
5 minute read
The role of charcoal in ironmaking
cannot be determined. The sulphur content of the slag was 1.2% suggesting the iron would be unsuitable for refining to bar iron in the charcoal hearths in use at this time, the major market for blast furnace iron. According to Dudley, his trials were terminated by rioters and lawsuits and his patent was not renewed in 1660. Nearly 50 years later, in 1709, Abraham Derby Ist was the first to make a commercial success of smelting with coal which he initially converted to coke. Having experience in using low sulphur coal from an earlier role as a malt maker, he recognised the value of the low sulphur Shropshire coals (0.500.55% S) taken from the upper strata. Also, his need was for an iron for casting to make thin-walled pots, previously made in expensive brass, and his high phosphorus iron produced a fluid metal ideal for such thin-walled casting which solidified to the more ductile grey iron.
A modest blast furnace producing 100 tonnes a year required about 36 hectares of woodland to supply sufficient charcoal.

The demand from refining forges was also high; while the finery hearth had to use charcoal, it was possible to use coal in the chafery hearth where the refined ‘loup’ of iron was reheated for consolidation under the hammer. In the chafery, the lower surface area of the metal reduced the risk of sulphur pick-up. Later, the Lancashire Hearth, popular in Sweden and for the tinplate industry in South Wales, provided an enclosed ‘oven’ for refining pig iron, making more efficient use of the charcoal required. It was not until the principle of the reverberatory furnace arrived with John Wood in 1761, that coal could be used as the fuel for refining since the fuel was kept separate from the iron, heat being transferred by ‘bouncing’ off the roof of the furnace. This was later developed into the puddling furnace by Cort in 1816.
Charcoal iron was still in demand for the forges and it would take many years for charcoal blast furnaces to be replaced by coke furnaces. Indeed, on the Weald of Sussex, coke was never used and the
*Consulting editor, Steel Times International and a member of the Historical Metallurgy Society last furnace did not close until 1813. In Cumbria, the Duddon furnace operated until 1871 using charcoal. The Backbarrow ironworks in Lancashire did not convert to coke until 1921. Elsewhere, in Sweden, where charcoal was readily available, some furnaces still used charcoal until the 1960s. Indeed, even today, charcoal blast furnaces operate in Brazil producing some 3Mt/yr using wood taken from Eucalyptus plantations – although evidence shows that some virgin wood from the Amazonian forests has found its way into charcoal production. Here, massive kilns that enable a lorry to back into them to discharge its load are used.
As late as 1864, John Percy, in his threevolume treatise ‘Metallurgy’(2) devotes 58 pages to the properties and manufacture of wood charcoal, with further pages on torrefied wood (‘white’ or ‘brown’ charcoal produced at a lower temperature) and on peat charcoal.

Percy summarises production using earth clamps, the general method of the day. In this case, mid-age wood (a coppicing cycle of 15-19 years was common) is used as the source, cut in winter when free of sap. This should be de-barked and air-dried and left for some months before charring. The best results are obtained before the wood is completely dry to slow down the rate of charring which improves the yield and quality. Steam must be free to escape. Rotten or worm-eaten wood should not be used as the result is too friable for the blast furnace. Water-logged wood, such as from wood stacks not protected from rain, or timber floated down rivers for more than 10 days, should be avoided. The ground on which the clamp is built must be level and impervious to air to avoid too much air ingress which will consume part of the charcoal product. A layer of charcoal dust can make the base air-tight. A clay ground is unsuitable as fissures may form by shrinkage from the heat of the burn enabling ingress of air. On moist ground, a foundation of wood covered by soil should be made. The pile must be covered in fine soil and protected from wind by either a sheltered location or by erecting hurdles to prevent uneven burning. The wood consumed on lighting the clamp should be replaced with more wood or charcoal browns to fill in the gaps.
Charcoal, he states, should not be used in blast furnaces or forges immediately after burning, as it has been found to improve by keeping for at least several months. With the same charge of ore and flux in a blast furnace, the same quantity of freshly burnt charcoal was found to be less effective than charcoal which had been kept during two years well under cover. The workmen, as well as the masters, of the Catalan forges in the French Pyrenees, were of the opinion that it was desirable to leave charcoal ‘at rest’ for a while, even if in a slightly damp place, from the belief that after such treatment it supports the blast better and is less quickly consumed. Coppiced charcoal from younger wood transports better, producing less waste than charcoal made from split thick woods, but this is the reverse of the needs of the storehouse.
In the charcoal barn, charcoal in contact with walls or the ground may absorb saline matter and deteriorate. The waste of charcoal in the store-house from this and other causes is very variable, and has been estimated at 8 – 11%. Percy states he is at a loss as to why the quality of charcoal should improve on keeping.
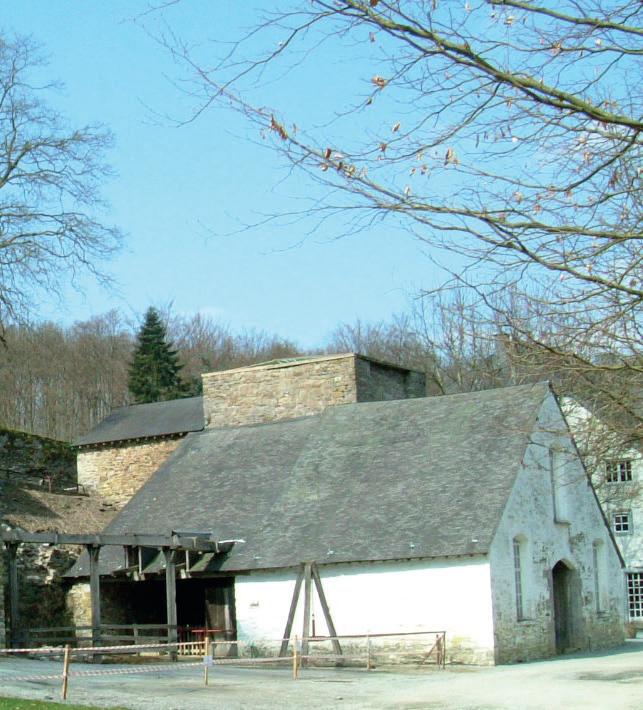
Not addressed by Percy, however, is the risk of spontaneous combustion. Evidence of this is seen in some charcoal stores where fire has damaged the walls. To reduce the risk of fire, charcoal was stored in piles often in separate bunkers. This necessitated the charcoal store being the largest building on the site.
The reason for debarking the wood prior to charring is partly because of a higher phosphorus content in the bark in certain woods such as fir. Also, oak bark was held in value for the leather tanning industry.
Is there a revival in use?
Charcoal is carbon neutral when burnt as it releases the carbon which the tree had absorbed from the atmosphere during growth. Because of this, the use of charcoal in certain modern steelmaking practices have been considered. In September 2021, worldsteel prepared a ‘Fact Sheet’ on the topic ‘Biomass in Steelmaking’. Tests have been made in Australia to substitute pulverised coal injection in the blast furnace with suitably charred wood waste. At Arcelor Mittal Ghent, the use of torrefied wood waste – produced at a lower temperature than traditional charcoal – has been undertaken. Two reactors have been built to produce 40kt/yr of ‘bio-coal’.
However, a major concern is the sustainable supply of wood waste in particular following an increasing demand for wood pellets as an alternative fuel for space heating and power generation. Worldsteel quote the conversion of four of the six generating units from coal to wood pellets at UK’s Drax power station. This now supplies 5% of the UK’s electricity and accounts for 10% of its renewable energy supply – attracting a Government subsidy so far amounting to £6bn(3). But, although waste wood is part of the supply, imported from Canada with associated transport emissions, the demand of 500 tons per day cannot be met without felling Canadian virgin forests as revealed in a BBC documentary(4). Hence, before reverting to charcoal as a modern bio-fuel, take a look at the biomass supply chain(5) to check if a supply is sustainable or is ‘greenwashing’.�
References
1 A History of Metallurgy by R F Tylecote p105
2 J Percy ‘Metallurgy The Art of Extracting Metals from Their Ores’ Vol 1 Introduction, Refractory Materials and Fuel’ pp 354-411 available as a Google scan at https://books. google.dk/books?id=nhZKAAAAMAAJ
3 https://grid.iamkate.com/
4 https://www.bbc.co.uk/news/scienceenvironment-63089348
5 www.worldbioenergy.org