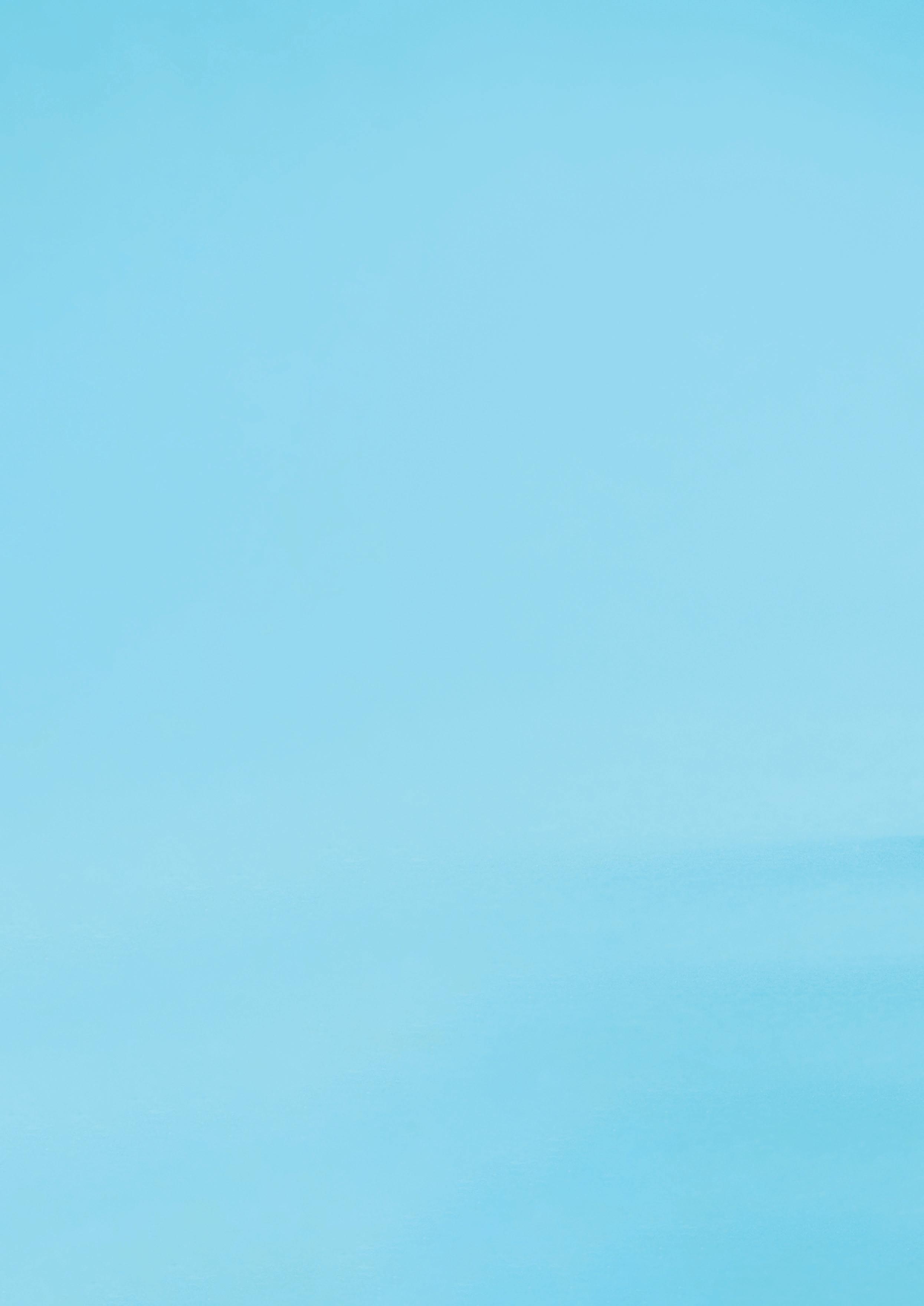
9 minute read
Increasing the value of deepwater wells
Kenneth J. Kotow, Steven M. Rosenberg, Nitin M. Kulkarni and
James P. Wakefield, Subsea Drive LLC, USA, explain how deepening the structural casing in the riserless section using casing drilling can lead to improved well integrity and economics.
Asignificant improvement in deepwater well integrity and value can be accomplished by deepening the structural casing creating its dual functionality. This results in the structural casing providing both axial and bending loading requirements and having a stronger casing shoe strength to drill any subsequent shallow drilling hazards. This, in turn, reduces at least one casing string in the riserless section to place the high-pressure wellhead housing (HPWH) casing significantly deeper than is possible with conventional methods. The result is fewer casing strings to reach planned well depths with placement of larger casing diameters with larger annuli deeper than current practice allows (Figure 1). This improves the likelihood of attaining the deepwater well objectives by enabling larger drilling operating pressure windows to minimise the risks associated with the loss circulation/well influx cycle.
The method proposed for deepening the structural conductor is casing drilling technology utilising the Subsea Drive Casing Drilling System. Casing drilling technology facilitates drilling casing to deeper depths than are currently possible with the practice of jetting, while mitigating the hazards of shallow drilling with a single trip.
Casing drilling on land or offshore is not new, having been applied frequently to improve drilling operations through greater drilling efficiency and mitigation of drilling hazards. However, casing drilling has never been used in a subsea environment since the technology was not available. Subsea Drive, LLC has developed the concept to deepen the structural casing to improve deepwater well design, using casing drilling as the means to achieve the objectives.
The deepened structural casing is part of a specially designed system – which includes casing with high torque capacity connections, casing bit, cementing inner string and a running/drilling tool – called the Subsea Drive. On top of the casing of this system is the low-pressure wellhead housing (LPWH), which is out of the torque path. This system is run on drill pipe to the seafloor with rotation
provided by the rig’s top-drive, drilling to the required depth of approximately 1500 to 2000 ft below the seafloor. This is much like a liner installation, due to the depth of the water being greater than the casing string.
Drilling continues with circulation of the drilling fluid as in current riserless operations through the drill pipe, cementing inner string and returns on the outside of the casing to the seafloor. This technique uses a sacrificial ‘heavy’ drilling fluid with returns to the seafloor in a process known as ‘pump and dump’. This is a dual gradient operation of the heavy mud in the annulus and the seawater above. The density of the heavy drilling fluid is determined for the dual gradient drilling density to be slightly higher than the prevailing pore pressure. It has been established by global casing drilling experience that if the casing diameter is about 80 to 90% of the hole diameter the narrow annulus created is ideal for plastering and grinding the drill cuttings into the wellbore as they are circulated up to the seafloor. This phenomenon mitigates shallow hazards, such as gas and water flows, by decreasing the effective permeability in the wellbore area. The ‘plastering effect’ increases wellbore formation strength, mitigating wellbore instability which is prevalent in the shallow offshore formations.
The principal benefit of this well design approach of significantly deepening the structural casing, the first casing, beyond current practice is decreasing the total number of casing strings required to reach planned depth. This allows for larger casing-to-formation-annuli, which increases the drilling operating pressure window between pore pressure and fracture pressure gradients. Deepwater environment operating pressure windows are narrow, causing significant drilling problems and often leading to failure to reach well objectives. A secondary, but also valuable benefit is the improvement in drilling efficiency, since fewer casing strings equals less rig operating time, with casing drilling technology the means to mitigate shallow drilling hazards.
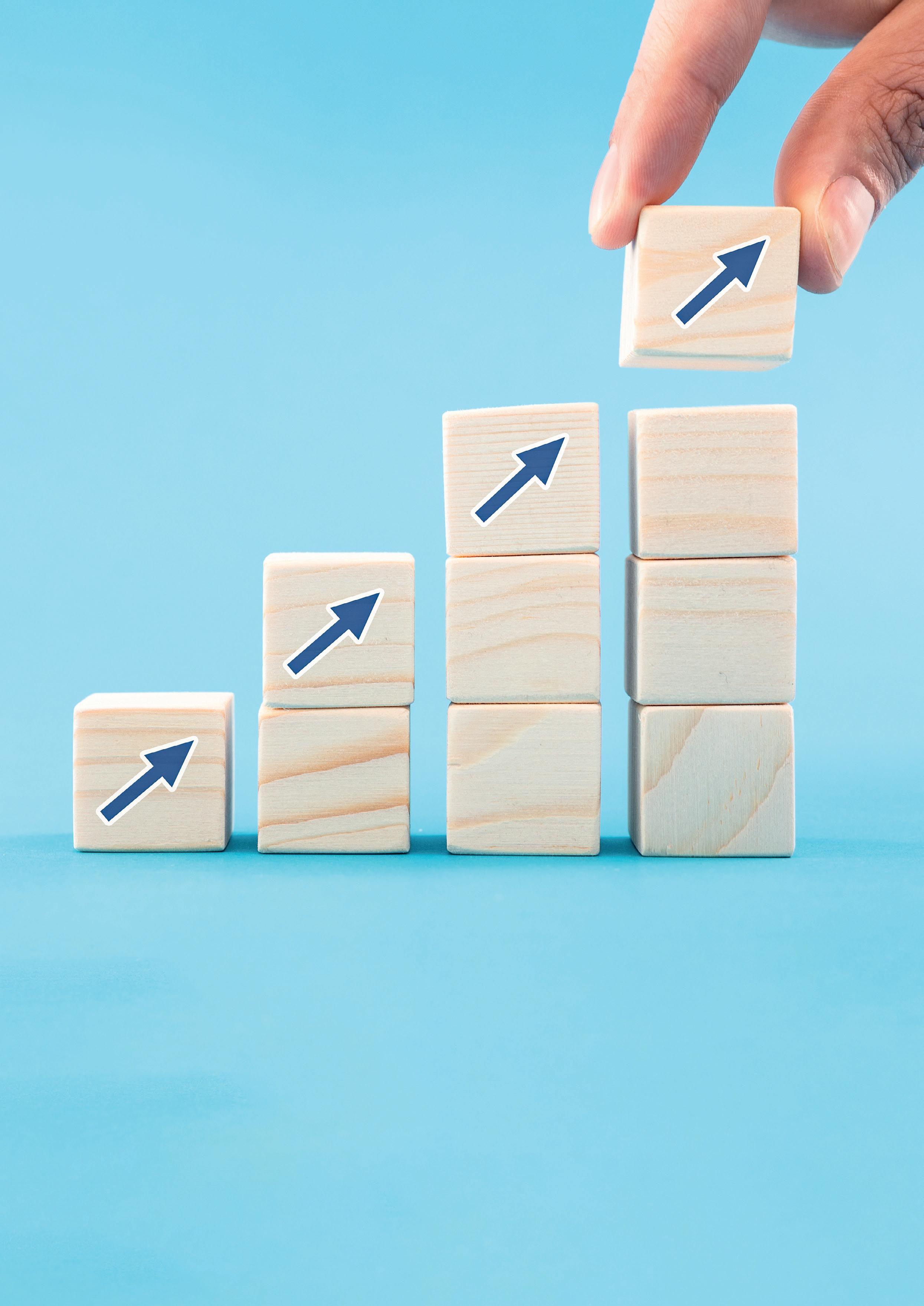
The application of casing drilling in the riserless sections has the following advantages: Ì Facilitates simultaneous drilling and running the structural casing to significantly deeper depths. Ì Improves drilling efficiency by drilling and running casing in a single trip. Ì Wellbore strengthening. Ì Mitigation of shallow drilling hazards with a single trip. Ì Better cementing and zonal isolation, as casing can be cemented immediately upon reaching setting depth.
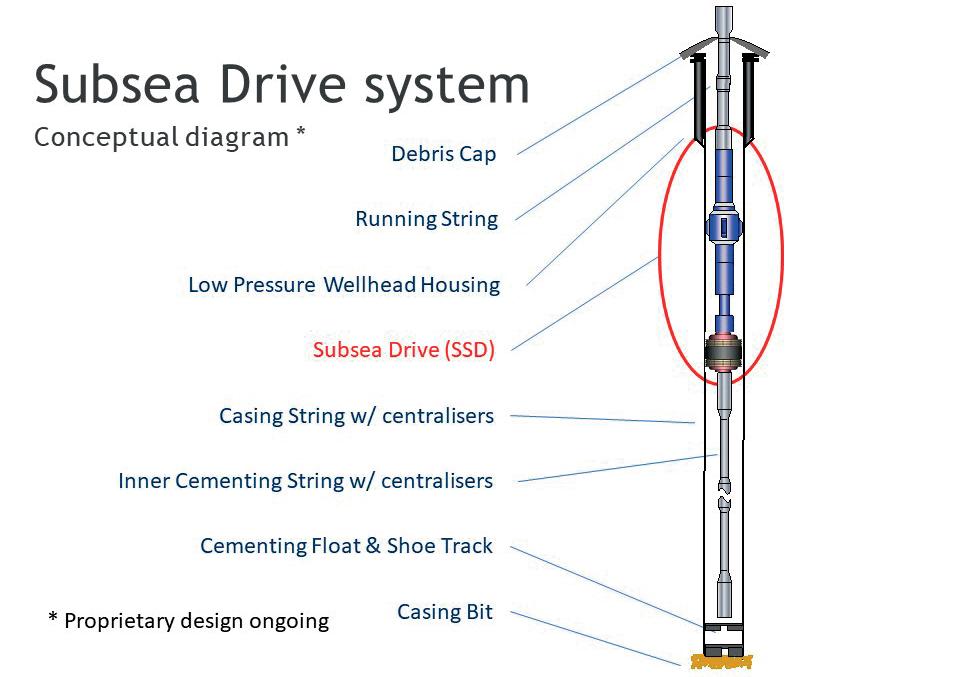
Figure 1. Reduction of casing strings.
Figure 2. Subsea Drive system.
Conventional drilling practices are not suitable for drilling and casing offshore shallow formations due to inherent wellbore instability, which does not allow enough time to drill and then run and cement the casing; there is high potential for hole collapse. Drilling with casing mitigates the wellbore instability and allows for immediate cementation upon reaching casing setting depth, thus eliminating the time off bottom where hole instability is problematic. The easily drillable nature of offshore shallow formations lends itself well to the application of casing drilling and the use of PDC drillable casing bits. It is the soft and unconsolidated nature of the shallow offshore and deepwater environments that made the jetting practice common for placement of the first casing. However, it has a technical limit of between 200 to 300 ft below the mudline for penetration. It is this shallow setting that is an impediment to deepwater well design improvement as proposed by Subsea Drive, LLC. It is hoped that the Subsea Drive system, using casing drilling, will replace jetting as the industry standard.
Wellbore strengthening
Wellbore strengthening resulting from casing drilling is a well-known phenomenon, sometimes called the smearing or plastering effect. There are many examples illustrating the quantitative value. One such example is in the Alaskan Kuparuk field, which clearly indicates a significant increase in effective fracture gradient from 12.7 ppg before to 14.4 ppg after casing drilling. This phenomenon can mitigate or prevent circulation losses while drilling and cementing. It has been estimated that formation strengthening is most effective when the ratio of casing to hole diameter is approximately 0.8 to 0.9.
Mitigation of shallow drilling hazards
Rotating the casing while drilling has significant advantages for mitigation of drilling hazards such as shallow water and gas flows, gas hydrate flows and wellbore instability. The smearing or plastering effect caused by the rotation of casing grinds and smashes the return drill cuttings into the wellbore, hardening the wellbore and plugging off permeability to mitigate loss of circulation, shallow water and gas flows – improving wellbore stability. Once the drilled casing reaches the required casing setting depth the cementing operation is initiated immediately.
Better cementing and zonal isolation
Cementing the conductor and/or surface casing strings in regions of shallow water flow is potentially one of the biggest challenges of deepwater drilling. During the transition stage, the hydrostatic pressure of the cement slurry can decrease to the density of mix water. This reduction in hydrostatic pressure can allow water and gas from geopressured zones to flow and disturb the cement before it sets up, causing uncontrolled flows of massive amounts of formation water to the seafloor. The wellbore strengthening from the casing drilling smearing
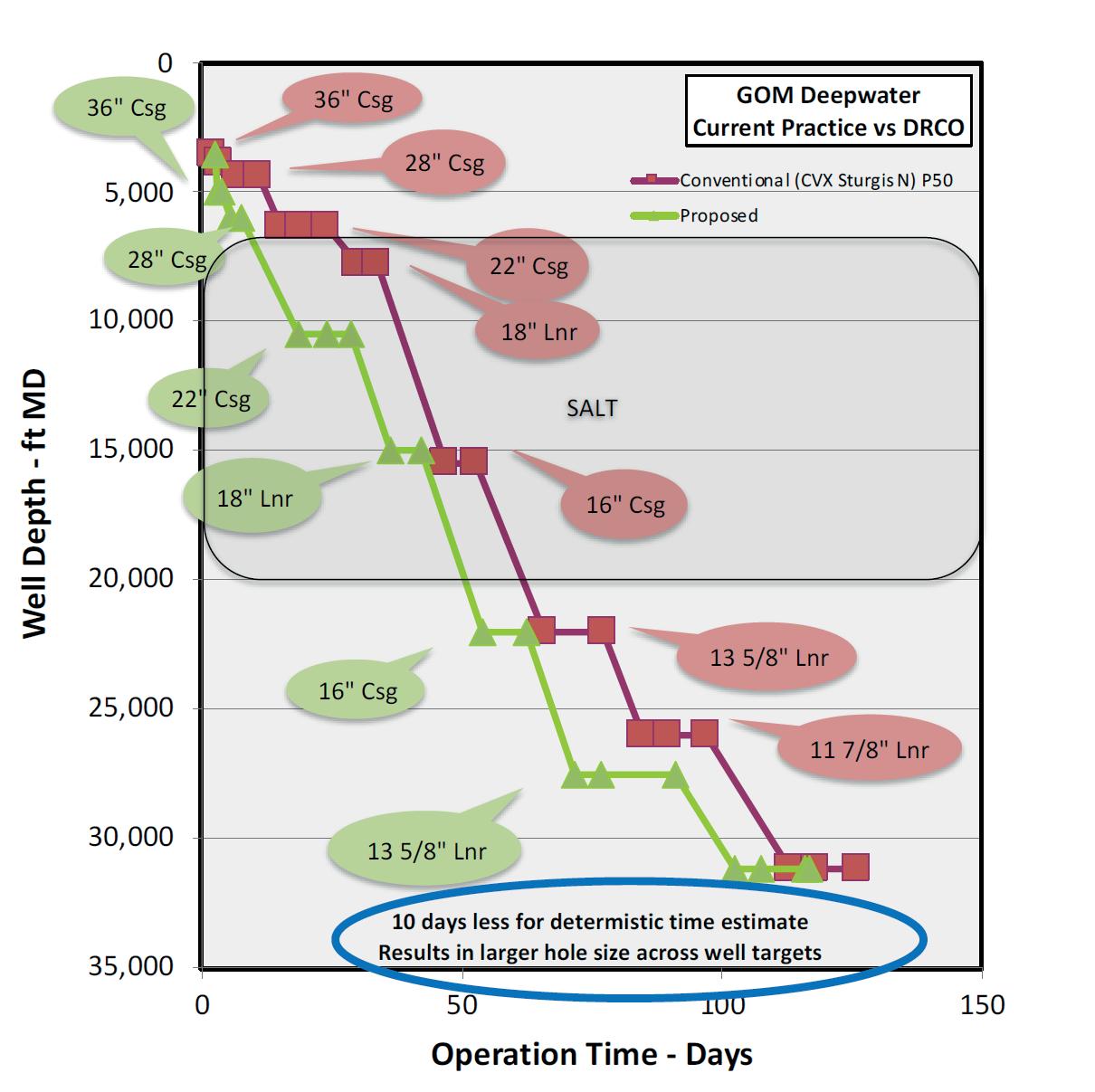
Subsea application
The use of casing drilling for the installation of the deepwater structural casing is an innovative application of this proven technology in the subsea environment. The technology will support the axial loading requirement for the 800 000 lbs structural casing and is capable of applying more than 50 000 ft-lbs of torque to rotate the casing for drilling. The casing would be run like a liner on drill pipe with a purpose-built subsea drive tool. This subsea drive tool allows the use of existing LPWH systems without any modifications, since the tools inserts engage the structural casing internally below the LPWH. This takes the wellhead assemblies out of the torque path. The casing is drilled to the depth placing the LPWH just above the seafloor. This system uses a custom-built PDC casing bit, in which the bit’s drill-out path is made of PDC drillable material for easy removal with a PDC or roller cone bit that is suitable for drilling the next hole section. A dedicated drill out trip is not required.
Due to the large casing volume, an inner string is required to efficiently circulate the cement in place once drilled to planned depth. Subsequent hole sections could be drilled as per current practices by drilling through the casing bit or with continual use of the subsea drive tool with a bottomhole assembly (BHA) inner string. This would be similar to current casing drilling practices. The concept of the system is illustrated in Figure 2, indicating the main required components and functionality of the assembly. This technology is an extension of existing casing bit and casing running technology, allowing for easy adaption by the industry to a subsea riserless drilling environment.
The deepwater Subsea Drive system will be deployed from existing floating drilling rigs to be run in a manner similar to current liner deployment methods. Once the first structural casing is drilled into place and cemented, the drilling operation will continue with current conventional practices to set each subsequent casing as per the pore pressure and fracture gradient environment.
Conclusion
The current limitation of structural casing setting depth is predetermined by the jetting practice, which is at its technical limit for setting depth. Subsequent riserless casings are set above shallow geological hazards for the utilisation of sufficient drilling fluid density for mitigation of shallow geological hazards (e.g. shallow flows, faults, wellbore instability) in the riserless interval. This practice in itself is self-defeating. The deepwater well design is based upon the ‘Top-Down’ casing design approach, where the diameter and setting depth of the first casing determines the number of subsequent casing strings and the resulting diameter of the wellbore annuli. The deeper the first string is set, the fewer casing strings are required and the wider the drilling operating window becomes.
The proposed casing installation process takes advantage of the rapid increase of the overburden and fracture gradients of shallow formations, allowing for the optimisation of riserless casing seats with casing setting depths predicated on pore pressure and fracture gradients.
The result is fewer casing strings, larger wellbore (casing/annular) geometries with lower equivalent circulating densities, leading to a higher probability of reaching well objectives with improved well economics.
Review new trends and technologies
Download technical white papers for free from companies across the upstream industry
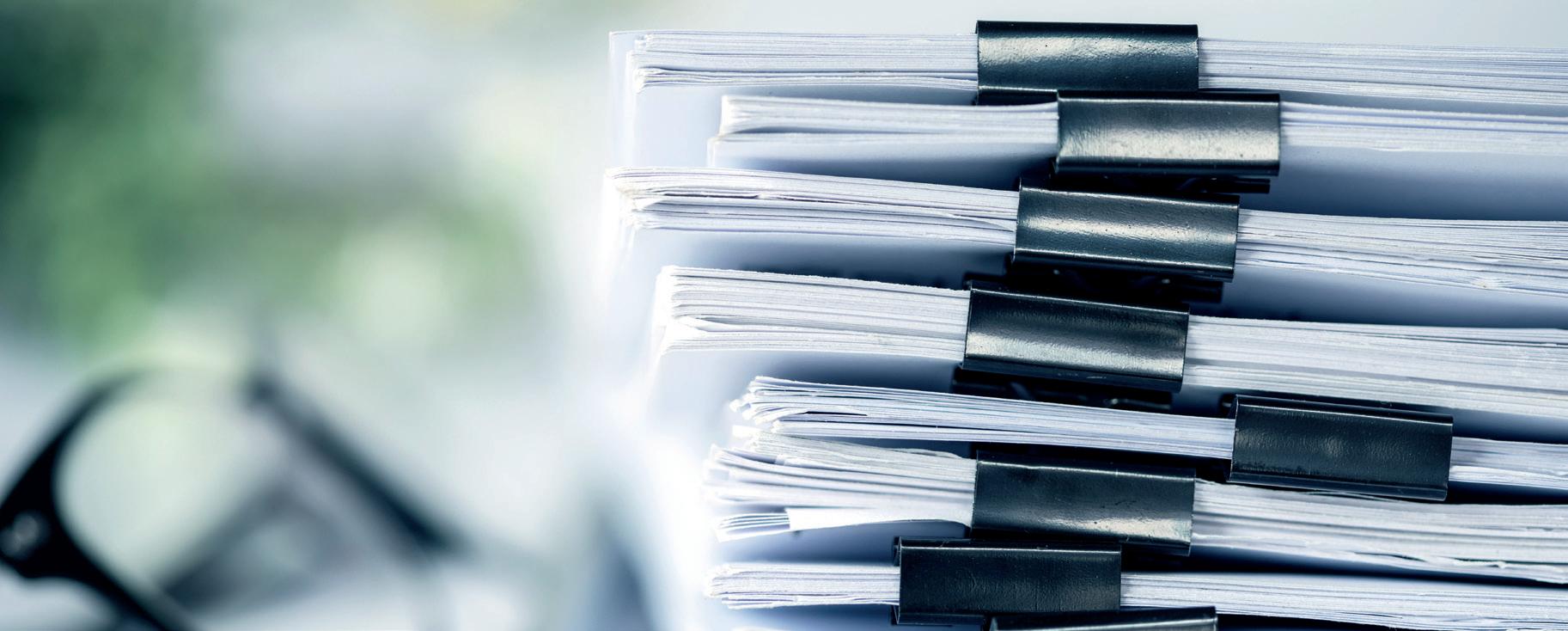
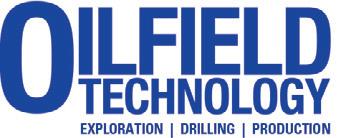