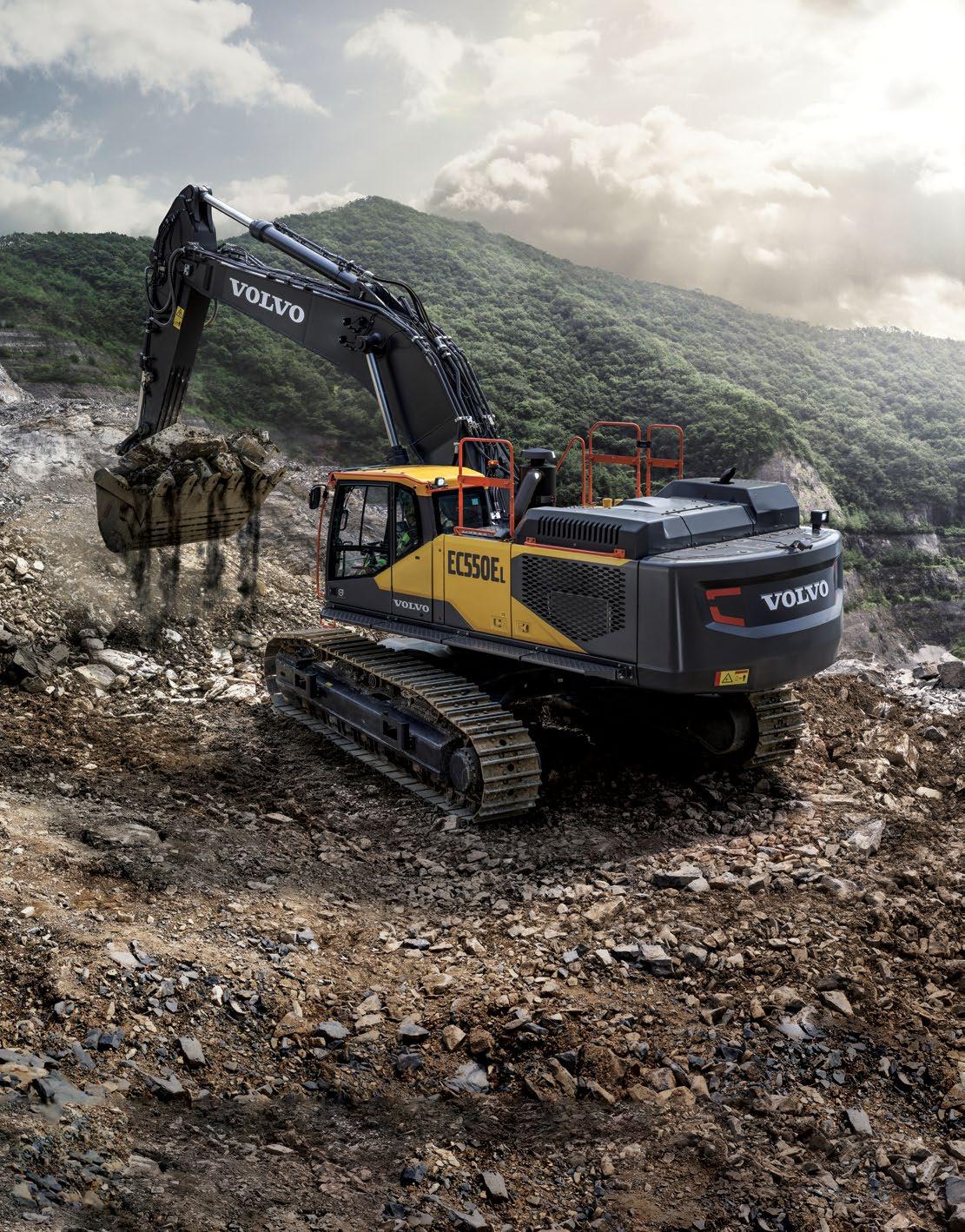

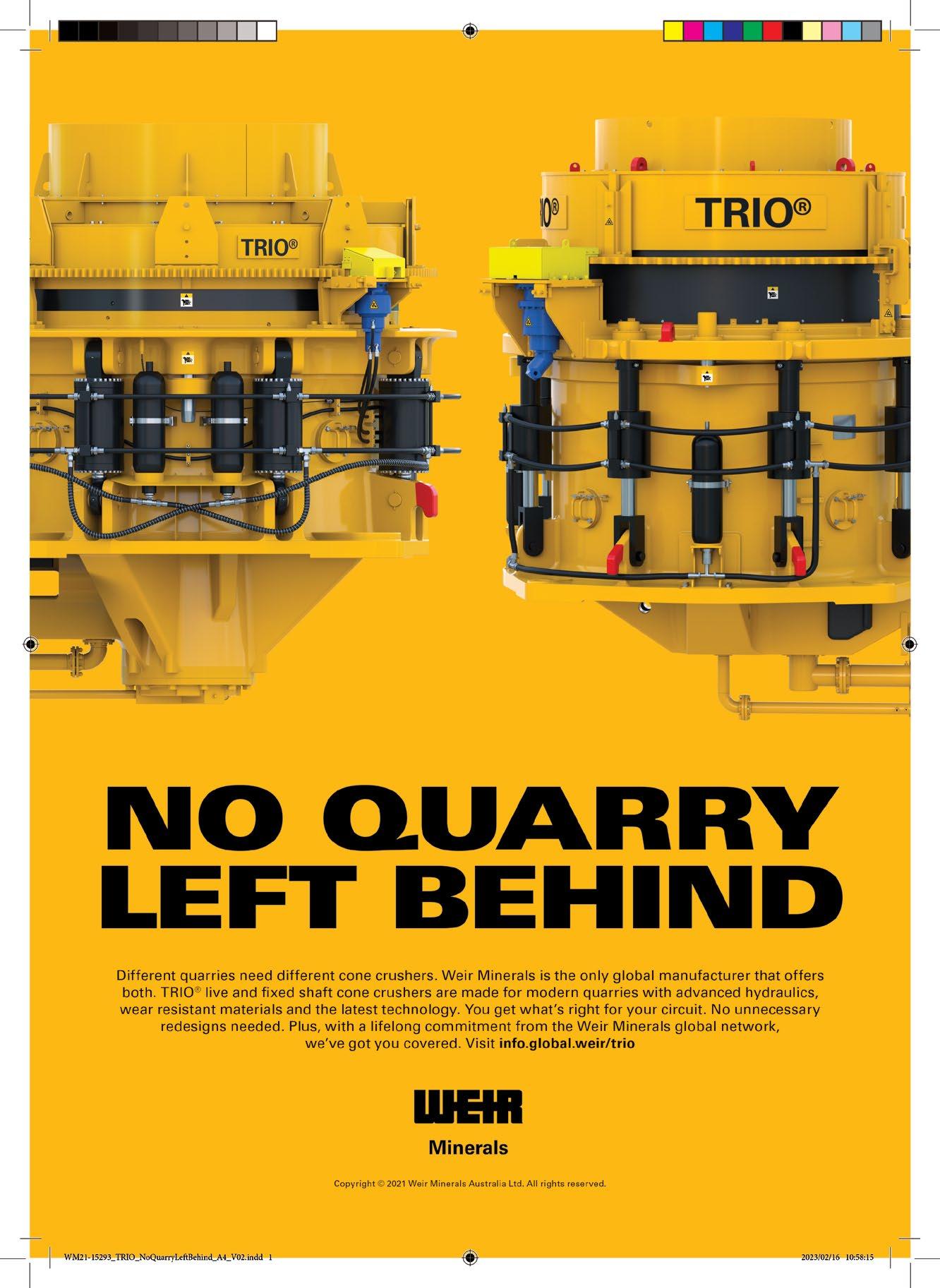
For years, there has been a clarion call from role players in the infrastructure sector for enhanced public infrastructure development to spur industrial growth and employment creation. While Africa’s infrastructure investment deficit is staggering, standing between US$68-billion and US$110-billion per year, it is however encouraging to see several African governments prioritising infrastructure development as a catalyst for economic growth.
In fact, leaders across the continent understand that infrastructure development is a key driver for the much-needed progress in Africa and a critical enabler for productivity and sustainable economic growth. A case in point is southern Africa, where countries such as the Democratic Republic of Congo, Zambia and Zimbabwe are showing a renewed focus on infrastructure development.
After years of neglect, Zimbabwe’s infrastructure is seemingly under renewal. It starts right at the Beit Bridge border post, where the US$300-million modernisation project has been commissioned. This project has not only changed the face of border management, but has had immense positive and sustainable impact, particularly for commercial trucks as the time spent at the border has decreased and has helped the movement of goods in the region.
Away from the border, work on the 580-km Harare-Masvingo-Beit Bridge highway continues unabated, with 400 km –almost 70% of the project – completed and now open to traffic. Part of the North South Corridor, which begins in Durban, South Africa, passing through Zimbabwe and ending in Lubumbashi, DRC, the project is divided into three sections: the 580-km HarareMasvingo-Beit Bridge highway with its eight toll plazas, the 342-km Harare-Chirundu highway, and the 59-km Harare Ring Road with three toll plazas.
As you will see in this edition of Quarrying Africa, the supply chain is also seeing some green shoots in the DRC and Zambia. A case in point is Pilot Crushtec, which has supplied four greenfield modular plants in the past six months. The majority of sales are coming from greenfield quarry and aggregate crushing projects. The bulk of these projects are aggregates operations for mining
companies establishing their own quarries or borrow pits for their own road builds and structures on mines.
West Africa is yet another region where well-targeted infrastructure programmes are expected to play a significant role in improving poor economic performance and boosting economic transformation. A region of 17 countries, West Africa will see its combined population rise from the current 412-million to 526-million over the next decade.
Notwithstanding the havoc wreaked by the Covid-19 pandemic in the past two years, the region has made significant strides in the past decade to improve its infrastructure across sectors, all the way from transport and energy to real estate and social development.
According to ABiQ, a business intelligence provider of all matters Africa and the Middle East, there are more than US$380-billions’ worth of active projects in West Africa, with US$230-billion already under construction and US$150-billion in the pre-execution phase. The majority of active projects by value are in Nigeria (34%) and Ghana (20%). Despite the optimistic trajectory of infrastructure development on the continent, there is an apparent lack of appetite to develop new commercial quarries to meet the aggregates needs of these projects. Apart from South Africa, which has a developed quarrying sector championed by a capable association, ASPASA, the rest of the continent still grapples with a lack of sustainable aggregates capacity.
Population growth on the continent –which is forecast to rise to at least 2,4-billion by 2050 – will surely create enormous and ever-growing demand for construction materials to construct new homes, cities, roads and other infrastructure. For much of the infrastructure stakeholders, it is easy to ignore the issue of where these materials will come from. The quarrying industry, though very critical, is often out of sight, out of mind. But that is going to have to change.
Many more quarries, or extensions to limited existing ones, will be needed to supply the aggregates to enable the continent’s infrastructure growth. The high cost of transporting materials is a good reason for these quarries to exist near where the material will be used, which means being sited close to cities and infrastructure hubs. a
STATEMENT OF PROMISE
RISING DEMAND FOR MODULAR PLANTS IN SOUTHERN AFRICA
UPWARD TRAJECTORY FOR MODULAR PLANTS
TEREX MPS PROCESS PLANT FOR SENECA CRUSHING AND SCREENING
MAXIMISING AVAILABILITY AND LONGEVITY
ROLLING OUT DIGITAL SOLUTIONS
EXPLORING CONTINUOUS SURFACE MINING TECHNOLOGY
Publishing Editor: Munesu Shoko
Sub Editor: Glynnis Koch
Business Development Manager: Elmarie Stonell
Admin: Linda T. Chisi
Design: Kudzo Mzire Maputire
Web Manager: Thina Bhebhe
Quarrying Africa is the information hub for the sub-Saharan African quarrying sector. It is a valued reference tool positioned as a must-read for the broader spectrum of the aggregates value chain, from quarry operators and aggregate retailers, to concrete and cement producers, mining contractors, aggregate haulage companies and the supply chain at large.
Quarrying Africa, published by DueNorth Media Africa, makes constant effort to ensure that content is accurate before publication. The views expressed in the articles reflect the source(s) opinions and are not necessarily the views of the publisher and editor.
The opinions, beliefs and viewpoints expressed by the various thought leaders and contributors do not necessarily reflect the opinions, beliefs and viewpoints of the Quarrying Africa team.
Quarrying Africa prides itself on the educational content published via www.quarryingafrica.com and in Quarrying Africa magazine in print. We believe knowledge is power, which is why we strive to cover topics that affect the quarrying value chain at large.
Printed by:
Contact Information
Email: munesu@quarryingafrica.com
Cell: +27 (0)73 052 4335
Having introduced the first Volvo EC550E unit late last year, Babcock reports increased demand for the new 55-t class excavator. A major talking point is the new Independent Metering Valve Technology hydraulic setup, which allows the machine to punch well above its weight with production more in line with 60-65 tonne (t) class machines. Customers can also expect 40% more productivity and a 25% improvement in fuel efficiency, writes Munesu Shoko.
Following its global introduction in January 2022, the Volvo EC550E crawler excavator made its southern African debut in October last year. Since then, a total of six machines – deployed in coal, diamond and hard rock applications – have been delivered to customers, with some repeat orders already placed.
At a time when productivity and efficiency have become non-negotiables for mining and quarrying projects, customers have been impressed by up to 40% more productivity and up to 25% increase in fuel efficiency. In addition, the machine also punches above its weight with production capabilities well in line with machines in the 60-65 t range.
Ideal for mining, quarrying and large infrastructure projects, the new 55-t excavator breaks the industry norm of production having a direct link to operating weight. This is achieved through Volvo CE’s ground-breaking Independent Metering Valve
Technology (IMVT) hydraulic setup, in conjunction with a totally new engine trim on the D13 block and electrohydraulic command for the joysticks.
“As a result, the machine ‘fights’ well outside its weight category, offering production in line with bigger class machines in the 60-65 t range, despite the decals only stating 55-t,” explains Lance Mannix, GM Sales at Babcock’s Equipment division.
“The machine fits in between our existing 48-t Volvo EC480D and the 75-t Volvo EC750D models. While the EC480D model is aimed at customers looking for an efficient and reliable 50-t class excavator, the EC550E offers 40% greater production than the EC480D in typical dig and dump applications, meaning it is closer to the EC750D and so challenges the 60-65 t excavator class,” explains Mannix.
The increased size and weight of the undercarriage gives the machine greater stability, allowing it to accommodate a larger bucket (2,4-4,2 m³) capacity. By load distribution surface/ footprint of the undercarriage, the EC550E has
40%
The EC550E offers 40% greater production than the EC480D in typical dig and dump applications, meaning it is closer to the EC750D and so challenges the 60-65-t excavator class
4-6
The machine can fill a 35-40-t hauler or highway truck with just four to six passes. The result is optimum pass-matching and high production at a lower cost per tonne of operation
Following the launch of the Volvo EC550E in southern African late last year, a total of six machines have been delivered to customers, with some repeat orders already placed
Customers have been impressed by up to 40% more productivity and up to 25% increase in fuel efficiency
The machine punches above its weight with production capabilities well in line with machines in the 60-65-t range
By offering a direct portal to tailor-made financing, Volvo Financial Services helps Babcock customers address financial challenges and grow their equipment fleets, through a personal hands-on approach that extends far beyond conventional financing services
The machine fits in between our existing 48-t Volvo EC480D and the 75t Volvo EC750D models. While the EC480D model is aimed at customers looking for an efficient and reliable 50-t class excavator, the EC550E offers 40% greater production than the EC480D in typical dig and dump applications, meaning it is closer to the EC750D and so challenges the 60-65 t excavator class.
We have over the years built our business on the back of our aftermarket offering. In fact, our aftermarket business, including parts and service, had a record year in the last financial year. One of the major talking points is the growth of our service/maintenance contracts portfolio. We now have more machines on service/maintenance contracts than ever before.
almost an identical size to some competitor 70-t machines.
In mass excavation (ME) configuration, it can even challenge bigger class competitors. For a typical ME machine, at 6 m reach, 1,5 m elevation – in other words where stability really counts – you have a lift value of 17 910 kg across tracks. This is, by kilos, comparable to certain 70-t competitor offerings.
The 2 071 Nm (320 kW) engine, with rated power at 1 600 rpm, is also well in line with certain competitor 70-t machines. This, coupled with the large displacement pumps (832 l per minute), results in faster cycle times. For most competitor offerings in the bigger class, one needs to rev the engine at 1 800 rpm to reach the maximum power. Low revs are generally good, so the EC550E has the upper hand here.
Experienced people tend to be relatively more interested in torque than power when it comes to large excavators. Torque is more about force, and power is more about speed – and typically excavator force can be more of a priority than speed, subject to application. However, one cannot see torque in isolation. The EC550 is fitted with large displacement pumps, matched to the capabilities of the engine. Customers can therefore get high flow/ fast cycle times at the same time as when operating at a high torque.
Productivity is a parameter of absolute significance to excavation applications. With that in mind, Volvo CE paid particular attention to increased productivity when developing the EC550E. Customers can brace themselves for up to 40% more productivity.
The machine can fill a 35-40-t hauler or highway truck with just four to six passes. The result is optimum pass-matching and high production at a lower cost per tonne of operation.
“The EC550E can fill a Volvo A35G or A40G articulated hauler with four to six buckets, which is considered a well-balanced match in the industry. It also means that Babcock now offers two perfect match excavators for A35G or A40G haulers in southern Africa – the EC750D and the EC550E,” says Mannix
As quarry and opencast mine operators seek to increase their tonne per hour and lower their cost per tonne, while reducing their environmental impact, pass-matching is especially important. Matching the size and capacity of the loading machine to the hauler shortens cycle times and minimises idling for greater productivity, lower fuel consumption and lower emissions. Essentially, it avoids unnecessary waste of time, fuel and money.
Away from the machine, the EC550E is available with a range of optimum-sized heavyduty rock buckets designed for use in abrasive conditions, with the Volvo Tooth System making light work of teeth replacements thanks to its place, push and click functionality.
Customers can further take control of their productivity with On-Board Weighing, helping to ensure the optimum amount of material is loaded. The optional system provides real-time information to eliminate under and overloading of haul trucks and records total tonnage for complete production management.
Thanks to the next generation electro-hydraulic system with IMVT and engine/pump optimisation,
which lowers engine rpm while optimising power, customers can take fuel efficiency to a whole new level. The main control valve uses IMVT, the latest pioneering innovation from Volvo, said to be the most high-performing hydraulic system in the industry. It provides significantly more precise control compared to a conventional system and contributes towards up to a 25% improvement in fuel efficiency.
“The IMVT is probably the biggest news as it is an industry first in this excavator size class. It involves a new concept main control valve (MCV). Instead of a conventional spool-type MCV, Volvo has built an MCV with dedicated valves – one each for feed and return for each actuator. This means that the pumps pump exactly according to demand at any given time, subject to the precise and exact requirement of oil for any specific actuator,” says Mannix.
from Babcock. At the core of Babcock’s eminence in southern Africa is its unparalleled aftermarket regime.
Guiding the company’s aftermarket philosophy, says Vaughan, is Babcock’s understanding that in today’s operating conditions, equipment owners expect suppliers to meet their needs and respond to their problems effectively and swiftly. This is most certainly the case when it comes to big-ticket, mission critical assets such as mining and quarrying equipment.
“We have over the years built our business on the back of our aftermarket offering,” he says. “In fact, our aftermarket business, including parts and service, had a record year in the last financial year. One of the major talking points is the growth of our service/maintenance contracts portfolio. We now have more machines on service/maintenance contracts than ever before,” says Vaughan.
A benefit of Babcock’s service contracts is that they are flexible and tailored to meet each customer’s unique needs. “A major advantage of Babcock’s repair and maintenance (R&M) contracts is increased machine uptime. The machines are serviced by experts, thus the scheduled downtime related to maintenance is kept to a minimum.
Since its inception in 2017, Volvo Financial Services South Africa has continued to go beyond traditional financing to offer Babcock’s customers access to fast and flexible finance solutions
This eliminates hydraulic losses, delivers increased fuel efficiency and unparalleled level of command of the machine. The system does not only cut fuel consumption, but it also reduces carbon (CO2) emissions significantly. Operators can achieve production that is close to the 70-t mark but without the fuel consumption that comes with a 70-t class machine.
To support the fuel-efficient performance of the machine, Babcock offers a range of Volvo services to help customers reduce the fuel expenditure and carbon emissions of their operations even further, including Fuel Efficiency Reports and operator training initiatives.
To further boost customer profitability, the EC550E benefits from the proven high level of local support
Machines are also serviced according to OEM specifications all the time, resulting in longer asset lifecycles,” says Mannix. Volvo machines on service and R&M contracts are monitored via CareTrack, Volvo CE’s telematics system. CareTrack gives Babcock a wide range of machine monitoring information designed to save customers time and money.
Fleet owners can also take advantage of Volvo Financial Services’ flexible finance options.
Volvo Financial Services, the global captive finance company of the Volvo Group, started operating in South Africa in 2017, and has over the years seen increased growth of its portfolio. Since its inception in 2017, Volvo Financial Services South Africa has continued to go beyond traditional financing to offer Babcock’s customers access to fast and flexible finance solutions. As part of Volvo Group, Volvo Financial Services has in-depth knowledge of the yellow metal equipment market, allowing the captive financial service provider to offer clients a customised solution.
By offering a direct portal to tailor-made financing, Volvo Financial Services helps Babcock customers address financial challenges and grow their equipment fleets, through a personal handson approach that extends far beyond conventional financing services. a
The significance of quality assurance in aggregates production cannot be stressed enough. In a one-on-one with Quarrying Africa , Barry Pearce, who leads ASPASA’s Technical Quality Committee, says it is unfortunate that quality often receives the least attention, yet it should be the parameter that governs all the other activities.
The construction sector, a key pillar to economic and infrastructure development, requires an abundant and dependable supply of quality aggregates. While there is no specific legislation that governs quality – with a wide variation in what different contracts consider suitable aggregates for specific applications –quality control/assurance is absolutely critical to the production of aggregates and crushed granular material produced at a quarry.
“Without some form of quality assurance, you have no idea of where you are in real terms, besides the ‘gut feel’ which often depends on an individual’s experience. This can be a good starting point if one is experienced but without a definitive test result, one cannot determine if the quality of the product is tending towards the edge of the specification limits,
By Munesu Shoko .which is problematic,” says Pearce.
Trending of results on a daily basis, he adds, helps aggregates producers get a feel of how consistent the crushed material is and whether any adjustments are required in the production process. If done well, one should be able to determine the rate at which the material is changing and make adjustments accordingly before any major issues occur.
“Paying attention to quality allows producers to sleep peacefully at night as they are confident that their product complies with the specification. Capital channelled towards quality control/ assurance is money well spent; it can lead to overall cost reductions based on lower percentages of materials produced that are out of the product specification limits. The investment pays for itself by reducing the percentage of rejected materials
Quarries belonging to ASPASA can now participate in an annual audit designed to measure compliance of testing facilities, including their apparatus calibration and personnel competence, against an abridged ISO 17025 format, to ensure the correct classification of products
ASPASA introduced its own guidelines and auditing systems to ensure testing of aggregates and crushed granular materials is carried out in accordance with the South African National Standards (SANS) 3001-AG and -GR series test methods
Quality control/assurance is absolutely critical to the production of aggregates and crushed granular material produced at a quarry
Trending of results on a daily basis helps aggregates producers get a feel of how consistent the crushed material is and whether any adjustments are required
Quality assurance helps ensure that quarries supply products that meet the required specification
Capital expenditure on laboratories at quarries is often regarded as an unnecessary expense. The perception of where the laboratories fit into the overall management organogram needs to be revised
per annum, thus helping meet the needs and expectations of customers, and those invested in the quarrying activities,” says Pearce.
Consistent aggregates quality is a key competitive edge for producers. Quality assurance helps
Paying attention to quality allows producers to sleep peacefully at night as they are confident that their product complies with the specification. Capital channelled towards quality control/assurance is money well spent; it can lead to overall cost reductions based on lower percentages of materials produced that are out of the product specification limits.
ensure that quarries supply products that meet the required specification. High-quality products result in satisfied customers, which can result in customer loyalty, repeat orders and positive references. Quarry operators by their nature tend to pay more attention to production, driven by the perception that the more they produce the bigger the income. However, Pearce points out that if production is driven too hard, the risk of losing quality, possibly resulting in materials that are out of spec and ultimately rejection or reclassification to a lower
If quality is the major driver, production is controlled within acceptable limits to ensure material conforms to specifications.
quality material and a lower sales price per tonne. “This is the one aspect that any primary or secondary supplier wants to avoid due to the potential loss of income and reputational damage,” he says.
Quality assurance is about people and processes; people must define a process workflow and oversee its implementation. Pushing production too hard can result in longer working hours, which creates an unsafe environment due to fatigued personnel and/or the taking of shortcuts. This often results in unsafe practices or changes in the testing methods so as to allow the acceleration of production to meet the adjusted targets.
“Unfortunately, shortcuts often lead to incorrect and inaccurate results, which is the one thing operations cannot afford as all decisions on material compliance in aggregates manufacturing are based on test results,” says Pearce.
The second activity that normally receives the greatest attention in aggregates production is Health, Safety and Environment (HSE). Given that it is a legislative requirement for compliance, it gets the attention due to it as quarry owners want to keep on the right side of the law.
“If HSE is your main driver, very little will get done in terms of quality and the quarry will start losing money,” he says. “If quality is the major driver, production is controlled within acceptable limits to ensure material conforms to specifications and HSE is kept in hand as everyone is not rushing around trying to meet fast-tracked production targets.”
The major downside of poor quality control, states Pearce, is rejected material that is out of specification, which results in loss of income and the resultant loss in reputation. The cost of such a failure is not just the replacement cost of the material, it is also the removal of the rejected material, the delivery and reworking of the new material. The big argument is always who then pays for these additional incurred costs?
“Further to this is the breakdown in trust between contractor and supplier, as well as the lack of faith from the engineers who
approve the material and ultimately release the money that pays for it,” says Pearce. “Confidence in one’s product is also in question, so selling/ marketing can be problematic as one may oversell and underdeliver, which is not great for marketing with confidence of one’s brand.”
Increasing requirements for certified quality aggregates has led surface mining industry association, ASPASA, to introduce its own guidelines and auditing systems to ensure testing of aggregates and crushed granular materials is carried out in accordance with the South African National Standards (SANS) 3001-AG and -GR series of test methods.
ASPASA’s Technical Quality Committee’s mandate is to keep members up-to-date with the latest changes in any standard specifications and testing methods; to allow members to give input in any revision of these standards; and to ensure quality processes are followed, through good laboratory practices (GLP).
Members of ASPASA can now participate in an annual audit designed to measure compliance of testing facilities, including their apparatus calibration and personnel competence, against an abridged ISO 17025 format, to ensure the correct classification of products.
The audits complement the association’s well established environmental and health and safety (ISHE) audit systems, which have contributed to the association’s recognition internationally as a leader in these fields.
“The idea is to help ASPASA members to produce better quality products that are tested consistently to meet the specifications of their clients as well as to meet national standards – where required. It entails the inspection of the laboratory including the testing apparatus and the verification of apparatus used,” says Pearce.
Unfortunately, says Pearce, with production being seen as the main driver behind profitability, it often gets the lion’s share of the attention, while quality tends to be overlooked. Consequently, laboratory setups at many quarries remain understaffed, underequipped and are just there to provide results that preferably always pass.
“Capital expenditure on laboratories at quarries is often regarded as an unnecessary expense that could be used elsewhere with greater benefits to production. The perception of where the laboratories fit into the overall management organogram needs to be revised. The laboratory actually underpins all production decisions regarding the adjustments to the crushing process and maintenance routines. In my opinion, the value of a strong laboratory on such facilities is one of the biggest cost-savers compared to any other aspect of the operation,” concludes Pearce. a
Investments in plant upgrades in recent years have put AfriSam’s Pietermaritzburg Quarry in good stead to meet growing aggregates demand from a diversified project base in its area. Munesu Shoko was recently on site and filed this report for Quarrying Africa.
12,75 mm/s
The ground vibration data recorded low PPV’s at all measuring points and all the values were below the conservative limit of 12,75 mm/s
2020
To meet high demand for sand, PMB Quarry invested in a vertical shaft impactor for its Tertiary Plant in 2020
Having endured tough market conditions for several years, exacerbated by the recent Covid-19 pandemic, Pietermaritzburg (PMB) Quarry has seen a change of business fortunes, recording double-digit year-on-year sales growth over the past two years.
This has largely been driven by a diversified project base in the area, ranging from national and municipal road projects to private sector real estate developments, works manager Ernest Sebeelo tells Quarrying Africa
A project of note in the area is the 80-km N3 road upgrade between Durban and Pietermaritzburg.
Part of government’s 62 Strategic Integrated Projects (SIPs) gazetted
as part of the Infrastructure Investment Plan approved by Cabinet in 2020, the project comprises 14 packages estimated to be worth in excess of R20-billion.
Aimed at strengthening the logistics and transport corridor between South Africa’s main industrial hubs, Johannesburg and Durban, the project will also improve access to Durban’s export and import facilities and raise efficiency along the corridor.
While the current package – the stretch between the Dardanellas Interchange and the Lynnfield Park Interchange – is located some 30-40 km away from PMB Quarry, the operation has already supplied considerable volumes of G2, G4 and G5 products to the project.
In addition, municipal road projects in the KwaZulu-Natal capital have contributed to an increased
In anticipation of a projected rise in demand, especially on the back of the N3 road upgrade, AfriSam embarked on plant upgrades at its Pietermaritzburg Quarry to ensure reliability of supply
“
significantly
As far back as 2017, we were aware of the planned N3 road upgrades and these plant upgrades were in preparation for these and other projects in the area. We have therefore created enough capacity to manage the aggregates demand.
The
significantly
In anticipation of the projected rise in demand, especially on the back of the N3 road upgrade, AfriSam embarked on plant upgrades to ensure reliability of supply.
demand for aggregates. This comes on the back of the KwaZulu-Natal Department of Transport’s commitment to upgrade 183 km of the provincial roads network in the 2022/2023 financial year. As part of this commitment, several multimillion-rand municipal road upgrade and rehabilitation projects have come to market.
“Apart from ongoing national and municipal road upgrades, we are supplying a diverse range of projects, including community developments, lowcost housing and student accommodation projects in the area. We have also experienced increased demand from concrete products manufacturers (CPMs) and asphalt producers servicing road contractors in the area,” says Sebeelo.
In anticipation of the projected rise in demand, especially on the back of the N3 road upgrade, AfriSam embarked on plant upgrades to ensure reliability of supply. The quarry operates three plants – A Primary Plant, Tertiary Plant and B Primary Plant. The B plant produces G products, while the A plant produces the road and concrete stone products, among others.
Due to the geological characteristics of the dolerite rock found at PMB Quarry, the operation has been challenged with its primary jaw crusher at A Primary Plant. To provide context, an existing jaw had to be replaced in 2016, following a broken swing stock shaft. In 2018, the new jaw crusher installed in 2016 developed cracks to its main frame and substructure.
Post various engineering investigations, structural modifications were implemented through Finite Element Analysis to design a new under structure. A Nordberg C120 jaw crusher from Metso was selected due to the crusher’s dampening
characteristics supporting complex dynamic and static loadings. Supplied by Pilot Crushtec International, the new jaw was commissioned in December 2021, and has thus far risen to the challenge and proven to be the perfect fit for the application.
To meet high demand for sand, PMB Quarry invested in a vertical shaft impactor (VSI) for its Tertiary Plant in 2020. Supplied by Techroq, the VSI has increased sand production significantly.
“We previously had a challenge with sand production on site, with demand outstripping production capacity. With the new VSI, we are able to generate more sand than conventional crushing and screening. In fact, the VSI installation has resulted in a substantial increase in sand throughput,” explains Sebeelo.
In addition, the VSI provides the much-needed flexibility to produce specific base products. An added advantage when producing G2 is the VSI’s ability to improve the flakiness index. If the market requirements for G2 increases, the quarry is now able to manufacture this product on the Tertiary Plant, complementing the current B plant production.
“As far back as 2017, we were aware of the planned N3 road upgrades and these plant upgrades were in preparation for these and other projects in the area. We have therefore created enough capacity to manage the aggregates demand,” he adds.
Located some 8 km from the Pietermaritzburg CBD, PMB Quarry mines a dolerite material. From the dolerite rock, the quarry processes several material sizes including unwashed crusher sand, 10-mm concrete stone, 14-mm road stone, 20-mm
Production starts with drilling and blasting in the pit. This function has been outsourced to leading KwaZulu-Natal-based drilling and blasting contractor, Brauteseth Drilling and Blasting. Given the challenging geology in the quarry, which is characterised by blocks of fractured rock, the quarry is challenged with big boulders in its blasts. This calls for secondary mechanical breaking using an excavator which has a hammer attachment.
“In the quest to improve fragmentation, we have previously tested stemming plugs with no marked success. Blasting reports showed no significant improvement in fragmentation. However, we are investigating other options on a different mining level to see if we can achieve different results, using information learnt from other AfriSam quarries which have successfully implemented this technology,” says Sebeelo.
With two townships (Copsville and Panorama) and a suburb (Orient Heights) within close proximity of the quarry, managing issues such as blast vibrations and noise are of great importance to Sebeelo and his team at PMB Quarry.
“We have traditionally had issues with dust emissions to Panorama Gardens, with dust generated by mine operational activities such as material handling, crushing and screening and vehicle movement. Dust generated in this manner is carried on both light and strong winds (Katabatic breezes and Berg winds). Under Katabatic conditions, dust rises into the atmosphere and is trapped under the inversion
To meet high demand for sand, PMB Quarry invested in a vertical shaft impactor (VSI) for its Tertiary Plant in 2020. Supplied by Techroq, the VSI has increased sand production significantly.
layer, which lowers in the evening with the dust drifting down the valley and settling in Panorama Gardens. Under Berg wind, dust will be generated when wind speeds are high to lift dust from the exposed surfaces and be carried down.
“The mine implemented additional measures to improve our dust management plan. The dust management involved installation of a dust extraction system, replacement of old dust suppression spray nozzles with mist spray nozzles, installation of conveyor belt curtains to clad the screen tower and additional water carts dedicated for supressing dust generated from the haul roads and product stockpiles,” says Sebeelo.
Noise has previously been a problem for Orient Heights, which is located some 250 m from the A Primary Plant. “The noise from the jaw has traditionally presented challenges, however this has been overcome by installing cladding to mitigate both noise and dust,” says Sebeelo.
A new property development, Surrey Park, which is set to be built some 100 m from the pit, will likely pose dust and blast vibration challenges for the quarry. AfriSam has, however, implemented modern blasting techniques and technology to mitigate the risks of encroachments.
“We have made several advances so as to improve the blast designs, timing modification and other blasting optimisation measures to mitigate the negative effects of blasting. We have also installed blast vibration monitors at strategically selected points in order to closely monitor each and every blast,” concludes Sebeelo.
The ground vibration data recorded low PPV’s at all measuring points and all the values were below the conservative limit of 12,75 mm/s. Therefore, there will be no risk of damages to any structure due to ground vibration. a
While contract mining is generally regarded as a mining role, there are, however, a number of operational functions conducted on a quarry or mine that fall within the civil engineering scope, which thus compel companies to register with the Bargaining Council for the Civil Engineering Industry (BCCEI). In a one-on-one with Quarrying Africa, Lindie Fourie, operations manager at the BCCEI, outlines some of these activities and why concerned parties should comply.
The use of mining contractors is a common approach in the local quarrying sector and the surface mining industry at large. Given that the functions they undertake happen in a mining environment, there is a general industry perception that all the activities are therefore classified as mining. According to Fourie, that is not always the case, as some of the activities are actually civil engineering functions.
Perhaps the most important of these are loading, hauling and dumping of mineralised material or waste material, as well as any excavations and bulk earthworks, which all fall under the BCCEI’s scope of application. The range of these activities is determined by the National Economic
Development and Labour Council (NEDLAC) and was accepted by the Department of Employment and Labour. Therefore, any company performing these activities is required by law to register as a member of the BCCEI.
The BCCEI is a statutory body created under the Labour Relations Act (LRA) 66 of 1995 to provide for the co-regulation of stable and productive employment relations in the civil engineering industry. The council is an industrybased forum of organised business and labour that regulates employment conditions and labour relations in the civil engineering industry. It furnishes the necessary administrative infrastructure and technical expertise to ensure effective collective bargaining, industry compliance, dispute resolution and social protection services.
The BCCEI is a statutory body created under the Labour Relations Act (LRA) 66 of 1995 to provide for the co-regulation of stable and productive employment relations in the civil engineering industry
The most important functions that fall under the BCCEI are loading, hauling and dumping of mineralised material or waste material, as well as any excavations and bulk earthworks.
14
If an agent gives a compliance order and determines outstanding amounts owed to the Council or employees, the company has 14 days to pay
The use of mining contractors is a common approach in the local quarrying sector and the surface mining industry at large
Given that the functions they undertake happen in a mining environment, there is a general industry perception that all the activities are therefore classified as mining, but that is not always the case, as some of the activities are actually civil engineering functions
Perhaps the most important of these are loading, hauling and dumping of mineralised material or waste material, as well as any excavations and bulk earthworks, which all fall under the BCCEI’s scope of application
Non-compliance can result in severe consequences for companies, such as fines and damage to their reputation
“This is where conditions of employment are negotiated for employees operating in the civil engineering sector,” Fourie says. “Our registered scope entails those operating in the civil engineering sector, listing common activities such as construction of roads and bridges, among others. However, our scope is wider than that – it also deals with a specific portion of civil engineering activities that are found on a mine or quarry.”
Fourie explains that the Labour Relations Act gives certain powers to the BCCEI to ensure that it executes on its mandate, which is to ensure that every company within its scope complies with the various collective agreements. These agreements
We have found that many of the companies operating on mines and quarries are not necessarily aware that some of their activities fall under the civil engineering jurisdiction. Part of our focus this year is to reach out to them and make them aware of this requirement.
Lindie Fourie, operations manager at the BCCEIwere entered into by and between the members of the employer organisations and the members of the trade unions after industry national wage negotiations undertaken under the auspices of the BCCEI were concluded.
According to Fourie, a major reason for noncompliance by many mining contractors is that the most of these companies are not actually aware of the need to comply with the BCCEI. She believes there is still a need for educational awareness, especially on mines and quarries.
“We have found that many of the companies
operating on mines and quarries are not necessarily aware that some of their activities fall under the civil engineering jurisdiction. Part of our focus this year is to reach out to them and make them aware of this requirement. The approach is not to punish organisations, but to work closely with them to ensure that they become complaint. The risks of non-compliance can be damaging to businesses,” says Fourie.
She urges concerned parties to approach any of the Bargaining Council’s offices in Cape Town, Durban, Port Elizabeth, East London or Bloemfontein. In addition, the council has several agents operating across the country.
There are considerable benefits of being a member of the BCCEI – both to the company itself and to the industry at large. Fourie draws attention to the philosophy behind the establishment of bargaining councils, which is to ensure a stable, fair and sustainable working environment – a good outcome for all stakeholders. The key function of the BCCEI is the facilitation of industry-wide wage negotiations between the main players – employers and trade unions.
“This is all about creating our own destiny as an industry, together through collaboration,” says Fourie. “While many companies in the sector do not have the time and resources to conduct satisfactory negotiations on wages and benefits with their own employees, the skilled and experienced representatives of the parties to the BCCEI have been doing this for years on behalf of the whole sector.”
In addition to the multi-year wage negotiations, the BCCEI regularly brings together the parties to the Council, to discuss issues affecting the civil engineering sector. “The parties’ professional and dedicated negotiation expertise ensures that working operations for all members can continue smoothly based on the security of having a multiyear wage agreement from the parties,” she says.
“This creates the right environment for companies to plan their costs and prices, and to focus on their operations instead of negotiating every year or sometimes more often. With negotiations being taken care of by skilled negotiators and facilitators, the industry can rest assured that there will not be emotional compromises made to the detriment of a fragile industry and economy.”
She also notes that the BCCEI offers other services such as high-quality dispute resolution. Through its Dispute Resolution Centre (DRC), dispute referrals are resolved as quickly as possible to meet the accreditation standards of the Commission for Conciliation, Mediation and Arbitration (CCMA). For the client, it gives them a sense of security that they are dealing with a reputable contractor. This reduces the risk of disruption on site through industrial action. Using a non-compliant organisation with questionable ethics also reflects badly on the client itself.
Non-compliance, says Fourie, can result in severe consequences for companies, such as fines and damage to their reputation. If, for example, a company has been non-compliant for a number of years – which might be true for most of the cases –or an employee approaches the Bargaining Council, a BCCEI agent may conduct an assessment and issue a compliance order which can be backdated for a number of years. The financial risk, through interests on outstanding amounts and fines that could be levied against a company, could be damaging.
“If an agent gives a compliance order and determines outstanding amounts owed to the Council or employees, the company has 14 days to pay. Failure to comply with the order results in the agent taking the matter to arbitration where the company will be required to appear before a commissioner. If the commissioner finds against the company, he can also levy fines on top of the interest payable, which might leave a company in a precarious financial position,” says Fourie.
Apart from the financial risks, being noncompliant comes with a reputational risk because a company will be non-competitive.
In conclusion, Fourie says that, since inception, the Council has never had a ‘stick’ approach to compliance. However, there have been many instances where companies are aware of the Bargaining Council but choose to dodge complying, which of course is unfair competition to those who are compliant.
“We urge companies to get in touch with us or one of our agents to come and verify if there is need to comply, especially in instances where companies are not sure whether what they are doing falls within the civil engineering scope,” concludes Fourie. a
With a long history of success on the African continent, dating as far back as the early ‘90s, Lintec & Linnhoff, a global leader in asphalt and concrete batching plants, seeks to build on its successful legacy on the continent to safeguard a stronger future. With a distinct focus on infrastructure development as a cornerstone of the continent’s economic development plans, Africa offers concrete growth prospects and remains a key market for the company.
To stimulate their economies, several African governments realise the significance of infrastructure development as a catalyst for economic growth. Well-targeted infrastructure programmes are expected to play a significant role in improving poor economic performance and boosting economic transformation across the continent.
With its wide and proven range of asphalt and concrete batching plants, Lintec & Linnhoff expects to play a leading role in the continent’s infrastructure development drive. Speaking to Quarrying Africa, Tony Chakra, regional sales manager, Middle East and Africa at Lintec & Linnhoff, says Africa has always been one of the company’s key markets, simply because of its enormous potential and the large-scale demand for asphalt and concrete in its infrastructure development. Chakra notes the extensive programmes of construction planned all across the continent for roads, airports, housing and more.
By Munesu Shoko.“In recent years, we have seen work really gathering pace as countries in Africa implement more ambitious projects and look to catch up with global counterparts. According to Research and Markets, the African asphalt plant market is expected to see significant growth and the concrete plant market is expected to reach US$35.6-million,” he notes.
Chakra points out a number of countries on the continent that really stand out in terms of infrastructure development. For example, Ethiopia is predicted to be one of the world’s most rapidly developing countries. Estimates suggest 25% of the state’s infrastructure budget is currently earmarked for roadbuilding as the plan to extend the nation’s road network to 20 000 km gathers momentum.
Angola, he adds, is another country where there is a significant scope for progress, as the road network undergoes extensive upgrading, with more than 13 000 km scheduled to be paved.
“Nigeria is also becoming an increasingly important market for us, with several large-scale projects in
Over the past 30 years, Lintec & Linnhoff has provided plants for numerous projects across Africa, with several flagship projects under its belt
25%
Estimates suggest 25% of Ethiopia’s state infrastructure budget is currently earmarked for roadbuilding as the plan to extend the nation’s road network to 20 000 km gathers momentum
With its wide and proven range of asphalt and concrete batching plants, Lintec & Linhoff expects to play a leading role in Africa’s infrastructure development drive
Africa has always been one of the company’s key markets, simply because of its enormous potential and the large-scale demand for asphalt and concrete in its infrastructure development
The company has in recent years seen growing demand for its asphalt and concrete plants on the continent, varying however, from one country to another
According to the latest information from the World Bank, in addition to the projects that have already been commissioned, we know that several African countries will see further development in construction during the coming years, and this will be an excellent opportunity for us. Africa is a dynamic market that is always changing and growing, and that is one of the main reasons we love working here so much.
Its range can reach any requirements, from continuous to containerised batchtype Lintec asphalt plants, and mobile or stationary Linnhoff asphalt plants
the pipeline as part of the Nigerian Government’s infrastructure drive. We have recognised Ghana as a critical market for our range of concrete plants from our Lintec and Eurotec brands,” says Chakra.
Lintec & Linnhoff has been present in Africa since the early ‘90s, with an initial presence in East Africa. Over the years, the company has expanded to the West, Central and Southern Africa. Its distribution channels have also grown, with a dealer footprint in several countries such as Egypt, Libya, Ethiopia, Congo, Nigeria and South Africa, amongst others.
“Not only does our distributor network provide sales and after-sales support to our customers, but it also allows us to maintain our strong foothold in local markets and give us a platform for future growth,” says Chakra.
The company has, in recent years, seen growing demand for its asphalt and concrete plants on the continent, varying however, from one country to another. Its range can reach any requirements, from continuous to containerised batchtype Lintec asphalt plants, and mobile or stationary Linnhoff asphalt plants.
On the other hand, the company also supplies Eurotec concrete plants that can be either portable or stationary. It has also launched its ECOlite model, especially for African countries; this model is ideally suited for small to medium-sized job sites.
the needs of the project and client requests. Most recently, ZFM took delivery of a brand-new Eurotec ECO90. Installed in the Mali capital, Bamako, the plant commenced operations in January 2023, supplying readymix concrete to local contractors – many of whom will be involved in supporting the nationwide push to increase public housing construction.
Another installation of note was a Linnhoff TSD 1500 MobileMix asphalt plant delivered to a customer for use on a grade separation project on the Tema Intersection in Ghana. The company has also supplied several plants of the same model to major Ethiopian Roads Authority projects, where they have helped to develop and upgrade the road network.
“The Linnhoff TSD 1500 MobileMix asphalt plant is a perfect option for our African customers as it is designed to provide high asphalt production and optimal mobility, which is a great combination for large-scale road projects in landlocked countries,” says Chakra.
In terms of concrete plants, one of Lintec & Linnhoff’s long-time customers was so impressed with the performance of its Eurotec ECO60 concrete batching plant they ordered a second model to support its work on the Toamasina Port Development Project (Phase 2) in Madagascar.
The Japanese contractor was already familiar with the ECO60 as they had previously been using the same model. When they needed a new plant for a port extension project, it was an easy choice for them to purchase the same model. The decision to buy the second plant was made after being convinced of its quality and reliability, as well as the contractor having been impressed with the superb level of aftersales support from the Eurotec team.
Angola is another country where there is a significant scope for progress, as the road network undergoes extensive upgrading, with more than 13 000 km scheduled to be paved
Over the past 30 years, Lintec & Linhoff has provided plants for numerous projects across Africa, with several flagship projects under its belt.
A case in point is the recent purchase of an ECO90 stationary concrete batching plant by Z For Mining (ZFM), a Mali-based contractor that now owns three of the four units that make up the Eurotec ECO range.
ZFM has been an enthusiastic advocate of Eurotec machinery ever since it acquired its first model, a second-hand ECO30, from a local contractor in 2013, and a brand-new ECO50 model that was also installed at the Syama gold mine, where it supported the shotcreting of underground tunnels.
Daily production output of both the ECO30 and the ECO50 varied between 10-100 m³ in response to
In Tanzania, a customer selected the Eurotec 3ECO50 concrete plant along with the Eurotec Pan Planetary concrete mixer, to build the Tazara Overpass, the first flyover in Dar es Salaam. In addition, several Lintec asphalt plants have been involved in major projects in Africa. These include a Lintec CSM4000 containerised asphalt plant that was involved in the Yaounde-Douala highway project in Cameroon, and a Lintec CSM4000 that worked on the Addis AbabaAdama Expressway project in Ethiopia.
“According to the latest information from the World Bank, in addition to the projects that have already been commissioned, we know that several African countries will see further development in construction during the coming years, and this will be an excellent opportunity for us. Africa is a dynamic market that is always changing and growing, and that is one of the main reasons we love working here so much,” concludes Chakra. a
To preserve uptime in loading operations, quarry owners should take advantage of the array of benefits offered by modern on-board weighing systems. Glen Webster, sales director at Loadtech Load Cells, the Loadrite distributor in sub-Saharan Africa, points out that three elements need to be considered to get the most uptime out of these systems – data, service time and support, writes Munesu Shoko.
20-25%
Loadtech has seen business growth of 2025% in the past two years
The new Loadrite system, particularly the L1380 Smart Scale, features an angle sensor instead of the traditional rotary triggers 24/7
To ensure customers get the best out of their data, Loadtech employs a data specialist who is available 24/7 to support customers
For any quarry owner, uptime is a key parameter that influences both productivity and, ultimately, also the bottom line. As the current challenging economic conditions continue to pressurise an already constrained construction materials market, quarry owners are well aware that maximising uptime is largely the basis on which they can survive these ongoing turbulent times.
“Loading operations are a key function of the quarrying and mining value chain at large. It is therefore important to know what’s happening at these operations in real time. The importance of weighing products to eliminate guesswork cannot be stressed enough,” says Webster.
Having access to data, in real time, is a key to ensuring efficient and productive loadout operations. According to Webster, it starts with deriving insights that can be turned into actionable change. “The availability of data arms quarry managers with the kind of insights that enable them
to improve productivity and impact the bottom line,” he says.
Loadrite onboard weighing systems can be configured to provide the data needed for any operation. Loadtech’s expert installers work with site managers to identify the configuration that will give them the information they need.
“We work with fleet managers individually to ensure the system meets the needs of their business. Our aim is to ensure that data collected provides real value to increase productivity and profitability over the lifecycle of the machine,” says Webster.
The first step, continues Webster, is to understand how productive machines are, including how much fuel they use and how much material they move. The next step is using that information to make changes where necessary to improve uptime, efficiency and reduce costs.
By tracking the amount of material moved per hour to measure productivity and set benchmarks, operators can see underperformance and make appropriate adjustments to
ensure all equipment is working at its optimum efficiency.
A Loadrite onboard weighing system such as the L3180 can be used to calculate the weight of material in an excavator’s or loader’s bucket, relay this information to the operator and record the weight for later use. Being able to track the amount of material moved per hour can then be used internally as part of an overall business analysis to measure productivity and set benchmarks.
“Once you know your benchmark productivity rates, it’s also easy to identify equipment that is underperforming, which sets off a trigger for an investigation into the underlying causes. These causes can vary widely, from operator error to equipment failure.”
Once productivity benchmarks are set, fleet managers can customise the Loadrite system to capture a wide range of other data such as cycle times, which can then be used to identify process bottlenecks and inefficiencies. By resolving these issues, managers can
To ensure peace of mind for its customers, Loadtech offers Service Level Agreements, which define specific metrics for ascertaining service quality.
To maximise uptime in loading operations, quarry owners should take advantage of the array of benefits offered by modern on-board weighing systems
Having access to data, in real time, is a key to ensuring efficient and productive loadout operations
Reducing service time maximises machine uptime. With that in mind, the new Loadrite systems’ design does away with moving parts
To ensure peace of mind for its customers, Loadtech offers Service Level Agreements (SLAs), which define specific metrics for ascertaining service quality
improve productivity and reduce operating costs.
The Loadrite system can also measure the cycle times between each loading event, which can show how efficiently the material is being moved. Shorter cycle times generally point to a more efficient and therefore more profitable operation.
To ensure customers get the best out of their data, Loadtech employs a data specialist who is available 24/7 to support customers. “The data specialist is complemented by four technicians and two truck drivers – the team is big enough to run and support our installed base,” says Webster.
As part of the SALs, a technician visits a customer once a month, where they conduct inspections to ensure that the load weighing systems are functional.
Reducing service time maximises machine uptime. With that in mind, the new Loadrite systems’ design does away with moving parts. The old systems feature rotary triggers and pins, which are susceptible to wear.
In contrast, the new system, particularly the L1380 Smart Scale, features an angle sensor instead of the traditional rotary triggers. This allows the system to offer accurate weighing in tough conditions, while reducing the need for maintenance due to the absence of moving parts.
“Customers are guaranteed more uptime with the L3180 SmartScale. The mew multi-axis IMU sensors are more robust with no moving parts, reducing the need for repair and maintenance. They are also faster and less invasive to install, with no need to customise mounting brackets or to weld,” explains Webster.
The Loadrite L3180 SmartScale uses weighing intelligence and solid-state sensors for more accurate, precise and faster loading. It also connects machines and devices for the collection and syncing of data via the built-in WiFi to the InsightHQ reporting portal. When using Trimble’s cloudbased InsightHQ quarry reporting portal, personnel can gain access to site production and operator performance KPIs on desktop or mobile devices.
In addition, Loadtech offers rebuild services for all its load weighing systems, allowing customers to upgrade their old systems with new software if need be. The company also offers trade-ins for older systems.
Product support also plays a key role in maximising uptime, points out Webster. To ensure
peace of mind for its customers, Loadtech offers Service Level Agreements (SLAs), which define specific metrics for ascertaining service quality.
According to Webster, SLAs are concrete, measurable standards that Loadtech promises to uphold. Examples include customer support response time and service uptime, amongst others.
As part of the SALs, a technician visits a customer once a month, where they conduct inspections to ensure that the load weighing systems are functional. On the day, Loadtech provides certified test weights for calibration purposes. In addition, Loadtech also provides additional operator training to any new operators on site.
“We also use these monthly visits to look at the data fields to ensure they input correctly. We then generate a report on the findings and also provide the customer with a new calibration certificate, which shows that the instrument is measuring correctly,” explains Webster.
Loadtech reports increased uptake of its SLA offering, largely driven by the industry’s push for more uptime. The increased uptake coincides with the general growth of the company’s business. Loadtech is a preferred supplier for big mining clients such as Glencore, B&E International, Danoher and M Civils, as well as big transporters such as Reinhardt Transport.
The company also partners several equipment suppliers such as Burgers Equipment & Spares (LiuGong dealer), Dura Equipment (Lovol dealer) and Babcock (Volvo CE dealer).
“We have seen incredible business growth of 2025% in the past two years,” says Webster. “During the same period, our SLAs have grown to a point where we had to invest in a new truck to move the certified test weights between sites.” a
The new L 580 has a 27-t operating weight, which allows for a 4% standard bucket capacity increase from 5 m³ to 5,2 m³.
Having introduced the new generation Liebherr 5.1 wheel loader range late last year, an upgrade of the previous 5.0 generation, Liebherr-Africa reports increased local demand for the three new models – the L 550, L 566 and L 580. Key talking points are the performance increases – increased tipping load, larger bucket sizes and more engine power – resulting in 25% less fuel burn per hour and 15 % higher production. By Munesu Shoko.
25%
Renowned for its efficiency, Liebherr’s proven hydrostatic travel drive achieves a reduction in fuel consumption of up to 25% 6%
The new L 550 has a 6% bucket capacity increase from 3,2 m³ to 3,4 m³
4,2 m³
While the L 556 retains the same axle as its predecessor, the model however benefits from a standard bucket capacity increase of 4% (4 m³ to 4,2 m³) 27-t
The previous generation L 580 weighed in at 25 t, while the new improved model has a 27-t operating weight, which allows for a 4% standard bucket capacity increase from 5 m³ to 5,2 m³
Following the global introduction of the new generation wheel loaders in January last year, the first units of the new L 550, L 566 and L 580 arrived in South Africa during the fourth quarter of 2022. Since then, several machines are already in operation at local sites across applications, including quarrying, construction, contract mining and port handling, confirms Lavell Ruthman, Head of Sales – Earthmoving Technology at Liebherr-Africa.
Developed at Liebherr’s Bischofshofen plant in Austria, dubbed the company’s Technology Centre for Wheel Loaders, the new range benefits from the company’s decades of experience in designing wheel loaders. Central to the development of the new wheel loader series, Tendayi Kudumba, General Manager Earthmoving Technology at Liebherr-Africa, points out, was the ‘voice of the customer’.
As part of the development process, Liebherr observed its customers’ wheel loader operations around the world, including Africa. Customers’ experiences were crucial to the development of
the new wheel loader series. Some of the key improvements influenced by this exercise include a sustainable performance increase in the two new models and a new electrohydraulic pilot control for increased safety and productivity. The performance of the L 566 in terms of engine power has remained the same while the bucket capacity has increased.
The new L 550, L 566 and L 580 wheel loaders feature Liebherr’s proven hydrostatic travel drive, which is renowned for its efficiency. The Liebherr driveline achieves a reduction in fuel consumption of up to 25%. Given that fuel is a major cost driver for loading operations, this reduces operating costs significantly.
Thanks to increases in engine power, the travel drive is even more powerful while maintaining lower levels of fuel consumption. While the L 566 has maintained the same level of engine power (200 kW) as its predecessor, the L 550 and the L 580 benefit from a power increase of 13% (168 kW) and 9% (219 kW), respectively.
“This is advantageous when
Following the global introduction of the new generation wheel loaders in January last year, the first units of the new L 550, L 566 and L 580 arrived in South Africa during the fourth quarter of 2022
Several machines are already in operation at local sites across applications, including quarrying, construction, contract mining and port handling
The new L 550, L 566 and L 580 wheel loaders feature Liebherr’s proven hydrostatic travel drive, which is renowned for its efficiency
Thanks to increases in engine power, the travel drive is even more powerful while maintaining lower levels of fuel consumption
accelerating or penetrating material and lowers fleet fuel costs. Liebherr has installed the diesel engine in the rear, where it also acts as a counterweight thereby increasing the tipping load for the wheel loaders,” explains Kudumba.
Continuous tractive force, combined with automatic limited slip differential, prevents wheelspin, thus increasing productivity, while reducing tyre wear by up to 25%.
In addition, the new range benefits from larger and stronger axles as well as increased operating weights, allowing for a marked increase in bucket capacities and ultimately productivity. The previous generation L 580, for example, weighed in at 25 tonnes (t), while the new improved model has a 27-t operating weight, which allows for a 4% standard bucket capacity increase from 5 m³ to 5,2 m³.
“The new L 550 has a 6% bucket capacity increase from 3,2 m³ to 3,4 m³. While the L 556 retains the same axle as its predecessor, the model however benefits from a standard bucket capacity increase of 4% (4 m³ to 4,2 m³),” explains Ruthman.
With the new range, Liebherr has two lift arm versions on offer. Firstly, the Z-bar kinematics, which come to the fore particularly in the lower lifting range and for the break-out force. Secondly, the industrial kinematics, which have been
designed for working with heavy working tools such as high dump buckets and log grapplers.
Finally, Liebherr also offers the High Lift arms – an extended version of the Z-bar kinematics with the longest lift arms in this wheel loader segment. These ensure greater reach and more productive loading procedures at great heights, which is beneficial when loading railway wagons or trucks with high sides.
The working hydraulics of the wheel loaders have impressed local customers with their larger components and new electrohydraulic pilot control. This technology ensures responsive movements of the lift arms, independent of the size or weight of the working tool.
Liebherr also offers a new, optional weighing device on the basis of the electrohydraulic pilot control. The assistance system works automatically as a check scale and provides real time information about the loading procedure. This data helps machine operators to fill dumpers very precisely with the specified quantities and to avoid overfilling.
The new range offers increased safety thanks to the electrohydraulic pilot control. “The electrohydraulic pilot control enables operators to perform individual adjustments on the new wheel loaders. For example, they can set lift limitations and maximum tilt-out heights, thus reducing the risk of accidents in areas where space is restricted. The tilt-out speed can also be programmed to protect lift arm components and the installed equipment,” says Kudumba.
In addition to these optimisations for operating safety, Liebherr has also invested in the operational reliability of the new wheel loaders, given that they are faced with an abundance of challenges: remote
operating areas, extreme climates, demanding loading materials and multi-shift operation over a long period, all demand a high degree of reliability.
“For this reason, Liebherr has installed larger axles than were fitted on predecessor models. Liebherr has drawn on proven components from its other wheel loaders for the core components and steel construction,” says Ruthman.
When designing the new wheel loader range, Liebherr paid particular attention to operator comfort, which is a key parameter in enhancing productivity. The clean lines on the rear as well as the large glass surfaces in the cab facilitate good all-round visibility. Furthermore, the new reversing camera, which is installed in a protected position in the engine bonnet, assists the machine operator to keep an eye on the area to the rear.
Numerous details that have been seamlessly integrated in the wheel loaders’ exterior design make service work easier. For example, on the L 566 and L 580, the engine bonnet opens to the rear, making the diesel engine freely and safely accessible.
A sturdy cab access leads to the redesigned and spacious operator’s cab. One of the special features of the cab is the height-adjustable 9-inch touch display with intuitive menu navigation. The highresolution display provides a clear overview of all the wheel loader’s operating information.
“The new Liebherr control lever enables the highly sensitive control of work movements as part of the modern operating concept. Hydraulic working tools, such as the log grappler, can also be precisely controlled with the optional mini joystick on the control lever,” concludes Kudumba. a
Ever Star Industries (ESI) has introduced a standard 5-Year/ Unlimited Mileage warranty on all its FT Series M4 spec models. National brand manager Justin Bennett tells Quarrying Africa that the new warranty is a statement of promise on the ability, performance and quality of the product. By Munesu Shoko.
For any big-ticket purchase, end users want to know before they checkout that if anything goes wrong, they can turn to the supplier for support. Warranties, therefore, provide definite value to consumers – they are an assurance that the company stands behind its product and is ready to support it for the long haul.
It is for this reason that leading truck importer, ESI, is rolling out a standard 5-year/ Unlimited Mileage warranty on all FT Series M4 spec models.
Bennett says the offering is prompted by the demands of the consumers, especially when one views the high cost of purchasing capital equipment/assets such as trucks. With the influx of more competitors, each brand is being pushed to offer that extra added value.
“In a pioneering development, we are offering a standard 5-Year/Unlimited Mileage warranty on all of our FT Series M4 spec models,” he says. “With this warranty, our customers will get peace of mind and assurance that they will get lasting value from the product.”
The first year of the warranty covers all the mechanical functions, from bumper to bumper. The second year covers the driveline – engine, gearbox, diff and propshaft. Years three, four and five cover the base engine –the heart and soul of the engine, including the block, the pistons, and the crankshaft – for an unlimited mileage, and/or duration, whichever occurs first. This, however, excludes bolt-ons such as the turbo, alternator, oil and water pumps.
A thorough research and development
The 5-Year/Unlimited Mileage warranty speaks volumes about the quality of the product and the support behind it
Ever Star Industries is rolling out an industry-first, standard 5-year/ Unlimited Mileage warranty on all FT Series M4 spec models
With this warranty, customers will get peace of mind and assurance that they will get lasting value from the product
In addition to the new warranty, Ever Star Industries is expanding the FT Series range with the addition of the new FT9 model
Armed with a simple, well-priced and rugged product that is complemented by good aftersales support, the FT range has gained considerable ground in the medium commercial vehicle market since its local introduction in 2018
(R&D) regime, says Bennett, has established that the product is rugged enough to carry the groundbreaking warranty. Once dismissed as lowend upstarts, Bennett argues that Chinese truck makers have built up their capabilities and now compete head-to-head with the Japanese product.
“The 5-Year/Unlimited Mileage warranty speaks volumes about the quality of the product and the support behind it, which adds great value, and gives us a competitive edge. It gives our customers the peace of mind knowing that they won’t have to deal with costly repairs due to relevant breakdowns,” he says.
In case of a breakdown, he adds, the OEM and the dealers will provide highly skilled technicians who are specifically trained to repair the trucks. This means that repairs will always be done right the first time without slow turnaround times and inaccurate diagnoses, thus maximising truck uptime, and subsequently maximising profitability.
In addition to the new warranty, Ever Star Industries is expanding the FT Series range with the addition of the new FT9 model. The new model offers 15-21 t of payload, depending on configuration.
3-13 t
While the focus is on on-road applications, he also sees opportunity in construction and quarrying, where the FT Series range – with a payload range from 3-t to 13-t – can act as a backup vehicle
The 5-Year/Unlimited Mileage warranty speaks volumes about the quality of the product and the support behind it, which adds great value, and gives us a competitive edge. It gives our customers the peace of mind knowing that they won’t have to deal with costly repairs due to relevant breakdowns.
Justin Bennett, national brand manager: FT at Ever Star IndustriesA major talking point, says Bennett, is the Cummins four-cylinder engine, which he believes changes the game in this size class. The Cummins ISF4.5 E3210 engine (Euro 3) delivers 154 kW of power at 2 500 rpm. While the 210 hp is some 10 hp less than the six-cylinder engine commonly found on competitor offerings in this size category, it still offers the same level of performance with reduced fuel consumption.
“The four-cylinder engine is a game changer for us. Firstly, it offers better fuel consumption
compared to the older six-cylinder run by some of our closest competitors in this size class. Secondly, two cylinders less means reduced service and maintenance costs,” he says.
Another key feature is the ZF six-speed Ecolite manual gearbox featuring a light aluminium alloy shell and optimised gear ratio for reduced fuel consumption, as well as an updated helical tooth design for ease of operation. Closest competitors, says Bennett, run an eight-speed splitter gearbox, which is complex to drive compared with the sixspeed offering. “Not everyone is able to operate the splitter gearbox, which makes the risk of damage very high,” he says.
“The model comes with cruise control as standard. Air conditioning is also standard, as well as the MP3 radio with a USB port to allow drivers to charge their cell phones on the go. Driver comfort is a key focus area in today’s operating conditions. In fact, drivers do influence purchasing decisions, which is why the FT9 places the driver at the centre of its design,” says Bennett.
Armed with a simple, well-priced and rugged product that is complemented by a good aftersales support network, the FT range has gained considerable ground in the medium commercial vehicle market since its local introduction in 2018.
Key to the range’s growth, says Bennett, is that it strikes a good balance between quality, price and effective backup support.
The medium commercial vehicle segment is a tightly contested market in South Africa, with Japanese manufacturers traditionally known to be the leaders in this market segment. In recent years, Chinese OEMs have aggressively started to challenge the status quo for market share with products that have continuously evolved and improved rapidly over the years.
Improved build quality and better aftermarket footprints are some of the key pillars of growth. The
simple, rugged product speaks directly to the needs of the ‘value-driven’ consumer seeking quality, value, and reliability at a lower price point.
The FT range has fared very well over the past five years. “Over the years, we have seen constant sales growth. In 2019, we sold some 64 units, before growing our sales to 146 the following year. We saw a slight growth in 2022, with a total of 173 units sold. Last year was good for us, with 244 units sold, representing a 25% year-onyear growth rate,” says Bennett. “We have made strong inroads into big-fleet clients, which further promotes the capabilities of the truck and the support behind it.”
Backed by the new 5-Year/Unlimited Mileage warranty, Bennett is confident that the FT range will see a far greater growth in the coming years. While the focus is on-road applications, he also sees opportunity in the construction and quarrying sectors and/or industries, where the FT Series range – with a payload range from 3-t to 13-t – can act as a backup vehicle, and/or more efficient vehicle to run the shorter and smaller loads.
Having a good product is one thing, but being able to offer crucial backup and parts support once the product is operational in the field, is quite another. Based on a clear understanding of this notion, ESI has, over the years, invested in a strong and focused dealer network across the region (South Africa, and some of the other southern African countries).
The dealer network is complemented by ESI’s ability to hold a large inventory of parts and has even established another two parts warehouses in Pietermaritzburg, near its assembly plant. All of this ensures better service to its customers operating both within and near that region.
“It must also be appreciated that this dealer network is always evolving, with the addition of more dealers, and focused training from both Cummins and ZF, as well as the OEM itself (ESI/ Foton),” concludes Bennett. a
The Pilot Modular range consists of standardised modules which are reconfigurable and scalable, allowing customers to start small or change and grow their processing plant.
Amid increased focus on infrastructure development largely driven by mines in selected southern African countries, Pilot Crushtec International reports growing demand for its modular plants in the region. By
Traditionally, South Africa has always constituted the bulk of Pilot Crushtec’s business. However, the company reports massive growth in the rest of southern Africa in the past year, with countries such as the Democratic Republic of Congo (DRC), Zambia and Zimbabwe showing the desire to invest in infrastructure projects.
At the moment, the amount of work coming from southern Africa is about 60% of the company’s business, with the other 40% coming from South Africa. Traditionally, it has always been the other way around.
Speaking to Quarrying Africa, Francois Marais, sales and marketing director at Pilot Crushtec, says for the first time in a long period, the modular plant market has surpassed the mobiles market in terms of demand.
“Our modular crushers, screens, conveyors and feeders are doing extremely well; we are
Munesu Shoko.KEY TAKEAWAYS
Pilot Crushtec reports growing demand for its modular plants in southern Africa
The bulk of projects taking delivery of Pilot Modular solutions are aggregates operations for mines
A case in point is a greenfield modular crushing and screening plant to process aggregates for a DRC mine – the biggest ever in Pilot Crushtec’s history
In recent months, Pilot Crushtec has also recorded remarkable success with its small, turnkey sand making plants, ranging from 30-300 tph
60%
At the moment, the amount of work coming from southern Africa is about 60% of the company’s business, with rest coming from South Africa
The Pilot Modular conveyor range is cost effective, fit-for-purpose and easily adaptable for the transfer of materials between feeders, crushers and screens.
While the rest of southern Africa is taking delivery of larger modular plants in the 200-250 tph region, South Africa is chipping in with demand for smaller modular solutions
“We have supplied four greenfield modular plants in southern Africa in the past six months. The majority of sales are coming from greenfield quarry and aggregate crushing projects. However, we have also sold a couple of units to existing plants where operations seek to upscale or diversify their processes.
moving them in fairly decent volumes,” he says. “To provide context, we have supplied four greenfield modular plants in southern Africa in the past six months. The majority of sales are coming from greenfield quarry and aggregate crushing projects. However, we have also sold a couple of units to existing plants where operations seek to upscale or diversify their processes.”
The bulk of projects taking delivery of Pilot Modular solutions are aggregates operations for mines. This is particularly the case in the DRC and Zambia, where mining companies are establishing their own quarries or borrow pits for their own road builds and structures on mines.
A case in point is a greenfield modular crushing and screening plant to process aggregates for a DRC mine – the biggest ever in Pilot Crushtec’s history. To be commissioned later this year, the 250-tonne per hour (tph) plant will include a primary crushing station, two secondary cone crushers, four triple deck screens and a tertiary cone crusher. Meanwhile, the company recently commissioned another modular solution in Zambia. “The Zambian plant was for a mine which had experienced a critical failure on the primary section of the existing plant and needed to supplement with a secondary line, with feed material coming from the existing first line post the primary stage. We added a feeder to accept material post the existing primary crushing stage,” says Marais.
While the rest of southern Africa is taking delivery of larger modular plants in the 200-250 tph region, South Africa is chipping in with demand for smaller modular solutions. For example, Pilot Crushtec recently supplied a 30 tph sampling
plant in the country.
“It’s the kind of setup that we believe is unique to us,” says Marais. “From point of order to delivery was only a matter of six weeks. Within such a short period, the client had a fully functional plant to sample product that they are mining for export purposes. The turnaround was extremely quick and the maintenance of operations of the plant are easy. The capital outlay was also very reasonable, which made sense for the client.”
In recent months, Pilot Crushtec has also recorded remarkable success with its small, turnkey sand making plants, ranging from 30-300 tph. These incorporate locally manufactured components only, with nothing imported.
“The sand making plants are complete Pilot Crushtec designed and built solutions, all the way from feeding to material stockpiling,” he says. “We have had a lot of success with this offering, particularly driven by small scale sand producers. With high demand for manufactured sand, we believe that these plants will continue to generate a lot of interest in the market.”
The Pilot Crushtec sand-making plant generally entails a feeder that feeds into a horizontal shaft impactor (HSI). From here, material goes over a screen, with any oversize material recirculating through a vertical shaft impactor (VSI), then back to the screen to produce largely -6 mm sand or any other aggregate sizes required.
The modular solution offers an array of benefits to the customer. Firstly, from a design perspective, customers can select the components they need to suit their specific application. These units are then interlinked with conveyors and a solution is tailored to their specific needs and site specifications. Once the design is defined, all the modules and individual components are sent to site, lifted into place and bolted together.
Marais says modular systems are readily available modules that can quickly be on site and operational within a day or two. Traditionally, bespoke plants have lead times of at least two years and more. “Just
the design and engineering of traditional bespoke plants takes 12 months, all the while costing customers a fortune. With modular solutions, the lead times are noticeably short, which is critical for most infrastructure projects,” he says.
Speaking of costs, modular plants generally have a lower capital cost compared with their bespoke, static counterparts. From an operational cost point of view, these solutions also work out cheaper than their tracked counterparts because they do not rely on diesel power. “They are far cheaper to operate and can still be quite easily relocated,” says Marais.
The modular solution is also a cost-effective option in terms of maintenance. Marais points out that with bespoke plants, getting replacement parts takes a bit longer, whereas in a standardised solution, parts are off-the-shelf in most instances. “With these solutions, our objective is the same as our customers’ – to maximise their uptime. Breakdowns and downtime related to maintenance are big enemies of production, and ultimately, profitability.”
Additionally, should requirements change at any point within the design process, customers are able to tweak the requirements, so they have exactly the right layout, equipment and capacity to get the job done at all times. “You get to choose what you need, when you need it, and can add modules as and when required,” he says.
Looking ahead, Marais believes that the mining sector will continue to drive demand for modular plants in southern Africa for the foreseeable future, given the thriving commodities market.
“The construction sector generally remains challenged, especially in South Africa,” he says. “Consequently, even some of the traditional construction contractors that we have dealt with for decades are diversifying into contract mining or doing more construction jobs on mines. The commodities side of the industry remains the biggest contributor to southern African economies and certainly our business. That I believe will remain the status quo in the short to medium term.” a
The new line of Liebherr wheel loaders draws upon the proven Liebherr quality of the past and combines it with the innovations of the future. The all-new wheel loaders deliver modernized design, proven components, and flexible configurations. Additionally, even more operator comfort has been realized thanks to increased technological integration. www.liebherr.com
One of the major trends in the quarrying and mining industry is the move towards the design and construction of modular plants. Key drivers behind the growth of these solutions, Ricardo Isaacs, regional sales manager at Astec Industries Africa Middle East (AME) tells Quarrying Africa, are largely the lower capital costs and the short lead times.
Building a new processing plant can be an expensive endeavour. Therefore, quarrying operations are turning to modular plant systems for their array of advantages, essentially the low capital costs that are reflected in a higher return on investment and improved cost to recovery ratios.
Additionally, modular systems offer quick lead times because they comprise quick and easily available modules that can be on site and operational within a short space of time. Original equipment manufacturers can build these self-contained, high recovery plants for minimal start-up capital, using high-quality components and in-house expertise.
“We have observed that customers are increasingly looking for faster and more costeffective solutions compared to conventional, bespoke structures. Modular plants by their nature require a smaller site footprint with minimal civil works, which gives the customer
By Munesu Shoko.the option to have the equipment relocated to a new location at a later stage. Time, available real estate and moveability are some of the key factors behind their uptake, especially for expansion projects or extending the life of mine,” says Isaacs.
The short timeframe for manufacture and erection on site is a big benefit for customers. In addition, modular plants allow for ease of plant extensions. Subject to the lifespan of the operation, the modular concept also allows for decommissioning and reinstating on alternative sites.
“Astec modular solutions are meticulously designed for easy erection and transportation, which allows them to be broken down to fit into standard shipping containers if needed. It is a compact but sturdy, heavy-duty design built to last and provides easy access for maintenance,” he says.
Astec’s excavator feed hopper modular
Quarrying operations are turning to modular plant systems for their several advantages, but essentially the low capital costs and short lead times
In addition, modular plants allow for ease of plant extensions
Subject to the lifespan of the operation, the modular concept also allows for decommissioning and reinstating on alternative sites
Astec modular solutions are meticulously designed for easy erection and transportation, which allows them to be broken down to fit into standard shipping containers if needed
jaw plant requires no retaining wall. However, the company’s truck dumping hopper will require one. The company also offers skid-type structures complete with walkways, handrails, access ladders, guards and all fasteners.
“Our modular structures are erected at many southern African quarrying and mining sites. One of our flagship projects is the recent supply of a 400 tonnes per hour (tph) primary modular jaw system to a top quarry in Cape Town,” he says.
The structure was easy to assemble and was erected in a matter of days with a mobile crane and only a single technician and an assistant. The client is
now able to shut down and dismantle the old plant and access saleable rock beneath the old plant. At the time of ordering, the quarry opted for a larger jaw crusher to increase its primary plant capacity.
While quarries are generally pressed for time and cost, Isaacs cautions that there is need for due diligence and careful consideration of the manufacturer, safety, quality and durability and not always the cheapest solution when it is buying time.
However, Isaacs believes that the modular growth will always be driven by cost, efficiency and safety. This, he believes, is going to be a growing opportunity in both the mining and aggregates spaces. Astec is an industry leader and has over the 100 years of its existence demonstrated its capability of manufacturing world-class products and of being compliant to standards in the mining and quarrying sector.
“At Astec Industries South Africa (previously Osborn), we are a triple ISO certified manufacturer. Our modular solutions are in operation worldwide and we can supply complete plants with various feed or surge hopper sizes up to 50 t live capacity, as well as inter-connecting and product conveyors for primary, secondary and tertiary applications. The standard sizes we offer range from 150 tph to 800 tph, however, we customise as per customer requirements,” concludes Isaacs. a
As part of its
and Operate (DBOO) operating model – a 2020 extension to its traditional crushing and screening business – leading South African contractor, Seneca Crushing and Screening, recently opted for a turnkey, bespoke process plant from Terex Mineral Processing Systems (MPS) for a Northern Cape contract. Despite the short lead time, Terex MPS successfully commissioned the 550 tph plant on time, with a layout that fitted within the limited footprint available on site. By Munesu Shoko.
Predominantly a crushing and screening (comminution) contractor in the mining, civils construction and recycling industries, Seneca Crushing and Screening cut its teeth in demolition waste recycling, before expanding its foothold into the mining industry, with a special focus on iron ore in the Northern Cape province. The company entrenched itself in this market and quickly became a preferred supplier to many mining houses within the iron and manganese resource areas. The processing of these ores, says Gareth Nettmann, Group Contracts Manager at Seneca, is demanding on the equipment and calls for sound management of maintenance and plant availability due to the hardness, abrasiveness and work indexes of the ores. Seneca has over the years excelled in these difficult applications.
“We have been able to deliver consistent performance on our contracts with our clients and by extension, we have been instrumental in their being able to conform to their KPIs and thus honour their
offtake and logistics commitments thereby ensuring delivery of product and feasibility of the mine,” says Nettmann.
Over the years, the company has grown its order book and subsequently its fleet to execute the growing number of jobs. Despite the recent Covid-19 setback and the current power crisis in South Africa, Seneca has experienced consistent annual growth in the past few years.
“We have a large client base within the civils construction industry and are encouraged by the uptick within this industry after a few years of dormancy. We have a large market share and substantial presence in the coal, chrome, platinum, gold and manganese mining industries and are the forerunner in the iron space, where we process in excess of 350 000 tonnes per month (tpm) of ore alone,” explains Nettmann.
In 2020, the company decided to extend its service offering to include Design, Build, Own and Operate
With particular site-specific requirements, Seneca needed a plant designed, engineered and built in a short timeframe to deliver a minimum of 550 tph
The plant was completed in the third quarter of 2022 and is delivering beyond expectations
and overall mine management, knowing that the comminution and beneficiation processes are managed by an expert company of Seneca’s stature. In essence, the difficult and capital extensive crushing, screening and beneficiation boxes have been ticked, allowing mines to concentrate on the balance of their operations.
Since its corporate decision to increase its service offering, the company now runs five magnetic separation plants on toll treatment basis for various clients within the manganese space and will be building its first 250 tph High Density DMS separator for one of its iron ore clients in the Northern Cape in 2024.
Part of this growing plant base is the recent DBOO crushing and screening plant for an iron ore client. Supplied by Terex MPS, the plant was completed in the third quarter of 2022 and is delivering beyond expectations, says Nettmann.
Located just outside Postmasburg, the mine is notorious for some of the toughest ore in Africa. With particular site-specific requirements, Seneca needed a plant designed, engineered and built in a short timeframe to deliver a minimum of 550 tph, explains Willem du Plooy, Regional Business Development Manager –Africa, Terex MPS.
Terex MPS recently commissioned a turnkey, bespoke processing plant for Seneca Crushing and Screening
In consultation with the experienced Seneca Crushing and Screening, Terex MPS developed a solution suited to the variable feed characteristic expected from the mine with a layout that fitted the limited footprint available on site
At the heart of the plant are two Terex MPS MC320 modular cone crushers – a TGS320 secondary and TG320 tertiary
The plant was designed to manage a feed of three different iron ore run-of-mine characteristics – detrital ore, on-grade DSO ore and sub-grade ore
(DBOO) and Build, Own, Operate and Transfer (BOOT) operating models, thus moving into both comminution and beneficiation spaces. The new models have been met with great interest by customers, confirms Nettmann.
By going this route, Seneca is now able to offer its clients the luxury and value of its wealth of experience, through guiding the design of the plant and process. Clients are also able to save some of their capital as Seneca finances the processing plants, allowing for cashflow flexibility for the client. These models also give clients enough room to concentrate on better understanding their resource, mining plan, logistics
“In consultation with the experienced Seneca Crushing and Screening, Terex MPS developed a plant suited to the variable feed characteristic expected from the mine with a layout that fitted the limited footprint available on site,” says Du Plooy.
According to Nettmann, the plant was designed to manage a feed of three different iron ore run-of-mine (ROM) characteristics –detrital ore, on-grade DSO ore and sub-grade ore – all with varying minerology, particle size distribution (PSD), feed size, crushability work indexes, hardness and abrasive index characteristics, as well as varying product size specifications for preparation for beneficiation.
“Consequently, we had to go for a three-stage crushing and three-stage screening plant, with screening prior to every crushing stage, all recirculated within a closed circuit. The result is an incredible plant that has benefitted from years of Seneca’s operational experience working within varied applications, coupled with a sound understanding of iron ore, as well as our experienced and motivated staff and our close relationships with OEMs such as Terex MPS,” says Nettmann.
Terex MPS is built on a very long history of crushing and screening, encompassing some of the oldest crushing names in the world, such as Cedarapids, Simplicity, Jaques, Canica and more, all available on static, modular and portable (wheeled) platforms.
At the heart of the Seneca process plant are two Terex MPS MC320 modular cone crusher stations – with a TGS320 secondary and TG320 tertiary respectively, explains Du Plooy. The TG-Series cone crusher is known for its flexibility and high production rates and is perfectly suited to application requirements at this mine. Equipped with the Terex MPS AIC control system with touch screen, both cone crushers were set up to ensure high reduction and maximise capacity to over 650 tph.
“With a wide range of crusher liner options and adjustable throws, the Terex MPS TG-Series cone crusher can be set up
to meet customer requirements and optimise feed rate performance, feed size and product quality required,” says Du Plooy.
In addition, two Terex MPS triple shaft horizontal screens are deployed. With high screening efficiencies in a small footprint, the screens deliver maximum product yield. The 1 800 mm x 6 100 mm Terex MPS TSV6203 triple deck final product screen is running at about 1 000 tph in closed circuit with the Terex MPS TG320 cone crusher. Triple shaft technology allows for high G-forces, adjustable throw angles, adjustable amplitudes, adjustable input speeds and the screen box angle itself can also be adjusted, which allows for the set up of screens to precisely meet the production and product requirements.
Feeding the plant is a Terex MPS JW55 single toggle jaw crusher, mounted on a custom-built crushing station with a double deck, grizzly pre-screen to remove any contaminated or clay material from the ROM feed stockpile. Measuring 1 400 mm wide, the Terex MPS JW55 single toggle jaw crusher produces a suitable product for the TGS320 secondary cone crusher.
Terex MPS not only boasts the TG-series cone crushers, but also the TC Series range, which is known for its ability to produce high quality product with a high fines content and quality shape for road stone product. The Terex MVP boasts the best hold-down force in the industry. The Terex MPS MVP series cone crusher can produce quality products and fines content in the toughest of crushing applications.
From the smallest of projects to the largest with complex crushing, screening, washing and even DMS requirements, Terex MPS and its extensive Africa dealer network, can provide and support Mineral Processing Systems to its customer, meeting their specific requirements no matter how remote or where in Africa.
Willem du Plooy explains, “At the end of the day we need to listen to what our customers’ needs are, they do know their customers and site requirements from a business perspective and match that with the correct processing equipment for the application, product and capacity needs, but most of all, delivery of what we promised and even more. We provide solutions not just crushing and screening equipment.”
“For this project we chose Terex MPS crushing and screening equipment. With the OEM’s proven track record, coupled with Seneca’s knowledge and experience with Terex crushers and screens in iron ore, we were comfortable with our choice and have not been disappointed,” says Nettmann.
“The plant delivers in excess of 550 tph average production and with our preventative maintenance schedules and wear management strategies, we achieve in excess of 140 000 tpm. We are in discussions with our client to increase the monthly minimum production requirement to 160 000 tpm.”
Looking ahead, Nettmann confirms that the company is in the design phase of a crushing and screening plant for two separate contracts, one in the mining space and another in the coal industry. Leveraging close collaboration with OEMs such as Terex MPS, he is confident that growth will continue for Seneca in an industry that places a premium value on productivity and efficiency.
Seneca’s processes are always targeted at the best cost solution, enabled by a strong understanding of the resource, its geology and minerology, and thus able to maximise on the resource value and the extension of the life of mine for the benefit of clients.
“Crushing and screening equipment is both capex and opex intensive. As such, Seneca, throughout its 12 years of existence, has always realised the value of building strong relationships with OEMs in the industry. Leveraging these strong relations with our OEMs and suppliers, we can manage our costs as efficiently as possible in order to remain competitive in the market, while offering a superior, professional, efficient and guaranteed service to our growing client base,” says Nettmann.
By working closely with OEMs, Seneca strives to equip its growing fleet of equipment with the very latest in crushing and screening technology. The relationship with OEMs is of paramount significance in retaining good product support, managing spares holding and availability, managing of wear parts and wear rates, as well as consideration and maximisation of capex and opex. a
A fleet of LiuGong wheel loaders is proving its mettle on a taxing 24/7 aggregates operation where downtime is out of the question. A proactive maintenance strategy is not only helping to maximise uptime, but also to extend equipment life. To provide context, two of the eight LiuGong CLG856H wheel loaders currently on site have already clocked 30 000 hours and counting.
Munesu Shoko was recently on site and filed this report for Quarrying Africa.
Afrigrit, an Emalahleni, Mpumalanga family-owned business, was established in 1996, initially specialising in the production of sandblasting sand from slag, a constant by-product of the steel industry. The slag is sourced from Ferrometals, one of the largest individual ferrochrome plants in the world which produces charge chrome for steel markets.
Over the years, the company has expanded its scope, to include the recovery of chrome from slag and eventually production of aggregates for a range of industries, including road construction, brick manufacturers and
concrete producers, among others.
Metallurgical oxide slag has stone-like properties and thus its major applications are in the civil engineering field. Due to the high cost of natural stone and the rising emphasis on sustainable construction, the construction industry is using these aggregates as a viable alternative.
To execute its mandate, Afrigrit has erected a processing plant at the Ferrometals dump to process the slag. Part of the plant recovers the rich material, which is transported to Afrigrit’s premises to produce sandblasting sand. The other part of the plant recovers chrome for Ferrometals and also produces varied sizes of
17-t
Two
Having bought its first LiuGong wheel loader in 2008, Afrigrit has over the years standardised its loading fleet with the LiuGong CLG856H machines, with a total of eight currently running in its fleet
Of note is that two of the current eight loaders have already clocked in excess of 30 000 hours, translating into about 4 300 hours a year or 360 hours a month
This feat speaks directly not only to the durability and reliability of the machines, but more importantly to the stringent 250-hour service intervals that have been maintained since their acquisition in 2017
Parts availability and good response times from Burgers Equipment & Spares are key to the success of Afrigrit’s operations
aggregates for the local market.
Speaking to Quarrying Africa , Marius Pick, logistics manager at Afrigrit, says maintaining optimal equipment availability is key to ensuring continuity in achieving production targets. Therefore, reliability and consistently available equipment is non-negotiable. This is exactly what a fleet of LiuGong wheel loaders, supplied and supported by Burgers Equipment & Spares, is offering at this 24/7 operation.
We run a 24/7 operation throughout the year. Uptime is especially important for us and our decision to standardise our fleet with LiuGong wheel loaders has paid dividends. Apart from high availability, both the capital and running costs are competitive, which is very much in line with our expectations.
Afgririt bought its first LiuGong wheel loader in 2008, and never looked back. In fact, the company has standardised its loading fleet with the LiuGong CLG856H model, with a total of eight currently running in its fleet. The decision, says Pick, has paid dividends, with these machines providing availability of about 80%, working around the clock.
“We run a 24/7 operation throughout the year, even during the December period. Uptime is especially important for us and the decision to standardise our fleet with LiuGong wheel loaders has paid dividends. In addition to 80% availability, both the capital and running costs are competitive, which is very much in line with our expectations,” says Pick.
Of note is that two of the current eight loaders have already clocked in excess of 30 000 hours, translating into about 4 300 hours a year or 360 hours a month. This feat speaks directly not only to the durability and reliability of the machines, but more importantly to the stringent 250-hour service intervals that has been maintained since their acquisition in 2017. The two machines are expected to continue operating reliably well into the future.
“Being proactive in our heavy equipment maintenance schedule has helped prevent expensive downtime and to extend equipment life. Our machines are serviced by the dealer, Burgers Equipment & Spares, at OEMrecommended maintenance intervals of 250 hours. This means that each machine is serviced at least once a month,” says Pick. “In addition to routine maintenance, the machines are subjected to a 2 000-hour major service.”
The 250-hour routine maintenance also allows Burgers technicians to spot potential problems before they escalate into major failures. Corrective actions are taken immediately to ensure reliability and performance of machines.
While the stringent service strategy is keeping machines in great working shape, Pick points out that this is only achievable when parts availability and dealer support are non-issues. This is where Burgers Equipment & Spares has excelled, even going the extra mile to meet Afrigrit’s needs.
“Parts availability and good response times from Burgers Equipment & Spares are key to the success of our operations. Burgers is very much on top of its game. We have never had issues regarding spares availability since we have dealt with them,” he says. To further ensure maximum equipment uptime, Afgririt also keeps critical spares on site, such as water pumps and prop shafts, among others.
One of the major factors in the decision to purchase LiuGong loaders was the price point, says Pick. He says that the LiuGong offering is competitively priced, yet boasts a range of tried and tested components that make it a competitive offering in arduous mining conditions.
The LiuGong CLG856H wheel loader is a 17-tonne (t) machine with a 5-t lifting capacity and comes standard with a 3 m³ bucket. The machine is equipped with a ROPS & FOPS cab, ZF transmission and ZF limited slip differentials.
“The powertrain, for example, comprises a 6LTAA9.3L Cummins engine, Kawasaki pumps and a ZF drivetrain. These are not foreign to us; these are components we understand and trust, and are well equipped to service them,” says Pick.
With efficiency in mind, the LiuGong wheel loader is powered by the latest fuel-efficient Cummins engine, delivering a net power rating of 160 kW (215 hp) at 2 000 rpm. For operational efficiency, the engine uses a precise, high pressure common-rail fuel injection system, turbo charger (VGT) and air- to-air intercooler, along with electronic engine controls to deliver optimal performance in every cycle in every shift.
A special focus on the well-being of operators not only ensures high productivity, but also equipment longevity. “Operator welfare is particularly important to us. We always ensure that air conditioners are in good working condition,” says Pick. The LiuGong CLG856H comes with an advanced climate control system with eight all-round vents, five selection modes and 6 kW of cooling capacity, creating the perfect working environment whatever the weather.
Afgririt’s machines are equipped with mine-spec LED lights, which produce stronger light, and the lifetime is much longer than the standard halogen. This comes in handy for a 24/7 application where downtime related to any light-changing exercise is unacceptable. a
Installations conducted worldwide have left customers satisfied with their newfound ability to control loads moved and drive down costs per tonne, achieving an increase in production of 15% –purely through payload monitoring
Trysome has seen a marked uptick in interest in its VEI load-weighing products.
Having entered into a partnership to bring digital solutions to the local mining and transportation industries, Trysome Auto Electrical Engineering and Dynamic Weighing Systems (DWS) have successfully rolled out and commissioned a wide range of VEI payload management systems across industries. Case studies show that customers are experiencing an increase in production efficiency, reduced maintenance costs, and safety improvements. By
Munesu Shoko.Five years ago, Trysome and DWS collaborated to distribute and support VEI onboard weighing and payload management systems in the local mining, quarrying, and transportation industries. Speaking to Quarrying Africa , Johan Momberg, Category Manager: Real-time Monitoring at Trysome, says that
Five years ago, Trysome and Dynamic Weighing Systems collaborated to distribute and support VEI onboard weighing and payload management systems in the local mining, quarrying, and transportation industries
Leveraging Trysome’s substantial branch network in South Africa and subsidiaries in Botswana, Mozambique, and Zambia, the partnership has recorded significant success with a number of systems installed across a wide range of industries
Several flagship quarries such as Midmar Crushers and Blue Rock quarries in KwaZuluNatal now VEI products exclusively
Quarry clients are becoming less tolerant of vehicles turning numerous times within the plant and are demanding that trucks be loaded correctly from the onset
96%
99-100%
VEI, the global maker of no-load-cells weighing technology, offers accuracies of between 99% and 100% on properly calibrated machinery
On one site, the same system has been operational for 12 years with no repairs or replacement of parts needed. At Marble Hall, the system improved the throughput of the quarry by 96% by reducing returns from the weighbridge by 99%.
“There has been a marked uptick in interest in load-weighing products,” he says. “Amid a constrained business environment and resultant shrinking margins, quarries continue to feel the pinch. With a return on investment (ROI) of about four to six months, depending on how busy the quarry is, payload management systems are rapidly becoming a no-brainer.”
Quarry clients, he adds, are also becoming less tolerant of vehicles turning numerous times within the plant and are demanding that trucks be loaded correctly from the onset. Digitalisation is also becoming more important, with having an electronic record of hours worked and operator performance, amongst others, becoming crucial within this environment.
with the emphasis and focus on real-time monitoring, the collaboration can be rolled out to almost every industry where loading and load-and-haul operations take place.
“At Trysome, we thrive in delivering optimal uptime, which is the ultimate goal of every business. What is imperative, however, is that maximum productivity is not achieved to the detriment of safety or loss of life,” says Momberg. “Our technical depth gives us the competitive edge, ranging from being autoelectrical journeymen and OEM fitment specialists to internationally accredited safety, weighing, and kinetic mesh network installation specialists.”
Leveraging Trysome’s substantial branch network in South Africa and subsidiaries in Botswana, Mozambique, and Zambia, the partnership has recorded significant success with a number of systems installed across a wide range of industries, offering customers the benefit of consistent accuracy and ultimately increased profits.
The uptake of the VEI systems, says Momberg, has been good in the local industry. “Several flagship quarries such as Midmar Crushers and Blue Rock quarries in KwaZulu-Natal now use our products exclusively. They have been impressed by the reliability and robustness of the units,” says Momberg.
Available is a full range of VEI weigh solutions for a wide range of sectors, including but not limited to the mining and quarrying industry. Agricultural, recycling, and timber industries are also serviced with application-specific solutions. Other target applications include scrap metal and refuse loading and monitoring. “Essentially, if it has a hydraulic piston or a suspension, we can tailor a weighing solution,” declares Momberg.
VEI, the global maker of no-load-cells weighing technology, offers accuracies of between 99% and 100% on properly calibrated machinery. The technology has been licensed as “legal for trade” in Europe and many other countries and is being processed in South Africa.
Commenting on some flagship offerings, Momberg cites the HelperX, which provides connectivity options to suit every site-specific requirement. Wi-Fi or LTE connectivity is available, allowing one to analyse data in real-time. The device incorporates all necessary components without needing any external black boxes, which are often damaged by harsh working and climate conditions.
“More importantly, all our products are upgradeable to the next level via a simple software patch. This means that as the client’s needs change,
the software system can be updated without having to replace an entire head unit. This is a unique offering in the industry,” he says.
The VEI systems come with a three-year warranty, which is said to be rare in the high-use, harsh environments in which the machinery operates. “For example, we have machines operating at Letseng at 3 000 m above sea level and units deployed 2 900 m underground,” says Momberg.
“The accuracy of the units and their ease of use means that loading efficiency is greatly increased, especially in the thirdworld environment in which we operate. They can be coupled to VEI’s range of high-speed thermal printers, memory sticks, and either RF, Wi-Fi, or cellular modems,” he adds.
The latter allows for real-time tracking of the client’s production, often important in remote locations where an office may not be present. VEI also provides powerful, multi-user payload management software which quickly puts information at managers’ fingertips. VEI onboard scale solutions can streamline and improve loading efficiency, leading to rapid ROI and increased profitability.
Payload monitoring saves money, reasons Momberg. Haulage costs, he says, are a headache for many mining and quarrying companies who seek the maximum payload and productivity per haul, at the lowest cost per tonne moved. A four-pass load might be less expensive operationally than say, a seven-pass load. So, if available, a larger truck should be used.
With onboard weighing solutions and payload monitoring, VEI can drive down haulage costs with a range of high-tech devices mounted onboard the loader, haulage truck, or excavator. Payload monitoring is delivered by easy-to-use software applications
wirelessly linked to the onboard device, or by connecting the VEI device with any make of onboard fleet monitoring system.
“Installations conducted worldwide across Russia, India, Colombia, South Africa, and Brazil for example, have left customers satisfied with their newfound ability to control loads moved and drive down costs per tonne, achieving an increase in production of 15% –purely through payload monitoring,” says Momberg.
The systems enable them to efficiently plan equipment size, quantity, and availability and improve maintenance procedures and operator training. With reports of overloads being reduced to zero, the result is more efficient equipment usage.
VEI’s new generation Millennium5 and HelperX take into consideration cabin space ergonomics, visibility, ease of use, and connectivity while reducing the amount of componentry. In-cab space is optimised by innovative design and applied electronics, with a sophisticated CPU controller board to work with any other peripheral board. The casing design has gone through various stages of prototyping and test application on the machines. The protective upper casing surrounding the display significantly cuts glare.
The optional printer casing, incorporated on the bottom of the device, requires minimum space and the vertically fitted unit allows excellent visibility from the machine when attached to the cabin pillar, enabling ease of manoeuvrability, without being obstructive.
The components of the display have been chosen from existing components and the screen provides clear visibility in bright sunlight. VEI’s extensive technological expertise has developed a powerful CPU to drive the detailed display graphics and, coupled with the user-friendly interface that assists in accurate navigation, the device has found popularity amongst customers and operators. This is especially important in third-world countries where the cell-phone-type keyboard is intuitive to use. a
As surface mines explore ways to run profitable operations, continuous surface miners offer an alternative mining approach that can benefit an array of commodity areas. Speaking to Quarrying Africa, Frank Beerthuis, MD of Vermeer Equipment Suppliers, says that, just like any other mainstream commodity areas, the quarrying sector, and, in particular, the limestone/cement industry, can largely benefit from this technology. By Munesu Shoko.
The surface mining industry is an important contributor to the African economy. That the industry needs to explore newer technologies to maximise its potential is no overstatement. This is particularly the case in small-scale surface mining operations such as limestone quarries, where continuous surface mining technology has played a key role throughout the world in increasing production and reducing operational costs.
Traditional surface mining methods, says Beerthuis, have left untold tonnes of minerals underground, simply because there was no
way to get to the detritus safely and efficiently. The Vermeer innovative Terrain Leveler surface excavation machines can work where explosives can’t, with top-down cutting that lets miners reach valuable deposits and get the most product out of the ground as possible.
“Other than the safety benefits stemming from the elimination of drill and blast (no explosives needed), less noise, reduction of dust, no nitrogen emissions into commodities and into ground water, there are significant operational efficiency benefits to the surface excavation machines as a consequence of the smaller and more uniform particle size distribution (PSD),” explains Beerthuis.
20%
Vermeer continuous surface miners come with fully hydrostatic drives, thus doing away with traditional mechanical transmissions. The result is minimum energy loss between the cutter and the drum, thus increasing machine performance by up to 20% compared with mechanically driven counterparts
66%
By deploying a Vermeer surface miner, Letseng Diamond Mine exceeded the 66% effective productivity it had planned for its overall works programme
The Vermeer T1255IIITL’s mining drum has a cutting width of 3,7 m
The single-sided direct drive drum on the T1255III allows the operator to cut an 80° high wall to provide slope stability that is desirable in high-wall mining applications.
These benefits, he adds, include higher payloads on haul trucks (thus reducing haulage expense), reduced processing costs (mined product can bypass primary crushers for further processing), and higher throughput, through secondary crushers and processing lines.
Vermeer continuous surface miners come with fully hydrostatic drives, thus doing away with traditional mechanical transmissions. The result is minimum energy loss between the cutter and the drum, thus increasing machine performance by up to 20% compared with mechanically driven counterparts.
The Vermeer T1255III surface excavation machine (SEM), for example, delivers enhanced production and efficiency. It has a fully hydrostatic motor mounted to the side of the cutting head, which provides direct drive power and delivers more horsepower to the cutting drum, resulting in enhanced efficiency when working in soft, medium or hard rock conditions.
The single-sided direct drive drum on the T1255III allows the operator to cut an 80° high wall to provide slope stability that is desirable in high-wall mining applications. The SmartTEC control software displays the status of critical elements of machine performance, alerting the operator to recommended control adjustment.
In a recent success story, Vermeer surface mining technology addressed the need for safer, more environment-friendly, effective and efficient mining
Traditional surface mining methods have left untold tonnes of minerals underground, simply because there was no way to get to the detritus safely and efficiently
The Vermeer innovative Terrain Leveler surface excavation machines can work where explosives can’t, with top-down cutting that lets miners reach valuable deposits and get the most product out of the ground as possible
In a recent success story, Vermeer surface mining technology addressed the need for safer, more environment-friendly, effective and efficient mining for Letseng Diamond Mine in Lesotho
The surface miner has given the mine the opportunity to effectively mine from the pit and produce a product that is similar to those two steps of drill and blast and primary crushing
for Letseng Diamond Mine in Lesotho. The mine conducted a trial to find an alternative technology that could result in reduced damage to the diamonds and ultimately recover higher value from them.
Vermeer Equipment Suppliers’ T1255IIITL surface miner was used as part of a series of trials.
According to Jaco Houman, senior manager Technical and Projects at Gem Diamonds Technical Services, using a surface miner showed potential against the conventional drill and blast process which was followed by a primary crusher.
“The surface miner gives us the opportunity to
Suppliers’ T1255IIITL surface miner was recently trialled at Lesteng Diamond Mine in Lesotho.
effectively mine from the pit and produce a product that is similar to those two steps of drill and blast and primary crushing. From that perspective we are able to have a process that is potentially more costeffective, and a process that is more complementary to the rest of our diamond processing flowsheet,” he says.
The trial took place from June 2022 to September 2022 and had the following outcomes: environmentally friendly; replacement of primary drill and blast as well as secondary pecking activities; more cost-effective on a cost-per-tonne basis; more stable processing due to greater consistency in product size distribution to the plant and more productivity and efficiency.
The trial period initially started on a single shift basis and then moved to a 24-hour basis. “The effective productivity that we had planned for in our overall works programme for the production period was around 66% effective in cutting time,” Houman says. “We exceeded that target with the deployment of the surface miner. He adds that the instantaneous cutting rate was within the expected target. “Overall productivity in the trial was certainly in line with our expectations.”
Although the machine was a new one on site, no mechanical issues were experienced, and production was not affected. “The machine performed very well mechanically,” says Houman. He adds that short-term challenges that did arise were easy to overcome, such as the inclusion of a dust suppression or dust extraction system in the full production unit.
The minor challenges encountered during the trial provided key considerations which could lead to increased efficiency when considered. They include mining/cutting through different geological domains with varying hardness, working on existing benches and in close proximity to bench crests, and mine planning, among others. “If you are putting this into a mine where you are starting from scratch, I think it is a
lot easier putting a surface miner in there and reaping success earlier,” says Houman.
The Vermeer T1255IIITL Single Side Direct Drive (SSDD) is powered by a CAT C18 Tier 3 diesel engine. The mining drum on the machine has a cutting width of 3,7 m. Beerthuis explains that the unique features of the machine include the full hydrostatic direct drive of the mining drum which maximises the energy that is being transferred to the ground engaging tools (GETs) and thereby increasing productivity. Another feature is the elimination of wear items in the driveline such as chains and sprockets, allowing for a significant reduction of operational expenditure.
“Another unique feature is the tilt function of the mining drum. This patented design feature allows for automated three-dimensional cutting of a smooth mining floor while cutting direction, cutting depth and slope angle are being controlled through GPS automation,” explains Beerthuis.
The machine also has a down-cut design which reduces the re-grind of mined rock. “As a result, clients will experience a more uniform PSD, reduced wear of GETs and higher production rates.”
Following three days of classroom training and a week of equipment operation with an instructor, the operators were deemed fit to run the equipment on their own. Vermeer Equipment Suppliers was on site during the full period of the trial. Beerthuis explains that on two-week rotations, senior service technicians from Vermeer carried out the preventative maintenance of the machine and replacement of any worn items during the full period of the trial.
This trial showed that using the Vermeer T1255IIITL surface miner is a viable option for an open pit diamond mine. “The key factor for us is potentially generating more revenue per tonne and the fact that we further mitigate the risk of potential damage to our diamonds,” concludes Houman. a
From being a hands-on, artisanal industry founded on mechanical engineering and chemical processes, the quarrying sector has become a hi-tech industry that uses vast amounts of data and data insights to enhance efficiencies and improve safety.
Gathering this data is the province of the Internet of Things (IoT), where smart devices, cameras, wearable health tech, satellites, drones, sensors, and onboard computers are used to track vehicles, material, staff and equipment. All of this technology enables insights that can enhance safety, boost production, and ensure legal compliance.
Globally, telematics and data technology are taking root in the quarrying sector. For operations to be viable, teams must move earth as efficiently as possible by monitoring fleets constantly, designing routes and usage rosters, conducting training, and managing performance output in order to ensure the most effective deployment of staff, equipment, and fleets in real time.
Quarries are dangerous environments, and numerous stringent Department of Mineral Resources and Energy (DMRE) health-and-safety regulations are specifically geared to protecting employees against collisions with trackless mobile machines. This has made some level of collisionavoidance systems mandatory for all vehicles in the surface mining and quarrying space.
Netstar’s Collision Avoidance Proximity System (CAPS) uses sensors that can trigger automatic slowing down (level 8) and stopping and/or avoidance (level 9) when pedestrians, vehicles and machinery enter a certain proximity. The system also collects real-time data,
interprets it, and then audibly and visually warns vehicle operators of a potential collision (level 7 intervention). Human error accounts for 90% of driving accidents, often due to fatigue. Wearable IoT technology, such as health monitor watches and AI-based driver-fatigue monitoring systems, addresses this. Wearable tech protects drivers and other users of mine roads, warning of possible worker fatigue and providing alerts before it becomes a safety risk.
Through IoT data-gathering technology and the use of artificial intelligence (AI), quarry owners can manage risk and avoid unnecessary downtime due to misuse or repairs. AI can also support predictive maintenance, proactively notifying quarry and fleet managers when equipment is faulty, due for service, or needs to be replaced.
Increased safety also means fewer events and lower investigations and claims costs. Health monitors provide data that the back office can view on a cloudbased software platform. Quarry managers can then review this to plan better routes, traffic, and employeeequipment interactions.
The use of smart devices and other IoT technology is growing at a rapid rate, and quarry operations across the world cannot afford to ignore the benefits of using the latest technology to extract as much performance data as possible.
It is not only about making operations safer, but about building a more efficient, more effective, and more profitable business. a
A wheel loader is an essential piece of equipment at a quarry site, and the significance of choosing the right machine for the job cannot be stressed enough. Quarrying Africa unpacks some of the key factors to consider when picking the correct wheel loader for the operation.
By Munesu Shoko.Wheel loaders are considered essential pieces of equipment for many quarry operators as they fulfil various important functions, perhaps the most common being stockpiling material and loading haul vehicles. They are also the ideal machine to feed crushers with material and for housekeeping under conveyor belts and around the worksite in general, says Petrie du Toit, sales product manager at Bell Equipment.
“It is important for quarry operators to choose the right machine to promote efficiency in the quarry. It should be a reliable workhorse that offers the lowest cost per tonne solution. It needs to be able to comfortably handle the production targets and other tasks it will be used for,” says Du Toit. “If the wheel loader is too small, its work pressures could cause undue stress that could negatively affect the machine’s longevity. At the same time, a machine that is too large will not be economical to run.”
Warren Alexander, branch manager, Isando, at CASE Construction Equipment SA, shares the same view, pointing out that a wheel loader plays a vital role in quarry operations due to its versatility and efficiency in handling a wide range of tasks. It serves as a reliable workhorse for material handling, such as loading and transporting various types of aggregate, gravel and other materials.
“The right wheel loader can significantly enhance productivity, reduce downtime and optimise overall quarry operations. Choosing the right machine is crucial as it ensures optimal performance,
Bench height and bench width play a key role in any face loading machine selection. If the face is too high, then it becomes too dangerous to work under the face with a wheel loader, and an alternative loading tool will have to be selected. For safety, the face height should not exceed the maximum lift height of the wheel loader bucket.
8,7l
R110-million
Bell
durability and cost-effectiveness, leading to improved operational efficiency and profitability for quarry operators,” says Alexander.
Gary Martin, senior market professional for heavy construction and quarry industries, Caterpillar, says quarries are large areas with typically two or more different faces being worked at any given time. Unlike the excavator, the wheel loader has the mobility to move easily from face to face to load the trucks and requires no clean-up machine to follow it.
“The fragmentation of the material needs to be correct for the wheel loader to be productive, and in these conditions it is unbeatable. For the midsized wheel loaders, mobility is key when working around the screening plants in operations such as load and carry, as well as for carrying the material from the conveyor stockpile to the main stockpile,” says Martin.
Given the importance of the wheel loader on a quarry site, what are some of the key factors to consider when choosing the right machine for one’s operations?
CASE’s Alexander says that the machine’s size and bucket capacity should match the specific requirements of the quarry site, considering the volume and weight of materials to be handled.
Power and performance, adds Alexander, are also crucial parameters to consider. “Evaluate the engine power, hydraulic system efficiency and lifting capabilities to ensure the wheel loader can handle the demanding tasks efficiently,” he says.
Durability and reliability are also non-negotiables, says Alexander. Quarry environments are rugged, so it is important to choose a wheel loader built with robust construction and high-quality components
that can withstand the harsh conditions.
Given the high local fuel prices, fuel efficiency is an important factor. Quarry operators, says Alexander, should therefore choose machines that offer optimum fuel efficiency to minimise operating costs and reduce their environmental impact.
The correct wheel loader for an operation should also tick the operator comfort and safety box. This should consider features such as an ergonomic cab design, intuitive controls and advanced safety systems to enhance operator comfort, productivity and overall site safety.
“After-sales support is crucial for maintaining the optimal performance and uptime of the wheel loader. It is important to partner with a construction equipment company that offers comprehensive after-sales support. This includes timely maintenance, spare parts availability, technical assistance and
The right wheel loader can significantly enhance productivity, reduce downtime and optimise overall quarry operations. Choosing the right machine is crucial as it ensures optimal performance, durability and cost-effectiveness, leading to improved operational efficiency and profitability for quarry operators.
WarrenAlexander, branch manager, Isando, at CASE Construction Equipment SA A Cat 992 large wheel loader loading a Cat 777G rigid dump truck.
training programmes. It also provides peace of mind knowing that the company is committed to supporting the customer throughout the lifecycle of the equipment,” says Alexander.
According to Martin, one of main factors when selecting the right loader for either working at the face or at the processing plant, is ensuring that it meets the expected production targets. That has a direct impact on correctly sizing the loader.
“Bench height and bench width play a key role in any face loading machine selection,” says Martin. “If the face is too high, then it becomes too dangerous to work under the face with a wheel loader, and an alternative loading tool will have to be selected. For safety, the face height should not exceed the maximum lift height of the wheel loader bucket. The wheel loader needs room to manoeuvre when loading the truck, so bench width and an open area are very important for a productive wheel loader operation.”
Du Toit maintains that productivity or tonnes per hour required from the machine is a key factor. Other factors include the underfoot conditions that the machine will operate in and the SG (specific gravity) of the material/s to be loaded or stockpiled.
“The underfoot conditions will impact the tyre and axle choice, for example, diff lock or limited slip. Typically, wheel loaders are fitted with L3 or L5 radial tyres in quarrying applications. The SG will determine the type of bucket the machine should be fitted with. Safety features that protect the operator and the machine, as well as operator comfort are other important considerations since a comfortable operator is a productive one,” says Du Toit.
country. Currently, Bell holds over R110-million worth of JCB spare parts, including new, used and reman parts,” he says.
The benefits of choosing the right machine for the right application abound. Caterpillar’s Martin says the right machine ensures high production in a truck loading application and a low cost per tonne moved, with no supporting machine needed.
CASE’s Alexander tells Quarrying Africa that the benefits of choosing the right wheel loader for quarry operations are manifold. Among them is increased productivity – a well-matched wheel loader can handle more materials efficiently, reducing loading and transportation time as well as improving overall productivity.
“The right machine for the job also results in cost savings. Optimal machine selection leads to improved fuel efficiency, reduced maintenance costs and decreased downtime, resulting in significant cost savings over time,” he says. “In addition, the right wheel loader offers advanced safety features, reducing the risk of accidents and injuries, thus prioritising the well-being of operators and site personnel.”
By selecting a wheel loader built to withstand the rigours of quarry operations, Alexander points out that quarry operators can benefit from extended machine life and reduced replacement and repair expenses.
According to Bell’s Du Toit, choosing the right wheel loader can increase productivity in a quarry by enabling faster cycle times and improved material handling, which leads to increased production. “A high-quality machine, designed for the rigorous demands of quarrying applications will provide durability and longevity. At the same time, a wheel loader suited to the specific application and terrain will minimise downtime and maximise utilisation,” says Du Toit.
The new Cat 950 and 962 Next Generation wheel loaders feature standard simple-touse technologies that boost operator efficiencies, provide consistent bucket-fill factors and increase productivity by up to 10% over the previous models
Selecting the right wheel loader, adds Du Toit, can simplify maintenance and improve serviceability, reducing downtime for repairs and maintenance. In addition, the rightsized machine with a modern, fuel-efficient drivetrain can save on expensive fuel costs.
While most machines in the market have very similar attributes, adds Du Toit, the most important factor to keep the quarry running is the support network. Having a support centre close to the quarry with fully trained technical experts and parts stock to ensure quick turnaround is crucial.
“Bell prides itself on offering sound support to our customers through continuous training of new and old technicians and by holding high levels of parts stock both at branches around the country and at our Global Logistics Centre that can deliver within 24 hours, to anywhere in the
To ensure that quarries meet their production targets, CASE loaders are designed with a strong focus on efficiency, reliability and comfort, with several features that speak to these important parameters. Key among them is the engine, which was developed and manufactured by CASE’s award-winning sister company, FPT Industrial, which produces over 500 000 engines per year and powers world record winners.
“The in-house design leverages advanced technologies developed for commercial vehicles and agriculture, and introduces specific tailored solutions for off-road applications,” says Alexander. “Our engine technology is so reliable that it is trusted by the French Sea Rescue service for their boats: what better guarantee could you wish for?”
CASE’s 1021F wheel loader’s 8,7l cursor engine ensures better engine control at all runs per minute. The multiple
injection technology ensures optimum combustion control, while the 1 600-bar injection delivers best-in-class torque performance. The combustion is optimised for maximum efficiency, at high temperatures using 100% fresh, cool air, as the air intake is separated from the exhaust. The turbocharged engine with an air-to-air intercooler relies on a three-step injection technology to maximise responsiveness and fuel efficiency with reduced engine noise and vibrations.
With reliability in mind, the heavy-duty axles of the CASE wheel loader are tough, big and easy to service thanks to the three-piece housing design. Wet multiple disc brakes are located in each wheel hub. The heavy-duty axles are engineered to support L5 or solid tyres for very abrasive environments. Solid tyres can be factory-fitted.
The axle differential locks reduce tyre spin and provide 2030% lower tyre wear, improving tractional force and bucket penetration, reducing loading cycle times and improving fuel efficiency and tonnes per hour.
The unique design of the CASE cooling cube, with five radiators mounted to form a cube instead of overlapping, ensures a constant flow of fresh and clean air from the sides and from the top, to maintain constant fluid temperatures. The cube structure provides easy access to radiators for a more effective cleaning and serviceability; additional cleaning can also be easily done manually, with separate access to each radiator.
Bell Equipment has three JCB wheel loaders in its range that are ideally suited to quarrying applications, namely the 15-t JCB 436ZX, the 18-t JCB 455ZX and the 24-t JCB 467 ZX, all of which have high power-to-weight ratios for class-leading climbing and stockpiling capability. The Z-bar loader design supports productivity by providing great penetration into the pile, high breakout forces, good rollback angles and faster digging times.
The JCB 467 ZX has a smooth ride suspension system that reduces material spillage and structural stresses while delivering superior operator comfort.
“The three models all have ergonomic ROPS/FOPS-certified cabs with air conditioning for comfort and joystick controls for ease of operation. All come standard with JCB’s LiveLink telematics solution, which monitors machine hours, fuel consumption, servicing intervals and fault codes, among other parameters, from a laptop or mobile device,” says Du Toit.
Various buckets are available, including options suitable for high SG and abrasive materials. Bell also retrofits strobe lights, fire extinguishers and stop blocks on its JCB wheel loaders as required.
The Widecore cooling pack keeps the machine operating at an optimum temperature by allowing large debris to pass through, while the reversible fans are ideal for working in dusty quarry environments. In addition, ground-level servicing promotes ease of maintenance.
JCB wheel loaders carry a 12-month/unlimited hours warranty and finance options are available through JCB Finance.
Caterpillar’s medium wheel loader offering ranges from the Cat 950 to the Cat 982. The ease-of-use features
integrated on the next generation platform improve performance and efficiency for expert or non-expert operators.
Cat Large wheel loaders (986K to 995) set the standard for optimised productivity, minimising downtime, enhancing operator comfort and protecting people on jobsites through key safety.
The large Cat wheel loaders come with Operator Coaching so operators can be trained on the go or as required, without the intervention of a trainer, so increasing efficiencies on the go or when needed.
Large Cat wheel loaders also include assist features that partially take the control of the complex operations during the dig phase (Rimpull modulation, lift command) and help close the gap between new and experienced operators and help increase the efficiency levels for all.
All Cat Performance series medium wheel loaders today come with a factory installed payload system fitted as standard to help increase loading accuracy. Our Standard models have the option to have a similar Cat payload system fitted at the Cat dealership, giving the same capabilities. For the larger wheel loaders, a factory payload system is also available. a
It is important for quarry operators to choose the right machine to promote efficiency in the quarry. It should be a reliable workhorse that offers the lowest cost per tonne solution. It needs to be able to comfortably handle the production targets and other tasks it will be used for.
With increasing infrastructure developments on the horizon comes a growing demand for raw materials, beginning at the core with mines and quarries throughout the world. By Steve
Fair, Haver & Boecker Niagara Tyler Engineered Media manager.Making sure equipment is running efficiently is a top priority, but it is also important to evaluate your screen media to ensure you are using the best tools for the job. Here are four things to keep in mind:
Consider the types of materials going through the vibrating screen. Factors such as material size, weight and abrasiveness all come into play during the selection process. Materials with top sizes as large as 250 mm require more durable screen media to handle heavy impact. Abrasive material, such as granite, typically requires screen media with higher wearability whereas higher open area plays a larger factor for softer material, such as limestone.
Next, look at your screen deck. There are three phases material goes through in the screening process, from layered to basic to sharp. Equipping the screen deck with a single type of media overlooks the fact that each of these phases has very different needs.
By recognising and analysing each phase, you can customise your vibrating screen’s deck with various types of screen media for the best combination of wear life and open area.
Using the wrong screen media can lead to increased maintenance costs and downtime. Start by looking in the boneyard at the discarded screen media. Problem areas, such as broken wires, wear areas, pegging or blinding, are often a sign of carry-over or contamination, resulting in unwanted material in the screened material pile, as well as the added cost of rescreening.
Engineered screen media used alone or blended with other options such as woven wire cloth or self-cleaning screens can provide the ultimate combination of wear life and open area.
Polyurethane screen media offer extended wear life. The polyurethane is poured open cast, offering up to two times the wear life of injection-moulded screen media. It is often ideal for handling impact at the feed end during the layered phase of screening. Hybrid screens are an option that combines woven wire with polyurethane to provide a higher open area than polyurethane, while extending wear life four to seven times beyond woven wire – often a good solution on that difficult-to-access second deck. a