
13 minute read
A Chain Reaction
The supplier as the fi rst link in the value chain
Several ‘end-users’ are far more interested in the CoC of the products that they purchase than the suppliers are. In all cases, even if the end-user is the direct customer of the system, the first act is to create a ‘supplier’ within their CoC.
Aft er the creation of the supplier within the system, all subsequent supply chain interactions are fully in the hands of the participants to the CoC, who in turn and in a controlled manner, will be the custodian of the raw materials and of the manufactured (semi) finished products.
The original raw material supplier steps in
The supplier has to generate a supply in supply lots (i.e. on a daily basis, equivalent to some thousands of tons of raw coal per day); this act generates one quick read code (QRC) per day associated to the actually extracted quantity of raw coal.
The supplier’s task, once the initial set-up is complete, only consists of: Defining the material to supply: a one-off activity. Creating the transporting company and the next user of the coal in the system (in this case the next user is internal – the refinery, and just transportations over conveyor belts are used). Defining an actual supply lot for that day’s raw coal production. Assigning that lot to the transportation via conveyor belt.
Every time that a new user is created, an automatic email is sent to the email address provided by the supplier. The concept of CoC fully applies here: the supplier, the very first custodian, knows perfectly well to whom the material must be delivered and who is going to carry out the transportation, so the next two custodians in the CoC have been easily identified.
Figure 1. Guaranteeing the full traceability of the origin of coal.


Figure 2. Tracking each transportation step individually. Generating QRCs
The step of creating an actual supply for the raw coal lot generates a master QRC: every subsequent QRC generated along the CoC will be linked to this one via a series of unchangeable links, all mastered by the web-based system, and this constitutes the guarantee about the solidity and the continuity of the CoC.
Also, assigning the lot for transportation to a logistics provider generates a QRC that will be readable exclusively by the transporting entity (the ‘custodian’ dedicated to that transportation, i.e. the captain of a vessel or a truck driver) and by the receiver.
If transportation occurs via trucks, the truck driver will need to install a dedicated application on their mobile phone, by simply inserting their telephone number and nothing else. As the logistics provider knows all needed transportation details, the information provided is enough to identify, without margin of doubt, the custodian for the trip. Once the application is installed, the truck driver must scan the QRC provided by the supplier for that lot. The application will record the geolocation of the scanning, the timestamp, and will consider the driver as the new custodian of the raw coal lot.
Geolocation and security
Some companies need to know where their lot is at any moment during the trip, or want to ensure that the journey does not cross unwanted borders (i.e. in the case of sanctioned countries). Although several expensive systems exist to accomplish this task, such as container shipments, VAREYE has implemented a premium feature in its smartphone application to allow for GPS tracking of the smartphone position during the journey from the port of loading to the port of discharge, assuming that the custodian must be present during the trip as the responsible person for the lot.

Reaching the transformer – the refi nery
In this case, the raw material reached the receiving refinery via conveyor belt, while a sub-lot of the original lot was sent to an internal warehouse for raw materials: the corresponding QRCs can be coupled later to a single code without losing the CoC properties. The receiver’s user at the refinery can acknowledge receipt of the lot by accessing the web database or by scanning the corresponding QRC directly from the smartphone application. This would trigger the following two actions: The quantity received by the refinery’s user is deducted from the original quantity of the full lot. The refinery’s user is the new custodian of the in-taken volume.
Transforming the raw coal
The QRC is then moved to the ‘production’ area of the system. This environment, available to transformers, keeps track of the transformation of a raw material (input) into a product (output), in terms of mass balance.
Joining QRCs from several sources is possible, thus preserving the full quality of the CoC and keeping full operating control of the transformed quantities of raw materials. This is especially relevant to cases in which the alignment of volumes across multiple storage places and production is a cause of book-keeping concerns, because the mass balance control is guaranteed.
The recipe to convert raw coal
When processes run very regularly and in a predictable way, the transformer can use a standard recipe for the transformation of raw coal into several types of anthracite. When processes are unstable for any reason, the transformation can be carried out on the basis of actual weights in eff ect obtained during the transformation of each single lot, including the formation of solid and liquid waste and other losses.
Moreover, the actual process needs the addition of water to facilitate the segregation of coal; water (or any other material) can be added as a non-CoC material to the raw coal, thus fully preserving the CoC of the products obtained at the refinery and fully reflecting the mass balance requirements for the CoC.


Figure 3. Personalise tracking while maintaining full control of the CoC via mass balance. Operational tools
The refinery needed some improvements in the operational control during the separation phase. The addition of water causes a mass imbalance that has to be corrected manually per each lot on the basis of hygroscopic measurements from the laboratory, in order to report back the adjusted weight of anthracite products in respect to the original humidity content of the raw coal. Dedicated tables are embedded into the system, where actual data can be input on a day-by-day basis and calculations are carried out automatically.
As information is stored for a contractually agreed timeframe within VAREYE, the customer can use the historic data base to measure the performance of the separation processes over time, and to analyse it in search of opportunities to improve and optimise.
Unshipped fi nished products, rejects, residues
Products that are not directly shipped to customers can be stored within an internal warehouse for shipment in the future, or for future blending with diff erent semi-finished products to conform to customers’ requirements, or, being defective, for recycling back into the production process.
The CoC mechanism also applies to by-products, i.e. for the management of solid waste, which is subject to controls due to its potentially harmful nature. The supplier can demonstrate not only how much solid waste is produced from each lot in a firmly measured quantity, but also how it is shipped and received by the end-user; this constitutes a relevant advantage facing inspections by controlling environmental authorities.
Mixing fi nal products and shipping
Occasionally, types of anthracite are blended to obtain a final product exactly matching the characteristics required by customers. In order to maintain a full CoC traceability, this feature is also incorporated into the system.
Each lot of product ready for shipment is entitled to its own QRC, still linked in the CoC with the
original master QRC from the mine. Again, the refinery knows exactly who is going to transport each anthracite type, and where it is going to go. Those constitute the next links in the CoC.
Shipping by train
The system is also able to cope with types of logistics where no actual custodian can be identified; for those means of transportation, the custody of the product is maintained by the shipping entity until it reaches the next user, because, for example, a national railway system might be unwilling to take custody under a CoC scheme for any material. The concept of a CoC is fully maintained anyway, as long as the QRC is in the hands of the refinery and until it reaches destination.
Shipment tracking
Each transport has its own QRC that can be read by the logistics provider and, upon arrival, by the end-user. Additional features include the splitting of shipments among several logistic providers, by maintaining the traceability of each single QRC and the tracking of each shipment, designed in principle for trucks and ship, by using the geolocation feature available on all smartphones.
The end of the journey
The end-users can take custody of the incoming QRCs via the application or the web-based interface; only aft er the QRCs acquisition and weight confirmation can the end-users download a CoC certificate for each single lot received via truck, ship, or train. The certificate is automatically generated by VAREYE when there is no detected interruption in the CoC.
Conclusion
A CoC system, similar to the one analysed in this article, is able to satisfy all of the main requirements provided by a coal producing customer. In particular, it generates a solid CoC certificate based on the mass balance of input and output materials and helps maintain full traceability of the streams of products deriving from the raw coal, as well as granting online access to transformation parameters of raw coal into anthracite and tracking shipments in break bulk mode.
This system might therefore constitute a solid alternative to some of the more expensive and more complicated systems that are available today on the market, thus contributing to and reinforcing the sustainability image of companies adopting it.
Eliminate Carryback.
Richwood Belt Cleaners Provide Immediate Return on Investment. Even in severe environments, Richwood belt cleaners provide a real return on investment through increased belt uptime, decreased clean-up costs, low maintenance and longer component life.
What would it mean for your productivity if carryback issues were eliminated?
Contact Richwood today for an on-site evaluation info@richwood.com.
Rely on
RICHWOOD BELT CLEANING SYSTEMS

www.richwood.com




James Trevelyan, Speedcast, UK, outlines how mining automation can help deliver business results.
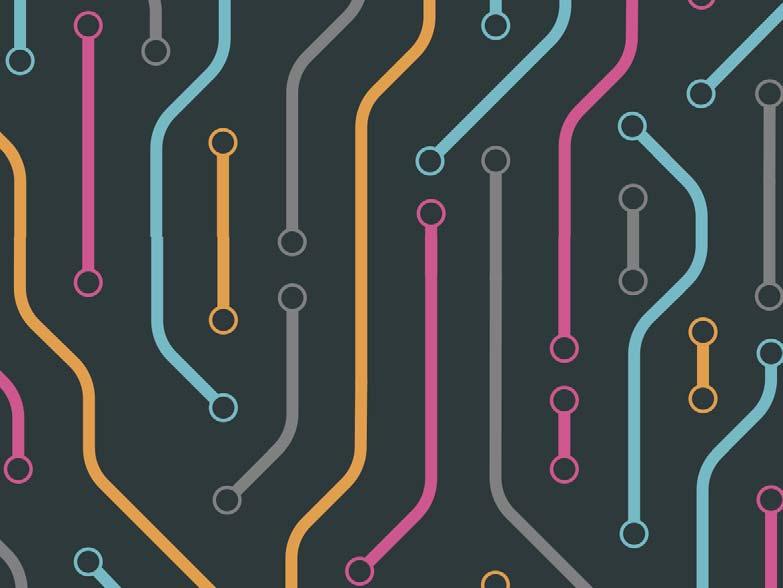
In 2019, Internet of Things (IoT) specialist Charles Towers-Clark wrote that “mining is now at a critical junction in which it will either adopt new technologies or be left behind.”1 He noted that second tier operators, more agile than the giants of the industry, are already acting on opportunities to use emerging technologies to enter markets they have been largely blocked out of.
The giants have apparently been paying attention, with Grand View Research reporting that the global mining automation market was worth US$3.6 billion in 2017 and will grow at 7.3% compound annual growth rate (CAGR) through 2025.2 At the beginning of 2019, Rio Tinto announced the launch of the world’s first autonomous long-distance railway network



to transport iron ore to the company’s ports in the Pilbara Region of Western Australia. In southern Mali, Resolute Mining uses automated vehicles and drill equipment to extract 300 000 oz/y of gold from the Syama Complex.
On the hunt
The established leaders of the business are now moving into automation for reasons other than just ‘being left behind.’ Coal is the largest revenue-generating material mined today, but its dominant share is levelling off as natural gas and renewables continue to grow. With volume growth increasingly unable to boost revenue and profits, investments that improve operations and productivity look more appealing by the year. According to McKinsey & Co., worldwide mining operations are approximately 28% less productive today than they were a decade ago.3
In a March 2020 interview, the CEO of Resolute Mining, John Welborn, cited several benefits that automation delivers.4 The first is safety; the company’s policy manual forbids manual interaction with automated equipment onsite to keep people out of harm’s way. Robotic systems, which never need to rest, also enhance productivity delivering an approximate 30% gain in operational eff iciency. He cited a third benefit that may surprise people: simplifying the operation using robotics allowed the company to train native Malians to do the work, rather than rely on expatriate miners with training and experience in drill operations.
Putting automation to work
The range of automated systems in use today is broad. Automated drills scan the coal face and prepare it for blasting with far greater precision and speed. Automated vehicles haul material, navigating confined space and rough roads using GPS and signals from wireless beacons on the ground. Asset trackers mark the location of hundreds of millions of dollars of equipment and can trigger alerts in the event of theft or misuse. More sophisticated versions transmit telematics data from engines to predict maintenance needs and increase uptime.
Video surveillance cameras feed data analytics that can automatically identify and flag human errors that may endanger people and operations, from missing hard hats to unsafe handling of explosives. Drones capture video feeds of mining waste, which can be rendered into 3D models of piles to assess their safety and stability.
The most advanced companies are developing ‘digital twins’ of their operations. Using data from construction and operation, they create a digital replica that uses real time data from the field. As additions and changes to the facility are proposed, the digital twin can test the decision’s accuracy before installation. By eliminating errors, the technology can save millions of dollars on field implementation.
When carefully implemented, each of these technologies can generate a reduction in risk, cost savings, or productivity improvement that off ers a material improvement in business results.
The connected mine
It is a vast array of new solutions – and it rests on something in short supply at mine sites: reliable, aff ordable, high-capacity communications. To achieve breakthroughs in safety, productivity and profitability, data must flow at high volume with no interruptions or degradation of service. While miners focus on pulling raw materials from the ground, managers rely on the system’s ability to draw massive amounts of data from those same processes.
The design of communications infrastructure – and the management of operating networks – has become critical to the safe and profitable operation of a coal mine. The remoteness of mining sites requires the integration of multiple communication technologies into a high-performance whole. Key elements in connectivity for the connected mine include:
Mine site communications
Wi-Fi is essential for communications, in order to enable every computer, tablet, and mobile phone on the site to access daily operations. That accessibility is balanced by short range and lower power, however, which is particularly problematic for underground mines. To overcome this, private long-term evolution (LTE) technology is becoming increasingly popular for its long-range ability to penetrate walls and barriers, high bandwidth, and reliability. Nokia has introduced a digital automation cloud that uses LTE to interconnect every aspect of operations and enable the full range of automation and IoT applications.
Backhaul access terminals
These are multi-mode terminals that support multiple satellite bands, microwave links, cellular service and optical fibre, and connect seamlessly with mine site networks. Terminal soft ware manages the logistics of making and breaking connections, from virtual SIM cards to least-cost routing.
Backhaul network
Satellite can off er the most cost-eff ective way to reach remote mine sites. Depending on the location, a productive mine may also be able to integrate optical fibre as the primary path and retain satellite as a backup. Providing the backhaul requires a network of satellites, teleports, fibre and high-performance cellular base stations in strategic locations, as well as high-capacity peering with wired and mobile networks, in order to ensure connectivity to the rest of the world.