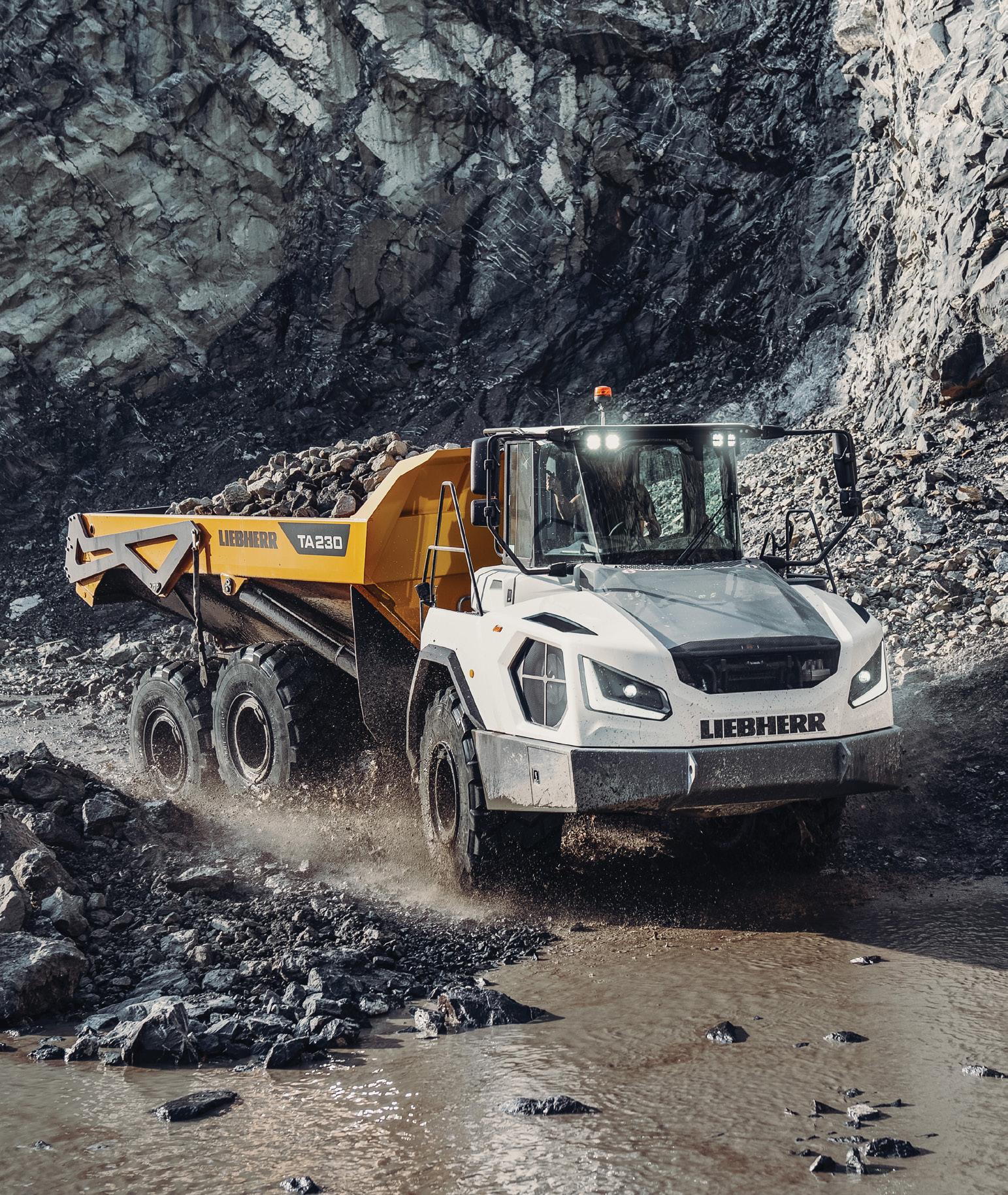
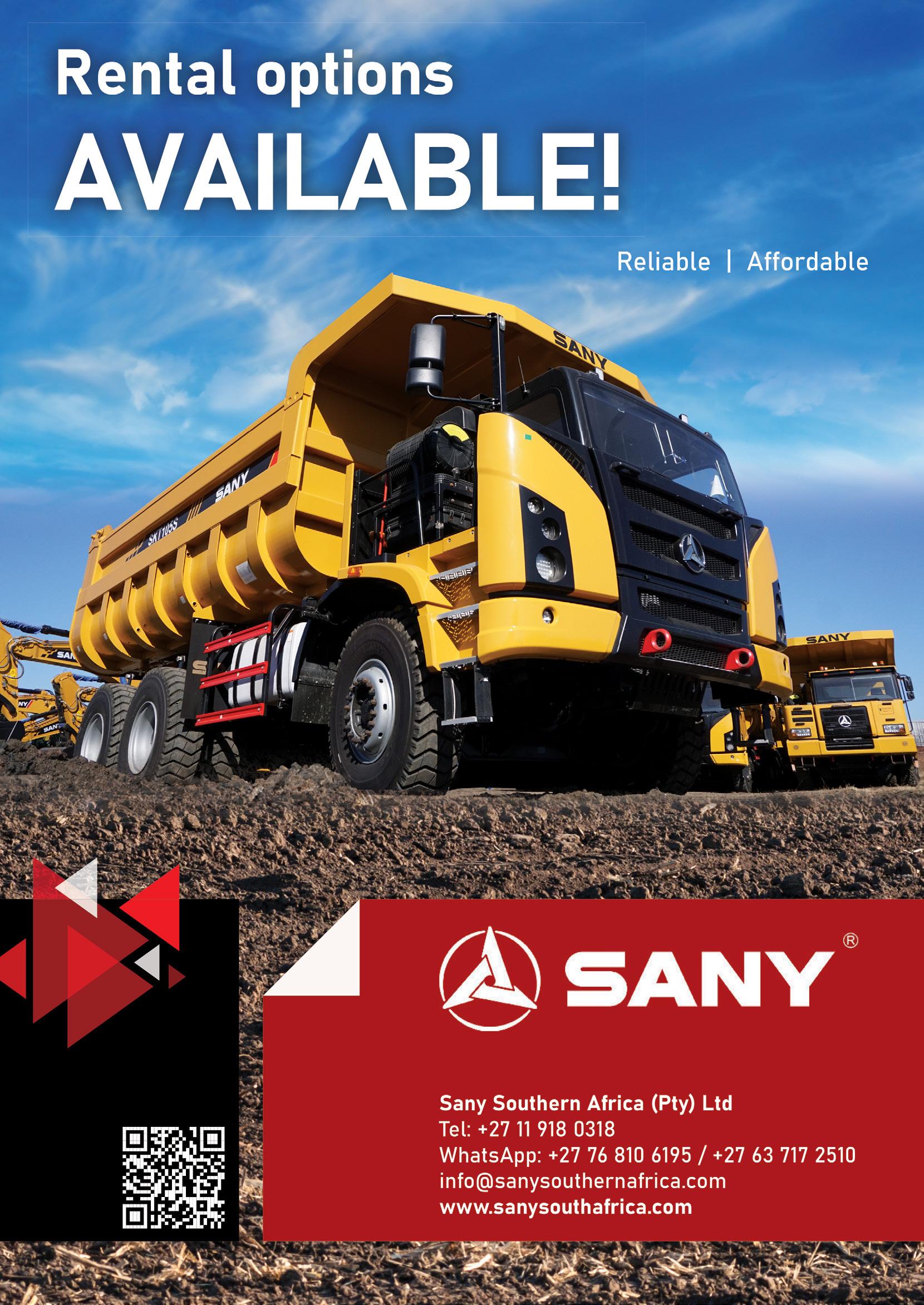
WHILE quarrying is undoubtedly an economically essential part of the modern economy, the adverse environmental impacts associated with this important industry cannot be ignored. As regulators and communities continue to demand that extractive industries place more emphasis on environmental issues, this might be the perfect time for quarries to start taking active steps on their environmental protection agenda.
Many quarries by nature are located close to communities. The existence of quarries near or even within the boundaries of urban centres is the cause of many environmental problems, despite their significant contribution to urban development. Given this proximity to communities, sustainability improvement therefore is no longer simply an option, but an imperative, for quarrying companies.Quarrying can have a negative impact on surrounding environments, but in recent years, efforts have been made to make this industry more sustainable. At the forefront of this environmental revolution stands surface mining industry association, ASPASA, with its Environmental Audit designed to champion sustainable mining practices.
The long-running environmental auditing programme has recently been revamped to become an invaluable tool to assist mines and quarries to meet their Environmental and Social Governance (ESG) targets. The association believes that environmental compliance and ESG at large have become important components of the modern business environment and should therefore be high on the agenda of every organisation in the industry.
As local quarries seek to play their part in the circular economy, I have also seen a growing appetite for recycling. As you will see in this edition of Quarrying Africa, we visit AfriSam’s Jukskei Quarry, where recycling, especially of readymix concrete waste, continues to grow in importance. This not only addresses environmental issues, but also allows the quarry to meet the growing demand for lower-spec material at a more economical cost of production.
While in the past there was some resistance from construction customers to using recycled aggregates, now the buyer barely bats an eyelid at the quality of the material. Due to affordability, the construction contracting fraternity is also buying down on quality of aggregates, which bodes well for recycled material.
Water is another sensitive environmental aspect that requires careful management at quarries. The world’s most essential commodity is, without doubt, water. Yet despite its critical significance to the global economy and to human life, water has for centuries been taken for granted, with the issue of water scarcity remaining largely neglected. As long ago as 2011, a report by the EIRIS Foundation noted that under a business-as-usual scenario at the time, water demand would outstrip supply by 40% by 2030. This had the potential to put US$63-trillion of global GDP at risk by 2050.
In an interview with the Mineral Policy Centre, renowned mining expert Dr James Lyon once said, “Water has been called mining’s most common casualty”. Mines and quarries use water for mineral processing, including comminution practices, classification by screening and hydrocyclones, dust suppression, slurry transport and employees’ needs, among others. One of the greatest challenges facing operations is the development and management of water resources. It is therefore essential that every single operation prioritises the most efficient control and management of valuable water resources in order to maximise proficient ‘use and reuse’ of every drop of water used in mining site operations. This would also minimise long-term environmental liabilities which could result from the mismanagement of water resources.Itis,however, encouraging to see that industries’ attitude towards water management has, in the past few years, improved significantly. Industry-led initiatives related to water risks have begun to gain momentum. Water plays an essential role in most mining and extractive processes, and responsible water management is a critical business case for the quarrying and mining sector at large. a
Publishing Munesu Shoko
Sub Glynnis Koch
Admin: Linda T. Chisi Kudzo Mzire Maputire
Web Thina Bhebhe
Quarrying Africa is the information hub for the sub-Saharan African quarrying sector. It is a valued reference tool positioned as a must-read for the broader spectrum of the aggregates value chain, from quarry operators and aggregate retailers, to concrete and cement producers, mining contractors, aggregate haulage companies and the supply chain at large.
Quarrying Africa, published by DueNorth Media Africa, makes constant effort to ensure that content is accurate before publication. The views expressed in the articles reflect the source(s) opinions and are not necessarily the views of the publisher and editor.
The opinions, beliefs and viewpoints expressed by the various thought leaders and contributors do not necessarily reflect the opinions, beliefs and viewpoints of the Quarrying Africa team.
Quarrying Africa prides itself on the educational content published via www.quarryingafrica.com and in Quarrying Africa magazine in print. We believe knowledge is power, which is why we strive to cover topics that affect the quarrying value chain at large.
Email: munesu@quarryingafrica.com
Cell: +27 (0)73 052 4335
Looking beyond the economic squeeze in which South Africa’s construction sector finds itself, there is still a need to inspire young people to join the industry. AfriSam’s Avi Bhoora highlights the strategic importance of the construction supply chain, which offers exciting careers for those with vision and a strong work ethic.
Having spent a very busy 40-year career in the construction business, Bhoora is concerned by the negative attitude of many young people towards this field of work.
“I do worry about the number of young South Africans who seem to have taken a conscious decision not to enter an industry like ours,” says Bhoora. “There appears to be a strong preference for an ‘office job’ rather than the often difficult conditions of working on a construction site, for instance.”
Such attitudes make it difficult for companies like AfriSam to compete for the best talent among school leavers or college graduates, he says. It is therefore vital for the industry to change this view among potential new entrants, and to highlight the potential for meaningful and rewarding careers.
“It might not be obvious to many people how vital our work is to every citizen’s quality of life,” he says. “If we could better convey the importance of what we do, it could inspire more youth to consider the opportunities and get involved.”
This might need a concerted rebranding of the industry’s image, to emphasise the many avenues that are open to new entrants. His concern is that construction related careers have become a ‘blind spot’ to many young people, blocking any
possibility of exploring these options.
“I have spent my whole life in construction, and as I approach retirement, I am inclined to reflect on how the sector is going to renew itself – so that it can continue delivering into the future,” he says.
An important starting point is for the public to appreciate more clearly that every city, road, bridge, dam, school, hospital or other engineered structure comes from the work of skilled contractors and their supply chain.
“Materials like aggregate must be extracted from the earth to make the concrete for this infrastructure; it is difficult work, but essential for progress,” says Bhoora. “If the youth can be inspired by these messages, perhaps we can start changing the value they place on the occupations this field offers.” a
Surface mining industry association, ASPASA, has voiced its concerns at the lack of industry buy-in to fight the scourge of crime at operations.
The association says it has been disappointed by the lack of support for the stellar work being done by mining industry organisations in collaboration with the National Intelligence Coordinating Committee (NICOC) to identify and stamp out crime.
While formal letters were circulated to mines and quarries, only two
responses were received. “We receive reports almost daily of crimes being committed, yet when we ask the industry for information to prevent these crimes, we get no response.
“Too often in our society we become indifferent, and it is only until we are directly affected that we start to respond. The idea behind the NICOC initiative is to gather information and intelligence to proactively prevent crime and nab the masterminds that seem to operate with impunity behind the scenes.” a
Even as South Africa’s construction sector struggles through difficult cycles of low profitability and declining capacity, it needs responsible and sustainable companies to maintain momentum.
After almost nine decades in business, AfriSam’s legacy has been to demonstrate the value of good corporate citizenship, according to the company’s sales and marketing executive Richard Tomes. AfriSam began its journey as Anglovaal Portland Cement Company in 1934, with a cement plant in Roodepoort.
“The time since then has seen many changes and we are proud to have grown stronger, with our customers confirming that we are still their preferred choice,” says Tomes. “Even with the depressed state of the construction sector, our focus on quality and sustainability means that we can continue to serve the market to world class standards.”
Tomes argues that the extensive investment in cement plants, readymix facilities and quarries over the years laid the groundwork for AfriSam’s considerable contribution to the country’s infrastructure. As Anglo Alpha, it had become a fully verticallyintegrated construction materials business in the 1990s through the strategic incorporation of aggregate producer Hippo Quarries and readymix company Pioneer Concrete. When the country re-entered the international community post-democracy, the company was acquired by the multinational Holcim group, further augmenting its access to world-class expertise and best practice. a
ASPASA industry participation in fighting crime Avi Bhoora, AfriSam Construction Materials Executive.Women in mining and quarrying still face numerous challenges in the workplace and at home. With that in mind, surface mining industry association, ASPASA, continues to address these issues as they arise and is encouraging its members to establish platforms that make it easier for employees to voice their concerns andDuringexperiences.theassociation’s latest Gender Justice – Women in Mining Workshop, ASPASA chairperson of the workshop, Letisha van den Berg, explained that setting up platforms to address gender issues should be regarded as a positive step towards improving the workplace.
“It is also important to note that the initiatives should not be run in isolation of management, as psychological safety
doesn’t mean a person only feels safe, but rather that they should feel safe to voice an opinion.”
Guest speaker, Marinda Hawthorn of Leadership 365, underlined the fact that almost daily women across the industry report incidents of physical assault, verbal abuse, being asked to trade sexual favours for employment or other benefits or being placed in more junior positions with less pay than their male counterparts.
Not surprisingly many of these women can be left traumatised or insecure and programs like the company’s Women’s Renaissance Life Transforming Coaching provides women with the tools to overcome past trauma and to empower themselves and transcend the status quo and fulfil their actual worth. a
Afrimat, the JSE-listed open pit mining company providing industrial minerals, bulk commodities and construction materials, has released the findings of the Afrimat Construction Index (ACI) for the second quarter of 2022. The ACI is a composite index of the level of activity within the building and construction sectors compiled by economist Dr Roelof Botha on behalf of Afrimat.
According to Dr Botha, the construction sector managed to increase the value added to the economy by an impressive 4,1% in real terms, compared with the previous quarter. “This is despite a series of unfortunate events putting additional pressure on levels of economic activity during the second quarter, including the KwaZulu-Natal floods and lengthy strikes at major mining companies, combined with general economic factors such as weaker prices for precious metals and iron ore, high fuel costs, extensive loadshedding, inefficiencies in rail transport and increasing inflation.”
He adds that the ACI also recorded a modest 2,4% increase over the first quarter of the year, saying that one of the most encouraging features of the second quarter performance was the positive trend for both the volume and the value of building material sales, which may be regarded as leading indicators for future construction activity.
“The best-performing indicator, however, was the value of buildings completed in the metros and larger municipalities, with a 21% year-on-year rate of increase. The increase in employment in construction during the second quarter was also encouraging and will hopefully continue as government starts embarking on more public/private partnerships as part of the promised infrastructure drive.”
Afrimat’s CEO, Andries van Heerden, acknowledges that while South Africa is not an easy environment to operate in at the moment, given loadshedding, increasing input costs
The construction sector managed to increase the value added to the economy by an impressive 4,1% in real terms in Q2, compared with the previous quarter.
such as diesel and what was a poor performance from Transnet, Afrimat’s strength lies in its ability to be nimble, underpinned by the diversification of products, commodities, location and foreign exchange income streams, all of which enable the Group to overcome and work through these operational detractors.
“Although there has been an uptick in the performance indicators of this edition of the ACI, we can attest to the fact that construction and infrastructure activity remains low. Thankfully, the Construction Materials segment continues to benefit from being located in strategic places across the country, efficiency drives, and product diversification. Similarly, in the Industrial Minerals segment, sector diversity, especially in support of the agricultural sector, is proving to be a solid support to the segment,” says Van Heerden. a
Letisha van den Berg, chairperson of ASPASA’s Gender Justice – Women in Mining Workshop.To help nurture young talent in the quarrying industry and mould them into future leaders, Pilot Crushtec International recently hosted the Institute of Quarrying Southern Africa’s (IQSA) Young Members Network for a facilities tour and presentations by subject matter experts.
Held on 25 July 2022, the technical meeting started with a tour of workshops and facilities, before the Pilot Crushtec team of experts shared their knowledge on a range of topics, including process design, design engineering for crushing and screening, as well as sand production using vertical shaft impact crushers, among others.
To attract young people in the quarrying industry, IQSA established a Young Members Network to create awareness of the global network opportunities between the Institute of Quarrying member countries and other stakeholders such as original equipment manufacturers (OEMs).
Speaking to Quarrying Africa, IQSA chairman Jeremy Hunter-Smith says the recent technical meeting at Pilot Crushtec was aimed at giving young members the much-needed exposure
to the technical aspects of crushing and screening.“Oftencompanies are in their own
islands. These regional and technical meetings give young members an opportunity to network and learn more about the various aspects of the industry. This is important in preparing for future leadership roles in our industry. I am encouraged to see many great young people coming through the pipeline. With the right mentors, they will be able
ASPASA’s long-running environmental auditing programme has been revamped to become an invaluable tool to assist mines and quarries in meeting their Environmental and Social Governance (ESG) targets.
Surface mining industry association ASPASA advises that environmental compliance and ESG have become important components of the modern business environment and are high on the agenda of organisations locally and internationally.
Sustainable mining is critical to the continued existence of the small-scale mining industry whether it be aggregates, sand, dimension stone, clay, salt or any other commodity that is mined in the sector. The audits comprise online and physical audits, both of which are designed to establish the level of compliance and to assist the various operations and managers to improve their knowledge of environmental issues and the compliance requirements.
Managers do not always have the luxury of an environmental specialist readily available on site and for this reason it is necessary for them to have a good working knowledge of compliance requirements in order for them to be able to deal with any of the day-to-day issues that may arise at their operations.
to develop and take the industry to the next level,” says Hunter-Smith.
Francois Marais, director of sales and marketing at Pilot Crushtec, says the company has for the past 25 years supported IQSA’s programmes. “It is our way of giving back to the industry,” says Marais. “With the experience we have in our ranks, we are able to pass on the necessary knowledge that can help mould these young members into industry leaders of tomorrow.” a
Environmental compliance has become an important component of the modern business environment. [Pic courtesy of AfriSam]
The credibility of ASPASA is dependent on its member companies being above reproach. That’s why the association encourages all its members to participate and invite nonmember companies to find out about the programmes and audits that are provided. a
IQSA’s Young Members Network visiting Pilot Crushtec International. Pilot Crushtec International has for the past 25 years supported IQSA’s programmes.Following its world premiere last year, the much-awaited, award-winning Liebherr TA 230 Litronic articulated dump truck (ADT) has finally arrived in southern Africa, marking Liebherr-Africa’s debut in the highly contested ADT market.
By Munesu Shoko
There is a new player in the local ADT market, following Liebherr-Africa’s official launch of the Liebherr TA 230 Litronic at an open day held on 24 June 2022. The new 30-tonne (t) class articulated hauler fits the bill for quarrying, coal mining and large infrastructure projects, confirms Tendayi Kudumba, General Manager: Earthmov ing, at DespitLiebherr-Africa.ethefiercecompetition in the local ADT market, Kudumba is confident that the Liebherr TA 230 Litronic will immediately challenge for a sizeable share of the market. At the time of the launch, Liebherr-Africa had brought in the first five units. A prominent contractor operating in Zimbabwe had just taken delivery of the first three units, while the remaining two had been deployed at a
For the very first time, Liebherr-Africa will offer an articulated dump truck to its local customers the official launch of Liebherr
A major talking point is the new machine concept, which has been developed especially for challenging off-road applications
The newly designed articulated swivel joint creates sound off-road capability; it allows independent movement of the front and rear ends, thus ensuring maximum manoeuvrability
The front of the trough – designed for the effective transport of a 28-tonne payload – is straight and the sills are low so that loading with a wheel loader, for example, is easily possible across the entire length
reclamation project at a mine in South Africa. Local customers have shown immense interest in the new ADT, says Kudumba, with pre-orders dating as far back as last year soon after its global launch. The Liebherr TA 230 Litronic made headlines after winning the coveted Red Dot Award: Product Design 2021 for its high design quality just a few months after the machine was first unveiled to the public. The award is widely considered to be one of the most important international accolades in the field of design.
A major talking point is the new machine concept, which has been developed especially for challenging off-road applications. Modern designs in the front-end area, says Kudumba, create maximum ground clearance for greater off-road performance.
The newly designed articulated swivel joint creates sound off-road capability; it allows independent movement of the front and rear ends, thus ensuring maximum manoeuvrability. The positive-locking swivel joint with tapered roller bearing is perfect for the shear stresses associated with tough underfoot conditions, while it also withstands maximum loads and provides optimal force distribution.
The front and rear axles of the machine are
The new 30-tonne class articulated hauler fits the bill for coal mining and large infrastructure Liebherr 230 Litronic won the coveted Red Dot Award: Product Design 2021 for high design quality after the machine unveiled to the publicsecured using sturdy A-rods at the articulated swivel joint and at the rear end. On front, the truck uses hydro-pneumatic suspension for maximum comfort, which is key to the smooth driving. The shock absorbers at the articulated swivel joint and the position of the separate and oscillating A-rods of the rear axles at the rear end, provide maximum ground clearance.
When developing the new ADT, Liebherr also paid particular attention to the performance of the machine. Powered by a 6-cylinder Liebherr engine with a 12-l displacement, producing 265 kW of power, the TA 230 Litronic is driven by an automatic 8-speed powershift transmission which ensures optimal force distribution.
The new Liebherr dump truck impresses with great driving performance and massive pulling force, even in the most difficult ground conditions and on challenging gradients. “A combination of balanced weight distribution, permanent 6x6 all-wheel drive, solid, flexible mounting and large bank angle as well as the machine’s high ground clearance, enable the TA 230 Litronic to deliver unparalleled performance on uneven terrain,” says Kudumba.
The actively controlled inter-axle differential locks mean that the Liebherr TA 230 has automatic traction control. As soon as one axle experiences wheelspin, it is decelerated, and the traction is intelligently redistributed to the other axles. In addition to maximum forward drive, this reduces the power requirement and therefore translates into lower fuel consumption.
Efficiency is further enhanced by the smart gear selection, which enables the machine to adjust automatically to its current speed and load to ensure optimum torque and fuel consumption at all times. The machine therefore automatically reduces its fuel consumption per
tonne of transported material.
In addition to hydraulic multi-disc brakes on all axles, the TA 230 comes with a zero-wear upstream braking system. This consists of an engine brake and a hydrodynamic primary retarder. The continuous operation brake is activated automatically as soon as the operator steps on the brake pedal. It is highly controllable, protects the components and provides additional safety due to the significant deceleration on gradients.
As quarrying and mining companies work to rebuild profitability, improving productivity is high on the agenda. With that in mind, Liebherr focused its efforts on maximum productivity when designing the TA 230 Litronic.
The optimised trough ensures that more material can be moved in a short time. The front of the trough – designed for the effective transport of a 28-t payload – is straight and the sills are low so that loading with a wheel loader, for example, is easily possible across the entire length.
A standard Liebherr weighing system shows the current payload during loading on the display in the operator’s cab, helping eliminate guesswork in loadout processes. An optional loading light on both sides at the back of the operator’s cab shows the loading level outdoors.
In order to accelerate the release of the material during unloading, the inner edges of the new trough are tapered. The two tipping cylinders at the side give the TA 230 Litronic high tipping pressure. The load can be tipped against the slope easily and quickly.
“During transportation, the long chute at the end of the trough ensures minimal material loss. The trough volume can be increased with the optional tailgate,” explains Kudumba. “Thanks to the large opening width, tipping of large and
Thebulky transported material is easily possible. Even with the tailgate the overall width of the TA 230 Litronic is still below 3 m, which allows the machine to be easily and quickly transported on a lowbed truck.”
In a world where data is king, the TA 230 comes with LIDAT, Liebherr’s data transfer and location system, allowing fleet operators to manage, monitor and control their fleets efficiently. All the main machine parameters can be viewed at any time using a preferred web browser.
Apart from productivity and efficiency, the development of the TA 230 Litronic focused on operator comfort and safety. During the design of the machine, Liebherr paid specific attention to visibility, which is a critical aspect in boosting operator productivity and safety. In fact, the machine’s workstation was one of the key design aspects central to the Red Dot Award win.
“The newly developed driver’s cab features panoramic windows without any obstructing struts, and a short, inclined bonnet, giving the machine driver an optimal view of the driving, working and articulated joint area of the machine,” says Kudumba. “At the same time, the spaciously designed workstation impresses with its sophisticated interior equipment, including numerous stowage compartments, storage options, a mobile phone bracket, USB charging ports and an air-sprung driver’s seat as standard for maximum comfort.”
The operating concept of the TA 230 is well thought-out and impresses with its automobilelike feel. The logically and artfully arranged control elements and the numerous assistance systems such as hill-start assist, speed-retention assist, or automatic traction control, support the operator in everyday work.
Additional driving comfort is provided by the
speed-dependent steering, which allows light and precise manoeuvring at low speeds and sensitive steering at high speeds. In addition, fewer steering corrections are needed when cornering.Thenew lighting concept features LED headlights, ensuring improved visibility and safety, both for the machine operator and for everyone in the vicinity of the machine. LED dipped-beam headlamps with integrated high beam illuminate the haul road and the extra powerful, optional LED headlights on the front of the cab illuminate the entire working area. The L-shaped multifunction light with animated light functions is said to be a homage to the Liebherr brand name – a novelty in the construction machine sector.
Ease of machine maintenance is a key factor in today’s buying decisions. With that in mind, the TA 230 employs a simplified maintenance concept, explains Kudumba. Thanks to the clever sensor technology, the machine automatically performs the daily check itself. The machine runs through an inspection catalogue at the start, where levels of engine oil, coolant and the central lubrication system, for example, are checked for the nominal state. Any deviations are shown on the display in the operator’s cab. As a result, the daily setup times can be reduced, costs can be saved, and the durability of the components can be extended.Themachine also comes with an electrohydraulic bonnet and an access ladder with nonslip steps, thus providing mechanics with safe, clear access to the entire engine compartment. All the service points are clearly visible as well as easy to reach, and all maintenance work can be conducted conveniently from a standing position. a
The likeitsimpressesthought-outTAconceptoperatingofthe230iswellandwithautomobile-handling.
CEO of Danoher Group.
Given that
Since
The
The
Danoher
Danoher’s focus during the first six months has been firmly on Kgale quarry, which currently constitutes the bulk of the commercial quarrying business in Botswana
Danoher has invested in a new 350 tph plant at Gaboronebased Kgale quarry
With its roots firmly planted in Botswana, the Danoher Group has a strong focus on growing its commercial quarrying and contracting businesses in the country. The recent acquisition of PPC Aggregates Botswana’s three quarries and a further big-ticket capital investment in Gaborone-based Kgale Quarry, is testament to the company’s commitment to its Botswana business, CEO Scott Danoher tells Quarrying Africa’s Munesu Shoko.
Since its inception, the Danoher Group (Danoher) has established itself as a household name in the southern African quarrying/min ing industry, providing a full bas ket of contracting services from drilling and blasting t o crushing and screening (mobile andAlthoughstatic). the company has grown its footprint across the whole southern African region over the past few years, Danoher retains
a strong presence in Botswana, the country where the business was founded in 2011. Having previously contracted for PPC, Danoher took control of the cement giant’s commercial quarry assets in October 2021, following the conclusion of the sales agreement between the two companies. The deal entailed the acquisition of three quarries – Kgale, Mokolodi and“GivenFrancistown.thatquarrying is our core business, it was therefore a natural fit for us to take over PPC’s aggregates business. The deal reinforces our commitment to Botswana – both from a commercial quarrying and a contracting perspective,” explains Scott.
Following the conclusion of the transaction, Danoher says all three operations needed a bit of attention. Consequently, the company has stopped using the fixed plant at the Francistown quarry and deployed a mobile crushing and screening train to process material. The Mokolodi operation has always been operated using Danoher’s contracted mobiles, and this will continue for the foreseeable future.
At Kgale, Danoher has also decided to start on ‘a clean slate’ by erecting a completely new plant. At the time of writing, construction of the new plant was almost halfway complete. The tertiary section was already up and running, with the front-end (primary section) still under construction. The total capital investment in the 350 tonnes per hour plant, as well as the associated mobile equipment, is about
Danoher has invested in a new processing plant at Kgale Quarry in Gaborone, Botswana.BWP50-million (about R70-million).
“Our focus during the first six months has been firmly on Kgale quarry, which currently constitutes the bulk of our commercial quarrying business in Botswana. We have decided to run our mobiles at Francistown because the current market conditions do not justify a big capital investment in a new fixed plant,” says Scott.
“We remain flexible; however, we will change our approach if market conditions change. At the moment it makes business sense to run mobiles. Another big advantage is that whenever we have crushing contracts in the area, mobiles can be easily moved between projects and our commercial operation. We have recently completed a contracting project in Francistown and are in the process of producing stock to have material on the ground for the next six months,” he adds.
With not many government infrastructure projects coming to market, the aggregates industry has had to contend with constrained market conditions in recent years. Francistown is particularly quiet at the moment, with very few active projects in the area.
While the Gaborone market, where Kgale quarry is a key player, also has no significant infrastructure projects underway, Scott says there is some activity to keep the quarry ticking. The brick and block manufacturing sector is currently the biggest market driver for Kgale, followed by readymix concrete producers involved in massive water related projects as well as providing services to the commercial and residential housing market.
“Botswana is currently driving its water infrastructure projects, with pipelines and reservoirs under construction to service water-stressed areas within the Greater Gaborone corridor. We are also supplying a few road projects as part of the
ongoing upgrading of Gaborone roads’ network infrastructure project. One of the notable projects underway is the construction of three interchanges along the Western Bypass intended to ease the flow of traffic,” says Scott. “However, with two years still to go before the next elections, we believe that we will start seeing significant infrastructure projects being rolled out.”
Looking ahead, Scott says the company’s focus is on maximising customer satisfaction through reliable supply of quality products. “Since taking over, we have adopted a customer-centric approach to the business. We have a strong commercial sales team that takes every customer seriously, irrespective of whether they buy 10 000 t or 300 000 t of material per month. Every single customer is treated the same, all the way from the driver to the business owner. It’s these small interventions that make a huge difference,” concludes Scott. a
A train of mobile crushing inDanoher’sataggregatestodeployedequipmentscreeningandproduceoneofsitesBotswana. The newly-built plant at Kgale Quarry.An aerial view of AfriSam Jukskei Quarry.
As part of AfriSam’s response to a lowvolume market, Jukskei Quarry has adopted a demand-driven strategy
Recycling, especially of readymix concrete waste, continues to grow in importance at Jukskei. This not only addresses environmental issues, but also allows the quarry to meet the growing demand for lower-spec material at a lower cost of production
Key to the ability to produce some of the new material specs is the flexibility of both the plant and personnel
In its quest to blast for safety, the quarry has tweaked a number of blast parameters such as burden, spacing, powder factor and stemming, among others
“In such a highly developed area, the ability to adapt is crucial. About four years ago, we started visiting all our neighbours to acquaint them with the activities of the quarry. We also have quarterly community meetings to keep them informed of some of the developments and changes at our operation.”Mohamed Docrat, works manager at AfriSam Jukskei
“
110
With some of the buildings as close as just over 110 m away from the quarry, it is therefore
Given the extraordinary shift in the aggregates market, adaptability and flexibility are key to riding the winds of change. This was the overarching reflection from Quarrying’s Africa’s recent visit to AfriSam Jukskei Quarry, where several initiatives have established resilience in the face of a rapidly changing business landscape. By Munesu Shoko.
Having enjoyed a thriving construction materials market for the better part of the last decade, AfriSam’s Jukskei Quarry has had to contend with a drastic dip in demand in recent years. When first established in the late 1950s, the quarry was considered to be far flung from any meaningful construction development at the time.
However, due to rapid urbanisation in its vicinity in recent years, anchored by the R16billion Waterfall City mixed-use development, Jukskei became one of AfriSam’s busiest quarries between 2015 and 2018. Apart from the thriving commercial development activity in the area, the quarry was at one point the principal construction materials supplier for major infrastructure projects in the area, including highways and bridges.
Mohamed Docrat, works manager at AfriSam Jukskei, says the market has changed significantly in the past four years. While the post-Covid volumes have started picking up slightly, they are still nowhere near the 20152018 levels.
One of the major trends, notes Docrat, is the noticeable increase in small and medium enterprises (SMEs) being contracted to execute government infrastructure projects.
TheTo provide context, a 40-km road project that would traditionally be undertaken by a single large contractor is now allocated to about four emerging contractors.
One of the emerging contractors’ operating models is to shop around for “cheaper” construction materials, resulting in what Docrat calls a “price war” in the market. Due to affordability, emerging contractors are also ‘buying down’ on quality of aggregates. In fact, this trend is prevalent across both public and private construction projects.
“The dynamics of the market have changed completely,” says Docrat. “High-spec material such as G1 is now being replaced with lowerspec products like G2. This approach is not only driven by contractors, but the concept is even being embraced by developers and consultants. While we have adapted to these new realities, the challenge is that our production processes for either high or lower spec material remain the same, which impacts our bottom line.”
Another major trend, notes Docrat, is the emergence of resellers. Previously, he says, resellers were largely suppliers of sand, but in the past two years, they have spread their wings to other areas of the market.
“This is traditionally common in Cape Town, but in the past two years we have seen it taking root in our market as well. The emergence of resellers has to some extent resulted in the price war. Armed with large fleets of trucks, they are able to shop around and influence prices. The rules of the game have therefore changed significantly. We believe it’s a buyer’s market at the moment, with customers dictating the price of aggregates,” says Docrat.
In such an everchanging market, Docrat believes it is imperative to grasp the new trends, understand their implications and act accordingly. Adaptability and flexibility, he says, are the most essential skills to respond to such
an evolving and cut-throat trading environment.
As part of the company’s response to a lowvolume market, Jukskei has adopted a demanddriven strategy, where production is based – as far as possible – on actual customer orders rather than market projections. In fact, this strategy has been adopted across all AfriSam operations.
In addition, recycling, especially of readymix concrete waste, continues to grow in importance at Jukskei. This not only addresses environmental issues, but also allows the quarry to meet the growing demand for lower-spec material at a lower cost of production.
“As part of our contribution to the circular economy, we take all the waste material, mainly return concrete from the readymix trucks, and stockpile it to dry. We then employ a hydraulic hammer to break down some of the big blocks of concrete into smaller, manageable sizes that can be fed into the processing plant. The recycled concrete is blended with some of the virgin material to produce lower-spec subbase products such as G5, G6 and G7,” says Docrat.
Key to the ability to produce some of the new material specs is the flexibility of both the plant and personnel. “We have good flexibility at our Plant B, which allows us to switch between products. For example, within two days, we can change over to either aggregate or G-mode, which is crucial, especially in the current market conditions,” says Docrat.
Key to realising the flexibility of the plant is a team of experienced personnel willing to adapt to meeting the ever changing market requirements, says Zielas du Preez, regional manager Gauteng and Cape Operations at AfriSam.
“One of the key trends in the market is the constant request for new material sizes, especially specific sand grading envelopes with reduced fines on the -75 micron envelope to assist clients with water demands on mix designs. Thanks to our experienced team, we have successfully managed to trial different types of sands without incurring huge costs. The flexibility
As part of trucks.theconcreterecyclesAfriSameconomy,tocontributionitsthecircularJukskeireturnfromreadymixof our plants, matched by that of our team on the ground, gives us the edge to address any special requests,” says Du Preez.
Contractor partners working on site have also heeded the call for agility and flexible operation, adds Du Preez. “Despite all the changes we experience in our business, our service providers have been understanding and accommodative. We have, for example, agreed to remodel our contract with the load and haul contractor to accommodate our demand-driven production model. The contractor is willing to make changes to the fleet at short notice,” he says.
The same flexible and cooperative approach has been adopted by the drill and blast contractor. “With all the uncertainty in the market, sizes and frequency of blasts vary significantly. We have therefore remodelled our contracts to be able to navigate the market uncertainty. Our contractor partners have been supportive and have assisted us in finding our way through the ups and downs of the market,” says Du Preez.
While the rapid urbanisation in the Midrand area has previously boosted the quarry’s business, it has also meant that the operation now finds itself bordered by communities – a business park to the north and a residential area to the south. With some of the buildings as close as just over 100 m away, it is therefore important to forge strong community relations.
“In such a highly developed area, the ability to adapt is crucial,” says Docrat. “About four years ago, we started visiting all our neighbours to acquaint them with the activities of the quarry. We also have quarterly community meetings to keep them informed of some of the developments and changes at our operation,” saysTheDocrat.closest development is only 110 m away from the northern face of the quarry. Here, AfriSam has entered into a special agreement to finalise mining on this face and change the mining footprint. The mining team has already
sterilised three benches, with the fourth one almost complete.
For an operation that is close to communities, blasting poses major challenges. “We have over the years adapted our blasting practices. In our quest to blast for safety, we have tweaked a number of parameters such as burden, spacing, powder factor, timing design and stemming, among others,” says Docrat.
To further improve its blasting practices, Jukskei was one of the early adopters of the Varistem stemming plugs in the local quarrying industry. Docrat says the most important factor in achieving a safe and efficient blast is to contain energy in the hole, and good stemming creates more resistance at the top of the blast hole and directs the energy to where it’s needed – the rock mass.
Docrat says the Varistem stemming plugs have proven to be key to good blast outcomes. On the health and safety side, there has been a reduction in flyrock, noise and airblast. From a productivity point of view, there has been a marked improvement in fragmentation.
Apart from these blast improvements, three fixed vibration recorders have been installed at some of the closest neighbours’ premises to monitor the impact of blasts. Two portable recorders are also planted at different locations to monitor issues such as airblast and ground vibrations. These are monitored by a third party, Blast Analysis Africa, which provides an independent report every month.
A strong focus on safety is paying dividends, with no lost time injury (LTI) recorded in the past four years, confirms Docrat.
“Safety is one of the main drivers on site. Our Competence Based Safety programme is at the heart of our safety achievements. This is an employee-driven safety programme, where they are allowed to take ownership of safety on site. Good safety behaviour is recognised, while unsafe behaviour is quickly addressed through coaching,” concludes Docrat. a
One of the key trends in the market is the constant request for new material sizes, reducedenvelopesgradingspecificespeciallysandwithfines.
The first Anaconda machine in southern Africa, a DF518 scalping screen, has been deployed to process old gold dumps in Gauteng, South Africa.
South African crushing contractor, Crushing & Screening Systems (CSS), has taken delivery of the first ever Anaconda machine in southern Africa, a DF518 scalping screen. Deployed to process old gold dumps in the Benoni area of Gauteng, the machine is performing beyond the client’s expectations. Munesu Shoko was recently on site and filed this report for Quarrying Africa.
Having signed the exclusive distributorship for the full Anaconda Equipment range of crushing, screening, feeding, washing and conveying equipment in southern Africa last year, Vermeer Equipment Suppliers has sold its first machine – a DF518 scalping screen.
The large-sized scalping screen has been deployed at one of CSS’s latest contracts,
where the company is processing about 5-million tonnes (t) of old gold dumps. The company has been on site since February this year, and, by end of June, had already processed nearly 1-million t.
At the time of Quarrying Africa’s visit in July, the Anaconda DF518 scalping screen had been on site for three weeks, during which time it had already processed in excess of 50 000 t, proving to be a hit with the team on site.
Equipped with a steel apron feeder, the machine is punching well above its 375 tph capacity, taking up to 400 tph of feed
The DF518 is extremely easy to commission and can be up and running within 20 minutes of arrival on site
Speaking to Quarrying Africa , Stan Fischer, MD and owner of CSS, says the machine has performed beyond expectations. To provide context, the original equipment manufacturer (OEM) states that the screener has the ability to cope with tonnages of up to 375 tonnes per hour (tph), depending on application and feeding method. Equipped with a steel apron feeder, CSS’s machine is punching well above this OEM capacity, taking up to 400 tph of feed.“We are feeding anything between fines and 400 mm size material. We screen out oversize to extract -20 mm material, which is transported to the client’s processing plant, located off site, for further processing. The DF518 is proving to be a powerful scalping screen to run; equipped with a high energy 5,49 m x 1,52 m screen box, the machine is processing in excess of 400 tph,” says Fischer.
Due to its high capacity, the production team on site had to change the bucket size on the feeding excavator from the standard 1,5 m³ to 3 m³ to allow the loading tool to keep up with the screen’s capacity.
Within three weeks of commissioning, the machine had already processed in excess of 50 000 t
Crushing & Screening Systems has taken delivery of the first ever Anaconda machine in southern Africa – a DF518 scalping screen
The large-sized scalping screen has been deployed at one of CSS’s latest contracts, where the company is processing about 5-million tonnes (t) of old gold dumps
Taking in excess of 400 tph feed material, the DF518 is delivering more than the expected 375 Vermeertph
Equipment Suppliers’ aftermarket regime was a key consideration in CSS’s buying decision
“The DF518 has a larger feeder box and is quick to screen. With a 1,5 m³ bucket, the excavator had to feed up to four buckets per minute to keep up with the screen, which was quite difficult. The 3 m³ bucket is matching up, because it achieves double the amount with just two scoops. Because of its high performance, we have also managed to replace two competitor screens that were previously working on site,” says Fischer.
Shaun O’Toole, sales manager – Mining, Crushing & Screening at Vermeer Equipment Suppliers, is pleased that the machine is proving itself, which bodes well for the brand still trying to make its big break into such a competitive market landscape.
“We are glad that the machine is delivering more than expected. The DF518 is a powerful and economical screen to run. With productivity at its core, the scalping screen has the ability to become the heartbeat of any large screening operation in the local market,” says O’Toole.
Commenting on why CSS opted for Anaconda, Fischer says the machine is built ‘Africa tough’. The Anaconda product, he says, is robust, yet easy to operate and service, which is key for 000 t
African contractors who often find themselves operating in remote locations.
More importantly, adds Fischer, Vermeer Equipment Suppliers’ aftermarket regime was a key consideration when making the buying decision. “Backup support is the most important consideration in this industry, especially given the importance of machine uptime in contracting. We need to maximise uptime to be able to earn money. This is a bigticket purchase, and any form of downtime is therefore out of the question,” he says.
“Vermeer’s track record in the provision of parts and services was a key consideration for us. The company has established itself for the past 20 years as a reliable partner with strong relationship building and dedication to its customers,” he adds.
Jan Kern, production & technical manager at CSS, was impressed from the onset by
the machine’s ease of serviceability and commissioning, which spoke directly to the contractor’s drive for uptime. Complete with a two-deck screen box, hydraulic folding hopper, main conveyor and two hydraulicallyfolding stockpiling side conveyors, the DF518 is extremely easy to commission and can be running within 20 minutes of arrival on site.
“All the service points of the machine are easily accessible. There is no need to strip the machine to get to certain components, thus our service-related downtime is very minimal. We also like the fact that it’s an easy machine to use and service; it’s a simple screen with no complicated electronics,” says Kern.
O’Toole adds that the machine was designed with uptime in mind. “On close inspection, one can see the attention to detail with little things such as collars around the clamp bar bolt heads to make changeout easier – something
that the guys in the field will appreciate,” says O’Toole.
As part of its distributorship agreement, Vermeer Equipment Suppliers offers the full Anaconda Equipment range of crushers, scalping and finishing screens, as well as trommels, washing equipment and mobile and tracked conveyors.
The crusher range comprises the J12 jaw and I12 impact crushers (open and closed circuit). This is complemented by a range of three scalping screen models and a fourmodel finishing screen line, as well as a mobile conveyor and feeder conveyor range of six models.Akeycompetitive edge, which O’Toole believes will be key in the brand’s breakthrough in such a competitive marketplace, is that the Anaconda is the only crusher range in the market that comes with interchangeable chambers. Core to the concept of the Anaconda tracked crusher range is that the same running chassis can be integrated with either an interchangeable, hydraulically driven, jaw or impact crusher chamber.
“The generic chassis is the backbone of the Anaconda crushing range. It allows for the placement of either crushing chamber, giving the customer immense flexibility in their fleet and the ability to reduce inventory costs. It increases fleet utilisation by allowing customers the versatility of converting the machine from a jaw to an impactor and vice versa in minimal time,” says O’Toole. “Anaconda has therefore created a machine where one can lift out the chamber and create either a jaw or impact crusher on the same chassis, and no other
manufacturer has ever done that in the market.”
To feed these crusher chambers, Anaconda has provided its crushers with a wide and heavy-duty grizzly feeder that can deal with the harshest of feed materials. The feeder is lined with replaceable wear resistant plates and has a robust grizzly screen as standard. This will remove fines from the feed material and improve the performance of the crushers while reducing the wear on the crusher plates and blow
Thebars.Anaconda mobile scalping screen range – including the DF410, DF514, DF518 and FSL100 – has been designed to deal with heavy duty applications where scalping away bulky oversize at the first stage of screening is a key aspect. The finishing screen range – comprising the two and three-deck SR520 as well as the two and three-deck SR514 – has been designed to deal with applications where separating fines is of utmost importance.
The Anaconda range of trommels – the TD516 and the TD620 – helps end users produce up to 75% more fines in the first pass compared to a standard scroll drum. This is because a scroll drum can cause the material to ball and bind together and increase the need for reprocessing.Thethree-model
Anaconda tracked conveyor range – the TR60, TR75 and TR100 – has been designed to minimise operating costs while maximising stockpile capacity. Key talking points on the range are the exceptional build quality and rapid set-up time, complemented by competitive pricing and versatility.
The wheeled conveyor range comprises three models – the ST50, ST60 and ST80. Designed for material handling, the ST range aims to reduce production time and save stockpiling costs. a
The SR520Anacondaisideally suited for fine applications.screeningWater plays an integral role in quarrying.
For both economic and environmental reasons, water management should be a priority for every quarry operation. This is the overarching message from ASPASA’s recently published best practice guideline for water management. By Munesu Shoko.
Traditionally, water management was never the first thing that came to mind when thinking of quarries. In recent years, however, this has all changed. In its Best Practice Guideline: Water Consumption, Treatment & Reuse, surface mining industry association, ASPASA, notes that water management is integral to achieving sustainable practices and is increasingly becoming a high priority in any industry. This is due to new and existing water resources becoming scarcer in many regions throughout the world. Per capita water consumption is increasing annually; water and sewerage rates have increased significantly over the last decade (100-
400%), while new water supply options are too costly or even unavailable.
Water plays an integral role in quarrying. Multiple quarry processes use water; in fact, it is a part of almost every step, all the way from extraction and dust suppression to wet processing, amongst others. It is therefore clear that efficient use of water at quarries is essential.
“The guideline document’s intention is to introduce information on existing procedures and strategies for improvement and conservation. Methods for increased efficiency, recirculation and reuse not only reduce the environmental impacts of production, but also lead to cost savings.”
100-400%
Per capita water consumption is increasing annually; water and sewerage rates have increased significantly over the last decade (100-400%)
Paving access paths of the quarry with sediment reduces the amount of loose particulates on roads, thus decreasing the amount of water required for dust suppression
Facilities with a high water demand may find settlement ponds the most effective solution for supplying the needed water as well as providing a sufficient storage area for effluent.
Water management is integral to achieving sustainable practices and is increasingly becoming a high priority in any industry
Methods for increased efficiency, recirculation and reuse not only reduce the environmental impacts of production, but also lead to cost
methods for streamlining water usage in quarries exist, including modifications to site landscape and investment in efficient
energy costs is another major benefit of good water management practices at quarry sites
Several methods for streamlining water usage in quarries exist, including modifications to site landscape and investment in efficient equipment.
For example, reseeding the quarry site with native grasses, indigenous and drought-resistant plants reduces the need for dust suppression. In addition, maintaining vegetation at an active quarry eliminates the future need to dedicate finances towards this aspect of site closure and reclamation.Pavingorcovering the access paths of the quarry with sediment also reduces the amount of loose particulates on roads, thus decreasing the amount of water required for dust suppression.
Updating equipment regularly can also greatly reduce water consumption on site. Pumps and
pipes wear with age, leading to wasted water via material deficiencies. Aged machines used in cutting and extracting can also waste water by overheating too easily or by creating more dust than newer technologies.
The use of automated systems – including variable-speed pumps – results in streamlined, consistently lowered use of water in facilities.
Primary water treatment and reuse at the quarry or processing facility can be accomplished in a number of ways. Filter presses, cyclone separators, sedimentation systems, retention basins and combinations of these systems are all viable solutions. In selecting an appropriate scheme for a site, several factors must be considered, including water demand, physical limitations, time and climate.
Facilities with a high water demand may find settlement ponds the most effective solution for supplying the needed water as well as providing a sufficient storage area for effluent. A filter press or cyclone separator alone may not be as capable of handling especially high flow rates.
If space is limited or other geographic obstacles exist, filter presses, inclined plate clarifiers, or cyclone separators (hydroclones) may be the best option for filtration, followed by storage in a tank or basin. These machines typically utilise a smaller area than a series of ponds and eliminate the need for excavation as they are installed on the ground
“Additionally,surface.settlement systems provide a relatively easy and effective method for collecting, treating, and reusing water at a quarry operation. This is in part due to the fact that natural stone
July/August Vol.
operations have little need for potable water; depending on the application, the water may need only to have the sediment removed. As such, stormwater runoff, dewatering water and process wash water can all be collected for treatment and subsequent recirculation.”
Further remediation of the water can be performed with an automated flocculent injection system. Flocculation is the process by which fines (relatively small particles) are induced – through the addition of an appropriate chemical solution – to clump together into masses referred to as floc. The floc is manually or mechanically filtered from the water, resulting in an efficient and effective system of particulate removal, particularly for very small-diameter particles. Other methods of filtration include geotextiles and filter devices installed in a series of discharge points within the water’s flow path.
Sludge accumulated in a settlement pond system, hydroclone, filter press, or inclined plate clarifier must also be disposed of properly. In the case of a pond system, the material must first be extracted and dewatered.
The former can be achieved with draglines, a vacuum/pumping system, or scooping machinery, such as a backhoe. Several options are available for dewatering pond sludge, as well. A centrifuge or filter press can be implemented, but to conserve energy, gravity is recommended.
With regards to the latter, the sludge can be placed in a hopper (or even an inactive quarry hole) until it dries. The draining water should be directed back into the settlement pond system.
Several uses for sludge exist both on- and off-site. At the quarry, dewatered sludge may be used to construct light-duty roads, coupled with vegetation to establish ditches or berms to collect and direct runoff, or laid as a liner in the construction of new settlement ponds.
Agricultural operations may utilise sludge as a type of soil fertiliser, and public or private groups
can use the material in road construction as a binder for gravel. In any case, the material does have multiple applications that will prevent the need for it to be disposed in landfills.
When it comes to water reuse, once the water has been treated, it can be directed back through operations for washing, dust suppression, extraction and cutting, finishing and irrigation. It may also be possible to use this water in a site greywater system, such as for toilet water.
The best practices outlined above bring a multitude of advantages to a quarry facility. One of the key advantages is revenue generation; collected sludge may be sold for use in road construction and agricultural applications, thereby generating a new form of revenue.Operations
can also greatly reduce their water expenses. Collecting, treating and reusing rainwater and runoff lowers the expense of water and sewerage bills. In addition, quarries can also avoid expenditures for well maintenance and upgrades.
Reduction in energy costs is another major benefit of good water management practices at quarry sites. Retention ponds facilitate a surface water supply, thus eliminating the expense of pumping from a deep groundwater well.
Retention ponds can function as a storage area for water generated from quarry dewatering, rainwater, and runoff. By collecting and retaining water, stress on the local water table and drinking water supply is avoided.
“Water is a finite resource, and proper water management is critical to sustain quarry operations. The best practices identified in the best practice document provide options in which a quarry can reduce its overall daily water demand.
Implementation of even a few of these suggestions can potentially result in cost savings, in addition to an improved environmental profile.” a
operation.atreusingtreatingcollecting,methodandasystemsSettlementproviderelativelyeasyeffectiveforandwateraquarryLike many other sectors of the economy, the aggregates sector is undergoing an intense period of change. In a one-on-one with Quarrying Africa, Tiisetso Masekwameng, GM – Comminution at Weir Minerals Africa, unpacks some of the emerging trends and how the company is responding to this shift in the market.
By Munesu Shoko.
With the industry facing the toughest market environments in recent years, the African quarrying sector is reinventing itself to achieve maximum growth and sustainability. Among the most significant trends in recent times, says Masekwameng, is the cost-sensitive nature of the aggregates market.
In a tough business cycle, it is clear that construction material suppliers are
holding their purse strings tight and are being much more conservative in their spending.“Theindustry is grappling with low demand due to a lack of significant infrastructure spending and the incessant tough economic times. This has provoked changes in how the aggregates sector approaches its procurement decisions. The market has become increasingly cost-sensitive, with a big drive to reduce capital expenditure (capex),” explains Masekwameng.
Trio cone crushers have formaintenanceuptimeincreasedandreducedcostslocalcustomers.The aggregates market is typically driven by two and threestage crushing plants in the 100-250 tph capacity region
6-8 weeks
The designs and drawings for the complementary conveyors and skids are readily available, allowing for fabrication and delivery of plants within 6-8 weeks
With the industry facing the toughest market environments in recent years, the African quarrying sector is reinventing itself to achieve maximum growth and sustainability
Among the most significant trends in recent times is the cost-sensitive nature of the aggregates market
The market is moving away from traditional stationary plants to semi-modular solutions that can be supplied and commissioned
Toimmediatelyrunefficient and profitable operations, aggregate producers in Africa are demanding maximum plant uptime, with unplanned downtime out of the question
Due to this cost-sensitivity, Weir Minerals has in recent times seen a move towards smaller sized plants that require less capex. “The aggregates market is typically driven by two and threestage crushing plants ranging from 100-250 tonnes per hour (tph),” she says.
Apart from cost, the market is also timesensitive, with aggregate producers demanding quick lead times and flexibility. Consequently, the market is moving away from traditional stationary plants to semi-modular solutions that can be supplied and commissioned rapidly.
“At Weir Minerals, we have answered the call with our standard Trio range of crushing and screening equipment that speaks directly to the need for 100250 tph plants,” she says. “Trio is a well-established brand within the quarrying industry globally. We offer a robust and reliable range of Trio crushers (jaw, cone and impact crushers), as well as a standard range of screens, feeders and washers. These are complemented by conveyors and skids to offer full modular plant solutions to our quarry customers,” says Masekwameng.
To respond to the call for quick lead times, Weir Minerals Africa keeps Trio crushers and screens for the 100-250 tph plant range available ex stock at its local warehouses. The designs and drawings for the complementary conveyors and
The industry is grappling with low demand due to a lack of significant infrastructure spending and the incessant tough economic times. This has provoked changes in how the aggregates sector approaches its procurement decisions. The market has become increasingly costsensitive, with a big drive to reduce capital expenditure.
“Tiisetso Masekwameng, GM Comminution at Weir Minerals Africa. Watch: Tiisetso Masekwameng discusses new industry trends.
skids are readily available, allowing for fabrication and delivery within 6-8 weeks.
“We tackle the need for easier mobility through semi-mobile skid-mounted plants. Our conveyors and skid structures are mounted on low ground pressure footings/skids and are self-contained (the internal structural loads are contained by the structure). The structures therefore do not require extensive conventional spread-footing foundations, but only minimal floating raft-type foundations with anchor bolts. This results in reduced costs related to civil works, while offering greater flexibility should the plant need to be relocated to a different quarrying site,” explains Masekwameng.Moreimportantly, Weir Minerals’ skids are preassembled in purpose-built workshops which follow strict Safety Health Environment and Quality (SHEQ) guidelines, ensuring maximum safety and peace of mind for clients and their operational teams working on site.
The Weir Minerals Trio team – consisting of qualified design and process engineers, as well as service support technicians – gives particular due diligence to the design of these modular solutions, with priority to safe operation, ease of operation and maintenance of products.
To run efficient and profitable operations, aggregate producers in Africa demand maximum plant uptime, with unplanned downtime out of the question, says Masekwameng. They are therefore looking to partner with original equipment manufacturers (OEMs) that can ensure them maximum uptime, efficiency and profitability.
“We support the need for uptime through Service Level Agreements (SLAs) and our experienced service technicians. SLAs are our commitment to the customer’s uptime, giving them that peace of mind that their best interests are always top of our priorities as the original equipment manufacturer,” she says.
Weir Minerals Africa further uses its extensive
branch network across Africa to ensure quick provision of spares and technical support. Whether a customer operates in Kathu, South Africa or Kitwe in the Zambia, the company has a branch with qualified personnel to ensure equipment is maintained and running at all times. Weir Minerals has invested heavily in its stockholding and branches around the continent to ensure their capabilities remain in sync with customer requirements.“Themoment a client buys a plant from us, we make sure that there is close interaction between them and the branch team located close to their operation. We also ensure that the branch is geared to support the customer and their particular needs,” she adds.
Masekwameng notes that Weir Minerals has a good or in-depth understanding of the innovation imperative in the aggregates industry. The quarrying industry is increasingly seeing value in digital solutions such as the Synertrex intelligent platform, which gives them visual access to actual costs of operating a piece of equipment, data to develop strategic improvements to their operations and the opportunity to performance benchmark every part of their operations.
Masekwameng says there is a complete mindset shift. There is a growing need for digital integration and Internet of Things (IoT) is the answer. Today, aggregate producers invest in digital technologies to enable them to make informed decisions, which ensures greater uptime, efficiency and productivity.“OurSynertrex intelligent platform can be fitted to our Trio range of crushing and screening equipment, thus providing a smart analytics platform that is easily integrated into customers’ existing systems. This means that health and performance analytics are conveyed through a digital interface, making sure our clients have all the indicators delivered to their devices with accuracy and in real time,” says Masekwameng. a
The Trio range of inclined screens is designed for applications.demandingoperationreliablecontinuous,in
Following years of a protracted downturn, the construction industry is rising from the ashes. This is the view of Maretha Gerber, vice president: Sales and Marketing at Daimler Truck Southern Africa, who tells Quarrying Africa that the company has seen increased demand for its construction range in the past 12 months, not only in South Africa, but also in the region at large. By Munesu Shoko.
Demand for 6 m³ concrete mixers has increased significantly in the past six months
In response to the growing demand for 6 m³ truck mixers, Daimler Truck Southern Africa introduced the FUSO FJ26-280C HYP in April 2021
The South African construction industry has been struggling for the past five years, if not more. However, if demand for construction-type trucks is anything to go by, the industry is on an upward Construction,trajectory.saysGerber, has been part of Mercedes Benz Trucks’ ‘DNA’ for many years, and remains a big focus for the brand. In fact, some ten years ago, the construction industry constituted 50% of Mercedes Benz Truck sales in southern Africa. During those years, the company actually had a stronger focus on its construction range than on long haul vehicles, with the previous Axor range enjoying a good run in the market.
“While the protracted slump in the construction environment hit us hard in the past few years, we have always believed that the market would rebound at some point,” says Gerber. “We are glad that construction is starting to show signs of recovery, with almost every original equipment manufacturer (OEM) struggling to meet demand.”
Despite a long market slowdown, Daimler Truck Southern Africa has in recent years boosted its offering with a range of models and solutions that speak directly to the needs of construction customers, further reiterating its commitment to the sector.
The arrival of the Arocs in early 2019 marked a new era in the company’s construction portfolio. Unfortunately, the range arrived at the height of the
hasConstructionbeenpart of many years, remains a big focus for the brand.
If demand for construction-type trucks is anything to go by, the construction industry is on an upward trajectory, not only in South Africa but also the region at large
Despite a long market slowdown, Daimler Truck Southern Africa has in recent years boosted its offering with a range of models and solutions that speak directly to the needs of construction customers, further reiterating its commitment to the sector
One of the new trends in the construction/ quarrying market is that end users are now looking beyond the truck – they are looking for efficiency, productivity, bodybuilder friendliness and value for money
Moving towards cleaner fuels is imperative for the construction/quarrying industry and the automotive industry at large
construction downturn and therefore struggled to gain the traction that the company had envisaged. However, sales of Arocs have been growing by more than 30% year-on-year, over the past three years.
The complementary FUSO range, which was brought in to meet the growing demand for value offerings in the construction space, is also enjoying good sales growth. In the past six months, says Gerber, demand for the 6 m³ concrete mixers in particular has increased. However, supply chain issues and bodybuilder backlogs remain a challenge for every OEM.
“It is encouraging to see our customers starting to enquire more about the Arocs and the FUSO FJ construction ranges. The challenge, however, is that when construction customers want their trucks, they want them ‘now’, irrespective of the supply chain disruptions. On the one hand, we are trying to manage customer expectations, and on the other, to be proactive. For example, some of the dealers, in collaboration with body builders, are proactively buying their construction trucks
While the protracted slump in the construction environment hit us hard in the past few years, we have always believed that the market would rebound at some point. We are glad that construction is starting to show signs of recovery, with almost every OEM struggling to meet demand.
“Maretha Gerber, vice president: Sales and Marketing at Daimler Truck Southern Africa
and bodying them up, so that when a customer walks in and wants a truck now, they have a standard offering available immediately,” explains Gerber.
One of the new trends in the construction/ quarrying market, says Gerber, is that end users are now looking beyond the truck – they are looking for efficiency, productivity, bodybuilder friendliness and value for money. When it is procurement time, she adds, they look for products that tick all the boxes for all involved parties in the decision-making process, all the way from the CEO to the operational manager.
The Mercedes-Benz Arocs range for construction is optimised for reliability, robustness and bodybuilder friendliness. The company initially launched two construction models in 2019 – the Arocs 3336K/36 Tipper Chassis and the Arocs 3236B/51
8x4 Mixer Chassis. These were later augmented by a further three models: an 8x4 tipper (the Arocs 4152K/51) and two all-wheel drive off-road vehicles (the Arocs 1836AE/45 and the Arocs 3352AE/48).
Drive programmes are available which have been specifically developed for the vehicles’ varied ranges of applications. For construction vehicles the “Off-Road Drive” programme is standard. Off-road drive mode offers the Standard, Economy, Off-road and Manual driving set-ups. It is optimised for the special requirements of construction-site traffic and
supports economic driving styles just as much as improved handling when pulling away or manoeuvring on building sites or when driving slowly along challenging terrain.
On gravel roads or off-road, the abovementioned drive modes offer ideal performance in terms of dynamism when pulling away under high loads, gearshift points and shift dynamics.
The Arocs 3236B/51, an 8x4 concrete mixer with 35-t gross vehicle weight (GVW), features a weight-optimised hypoid rear axle, light-weight aluminium fuel tank, disc brakes and aluminium rims to reduce kerb weight and increase payload. This enables the 8x4 mixer chassis to supply 8 m³ of ready-mixed concrete on everyThetrip.Arocs 3336K/36 is a versatile tipper chassis with a short rear overhang featuring robust planetary axles, a double disc clutch, robust drum brakes, optimised for off-road use and a 16-speed Powershift 3 automated transmission with the “Off-Road Drive” programme as standard.
The application-specific mounting elements provide for a bodybuilder-friendly and fast-mounting process. All mixer chassis are standard with the mixer mounting brackets and all tipper chassis come standard with the tipper mounting brackets, together with the modular bolted frame and the 50 mm chassis hole pattern. With the new generation Parameterisable Special Module (PSM), the turnaround time at a bodybuilder is significantly reduced.
The Arocs benefits from a number of innovations such as electronic parking brake,
The Sales of Arocs have been growing by more than 30% year-on-year over the past three yearsmultifunctional steering wheel and keyless start, amongst others. The electronic parking brake activates automatically when switching off the engine, but can also be switched on and off manually, using the lever in the cockpit. The integrated HOLD function activates when the vehicle is at a standstill simply by pressing the brake pedal more firmly, for example, at a red traffic light or on an uphill gradient.
While the Arocs is a top of the range offering for the high-end construction market, the FUSO plays in the value end of the market, speaking directly to the emerging construction contractor market and small-scale quarries.
In response to the growing demand for 6 m³ truck mixers, Daimler Truck Southern Africa introduced the FUSO FJ26-280C HYP in April 2021. This model is specifically fitted with hypoid rear axles (single reduction axles), contributing extensively to low fuel consumption and reducing the tare weight of the vehicle. This is to ensure that the vehicle can accommodate a 6 m³ concrete mixer and still comply with the permissible axle loads.
Traditionally, most construction truck owners have never taken a total cost of ownership (TCO) approach to their truck purchases. While many still largely consider the capital cost of the product, Gerber says several industry players are starting to develop a much better understanding of TCO, showing interest in not only purchase costs but also in the costs related to keeping the equipment running.
There are several pillars to TCO. For Gerber, it’s all about the reliability and efficiency of the truck, as well as the aftersales care that comes with it. Daimler Trucks Southern Africa makes sure
that when a customer walks in, they walk out with a solution that meets their needs, not just a truck. For example, the company offers a service contract as a maintenance option. Together with its dealers, the OEM makes sure that the truck is kept in good condition throughout its lifespan. Customers also have access to the OEM’s inhouse finance solution, among other offerings such as driver training.
“For us it boils down to value for money, efficiency and productivity. It’s also about building a modular solution that meets the customer’s needs. Some customers, for example, might not want a service contract, but finance would be important to them. One doesn’t necessarily have to take the full basket of solutions to put together a TCO solution. We can come up with a solution that speaks directly to the customer and their contracts,” she says.
Looking ahead, Gerber says moving towards cleaner fuels is imperative for the construction/ quarrying industry and the automotive industry at large. Going the Euro 5 or Euro 6 route exposes the industry to a wide product range and an array of other operational benefits such as better fuel efficiency and reduced environmental impact.
“If customers are willing to move to Euro 5 and Euro 6, we are able to bring in a broader product offering because these have become a priority for many of our source plants across the world. I believe that the next four years are going to be interesting for the South African market. Neither we nor our customers are waiting for legislation. The industry needs to evolve, and fast,” concludes Gerber. a response to the
As part of the rollout of its production class equipment in Africa, John Deere Africa Middle East (AME) has launched the 460E-II articulated dump truck (ADT) in southern Africa. Targeted for quarrying and high-production mid-tier mining operations, the new ADT has a distinctive design focus on increased productivity, economy, performance and lower total cost of ownership – parameters of principal significance to every quarry or mine owner. By Munesu Shoko.
Having successfully completed the first phase of the rollout of its John Deere-branded construction equipment in Africa, John Deere AME has turned its focus on its production class equipment, including largesized wheel loaders, excavators, dozers and ADTs.Latest on the arrival lounge is the 42-tonne (t) class John Deere 460E-II ADT, which made its debut on 26 July 2022 at a launch event held at
AfriSam’s Jukskei quarry in South Africa. Griffiths Magkate, sales manager Construction and Forestry AME, tells Quarrying Africa that the 460EII ADT is the culmination of a thorough research and development (R&D) regime, informed by customer needs.
“Given the importance of the ‘voice of the customer’ in today’s equipment designs, the development of the 460E-II ADT was informed by customer feedback. John Deere spent considerable time talking to customers to find out
The 42-t class John Deere 460E-II ADT made its debut on 26 July 2022 at a launch event held at AfriSam’s Jukskei quarry in South Africa.7%
In a comparison between the E Series truck and the new E Series II, it is apparent that customers can enjoy up to 7% fuel efficiency gains in Normal Mode
12%
Eco Mode, which conserves fuel by managing engine power delivery and enhancing transmission response for applicable conditions, further improves fuel consumption by up to 12%
The new ADT is targeted for quarrying and high production opencast mining.
Having successfully completed the first phase of the rollout of its John Deere-branded construction equipment in Africa, John Deere AME has turned its focus on its production class
lounge is the is the 42-tonne class John Deere 460E-II ADT, which made its debut on 26 July 2022 at a launch event held at AfriSam’s Jukskei quarry in South
the enhancements that will be of great interest to mines and quarries is the ADT’s fuel
is said to be the largest bin capacity and payload of all ADTs in this size class, the 460E-II has a special design focus on increased productivity
what they needed, wanted and expected from the product. We believe that the 460E-II ADT is everything that the market wants from an ADT today, ticking all the right boxes, from increased productivity and uptime to efficiency and lower total cost of ownership,” says Magkate.
ADT engineer Ian Marshall adds that John Deere’s R&D regime is driven by the company’s Customer Advocate Group – a team of experts drawn from experienced ADT operators, owners, dealers, technical support staff and factory
We believe that the 460E-II ADT is everything that the market wants from an ADT today, ticking all the right boxes, from increased productivity and uptime to efficiency and lower total cost of“ownership.
Griffiths Magkate, sales manager Construction and Forestry AME
engineers. As part of John Deere’s design process, members of this group of ADT specialists gather before and during the design of any model to give their input.
This design approach has been at the centre of the continued evolution of the John Deere ADT over the years. The company, says Marshall, started selling ADTs some 25 years ago in North and South America – the Richards Bay, South Africa-made C-Series. In 2004, John Deere began manufacturing the D-Series ADTs at its Davenport, United States factory, before rolling out the E-Series in 2012.“Last year, the E-Series range was upgraded with several enhancements. The range boasts all the latest electronic features of any contemporary ADT, thus driving new levels of productivity, economy and performance required on any jobsite,” saysTheMarshall.newADT is targeted for quarrying and high production opencast mining. According to Magkate, the truck is meant to address the rising demand of 40 - 45-t offerings in the mining sector. “The mining environment is changing. To provide context, hauling at high production mines has always been reserved for largesized rigid dump trucks. This is all changing, with customers moving towards smaller hauling solutions. The reasoning is that running a big fleet of smaller trucks reduces the risk of downtime. For example, if a single 400-t truck breaks down, production stalls. On the contrary, if you are running smaller 40-t trucks and one breaks down, you can still produce with minimal impact to your overall production,” he explains.
One of the enhancements that will be of great interest to mines and quarries is the ADT’s fuel efficiency, especially considering the high fuel prices in South Africa and the region at large. To give some background, the cost of diesel (50 ppm) has risen by almost 134%, from R10,33 per litre in 2010 to R24,15 in 2022.
Five years ago, we embarked on a complete channel redesign, which we implemented 18 months ago, with remarkable success to date. We selected what we believe are the strongest dealers, based on their wide support footprint, closeness to their customers, investments in their infrastructure, personnel, tools and training.
“Jaco Beyers, MD of John Deere Africa Middle East
“Key to increased productivity is the redesigned dump body, which is wider and has a lowered and levelled rail height to improve material retention and allow it to be easily loaded. Additionally, the bin rail features an angled top, helping to reduce material spillage while travelling.
PowerTech 6135 engine which is also fitted in other large John Deere construction machines, agricultural tractors and combined harvesters for greater parts commonality. The transmission is a ZF 8 EP 420 designed specifically for ADT applications and thrives in long, hard and fast hauling. The top gear sets are countershaft type, more suited for high RPM, low torque from the engine. The lower gear sets are planetary type and are suited to lower RPM and high torque generated by the transmission,” explains Marshall.
At the centre of the truck’s fuel economy are the three different drive modes – Normal, Economy and Traction – which help optimise the drivetrain, reduce input from the operator and enable easy customisation.Inacomparison between the E Series truck and the new E Series II, it is apparent that customers can enjoy up to 7% fuel efficiency gains in Normal Mode. Its Eco Mode, which conserves fuel by managing engine power delivery and enhancing transmission response for applicable conditions, further improves fuel consumption by up to 12%. Eco Mode is ideal for instances where the ADT does not always have to travel at full throttle moving at top speed. This is often the case when there are many trucks in a normal haul cycle.
The 460E-II also has a special design focus on productivity. The machine, says Marshall, has the largest bin capacity and payload of all ADTs in this size class. With a payload of 41 820 kg, the truck has 800 kg more payload than the nearest competitor offering in this size“Keyrange.toincreased productivity is the redesigned dump body, which is wider and has a lowered and levelled rail height to improve material retention and allow it to be easily loaded. Additionally, the bin rail features an angled top, helping to reduce material spillage while travelling,” withcanareaoverMarshall.explainsThe460E-IImodelisalsoavailablewithanewejectorbodysolution,whichallowsoperatorstospreadaloadagivenandwhichbeusedinareasoverheadpower
In Traction Mode, the truck locks up four differential locks –one in each axle and one in transmission, thus allowing a fully loaded ADT to travel as smoothly and efficiently as possible, even in tough underfoot conditions. The new wheel-speed sensors also provide a more accurate reading than the groundspeed radar to confirm that the traction-boosting autodifferential lock engages when needed.
“The 460E-II is powered by the 13,5- l John Deere
line concerns or where the risk of rollover is high due to steep grade unloading.Basedon John Deere’s understanding that a comfortable operator is a productive one, the 460E-II casts the spotlight on operator comfort. The cab, says Marshall, is the most important part
With a payload of 41 820 kg, the truck has 800 kg more payload than the nearest competitor offering in this size range Watch: Ian Marshall unpacks some of the key features and benefits of the new ADT Ian Marshall, ADT engineer at John Deereof the truck for operator comfort.
“Operators are in their cab all day long – spending anything between 10-12 hours in it. It is therefore important that their working environment be comfortable, which is also key to productivity on site. With that in mind, the 460E-II’s updated operator station includes features that promote increased productivity and all-round comfort. One of the notable features is the single switch model, which reduces the number of switches by 25% compared with previous models,” explains Marshall.
The quiet, pressurised cab also features a new, easy-to-read monitor and rear camera display, along with options such as the premium heated/ventilated seat and automatic control (ATC) system.
In addition, subscription to John Deere’s JDLink™ telematics system is available free of charge to users. JDLink allows owners and managers to connect to their machinery remotely, to help monitor and track operations and productivity.
With uptime in mind, John Deere paid particular attention to ease of service during the design of the new ADT. All service points are reachable from ground level. At the front of the truck are side doors, a front panel and a bonnet, which provide access to all major service points.
To further improve service access, the front suspension travel can be decreased at the push of a button to bring service points closer to the ground. As part of the enhancements to the new range, John Deere has also reduced over 10% of the hose connections and electrical routings, making the 460E-II one of the most serviceable trucks on the market.
An optional factory-installed auto lube system with ground refill is electrically powered and integrated with machine diagnostics in order to help verify daily maintenance is being performed. In addition, diesel exhaust fluid (DEF) refills are also easily accessible at ground level.
Machine reliability and durability are principal considerations in buying decisions. The John Deere 460E-II axles are designed for heavy-duty hauling and long life. They are lubricated, filtered and cooled to extend their service life, while the spring-applied, hydraulically released park brake is also highly reliable.
The oscillation tube adopts a revolutionary contemporary design. “While it appears conventional and similar to competitor offerings, it does not a have a cast tube or plastic/bronze bushes. Instead, it features a cast beam with excavator carriage-type roller bearings at each end. This is factory set up and does not require regular service adjustments. The new lowmaintenance oscillation design should provide twice the life of conventional bushes, possibly up to 20 000 hours,” explains Marshall.
In addition, the inboard wetdisc brakes run cool, clean and unexposed. The brake axles are each force-cooled and filtered separately. The cooling oil is separate and not shared, thus eliminating the possibility of cross contamination.
Meanwhile, the hose and wire routing on the ADT has been simplified to reduce rubbing and improve reliability. A 10% reduction of electric and hydraulic routings reduces leak points, thus maximising machine reliability and uptime.
“
We have made the investment and our dealers have also invested in order for our customers in the region to receive support. We will continue to add part numbers as more construction models become available for our market.Glenys Millingham, manager Aftermarket Sales, AME
According to Jaco Beyers, MD for John Deere Africa Middle East, the production class equipment range comes at a time when John Deere’s construction equipment channel partners, appointed in the last 18 months, have made substantial investments to be able to support the range in the market.
“Five years ago, we embarked on a complete channel redesign, which we implemented 18 months ago, with remarkable success to date. We selected what we believe are the strongest dealers, based on their wide support footprint, closeness to their customers, investments in their infrastructure, personnel, tools and training, which are all key to supporting our construction equipment range, not only now, but well beyond the next 50 years,” says Beyers.
As part of the exercise, AFGRI Equipment was appointed the distributor of selected areas in South Africa, namely Gauteng, Limpopo, part of Mpumalanga, part of the Free State and the Western Cape, as well as Botswana and Zimbabwe.
Senwes Equipment is the authorised distributor for selected areas in South Africa (North West, part of Free State and the Eastern Cape) as well as Namibia. The Mascor Group is responsible for KwaZulu Natal and part of Mpumalanga in South
Africa, as well as Uganda and Kenya in East Africa. The TATA Group is the sole custodian of the brand in Tanzania, Zambia, Malawi, Nigeria and Ghana.
Glenys Millingham, manager Aftermarket Sales, Africa and Middle East, says John Deere is dedicated to keeping its dealers equipped with the necessary parts. This is made possible by the company’s worldwide distribution network. The key distribution centres for Africa and Middle East comprise the Regional Distribution Centre (RDC) in South Africa, the Parts Distribution Centre in Europe and the parts facility in the US. Combined, these facilities stock 900 000 part numbers, with more than 120 000 parts shipments despatched on a daily basis.
“We have made the investment and our dealers have also invested in order for our customers in the region to receive support. We will continue to add part numbers as more construction models become available for our market,” concludes Millingham. a hours000
Located in Kempton Park, South Africa, the 20 000-m² RDC serves the southern part of Africa. It stocks 86 000 stock numbers worth R1,5-billion, averaging 600 shipments a day. With the integration of the construction business last year, John Deere AME added 17 000 more part numbers to the RDC.
The 460E-II is powered by the 13,5-litre John Deere PowerTech 6135 whichengineis also fitted in other large John commonality.forharvesterscombinedtractorsagriculturalmachines,constructionDeereandgreaterparts
Handax Machinery, the sole distributor of Shantui construction and mining equipment in southern Africa, used Electra Mining Africa 2022 to unveil its new DH13-B2 dozer in southern Africa. Key talking points, Equipment sales manager, Marcus du Toit, tells Quarrying Africa, are the hydrostatic transmission, the PAT blade and the favourable price point. By Munesu Shoko.
Traditionally, exhibitions have always afforded the ultimate platform to introduce new products and solutions to the market. For Handax Machinery, Electra Mining Africa 2022 proved to be the ideal launchpad for the new Shantui DH13-B2 dozer. Suited for agricultural and small-scale quarrying appli cations, the new dozer has already generated signif icant attention from the local market, with at least six customers interested in taking the very first unit locally, confirms Du Toit.
The 130 HP class Shantui DH13-B2 dozer is a radical upgrade of the previous SD13 model.
A major differentiator is the new hydrostatic transmission, which is a major upgrade to the previous model’s mechanical transmission. In addition, the new dozer employs a flexible and versatile Power-Angle-Tilt (PAT) blade, moving away from the traditional U-blade found on the previous model.
While hydrostatic transmissions are not necessarily new to the market, it is only in the last ten years that the migration to this type of transmission has taken root, and the reasons are simple: hydrostatic transmissions
The Shantui DH13-B2 dozer made its southern African debut at Electra Mining Africa 2022.10-15%
Shantui’s innovative hydrostatic drive optimisation technology achieves higher efficiency and energy saving. Customers can expect 10-15% in fuel savings compared with the previous model and other mechanical transmission dozers of the same horsepower range
25%
Unlike the normal U-blade, which has limited movement, the PAT blade can swivel in nearly all directions, offering 25% better angling of the blade
Handax Machinery, the sole distributor of Shantui construction and mining equipment in southern Africa, used Electra Mining Africa 2022 to launch the DH13-B2 dozer in southern
model comes with a hydrostatic transmission, which is a major upgrade to the previous model’s mechanical one
Another major talking point on the new Shantui DH13-B2 dozer is the innovative PAT blade, said to be the most versatile dozer blade on the market
To further boost its aftermarket regime, Handax Machinery will embark on an aggressive rollout of service dealerships in the next 24 months
provide greater operational efficiency and make machine operation so much easier and smoother than the conventional mechanical counterparts.
One of the greatest benefits of the hydrostatic transmission, says Du Toit, is that it is extremely efficient. Hydraulic servo pressure and flow are based on demand, while the electronic control of the system adjusts travel speed and drawbar pull to match load conditions. If full flow and pressure
are not required, the load-sensing system automatically dials back hydraulic output and conserves energy. Likewise, in low power demand situations, the pump can increase output and let the dozer move at high speed without increasing engine speed, resulting in greater fuel efficiency.
With the hydrostatic transmission, explains Du Toit, the engine generally operates at its most efficient power output, while the hydraulic pumps and motors constantly adjust to vehicle power and load requirements, thus ensuring optimal fuel consumption at all times.
“Shantui’s innovative hydrostatic drive optimisation technology achieves higher efficiency and energy saving. Customers can expect 10-15% fuel savings compared with the previous model and other mechanical transmission dozers of the same horsepower range,” explains Du Toit.
A key propositionvalue of the dozer is its favourable price point, which bodes well for markets.andconstructionincontractorsemergingbothquarryingMarcus du Toit, Equipment sales manager at Handax Machinery, unpacks the key features and benefits of the new dozer.
Another big benefit of the hydrostatic transmission, he adds, is smooth operations resulting from the absence of gears. Smooth machine operation means improved control of loads during straight-line dozing and especially during power turns, where the machines automatically increase throttle to maintain the dozer’s ground speed. Consequently, hydrostatic dozers have been proven to be significantly more productive in most applications compared with their powershift counterparts.
Because it is easier to operate, the hydrostatic transmission also helps novice operators become productive faster, and makes experienced operators even more productive, adds Du Toit. The transmission also comes with fewer components, translating into reduced cost of maintenance.
Another major talking point on the new Shantui DH13-B2 dozer is the innovative PAT blade, said to be the most versatile dozer blade on the market. It can angle and tilt in six directions. The versatility in movement makes it ideal for spreading soil and clearing debris. “Unlike the normal U-blade, which has limited movement, the PAT blade can swivel in nearly all directions, offering 25% better angling of the blade in the process,” says Du Toit.
Apart from new machine features, Du Toit tells Quarrying Africa that another value proposition is the favourable price point, which bodes well for emerging contractors in both construction and quarrying markets.
“Our price point is one of our key competitive edges in the market. Pricewise, we are 40% competitive than some of the so-called
‘premium’ offerings, yet we offer the same quality and features. Testimony to our confidence in the quality of the product is the two-year/4 000-hour warranty,” says Du Toit.
With the arrival of the new DH13-B2, Du Toit is confident that Shantui will further gain more market share in the local dozer market. Since its arrival in the southern African market back in 2007, the Chinese maker has proved its mettle in this competitive market which has traditionally been dominated by premium OEMs.
In fact, Shantui is a force to be reckoned with in the global dozer market. With a whopping 60% share of its domestic Chinese dozer market, the company holds a 15-20% share of the global dozer market, confirms Du Toit.
In 2010, Shantui went on to become the largest producer by volume of bulldozers globally, making over 10 000 units that year, thus representing two in five crawler-type dozers produced in the world. Currently, the company produces in excess of 15 000 units a year.
“Locally, our market share continues to grow at a rapid pace. With the arrival of the new hydrostatic dozer, coupled with the competitiveness of our pricing, quality of machinery and aftermarket support, we expect to substantially increase our local market share in the next two to three years,” says Du Toit.
To further boost its aftermarket regime, Handax Machinery will embark on an aggressive rollout of service dealerships in the next 24 months. These will be established across South Africa and neighbouring countries, including Namibia, Botswana and Zimbabwe, as well as Zambia and the DRC. a
A major talking point on the new market.bladeversatiletoPATisDH13-B2Shantuidozertheinnovativeblade,saidbethemostdozerontheSandvik Mining and Rock Solutions has effectively transitioned its operations to Khomanani, its new high-tech head office facility, workshop and manufacturing complex in Kempton Park, Johannesburg. The facility was officially opened by his Excellency President Cyril Ramaphosa on 09 September 2022.
Representing an investment of R350-million, Khomanani – which accommodates approximately 500 Sandvik employees – consolidates the operations previously undertaken at five separate sites. Sandvik’s fulltime equivalent (FTE) forecast is 39 by end of December 2022 representing an 8% growth.
For the first time ever, the company now has its soft rock, hard rock and surface businesses all under one roof. Khomanani, which occupies a 62 000 m² site, is one of Sandvik’s biggest and most advanced facilities globally and has the ability to produce underground
Epiroc has signed an agreement to acquire AARD Mining Equipment, a South African mining equipment manufacturer.
AARD, based near Johannesburg, South Africa, designs, manufactures, services and supports a wide range of mining equipment, specialising in lowprofile underground machines for mines with low mining heights.
The high-quality products include drill
loaders with over 60% local content, allowing them to be designated as ‘Proudly South African’.
Developed in conjunction with Equites Property Fund, Khomanani is a bespoke facility comprising an office building and three workshops. Two of the workshops are dedicated to the refurbishment and rebuilding of Sandvik machines – to OEM standards – from throughout the southern African region while the third is designed to assemble equipment locally.
The workshops are equipped with 23 docking bays and a combination of cranes up to 30-t capacity to facilitate the handling of equipment. The floors can support very high loads, including continuous miners weighing over 100 tonnes. The spacious site has a carefully designed road layout which allows heavy transport vehicles to move in and out of the property easily without the need for time-consuming manoeuvring. a The workshops are equipped with 23 docking bays and a combination of cranes up to 30 t capacity to facilitate the handling of equipment.
Epiroc has introduced its new Automatic Bit Changer (ABC) for hands-free bit changes on Pit Viper 270 and Pit Viper 290 series drill rigs used in rotary drilling. The ABC option is designed to change rotary tricone bits significantly faster than manual exchanges and eliminates human interaction with the drill string for a safer, more efficient way to operate a drill fleet.
The ABC makes it possible for operators to complete hands-free drill bit changes with the single touch of a button and to stay informed on their screen. Operators can make or break joints, select drill bits, and add or remove them. This can be done from either a remotely-based control room or from the comfort of the cab. The ABC optimises productivity and efficiency of the drilling operation and improves safety by eliminating exposure to live work environments.
“The early collaboration with customers and cross-functional teams resulted in an auto bit changer that is repeatable, keeps the operator out of the line of fire, and improves machine uptime,” says Matthew Fosler, senior design engineer, Surface division.
rigs, bolters, loaders, scalers and more. The company’s customers are mainly in the southern Africa region. AARD has approximately 200 employees.
“AARD has reputable and reliable products that complement our underground product portfolio well,” says Helena Hedblom, Epiroc’s President and CEO. “This acquisition will further strengthen our growth ambitions in Africa and beyond. a
Epiroc’s ABC decreases downtime and eases operator workloads. The carousel design allows up to four bits to be easily changed significantly faster and safer than a single manual exchange. The removable bit carousel can store rotary tricone bits in varying sizes and cutting structure, for a total of four on-board bits, for flexibility and versatility on a drill site. Featured in the unique carousel design, the ABC gives users the ability to safely replace the worn drill bits with a range of bit types and sizes from a safe distance without exposure to live work. a
Representing an investment of R350-million, Khomanani – which accommodates approximately 500 Sandvik employees – consolidates the operations previously undertaken at five separate sites.Epiroc to acquire SA equipment manufacturer
Latest from Pilot Crushtec International is Metso Outotec’s Lokotrack ST4.10, the largest model in the Lokotrack mobile screen range. With a nominal capacity up to 600 tonnes per hour (tph), it is ideally suited for high-capacity aggregate screening in a closed-circuit crushing process.
While static plants have always been preferred in high-volume aggregate applications, mobility and flexibility have become principal factors for aggregate producers, prompting the migration to mobile screens at several operations.
A major talking point is the plant’s extensive 9 m² screen area with three 6 060 mm x 1 520 mm screen decks producing up to four end products. The wide feed box with an 8 m³ capacity and the 10 m side conveyors with adjustable angles and speeds, enable the unit to be deployed as part of a multi-stage crushing process in closed circuit with large scale crushing plants such as the Lokotrack LT120 or LT300HP.
The wide grizzly rock box also makes loading with a wheel loader easy when using the Lokotrack ST4.10 as a stand-alone unit in sand and gravel applications. Despite its large size and its 33 000 kg weight, the new mobile screen is fast and easy to set up. With its 19 650 mm (length) x 3 040 mm (width) x
The Lokotrack ST4.10 features a large 6m x 1.5m screen box which is rated to handle up to 600 tph.
3 560 mm (height) transport dimensions, it can be transported between sites as a single unit on a low bed truck.
The screen is equipped with a diverter chute that enables blending of products from different decks. Side tensioned top and middle decks make changing screening media quick and
Metso Outotec has closed the acquisition of Global Physical Asset Management, a technology provider based in North America. The acquisition will further strengthen Metso Outotec’s capabilities in digital field service inspections for grinding.Theinnovative technologies and the digital inspection method of Global Physical Asset Management are patented and fully complementary to Metso Outotec’s current service offering for grinding. This will bring more value to customers and support them in achieving reliable plant performance. The acquired technology enables 60% faster gear inspections with outstanding accuracy when compared to the use of conventional methods.
“I am very pleased about this important step toward our strategic target to become the preferred services provider in our industry. The unique technology and digital inspection method fit excellently with our services strategy and grinding offering and will also bring potential to further develop our
easy, thus maximising uptime on site.
As all Lokotracks, the Lokotrack ST4.10 can be equipped with the optional Metso Outotec IC process control system, which offers a safe single-button start-up and the possibility to interlock the screen with other Metso equipment in a train. a
inspection capabilities for our crushing solutions. I warmly welcome our new colleagues to the Metso Outotec team,” says Sami Takaluoma, President, Services business area at Metso Outotec. a
Despite its large size and its 33 000 kg weight, the new mobile screen is fast and easy to set up.Lack of attention to maintenance on heating, ventilation and air conditioning (HVAC) systems on mobile mining equipment such as dump trucks, excavators, dozers and drill rigs can cost mines dearly. Booyco Engineering provides these a range of support services for these HVAC systems, either long or short term, and is happy to negotiate appropriate arrangements with customers.
“The fact of the matter is that an HVAC system that is malfunctioning can result in a multi-million rand mining vehicle being taken out of service, resulting in hours of downtime and possibly hundreds of thousands of rands of lost production,” says Spies. “Modern health and safety laws in South Africa are very demanding and operators are entitled to stop work if ambient temperatures in the cab are too high or, for that matter, too low.”
Booyco Engineering has an unparalleled track record of supplying and maintaining highly efficient HVAC systems for customers in the railways, defence and mining sectors. Its clients over the years have included Transnet, General Electric, Alsthom, Bombardier and, in the mining
sector, Seriti’s New Vaal opencast coal mine. Booyco has supplied maintenance services continuously to New Vaal for more than two decades.
The company’s HVAC systems are locally designed and manufactured and are specifically designed for Africa’s rugged conditions. The units are assembled in Booyco Engineering’s 3 000 m² Meadowdale premises in Germiston. “We outsource most of the fabrication, but all design is undertaken by Booyco Engineering’s engineers and technicians at our premises using the latest software and specialised tools,” says AccordingSpies.toSpies, the standard
HVAC systems used on many offroad mining vehicles are unable to cope with the constant vibration, extreme temperatures and dust that are encountered in mining environments. “Our customised units are more expensive than these products, but they are durable and can function for 20 years, or even longer, if maintained correctly,” says Spies. “By contrast, the life of standard units can be short – no more than two or three years. Buying them is false economy.” a
The true test of effective customer support is its ability to lower the total cost of ownership of equipment.
According to vibrating screen specialist Kwatani, this means accurately predicting the customers’ future needs. It also means regular and detailed measure of costs and output.
While low total cost of ownership (TCO) is a function of product quality, it is also about predicting maintenance intervals and optimising uptime.
“Prediction and planning have become the pillars of quality aftermarket support,” says Jan Schoepflin, GM sales and service at Kwatani, now part of the global Sandvik engineering group. “More than ever, OEMs must support customers with systems and services that pinpoint future needs.”
Schoepflin highlights that when equipment users adopt a TCO approach, they realise cost savings through smoother operations and less disruption, as there are fewer unplanned stoppages.
“This approach should also extend the life of equipment, making it not only more cost effective but more environmentally sustainable,” he says. “As the name suggests, capital equipment is a significant investment and should last as long as possible.”
An important part of an OEM’s support role, then, is to help customers measure the condition and performance of equipment. a
Booyco Engineering’s HVAC systems are locally designed and manufactured and are specifically designed for Africa’s rugged conditions.One of several world premieres from Doosan at Bauma 2022 will be the launch of the company’s new 4x4 articulated dump truck (ADT). Complementing the company’s standard range of 6x6 ADT models, the new 4x4 version of the DA45-7 ADT is intended to compete with rigid dump trucks (RDTs) in the 40-tonne (t) class.
The new 4x4 DA45-7 ADT complements the current range of 6x6 ADTs from Doosan, which includes the DA30-7 and DA45-7 models with payloads of 28 and 41 t, respectively.
In the new 4x4 ADT, the front truck and cab unit is the same as in the original 6x6 model, with modifications being made on the rear dumper unit only. Featuring a ZF EP8-420 transmission, the 4x4 DA45-7 is a two-axle ADT with twin wheels at the rear, and with a dumper section similar to that on RDTs in the 40-tonne class.
“With superior operation on poorer roads, smoother surfaces and steeper terrain, the aim of our new 4x4 machine is to challenge RDTs in the 40-t class, by providing a dumper product that delivers much more than RDTs,” says Beka Nemstsveridze, ADT
After seven successful years of growth and evolution, pumping specialist Integrated Pump Rental has rebranded as IPR.
Announcing the rebranding at the popular Electra Mining Africa 2022 show in Johannesburg, IPR MD Lee Vine says the fresh new look reflects the company’s expanded range of offerings. It has made a solid name for itself as a rental operation in dewatering and dredging – having significantly grown its rental fleet over the years.
This rental success has led to a move towards selling pump solutions where this made sense to the customer’s particular operating conditions. By prioritising the total cost of ownership, IPR is able to offer the most costeffective choice between renting and
product manager at Doosan. As well as performing better in conditions that are tough for RDTs, the new 4x4 DA45-7 ADT has a width of less than 4 m to avoid the need for special transportation and offers a better turning radius than a comparable RDT. The shorter turning radius and the design of the rear dumper unit, which is more suited to carrying flat and heavy rocks, provide particular advantages in the mining and tunnelling industries.
The latter are growing markets for ADTs, and include pioneering, shortterm mining projects, quarrying and contract mining industries, especially those in southern Africa, the UK and Australia. Construction and bulk earthmoving contractors involved in roads, dams, airports, landfills and development projects are also large users of ADTs. Together these areas make the ADT market a wide and varied one, thereby ensuring a large customer base. a
purchasing.
“In responding to customer needs, we have also naturally evolved into the manufacture of custom pump sets for specific applications,” says Vine. “With our extensive experience and engineering expertise, this was a logical step which our new brand can now embrace.”Heemphasises that IPR boasts the same expert team that customers have relied upon and continues to deliver their well-known standards of service excellence. As the sole agent in southern Africa for Sykes diesel-driven pump sets, IPR also deals with various global pump brands including Grindex, Flygt, Godwin and Atlas Copco.
“Among the products that we have developed locally – to great acclaim in the local market – are the SlurrySucker
and SlurryBlaster,” he says. “These are designed for dredging silted-up ponds and for removing accumulation of slurry and sediments on dam walls and inside dams.”
He credits hard work from the IPR team as the force behind becoming synonymous with pump dewatering and dredging solutions across industries, especially in challenging conditions. Existing customers as well as the broader marketplace today recognise the company as IPR, so it was appropriate to update its branding and launch a new look.
The vision, he explains, continues to be aimed at becoming the leading pump dewatering and dredging specialist – with a focus on assisting customers to reduce their total cost of ownership. a
Doosan 4x4 DA45-7 ADT to make Bauma 2022 debut at Mining The new 4x4 DA45-7 ADT complements the current range of 6x6 ADTs from Doosan, which includes the DA30-7 and DA45-7 models with payloads of 28 and 41 t, respectively. The new 4x4 version of the DA45-7 ADT is intended to compete with rigid dump trucks in the 40-t class.While the mining industry is making great strides in achieving greater gender equality in terms of women at the middle and senior management level, the real impact of achieving gender inclusivity lies at grassroots level. By Ricardo Ribeiro, MD of Rosond and Advisory Board Member of WiMBIZ, SA.
At board level, women representation may reach as high as 50%, but at the lower em ployment levels in the mining industry there is still a lot of work to be done. At Rosond, we have been very passionate about making a difference at this level and our efforts are starting to reap realTherewards.issueis what constitutes gender equality at a grassroots level in the mining industry? What are the specific hurdles that have to be overcome at such a basic level? And how do we achieve this within the framework of the existing Mine Health and Safety Act legislation and regulations? How do you transfer knowledge and skills to allow women to become integral members of the mining workforce? Answering these key questions is what will drive the achievement of real as opposed to token gender equality.
Achieving gender equality in the industry is challenging. Our experience on the ground has shown us that the focus should not only be on increasing the number of women in skilled positions, but also on how to support these women through the intelligent design of programmes that enable them to grow and achieve greater success at work.
At Rosond we are proud of the work we do in upskilling women and creating opportunities for them to be successful in roles traditionally performed by men. Apart from creating greater access to these positions and making significant progress in increasing the number of women working at operational level, we believe that progress will be optimised through driving Mine Health and Safety Act policy change by taking aspects such as technology and automation into consideration.
In our view, this requires even greater upskilling and a sensitivity to the particular socioeconomic and family issues women face on a daily basis. Through adopting a sensitive and appreciative view of the reality women are confronted with, Rosond has been able to create a more inclusive work environment. A lot of these women were sitting at home with no job prospects. Developing them further, in conjunction with family planning and financial planning, is key to their career success as well.
As part of Rosond’s commitment to addressing these gaps, we are establishing an inaugural women’s forum at one of our drill sites in the Northern Cape to
provide a platform to address ancillary issues such as family planning and financial literacy. There is a lot of responsibility involved in promoting gender equality in the mining industry, especially as we afford women the opportunity to be financially independent and to have viable careers.
The women’s forum will consolidate all of our learnings on-site in terms of gender diversity and inclusivity, allowing us to continue to offer a sustainable and empowering career path for women in mining. We invest a lot of time and resources in training women to become proficient in the drilling industry. In this regard, we have embarked on a gender inclusivity programme that includes workshops on gender sensitivity.
Apart from the female drill rig crews themselves, another way for us to promote gender diversity and inclusivity in the mining value chain is to support small and medium enterprises (SMEs) that are established and driven by women. Of course, we have to balance this requirement against our own impetus to maintain market share.
One means to achieve this is to empower such SMEs by providing them with the equipment and services they require so that they essentially become our accredited partners. Rosond is making significant progress in this area as part of our partnership with WiMBIZ, SA.
This is an organisation established to create a platform for women entrepreneurs, businesswomen and professional women to speak in one voice and access procurement opportunities and equity transactions in the mining sector.
We are adding great value to WiMBIZ, SA through our knowledge of the industry, networks and valuable strategic input. In addition, we recently concluded a Memorandum of Understanding (MOU) with two WiMBIZ, SA members as part of its enterprise development initiatives in exploration drilling.
Not only does it allow these smaller, women-led players to tender for bigger projects, but it also gives the mining houses themselves the confidence that there is a major player such as us in the background driving the process.
Transformation does not happen overnight. Therefore, we will continue to be creative and find ways to support our women employees in ways that make a real difference to their lives.
Ricardo Ribeiro, MD of Rosond and Advisory Board Member of WiMBIZ, SA.While slope failures in open pit mines occur mainly due to kinematic instability or shear stresses within the slope exceeding rock mass strength, the concept of foundation failure can prove useful in cases where ground profile anomalies occur.
This was the message from John Kwofie, principal geotechnical engineer in SRK Consulting’s Ghana office, when he delivered a keynote address to the recent Rocscience Africa Conference 2022 in Accra. Kwofie noted that he had encountered three instances over a span of a decade, where the cause of slope failure could not be determined using the usual well-known methods.
“In these cases, slope stability analyses conducted on the slope design showed that the Factor of Safety (FoS) was above the recommended minimum value,” he said. “At the same time, analyses of the orientations of geological structures did not point to any kinematic admissibility.”
Nevertheless, he said, the slope had failed – and it was difficult to recommend remedial measures because the cause of failure had not been established. After close observation, though, it appeared that the ground profile was not typical. Instead, it was found that that there was weak material embedded within strong layers below the toe elevation of the slope – such as completely weathered layers in otherwise unweathered rock.
“The weak foundation material appeared to be overstressed, evidenced by the heaving of the ground at the toe of the slope failure as encountered in general geotechnical shear failure,” he said. “Reassessment of the cause of instability – from the perspective of bearing capacity failure – made it easier to see why the slope would fail when conventional methods did not predict such behaviour.”
Kwofie noted that the existence of weak and compressible materials within competent rock introduces different stress behaviour into slope stability. Differential settlement introduces tensile stresses into the rock mass causing cracking and dilation, which lead to failure that would not have occurred if not for the ground profile anomaly.
“The excavation of the pit itself results in a progressive loss of confining pressure in the weak compressible material underlying the slope, making it even weaker,” he argued. “Even though the stresses on a weak foundation material are unlikely to increase, the reduction in the strength of the material with mining –due to the loss of confining pressure – is analogous to increasing loading intensity.” a
The existence of weak and compressible materials within competent rock introduces different stress behaviour into slope stability.