
4 minute read
Meeting the challenges of the Haynesville
Donya Blakney, Drilformance, USA, outlines the impact that meaningful pairing of bit design and cutter geometry can have on drilling performance in over-pressured shale plays such as the Haynesville.
As the shale market continues to accelerate, so does the need for drilling technology development to keep up so that performance can be optimised and operator costs reduced.
Over-pressured shale plays, such as the Haynesville in the US, present a unique challenge. High mud weight and elevated temperatures can wreak havoc on downhole tools, increasing the risk of unplanned trips and non-productive time (NPT). Choosing the proper drill bit and complementary bottomhole assembly (BHA) to address these challenges can provide notable gains in performance. Bit design and ‘fit-for-purpose’ cutter geometry affect bit response. The bit response must be understood in order to identify the appropriate motor configuration and torque output. Meaningful pairing of these two BHA components ensures success.
Drill bit platform
The Badger Drill Bit Platform presents three drill bit options to target specific requirements within the application. Design elements include Badger cutters, TruSteer cutters, TruSteer back rakes, a gauge design that enhances lateral stability and hole quality, blade stand-off and a nozzle placement that increases hydraulic efficiency. Operators have used the platform on over 75 runs.
Cutter technology
The Badger cutter is designed for operators drilling over-pressured shales. The cutter’s relieved face geometry is more sensitive to weight on bit, providing better point loading and shearing capability in high mud weight applications. The relieved cutter face reduces the confining pressure of the formation more effectively than a flat face or wedge style cutter. The geometry also reduces friction along the cutter face, changing the cutting’s structure and resulting in faster cuttings evacuation and reduced heat generation at the cutter tip. Lower temperatures

Figure 1. Badger cutter.
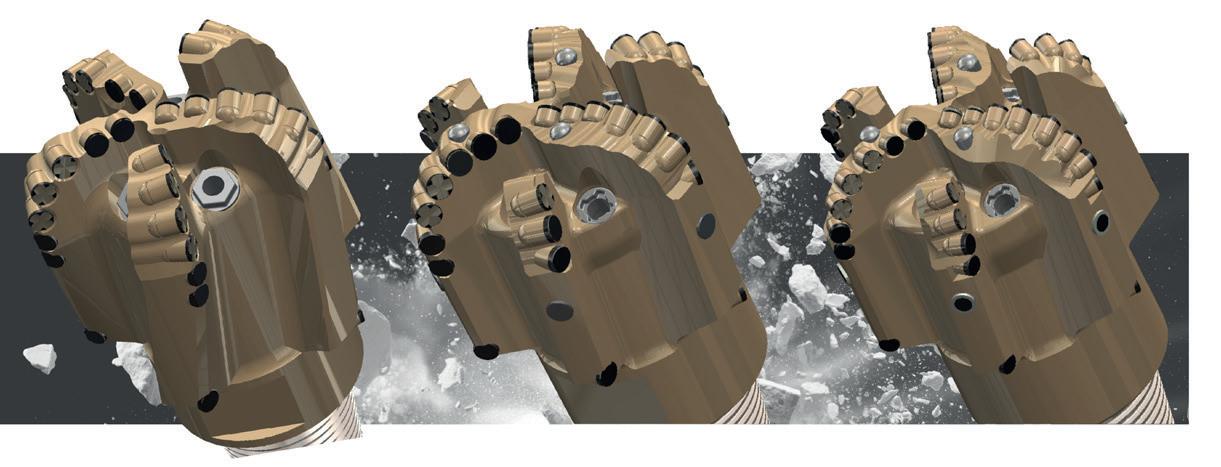
Figure 2. Badger Bit Platform 6.75 in. DF513, DF613, DF611.
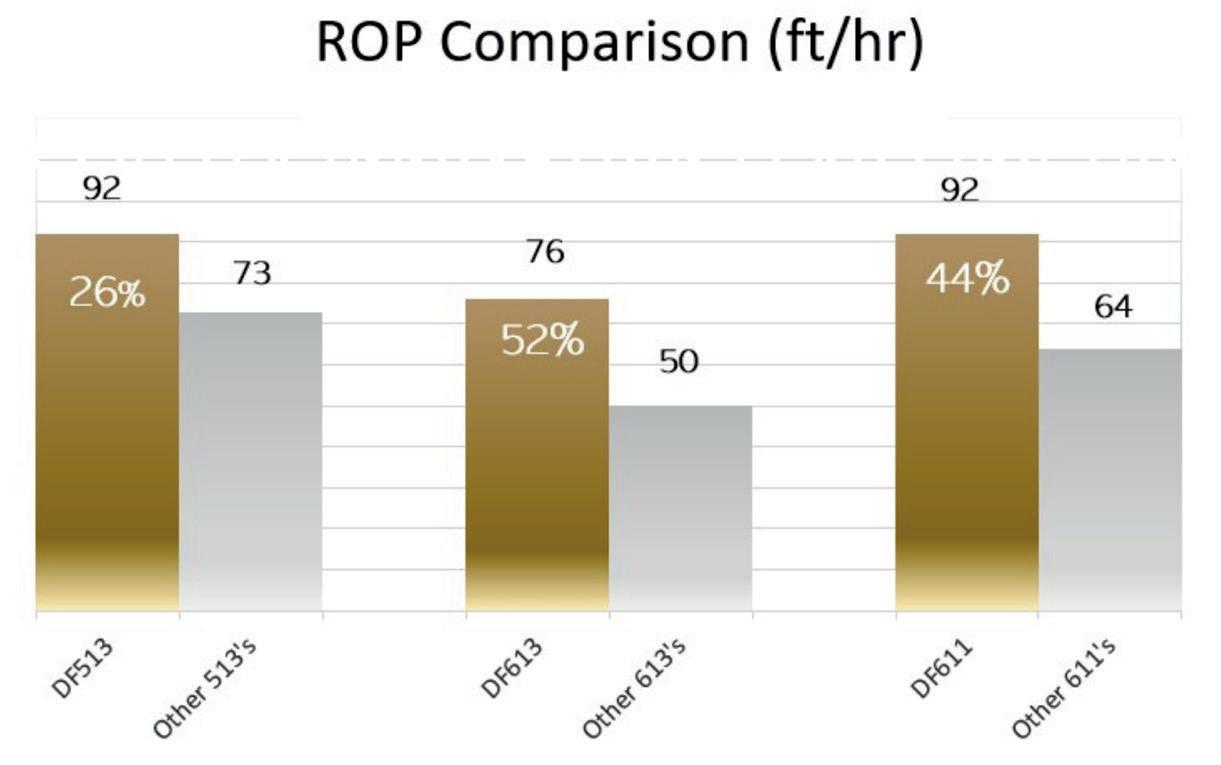

at the cutter/rock interface mean reduced thermal degradation and wear.
TruSteer utilises a bimodal geometry that effectively shifts a portion of the rock failure mechanism from a shear failure to that of a compressive failure. When combined with TruSteer bit design elements, the result is improved tool face control and reduced torque fluctuations while sliding, resulting in higher slide and overall rate of penetration (ROP) without compromise.
Traditional tool face control mechanisms typically involve overly passive back rake schemes and secondary torque control features that occupy critical blade top area and limit junk slot area. TD cutters are effective with more aggressive back rake angles. These features offer directional drillers the ‘best of both worlds’ in the pursuit of responsive build rates and high rotating and sliding ROPs. Operators using the Badger Bit platform have reduced slide time in the lateral to less than 5%.
Performance results
The DF611 and DF613 are designed to maximise build rate capability but continue to drill the lateral effectively. When a trip is required, the more aggressive DF513 can be run to complete the interval. However, all three designs have been proven in both the curve and lateral.
A recent DF613 run drilled the curve and lateral utilising the Drilformance Haynesville motor. After drilling 8329 ft at 110 fph, the bit was tripped due to a measurement-while-drilling (MWD) failure and was dull graded a 0-0. The operator then picked up another manufacturer’s 613 and motor to complete the lateral. This second BHA drilled 3253 ft at 40 fph. The bit was pulled and dull graded a 2-2.
Haynesville motor
A motor with a 5.5 in. outside diameter (OD) can be used in order to provide higher torque and flow rate. This OD size can, however, inhibit hole cleaning, potentially create higher drag and present geometry challenges while drilling build sections. In the high temperatures of the Haynesville, the actual operating specifications are reduced. The company’s Haynesville motor is offered in a 5 in. or 5.25 in. OD. The system’s hybrid transmission and proprietary radial and thrust bearing design allows for reliability and longevity in a smaller package. In addition, the motor provides 8.7% faster revolutions per gallon and a maximum flow capability that is 14.3% higher.
Conclusion
All rock removal begins at the drill bit. In an over-pressured formation, the drill bit should complement the mud motor to fracture rock with optimal depth of cut to maximise rock and cuttings removal. This is achieved with collaboration when designing the motor configuration and drill bit. Bit design and cutter geometry, along with motor speed and torque output, are crucial variables to consider. Meaningful pairing of these two BHA components ensures greater control, less sliding and higher ROP. Choosing the proper drill bit, complementary motor and BHA design for a specific drilling environment provides significant performance improvement.
Advertising with us
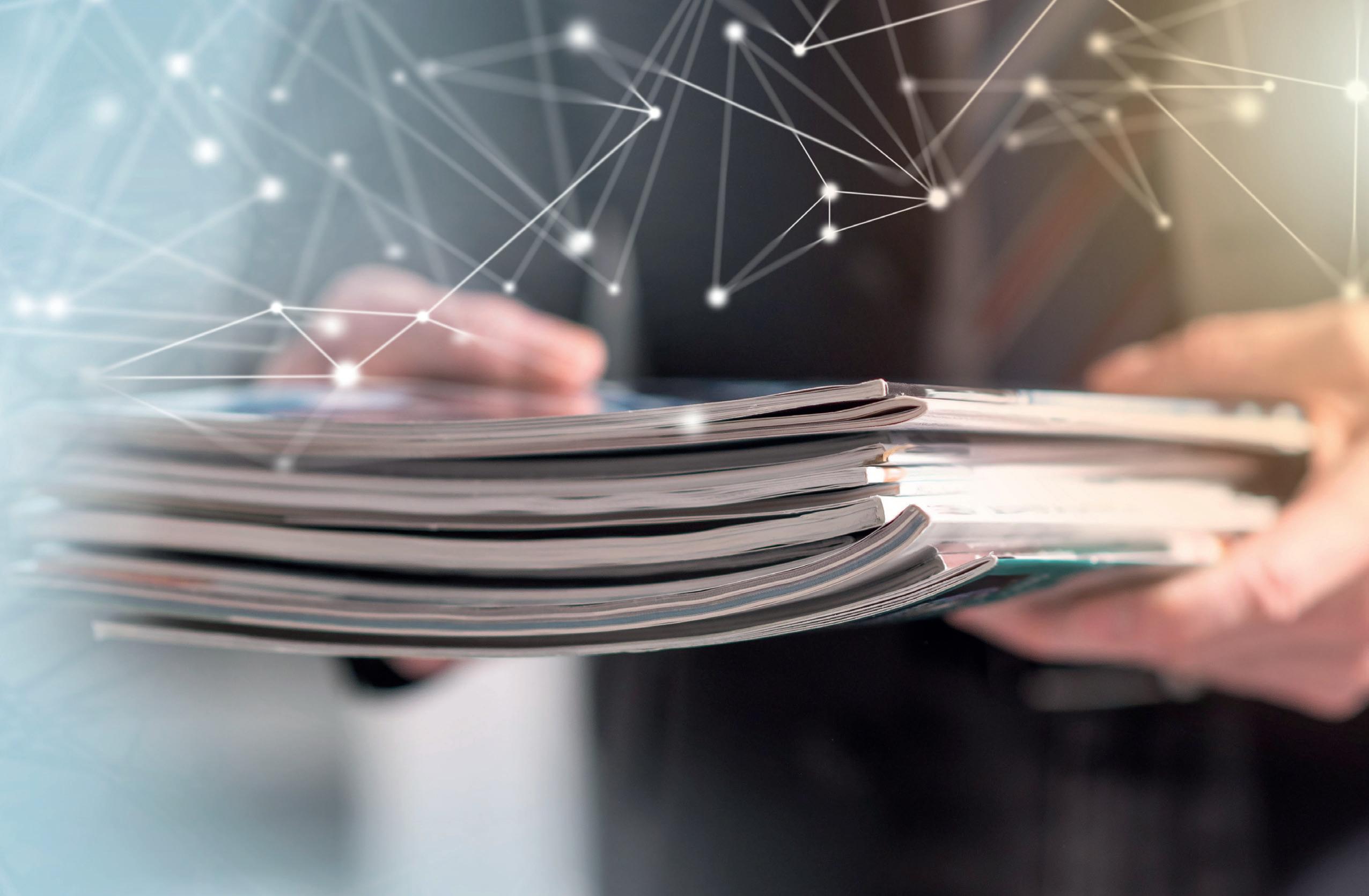
Learn more about our advertising opportunities
• Brand exposure • Lead generation • Premium packages
