
7 minute read
It’s Next Level
Figure 1. Continuous level measuremt solution for mining freight train coal with contact-free radar.
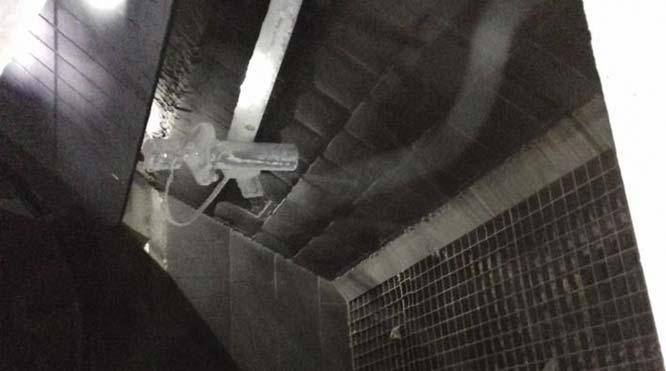
Figure 2. Installation of NivoRadar NR 3000 with aiming flange within the mining process.
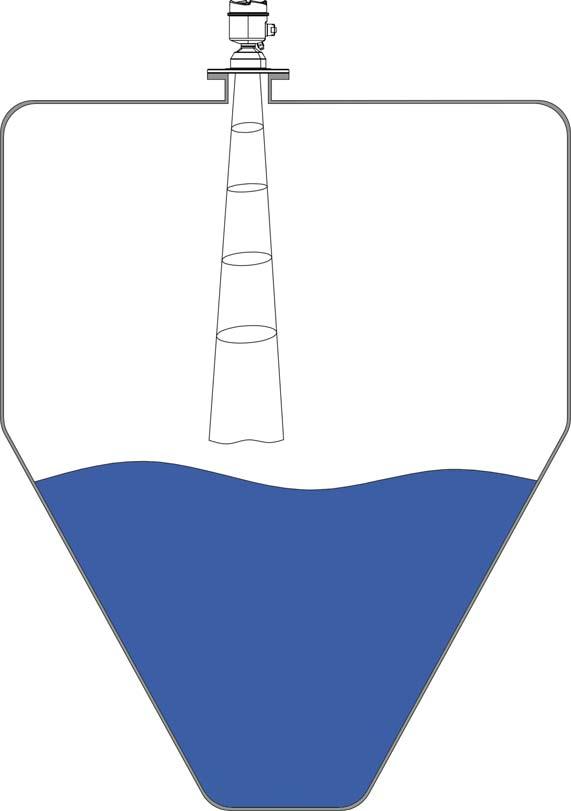
Figure 3. Multifunctional FMCW radar level transmitter for continuous monitoring of solids and liquids with two-wire technology.
The radar is certified for hazardous locations (Zone 20/21) and the stainless steel construction makes the continuous level measurement suitable for these kinds of application. The unit operates at a high frequency of 78 GHz and delivers a small beam angle of 4˚, which eliminates any signal interference at the flange but allows for optimum reflection of the bulk solids material. Distances of up to 100 m (328 ft ) can be measured, and the sensor can be used in very fine as well as rough-grained solids due to the high sensitivity range. The radar also off ers a flat flange and aiming flange version.
Using the adjustable aiming flange, the radar was perfectly aligned since the probe could be fixed to the desired point, and the angle of the beam can be set to the desired point. Therefore, the installed radar sensor could be exactly placed over the trippler hopper and adjusted for continuous level detection of the material without delay and spurious echo, even within the limited space. The non-contact technology sided cones did not influence the measuring results. The lens antenna is highly resistant to material deposits and off ers a self-clean function for the sticky solids using an air flush connection. Even within applications where condensation occurs, the flushing connection provides functionally reliable measurements.
The device uses a two-wire technology and is kept simple, in order to operate via a local programmer with Quick Start Wizard and a plug-in display that allows programming and diagnostics onsite. The unshielded radar sensor has a completely dustproof design and provides reliable measurement results in high process temperatures up to 200˚C (392˚F).
More effi cient silo management by visualisation of stock level
The next consideration for the plant operator at this point of production was to connect the radar sensor to a complete system for level monitoring, in order to achieve improved transparency concerning silo management. The measurement system devices communicate directly with PLC control systems via an analogue ***4…20ma*** signal, or even a MODBUS RTU or Profibus digital protocol. The level signals of the installed radar sensors on each silo could be bundled by the visualisation soft ware NivoTec®, combined with a Wago WebController. The plant could securely access this information (password-protected), at any time of the day, via any internet browser over a predefined IP address using the visualisation soft ware. It is possible to include any number of other measuring points in the visualisation system – without additional hardware costs. By utilising this level monitoring and visualisation, the plant operator established a complete system for fill level and trend display, data storage, and remote fill level information.
Historical digression
Coal mining has an interesting history to be told. One of the largest mining industries, mining for coal started out in the 18th century and boomed all the way to the 1950s. Today, although maybe not as prevalent as some other
mined commodities, coal is still a valuable form of energy for opencast extraction.
Interestingly, the initial method for coal extraction was tunnelling into the earth, but this had to be stopped due to the perilous vapours that were emitted, for example: carbon monoxide, carbon dioxide, and hydrogen sulfite – deadly to say the least. The sensors now used in the coal mining process have helped with detecting these harmful vapours, and have thus helped progress the industry away from the traditional miner’s canary method.
What is the miner’s canary?
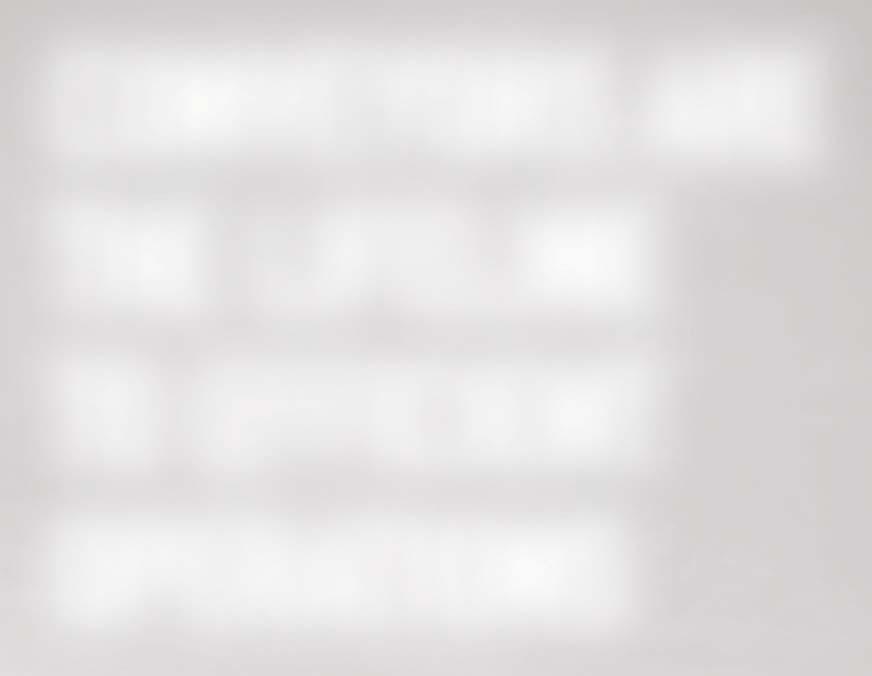
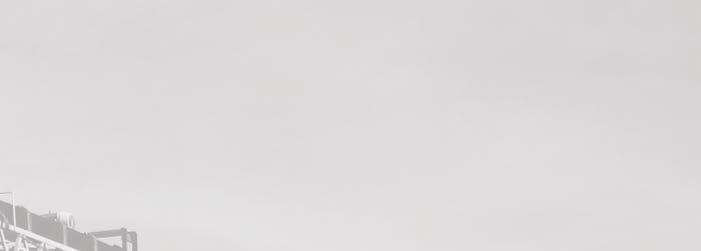

Very simply put, miners used to take a canary in a cage down into a mine with them. Canaries were known to be very sensitive to odourless vapours, such as carbon monoxide, and they would show eff ects of distress, rocking from side to side, before falling off their perches.
While not a very safe procedure for the animal, it was known to have saved many human lives. Aft er a time, the canary method of detection was stopped as it proved to be less eff ective than initially assumed.
The Pellistor was introduced as a replacement – a catalytic sensor able to detect a very wide range of toxic vapours and flammable gases. Due to high maintenance costs and limitations – such as malfunction when exposed to chemicals made with chlorine, sulfur or halogen, as well as any metals containing silicon or lead – this method was also withdrawn aft er a time. The more modern and more eff ective method is the infrared LED–based gas sensor.

CONVEYORS ARE THE LIFELINE TO EFFICIENT OPERATIONS
Belt conveyors are the basis for your

Conclusion: measurement technology off ers critical support
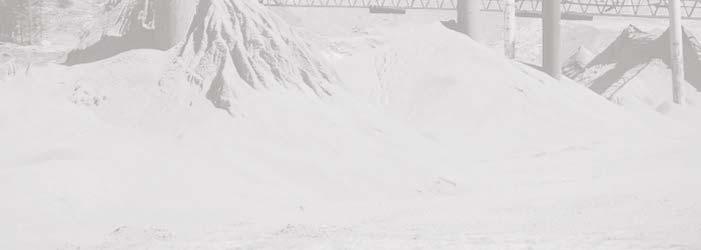
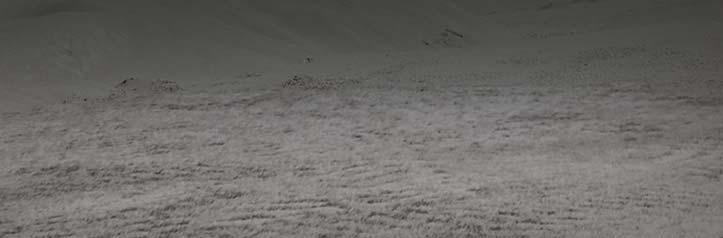
Level measurement technology is multifaceted and rarely stands still. Exciting and challenging developments in diff erent applications mean that the product range continuously has to grow and develop to meet these requirements. For continuous and point level measurement technology plant operators oft en need individually tailored solutions for their material manufacturing processes. Each process has specific requirements or demands for the sensors involved.
With particular attention to single steps during the manufacturing of the cement producing company in South Africa, the customised level measurement was a crucial component to supporting continued smooth running process flow – avoiding overfill protection, responding quickly when it comes to silo emptying, and providing transparency and control over content level within the vessels at any time.
With application-oriented product design of the installed radar sensor and paddle switch – supported by the level control visualisation system – a high degree of compatibility for the silos and vessels was given, so that they could be seamlessly integrated into the installations ensuring optimal silo management.
systems lead to downtime, lost production, and increased maintenance and expenses. Your bottom line depends on a reliable conveyor system, and Martin Engineering will keep your operation running at full capacity.
Visit our website to learn more today.
martin-eng.com
® Registered trademark of Martin Engineering Company in the US and other select locations. © 2021 Martin Engineering Company. Additional information can be obtained at www.martin-eng.com/trademarks and www.martin-eng.com/patents
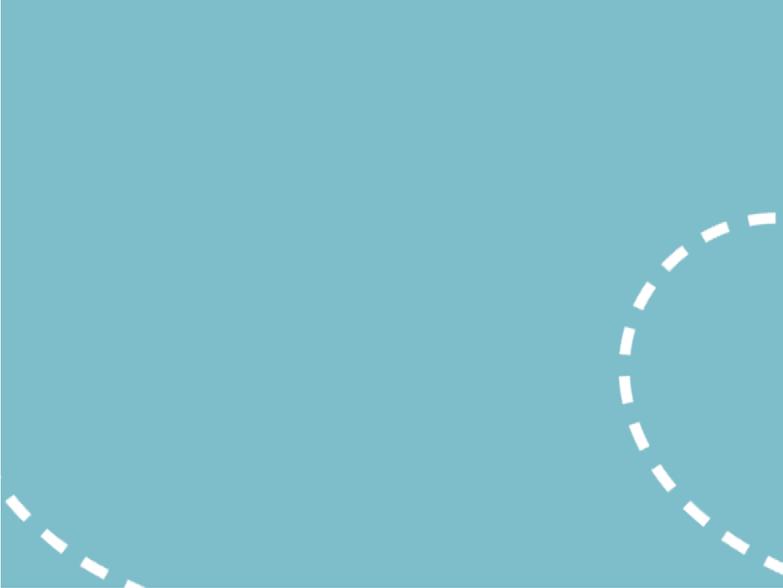
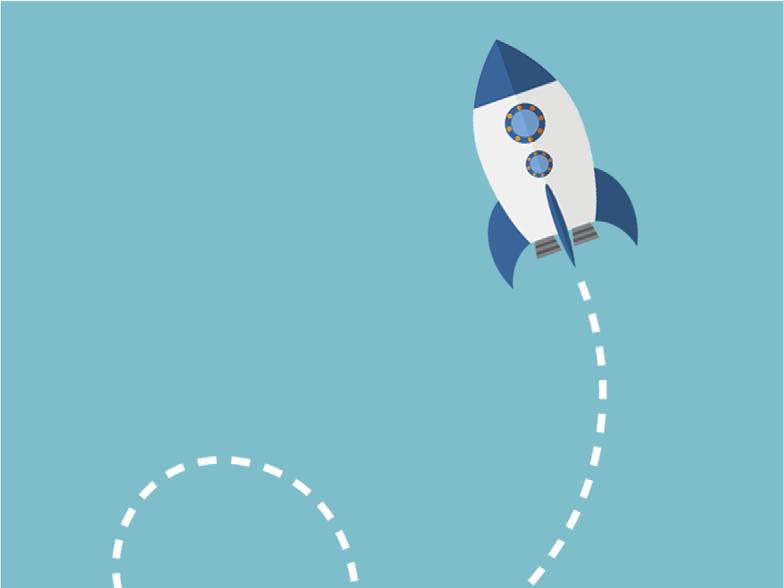
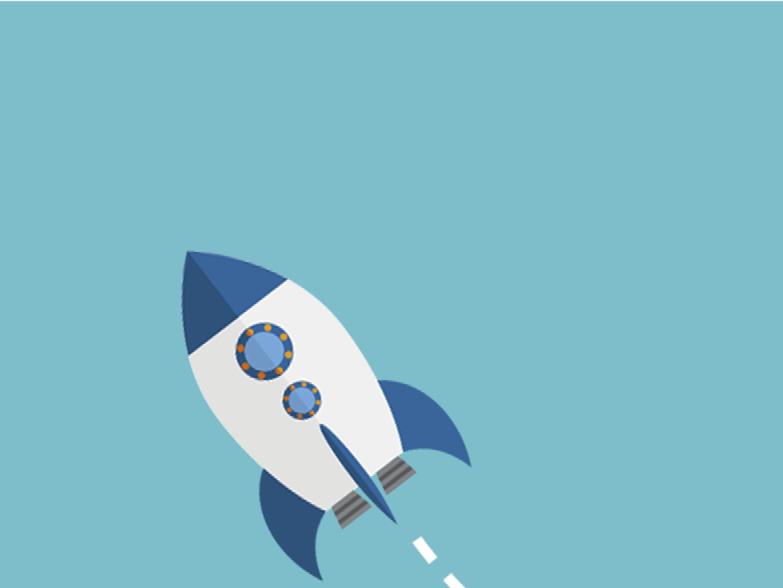
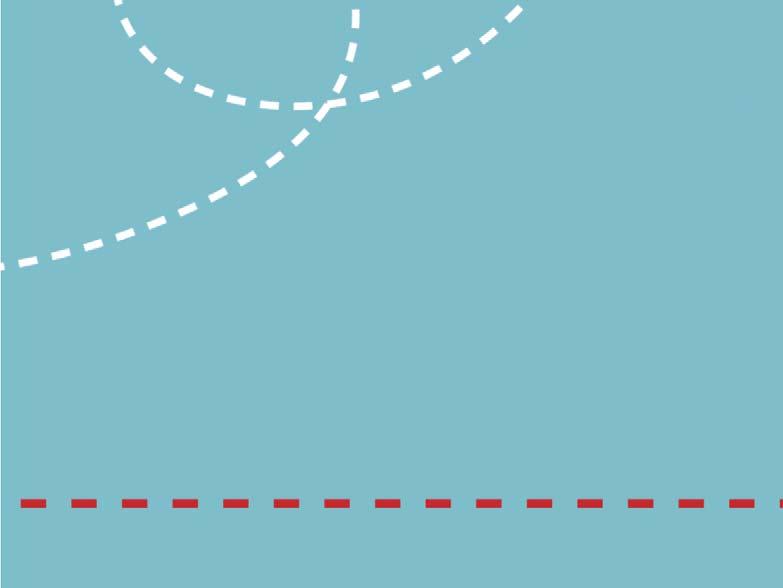
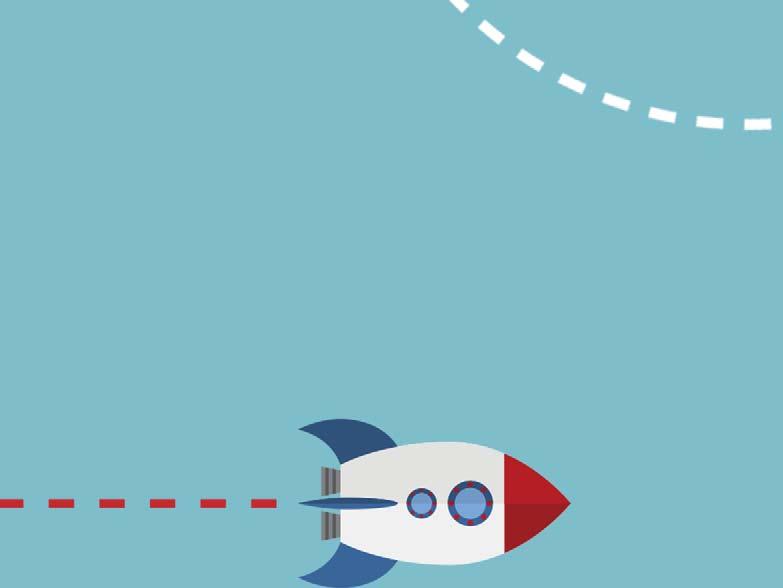
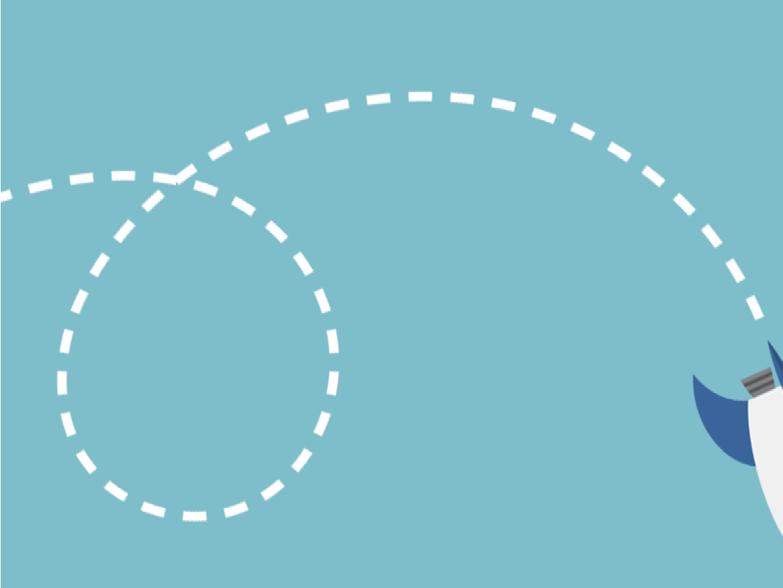
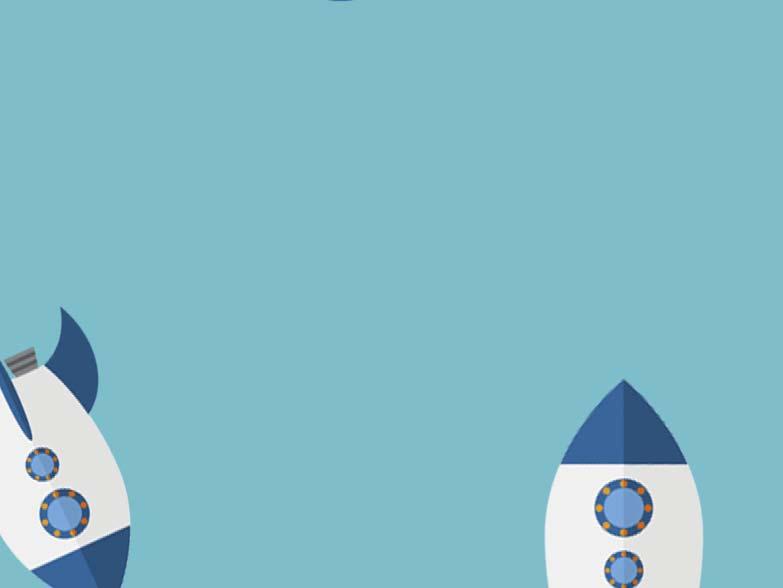
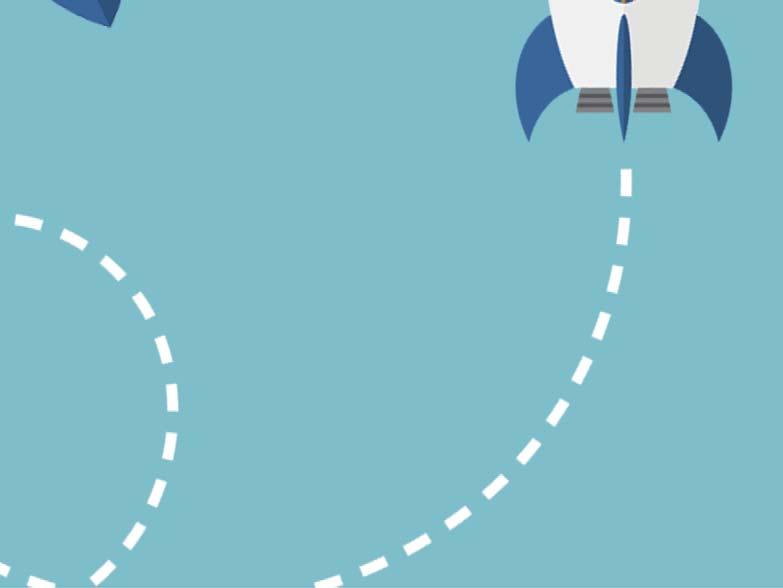
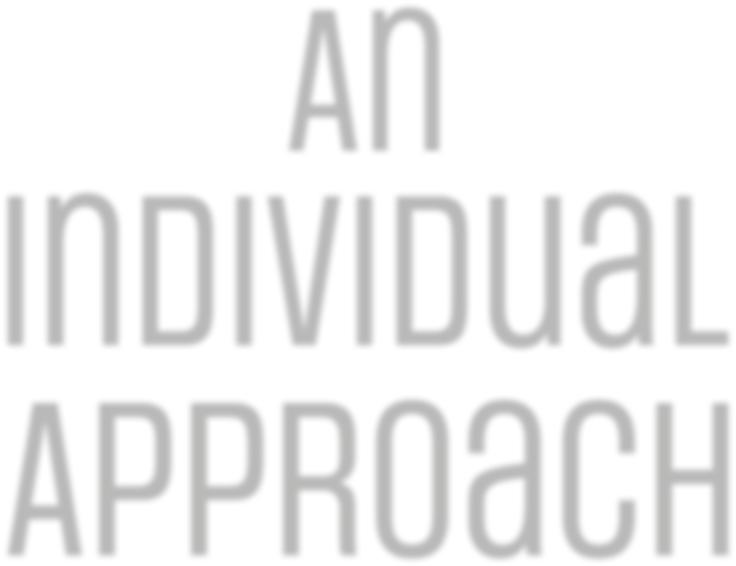
Łukasz Gonsior, FAMUR Group, Poland, outlines an approach to client requirements in relation to highly customised gear products.
Starting with an analysis of customer requirements and progressing to the supervision of a deployed device, this article presents a life cycle assessment (LCA) path study of a bucket wheel drive gear mounted on a lignite excavator.
One of the product branches of the FAMUR Group is drive sets and gears used in industrial surface transport systems and equipment for mining in a broad sense. Apart from output transport technology, the company’s gears are used in the drives of running gears and boom rotation systems of lignite excavators, running gears, and conveyors installed on loaders and loader-reclaimers of loose materials.
Power transmission
The market for power transmission products can be divided into standard products and products that are highly customised to meet the specific requirements of a particular application.
In the first case, applications generally do not require expert advice from the drive manufacturer. The interaction between the customer and the gear manufacturer is limited to confirming the correctness of a solution.
The second group of products is characterised by the presence of multiple product LCA phases and it requires: Design skills and experience, as well as access to commercial and proprietary design tools. Research and development activities. Optimised and reliable technological processes. Experienced technical and production staff. A specialised machine park. Enforcement of a uniform quality control policy. A consistent purchasing policy and proven supplier base. Resources to perform load motion testing prior to the delivery of equipment to the customer.
