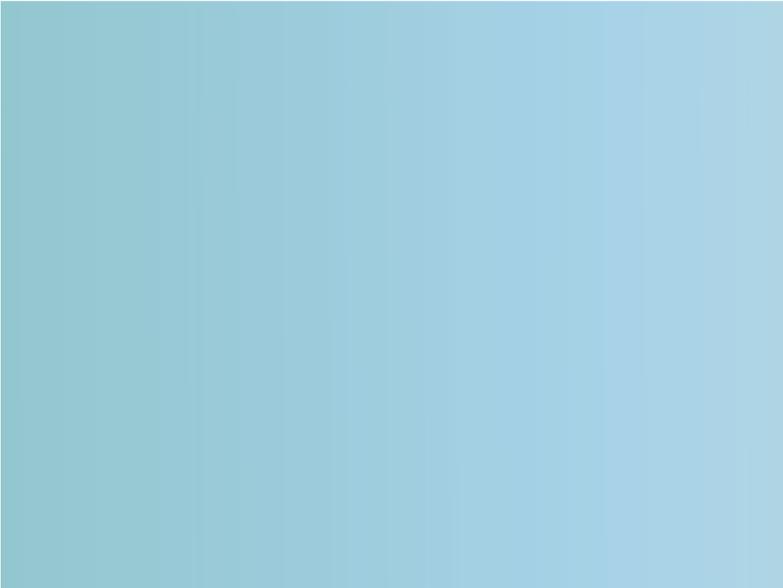
7 minute read
Access To The Once Unaccessible
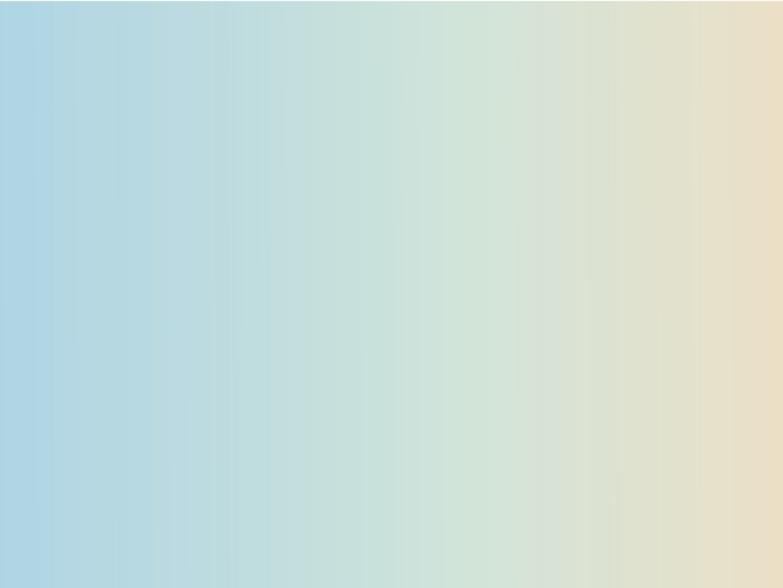

Ellie Langdon, Nectar Group Ltd,
UK, describes how transport corridors can be opened through the use of quayside bagging.

In the early 1980s, UK company Nectar Group Ltd changed the bulk commodities handling industry in developing ports around the world with the invention of the world’s fi rst mobile bagging system known as the MOPACK™; now superseded by the COMPAC range. The mobile bagging concept was completely new and designed specifi cally to work alongside the vessel on the quayside. This innovative and radical approach offered improved flexibility of discharge
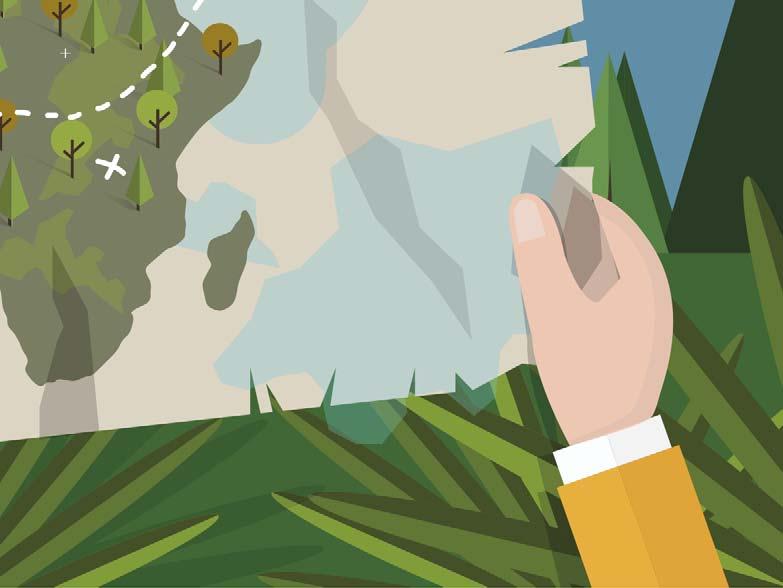
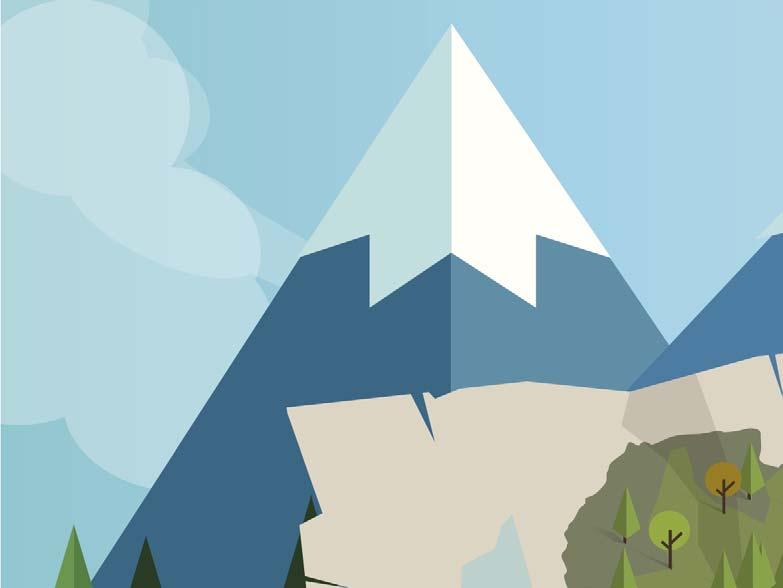
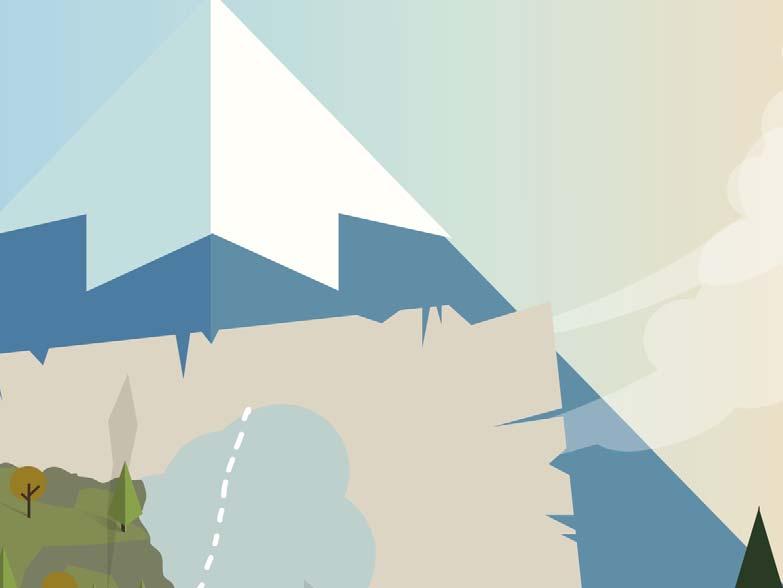
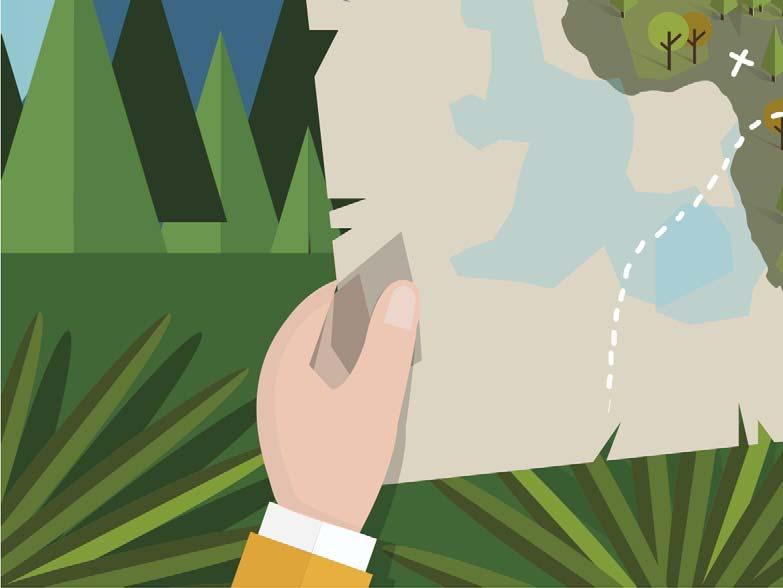
and distribution of bulk cargoes in ports where facilities were not available, and therefore dramatically reduced the overall cost of the end-to-end logistics chain.
Although the concept of quayside bagging is not new, mobile bagging equipment continues to transform how cargoes are handled in developing countries. The design – which incorporates receiving, weighing, stitching, and conveying systems – is housed in two 20 ft ISO containers, allowing for the system to be completely self-contained and easily transported between locations using approved container handling equipment. Today, this continues to prove vital in assisting major organisations such as aid agencies and commodity traders to deliver food-grains and fertilizers into ports globally that lack the existing infrastructure to handle bulk cargoes. In many cases, due in part to its mobility and affordability, mobile bagging equipment is now the preferred solution over fi xed bagging infrastructure.
The use of mobile equipment has continued to remain popular, with operations taking place around the globe for a wide range of free-flowing commodities including, but not limited to, grains, pulses, fertilizer, sugar, soda ash, and sulfur. Today, annual volumes equate to many millions of tonnes per year.
Almost 50 years on from Nectar’s inception, quayside bagging still brings a huge range of benefi ts to ports worldwide. These include: Faster loading speeds: Cargo can be sourced from bulk export terminals allowing for extremely fast vessel loading, making it an increasingly popular choice over pre bagged/pre slung cargo, especially with increasing freight rates. Faster discharging speeds: Cargo is discharged in bulk using grabs into the bagging units, which are capable of handling more than 1500 tpd per machine. Speeds in excess of 5000 t per weather working day are achievable for well managed operations. Reduced risk of cargo loss and damage: As the product remains in bulk throughout loading/discharge there is no damage to the bags when stowing/ unloading, reducing cargo losses, and ensuring correct bag weights. Marketing of cargo: Bags are clean and new on dispatch from the port. This also means that cargo can be sold on the water and bagged into the clients' specific bags upon arrival, reducing double handling and costs for re-bagging. Service provider guarantees: Some service providers are able to provide guarantees on operational aspects such as discharge speeds (in line with Charter Party terms), cargo loss, and bag weight accuracy. This helps the shipper/receivers manage and mitigate their risk.

Figure 1. Commissioning and testing of Nectar COMPAC XL120.
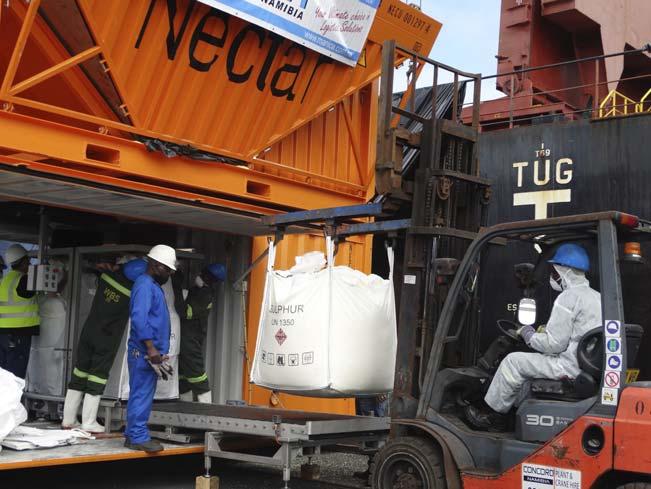
Figure 2. Training of personnel.
Diversifying the bagging
As the availability of handling equipment across supply chains in developing nations has increased, so has the possibility of diversifying from the standard 50 kg output in most quayside bagging operations. Demand for larger bag weights is now becoming more popular, with receivers utilising more widely available handling equipment to support their operational requirements. Flexible intermediate bulk containers (FIBCs) or 1 t bulk bags, a staple across Europe, are now seeing far more widespread use across developing markets, especially where commodities must travel a long distance by road into remote areas away from the coast and/or major rivers.
One such location that has used quayside FIBC bagging to great effect is the port of Walvis Bay, Namibia. Walvis Bay has long been used as a transport corridor for commodities into Botswana/Zambia, most commonly for the transport of products to/from the mining regions. However, its increased distance from the usual hubs of Beira, Maputo, and Durban placed it at a signifi cant disadvantage. One of the major disadvantages is the availability of return journeys for trucks and trailers that are used on the transport corridor, with empty return runs driving costs higher than viable for most receivers. In 2020, a local logistics operator in Namibia, in co-operation with its clients at both the shipping and receiving end of
the supply chain, purchased COMPAC XL120 bagging machines for operation on the quayside. This signifi cantly reduced the double handling of cargoes and removed the requirement for warehouse operations to manually bag the cargo for onward transport. The fi rst operation took place in January 2021 and was a resounding success, achieving speeds of approximately 3000 t PWWD and completing a shipment of 20 000 t, bagged and dispatched, within one week.
Previously, the type of truck/trailer available at the time of transport dictated what could and could not flow out of the region. By introducing FIBC quayside bagging, the bags can now be loaded onto bulk, curtain side, or flatbed trucks – tripling the options for transport and mitigating one of the major historical bottlenecks on the transport corridor. The same logistics operator is also effectively reducing the transport of empty bags within the region, a smart cost saving method that is completely unique to the market. The now streamlined process starts by bagging sulfur on the quayside for transport to the mining region, where they subsequently discharge, clean, and reuse the bags for return transport of copper concentrate. A simple solution, leading to major cost savings for the operator and its receivers.
Namibia’s principal port is strategically located and supported by a network of well-maintained roads that extend across Namibia into Angola, Botswana, South Africa, Zambia, Zimbabwe, and the DRC. In addition to accessibility and effi ciency, Walvis Bay is closer to the Americas and Europe than any of the East Coast ports, with Botswana, Zambia, and Zimbabwe having developed dry port facilities in Walvis Bay. The capacity of the port is expected to continue to grow as a result of ongoing investment projects with greater attention required in managing logistics sustainability. By 2025, Namibia is expected to become a logistics hub for the Southern African Development Community, with emphasis on developing dry port facilities and subsequent growth of quayside FIBC bagging.
Another recent bagging assignment undertaken by Nectar Group Ltd involved the discharge and bagging of 12 000 t of rice in West Africa. In this instance, the Group was responsible for handling the bulk discharge of the cargo, bagging into 50 kg and 25 kg, and loading on the client’s trucks. Nectar co-ordinated with the supplier of the cargo, the ships agent, and provided on-site monitoring and daily reporting on the vessel’s discharging operations and post-operation follow up with all parties. A new concept to the client in question, the Group’s involvement produced an impressive reduction in damages and losses saving the client over US$150 000 in costs. The Group’s expertise ensured that the whole process ran smoothly from beginning to end and paved the way for the client to reduce operating and insurance costs substantially on future shipments.
Conclusion
With faster loading and discharge speeds, reduced risk of cargo loss and damage, and several providers now including service guarantees, it is no surprise that quayside bagging has continued to remain popular. 40 years from its invention, quayside bagging is still opening transport corridors and providing signifi cant cost benefi ts to its users. The concept continues to develop alongside global supply chains, with receivers widely utilising the availability of handling equipment to support their operational requirements and subsequently providing opportunities to diversify from the standard 50 kg output to larger bag weights. The result is cheaper bag rates for the end user with savings achieved within a number of aspects of the supply chain.
The versatility of bagging equipment has ensured that many bulk shipments can be discharged and bagged successfully despite challenging markets and port conditions in many locations. The key for successful operations in many cases is down to a wealth of knowledge, experience, and high levels of communication between providers and receivers. With better communication comes a greater understanding of bottlenecks and operational requirements/challenges to mitigate risk and provide end-to-end benefi ts through smarter and streamlined operations, however big or small the project may be.
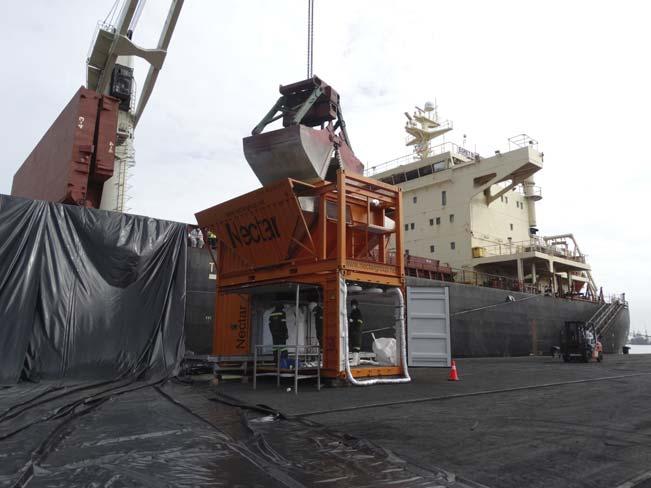
Figure 3. First grab discharge into Nectar bagging machine.
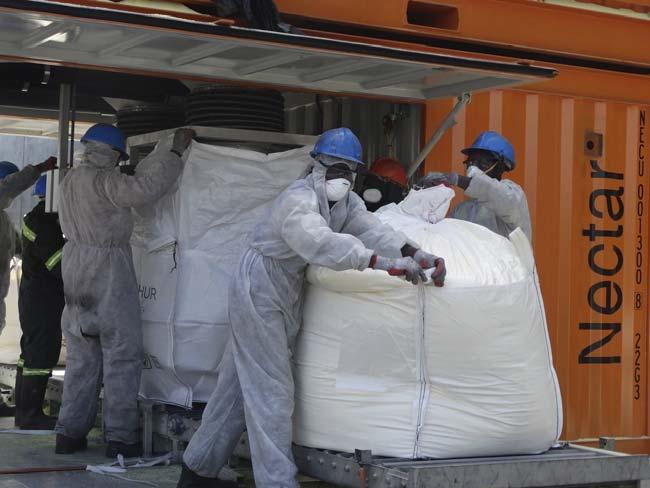
Figure 4. First 1 t bag from Nectar bagging machine.