
10 minute read
Tackling The Plastic Problem
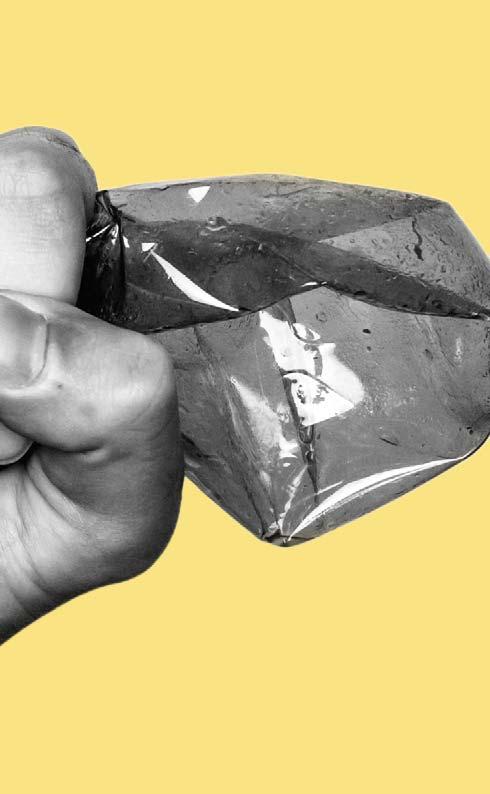
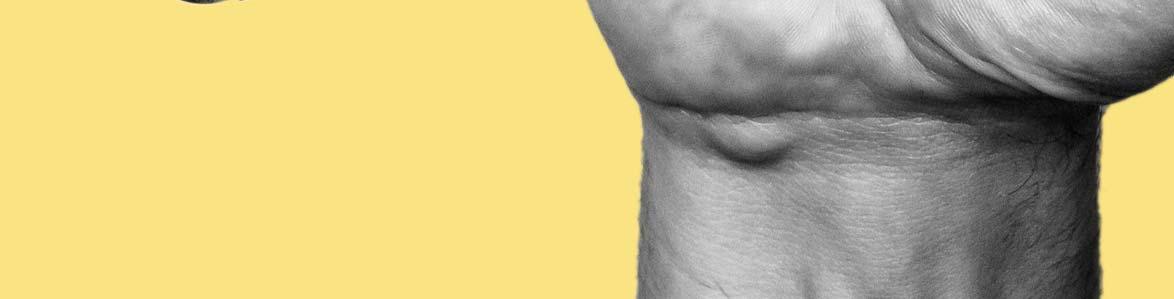
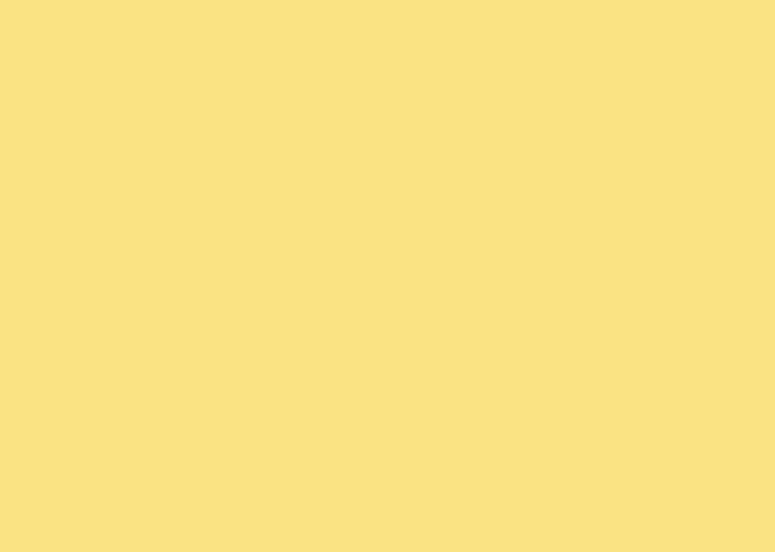
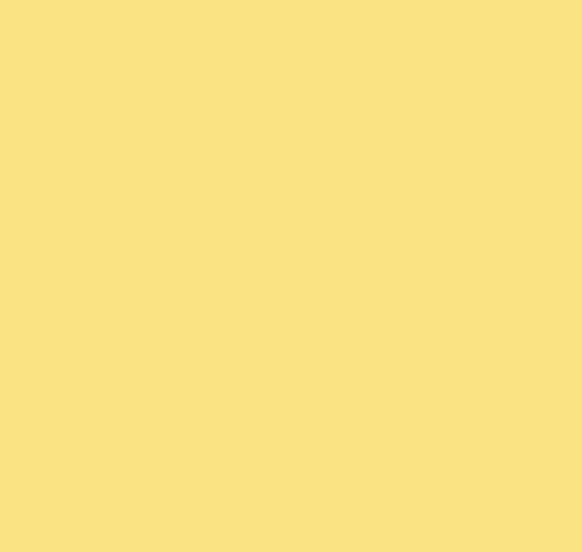


Sigrid Eder-Ince and Reinhard Lechner, Starlinger & Co. GmbH, Austria, explain why FIBCs made from PET can help boost the circular economy as countries introduce more stringent legislation on plastic.

The UK’s proposed Plastic Packaging Tax could set an example for governments worldwide to follow in order to meet sustainability goals and promote recycled content in plastic packaging. In the area of heavy-duty bulk packaging, flexible intermediate bulk containers (FIBCs) made of PET tape fabric provide an economically viable solution to comply with such legislation.
Parallel to the EU’s Single-Use Plastics Directive and the EU Plastic Packaging Levy, the UK plans to tackle plastic waste and promote the recycling of it by taxing plastic packaging that contains less than 30% recycled content.1 The HM Revenue & Customs – the UK’s tax, payments, and customs authority – has drafted a legislation defi ning chargeable types of plastic packaging, thresholds of recycled content, tax rates, and liability, which will take effect from 1 April 2022. The aim of the tax is to provide a clear economic incentive for businesses to use recycled material in plastic packaging, which will create greater demand for this material and in turn stimulate increased levels of recycling and collection of plastic waste, diverting it away from landfi ll or incineration.
Once in force, this tax will also affect FIBC producers who export their bags to the UK. Importers will have to pay a tax of £200/t in addition to the customs duty if the FIBCs do not contain the defi ned amount of recycled content, which will make them uncompetitive.2 If other countries follow, exports to these countries will also be affected.
FIBCs are generally made of polypropylene (PP), and although PP can be recycled, it degrades in the process. Low



Figure 1. A PET FIBC produced at a Starlinger customer in Asia.

Figure 2. Starlinger circular looms produce PET fabric for FIBCs. quality recycled PP cannot be used in tape production for heavy-duty FIBC fabrics. As a result, in order to achieve a certain amount of recycled content in PP FIBCs the recycled material has to be of high quality. This strongly depends on the quality of the recycling process and the amount of foreign substances and polymers – additives such as CaCO3, or polymers like polyamide used for seams – in the input material for recycling.
In addition, there are no existing legal requirements and defi nitions for using recycled PP in FIBCs for food and pharmaceutical grade applications yet, although the industry is working on solutions.
Up to 100% recycled material
An alternative for FIBC producers is FIBC fabric made of PET tapes. Besides its high strength and form stability, which makes PET fabric ideal for heavy-duty applications, PET can be recycled and refi ned so that its properties are restored to those of virgin material. For FIBC producers, this means that with PET they can kill two birds with one stone: produce high-quality FIBCs, and meet sustainability criteria which are likely to become a must in the near future. With PET, the recycled content of an FIBC can even be up to 100% – with PP, this high rate can never be reached.
Advantages of PET
Making new products out of PET waste is not a new approach. For many years, PET flakes have been recycled into new PET bottles or sheet for food trays, and the unique properties of PET recommend it for other applications as well. Austrian manufacturer Starlinger & Co. GmbH, which has been exporting machinery for the production of woven polypropylene fabric since the 1970s, has developed the technology to turn flakes from used PET bottles into fabric for sacks, bags, and FIBCs. PET offers a whole range of advantages that can benefi t the logistics industry, and with millions of FIBCs being produced worldwide every year, the potential to save resources through the use of recycled material is enormous.
The production of packaging from waste (i.e. PET flakes) allows for a closed loop production. PET has an edge over other plastics because of its advanced recyclability. With a method known as solid-state polycondensation, the molecular weight of recycled PET can be restored to its original level, thereby yielding material that is as good as new, even after being recycled many times. Furthermore, due to its high decontamination performance, this process opens up multiple possibilities for food-grade packaging and broadens the customer base of FIBC manufacturers.
Applied to heavy-duty fabrics
High form stability and a high melting point are the main reasons why PET strives to achieve a better performance and can withstand higher working temperatures than other polymers used for fabric production. A fi eld where these advantages are particularly useful is bulk material logistics, as the properties of PET benefi t heavy-duty fabrics in a number of ways, as outlined next.
Positive characteristics of PET FIBCs include:

Form stability: PET FIBCs are an ideal combination of strength and flexibility. They are flexible compared to cardboard octabins, but due to the high creep resistance of PET, they maintain their form over long periods of time. This stiffness of PET prevents bulging and therefore allows big bags to be stacked on top of each other without the risk of toppling over. As a result, PET FIBCs are highly suitable for multiple stacking and long-term storage of goods with little inter-particle friction, such as polystyrene beads or polymer chips with slip additives.
Moreover, the strength of PET makes FIBCs resistant to abrasion – an advantage during rough handling. High melting point: PET maintains its modulus and strength at temperatures up to 80˚C. PET FIBCs can therefore be used in an environment with extremely high or low ambient temperatures, and because of the high melting point of PET, PET FIBCs are ideal for hot-fill applications. Price and availability: PET bottle flakes are available at a reasonable price as compared to other raw materials (Figure 3). In many countries, public and/or private collection systems have been set up that satisfy the growing demand for washed and sorted flakes. Some companies even operate their own sorting and washing equipment. Sustainability: Post-consumer bottle flakes are turned into FIBCs that are in turn recyclable. Starlinger calls this concept ‘bottle to bag’, as PET bottles are used to make new bags or big bags. If collected and reprocessed with the right equipment, PET FIBCs can be recycled indefinitely due to the recyclability of PET.
Truly eco-conscious producers can now transport their recycled goods in recycled FIBCs as well. Waste reduction: PET FIBCs are highly suitable for multiple use, which saves valuable resources. Food safety: Equipment for PET decontamination makes bottle flakes and consequently, the recycled fabric, safe for food contact, so that FIBCs can be used to transport food products such as seeds.
Since Starlinger circular looms do not have sliding parts, no oil/grease is needed in the weaving process that could potentially contaminate the fabric. Visual appeal: First impressions count – packaging is the business card of the finished product and conveys an impression of superior quality. PET has a shiny surface and good printing properties; this visual appeal gives PET an edge over other materials, as it permits sophisticated packaging designs.
Investing in technology
Starlinger has been working since 2010 on developing the process and equipment for converting PET into woven fabric – initially from virgin material, then recycled pellets, and ultimately, from PET flakes. This was something that no technology provider had managed to achieve up until this point, as the conversion of PET to plastic tapes is not a straightforward process and entails many challenges that need to be addressed. In doing so, Starlinger was able to draw on its knowledge and experience in the area of PET recycling, as the company has been developing recycling technology for more than 30 years. Building on this foundation, Starlinger spent considerable time and resources on research and development, perfecting the technology for PET tape fabric until fi nally presenting the fi rst PET FIBC at K show 2016 in Düsseldorf, Germany.
The investment cost for PET FIBC fabric manufacturing equipment can vary greatly and depends on the type of FIBC
Figure 3. Raw material prices in Western Europe, January 2018 - February 2021. Image courtesy of KI Kunststoff Information Verlagsgesellschaft mbH.
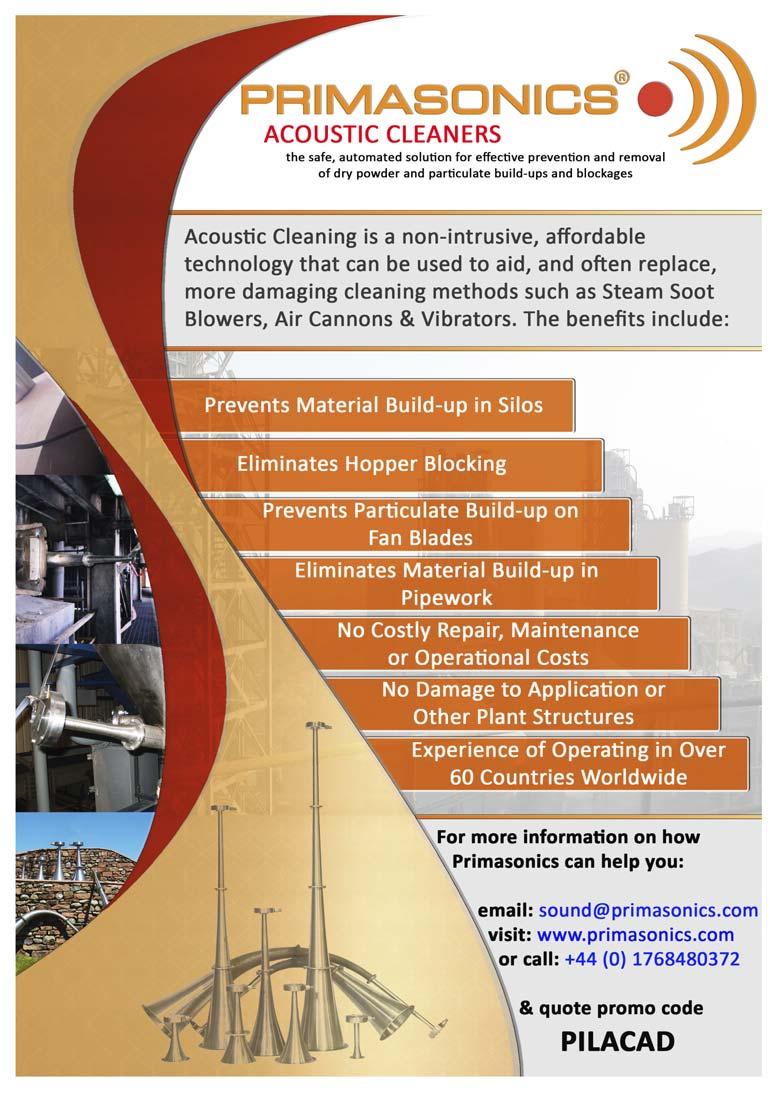
(size, food safety, coating, printing) as well as the required production capacity. Because the manufacturing process of PET FIBCs is more complex, the investment is higher as compared to PP fabric, but this difference is more than compensated for by cost savings in input material (i.e. flakes instead of PP granules). Figure 3 compares the price development of fi ve types of raw materials, namely PP homopolymer suitable for fi lm production, virgin PET for packaging applications, as well as recycled PET granules and clear and coloured PET bottle flakes, between January 2018 and February 2021 on the Western European market (prices are given in €/t). The graph clearly shows that the purchase price of PP is consistently well above the price of PET flakes; especially coloured PET flakes which cannot be used in PET bottle production provide input material at a very favourable cost. The applicable price difference at the time of purchase determines the manufacturing cost of the end product.
An important consideration in this respect is that PET flakes as a secondary resource are less dependent on the development of the oil price. This cost advantage in combination with the favorable properties of PET causes an increasing number of FIBC producers to look into a bag project for PET fabric. Such a project is an especially attractive investment opportunity for companies that already sort and wash flakes, and would like to expand their business into related areas of activity.
Conclusion
The proposed Plastic Packaging Tax the UK is planning to implement by 1 April 2022 might be an example other countries are deciding to follow. According to the tax, plastic packaging that does not contain a minimum of recycled content will be charged with an additional tax when sold. This also affects FIBC producers and importers of FIBCs. Starlinger has developed the technology for a very competitive alternative: FIBCs made of PET. This polymer achieves the same properties as virgin material after recycling and thus can be used to produce heavy duty fabrics for FIBCs containing up to 100% recycled content.
FIBC producers thus will not only be able to comply with government regulations such as the UK’s, they will also benefi t from the unique characteristics of PET that makes it an ideal material for heavy duty applications. As sustainability goals are on the agenda of many governments worldwide, it is to be expected that similar regulations will be put into place in the upcoming years. The use of PET for FIBC production provides producers with an ecologically and economically viable solution for this future challenge.
References
1. HM Revenue & Customs, Introduction of Plastic Packaging Tax from
April 2022, 3 March 2021. 2. Ibid.
ADVERTISER’S INDEX
OFC Bedeschi S.p.A
29 BEUMER Group
37 BULKEX
09 BulkHandlingMaterials.com
22 Coaltrans Asia
21 DCL
33 Dry Bulk
45 European Bulk Services (EBS) B.V.
IBC GEAPS Exchange
13 Jotun A/S 17 Kumera Corporation
IFC Liebherr-MCCtec Rostock Gmbh
46 MRS Greifer GmbH
OBC NEUERO
55 Primasonics
33 Samson Materials Handling Ltd
05 Telestack
02 Thiele GmbH
25 VIGAN
07 Vortex Valves
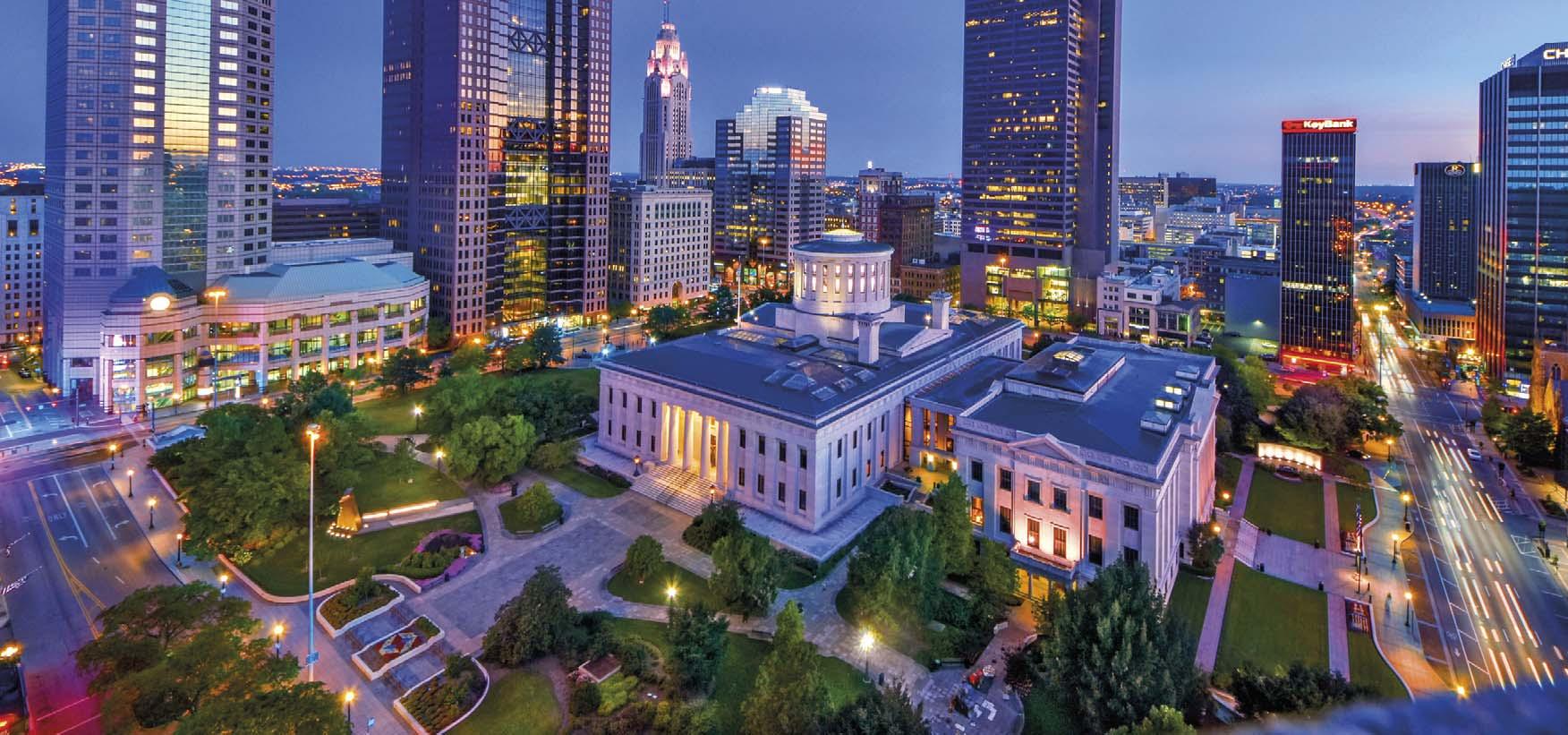
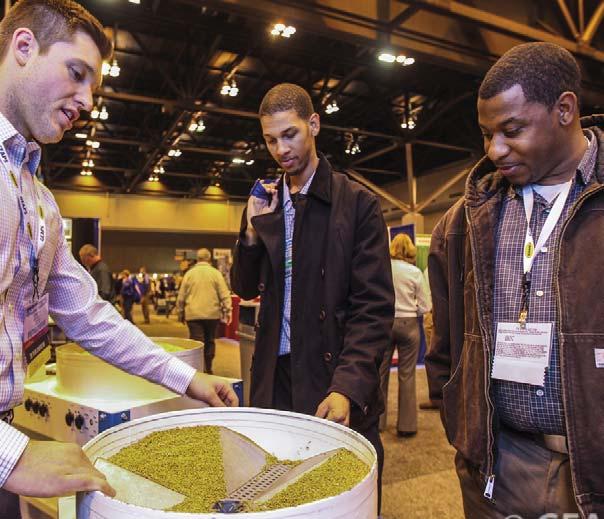
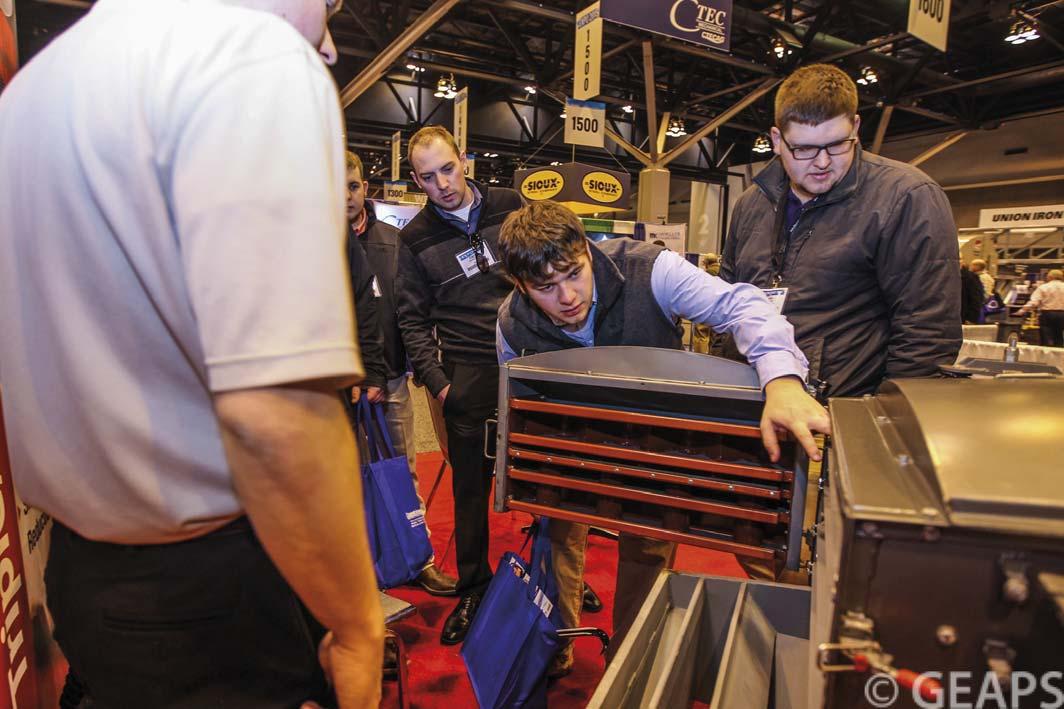
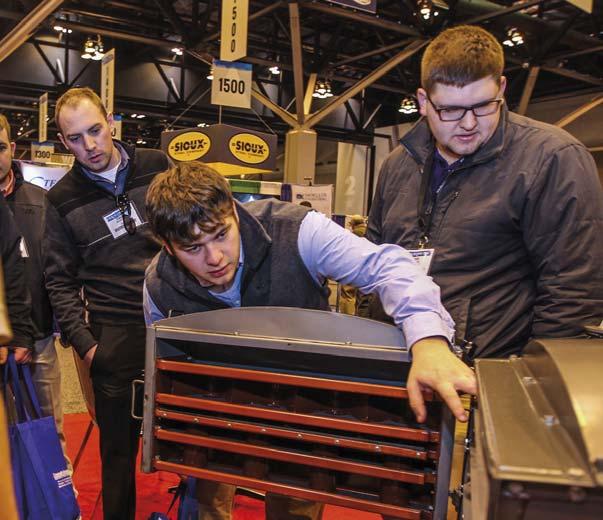
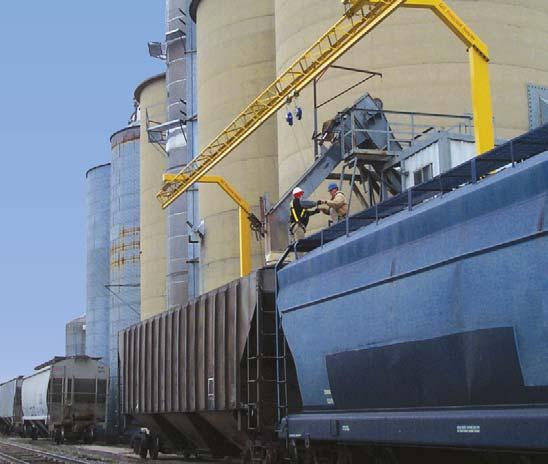