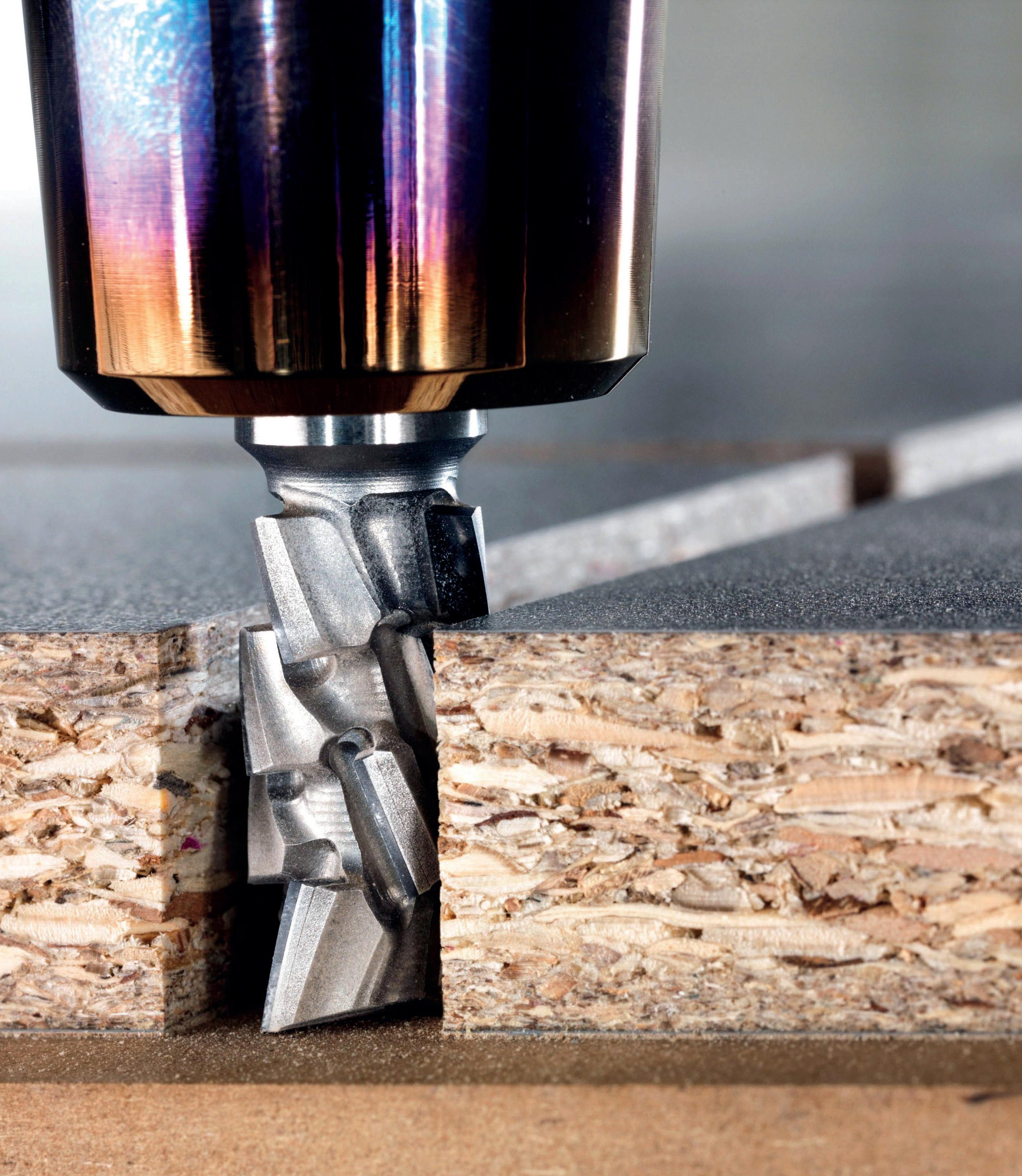
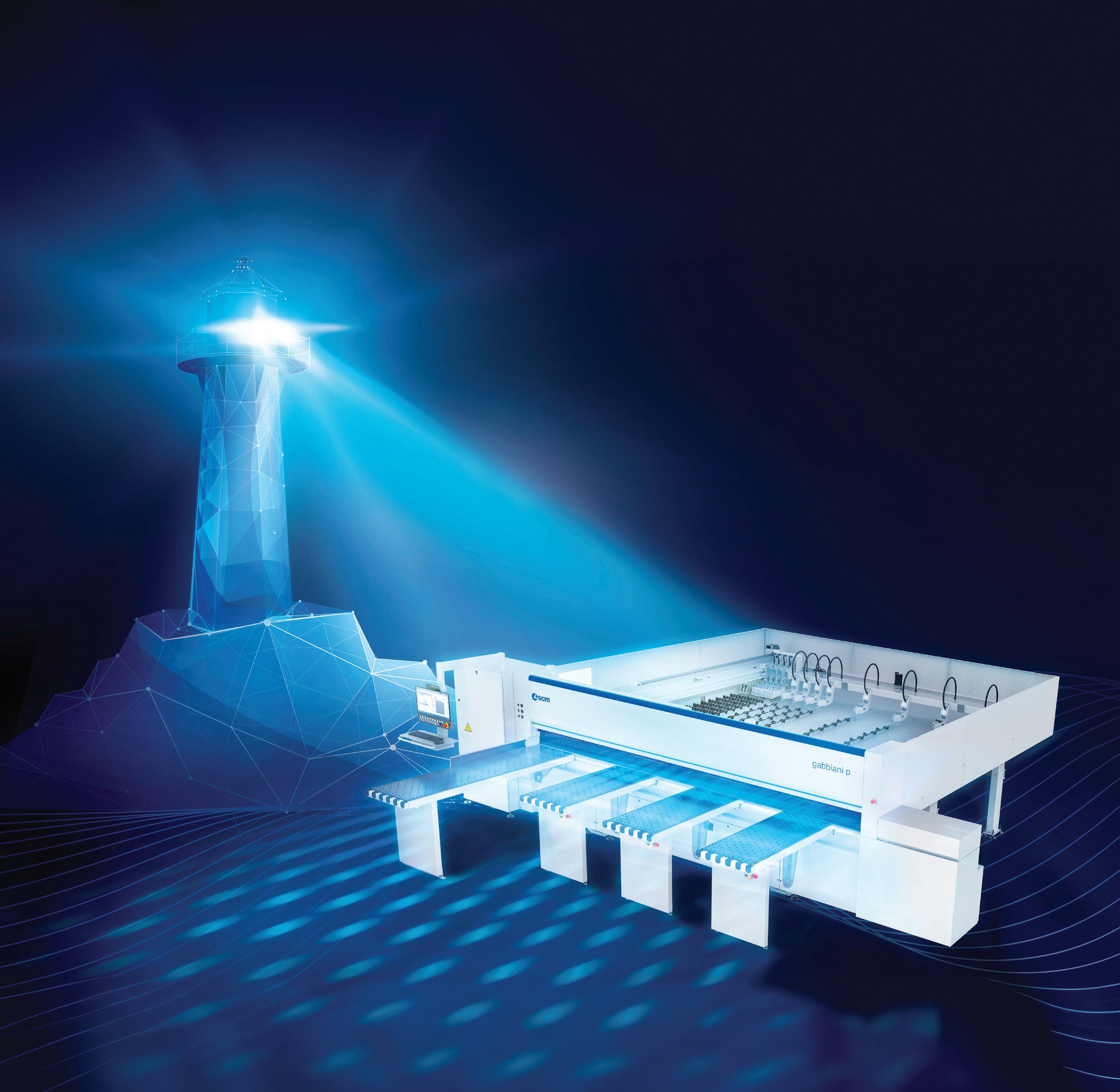

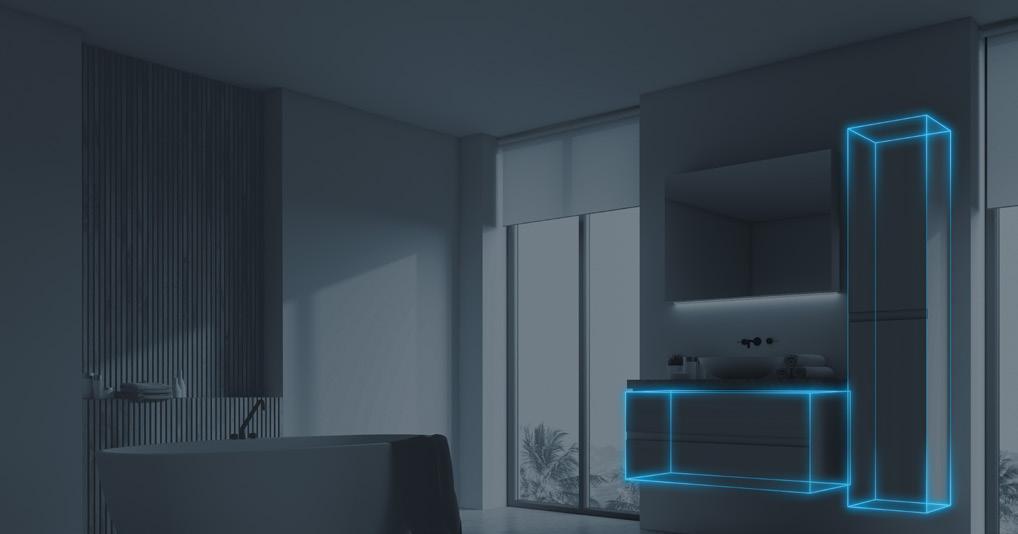
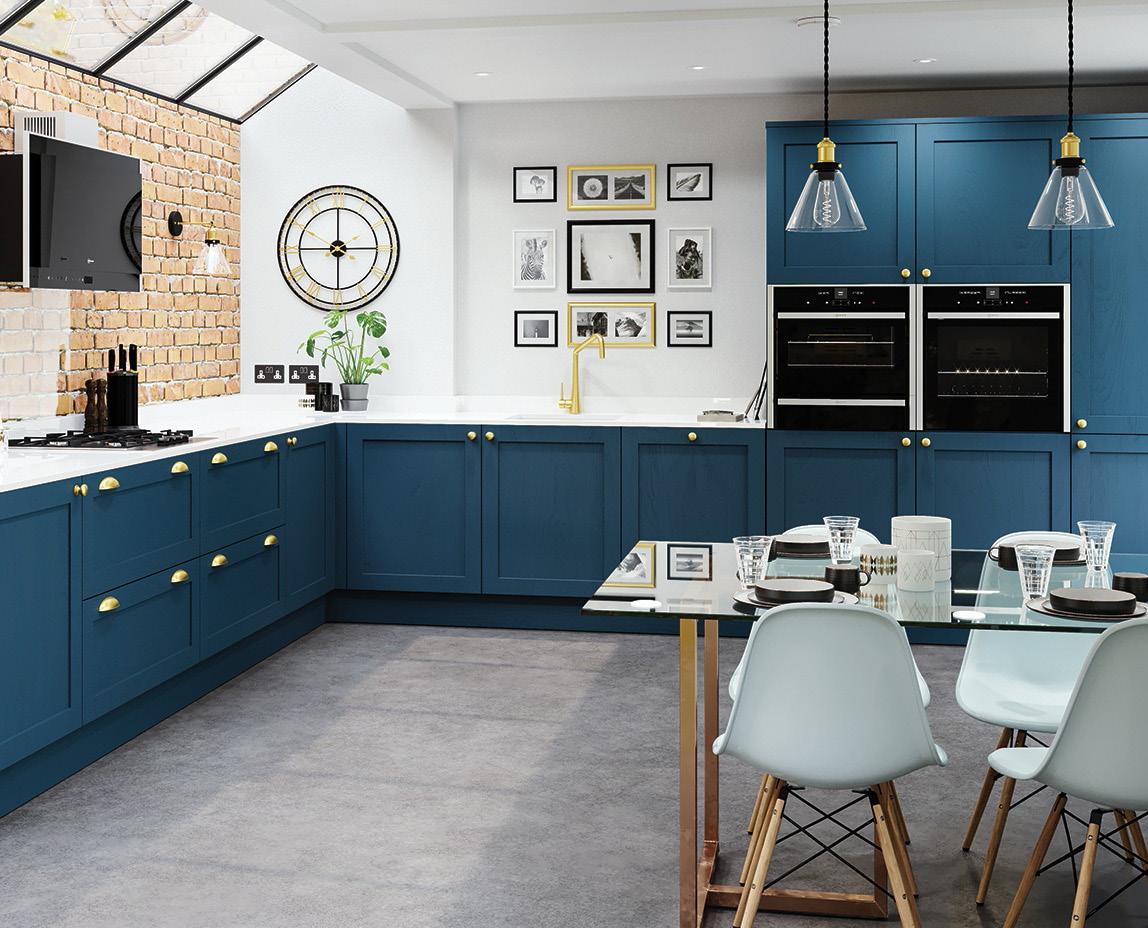

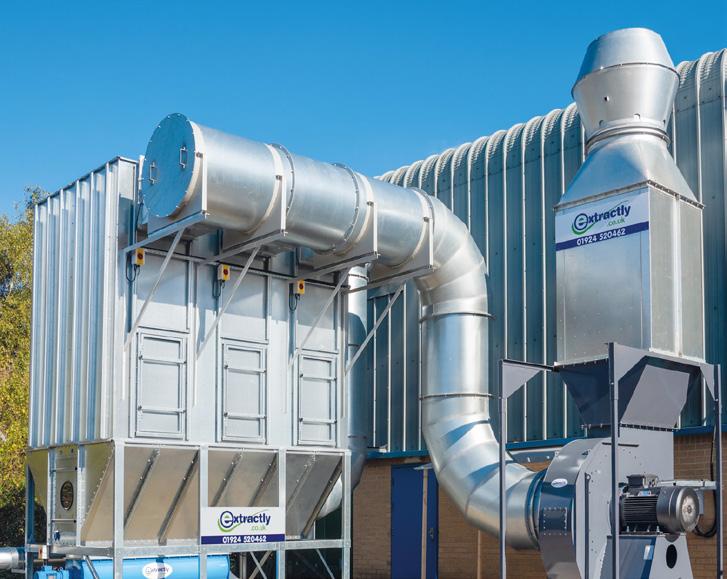
Combilift, the global leader in material handling solutions, has been awarded Company of the Year at the prestigious Business & Finance Awards 2024, in association with KPMG Ireland. This remarkable achievement marks Combilift’s 9th major win in the last three months, solidifying its position as an industry leader.
The Company of the Year award, presented to Combilift’s CEO Martin McVicar by Seamus Hand from KPMG at the 50th Business & Finance Awards ceremony - held in Dublin, is a testament to the company’s significant impact on both the Irish economy and the global market. Combilift, with annual revenue exceeding €500 million, has continued to thrive with its export-focused business model, with 98% of its operations serving international markets.
Since its founding in 1998, Combilift has built a global reputation as the largest manufacturer of multi-directional, articulated, and sideloading forklifts, as well as large material handling equipment such as straddle carriers, with over 85,000 units in operation across 85 countries. The company’s commitment to innovation, sustainability, and research and development has been pivotal to its exceptional growth, making it a true leader in the material handling industry.
L-R. Kevin Hughes, Kenny Gilmour, Lisa Mc Crudden, Fintan Sherry, Ian Hyland, Martin McVicar, Seamus Hand, Patrick McMeel, Colin Gray, Donna Rutledge, Margaret Courtney & Peter Campbell
Martin McVicar, CEO of Combilift, said:
“This award reflects the bold vision and relentless drive that has been at the heart of Combilift since Robert Moffett and I started in 1998. Every forklift, every innovation, and every milestone reflects our commitment to pushing boundaries and transforming material handling worldwide. This moment belongs to our employees, our dealers, and our customers, who rely on us to deliver quality material handling solutions to optimise their warehouse space.”
Joining a Legacy of Excellence
Winning this award places Combilift among an elite group of previous winners, including industry giants Glen Dimplex, Kingspan, Primark, Google, and Intel. As a homegrown Irish business with a global footprint, this latest recognition serves as a powerful reminder of the company’s ongoing success and its critical role in shaping the future of the material handling industry.
Ian Hyland - Business & Finance, Martin McVicar -Combilift, Seamus Hand - KPMG
Scm Group, leading multinational in technologies for machining a wide range of materials, signed the closing deal for the purchase of 51% of Mecal Machinery, specialising in the production of machinery and systems for processing aluminium, PVC and light alloys.
Mecal Machinery, based in Pavia, is a vertically integrated company with a 100% made in Italy production with 190 employees and a turnover of 45 million Euro.
‘The entry of Mecal Machinery into the group,’ emphasises Marco Mancini, CEO of the Scm Group, ’allows us to enter a new market segment, enhancing the range of technologies and services already offered by the Group. The Partnership with Mecal Machinery, like the one signed in June with Tecno Logica in the highly innovative industrial plant sector, opens up important new business opportunities for us at international level’.
Ennio Cavezzale, owner-partner of Mecal Machinery, adds:
‘Becoming part of a solid multinational company like Scm Group guarantees Mecal a role as a global leader in its sector, leveraging the Scm Group’s capillary sales and service organisation’.
Cavezzale remains a shareholder of the Lombard company with the role of Chairman of the Board.
Leading woodworking machinery manufacturer, Weinig, has appointed Fortitude Communications to manage its public relations and marketing.
The WEINIG Group is one of the world’s largest manufacturers of machines and systems for processing solid wood and derived timber products. Fortitude Communications will represent the UK arm of the German machinery business, which includes the brands Weinig, HolzHer and Essetre.
It appointed Fortitude as its retained agency following a competitive tender process. Award winning Fortitude will devise and deliver an integrated service with a strong focus on trade press, social media and video production.
Malcolm Cuthbertson, managing director at Weinig said: “We’re proud to be market leaders in the wood machinery manufacturing industry with our reputation based on maintaining exceptional standards and continuous innovation.
“We have exciting plans for 2025 and needed an agency to ensure we maintain our market position and support our vision for continued growth in our key markets.
“Fortitude is an excellent fit for us to take our communications forward and enhance our profile. The agency is nimble, excel at storytelling and deliver a rounded communications service.”
Greig Box Turnbull, founder of Fortitude, said: “Weinig is an exceptional brand that is innovative and highly respected and we’re proud to represent the business.
“It has a strong heritage, first-class standards and provides market marketing leading machinery for the UK wood processing sector manufacturing market and we’re looking forward to partnering with the team for years to come.”
Fortitude was founded by Greig Box Turnbull, who is a former Oxford United managing director and Daily Mirror journalist. Based on Oxford Business Park it has clients across a range of sectors including corporate, transport, sustainability,hospitality, charity and sport.
Based on Abingdon Business Park in Oxfordshire, Weinig UK is part of the worldwide WEINIG Group, synonymous for providing solutions and the latest in technology to solid timber processors. Weinig UK provides UK and Ireland sales and service solutions via an experienced work force.
Mirka® DEROS RS 600 is a rotary sander designed for heavy-duty, coarse sanding applications. Its lightweight, compact design provides a smooth operation and enhances user comfort and productivity. The Mirka® DEROS RS is the perfect solution to tackle paint removal, furniture restoration, cabinetry, solid surface and wooden flooring projects with ease. For further information or to arrange a demonstration, please contact Customer Services on 01908 866100.
Panel & Joinery Production were delighted to accept an invitation from Mirka, a global leader in tools, abrasives, and polishing solutions, to their UK HQ in Milton Keynes to discuss Mirka’s commitment to sustainability and the new tools that have joined its constantly growing product portfolio to meet the demands of the industry.
Clare Hollister said: “This was my first visit to Mirka UK and it was a pleasure to meet Neil Newbrook and the team. It was a great opportunity to find out more about their new product development and continued commitment to the environment and sustainability. Getting hands on experience of their products demonstrated the usability and flexibility of their products and was a great way to end the day.”
The first area that was covered was sustainability, which is a hot-button topic in every sector Mirka works in. Neil Newbrook, business sector manager Wood, explained that Mirka was commited to sustainability, anchored by three key pillars: societal impact, environmental cleanliness and resource efficiency. The pillars cover vast areas but Neil broke them down into manageable chunks.
Neil says, “For environmental cleanliness, we are aiming for a 55% reduction in greenhouse gas emissions by 2035 and are aiming to achieve net-zero emissions by 2050. We believe we are on the way to meeting these targets and are always looking into options to help us get there. With resource efficiency, we are talking about the lifecycle of the product and what happens to it when it is ‘finished’. As a business, we want to ensure we get the most out of our products and this is highlighted by the fact that we are looking to have 70% of Mirka’s products recyclable by 2035. This aim is supported by a €25 million circular grain manufacturing plant in Finland, which is scheduled to be operational by December 2025. The site has been designed to sort, clean and prepare incoming recycled materials as well as screen and classify grains for reuse. This will aid in maximising the lifecycle of products and reducing waste both internally and from external sources.
“For societal impact, we are aiming for zero workplace accidents and the provision of dust-free work environments because, as we know, the dust produced can affect the health of employees and be detrimental to jobs being performed in the workshop,” he adds.
We then moved onto talking about tools and this is where things got particularly interesting. When it comes to the development of new tools, the R&D team in Jeppo, Finland is the brain behind the innovation, but Mirka UK’s technical experts are in constant dialogue with customers to understand their needs and requirements. The insights from these conversations are circulated to the R&D team to help them design innovative and versatile tools tailored to industry needs. In 2024, the main product launched for the wood sector is the DEROS RS 600 Rotary Sander.
This tool has been designed from the ground up to make easy work of multiple applications from paint removal and furniture restoration to cabinetry, solid surface, and flooring projects. In addition, its lightweight, compact design provides a smooth operation and enhances user comfort and productivity, despite it being a powerful heavy-duty sander. Furthermore, it has Bluetooth connectivity, so when it connects to the myMirka app, users have access to real-time data about the tool and how it is being employed.
When it came to talking about dust-free sanding, Neil introduced the new Mirka® DEXOS 1217 M Class AFC dust extractor. He says, “This extractor is the latest addition to Mirka’s extractor range and it stands out from other extractors on the market in terms of its looks and what it provides the user. This is highlighted by the 1200-watt brushless electric motor that ensures dust is quickly and efficiently removed from surfaces.”
In addition, Neil highlighted the fact it can handle both wet and dry applications and is compatible with multiple tool types, so there is less downtime as tools do not need to be switched from job to job. This leads to increased productivity which is something businesses and users alike are looking for.
Neil also highlighted some of the DEXOS’ USPs. The first is the adjustable automatic filter cleaning capabilities, which ensure consistent suction. The second is an additional power socket on the front which allows the user to operate a second tool to speed up the job, or put their phone on charge while working. The third is a Bluetoothenabled remote control (sold separately) that is strapped around the dust hose and senses tool vibrations meaning the auto-start function can still be used with cordless or pneumatic tools, and offers the user two operating modes.
Overall, Mirka is prioritising sustainability and innovation at the forefront of its business practices and by doing so, it is embracing environmental responsibility while still producing high-quality tools that meet the needs of the industry in the short, medium and long term.
We cannot wait to see what Mirka is going to do in 2025 and beyond.
https://www.mirka.com/en-gb/
Rack-clad warehouses where the rack installation columns also act as a supporting structure for the roof and sidewalls are an attractive option for companies that quickly need weather-protected storage capacities. They offer a significant cost advantage over standard buildings with separate rack systems. OHRA also enables its customers to reduce costs further by performing work themselves. Hungarian companies Farkas-Fa, a woodworking business, and timber dealer Sarok-Fa made and mounted the roof constructions for their OHRA rack-clad warehouses with their own wood.
New storage capacities in no time
Both companies quickly needed new capacities for storing planks, beams and other wood protected from the weather. Farkas-Fa and Sarok-Fa opted for rack-clad warehouses based on cantilever racks. Warehouse construction and rack assembly are done at the same time and not separately, enabling significantly faster construction times.
Custom solutions
At Farkas-Fa, two cantilever racks each measuring 12.4 metres in length form the walls. As the columns of the OHRA racks are made of hot-rolled steel profiles, offering high load bearing capacities, they enable large spans for the roof construction: At Farkas-Fa, the distance between the two rows of racks measures 15 metres. A third row of
racks can easily be placed in the centre of the warehouse at a later time. By contrast, Sarok-Fa opted for a rack-clad warehouse without sidewalls, allowing air to flow freely through the stored wood and dry it further. Three rows of two-sided cantilever racks act as the supporting structure. For Sarok-Fa, one important feature of the OHRA racks was that the flexibly suspended cantilever arms can be adjusted in a 100-millimetre grid without any tools. The racks can be adapted to a changing product range at any time.
Roof construction
Both companies had the workforce and expertise to build the roof construction themselves. OHRA simply tailored the supports at the racking columns to the respective roof construction in consultation with the two companies.
Increased capacity and efficiency
Thanks to the rack-clad warehouses from OHRA, Farkas-Fa and Sarok-Fa were quickly able to create new, sheltered warehouse capacities. Before constructing the rack-clad warehouses, both companies stored their wood, or at least some of it, on the ground. Thanks to storage in cantilever racks, they have significantly expanded their storage capacities in the same floor area. They also benefit from easier, faster access to the goods, improving warehouse efficiency significantly.
Manufacturers constantly seek solutions that enhance production efficiency while maintaining superior product quality. The innovative Quickfit TL5 “Full Metal Jacket” dowel from cabinet hardware expert Titus delivers on both fronts. It offers a versatile solution that streamlines assembly processes while ensuring longlasting joint integrity.
One of the most significant advantages of the Quickfit TL5 dowel is its universal applicability across different materials. Furniture manufacturers no longer need to maintain multiple dowels for various materials, as this single solution creates strong, reliable joints in MDF, chipboard and solid wood. This versatility eliminates the traditional need for supplementary wooden dowels, simplifying inventory management and reducing production complexity.
The system’s tool-free insertion capability represents a major breakthrough in assembly efficiency. This can reduce assembly time by up to 50% for home-assembled furniture, offering a considerable competitive advantage in the retail-ready furniture sector. For manufacturers focused on volume production, the dowels can be inserted automatically using Titus FastFit machines, further optimising the production process.
Used with Titus Cam5000 cams, the Quickfit TL5’s expanding steel sleeve delivers exceptional resistance to both torsion and pull-out forces. This engineering innovation ensures rigid furniture construction while addressing one of the most common consumer complaints – joints that loosen over time. Its robust design maintains joint integrity even through multiple cycles of assembly and disassembly, which is essential for furniture that may need to be moved or transported frequently.
Quality control is vital in furniture manufacturing, and the Quickfit TL5 significantly contributes to consistent production standards. The system’s reliable cam locking mechanism consistently engages at the 2 o’clock position, ensuring a smooth, firm tightening action and superior dowel pull-up strength. This predictable performance helps manufacturers maintain high-quality standards across their production lines while reducing the need for extensive operator training.
The system’s tolerance to manufacturing variations and positive engagement features set it apart in realworld applications. The specially designed dowel head accommodates edge-to-hole-centre (ETHC) tolerances of up to ± 1 mm, effectively managing both drilling inconsistencies
and the natural movement of wooden panels. When inserted into a 5 mm hole, the dowel immediately and securely engages, simplifying subsequent assembly steps. During edge insertion, the dowel engages positively with the cam and maintains its position until tightened, ensuring consistent assembly quality regardless of operator experience. This reliability reduces waste and rework in the production process, improving manufacturing efficiency and cost control.
The Quickfit TL5’s versatility makes it equally valuable for both large-scale manufacturers and smaller custom cabinet makers. For highvolume producers, the system’s compatibility with automated insertion equipment and consistent performance characteristics enable streamlined production flows and predictable assembly times. Meanwhile, custom manufacturers can feel confident in the system’s flexibility across different materials and panel thicknesses, allowing them to maintain consistently high quality while working with varied specifications. This adaptability is particularly valuable today, where manufacturers often need to switch between different product lines and materials to meet changing customer demands.
The system’s versatility is further demonstrated by its availability in versions suited to ETHC dimensions of both 24 mm and 34 mm, accommodating different panel thicknesses and construction requirements. The standardised drilling specifications – 5 mm diameter for the face board and 8 mm for the edge board, with a minimum face board hole depth of 12.5 mm – allow for straightforward integration into existing manufacturing processes.
In an industry where profit margins are increasingly under pressure, the Quickfit TL5’s contribution to manufacturing efficiency can significantly impact the bottom line. Beyond the immediate benefits of faster assembly and reduced material requirements, the system’s reliability helps minimise waste and rework. The universal compatibility across different materials allows manufacturers to streamline their purchasing processes and reduce inventory holding costs. Additionally, the system’s durability and consistent performance can reduce warranty claims and enhance customer satisfaction, contributing to a stronger brand reputation and repeat business.
As the industry continues to evolve, solutions like the Quickfit TL5 demonstrate how innovative hardware can drive improvements in both manufacturing efficiency and product quality. For manufacturers seeking to optimise their production processes, its ability to create reliable joints across multiple materials, combined with significant assembly time reductions and tolerance to manufacturing variations, positions it as a valuable tool in modern furniture production. https://uk.titusplus.com/
The UK’s soaring energy prices are already causing financial strain to some small businesses, and yet the energy price cap is set to rise in early 2025.
Managing spiralling operational costs in an already uncertain market is crippling some small businesses, with the only possible solutions being to raise prices for customers or absorb the losses themselves.
There are already signs that people are tightening their belts in this current economic climate. With both household and commercial budgets already being squeezed, many business owners are fearful of increasing prices in case it alienates their clientele.
Over the past few years, UK energy prices have surged. For small businesses with energy-intensive operations, such as manufacturing companies, this sharp increase has a huge effect on the bottom line.
Despite the bleak landscape, some businesses are managing to find alternative solutions. Those companies that generate or have access to waste wood could benefit from purchasing a wood waste heater. Wood waste heaters allow businesses to convert waste wood into affordable and renewable energy, slashing energy and waste disposal costs simultaneously.
Whilst the purchase of a wood waste heater requires an initial investment, the payback period can be quite short. Businesses that generate waste wood are urged to find out more and do some calculations, as with the savings on energy and waste disposal costs, some businesses can get payback on their investment in a wood waste heater in less than 12 months.
Wood Waste Technology offers a range of durable, reliable and easy to use wood waste heaters to suit all sizes of businesses. By investing in a wood waste heater, a business can benefit from free factory heating whilst saving money on skips and other waste disposal charges, as well as helping reduce a company’s carbon footprint
• Enormous melting capacity of 12 kg / hour
• Range over 400 metres with one charge (with 18 mm plate)
• Motorised height adjustment
With a substantial 2 kg cartridge capacity, businesses can achieve significant cost savings, utilising cheaper-priced PUR adhesive without compromising finish. Delivering near-invisible, waterproof joints that meet the highest quality demands.
Just-in-time heat-up
From zero to operating temperature in only 3 minutes and back to zero just as quickly.
• Can be pulled out on linear guides for easy cleaning
• 3 minutes heat-up time, low energy consumption
• Processing of commercially available 2 kg PUR glue cardridges
• Processing of PUR or EVA granulate possible
Sustainability is a term that is becoming increasingly important for many companies worldwide. “Green” is no longer just a colour; it has turned into a symbol, as businesses strive to showcase their commitment to being environmentally friendly. Combilift’s original green company colour reflects its Irish roots and has become globally synonymous with the brand since its establishment over 26 years ago. Recently, Combilift expanded its green colour palette by introducing the new vibrant Combi-Eco green, which enhances truck visibility in all conditions.
Reducing your company’s carbon footprint benefits society and the environment, and transitioning to electric-powered equipment can ensure a more sustainable business model. With the growing demand for greener technologies, 98% of Combilift’s R&D focuses on energy-efficient and electricpowered equipment, with over 70% of its production now electric.
Combilift’s CEO and Co-Founder Martin McVicar explains: “Sustainability is at our core – we’re highly focused on making our vehicles more environmentally friendly and helping our customers maximise their warehouse efficiency,”
Moreover, Combilift’s products are designed to maximise efficiency, storage capacity, and safety. The multidirectional “3 forklifts in 1” models, such as the C-Series or CB range, can replace various types of trucks, significantly reducing the size of the required fleet. They operate in narrow spaces while carrying long loads, potentially creating up to
50% more space and avoiding an unnecessary greenfield expansion during growth periods. Maximising space use also leads to lower energy consumption for utilities like heating and lighting.
Combilift’s multidirectional models are especially popular for handling long, heavy, or bulky timber products, as they enable safe and space-saving transportation of these loads in confined spaces.
In addition to using electric power, optimising warehouse space contributes to a sustainable supply chain. Before considering facility expansion or relocation during periods of growth, it is worth exploring space-saving strategies to optimise your existing facilities. Narrowing aisles and using higher racking are two methods that Combilift’s design engineers can recommend as part of the company’s free warehouse planning consultancy service. They provide diagrams and 3D simulations to help visualize how to increase extra storage capacity, and enhance workflow efficiency. Using Combilift’s versatile trucks, which can operate both indoors and outdoors, reduces the total number of forklifts needed, the energy consumed, and, in turn, the carbon footprint.
Martin McVicar said: “Almost every model in our extensive range of products is now available with electric power. The ever-increasing lift capacities will answer the demand for more powerful products, which at the same time help companies to achieve their aims for more sustainable operations”
When it comes to fitted furniture, the drawer is the big pull according to Hettich, even if it sometimes hides from view.
Fitted-furniture styles and finishes might evolve or retreat, inspire or reassure, but for quality the only way is forward. In the kitchen, bedroom and other areas of the home, the sensation of opening and closing a door or drawer is the differentiating factor which continues to delight long after the fitters have left the building.
Likewise, sharply-defined, even gaps between drawers are the mark of quality cabinetry, and Hettich’s Quadro V6 fullextension drawer runner has become the acknowledged way to achieve this visual perfection. The addition of Quadro has always given a meaningful uplift to a range of furniture without adding significant cost. As soon as the customer uses or sees the drawer with Quadro as opposed to a more basic alternative, the added value is immediately apparent and that can make all the difference.
Add Quadro, add value
But Hettich has now set the bar even higher for drawer system performance with Quadro V6 5D, which has a loading capacity up to 30 kg and uses slide-on assembly. It comes with Silent System and Push to Open, with Push to Open Silent being optional. The significant difference is that Quadro 5D is adjustable in five dimensions as opposed to four. The new plane of adjustment is radial, which is
fine-tuned using the drawer-box adjuster on the runner, in addition to tilt. Vertical and horizontal movement remain adjustable in the catch, while depth is determined in the plug.
With quick and easy tool-less adjustment in five dimensions – horizontal, vertical, depth, tilt and radial – Quadro V6 5D provides the best route yet to dependable and accurate alignment.
With slide-on assembly and quick-release, Quadro’s ease of installation belies its sophistication. Its design even removes the need for a door damper: simply minimise the drawer front gap without letting the front panel contact the carcass. In the Quadro range, you’ll find further universal benefits such as the option to use in conjunction with up to 18mm wood or fibreboard in applications where KA runners fitted to the side of the drawer box would more typically have been used. For a small uplift in price, manufacturers can offer the superior performance of Quadro, plus the fact that it is concealed under the drawer box.
Quadro features high-precision, maintenance-free steel ball bearings, and the whole assembly is made from galvanised steel and therefore suitable for rooms exposed to moisture. Its profile geometry makes for high tracking stability and strength. The result is a well-balanced, smooth-running action which is bound to impress end-users.
Quadro also benefits from Hettich’s platform concept, providing many options for differentiating furniture using the same drawer and carcass. Choices include partial and full-extension runners, plus soft close and the innovative synchronised Push-to-open silent mechanism for handleless furniture.
For highly-distinctive furniture design, with narrow reveals and large front panels, Hettich also has the answer in the Actro 5D drawer runner. As with Quadro V6 5D, Actro 5D adjusts in five directions, but with the distinction of providing extremely narrow reveals with large drawer fronts, with smooth, synchronised running, incredible stability and capacity up to 70 kg.
Give it wings
Drawers are not the only storage solution, or sometimes the interior scheme demands that they be hidden. In which case, if you’re looking for something fresh and innovative to offer customers, then it’s time you met WingLine L from Hettich.
These trend-setting bi-folding doors from Hettich’s sliding and folding doors range have recently received a major upgrade. They are a sleek and elegant solution creating an
impressive panorama of the cabinet’s contents (up to 6m²), making sure everything is visible and accessible.
In multi-functional spaces encompassing kitchen areas and working-from-home for example, WingLine L can bring food preparation zones, appliances or workstations into action or hide them from view with minimal effort.
Manufactured in Germany by Hettich, WingLine L brings a fresh and innovative approach to flexible storage in the kitchen, bedroom, office or indeed any living space. With optional handleless, push or pull-to-move technology, customers are sure to experience a moment of pure magic that will stay with them as they specify their project.
WingLine L comes with optimised running performance, optional soft opening and closing operation, and without the distracting bottom-panel profile, making it a versatile allrounder for beautiful kitchens, bedrooms and other spaces in the home.
Whether you’re an architect, interior designer, trend expert, colour specialist, or simply passionate about surface design, Surface Design Show 2025 is your destination for fresh ideas, cutting-edge materials, and unparalleled insights.
The 2025 show speaker lineup features experts from the forefront of architecture and design, including:
• Christos Passas, Director, Zaha Hadid Architects: Explore AI-driven design and the evolution of luxury in hospitality
• Kate Watson-Smyth, Founder, Mad About the House: Get exclusive insights on interior design trends—what to embrace and what to leave behind
• Vanessa Champion, Founder, Journal of Biophilic Design: Learn how biophilic principles are transforming spaces into havens of well-being
• Tina Norden, Principal, Conran and Partners: Discover the materials and trends shaping the future of hospitality design
• Asif Din, Director of Regenerative Design, Perkins and Will: Uncover innovative approaches to sustainable and circular design
Registration is now open 4th - 6th February 2025
Business Design Centre, London
What You’ll Experience:
• Inspiring Content: Over three days, explore thoughtprovoking sessions on topics like AI in design, circularity, biophilia, and designing for wellness.
• Product Launches & Trends: Be the first to discover innovative surface materials, technologies, and design solutions from emerging brands and established exhibitors.
• Networking Opportunities: Connect with architects, interior designers, and design professionals in our exclusive Designers Hub, a vibrant space to collaborate and share ideas.
Featured Sessions to Watch Out For:
• Material Passports: Dive into sustainable and transparent material sourcing with leaders from Perkins and Will and John Robertson Architects.
• Trends: Should You or Shouldn’t You?: Join Kate Watson-Smyth for a lively discussion on the evolution of interior design trends.
• The Power of Biophilic Design: Vanessa Champion explores how nature-inspired design enhances wellbeing and sustainability.
• Partners in Circularity: Hear from experts like Alex Johnson (SGP) and Deepthi Ravi (PLP Architects) on tackling adaptive reuse and circularity challenges.
www.surfacedesignshow.com
This Joinery Network event, hosted by partner Teknos is the perfect opportunity to increase your profitability when manufacturing timber windows and doors.
If you manufacture timber windows or are interested in manufacturing timber windows, this event will show you how to increase profitability, address manufacturing challenges and overcome changing legislation like PAS:24 or new building regulations.
The day features two demonstrations: machining a sash window with Leitz & The Joinery Network and a paint spray application session from Teknos.
Leaders from across the industry will be present to network, discuss all things joinery including The Joinery Network, Leitz, BJ Waller, Fedler, JoinerySoft, Hi-Tech Spray, Owen Dare Consultants and more...
Tickets available through Eventbrite:
Why attend:
• Demonstration of the innovative sash window Lignum tooling system on a Felder Spindle Moulder.
• Demonstration of paint applications for the best finish quality.
• Pick the brains of industry experts - we’ve brought together experts from across the industry to answer such as Leitz, Teknos, OTD Consultants, BJ Waller, Felder & more...
• Question and answer session form Hi-Tec Spray, the finishing solution specialists.
• Understand and get ahead of changing legislation like Pas:24 and Secured by Design.
• Learn how to increase your profitability by getting it right the first time: no more test cuts, reduce sanding, correct finishing spray application ad more...
Teknos & The Joinery Network Live Event Tickets, Wed, Mar 26, 2025 at 9:30 AM All ticket proceeds will be donated to our partner charity – Northern Ireland Air Ambulance Charity.
Teknos, 7 Longlands Rd, Bicester, Oxfordshire OX26 5AH.
Creative Homes Scotland is a five star rated furniture company based in Glenrothes, Fife. The company designs, manufactures and installs high quality and bespoke furniture across Scotland. Creative Homes has been working closely with its key supplier, Leitz Tooling, to develop the business, streamline manufacturing and ensure top quality products. Alan Goodsir, the companies owner and director, has developed a close relationship with Leitz over the last 3 years.
Creative Homes recently started their manufacturing journey. They are a new player to the industry and Leitz was able to offer meaningful recommendations and setup support that helped the business to get started. “Steven from Leitz offered us valuable tooling advice and he worked closely with our machinery supplier to get us set up with the correct tooling, including recommendations on cutting speeds and RPM’s. Leitz also introduced us to a system to avoid downtime and ensure there is always a tool on the machine, one ready for use and another tool off for sharpening. We don’t have to worry about the tooling side of the business anymore.” Alan noted.
Once Alan had setup his machine shop and processes, Leitz continued to support Creative Homes by offering innovative tooling solutions to address challenges in production as they arose. As part of their kitchen offering, Creative Homes manufacture kitchen surface tops with Krion® solid surface. Like many solid surface materials, Krion® can be difficult to machine due to its composition and properties. Its non-porous nature can cause excessive heat build-up when machining which can lead to melting of the material, excessive tool wear and chatter or burn marks. To solve this challenge, Leitz Tooling introduced Creative Homes to the BrillianceCut sawblade. Featuring a pioneering tooth geometry, the BrillianceCut achieves excellent cutting results even in polymer-bound mineral materials such as Krion®
The tooth geometry ensures finish cut quality and breakout free cutting, even on tough materials. Alan commented that “The new blades cut through material like butter, with much less wastage and no chipping. Doing it right the first time has been invaluable”. Higer quality finishes lead to huge cost and time savings through eliminating rework. With up to 20 sharpens, the BrillianceCut offers a sustainable and very economical solution to solid surface and plastic sawing.
After noticing an increase in tool wear, breakage and damage; Leitz recommended that Alan swap from using Leitz UK-made carbide spiral router cutters to the Diamaster Pro3 diamond nesting router. This led to a large increase In efficiency thanks to the fast cutting speeds of the Leitz Diamaster. Thanks to the Real Z3 design, it cuts up to 50% faster than standard diamond routers, allowing for reduced cycle times. “Introducing the Leitz PCD routers on our CNC has had a positive impact on quality thanks to greatly reduced chipping. The finish quality also means we get better cuts when edgebanding.” Additionally, the Diamaster’s long tool life reduces downtime from tool changes and has resulted in a massive decrease in sharpening costs as they can be sharpened multiple times and used for longer. “Leitz are the best in the business and the support given is above everyone else. Even setting expectations on tool life”. The Diamaster also features gullets in the tool body to support efficient chip extraction and avoid resin build up on the cutting edge.
To improve the efficiency and tool life even further, Creative Homes mount their Diamaster router cutters in the ThermoGrip heat shrink chuck. The ThermoGrip clamping system combines the tool and chuck into one tool body through thermal shrinking. It plays a decisive yet often overlooked role in the machining process as it’s stress resistant body can help achieve up to 50% higher feed rates compared to collet chucks. With a 6 fold higher clamping force than conventional collet chucks,
the ThermoGrip’s perfectly balanced geometry reduces vibrations, noise and therefore tool wear. This vibration reducing technology extends the life of mounted tools by up to 3 times and supports fast RPM’s of up to 36,000 min-1 for high performance cutting, faster than most machinery. Leitz measures tooling to 3 decimal points for height and diameter. This accuracy assists setting up and to aid the tool life, test cuts are not required. The small “nose” of the ThermoGrip chuck supports efficient extraction and chip removal.
Creative Homes has also benefitted from the Leitz tool service programme. The sharpening service has also addressed many manufacturing challenges faced in the factory and ensures Creative Homes’ tooling is costeffective and operating at maximum performance. The sharpening service extends tool life whilst improving cutting performance, making tooling more efficient and sustainable. This helps Creative Homes to maintain reliable cycle times
and a consistent finish quality. Leitz has 8 service centres in key locations across the UK for tool sharpening and repair. With a growing range of advanced machinery and the UK’s most sophisticated saw sharpening setup to date; Leitz is uniquely positioned to support Creative Homes as a sole supplier. Leitz sharpening services are accurate to microns and the intricate sharpening process revitalizes tools so that they perform at their best, offering a consistent finish quality.
Overall, support from Leitz has enabled Creative Homes to stay focused on what they do best: manufacturing high quality kitchens, bedrooms and bathrooms. Creative Homes Scotland has experienced a significant transformation thanks to its strategic partnership with Leitz Tooling. By leveraging Leitz’s innovative tooling solutions and expert sharpening services, Creative Homes has streamlined its manufacturing processes, reduced costs, and enhanced the quality of its bespoke furniture.
“Leitz are the best at what they do, that’s why we have developed a great working relationship.”
For more than four decades, the Holz-Her Glu Jet system has set the benchmark in glue application technology for edgebanders, redefining industry standards with its innovative approach.
Renowned for its versatility and efficiency, the Glu Jet system has built a global customer base of almost 60,000, thanks to its ability to apply high-performance PUR glue with precision, delivering near-invisible, waterproof joints that meet the highest quality demands, without the need for a nitrogen tank or lengthy glue pot clean-down.
Key features include:
• EVA or PUR
• Granulate or cartridge
• Three-minute heat up time, low energy consumption
• Four-minute clean down, saving time and money
• Program recall
• Glue usage metering, impossible to run out of glue
• Perfect results, bench time erased
Introducing the Glu Jet GJ730 PUR 2000
The recently launched Glu Jet GJ730 PUR 2000 builds on the legacy of the Holz-Her Glu Jet, offering enhanced efficiency, precision, and cost-effectiveness.
It delivers the perfect combination of performance, durability, and aesthetic appeal for a flawless finish on panels, boards, and furniture components. Designed to meet the evolving needs of modern production environments, the GJ730 PUR 2000 combines all the renowned features of its predecessor with advanced capabilities that enhance performance and usability.
At the heart of the GJ730 PUR 2000’s appeal is its economical use of PUR adhesive.
With a substantial 2KG cartridge capacity, businesses can achieve significant cost savings, utilising cheaper-priced PUR adhesive without compromising quality.
Each 2KG cartridge, compliant with commercial specifications (120 – 126 mm diameter), provides the capacity to cover over 400 metres of board (18 mm thick) with ease, ensuring extended operation and reduced downtime.
The machine’s impressive melting capacity of 12 KG per hour ensures it can handle high-volume production demands efficiently, making it an invaluable asset for businesses aiming to boost productivity while maintaining superior glue application standards.
Ease of use is a cornerstone of the GJ730 PUR 2000’s design. The system features linear slideways that provide straightforward access to the nozzle, simplifying cleaning and maintenance tasks. This design reduces downtime associated with routine upkeep, enabling businesses to maximise operational efficiency and maintain consistent performance.
Precision in glue application is critical, and the GJ730 PUR 2000 excels in this aspect with its motorised height adjustment.
This feature allows users to fine-tune the application process, ensuring optimal results across a variety of materials. The system’s adaptability to different production needs further underscores its value as a versatile solution for diverse wood manufacturing requirements. Advanced Automation with iTronic Technology
Incorporating iTronic technology, the GJ730 PUR 2000 offers programmable pneumatic setting recall, allowing users to store and retrieve settings effortlessly for different applications.
This automation not only reduces setup time but also ensures consistent, high-quality results, enhancing workflow efficiency and vastly minimising the potential for human error.
Meeting stringent commercial compliance standards, the GJ730 PUR 2000 provides businesses with the confidence to operate within regulatory frameworks. Its compatibility with 2KG cartridges ensures it adheres to industry specifications, making it a reliable choice for any production setting.
Glu Jet PUR 2000 and 2 KG PUR cartridge in situ on Accura 1556 edgebander, allowing for extremely shallow infeed angle, especially important for solid wood lipping application
Conclusion
The Holz-Her Glu Jet GJ730 PUR 2000 represents the pinnacle of glue application technology, offering businesses an unrivalled combination of efficiency, precision, and cost-effectiveness.
With its advanced capabilities, including cost-saving adhesive use, high melting capacity, user-friendly maintenance, precision adjustments, and advanced automation, the GJ730 PUR 2000 is the perfect solution for businesses seeking to optimise production processes and achieve exceptional results consistently, whilst saving money.
Jet PUR 2000 with robust, extremely stable base mount and precision linear guides for easy access to glue nozzle
Decorative Panels Lamination is proud to unveil dpslim—a revolutionary acrylic surface solution that combines cutting-edge technology with elegant design. Newly launched, dp-slim offers a versatile and durable option for manufacturers creating bespoke kitchens, bathrooms, and other modern interior spaces.
At just 4mm thick, dp-slim redefines possibilities with its lightweight yet robust composition, delivering a sleek, seamless finish that’s perfect for high-demand environments. Part of the dp- slim Crystal Collection, this innovative product includes over 16 stunning designs from REHAU Rauvisio Pure, Strong, and Deep portfolios. The collection has been further enhanced with the exciting addition of REHAU Crystal Mirror, offering a reflective, sophisticated touch ideal for contemporary designs.
Designed for Kitchens and Bathrooms
dp-slim is purpose-built to meet the specific needs of kitchen and bathroom manufacturers. Its exceptional durability, easy maintenance, and aesthetic appeal make it the perfect surface solution for:
• Backsplashes: A modern, grout-free alternative that’s both practical and visually
• striking.
• Shower Walls: Adds durability and style to wet areas with a seamless, luxurious finish.
• Wall Panels: A sleek and contemporary option for feature walls in bathrooms and kitchens.
Whether designing for high-end residential kitchens, elegant hotel bathrooms, or multi-unit developments, dp-slim delivers a combination of style and performance that you can rely on.
Key Benefits
Engineered for ease of fabrication, durability, and outstanding results, offering several key benefits:
• Lightweight and Durable: At 50% less weight than standard glass and 10 times more resistant to breakage, dp-slim ensures easier handling and reduced damage during production and installation.
• Scratch-Resistant UV Coating: Guarantees long-lasting beauty and protection in high-use areas.
• Hardcoat Finish: Delivers enhanced resistance to chemicals and abrasions, ideal for kitchen and bathroom applications.
• Hygienic and Easy to Clean: A dirt-resistant coating simplifies maintenance, offering end-users a lowmaintenance solution.
• Flexible Processing: Fabrication is simple with standard woodworking tools, enabling precise cuts and customisation without the risk of shattering.
Why Choose dp-slim for Kitchens and Bathrooms?
As a groundbreaking innovation in surface design, dp-slim offers a contemporary alternative to traditional tiles. Its lightweight construction and exceptional durability address the challenges of creating stylish, low-maintenance interiors, making it ideal for both large-scale manufacturing and bespoke projects.
dp-slim eliminates the need for grout lines, providing a seamless, hygienic surface that is easy to clean and maintain. Perfect for modern kitchens and bathrooms, its applications include sleek backsplashes, sophisticated shower walls, and durable wall panels. By combining aesthetics with practicality,
dp-slim enables manufacturers and designers to meet the rising demand for functional yet visually stunning interior solutions.
Order and Customise
dp-slim is available in laminated acrylic sheets with dimensions of 2800 x 1300 x 4mm, making it ideal for a variety of production scales. With minimum orders starting at just one sheet, dp- slim offers flexibility and accessibility for manufacturers of all sizes.
Be at the Forefront of Innovation
dp-slim is the latest advancement in acrylic surface design, crafted to empower manufacturers with a product that’s as versatile as it is beautiful. Discover the new dp-slim Crystal Collection today and revolutionise your kitchen and bathroom designs with style, durability, and ease.
New gabbiani P95 and PT95 range: Full control of the production process
gabbiani p expands the range with the new p95 and pt95 models, suitable for both batch one and mass production. Automated machines, affordable to all users, thanks to guiding technology, making the production process intuitive and safe.
These new models are equipped with all the higher-end features and options that the market demands:
- FLEXCUT 1/S: more cuts in less time. High performance enabled by the use of two fully independent pushers.
Dramatic reduction in machine cycle time due to simultaneous processing of multiple bars with differentiated cuts (with a maximum number of two side-by-side 600mm bars).
• Cutting with high finishes up to 50 m/min. thanks to blade motors with power up to 18.5 kW.
• Led indicators of both front and rear loading in the presence of lifting table: an intelligent led bar system guides the user during the processing stages for intuitive and safe production monitoring. In the version with the lifting table, the system guides the user to the correct forklift loading of the panel stack, signals the need for a stack change, and signals, if present, the removal of the pallet/martyr.
• Led device for guided positioning of movable air floating tables: an intelligent led system that indicates to the user the correct positioning of the movable air floating tables with respect to the format of the panels being processed.
• Angular cutting device provides for inclination of the squaring guide by handwheel and automatic positioning at panel dimension by a linear stop positioned on the main pusher.
The key words of this new project are productivity, quality and price.
A state-of-the-art solution designed to increase efficiency and productivity. The system uses advanced algorithms to analyse and optimise piece stacking during the made-tomeasure cutting process, ensuring that they are strategically placed to achieve maximum efficiency, reducing scraps to a minimum and maximising return.
In the manufacturing industry, competition is not just based on its ability to offer a quality product. Nowadays, being able to rely on sustainable processes which optimise both the consumption of raw materials and relative costs as much as possible, is an increasingly decisive factor. A requirement which has become ever more pressing for companies working with wood. Panel cutting is a particularly crucial part of the production cycle and any improvement in this area could have a very significant impact on profits. This is why SCM has developed its Maestro optiwise optimisation software for panel saws. Let’s take a look at its main advantages.
One of the most significant advantages in using Maestro optiwise is its ability to maximise the use of material. SCM’s software was designed to optimise panel cutting diagrams, reducing waste to a minimum. The software intelligently arranges the cuts by ensuring that as much as possible of each sheet of material is used.
As part of its ongoing commitment to give back to the community in which it works, staff at leading specialist supplier IronmongeryDirect have raised over £6000 in 2024, to support a number of local and national charities, including Basildon Mind and Macmillan Cancer Support.
Employees at the Essex-based company took part in fundraising, giving, and volunteering activities across the year to support the worthy causes that had been nominated by the WOW Team at IronmongeryDirect.
The WOW Team comprises a group of employees who represent each department and work together to organise company and charity events. As the voice for all staff across the business, the team selected a range of local and national causes to support over the course of the year. Basildon Mind, Basildon Food Bank, St Luke’s Hospice, and Wat Tyler Country Park in Basildon were all recognised as part of the company’s mission to help local causes, as well as the Alzheimer’s Society and Macmillan Cancer Support.
By hosting various fundraising activities, which included an employee Christmas raffle, and a charity bake sale, the company raised a combined total of £6,575 for the charities during 2024. Additional activities included over 30 employees spending 6 hours volunteering at Wat Tyler Country Park to undertake litter picking and grounds maintenance. Plus, a donation of 60kg worth of food and toiletries to Basildon Food Bank to aid people in crisis.
A key fundraising highlight of the year was hosting the UK’s first ever inter-trade football tournament held at Chelsea’s Stamford Bridge, which saw 50 tradespeople from different sectors compete in ‘Match for the Mind’. Organised by IronmongeryDirect, the event which coincided with Mental Health Awareness Week, raised over £4,000 alone for Mind, the national mental health charity.
Jayke Ingram, HR Business Partner and Chairperson of the WOW Team at IronmongeryDirect commented, “We are delighted to have raised over £6,000 to help support these brilliant organisations and the valuable work they do. A huge thank you goes out to all the IronmongeryDirect staff for their efforts throughout the year, in raising this fantastic sum of money, and donating their time to these causes.” Jayke continued, “Giving back to the community is integral to who we are as a business, and we are very proud to be able to contribute in this way and look forward to doing even more in 2025”.
IronmongeryDirect is the UK’s leading online ironmongery specialist, with over 50 years of trusted experience and over 18,000 products in stock. Partnered with leading couriers, customers can order by 9pm for next day delivery (4pm on Saturdays) or choose Click & Collect from over 10,000 DPD parcel shops nationwide.
Since the acquisition of the Cascamite brand by Ureka in April 2023, the brand has gone from strength to strength. Ureka has seen a substantial increase in brand engagement and robust revenue growth. Their mission remains steadfast: “Enabling access to industrial adhesive technology in the resale market through a simple retail brand”. Growth in demand has been observed across the UK market, accompanied by promising signs for future expansion.
Taking a broader perspective, it’s important to remember that Cascamite was once successfully traded in America, Australia, and several European markets. This highlights the brand’s distinction and the strength of its reputation. From its origins in America in 1937, Cascamite has come a long way, and Ureka is revitalising the brand with ongoing investment. This commitment signals sustainable growth and a return to a global presence.
This commitment to growth is why Ureka was thrilled to accept an invitation to participate in the Welsh Government’s 2024 Export Commission to the Netherlands. “We are delighted to be participating in the Welsh Government Export Commission to the Netherlands”, said Alex Nunn, Managing Director of Ureka. “We already have several direct customers in the Netherlands, so the programme aligns perfectly with our current export activity”.
Participation in the Export Commission is a key part of Ureka’s broader strategy to enter European markets, re-establishing Cascamite as the preferred choice for professional wood adhesives in both retail and industrial sectors. The focus on sustainability and high performance, which are hallmarks of the Cascamite brand, aligns well with the growing demand for environmentally responsible adhesives.
“The Export Commission presents an unparalleled opportunity to further expand our reach and strengthen the Cascamite brand among European buyers who value the quality and durability of adhesives in the range”, said James Shepperdley, Marketing Manager at Ureka Global.
As Ureka continues to innovate and push the boundaries of adhesive technology, the company remains committed to its tagline: “Solving Sticky Problems Simply”
Compass Windows & Doors, based in Londonderry, stands as Ireland’s premier manufacturer of Timber, Aluminium, PVCu, and Alu-Clad windows and doors, catering to both residential and commercial sectors. Established in 1977, the company has seen significant growth and development over the past four decades, driven by substantial investments in both their workforce and advanced machinery.
One notable development includes the acquisition of two state-of-the-art machines from SCM, a leading producer of woodworking equipment. The new CNC Router and complex Windowflex machine, are capable of performing all necessary operations for producing window frames from solid timber.
With the integration of these machines, Compass Windows & Doors recognised the need to re-evaluate their dust extraction systems. They enlisted dust extraction specialists, Dust Control Environmental (DCE) Ltd. to design, manufacture and install a compliant dust extraction system in line with health and safety and environmental standards, maintaining a healthy workspace.
• Additional new machinery, meant the current cyclone dust collectors at Compass were now undersized, no longer providing effective and compliant dust extraction. A more efficient system was required.
• Compliance needed to align with the latest EPA (Environmental Protection Law), mandating improved control of pollution from certain industrial processes. This includes managing dust that can be harmful to health or a nuisance to the public.
• A requirement to manage energy consumption and sustainability goals.
• Safe operation of the extraction equipment in a combustible atmosphere was essential.
• The machinery commissioning was scheduled to take place before the new tailored dust extraction system from DCE was ready. This was to minimise downtime and gain a quick return to production.
• Machines already on site needed to be integrated into the new extraction system.
• Removal of the old cyclone units from the site would be necessary.
Dust Control Environmental set about planning the new dust extraction and installation with as little interruption as possible to the production at Compass.
In order for Compass to enable the commissioning of the CNC and Windowflex to the required timescale, DCE loaned a stock ATEX dust extraction filter at short notice. The machines were therefore productive whilst waiting for the permanent extraction filter.
Enhanced dust control was ultimately provided in the form of A DCE Envirojet W – Series. This negative pressure filter unit provides high-performance extraction. Manufactured with ATEX adaptions ensures safe operation in this explosive risk environment.
The Envirojet W has an innovation E-performance panel to monitor machine use and tailor the cascading fan function to operational requirements. This process can provide energy savings of up to 50% without loss of suction to the system. The incorporation of a waste pre-separation chamber and the use of oval filter bags extends the lifecycle of the filter media.
Whilst installing the Envirojet W –Series, along with control panels and ducting, DCE were able to link into the system’s older machines already in operation. The removal of the two old cyclone filters was carried out, free of charge, by DCE fitters whilst on site.
The Benefits
Dust Control Environmental delivered a comprehensive “one stop service” from start to finish. Their expertise in design, manufacture, and installation (including ducting, monitoring, and controls) ensured a seamless and complete project. With the installation of the DCE Envirojet W –Series, Compass will experience highly proficient dust- extraction throughout processing areas, providing healthy, clean air for the workforce. Equipment and machinery will also be protected from detrimental dust ingress, saving time on maintenance and housing keeping.
The E-performance monitoring will regulate the speed and number of fans required to facilitate optimum dust extraction in line with the number of machines operational. By only activating what is necessary, a year on year saving in energy will be made, assisting Compass to achieve environmental goals. The reduction in filter bag changes, with less going to land waste, provides another financial and environmental win.
Production downtime was reduced greatly with the loan, from DCE, of the ATEX filter resulting in a smoother
operating transition from the old to the new dust extraction system.
Conformity to EPA will be achieved with the advanced dust extraction supplied by the Envirojet W-Series dust collector with the ATEX modifications providing the assurance of safe operation.
Client’s Comments Compass Window & Doors Managing Director Michael O’Kane said of the project “The management team at Compass are extremely pleased to have appointed Dust Control Environmental Ltd. to carry out a complete and comprehensive renewal of their dust extraction system in 2024.
“We found the staff at DCE to be most professional, informed, helpful and accommodating throughout. “From advice on the initial design, through to installation and commissioning the entirely new extraction system, DCE surpassed our expectations.
“For example, to avoid any interruption to our production, DCE proposed and installed a temporary dust extraction system whilst the new system was being installed and commissioned.
“Most importantly, the overall project was delivered successfully, both on time and on budget.
“We are delighted with the performance of our newly installed Dust Extraction System and would have absolutely no hesitation in recommending Martin (Gill), Steve (Bukowski) and their team to any prospective clients.” https://dustcontrolenvironmental.com/
Global acrylic solid surface manufacturer Durasein is now officially a Partner of Panelco. This exclusive distribution agreement is a further premium addition to the highquality surface brands. This creative collaboration is a welcome addition to the diverse and innovative product ranges that Panelco continues to offer. In Durasein’s own words, Durasein is making a solid surface for people with bendy and twisty ideas. Alongside a range of surfaces in a contemporary palette of colours, a selection of acrylic sinks is also available to support the offer.
The heart of Durasein is a solid surface driven by creativity and purpose, manufacturing a versatile and durable product that stuns in its design capabilities and premium functionality.
Benefits include scratch and dent resistance, plus a nontoxic, non-porous finish that is easy to clean. These surfaces are ideal for commercial and residential applications requiring something special.
Stringent demands in hospitality and retail environments do not mean you have to limit your creative aspirations. You can achieve your inspired visions with a range of solid high whites, soft muted grey and cream tones with subtle flecks and veins, or the more striking dark grey and black tones with added sparkle.
Products that are easy and durable to use are a major advantage when it comes to sourcing materials, and Durasein is no exception. The ease of fabrication and the
ability to curve shapes using thermoforming methods ensure that this product can be twisted and formed to really deliver your shape ideas!
Functionality is key, and the food-safe material is ideal for style and meeting strict food regulations while creating a seamless, clean look.
With years of experience in designing sinks the high-quality acrylic sinks are a cohesive addition to the surface range.
It is ideal for a simple, clean, and functional solution for modern bathroom vanity or applications such as hospitals and food environments. All available in a fresh glacier white tone and in assorted sizes and shapes, the Durasein sinks will undoubtedly add a luxury finish to your bathroom and leisure requirements. All sinks and bowls are CE and UKCA compliant, easy to clean, non-porous, and stain and mildewresistant.
Panelco continues to enhance its product offerings with the latest trends and new partnerships to ensure consistent evolution. It also continuously evaluates services and facilities to support the growth and development of innovations.
Leading dust and fume extraction specialists, Extractly Limited, have recently completed the installation and commissioning of new dust extraction and filtration plant for a major UK furniture manufacturer based in Rotherham, South Yorkshire.
Originating from the village of Staverton, in South Devon, and with almost a century of history behind it, the Staverton brand has become synonymous with high-quality contemporary office furniture. In the late 1920s, a team of craftsmen, including joiners and cabinet makers, was recruited to undertake works on the Dartington Hall estate and, in 1931, Staverton Builders Ltd was incorporated. Over the decades the business has ridden the storms of change but, throughout its various phases and guises, has continued to be design-led and, today, Staverton (UK) Ltd enjoys an enviable reputation as a responsible and reliable, awardwinning British manufacturer.
Whilst Staverton’s showroom and sales team are based in the heart of London’s creative Clerkenwell district, its design,
15kW transport fan blows waste into storage container
33,000 m 3 /hr capacity ATEX filter unit with main fan fitted to ‘clean side’ of the filter unit for maximum efficiency. Noise is attenuated by the silencer fitted above the fan
manufacturing and admin functions are accommodated in a strategically-located 38,000 sq. ft. facility, alongside the M18 motorway, on the outskirts of Rotherham. In the busy workshop, responsibility for supervising and managing machining operations is the duty of Production Manager Mark Powell. “When it comes to dust producing machines, we’ve got some big hitters here”, says Mark, who’s been with Staverton for just a quarter of a century.
“There are three high-speed CNC machining centres requiring around 15,000m3 of extraction an hour between them, plus a couple of big saws and an edgebander that together need about 10,000m3. On top of that we have a snip saw, spindle moulders and BHX drilling centres; all of which can easily add another 5,000m3 an hour if they’re all being used at the same time.”
Staverton’s previous main fan and filter unit were both nearing the end of their service life and, although the extraction system had been upgraded back in 2015 to take advantage of Ecogate® ‘on-demand’ energy-saving technology, the company’s additional investments over the years in newer, high-speed machinery meant that the system was now operating close to its maximum capacity. Extractly Ltd is also the Master UK Distributor and Installer for Ecogate® in the UK and, as a result of a timely customer relationship interaction with Staverton, sales director, Jake Oldfield, was invited to visit the Rotherham factory to survey the site and assess Staverton’s current extraction requirements.
As Jake explains: “Since Staverton already had Ecogate® technology installed across the factory, it was evident from recorded system data that the old filter unit and fan were
being stretched to the limit and now clearly lacked the power required to efficiently extract dust and wood waste from all the machinery being used.”
With the old fan and filter being rather long in the tooth, the only satisfactory solution was to install a modern, efficient replacement filter unit, with greater capacity, together with a more powerful main fan.
“Extractly put together a compelling proposal”, added Mark Powell. “We previously had a 37kW fan, running flat out, but Jake recommended replacing this with a 55kW fan which would easily cope with today’s requirements, but also give us plenty of leeway for future expansion. Compared with our previous fan this is quite a step up in power but, with Ecogate® already installed, it means the fan only consumes the energy needed to extract from machines that are operating at any point in time.”
For dust collection and filtration, Extractly installed a new ATEX filter unit with sufficient capacity to filter 33,000m3 of dust-laden air every hour. “To achieve maximum extraction efficiency from the new system we’ve installed the fan on the ‘clean’ side of the filter unit,” says Jake Oldfield, “and,
since dust and wood waste doesn’t pass through the fan, a more efficient impeller design can be used. As a result, the fan consumes less electricity, and ongoing maintenance is minimised due to the inevitable reduction in wear and tear.”
Dust and woodwaste is removed from the airflow as it’s drawn through an array of tubular filter bags, which in turn are cleaned by three 1.5kW regeneration fans. Collected waste is then removed, pressure-free, from the filter unit by a rotary valve before being blown by a 15kW ATEX transport fan into an adjacent storage container.
Of benefit to personnel working in the Staverton factory, as well as those in neighbouring businesses, the silencer Extractly fitted above the main fan is very effective in keeping noise to a minimum. In addition, and to comply with ATEX regulations, Extractly installed an explosion isolation valve into the main ductwork, close to the filter unit. “We always recommend the inclusion of a non-return valve”, Jake Oldfield explains. “In the unlikely event of an explosion occurring in the filter unit, the valve prevents a pressure wave and flames travelling through the ductwork and into the factory.”
In conclusion, Mark Powell confirmed: “The new extraction works really well – the new filter unit has made a significant difference to the efficiency of our waste collection and Extractly managed to complete the whole installation with minimal machine downtime.”
Chris Franklin MD at Ranheat Engineering Ltd., a leading UK manufacturer of wood combustion equipment, continues his series of articles exclusively for Panel and Joinery Production. This month he remembers, and writes about, one of the pioneers of industrial wood-waste heating systems in the UK, Bob Talbott.
“I first met Bob in the 80’s when I worked for Scanfield boilers in Ashford in Kent. I visited Bob having driven 5 hours to get to his office. I had just sat down when his pager went off. Sorry said Bob but I have to go! (Bob was also a serving fireman for many years)
We always met up at the “woodmex” exhibitions and over the many years we knew each other we became friends, partly due to our common love of skiing.
Bob was an excellent skier (far better than me) and loved the French Alps.
It was with much sadness that I saw on Linkedin that he had sadly passed away on the 20th of July last year 2024. At the age of 76.
Bob was passionate about the use of industrial woodwaste to use on site to heat factories within the woodworking industry.
Ranheat’s origins were in Randers a small city in Denmark, where wood was a fuel for Danes as they had no reserves of Coal, Oil or Gas. The Danes could not understand why the UK woodworking industry literally sent tonnes of wood-waste to landfill each year.
Bob had a similar vision, zero wood-waste to landfill. As such warm air space heaters for industrial wood-waste did not exist so Bob Talbott set about designing a range of hand loaded warm air heaters, specifically for the UK woodworking industry.
The original units were manufactured in a small village called Eccleshall in Staffordshire. The Talbott T range soon became synonymous with industrial wood-waste heating as Hoovers were to vacuum cleaners.
As the years passed Talbotts moved into boiler-based systems with a link with Farm 2000 owned by Peter Teisen, (Peters’ father was a Dane)
Bob went on to develop his own range of boilers and Ranheat developed a range of warm air heaters, mainly automatically fed rather than hand loaded. It was inevitable that the two companies would overlap, but Bob and I remained friends throughout.
Talbott systems were sold all over the world not just in the UK. I remember Bob towing a T500 warm air heater down to the Ligna exhibition in Germany. His Ford Sierra was struggling to drive up the loading ramp in Dover to get on
the ferry. So they waited until everything else was loaded then lifted the ramp to level so Bob could drive onto the ferry!
We would sometimes accidently meet up in Belfast International airport and sit next to each other on the flight home ( no doubt we had both been visiting the same customers in Ireland! )
Sadly, Bob was diagnosed with Parkinsons Disease and Talbotts were taken over by the Smiths group based in Leicestershire and became part of Airplants Dust Extraction.
The name however remains in Bob’s memory. He was a true Pioneer of the wood burning industry in the UK.
The team at PJP send their condolences to the family and friends of Bob Talbott.
For 25 years, Combilift has been revolutionising the way companies handle and store goods. We help companies of all sizes and from every industry to maximise the capacity, safety and efficiency of their warehouse and storage facilities.
Our pioneering product range of multidirectional, articulated and pedestrian forklifts, straddle carriers and container loaders allows you to manoeuvre long loads safely, reduce aisle widths and increase the amount of space available for storage.
To find out how Combilift can help you unlock every inch of your storage space.
Founded in 2005, TEK Contracts is a family-owned business based in Burntwood, specialising in bespoke joinery and shopfitting for diverse sectors, including leisure, retail, and healthcare. With a 13,000 sq. ft. facility and a skilled team of 19, TEK delivers tailored solutions that not only meet each client’s unique requirements, but meets them in style.
TEK’s commitment to quality, which they have maintained for 19 years, has ensured their continued growth. To keep pace with their own success, however, they needed to fully embrace an automated workflow by investing in machinery that was up to the task. Waiting in the wings was HOMAG.
The shift to automation
For Chris, TEK’s Managing Director, the journey began with the implementation of a new software system, Microvellum, which automated TEK’s previously manual processes. “Microvellum was transformative,” Chris explains, “but the issue was that our machines weren’t equipped to work at that level. To fully commit to automation, we needed machines that were on technological par with the Microvellum software.”
Selecting the right machines for future growth
After evaluating several manufacturers over six months, TEK found that HOMAG’s exceptional service distinguished them from competitors. “Good service was one of our main criteria – we suspected that we could do better than what we were currently getting.”
As for the machines, TEK initially considered the DRILLTEQ V-200 but set their sights instead on the V-310 after witnessing its capabilities firsthand at HOMAG’s Castle Donington workshop. “Despite it being a bigger machine than what we actually needed at the time, we couldn’t resist the V-310. We knew that it would open a lot of doors for the future growth of the business.”
To support their vision, TEK also upgraded their edgebanding process with the EDGETEQ S-300, consolidating all machinery under the HOMAG brand for consistency. And as Chris explains, TEK have no intention of stopping at just a drill and edgebander: “Our next purchase will be HOMAG’s CENTATEQ N-210, a CNC machining center – we’re itching to press go on that one!”
Immediate impact and future potential
“The machines have made our lives easier and improved our operation in every conceivable way,” praises Chris.
“Our previous workflow was a little on the awkward side, requiring manual adjustments at almost every stage of the process. With HOMAG’s machines working alongside Microvellum, we’ve streamlined our operations and have become a lot more efficient.”
The new machines have also unlocked future opportunities. “For example, we’re now able to essentially provide flatpacks of furniture – with the parts pre-cut, edged, and drilled – as well as pre-assembled furniture, which has increased our potential client base significantly.”
Chris and his team have also been pleased with the service. “As I mentioned, one of our main reasons for choosing HOMAG was their reputation for top quality service – and they didn’t disappoint. It’s been outstanding. If ever there’s a fault or issue, a HOMAG technician arrives within 24 hours of us flagging it, without fail.
“And I’d like to give a special mention to Jon, our HOMAG sales rep. He was really on the ball, happy to answer any questions or queries, and if he didn’t know something he went and found out and came back to us with an answer. We still speak with Jon; he checks in on how we’re getting on with the machine. You do get the sense that HOMAG genuinely cares about your business.”
Both the EDGETEQ S-300 and DRILLTEQ V-310 were installed at the start of 2024. Chris reflects: “The installation was smooth; we wanted both machines to arrive at a similar time, which HOMAG were happy to accommodate.”
Next came four days of training for each of the machines. “I can’t fault the training, either,” says Chris. “It’s a lot of information to take in, but HOMAG presented it very well and took the time to ensure we were comfortable with everything.”
With HOMAG’s ongoing support and machinery that enhances productivity and product quality, TEK Contracts is well-positioned to meet future demands, increase production capacity, and capitalise on new market opportunities.
“We’re thrilled with both the machines and the service,” Chris concludes.
“We’ve found a great partner in HOMAG and we’re excited to see what the future holds with their continued support.”
As 2025 begins, the industry is looking forward to growth, innovation and leadership. AJB Group has positioned itself for a new era through the launch of their new brand; Integra Fire Doors and Panels.
Already well established for its high-quality door frames, the company has expanded its product range to offer the complete package of fire doors and frames. This was not a decision which was made lightly but came from discussions with the industry and ultimately from customer demand. Their order book for 2025 is looking extremely healthy and the addition of Integra to their already strong manufacturing reputation has further enhanced their position within the UK’s woodworking sector. Leading companies in the fit out market have responded enthusiastically to the expansion of this side of the business.
A Bold New Step for AJB Group
Integra Fire Doors and Panels has introduced a comprehensive range of fire doors to complement its established door frames fulfilling the needs of customers who have been asking for a unified solution with the manufacture of both the frames and the doors in house at their Corby factory. The company’s decision to venture into fire door production is a direct response to customer feedback, cementing their commitment to meeting the industry’s evolving demands.
The integration of fire doors into AJB’s offer comes at a crucial time, with the UK’s construction industry seeing a greater emphasis on safety standards and fire compliance. This strategic expansion is not just a product addition but a reflection of the company’s confidence and capability to provide complete, high-quality fire safety solutions.
A significant part the successful transition into the fire door market is the company’s rigorous attention to testing and certification. All manufacturing processes have been certified to the highest industry standards, ensuring that Integra’s fire doors meet or exceed fire safety regulations. The company has completed all required fire resistance tests, with the doors passing all security tests that are mandatory in the UK market.
Integra’s fire doors have full BM Trada Q Mark certification—a recognised symbol of quality in the fire door sector. This certification is vital for ensuring that the company meets stringent regulatory requirements, making Integra’s products a reliable choice for architects, specifiers and contractors across the industry. The company’s fire doors are now ready for installation in both residential and commercial projects, providing peace of mind and superior fire protection.
State-of-the-Art Manufacturing Process
Integra’s fire doors are manufactured using cutting-edge technology and equipment sourced from industry-leading suppliers. The company’s operations include advanced machinery, such as HOMAG’s beam saw, edge bander and CNC machines for precision door production coupled with Kündig sanding machine for the preparation of flawless fire door assembly.
This combination of machinery, expertise, and process is a cornerstone of Integra’s ability to produce high-quality fire doors efficiently. The use of top-tier equipment ensures that every door meets the exacting standards expected of fire-resistant solutions.
The Leadership Team Behind the Brand Integra’s expansion into the fire door market is being guided by a team of industry veterans with decades of experience. Lead from the front by CEO, Amarjit Binji, the company has recently appointed two new directors: Sarb Marwa, as Commercial Director with over 30 years of experience in construction, joinery and fire door manufacturing, and Umesh Tailor, as Technical Director with over 37 years of industry experience. Their combined expertise strengthens AJB’s capabilities and reinforces the company’s commitment to becoming a leading player in the fire door sector.
Integra is committed to continuous improvement, ensuring that it remains at the forefront of the fire door industry. Both new directors bring invaluable knowledge in commercial strategy and technical excellence, enabling Integra to navigate the complexities of fire door production while maintaining its focus on quality and compliance.
AJB Group’s shift into fire doors is also a natural extension of its long-standing reputation for quality door frames. For over 20 years, the company has been supplying some of the UK’s leading construction firms with durable, high-performance door frames. The decision to add fire doors to the portfolio strengthens their ability to meet the diverse needs of its customers.
“Many of our customers asked us to manufacture the doors as well as the frames,” said Amarjit Binji. “This move allows us to provide a complete, end-to-end solution for fire safety and confidence, all while maintaining the high standards of quality we’ve built our reputation on.”
Integra has already received positive feedback from top contractors in the UK, including some of the leading players in London’s fit-out market. These endorsements underscore the demand for a reliable, comprehensive fire door offering that meets both safety and aesthetic requirements.
As AJB Group begins 2025, it is poised for significant growth within the fire door market. With a full range of certified fire doors, cutting-edge manufacturing capabilities, and an experienced leadership team, the company is ready to take on new challenges and opportunities.
Their future is about building on its legacy of excellence and expanding its reach in the fire safety sector. By focusing on the quality of its products and the needs of its customers, Integra Fire Doors and Panels is set to be a key player in the ongoing evolution of fire safety standards across the UK.
As the company continues to expand its offerings and refine its production processes, there is little doubt that Integra Fire Doors will be at the forefront of the fire safety industry for years to come.
Based in Northern Ireland, Fabtops Solid Surfaces is a specialist fabricator offering high-quality solid surface solutions for residential, commercial, and healthcare projects. The company, while purposefully small in number, combines over three decades of shopfitting expertise with a passion for craftsmanship. Their bespoke services, from DuPont Corian® to LG Hi-Macs and more, have earned them a loyal, high-end customer base and accolades like the “Modern Homes” photo of the month.
Despite their strong reputation, Fabtops recently faced challenges with their aging equipment, leading to inefficiencies and limitations in production capabilities. To overcome these issues, they turned to HOMAG for a state-ofthe-art solution.
Out with the old Fabtops’ older machinery was becoming a bottleneck in their production. Managing Director Patrick Hannaway explains, “The clamping system was outdated, leading to movement and sizing errors. It was inefficient, a nightmare to operate, and we were afraid to push it too hard for fear of breaking something. It felt like we were stuck.”
Recognising the need for a modern solution to maintain their high standards while improving efficiency, Fabtops began searching for a machine that could meet their current and future needs.
After hearing positive feedback from similar businesses using HOMAG equipment, Fabtops initiated their search. Their first point of contact was Paul from HOMAG, whose hands-on approach made a lasting impression.
“Paul was fantastic,” recalls Patrick. “He cut out samples and sent them to us, and we couldn’t believe the quality. He took the time to understand our business and recommended exactly what we needed – and what we didn’t. Without Paul, we might have overspent. HOMAG genuinely wants what’s best for you.”
After evaluating their options, Fabtops chose the CENTATEQ N-210, a CNC gantry-processing center designed to handle high-precision tasks with ease.
The installation process was smooth and efficient. “It couldn’t have been better,” says Patrick. “We were given clear timelines months in advance, and the machine arrived exactly on schedule.”
On-site training was equally impressive: “Aaron led the integration, and my team loved the training. They couldn’t wait to get started with the machine. We were treated like
kings at their training centre – the catering was especially fantastic! HOMAG’s professionalism is unmatched.”
Immediate benefits
Since installing the CENTATEQ N-210, Fabtops has seen transformative improvements in their operations. The increased speed of production has been a standout benefit, as Patrick explains: “The speed is incredible. We only need to run the machine 3-4 hours a day, and it’s doing far more than we ever managed before.”
In addition to faster production, the machine has significantly lowered operating costs. “The machine uses less power and has reduced our operating costs. The ability to turn it off when tasks are complete is a big saving.”
Precision has also improved dramatically. “We can handle big sheets with big rigging easily, and the accuracy is unmatched. It’s easier to program and run, making production smoother than ever.”
Outstanding service
Fabtops’ experience with HOMAG didn’t end at the point of sale. Their ongoing support has been a standout feature. “The machine has been so reliable that we’ve only had to call HOMAG once since installation. In fact, they rang us the other week because they hadn’t heard from us and wanted to make sure we were getting on OK! I’ve been in this industry long enough to know – that level of service is rare indeed.”
“I also want to give a special mention to Derek Reid, the HOMAG agent in Ireland. From the moment we met, Derek’s service was first-class. He got us on track right away, inviting us to the HOMAG HQ in England and introducing us to Paul. Within two weeks, they had our programmes ready to run on our Corian surfaces, which was just so impressive.”
While Fabtops remains content with their niche market and manageable size, they’re already considering expanding their product range.
With the CENTATEQ N-210 as the cornerstone of their workshop, their next move will undoubtedly involve HOMAG.
“We’re not chasing wild growth, but when it’s time to expand, HOMAG will be our first choice. For now, the CENTATEQ N-210 is helping us do what we’ve always done – only faster, better, and more efficiently. We couldn’t be happier with the investment.”
In a groundbreaking move, Hettich UK unveiled its first Innovation and Training Centre at its headquarters in MediaCityUK, Manchester in the final quarter of 2024.
This state-of-the-art facility is a commitment to pushing the boundaries of furniture technology. The space is meticulously designed to showcase Hettich’s furniture technology solutions, arranged thematically by use and application. From kitchens and bedrooms to flexible, multipurpose living spaces, the centre is brimming with innovative ideas and surprises that add functionality and value.
Adjacent to the Innovation Centre is the Training Centre, a dedicated space for hands-on education and instruction.
Here, fitters and manufacturers can learn the practical aspects of using Hettich’s products to create unique interiors. This dual approach ensures that visitors not only see the potential of Hettich’s products but also understand how to implement them effectively.
Simeon Gabriel, Managing Director of Hettich UK, expressed his excitement about the new facility: “I was thrilled to open the doors to Hettich UK’s new Innovation and Training Centre. Visitors are already seeing how our market-leading furniture fittings can be used in novel ways, in real-life situations, to delight end-users. For those new to Hettich, they can see the value and magic we can bring to their business. For those already familiar with Hettich, they can discover something new and different. They will find not only innovation but inspiration!”
Patterson, Technical and Health & Safety Manager of Hettich UK, emphasized the practical benefits of the new facility: “The new Innovation Centre and Training Centre at Hettich UK is a priceless resource for ourselves and our customers. We took our time to get it right and are delighted with the result. Not only can we add value through market-leading technology, but we can back it up with technical support to turn ideas into practical reality.”
Among a host of solutions, the Innovation Centre features two standout examples of Hettich’s forward-thinking approach to furniture design: FurnSpin and LightTower.
FurnSpin: A Glimpse into the Future of Furniture Design
FurnSpin, conceived by Hettich, revolutionizes cabinet design by revealing or concealing the contents of furniture with a simple 180-degree rotational movement. This innovative concept eliminates the need for traditional doors or flaps, allowing for flexible use of space. Whether you want to display the contents of a cocktail cabinet during a party or hide them during a work meeting, FurnSpin makes it possible.
Jonathan Hunt, Head of Marketing at Hettich UK, explains, “FurnSpin gives a glimpse into the near future of furniture design. As innovators in the sector, we have introduced the concept to customers to spark the imagination and initiate discussions. We want to explore how FurnSpin can play a part in the future of high-end cabinetry throughout the home.”
Making FurnSpin a workable reality required perfected kinematics to prevent any collision with furniture edges and to cancel out centrifugal force to ensure that even light objects stay put. The Interzum award-winning, door-free concept is demonstrated at the Innovation Centre and really needs to be experienced to be believed.
LightTower: Illuminating the Future of Kitchen Storage
The same could probably be said of LightTower by Hettich which is a practical tower unit larder storage concept featuring hassle-free, no-connection illumination using the exceptional AvanTech YOU platform drawer system. It’s been installed as a stand-out feature in studios up and down the country, one of which is Kitchen Flair, which
factor: “It’s that sleek design, you know? You open the drawer, and it’s the ‘Oh!’ reaction that is so satisfying: that element of surprise that comes with it.”
Each drawer in LightTower is individually illuminated, providing even, 4,000K light without the need for complicated connections. This innovative design ensures smooth, effortless drawer opening and closing, making it a perfect addition to both new kitchens and retrofits. With the option of glass drawer sides and fronts, LightTower offers a new realm of design opportunities and flexibility.
In conclusion, Hettich UK’s new Innovation and Training Centre is a beacon of innovation in the furniture industry. By combining cutting-edge technology with practical training, Hettich is setting new standards for customer experience and product presentation. Whether you’re a seasoned professional or new to Hettich, the Innovation Centre promises to be a source of endless inspiration and practical solutions.
The Future of House Building - JJ Smith & Co
Knowsley Industrial Park, Kirkby
Surface Design Show
Business Design Centre, London
Internationales Wood BioEconomy-Forum
Rosenheim Technical University of Applied Sciences, Germany
Wood Tech Expo
PTAK Warsaw Expo, Poland
Saloni del Mobile Milano
Fiera Milano, Milan, Italy
Dubai Wood Show
Dubai World Trade Centre, Dubai, UAE
Fit Show
NEC Birmingham, UK
Interzum
Cologne, Germany
Messegelände, D 30521, Hannover, Germany
Furnitech
Poland
(AWFS) Association of Woodworking & Furnishings Suppliers Fair
Las Vegas Convention Centre, Nevada, USA
Saudi Wood Expo
Riyadh International Convention & Exhibition Centre (RICEC), Saudi Arabia
Woodtech Tüyap Fair and Congress Centre, Istanbul
Eurobois
EurExpo, Lyon, France
Materials & Finishes Show
NEC, Birmingham, UK
3 Feb - 6 Feb 17 May - 19 May 25 Aug - 28 Aug
International Woodworking Fair
Georgia World Congress Centre, USA
Nov - 13 Nov
Fimma + Maderalia
Fiera Valencia, Spain
glass designs with the
Designed for vertical indoor use, dp-slim Crystal is perfect for splashback and wet wall applications. With its easy to clean, hygienic surface, dp-slim Crystal is a suitable replacement for traditional bathroom and kitchen wall tiles. dp-slim Crystal is the ideal glass, tile or traditional stone and marble substitute for all hospitality and retail environments.
Available to order in quantities from as little as just one laminated acrylic sheet with dimensions: 2800mm x 1300mm x 4mm.
Visit www.decorativepanels.co.uk to explore the full dp-slim collection within our dp-limitless portfolio.