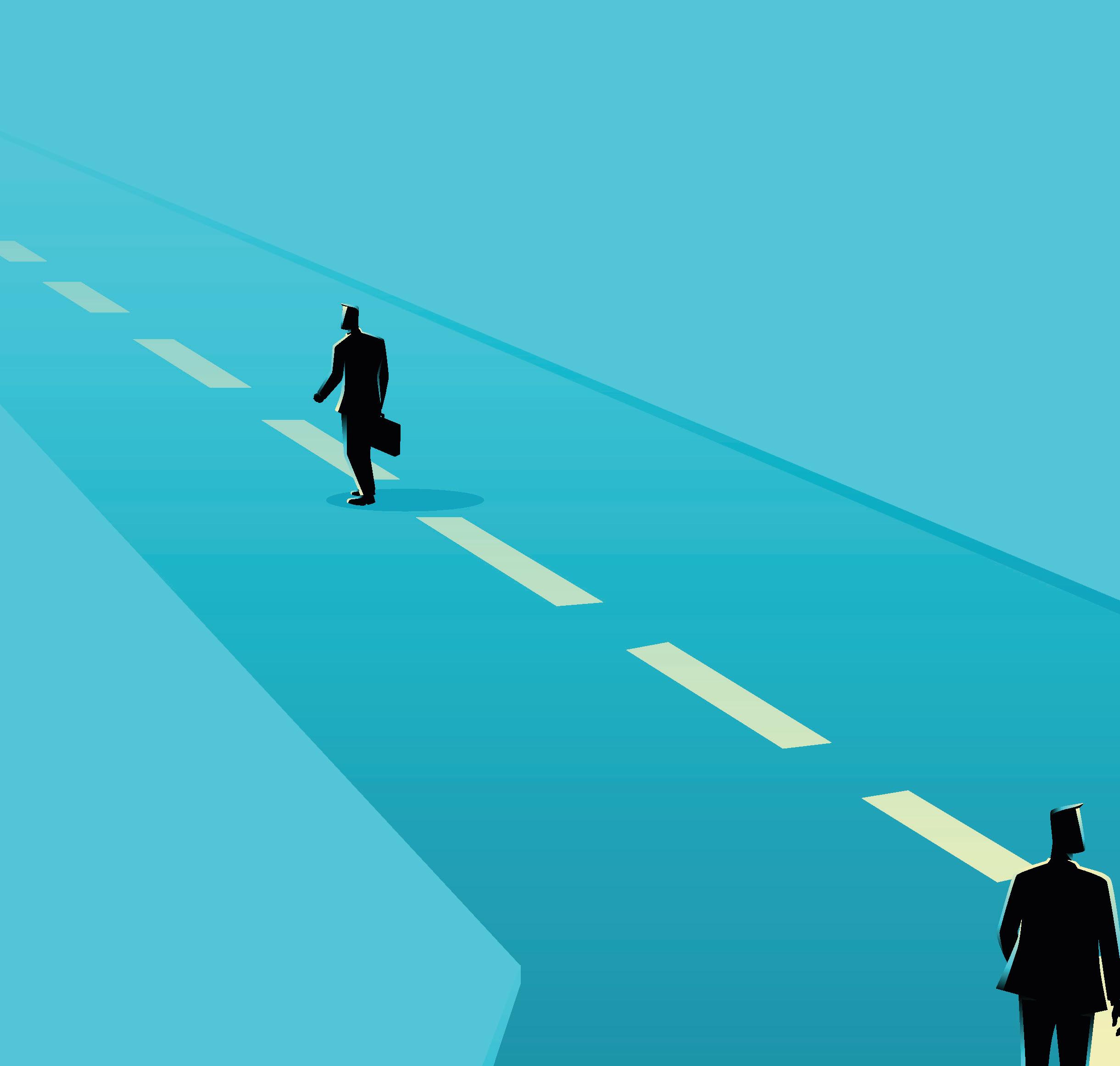
7 minute read
Unconventional times call for unconventional measures
Bryan Holleyman, Extract Production Services, USA, reports on a new permanent magnet electric submersible pump design created for unconventional wells and stricter ESG requirements.
Since the invention of the electric submersible pump (ESP) in 1918, this pump design has been a bedrock of oil production. But, other than some tweaks in design and materials, it has changed little in about 100 years. For a long time this was acceptable.
In conventional wells, decline curves were long and slow, meaning one pump size could work well for years. Wellbore casing remained at 5 1/2 in. – 17 lb/ft, giving the 4.56 in. outer diameter (OD) ESPs plenty of room to operate. And when the times themselves were conventional, there were few concerns about carbon footprints involved in electricity use or steel production for a large piece of equipment.
But the rise of unconventional wells since the early 2000s has created challenges for the standard design. Decline curves that drop precipitously within 2 years require more frequent pump resizing, as standard ESPs have a narrow operating range.
With longer laterals and higher frac pressures requiring thicker, heavier casing too, conventional ESPs began to face efficiency

challenges, as they were required to provide more horsepower in smaller spaces.
Longer and more expensive laterals and completions have also stretched completion budgets at the same time that investment money has tightened. This has led producers to seek ways to obtain faster returns on their investments by boosting initial production ahead of steep decline curves. More powerful and efficient ESPs could help achieve these return on investment (ROI) goals.
Furthermore, gas locking due to low-functioning gas separators has always been the bane of ESPs, wasting energy and overheating pumps and motors to the point of damage or destruction.
Finally, increasing awareness and understanding of climate change and environment, social and governance (ESG) issues since 2019 – 2020 has required the oil and gas industry to find ways to reduce its carbon footprint from the drill pipe all the way to the tail pipe. A substantially new ESP design became a glaring need.
Something needed to change
During the downturn of 2015 – 2016, David Zachariah (now Extract’s Chief Technology Officer) began to see producers move to survival mode. They were cutting drilling costs by drilling fewer wells, but those they did drill had longer laterals to expose the site to more producing rock. Those longer laterals required higher frac pressures. To accommodate those pressures they thickened casing walls, using 5.5 in. 20 lb/ft and 23 lb/ft types instead of the older 17 lb/ft variety.
Since the OD remained at 5.5 in., making the casing heavier had the effect of reducing its inner diameter (ID). This, in turn, required ESPs to be reduced to 3.75 in. diameter instead of the previous 4.56 in.
At the same time, the longer laterals required more horsepower to increase the flow from the greater exposure to the producing zone. The maximum power that can be squeezed from a 3.75 in. motor is approximately 108 hp – significantly less than the 260 hp available from the 4.56 in. motor. Up to three of the slimline 3.75 in. motors can
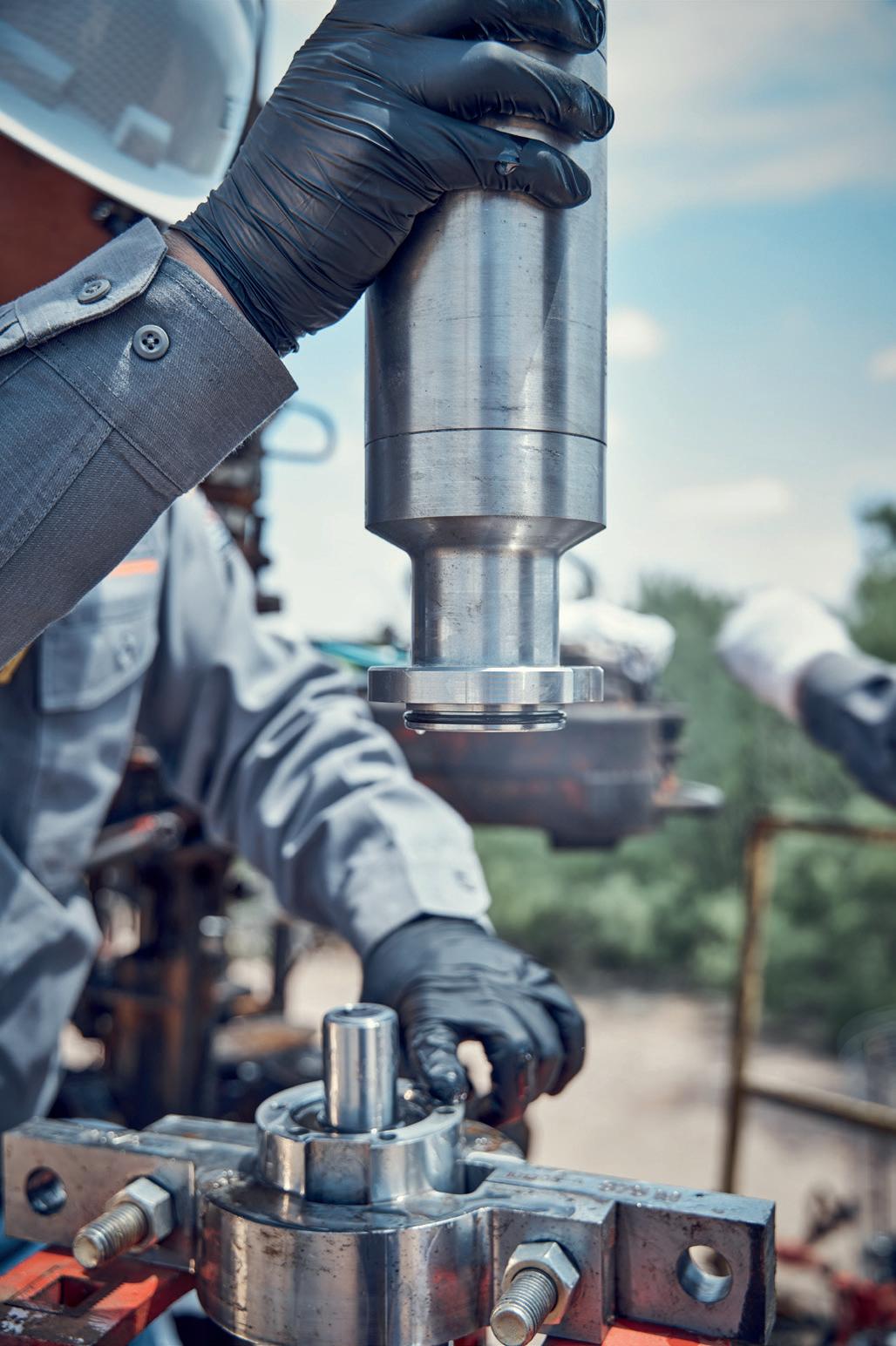
Figure 1. The SpeedFreq’s smaller size means it can be installed quickly onsite.
Something had to give
Some companies that tried shaving down the housing and back iron of a 4.56 in. induction motor experienced more loss of speed through slippage. This required more stages to achieve the needed results, which added expense, used more steel and ultimately required more horsepower.
In searching for a different solution, Zachariah and his associates landed on a modular permanent magnet motor design that would create more than 400 hp in the smaller 3.75 in. size. With this development, a decision was made to start Extract Production. The company’s first step was to manufacture and sell standard ESPs to create cash flow for developing the high-speed permanent magnet motor now known as SpeedFreq.
After 3 years of development the first field trials were rolled out in the autumn of 2019.
Basic design features
The use of permanent magnets allows the SpeedFreq system to deliver up to 10 000 rpm and 400 hp from a package that has a diameter of 3.75 in. and is less than 50 ft in length, as opposed to 3500 rpm from 170+ ft for standard ESPs. With a bottom speed of 3000 rpm, it can accommodate greater decline curves without the need for re-sizing.
This short length has the effect of better accommodating wellbore variations in deeper wells. Ì Other advancements include: Uses 20 – 35% less power than induction ESPs. Ì Arrives onsite ready to install rather than in multiple sections, saving time.

ÌGas separator operates at 75% efficiency and up to 95% in some cases. This means less gas locking, less opportunity for pump cavitation and damage and longer run-life.
Most importantly, the higher horsepower and high-speed capability helps operators realise greater early production returns when bottomhole pressures begin to drop.
ESG design
Reducing the carbon footprint of production is becoming more important – and more possible as research continues. The system reduces this type of carbon footprint in the following ways: Ì Uses 75% less steel than equivalent slimline induction ESP units. Steel production accounts for 7 – 9% of greenhouse gas emissions, according to the World Steel Association.1 Ì Smaller size and fewer components means less fuel expended in logistics and inventory handling – lower tailpipe emissions from fewer miles/trips (Figure 1). Ì Uses up to 35% less electricity per barrel than standard
ESPs. Figure 3. Power use comparison: SpeedFreq versus induction ESP.
Table 1. Power usage comparison Unit Average KW usage Average bpd Depth KW/bbl/1000
Induction 200 3194 7050 0.213
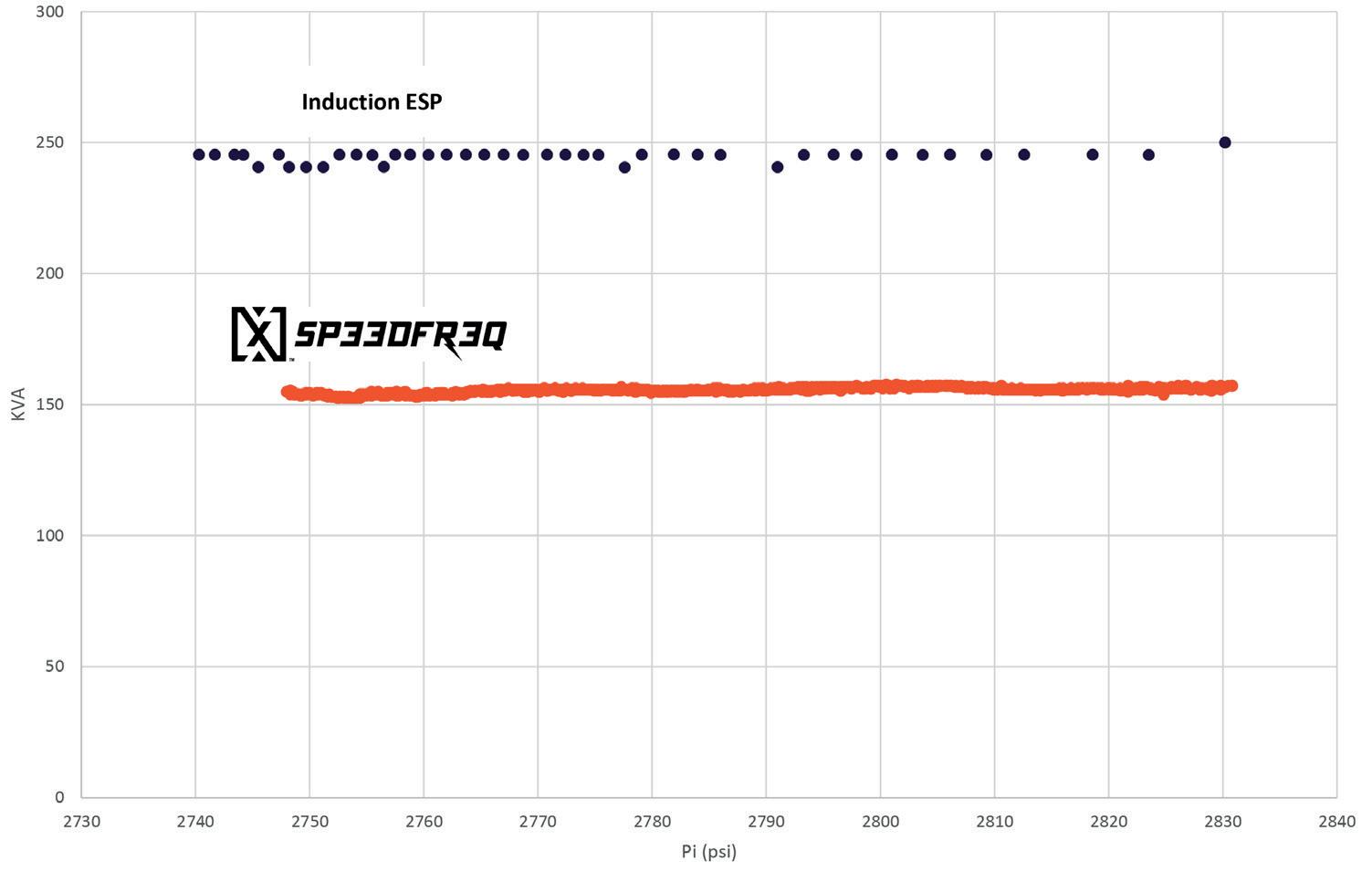
Case study: energy consumption reduction
Basing the SpeedFreq motor on permanent magnets allows the unit to deliver more power with much less equipment than is required by standard ESPs (Figure 2). A conventional ESP’s equipment includes six pumps, two gas handlers/separators, two protectors and two or more motors. On the other hand, the SpeedFreq includes a single pump and gas separator, two seals and one modular motor capable of up to 400 hp at 10 000 rpm.
In 2020 a customer in Texas’s Permian Basin installed the unit alongside a conventional induction unit in a well on the same pad, then compared power usage between the two. For starters, the unit was installed 4.5 hours faster than the conventional pump.
Because the wells were in the same formation, on the same pad and of similar depths and flow rates, the test was expected to provide useful information. Figure 3 shows the power consumption comparison at similar pump intake pressures.
And, as shown in Table 1, Extract converted KVA into KW usage by utilising the efficiencies of each motor at load. This shows the difference in KW usage, normalising for minor differences in production rates and depths.
By converting consumption into a metric for the kilowatts required to lift a single barrel by 1000 ft, Extract demonstrated that SpeedFreq consumed 35.2% less power than an equivalent conventional unit. At US$0.06/KWh, the power savings are close to US$2800 per month and US$33 600 per well on an annualised basis. Exact savings will vary with changes in power costs, and the percentage may vary by field.
Case study: greater upfront production through high-speed operation
With development and completion costs skyrocketing, producers find themselves needing a faster return from each well. SpeedFreq’s motor and horsepower output help speed upfront production by sustaining higher production rates longer as bottomhole pressure declines.
In early 2021, a producer evaluated the unit’s production capabilities in a declining well after replacing a competitor’s induction unit.
The previously installed unit’s production had dropped significantly over its final 7 days in use. That pump showed signs of reaching Q-min, where a pump can no longer draw down bottomhole pressure and sustain production rates.
On its last day this previous pump’s intake pressure was 1863 psi, producing 2846 bpd of liquid and requiring 250 brake horsepower (bhp).
Once the SpeedFreq was optimised for the well, it reached similar pump intake pressure while boosting liquid production to 3541 bpd, a 24% increase. The bhp required was 200 hp, a 20% reduction. The company continues field testing to further confirm these results.
SpeedFreq 133 3218 7170 0.138
Conclusion
Financial realities and ESG requirements are pushing unconventional producers into ever more unconventional situations, which standard equipment and procedures struggle to fulfill. The days of small tweaks and updates are quickly disappearing. New thinking and ground-up redesigns of many processes and machines will be necessary for the oil industry to survive and thrive.
Reference
1. World Steel Association, ‘Steel’s Contribution to a Low Carbon Future and Climate Resilient Societies’, https://www.worldsteel.org/en/dam/ jcr:c4532192-07eb-43ba-955c-cec8aead6763/Climate+Change+Position+Pa per+FINAL+WEB.pdf, p. 4.