
3 minute read
Figure 20: Distress due to temperature segregation causing inadequate compaction [50
temperature differentials [46]. Temperature segregation can also be found in the accidental discharge of asphalt from a haul truck on the base surface to be later paved over. The dropped material will cool quickly and will not compact properly when fully paved over [48]. Asphalt pavement is one continuous material and therefore nonstop paving is preferred. However, mechanical or hauling issues can lead to the paver stopping for several minutes. Waiting too long between hauls can lead to a cyclic temperature segregation where the mat temperature has the potential to fluctuate up to 86°F (30°C) before paving continues [46]. This creates a strip of temperature differentials that may be significant enough to effect density if it is a long delay.
A high-severity temperature segregation can reduce a pavement life by up to 50%. Cold spots in asphalt pavement causes nonuniform compaction which can lead to accelerated distresses (Figure 20) under traffic loading and environmental effects [47,48]. Common distresses that occur due to temperature segregation are oxidation and moisture damage caused by density differentials creating excess air and water exposure. There can also be a decrease in bond strength between pavement sections caused by the cooling caused by paver stoppage which can lead to transverse cracking [48]. Edges and joints are already especially susceptible to distresses due to the temperature differential created by being exposed to more air than just the surface [47]. This can result in a low density at the edges and joints, increasing the vulnerability of this location [49].
Figure 20: Distress due to temperature segregation causing inadequate compaction [50].
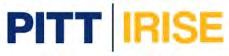
27
Taking care to reduce temperature segregation removes distresses related to the nonuniformity caused by the temperature differentials [51]. Quality control is needed to ensure proper asphalt temperature so that action can be taken if temperature segregation occurs. Recent advances in technology can be used to mitigate segregation to improve pavement performance.
There are several traditional methods to determine asphalt temperature. Thermal couples have been used but are reported to have breakage issues and can only be placed in so many locations [47]. Temperature probes and gun-type thermometers are another common practice however these can only measure one point at a time [47,48]. These traditional methods are also performed randomly which does not guarantee temperature segregation will be noticed [47]. In addition, conventional methods require active presence of workers and inspectors directly in the paving area. That creates several safety hazards as workers and inspectors are close to heavy moving equipment, passing traffic, and hot asphalt concrete.
3.1.1 Proposed Technology 1: Automated Real-Time Thermal Profiling for Asphalt Paving
Recent development in technologies can allow for more comprehensive profiling through high precision portable infrared thermal imaging [46]. Over the past 20 years, infrared cameras have been used to measure temperatures of newly paved asphalt pavements. Infrared is a method of evaluating materials based on their temperature to determine surface of subsurface defects [8]. Originally, this technology was used alongside the roadway creating images such as Figure 19. However, this method has a narrow field of vision, and the images must be merged together to see the entire project. There are also issues on accurately locating the identified problem areas to the correct location on the pavement surface [51].
To address these shortcomings, infrared technology has been farther used to provide comprehensive thermal profiles by attaching a scanning device directly on the paver as shown in Figure 21. This provides real time access of temperature data to the operator and on-foot inspectors. Inspectors can receive and analyze the information from a safer distance reducing exposure to hot materials and heavy equipment. This method of quality control provides nondestructive, diagnostic monitoring that provides quantitative and visual feedback. Infrared
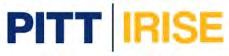
28