
7 minute read
Dust Busters
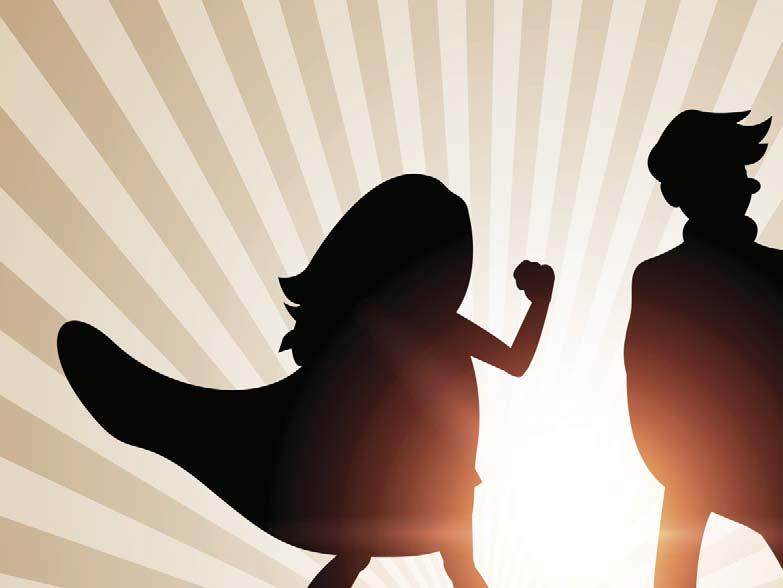
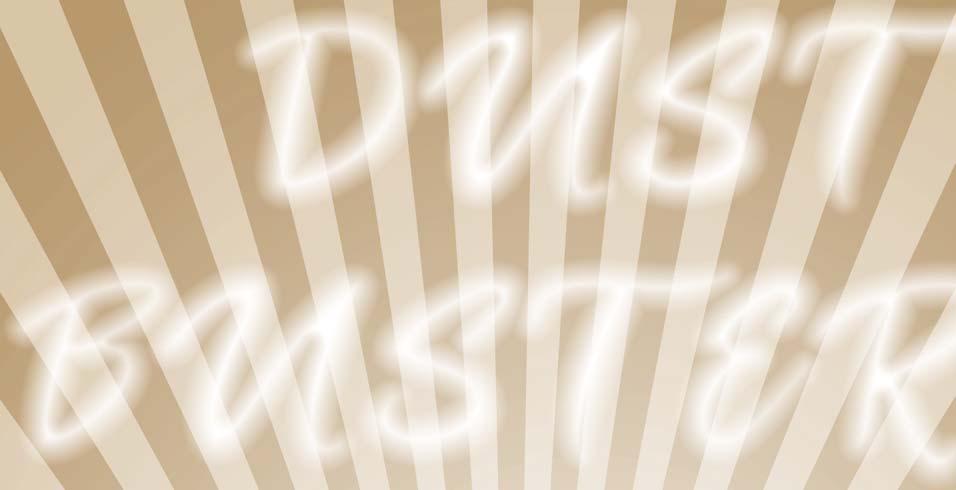
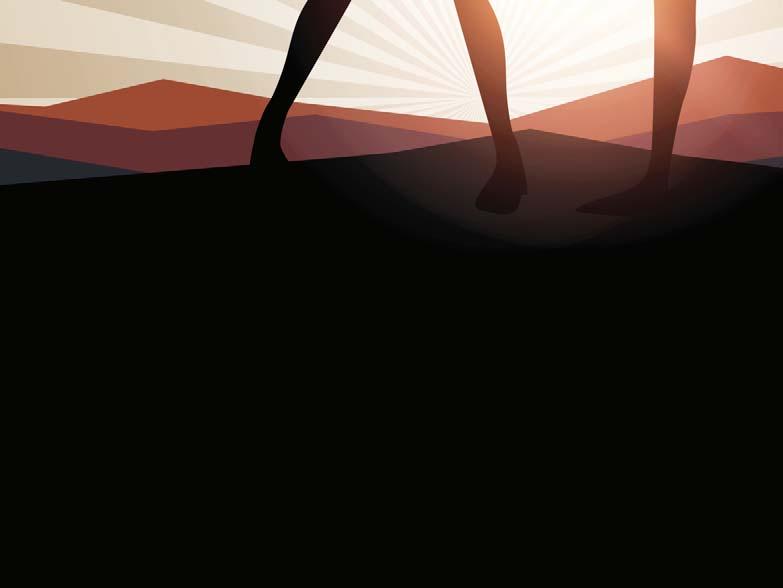
Austin Anderson, Vortex Global, USA, discusses ways to address safety concerns surrounding dust in the workplace.
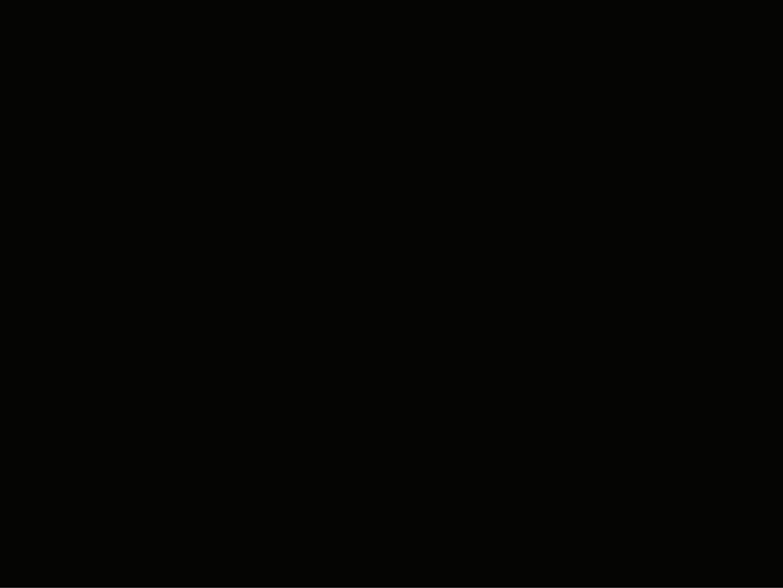
Material dusting and equipment leakage plague factories across the globe. The hazards generated by dust increase the risk of explosion, material waste, and loss of profi t. The rogue dust also imposes potential health and safety concerns for employees and environmental consequences for nearby communities and ecosystems.
Employees of manufacturing plants and factories face potential exposure to these hazards on a daily basis. In recent years, these facilities have faced tighter regulations and restrictions by federal and local agencies to protect their employees and prevent environmental pollution.
Common issues faced by employees in dust-ridden environments include irritated skin due to allergic reaction, irritation of the lungs due to inhalation of potentially toxic materials, and slips, trips, and falls due to dust accumulation on surfaces. Fugitive dusts can also accumulate to form a dust cloud that can ignite, burn, and in some instances, explode.
Employee and plant safety are key components in dust control. In many applications, dust-tight valves can help mitigate some of these concerns by drastically reducing the percentage of fugitive dusts.
Dust-tight valves can help facilities mitigate potentially detrimental effects simply by the way they are designed. Dust migrates through the path of least resistance. This can be a challenge when using soft polymers and packing as seals. Many dust-tight valves designed today feature hard polymers as a sealing surface, because they tend to offer better wear characteristics for most applications.
When replacing a regular valve with a dust-tight valve, it is important to verify that the connections between the valve and what sits above and below are tight. For example, transition flanges need to be true and flat, with
no bow, and gaskets need to be inspected and replaced if necessary. Keeping a good seal on every connection, minimising the escape of dust from process equipment, and inspecting and cleaning dust residues at regular intervals are all part of a robust dust control safety plan.
Dust control
Vortex designs slide gates, diverter valves, and loading spouts specifi cally to address material leakage and dusting concerns. Facilities have an ethical obligation to protect against the hazards of manufacturing. Vortex closely studies trends in air quality, environmental dust emissions, workplace safety, and evolving regulations, and develops its components to comply and address these concerns.
The patented sealing technology in Vortex products has evolved over four decades and is utilised in manufacturing processes across the world. Vortex utilises hard polymer seals in its products with a strategically placed compressed rubber backing to decompress as the polymer wears, making the seals compensate for wear. This applies constant force against the blade, creating a positive seal of fi ne dust and powders and keeping factories clean with minimal maintenance over time.
The fundamental difference between Vortex’s designs from typical slide or knife gates is that Vortex valves are designed specifi cally for handling dry materials. Many valves used in dry bulk processing utilise soft elastomers to create the seal between the internal process and the factory atmosphere. When handling dry materials, these valves suffer from major sealing problems as material wears through the seals on every actuation.
Over the past 40 years, Vortex has provided dust-free solutions to customers in a variety of industries where dusting and material leakage is a concern, including the cement, chemical, food and beverage, milling, and mining and minerals industries. While each industry has its unique challenges when it comes to dust, the principles used to develop Vortex products can be applied in a variety of applications.

Figure 1. Vortex Orifi ce Gate incorporated into a manufacturer’s dust collection system.
Figure 2. Vortex Titan Slide Gates sourced by steel producer to dispense material into containers.
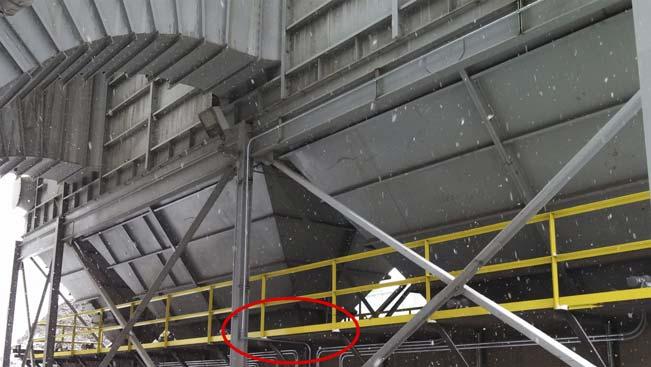
Case study 1: fi ne metal dust
A manufacturer of welded steel pipe contacted Vortex to solve a problem with material leakage onto their factory floor, which was creating safety concerns within the workplace. The challenge was to source a lightweight valve that could maintain a positive seal under full vacuum.
Application
In this application, seven Vortex Orifi ce Gates were sourced to incorporate into the manufacturer’s dust collection system to solve the problem of fi ne metal dust leakage onto the factory floor.
Features and results
When the plant manager was instructed to improve the air quality within the facility, he knew the fi rst areas that needed to be addressed were the seven individual stations where the manufactured pipes were cut to length. The fi ne metal dust created by the cut-off saws became suspended in the air and migrated into every corner of the plant.
A Vortex sales representative suggested that a Vortex Orifi ce Gate could be installed on each station to isolate them. The slide gates were capable of sealing the differential pressure involved and could be equipped with
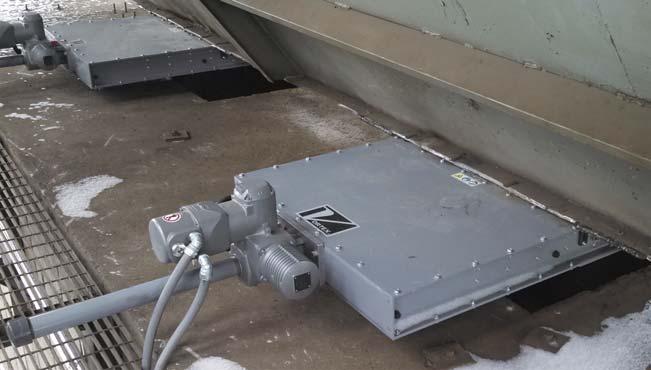
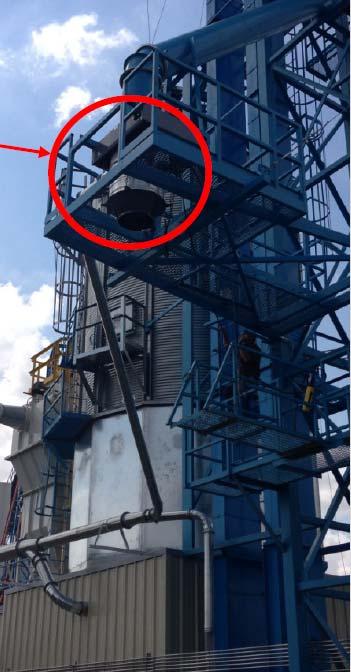
Figure 3. Vortex Loading Spout utilised by hybrid seed producer for the loading of corn.
a solenoid valve to open and close the gate in conjunction with the use of the cut-off saw. When the cut-off saw was not being used, the valve was closed and the demand on the industrial vacuum was greatly relieved.
At the representative's suggestion, hoods were fabricated to collect the fi ne metal dust around the cut-off area, the industrial vacuum and hoses were placed, and the Vortex valves were installed. The result of the project was a signifi cant improvement in the plant environment.
Case study 2: furnace dust
A steel producer required new slide gates to replace existing slide gates in their process to handle electric arc furnace dust and slag. The existing slide gates were very diffi cult to access and actuate and did not seal material well, leading to material leakage within the facility and into the atmosphere.
Application
Five Vortex Titan Slide Gates were sourced to solve this producer’s access problems when dispensing material into containers for future recycling.
Features and results
This producer utilises electric arc furnaces to melt scrap steel. The melt is then poured to form carbon steel bar, which is marketed to industries across the globe. The original gates located at the bottom of the collection bins were pneumatically operated and did not seal material well. This allowed the material to escape to the atmosphere. Air lines would freeze up in the winter time and eventually the gates quit working altogether.
Due to the success they experienced with other Vortex gates and diverters, the producer ordered fi ve special Titan Slide Gates manufactured to match the size of the bin openings. The gates were ordered with 460 V, three-phase electric actuators to eliminate any future issues with winter weather.
In a follow-up visit to the facility, the production and maintenance managers commented that “We should have replaced those gates a long time ago. The Vortex gates work well, contain the material, and have already provided big savings with our labour costs.”
Case study 3: Handling corn
A hybrid seed producer required a solution for the loading of materials at their new hybrid corn railcar loadout station. When developing the new loadout station, the client’s primary concerns were loading effi ciency and dust management, in order to address workplace and environmental health and safety best practices.
Application
A Vortex Loading Spout was sourced as part of a dustless loading system to handle corn in this client’s process.
Features and results
In addition to the Vortex Loading Spout, the client also sourced Vortex Aggregate Gates, Vortex Maintenance Gates, and Vortex Roller Gates as part of this system. Since beginning operations, the client has enjoyed low maintenance and spare parts costs, and the loading system has exceeded their expectations for loadout speed.
Features of the Loading Spout include a material level-sensing device with auto-raise system, to avoid overfi lling. Together, these systems eliminate the need for visual monitoring throughout the loading process. Other features included stacking cones constructed from abrasion-resistant steel and a handheld remote-control pendant.
The spout also includes three-piece, CNC-machined pulleys with rounded edges and precision cable grooves, to signifi cantly reduce cable wear and backlashing. For these reasons, Vortex lifting cables carry a 10-year warranty for wear, tear, and workmanship.