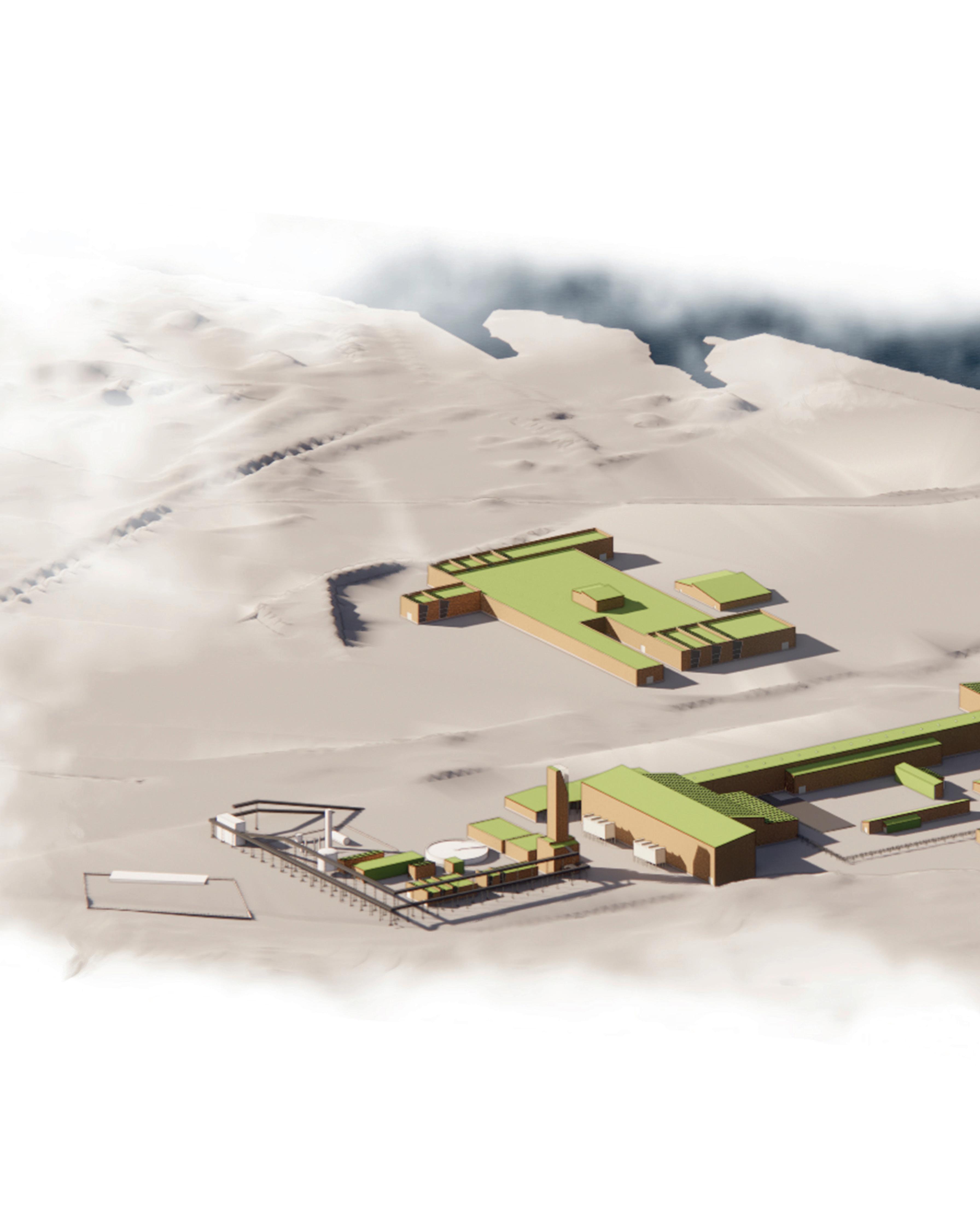
5 minute read
Greening the value chain
SEVERAL steel-producing companies are active in the Nordic region, which is known for its green technology, innovation, and fossil-free energy. Blastr Green Steel is one of them. Established in 2021, it aims to become an integrated producer of ultra-low CO2 steel, leveraging Nordic advantages, and is estimated to grow into one of the largest industry start-ups in the Nordic region.
Blastr Green Steel´s vision is to decarbonize the entire steel value chain. Its concept is based on locating its activities adjacent to attractive European markets, accessing raw materials locally, and utilizing ice-free ports with efficient and green logistics. With this integrated approach, the company aims to produce steel with ~90% lower CO2 emissions across scopes one to three than average steel producers today. Emissions will be reduced throughout the entire value chain and in areas such as logistics, heat recovery, and circular economy in addition to the use of hydrogen and fossil-free energy in the production processes. By developing local, sustainable, and scalable value chains for ultra-low CO2 steel production, the company is setting out to challenge the status quo of the steel industry.
Inkoo – an ideal location for ultra-low CO2 steel production
Finland offers an ideal environment for energy-intensive green steel production, with abundant renewable energy resources, a robust infrastructure, and a commitment to sustainability. Blastr evaluated several sites for its steel plant in Northern Norway and Finland, and ended up selecting Inkoo, located approximately 50 kilometres southwest of Helsinki, the capital of Finland. The country offers several benefits for developing green industries: it has abundant fossil-free energy, supportive and predictable operating conditions, and a highly qualified workforce. Furthermore, Finland´s ambitious political energy transition agenda facilitates stable and competitive prices for its fossil-free energy, providing a cost advantage for steel and hydrogen production.
Blastr Green Steel, a Norwegian steelmaker of the future, discusses plans to establish a pellet plant in Gildeskål, Norway and a steel plant with an integrated hydrogen production facility in Inkoo, Finland.

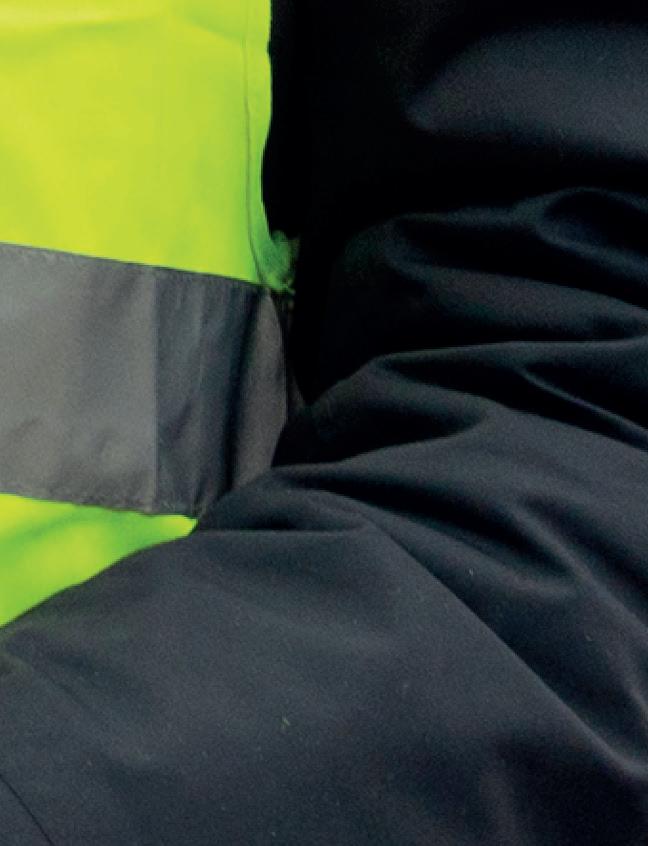
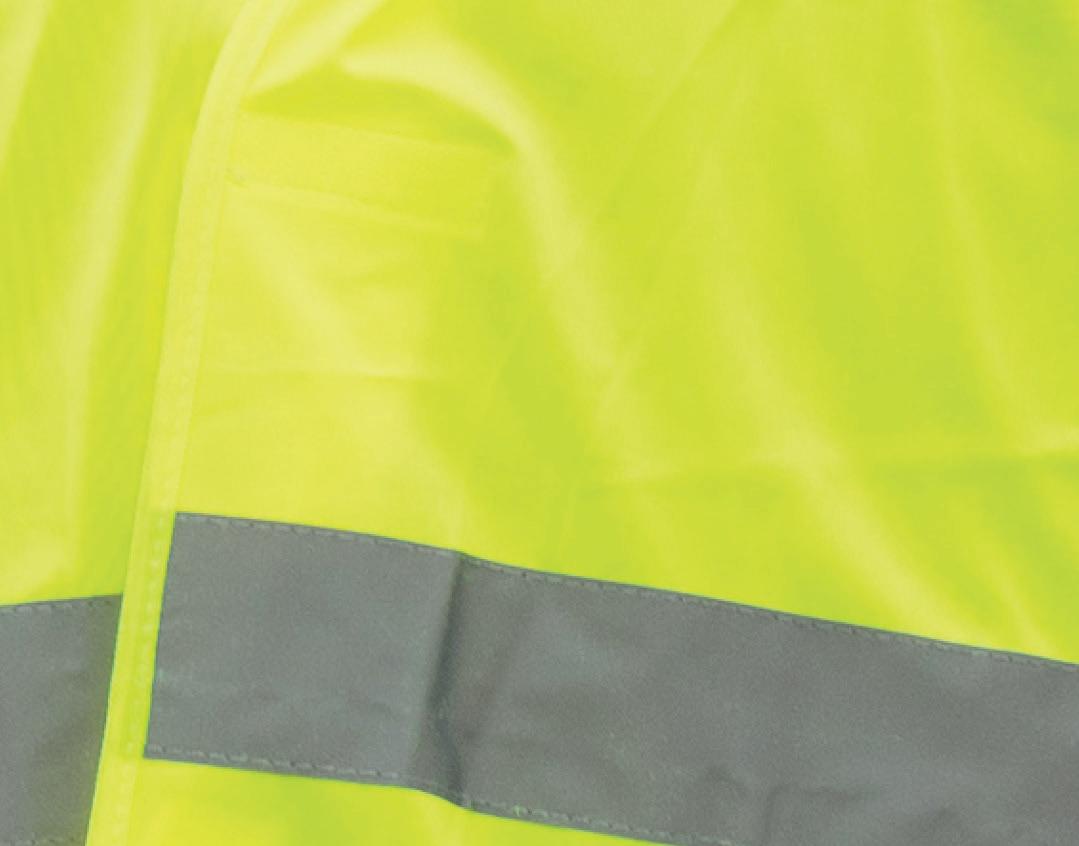
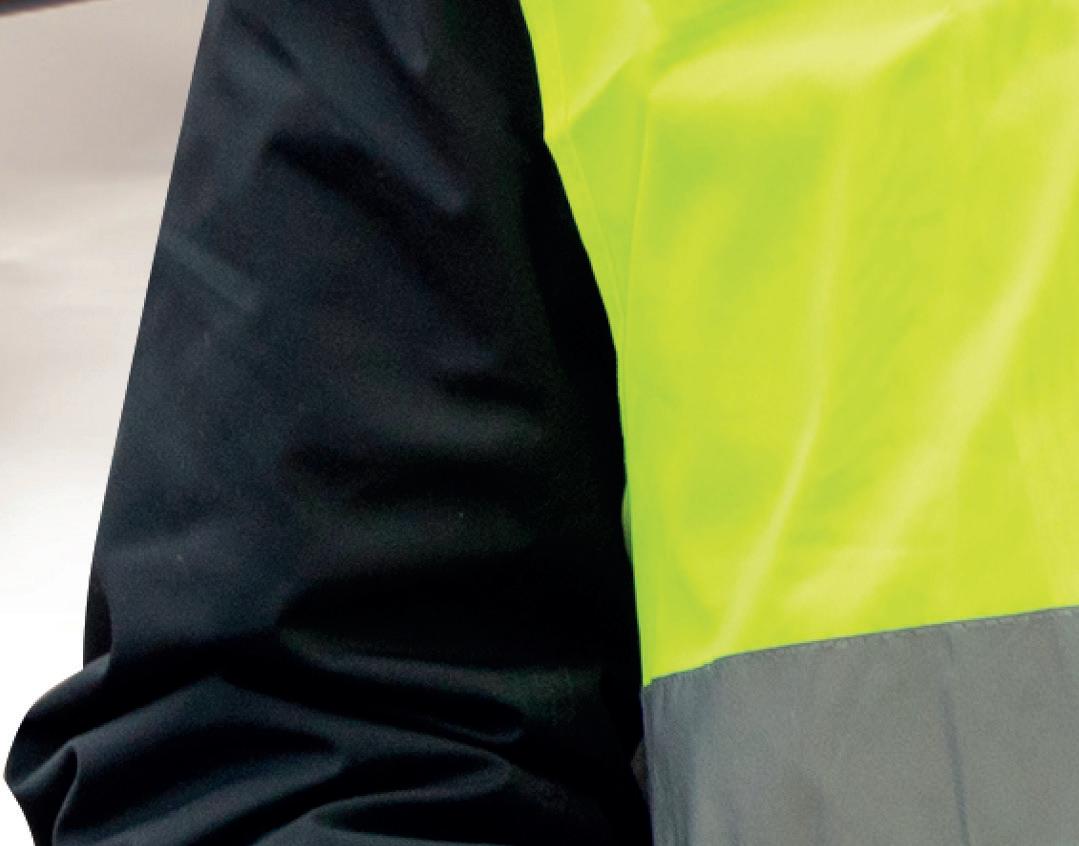
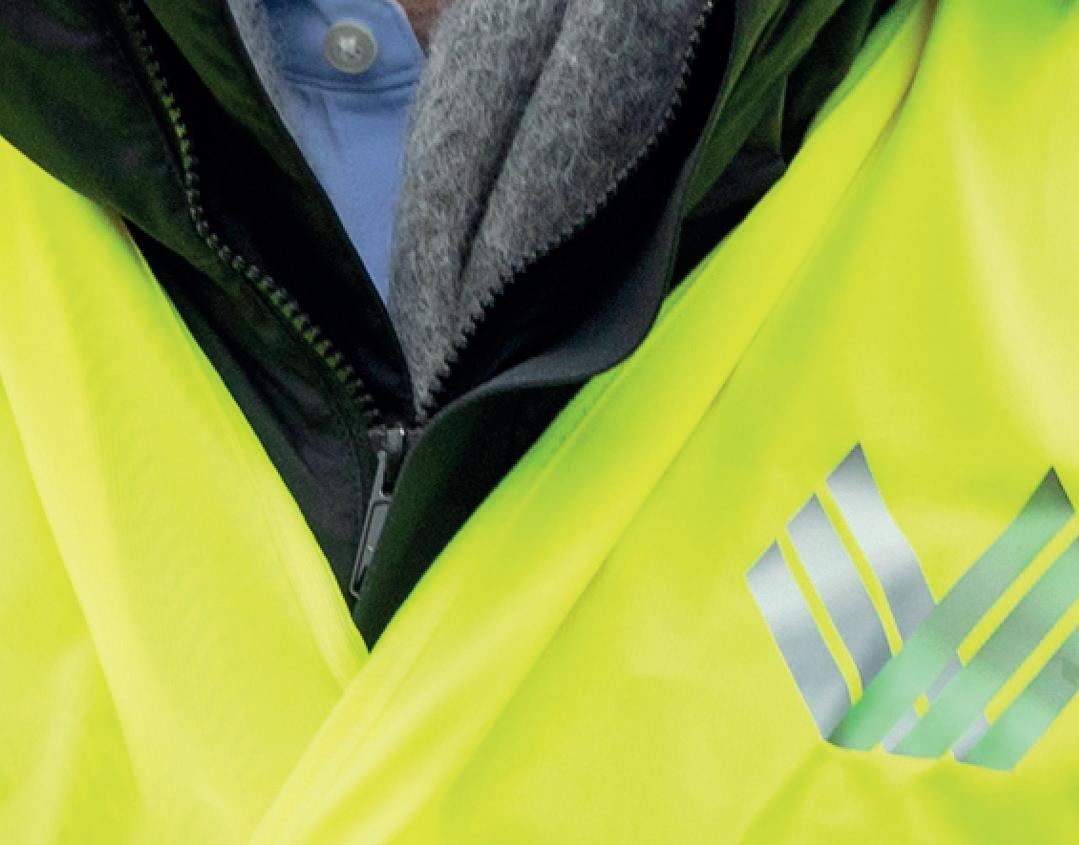
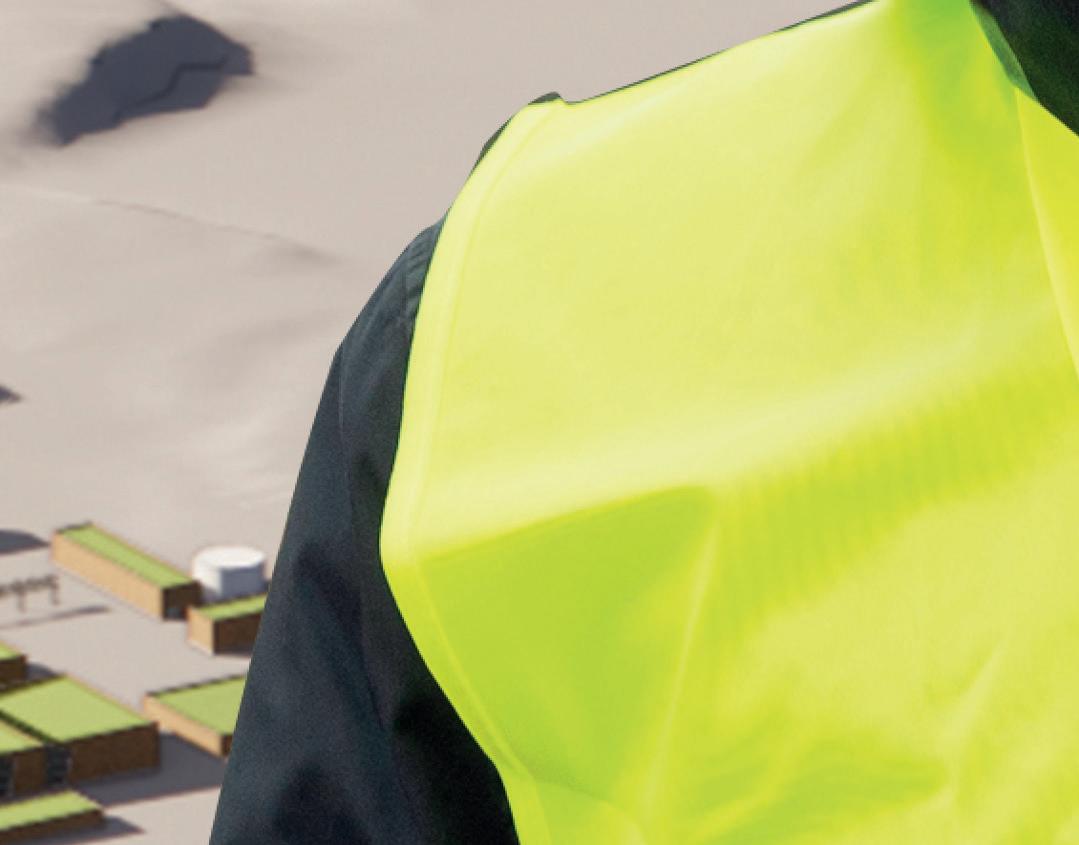
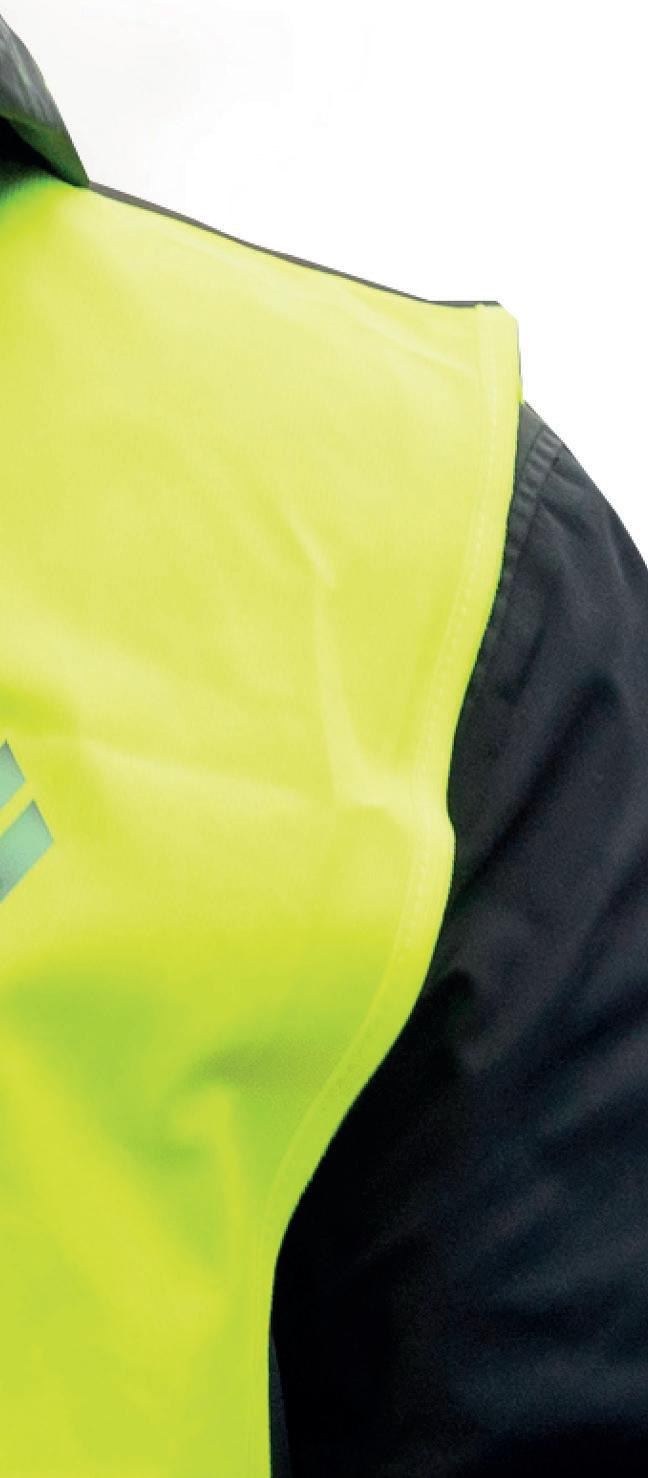
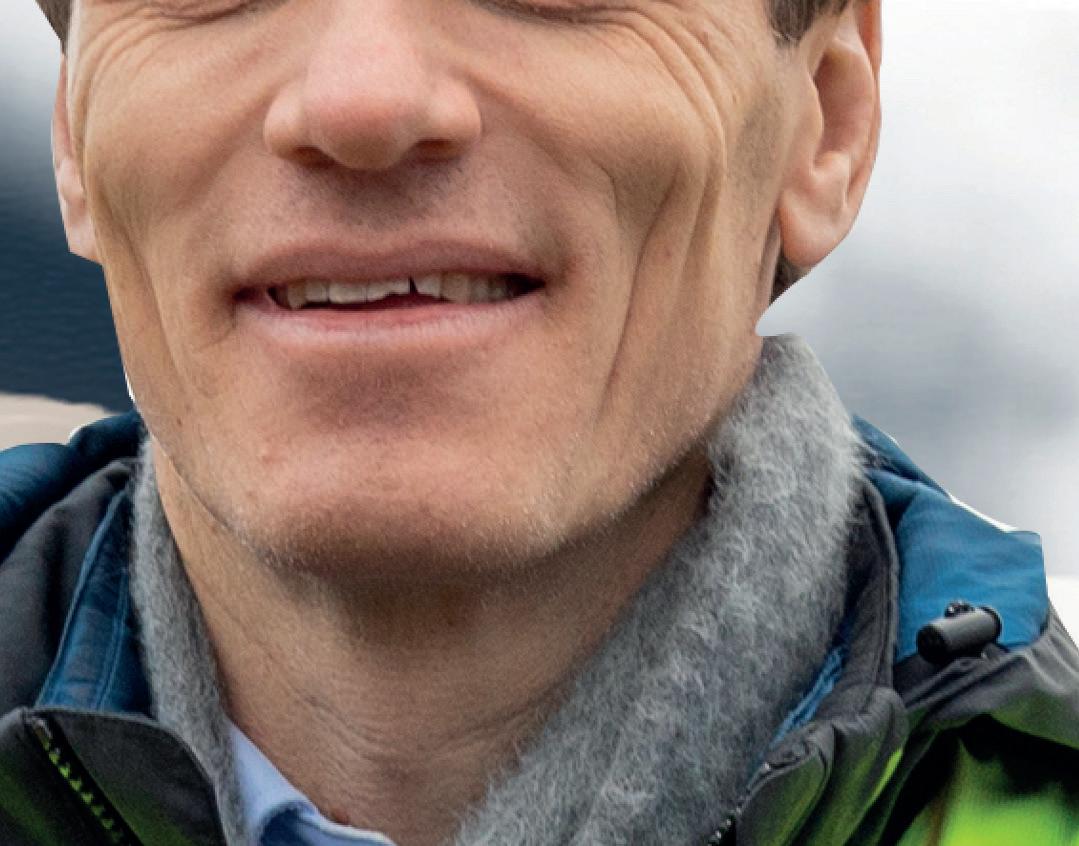

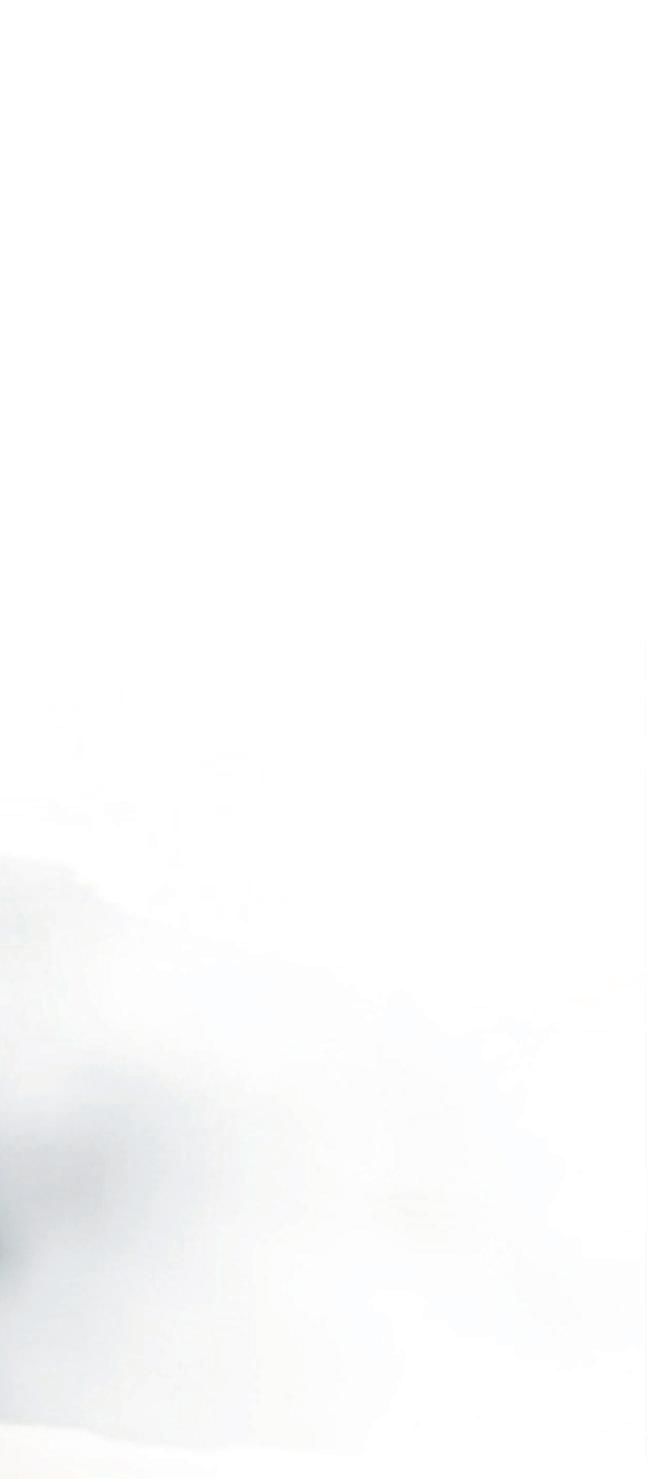


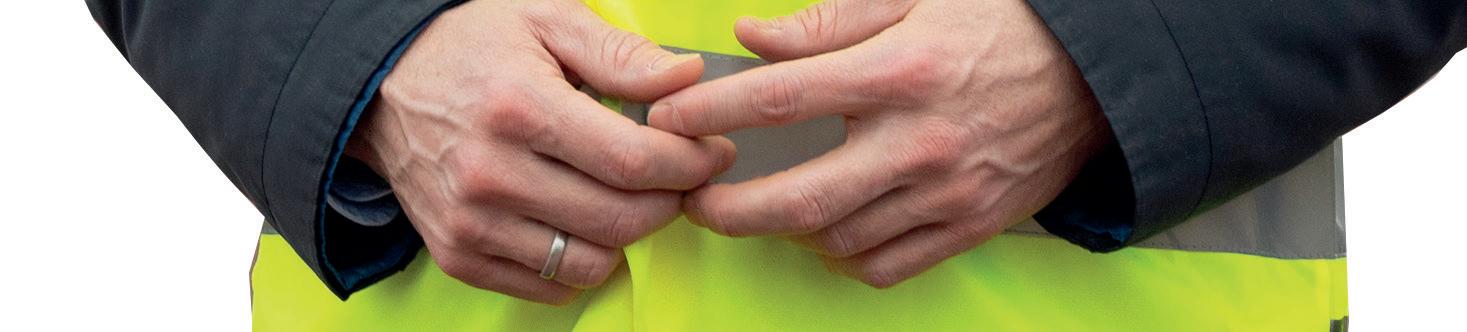

The Inkoo site is well-suited for a steel plant. The southwest region of Finland has a long industrial history, also in steel production. Closeness to the capital with its highly skilled labour force and strong transport connections enables attracting the needed 1,200 employees for the steel plant. Blastr´s €4 billion investment will bring not only direct but also significant indirect opportunities for employees and businesses, and economic effects for the municipality and the region.
The brownfield area planned for the steel plant previously hosted a now dismantled coal-fired power plant. The site has strong access to Finland’s main energy grid with direct connection to several 400 kV and 110 kV power lines and a pre-existing high- voltage substation at the site´s boundary. The deep ice-free port enables efficient, low-carbon logistics all-year round, as well as smooth international, as well as regional access to raw materials, such as recycled scrap metal and direct reduction pellets to be used in the process. The growing European market for Blastr’s finished ultra-low-CO2 steel products is also wellaccessible.
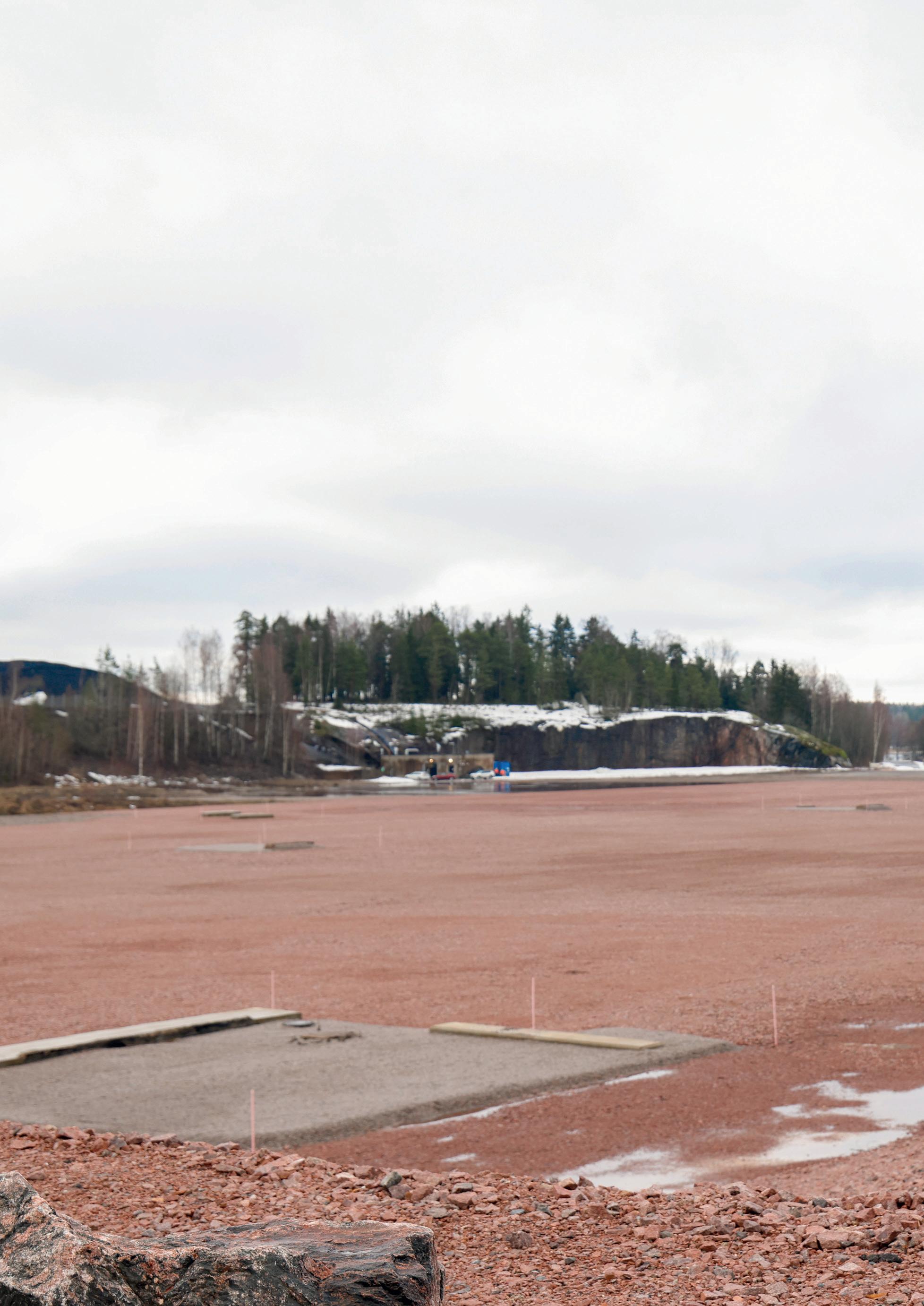
The Inkoo site is currently owned by Nordic energy company Fortum, with which Blastr is developing a strategic partnership for site development and energy sourcing. In addition, Blastr’s ambition is to secure a significant share of its own power needs from directly or indirectly owned wind parks, advancing clean energy production in Finland.

Steel production based on fossil-free hydrogen Blastr will employ the so-called mini-mill concept with state-of-the-art technologies across all key areas. The steel production process will use fossil-free hydrogen instead of coal. An integrated hydrogen facility to be linked to the steel plant will ensure a constant supply of hydrogen. Large-scale electrolyzers will produce hydrogen at scale with a capacity exceeding 500 MW.
The hydrogen-based direct reduction iron (DRI) plant will have a capacity matching the largest reference projects to secure economies of scale. Hot DRI will be transported to the electric arc furnace (EAF) melt shop, ensuring the lowest possible electricity consumption. The process route includes a ladle furnace and degassing station before feeding the alloyed steel to a direct casting and hot rolling mill, fully avoiding the use of fossil energy for slab reheating to minimize CO2 emissions and energy consumption. This line can produce hot-rolled coils thinner than conventional mills, which eliminates the need for cold rolling for part of the product portfolio.
Part of the hot rolled coils will be further processed in the downstream processing lines providing additional thickness reduction, surface treatment, and protective coating to meet the most demanding end-product requirements. Automation and digitization will be leveraged across all processes to ensure an end-to-end optimization of the plant.
The steel plant will produce 2.5Mt of hot-and cold-rolled coils, and hot-dipped galvanized coils made from self-produced high-quality direct reduction pellets and recycled scrap steel from Northern Europe. The product offering will be targeted to European customers, for example, in the automotive and construction sectors seeking sustainable products to support their ambitious CO2 reduction goals.
Project development progressing at full speed
The steel plant project is progressing at full speed on many fronts. The land use planning of the Inkoo site is currently ongoing, as well as the Environmental Impact Assessment. These are prerequisites for acquiring the necessary permits for plant construction and operations. Also, the pre-feasibility study is ongoing to deepen the engineering and support the permitting process with necessary technical input.
Blastr is in the process of building up its organizational capabilities and has already secured strong steel industry expertise on the company and its Board. The start-up is currently owned and funded by Vanir Green Industries, a Nordic investment company that invests in, develops, and scales green businesses that are needed to accelerate the energy transition. Blastr has recently initiated its Series A financing with the aim of attracting strategic and financial investors. The target is to close the first financing round in late 2023 to secure funding to complete the engineering and feasibility studies for the plants, as well as the organizational build-up. In 2024, the project will move into a feasibility study and permitting phase. The Series B financing is aimed to be closed towards the end of 2024. The final investment decision is planned to be taken in 2025, around the time of receiving the permit decisions. The production is planned to start commissioning in 2027, with the ramp-up of the integrated value chain to full capacity taking pkace between 20282030.
Raw material supply secured through own production
A key aspect in ensuring a high quality of the raw material will be the self-owned direct reduction pellet plant, currently planned to be located in Gildeskål municipality in Northern Norway. Blastr is developing a partnership with Cargill for sourcing iron ore feedstock for the pellet plant.
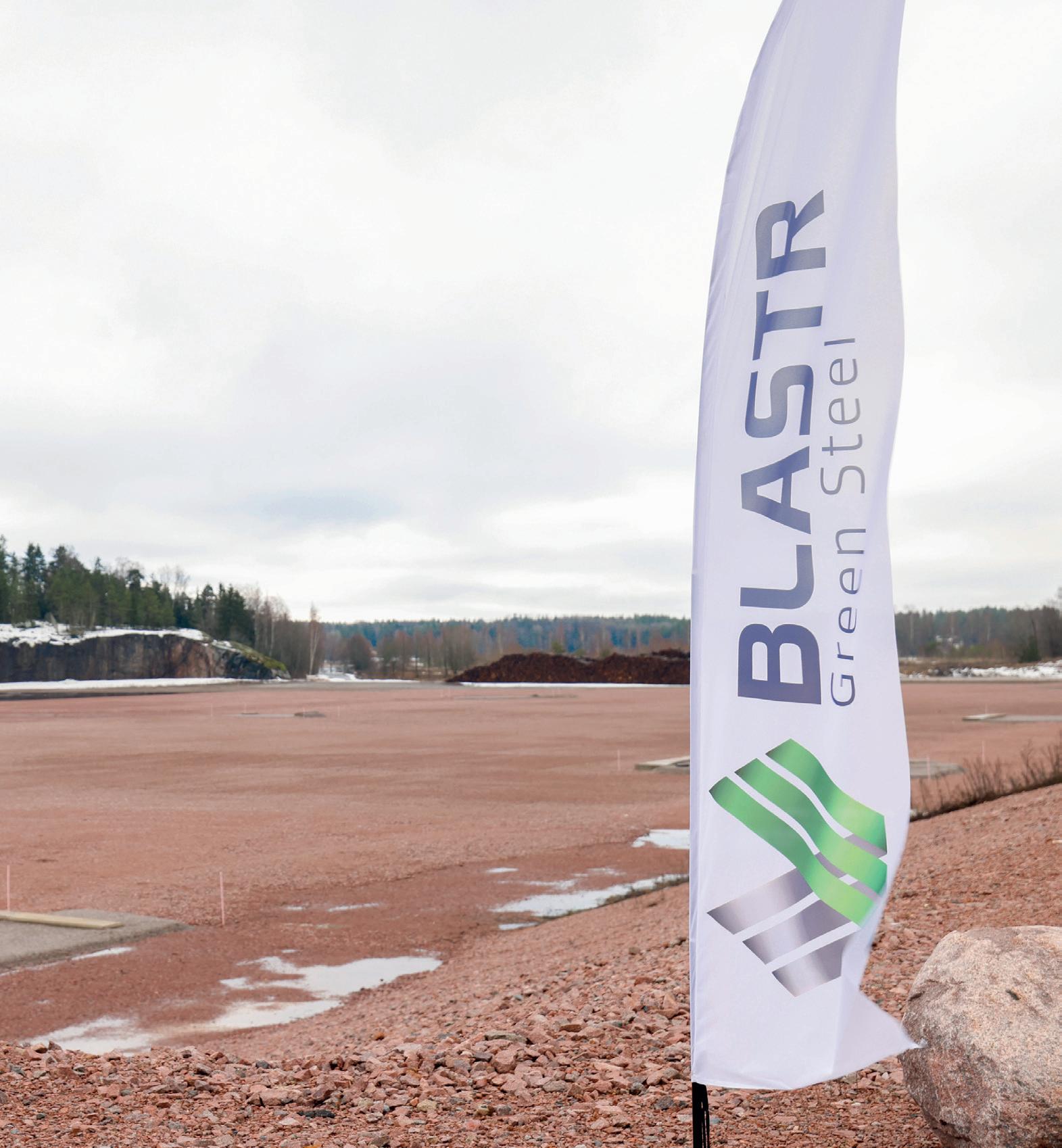
The coastal location of Gildeskål provides an ice-free harbour with access to the seaborne iron ore market. In the pellet plant, Blastr will convert the iron ore pellet feed into high-quality direct reduction pellets, producing 6Mt of raw material annually. Part of this volume will be feedstock for Blastr’s ultra-low CO2 steel production at Inkoo, and the rest will be sold on the growing world market for direct reduction pellets.
The pellet plant will utilize hydropower from the Norwegian grid. The plant will require a more than €1 billion investment and will offer approximately 120 direct jobs when operational. Blastr is expecting to make a final investment decision on the pellet plant in 2025, subject to relevant permits and agreements being in place by then. The plant is planned to start production in 2027-2028.
Future scaling to additional steel plants
Blastr’s long-term plan is to set up additional steel plants, utilizing the feedstock capacity of its own pellet plant. The company believes that its vision will be reached by working closely with different industry players and customers to find solutions to decarbonize steel production. This will be accomplished through developing strong, long-term strategic partnerships along the value chain. All in all, it´s all about taking a quicker leap together to a more sustainable future. �