
7 minute read
Subsea pipe repair in the Middle East
the Middle East
Vincent Ribouleau, 3X ENGINEERING,
Monaco, uses a case study from the Middle East to demonstrate how composite wrapping is transforming the pipeline repair industry.
Maintaining offshore assets or subsea pipelines to ensure that the extraction and production of oil and gas is carried out effectively is one of the key challenges that petroleum engineers have faced over the years.
The use of inappropriate technology or difficulty in procuring the right solution (especially in response to an emergency situation) often leads to a rise in the cost of maintenance, loss of production and even delays in the delivery process. This necessitates the introduction of innovative technology that can enable workers to perform their duties in harsh environments, as well as increase the longevity of various parts of a facility for maximum usage.
Subsea pipelines often experience harsh conditions that lead to quick deterioration, whether from the chemical composition of oil, gas, chemicals or water, the sea /seabed conditions or other activities (e.g. anchors, drag force, pipelines crossing etc.).
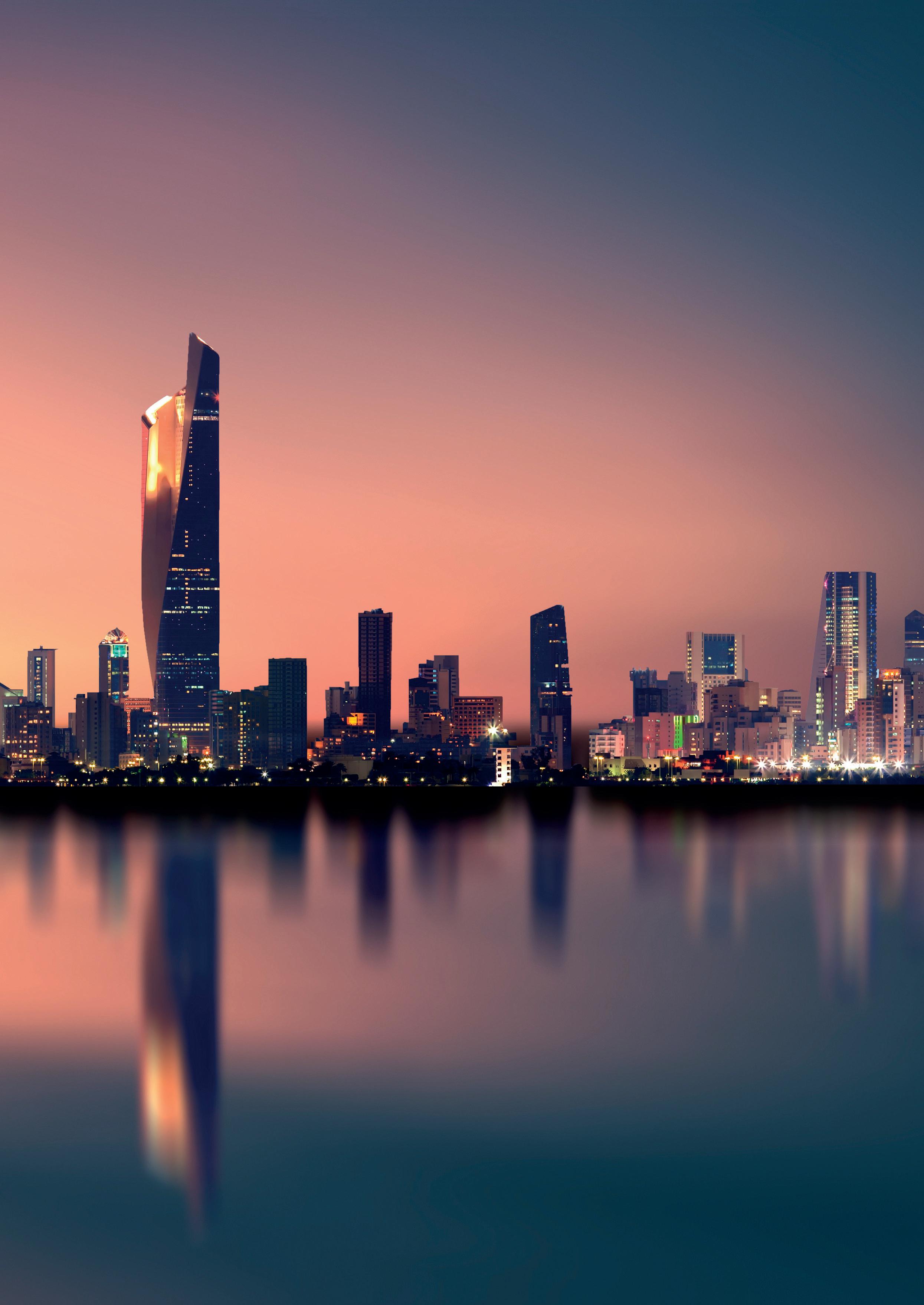
Today, for many pipeline owners, the challenge is no longer how to expand their subsea pipeline network but rather how to maintain in service an ageing subsea pipeline network. What strategies are available to extend the life of a network by reducing the time of maintenance and reducing the risk and cost of heavy equipment mobilisation?
Composite repairs are now a mainstream solution in the oil and gas industry, with an extensive track record onshore and offshore. The benefits of composite repairs for the industry have been proven to a level where the major oil and gas companies have standardised and integrated the use of this solution. They extend the life of assets by providing strength, corrosion resistance, a light weight, design flexibility and durability.
The requirements of the emergency pipeline repair systems (EPRS) divisions of the major oil and gas companies have converged on the development of a solution that has to be on shelf, ready to be used with a standardised design, applicable on any geometry and has a minimum impact on service and production.
A new product is now able to reinforce a pipe experiencing external or internal corrosion, a dent, a leak, a weld defect, a crack, a delamination and much more, regardless of the diameter, geometry, operating condition or environment.

Figure 1. Composite wrapping in progress using subsea handles (control room screenshot).
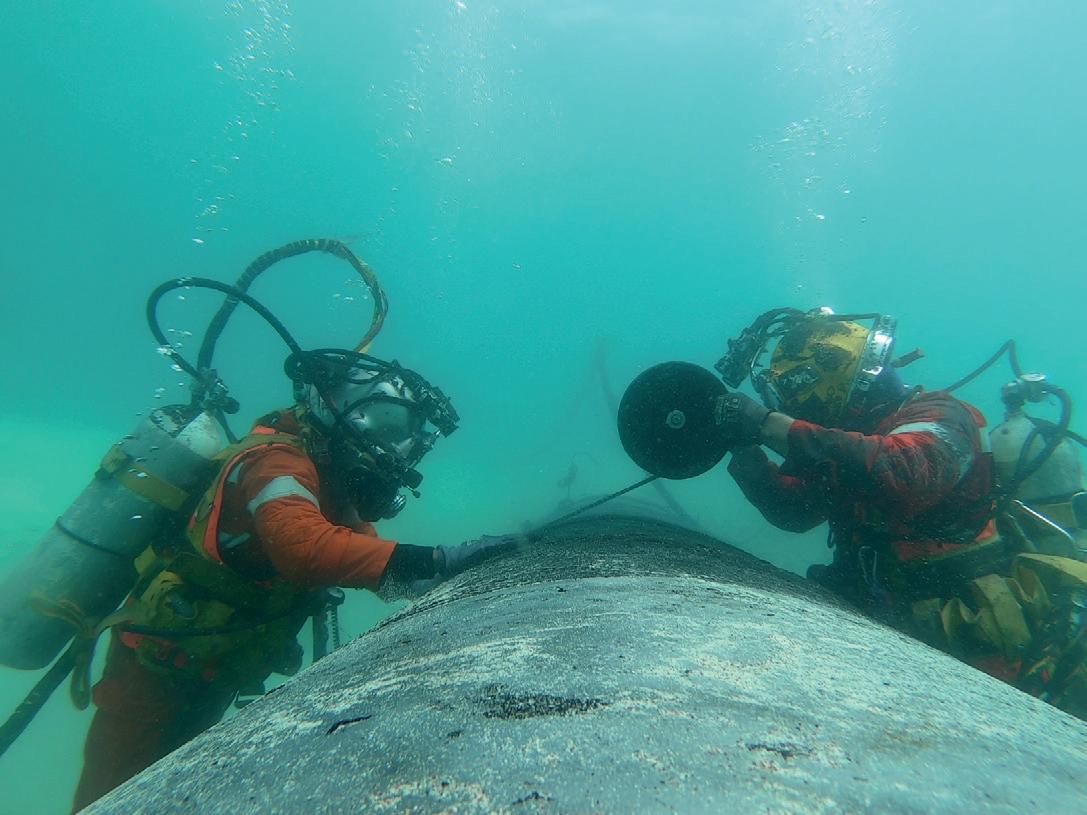
Figure 2. Subsea repair performed by trained and certified divers (illustrative picture).
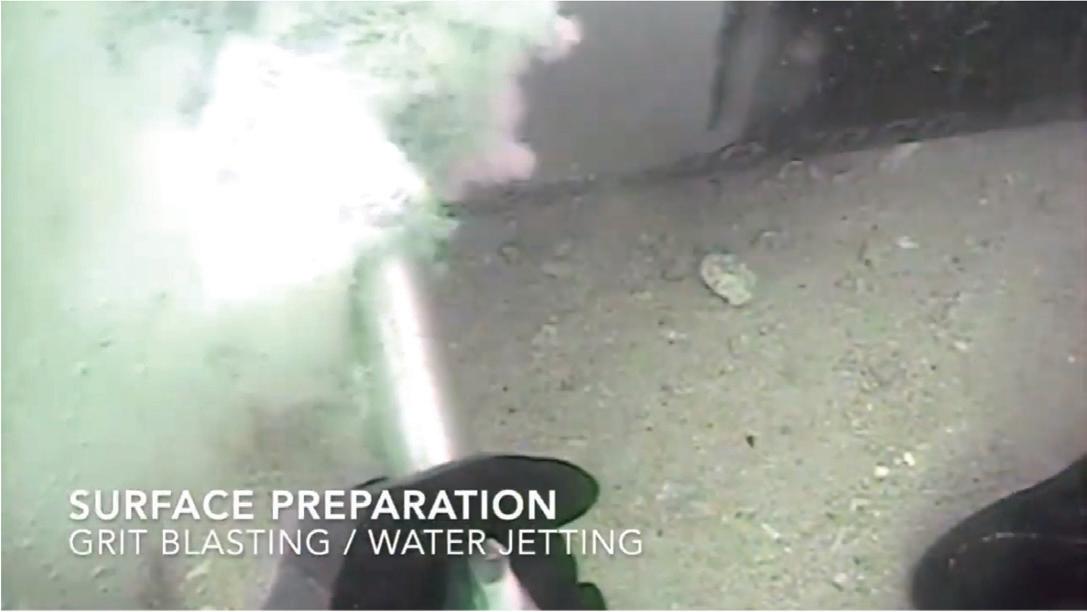
Figure 3. Surface preparation (illustrative picture).
Case study
What is the performance of this product? And what are the benefits of using composite wrapping in the repair of a subsea pipeline?
These questions can be answered by the review of a project carried out in response to the bursting of a 32 in. subsea gas pipeline due to hydrogen-induced cracking (HIC) in the Middle East.
Subsea inspection identified two cracks, including one opened through wall that initiated a severe gas leak of 1160 psi (80 bar).
Of particular importance for the client was sealing the leak from the crack, stopping the crack propagation and, finally, rehabilitating the original integrity of the pipeline in order to operate it again at the design pressure.
The major challenge was to seal the cracks in situ at the given depth with non-metallic material that was resistant to corrosion and had sufficient strength to sustain mechanical and structural stresses.
This particular repair performed by 3X ENGINEERING used computer software based on ISO 24.817:2017 and ASME PCC-2, as well as finite element analysis (FEA), to define the length and the thickness of REINFORCEKiT® 4D SUBSEA (the company’s composite wrapping solution) required for the project. Composite layers are produced from the impregnation of an aramid fibre with an epoxy resin to achieve the mechanical and structural rehabilitation of the original integrity.
In this particular project, the 70-m depth required saturated diving in order to be convenient for operations.
Before the main work could begin, excavation underneath the laid pipeline at the defect’s location – to generate a 40 cm clearance area – was required. Removal of the concrete coating, in order to reach the bare metal, was also performed through water jetting.
Stages of installation
Preliminary operations involved the achieving of a desired surface profile through the means of sand blasting, with a roughness of between 60 µm and 100 µm needed in order to conform with the bonding requirement. This was a crucial stage, with all axial and circumferential mechanical efforts borne by the REINFORCEKiT 4D SUBSEA. Adhesion between the composite and the substrate was one of the key points.
The second step was to stop the crack propagation. This was a mechanical operation performed by drilling the edges of the cracks using a pneumatic driller.
The two cracks then had to be sealed with the application of epoxy filler in addition to a factory-made composite plate. Epoxy filler is the most appropriate substance for such a task, as it ensures the surface regains its original conformity and the pipe regains its original geometry.
Once the cracks were sealed, the next step was to restore the original integrity of the pipe by bringing the necessary strength from the composite wrapping to compensate for the weakness of the defective pipe.
Epoxy primer was applied on the whole surface to be repaired. The primer was used to ensure that proper bonding was achieved between the surface of the pipeline and the composite to be wrapped.
Application of the composite layers was carried out by the divers during the wrapping stage. Composite was pre-impregnated on the diving support vessel (DSV) with an impregnation device and sent to the divers through a messenger cable. This task was facilitated with the use of a dedicated coil fitted with controlled tension handles.
The final step was linked with the curing of the composite. As a bi-component material, the product is entirely reliable when full polymerisation is achieved. Chemical composition and temperature are the two main factors to be considered during this process. A Shore D durometer was used onsite to evaluate the hardness during curing. When the hardness reached the specified minimum value, the resin was considered cured and the composite repair was able to sustain fully mechanical stresses.
As a result, the client received the repaired pipeline after a fast mobilisation, as a composite application does not require the manufacture of a specific structure – such as a metallic clamp or a spool replacement – in advance. 3X ENGINEERING is testing the development of its solutions with reputed third-party laboratories to ensure they are safe to use and deliver the expected operational results and necessary standard requirements.
The subsea environment is challenging for composite repair, as many factors have to be contended with, such as the temperature of the water and pipe, salinity and depth. With each case being unique, so the solution must be as versatile as possible. The epoxy components are chosen carefully to be the least sensitive to water aggression during polymerisation.
Studies in a hyperbaric room under a hydrostatic pressure of 300 bar have been performed to simulate the deep offshore configuration, demonstrating the good performance of REINFORCEKiT 4D SUBSEA. The bonding of the primer is critical to transferring the loading to composite. It implies the primer needs to be able to wet properly the substrate, polymerise at a specified temperature and, once cured, transfer the loading to composite. Even when applied in seawater, the shear adhesion strength of the solution is twice (10 MPa) that of the minimum requirement of the applicable standard (4 or 5 MPa).
Epoxy curing is followed up by checking thermal and mechanical performance simultaneously, using dynamic mechanical analysis (DMA) or a combination of a tensile bench and differential scanning calorimetry (DSC). Epoxy chemistry is governed by the Arrhenius equation, meaning that a higher temperature leads to faster curing.
The challenge now is to bring this experience to the next level of depth, from shallow (0 to -100 m) to deepwater areas where the constraints will be the key factor in an important transformation in the maintenance market.
Your Global Partner for Tungsten Carbide Solutions
▲ High-end carbide grades, tailor-made for drilling and flow control applications
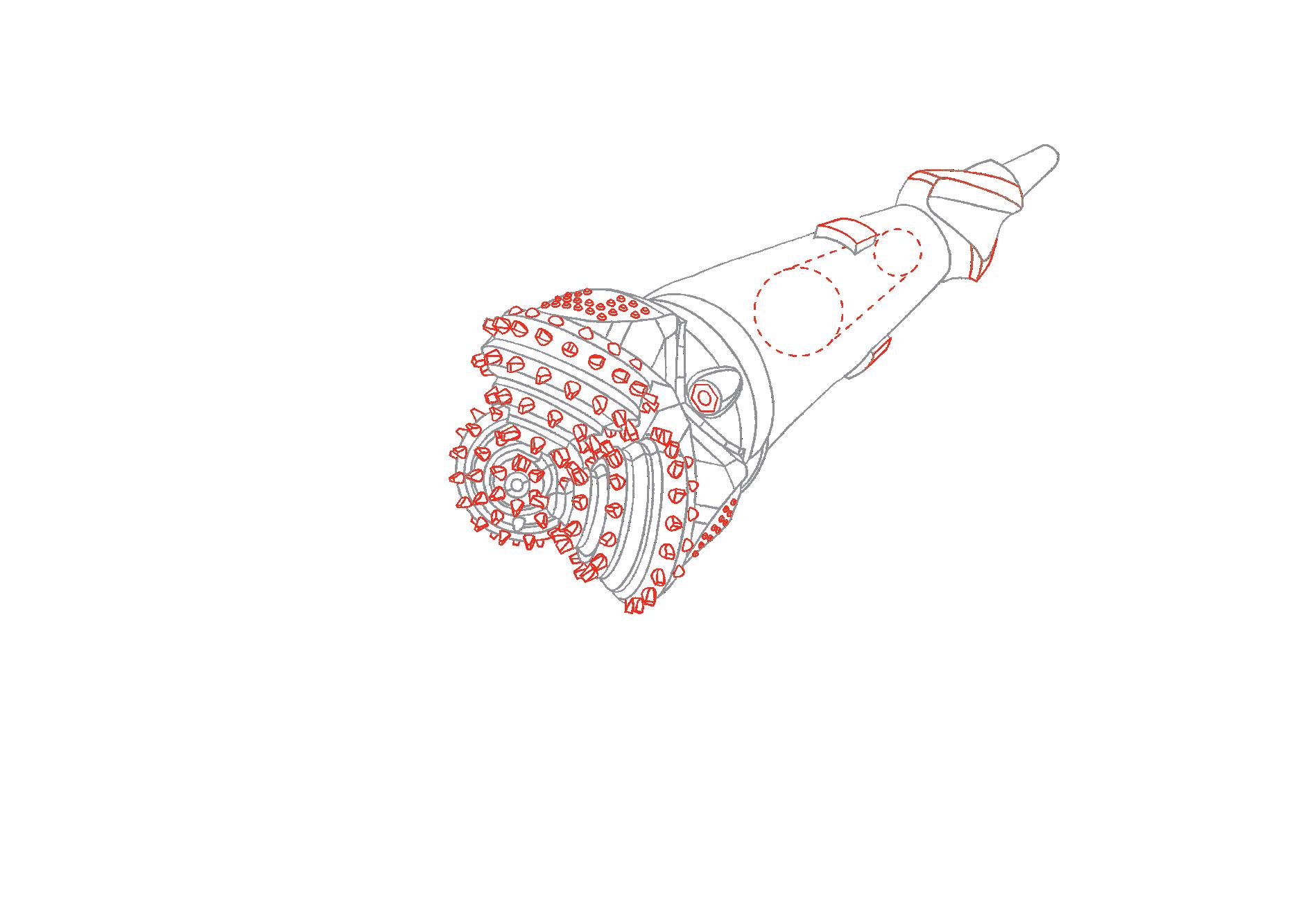
▲ Flexible production capabilities to fulfil most extreme geometry needs

Send your inquiry today: E. hardmaterialsolutions@ceratizit.com
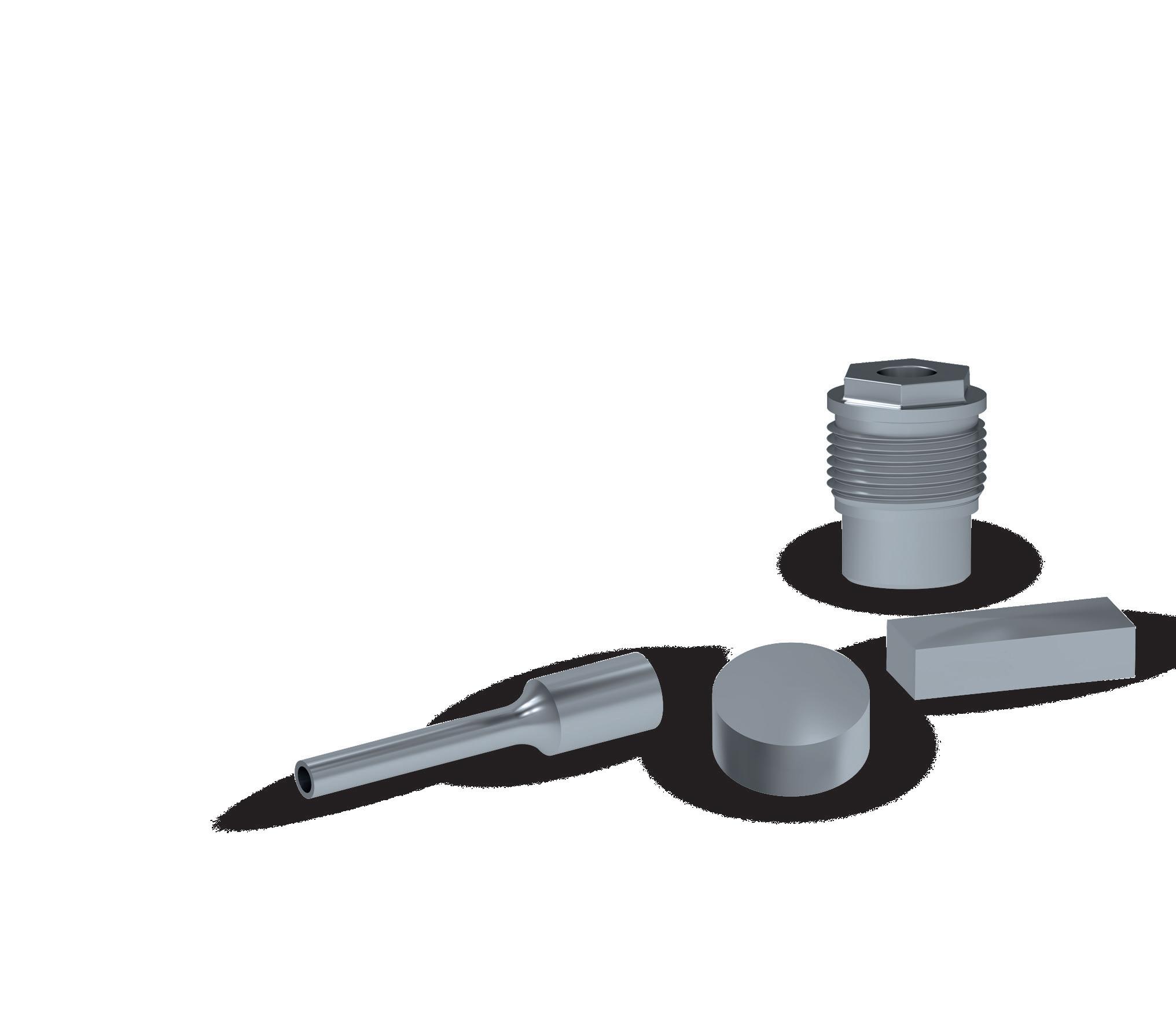
CERATIZIT is a high-tech engineering group specialised in tooling and hard material technologies.