
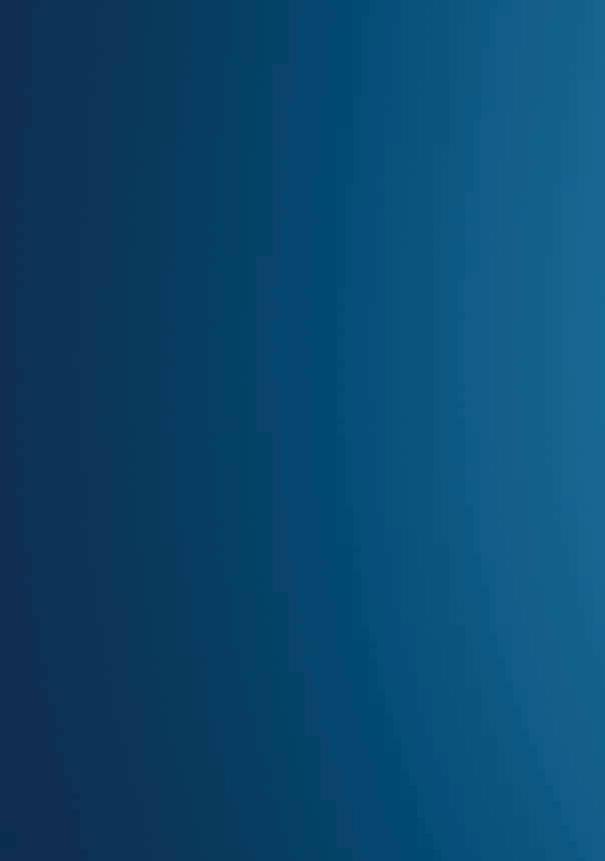
News
Blum UK’s Sustainability Initiative
Specialist Office Furniture Manufacturer Increase Capacity With HOMAG
Ostermann now offers a new PUR hotmelt
Lamello: A Work Shop Essential
So Simple, So Sustainable, So Space Plug
Build A Sanctuary Of Luxury With Hranipex And Partners
Weinig’s Cube3: Plane & Simple
Timber Business Invests In Wood Waste Heater
SCM Opens The New Digital Home For Woodworking Innovation
Q&A Decorative Panels
Take Control With Striebig
AFS Biomass
Front Cover Feature – HOMAG Software Solutions
The Laminate Which More Than Washes its Face
OVVO Partner With Proedge Technology
Materials & Handling Show Q&A
Loading Lumber Is Quicker And Way More Efficient With A Combi-CSS
James Latham Continues Support for Rycotewood College
HOMAG’s CENTATEQ P-110 Creates Secure Fire Doors For JLA Fire & Security
Hoffmann - As Accurate As The Day It Was Installed
Tiflex’s Implementation of AXYZ and WARDJE Tailored Cutting Solutions
Investment Keeps Automotive Supply Chain Agile
Ostermann With Two New Catalogues
Joinerysoft Helped Me Fall in Love with Joinery All Over Again
PUBLISHED BY:
TELEPHONE:
EMAIL:
WEBSITE:
PUBLISHER:
DESIGNER:
PRINTER:
EC Media 21 Cedric Road Westgate on Sea Kent CT8 8NZ 0771 314 8831
ecmedia@btconnect.com
www.p-j-production.com
Clare Hollister
Russel Goldsmith
TRACE Creative Agency www.tracecreative.co.uk
The Magazine Printing Company www.magprint.co.uk
Reproduction of articles: All material appearing in Panel & Joinery Production is strictly copyright, and all rights are reserved.
No part of the publication may be copied or transmitted in any form whatsoever, including photocopying without prior permission of the publishers.
Publishers note: The editorial opinions expressed in Panel & Joinery Production are not necessarily those of the publishers, who shall be under no liablity with respect to any article published herein.
British Furniture Manufacturers’ new Furniture Component Expo is continuing to go from strength to strength, with the announcement of a second headline sponsor.
BeA UK (Fastening Systems Ltd) has pledged support for the event, joining the Vita Group as the two leading names behind the show, which takes place at the Telford International Centre on 24 and 25 April, 2024.
The British Furniture Manufacturers (BFM) Furniture Component Expo provides an opportunity for furnituremakers to connect in a one-stop-shop format.
Manufacturers of furniture will be able to review, network and purchase products in the whole supply chain from leading suppliers, all under one roof.
The expo features a seminar theatre where exhibitors and visitors can gain industry insights and where exhibitors will launch new products and services.
BFM members will have free access to Club BFM, an exclusive lounge where refreshments will be available.
https://fcexpo.co.uk/
JAMES LATHAM INTRODUCES SWISS KRONO’S ONE WORLD, A UNIQUE SELECTION OF MELAMINES SPECIFICALLY FOR THE UK AND IRELAND.
James Latham, one of the UK’s leading independent distributors of architectural materials and finishes, has announced the UK and Ireland launch of Swiss Krono’s One World collection.
Specially curated for James Latham, One World brings together 37 of Swiss Krono’s highly sought-after, premium melamines in one place.
Offering a near-unrivalled variety of patterns and textures, One World covers all the bases, including monotone, woodgrain, material reproduction and design surfaces.
Unlocking creativity, One World’s surfaces can be continually combined in new and interesting ways, opening up a diverse range of design possibilities and firing the imagination of any specifier, daring them to mix, match and experiment.
Available across all James Latham’s 14 UK and Ireland depots, the distributor possesses a full stock holding of black, white and standard carcass decors, with three distinct collections: UNI, Woodgrain and Camustyle TX.
UNI: From subtle to bold, and beautiful in their simplicity, this collection comprises a wide variety of on-trend colours, updated on
a regular basis to ensure everything ‘in fashion’ is always available. Woodgrain: features realistic oak, elm, chestnut and walnut finishes with a timeless and elegant finish that will enhance any style.
Camustyle TX: Inspired by limestone and textile surfaces, these sophisticated decors feature an impressive vintage look and a rugged texture, offering massive creative potential for furnishings and interior design at an affordable price point.
The quality of the One World range is not just skin deep. Lightweight and simple to fabricate and install, it’s suitable for a variety of commercial and residential internal surfacing applications, from furniture and shop-fittings to kitchens, bedrooms, hotels, and offices.
PEFC™ certified, the range meets the new low-emission class of ED2020 (E0.5), halving the formaldehyde content of E1 melamines.
Available in the UK and Ireland from James Latham, One World comes as 2800 x 2070 x 18mm sheets.
For more information:
https://www.lathamtimber.co.uk/products/melamine/swiss-krono https://www.lathamtimber.co.uk/
Leading components and fittings manufacturer Blum is proudly committed to sustainability and to the continual movement of ideas and innovations.
A family-run Austrian company whose aim is to preserve natural resources for future generations, Blum utilises sustainable methods in everything from energy and resources to transport and mobility.
Blum believes that a successful sustainable business strikes the right balance between ecological and economic progress and, along with its environmental and energy policy, a crucial component is the promotion of renewable energy. With this in mind, the company has recently installed 904 solar panels on its UK headquarters’ roof, generating 75% of the building’s power needs and estimated to save 94 tons of carbon per year.
One of the project leaders, Matthew Glanfield, says, “At Blum UK, sustainability lies at the heart of everything we do. Now we have gone the extra mile by installing a magnificent solar farm, embracing renewable energy as much as we can and nurturing a brighter tomorrow. Our passion for sustainability has driven these steps, as we ramp up our efforts and continue to live by our values.”
The solar panels will generate energy during both working hours and out of hours, as well as weekends, and any excess energy will be sold back to the main grid.
Another part of the sustainability plan has been the inclusion of a beehive installation at the rear of the Blum UK warehouse. Three have been added so far with plans for a further seven. “We are so excited to announce our beehive installation as part of our sustainability journey,” says Raj Tanna, Blum Warehouse Manager. “We all have a responsibility to take care of nature and the environment and this is one of our contributions towards that goal. Our commitment to nature and the environment continues to expand and now, with the introduction of purely pollinator-friendly beehives, we are ready to make a real difference. We are so proud of our efforts to protect the environment and create a more sustainable future and could not be more thrilled to welcome our buzzing friends to our site.” So, remember, BEE is for Blum!
Blum’s sustainability focus also includes the entire life cycle of its products, from the production of the raw materials to the manufacturing and assembly until its usage and final disposal. “We hope to achieve all of our sustainability goals with a combination of partnership, inspiration and creative solutions,” says Cara Lee, Marketing & Communications at Blum UK.
For further reading, Blum has also produced a sustainability brochure to illustrate its commitment and measures taken over the past business year. The 80-page brochure features the new sustainability logo (below) and makes operational, ecological and social figures transparent and easily comparable.
You can view it https://www.blum.com/gb/en/company/ sustainability/overview/
Staverton (UK) Limited has been making quality furniture since 1928. Today it is known for solving clients’ workspace challenges with innovative design, quality craftsmanship and unbeatable customer service. The company’s 60-strong work force is based in its 26,000 sq. ft. manufacturing plant in Rotherham. Staverton also has a prestigious London showroom in Clerkenwell where the sales team is based.
“The foundation of our business has always been built on innovation, quality and first class service,” explains Staverton’s operations director, Ian Samuel. He continues, “The woodworking machinery we’ve invested in over the years is one of the cornerstones of the business. We have been buying HOMAG equipment for over 20 years and today our manufacturing facility is 100 percent HOMAG.
“As the world slowly emerged from the COVID crisis we began to question what the best strategy would be to grow the business. Whilst many manufacturers looked to take cost out of their operations, we decided to be more bullish and invest in our factory to give us more capability and capacity.
“We believed this positive approach would provide a better proposition to take to the market in the post-COVID, postBrexit period, particularly with our OEM (original equipment manufacturers) customers.”
“With the decision to invest in new machinery made, we turned our attention to finding the best machine manufacturer to partner with. Although we had a longstanding history with HOMAG, we evaluated two other Italian manufacturers before making the final decision.
“Obviously, machine build quality is a very important factor in the purchasing process for new equipment. However, whilst HOMAG is renowned as the best woodworking machinery brand in the world, we believe the key to making significant capital investments in machinery is the service levels the manufacturer can deliver. And ultimately, that was the deciding factor for us; HOMAG’s service levels, relative to the competition, remain far and away the best in the industry.
“Our HOMAG area manager, Alan Betteridge, is a key component in our relationship with the company. He understands our business and we can rely on him to be candid and give us unbiased advice. Consequently, we briefed Alan on what we were looking to achieve with the new equipment and he helped us specify the right models.”
”The existing HOMAG CNC machining centre had been a real asset for the business. We felt, however, it was vital to move with the times and take advantage of the changes
taking place in the office furniture market. There was a shift from single work stations to larger meeting tables and so Alan recommended the 5-axis CENTATEQ E-310 to increase throughput, provide flexibility and improve our production capabilities, particularly of curved parts.
“To strengthen our inserting and drilling capacity Alan steered us towards the DRILLTEQ V-200 which has proved to be an excellent choice. For edge banding, he suggested the EDGETEQ S-300 with a LOOPTEQ O-300 automatic return system and XES 200 glue station. The S-300 edge bander is equipped with the latest airTec glue technology and this has proved to be a game-changer, eliminating any issues with the quality of the glue line.
“The LOOPTEQ return system and the XES glue station have further improved our throughput speed. The LOOPTEQ system means the edge banding cell is now a one man operation. Meanwhile the glue station enables us to eliminate downtime associated with changing glue types and cleaning glue pots.”
SMOOTH, EFFICIENT INSTALLATION AND TRAINING
“The installation process for the machines went smoothly. Our production manager, Mark Powel, worked closely with Alan Betteridge and the team at HOMAG to coordinate everything. As a result, we were operational within ten days of the machines being delivered.
“In preparation for the installation of the new machines we sent three of our operators to HOMAG UK for a week’s training prior to delivery. The remainder of the training was done onsite in Rotherham by the HOMAG installation engineers and I have to say, they did an excellent job.
“We reckon the new machines will probably pay for themselves within a 3 to 5 year window. What’s more important, however, is that the improved capabilities and delivery times have enabled us to grow our existing customer business. In addition, we are attracting new customers with the quality, flexibility and value for money we provide.
“By working closely together with HOMAG we have established a strong partnership which has enabled us to constructively work through any issues. All in all, we’re delighted with our new HOMAG machines. They have improved nearly every aspect of our manufacturing processes and increased our throughput by well over 40 percent. The consistent quality, particularly of the glue line, is fantastic and HOMAG’s service levels remain the best in the industry,” concludes Samuel.
If you would like a demonstration or further information on HOMAG woodworking machinery or software, please contact Adele Hunt at HOMAG UK
With REDOCOL Kantomelt PUR LM, Ostermann now offers a new PUR hotmelt adhesive with low monomeric isocyanates content.
When processing edgings, hotmelt adhesives based on polyurethane (PUR) ensure a particularly good, durable and water- and heat-resistant bond. Since the requirements for occupational safety and environmental protection are increasing in the area of PUR adhesives, Ostermann has now included a PUR hotmelt adhesive with a reduced monomeric isocyanate content in its range. The new REDOCOL Kantomelt PUR LM is the first non-labelled PUR product of the REDOCOL brand. It is available as a 2 kg block and in two colours (natural and white). For more information, type in the search term “#REDOCOLLM” on the Ostermann website www.ostermann.eu.
NEW PRODUCT GROUP: REDOCOL PUR LM
LM is short for “Low Monomer”. This means that the new REDOCOL products labelled as such have a low content of monomeric isocyanates - products with an isocyanate content of less than 0.1 % require no training for the user. As with all PUR hotmelt adhesives, the new product is characterised by its high initial strength and excellent water and heat resistance. The first product in the new line is the 2 kg block; further adhesive versions are to follow.
As a service for the trade, Ostermann has already created an information page regarding the compulsory PUR training and informed their customers about the upcoming training obligation in newsletters. This information is compiled in a user-friendly way on the Ostermann website https://www. ostermann.eu/en_GB/page/pur-training-obligation.
E: s.parsons@ostermann.eu
T: 01905 793550
Furniture makers who also place high demands on occupational safety and environmental protection when it comes to cleaners on the edgebanding machine should be familiar with REDOCOL greenline Teclinex One For All. The cleaner is based on organic alcohol and can be used on all spray units in the formatting, glue and pressure, post-processing and finishing zones. This reduces storage costs and simplifies the work.
With over 130,000 Instagram followers and an equally impressive following on YouTube, Facebook and TiKTok, Derek Barett, owner of Buckinghamshire-based Derek Barret Design Ltd, is a man that knows what it takes to get noticed. But, like all good furniture designs, it’s often what you can’t see that proves most impressive. For Derek, this is Lamello’s innovative fixings.
“Lamello has was always been on my peripheral but it wasn’t until 2020 that I became the owner of my first Zeta P2,” admits Derek, Managing Director Derek Barret Design Ltd. “I’m a big fan of trying new things and I’m always on the hunt for innovative solutions that can not only help me create beautiful pieces of furniture for my clients but also standardise and simplify my manufacturing processes. For me, this is exactly what the Zeta P2 does.”
Derek admits that the benefits were seen immediately. “From day one, I used it on every job and within a few months I’d purchased a second one. Teamed initially with the Clamex P-14, we not only saw an increased level of speed and accuracy in the workshop but we were also able to transport pre-fixed panels easily to site and erect them quickly with little more than an allen key. It was unbelievably quick and the whole team, which all have different backgrounds and competencies, found it a straightforward, easy to follow process. Now, Lamello is engrained into our business and we use a range of fixings on everything we make.”
Take draw boxes for example. In the past, I would Kregg my draw boxes together. The process worked well but it required a certain level of skill to guarantee the panels remained flush. An experienced furniture maker would know to expect some movement and how much torque to apply. This level of skill isn’t needed when using Lamello’s fixings. With the Clamex P-14, you simply create the grove using the Zeta P2, insert the fixing and click it in place. It’s child’s play. The cost of using Lamello is far cheaper than having to remake a draw box due to a mistake and it’s 50% quicker. Site work and assembly time has also reduced and they remain strong, even when disassembled and reassembled multiple times.”
Derek is also a fan of the Tenso P14. “They offer a seriously strong hold. In fact, they are so strong that we were able to use them on a hidden door that was designed to show no fixings when open. We didn’t want to clad over the fixings – this would have made the door really heavy and prone to dropping – so we used the Tenso P-14 self-clamping gluing aid instead to create the same effect with no visible holes. The results were beautiful.”
Then there’s the K20 – which Derek admits is his favourite. “I’d be an ambassador for the K20 if I could,” laughs Derek. “We use them a lot on our fillers – the scribes around the wardrobes – as they’re stronger than a Bisco so you are guaranteed a really good bite. You don’t need to add any glue during the process because you just know it has the right amount of strength to do the job but if you do need to pull off a filler once fitted, you can without causing any damage. This makes it an extremely flexible option.”
Two years on from the purchase of Derek’s first Zeta P2, he’s invested in the new Zeta Cordless. “As soon as we tested it on MDF, we wanted it,” says Derek. “We predominantly use it on Egger, Kronospan and Finsa MDF board and very occasionally on Xylocleaf textured board. We also use it on solid wood – although we prefer to use a TCT blade on solid wood which is actually cheaper than a diamond tip blade.
“The only problem is, we now fight to get to the Zeta Cordless first. Just like the original Zeta P2, it’s quickly become an essential part of our tool kit and using it onsite – without the restrictions that come with an extraction hose and cord – makes life so much easier, especially when working in confined spaces. The guys are already asking for a second one.”
Derek is also keen to disperse any myths about the Zeta cordless. “People always question the battery life and extraction power on tools like this. With the Lamello Zeta Cordless, you don’t need to. We use two four-amp batteries because they’re lighter and easier to handle than the six, eight or 10amp options that are also available. They obviously don’t have the same battery life as the bigger ones but we can easily make 300 cuts – a whole box of fixings – without needing to recharge.”
Derek continues, “The extraction is also effective. It has a good amount of air-draft blowing into the bag at all times. You just need to remember to turn the machine on before doing a downward cut as the sawdust will fall out. That’s gravity for you!”
Derek’s latest efforts to standardise his production processes and combat the skills shortage has seen him became the proud owner of his first CNC router - a Homag Drilteq V-200 - which features software designed to work with Lamello’s P-System. “It features pre-loaded settings for Lamello’s P-System within its WoodWop software package. It has a disc and two router cutters that clear the hole and machines the t-section. As it’s a four-axis machine, it will do all our Lamello cutting on the face, top and side of a panel. This was a huge selling point for us as we look to streamline our business, whilst maintaining our standards.”
This purchase, whilst extremely new to us, will help us take our production to the next level. The core of the business won’t change and it will never take away our need for Lamello’s handheld machines because of the site work and bespoke pieces we do - but if this machine can alleviate some of the manual processes we’re currently having to do, it will have an extremely positive impact on the business and ultimately, how many projects we can complete every year.”
Derek continues, “We are still learning how to use the machine but Homag’s partnership with Lamello sealed the deal for us. It’s just another example of how integrated Lamello has become in our business and the wealth of possibilities available to Lamello users. It’s now a way of life and is central to the company’s best practise. Come back next year and we’re confident the results of incorporating a Lamello-ready CNC into our workshop will speak for themselves.”
For more information please visit lamello.co.uk
The brand new Cube 3 compact four-sided planer is more affordable than ever thanks to Weinig’s exclusive CUBE Rental Plan.
The low cost, risk free route to owning a Weinig CUBE 3
YOURS FROM £170 PER WEEK* *Subject
Sustainability, Intelligent Design, Manufacturing Innovation, Production Economics, Customer Experience. All of these are addressed when a manufacturer embraces “Space-Plug Evolution”
The last 10 years has seen Space-Plug become the brand synonymous with fast effective fittings for kitchen base units and tying back all manner of KBB furniture. With the launch of their new system, “Evolution”, manufacturers will now be, “More Sustainable” whilst, “Saving Money” and including brand new, “Fast-Fit” technology.
It’s a simple idea. The cabinet is made with shorter Side Panels that no longer have to reach the wall. This strip of material is now saved in manufacture and replaced with the addition of their, “Datum Pegs” - 2 grams replaces 500! This handy measuring stick replaces the excess material manufacturers have included unnecessarily for decades! Manufacturers now save this material which more than covers the cost of a set of Evolution components and so Space-Plug guarantees to save money overall and offer much more to their fitters and more importantly, their customers!
The reason? These strips of board are in the way for fitting a kitchen. “The industry thinks installers want them” said Cliff Petit, Inventor and MD at Space-Plug. “Installers currently think that, because manufacturers provide them and they are needed to create the service void. But both the manufacturers and the installers haven’t seen Evolution cabinets … Yet!”
Fitters time is wasted and customers cabinets’ edgebanding is sacrificed as these machined edges don’t marry to meandering walls let alone around surface mounted services. Fitters have to scribe round these pipes or cut away large sections to get the unit in place. Modifying the units on-site, causing more work, more dust and more risk … often contrary to the manufacturer’s warranties! These leave brand new cabinet material in the skip, wasted and customers board edges now exposed compromising the new unit’s integrity.
“All of this is negated by Evolution” states James Marchant their Director of Marketing, “Not forgetting that all of these benefits are accompanied complete with a SpacePlug Adjustable Spacer Fixing the Five star fast, purposeful professional fixing… basically Free of Charge”
The system is already in manufacture in the UK and taking orders. With Sustainability and customer experience at the forefront of its benefits of Evolution is set to eclipse the 8 million adjustable spacers Space-Plug has already sold.
Interior design is at the heart of people’s lifestyles and with Hranipex renowned brand Riex, you can create additional storage space, new possibilities of usage and exceptional bedroom architecture.
In the world of interior design, partnerships between trusted suppliers and distributors play a focal role. Hranipex takes pride in being a stockist of HAWA Combino Sliding Doors solutions, a family-owned company with more than 50 years Swiss quality. This collaboration signifies a commitment to delivering excellence in interior design by providing access to products that blend innovation and craftsmanship. One of the most impressive features of the HAWA Combino Sliding Doors is their robust load capacity. Each door can bear a weight of up to 50 kg, ensuring that even larger and heavier doors can be effortlessly maneuvered. This load capacity not only speaks to the high-quality engineering of the system but also adds an element of reliability that is crucial in any interior application.
Hranipex’s decision to stock the HAWA Combino Sliding Doors reflects the dedication to offering solutions that meet the highest standards of quality and reliability.
Jason Southam, Hranipex product manager confirms “With Hranipex extensive experience and expertise in the industry, to align with a premium brand such as HAWA highlights the commitment to delivering value to our customers.”
To complement the Hawa systems, Riex NC70 hinges are suitable for a wide range of doors and Hranipex are proud to confirm Riex has evolved the range and is now available in a sophisticated dark grey hue. This elegant colour choice positions these hinges as the perfect companion when crafting luxury furniture. Available in inset, half, and full overlay options, each variant boasts a soft-close mechanism, guaranteeing a consistent sense of luxury. Jason Southam, Hranipex product manager confirms ‘’The blend of luxurious quality with affordable prices allow to you offer the perfect solutions to your customer with the NC70 range”.
Complete the look with Additional Riex components in dark grey
Optimise wardrobe space with Riex VX95 Aluminium Frame with Storage Mesh Basket in dark grey! Designed with functionality and style in mind, this aluminium pullout wardrobe frame is the essence of modern storage innovation.
A standout feature in the VX95 is that it effortlessly glides on concealed soft-closing slides, ensuring a seamless and quiet operation. Available in widths ranging from 600mm to 900mm, the Riex VX95 Aluminium Frame with Storage Mesh Basket is a versatile choice that complements various wardrobe styles and sizes.
Experience systematised dark grey wardrobes and create a coherent design with Riex VX75 aluminium trousers rack. A sleek aluminium frame that glides on hidden soft-closing slides, accompanied by aluminium profile trouser hangers for a refined and efficient wardrobe solution. VX75 offers versatility with widths available from 600mm to 900mm. Riex VX47 pull-down wardrobe bar has an impressive load capacity of 25kg making it an ideal solution for heavy loads to be lifted comfortably with the spring lifting mechanism. VX47 comes with soft-close mechanism in both up and down positions and is easy to assemble and install.
To complete the realm of luxury, the finishing touches include handles and knobs on the cabinets. Within the Riex comprehensive collection you can choose between traditional or modern design, the handles will always be durable and perfectly made to coherently complement the luxury feel of your designs.
Jason further explains “focusing on craftsmanship, quality, and cohesion Hranipex can offer the perfect solution”.
For many manufacturers, time and money are two of the biggest factors to consider when running a profitable manufacturing business. For Reigate-based Boxhill Joinery, their continual quest to increase productivity and tackle the growing labour shortage influenced the decision to purchase a Cube 3 four-sided planer from Weinig UK and in the process, become the first company in the UK to have the new model installed in their workshop.
“I have always seen Weinig as a brand to aspire to and as such, their machinery has always been on my radar but when I started Boxhill Joinery with my business partner, Jon, we only had £5,000 to spend on machinery,” begins Ashley Hook, Director of Boxhill Joinery. “We could only afford an old sliding table saw, a spindle moulder and a manual planer and thicknesser. It wasn’t a lot but it was enough to get us started. As we made more money, we’d reinvest it into the business and upgrade our machinery. Three years later, we purchased our first Weinig – a 35-year-old Profimat moulder. It might have been old but it ran smoothly and it helped us make huge strides in our production capability. Results were good and its build quality was exceptional but like all machines from the 1980’s, it required a lot of manual set-up and a certain level of skill and understanding to run effectively.”
In 2022, the decision was made to upgrade the Weinig Profimat to a brand-new Cube 3 four-sided planer – a model that’s been proven to be ten times faster than conventional
machines and requires minimal skill to operate. “Thanks to the level of automation, we experienced immediate timesavings,” admits Ashely. “We no longer had to contend with manual levers or old synchro units that made dimension changes long and laborious. Instead, to plane a piece of material on all four sides in one pass, we simply had to punch in the finished size and how much we wanted to take off the bottom and side. The machine did everything else for us.”
Whether machining one-off pieces, small batches or a complete project with varying size and material requirements, the Cube 3 offered the joinery company much-needed flexibility and performed the tasks easily with just one operator.
“The Cube 3’s large standard working dimensions were a big selling point for us as we machine a variety of sizes,” says Ashley. “Our solid wood drawer boxes measure up to 200mm wide and 13mm thick. Other furniture designs require a width of up to 260mm. The Cube 3 can work with working heights of 8-160mm and widths of 15-260mm where our old planer was restricted to a width of 210mm. This meant we would often have to join two pieces of wood together. A slight step in the join was all it took for one of my team to waste time sanding it down when they should have been moving on to the next job. We’ve easily saved more than 30 minutes per piece by not having to flush up a joint or put it thorough a drum sander and we’ve reduced labour.”
Due to its simple set-up, the joinery’s batch run times have been halved as oak draw boxes and Shaker door components are planed perfectly on four sides in a single pass. Intuitive operation has also made the machining of multiple sizes quicker and easier. “You don’t need to wait for a piece to exit the machine before programming the dimensions of the next piece and that speeds up the operation. The machine only actions the new size once the existing piece has been completed and because the process is automated, we don’t have any size discrepancies that, in the past, could have led to material wastage.
“To make life even easier, the Cube’s memory function stores common sizes so we don’t need to re-enter the same dimensions over and over again. And, if you think the laser is more of a gimmick than a functional feature, think again. It speeds up the measuring process no end.”
The variable feed speed of 6-12m/min means it’s easy to achieve a high-quality finish: “The finish you get off the machine is really nice,” confirms Ashley. “We tend to run most things through on the slowest speed to minimise any chatter. This ultimately reduces the amount of hand finishing needed and increases the volume of work we can complete in a shorter timeframe.”
When it comes to running costs, the plug and play machine offers excellent low-maintenance credentials: “There’s next to no maintenance required – just some regular greasing and a service from Weinig once a year,” says Ashley. “On the rare occasions we do need to do something, like change the reversible knives, it’s really quick. We would have had to spend half a day changing the knives on our old machine but we can replace all four sets in under 30 minutes thanks to the Cube 3’s EasyLock system. This doesn’t just save on labour, it gives us extra machining time. It’s a huge double saving.
“Like many workshops, we’re struggling to employ the right people but high-quality machines can compensate for the labour shortage, ultimately shaping your workforce while increasing productivity. The Cube 3 does this exceptionally well. I have a great team of experienced joiners. I don’t want their time being spent running or maintaining machines for long periods of time unnecessarily. The quicker and more efficient the machine, the better the outcome. If we get to a point where our machines are needing to be run more frequently, the opportunity to employ a lower skilled worker is now a viable option thanks to the Cube’s automated machining and ease of use.”
Ashley add, “As a small business owner, Weinig is only ever a phone call away. Weinig’s service throughout the buying process was quick and easy and the continual support and guidance we continue to get from their after-sales team is great. We have every confidence in our Cube 3 and equal amounts of confidence in Weinig’s staff. They know their products and they know what they are doing. This makes them a great manufacturer to invest in.”
https://cube3.weinig.co.uk
A timber products manufacturer in the Southwest of England has purchased a wood waste heater from Wood Waste Technology to save money on heating and waste disposal.
Face Edge Ltd manufactures bespoke timber products for retail and office refits. Its manufacturing operation is split across a number of individual units at its head office in Bideford, North Devon.
With the increasing energy bills, Director at Face Edge, Des Brown decided to look into other options to heat the workshop. He explains: “After some research, we realised that investing in a wood waste heater made good business sense, as our manufacturing process results in lots of wood offcuts. Feeding these offcuts into a wood waste heater would not only save money on waste disposal and prevent more waste going to landfill, but would also create free heating for the factory in the process, reducing our energy bills and benefiting our bottom line. “
The team at Face Edge ordered a WT10 wood waste heater, which was installed by Wood Waste Technology’s experienced engineers.
Des explains: “In today’s economic environment, businesses need to operate as efficiently as possible. Investing in the wood waste heater will help us to control our costs and save money, whilst maintaining a comfortable temperature in the workshop.” As the wood waste heater is perfectly located to serve all the individual units, including the offices and machine shop, goodsin-and-out areas, canteen, stores, assembly, materials storage and spray shop, the heat generated will benefit not just the people working in the business, but also help to offset the damp atmosphere in the cold winter months that can negatively affect any stored wood and spray-painted items.
Kurt Cockroft says: “Whatever the primary reason for purchase, whether it’s to generate heat, reduce waste disposal, or both - a wood waste heater is a cost effective and productive solution for companies that generate waste wood, and the investment can pay back in less than 12 months.”
Wood Waste Technology’s years of expertise in wood waste solutions have helped many companies reduce their waste disposal and heating costs. As well as offering site survey, design, manufacture, installation and on-going maintenance for new units, the company also services all types of wood waste heaters and supplies genuine spares up to 60% cheaper than other suppliers.
In addition, Wood Waste Technology is the UK official distributor for Gross Apparatebau GmbH, a German manufacturer of dependable, precision engineered shredders and briquetters, available in various size and specifications to suit all business applications.
ORDER A SAMPLE CONNECTOR!
Detachable furniture connector for 4 mm grooves
– Universal connector for all biscuit joiners
Connection of workpieces at every angle
Minimal connector breadth in materials from 8 mm
The Grand Opening of the new Technology Centre in Rimini takes place from 28 to 30 September. It is an opportunity to discover how SCM’s latest technological and digital innovations can assist the client with developing their business.
These include the innovative automated Cargo system for machining centres, the new Maestro Lab software and the advisory services enabled by Maestro Connect for a new standard of relations with the client.
SCM is confirmed as a solid group which continues to grow and innovate, investing in its industrial sites in Italy to increase its production capacity and further enhance its relationship with its clientèle. One clear example is the new Technology Centre created as part of an expansion and modernisation programme at the Headquarters in Rimini, which will be opened from 28 to 30 September 2023 with a Grand Opening aimed at companies and stakeholders from the entire wood-working industry at global level.
It is a space of 4,000 m2 which, for all intents and purposes, is the new digital home for woodworking innovation: every detail has been planned to offer the client the widest range of technologies and services possible and provide integrated, connected, flexible, more sustainable and optimised processes at each stage of secondary wood processing.
The event will be an opportunity to discover the latest solutions developed by the Group which combine the strong technological skill for the production of solutions for furniture, doors and windows, timber construction and artisan joinery with the development of software and services, to accompany the client at each stage of their production process. Some of the main new entries include those applied to machining centres, which will be the subject of a specific training event: Cargo, innovative automatic system for loading and unloading doors and panels, and the new CAD-CAM Maestro lab programming software. Cargo will be presented integrated with the morbidelli m200 pods & rails machining centre: it is a fully automated cell that requires no operator supervision, and it is unique in the market for its ability to continuously load and unload pieces in masked time while the machine performs drilling and routing operations. This exclusive solution allows for maximum efficiency by avoiding manual work phases and their associated costs and unproductive time, in addition to an unprecedented ease of use: both the machining centre and Cargo are directly managed with Maestro active HMI interface.
However, if it is true that the technology remains the heart of SCM’s experience, the software and services are increasingly the guarantor element of a continuous and shared relationship with the client.
Maestro lab is the new state-of-the-art CAD/CAM programming software for both the office and machine use. Intuitive and dynamic, it allows you to easily transform an idea into a finished product, thanks to intelligent and technologically advanced programming functions and more than 150 already integrated apps. So, from the office to the factory in a flash via an enjoyable and fast user experience.
The contextualised and continuous exchange of information from the machine to the cloud thanks to the IoT Maestro Connect platform means SCM can provide clients with rapid access to answers and specific advice which will support the operators and maintenance workers with their challenges and needs for autonomy when using, carrying out maintenance and programming the machine and software. On the subject of this, a specific area has been created inside the Technology Centre which will demonstrate how the data is transformed into bespoke assistance and advisory services of a proactive and predictive nature with a view to guaranteeing the client operational continuity thanks to the most evolved digital technologies and constant attention by the SCM Service team.
SCM continues to invest in the excellence of its customer service and, for the event, will open the doors to its new automatic storage for spare parts, Autostore, an innovation which has allowed SCM to increase fivefold the pick-up speed of the codes and increase the number of orders handled within 24h by 26%. All this with an energy consumption of less than 0.1 kWh per robot, confirming the Group’s focus on sustainability.
Sustainability which also means ergonomics and ease of use, made available to the operators of all the SCM machines by the renewed eye-M control panel, which makes the operator’s work easier and offers a modular programming and a higher calculation power.
FURNITURE INDUSTRY
The new SCM Technology centre will see flexible cells integrated with the unmanned AMR shuttles: for beam saw, gabbiani gt2 with robot for loading and unloading; for edgebanding, stefani cell E with gantry panel return system; for drilling and dowelling, morbidelli cx220 which can be used either with just the robot or partially manned. Also highlighted is a beam saw and nesting cell for batch 1 with flexstore hp automatic storage and robot to unload the finished pieces, small pieces and waste, a gabbiani p80 panel saw and a morbidelli x200 nesting machining centre integrated into the same storage. Worth highlighting for edgebanding is the new olimpic 500plus which can achieve even higher productivity, to machine edges in solid wood up to 12 mm and glue plastic edging using hot-air technology for a line of invisible glue. For assembly, worth pointing out is action e with a new loading and unloading system which greatly helps the work of the operator and the action p loading and unloading electromechanical clamp with a new HMI which allows work programs, production data and general database to be imported and exported.
SURFACE TREATMENT
The latest in the dmc eurosystem will be present for sanding and calibration for machining work on unfinished and painted panels. These include the new 15” eye-S control panel to handle all the functions directly from the touch screen; the new HMI Maestro active sand for ideal handling of the tool storage; the new planetary unit for an accurate finish on any surface.
Also on display are the new dmc sd 90 functions, a highly customisable solution, available in 12 versions, to guarantee the best results on solid, lacquered and painted wood.
It will be possible to request a specific demo at the Surface Lab at Villa Verucchio (Rimini) on the new dmc system with laser unit, for exclusive productions and three-dimensional scorings on parquet, wooden elements, mdf panels to be veneered, fibre cement panels and solid surfaces of any length.
In a link up with Superfici’s Technology Centre, there will also be demos of the latest new entries for painting and finishing like the compact xl sprayer for high capacity productions and a more efficient paint recovery system; the innovative Uv led polymerisation system for performances on a par with conventional Uv polymerisation, while keeping the advantages of led; Excimatt, the Superfici excimer technology for the finishing on different finished products and materials, capable of providing extra-opaque effects that are surprisingly smooth with no more compromising on the surface resistance; the Cartesian and articulated robots for painting windows and doors and panels, designed to guarantee production speed and continuity together with a very high level of precision and machining quality.
During the Grand Opening, you will have a chance to discover, in a world preview at the expanded production site in Rimini, the new system 9 integrated range for the production of windows and doors with an absolute new entry: the celaschi action bilateral tenoner. The SCM range stands out for the high speed at which it changes configuration and the extreme flexibility in handling the piece lengths. This makes it possible to produce up to 200 complete windows per shift, even with medium-small batches. The new celaschi action, in particular, allows for two elements of differing lengths to be machined simultaneously, making the most of the principle of machining with the transfer of the motors when the pieces are stopped. Some of the advantages include the presence of 4 electro-spindles, each one subjugated by an 8-position tool change.
Windorflex, the new automatic cell for complete windows and doors which optimises productivity by keeping a high flexibility and machining quality will also be on show at the plant in Rimini.
The automatic superset nt throughfeed moulder will be on show at the Technology Centre for the first time complete with SCM’s Maestro connect IoT platform, for an intelligent and connect production of profiles for windows, doors, staircases, matchboards and furniture parts.
The new entries also include Connexus fj: tenoner-mortiser that meets all the machining demands for different kinds of solid wood or coated MDF, including complex joins such as miter doors, face frames and French joints on cabinet doors and shutters.
SCM’s machines best suited to artisan work on show. Stand-alone as well as integrated solutions like those for beam saw, edgebanding and drilling of the Smart&Human Factory integrated cell dedicated to flexible and bespoke production from raw materials to finished furniture and enhanced by the integration with MES software.
Other new entries will include: “blade off”, SCM’s innovative safety system applied to circular saws which, thanks to the smart sensors, prevent accidental contact between the human body and the blade; startech cn k, compact 3-axis machining centre for routing of any kind, decorations, engravings, production of signs and 3D model prototyping.
The Decorative Panels Group is proud to be Europe’s leading supplier of decorative faced sheet materials, panel components and flat pack furniture. Julian, who heads the group design team has always been focused on designing and selecting products that can adapt to the varied needs of today’s consumers. Keeping an eye on trends ensure that products, from surface coverings to furniture ranges, meet the quality and style demanded by their customers for the retail market. Generating fresh and exciting product design, specifying what processes are required, suggesting easier solutions for furniture assembly, or recommending different substrates or surface finishes - these are all part of the design department service offering.
Vertical integrations across all three of our businesses enables us to supply the most flexible and cost effective solutions to our customers. Our integrated approach allows us to manage design, production, and logistics at every point of the process. This along with our diverse stock of surface materials from economical options to high end, exclusive surfaces, mean we are able to supply the many different market areas from manufacturers to retailers.
Matt Metallics within kitchens have been gaining ground and now feature among the top-selling décors. It has always been difficult to achieve consistency within the colour for metallics but one of our recent collection launches, Fineflex metallic surfaces do just that. We are also seeing even more surface textures coming through including woodgrains and more sculptural designs, perfect for bedroom furniture. Continuing the trend for matt unicolours we are introducing even more warm tonal palettes rather than the cool greys which have dominated for years.
With growing awareness and an increased drive to supply sustainable options for their own customers, we are seeing preferences for more environmentally friendly product solutions. As a fully certified FSC and PEFC business, raw materials such as board substrates and foil laminates are only sourced from responsible suppliers ensuring they are as environmentally conscious as possible. Our furniture business has recently achieved certification to the environmental standard ISO 14001. Showing that we are committed to continually improving our environmental footprint is an essential for us as a business and of course
for future generations. This is a process that started in June 2022, and is the first step in our 3 stage Group Certification.
What are the latest advancements in surface technology and what are the benefits to your customers?
Paper foil technology has come a long way particularly digital technology used in the creation of the artwork and the engraving of the printing cylinders, this combined with developments in lacquering technology have contributed to both the visual appeal of designs and the tactile quality of the surface. The surface resistance of paper foils has also increased with the majority of designs from our dpdecor range now being able to meet the FIRA 6250 and BS6222 severe use categories for kitchens, bathrooms and bedrooms- suitable for all applications except worktops. We are currently investigating options into digital printing for paper foils. This would give us more design scope and the possibility of unique surface patterns for customers with the added benefit of market testing new designs without committing to significant volumes of stock.
WHAT INTRODUCTIONS TO THE RANGE OF SURFACE FINISHES CAN CUSTOMERS EXPECT TO SEE NOW AND OVER THE COMING MONTHS?
As already mentioned, we have recently introduced a collection of Fineflex Metallic designs to our dp-specialist range. The PET surface is made with a percentage of recycled PET and the iridescent shimmer is visible throughout the pigment creating a luxurious finish to both the eye and the touch.
To meet the demand for matt unicolours our Serica Collection is constantly evolving with brand-new colours being introduced all the time. These are following the trend for warmer shades bringing a new energy to the collection.
Within our dp-limitless range of specialised and highperformance surfaces we have partnered with Rehau to offer their RAUVISIO Crystal and Noble Matt collections. Surfaces like these add a special touch of luxury to any interior. Look out for new colour introductions soon. All of these products and more are on display in our Group Marketing Suite.
If you’re looking to manufacture your own kitchen cabinets, where do you begin? For award-winning kitchen retailer, Stoneywell Kitchens, the process of bringing its complete manufacturing cycle in-house began with the purchase of a Striebig Compact vertical panel saw from TM Machinery.
“I’ve been designing kitchens for over 20 years and during this time, I’ve always outsourced my kitchen cabinets from large-scale cabinet maker,” explains Paul Durant, MD of Stoneywell Kitchens and Stoneywell Cabinetry. “For smaller businesses and start-ups, it makes sense to do this. I was getting a good quality product and reliable service but as my kitchen designs became more bespoke and demand for unique cabinet sizes increased, my supplier could no longer accommodate my needs. Massproduction cabinet makers are simply not geared up for what my business needs and as a result, I had to pay a premium and wait longer to get it.”
Paul and his team were not the only ones in this position: “We knew several kitchen fitters and independent retailers who were experiencing the same problem and needed a more flexible service that offered premium quality, bespoke sized cabinets more quickly.”
It was this that led Paul to start a second company, Stoneywell Cabinetry. “It was clear that I needed to gain more control over my production. I needed continuity and the guarantee of quality products that worked around my schedule. This could only be done by manufacturing my own kitchen cabinets,” explains Paul.
The shift towards cabinet manufacturing required the Staffordshire-based company to source new machinery. “I’m fastidious when it comes to researching products,” admits Paul. “I want to know everything there is to know about a product before I buy it. I started looking at sliding table saws but I soon realised that space in my 1800sqft workshop would be an issue and the team would struggle to handle and cut jumbo Egger boards easily due to their size and weight.”
A vertical panel saw seemed like the best option for the business. It not only fit into a 70sqft space but would cut 18mm-50mm thick boards quickly, accurately and cleanly thanks to a rigid, self-supporting frame, powerful 3.9kW motor and scoring unit.
“After reading about Striebig’s vertical panel saw range and watching videos of the machine, I knew I wanted one before I saw the machine in action at TM Machinery’s showroom,” says Paul. “Like my kitchens, Striebig is a premium brand and that comes at a price but my customers are buying a high-end kitchen in the region of £45,000 and expect a high-end finish and service to match. I had no intention of skimping on the machinery I was buying because I didn’t want it to impact on the quality of product I wanted to produce.”
Installation and training on a Striebig Compact soon followed. “It’s extremely simple to use,” says Paul. “My team has little-to-no experience using woodworking machinery but they picked this up extremely quickly. It’s second nature for them now to cut jumbo sheets to size on the Striebig before feeding each panel through an edgebander and performing horizontal and vertical drilling on a Blum MiniPress. It’s an extremely effective, streamlined production cycle that allows us to complete two kitchens a week and still have time to fulfil cutting lists for smaller companies looking for a high-quality cutting service.”
Paul explains, “After my own experience, the idea of offering smaller retailers a design consultancy and cutting service made complete sense and has proven to be a great revenue source. After all, I have become well versed in the design and manufacturing of my own kitchens purely because there wasn’t a more personal service available to me.
“Now, thanks to the introduction of machinery like the Striebig, I can deliver standard and custom cabinetry, cut-to-size in a concise timeframe for both myself and others. What’s more, the service I offer is human. In the past, if a part got damaged or a mistake was made, waiting for a replacement panel could delay the completion of a kitchen by three to four weeks. I understand how costly this can be. That’s why I offer a flexible service and help to rectify any problems quickly. It’s the service I always wanted and its proving to be very successful.”
Paul concludes, “By investing in a Striebig vertical panel saw, I now have control over my manufacturing processes and I’m busier than ever. The saw is certainly not running to capacity but it doesn’t need to be machining constantly to be a cost-effective addition to my workshop. It’s a great piece of machinery that requires very little maintenance. It’s well built, accurate and is helping me create beautiful, bespoke kitchens to an exceptional standard.”
The latest state-of-the art technology can generate electricity and heat from your waste including off-cuts, shavings and sawdust.
The pyrolysis thermal combustion unit produces consistent temperature hot gases at approx. 950ºC. These gases pass through an air to air heat exchanger from which the pressurised clean hot air powers a hot air turbine to generate electricity. The hot flue gases and hot clean air, still at approx. 450ºC, can then be used to generate heat through an air to water heat exchanger, steam through a steam generator or more electricity through an ORC (organic rankine cycle) waste heat electricity generator. The only waste, or bi-product, is biochar. Often referred to as “carbon gold” or “black gold”, biochar is a carbon rich material with compelling environmental benefits.
Normal thermal combustion of wood produces ash which needs to be disposed of ethically. Pyrolysis thermal combustion, or pyro-gasification, produces INDUSTRY biochar, which is a highly sought after product in various different markets including agriculture, water purification and construction. Top quality biochar can sell for more than £1,000/tonne.
A carbon credit represents either the permanent removal of a tonne of CO2 from the atmosphere, or the avoidance of one tonne of CO2 being emitted in the first place, through changes in energy generation or carbon capture. Biochar produced from pyro-gasification is recognised as a carbon sink, i.e. it captures or locks away carbon permanently. Biochar attracts CORCs, CO2 removal certificates, which can be traded on carbon exchanges or retained in the expectation of future growth. Grade “A” biochar currently attracts 2.75 credits/tonne.
There are compelling reasons to invest:
• Become self-sufficient for electricity and heat
• Massively reduce electricity bills
• Save money on fossil fuel heating
• Use manufacturing waste as fuel
• Sell the only waste/bi-product - biochar
• Earn from trading carbon credits
• Become carbon neutral
The demand for bespoke furniture items, and ever shorter manufacturing and delivery schedules puts significant pressures on furniture manufacturers. Recently, this has been exacerbated by delays in the supply of raw materials and components. Together, these issues have made the challenge of maintaining an overview and control of production increasingly difficult.
“Software solutions have become a critical element of furniture manufacturing,” says HOMAG UK managing director, Simon Brooks, “Without intuitive and powerful software it is almost impossible to provide the level of service demanded by customers.
“HOMAG has always been at the forefront of software development in the woodworking industry. From the early days, the company has invested heavily in the development of programs that improve the efficiency and performance for furniture makers. The latest software solutions, including SmartWOP, productionManager and productionAssist Feedback, integrate with the industry market leading woodWOP control software from HOMAG.”
SmartWOP – The simple way to design furniture Designing bespoke furniture items requires a software application that is not only easy to use, but also offers total design flexibility. The latest SmartWOP software from HOMAG is a simple ‘drag and drop’ solution that enables the fast and straightforward design of furniture items.
The individual components of a cabinet are simply drawn into a previously selected volume. As well as the standard rectangular shapes, special designs such as sloping ceilings or corner cabinets are also available. Existing furniture designs can be stored in a library and called up or changed at any time.
A ‘room planning’ feature enables the user to quickly design entire layouts for bedrooms, offices or kitchens. The beauty of SmartWOP is that a user doesn’t need to have any previous CAD knowledge or skills, it is that easy to use.
The opening of doors and drawers can be simulated, avoiding potential collisions with neighbouring components. The scope of delivery includes a large library with all common fixtures from the well-known manufacturers. Even customers’ own woodWOP components can be added to the furniture without any problems.
Visually, SmartWOP offers a realistic view of the furniture items being designed. An integrated material library with a range of designs for panel and edge materials enables the user to assign the corresponding material to each component quickly and easily. This gives a realistic representation of the piece even during the planning stage.
The interaction between woodWOP and SmartWOP offers
a special feature of selecting single parts of an individual item of furniture in SmartWOP and opening it directly in woodWOP. Processing steps can then be added and saved in woodWOP. And importantly, any changes made in woodWOP are transferred directly to SmartWOP and visualised there. So special parts and standard parts can be designed and then manufactured with ease.
The CNC programs and cutting lists for a HOMAG beam saw are generated directly in SmartWOP and contain all of the processing steps from both software programs. This unique CAD/CAM feature opens up a range of possibilities in the design stage and, above all, on the factory floor.
Production data such as CNC programs, parts lists for panel cutting, fixture lists or technical drawings are generated at the touch of a button. The data generated can then be passed seamlessly to the HOMAG apps and the digital assistant, productionManager and HOMAG’s nesting and saw optimising software.
As soon as a job has been transferred to productionManager, the parts lists and drawings can be accessed from anywhere. This means that all employees working on the job have access to all the job details, at all times. The days of issuing and then re-issuing paper based changes and revised designs to the shop floor are over. By equipping each employee or station with a tablet, the shop floor always receives the correct information for the job in hand.
Furthermore, by equipping the nesting machine and/ or beam saw with a label printer, the combination of SmartWOP, label printing and productionManager can control all downstream operations of the production process. SmartWOP can output the edge data required for each part and each edge, this is printed on the label along with a barcode. Downstream drilling machines equipped with a barcode scanner can then select the necessary programme automatically, saving time and money.
If at any time the operator is unsure about a part, he can always refer to the specific part data – in both a single or an exploded view – using the tools provided in productionManager. This saves time for both the operator and the production staff as it reduces the mistakes made on the shopfloor. The volume of reworks is reduced and efficiency is improved resulting in increased output and profitability.
The digital job folder in productionManager clearly shows the progress of every single part or the entire job, bundling all the important information about a job in one place.
The user can report single parts as ‘finished’ for each process step (e.g. sawing, CNC, edge, assembly). HOMAG machines with a connection to tapio have the option of
reporting production progress back to productionManager automatically.
With HOMAG’s optimisation software, the cutting patterns for the saw or the nesting patterns for the CNC machine are calculated automatically. The software can then calculate several alternative solutions simultaneously, for example, optimised for minimum waste, minimum material costs or minimum production time. The user simply selects the result that is right for them.
The productionManager job management system allows jobs to be displayed clearly and ensures that the job details are quickly and easily visible. In addition, the job status is displayed directly for each component and each item for both HOMAG and non HOMAG machines or stations. To give an even better overview of jobs, the job archive is in the navigation area of productionManager. One or more jobs can be moved from job management to the archive with just a few clicks. All information relating to a job, including information from production, is archived and made available to view at all times and for all employees. This makes job management clearer; for example, completed jobs are removed from this view and placed in the job archive. Entire jobs or individual parts can also be reproduced. For example, if further production is required, the selected job is
simply copied from the archive and is then ready for further processing.
The digital job folder can be integrated into any existing workshop environment with very little effort. No significant adjustments are necessary in the software landscape or in the machine portfolio. Although machine portfolios are usually made up of machines from different manufacturers, this is no obstacle to using the software.
In conclusion Simon Brooks said: “HOMAG has developed an all-encompassing range of software apps that make the control of furniture manufacturing easy and fool proof. All the details are kept up to date across the various digital apps so that everybody in the organisation always has the very latest information about a job.
“If you haven’t yet considered HOMAG’s software solutions now really is the time to do so. They will make a significant impact on the performance and profitability of any furniture manufacturing business.”
For a demonstration or more information on the market leading software solutions from HOMAG or on any HOMAG machinery, please contact Adele Hunt at HOMAG UK on 01332 856424.
James Latham, one of the UK’s leading independent distributors of architectural decors adds Pfleiderer’s premium Compact Grade (CGL) and High Pressure Laminates (HPL) to its signature Washroom Collection.
Available through James Latham in the UK and Ireland and perfect for any commercial, hospitality, leisure or education washroom project, Pfleiderer laminates are available in 40 different colourways, patterns, and textures, offering specifiers an incredible choice of visually appealing decors.
This exceptional level of style is also complemented by impressive performance attributes. Robust and durable, all laminates in the collection are able to meet the demanding, high-impact setting of a busy washroom.
Moisture, scratch, and stain resistant, Pfleiderer laminates achieve a very hygienic surface that is easy to clean. This results in lower maintenance and longer-lasting surfaces, futureproofing the washroom by slowing down the refurbishment cycle.
Going further, the range also includes Moisture Resistant Melamine Faced Chipboard* (MR MFC) and the innovative Melamine Faced High Density Fibreboard* (MFHDF) featuring a black core. This increased durability makes these two products particularly useful for high-footfall, frequently-used environments such as leisure centres and educational establishments.
And that’s not all. These surfaces’ inherent hygienic properties can be further enhanced with Pfleiderer’s proprietary MicroPLUS® antimicrobial surfaces. Available across the brand’s entire laminate portfolio, this added protection means the range can be specified for specialist applications in sensitive environments including healthcare, pharmaceutical, and laboratory facilities.
For fabricators, Pfleiderer laminates are also incredibly flexible. Their availability in four core substrates means they can be specified to the different performance requirements of myriad features across the washroom environment, from toilet cubicles and vanity units to IPS Systems and lockers; all within one product range.
Produced in many different dimensions, sheets can easily be cut to size or applied in their entirety, according to the specification requirement. This variety of formats, including half size sheets, means you can maximise yields and reduce waste and, in turn, the project’s carbon footprint.
Specifiers and fabricators are also making a sustainable material choice when they choose Pfleiderer laminates. Manufactured using recycled materials, all products have a circular lifecycle, delivering uncompromising results with minimum environmental impact.
www.pfleiderer.com/ www.lathamtimber.co.uk/products/washroom-collection
Powerful performance, extensive battery life and unrivalled ergonomics combined with all the advantages of the Combi-CB range - the new COMBi-CB70E electric multidirectional forklift is the most compact 7,000kg counterbalance truck on the market. Its ability to handle long and bulky loads maximises the safety, storage & efficiency of your logistics.
Features incorporated in the Combi-CB70E that greatly enhance operator comfort include excellent all-round visibility, a spacious gas-strut suspension cab, independent electric traction and our newly developed Auto Swivel Seat which intelligently swivels 15°in the direction of travel.
To find out how Combilift can help you unlock every inch of your storage space.
2 5 combilift.com
OVVO recently announced a strategic partnership with ProEdge Technology, a leading vendor in CNC insertion machines.
The PET CNC OVVO is the only machine in the industry with VERTICAL ROUTING CAPABILITIES on the bottom surface of the panel which guarantees accuracy of +/- 0.05mm of router depth by making the bottom of the panel a TRUE zero reference point. This machine removes the need for expensive floating head aggregates or a live Z-axis laser measurement device on a flat table router.
https://www.youtube.com/watch?v=1SMwmSXcz5w
Established in Ireland in 2014, the OVVO brand has gone from strength to strength, picking up numerous highly regarded industry awards along the way. Most recently awarded “Outstanding Furniture Accessories” award at Interzum-Guangzhou in April 2023 for the innovative connection system, the relentless quest to make life easier for people ensures that simplicity is at the heart of every new product: with each new product developed, the OVVO range has become more accessible to manufacturers, with the ability to be integrated into existing production processes, and suitable for a wide range of production capabilities.
All OVVO connectors are designed for high-volume, automatic insertion, and ongoing partnerships with leading software providers Cabinet Vision, TopSolid, iFurn, Swood and Cabinet Sense ensure that manufacturers can easily incorporate OVVO into their existing processes, and also into new product design and development.
All OVVO connectors can be installed into a variety of materials ranging from high-quality hardwoods to low-grade particle board, and our recyclable plastic means any waste is put back into the production of our product.
OVVO products are a range of cleverly engineered, awardwinning, invisible connectors that make joining wood simple. The connectors are installed during the manufacturing process so the end-user can simply click/push together cabinets, shop fit-out components, door frame assemblies or furniture without the need for tools, screws, or glues.
The result is an accessible, sustainable product that saves time, money and effort for consumers and manufacturers alike. Manufacturers can also benefit from significantly reduced shipping costs, as items can be shipped flat-packed. The latest addition to the OVVO product family is the incredible OVVO DOWEL (OD30) which is specifically designed to work in standard drill patterns. The OD30 is inserted into the panel without any glue to form a permanent joint in 15mm panels and above. These new connectors make it even easier for manufacturers to incorporate OVVO into their standard processes, saving time and money by eliminating glue and case clamping time. No additional equipment or capital needed to deliver tools free assembly products to the end customer.
This new self clamping, glueless, invisible OVVO Dowel (OD30) is designed for connecting cabinet parts and all types of furniture using standard drilled holes on BOTH sides of the joint, thereby simplifying the panel processing operations while continuing to provide all of the benefits of OVVOs’ proven tools-free assembly methodology.
OVVO works best in boards >12mm thickness and is available in a range of sizes to perfectly match your requirements. All connector sizes are available in both PERMANENT and RELEASABLE options, extending the range of materials and opportunities to inspire creative design and innovative development.
Consumer demands are shifting more and more towards convenience and sustainability.
OVVO helps you meet those demands and give your products a competitive edge. Our team is on hand to support your switchover to OVVO and help you take the next step of innovation.
Furniture Assembly made simple –no need for tools, glue or screws.
SIMPLY PUSH, CLICK AND CONNECT.
With less than a year to go until Materials & Finishes Show (formerly W Exhibition) returns to the NEC (May 19 - 22, 2024.) We catch up with event director, David Todd to find out how he’s settling into his new role at the helm of the reimagined show and explore how preparations for the May event are shaping up.
David, you’ve had a few months to find your feet and familiarise yourself with the furniture manufacturing and joinery industry. How’s everything going?
I’ve worked in exhibitions for over 15 years, working across a variety of sectors for industry shaping events around the globe so I’ve not found the move across to Montgomery Group’s ‘design and build division’ too dissimilar to my previous roles. What is very apparent is the abundance of passion, enthusiasm and the genuine appetite that there is for us to continue to deliver an event platform for the sector and I’m excited to be part of bringing Materials & Finishes to market next May.
How is the floorplan shaping up for Materials & Finishes Show next May?
We’re in a really strong position as we move into September, with a good mix of legacy brands that people will be familiar with from the W Exhibition lineup, as well as a raft of completely new brands who have joined the lineup in recent weeks. What’s interesting is the broad mix of brand products
and services that the Materials & Finishes Show 2024 lineup presents, with which includes the likes AES, Fen, Quin Global, Amicus and Machinery Services to name a few. The full exhibitor lineup, which is growing weekly, is available on our website - www.materialsandfinishesshow.com.
Visitors will still be able to see the running woodworking machinery that they expect at the show, but this will be significantly enhanced with a wide materials and finishes offering. The KBB market is a key growth area for us, with brands such as Hanex signing up to exhibit in recent weeks.
We’ll also be growing the ‘elements’ section of the show, which will include brands such as our relaunch partner, Hranipex. To have secured the support of such a forward thinking and ambitious company as a relaunch partner is a real coup for the show and will perfectly complement the machinery and materials brands who are already part of the exhibitor lineup.
There’s a long gap between the incumbent W Exhibition in 2018 and the new Materials & Finishes Show next May. What changes are you making and how is the campaign shaping up?
I think it would be naive of us to say that the run into the relaunched show hasn’t been challenging - from Covid delays and the negativity that this brought, through to an
ever changing industry landscape. The main pain-points from the previous exhibition have been very simple and quick fixes for us and we’re now in a very stable timeline, with dates secured for Materials and Finishes Show in 2026 after our return next May. This has allowed us to focus our attention on growing the event. The success of any trade exhibition hinges on the quality of the people in attendance, so this is by far our top priority. Building and enhancing our data, partnering with new associations and media partners to ensure we are attracting the right people to do business.
You’ve mentioned new brands joining the lineup, what else can people expect to see when they visit the show next May?
There are so many new and exciting features in development in the background. We’ve been working really closely with our community to ensure that Materials & Finishes Show really delivers above and beyond expectations next May.
Alongside new show features, such as the CPD certified learning programme, live demonstration zone and hosted buyer meetings programme, we are revising the show opening hours to include a new late night feature on Tuesday (May 21, 2024) of the show. This will allow an extra opportunity for out of hours networking, and extended hours for people to attend out of hours, which we know from experience works well on B2B trade shows.
If there are brands out there who haven’t yet joined the lineup for Materials & Finishes Show 2024 but who are perhaps considering joining, what would you say to them?
If you work in the joinery and furniture manufacturing industry and are involved in the wood or timber processing chain, you need to be part of Materials & Finishes Show 2024.
Nothing brings a brand, its products or services to life like being able to see, touch and speak to the people behind them face-to-face at a live event.
Materials & Finishes Show will bring together every corner of the joinery and furniture manufacturing industry. If you are involved in the wood or timber processing chain and are looking to connect with furniture manufacturers, joiners, carpenters, machinists and installers - Materials & Finishes Show is the perfect platform for you.
People can either contact me directly, or our Commercial Manager, Ranju Singh if they have an enquiry about exhibiting. Visitors can see what’s on offer, including our list of exhibitors, via the new website: www.materialsandfinishesshow.com.
For more information: please contact Materials & Finishes Show PR & Comms Manager, Jess Hardisty (jess.hardisty@montgomerygroup.com) or 07871544330.
Located in the Appalachian foothills of Virginia, Meherrin River Forest Products produces over 40 million board feet of green and kiln dried lumber each year for its global customer base. Business is growing month by month across the five sites in Virginia and North Carolina and the company aims to double its exports within the next five years. The streamlined journey of products from sawmill to container and finally to ship is therefore a key issue for President Don Bright, who has found a piece of equipment that has dramatically increased efficiency when loading a consignment into a freight container.
Don came across the Combi-CSS Slip-Sheet during an event at the Virginia Forest Product Association when Combilift product Manager Patrick Keenan introduced him to this automated and very fast method of stuffing containers. “I had been planning to get some new forklifts in for this task, but realized the concept, design and performance
of this device was far superior in terms of time and use of manpower and resources,” he said.
The Combi-CSS is a low level free-standing platform with a dual-directional motor-driven pulling mechanism, on which a steel sheet rests. This enables a full load of product to be prepared behind the container before the four hydraulic cylinders pull the sheet forward into the container. Once fully loaded, a hydraulic rear barrier gate swings across the container opening and holds the load in place while the sheet is slipped out from underneath. The machine can load containers in lengths between 6.1m / 20 ‘feet and 12.2m / 40 ‘feet and has a capacity of 30,000kg/ 66,000 Lbs
This has many advantages over the traditional “push-pull” method using forklifts, as Don has discovered since his Combi-CSS has been in operation. “What used to take a good half an hour per container and involve two forklifts and 2 operators can now be done in less than half the time, with
half the resources – freeing up personnel and equipment for use elsewhere on site.” A further major advantage is the much lower risk of damage to the product as well as the container during loading. “This improves quality and therefore enhances customer service and is also a major advantage when you are dealing with very valuable lumber,” said Don.
Meherrin River is unique in that it is the only North American forest products company to have an on-port facility, and having the Combi-CSS based within the Richmond Marine Terminal means that drayage charges are not applicable on each container that is loaded there. This represents substantial cost savings and also gives the company a competitive edge as half of the current weekly tally of around 20 containers is loaded with lumber transported from other Meherrin sites. All personnel here are trained to use the Combi-CSS and they find it very easy and straightforward to operate.
Don has been impressed with the build quality: “it’s a tough and heavy duty machine built for an industrial environment and what’s more it takes minimal service to keep it running smoothly. It’s cheaper to maintain than the second forklift I was originally thinking of getting too.” He is also full of praise
for the people at Combilift who he believes are as good a team as he has ever come across. “They are passionate, capable and totally committed to getting things 100% right for the customer. Combilift’s drive for innovation is also incredible. I visited the global HQ and factory in Ireland a few weeks ago as part of a trip to Europe for a trade fair and from the CEO down, everyone is focussed on not just building trucks but on getting a better understanding of the challenges facing customers and the solutions they really need. At Meherrin we believe we are a great company built around good people and the same can be said of Combilift.”
By the end of the year the plan is to be loading 75% of containers within the on-port location and to offer this service to other exporters in the region. The first CombiCSS has been an integral part of the company’s growth plan and Don is hoping that business will continue to expand to justify getting a second unit for Richmond so that 100% of Meherrin’s products can be conveniently and cost effectively loaded port-side.
www.combilift.com
http://meherrinriver.com
Our two new catalogues will be published in September!
In these reference books you will find our entire product range and numerous inspirations for your new projects. Of course, they are also available digitally in the download centre of our online shop.
For further information, go to www.ostermann.eu and type in SERVICE, DIVERSITY AND SPEED - THAT IS OSTERMANN. #catalogues
Since first importing hardwoods into the UK in 1757, James Latham has been a longtime champion of the British furniture industry. So, when Rycotewood College (Rycotewood), Oxfordshire, one of the country’s top institutions for furniture-making vocational training, approached them to support its student competition for the second year running they were delighted to accept.
Building on the success of 2022, this year also challenged the students to focus on the captivating dual concepts of colour and curve within the overarching theme of storage.
To assist the students, James Latham donated a quantity of HIMACS and Valchromat, providing them with the opportunity to demonstrate their skills and initiative when working with these non-traditional materials to meet a challenging creative brief.
Following a 10-week entry period, in which 12 Rycotewood Degree students participated, judging took place ahead of the College’s end-of-year celebratory show, on Monday 18th June, where the winning and commended entries were announced.
This year’s competition proved to be a showstopper, with a collection of remarkable pieces that perfectly showcased the students’ ability to adapt, experiment, and transcend traditional furniture design.
Joe Fortune, who won the HIMACS category, created a visually striking and artistically ingenious shelving unit for indoor plants. Pushing the material to its limits, the smooth, delicate twists within the piece, seamlessly joined, demonstrate the thermoformable nature of the solid surface and its ability to retain its original rigidity post-heating. He went further, using CNC to cut out a series of holes within the curved pieces to evoke the cellular structure of a leaf.
The judges were particularly impressed with the range of different skills displayed. From the seamless curvature, invisible joints, and extensive cut-outs they felt it demonstrated technical mastery without compromising structural integrity; a remarkable example of how HIMACS can surpass initial expectations, creating visually stunning and functional features.
Commenting on working with HIMACS, Joe said, “HIMACS’s ability to be heated and twisted without visual or structural compromise proved the perfect material to achieve what was, from the outset, a very ambitious design. The results speak for themselves. Personally, I was pleased with the
seamless joins I was able to achieve, creating an appealing visual continuity within the finished piece.”
Unparalleled Versatility for Valchromat
Benjamin Scott was the competition’s other winner, using Valchromat to breathtaking effect in a sophisticated storage cabinet. A stunning fusion of yellow and grey Valchromat with oak, the modern day parquetry on the cabinet has over 1,000 precisely arranged, extensively sanded, and polished Valchromat pieces, forming elegant herringbone-patterned panels, showcasing Ben’s incredible attention to detail.
The judges felt the piece truly exemplified the creative potential of Valchromat, representing a massive leap forward compared to its use in the previous year’s competition. Importantly, they felt it encapsulated Rycotewood’s growing proficiency in working with the material.
As Benjamin explains, “Valchromat’s superior sanding and finishing capabilities are remarkable. It outshines alternative materials, effortlessly achieving a flawless surface. Additionally, it retains sharp edges when shaped by hand, offering a more refined look.”
RAISING THE BAR
Emma Harris was also commended for her chic drinks cabinet, which combined black HIMACS and solid oak for a cool, contemporary piece of furniture. Attractive, yet eminently practical, the addition of a mirrored interior adds an extra touch of luxury.
The judges praised its refinement and harmonious combination of textures and colours to achieve a cohesive composition. They also felt it demonstrated Emma’s keen understanding of HIMACS’ versatility, and its ability to complement and enhance other materials.
Commenting on the success of the competition, Josh Hudson, Furniture Lead at Rycotewood, says, “We’re thrilled to witness the tremendous growth of the students in their ability to work with new materials, as demonstrated through the ambitious and captivating pieces submitted for this year’s keenly-anticipated and hotly-contested competition. Partnering with James Latham has been fantastic and our ongoing collaboration allows the students to push their creative boundaries and showcase their talent to the full.”
Aside from the winning and commended projects, all other submissions showcased the massive potential of the materials donated. To see them all, https://youtu.be/XETth10bMqk
To find out more about Rycotewood School and its work https:// www.rycotewoodfurniture.co.uk/
For more information about HIMACS and Valchromat, as well as James Latham’s wider material portfolio, https://www.lathamdigitalshowroom.co.uk/
The JLA Fire & Security family now incorporates some of the UK’s most widely known and respected names in fire safety. Headquartered in Ripponden, West Yorkshire and formed in 2019, the division employs over 1000 people. Unable to find a consistently premium quality fire door supplier, JLA opted to manufacture its fire doors inhouse.
“Our reputation is built on keeping people and premises safe when fire strikes, and high performance fire doors are one of the key elements that help us achieve this,” enthuses JLA Fire & Security’s National Operations Manager, Chris Fox.
He continues, “The initial machinery the business purchased wasn’t ideally suited to the manufacture of fire doors. As the department grew, we recognised the need to invest in equipment that was more advanced and could do everything required to produce first-class fire doors. “With the old machine we had to do much of the routing for locks and finishing by hand. This was not only timeconsuming and inefficient, but also prone to human error. To ensure we found the best machine for our needs now and in the future, we asked five companies to tender for the supply of the new CNC machining centre.
“When the responses came back HOMAG’s was outstanding. I’ve always been well aware of the reputation HOMAG has in the market, so it came as no surprise that its sales team was so professional. From the way they conducted the initial site visit, through to the recommendations they made and the pricing for the package, everything was totally professional.
They never once tried to over-sell us with options we didn’t need and they never talked-down the competition; it was very refreshing to deal with a company with similar ethics to our own and it gave us tremendous confidence in them as a potential business partner.”
“HOMAG eased the potentially challenging task of specifying the machine. We told them what we wanted to achieve with it, and they came back with a couple of options including a tandem load model.
“In the end we opted for the 5-axis version of the CENTATEQ P-110 CNC machining centre with the woodWOP control software and tapio (which opens up a host of digital solutions including faster service for machine issues, live video diagnostics and cost savings on maintenance).
“The package we agreed with HOMAG included comprehensive training for our operator and a trainee both of whom attended a week-long course at HOMAG UK’s Castle Donington head office. This was extremely thorough and gave our people the tools to maximise the features of the P-110.
“The new CNC enables us to manufacture our fire doors quicker and to a much higher quality than before, with no need for hand-finishing. This has freed up skilled team members who can now be employed more effectively elsewhere in our factory.”
“Before we could have the new CNC installed we had to have the old machine dismantled and removed from site. There were a few delays with this process, but to their credit the HOMAG installation engineers were able to claw back the lost time to ensure the new CENTATEQ was in place and commissioned on time.
“Since it has been operational we have been able to stand toe to toe with any other manufacturer of fire doors in the country. Given the throughputs we are achieving and the potential we will have when a new HOMAG edge bander arrives, we believe the CENTATEQ P-110 will have paid for itself within 18 months.”
“Although the CENTATEQ P-110 takes up a bit more space than the old machine, for its capabilities and power, it has a relatively small footprint. This was a key consideration for us as our manufacturing facility is only 1,832 sq. ft.
“The old CNC and edge bander limited our production capacity to six doors a day. With the new CENTATEQ machining centre and soon to be installed HOMAG edge bander we will be capable of manufacturing 80 doors a day. Not only that, but the quality of those doors will be much higher and more consistent than before.
“Our new set up is already enabling us to attract bigger customers because we are confident we can meet the higher volumes and premium quality they demand. That is only going to improve further once we have the new edge bander in place,” concludes Fox.
Ahmarra Door Solutions manufacture performance architectural doorsets across all sectors including education, commercial, hotel, airport and luxury residential. They specialise in manufacturing performance doorsets for projects where complex fire resisting, acoustic and security requirements exist including timber glazing bead cassettes for fire rated doorsets and timber panel mouldings for their range of bespoke Artisan Panel Doors. A combination of precision machinery and fine craftsmanship enables Ahmarra to meet the highest quality, performance and certification requirements. One of these precision machines is the Hoffmann MS 35-SF combination double mitre saw and router.
As an absolute innovation the Hoffmann MS 35-SF delivers two clean precision mitre cuts without break-out, to an exact length in one machine cycle. When both pieces are to be joined together or in a frame, then they can be prepared with one or two dovetail slots in precise positions in the cut faces for jointing with Hoffmann Keys. Suitable for workpiece sizes maximum 90 x 90 mm. The machine can be fitted with router cutters for processing Hoffmann Key sizes W-1/2/3. Ideal for cutting profiles for glazing beads, cornices, plinths etc. in wood, aluminium or plastic at 45°. It can also be used solely as a Double Mitre Saw. The technology, developed by Hoffmann for damping vibrations of the blades ensures the high precision cut of the MS 35-SF and the almost vibration free running of the machine ensures that no further work is required prior to joining. The range has now evolved to include the MS40-SF. A larger saw blade (400mm) increases the cutting width to 105mm and a new waste ejector automatically removes off cuts at the front of the unit. Automatic router positioning is also available via NC axis and touch screen adjustment.
Tim Doran – MD stated: “Our Hoffmann MS 35-SF has been extremely reliable and efficient. Over the many years of manufacturing, many of our machines have required replacing and updating as expected, but the Hoffmann MS 35-SF has continued to manufacture a precision product with only routine maintenance required, and we see no reason to replace it in the near future. This combination
machine not only cuts the perfect mitres but simultaneously routers the dovetail slots for the Hoffmann Keys. Ahmarra have a long relationship with Hoffmann, and our current Hoffmann MS 35-SF has been in operation for over 20 years, and still performs with the expected accuracy and precision that it did the day it was installed”
Ahmarra works very closely with architects and interior designers to meet their requirements, allowing flexibility in design while retaining comprehensive fire certification in accordance with Building Regulations. Hoffmann Dovetail Keys are all accredited with FD30 / FD60 ratings. As a leading manufacturer of fire door solutions, they believe in maintaining the traditions of their craft by preserving the skills and value of time-served, traditional bench joiners, whilst utilising the very latest technology in design and production methods. This way, their customers get the best of both worlds.
“Our many years’ experience of manufacturing timber doors has led us to produce a number of sector specific product ranges to include Education, Hotels and Panelled doors. We specialise in working with clients who recognise the importance of developing doorset standards throughout their facilities. Significant client cost savings can be made by eliminating the need to redefine doorsets and ironmongery for each new project. We offer intelligent advice on how to make this process cost effective, simplifying what can be a very complex issue.”
A similar principal is held by Hoffmann Machine Company Ltd. When specifications such as optimization, rationalization and cost savings are essential aspects of your production, then help can be found in our engineering services dept. We can develop a package of measures that will result in a machine, designed to your requirements. Offering efficiency, quality assurance and cost minimization.
T: 01524 841500
E: info@hoffmann-uk.com
www.hoffmann-uk.com
Tiflex Ltd is a British company that has been manufacturers of cork and rubber bonded materials for over 70 years.
The company specialises in the design, manufacture and distribution of industrial rubber products, including rubber sheeting, matting, and gaskets. Tiflex’s products are used in a wide range of industries, such as construction, transportation, marine and agriculture. The company has developed a reputation for high-quality products, which are designed to be durable, reliable and cost-effective. Based in Cornwall and employing 160 people, Tiflex has four divisions TRACKELAST, TREADMASER, TICO and Oxbridge cricket balls and has a strong presence in the UK market, as well as a growing international customer base. Tiflex has a strong commitment to quality and the company was accredited to ISO 9001 in 2015 and offers custom design and manufacturing services, which allow customers to create bespoke products that meet their specific needs.
Historically, the company faced challenges in manufacturing shaped parts due to the high cost and low production rates associated with traditional moulding methods. As the business expanded, they recognised the limitations of this approach, particularly for bespoke and low-volume parts. The company sought innovative solutions to improve production capabilities and cater to a more diverse customer base.
In 2007, Tiflex decided to adopt AXYZ routers, part of AAG, a leading global manufacturer of CNC routers and waterjet cutting solutions, focused on helping companies of all sizes improve their automation. With over 30 years of experience, they have built and installed thousands of CNC routers and waterjet cutting systems across a wide array of industries. Tiflex started with a router to revolutionise their production process and offer a broader range of cutting services to their customers. The success of the first router led to the acquisition of a second machine in 2013, enabling the company to enhance productivity and efficiency significantly.
The primary use of these automation machines was cutting rubber sheets and pads into specific shapes. Over time, the scope expanded to include cutting large volumes of plastic sheets as well. Although the routers were occasionally employed for cutting small metal parts or moulds for internal use, this was not their primary function.
“The integration of AXYZ routers significantly improved Tiflex’s productivity and efficiency,” said Matthew Orton Operations Director at Tiflex Ltd. The routers allowed the company to cut parts much quicker than traditional moulding methods. This improvement in production speed opened up opportunities to offer a wider range of products, which was not feasible before due to limitations in moulding sizes.
The implementation of AXYZ routers required some changes for Tiflex. Employees needed to learn how to operate the
machines and understand their capabilities effectively. Additionally, cutting a diverse range of materials required learning optimal settings and techniques for each material. With the invaluable support and advice from AXYZ, Tiflex made these changes and fine-tuned their processes for improved productivity and efficiency.
The use of AXYZ routers led to substantial cost savings for Tiflex. The high cost of moulds for low-volume parts was eliminated, making it feasible for the company to produce a broader range of parts at lower volumes.
This capability enabled Tiflex to secure orders that were previously unattainable, ultimately contributing to increased profitability. With AXYZ routers, Tiflex achieved greater accuracy and precision in cutting, resulting in significantly improved product quality. The company could offer a wider range of products with shorter lead times, meeting customer demands more effectively.
“Employees at Tiflex welcomed the introduction of AXYZ routers, as they significantly improved production techniques and offered solutions to customer problems. The machines have become a key part of the company’s operations, and more staff have been trained to operate them across all shifts, including the night shift. The introduction in 2022 of the WARDJET waterjet has opened up even more markets enabling us to cut extremely small product with precision and accuracy would not be possible with more traditional cutting methods. We are able to produce one offs or volume runs quickly and efficiently. We were blown away by with the results that the WARDJET waterjet cutter delivered,” said Matthew Orton Operations Director at Tiflex Ltd.
To ensure smooth operation, Tiflex invests in annual service plans offered by CNCSHOP the after-sales service and OEM supplier of consumables, spare parts and upgrades for AXYZ CNC routers and WARDJet waterjets. The company remains open to future integration of automation in their processes. Another AXYZ router is being considered to increase cutting capabilities for larger pieces of material, demonstrating Tiflex’s commitment to continuous improvement and innovation.
The adoption of AXYZ and WARDJET machines has been a transformative journey for Tiflex. With the routers and waterjet, the company has achieved higher productivity, cost savings, and improved product quality. By embracing automation, Tiflex has positioned itself as a leading player in the manufacturing industry, catering to a diverse customer base with a wide range of products and cutting services.
The future holds great promise as Tiflex explores additional automation opportunities to further enhance their production capabilities and maintain their commitment to delivering top-quality products and services.
T: 01579 320808
www.tiflex.co.uk
AXYZ: www.axyz.com
WARDJET: www.wardjet.com
E: enquiries@axyz.com
T: 01952 291600
Our unique and flexible drop-down vacuum cups are the most powerful upgrade for your CNC machine. Just drop the vacuum cup in the desired position for maximum hold of the work piece.
Tooltec vacuum cups feature the unrivalled vortex acceleration technology.
Tooltec’s vast range of powerful vacuum cups to fit the following CNC machines:
SCM
Homag
Biesse
Masterwood
Felder
Holzher
Unrivalled power for your CNC work station.
William Hughes, a specialist manufacturer of springs and wire components, has adapted quickly to a serious increase in demand from a tier-one automotive seating customer, thanks to a major new investment in robotic welding cells and associated tooling and fixtures.
The investment at its plant in Bulgaria is in reaction to the ramp up in popularity for a recently released sports utility vehicle (SUV). Currently selling beyond production capacity, the vehicle is available with multiple seating configurations, so the demand for seating frames and hardware has seen commensurate growth.
According to Ben Cox, Manager of William Hughes Bulgaria: “The output for the various seating modules and formats is now about 30% higher than the original anticipated peak production plan. And with the automotive industry relying on just-in-time delivery for primary modules, such as seating, we knew that we had to pull out all the stops to ensure our tier-one customer would not disrupt production.
“The seat frame for this model is unusually heavy duty –being a welded-wire assembly designed to complement the vehicle’s impressive off-road reputation,” Cox continues. “The new welding cells, Fanuc robots and additional tooling have enabled us to meet our delivery quotas for this model and, indeed, other projects in the future, which will also benefit from the added efficiencies we can bring through automation and fabrication at scale.”
Demand for the new SUV is showing no signs of slowing so there is the potential for additional investment in the future. “The Bulgarian factory is ideally placed to satisfy the demands of the Eastern European OEMs,” Cox concludes.
“With hand-to-mouth delivery, being on their doorstep – or at least in the same neighbourhood – removes many of the logistical hurdles. And from a technological standpoint, investment like this, and in wider capabilities such as spotwelding for back frames, puts us in a perfect position to satisfy a huge array of OEM demands.”
The investment in its Bulgarian facility cements the company’s commitment to its customers and Eastern European operations. Indeed, the plant is already being asked to investigate newer seating variants, with its customers being confident that William Hughes can quickly ramp up and scale production to cater for any demand level – now and in the future.
Two new Ostermann catalogues will be published in September. The comprehensive reference books Creative Design [CD] and Edgings | Practical Processing [PP] show the entire diversity of the Ostermann range and offer inspiration for new projects.
As in all creative professions, an integral part of a furniture maker’s work is to be regularly re-inspired. Customers therefore like to pick up the Ostermann catalogues: when you leaf through the several hundred pages of the reference books, you are bound to find new products or ideas. As a service and inspiration for their customers, the company has worked hard to launch a new edition of the strong tandem. In addition, both reference works can also be found digitally at the download centre at www.ostermann.eu.
As before, the catalogues are divided based on the two elementary steps in furniture making - the first being the design and the second the practical processing in the workshop. Accordingly, the new editions are titled Creative Design (CD for short) and Edgings | Practical Processing (PP for short).
The newly launched grey catalogue is called Creative Design [CD]. It includes design items such as handles and furniture luminaires or surfaces for furniture and wall design. It is ideal for presenting the manifold design options in the showroom or on site at the customer’s premises. In the “Made to Measure” section, you can learn all about the different customisable elements that Ostermann delivers according to personal specifications.
The new red catalogue is called Practical Processing [PP]. Here you will not only find Europe’s largest immediately available range of edgings and lots of background information on “everything edging”, but also the matching workshop supplies, such as adhesives and cleaners. What is the ideal processing temperature for my adhesive? Which surfaces can I clean with the product? Such detailed information makes the new catalogue a perfect companion for the workshop.
First of all, there are many new products in both catalogues. In the [PP] catalogue, for example, the new linoleum edgings make their first appearance. The continuously growing range of profiles is also to be found here. In the [CD] catalogue, readers can expect new surfaces for naturalistic wall design, such as moss. In addition, table fittings and furniture castors are also included for the first time. Also worthy of mention are the inspiration pages in the Creative Design [CD] catalogue, where various spaces were designed using Ostermann products. In short, there is a lot to discover!
Daniel Walker started his journey into traditional joinery at the age of 15 as an apprentice with a small local joinery company. Making traditional joinery including box sashes, staircases, windows, doors and cabinets Daniel set up his own business, DW Interiors in Godalming, Surrey around 10-12 years ago.
A small joinery company with 2 bench joiners yet Daniel is able to compete with much larger companies due to investment over the last 18 months in new software for the workshop. Previous experience of Joinerysoft’s Joinery Management Software (JMS) at other joinery manufacturers made it inevitable that Daniel would consider JMS for his own business once he realised that quoting was taking too long.
Joinerysoft’s Joinery Management Software has been a market leader in the joinery industry for nearly 20 years helped by continuous development and an expanding product offering. With a range of products targeting all areas of the industry, Daniel chose to purchase Joinerysoft’s standard JMS, on a rent to buy option, making it affordable with fixed payments and avoiding the large initial outlay that you might expect.
Previously quoting by hand, Daniel confirms that, “JMS quotations look far more professional than our previous description of works. Everyone loves the new drawings which confirm all the details, including side hanging”. He adds, “We’ve won more work and our windows and doors business has grown significantly since having the software”.
Daniel’s ability to quote quickly has made such a difference. He says, “I can sit in a client’s house and price as I go around the site. Before I leave I can send the client the quote, there and then.” Alternatively, when quoting back at the office it takes him only 3 to 4 minutes with all the information in front of him and JMS automatically adds all the terms and conditions, and provides confirmation of order paperwork for clients to sign and return.
One of the main bonuses for Daniel is the time the software has saved him throughout his business. As soon as the quote has been prepared all other workshop requirements and material ordering is ready to go at the press of a button. “JMS is so accurate that the same day I win the work I can print the glass
order, ironmongery and timber orders and workshop cutting sheets. Everything is there ready to go straight away. That is the biggest benefit; there is no down time, no guesswork,” he says.
With customisable reports, JMS enables joinery manufacturers to select which reports are most suitable for their business and choose what is displayed, meaning you can print cutting sheets easily for different areas of the workshop or even fitting sheets for the fitters on site, so they know exactly what they are doing and each window’s placement on site.
Initially concerned about how he would fit in installation and training on how to use the software while still running his business, Daniel was pleasantly surprised to find that the regular small bite sizes of online training made it easy for him to fit it in. It also provided him the time to add his own data to the software in between training sessions. He admits it was quite daunting letting the software take over all his quoting but he says the software has proved itself and he is confident of its accuracy. He adds, “the Joinerysoft support team is friendly and knowledgeable. Having a time served joiner on the end of the phone means we speak the same language. With continued support I’m still learning ways to speed up my business”.
After 18 months using the software, there have been so many benefits for his business, including winning work, increased efficiency and improved profit margins, that Daniel
would not go back to how he did things before. He says, “JMS has freed up so much of my time. It’s made us more efficient as a company and allowed me to fall back in love with joinery again.”
He adds, “I believe software is important because efficiency is the key to success. JMS has helped the business to grow. I’d tell others considering buying JMS, ‘Just buy it. You won’t regret it. It is really advanced software for the smaller joinery company, or in fact any sized joinery company’”.
Not only do we stock Reactive HotMelt Adhesive for Prole Wrapping and Edge Banding Applications.
We also stock Nordson compatible spare parts for EB 60V Slot Nozzles , Heated Hoses , Platen Seal for BM 200 and BM 20 Systems and generally anything to do with Prole Wrapping!
We also supply Slitting Blades, Moulder Wheels, Heat Guns, Elements and Brushes for Heat Guns
We have one of the largest stocks of Wrapping Wheels in the UK ! Stocking 30 different types and 8 different shore hardness! So literally thousands on stock at all times!!
With the SAWTEQ S-320 flexTec, HOMAG revolutionises cutting for batch size 1 production and allows highly flexible order-based or customer-specific production. The innovative cutting cell is designed specifically for processing single panels and completely redefines the flow of parts — whether as a standalone machine or an integrated solution. The SAWTEQ S-320 flexTec allows fully automated processes and unlimited recuts. This model can also operate completely autonomously over long periods allowing man power to be used elsewhere in the production process, freeing up resources for an extremely efficient work flow