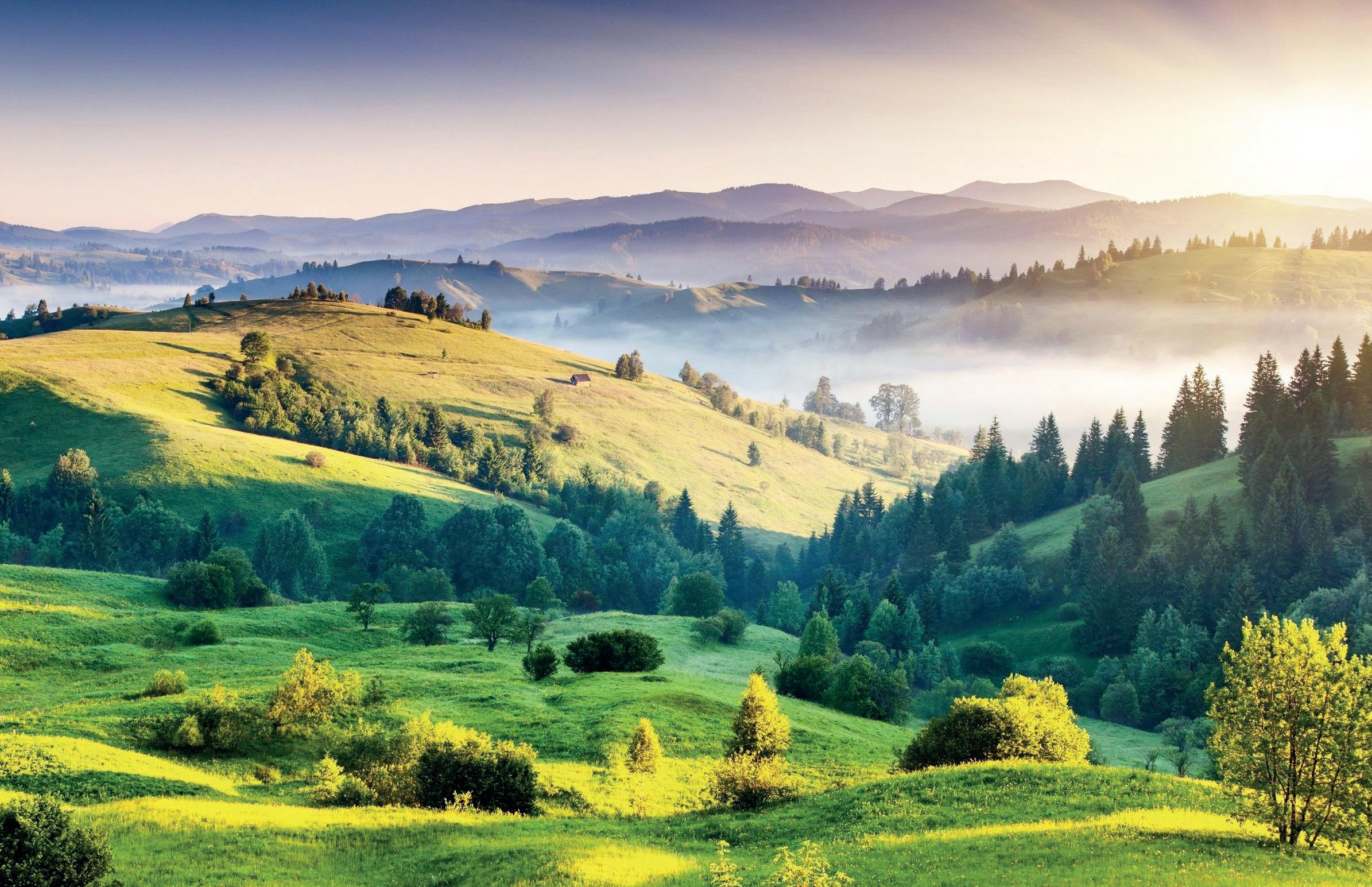
6 minute read
Winds of change
Amid infrastructure headwinds, India is tackling its greatest challenge head on – as the country attempts to decarbonize production while ramping up production.
STEEL consumption determines the economic growth and prosperity of a nation, which is directly linked to its infrastructure development. With the Reserve Bank of India estimating 6.5% of India’s gross domestic product (GDP) growth, the country’s steel consumption is expected to grow at 7-8% in FY2023–24 (April – March). However, India’s steel consumption is estimated to have grown by a staggering 12.7% to a record 119.17Mt/ yr in FY2022-23, at a 6.4% growth of the GDP. At 120Mt/yr of crude steel production in FY2021-22, India surpassed Japan as the second-largest crude steel producer after China.
This being said, economic growth and prosperity bring in a lot of carbon emissions. The steel sector in India has a high carbon footprint and contributes almost a third of direct industrial CO2 emissions, contributing 10-11% of the total release of this obnoxious gas in the country. This remains a concern considering that the Indian steel industry will grow at high rates, increasing production by 40Mt in the next five years. Therefore, if adequate measures
By Dilip Kumar Jha*
India’s green steel fact file
Particulars
Total crude steel production in the financial year FY 2022-23
Total finished steel consumption in the financial year FY 2022-23
Present crude steel production capacity
Target to achieve by 2030
Per tonne energy consumption in an integrated mill average per tonne energy consumption
Average carbon emissions by steel mills (2005)
Target achieved by Indian steel mills (2020)
Commitment to reduce carbon emissions in steel mills by 30-35% by 2030
India’s cumulative target up 4.2% from the previous year up 12.7% from the previous year giga calorie in 2015 in 2020
To achieve carbon neutrality by 2070
Source: Ministry of Steel, Government of India; Mt/yr = Million tonnes per year; T/tcs = Tonnes/ tonne of crude steel; Financial year runs in India from April 1 to March 31 are not taken to reduce its carbon footprint at the earliest, it will be responsible for huge carbon emissions in the coming years.
As per a 2020 report by the International Energy Agency (IEA), Indian crude steel production will increase to 180Mt/ yr in 2030 and 350Mt/yr by 2050. The government of India, in its National Steel Policy, targets India’s crude steel production at 300Mt/yr by 2030. To achieve this target, the government of India is working on the Production Linked Incentive (PLI) scheme to
*India correspondent, Steel Times International boost investment in the steel sector. With a massive production plan in place, the carbon emission volume in India is estimated to rise by 2.5 times by 2030, contributing to more than 5% of the country’s greenhouse gas (GSG) emissions. According to an estimate, steel mills across India consume an average of 6-6.5 gigacalories of energy compared to the world’s average of 4.5-5.0 gigacalories. With such a high energy consumption, average carbon emissions by integrated steel mills in India were measured at 3.1 tonnes per tonne of crude steel (T/tcs) in 2005, which was brought down to 2.65T/tcs in 2015 and further to 2.5T/tcs in 2020 through several efforts made by the government. Carbon emissions by the average integrated mill are again targeted to reduce by at least 30-35% from its 2005 level to 2.4T/tcs by 2030.
Therefore, India’s steel industry needs to set an impactful pathway to evolve into a low-carbon yet growing manufacturing sector. The entire value chain in the steel industry, i.e. producers, distributors, exporters, importers, suppliers, and consumers, needs to go green. Owing to India’s heavy reliance on coal throughout various steelmaking processes, the task is not easy. The Indian steel mills are heterogeneous and plagued by using a wide range of equipment, with some dated and insufficient technologies. There are numerous players from small-to-medium steel mills that are often less efficient and more polluting.
Green initiatives
To make the policy prudent, the government of India recently introduced the Green Hydrogen Mission to promote the utilisation of green hydrogen instead of fossil fuels like coal and reduce carbon emissions in the steel industry. However, this mission continues to face headwinds such as poor infrastructure for producing green hydrogen, storage, and transportation from the production centre to the fuelling spots. Despite the government working overtime to encourage investment in the entire hydrogen channel, the plan remains on paper. As one of the largest polluters, the steel industry needs to adopt green hydrogen technology and reduce carbon emissions for the sector’s sustainable growth. Green hydrogen is projected to mitigate an overall 50Mt of carbon emissions and save India’s fuel imports INR 1 trillion by 2030.
Meanwhile, the Steel Association of India (SAI) has prepared a list of policy enablers that can push green steel investment in India. These include preferential public procurement of green steel, the introduction of standards, and incentives across the value chain sectors, i.e. from production and transportation to consumption sectors.
Steel mills in India have already started taking voluntary measures to reduce carbon emissions. For example, Tata Steel, which has a production capacity of 34Mt/yr, has a mission to bring down carbon emissions to 1.8T/tcs by 2030. The company now aims to become water-neutral by 2030 for all its sites and a zero-effluent organisation by 2025. In addition, it plans to produce a major portion of its steel from scrap-based production processes in the coming decade. The scrap-based steel production process is less carbon-intensive than the traditional blast furnace or oxygen furnace route.
Leading from the front, Tata Steel has set up a 0.5Mt/yr scrap processing plant in Rohtak, Haryana. For the existing process, Tata Steel looks forward to enabling hydrogen-based sustainable steel production as a step towards achieving the company’s vision of net-zero emissions. It also undertook a trial for the continuous of India (SAIL) has a total production capacity of 21Mt/yr. The Ministry of Steel has already submitted the Intended Nationally Determined Contributions (INDC) for reducing GHG emissions in the iron and steel sector, while projecting CO2 emissions of 2.2 - 2.4T/tcs in the blast furnace route and 2.6-2.7T/tcs in the direct reduced iron (DRI) – electric arc furnace (EAF) route by FY2030, from 3.1T/tcs during 2005. SAIL has set a target of reducing carbon emissions by 2.30T/tcs by FY2030. injection of coal bed methane in the blast furnace of its largest plant at Jamshedpur, Jharkhand, to reduce carbon emissions.
Jindal Steel and Power Ltd (JSPL), which has a production capacity of 8.6Mt/yr in India and 2.4Mt/yr in Oman, aims to significantly reduce its carbon footprint by almost half as part of its ESG objectives. At its site in Angul, Odisha, JSPL adopted the DRI-BF-EAF route for manufacturing steel. To overcome the challenge of the nonavailability of natural gas and coal, the steel mill set up a gas plant on its site and used locally available high-ash coal to convert it into synthetic gas (Syngas).
With its annual production capacity of 18Mt/yr, JSW Steel focuses on a circular economy by optimizing water, waste, carbon, and energy footprint. The company has set a target of achieving CO2 emissions of 1.95T/tcs by 2030. JSW Steel secured a power purchase agreement for 2.5GW renewable projects and commenced operations at a 225 MW solar power plant in Vijaynagar, Karnataka, in April 2022. The firm also secured tie-ups with various states for 5-gigawatt hydro-pumped storage projects. Furthermore, the company has 1.26 GW of wind projects in the pipeline to start operation by FY2023. In an optimistic scenario, the company’s renewables-led growth may reach 10 GW capacity by FY2025 and 20 GW by FY2030.
The government-owned Steel Authority
Rashtriya Ispat Nigam Ltd (RINL), also known as Vizag Steel, has a production capacity of 7.3Mt/yr. Now, the company is striving to reduce CO2 emissions in all stages of steelmaking by installing state-of-the-art cleaner technologies, improving processes, recycling waste, and afforestation. The company claims a reduction of 1.3Mt/yr of CO2 emissions is possible as a result of using state-of-the-art cleaner technologies during the design stage, as well as a reduction of about 3Mt/yr of carbon dioxide by installing energy-efficient technologies, modifying processes, enhancing the capacity of sinter plants, and rebuilding blast furnaces.
Conclusion
In India, the government has drafted a ‘master plan’ and outlined an investment of $1.3 trillion in infrastructure development. According to Ernst & Young, this along with future investments would help India become a $5 trillion economy by FY2025 and $26 trillion by FY2047 when India will be celebrating its centenary year of independence. Amid the government’s continued focus on the construction of roads, railways, ports, and airports, Moody’s Investors Service estimates India’s steel consumption growth to rise by 10% until FY2026. Therefore, India is now considering implementing a law to curb carbon emissions, that will require steel mills to dedicate a portion of their annual production through green routes. �
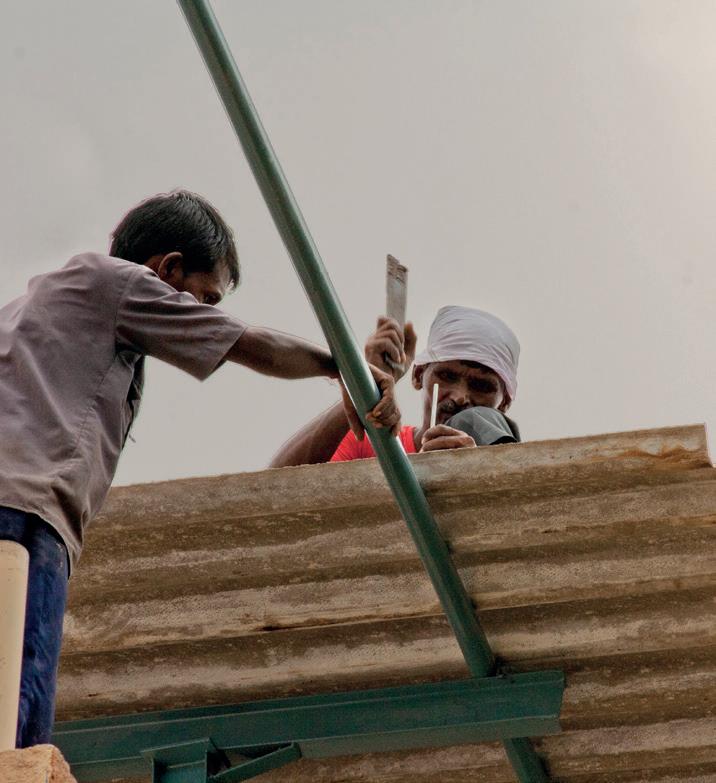