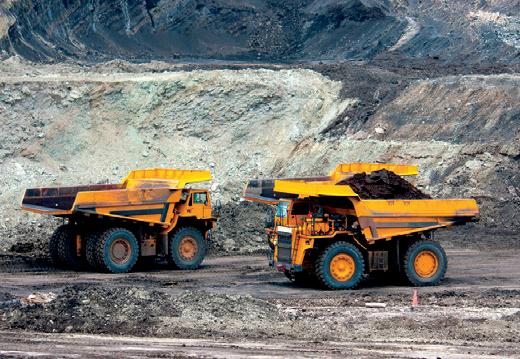
3 minute read
LEADING A CLEANER INDUSTRIAL FUTURE
Walk away informed and inspired about your company’s sustainability journey. SIM Europe in Maastricht offers attendees a deep-dive into the latest solutions for sustainable manufacturing, break-through technology, and the future direction of industrial processes.
INCLUDING SPEAKERS FROM:
China Hongqiao Group
Henkel Global Supply Chain
General Electric
British Glass
Linde PLC
Titan Cement Interational
Holcim
SABIC
Heidelberg Materials Group
Schneider Electric
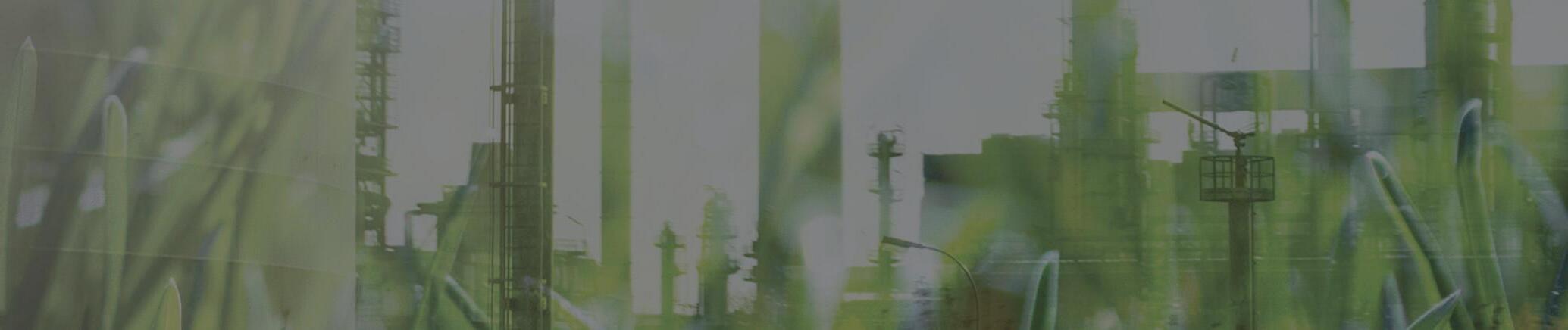
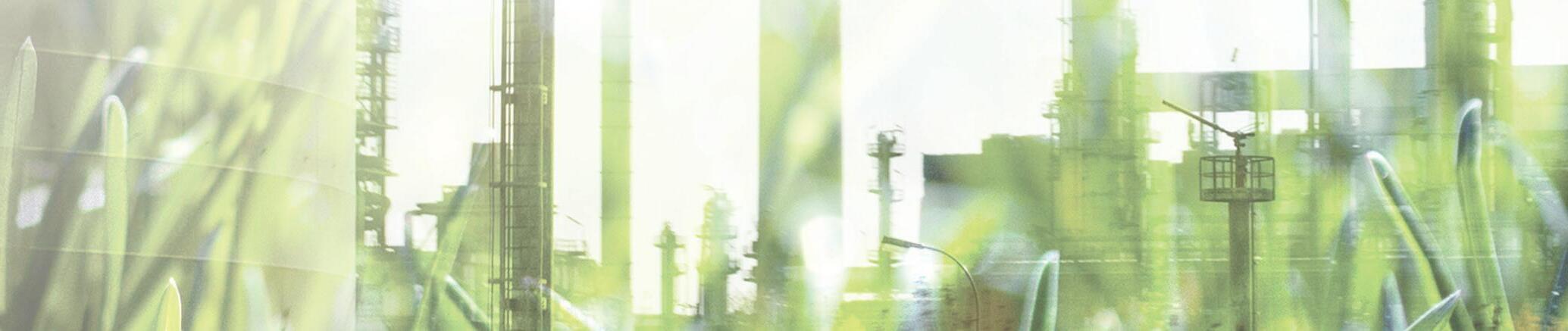
AGC Glass Europe
ABB Process Industries
Thyssenkrupp Steel Europe
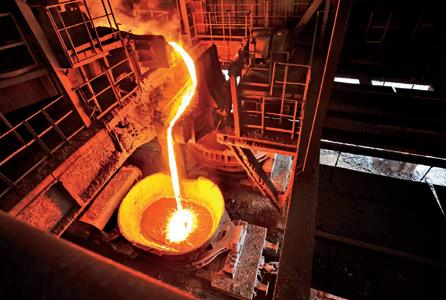
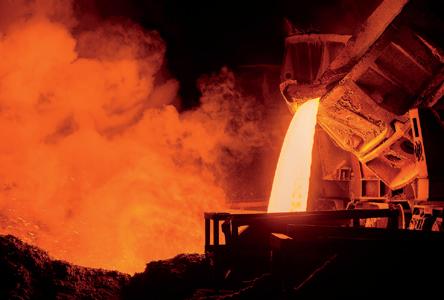
Plus a whole host of NEW tech disrupters including Net0, CemVision, BioBTX, Magsort, Carbon Clean and many more…
100+ SPEAKERS
Follow our LinkedIn group for updates
ROUNDTABLE DEBATES
NETWORKING EVENTS
Europe’s only event dedicated to the met coke, coal and steel industries
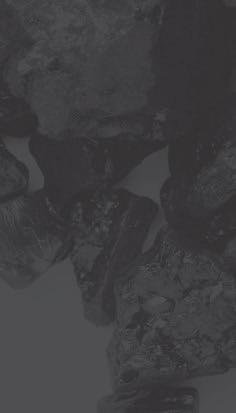
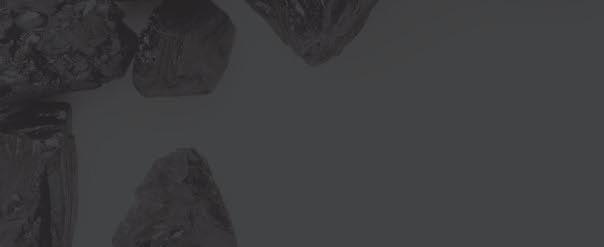
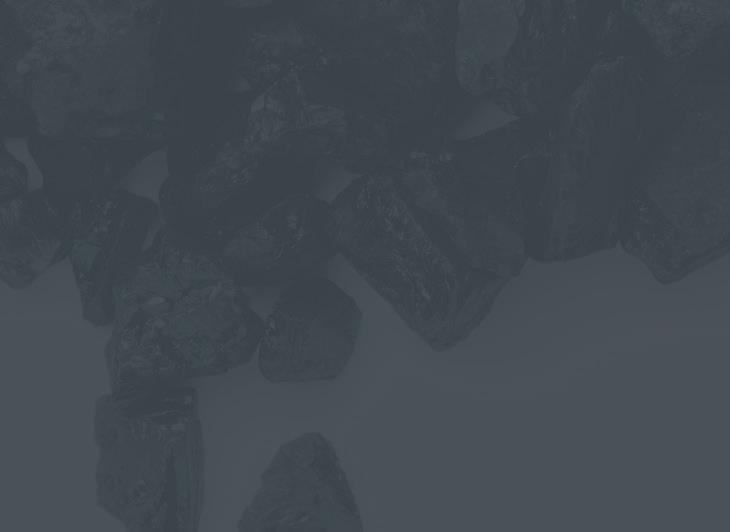
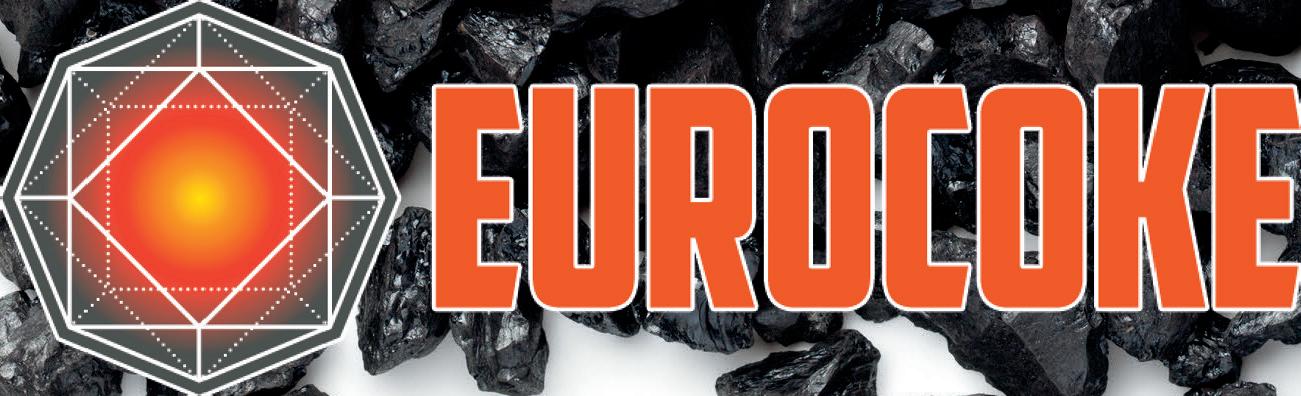
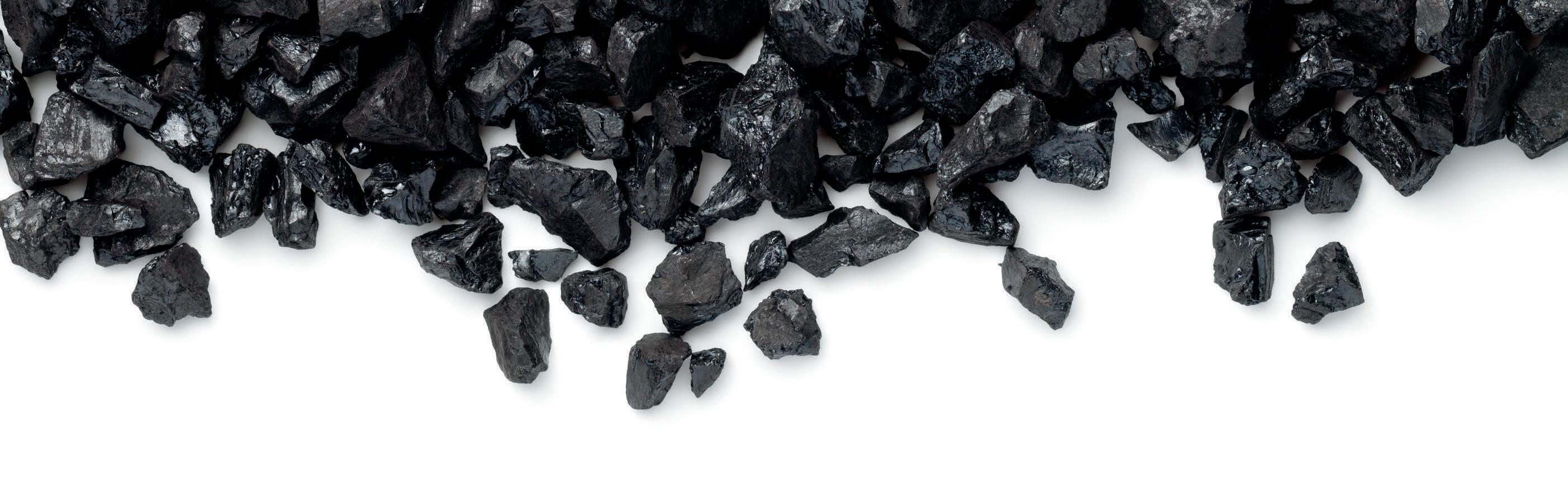
With over 300 attendees and 28 expert speakers at the 2022 event, can you afford to miss out?
Eurocoke is a fantastic platform for people in the met coke industry from all over the world to exchange ideas and information - ACRE www.eurocokesummit.com
SAVE 10% WITH CODE ECOKE23STI
HBI or green pig iron from Australia or the Middle East into countries where steel is produced but energy is expensive.’’ This, said Fleischanderl, ‘will have impacts on the value chain and employment rates, and it’s likely it’s going to happen in the mid-term’.
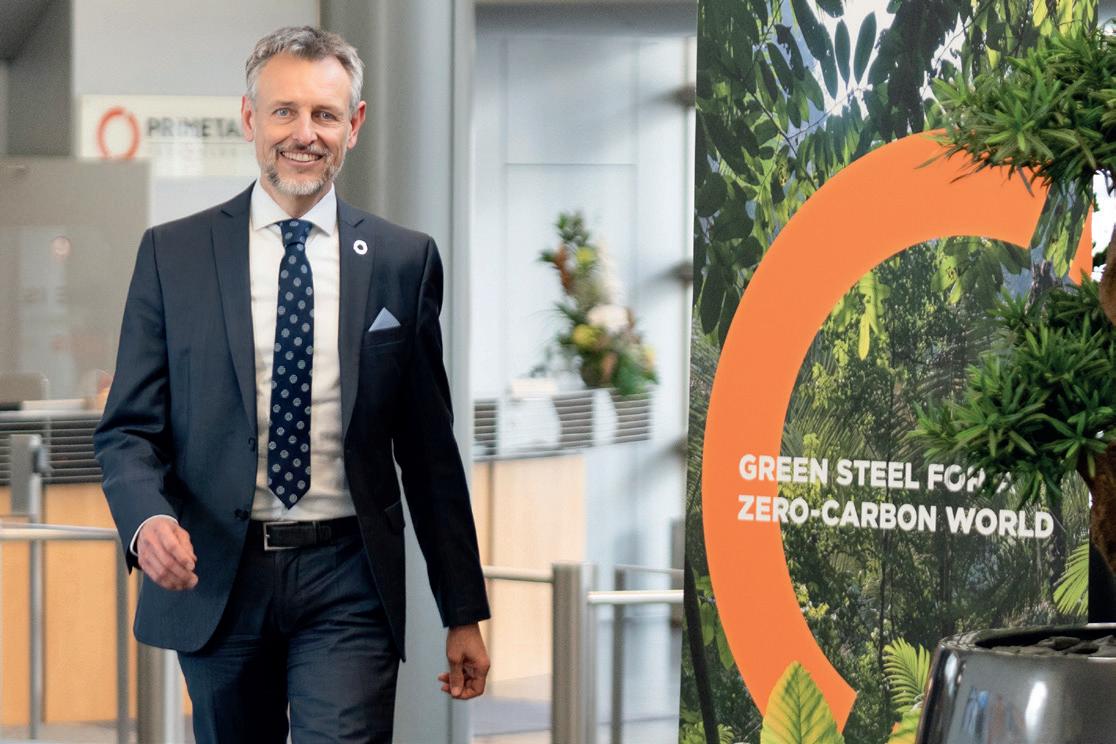
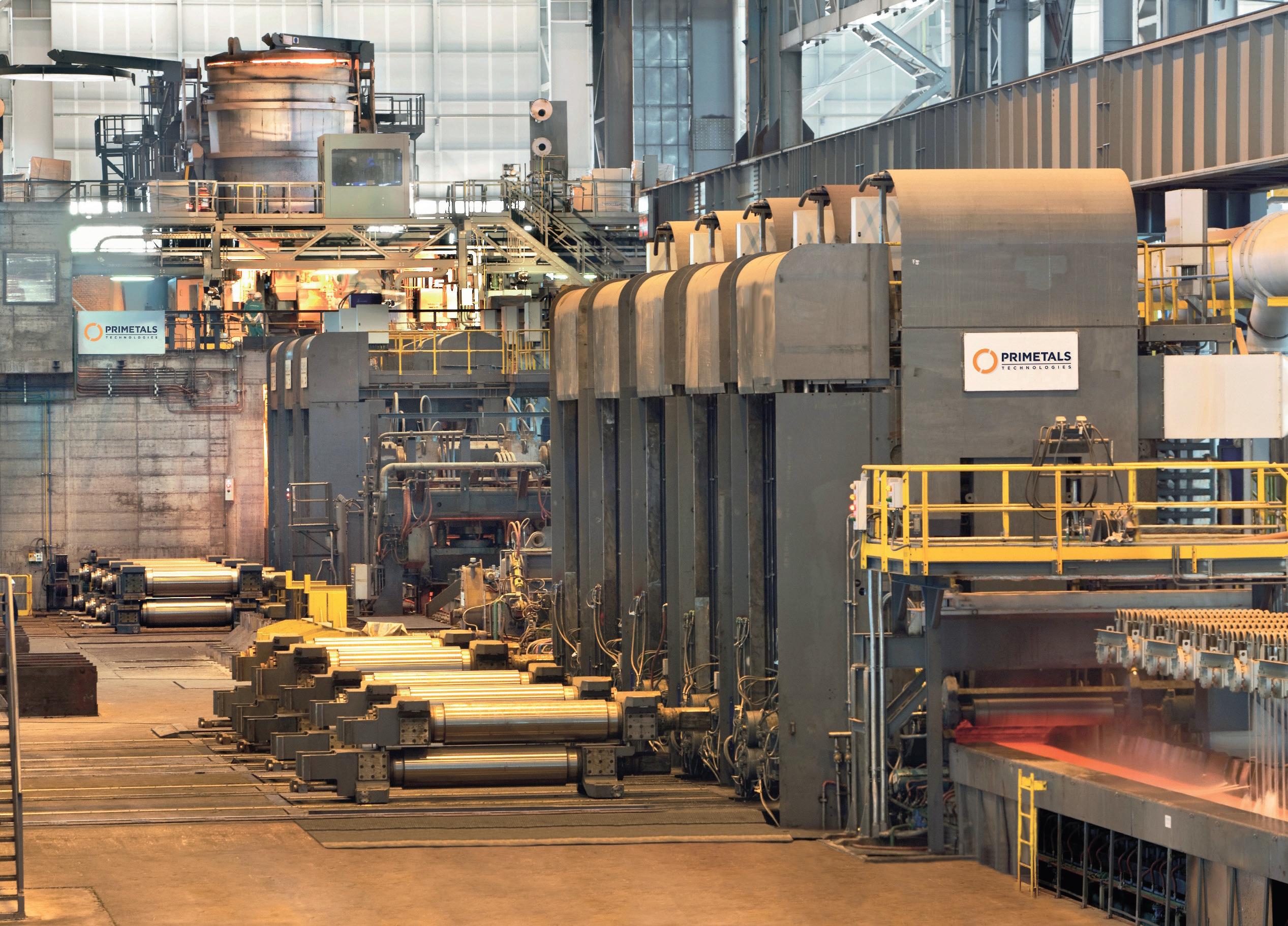
Despite the ongoing efforts to convert to green steelmaking, all the clichés of smokestacks pumping out fumes exist for a reason, and a huge discrepancy continues to plague the industry – of blast furnaces still being built, while other regions are converting to cleaner production processes. ‘‘It’s no secret that the lifetime of a blast furnace is 50 years plus’’, said Fleischanderl, and so in his view, the only way out for regions such as Southeast Asia and China continuing to invest in emissions heavy production is carbon capture and utilization; ‘it’s one of the passways to solve the issue and come closer to netzero’. Other than that, it’s a waiting game for legislation to catch up with the remaining blast furnace stronghold, with the ‘introduction of mechanisms’ such as CBAMs and emissions trading schemes, as well as market incentives to switch to greener production methods.
While this fight continues, Fleischanderl turns to the 20 strong task force he works within, which after a year since its commencement, has ‘never been better integrated’, nor more passionate about the drive to decarbonize the industry. The ‘one disadvantage’ of working within the task force, said Fleischanderl, is ‘not doing the deep dive work’ that has given him over 100 patents to his name, but that research is ‘now with the next generation’– one that he feels is inspired to propel deep and meaningful change through the steel industry. Looking back to his beginnings, Fleischanderl refers to a childhood that was spent ‘playing around with chemical tools, changing colours, and making reactions’–always with the underlying thought of ‘cleaning things up’. One of his proudest moments to date is the development of MEROS; a maximised emissions reduction system for sintering and pelleting plants. Designed as a modular system, it removes almost all harmful substances found in the off-gas of sinter plants and other steel production units. This includes elements such as sulfur oxides, nitrogen oxides, dust with particle sizes as tiny as 2.5 nanometers, dioxins, furans, polyaromatic hydrocarbons, heavy metals like lead or mercury, acidic gases, and various other harmful organic compounds. It’s a gamechanging innovation, with a surprising backstory. Fleischanderl recalls holidays in Italy with his family, where they stayed near a steel mill that had a ‘brown plume always hovering over’, a sight he said which ‘threatened’ and disturbed him as it continued to billow out into the nearby town, causing illness, dense clouds of pollution, and damage to the wildlife.
‘‘99% of all dioxin emissions from Italy were from that one stack’’, he said, which led him to stage a return to his holiday haunt in 2005 – where he and his team built a MEROS pilot plant and waited with bated breath to see the community’s reaction once it commenced operations in 2007. As it turned out, it was worth the wait.‘‘If you look now at that stack, all the people in the city love to see it – you don’t see [fumes], it’s zero emissions. This is why I love to work in sustainability, because it’s contributing to society and the well-being of people...it was a city with some of the highest cancer rates, and hopefully this is gone now.’’
It’s not just about steel then, for Fleischanderl, it’s the knock-on effects of an industry that, for a long time, has existed in contradiction – both contributing to the development of society, and causing detrimental effects to the world in which it functions. Yet, with the advancements of systems that work to offset the costs, the unlikely neighbours of ‘sustainable’ and ‘steel’ might finally be able to exist in an unexpected, and indeed crucial alliance. �