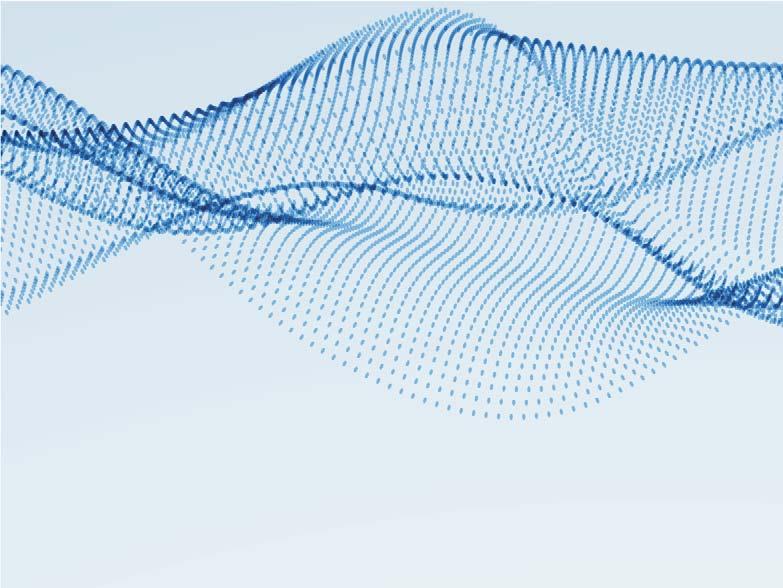
9 minute read
Sounds Of Pure Cleanliness


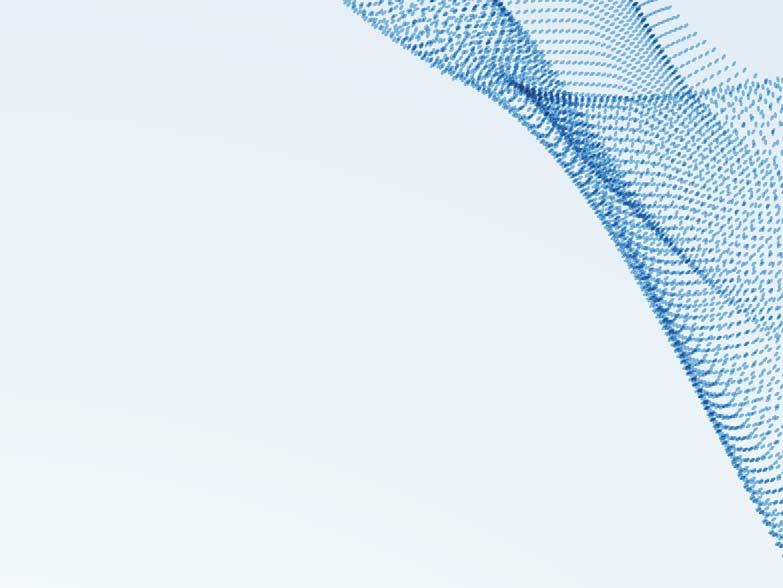
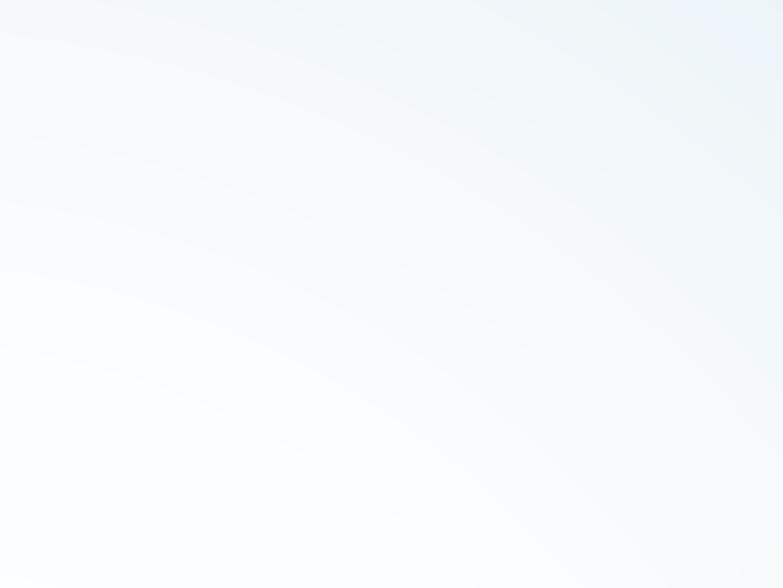
James Swindlehurst, Primasonics, UK, explains how acoustic cleaners can help maintain maximum continuous material flow in many industrial processes including silos and hoppers.

Acoustic cleaners are widely employed wherever ash, dust, and powders are generated, processed, stored, or transported. Primasonics acoustic cleaning systems ranging from 60 - 420 Hz in fundamental frequency have been benefi cial in both preventing material hang-ups and maintaining maximum continuous material flow in a range of industrial processes including silos and hoppers. Indeed, some of Primasonics’ most challenging but successful applications have been within silos which contained dry materials such as cement, carbon black, and fly ash, to name a few common examples. It is important to understand several main advantages that acoustic cleaners have over the alternative cleaning and material handling methods which have been employed to try and aid material flow.
Primasonics’ acoustic cleaners operate at fundamental frequencies much higher than the natural frequency of the silo construction, thus
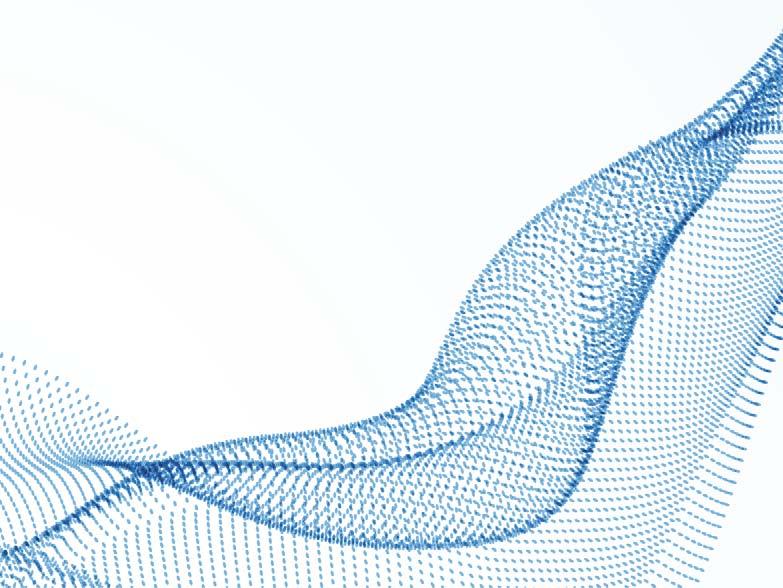
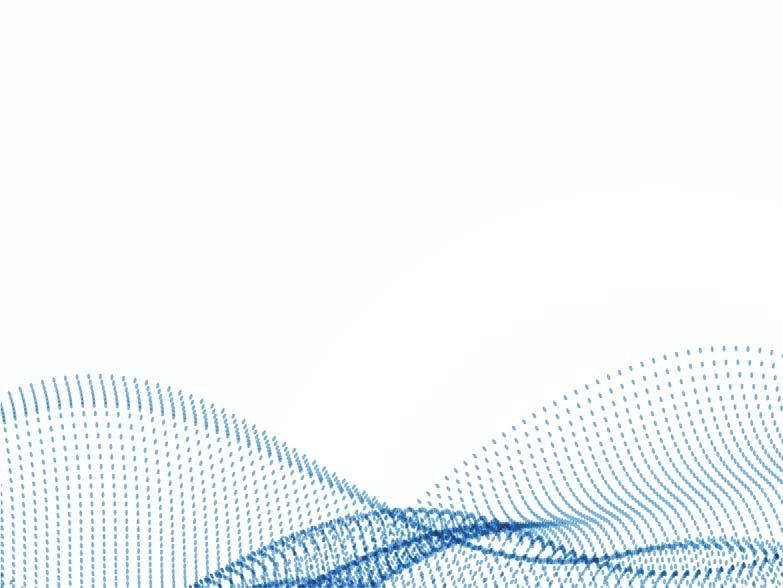

Figure 1. Twin PAS75 on a silo.

Figure 2. Twin PAS75 on a 6000 t cement silo in Haiti.
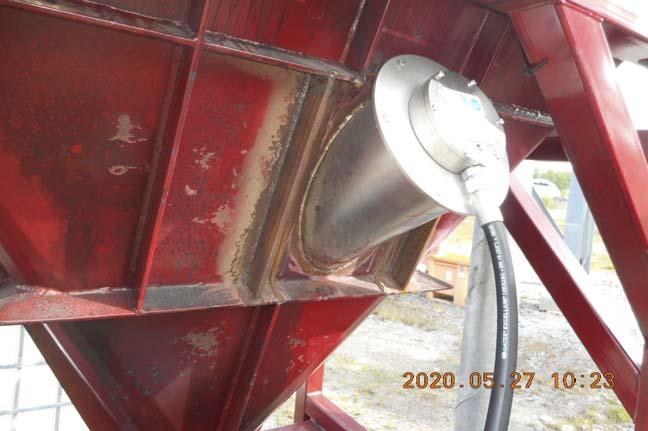
Figure 3. PAS350 housed within mounting tube for bridging hopper. preventing resonance leading to vibrational/structural damage. Instead, sound at an extreme sound pressure level is focussed into the bulk material directly, which is used to break the adhesive and cohesive bonds between the bulk material particles and the walls of the application. This is quite unlike vibrators which by their very nature and method of installation cause vibration and stress weaknesses within the vessel or structure to which they are attached. The vibration resonances from the vibrators first have to pass through the vessel wall before reaching the material. With the acoustic cleaner the sound is not used to ‘drive’ the vessel, with 100% of the sound energy focussed into the material itself.
Air cannons/blasters seek to provide a very localised cure for a blockage problem which has already occurred. In many cases the air cannon simply ‘blows’ a localised hole through the blockage, necessitating the installation of many air cannons within the general problem area. This differs from acoustic cleaning as the problem is approached with an entirely different philosophy – by preventing the build-up from occurring in the first place.
Primasonics’ audiosonic acoustic cleaners aid material flow from hopper and silos in industries including, but not limited to, cement, gypsum, carbon black, MDF and other wood products, chemicals, food, pharmaceutical, and power generation plants. The cleaners are also employed in a range of ancillary plant such as baghouse filters, cyclones, ID fans, ductwork, as well as extreme temperature boiler applications for steam/power generation plants.
How does the cleaning process work in silos and hoppers?
Primasonics’ audiosonic acoustic cleaners have been designed to be simple in their operation, requiring only normal plant compressed air for their initial energy source. Compressed air enters the wave generator and forces the only moving part, the ultra-high-grade titanium diaphragm, to reverberate very rapidly within its specially designed housing. These rapid reverberations set up the standing sound waves which are then amplified from the base tone to the selected key fundamental frequency set by the bell section itself. The current range of models produce set fundamental frequencies between 60 - 420 Hz.
Irrespective as to whether the bulk storage facility is under 500 kg or over 10 000 t capacity, Primasonics’ audiosonic acoustic cleaners can be used to eliminate the three key problems that occur in silos.
The fi rst of these is ‘bridging’, which is caused when the design of the conical section has insuffi cient angle of repose, side walls with excessive frictional properties, or an insuffi ciently sized outlet for the material being contained. Consequently, these problems can become severe if a silo is used for materials different to those it was designed for, either through process or plant layout changes over time.
To combat bridging, an acoustic cleaner is mounted close to the outlet just underneath where the bridge is known to typically form. When the unit sounds, single particles and clusters of particles move at different speeds, therefore causing the bridge to collapse and material flow restored. Once the acoustic cleaner has ceased to sound new bridges will begin to form.
To counter this, the sounding may be controlled in one of two ways, either simply on a timer device typically set for a few seconds every 5 - 10 min. during material discharge only, or alternatively it can be controlled automatically via a flow sensor downstream of the outlet or even from load cells.
The next problem associated with material build-up in silos is ‘ratholing’ or ‘funnel flow’ which, as the name suggests, is material adhering to the side walls causing reduced working capacity within the silo itself. This usually occurs with material that displays mechanical interlocking properties or very quickly bonds without compaction, for example by means of solvent evaporation. To defeat ratholing, acoustic cleaners with a long wavelength are placed on the top of the silo – usually through an available existing manhole or inspection hatch. If there is a large amount of hardened material that has built up over an extended period of time then the silo should be cleaned offline prior to the installation, using a cleaning method such as the GyroWhip system. This is because if an acoustic cleaner were to be sounded in a silo with these thick hardened build-ups, and the adhesion forces between particles were greater than those between the side walls of the silo, there may be a chance that the material be dislodged in slabs and cause an obstruction to the outlet. This is due to the power of the low frequency acoustic cleaners which continue to sound their transmission through the bulk material until the reflective surface of the silo is reached.
If considering a full silo which is prone to ratholing being slowly discharged and emptied, the central core of the material can be imagined lowering a small amount, while an outer ring close to the side walls remain at the same height. Without acoustic cleaning this process would continue until eventually the central core was discharged and the outer ring was left adhering to the side walls. The control engineer must determine whether to remove the silo from active process lines while offline cleaning takes place, or to refill the silo and risk lower control over the quality of product as older adhered material mixes with new material entering.
When using acoustic cleaners, once the central core has lowered slightly, the cleaner will sound and the bonds holding the outer ring of material will collapse. This will form a flat surface along the top of the material in the silo. This pattern is repeated as the silo empties, even if the silo refills before complete discharge has taken place. This now allows a first in, first out mass flow pattern. Again, the acoustic cleaner
SOME THINK THAT RAW MATERIALS EXTRACTION MEANS TRUCK TRANSPORT. WE THINK DIFFERENT.

can be controlled by a simple solenoid valve and timer arrangement or via PLC of central DCS system.
The third area in silos and hoppers where acoustic cleaners can be employed is preventing material batch cross contamination. Considering the example of a weigh hopper, sometimes not all material is discharged before the next batch enters. This can lead to product contamination, which can in turn lead to quality control problems. The reasons for material failing to discharge from hoppers are similar to those already mentioned, but in weigh hoppers or similar batch filled vessels, an additional problem occurs. Material can make contact with cold side walls and moisture precipitates from the bulk material onto the side wall. This moisture forms a meniscus between the side wall and the particles which holds the powder in place so that even after discharge, a thin layer of powder remains. In this instance, the acoustic cleaner is activated when the bin is being emptied, the alternate compressive and rarefactional forces break the surface tension of the moisture and allow this material to flow out, leaving the vessel to completely empty.
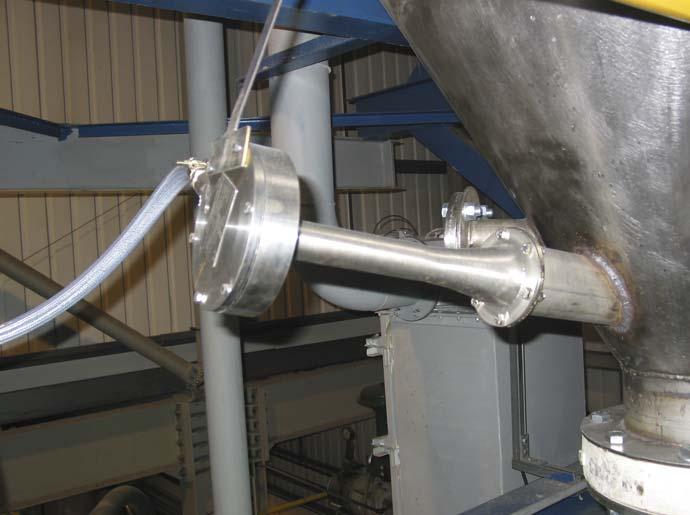
Figure 4. PAS420 mounted at hopper outlet to prevent bridging.
Figure 5. Workers in Mumbai, India, at a cement plant.
Case study
A company involved in the production of carbon black additives was finding it concerning that employees had to enter the inside of a tank to remove the carbon black on the bottom shell of the silo. One of the company’s sites in Hungary has already installed the Primasonics acoustic cleaner model PAS60, thus the plant in question in a different country was also interested in following suit.
The previous cleaning routine carried out by the company involved outside hammering and also manual entry of the silo for cleaning with a scraper.
By implementing one of Primasonics’ acoustic cleaners, the company is able to save on cleaning costs, equating to an annual saving of US$45 000. Furthermore, employees are no longer required to enter the silo for manual cleaning, which is hugely beneficial to the company.
The system
Acoustic cleaners are very easy and simple to install by either using Primasonics’ standard connecting flange, mounting tube assembly, or custom mounting arrangements designed specifically to suit the application. The fundamental frequency and therefore model required along with the quantity are determined on a case-by-case basis, dependent on a number of factors and parameters within the application itself. A dimensional drawing outlining each elevation of the application, along with a specific questionnaire, are requested prior to being able to quote. The possible mounting positions are also taken into account in being able to calculate the unit(s) required for effective coverage.
The acoustic cleaning systems are extremely low maintenance with the only consumable part being an aerospace specification titanium diaphragm, which should provide a minimum of two years of uninterrupted service before requiring replacement. This is then a simple and short task taking approximately 10 min. to remove and replace, and can usually be undertaken while the system remains online with acoustic cleaner isolated.
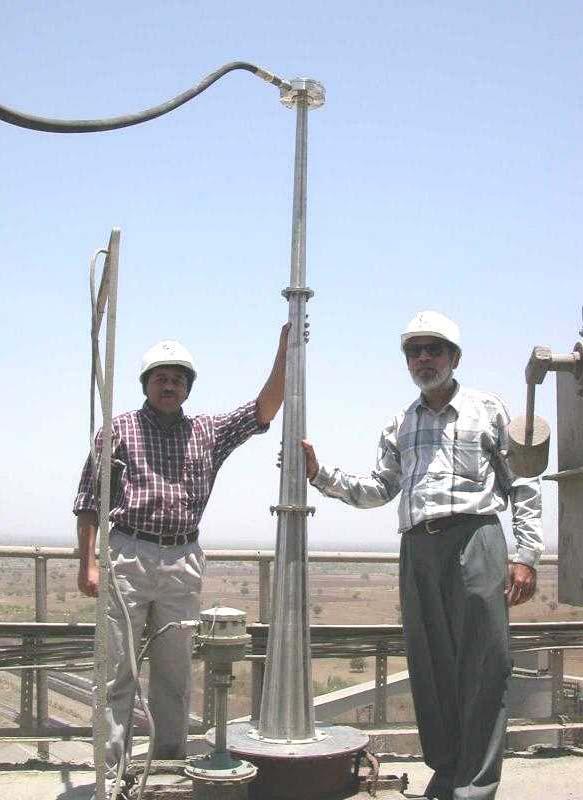