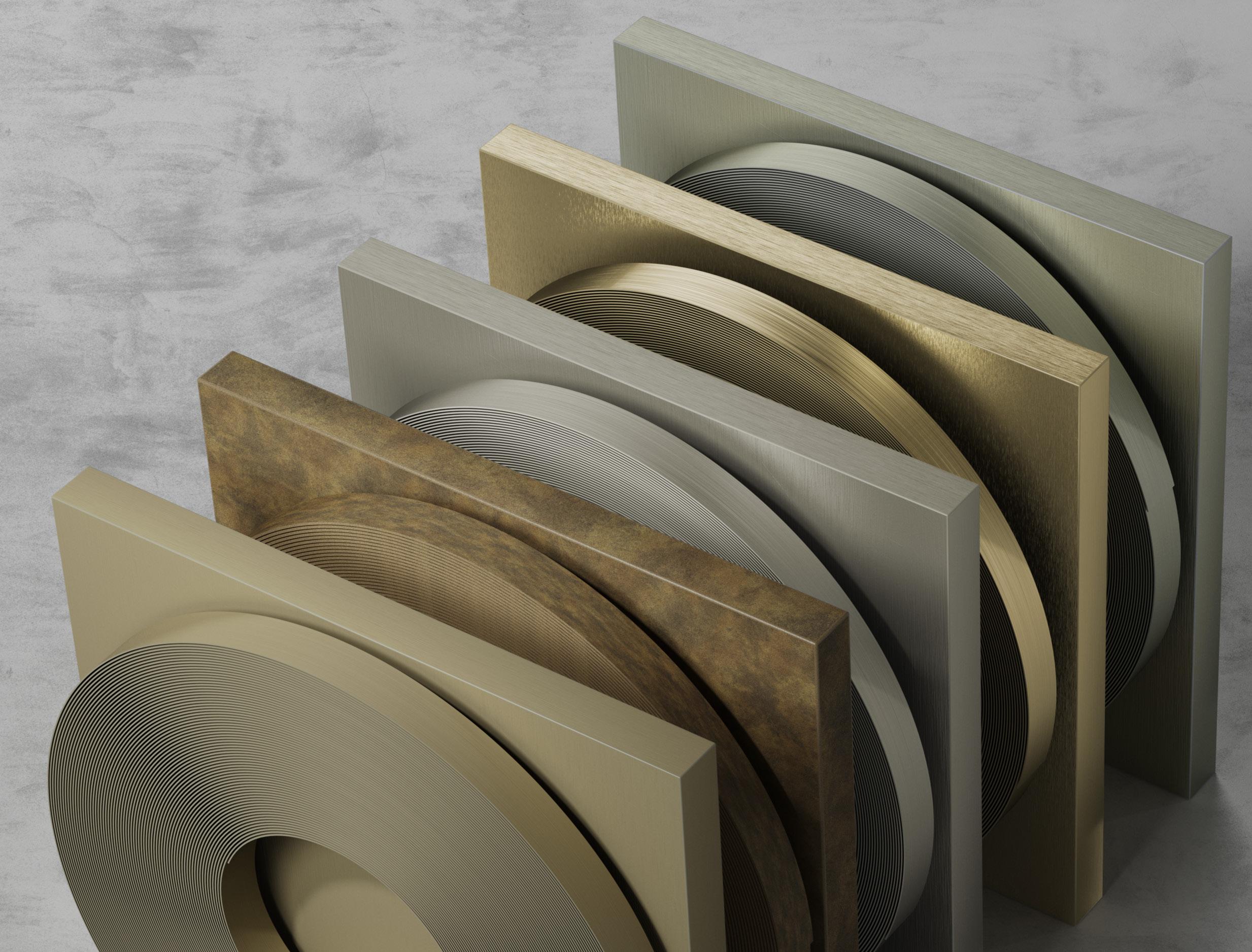
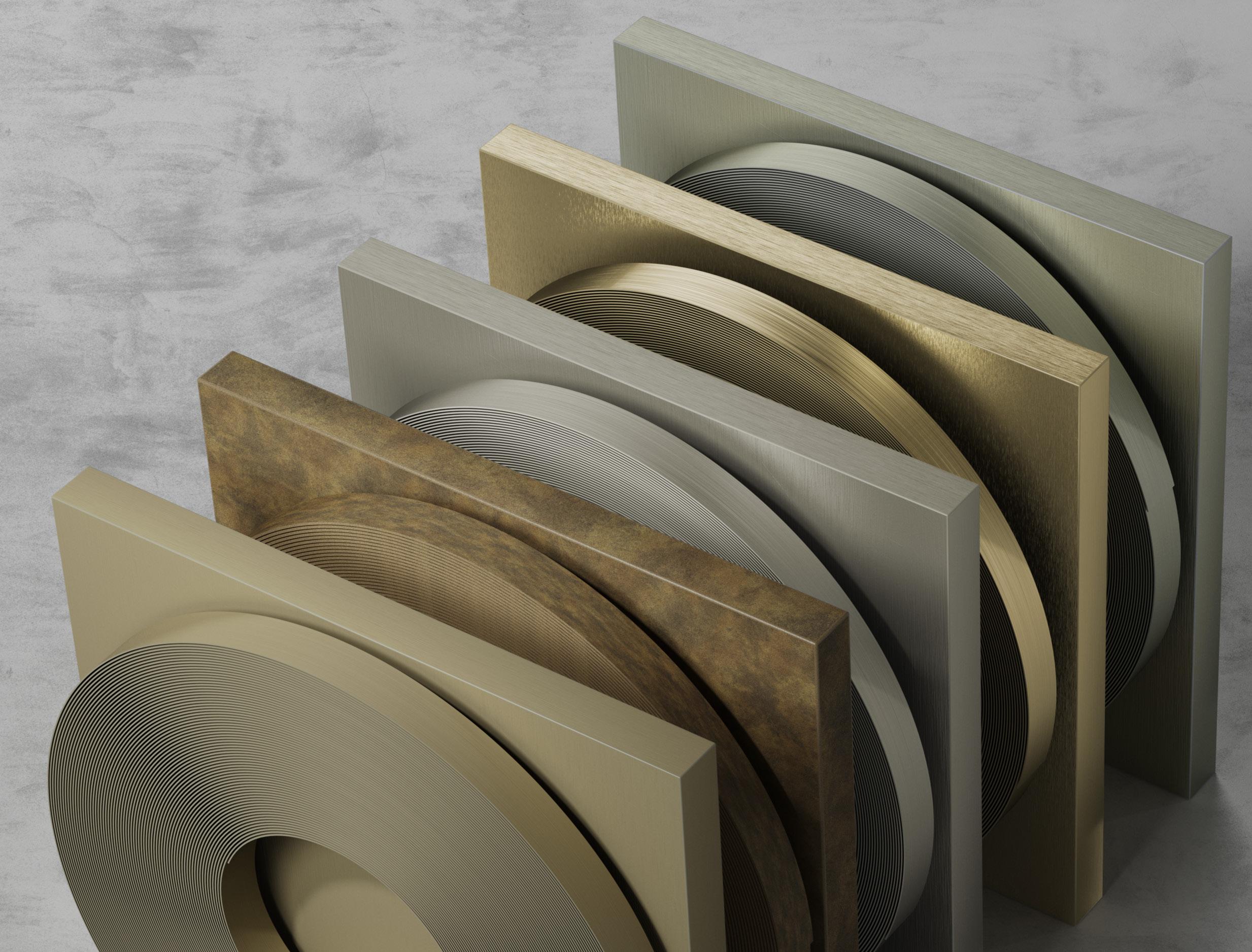
STEFANI SBX
PRECISE SQUARING FOR HIGH-QUALITY EDGE
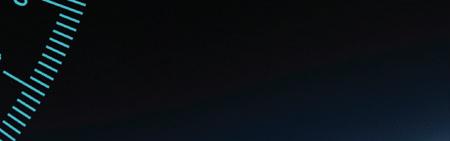
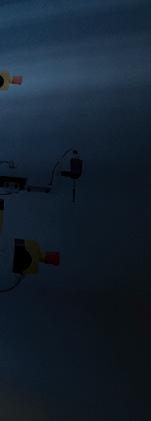

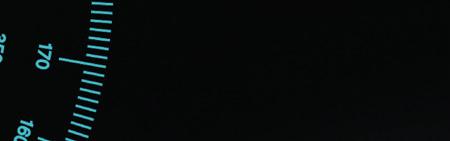
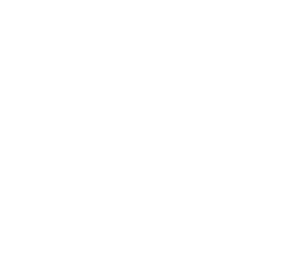
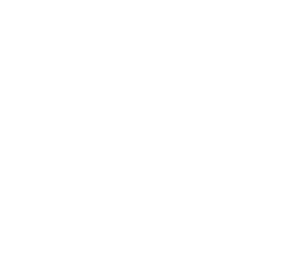
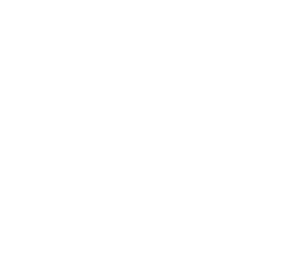
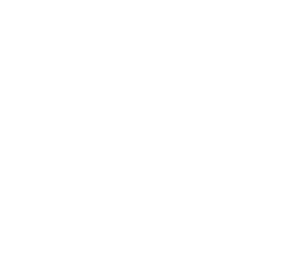





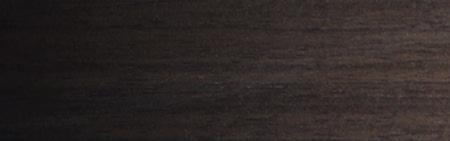
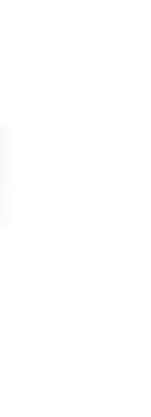
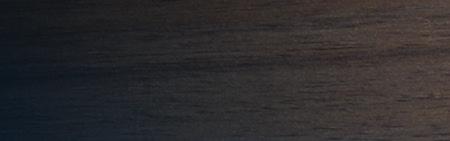
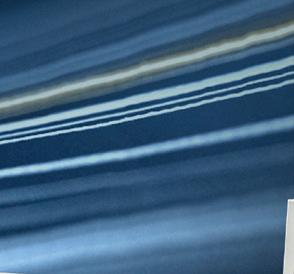
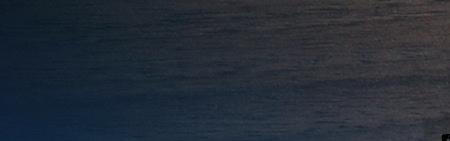
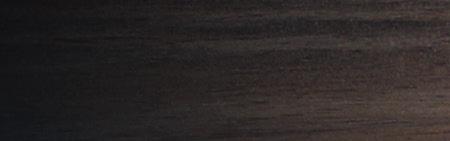
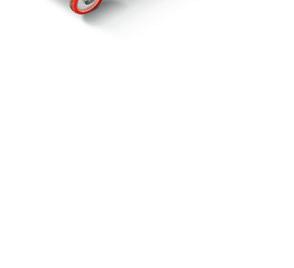
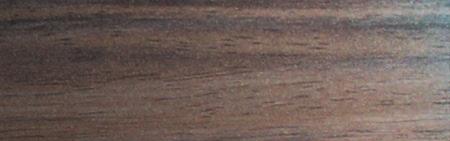
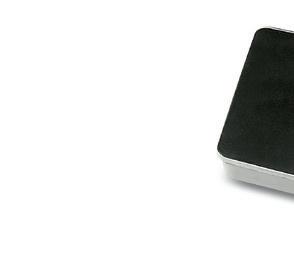
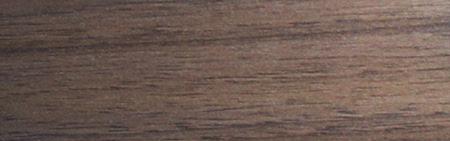

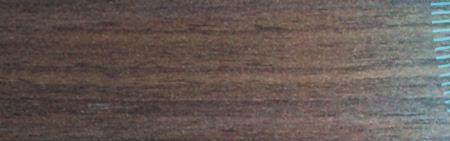
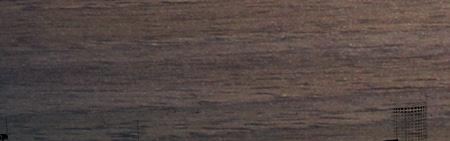
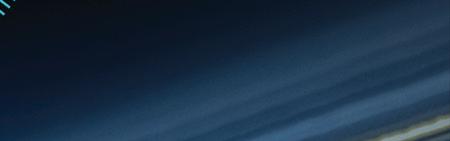
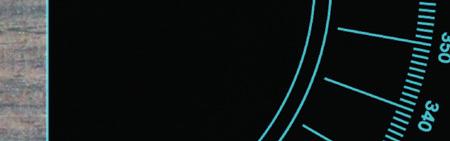
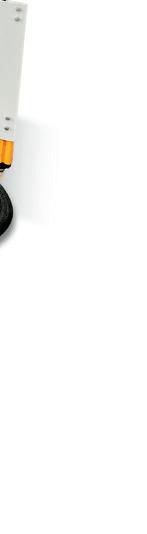
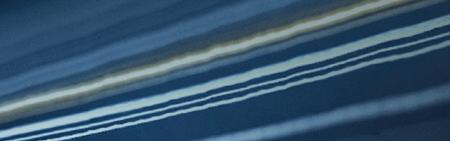
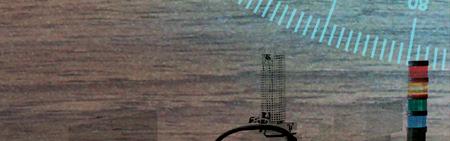

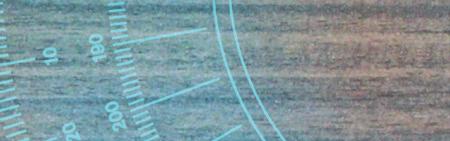

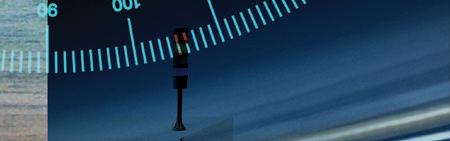
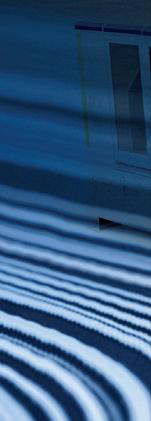

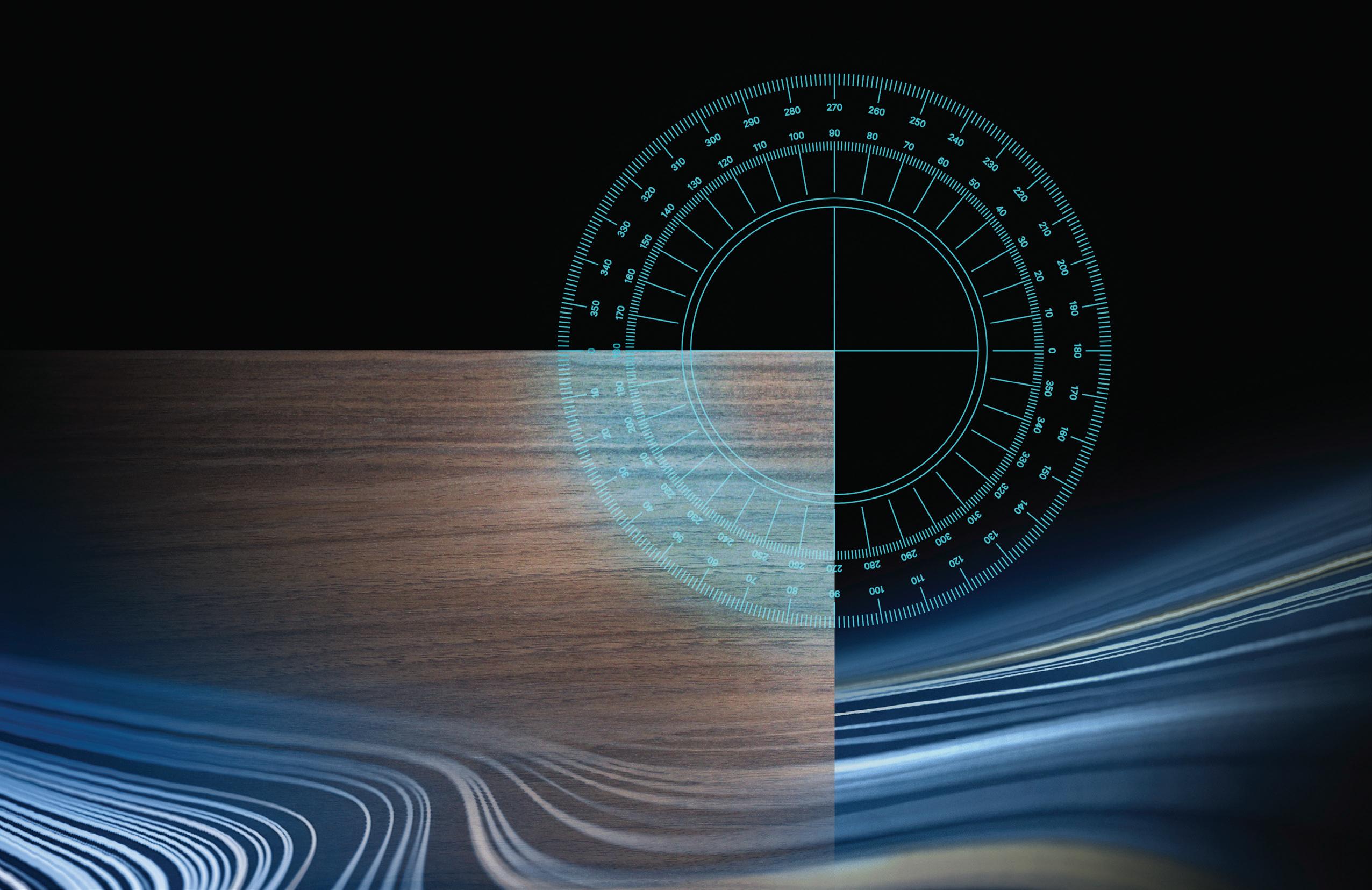
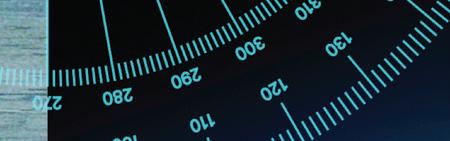
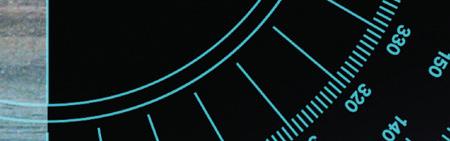
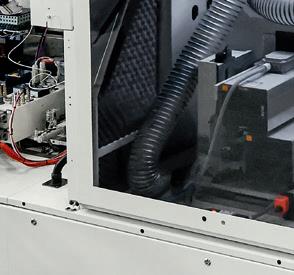

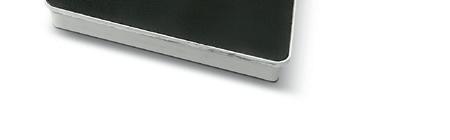
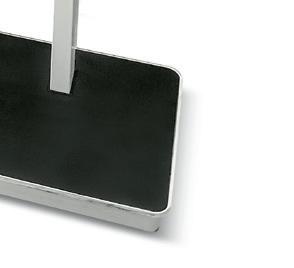
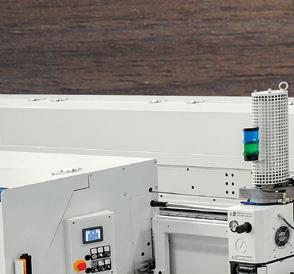

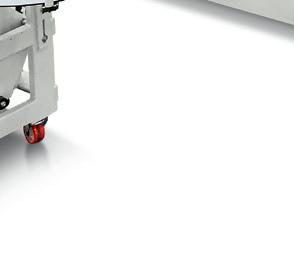
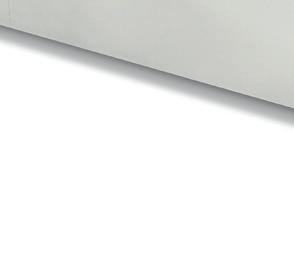
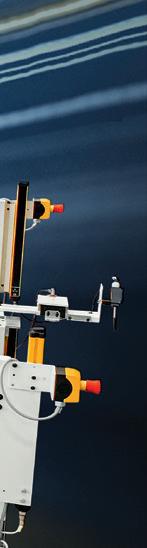
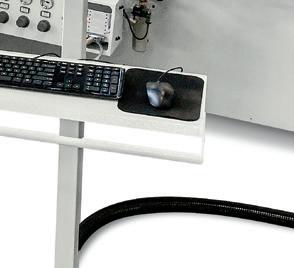
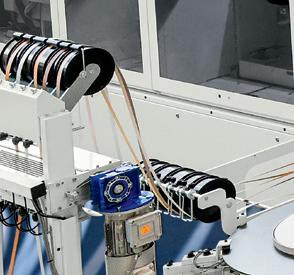


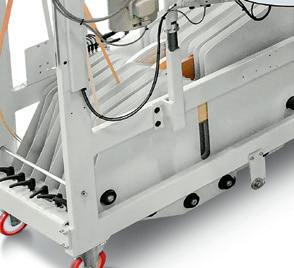
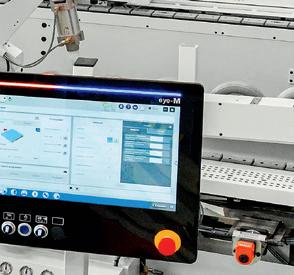
T h e s tefani sbx squaring-edgebanding machine combin es perf ec tion in panel sizing a n d s q u a ring with flawless finish quality , ideal for the furniture industr y t ha t r eq uires h i g h l y c o n figurable solutions.
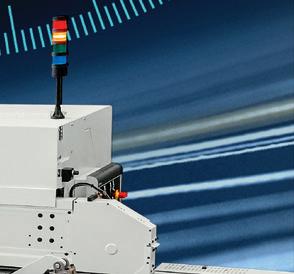
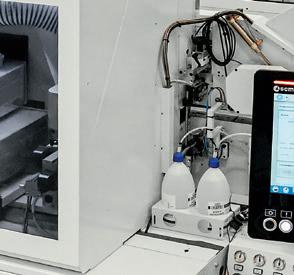

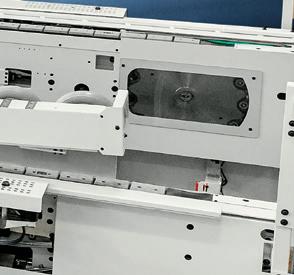
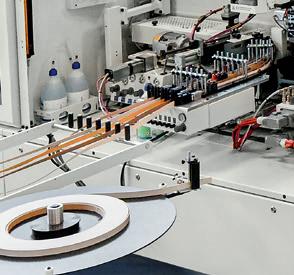
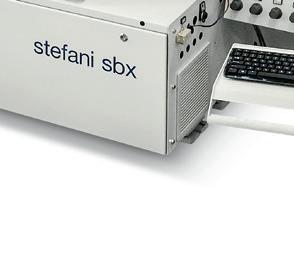
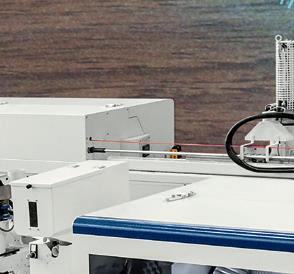
T h e rigid structure , together with the reliable an d constant system of panel tr ansport are key to preci se squaring and high-productivit y. Th e sq ua red p an el is ready to move on t o th e more delicate process of edg e gluin g, with zerod o wn time automatic glue ty pe / co l ou r c ha ng eo ver, and the finishing with state-ofthe-ar t e l ectronic units. The re sult is stefani sbx, the ou ts tanding s olution for highly demanding workflows and top-level finis he d pr od uc ts .
SCM UK
Tel. +44 (0)115 9770044 scmuk@scmgroup.com www.scmwood.com

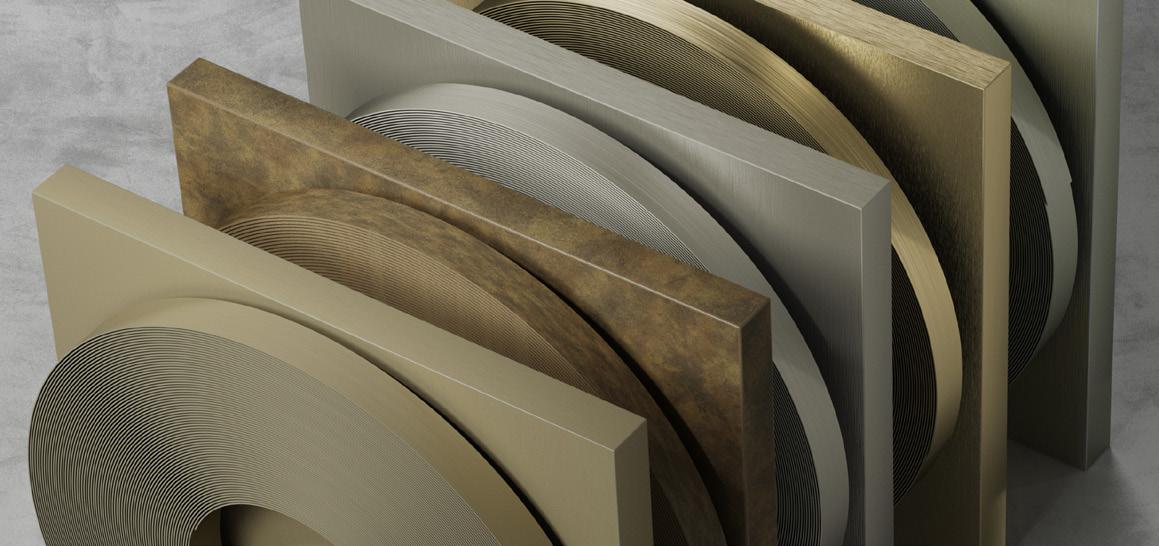
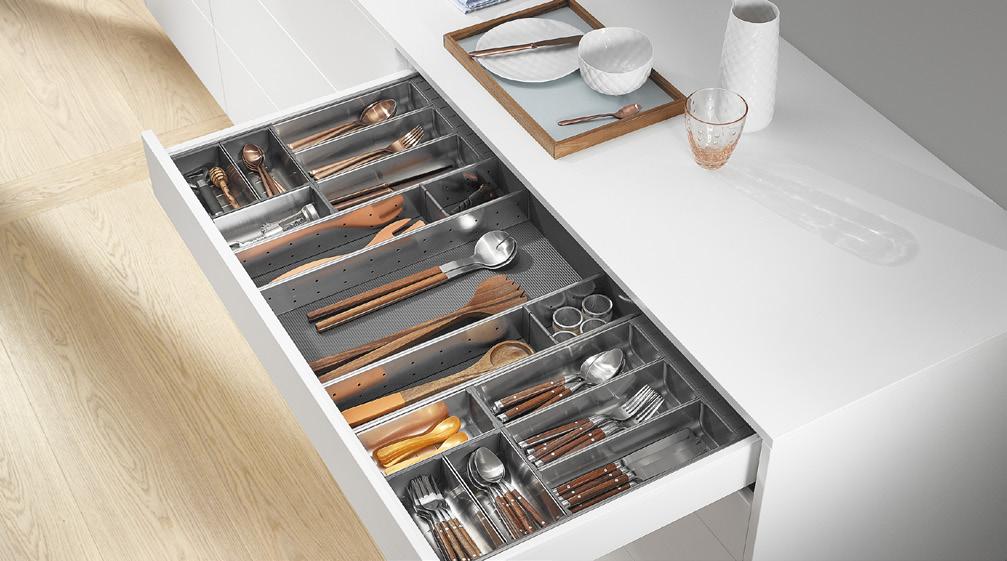
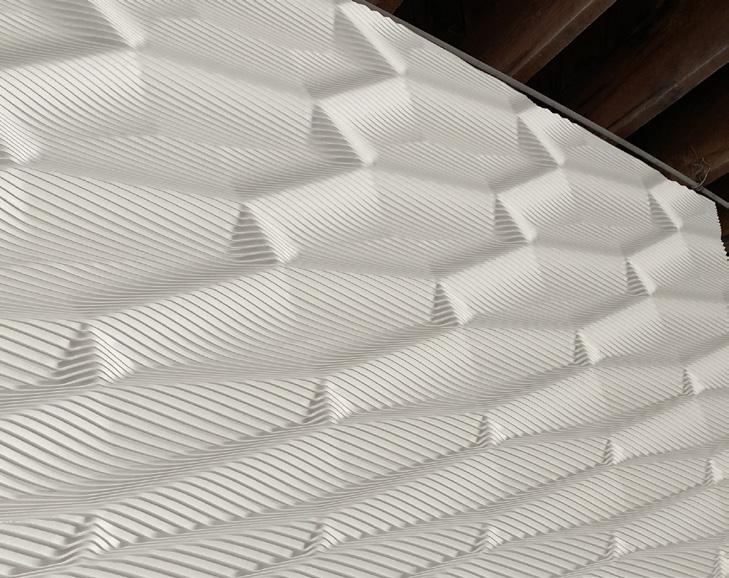
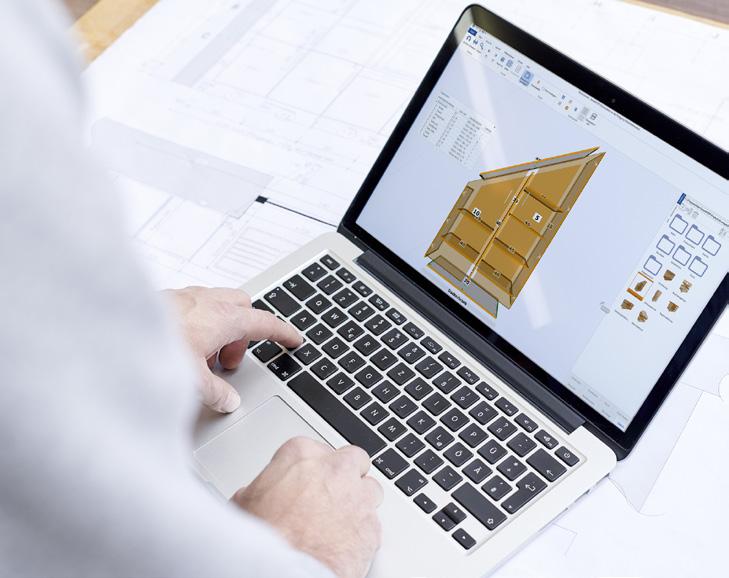
IDS EXPANDS ITS SENIOR PANEL TEAM
Specialist surface materials distributor IDS has appointed Kevin O’Donnell as Regional Sales Manager, as part of the expansion of its dedicated decorative panel division.
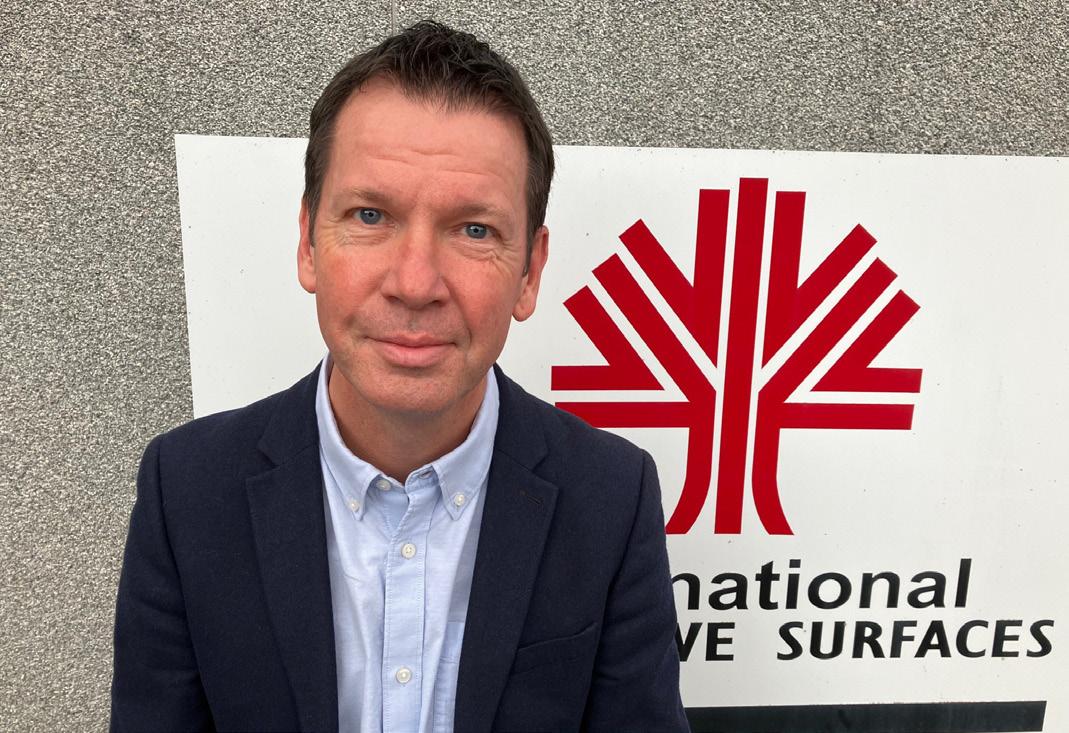
Based at the company’s branch in Ely, Cambridgeshire, Kevin will play a key strategic role in driving sales growth of decorative panel products in the south-east region. He will be responsible for driving the panel sales strategy and developing new business opportunities in the region.
Kevin joins IDS with a wealth of sector experience having previously worked in National Sales Manager roles at Twyford Bathrooms and more recently Gerfloor. His expertise will complement the existing senior panel team headed up by Dave Huggins, Business Development Director and Michael Davis, National Panel Sales Manager.
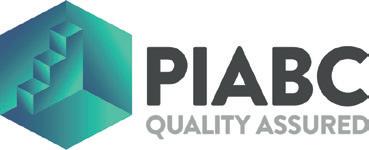
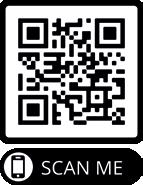
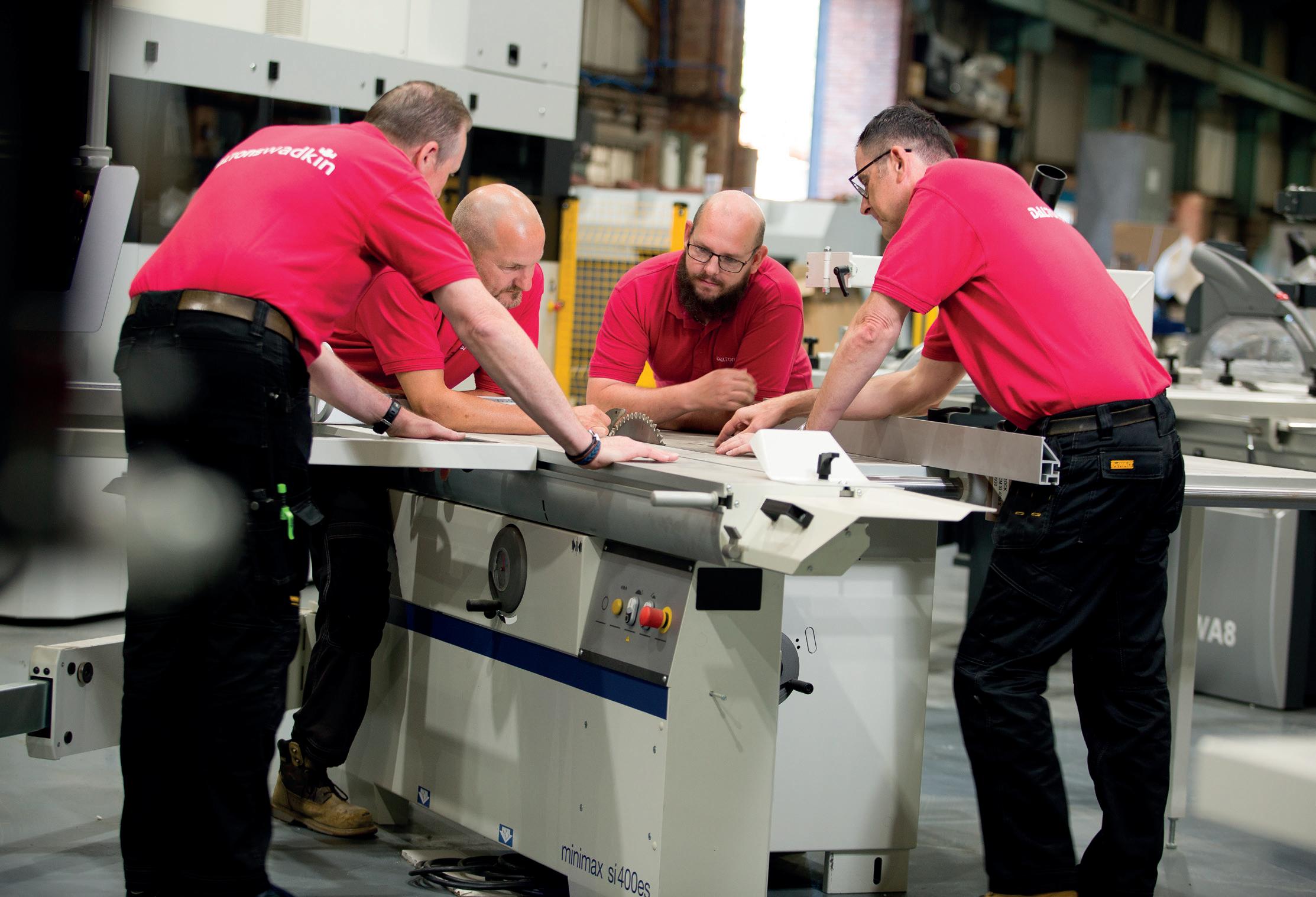
The appointment comes at a time of expansion for IDS’s panel division. The business has recently invested in extra racking at both its Ely and Blackburn distribution centres, expanded its fleet of delivery vehicles and added new products to its portfolio which spans raw boards, MFC, MDF, CDF and more.
Dave Huggins, Business Development Director at IDS, says: “IDS has continued to invest in its specialist panel business and I’m delighted to welcome Kevin at a time of strategic growth. His track record for being professionally tenacious and renowned as a solutions provider will benefit both IDS and customers alike. Having Kevin on board will afford IDS Ely the capability to spend more time with our customers in the south-east, deep diving into all issues surrounding customers decorative panel product and service requirements, ensuring we are continuously aligned with the needs of new and existing customers.”
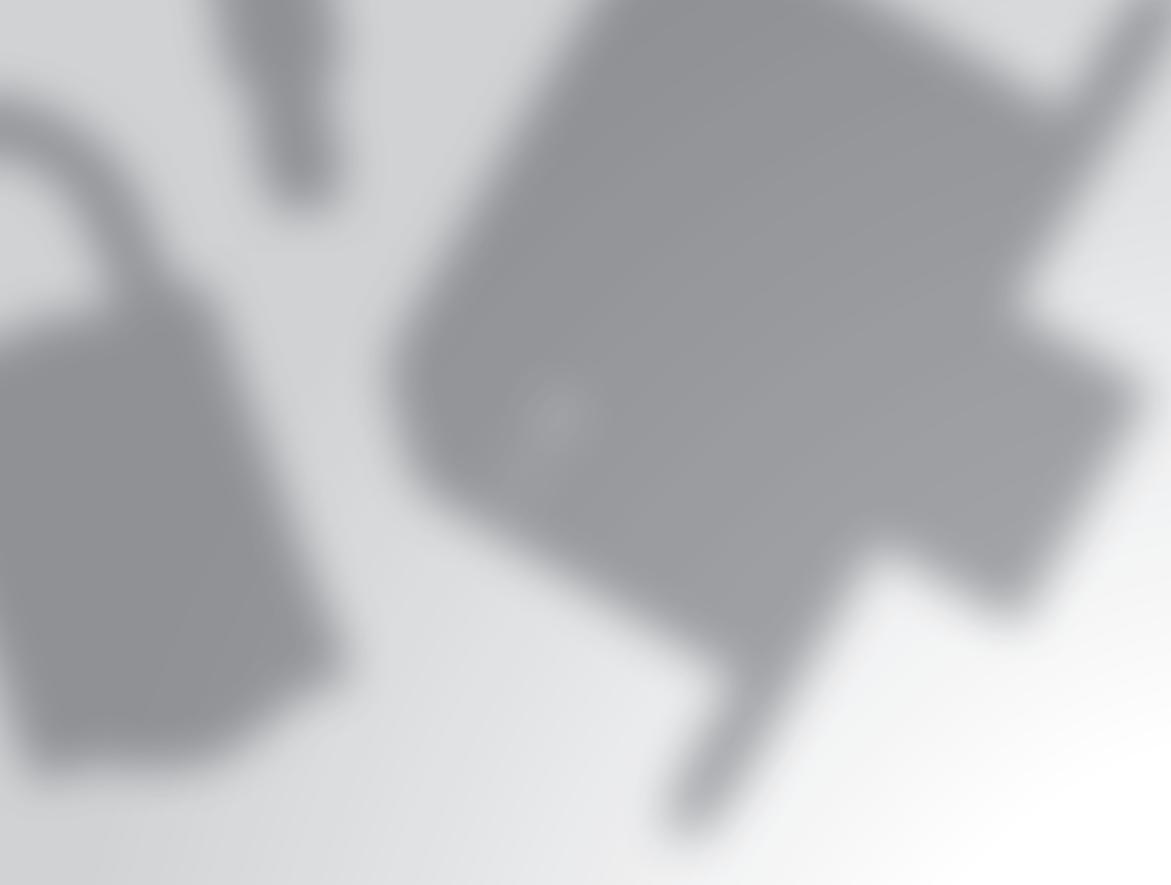
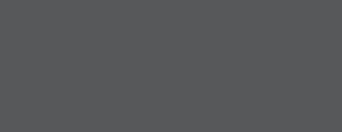
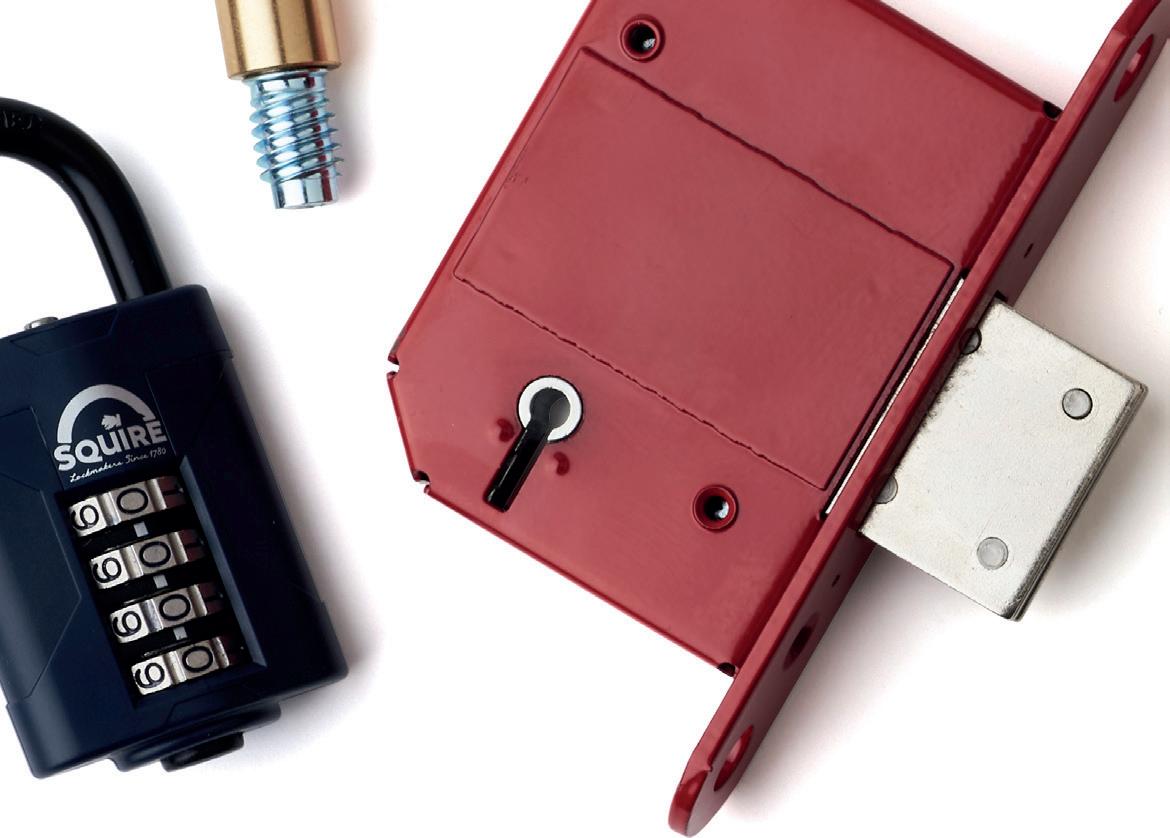
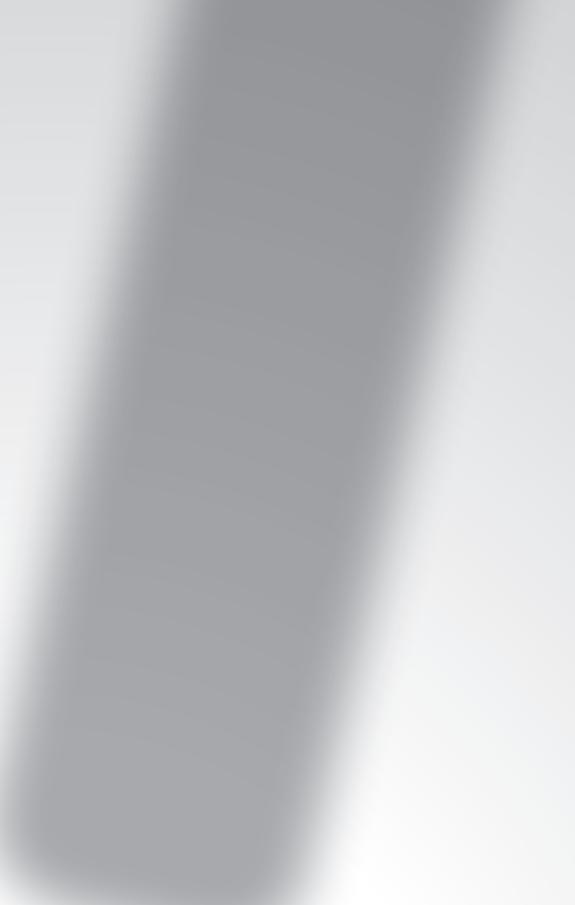
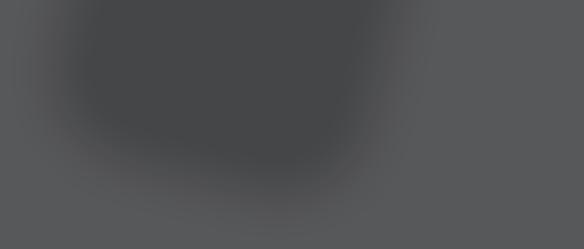
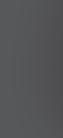
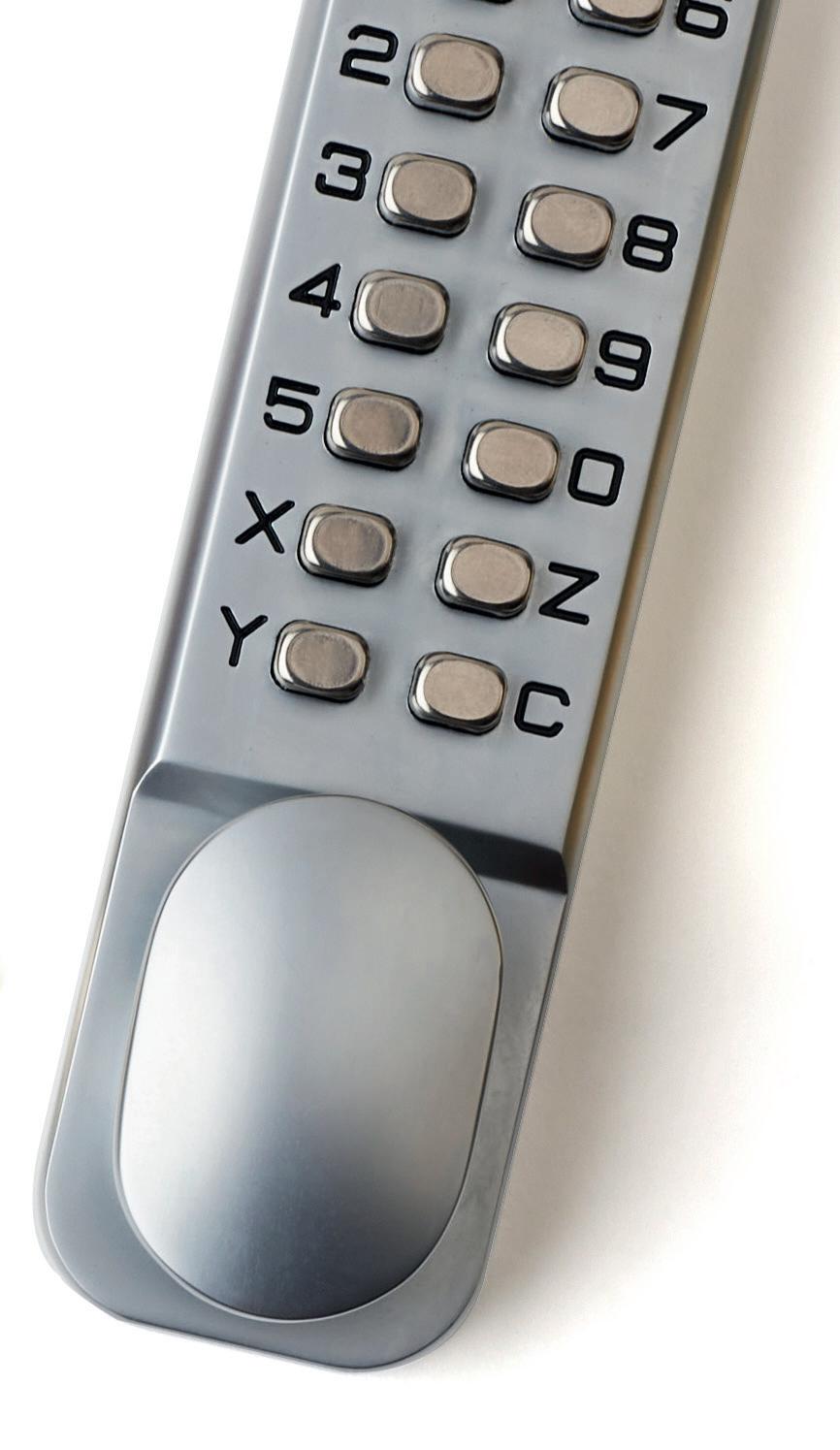

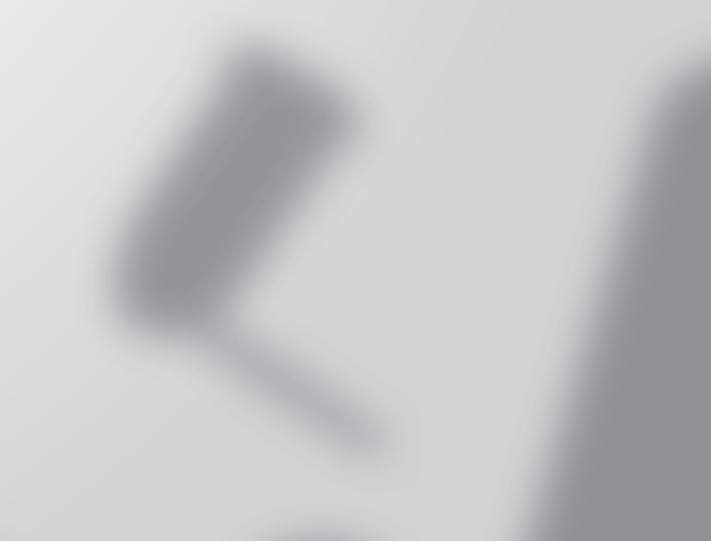

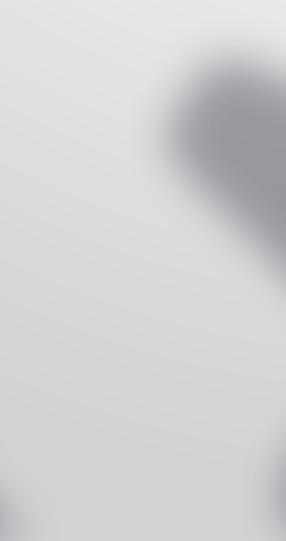
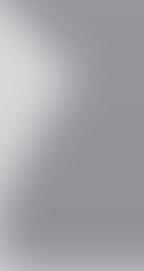

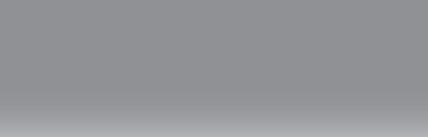
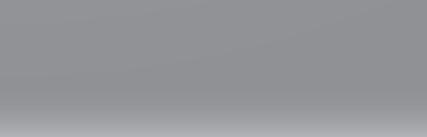
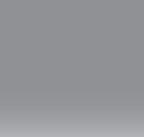
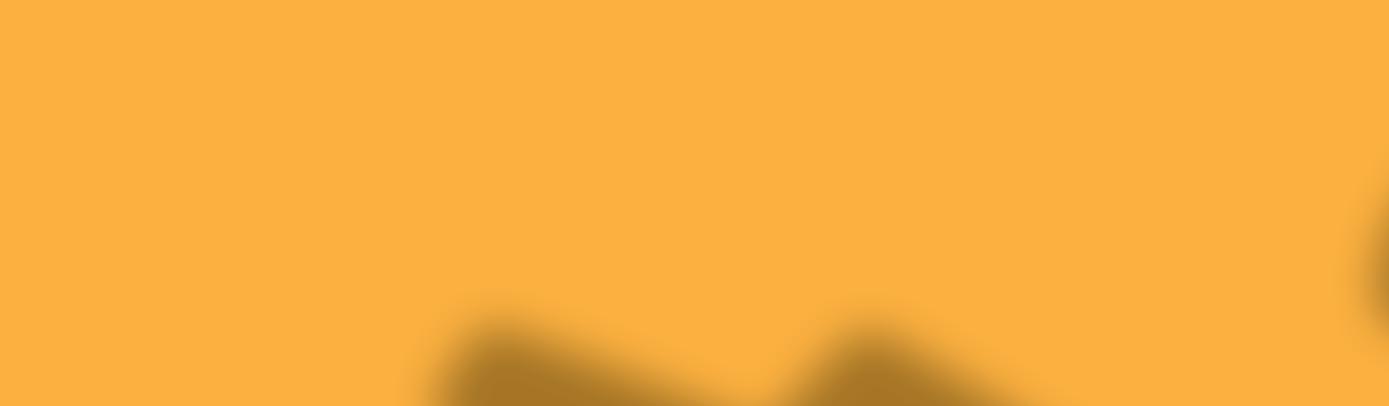
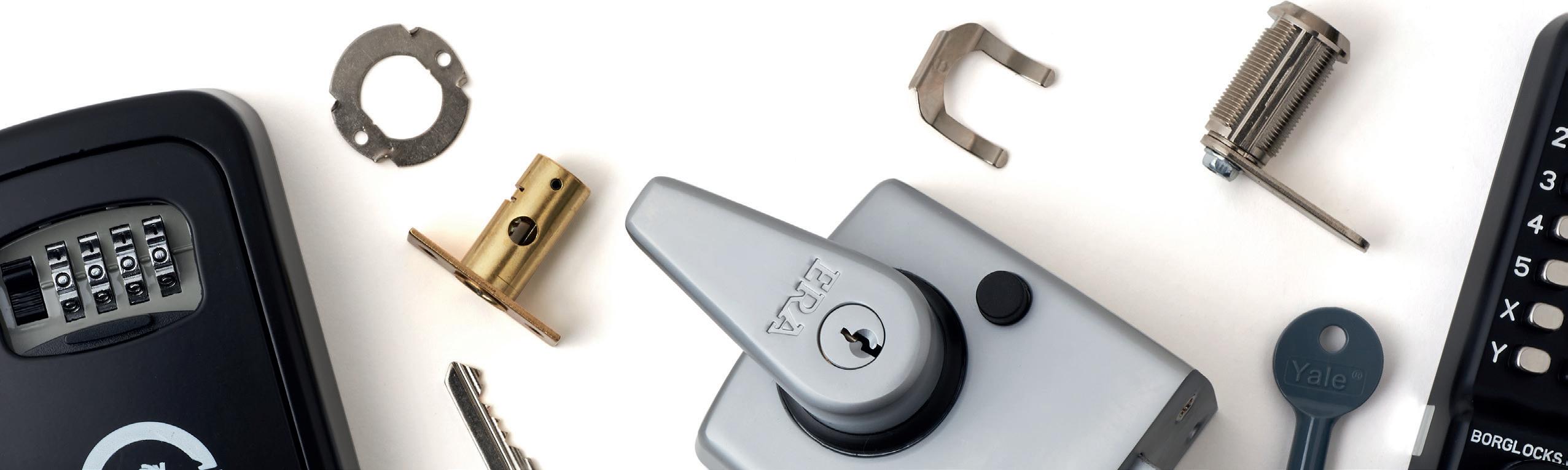

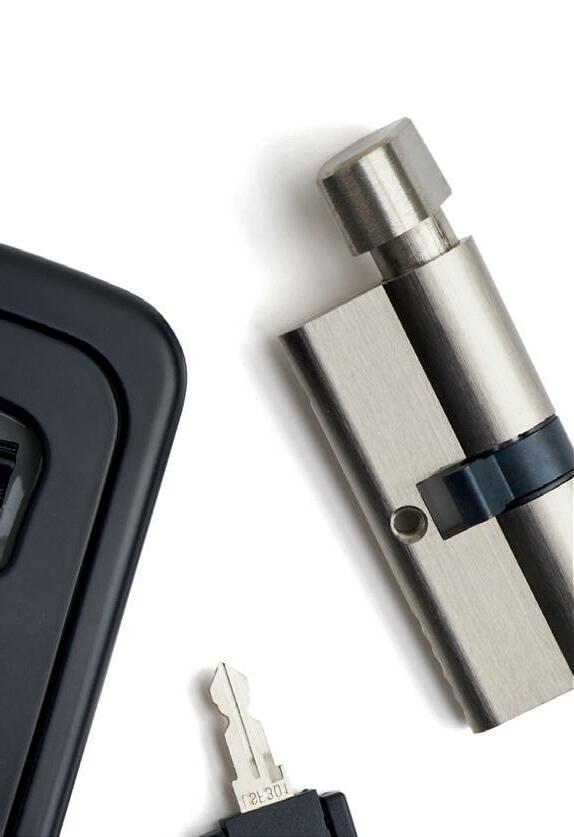
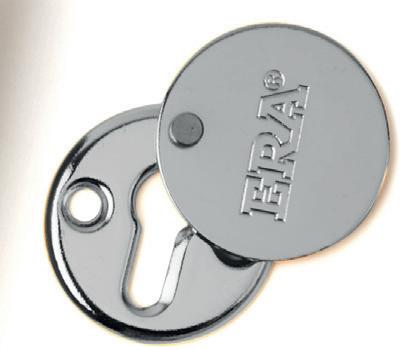
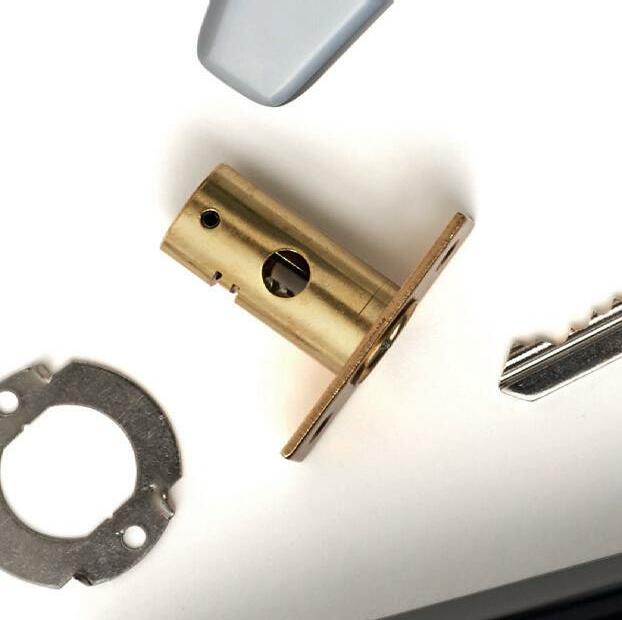

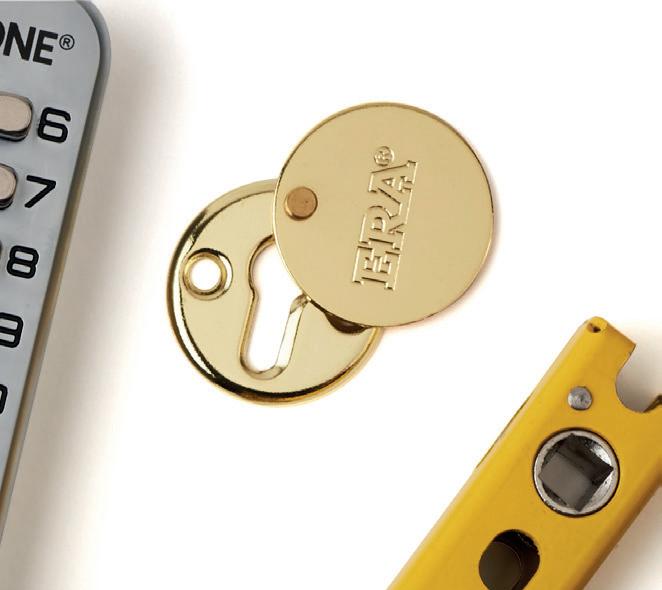
“A SURPRISING XYLEXPO!” SAYS SALVAMAC
“We did not expect the results that this Xylexpo 2022 has given us instead”. Christian Salvador and Ziemowit Dolkowski, owners of Salvamac Group, the Italian-Polish company that is also in Milan has shown great vitality and an uncommon vision, presenting itself to the visitors of the international exhibition in a collective stand with Sia, partner in dust extraction, and Paoletti Engineering, specialist in solid wood processing.
“We are absolutely satisfied not only with the quantity of contacts we have established, but also with the quality and concrete interest we have gathered among the visitors,” added Ziemowit Dolkowski. “Showing ourselves in a booth of “important” dimensions, investing in an image that would tell of our determination and putting, above all, our team on the field once again rewarded us”.
“We breathed a positive atmosphere, the desire to reconnect those human relationships that the pandemic had cooled, returning to talk about our machines and our ideas face to face, in front of plants and solutions that it was finally possible to touch”, adds Christian Salvador, who then concluded: “We signed orders and even received downpayments, something that hasn’t happened for some time.”
Great attention has been paid to the “Salvacut 5000”, a high-speed pass-through optimizing saw with electronic cutting and handling that allows the optimization of up to 3,500 linear meters of profiles per hour: important performances, achieved thanks to technical innovations and the development of electronics from which this machine was born.
Once again, the already mentioned partnership with other “co-exhibiting” companies - Sia and Paoletti – which was awarded the Xia-Xylexpo Innovation Award for solid wood processing, is a further confirmation of the validity and quality that the partnership and sharing project that Salvamac Group has always carried out, is an absolutely winning recipe.




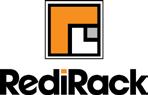

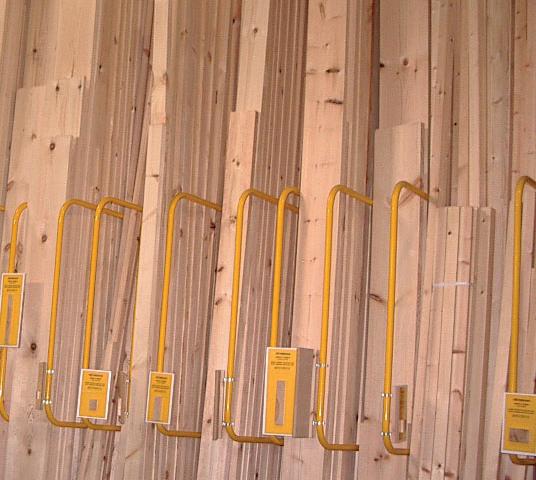

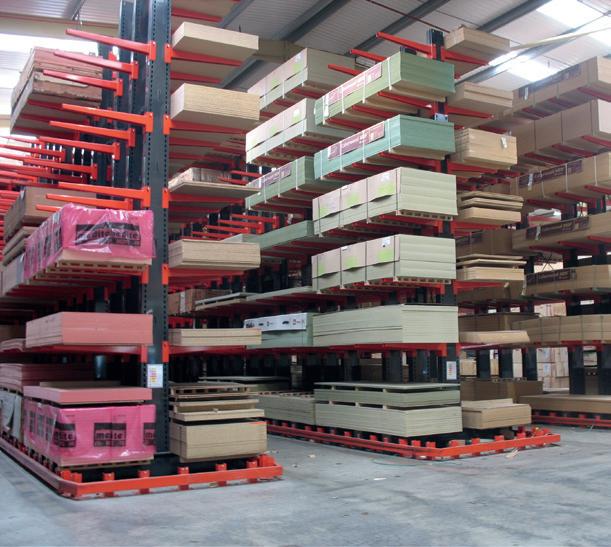
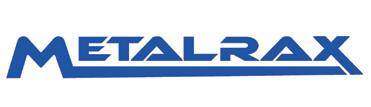

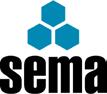
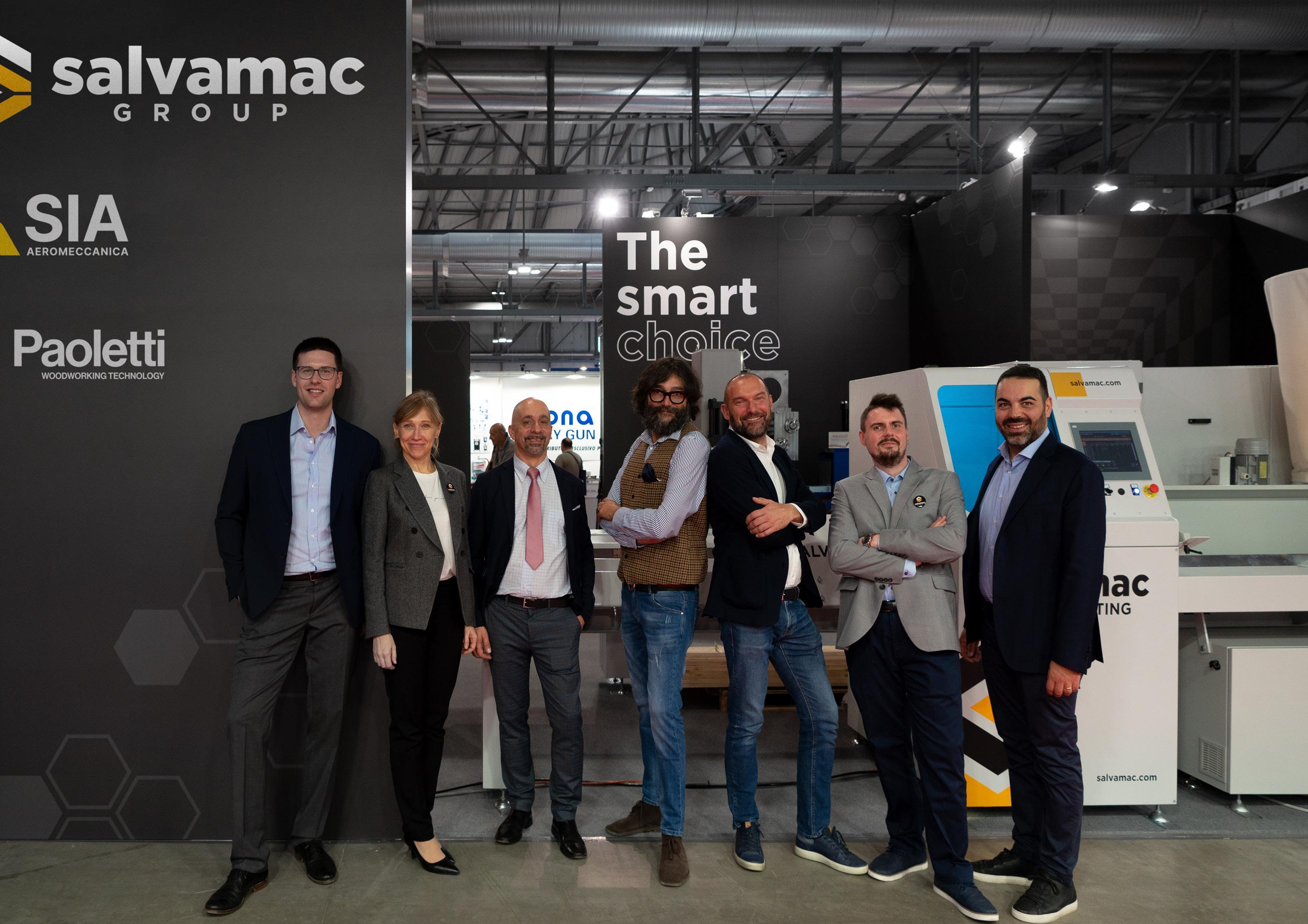
In conclusion, a fair that has certainly given new energy and ideas to better face the challenges that will not be lacking in the near future.
www.salvamac.com
XYLEXPO 2022: SUCCESS BEYOND EXPECTATIONS
Clare Hollister from Panel & Joinery Production, visited the 27th Xylexpo Exhibition in October and can attest to the success of the exhibition. There was an air of optimism among both exhibitors and visitors which bodes well for the future of the industry and, of course, future Xylexpo exhibitions.
In October and can attest to the success of the exhibition. There was an air of optimism among both exhibitors and visitors which gives rise to hope for the future of the industry and, of course, future Xylexpo exhibitions.
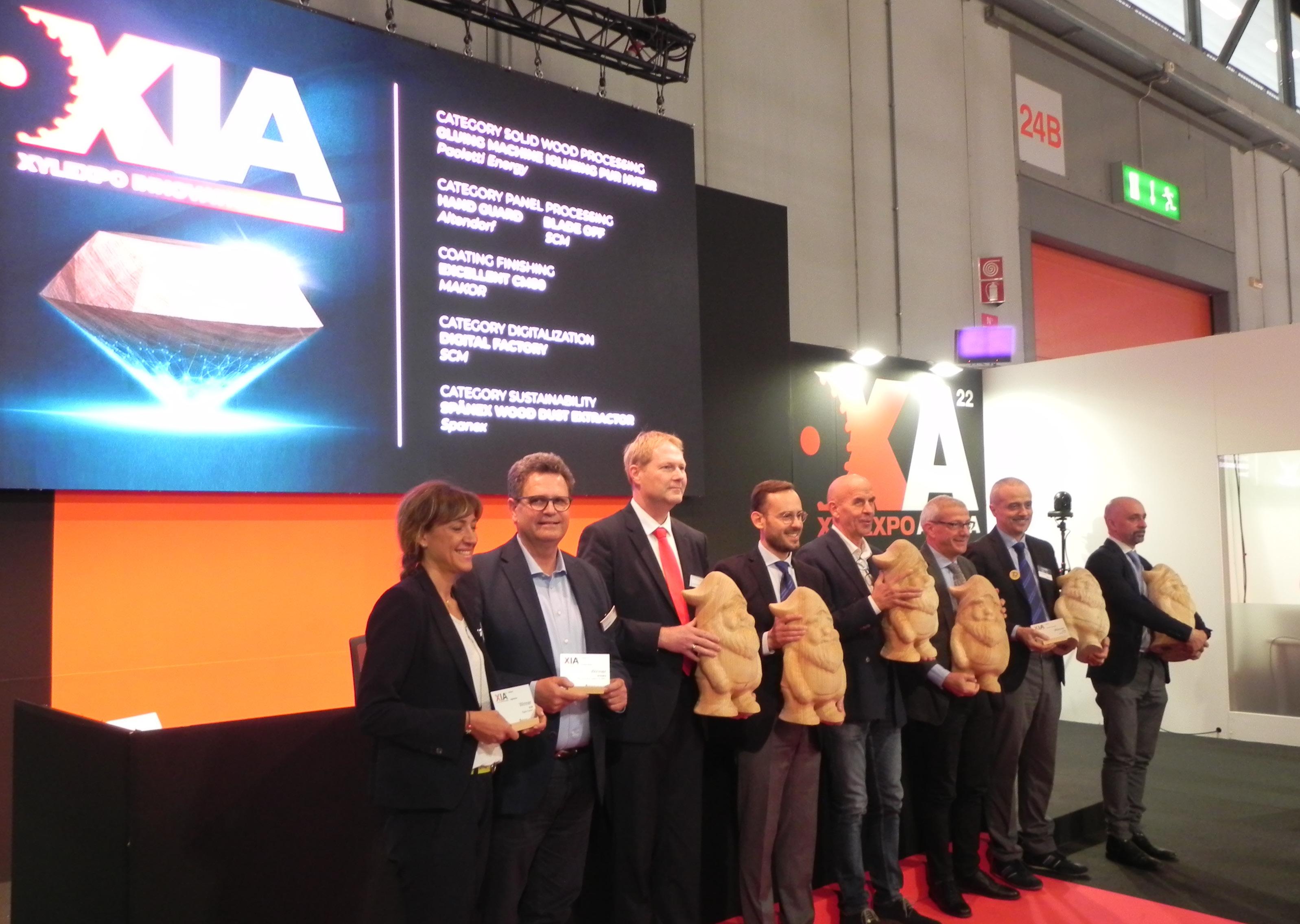
The biennial international exhibition of technology for the wood and furniture industry, closed with great satisfaction after four busy days in thalls 22 and 24 of FieraMilano-Rho. Satisfaction was tangible from the very start, supported by the desire to restore personal meetings and handshakes, which ultimately translated into positive figures for the exhibition.
Xylexpo 2022 was attended by more than 16 thousand unique visitors, a figure that reaches up to over 22 thousand visits if you consider that a single visitor came back several times over four days. Out of 16 thousand unique visitors, 12,356 were recorded at the entrance turnstiles, while at least 4 thousand – according to early but accurate estimates – came in from Viscom Italia and most of all from 33.Bimu. this was, of course, the first time that the biennial exhibition of wood and furniture technology was held concurrently with the digital communication show and, leveraging a much more effective synergy, with the machine tools
exhibition organized by Ucimu. The two events dedicated to manufacturing technology really created a virtuous circle, generating an impact that was immediately clear to the organizers during the exhibition days, and already announced in the preregistration phase, when most visitors had declared their intention to visit the parallel show.
Satisfaction was also supported by the fact that Xylexpo is probably the only post-pandemic exhibition that has achieved a number of unique visitors in line with the last pre-Covid event in 2018. The share of international visitors decreased by a few percent points (from 28 percent in 2018 to 25 percent in 2022), in line with the expectations of organizers due to the closure of markets like China, Russia and Ukraine, traditionally interested in Italian technology.
“The figures have confirmed not only the role of Xylexpo –said Luigi De Vito, president of the exhibition and Acimall – but also the decisions we made for this edition, aimed at redesigning the layout and focusing on the elements that will be the pillars of future exhibitions: a different strategy in product presentation and a strong focus on new digital services that can only expand the scope and function of an exhibition”.
T: press@xylexpo.com www.xylexpo.com
XIA-XYLEXPO INNOVATION AWARDS

PRESENTED
IN MILAN
The XIA-Xylexpo Innovation Awards were again presented this year. The awards have become a traditional event of the biennial international exhibition of wood and furniture industry technology which took place in October.
The award included five categories – solid wood, panels, finishing, digitalization and sustainability – and required an intensive work for the jury who accurately evaluated all the entries to assign the Xylexpo “Oscar”, a “dwarf” designed in 2014 – when the award was originally introduced – by Elio Fiorucci for Riva 1920.
The award for the “Solid wood processing” category went to Paoletti Energy from Borgo Valbelluna (Belluno) for the gluing system “Iglueing PUR Hyper”. The justification: “It is an innovative system for the application of polyurethane adhesives in finger jointing. The innovative features include a massive reduction of applicator cleaning time, a more efficient use of adhesive, and easy integration with several machines”.
For the “Panel processing” category, the jury decided to reward two solutions “…which solve the same problem with different approaches but equivalent results”. The winners were “Hand Guard” by Altendorf in Minden (Germany) and “Blade Off” by SCM in Rimini. “The innovative features include a significant improvement of operator safety in squaring machines, potentially applicable also to other types of machines”, the jury commented.
In the “Finishing” category, “…the jury identified the automatic spraying machine “Excellent Cm80” by Makor in Sinalunga (Siena), the winner in this category. The innovative features include enhanced belt conveyor cleaning, greater efficiency in paint use as a result of more effective overspray recovery”.
The “Digitalization” award went to the “Digital Factory” system of SCM in Rimini. The justification states: “…although this has been an established trend in the furniture industry for a few years, the jury recognized the innovative features of this eco-system, as it offers the possibility to capture information and data from a production environment, with the capacity to monitor a product from order, through production, up to after-sales. This solution offers a range of services that enable the OEM to leverage new business models in line with the current market trends”.
The award for the “Sustainability” category went to the wood dust extractor by Spänex in Uslar (Germany). “The jury recognized that the product represents a real innovation, as the approach to sustainability is clear since the early design phases and consistently translates into the environmental, social and economic aspects.
In detail, energy saving, environmental protection and the integration with existing recycling systems were recognized as environmental benefits; the protection of workers with a versatile, scalable and flexible system, adapting to different business requirements, were recognized as social benefits; for the governance, improved maintenance and reduced business risks are achieved through the reduction of fire risk and more efficient system control options”
THE JURY
The XIA-Xylexpo Innovation Awards are assigned by a jury that select the winners independently. The working group includes the following members, in alphabetical order.
STEFANO BERTI, chairman of the jury, former director of IRL, merged into CNR IBE, professor of wood technology and forest applications at the Agriculture Department of the University of Palermo, and professor of wood and woodbased material industries at the Agriculture Department of the University of Florence.
ANNA BORTOLUZZI, qualified Management Consultant at ICMCI, with a MA in chemistry and material technology, she has developed significant experience in industrial plant management and statistical analysis. Since 2006, she has been working as lifecycle analysis (LCA) expert in international projects and in the development of PCRs (Product Category Rules). For twenty years, she was visiting professor at the University of Milan. She is a founding member and partner of MAPPING LCA.
FILIPPO BOSCHI, project manager for innovation, industrial research and experimental development.
MADE s.c.a r.l., Competence Center Industry 4.0. Consultant of the Italian Ministry of Economic Development for Industry 4.0 topics.
FRANCO BULIAN, director of CATAS, Italy’s major laboratory for certification, research and testing in the wood-furniture industry. Professor of the course Materials and technologies of the furniture industry in the double-degree track of the Universities of Trieste (Italy) and Lippe (Germany).
GIANNI CAMPATELLI, associate professor, University of Florence. Department of Industrial Engineering. Manager of the “Manufacturing Technology Research Lab”.
GIACOMO GOLI, associate professor, University of Florence. Wood technology and forestry applications. Agricultural, food, environmental and forest sciences and technology (DAGRI).
FELICE RAGAZZO, visiting professor for the wood module of the international Master course “Architectural restoration and asset culture”, Department of Architecture Roma 3, former High Qualification Professor at the Industrial Design course of the University “La Sapienza” in Rome.
FRIEDER SCHOLZ, former professor at the Hochschule Rosenheim - University of Applied Sciences. Head of the Master course in wood technology and manager of the machine tools, machining and equipment dynamics laboratory.



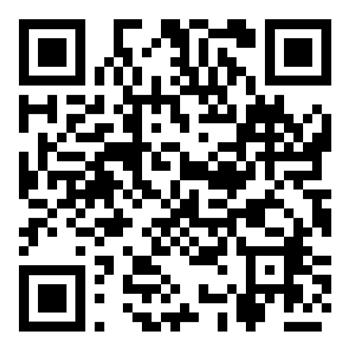
GREAT SUCCESS FOR THE LATEST SCM INNOVATIONS AT XYLEXPO
Standalone technological solutions and integrated, intelligent and sustainable processes. There was much on the SCM stand that was new to meet any production requirement. Two XIA – Xylexpo Innovation Awardswere granted to SCM’s Digital Factory and Blade Off.
SCM was once again a key player at Xylexpo, on a special occasion for the Italian Group, as it celebrated 70 years of innovation and success alongside the entire woodworking sector.
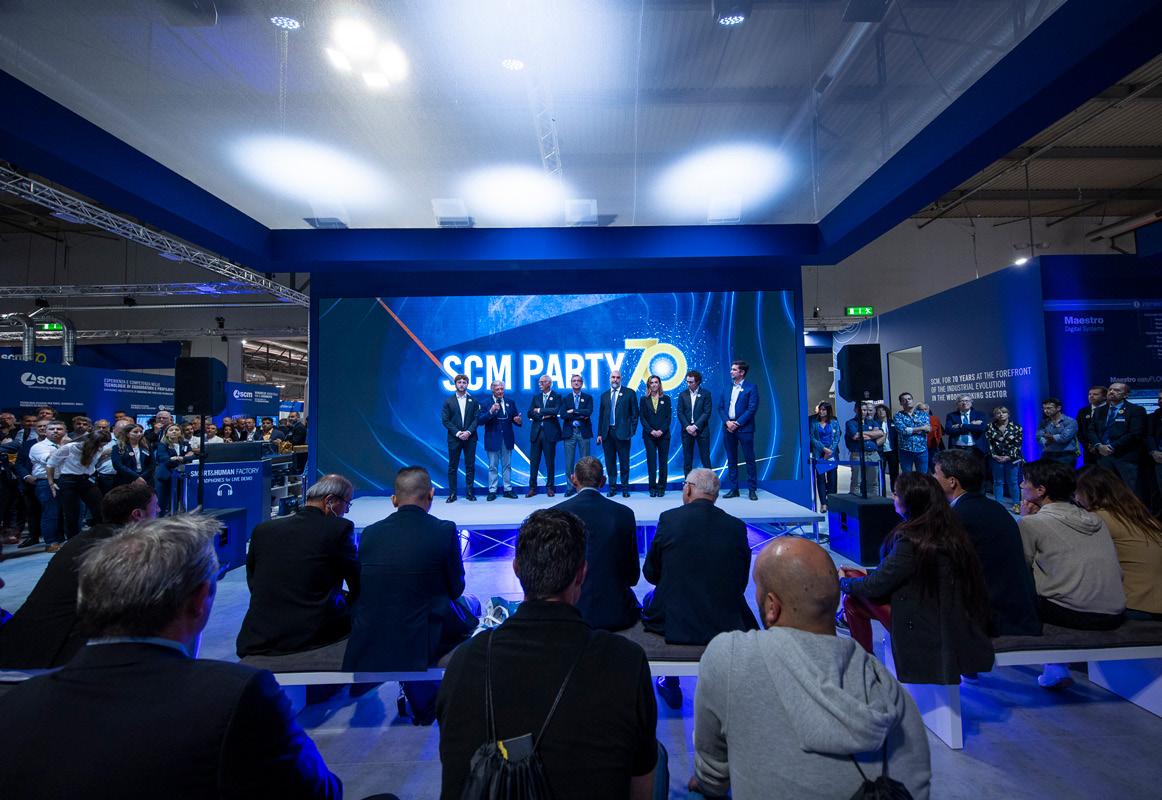
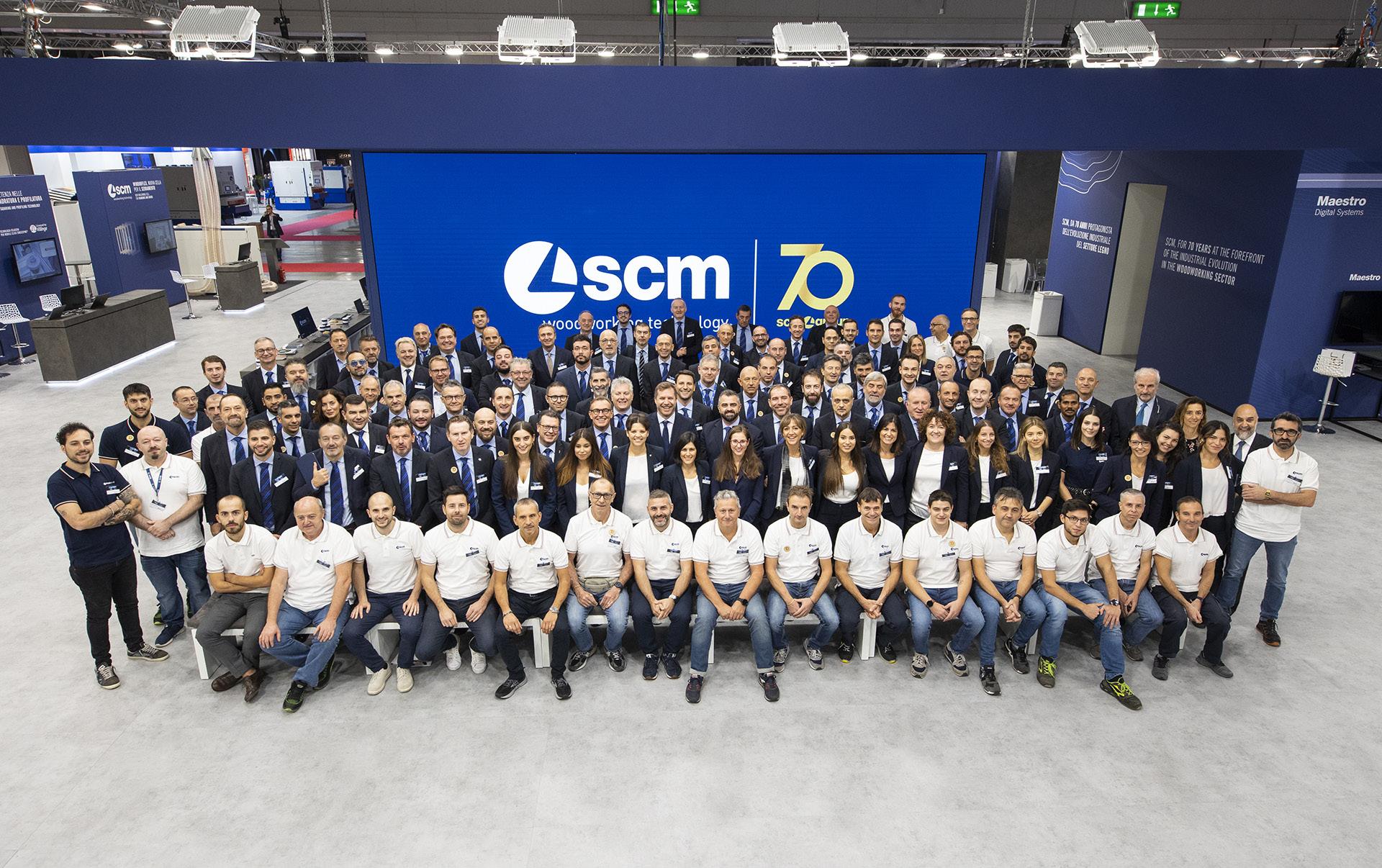
SCM offered its vision for digital, connected and integrated production: a Digital Factory model that was also recognised at XIA, supporting customers with the most complex challenges of mass customisation, making the processes faster and more sustainable, keeping down costs, consumption and waste and simplifying management. Smart&Human Factory is a system with flexible, automated and modular cells that was on show for the first time with two distinct versions for industry and the joinery.
Flanking both the processes is an integrated offering of software, MES and digital services on display in the “Digital

Integrated Woodworking Process” area. Software and services that support the customer at each stage: data preparation, planning, production, monitoring and aftersales assistance, by increasing efficiency and connecting the office and factory.
For planning, optimisation and production control, the new MES Maestro easyFlow is the plug&play solution integrated with all of SCM’s software and machines, combined with both Smart&Human Factory for both industry and the joinery to handle the programming, management and 4.0 interconnection of the entire production flow.
Maestro optiwise for the gabbiani single blade and angular beam saws ensures you get the best out of cuts with a minimum amount of waste for both large and small production batches.
Maximum performance for woodworking with the mobile app SCM Thundercut: this optimiser-sequencer is the only one that provides the operator with a step-by-step guide to inserting the panel into the machine and making the cut.
Maestro Power TMS, the software that simplifies and optimises the management of tools inside the solid wood CNC machining centres’ warehouses also made its début. Depending on the machining required, the software operates to maximise the capacity of the warehouses and to speed up the tool change according to the production mix.
The HMI software and Maestro active line supervisors have also been updated for an even simpler, optimal control and interaction with all the SCM machines.
In support of the production monitoring stages, machine maintenance and after-sales services, the digital services enabled by the IoT Maestro connect platform have been further enhanced. It aims to guarantee maximum return on the machines and plants in conjunction with support from SCM technicians. This IoT platformintegrates into the “Woodworking made Izy” project led by the most important machinery manufacturers.
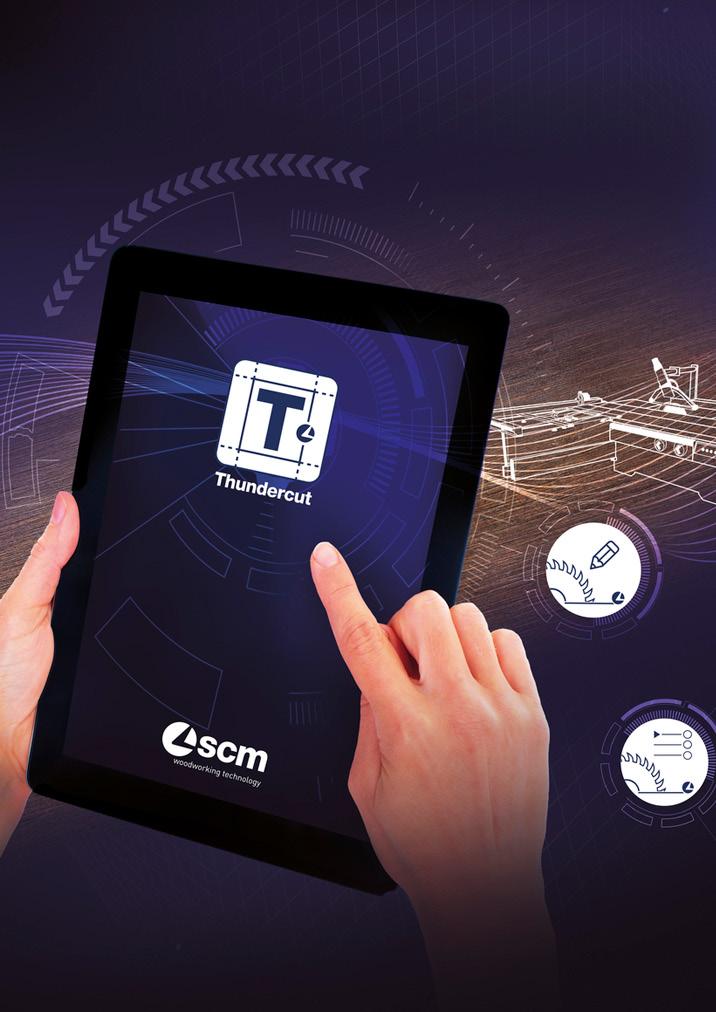
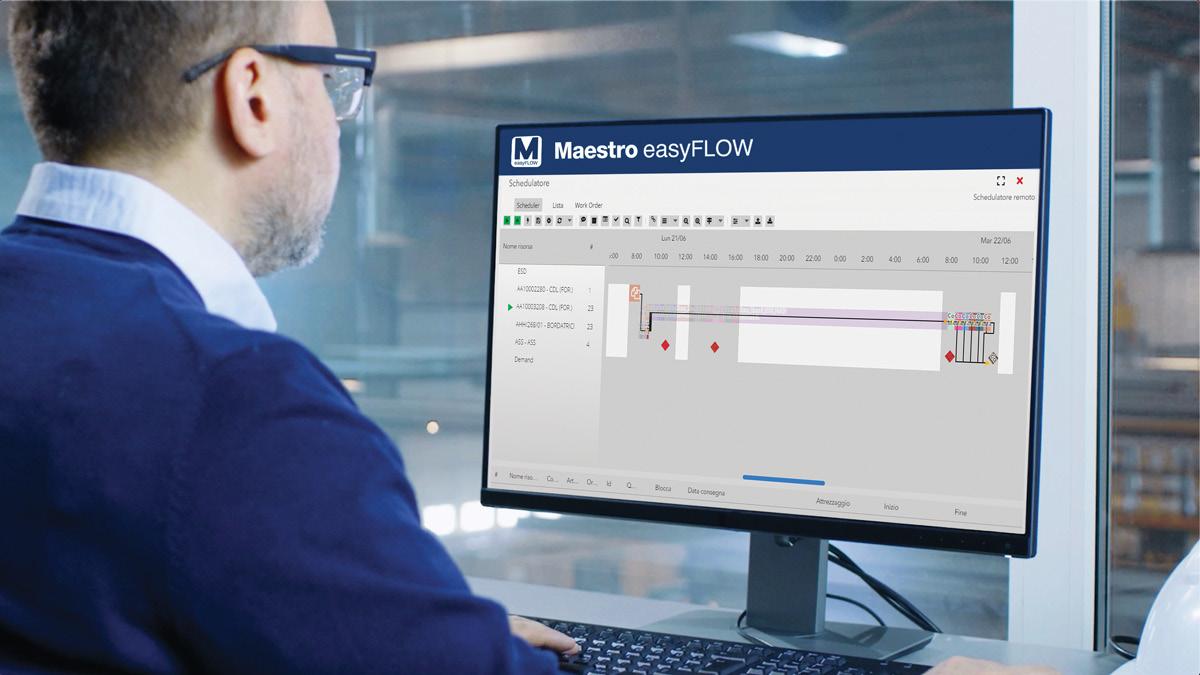
The Smart&Human Factory for the furniture industry
The flexible integrated line produces around 400 furniture parts per shift and shows two alternative flows for the manufacturers of assembled or kit furniture.
This is only one of the many configurations that the Smart&Human Factory can deliver. The cells are integrated with articulated robots and interconnected by unmanned AMR shuttles.
For edgebanding there’s a new model of stefani cell E flexible cell that combines the numerous advantages of the stefani x industrial edgebander in terms of productivity and machining quality with the new Fastback 27 automatic panel return system.
New this year was the morbidelli cx220 drilling and dowelling flexible cell that creates all the parts of the piece of furniture more efficiently.
SMART&HUMAN FACTORY FOR THE JOINERY
Centre stage was an integrated cell for flexible and customised production from raw material to the finished piece of furniture.
The invincibile si x circular saw enhanced by the SCM Thundercut cutting optimiser-sequencer. Startech cn plus CNC drilling centrewhich produces flexibly produce furniture parts without repositioning the tools or operator intervention.
The me 40tr edgebander allows you to achieve excellent quality finished products, without further machining.
OTHER NEW PRODUCTS:
Edge banding
The new olimpic 500 offers excellent machining versatility in a limited amount of space
SCM Surface Technologies
The integrated dmc technologies for sanding, sergiani 3d form for three-dimensional panels and superfici for finishing has been further enhanced.
Doors and windows production and solid wood machining
A first for Xylexpo was the accord 600 CNC machining centre for the production of doors, staircases and windows in solid wood: it offers 30% more productivity compared to market standards and an intelligent management with Maestro power TMS.
A special feature was windorflex, the new automatic cell for machining complete fixtures designed to optimise productivity while simultaneously maintaining a high level of flexibility and machining quality, irrespective of the kind of window or door.
The solutions for solid wood were rounded off with the automatic superset nt throughfeed moulder complete with high-efficiency motors that guarantee a considerable benefit in terms of energy saving; the balestrini idea CNC machining centre for chairs and tables and the automatic balestrini pico md tenoner-mortiser, ideal for creating “Miter Door” joints.
Joinery machines
There was a debut for startech cn k compact 3-axis machining centre, ideal for any kind of routing, decorations, scoring, creation of signs and 3D model prototype. The only one in its category to have a 2.4 kW electro-spindleIt is east to program thanks to the virtual “open” Human-Machine Interface.
SCM highlighted the eye-S compact touch controls on edgebanders and the exclusive “Blade Off” technological solution (XIA winner) applied to circular saws and fitted with exclusive smart sensors to machine in complete safety.

Squaring, tenoning and profiling
Xylexpo showcased celaschi products. For the production of both traditional and gradient board (chevron) wooden floors, the new celaschi tmc transversal tenoner with automatic loading system. Versatile and precise, it offers the utmost in terms of technical solutions for line profiling of boards with different gradients.
The celaschi innovations also referred to the creation of Threespine® click panels and the production of drawers, with the option of machining pieces of less than 60 mm in width.
Stakapal are full members of SEMA (Storage Equipment Manufacturers Association) who are the industry body responsible for developing the safe design, installation and use of storage equipment manufactured and supplied by its members. The company therefore play a very proactive role in the development of industry standards and their knowledge and commitment to creating awareness of relevant Health & Safety issues is very high on their agenda.
As manufacturers and suppliers to the panels and joinery industry for over 55 years, Stakapal design bespoke storage solutions that really do stand the test of time if correctly maintained. The industry is predominantly very safetyconscious, however Stakapal would question whether businesses are fully aware, or perhaps decide to dismiss their priorities when it comes to maintaining their racking. It is common knowledge that if racking is subjected to any form of damage it could be at risk of collapse and there are many examples of sometimes catastrophic collapses that can be viewed online.
PUWER REGULATIONS AND PRRS (PERSON RESPONSIBLE FOR RACKING SAFETY)
Any warehouse should have its storage equipment regularly assessed and your company should have a maintenance programme in place that is overseen by a nominated PRRS (Person Responsible for Racking Safety). Having a PRRS will help to ensure the requirements of PUWER (Provisions and Use of Work Equipment Regulations 1998) are met. PUWER dictates that as your storage equipment is classified as work equipment it must be regularly monitored and your onsite PRRS should have attended an appropriate course such as one of SEMA’s Rack Safety Awareness Courses. SEMA offer courses for either Cantilever Racking or Pallet Racking or both dependent upon the type of storage systems that are installed in your operation. Their courses cover every aspect that is required to educate and enable your staff to perform in-house rack inspections, information for the ongoing safe operation of your racking systems, explanations about load notices that should appear on all of your equipment plus excellent pictorial examples of damage categorisation and prevention.
All staff operating in your warehouse should be actively encouraged to report any damage immediately, and your PRRS should be able to take the appropriate action required. In possessing the capability to assess how serious the damage is and whether racking needs to be cordoned off and unloaded should ultimately help your company minimise any risk to your employees.
MEETING THE REQUIREMENTS OF THE HSE
Remember - if the HSE pay you a visit and you are found to be in breach of the Health and safety at Work Act it could have very serious consequence for you and your business. Prevention is definitely better than cure - companies do not want to be in the position of dealing with the impact of an employee getting seriously hurt or worse.
Following the installation of Stakapal’s racking systems by their in-house SEIRS (Storage Equipment Installers Registration Scheme) installers, the company also offers their customers an annual inspection by one of their inhouse SARI’s (SEMA Approved Racking Inspectors). They visit each site and undertake a comprehensive racking inspection preparing a detailed damage report highlighting any issues with recommended timescales for any corrective action to be implemented. A SARI satisfies the HSE’s criteria for a technically competent person to carry out an annual inspection as per HSG76 guidance.

DAMAGE REPLACEMENTS OR REPAIR
As full SEMA members it means that Stakapal’s products are independently tested which guarantees they have been designed to rigorously defined standards. If any repairs are undertaken on your site using third party materials or unqualified installers it could seriously affect the original specification and verification of your systems, rendering any company warranty as null and void.

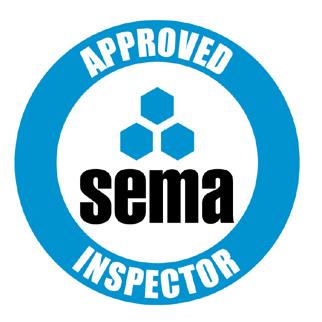
As part of any ongoing maintenance Stakapal strongly advise that companies should not try to cut corners in order to save money, investing in the correct upkeep of their systems will only prove beneficial in the long term, both in terms of safety and costs.
A COMPLETE SERVICE
Stakapals’ commitment to design excellence, quality manufacturing and accurate and safe installation procedures provide their customers with strong, safe and high-quality racking and storage solutions. Their in-house design and project teams support a concept to completion service. This includes a free site survey to discuss your requirements in detail, through to design, manufacture and installation plus ongoing inspections and maintenance.
UK Storage Manufacturers Stakapal ask do you have the correct maintenance procedures in place for your Racking Systems?
SO, WHAT DO SARI’S LOOK OUT FOR THAT WOULD BE REQUIRED BY THE HSE?
Load notices - all racking structures require a visibly displayed load notice that shows the date of your installation and who your supplier is plus relevant loading limitations etc. If you haven’t got any load labels whoever supplied your equipment must undertake a physical inspection that verifies the correct configuration of your racks and their condition.
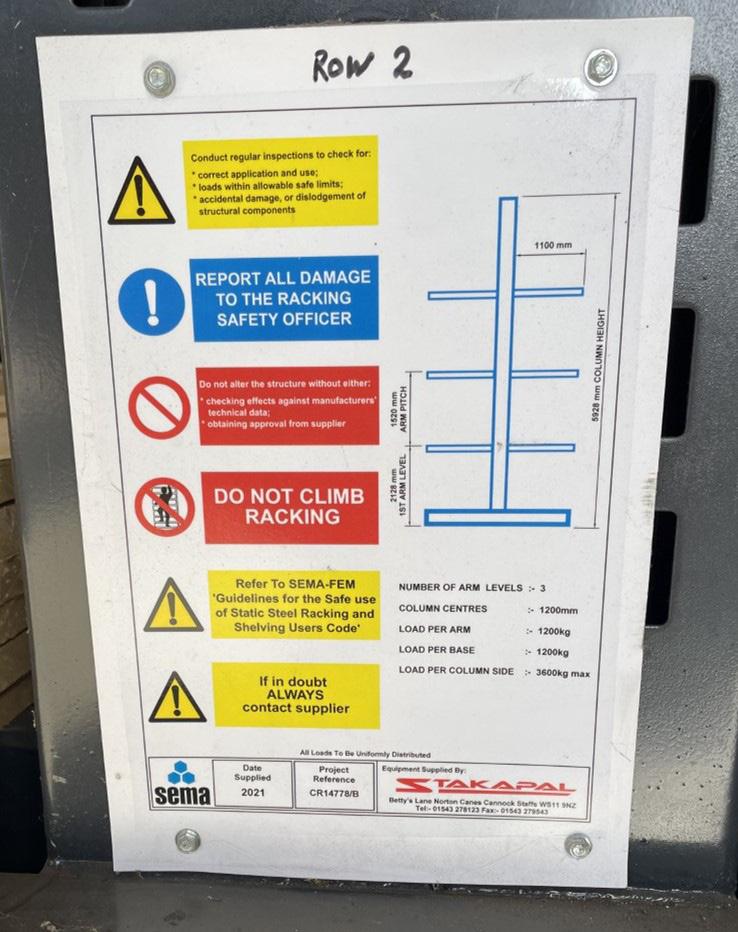
Pallet Racking - a RED Risk requiring immediate offloading and repairing or replacement that their SARI’s will look out for are Post damage, Bracing damage and Beam damage or dislodgement.
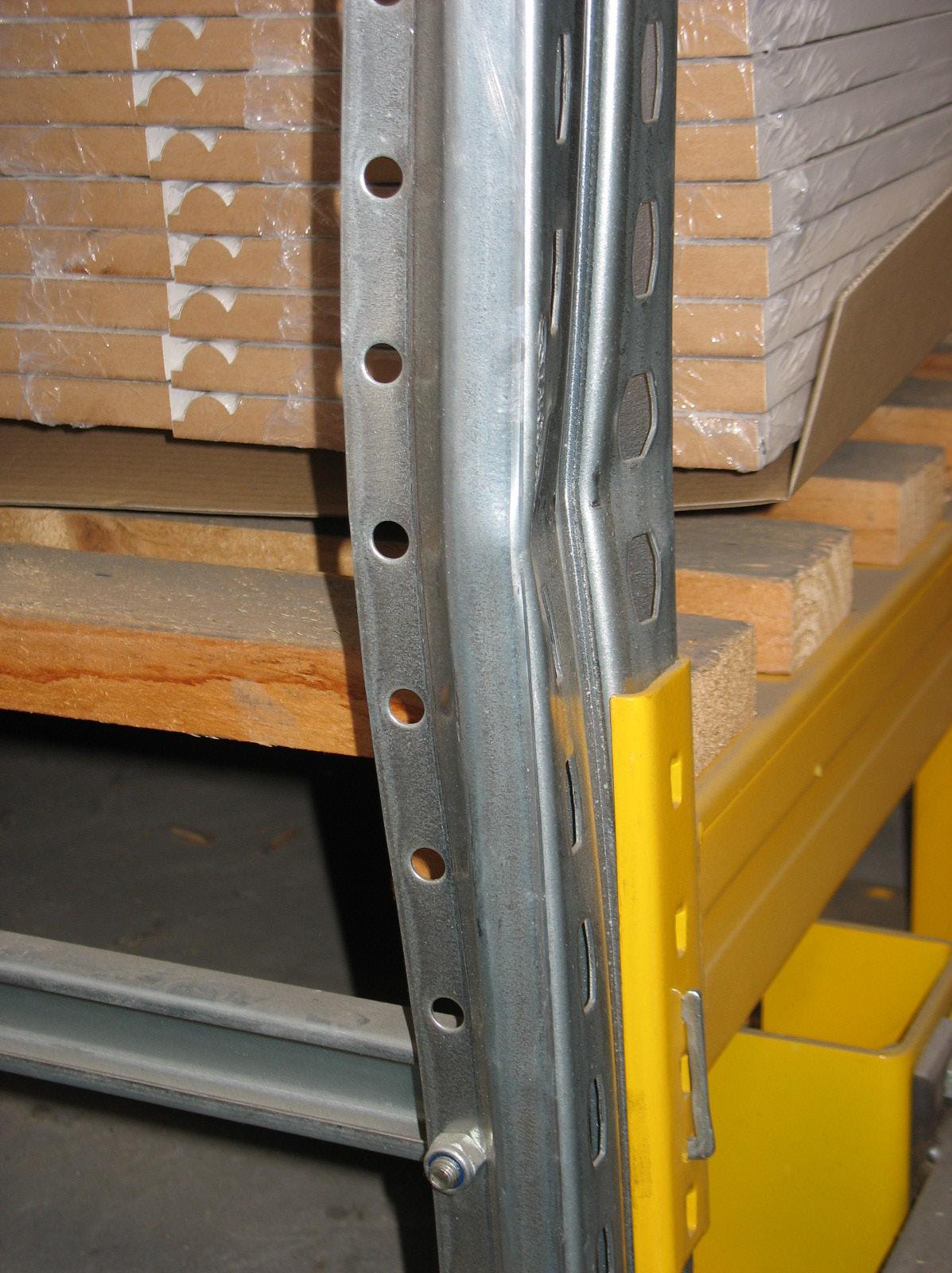
Cantilever Racking - Stakapal operate to SEMA’s traffic light system which means anything that is classified as a RED Risk requires immediate offloading and repairing or replacing. Their SARI will be looking for damage to Cantilever Columns, Lateral Arm damage, Horizontal Arm damage, Rotational Arm damage, Bracing damage or Base damage.
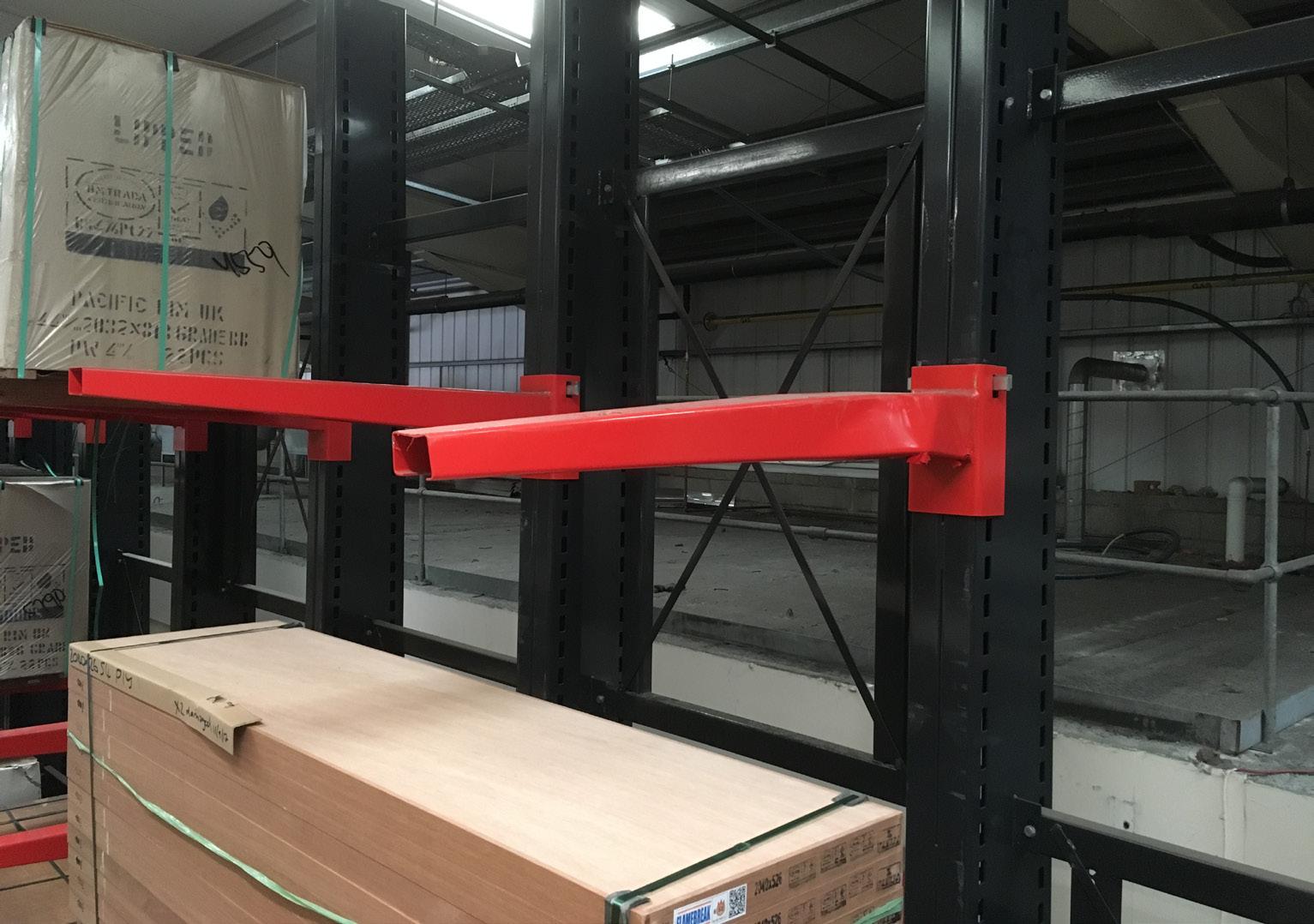
STUDY
LUCABELLA FURNITURE INVESTS IN COMPLETE HOMAG SOLUTION
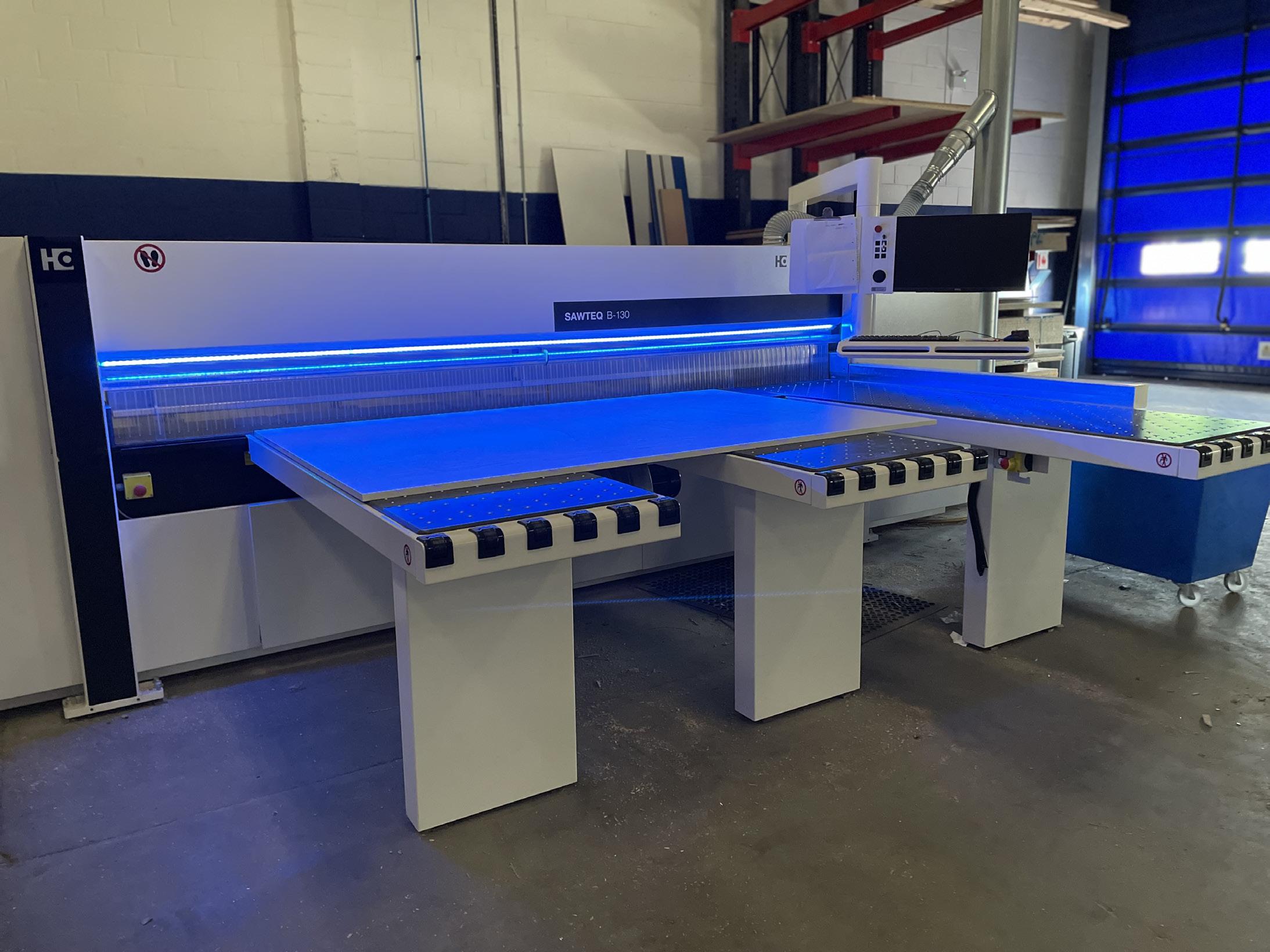
Based in Waltham Abbey, Lucabella Manufacturing is a division of New River Holdings Ltd. Lucabella was set up to manufacture quality bathroom furniture and trades under the Lucabella Furniture brand name.
“Previously the sister company, Robert Lee Ltd, had always bought finished bathroom furniture products from Europe and the Far East,” explains Will Burn, Lucabella’s managing director. He continues, “The last few years, however, have seen significant pressures on the supply chain, particularly regarding the cost of transporting finished furniture items to the UK. Brexit, the pandemic and now the energy crisis have meant transportation costs have gone through the roof. “Given these difficulties, we started to look at the viability of manufacturing the furniture here in the UK. At the same time, the ‘Made in Britain’ campaign was providing considerable encouragement for companies to produce in this country. As a consequence, we did preliminary ballpark calculations and concluded that we could manufacture competitively here provided we had the right machinery.”
FINDING THE BEST MACHINERY SUPPLIER
“In a prior position, I had purchased equipment from HOMAG UK and so they were the first company we
considered. As part of our due diligence, however, we included a couple of Italian machinery suppliers on our shortlist.
“From the outset, one point we were clear on was that whichever brand we chose, we would purchase all of the machines from them; we wouldn’t have a mix of machinery suppliers. There are several reasons for this: first, we wanted to keep things straightforward so dealing with just one supplier made sense; secondly, we wanted to have software that was common to each machine to simplify the learning process for our operators and thirdly, we felt we would get a better deal overall.
“One of the advantages of HOMAG was the ease with which we could collect all the qualitative and quantitative information for each machine. This was particularly important for us as we needed everything including the minimum and maximum speeds of the machine, the recycle times between operations and also to a lesser degree, the kW (kilowatt) output data. This information enabled us to accurately calculate the production cost, capabilities and the throughputs of each machine.
“After careful consideration the decision was made to partner with HOMAG UK. Ian Woodall, the area sales manager for HOMAG, was a key factor in this decision. From the outset he demonstrated his knowledge and understanding of our business and what we were looking to achieve with the setup of the new furniture workshop.
“Whilst we were clear we wanted a beam saw, edge bander and vertical drilling CNC, Ian was able to suggest specific options, such as the airTec system on the EDGETEQ S-240 edge bander. In fact, all his recommendations proved to be exactly what we needed. The machines we ordered, a SAWTEQ B-130 beam saw, a DRILLTEQ V-200 vertical CNC and the EDGETEQ S-240 edge bander, have made a real difference to our manufacturing capabilities and capacity.”
A TRUE PARTNERSHIP FOR THE LONG TERM
“The relationship with HOMAG has grown stronger as time passes. Both companies have learnt from the partnership. HOMAG has an excellent checklist for the installation process of new machinery. As a completely new operation, however, we were able to add additional items that have strengthened that checklist.
“Because of the importance of ensuring we would be producing the furniture in the most cost effective way, we allocated a six week period to comprehensively test each machine. We tried different combinations of tooling and drill sets, different panels and edging; everything was done to make certain that when we started production there would be no surprises and no glitches.
“This foundation work has paid dividends. We are now fully operational with each machine running efficiently and quickly. The accuracy of the processing means we are able to construct high quality furniture at competitive rates. Long term, this will enable us to attract a lot more business from the UK market which is definitely one of the key goals we want to achieve,” concludes Burn.
If you would like a demonstration or further information on HOMAG woodworking machinery or software, please contact Adele Hunt at HOMAG UK on 01332 856424 or email: info-uk@homag.com
T: 01332 856500 E: info-uk@homag.com www.homag.com
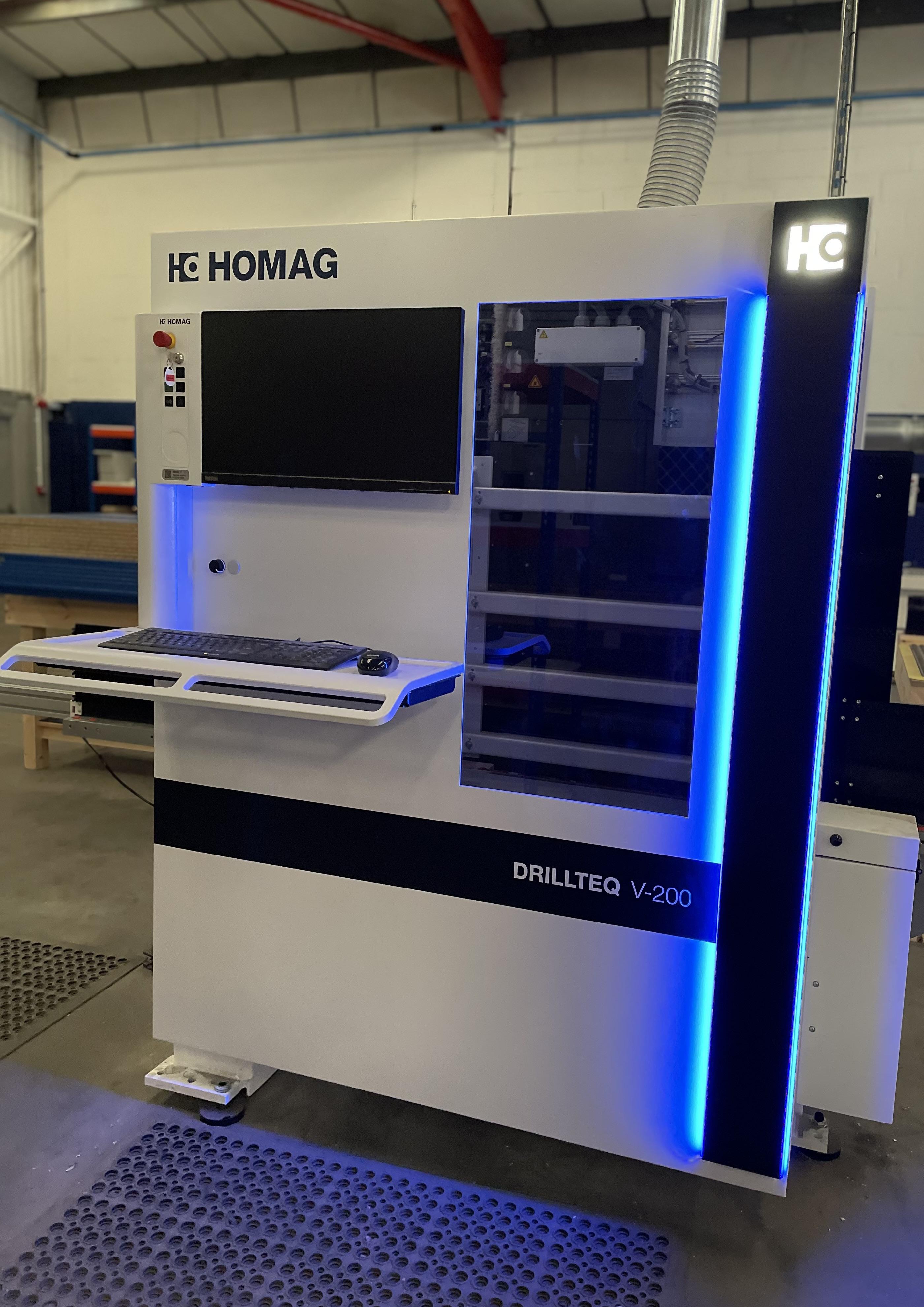
CASE STUDY
TIMBER MANUFACTURER SAVES MONEY BY INVESTING IN WOOD WASTE HEATER
A timber manufacturer has purchased a replacement wood waste heater from Wood Waste Technology to continue to save money on waste disposal bills and heating costs.
Stoneleigh Timber Engineering Ltd is an independent manufacturer of roof trusses, floor joists, stairs and timber wall components based in Wiltshire.
The business manufactures its products from a 1940’s building that used to make spitfire components. Although the large building provides the business with lots of manufacturing space, it’s a cold, draughty building to work in during the winter.
When Managing Director, Adrian Hall took over the business 5 years ago, the building already contained a wood waste heater, but it was quite old and hadn’t been very well looked after. Adrian didn’t want to be without a wood waste heater, having become reliant on it to dispose of waste wood and generate free heating, so he decided the business needed to replace it with a newer model. As Wood Waste Technology had been out to service the original boiler, Adrian contacted Kurt Cockroft at Wood Waste Technology to purchase a replacement.
Adrian explains: “We generate 40 cubic metres of waste wood each year, so a wood waste heater is vital to our operation, especially as we aim to make our business as carbon neutral as possible. The WT15 burner ticks a lot of boxes for us, as it’s a good piece of kit at the right price – plus we’ve always found the team at Wood Waste Technology to be especially helpful. The new heater is fantastic, and performs even better than we hoped it would, giving us greater heat output than the original burner. We’re delighted we purchased a new one from Wood Waste Technology.”
MD of Wood Waste Technology, Kurt Cockroft says: “Wood waste heaters help businesses to save money on heating, reduce waste disposal costs and provide carbon neutral energy, which are all extremely important factors in today’s economic climate.”
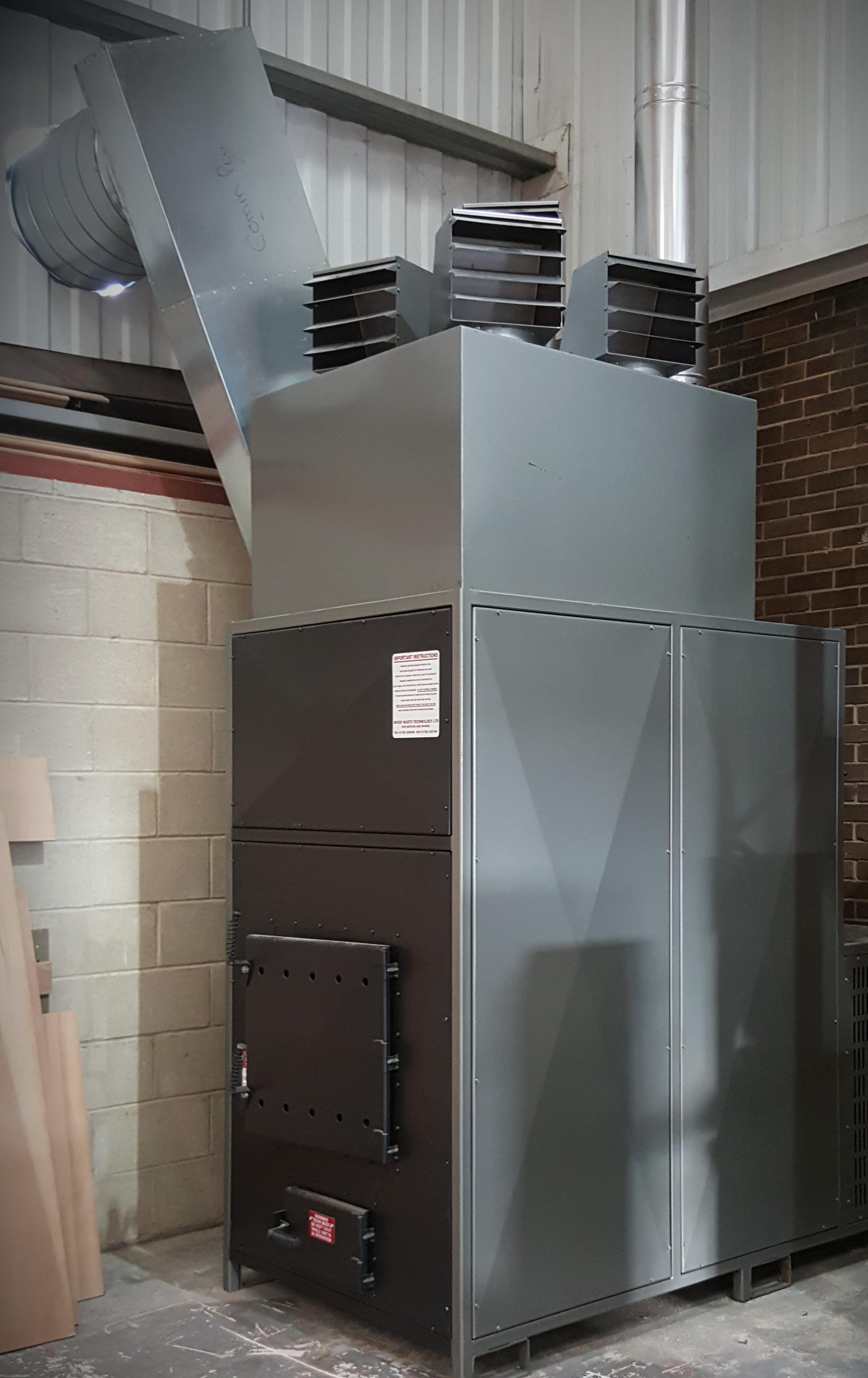
Wood Waste Technology’s years of expertise in wood waste solutions have helped many companies reduce their waste disposal and heating costs. As well as offering site survey, design, manufacture, installation and on-going maintenance for new units, the company also services all types of wood waste heaters and supplies genuine spares up to 60% cheaper than other suppliers.
In addition, Wood Waste Technology is the UK official distributor for Gross Apparatebau GmbH, a German manufacturer of dependable, precision engineered shredders and briquetters, available in various size and specifications to suit all business applications.
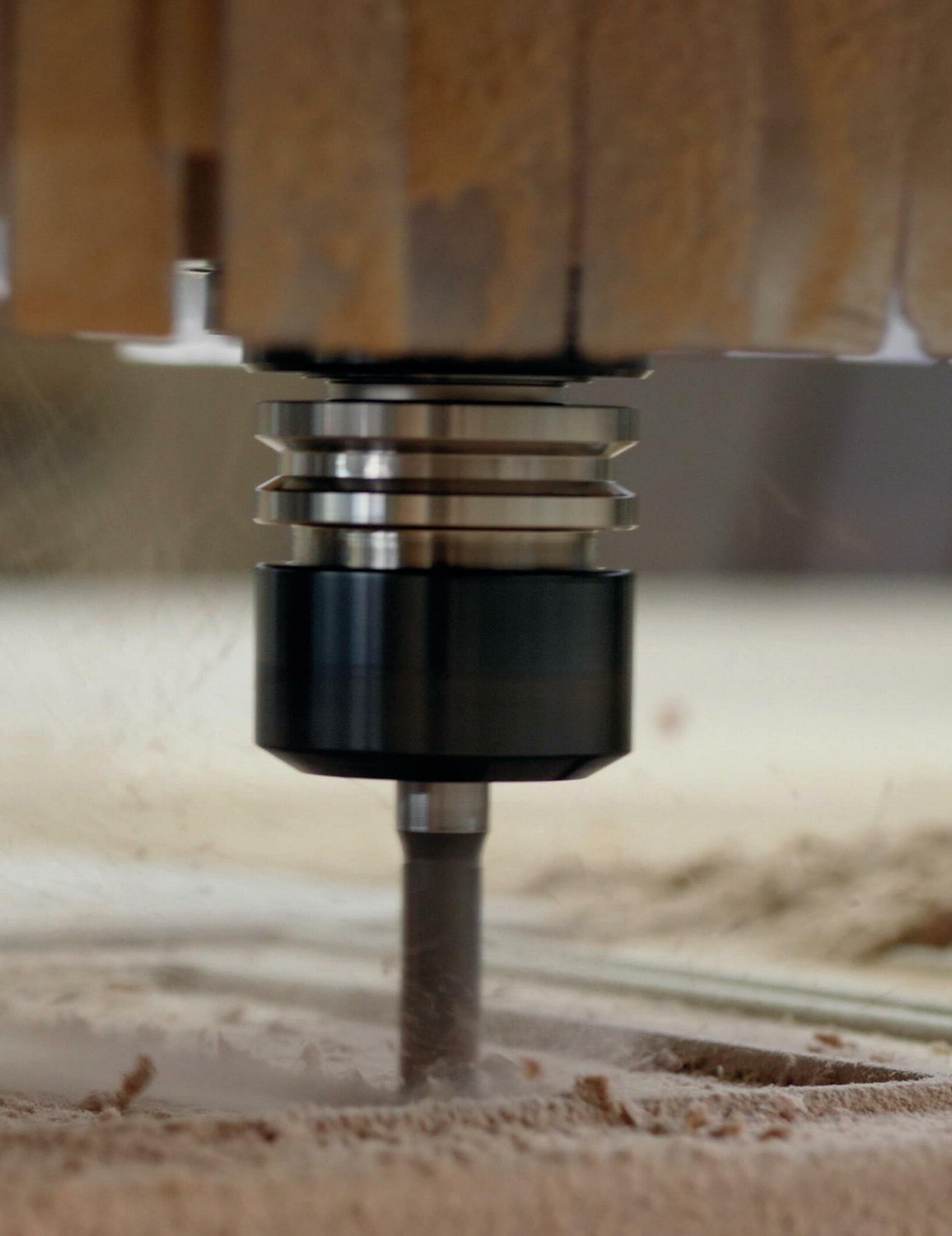
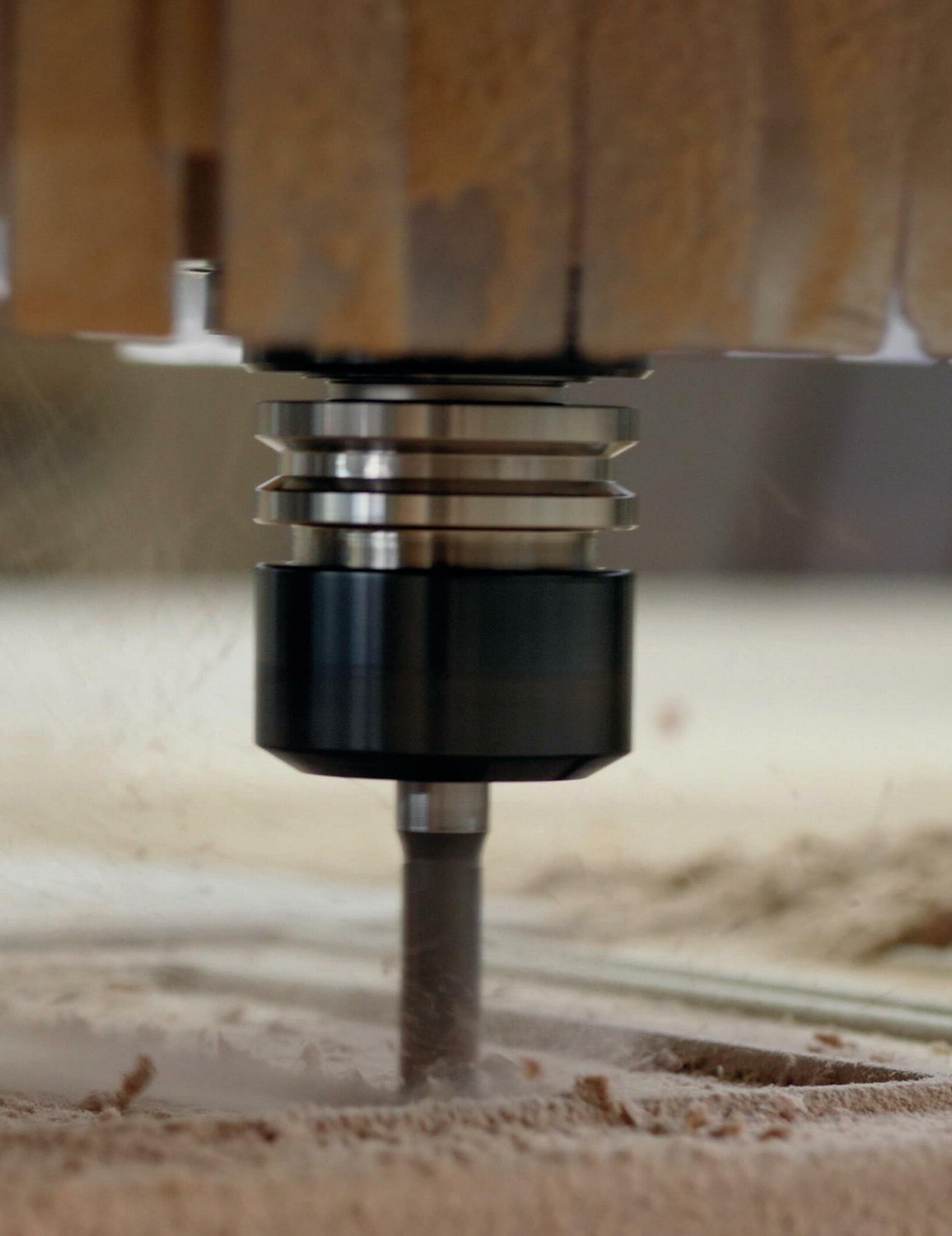
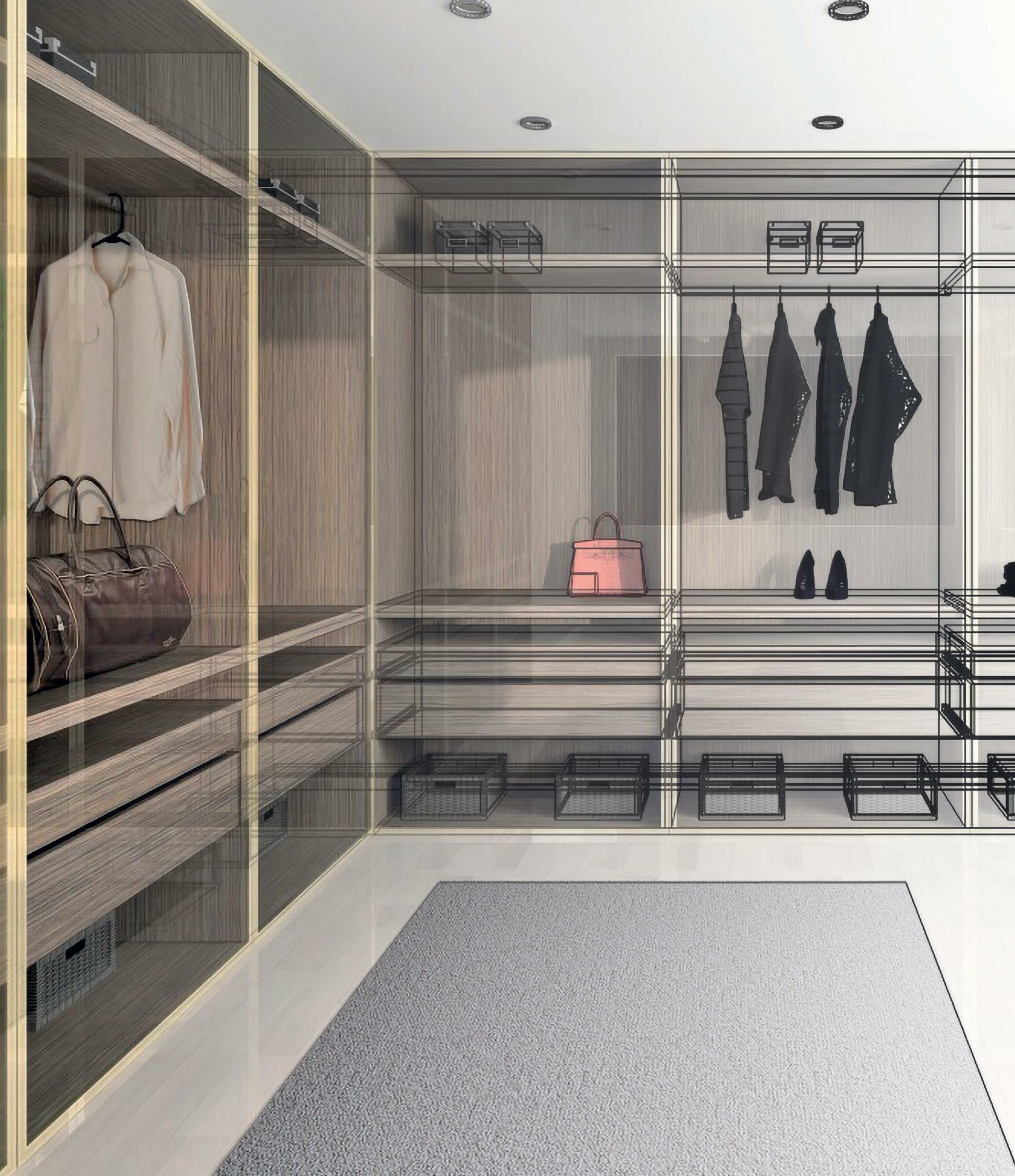
INDUSTRY
SELCO BEAM SAWS
AUTOMATIC PANEL LABELLING AVOIDS STICKY SITUATIONS
Biesse can now supply its SELCO machines with an automatic labelling system on the beam saw, for factories looking to drive down waste and enhance workflow efficiency.
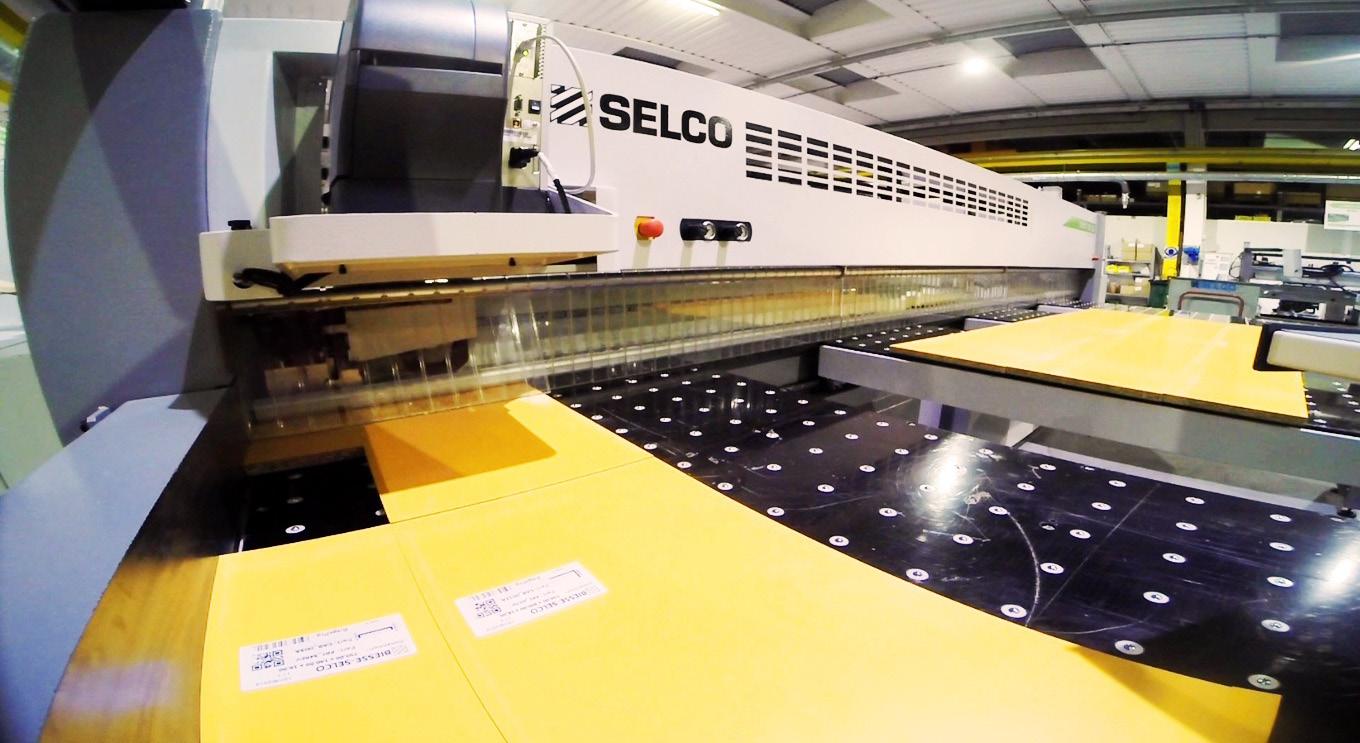
HOW DOES AUTOMATIC LABELLING WORK?
Labelling cut panels for internal information and identification purposes is a key component of a functioning workflow. Normally, this involves siting a labelling station next to the beam saw to print off individual labels and apply them manually to each panel after it has been sized.
However, this slows down the process and introduces the risk of human error: what if the wrong label is applied or the operator forgets to apply the label altogether?

The automatic labelling option integrates Biesse’s proprietary OptiPlanning cutting pattern optimisation software with an automatic labelling system that is mounted on the pressure beam. From cutting pattern information generated via the software, the labelling system moves rapidly along the beam to apply an individual label to a specific piece whilst it is being cut.
The process starts with the optimisation of the cutting list. This list includes individual piece sizes and other optional information including subsequent drilling, CNC and edgebanding programmes. It may also include information that can be used to create a schematic drawing of the piece cut on the label, showing what sides need to be edged, as well as the type of edge to be used for each side. This provides a visual aid to the edge-bander operator, reducing the risk of placing the panel into the edge-bander machine in the wrong orientation.
Once this is completed, the cutting optimisation is processed in the software and production files are generated and sent to the beam saw. These files contain the optimised cutting pattern for the cutting list and any additional information selected.
The final step is for the operator to configure the layout of the label - depending on the information required for that job. This ensures that the labels are individually customised with the correct data - no further operator intervention is required.
WHAT ARE THE BENEFITS OF AUTOMATIC LABELLING?
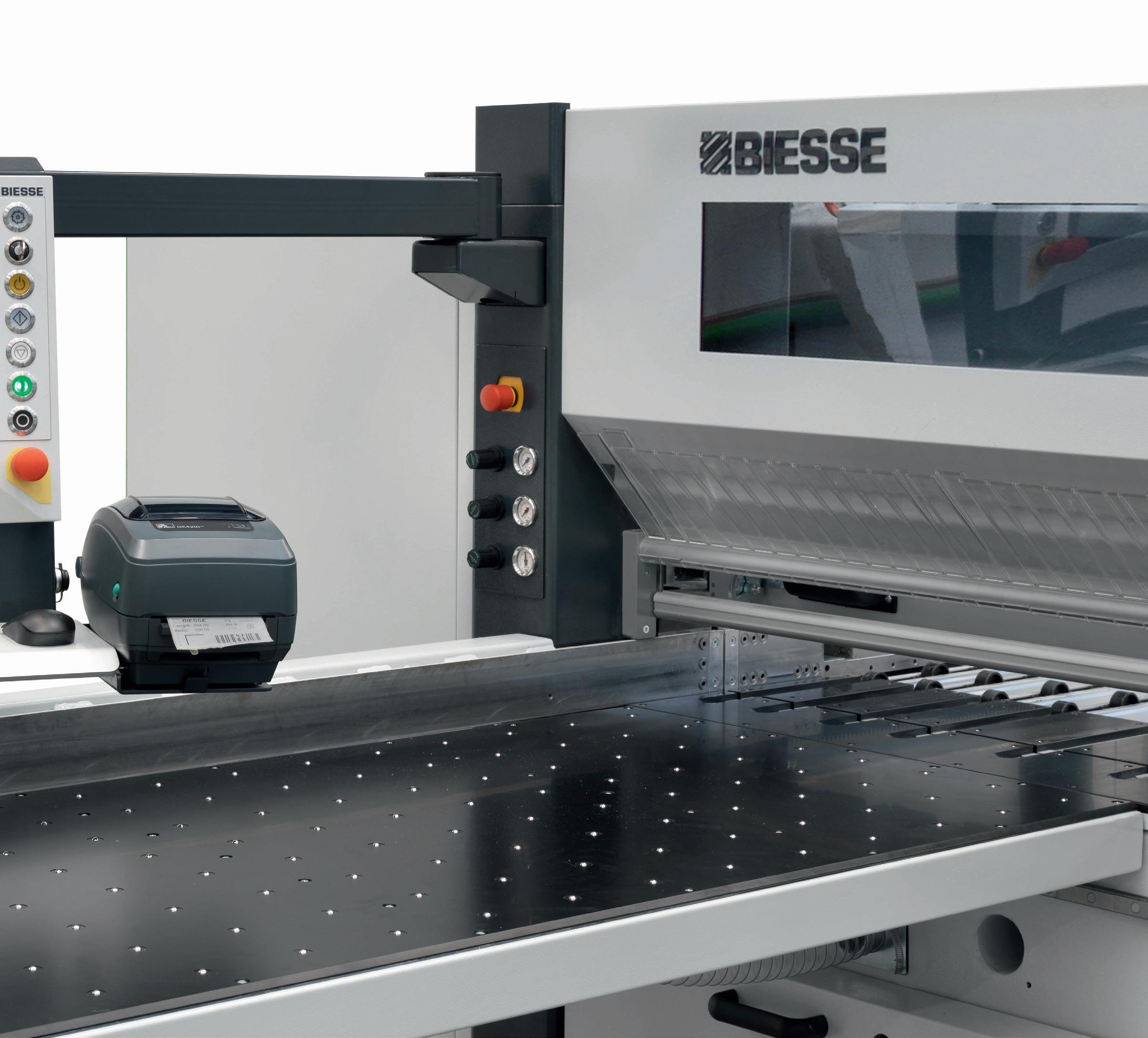
The primary benefit of this approach is that it achieves an error-free production process by creating a continuous, automated information flow.
When the panel is presented at the next work station, be that drilling or edge banding, the operator simply scans the barcode or QR code to recall all the information associated with that panel. This could include a visualisation of the panel, showing which sides need to be edged or where holes need to be drilled. Without this instruction, there is the risk of workers using the wrong machine programme on a panel that could result in, for example, a panel with the wrong number of holes drilled in it, creating a reject panel.
Therefore, harnessing automation to match the correct panel with the correct manufacturing step locks out the potential for human error, driving down waste, boosting productivity and guaranteeing a defect-free workflow. As well as printing barcodes, the labeller can be programmed to print additional data such as job name, customer name and panel dimensions. Although more basic than the type of data that can be accessed via a barcode, this information is still extremely valuable for fast and accurate panel identification and reconciliation.
ECOGATE ENERGY-SAVINGS CALCULATOR
With electricity prices at an all-time high, there will never be a better time to invest in Ecogate’s energy-saving technology… and now you can see the potential savings for your business at the click of a button!
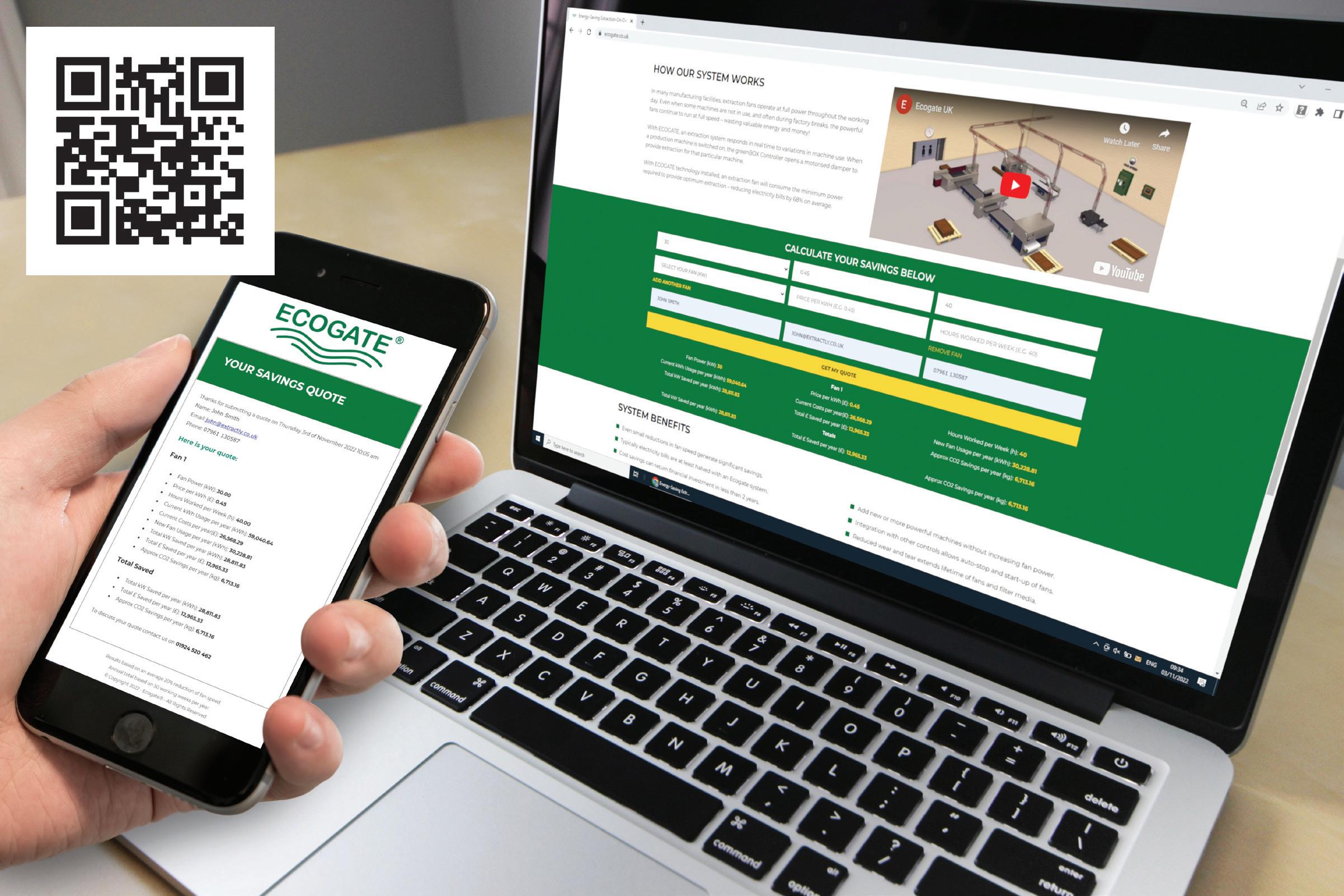
Ecogate has been making headlines in the UK for over 10 years now, and this innovative energy-saving technology has been proven worldwide to significantly reduce energy usage for process industries. In the woodworking industry, cost savings in excess of 50% are easily achievable – that’s half price electricity – and, with a payback on investment being typically less than 2 years, the savings will just keep on coming.
Ecogate equipment can be fitted into any existing extraction system, and the installation process can be undertaken with only minimal interruption to your production. Ecogate’s automatic dampers are connected into the ductwork serving each of your machines, and sensors attached to each machine signal the Ecogate “greenBOX” controller to open
and close the dampers as machines come on or off-line. Simultaneously, the greenBOX instructs the PowerMASTER variable speed drive unit to adjust fan speed to exactly match the new demand for extraction.
With Ecogate installed the fan no longer runs continuously, at full speed, for 8 hours a day. Since machines constantly stop and start during production, as well as at break times, the extraction only needs to operate at 80% of capacity, on average, but the 20% reduction in fan usage generates a huge 50% reduction in power consumption.
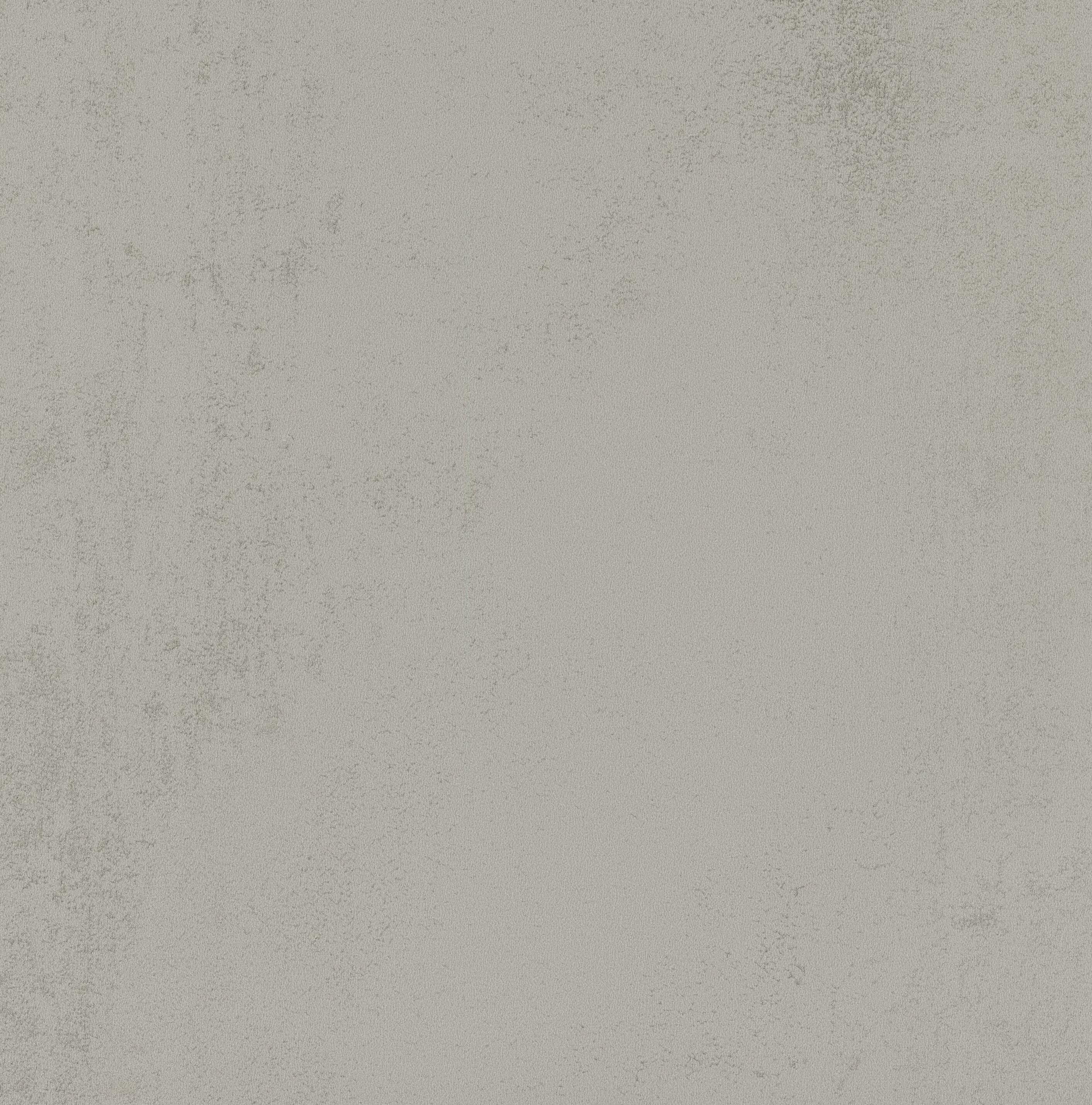
T: 01924 520462
E: info@extractly.co.uk www.extractly.co.uk
Whatever your design ideas, you’ll find inspiration to complement and elevate them in the dp-fantasy collection from Decorative Panels Lamination. A range of finishes that nature cannot provide, fantasy represents the best in material technology from the printing industry with levels of design realism like never before.
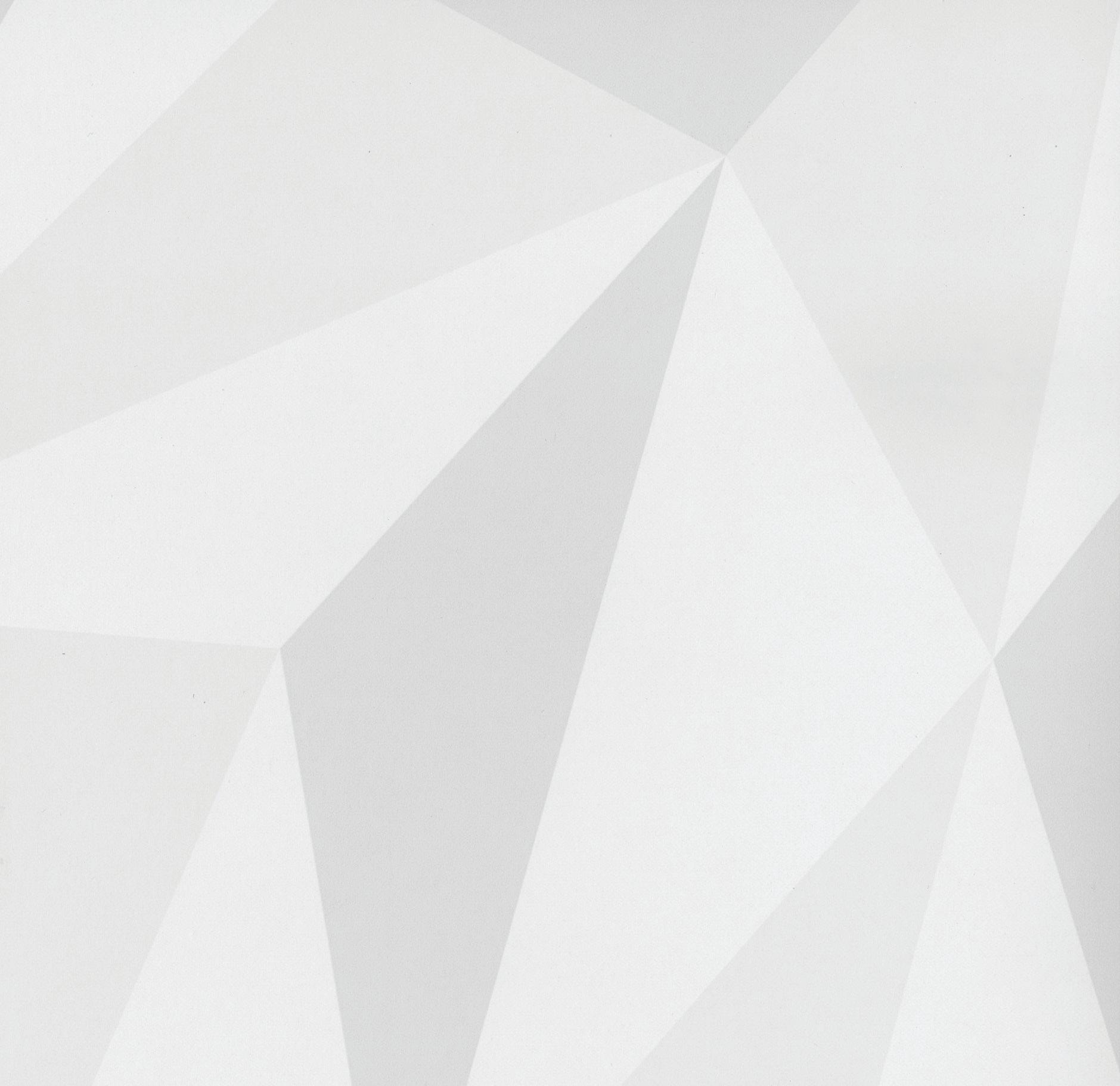
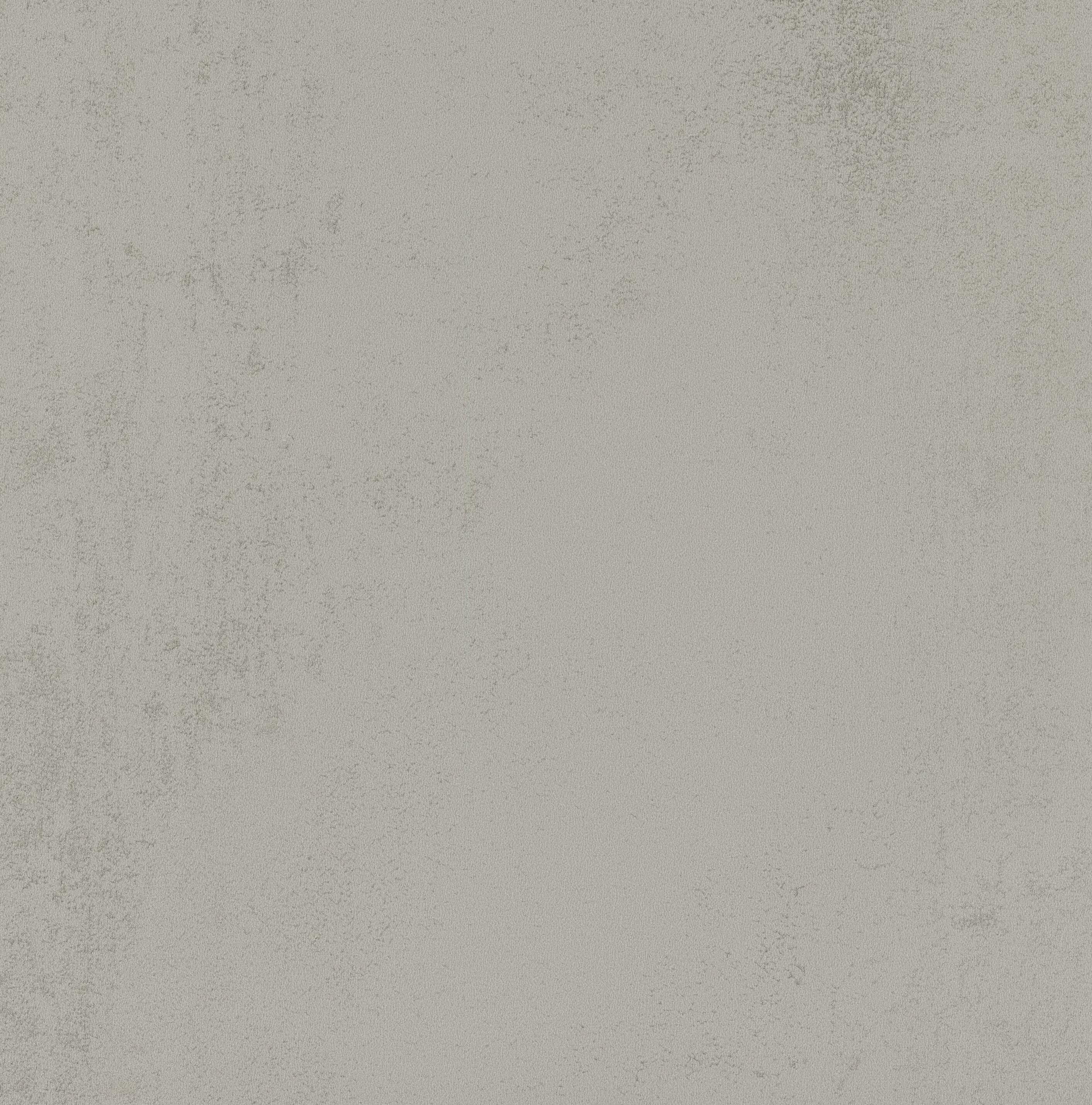
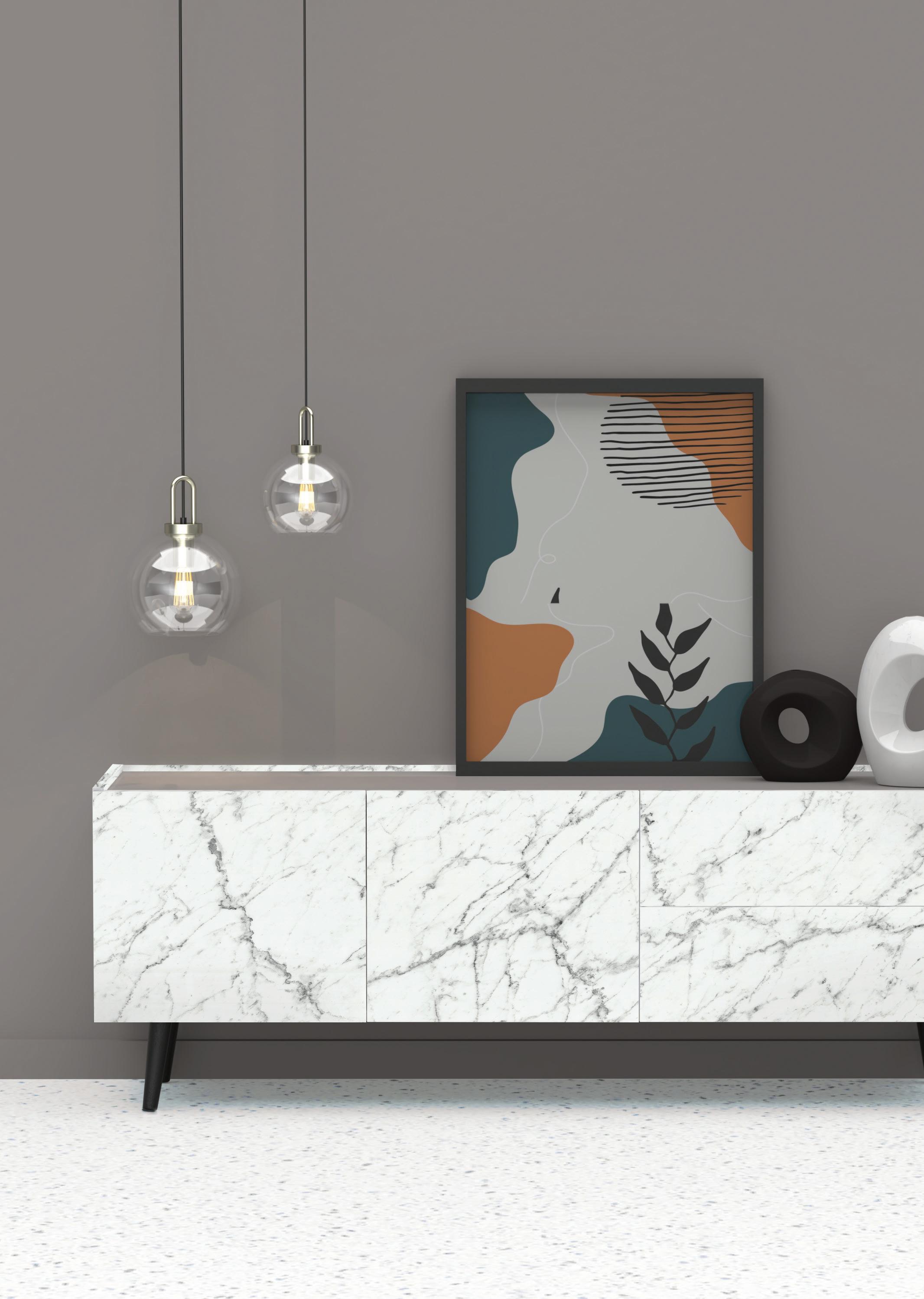
BLUM HAS HOME ORGANISATION SORTED
AS ‘STORAGE’ TOPS SOCIAL MEDIA SEARCHES
As more and more consumers look to social media for interior inspiration and ideas, it seems that kitchen storage comes out on top. From TikTok and Instagram to YouTube and Google, #kitchenorganisation and #kitchenstorage are some of the most popular hashtags with users searching for the best and most innovative ways to clear the clutter, create more space and give rooms a calm, orderly feel.
“Watching reels, shorts and videos of a wellorganised drawer or cupboard being achieved also taps in to the trend for an autonomous sensory meridian response (ASMR), a relaxed feel for the senses that viewers can experience when watching,” says Amanda Hughes, Blum Expert for Ergonomics at Blum UK. Blum knows all about organisation with its precision engineered fittings, drawer runners, pull-outs and lift systems that allow for flexible and space-saving storage in not just kitchens but living spaces, bedrooms, children’s rooms, bathrooms, hallways and home offices too.
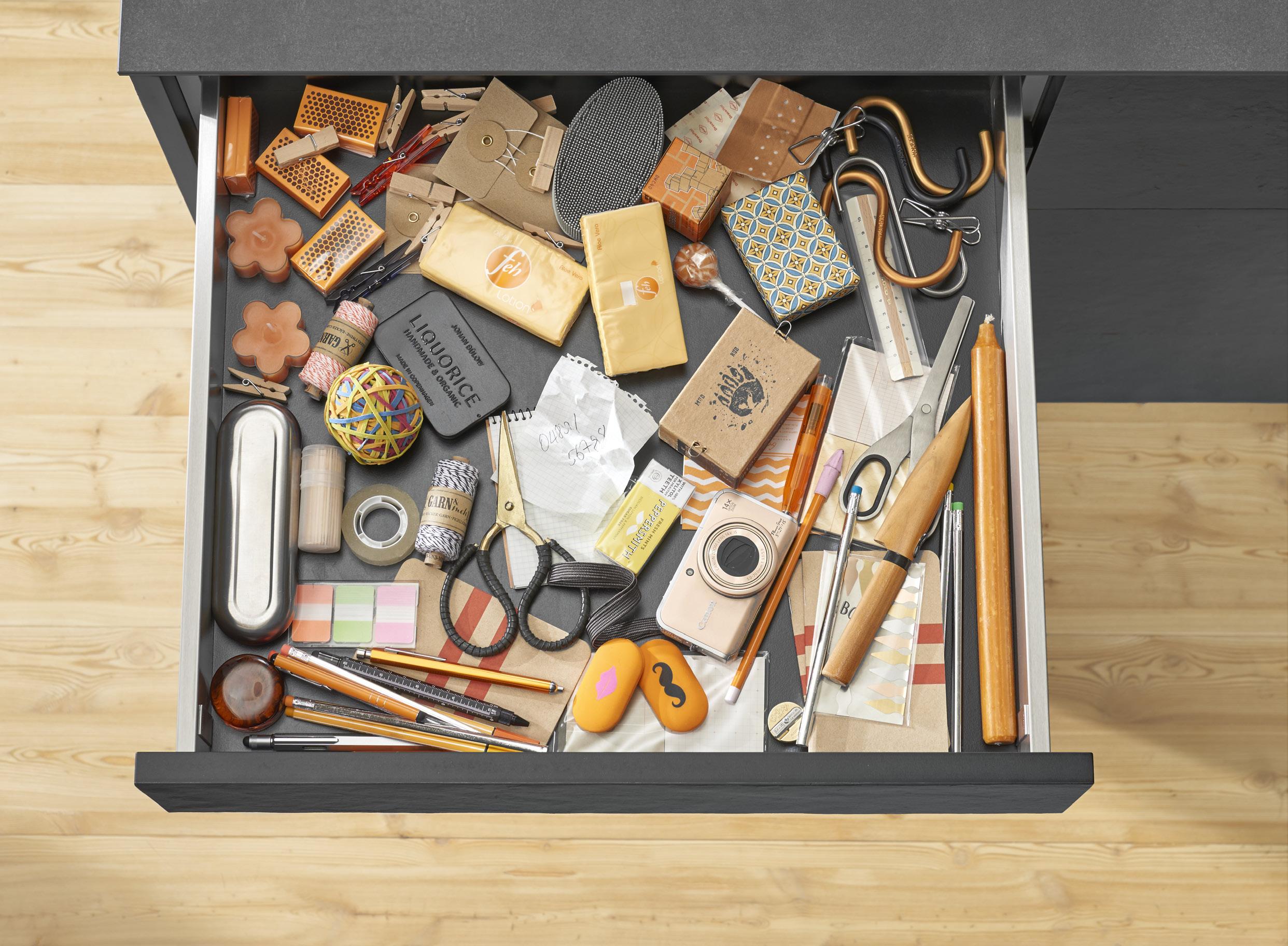
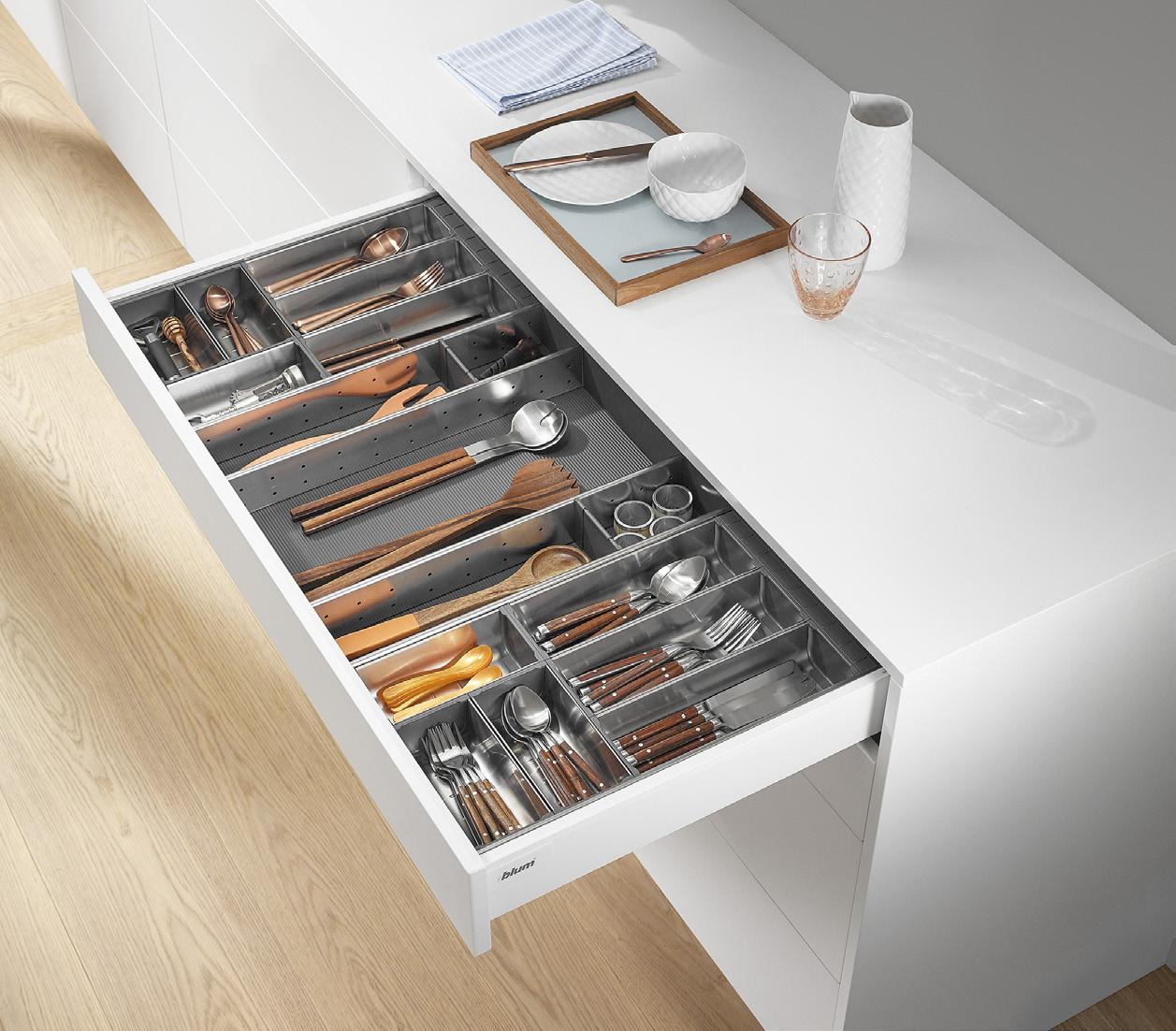
BLUM ORGA-LINE FOR TANDEMBOX
Perfect for organising everything from cutlery and utensils to pots, pans, bottles and chopping boards, ORGA-LINE is a high-quality stainless steel inner dividing system that can be used within drawers and highfronted pull-outs. Users can see instantly what’s inside with quick and easy access to items needed. There’s also a cling film dispenser and spice, knife and plate holders and for added versatility, ORGA-LINE also includes containers and cross dividers that can be arranged to suit all storage needs. As well as keeping items organised and easy to locate, it also holds things securely in place while inserts are dishwasher-safe for easy cleaning.

BLUM AMBIA-LINE FOR LEGRABOX
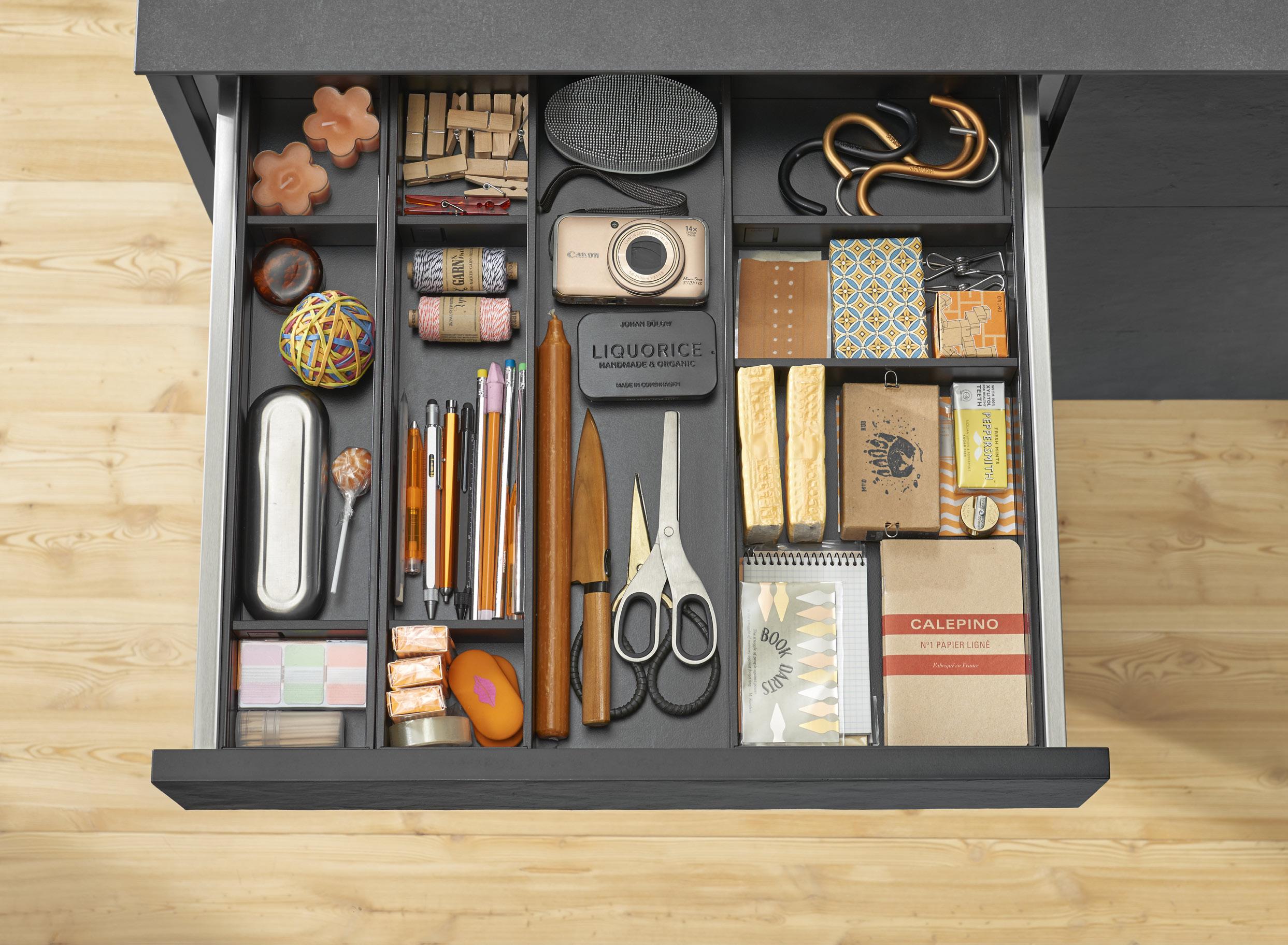
Drawers are a much better use of space than cupboards, as Amanda Hughes, Blum Expert for Ergonomics at Blum UK, confirms, “Drawers are so much easier to find things in, especially when it comes to the kitchen. No more feeling around the back of cupboards in the dark and dragging out all its contents to find that elusive item. Full extension drawers allow users to fully open them up to instantly see what’s inside. As well as saving time, which is something everyone could do with, it also saves space, allowing more contents to be added without overcrowding.
AMBIA-LINE is the inner dividing system for LEGRABOX. A sleek black design with a minimal look, it features slim and straight sides to the box system with frames that can be positioned wherever needed. Held in place next to other frames by magnets, it also comes with anti-slip feet to keep everything securely in place with cross dividers that can be adapted to suit different sized items.
INDUSTRY
THE BENEFITS OF AUTOMATIC AND ROBOTIC SPRAY TECHNOLOGY FROM HOMAG AND MAKOR
Providing products with a premium quality finish is absolutely vital in the competitive world of bedroom, bathroom, kitchen, office furniture, door and window manufacturing. Achieving the perfect finish relies on several elements, the most important of which are surface preparation and the painting or varnishing of each piece.
The HOMAG Group is a world leader in surface finishing and offers a range of sanding machines to prepare work piece surfaces. For spraying solutions, HOMAG has partnered with the Makor Group to provide a range of advanced automatic and robotic spray machinery. Together, the two companies provide the very best surface finishing solutions.
THE BENEFITS OF AUTOMATIC AND ROBOTIC SPRAY TECHNOLOGY
For any manufacturer that processes solid wood, woodbased, PVC or metal components, automatic spraying delivers a host of benefits including:
• High quality, flawless surface finishes
• Significant cost savings – economical use of coatings & reduced overspray
• Batch size 1 flexibility
• Fast colour changes
• Process consistency
• Simple operation
Makor has been perfecting spray technologies for over 40 years and offers a full range of automatic and robotic
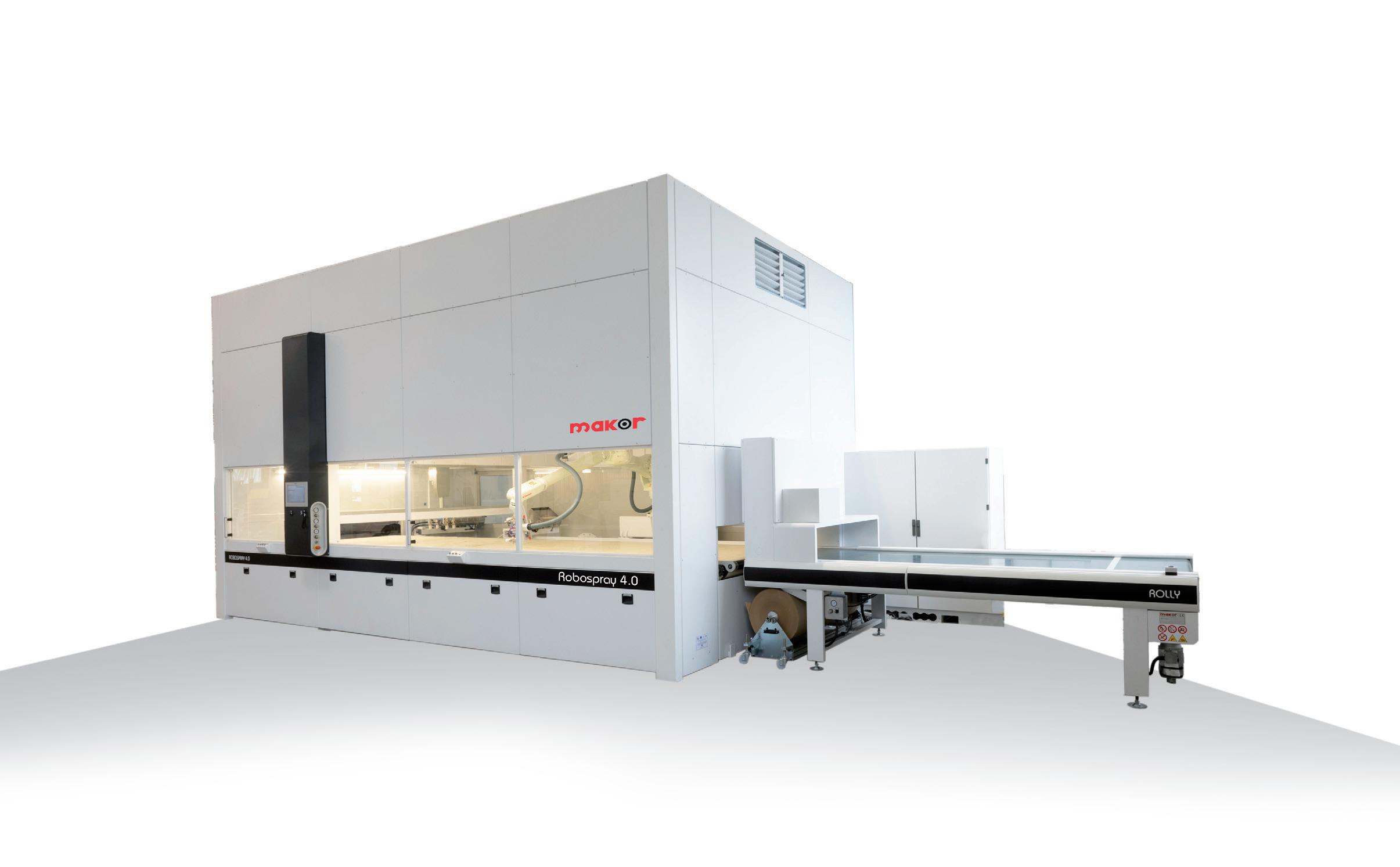
spraying solutions for profiles, panels and 3D parts. The investment it has made in continuous research and development has resulted in a portfolio of high quality machinery that is reliable, long-lasting and easy to use.
START ONE – ENTRY LEVEL AUTOMATIC PANEL SPRAYING
The Makor Start One is an ideal option for companies making their first venture into automatic panel spraying. It is suitable for manufacturers that need to spray medium to small batches with water or solvent based paints, or glue for veneered components.
It is a reciprocating spray machine which means the spray head moves backwards and forwards in a straight line. An electronically controlled drive ensures the smooth movement of the spray head and delivers a consistent application across the entire working width.
With a touch screen monitor, the Start One is very easy to operate and features an electronic bar to automatically read work piece sizes. The paper transport system renders the machine self-cleaning, minimising maintenance expenses and all but eliminating downtime. The machine delivers higher productivity, paint saving, coating uniformity and higher, more consistent quality with low operational and investment costs.
IRIDE 306 – FOR A HEALTHIER WORKING ENVIRONMENT
The IRIDE 306 has been designed and built to satisfy the present anti-pollution requirements and provide protection for employees in the work environment. It enables the automatic spraying inline of varnishing products on picture
frames, architectural mouldings, matchboards, valances, door and window parts.
The IRIDE’s spacious cabin offers full protection from noxious exhalations in the working zone and is kept under depression by means of a highly efficient suction and filtering system. The suction chamber is equipped with a differential manometer for monitoring the state of the filters. A wide front door enables easy access for quick setup and effortless maintenance. There is also bright lighting inside the unit for clear visibility.
With a robust steel plate and tubular steel construction, the IRIDE 306 offers variable forward feed speeds by means of strong poly-urethane belts. A pull-out trolley at the front of the machine holds large spray tanks which are coated with special non-stick material for easy maintenance and cleaning. The tanks are positioned in line with the spraying zones to collect excess spray material.
and select the type of coating required via the simple ‘EasyTouch’ operator panel.
The machine can be equipped with a self-cleaning belt, a paper transport system or a hybrid belt with both solutions. As part of the complete package Makor has developed its own CAD-MAk software; this controls the management of the trajectories and the 3D parts to be coated. The new software has extended the boundaries of what is possible with automatic coating. Every piece of any 3D shape can be painted by ROBOSPRAY 4.0, guaranteeing not only high, but also consistent quality of the most complex of 3D shapes.
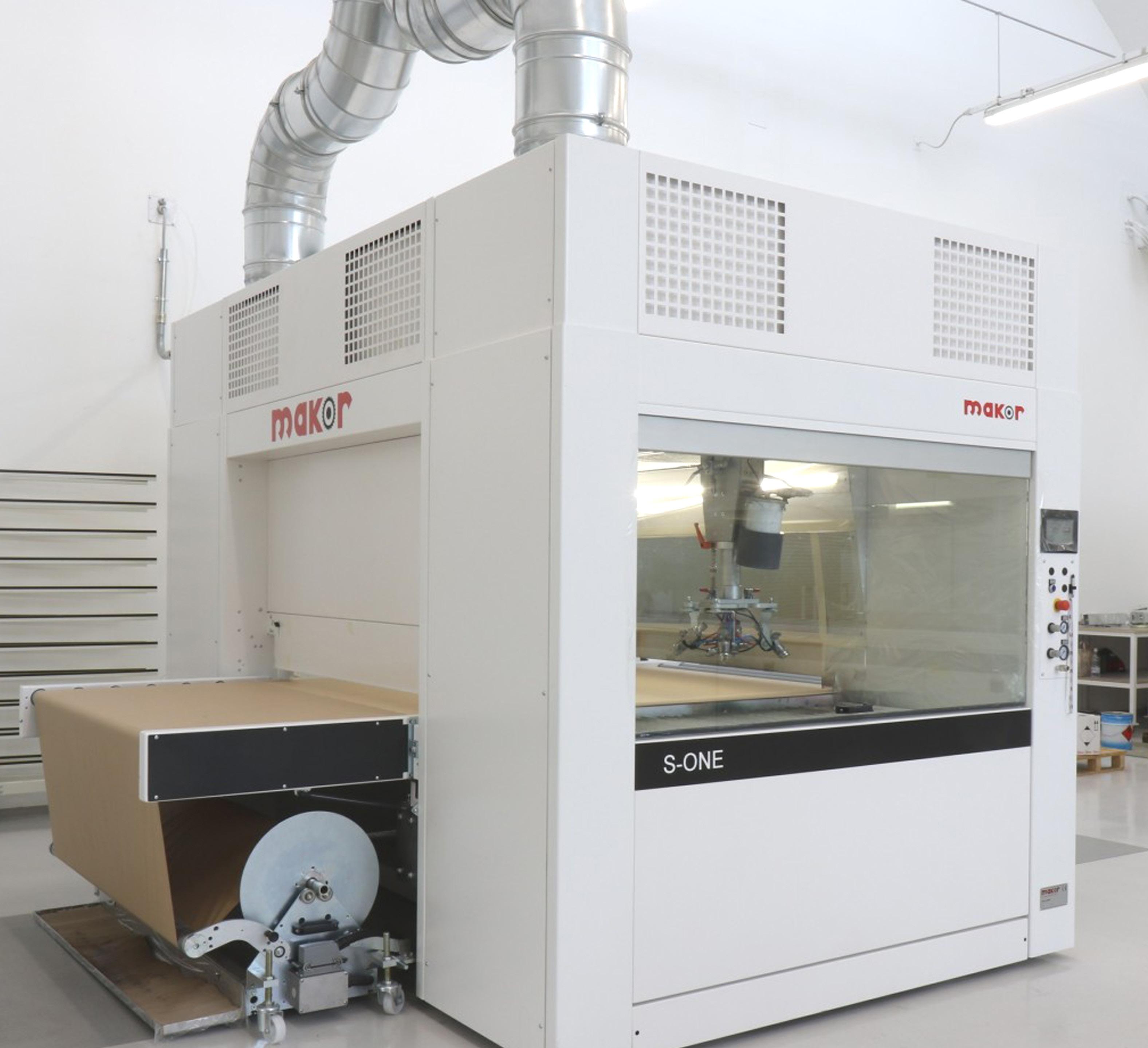
HOMAG & MAKOR – A PARTNERSHIP GOING FROM STRENGTH TO STRENGTH
ROBOSPRAY
4.0 – THE SECOND GENERATION OF THE ANTHROPOMORPHIC ROBOT FAMILY
Makor’s latest anthropomorphic (having human characteristics) robotic spray machine replaces the extremely successful ROBOSPRAY-TWIN. The ROBOSPRAY 4.0 offers premium quality finishing solutions for flat and complex 3D shapes.
The advanced technology in the ROBOSPRAY 4.0 combines flexibility and productivity. Its 3D scanning system features a blue laser that enables the machine to detect any shape
Commenting on HOMAG’s partnership with Makor, Simon Brooks, HOMAG UK’s managing director said: “The HOMAG Group has a heritage in high quality finishing machinery and it makes complete sense for the Group to partner with Makor. Its comprehensive range of hi-tech automatic and robotic spray solutions provides a valuable extension of our own product offering.
“The distribution partnership continues to be very beneficial for both parties. HOMAG is delighted to be associated with such an established market leader of premium automatic and robotic spray equipment.”
For a demonstration or more information on the Makor or HOMAG machinery and software solutions, please contact Adele Hunt at HOMAG UK on 01332 856424.
FEATURE
IDS’S DECORATIVE PANEL BUSINESS INVESTS IN FACILITIES, PEOPLE AND PRODUCT
IDS is continuing to grow its decorative panel business at a pace with new additions to its portfolio, investment in facilities and fleet, and new appointments to its dedicated national panel team.
Under new ownership since June, the specialist surface distributor remains committed to investing in the panel division which has been a key part of the business for more than 35 years.
Dave Huggins, Business Development Director at IDS, comments: “It’s been a very busy year for panel with a raft of new products available, new racking to enable us to meet growing demand and new team members on board giving us extended reach across the UK.
“We’re delighted that our new owners, Chiltern Capital, recognise panel as a key part of the IDS portfolio and have committed to investing in this area. We’re continuing to do what we’ve always done which is to evolve the business in line with the needs of a diverse customer base.”
INCREASED WAREHOUSE CAPACITY
Responding to market needs, IDS has invested in extra racking at both its Ely and Blackburn distribution centres. Between the two locations, IDS now has increased capacity of decorative panel, equating to more than 6,000 tonnes, available for tailored delivery and any order quantity across the UK.
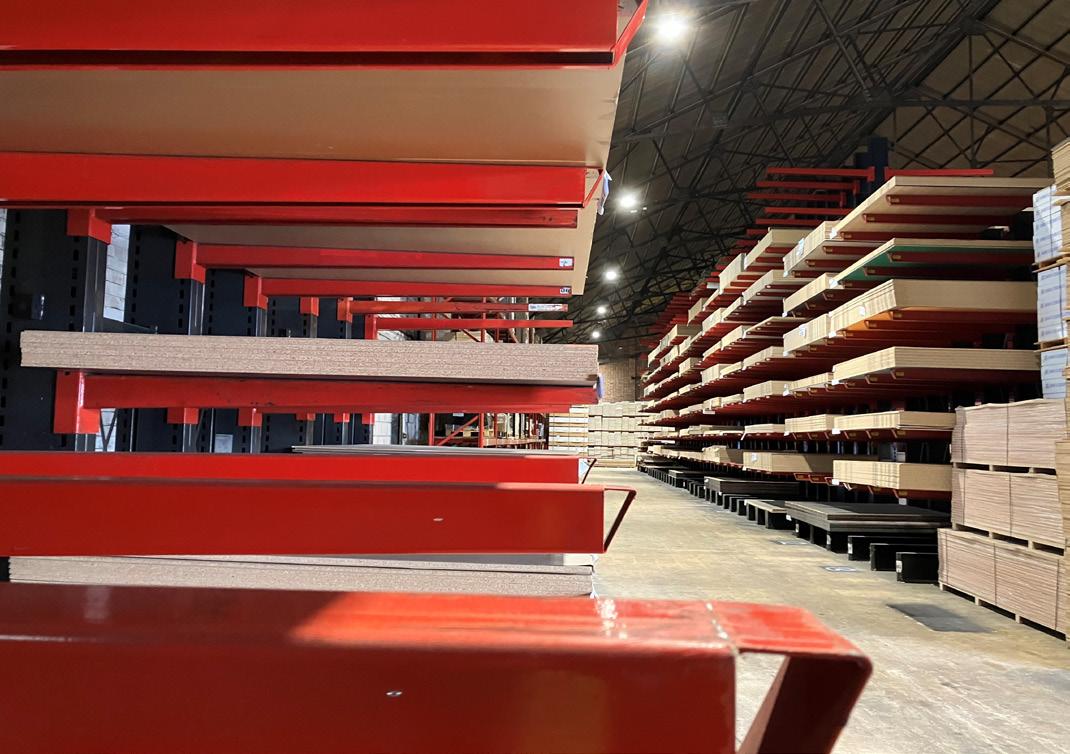
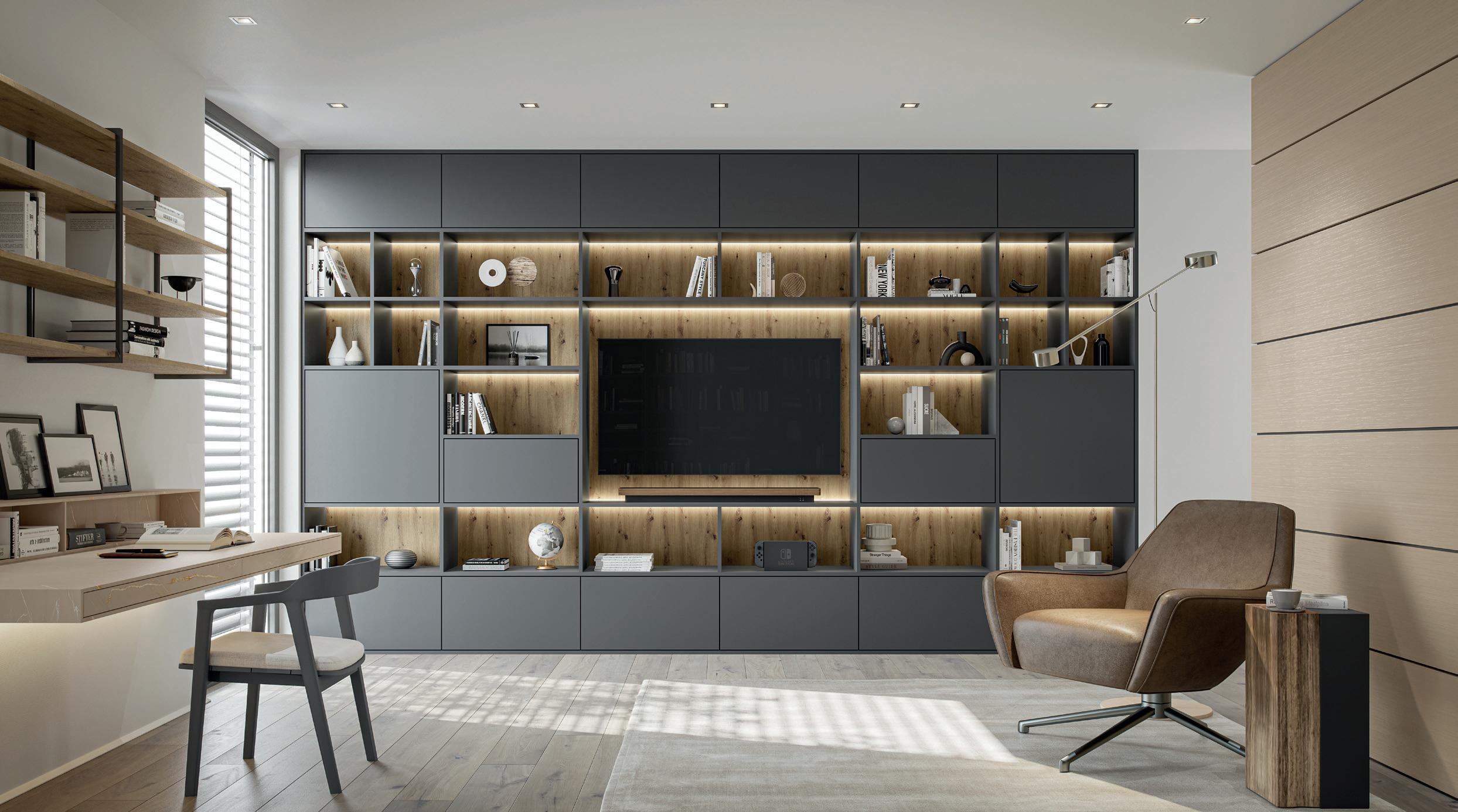
The stocked offer spans, Swiss Krono One World, Fundermax Premium Star, Finsa Superpan, and Fibralux coloured through MR MDF, which are all available from stock. Among the new ex-stock items are 16 trend-led
decors in 25mm thickness selected from the Swiss Krono One World Collection. This is a range geared towards the evolving needs of the office furniture sector, giving them the option of low volume orders on design-led decors serviced next day. 25mm has become an increasingly important thickness as it also offers cost engineering benefits being more widely used for shelving and partitions. IDS also exclusively stocks the entire Swiss Krono One World range in 18mm thickness for UK-wide delivery too. Featuring bestin-class environmental credentials, the Swiss-made range meets the growing requirement for responsible sourcing among furniture manufacturers, fabricators and designers.
INVESTMENT IN FLEET
IDS has also invested in five new vehicles, ensuring the business has a nimble approach the length and breadth of the UK. The new vehicles comprise one 12 tonne, two 26 tonne and two articulated lorries giving the flexibility to access all customer sites, as well as handle a wide range of orders and customer requirements.
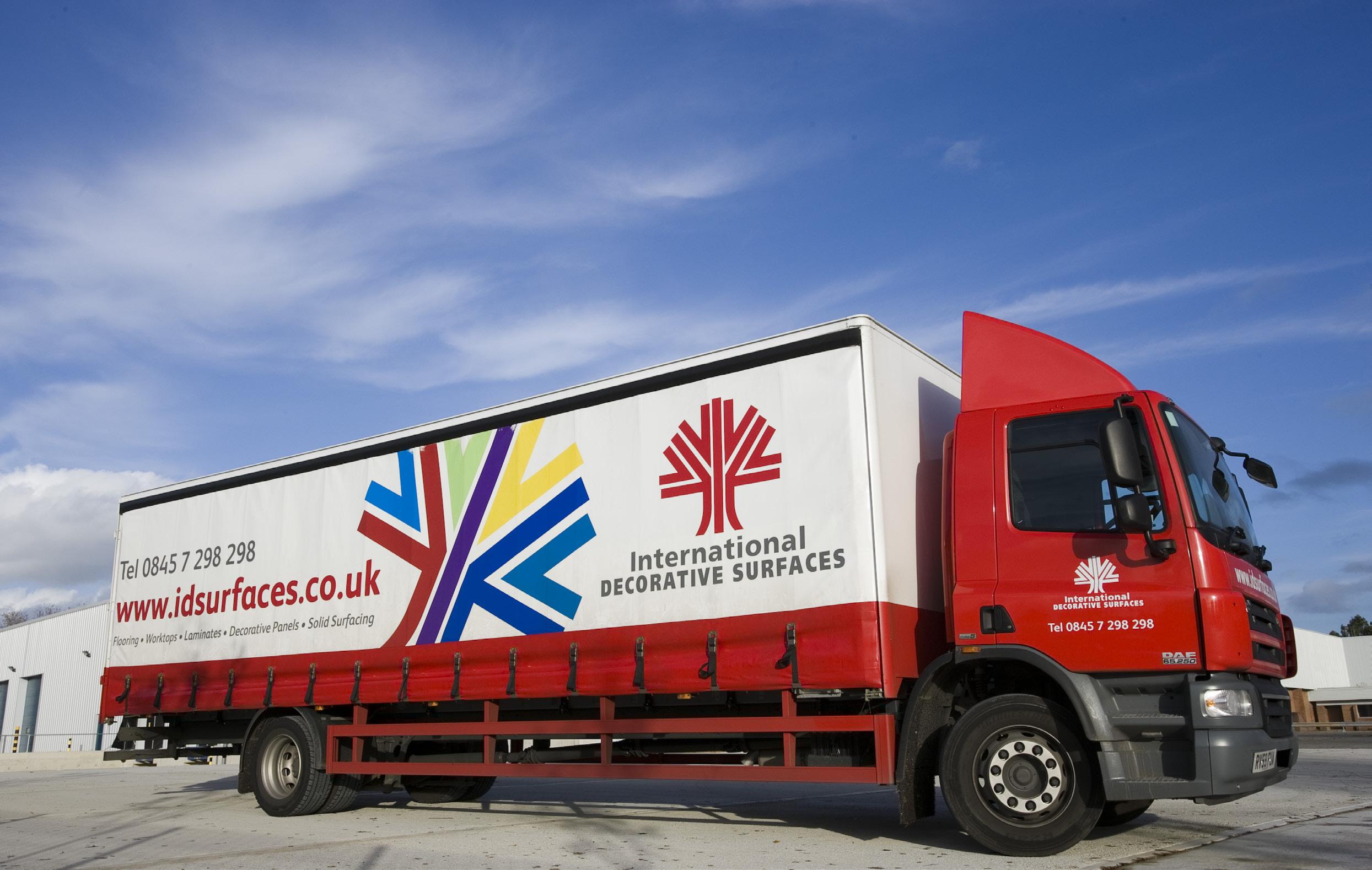
EXPERT TEAM
With a dedicated national panel team that service customers across the UK, IDS has continued to invest in its specialist team and recently welcomed Kevin O’Donnell as Regional Sales Manager based in Ely. With significant experience gained in National Sales Manager roles at Twyford Bathrooms and more recently Gerfloor, Kevin will play a key role in driving the sales growth of decorative panel in the south.

Huggins comments: “I’m delighted to welcome Kevin to the panel team with his strong track record. His appointment will afford IDS Ely the capability to spend more time with our customers in the south-east, deep diving into all issues surrounding customers decorative panel product and service requirements, ensuring we are continuously aligned with the needs of new and existing customers.”
BROAD PORTFOLIO
IDS continues to invest in product development and innovation to provide customers with the latest decorative panel products and broadest portfolio possible.
New to the range is the Fundermax Premium Star range of super gloss and super matt anti-fingerprint panels. Suitable for a wide range of furniture manufacturing and shopfitting applications, the exclusive UK collection offers a choice of five popular decors across both finishes available from stock in 24-48 hours, with additional decors and thicknesses available on extended lead times.
Also new to the portfolio is the premium Fibralux coloured through MR MDF panels which are suited to a wide range of interior decoration and furniture manufacturing applications.
As the exclusive UK distribution partner for Swiss Krono’s decorative panel products for over 30 years, the One World Collection continues to be a mainstay of the IDS portfolio, offering a choice of 134 decors available for next day delivery. The FSC® and PEFC™ certified panels feature a virgin wood core and are rated E D2020 as standard for low formaldehyde emissions.
Huggins adds: “These new ranges complement the existing panel portfolio and bring popular products into the IDS offer. At the same time, we’re very proud of our longstanding partnership with Swiss Krono for their genuine Swiss-made products. The brand’s strong environmental credentials give a genuine USP which can create business opportunities with customers who work to environmental or ethical principles. We’re thrilled to be number one for Swiss Krono One World in the UK.”
A TOUCH OF GOLD
CUTTING-EDGE TREND BY OSTERMANN
Furniture in gold or with decorative elements in gold is back in style and we will soon see a lot more of it. In line with this trend, Ostermann offers various matching solutions for the narrow surface of the board.
We have already gotten used to the sight of gold-coloured accessories in interiors again. In the future, you will even find the elegant colour again on entire furniture surfaces. Ostermann has the right edgings in store to cover the narrow surfaces. Among these, ABS edgings with a real aluminium finish are a particularly high-quality solution. They are just as easy to process as standard ABS edgings. A thin layer of real metal gives their surface a realistic look. But even with ABS material alone, soft gold tones can be created. In the following, the Ostermann experts present five selected solutions that round off golden surfaces or highlight furniture when used as accentuating edging. All versions presented here are available directly from stock and can be shipped in small quantities from 1 metre. Furniture makers will find more information under the search item “#Highlights10” on the Ostermann website www.ostermann.eu.
HOW TO BLEND IN PIECES OF GOLD
Touches of gold look particularly elegant on anthracite grey or black plain boards. Whether you combine them with glossy or extremely matt surfaces does not matter. What counts is the end customer’s personal taste and, of course, the setting in which the furniture is supposed to be placed. A golden edging can also be applied to dark wood decor boards, giving them a stylish finish.
WITH REAL ALUMINIUM FINISH: ALU ORO CORTEZ
With the ABS edging Alu Oro Cortez exclusive matt brushed, you get an unusual furniture edging which is not only in line with the “gold” trend but at the same time meets the trend for matt surfaces. The 1 mm thick ABS edging matches the Fenix NTA matt metal finish of the same name. The metal finish gives it a particularly high-quality look.
WITH REAL ALUMINIUM FINISH: ALU GOLD BRUSHED
If you prefer your golden edging to shimmer and are looking for a quality solution, you should seek out the ABS edging Alu gold brushed. Just like Alu Oro Cortez, it has a highquality real aluminium finish. The brushed texture and metallic sheen add a warm hue. This edging is available from Ostermann in 3 different thicknesses (0.5, 1 and 2 mm) for a wide scope of possible designs.
VELVET GOLD LOOK: ABS EDGING BRUSHED BRASS
With its fine Linea structure and its restrained, warm colour, the ABS edging, available in thicknesses of 1 and 2 mm, appears very realistic even without a metal finish. The velvety gold shade not only matches Egger’s decor board of the same name, but also goes excellently with wood decors, especially boards with a slightly reddish base tone.
ABS EDGING SIERRA GOLD
The ABS edging Sierra Gold gets a slightly antique look due to its cloudy colour play. It is available in 2 mm thickness and perfectly matches Pfleiderer’s surface of the same name.
ABS EDGING GOLD BRUSHED
The ABS edging Gold brushed wood pore is slightly darker than the velvet-gold brushed brass variant and significantly lighter and calmer in decor than the Sierra Gold edging. With its warm gold tone, the 1 mm thick edging can also be used perfectly as an accentuating edging on plain-coloured boards.
EUROPE’S LARGEST IMMEDIATELY AVAILABLE RANGE OF EDGINGS
Ostermann has all furniture edgings readily available in their own warehouse. As stock items, they can be ordered by 4 p.m. to be shipped on the same day. In order to maintain this pace even with the growing variety in the product range, the company is continuously investing in state-of-the-art storage and shipping technology.
OSTERMANN SERVICES AT ONE GLANCE
• Edgings from 1 metre
• Edgings in every width up to 100 mm
• Edgings in various thicknesses
• Edgings in ABS, Melamine, 3D-acrylic, Aluminium, Real wood veneer
• Airtec edgings despatched after 2-4 working days
• Laser edgings despatched after 2-4 working days
• Infratec edgings despatched after 2-4 working days
• Edgings pre-glued with hotmelt adhesive upon request
• Europe’s largest immediately available edging range
• All orders placed before 4.00pm are delivered within 24 hours
GOLD TONE DIVERSITY:
Ostermann supplies the trendy gold-coloured furniture edgings in many variants. Here in the picture you can see from left to right the ABS edging Gold brushed wood pore, the ABS edging Sierra Gold Stone Finish, the ABS edging Alu Oro Cortez exclusive matt brushed, the ABS edging Alu gold brushed and the ABS edging Brushed Brass linea structured.
CUSTOMERS APPRECIATE OSTERMANN’S EDGING SERVICES
In Ostermann’s Edging Expertise Centre, a whole team is tasked with referencing the exactly matching edging to each board. The result can be found in the convenient online shop or in the Ostermann app. If you enter the board name or the board number in the search field on the home page, an image of the decor you are looking for will immediately appear. One click and you can see the assigned edgings to this board and choose thickness, width and the required length of the edging. You can also request any individually required width up to 100 mm.
The pre-coating of the selected edging with hotmelt adhesive is just as much part of the Ostermann service as the delivery of so-called TPU zero bondline edgings. These are edgings which are suited to be processed with zero bondline technologies. In line with the 3 machine technologies currently available on the market, the Laser, Airtec and Infratec edging each offer a solution specially tailored to the respective technology.
For all 2 mm strong edgings, Ostermann offers the retrofitting of a T-bar - a good choice whenever you need to apply an edging without an edgebanding machine, for example directly on site or to mend already assembled furniture.
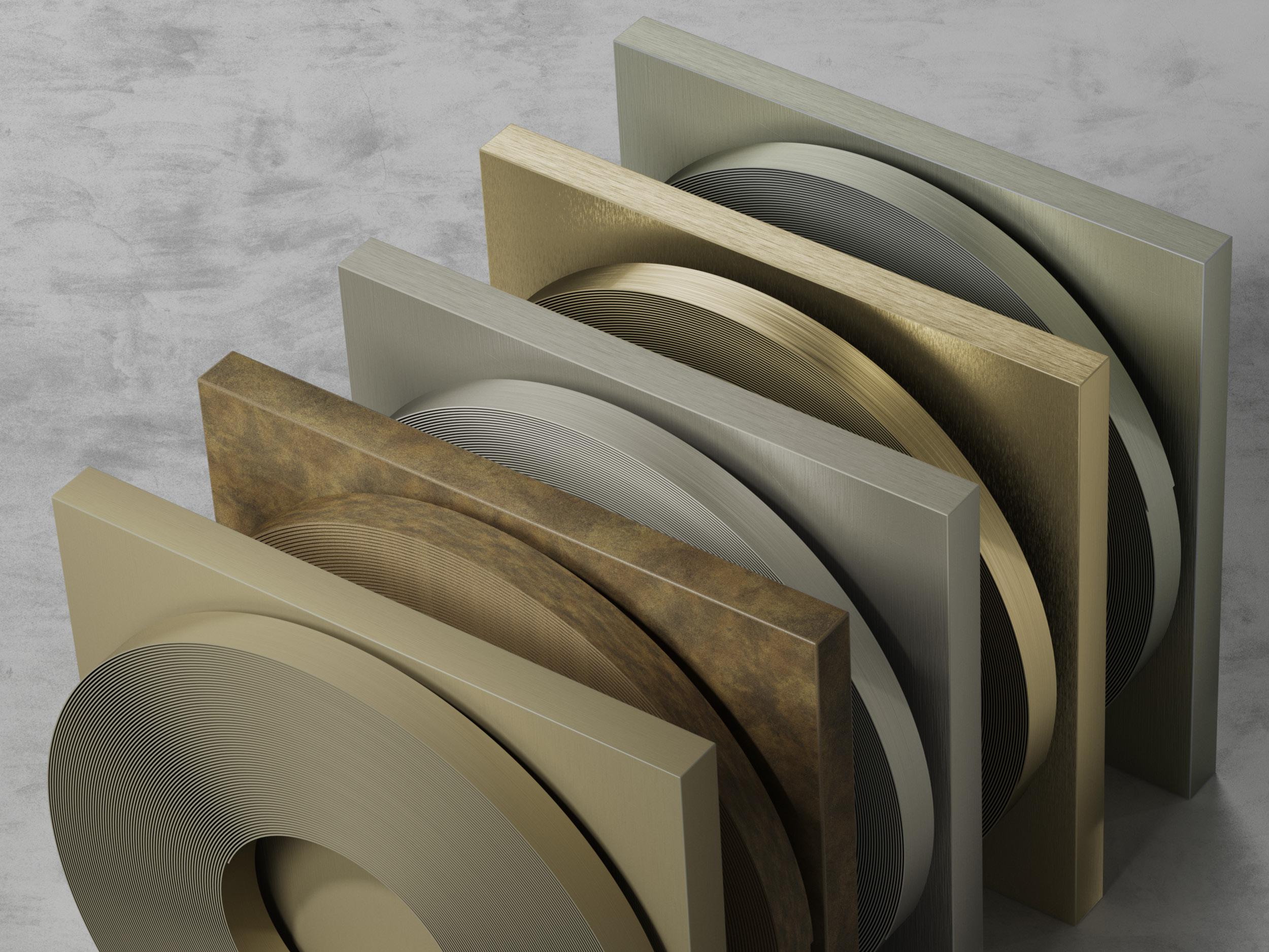
INDUSTRY
DIGITAL TOOLS OF THE TRADE USING CAM SOFTWARE TO ARTISTIC EFFECT
Beating the clock without sacrificing quality is the primary goal of every manufacturer, so it makes sense that the development of computer-aided manufacturing (CAM) software was more about increasing output than providing specialised design-to-manufacturing tools.
Nowadays, businesses that produce high-volume commercial work — such as cabinetry and furniture for schools and medical offices — use CAM software to boost production efficiency and take advantage of digital tools that broaden capabilities and potentially add value to products. Businesses that produce one-of-a-kind products for commercial and residential clients, on the other hand, benefit from CAM tools that help them remain competitive despite the highly custom nature of their creations. The growing availability of these types of tools help manufacturers use CAM systems to design and produce ornate products with consistent quality and efficiency.
CHOOSING THE RIGHT DIGITAL TOOLS
The painstaking process of bringing a project to life without the right digital tools can quickly remove the sparkle from a bright new idea. While the imagination may be limitless, the capabilities of CAM software systems may differ greatly — and some may be too limited for certain applications. While a CAM system compatible with a wide variety of computer-aided design (CAD) file formats should be a minimum requirement, it’s best kept in mind that CAM software with robust design tools can significantly improve
workflow even if CAD software is used in tandem. The ability to seamlessly import a wide range of CAD files ensures that design data remains intact and that the part can be programmed for CNC (computer numerical control) production without editing the imported design. However, if a problem does occur during import or if a last-minute change to the design is required, CAM systems that offer design tools eliminate the need to use a separate CAD system to make those changes.
Software with advanced engraving functions simplifies the production of artistically detailed products, and some CAM systems are even capable of generating engraving toolpath from just about anything. A system capable of converting scanned images into the G-code needed to drive a CNC router makes it possible to, for example, transform photographs or sketches into engravings.
The applications for this capability are countless and include the ability to, for instance, scan a child’s artwork, save it as a bitmap or JPEG, and import it into CAM software. From there, digital tools can be used to generate the toolpath needed to engrave the images into furniture, panelling, mouldings, and more.
Software that provides drawing and layout tools for converting images into machinable geometry, adding borders, scaling, sizing, and positioning, simplify the manipulation of images for desired effect. By offering digital
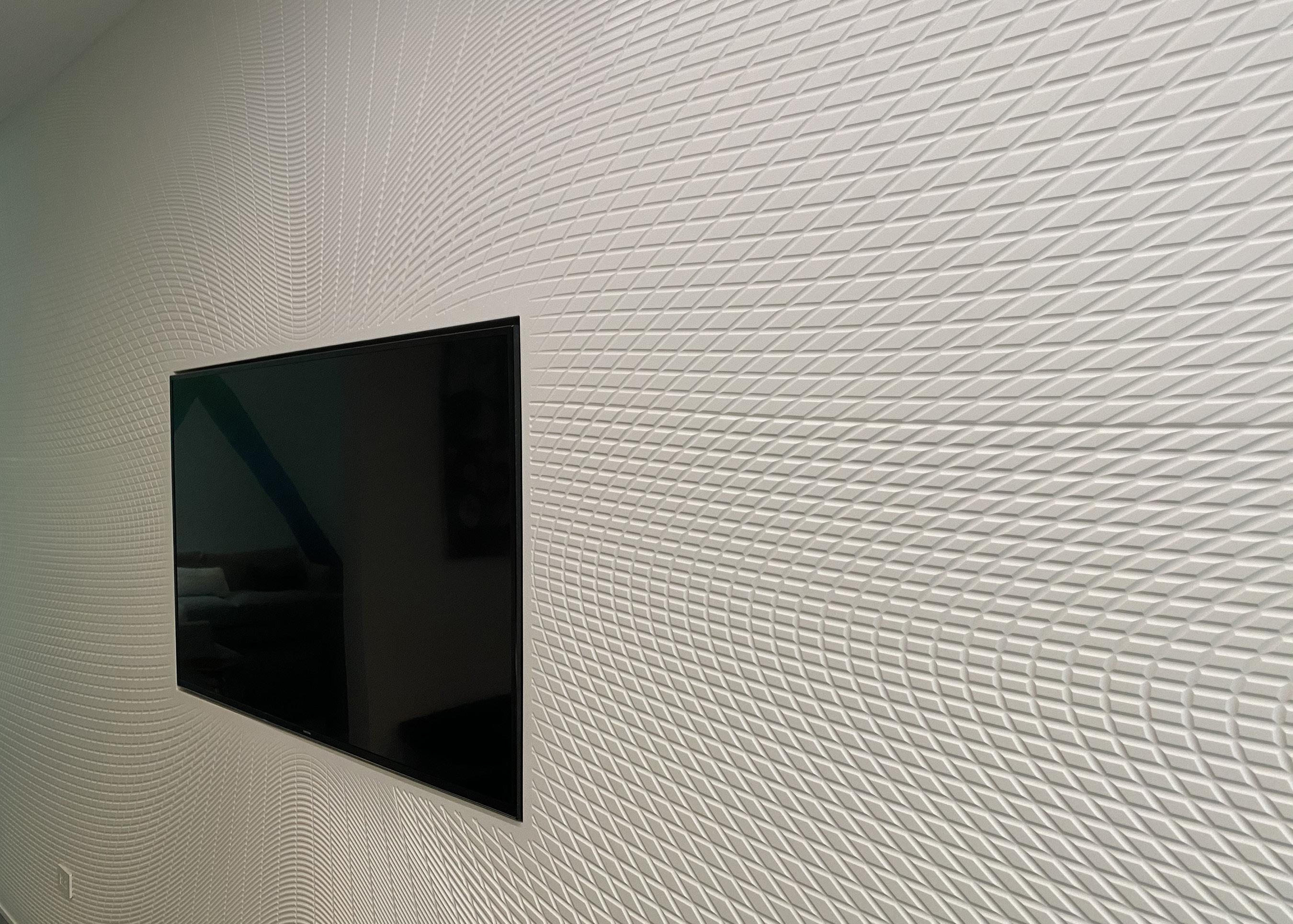
tools that support interactive sculpting and blending, as well as the ability to create 3D textures from images, CAM systems can help manufacturers bring unique designs to life.
MAKING WAVES
The machining of complex surfaces is a challenging art and science regardless of the material used. Creating artistic effects in wood, MDF, and solid-surface materials, such as Corian®, can be achieved by using CAM software to machine at various depths with any number of tools.
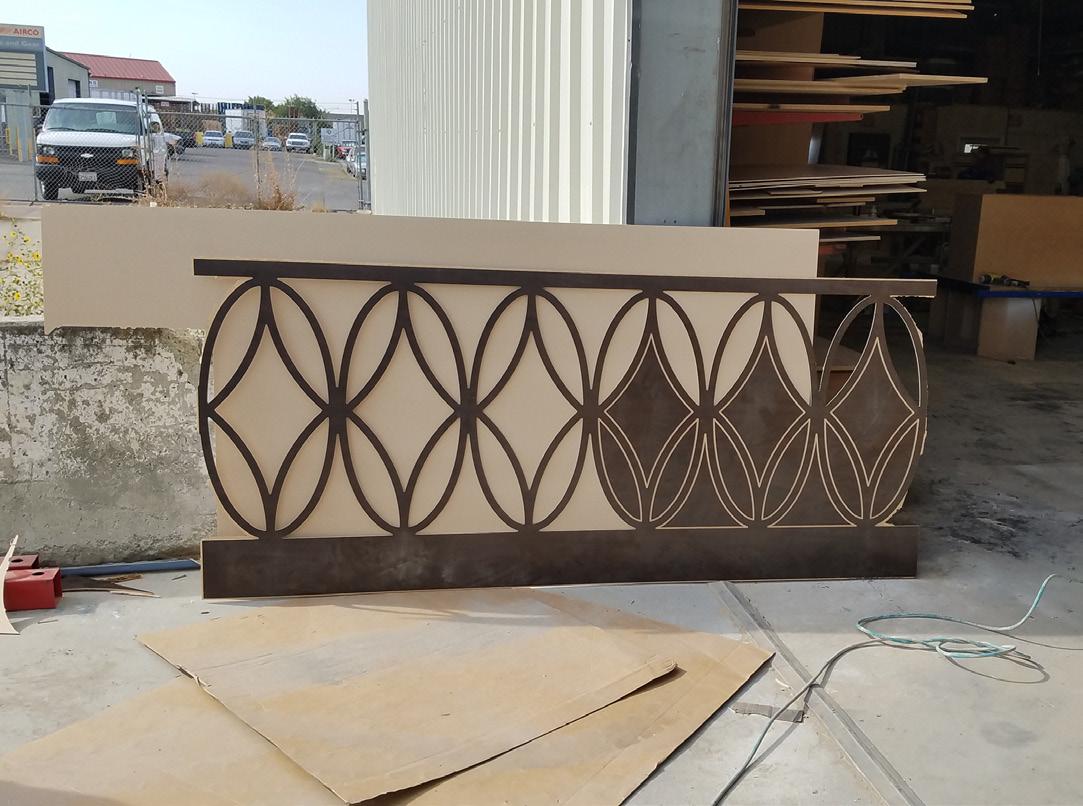
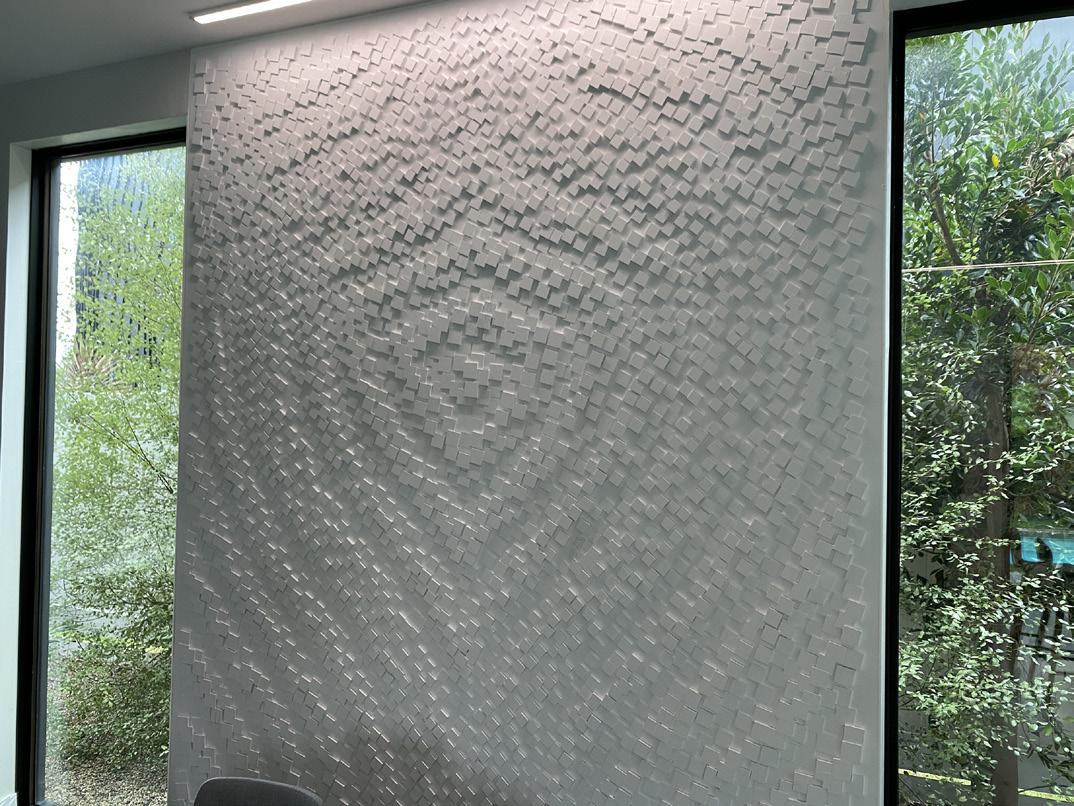
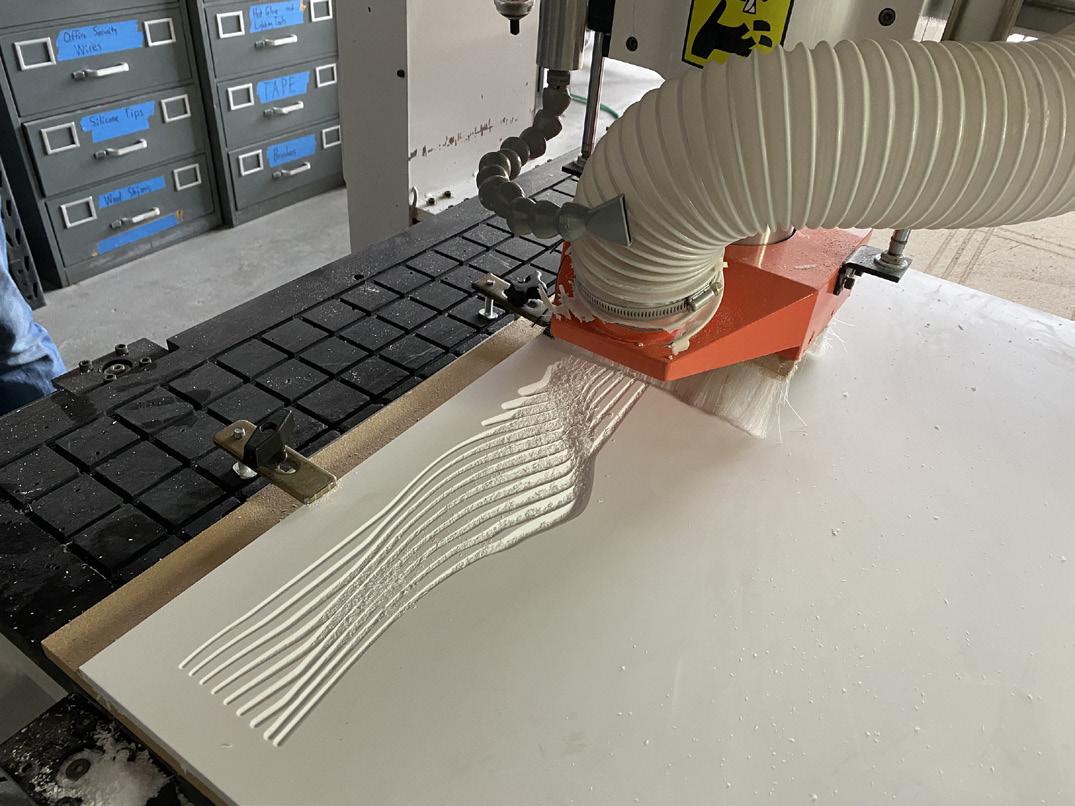
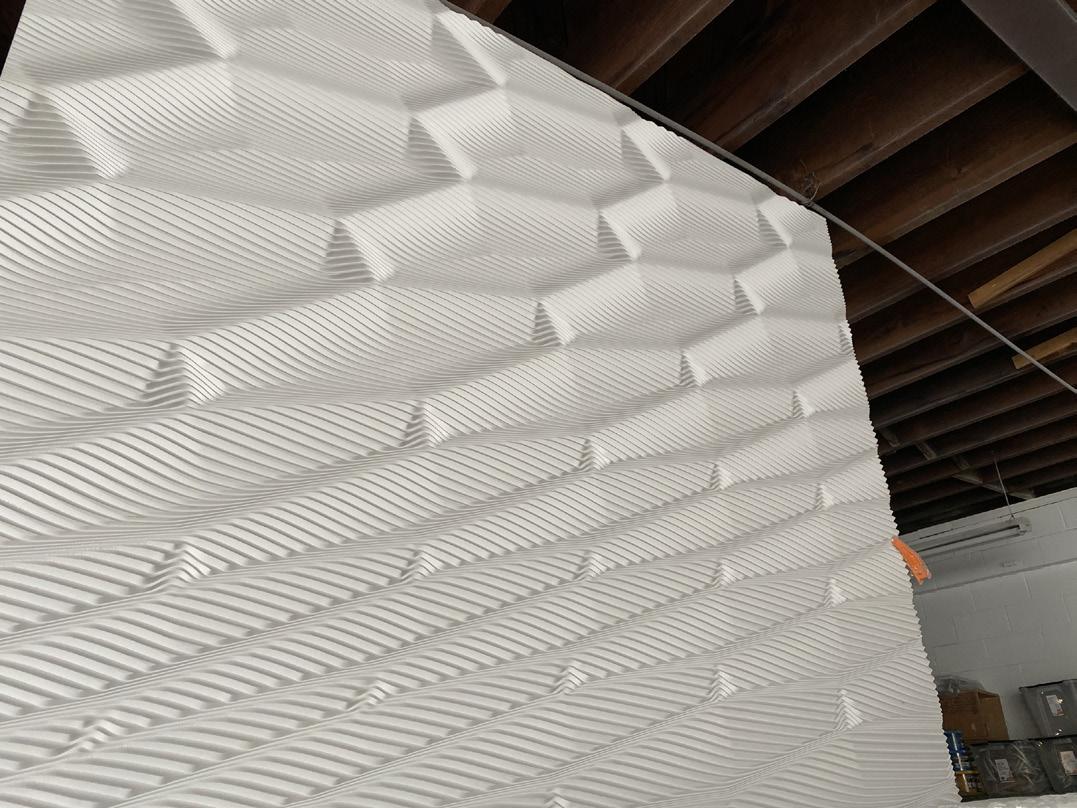
M.R. Walls, a California-based producer of solid-surface walls, is a pioneer in the design of multi-dimensional, carved, and textured products. The company uses CAM software to program intricate designs that are machined into solid-surface panels to dramatic effect, and many of the company’s products include backlighting that dramatically highlights varying degrees of material transparency.
Achieving these effects requires a CAM system and CNC machinery that can be programmed to machine at variable Z-depths to create one-of-a-kind surfaces. The ability to simulate surface machining and verify toolpath before jobs are sent to the shop helps users identify potential problems and prevent machine crashes.
WAINSCOTTING AND APPLIQUES
While detailed wainscotting and appliques aren’t especially challenging to tackle manually, achieving ideal results in a profitable timeframe without the help of CAM software would surely entail more than one sleepless night. Software that’s robust and easy to use significantly simplifies the production of complex profiles in plywood or MDF.
Stair Systems of California used CAM software to manufacture 200 linear feet of wainscoting with complex cutouts, as well as a set of mirrored barn doors in MDF that feature an intricate design. The ability to fulfil customer requests for pieces that feature personal flair is one of the strengths that differentiates the company from its competition and keeps it busy with varied requests for artistic projects.
While turning out products imbued with the qualities of traditional craftsmanship is the goal of any woodworker, artistry often takes a backseat to profitability. The ability to create products that reflect the interests and unique tastes of clients is a strength that helps win jobs, increase demand for your work, and ultimately boost profits. The growing availability of powerful and easy-to-use digital tools have made thriving while creating one-of-a-kind products more achievable than ever before.
RENAME IS THE GAME, LET’S TRY A DIFFERENT OUTLOOK
Most magazines in the wood working industry regularly host a “Wood Waste and Dust Extraction feature” This publication included.
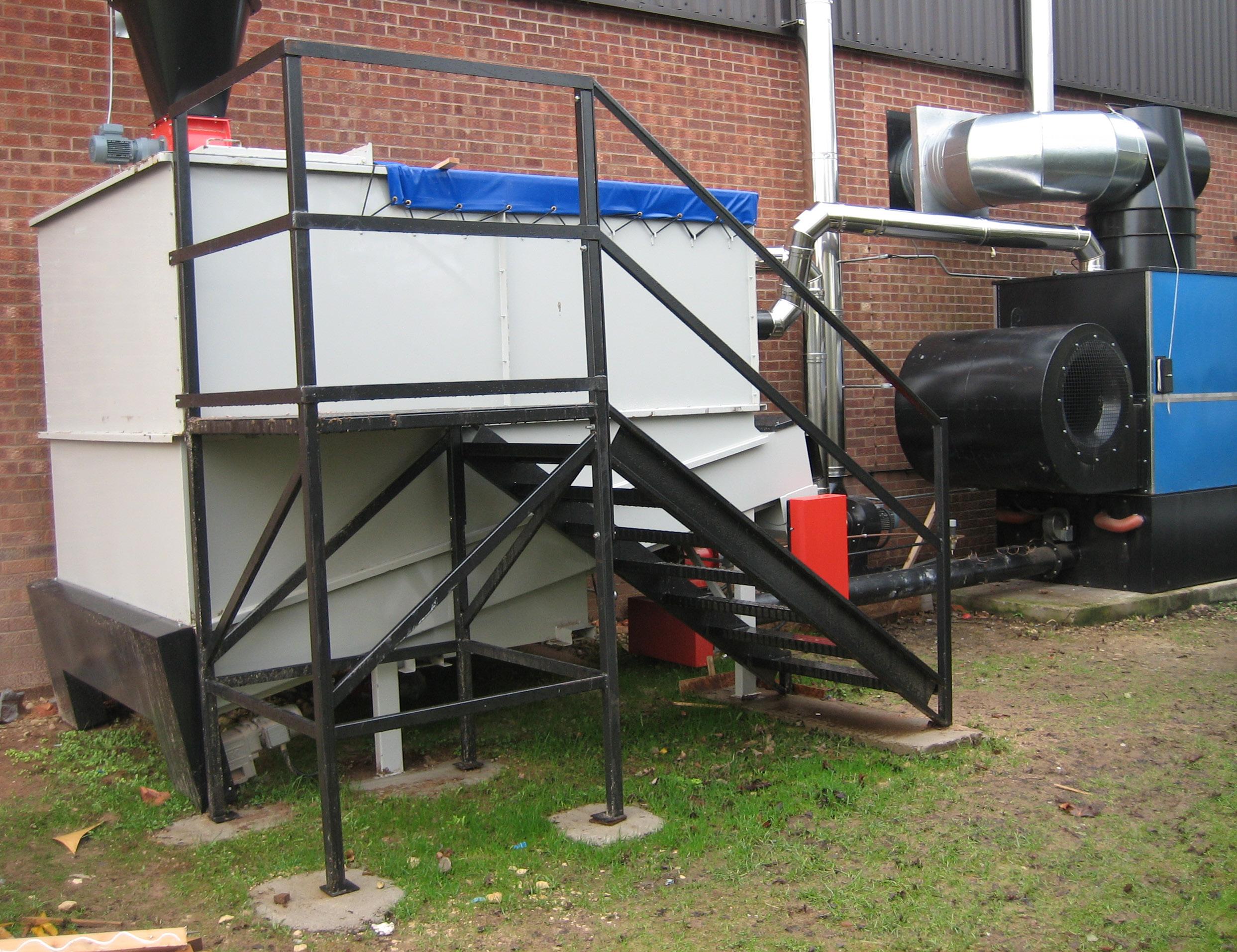
Chris Franklin Managing Director of Ranheat Engineering Ltd. Leading UK manufacturers of Biomass boilers and heaters suggests it is time to re-address the terminology used in the woodworking industry in the United Kingdom. For many years wood fuel as a by-product of a wood manufacturing process has been described as waste. When we think of waste at home, Domestic waste, we think of household rubbish collected by the bin-men and taken away to landfill or re-cycling.
It is time to think again: the wood by-product from our woodworking industry should be looked at as wood fuel and not wood waste.
All wood working companies both big and small should use this valuable resource as a clean renewable fuel that the industry produces tonnes of every day.
WASTE
NOT WANT NOT
We all know the hazards that can be caused by our industry when we machine or process wood or wood-based
products. Good LEV to a central location outside creates a safe working environment for the workers inside the factory. Many of these dust extraction systems then deposit the extracted wood into plastic bags. The removal of the bags means that the extraction system has to be turned off and literally “let the dust settle”. This involves the workers having to put on PPE including face masks, it can be a horrible dusty job especially if outside on a windy and rainy day. Downtime on production and itchy workforce.
The bags are then removed, often overfilled, then they have to be sealed using sealing tape and then put in a dedicated skip for specialist disposal.
So, let’s not call it wood-waste but wood fuel. It’s no longer a waste but a valuable asset.
By linking the dust extraction system directly to a metal sealed storage silo the wood-fuel is then stored, with no manual intervention, into a safe external energy store, ready to be automatically fed into a warm air heater or boiler to utilise this valuable resource to heat the factory.
The war in Ukraine has seen unprecedented rises in energy costs, the government has stepped in and capped the price
per kW hour that can be charged and introduced direct rebate schemes for domestic users. Some help is coming for industry, but nobody is certain how much and for how long?
Hand loaded heaters for wood-waste can only deal with solid off-cuts not dusts, the equipment generally is not fitted with any particulate abatement or flue gas recirculation to reduce NOx. Often the extracted dust from the woodworking machines is harder to dispose of but for a properly designed wood fuel combustion system it is an excellent fuel in it’s extracted form, requiring no further processing or energy input to convert it into fuel. (as opposed to briquetting dusts into briquettes needing further energy).
NOx and particulate, which are produced by diesel engines has seen the decline in sales of diesel cars with a swing back to petrol or petrol Hybrids or full electric cars. But how is the electricity produced? Electric cars in China would be of no advantage if the electricity used is generated by coal fired power stations.
Hydrogen production could be a way forward, but it only seems to stack up if the electricity used in the production is from renewables.
So, for an immediate solution to the heating energy needs of factory, with a wood machining process direct linking of the LEV dust extraction system to a wood fuel storage silo or bunker with an automatic feed system into a wood fuelled heater or boiler is the answer.
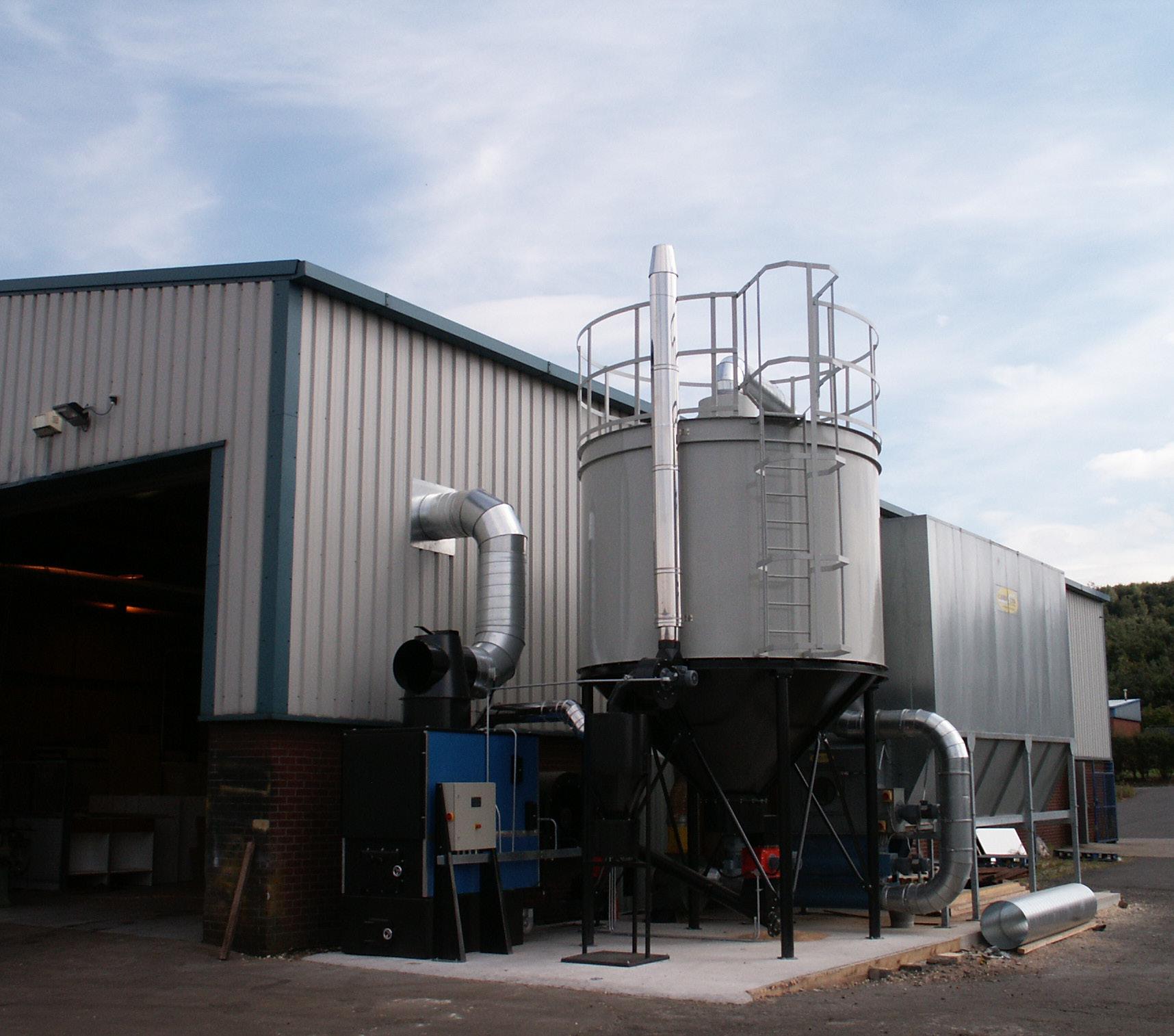
With the installation of a woodchipper any off-cuts are turned into granulate and mixed with the other extracted materials to form a completely self-sufficient heating plant. Minimal emissions from a self-adjusting, self-responding system that automatically adjusts the feed rate of the wood fuel depending on heating demand on the system.
Ranheat systems can come with remote interrogation of the system enabling the rate of use of wood fuel to be adjusted from the operator’s phone. They can also receive text or e-mail alerts for alarms or low fuel alerts giving full control over the system.
T: 01604 750005
E: sales@ranheat.com www.ranheat.com
ROBOTIC SANDING
BY MIRKAMirka® AIROS
Sanding for industry workers can often be associated with health risks due to being exposed to dust and vibrations. Increasingly, the solution to sanding is automation.
Mirka® AIROS is the first smart electric sander for industrial robots. Designed by dedicated surface finishing professionals, this automated industrial random orbital sander is easy to integrate and suits the requirements of different manufacturing industries.
For further information, please contact Customer Services on 01908 866100
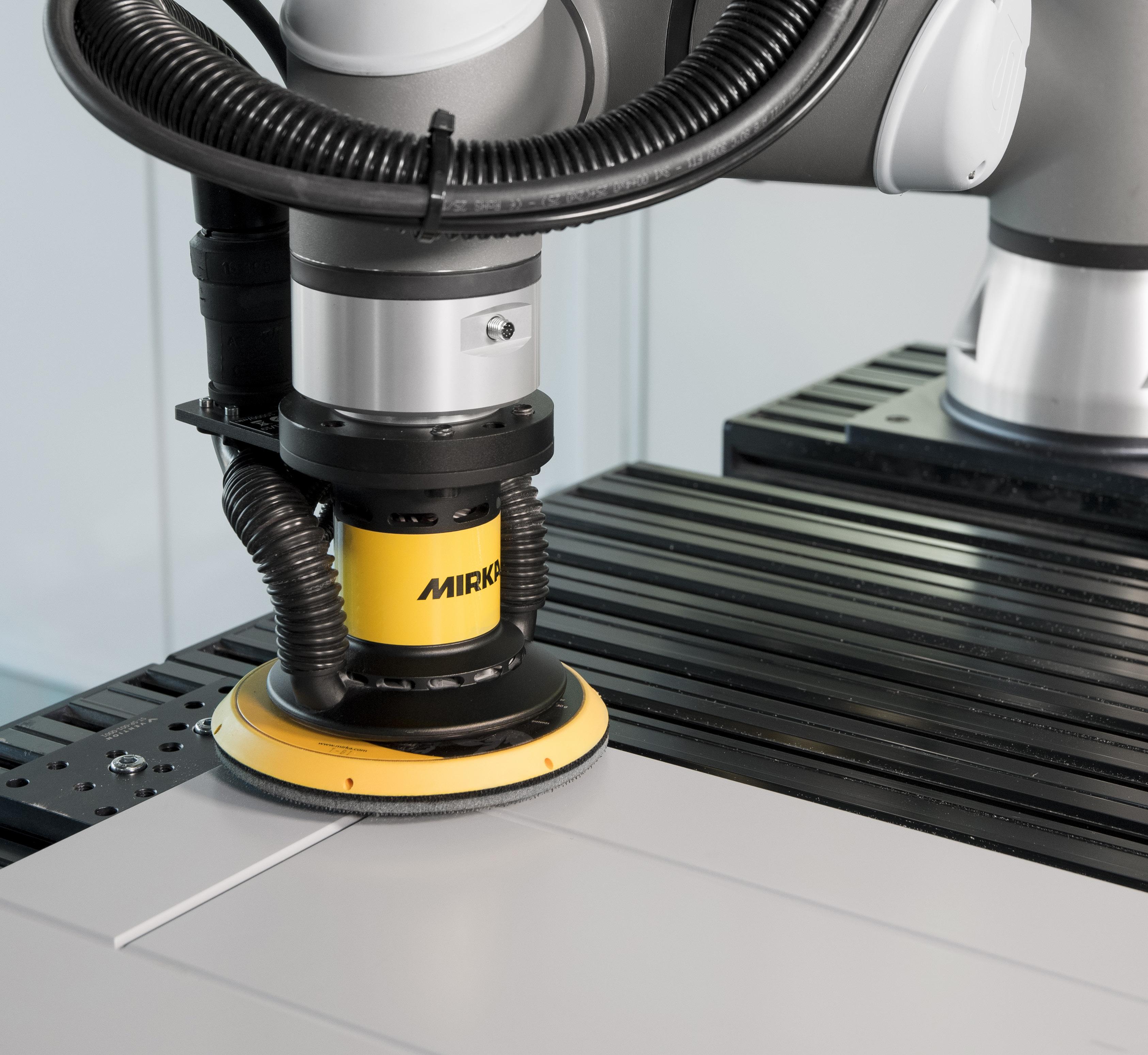
ENERGY FROM WASTE WOOD
Holzbau Rohrmoser relies on UNTHA shredding technology to heat its business premises as well as the adjacent residential building
The Rohrmoser carpentry and timber construction business based in Flachau/Salzburg appreciates the quality of the UNTHA LR700 shredder. The waste wood from the company’s production as well as building sites is processed by the compact shredder into high-grade fuel for a woodchip heating system. The business and the residential building that joins it cover their energy needs for the winter with the material produced in-house.
Wood is a precious resource and a fuel source produced in Austria, making it crisis-proof and renewable. This not only means that value creation stays in the region, but also constitutes a possibility for woodworking and timberprocessing businesses to use their waste wood efficiently – as is the case for Holzbau Rohrmoser in Flachau. “By utilising and shredding the waste wood from our production and building sites as well as from disposable pallets, we are able to dispose of waste wood quickly and use 100% of it as an energy source”, says proprietor and master carpenter Johann Rohrmoser. The business was founded in 1992, employs six people and does general carpentry work, builds wooden houses, car ports, roof structures, balconies and “anything else that comes along”, as Johann Rohrmoser puts it.
LR700: ROBUST, COMPACT, CRUCIAL
Rohrmoser first began to use an LR700 unit from UNTHA shredding technology for the shredding of waste wood around Christmas 2016. Johann Rohrmoser sees the benefits of the unit in the cutting system with a swivelling pusher and the low maintenance requirements. Waste wood from joinery constructions, splinters from circular saw operations and waste wood from the construction sites are all fed into the shredder and are mixed with wood shavings, resulting in a particularly productive heating material. The chips are extracted into the chip silo straight after the shredding process, where they are stored until the winter, when they are fed into the wood chip heating plant via a discharge system.
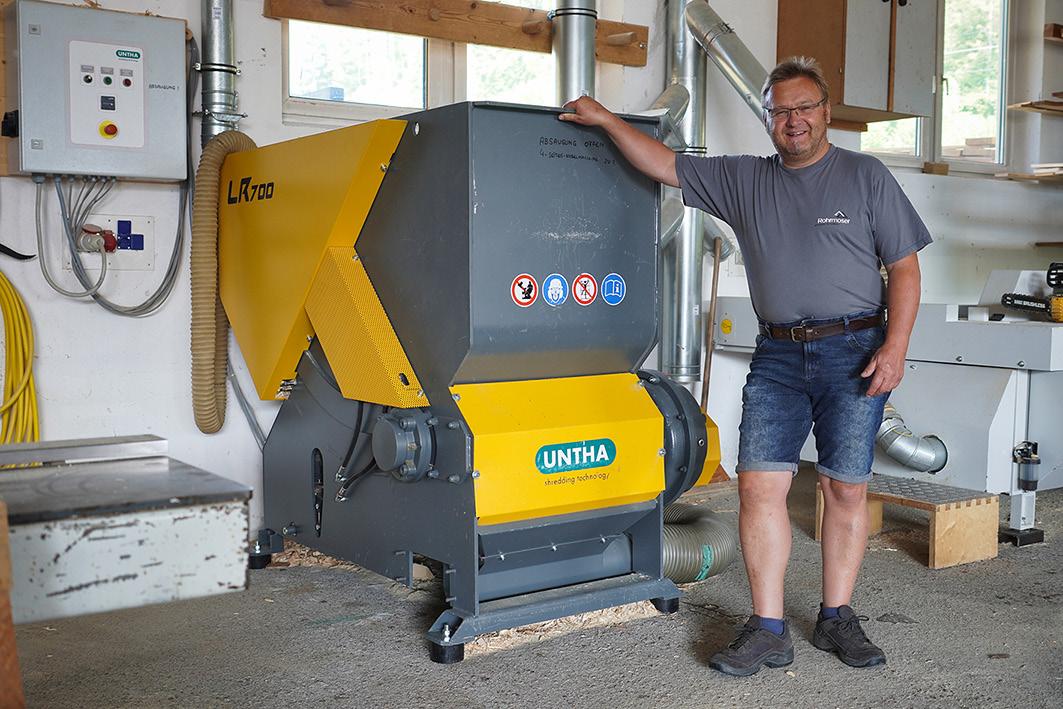
FLEXIBLE LR SERIES
With the LR series, UNTHA offers a family of machines that ensure compact shredding for carpentry workshops, cabinetmakers, joiners, sawmills and timber industry businesses of all sizes. These shredders with tried-andtested single-shaft technology come with rated capacities from 11 to 60 kW and fulfil the needs of smaller as well as larger players. Overall, the LR series stands out for its efficient cutting system, longevity and reliability. All models of the LR series have a high level of efficiency and economy and are maintenance-friendly. For users, this translates into homogeneous wood chips ranging from 12 to 80 mm, at a low cost and with little effort in terms of operation. The final product is suitable for wood-chip heating plants and for briquetting, which offers yet another layer of energy efficiency for users who are able to recycle their own residual wood. Thanks to UNTHA shredding technology, users of the LR series are able to make an important contribution to the sensible use of precious raw materials that nature provides.
UNTHA SHREDDING TECHNOLOGY
Reliable shredding technology that goes back more than 50 years!
“The
chips
Rohrmoser,
us
winter”,
not just for his business, but also for his home that adjoins it. The LR700 shredder is filled twice a day and runs for an hour each time. In the three and a half years since the unit was first put into operation, it has completed approximately 250 operating hours. It is the second UNTHA unit in operation at Rohrmoser, where a smaller, two-shaft shredder provided a valuable service over many years. Johann Rohrmoser is more than happy with the purchase he made in 2016. He sums up the main features of the unit: “It is robust, compact, and crucial to us in our daily workflows”.
UNTHA shredding technology develops and manufactures customised, reliable shredding systems that are used in a wide range of applications, from material recycling to processing of residual and waste wood and the reprocessing of waste to produce alternative fuels. In this way, the company makes an important contribution towards the conservation of resources and the sustainable processing and reduction of waste.
The company was founded in 1970 and is headquartered in Kuchl near Salzburg. UNTHA has more than 250 highly qualified employees and a worldwide sales network that spans 40 countries on all continents, placing it among the world’s leading manufacturers in this growing, futureorientated industry.
SAVE ENERGY REDUCE COSTS
In many manufacturing facilities, extraction fans operate continuously, at full power, throughout the working day.
Even when some machines are not in use, and often during factory breaks, the powerful, energy-consuming fans continue to run at full speed – wasting valuable energy... and money!

With ECOGATE, the extraction system responds in real-time to variations in machine use. When a production machine is switched on, the greenBOX Controller opens a motorised damper to provide extraction for that particular machine.
With ECOGATE technology installed, an extraction fan will consume the minimum power required to provide optimum extraction – reducing electricity bills by 68% on average.
WS WOODMACHINERY
WS Woodmachinery was established in 1985 by founder Walter Scott Snr who was joined by his son Walter Scott Jnr in 1987. Together they established themselves as a knowledgeable and technical machinery dealer in Scotland.
They first worked with two large woodworking machinery manufacturers until making the decision in 2007 to go independent as a complete machinery importer into the UK. Their machine portfolio is very much based on independent specialist machinery manufacturers who only manufacture and invest in one main product which allows them and W.S. to bring the best technology and service to the market year after year.
W.S. Woodmachinery’s main products include Cosmec CNC Technology, Cehisa Industrial Edge Banders, Casadei Heavy Duty Beam Saws, Harwi Saw Solutions and Martin Quality Panel Saws.
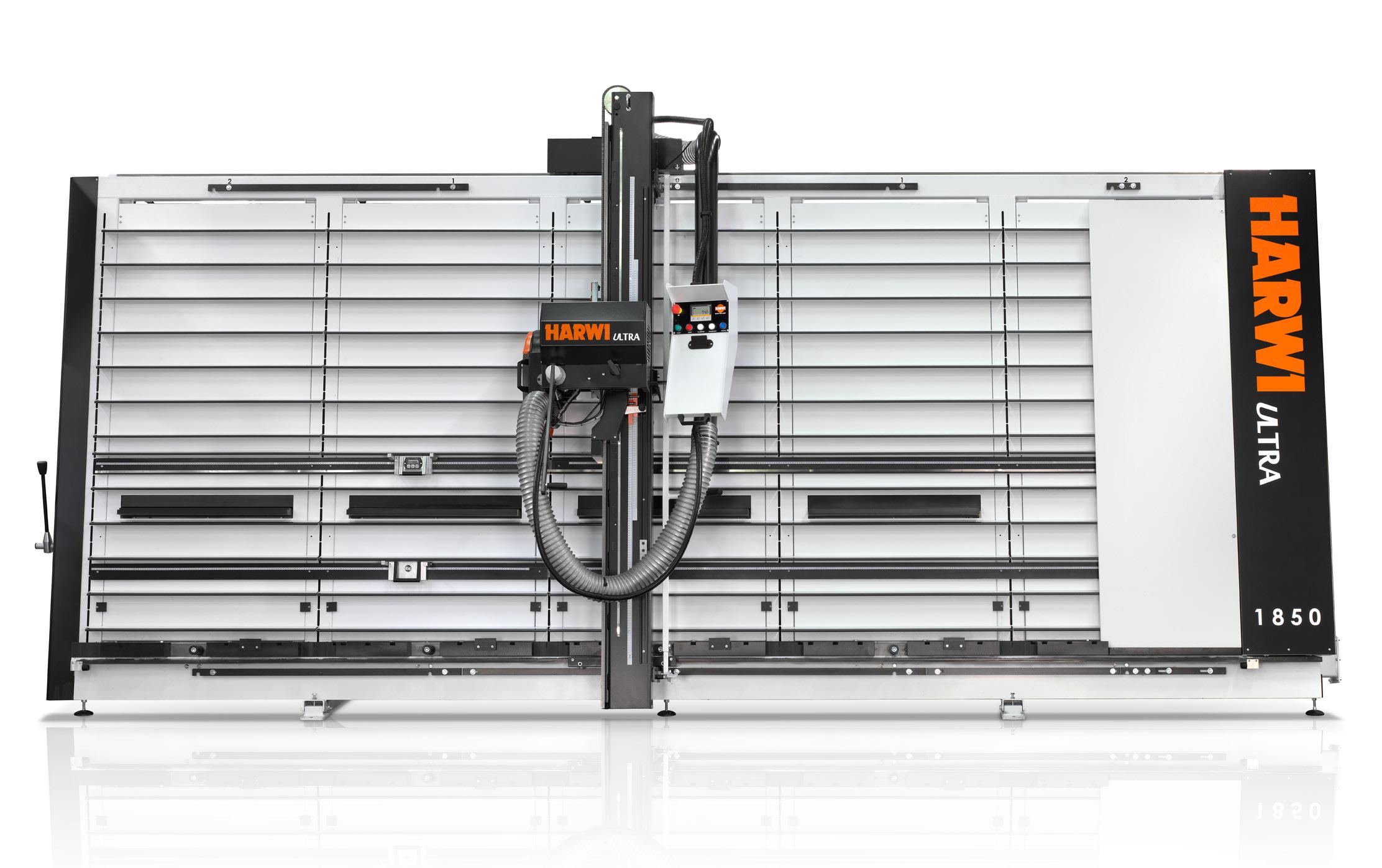
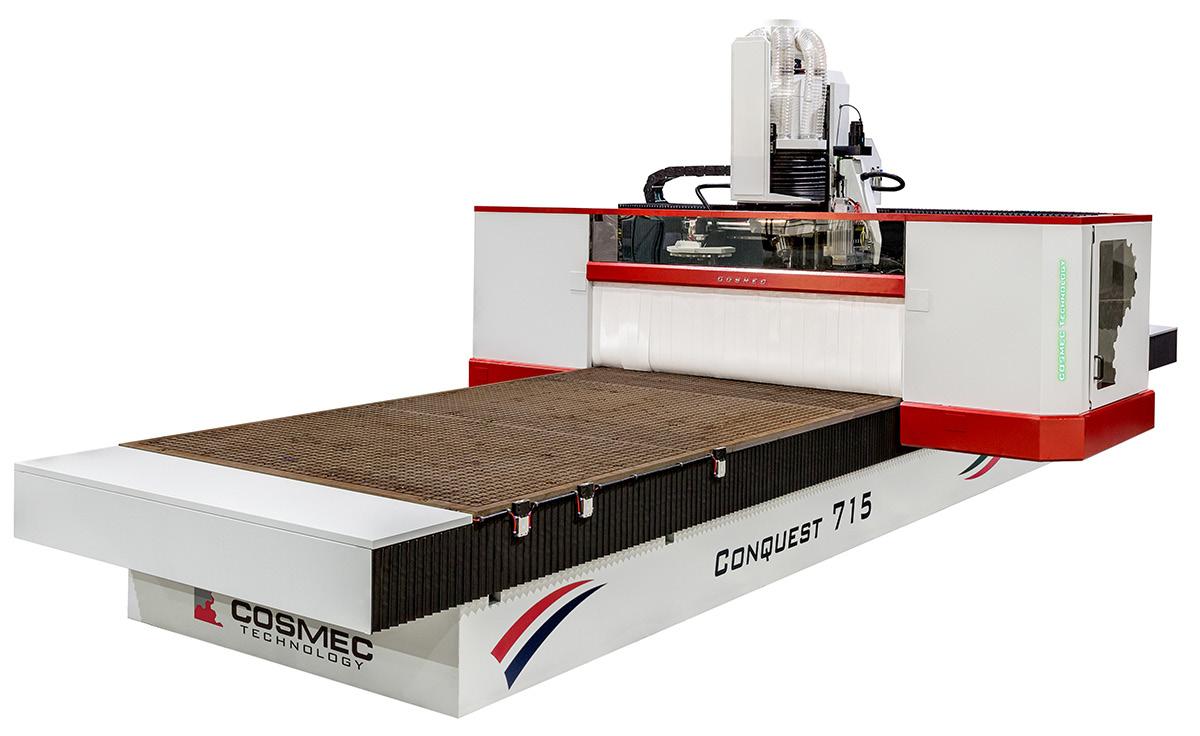
They also supply a full range of auxiliary machinery which allows them to offer complete installations including Dust Extraction and Air Compressor systems. Their strength lies in the fact that they are a “ONE STOP SHOP” supplier who can offer complete packages to their customers, combined with low cost finance to make the process simple. The company continues to grow with 12 people, who with their combined knowledge and experience gained within the woodworking industry are able to assist their growing customer base across the whole of the UK, both with their technical product knowledge and their general industry experience.
By sourcing the best quality machinery across Europe at competitive prices they are able to offer customers very competitive deals as well as the very latest in machine technology. Whilst their main showroom is based in Coatbridge, Scotland they have full UK coverage with Technical Managers based both in Coventry and North of England.
Aside from their large portfolio of new machinery, they also supply used machinery from various manufacturers which is ideal for new start companies where budgets are sometimes challenging.
W.S.Woodmachinery also offer these additional services: Machinery Service, Telephone Assistance, PPM Schedules, Braking System Installation, Bespoke Guarding, Electrical Interlocks and Machine Training.
Other complementary machinery supplied includes, Martin Classical high end machinery, ACM Narrow Bandsaws, Houfek Wide Belt Sanders, Salvamac cross cut solutions, Italpresse Heated Presses and complete lines, Alberti Drilling Solutions, Maggi Manual and CNC Drilling solutions, Rojek Quality Standard Classical machines and our Environmental Range of equipment from WWT Wood Burning Heaters & Systems, CO.MA.FER Briquetting Systems and Untha Industrial Shredding machines.
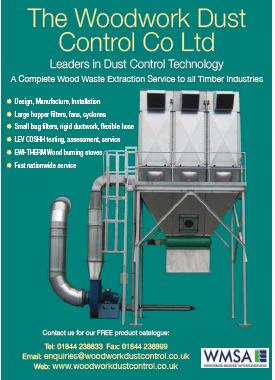

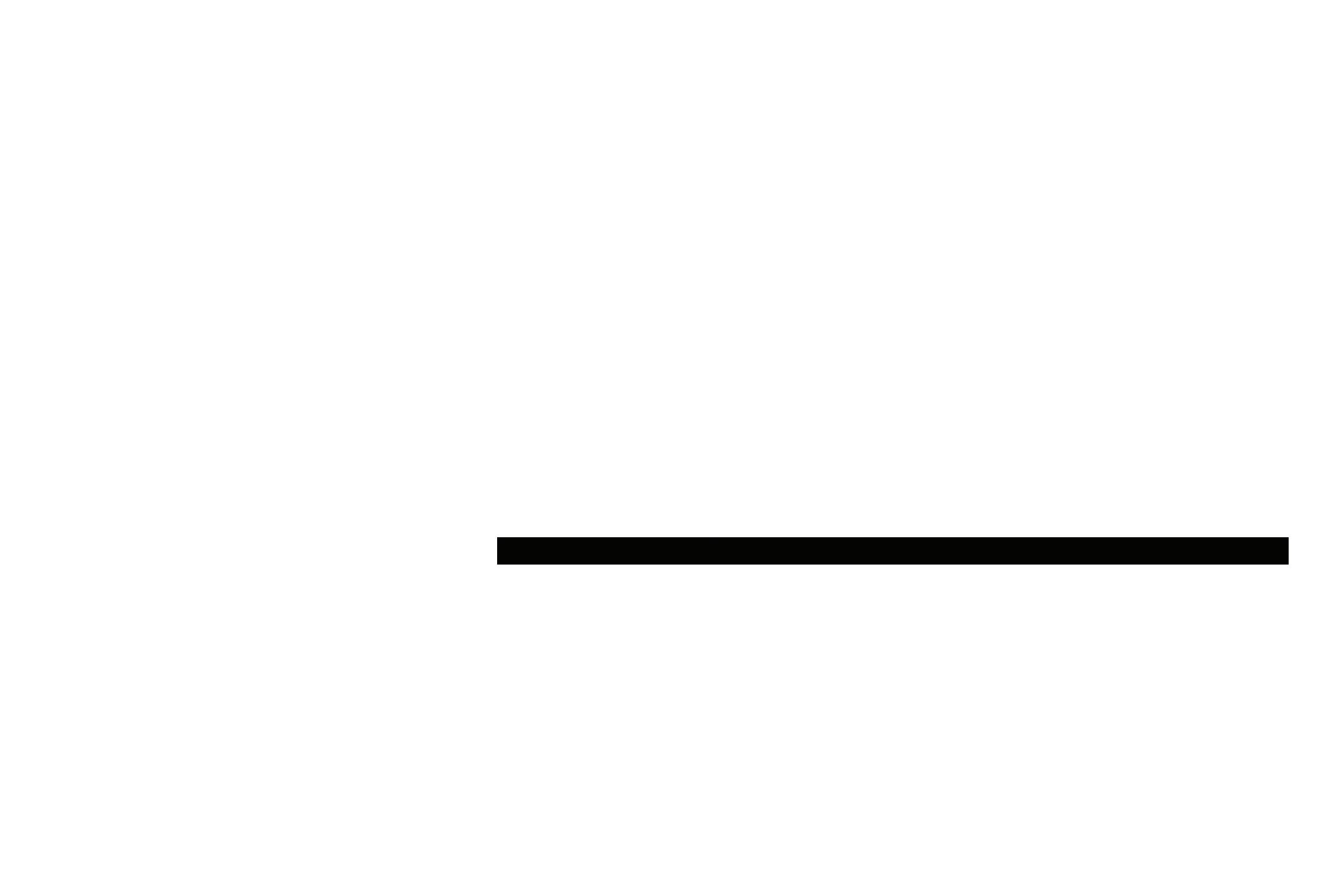
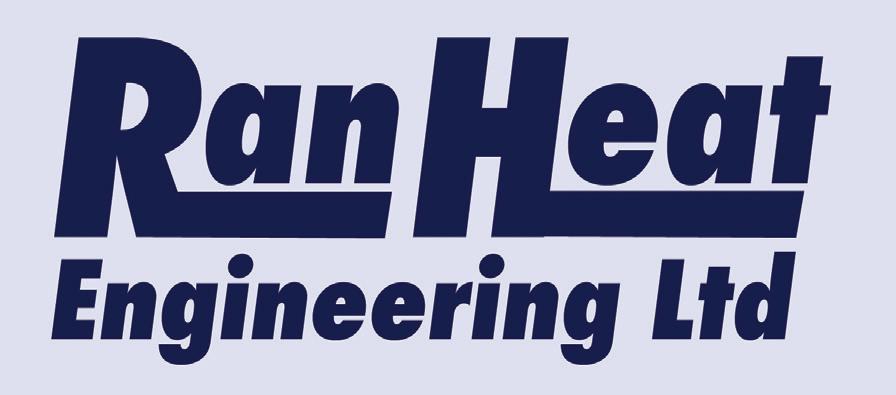
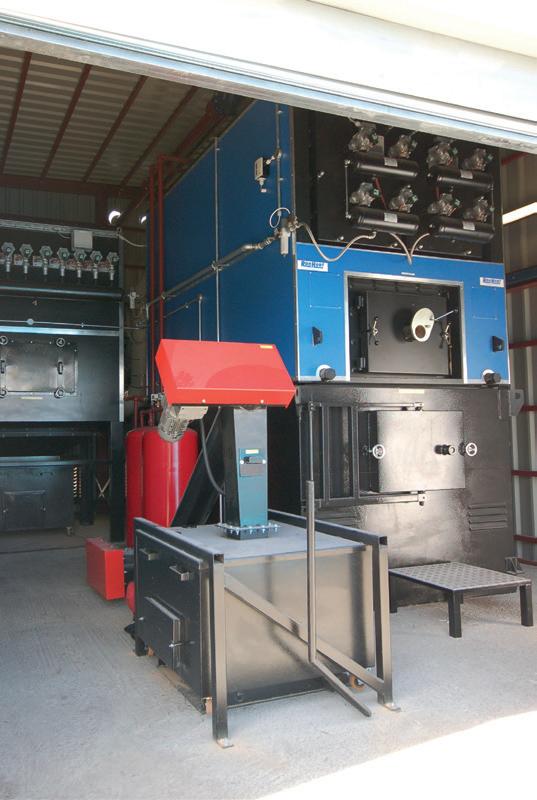
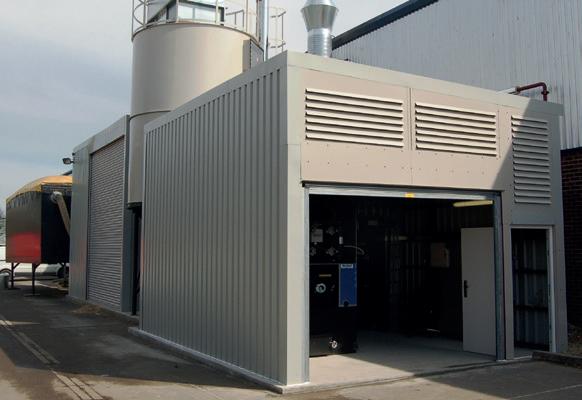
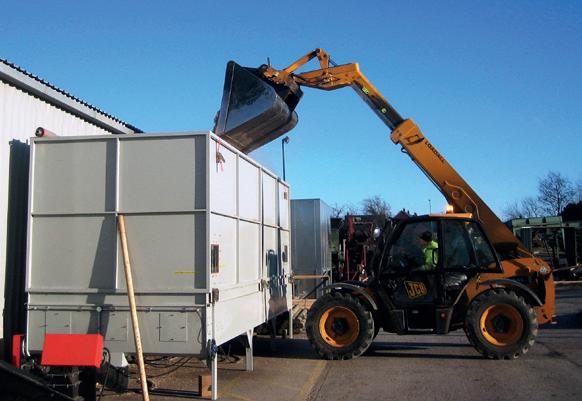
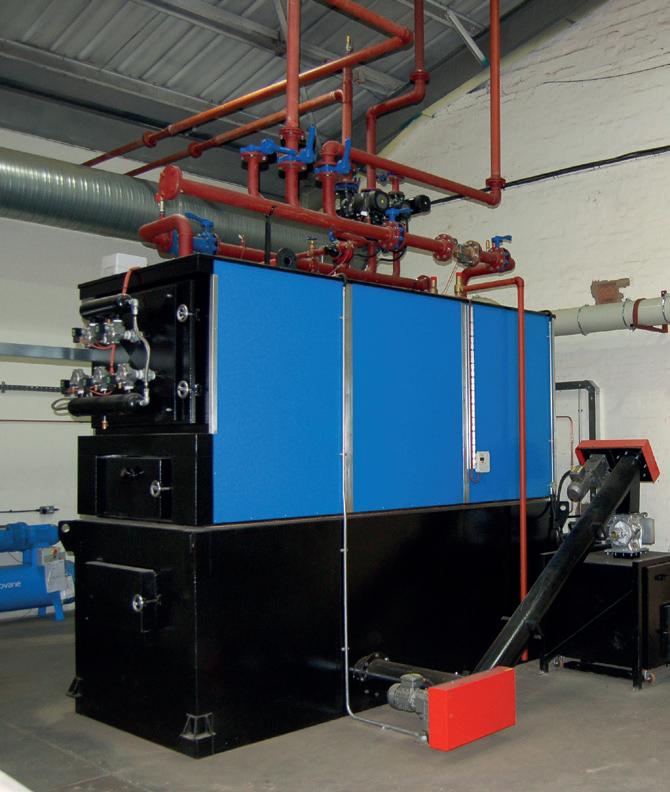
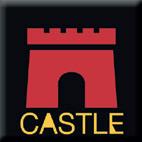

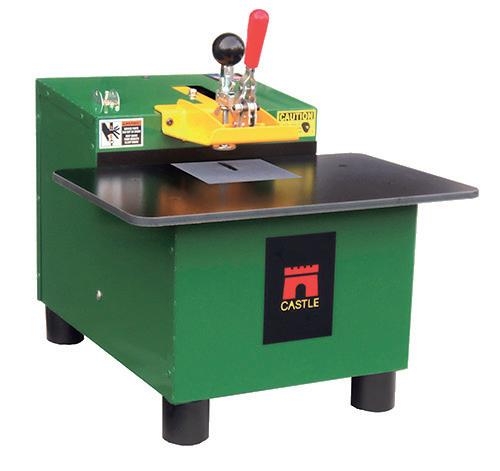
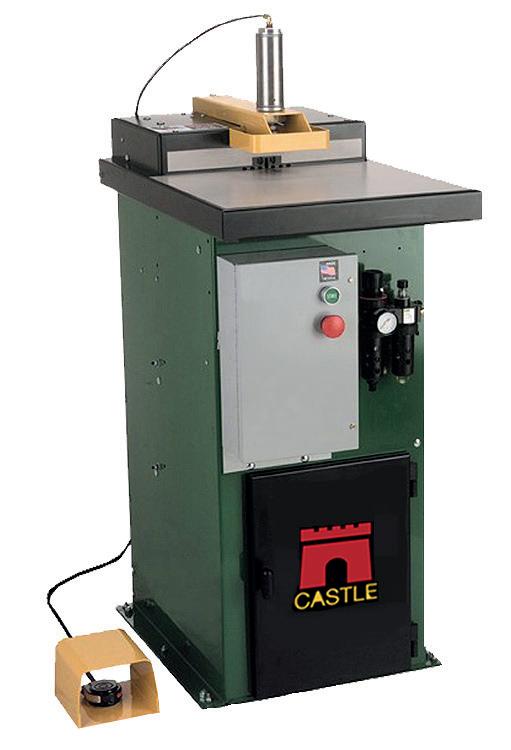
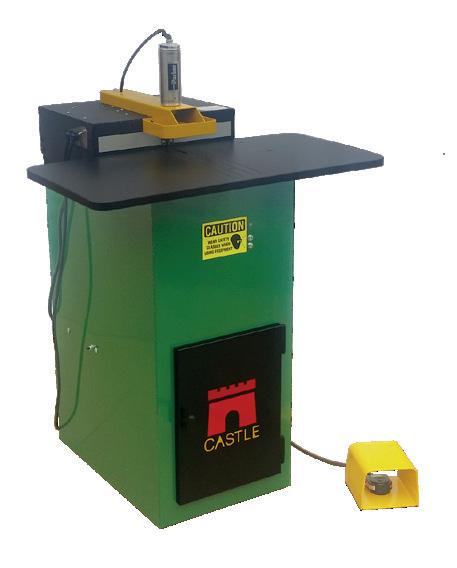
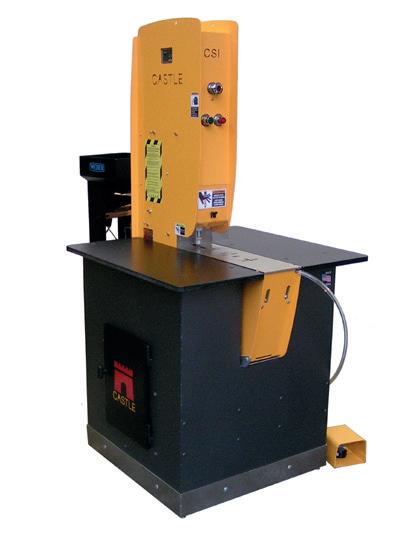
INDUSTRY
S mart WOP FROM HOMAG : THE SMART WAY TO DESIGN FURNITURE
The HOMAG Group, the world’s leading provider of integrated production solutions for the woodworking industry, has launched a new design software package. Named SmartWOP, the software has been specifically created to provide furniture manufacturers with a simple to use design tool that is intuitive and flexible.
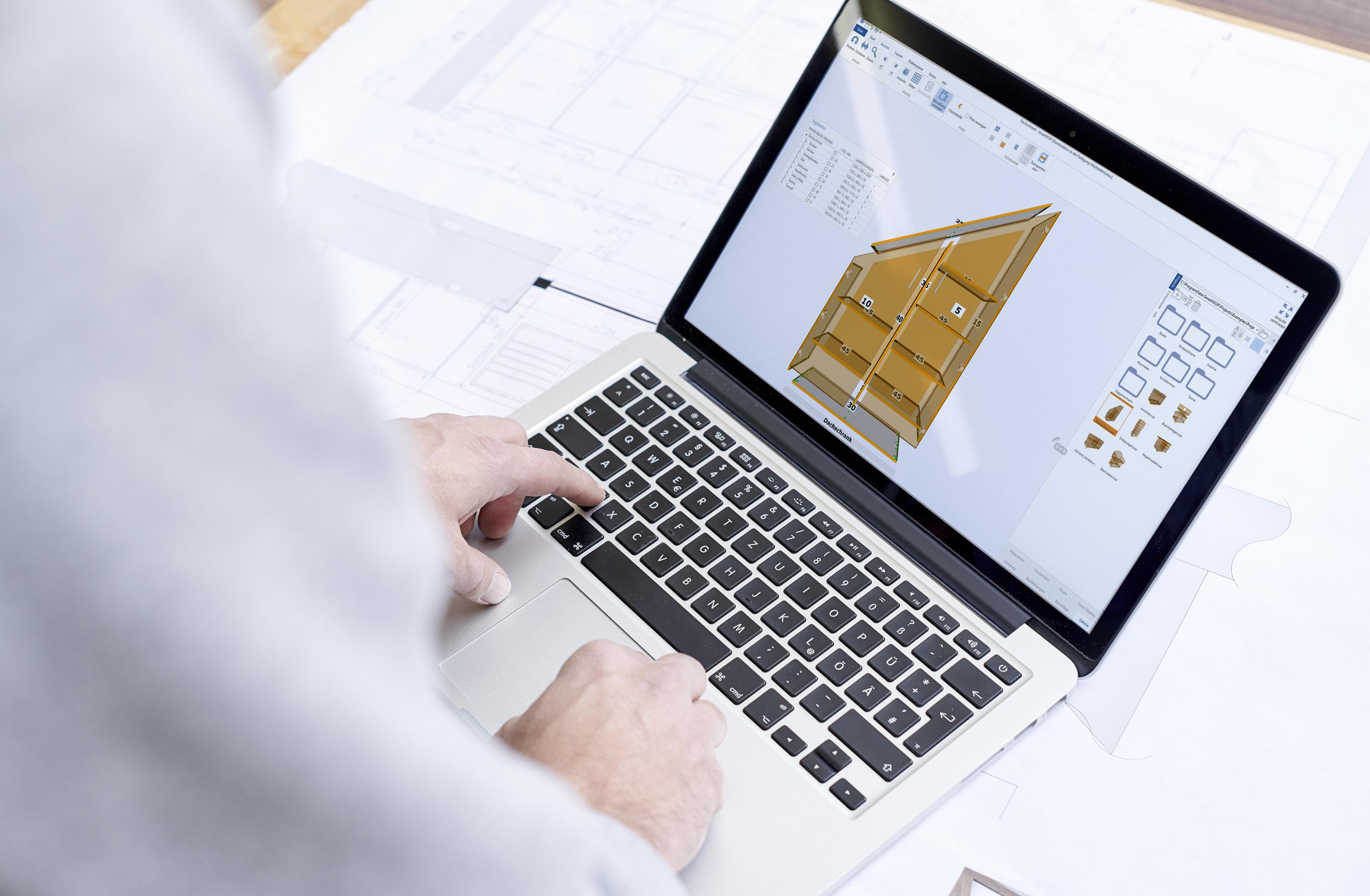
SmartWOP is powerful CAD/CAM system for designing individual furniture quickly and spontaneously using the drag and drop method. Ideal for kitchen, bedroom, bathroom and office furniture manufacturers, its intuitive nature requires no previous CAD knowledge to operate.
FROM INDIVIDUAL ITEMS TO COMPLETE ROOMS
Using the room planning feature, users can design both individual pieces of furniture and entire rooms. Once the furniture has been designed, the operative can create all essential data such as CNC programs, parts lists for panel cutting, fixture lists and technical drawings at the touch of a button.
This information can be passed directly to HOMAG digital assistants and apps, including production Manager. To ensure everything works as it should without the need to make prototypes, there are numerous simulation options. These allow the user to check such things as the opening of doors and drawers or possible collisions with neighbouring components.
The software enables the easy allocation of fixtures and connectors thanks to a large library featuring all the common parts available from established manufacturers.
INTEGRATION WITH WOODWOP
The integrated interaction between woodWOP and SmartWOP permits operators to select a single part of furniture in SmartWOP and open it directly in woodWOP. Processing steps can then be added and saved in woodWOP. For clarity, all changes are transferred directly to SmartWOP and visualised there.
Furniture previously designed is stored in a separate library and can be called up or changed at any time. Original woodWOP components can also be added to the furniture very quickly.
VERSATILE AND EASY TO USE
Whether designing standard regular shaped furniture or more complex items to fit sloping ceilings or corners, SmartWOP makes it a simple task. The software also offers various display options such as exploded views of furniture items or finished rooms illustrating how all the pieces of furniture will look.
HOMAG SOFTWARE – THE INDUSTRY STANDARD
Commenting on HOMAG’s new SmartWOP design software, Simon Brooks, HOMAG UK’s managing director said: “Over the years, many of the HOMAG Group’s software solutions have become the industry standard and this simple to use design software is destined to follow in their footsteps.
For a demonstration or more information on the new SmartWOP or other HOMAG software solutions, please contact Adele Hunt at HOMAG UK on 01332 856424.
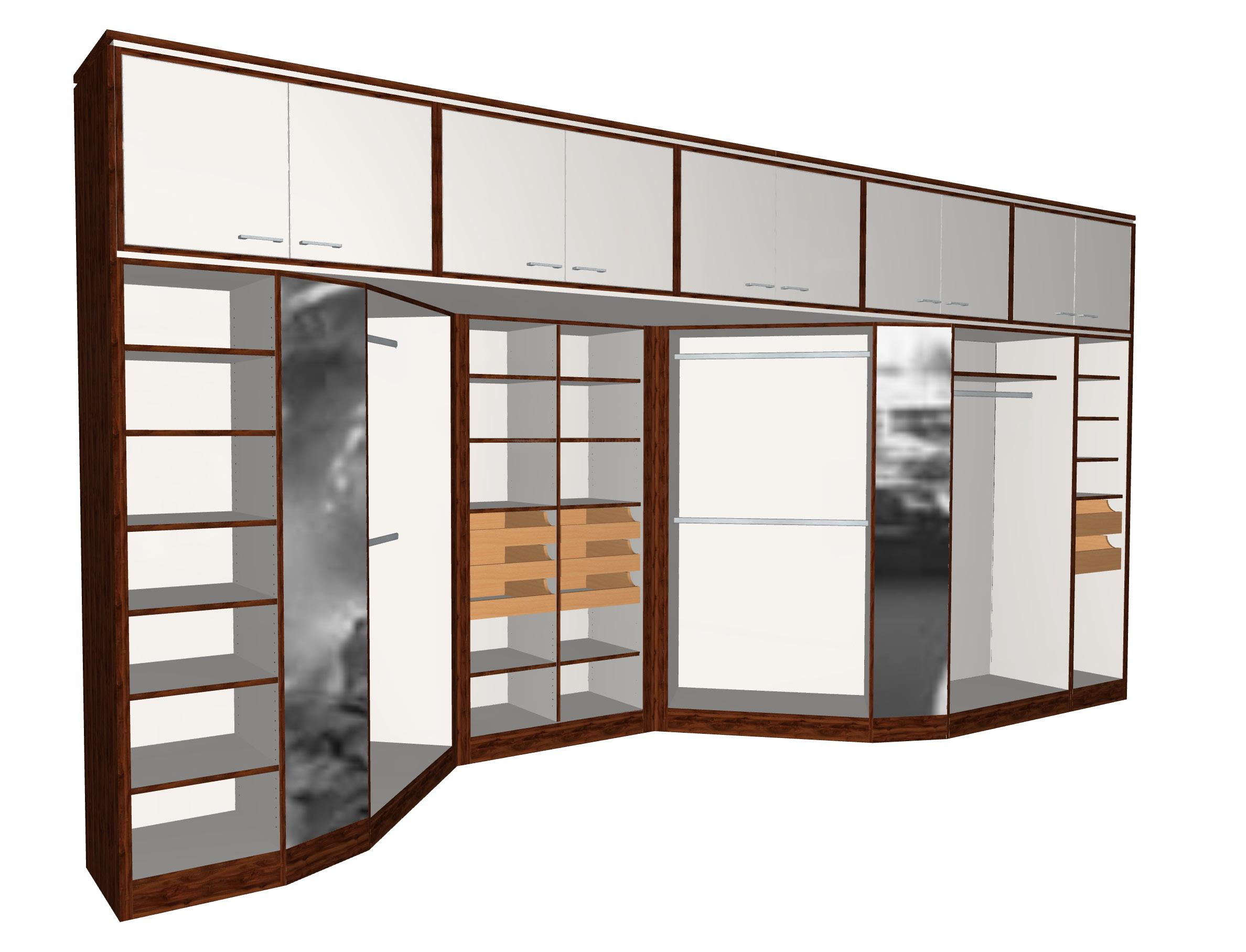
Testing LEV efficiency at source
LEV… EXTRACTLY HOW IT SHOULD BE
Dust… it’s a dirty subject but, if not controlled effectively, wood dust has the potential to cause serious health problems for workers exposed to the hazard, and it’s something we all have a responsibility to deal with in this industry.

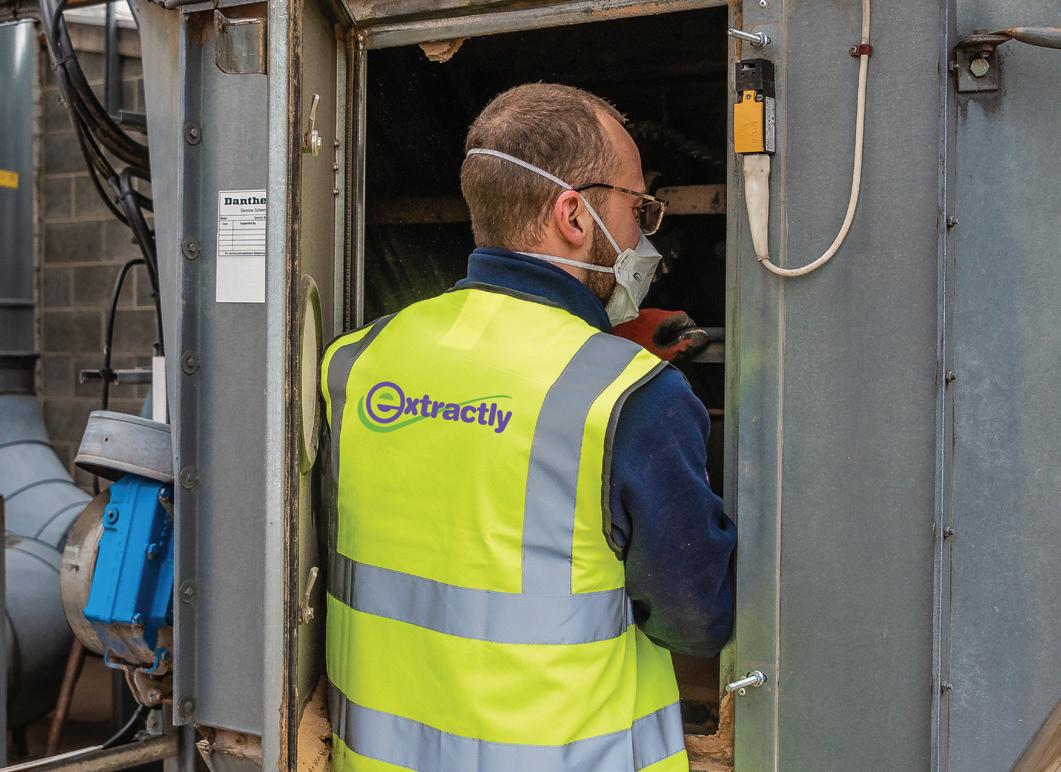
The specific health hazards associated with wood dust are well-documented and regularly reported through the pages of our industry’s media, and the Control of Substances Hazardous to Health (COSHH) Regulations require employers to ensure that the exposure of employees to substances that are hazardous to health is either prevented or, where this is not reasonably practicable, adequately controlled. However, despite all the publicity and the seriousness of potential problems, the Health and Safety Executive continue to report a high incidence of dust exposure regulations being breached by woodworking businesses.
Regulations stipulate Workplace Exposure Limits (WEL) for wood dust based on the average amount of airborne dust present during a nominal 8-hour shift. Since 2020, the maximum WEL for softwood dust has been set at 5 milligrams per cubic metre and, where hardwood dust is prevalent, or a mixture of both softwood and hardwood dust exists, the current limit is 3 milligrams per cubic metre; expected to be reduced to 2 milligrams in 2023.
Since wood dust acts as a respiratory sensitiser, it’s essential that employees’ exposure to dust is not just maintained below the relevant WEL, but that any exposure to wood dust is minimised as far as is reasonably practicable – a respiratory sensitiser is a substance which, when inhaled, can trigger an irreversible allergic reaction in the respiratory system and, once such a reaction has occurred, even the
slightest repeat exposure to the substance may produce symptoms.
In a woodworking factory it’s the fine particles of wood dust that are most likely to cause lung damage but, when fine wood dust is airborne, it’s practically invisible. Just to put the exposure limits into perspective, one teaspoon (5ml) of dry sawdust typically weighs in at around 1 gram, or 1000 milligrams; which means that 5 milligrams of sawdust per cubic metre equates to around one fiftieth of a teaspoon (0.1ml). When measured in those terms, it’s not hard to appreciate why such a small amount of dust is difficult to see when it’s floating around in a million cubic centimetres of air, and just how effective dust extraction needs to be to control the hazard.
In order to capture the harmful dust at source, and remove it before it can spread, adequate dust extraction, or Local Exhaust Ventilation (LEV), must be provided wherever woodworking machines are in operation and, crucially, it must be maintained in tip-top condition. There’s a legal requirement for LEV systems to be examined and tested, by a competent person, at least every 14 months and, especially for complex systems, more frequent checks are strongly recommended. A reputable dust extraction provider will advise on LEV Testing requirements for an individual system based on how complicated the system is, how likely it is to fail, and the consequences if it does.
Extractly Ltd have a highly-dedicated and experienced in-house service team to support its customers in the woodworking industry. The team’s knowledge and skills have been honed and developed through years of experience with countless LEV system configurations and extraction equipment from a myriad of manufacturers. Whether your dust extraction was installed by Extractly or another provider, the service delivered will be customised to meet your specific needs; ensuring maximum uptime and optimum performance from your system, and safeguarding the health of your workforce.
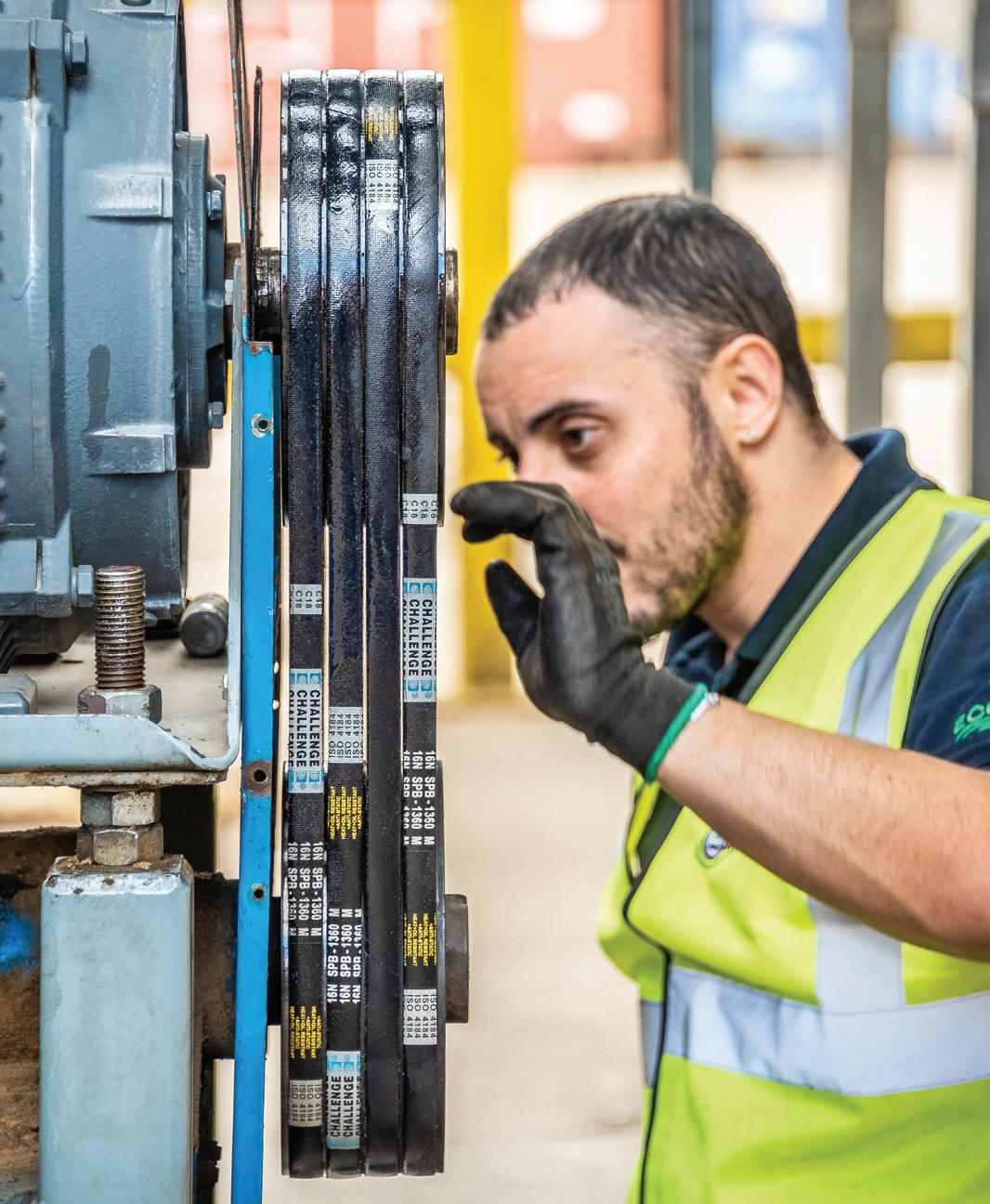
Extractly have the capability to meet all your LEV requirements: whether it’s for regular testing and maintenance, updating an existing system to provide additional extraction capacity for new machine installations, to design, install and commission a new and efficient dust extraction system, or simply to reconfigure ductwork to accommodate a machine replacement or relocation.

In addition, as the sole UK Distributor of Ecogate® energysaving extraction equipment, Extractly is uniquely-placed to provide a one-stop-shop solution, covering all your dust extraction requirements. Ecogate® technology is highly effective when it comes to maintaining optimum airflow in an extraction system and, with fan speed automatically and continuously adjusted to exactly match extraction demand throughout the working day, it is guaranteed to significantly reduce your system’s power consumption and running costs.
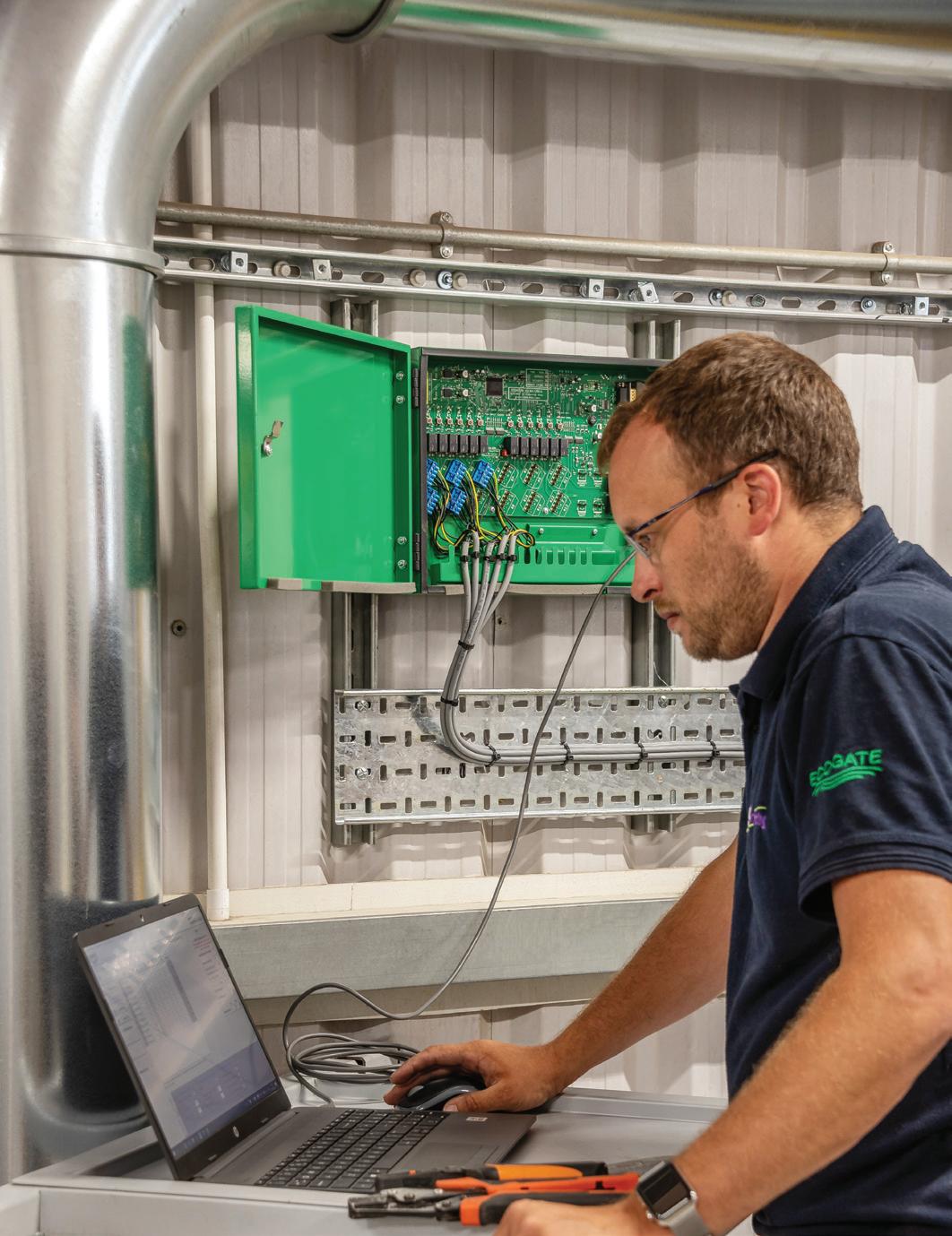
FEATURE
A FAMILY COMPANY LEADING THE WAY
Established 16 years ago Joinerysoft, a family run business, has been involved in the industry for nearly 40 years. It provides innovative and industry leading software for joinery companies in the UK and across the world. Now with over 1100 customers it continues to expand, committed to development, further enhancing its products and services.
With ever changing economic climates, market trends and industry practises Joinerysoft’s solutions have changed a lot from its single product, JMS, back when it launched in 2006. This includes the introduction of automatically calculated u-Values, JMS2D, JMS 3D Pro, and JMS Cloud just to name a few of the most significant changes.
JMS 2D is the product aimed at the entire bespoke joinery market - whether you are a one man band or you have 10 joiners or more, this is the product designed specifically for bespoke joinery. Including 6 modules; Windows, Sliding Sash, Doors, Screens, Stairs and Bill of Materials, it gives you everything you need to successfully quote and manufacture, right through to delivery. Our software saves you time, makes you more professional, reduces waste and makes sure each and every job is profitable.
“As soon as I saw a demonstration I could see how fantastic JMS was going to be. The setting out, diagrams, ease of use, the hours that you save by pulling up the saved details; JMS solves all those problems. It’s good value for what it does.”
James Selby, James Selby Joinery
The newest software solution is JMS Cloud, a fully online based system that provides a wealth of tools for your company available 24/7, 365 days a year. This integrates
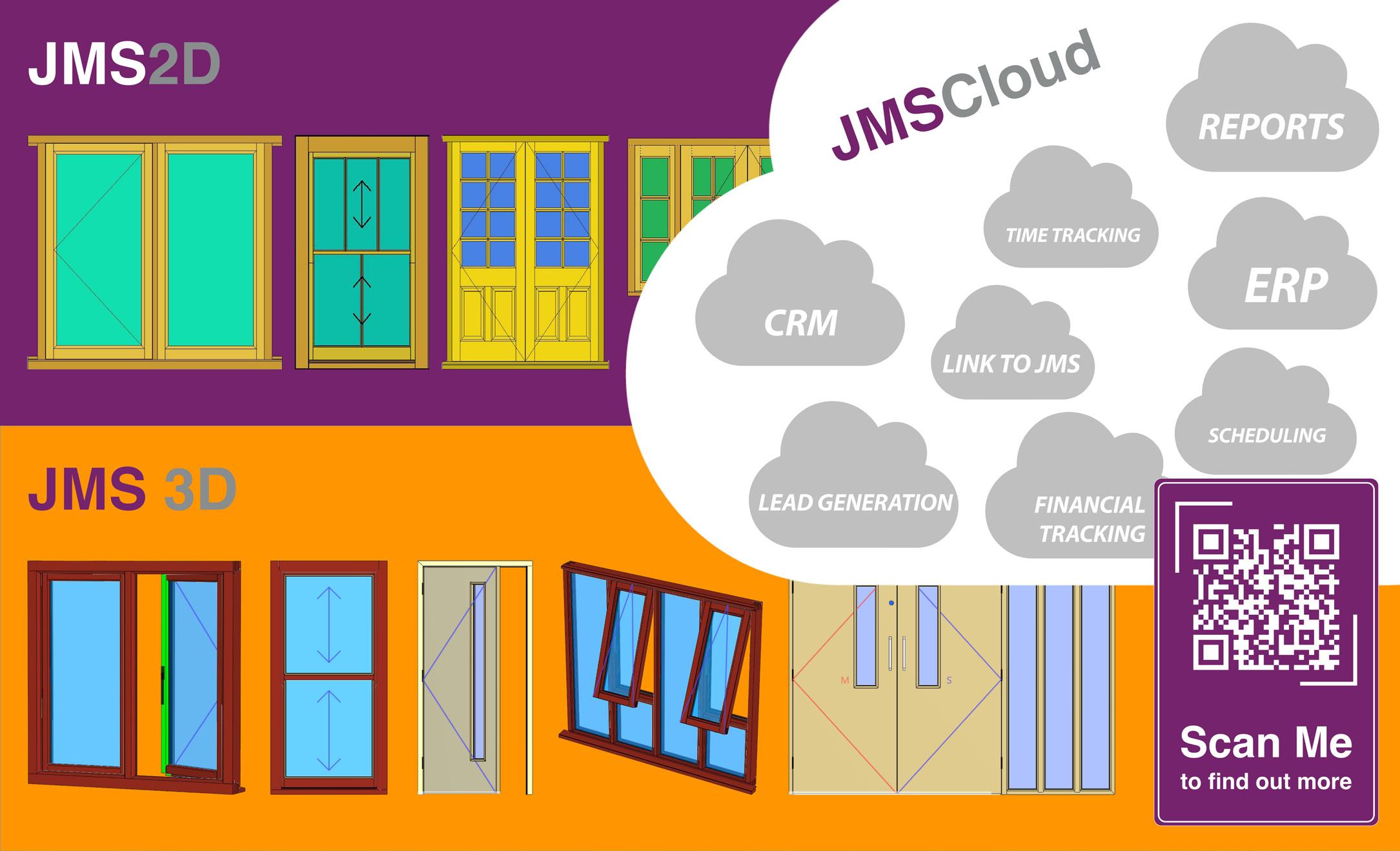
with both JMS2D and JMS 3D Pro syncing seamlessly to these desktop solutions and extending their features. JMS Cloud gives you tools such as customer relationship management, file storage, lead generation, scheduling, time tracking, real time reporting and much more.
JMS 3D Pro is Joinerysoft’s largest and most powerful development yet. 3D Pro is designed for larger joinery manufacturers and/or commercial door manufacturers. It mimics your own tooling, joints and profiles meaning you can literally make any type of joinery, and visually see cross sections and cut outs using 3D modelling. All of this incredible 3D detail uses Joinerysoft’s custom built solid modelling engine - even showing things like fixtures, fittings, ironmongery and signage.
JMS 3D Pro includes specific development for commercial door manufacturers, whether that’s a fire door, x-ray door, acoustic door, hygienic door, post wrapped, multiple cores or any material – JMS 3D Pro can handle it. Including features such as Excel import and export, the level of detail and accuracy, even in pricing, is unparalleled. JMS 3D Pro comes with a subscription to JMS Cloud free of charge, so you get all of the amazing tools and features of JMS Cloud as standard!
Joinerysoft has over the years linked their software solutions to most of the big machine manufacturers, whether its a 5 axis CNC or a cross cut, customers can simply send jobs or items straight to their machine, making the manufacturing process as seamless and efficient as possible.
“I’ve used JMS for a number of years and like their quoting and production software; other software can’t offer the continuity and support across my business that Joinerysoft can. Joinerysoft has fallen over backwards to meet my requirements and worked closely with me to create my 5 axis link. I’ve been impressed with their professionalism and commitment to getting the link working as quickly as possible. It’s early days in configuration but they have worked tirelessly to ensure minimal disruption to my business and have certainly given me confidence in their ability.”
James Tanner, James Tanner Joinery“I don’t want joinery manufacturers to be constrained by their software and only have limited connectivity to a select number of machines. Our aim is to ensure that our software can link to any machine in the future and enable manufacturers to grow their business at the right time for them with ease.”
Alan Turner, Joinerysoft Ltd“It’s made us a more multitasking office. Instead of one of us doing the quoting, another doing the drawings and a third doing the cutting lists, now all of us can do every job. So I can now do the quotes, order acknowledgments, cutting lists, and client drawings - which was impossible before JMS 3D Pro”
Louise Sheppard, JCK
Joinery/Unity Group
“All our jobs are processed through JMS now. With consistent and clear pricing, customers have been impressed with our quotes and our quick response helps us to win work”
Karen Kebby, Churchview JoineryPROFILE
THINK CNC … THINK MASTERWOOD
OUR HISTORY:
Masterwood Spa is one of the leading suppliers dedicated to CNC solutions, supplying machines to over 100 countries globally. Masterwood has been producing woodworking machinery for over 60 years, initially under the names of the three Italian families; Muti, Zangheri, and Boschetti. The company has now become part of the KDT Machinery Group, one of the largest manufacturers of woodworking machines in the world.
Our range of CNC routers, CNC drilling machines, and oscillating chisel mortises are all built in Italy, using proven designs and leading suppliers for components such as; HSD, Beckhoff, Yaskawa, THK, Schmalz, and Becker. These are now joined by edgebanders, high speed drilling machines, and beam saws, in partnership with KDT.
POD & RAIL CNC’S:
Starting with an entry level Project 250, moving through the larger 300 and 400 Project series, to the top end Project 500 range, these CNC machines can be supplied in all formats for solid timbers, panels, composites, and other materials. This includes long or short beds, cantilever or gantry designs, manual or automatic beds, in 3, 4 or 5 axis formats.
FLAT BED CNC’S:
To compliment the pod and rail range, Masterwood has increased the choice of matrix beds for nesting and special works. These range from the entry 2500mm x 1250mm bed, through a large range of sheet sizes up to beds of 7500mm in length.
These machines are built with a solid frame bed, the gantries driven on both sides of the matrix bed for added accuracy and long-lasting reliability.
The flat bed range can have infeed and outfeed systems to automate the production, allowing full sheets to be loaded, fully machined, finished panels pushed out, and the bed cleaned, all before the next sheet is loaded. On top of this, a manual or fully automatic arm can be added, for sticking labels on to the sheets prior to, or after, machining.
SPECIAL CNC’S AND PRODUCTION LINES:
To add to the main CNC range, Masterwood produces dedicated machines like the 4WIN (windows), Project Door (full size doors), DoorLine (door locks and hinges), Teknomat (window and frame components). These machines can be manually fed, or in most cases, supplied with a mixture of automatic loading and unloading equipment, including Robots. Masterwood can also offer multiple layout options for complete production lines for drilling and routering.
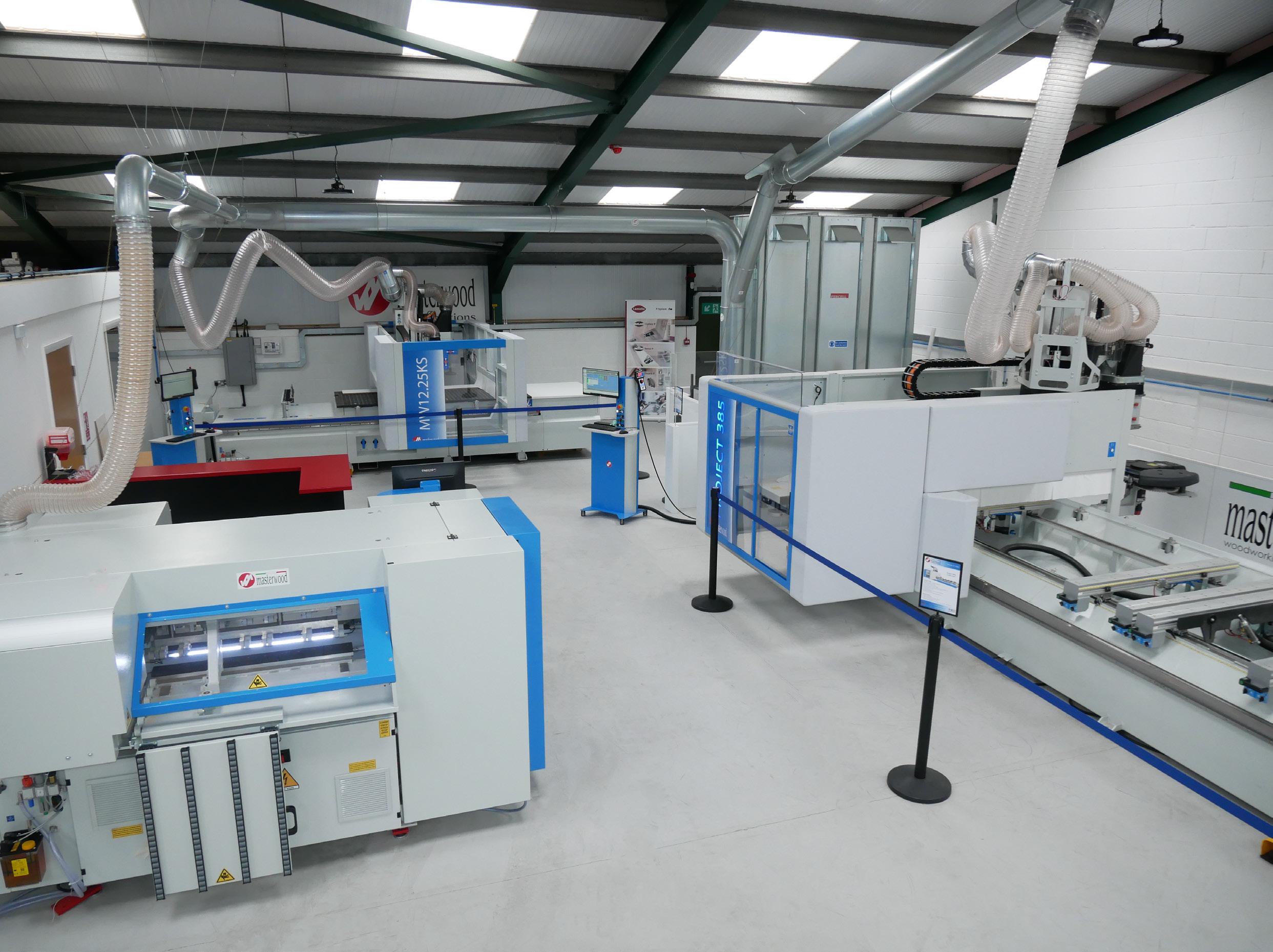
DEDICATED SOFTWARE:
Developments and improvements to the CNC machines are one thing, but the biggest innovations have been with software. As PC’s have become more powerful, the software has too. This allows customers to produce programmes that consist of thousands of lines of code in just minutespermitting carvings and intricate work to be produced on the very basic 3 axis machines, often dismissing the need to go to more expensive 5 axis machines and software.
Masterwood has always produced software with their own companies, but, to move to a higher level, we now work under contract with some of the leading software houses; meaning that machines and software are always fully compatible.
All our machines are supplied with the tried and tested MasterWorks Cad/Cam; an easy to use but powerful package, for most CNC work.

In addition, there are dedicated packages to cover Staircases, Windows, Door Sets (timber frame & solid core), Traditional Box Windows, Cabinets, Furniture, Louvres, and the latest 3D software for 3, 4 and 5 axis work. Any of the packages can be added to a customer’s machine at any time, giving them the ability to change direction or production methods if required.
All the Masterwood software packages come with full on-site installation and training to meet the customer’s manufacturing needs.
SUPPORT:
Masterwood doesn’t just sell and supply machines, we also support and help our customers in the next stage; from our point of view - the most important.
For first time buyers CNC is likely to be the biggest investment their company makes, so it’s important that they see the results on their production as soon as possible, and feel comfortable with the direction they have taken.
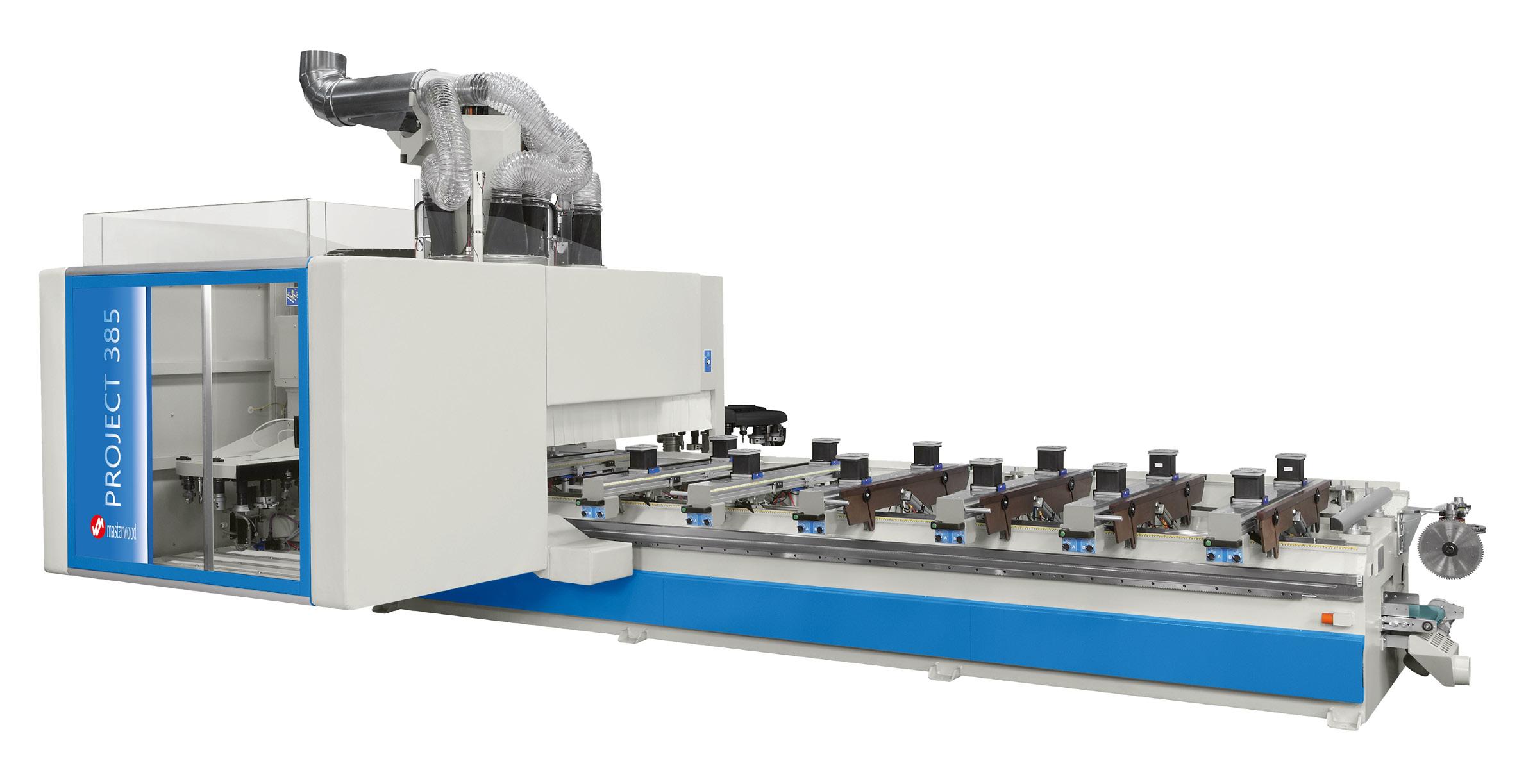
Masterwood GB has a team of experienced technicians in the UK and Ireland; they cover the installation and training on new and old CNC machines and software, support & back up, servicing, repairs, and breakdowns, plus upgrading old machines to be more compatible with the new machines when installed. We also have the expertise of our Italian company staff to help with the more specialised jobs when required.
www.masterwood.com
CASE STUDY
HERMAN MILLER EXTENDS HOMAG RELATIONSHIP WITH NEW CENTATEQ E-310 EDGE BANDER
Founded in 1905 in Michigan, USA, Herman Miller is a design led office and home furniture manufacturer. The company’s purpose reflects the desire of all its brands to leverage the power of design to improve people’s lives – its mission is to pursue design for the good of humankind. In line with this, the UK division recently invested in a HOMAG CENTATEQ E-310 CNC edge bander with a powerEdge Pro Duo gluing unit.
“The ethos of Herman Miller demands that every product we manufacture has to be premium quality, and to achieve that, we have to invest in the best machinery available,” explains the UK company’s Head of Engineering, Martin Waller.
He continues, “Here in the UK we have been investing in HOMAG product for over 25 years and we now have six HOMAG models on our plant list.
“Our latest asset is the CENTATEQ E-310 CNC edge bander with a Pro Duo gluing unit. There were two key reasons we wanted this machine: the first was to replace an ageing CNC from another manufacturer and the second was to provide us with the flexibility to offer real wood edge finishes in addition to our standard edged products.”
ZERO JOINT EDGES WITH HOMAG’S HOT AIR SYSTEM
“Our sales team was seeing an increasing demand for real wood premium edge finishing and our old process to achieve this was very rudimentary. It was labour intensive and had a high cycle time, making it very inefficient.
“The CENTATEQ E-310 CNC with the Pro Duo unit offers us the versatility of being able to produce real wood edged products in a one step process. At the same time, the same Pro Duo unit has a hot air facility giving us the ability to costeffectively apply our standard edging as well.
“For us, the hot air option on the powerEdge Pro Duo gluing unit offers a big advantage; it achieves a zero joint finish but with significantly lower running costs than our larger, high volume laser edging machines. This means we get the same high quality end product but with a much lower capital cost.
“Additionally, this latest generation of head has a number of technical advances which produce a more accurate application of the edge tape, especially when it comes to butt joint features.”
TRUST IN HOMAG SOLUTIONS
“Although we are a single manufacturing site in the UK, globally as part of the Herman Miller group, we have over 30 HOMAG machines including many edge banders. This gives us a real confidence in the HOMAG brand and is one of the reasons we didn’t hesitate to invest in the new CENTATEQ E-310 CNC.
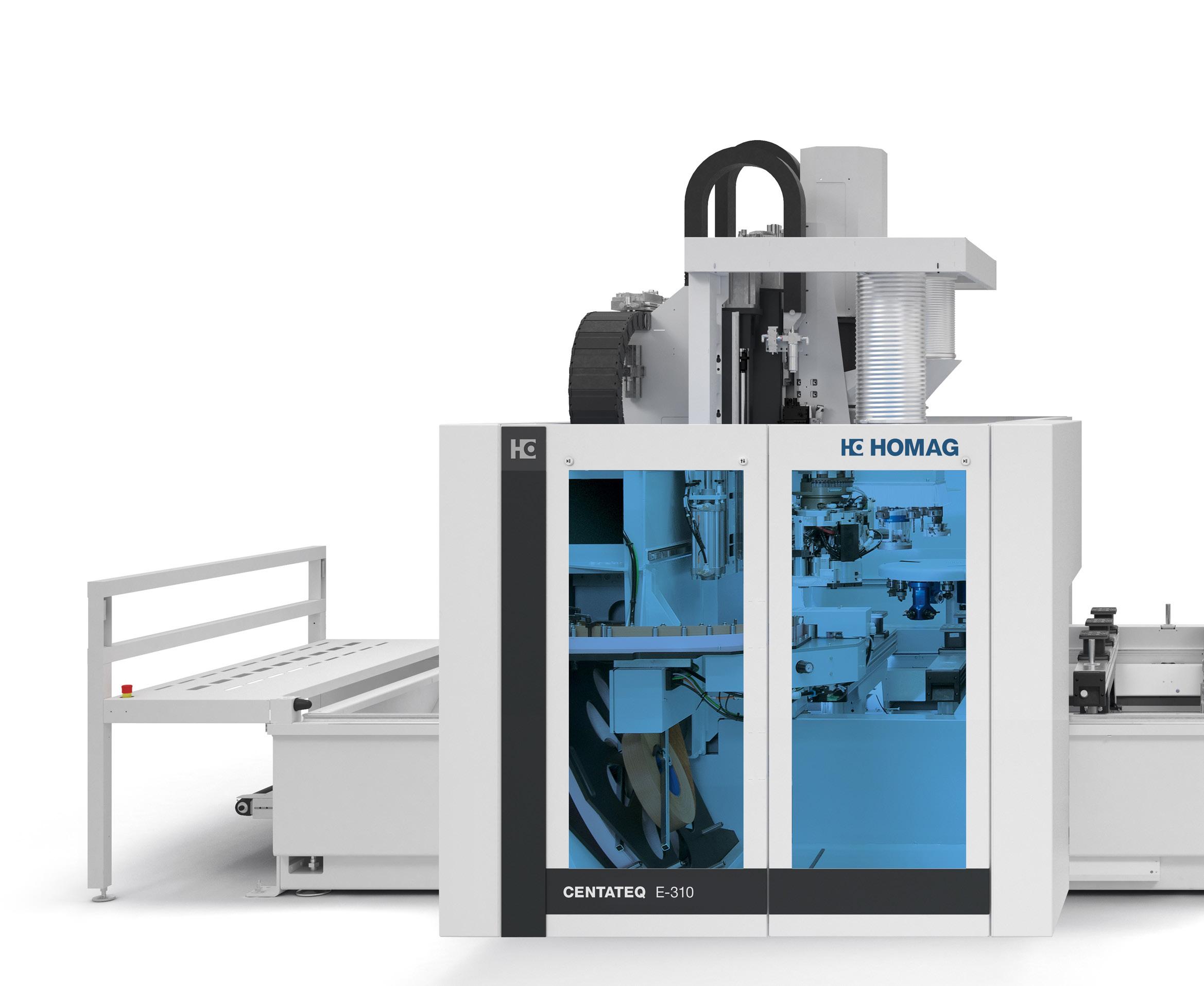
“The E-310, however, stood out on its own due to its performance capabilities, lifetime value, accuracy and the quality of finished work pieces. And, because it is controlled with HOMAG’s woodWOP software, it was much easier and quicker for our operatives to become proficient running it. If we’d bought another brand of machine, it would have been much harder to get to grips with.
“Another benefit of the woodWOP software is that we program work remotely from the office and, because the CENTATEQ uses woodWOP, it is easy for our programming team to adapt to the new machine rather than having to learn something very different.”
RESPONDING TO CUSTOMER DEMAND
“From the company point of view, we are now more able to support our sales team who are being asked to make special products or enhance our standard items with real wood edge banding. The CENTATEQ CNC gives us the capacity to fulfil this demand more efficiently.

“What’s more, the UK government’s Capital Allowances –Super Deduction – currently offers 130% first-year relief on qualifying plant and machinery investments until 31 March 2023. This makes investing in new machinery very attractive, and we wanted to take advantage of this before it ends.”
FLEXIBLE TRAINING SCHEMES
“The training options from HOMAG are another plus point from our perspective. They give us the opportunity to ’pick and mix’ between different training methods to suit the operators’ skill levels.
“For the CENTATEQ E-310 CNC we sent two people to HOMAG’s Schopfloch headquarters in Germany for the full training, whilst three other operators undertook remote woodWOP training with HOMAG UK. This flexibility enabled us to maximise the training opportunities for our team.”
THE COMPLETE PACKAGE FROM HOMAG
“We didn’t buy the new edge bander on a ‘return on investment’ basis, rather it was a business continuation decision with the added flexibility that came with the performance capabilities of the Pro Duo gluing unit.
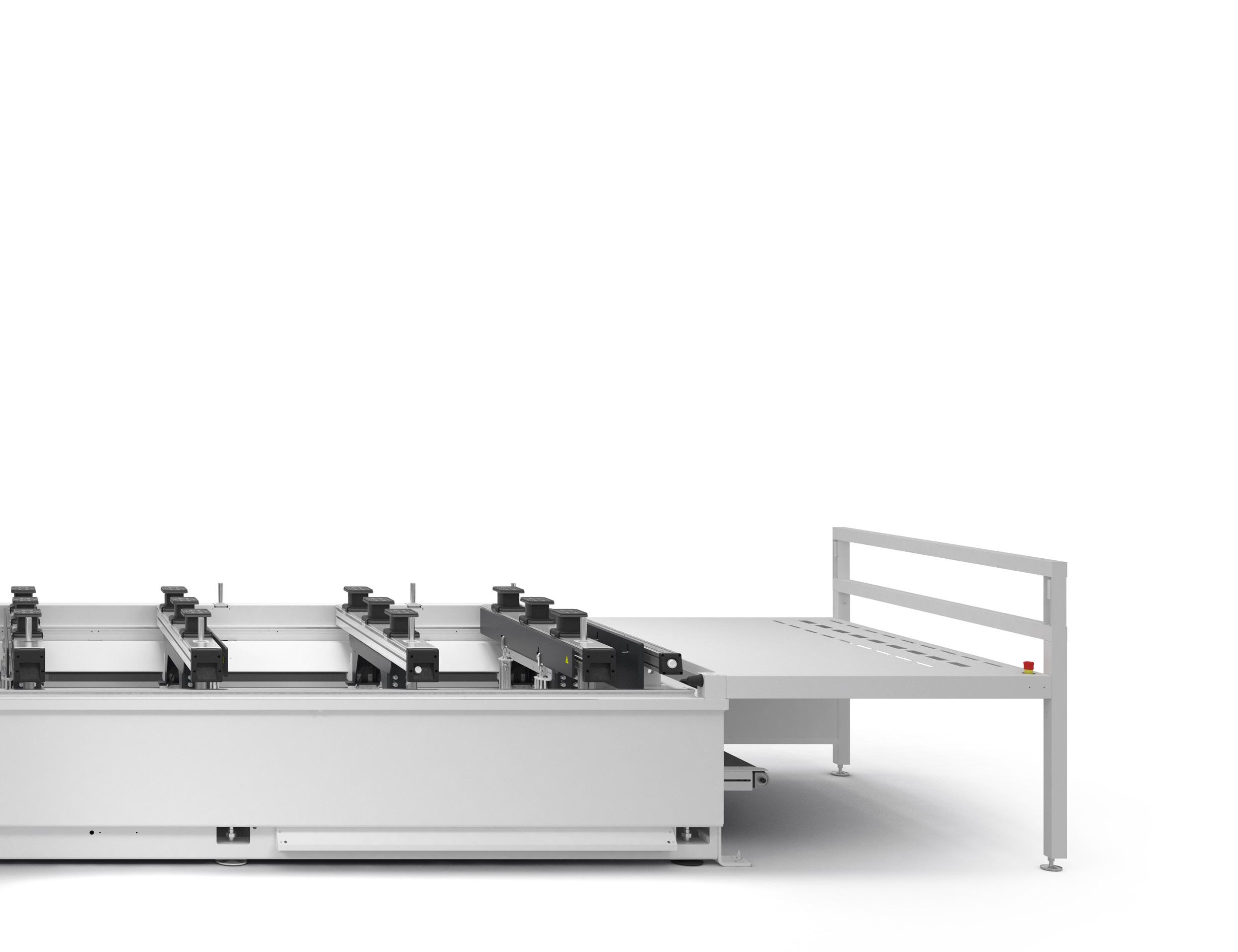
“Because we spent a lot of time at the front end refining the specification of the machine and conducting performance trials with several potential machine suppliers, we knew exactly what the CENTATEQ would deliver. And it has not disappointed. In fact, based on the success of the E-310, we have ordered an additional HOMAG machine; the new machine is a 5-axis CNC processing centre which is due for delivery in September.
“Ultimately, HOMAG offers us a one stop shop. All the staff in the UK and Germany, are extremely knowledgeable and helpful. Consequently, we have strong relationships with people in both locations, and they’re always on hand to discuss our needs,” concludes Martin Waller.
If you would like a demonstration or further information on HOMAG woodworking machinery or software, please contact Adele Hunt at HOMAG UK on 01332 856424 or email: info-uk@homag.com
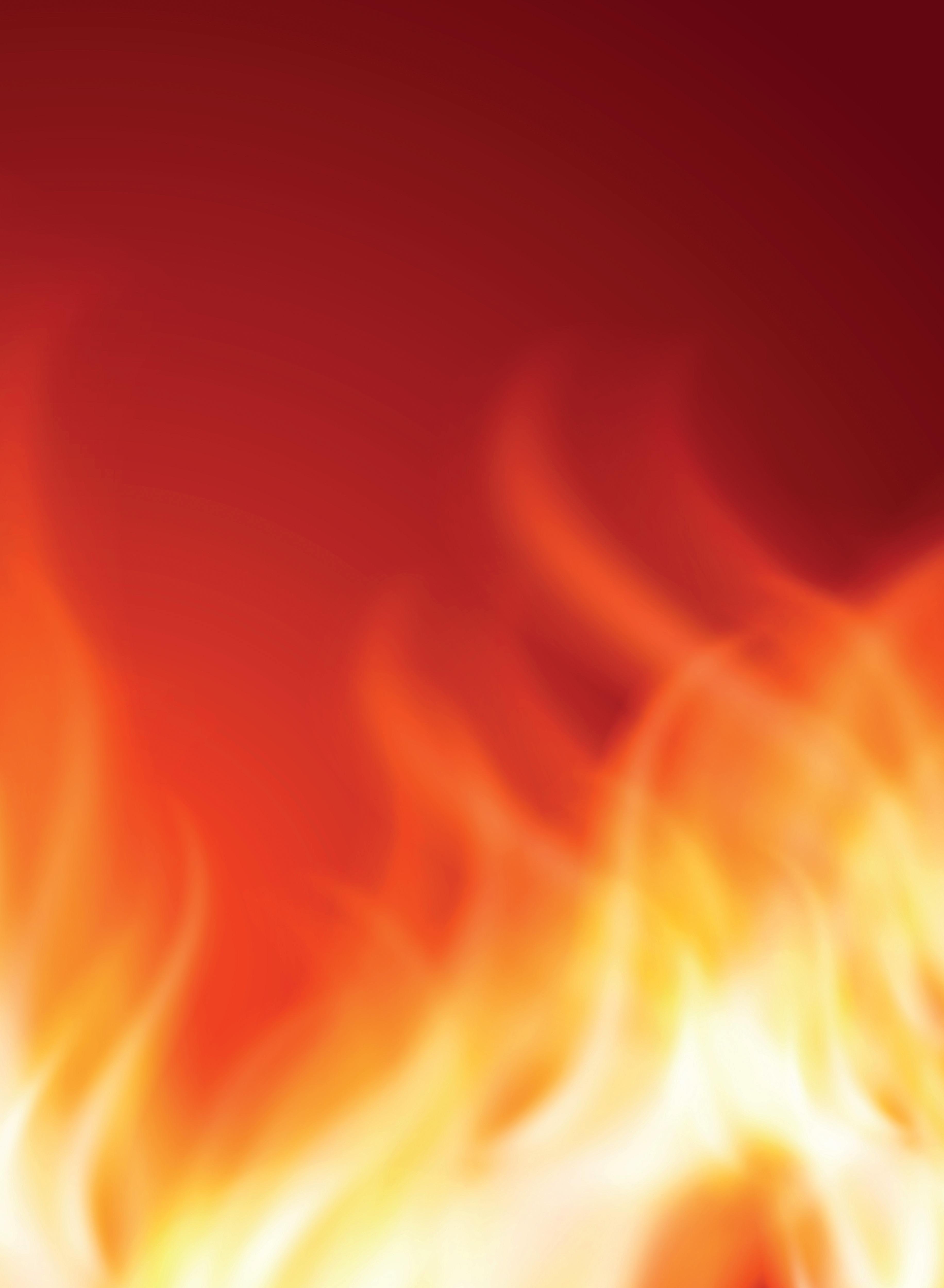
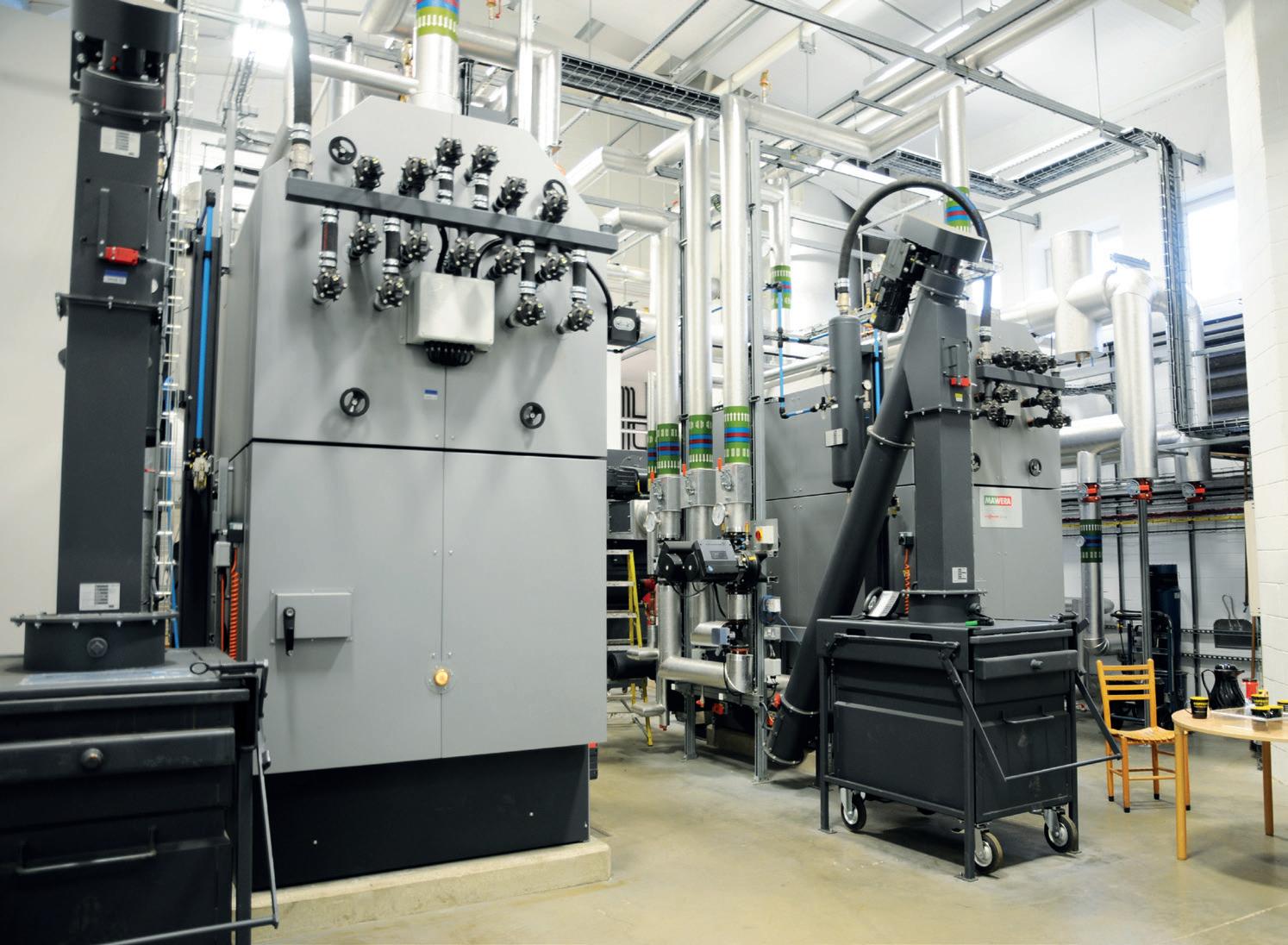
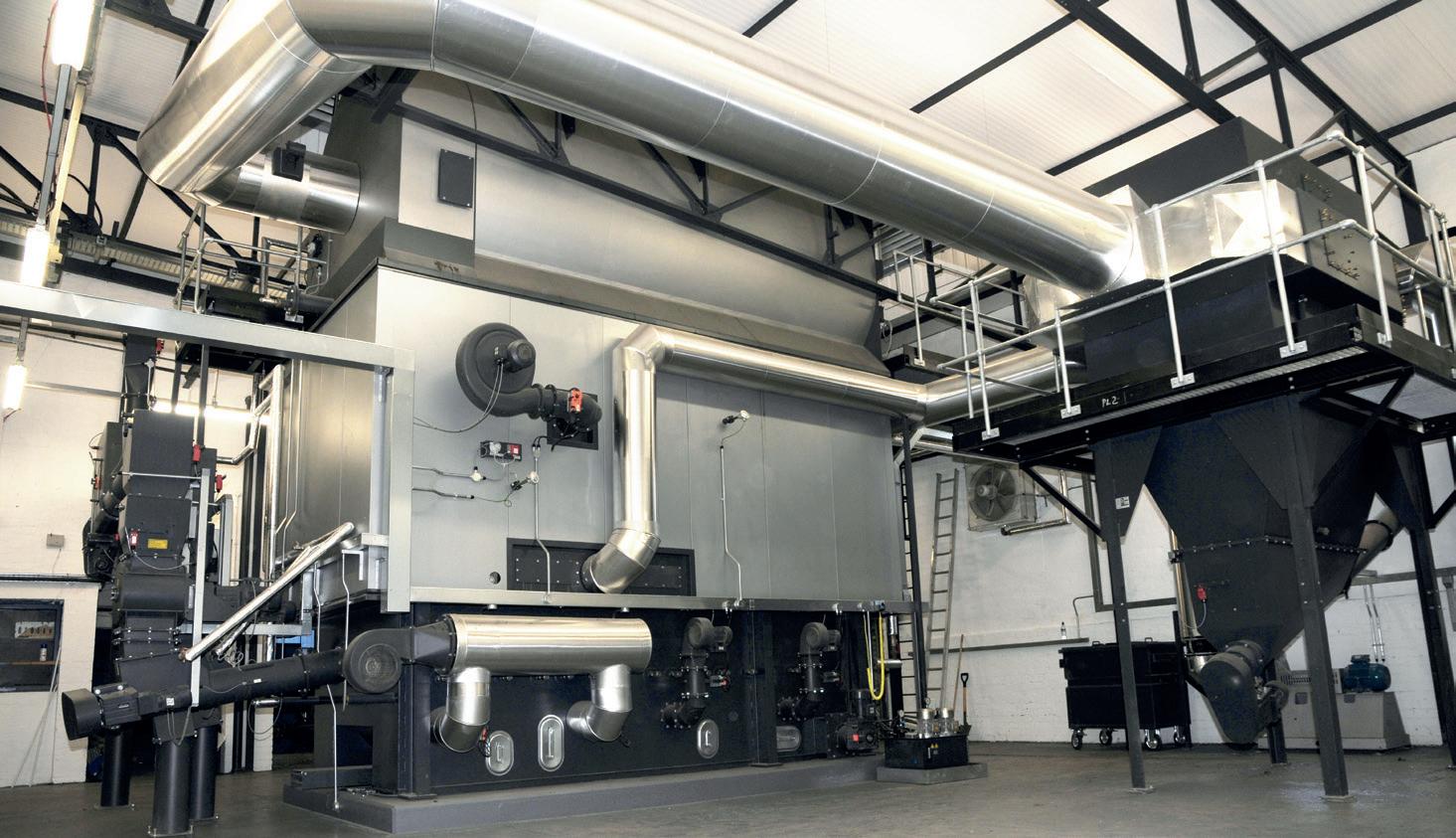
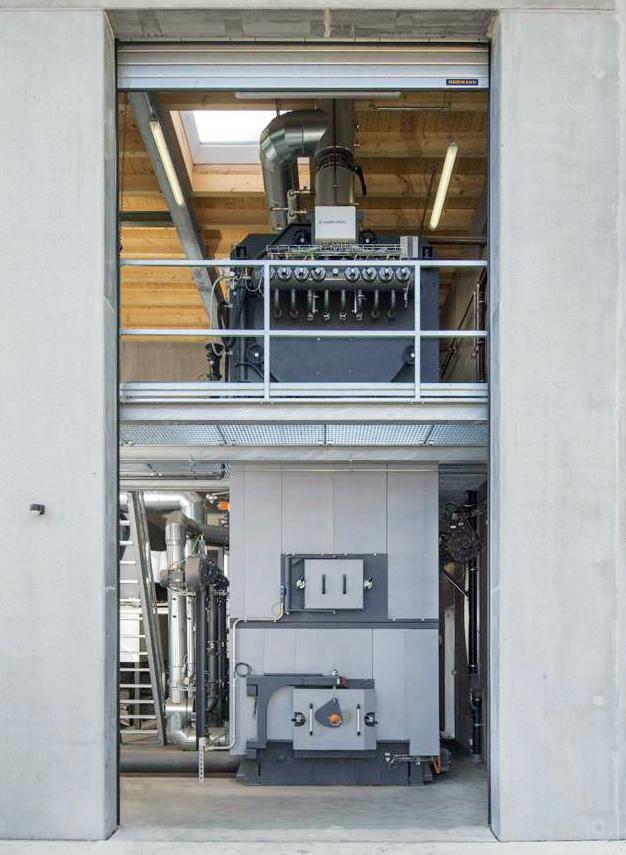
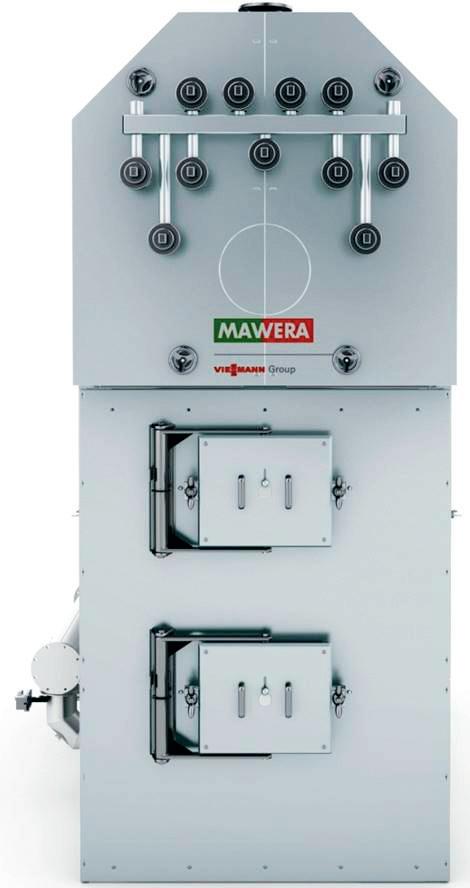


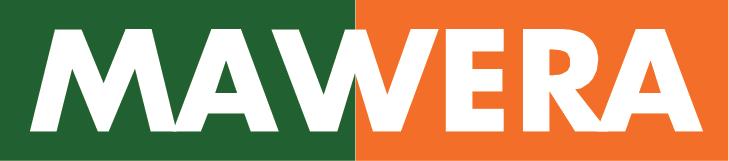
VISITOR REGISTRATION IS NOW LIVE!
Here are just some of the highlights you will experience at Surface Design Show:
• More than 180 exhibiting companies
• A Stone Gallery featuring some 30 natural stone suppliers
Welcome back everyone!
Visitor registration for Surface Design Show 2023 is now live - and it’s FREE to professional and industry colleagues.

Get your entry badge now to make sure you don’t miss the UK’s only event dedicated to surface material innovation where the architectural and design community come together in one place for 3 days.
WHERE AND WHEN?
7-9 February 2023
Business Design Centre Islington, London N1 0QH
Tuesday 7 February: 6pm-9pm (Preview Evening)
Wednesday 8 February: 11am-8pm
Thursday 9 February: 11am-5pm
• More than 30 ‘New Talents’ bringing an exciting new dynamic to the Show
• Our Surface Spotlight Live area displaying and explaining the most innovative of surface materials
• 18 presentations and over 40 speakers on our Main Stage - The Home of Headline Acts
• The highlight of our Preview Evening on Tues 7 Feb - our Opening Night Debate entitled ‘Design Solutions for Place and Sustainable Living: the work of many hands’
• Our PechaKucha Evening on Wed 8 Feb will have 7 speakers each showing 20 slides... for 20 seconds each!
www.surfacedesignshow.com

Furniture Assembly Made Simple
OVVO products are a range of cleverly engineered, award-winning connectors that make furniture assembly simple.
Connectors are installed during the manufacturing process so the end-user can click together furniture without the need for tools, glues or screws.
The result is a more accessible, sustainable product that saves time, money and effort for manufacturers and customers alike.
www.ovvotech.com
TRAINING
RECORD TRAINING GROWTH FOR DALTONS WADKIN
The Daltons Wadkin “red team” of trainers is celebrating a significant milestone in the delivery of certificated operator training courses throughout the UK and Ireland.
The past 12 months has seen a record 1250 individual learners successfully trained across all types of woodworking machines, abrasive wheels and hand operated power tools.
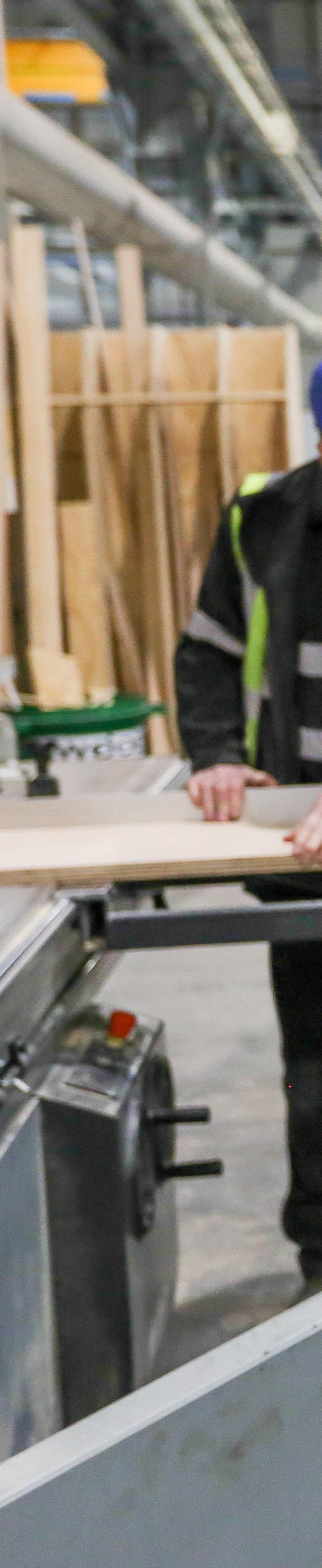
Daltons Wadkin are a PIABC Quality Assured training provider and have been providing industry led courses for over 15 years, continually honing the content to meet both customer and legal requirements
One of the fastest growing departments within the company, Daltons Wadkin has expanded its training team to 4 full time trainers to keep pace with demand and are now recruiting a fifth. Each trainer is a qualified teacher and assessor and has a minimum of 10 years experience in the woodworking sector operating industrial machinery.
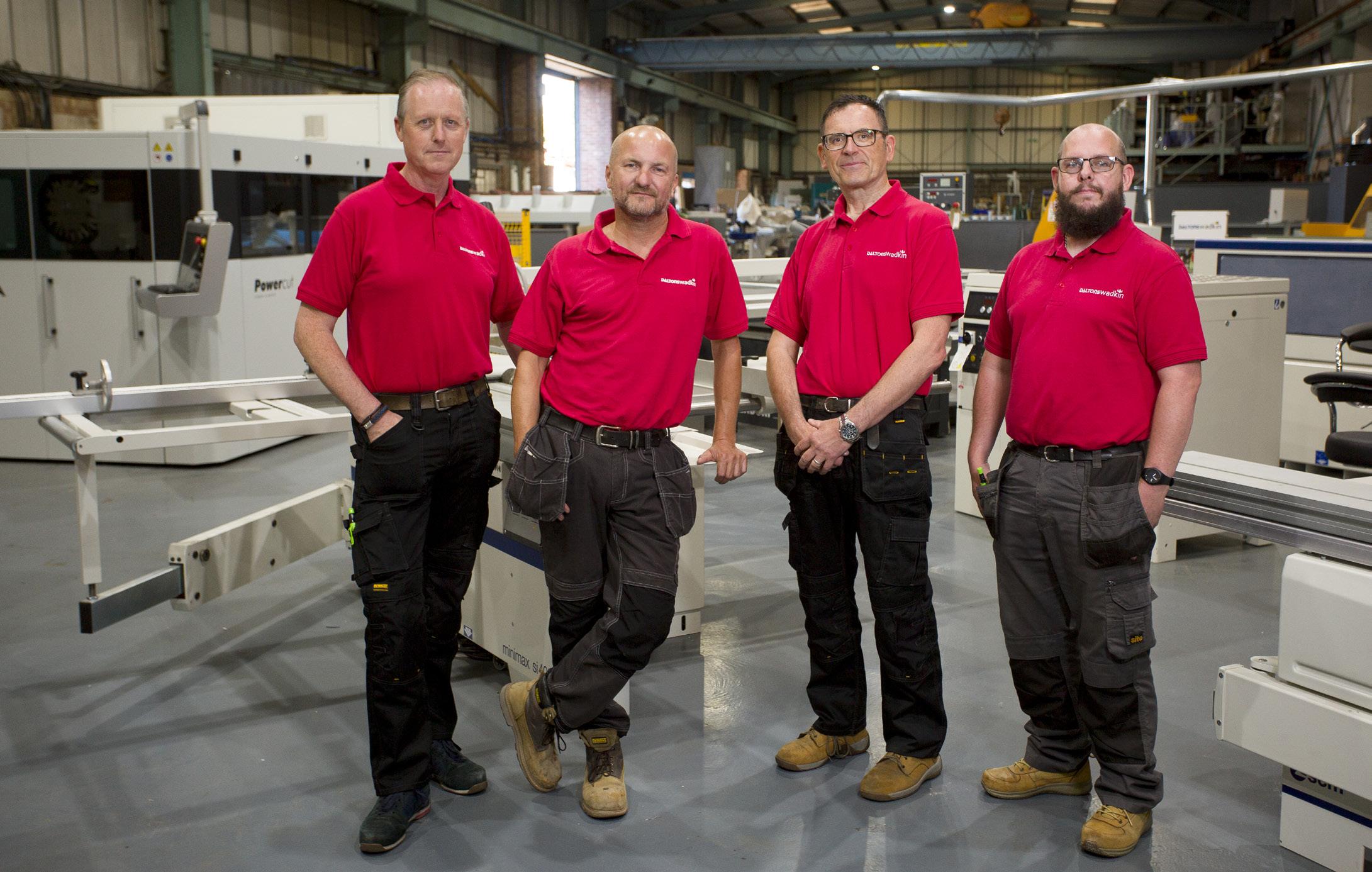
“Our standards are extremely high when it comes to recruiting trainers”, comments Managing Director Alex Dalton. “Our customers look to us for a professional, reliable service. The stakes are extremely high. We are working in one of the most dangerous industries with regards to accident rates and it is imperative that our trainers are suitably qualified, experienced, and confident in their knowledge.”
Training is tailored to individual requirements, whether an experienced operator or novice learner. With absolutely no PowerPoints, courses are delivered on and around customers own machinery. This hands-on approach ensures teaching and assessment is relevant to the customers workplace and production.
Each machine type is covered by an individual training unit. The aim of each course unit is to inform, access and certify the learner in Safe Setting and Operator Training on each woodworking machine in accordance with the Management of Health and Safety at Work Regulations, the Workplace Health Safety and Welfare Regulations 1992 and the Provision and Use of Work Equipment Regulations 1998. A key component to the success of the Daltons Wadkin training department is the course material. Every machine unit is accompanied by a detailed training book. Developed in house, the course material serves as a training tool during course delivery and is kept by each learner for future reference.
“We are very proud of our course material; it is unique in the industry. Working with the HSE we are continually honing the content to ensure the latest rules and regulations are reflected”
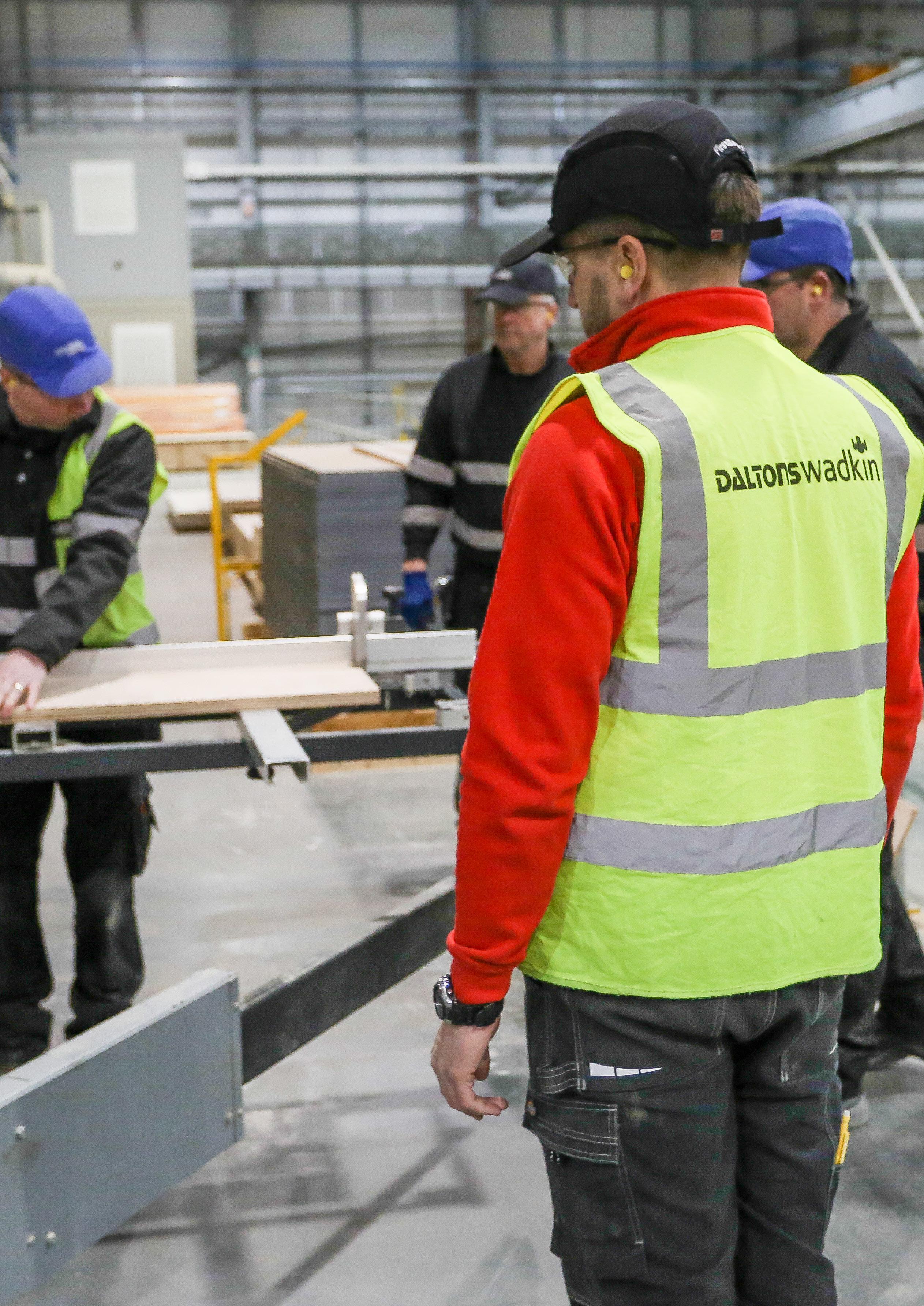
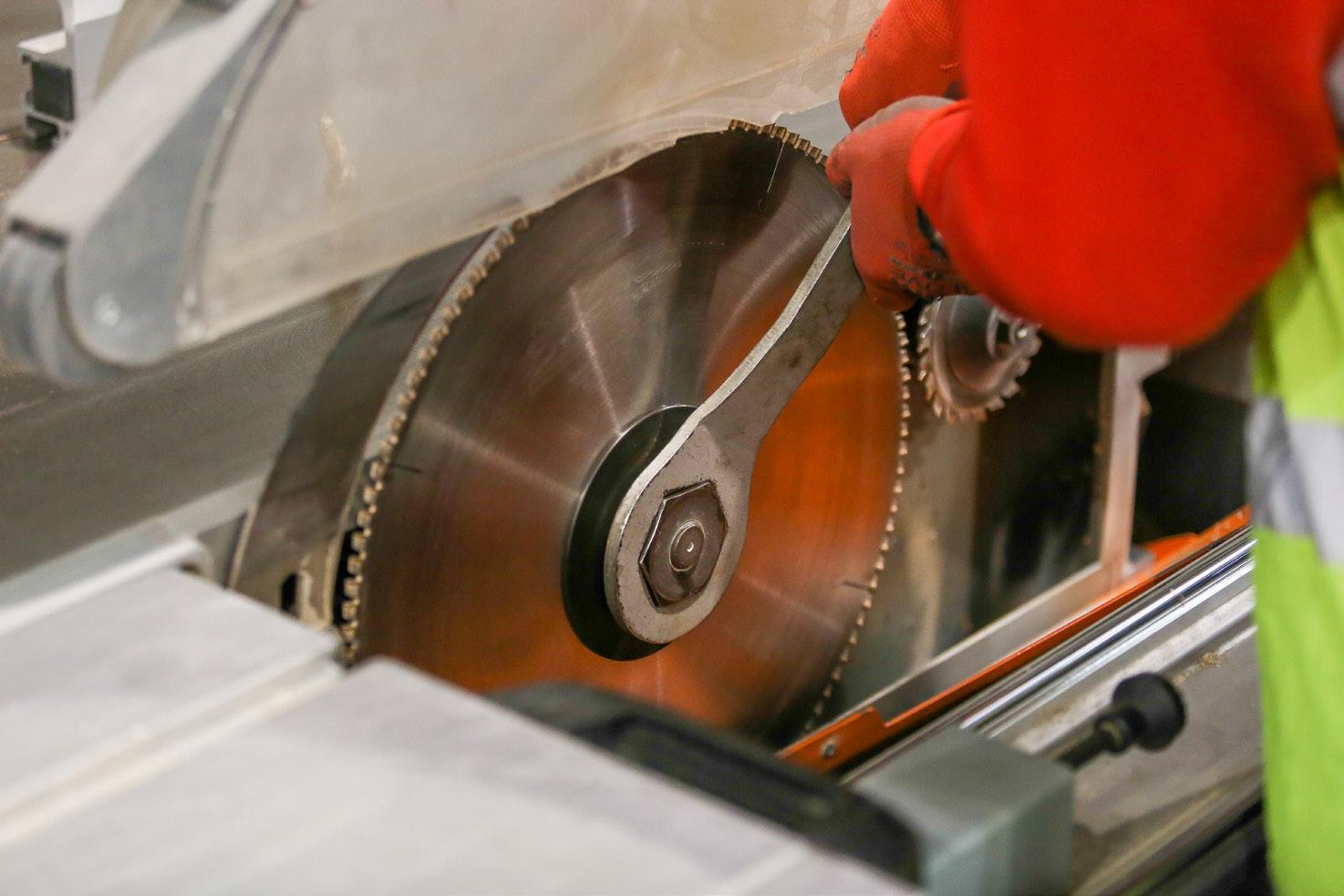
IMA SCHELLING – The Elite New Offerings
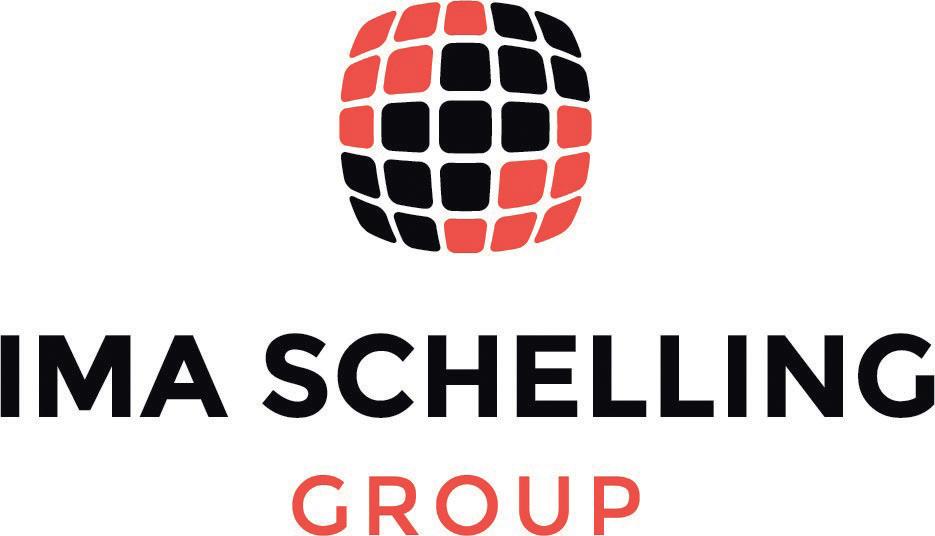

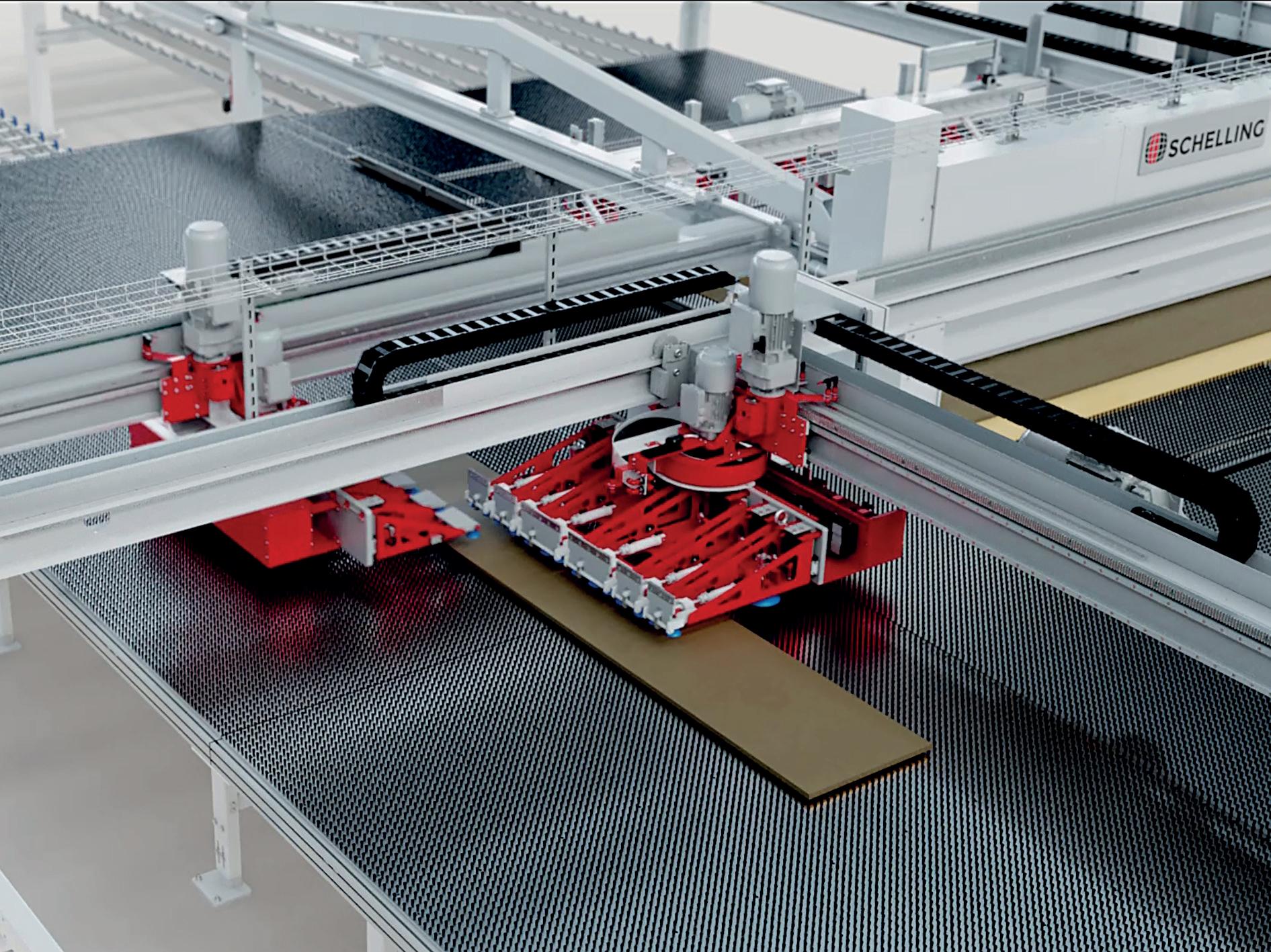
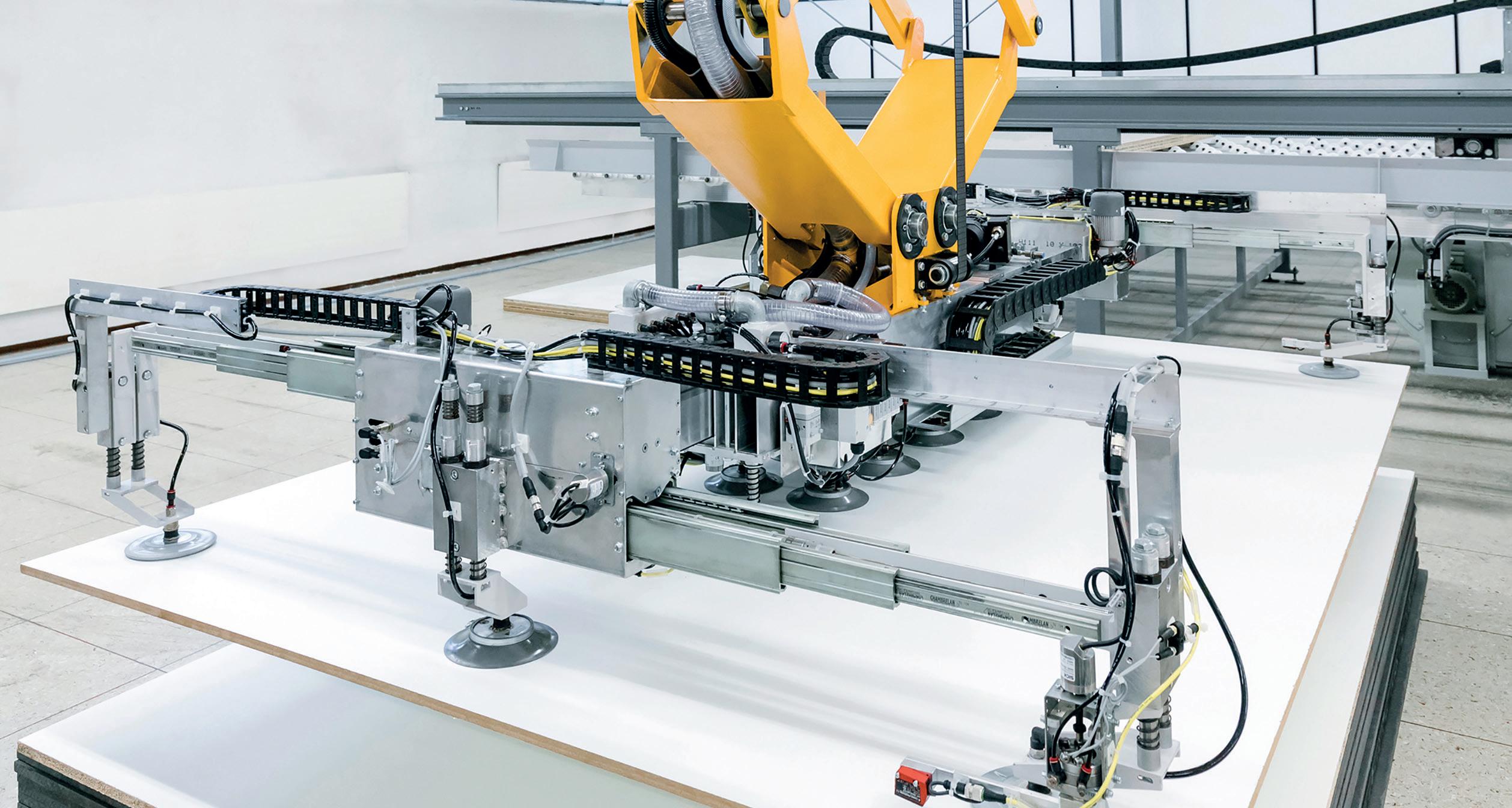
The new VS Area Storage System and LS1 range from Schelling are just showing how well they are adapting to the climate in the market. The LS1 is making batch size one production even more eicient and the VS can be adapted to suit any requirements. It can even be over multiple levels for those short of space! Get in touch for more information on the VS or LS1. at sales.uk@imaschelling.com
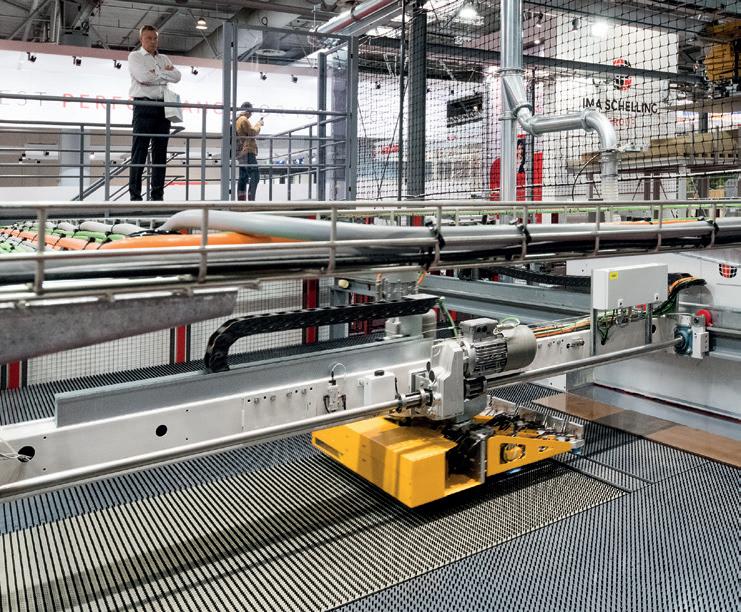
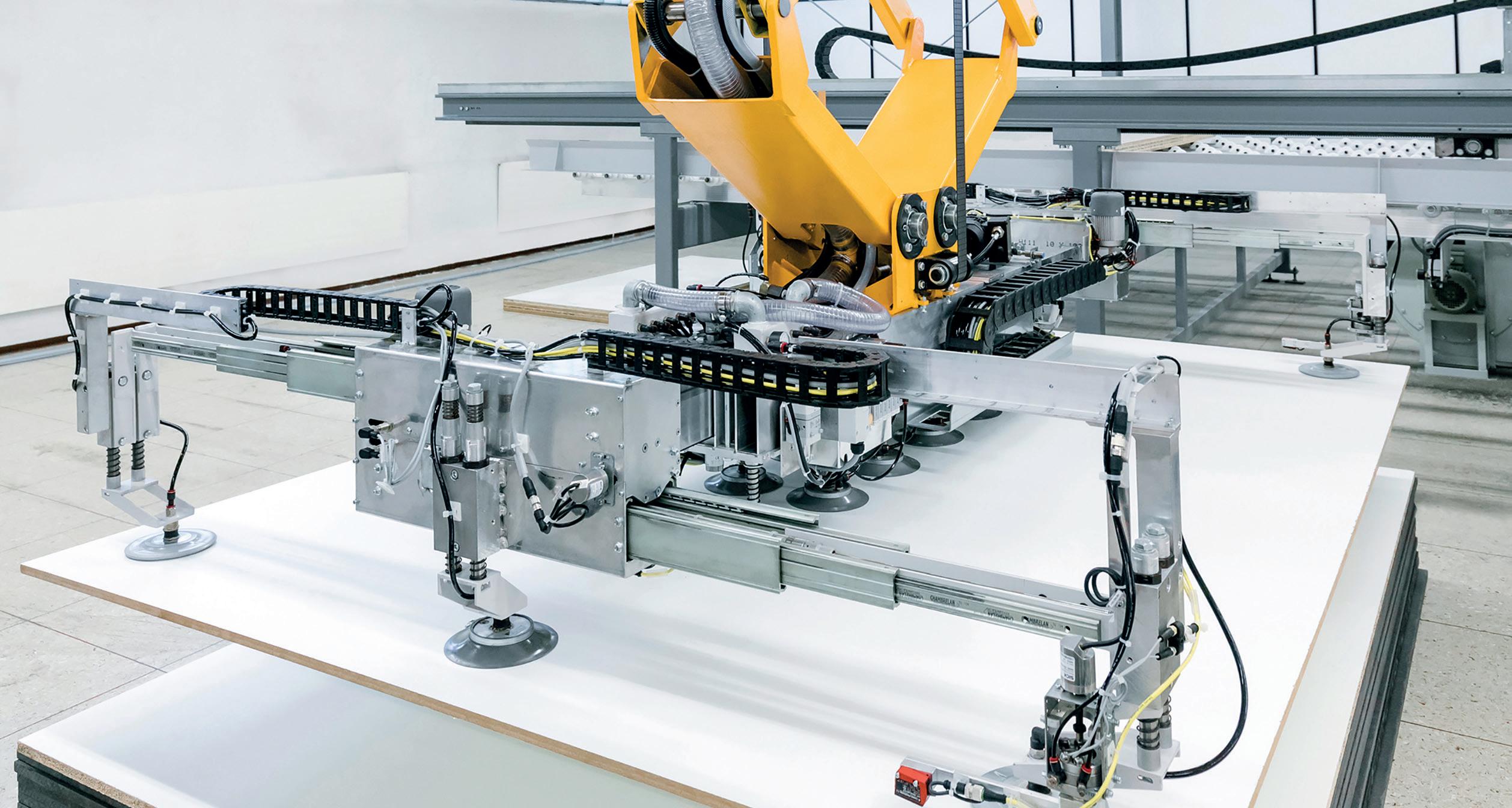
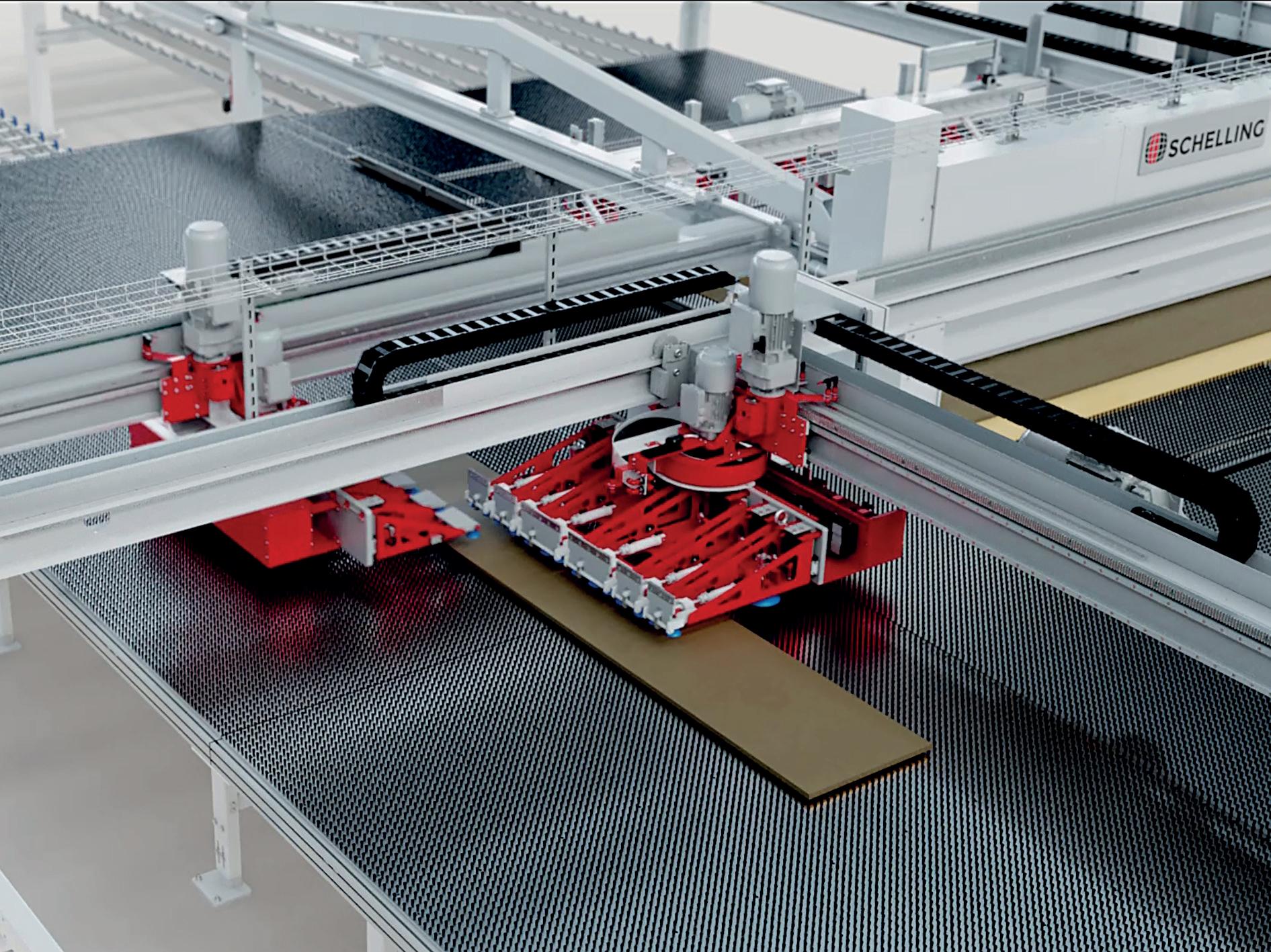
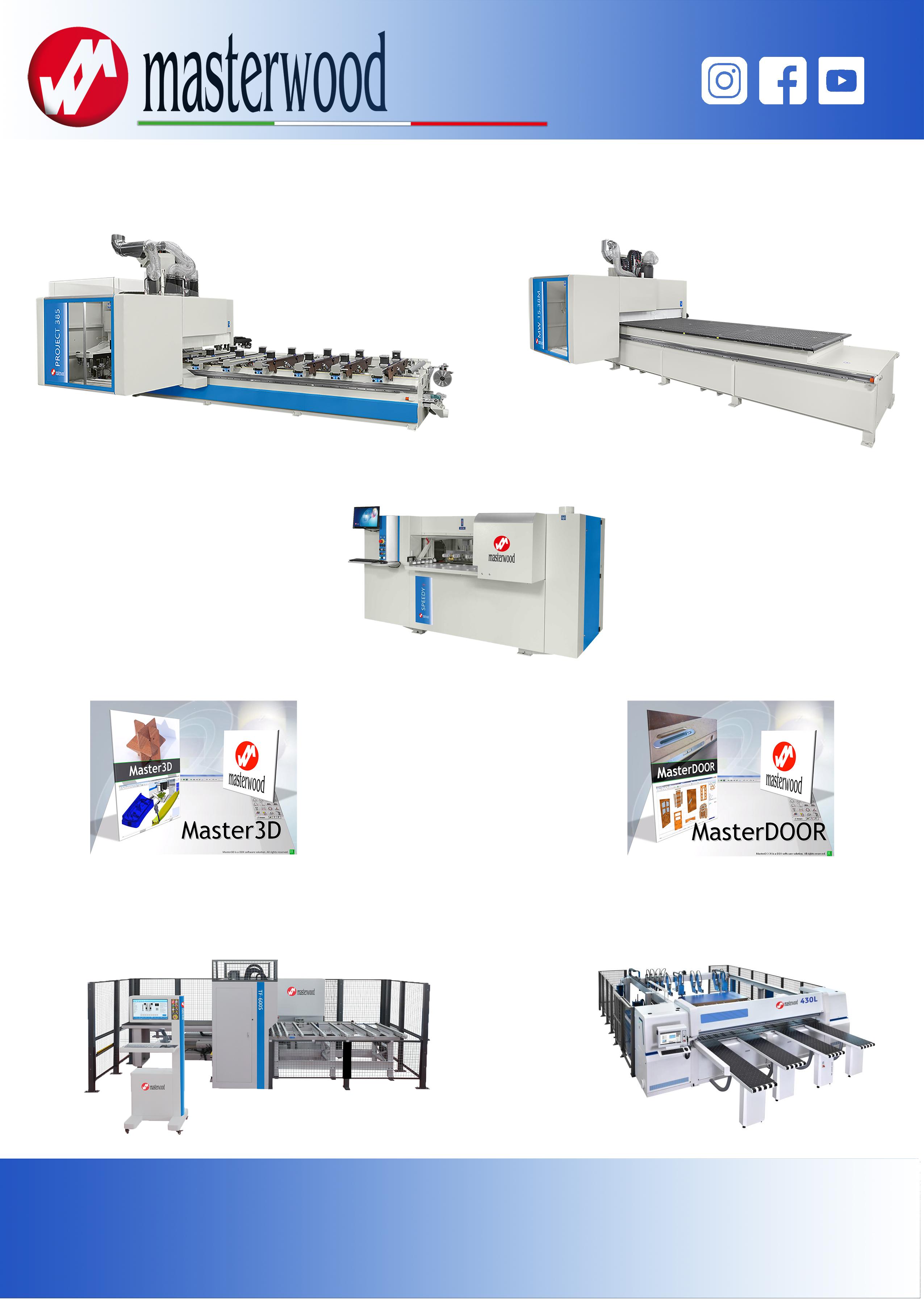

