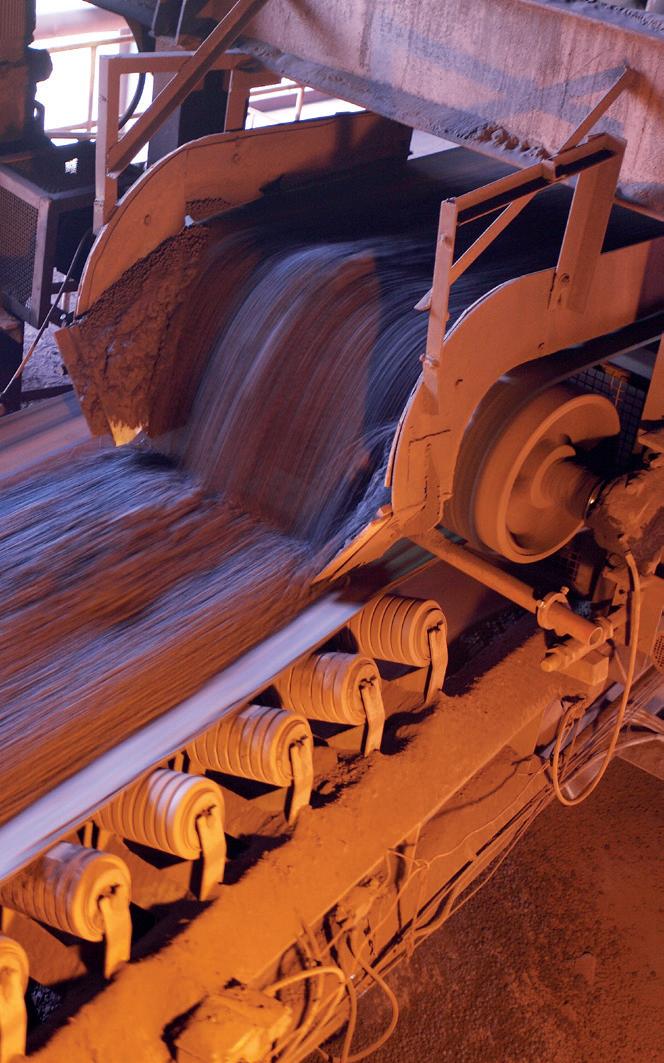
6 minute read
and technology
Making smart decisions around automation
Like mining, steelmaking is traditionally a conservative, risk-averse sector that relies on systems and processes that have been established over many decades. However, while perennial challenges such as optimizing production and reducing raw material costs remain, the landscape has changed; steel operators face a host of new requirements around environmental certification, energy costs, plant and furnace design, and the implementation of advanced process control (APC) and digital technologies.
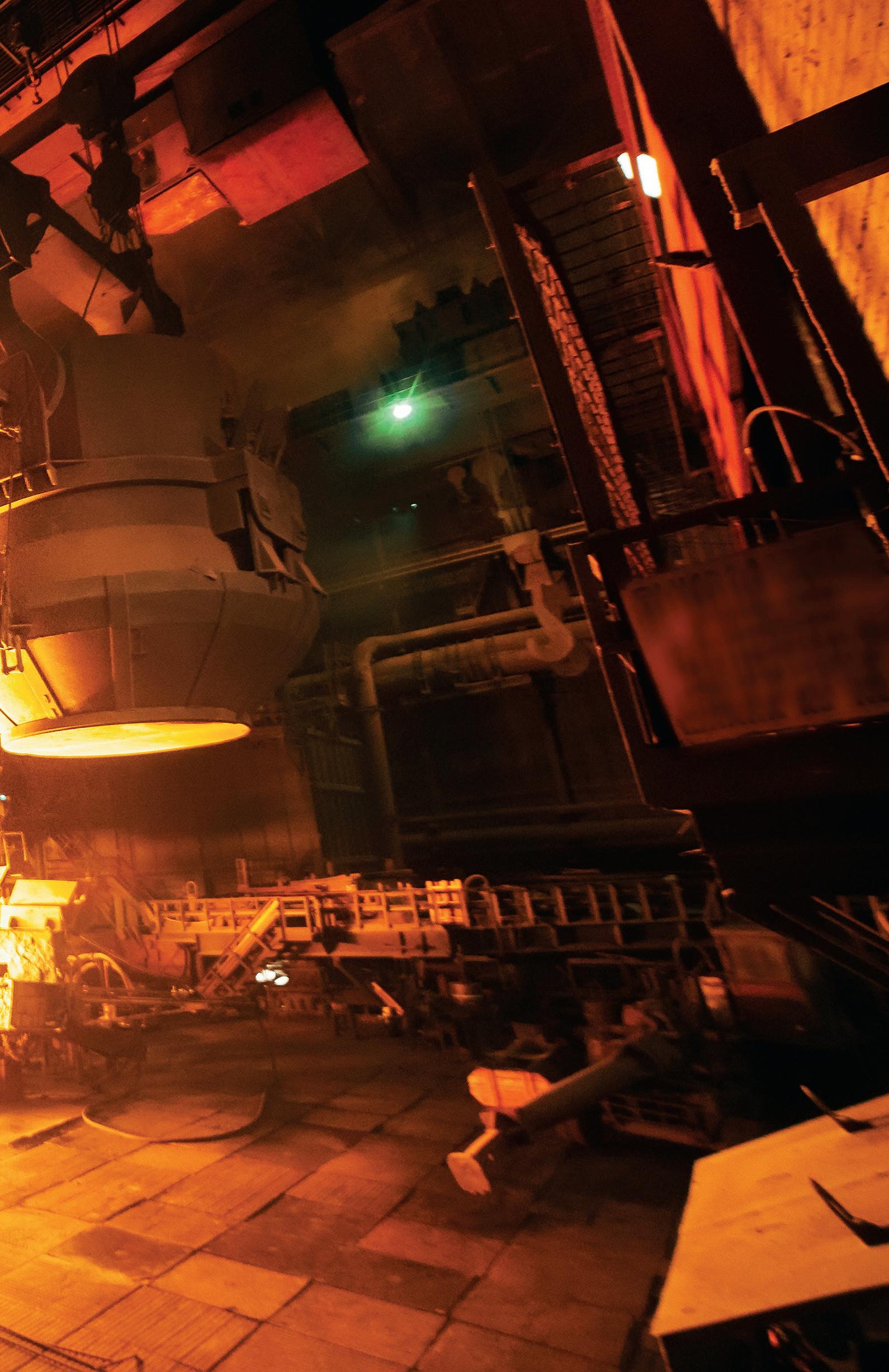
Steel melt shops, for instance, are under increasing pressure to produce the same tonnage while reducing operating expenditure (OPEX). This can be achieved by fingerprinting the operation to identify ‘dead time’ when processes are not being optimized, and then deploying digital solutions that eliminate equipment and process bottlenecks, improve throughput, and reduce energy usage and carbon footprint.
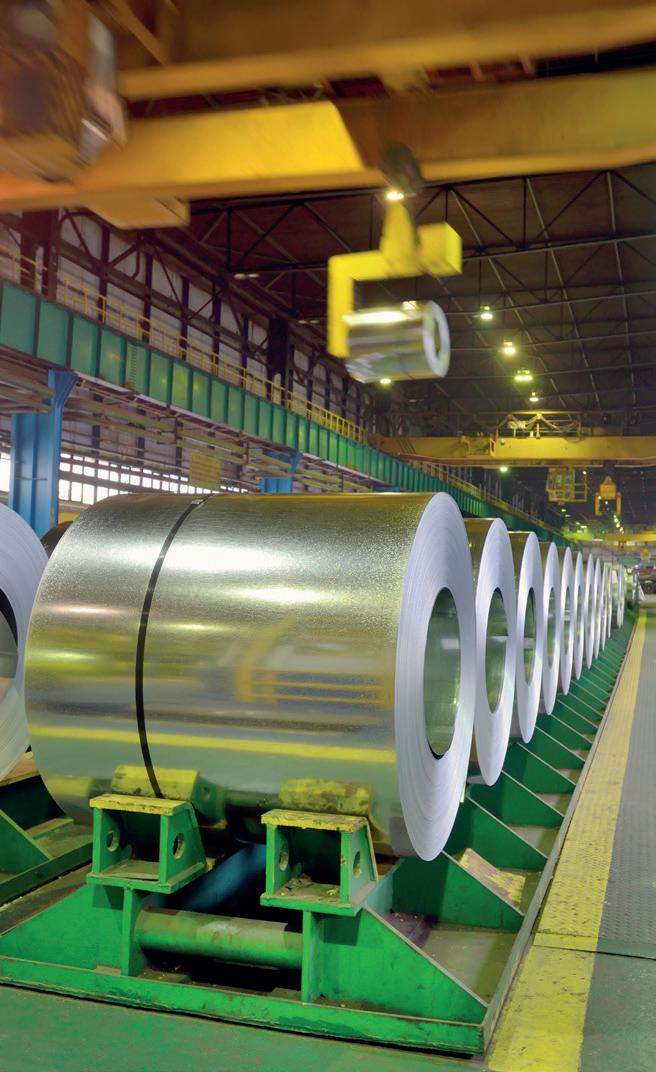
Such environments are typically characterized by high temperatures and batch processing, which means installing sensors throughout the factory to gather performance data can be a challenge.
on developing technology solutions that reduce energy consumption, costs and waste, while also formulating a strategic digitalization and decarbonization road map ahead of the impending hydrogen transition.
In this article, we discuss why collaborating with a partner with an indepth understanding of metals processes is key to making this happen, why technology must be supported by the transformation of processes and people, and take a closer look at solutions provided by specialist technology providers like ABB around energy recovery, reduction, substitution, management, and optimization.
ABB AbilityTM Smart Melt Shop integrates more pragmatic, customized data solutions on top of generic internet of things (IoT) sensors and optimization apps, thus enabling the move towards a fully connected, autonomous and optimized steel melt shop. It does this by connecting operations with both ladle tracking and crane scheduling based on data including thermal modelling1. The industry-first smart factory solution has been deployed at JSW Steel’s Dolvi Works plant in India, boosting profits by an estimated $2m through 4% higher casting speeds and additional output of 24kt a year2
Meanwhile, considerable savings can be made regarding machines and raw material. Sandvik, SSAB, Ovako, University of Gävle and ABB are co-developing methods for predictive maintenance in an example of digital and analytics solutions maturing for plant reliability and efficiency.
Another of our steel customers is working with ABB and Microsoft on energy optimization, and to improve reliability by 5%, through the use of digital technologies, so there is real evidence that the industry is engaging with the digital/automation and hydrogen transition, as well as an awareness from manufacturers that they must start laying the groundwork now to future-proof their operations.
ABB is committed to improving efficiency and reducing the carbon footprint of its industrial products at every stage of the production chain. This holistic view digitalization and automation, technology solutions must be supported by the transformation of processes and people. What do we mean by this? Well, when
Towards the circular economy
As we mentioned at the outset, partnering with a technology provider with deep domain expertise in metals can help prepare steel manufacturers for the hydrogen transition, while simultaneously ensuring they optimize production and maintain a critical competitive edge in the here and now.
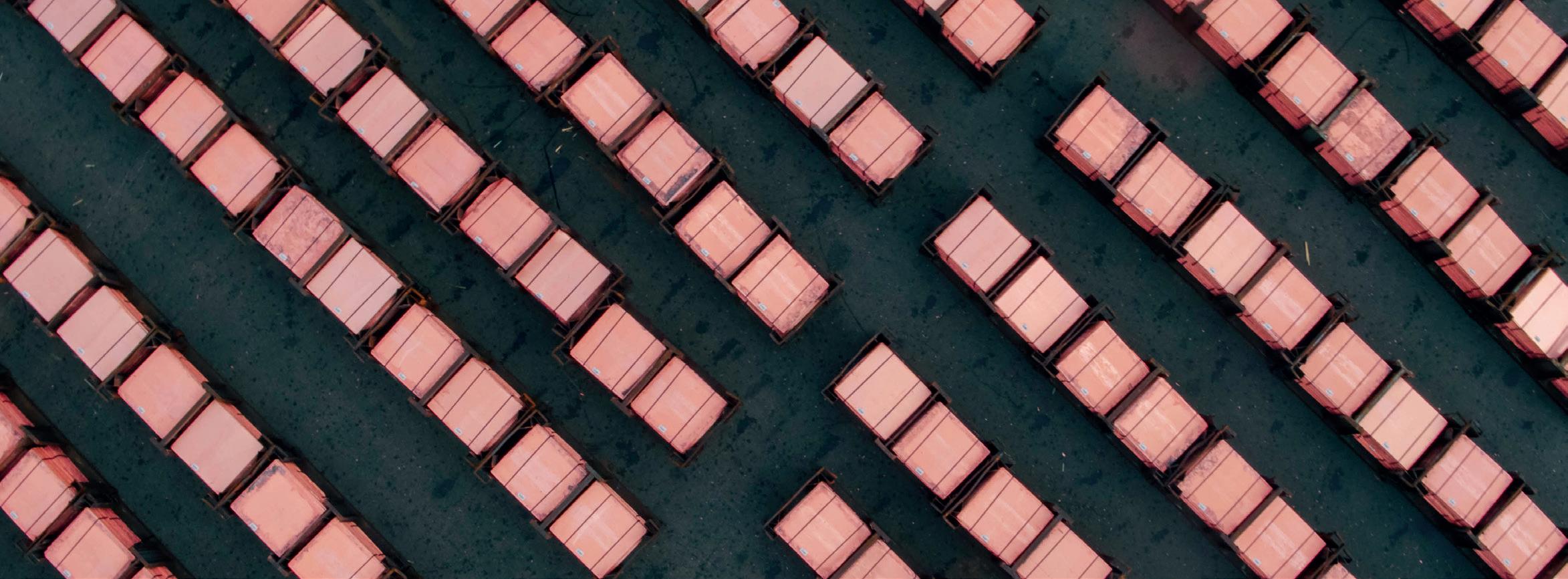
Consteerrer® was developed as part of a collaborative project between ABB and Tenova. Based on ABB’s ArcSave® technology, this electromagnetic stirring (EMS) solution for continuously charging electric arc furnace systems is already paying dividends at Italian steelmaker Acciaieria Arvedi’s record-breaking melting unit (furnace tapping size 300Mt). EMS has boosted productivity by 5%, reduced electrical energy consumption by 3.6%, and significantly improved metallic charge yield3 extends to circularity; for example, recycling copper, aluminium and steel offers energy savings of 75–95% compared with virgin production. To this end, ABB is using Boliden’s certified recycled and lowcarbon copper in its electric motors and electromagnetic stirring technologies. The ultimate goal? To improve performance and product quality in electric arc furnaces, reduce greenhouse gas emissions and drive the transition to a more circular economy.
Solutions such as these and furnace optimization control systems that improve reheat furnace control to reduce heat losses and optimize the energy consumption, as well as an advanced process control that communicates with installed level one distributed control system (DCS) controllers, are designed to help steelmakers meet the dual challenges of maximizing yields and hitting sustainability KPIs. Combining them with ABB’s Energy Management System4 offers operators even more value by enabling them to manage energy demand, supply and price volatility, as well as reduce costs by as much as 15%.
That road is a long and winding one, however. Let’s take something as fundamental as the blast furnace as an example. Many manufacturers, particularly those located outside of Europe, are still building and installing blast furnaces powered by coal as opposed to newer electric arc furnaces.
These blast furnaces will likely be in use until around 2080. Stringent environmental regulations in the EU are welcome, but if steelmakers in Europe import steel from other countries with less strict rules while being penalised for their emissions at home, any benefits in terms of circularity are lost. So, for the circularity concept to really work, governments must also work to level the playing field when it comes to legislation, import and export rules, and knowledgesharing between countries.
A question of culture
Earlier we mentioned that steelmaking is a conservative industry, and that for customers to really reap the benefits of we talk about the digital transformation, rather than just frame that conversation around futuristic technology, we should also talk about how it is a commitment to continuous improvement and perpetual change.
The hydrogen revolution will inevitably require new skillsets to allow personnel to make sense of as well as augment technological innovations such as IoT, advanced process control and artificial intelligence (AI). Successful change management is, therefore, key to upskilling and preparing the workforce for new models and processes, not to mention attracting and retaining a new generation of digitally literate talent for whom sustainability is a priority.
Encouragingly, we have detected an identifiable shift in the industry from a digital and sustainability perspective in the past few years, with manufacturers really recognizing the benefits of innovations in process control solutions and products like high efficiency motors. Many companies now have dedicated and independent digital teams with a mandate and budget to invest and develop digital technologies. Maybe a decade ago, these issues were only being engaged with at leadership level; now, we see them trickling down to the lower levels of businesses as well.
It is not just multinationals such as ArcelorMittal and Tata Steel that are partnering with start-ups and established vendors such as ABB; the smaller players in steel, of which there are countless numbers, of course, are also becoming much less resistant to change. Instead of settling for just small energy efficiency changes, for example, they are beginning to understand the power of new technologies to not only improve their production, but also emissions and regulatory compliance.
Collaboration on the road to green steel
At ABB, we realise that our environmental responsibilities extend beyond developing technology solutions that help our customers. With our 2030 sustainability strategy, we are actively enabling a lowcarbon society as well as working with our customers and suppliers to implement sustainable practices across our value chain and the lifecycle of our products and solutions. As a company, we also place great importance on the power of industrywide knowledge-sharing and collaboration5 Three ongoing projects illustrate this best in the context of green steel production and the hydrogen revolution. In Sweden, our electrification and automation solutions are part of HYBRIT (Hydrogen Breakthrough Ironmaking Technology), the world’s first large-scale, fossil-free steelmaking plant. In the realm of carbon capture, ABB has equipped a team at Imperial College London with the latest control technology and control room equipment to provide students with the skills they need to run tomorrow’s industrial processes, including steelmaking. In France, the company is supplying a control solution for automation of Lhyfe’s first ever green hydrogen clean energy production facility. Lhyfe designs, installs and operates hydrogen production units.
Conclusion
With energy costs and global demand for steel increasing in tandem, manufacturers are faced with the challenge of maintaining steel production while simultaneously preparing for the impending industry transition from using fossil fuels (coal) for both fuels and feedstock to using hydrogen.
Digital, automation and electrification technologies are key to achieving these goals, offering unprecedented visualization, control, and optimization of steelmaking processes across the entire value chain. However, they should not be viewed as a silver bullet.

Collaboration, and a willingness to invest meaningfully in new innovative working models and practices, as well as in human capital to ensure that as the current generation retires, new, forward-thinking employees take their place.
By addressing company culture, replacing entrenched ideas with innovative thinking, and deploying the latest emissions-saving technologies, the steel industry can continue to provide the materials that are so vital to modern life – and contribute to a cleaner, safer world for future generations.�
Sources:
1. ‘The steel melt shop is getting smarter’ – Tarun Mathur, Steel Times International, 2021
2. https://new.abb.com/news/detail/79684/ abb-completes-melt-shop-digitalizationproject-with-indias-leading-steel-companyboosting-productivity-and-profitability
3. https://new.abb.com/news/ detail/90023/abb-and-tenova-receivefinal-acceptance-for-innovative-chargingmelting-and-electromagnetic-stirringsolution-on-a-large-electric-arc-furnaceeaf#:~:text=Leading%20metals%20 industry%20suppliers%20ABB,the%20 world’s%20highest%2Dyielding%20EAF.

4. https://new.abb.com/industrial-software/ sustainability/energy-management-systemenms
5. https://global.abb/group/en/sustainability/ sustainability-strategy-2030