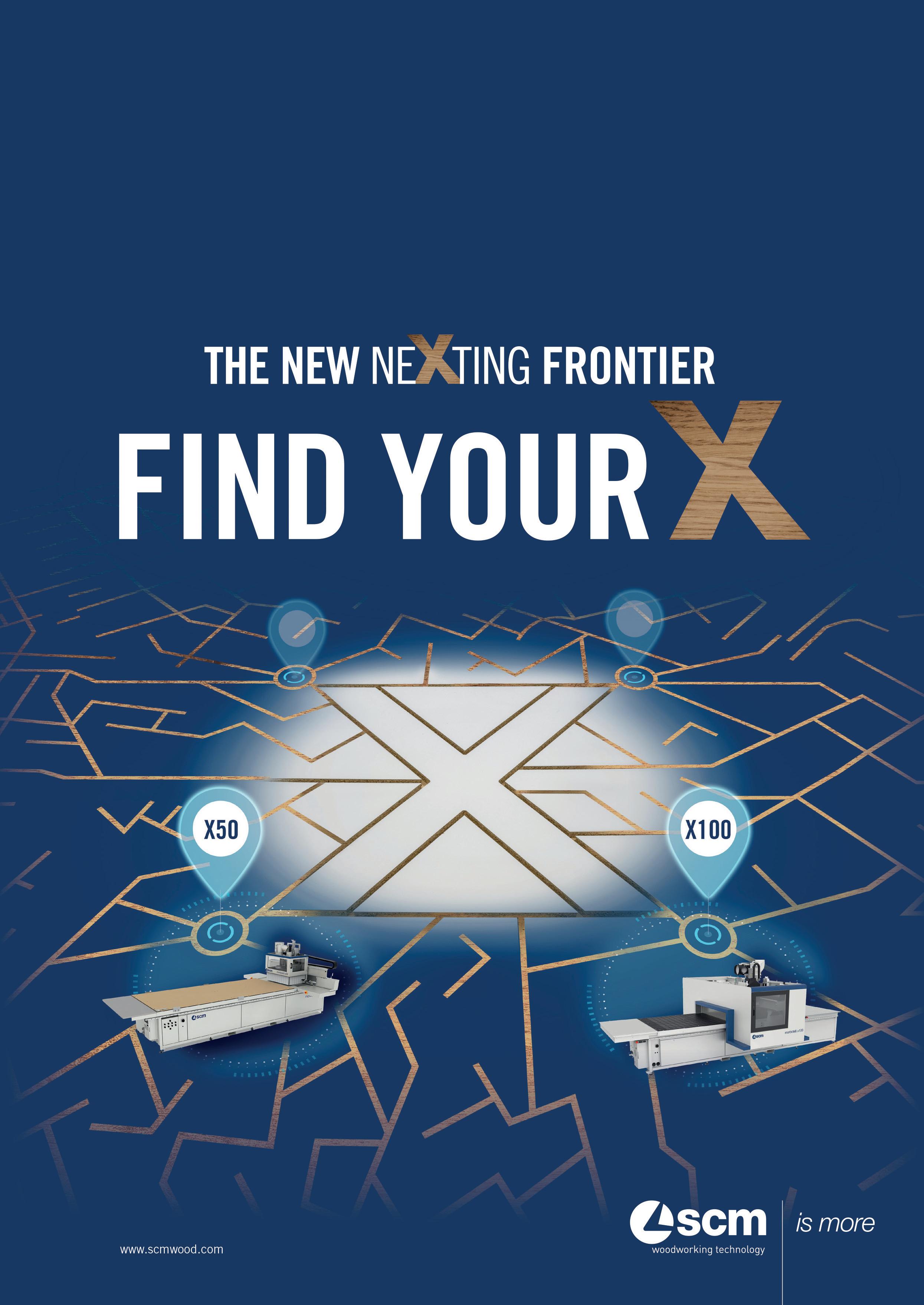
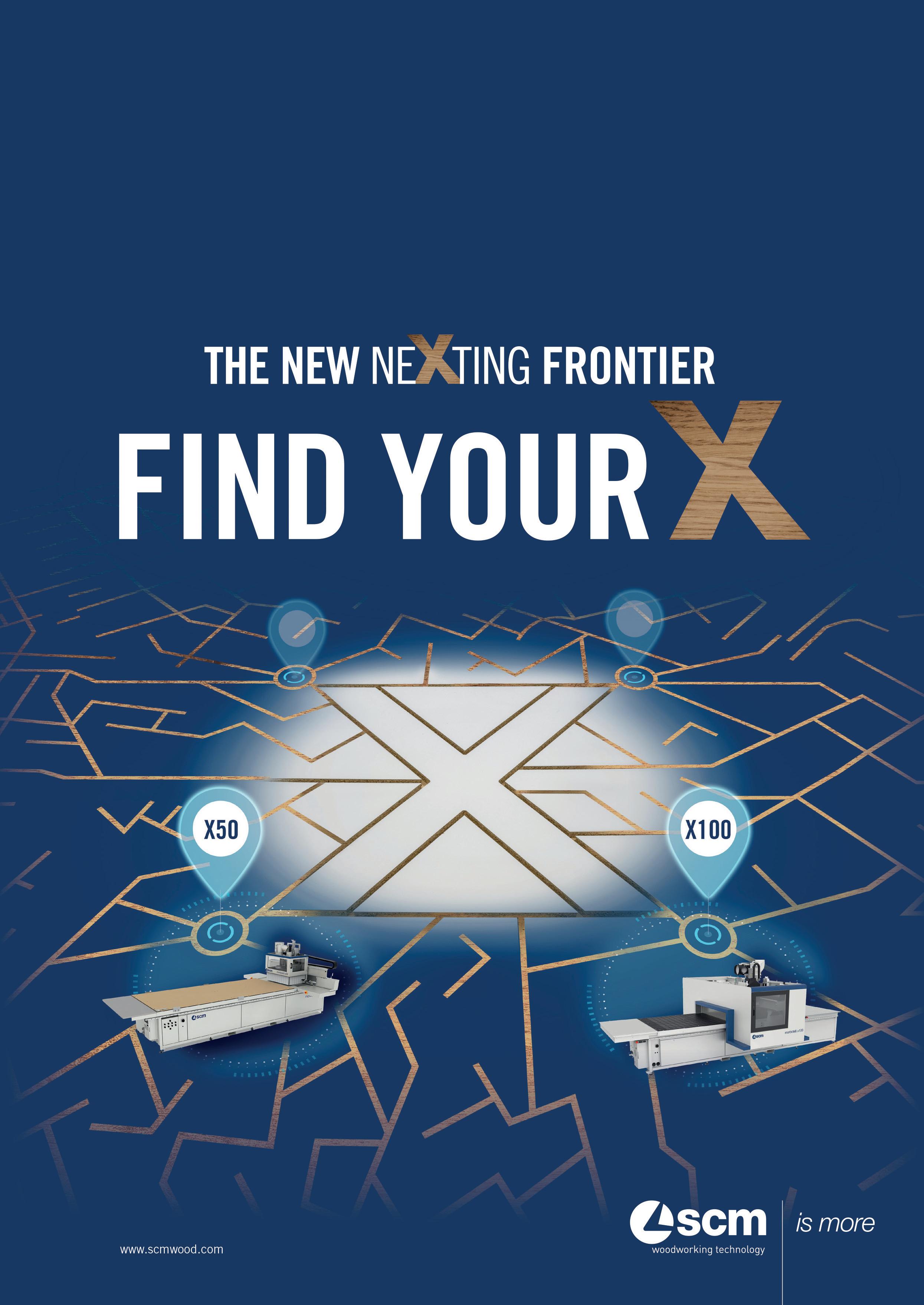
Holz-Her’s Glu Jet
Invisible joints with thin film technology
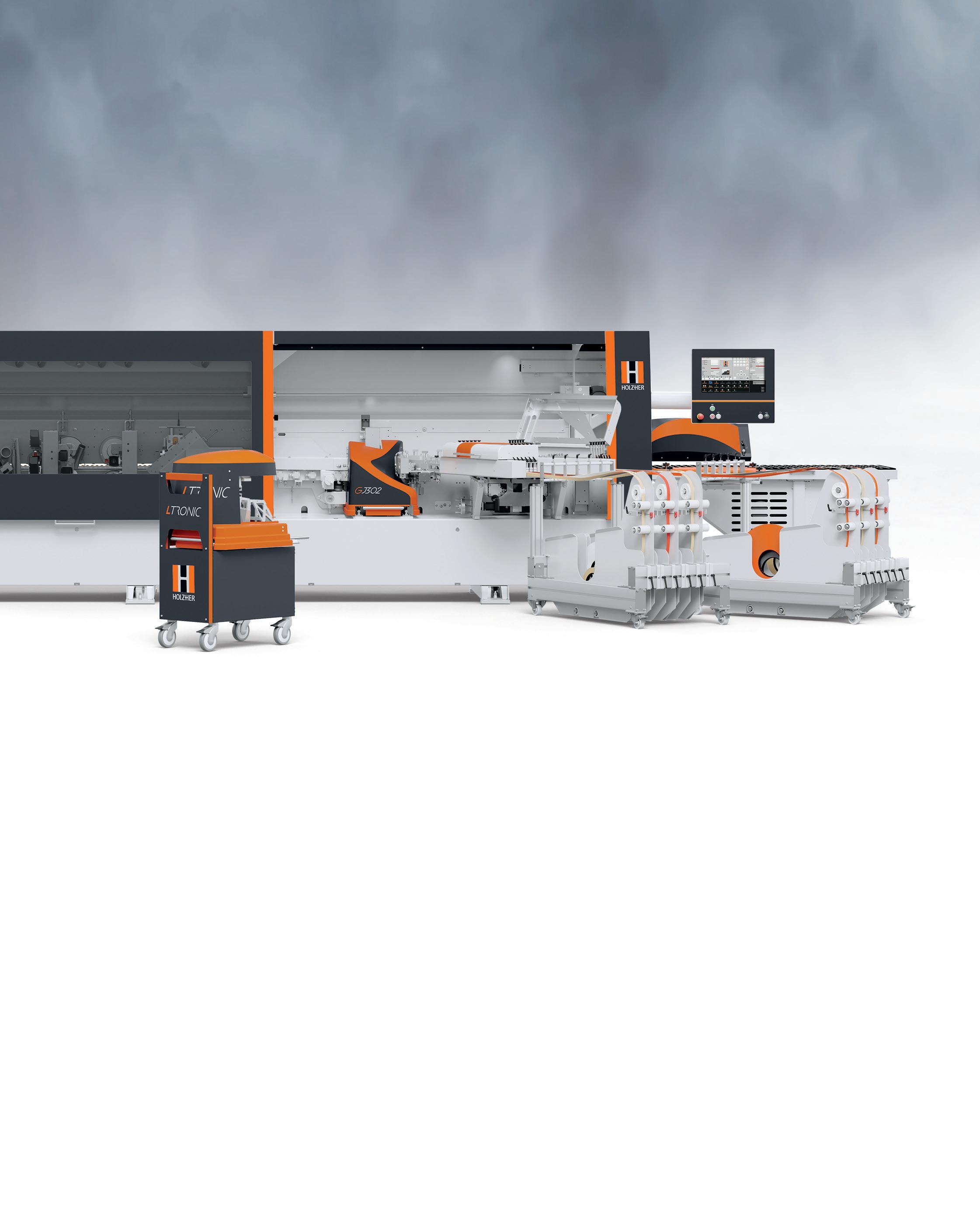
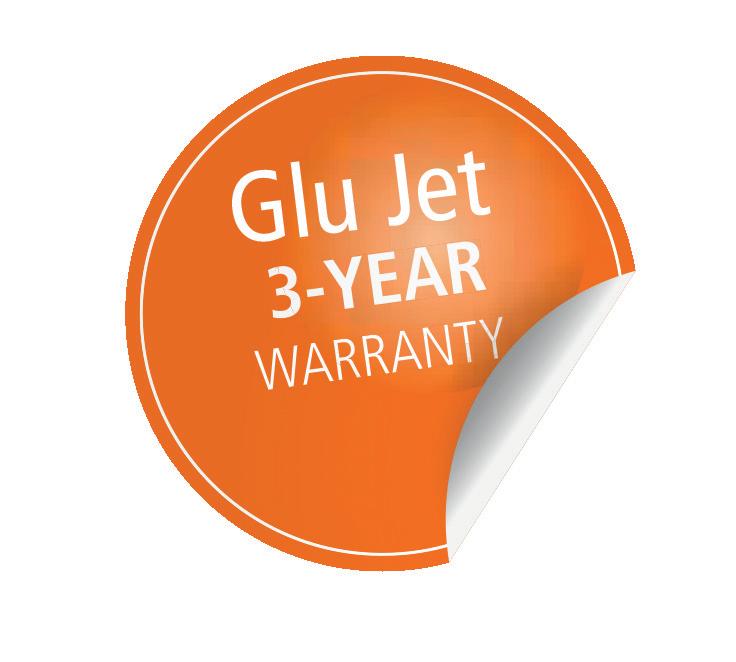
• Laser equivalent at a fraction of the price ❱❱
Robust, precise and repeatable. Holz-Her’s patented Glu Jet system is your solution to flexible edgebanding.
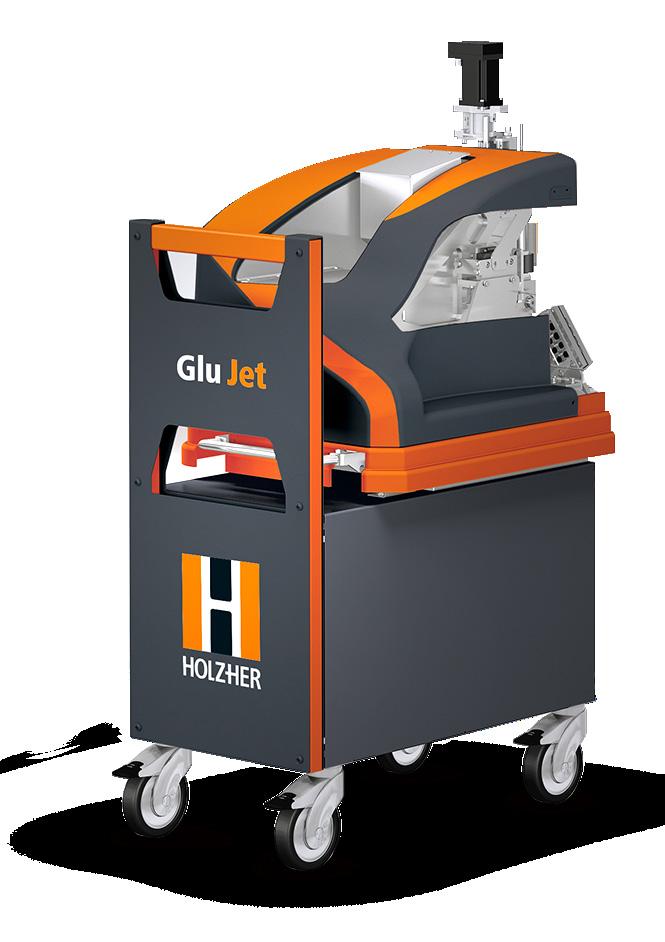
• 100% glue strength at all times
• Ready to run in 3 minutes
• 4 minutes change over from EVA to PUR
• Automatic cleaning at the touch of a button
• Touch nozzle for precise adhesive application
• Flexible application possibilities
• Cartridges or granules
• Simple colour change
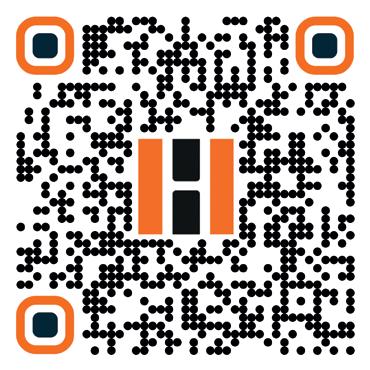

Watch the Glu Jet in action! just scan the QR code...
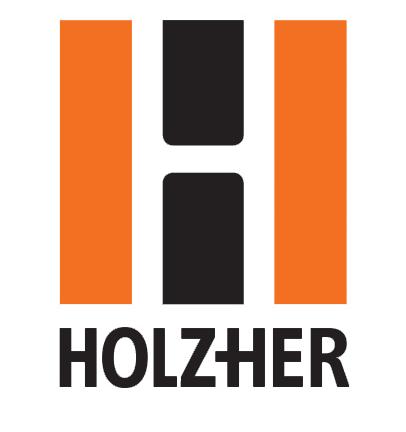


OHRA Overview And Products
Titus T-Type Hinges: Setting New Standards
“Wood Waste Heater Will Have Paid For Itself In Around A Year!”
Unitech Oxon Advances With Biesse Rover B Ft Hd
Strathallan School Perth and AXYZ Automation Ltd Routers in Education
Mcevoy & Rowley Brings Kitchen Manufacturing In-House With HOMAG
Martin Mcvicar Talks About The Journey Into The Global Market.
New Nesting Frontiers With SCM
Possibilities Are Endless With Dp-Slim From Decorative
OVVO Expands Its
Holz-Her’s Sprint. A Game Changer In Edgebanding
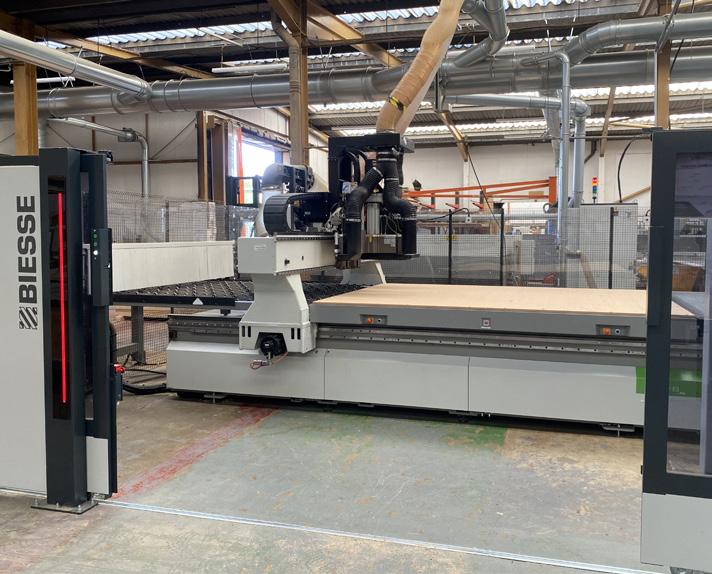

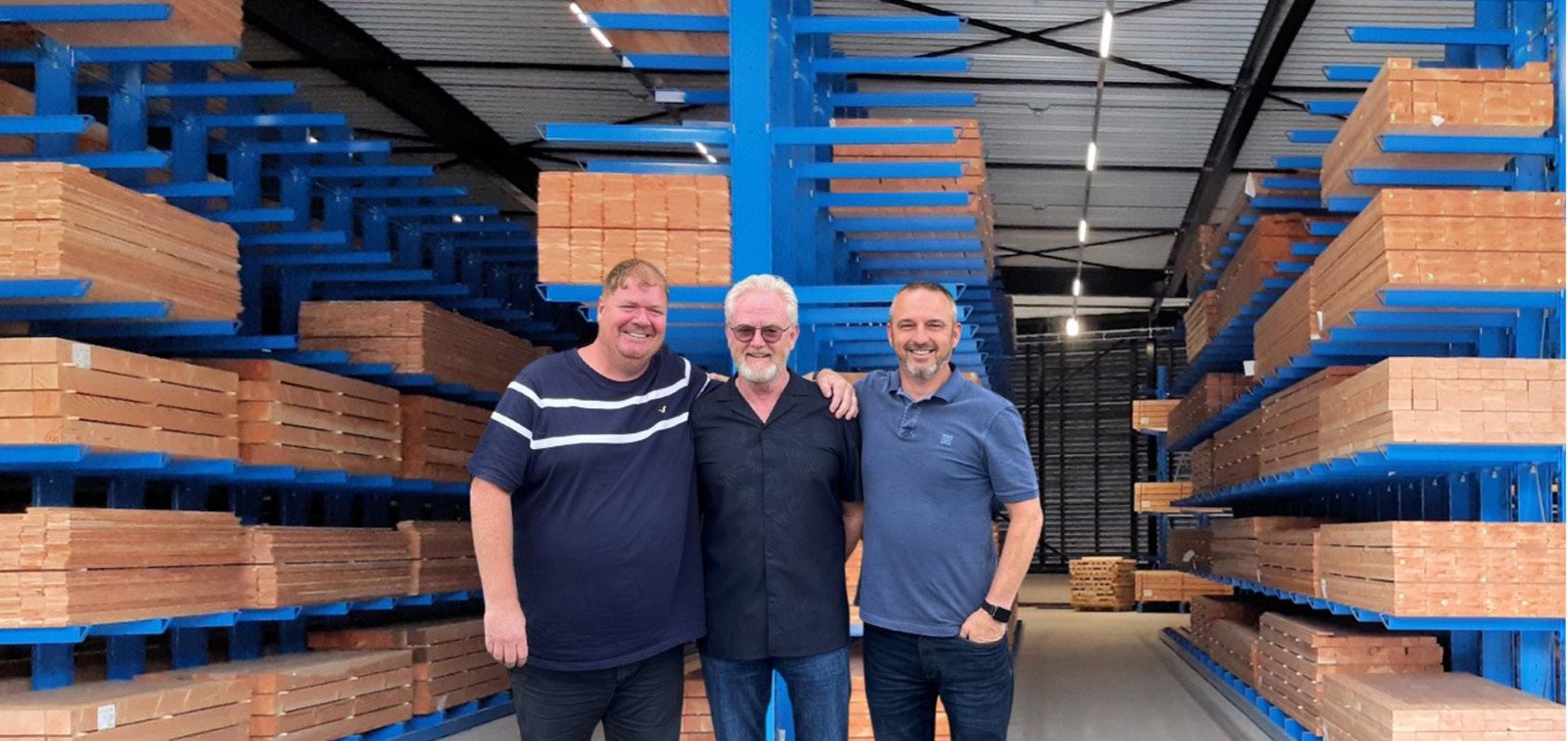
HOMAG UK Presents Makor’s Latest Automatic Oscillating Spraying Machines
Mirka Continues To Clean-Up With Its New Extractor From Little Acorns Grow Great Oaks
Reproduction of articles: All material appearing in Panel & Joinery Production is strictly copyright, and all rights are reserved.
No part of the publication may be copied or transmitted in any form whatsoever, including photocopying without prior permission of the publishers.
Publishers note: The editorial opinions expressed in Panel & Joinery Production are not necessarily those of the publishers, who shall be under no liablity with respect to any article published herein.
“SMAU Innovation” Award To Scm Group
The “SMAU Innovation” Award awarded to Scm Group is for the new “Solutions Library” project, a digital library of technical solutions which makes the most of artificial intelligence to process and share the group’s wealth of knowledge, acquired over 70 years in the technologies sector for machining wood and other materials.
Scm Group is one of the “Made in Italy” entrepreneurial excellences to be honoured at the most recent edition of Smau, the annual Innovation trade fair held in Milan. The Italian group is a global leader in technologies for machining a wide range of materials and industrial components and won the 2024 Innovation Prize for its “Solutions Library” project.
Digital transformation and open innovation, key topics at the 2024 edition of Smau, are also the concepts at the root of this new service devised and developed by Scm Group: a library of technical solutions for co-workers and customers, which makes the most of artificial intelligence to process the company’s technical know-how, effectively classify it and make it available, as and when it is required, to those it may be of use to.
The purpose of the project, which is part of the group’s digital transformation programme, is to activate the process and enhance the wealth of know-how acquired over seventy years of experience in the technologies sector for machining wood and other materials.
Alessandra Benedetti, Digital Transformation&Business Remodelling Director picked up the prize on behalf of the group and she explained the purposes and advantages of the new, winning project during the Live Show on “Innovative tools to support and enhance employees’ work”.
“Solutions Library is part of a wider strategic plan - she explained - which involves offering customers, not only the product but also software and services beneficial for building a continuous and shared relationship”.
An example of innovation which highlights how digital technologies can transform business models by also creating sustainable worth.
Smau was an opportunity for networking with the key players and stakeholders of the Made in Italy innovation eco-system. Together with Sara Iaconianni, Scouting&Idea Generation Manager, and Lorenzo Monti, Digital Projects Manager, Scm Group took part in the “Startup Safari” initiative for examining open innovation ideas and potential opportunities.
www.scmgroup.com
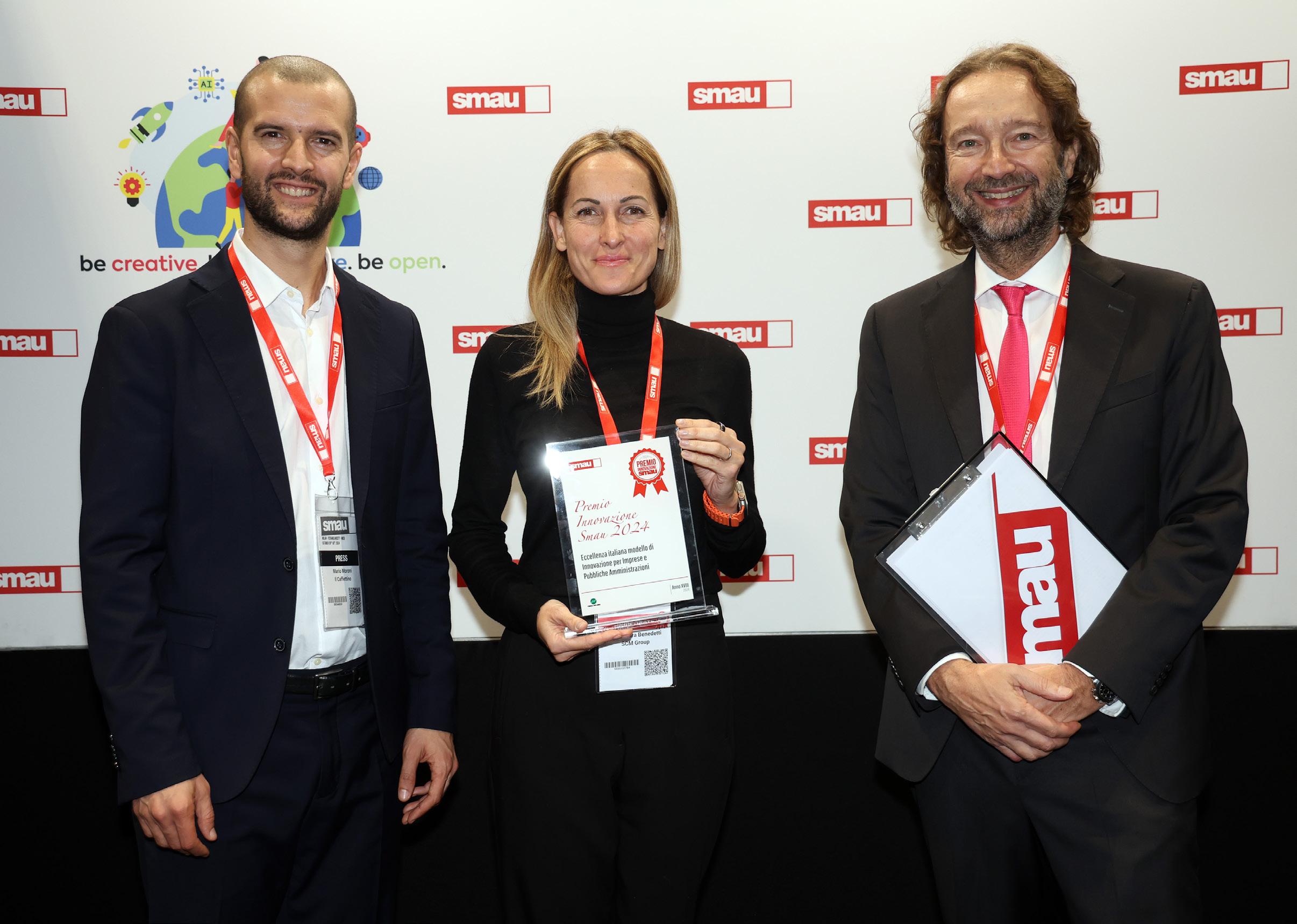
New Mirka ® DEROS Rotary Sander TacklesTough Sanding Jobs With Ease
Mirka UK is introducing its new Mirka® DEROS RS 600, blending power, precision and user-centric design to tackle paint removal, furniture restoration, cabinetry, solid surface and flooring projects with ease.
The versatile Mirka® DEROS RS 600 has a robust 750W brushless motor, ensuring it can be employed to sand a wide variety of materials and applications efficiently, while minimising vibrations and noise.
The rotary sander effectively contains the dust generated through its suction system that is distributed around the backing pad to ensure optimal performance beyond hole alignment, reducing health risks.
Its lightweight, compact design provides a smooth operation and enhances user comfort and productivity, despite it being a powerful heavy-duty sander.
In addition, the DEROS RS is equipped with Bluetooth technology providing monitoring and configuration options for the end user.
Neil Newbrook, business sector manager - Wood for Mirka UK, says, aggressive sanding making it ideal for tackling tough materials and heavy-duty applications ensuring fast and high material removal rates in a compact, lightweight sander.”
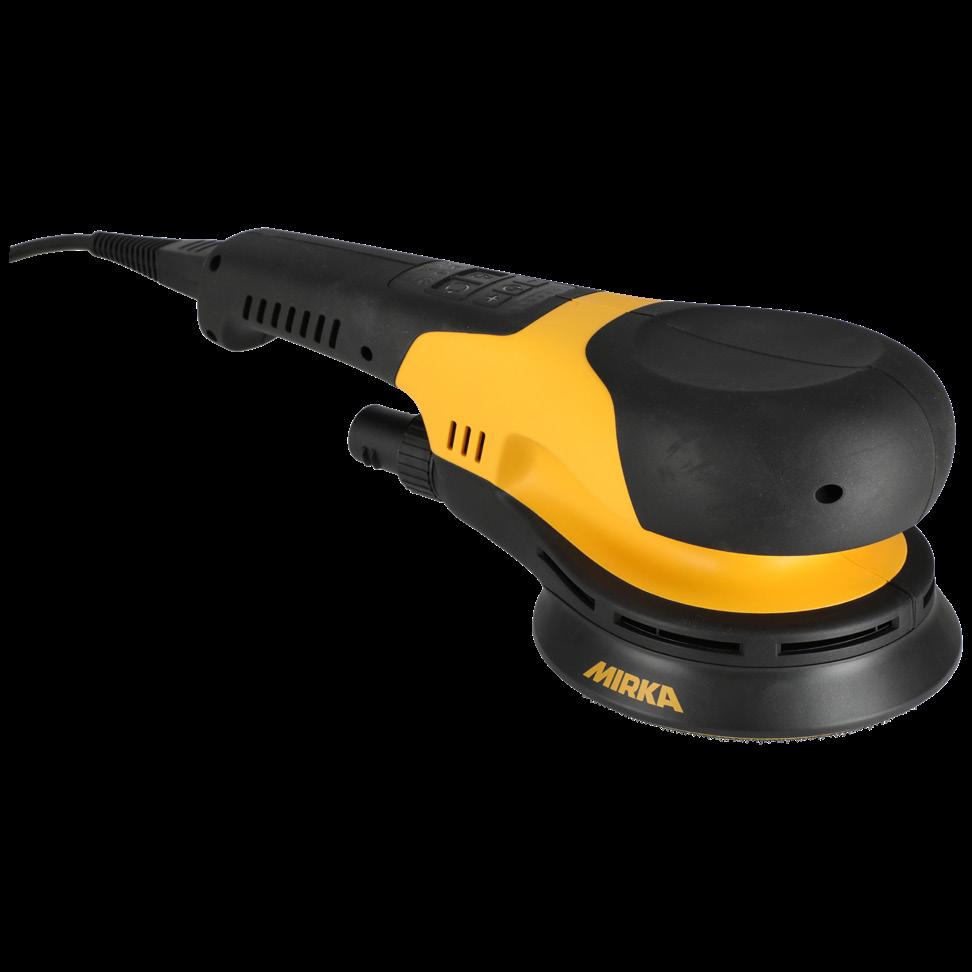
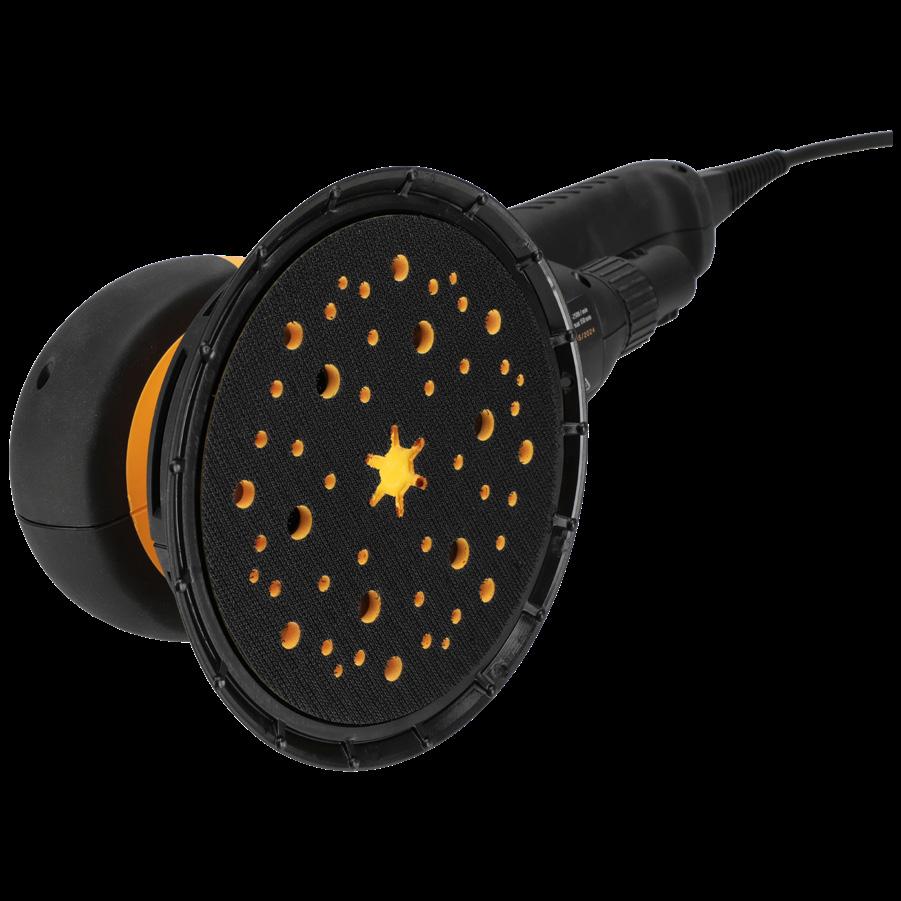
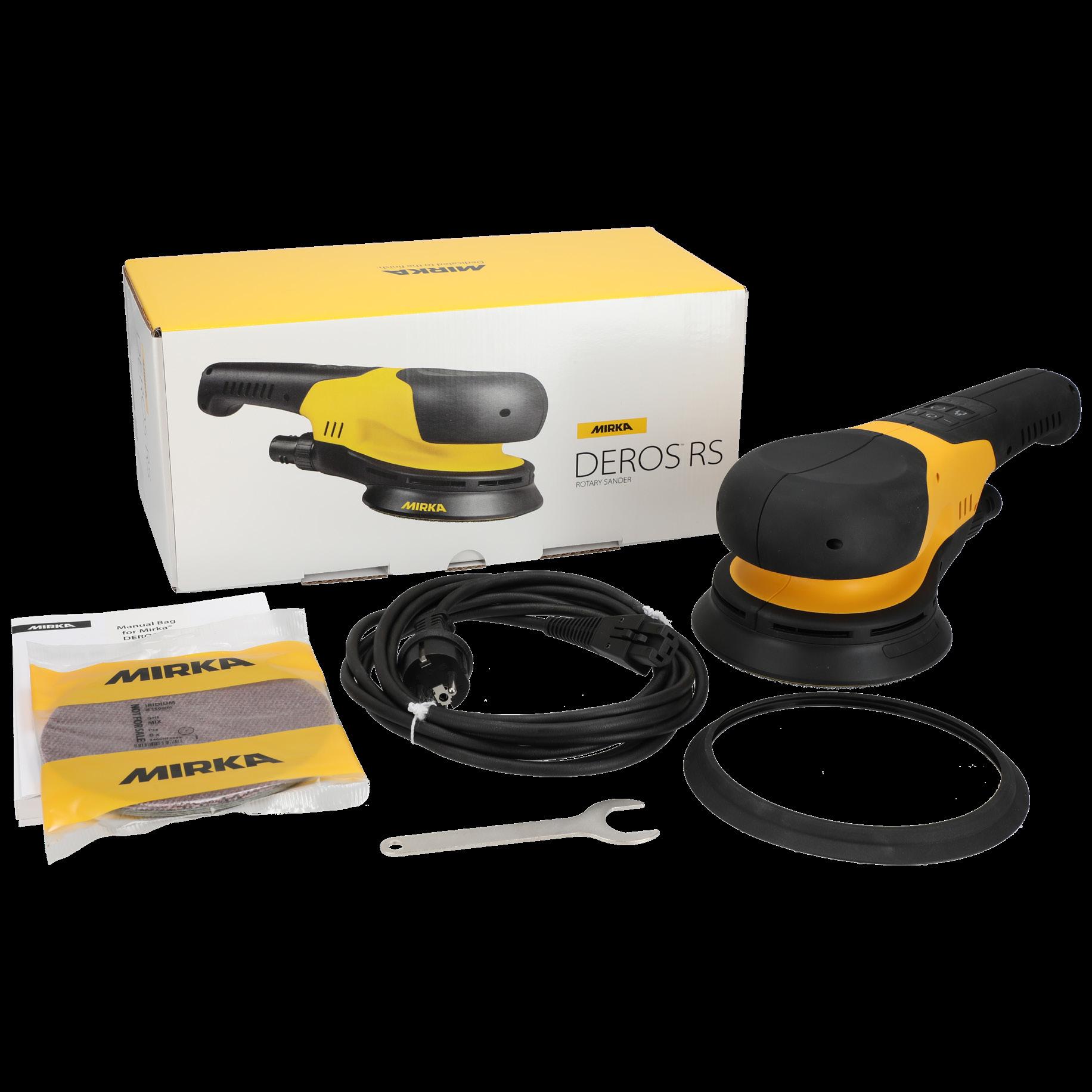
https://www.mirka.com/en-gb/products/top-brands/mirka-deros-rs-rotary-sander
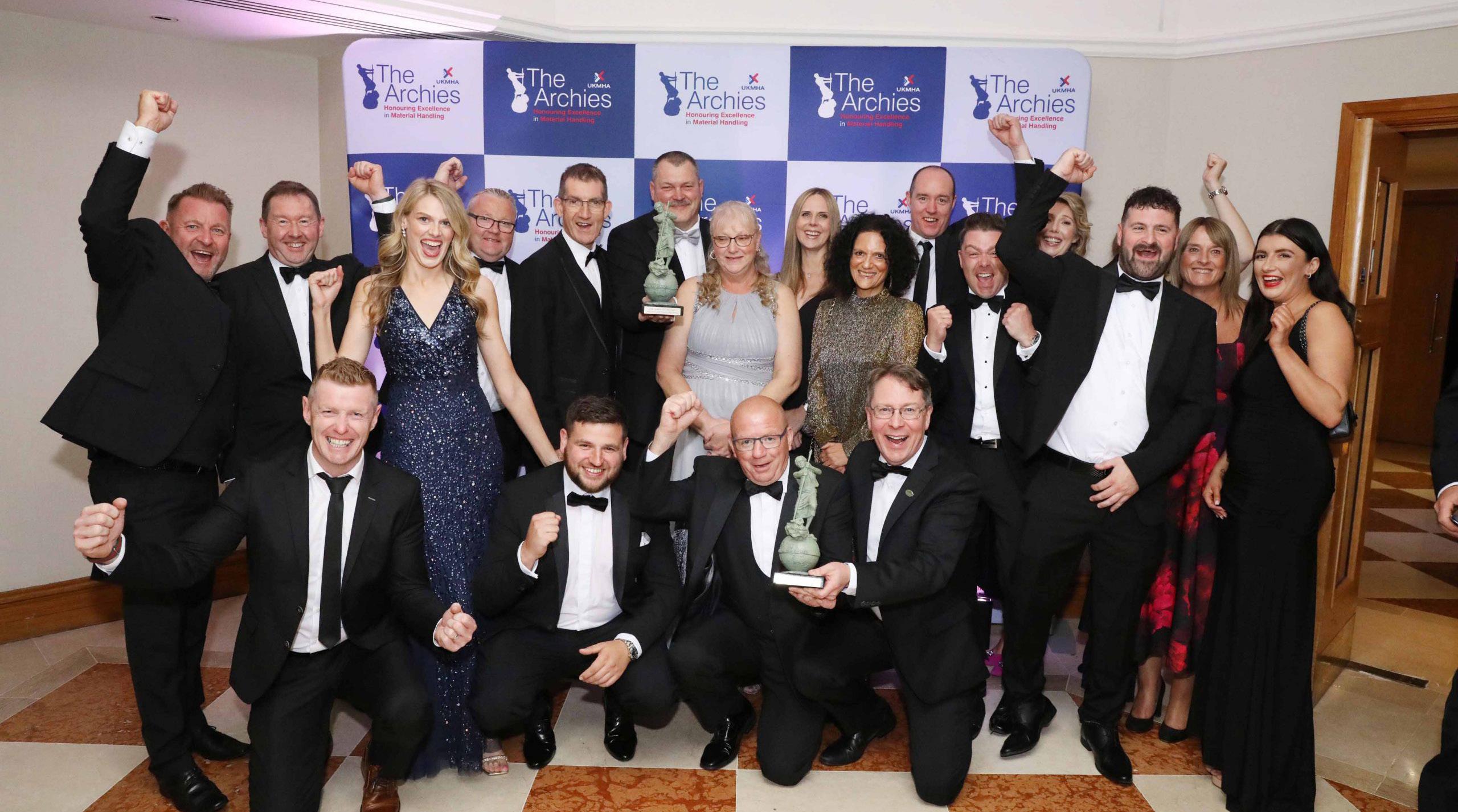
Innovative And Award-Winning Material Handling Solutions AWARDS
Combilift, the largest manufacturer of multidirectional trucks, side-loading and articulated forklifts, has been helping businesses enhance the safety and productivity of their material handling operations while increasing storage for over 26 years. Since the first C4000 multidirectional forklift was produced in 1998, more than 85,000 units have been exported to over 85 countries.
The Irish-based manufacturer is also renowned for its innovative material handling solutions and has received numerous awards for its groundbreaking products.
The Combi-CB70E is one of the latest additions to Combilift’s evergrowing range of electric models, offering powerful performance, extensive battery life and unrivalled ergonomics.
This multidirectional model has a lifting capacity of 7 tons and boasts the distinction of being the most compact counterbalance truck in its capacity category. Its small footprint and multidirectional movement capabilities enable effortless navigation through confined spaces and narrow aisles, making it ideal for transporting timber panels, which are usually bulky and long.
Occupational health and safety requirements mean that the welfare of the workforce has become ever more important over the years. Drivers of industrial vehicles usually spend extensive periods operating machinery and expect high levels of comfort and safety. In response, Combilift’s designer engineers have prioritized advanced ergonomics and high-quality components in their latest models to create a stress-free in-cab environment.
The Combi-CB70E, designed with a focus on driver comfort and safety, recently received the prestigious ‘Ergonomic Innovation of the Year’ award at the UK Materials Handling Association Awards. It boasts a spacious cab with floor-to-ceiling panoramic glass, providing exceptional visibility and safety for operators. One of its standout features is the Auto Swivel Seat, which automatically adjusts 15 degrees to the left or right based on the travel direction, significantly reducing driver strain, especially during reverse manoeuvres.
The CB70E is equipped with a gas strut suspension system typically found in larger industrial machinery. This advanced suspension, combined with large super-elastic tires, ensures a smooth ride over rough or uneven terrain, making it suitable for long shifts.
Additionally, it incorporates Red Dot award-winning Independent Traction, which eliminates the need for a differential lock on slippery
surfaces and minimizes the twisting effect of long loads when travelling sideways, regardless of ground conditions.
Presented in the new Combi-Eco green colour, this model is fully electric and aims to make operations more environmentally friendly. Sustainability is a top priority for Combilift, and this electric model showcases that commitment.
Combilift CEO and Co-Founder Martin McVicar said: “The increased capacities that we are offering in our electric range will answer the demand for ever more powerful products which at the same time help companies to achieve their aims for more sustainable operations.”
Combilift emphasizes sustainability not just by producing more electric equipment, but also by maximizing space utilization. As land prices rise, optimizing existing warehousing facilities becomes crucial and often the most cost-effective solution for companies considering expansion. The Irish company has the expertise to help businesses enhance the capacity, safety, and efficiency of their warehouse and storage facilities.
CEO and Co-founder Martin McVicar, “We have always seen Combilift as much more than a designer and manufacturer of forklifts and other handling solutions. Space is one of the most valuable assets our customers possess, and if our trucks can make it work better for them in terms of storage density, then everyone benefits. The ongoing demand for warehouse space coupled with ever-rising business costs means that space optimization is now more important than ever. Additional benefits of course also include avoiding the operational headache for management and the workforce of relocating to new premises, the lack of bureaucracy associated with new builds or extensions, and the expense of leasing extra offsite storage.”
Combilift offers a free-of-charge warehouse design and layout service, provided by a team of experienced design engineers. This service demonstrates how warehouse space can be configured to maximize the capabilities of its products, which in some cases can double available space.
Discover how Combilift can improve the safety and efficiency of your material handling operations, while optimizing your storage space. For more information on the Combi-CB70E and Combilift’s extensive range of products, please visit Combilift.com.
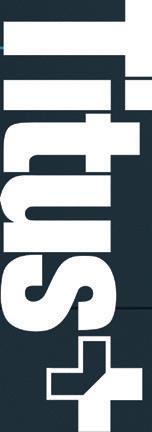
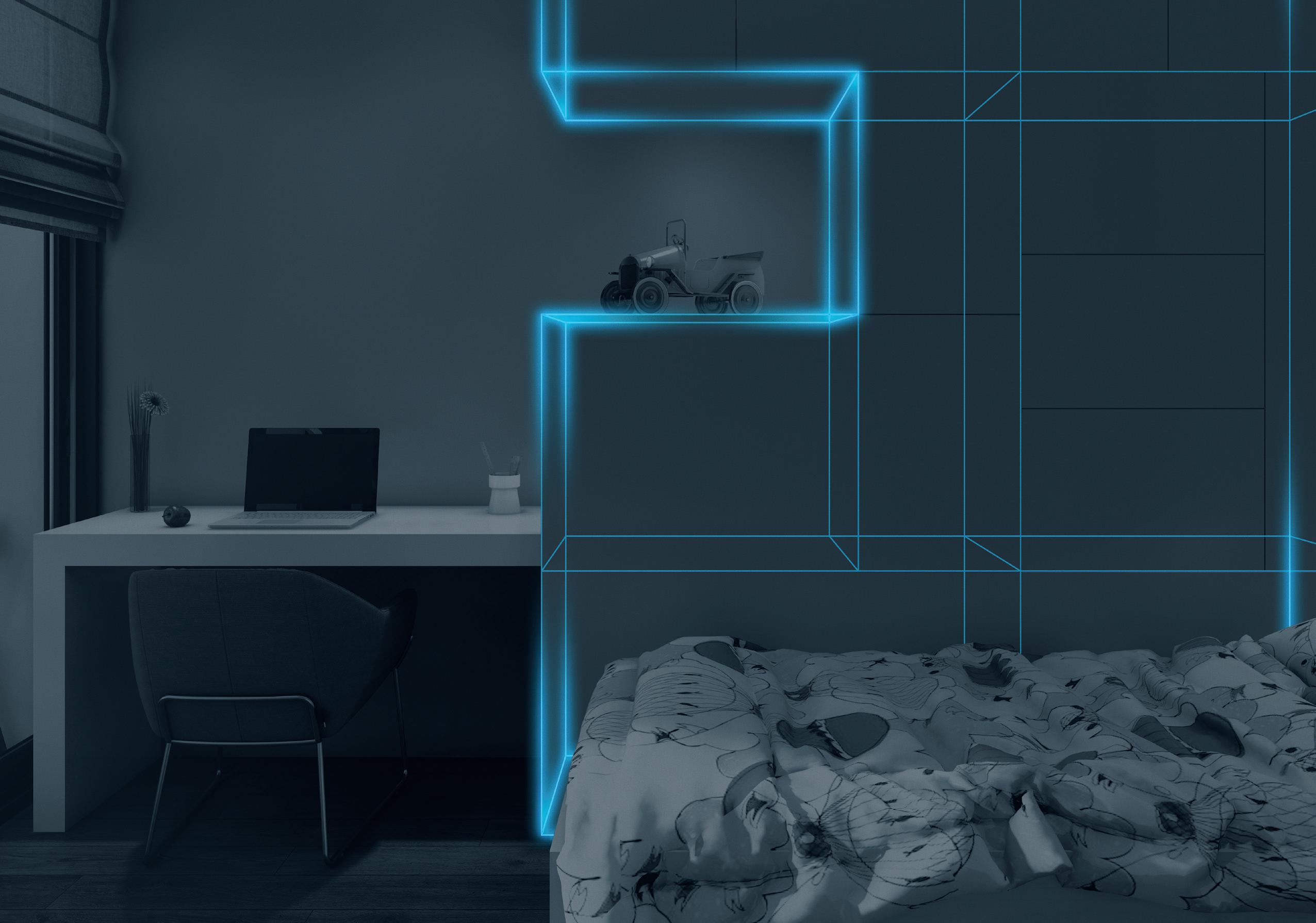
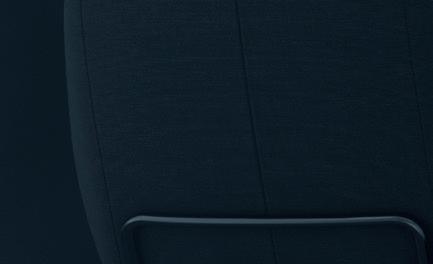
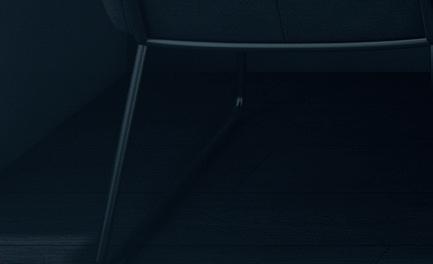
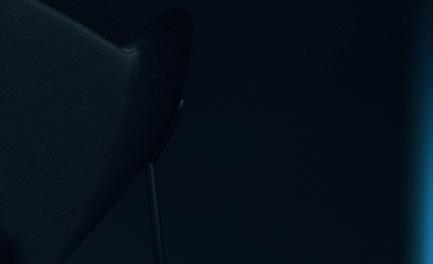
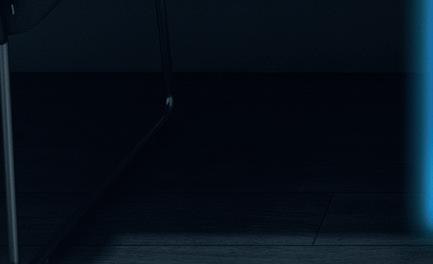

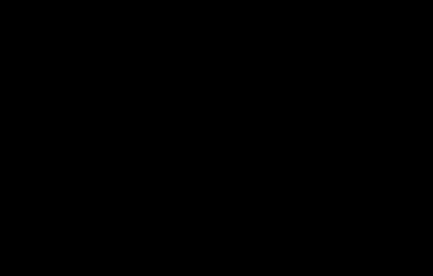
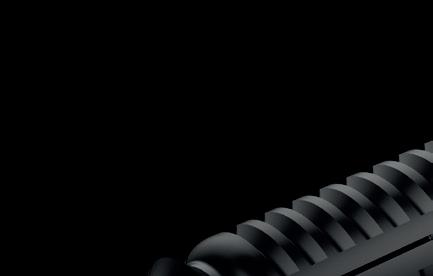
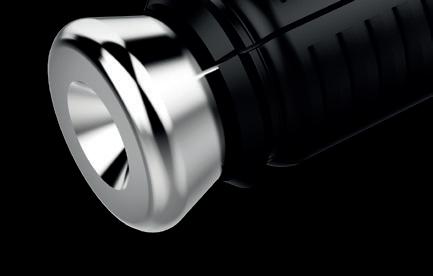
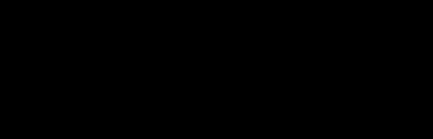
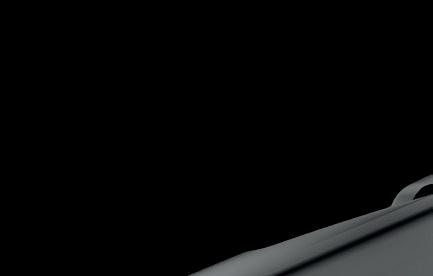

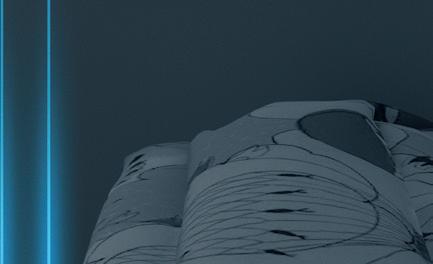
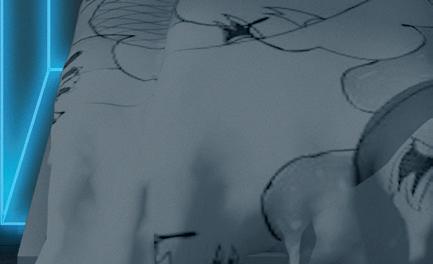

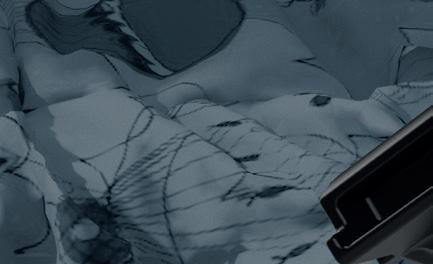


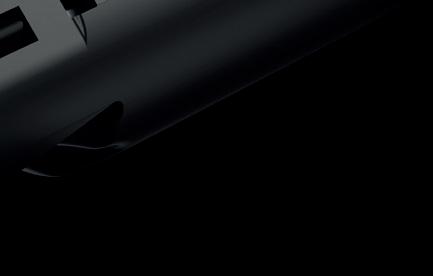

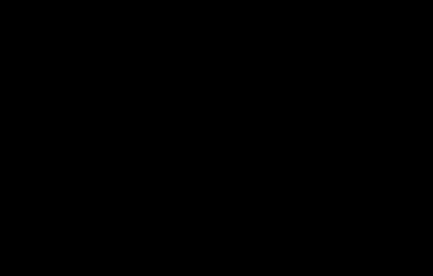
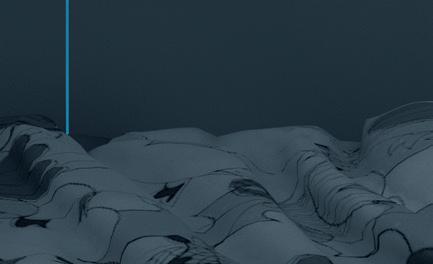
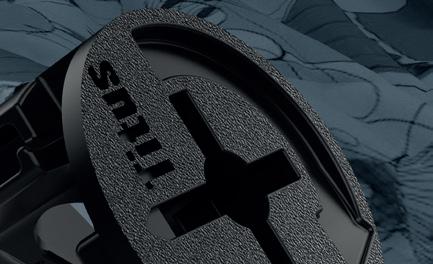
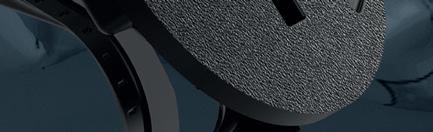
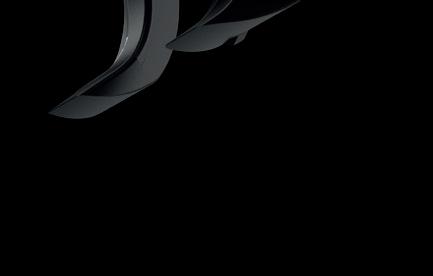
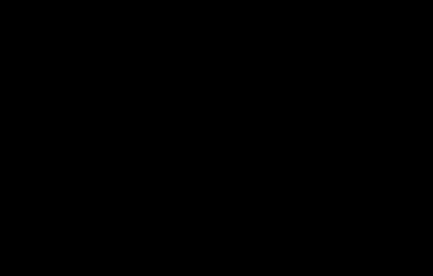

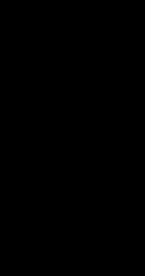
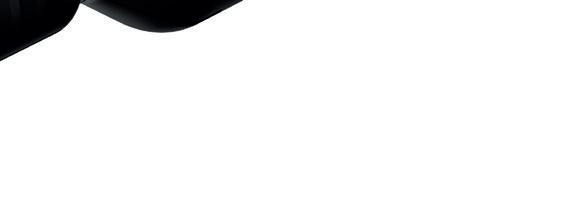
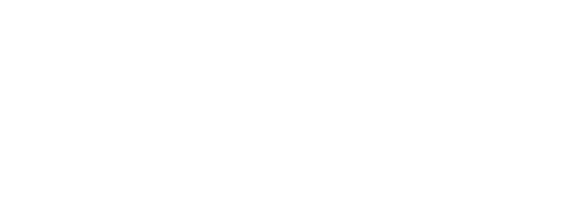



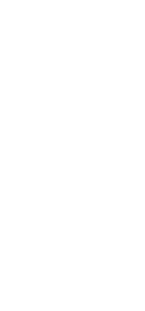
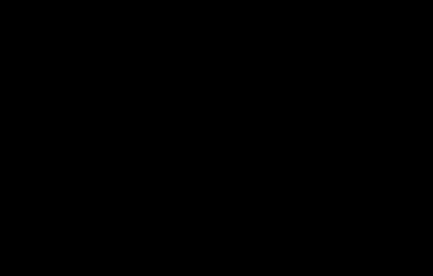
Exceptional Quality As Standard PROFILE
Our company philosophy is simple: OHRA customers deserve 100% confidence that their storage system is safe, reliable and built to last. That’s why we use solid-walled, hot-rolled steel profiles instead of thin sheet metal parts, to ensure our storage has high load-bearing capacity without taking up too much space. All OHRA racking systems are individually produced and high-grade powder-coated based on the requirements of your warehouse and your stored goods.
OHRA was one of the the first racking companies to meet the high safety standards of TÜV Süd. So, when you’re looking for a storage solution, you’re in safe hands with us.
FIVE DECADES OF EXCELLENCE
Our success story begins in 1979 in Germany, when Ottokar Hölscher founded OHRA Regalanlagen GmbH. Thanks to his innovative cantilever racks, his racking company quickly established itself as a market leader for high quality storage systems. OHRA’s patented adjustable cantilever racking arms gave it the competitive edge over other systems, and the OHRA became a guarantee for load-bearing ability, flexibility, quality and longevity. Today, OHRA storage and racking systems and warehouse technology are used in a variety of different sectors and industries and are available throughout Europe.
10
REASONS TO CHOOSE OHRA STORAGE SYSTEMS
• Outstanding quality: hot-rolled steel profiles instead of sheet metal
• High-quality powder coating instead of wet painting
• Made-to-measure individually configurable racking systems
• Suspended cantilever arms ensure total flexibility
• 20-year warranty against perforation corrosion on hot-dip galvanised finishes
• Made in Germany: five decades of storage experience
• International sales offices and OHRA sales advisors in 14 countries
• Economic storage solutions for every industrial sector
• Full consulting, planning, manufacturing, assembly and after-sales service
• The European market leader for cantilever racks
OHRA, a leading specialist in heavy-duty storage technology, is enhancing its UK sales team with the addition of two key
MEET THE TEAM:
L-R Barry Lappin
Sales Manager
E: lappin@ohra.de
Steve Morrison (middle) Sales Manager
E: morrison@ohra.de
Stephen Dimond (right)
Sales director UK
E: dimond@ohra.de
T: 132659898999997
www.ohra.co.uk

personnel. Stephen Dimond, appointed as Sales Director UK, will now oversee customer relations across the Midlands and Mid and North Wales, operating from Birmingham.
Meanwhile, Barry Lappin, based in Wigan, has joined as Sales Manager, focusing on the North of England and Scotland. Steve Morrison, a long-standing member of the OHRA team, continues to lead efforts in southern England, the Home Counties, and South Wales. This strategic restructuring allows OHRA to respond more quickly and efficiently to market demands, while offering customers highly personalized support in the development of their warehouse solutions.
SERVICE AND QUALITY
“In recent years, we’ve focused on strengthening our presence in the European Union, where we’ve solidified our position as a leading manufacturer of cantilever racking,” says Raymond Wolsey, Export Sales Director at OHRA. “We now aim to further tap into the UK market and establish a leading position here as well.”
Stephen Dimond, with over 20 years of experience in the mezzanine industry and factory equipment, is committed to providing close, personal service along with the proven reliability of OHRA racking systems. “Our racking is produced entirely in-house, ensuring the highest quality standards,” says Dimond. Unlike competitors, OHRA uses full-walled, hot-rolled steel profiles rather than thin sheet metal, enabling high load capacities with a slim, efficient design
Barry Lappin adds, “This approach has made us the European market leader in cantilever racking. Our next goal is to enhance OHRA’s brand recognition and profile in the UK.” Lappin, who holds a degree in sales and marketing from Dublin, has extensive experience as a key account manager in the mezzanine industry.
SOLUTIONS FOR AUTOMATION
OHRA’s initial focus will be on the construction and woodworking industries, where the company already counts major EU players as clients. “We’re also expanding our offerings in warehouse automation, particularly for long goods,” explains Wolsey. “As this becomes an increasingly vital topic for our customers, we aim to provide real added value through our expertise and partner network.”
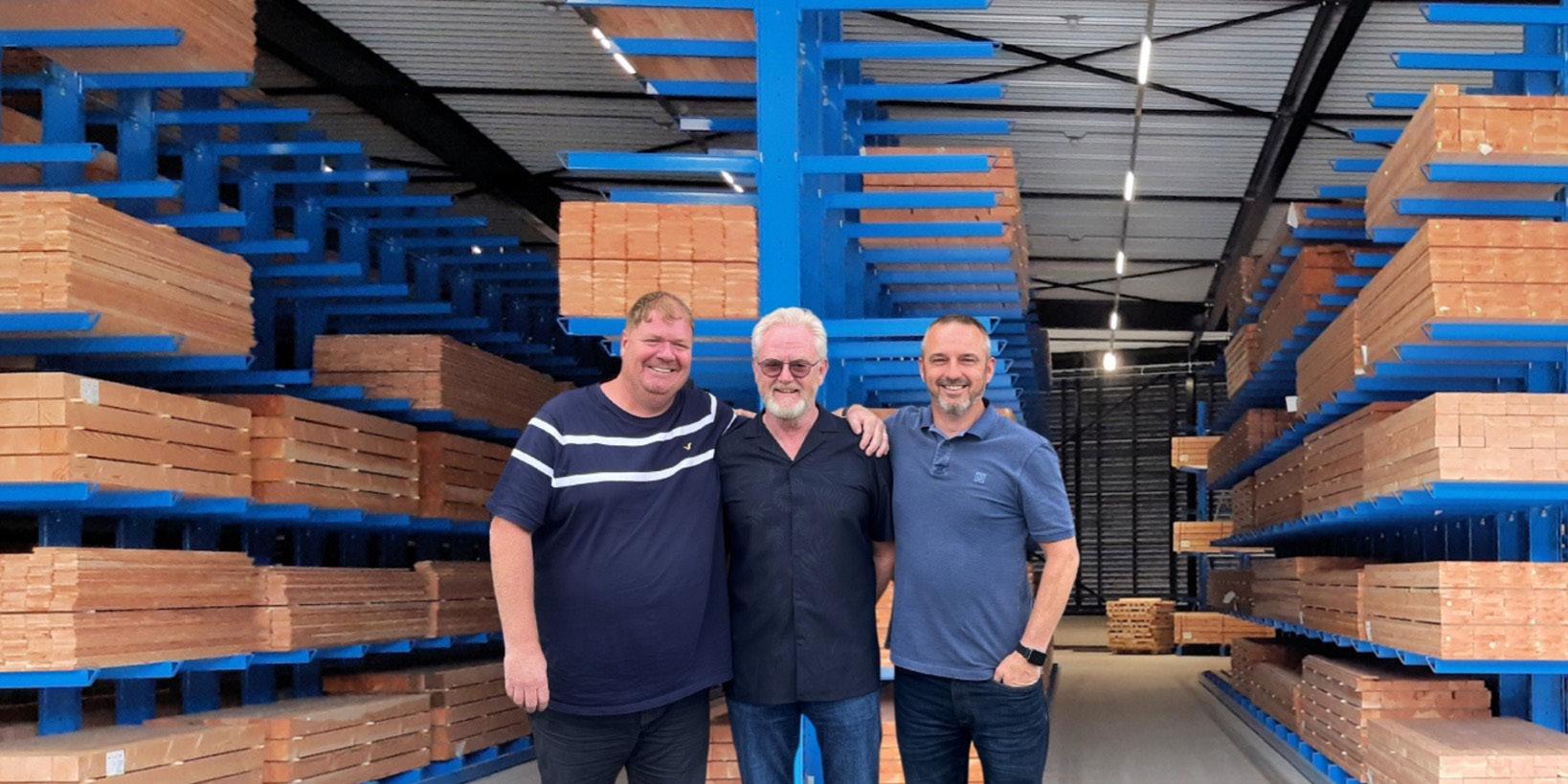
Our company philosophy is simple:
OHRA customers deserve 100% confidence that their storage system is safe, reliable and built to last.
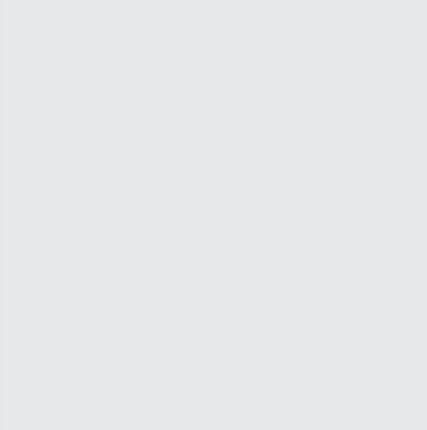
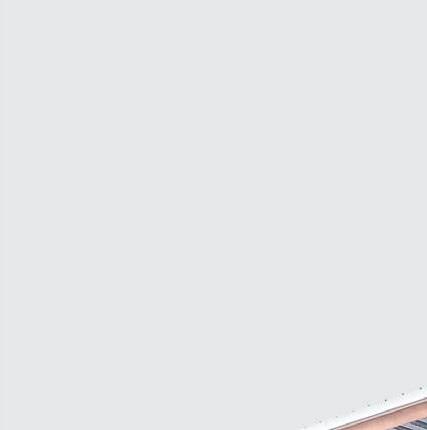
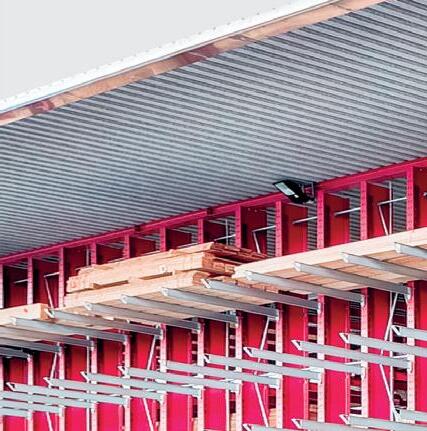
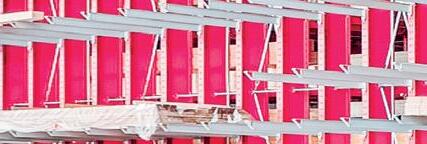
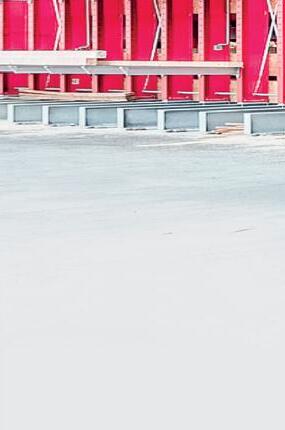
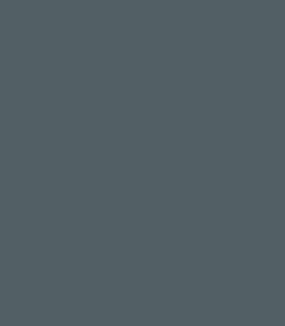
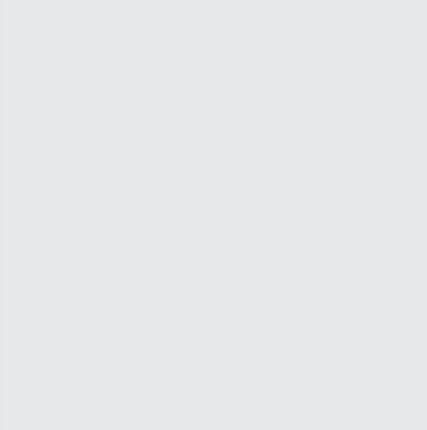
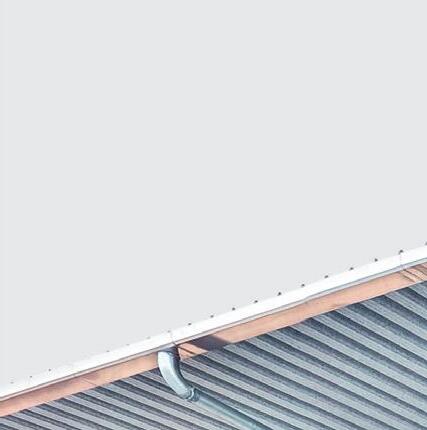
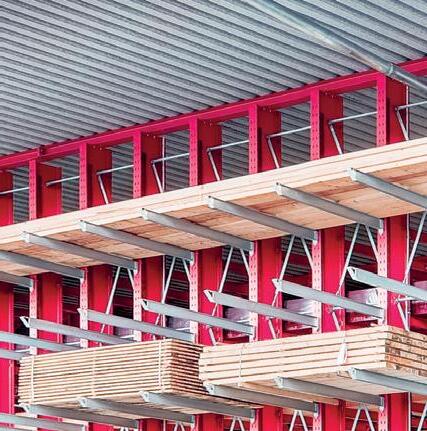


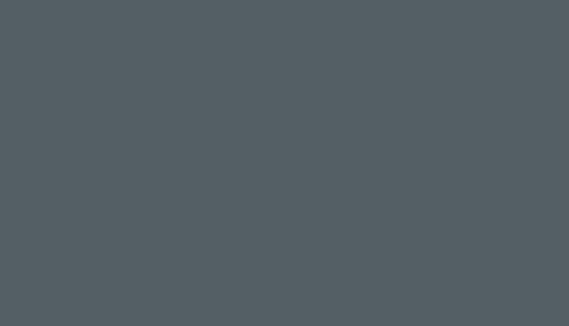
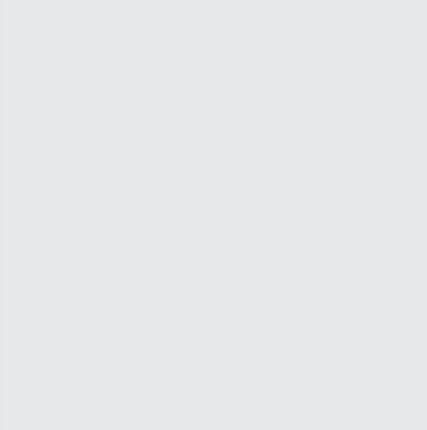
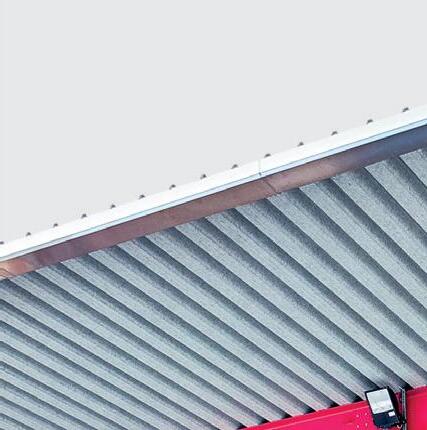
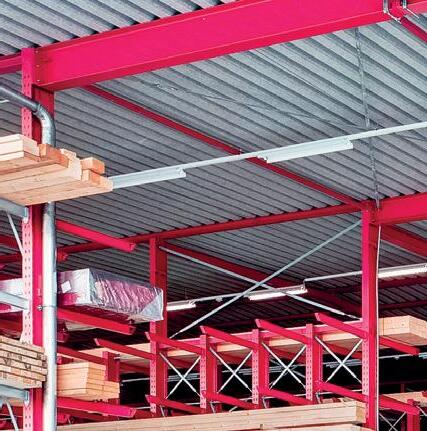

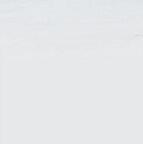
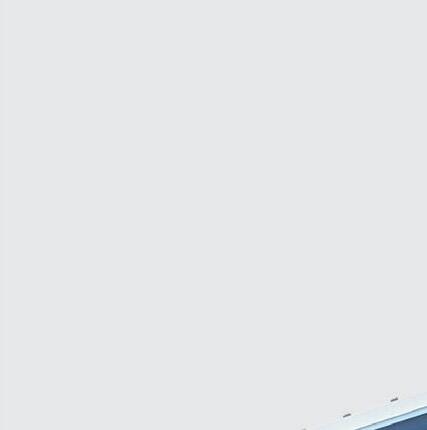

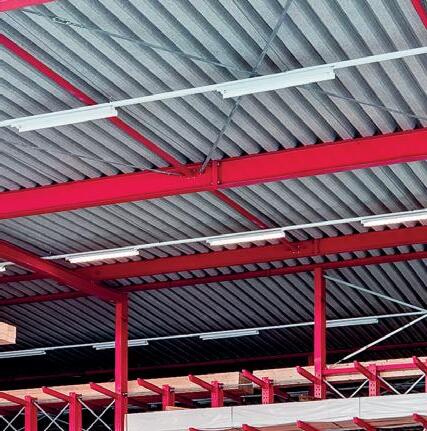
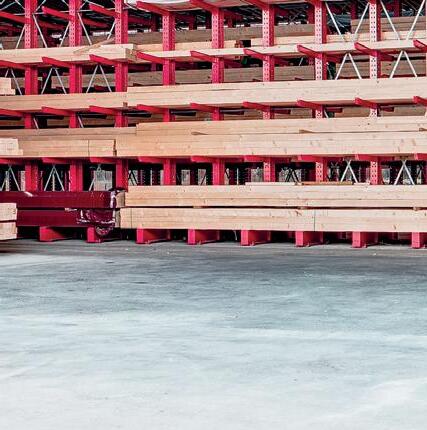
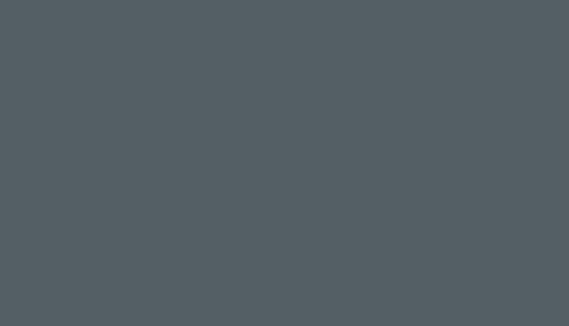
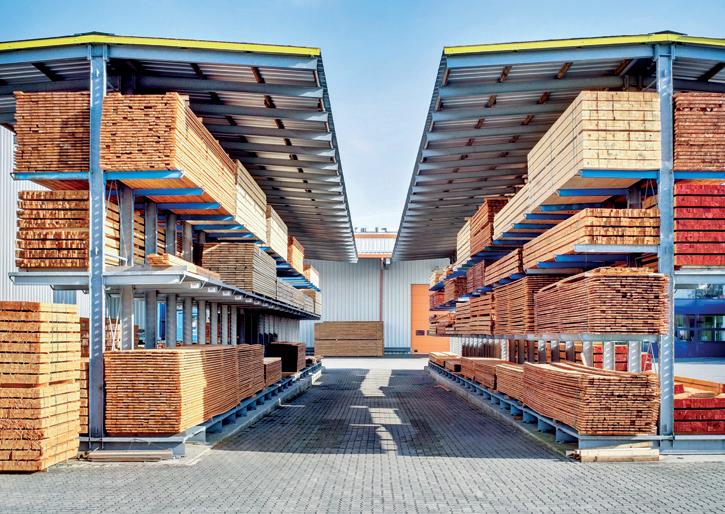
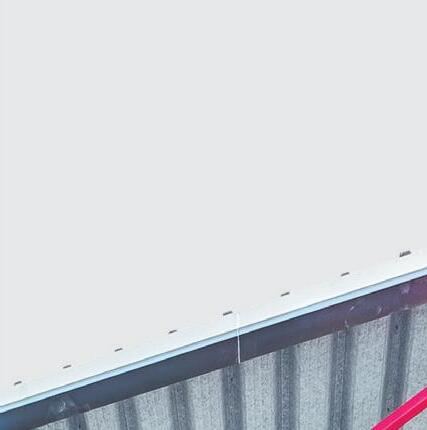
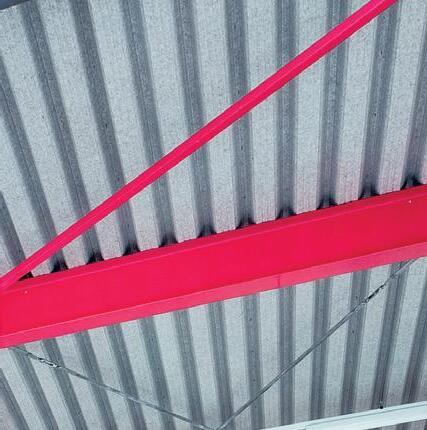
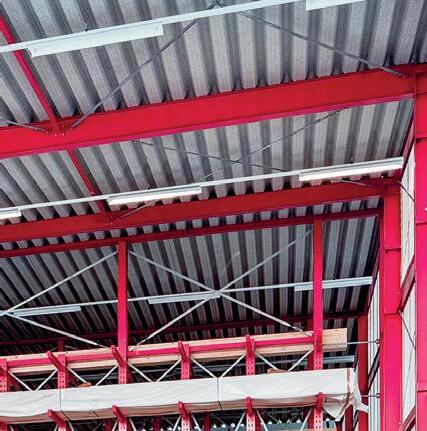
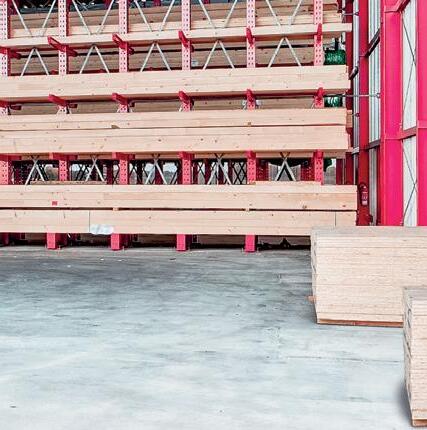
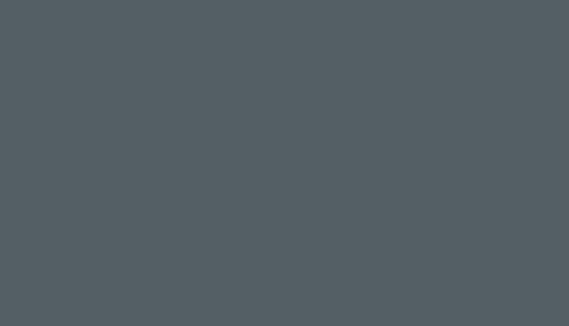
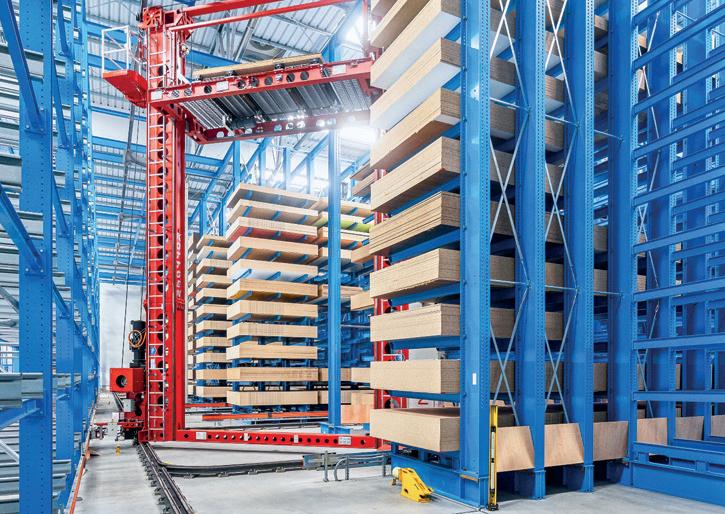
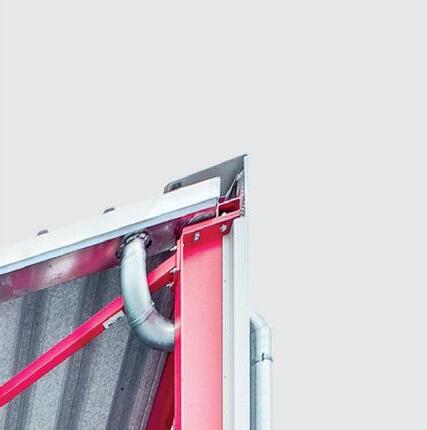
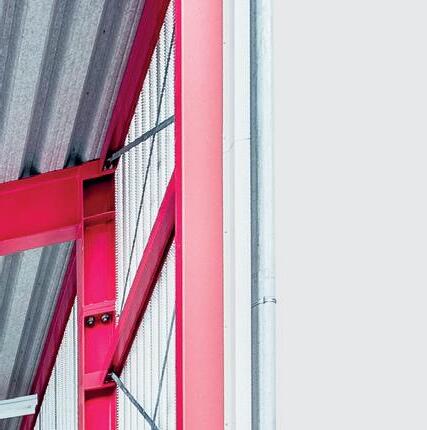
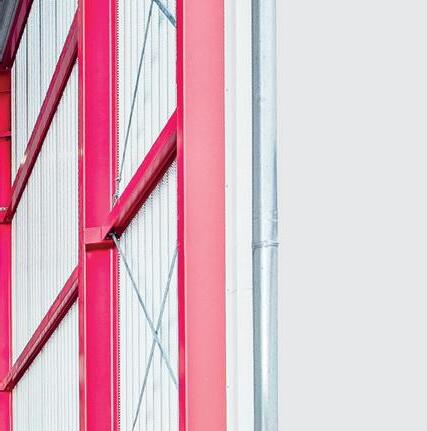

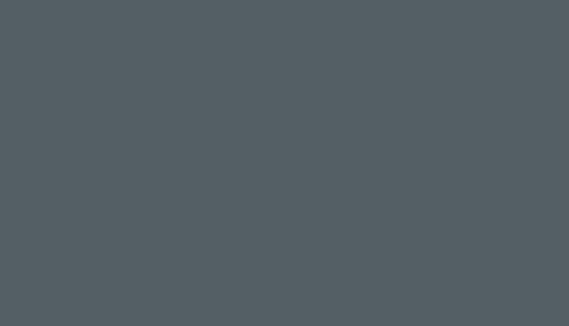
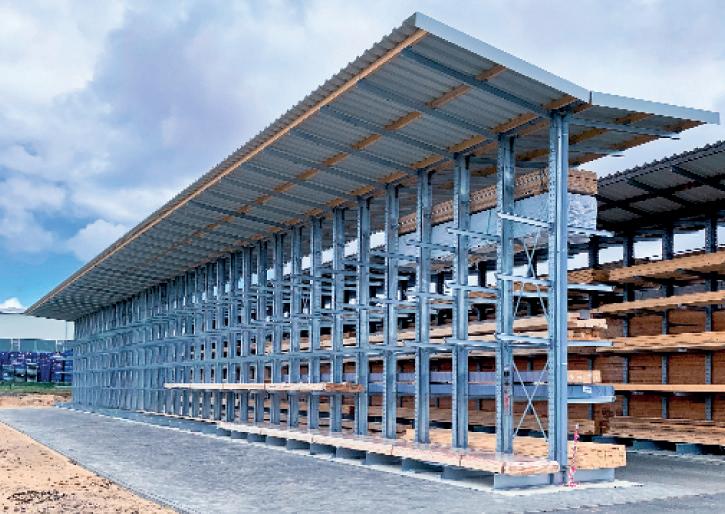
Mobile Racking
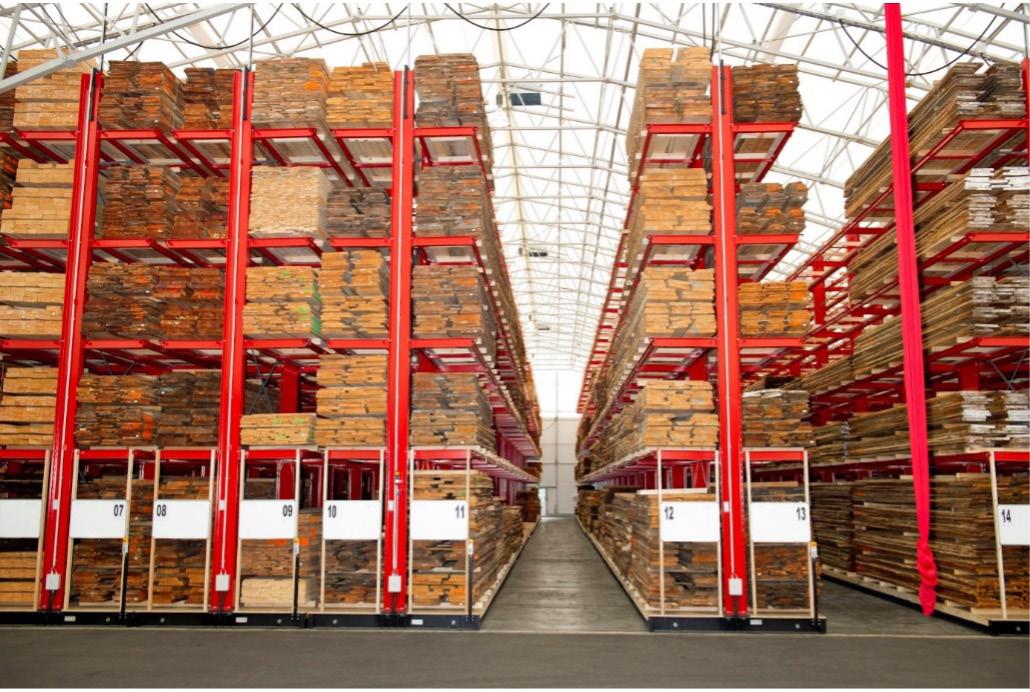
Mobile racking systems can help transform the storage options in a compact warehouse. Our single racks are mounted on traversing carriages that can be pushed together using rails and rollers. For stock storage and retrieval, aisles are opened by an electronic controlled drive train. This can double available storage capacity compared to fixed racks and drastically reduce transport routes.
• Increase storage capacity by up to 100%
• Highly cost-effective way to maximise available space
• Remote control operated
• Mobile rails can be installed in existing buildings

Automatic storage systems
The basis for an automated warehouse comes with choosing a suitable automated racking system that ensures the the advantages of automation: speed, dynamics, safety, energy and cost savings. At OHRA, we believe almost all racking systems, including shelving for small parts, can be automated, but the key factor is to determine which goods are being stored and moved (long and bulky goods are best suited for cantilever racking, whereas the pallet rack is the first choice for palleted goods).
• Storage and equipment planning from one source
• Wide range of equipment types
• Warehouse management software available
• Up to 8,000 kgs load capacity
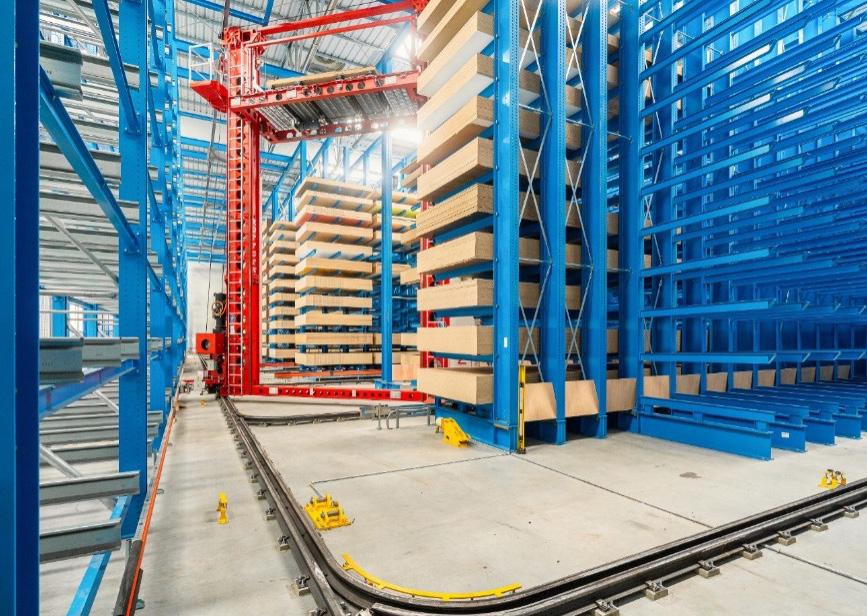

Cantilever Racking

The cantilever racking is a storage systems for long and/or heavy loads. The main elements are vertical steel columns with horizontally inserted cantilever arms. The stored goods are placed on these arms. They are used for the storage of especially long objects such as pipes or beams (long goods).
• Columns and cantilever arms made of solid, hot-rolled steel profiles
• Available as single- or double-sided racking system
• Outdoor storage design includes roof, rear panel and rain gutter – hot-dip galvanised
• Height-adjustable cantilever arms
• Arm loads of up to 2,000 kgs

Rack-Clad Buildings
Our rack-clad buildings deliver significant cost savings compared to conventional warehouse structures with additional racks installed. As well as offering superior storage, the uprights of our racking system act as a load-bearing substructure for the roof, and give you the option of attaching side walls to the building.
• Saves space, offers flexible storage options and delivers significant cost benefits
• Depending on your requirements, we can supply open or closed constructions
• Detailed sections, drawings and assembly plans provided
• Large range of accessories available
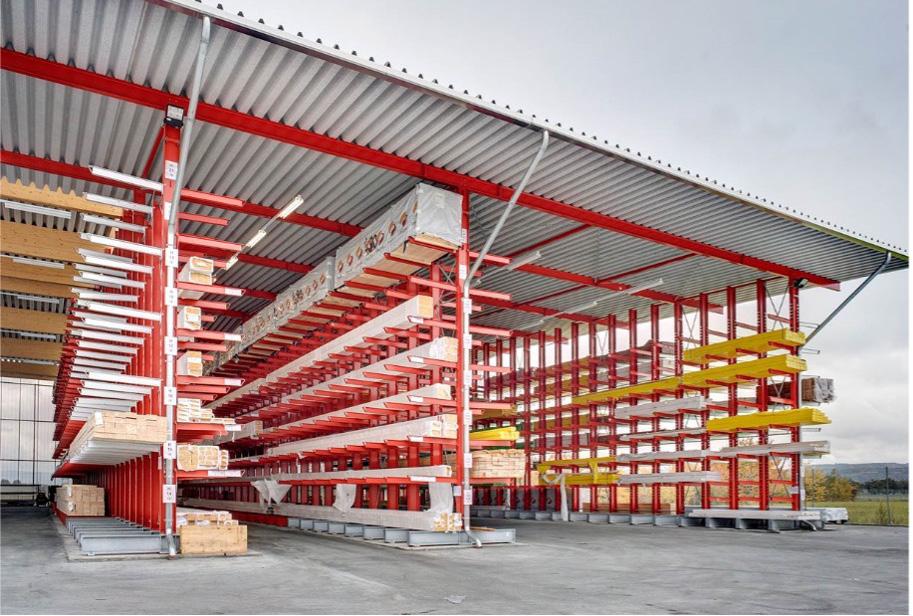

The complete solution for sliding soft-close FEATURE
In today’s market, consumers of domestic furniture and appliances have become increasingly discerning and demanding. This shift has sparked a robust trend towards ‘engineered’ construction in furniture and appliances. Manufacturers are now leveraging the latest technological advancements to enhance their products’ aesthetic appeal and functional convenience. Titus, a globally recognised leader in furniture hardware development and supply, is at the forefront of this movement.
Titus places a strong emphasis on research and development, with a laser focus on addressing the realworld needs of both its customers and end-users. As part of its strategic vision to expand into wider and complementary markets, Titus acquired the Slidix range and its associated intellectual property. This acquisition has proven fruitful, with one of the most recent outcomes being the Slidix range of soft-close sliding door damper mechanisms.
The Titus hydraulic damper, renowned for its performance and versatility, forms the core of all products in the Slidix range. This advanced hydraulic damping technology offers a fully controllable damping curve, allowing users to define forces and their distribution with precision across the entire range of the damping action. This capability enables accurate fine-tuning of the damper’s performance to match the exact requirements of each application. The dampers can be easily configured to provide flat, progressive, multistage, or final release damping, offering unparalleled flexibility to manufacturers.
Soft-close technology has revolutionised user expectations for interactions with furniture, doors, and white goods in residential settings. Mere functionality is no longer sufficient; users now demand convenience and a touch of luxury. By incorporating Slidix products, manufacturers can efficiently and cost-effectively meet these expectations. The soft-close sliding door damper mechanisms effectively eliminate noisy slamming doors and drawers, offering a smooth, controlled motion that elevates the product’s perceived quality.
The Slidix range offers damping mechanisms with strokes of 50 mm or 100 mm, suitable for use on a wide range of materials including wood, glass, hollowcore, and plastics. The applicable weight range spans from 5 kg to 120 kg, accommodating diverse design requirements. Users can select from various sizes and three damping arrangements: damping from inside out, damping from outside in, or damping in both directions. These choices are influenced by factors such as the mounting location of the Slidix mechanism, space limitations, closing speed, weight, and the level of friction. Regardless of the configuration, all Slidix solutions feature compact construction that occupies minimal space, making them easy to integrate without compromising the aesthetic appeal of the product.
The versatility of Slidix products allows them to enhance the performance and end-user appeal of a broad spectrum of applications, including:
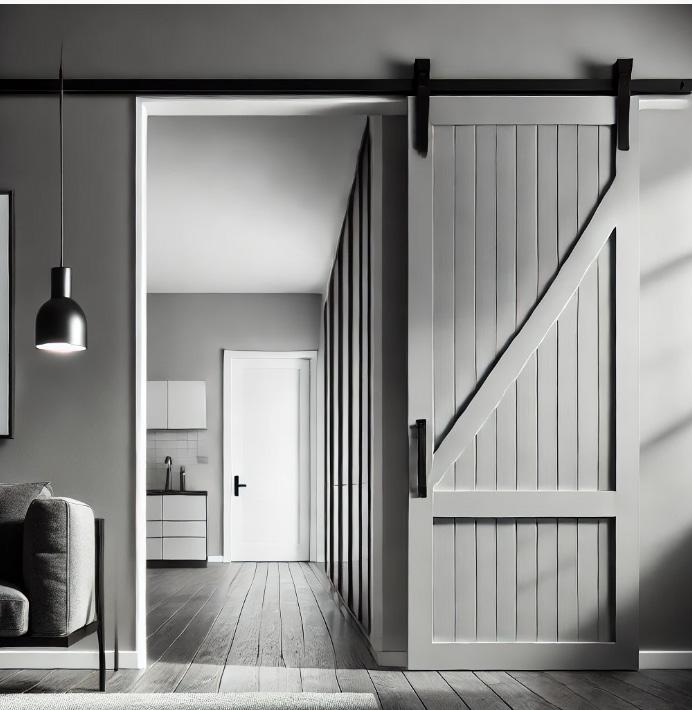
• Furniture, including wardrobes, three-door wall partitions, walk-in closets, drawers, two-way runners in draw cabinets and storage systems with pull-out units
• Interior sliding doors, including pocket doors, barn doors and wall partitions
• Exterior sliding doors, plus sliding windows for balconies and summer houses
• Bathrooms, including shower screens
• Appliances and white goods, including refrigerators, wine coolers and under-counter refrigerator/coolers
In all these applications, Slidix damping mechanisms offer significant benefits. They provide reliable damping at any speed while eliminating rebounce, regardless of door weight and material. The mechanisms ensure full door closure even at minimum speed, complementing this reliable closing action with effortless, smooth opening and a low pull-open force that requires minimal user effort.
The flexibility of Slidix damping mechanisms and their modular construction allow for precise matching to specific application requirements. The damping curve can be adjusted to meet particular needs, and multiple options are also available for spring and damper force. This adaptability extends to mounting, making it easy for users to incorporate the mechanisms into existing designs. The consistent performance over a wide temperature range is particularly valuable in appliance-related and outdoor applications.
A standout product in the Slidix range is the innovative Slidix Centro, which provides soft opening, closing, and centring of middle sliding doors. Its integrated dampers ensure reliable soft closing in both directions with minimal rebounce. Like all Slidix products, it can be fine-tuned to meet specific application requirements and features compact construction
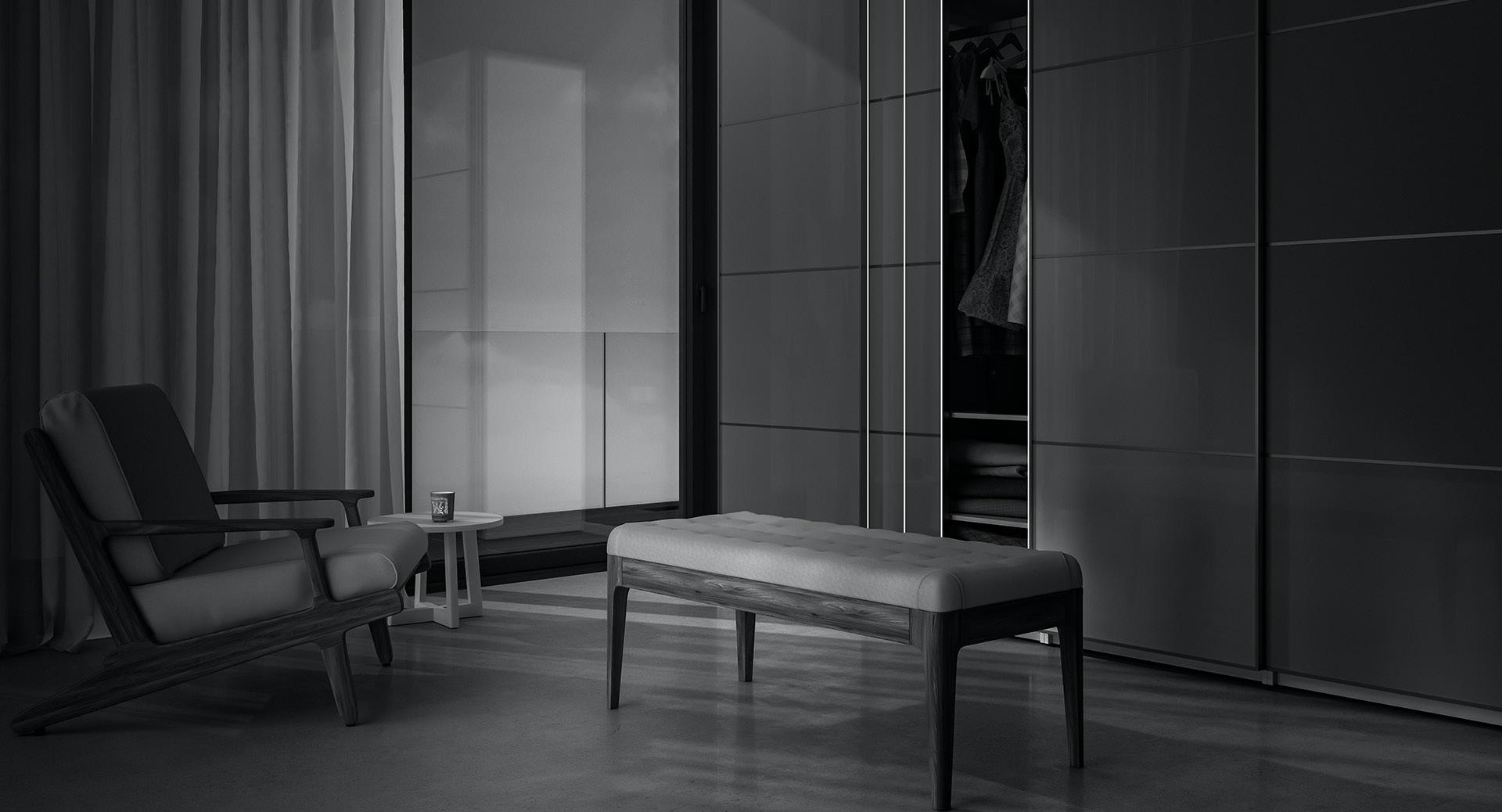
that minimises impact on product design and aesthetics. Suitable for doors weighing 10 kg to 40 kg, the Slidix Centro has a dedicated actuator that works in conjunction with other Slidix mechanisms to offer a complete set of soft closing systems for large wardrobes. It can be easily added to any two-way runner system, such as those in kitchen island drawer cabinets and double-sided pull-outs in shop displays.
THE SLIDIX RANGE ALSO INCLUDES:
• Slidix II for general applications with drawers and sliding doors
• Slidix TA for heavy sliding doors
• Slidix TB, a 100 mm stroke product for wardrobes with sliding doors
• Slidix TC, a 50 mm stroke product for wardrobes with sliding doors
• Slidix TE for sliding and shower doors
• Slidix TF for interior sliding door applications

The newest addition to the range is a push-to-open solution that combines soft closing and touch opening in the same mechanism. It’s currently the only system available that combines these functions in a single unit, making it ideal for use with wall pocket sliding doors.
The Slidix range from Titus represents a comprehensive solution for manufacturers looking to elevate their sliding door and drawer systems. By offering a perfect blend of functionality, adaptability, and user comfort, Slidix products enable manufacturers to create furniture and appliances that meet and exceed the expectations of today’s demanding consumers. As the trend towards more engineered, high-quality home products continues to grow, incorporating Slidix solutions into product designs presents a clear opportunity for manufacturers to position themselves at the forefront of this evolution in domestic furniture and appliances.
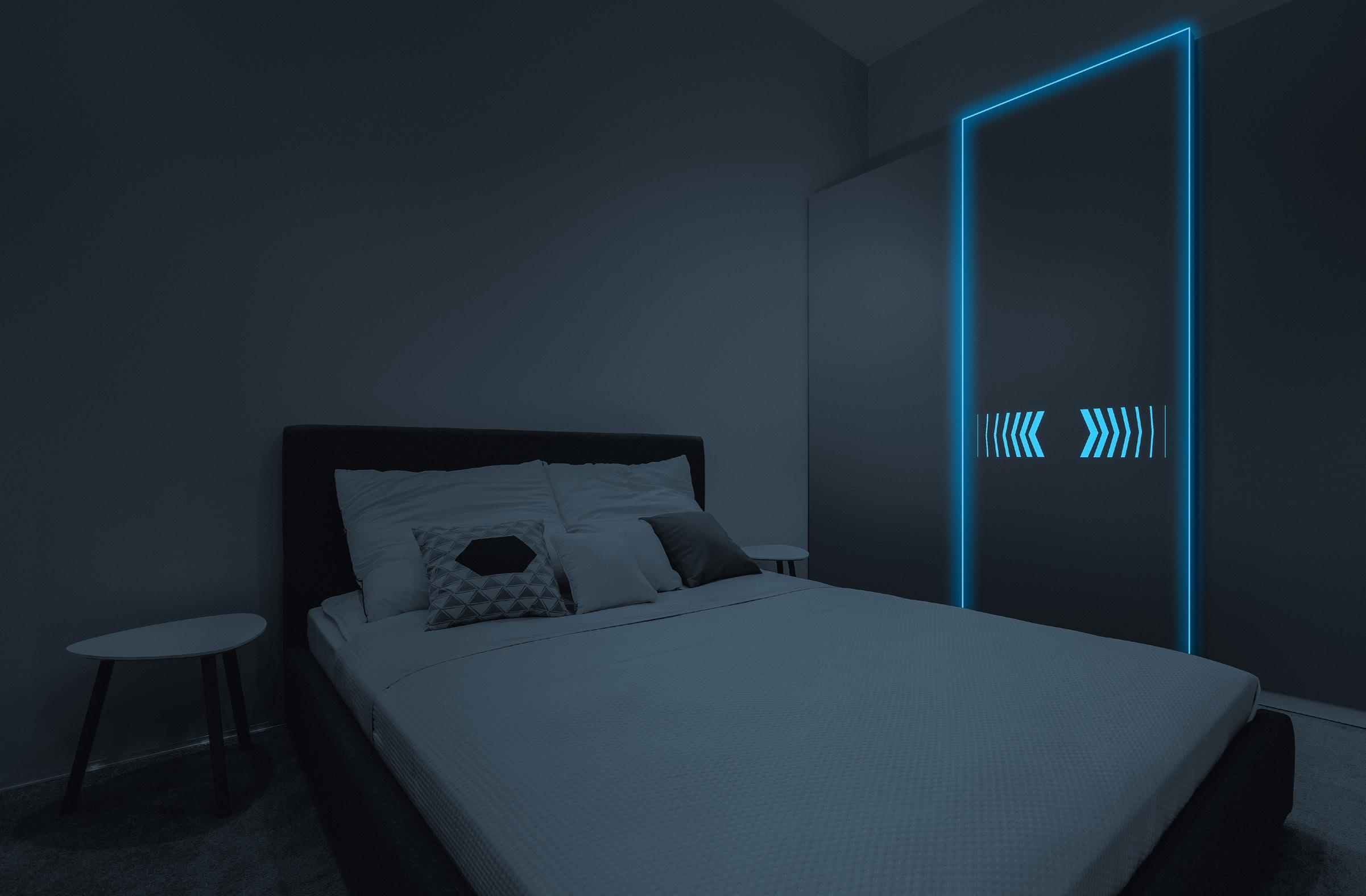
https://uk.titusplus.com/
CASE STUDY
“Wood Waste Heater Will Have Paid For Itself In Around A Year!”
A joinery company in Suffolk has purchased a wood waste heater from Wood Waste Technology to save money on its operating costs.
Cleveland Joinery (East Anglia) Ltd has been producing high quality bespoke joinery from its workshop for over 30 years, for both commercial and private customers. Having previously experienced the benefits of a wood waste heater, the management team at Cleveland Joinery (E.A.) Ltd started looking for a model that complied with the Clean Air Act, due to the workshop being surrounded by residential properties.
Cleveland Joinery (E.A.) Ltd operates out of two buildings that were previously boat sheds, which have been connected to form one working workshop. With no in-built source of heating, the only options to keep the employees warm in winter was bottled gas or electric heaters - both of which could be quite costly to use in today’s economy.
Operations Manager, Andrew Cleveland saw an advert in the trade press from Wood Waste Technology, and got in touch to find out more.
Following a conversation with Kurt Cockroft, MD at Wood Waste Technology and a site survey, a WT5 heater was ordered and installed at the company’s 4500 sq. ft unit in Lowestoft by Wood Waste Technology’s experienced engineers, who were able to duct the heat to warm both the workshops from one heater.
Andrew says: “The heaters are great value for money, and ideal for wood working companies like ours. Wood is a natural by-product of our business, so it’s great to be able to save money on waste disposal costs by burning our wood offcuts and turning them into free heating. And given the increases in fuel costs recently, we purchased a wood waste heater at exactly the right time! We think the heater will have paid for itself in around a year because of all the savings it is providing.
“We’ve been delighted with the advice from Wood Waste Technology about the size of heater to buy and the best place to locate it within our building, and the on-going service. Coming to work in a warm environment makes everyone happier, plus we’re saving money, so the wood waste heater is proving very effective.”
Kurt Cockroft, MD of Wood Waste Technology says, “We’re delighted that the company is enjoying the benefits of its wood waste heater. Any businesses that are generating waste wood should investigate the benefits of biomass technology, to reduce operating costs and improve the bottom line as, similar to Cleveland Joinery (E.A.) Ltd, some companies get payback on the investment in less than 12 months.”
Wood Waste Technology’s years of expertise in wood waste solutions have helped many companies reduce their waste disposal and heating costs. As well as offering site survey,
design, manufacture, installation and on-going maintenance for new units, the company also services all types of wood waste heaters and supplies genuine spares up to 60% cheaper than other suppliers.
In addition, Wood Waste Technology is the UK official distributor for Gross UK, a German manufacturer of dependable, precision engineered shredders and briquetters, available in various size and specifications to suit all business applications.
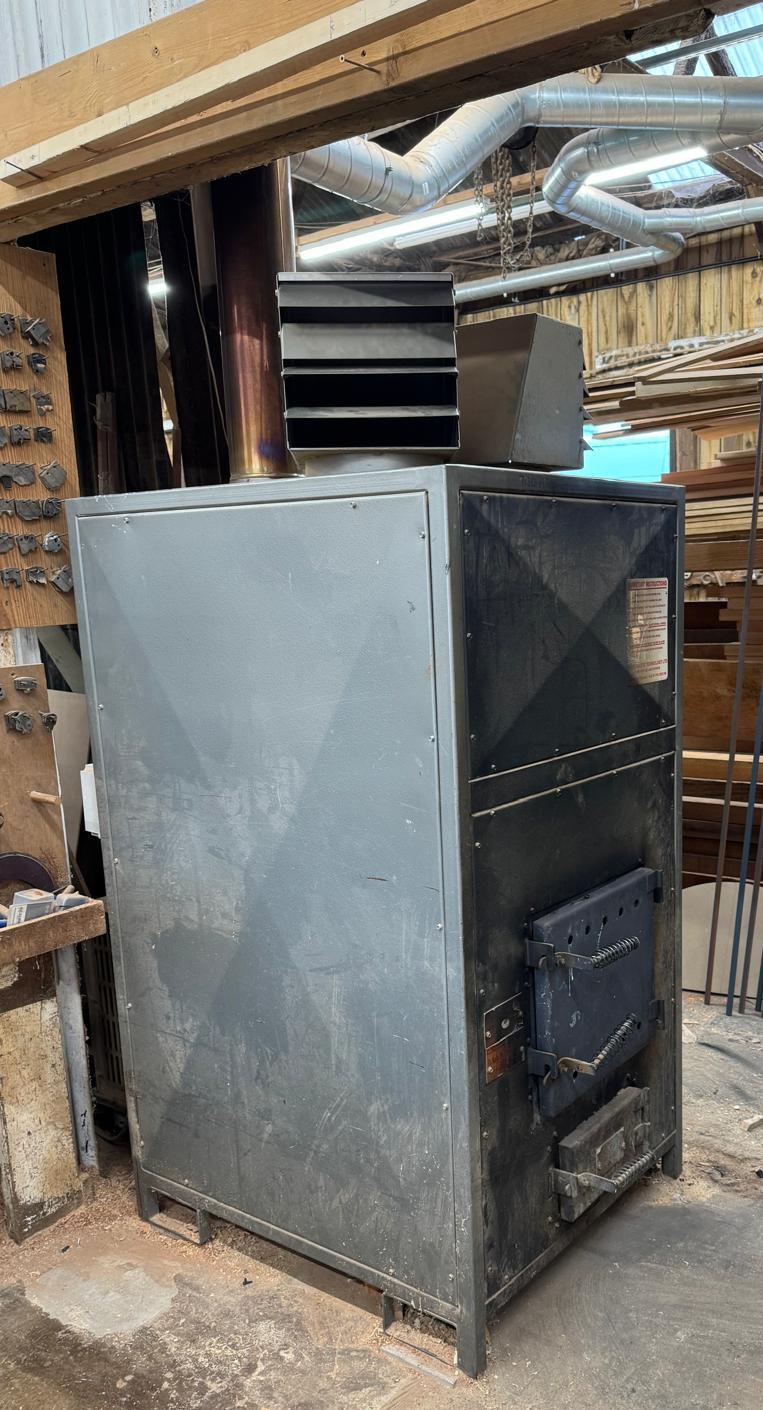
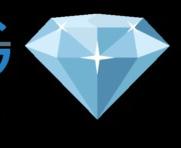
EDGE TECHNOLOGY

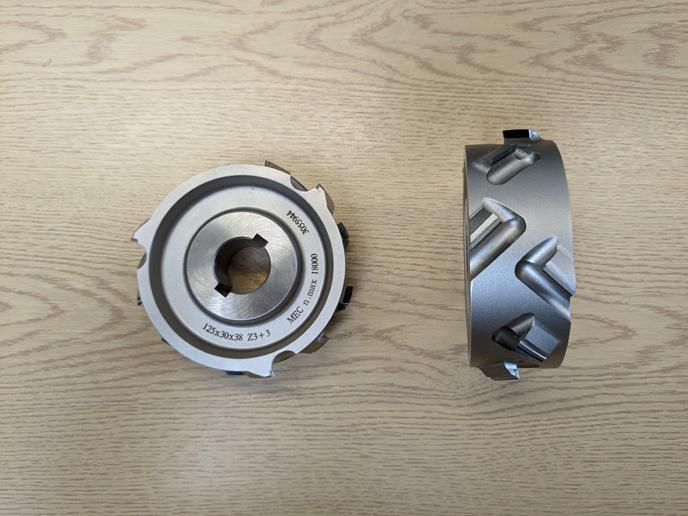
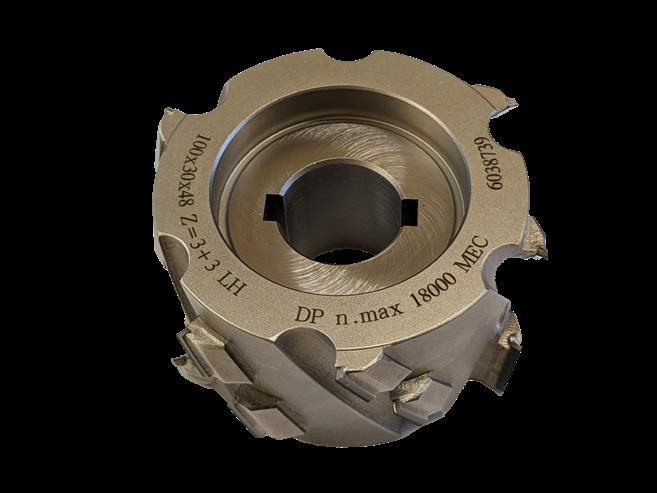
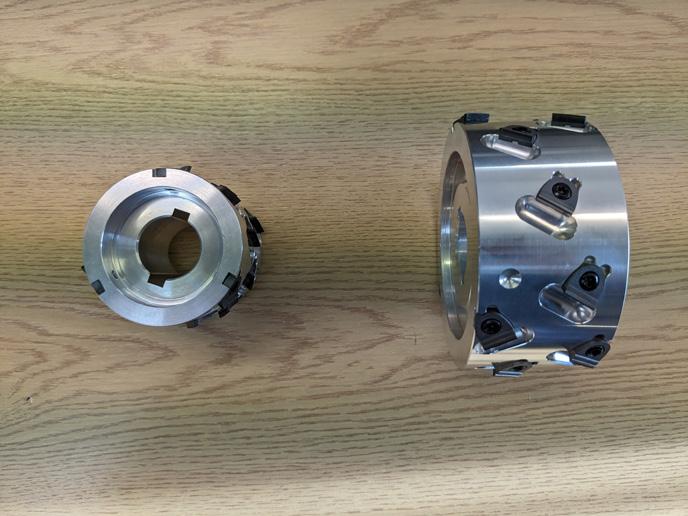
Pre milling cutter blocks for edgebander and double end tenon machines.
Many sizes are ex stock in braised tip style with high shear and super quiet whisper insert style.
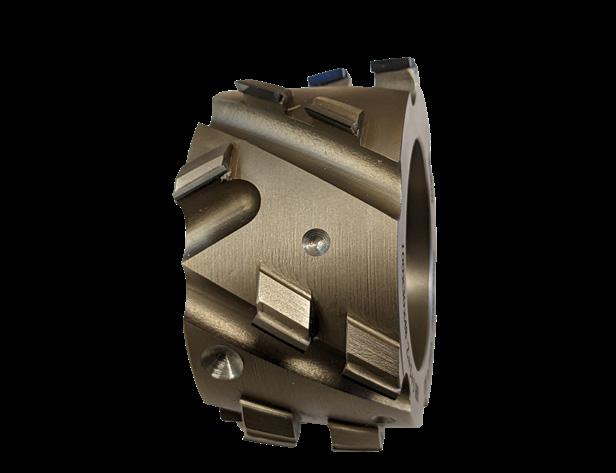
Sizes to suit all major brand machines e.g. Homag, Holzher, SCM. Felder. Brandt IMA. Special widths and tip configuration can be made to order.
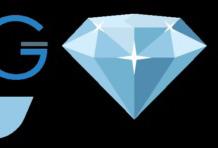
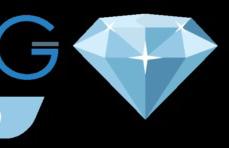
We offer a full repair and sharpening service on all types of Polycrystalline Diamond blocks and tooling with a one week turnaround.
YOUR MACHINE AND PRODUCT CAN ONLY BE AS GOOD AS THE TOOLS YOU USE
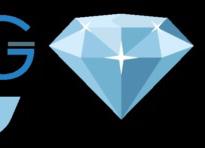
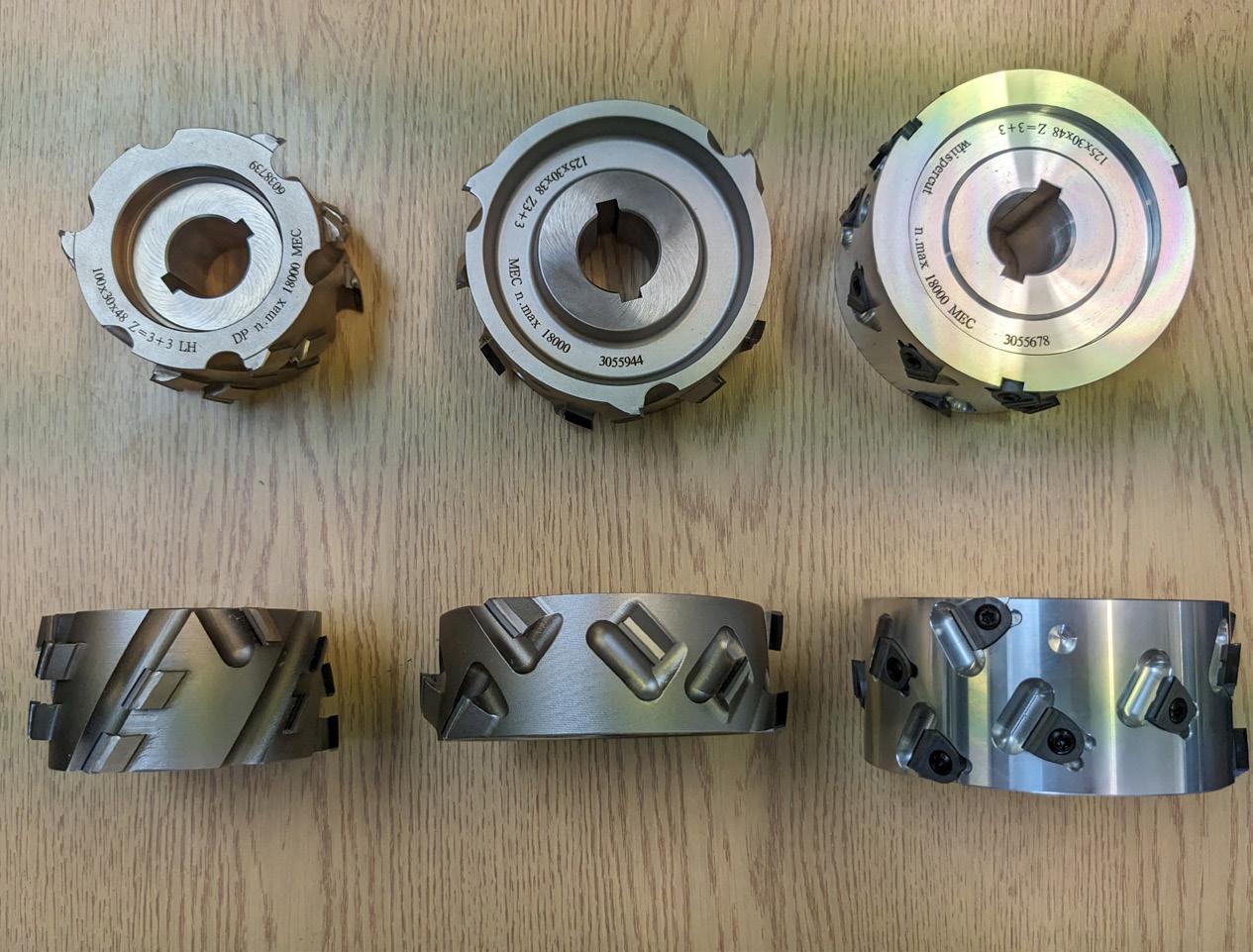
STUDY
Unitech Oxon Advances With Biesse Rover B FT HD
The addition of the high-performance Biesse Rover B FT HD has significantly transformed Unitech Oxon’s kitchen manufacturing process, enabling the Banbury-based company to achieve faster production times and a vastly improved working environment. Founded by Kevin Crouch over 20 years ago, this family-run business is known for its high-end, bespoke kitchens and bedrooms, with a mix of clientele that includes direct-to-public customers, trade retailers, and fitters. More recently, Unitech Oxon has expanded into the contract market, producing kitchens for new housing developments—a strategic move that called for greater production capacity.
In late 2022, a booming demand for contract work created an urgent need for a faster CNC machine. The company identified Biesse’s high-speed Rover B FT HD as the optimal choice due to its innovative design and unmatched productivity for nesting operations. By rethinking machine design, Biesse has achieved a 30% faster cycle time, enabling Unitech Oxon to accomplish in three days what previously took five. The Rover B FT HD’s structure includes a self-contained enclosure that allows operators to work safely while the machine operates at higher speeds. Key components, including the machine’s motors, rails, racks, and pinions, were upgraded to handle the added inertia that comes with increased speed.
STREAMLINING WORKFLOW AND REDUCING COSTS
Just after installing the Rover B, Unitech Oxon faced a shift in the property market as rising interest rates began to cool demand. To adapt to these new conditions, the company restructured its CNC workflow to take full advantage of the Rover B’s productivity. By consolidating CNC work into three days, Unitech Oxon reduced energy costs and operating expenses while redeploying labour to other areas of the business.
“We had less work to process but a much faster machine,” explains Adam Watts, Unitech Oxon’s head of sales and business development. “Instead of running the machine and extraction systems for five days, we compressed operations into three days, which helped reduce costs like electricity and freed up labour for other tasks.”
However, this increase in speed required the team to rethink how they handled loading and unloading, as well as general workflow management. With the new machine’s speed, efficiency in these supporting tasks became crucial to keeping up with production demands.
ENHANCED DRILLING EFFICIENCY
Biesse provided valuable support in optimizing the Rover B’s efficiency by equipping it with a 32-spindle drill block, allowing for a dramatic improvement in drilling productivity. Drilling can account for up to 60% of nesting time, and maximizing this part of the process was essential. According to Biesse’s area sales manager, Mark Trapnell, having an efficient drilling setup is crucial for high-speed operations like Unitech Oxon’s.
Previously, Unitech Oxon’s old machine required individual drilling for each hole, which was time-consuming. Trapnell showed Unitech Oxon how to make better use of multidrilling capabilities: now, when multiple holes are needed, the drill block can drop down multiple drills to drill them simultaneously. This adjustment saves about one minute per panel, which adds up over the course of the day.
“With these optimizations, we’re saving up to an hour a day in drilling time alone,” notes Adam.
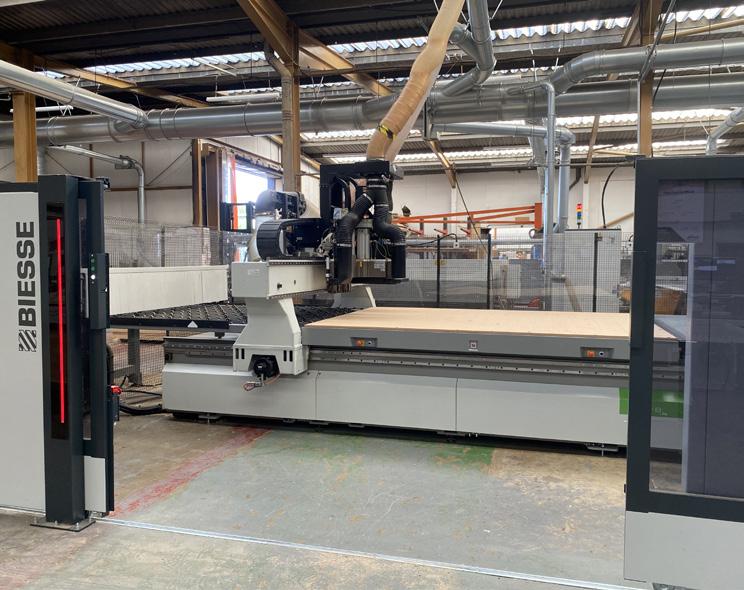

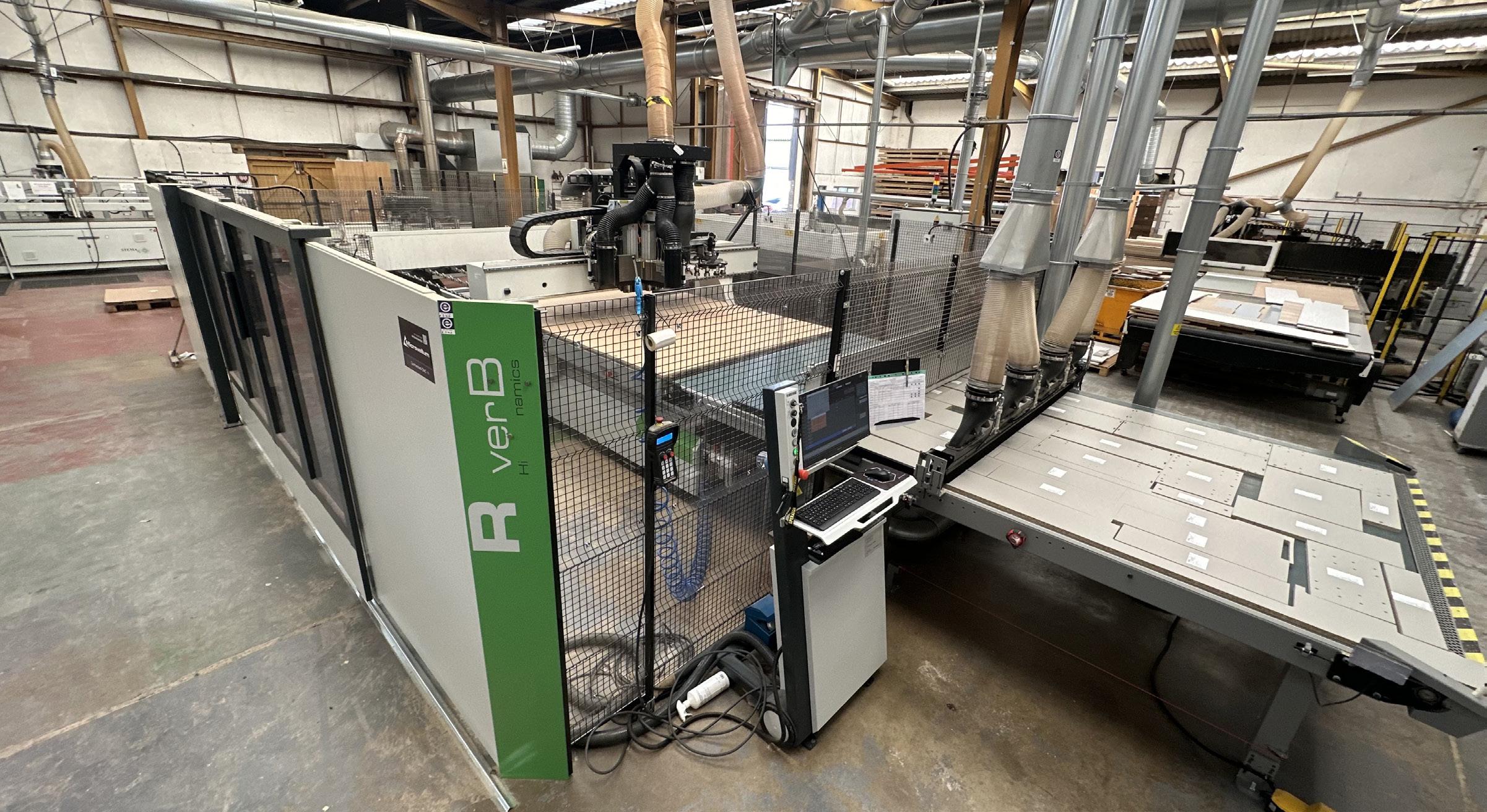
CUMULATIVE TIME SAVINGS AND INCREASED OUTPUT
When the drilling time savings are combined with the improved loading and unloading efficiency, Unitech Oxon saves up to two hours per day, in addition to the Rover B’s faster processing capabilities. With the new machine, they’ve seen a remarkable increase in output. According to Kevin Crouch, where an operator could previously process 40 sheets of board in a day, they can now handle more than 60 sheets with the Rover B.
The company plans to maintain this efficient three-day production schedule when demand increases, allowing flexibility in production planning. “The Rover B has essentially forced us to work smarter, giving us flexibility to manage fluctuations in workload,” says Adam.
Enhanced Dust Control and Work Environment
With the Rover B installation, Unitech Oxon also invested in a new dust extraction system to improve the workspace environment, addressing the considerable dust generated by machining MFC and MDF panels. This addition, combined with Biesse’s T-JET feature, has proven to be transformative. The T-JET system, which uses high-pressure nozzles to clean the cut line as dust is produced, mitigates dust buildup directly at the cutting channel. This advanced air jet system dislodges dust before it accumulates, allowing the extraction system to efficiently remove it. “It’s a different workplace now,” says Kevin. “Previously, dust was everywhere—in the offices and on screens. With the T-JET and our new extraction setup, dust in the workspace is no longer an issue.”
The T-JET system not only improves air quality but also saves time. Without dust settling on the bed, operators no longer need to clean between programs, allowing them to immediately start the next job, increasing overall workflow efficiency.
ADDING THE STREAM A SMART EDGEBANDER
Following the positive experience with the Rover B, Unitech Oxon has invested in a Biesse Stream A Smart edgebander with the innovative AR70 corner rounding unit. This addition will enhance the finish on doors for the contract market and further improve efficiency. Historically, the company used coloured glues, which required frequent colour changes based on board types. The Stream A Smart will facilitate the switch to transparent PUR glue, which is suitable for all
colours, resulting in a thinner, moisture-resistant glue line. The decision to switch glues and upgrade equipment stemmed from a Biesse Edgebanding Masterclass. Kevin acknowledges that despite his years of experience, learning directly from Biesse’s experts has been invaluable: “There’s no ‘university of edgebanding.’ The team at Biesse has been generous in sharing their expertise and has guided us at every step.”
Both the Rover B and Stream A Smart represent part of Unitech Oxon’s broader investment strategy, aimed at streamlining operations and positioning the business for growth. “These investments have set us up to operate more efficiently, giving us the best chance to expand and take on new projects,” says Kevin.

STUDY
Strathallan School Perth And AXYZ Automation Ltd Routers In Education
INTRODUCTION TO STRATHALLAN SCHOOL
Strathallan School, Edinburgh, is known for its commitment to fostering creativity and innovation in education, and has embarked on a journey to enhance its educational offerings through the integration of AXYZ routers.
Adoption of AXYZ Machines: A Thoughtful Decision
In the summer of 2022, Strathallan School made a significant investment in an AXYZ INNOVATOR router. The decision to invest in AXYZ routers came after an exhaustive four-month consultation period. The CNC purchase represented a forward-thinking move, aligning with the school’s commitment to providing cutting-edge educational experiences and this decision was driven by the desire to introduce modern CNC technology to their educational setting.
CHOICE OF AXYZ AS PREFERRED SUPPLIER: BUILDING ON PAST SUCCESS
Strathallan School’s choice of AXYZ as their preferred machine supplier was grounded in positive past experiences. “I had previously installed a similar machine back in 2018 at a previous school, Yarm in North Yorkshire”, explained Ian Barrett Head of Design Technology. This familiarity with the brand’s reliability and performance was very much a positive influence on the selection, cementing confidence in the AXYZ router range.
The Machine and its Core Use at Strathallan School: There are five models in the AXYZ Routers range, all with their own unique options and versatility to cross over infinite markets. The routers are controlled by AAG’s industry leading control interface MOVE™ that drives all machine tasks and is designed to optimise the operation of the CNC machines, perform tool changes, set up work offsets, call up a new file or optimise the cutting speed. MOVE™ is designed to make machine operation easy and intuitive.
The INNOVATOR Router offers standard Option Ready Installation Packages, allowing the operator to expand the capabilities of the machine as one’s needs or business grows. With its advanced technology and cutting-edge features, this machine is the ultimate choice for educational establishments or businesses looking to take their operations to the next level. The AXYZ INNOVATOR, is optimised for prototype, signs and graphics, woodworking shops and educational institutions. It is equipped with powerful integrated servo motors, an optional tool changer and standard helical rack. Choose from two standard sizes that fit the most common sheets sized for this market.
The INNOVATOR has a robust design using high-quality components. This includes a welded steel frame, integrated servo motors and helical rack & pinion. This design ensures the router can deliver an excellent quality of finished product. The INNOVATOR uses AXYZ’s highly intuitive Smart Console and A2MC CNC controller. These machines integrate with the most popular CAM software and automatic tool
changer making it easy to switch tooling without stopping production.
The INNOVATOR is able to process plastics, woods, foams, and non-ferrous metals. This versatility, combined with a compact footprint, makes it ideal for R&D labs, schools and universities. AXYZ also offers an education curriculum which can be taught with this machine.
The Innovator is designed to be upgraded whenever the user is ready. For example, one can add productivity with an optional automatic tool changer or versatility with a highspeed knife cutter. This allows the machine to keep up with the company or establishment growth.
Strathallan predominantly utilises the Innovator machine to manufacture furniture designed by students for their exam projects. The machine efficiently handles materials such as Birch-faced ply, MDF and laminated decorative boards. “The AXYZ INNOVATOR machine at Strathallan School primarily handles profiling, pocketing and occasionally skimming tasks. These capabilities are vital for creating components used in various projects, including the popular resin river tables”, said Ian Barrett.
Impact on Productivity, Efficiency and the Education Syllabus
The implementation of the AXYZ router has had a profound impact on productivity and efficiency at Strathallan School. The introduction of CNC technology has not only streamlined the manufacturing process but has also significantly affected the education syllabus. The INNOVATOR router has been tailored to meet the specific needs of the curriculum. This capability has empowered students to turn their design concepts into tangible, high-quality products. By utilising CAD designs directly for cutting, the school estimates a remarkable 75% reduction in making time, providing an additional 50 hours of teaching time.
INITIAL CHALLENGES AND SOLUTIONS
The integration process, overseen by experienced personnel who had prior knowledge of the AXYZ machine, proved to be relatively straightforward. Any challenges faced were swiftly addressed with the assistance of Chris Perry from AXYZ, providing guidance on installation logistics, room layout and power requirements.
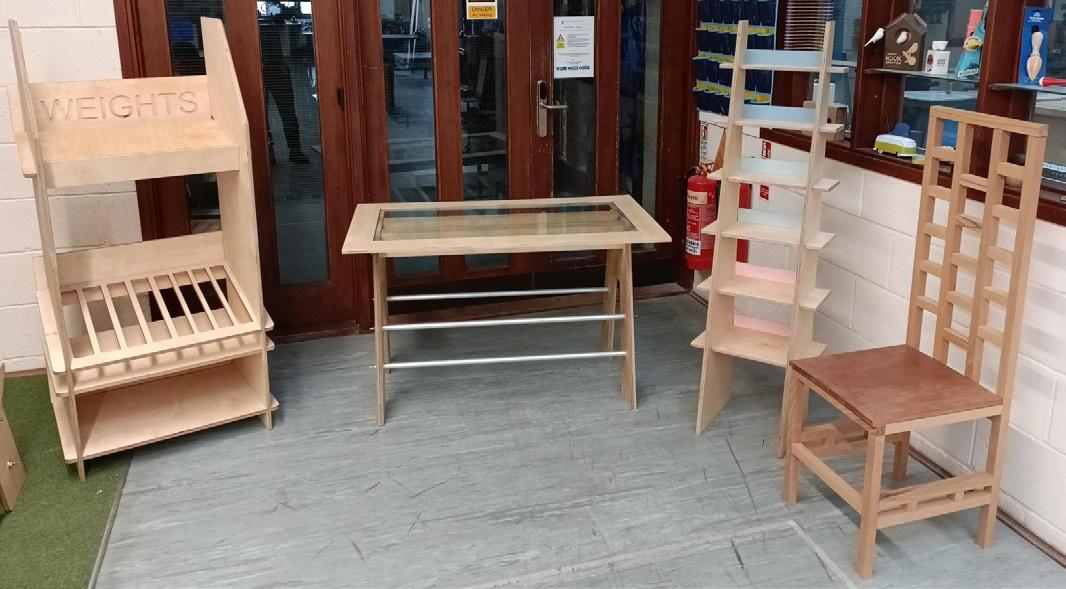
CASE STUDY
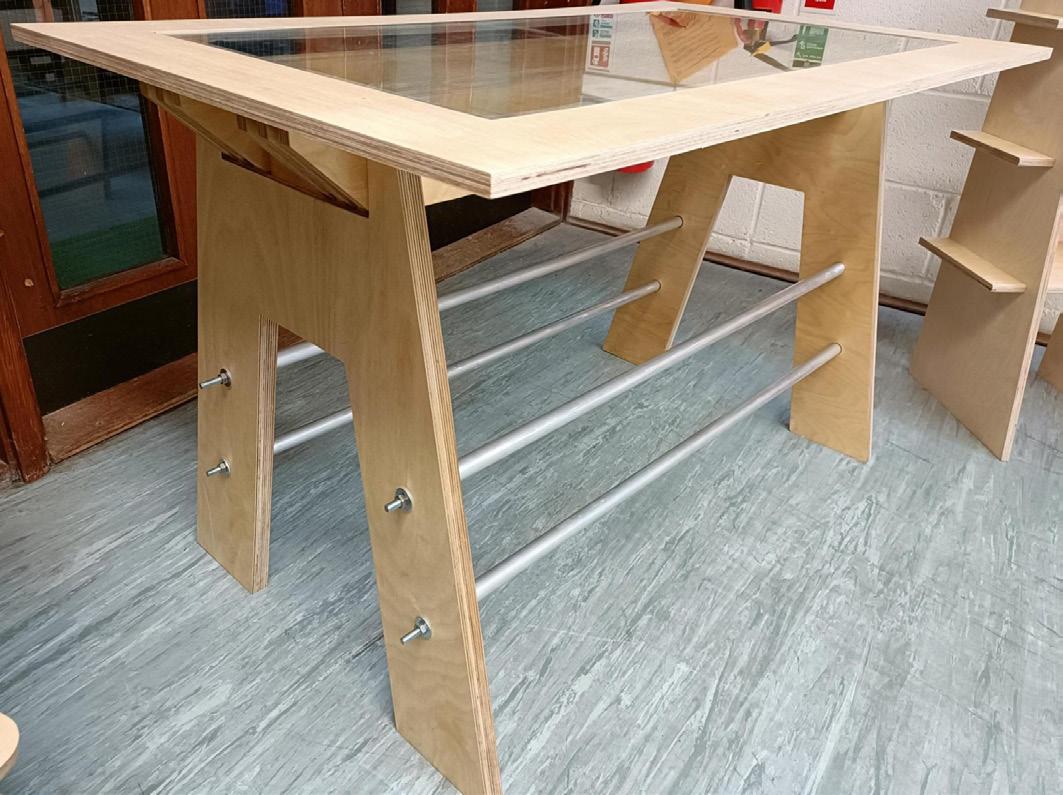
COST SAVINGS, CREATIVITY AND EXPANSION
While cost savings have been realised through reduced material waste and fewer errors, the adoption of AXYZ machines has led to an interesting dynamic. The students’ growing confidence and creativity, fuelled by the possibilities the AXYZ machine offers, have resulted in a potential increase in material usage. However, the overall impact on efficiency, creativity and educational value remains substantial.
QUALITY IMPROVEMENT IN PROJECTS
The quality and accuracy of finished projects at Strathallan School have been elevated and it can safely be said have reached industry standards, leaving parents impressed with the high-calibre and professional-grade outcomes created by their children.
USER-FRIENDLY
EXPERIENCE AND BENEFITS: SIMPLIFYING OPERATIONS
Operated by the department staff, the AXYZ machine’s user-friendly operation, has simplified the manufacturing process. “With minimal glitches, the machine’s introduction has provided tangible benefits, in terms of simplicity and efficiency, making it an integral part of the educational landscape”, said Ian Barrett.
STUDENT INVOLVEMENT AND EDUCATIONAL PURPOSE: A HANDS-ON APPROACH
Students actively participate in every stage of the process, from the setup of materials to programming cutting operations. While they may not physically press the button, their involvement in planning and executing tasks ensures a hands-on learning experience that goes beyond theoretical knowledge.
MAINTENANCE AND FUTURE PLANS
An introductory 2-year maintenance plan was included with the purchase, given the relatively light usage compared to industry standards, biennial site visits are deemed sufficient to ensure optimal machine performance. Although currently exploring the capabilities of the existing AXYZ machine, Strathallan School remains open to future possibilities and expansions in their CNC portfolio.
In conclusion, the collaboration between Strathallan School and AXYZ exemplifies how advanced technology can enhance both educational experiences and practical
outcomes and is a testament to the transformative power of advanced technology in an educational setting. Beyond the tangible benefits of efficiency and cost savings, the seamless integration of CNC technology has enriched the creative and educational endeavours of students at Strathallan School. The integration of AXYZ machines has provided students with hands-on skills, creative confidence and additional teaching time that will undoubtedly shape their future endeavours. The ongoing partnership between Strathallan School and AXYZ stands as a beacon of innovation in education, demonstrating the profound impact technology can have on both the present and future of learning.

T: 01952 291600 E: enquiries@axyz.com www.axyz.co.uk
INDUSTRY
What’s NEXT? HOMAG UK Presents Makor’s Latest
Automatic
Oscillating Spraying Machines
HOMAG UK is proud to introduce the NEXT series from Makor, a new generation of automatic oscillating spraying machines pushing the envelope of surface coating for furniture and cabinetry. As the exclusive UK distributor for Makor, HOMAG UK provides local customers with access to this innovative technology and specialist support, offering the latest advancements in surfacing solutions.
The NEXT series comprises four models: NEXT-ONE, NEXTTWO, NEXT XL, and NEXT XL HYBRID. Each machine is engineered to deliver a host of benefits, including increased
productivity for medium production volumes, greater control over overspray for cleaner operations, and ergonomic design for optimal operator comfort.
“Makor have outdone themselves with the NEXT series,” comments Simon Brooks, Managing Director at HOMAG UK. “The technical advancements are astounding – we can’t wait to share these machines with our customers.”
With access to the latest in coating technology, HOMAG can continue to meet the diverse needs of manufacturers, whether for high gloss or matt finishes, on everything from furniture components to cabinets.
INTRODUCING THE NEXT SERIES
NEXT-ONE: AUTOMATIC OSCILLATING SPRAYER FOR PANELS
NEXT-ONE is the perfect solution for medium production volumes. With its spacious booth and versatile design, it excels in applying both base and top coats with high precision. Key features include:
• Paper transport system with up to 3000 meters of autonomy
• Single spray arm with a quick release system
• Pressurised booth with a high-efficiency filtering device
• Maki virtual assistant for optimised machine control
NEXT-TWO: ENHANCED FLEXIBILITY AND PRODUCTIVITY
NEXT-TWO builds on the capabilities of NEXT-ONE with increased flexibility for medium production volumes. It features:
• Double spray arm with 4+4 guns for enhanced coverage
• Up to 4 circuit configurations to meet various coating needs
• Advanced touch-up tank with up to 6 Bar pressure
• High precision reading bar for accurate performance
NEXT XL: HIGH-VOLUME SOLUTION FOR LARGE OPERATIONS
NEXT XL is sized up for large scale production and is designed to deliver exceptional performance with its self-cleaning transport belt and high-efficiency recovery system, minimising solvent consumption. Highlights include:
• Double spray arm with 4+4 guns for optimal coating
• Booth with a new design to ensure maximum transference efficiency
• Pressurised environment for controlled operations
• Comprehensive virtual assistant for intuitive machine management
NEXT XL HYBRID: THE ULTIMATE IN CAPACITY AND FLEXIBILITY
Combining the best features of its predecessors, NEXT XL HYBRID offers the ultimate, all-in-one solution for large scale production, boasting both self-cleaning transport and paper transport capabilities. This hybrid model ensures a cleaner operation and greater adaptability:
• New high-efficient recovery system for low solvent use
• Double spray arm configuration for uniform application
• Predictive alerts and faster maintenance options for maximum uptime
• Ergonomically designed interface for ease of use
MAKI: THE VIRTUAL ASSISTANT THAT’S ONE STEP AHEAD
One of the standout features of the NEXT series is the integration of MAKI, a state-of-the-art virtual assistant that supports operators in managing the entire automatic painting process. MAKI provides real-time documentation and responds instantly to operator queries, offering guidance and troubleshooting based on AI-powered data. The virtual assistant continuously updates with manuals, global data, and a knowledge base built from service tickets, ensuring that operators always have access to the most up-to-date information.
THE PARTNERSHIP PACKAGE
With the NEXT series, HOMAG UK and Makor’s partnership continues to blossom, providing manufacturers with cutting-edge machines and the expert support to keep them working at their best.
As Simon Brooks summarises, “The fundamental idea behind HOMAG UK’s collaboration with Makor is to ensure that UK manufacturers not only have access to the latest in surface finishing technology but also receive the first-class service for which HOMAG is known. The NEXT Series is a continuation of that idea – and I have no doubt it will benefit our customers for years to come.”
For more information about the Makor NEXT series or to explore how HOMAG UK can support your surface finishing needs, please contact Adele Hunt at HOMAG UK on
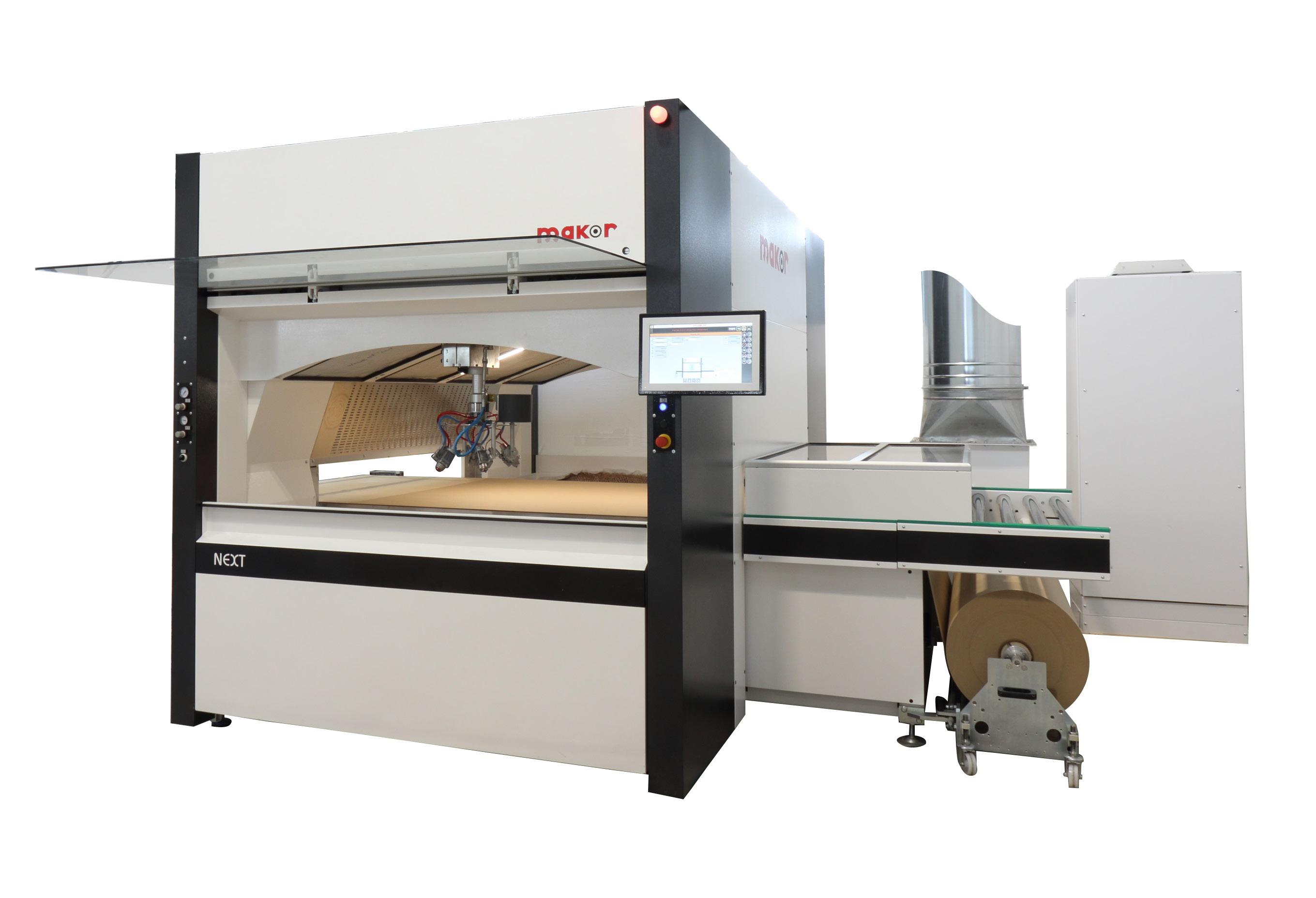
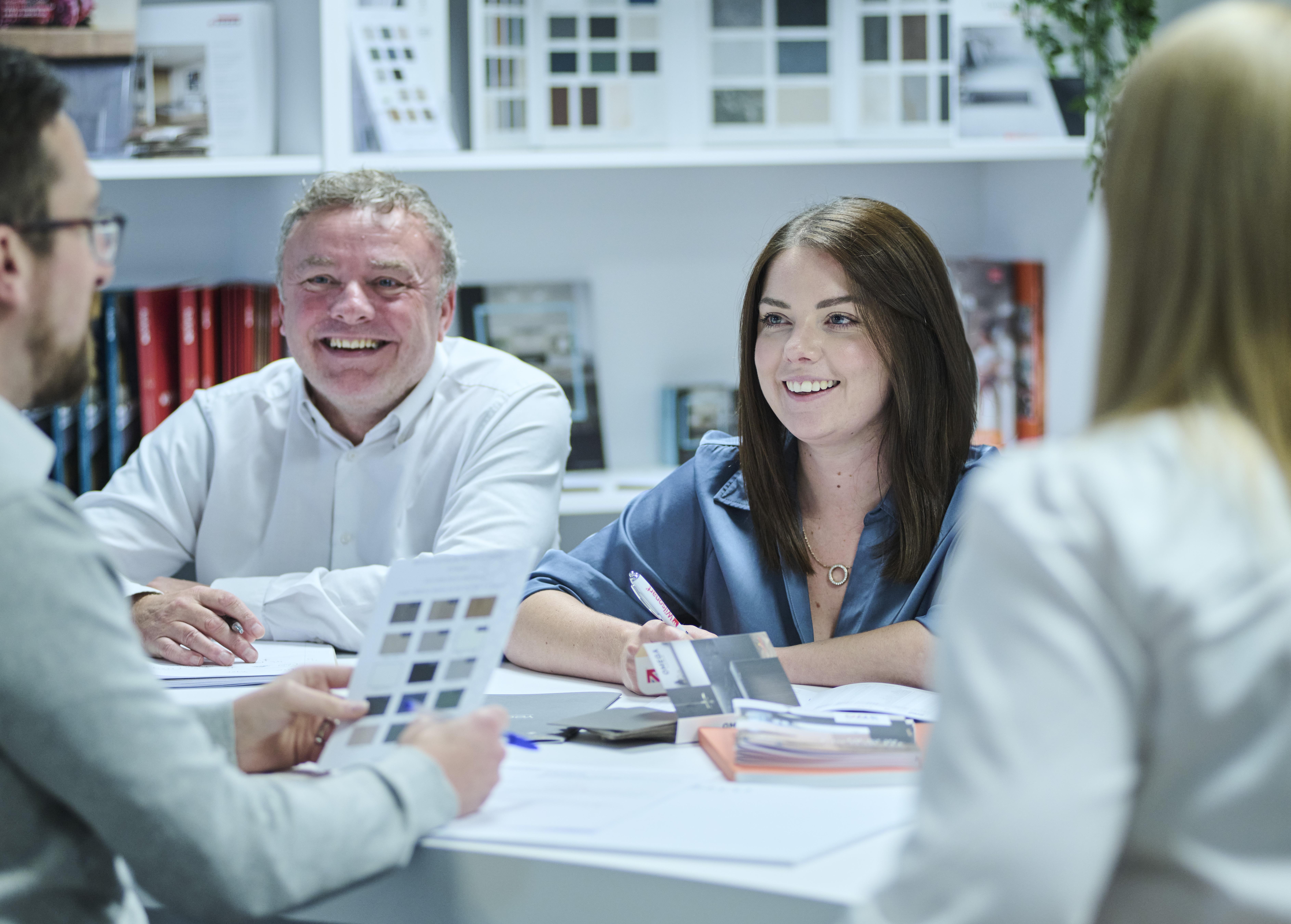
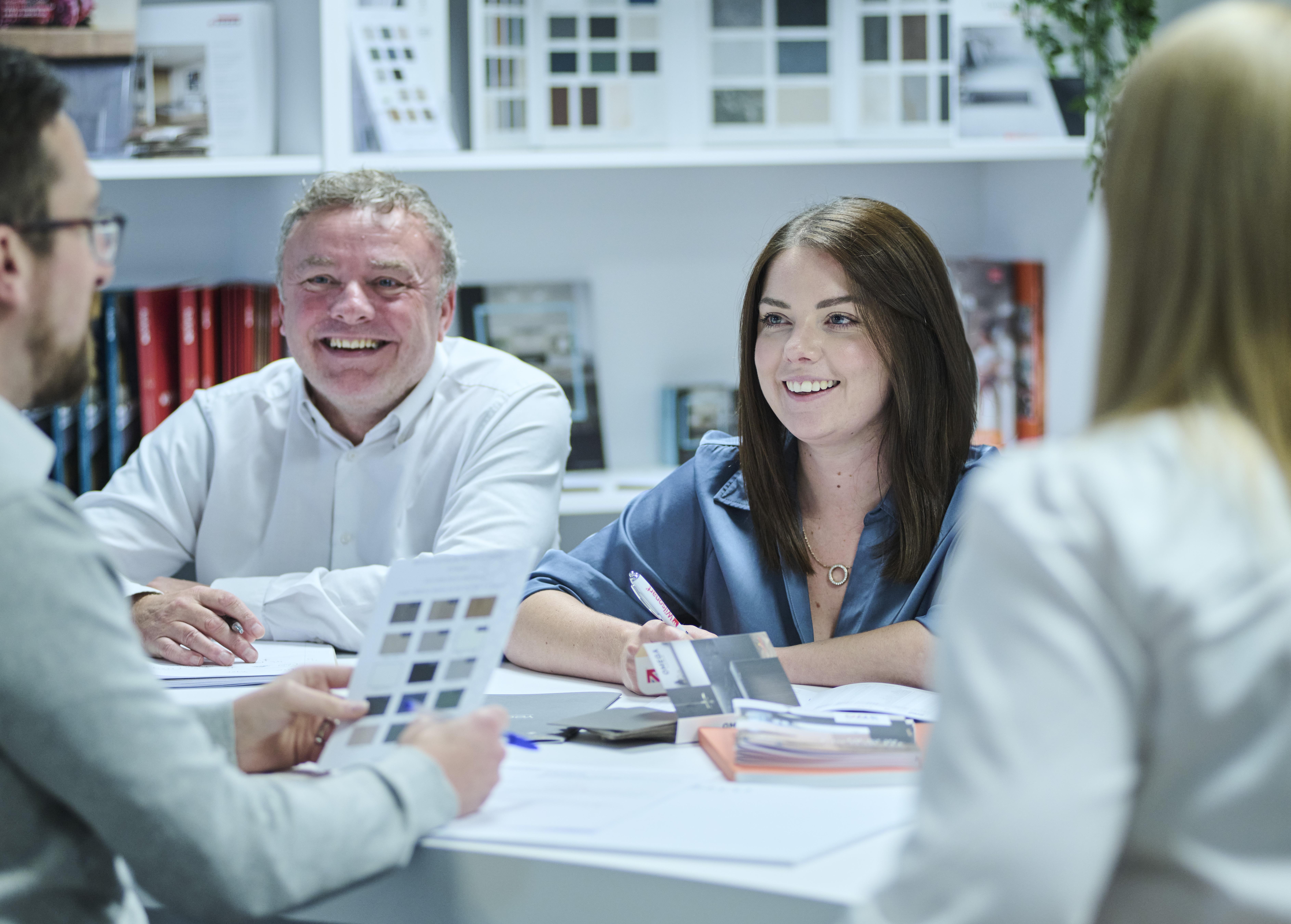
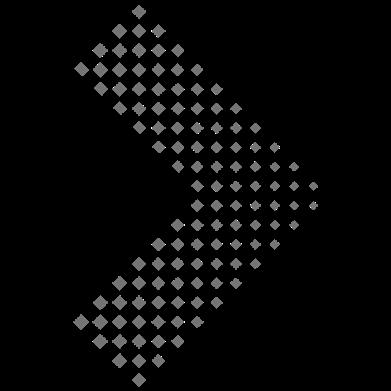
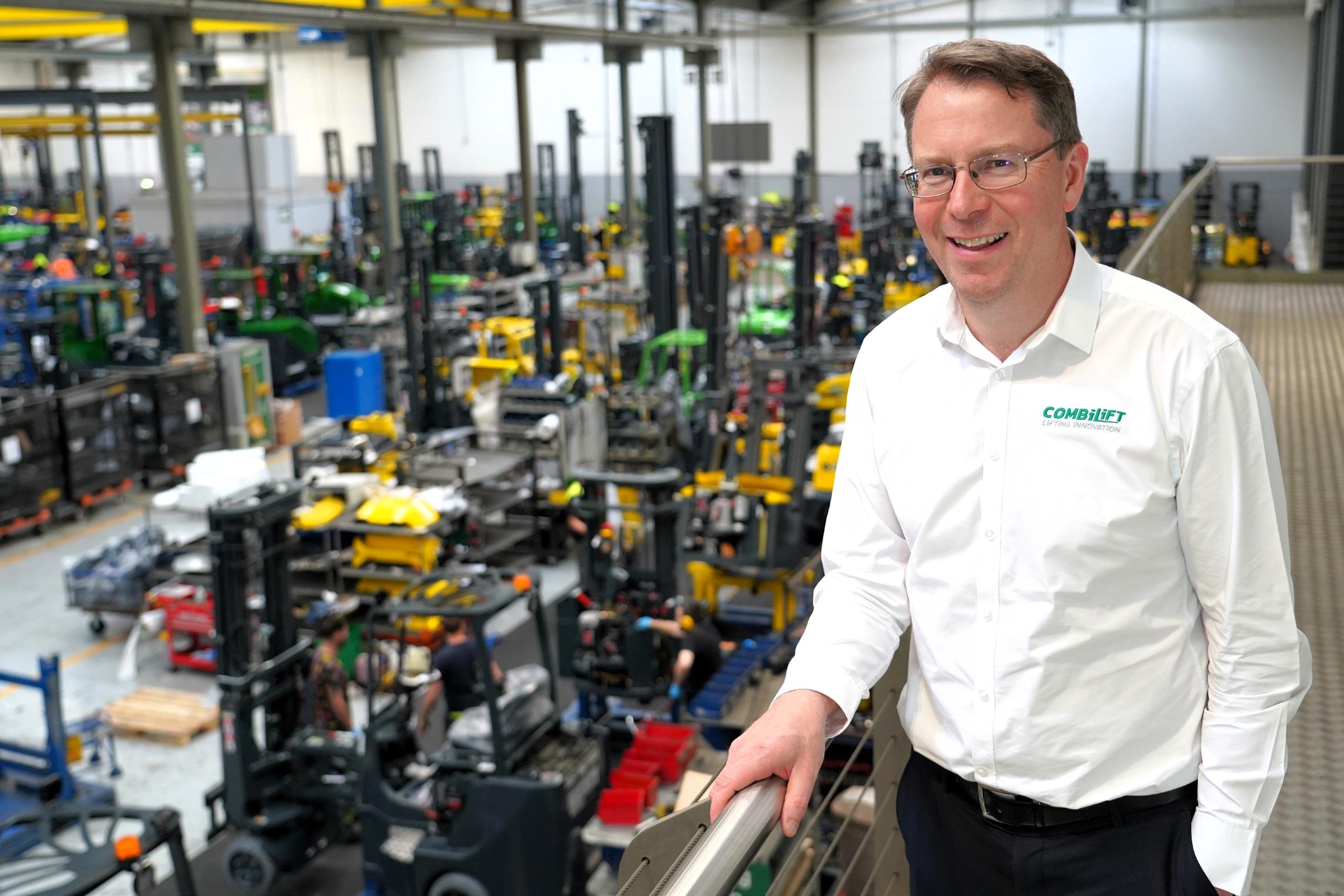
Winning Irish Exporter of the Year, Combilifts CEO Martin McVicar talks about the journey into the Global Market
HOW IT ALL STARTED
In 1998, Robert Moffett and I co-founded the business with a unique forklift concept. We designed a truck that could move forwards and backwards like any regular forklift but, at the flick of a switch, could also travel sideways. Our first model, the multidirectional 4-tonne C-Series, is still in production 26 years later. Its innovation in long-load handling, which can be risky with standard forklifts, made the concept and its advantages easy to visualise and sell—even before we had a prototype.
We started in March 1998, and by July, we had completed three units for customers in Norway. I told my girlfriend, now my wife, that we were taking a week’s holiday to Norway. In reality, we were there so I could oversee the delivery of those first trucks. By the end of that year, we had produced 18 Combilifts, 17 of which were exported. From day one, exports were our primary focus, and as of today, they account for 97-98% of our business.
TRANSPORTING LARGE GOODS
When you’re focused on exporting, minimising transportation costs becomes a priority. Shipping efficiently is key, so from the start, we designed compact, multidirectional trucks that fit into containers, reducing freight costs. Our larger products, like straddle carriers, which can reach up to 14 metres tall, are designed like a Lego Meccano set, so after testing, they can be disassembled and shipped within containers. For oversized equipment, we use roll-on, roll-off shipping, where the vehicle is loaded in our yard and driven directly onto the ship and then off again at its destination. So far, we’ve never had a vehicle we couldn’t ship.
NAVIGATING EXPORT RULES AND REGULATIONS
When starting a business, ignorance of export rules can actually be a blessing—knowing too much might have discouraged us from pursuing the global market. The regulations we faced were diverse and complex, depending on the market, but strong customer relationships, and a bit of hand-holding, helped us navigate these challenges. Our customers often guided us through their country’s specific requirements.
Back in 1998, we were a team of 13 engineers and fabricators. Today, we have 850 employees, including an expert team dedicated to handling exports, so thankfully I no longer need to worry about the finer details. Our logistics team of over 30 people ensures that, from pre-delivery inspections through final testing and shipping, everything runs smoothly.
GLOBAL SUPPORT NETWORK
Like any moving vehicle, forklifts need servicing to keep running efficiently. For Combilift, our route to market is through a global dealer network with skilled service engineers. We provide comprehensive in-house training and also offer service training in local markets. Having professional local service on the customer’s doorstep is crucial, along with rapid access to parts, and today Combilift has more than 300 dealer distributors around the world.
WHAT WINNING EXPORTER OF THE YEAR MEANS
Over the years, we’ve been fortunate to receive various awards, but being named Irish Exporter of the Year is a significant achievement. Competing with industries across
the island, including large global manufacturers in sectors like pharmaceuticals and medical devices, was no easy task. This award wasn’t just about submitting an application; it also involved two rigorous interviews in front of a panel of 14-15 independent judges from diverse industries. Winning this award shows that we’ve been recognised as a fullyfledged manufacturing company that truly exports globally. We don’t simply rebadge products—we design, fabricate, paint, and assemble our vehicles from start to finish before exporting them worldwide.
For Combilift, this recognition feels like winning an Olympic gold medal. It’s a stamp of approval that we’re doing, and continue to do, things right.
LOOKING AHEAD
Like many entrepreneurs, Robert and I came from humble beginnings, growing up on a farm where hard work was essential. I was never handed anything, and that work ethic has stayed with me. Today, we are in a strong market position as a debt-free, privately owned company with over €500 million in revenue. The only downturn we’ve experienced in the last 26 years was during the financial crisis of 2008/09; every other year has seen continued growth.
Innovation has been key to our success. Our team continues to design new, exciting products, which keeps us ahead of the market. That’s what really drives me—knowing that Combilift’s innovation keeps us moving forward.
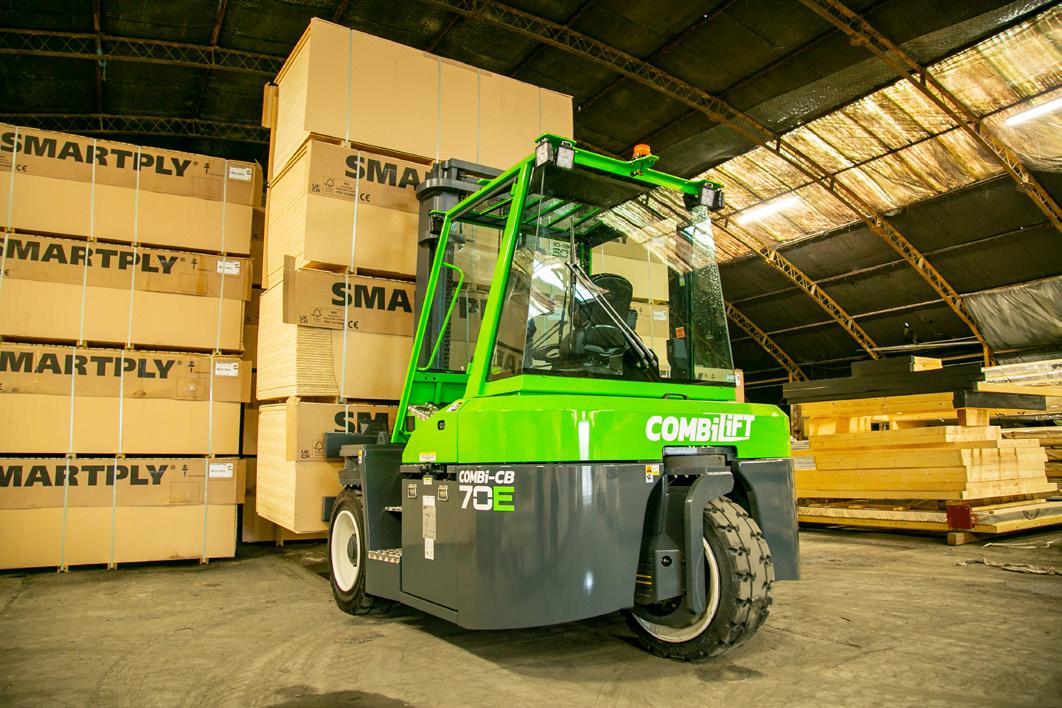
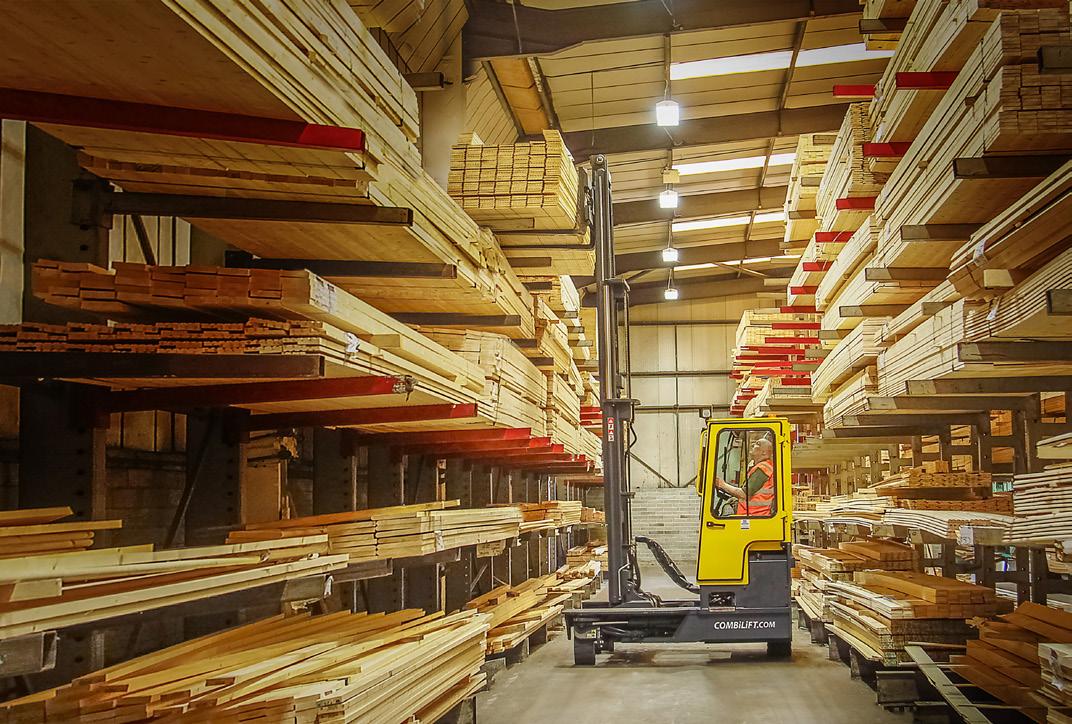
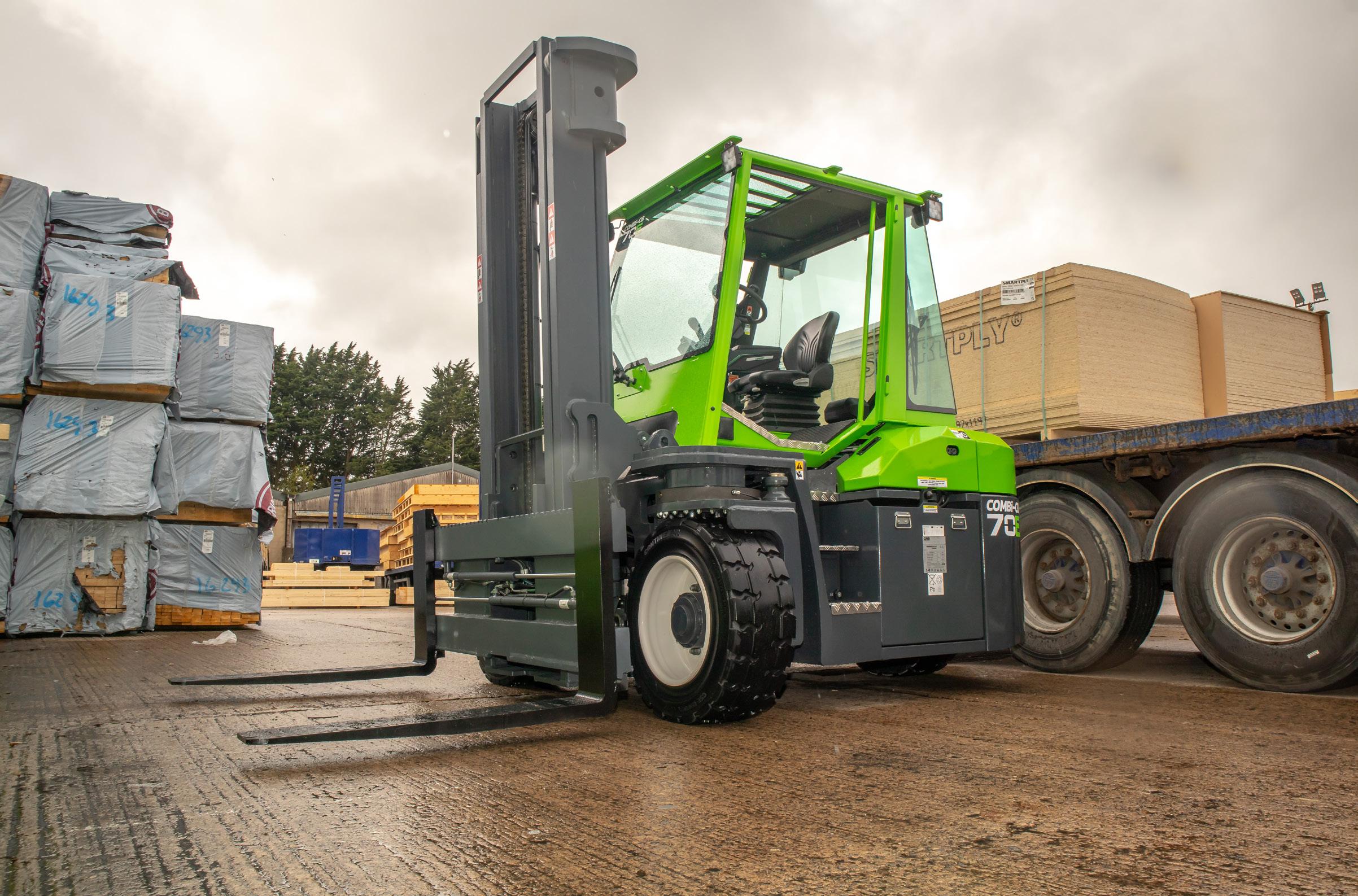
FRONT COVER
New Nesting Frontiers With SCM
SCM presents two new CNC machining centres to enhance and integrate its range for nesting processing: “morbidelli x50” and “morbidelli x100”.
The new nesting frontiers start in Rimini. It is here, at SCM’s Headquarters, that two new CNC machining centres were presented on the 13 and 14 September for the sector: “morbidelli x50” and “morbidelli x100”.
The two solutions further enhance and integrate the “morbidelli x” range already chosen by leading market clients thanks to its capacity to apply high speed and maximum flexibility to nesting machining to meet a market demand that is increasingly focused on “batch one”.
SCM has once again shown, with these new CNC machining centres, its ability to transfer high performance even onto “entry level” solutions, guaranteeing a number of advantages which differentiate its nesting range at highly competitive prices. Every detail has been scrupulously designed with a view to making all the necessary features accessible from an efficiency, machining quality and predictive maintenance point of view.
From a software point of view, it not only has the new Maestro Lab intuitive and dynamic CAD/CAM design system, for programming both from the office and machine, but “morbidelli x50” and “morbidelli x100” also have a stateof-the-art SCM Smart cut algorithm. Elimination of both unproductive times and waste and a reduction in energy consumption and material scraps are the main advantages of this optimiser which proves ideal for the nesting cut of even the smallest pieces. SCM Smart cut applies sequences and cutting technologies which, without affecting either the speed or arrangement of the pieces in the program, improve the finishing quality and reduce cycle times.
Highlighted for both machining centres, we also find the SMS - Spoilboard Management System software, an advanced solution which, thanks to an exact calculation carried out
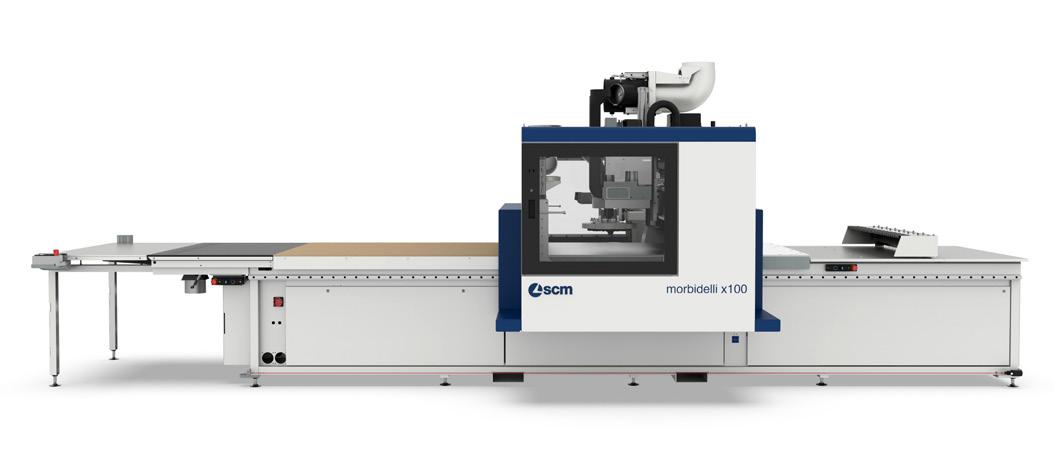
on the machine, makes it easier for the operator to manage the spoil panel signalling pro-actively when it needs to be rectified or replaced.
IMPORTANT
INNOVATIONS CAN ALSO BE FOUND IN THE MECHANICAL CHARACTERISTICS.
One example is the worktable with High Grip Vacuum technology on the “morbidelli x50”: practical and sturdy, it is the only one of its kind to guarantee the best grip on the piece thanks to an exclusive SCM patented deflector which distributes the vacuum across the whole surface thus maximising the grip even in the case of panels that are smaller than the machine’s overall area.
Another significant advantage of “morbidelli x50” is its flexibility thanks to XS Device, a device that makes it easier for the operator to refer and machine all the pieces directly on the spoil panel, even the smallest ones.
Also taking priority of place is the SAFE - Safe Advanced Fixed Equipment protection system, one of a kind on the market for ensuring maximum operator safety at all times. This occurs thanks to a perimeter photocell system which provides free access to all four sides to machine right across the board.
The advantages of “morbidelli x50” are rounded off with the top performances of the drilling units, with 8000 rpm RO.AX technology, and boring units capable of machining in nesting up to 40 metres per minute.
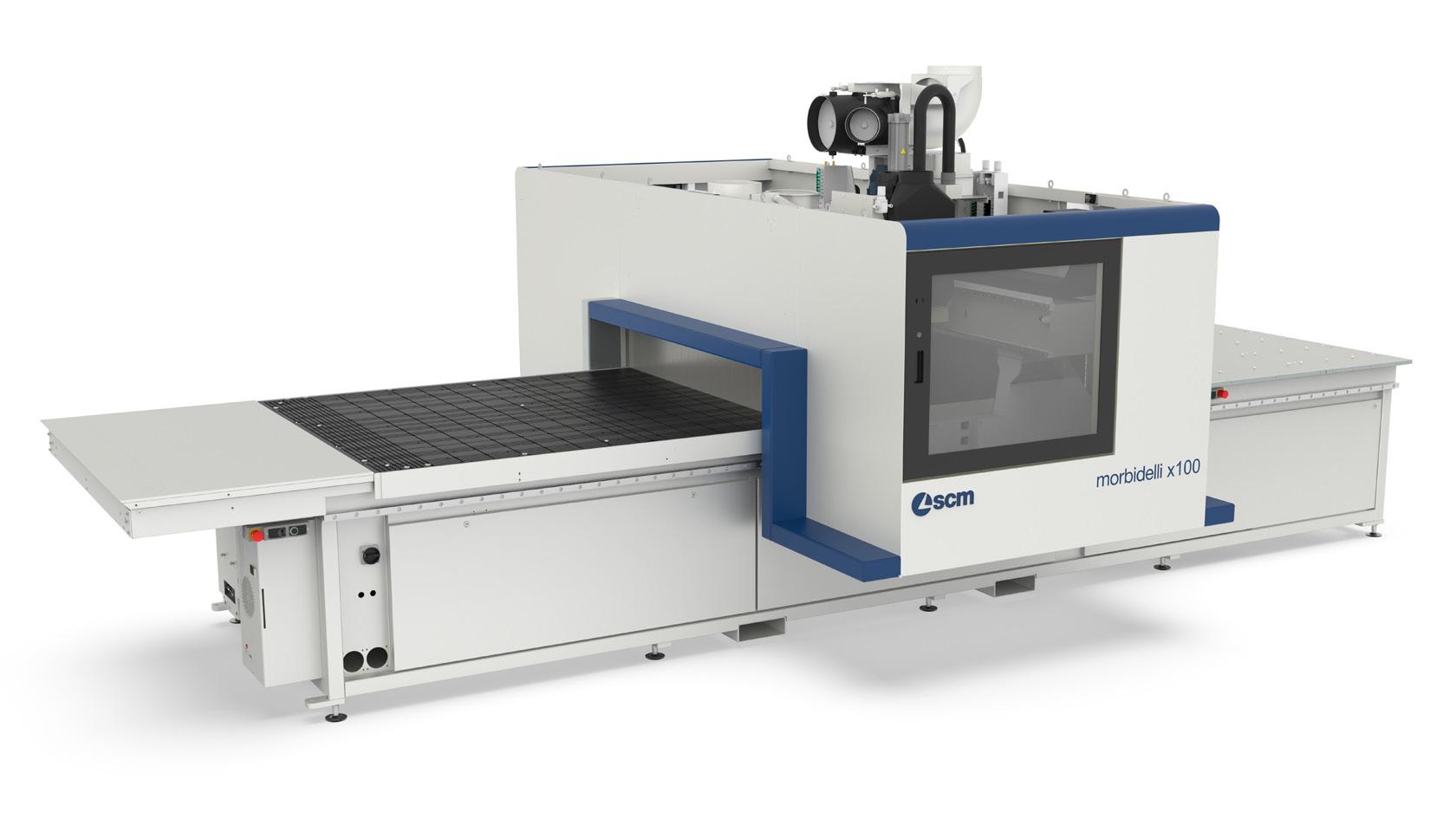
The innovation at the heart of SCM’s new machining centres for nesting is further amplified with “morbidelli x100”.
Some of the advantages being highlighted include its excellent configuration versatility: the model is available in different versions, from stand-alone machine to integrated cell with automatic “flexstore” magazine, right up to the “push” and “mat” versions respectively fitted with automatic pusher and motorised unloading belt to simplify and speed up the exit of the pieces in complete safety and, in this latter case, even without manual interventions.
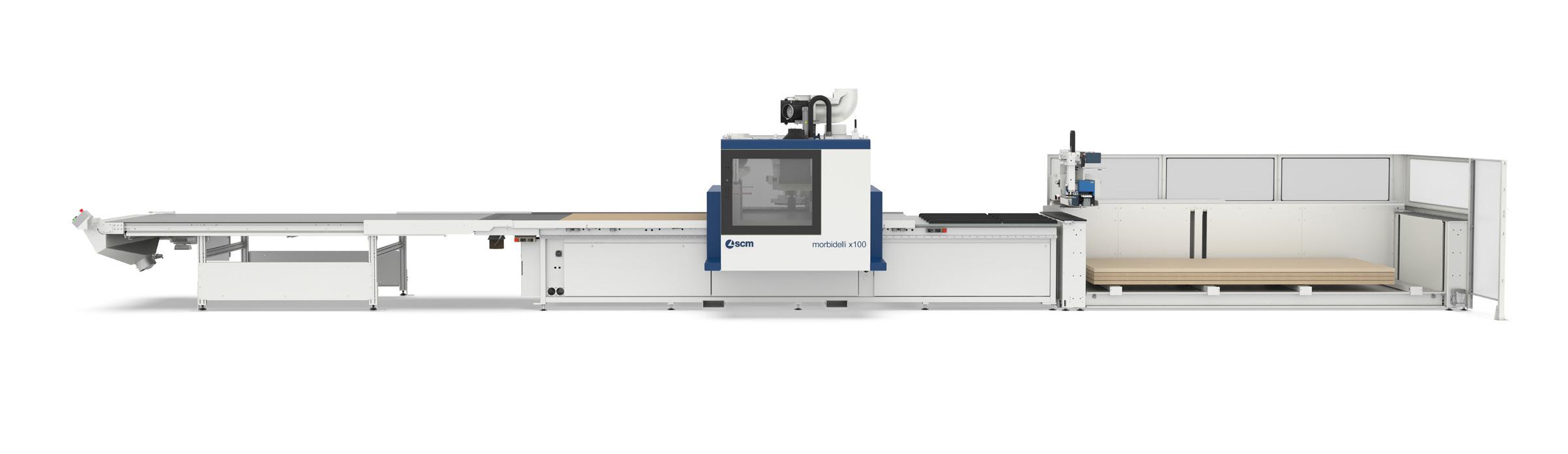
Not just nesting: the other new entries for “accord” CNC machining centres dedicated to the furniture industry
SCM is, therefore, capable of offering the most suitable solution to the client irrespective of their investment abilities.
Another distinctive feature is the maximum grip on the piece guaranteed by Smart vacuum, the system which concentrates the vacuum only in the parts still to be machined, thus avoiding dispersion in the areas already nested. An innovation that has been added to an already high-performing worktable with PHE - Phenolic High Efficiency technology especially designed for use with the spoil panel.
The event held on 13-14 September in Rimini was also an opportunity to present the latest new entries in the range of “accord” CNC machining centres.
Three years after the launch of “accord 500” and “accord 600”, solutions which have dramatically changed the rules of play in the production of doors, windows, staircases and solid-wood elements, SCM is presenting new finishing upgrades to the range, for machining the panel and the furniture world, but always “According to wood”, starting from the intrinsic peculiarities of the material machined and the client’s most pressing demands.
The strong points of this range which has conquered leading clients at international level, remain unvaried such as the dual motorised “gantry” structure, the 5-axis operator unit with excellent performance, the innovative suction systems to guarantee maximum cleaning of the machine and the surrounding environment, the high-capacity tool magazines with Maestro power TMS intelligent management system and the CAD/CAM Maestro Lab software for designing and programming.
THE LATEST NEW ENTRIES FROM SCM REGARDING:
“Optizone” patented system connected to the Maestro Lab software is revolutionising the CNC bar machining centres: with a simple click, the size of the two work areas can be defined as early as the programming stage, based on the pieces to be machined. This function is also available for the clamps.
New SVP – Single Vacuum Pods function to independently secure the pieces on each semi-table: it is possible to have several separate vacuum areas, and the pieces can be loaded onto the machine by activating one suction unit at a time. This allows for excellent management of the scraps. The two functions mentioned, developed to deal with the vacuum, are particularly useful in the case of asymmetrical machining areas.
Increase in the length of the 1900 y-axis work surface compared to the current 1600 y-axis to carry out horizontal machining more effectively and simply inside the pieces blocked with clamps with the 5-axis electrospindle.
Greater configurability of the operator unit with new boring and drilling heads and new multifunction units.
New chain tool magazine, Quadro 35, positioned on the rear side of the mobile gantry-type structure, ideal for those always needing numerous tool positions easily and rapidly to hand in a reduced space.
As Bruno Di Napoli, Business Unit Manager for SCM’s machining and drilling centres explains: “Once again leading all the developments in these new solutions is the will of the company to place the client and their experience in using the machine at the centre of everything.
Whether we are dealing with aspects of software programming, digital connectivity or ergonomics and ease of use, we aim to ensure the operator always works under maximum safety conditions without compromising in any way on practicality and production efficiency”.
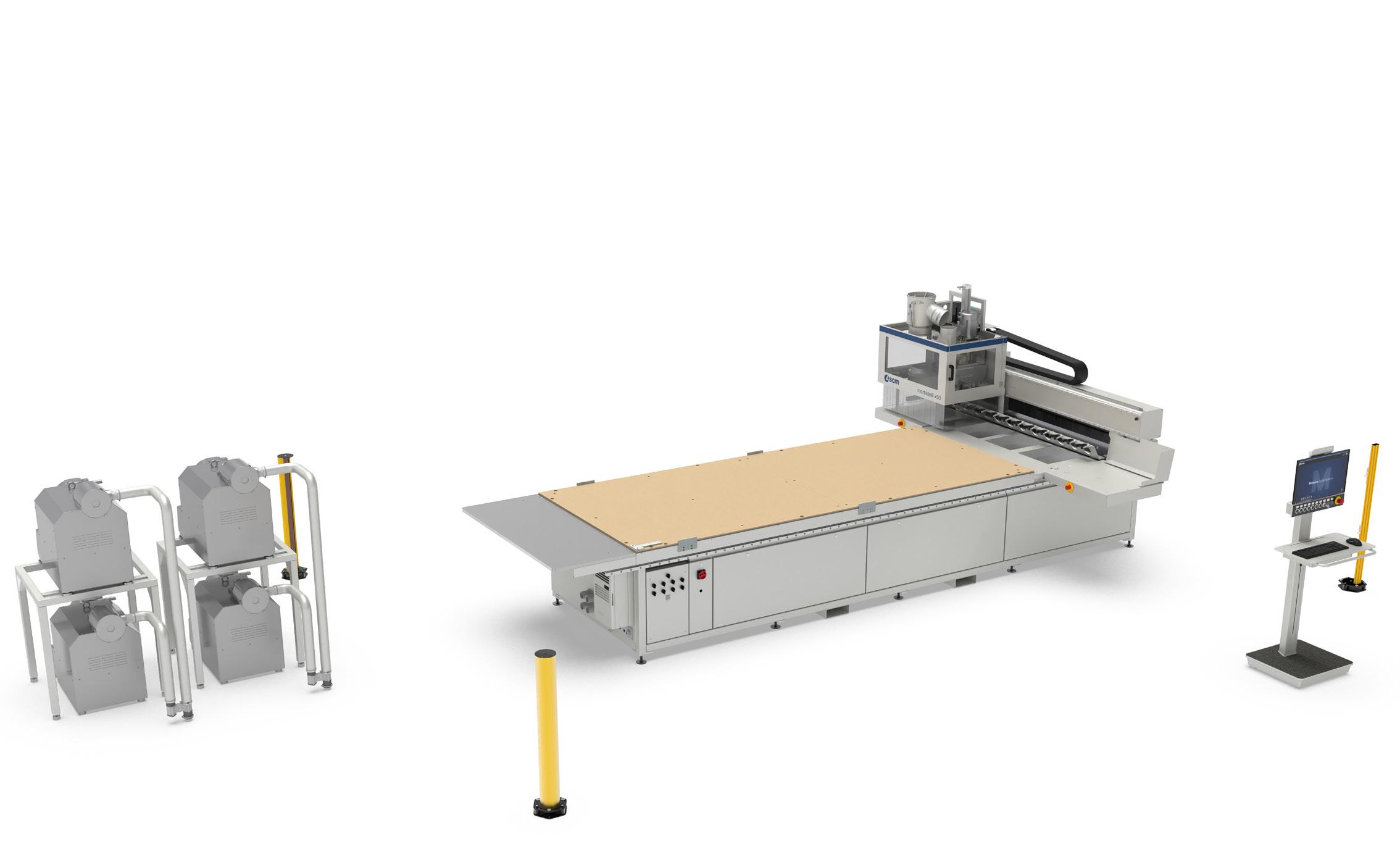
Possibilities Are Endless With dp-slim From Decorative Panels FEATURE
Are you in search of a statement piece that combines elegance, durability, and timeless design? Look no further than the latest innovation from Decorative Panels Lamination: dp-slim – a revolutionary 4mm thick acrylic surface collection that combines the elegance of REHAU Rauvisio Crystal glass with the unparalleled strength of crystal.
dp-slim Crystal collection includes over 16 designs from REHAU Rauvisio Pure, Strong and Deep portfolio.
Decorative Panels Lamination recently added REHAU Crystal Mirror to their dp-slim Crystal collection. The newest addition to the dp-slim collection adds a touch of sophistication and modern look that complements any décor style. Its unique combination of elegance, durability, and functionality makes it the perfect solution for designers, architects, and contractors looking to create stunning, oneof-a-kind spaces.
Whether you’re working on a high-end residential project, a commercial development, or a hospitality design, dp-slim Mirror is sure to inspire and impress.
This beautiful decorative surface has the look and feel of a real mirror and has the advantages of weighing 50% less than standard glass mirror and boast a real glass reflection whilst being 10 times less susceptible to fracture.
Here are some of the benefits using dp-slim Crystal product: scratch resistant UV coating, hardcoat finish for increased chemical and abrasion resistance, extremely hard wearing, flexibility to drill holes without shattering, flexible production – can be processed with common wood working tools, dirt resistant coating meaning it is easy to clean. Additionally, dp-slim Crystal also offers enhanced thermal resistance, making it an ideal choice for applications exposed to high temperatures. Its lightweight yet durable composition reduces the risk of breakage, ensuring a longer lifespan and minimizing the need for frequent replacements.
Furthermore, the product’s advanced manufacturing process allows for precise colour consistency, resulting in a uniform appearance that maintains its vibrancy over time. With dpslim, you can enjoy a low-maintenance, high-performance solution that meets the demands of various industries, from construction and architecture to interior design and beyond.
The new dp-slim Crystal collection from Decorative Panels Lamination is designed for vertical indoor use. dp-slim is perfect for frontal and backsplash applications. With its easy to clean, hygienic surface, dp-slim is a suitable replacement for traditional bathroom and kitchen wall tiles. dp-slim Crystal is the ideal glass or tile substitute for all hospitality and retail environments.
Available to order in quantities from as little as just one laminated acrylic sheet with dimensions: 2800 x 1300 x 4mm.
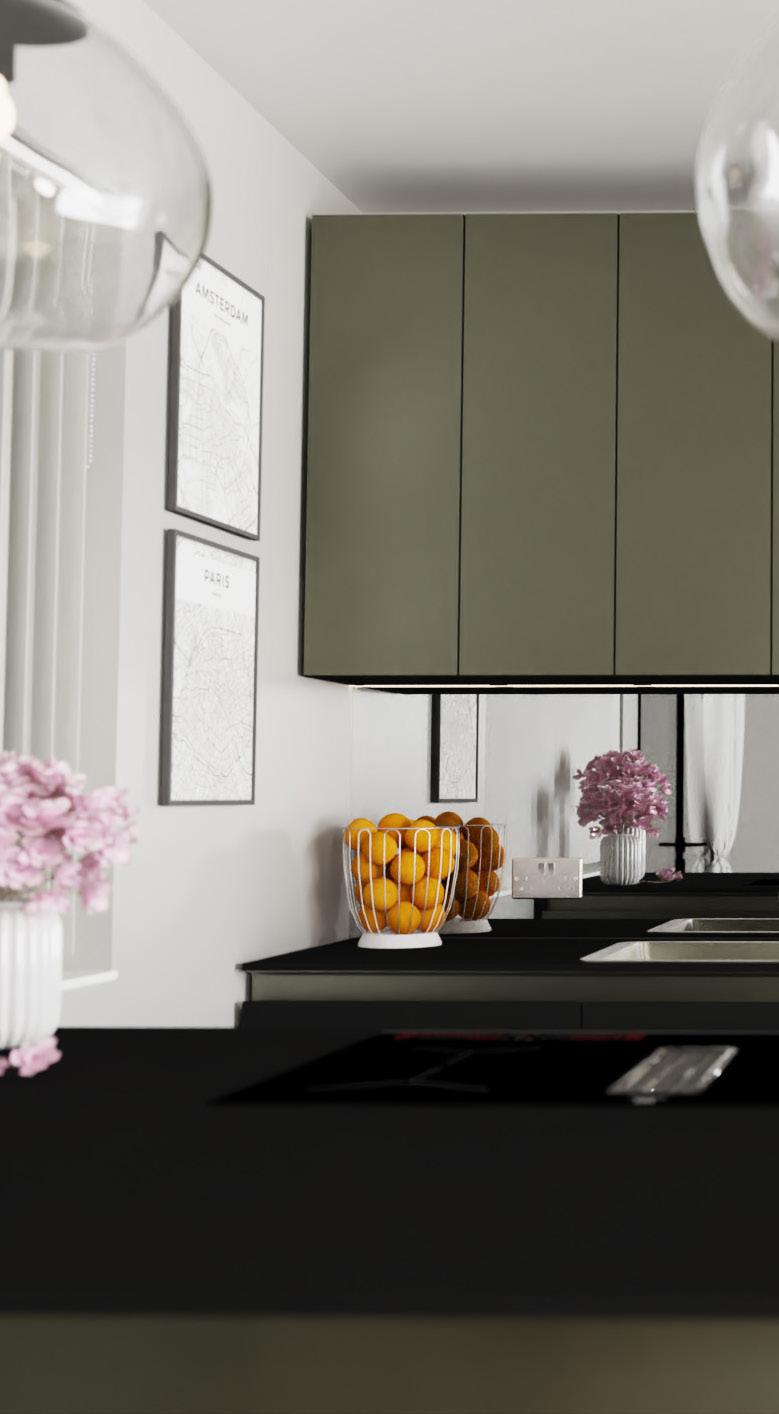
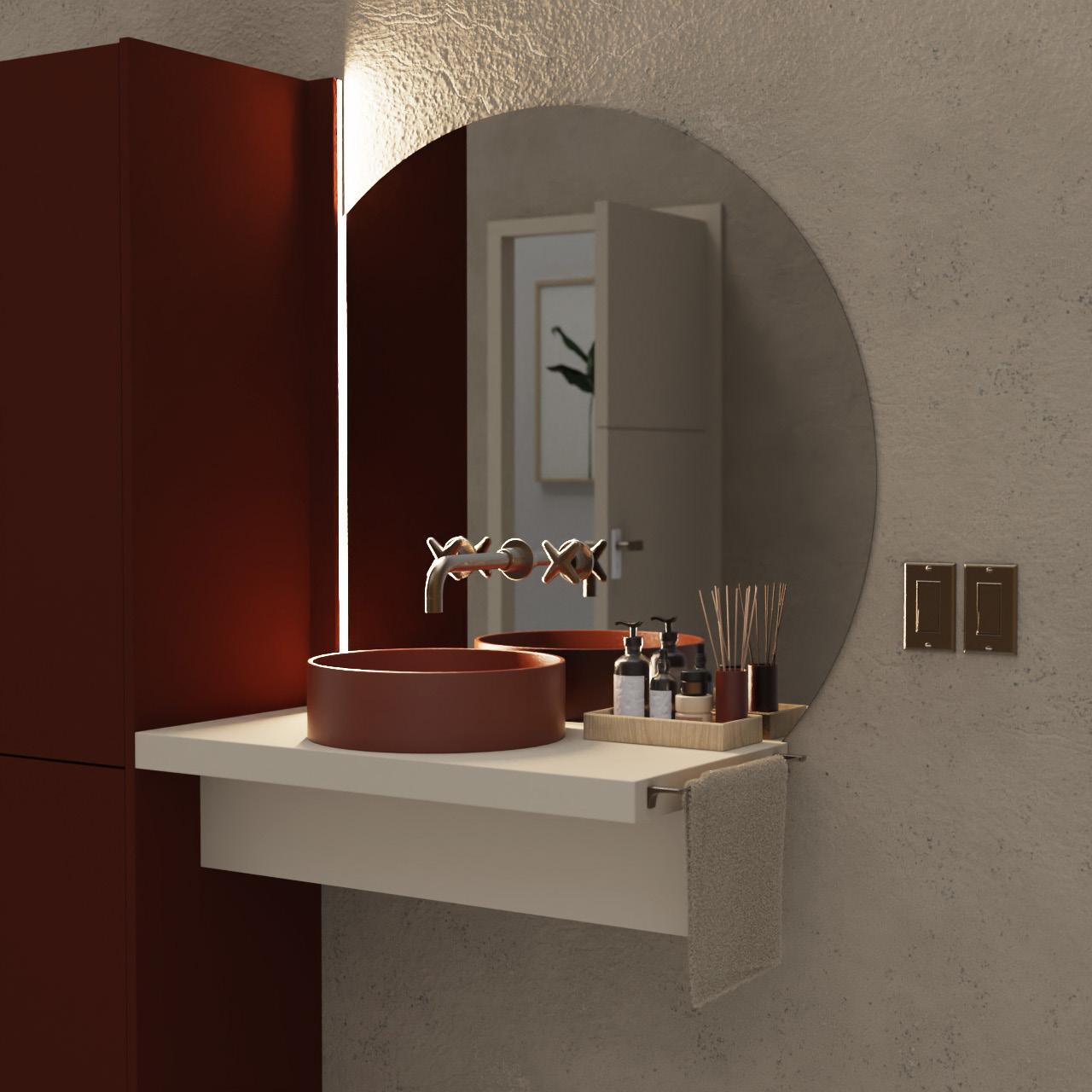
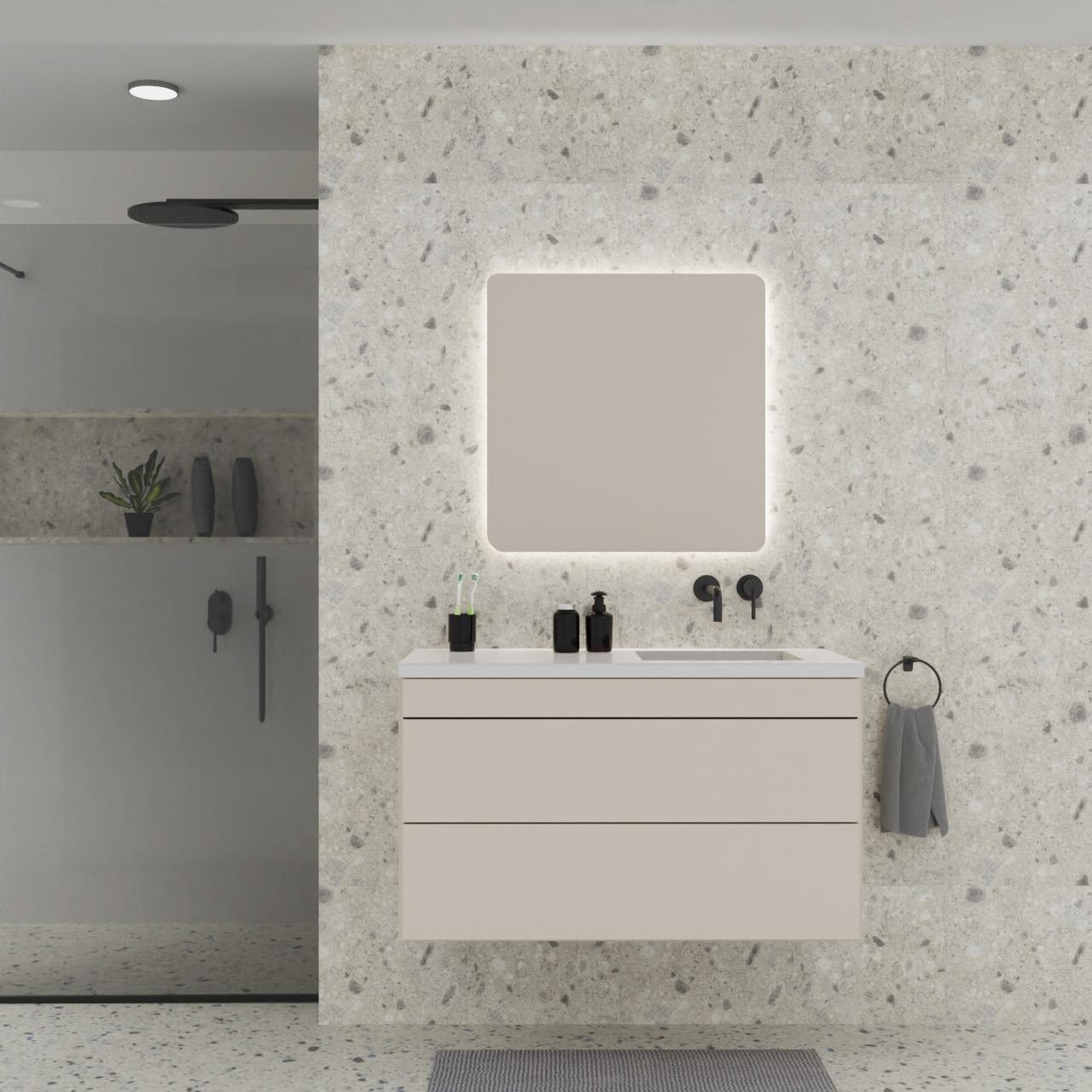


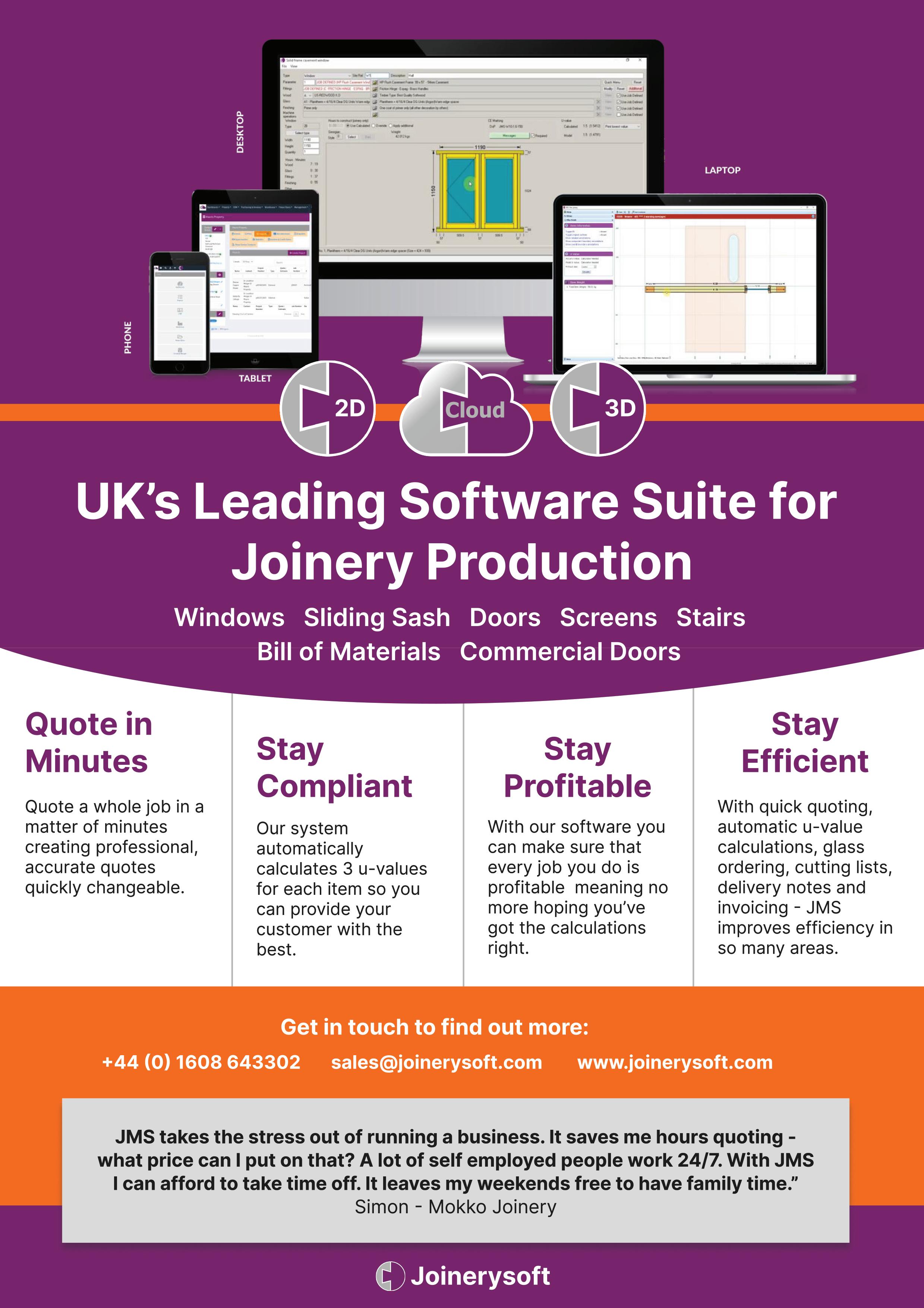


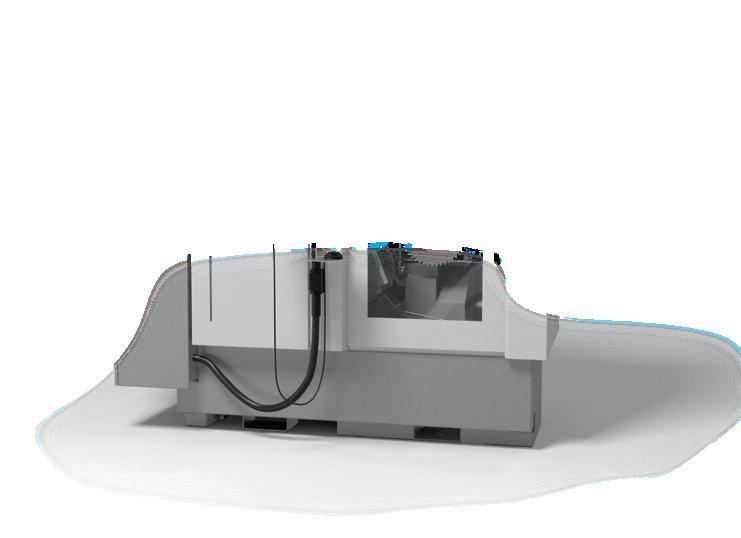
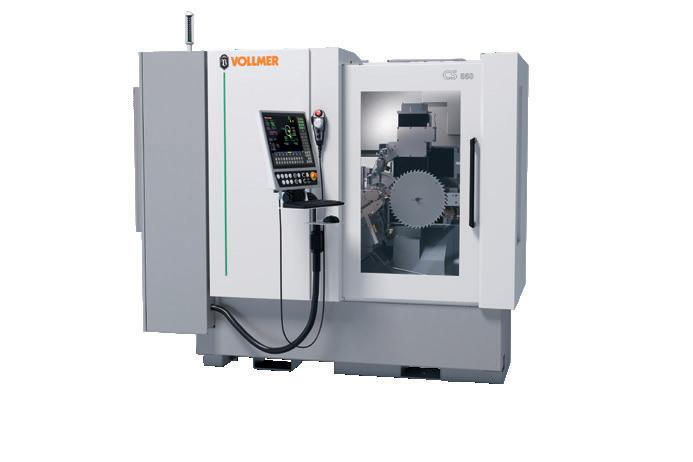
Simple, Flexible and Absolute are three words that describe the CS 860 & CSF 860 from VOLLMER. Perfect for machining the sharpest clearance angles and sides, the new arrivals are easy to use and incredibly flexible. This gives you outstanding grinding results with optimal processes for all your circular saw blade requirements. The CS 860 & CSF 860 deliver the highest level of quality, productivity and user-friendliness with maximum flexibility.
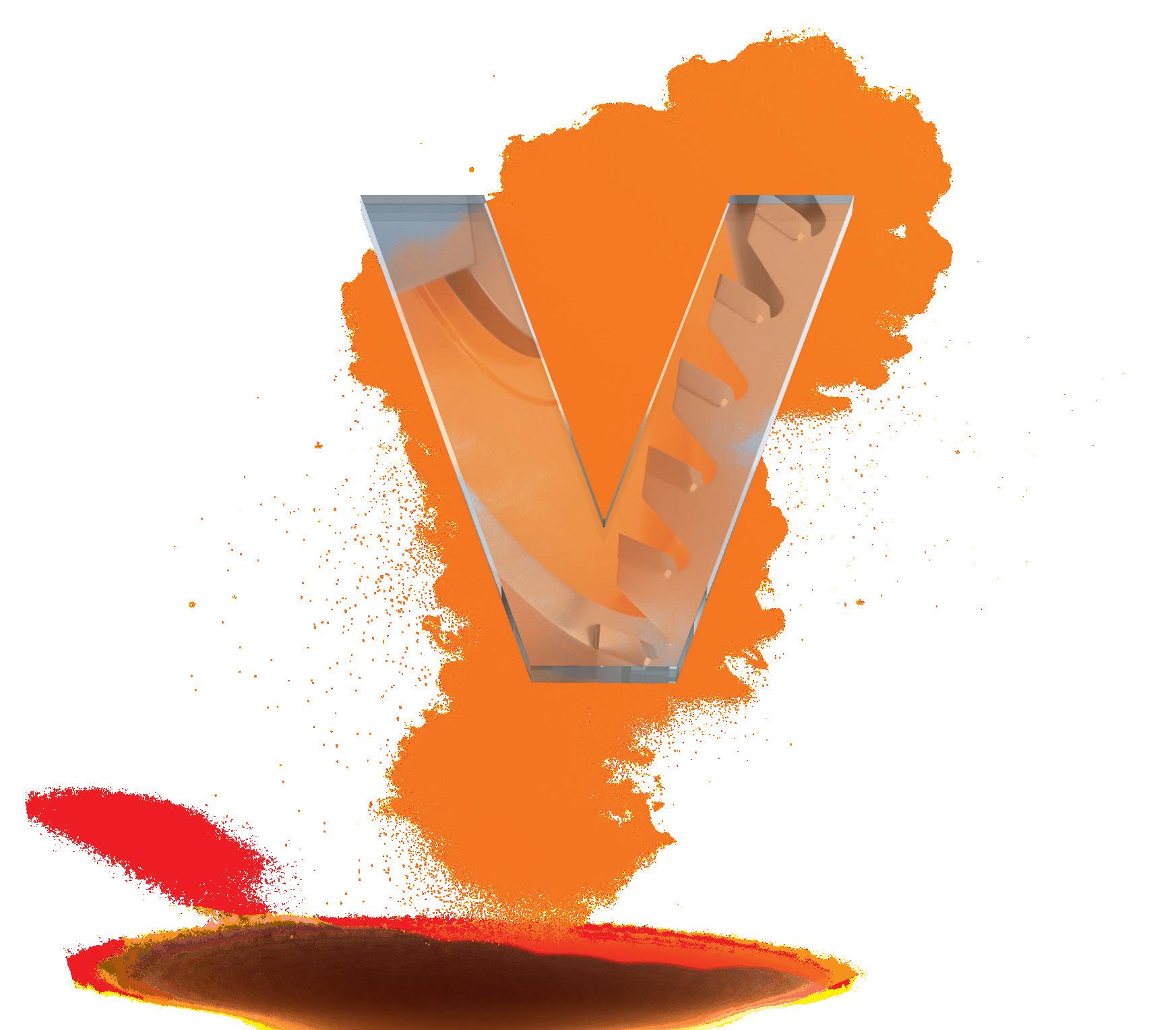
www.vollmer-group.com
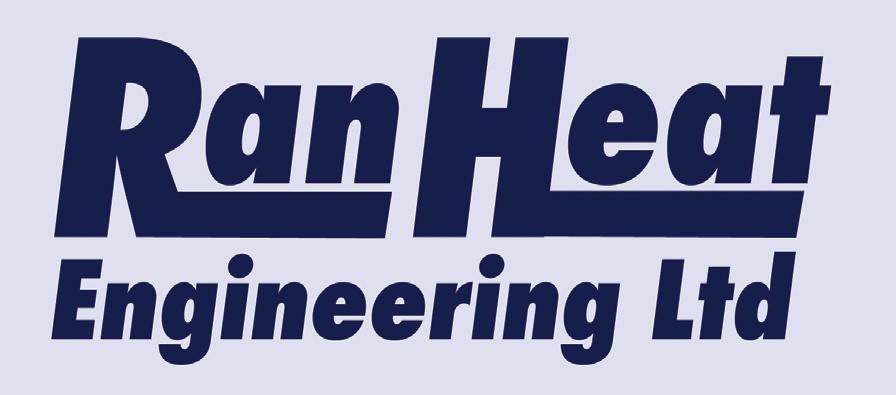
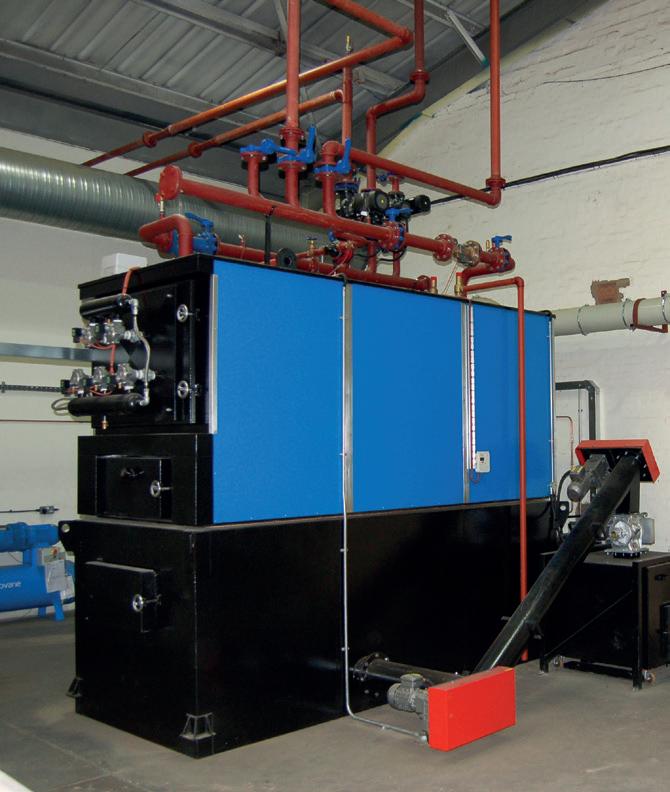
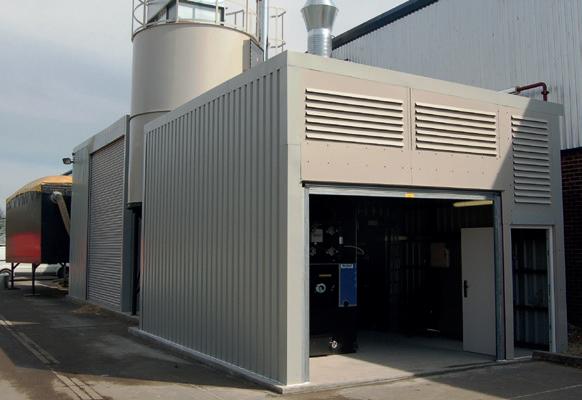
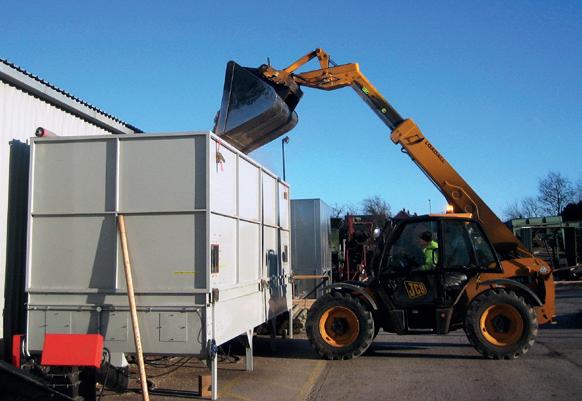
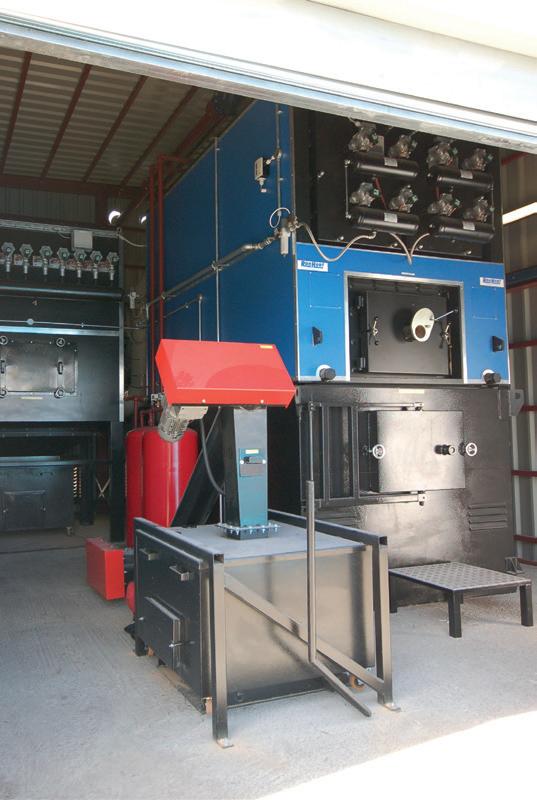
CASE STUDY
Extractly Applauded For Sweet Extraction
Dust and fume extraction specialists, Extractly Ltd, have recently completed the installation and commissioning of a comprehensive new dust extraction system to maintain a safe, clean workspace for North Somersetbased Sweet Joinery Ltd – one of the most successful and respected joinery firms in South West England.
Although Sweet Joinery Ltd was incorporated as recently as 2017, the business has family roots going back over 5 decades. Company founder, Dan Sweet, started his career in the early 2000s as an apprentice carpenter for his grandfather’s company, H. Sweet & Sons, and later went on to manage the firm’s specialist joinery shop. In 2019, Sweet Joinery’s rapid expansion was bolstered with the acquisition of Woodhill Joinery; another local family concern, also established back in the 1970s.
In addition to a collection of traditional woodworking tools that are typically employed in the crafting of bespoke kitchen cabinetry and window frames, the company’s workshop, located just a few miles southwest of Bristol, houses a comprehensive range of high-performance production machinery, including a Biesse Rover machining centre,
Ecogate® motorised dampers open and close automatically as machines come on or off-line.
Hebrock Edgebander and Altendorf F45 Panel Saw, along with SCM Spindle Moulder and Planer Thicknesser, and a Sedgwick Tenoner. This comprehensive set-up, teamed with a dedicated and experienced workforce, has enabled Sweet Joinery to build an enviable reputation for high quality bespoke joinery for their clients in the retail, education and transport sectors.
As Dan Sweet explained: “To eliminate our wood waste disposal costs, and to get ‘free’ heating for the workshop in the process, we wanted to install a modern, efficient, waste wood burner. However, to effectively filter and collect all the wood waste material our machines were producing, which was necessary to make the installation viable, it was obvious that our existing extraction would require something of an upgrade. After discussing our requirements with other colleagues in the industry, it was recommended that we should contact Extractly for advice.”
The advice was provided by UK Sales Manager for Extractly and Ecogate, Ian Rayner: “This was a challenging but really interesting project to be involved with”, says Ian. “Key to the success of the installation was going to be a new and
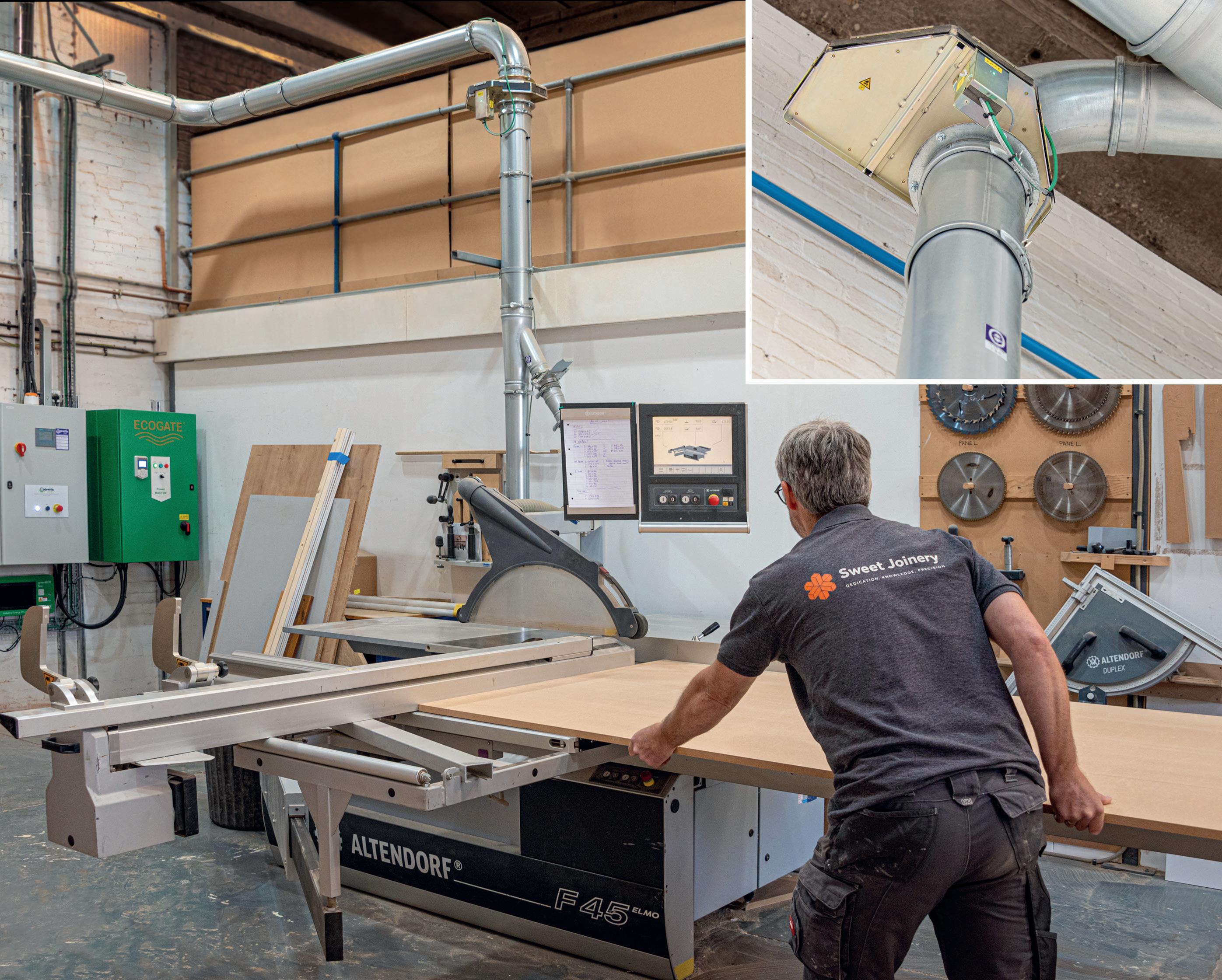
more efficient filter unit, including a more powerful main fan, but space and access at the site was particularly restricted. The wood burner was being installed internally, at the rear of the workshop, along with a high-powered Reinbold Shredder, and there was just enough space here to site the 30kW ATEX fan unit we’d specified to provide the necessary maximum airflow volume of 17,000m³/hr. This would provide effective extraction from all the current machinery, plus a margin of extra capacity for future additions, but siting the filter was going to require a more complex operation; as space in front of the factory needed to be kept clear for delivery vehicles and personnel access, and a narrow passageway to the rear of the premises had already been earmarked for a vast, externally-located silo which would store the collected waste before feeding it to the new burner.”
The solution Extractly’s design engineers provided was for the new filter unit to be mounted on top of the silo. The unit selected for the task was an LBR-S HJ2 reverse air baghouse weighing in at around 2 tonnes. The unit is fitted with XT15 ‘Superbag’ filter media, and two 1.1kW regeneration fans provide filter cleaning. The modular, galvanised steel housing, with a 2.4m x 2.4m square footprint and around 6 metres tall, was craned-in over the roof of the factory and fixed into place above the silo. “The positioning of the filter unit is actually ideal”, Ian Rayner remarked. “Collected waste is discharged from below the hopper, then delivered directly into the silo, pressure-free, via an ATEX rotary valve.”
The installation not only provides Sweet Joinery with a renewable heating source and cuts the cost of woodwaste disposal, but it’s also a great way for the business to reduce its carbon footprint. And, to ensure the company derives maximum cost savings and reduces its carbon footprint even further, Ian Rayner also put forward a proposal to include Ecogate® energy-saving technology to control the dust extraction system. “In common with all workshops involved in the production of bespoke joinery, the machines at Sweet Joinery are never all in use at the same time, so demand for extraction is continually changing throughout the working day.”
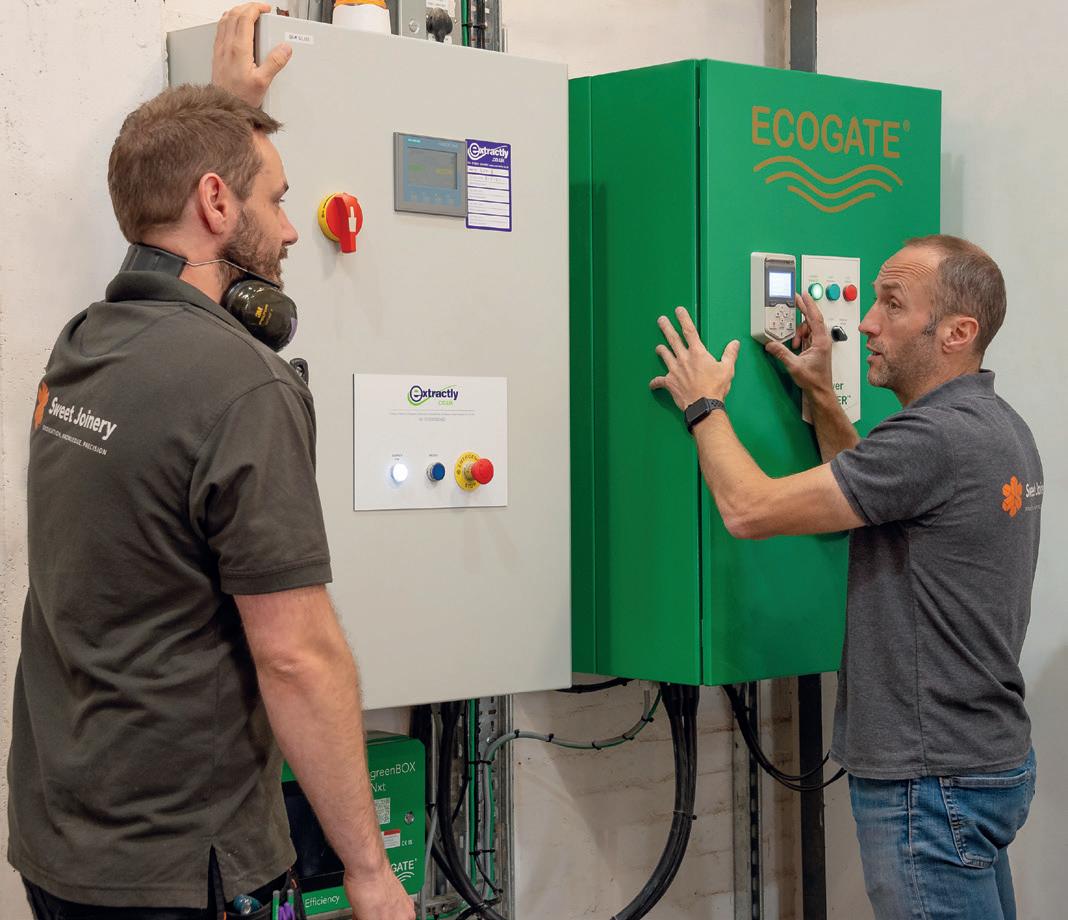
Mounted above the storage silo, the 17,000m3/hr capacity filter unit delivers collected waste, pressure-free, via a rotary valve.
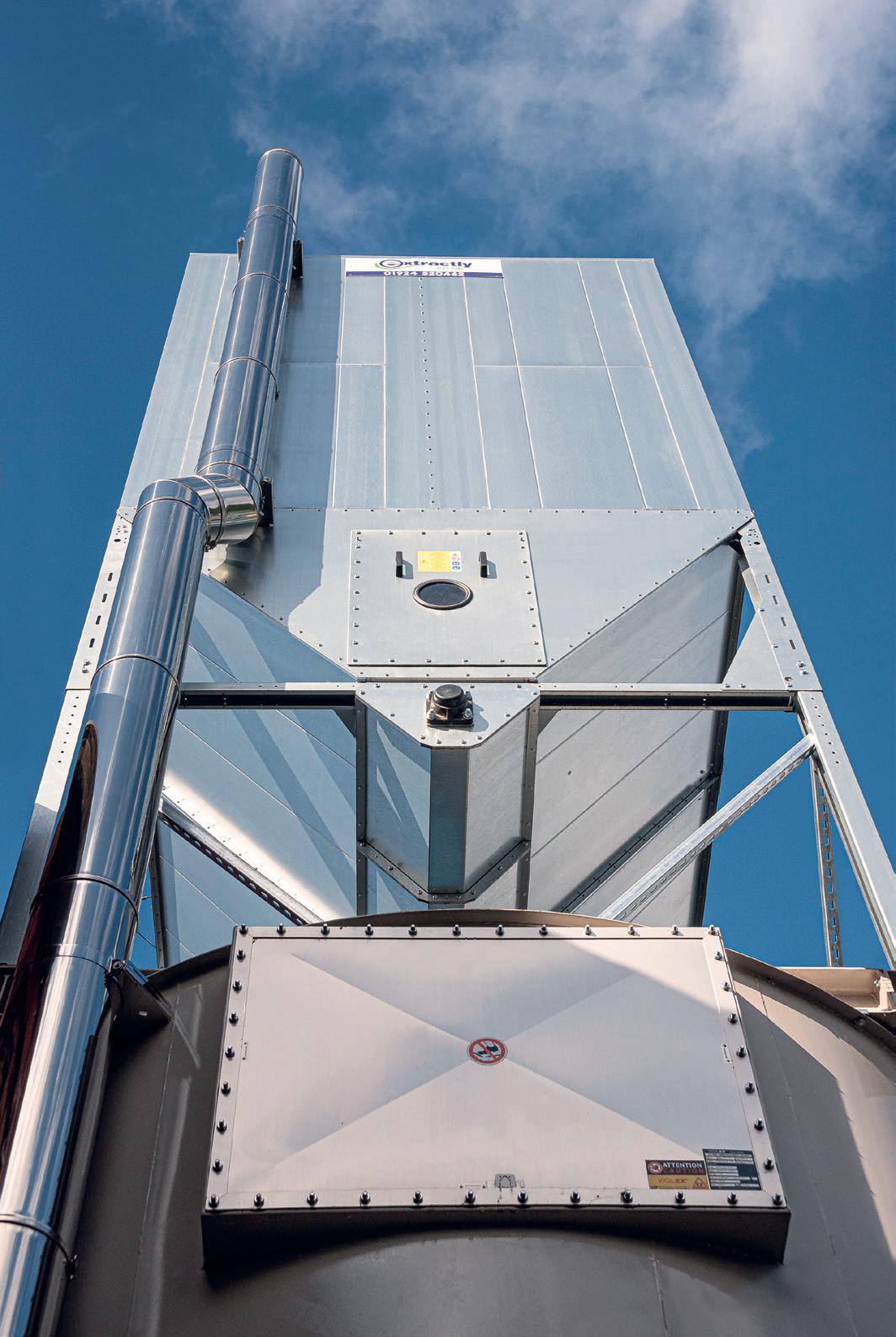
With an ‘On-Demand’ Ecogate® system controlling the extraction system, a sensor fitted to each machine monitors machine usage and sends a signal to the Ecogate® greenBOX controller whenever an individual machine comes on or off line. In turn, the greenBOX controller, via the Ecogate® PowerMASTER™ Variable Speed Drive unit, immediately adjusts the fan speed to exactly match the change in demand; reducing power consumption, and obviously saving on electricity costs. However, the level of savings a company like Sweet Joinery can achieve are quite significant, as Ian went on to explain: “By taking advantage of the Laws of Physics, Ecogate® technology can typically reduce electricity usage by at least 50% when the fan speed is reduced by as little as 20%. This sort of saving is easily achieved when machine usage is varying throughout the day and, when it’s break-time and all machines shut down, the fan also shuts down – automatically.”
In conclusion, Dan Sweet commented: “We were really pleased with the installation team from Extractly; they worked efficiently around us, and I found them to be professional and very flexible when delays on other equipment installations inevitably impacted their installation work schedules.”
Company founder Dan Sweet (right) with CNC programmer and operator, John Merchant, reviewing and discussing machine usage and power savings data collected by the Ecogate® system.
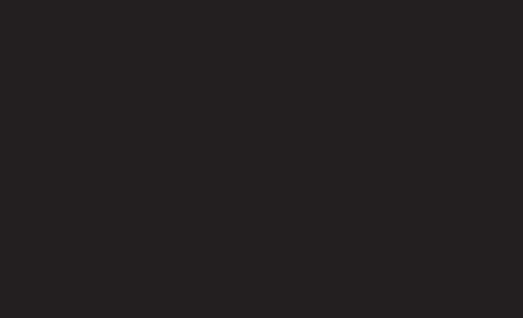
WASTE WOOD IS WOOD WASTED
Disposal of timber offcuts, shavings, chips and sawdust can be costly, yet these inevitable by-products of the woodworking industry can become a valuable commodity when converted into briquettes, or used directly as a fuel for heating.

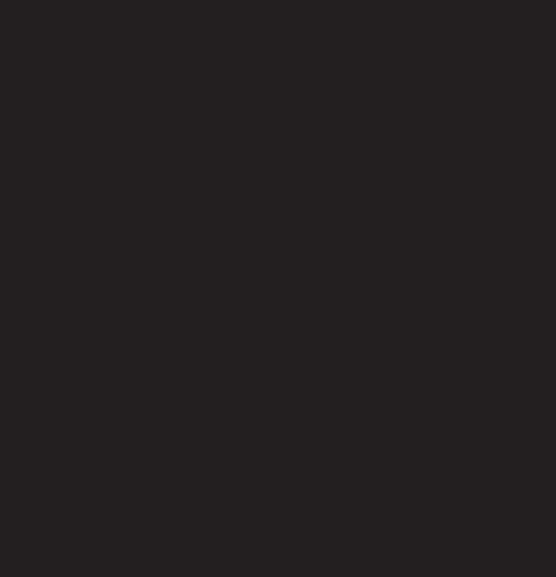
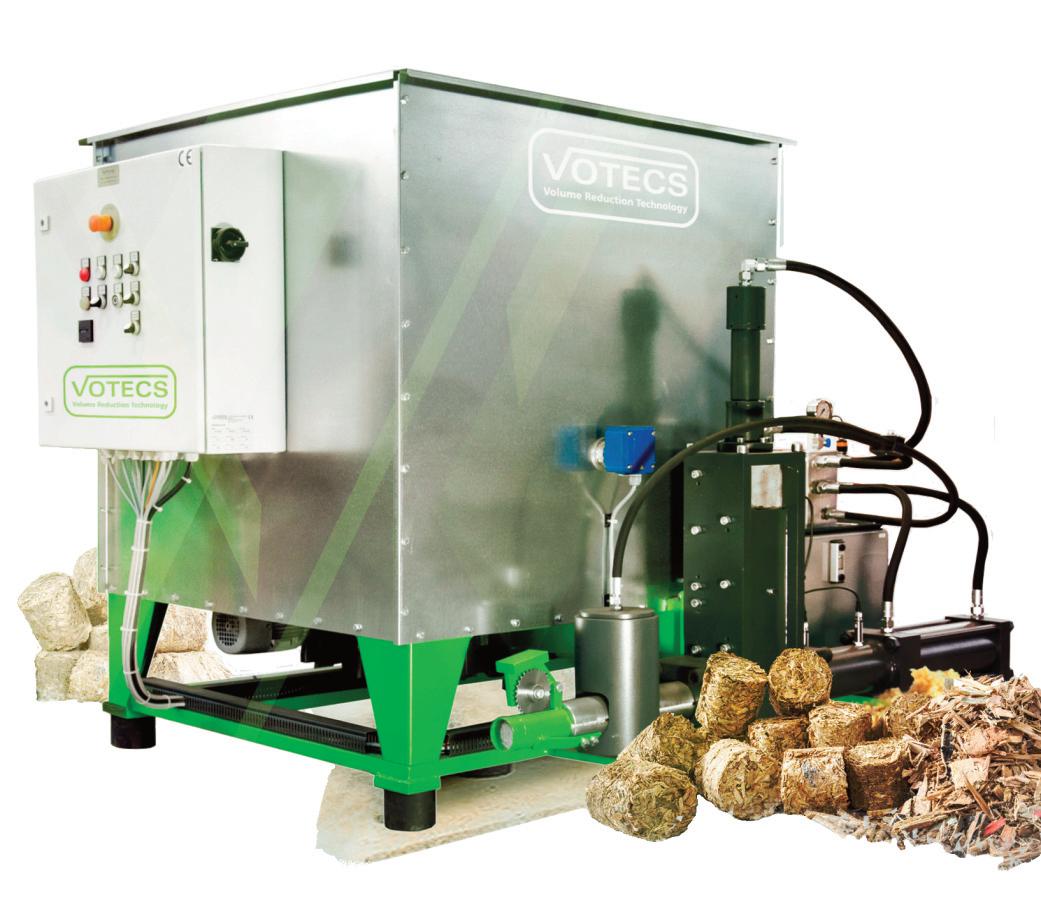
With multiple machine sizes, power specifications and accessory options, the wide range of VOTECS briquetting presses and shredders has the capacity to deliver efficient solutions… whatever your waste reduction needs. EXTRACTLY has teamed up with
–
in volume reduction technology and precision-engineered shredding and briquetting equipment for the woodworking industry.
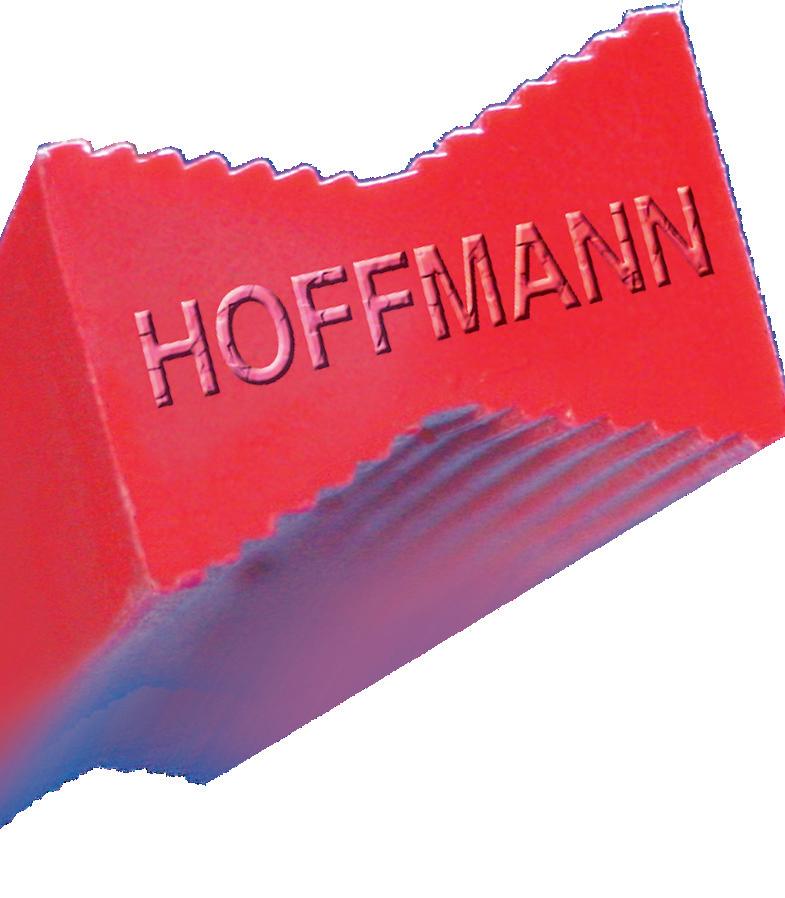
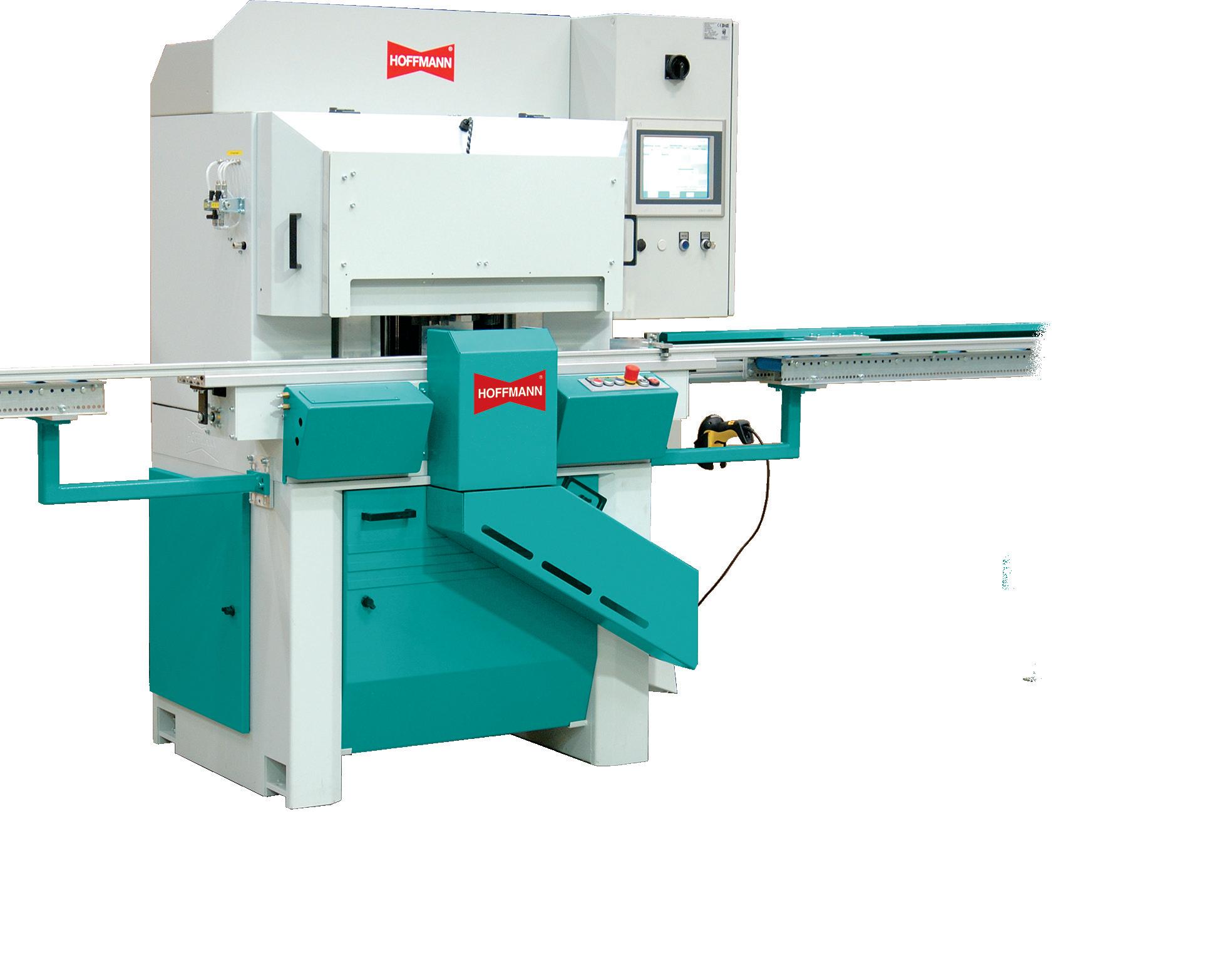
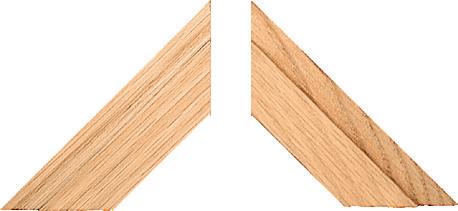
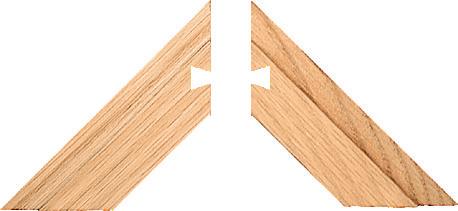
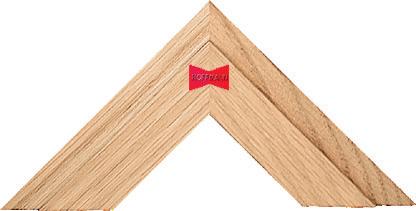
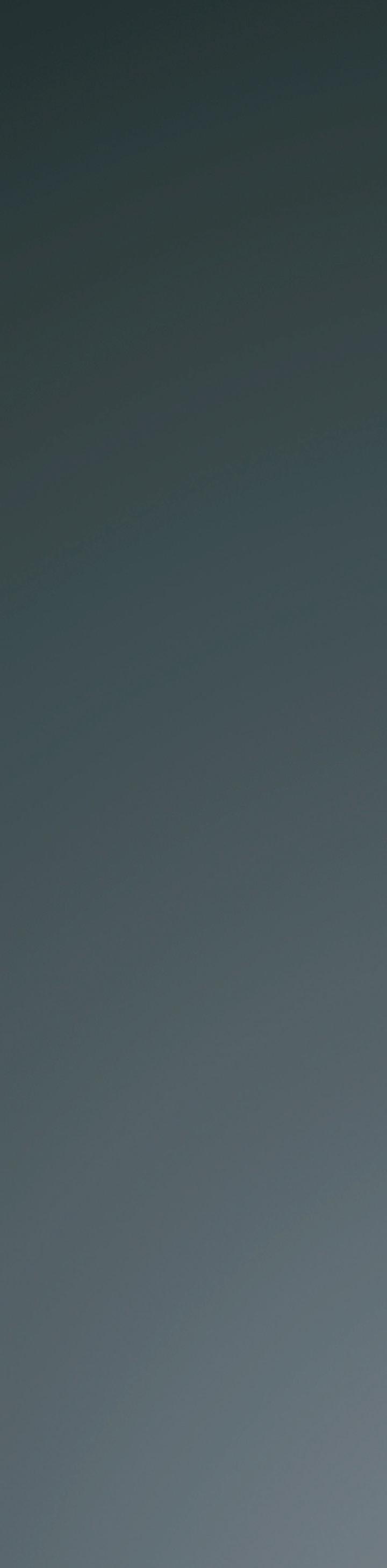
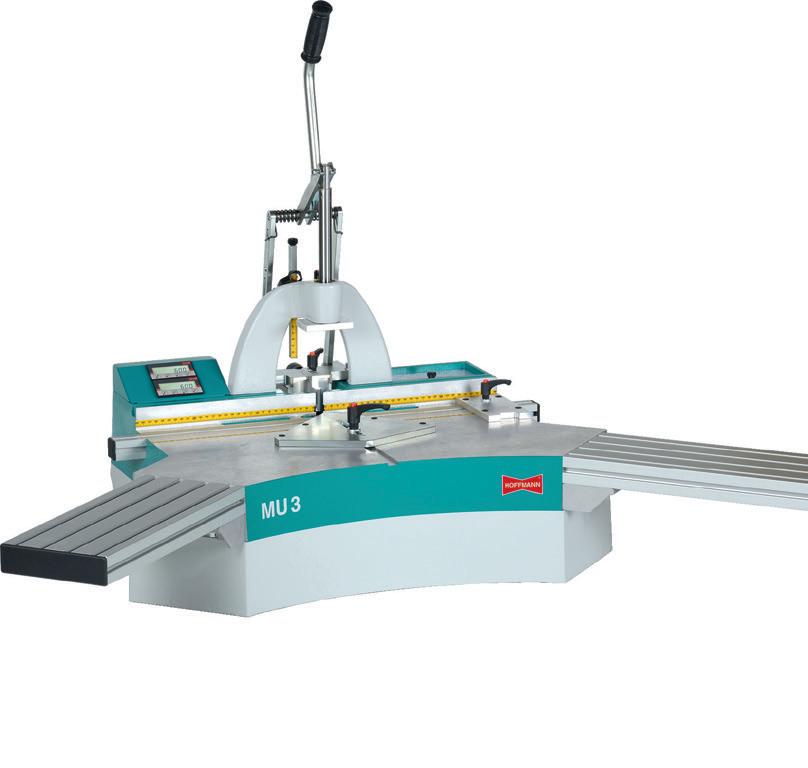
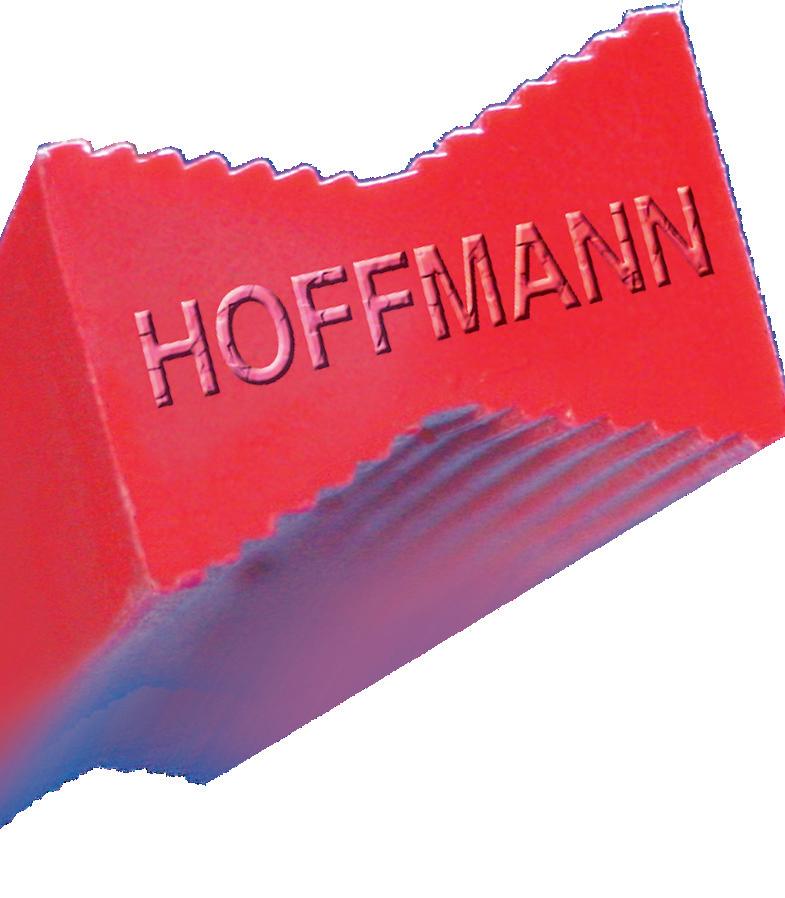
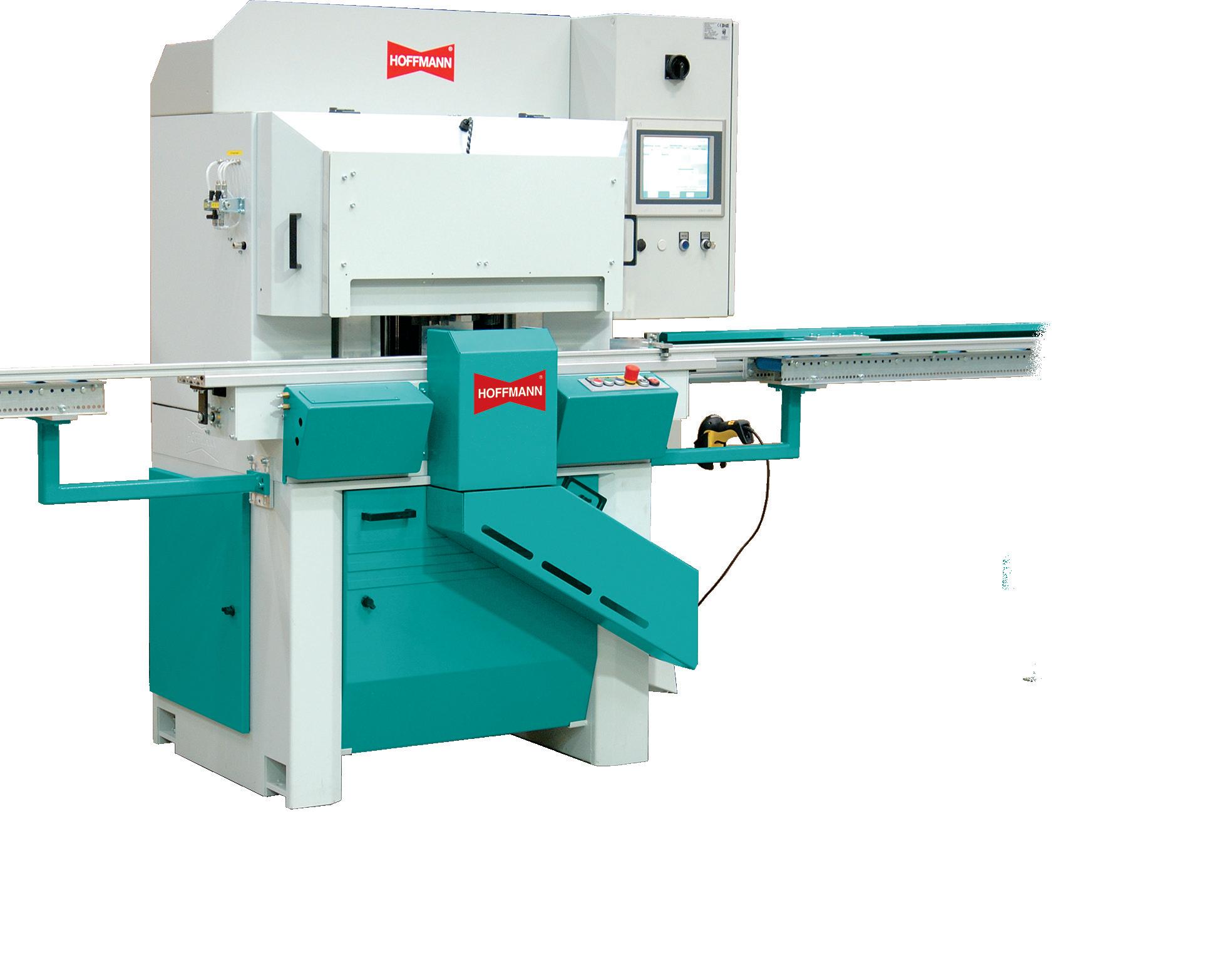
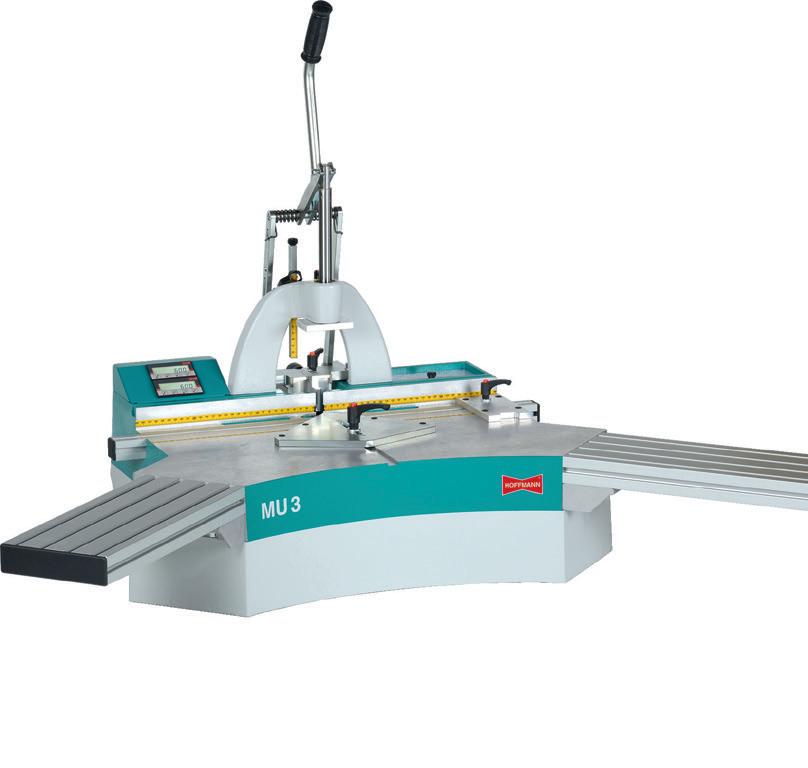
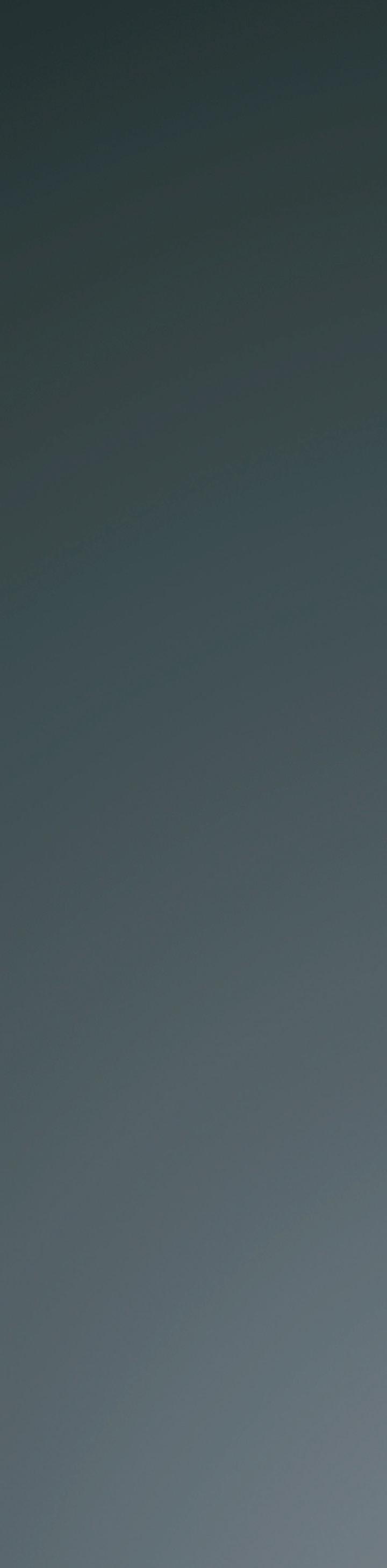
New From Ostermann Aluminium Suspension Profile: Now
Also Pre-Drilled
The aluminium suspension profile is perfect for covering large surfaces with decorative boards, or to attach displays and lightweight furniture with a floating appearance to the wall. Ostermann will also offer the profile in a pre-drilled version from mid-September.
With the aluminium suspension profile, Ostermann has a quick and easy solution for mounting wall coverings or lightweight furniture in its range. The profile can be used for both the wall and for the element to be suspended. It is suitable for all applications in which furniture or wall elements are supposed to be hung. Due to the floating look and easy handling, the item is often used in shopfitting for
Ostermann’s aluminium suspension profile allows you to attach decorative boards to the wall without visible screw or plug holes.
attaching wall panels, displays or backrests of benches. Thanks to its high material stability, even large boards can be mounted stably and without visible screws or drill holes. Compared to self-produced hardwood mouldings, the profile scores points with its low installation height of 6 mm. It is supplied in straight lengths of 5000 mm. From midSeptember, Ostermann’s aluminium suspension profile will also be available pre-drilled, which allows for an even faster installation on site.
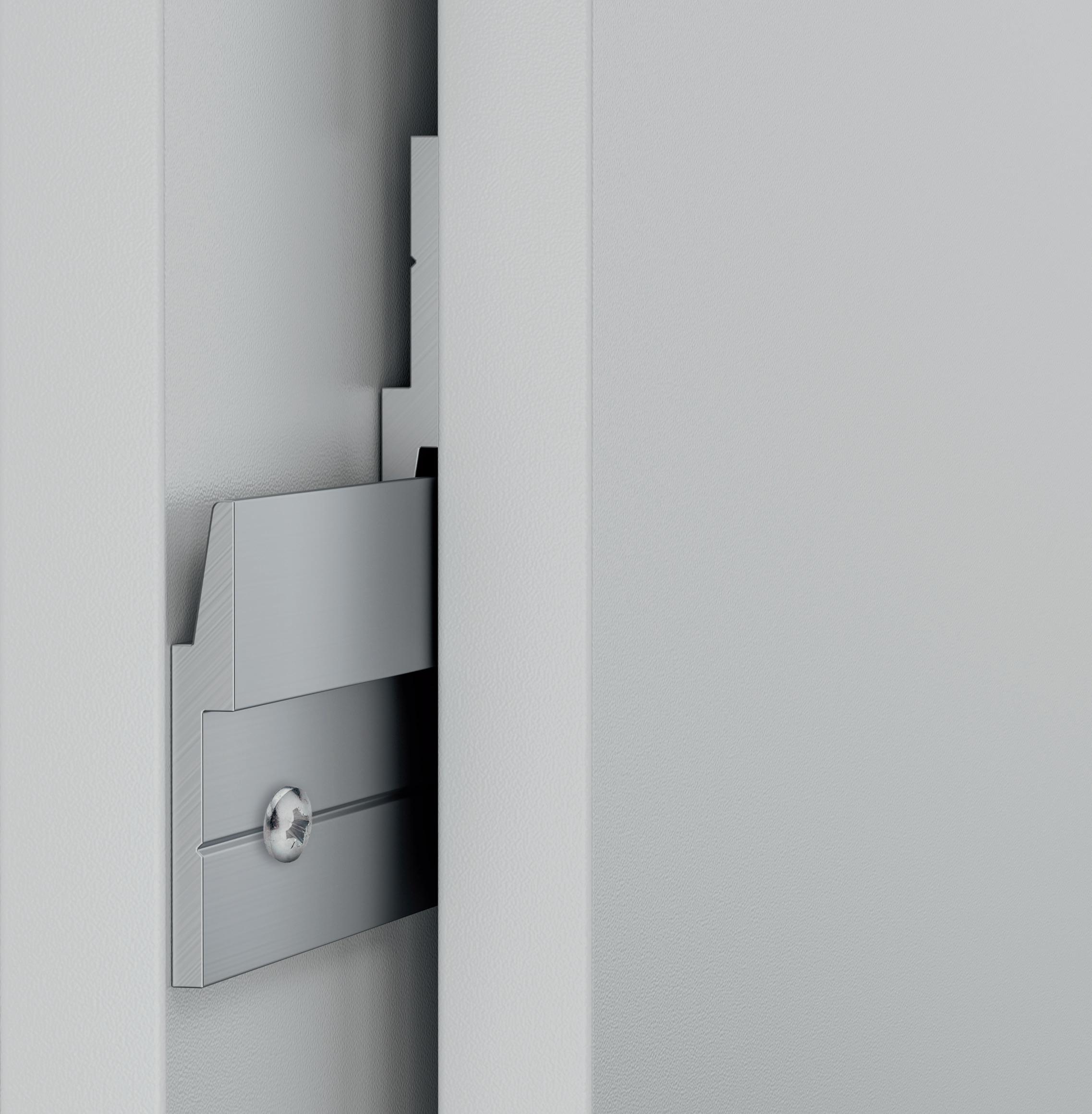
Find all information on the product under the search term “#suspensionprofile” on the Ostermann website www.ostermann.eu
ALTERNATIVE
As an alternative, the Ostermann experts recommend the Hettich suspension brackets SAH 215 or SAH 216 with a load capacity of 45 and 55 kg. The suspension brackets are hooked into the Hettich universal suspension rail, type B.
PROFILES FOR EVERY APPLICATION
The aluminium suspension profile is just one out of many useful products and problem solvers among the Ostermann profiles range. Carpenters / cabinet makers can find many more construction, functional and decorative profiles in the construction category under www.ostermann.eu
DON’T FORGET THE PLUGS AND SCREWS
For simple and secure fixing of the moulding to the wall, the Ostermann experts recommend the Duo Power plug with matching Fischer Power Fast screws, which are best ordered together with the suspension profile in the Ostermann online shop. Plugs and screws are available in many lengths, models and pack sizes.
OSTERMANN: SERVICE, DIVERSITY & SPEED
• everything for furniture making from one source
• largest immediately available edging range in Europe
• edgings in every length from 1 metre
• all edgings also for zero bondline technologies
• Furniture elements made to measure
• personal service & online shop
• expert advice & inspiration
• all stock items ordered before 4 p.m. are dispatched on the same day
T: 01905 793550
E: s.parsons@ostermann.eu
www.ostermann.eu
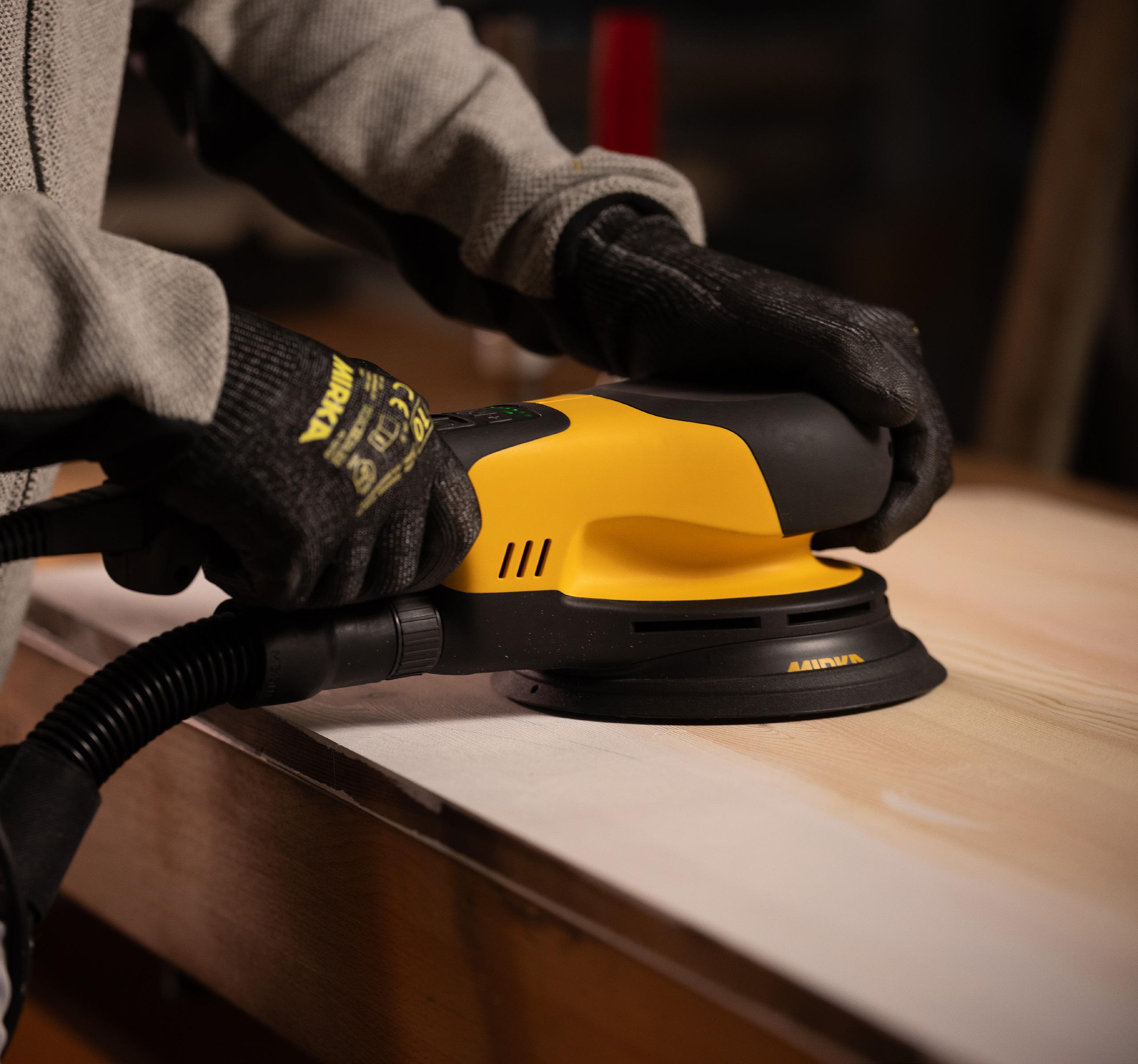
Mirka® DEROS RS 600 is a rotary sander designed for heavy-duty, coarse sanding applications. Its lightweight, compact design provides a smooth operation and enhances user comfort and productivity. The Mirka® DEROS RS is the perfect solution to tackle paint removal, furniture restoration, cabinetry, solid surface and wooden flooring projects with ease. For further information or to arrange a demonstration, please contact Customer Services on 01908 866100.


OVVO Expands Its Range
The OVVO range of invisible, glueless and self clamping dowels continues to expand, now with the addition of a new 8mm x 40mm Dowel.
OVVO continues to expand its range of wood joining connectors leading the way in furniture ‘Tools free’ assembly components, making life easier for consumers and endusers, and delivering a more profitable and efficient solution for manufacturers.
OVVO products are a range of cleverly engineered, awardwinning, invisible connectors that make joining wood simple.
The connectors are installed during the manufacturing process so the end-user can simply click/push together cabinets, shop fit-out components, door frame assemblies or furniture without the need for tools, screws, or glues. The result is an accessible, sustainable product that saves time, money and effort for consumers and manufacturers alike. Manufacturers can also benefit from significantly reduced shipping costs, as items can be shipped flat-packed.
The latest addition to the OVVO product family of Dowels is the 8mm x 40mm version, namely the OD840 which is specifically designed to work in standard 8mm drill patterns. The OD840 is inserted into the panel without any glue to form a permanent joint in 15mm panels and above. These new connectors make it even easier for manufacturers to incorporate OVVO into their standard processes, saving time and money by eliminating glue and case clamping time. No additional equipment or capital needed to deliver tools free assembly products to the end customer.
This new self-clamping, glueless, invisible OVVO Dowel (OD840) is designed for connecting cabinet parts and all types of furniture using standard drilled holes on BOTH sides of the joint, thereby simplifying the panel processing

operations while continuing to provide all of the benefits of OVVOs’ proven tools-free ‘Push-Click-Connect’ assembly methodology.
All OVVO connectors are designed for high-volume, automatic insertion, and ongoing partnerships with leading machine vendors such as Pro-Edge Technology and software providers Cabinet Vision, TopSolid, iFurn, Swood and Cabinet Sense ensure that manufacturers can easily incorporate OVVO into their existing processes, and also into new product design and development. The PET CNC OVVO is the only machine in the industry with insertion capabilities for ALL OVVO connectors.
All OVVO connectors can be installed into a variety of materials ranging from high-quality hardwoods to low-grade particle board, and our recyclable plastic means any waste is put back into the production of our product. OVVO works best in boards >12mm thickness and is available in a range of sizes to perfectly match your requirements.
All connector sizes are available in both PERMANENT and RELEASABLE options, extending the range of materials and opportunities to inspire creative design and innovative development.
Consumer demands are shifting more and more towards convenience and sustainability. OVVO helps you meet those demands and give your products a competitive edge. Our team is on hand to support your switchover to OVVO and help you take the next step of innovation.
FURNITURE ASSEMBLY MADE SIMPLE –NO NEED FOR TOOLS, GLUE OR SCREWS. SIMPLY PUSH, CLICK AND CONNECT.
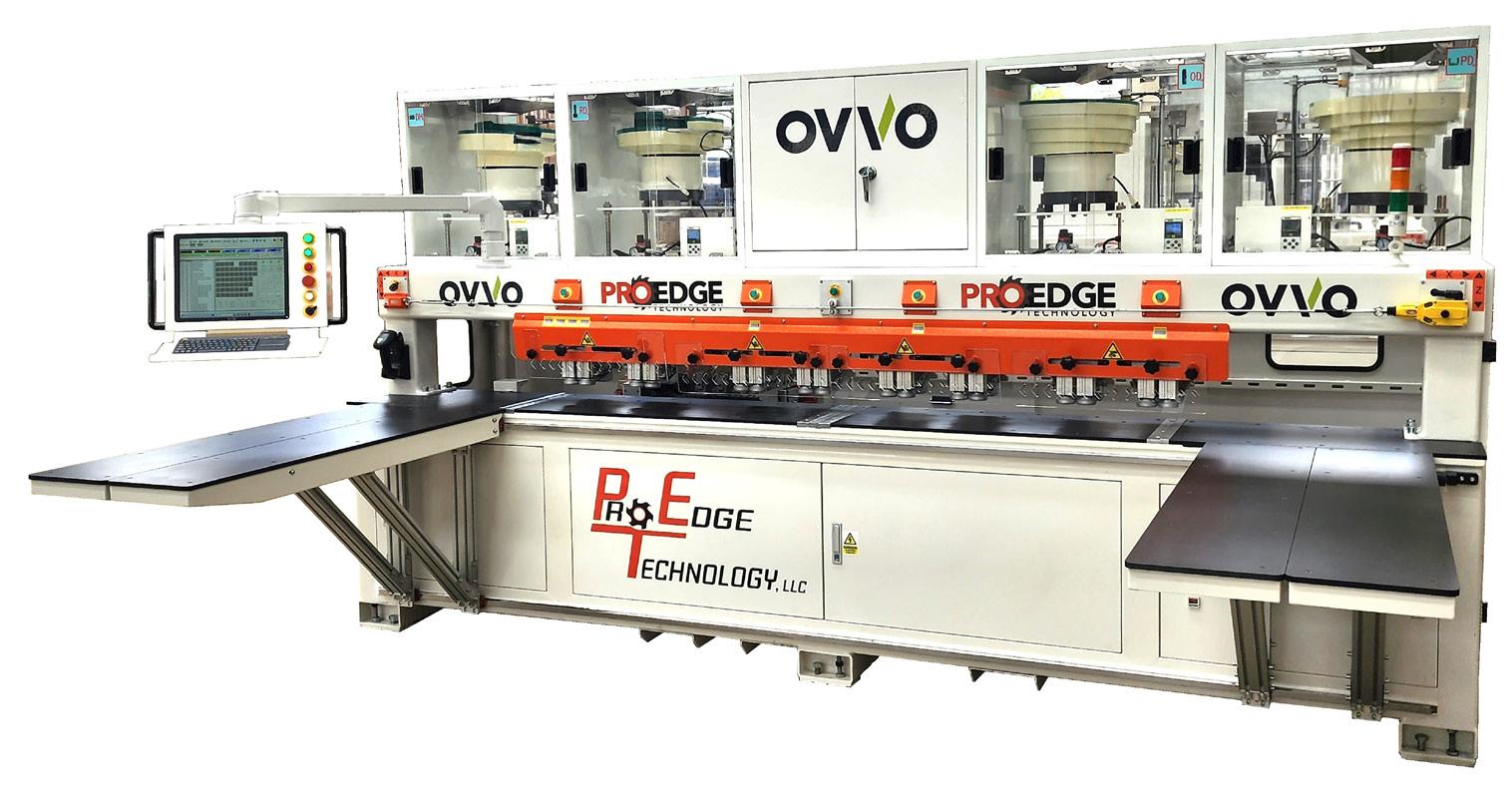
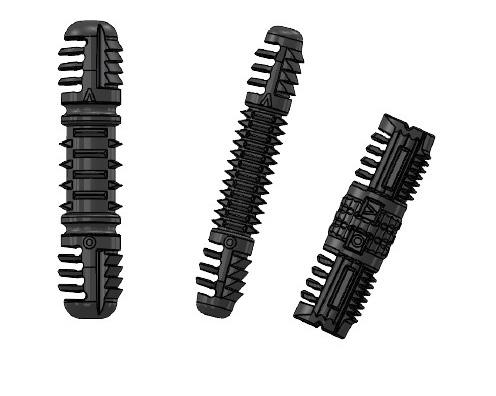
Holz-Her’s Sprint. A Game Changer In Edgebanding
Working with retail giants like Tesco, KFC and The Fragrance Shop, specialist architectural joinery company, Adams Joinery Ltd, knows all too well the importance of producing consistent, high quality edging. When their old edgebander’s performance started to impact production, the Londonbased joinery invested in a Sprint 1329 edgebander from Holz-Her UK to increase efficiencies throughout the edging process.
“The right machine in any workshop should be a help and not a hindrance to your production,” begins Alex Adkin, Senior Production Manager at Adam’s Joinery. “This simply wasn’t the case with our old edgebander. We knew we needed more control over our edging. This meant being able to quickly and easily change glue colours when required, reduce the amount of manual set-up involved and eradicate the hand finishing of panels once they’d been edged.” It was clear from the off that Holz-Her’s Sprint offered Alex and the team the complete package, thanks to its sturdy German build quality and wealth of automated features designed to simply operation and guarantee repeatable, near invisible glue lines.
“We could see how it’s multi-function milling, fa.s.t (fast setting technology) and integrated finishing units could deskill the operation for us, whilst its ability to applying solid wood, melamine, HPL, real wood coil and veneer lippings up to 15mm thick onto work pieces up to 60mm thick offered us the flexibility we were after.
“Then there was the Glu Jet system it came with,” adds Alex adds. “We’d read about its insanely quick heat-up times, its ability to switch between EVA and PUR and easy cleaning but it all sounded a bit too good to be true. How wrong were we? When we saw the machine in action, we were immediately sold. No other manufacturer could offer anything like it. We knew it would be a gamechanger for our business and we were right.”
“Due to the bespoke nature of our work, we can easily perform 20 different set-ups on the machine in a week which, on our old edgebander, was difficult to say the least. Everything needed to be set by hand – requiring a certain level of skill and patience - and changing glue colours was one of the most painful experiences of them all,” admits Alex.
“With the Glu Jet, it takes just five minutes to change from one glue colour to another and only requires 250g of slugs to complete the process. It was taking us three hours to change the glue on our old edgebander and 5kg of slugs to guarantee a good job,” explains Alex “Because the old machine would be out of action for so long, we’d have to make the decision to swap the glue the night before and be in a position to halt work on the machine. It was our biggest headache. If we didn’t do it, we’d risk producing poor quality edging and an ugly glue line. Now, we simple use the automatic cleaning function to purge the machine until the solution runs clear. This saves us three hours of downtime,
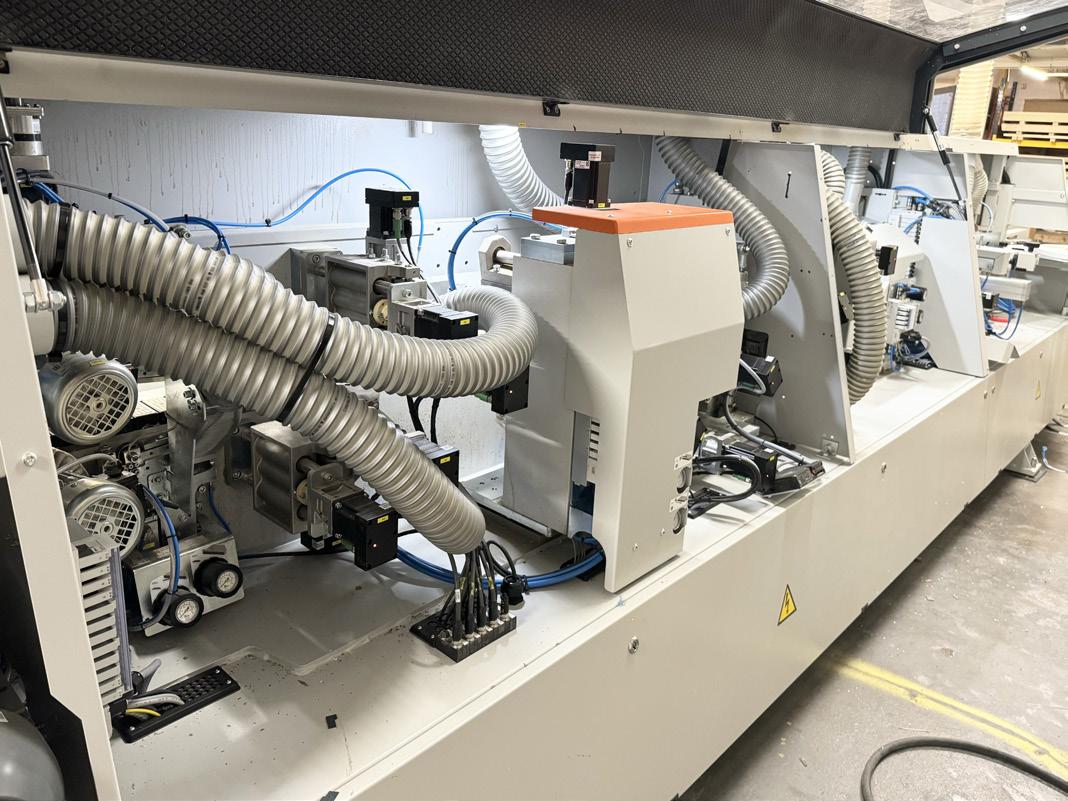
as well as wasted labour and a potential production back log.”
Then there’s the automatic set-up functions. “Each job we work on may require a different panel type or lipping thickness but the set-up on the Sprint is exactly the same. If you’re running a job and you’ve got 12mm, 25mm and 60mm thick work pieces, you can click a button and the machine will automatically change its settings to accommodate the different sizes in seconds, without you having to stop and re-set the machine. Plus, thanks to its smart pre-milling features, it compensates for any discrepancies on the board and allows you to make fine adjustments between 0.1–0.01mm yourself.”
The finishing units and automated anti-static spray on the Sprint have also eradicated hand finishing and, thanks to the machine’s buffers, it works effective on even the most delicate veneers. “As well as buffers, scraper and four different cutter types, we opted for spray units on the front and back to avoid any additional finishing, especially on high gloss melamine. Not having to scrape off excess glue from every panel saves us two to three minutes per board, which soon adds up when you’re running thousands of pieces through it. It also means the risk of human error –like digging a chisel in too deeply and marking the panel – is no longer an issue. No glue spills on the face, no poorly cut edge, just a perfectly clean, flat board.”
On top of this, the Sprint also aids the operator in other ways. “It tells you how much glue you have left and you how much edging you’ve used. It takes the guess work out of the process and doesn’t lead to any downtime whatsoever. This is particularly handy when working on larger shopfitting projects where we might require 1,000m of edging at a time as you don’t need to stop the machine to check.”
Alex continues, “Heat-up times have also gone from anywhere between 30 minutes and one hour, to just five minutes. This not only saves on energy but production time, too. It also means we can be more reactive if an unplanned
board needs to be run through. Now we can just turn it on and go. This level of flexibility cannot be underestimated in any joinery business.”
When it comes to labour, there is also no longer a reliance on skilled operators. “We had two primary operators on the old edgebander because of the level of skill required to use it. Now, we have eight people that can use the Sprint easily. The difference is night and day and, if somebody retires or leaves, it doesn’t leave us in a vulnerable position to find an experienced replacement.” Alex adds, “Following the visual prompts on the screen and operating the machine really is child’s play.”
Following a smooth installation process and three-days of training on the machine, the edgebander has now been in use for 12 months. “I started by saying this machine was a gamechanger and it has been. The Sprint has given us the confidence to complete jobs to a much higher stranded and has reduced production times,” says Alex. “On the face of it, it’s not a cheap machine but its build quality, speed, accuracy and simple set-up will pay us back over and over again. All these areas positively impact our labour and material costs, as well as the ability to future proof our business. These areas cannot get overlooked.”
Alex continues, “Some machinery manufacturers try and sell you a machine with this idea that it can do everything but inevitably, you don’t end up using most of the features on it. It’s safe to say we use everything on the Sprint and everything it does, it does well. The ongoing service with Holz-Her has also been the best I’ve experienced from a machinery manufacturer and their troubleshooting has been exceptional. The Sprint is really straightforward but if I need help or support, I can WhatsApp one of the edgebanding experts in Abingdon and within five minutes he’s telling me what I need to do to resolve the problem. That’s unheard of in this industry. It’s actions like this that give us resounding confidence in Holz-Her and peace of mind in both the edgebander and the aftercare going forward.”

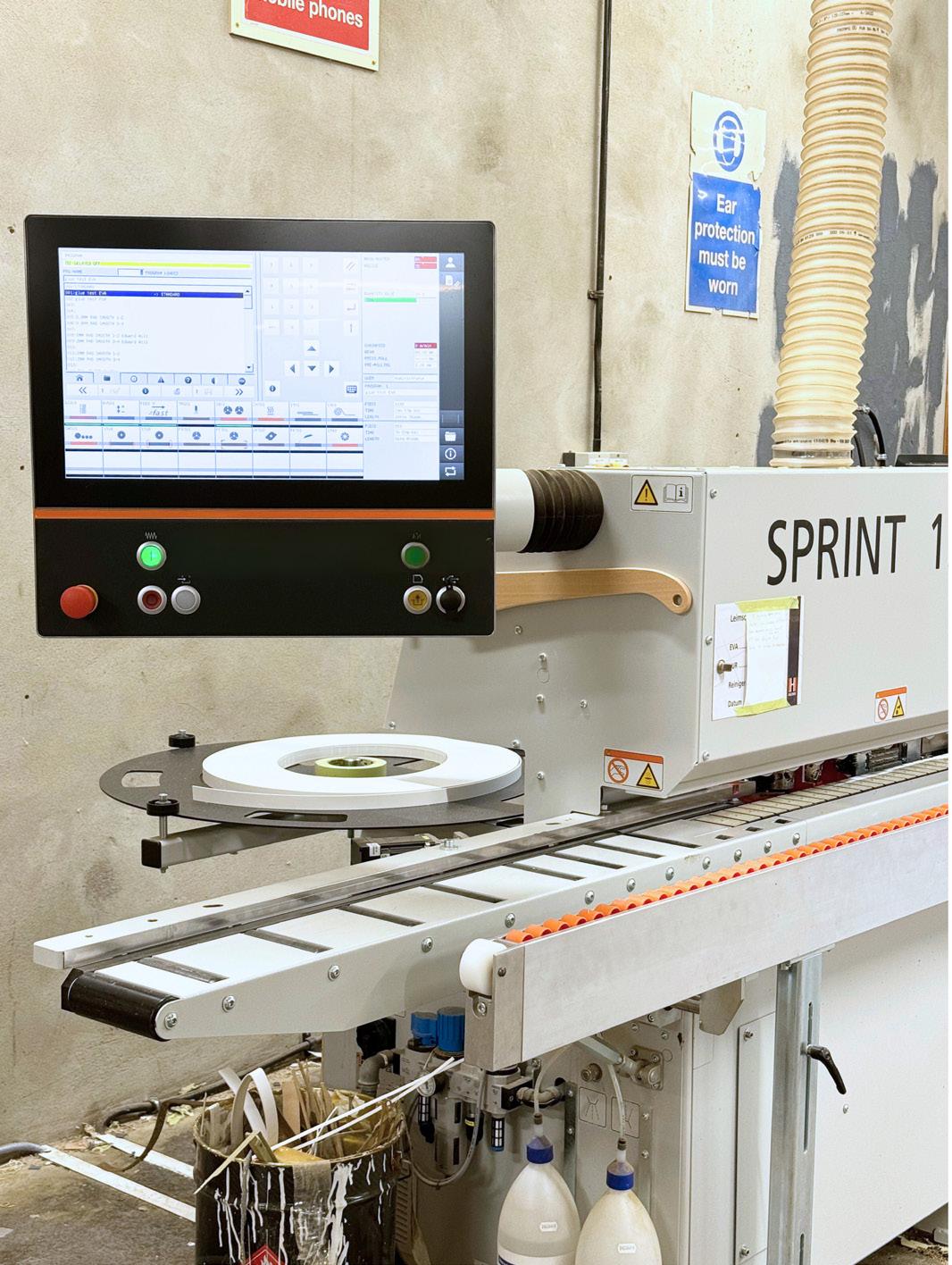
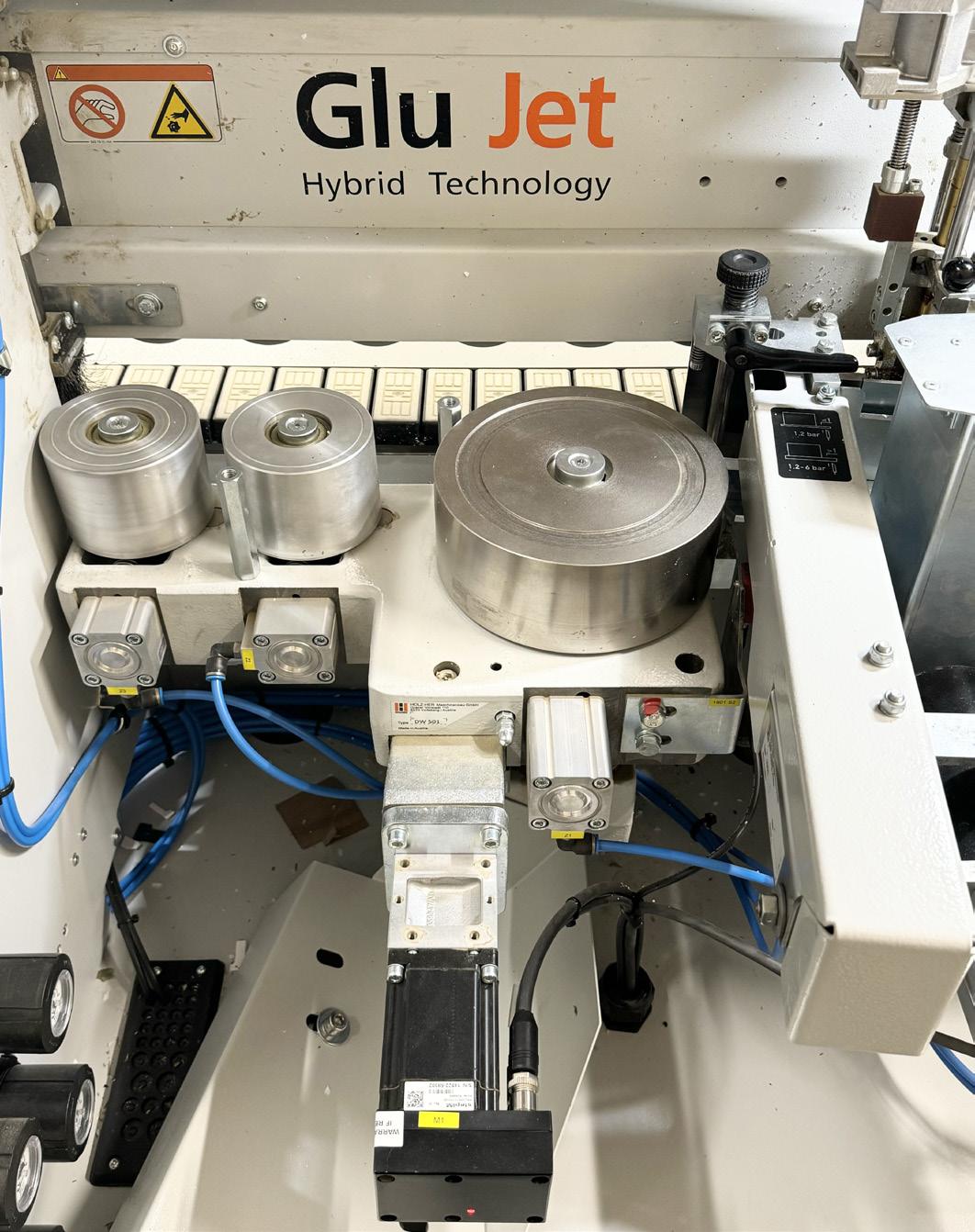
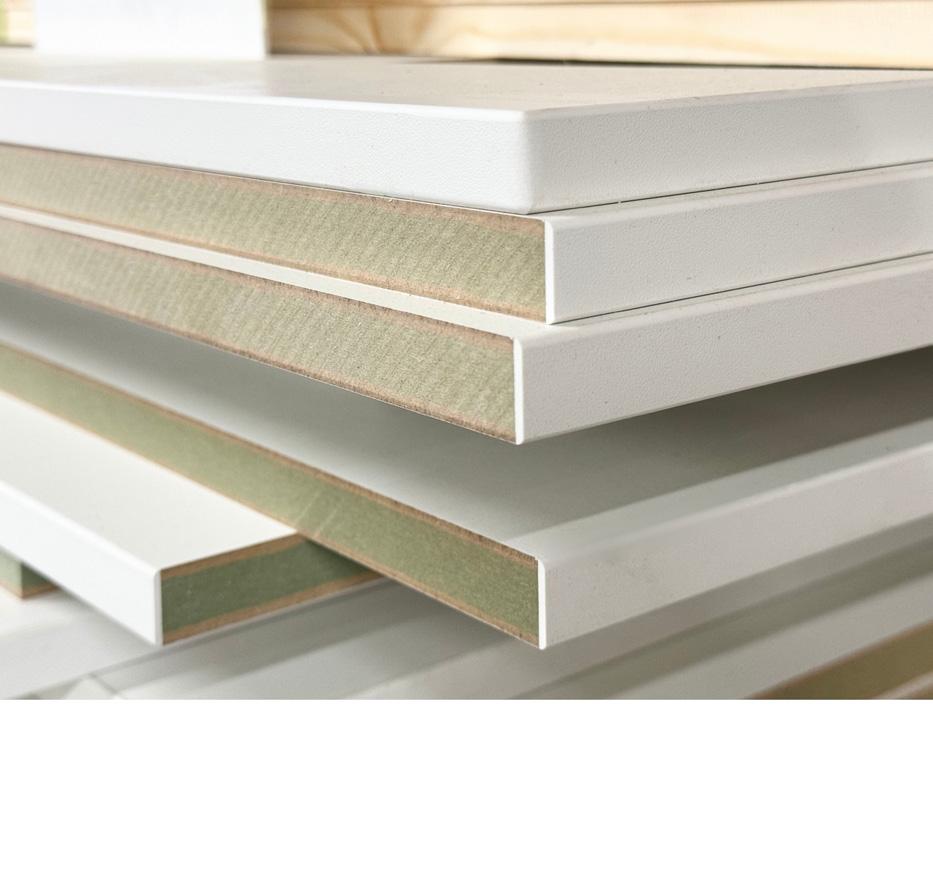
McEvoy & Rowley Brings Kitchen Manufacturing In-House With HOMAG Machinery
McEvoy & Rowley, a family-run business with over 50 years of history, has long been a staple in the Maidenhead community, offering top-tier kitchen designs and appliances. Originally, they relied on suppliers from Scotland and Germany to provide their kitchen products. However, the disruptions brought on by the COVID-19 pandemic exposed critical vulnerabilities in their supply chain, leading to issues with quality, lead times, and overall customer satisfaction.
Faced with these challenges, McEvoy & Rowley made the strategic decision to take control of their manufacturing process by bringing it in-house. To achieve this pivotal move, they turned to HOMAG, who stood ready with a bespoke solution consisting of no less than nine machines.
CHOOSING HOMAG
The transition from purchasing kitchens to manufacturing them required careful planning and investment in the right machinery. McEvoy & Rowley needed a solution that would allow them to produce high-quality kitchen units quickly and accurately, without the common issues they had experienced with supplier-made products, such as units arriving out of square.
Jake Howard, the Factory Manager at McEvoy & Rowley, recalls the company’s initial approach: “We were new to manufacturing, so we spoke with several of the big
manufacturing giants to explore our options. As you’d expect, HOMAG were on that list – and after our meeting with Ian Woodall, their Sales Manager, we were more or less convinced that they were the best choice for us.
“What set HOMAG apart was their willingness to listen to our specific needs and provide tailored advice. They didn’t just give a big sales pitch – they genuinely wanted to ensure we had the right equipment for our operations.”
TO THE NINES
After detailed consultations, HOMAG recommended a suite of machines that perfectly aligned with McEvoy & Rowley’s goals. Rather than pushing for CNC machines, which are commonly used but might not meet the speed and precision requirements for their specific needs, HOMAG guided them towards beam saws and edgebanders.
“A lot of manufacturers seem to go down the CNC route. But we’ve found that, a lot of the time, you can attribute faults in products back to the CNC machine being used. We also wanted machines that could work faster. So Ian introduced us to HOMAG’s beam saws, which promised perfect cuts 99.9% of the time – and at speed. This would solve a lot of the issues we had when we were buying kitchens from suppliers.”
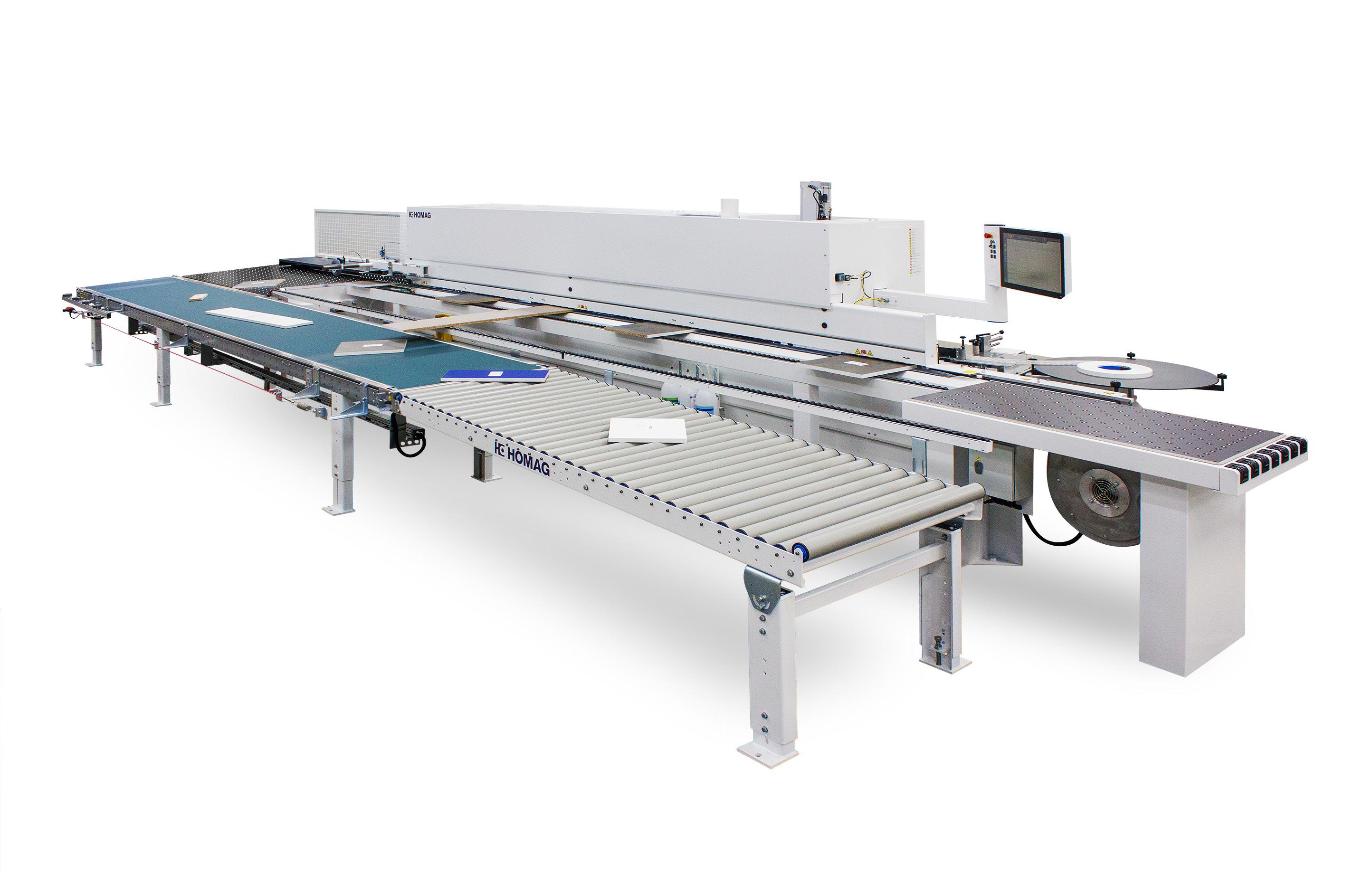
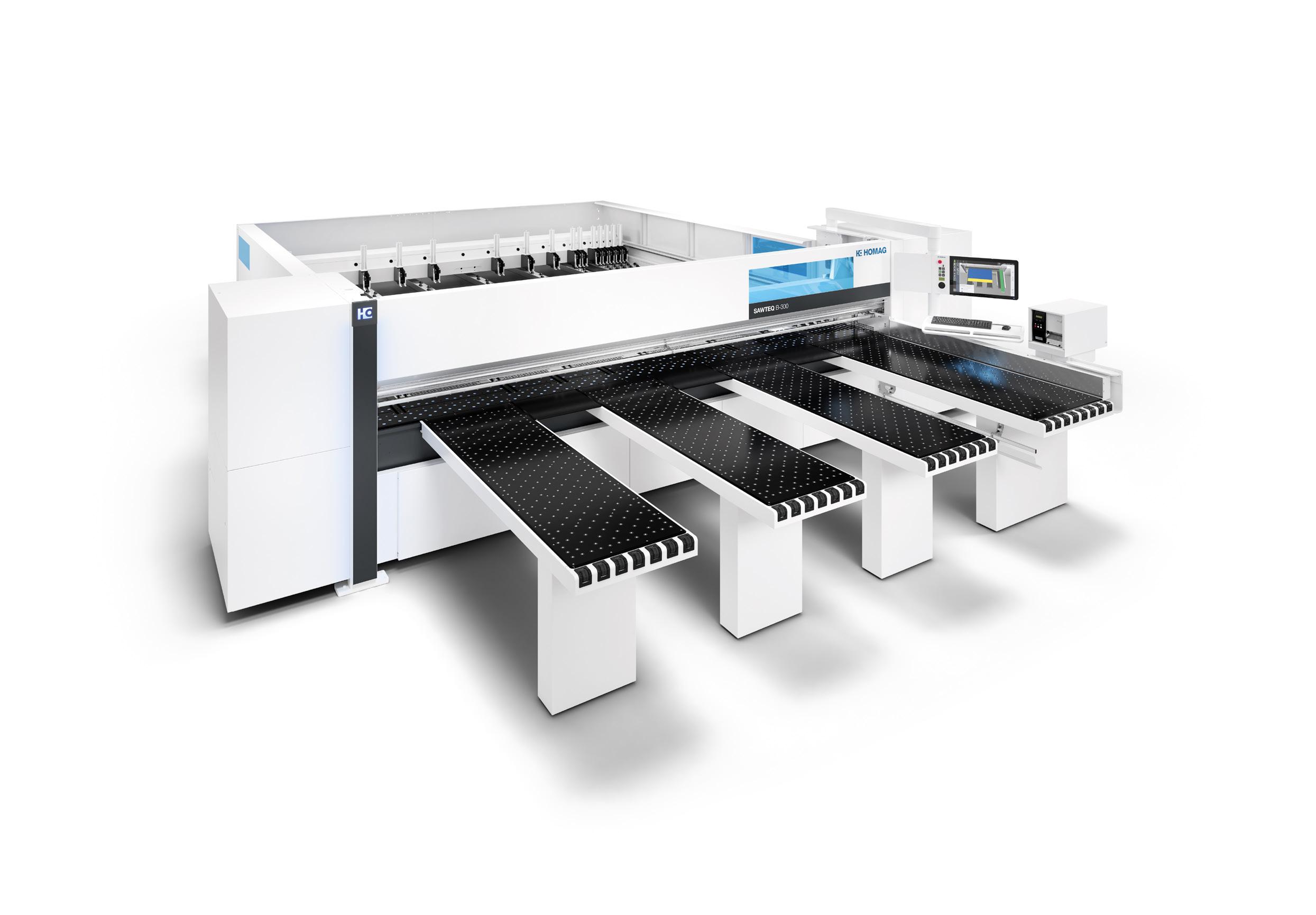
The SAWTEQ S-300 panel saw was therefore selected, but this was just one piece of the puzzle. Also purchased were two EDGETEQ S-300 edge banders, a LOOPTEQ O-300 return conveyor, a Makor Start One spray machine, two DRILLTEQ models (V-200 and V-500) for drilling and doweling, an XES Glue Service Station, and a CABTEQ T-200 case clamp.
“The advice given by HOMAG was absolutely spot on. It was the first time our company had gone into any kind of manufacturing, so it was great to have their expertise at hand, and we couldn’t be happier with how all nine machines are performing.”
IMPLEMENTATION
The implementation process was smooth and wellcoordinated, beginning with a thorough site survey conducted by HOMAG. “They were very clear on who was going to arrive and when,” Jake noted. “The entire installation was very professional, and HOMAG had a great presence onsite, which really put us at ease.”
Training was another critical aspect of the transition. HOMAG provided comprehensive training sessions for McEvoy & Rowley’s team, ensuring they were fully equipped to operate the new machinery. This training allowed the company to gradually shift their production in-house, significantly reducing their reliance on external suppliers.
BENEFITS REALISED
Since bringing the manufacturing process in-house, McEvoy & Rowley have seen numerous benefits.
“Cost savings is the obvious one. We were spending crazy money on kitchens from external suppliers. Moving everything in-house will save us a fortune in the long run. “Equally, if not more beneficial is the quality assurance we’ve gained. We now have full control over the product we sell, and when you’re working with such accurate and
reliable machinery, that’s a great position to be in. It also means we can make tweaks to products as and when needed, which customers always appreciate.”
Additionally, McEvoy & Rowley now have the ability to invite customers to view their kitchens being made, providing transparency and boosting confidence in their products. “We’ve enjoyed showing customers around our factory to see the HOMAG machinery in action. It’s made a huge difference to how our guys can sell our kitchens – and it’s improved the customer experience as a whole.”
FINAL THOUGHTS
One of the standout aspects of working with HOMAG, according to Jake, was their honest and consultative approach. “They even challenge us on things to make sure it’s the right decision. We’ve always appreciated that they won’t just let you spend your money on something you don’t actually need.”
He concludes, “Bringing our manufacturing in-house was a huge decision – daunting, to say the least. HOMAG not only made it possible but they also made it as seamless as can be. From start to finish the service was excellent, and we’re glad to consider them a partner as our business continues moving forward.”
If you would like more information or a demonstration of any of the HOMAG machinery and software, please contact Adele Hunt at HOMAG UK on 01332 856424.
SAWTEQ-B-300
Mirka Continues To Clean-Up With Its New Extractor FEATURE
Mirka UK is expanding its extractor range with the introduction of the new Mirka® DEXOS 1217 M AFC dust extractor. This M class extractor blends power and versatility to ensure users have a dust-free work environment when working on a variety of jobs from flooring projects to paint removal and restoration work.
The Mirka® DEXOS 1217 M AFC is powered by a 1200 watt brushless electric motor, designed by the R&D team to be durable and to ensure dust is quickly and efficiently extracted. Alongside the power, the new extractor is versatile because it can handle both wet and dry applications as well as being compatible with multiple tool types. It also comes with two sockets with auto start capabilities. This feature ensures the dust extraction system activates simultaneously with the power tool, so any dust and debris is captured by the extractor as soon as the tool is in use.
To ensure the DEXOS can work for long periods without a break, it has automatic filter cleaning capabilities, which ensure consistent suction from the first use to the last. In addition, there is an integrated airflow sensor that provides users with real-time feedback on its performance via the MyMirka app, so they are aware of any deviations from the optimal flow rates of the tool.
The extractor’s ergonomic design makes it easy to handle and manoeuvre around job sites and its built-in storage space accommodates the 4 metre hose. It is also compatible with the Mirka case and toolbox as well as existing Mirka hoses. This enables users to have everything they require in one place. In addition, it has an easy-to-clean construction that ensures hassle-free maintenance as and when required.

One of the DEXOS’ innovative features is the Bluetoothenabled remote control (sold separately) that is strapped around the dust hose and senses tool vibrations to start the extractor and offers the user two operating modes: auto sense and manual. The remote control has a Bluetooth range of up to 20 metres, and it eliminates the need for a pneumatic box.
The extractor’s bluetooth connectivity also enables it to connect to the MyMirka app. Via the app, the user will be able to access numerous insights from air flow indication to a running time display and a hot PCB alarm. These insights provide the user with comprehensive monitoring of the tool, so it can perform at optimal level and users are aware of any issues.
Neil Newbrook, business sector manager – Wood, Mirka UK, “In the woodworking sector, we know from experience there is a lot of dust produced during the sanding process, so it is important to have an extractor that can quickly and efficiently remove the dust. To combat the dust being produced, we are introducing the DEXOS, the next step in the evolution of our extractor line-up. This extractor has been designed in response to feedback from our customers in order to give comfort, convenience and efficiency during all sanding applications, with new features like multiple sockets and improved storage”
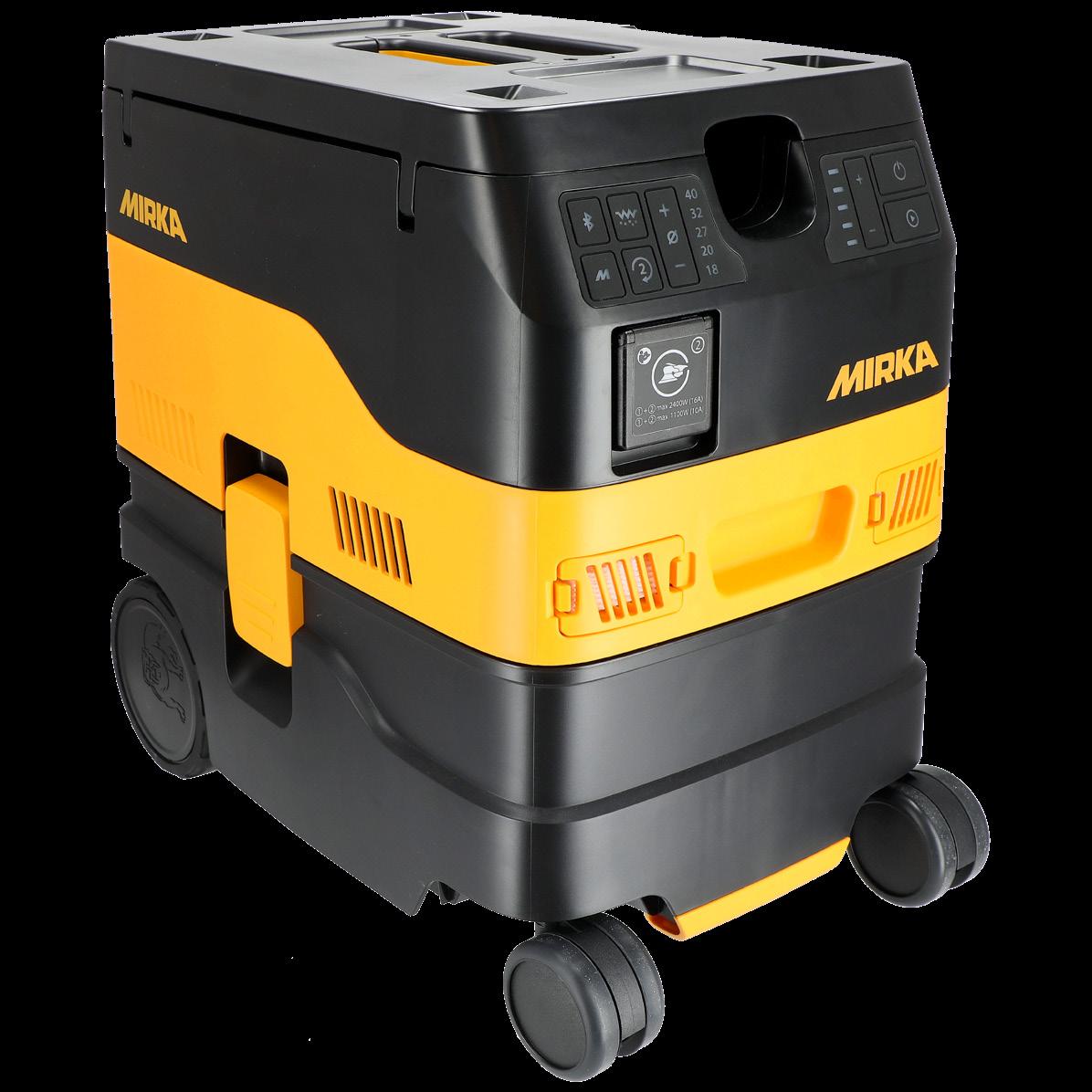
https://www.mirka.com/en-gb/products/top-brands/mirka-dexos-dust-extractor
dp-lite. the lighter choice.
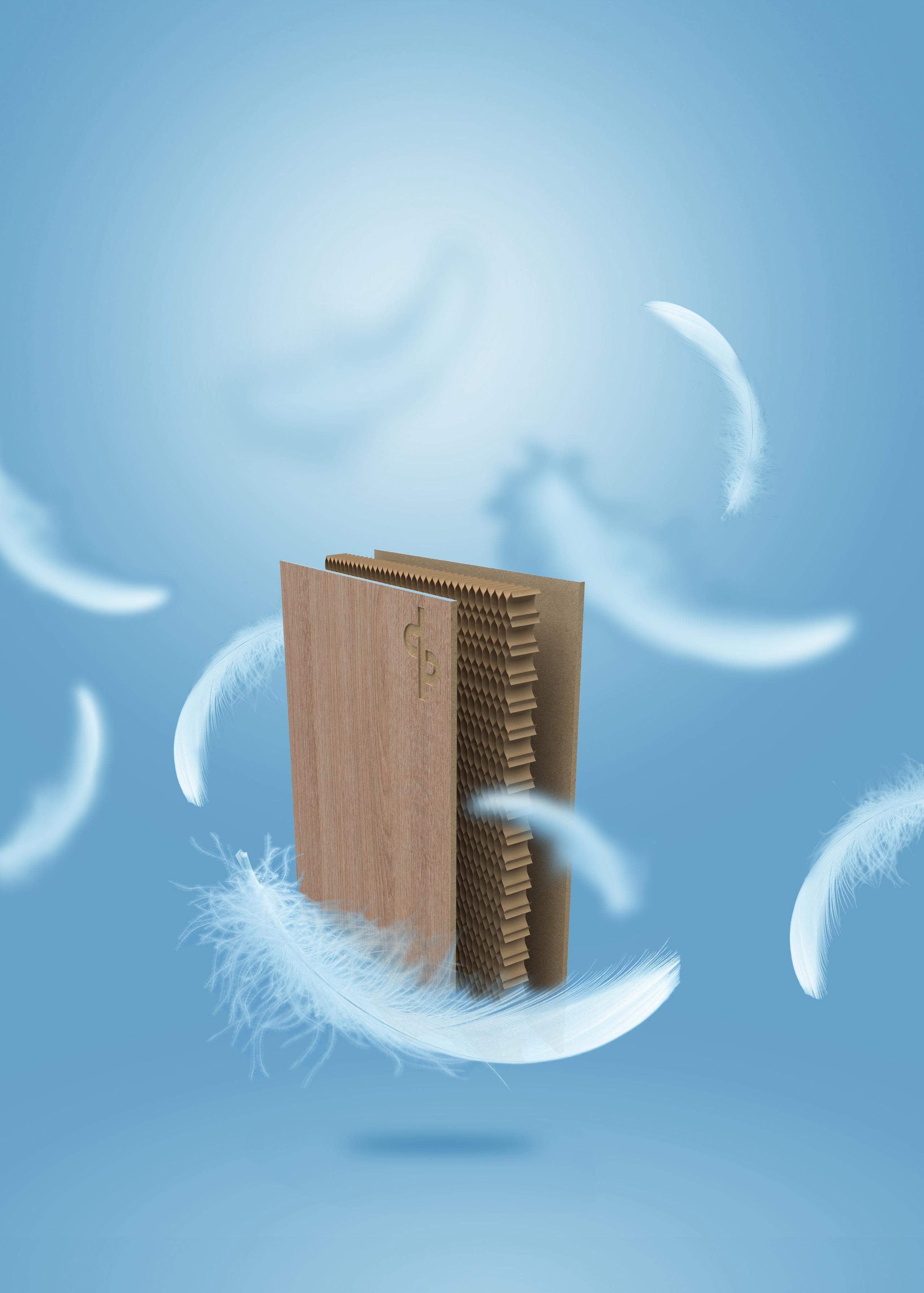
Extremely low in weight and has excellent stability allowing vast creative freedom. Offers weight savings compared to chipboard of some 60%.
Manufactured in a range of sizes and thicknesses – can be supplied raw or laminated.
A full range of competitively priced fixings available.
Can be supplied with longitudinal rails or completely frameless
Plywood skins can also be applied for extra weight savings.
From Little Acorns Grow Great Oaks INDUSTRY
When ECC Timber Products was founded by PJ Fahy in 1992, the company could only dream of becoming the success it is today. Over 30 years later, the company has evolved into a €100m+ turnover business with over 150 staff employed at their facility in County Galway on the west coast of Ireland. Despite the exponential growth the company has enjoyed, one thing has always been a constant: its saw blade sharpening technology from Vollmer UK.
As the Corr na Mona based company has grown, its portfolio has evolved to encompass products for construction, fencing and landscaping, pallet and packaging, motorway fencing, acoustic panel products and much more. The manufacturer processes more than 600,000 tons of timber every year.
Soon after its inception, the company invested heavily in its saw-sharpening facility. During those early days, ECC purchased a CAS bandsaw sharpening machine, an EMS twin-head side grinder, a first-generation bandsaw stellite tipping machine and a VWM bandsaw rolling bench, all from Vollmer. The circular section of the Sawshop was also augmented and propelled forward with the purchase of a Vollmer CHC22H TCT grinder and an FS2A side grinder. This investment was copper fastened over the following years with additions and updates, including CA200 profile grinders, an Alligator stellite tipping machine and more recently, an RC100 automatic levelling and tensioning machine- all from Vollmer. Many of these Vollmer machines are still in active service today – demonstrating the longevity and quality of the brand.
As part of a strategic plan, ECC is currently planning the next phase of their Sawmill upgrade and as an initial part of this, the saw shop that services and maintains circular saws and band saw blades needed to be moved from its previous location. As ECC Timber Products Maintenance Manager, Mr Pat Mullarkey, says: “We needed to move the saw shop on site, and we saw this as an opportunity to invest in a brand-new purpose-built facility. We also saw this as an opportunity to improve quality and create efficiencies. Many of our previous Vollmer machines were 25 years old and had more than served their time. The all-new facility allowed us to invest in the next generation of technology. After the proven performance of Vollmer, we had no intention of looking anywhere else.”
ECC took delivery of a Vollmer CHF840 side grinding machine. This was accompanied by a fully automated CS860 for universal tooth face and top grinding of TCT saw blades with an ND320 robot loading automation system. ECC placed the order in November 2023. Landing in March 2024, the new arrivals have significantly benefitted ECC.
The previous Vollmer circular machines were manually operated and labour-intensive. Pat continues: “We only service saws for our own site. However, we have evolved over the years, and along with many other changes, we currently have a USNR Versagang that takes a box of 25 guided 28” saws per shift. In addition, we have four multi-head cross-cut lines, two board edgers, an 18-saw trimmer and a Ledinek high-speed planer with a splitting
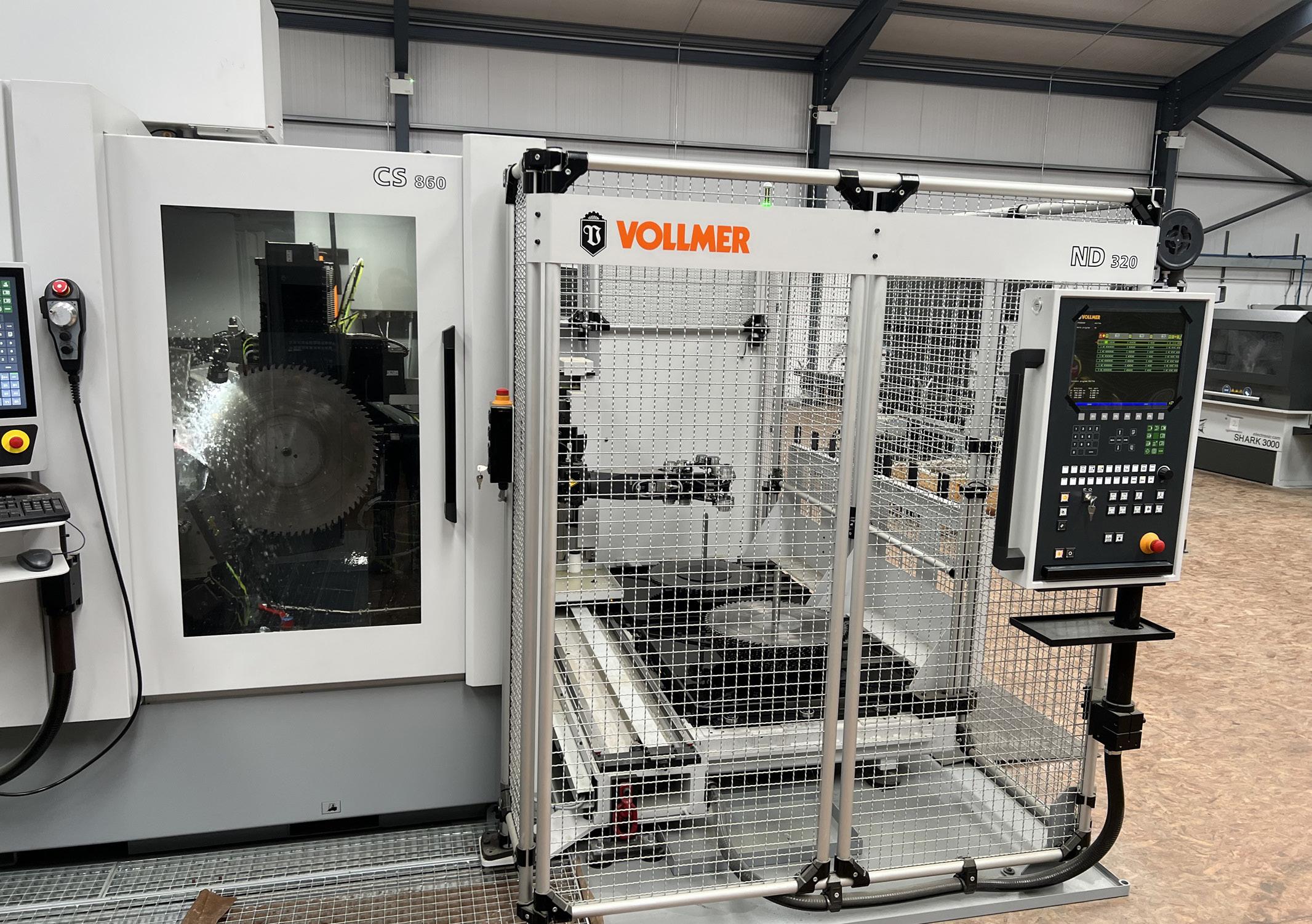
module. These machines all run two shifts daily, and many workstations require daily saw blade changes. This means we go through a lot of saw blades. This placed significant demands on our saw shop, the old Vollmer machines and our ability to service the fast-paced production department with the quality required.”
Pat continues: “We we wanted to introduce automation to alleviate bottlenecks and to aid staff in achieving throughput. Previously, we had an operator constantly loading, unloading and tending to the manual machines. Now, our operator can fully load the ND320 with upward of 25 heavier circular saw blades with a diameter of up to 840mm and a weight of up to 20kg. Once loaded, the automated measuring and probing of the saw blades inside the machine enable the operator to load the ND320, select the preset recipes, press start and let the machine do the rest. This means the new CS860 can run for an entire shift unmanned.”
Concluding on the investment in the two new Vollmer machines, Pat says: “The automated CS860 and the CHF840 have made a massive impact on everything from labour, manufacturing efficiency and productivity in the saw shop to precision, quality and improved saw service life in the sawmill. We have had the machines for a few months, and we still haven’t fully challenged or utilised the benefits of Vollmer’s latest CNC technology.”
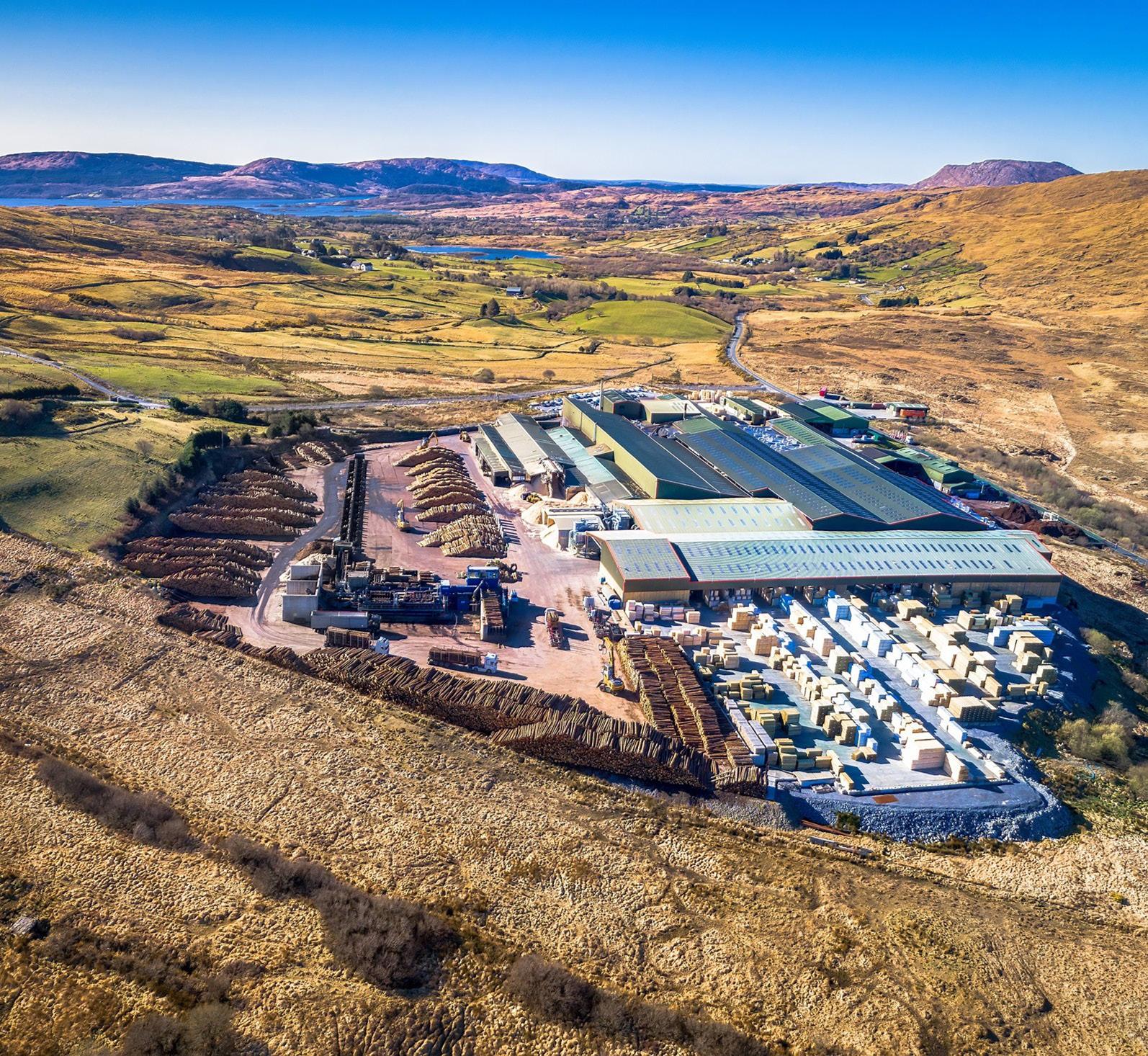
https://www.vollmer-group.com/en-uk/
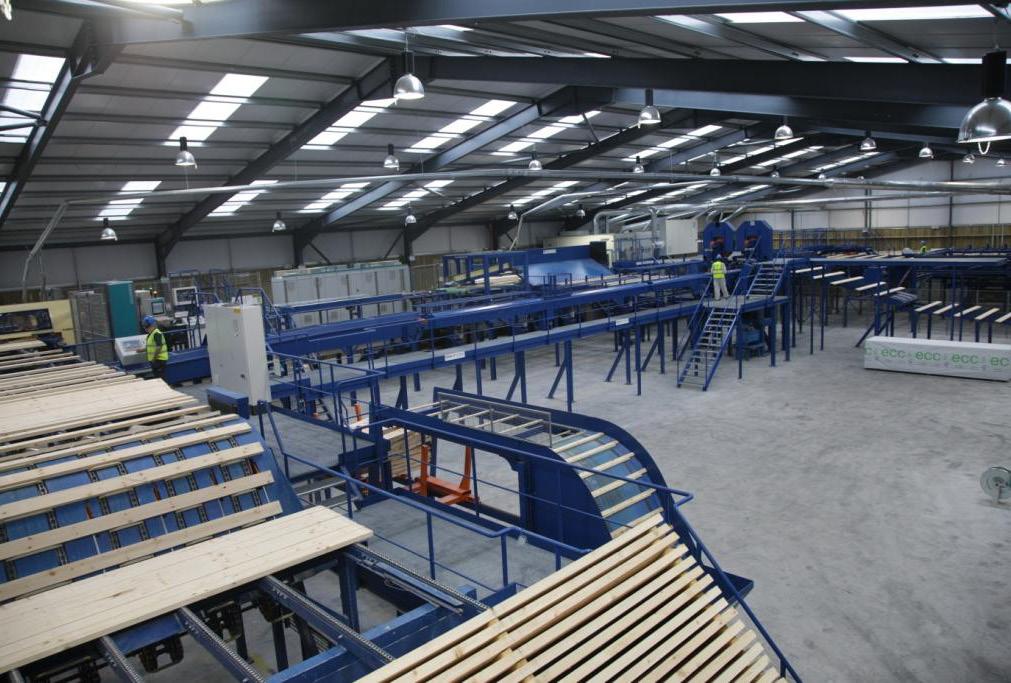
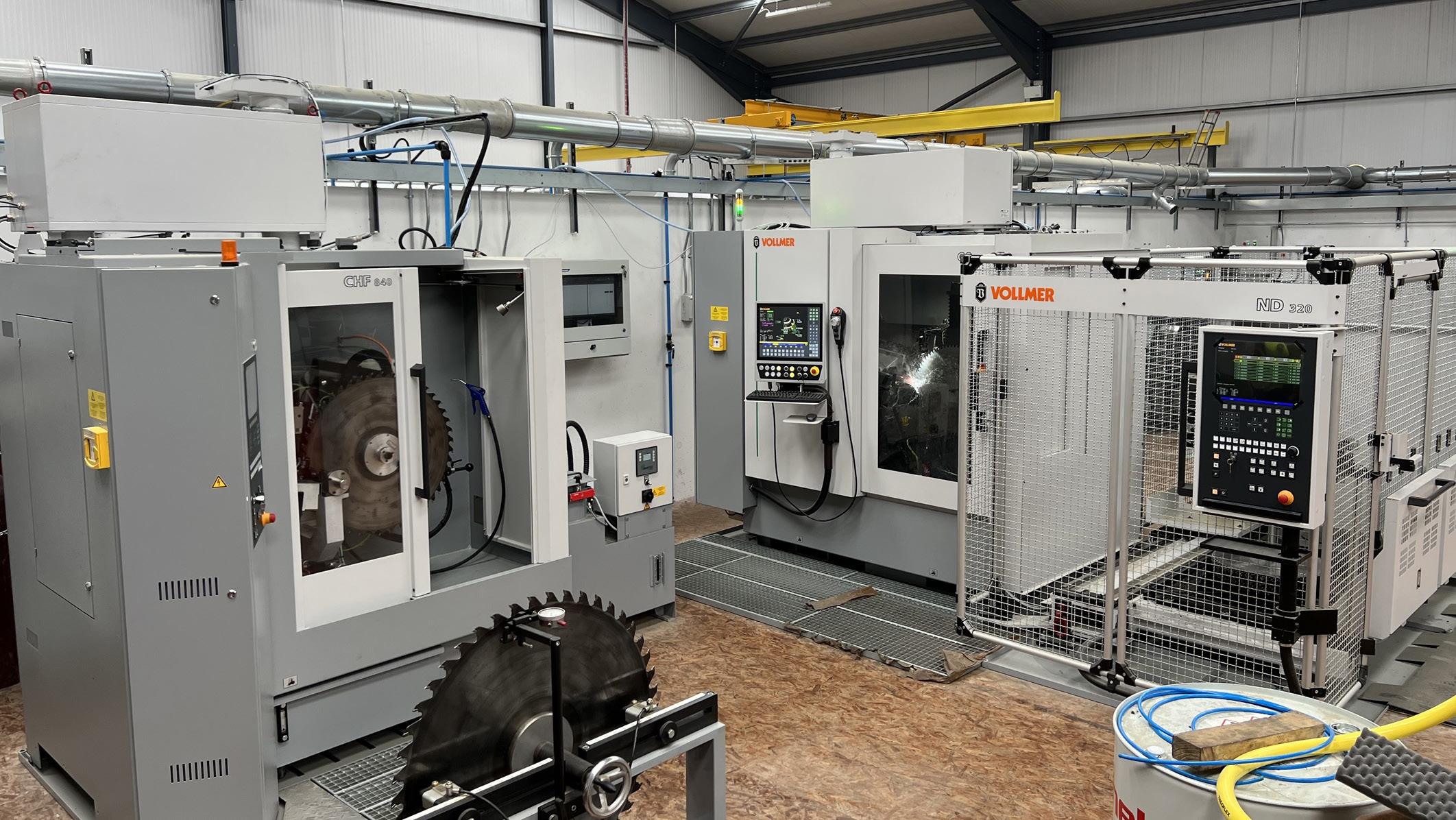
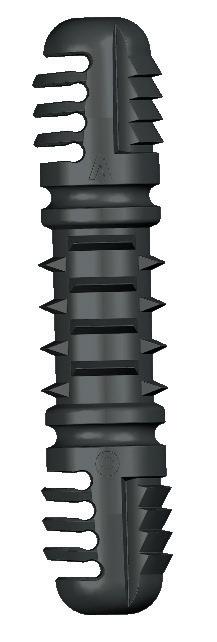
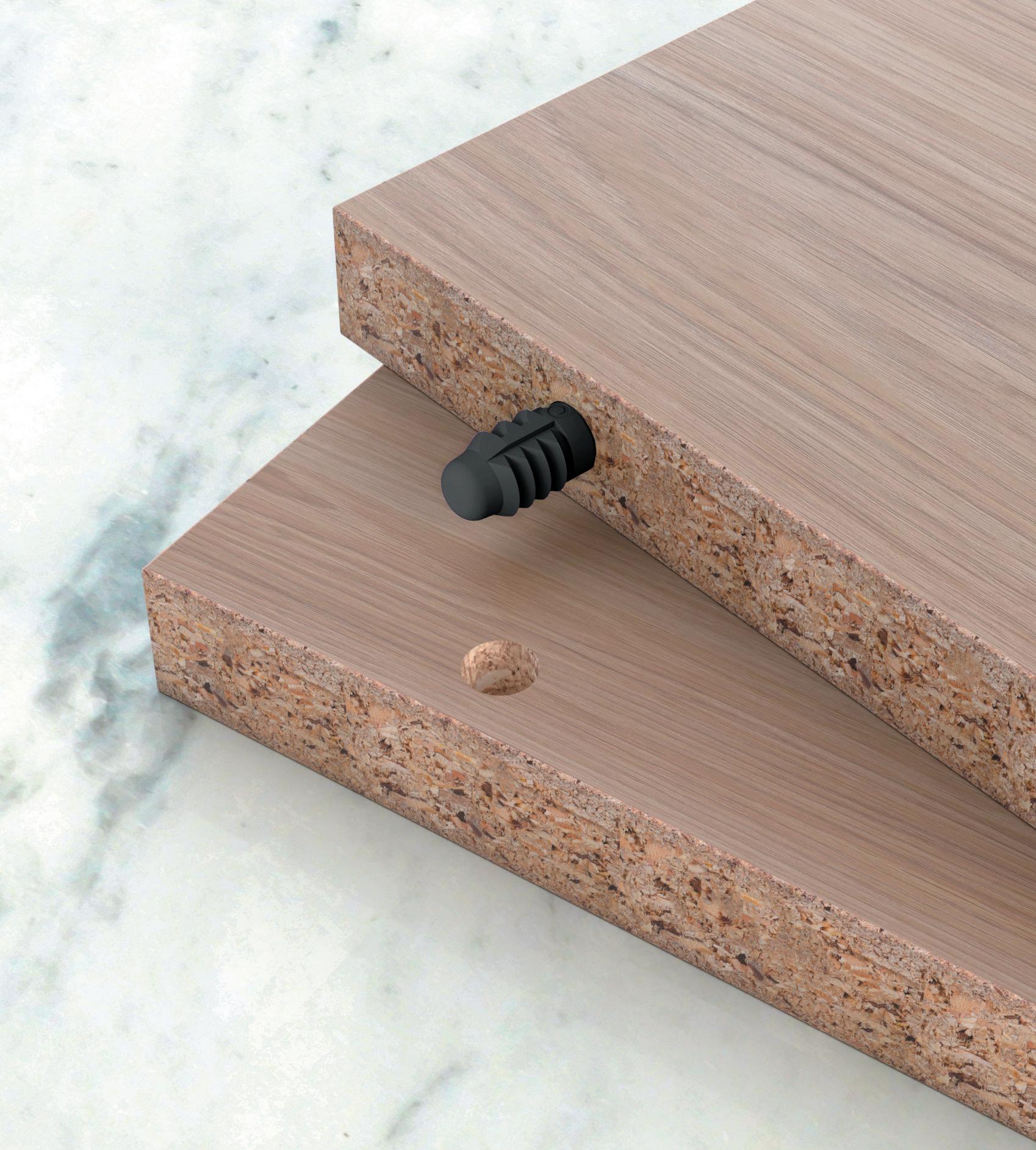
The Japanese Experience, In Timber Framed Buildings
Chris Franklin MD at Ranheat Engineering Ltd. a leading UK manufacturer of wood combustion equipment-continues his series of articles exclusively for Furniture and Joinery Production. In previous month’s editions he looked at how timber framed housing could help meet the UK Governments targets on new builds.
This month’s article was written by Chris, whilst researching into timber framed housing in Japan, in October 2024. He looks at how, for many years, the Japanese have successfully built timber framed buildings that not only make great homes but can also withstand earthquakes!!
One of the fears with timber framed housing is longevity in use. Modern manufacturing methods and environmentally friendly treatment of the timber ensures this happens.
His recent Japanese experience showed that the buildings had a long life even if not made of modern timber construction methods and using modern materials, buildings were still made of wood. Houses and other buildings including shrines, still stand that were made in the 18th century and before.
One of the few buildings to remain in Tokyo, that survived the intense bombing of the second world war, is a Shrine made of timber.
The other major fear with timber framed houses is fire, as wood burns. However, there are fire retardant treatments available, and have been available in the UK for many years for treating roof trusses and other structural timber. Also, timber has a natural protection when the outer surface becomes charred this protects the timber within and retains structural strength.
Timber framed housing looks like the only way to meet Government targets with regards to the number of houses needed in the UK and maintaining Carbon Neutrality. With the use of timber framed houses, housing can be erected quickly as well as being well insulated. They can be made in a quality-controlled environment using the latest in timber technology, including engineered sections. By embracing this new approach to housing (although others have used timber for centuries) the ambitious targets set by the new Government, and in the recent budget, could possibly be met.
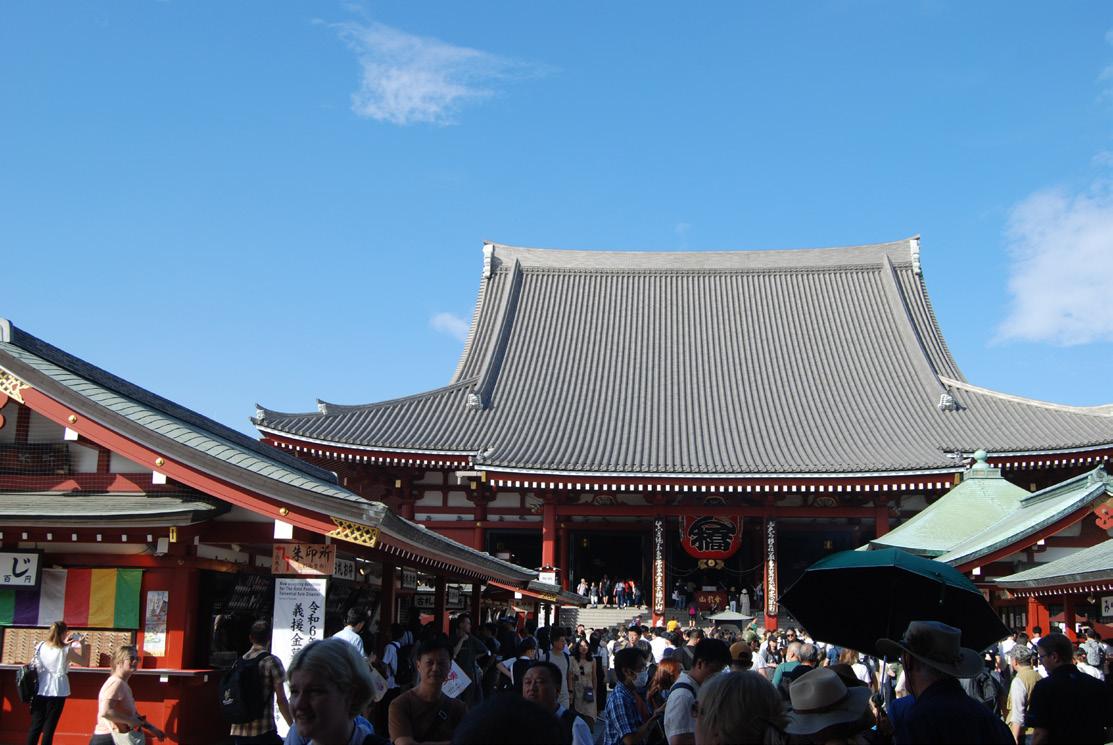
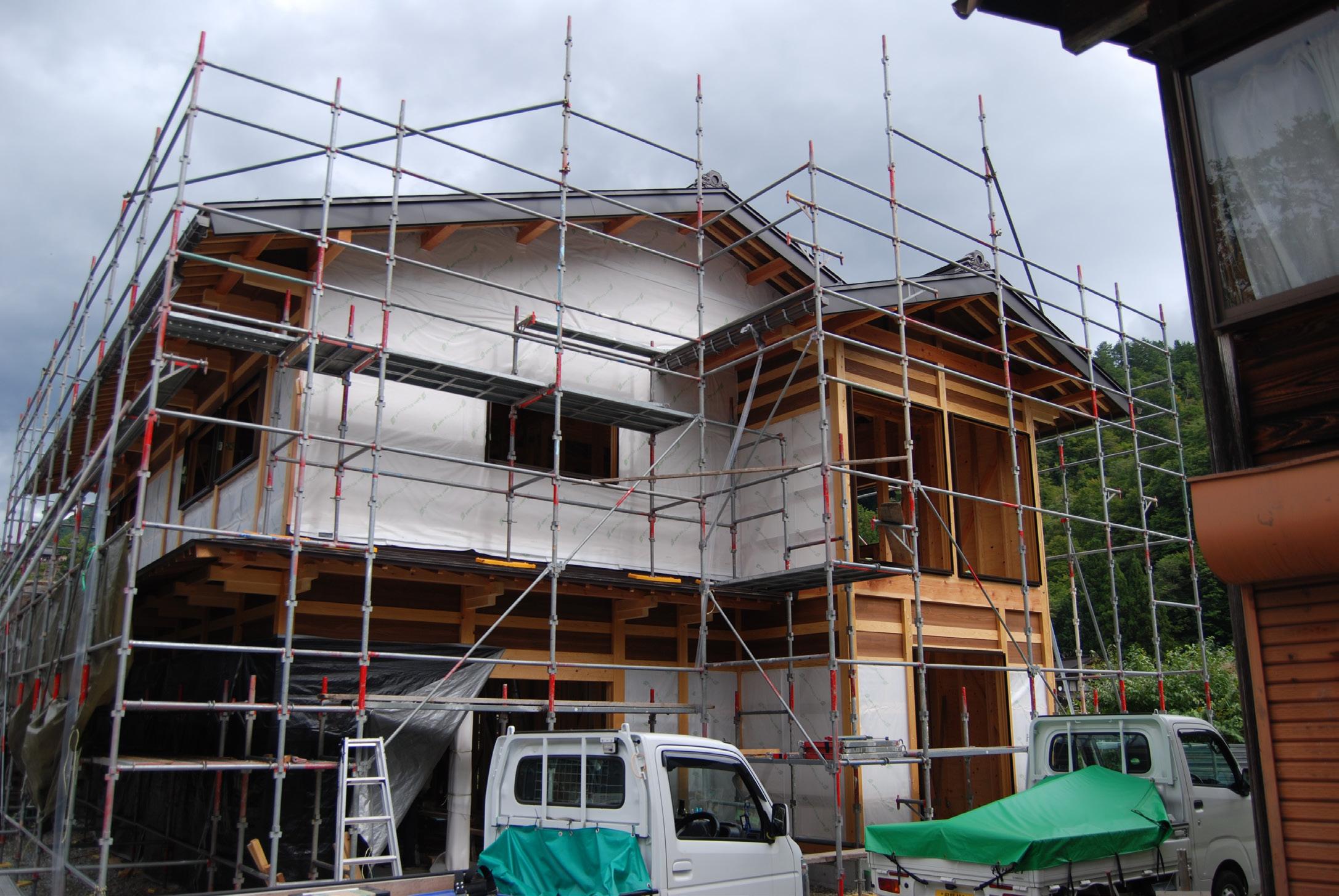
New-build Japanese Timber Framed House under construction
Old Japanese Timber framed house
A HOMAG Homage, Courtesy Of A Small Business Owner INDUSTRY
Ian Woollard, Owner of the family-run Woollards of Mildenhall, was recently interviewed regarding the purchase of HOMAG’s EDGETEQ S-300. He spoke with such eloquence not just about machinery, but about HOMAG in general, that he more or less encapsulated what it means for a small business to partner up with the woodworking giant. With a special thanks to Ian, here’s the full story.
ABOUT THE COMPANY
Woollards of Mildenhall is a small family-run business that has been creating high-quality, bespoke kitchen, bathroom, and bedroom interiors for over 75 years. With a reputation for personal, dedicated service, Woollards has always prided itself on delivering exceptional craftsmanship.
MACHINE LEARNING
When the time came to upgrade their machinery, the company’s first thought was HOMAG. “We needed a new machine to replace an old faithful,” Ian Woollard explains.
“We had a HOMAG edge bander 17 years previously which had worked pretty much flawlessly throughout that period of time.
“Right from the get go, going back to when we purchased that original machine, it was always the HOMAG way to understand a business before they recommended the machines to be considered – machines which would lend themselves to current need as well as potential need for a growing business.
“When you start off with an edge bander, or any machine, when you haven’t had the benefit of it before, you don’t really appreciate the true value that machine brings to your business – until you’re using it. HOMAG, of course, know exactly what their machines are capable of, and they share this wisdom with you in a way that doesn’t feel forced. These machines open doors, but it’s the people behind them who show you the way through.
“Anyway, after 17 years of it, we were no strangers to edge banding and all the benefits it brings to our small business. But nothing lasts forever, and the time came for us to invest in something new. Although, having said that, our old edge bander has since been recommissioned, and is now with another small business over in Norfolk. They’re thrilled with it, and for us it’s great knowing its lifespan has been expanded with another family business. But I digress!”
DISCOVERING THE EDGETEQ S-300
“So we were in the market for a new machine, and to be frank, there was never any question of looking anywhere other than HOMAG – we’d been so delighted with everything they had done for us up until that point.
“Our minimum requirement for the new edge bander was that it needed to do everything the old one did. We also suspected there may have been one or two
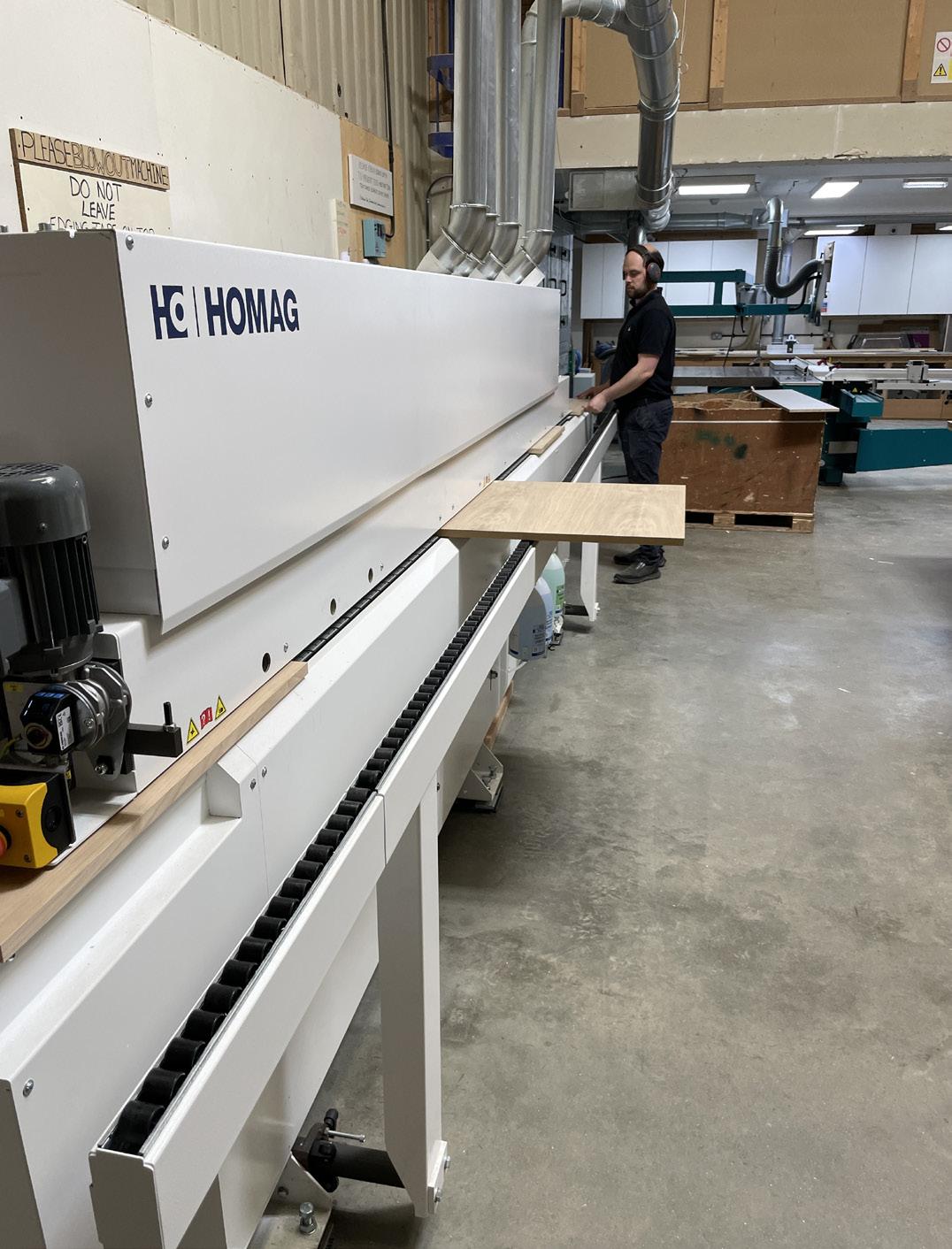
advancements in edge banding technology since the early 2000s, so we were more than happy for HOMAG to educate us on those advancements and the benefits they could bring.”
For Woollards, the relationship with HOMAG has always been more than just about the machines. “As a HOMAG customer, you benefit from a gentle relationship of service. Not only do they keep your machines in good nick, they’re also a great source of information with regards to recent developments in the market.” Guided by the expertise of HOMAG technicians, it wasn’t long before Woollards had their sights firmly set on the EDGETEQ S-300.
THE TECHNICAL EDGE
The EDGETEQ S-300 offered not only familiarity but also added benefits, thanks to the advancements in edge banding technology. “The most noticeable improvement with the EDGETEQ S-300 is a greater level of accuracy. The fine tuning of all the tooling, the output of the machine, the consistency… it’s next level. We were really impressed.
“We’re also really enjoying the ease of use and the adjustment. The software probably deserves an article of its own – honestly, it’s a delight. Remarkably intuitive. Altogether, in our experience, the system is flawless. From start to finish the edge banding process has become seamless.”
INSTALLATION AND TRAINING
The installation process was equally as smooth. Ian recalls, “The guys who delivered and installed the machine were highly professional individuals. And very friendly – they didn’t mind us being specific and awkward! For instance, we asked them to reposition the machine three times, which they did without complaint. In fact, like us, they were determined to get the positioning just right, down to the millimetre.
“HOMAG then disseminated two tiers of training – an advanced level of training for myself and my eldest son David, covering the administrative detail of the machine which we didn’t want to burden the wider team with, and a more basic level which provided the necessary information for our operators to use the machine effectively.”
This programme was devised and co-ordinated by Carl Mullins from HOMAG. “Carl was exceptionally good at understanding our operation,” Ian reflects. “We were honestly amazed at the extent to which he tailored the training to our specific needs.”
PRAISE FOR THE PEOPLE
“Everyone from HOMAG, particularly those we dealt with directly, is worthy of praise – Punit Hirani, Charles Smith, Marie Harrison, Kyle Smith, to name a few. But I want to give a special mention to Carl Mullins. He really embodies the professionalism of the HOMAG brand, working with a
level of care and attention that has benefited our business beyond measure.
“No matter who you deal with at HOMAG, the calibre of the people is a great reflection of the calibre of their machinery. We’ve never encountered someone who hasn’t made time for us, who hasn’t been patient, who hasn’t either been able to answer a question or ask us to bear with them as they seek the solution that’s right for us.”
FINAL THOUGHTS
Ian Woollard concludes, “We found in HOMAG a partner who we can readily identify with, who understands our needs, wants, and our direction of travel, who can even help with the steering of our business moving forward. For us, HOMAG was, is, and always will be the staple choice.”
If you would like more information or a demonstration of any of the HOMAG machinery and software, please contact Adele Hunt at HOMAG UK on 01332 856424.
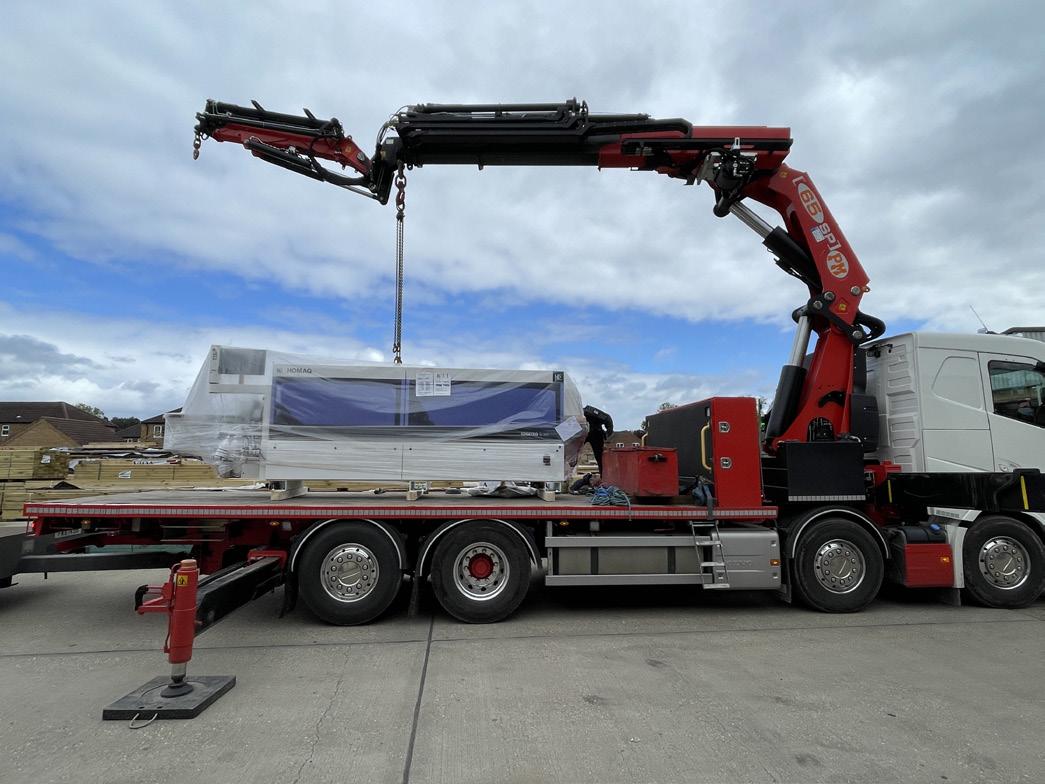
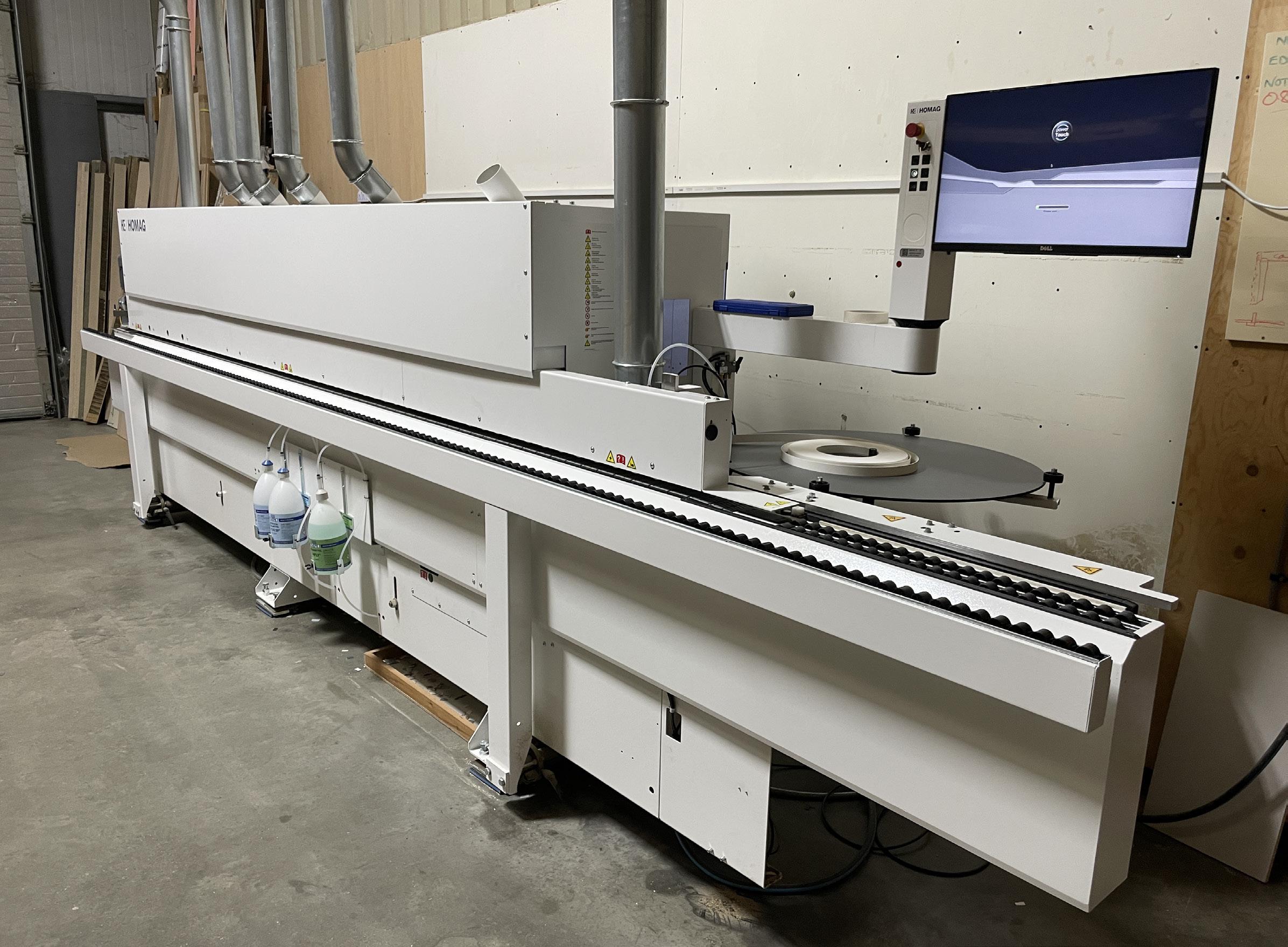
By
ONLINE AUCTION
Woodworking Equipment & Display Kitchens
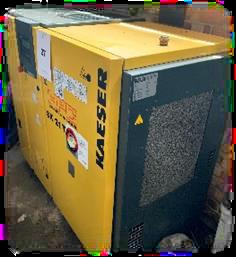
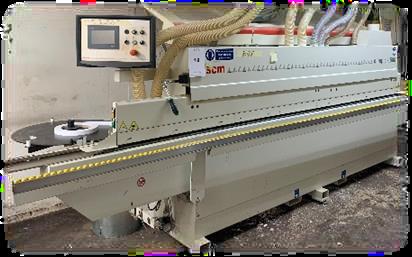
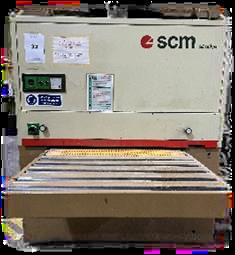
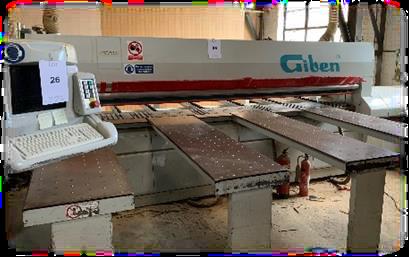
including: SCM K560 edge bander, SCM MiniMax spindle moulder, SCM Sandya CS110 wide belt sander, SCM MiniMax Unilev-150 edge sander, Biesse Rover 20 CNC machining centre, Giben 2 SP H.100 beam saw, a Rojek table saw, Blum Minipress P drilling/insertion machine, Magic MT3 spindle moulder, 3 Fercell vacuum tables, a large quantity of hand power tools DeWalt, Festool, Makita, Bosch, Mac Allister, Draper, dust extraction systems and air compressors, work trolleys, paint spray booths and equipment, a large quantity of stock including Blum fixings, wood profiles, sheet material and edge banding materials, Various quality fitted kitchen & furniture displays and Italian leather designer chairs
On view by appointment only on Tuesday 3 December
At: Hyperion Wall Furniture Limited (In Liquidation), Business Park 7, Brook Way, Leatherhead, Surrey KT22 7NA
Bidding Closes: Wednesday 4 December from 3pm
Further information, registrations and online bidding available at: www.marriottco.co.uk/auctions
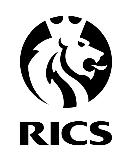


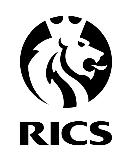
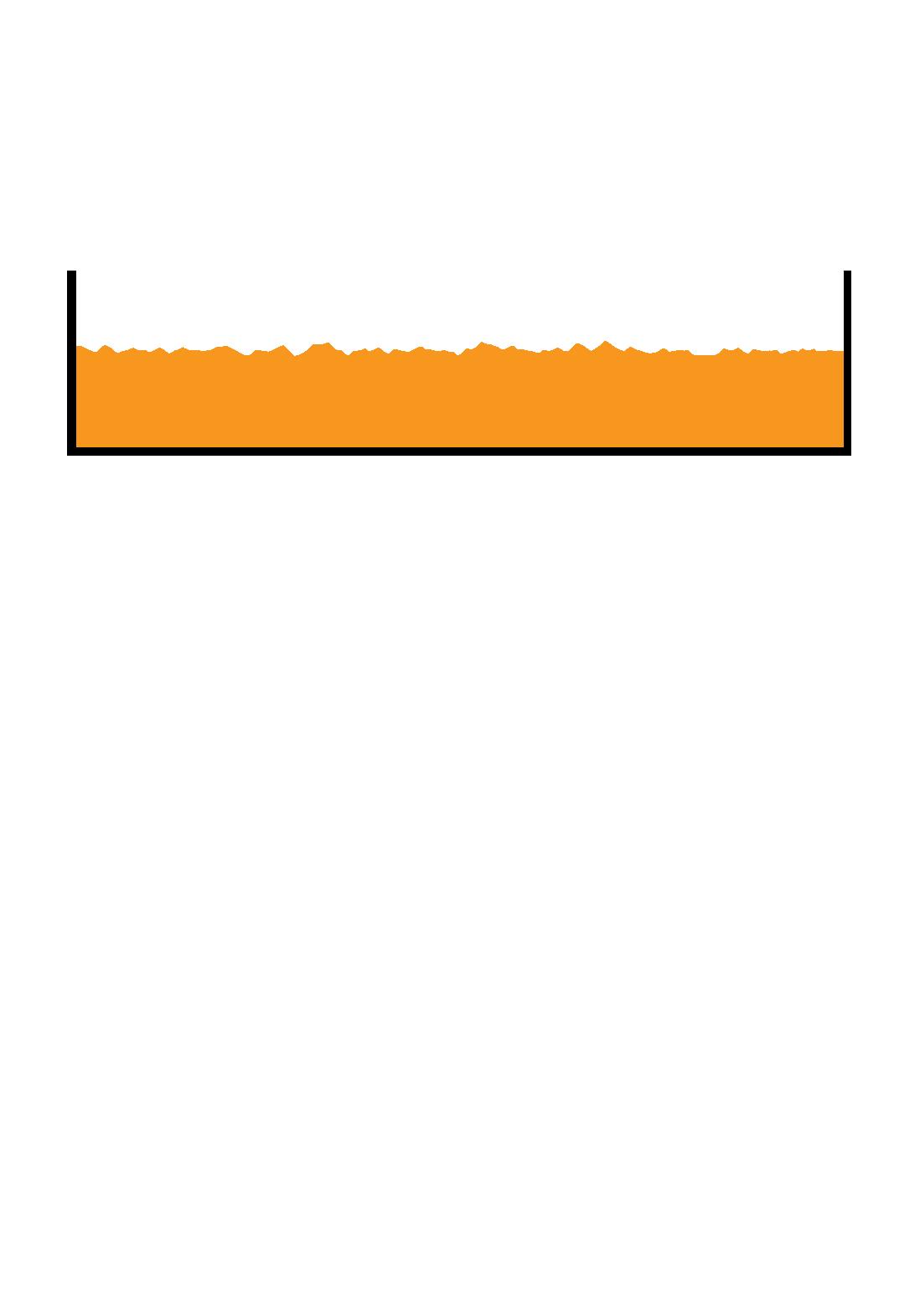
Driven By Passion, Powered By People.
People, investment, and growth are the three key factors in the enhanced strengths of the Panelco team this year. Add extensive premium product collections, prominent levels of service, and superior facilities on site, and you have a winning combination for the latest enrichments to the already well-established teams.
Working together so closely is the real success behind the development of the Panelco team. With multiple new members across all parts of the business and branches, this is an exciting time for all at Panelco. Collaboration and support for each other are vital to our communication, as this ensures clear feedback and insights so we can provide a collaborative environment where everyone has a role to play. Consistency is vital; an open channel environment ensures clarity and successful strategies.
Always with common goals, the Panelco team works well together, sharing insights, thoughts, and ideas to motivate each other for collective success.
Training and development within the business mean that we are fully up to speed with new products and services within the Panelco group. Innovation is key, and given the latest product developments in 2024 alone, our teams have
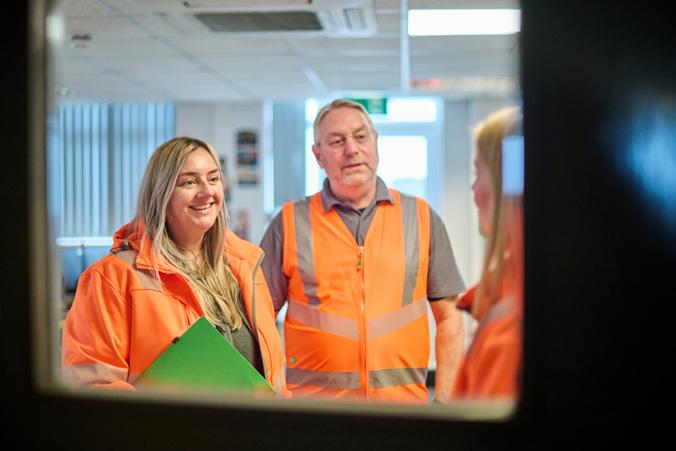
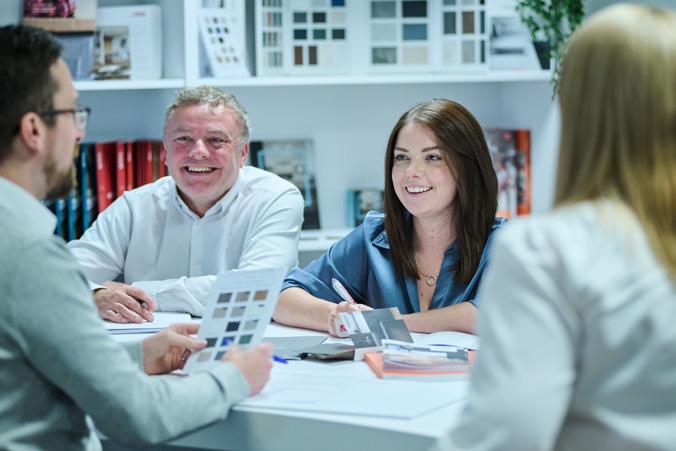
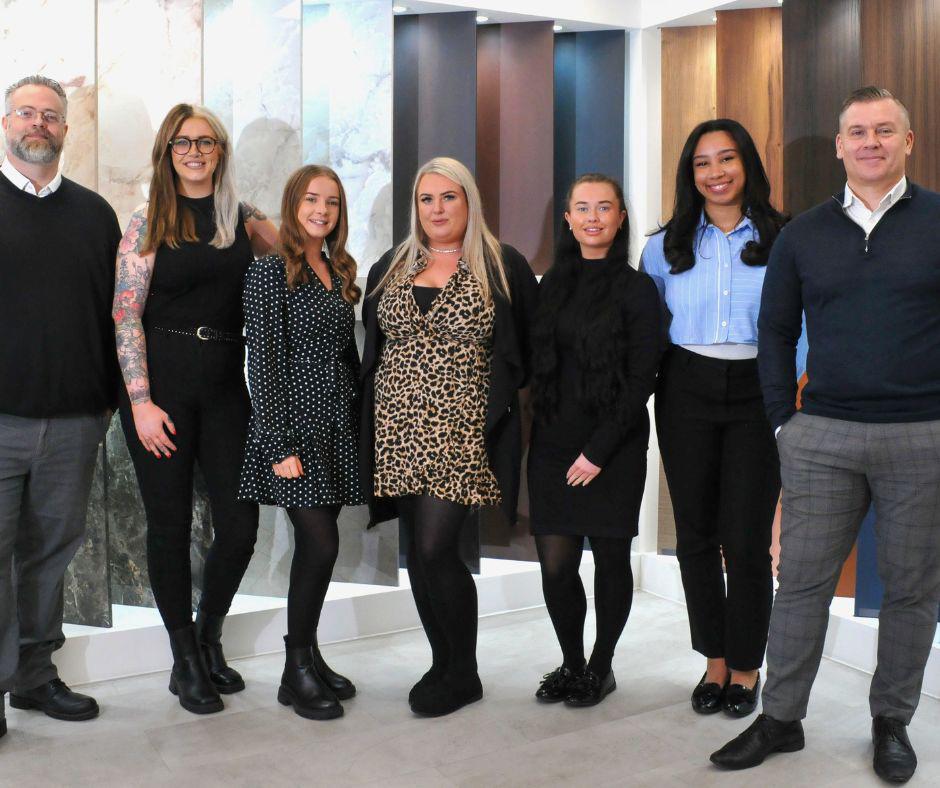
worked tirelessly together to provide the latest updates to our collections.
A positive culture encourages motivation and teamwork, and our close-knit team is apparent to everyone who visits and spends time at our facilities. This encourages seamless relationships among all involved and enhances a thriving work environment, increasing productivity.
Building solid relationships is a time-honoured focal point. Understanding customers’ needs and preferences is critical to long-term loyalty and mutual trust. We strive to improve consistently and always listen to our customers’ needs. Now, with our most substantial teams across four branches, we can support and help more than ever. Partnered with the leading manufacturers in our sector, we continue to provide the latest and most innovative products with what we believe is the strongest and friendliest team.
Panelco, the Perfect Partner
To contact Panelco regarding any of our latest products, to book a visit to our design facilities or for a chat, contact your local branch.
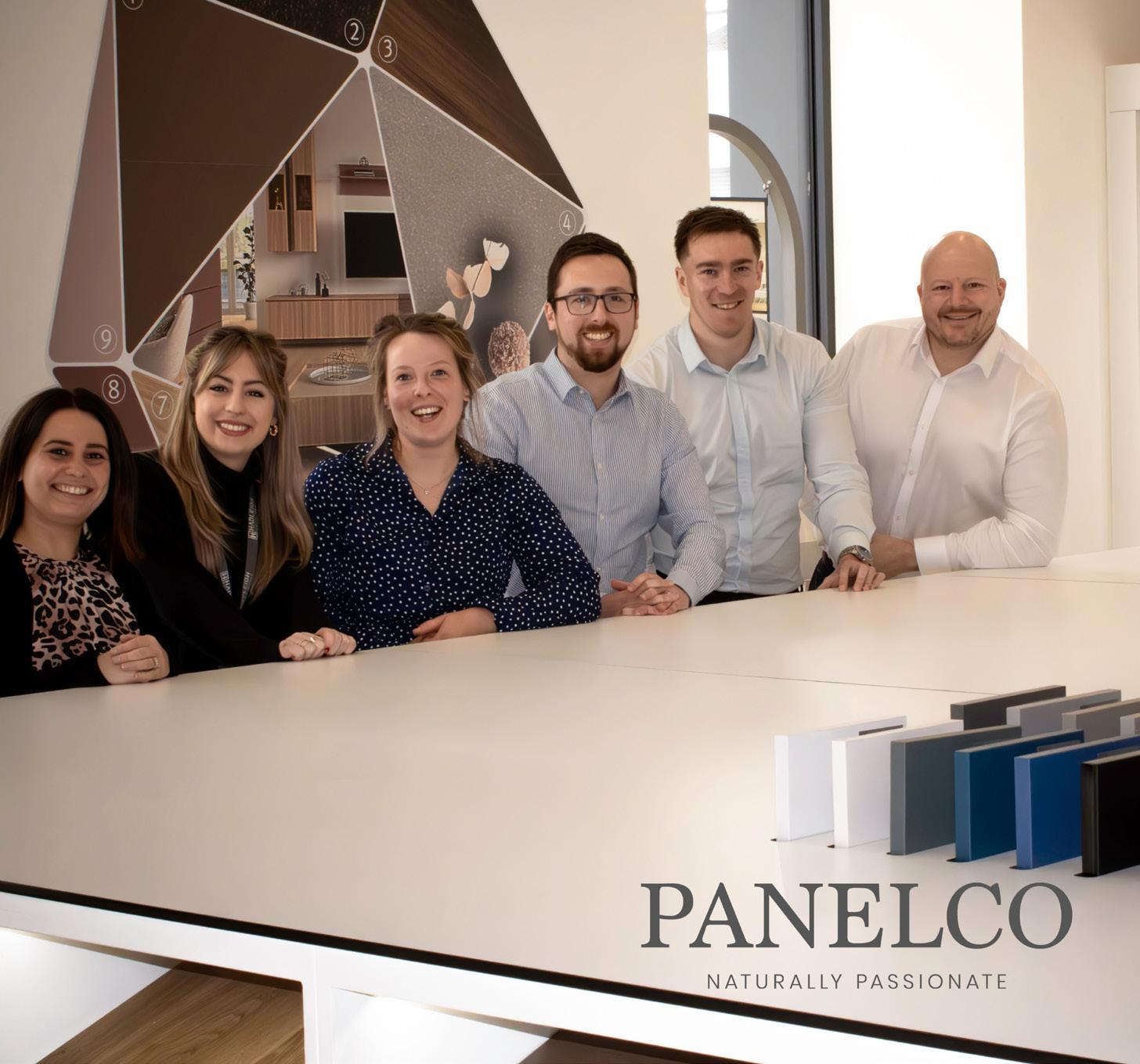
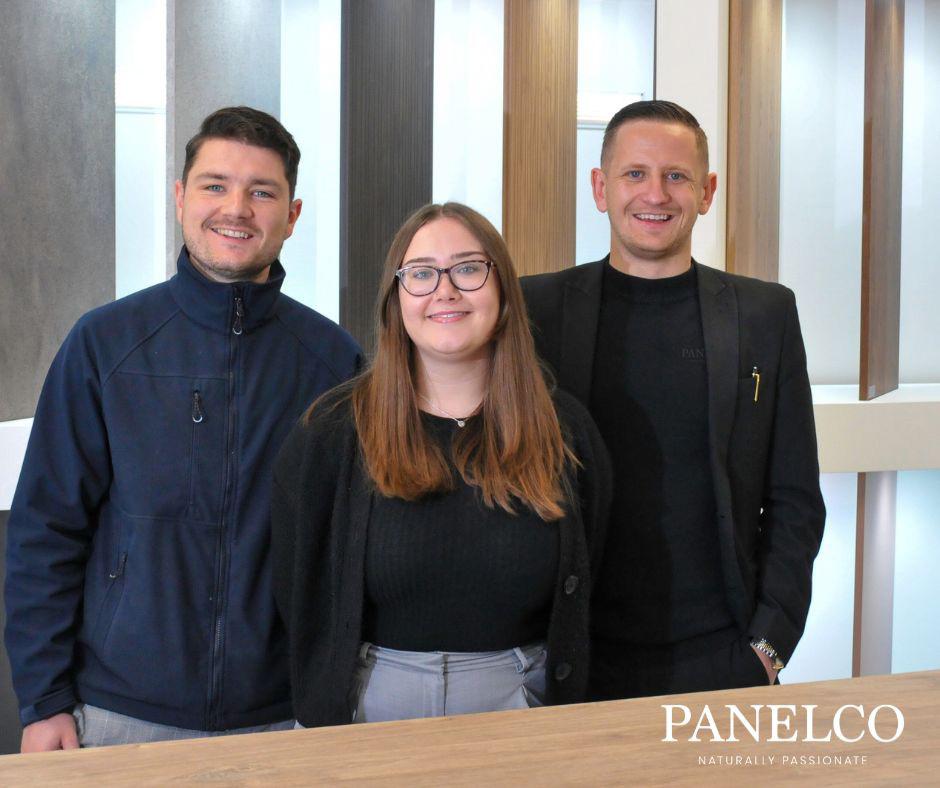
Introducing Latham Timber Manufacturing INDUSTRY
Dresser Mouldings rebrands to Latham Timber
Manufacturing with a refreshed proposition, an upgraded plant, and a new, cutting-edge cladding visualiser. Today, James Latham, the UK’s leading independent distributor of timber, panels and decors, announces the rebrand of their Rochdale-based timber mouldings and cladding specialist, Dresser Mouldings (Dresser) to Latham Timber Manufacturing (LTM).
This move is a key milestone in the James Latham Group’s strategic objective to bring all its subsidiaries in line with the overall family of brands, creating a holistic package that will straddle the distribution services supply chain.
James Latham acquired Dresser in 2019 to meet the rising market demand for machined mouldings and cladding, a trend that has only continued to grow since. Over the past five years, the business has built on its unrivalled reputation for quality, creativity, and consistency, working with high-profile clients to develop decorative and finishing solutions across a wide variety of sectors. This ranges from intricate bespoke carving and cornicing to Award Winning cladding products and through to high-performance, ultrasustainable curtain wall systems.
As LTM, the business will continue to deliver the same best-in-class services customers have come to expect, whilst benefitting from significant investment provided by the James Latham Group. This has been seen in the major upgrades made to plant equipment, which now possesses the very latest state-of-the-art machinery, increasing capability and efficiency without compromising on finesse. David Johnson, General Manager at LTM says, “Since James Latham acquired Dresser, they’ve provided incredible support to help enhance the business and broaden both our scope and ambition. Put simply, these experts are deeply rooted in the timber trade, fully understanding the challenges we face and recognising opportunities as they arise. They continue to help us, whether physically or digitally, to evolve our proposition, maintain our appeal, and make serious in-roads into existing and emerging markets.”
VISUALISING SUCCESS
James Latham has long been a leader in digital innovation, and to mark its new brand identity, they have introduced a cutting-edge online tool: the James Latham Cladding Visualiser. A powerful new platform, it builds on the success of the distributor’s award-winning Digital Showroom,
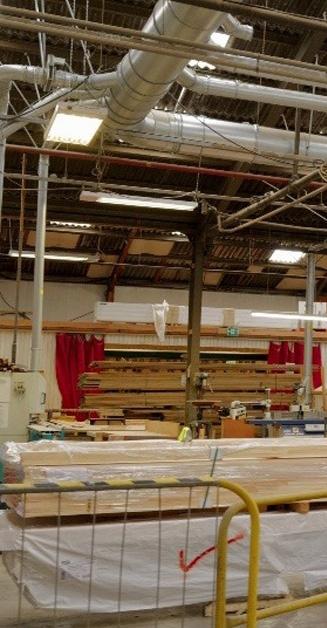
providing architects, designers and contractors with an opportunity to see how its cladding portfolio looks in application, ahead of specification.
Developed with long-time design partner, Cyon Agency, the site empowers James Latham’s influencers and purchasers to see a wide array of materials, tones and colours under a variety of lighting conditions on different building types. Featuring leading brands, including Accoya, Shou Sugi Ban, and James Latham’s own multi-award-winning Finish Line collection, users have a near unrivalled scope and freedom to see what the exterior finish of their development will actually look like.
TAKING IT UP A NOTCH
Whilst other cladding visualisers exist, what sets James Latham apart is its use of high-definition photographic renders of the actual materials, resulting in a true-to-life replica of what each product will look like on a building façade.
The authenticity of the in-person specification journey is another advantage. Many visualisers already on the market have poor functionality and, as customer experience is at the heart of the James Latham proposition, ensuring that showroom feel, was at the heart of the project. That’s why users have wide-ranging freedom to explore different materials, colourways, and lighting conditions. By creating a user profile, visitors can save their concepts, arrange sample deliveries, and even schedule a video meeting with a LTM cladding expert to discuss their selections.
As James Latham’s Timber Director, Andy Duffin says, “The new visualiser is the perfect calling card for LTM, and the services it has to offer. Crucially, it shows how we’re constantly listening to our audience’s requirements and looking for ways to give them exactly what they need to make the most informed choice possible, regardless of time or location. As we continue to grow our share in the facades market, the new identity and cutting-edge visualiser platform positions us to compete for more business, ethically and sustainably.”
As of 00:01 on Monday 4th November 2024, Dresser Mouldings assumes the name Latham Timber Manufacturing. The division will continue to be headed up by David Johnson reporting to Andy Duffin at James Latham Group. There have been no personnel or day-to-day operational changes.
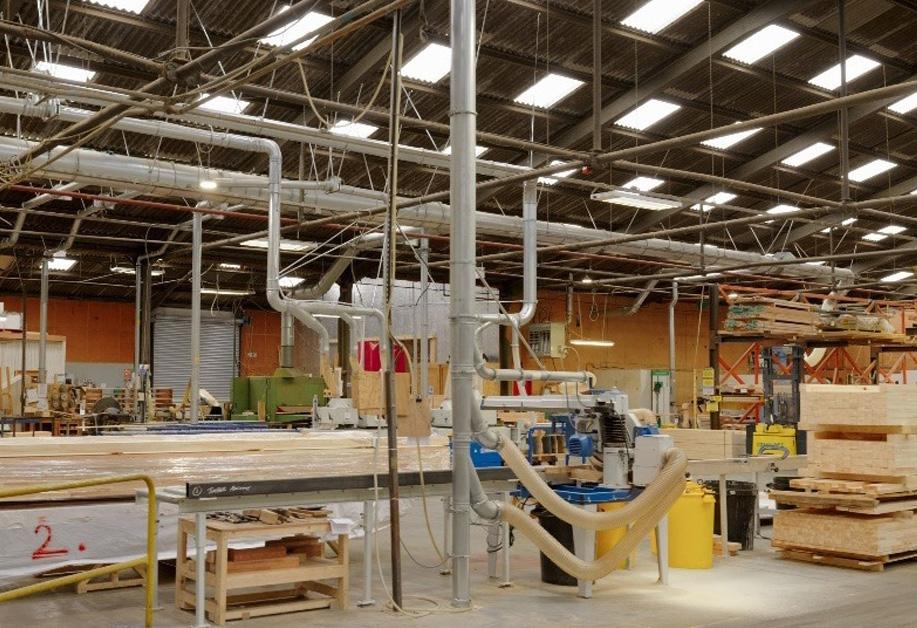
EVENTS 2024
November 2024
17 Nov - 19 Nov
North of England Woodworking Show
Yorkshire Event Centre
Harrogate
December 2024
6 Dec - 7 Dec
VWM Open House
VWM Ltd, Lodgeholme, Skipton Road, Trawden Nr. Colne, Lancashire BB8 8RA
EVENTS
2025
January 2025
19 Jan - 22 Jan
January Furniture Show
NEC, Birmingham
March 2025
19 Mar - 20 Mar
Furniture Component Expo 25
Telford International Centre
May 2025
20 May - 23 May
May Interzum Cologne, Germany
26 May - 30 May
May Ligna Hannover, Germany
October 2025
12 Oct - 15 Oct
Decorex
Olympia Events, London
14 Oct - 17 Oct
SICAM 2025
Pordenone Fiere, Italy
2026
May 2026
17 May - 19 May
Materials & Finishes Show
NEC, Birmingham
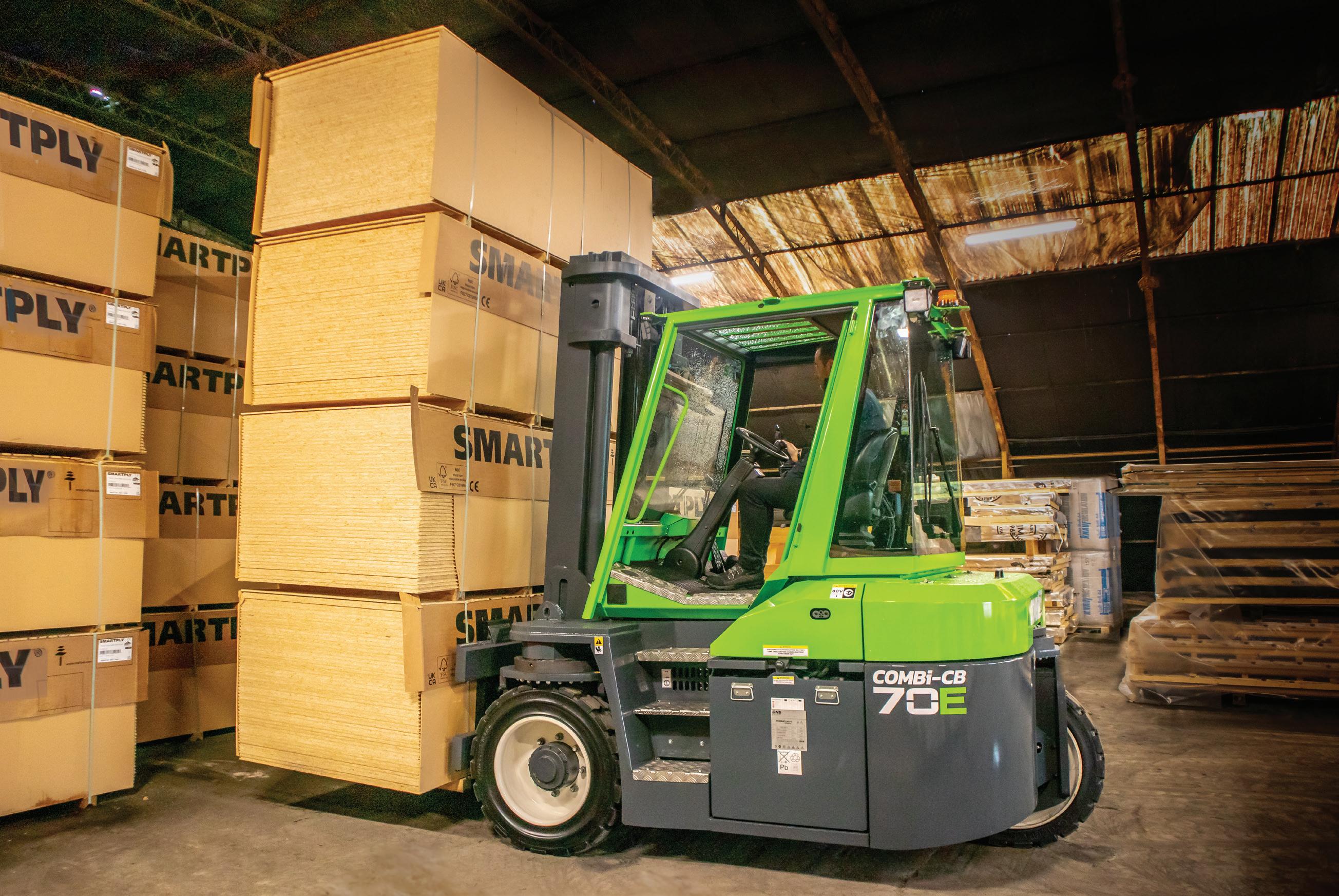
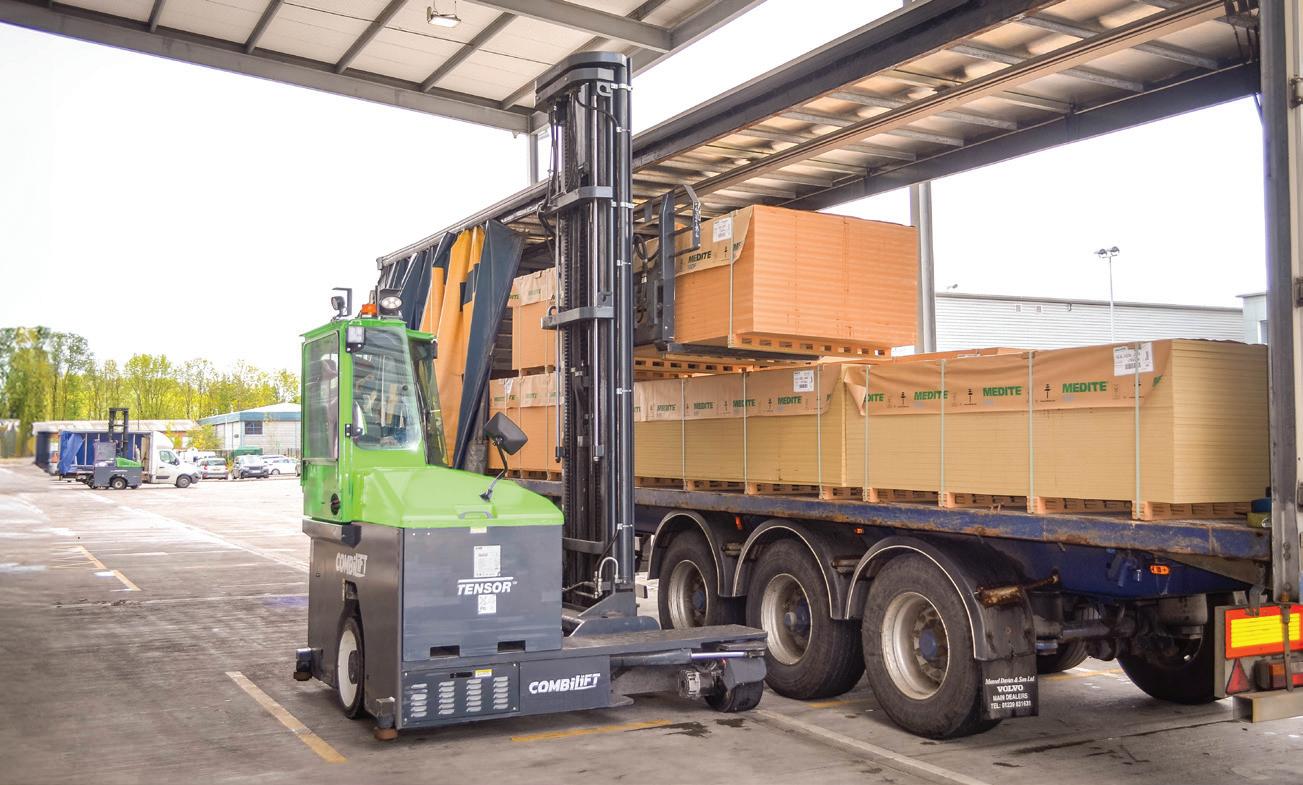
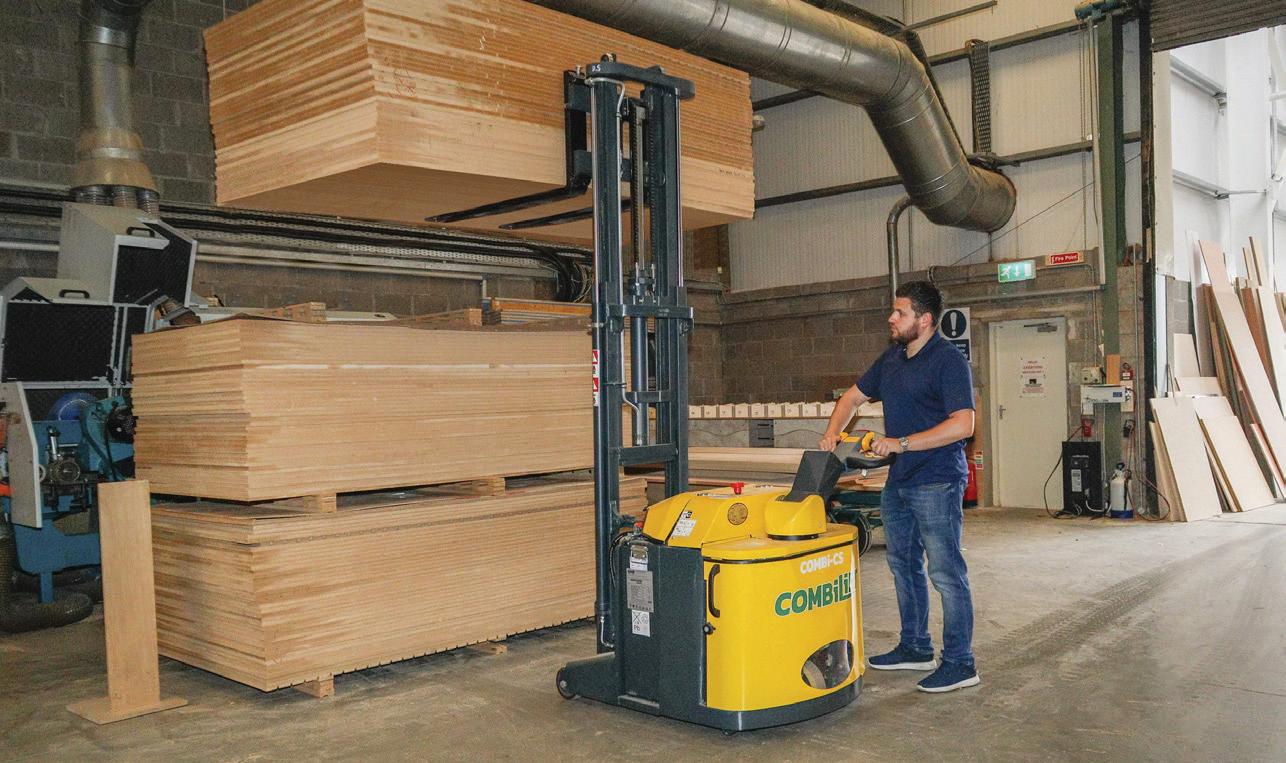
ENHANCE THE SAFETY, STORAGE AND EFFICIENCY OF YOUR LOGISTICS WITH COMBILIFT
For 25 years, Combilift has been revolutionising the way companies handle and store goods. We help companies of all sizes and from every industry to maximise the capacity, safety and efficiency of their warehouse and storage facilities.
Our pioneering product range of multidirectional, articulated and pedestrian forklifts, straddle carriers and container loaders allows you to manoeuvre long loads safely, reduce aisle widths and increase the amount of space available for storage.
CONTACT US TODAY
To find out how Combilift can help you unlock every inch of your storage space.
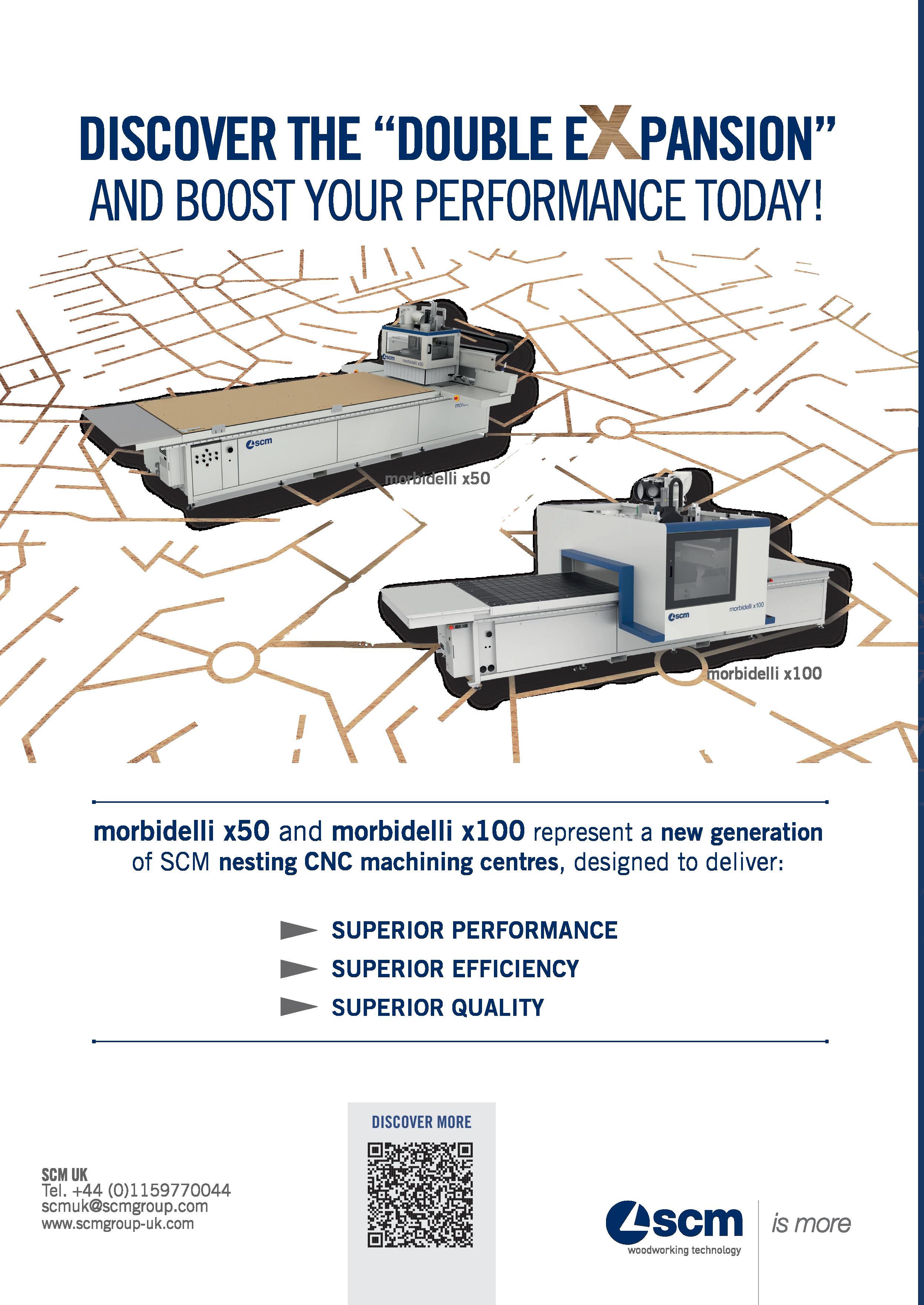