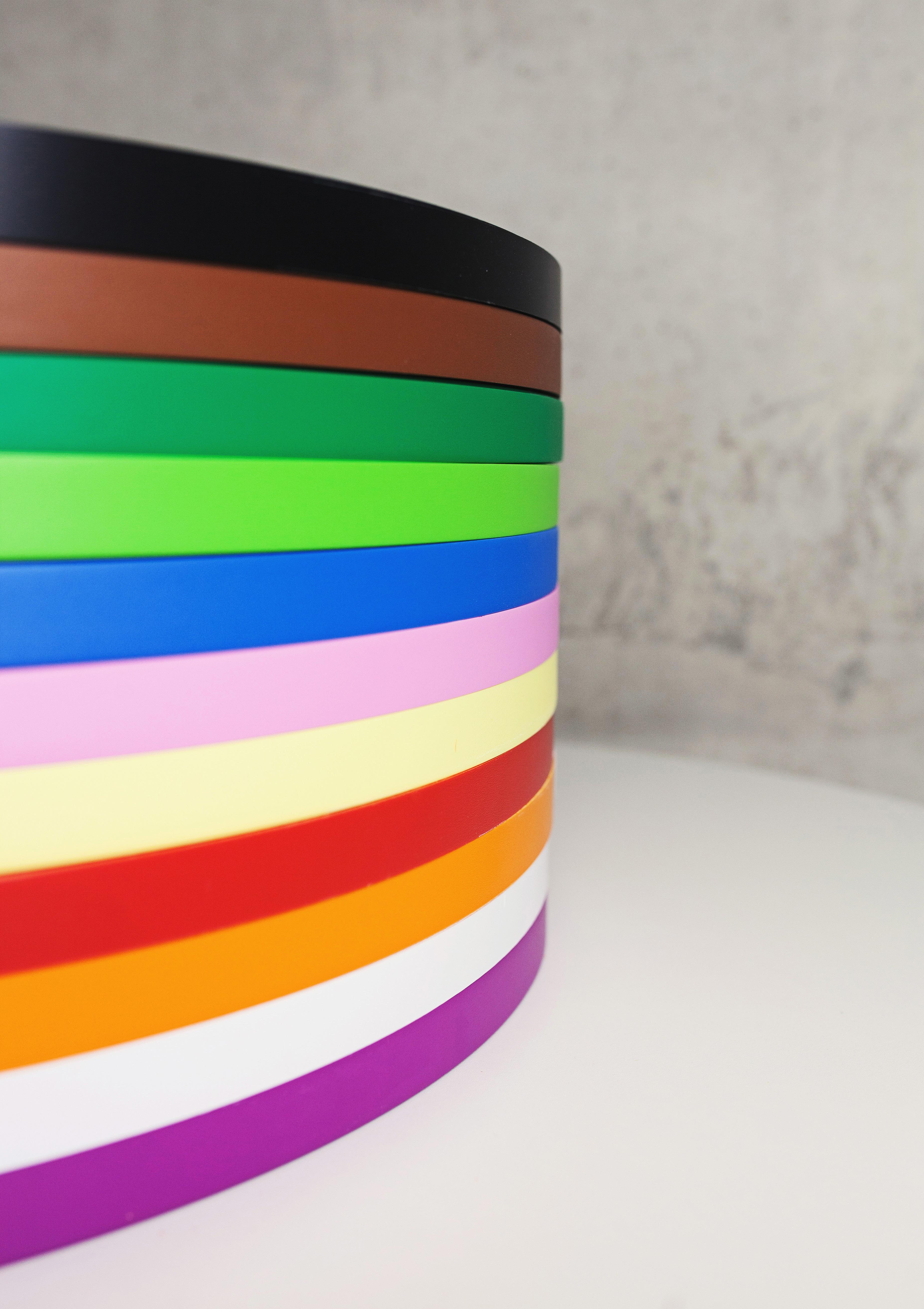
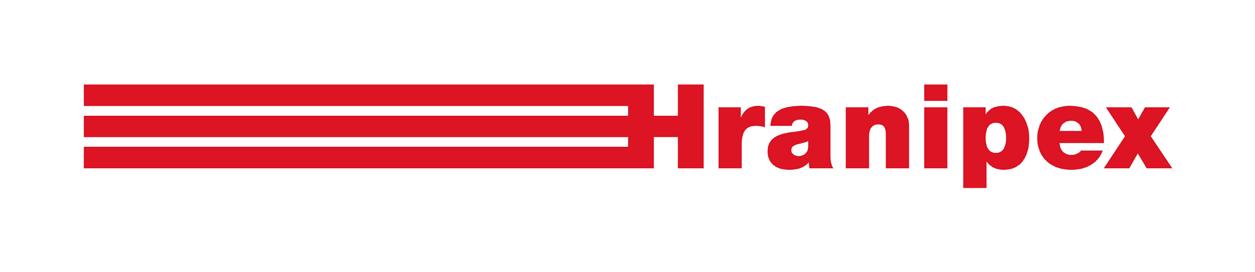
SCM creates high technology CNC machining centres for timber construction of structural beams, X-Lam/CLT wall elements and curved beams.
Innovative solutions allow extreme accuracy and speed when machining CLT panels and curved beams up to 16,000x3,600x400 mm , or glulam beams and columns of sections up to 1,250x610mm.
With Maestro beam&wall , SCM’s proprietary interface, importing data files from the main design software package is simple and flexible.
SCM UK
Tel. +44 (0)115 9770044 scmuk@scmgroup.com www.scmwood.com
Precision Made Joinery, based in Suffolk, has won the British Woodworking Federation’s Woodworking Project of the Year Award.
Sponsored by National Timber Group, the Woodworking Project of the Year Award champions innovation and the very best in design, application and ability in joinery manufacture. The BWF Awards celebrate the outstanding skills and talent in the woodworking and joinery sector, and the milestone achievements of the past year.
Precision Made Joinery was chosen as the winner of the prestigious award in recognition of its multifaceted renovation of a heritage property in Suffolk. The BWF Award judges recognised the project as an example of great capability and skill, which used modern joinery techniques to sympathetically blend structures into the existing fabric of the building.
Helen Hewitt, Chief Executive of the BWF, said:
“The quality of entries for the Woodworking Project of the Year were of an incredibly high standard but the craftsmanship of Precision Made Joinery’s work stood out. The BWF Awards judges commended how they were able to seamlessly blend old and new together – a real achievement.
“The BWF Awards allow us to come together and take pride in all that has been achieved over the past year. Our sector has overcome a great deal this year, with supply chain interruption as well as the increase in energy costs and the continued skills shortage. The Awards are a welcome opportunity to celebrate the hard-earned achievements of the past year and showcase the skill and technical expertise in the sector. Every year I’m amazed at the hard work, innovation and incredible skill of all of our finalists, and I want to congratulate all our winners on their achievements. It was fantastic to bring the industry together once again and celebrate the successes of our ever-evolving profession.”
Scott Grimwood, Director at Precision Made Joinery, said: “The whole team is incredibly proud of the end result of this project, and we’re delighted that our hard work has been recognised by the BWF Awards.”
A full list of the winners at this year’s BWF Awards can be found at: https://www.bwf.org.uk/awards-2022/
Multi award-winning timber window and door manufacturer Gowercroft Joinery has ended 2022 on a high as winner of the first ever British Woodworking Federation (BWF) Heritage Project of the Year Award.
This newly introduced award category, sponsored by Remmers UK, recognises outstanding design, craftsmanship and innovation in restoring and developing period properties.
Gowercroft Joinery scooped the top prize for the central part its range of Winston sliding sash windows played in the complex retrofit of Mews House, a low energy Victorian listed mews property in West London, which has already won a raft of architectural awards.
Set in a conservation area, Mews House demonstrates how deep sustainability can go hand in hand with building conservation.
Gowercroft worked closely with Prewett Bizley architects to provide replacement sash windows that would maintain the integrity of the historic facades whilst helping to drastically reduce the carbon footprint of this draughty nineteenth century property to better than that of a newly built home with an 82% measured reduction in the overall energy consumption.
Made from sustainable Accoya timber, the Winston sliding sash windows combined traditional joinery features with vacuum glazing
to match the appearance of the single glazed windows, whilst delivering whole window U values of 1,5 W/m2K (since improved to 1.2 W/m2K).
Andrew Madge, Managing Director of Gowercroft Joinery said, “We are proud of our work on Mews House. This landmark retrofit demonstrates how sustainability can be achievable within conservation projects, and the important role that vacuum glazed timber windows can play in bringing their energy efficiency levels up to modern standards.”
Helen Hewitt, Chief Executive of the BWF said: “Heritage projects require specialist skills and knowledge, and this award celebrates the achievements in this unique sector. With the launch of this award taking place this year, we had a significant number of entries, and it really was a close call - the quality of entries was outstanding. Gowercroft Joinery were selected as the first winners for the BWF Heritage Project of the Year Award for demonstrating how listed properties can clearly benefit from the latest technology and be more sustainable - a showcase of craftmanship and expertise.”
After a career spanning more than 40 years of service, John Bagshaw, the Managing Director of International Decorative Surfaces, IDS, has decided to retire.
John was instrumental in establishing IDS in 1999 and he has built IDS into the UK’s leading specialist distributor of decorative surfaces, generating well over £100 million in annual revenues and employing over 500 incredibly committed and capable team members across 16 sites in the UK.
Having led IDS through the Covid pandemic and its recent buyout by Chiltern Capital, John will now hand over the reins to Andy Sutton, IDS’s long-standing Commercial Director, who moves into the role of CEO. Andy will be well known to many of IDS’s customers, suppliers and employees, having worked closely with John over the past 21 years.
John Bagshaw commented: “I would like to thank everyone who has supported me over the last 22 years, during which we have successfully managed through some challenging times and wish you all good luck for the future.”
Andy Sutton commented: “On behalf of all the employees at IDS, past and present, I would like to thank John for his commitment and hard work, and we wish him all the best in his retirement. It is a privilege to be taking on the role of CEO and I am committed to building on the many successes to date and look forward to taking IDS through the next stage of its journey. We have a talented team, enduring and innovative suppliers and valued customers, and I am delighted and humbled to have been chosen to lead the business into the future.”
Tony Buffin, Chairman, commented: “John has played a fundamental role in building IDS and guiding it through unprecedented times. We are, however, extremely pleased with the deserved appointment of Andy as CEO. He has built strong relationships with both customers and suppliers over many years and has ambitious plans for the business. We look forward to giving him our full support.”
The new modern look reflects the company’s full dedication to its family of tailored cutting solutions across routers, waterjets, and parts & services.
AAG, a leading global manufacturer of CNC AXYZ routers and WARDJET waterjet cutting solutions, announced today the completion of its brand refresh, the introduction of its new AXYZ website and the refresh of all AAG logos, including redesigns for AXYZ, WARDJET, and CNCShop logos. With the continued growth and evolution of our over 30-year history in the router and waterjet industries, AAG brings its family of brands together with logos that demonstrate the cohesive link between each of the companies.
The logo refresh brings a consistent look to the AAG family of brands by using a unified colour palette, revised logo design, and a common brand icon. This update reflects our continued commitment to providing customers with the best cutting solution to keep your business growing.
The updated AXYZ website amplifies the connection between the AAG corporate site, and the AXYZ & WARDJET brands, and provides easier access to information about our growing line of routers, along with router options, software, and support. The new website features a modern design, is easier to navigate, faster, and more intuitive. The new look will be visible throughout the company’s marketing materials and social media platforms.
AAG is a leading global manufacturer of CNC routers and waterjet cutting solutions, focused on helping companies of all sizes automate better. With over 30 years of experience, we’ve built and installed thousands of CNC machines across a wide array of industries. From metals, plastics and foams and everything in between, you won’t find a better cutting system that will help your business grow and expand to exciting new levels. We currently have factory direct offices, support personal or channel partners in North America, Europe, Africa and Asia-Pacific. Every one of our team members is dedicated to keeping our clients growing better.
Hranipex Ltd is a leading European manufacturer and supplier of products and expert consulting for the furniture industry. The group, which is headquartered in the Czech Republic, was founded in 1993, and today is active in more than 60 countries around the world. Hranipex has a physical branch in 13 countries within Europe including UK and is expanding this continually. It’s wide product portfolio includes furniture fittings, edge banding, adhesives, cleaners and other components for furniture production.
PJP spoke to Simon Mitchell, Managing Director of Hranipex Ltd to get an insight into the ethos of the company.
Simon Mitchell joined the company 10 years ago when the UK branch first opened back in 2012 where he managed the East of England. Within his first five years at Hranipex he built up a solid customer base by creating sustainable relationships with small, medium and large manufacturers.
After his promotion to Managing Director five years ago he made sure that this ethos has continued ensuring equality, positivity, and teamwork throughout the branch.
Here Simon talks about his role in the business and helps us understand Hranipex and how the company differentiates within the industry.
Q: Talk us through who you are and how you achieved your role as managing director?
A: I started as an Area Sales Manager, using my own experience and gathering more knowledge and skills from experts within the industry which meant I was able to achieve local success for Hranipex. I always knew that the business would be able to grow as our product and service offering in the industry is second to none. Taking into account the local achievements and coupled with other learning obstacles, I felt it right to make small adjustments to the way we worked in the UK. The goals we set were fairly ambitious but despite that we achieved them
Q: What makes Hranipex different within the industry?
A: From an edge perspective being a manufacturer is a huge benefit for us, moreover, being a smaller manufacturer gives us more flexibility in the marketplace. With the new fittings range, and the fact that the products are mostly our own, we can have a more flexible way of working to the industry. We pride ourselves in customer service and being seen as a partner, rather than a supplier.
Q: What is Hranipex mission statement and the importance?
A: Hranipex is a leading European manufacturer and supplier of products and expert consulting for the furniture industry. The group, which is headquartered in the Czech Republic, was founded in 1993, and today is active in more than 60 countries around the world. Its wide product portfolio includes furniture fittings, edge banding, adhesives, cleaners and other components for furniture production.
Q: What steps do you take to ensure Hranipex staff are happy and motivated and how does this reflect on the customer experience?
A: The company’s corporate culture is based on the solid values that have accompanied the company throughout its history. Taking care of employees, customers, business partners and suppliers creates long-term relationships and successful teamwork. An integral part of life in the Hranipex group is extensive charitable activities and support for cultural and sports activities.
Q: What is the Hranipex approach to creating sustainability within the industry?
A: Hranipex is aware of its social responsibility and adheres to the highest ethical principles and to the principles of sustainable development. It pays attention to investments in research and development, safety and quality, and promotes new technologies leading to energy savings and emission reductions. It reinforces its commitment to protecting the environment.
With a passion for continuous development and innovation, as well as high added value of products and services, the Hranipex Group is setting new standards, strengthening its market position and becoming the number one choice for its customers.
Q: In the last two years what has made the biggest difference in operations to Hranipex UK and how does it benefit your customers?
A: In July 2021 we moved from our original site to our new facility which is three times bigger with more technologically advanced capabilities to ensure a smooth pick, pack and ship process.
The pandemic in 2020 made us review and quickly adapt to a new style of working, our office team are now working hybrid, in-between office and home, and in 2023 will be capable of carrying out their roles from home 80% of the time. This ensures our team has a good work-life balance and are able to give exceptional time and attention to detail for every customer contact.
Q: Where do you see Hranipex in the next 5 years?
A: At Hranipex we want to be recognised in the UK as being a leading supplier of furniture components and not just “the edging people”.
Our outstanding customer service will continue. We always aim for a 6-star service that is something that is always uppermost in our minds and we will continue to strive to make improvements. Our HQ are always looking at new and exciting opportunities, some will happen sooner than later, but I cannot discuss these at present.
www.hranipex.co.uk
“
“The quality and attention to detail really sets our shepherd huts apart,” claims Blackdown’s design engineer, Ross Colenso. He continues, “We get inspiration from the original shepherd’s hut concept and create bespoke designs for our trade and private clients.
“Our craftsmen take the best of the old and combine it with the experience of the new to create a unique space. It could be a living or working space, a kitchen, bedroom or even a sauna, whatever the customers’ heart’s desire.”
As a company, we are known for high quality shepherd huts and making all our joinery in-house. This means we can customise to our client’s requirements and maintain the finish we are known for.
“As the business grew, we found ourselves needing repeat pieces more often, in addition to the specialist joinery skills for the more complicated bespoke items. For us, therefore, the obvious choice to increase throughput was to use our joinery skills to craft the specialist pieces and to look at investing in CNC technology for the repeat items.
“It has always been our dream to invest in a CNC machining centre as part of our growth plans. So, with order books full, we decided the time was right to address this and purchase a 5-axis CNC. Our managing director, Will Vickery, carried out the initial research and settled on HOMAG as the best company to approach, given the heritage and reputation of the brand.
“At this point, I was assigned responsibility for the selection process which meant liaising closely with HOMAG UK’s CNC product manager, Phil Pitchford. Phil arranged for us to visit Ahmarra Door Solutions, a Hampshire based company who were already operating a couple of HOMAG CENTATEQ 5-axis CNCs.
“Seeing the 5-axis HOMAG CENTATEQ P-310 in action and talking with the operators was extremely helpful. In fact, it influenced the specification of the model we eventually opted for. There was a great deal of productive ‘back and forth’ between Phil and I to nail down the right specification for our needs.
“Phil’s knowledge of CNCs combined with his understanding of our production processes meant that together we created a solution that would serve our needs both now and in the future.”
A well organised installation with first-class training “The installation procedure for the CENTATEQ P-310 was very well organised by HOMAG. They took all the weight off our shoulders, leaving us to get on with our day jobs. Before the machine was delivered they carried out a site survey.
This highlighted the need for a new concrete slab to be laid to give the machine a solid, level foundation; this we were able to arrange prior to the CENTATEQ being delivered.
“Once on site, the HOMAG engineers worked tirelessly to install the machine. In total they were with us for around eight working days; the first three days were spent installing the CNC and getting it operational.
“The engineers then concentrated on training our team on site and I have to say they did an excellent job. They took time to ensure our guys understood each and every aspect of the machine so that when they finished the training we were able to start producing on the CNC straightaway.
“We also had training on HOMAG’s woodWOP software; this was done online with Ryan Beard and that was great too, he is a really good trainer.”
“The 5-axis HOMAG CENTATEQ P-310 has delivered significant time savings to the business as well as giving us the consistency of quality that we were looking to achieve. From the outset, it has created time for us as a business, allowing us to harvest efficiencies and use our existing skills to help us grow the company further.
“Another advantage of the CENTATEQ is its robust build quality which is exceptional. Despite it being a cutting-edge CNC, it is totally reliable and as a consequence, we have little or no downtime.
“That’s one of the great benefits of dealing with HOMAG, we hardly ever need to talk to them. I mean that in a very positive way – when you partner with HOMAG you have the peace of mind that not only does the company have a nationwide network of service engineers, but also there are engineers at the Castle Donington head office who can remote-in online and fix issues quickly,” concludes Colenso.
Specialists from Lustenau deliver know-how for smart innovations Blum is acquiring a 75.1% stake in the Austrian company System Industrie Electronic GmbH (S.I.E), based in the town of Lustenau, Vorarlberg. System integrator S.I.E generated an annual turnover of 24.8 million euros in 2021 with 125 employees in three sites. Blum’s Managing Director Martin Blum explains: “S.I.E’s focus is on the interaction of mechanical engineering, electrical engineering and information technology. At Blum, we develop product innovations for electric and intelligent furniture. Together, we can further expand our competencies in the business segments of S.I.E and in our mechatronic and smart development projects.” The close partnership also creates new synergies in the procurement of electronic components and the flexible use of resources in research and development.
Smart furniture – Applications for the furniture of the future Blum has been focusing on the potential of smart furniture for a long time, and was early to start developing mechatronic products for the “furniture of the future”. For example, the fittings manufacturer has been offering the SERVO-DRIVE electrical motion support system for wall cabinet fronts and pull-outs since 2006. The latest product solution from Blum, AMPEROS, equips furniture with lights and charging facilities for smartphones and household appliances, and there are more electronic applications in the pipeline. It was
presented at interzum, the world’s leading trade fair for furniture manufacturing and interior design, in 2021. In contrast to Blum’s core business of mechanical systems, the innovative discipline of mechatronics is very fast-moving and dynamic. S.I.E’s employees are deeply focused on this technology, so their know-how is invaluable to Blum. So now, Blum is combining its own competencies in the field of mechatronics with those of the Lustenau-based specialist for embedded systems. S.I.E will retain its status as an independent company with its 125 employees and continue to operate the Vorarlberg site plus two sites in southern Germany.
Interestingly, the founder and owner of S.I.E is Udo Filzmaier, a former Blum apprentice.
SCM attended last years IHF together with the most important players in the production business - architects and designers, machinery suppliers and builders - to present its latest products for the industry. They highlighted well established technologies that, together with the SCM team’s exclusive skills, are empowered by the seventy years of experience acquired by the Italian group in developing and producing advanced, and flexible solutions for wood machining.
The area and oikos CNC machining-centre ranges are an example of this as they are continually improved with new specific models for the production of timber construction components, and the launch of a completely new entry in terms of finishing: dmc system xl, an automatic sandingcalibrating machine specifically designed for machining X-lam/CLT panels and walls. Another good example is the trade partnership forged with the Swedish company, Randek AB - another key player at Forum Holzbau - to supply the widest range of solutions for beams, walls, frame walls and X-lam/CLT panels at international level.
At the Forum in Innsbruck, together SCM showcased the specifics of the area x, the new 5-axis CNC machining centre with mobile gantry-type structure for SMEs in the timber construction industry.
The key advantages of this new model include exceptional machining quality and maximum reliability that allow for finished elements to be produced, ready for assembly at the work site, completely eliminating potential down times caused by any problems.
Area x positions itself at the centre of the SCM 5-axes CNC machining centre range with a mobile gantry-type structure and PRO worktable dedicated to the production of X-lam/ CLT panels for walls and flooring as well as curved beams. This solution allows you to machine elements of up to 3,600 mm in width and 360 mm thick, while the length can reach up to 36 metres.
The PRO version worktable is the key feature of this new model. The high level of configurability comes from the availability of five different bases (from 16,000 to 36,000 mm) that can be fitted with automatic systems for reference and piece locking, together with innovative systems for cleaning the work area.
AREA X can have a simpler worktable for a stand-alone version or a more complete one for a version that can integrate into automatic production lines.
The 30-kW working unit guarantees excellent performance even under severe working conditions and is supported by a specific suction system for completely dust-free operations. The tool magazine can hold up to 15 tools and/or special supplementary ones to cover all possible machining work: squaring, end stop milling, slots, drilling, nesting cut, creation of sharp edges, laps and notches.
Area X, as is the case with all SCM cnc machining centres for the timber construction, is fitted with Maestro beam&wall, the software that allows you to program and control the entire workflow easily and quickly.
SCM has new project dedicated to machining X-lam/CLT panels.
Dmc system xl, is a solid, reliable and highly technological solution that offers configuration versatility and unification of the components and parts in common to optimise management costs. This new solution involves a solid steel structure capable of machining the upper side of the panels up to 3700 mm wide and 500 mm thick. Its strength is the modularity that for decades has been one of the most popular advantages of the range for dmc sanding. At this initial stage, three modules have been developed (roller unit, pad unit and transversal unit) that can be combined with one another based on specific production needs.
At the planning stage, top quality materials and components have been selected that have been designed to last long and support the most intense machining work. Furthermore, the heart of the dmc system xl technology was developed to make the operator’s maintenance work easy, fast and always safe.
SCM’s approach to X-lam/CLT sanding is to help customers distinguish themselves on the market with solutions aimed at improving the surface finish and increase the value of the finished product.
SCM presented the latest 3.0 version of its Maestro beam&wall software at Forum Holzbau, designed to machine structural elements and, more specifically:
The new 3.0 software version features a fully updated graphic programming interface and is aligned with the design CAD systems used by architects.
Its new functions are: “Advanced” nesting function for machining beams and panels that tells you in advance the amount of material needed to complete the project and achieve an increasingly more significant reduction in waste.
2D freehand drawing function to create particular shapes not included in the macro standards of BTL language.
The most recent feature is the option of using Maestro beam&wall both on PCs in the office and on the eye-M operator console, that is, directly on board the machine even at the programming stage, an important advantage for companies that rely on flexibility of use to increase their productivity.
www.scmgroup.com
Salford-based furniture installation and interior fit out specialist First Install has underlined its plans for growth next year with a trio of new appointments.
Part of The First Interiors Group which operates nationally and also has a manufacturing base in Ipswich and furniture business in Leighton Buzzard, First Install has ambitious expansion plans for 2023 and the new team is tasked with ensuring these growth objectives are achieved.
Based at First Install’s warehouse on Fairhills Industrial Estate in Irlam, the three new appointments are Liam Croft, Tom Hindle and Tom Sexton. All three will report into head of group sales and operations Mike McVey. Previously operations manager, 29-year-old Liam Croft has been with First Install for three years and has been promoted to head of operations. He will now oversee the day-to-day operations of the Irlam base, from warehousing and logistics to the installation teams working for clients out on site.
44-year-old Tom Hindle joins as commercial manager responsible for developing and implementing an effective commercial strategy that delivers on the growth aspirations of the rapidly expanding business and ensures continued success.
Finally, 33-year-old Tom Sexton assumes the role of key account manager with the brief to retain and nurture key relationships and support the growth of the company by identifying new opportunities and maximising new prospects and leads.
All three bring a wealth of experience to their new roles having worked in the industry for many years in similar roles for competitor businesses.
Head of group sales and operations at The First Interiors Group, Mike McVey, commented: “It’s great to welcome Tom and Tom to the team and I am delighted with Liam’s promotion. All three appointments will strengthen our team and service offering as we prepare for a concerted period of growth and expansion early next year. I’m looking forward to working with them and am confident that they will help us achieve our goals.”
The First Interiors Group comprises four businesses that are experts in their field of operation and have been established for more than 20 years. Offering design, manufacture and specialist interior fit out, First Install and Specialist Interiors Division deliver beautiful interior fit out projects and professional furniture installation services in the retail, hospitality, leisure and corporate sectors supported by Apex Joinery providing bespoke solid wood aesthetics and the expertise of MBS Workplace Environments in the furniture sector.
www.firstinteriorsgroup.com
Demand for warehouse space continues to outstrip supply which is driving up rents, according to industrial and logistics property experts Colliers. The situation is particularly acute in certain hotspots such as London, the home counties and locations in the midlands near major motorway networks.
“Improving not moving” could therefore be the answer to warehouse woes – assuming you know where to start with what can be a daunting task. This is all in a day’s work for materials handling specialist Combilift, which has over two decades of experience in helping companies of all sizes and from varied industries maximise the capacity, safety and efficiency of their warehouse and storage facilities. A team of 10 design engineers work on this very popular, free of charge warehouse design & layout service, and provide diagrams showing how warehouse space can be configured according to the capabilities of Combilift’s products – which can in some cases enable a doubling of available space.
CEO and Co-founder Martin McVicar: “We have always seen Combilift as much more than a designer and manufacturer of forklifts and other handling solutions. Space is one of the most valuable assets our customers possess, and if our trucks can make it work better for them in terms of storage density then everyone benefits. The ongoing demand for warehouse space coupled with ever rising business costs means that space optimisation is now more important than ever. Additional benefits of course also include avoiding the operational headache for management and the workforce of relocating to new premises, the lack of bureaucracy associated with new builds or extensions and the expense of leasing extra offsite storage.”
One company that let Combilift do the hard work for them was Farrell Furniture, which designs and manufactures quality contract office and residential furniture from its base in Ardee, Co. Louth, Ireland. Just a few years after Combilift
was established, Farrell’s Joint CEO Brendan Farrell started to investigate how they could improve storage and access to various products in the 150 x 60ft warehouse.
“We were using a 3t conventional counterbalance truck which wasn’t overly efficient and when I got talking to Combilift they took a wholly different approach from other companies that want to sell you something, I’d call it more solution based. We gave them the plans of the warehouse, the dimensions of the sheet materials, the sizes of the crates of veneer and aluminium that we use in production. They came back with detailed plans that showed us how using one of their trucks could make a massive difference to the management of our space. So, before we had even decided to go with their products, they had proved to us that we could generate over 30% more valuable storage in our warehouse – which was a pretty persuasive argument and a refreshing attitude as to how to get customers on side!”
Reconfiguring Farrell’s warehouse layout also enabled efficient and easy access to stock, which had been a bit of a slow process with the old system. Brendan reckons they now stock over 50 different colours and finishes compared to around just 4 or 5 twenty years ago, so as a rule he aims for a quick turnaround. As a major supplier of furniture for student accommodation there is also the need to be very flexible as 75% of annual company turnover is generated in just five or six months.
“Ideally a truck comes in, its load is taken to the warehouse and it’s cut next day. The less time we have the product in store the better value it represents. Our premises are around 100,000 ft², with as little as possible - just 15,000 ft² - being given over to storage. The warehouse is the same size as it was when we got our first Combilift, but over the last few years we have quadrupled in growth. This is testimony to how Combilift’s original layouts futureproofed us. Due to the lift height of 6m of our C4000 model we have been able to go up not out. The truck’s ability to travel sideways as well as block stack, plus its inherent stability means that even our largest loads – 3.6 x 2m for example - can be very safely moved around and easily accommodated in the space available.”
“For any company experiencing growth I’d recommend talking to Combilift first before they even think of moving or building new facilities – they could potentially save themselves a lot of money and hassle,” said Brendan.
“Getting help from the experts to improve the performance of our warehouse was an absolute eye opener. There’s a bit of a communality between us and Combilift too. Alongside our ‘making furniture work better’ slogan we have another one - ‘making spaces work better’ – and that’s definitely what Combilift have done for us. And we like to think employees in the offices in Monaghan appreciate the quality of the desks we provided them too!”
“The warehouse is the same size as it was when we got our first Combilift, but over the last few years we have quadrupled in growth. This is testimony to how Combilift’s original layouts future-proofed us.”
Furniturewww.combilift.com https://farrell-furniture.com/
When it comes to carefully planned storage, kitchens are where it matters most. With everything from crockery, cookware and cutlery to utensils, gadgets, food and all those bits and bobs such as scissors, batteries, chargers and pens, there’s a lot to fit in. That’s where kitchen drawers can help. While cupboards and shelves are commonly used to create storage both above and below the worksurface, it’s the drawers that offer extra space with the option to organise thanks to dedicated fittings and inserts. As the leading name in precision engineered fittings, drawer runners, boxes, inserts, pull-outs and lift systems, Blum knows all about making the most of every inch.
“Drawers are definitely the way to go with kitchen storage,” says Amanda Hughes, Blum Expert for Ergonomics at Blum UK.
“They may be more of an investment piece than cupboards and shelves but they fit more in. This allows users to do away with wall units altogether if they wish – especially if they want to make a small kitchen feel larger – without worrying about the cost, as the total price tends to be about the same. Drawers provide more usable storage space and they are much more future-proof, as they are easier to access for all ages and abilities.
There are so many advantages to planning a kitchen with drawers rather than cupboards and shelves. Doing away with wall units altogether prevents the space from feeling cramped and closed in. It’s a great way of making a small kitchen instantly feel lighter, brighter and larger plus there’s the bonus of being able to find everything quicker and easier. No more hunting around the back of dark cupboards for that elusive colander. With drawers, nothing is lost at the back and everything is instantly accessible, saving time and energy.
Drawers also fit a lot more in and the bigger, the better. Extra wide 1200mm drawers for instance provide 15% more storage space than two standard 600mm drawers. Weight is also nothing to worry about, especially with Blum drawer boxes. Depending on the width and runner system, LEGRABOX can hold 70kg and TANDEMBOX, 60kg. Use all around the kitchen, including the island.
For anyone looking to be more organised in their kitchen, Blum’s AMBIA-LINE inner dividing box system for LEGRABOX is a quick and efficient way of keeping loose bits and pieces in their place. Style-wise it’s sleek and streamlined with an on-trend black finish and slim frames that can be slotted wherever needed. Its fussfree design allows users to hold the frames in place with magnets while anti-slip feet keep contents securely in place. The ‘before’ and ‘after’ images below show how easy it is to clear the clutter and ensure the kitchen drawer is a joy rather than a dread.
Drawers can also be used to make the undersink space much more usable, too. Perfect for recycling bins, cleaning products, bin bags, dustpan and brush and all the paraphernalia that kitchens need to keep them clean and working efficiently.
Blum storage solutions can be found in all good kitchens, living spaces, bedrooms, bathrooms, hallways and home offices.
With 50 years’ experience in shredding technology and more than 13,000 reference facilities worldwide, Untha shredding technology (headquartered in Kuchl near Salzburg) provides not just a reliable partner for woodworking and timberprocessing businesses, but the undisputed first choice when it comes to shredding residual wood.
Untha is represented in the UK by Ima Schelling and one of the company’s most popular models (both in the UK and further afield) is the compact, robust LR700 which enables waste wood from joinery workshops to be fed into the shredder and mixed with wood shavings to produce a particularly productive heating material.
With the LR series, Untha offers a family of machines that ensure compact shredding for carpentry workshops, cabinet-makers, joiners, sawmills and timber industry businesses of all sizes.
These shredders offer tried-and-tested single-shaft technology, come with rated capacities from 11 to 60 kW and fulfil the needs of both smaller and larger operations . Overall, the LR series stands out for its efficient cutting system, longevity and reliability. All models of the LR series provide a high level of efficiency and economy and are maintenance-friendly.
This translates into homogeneous wood chips ranging from 12mm to 80 mm, which can be produced at a low cost and with little effort in terms of operation.
The final product is suitable for wood-chip heating plants and for briquetting, which offers yet another layer of energy efficiency for users who are able to recycle their own residual wood.
Users of the LR series of Untha shredders are able to make an important contribution to the sensible use of precious raw materials that nature provides.
Untha shredding technology develops and manufactures customised, reliable shredding systems that are used in a wide range of applications, from material recycling to the processing of residual and waste wood and the reprocessing of waste to produce alternative fuels, thus making an important contribution towards the conservation of resources and the sustainable processing and reduction of waste.
T: 1937 586340
E: sales.uk@imaschelling.com www.imaschelling.com www.schelling-solutions.co.uk
Now part of the dp-limitless range
RAUVISIO Noir HPL - 12 matt finishes with a robust HPL surface perfect for horizontal application.
RAUVISIO Brilliant Matt - A matching collection of matt acrylic finishes suitable for vertical application.
For cut and edged panels, contact us for your regional conversion perfect partner.
Available laminated on single sheets up to full load quantities. Standard sheet size 2800mm x 1300mm x 15mm or 18mm MDF. Double sided or with matching balancers on all designs.
High impact resistance
Soft touch finish
Easy clean and antibacterial
Anti-fingermark technology
Contact us for more information.
Century House, Premier Way, Lowfields Business Park, Elland, West Yorkshire, HX5 9HF
High water and heat resistance
High scratch and micro-scratch resistance
Shown in Boxcar Blonde 2464L
Matching Rehau edging
T: +44 (0) 1484 658341 E: info@decorativepanels.co.uk www.decorativepanels.co.uk
For over forty years, A.S.H. Plastics has been producing premium quality point of sale displays and precision components for sectors ranging from retail to defence and beyond. Located in Wolverhampton and with a turnover of £4.2 million, the ethos of the company is based on combining engineering excellence, a commitment to customer service and an insistence on utilising the latest in technology.
Its ethos was a key reason the company invested in a HOMAG SAWTEQ B-200, as managing director David Archer explains: “Our pledge to always provide our customers with the very best products and solutions requires we invest in the most advanced technology available.”
He continues, “We decided to purchase a HOMAG beam saw to enable us to bring under our control the tolerance accuracy of cut parts. For us to supply the best point of sale material, every part must fit together perfectly, but if there are even minor variances in the cutting accuracy it makes it almost impossible for us to consistently produce the high standard of finish we strive for with all our products.
“Previously, we had contracted out the cutting of our plastic sheets, but it was hard for us to control the quality of the cutting. Consequently, we decided to invest in a beam saw from what, in our industry, is considered the best machinery manufacturing brand on the market.”
SPECIFYING THE HOMAG SAWTEQ B-200
“As part of the selection process we looked at a few brands including an Italian manufacturer and HOMAG. We chose HOMAG for a number of reasons. Firstly, its reputation as the global brand leader gave us a great deal of confidence. Secondly, the company’s representative, Matt Long, was extremely helpful and knowledgeable. We felt he understood our business needs and, more importantly, we could trust him to specify the right saw for our current and future requirements. Matt recommended the entry level SAWTEQ B-200 and it has proved to be the perfect machine for our production demands.
“Finally, the SAWTEQ’s consistent quality of cut, with regards to both accuracy and a clean finish, were very impressive. The HOMAG saw has added a new string to our bow; it has not only given us independence, but also much improved quality control.”
The SAWTEQ B-200 is designed to cut panels horizontally with power, precision and above all flexibility. It is available in a choice of two standard models and a wide range of technology options. This enables customers to specify the machine to meet specific requirements and yet remain flexible, so the saw can grow depending on the business’ needs.
The B-200 is operated by CADmatic 5, the state-of-theart, high-performance control system from HOMAG. It features an intuitive operating concept and is open for
communication with other machines and software solutions. This latest generation of HOMAG’s saw control system has a new assistance graphic that clearly shows the machine operator all the steps in sequence. The 3D assistance graphic supports the operator directly at the saw. Its intuitive operation shortens the training period required and reduces errors to a minimum.
The new powerTouch 2 user interface features a 24” full HD multi-touch widescreen display which is easy to use by swiping, scrolling and zooming. Many of the functions are similar to those of a smartphone or tablet and are therefore familiar to most users. Even beginners will feel immediately at ease and will soon be able to control the machine comfortably.
EFFECTIVE TRAINING AND EASE OF USE
David Archer again: “HOMAG’s installation engineers were very helpful and provided the training for our staff on the SAWTEQ B-200. The saw is easy to operate and the quality of training meant that from day one our guys were able to hit the ground running.
“The machine has proved to be extremely reliable; on the odd occasion we have needed support, however, HOMAG has always responded quickly and effectively. Overall, we would expect the SAWTEQ to have paid for itself within five years and still have many more years’ service to give.
“Not only has the saw delivered cost savings and efficiencies to our production, but it has also enabled us to attract new customers,” concludes Archer.
Specialist surface materials distributor IDS has introduced the Fundermax Premium Star range of super matt and high gloss lacquered decorative panels, combining sophisticated technology with superior visual effects.
Premium Star UV-coated panels offer significant design scope in high-end residential and commercial settings, thanks to the multi-layer lacquer which ensures long-lasting colour and a luxurious look and feel. The panels are ideal for a wide range of vertical applications including furniture, kitchen fronts, partitions and more.
The exclusive UK collection offers a choice of five popular decors in both the super matt and high gloss finishes, which are available from stock in 24-48 hours with no minimum order quantity. Seven further decors and additional thicknesses are also available on extended lead times. The range spans classic whites, earthy neutrals, grey in varying shades and elegant black.
The super matt Aptico (AP) single sided 2800 x 2070mm panels feature patented anti-fingerprint technology to ensure a luxurious yet hard-working surface. The panels
have an FSC® certified chipboard P2 core which meets emission class 05 and are coated with UV resistant multilayer coloured through lacquer, which provides the opportunity to match any Pantone or RAL colour on a made-to-order basis (MOQs apply). The super matt panels are resistant to solvents, household cleaners, scratches and abrasions. They are available in 10-25mm thicknesses with 19mm available from stock.
Premium Star’s super gloss (SG) panels feature a high gloss mirror finish which guarantee maximum aesthetics. The single sided panels are resistant to heat, chemicals, solvents and scratches. They feature an FSC® certified MDF class E1 core and the high gloss effect is achieved through a UV resistant multi-layer coloured through lacquer which includes a flexible primer layer to provide a much-improved edge when cutting. Also measuring 2800 x 2070mm, the super gloss panels come in 10.3-25mm thicknesses with 19.3mm available from stock.
Fundermax Premium Star is available from IDS’s 16 regional branches, with stocked decors available for nationwide delivery in 24-48 hours.
IDS is now the exclusive UK stockist for Fundermax Premium Star range of super matt (AP) and high gloss (SG) lacquered decorative panels, suitable for a wide range of vertical applications including furniture, kitchen fronts, partitions and more.
The 2800 x 2070mm panels are available from stock in 19mm (AP) and 19.3mm (SG) in five decors, while seven further decors and additional thicknesses are available on extended lead times. Pictured is the City Grey decor in the super matt finish.
With a heritage spanning over 150 years, the upholstery specialist, Alstons, has become one the best-known sofa manufacturers in the UK and continues to provide furniture outlets with British-made sofas from its premises in Colchester. Following the sale of the business in 2015, the award-winning manufacturer has continued to invest in its 8,000 square meter manufacturing facilities, purchasing a new Weinig Opticut S90 Cross Cut Saw and Powermat 1500 Moulder with EM100 feeder to increase output and reduce running costs in its saw mill.
In 2020, the decision to replace two of the companies most integral machines in its sawmill was taken. “After 23 years of service, our trusted Weinig Opticut 200 roller-feed cross cut and Weinig 23E moulder – which we had been using to manufacturer Birch piece parts for sofa frames – were showing signs of age,” begins Michael Parker, Facilities Manager at Alstons. “We look after our machines and make sure a Weinig engineer comes to service them each year but there comes a time when you have to weigh up the practical implications of running an older machine. At some point, they will become obsolete and spare parts will be impossible to find. The fact that Weinig still holds parts for a 23-year-old machine is testament to the build quality of these machines but we needed to think longer term and the knock on effect a failing machine could have on production at a later date. Then there was a question of technology, speed and automation. Machinery has come a long way in 23 years and we didn’t want to get left behind.”
In 2020, the cross-cut saw was replaced with a brand new Weinig Opticut S90 push-feed Cross Cut Saw, which removed the manual work involved in passing timber through the old saw, providing more accuracy to the ‘cut-to-length’ product and avoiding a further secondary cross-cutting process later in production. With a clear distinction between the output, quality and cost-savings associated with the new machine, the Weinig 23E moulder followed suit. In the summer of 2022, it was replaced with a Powermat 1500 and EM100 feeder. “The cost and time-saving benefits of running the two new machines side by side was immediate,” recalls Michael “The set-up times on both machines were more than halved and the need for manual set-up and regular adjustments were a thing of the past.”
Alston’s moulder took the longest to set-up when working on small batch runs that required one of five different radiuses and profiles. “It was a laborious process and required a certain level of skill,” says Michael. “The operator had to change the cutter blocks, wind the heads up and down and amend the top, side and bottom pressures every time we wanted to complete a short production run. Now, the Powermat 1500 is pre-programmed and ready to go at the touch of a button.
“Weinig’s Powerlock clamping system also allows us to change tools within a matter of seconds safely and it’s really easy to do. This has seen the set-up times on this machine reduce from 20 minutes to just five. When you think we could be running 10 different jobs on the moulder in one day, the easy set-up process alone saves us over three hours a day and that’s before calculating the increased speed of the production cycle and reduced handling associated with EM100 feeder we installed alongside it.”
Each of the Powemat 1500’s energy-efficient IE3 motors offer Alstons a 15% saving Weinig Powermat 1500
Additional time saving has also been put down to the moulder’s user-friendly design, which includes its intuitive machine controls and tool accessibility, and the additional EM100 feeder. “The EM100 feeder allows for cut to length material to be fed via the hopper feeder rather than feeding long lengths and then cutting afterwards. The long timber lengths caused some slippage from time to time and made working with timber as long as 4.8 metres labour intensive. Now, operators are not pushing timber through. They simply load the hopper and the machine does the rest. This not only streamlines the production but also feeds the machine uniformly, which eliminates marks on the timber.”
Intelligent tooling options were also included on Alston’s Powermat 1500 and supplied by an external tooling specialist. “We opted for a reversable Tip Tooling system with constant radial settings,” says Michael. “This allows the machine to run at higher speeds of 8,000rpm and not 6,000rpm and, if required, gives us the flexibility to remove more material more quickly, accurately and to a better finish, adding to our efficiencies. This was an upgrade but we knew it would allow us to effectively machine lower grade timber suitable for sofa frames.”
The intelligent inverter-driven motors also simplify the running and maintenance of the moulder. Michael says, “Like many manufacturing companies, skilled labour is often difficult to come by. The Powermat 1500 offers a solution. The machine monitors the complete machining process, including the top pressures and notifies the operator if it detects any potential problems, avoiding damage and expensive maintenance costs. The machine also comes with a remote monitoring package that allows engineers to dial into the PLC and access the machine’s diagnostics remotely to reduce any future repair costs. We’re yet to use this but it’s something we’re looking to use on both machines in 2023.”
Alston’s energy consumption has also greatly improved. “We couldn’t have foreseen the energy crisis but we’re pleased we made the changes when we did,” admits Michael “The overall running cost of the moulder has reduced from 74kW to 58kW per hour and the speed each batch is completed has reduced by 20%. Plus, each energy-efficient IE3 motor offers us a 15% saving. It soon adds up. We’re also able to turn the motors down to reduce energy consumption when performing simple jobs like ripping.”
Due to the speed and accuracy of both machines, the sofa manufacturer now machines the same amount of timber in four days as it previously did in five – not only reducing energy consumption but also giving Michael the flexibility to use his operators in different areas of the mill. “Our wood mill is the most labour-intensive part of our business but thanks to machines like these, we see this changing. We will always need a skilled team of frame-makers and upholsterers on the floor but technology will allow us to create a more streamlined production process that makes our employees’ lives easier.”
Michael adds, “In my eyes, Weinig is one of the best machinery manufacturers in the world and they offer the best after-sales service we’ve had. You often read about happy customers saying all the right things but in our case, this is the honest truth. Weinig’s spare parts team and engineers are highly knowledgeable and really helpful – the best I’ve come across in 20 years. We’ve built a brilliant relationship with the team in the UK and they understand our business. The spare parts team know what we need, even when we don’t. They are like a family to us and that’s how it should be. They’ve even been happy to take calls on a weekend when we’ve needed advice. You simply don’t come across this level of service anywhere else. You might think you’re paying a premium for Weinig machines but when they last over 20 years, this pales into insignificance. You get what you pay for, so why would you look anywhere else?”
Machine set-up times have reduced from 20 minutes to just five
Digital readout
www.weinig.co.uk
A North East joinery company has purchased a second wood waste heater to save money on its operating costs.
Whitehart Joinery, based in Stockton on Tees is a British Woodworking Federation (BWF) registered licensed door processor for fire doors.
Whitehart Joinery has a wood waste heater in its original building, but needed a second one when the company expanded into an adjoining building to extend its manufacturing space. The new area didn’t have any existing heating, so had to be warmed using gas heaters on cold winter days.
Managing Director of Whitehart Joinery, Peter Fitzpatrick explains: “Having already experienced the benefits of a wood waste heater, we had no hesitation in purchasing a second one, so contacted Kurt Cockroft at Wood Waste Technology to give us a quote. We have plenty of wood offcuts from the frames, doors and vision panels we manufacture, enough to run the two wood waste heaters, so it was an easy investment decision to make.”
The WT5 was installed by Wood Waste Technology’s dedicated engineers, who fitted the burner into the new building and also managed to duct some of the warm air into a separate storage area, to keep the stored wood at a suitable temperature.
Peter continues: “The wood waste burners keep the factory warm, are easy to use and save us a fortune on heating and waste disposal. They’re a great investment with a good payback. We’ve been really impressed with the service from Wood Waste Technology too. From quote to installation, the team at Wood Waste Technology has delivered everything promised.”
MD of Wood Waste Technology, Kurt Cockroft says: “There are a number of businesses who purchase additional wood waste heaters for their premises once they’ve experienced the benefits of having one, especially in the current economic climate when businesses are trying to reduce operating costs and expenditure.”
Wood Waste Technology’s years of expertise in wood waste solutions have helped many companies reduce their waste disposal and heating costs. As well as offering site survey, design, manufacture, installation and on-going maintenance for new units, the company also services all types of wood waste heaters and supplies genuine spares up to 60% cheaper than other suppliers.
In addition, Wood Waste Technology is the UK official distributor for Gross Apparatebau GmbH, a German manufacturer of dependable, precision engineered shredders and briquetters, available in various sizes and specifications to suit all business applications.
HOMAG’s PAQTEQ cardboard box cutting machines automatically produce resource-friendly, madeto-measure cardboard boxes. The state of the art technology significantly reduces the amount of cardboard and filling materials required for packaging products. It lowers packaged product transportation volumes and costs, and its just in time operation eliminates box storage requirements.
PAQTEQ machines produce packaging to exact requirements – in the optimal shape, with high volume utilisation and a minimum unit cost. A core part of the technology is flexible tools that cut cardboard boxes to size automatically.
The packaging technology has an adaptable cardboard feeding system with automatic access to a maximum of 12 different track widths. This multi-line system enables the processing of complex multi-piece packaging solutions.
The machine’s software also offers the option of using a vast array of ready-made packaging designs. These are readily available to purchase from the PAQTEQ online shop. Performance, quality and safety are all increased with PAQTEQ technology when compared to that of manual packaging systems.
HOMAG’s PAQTEQ C-200 model is designed for standalone operation, while its PAQTEQ C-250 model can be integrated into packaging lines. It can be supplemented on an individual basis with a folding machine, sealing machine, robot insertion station or robot palletising to create a complete packaging line.
Displaypro is one of the many companies to have benefitted from the technology of PAQTEQ C-250. Displaypro is a leading UK manufacturer and fabricator of retail displays, signs, catering and office equipment. The company’s products are sold worldwide and it operates from three branches across Norfolk and Lincolnshire. It has ambitious plans to expand nationwide.
To increase the speed, accuracy and control of its packaging production the company’s managing director, Chris Bowles, chose to invest in HOMAG’s PAQTEQ C-250 cardboard-box cutting machine.
Commenting on the investment, Bowles said: “The HOMAG cardboard-box cutting machine enables us to produce our packaging with far less effort, more accuracy and more safely than had been previously possible using manual cutting.
“It has also the added benefit of significantly reducing our damage in transit costs and improving our customer experience. The benefits this new equipment brings will therefore assist our company’s growth plans.”
When selecting the new equipment Bowles reviewed the specifications of three specialist cardboard-box cutting machine suppliers at various trade shows. He selected the HOMAG machine as it had the right features for his company’s requirements. This included the machine’s adaptability and inline printing upgrade facility. Bowles also had previous experience of using HOMAG equipment and so trusted the brand’s product quality and reputation.
Enthusing about the service he received from HOMAG, Bowles went on to say: “HOMAG’s customer care was exceptionally good. Throughout the buying process, I received regular communications from HOMAG.
“As a result, they made sure that I got exactly the right product specification for our company’s requirements. HOMAG also made certain that our staff were adequately trained to effectively operate the machinery from day one.”
With its worldwide cooperation partners, HOMAG offers appropriate financing solutions for all of its high-tech products. So, if cash flow is an issue right now, it need not inhibit investment in a PACTEQ solution that will help you grow your business.
Decorative Panels Lamination, one of Europe’s leading suppliers of decorative faced sheet materials are launching a collection of FineFlex Metallic Designs from premium surfacing brands FineDecor and Schattdecor, to its dp-specialist range.
The dp-specialist range is a comprehensive set of quality gloss and matt surface finishes from market leading brands all of which are laminated straight from the roll onto MDF or dp-lite, perfect for trade and volume customers. With the merge of two premium surfacing brands; Fine Decor and Schattdecor, years of design expertise in the field of solid colours and decor printing have come together, along with pioneering technology to produce sustainable lacquer laminate surfaces. The two companies are united in their first joint product – Fineflex. A quality surface made with a percentage of recycled PET.
Through a patented lacquering process, a surface with a unique feel and anti-fingerprint technology has been achieved. Fineflex is particularly easy to clean and conforms to 6250 and 6222 standards. Thanks to its moisture resistance, the surface is not only ideal for furniture surfaces, but is also particularly suitable for use in humid areas such as kitchens and bathrooms. With outstanding processing properties, Fineflex is an environmentally conscious alternative for 2D lamination, as a thermoforming film for three-dimensional surfaces and wrapping or postforming.
With growing awareness and an increased drive to provide sustainable options for the market, Decorative Panels Lamination are certain the addition of 6 FineFlex metallics will be welcomed by their customers. Metallics have been coming into trend for some time now, but it has always been difficult to achieve consistency within the colour. Fineflex metallic surfaces do just that, their iridescent shimmer is visible throughout the pigment creating a luxurious finish to both the eye and the touch. The super matt finish is distinguished by the 6 warm and subtle earthy tones perfectly suited to create focal points and feature panels throughout the home.
Schattdecor and Fine Decor have a unique process to recycle the manufacturing scrap from their own production cycle into new raw material, thus bringing it full circle back into the production process. Decorative Panels Lamination are now part of the solution offering the perfect combination of first-class design and surface quality with increased sustainability.
Available on 1220mm wide laminated on MDF and dp-lite Hollowcore board in a range of thicknesses.
The Government has announced that it will be reducing support for industry with soaring energy prices continuing what can be done?
Now more than ever, companies within the UK woodworking industry need to use their own resources to overcome the energy crisis in 2023.
Chris Franklin, Managing Director at Ranheat Engineering Ltd, one of the UK’s leading manufacturers of Industrial wood-waste burning equipment. Continues his series of articles exclusively for Panel and Joinery production. This edition he looks at industrial wood fired heaters as well as boilers.
The best way to save money on energy is to use less in the first place. But within our industry there exists special requirements for making things from wood and wood-based products.
Over the last decades there has been increased use of manmade boards as opposed to natural timber. But man-made boards come with low moisture contents and therefore can be hydroscopic. i.e., they can absorb moisture from the atmosphere so need to be stored dry.
Once made into an item that item needs to be kept dry and protected from inherent moisture present in the atmosphere particularly in the winter months. Higher external ambient winter temperatures do not mean that the air is dry, so heating within a wood-working factory is needed.
Our industry also has other special needs when wood or wood-based products are cut or machined fine dusts are produced, so the workforce needs protecting from these fine dusts, so a safe working environment is provided. So, to meet COSHH regulations effective dust extraction systems from the wood working machinery is needed. This causes large amounts of air movement within the factory.
The extraction system draws the air to a central filter to separate the wood-waste from the transport air. Having got this wood-fuel to a central point there are two ways that the fuel can be turned into useful heat, an air to air heat exchanger (Warm Air Heater) or an air to water heat exchanger (Boiler)
All Ranheat boilers and warm air heaters are based on multitube heat exchangers with the hot flue gasses passing down the centre of the tubes and then the tubes having the heat extracted by surrounding them with water (Boiler based System) or with air (Warm air System)
The more tubes and the more passes down the tubes the more heat that is extracted from the hot combustion gasses and the higher the efficiency of the heat exchangers. Ranheat apply the same technology to both types of heat exchangers, boiler or warm air.
So, which is best? Generally speaking, both Ranheat types run with flue temperatures below 180oC. As the heat exchanger tubes get dirty then the flue temperature rises, a sure indication that the tubes need cleaning. Automated tube cleaning systems using compressed air can be included on most models greatly reducing the number of times the unit has to be off for cleaning.
Ranheat’s 6 figure investment in a new CNC plasma cutter in 2022 ensures that the tube nests for both Warm Air and Boilers are quickly and accurately cut. Keeping the work inhouse reduces manufacturing costs.
The lates Esprit CNC plasma cutter is the third such machine that Ranheat have purchased since 1990, this one is able to cut 25mm plate and takes a 3,000mm x 1,500mm sheet of steel.
As suppliers of parts and materials, across all industries, endure the ongoing global struggle, Masterwood GB was facing delivery times of up to six months for new machines. As the demand for these is still going strong, Masterwood GB have pre-ordered a range of machines, to go into production at the Rimini factory in Italy.
The machines are built to mid-range specifications, with the ability to retrofit additional options, such as waste conveyors and a fourth axis, so every machine can meet the customer’s requirements without the need to compromise. Alternatively, items initially added to the machine can be removed if not required, to avoid unnecessary costs for the customer.
When a Masterwood customer in Northern Ireland found their 18-year-old CNC was no longer viable for repair, the decision was made to purchase a new Masterwood Project 470L. As the machine was near completion when the order was placed in early October, delivery from Italy and installation was completed in just 4 weeks.
The current range of stock machines available from Masterwood GB includes the versatile 4-axis Project 470L, also available as 3-axis.
Winner 250 - Masterwood’s entry level short bed CNC; suitable for doors, windows, cabinets and other bespoke work.
Winner 485L – Fixed specification full 5-axis long bed CNC.
TF 600 KT – The latest addition to the Masterwood CNC drilling range. High speed drilling on all six faces of a panel, plus routering above and below with a six-position tool changer.
Masterwood continues to develop its full range of CNC machinery, as well as the recently added beam saws and panel saws, which have already been selling well across Europe and received high praise from customers for their quality and build strength. Special machines for doors, windows, and frames are still an integral part of the Masterwood range, and with the option of automation and full production lines, Masterwood can provide solutions to business, large and small.
With the support of KDT Machinery and Masterwood’s own software house, the Italian manufacturer is moving forward with upgrading existing software design packages, as well as creating new packages. The software available covers standard windows, traditional box windows, door sets, staircases, cabinets, nesting, and 3D, for three, four and five axis machines. A new version of the long-established MasterWorks CAD/CAM system is under development and will be available on new machines, and as an upgrade for existing customers.
Masterwood GB can offer bespoke demonstrations on a range of products and software at our showroom near Gatwick Airport. On show we have a 5-Axis pod & rail, 4-axis matrix bed, compact drilling machine, high speed drilling machine, and a beam saw.
The new CSC SYS 50 cordless table saw will be available from selected retailers from February 2023. With its modern and sophisticated design, including digital technologies, the cordless table saw redefines industry standards. What’s more, the new cordless table saw is so compact that it fits perfectly into a Systainer.
This means that the new CSC SYS 50 delivers the same cutting precision on construction sites as a mainspowered panel saw does in a workshop. It performs excellently in every discipline, with parallel cuts up to 280 mm, a cross cut width of up to 450 mm and angled cuts of -2° to 47°.
The new CSC SYS 50 provides precise cuts at the press of a button, compact dimensions and a state-of- the-art operating concept. These features make it an indispensable aid for interior finishing, as well as for carpenters and floor layers. Its centrally positioned and easy-to-read display allows you to adjust the height and angle with absolute precision and in next to no time. You can make even the most demanding cuts with maximum precision with the robust stop system made up of a parallel side fence, angle stop and sliding table.
“The CSC SYS 50 is the world’s first portable table saw with electric height and angle adjustment and a display with menu navigation. This means that the new CSC SYS 50 marks a step towards digitalization. However, when we implement digital technology, we always focus on the benefits to customers. The CSC SYS 50’s digital functions aren’t a gimmick but offer real added value with respect to precision and enable a cutting quality of unprecedented consistency in a portable saw. Essentially, the CSC SYS 50 offers all the qualities of a contemporary panel saw but you can also take it with you onto construction sites,” explains Wolfgang Reines, Product Manager of the new cordless table saw.
The key feature of the CSC SYS 50 is the centrally positioned display, with its non-slip dial and two buttons at the side. This enables you to effortlessly save up to four saw blade positions in just a few steps. Another clever detail is that linking the table saw to the Festool Work App enables additional saw blade positions to be saved. You can use the display to electrically adjust the height and angle at the press of a button – accurate to a tenth of a millimetre. The height and angle (available in millimetres and inches) are set parallax-free via the digital display and are therefore more accurate than any visual judgement. In addition, you can preselect speeds appropriate for the material via the digital display.
In addition to its state-of-the-art operating concept, the new Festool CSC SYS 50 typically impresses customers with extremely precise sawing results, which are in no way inferior to a mains-powered saw when it comes to precision and quality. This is thanks to, among other features, the high- precision parallel side fence with double clamping (via a single lever). Moreover, it has a highly precise angle stop, which can be optimally aligned and centrally clamped via a groove on the slide and enables mitre angles of between -70° and +70°. The ball bearing-mounted slide can be moved completely smoothly and ensures parallel and angled cuts with maximum precision. Another practical detail is that, in the limited range of a cutting height of 35 mm, it is even possible to make angled cuts of up to -10°. This is ideal for undercutting infill panels because the field of vision in which the workpiece is to be cut is at the top. You can saw long workpieces exactly, safely and easily in combination with a slide, preset profile setting rail and additional underframe support. You can also use a groove in the slide to safely clamp workpieces together with the Festool FSZ clamp clips, which are available as an option.
Nor is the CSC SYS 50 in any way inferior to a mains-powered tool when it comes to power. The CSC SYS 50 is powered by a brushless EC-TEC motor and a dual battery system with two 18 V battery packs (from 4.0 Ah). This combination ensures a long runtime. For example, the brushless ECTEC motor is long-lasting, maintenance-free and, on top of that, powerful. With high speeds of 6800 rpm, it enables fast sawing progress and perfect cutting results in equal measure. The dust collection bag allows work with low levels of dust, even without a mobile dust extractor. The table saw is an ideal partner for the new Festool CTC SYS, CTC MINI and MIDI cordless dust extractors.
The table saw is as surprisingly versatile as it is convenient due to its size and cutting capacities, with parallel cuts up to 280 millimetres, a cross cut width of up to 450 millimetres and angled cuts of 2° to 47°. The simple space wedge changes for hidden cuts and rebates is another feature which extends the saw’s range of applications. Moreover, you can reinstall the spacer wedge with the guard in an instant.
Work is made even more convenient with the UG-CSC-SYS underframe specially developed for the CSC SYS 50. You can use this folding underframe to set the cordless table saw to the ideal working height in an instant. At the same time, it also serves as the ideal solution for transport from the vehicle to the construction site. The CSC SYS 50, packed in a Systainer, is compatible with bott vehicle equipment. However, even when away from the vehicle, the CSC SYS 50 can also be transported easily in one hand in a Systainer.
Another practical detail is that saw blades, a spacer wedge and a dust collection bag are securely stowed in the lid of the Systainer. It has a three-year warranty, which also covers the battery packs and chargers.
“Battery technology and battery-powered devices are an extremely significant trend on the tools market. We have tailored our strategy to reflect this and are continuously expanding our portfolio accordingly. We want to take a more purposeful approach to ascertain how battery technology might best serve the application in question. We want to optimise the results so that the products are perfect for their applications, and we want to make work easier, safer and better for tradespeople,” says Sascha Menges, CEO of Festool GmbH.
T: 01284 727271 www.festool.co.uk
The new VS Area Storage System and LS1 range from Schelling are just showing how well they are adapting to the climate in the market. The LS1 is making batch size one production even more eicient and the VS can be adapted to suit any requirements. It can even be over multiple levels for those short of space! Get in touch for more information on the VS or LS1. at sales.uk@imaschelling.com