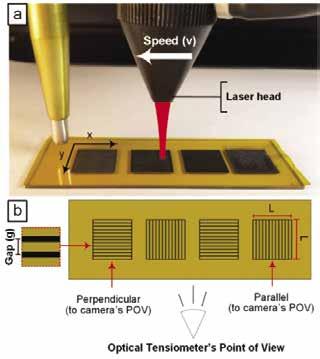
11 minute read
Laser-induced nanocarbon formation for tuning surface properties of commercial polymers
Angela J. McComb a , Moataz Abdulhafez a and Dr. Mostafa Bedewy a a NanoProduct Lab, Department of Industrial Engineering University of Pittsburgh, PA, USA
Angela McComb
Angela McComb is a sophomore undergraduate researcher (SSOE Fellow) in the Industrial Engineering department at the University of Pittsburgh. She is pursuing a degree in Industrial Engineering.
Moataz Abdulhafez is a PhD student at the Industrial Engineering department at Pitt. His research interests include laser material processing and in-situ characterization of nanomaterials.
Moataz Abdulhafez
Dr. Mostafa Bedewy is an Assistant Professor of Industrial Engineering, Chemical & Petroleum Engineering, and Mechanical Engineering & Materials Science at the University of Pittsburgh, where he leads the NanoProduct Lab. Before that, he worked as a Postdoc at the Massachusetts Institute of Technology (MIT) in the area of bionanofabrication with Professor Karl Berggren in the Research Lab for Electronics. Also, he was previously a Postdoc at the MIT Laboratory for Manufacturing and Productivity, working with Professor John Hart on in situ characterization of carbon nanotube growth. In 2013, he completed his PhD at the University of Michigan in Ann Arbor, where he worked with Professor Hart on studying the population dynamics and the collective mechanochemical factors governing the growth and self-organization of filamentary nanostructures. He holds a Bachelor’s degree (honors) in Mechanical Design and Production Engineering (2006) and a Master’s degree in Mechanical Engineering (2009), both from Cairo University. Dr. Mostafa Bedewy
Significance Statement
Laser-induced nanocarbon (LINC) is a directly graphitized carbon nanomaterial on polyimide using laser irradiation. It has high potential for applications in antibacterial and antifouling surfaces. We demonstrate that controlling the laser parameters enables tuning the surface properties of LINC.
Category: Experimental research Keywords: Laser-induced nanocarbon (LINC), Tunable properties, Laser writing, Nanocarbon
Abstract
The manufacturing of flexible materials with patterned functional nanostructures is required for wearable electronics and conformal devices. Laser-induced nanocarbon (LINC) is a typically porous material prepared by direct laser writing with an infrared laser on polymers like polyimide in ambient atmosphere. The resulting material is graphitic and hence conductive, making it suitable for applications in broad fields, such as microfluidics, sensors, and electrocatalysts. This paper aims to expand the range of surface properties for LINC by tuning laser processing parameters. While it was previously shown that different wetting behavior of LINC can be achieved by lasing in inert atmospheres, we uniquely fabricate hydrophobic and hydrophilic LINC by lasing in air, which underlie the simplicity, scalability, and cost-effectiveness of our process. We demonstrate that by varying laser speed, power, and line-to-line gap sizes, considerable changes in water contact angle can be obtained. Upon examining tensiometer, optical, and scanning electron microscopy (SEM) images, it is clear that different surface properties are due to the different morphologies of LINC. Additionally, it becomes evident that increasing gap sizes leads to an increase in contact angles and thus an increase in the hydrophobicity of the surface. The results demonstrate that simple changes to the lasing parameters, the sample hydrophilicity and hydrophobicity can be controlled without special environment control setups. The results also provide insight into the underlying mechanisms behind the various wetting behaviors of LINC.
1. Introduction
The applications of commodity polymers are ubiquitous in almost all aspects of modern life. Recently, it has been shown that nanoscale graphitic structures can be synthesized through the lasing of polyimide, a popular commodity polymer, with commercially available low-cost IR lasers [1]. These laser-induced nanocarbon (LINC) structures have been shown to exhibit excellent electrical and thermal conductivity as well as high surface area [1]. In addition, different morphologies have been observed at the microscale for LINC material, ranging from porous to fibrous [2]. Accordingly, wide-reaching potential applications of LINC such as anti-fouling [3], anti-icing [4] and antimicrobial [5] surfaces have been investigated. Recent research has shown that LINC surface properties depend on lasing parameters such as laser power and speed [6]–[8]. For example, it was shown that by changing the lasing environment, namely the process gas, the contact angle between water droplets and LINC surfaces can be switched between superhydrophobic (>150°) and superhydrophilic[8]. To fully exploit this feature, we generate nanostructured carbon directly on the surfaces of the commercial Kapton films by surface lasing with the objective of tuning surface properties and morphology in a large range of contact angles based on changing laser power, speed, and line-to-line gap in the LINC process. We explore the lasing parameter space to achieve control over the resulting contact angle of direct written LINC areas. Here, we test the hypothesis of whether it is possible to achieve contact angle control by only changing the lasing parameters in an air
Figure 1: (a) Image of laser head and polyimide with LINC. (b) Schematic of experiment slide with LINC patches at different orientations.
environment. By showing this, we simplify the process since no special environmental setup is needed. Additionally, we propose a potential mechanism to the observed difference in contact angle measurements at different parameters by comparing it with SEMs of the LINC areas.
2. Methods
2.1 Sample preparation
The experiment was conducted by laser scribing on polyimide (PI) tape, also referred to as Kapton, (Grainger, Cat. No. 15C616, thickness: 3.5 mil), which was applied to a glass slide with a rubber roller to eliminate air bubbles. A chemical wash consisting of acetone and isopropyl was applied and then quickly dried off with compressed air to clean the PI surface.
2.2 LINC Processing
The laser scribing was conducted using a CO 2 laser system (Full Spectrum Laser Pro-Series 20x12, 45 W, 3.81 cm focus lens) with 10.6 µm wavelength and 45W laser power. The system allows tuning the power by controlling the laser current. The beam diameter (1/e 2 ) was measured to be 110 µm. The samples were placed on an XYZ stage with a maximum horizontal rastering speed of 500 mm/sec.
2.3 Experiment design
As shown in Figure 1a, each slide has 4 square patches (1.27 cm x 1.27 cm) that are lased at different conditions. A single LINC patch is formed by lasing in the positive x-direction a distance (L), then shifting by an increment (g) in the y-direction, followed by lasing in the negative x-direction by the same distance (L) (Fig. 1b). This sequence is repeated until the square is completed. The laser machine input design file is generated by programming a MATLAB script with lines and a certain number of pixels gap between each line, which represents a single patch. The study was conducted by varying power (28W and 12W), speed (v, 500 mm/sec, 350 mm/ sec), and the distance between lines lased (g, 0 pixels, 3 pixels, 5 pixels, 7 pixels), where one pixel represents a shift of 0.00508 cm (Fig. 1). Finally, the patches were rotated 90° for a total of two orientations in order to investigate contact angle anisotropy (Fig. 1b). Four drops are dispensed for each condition. A control sample without any lasing was also used to establish an experimental control measurement. 2.4 Characterization methods
Quantitative results were obtained by measuring the Young-Laplace’s contact angle using a Biolin Scientific Optical Tensiometer. The process included ejecting four 5 µl water droplets on each sample and recording the results at 6.9 frames per second for 20 seconds. Afterwards, the program OneAttention was used to analyze each droplet by curve fitting the Young-Laplace equation to the droplet to yield a contact angle for each of the 140 frames. The average of the 140 contact angles was then recorded as the contact angle for the droplet.
To explore the morphology of the LINC patches, SEM images were taken with a Zeiss SIGMA VP Scanning Electron Microscope.
Figure 2: Box plot representing the contact measurements resulting at different laser powers, speed and line gaps. Insets represent images of contact angle measurements at a wicking condition and a hydrophobic condition.
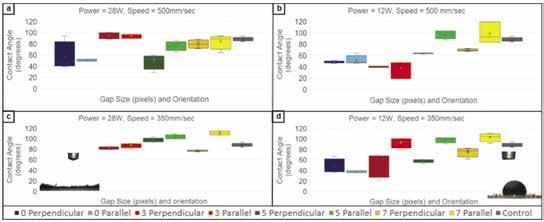
3. Results
The control sample had an average contact angle of about 88°.
As shown in Figure 2, the parallel orientation almost always had a higher contact angle measurement than its perpendicular counterparts. The lowest contact angle measured was 0°, at power 28W, speed 350 mm/sec, g = 0 pixels, both orientations (Fig. 2c, inset). The highest contact angle measured was 111°, also at power 28W, speed 350 mm/sec, but this time at g = 7 and the parallel orientation (Figure 2d, inset). It is observed there is a general trend that as gap size increases, so does contact angle. Optical tensiometry of drops at two selected patches at identical power and lasing speed (28W power, 500mm/ sec speed) but different gap sizes (0, 3) exhibit significantly different contact angles as shown in Figure 3a-b (ANOVA test, CA g=0 =56.70,CA g=3 =94.65, n==4, p = 0.0271). Optical images of the patch show that the patches have different colors and different surface appearances. In the higher gap sample (Figure 3d) the patterns representing the dried water spots can be noticed, whereas in the lower gap case, (Figure 3c), they are not noticed. Further investigation using SEM showed that there are vast differences in the morphology of the structures, even between g = 0 and g = 3 at the same settings. The sample with g = 0 has a porous appearance, whereas sample with g = 3 has a fibrous appearance.
4. Discussion
For some samples, such as power 28W, speed of 350 mm/ sec, g = 0, wicking behavior was observed. When wicking occurs, the water is absorbed spontaneously into the LINC patch, driven by capillary forces.
To explain the difference in contact angle with the different lasing conditions, we relate the observed behavior with the morphology of the patches observed in SEM images. It is evident from the differences between the samples with g = 0 and g = 3 that gap size plays an important role in morphology. The sample with g = 0 has high overlap between lines (Fig. 3c, e) whereas the
70 Undergraduate Research at the Swanson School of Engineering Figure 3: (a-b) Contact angle measurements of power 28W, speed 500 mm/sec, gap (a) = 0, gap (b) = 3. (c-d) Top view optical images of (a) and (b). (e, g, i) SEM images of (a) at 250x, 5,000x, and 25,000x, respectively. (f, h, j) SEM images of (b) at the same magnification.
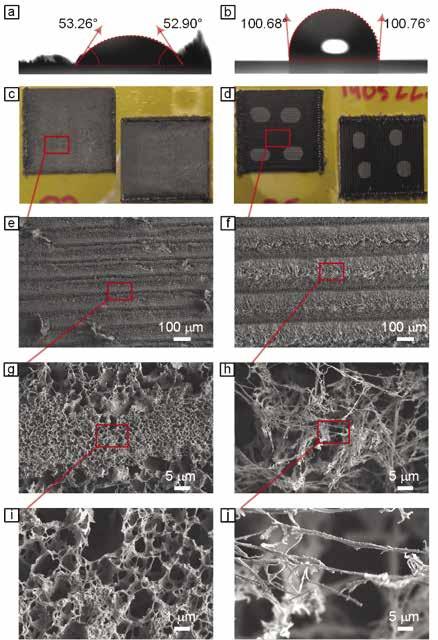
sample with g = 3 has less overlap (Fig.3 d, f). High overlap occurs when distance between the lased lines is smaller than the laser spot size. In this case (g = 0) since the spot diameter is around 200 m, and the distance between the lines is around 50 m, each spot on the line is lased multiple lines due to the overlap between the lasing runs. The high overlap in the sample with g = 0 resulted in a porous morphology, looking much like a sponge (Fig. 3g, i). This potentially enhances water absorption through capillary effects, leading to lower contact angles (~53°) as opposed to the sample with g = 3 that has a smaller overlap, which exhibited a larger contact angle (~100°) and a more fibrous morphology (Fig. 3h, j). The results show that diverse morphologies are possible with changing the laser parameters, which in turn clearly affect the contact angle. Further work is needed to explore the different morphologies and the mechanism by which they are formed and affect the surface properties of LINC.
5. Conclusion
We demonstrate that varying the gap between nanostructured carbon lines obtained by laser-induced nanocarbon formation (LINC) on polyimide surfaces has a significant impact on the contact angle of water. Our results show that a wide range of contact angles can be achieved, ranging from hydrophilic approaching 0° to hydrophobic surfaces approaching 120°. Characterizing the morphologies using a combination of optical and electron microscopy also related these properties to the structure of LINC. This highlights the versatility of our technique, which is promising for tuning the surface properties of commercial polymers for various applications, such as self-cleaning, anti-fouling, and water-repellant surfaces.
6. Acknowledgements
This research was funded by the Swanson School of Engineering and the Office of the Provost.
7. References [1] J. Lin et al., “Laser-induced porous graphene films from commercial polymers,” Nat. Commun., vol. 5, pp. 1–8, 2014. [2] L. X. Duy, Z. Peng, Y. Li, J. Zhang, Y. Ji, and J. M. Tour, “Laser-induced graphene fibers,” Carbon N. Y., vol. 126, no. 7, pp. 472–479, Jan. 2018. [3] S. P. Singh, Y. Li, J. Zhang, J. M. Tour, and C. J. Arnusch, “Sulfur-Doped Laser-Induced Porous Graphene Derived from Polysulfone-Class Polymers and Membranes,” ACS Nano, vol. 12, no. 1, pp. 289–297, Jan. 2018. [4] D. X. Luong et al., “Laser-Induced Graphene Composites as Multifunctional Surfaces,” ACS Nano, vol. 13, p. acsnano.8b09626, Feb. 2019. [5] S. P. Singh, Y. Li, A. Be’er, Y. Oren, J. M. Tour, and C. J. Arnusch, “Laser-Induced Graphene Layers and Electrodes Prevents Microbial Fouling and Exerts Antimicrobial Action,” ACS Appl. Mater. Interfaces, vol. 9, no. 21, pp. 18238–18247, May 2017. [6] L. Andrea et al., “New insights on laser-induced graphene electrodes for flexible supercapacitors: tunable morphology and physical properties,” Nanotechnology, vol. 28, no. 17, p. 174002, 2017. [7] E. Vasile, S. M. Iordache, C. Ceaus, I. Stamatin, and A. Tiliakos, “Morphic transitions of nanocarbons via laser pyrolysis of polyimide films,” J. Anal. Appl. Pyrolysis, vol. 121, pp. 275–286, 2016.
[8] Y. Li et al., “Laser-Induced Graphene in Controlled Atmospheres: From Superhydrophilic to Superhydrophobic Surfaces,” Adv. Mater., vol. 29, no. 27, pp. 1–8, Jul. 2017.