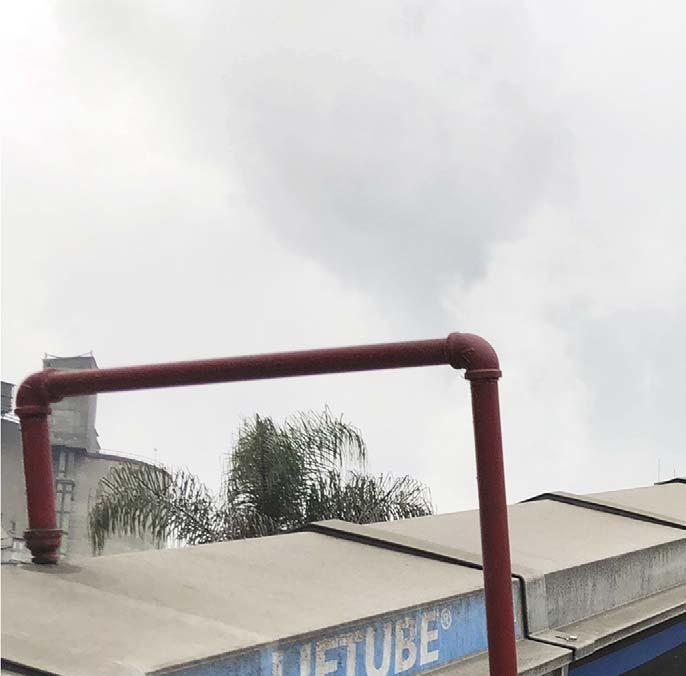
7 minute read
Keep It On The Conveyor
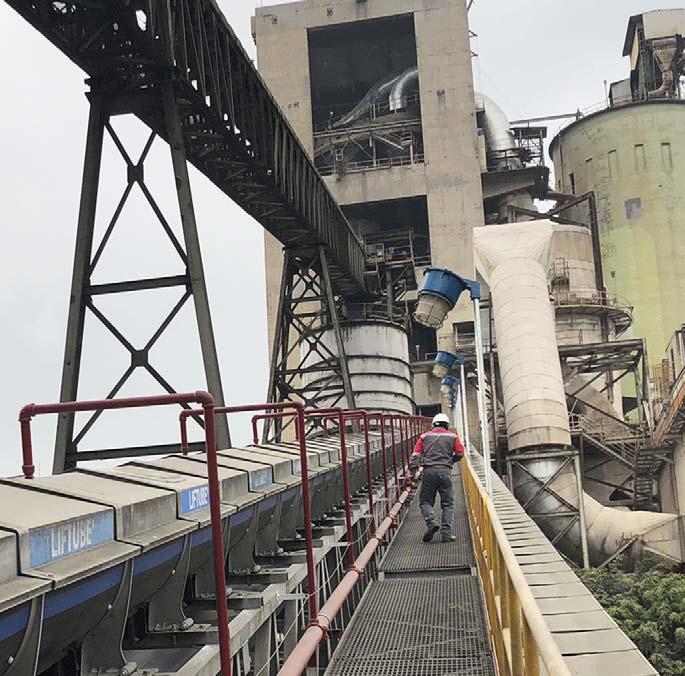
Figure 1. Lafarge waste conveyor with LIFTUBE® to supply the kiln.


David Fregez, Standard Industrie International, France, outlines how material losses and dust emissions can be reduced through the addition of conveyor belt accessories.
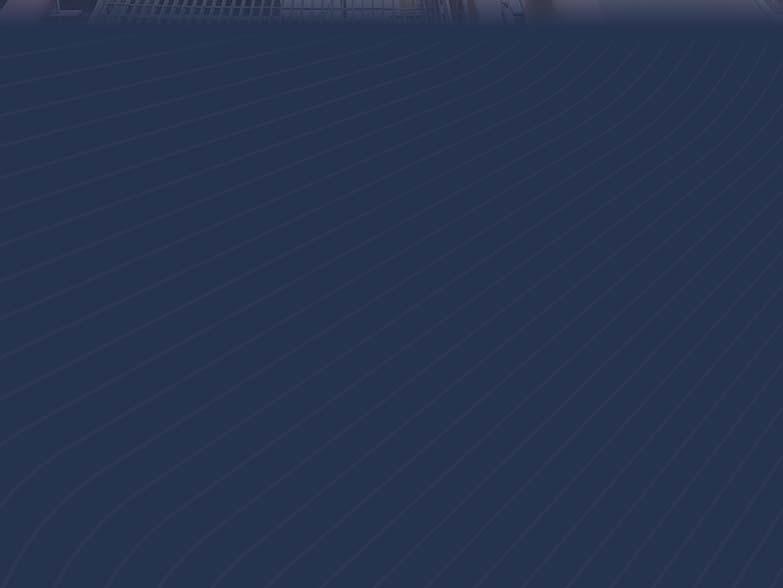
Optimising production tools can enable a reduction of atmospheric emissions, improved visibility, staff safety, and reduced maintenance costs. Standard Industrie International has been a specialist in the design and manufacture of solutions aiming to facilitate the handling of bulk products by combining safety and respect for the environment, thus this article outlines several of the company’s solutions regarding dust control.

Reducing material losses and dust emissions
The LIFTUBE® is a solution from Standard Industrie that is designed to optimise the sealing of any conveyor belt – smooth or cleats, rubber or PVC, vulcanised hot or cold. It comes as a replacement to stations equipped with three rollers on the conventional conveyors. These are standard 1 m modules that are scalable and easy to install on all or part of a

new or existing conveyor, while keeping the belt, chassis, and motorisation of origin. It is installed between the point of loading and unloading. Available in widths from 500 - 1400 mm, and in high temperature, explosive, or self-extinguishing versions, the LIFTUBE is designed to avoid any contamination of the product transported with the outside environment. This seal-proof system enables simple tilting of the glide boards and the central roller for easy and minimal maintenance. As a result of its pinch point protection, the LIFTUBE aims to signifi cantly improve the working conditions for the operators.
Installation 1: Cement plant in Mexico
Standard Industrie was contacted by a leading cement manufacturer in Mexico, where the plan was to improve one existing conveyor in the plant and to replace the 600 mm conveyor belt with an 800 mm belt – with the whole system upgraded with LIFTUB2-800 (Figure 1).
The cement manufacturer was looking for a solution that would also be combined with a drastic reduction in the plant’s fuel consumption. In order to reduce the average yearly energy costs, the target has been set to reduce the traditional fuel used, such as coal, to AFR – fluff fuel such as shredded plastics and cardboard.
Opting for these new fuel types meant that the conveying system needed to be largely redesigned. AFR material – for instance, tiny plastic particles – needs to be conveyed in a totally sealed system because wind or any turbulent weather conditions have the potential to blow these particles away, thus impacting the immediate environment. The product density is very low at 0.3 - 0.5 t/m3, with moisture of 5 - 20% and high risks of toxicity and inflammability of the AFR. Last but not least, the belt needs to run around the clock, regardless of the slow velocity of the belt at 1 m/s.
LIFTUBE was found to be the solution most adaptable to the necessary requirements. Since its design offers complete sealing, AFR is thus entirely enclosed and contained in the conveyor. After a study was conducted on-site, several visits to the plant and a comprehensive adapted design solution of LIFTUBE was offered. Standard Industrie Mexico co-operated with the customer’s installation company and all details for energy consumption, design of tumblers and hooding, and 136 m of LIFTUBE were delivered. The installation was a success, and the cement manufacturer is already reaping the benefi ts.
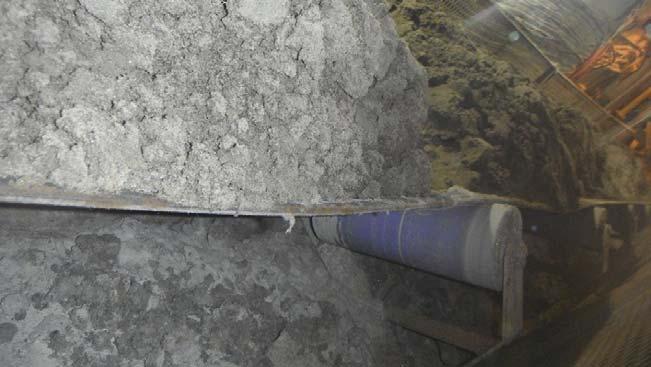
Figure 2. Platinum plant without LIFTUBE – a conveyor of fi ne density materials causing volatile dust emissions, material spillage, and need for cleaning.
Figure 3. Platinum plant with LIFTUBE. Conveyor sealing: no overflow of material or dust emission, easy maintenance, and reduced cleaning costs.
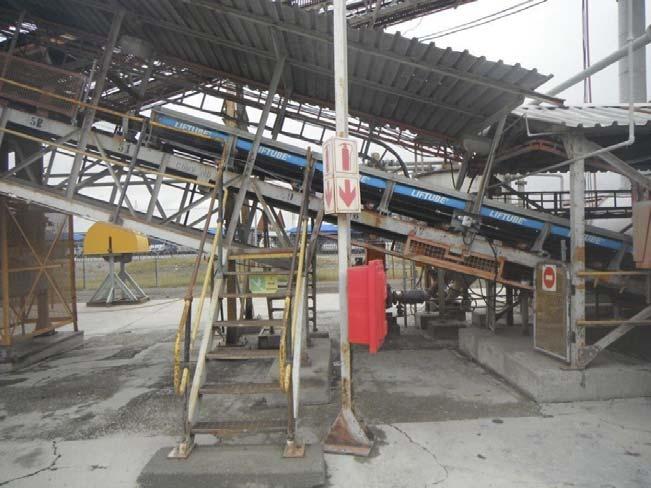
Installation 2: Platinum factory in South Africa
Standard Industrie’s customer was facing a loss of 2 - 3 tpd of material on its mill feeding conveyor. This required putting in place signifi cant resources in terms of cleaning: between four to six hours of cleaning per day was carried out by four to six workers. The extent of this cleaning meant that considerable time and money was wasted, as well as disruption to the production process.
To solve this problem, 30 m of LIFTUBE has been installed at the platinum factory, with a belt width of 900 mm to fi t the dimensions of the conveyor. An inspection hatch has also been installed on one of the covers so that the customer can easily control the routing of the product to the mill.
The customer has regained its productivity and the routine daily cleaning cancelled, replaced instead by a routine maintenance check and a monthly planned quick cleaning campaign.
Installation 3: Limestone quarry in Switzerland
At a limestone quarry, the operator wanted to integrate the LIFTUBE solution and a dust collector in its new installation project – which included conveyors, an impactor, and crusher (Figure 4). The size of the conveyor equipped with LIFTUBE is 27 m, with a belt width of 800 mm, a hopper cover, and a dust collector. The conveyor is located just below the crusher, which creates a dusty air stream between the feed hopper and the chute.
The speed of the belt pulls this charged air into the conveyor and can create dust emissions at the outlet. To solve the problem, there are several solutions, including: installation of decompression boxes; fogging; vacuuming; and dust removal. This latter solution, dust removal, was chosen by the customer as being the most compact and economical.
Fixed on only 2 m of the industrial solution, the dust collector is installed after the last chute, capturing the suspended particles due to the vacuum created by the fan. The multi-pocket fi lter retains these particles, which then fall back by gravity onto the belt during the automatic cleaning cycles. Standard Industrie’s solution is also suitable for flammable and explosion-prone products, while also meeting various European and international standards.
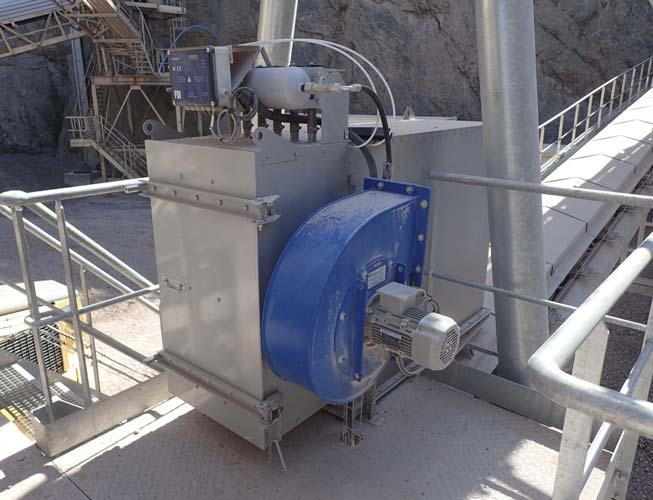
Figure 4. LIFTUBE solution with a dust collector.
Figure 5. The patented LIFTUBE system for the conveyor belt.
Figure 6. The vacuum cleaner on the trailer enables cleaning operations to be carried out as well as heavy pumping – offering a large scope of cleaning possibilities.
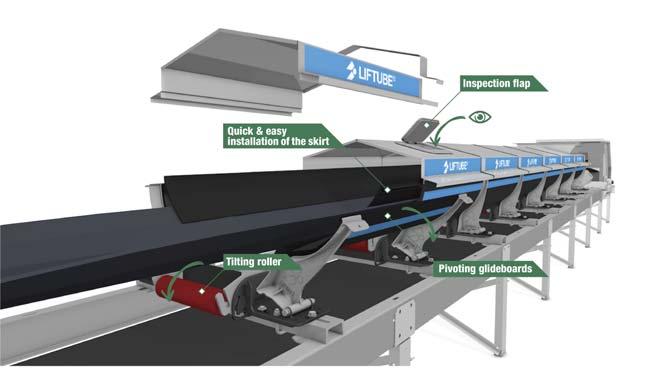
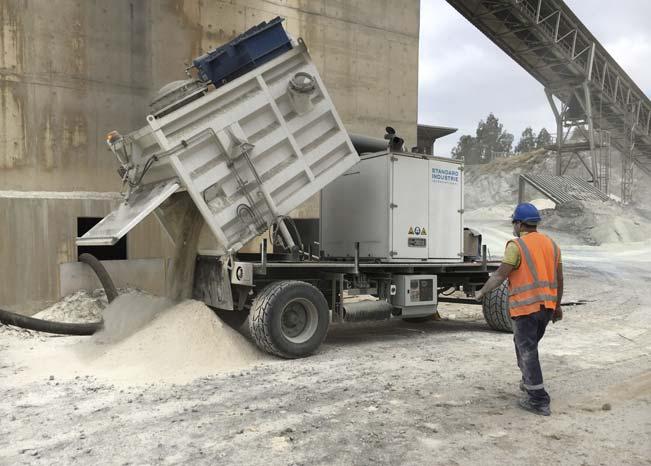
Conveyor belt accessories
The patented LIFTUBE and the dust collector are accessories for conveyor belts. The dust collector has been developed to increase the containment effect of the material and to minimise dust emissions.
The LIFTUBE system enables the belt to run on a central horizontal tilting roller and to slide on the edges, which also tilt.
A removable hood can be adapted to the equipment to reduce belt conveyor dust emissions. Only the size of the hood and the central horizontal roller depends on the width of the conveyor. The conveyor belt and rollers can be easily accessed as a result of innovative tilting legs. Belt width: From 500 - 1600 mm. Belt speed: From 0.05 - 5 m/s. Output: Up to 1500 tph. Particle size: Up to 500 mm. Density: Up to 4. Product temperature: Up to 300˚C. Modules: Standard and evolutive. Installation: Suitable for both new or existing conveyors.
Vacuum cleaning machines
To meet its clients’ industrial cleaning requirements, Standard Industrie also offers a complete range of equipment and vehicles that combine safety and performance. All industrial vacuuming problems can be covered by the company’s vacuum vehicles to mobile vacuum units.
Example
An integrated cement plant and all its surroundings (bagging, tunnels, conveyor belts, cement grinding, and coal workshop) require a huge demand on cleaning to make sure the whole facility is kept at an acceptable cleaning level. The plant was already equipped with Standard Industrie’s AIRCHOC® WIRELESS. This time, the cement producer turned to Standard Industrie International which supplied several vacuum machines and purchased a UMA3000DMX (Figure 6).
The UMA was determined to be the best solution to tackle the diffi culties and constraints associated with a heavy vehicle. Powerful, mobile, and adaptable, the UMA is equipped with explosion vents. It can therefore vacuum coal and petcoke. The older equipment on site could not tackle this need. Standard Industrie International was also responsible for the installation of a fi xed pipe network in the bagging area. The nine suction inlets of the network made it possible to optimise the cleaning of three existing buildings.
These innovative and reliable solutions proposed by the design offi ce of Standard Industrie International have been adopted by many plants of bulk industry, worldwide.
Conclusion
Dust collection is an important issue for factories. Especially in certain sectors of activity where health and safety standards are developing, as has recently been seen with the risks linked to the propagation of crystalline silica dust.
Standard Industrie International assists its bulk customers in fi nding the best solutions for the safe storage, transport, and collection of materials.