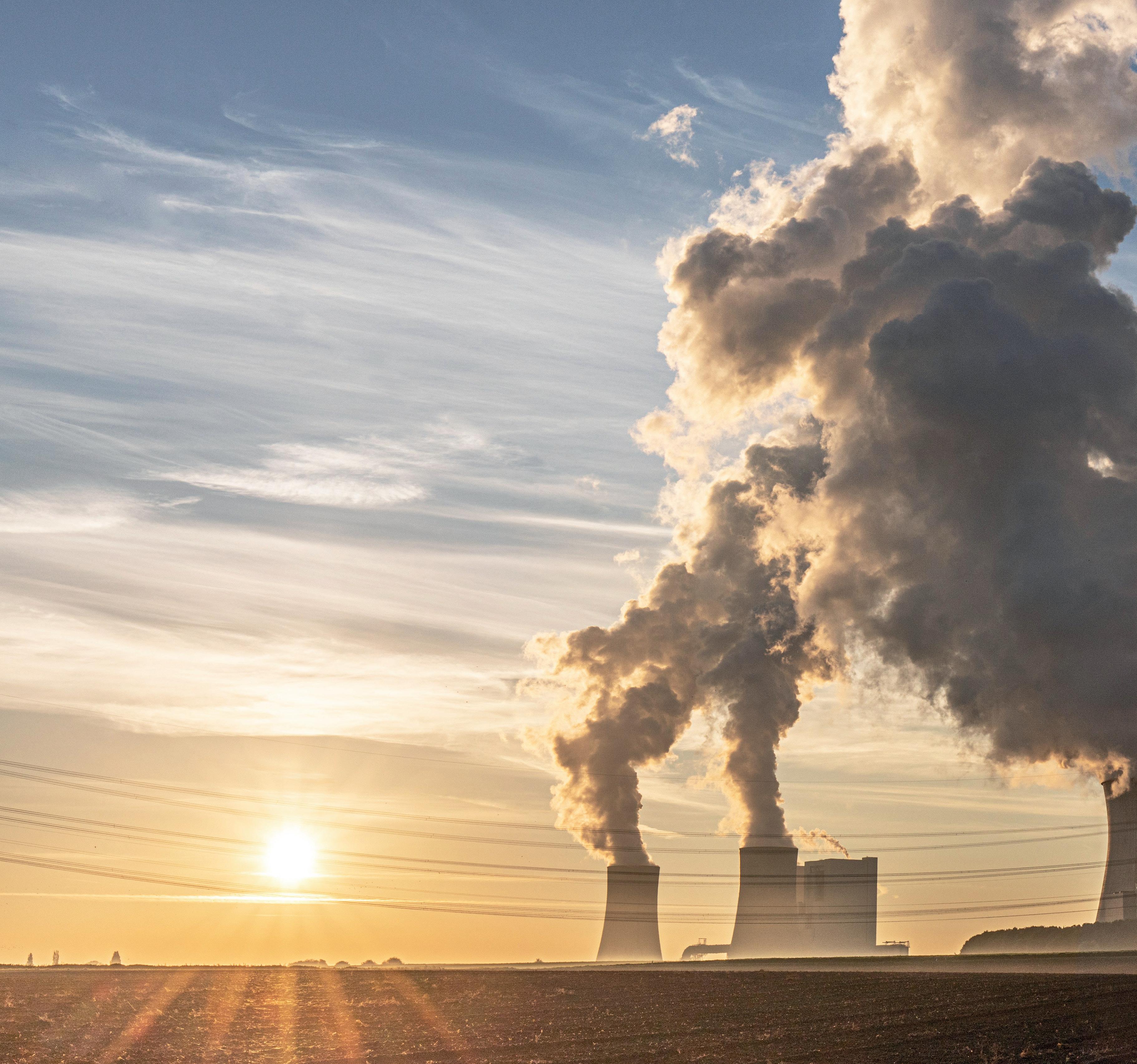
9 minute read
Green steel for a green planet Green steel for a green planet
The Centre for Advanced Steels Research (CASR) discusses its current projects, which aim to enable a hydrogen economy and streamline the transition to decarbonized and digitalized steel production. By Pentti
IN the Glasgow Climate Pact 2021, 197 countries agreed to limit the global temperature increase to 1.5°C by reducing greenhouse gas emissions. This calls for a climate-neutral Europe by 2050 and Finland has an ambitious aim to become carbon-neutral already by 2035 and carbon-negative soon thereafter. The steel industry is responsible for ≈7% of annual CO2 emissions globally. Therefore, the steelmaking and mechanical engineering industries have an important role to play in addressing the challenges arising from the long-term strategy on climate goals. Replacing carbon partially or even completely with hydrogen and non-fossil renewable electricity generation are the key factors, by means of which the universal targets of CO2 emissions and climate change could be achieved. The EU Green Deal identifies clean hydrogen as a priority in the green transition and electrolytic water splitting using sustainable electricity is at present considered as the primary preference for green H2 production, but it fails in covering the huge demand. Furthermore, hydrogen, as causing hydrogen embrittlement, is detrimental to the properties of high-strength steels, needed as a critical construction material to reduce the CO2 emissions.
Advanced steel research at CASR
In Finland, the Centre for Advanced
Steels Research (CASR) was founded in the University of Oulu in 2006 in order to co-ordinate steel-related research (https://www.oulu.fi/casr/). Currently CASR consists of 10 members, seven research units from the University of Oulu, and a unit from LUT University, Turku University and Åbo Akademi, with a total of about 140 researchers. CASR is currently headed by Professor Jukka Kömi. Well before the age of the CASR, in the early 1990s, research related to thermomechanical processing of high strength steels was initiated, particularly focused on physical simulation and direct quenching technology in processing high-strength plate steels. It is estimated that the use of advanced ultra high-strength steels can decrease total CO2 emissions worldwide by up to 15%. The direct quenching technology was adopted by Rautaruukki (now known as SSAB Europe Oy) in Finland in the early

1990s. For potential future technology, based on the physical and laboratory rolling simulations of quenching and partitioning (Q&P) processing, a novel direct quenching and partitioning (DQ&P) process has been proposed by CASR.
Currently, in the line of numerous research groups globally, CASR focuses very closely on the challenges of targeting carbon-neutral/carbon-free green steel processing and the manufacturing of ultra high-strength steels for weight reduction. In this research field, some projects have already been completed but numerous ones are currently going on and are planned.
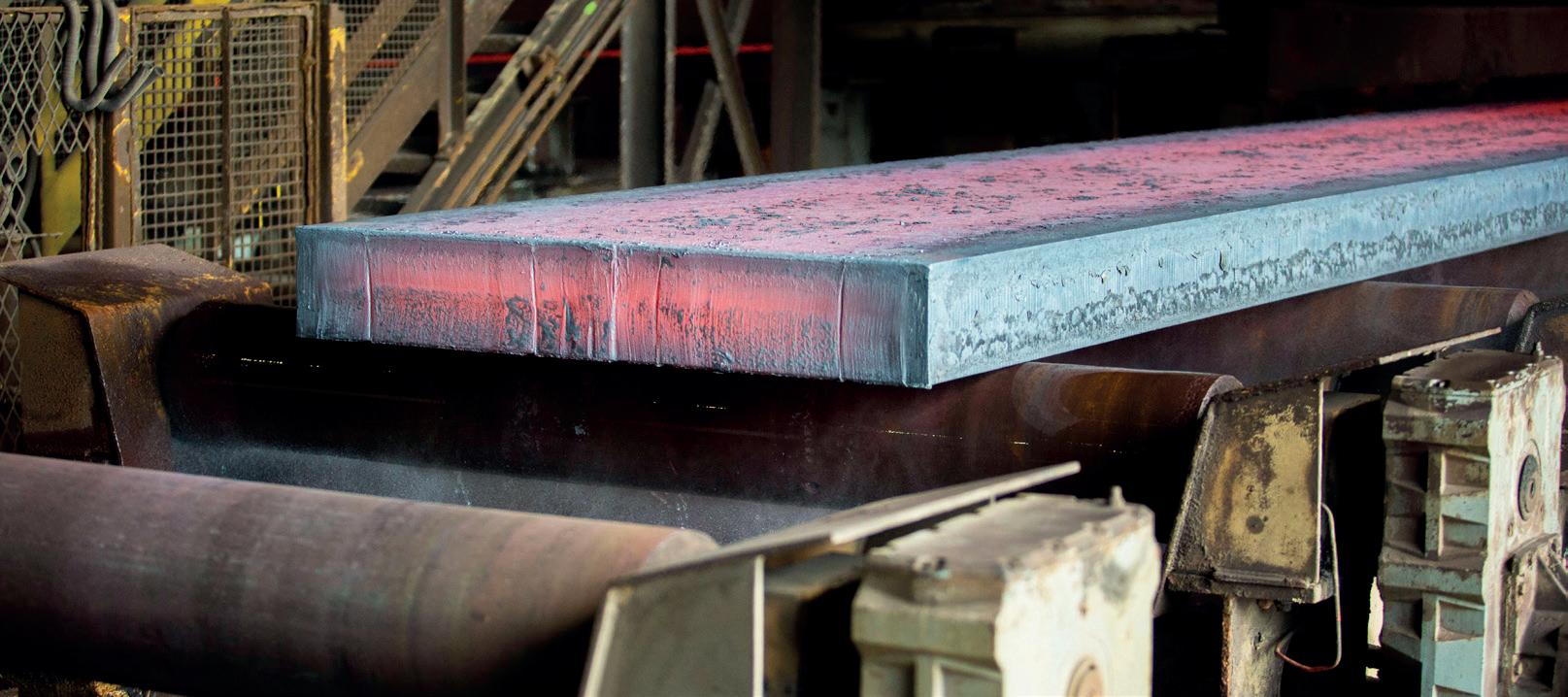

As a starting point for the current efforts, a five-year-long academic project entitled Genome of Steel – Physics for strong, tough, and sustainable steel, funded by the Academy of Finland, was conducted over the years 2017–2021. In the Genome of Steel (GoS), the co-operation of material physicists and steel researchers formed a successful integration of experimental and theoretical physics with process and physical metallurgies. The multidisciplinary approach pushed the traditional engineering research towards novel physics-based atomic-level understanding of metallurgical routes and microstructure evolution under the influence of processing parameters for realizing sustainable ultra high-strength steels; and boosted steel research utilized to-day in projects concerning the hydrogen transition of steelmaking. The multi-disciplinary research has been and will be further utilized in several hydrogen-related projects (see Fig 1). The short descriptions of the projects can be found on the webpage of CASR: https://www.oulu.fi/en/research/researchinfrastructures/centre-advanced-steelsresearch/research-projects-casr)
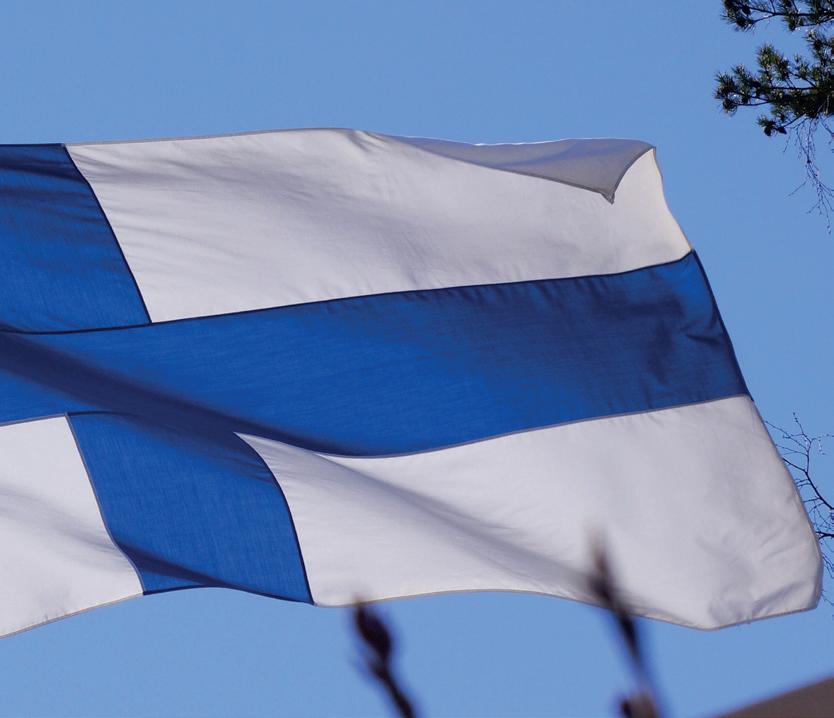
Most of the projects are concerned with carbon neutral steelmaking using hydrogen reduction.
Digital TWINs for a green hydrogen transition in the steel industry (TWINGHY) is an RFSC-funded project aimed at demonstrating new ways to use, monitor and control hybrid NG–H2 burners for reheating furnaces, progressively decarbonizing the reheating process through an increase of H2 in combination with O2 and monitoring and controlling it through a digital twin. TWINGHY will contribute to the synergetic green and digital transitions of the steel industry.
Hydrogen technologies for the decarbonization of industrial heating processes (HyInHeat) is a Horizon EUIA funded gigantic project, with the participation of 31 beneficiaries, aiming to demonstrate how 100% H2 can be used in industrial high-temperature heating processes. HyInHeat contributes to the objectives of decreasing CO2 emissions of the processes while increasing energy efficiency in a cost competitive way, keeping NOX emission levels and resource efficiency at least unchanged.
Two big national projects, Advanced Steels for a Green Planet (AS4G) and Hydrogen Future as a Climate Change Solution (H2Future), funded by two Finnish foundations (with a budget of €2m for four years) and the Academy of Finland for six years together with the University of Oulu (with a budget of €8m) will be initiated shortly. Researchers are working on these two projects with the common objectives of the transformation to a hydrogen economy and the conceptualization of a zero waste plant. These objectives are anticipated to be achieved through effective clean hydrogen production solutions; carbon-free steel manufacturing, advanced steels and the utilization of industrial side streams. Accordingly, the AS4G is organized in five themes as follows: (Fig 2)
Sustainable green hydrogen in industrial applications

(led by Professor Marko Huttula)
At present and in the near future, the supply of renewable green electricity is not realistically sizeable enough to support electrolytically driven processes required for generating green hydrogen. The photocatalyst, sun light-assisted hydrogen electrolysis, can be anticipated to serve as the core technology for a truly sustainable hydrogen economy in the future, powered by direct sunlight.
Based on some previous investigations, novel high-efficiency photocatalysts for hydrogen evolution will be developed and applied to iron ore reduction processes. The timeline of the development of high efficiency catalysts is between three-to-five years, piloting in five-to-seven years, and having industrially-scaled readiness in seven to 10 years.
Carbon-free steelmaking by hydrogen use
(led by Professor Timo Fabritius)
The study focuses on the replacement of fossil carbon with hydrogen as the reducing agent. Iron ore reduction will be accomplished by using varying mixtures of CO-H2 atmospheres, followed by a continual increase in H2 content until reaching a pure H2 atmosphere. Globally, CO2 emissions from iron ore-based steelmaking (~1,200Mt of steel per year) could be decreased to nearly zero using this step-by-step approach.
Industrial collaboration is based on very close connections with companies in their own business areas: SSAB (hydrogen reduction of iron ore in a shaft furnace), Hybrit (fundamentals of hydrogen reduction), Outokumpu (hydrogen plasma reduction), Ovako (hydrogen in electric arc furnace steelmaking), Metso Outotec (electric arc furnace process development) and Fortum (hydrogen reduction of multi element systems).
Metallurgy of advanced steels for sustainable applications
(Led by Professor Jukka Kömi)
The objective of this study is to develop the 3rd and 4th generation hot- and coldrolled ultra-high-strength steels without the excessive use of expensive alloying elements. The yield strength is targeted in the range of 900Mpa to beyond 2000 MPa, with elongation exceeding 20% and having good low-temperature toughness and high sustainability.
Two kinds of steel will be investigated: nanostructured medium-carbon martensitic and bainitic steels and medium-Mn steels, both having ultra-high-strength for weight reduction as well as good resistance against hydrogen embrittlement for service in a hydrogen society.
Optimizing ultra-high-strength steel solutions (a) develops testing technique(s) for detection and analysing the detrimental influence of atomic H in iron lattice, (b) develops novel microstructure(s) for enhanced local H-trapping and crack propagation resistance, and (c) improves the understanding and modelling of H-steel interaction from atomic to macro scale and vice versa
Virtual steelmaking novel models
(Led by Professor Jari Larkiola)
The Virtual Steelmaking platform (VSP) makes it possible to consider new and changed process steps before the actual production begins. The impact of hydrogenbased steelmaking on process efficiency, potential bottlenecks, the formation of desired side streams, final mechanical properties of the steel, and carbon footprint can be solved virtually.
Future side streams for future cement

(Led by Professor Mirja Illikainen)
A transition to hydrogen-based ironmaking will hugely change the amount and composition of the slags, which in turn will pose a challenge for their future use. Moreover, full capture and utilization of steel production dusts and sludges are inevitably needed to achieve the concept of ‘zero waste plant’.
Slags will be treated by CO2, resulting in carbon capture and utilization. After that, the carbonated slags will be benefited as supplementary cementitious material. This will not only support and advocate the idea of a zero waste concept but would also offer the possibility of globally alleviating the carbon footprint emerging from cement production.
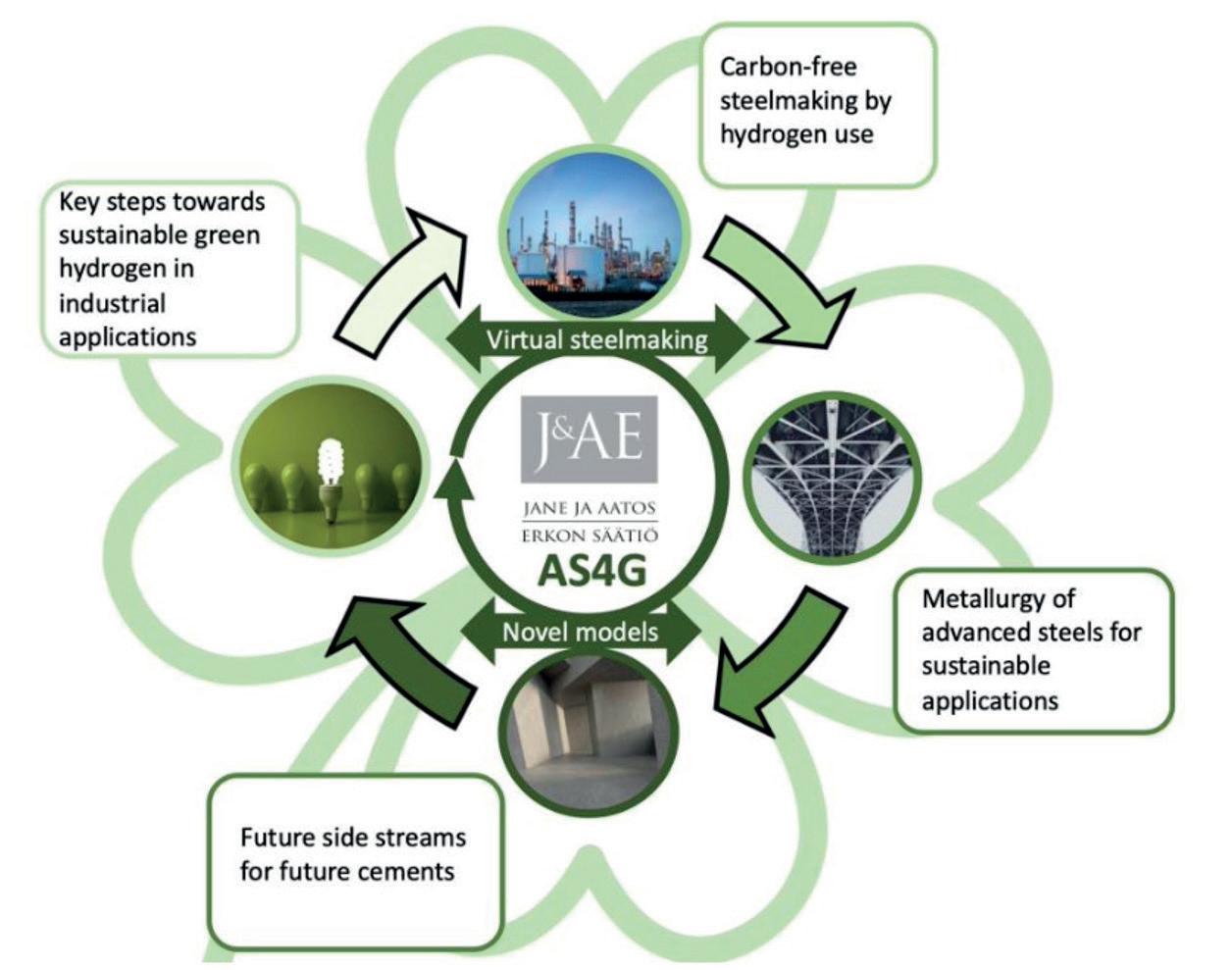
Testing and characterization of green steels
An example of a result of recent research is a special testing method developed by Dr Renata Latypova in her doctoral studies to assess the risk of hydrogen embrittlement; a novel tuning-fork test (TFT). TFT utilizes an integrated loadcell system used during hydrogen charging that allows tracking of the applied force throughout the tests, enabling the detection of initiation and propagation of cracking and time-tofracture. A trustworthy threshold stress level can be determined with a longer testing period. (Renata Latypova: Development and Application of a Tuning-Fork Test in Studying Hydrogen-Induced Fracture in As-Quenched Martensitic Steels, Acta Univ. Oul. C 856, 2022. https://cc.oulu. fi/~kamahei/z/tkt/vk_RenataLatypova.pdf – see Fig 3)
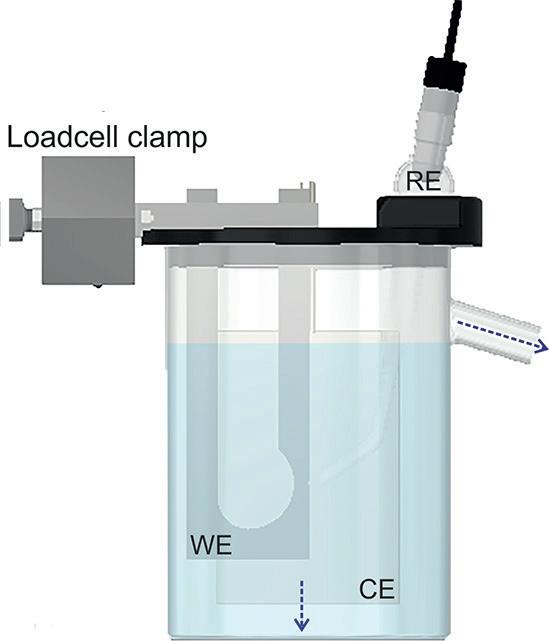
In addition to an existing Linseis furnace for reduction experiments with H2 and a small-scale EAF furnace for melting of DRI, two special devices for novel state-of-theart sample environments are aimed to be developed in the ongoing projects:
In situ SR dilatometer
A synchrotron radiation dilatometer will be designed together with CASR and MAX IV laboratory for employing the hard X-ray beamlines at MAX IV for following up phase transformations as a function of temperature and time, while monitoring the changes in macroscopic properties of the material.
Ambient pressure x-ray photoelectron spectroscopy (APXPS) unit for photocatalysis and high temperatures This is the combination of advanced characterization of a photocatalyst with real time measurements of its activity and selectivity under real working conditions. The new sample environment will be specifically suited for the characterization of photocatalytic processes such as hydrogen production, hydrogen-based reduction processes, as well as high temperature steel studies in reactive atmospheres.
Other related activities at CASR
In addition to research projects, there are numerous activities regarding hydrogen economy with steels, in which CASR’s members have also been involved. One is the Hydrogen Research Forum Finland, co-ordinating hydrogen-related academic research in Finland. An international hydrogen conference in 2024 is also planned. The activities of CASR are also firmly embedded in the Oulu Innovation Alliance, a regional strategic coalition aiming to promote innovations and sustainable growth both locally and globally, including a robust steel and mechanical engineering industry value chain.
The targets towards the transition to green steel are parallel to planned changes in steel production taking place in the near future, where CASR will have its role.
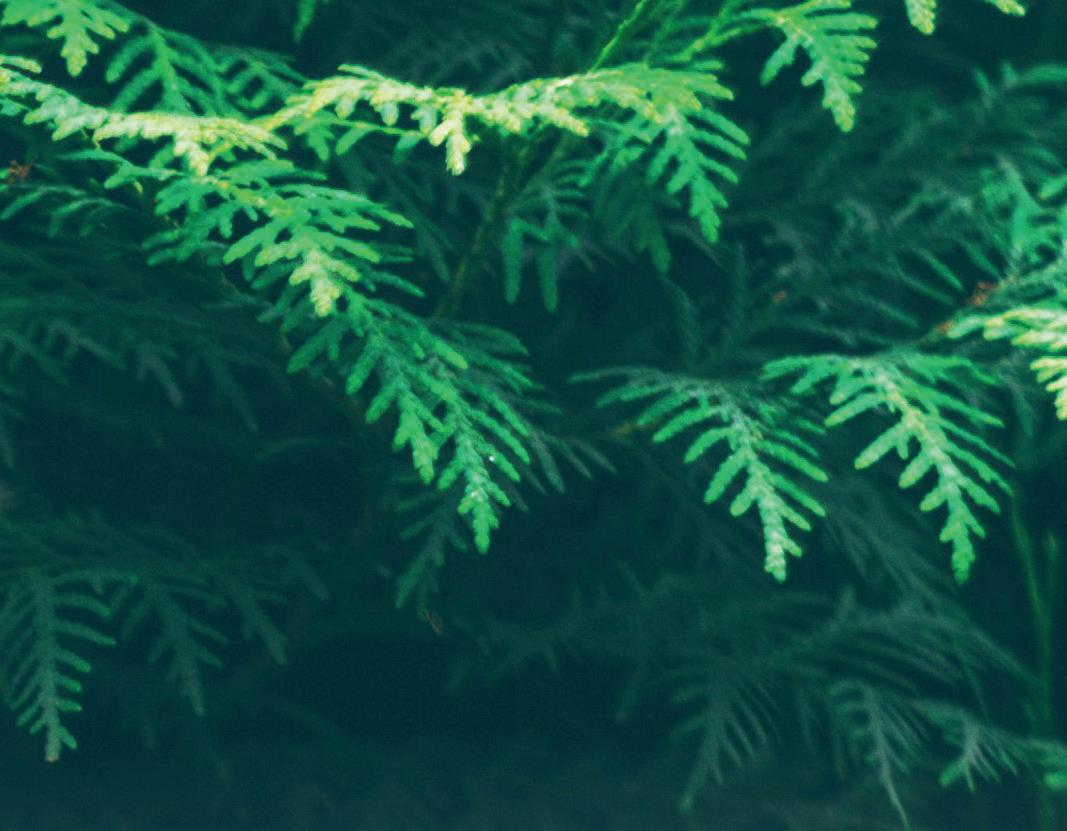
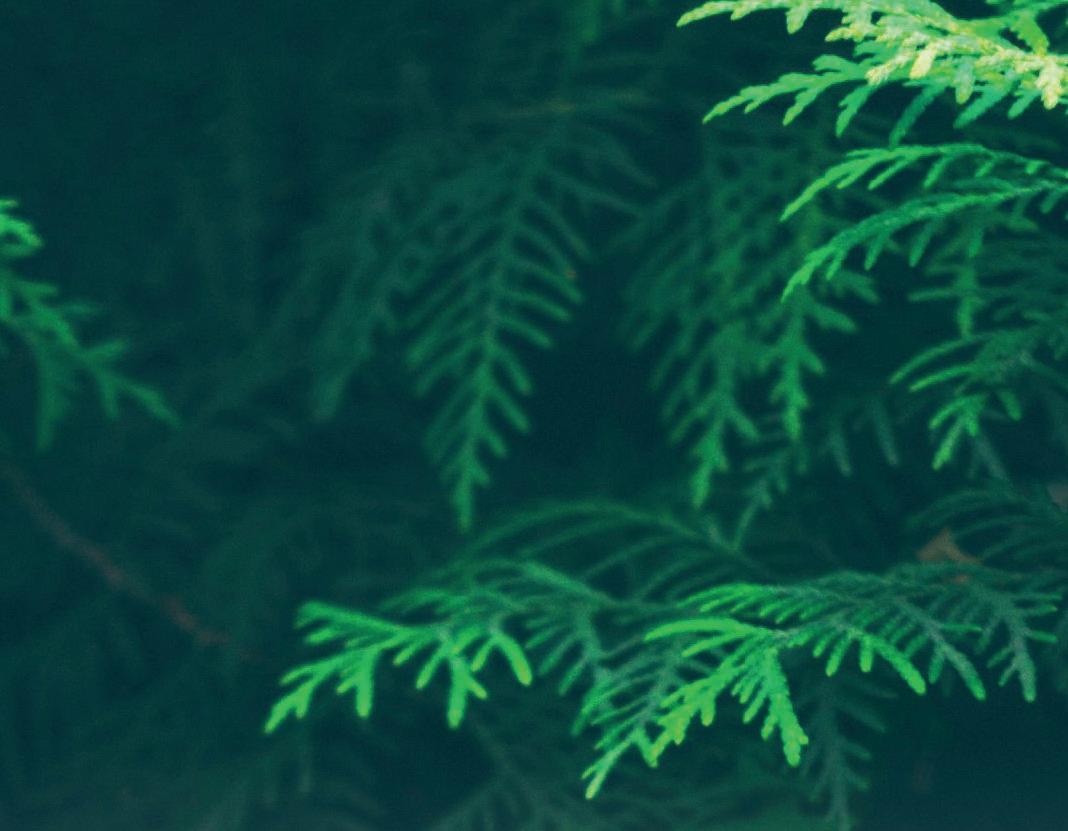
Conclusion


In 2021, SSAB announced an extensive research project to replace fossil fuels with renewable hydrogen in steelmaking, and publicized plans for a new steel production concept based on carbon-free technology in Sweden and Finland.
This would lead to a reduction of around 7% in the total CO2 emissions of Finland.
Further points include Nordic collaborations on steelmaking and a hydrogen economy, including Hybrit, a joint venture company aiming to have a completely fossil-free process for steel making by 2035, and BotH2nia, an international initiative for around the Gulf of Bothnia and the Baltic Sea.
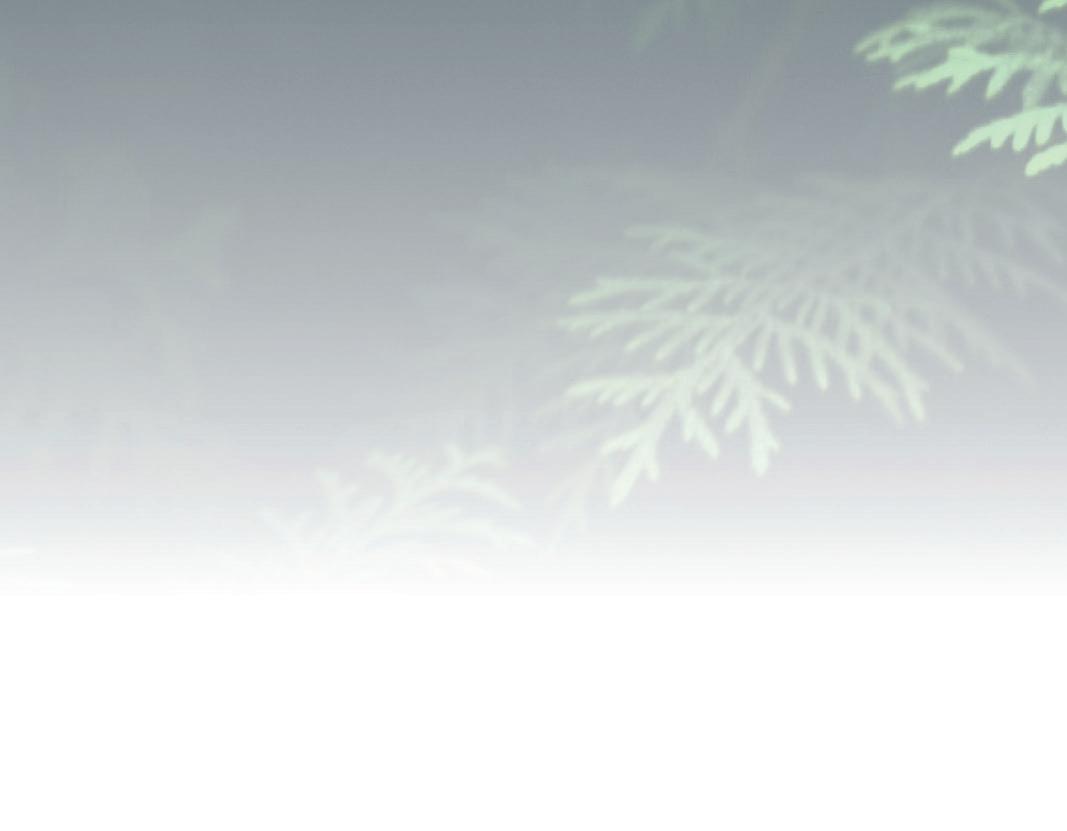

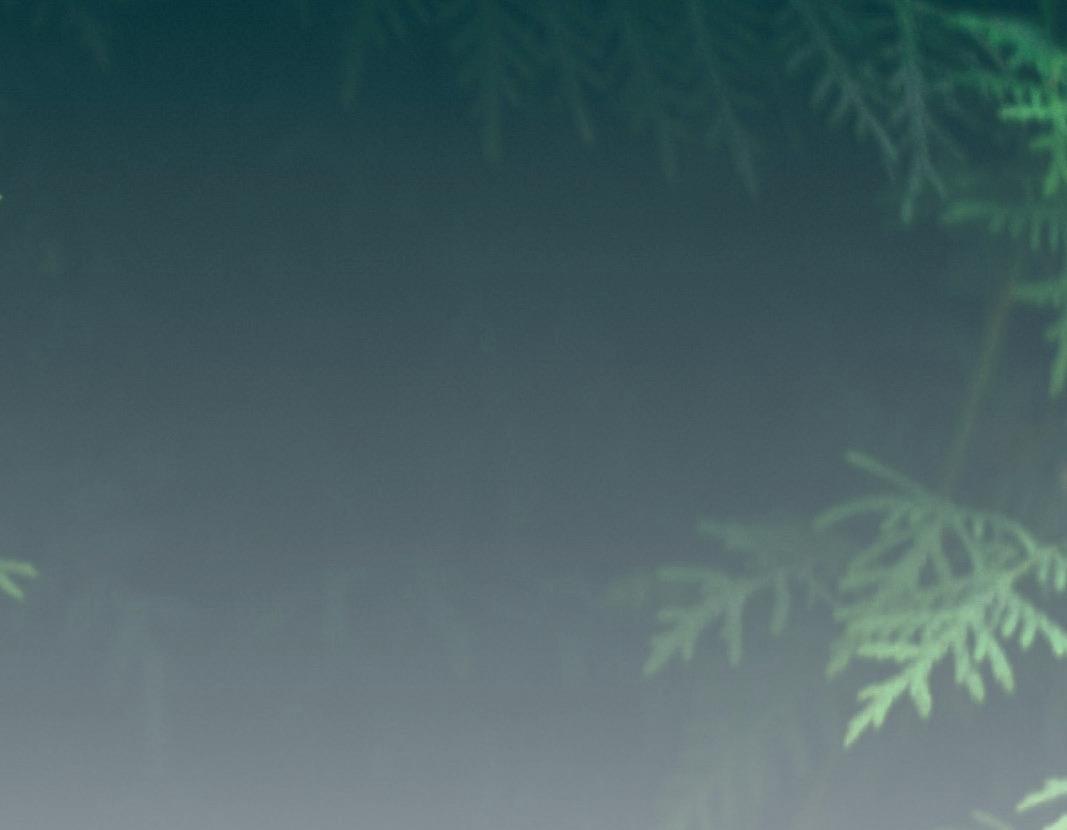
in Nickel-Based Plasmonic Core@Shell Hybrid Nanostructure for Photocatalytic Water Splitting, Applied Energy 322, 2022, 119461
Shi, X., Zhang, M., Wang, X., (...), Cao, W., Huttula, M., Nickel Nanoparticle-Activated MoS2 for Efficient Visible Light Photocatalytic Hydrogen building a large-scale hydrogen economy
Evolution, Nanoscale 14(24), 2022, 8601-8610
Heidari, A., Niknahad, N., Iljana, M., Fabritius, T., A Review on the Kinetics of Iron Ore Reduction by Hydrogen, Materials 14(24), 2021, 7540; https://doi.org/10.3390/ma14247540
References:
Singh, H., Alatarvas, T., Kistanov, A., Aravindh, S., (…), de Groot, F., Huttula, M., Cao, W., Fabritius, T., Unveiling Interactions of Non-Metallic



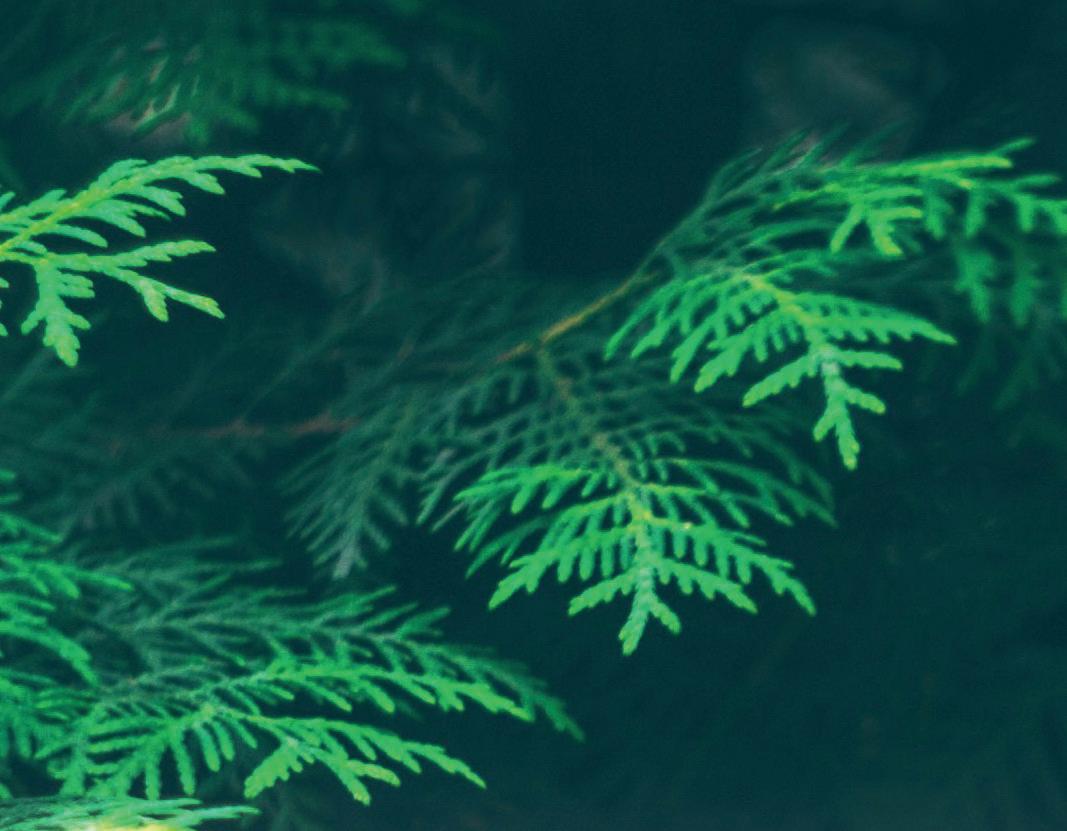
Inclusions within Advanced Ultra-High Strength Steel: A Spectro-Microscopic Determination and First-Principles Elucidation, Scripta Materialia 197, 2021, 113791. https://doi.org/10.1016/j. scriptamat.2021.113791
Wang, S., Kistanov, A., King, G., Ghosh, S., Singh, H., Pallaspuro, S., Rahemtulla, A., Somani, M., Kömi J, Cao, W., Huttula, M., In-situ Quantification and Density Functional Theory
Elucidation of Phase Transformation in Carbon Steel during Quenching and Partitioning, Acta Materialia 221, 2021, 117361. http://doi. org/10.1016/j.actamat.2021.117361
Talebi, P., Kistanov, A.A., Rani, E., (...), Huttula, M., Cao, W., Unveiling the Role of Carbonate
Latypova, R., Seppälä, O., Tun Nyo, T., (...), Kömi, J., Pallaspuro, S., Influence of Prior Austenite Grain Structure on Hydrogen-induced Fracture in As-quenched Martensitic Steels, Engineering Fracture Mechanics 281, 2023, 109090
Latypova, R., Seppälä, O., Nyo, T.T., Kauppi, T., Pallaspuro, S., Mehtonen, S., Hänninen, H., Kömi, J., Hydrogen-Induced Cracking of 500 HBW Steels Studied Using a Novel TuningFork Test with Integrated Loadcell System, Corrosion 76(10), 2020, 917-966. https://doi. org/10.5006/3592
Abdelrahim A., Nguyen H., Omran M., Kinnunen P., Iljana M., Illikainen M., Fabritius T., Development of Cold-Bonded Briquettes using By-Product-Based Ettringite Bindere from Ladle Slag, Journal of Sustainable Metallurgy 8(1), 2022, 468-487, DOI: 10.1007/s40831-02200511-1