
11 minute read
Conveying The Need For Dust Suppressants
smaller dust particles to become airborne more easily, as a result of the increased air flow and speed of the system. A fugitive dust issue is thus created and needs to be addressed throughout the entire system.
Dust control techniques
There are a variety of dust control techniques used to curb the amount of fugitive dust generated from a mining operation. Water sprays are the most common and eff ective method employed. They can be used for both dust suppression and re-directing air flow. With this in mind, they are installed to suppress dust at all major dust sources, including: cutting, loading, and material transportation sites. While operational changes and mechanical means are standard for most operations, the use of chemical suppressants should be considered to compliment engineering controls. There are various types of chemistries used to control dust dependent upon the application. Though there are several combinations of chemicals used to achieve the desired results, all products primarily try to bind dust particles together, create a seal over the dust, or increase the weight of the particles to the point that they cannot become airborne.
Water spray
For conveying applications, dust is generally controlled with a water spray system that continuously wets the material throughout the transportation process. Though eff ective in most circumstances, increased amounts of water can aff ect moisture specifications and the ability to transport the ore eff iciently. The use of water can be made more eff ective by atomising the water used, as well as adding a surfactant to change the water’s chemical make-up.
The principle of surface tension can be seen when liquid spreads onto a surface. An example is water spreading over an area of perfectly clean glass. The degree of wetting is a balance between two forces within the liquid. The liquid’s adhesive force (attraction to another substance) encourages it to spread onto the glass while the liquid’s cohesive force (attraction to the same substance) tries to form into a ball. Surfactants (also known as wetting agents) have a direct eff ect on these forces. Surfactants increase the adhesive force and lower the cohesive force which allows the liquid to easily spread. The eff ects any surfactant has on these forces can be measured by determining the surface tension of the liquid.
Water typically maintains a surface tension of approximately 72 dynes/cm, depending on its temperature. By adding the appropriate amount of surfactant to the system, surface tension can be reduced below 45 dynes/cm, considered the point where maximum wetting of dust occurs. When the surface tension is reduced, it will allow the droplet to absorb many small particles of dust and wet them more easily. This will increase the weight of the dust particles and reduce their ability to become airborne. When enough small particles of dust stick together, they increase in weight and fall to the ground. In a normal spray system, the size of a water droplet can remain large and collide with or create a slipstream eff ect with smaller dust particles, limiting its eff ectiveness. Reducing surface tension also has an atomising eff ect on water droplet size, eff ectively reducing overall circumference. The weight and size of the dust particle are not able overcome the surface tension of the water droplet and, in some cases, the water droplet may increase the suspension process.
Table 1. Respirable dust
Applications Prior to DUSTGRIP® JFP-95
Aft er DUSTGRIP® JFP-95 Continuous miner operation 0.326 0.221 Shuttle car 0.317 0.169 Shuttle car 0.350 0.221 Scoop 0.372 0.152 Roof bolter 0.228 0.168
Table 2. Quartz
Applications Prior to DUSTGRIP® JFP-95
Aft er DUSTGRIP® JFP-95 Continuous miner operation 33.8% 5% Shuttle car 6.9% 4.3%
Shuttle car 22.9% 4.1%
Scoop 4.4% 4.1% Roof bolter 14.2% 7.1% Surfactants
In practice, both liquid and solid forms of surfactants are commonly used, dependent upon available equipment and operation preference. Both forms have the same function and are applied via dilution in the water source that supplys the spray nozzles. The process can be introduced in a mine wide water system to control dust in all areas of the mine, or locally to control one specific area.
In a conveying system, transfer points become a focal point for fugitive dust as the material is agitated during the process. This is the area at which the mined material becomes airborne itself when it transfers from one conveyer to the next. At most 90˚ transfers, the mined material impacts a deflector plate that is used to direct the flow of material onto the centre of the next conveyer. The physical movement of the material allows untreated dust particles to become airborne and create float dust. Though water sprays are used
continuously at these points, the function of the spray system is only intended to act as a ‘curtain’ to limit the flight of dust. The addition of a surfactant to the water system allows a curtain to be maintained, while also eff ectively wetting the material as it becomes airborne. The combination readily produces a 50% reduction in measured fugitive dust, whether at a specific location or as measured by operators on specific pieces of equipment. Tables 1 and 2 present examples of how a coal mine in the US significantly reduced dust readings across all equipment and areas by adding a surfactant to their current controls.
Conclusion
Respirable dust rule
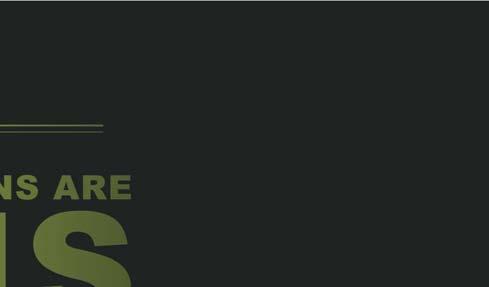
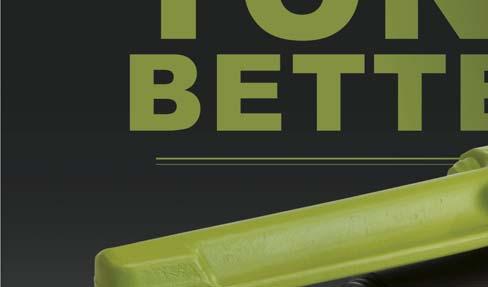
and specific operational changes can be enforced to protect workers from the elevated levels. Tables 1 and 2 show results from samples taken following MSHA guidelines at an underground coal mine. Samples were taken both before and aft er the addition of DUSTGRIP® JFP-95, Quaker Houghton’s solid cartridge dust suppressant. The generation of dust is an unavoidable consequence of mining activity. Whether generated from mining processes or reoccurring issues from where dust accumulates, fugitive dust is a health and safety hazard that must be managed eff ectively. Careful consideration On 1 August 2016, Phase III of the should be given to the use of engineering controls, Mine Safety and Health Administration’s (MSHA) mechanical means, and chemical aids available to respirable dust rule went into eff ect. The concentration reduce worker exposure and increase mine safety. limits for respirable coal mine dust were lowered from Current industry best practices include a combination 2 mg/m3 of dust of air to 1.5 mg/m3 at underground of all these controls to increase the eff ectiveness of their and surface coal mines counterparts.
The concentration limits for respirable coal mine dust were lowered from 1 mg/m3 to 0.5 mg/m3 for intake air at underground mines and for part 90 miners (coal miners who have evidence of the development of pneumoconiosis)
Within the dust levels recorded, quartz must be 0.10 mg/m3 or less of the total make-up.
Lowering the concentration of respirable coal mine dust in the air that miners breathe is the most eff ective means of preventing diseases caused by excessive exposure to such dust. MSHA requires quarterly sampling be performed by qualified mine personnel at specific equipment and worker locations.
Personal Dust Monitors (PDMs) are used to collect coal dust readings while volumetric cassette pumps are utilised for quartz measurements. The samples are measured portal to portal and can result in reduced dust standards if over the maximum 1.5 mg/m3 of coal dust and 0.10 mg/m3 quartz content. Cincin nat i D ual Sp roc c ket Conveyor Cha hains are prov ven to be bett er tha an o t he r
If high levels of respirable mining chains. Tons bett et er, in fact. Tests confirm m our c h a in s de liv e r 20 perce nt coal mine dust or quartz mor e stre n g t h . The h re sul t i t i s g s g rea e ter durabi lit y, m a x im u m availability and a are found, a reduced total t roub l e -f ree se rvi ce lif e . Th a t’s how we deliver the lowest cost per ton. respirable coal dust standard For 90 y ears , C incinnat i h a s proven to b e T HE S TR O N G E S T LI N NK .
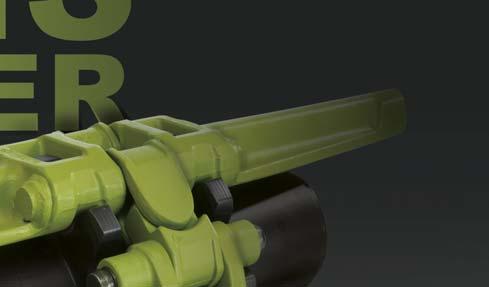
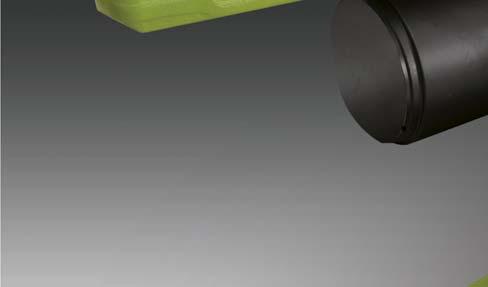
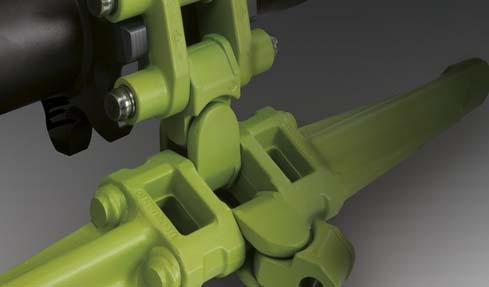
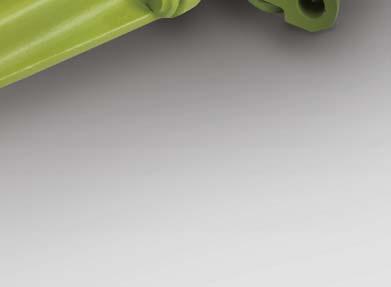
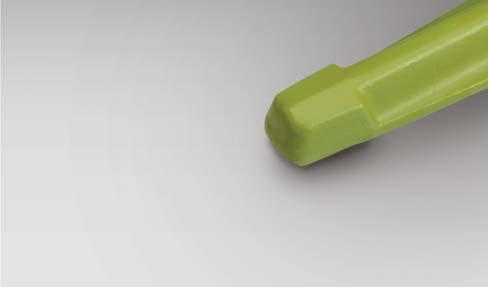
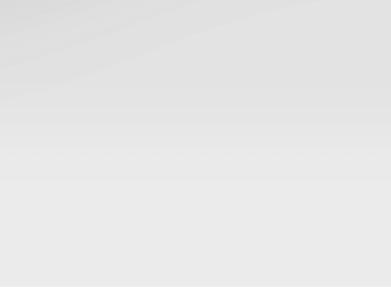
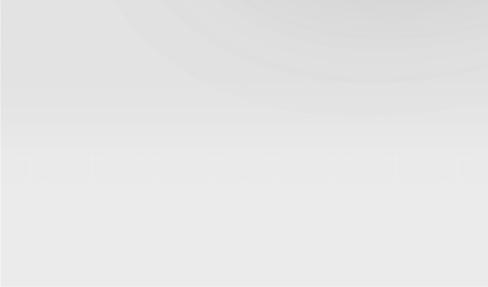

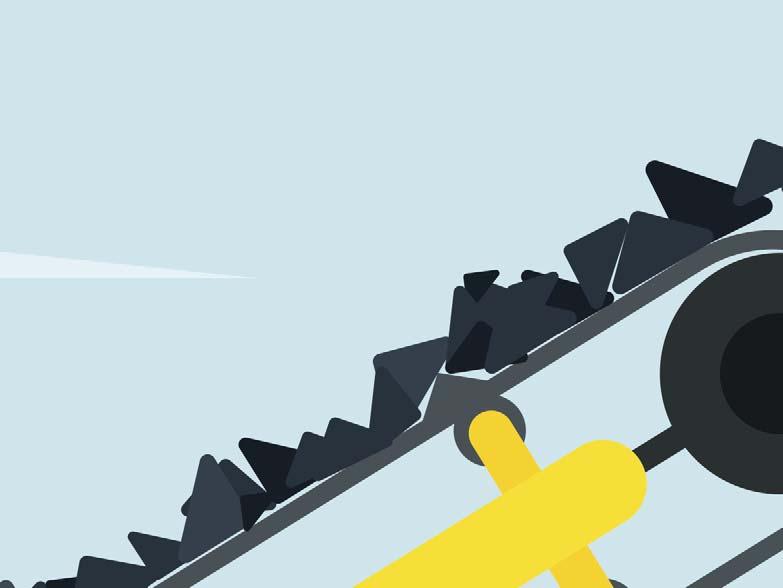
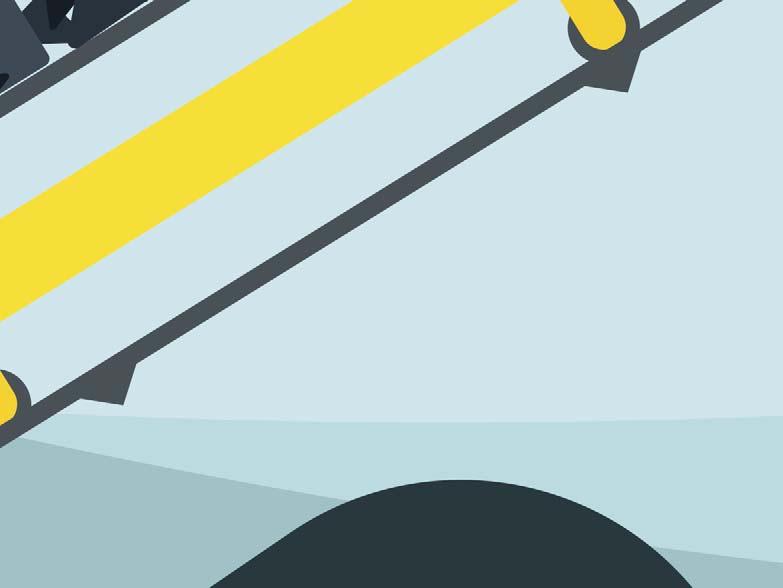
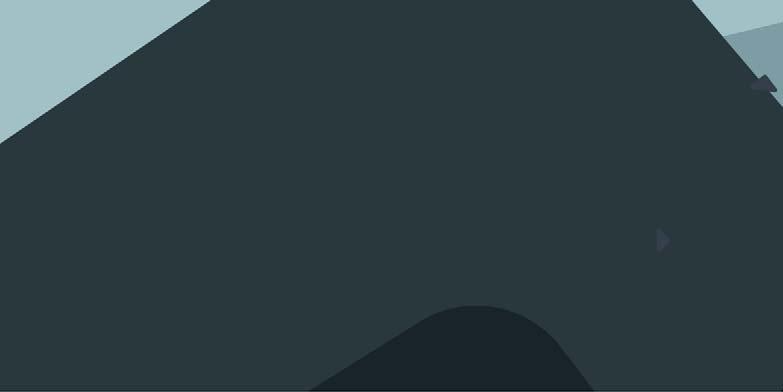
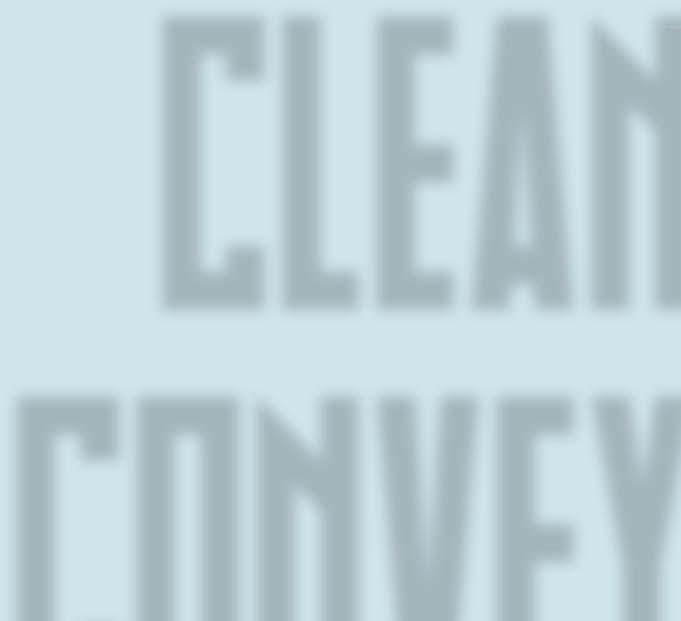
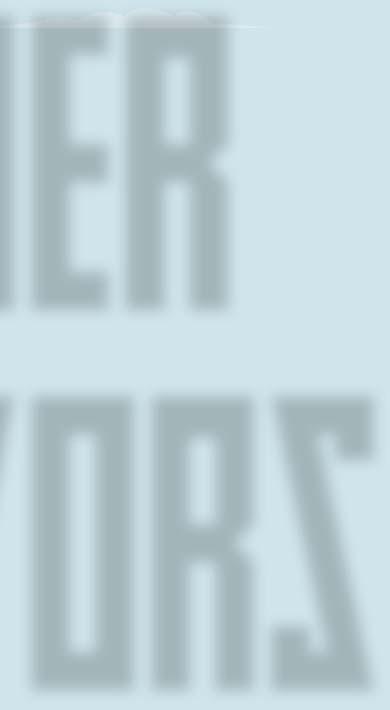

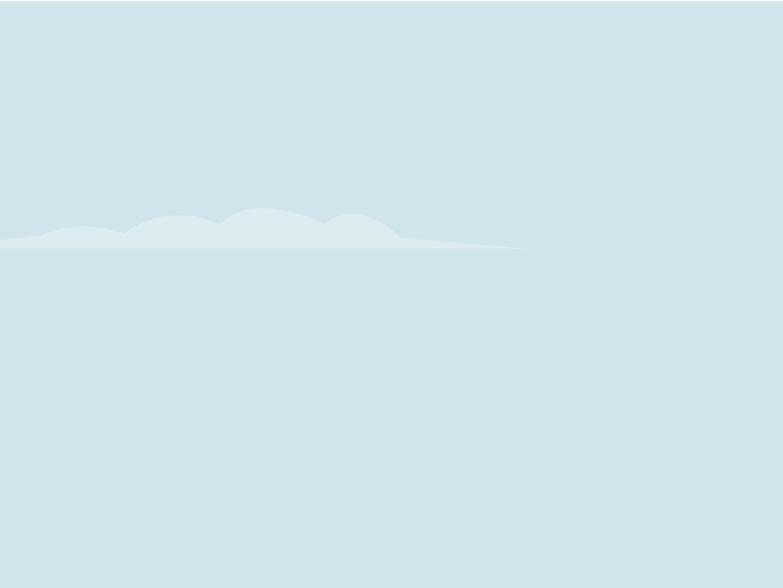
Todd Swinderman, Martin Engineering, USA, details how to achieve a return on investment for the control of conveyor dust.

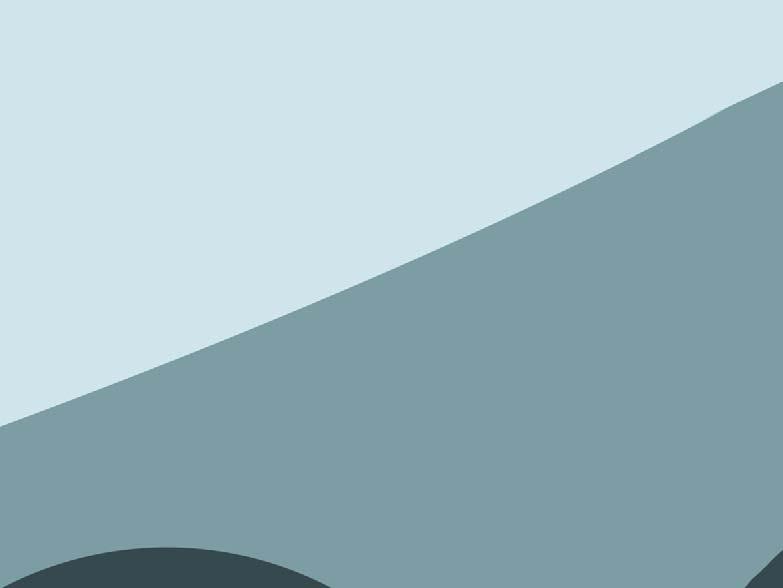
Most conveyors handling bulk materials have some amount of material loss from spillage, leakage, dust and carryback emissions, collectively called fugitive materials. The root causes are often obvious, but rarely addressed. Rather, the standard approach is to treat the symptoms. The consequences of failing to control fugitive materials include: unplanned downtime, excessive cleaning costs, regulatory actions, poor public relations, and safety incidents. Addressing the issues with workable long-term solutions improves availability, housekeeping and safety, ultimately enhancing the company’s cash flow.
Perhaps the most insidious of all forms of fugitive material is dust. Some of the issues are obvious – accumulations on floors and structures, premature bearing failures, and even explosion risk – but some are less noticeable, such as the long term physical and mental health issues caused by respirable and nuisance dust. A particle is considered respirable if it is 10 µm or smaller, which can penetrate into the gas exchange regions of the lungs and cause serious lung diseases.
Nuisance dust is generally understood as inhalable particles from 10 – 100 µm that are known to irritate the airways and cause inflammation, which can affect breathing and lead to chronic conditions, such as chronic obstructive pulmonary disease (COPD). It is estimated that for every accidental death in industry, there are 20 deaths due to the long-term effects of dust exposure. These deaths are not as sudden, but are just as traumatic, and often do not show up as fatalities in the company injury statistics because a worker can be on disability for years before passing.
Reducing visible dust emissions (usually defined as ≥40 µm) from conveyors is typically a primary goal, partly because it attracts the attention of workers, neighbours, and inspectors. The Occupational Safety and Health Administration (OSHA) provides a list of hazardous dusts in 29 CFR 1910.1000 Z and recommends wet or vacuum cleaning, while prohibiting the use of compressed air, dry sweeping, or brushing in most situations (see 1910.1053[h]). For dust management, OSHA requires engineering controls, such as enclosures and dust collectors, be considered first. If not practical or effective, work practices or respirators are needed to limit exposure. Quite often the use of respirators is seen as an acceptable alternative, but a closer evaluation will show respirators reduce productivity by as much as 19%, and prolonged use can affect cognitive and sensory abilities significantly. These decreases in productivity alone can justify improvements to conveyor dust containment to reduce emissions.
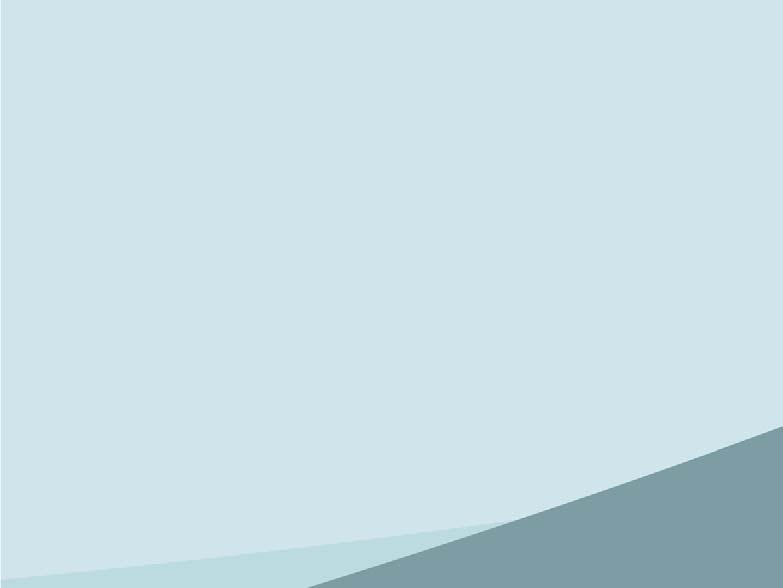

Skirtboards
The skirtboard enclosure is essentially a low-efficiency settling chamber. The basic concept is that a dust particle will settle out of a laminar air stream based on the speed of the air flow, Vair, and the terminal velocity, Vt, of the dust particle (Figure 1).
There are many rules of thumb, along with traditional and industry-based practices for skirtboard sizing and dust curtain placement, in an attempt to contain the dust in the skirtboard enclosure. Most of these practices are without proof of performance other than having always being done that way.
Current practice for conveyor skirtboard enclosures is to design for Vair ≤ 1.0 m/sec. by increasing the height (H) of the enclosure. Two common rules of thumb for the enclosure length are two times belt width, or 0.6 m for every 1 m/sec. in belt speed. It is interesting to note that if H is increased, the distance (L) that the average dust particle must travel also increases. A detailed design study of air flow and particulate settling was performed using SolidWorks 2019 Flow Simulation software.
A ‘standard conveyor’ was established as the baseline for the study (Figure 2). The standard conveyor is a 1200 mm wide belt with a 35˚ trough angle, travelling at 2 m/sec. A generic material was used to produce the baseline data, with a bulk density of 1442 kg/m3 and a nominal 50 mm minus particle size distribution with a 20˚ surcharge. The discharge chute was sized based on the rule of thumb: material volume equal to or less than 40% of the chute cross section. A drop height of 3 m, an open area of 0.9 m2, an average particle size of 25 mm, and bulk flow of 1680 tph were used to calculate the induced air volume.
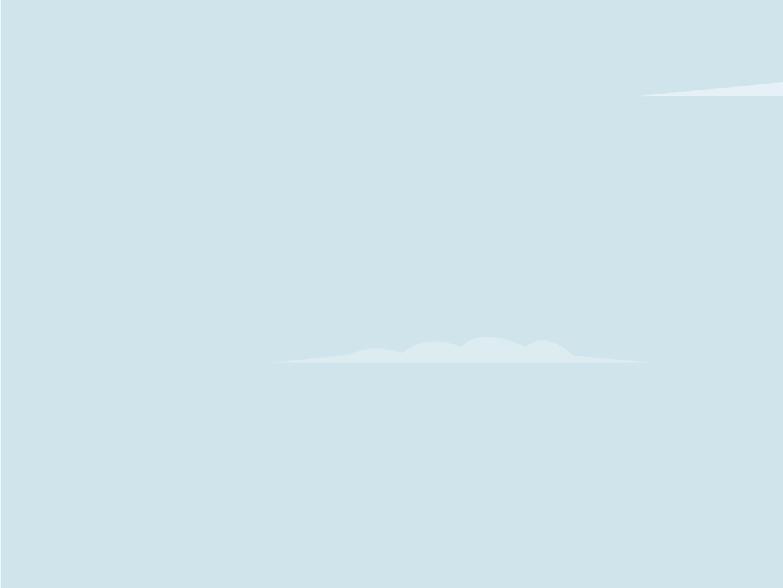
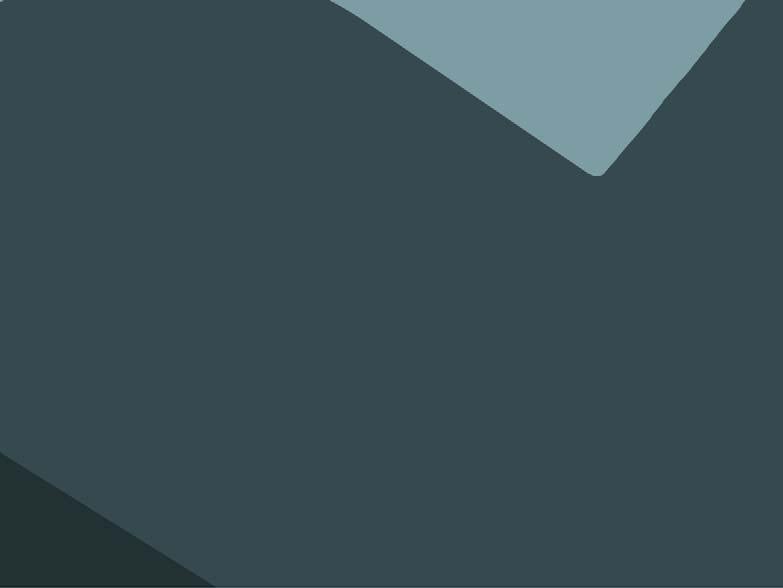
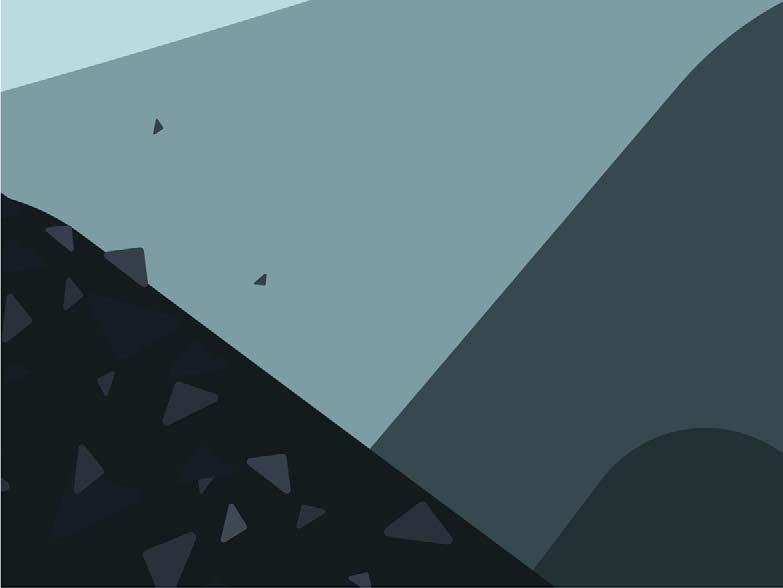