Timeless glass designs with the unrivalled strength of crystal
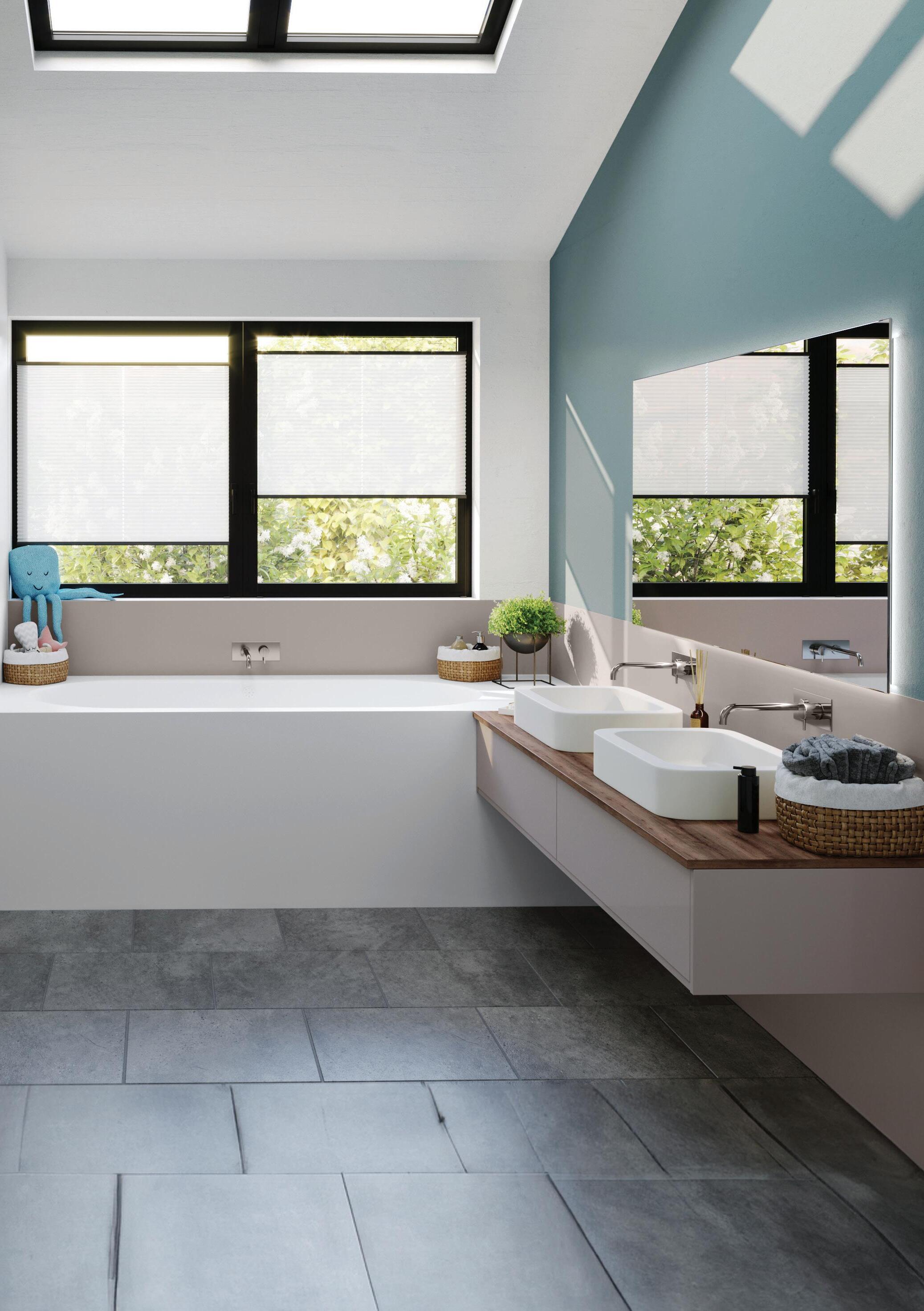
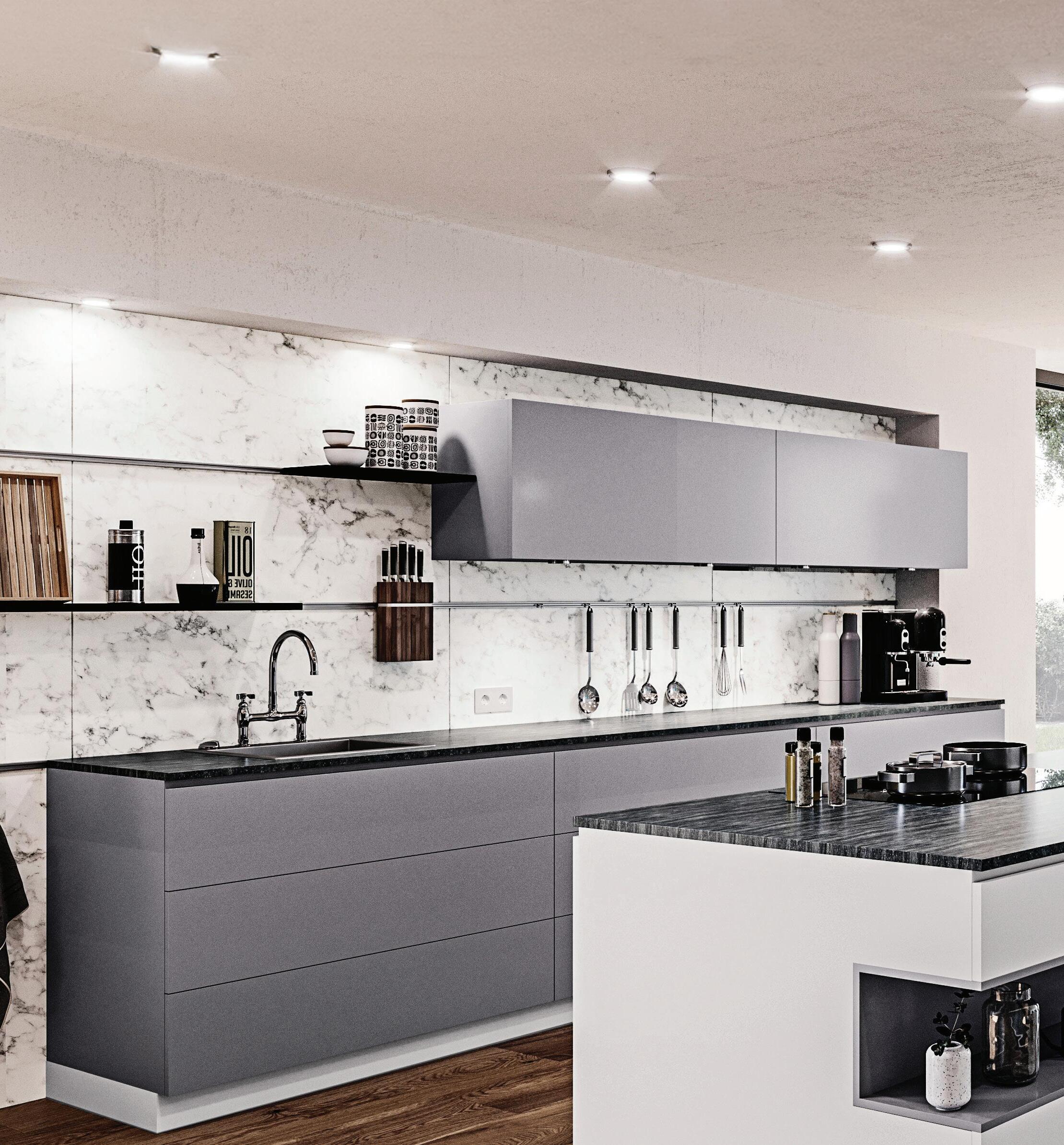

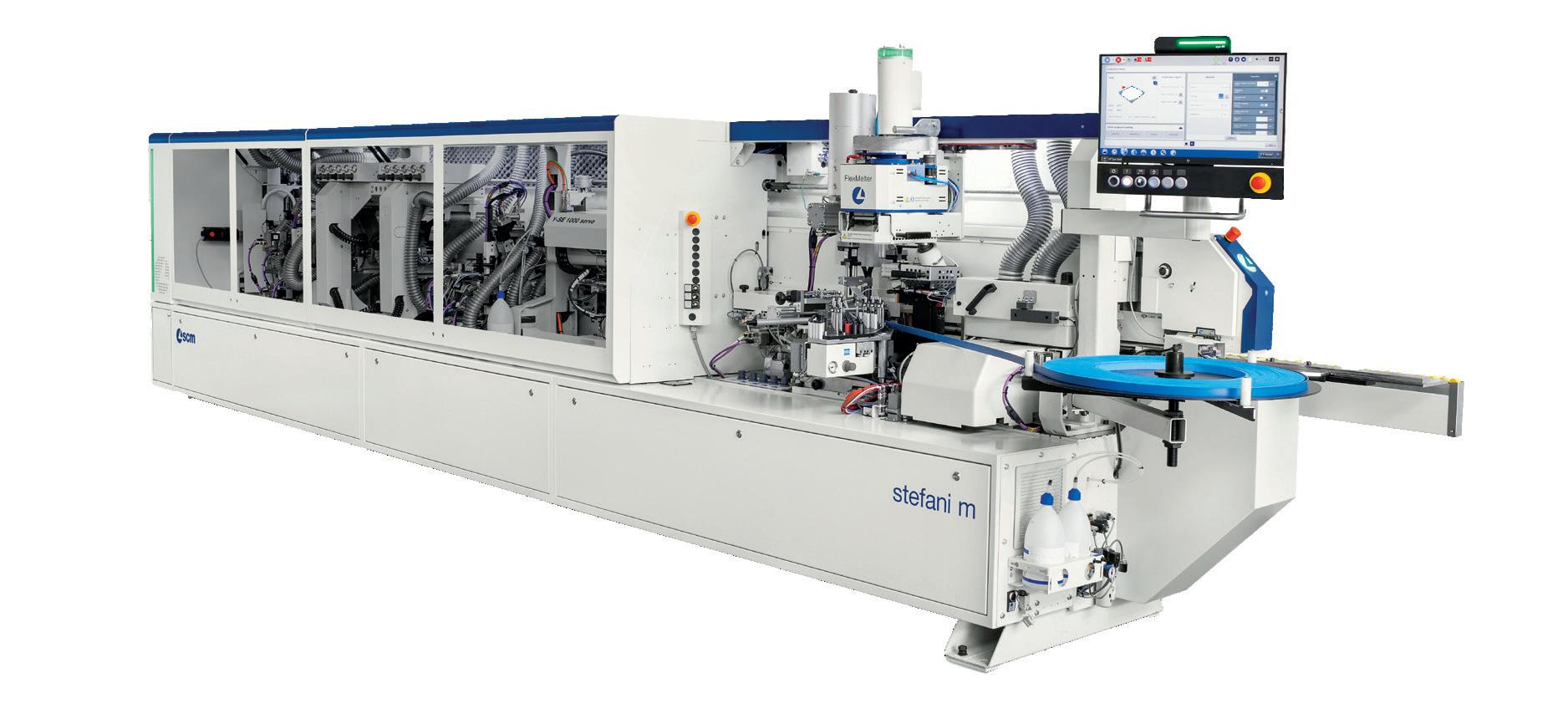


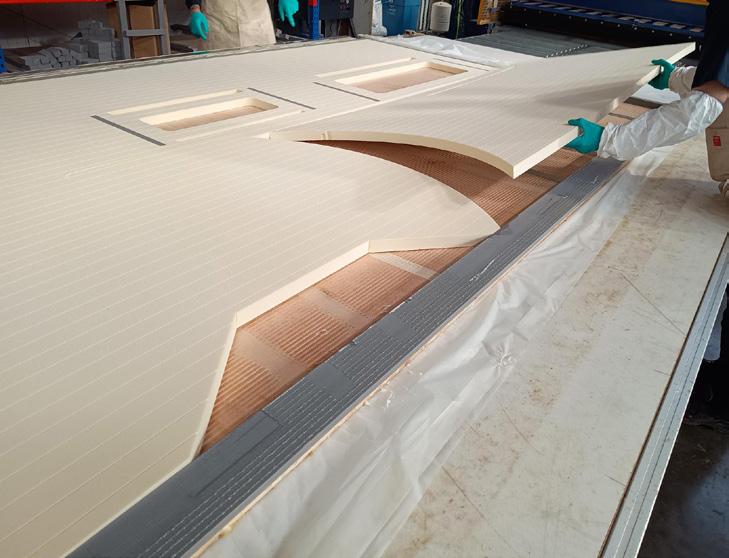
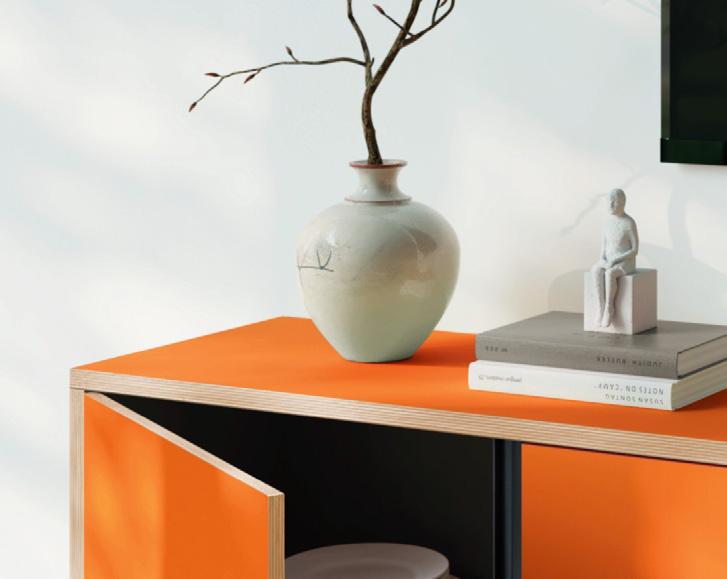
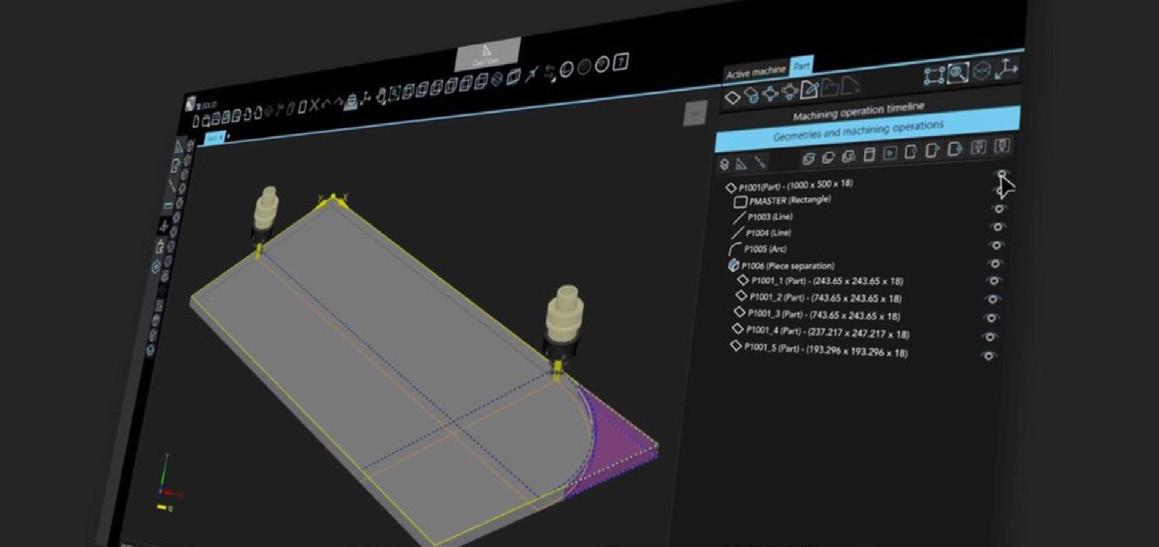
Timeless glass designs with the unrivalled strength of crystal
Matthew Rutherford, an apprentice carpenter from Bangor, County Down, wins national award. The apprentice carpenter wowed judges with his passion for restoring older buildings. Matthew takes home the Screwfix Trade Apprentice 2024 title and a careerboosting £10k prize bundle including tools, technology and training.
Matthew Rutherford, currently employed by Laird Contracts Ltd, has been named Screwfix Trade Apprentice 2024 champion.
At just 19 years old, Matthew successfully competed in the national final against nine other top apprentices from across the UK and Ireland. Fighting off fierce competition, Matthew walked away with the coveted trophy and a career-boosting prize bundle of tools, tech and training worth £10,000.
During the two-day final, which took place in London, UK, Matthew wowed the panel of industry judges, including representatives from Screwfix, the National Inspection Council for Electrical Installation Contracting (NICEIC), the Chartered Institute of Plumbing and Heating Engineering (CIPHE) and the Federation of Master Builders (FMB. After A-levels knowing his passion was in carpentry, he enrolled at South Eastern Regional College in Newtownards to study Carpentry and Joinery.
During the final, Matthew spoke passionately about preserving and restoring the UK’s existing buildings, particularly residential properties that would otherwise be demolished. Hoping to breathe new life into older properties, Matthew sees his future in the renovation market and wants to build his own portfolio of renovated properties for the Northern Ireland rental sector.
Matthew also won the judges over with his thoughtful response to the pre-final task – designing a tool that would make a tradesperson’s life easier. Matthew devised a proposal for a product called ‘DoorMate’ which addressed the common problem of hanging doors correctly.
Matthew said: “I’m so honoured to be Screwfix Trade Apprentice 2024. When they announced my name as the winner I couldn’t believe it, it felt completely surreal. I just love my job and I am constantly inspired by my surroundings.
“I think a lot of people believe a career in the trades is for those who can’t get into university, but I’ve chosen to follow my passion for carpentry – I get to work on something different every day and it’s helped me grow my confidence and skills so much.
“I’m the first Screwfix Trade Apprentice from Northern Ireland, so it feels great to be representing my country. I’d love to inspire others to take up a career in the trades, and I hope to be able to take on my own apprentices one day.”
With an incredibly high standard of finalists in this year’s competition, for the first time, the judges decided to award two Highly Commended recognitions at the final to Jindara Scott and Ethan Wynn.
Simon O’Mahony, Director of Marketing Communications for Screwfix, who also was a judge at the final, said: “We are now in the tenth year of Screwfix Trade Apprentice, an important award that recognises the very best trade apprentices in the UK. This year more than ever, the calibre of entries were particularly high. Every one of our finalists is a credit to their trade and the future of the industry.
I’m really looking forward to Matthew being an ambassador for Screwfix and for apprenticeships in the trades. We urgently need to address the skills gap in the construction industry and nurturing fresh, new talent is key to achieving this.”
Screwfix Trade Apprentice 2024 received 1,800 entries this year.
To find out more about the award please visit www.screwfix.com/landingpage/tradeapprentice
AJB Group are delighted to announce the launch of Rockingham Doors, an exclusive range of high end bespoke timber doors; hand made to order and designed to compliment and enhance beautiful homes. Their internal door collections are carefully crafted by their skilled team with all their timber sustainably sourced and carefully selected to ensure the highest possible finish. All Rockingham Doors are made in the United Kingdom in their Corby based factory.
The bespoke range of doors are made to order with an estimated delivery time frame of 3-6 weeks and the company also offers bespoke door frames to compliment the doors. AJB Group pride themselves on delivering a unique and bespoke finish to all their products.
Amarjit Binji, CEO of AJB Group, quoted: “We are delighted to add Rockingham Doors to our portfolio. Complimenting and enhancing beautiful homes is our expertise. We invite potential customers to visit our website to find our more and we are always happy to answer any questions they may have.”
Angie Rains, Interior designer, said: “Quality of craftsmanship and finish are at the heart of Rockingham’s ethos. Careful consideration is given to every detail of your door requirements to ensure a superb, bespoke product is delivered to site every time.”
Strategic closing with a view to enhancing the offer in the field of nindustrial systems with high innovation, productivity and flexibility.
Scm Group, a leading multinational in technologies for machining a wide range of materials, signed an agreement with Tecno Logica to take over control of its share capital.
This is a strategic operation which expands the range of products and services offered by the group from Rimini with integrated modular and scalable systems, for large automotive, furniture and door production manufacturers.
Tecno Logica is based in Treviso and is one of the main manufacturers of highly productive and flexible systems for a wide range of industrial processes, with over 200 installations in Europe, the Middle East, Mexico and the USA and has a turnover of more than 30 million Euro.
Marco Mancini, Scm Group’s CEO points out that “this buyover further enhances our leadership in the aluminium, composite and wood machining sectors where we are already present with our Cms and Scm brands. Further options at the top end of the market open up with an opportunity to get ahead of new trends and innovate our offer even more strategically”.
“Becoming a part of a solid multinational organisation like Scm
-
Piasentin, CEO of
will provide greater access to leading clients around the world thanks to the group’s direct presence and capillary sales and assistance organisation”.
www.scmgroup.com
Over 400 tools added
Delivering a choice of high quality hammers, wrenches, hand saws, circular saws and screwdrivers through to tapes, abrasives and much more!
The BWF Awards recognise those leading the charge on sustainable practices with launch of new BWF Sustainability Award category
Entries have now opened for the British Woodworking Federation’s (BWF) Awards, with the event set to recognise and celebrate the outstanding skills and talent, projects and manufacturing achievements within the woodworking and joinery sector of the last year.
This is the 16th year that the prestigious annual awards have taken place, with this year marking the launch of a new category– the BWF Sustainability Award.
Helen Hewitt, Chief Executive of the BWF, said: “We’re excited to introduce the BWF Sustainability Award to honour those leading the charge with sustainable practices.
“Our profession is in a unique position with timber being the only truly renewable building material, and through the Timber in Construction Roadmap we can play a key role in the Government’s net zero ambitions by safely increasing the use of timber and reducing embodied carbon in the built environment.
“To support this low carbon vision, it’s also important to champion the woodworking and joinery businesses taking a proactive approach to sustainability. The new BWF award will recognise the significant achievements of woodworking and joinery businesses that have reduced their carbon emissions or implemented new and better processes to improve their energy efficiency.
“We’re looking forward to coming together in November to celebrate the very best of the UK’s woodworking and joinery sector.”
Entries for this year’s BWF Awards close on Friday 30th August
2024. Those shortlisted will be invited to attend the prestigious BWF Awards Dinner on Friday 22nd November at The Langham, London –Europe’s first ‘Grand Hotel’.
Businesses can nominate themselves or be nominated by a client or supplier, and there are no limits on the number of categories that can be entered. The categories for this year’s awards, which are free to enter, are:
BWF WOODWORKING PROJECT OF THE YEAR AWARD –SPONSORED BY IMPRA
This award recognises innovation and the very best in design, application and ability in joinery manufacture. Judges are looking for a project that demonstrates excellence in woodworking and joinery and exceeds the usual requirements of joinery products.
BWF INNOVATION AWARD – SPONSORED BY ANKER STUY
This award recognises excellence in technical innovation, product development, design, manufacturing or application. The judges are looking for a product or process development that showcases or extends the opportunity and application of timber joinery by overcoming technical or process difficulties or by introducing new concepts to produce the desired joinery solution.
BWF HEALTH AND SAFETY AWARD – SPONSORED BY NFU MUTUAL
This award acknowledges an individual or collective effort, or initiative, which has made a notable difference to the health and safety practices and culture within a business. The judges are looking for an initiative or action that has improved safety in an organisation.
BWF RISING STAR AWARD – AVAILABLE TO SPONSOR
This award recognises an individual whose dedication and hard work has made a real difference to either the organisation in which they work, or to the wider woodworking and joinery community. The judges are looking for an individual who goes the ‘extra mile’ to ensure that customers receive the best possible experience and has had a positive impact on the performance or efficiency of the business.
BWF HERITAGE PROJECT OF THE YEAR AWARD – SPONSORED BY REMMERS
Recognising excellence in a conservation, restoration or renovation application, for this award the judges are looking for a heritage joinery project that demonstrates excellence in woodworking/ joinery, and evidence that the company contributed to the conservation, restoration or renovation of a heritage project.
NEW: BWF SUSTAINABILITY AWARD – AVAILABLE TO SPONSOR
This award recognises outstanding projects, initiatives or individuals that demonstrate a commitment to improving the company’s environmental sustainability performance. The judges are looking for organisations or individuals that have identified and secured lasting sustainability improvements, demonstrated through evidence that sustainable environmental improvements have been made, and committed to continually improving sustainability through clear processes.
BWF APPRENTICE OF THE YEAR AWARD – SPONSORED BY CITB
Celebrates the achievements of all apprentices within the woodworking businesses. The judges are looking for quality of work to agreed quality targets and standards, a safety-first attitude and extraordinary commitment that has added value to the apprentice’s place of work.
Whether you need edgings and glues, fittings, handles, luminaires, or workshop supplies ... we are your one-stop shop. Are you already familiar with our entire product diversity and appropriate services?
For further information, go to www.ostermann.eu and type in
Organisers of Materials & Finishes Show (formerly W Exhibition) are celebrating after the hugely successful return of the UK’s trade show for the furniture manufacturing and joinery industries (Birmingham NEC 19 - 22 May 2024.)
Over 6,000 visitors attended Materials & Finishes Show marking a conversion rate of over 55% from pre registrants. The audience was made up of joiners, furniture manufacturers and professionals, carpenters and cabinet makers, and business owners and executives who had come to source the latest products and technology on the market.
The event marked the first time that every corner of the UK woodworking sector has had the opportunity to come together, see the latest products and innovations on offer all under one roof, network and do business, since 2018.
Visitors had over 160 brands to choose from on the show floor, with running machinery displayed alongside the latest materials, components, software, tools, fixtures, finishing products and innovations for the woodworking sector.
Over 45% of the exhibitors were overseas brands who had recognised the opportunities that having a presence at the UK’s trade show for the furniture manufacturing and joinery industries presented.
Visitor Josh Hudson, furniture lead for Rycotewood Furniture Learning Centre, said: “It’s great to be able to meet so many people in one place. You’ve got everybody here which means you’re not trekking around the country to meet everybody and it’s the perfect place to make connections with the industry.”
New features, such as the Live Demo Zone and CPD certified learning programme proved a big draw for visitors who were able to participate in over 40 hours of live demonstrations from brands including AMS, Leitz Tooling, The Joinery Network, Lamello, GreCon, Trend Tool Technology and Rubio Monocoat, as well as panel debates and seminar sessions.
Al Parra, BLOQS co-founder and Materials & Finishes Show speaker, said: “We’re really impressed that Materials & Finishes Show is thinking ahead about the future of furniture manufacturing, what that looks like, and were delighted to be invited to participate in the show and discuss this topic in particular.”
The presence of Materials & Finishes Show brand ambassadors, which included self-confessed carpentry, joinery and building fanatic, Robin Clevett, media personality and carpenter, Tibby Singh and fellow online content creators; Peter Millard, Alastiar Johnson (Freebird Interiors), Derek Barrett Design and the Welsh Woodworker, increased the event’s campaign reach by over one million and added a new dimension to the show.
Peter Millard, Materials & Finishes Show ambassador, and owner of 10 Minute Workshop, said: “What a great show this has been! We had a fabulous demo area set aside for us where I worked alongside my fellow content creators. We had some fantastic questions from the audience and I was able to demo my latest 10 Minute Workshop multi jig as well as talk about all of the great technology, such as CNCs, which help smaller makers / installers like me to work more efficiently.”
Event director, David Todd comments: “We’re absolutely delighted with the success of Materials & Finishes Show 2024. We set out to deliver an engaging event, with a broad lineup of brands showcasing thousands of the latest products and innovations for the UK’s furniture manufacturing and joinery industries - and Materials & Finishes Show did just that!
“The feedback we have received from the industry has been hugely positive. The new features that we developed, including the Live Demo Zone, CPD certified learning programme and networking bar, were all really well received by exhibitors and visitors alike. Over 115 people turned up for the first seminar session with Robin Clevett - his involvement as a brand ambassador in the run up to and during the show was invaluable in helping us to curate a programme that would resonate with joiners and carpenters specifically.
Running machinery proved to be a big pull for visitors, with brands such as Advanced Machinery Services, AES Group, Felder, FEN, Vertongen, Kundig, Robland, MARTIN and VWM putting on a fantastic showcase of the latest CNC, drilling, nesting, routing, sanding and cutting solutions. These brands received high levels of interest throughout the show, with four machines sold by the end of the first day of the event.
Owen Dare, joinery consultant for The Joinery Network, delivered a live demonstration of the end-to-end production of a timber window frame utilising an AMS distributed Wadkin Bursgreen woodworking machine and Lignum tooling supplied by Leitz Tooling. Owen said: “Our demo was designed to help joiners become more efficient so that they can make more profit with a very low investment model to grow their business portfolio.
“Materials & Finishes Show provided an ideal platform for joiners to see the latest products and innovations, as well as stay abreast of the latest legislation and regulations for the industry.”
Event director, David Todd concluded: “I’d like to extend my gratitude to our stakeholders, including our exhibitors, visitors, media partners, content creators, speakers and the trade associations who threw their support behind Materials & Finishes Show 2024.
“We’ve set extremely solid foundations in place to build on and deliver an even more successful event when Materials & Finishes Show returns for its next instalment in 2026. We’re increasing the footprint of the show by 30% for 2026 and have already secured a high percentage of rebookings which we’ll be announcing over the coming weeks!”
LEITZ MAKES A STRONG SHOWING AT THE MATERIALS & FINISHES SHOW 2024
Leitz Tooling actively participated in the recent Materials & Finishes Show 2024, held at the NEC, Birmingham. Their presence focused on showcasing their latest innovative tooling solutions for the furniture & joinery markets alongside a heavy focus on their Lignum window and door tooling system with The Joinery Network.
Tooling from Leitz was also featured on Vertongen & Martin machinery on their respective stands.
In addition to exhibiting at the show, Leitz was heavily involved with the new demonstration zone, the seminar theatre and in 2026 will be the official partner to the Materials & Finishes Show.
LEITZ UNVEILS INNOVATIVE NEW TOOLING SOLUTIONS FOR JOINERY AND EDGEBANDING:
The Leitz Tooling stand was very busy over the four show days with a lot of interest over the new HeliCut Monoblock system – a versatile tool designed for drilling and milling within one tooling solution. Taking the concept of shrink fit collets chucks one step further, this unique tool boasts a monolithic design, making the tool very stable and dampening vibrations for lower noise and longer tool life. Equipped with 4 sided turnblade knives for fast knife changes and reduced downtime, the HeliCut Monoblock can be used for various applications such as drilling holes, pockets, tenons and rebates in perfect quality. Eliminating downtime from tool changes between applications and increasing productivity.
Suitable for all types of joinery machines, this tool comes in many variations for mounting on machines; such as HSK variants or a S30 shank. Contact Leitz to learn more.
For edgebanding operations, Leitz Tooling showcased the award winning FlexTrim profile cutter for Homag Edgebanders. Machinists in furniture production today work with a mix of different types of edgebanding materials and thicknesses. With batch sizes becoming ever smaller, this mix of materials and profiles can only be mastered economically with fast profile changes in edge refinishing. Leitz FlexTrim profile cutters allow simple profile changes via the machine control due to the multi-profile technology. This saves time and increases finish quality. With the FlexTrim3, the higher productivity through less adjustment effort is supported by a possible combination of tools running with and against the feed.
The Joinery Network’s Owen Dare demonstrated machining a timber sash window on two Wadkin Bursgreen spindle moulders provided by AMS, twice a day. With one machine set up for profiling and another for tenoning, each demonstration lasted just over an hour and showcased the efficiency and quality of the Leitz Lignum tooling system as well as covering the changing legislation in the industry such as PAS24 and changes to relevant building legislation. “The demonstration zone was probably the biggest success of the show” argues Ben Mitchell, Marketing Manager at Leitz Tooling “It was great to see how much interest there
was for our window making demonstration. We had people from all over the industry attend our demonstration, from joiners and students to kitchen manufacturers.”
The demonstration zone was so popular for The Joinery Network, AMS and Leitz that they ended up running extra slots throughout the week, despite only being scheduled for two demonstrations per day.
“One thing that stood out was the interest from nonjoiners, I think a lot of the topics we covered such as removing the need for sanding and efficient set ups really spoke to pain points from across the industry, regardless of product.”
LEITZ AND THE JOINERY NETWORK DELIVER SEMINAR ON “MAXIMISING EFFICIENCY & MINIMISING COSTS IN JOINERY”
Taking a step back from promoting their own products, Leitz tooling accompanied by Owen Dare (The Joinery Network) and Steve Windscott (Nine Zero Joinery) discussed how joiners can reduce costs and increase profitability through a wide range of topics. The panel discussed preventative maintenance, efficient factory set up, impact of tool sharpening and the future of joinery within their talk at the seminar theatre.
“I think that our talk opened a lot of eyes” says Brian Maddox, National Sales Manager of Leitz Tooling “the problem is, you don’t know what you don’t know. Hopefully today we have been able to pass on some of our experience and knowledge to the market and get woodworkers thinking about the entire set up and production process.”
The UK’s leading laminate supplier All delivered straight to your hands
Dust and fume extraction specialists Extractly Ltd, along with the award-winning ‘extraction-on-demand’ Ecogate® system, were highly visible to potential customers who attended the inaugural Materials and Finishes Show, and gave visitors a double opportunity to meet the team and see the products in action.
As well as displaying equipment and meeting visitors on their own stand, Extractly also supplied, installed and maintained the dust extraction system for the show’s Demo Zone. The centrepiece of the demonstration area was a modular filter unit, powered by an 18.5kW fan, to provide a total extraction capacity of 10,500m3/hour. With Nordfab QF ductwork neatly connecting everything together, including a non-return valve, all dust and woodwaste was safely removed from the working machinery. Perhaps not quite as noticeable to most visitors watching the machine demonstrations, but making a big impact all the same, was the energy-saving Ecogate® technology that Extractly had included in the system.
Although Ecogate® was first introduced to the UK market 14 years ago, at the W10 exhibition, and despite the countless successful installations featured in the woodworking press since then, this is the first time an audience has had the opportunity to see it operating in public, under realistic working conditions. Ian Rayner, UK Sales Manager for Extractly & Ecogate, commented: “With MAFS providing what was, as near as practicably possible, a real working environment for the live demonstrations, it was the perfect opportunity for us to showcase Ecogate’s capabilities and versatility to a much wider audience.”
Technical Director, William Keyon, was in complete agreement: “The setup at MAFS allowed us to demonstrate to everyone involved in the woodworking industry that Ecogate® technology can cut your electricity bills by at least 50%... whether you’ve got just a handful of machines, or a large factory with dozens of machines, the same formula for achieving significant savings can be applied across the board.”
The Demo Zone at MAFS had just four operational machines but, as in the majority of manufacturing facilities, they were rarely all in operation at the same time. However, the total extraction capacity had to match the requirement of all the working machines combined, so the system was designed to extract up to 10,500 m3/hour if required. In reality, since an Ecogate® greenBOX Nxt Controller was managing the system’s operation, although extraction was fully operational throughout the demonstrations, fan speed was continually varied, in real-time, to exactly match the extraction demand.
Without Ecogate® technology optimising extraction the fan would have been running at full power during each demonstration period, consuming around 17kW for every hour of operation, and Ian Rayner was keen to emphasise the fact that: “With Ecogate® installed, the reduction in energy usage for the working demonstrations effectively reduced the show’s carbon footprint and, an additional bonus appreciated by neighbouring exhibitors as well as the audience, the lower fan speeds meant less noise!”
Last month saw TM Machinery exhibit at the first Materials and Finishes Show at the NEC, Birmingham. As the first major UK event for the furniture manufacturing and joinery industry since the W Exhibition in 2018, the Leicesterbased machinery supplier was keen to support efforts to re-establish a woodworking show with real value-added appeal and create an opportunity to connect with industry professionals.
While the show did not see the footfall of previous years, especially from mid to large-sized businesses, TM Machinery were able to demonstrate an exclusive range of cutting-edge filtration systems and dust extractor units from AL-KO and market leading vertical panel saws from Striebig to a steady stream of visitors from around the UK. As well as presenting advanced and energy-efficient solutions for streamlining operations and building scalable growth, the stand also presented the very latest design features created to enhance productivity and reduce operational costs – affirming the two machinery manufacturers as ‘go to’ brands for businesses looking to scale their processes efficiently.
“Despite the lower-than-expected attendance to the show, the engagement we experienced on our stand confirmed the importance of these events and paved the way for positive collaborations in the future,” says Matt Pearce, Managing Director of TM Machinery Sales and TM Services. “They provide us with an invaluable opportunity to connect with businesses of all sizes and to work together to meet the needs of the woodworking industry in the UK. While online communication has many benefits, nothing beats face-toface interactions.”
Matt concludes, “A huge thank you to everyone who visited our stands and to our hardworking team for their commitment. Let’s continue to drive the woodworking industry forward. There’s a long way to go in creating a large exhibition but we’re excited about the future and look forward to new opportunities to connect with our industry peers.”
Wood Combustion Equipment
Industrial Heating Systems
Specialist Metal Fabrications
Ranheat design and manufacture the complete range of equipment including Boilers, Heaters, Stokers, Grit Arrestors, Chimneys etc.
Manual & automatic woodburning systems, gas & oil fired, turnkey installations for disposal and/or heating purposes, outputs up to 10 million BTU/HR
RANHEAT ENGINEERING LTD
62-64 St James Mill Road, St James Mill Industrial Estate, Northampton NN5 5JP Tel: +44 (0)1604 750005 Fax: +44 (0)1604 757300
Web: www.ranheat.com Email: sales@ranheat.com
CS 860 & CSF 860.
Simple, Flexible and Absolute are three words that describe the CS 860 & CSF 860 from VOLLMER. Perfect for machining the sharpest clearance angles and sides, the new arrivals are easy to use and incredibly flexible. This gives you outstanding grinding results with optimal processes for all your circular saw blade requirements. The CS 860 & CSF 860 deliver the highest level of quality, productivity and user-friendliness with maximum flexibility.
Andy Ball, Founder Director at The Joinery Network shares his key takeaways from the Materials & Finishes Show (MAFS) at the NEC in Birmingham, and why The Joinery Network is returning as an exhibitor in 2026.
When the W Exhibition relaunched as Materials & Finishes Show (MAFS), its organisers, Montgomery Group, said it was a ‘reimagined concept developed to provide a platform for manufacturers, processors and installers of timber, components and supporting services, alongside complementary materials such as stone.
The show began life in 1974, at first solely as a woodworking machinery exhibition, then evolving and covering the full range of technology and materials for industrial woodworking.
The decision to exhibit at the newly revamped show, which hadn’t taken place since 2018, was a no-brainer for The Joinery Network.
Being a conglomerate of companies that specialise in bringing together a complete range of services for businesses who manufacture or install timber windows and doors, a good opportunity to speak to joinery companies to demonstrate all that The Joinery Network had to offer under a single roof, or exhibition stand as it was here.
The event gave Joinery Network partners Woodge Software, business coach Erin Woodger, full-service marketing agency Balls2 Marketing, and new partner, systems manufacturer Gutmann showing the new GUTMANN LIGNUM woodaluminium window and door system, plus some of our Affiliate Partners, a chance to collaborate on a joint exhibition stand that was a ‘one-stop shop’ for all those that that manufacture and install timber windows and doors. And that ‘one-stop shop’ proved to be a hit for visitors, with the stand attracting vast amounts of interest throughout the four days.
The Vacuum Glazing Network’s PassivGlas brought its heat booth that was a big pull for visitors. The cleverly designed glass unit means that despite a heat lamp at the centre, the outside pane was comfortable to touch, and clearly demonstrated the energy performance of the glass. There was also information on how to achieve 2025 Building Regulations thermal performance with its super-slim glazing offering a true energy saving solution for conservation areas. RegaLead added colour to the stand with its new decorative glass range for timber doors, plus visitors to take away the beautiful brochure that includes all the designs, styles and sizes.
JFJ Wood Flooring offered joiners a simple way to increase profit from projects with John Fanthorpe from JF Joinery was also on hand to give practical manufacturing advice.
Woodge software showcased its practical software solution for joinery and kitchen manufacturers.
And lastly my co-director Sarah Ball and me were on hand to discuss the services Balls2 Marketing with our specialism in the glazing industry and specific interest in timber. Sarah also provided information about the People in Glazing Society, AKA PiGs, a networking event held four times a year across the UK for those in the glazing and fenestration sector.
But it wasn’t just the stand that proved to be a success for the Joinery Network. The ‘Demo Zone’, which MAFS organisers said gave visitors a chance to ‘see products come to life’ was well-received throughout the event. Alongside influencers from the joinery and carpentry sectors such as the BBC’s Carpenter of the Year, Tibby Singh, and popular YouTuber Robin Clevett, was Joinery Network Founding Partner Owen Dare.
Owen, a joinery manufacturing consultant with more than 35 years’ experience working in the industry, provided a live demo twice a day showcasing how to make a Lignum window using Leitz tooling. Leitz Tooling UK is also a partner of the Joinery Network had its own stand during the show. Owen’s demos proved to be one of the most popular throughout the duration of the show, and he demonstrated to packed aisles every time.
And being ideally situated close to the ‘Demo Zone’, Owen could send visitors watching to the nearby Joinery Network
stand, to discuss the Lignum window, and the support available to joinery companies, in more detail.
The Joinery Network demo was designed to help joiners become more efficient so that they can make more profit with a low investment model to grow their business portfolio.
“MAFS provided an ideal platform for joiners to see the latest products and innovations, as well as stay abreast of the latest legislation and regulations for the industry.
The show was a success all round. The organisers said they are increasing the footprint of the show by 60 percent for 2026 and have already secured a high percentage of rebooking. And we are testament to that success. We took more than 200 enquiries throughout the show for The Joinery Network
Over the coming months, Joinery Network partners and affiliates will be hosting manufacturing days to demonstrate the benefits of manufacturing and installing the Lignum timber window and door system.
www.thejoinerynetwork.co.uk
The Department of Furniture Design & Technology, School of Design & Creative Arts at The Atlantic Technology University in Connemara is regarded both nationally and internationally as a leading provider of third-level courses in furniture, wood products and teacher education (Design Graphics and Construction).
The campus educates over 240 students a year, studying different degree courses and apprenticeships in its state-of-the-art workshop facilities featuring the most advanced machinery and computer technology.
With links to major furniture design and manufacturing companies around the globe, this allows students to avail of work placement opportunities with leaders in furniture design and manufacture and interior fitout sectors.
Graduates are recognised for their innovative, creative and responsive approach to projects. They frequently win, and are shortlisted for, national and international awards that influence and develop the industry.
“In recent years, along with our undergraduate degree programmes, we have expanded our offering to include teaching apprentices in Wood Manufacturing and Finishing,” explains Paul Leamy, Head of Department of Furniture Design & Technology. He continues, “It is vital that we train all our students on the most advanced technologies available so that when they leave, they have been exposed to the most up-to-date equipment, giving them the best opportunity to gain employment and providing industry with much needed talent.”
THE PROCESS TO ACQUIRE A NEW CNC MACHINE
“As part of our commitment to have the latest machinery, we recognised the need to replace one of our aging CNC processing centres. When looking to acquire new capital equipment, ATU has a fair and transparent European-wide tendering process in place which must be strictly adhered to.
“We drew up our required specification for the new CNC processing centre – size, 5-axis head, table types, software, cost, etc. – and then we uploaded the invitation to tender on www.etenders.gov.ie so all interested parties were free to apply.
“Each company that tendered had exactly the same information; they had to demonstrate their machine was compliant with our clearly defined requirements. At the end of the process, it was Electro-Tech (HOMAG UK’s partner in Ireland) that won the tender, with the HOMAG CENTATEQ P-110 CNC.”
“Following Electro-Tech’s successful tender, our procurement department issued them with contracts. The delivery and installation process were handled superbly by Electro-Tech and HOMAG. To minimise disruption, we specified that the installation had to take place in the first two weeks of January when the least number of students would be on campus.
“This was adhered to and the whole process went very smoothly, including the online and onsite training of our staff by the installation engineers. For the first time we can train students on a 5-axis CNC which opens up new and exciting possibilities for the students, apprentices and lecturers alike”
“This means that when students graduate from our programmes, they have the very best qualifications and a good level of experience to enable them to pursue a career in the woodworking industry. That is so important to us; it is the fundamental reason we exist.” concludes Leamy.
The CENTATEQ P-110 model is used by kitchen, office and solid wood furniture manufacturers, as well as by joinery workshops for the construction of stairs, windows and doors.
If you would like more information or a demonstration of any of the HOMAG machinery and software, please contact Adele Hunt at HOMAG UK on 01332 856424.
T: 01332 856500
E: info-uk@homag.com www.homag.com
Expanding its already impressive range, leading specialist trade supplier IronmongeryDirect now stocks high-quality hand tools and tool accessories – all the essentials required to complete panel and joinery production projects, whether it is for furniture making, kitchen or bathroom work.
IronmongeryDirect is committed to ensuring customers have everything they need to complete a project from start to finish, and has introduced over 200 tools from OX Tools. Renowned for its superior engineering, this trusted brand is relied upon by trade professionals.
For complete accuracy to ensure components fit together perfectly, there are tape measures and combination squares together with marking tools, and spirit levels including magnetic options. For the most precise readings there is also the new Self-Levelling Green Cross Beam Laser Level, which features a tough shock proof casing that can easily withstand the environment of most job sites.
The efficiency theme continues with the range of hand saws, hacksaws and circular saw blades now available. The OX Pro Hand Saw is particularly reliable. There are integral 45° and 90° angles built into the handle for versatility, making this product perfect for universal cutting. Its robust build provides stability when making precise cuts and the soft grip handle allows users to comfortably saw for long periods.
Also on offer is the new range of screwdrivers, featuring the most common head types to cover a variety of tasks. Each screwdriver comes with comfortable soft grip handles which are colour coded for easy identification. The OX Pro Diamond Tipped Hex Key Set features 9 hex keys from 1.510mm as well as ball-end designs that help access bolts in hard-to-reach places.
Another new addition is the OX Pro Heavy Duty Bar Clamp, which is available in various lengths. Robust in its construction, the clamp ensures workpieces are held secure with an impressive clamping force of up to 150kg. Its toolless, quick-change feature enables seamless conversion from clamp to a spreader when required. The jaw pads, made from Thermoplastic Rubber (TPR), will protect surfaces from damage.
IronmongeryDirect has also added a variety of individual chisels and chisel sets to its stocked range including the Pro Heavy Duty Wood Chisel. A forged steel core and high-quality blade make it a strong, highly durable tool that delivers sustained performance and edge retention. Its soft grip and split-proof acetate handle are designed to withstand the toughest conditions. There are several blade width sizes available, from 6mm up to 38mm, as well as 3-piece and 5-piece set that come with a high quality Velcro case.
For tapping chisels and fitting joinery together, a selection of hammers and mallets are available. The OX Trade Combination Mallet is a versatile option for soft and hard surfaces thanks to its two-sided construction. Specifically, it features a standard black face for general work, and a semi-hard, white face that will not mark or discolour surfaces, ensuring the quality and accuracy of work is not compromised. It is also equipped with a strong and lightweight fibreglass soft grip handle making the mallet comfortable to use, even for extended periods.
Award-winning online supplier, IronmongeryDirect, has over 18,000 products in stock All products are regularly reviewed to ensure customers are offered competitive prices, including bulk buy savings on over 12,000 products. Flexible delivery options to meet busy schedules are offered, including next-day delivery, 2-working-day delivery, sameday delivery to postcodes in selected areas of London and the East of England, as well as click and collect from 6,500 pick-up points across the UK.
DP Lamination stays ahead of ever-changing market. Having pioneered the use in the UK of lightweight paper foils as decorative overlays, dp-lamination now have the largest and most diverse portfolio of decor materials available in the UK.
The newest product, DP-Crystal Slim is a collection of over 16 Rehau designs from their Pure, Strong and Deep ranges and has been designed for vertical indoor use, perfect for splashback and wet wall applications. Easy to clean, hygienic surface, DP-Crystal Slim is a suitable replacement for traditional bathroom and kitchen wall tiles. It is an ideal glass, tile, or traditional stone and marble substitute for all hospitality and retail environments.
Crafted with precision and attention to detail, each piece in the DP-Crystal Slim surface collection is designed to elevate any space with its timeless beauty. The crystal-clear finish adds a touch of sophistication, while the slim profile creates a modern, minimalist look that complements any decor style. Whether used in kitchen or bathroom these surfaces are engineered to withstand daily wear and tear while maintaining their flawless appearance.
DP-Crystal Slim boasts exceptional durability, resisting scratches, heat, and chemicals, making it an ideal choice for high-traffic areas. Its sleek and modern aesthetic will elevate any space, while its low maintenance requirements
ensure a hassle-free experience. The crystal glass surface is non-porous, preventing the growth of bacteria and mould, making it a hygienic choice for kitchens, bathrooms, or even healthcare facilities.
The versatility of DP-Crystal Slim knows no bounds. Is suitable for kitchen walls under cupboards, shower walls, basin splash backs, kitchen splashbacks. DP-Crystal Slim is perfect as a centre panel for furniture or media units. Its acrylic surface is only 4mm thick, is 50% lighter than real glass and 10x less brittle. It is perfect for hospitality and retail interiors. DP-Crystal Slim can be easily machined on site using conventional woodworking tools, no need for templating, off site working and revisiting to install at a later date. Suitable replacement for traditional bathroom or kitchen wall tiles.
It can be used to create stunning feature walls, elegant backsplashes, or sophisticated cladding for columns and walls. Its slim profile and lightweight design make it easy to handle and install, reducing labour costs and minimizing environmental impact.
In addition to its functional benefits, DP-Crystal Slim is also a design statement. Its crystal-clear glass surface is available in a range of colours and finishes, allowing designers and architects to unleash their creativity and bring their vision to life. Whether you’re looking to create a luxurious ambiance
in a high-end hotel or a modern, sleek look in a trendy restaurant, DP-Crystal Slim is the perfect solution.
DP-Crystal Slim is not just an ordinary surface finish. It is a masterpiece crafted with precision and care to deliver a product that is both visually stunning and incredibly durable. The slim design adds a touch of sophistication to any setting, making it the perfect choice for those who appreciate the finer things in life. But what truly sets DP-Crystal Slim apart is its unrivalled strength. Made with the highest quality materials, this product is built to last. Say goodbye to fragile surface that shatters at the slightest touch - DP-Crystal Slim is here to stay. Its timeless design seamlessly blends with any decor style, adding a touch of elegance to every setting.
Julian Tatham, Group designer:
“We’re excited about the potential of DP-Crystal Slim. At Decorative Panels Lamination, we’re committed to providing innovative solutions that meet the evolving needs of architects, designers, and builders. With DP-Crystal Slim, we’re proud to offer a game-changing product that redefines the boundaries of glass design.
With our unparalleled range of decorative panels and laminates, combined with our expertise and commitment to customer service, dp-lamination is the ideal partner for any design project’’.
At dp-lamination, they are committed to helping clients bring their design concepts to life. Their team of experts is dedicated to providing exceptional customer service, offering technical support, and ensuring timely delivery of our products. Whether you’re working on a large-scale commercial project or a bespoke residential design, Decorative Panels are here to help you achieve your creative vision.
Experience the unparalleled strength, durability, and style of DP-Crystal Slim – the ultimate solution for your next project.
Upgrade your interior design with a touch of luxury - choose the DP- Crystal Slim Surface Collection for a lasting impression that will never go out of style.
To experience the benefits of DP-Crystal Slim for yourself, head over to Decorative Panels website now to learn more about this innovative product or speak to their friendly team today to see how they can help with your next furniture project.
DP-Crystal Slim is available in high-gloss and matt versions in quantities from as little as just one laminated, acrylic sheet with dimensions: 2800mm x 1300mm x 4mm.
Visit www.decorativepanels.co.uk
Established in 1995, SAM Cases has evolved into a prominent player in the field of flight case manufacturing. Founded by a team of qualified professionals with a deep understanding of packaging and delicate equipment transportation, the company quickly gained recognition for its commitment to quality and innovation. Specialising in packaging and transporting fragile equipment, the company boasts an impressive client roster including renowned names such as BBC, Dyson, Chelsea Football Club, LG Electronics, Aardman Animation, Procter and Gamble, BT, the MOD, and various other organisations. SAM Cases is committed to delivering cutting-edge solutions that meet the highest standards of protection and security. Throughout its journey, SAM Cases consistently incorporated the latest technology and materials into its products. This dedication to innovation became evident in the range of offerings, from sample and demonstration cases to tough and rugged transit/ flight cases. The company embraced waterproof options, integrating renowned case ranges such as Peli, Explorer, Peli Air, Peli Storm, and Peli-Hardigg.
AXYZ MACHINE ADOPTION:
Since 2009, SAM Cases has been utilising AXYZ machines, starting with the purchase of their first machine. Recognising the efficiency and reliability of AXYZ technology, SAM Cases expanded its capacity by adding a second machine within a few short years. In 2023, the company took another leap forward, investing in two brand new AXYZ Infinite series machines equipped with multiple heads. This strategic move aimed to enhance production capacity, reduce machining time, and leverage the latest advancements in CNC technology.
The INFINITE router is a highly configurable CNC machine that is suitable for one-off, small batch production as well as high volume and high productivity applications, including woodworking, plastic fabrication, engineered plastic machining and so much more. For a wide range of routing operations, one can choose from high-speed spindles ranging from 5HP to 15HP. For knife cutting, choose from a tangential knife, which can be used for creasing and folding applications or an oscillating knife which can be used to process soft goods material.
AXYZ AS THE PREFERRED SUPPLIER:
AXYZ became SAM Cases’ preferred machine supplier in 2009 and continues to hold that position. “The decision to choose AXYZ as the preferred machine supplier was not only a strategic one, but the choice was also influenced by recommendations from other manufacturers in the industry”, said Mathew Addy Technical Director. SAM Cases serves diverse industries worldwide, producing high-quality packaging with no limitations. They are recognised for offering top-notch foam inserts, a testament to the quality of AXYZ machines. AXYZ machines at SAM Cases handle the production of custom foam inserts and cutting various plastics used in packaging manufacture. They recently created their first 3D foam insert with a rounded bottom pocket for a Rolls Royce project.
IMPACT ON PRODUCTIVITY AND EFFICIENCY:
The implementation of AXYZ machines has significantly enhanced productivity and efficiency at SAM Cases. “The inclusion of an oscillating knife on one of the machines has resulted in a cleaner and faster cut with minimal mess,
improving lead times for certain projects, enhancing overall operational efficiency”, said Mathew Addy Technical Director. Bringing CNC manufacturing in-house has empowered SAM Cases to control and enhance the quality of their products, establishing them as leaders in the industry. Prior to the adoption of AXYZ machines, the company relied on external manufacturers for foam inserts, limiting their ability to control product quality. Since the integration of AXYZ technology, SAM Cases has achieved unparalleled control over the quality of their products, setting industry benchmarks.
The initial challenges faced by SAM Cases during the integration of AXYZ machines revolved around finding adequate space and addressing power and air requirements. AXYZ responded with comprehensive documentation detailing space requirements and power ratings. The successful resolution of these challenges for the first machine paved the way for the seamless integration of the second machine, highlighting the collaborative partnership between AXYZ and SAM Cases.
While cost savings primarily stem from avoiding markup on outsourced foam inserts, the overall streamlining of operations through AXYZ machines has contributed to enhanced profitability. The CNC technology allows SAM Cases to have greater control over their production processes, resulting in a more cost-effective and efficient operation.
Employees at SAM Cases welcomed the introduction of automation in their workflow. The presence of AXYZ CNC machines has not only increased efficiency but also allowed employees to focus on more intricate manual tasks, fostering job satisfaction and a positive work environment.
While there is a learning curve for programming, SAM Cases has grown its workforce to meet the increased demand since the initial machine purchase. The user-friendly nature of the AXYZ control system makes it accessible to all staff members. While there is a learning curve for programming to optimise cut quality and processing time, the ease of use has allowed SAM Cases to grow its workforce significantly to meet escalating demand since the initial machine purchase.
Ensuring the maintenance and smooth operation of AXYZ machines is crucial for SAM Cases. Recognising the impact of downtime on their workshop schedule, the company emphasises the importance of AXYZ service contracts, ensuring that the machines are consistently maintained at peak performance levels.
Future Plans for Automation: Expanding Horizons with AXYZ Looking ahead, SAM Cases envisions further integration of automation into their processes. Plans include the acquisition of another machine, housed in a separate facility, to process rigid plastics and wood. This strategic move aims to enhance yet another aspect of SAM Cases’ production capabilities, showcasing their commitment to continuous improvement and innovation.
In conclusion, SAM Cases’ partnership with AXYZ has been pivotal in elevating their precision and efficiency, establishing them as leaders in the competitive world of flight case manufacturing. The commitment to quality and continuous improvement is evident in their successful integration of AXYZ CNC routers into their operations. The symbiotic relationship between SAM Cases and AXYZ has not only withstood the test of time but has propelled the company to new heights in packaging precision. The adoption of AXYZ CNC routers has been a cornerstone in SAM Cases’ journey of excellence, setting them apart as industry leaders and paving the way for future advancements in automation and efficiency. SAM Cases continues to be the leading force in the case manufacturing industry, renowned for its precision, durability, and commitment to excellence. The company’s journey is a testament to its continuous pursuit of innovation and its ability to meet the evolving needs of clients across various industries.
T: 01275 866 366 E: sales@samcases.co.uk www.samcases.co.uk/
For more information on the AXYZ range of routers: Tel: 01952 291600 www.axyz.com
As furniture manufacturers adapt to demand for smaller batches, this software innovation promotes efficient processing of bespoke orders and varied workloads by enabling multiple panels to be handled in pendulum mode.
Pendulum loading is well established as an approach for maximising uptime and productivity in CNC machining. Pendulum mode allows an operator to load and unload parts at one end of the bed while the machine works at the other end. This means the machine is never sitting idle, and the operator isn’t wasting time watching the machine and waiting for it to finish its cycle. A standard CNC machine has to pause between cycles to allow the operator to swap workpieces in and out. With pendulum loading, an operator can go an entire shift without having to stop the machine, allowing more parts to be processed in a shorter space of time.
What if, instead of being limited to single-panel pendulum loading, CNC machines could handle two, or even more workpieces simultaneously in pendulum mode? This would enable furniture manufacturers to make seismic efficiency gains and would make ‘batch one’ production commercially viable.
UNDERPINNED BY SOFTWARE ADVANCEMENTS
Biesse has drawn on its in-house software engineering expertise to make multi-panel pendulum loading a reality
on its Rover series of CNC machines. By further developing its proprietary B_Solid software, which makes high-tech operations intuitive and accessible by allowing the user to view the machine in virtual reality, Biesse has taken the complexity out of multi-panel pendulum loading.
For some time, there have been solutions on the market for machining multiple parts on one bed simultaneously. But not in pendulum mode. Now, thanks to this breakthrough, manufacturers can run multiple programmes whilst performing pendulum loading. The number of parts that can be worked on at any given time is limited only by the physical size of the bed or the number of pods and rails - a large machine may be able to accommodate up to eight workpieces (four on each side) at a time.
The long-term trend in cabinet making is towards smaller batch sizes and bespoke units. Rather than producing a batch of 500 identical base units or panels, for example, furniture manufacturers might produce just a few of one cabinet type or part before switching over to a different programme. Whilst introducing greater variability into furniture manufacturing has advantages for inventory management and waste levels, the frequent changeovers present a challenge for productivity.
Biesse’s multi-panel pendulum loading solution can help manufacturers to maintain efficiency whilst adapting to increasingly varied workloads. It turns traditional production
principles on their head. It makes it viable to machine an entire unit (a cabinet for example), as a single batch rather than machining multiple quantities of each component part one after the other.
This is a particularly attractive proposition for shop fitters and manufacturers of ‘bespoke’ kitchen, bedroom, bathroom and home office furniture. For example, a machine in multi-panel pendulum mode will make light work of a kitchen order for cabinets of varying dimensions in different materials and colours, by treating every cabinet as a ‘batch one’ and producing it in its entirety before moving onto the next. This flexible approach to production eliminates the need to hold stock and has the potential to increase profit margins on bespoke work.
In light of successful partnerships with Heesemann and Makor, HOMAG UK is able to offer a comprehensive range of sanding and spraying solutions to the UK market. The agreement sees all the sanding and spraying machines branded as ‘Heesemann’ and ‘Makor’ respectively, with HOMAG serving as the UK agent.
Two standout models that are available to UK woodworking manufacturers as a result of this agreement are the Heesemann SWT-100 wide-belt sander and the Makor Start One spraying booth. “These machines,” explains HOMAG UK Managing Director, Simon Brooks, “exemplify the quality, precision, and efficiency that customers have come to expect from the HOMAG brand.”
With the equipment of Heesemann and Makor to hand, HOMAG UK is now a one-stop hub for service and support, providing customers with access to the latest in surfacing technology as well as the specialist assistance of all three companies. “Heesemann and Makor have both been great companies to work with,” Simon Brooks continues. “They align with our values and culture, and their co-operation has enabled us to expand our surface solutions offering for new and existing customers.
“It’s a collaboration that brings together the expertise of three industry leaders to deliver top-of-the-line surface solutions to woodworking businesses across the UK.”
The Heesemann SWT-100 wide-belt sander is tailored for the needs of small and medium-sized businesses seeking precise
sanding solutions. Offering customer-specific sanding tasks with remarkable precision and speed, the SWT-100 features five pre-defined configurations. Its independently driven units ensure rapid and high-quality sanding results, making it ideal for craftsmen engaged in the manufacture of kitchen, office, and solid wood furniture.
Designed for companies engaged in small batch production, the Makor Start One is an automatic panel and reciprocating spraying machine. It offers precision and efficiency in spraying operations, accommodating waterbased or solvent-based paints, as well as glue for veneered components or PVC. The Start One enhances productivity, facilitates paint savings, ensures coating uniformity, and maintains consistent quality. Featuring a touch screen monitor and electronic bar for reading piece sizes, it simplifies spraying processes while delivering impeccable results.
“HOMAG UK is committed to providing the most advanced woodworking machinery solutions available on the market,” concludes Simon Brooks.
“With the addition of Heesemann and Makor’s specialist machines to our portfolio, we’re even better positioned to meet the diverse needs of our customers.”
For a demonstration or more information on the Heesemann SWT-100, the Makor Start One, or any HOMAG machinery and software, contact Adele Hunt at HOMAG UK on 01332 856424.
For two decades, Chemique Adhesives has been the trusted supplier of adhesives to Mannok, a leading building products manufacturer, for its thermal laminate plasterboard manufacturing facility in Ireland. Since the beginning, Chemique has been actively involved in the bonding process of its thermal laminate composite board, which has evolved over the years into a state-of-the-art fully automated bonding line.
In 2012, Chemique Adhesives collaborated with both Mannok and Finishing Design Services (FDS), a specialist machinery manufacturer, to develop an automated process for bonding plasterboard to PIR insulation. This twocomponent polyurethane adhesive system proved successful for many years, however, advancements in adhesive and machinery technologies led to the creation of a new, stateof-the-art production line.
Considering future requirements for output and environmental impact, Mannok, FDS, and Chemique Adhesives collectively determined that adopting a PU bead system would be the optimal choice for the new process.
James Thorpe, Sales Manager at Chemique Adhesives commented on the new adhesive, “During the initial testing stages, we were pleased with the performance of the singlepart polyurethane adhesive and its excellent bond to the laminated panel. Tailoring the open time and cure time to meet the specific requirements of the application proved successful, and we were delighted with the final outcome.” The adhesive used is from the Solfre range of polyurethane adhesives and its unique formulation provides superior resistance to chemicals, heat, humidity, and thermal shock. The switch from a two-part to one-part PU adhesive has provided several benefits to Mannok’s manufacturing process, creating a simplified application process, improved environmental conditions, and the elimination of solvent cleaners.
FDS successfully designed a new laminating production line incorporating the latest technology, and providing a robust, efficient system for Mannok to meet the growing demand for high-quality bonded PIR insulation for their clients. This new machine integrates the latest adhesive technology from Chemique, ensuring the efficient production of panels of the utmost quality.
The new manufacturing system boasts numerous improvements over its predecessor, providing reduced adhesive coat weights with higher bond strengths, lower heating costs, increased production capacity, and an improved working environment for employees. The system also ensures a more even distribution of adhesive onto each board and the improved manufacturing control capability allows for less employee intervention and reduces downtime.
Gordon Wiggins, Production Manager at Mannok, PIR Insulation facility commented: “Throughout this entire process, the advice and guidance from both Chemique and FDS has been exceptional. “The implementation of the new line aligns closely with the Mannok 2030 Sustainability Vision and our commitment to the three pillars of our people, the planet, and our partners. It has greatly enhanced our overall manufacturing efficiency, allowing
us to produce a resilient PIR laminate plasterboard using 50% less adhesive per unit and requiring 60% less electrical energy compared to the previous system.
“It also facilitates an improved working environment during manufacture for employees as well as reduced long-term environmental impact and zero chemical emissions from the production process.
“Furthermore, it has also increased our laminate plasterboard production capacity meaning we can manufacture higher quality laminate composite products which are more readily available for our customers and to meet market demand.
“Mannok would like to offer a huge thank you to the entire team at Chemique Adhesives and FDS for their communication, collaboration and successful completion of this transition, we look forward to working together on future initiatives that align with our sustainability goals.”
T: 01922 459321
www.chemiqueadhesives.com
www.mannokbuild.com
Top quality machining and productivity on any kind of panel or material and in full sync with the demands of a digital, connected and integrated factory: these are the main advantages of SCM’s new industrial edgebander.
Bolstered by its R&D experience and the market success achieved with the launch of the “stefani x” two years ago, SCM is launching another new industrial edgebanding product: “stefani m”.
It aims to cater to the latest trends in furniture and design in terms of flexible production, Industry 4.0 and now, even Industry 5.0.
The new “stefani m” industrial edgebander has everything it takes to position itself as a very strong competitor on the market. Every detail has been designed to offer a solution in line with the industry’s more complex demands: from the machine’s structure to the digital and electronic control systems; from the machining units with power assisted movement to the latest gluing devices, for an even faster, more efficient glue change.
The result is a highly configurable, customised edgebander, designed to work reliably and provide top-quality machining,
both in the stand-alone version and in integrated cells.
One other important advantage is its ability to achieve maximum quality standards easily and without interruption, even on the most delicate, state-of-the-art materials, thanks to SCM’s new electronic touch technology.
Furthermore, in an attempt to meet the increasingly more widespread demands for flexible, connected and integrated production, “stefani m” comes with a “Maestro active edge” control system which means it can operate in perfect synergy with the Maestro edgestore manager software, other SCM technologies and MES IT and management systems used in the factory.
The new “stefani m” can machine panels at a speed of up to 25 m/min and with a minimum distance between the panels of 350 mm. All this, thanks to reliably tried-and-tested units and a new, highly rigid mechanical structure.
EXCELLENT VERSATILITY IN GLUING SOLUTIONS
Another significant new feature of “stefani m” is the new gluing unit which ensures the three key technologies are always ready to hand - PUR glue, EVA glue and Hot
Air AirFusion+-, up to 6 rolls with automatic change of machining edge and height adjustment of the edge table to ensure the edge is always in the right position on the panel side.
A new, innovative FlexMelter “all-in-one” pre-melting device which uses EVA and PUR glue in slugs and granules, as well as a fast glue change and without waste thanks to the removable container.
The “stefani m” electronic units are designed to meet two objectives that are key to the market: ease of use even for more complex machinings on delicate, in-vogue materials, thanks to an automatic, flexible set-up, and repeatability, quality and accurate production processes, thanks to the electronic touch.
1. Y-SE 1000 SERVO END TRIMMING UNIT
For constant precision when cutting, irrespective of the amount and type of panels machined, to optimise machining work even on the most delicate panels, automatically control adjustments and correct any machining errors on the spot.
2. ROUND 2 SERVO ROUNDING UNIT
Guarantees top quality machining on any profile and optimises the processes even on three different edge thicknesses.
www.scmgroup.com
High-quality fire doors require top-quality finish especially when it comes to the vision panel cassettes. When producing Vision Panel cassettes, the need for an accurate mitre joint cannot be overstated. Accurate mitre cuts reduce the need for further finishing work prior to joining. Creating an accurate, tight joint is also key in maintaining the frame’s integrity as well as reducing the need for filling once joining is complete.
With the correct equipment, a skilled Joiner can produce accurate mitre cut profiles. Using the HOFFMANN Dovetail Router to complete the joint is a cost-effective way of completing the process of producing accurate, high-quality, vision panel cassettes.
Once all the pieces have been mitred (this can be done with a mitre saw or a guillotine, as long as all the 45° angles and the lengths of the workpieces are 100% accurate), the workpieces are transferred to the Hoffmann MU3 for processing the dovetail slots. The Hoffmann Keys are then inserted in the mitre joints to complete the vision panel cassette.
THE HOFFMANN MU3 DOVETAIL ROUTER IS AVAILABLE IN 4 MODELS.
MU-3 Entry Level version for the quick and precise routing of dovetail slots.
MU-3 D Digital version, with electronic two-axis display for the adjustable routing depth as well as the positioning of the centre fence for the routed slot location. It is ideal for high precision work.
MU-3 P Pneumatic version for series production and high throughput. Pneumatic workpiece clamping and controlled router feed. The MU-3 P is operated by foot-pedal control. MU-3 PD Pneumatic and Digital version – the top machine with the highest operating comfort for a wide range of
requirements. Functional features are similar to MU-3 D with a digital two-axis display for the adjustable routing depth as well as the positioning of the centre fence for the routed slot location.
The MU-3 and the MU-3 D have a workpiece thickness capacity of up to 140mm – in the versions MU-3 P and MU-3 PD this increases to 170mm. Infinitely adjustable routing depths up to 95mm and protection against break-out of the finished surface. The dual-function hand lever ensures quick machine cycles when routing smaller workpieces. The scale tapes in the table and the rear fences assist the quick and precise positioning of the workpieces. All versions of the new MU-3 routing machine are equipped with a motor carriage which has vernier adjustment for the precise setting of the router cutter and hence the adjustable tension of the joint.
MACHINE PROCESSES
MU3 / D – The Fence plate is secured in the required position (digital positioning with the “D” version) and the workpiece is laid against it. The router depth gauge is selected (Digitally with the “D” version). By drawing down the hand lever, the work piece is clamped, and the router motor starts. Continued pressure on the lever brings the router up into the workpiece, to the pre-set routing depth. Returning the hand lever to its starting position automatically returns the carriage to its home position, switches off the router motor and releases the workpiece.
MU3P / PD - – The Fence plate is secured in the required position (digital positioning with the “D” version) and the workpiece is laid against it. The router depth gauge is selected (Digitally with the “D” version). Pressing the foot pedal clamps the work piece in place pneumatically and the router motor starts. The router then rises up into the workpiece, when the pre-set routing depth is reached the router carriage returns to the start position, switches off, and the work piece is released.
Once the dovetail slots have been cut into all the mitre faces, the mitres can be locked together by inserting the Hoffmann Dovetail Key all the way into the slot. Optionally, a thin layer of glue can be applied to the surfaces before bringing them together. Once the Hoffmann key is inserted, the joint is secure. NO DRYING TIME IS REQUIRED. So long as the mitres are accurate, work can instantly continue. Frames can be sprayed or lacquered before fitting into the door.
When producing fire doors, all the component parts are essential in ensuring the door maintains its integrity. Hoffmann Dovetail Keys are an integral part of many fire doors. They have been accredited with FD30 / FD60 fire safety ratings for securing the joints in vision panel cassettes. Hoffmann keys have also been successfully tested in composite fire door blanks and solid wood door frames.
Chris Franklin MD at Ranheat Engineering Ltd. a leading UK manufacturer of wood combustion equipmentcontinues his series of articles for Panel and Joinery Production.
This edition he looks at how the wood burning industry has grown and developed over the last 40+ years that he has been in the industry.
“It’s hard to imagine that Medium Density Fibreboard was once considered a “New Material” where would the industry be without MDF?
When MDF first came onto the scene it was considered a new Material and not a lot was known about. Around 1990 a new company, part of the JS Hickman Sawmill group was founded called Fibercill. As the name suggested it was to make windowsills using MDF board shaped and primer painted.
This proved successful so the range of products was extended to include skirting boards and architraves. At the time the machining of MDF using profiled cutters was a new concept Fibercill developed the technique of cutting, machining, sanding painting and drying of the product and then packaging.
Ranheat was approached as a specialist manufacturer of wood burning equipment able to produce a system that could burn this new material. Once MDF is machined it produces what we called MDF Flour. This was a very fine dust that nobody wanted to handle or take away.
Fibercill had installed a 300 kW plant installed by another company but they could not get it to work.
Ranheat were tasked with removing the 300 kW plant and installing a 1,000kW plant as production was on the increase and much more dust was being produced than a 300 kW system could cope with.
Ranheat’s system was a complete success and worked extremely well with the MDF Flour.
Shortly after Ranheat were commissioned to install a second 1,000 kW plant alongside the first one as production of MDF products was on the increase.
It wasn’t long before Ranheat were again approached to install an additional boiler this time an extra 2,000 Kw boiler was added.
The growth in demand for MDF products continued and an additional 2,200 kW boiler was added.
Fibrecill now had a total boiler capacity to run at full output of 6.2 MW on 100% MDF Flour. Most of the heat produced was dissipated to atmosphere.
The installations were fully permitted by the local authority under the then new Environmental Protection Act under guidance note PG1/12.
With current energy prices it would now seem incredible to waste all that heat, but at the time disposal was the main problem, so the heat produced was never utilised. As with most innovative ideas it was not long before other companies started up machining MDF for use in housebuilding.
Other forms of MDF came along including fire retardant and water retardant.
“Chris recalled getting a phone call from another customer who normally used standard MDF but was given a project that needed fire retardant MDF to be used.”
He called and said “Chris, I’m having one hell of a job burning this fire retardant MDF”
Then silence on the phone,” I think I have just answered my own question”
Ranheat were able to help by adjusting all of the settings on the machine although fire retardant it is not fire proof so can be burned. That customer never took on another job using FR MDF.
Long-life and antistatic: the new Mirka Ultimax® Black takes belt sanding to the next level. With a strong backing paper and a special silicon carbide grain, it performs exceptionally well for the life of the belt.
For further information or to arrange a consultation, please contact Customer Services on 01908 866100.
Painted Ltd, a spray paint business that recently ventured into woodworking, has rapidly expanded its capabilities and market presence. Founded just three years ago in a modest garage, Painted Ltd has grown into a thriving enterprise offering a range of services for furniture and kitchen needs. “I’ve always aspired to lead a business, to invest my time and dedication into something meaningful,” explains Emilia Dlutowski, the owner of Painted Ltd. “We started off small in 2021, but from the outset I had big plans. Once we’d become established in the spraying side of things, the time came to expand into joinery.”
With a team of dedicated professionals, a commitment to quality, and a customer-centric approach, Painted Ltd has become a go-to destination for bespoke and end-to-end furniture solutions.
Prior to investing in their own woodworking machinery, Painted Ltd relied on various suppliers to handle manufacturing processes. “We were having to outsource everything and it was eating into our margins. Not to mention the lack of control. Clearly, something had to change.”
Emilia saw the potential in bringing everything in-house and being self-sufficient as a business. “Ultimately, we wanted to be a one-stop-shop, the go-to place for quality joinery with a quick turnaround.”
As Painted Ltd sought to expand its woodworking operations, they faced the challenge of finding reliable and efficient machinery to meet their growing demands. Emilia
recognised the need for advanced woodworking equipment that could enhance productivity, quality, and versatility. “I wanted to get something that would do a lot more than basic joinery,” Emilia explains. “I needed something bigger and better.”
After extensive research, Emilia discovered HOMAG, a global leader in woodworking machinery, systems, and software solutions.
“Inevitably we came across HOMAG. As I was new to this industry I hadn’t heard of them before, but after thorough research, they seemed like the perfect fit for our needs.” Impressed by HOMAG’s reputation for innovation and quality, Emilia arranged to see the machines for herself.
Painted Ltd were in the market for a combination of machines tailored to their specific needs:
1. SAWTEQ B300 - Panel Dividing Saw: Known for its high performance and compact space design, this panel dividing saw facilitates precise cutting for batch production or custom projects.
2. EDGETEQ S-300 - Edge Banding Machine: Equipped with multi-level technology and high automation, this machine ensures efficient processing of different profiles, offering flexibility and ease of use.
3. CENTATEQ P-110 - CNC Machining Center: With its versatility and compact design, this CNC machining center
provides the flexibility to handle various woodworking tasks, from intricate fretwork to commercial installations. “The CNC machine was essential for us, especially for fretwork doors and making shaker style with moulds,” Emilia emphasises. “I don’t think any other CNC machine would have been able to do that.”
Emilia’s decision to choose these specific machines was driven by her desire to offer diverse woodworking services, from intricate fretwork to commercial installations. She valued HOMAG’s reputation for quality and innovation, and the machines’ capabilities aligned perfectly with Painted Ltd’s ambitions.
In addition to the machines, Painted Ltd also acquired HOMAG’s smartWOP software, a powerful tool that enhances the functionality and efficiency of woodworking operations. This software allows for easy programming of workpieces in 3D, offering a modern and intuitive interface for CAD, CAM, and WOP programming combined.
“smartWOP is very easy to use and offers improved programming reliability thanks to its modern 3D interface,” notes Emilia. “It’s fool-proof software that has been an essential tool in streamlining our workflow.”
Emilia fondly recalls her experience visiting HOMAG to see the machines in person. “From the minute we walked in to the minute we walked out; I was like a kid in a sweet shop. It was love at first sight. I couldn’t wait to own the machines. They just looked amazing.”
The HOMAG team also left an impression. “Everyone we encountered, from James Mason, our local Sales Manager, to the software and showroom teams, were just so friendly and knowledgeable. We felt very welcome, and better yet we never felt pressured to buy anything. The machines don’t need anyone to sell them, anyway; they sell themselves!”
The installation process was seamless, with HOMAG’s delivery team ensuring a smooth transition. “It wasn’t
disruptive in the slightest,” Emilia reflects. “We knew exactly what to expect and when to expect it. The delivery guys were great, and the training provided, namely by Ryan, was absolutely excellent.”
Broadly speaking, Painted Ltd have fulfilled their goal of becoming an end-to-end provider of bespoke furniture solutions. Since integrating HOMAG machines into their operations, the business has experienced increased efficiency, reduced production costs, and enhanced product quality.
“The acquisition of HOMAG machines marked a significant milestone for Painted Ltd,” explains Emilia. “The transition from relying on various suppliers to in-house manufacturing has not only improved quality and efficiency but also reduced costs significantly. We’ve sliced roughly 60% off the cost of a sale, and the results are perfect every time. Since using HOMAG equipment, we’ve never had a dissatisfied customer or missed a deadline.”
Emilia is confident that these investments will propel Painted Ltd to new heights, enabling them to compete with industry leaders and fulfil ambitious growth targets. “Already we’ve increased our brand awareness, and even more excitingly, we’re starting to win some big contracts. Truly, this is all possible due to the HOMAG machines.”
She concludes, “If anybody’s considering buying joinery machines, no one should waste time with manual machines. Make the investment; it’s worth it and I would definitely recommend you buy HOMAG machinery and software.” If you would like more information or a demonstration of any of the HOMAG machinery and software, please contact Adele Hunt at HOMAG UK on 01332 856424
T:
E: info-uk@homag.com www.homag.com
From the wide choice of filter types and technologies available, we source the most appropriate and cost-efficient system to meet your requirements and, from initial consultation and design, all the way through to installation and commissioning, we will be with you at every stage of the process.
The wealth of practical experience within the company, together with an extensive range of proven products, allows Extractly to offer extraction systems which are individually tailored to customers’ specific needs.
Whether you need a small mobile extractor, or a high-capacity modular filter unit, an energy-efficient shredder or briquette press, or perhaps a modern spray booth or enclosure… from simply adapting ductwork to suit a new machine installation, to commissioning a complete waste-to-energy system, Extractly’s experienced engineers deliver the optimum solution.
Coated multiplex boards give furniture a high-quality character. If the boards are not available or too expensive for a project, the popular look can also be achieved with real wood edgings in multiplex look. Ostermann has a large selection of these available.
From designer furniture in the office or living room to robust pieces in the children’s room - coated multiplex boards are a well-received item in furniture making. One reason for their popularity is the multi-layer look at the narrow sides that endows furniture with a high-quality and warm appearance. The open cut surface can be waxed, stained or lacquered to further embellish it or to adapt it to a specific look. It is equally possible, though, to achieve the look with other wood-based boards if you combine these with real wood edgings in a multiplex look. This is particularly helpful when multiplex boards are not available or too expensive for a project. The edgings are available from Ostermann in birch or beech, and in many widths and thicknesses. On request, they are supplied with a hotmelt adhesive coating or a functional layer for processing with zero bondline technologies. To save time it is always a good idea to order the edgings together with other materials for furniture making. All information on the individual variants can be found under the search term “#Highlights06” on the Ostermann website www.ostermann.eu.
Depending on quality requirements, application and budget, there are various options to obtain the multiplex effect without using an actual multiplex board. An MDF or particle board can be given a high-quality finish by first applying a solid real wood edging with a multiplex look and then pressing the workpiece with an HPL or a linoleum surface. Ostermann has the 2.65 mm thick wood veneer edging Real Multiplex Birch in its range for this purpose. It is supplied in two widths (23 and 43 mm) and in straight lengths of 4 metres. There is a milling margin of 4 mm on each side of the edging, which leaves sufficient space for radius processing.
The quicker and more economical way on the other hand is to apply a classic multiplex wood veneer edging (delivered in rolls) to an already coated particle board. The latter is available from stock at Ostermann in birch and beech, each in 4 widths (24, 30, 33 and 43 mm) and 3 thicknesses (0.5, 1 and 2 mm). For companies that do not want to machine their wood veneer edging, the company has a 0.5 mm birch variant precoated with hotmelt adhesive in stock. The other two thicknesses (1 and 2 mm) are primed. On request, Ostermann also offers subsequent coating with hotmelt adhesive or a functional layer for processing with zerobondline technologies.
The veneer edgings in birch and beech differ not only in the type of wood used, but also in the look they produce. While the individual stripes (layers) of the birch edging are much more irregular and delicate, those of the beech edging are somewhat wider, straighter and more clearly delineated. Both edgings are supplied with a sanded surface and are given their final colour and effect by the furniture maker’s individual surface finishing.
Of course, Ostermann also supplies the appropriate white glues or hotmelt adhesives for processing the edgings mentioned. For the manual bonding of wood veneer edgings in straight lengths, the Ostermann experts recommend the REDOCOL Kombicoll Super-N D3 white glue. A variety of EVA and PUR hotmelt adhesives from well-known suppliers are available for processing with the edgebanding machine. Products from the REDOCOL range are of high quality and at the same time economical to use.
Over its 45-year history, family-run Allied Tooling has navigated its route to success with a reputation for quality and innovation that has foundations built by longstanding staff with unsurpassed expertise – and of course, industry-leading technology from Vollmer UK.
The foundation blocks have been laid for more than a generation, but in the last six years, the Poole-based company has more than doubled turnover to over £7m – and growth is destined to continue at pace. Central to this expansion has been a company re-branding, the introduction of PCD round tools and saw blades, becoming the UK’s exclusive AKE saw blade partner, and also a rapid expansion of available product lines. This has all culminated in the Dorset manufacturer winning long-term supply contracts with prestigious brands such as Princess Yachts and Wren Kitchens. The 60+ employee manufacturer for the woodworking and kitchen, marine, construction, composite and motorsport sectors has ramped up its investment in grinding and erosion machines from Vollmer.
The first Vollmer machine arrived in the 1990s and the company has purchased more than 20 Vollmer machines over the years. In the last six years, the company’s entry into PCD tool production has seen it acquire two Vollmer QXD250 6-axis disc erosion EDM machines with H5 loading stations, a CHD270 8-axis TCT circular saw blade sharpening machine, a VPulse 500 wire EDM with 5-axis simultaneous interpolation, a QR270 erosion machine for finishing the tooth tops of saw blades, and the most recent installation, the Vollmer QM ECO Select. This investment adds to Vollmer machines that already include Loroch KBN and KSC HSS saw blade machines, a CHHF 21H TCT saw blade repair machine, TCT
saw blade machines such as the Vollmer CHD250R2, CHD251 and CHD270 with ND340 automated loading, a CHX840 HS and a CP200. These machines manufacture everything from solid carbide and PCD tooling, TCT and HSS saw blades, bandsaw blades, drills, endmills and many more products.
Commenting upon the business growth, Allied Tooling Managing Director, Mr Wes Hacker says: “We have always endeavoured to cater for the diverse demands of the industry whilst building a high-quality brand with sustainable growth. This has seen Allied move away from ‘cottage-industry’ work like hand tools, planer knives, lawn mower blades - stepping into more complex, higher value and higher volume solutions. This has seen us fill our factory with state-of-the-art machines to adopt greater levels of automation and technology. In the last five years, TCT saw blade servicing and sales are up 100%, carbide round tooling sales are up 100% and our diamond tooling that was once outsourced is now produced in-house with growth beyond 400%.”
It’s not a coincidence that Allied has been the exclusive UK dealer for AKE since 2019, or that it has won major contracts with multinational companies – it’s the propensity to work tirelessly to deliver on its promises, pivot and invest when required.
The 16,000sq/ft Allied facility is crammed with Vollmer machines, so Allied is adopting a ‘one-in and one-out’ policy until it finds a suitable facility for expansion in the North East to service Wren Kitchens. The latest tranche of Vollmer machines commenced when PCD tooling went from being
an outsourced solution to a serious addition to the product range. Identifying the industry trend at an early stage, Allied invested in two Vollmer QXD250’s with the H5 28-tool automation solution in June 2018 and a VPulse 500 in March 2023.
Alluding to this, Wes says: “The QXD 250 is perfect for TCT saws up to 320mm diameter, but it also has the flexibility to process all our PCD end mills, drills and cutters. With our in-house brazing facility, the QXD250 may be a machine designed for manufacturing new tools, but we also take advantage of its flexibility to service tools. With the 28-tool chain magazine, we can set the QXD250 to run around the clock, giving us a combination of lights-out productivity with flexibility. The arrival of the QXD for PCD tools certainly enhanced our reputation as a serious player in this niche and the lights-out automation reduced our lead times by more than 2 weeks on bespoke tool solutions.”
The same HC5 28 tool external workpiece storage system is also on the VPulse 500 machine that arrived in March 2023. Discussing this, Wes adds: “We purchased the VPulse 500 for its flexibility. The simultaneous 5-axis kinematics and polymer concrete base deliver unsurpassed precision
with astounding flexibility. This flexibility is derived from an EDM wire that can access areas of a tool that a disc erosion machine cannot. Furthermore, the new VPulse EDM generator significantly improves productivity.”
In October 2021, a Vollmer CHD270 sharpening machine with a four-station ND340 automation system was installed. Adding to their CHD251 and CHD250, the new arrival increased productivity by more than 30%.
The success of the CHD270 was followed in January 2023 with a QR270 erosion machine for processing the tooth tops of PCD circular saw blades. Discussing this machine, Wes says: “HSS and TCT saw blades are long established, but like the uptake in PCD shank tools, PCD saw blades are now becoming a growth market as the industry recognises the benefits of PCD on particular materials and applications. As this market shift develops, Allied will be well positioned to service customers.”
It is this strategic foresight that led Allied to bolster its PCD saw sharpening technology with a Vollmer QM ECO Select machine that was installed in January 2024. Whilst capable of processing PCD round shank and circular saw blades, this most recent arrival was acquired for saw blade servicing. As Wes says:
“The QM ECO Select was bought for its flexibility, replacing an older machine for large saw blades. The QM ECO can do anything with diamond tooling up to 600mm diameter and it’s this flexibility that appealed to us.”
6 – 9 August
IWF
Atlanta, Georgia
17 – 19 September
HOLZ-HER UK – CONTENT EVENT, EDGEBANDING WITH EFFICIENCY
Abingdon, Oxon OX14 1DY
8 – 10 October
WEINIG UK CONTENT EVENT, PERFORMING WITH POWERMAT
Abingdon, Oxon OX14 1DY
10 – 11 October
MARKFIELD AUTUMN IN-HOUSE SHOW
– HOLZ-HER
Unit H Chill
Leicestershire LE67 1TU
19 – 20 March
FURNITURE COMPONENT EXPO 25
Telford International Centre
20 – 23 May INTERZUM Cologne, Germany
26 – 30 May LIGNA Hannover, Germany
17 – 19 May
MATERIALS & FINISHES SHOW NEC, Birmingham
In response to customer feedback, IDS has introduced a brand new 665mm wide breakfast bar size as part of its Finesse by Kronodesign® laminate range.
60 laminate decors are now available in the deeper 665mm width in 4.1m lengths and 38mm thickness, these round and square profile breakfast bars are edged on both long sides increasing the design flexibility of Finesse® worktops for both new and renovation projects.
665mm is a versatile size that can be used in multiple ways. It’s ideal as a narrow breakfast bar in compact kitchens or it can be cut down to 650mm giving a deeper single sided worktop to accommodate plumbing and electrics typically installed on a sink run. The extra width also means it can be scribed into walls that aren’t square to give a neat linear run of cabinets.
The new size is available for delivery in 24-72 hours nationwide from IDS’s 10 branches.
The full Finesse range offers over 60 decors in a curated range of round and square edge profiles, thicknesses in 38mm and 22mm, together with 12mm Slim Line compact laminate decors. Worktops come in 3m and 4.1m lengths in 600mm widths, with 665mm and 900mm wide breakfast
bars, plus matching upstands and double-sided splashbacks across all designs. They are manufactured in the UK by Kronodesign®, a global leader in engineered wood products.
Designed for vertical indoor use, dp-crystal slim is perfect for splashback and wet wall applications. With its easy to clean, hygienic surface, dp-crystal slim is a suitable replacement for traditional bathroom and kitchen wall tiles. dp-crystal slim is the ideal glass, tile or traditional stone and marble substitute for all hospitality and retail environments.
Available to order in quantities from as little as just one laminated acrylic sheet with dimensions: 2800mm x 1300mm x 4mm.
Visit our website, www.decorativepanels.co.uk to explore the full dp-crystal slim range within our dp-limitless portfolio.