
5 minute read
Keeping it rolling
Too many companies got caught up in the ‘early hype’ of digital transformation, says Joe Maczuzak*, leading to conservative views on its potential, but the results speak for themselves – as the uptake of industry 4.0 offers energy efficiency, increased sustainability, and even improved safety.
1. How are things going at ROVISYS? Is the steel industry keeping you busy?
The steel industry got hot in February 2021 and has been rolling ever since. Modernization investments in automation and projects in the information space have made up the bulk of our work since coming out of the COVID-19 slowdown.
2. What is your view on the current state of the global steel industry?
From our view we see the US steel industry busily updating its facilities. Energy efficiency and environmental improvement projects currently have priority. Somehow the industry continues to roll through the ongoing global geopolitical and economic uncertainties.
3. In which sector of the steel industry does ROVISYS mostly conduct its business?
Cokemaking, ironmaking, and steelmaking on the primary side are key for RoviSys. Our headquarters in the US Great Lakes Region is located near many integrated steel mills.
4. Where in the world are you busiest at present?
We are busiest in the US, but we provide solutions globally from our offices in Asia and Europe also.
5. Can you discuss any major steel contracts you are currently working on?
Without specifics, our current major steel projects include large-scale drives/PLC/ DCS/SCADA modernization projects in the cokemaking and ironmaking segments.
6. Where does ROVISYS stand on the aluminium versus steel argument?
Producers of both of these metals continuously innovate and improve their products which is healthy competition that benefits us all. RoviSys works with customers in both metals industries, so we’re open-minded.
8. Hydrogen steelmaking appears to be the next big thing. What’s your view?
There is a long road ahead in steelmaking’s decarbonization transition, to fully realize the potential of hydrogen steelmaking and to build the required infrastructure. It is encouraging to see the journey has begun with significant investments in these processes and others.
9. In your dealings with steel producers, are you finding that they are looking to companies like ROVISYS to offer them solutions in terms of energy efficiency and sustainability? If so, what can you offer them?
Energy efficiency and sustainability projects are certainly top-of-mind for our customers. These types of projects often include analytics, IoT devices, historians, and/or machine learning.
7. What are your views on Industry 4.0 and steelmaking and how, if at all, is ROVISYS using it?
RoviSys assists customers with all aspects of industry 4.0, from road mapping, to design, to implementation, to organizational change management and deployment. We have a systematic approach to industry 4.0 that tackles each aspect of digitalization and building one project onto another to reach a true digital transformation.
We look at networking modernization, data infrastructure, data consolidation and warehousing, OEE/KPIs, visualization, MES, analytics, and AI to create a holistic strategy that’s tailored for each of our customers, ensuring the right priorities are put in place which keeps things running smoothly.
RoviSys offers all of these services, and we work closely with our vendor partners who provide the hardware and software tools for successful projects.
10. How quickly has the steel industry responded to ‘green politics’ and are they succeeding or fighting a losing battle?
Many readers will know that steel accounts for 8% of global GHG emissions, emitting at a rate of 1.8 tons CO2 per ton of steel. Innovative minds in the industry have solutions in development today that can reduce emissions; however, each technical solution requires supporting solutions to be viable.
These latter challenges may be more daunting than the technical. We all have a stake in this fight and its outcome.
11. Where does ROVISYS lead the field in terms of steel production technology?
RoviSys has a unique approach to industrial AI called Autonomous AI. It incorporates the best of existing machine learning with the most advanced techniques, including deep reinforcement learning. It typically leverages both historical data and simulation to provide significant improvements to existing processes –especially processes that currently have heavy operator involvement.
12. How do you view ROVISYS’s development over the short-tomedium term in relation to the global steel industry?
RoviSys’ investments in artificial intelligence, cyber security, and digital transformation consulting knowhow are complementing our core control and information systems expertise.
These investments benefit our customers as they modernize and take their operations to the next level.
13. Where do you see most innovation in terms of production technologies – primary, secondary or more downstream?
Right now, there are low-cost IoT devices which offer many new capabilities to downstream producers, for example, by improving the ability to track and trace material through production in discrete processes in real time. At the other end, complex primary steelmaking processes will benefit from DRL artificial intelligence solutions by augmenting the knowledge the industry already possesses.
14. How optimistic are you for the global steel industry going forward and what challenges face global producers in the short-to-medium term?
We’re optimistic that in the short term, the steel industry will remain healthy and opportunities for investment will continue. However, our customers are approaching the short-to-medium term with caution.
15. What exhibitions and conferences will ROVISYS be attending in over the next six months?
RoviSys just presented at the AIST Digital Transformation Forum in Pittsburgh. We also regularly attend vendor conferences hosted by partners such as Schneider Electric, Rockwell, AVEVA, and SAS.
16. ROVISYS is headquartered in the US but what’s happening steel-wise in the country?
We see many projects related to improving OT connectivity and cyber security. Making process data available for use, securely, is the first step in any successful digitization effort.
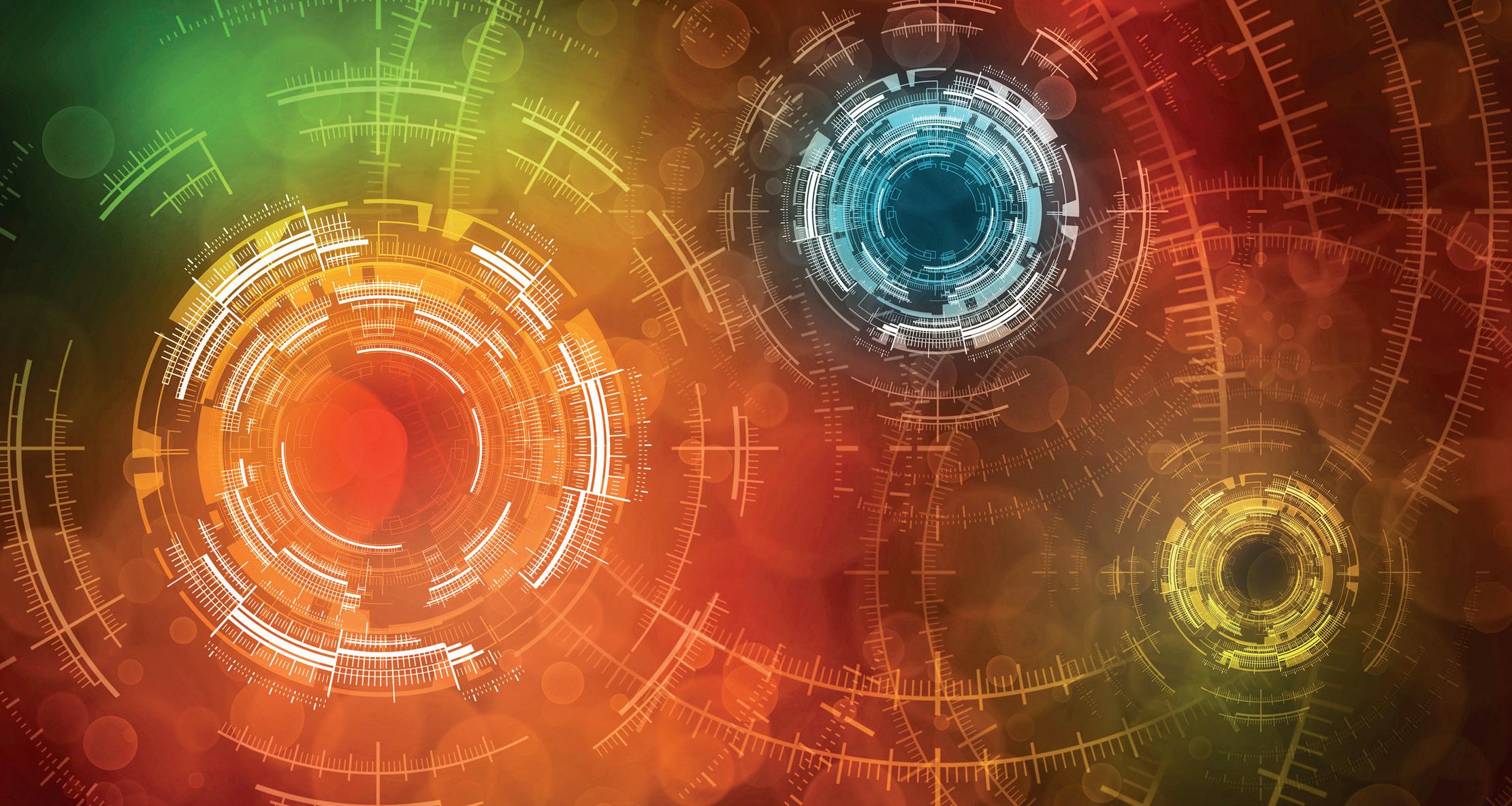
17. Apart from strong coffee, what keeps you awake at night?
Missed opportunities for digital transformation. Too many companies got caught up in the early hype with digital transformation, were sold a story by highpaid consultants, then had little to show for their investment.
This has made many companies too conservative, and stalled real grassroots digital transformation projects that could have a large positive impact on productivity and revenue.
18. If you possessed a superpower, how would you use it to improve the global steel industry?
No question, the answer would be to improve safety. By its nature, steel production is a dangerous process. We take the benefits of steel for granted, but visiting one of these plants shows you how violent the process is for human beings to shape raw materials into steel.
As much as possible, if we can reduce the danger to humans by improving automation, leveraging robotics, or using AI to minimize unsafe conditions, that would be a win for the industry. �
WOOD charcoal was, from the Iron Age to the 18th century, the only successful combined fuel and reductant for the extraction of iron from its ores. Although coal was recognised as early as Roman times as an alternative fuel to wood, or the hotter burning charcoal, attempts to employ it for the reduction of iron ore had little success. In Britain, patents(1) were granted to smelt with coal as early as 1611 to Sturtevant, and in 1613 to Rovenson, but with no evidence of success. Later, in 1622, Dudley took out a patent for the use of coal in the blast furnace. This followed the application of coal in copper and lead smelting and glass making. Dudley has the more credible claim for success having made changes to his furnace, and was fortunate in using low sulphur coal, and limestone as flux, from his residence in Staffordshire. Examination of residues of one of his furnaces at Himley, Staffordshire, showed that the slag contained coked coal, but whether this was from coking in the furnace, or it being charged to the furnace,