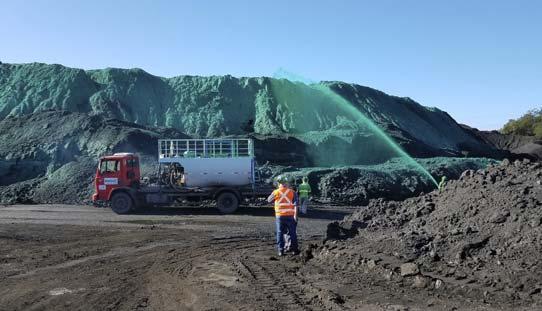
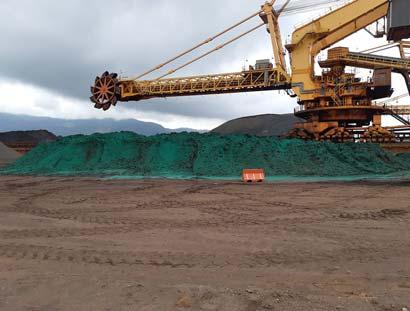
material flow and minimising entrained air along with soft loading and centre loading of wood pellets onto the receiving belt, the dust and risks of fi re or explosions are reduced well below the acceptable level.
Course and fi ne ore storage and transfer
These materials are abrasive and aggressive for material handling equipment and can generate signifi cant dusting in both handling and storage applications.
These materials require robust components and systems to handle rigorous wear and heavy-duty loading requirements.
Bulk storage is also a concern for local NGOs, neighbours, and regulatory pressures.
One of Benetech’s larger clients, a Brazilian producer in the iron ore industry, has adopted many of Benetech’s systems and technologies to improve its operations at mine and port facilities. Benetech has also developed the GreenTarp™ pile sealant, which has solved the dusting issues as well as provides major PR benefi ts within the local communities. Figure 4. Pile colour changed to show support for various causes.

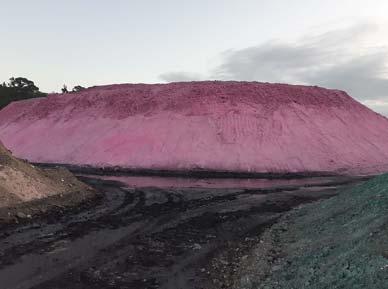
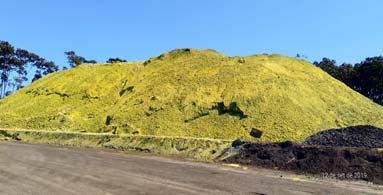
Figure 5. Stainless steel engineered chute and MaxZone® modular load zone.
Problems and solutions
The pile in Figure 3 is now sealed and eliminates leaching and material run-off during storage. The coating also prevents wind erosion that can carry dust from storage piles to neighbouring structures or sensitive coastal environments.
In addition, the colour of the GreenTarp protective seal can be varied to reflect the needs of the end user. In the case of this client, storage pile colour will vary as they use this as a means to show support for local causes. For instance, the pile colour was changed to pink during breast cancer awareness month, blue for prostate cancer awareness month, and yellow for suicide prevention awareness, all to show support for the causes and heighten public awareness, as shown in Figure 4.
Engineered chutes and modular load zones
Problems Spillage and plugging issues. Extremely sensitive environmental conditions. Throughput, capacity, and demurrage issues. Difficult for maintenance. Regulatory pressure from agencies, NGOs, and local community.
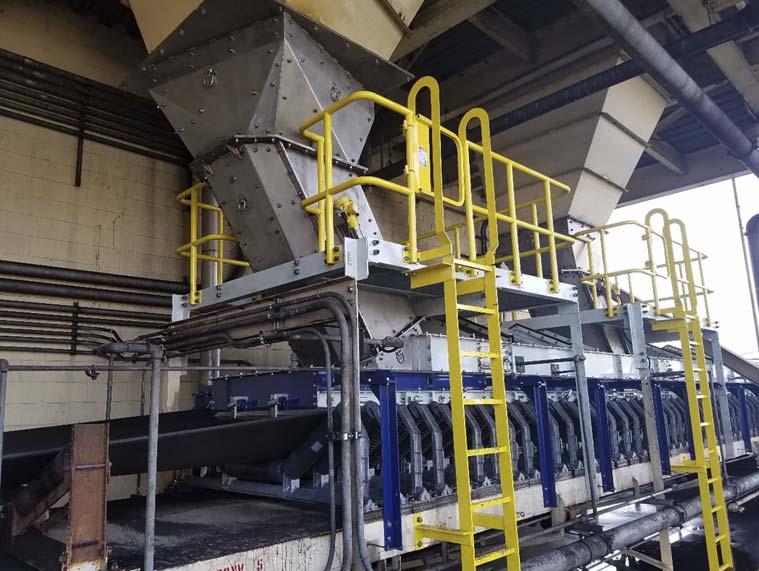
Solutions provided
Fully engineered chute. Increased capacity and smooth flow capability. Improve belt loading and eliminate plugging (soft load and centre load belt). Eliminate spillage with MaxZone® load zone and XN
Liners (internal liners/external adjustment). Service and replacement now possible by one person.
The heaviest section is 37 lb. Reduce dust and spillage with improved load zone and sealing. Baffles in load zone to control air velocity and dust settling. BXS5 belt cleaners to eliminate carryback (spillage). Easy to service by one person. No hot work is required after installation. All bolted connections and external serviceability are made possible in tight spaces. Demurrage charges are reduced, and ships can be loaded without interruption and at desired capacity.
In conclusion, the Benetech toolbox offers many products and services to help with total dust management and easy maintenance to keep port facilities cleaner, more profi table, and meet stringent environmental pressures.