MATERIALI E SOLUZIONI DI
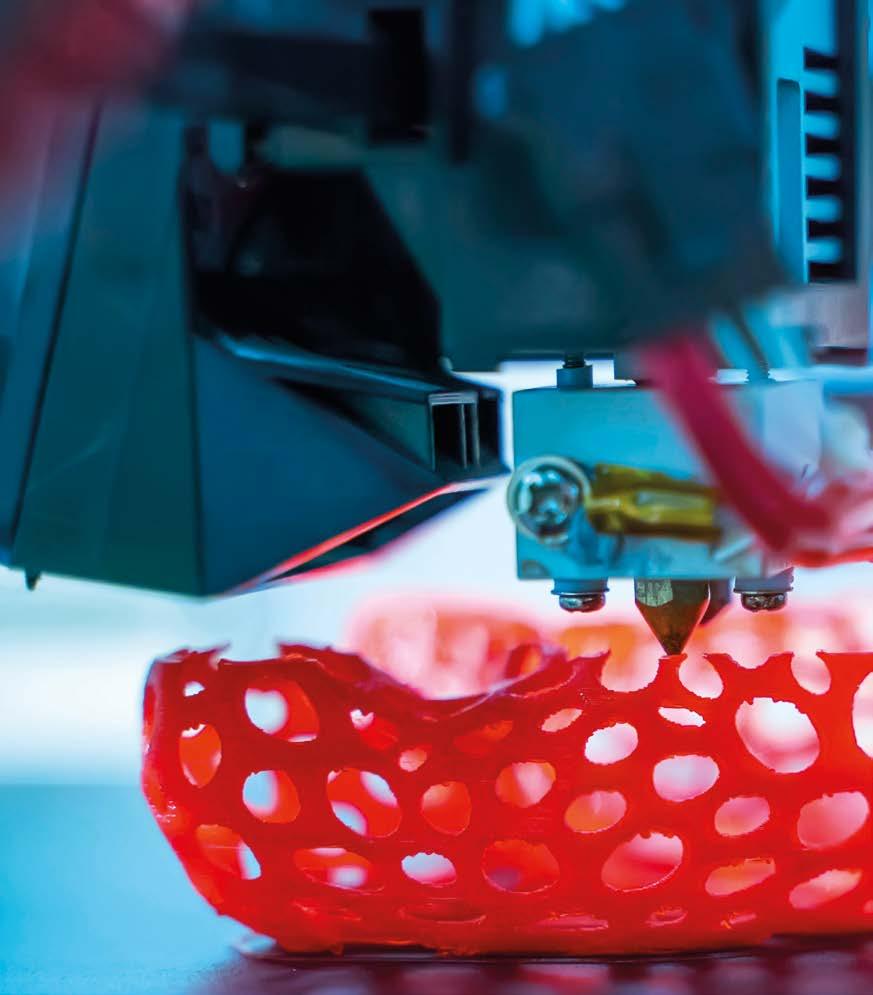
I MATERIALI PIÙ INNOVATIVI PER PROGETTARE PEZZI 3D PIÙ RESISTENTI, LEGGERI, FLESSIBILI O DUREVOLI E I TRATTAMENTI E LE FINITURE PER SODDISFARE I VINCOLI E I REQUISITI DI SETTORI PARTICOLARMENTE ESIGENTI di Patrizia Ricci
Grazie alla stampa 3D è possibile realizzare prototipi e produrre parti per un’ampia gamma di applicazioni in modo rapido ed economico. Tuttavia, per ottenere parti che abbiano l’aspetto desiderato o proprietà meccaniche, chimiche e caratteristiche funzionali specifiche, non basta scegliere il giusto processo di stampa 3D perché il risultato finale dipenderà in gran parte anche dai materiali scelti.
I recenti progressi tecnologici ottenuti per i materiali e i processi produttivi hanno permesso all’industria della produzione additiva una continua crescita, sotto ogni punto di vista. Attualmente, la stampa 3D sta riscuotendo un successo sempre maggiore, venendo incorporata e consolidata da diversi settori applicativi. Infatti, anche se il mercato della produzione additiva è stato indebolito dalla crisi sanitaria, è riuscito a resistere, dimostrando i suoi punti di forza e rivelandosi in crescita nell’anno appena concluso con buone prospettive per il 2023. Come già anticipato, i materiali, insieme ai trattamenti e alle finiture, sono una componente chiave del mercato della stampa 3D. Sulla base dell’andamento del 2022, per il nuovo anno si prospettano importanti novità per ognuna delle quattro famiglie di materiali - polimeri, metalli, ceramiche e compositi – destinati alla produzione additiva che contribuiranno
alla crescita del settore dell’AM. Nel caso dei polimeri, ad esempio, la sostenibilità e reperibilità stanno diventando sempre più importanti e i produttori spingono sempre di più verso filamenti, resine o polveri provenienti da risorse naturali e rinnovabili. D’altra parte, anche gli utenti sono indirizzati verso la produzione di parti riciclabili o almeno riutilizzabili, con un impatto sempre minore sull’ambiente.
Infatti sia nel mercato dei filamenti, sempre più spesso realizzati a partire da risorse naturali, materiali riciclati o scarti di produzione tecnica delle aziende, che nel segmento delle polveri, i cui produttori cercano di migliorarne continuamento il tasso di riutilizzo e di sviluppare plastiche che possano essere riciclate, la sostenibilità sta assumendo un ruolo centrale.
Parlando di filamenti e quindi di processi di stampa a estrusione, viene spontaneo pensare alla tecnologia FDM. La FDM, o modellazione a deposizione fusa, è spesso considerata la tecnologia di stampa 3D più semplice in quanto consta essenzialmente di tre elementi fondamentali: un piatto di stampa sul quale viene stampato il pezzo; una bobina di filamento che funge da materiale di stampa e una testina di estrusione, anche chiamata estrusore. Il processo consiste nella fusione del filamento dall’estrusore della stampante, che deposita il materiale strato per strato sul piatto.
In questa tecnologia, tuttavia, i filamenti non sono l’unico materiale utilizzabile. Sono sempre più presenti sul mercato stampanti 3D alimentate con pellet. I pellet sono dei granuli utilizzati per lo stampaggio a iniezione che stanno diventando sempre più popolari nella stampa 3D perché consentono un risparmio sui costi e offrono anche una gamma più ampia di materiali rispetto ai filamenti.
I metalli sono tra i materiai più utilizzati nella stampa 3D industriale, soprattutto nei settori aeronautico, automobilistico e bio-medico. Le tecnologie additive a metallo più importanti sono sicuramente la Laser Powder Bed Fusion (LPBF) e l’Electron Beam Melting (EBM, fusione a fascio di elettroni) o Directed Energy Deposition (DED).
Tuttavia, anche per quanto riguarda i metalli, occorre sottolineare la crescita della tecnologia FDM nota anche come fabbricazione a fusione di filamento (FFF), ispirata allo stampaggio a iniezione dei metalli (MIM). Il vantaggio principale di questo processo, che permette di fabbricare una parte metallica con le sole tre fasi di stampa, sformatura e sinterizzazione, è il suo basso costo rispetto alle soluzioni di fusione laser a letto di polvere dotate di uno o più laser, o anche di un fascio di elettroni. Per questo motivo i suoi produttori sono in continuo aumento sul mercato.
Il mercato offre anche composti di rame, caratterizzati dalla presenza di particelle fini e medie che offrono un’elevata conducibilità termica ed elettrica, consentendo un migliore trasferimento di calore e una migliore corrispondenza del coefficiente di espansione termica; polveri di origine biologica e neutrali dal punto di vista climatico o a basso contenuto di carbonio; filamenti che offrono una diversa permittività elettrica e che sono caratterizzati da basse perdite dielettriche con i quali progettare forme più complesse e variare la permittività del pezzo; polveri di titanio a basso contenuto di ossigeno che consentono
agli utenti di progettare parti di migliore qualità e durata, poiché è necessario meno ossigeno per produrre la polvere.
Le innovazioni sui materiali per la stampa 3D non si limitano ai polimeri e ai metalli, ma riguardano anche soluzioni più rare come il silicone o la ceramica. Grazie a queste novità, gli utenti della manifattura additiva sono in grado di progettare pezzi più resistenti, più leggeri, talvolta flessibili o addirittura più durevoli. Il silicone, ad esempio, è un materiale sempre più popolare nel mercato della produzione additiva, con proprietà interessanti per molti settori. Sul mercato sono presenti siliconi per i processi basati sul Liquid Deposition Modeling (LDM) e nuovi materiali di supporto idrosolubile che consentiranno agli utenti di immaginare geometrie ancora più complesse, così come stampanti 3D con le quali stampare pezzi con diversi siliconi contemporaneamente.
Perché migliorare la qualità delle superfici delle parti stampate in 3D
Il mondo della stampa 3D è in continua evoluzione, nonostante la sua “giovane” età, anche a seguito delle necessità che con il progredire delle tecniche si delineano tra gli utilizzatori di questa tecnologia, ossia ingegneri, produttori e industrie, ognuno dei quali si trova ad affrontare difficoltà più o meno specifiche in relazione al proprio ambito di attività.
I manufatti ottenibili mediante tecnologie additive hanno raggiunto ormai una qualità molto elevata, basti pensare a quella del-
le microfusioni ottenute mediante fusione a letti di polvere; anche i polimeri lavorabili presentano caratteristiche sempre più elevate, come la resistenza al calore e alle sollecitazioni meccaniche e chimiche. Tuttavia una delle caratteristiche dei processi additivi, in particolare con tecnologie LPBF (Laser Powder Bed Fusion), è proprio la non ottimale qualità superficiale dei componenti dopo la fase di stampa. Questo è dovuto all’utilizzo di polveri come materia prima, alla realizzazione del componente strato su strato (staircase effect) e alla presenza di supporti necessari alla produzione del componente stesso. Anche se la risoluzione ottenibile ha raggiunto livelli molto alti, si va dai decimi di millimetro della tecnologia FFF ai centesimi della stereolitografia ai micron della fusione a letti di polvere dettata delle dimensioni del granello di polvere metallica, tali tecnologie additive non presentano ancora la possibilità di produrre particolari estetici senza alcun trattamento successivo e quindi non si può prescindere dal ricorso a trattamenti estetici e funzionali. A seconda delle specifiche esigenze di ogni singolo componente vengono applicate tecnologie e soluzioni differenti.
Uno dei temi più attuali , quindi, riguarda la continua ricerca della finitura perfetta. Anche perché molto spesso determinate industrie o settori industriali hanno una serie di standard obbligatori da soddisfare per garantire il corretto funzionamento di determinate parti, sistemi o servizi. Il che costringe, nel caso di
pezzi o parti prodotti con stampa 3D, al controllo delle proprietà delle parti stampate in 3D, sia in termini di prestazioni che di biocompatibilità, per il soddisfacimento di questi requisiti. In tal senso, è fondamentale la post-produzione delle parti grezze realizzate con produzione additiva. Si tratta di passaggi successivi alla fase di produzione in cui vengono eliminate le imperfezioni inevitabilmente presenti sul pezzo stampato mediante i quali gli utenti riescono a conseguire la finitura desiderata o richiesta dagli standard. Accade spesso, infatti, soprattutto quando si utilizza la tecnologia di stampa FFF, che l’oggetto che esce dalla stampante 3D necessiti di ulteriori trattamenti superficiali.
Per questo motivo sono nate diverse soluzioni di postproduzione per le parti stampate in 3D atte al conseguimento delle certificazioni necessarie per le diverse applicazioni, che consentono di competere direttamente con i processi tradizionali, come lo stampaggio a iniezione. Come naturale conseguenza, i principali attori dell’Additive Manufacturing stanno mostrando un crescente interesse per il post-processing grazie al quale ottenere l’alta qualità delle superfici finali, le ottime performance e una buona estetica.
Le più attuali tecniche di post- processing della stampa 3D
Le soluzioni di post-lavorazione disponibili sul mercato vanno dalla pulizia del pezzo, intesa sia in termini di rimozione del materiale in eccesso e/o dei supporti, alla finitura superficiale, e infine alla colorazione. Per quanto riguarda la pulizia della parte, occorre precisare che una volta stampato il componente, raramente è utilizzabile così com’è. Il più delle volte, è necessario un passaggio per rimuovere il materiale in eccesso. Nel caso delle tecnologie a letto di polvere – metallo o plastica – il processo viene chiamato de-powdering, mentre nel caso delle tecnologie a resina, pulizia. Qualora sia necessario rimuovere anche i supporti di stampa, in alcuni casi si interviene a mano, in altri, come nel caso dei processi metallici, occorre una macchina specifica in quanto i metodi di rifinitura a mano sono costosi, irregolari e non riescono a stare al passo di una produzione di massa.
Una delle sfide più attuali della post-elaborazione è la riduzione del tempo necessario per completarla, che mediamente richiede tra l’11-25% del tempo totale di produzione. Indipendentemente dal processo utilizzato, infatti, la richiesta dei produttori è quella di ottenere soluzioni più rapide, accessibili e automatizzate. Per questo motivo, oggi, l’evoluzione della tecnologia e in particolare delle tecniche di post-processing sta portando sempre di più all’utilizzo di metodi automatizzati per la finitura dei componenti. Il processo di rifinitura delle superfici per la produzione additiva può essere automatizzato, ad esempio, con soluzioni tecnologiche, in alcuni casi ancora in fase di brevetto, che integrano hardware e software proprietari con la chimica, garantendo che ogni componente stampato abbia la Ruvidezza Media (Ra) e la consistenza dimensionale desiderata, e conservi intatta la rifinitura dei dettagli delle stampe in 3D. Queste tecnologie innovative, che assicurano la rimozione coerente e totale dei supporti da ogni componente senza rotture e garantiscono la sicurezza che ogni componente
risulti identico, ogni volta, eliminano i “rallentamenti” del postprinting manuale, combinando combustibili eco-sostenibili con l’uso di software e hardware proprietari, per portare a termine una rimozione dei supporti automatizzata e intelligente.
La rimozione dei supporti non è l’unica esigenza alla quale provvedere. Infatti, per alcuni settori particolarmente esigenti in termini di qualità dei componenti, sicurezza e prestazioni, come ad esempio quello sanitario, più tipicamente quelli medico e dentale, il problema maggiore risiede nella difficoltà di ottenere finiture lisce nei canali interni del pezzo, che rimangono quindi esposti alla possibilità di intrappolare potenzialmente batteri e contaminare il processo produttivo. Lo stesso dicasi per il settore automobilistico che richiede il raggiungimento di standard molto elevati per le parti stampate in 3D.
Come già detto, quindi, le caratteristiche delle superfici prodotte, in determinate condizioni, possono influenzare le proprietà finali dei manufatti. Questo vale anche nel settore degli stampi, per i quali le opportunità di creare canali di raffreddamento con geometria complessa (conformal cooling) fornita dalla stampa 3D rappresenta un valore molto importante e innovativo per un miglioramento delle loro performance, e le finiture sono determinanti. Le ricerche attualmente in corso hanno come scopo proprio il conseguimento di una soluzione al problema del trattamento superficiale di configurazioni complesse e il condizionamento delle superfici interne di tali canali. La libertà nel design del pezzo ed in particolare la facilità di creare camere, cavità e canali interni non altrimenti ottenibili, resa possibile dalle tecnologie additive, rappresenta indubbiamente uno degli aspetti più interessanti ed apporta numerosi vantaggi alla produzione, ma l’elevata rugosità dei componenti prodotti, che per alcuni di essi costituisce di per sé un requisito voluto, rimane, nella maggior parte dei casi, ancora uno dei limiti principali e un elemento penalizzante, specialmente all’interno dei canali e delle camere. L’industria della manifattura additiva è quindi alla ricerca di tecniche e processi di levigatura delle superfici che permettano di raggiungere livelli di rugosità ottimali.
Una possibile soluzione viene fornita dal sistema di postproduzione automatizzato di AMT chiamato Vapor Smoothing, che fornisce una finitura superficiale liscia e sigillata per le parti stampate in 3D. Questo metodo di post-produzione, di cui si fa cenno in una delle soluzioni di seguito presentate, permette alle parti di superare diversi test che dimostrano che esse soddisfano gli standard e le normative per le applicazioni industriali in numerosi campi. Il metodo di Vapor Smoothing consiste nell’introduzione in sospensione di una serie di lotti di parti in una camera di lavorazione sigillata, e nella successiva immissione sotto forma di vapore in un sistema a circuito chiuso di una miscela di solventi proprietaria. Il vapore, entrando in contatto con le parti, le sigilla eliminandone le irregolarità superficiali. Sigillando completamente la superficie ed eliminando le possibili crepe, il processo di Vapor Smoothing comporta un aumento dell’allungamento a rottura del pezzo senza perdita di resistenza
nella trazione finale.
Questo processo può essere utilizzato per ottenere la rugosità superficiale desiderata nelle parti create utilizzando tecnologie di produzione additiva come SLS, Multi Jet Fusion (MJF), Selective Absorption Fusion (SAF) e Fused Deposition Modeling (FDM). In termini di materiali, le soluzioni di AMT sono compatibili con un’ampia gamma di polimeri, tra cui poliammidi (PA12, PA11 e PA6), materiali flessibili come TPU e materiali più standard come l’ABS, tra gli altri.
La peculiarità di questo processo consiste nella possibilità di levigare geometrie complesse senza influire sulle proprietà meccaniche del pezzo e nella controllabilità e ripetibilità. Nel settore del medicale, i vantaggi del Vapor Smoothing risiedono soprattutto nell’impedimento dell’accumulo di batteri e nella maggiore sterilizzazione del pezzo oltre che nell’importanza che la levigatura della superficie assume per le parti soggette a contatto con la pelle, come protesi, tamponi nasali, applicazioni dentali, ecc. il metodo consente anche di sigillare le superfici contro l’ingresso di liquidi e gas.
Tornando tecniche di post-processing, quindi, per finitura superficiale si intende un processo che assicura che ogni parte soddisfi le sue specifiche, come la rugosità media desiderata e la coerenza dimensionale, mantenendo intatti i dettagli fini della parte stampata in 3D, mentre con la colorazione, detta anche tintura, si fa riferimento al terzo passo della post-elaborazione delle parti stampate. Le parti bianche sono quelle più adatte alla colorazione.
Per molti versi, il post-trattamento rappresenta ancora una sfida. La finitura di componenti ottenuti da Additive Manufacturing richiede tuttavia un’analisi dell’intero flusso di processo per poter garantire la qualità superficiale desiderata, sia che avvenga tramite operazioni di rimozione delle strutture di supporto, che di rottura degli spigoli, di lucidatura ad alto gloss, di levigatura, raggiatura o di preparazione alla verniciatura. Già da diversi anni, alcune aziende del settore hanno messo a punto numerosi processi di levigatura, lucidatura e granigliatura sviluppati specificatamente per questo scopo: in questo modo, è possibile trattare praticamente qualunque materiale, dalla plastica al metallo, e pezzi ottenuti con le più svariate tecnologie. Il ventaglio delle opzioni disponibili spazia dall’omogeneizzazione delle superfici alla lucidatura con bassi valori di rugosità e persino ad alto gloss. I fattori da prendere in considerazione sono la tecnologia di produzione additiva impiegata, la granulometria, le tolleranze degli strati di materiale applicati e la posizione del pezzo nella camera di produzione. La finitura di massa, ad esempio, è la tecnologia di riferimento per i pezzi in plastica o metallo. A seconda della forma e dimensione dei componenti e delle loro specifiche tecniche, è possibile ottenere le finiture desiderate con un trattamento in batch o individuale. Anche se, in ogni caso, sarebbe importante prendere in considerazione il grado di finitura richiesto già a partire dalla fase di progettazione.
Le polveri metalliche per la stampa additiva devono rispettare alcune caratteristiche per garantire la qualità e le specifiche del pezzo stampato, particolarmente quando utilizzate in processi che prevedono la fusione in letto di polvere (Powder Bed Fusion) sia mediante sinterizzazione selettiva al laser (Selective Laser Sintering o Selective Laser Melting) o con fascio di elettroni (Electron Beam Melting).
Le caratteristiche essenziali di una polvere metallica per stampa additiva sono le seguenti, e andrebbero verificate per ogni lotto in modo da garantire una qualità costante dei prodotti stampati:
• La composizione chimica con un basso livello di ossidazione, in particolare per leghe di titanio o a base di nichel
• La distribuzione granulometrica adattata sia al processo che alle esigenze operative e di finitura
• La morfologia delle polveri, ovvero particelle di polvere il più possibile sferiche, senza aggregati o satelliti
Le polveri metalliche possono risultare costose, pertanto nei processi di Powder Bed Fusion, vengono di solito riciclate più volte, effettuando diversi cicli produttivi con lo stesso lotto o aggiungendo una porzione di polvere vergine. Il riutilizzo continuo della polvere modifica le sue caratteristiche e può influire sulla qualità costruttiva, con conseguenti potenziali difetti nella parte prodotta ed eventuali fragilità, introducendo un grave rischio per la sicurezza a seconda dell’uso finale della parte stessa. In termini pratici, la densità di impaccamento della polvere deve risultare sufficientemente elevata per evitare la formazione di spazi vuoti, mentre per garantire un componente uniforme, la polvere metallica deve scorrere migliaia di volte in maniera consistente e coerente sulla piattaforma di costruzione. Queste due proprietà, densità di impaccamento e scorrimento della polvere, sono controllate dalla dimensione e dalla forma delle particelle
In Alfatestlab usiamo una tecnologia dedicata che fornisce la granulometria in volume e in numero della polvere, oltre a numerosi parametri morfologici come la circolarità, l’elongazione, la convessità, ideali per quantificare l’irregolarità della forma delle particelle. Rispetto alla classica microscopia elettronica a scansione il numero di particelle misurate automaticamente è estremamente elevato (fino a
100.000), rendendo l’analisi statisticamente rappresentativa. A titolo di esempio riportiamo in figura 1 la percentuale in numero e in volume di particelle sferiche e aggregati misurati su 10 lotti di polvere di una lega di AlSi10Mg prodotte con lo stesso processo di atomizzazione a gas. Il nostro cliente ha fissato i limiti di accettabilità in termini di sfericità delle particelle e presenza di satelliti. Con una singola misura della polvere possiamo fornire la percentuale per ogni lotto di particelle altamente sferiche, che secondo specifiche indicate non deve scendere al di sotto del 50% per un lotto vergine, e la percentuale di particelle con satelliti che non deve superare il 40% in numero di particelle (i limiti sono fissati rispettivamente a 30% e 50% in volume).
Nell’esempio fornito abbiamo introdotto n.1 lotto processato più volte, il lotto n.5, per valutare la capacità della tecnica di rilevare le differenze rispetto ai lotti di polvere vergine. Le percentuali di particelle altamente sferiche e di particelle con satelliti appaiono immediatamente fuori specifiche quando valutate in numero (figura 1 - sinistra).
L’analisi effettuata su ciascun lotto permette di rivelare qualsiasi deviazione o alterazione della qualità della materia prima. L’analisi in volume di particelle, equivalente a quella fornita dalla granulometria laser, consente di controllare le caratteristiche della polvere ma è meno sensibile alle variazioni tra lotti. In conclusione, controllando la morfologia oltre alla granulometria delle particelle, è possibile garantire una qualità costante tra i lotti di polvere, e controllare la variazione dei parametri di controllo ciclo dopo ciclo in modo da aggiungere solo la quantità richiesta di polvere vergine per rientrare in specifica.
Alfatestlab fornisce un servizio di analisi express con consegna dei risultati entro 24 o 48 ore dalla consegna della polvere presso il nostro laboratorio di Cernusco sul Naviglio (MI). Per maggiori informazioni contattateci scrivendoci a info@alfatestlab.com
L’additive manufacturing sta rivoluzionando il mondo della manifattura, con una disponibilità di tecnologie e materiali utili a rispondere a molteplici esigenze, ma soprattutto con un significativo cambio di paradigma: dal design per rispettare i canoni di produzione alla libertà di design e alla progettazione in funzione delle performance da ottenere, dalla standardizzazione alla customizzazione di massa. Per quessglio le opportunità offerte da queste nuove tecnologie, abbassandone le barriere di fruizione e trasferendo cultura additiva e competenze.
Diverse tecnologie, un solo obiettivo
Nonostante l’ampiezza del portfolio di tecnologie additive e, di conseguenza, del ventaglio di materiali, l’obiettivo resta unico: sfruttare la stampa 3D per progettare componenti capaci di rispondere a un bisogno o risolvere un problema specifico, senza i limiti dei sistemi produttivi tradizionali. Realizzare, per esempio, parti con geometrie prima impensabili; produrre solo se, quando e dove è necessario grazie al paracadute offerto dal sistema del digital inventory; risparmiare sfruttando la natura stessa dell’additive che crea aggiungendo materiale e non sottraendone dal pieno.
Le tecnologie selezionate da Elmec3D
Ciò che contraddistingue l’offerta di Elmec3D è una selezione di tecnologie sviluppate per l’industria. Si parla quindi di stampa 3D industriale: macchinari, materiali e produttività non paragonabili con le FDM che si trovano online.
Nello specifico, l’azienda Varesina ha scelto come suoi Partner HP 3D Printing per la stampa di polimeri ed elastomeri, Desktop Metal per la stampa a metallo e 3D Systems per quella a resine termoindurenti.
HP 3D Printing. La tecnologia Multi Jet Fusion di HP dà forma a polveri polimeriche: termoplastici ed elastomeri. In estrema sintesi, su un letto di polvere vengono rilasciati degli agenti proprietari che disegnano e definiscono la parte da realizzare strato per strato; a ogni gettata questi vengono riscaldati e fusi con la polvere. A fine processo si ottengono dei componenti isotropi e altamente definiti, stampati in PP, PA 11, PA12, nonché TPU o TPA. Si tratta di una tecnologia con una automazione e una produttività rivoluzionarie nel mondo dell’additive, capace di realizzare vere e proprie produzioni di livello industriale. Post processi sviluppati ad-hoc, ma funzionali
indipendentemente dal metodo produttivo del pezzo, hanno notevolmente contribuito alla diffusione di questo sistema: il trattamento Vapour Smoothing di AMT, per esempio, attraverso la levigatura chimica, conferisce finiture superficiali paragonabili a quelle tradizionali ma dal costo decisamente più contenuto.
Desktop Metal. La mission dell’azienda americana è quella di rendere accessibile la stampa 3d a metallo, fino a poco tempo fa esclusiva di settori industriali di nicchia quali l’aerospaziale o il medicale, attraverso l’abbattimento dei costi di produzione, la semplificazione dei processi e la possibilità di accedere alla customizzazione di massa. Nello specifico, Elmec 3D, ha scelto di internalizzare i sistemi Studio, tecnologia Bound Metal Deposition che depone materiale estruso, e Shop, un binder jetting che stampa le cosiddette parti verdi legando tra loro polveri metalliche con un binder, parti che vengono poi sinterizzate nella fornace proprietaria e parte del sistema, divenendo funzionali. Si tratta di tecnologie che possono accelerare l’evoluzione delle imprese verso una produzione 4.0 e che dispongono di una ricca gamma di materiali, tra cui diversi tipi di acciai come il 17-4 PH, il 316L, legati come il cromo cobalto, il titanio o il rame. Naturalmente, le parti in metallo così prodotte possono essere sottoposte ai più diffusi processi di trattamento superficiale e termico per ottenere un elevato livello qualitativo e di resistenza meccanica. Lo stesso brand ha recentemente lanciato Forust, una macchina che stampa il legno e che promette di dare una
scossa al mondo dell’architettura e del design.
3D Systems. Si tratta di un player storico e non poteva mancare nell’offerta di Elmec 3D che propone al mercato le soluzioni Figure 4, complementari rispetto alle altre tecnologie. In particolare, è stata selezionata per la varietà di materiali disponibili e la velocità con cui il produttore ne sviluppa di nuovi restando in ascolto del mercato. La stampante, una DLP, permette infatti di lavorare con una vasta gamma di fotopolimeri dalle caratteristiche più varie – autoestinguenza, biocompatibilità, alte temperature e molte altre – e garantisce un’ottima finitura superficiale.
Non solo tecnologia, soprattutto competenze.
Recitava un famoso spot “La potenza è nulla senza controllo”. Ed è esattamente per questo motivo che Elmec 3D ha sviluppato delle linee di business che puntano a educare il mercato, con l’obiettivo di padroneggiare le tecnologie additive, massimizzandone i benefici. Formazione cucita addosso alle esigenze dei clienti e calata in un contesto industriale ben preciso e una metodologia di apprendimento che passa attraverso il fare. Il Training Progettuale è un sistema di apprendimento ibrido che alterna momenti di formazione a momenti di progettazione: i progettisti del cliente imparano il Design for AM sul campo e, alla fine del percorso, hanno ingegnerizzato od ottimizzato un proprio componente, internalizzando le competenze necessarie per replicare in autonomia.
Resina iglidur i3000 per la stampa 3D di parti e ingranaggi soggetti a usura . iglidur i3000 è la prima resina igus sviluppata specificamente per la stampa 3D DLP di parti e ingranaggi soggetti a usura. Le parti in resina sintetica polimerizzata realizzate strato per strato con luce UV presentano dettagli molto fini e una durata d’esercizio estremamente lunga. Dai test di laboratorio è emerso che la durata d’esercizio di iglidur i3000 è almeno 30 volte superiore rispetto ad altre 10 tradizionali resine per la stampa 3D. In alcune applicazioni, si evidenzia addirittura una durata d’esercizio 60 volte maggiore. Inoltre, non richiedendo lubrificazione, non serve manutenzione. Infatti, nel materiale sono incorporati lubrificanti solidi microscopici, che vengono rilasciati man mano durante il movimento. Oltre alla resina stessa, i clienti possono ordinare componenti realizzati con questo materiale direttamente da igus. L’azienda sta infatti ampliando il suo servizio di stampa 3D. Mentre prima i clienti potevano scegliere tra la stampa 3D tramite sinterizzazione laser selettiva (SLS) e la
modellazione a deposizione fusa (FDM), in futuro potranno scegliere anche parti prodotte tramite fotopolimerizzazione con stampanti DLP 3D per per realizzare componenti con dettagli molto fini e persino con scanalature interne.
iglidur® i6-BLUE, compatibile al contatto con alimenti grazie alla sinterizzazione laser. La polvere per sinterizzazione laser iglidur i6-BLUE è una plastica per stampa 3D resistente all’usura, testata e conforme al contatto alimentare secondo i requisiti FDA e EU 10/2011. Il colore blu rende i componenti rilevabili otticamente. Parti speciali, prototipi e componenti per applicazioni nel settore alimentare e delle bevande possono essere realizzati in soli tre giorni, in quantità che possono variare da 1 a 10.000 pezzi. I produttori di macchine che non dispongono di una propria stampante 3D possono utilizzare il servizio di stampa 3D di igus, senza un minimo d’ordine. Tutto ciò che devono fare è inviare un modello 3D del proprio componente. La stampante a sinterizzazione laser lo produce quindi in strati con il nuovo materiale in polvere i6-BLUE iglidur - un processo decisamente più veloce rispetto ai più classici metodi di produzione, come la tornitura o la fresatura. Grazie ai lubrificanti solidi incorporati, i componenti non richiederanno alcun intervento di lubrificazione e la speciale composizione
del materiale permetterà di ridurre il livello di abrasione fino a 50 volte. Le eccellenti proprietà di scorrimento lo rendono particolarmente adatto alla stampa di viti senza fine e ingranaggi in 3D destinati a macchine dell’industria alimentare e delle bevande. Il materiale è resistente a temperature comprese tra -40°C e +80°C. I test condotti nel laboratorio interno di igus hanno dimostrato che gli ingranaggi stampati in 3D con iglidur i6-BLUE hanno una durata d’esercizio molto più lunga rispetto alle ruote fresate in resine acetaliche (POM) e sono almeno nove volte più resistenti all’abrasione rispetto al PA12 (SLS). Grazie all’elevato allungamento a rottura, il materiale di stampa a sinterizzazione laser è adatto anche alla produzione additiva di elementi di collegamento a scatto.
igumid P190 per la stampa 3D: con ottime proprietà di rigidità e resistenza. Il nuovo filamento per stampa 3D rinforzato con fibre igumid P190 è stato sviluppato appositamente come materiale da associare a iglidur i190. Grazie ai lubrificanti solidi incorporati nel
materiale, iglidur i190 si distingue per l’elevata resistenza all’usura e l’eccellente durata d’esercizio. La sua resistenza all’usura è fino a 50 volte superiore a quella dei normali filamenti per la stampa 3D. Il nuovo igumid P190, rinforzato con fibre, offre invece una resistenza doppia e una rigidità cinque volte superiore rispetto al materiale iglidur.
La combinazione dei due materiali garantisce la produzione di componenti particolarmente resistenti e a basso attrito, realizzati tramite processo di stampa multimateriale . La grande resistenza e rigidità di igumid P190 lo rendono adatto alla stampa di parti strutturali molto resistenti, ma anche di strutture leggere con l’impiego di meno materiale.
I test condotti secondo lo standard DIN EN ISO 178 nel laboratorio igus di 3.800 metri quadrati hanno dimostrato che, grazie alle fibre di rinforzo, il filamento vanta una resistenza alla flessione altissima che arriva fino a 237MPa e un modulo di flessione di 11,5GPa (stampato in piano, linee di stampa allineate in base alla resistenza ottimale, direzione di riempimento ottimizzata).
Un materiale nuovo, completamente bianco, caratterizzato da ottime proprietà meccaniche e una grande versatilità nelle applicazioni. Adatto all’utilizzo nella stampa 3D HP MJF in applicazioni prima limitate all’uso dello stampaggio a iniezione o della lavorazione CNC: parliamo del Nylon PA 12 Bianco (HP 3D High Reusability PA 12 W) da poco presente sulla piattaforma di Weerg, il primo service italiano di manifattura nell’ambito delle lavorazioni CNC e stampa 3D online.
L’innovativo materiale è stato presentato in versione beta, in collaborazione con HP, al Formnext 2022 di Francoforte, insieme alla stampante 3D HP Jet Fusion 5420W, nata con lo scopo di accelerare la produzione di applicazioni con polimeri e consentire la produzione costante, e di alta qualità, di parti bianche ideali per il mercato dei beni di consumo sanitari, industriali e automobilistici, oltre che in architettura e nel fai da te. Lavorato mediante Stampa 3D, il Nylon PA 12 Bianco permette totale libertà al progettista in fase di design aprendo a nuove possibilità di mercato, come ad esempio il mondo del medicale, e alla colorazione per poter soddisfare ogni fantasia di design.
Il Nylon PA 12 nasce in grigio e ora si evolve anche in bianco conferendo al materiale un aspetto premium in grado di assorbire tinture di differenti pigmenti. Dal prototipo alla produzione di massa, questo materiale ha tutte le caratteristiche per garantire al progettista piena libertà. Con proprietà meccaniche molto buone, ottima resistenza agli agenti chimici come oli e grassi, e una buona resistenza agli agenti atmosferici e all’umidità, il materiale è ideale per nuovi mercati come quello ortopedico e sanitario che per regolamentazione richiede che le componenti siano tutte di colore bianco.
Così come la versione originale, il Nylon PA 12 Bianco è realizzato tramite tecnologia HP Multi Jet Fusion che permette di stampare anche parti complesse senza necessitare di supporti e garantendo, allo stesso tempo, proprietà meccaniche di buon livello su tutti e tre gli assi. La sua versatilità e il costo di produzione contenuto lo hanno reso uno dei materiali più adoperati nell’industria manifatturiera.
“In qualità di uno dei principali Online Service della tecnologia HP Jet Fusion, siamo entusiasti di collaborare con HP nel lancio sul mercato della nuova soluzione Jet Fusion 5420W
- commenta Matteo Rigamonti, Fondatore e Presidente di Weerg - Siamo inoltre orgogliosi di essere stati scelti per le nostre potenzialità e per l’alto numero di macchine a nostra disposizione, che abbiamo ulteriormente ampliato per poter sfruttare al massimo le qualità di Nylon PA 12 Bianco. Crediamo molto nelle potenzialità di questo materiale e ci aspettiamo che molte linee produttive si accorgano della sua versatilità di utilizzo, accelerando l’adozione della stampa 3D per i propri progetti.”
Una novità, ancora in versione beta, ma che promette di essere rivoluzionaria per molti settori industriali. Nel Nylon PA 12 Bianco i progettisti, oltre alla piena libertà di esprimere la propria inventiva progettuale, possono ritrovare le seguenti caratteristiche: densità di 1,01 g/cm3, carico di rottura a 44 MPa, allungamento a rottura del 12%, modulo elastico a 1.600 MPa, resistenza alla flessione di 70 MPa, modulo di flessione a 1.800 MPa e resistenza all’impatto di 45 kJ/m2
Weerg, grazie alla propria potenza produttiva, è stata scelta da HP per testare la messa in commercio del prodotto e le proprie potenzialità progettuali. L’headquarter di Scorzè (VE) conta infatti una superficie di 6.000 m 2 e un parco di oltre 45 macchine che lavorano su turni 24/7. La capacità produttiva in costante crescita permette all’azienda di poter dedicare un macchinario esclusivamente al Nylon PA 12 Bianco per poterne esaltare le proprietà cromatiche senza correre il rischio di contaminarne il colore. Inoltre, il servizio clienti in 5 lingue e sempre disponibile permette ai progettisti di approcciarsi a questa novità con maggior consapevolezza e attenzione ed essere guidati per poterne sfruttare al meglio le potenzialità.